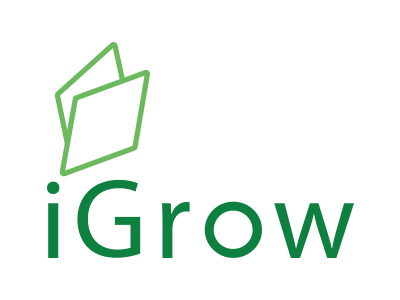
Welcome to iGrow News, Your Source for the World of Indoor Vertical Farming
British Soil-Free Farming Start-Up Prepares For First Harvest
British Soil-Free Farming Start-Up Prepares For First Harvest
British start-up Airponix will later this month harvest its first large crop of potatoes grown without soil, in a promising sign for a technology that claims it can deliver high vegetable yields with minimal costs and environmental degradation.
At its new 1,000 square metre greenhouse in Norfolk, Airponix has ditched soil to grow potatoes using a nutrient-rich "fog" sprayed out of modified inkjet printers down long polythene tunnels of crops.
"Trials of our breakthrough technology means that we can produce crops, such as potatoes, with lower production costs and higher quality, competing strongly against conventionally grown new baby potatoes," said co-founder Michael Ruggier in a statement.
"The potential cost of the system is very low and requires little energy to operate," he added. "Manual labour is also greatly reduced because harvesting is a simple clean process and root crops don't need washing. This means that everyone can benefit from our technology and it has the potential to guarantee high-yield high quality food production independent of external environmental conditions."
The technology is suitable for food production even in arid or degraded regions, and without the need for herbicides, fungicides or pesticides, Airponix claims.
The company says its system is an improvement on rival aeroponic growing methods thanks to its fine spray technology, which produces tiny water droplets better suited to staple food crops such as rice, wheat or potatoes.
The first crop of potatoes from its Norfolk greenhouse will be harvested at the end of the month.
Source: Business Green
Publication date: 5/1/2018
Key Factors For Optimal Crop Production In Greenhouses And Vertical Farms By Professor Leo Marcelis of Wageningen University
Key Factors For Optimal Crop Production In Greenhouses And Vertical Farms By Professor Leo Marcelis of Wageningen University
By urbanagnews
April 16, 2018
Greenhouses and vertical farms around the world are faced with many of the same questions and obstacles when learning to manage crop production in controlled environment agriculture systems. Listen to Professor Leo Marcelis discuss trends, opportunities and other key factors in creating optimal crop production systems for greenhouses and vertical farms.
CA: Similarities Between Running A Marathon And Running A Company
Bert Mucci, Mucci Farms
CA: Similarities Between Running A Marathon And Running A Company
It all began with two brothers throwing caution to the wind. Today Mucci Farms is a massive producer of greenhouse vegetables.
A challenging climate
Lake Erie, one of the five Great Lakes of North America, sits on the Canadian-US border. It is a place where strong winds blow and temperatures fluctuate from minus 20°C in winter to plus 30°C with 95% humidity in summer. But that hasn’t stopped a long line of growers trying their luck.
On its north shore, the Leamington and Kingsville region of Ontario is today home to the largest concentration of greenhouses in North America. It is here that brothers Gino and Tony Mucci decided to throw caution to the wind when they arrived from Italy. After leasing their first piece of land they bought some of their own and then expanded one plot at a time around the great lake. When they built their first greenhouse complex in the mid-1970s, people thought they were crazy.
Now three of their sons, Bert, Danny and Gianni, work alongside Vice Marketing Manager Joe Spano to run an ever-expanding, state-of-the-art greenhouse cultivation business, which includes a range of proprietary fruit and vegetables. Mucci Farms today covers an area of more than 1.5 million square meters in Ontario. And they are planning a major expansion in Ohio. At the sprawling plant in Kingsville, just a few steps from Lake Erie, long lines of cucumbers, tomato vines and heads of lettuce thrive in uniform, pleasant light.
Ideal greenhouse conditions with the help of climate screens
CEO Bert Mucci tells us how the climate screens Svensson supplies help Mucci Farms to create the ultimate indoor climate and maximize production. “No other suppliers come close to the quality of Svensson climate screens,” he says, and then lists the advantages.
“These screens help to maintain the perfect climate year-round – both during the ice-cold winters and the hot summers. When the sun rays are at their strongest, they give us soft, diffuse light and a very comfortable indoor climate.” Mucci Farms also saves up to 20% on its energy bill. “We use Luxous screens on cold winter days because we can save a lot of energy that way without losing too much light,” Bert continues. “Harmony, on the other hand, provides us with a diffuse light that softly showers perfect quality light evenly into the entire plant. It also provides us with the shade we need. And finally, we use Obscura, both to save energy and to prevent light from escaping the greenhouse when it is dark outside.”
"Svensson screens in combination with the greenhouses’ protective shell create the ideal conditions for Mucci Farms to increase its productivity and profits. And this method of cultivation is clearly a trend for the future in light of the environment and the need to grow more food with less land. The difference in cultivation efficiency of growing in a climate screen-controlled environment such as this compared to plants directly exposed to the elements is simply huge."
Mucci Farms has a few more environmental tricks up its sleeve, too. For example, it recently introduced a sustainability programme called GreenERhouse, which includes recycled water. But for now business is blooming and Bert Mucci has more and more rows of vegetables to inspect.
Mucci Farms has come far since Bert’s father and uncle built their first greenhouse. Bert Mucci isn’t afraid to take the long road either when he has his sights set on a goal. He’s been a keen marathon runner for many years. Are there any similarities between running a marathon and running a company that grows greenhouse vegetables? Bert replies without hesitation: "Sure! Both require perseverance, a strong work ethic, dedication, and strategy."For more information: Ludvig Svensson
Netherlands: 9 Hectares Indoors Compared To 90 Hectares Outdoors
Netherlands: 9 Hectares Indoors Compared To 90 Hectares Outdoors
Siberia is an innovative enterprise that grows greenhouse vegetables in Maasbree. It was established in early 2016 by Peter van Dijk and Luc Willemssen who also own Van Dijck Groenteproducties, one of the largest suppliers of outdoor-grown leafy greens to the retail and processing sectors in The Netherlands. The partners established Siberia to meet the increasing demand for fresh produce in the winter. Lettuce and leafy vegetables are grown in a mobile gutter system in a new, hypermodern greenhouse. Siberia’s innovative and unique cultivation strategy means that a virtually identical volume of produce can be grown on 9 hectares compared to the 90 hectares that would be required to grow the same amount of lettuce outdoors.
