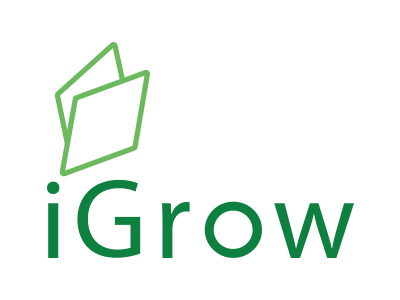
Welcome to iGrow News, Your Source for the World of Indoor Vertical Farming
World Vegetable Map 2018: More Than Just a Local Affair by Rabobank
World Vegetable Map 2018: More Than Just a Local Affair by Rabobank
FEBRUARY 1, 2018 URBAN AG NEWS
The 2018 World Vegetable Map shows essential vegetable trade flows and highlights some key global trends in the sector, such as the growing importance of production in greenhouses and vertical farms, as well as the popularity of organic vegetables.
Download
> Click here to download the World Vegetable Map
Poster versions of the World Floriculture Map are exclusively available to Rabobank clients. To receive one, please contact your relationship manager.
Map summary: more than just a local affair
The global vegetable market is still predominantly a local market. Only 5% of the vegetables grown are traded internationally. But that share is increasing. Easy market access is vital for export-focused vegetable-producing countries like Mexico, Spain, and the Netherlands. Over the last decade, Mexico has further expanded its prominent position on the North American market, and internal EU trade has continued to grow.
Market for fresh (prepared) vegetables up, demand for canned vegetables down
An estimated 70% of all vegetables grown in the world are sold as whole fresh vegetables. This market is still on the increase, mainly outside of the US and the EU. Processing of vegetables (freezing, preserving, and drying) is a good way to prevent wastage, but global consumption of preserved (canned) vegetables has decreased over the last decade. At the same time, demand for frozen vegetables has increased by an average of 1% per year. Demand trends seem most favourable for vegetables that are convenient to eat and prepare and/or do well on (social) media because of considered health effects or their visual appeal. Examples are all kinds of (prepared) salads as well as sweet potatoes. EU imports of sweet potatoes (mainly from the US) have tripled in just four years’ time.
Organic vegetables most popular in wealthy nations
Organic foods are gaining market share around the world. The share of organic fruit & vegetable sales (in total fresh fruit & vegetable sales) has already passed 10% in wealthy countries such as Switzerland, Sweden, Austria, and Denmark (see Figure 1). In the US, this share is 9% and quickly growing. Income is not the only determinant for organic vegetable consumption. In the Netherlands, where the average income per capita is similar to that of Sweden and Austria, the market share of organic vegetables is only 5%. The reasons behind this are not clear, but it is likely related to supermarkets’ decisions on the category, price, availability, and quality of conventional vegetables, as well as cultural factors.
Sources: UN-Comtrade, Eurostat 2017
Figure 1: Share of organic fresh fruit and vegetable sales vs. income, 2016
Free trade agreements vital
As most fresh vegetables are highly perishable, easy market access is essential. In Latin America and Africa, vegetables are mainly sold regionally. Growing circumstances (climate, water availability), production costs, exchange rates, and trade agreements can trigger vegetable trade flows. Distortions in NAFTA or EU trade agreements (such as Brexit) will negatively affect vegetable trade. In the last decade, Mexico has further extended its very prominent position as North America’s vegetable garden. Spain and the Netherlands are key vegetable exporters within the EU (see Figure 2). Morocco has emerged as an up-and-coming vegetable supplier for the European market.
Figure 2: Intra-EU trade
Source: UN-Comtrade, Eurostat 2017
Up-and-coming import markets
A significant change in the world of vegetables is the rise of new vegetable-importing nations. Vegetable imports used to be concentrated in North America, western Europe and Japan. But gradually, countries like India, China, and the United Arab Emirates have upped their vegetable imports. Russia has also shown an increase in trade, despite the 2014 import sanctions for vegetables from the EU, the US, and a number of other countries. Currently, Belarus, Morocco, China, Armenia, and Azerbaijan are important vegetable suppliers to Russia.
The rise of controlled production in greenhouses and vertical farms
Globally there is a growing need for vegetables that are available year-round, produced in a safe and resource-efficient manner, and are of a consistently high quality. Consequently, vegetable production in greenhouses and vertical farms is rising. The area of greenhouses is estimated at 500,000 hectares, including roughly 40,000 hectares of glasshouses. Recently, we have seen vertical farms popping up in various places around the world, mainly in the Northern Hemisphere close to large consumer concentrations.
Vertical farming entails growing crops (often leafy vegetables) in a controlled environment using artificial lighting. As investments and electricity costs are relatively high, it is (still) challenging to run an economically viable vertical farming business. That said, discerning customers are willing to pay a premium for locally grown vegetables grown in a contained environment.
For more: https://research.rabobank.com/far/en/sectors/regional-food-agri/world_vegetable_map_2018.html
North American Growers Welcome New Tool To Manage Light
North American Growers Welcome New Tool To Manage Light
JANUARY 26, 2018 URBAN AG NEWS
“Giving growers the tools to manage light quality is one of our specialities,” says Chris Higgins, General Manager of Hort Americas. “For example, we were one of the first suppliers of LED grow lights in the US. At that time, we saw the crop advantages that growers realised when they had the ability to manipulate spectrum along with intensity.”
The company recently started a partnership with Sudlac. Sudlac’s shading products were introduced in the US last year and received much interest from a wide variety of growers. “We’re giving North American growers a new tool to manage light.”
Hort Americas was founded in 2009 although the team has been actively involved in commercial horticulture for much longer. Strategically positioned in Dallas, it is centrally located to serve its customers in the US, Canada, Mexico and the Caribbean. It has also partnered with the Dutch supplier Horticoop which provides access to knowledge and products developed by leading European horticulture companies.
Proven products
The decision to partner with Sudlac was based on the European manufacturer’s proven ideas and concepts to manage light and protect the greenhouse structure, says Chris. “As a company we spend a significant amount of our time managing light in greenhouses and other horticultural production facilities.”
In the past shading products were designed to reduce the amount of light when the sun was at its brightest. “However, when we started talking to Sudlac we weren’t only looking at shading products. Additionally, we were looking at tools that would complement our product range and that would allow growers to manipulate light quality as well as light intensity in the greenhouse. Sudlac’s product portfolio includes such products and as a result has been enjoying growing success in Europe,” says the general manager.
Once Chris and his team had indeed established that Sudlac had the sort of high-quality products they were looking for the decision to form a partnership came down to people. “We also considered competitive products but ultimately it was Sudlac’s team that won us over. They are very open and easy to talk to. They have a simple philosophy, when their business partners do well, they do well. And working together for shared goals is something we always strive for.”
Wide range of climates
The main shading products imported to North America from Europe are Eclipse LD, Optifuse and Transpar. Eclipse LD is a removable shading agent that protects crops against excessive light and heat; Optifuse is a removable diffuse coating; while Transpar is a shading agent that reflects heat radiation.
“Our growers experience a vast variety of climate conditions and grow a wide variety of crops. These products are best suited to cover all possibilities,” says Chris.
The customers also range from very large to small growers with high value crops. “We want all growers to be able to enhance their crops using shading products. Early interest has come from growers with high value crops such as tomatoes, cucumbers, leafy greens and herbs as well as ornamental potted crops. We are also hearing from growers with a wide variety of niche crops that range from general ag research to high end medicinal and biopharmaceutical crops.”
Hort Americas introduced the first products to the North American market in the middle of 2017. “We are still in the process of convincing growers that this technology is going to work, and we have had a huge amount of interest so far. We expect demand to take off when the shading season starts this year!”
For more information:
Hort Americas
2801 Renee St
Bedford, Texas 76021
469-532-2383
hortamericas.com
Motorleaf's Agronomist.ai Software Cuts SunSelect's Yield Prediction Error Rates In Half
Motorleaf has come out of private BETA with a commercially available yield prediction service for commercial greenhouses, after working closely with SunSelect (150 acres in California & B.C.) with results that disrupt how commercial greenhouse farms worldwide can now operate their business, adding significant dollars to their client’s bottom line.
Motorleaf's Agronomist.ai Software Cuts SunSelect's Yield Prediction Error Rates In Half
Motorleaf, Montreal, Canada
Motorleaf has come out of private BETA with a commercially available yield prediction service for commercial greenhouses, after working closely with SunSelect (150 acres in California & B.C.) with results that disrupt how commercial greenhouse farms worldwide can now operate their business, adding significant dollars to their client’s bottom line.
Motorleaf has launched it’s Agronomist.ai platform with a world first for greenhouse owners/operators, allowing for accurate Yield Prediction.
“After 8+ months of private BETA testing with one of North America’s premier greenhouse operators SunSelect, our latest algorithm has cut the accuracy error rates of SunSelect by half. For such a high tech greenhouse- they’ve tried every method that’s out there,” – Alastair Monk, Motorleaf CEO/Co-Founder.
SunSelect’s co-owner Victor Krahn agrees, saying: “For us (and any commercial size operation) knowing/predicting exactly what quantity of product we'll have each week is one of the top metrics we obsessively track. This data feeds into all critical areas of our operation, from labour management to price negotiation, to buyer relationships and even trickling through to in-store marketing budgets. Like most commercial greenhouses, our ability to predict something so dynamic as yield is almost impossible to get right. Our error rates bounce between 5% to over 35% in some weeks. Motorleaf is now our new standard for predicting yield.”
With the emergence of so many AgTech companies in the past couple of years, Motorleaf has been building its suite of hardware and software to leverage the data it collects via its own hardware, but can also leverage data already been collected by greenhouse clients, which in most cases is not being leveraged to its potential by the greenhouse.
Mr Krahn continues: “Working with our team of growers and VP of Operations we were impressed at the level of accuracy Motorleaf’s team provided through both touching the plants in the greenhouse and reaching through the cloud for the data our state of the art greenhouses provides every day! The integration was easy, non-invasive and I think shows amazing promise to become the new industry standard.”
Both companies are looking to expand their relationship, with Mr. Krahn adding: “I'm proud to say SunSelect is not only a client, but we will be helping Motorleaf roll out an increasing number of solutions to the benefit of every Motorleaf client worldwide. Their latest algorithm cut our yield prediction error rates in half, and goes without saying is a game changer that no one saw coming!"
Mr Monk adds: “You know your team is delivering exceptional work when the head growers at a client’s location literally don’t believe the results can be so much better than what’s normal in the industry. We have to thank the very long hours our team has put into making this a reality, especially Scott Dickson-Dagondon and Ramen Dutta (AI Director and CTO/Co-founder) – this is a very exciting time for our company and we feel for greenhouse producers worldwide.”
Find out how Motorleaf's Ai-powered yield predictions can help your business:
CONTACT US
About Motorleaf: Motorleaf is developing Agronomist.ai – a virtual agronomist for every greenhouse and indoor farmer in the world. With a varied mix of monitoring, control and predictive capabilities, Motorleaf is leveraging AI & Machine learning to deliver predictable, repeatable, improved crop production worldwide.
Greenhouse Technology Could Be The Future of Food
Greenhouse Technology Could Be The Future of Food
Published: Jan. 17, 2018 • By Trent Knoss
Professor Ronggui Yang (left) and Assistant Professor Xiaobo Yin. Photo by Glenn J. Asakawa / University of Colorado Boulder
CU Boulder engineers have received a $2.45 million grant from the U.S. Department of Agriculture (USDA) to develop a scalable, cost-effective greenhouse material that splits sunlight into the photosynthetically efficient light and repurposes inefficient infrared light to aid in water purification. The material can also split the light streaming into greenhouses into rays that plants can use more efficiently.
The four-year research program could yield next-gen technology capable of solving food, energy and water security challenges posed by global population growth and climate change.
