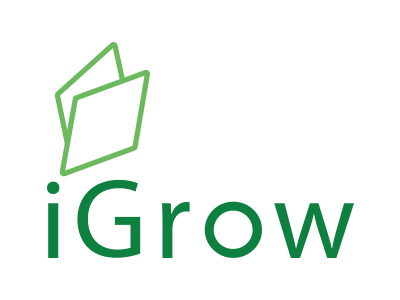
Welcome to iGrow News, Your Source for the World of Indoor Vertical Farming
US (IN): Greenhouse Workshop To Promote Sustainable Growing Practices
September 5, 2018 - West Lafayette. Indiana
US (IN): Greenhouse Workshop To Promote Sustainable Growing Practices
Purdue University’s Department of Horticulture and Landscape Architecture is offering a Greenhouse and Indoor Hydroponics Workshop on Sept. 5, 8 a.m. to 3 p.m., in Room 1159 of Pfendler Hall, 715 W. State St. Participants will learn about optimal conditions for growing hydroponic lettuce, including nutrient recipes, production systems, artificial lighting practices and optimal temperatures for lettuce.
Workshop attendees will also have the opportunity to tour the department’s greenhouse and hydroponic facilities where several hands-on activities will take place. Krishna Nemali, professor of controlled environment agriculture, will lead the workshop. Nemali’s research centers on enhancing sustainable growing practices in controlled environments, like greenhouse and indoor vertical farms.
Click here for more information and to register.
Publication date: 7/18/2018
Students Competing In The Greenhouse Challenge Are In The Final Sprint
While most students have been on holiday, some were hard at work in the basement of Atlas. Student team GreenWURks participates in the Urban Greenhouse Challenge and designed a vertical greenhouse in the old Bijlmer prison in Amsterdam. At the end of last week, they delivered their report. On 28 August, they present their work and the winner of the Challenge will be announced.
The student teams have been working on their designs since February. The GreenWURks team has fifteen members. "In the beginning, there were twenty of us, but a number of students have dropped out and a few have been added”, says Loes Mellink. As the team leader, she has overseen the work of the entire group for the last six months. “New people bring new perspectives. That makes decision-making difficult, but is also a breath of fresh air and motivates everyone to work.”
Community project
With their design, GreenWURks aims to have local residents become shareholders in the city greenhouse in the old Bijlmerbajes. The greenhouse must be installed in consultation with local residents and therefore the cultivation plants are modular. “We want people to bond with the tower and learn about food production. Above all, they must enjoy growing vegetables themselves in the greenhouse and we think that the best way to do that is if they are involved in its establishment”, says Mellink.
This is the atmosphere that the Bijlmer tower should have according to GreenWURks. Impression Shiyi Liu, Du Man and Fangyi Zheng.
Mellink feels that commitment from the surrounding area is important. The connection between the Bijlmerbajes and the surrounding area was already there when it was a prison. During a tour earlier this year, Mellink heard many stories of how prisoners and their family members communicated by standing on the roofs of student homes and yelling to each other. And the prison wardens lived in the adjacent village.
In 2016, the old prison was converted into a residence for refugees, who then started a hotel and a restaurant there. “These social developments characterize the Bajes neighborhood and we have taken this into account in our design”, says Mellink. “The restaurant should definitely remain and can even cook with the vegetables that are grown in the greenhouse.”
Investing in real estate
The students of the Greenhouse Challenge are now on holiday until the end of August. On 28 August, their hard work will culminate in a pitch and an award ceremony for the best idea. The winning team will receive ten thousand euros. Mellink already knows what she would do with the prize money. “If it were up to me, we would organize an educational trip for the whole team. And if anything is left over, we would invest in the renovation of the Bijlmer tower.”
Source: Wageningen University & Research
Publication date: 8/7/2018
MightyVine Tomatoes To Double Operations — Again — To Meet Growing Demand
Agricultural start-up MightyVine, the Rochelle-based hydroponic grower of tomatoes, plans to double its operation by building two more greenhouses. (Stacey Wescott / Chicago Tribune)
Greg TrotterContact Reporter Chicago Tribune
MightyVine, the Rochelle-based hydroponic grower of tomatoes, plans to double the size of its operation once again to help meet increasing demand from large retailers like Costco, Walmart, and Jewel-Osco, according to company executives.
Come September, construction will begin on two more 7.5-acre greenhouses in Rochelle, located about 80 miles west of Chicago, said MightyVine Chairman Jim Murphy. Once the $16 million project is complete,
MightyVine will have four adjacent greenhouses totaling 30 acres that will produce about 105 million tomatoes a year, Murphy said. That represents the second major expansion for MightyVine since launching in 2015 to offer fresh, locally grown tomatoes year-round in the Chicago area.
The agricultural startup has experienced some growing pains, too. In the summer’s hottest weeks, the greenhouses can get too hot, making it difficult to maintain the same size and quality of fruit, Murphy said.
Quantity has been the far greater challenge, though.
Deciding when to enroll in a Medicare prescription drug plan is a big decision and we can help. Check out helpful video tips on getting the most out of Medicare Part D at Walgreens.
“We can’t keep up with demand. … It’s hard to keep them in stores, so we have to build more,” Murphy said.
Much of the company’s recent growth has come through large retailers like Costco, Walmart and Jewel. MightyVine is poised to sell through a second Walmart distribution center, which will expand its reach throughout the state, said MightyVine CEO Gary Lazarski. And after a trial run in 10 Costco stores, MightyVine plans to expand to more than 50 stores by the end of the year. In true supersized Costco fashion, MightyVine tomatoes come packaged in a 3-pound box for $6.49.
Walmart and Costco did not respond to interview requests Monday.
At Jewel, one of MightyVine’s first retailers after Whole Foods Market, the tomatoes are typically available in all 187 stores — when they’re available, said Scott Bennett, produce sales manager for Jewel-Osco.
MightyVine, the Rochelle-based hydroponic tomato farm, plans to double its operation by building two more 7.5 acre greenhouses this fall.
Quality is never the problem with MightyVine, which leaves the tomatoes on the vine to ripen longer than most growers, Bennett said. After the tomatoes are harvested, they’re transported to Jewel’s distribution center in Melrose Park within a couple of hours, he said, and are in stores the next day.
“I’ve been doing produce for 35 years, and this is the best darn tomato I’ve ever had,” Bennett said. “They just don’t have enough product. They have enough to keep everyone hooked. It’s a great game they’re playing — we’re all hooked.”
Lazarski acknowledged there’s been tension with retailers as a result of supply shortages but said that ultimately, that’s a good problem to have. MightyVine has grown from being a “speculative venture” to an established brand, Lazarski said.
MightyVine is one of a handful of large-scale indoor commercial farms to enter the Chicago market in recent years. Others have also found a mix of successes and challenges. BrightFarms, a New York-based company that also has a hydroponic greenhouse in Rochelle, sells its leafy greens in Mariano’s stores. Gotham Greens, another New York-based grower of leafy greens, announced earlier this year that it would build a second greenhouse in the Pullman area on Chicago’s Far South Side.
They’re not all happy stories: FarmedHere, a pioneer of commercial hydroponic farming, closed its Bedford Park greenhouse last year, citing onerous costs and increased competition. Here Holdings, parent company of FarmedHere, instead shifted its focus to making food products — such as juices, salad dressings and spreads — under the Here brand at the company’s food processing plant in Carol Stream in DuPage County.
READ MORE: Coming to Englewood: Kimbal Musk's Square Roots urban farm in shipping containers »
When MightyVine began selling tomatoes in 2016, it almost immediately found high-profile allies among some of Chicago’s top chefs, including celebrity chef Rick Bayless who promoted the brand on social media. Today, MightyVine sells tomatoes to more than 200 restaurants in the Chicago area, including restaurants with the Lettuce Entertain You Enterprises and Four Corners restaurant groups.
MightyVine is backed by Grow Forward, Murphy’s investment and philanthropy firm. Local Foods, another of Murphy’s ventures, is the wholesaler that distributes the MightyVine tomatoes to restaurants. The Grow Forward portfolio also includes Handcut Foods, a food service company for schools and universities, and Carbon Green BioEnergy, a Michigan-based ethanol company.
Murphy, a longtime Chicago-area entrepreneur, called MightyVine his “baby.”
“Everyone in the business said we couldn’t brand a tomato,” Murphy said. “We’ve captured the marketplace.”
Twitter @GregTrotterTrib
Small Indoor Greenhouses Let Apartment Dwellers Grow Veggies
August 7, 2018 by Tracee M. Herbaugh
This undated photo provided by Harrison Lin shows what the completed version of the indoor greenhouse made by a group of six engineering students at Rice University. The students built three of these greenhouses, about the size of a small …more
You don't need a green thumb to grow vegetables indoors.
On the contrary, there are plenty of indoor greenhouses that take the work out of growing plants, from the amount of water they get to the right dosage of light.
One of these indoor greenhouses—or automated growing systems, as they're referred to—was created by six engineering students at Rice University. Aside from planting the seeds, the greenhouse does pretty much everything. It's about the size of a small bookshelf and operates anywhere indoors.
"We didn't want it to take up too much space in an apartment," said Harrison Lin, a student who worked on the project. He said they wanted to "make it not intrusive, but it could still grow a useful amount of plants."
There are push buttons on the device to designate how much light and water the plants get, and to determine the temperature inside it. If you're feeling extremely hands-off, there are three pre-set options: leafy greens, roots, and herbs. Select what you're growing and go about your business.