When they began building the Siberia facilities, Van Dijck and Willemssen were committed to creating an efficient and eco-friendly greenhouse. They consulted Cogas Zuid, a specialist in ultra-modern greenhouse installations and certified Philips LED Horti partner. Advisors from Philips Lighting’s Horticulture department provided input on the best light recipe to use and calculated potential yields and return on investment for the crops grown.
Siberia’s 9 hectare greenhouse would be used to grow lettuce and leafy greens like bok choy. The co-owners first considered using HPS (high pressure sodium) lighting, but Philips proposed using LED instead. With LEDs, growers can go to higher light levels, which are really needed for growing lettuce and they can produce more in the winter. LEDs also produce less radiant heat, so there are fewer quality issues with tip burn and inconsistent growth.
The first lettuce and bok choy crops were sown in the new greenhouse in January 2016. It is equipped with a mobile hydroponic gutter system that can be adjusted as the plants grow. The entire process - from sowing to harvesting - takes place under controlled conditions under one roof. A rainwater irrigation system minimizes water usage, and less crop protection products and fertilizers are used compared to outdoors.
The total growing area is 9 hectare. The greenhouse is 6 meters high with 4 meters of space between the LED grow lights and crops. Philips GreenPower LED toplighting modules are used to deliver a light level of 104 μmol/m2/s. According to Philips, these LEDs provide twice as much light output as HPS lights and the entire installation has an efficiency of 2.6 μmol/J. Siberia BV’s customers were so enthusiastic about the locally grown crops available in the winter that they immediately increased their orders. As a result, Siberia BV expanded their operations with another 4 hectares of greenhouse with LED grow lights which opened in June 2017 and has been running at full capacity since.
“Our customers are impressed with the high quality and longer shelf life of the greenhouse crops,” says Grower Tom Willemssen. “The red lettuce has a beautiful dark red color and we are getting heavier and more uniform plants thanks to the controlled growing environment which is what our customers want.” The high light output of the LEDs promotes very fast growth of the plants, shortening the growth cycles. “We can harvest excellent quality crops in about 7 weeks and they are not damaged by the weather compared to those grown outside,” Willemssen.
In the beginning of the project, plant specialists from Philips Lighting supported Siberia in choosing the right lighting set-up and the right light recipe for their crops. Willemssen says, “We know everything about growing crops but we are not experts on lighting so we really appreciated the advice that Philips Lighting gave us. All of their prognoses for yields and length of crop cycles have proved accurate.”
For more information:
Philips
www.philips.com/horti
Publication date: 4/23/2018
Designing Resilient Organic Greenhouse Production Systems For Europe
Designing Resilient Organic Greenhouse Production Systems For Europe
Greenhouse production is a highly intensive cropping system that guarantees out-of-season production in any climatic condition. The Greenresilient project, which was launched on April 2, 2018, aims to demonstrate the potential and feasibility of an agroecological approach to organic greenhouse production in Mediterranean, Central and Northern European organic production.
Challenge
The year-round production of high quality and tasty vegetables in unheated and low-energy greenhouses or polytunnels, using resilient, sustainable and local systems, is a challenge.
The main objective of the new 3-year Greenresilient project is therefore to design robust agroecosystems in protected conditions, which are able to maintain high and stable production with a low environmental impact.
While in Central and Northern European countries, the major challenge is to produce crops in low-energy systems under low temperature and low light conditions, in Mediterranean countries, the challenge is to reduce the use of plant protection products (for example copper).
The use of agroecological practices (biodynamic agricultural) in organic greenhouse production systems constitutes an innovative approach to a traditionally intensive system of organic production.
Sustainability
The project will also assess the environmental sustainability of the different cropping systems, using a Life Cycle Assessment (LCA) approach to calculate the environmental impact of two “extreme” strategies within the five experimental sites of the project.
In order to reach these objectives, a team of scientists with multidisciplinary competences (agronomy, agroecology, soil chemistry, entomology, plant pathology, weed science) from twelve research centres in eight European countries are involved.
During the kick-off meeting held on the 18-20th of April, 2018 in Capua, Italy, Greenresilient project coordinator, Dr. Fabio Tittarelli of the Italian Council for Agricultural Research and Economics (CREA), presented the timeline and the interactions among project activities. Work package leaders and participants detailed and planned the work to be done in the first year of the project.
The project is funded by CORE Organic Cofund funding bodies, which are partners of the Horizon 2020 ERA-Net project CORE Organic Cofund.
For more information:
Greenresilient
www.greenresilient.net
Netherlands: Students To Turn Former Prison Into Urban Greenhouse
Netherlands: Students To Turn Former Prison Into Urban Greenhouse
Twenty-three student teams from around the world have taken up the challenge to transform the former Amsterdam Bijlmerbajes prison and its surrounding area into an urban greenhouse. This innovation competition is a perfect match for the plans for this area as the prison district is earmarked to become a green, healthy and pleasant neighbourhood in which to live.
The renovation of this Bijlmertoren is part of a general repurposing of the entire prison complex, which envisages 1,350 private residences, art studios and start-up offices. The new tower is to provide a green touch to the area, possibly in the form of a vertical urban greenhouse.
WUR is organising the design challenge in the context of this year’s centennial. Whether the architect will incorporate the winning design in his renovation plans will be announced at the prize ceremony, which will be held on 28 August.
Source: Wageningen University & Research
Publication date: 5/7/2018
Turkish Growers In Love With Soilless Agriculture
Turkish Growers In Love With Soilless Agriculture
There is an emerging interest towards hydroponic growing in Turkey. Hydroponic growing has become popular globally in recent years and its popularity started to spread around Turkish growers as well. The first attempts for soilless growing started in Antalya around 1995 and nowadays it has been carried out approximately in a 100 million square feet area in total. 55% of this area is located in the Aegean region whereas 43% is located in the Mediterranean region of Turkey.