The study, administered under the USDA and National Science Foundation’s Innovations at the Nexus of Food, Energy and Water Systems (INFEWS) program, will be led by researchers from CU Boulder’s Department of Mechanical Engineering in collaboration with Michigan State University’s Department of Horticulture and Department of Mechanical Engineering.
“We are excited to work on a project that addresses one of the most important global challenges with our multidisciplinary colleagues at CU and MSU,” said Ronggui Yang, a professor of mechanical engineering who will lead the team.
Greenhouses have been used since the 1960s and remain the standard for effective plant productivity compared to open-field agriculture. But the structures carry high energy costs, requiring tremendous amounts of energy for heating, ventilation, electrical lighting and water for evaporative cooling. By the year 2050, current greenhouse capabilities will likely be unable to keep up with worldwide human consumption, making an increase in productivity an urgent mandate.
Under normal conditions, plants only use around 50 percent of incoming sunlight for photosynthesis while the remaining half goes unused.
“The new CU Boulder technology will take the form of a semi-translucent film that splits incoming light and converts the rays from less-desired green wavelengths into more desirable red wavelengths, thus increasing the amount of photosynthetically efficient light for the plant with no additional electricity consumption,” said Xiaobo Yin, an assistant professor of Mechanical Engineering and Materials Science and Engineering at CU Boulder.
The thin engineered material can be applied directly to the surface of greenhouse panels. The technology also makes use of the photosynthetically ineffective light by redirecting it to aid in solar-driven water purification.
“The near-infrared wavelengths can help clean brackish wastewater, allowing it to be recirculated in an advanced humidification-dehumidification interface and further reducing the greenhouse’s energy footprint,” said Yang, an American Society of Mechanical Engineers Fellow.
The innovation could help improve U.S. agricultural competitiveness and lead to new best practices for greenhouse systems in different climates, especially in arid regions with limited freshwater availability where crops cannot be grown profitably.
The technology expands on the researchers’ previous successful efforts to develop a suite of scalable engineered materials that can cool structures and improve solar panel efficiency, among other applications.
The researchers plan to create a pilot greenhouse facility to test the material’s properties over the course of multiple tomato production cycles and, later, expand the test to leafy greens such as lettuce and herbs.
New Technologies Allow Sustainable Farming In The Arctic
New Technologies Allow Sustainable Farming In The Arctic
Bambi Majumdar January 23, 2018
Eco-chef and foodie Benjamin L. Vidmar has used "polar permaculture" to grow food in the Arctic. (Image: Polar Permaculture)
In "The Martian," Matt Damon showed us how we can grow food even when stranded on the frigid surface of Mars. Back on Earth, this method has been successfully proven by eco-chef and foodie Benjamin L. Vidmar.
The small Arctic town of Longyearbyen is known for its spectacular Northern Lights. But now it is making news for the successful implementation of "polar permaculture" that Vidmar introduced here (which also happens to be the name of his company, Polar Permaculture).
For a long time, the town had to pay a hefty price to procure all its food and produce from outside. All that has now changed with the use of modern technologies like polar permaculture, which makes use of hydroponic systems, insulated greenhouses and compost-warmed geodesic domes.
They are also using the waste from the island to produce biogas and grow their food. The design keeps in mind the fragile ecosystem of the North Pole and ensures that the environment is well-protected. This shows how technology is changing the world of fresh produce and creating regional food security.
This emerging technology can grow fresh food even in the coldest and darkest regions on Earth. Scientists are hopeful that they can soon grow fresh food in an arid desert throughout the year.
Permaculture design techniques are inspired by nature. They have the potential to turn a simple garden into an ultraproductive food source. This could be a game-changer for those who want holistic and organic produce. With Vidmar's project, we now have evidence for indigenous growth in extremely cold climes as well.
There are many regions like Longyearbyen that suffer from poor soil and unsuitable conditions for growing food. Most of the food needs to be shipped into these areas while waste is dumped without recycling.
The polar permaculture technique looks at both these ends and offers a solution. It has helped Vidmar close the loop, reuse and recycle the waste to create a "circular economy." Food insecurity and food waste are worrisome issues. With the help of innovative technologies, it now seems a sustainable food culture is possible.
Vidmar's efforts are mirrored by Canadians Ben Canning and Stefany Nieto. They are working to produce affordable fresh food in the Arctic Canadian community of Naujaat. Remote locations like these suffer from lack of indigenous produce, and poverty is rampant, too.
Shocked by the conditions there, they partnered with organizations like Enactus Ryerson to bring about affordable, healthy food to the locals. They create greenhouses to grow fresh produce in otherwise harsh and impossible conditions. Much like Vidmar, they use techniques like insulated greenhouses hydroponic systems and compost-warmed geodesic domes, among others.
Other innovative strategies that defy the extreme climates include cold-weather container farms. Simple and brilliant, the technology transforms a shipping container into a hydroponic greenhouse.
Called the Arctic Growing System, this is slowly empowering remote Arctic communities to grow their greens on site. The future may see other remote locations benefit the same way, thereby lowering food insecurity around the world.
New Houses Built, Urban Farms Expanding As Bailey Green Project Pushes Ahead
Habitat for Humanity Buffalo has built five houses on Wende Street as part of the Bailey Green project. (Sharon Cantillon/Buffalo News)
New Houses Built, Urban Farms Expanding As Bailey Green Project Pushes Ahead
By Mark Sommer | Published 7:06 a.m. January 15, 2018
The Bailey Green project on the East Side was started by a major business, guided by an internationally acclaimed plan and has had the involvement of the University at Buffalo, community organizations, businesses, entrepreneurs and politicians.
The idea was to create affordable housing, green space and recreation, healthy food and job opportunities in an economically impoverished and long-neglected area, where the spaces between homes are often pockmarked with open space from previous demolitions.
Despite some setbacks, the plan to impact a seven-block, 33-acre area, located between Bailey Avenue and Leslie Street, and Genesee and Scajaquada streets, is pushing ahead.
"I think we have good forward motion," said John Somers, owner of Harmac Medical Products, a maker of single-use medical devices at 2201 Bailey Ave., which is spearheading the public-private effort.
"But the project is not always on a straight line," Somers said. "Some of the partners have dropped out, and some have moved faster than others. That's the nature of the process."
Here's what's happening:
- Habitat for Humanity Buffalo has built five ranch-style homes on Wende Street, has two more nearing completion and will start six more houses on Kilhofer Street in April. The nonprofit expects to build or rehab additional houses in the neighborhood in 2019.
- Groundwork Market Garden is growing organic produce on Genesee Street and has purchased a 40,000-square-foot building next door to its 2.5 acres of farmland. The building will be initially for packing, cold storage and youth education.
- Urban Fruits & Veggies plans to break ground in April for the first of two hydroponic greenhouses at Zenner and East Ferry streets. More funds will need to be raised for a second greenhouse, community garden, fruit orchard and wellness center that includes yoga instruction and a small medical practice.
- A carpentry training center by artist and architect Dennis Maher, working with Albright-Knox Art Gallery's Innovation Lab, is expected to begin rehabbing a building in 2018 that was removed from the city's demolition list, with help from Harmac and a grant from Lovejoy Council Member Richard Fontana.
Two key projects from the original plan are no longer involved.
Heart of the City Neighborhoods Inc. planned to build eight four-unit affordable apartments on four streets, but could not obtain funding.
And Algonquin Sports for Kids backed out of plans to build two mini-pitches for soccer over concerns about cost, maintenance and liability.
"If things like this were easy, it would have been done as soon as we talked about them," said Allison DeHonney, owner of Urban Fruits and Veggies. "You need to have partners who will be able to overcome the challenges. This is a big project in a severely neglected neighborhood."
Civic-minded business
Harmac has been the catalyst for Bailey Green. The company has been located on Bailey, near East Ferry Street, for 37 years.
The company has maintained a nearby, once-derelict stretch of Bailey from Genesee to Scajaquada for eight years. The company bought 20 blighted parcels, demolished broken-down houses, converted more than 4 acres to green space and planted 150 trees. Harmac still pays for the trash pickup.
Harmac owns some of the land being used for Bailey Green. It is working with the city's Division of Real Estate to obtain other parcels for redevelopment.
"It's a great public-private partnership," said Brendan Mehaffy, who directs the city's Office of Strategic Planning.
The company had an economic incentive to clean up the surrounding area, since it wanted its surroundings to look more appealing to out-of-town job applicants. At one time, Somers said Harmac considered moving out of the city past Clarence. But when Harmac realized 25 percent of its employees lived within its ZIP code, the company decided to rejuvenate the area instead.
Somers said Howard Zemsky, the Buffalo developer and state development head, suggested the creation of a 10-year plan to guide the neighborhood's revitalization. The company reached out to the University at Buffalo Research Institute, which, under the direction of Hiroaki Hata, an associate professor of urban design, became involved in fall 2014.
Three architecture and urban planning student teams helped create the first phase of a Bailey Green master plan that went on to earn second place in the 2016 International Making Cities Livable Design Competition.
Hata and urban planner Ji Dai remain involved with the project.
Harmac has helped its partners with startup funding and other kinds of assistance, Somers said. The company also has facilitated minor home repairs working with the Urban League of Buffalo. Prime Time Energy offered reduced-cost weatherization to homeowners, and Doyle Alarm Systems, based in Rochester, donated alarm systems last year and in 2018 for the Habitat homes.
Buffalo Peacekeepers and Stop the Violence Coalition also are involved.
"I think it’s about safety and stability, and rejuvenating the community," Somers said. "It’s a grassroots effort and building relationships one person and one partnership at a time. It's probably taking longer than people expected, but I think we are making a positive impact."
John Somers, owner of Harmac Medical Products, walks down Wende Street near the company's Bailey Avenue plant in this file photo from Feb. 29, 2016. (Derek Gee/Buffalo News)
This year saw the third annual Bailey Green Day, with several dozen community members attending.
"We were a stop on the Community Foundation for Greater Buffalo's bus tour of the city," Summers said, proud of the recognition.
The company's involvement outside the building is in league with what it does inside.
Educational programs, a scholarship, a fresh produce market in the summer and onsite mammogram testing are some of the extras Harmac makes available to its employees.
Urban Fruits & Veggies' DeHonney said Somers has been a big help and source of encouragement to her.
"I can't say enough about John," she said. "He is just so supportive, and he really wants this to come to fruition."
Urban Fruits & Veggies plans to begin work this spring on its first of two hydroponic greenhouses with Harmac's support and the support of the Community Foundation for Greater Buffalo and First Niagara Foundation.
At Bailey Green, an oasis emerges in neighborhood around Harmac Medical Products
By Mark Sommer:Owners of second-generation manufacturer Harmac Medical Products, which has stayed in the city and employs local residents, have decided to invest in their neighborhood as well...
Housing variety questioned
Not everyone is happy with the direction Bailey Green is taking.
Stephanie Simeon, executive director of Heart of the City Neighborhoods, a nonprofit that builds affordable housing, believes the project is too focused on owner-occupancy rather than including multifamily housing.
Her plans for eight four-unit apartments on four streets had to be abandoned after the group couldn't obtain the necessary funding.
"The way we were going to do sustainable development was unheard of," Simeon said. "We were going to address the issues of food access, recreation and affordable housing in three different ways."
Simeon said homeowners in the immediate area were going to be helped with small repair grants. Those wanting to own their own homes would be aided by Habitat. Renters would have places to move into as well.
"It's great Habitat has built its homes, but not everybody can afford to own their own home," and diversity of housing stock adds to a neighborhood's stability, she said.
Momentum for the project, and community engagement, waned after Heidi Rosmer, the company's community advancement liaison, left in 2017, Simeon said.
"She was the linchpin. We had the direction, we had the map, but we lost the conductor who helped us navigate the plan," Simeon said. "This is now a shell of a plan, and the only one standing – and they’re standing with shaky legs – is Habitat."