"In the most ideal circumstance, you plant your seeds, put on the correct settings and walk away until it's ready to harvest," said Jack Kaplan, another student on the team.
This undated photo provided by Harrison Lin shows the watering and lighting system inside the indoor greenhouse constructed by six engineering students at Rice University. The system measures water for specific vegetables and the lights …more
Most indoor growing systems are hydroponic, meaning plants are planted in water mixed with mineral nutrients, but this one uses a soil trough for planting. LED bulbs provide the plants with the red-blue spectrum of light needed to grow. The only maintenance is refilling the water tank every three weeks.
The students built three of these indoor greenhouses as a senior project. They were installed at the HSB Living Lab, a residential research facility at Chalmers University of Technology in Sweden.
This undated photo provided by Mary Leach shows George Reberio Brooks Jr. on his orchard in Tewksbury, Mass. Brooks Jr. has more than 45 years experience growing fruits and vegetables but still found it difficult to grow lettuce indoors. (Mary Leach via AP)
Growing food indoors, often in small spaces like city apartments, has become popular.
In 2017, indoor gardening was listed as a popular trend in a report by Garden Media Group, a marketing group that tracks industry. Apartment dwellers have less room for a traditional garden but still, want fresh veggies.
This undated photo provided by Mary Leach shows George Reberio Brooks Jr. on his orchard in Tewksbury, Mass. Brooks Jr. has more than 45 years experience growing fruits and vegetables but still found it difficult to grow lettuce indoors. (Mary Leach via AP)
Businesses are noticing the expanded interest in at-home gardening.
Aerogarden, owned by Scott's Miracle Grow and the Hawthorne Gardening Company, is another automated in-home growing system on the market. It's automated, hydroponic systems range in size and price point—the smallest retails for $99 and holds four plants, while the largest sells for nearly $700 and grows 24. Sales have grown over 20 percent year over year since 2013, and last year's sales grew by more than 30 percent, according to company numbers.
Automated systems take the guess-work out of gardening, said Clydette Alsup-Egbers, an associate professor of plant science at Missouri State University. The biggest reason that indoor plants die, she said, is over-watering. If an automated system is used, that risk is eliminated.
"People who are new to growing don't know what they're doing," she said. "A kit makes them feel more confident."
This undated photo provided by Mary Leach shows George Reberio Brooks Jr. touching some of the plants blooming in his orchard greenhouse in Tewksbury, Mass. Brooks Jr. has more than 45 years experience growing fruits and vegetables but still …more
Automating everything is what commercial greenhouses have done for years, said Julie Bare, an estate gardener at Meadowbrook Farm, located in Jenkintown, Pennsylvania, and owned by the Pennsylvania Horticultural Society.
Bare helps grow some of the hundreds of plants on display in the renowned Philadelphia Flower Show. To do this, greenhouses are necessary; the show is held annually in March, which means short days and cold temperatures.
Still, even the most seasoned gardener can run into problems with indoor vegetables.
A few years ago, George Rebeiro Brooks Jr., a retired mechanical engineer, tried growing lettuce in pots inside at his home in Tewksbury, Massachusetts. Brooks, who owns Green Hollow Orchards, has grown apples, tomatoes, and other plants for local farmers markets for more than 45 years. But his indoor lettuce turned out limp, not crispy.
"It's just my guess, but I think it didn't have the right air circulation indoors to make it toughen up," he said.
This undated photo provided by Mary Leach shows George Reberio Brooks Jr. in a greenhouse on his orchard in Tewksbury, Mass. Brooks Jr. has more than 45 years experience growing fruits and vegetables but still found it difficult to grow lettuce indoors. (Mary Leach via AP)
UAE developer Seven Tides To Use Hydroponics To Supply Its Hotels
Seven Tides is planning to expand a hydroponic greenhouse on the World Islands to supply its portfolio of three Dubai hotels
UAE-based developer Seven Tides is planning to expand a hydroponic greenhouse on the World Islands to supply its portfolio of three Dubai hotels, according to CEO Abdulla bin Sulayem.
Hydroponics, a subset of hydroculture, allows one to grow plants without the need for soil, using mineral solutions in a water solvent. According to bin Sulayem, the process will allow the company to grow almost any plant at any time of the year, meaning that climate and season will no longer present any limitations.
According to bin Sulayem, collectively, Seven Tides’ hospitality portfolio – which includes Anantara, DUKES and the Mövenpick Ibn Battuta Gate hotel – “consume a large amount of fruit and vegetables on a daily basis.”
“We already have a large greenhouse located on the World Islands, but we are currently working to upgrade the facility, with the intention of supplying all of our hotels with the majority of the fruit and vegetables they require within the next few months,” he told Arabian Business.
Sulayem added that hydroponics is cleaner and more efficient than traditional agriculture techniques.
“It also produces better tasting produce with more nutritional value and can reduce water consumption by up to 90 percent,” he said.
In addition to its hospitality portfolio, Seven Tides has an upcoming project on the World Islands, where the company is creating an exclusive resort of 60 one-and two-bedroom villas, as well as SE7EN CITY JLT, a mixed-use development in Dubai’s Jumeirah Lakes Towers.
For all the latest travel news from the UAE and Gulf countries, follow us on Twitter and Linkedin, like us on Facebook and subscribe to our YouTube page, which is updated daily.
Last Updated: Tue 31 Jul 2018
China Unveils High-Tech Indoor Farm That Can Feed 36,000 People
China Unveils High-Tech Indoor Farm That Can Feed 36,000 People
by Ryan General | July 9, 2018
A Chinese firm has unveiled an improved version of their “smart farm” which enables the growth of more vegetables without soil or natural sunlight in an automated environment.
Currently utilized in many parts of the world, the technology of controlled-environment agriculture via indoor farming is being improved upon by a company in Anxi, Fujian Province, called Sanan Sino-Science in hopes of setting the course for the future of agriculture in China.
The firm unveiled its most recent expansion project last Friday, featuring a high-tech indoor farm that has been in development for about two years, MailOnline reports.
The farm, which covers a 5,000-square-meter (53,819-square-foot) indoor space, produces eight to ten metric tons of vegetables daily while requiring only four staff members to manage it. Conventional farmlands would require about 300 farmers to produce the equivalent amount which can feed almost 36,000 people.
Equipped with advanced autonomous technology, the facilities grow vegetables and herbs in multilevel cultivation beds of hydroponic solutions in a controlled environment.
The smart farming method involves a strict system that regulates temperature, water source, humidity, nutrients and LEDs that replace sunlight in a confined indoor space. Such regulations allow the firm to significantly save on water, granting each plant only the right amount it needs.
Sanan Sino-Science’s first generation indoor farm is claimed to be the world’s largest vertical farming complex, covering an area of 1 hectare (2.47 acres).
“Compared with our first generation smart farm, this new plant yields even more effective results while reducing labor and environmental costs,” Sanan Sino-Science CEO Zhan Zhuo was quoted as saying.
Zhan explained that their revolutionary technique “maximizes the plant’s growth potential while maintaining a sustainable and continuous growth cycle.”
While vegetables in a conventional farm need about 40 to 60 days to reach maturity depending on weather condition, Sanan Sino-Science’s “vegetable factory” allows the harvesting of smaller-sized varieties in just 18 days and larger vegetables just between 33 and 35 days.
“This farming method is particularly beneficial in challenging environments such as deserts, mountainside towns, or in cities where labor comes at a high cost,” Zhan said.
Zhan claims that the smart factory can produce 3,000 to 3,500 metric tons of vegetables annually at full capacity.
The company plans to improve its farms by installing AI technology to be able to record and analyze growth data via sensors to identify the optimal growing condition for each specific kind of vegetable.
Vegetables produced from the high-tech farms are shipped to the rest of Fujian Province and Shanghai in supermarkets and high-class restaurants at around 30 yuan ($4.50) to 36 ($5.50) yuan per kilogram (2.2 pounds). These high-tech grown vegetables cost more than regular vegetables which are sold at a wholesale price of 2.85 yuan ($.50) per kilo in China.
Zhan, who expressed the company’s interest in bringing the concept of “produce locally, sold locally” to different cities worldwide, says their technologies have been shared with countries such as the U.S., Japan, and Singapore.
Bright Farms Takes Local Produce Model Nationwide With Hydroponics
It wasn’t too long ago when locally-grown produce evoked images of backyard gardens or roadside produce stands many miles outside of city limits. Now, the local produce movement has morphed into an urban-centered industry thanks to the rise of hydroponic greenhouses.
Read the complete article here
Way To Grow: Urban Farms Are An Amenity At Many Developments
Denver Construction & Development
July 12, 2018, Margaret Jackson, Bisnow Denver
As people increasingly demand to know where their food comes from, more developers are jumping on board to integrate urban farms into their projects.
Way To Grow: Urban Farms Are An Amenity At Many Developments Courtesy of Tracy Weil RiNo Art District Creative Director Tracy Weil grows heirloom tomatoes at Farm 39 in RiNo
Take S*Park. Named for its heritage as Sustainability Park, the 99-unit residential project in Denver’s Curtis Park neighborhood includes a 7,200 SF greenhouse with 340 aeroponic towers that will grow leafy greens.
The greenhouse will be operated by Altius Farms, which will offer residents a vegetable subscription program, greenhouse tours, and classes and community dinners with Denver celebrity chefs. Altius also will provide neighborhood restaurants with produce from the greenhouse.
Way To Grow: Urban Farms Are An Amenity At Many Developments Courtesy of Altius Farms Altius Farms will grow leafy greens on towers like these at Scissortail Farms in Tulsa, Okla.