Hydroponic growing is commonly used in Spain, France, Belgium, Germany, Italy, Japan, South Korea, USA, Israel, Colombia, and China but is most used in the Netherlands, with almost 95% of the greenhouses being utilized with this particular method of production. This contributes significantly to the Netherlands being the second biggest food exporter in the world after the US.
Turkey Association of Chambers of Agriculture Chairman Semsi Bayraktar: “The world population is increasing rapidly and is projected to reach 9.6 billion people in 2050. In order to feed this population, you need to utilize all the production methods, including greenhouse production and hydroponic growing in addition to the traditional field growing. The whole global industry is around 55 – 60 billion USD.
In the greenhouses, a lot of growers are experiencing problems with soil which caused a lot of growers to explore the soilless production methods. There are usually a few varieties grown in a greenhouse and they are grown without any break between them thus it causes soil fatigue. That’s why it is suggested you need to replace the top 20 cm of the soil in a greenhouse every 4-5 years.
Turkey has tremendous potential in soilless agriculture and we are located in a very advantageous position to be in close proximity to European, Russian and Middle Eastern markets. If we can use modern technology in soilless production, we can increase the productivity per square feet and contribute significantly to our country’s economy.
As the grower is not dependent on the soil and its characteristics for production, the grower is free to grow products anywhere they like. You can feed the products at the right amounts and at the right times and this way you can achieve total control in production. This method of production enables you to get the products ready earlier and at the right time where the grower can get better prices for their products. As the production area can be sterilized very quickly, you can have continuous production all year round.
Another additional benefit is the elimination of the soil based diseases with the absence of the soil. Moreover as there are no pests in the production, there is no need to use pesticide which makes the fruits and vegetables grown in this method more healthy for consumers. As there is no vaporization, the grower also saves on water expenses. If the grower also sets up his production with proper automation systems, they can also save on labor costs.”
Source: Sozcu
Publication date: 5/3/2018
Northwest Europe Discovers The Benefits of Coating
Northwest Europe Discovers The Benefits of Coating
Light is the limiting factor for a large part of the year in North-West Europe. This means that any improvement in the amount of light that reaches the crop immediately results in improved yield and quality. The general rule of thumb is: 1% more light = 1% higher production. This applies both to fruiting vegetables and cut flowers.
Normally some of the sunlight that hits the greenhouse roof is reflected and does not reach the crop. AntiReflect significantly reduces this reflection. More light enters the greenhouse as a result; allowing for a higher production and improved quality. The light gain is 3%. This was measured by the Light Lab of Wageningen University & Research.
The lower the sun, the more light reflects from an uncoated greenhouse roof. This means that the greater the angle of incidence, the greater the increase in the amount of light entering as a result of AntiReflect. Calculations by the Light Lab reveal that the light gain can increase to 5% at an angle of incidence of 60o. This angle of incidence is particularly common in North-West Europe and Canada.
Total package
AntiReflect was successfully introduced in the Netherlands in 2017. It was introduced to companies growing cucumber, tomato, bell pepper, roses, chrysanthemums, and lilies. The Light Lab in Wageningen measured the treated glass of all these agricultural companies and confirmed the light gain. The growers are enthusiastic about this new solution and report a higher production and quality of their crop.
Starting this year, companies in Belgium, France, England, Germany, Austria and Switzerland can also take part. Due to the good experiences in the Netherlands, Mardenkro is now offering this solution as a total package in these countries too. This package consists of three components: the product itself, the application and the light measurement.
Guarantee of light gain
The application method is crucial to the result. Mardenkro uses contractors in all cases, who are specially certified for the application of AntiReflect. They have proven that they are able to apply the layer uniformly and at the correct thickness.
Following application, the Light Lab in Wageningen will measure a number of treated panes and will determine the actual light gain in comparison to non-treated panes. The grower will receive a report of this measurement.
This controlled introduction ensures that Mardenkro can guarantee everything is done correctly and that a substantial light gain is indeed achieved. Mardenkro guarantees an increase in the incidence of light by at least 2.5%.
For more information
Mardenkro The Netherlands
Geerstraat 8
5111 PS Baarle-Nassau
The Netherlands
T: +31 (0)13 507 70 69
Email: sales@redusystems.com
www.redusystems.com
Publication date: 4/30/2018
Energy Is A Major Expense In Greenhouse Productions (between 10% and 25%).
Energy Is A Major Expense In Greenhouse Productions (between 10% and 25%).
Several solutions currently exist on the market to help reduce this energy bill. The dilemma is how to choose an optimal configuration adapted to the external climate, inner climate, and crop(s).
Hortinergy is the first online software that can simulate energy consumptions of an existing or planned greenhouse anywhere worldwide.
It is suitable for a diversity of clients, from growers to agricultural consultants or greenhouse equipment manufacturers. It takes less than 10 minutes to enter your parameters.
The library includes the major equipment available on the market: glass, plastic films, climate screens, etc. Equipment manufacturers can spotlight their branded products for select pre-set parameters to simplify the user experience.
Hortinergy is a decision-making tool to calculate the required dimensions of equipment and optimize the investment: users compare economical and technical scenarios with a simple online interface. A detailed report is sent for each scenario.
Hortinergy allows users to determine optimal configurations for energy savings, which can be up to 50% for renovations, and more than 70% for innovative greenhouse concepts.
In most cases, existing software programs offer only qualitative analyses. While a few are quantitative in nature, they are either not suitable for daily use or they provide limited modeling options.
Hortinergy is a real scientific breakthrough with:
ï Innovative algorithms that take into account greenhouse-specific parameters, such as: light transmission through the transparent cover, external and inner climate, canopy evapotranspiration, and crop types.
ï Dynamic calculations generated with GPS position anywhere worldwide.
ï Most of the functions of a climate computer regulation: day/night climate, screens, vapor pressure deficit, etc.