Somers said he's still hoping that apartments will be part of the Bailey Green mix. He also said there have been and will continue to be efforts to involve neighbors.
This is one of the houses that Habitat for Humanity Buffalo has built on Wende Street as part of the Bailey Green project. (Sharon Cantillon/Buffalo News)
Habitat expands role
Normally, Habitat for Humanity builds one new house for every three homes it works on. At Bailey Green, it's been all new builds.
Habitat has nearly completed seven houses with six more on the way. The potential is there to build 15 more, said Teresa Bianchi, the group's executive director.
Doing clusters of housing at a time, she said, helps create a closeness even before people have moved in. That's because each family is required to put in 500 hours of sweat equity. The first 250 hours are used to help others to build their home, and the second 250 is used to build theirs.
"If you're building together on one street, you're building community before you ever move into your house," Bianchi said. "That helps solidify the neighborhood."
A Harmac employee was able to become a homeowner through Habitat. Two people were hired by the medical devices manufacturer after moving into their new homes.
"Everyone thinks Habitat is about building houses, but we're really here to build communities," Bianchi said.
"That's what Bailey Green is. We'll stay committed to Bailey Green as long as there are houses for us to work on."
Explore urban farms like 5 Loaves, Groundwork Market
A farm in the city
Groundwork Market Garden wasn't initially part of Bailey Green when Mayda Pozantides and Anders Gunnersen began preparing their plot of land for organic vegetable production in 2016.
But their work in producing affordable and nutritious food – including more than 300 pounds of tomatoes weekly in a hoop house – within Bailey Green's boundaries ties in perfectly with the project's mission.
Groundwork Market also grows arugula, spinach, lettuce, kale, eggplant, squash, zucchini, turnips and radishes. The produce is sold to 10 restaurants, farmers markets and to 20 families through a small CSA program.
The small farm also is used as a teaching site, with children tending to a dozen raised gardens through a national organization for children.
"When I go to the quarterly Bailey Green meetings, I feel energized about the neighborhood and the initiative and the future of this area," Pozantides said. "There are more people getting involved at every meeting, and you can see the energy."
The Benefits of Supplemental CO2 Are Worth The Cost
The Benefits of Supplemental CO2 Are Worth The Cost
JANUARY 8, 201 8 | DAVID KUACK
The benefits of supplemental carbon dioxide (CO2) on greenhouse crops are easy to quantify. Faster production times, higher yields and larger fruit are some of the results of incorporating CO2 into the greenhouse atmosphere to optimize plant growth.
Greenhouse crop consultant Marco de Bruin at de Bruin Greenhouse Consulting never worked in a greenhouse operation that didn’t use supplemental carbon dioxide (CO2).
“I have grown a variety of tomatoes including, tomato on the vine, grape tomato, cluster tomato, Roma tomato, as well as cucumber, sweet pepper, lettuce and basil,” de Bruin said. “Supplemental CO2 was used in all of the facilities I have worked in. e modern glass and plastic greenhouse operations being built today all have CO2 systems in them.
“In traditional glass greenhouses, there can be a lot of air exchanges that occur through the roof. at can help to reduce the temperature and humidity in the greenhouse, but it can remove CO2 from the greenhouse as well. e roof vents start to function like a Venturi drawing the air and CO2 out of the greenhouse.”
de Bruin said it is best to distribute supplemental CO2 between the leaves of the plants.
“Growers will install lay-flat tubing in the greenhouses, particularly with row crops like tomatoes, peppers and cucumbers,” he said. “CO2 is then injected into the greenhouse environment, particularly into the microclimates around the plants.”
de Bruin said the growth response to supplemental CO2 is similar regardless of the crop being grown.
“CO2 is one of the building blocks for photosynthesis,” he said. “A grower always has to have the supplemental CO2 in combination with light, whether that is sunlight or supplemental light. If there is no light then there is no point in using supplemental CO2. So at night no supplemental CO2 is dosed into the greenhouse.”
Avoiding Plant Stress
de Bruin said the ideal levels of CO2 in the greenhouse vary with the crop, but they vary more due to the growing environment.
“During the summer when plants are actively growing, the CO2 level in a greenhouse can drop from ambient 380-400 parts per million to 50-100 ppm in a very short period of time,” he said. “ The sunlight intensity, the temperature and the humidity in the greenhouse are factors that are extremely important. If plants are stressed and their stomata, which take up CO2, are closed, then CO2 dosing should be greatly reduced or even stopped since there is no bene t to the plants under these conditions. A grower needs to make sure that the temperature and humidity levels are appropriate for dosing CO2 to maximize the rate of photosynthesis. e dosing level is very dependent on stress factors.”
de Bruin said there are certain times of the day and certain times of the year when a grower should actually reduce the dosing level of CO2 due to the stress level on the plants.
CO2 dosIng systems lIke these from Zantingh B.V. can transport flue gas containIng CO2 from natural gas-fIred boilers to greenhouse production areas.
“Heat stress is a combination of radiation and a grower’s ability to maintain the climate in the greenhouse,” he said. “Once the greenhouse starts to heat up and the grower starts to ventilate, some of the CO2 and a lot of the humidity is being pushed out. Humidity is the major driver in transferring the heat out of the greenhouse. As the humidity is lost, the plants start to transpire faster which increases the humidity. When the evaporation level gets too high for the plants to maintain, the stomata start to close and CO2 is no longer taken up by the plants. At that point, the CO2 is going straight out of the greenhouse. If a grower can keep his plants from undergoing stress, then CO2 can be dosed up to the most efficient level for both the plants as well as for the grower’s pocketbook. There are some really high tech greenhouses that are able to go to an extremely high level of CO2 before they encounter this stress situation.”
de Bruin said the level of CO2 can go as high as 1,000 ppm, but the rate of payback starts to flatten off after a grower achieves CO2 levels of 700-800 ppm.
“It is possible to achieve additional production above this rate, but it becomes a question of whether or not it is feasible,” he said. “Dosing capacity requirements go up, investment requirements go up and at the end of the day there is a certain price limit as to what a grower can receive for the product sold, whether his crop is tomatoes, peppers or cucumbers. How much a grower doses CO2 is determined by the cost of the CO2 and the selling price of his product.”
Sources of Supplemental CO2
de Bruin said the most common way for introducing supplemental CO2 into greenhouse vegetable and ornamental crops is to dose the flue gases from the boiler, which contain CO2.
“Basically the flue gases from the boiler are rerouted through the greenhouse so that the plants can filter out the CO2,” he said. “Some of the CO2 will still leave the greenhouses, but 100 percent of the CO2 would have been lost into the atmosphere if the flue gases would have been allowed to go out the chimney.
“What growers have done to use the CO2 is to install a heat storage tank. While they are producing heat they store it in an insulated water tank. They then can use the flue gases that come o of the boiler during the day when the sun is shining and the plants are actively using CO2. A computer system regulates the heat from the storage tanks to go into the greenhouses as needed. is can allow the boilers to turn o at night if no extra heat is needed. ese boiler systems are very efficient.”
de Bruin said growers can also use unit heaters, some of which are combined heaters that allow a grower to dose CO2 in the greenhouse as well as using the flue gases that the heaters produce.
Marco de Bruin at de Bruin greenhouse Consulting said supplementing with CO2 enables a grower to produce 20-30 percent higher yields. Installing the equipment to dose CO2 to raise ambient levels to 400-500 ppm is a very quick payback.
“In regards to noxious gases, the unit heaters and boilers that I’ve seen in most growing operations are designed to have extremely low NOx (nitrogen oxides) and burn very clean,” he said. “These are monitored very carefully.” de Bruin said for growers who are going to have to heat their greenhouses regularly with either unit heaters or boilers, it makes sense to use the CO2 in the flue gases. He said since propane costs three times as much as natural gas, a grower could quickly make a case for using liquid CO2 instead.
“If a grower is located in the South or on the coastlines the heating requirements may be considerably less,” he said. “In these locations, using liquid CO2 or a combination of flue gases and liquid CO2 could be more economical as well. With the liquid CO2 set ups, growers lease the tanks and the evaporator units. There are several companies that specialize in greenhouse applications that deliver a complete package.”
de Bruin said growers can figure they will harvest 20-30 percent higher yields when they dose CO2 versus relying on ambient CO2. “If a grower is going to produce 20-30 percent higher yields, installing the equipment to dose CO2 pays o quickly,” he said. “Going from ambient CO2 levels to 400-500 ppm is a very quick payback.”
For more: de Bruin Greenhouse Consulting, (507) 451- 0701; Marco@deBruinGreenhouseConsulting.com; http://www.deBruinGreenhouseConsulting.com. Editor’s note: For more information on the use, bene ts and costs of supplemental carbon dioxide see “Carbon Dioxide in Greenhouses” Factsheet from the Ontario Ministry of Agriculture, Food and Rural Affairs.
David Kuack is a freelance technical writer in Fort Worth, Texas; dkuack@gmail.com.
Urban Farming Key in Fight Against Hunger and Climate Change
The urban farms sprouting up and across cities around the world aren't just feeding mouths—they are "critical to survival" and a "necessary adaptation" for developing regions and a changing climate, according to a new study.
Urban Farming Key in Fight Against Hunger and Climate Change
The urban farms sprouting up and across cities around the world aren't just feeding mouths—they are "critical to survival" and a "necessary adaptation" for developing regions and a changing climate, according to a new study.
Urban farms—which include plain ol' allotments, indoor vertical farms and rooftop gardens nestled amongst busy streets and skyscrapers—have become increasingly popular and important as the world's population grows and more and more people move to cities.
The United Nations predicts that by 2030, two-thirds of the world's population will be living in cities, with the urban population in developing countries doubling. That's a lot of mouths to feed.
The new paper, published in the journal Earth's Future and led by the Arizona State University and Google, finds that this expected urban population boom will benefit from urban farming in multiple ways.
As the Thomson Reuters Foundation explained from the study, "Urban farms could supply almost the entire recommended consumption of vegetables for city dwellers, while cutting food waste and reducing emissions from the transportation of agricultural products."
According to the study, urban agriculture can help solve a host of urban environmental problems, from increasing vegetation cover (thus contributing to a decrease in the urban heat island intensity), improving the livability of cities, and providing enhanced food security to more than half of Earth's population.
After analyzing multiple datasets in Google Earth Engine, the researchers calculated that the existing vegetation on urban farms around the world already provides some $33 billion annually in services from biocontrol, pollination, climate regulation and soil formation.
The future of urban agriculture has even more potential, the researchers found.
"We project potential annual food production of 100–180 million tonnes, energy savings ranging from 14 to 15 billion kilowatt-hours, nitrogen sequestration between 100,000 and 170,000 tonnes, and avoided stormwater runoff between 45 and 57 billion cubic meters annually," the authors wrote.
"In addition, we estimate that food production, nitrogen fixation, energy savings, pollination, climate regulation, soil formation and biological control of pests could be worth as much as $80–160 billion annually in a scenario of intense [urban agriculture] implementation."
Others have praised urban farming for its many benefits.
"Urban agriculture won't resolve all food production and distribution problems, but it could help take pressure off rural land while providing other advantages," wrote environmentalist Dr. David Suzuki.
He cited an example of how one patch of Detroit land, where 12 vacant houses were removed to grow food, "has supplied almost 200,000 kilograms of produce for 2,000 local families, provided volunteer experience to 8,000 residents and brought the area new investment and increased safety."
"Local and urban agriculture can also help reduce greenhouse gas emissions and recycle nutrient-rich food scraps, plant debris and other 'wastes,'" Suzuki continued. "Because maintaining lawns for little more than aesthetic value requires lots of water, energy for upkeep and often pesticides and fertilizers, converting them to food gardens makes sense."