Altius Farms founder and CEO Sally Herbert said the tower system at S*Park will produce 75,000 pounds of leafy greens a year — the equivalent of 1.5 acres of conventional farming each month. The towers use 10% of the water of a traditional farm and produce 10 times the yield, and the produce is much fresher than what consumers find in grocery stores, she said. Colorado imports 97% of its produce, and after it spends seven to 14 days in transport, between 20% and 40% of it is discarded.
“When restaurateurs receive produce that’s come in from Arizona or California, it’s been harvested early and gets wilty or bruised,” she said. “You have to throw away the crappy stuff.”
NAVA Real Estate Development is taking a different approach at Lakehouse, its 12-story, 196-unit condominium project at Sloan’s Lake. The produce from its second-floor garden will be available only for residents of the 12-story building.
“We are growing a certain amount of vegetables and herbs on-site that will be professionally managed and harvested,” NAVA co-founder and CEO Brian Levitt said. “We’ll have a harvest room where people can be part of a harvest. There will be opportunities where people can reach over and pick something and put it in their salad. There will be a juicing center and sauna where people can sit and enjoy the juice.”
Way To Grow: Urban Farms Are An Amenity At Many Developments Bisnow/Margaret Jackson The greenhouse at S*Park will provide produce to residents and nearby restaurants.
The garden is just one component of NAVA’s efforts to ensure a healthy environment for residents of Lakehouse, which is seeking Well Building certification. It also must meet standards for air and water quality and fitness, among other things.
Urban Ventures has launched a wellness program that includes food production at Aria Denver development. Aria Denver has partnered with Regis University to launch the Cultivate Health program at its development in northwest Denver. Food production, in both gardens and greenhouses in the neighborhood, is just one component of the program, which is designed to support the health and wellness of residents living in the multi-generational, mixed-income community. Its food production partners are UrbiCulture Farms and Groundwork Denver.
Way To Grow: Urban Farms Are An Amenity At Many Developments Courtesy of Tracy Weil Farm 39 in RiNo sells about 8,000 tomato plants a year
Urban farming is a growing trend both in new developments and in city neighborhoods.
Artist Tracy Weil, creative director of the RiNo Art District, co-founded Heirloom Tomato Farms with Carolyn Jansen in 2004 when they weren’t able to find the produce they wanted. They started with 175 plants, which they sold and gave to friends. Weil was on the board of The GrowHaus, a nonprofit indoor farm, marketplace and educational center in Denver’s Elyria-Swansea neighborhood. The GrowHaus, based in a historic 20K SF greenhouse, agreed to give him enough space to expand to 1,200 plants.
But then aphids from the herbs in The GrowHaus infested Weil's tomato plants, so he built his own greenhouse — Farm 39 — on an eighth of an acre at 3611 Chestnut Place in RiNo. Jansen started The Sparrow in Capital Hill. The combined farms are known as Heirloom Tomato Farms. Now, people line up every spring to purchase some of the 8,000 plants the two farms grow before they sell out.
“It’s been kind of a nice supplemental income,” he said. “As an artist, I wanted to diversify my income stream.
See Also: Sopher Sparn Project Wins Community Building Award Related Topics: urban farming, Brian Levitt, RiNo Art District, Urban Ventures, S*Park, Altius Farms, Sally Herbert, NAVA Real Estate Development, Lakehouse, Aria Denver, Tracy Weil
Read more at: https://www.bisnow.com/denver/news/construction-development/way-to-grow-urban-farms-are-an-amenity-at-many-developments-90572?utm_source=CopyShare&utm_medium=Browser
Forbes List of Innovative Ag-Tech Companies Includes Greenhouse Producers
Forbes List of Innovative Ag-Tech Companies Includes Greenhouse Producers
Posted by Brian Sparks|July 8, 2018
BrightFarms is one of a few greenhouse companies on Forbes’ list of the top 25 most innovative ag-tech startup companies in 2018.
Forbes magazine recently posted a list of the 25 most innovative ag-tech startups in 2018, which includes a few companies involved in greenhouse plant production.
To compile the list, Forbes editors surveyed the agricultural technology landscape by speaking with experts, venture capitalists, and accelerators. Then they examined financials and each company’s agricultural credentials, with help from Seana Day at the Mixing Bowl, who did comprehensive research on the ag-tech environment.
“In 2017, ag-tech funding through investment or acquisition increased 32% to $2.6 billion, and half of the top 20 deals in the space exceeded $50 million,” the Forbes article states. “The bad news? There is now so much money flowing into the space, and so many entrepreneurial solutions coming to the market, that it’s harder than ever to cut through the noise.”
This year’s Forbes list features 12 alumni and 13 newcomers. The high degree of turnover is due in part to mergers and acquisitions, and to a number of companies making big gains in both technology and dollars.
The complete list is available here. Keep reading for a brief look at a few greenhouse-related companies that made the list.
• BrightFarms: This indoor farming outfit aims to help consumers buy local produce by building greenhouses in the communities it serves. So far, this strategy has resulted in leafy greens that take 80% less water, 90% less land, and 95% less shipping fuel than lettuce that is grown out west and shipped east. BrightFarms supplies some of America’s largest grocers, including Walmart, ACME, ShopRite, and Giant.
• Plenty: Plenty is an indoor farming company using machine learning, artificial intelligence, and crop science to optimize yields and give produce exactly what it needs to achieve optimal freshness and taste. Bezos Expeditions, SoftBank Vision Fund, and the Data Collective are among investors that have given Plenty and its vision $226 million in venture funding.
• Produce Pay: This supply chain startup with $12.5 million in funding connects wholesale buyers with produce sellers. The platform fixes cash-flow problems by paying for product the day after it is shipped, rather than the typical 30- to 45-day waiting period. ProducePay has provided liquidity to more than 200 growers and 50 distributors, financing more than $500 million of produce in its three years of operation.
Brian Sparks is senior editor of Greenhouse Grower and editor of Greenhouse Grower Technology.
Little Leaf Farms Keeps Growing And Growing
Little Leaf Farms Keeps Growing And Growing
July 8, 2018
By Paula J. Owen Correspondent
SHIRLEY — Little Leaf Farms is disrupting the lettuce industry and giving people in New England a high-quality product that is cut and delivered within 24 hours, taking a piece of the business away from the giant California lettuce conglomerates.
The business completed an expansion last month that doubled the size of its hydroponic greenhouses, going from 2.5 acres of totally controlled indoor automated, hands-free systems, free of pesticides, herbicides and fungicides, grown year-round, to 5 acres of greenhouse space.
The state-of-the-art operation at Little Leaf Farms, which opened in 2015, is on 12 acres in Devens and Shirley. The company specializes in local, fresh lettuces and salad greens, and is home to one of the most modern, technologically-advanced greenhouses in the world, with technology ranging from UV lights that disinfect water used to water plants, to soil-less trays that replace traditional soil.
The greenhouse technology at Little Leaf was developed in the Netherlands and the growing system in Finland, according to Paul C. Sellew, owner and CEO, who said Little Leaf just bought another 12 acres a few weeks ago, and plans to double its greenhouse capacity again next year. Little Leaf also hired a third grower.
“It is really a consumer-led expansion,” Mr. Sellew said. “People are buying and loving our product, and we were not supplying market level to meet demands.”
Still a small supplier compared to California, which dominates the industry and provides more than 90 percent of the region’s lettuces, Little Leaf is showing it can deliver a superior product year-round that doesn’t take weeks to transport to New England, making the product on the shelf fresher than what is grown on the West Coast.
“Prior to us, 100 percent of lettuce came from California and Arizona,” Mr. Sellew said. “We’re up against these billion-dollar California lettuce conglomerates. We’re a small local producer, and we had to win the battle in the marketplace by demonstrating we could deliver a superior product to California’s product.”
The only year-round lettuce supplier in Massachusetts, Mr. Sellew said the expansion costing “in the millions” was also an investment in the development of the local food movement still in its infancy.
“One crop we’re looking at seriously is romaine,” he said. “With the recent romaine scare from California and Arizona field producers, people have asked us to grow romaine that is safer to eat.
“A field with people and animals is not a controlled environment, and you don’t know what is running from the field. A greenhouse is a completely controlled environment. There is no way disease can enter the system, and you can have a safe product year-round. California growers can’t make that same claim. ”
Another distinction of Little Leaf is that it captures water from the roofs of the greenhouses and stores it in a lined pool and disinfects it for irrigation.
“In Massachusetts, we have water, and the West Coast doesn’t,” Mr. Sellew said. “They are pumping it out of the ground and putting it in a lettuce leaf and transporting it across the country. In a sense, you’re drinking California water in the form of a lettuce leaf, and it doesn’t make sense. It makes sense to grow it where you have 47 of inches of rain a year. California has less than 5 inches. Pumping out groundwater is completely unsustainable.”
Nikita D. Geovanis, order fulfillment manager at Little Leaf, said the business produces 8,000 pounds of lettuce a day in summer and about 7,000 in the winter.
“This is the most technologically advanced greenhouse in the world,” Mr. Geovanis said. “We’re here disrupting the industry and taking a market share share.”
Timothy K. Cunniff, co-founder and executive vice president of sales and marketing, said the first hurdle was getting a space on the retail shelf, “which is valuable real estate.”
“They cut us into the set, and we were getting noticed and repeat purchases,” Mr. Cunniff said. “Consumers know us and are actively talking about us. It’s been crazy.”