ï Models that simulate classic equipment (water tank, combined heat, and power (CHP), etc.) as well as innovative equipment (semi-closed greenhouse, active ventilation).
ï Outputs that include heating consumptions, dehumidification needs, photosynthetically active radiation (PAR) reaching canopy, etc. for hourly, monthly or annual periods.
ï Results validated by research centers with measurement campaign in classic and semi-closed greenhouses in France and in the Netherlands.
Multiple add-ons will complete our software.
For more information please contact us : alexandre@hortinergy.com - +33 (0)4 79 72 40 59 Agrithermic 17 avenue du Lac Léman – Savoie Technolac BP 60 269 -73 375 Le Bourget du Lac cedex - France
Aquaponics Enhances St. Kitts and Nevis Agricultural Sector
Aquaponics Enhances St. Kitts and Nevis Agricultural Sector
Recognizing that small developing countries like St. Kitts and Nevis face enormous challenges following the passage of category 5 hurricanes Irma and Maria in 2017, the Inter-American Institute for Cooperation on Agriculture (IICA) and the Caribbean Agricultural Research and Development Institute (CARDI) provided USD 37,000 to rehabilitate the sector and to enhance food security on the islands.
In doing so, both institutions were mindful of the fact that there was need to ensure greater resilience against climate change. They therefore collaborated with Garden Pool, a United States non-governmental organization (NGO), and the United Nations Food and Agriculture Organization (FAO) to construct an Aquaponics system.
“Aquaponics is the combination of aquaculture (raising fish) and hydroponics (the soil-less growing of plants) into one integrated system”, explained IICA’s National Specialist, Augustine Merchant.
Regarding this project, the Minister of Agriculture, Alexis Jeffers indicated that “IICA is doing the right things at the right time to ensure that they assist us in securing our future”.
The fish waste explained Merchant, provides an organic food source for the plants, and the plants naturally filter the water for the fish. The microbes nitrify bacteria, and this bacteria converts ammonia from the fish waste firstly into nitrite, and then into nitrates. Nitrate is a form of nitrogen that plants can uptake and use to grow.
“As climate change increases variability in weather patterns, large aquaponics systems have the potential to increase food security by changing the way food is produced.” In addition, he stated that in areas with climate challenges such as limited water resources, hurricanes, and flood, aquaponics can facilitate local food production and enhance food security.
The aquaponics system is located at the Government Experimental Station at Prospect Estate, Nevis, and will be used by IICA for demonstration and training.
Effects
The natural disasters devastated the agricultural sector of the Federation. Greenhouses, standing tree crops, vegetables, livestock feed, poultry, small ruminants, and irrigation pipes were lost or damaged by the unprecedented high winds and flood waters.
For a few weeks, there was a shortage of food on the island as some of the countries from which St. Kitts and Nevis import food were adversely affected by the hurricanes.
Both institutions recognize the challenge to increase productivity in the agricultural sector, enhance food and nutrition security and understand the implications of climate change.
For more information:
Inter-American Institute for Cooperation on Agriculture
www.iica.int
Publication date: 5/2/2018
Effects Of Temperature On Basil Growth: Some Like It Hot!
Effects Of Temperature On Basil Growth: Some Like It Hot!
Philips researchers all aspects that make up the ideal light recipe for a particular crop. But, did you know that we also study a much broader range of factors to come up with the ideal growth recipe? This means that besides LED growing lights, we look at climate, CO₂, nutrients, and substrates to see how we can make them work together most effectively. In this blog post, I’ll tell you more about the major role that temperature plays in the storage life and yields of basil.
by Thijs van den Bergh
Top performer
Basil, often called the king of herbs, is one of the classic crops that performs very well in a vertical farm. It can be grown year-round in a vertical farm where much higher yields can be achieved compared to a standard greenhouse application. Basil can be grown hydroponically on coco coir, Rockwool or mats.
A global favorite
Originally from India, basil is frequently used in Asian as well as Mediterranean cuisine. Fresh cut basil is highly valued by consumers across the globe and can be grown year-round in a vertical farm or city farm. We have tested several different varieties ranging from Thai and lemon basil to African Blue basil and a range of common Genovese cultivars. They all have very different flavors and characteristics and the breadth in taste and smell is staggering!
The ideal growth recipe for basil
We recently ran a series of experiments to establish a good growth recipe for basil. Philips Horticulture LED Solutions is a lighting supplier and investigating the effects of light on crop growth is one essential aspect of our research. To find a light recipe that achieves a certain set of desired crop characteristics as efficiently as possible, we often start by testing the performance of a crop under different light regimes (spectrum, intensity, day light hours). In this experiment, we broadened our research to also look at other aspects that influence plant growth and we call the combination of these factors a “growth recipe”.
Faster growth or longer shelf life
One of the most influential growth parameters for basil is temperature. Therefore, we grew a series of basil varieties under different temperatures, ranging from 22°C to 30°C. With every increase in temperature, we saw higher productivities (grams per mole). At the same time, however, the shelf life of the end product went down. This means a good growth recipe for basil will need to balance growth speed and shelf life and will greatly depend on how the end product will be sold. For instance, basil for pesto can be grown very quickly because its shelf life is not as important, whereas basil plants grown for fresh cut stems will need to be grown at somewhat more conservative temperature regimes.
Getting the best of both worlds
In the future, we will look at how we can combine faster growth and long shelf life. One approach might be applying a pre-harvest treatment to achieve both faster growth and long shelf life. Our experiments never focus on growth alone.
Thijs van den Bergh is a Plant Specialist at Philips Lighting. He is located at the GrowWise Research Center. His work focuses on setting up and carrying out trials aimed at developing growth recipes to efficiently grow crops with desired characteristics. He carries out research on light, cropping systems, climate and nutrients for a wide range of crops. In this series of articles, Thijs shares the latest results from growing trials carried out in a multi-layer growing environment without any daylight.