Writer and former Vancouver city councillor Peter Ladner also wrote in The Urban Food Revolution: Changing the Way We Feed Cities, "When urban agriculture flourishes, our children are healthier and smarter about what they eat, fewer people are hungry, more local jobs are created, local economies are stronger, our neighborhoods are greener and safer, and our communities are more inclusive."
RELATED ARTICLES AROUND THE WEB
- EcoWatch - These radical urban farms could feed the cities... ›
- Smart garden makes urban farming easy | Reuters.com ›
How This Greenhouse And Fish Farm Operation Is Fuelled
How This Greenhouse And Fish Farm Operation Is Fuelled By Bitcoin Mining
Local company using waste heat from bitcoin miners to operate new business in St. Francois Xavier
By Samantha Samson, CBC News Posted: Jan 04, 2018 5:00 AM CT Last Updated: Jan 04, 2018 6:34 PM CT
Myera Group uses waste heat from bitcoin miners to keep their building warm enough to grow plants like lettuce. (Lyzaville Sale/CBC News)
- Where to invest: Bitcoin or Canadian Tire money?
- Beyond bitcoin: How cryptocurrencies are changing the world
- Bitcoin's dirty secret: it wastes an incredible amount of energy
More than 30 computers sit on the second floor of a former car museum west of Winnipeg, quietly working to mine bitcoin.
The heat generated by those computers, which are verifying bitcoin transactions by solving cryptographic puzzles, helps warm nearby plants in a makeshift greenhouse.
To water, the trays filled with lettuce, basil and sprouted barley fodder, Bruce Hardy, the owner of this 20,000-square-foot building in the Rural Municipality of St. Francois Xavier, clicks a button.
A pump waters the plants with wastewater from tanks located on the first floor in which around 800 Arctic Char swim and breed. The wastewater from the tanks is rich in nitrates, a great fertilizer for the plants upstairs.
It's a complex operation but that's the beauty of it, according to the owner.
"It's all connected, much like Earth," said Hardy, president of Myera Group.
'A popular move'
His company's goal is to use technology to create sustainable food systems.
Hardy runs his own software company and has been in the bitcoin mining business for two years. He used to pay for air conditioning to cool off the computers but quickly realized there was a better use for the heat.
"When bitcoin came, they were an excellent proxy for what a server could do in terms of emulating heat, and whether we could use that heat for agricultural purposes," he said.
About a year ago, he opened his operation in the old Tin Lizzie Auto Museum and the former Grey Nuns convent located on Highway 26 just west of Winnipeg
The greenhouse operation is small right now, but Hardy says he hopes to create several greenhouses in St. Francois Xavier that are fuelled by waste heat from bitcoin mining. (Lyzaville Sale/CBC News)
"From what we've seen so far, it looks like a popular move for the community," says Dwayne Clark, the Reeve of the RM of St. Francois Xavier. "It's already cleaned up what used to be an eyesore for a number of years."
The company is still experimenting with using the heat from bitcoin mining in different ways. Right now, about one-quarter of the second floor is filled with computers and plants, but Hardy hopes to eventually fill the space.
Starting the operation would have been a lot more difficult without the bitcoin cash, said Hardy. The price of a bitcoin is hovering around $19,000 Cdn.
"The revenue from those bitcoins has helped me to keep staff on, it's helped me create these displays so we can show people what we're doing in agriculture innovation," said Hardy.
Hundreds of Arctic Char swim in these tanks at Myera Group's operation in St. Francois Xavier. (Lyzaville Sale/CBC News)
Ways to use 'Manitoba's gifts'
Hardy hopes his operation becomes a place where people can research and develop sustainable food systems while programmers work with bitcoin technology.
Australian researchers and Chinese investors have expressed interest in his operation, he said.
Manitoba is a prime location for electricity-intensive operations like this, said Hardy.
"Hydro is one of our best assets in the province," said Hardy.
Manitoba has the cheapest commercial hydro electricity rates in the country and among the lowest temperatures of major North American cities, making it attractive to bitcoin miners.
"If we can take our energy and use it here in Manitoba, we value-add that energy, and we can do all sorts of great things," he said.
Bruce Hardy, president of Myera Group, hopes to create a global campus in St. Francois Xavier for food sustainability. (Lyzaville Sale/CBC News)
Philips Lighting Installs LED Project At Madestein UK, Which Supplies Fresh Lettuce To Major UK Retailers
Philips Lighting Installs LED Project At Madestein UK, Which Supplies Fresh Lettuce To Major UK Retailers
Philips Lighting today announced that Madestein UK, in Chichester, UK, which supplies fresh lettuce and herbs to the UK’s major food retailers, food service companies and wholesale markets, is installing Philips GreenPower LED toplighting to improve the quality of its crops. Madestein UK became convinced about the benefits of growing with LED grow lights after trialing Phillips GreenPower LED Toplights and visiting several growers in The Netherlands and Finland.
“It’s great to see how our network of growers are ambassadors across the entire globe,” said Udo van Slooten, Business Leader Horticulture at Philips Lighting. “In this case, they were able to show how LEDs can help them speed up their crop cycles and grow more compact plants. That’s the real value of working with people who are passionate about their professions.”
Madestein UK was founded in 1982 and has introduced many innovations to the UK market, including curly leaf lettuce in the late 1980s and living mixed lettuce in 2001. They currently focus on producing glasshouse lettuce and growing fresh basil all year. In addition to conventional growing methods, Madestein UK employs sustainable growing methods such as an Deep Flow hydroponic system which makes efficient use of water and minimizes the chances of groundwater contamination.
The company has been investigating LED grow lights for a long period and carried out several LED trials at its site in Chichester from 2014 to 2017.
Jonathan Zwinkels at Madestein UK says, “We are seeing a strong demand for UK grown lettuce and herbs, so we’ve been exploring ways to raise our productivity. We were impressed with what we saw in our trials and confirmed those views with visits to growers in The Netherlands and Finland who are using LEDs to grow lettuce. Our aim is to use LED grow lights to improve quality, reduce the impact of adverse weather conditions, and improve the shelf life of our products.”
Peter Zwinkels and his grandchildren Noah and Grace.
The LEDs will be installed by Philips Lighting’s Horti LED partner Cambridge HOK.
Global Growables, Inc. Partners With DNM Farms
Global Growables, Inc. Partners With DNM Farms
The first Mobile Growable hydroponic container is growing herbs and greens to augment the Aquaponics and Greenhouse on a farm near Santa Fe New Mexico
San Juan Capistrano, Dec. 29, 2017 (GLOBE NEWSWIRE) -- Food deserts, food insecurities and lack of education are real issues facing many local communities nationwide and the partnership between Global Growables and DNM Farms provides a sustainable solution that feeds, educates and donates to the local community. This sustainable model does not require government funding or intervention and generates a recurring revenue stream for decades to come.
The first Mobile Growable unit is on location at DNM Farms which is owned and operated by George Budagher, a long-time New Mexico resident that has an existing Aquaponic farm and Greenhouse. DNM Farms has over 1,500 live fish in three large tanks. The fish feeds the community and provides a sustainable solution as the fish waste feeds and fertilizes the tomatoes, peppers, lettuces, and herbs in the 5,000 square foot greenhouse.
DNM Farms recently added the Mobile Growable container to grow high-quality greens and herbs to service the local chefs from private country clubs and restaurants. The Mobile Growable container is made from refurbished freight containers and grows micro-greens, herbs and leafy-greens indoors 24/7 365 days a year using liquid-cooled LED lights and sophisticated hydroponic technology.
The Mobile Growable container will grow over 10,000 pounds of fresh produce annually using 10% of the water of traditional soil-based farming and will provide the chefs at local private clubs, restaurants, and hotels with fresh, organic and local organic food. The combined yield from the Greenhouse, Container, and Aquaponics will feed hundreds of families, provide local jobs and provide financial support to the community with donations from the sale of fresh, healthy and locally grown food.
In addition, DNM Farms will host school field trips, provide fresh produce at farmers markets, provide culinary education and tours to help educate and feed the kids and families living in the community. In addition, local residents living in cities from Santa Fe to Albuquerque New Mexico now have a reliable source for affordable and locally grown fresh vegetables, leafy greens, herbs and fresh fish.
Click here to listen to a recent podcast with Rick Ladendorf, founder of Global Growables.
George Budagher, founder, and farmer explains, “We have over 1,500 Tilapia fish growing in three tanks and they provide our plants with natural fertilizers i.e. fish poop, which in-turn provides the plants natural fertilizers and nutrients for maximum yield and flavor. We deliver live fish to the chefs and grocers and we service the local chefs with specialty herbs, micro-greens and hard to find leafy-greens at local private country clubs, restaurants and hotels. A portion of the proceeds and product are donated to local schools, churches and food banks, which is our way of giving back to the community.”
Global Growables mission is to reduce childhood obesity, prevent and reverse chronic illnesses through education, provide access to affordable plant-based foods and more importantly create sustainable solutions that doesn’t rely on the government. Rick Ladendorf explains, “I recently asked a child if they could tell me where a carrot comes from and he replied, “Wal-mart”! While I was not surprised, I can honestly say his response is a reflection of our society where the lack of educational funds allocated to health in the schools and lack of nutritional knowledge in the home is a major contributing factor to the health crisis. And until we change behavior in the home, mom will continue to load the shopping cart with unhealthy options and the obesity epidemic will continue to get worse. The partnership with DNM Farms will provide local families access to affordable food and provide the education needed to change behavior.”
ABOUT GLOBAL GROWABLES, Inc.
Global Growables designs builds, installs and manages Mobile Growable Containers made from refurbished freight containers. Global Growables is strategically aligned with Prevo Health Solutions, the private club industry’s premier wellness experts and Executive Producer of America’s Healthiest Clubs certification program. Global Growables and Prevo Health work together to bridge the gap between the have’s and the have not’s, the private club with the community and the public and private sectors.
For more information call 888-321-1804 or visitwww.globalgrowables.com.
ABOUT DNM FARMS
DNM Farms is a sustainable farm located halfway between Santa Fe and Albuquerque New Mexico. The 8,500 square foot facility is comprised of a 5,000 square foot greenhouse, four 1,500 gallon aquaponic tanks and 3,500 square feet of production area that includes a designated area for growing mushrooms. DNM Farms grows and delivers mushrooms, leafy greens, micro-greens, vegetables and specialty herbs and greens.
For more information call George Budagher at 505-228-5318.
These Farmers Are Doing The Impossible: Growing Fresh Veggies in The Coldest Parts of The Planet
These Farmers Are Doing The Impossible: Growing Fresh Veggies in The Coldest Parts of The Planet
A plant sprouts in arctic conditions Milosz_G/Shutterstock
Dec. 21, 2017
Halfway between mainland Norway and the North Pole, the islands of Svalbard are a palette of blue, white and brown — from the Arctic Ocean to glaciers, frozen sea ice and permafrost mountains. Upon first glance, it’s not a destination that inspires much in the way of agriculture.
“This whole island is about extraction: whales, coal, animals, fish, gas, oil,” said Benjamin Vidmar, founder of Polar Permaculture Solutions, a small crew of people who produce locally grown food in Longyearbyen on the archipelago’s largest island of Spitsbergen.
(Editor’s note: The writer traveled to Svalbard with Visit Norway, who covered lodging and transportation.)
The challenge of growing food in a region where the average temperatures are subfreezing and where there are nearly four months of polar night is no simple task. Even during midsummer, when temperatures hover around 40 degrees Fahrenheit, mountaintops are still draped with snow and vast glaciers sweep across the islands.
But Vidmar, a chef who has lived in Longyearbyen since 2007, discovered that there is a history of growing food on the island, and started growing microgreens in an insulated room to use at home and in some local restaurants. He also researched what others in Arctic regions were doing and learned about using red worms to produce a natural fertilizer from food waste (vermicomposting).