Little Leaf is also growing in the food service sector, he said, with their lettuce in area colleges, hospitals and restaurants.
“It wasn’t our primary focus, but we’re trying to feed as many people as we can,” he said. “The majority of our food comes through the grocery store. We’re in over 1,000 grocery stores. It has been an emotional roller coaster, without a doubt — the first year — and now it’s like, we got a tiger by the tail. We’re not just targeting the intellectual elite who want to support the local food movement. We’re targeting everyone.”
Andy W. Kendall, executive director of the Henry P. Kendall Foundation, said the aim is to try to grow locally as much of the food consumed in New England as possible to make New England more resilient.
“Most of the food that comes to New England travels thousands of miles,” Mr. Kendall said. “We’re at the end of a long supply chain that originates in California, the West and other places around the world.”
In Boston alone, he said the market for lettuce is about $100 million, and 99 percent comes from California and out West.
“It is not rare that you will see it already going bad and literally have to rush to eat it,” he said. “It’s not a great experience. With Little Leaf, it may be 12 hours before it appears on the shelf from when it was actually growing. It looks better and tastes better, and the consumer gets the benefit of having it in their fridge for the three weeks it would take to get here from California.”
Italy: Tomato Grower Plans To Light 6 Hectares With LED
Italy: Tomato Grower Plans To Light 6 Hectares With LED
Prominent Italian tomato grower Gandini Antonio officially selected igrox srl as technological partner in LED supplemental lighting. Gandini is going to increase the LED lighted surface in their greenhouses with a new system, in order to improve yield and quality of crop. The first delivery of the LED systems is scheduled for week 39.
From HPS to LED
Gandini Antonio is the main tomato grower in the north of Italy; they currently have 16,000 m2 already lighted with HPS. Gandini wants to replace its 600W HPS with LED systems in order to increase PPFD (photosynthetic photon flux density) and improve the yield and quality of tomatoes, Alessandro Oliveri, CEO of igrox, tells us.
"In 2017 Gandini decided to test our a new LED fixture, a toplighting system of 300W and 2.35uMol/J efficiency with our HEx spectrum, specifically designed for supplemental lighting applications in greenhouses", Alessandro explains. "Our new system has been designed to get the best balance between efficiency and cost, ensuring high ROI and low investments per square meter."
In the test, Gandini compared different LED fixtures from other well known manufacturers. "Gandini selected our solution thanks to the best return on investment respect to the other tested LED fixtures. Our new systems produced the same yield but with 22% less power consumption respect to the other tested LED fixtures. In addition to this, the plants have a higher productivity and the fruits a superior quality if compared with the old HPS systems."
First phase: 7,500 square meters
The partnership with Gandini starts with a first order for substitution of HPS fixtures, getting a total LED lighted surface of 7,500 m2. Gandini aims to get to 60,000 m2 of LED lighted greenhouses in the next 2 years.
Cherry tomatoes during the test
igrox horticulture business
Horticulture is a relatively recent venture for the people behind igrox, but they have been around for a while, Alessandro says: "We have a history of 40 years in general lighting and, after 2 years spent in R&D, in 2017 we started the horticulture business with the new brand igrox.
"We develop LED lighting systems for plant growth in controlled environments, combining latest technologies and high quality LED chips to provide top class, cost-effective lighting solutions.
"Our team is composed of engineers, biologists and agronomists in order to optimize and integrate our solutions with the specific needs of controlled environments for plant growth."
For more information:
igrox
Via Vittorio Veneto 23b
20010 Bernate Ticino (MI)
Italy
info@igrox.com
www.igrox.com
For more information:
igrox
Via Vittorio Veneto 23b
20010 Bernate Ticino (MI)
Italy
info@igrox.com
www.igrox.com
For more information:
igrox
Via Vittorio Veneto 23b
20010 Bernate Ticino (MI)
Italy
info@igrox.com
www.igrox.com
For more information:
igrox
Via Vittorio Veneto 23b
20010 Bernate Ticino (MI)
Italy
info@igrox.com
www.igrox.com
For more information:
igrox
Via Vittorio Veneto 23b
20010 Bernate Ticino (MI)
Italy
info@igrox.com
www.igrox.com
For more information:
igrox
Via Vittorio Veneto 23b
20010 Bernate Ticino (MI)
Italy
info@igrox.com
www.igrox.com
For more information:
igrox
Via Vittorio Veneto 23b
20010 Bernate Ticino (MI)
Italy
info@igrox.com
www.igrox.com
For more information:
igrox
Via Vittorio Veneto 23b
20010 Bernate Ticino (MI)
Italy
info@igrox.com
www.igrox.com
For more information:
igrox
Via Vittorio Veneto 23b
20010 Bernate Ticino (MI)
Italy
info@igrox.com
www.igrox.com
For more information:
igrox
Via Vittorio Veneto 23b
20010 Bernate Ticino (MI)
Italy
info@igrox.com
www.igrox.com
For more information:
igrox
Via Vittorio Veneto 23b
20010 Bernate Ticino (MI)
Italy
info@igrox.com
www.igrox.com
For more information:
igrox
Via Vittorio Veneto 23b
20010 Bernate Ticino (MI)
Italy
info@igrox.com
www.igrox.com
For more information:
igrox
Via Vittorio Veneto 23b
20010 Bernate Ticino (MI)
Italy
info@igrox.com
www.igrox.com
For more information:
igrox
Via Vittorio Veneto 23b
20010 Bernate Ticino (MI)
Italy
info@igrox.com
www.igrox.com
For more information:
igrox
Via Vittorio Veneto 23b
20010 Bernate Ticino (MI)
Italy
info@igrox.com
www.igrox.com
For more information:
igrox
Via Vittorio Veneto 23b
20010 Bernate Ticino (MI)
Italy
info@igrox.com
www.igrox.com
For more information:
igrox
Via Vittorio Veneto 23b
20010 Bernate Ticino (MI)
Italy
info@igrox.com
www.igrox.com
For more information:
igrox
Via Vittorio Veneto 23b
20010 Bernate Ticino (MI)
Italy
info@igrox.com
www.igrox.com
For more information:
igrox
Via Vittorio Veneto 23b
20010 Bernate Ticino (MI)
Italy
info@igrox.com
www.igrox.com
For more information:
igrox
Via Vittorio Veneto 23b
20010 Bernate Ticino (MI)
Italy
info@igrox.com
www.igrox.com
For more information:
igrox
Via Vittorio Veneto 23b
20010 Bernate Ticino (MI)
Italy
info@igrox.com
www.igrox.com
For more information:
igrox
Via Vittorio Veneto 23b
20010 Bernate Ticino (MI)
Italy
info@igrox.com
www.igrox.com
For more information:
igrox
Via Vittorio Veneto 23b
20010 Bernate Ticino (MI)
Italy
info@igrox.com
www.igrox.com
For more information:
igrox
Via Vittorio Veneto 23b
20010 Bernate Ticino (MI)
Italy
info@igrox.com
www.igrox.com
For more information:
igrox
Via Vittorio Veneto 23b
20010 Bernate Ticino (MI)
Italy
info@igrox.com
www.igrox.com
For more information:
igrox
Via Vittorio Veneto 23b
20010 Bernate Ticino (MI)
Italy
info@igrox.com
www.igrox.com
For more information:
igrox
Via Vittorio Veneto 23b
20010 Bernate Ticino (MI)
Italy
info@igrox.com
www.igrox.com
For more information:
igrox
Via Vittorio Veneto 23b
20010 Bernate Ticino (MI)
Italy
info@igrox.com
www.igrox.com
For more information:
igrox
Via Vittorio Veneto 23b
20010 Bernate Ticino (MI)
Italy
info@igrox.com
www.igrox.com
For more information:
igrox
Via Vittorio Veneto 23b
20010 Bernate Ticino (MI)
Italy
info@igrox.com
www.igrox.com
For more information:
igrox
Via Vittorio Veneto 23b
20010 Bernate Ticino (MI)
Italy
info@igrox.com
www.igrox.com
For more information:
igrox
Via Vittorio Veneto 23b
20010 Bernate Ticino (MI)
Italy
info@igrox.com
www.igrox.com
For more information:
igrox
Via Vittorio Veneto 23b
20010 Bernate Ticino (MI)
Italy
info@igrox.com
www.igrox.com
For more information:
igrox
Via Vittorio Veneto 23b
20010 Bernate Ticino (MI)
Italy
info@igrox.com
www.igrox.com
For more information:
igrox
Via Vittorio Veneto 23b
20010 Bernate Ticino (MI)
Italy
info@igrox.com
www.igrox.com
For more information:
igrox
Via Vittorio Veneto 23b
20010 Bernate Ticino (MI)
Italy
info@igrox.com
www.igrox.com
For more information:
igrox
Via Vittorio Veneto 23b
20010 Bernate Ticino (MI)
Italy
info@igrox.com
www.igrox.com
For more information:
igrox
Via Vittorio Veneto 23b
20010 Bernate Ticino (MI)
Italy
info@igrox.com
www.igrox.com
For more information:
igrox
Via Vittorio Veneto 23b
20010 Bernate Ticino (MI)
Italy
info@igrox.com
www.igrox.com
For more information:
igrox
Via Vittorio Veneto 23b
20010 Bernate Ticino (MI)
Italy
info@igrox.com
www.igrox.com
For more information:
igrox
Via Vittorio Veneto 23b
20010 Bernate Ticino (MI)
Italy
info@igrox.com
www.igrox.com
For more information:
igrox
Via Vittorio Veneto 23b
20010 Bernate Ticino (MI)
Italy
info@igrox.com
www.igrox.com
For more information:
igrox
Via Vittorio Veneto 23b
20010 Bernate Ticino (MI)
Italy
info@igrox.com
www.igrox.com
For more information:
igrox
Via Vittorio Veneto 23b
20010 Bernate Ticino (MI)
Italy
info@igrox.com
www.igrox.com
For more information:
igrox
Via Vittorio Veneto 23b
20010 Bernate Ticino (MI)
Italy
info@igrox.com
www.igrox.com
For more information:
igrox
Via Vittorio Veneto 23b
20010 Bernate Ticino (MI)
Italy
info@igrox.com
www.igrox.com
For more information:
igrox
Via Vittorio Veneto 23b
20010 Bernate Ticino (MI)
Italy
info@igrox.com
www.igrox.com
For more information:
igrox
Via Vittorio Veneto 23b
20010 Bernate Ticino (MI)
Italy
info@igrox.com
www.igrox.com
Chicago's North Lawndale’s ‘Farm on Ogden’ Looks to Supply Fresh Produce, Jobs
North Lawndale’s ‘Farm on Ogden’ Looks to Supply Fresh Produce, Jobs
Alex Ruppenthal | June 19, 2018
A graphic rendering of the soon-to-be-completed Farm on Ogden, which opens June 22. (Courtesy Chicago Botanic Garden)
Angela Mason has spent decades running school and neighborhood garden programs in Chicago, but she’s never been part of anything quite like this.