For more information:
Philips
www.philips.com/horti
Publication date: 4/30/2018
Using Sun To Desalinate Water For Irrigation
Using Sun To Desalinate Water For Irrigation
By Gardy Chacha | Published Sat, May 5th 2018
Solar water desalination
Water efficiency in farming and food production, whether for traditional rural irrigation, arid regions or urban farms, represents a key metric in the face of global population growth and climate change.
As it is, 71 percent of the Earth’s surface is covered in water.
A big percentage of this water is salt water – in world’s oceans and seas. Scarcity of freshwater resources therefore makes a compelling argument for desalination. However, the process of desalinating seawater consumes large amounts of energy that some scientists have argued that more energy is lost than gained in the long term – relative to agricultural profit margins.
Sundrop Farms in Australia thus solved the problem by coming up with a solution that draws on one of the few renewable resources in even more abundant supply than seawater – sunlight.
Sundrop Farms harvests solar power to generate energy for desalination to supply hydroponic greenhouses. Requiring no freshwater, farmland or fossil fuels, this potential game-changer for sustainable farming is creating 300 jobs in Port Augusta, South Australia, with a 10-year contract won to grow tomatoes for Coles supermarkets.
RELATED TOPICS: food production farming Clean water Irrigation desalination
Building A Greenhouse On An Island Far, Far Away
Building A Greenhouse On An Island Far, Far Away
The island of Réunion is located in the Indian Ocean, east of Madagascar. The island is 63 kilometers long and 45 kilometers wide, covering a total of 2,512 square kilometers and housing over 860,000 inhabitants. Réunion is formed completely of volcanic rocks and combined with its tropical climate, vegetable production isn't that easy. "Greenhouse production answers the agricultural challenges on this island", Aurore Hoarau of JM Horti Consulting states.
Greenhouse production
Jean-Marc and Aurore were born on the island of Réunion. They both gained experience and an extensive background in horticulture, working as growers and advisors at several greenhouse companies and cooperatives in France, Réunion, Morocco and the UK. A couple of years ago they returned home, and with their company JM Horti Consulting, they are now helping Réunion farmers and growers optimize their operations and guide them on the way to produce more sustainably and responsibly, including the adaption of modern techniques and use of biological crop control.
Small greenhouses
The first greenhouses appeared on the island of Réunion in the late 1990s. Due to the hilly nature, many small nurseries have been established on the island, mainly in the southern part. "The challenge is to produce in a healthy and profitable way on a small agricultural surface", Aurore explains.
The average size of the operations is 5 ha with the vegetable greenhouse being 0.3 ha on average. The climate on the island is tropical. Combined with the demand from the local market for fruit, vegetables, and lettuce, JM Horti Consulting has decided to represent Asthor greenhouses on the island. "We want to work with the product that can be adapted best to the expectations and needs for the farmers, both in terms of quality and professionalism."
Greenhouse project
An example of the developments of horticulture on Réunion is shown in the recently erected greenhouse. "We've accompanied the grower from training in soilless cultivation techniques to realization of the greenhouse project: advising on the choice of the greenhouse, the irrigation system and the utilities to recycle drainage water."
With the application of all these techniques, the completed greenhouse is perfectly compatible with the agricultural development on Réunion: a grower starting a new experience by working in a greenhouse. "We will accompany him in running the greenhouse and growing the crops, knowing he can't wait to start the first harvest from the new greenhouse. Protected cultivation answers the challenges on the island."
For more information:
JmHorti-Consulting
Jean Marc Hoarau & Aurore HOARAU-Ferrante
jmhorticonsulting@gmail.com
Publication date: 5/2/2018
Author: Arlette Sijmonsma
Copyright: www.hortidaily.com
India - June 4-8, Pune: 3rd Greenhouse & Hydroponic Technical Management Course
India - June 4-8, Pune: 3rd Greenhouse & Hydroponic Technical Management Course
Delish Veggies, Graeme Smith Consulting and Future Farms have announced the 3rd Greenhouse and Hydroponic Training Program in Pune, India, after their two training courses in 2017.
The course will again be conducted by two highly experienced Australian industry presenters – Graeme Smith and Rick Donnan. Graeme consults throughout the world, Chairs the ISHS Working Group – Hydroponics and Aquaponics – and is a past Chairman of Protected Cropping Australia. Recent international greenhouse projects include Hyderabad, Abu Dhabi, China and Rajasthan. Rick is the co-principal of Growool Horticultural Systems and is the Q&A columnist for Practical Hydroponics & Greenhouses magazine and provides consultancy services.
Hands-on training at the first training course held in Pune, India
The course assists participants to improve their ability to understand the key principles in a commercial greenhouse and hydroponic production by:
- understanding the principles of controlled production systems
- using correct strategies and technologies to manage greenhouse climates and irrigation
- understanding plant growing requirements and plant production techniques
- developing new strategies for plant protection and integrated pest and disease management
- understanding plant nutrition and fertigation programs
- identifying the risks and opportunities of climate change.
Topics include:
- Media types and characteristics
- Nutrition and nutrient management
- Water quality and treatment
- Environmental management
- Greenhouse business and marketing plan
- Greenhouse design and layout
- Plant structure
- EC and pH
- Plant physiology
- Irrigation management
- Plant health
- Pest and disease control.
The location for the 3rd training course is again Pune, India, to be held from 4-8 June 2018. The course cost is Rs 50,000 excluding 18% GST. Lunch, morning and afternoon tea will be provided throughout the course.
To register your interest, contact the Course Coordinator:
Uday Mathapati on +61 9130098714
or email udaymathapati@gmail.com
or visit www.delishveggies.com for further information.
Publication date: 3/22/2018
Tradepoint Atlantic Welcomes Gotham Greens to Sparrows Point
Tradepoint Atlantic Welcomes Gotham Greens to Sparrows Point
From steel to greens: leading urban agriculture company expands to Baltimore with 100,000-square-foot state-of-the-art greenhouse facility at historic steel mill.
BALTIMORE, MD (May 08, 2018) – Tradepoint Atlantic, a 3,100-acre multimodal global logistics center in Baltimore, Maryland featuring an unmatched combination of access to deepwater berths, railroads, highways and storage space, announced today that Gotham Greens, a rapidly growing agtech startup and leading local produce brand, will open a state-of-the-art hydroponic greenhouse at the site of the former Bethlehem Steel mill.