An outdoor dome in the Arctic region surrounded by members of Polar Permaculture Solutions Polar Permaculture Solutions
Vidmar’s dream is to take it all outside and create a circular economy. “Everything here is based on taking things from the Earth. I feel like I have to do something for this town,” he said. He pressured the local government to let him start growing plants in an outside dome, necessary because there are many laws in the archipelago against agriculture and ranch animals, instituted in the late 20th century.
In 2015, more than 300 tons of household waste was registered in Longyearbyen, equal to approximately 331 pounds per person. This number is nearly one-third of the amount for the country of Norway as a whole. In Longyearbyen, food waste from households is ground up and washed out to sea, and it’s often not registered as waste.
Vidmar inside the dome Polar Permaculture Solutions
Vidmar’s microgreens are used in town on restaurant menus, and he composts unused produce with the worms, using their castings as a natural fertilizer that can help to grow more food. Vidmar has recently started to hatch quail from eggs, offering fresh, locally produced quail eggs to Longyearbyen restaurants. He’s also introduced a market within Galleri Svalbard, which includes handmade items from fish-skin leather. Vidmar wants to expand his growing space, continuing to show how the Longyearbyen community can be more sustainable than its old habits are.
Another community within the Arctic Circle is Inuvik, a town in Canada’s Northwest Territories. Converted from an old hockey arena 20 years ago, the Inuvik Community Greenhouse flourishes as a 16,000-square-foot garden that promotes community building through gardening, provides educational opportunities and reduces the cost of healthy food options.
Fish-skin leather products in Galleri Svalbard Polar Permaculture Solutions
While it began with 50 members, the greenhouse now has 250 members who use 149 community garden beds and 24 small beds. Members grow fruit, vegetables and even flowers. The community donates approximately 100 pounds of fresh vegetables to the local food bank each season, which runs from May through September, when the region gets 24 hours of sunlight.
The Inuvik Community Greenhouse also provides a convenient compost collection service in the greater community by charging a minimal fee ($5 CAD) to collect organic waste from homes on a regular basis. The effort helps reduce organic waste from the area, creates soil and supports the greenhouse projects.
Inuvik Community Greenhouse Inuvik Greenhouse
In Kotzebue, Alaska, just 33 miles north of the Arctic Circle, conventional farming isn’t possible. The Arctic Greens project, sponsored by the Alaska Native Kikiktagruk Inupiat Corporation (KIC), has been considered a game-changer for many of the communities in northern Alaska, where almost all produce originates from the Lower 48 by way of truck, barge or air cargo. By the time it’s available on grocery shelves, it’s already two to three weeks old.
The custom hydroponic farm containers allow remote communities to have a regular supply of fresh, affordable vegetables, grown without pesticides or other biological hazards.
The Arctic Greens project has been considered a game-changer for many of the communities in northern Alaska.
Arctic Greens plans to grow produce in 30 Alaska communities and sell the harvest in AC stores located in the same community, which will create jobs and ensure fresher and better-tasting produce no matter the season.
A Polar Permaculture Solutions dome captured at night under the Northern Lights Polar Permaculture Solutions
Back in Svalbard, Vidmar dreams of having more of his produce featured throughout Longyearbyen — in restaurants, hotels and even home kitchens. He’s stepped up his site tours for locals and visitors who are interested in what he’s doing, and he has also started to offer cooking classes. The next step on his list is to acquire a biodigester, which would be fed with the quail droppings as well as food waste in order to produce biogas, a mixture of different gases which are produced from raw materials like agricultural waste. That, in turn, would be used to heat the dome and produce electricity and fertilizer that would help grow more food. “We would like to connect people back to their food,” he said in an email. “And helping people to live here more sustainably.”
Greenhouse To Provide Fresh Vegetables At Bangor Restaurant, Regardless of the Weather
Greenhouse To Provide Fresh Vegetables At Bangor Restaurant, Regardless of the Weather
By Abigail Curtis, BDN Staff • December 19, 2017
Gabor Degre | BDN
Bob Cutler, the owner of Novios Bistro in Bangor stands at the restaurant’s new greenhouse in Hermon Monday. Cutler and head chef Dustin Cyr said they will run the greenhouse and will be able to plant and harvest vegetables based on the daily needs at the restaurant. The greenhouse will be operational in early January.
Gabor Degre | BDN
Dustin Cyr, the head chef at Novios Bistro in Bangor, stands in the laundry room of his home, where he has been testing various seeds and plants he intends to grow in the restaurant’s new greenhouse in Hermon. Cyr and owner said they will be able to plant and harvest vegetables based on the daily needs at the restaurant.
Everybody knows that Maine has a lot going for it, especially when it comes to what’s for dinner.
There’s the agricultural renaissance, the burgeoning farm-to-table movement and the willingness of farmers to grow all kinds of interesting produce.
One thing that Maine can’t boast about, though, is the length of its growing season.
With frosts possible even in the months of May and September, and basically guaranteed during our long, frigid winters, restaurateurs who want to serve locally-sourced produce all year long have a big challenge ahead of them.
But it’s a challenge that the team at the helm of Novio’s Bistro in Bangor believes they can handle, with a unique plan to make an end-run around the cold, hard reality of Maine weather.
This winter, Novio’s owner Bob Cutler, and Chef Dustin Cyr are busy constructing a 1,500-square-foot greenhouse near Cyr’s home in Hermon. In the greenhouse, which will be heated with an oil-burning furnace, they hope to grow 80 percent of the produce they serve at the restaurant within eight months. It’s an ambitious plan, but both achievable and worthwhile, they said.
“If you believe like I do, and like Dustin does, in cooking with the best possible ingredients, it’s a no-brainer,” Cutler said. “And if you believe the extreme weather patterns will continue, as Dustin and I both do, you want to have more control [over the produce supply.]”
Both Cutler and Cyr have a lot of experience in the restaurant industry. Prior to opening Novio’s in the fall of 2016, Cutler owned The Family Dog in Orono and two food trucks in the Bangor area (he has since sold those in order to concentrate on the Bangor bistro). And Cyr has plied his craft at many Bangor restaurants for more than a decade, including a long stint behind the stove at the acclaimed Fiddlehead Restaurant. Farming, though, is fairly new to both of them.
“I started last year,” Cyr said.
After a friend of his got him interested in growing super hot chili peppers, Cyr converted his laundry room into a grow room, and found success with his 100 or so plants.
“That was my crash course,” he said. “I don’t do anything small … and it got me thinking.”
He thought about ways to make sure that he could get the freshest, most delicious produce possible. And he thought about growing exactly what he wanted for his menus, researching how to use the greenhouse to make that happen. Although Novio’s has been transitioning to sourcing more produce locally, that has not always been easy, Cyr said. Growing his own just made sense to him, and he had an idea of how to scale up to grow enough to supply the small restaurant, which serves an average of 230 diners a week. To grow his super hot peppers, he dabbled in hydroponics, the technique of growing plants without soil. Instead of planting them in dirt, they grew in water with the help of mineral nutrient solutions. In the greenhouse, he plans to use a hydroponic system to grow vegetables including tomatoes and lettuces.
“Hydroponics is really interesting to me,” Cyr said. “Plants will be pest-free, disease-free. They’re clean [because they’re not grown in dirt] and you get more plants per square foot.”
He also is working on a design for a raised-bed system for plants such as beets and radishes that will be grown in soil.
Once the greenhouse is up, Cyr will get the chance to try out a much larger hydroponic system than the one in his laundry room and with special supplemental lighting that will let the plants thrive even in the short, dark days of December and January. He’s already started a batch of lettuce, tomatoes, cucumbers, eggplants and bell peppers in his house that he would like to move into more spacious quarters as soon as possible. He knows he is not as experienced as a farmer would be, but believes he can figure out the learning curve to make the project an eventual success.
“It’ll be a little experimental,” at first, he said.
That’s OK with Cutler, who is 100 percent in support of the venture.
“In my mind, I think we’re going to have some mistakes,” the Novios owner said. “We’ll probably grow too much of something and too little of something else. But if you don’t take risks, you’re never going to get better.”
Cutler said it’s likely the greenhouse will never be able to grow sufficient quantities of some vegetables such as garlic, potatoes, onions, and mushrooms. But it is exciting to him to think about having spinach, microgreens, unusual varieties of kale, eggplant and more, freshly picked at the height of ripeness, even in the wintertime.
“We want to be different, and we want to challenge ourselves,” he said.
Cyr is looking forward to having all that bounty close at hand, and turning it into delicious dishes to serve his customers.
“To me, it’s my ultimate opportunity as a chef,” he said.
Growing In A “Perfect” Greenhouse Climate
Growing In A “Perfect” Greenhouse Climate
NOVEMBER 30, 2017 | DAVID KUACK
Originally published in Issue 16
Although it may be difficult to create the perfect greenhouse climate for growing plants, there are variables growers can control to maximize plant growth.
Regardless of the type of crop being grown in a greenhouse, the climate a grower is trying to achieve requires controlling the same variables.
“Greenhouse growers are trying to control temperature, humidity, light level, carbon dioxide, and in some instances, airflow and air distribution,” said mechanical and agricultural engineer Dr. Nadia Sabeh, founder of Dr. Greenhouse. “Depending on the crop, these variables have different set points. They also might have different acceptable maximum and minimum ranges or levels.
Dr. Nadia Sabeh said carbon dioxide is most useful to plants when there is a lot of light and good temperature and humidity levels or vapor pressure deficit (VPD).
“Depending on the crop, these variables can be changed during different times of the day. For instance, a tomato crop wants a daily average temperature around 72ºF. If the plants experience high temperatures during the day, if the temperature is able to be cooled down during the night, as long as the average temperature is 72ºF, the tomato plants are happy. For lettuce, a grower may not be able to manipulate the day or night temperature to make up for exceeding the maximum temperature that occurs during the day or night. That’s one way these crops differ.”
Sabeh said when it comes to controlling the greenhouse environment growers usually focus first on temperature.
“The first line of defense against warm temperatures is not shading,” she said. “Growers are trying to maximize as much light into the greenhouse as possible. As soon as a shade curtain is closed the solar input is reduced. The first line of defense for cooling a greenhouse is ventilation, either natural or mechanical.
“If ventilation can’t achieve the temperature a growers needs, then some form of cooling is added. Typically cooling is done through evaporative cooling. This could be wet pads and a fan system, high pressure fog or a low pressure misting system in combination with mechanical and natural ventilation. If that doesn’t work, then a shade curtain can be pulled. A shade curtain is usually only drawn for two to four hours during the day. It’s pulled during the peak solar heat gain period. A shade curtain can cut the temperature by 2ºF-4ºF.”
The challenge of reducing humidity
Sabeh said between controlling the greenhouse temperature and humidity, humidity is the more challenging variable, especially if it is for dehumidification.
“If a grower is trying to remove moisture from the greenhouse, that presents a lot of challenges,” she said. “The standard method of removing moisture from the greenhouse is through ventilation. But that assumes that the moisture level or the humidity outside the greenhouse is lower than it is inside the greenhouse.
Evaporative cooling can be used in dry climates to increase the humidity and lower the temperature in a greenhouse.
“If a grower is looking to increase the humidity or humidification, for a greenhouse located in the southwest U.S. where it is very dry, moisture can be added to the greenhouse using evaporative cooling. Another benefit of evaporative cooling is a reduction in the temperature that cools the greenhouse temperature. Evaporative cooling works very well in a dry climate to do both of those things.”
Sabeh said growers in the Midwest and Southeast can experience more challenging climates because they have a high heat solar gain like growers in the Southwest experience, but they also have high humidity levels requiring them to ventilate.
“The climates in the Midwest and Southeast make it very challenging to grow plants in a greenhouse because of the humidity,” Sabeh said. “The only line of defense for growing plants in that kind of climate is ventilation. Growers want to exchange as much air as possible with the outside to remove moisture and solar heat gain during the day. Typically that is inadequate. If the outside temperature is 90ºF and the relative humidity is 90 percent, growers certainly don’t want those conditions in their greenhouses.