Neither has anyone else.
On Friday, two organizations that might seem to have little in common – the Chicago Botanic Garden and Lawndale Christian Health Center – will celebrate the opening of the Farm on Ogden, a 20,000-square-foot urban agriculture facility that aims to bring healthy foods and good-paying jobs to North Lawndale. Data shows that North Lawndale has some of the highest unemployment and poverty rates in the city, and residents there suffer from conditions such as diabetes and post-traumatic stress syndrome at rates far exceeding city and national averages.
Located in the heart of the Southwest Side neighborhood – at 3555 Ogden Ave., next to the Central Park Pink Line CTA station – the Farm on Ogden will allow the Botanic Garden’s Windy City Harvest to expand programs for job training, farming, food safety, cooking and nutrition, while also providing more fresh produce to community members and patients at Lawndale Christian Health Center.
Participants in Windy City Harvest's Corps training program construct a platform for the Farm on Ogden's aquaponics system. (Courtesy Chicago Botanic Garden)
Mason said the project is the culmination of 15 years of work in urban agriculture – and a giant step forward from the school and neighborhood-focused garden programs she once ran.
“We used to say that our programs served 10,000 kids per year,” said Mason, who has led Windy City Harvest since shortly after its founding in 2001. “But what does that really mean when you spend 20 minutes with one kid, put a plant in the ground and say, ‘Good luck,’ and then walk away?”
With the Farm on Ogden, Mason said Windy City Harvest will be able to grow its job training program – which targets people who have been incarcerated – from 250 to 350 people per year. Participants in the program can obtain industry-specific training certificates in a number of areas, including aquaponics and vertical farming, edible landscaping and rooftop farming.
Thanks to the new facility, Windy City Harvest will also be able to operate its Youth Farm job training program year-round as opposed to only during summer months.
“If you can pack and sort produce or perishable items, you can pack and sort car parts,” said Mason, noting that participants in WCH’s training programs have landed jobs at Whole Foods, Eataly Chicago, a number of food distribution warehouses and other companies. “It’s just figuring out how to transfer that skill to another industry.”
Tilapia tanks for the aquaponics system at the Farm on Ogden (Courtesy Chicago Botanic Garden)
The farm will also supply produce to patients at Lawndale Christian Health Center through the Veggie Rx program, which allows doctors to write prescriptions for healthy foods to combat diet-related conditions such as high blood pressure and diabetes. The program, which served 160 families last year, will now aim to provide boxes of fresh produce to 400 families, Mason said.
The space will also feature a 7,300-square-foot greenhouse, a commercial and teaching kitchen, a year-round farm stand and shared space for urban farmers – in addition to a 50,000-gallon aquaponics system, which will produce 2,500 heads of lettuce each week and 14,000 pounds of tilapia annually.
Once fully complete in several months, the facility will glow with special purple LED lights facing one of the city’s busiest streets.
“It’s no accident that we chose to put this on Ogden Avenue,” said Dr. Wayne Detmer, director of operations for Lawndale Christian Health Center. “We want this to be a place where people can see possibilities in a neighborhood where that’s not often the case.”
Detmer first envisioned something like the Farm on Ogden in 2010 after attending a seminar at Duke University’s Divinity School, where he met a theologian who made the case that providing residents with access to local foods is a societal responsibility.
Detmer and Mason connected soon after and eventually joined forces to try and make something of their shared vision for a new type of urban garden.
To Detmer’s knowledge, the project is the nation’s first to combine elements of a community health clinic, botanic garden, agriculture-focused jobs training program and a year-round farm stand.
An overhead view of the Farm on Ogden site during construction in summer 2017 (Courtesy Chicago Botanic Garden)
Detmer estimates that the new farm stand, or “healthy corner store,” could draw tens of thousands of residents each year, given the success of an existing farm stand stationed at Lawndale Christian Health Center, which sells out every week.
But he acknowledges that it’s difficult to project whether the Farm on Ogden will actually work – or, if it does, how anyone will be able to tell.
“I don’t know if we’ll ever be able to measure the direct impact on our community in terms of health indicators,” he said. “It doesn’t mean we’re not going to try.”
Researchers from the University of Illinois at Chicago are already on board to study the project’s effect on residents’ health and well-being, and other researchers could join the effort later, Detmer said.
Based on the project’s initial performance, Detmer said it could expand to serve a broader range of individuals by adding programs for those suffering from mental illness or substance abuse.
“Getting people doing things related to growing and being exposed to nature can be therapeutic in and of itself,” Detmer said.
The Farm on Garden will host an opening celebration and ribbon cutting on Friday from 10 a.m. to noon. A community celebration is scheduled for 10 a.m. to 4 p.m. Saturday.
Visit the Chicago Botanic Garden’s website for more information.
Contact Alex Ruppenthal: @arupp | aruppenthal@wttw.com | (773) 509-5623
Mucci Farms Expanding Its Greenhouse Operations
Mucci Farms Expanding Its Greenhouse Operations
BY KEITH LORIA | JULY 06, 2018
As a vertically integrated grower, packer, shipper and marketer of greenhouse-grown product, Mucci Farms owns more than 200 acres of tomato, Bell pepper, cucumber, lettuce and strawberry greenhouses in Kingsville, ON. In addition, the first 24 acres of a 60-acre expansion in Huron, OH, is now in operation.
Mucci Farms has added the first 24 acres of a 60-acre expansion in Huron, OH.
Kingsville is also home to a 24-acre strawberry farm, which will be 36 acres by this fall, and is among the largest indoor strawberry farms in North America. Including support growers in Canada, the U.S. and Mexico, the company markets for more than 700 acres.
Joe Spano, vice president of Mucci International Marketing Inc., noted a company needs to grow high-quality fruits/vegetables with premium flavor and consistent supply to be a success in this segment.
“You need to establish great relationships with retail partners and most importantly execute by delivering fresh product on time and of premium quality,” Spano said. “Offering marketing support through packaging, world-class branding and social media to assist with the sale of items and having the ability to manage unforeseen circumstances is also important.”
In 2018, Mucci Farms is enjoying a strong greenhouse harvest, as the crops look great and it is adding new automation equipment to improve packing efficiencies.
“We are introducing a Mucci Logistics App to allow retailers to track shipments in real time via GPS and communicate with dispatch or the driver through the app,” Spano said. “We also have several new packages coming out. One in particular is for a new cucumber variety, which includes a compartment that holds dip.”
In addition, the company is partnering with Henry Frose from Thermo Energy Systems to donate a greenhouse to be built on the site of Hotel-Dieu Grace Hospital in Windsor, ON, to serve as a place for the hospital to grow fresh produce and also for the greenhouse to serve as a healing garden for patients.
“Overall, we want people to know that we are a modern, forward-thinking company that is invested in the future of farming,” said Emily Murracas, director of marketing at Mucci International Marketing Inc. “In addition to business objectives, we also have social objectives that revolve around environmentally safe growing practices, social responsibility, sustainability and a high emphasis on corporate culture.”
Mucci Farms is also extremely involved in the community, hosting and sponsoring numerous events and initiatives throughout the year.
“We deliver fresh produce to multiple schools weekly, take part in fitness events and charitable fundraisers to raise awareness for health and wellness through the consumption of fresh vegetables,” Murracas said. “We want people to know that we are a family company that cares about more than just business. We are good corporate citizens that are keen on immersing ourselves into the community and take part in programs that encourage healthy living.”
Inside China's 'Smart Vegetable Farm': Autonomous Greenhouse Allows Plants To Grow Without Soil Or Sunlight
Inside China's 'Smart Vegetable Farm': Autonomous Greenhouse Allows Plants To Grow Without Soil Or Sunlight
- Futuristic farm maximizes the growth potential of plants and is 75 times more efficient than conventional farming
- 54,000 sq ft plant in Fujian, south-east China, can produce eight to 10 tonnes of vegetables every day
- The system automatically regulates temperature, water, humidity, nutrients and LEDs that replace sunlight
By KELSEY CHENG FOR MAIL ONLINE
PUBLISHED: 6 July 2018
These luscious leafy greens sprout from stackable trays in a confined room - without the need of a single drop of pesticide, natural sunlight or soil.