Gotham Greens’ expansion to Baltimore represents the third city in its growing network of high-tech urban greenhouses, after New York and Chicago. The initial phase of the new greenhouse facility will occupy over 100,000 square feet in the northern part of Tradepoint Atlantic, and is scheduled to open in early 2019. Gotham Greens’ Baltimore facility will create over 60 full-time jobs and will bring a reliable, year-round, local supply of fresh produce to serve retail, restaurant and foodservice customers throughout the mid-Atlantic region.
The climate-controlled farm will be powered by 100% renewable electricity and recycled irrigation water using proprietary methods that yield more than 30 times that of conventional farms, with higher levels of food safety and environmental sustainability.
"We are thrilled that Tradepoint Atlantic has attracted an innovative and growing company like Gotham Greens to Maryland," said Maryland Governor Larry Hogan. "Their unique approach to urban agriculture, in an area once known for steelmaking and shipbuilding, will be an asset to the community and our state's economy. Tradepoint's prime location provides a competitive advantage for fresh food businesses like Gotham Greens to reach a significant mid-Atlantic customer base. Gotham Greens' locating at Tradepoint is yet another example of how Maryland – and Baltimore – is open for business."
“Gotham Greens’ decision to locate at Tradepoint Atlantic is yet another step forward towards bringing 17,000 quality jobs to eastern Baltimore County,” said Baltimore County Executive Kevin Kamenetz. “Tradepoint Atlantic continues to establish itself as a major economic force for the region, attracting diverse businesses with their desirable proximity to the mid-Atlantic market.”
Gotham Greens’ flagship greenhouse, built in Brooklyn, NY in 2011, was the first commercial-scale urban greenhouse facility of its kind in the United States. After opening new locations in New York, the company expanded to Chicago in 2015 by building the world’s largest rooftop farm. Spurred on by its industry-leading agtech expertise and the growing demand for local and artisanal food, Gotham Greens has grown from a single urban farm operation into a multi-state greenhouse developer and operator, dedicated to bringing premium-quality produce to communities across the country. At the time of opening for the new Baltimore facility, Gotham Greens will own and operate 500,000 square-feet of technologically advanced greenhouses across eight facilities in five states.
“Baltimore is the ideal home for Gotham Greens’ expansion to the mid-Atlantic region. We’re thrilled to bring our brand of premium-quality, safe and sustainably-grown produce to supermarkets, restaurants and communities throughout the region,” said Viraj Puri, Co-Founder, and CEO of Gotham Greens. “We’re honored and humbled to join the rich heritage of Maryland farmers, growers, and food producers. Urban agriculture, at its core, is about reconnecting with the community through food, jobs, and economic development. To that end, we’ve found a great partner and are proud to be part of the American industrial turnaround story taking place at Tradepoint Atlantic.”
“We are very excited and extremely proud to welcome Gotham Greens to Tradepoint Atlantic,” said Eric Gilbert, Chief Development Officer of Tradepoint Atlantic. “Today marks a true milestone, in the continuing revitalization of Sparrows Point, where a community synonymous with the production of steel will now be home to a leading agriculture tech startup producing locally-grown, premium produce while bringing green jobs to the community. Gotham Greens is another example of the diverse tenant base we are bringing to a site once dominated by a single industrial user. This diverse tenant base will provide stability to a community hard hit by decades of decline in American industry.”
JLL, a professional services, and investment management firm offering specialized real estate services to clients seeking increased value by owning, occupying and investing in real estate, serves as the exclusive broker for Tradepoint Atlantic.
About Gotham Greens
Gotham Greens is a global pioneer in urban greenhouse agriculture and a leading consumer brand of premium-quality local produce and fresh food products. Gotham Greens’ produce is always locally grown using ecologically sustainable methods in technologically-sophisticated urban greenhouses. The company provides its diverse retail, restaurant, and food service customers with a reliable, year-round supply of fresh produce grown under the highest standards of food safety and environmental sustainability. The company owns and operates over 170,000 square feet of greenhouse across four facilities in New York and Chicago and currently has an additional 500,000 square feet of greenhouse under development in four US states. Gotham Greens employs over 150 full-time team members and was founded in 2009 in Brooklyn, New York. www.gothamgreens.com
About Tradepoint Atlantic
The 3,100-acre multimodal global logistics center in Baltimore, Maryland, offers a gateway to markets around the United States and the world, featuring an unmatched combination of access to deep-water berths, rails and highways. Ground-breaking agreements signed with federal and state environmental regulators in 2014 to remediate the legacy from a century of steel-making, and the financial backing of investment firms Hilco Global and Redwood Capital Investments, as well as the robust support of local and state government, enable the redevelopment of the site through further infrastructure improvements. At full buildout, Tradepoint Atlantic is projected to generate 11,000 permanent jobs, $2.9 billion in annual economic impact, and add a point to Maryland’s gross domestic product as one of North America’s most strategic commercial gateways. www.tradepointatlantic.com
LumiGrow Supplies LED Fixtures to Lettuce Work Foundation Greenhouses
LumiGrow Supplies LED Fixtures to Lettuce Work Foundation Greenhouses
April 20, 2018
By Maury Wright
Editor in Chief, LEDs Magazine
US lettuce grower with a caring social mission has installed LumiGrow SSL enabling full production of leafy greens during cold Ohio winters.
LEDs continue to thrive in horticultural lighting applications as a new lettuce-growing installation attests. LumiGrow has announced that the Lettuce Work Foundation in New Albany, OH has installed Pro 325e fixtures in its lettuce greenhouses that both provide fresh produce to local consumers year-round and aid young adults with autism in entering the workforce. The solid-state lighting (SSL) has enabled better yield during the cold and short days of winter.
Interested in articles & announcements on horticultural lighting?