“If the temperature and humidity are high, growers don’t have the opportunity to use evaporative cooling because they can’t reduce the temperature enough,” she said. “They can shade the greenhouses, but that only lowers the temperature by 2ºF-4ºF from outside conditions. If it is 90ºF and 90 percent humidity, pulling shade results in 86ºF and 90 percent humidity, and that is not going to provide the vapor pressure deficit a grower is trying to achieve.”
Sabeh said growers might consider closing up their greenhouses to avoid bringing in hot, moist air, but that creates additional challenges.
“Closing the greenhouse can cause the greenhouse to heat up from the sun plus the plants are releasing moisture resulting in the greenhouse just getting hotter,” she said. “So far I haven’t really seen anyone come up with a very cost effective method to mitigate that heat and moisture. Certainly a grower could use a refrigerant-based cooling system similar to an air conditioning system that would provide dehumidification. But the size and scale of those systems are cost prohibitive.”
Typically greenhouse cooling is done through evaporative cooling. This could be wet pads and a fan system, high pressure fog or a low pressure misting system in combination with mechanical and natural ventilation.
Sabeh said temperature and humidity are very closely linked through the vapor pressure deficit (VPD).
Maintaining the proper vapor pressure deficit
“As long as a grower is able to control the greenhouse temperature, that usually means he is able to control the humidity level to the point where the vapor pressure deficit is where it should be,” she said. “Even if VPD is not the target that a grower is going for, that is actually the target that he is trying to reach with temperature control with or without humidity control.”
VPD is the difference between the amount of moisture in the air and how much moisture the air can hold when it is saturated.
“There is an optimum level for VPD,” Sabeh said. “For leafy greens and culinary herbs, which prefer a lower VPD, the accepted VPD range is 0.65 to 0.9 kilopascal (kPa) with 0.85 kPA being optimum. Tomatoes, cucumbers and peppers tend to like it drier. The VPD range for tomatoes is 0.9 to 1.2 kPa.
“For leafy greens there is more surface area for moisture to escape the plants. The plants like to be in a more humid space so they don’t release too much moisture too fast.”
Providing adequate airflow
Sabeh said airflow in the greenhouse is really important for breaking up the layer of moisture around the leaf surface of the plants.
“If the leaves are transpiring water, the leaf surface itself is considered saturated,” she said. “The leaf surface is exchanging moisture with the air around it. The more moisture in the air around the leaf surface, the less tendency to transfer moisture from the leaf surface to the air around it.
“This is basically what the vapor pressure deficit is. It is the difference between how much moisture there is at the leaf surface at a given temperature vs. how much moisture there is in the air at that same temperature. If it is within the right range, then the plants are happy because the leaves are freely exchanging moisture with the air. If the vapor pressure deficit is too low that means the air has a lot of moisture in it so there is going to be less transfer of moisture from the leaves to the air. The plants can’t transpire as quickly and nutrients can’t be delivered as quickly to the rest of the plant. If the vapor pressure deficit is too high, the air is really dry, and the plants shut down. As a protection strategy, the plants will close their stomata so that they don’t transpire moisture to the air because it would occur too fast. The loss of water through transpiration would occur faster than the plants could take up water.”
Sabeh said horizontal airflow fans are the traditional method for producing airflow and air currents in a greenhouse.
“Horizontal airflow fans are usually suspended from the trusses or the structure of the greenhouse and blow air in a circular pattern over the tops of the plants without actually blowing directly down on the plants,” she said. “Just the circulation and motion is enough to create turbulence to cause air mixing around the plants to encourage transpiration and convection.
“By breaking up the little saturation pocket of air around the leaves, it facilitates that moisture transfer from the leaves to the air. Under more humid conditions, as air is blown over the leaf surface, a grower can facilitate more transpiration from the plants than if no airflow was blowing over it. Airflow is one of those variables not addressed as often as temperature and humidity control. It is sorted of neglected.”
With the increasing interest in vertical farms, Sabeh said growers are using large grow racks to try to create temperature and humidity conditions in three dimensions.
“Under these conditions it is very easy for air to get trapped over the center of a rack,” she said. “Vertical farmers are really cognitive of airflow because they see these hot spots or these wet spots in the middle of the grow racks so they know they need airflow.
“It is the same situation as if plants are grown in a greenhouse. If more airflow is provided in a greenhouse, more moisture could be removed from the plant surface and help the plant with cooling by convection.”
Maintaining the proper carbon dioxide level
Sabeh said although carbon dioxide is not necessarily impacted by the outdoor climate, greenhouse growers are controlling it relative to the outdoors.
“In a greenhouse where growers are burning fuel to generate carbon dioxide and ventilating at the same time there is a challenge of how much carbon dioxide should be delivered and how is it going to be retained? Is there a way to mitigate the carbon dioxide’s immediate loss to the outside air through greenhouse ventilation?
Tomato crops want a daily average temperature around 72ºF. Dr. Nadia Sabeh said if the plants experience high temperatures during the day, but the temperature can be cooled down during the night, as long as the average temperature is 72ºF, the tomato plants are happy.
“One strategy for not overusing carbon dioxide is to provide plants with a boost from carbon dioxide enrichment. Carbon dioxide can be provided first thing in the morning during first light before the greenhouse vents are open. Basically, the plants take a deep breath when the sun starts to come out and the stomata open. The sunlight or the supplemental lights are turned on and the plants take up that carbon dioxide. When a grower starts to ventilate because the moisture has built up overnight or the temperature starts to increase because the sun is rising, enrichment with carbon dioxide can be stopped so that it is not being blown out of the greenhouse through the vents and exhausted by the fans. Some growers use carbon dioxide enrichment all day as long as there is enough light from the sun or from artificial light.”
Sabeh said growers can mitigate the loss of carbon dioxide by trying to deliver it as close to the leaves as possible.
“Some growers use under-floor or under-bench ducts to deliver carbon dioxide,” she said. “Some growers may use PVC tubing or fish tubing to distribute carbon dioxide through the crop and directly to the leaves. This is ideal if a grower can find a way to deliver the carbon dioxide in an effective manner without getting in the way of all of the other equipment and people working in the greenhouse.
“This is why some people are looking at the potential advantage of growing in vertical farms. There is an enclosed space and in most cases, it is being done in buildings that are not leaky. There are some growers who have considered closed greenhouses. The cannabis industry is really interested in this, but the problem is there is an outrageous energy bill to try and close the greenhouse and not use any ventilation or mechanical cooling.”
Relationship between greenhouse climate variables
Sabeh said the optimum level of carbon dioxide varies for each crop. She said 700-1,500 parts per million carbon dioxide is the level that most growers are trying to use.
“Carbon dioxide is most useful to the plants when there is a lot of light and good temperature and humidity levels or a good VPD,” she said. “Carbon dioxide is transferred through the leaf stomata, the same as moisture through transpiration. At the right VPD the stomata are open to the maximum and are letting out moisture and gulping up carbon dioxide.
“The first thing is having the right VPD to maximize stomata opening. The second thing is photosynthesis, which is driven by light. If the air is being enriched with carbon dioxide, but the light level is very low, much of the carbon dioxide will be wasted. There has to be enough light to facilitate a high enough rate of photosynthesis or the plants can’t use the carbon dioxide. All three of these variables work together. A good VPD is needed for stomata opening. An adequate light level is needed for photosynthesis. And carbon dioxide is needed to maximize the photosynthesis cycle.”
For more: Nadia Sabeh, (916) 775-3724; nadia@doctorgreenhouse.com,
http://www.doctorgreenhouse.com.
How This Startup Produces 700 Tonnes of Fruits and Vegetables Without Soil
Triton Foodworks started as an experiment in urban farming in September of 2014 by four friends — Deepak Kukreja, Dhruv Khanna, Ullas Samrat, and Devanshu Shivnani.
How This Startup Produces 700 Tonnes of Fruits and Vegetables Without Soil
Foraying into urban farming, a group of friends has set up a green enterprise that is based on hydroponics.
There is growing concern in urban and semi-urban areas about the dangers of the pesticide-ridden food that is sold in the market.
Following the Green Revolution in the mid-1960s, the use of pesticides in India has increased. Although the period saw the boom in agriculture like never before, the flip side of this revolution has left the country consuming poisonous food. Food production in large quantities at the cost of their health has made people wary and look for alternatives.
In the confines of an urban setting, four youngsters from Delhi are venturing into hydroponics to provide an organic and healthier option for the urban populace.
Hydroponics is the method of growing plants in a water-based, nutrient-rich medium, without the use of soil. This method essentially cuts down the amount of water being used compared to the method in which plants are grown in soil. In some cases, up to 90 percent less water is used in the hydroponics method compared to the traditional soil-based agriculture — a boon for water-starved urban areas. One can plant four times the number of crops in the same space as soil farming.
An Experiment In Urban Farming
Triton Foodworks started as an experiment in urban farming in the September of 2014 by four friends — Deepak Kukreja, Dhruv Khanna, Ullas Samrat, and Devanshu Shivnani.
In early 2014, Ullas was exploring ways to develop his agricultural land in Mohali for his mother, who suffers from ILD, a degenerative disorder of the lungs. When the doctors told him that life on a farmhouse would in fact be counterintuitive for his mother due to dust and other issues related to farming, he became obsessed with finding a way to farm in a clean and hygienic manner.
Dhruv, who was in Singapore at the moment working on his tech startup, wanted to come back to India and start something here. On a catch-up call, the two got discussing how much fun it would be to start a business together; especially something that made sense economically and ecologically. Following a lot of research, they zeroed in on hydroponic farming, something that connected with both of them. Dhruv visited a few hydroponic farms in Singapore to see firsthand how it works. Ullas met Deepak online while researching on hydroponics. The team quickly realized that to make this thing big, they needed a formal structure and a financial disciple — which is when Devanshu was roped in.
“We were just a bunch of friends who wanted to do something in the space of food and agriculture. We were very excited by the opportunities of rooftop farming and farming within the limits of the city. We did a pilot to grow strawberries in Sainik Farm of Delhi. We used an open system with vertical towers to grow eight tonnes of strawberries out of 500 sqm of land. Eventually, we decided against setting rooftop farms due to feasibility issues. Instead, we set up full scale, commercial farms in the outskirts of cities,” says 38-year-old Deepak, technical Co-founder, who takes care of the farming aspect of the business.
Like any bootstrapped startup, Triton Foodworks also faced a huge number of issues at every step. Their farm at the Sainik Farm was demolished by the Municipal Corporation of Delhi (MCD) because the team refused to pay a bribe.
“We went to the Delhi government to ask for some sort of help in setting up farms in Delhi; we were called ‘food terrorists’ to our face. Quite a few vendors still owe us money for our early projects, something which is a huge issue in this industry. We had no previous data to map our progress against, no previous players who could be used as a yardstick in the field,” says 27-year-old Devanshu, who takes care of the finances and the financial modelling for the business.
Taking Hydroponics Ahead
“Toxic food is the biggest issue we are trying to resolve. People don't realise how toxic their food really is. We don't use chemical pesticides for our plants. The second issue is the fact that we are running out of land and water to grow food. Lastly, we are addressing the problem of traceability, consistency and, by extension, accountability in farming. You buy a bag of chips and you can trace it back to the field in which the potatoes were grown, but if you pick up a tomato from your vegetable vendor, there is no way to know where it came from, who harvested it, when was it harvested, and what all did he put in it to grow. We are teaching people to ask these questions by offering them answers even before they realise this information is important,” says 27-year-old Dhruv, who looks after operations and marketing.
The team relies on Ayurvedic recipes and bio control to fight off pests and other infections, as an alternative to pesticides and insecticides. The team grows the same amount of food grown under conventional farming with just about one-eighth of the area and using 80 percent less water.