In what could be the future of agriculture in China, a company in Anxi, Fujian province, has been developing a smart farm that enables vegetables to grow efficiently in an automated environment.
The firm's latest expansion project - a 5,000-square-metre (53,819-square-foot) indoor farm - has been under development for the past two years and was finally unveiled last Friday.
Eight to 10 tonnes of vegetables are produced every day on the farm, which is almost the size of a football pitch. That amount of vegetables would be enough to feed nearly 36,000 people, according to Sanan Sino-Science, the company behind the project.
In what could be the future of agriculture in China, a company in Anxi, Fujian province, has been developing a smart farm factory that enables vegetables to grow efficiently in an automated environment
The firm's latest project - a 5,000-square-metre (53,819-square-foot) indoor farm - has been under development for the past two years and was finally unveiled last Friday. The new farm can produce between eight to 10 tonnes of veggies daily
The massive incubation room requires only four staff members to manage - compared with about 300 farmers required in conventional farmlands to produce the equivalent amount.
People in China consume an average of 276 grams (9.7 ounces) of vegetables every day, according to the National Institute for Nutrition and Health.
'Compared with our first generation smart farm, this new plant yields even more effective results while reducing labour and environmental costs,' Sanan Sino-Science CEO Zhan Zhuo told MailOnline.
The company was founded in 2015 by San'an Group and the Chinese Academy of Sciences' Institute of Botany.
Its first generation plant factory, which covers an area of 10,000 square meters (1 hectare), is claimed to be the world's largest vertical farming complex.
The smart farming method, which practices growing vegetables and herbs in multilevel cultivation beds of hydroponic solutions in a controlled environment, is equipped with highly advanced autonomous technology.
The smaller-sized varieties can be harvested in 18 days while larger vegetables take between 33 and 35 days
An automated converter belt was also seen transporting the plates of crisp green veggies for packaging
Scientists donning a full biohazard gear with goggles, face masks, rubber gloves and boots while examining the veggies
The confined indoor space has a strict system that regulates temperature, water source, humidity, nutrients and LEDs that replace sunlight.
'This maximizes the plant's growth potential while maintaining a sustainable and continuous growth cycle,' Mr. Zhan said.
In the factory, the smaller-sized varieties can be harvested in 18 days while larger vegetables take between 33 and 35 days, he added. Vegetables in a conventional farm need about 40 to 60 days to reach maturity, which is also highly dependable on weather conditions.
At full capacity, when the energy cost is neglected, the smart factory can produce 3,000 tonnes to 3,500 tonnes of leafy greens per year.
Video footage of the gigantic smart plant shows factory workers donning a full biohazard gear with goggles, faces masks, rubber gloves and boots while examining and patrolling rows of rainbow-colored LED-lit shelves.
Various plants including lettuce, basil, and bok choy are seen growing on large white trays in tiny allocated slots, submerged in nutrient solutions that are essentially free of soil.
Sanan Sino-Science's first generation plant factory is claimed to be the world's largest vertical farming complex
These vegetables taste less bitter and possess higher nutritional value compared with other conventionally grown plants
The incubation room requires only four staff members, compared with about 300 farmers required in conventional farmlands
An automated converter belt was also seen transporting the plates of crisp green veggies for packaging.
'These vegetables taste less bitter and possess higher nutritional value compared with other conventionally grown plants,' Mr. Zhan said.
More importantly, the new technology greatly saves on water, which is a scarce resource in the country.
'We are working hard to attain a 1:1 ratio between the water used and the vegetables harvested,' Mr. Zhan said, meaning that one tonne of water used can ideally produce one whole tonne of vegetables.
'Currently, 80 percent to 85 percent of the water used could be recycled back into the plant. We hope to reach the 1:1 ratio goal by 2020.'
The company also plans to install AI technology in the facility that can record and analyze growth data through sensors.
The self-learning model will automatically design a template that illustrates the optimal growing condition for each specific kind of vegetable, Mr. Zhan said.
This will also help the farm produce a precise, stable, year-round supply of leafy greens, which means that market prices vegetables could also be more predictable.
More importantly, the new technology greatly saves on water, which is a scarce resource in the country
The smart, GMO-free veggies are sold around 30 yuan (£3.4) to 36 (£4) yuan per kilogram in China
'This farming method is particularly beneficial in challenging environments such as deserts, mountainside towns, or in cities where labor come at a high cost,' Mr. Zhan said.
A tightly controlled environment not only speeds up the growth cycle but also allows researchers to create vegetables that suit specific needs, he added.
For example, scientists can lower the amount of potassium in the greens for patients with kidney problems or increase zinc in cabbages for children.
Right now, the vegetables produced are being shipped to the rest of Fujian province and Shanghai in supermarkets and high-class restaurants.
The brand new technology could help transform China's rapid green revolution amid growing concerns about food safety and nutrition.
The country is also the largest producer of vegetables in the world, harvesting 78.7 million tonnes of vegetables in 2016. The number is expected to rise continuously, according to the National Bureau of Statistics.
The farm can produce a precise, stable, year-round supply of leafy greens, meaning market prices will be more predictable
Through the system, scientists can lower the amount of potassium in the vegetables for patients with kidney problems
The smart, GMO-free veggies are sold around 30 yuan (£3.4) to 36 (£4) yuan per kilogramme in China, while regular vegetables are sold at a wholesale price of 2.85 yuan (£0.32) per kg, according to the latest statistics released by the Chinese Ministry of Agriculture and Rural Affairs.
While this may be an eye-watering price tag to many, a recent food and health survey conducted recently by China Youth Daily on 2,001 Chinese residents shows that more than 76 per cent of participants are willing to spend more money on healthier food choices.
Another 66 percent of those surveyed agreed that they would now pay more attention to the product's nutritional value than its flavor and taste.
The smart factory's relevant equipment and technologies have been shared with countries possessing advanced technological capabilities such as the US, Japan, and Singapore, Mr. Zhan said.
'We hope to bring the concept of "produce locally, sold locally" to different cities,' he said. 'We have ambitious plans to expand.'
Gotham Greens Raises $29 Million In Growth Equity Funding
Gotham Greens Raises $29 Million In Growth Equity Funding
JULY 06, 2018
Gotham Greens, a leading urban greenhouse developer and grower of locally and sustainably grown produce, has announced the closing of $29 million in Series C equity funding last month. The new round brings the company’s total funding to $45 million, not including bank debt. Since its launch in 2011, Gotham Greens has grown from a single urban rooftop greenhouse in Brooklyn to a multi-state indoor farming leader and one of the largest hydroponic leafy greens producers in North America.
The round was led by the company’s existing investors, including the Silverman Group, along with a significant new investment from Creadev, a global private equity investment firm controlled by the Mulliez family.
“This funding enables us to continue on our path of rapid growth that is providing consumers with fresher, better tasting, locally grown produce while transforming urban real estate and promoting sustainable agriculture,” said Viraj Puri, co-founder, and chief executive officer. “We’re inspired every day by the dedication and talent of our team to grow and purvey exceptionally high-quality, nutritious produce while contributing to the better food movement.”
Gotham Greens grows fresh produce in technologically advanced, climate-controlled urban greenhouses in close proximity to retailers and food service providers. This ensures year-round supply chain reliability, transparency, and traceability. The company currently owns and operates four production-scale facilities in New York City and Chicago totaling 170,000 square feet and has another 500,000 square feet under development in five states. The company announced new greenhouses in Chicago and Baltimore earlier this year. The funding will help finance the expansion trajectory, widen distribution, grow its team, and enhance research and development in controlled environment food production techniques, data science, and machine learning.
“The oversubscribed financing is strong validation of our proven farm unit economics, efficient utilization of capital, growth rate, and best in class brand,” said Eric Haley, co-founder, and chief financial officer. “We are excited to welcome Creadev to the Gotham Greens family and for this next phase of growth to bring local produce nationwide.”
“Indoor farming is one of the most exciting and promising sectors in the world of food and ag-tech. Gotham Greens is a clear market leader and is positioned for significant growth. We were highly impressed by the company’s proven track record, greenhouse profitability, exceptional product quality and human-driven values,” said Delphine Descamps, managing director for Creadev USA. “We believe that the Gotham Greens team will continue to significantly influence how fresh produce is grown and distributed both in the U.S. and globally.
Gotham Greens’ business model combines proven hydroponic controlled environment agriculture together with proprietary cultivation techniques and the art of growing. The company reports best-in-class crop yields under the leadership of managing partner and plant scientist, Jenn Nelkin Frymark. Gotham Greens’ greenhouses are powered by 100 percent renewable electricity and yield up to 30 times more crop per acre than conventional agriculture while using 90 percent less water and eliminating agricultural runoff and the use of harmful chemicals.
The company’s growing methods and shortened supply chain reduce the risk of food-borne pathogens. By locating its greenhouse farms in cities, Gotham Greens eliminates the environmental footprint and food waste linked to shipping produce long distances while advocating for improved healthy food access, environmental education, and green collar economic development.
Growing 'Up' With Cucumbers
Growing 'Up' With Cucumbers
One Canadian family applies its expertise to guide Big Marble Farms, the largest produce greenhouse operation in Alberta, into the future.
From left to right: Eden, Brianne, Ryan and Rhys Cramer
Patrick Williams | Photos by Chasing Autumn Photography, except where noted
“I grew up in a cucumber crop,” Ryan Cramer says, recalling his formative years helping around his father Albert’s greenhouse. Now, Ryan has a cucumber greenhouse of his own, called Big Marble Farms.