The Lettuce Work Foundation began commercial growing operations in 2014 with a controlled environment agriculture (CEA) or greenhouse facility. The grower always sought to supply customers, including Kroger and Giant Eagle, with leafy greens for spring salad mixes year-round. But even in the CEA environment, yield suffered in the winter with crop cycles stretching from five weeks to ten, and some weeks transpiring with nothing to harvest.
We will cover CEA, vertical farming, horticultural lighting recipes, and many other topics at our 2018 Horticultural Lighting Conferences. The Horticultural Lighting Conference Europe is slated for May 14–15 in the Netherlands. The Horticultural Lighting Conference US is scheduled for October 9–10 in Portland, OR.
The winter slowdown was doubly troubling for the grower because the business had been created with the goal of providing opportunity to help young adults living with autism. Winter meant less work and fewer opportunities to help the youngsters transition from high school into the workforce. Short days, cloudy skies, and cold, snowy conditions reduced yield and increased mold and mildew in the crop.
Lettuce Work owners Doug and Julie Sharp and greenhouse manager Brent Langenkamp contemplated installation of lighting but found the evaluation of systems and technologies a daunting challenge. But LumiGrow took a proactive role in helping the operation plan an SSL installation, whereas other suppliers had expected the grower to know what they needed and how to install supplemental horticultural lighting.
Indeed, LumiGrow lighting specialist Ashley Veach created a custom plan for Lettuce Work based on the configuration of the operation’s four hydroponic bays. “She helped us figure out how many lights we needed as well as the optimal layout for our custom facility, unlike the other companies that asked us how many units we wanted,” said Doug Sharp.
The results through the first winter of operation with supplemental lighting have exceed the expectations of the Lettuce Work team. “Even though we're only currently using 75% of the space in the greenhouse, we're outperforming last winter,” said Sharp. “This January alone, our revenue was nearly 80% higher than it was that month last year. It's been phenomenal. The color is definitely better, too.”
The Lettuce Work Foundation has installed LumiGrow LED-based horticultural lighting, improving year-round produce yields while providing employment for young adults living with autism.
The results are being felt by the customer as well. Sharp said, “We don’t have to scale back the quantities we deliver in store. We had to ration cases last year. If you skip a store a week or two, you may not get back in there. We haven’t had to deal with that at all. Now, if someone wants extra, we can provide that. It’s really stable. It reduces the risk of us losing a customer because we can provide the same quantities we deliver in the summer.”
Of course, any installation of horticultural lighting comes with both an upfront investment and with the recurring cost of powering the lighting. And with LED-based fixtures, the upfront investment is significantly higher compared to legacy lighting — although the energy efficiency of SSL pays back that upfront premium over time.
Lettuce Work was able to get a state grant to cover part of the purchase of 195 Pro 325e fixtures. Moreover, the Columbus Foundation and Autism Speaks also provided funding to help benefit the student workers.
The choice of LED horticultural lighting proved critical in recurring costs. An electrical contractor had warned the Sharps that electrical costs might reach $1500 per month. But over the initial winter, the bills were typically in the $450 range. And that allowed the greenhouses to be lit for 13-hour growing days.
Of course, there are many methodologies to grow lettuce and other leafy greens indoors. We covered a project from Texas where a grocery store is growing its own greens and herbs just outside the back door using vertical farming in a recycled shipping container. And large-scale vertical farms are filling warehouses with layered crops. The greenhouse approach, however, allows you to turn off the lights in the summer.
Industry experts will deliver more details on horticultural lighting recipe research and system design topics at our upcoming Horticultural Lighting Conferences. To get insight into the content of our conferences, you can peruse the feature articles we published on the presentations at the US conferences in each of the last two years. The 2016 conference featured Robert Colangelo of Green Sense Farms and Cary Mitchell of Purdue University. The 2017 conference featured Steven Newman of Colorado State University and Tessa Pocock of the Center for Lighting Enabled Systems and Applications (LESA) at Rensselaer Polytechnic Institute.
Are Micro Leaves The Next Super Vegetable?
Are Micro Leaves The Next Super Vegetable?
Israeli company 2BFresh believes that the combination of a positive nutrient profile, functionality, and increased availability mean microgreens are set to be the new superfood on the block. Microgreens (or micro leaves) are young sprouts of seeds grown from a variety of edible plants harvested 7-20 days after the seedling emerges.
According to Avner Shohet, CEO and Co-Owner of 2BFresh, part of Teshuva Agricultural Projects, at this point in the plants life-cycle micro greens have the highest proportion of vitamins and minerals to weight. As plants age this ratio decreases, Shohet told FoodNavigator during a visit to one of the company's greenhouse facilities in Israel, which cover 1.6 hectares.
Small but strong 2BFresh cited 2015 research finding micro lettuce to be "significantly richer in minerals including iron, manganese, zinc, selenium, and molybdenum. Further studies confirmed similar results in the mineral content of micro broccoli and spinach.”
"These products are so healthy, they really should be more accessible," said Shohet. "Microgreens are a premium product and more importantly they are healthy.”
2BFresh is working to expand the availability of microgreens and build awareness of the properties of young plants.
Publication date: 4/17/2018
This Former Steel Mill Will Soon Be A Tech-Filled Greenhouse
- 05.07.18
This Former Steel Mill Will Soon Be A Tech-Filled Greenhouse
The next Gotham Greens location will convert old industry in Baltimore into a hydroponic farm, to provide local produce (and jobs).
1/8 [Photo: Gotham Greens]
For decades, a sprawling steel mill in Baltimore, Maryland was a key site for American industry, making steel for World War II battleships and the Golden Gate Bridge. By the year 2000, however, the industry was failing, and site owner Bethlehem Steel declared bankruptcy. Now, one corner of vacant land at the former mill will become an indoor farm growing pesticide-free lettuce in a sensor-filled greenhouse.
“I think what we’re doing is sort of representing 21st-century manufacturing,” says Viraj Puri, co-founder, and CEO of Gotham Greens, the Brooklyn-based urban agriculture company building the new greenhouse. “This, at one point, was the largest steel-producing facility in the world. It employed tens of thousands of people. Those jobs disappeared when the global steel industry changed . . . we’re coming in and helping to revitalize [the economy] and produce jobs that represent this innovative, technologically advanced way to produce food.”