The team has successfully set up more than 5 acres of hydroponic farms across three locations in India. The strawberry farm in Mahabaleshwar grows 20 tonnes of strawberries a year and a 1.25 acres facility in Wada district of Maharashtra that produces about 400 tonnes of tomatoes, 150 tonnes of cucumbers, 400 heads of spinach, and over 700 bunches of mint.
Triton also operates an acre facility in Shirval, Pune that grows tomatoes and cucumbers, which are used to feed farmers' markets in Pune. The team also advises companies in Hyderabad, Manesar and Bengaluru that are interested in incorporating hydroponics.
Triton currently has over 200,000 sqft of area under hydroponic cultivation in various locations in the country. Using hydroponics, it produces more than 700 tonnes of residue-free fruits and vegetables every year.
“Our systems enable us to save around 22 crore litres of water per year as compared to traditional agriculture. In terms of volume, our vertical systems grow food comparable to 10,00,000 sqft of land when using traditional agriculture methods, which translates into a saving of more than 800,000 sqft of land to grow the same amount of food. Since our farms are located within a 100-km radius from cities, our produce carries lesser food miles,” says 27-year-old Ullas.
The team is currently in the process of setting up stalls in farmers' markets in Pune and Mumbai.
Regina Food Bank Greenhouse Fills Shelves With Garden-Fresh Goods
Regina Food Bank Greenhouse Fills Shelves With Garden-Fresh Goods
Greenhouse project connects people with fresh food and the art of growing
CBC News Posted: Dec 09, 2017
The greenhouse features multiple towers that are similar to barrels, each with 72 pockets from which food can be grown. (Submitted by B. Paul)
The tastes and smells of garden fresh food is bringing light to the winter, as the Regina food bank plows onwards with its year-round greenhouse project.
From the light crunch of lettuce to the earthy flavours of sweet basil, the food bank's greenhouse is not only producing fresh food, but also putting people back in touch with where their food comes from, community greenhouse co-ordinator Kimberley Wenger told CBC's Saskatchewan Weekend.
- "Growing our own food as a food bank is a really good way to look at what we do on a bigger scale and provide not only fresh food but also education to the clients and community about where food comes from, what it looks like, what it smells like, what it tastes like," she said.
Ultra-efficient technology
The greenhouse launched its Four Seasons Urban Agriculture Project earlier this year, using garden towers. The technology is ultra-efficient, featuring multiple towers that are similar to barrels, each with 72 pockets from which food can be grown.The centre of each tower is filled with compost which is produced by red wriggler worms, who live in bins at the greenhouse. These worms are fed waste the food bank won't be using, with the worms converting 31 kilograms of inputs each week into fertilizer. This fertilizer, in turn, is fed back into the garden towers as nutrients for the plants.
Kimberley Wenger is the community greenhouse co-ordinator with the Regina Food Bank. (Submitted by B. Paul)
"It's vertical gardening and indoor growing. Controlled environments are definitely a popular thing right now," said Wenger.
Wanting to share community asset
Outreach is also a major part of the greenhouse project, she explained. In the launch of this outreach program, students from five schools learned all about the garden tower, with the food bank delivering students with their own garden towers and all the materials they would need to grow food in their own classrooms through the year.
"We have a lot of interest from people that want to extend their season. There's so many opportunities with this place. It's really an asset to our community and we want to be able to share that."
For herself, Wenger said she's learned a lot about gardening since getting involved in the greenhouse project.
"It's been a very transformative process for me," she said. "I never really grew up around gardening and so a lot of this information was new but it was just about being optimistic and tackling a challenge. And that's something I've always enjoyed doing."
With files from CBC Radio's Saskatchewan Weekend
Polar Permaculture Grows Fresh Food In One of The Coldest, Darkest Regions on Earth (Video)
We've heard about how holistic and nature-inspired permaculture design techniques can green a desert and transform ordinary gardens into ultra-productive "food forests." But what about practicing permaculture principles to help grow food in the cold Arctic region -- is it possible?
Polar Permaculture Grows Fresh Food In One of The Coldest, Darkest Regions on Earth (Video)
Kimberley Mok (@kimberleymok)
Science / Sustainable Agriculture
December 21, 2017
© Polar Permaculture
We've heard about how holistic and nature-inspired permaculture design techniques can green a desert and transform ordinary gardens into ultra-productive "food forests." But what about practicing permaculture principles to help grow food in the cold Arctic region -- is it possible?
That's something that American-born professional chef and foodie Benjamin Vidmar is exploring with his project, Polar Permaculture. Based out of Longyearbyen, a town of 2,500 that's located on Svalbard, Norway's archipelago of islands (yes, the same place with the so-called doomsday seed vault), Vidmar is experimenting with innovative ways to grow fresh food and creating a "circular economy" in a rugged, cold place that is dark for 3 months out of the year, and where most supplies have to be shipped in. Watch him explain in this short feature on NBC:
Vidmar is trained as a professional chef and has worked in hotels and cruise ships around the world. In 2007, he landed a job in one of Longyearbyen's hotels, and has stayed there since, raising his family. However, since childhood Vidmar has always been interested in sustainable agriculture, and a few years ago he got tuned into permaculture, recently getting trained in permaculture design practices.
© Polar Permaculture
He's since brought these skills back to Longyearbyen, setting up a geodesic greenhouse, and bringing in red worms to help with composting the locally produced organic waste, which can then be used to grow food here. This is an important point that's not to be taken for granted; on Svalbard, the soil is extremely poor and unsuited for growing food, so if it were not for the worms and compost, soil would literally have to be shipped in.
NBC/Video screen capture
On an island where everything is transported in, and waste is either dumped into the ocean or shipped back to the mainland for disposal, Vidmar's aim is to look for ways to close the loop, reusing and recycling outputs back into inputs whenever possible:
I had initially wanted to do a permaculture project in Florida where I presently spend a month each year, but something told me to do it here in Longyearbyen. There was a huge need for it is as we presently dump all sewage directly into the sea without any treatment facility. We also mine and burn coal. All produce is shipped and flown in, so I basically believe the place chose me to complete this mission, to help make this place more sustainable.
Surprisingly, one of the biggest obstacles has been local politics: the island is socially conservative and has no agricultural zoning regulations in place. It took Vidmar a year and a half to get permission to import his worms. "So with our permaculture project we are basically rewriting all of the history books, looking to change the laws and grow food here once again." says Vidmar.
NBC/Video screen capture
Polar Permaculture/Video screen capture
Currently, Polar Permaculture is the only supplier of fresh, locally produced food on the island, serving all the major hotels and restaurants. The greenhouse is used only when the sun is out, otherwise they grow their veggies -- mostly microgreens, chilies, tomatoes, onions, peas, herbs and so on -- inside their lab -- basically a converted room in one of the local hotels. They've also recently set up a small quail farm, and are producing eggs to eat. The future goal is to scale things up, and to increase food security and reduce waste on this remote island, says Vidmar:
Before we started this project, there was no one speaking about composting, or having locally grown food. All around the Arctic, many people are farming and growing food, but here we were only relying on shipments. After starting this, we now have much more support to expand and increase what we are able to produce. We want to install a biogas digester and also set up a system that can process most of the cities sewage and turn it into biogas that we can use to heat our greenhouses.
Growing food in one of the planet's harshest regions seems like an impossible task, but it appears that through the principles of permaculture, and a lot of dedication, it can be done. Besides growing food, Polar Permaculture offers courses, tours, and gourmet cooking classes. For more information visit Polar Permaculture.
Organic Hydroponics With Industry Pioneer Michael Christian
Organic Hydroponics With Industry Pioneer Michael Christian
DECEMBER 20, 2017 JIM PANTALEO
At Urban Ag News, we’re all about educating our readers with the goal of providing valuable input from a wide variety of industry professionals. Without question, Michael Christian, founder of American Hydroponics, fits that bill. I was delighted to sit down with him recently to learn of his 30-plus year career in the hydroponics industry and how his insight, in particular about the often contentious argument of what actually constitutes the definition of the word “organic,” pertains to growing plants.
Does a plant need to be grown in soil to be truly organic? Can all the biological elements required by the plant be safely replicated to meet the definition? Will soil purists ever find common ground, no pun intended, with hydroponic growers?
These questions are essential to continuing the debate over the word “organic” including the USDA National Organic Standards Board’s (NOSB) own definition written in April 1995: “Organic agriculture is an ecological production management system that promotes and enhances biodiversity, biological cycles and soil biological activity. It is based on minimal use of off-farm inputs and on management practices that restore, maintain and enhance ecological harmony.”
Seems like a fair definition, but not so fast. To say the least, the subject is a complex one and I’m hoping Michael will shed some light, pun intended, on the subject from his point of view. If anything, I’d like for an olive branch (yes, again pun intended) to be laid upon those soil purists who don’t believe hydroponic growers either have a heart nor are working, as they certainly are, at making the world a healthier and more verdant place for all.
(L-R) Fred Lau of Mari’s Garden and Fred Humphrey of Island Growers with Michael Christian at the AmHydro research greenhouse in Arcata, Calif.
Photo courtesy of AmHydro
For some background, Michael started the business in 1984 in the beautiful northern California agrarian community of Arcata, initially to meet the needs of small, hobbyist growers, and for full disclosure, those growing cannabis. Side note: Also known as the Emerald Triangle, the counties of Mendocino, Humboldt and Trinity make up the largest cannabis producing region in the United States. And perhaps the most often maligned by federal law enforcement over the past 40 years. This could all change in November when Californians will have the opportunity to vote on the ballot measure entitled the Adult Use of Marijuana Act.
As Michael states, in those early days he essentially moved to the top of a mountain to raise kids and make some money. It wasn’t until 1994 and a trip to Australia where he saw NFT (nutrient film technique) hydroponics everywhere. In his words, “That just blew me away as there was nothing like that in the U.S.” The following year he made the decision to target the commercial market. To this day AmHydro, as it is known, is a well-established and trusted provider of hydroponic equipment to commercial farms and greenhouses worldwide.
Success did not come easily however, and it’s only been within the last eight to 10 years that AmHydro found its groove with robust sales primarily of NFT systems into urban areas where demand for locally-grown produce is very high.
Michael recently sold a majority of his interests in AmHydro, but remains on staff to consult on various projects. He is now spending more time focusing on life’s more important endeavors, including his grand kids and fly fishing.
JP: Michael thanks so much for sitting down with Urban Ag News today, please tell us why you believe there is an (often) adversarial relationship between hydroponically grown (soil-less) produce versus soil-grown when it comes to the definition of “organic?”
MC: I think it’s in the interpretation. I don’t know if it’s in the DNA of people who have always seen plants come from soil. When they hear the word “hydroponics” they are kind of intimidated and whatever images they have, be they generated from media or who they talk to, has fortified their interpretation and they actually get angry at you. They say “No way I’d ever do hydroponics and give up my gloves!”
It triggers all kinds of madness, especially many years ago. However that all has changed in the last eight to 10 years. But usually it’s because of people’s ignorance as to what it is or the value of it or having never tasted it or thinking it’s chemical or synthetic or bad or unnatural. All these images are associated in their heads.
One of the contentions is the biological activity in the soil is fundamental because the plant is interacting through the roots by releasing compounds and nitrates and therefore it’s feeding and colonizing microbes. That’s part of the health of the soil but that also happens in hydroponics and NFT. The roots actually become a rhizosphere. It’s a predominant life form. It just shows up so all that biological activity whether in a foam cube or in a peat and coco plug; that biological activity is in the root zone. It really doesn’t have much to do with the mechanical structure that holds the plant up. And this is what they are getting down to in the “sand box” argument.
JP: I’ve previously read your reference to “a nitrogen atom is a nitrogen atom.” How would you directly address the naysayers that produce using soil-less methodologies are designated “organic” because all the inputs and amendments are also deemed “organic?”