In 2009, Ryan started Big Marble as a four-acre greenhouse near Medicine Hat in Alberta, Canada, with his father and his uncle, Rick Wagenaar. Ryan sticks close to his family — he also works with his wife Brianne, who is the company’s executive assistant, and they are raising their daughter, Eden, and son, Rhys, around the greenhouse.
Family was the foundation for Big Marble Farms, and it is now a huge operation. In less than a decade in the role of CEO, Ryan has expanded the business to its present 35 acres of glasshouses. This city of cucumber production, with 190 employees, is the largest produce greenhouse in Alberta, Ryan says. And fitted with high-pressure sodium (HPS) grow lights throughout its entire production area, “It is one of the biggest lit operations in Canada,” he says.
Several key practices have contributed to Big Marble’s success: marketing geared toward healthy diets, crop selection based on market demand, year-round production enabled by the use of supplemental lighting, near-total adoption of beneficial insects for the benefit of both crops and customers, and packing onsite and selling local to ensure freshness.
“You’ve got to be always moving forward,” Ryan says. “That’s a common thing. You always have to be constantly innovating and adapting to the changes — constantly becoming more efficient and looking for ways to produce better.”
From one generation to the next
Raising Ryan on a farm was a natural follow-up to Albert’s own childhood. Albert was raised on a dairy farm where he tended to crops such as alfalfa, timothy and wheat. In the mid-1980s, Albert opened Rolling Acres Greenhouses, an operation that has, at various points, produced cucumbers, peppers, specialty crops and tomatoes. Although Albert brought his experience to Big Marble as founder, he still operates Rolling Acres Greenhouses, which is currently situated on 9.5 acres in Medicine Hat. Albert splits his production between cucumbers and peppers.
“My dad was always close to home,” Ryan recalls. “He worked on the acreage [where we lived] — that’s where the farm was. And he was able to be around. But we were also in the greenhouse a lot. We learned how to work from a young age, from just small jobs like dumping the leaves out in the field to actually having to pick cucumbers when we got a little bit older.”
Big Marble Farms has 35 acres of cucumber production.
Photo courtesy of Big Marble Farms
Albert bought a quarter section (160 acres) of land in the early 2000s with the intention of growing on a larger-scale. He noted how Ryan, who had developed a serious passion for growing, needed an opportunity to advance in the business. “When we had started talking as a group about doing something, I said to my brother-in-law, Rick, and Ryan, ‘Let’s just start our own,’” Albert says. “There was nothing around here with year-round production, and I said, ‘Let’s do something completely different. We’ll put glasshouses up and put lights in it.’ We just had to pull the trigger, and we did, and there we go, and now we’re at 35 acres. It grew fast.”
With 20 years as a grower under his belt, Wagenaar wanted to try something new by 2007, when he sold his own produce greenhouse, Sunquest Growers. Originally, he and Albert had more of a hands-on role at Big Marble. But now Wagenaar, who performs public relations and marketing, and Albert leave most of the day-to-day decisions to Ryan. “[Albert and I] are not scared to take a leap of faith, and we’re not scared of debt — we’re not scared of risk and reward,” Wagenaar says. “Both of us being in that same position, but at an arm’s length to the day-to-day, is perfect. And Ryan, being youthful and spending his whole life within the greenhouse industry, was the perfect third partner.”
Cuke choices
With Ryan at the helm, Big Marble Farms grows Long English Cucumbers and Mini Cucumbers. The Long English Cucumbers fill about 21 acres of production space, and its Mini Cucumbers fill about 14 acres. The offerings and how the greenhouse space is divided are based on market demand, he says.
The operation uses rockwool starter cubes for both types of cucumbers. It then grows them in high-wire systems using bags containing coconut fiber, growing off the main stem of each crop and pruning off the side shoots. “We keep on lowering the plant down so that we keep the head in the same spot so that the cucumbers are always being harvested in the same spot,” Ryan says. “It’s much better for labor, it’s better for quality of the product and it also has potential to yield higher. But it’s a premium system. It’s more labor, so it’s a bit of a commitment, but it also gives you better product quality.”
Growing Mini Cucumbers and Long English Cucumbers are similar practices, Ryan says, but they differ in some ways. For instance, growers need to pick Mini Cucumbers every day, but they can get away without picking Long English Cucumbers for a day. “Mini Cucumbers will grow too fast in two days — they’ll just get too fat,” he says. “They’ll get too big, and then they’ll go to waste.”
Mini Cucumbers are ideal snacks for children’s and adults’ lunches, Ryan says, and Long English Cucumbers are well-suited for slicing up and including in larger dishes.
Growing year-round
Ryan (left) and Albert (right) Cramer
Photo courtesy of Ryan cramer
Photo courtesy of Ryan cramer
Ryan as a young boy
Big Marble Farms takes advantage of the sun’s rays at its location near Medicine Hat in Cypress County, Alberta. This part of the country receives the most annual hours of sunlight — it’s what Ryan calls the “sweet spot of Canada’s Sun Belt.”
In Medicine Hat on the Summer Solstice, the sun shines 16 hours a day, but on the Winter Solstice, it shines only eight hours, according to The Old Farmer’s Almanac. Big Marble Farms maximizes light transmission by using glass structures, Ryan says. And when the days get shorter, the farm increases the amount of light its crops receive by using HPS lighting throughout its 35 acres.
“Our tagline is ‘Always Growing,’ which is describing the fact that we produce all 365 days a year,” Ryan says. “It’s a summer-like product, even in the middle of winter. We’re able to turn on the grow lights once the fall light starts to set in, and we can actually push right through November, December, January, February, when most growers are changing crops and cleaning their greenhouses.”
On the marketing and sales side, Wagenaar sees major value in informing purchasers, produce managers and end consumers about the processes that go into a quality cucumber crop, such as supplemental lighting. He notes that not all customers have time to talk to food producers and learn about where the crop came from, but if he could tell all of them about the production systems at Big Marble, he’d be able to secure and maintain their business.
“When you explain it to them — the science of what it takes to grow a good cucumber and the effort of atmospheric computers and the lights and the waking up of the plant — they can’t help but grin,” Wagenaar says. “[They say] ‘You’re kidding? It’s not just a cucumber?’ ‘No, we wake them up in the morning, we put them to bed at night. We have to tickle their feet — tickle the roots — we call them the feet. We tickle them with the little sensations in the morning to get them active, to get them out of their sleepy slumber. And then okay, it’s worktime, let’s go.’”
Big Marble Farms grows its cucumbers in a high-wire system.
A biological approach
To fight pests and diseases, Big Marble Farms uses approximately 99 percent beneficial insects, Ryan says. The farm, along with other operations, takes the biological approach rather than using pesticides to assure customers that their food is safe. This is one of the main assurances about produce that is important to customers, he says, along with local and fresh.
In addition, growers are beginning to find more sense in using biological programs than using pesticides, Ryan says. “It might be more expensive, but it’s just easier on your crop,” he says. “If you’re always spraying pesticides on your crop, you’re damaging it, to a degree. Plants don’t like being sprayed. In the long run, people have realized that this is the better option.”
Big Marble Farms’ biological program manager scouts the entire farm for pests and diseases, Ryan says. “He’s got a really good eye for it, a real passion for it,” he says. “What he does is he orders the beneficial insects, and they come from Holland. He monitors on a weekly basis how many good guys and bad guys we have in the greenhouse, and then he makes decisions based on that for how many more good bugs he’s going to need for the next week.”
When it comes to educating end consumers on organics, Wagenaar says he tells them that it is far better that they are eating a vegetable rather than a processed food such as Pizza Pops or Crispy Crunch — Canadian junk food. He never says the product is organic, but he tells them, “Spraying pesticides is always, always, always the very, very last chink in the armor.”
Big Marble Farms packs its own product to avoid bruising and guarantee freshness and proper labeling.
Freshly packed
Once harvested, Big Marble Farms packs its own product to avoid bruising and guarantee freshness and proper labeling. The Mini Cucumbers can be packed in different ways, Ryan says, including six or eight packed together on a foam tray with a labeled plastic-wrap on top; or placed in one, one and a half or two-pound bags. The English Cucumbers are plastic-wrapped either individually or shrink-wrapped with others, placed in a box and sold in bulk.
Big Marble Farms uses grading lines, which Ryan says requires a lot of labor. Employees fill boxes with cucumbers and place the vegetables on trays by hand.
“All the big operations have been packing their product for a long, long time,” Ryan says. “But as far as Alberta goes, we are one of the only ones that do it. So [it’s] somewhat new to Alberta, because we never had big enough operations. We always co-packed.”
Big Marble Farms sells its cucumbers it through the RedHat Co-operative, a co-operative of about 30 growers near Redcliff, Alberta, “The Greenhouse Capital of the Prairies.” Ryan is a board member of the co-op, as is Albert, who chaired it for several years due to his roles at both Rolling Acres and Big Marble. The co-op sells Big Marble’s product throughout Canada — mainly in the Prairie Provinces of Alberta, Saskatchewan and Manitoba.
The importance of family
Family still plays an integral part at Big Marble Farms. As an executive assistant, Brianne helps with tasks such as marketing, branding and office work. And Ryan sees a benefit to having his children grow up around the operation.
“One of the things I think that I find very important from running a family business like this family farm, for my kids, is that I hope that they learn the same work ethic values that I learned and they have the same family life that I had,” Ryan says.