In New York City, the company pioneered using large rooftop greenhouses to grow greens with no soil, no pesticides, and far less space and water than traditional farming in fields. Most lettuce, grown in areas with limited water like Arizona and California, is shipped thousands of miles to consumers on the East Coast. Gotham Greens, like other startups in the urban farming space, wanted to offer consumers fresher produce that used fewer resources.
After opening its first Brooklyn greenhouse in 2011, the company built another on top of a local Whole Foods. A third greenhouse, in Chicago, sits on top of a sustainably designed factory on a former brownfield. A second Chicago location, next to the first, will be complete by the end of this year.
Gotham Greens Chicago [Photo: Julie McMahon/Gotham Greens]
In Baltimore, as in the other cities, the company will provide both low-skill farming and packing jobs and high-skill jobs in horticulture and engineering. The site, now run by a company Tradepoint Atlantic, will now include a mix of occupants rather than a single industry (Tradepoint Atlantic is the fifth owner since the steel mill closed in 2000; the first four tried to revive steel manufacturing there and failed.) UnderArmour and FedEx will use the site for distribution, and others are using it for vehicle importing. But Gotham Greens represents a different type of industry.
It won’t be the first indoor farm at a former steel industry site. In Newark, New Jersey, the vertical farming company AeroFarms grows baby greens where a former steel factory once operated. Because the farms use hydroponic systems–growing without soil, indoors–it’s possible to grow anywhere, including on the ruins of heavy industry.
The new greenhouse in Baltimore will create 60 jobs. That’s far fewer than the 30,000 jobs the former steel plant provided at its height in the middle of the 20th century (though steel mills now use only a tiny fraction of the labor they once did). Puri says that the operation in Baltimore could triple over time.
The company also plans to continue expanding to other cities, albeit slowly. “We are producing a lot of lettuce,” says Puri. “We’re doing about 20 million heads a year. So we’re definitely large-scale at this point. But in order to maintain product quality, consistency, and food safety, which is incredibly important, we didn’t want to rush into opening more facilities than we thought we could effectively, efficiently manage. It’s a measured, step by step approach. We’re assessing sites in other cities as well. Our vision is certainly to have a network of urban greenhouse farms in cities throughout the country.”
ABOUT THE AUTHOR
Adele Peters is a staff writer at Fast Company who focuses on solutions to some of the world's largest problems, from climate change to homelessness. Previously, she worked with GOOD, BioLite, and the Sustainable Products and Solutions program at UC Berkeley.
Australia's Largest Hydroponic Strawberry Glasshouse To Be Built In Victoria's Latrobe Valley
Australia's Largest Hydroponic Strawberry Glasshouse To Be Built In Victoria's Latrobe Valley
April 16, 2018
Mercus Group is about to release 12 new exclusive strawberry varieties following years of research at a Gippsland site.(Supplied: Gippsland Strawberries)
Strawberry growers say plans for Australia's largest hydroponic strawberry glasshouse, to be built in Victoria's Latrobe Valley, will oversaturate an already crowded market.
The Federal Government has provided $3 million towards the glasshouse to be built by Mecrus Group, which trades as Gippsland Strawberries and Berry Sensation. The glasshouse would be six times the size of the MCG.
It will cost $37 million, and will be capable of producing more than 2,000 tonnes of strawberries annually.
Mecrus Group already grows strawberries at Officer and Shady Creek near Warragul, east of Melbourne.
The new $37 million hydroponic strawberry glasshouse will be six times the size of the MCG.
(Supplied: Gippsland Strawberries)
Managing director Barry Richards said more than 120 ongoing jobs will be created after the 12-hectare glasshouse is constructed.
The glasshouse will be built in the Latrobe Valley, a region which has lost hundreds of jobs after a power station closure.
"We'll build it in three, four-hectare stages, just so that's more manageable," he said.
"It's a significant increase from where we are now.
"There'll be 122 full-time jobs after construction and they'll range from professional growers, quality control, harvesting, planting and crop maintenance."
Mr Richards said demand for the company's strawberries was growing locally and it had set its eyes on domestic markets moving forward.
"For the future it'll be interstate but right now we can't keep up with the demand in Victoria," he said.
"Glasshouse production of fresh fruit has grown dramatically over the last 15 years, particularly with tomatoes, cucumbers and eggplants, but glasshouse production of strawberries hasn't as yet developed."
Growers' association says glasshouse will be 'another nail in the coffin' for strawberry industry
Victorian Strawberry Growers Association president Sam Violi said the development of a large strawberry glasshouse in Victoria would kill the industry.
"For the industry, this will be like another nail in the coffin for the strawberry industry in Victoria," he said.
"Most of the strawberry industry in Victoria is family-oriented, husband and wife and maybe some children. There are quite a lot of smaller growers. With the competition, they'll probably be forced out."
Mr Violi said there was already strong competition in Victoria from strawberry growers in Queensland, South Australia and Western Australia.
"We are going to have a fair bit of fruit on the market. The fruit coming out of Queensland in the last few years has caused a glut and we've seen strawberries retail for 99 cents. I think this will have a detrimental effect," he said.
"The prices will go down and be uneconomical.
"We know that the cost of production in Victoria has been about $2 for a 250 gram punnet. It's all manual labour. The profit margin is diminishing and you can't stay in the marketplace for a loss. Bigger corporate people, using other money, can absorb the cost.
"I'm not sure they are tyring to force the closures of business, but it will have that effect."
New strawberry variety to be released
Mecrus Group is about to release 12 new exclusive strawberry varieties following years of research at its Shady Creek site in West Gippsland.
"We spent a number of years overseas working with overseas breeders to try to find newer varieties of strawberries that have a much sweeter taste, more fragrance, a greater shelf life," Mr Richards said.
"All the sorts of things the consumer in Australia is looking for in strawberries.
The first commercial variety to be released is called Desire.
"It has been out over the past year through our stalls at farmers markets and some fruiterers and proved very popular," Mr Richards said.
"It's a reasonably sweet, very red fruit."