MC: That’s a tricky statement because fundamentally in hydroponics all of those elements in a hydroponic nutrient solution or an inorganic mineral are elements. You can’t make elements. They are on the periodic table. You can only extract them from nature. And whether you’re growing chickens and collecting chicken poop, the food is being produced somewhere. Somewhere every input is coming from elsewhere.
It gets down into a difficult conversation or which is the most sustainable source for whatever input you are bringing in to develop whatever it is you are doing. If it’s an organic farm, what are you using in your soil? Where is it coming from? What’s feeding it?
I think fundamentally it goes back to the NOP (the USDA National Organic Program) and what their definitions are and what they think is correct.
Michael Christian visits with Pierre Sleiman Jr. at Go Green Agriculture in San Diego, Calif.
Photo courtesy of AmHydro
JP: That dovetail’s nicely into my next question: Do you believe the USDA (in a 2002 statement) was premature in designating the word “organic” without the mentioning of soil (in the definition)?
MC: That was then and this is now and we have a different set of constraints in the world. The word “organic” has lost a lot of credibility as big ag is now in it and of all the projects I’ve seen, there’s no way they are all organic. Somehow they jumped through the hoops and paid the fees and now they can benefit from the increased margin of organic produce. So really, the whole thing has shifted. It’s going more in the direction of localizing food production. That’s where the power is and that’s what people are starting to appreciate more. We have a different set of challenges now than we ever had before. The real problem is in the nitrogen cycle; there really isn’t enough nitrogen-fixing ability of the soil to support the number of people we have on the planet right now without synthetically producing it with natural gas and electricity. That’s where the really big problem is.
I read an article in Scientific American magazine, back in 1997, and I was pretty blown away with the information they were presenting. The fact is that when you look at population growth you look at a graph and then you look at ammoniacal nitrogen production.
There was a process in the late 1800s where they were actually using natural gas and electricity in making urea (which is ammoniacal nitrogen). You can have just junk soil and then put this nitrogen in there and plants grow.
It wasn’t until the 1950s when they began a process called the Haber-Bosch process in Germany and they were able to lower the cost (of creating nitrogen) by 90 percent. By the time they started making ammoniacal nitrogen, there was a direct correlation (and spike) with population growth.
The other method of nitrogen creation is from chicken or cow poop, for example, and the farmer is bringing that in and constantly adding it to the soil. When you look at the primary crops in the world which are basically legumes, grains and potatoes; those are the main crops that sustain the population. And this is where all the nitrogen tonnage is going into, not lettuce or tomatoes.
The scientific community believes there may be more than four billion people alive today because of synthetic ammonia. That’s a sobering thought when you think of the carrying capacity of the earth in that all these inputs are derived from somewhere and they are just moved around. At some point, phosphorous, for example, is just going to run out and when that does happen, how can you replace an element?
This little organic debate pales in comparison to all this other stuff.
JP: Why does the organic certification matter to the farmers and growers you know and work with?
MC: It allows them (to make) more margin. But that’s changing too. I’d say maybe eight years ago all the markets would ask “Is it organic?” And the response would generally be “No, it does not qualify as organic but it is pesticide- and herbicide-free.” That allowed farmers and growers to take ground as people would actually prefer that over the designation of organic, especially when it’s sitting next to some really ugly looking organic produce. This and the inability of produce managers (in grocery stores) to risk putting something on their shelves that people didn’t know about.
So it’s been an educational process that’s really been successful over the last eight years. I mean, a 25 percent extra margin is pretty decent.
JP: Do you believe the organic versus inorganic argument would hold true if the plants produced were flowers or medicinally-based?
MC: There’s a couple parts to this. One is inorganic or organic, is this in a sun-lit environment like a greenhouse or is this LEDs? Because one thing that I’ve come to understand through the years is when they talk about PAR light (photo synthetically active radiation) they don’t know (squat) about that! The electromagnetic spectrum of sunlight is so huge we only see a fraction of one percent. Our machines may be able to tell wavelengths and nanometers but as far as what a plant is actually taking in and what’s affecting it, we just don’t know. For me, having done a lot of LEDs inside, there’s no way that (plant) tissue is as healthy or as terse or as strong. I just haven’t seen it. Whether it is inorganic or organic in an artificially lit environment, I don’t see the health of the plant as I do with sunlit environments.
JP: Do you believe the adage that humans, for the most part fear what they do not know, has been a catalyst to the adversarial relationship between soil-grown and soil-less? Or is this fear based on the increase in indoor vertical farming operations and the soil growers essentially fear they will lose business and market share?
MC: I think it’s all of those. I think they do fear what they don’t know and a lot of these big guys, especially big ag with all their machinery, have been doing that (growing in soil) for hundreds of years. They know that they get so much per acre and they can get organic certification if they talk to “Jack” and they jump through hoops.
But meanwhile, all these localized, food production farms have such high production rates. In 8,000-square-foot greenhouses these guys are producing 6,000 heads of lettuce a week, year round. And when you look at 28 million heads of lettuce produced in the U.S. per year, you can see that all you need is maybe 15 or 20 acres located near cities and you’re going to put a hurtin’ on big ag. People prefer, instead of shipped-in produce at a lesser quality, they prefer locally grown. And the locally-grown guys are expanding like crazy because the market is just so open and ripe right now.
People prefer to know that the grower who is growing the food they are eating lives down the street. And why would he mess with them and put pesticides in their food? It’s becoming more of a community operation.
The whole issue of pricing, distribution and organic…people just want to get food from their neighbor. People don’t want to feel powerless and they can do something by going to their local store and buying something locally produced. They can make a difference by doing that. That’s an act of power and has more value than the word “organic”.
JP: Thank you Michael. You are a gentleman and a scholar and I hope you catch some big fish!
For more: AmHydro (American Hydroponics), 286 South G St., Arcata, CA 95521; (800) 458-6543; http://americanhydroponics.com/.
A Look Beyond the Glass at NatureFresh™ Farms
The company operates on a mantra that was coined by Peter Quiring “We don’t just grow produce, we grow people”.
A Look Beyond the Glass at NatureFresh™ Farms
Delta, Ohio | November 20th, 2017
On Wednesday, November 15th & Thursday, November 16th NatureFresh™ Farms opened their doors to the community for their first ever Open House.
“The Ohio community has been extremely supportive throughout the entire build and we have continuously received many inquiries from our neighbors wanting a chance to take a look behind the glass” explained John Ketler, General Manager. “Education is a key component of who we are and we wanted to ensure that our neighbors had a chance to see exactly how we grow; from seedling to harvest.”
The response to the NatureFresh™ Open House was both stunning and humbling. Within days of the registration going live, there was more interest than hours available in the day as well over 1000 people registered to tour the facility. The team had originally planned on the event lasting one day, however, had to extend the tour to two days in order to accommodate all those interested.
“For us, it’s more than just existing in Delta. We want to be an active partner in the community. It is important for us to show our neighbors how we grow and provide total transparency,” commented Peter Quiring, President, and CEO. “We had school groups, senior homes, care facilities, farming clubs, and many families come out. It was great to be able to show everyone exactly where the produce they have sitting on their kitchen table comes from”. With interactive sessions, the team was able to give individuals a firsthand understanding of greenhouse growing techniques such as the Integrated Pest Management (IPM) system & the growing medium.
The company operates on a mantra that was coined by Peter Quiring “We don’t just grow produce, we grow people”. In that spirit, NatureFresh™ partnered with JJ Safe House and Open Doors Delta to raise awareness and funds for the local charities. With produce being sold for $2 an item, approximately $2000 was raised in addition to over 3000 lbs of produce being donated to the charities to help support local families having a healthier and happier Thanksgiving.
“The feedback we received after the event was phenomenal,” said Ketler. “The community was amazed by everything from the scope and technology incorporated in the facility to the flavor of the tomatoes. Overall, we couldn’t have asked for a better event.”
To learn more about NatureFresh™ Farms, visit naturefresh.ca
Kara Badder
Marketing Project Manager
kara@naturefresh.ca
Phone: 519.326.1111;3215
Mobile: 226.936.2358
Is The Future of Farming in Public Schools?
Is The Future of Farming in Public Schools?
DECEMBER 17, 2017 URBAN AG NEWS
By Jennifer Prescott
On a chilly February 26, excited student greenhouse ambassadors of PS84 in Williamsburg, Brooklyn greeted a host of city and local dignitaries arriving to tour and cut the ribbon for the launch of their amazing 1,500-square-foot hydroponic greenhouse classroom rooftop facility. As New York City Council member Stephen Levin observed, “it’s 34 degrees out and we are in this beautiful greenhouse growing food!”
Principal Sereida Rodriguez-Guerra—observing the student ambassadors guiding each guest on a tour, with thorough explanations of each hydroponic system—was understandably proud of the students and the school community as she reflected on the last 4 years of work steering the development of the greenhouse along with NY Sun Works. “These guys”, she said gesturing to the students, “dressed in black and white, look at them, just listening to them, and this is just a small portion of our children. Our children have been working the green classroom, they know the hydroponic systems, they know how they work, and they’re just as excited to be up here and do it on a bigger scale, but I really really want to thank Diana Reyna, because we both grew up here in Williamsburg, and for her to believe in our vision, and really rallying everyone up to stand behind us and see this through, thank you so much.
The festivities continued as Principal Rodriguez-Guerra then introduced Brooklyn Deputy Borough President Diana Reyna to the podium. Reyna has been a significant force in galvanizing the will and funds for the traditionally underfunded public school’s educational programs in her borough. She is fighting for “21st-century technology and skills” for these kids. And to be sure, Borough President Adams and Deputy President Reyna recently allocated 2 million dollars to NY Sun Works for the development of 12 classroom greenhouse/labs over the next year.
“These are the scientists, the lab researchers, these are the academic visionaries and entrepreneurs that we need to invest in, and so we want to make sure they don’t fall short,” Deputy Borough President Reyna said at the opening. “Within each school district, we’ve mapped out what the options are so that when you graduate PS/MS 84 that you will have a high school to go to to have this same [greenhouse classroom] learning experience and a more challenging and rigorous curriculum within your own community, making sure that everyone understands that you will compete globally, and you will be prepared to do so.”
Technology and farming for the future are exactly what PS84’s greenhouse science lab represents. The systems include a large NFT (nutrient film technique) system for leafy greens, Dutch bucket systems for vine crops like melons, tomatoes and cucumbers, a state of the art aquaponics system, tower gardens for herbs, a vertically integrated growing system (a NY Sun Works proprietary design), and rainwater catchment and evaporative cooling systems, making the lab as environmentally friendly and efficient as possible.
NY Sun Works greenhouse/labs also include STEM and environmental science curriculum that can be integrated with existing science curricula at the discretion of the school. In addition to building an understanding of all facets of sustainability—pollution, contamination, bio-diversity and conservation—students that participate in a NY Sun Works greenhouse/classroom lab gain valuable experience in urban farming as they learn science.
Advocates for the development and expansion of the “Brooklyn Project” (as NY Sun Works has come to call it)—including council members Antonio Reynoso and Stephen Levin, as well as Borough President Adams and Deputy President Reyna—do not shy away from addressing the social justice issues these greenhouse labs help to address. For families with often limited access to healthy food, sharing urban farming knowledge with their families and community represents a powerful shift in the urban landscape with regard to the value of food. At the opening, student ambassador Olivia proclaimed “my favorite part [of the greenhouse] is that we grow food to make people healthy.”
Jennifer Prescott, School Liaison & Program Support, NY Sun Works
Photos courtesy of Daphne Youree
NY Sun Works is a non-profit organization that builds innovative science labs in urban schools. Through their Greenhouse Project Initiative, they use hydroponic farming technology to educate students and teachers about the science of sustainability.