The business’ marketing emphasizes the importance of nutrition for children. Images of children — including Eden and Rhys — playing and eating cucumbers are prominent on the company’s website. There are also old photos of Ryan as a child — one of him on a tricycle holding a cucumber and one of him standing beside Albert, who is kneeling.
Albert says he enjoys seeing his grandchildren growing up in Ryan’s greenhouse like Ryan grew up in his. “It’s pretty exciting to see them being involved with that, and the opportunity for them is pretty cool, if they want to go with it,” he says.
The farm’s name also refers to children. “The name Big Marble harkens back to a simpler time when kids would spend hours playing with their friends and family,” according to the company’s site, which offers instructions for playing the game marbles, as well as Jacks and Conkers, two other games. (Ryan says the name is twofold — it also refers to Earth. “The Blue Marble” is a nickname for the planet, and an image the Apollo 17 crew took of it in 1972.)
More developments are on the horizon for Big Marble Farms, which has an expansion plan for 2020. Consumer demand will determine the crop type, and acreage will increase by another 10 or 20 acres, enlarging the greenhouse space to more than 10 times its original four acres.
Big Marble completed its 2016 expansion — a whole 20 acres — within a year of breaking ground, and Ryan has the same plans for this next expansion. “It will be complete in 2020,” he states, confidently. “We would break ground [in] early 2020, and we would have plants in it by the fall of 2020.”
Rob Baan Looking For Help: Urban Greenhouse Should Become Health Centre
Rob Baan Looking For Help: Urban Greenhouse Should Become Health Centre
Two years after its founding, the urban greenhouse in The Hague went bankrupt last week. Rob Baan thinks it’s no surprise, he never understood the project. “Why would you commercially grow vegetables on a surface of not even 1,000 square metres, while just in the Westland and Bleiswijk vegetables are grown better and more cheaply on 35 million square metres? Tomatoes for 18 euro per kilo when the Westland’s right around the corner, and growing tilapia this close to Scheveningen. It was just a miscalculation and that annoys me.”
In December Rob was asked to help think of new ideas for the project for the first time. Rob: “I didn’t want to at first, but I became intrigued after a while. It gave me quite a start to see how badly the production was doing. In the Netherlands, we have very good production methods, but these weren’t used. Dutch consultants haven’t been heard either. How stubborn can you be?”
Educational centre
Because the greenhouse is there now, Rob would like to do something with it. “The greenhouse is in one of the poorest neighbourhoods in the Netherlands. Seven of the 20 underprivileged Dutch neighbourhoods are in The Hague, so it’s important to involve the neighbourhood in the project, so the people there can eat healthy. The project overshot its goal by selling expensive tomatoes. My plan is to turn it into an educational centre that involves greenhouse horticulture to show how easy it is to eat healthy.”
The urban greenhouse therefore fits into Rob’s dream to turn the Netherlands into one of the healthiest countries in the world. “The daily recommended amount of vegetables of 250 grammes can’t be reached just by eating dinner. Lunch should also contain many vegetables. The Netherlands is the only country in Europe that doesn’t have school lunches. But imagine an urban greenhouse in a neighbourhood where people cook, where schools receive school lunches and where they learn about the production of vegetables. That’s my plan.”
Help
Rob is emphatically looking for help from other parties for this plan. His appeal on Twitter received many responses. He’s now trying to bring these into line. “I can’t do this alone. I’m appealing to greenhouse horticulture, but also to politics and insurers. Which insurer is brave enough and joins me? In poor neighbourhoods in The Hague you can see many people with type 2 diabetes, mostly due to bad eating habits. I want to change that.”
More clarity in coming weeks
Curator Martijn Vermeeren confirms Rob’s interest in the project. “After the bankruptcy, we wrote to various parties on the market, and this plan was then announced to us. We’ve been talking to them ever since.” Whether this will be the final plan is unclear a few days after filing for bankruptcy. Other parties have also declared themselves to the curator, although those plans are less concrete.
In the meantime, production is continuing in the rooftop greenhouse, and the fish are also still swimming around. “The operation is continuing for now, but it’s important to quickly gain clarity. We’re working very hard on this: keeping in contact with stakeholders and parties who could mean something to the project.” He expects to be able to give more clarity about this in the coming weeks. The cause of the bankruptcy should also become clear.
A letter from an Alderman from The Hague has now also made clear that profitability of the greenhouse was under pressure from the first production year, 2016. UF de Schilde, which has now been declared bankrupt, rented the upper floor and the greenhouse. The building itself, The New Farm, is owned by Starterspanden Den Haag BV. They concluded in September 2016 that Urban Farmers were having difficulty meeting their payment obligations, and they arranged a provision for the annual account in 2017.
Publication date: 7/10/2018
Flying Greenhouse From Bremen Goes Into Space
Flying Greenhouse From Bremen Goes Into Space
Soon, a flying greenhouse could revolve around the Earth. This summer, a research satellite from Bremen should be launched into space with tomato seeds on board. In it, the plants should grow under different gravitational conditions; for half a year gravity like on the moon, then for half a year with the gravity of Mars.
Engineers work on a research satellite at the German Aerospace Center.
Photo: Carmen Jaspersen
"We will ultimately simulate and test greenhouses that could be put on the Moon or Mars (inside a habitat) providing fresh food for a crew by using a closed system to convert waste into manure in a controlled manner," says DLR biologist Dr. Jens Hauslage, who leads the science mission. For example, in a lunar habitat, the greenhouse would be inside - where even the astronauts are in an Earth-like atmosphere. One of the waste products that would be produced with great regularity would be the urine of the astronauts. The plants would have to adapt to the reduced gravity: the moon only has about a sixth of Earth’s gravity, Mars about one third.
Tomato farming under controlled conditions - Photo: DLR
Researchers from the German Aerospace Center (DLR) in Bremen and Cologne will be watching what goes on in the small ecosystem inside the satellite. The findings are important for future space missions to the moon and Mars, said project manager Hartmut Müller. The tests with the tomato plants in space would take one and a half years in all.
More information about project Eu:CROPIS can be found here.
Source: dpa/dlr
Publication date: 6/21/2018
Plenty of Production in The Future Exploration Greenhouse on Antarctica
Plenty of Production in The Future Exploration Greenhouse on Antarctica
Published on June 19, 2018
The most important element of the EU H2020 EDEN-ISS project is the simulation of a one-year "space mission" on Antarctica, in preparation of future space missions.
The business unit Greenhouse Horticulture of Wageningen University & Research has been involved in all preparations (from the design and dimensioning of the installations and necessary resources of the Future Exploration Greenhouse, through the selection of the crops, to the preparation of a crop handling manual for Paul, the space technician whose job is to produce fresh vegetables for the benefit of the "mission" crew.
The building blocks of the greenhouse arrived at the beginning of this year on Antarctica and, after assembly and testing, first crops were sown in the second half of February. In total there are now 10 people at the German station Neumayer III, completely isolated in the Antarctic night. In his growing task, Paul is assisted by an automated system developed by the bu Greenhouse Horticulture of Wageningen University & Research especially for this purpose, based on simple and inexpensive cameras.
Components of the system are: evaluation of the growth rate, prediction of harvest time and timely detection of deviations. Only when necessary the Wageningen experts are alerted to evaluate possible actions that are discussed with Paul. In the meanwhile he has harvested almost 100 kg of fresh tomato, cucumber, lettuce, spices and radish. Go to EDEN-ISS for beautiful Antarctica images, explanation and for updates.
Ivy Tech Greenhouse Dedicated
Thursday, June 14, 2018
Ivy Tech Greenhouse Dedicated
Facility reflects ag program boom
ASHLEY SLOBODA | The Journal Gazette
When Ivy Tech Community College Fort Wayne started its agriculture program about five years ago, officials were already pondering options for growing it.
Dreams of a greenhouse – a facility that could bridge the campus' agriculture and culinary programs – soon followed.
On Wednesday, Ivy Tech showed off its new greenhouse during a two-hour dedication event.
“This is really a community project,” said Chancellor Jerrilee Mosier, listing the numerous donors.
At more than 3,000 square feet, the facility cost about $498,000. It opened in January with hydroponics capabilities – growing plants with water and no soil.
“We want to train students on the same equipment they can expect to see with industry leaders today,” Kelli Kreider, agriculture program chair, said in a statement.
The greenhouse teemed with life Wednesday.
Tomatoes, carrots, hot peppers, sweet peas, kale, arugula, orange mint, pineapple sage, endive, spinach and basil were among the plants growing in the bright, roomy space.
At the dedication, Kreider noted she grew up as a soil farmer and credited Rob Eddy, an expert in hydroponics, as the mastermind behind the greenhouse.
The facility replicates a new trend in agriculture – vertical farming, Eddy said. It's a way to grow food locally in metropolitan areas, connecting consumers with fresher food.
Rebecca Marshall – one of the seven original agriculture students – attended the event, telling the crowd she's “very jealous” of the resources now available to students.
This year marked the program's largest graduating class – about 20 students. Enrollment for the fall has already surpassed 80, Kreider said, adding she's excited that enrollment continues to grow.
Agriculture education is important, Mosier said, sharing statistics about jobs available in agriculture.
Nationwide, nearly 58,000 job openings in food and agriculture are expected each year from 2015 to 2020, she said, but there's a shortage of graduates – about 35,000 annually.
Along with educating Ivy Tech students, the agriculture program is also benefiting Easterseals Arc students, who are taking classes this summer, college officials said.
Mosier said Ivy Tech takes the “community” in its name seriously.
“We need to be integrated and really support community efforts,” she said.