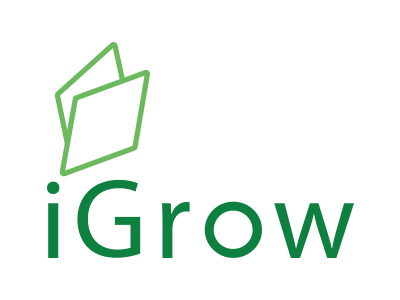
Welcome to iGrow News, Your Source for the World of Indoor Vertical Farming
South Africa: Soilless Farming Shows Potential
Farmers in the Central District; Messrs Olemogile Botsile and Lesego Obuseng have called on their peers to take to soilless horticulture.
The duo explained in an interview after Serowe Agricultural Show where they were exhibiting recently, that the practice, termed hydroponic had the potential to assist the horticultural sector turn the corner.
They said they took to the method after experimenting with traditional farming for a long time without much success, given the climatic condition of the country.
Mr Botsile explained that under hydroponic farming, vegetables are grown in soilless conditions, with cultivation taking place in an aquatic-based environment.
He said the system had become popular over the years because of its yields.
“We would like to advice farmers specialising in horticulture to consider growing hydroponically, as the plants here are of exceeding high quality, occupy less space and consume fewer resources than traditional growing methods,” he said.
He said after planting for three years without satisfactory yields, they decided to find out if there were other methods which they could utilise to make returns.
“Through our research and benchmarking in South Africa, we identified, hydroponic as the best. Traditional farming has proved an upset in our returns as we were spending more than we could benefit on aspects such as water, herbicides and fertilisers,” he said.
Mr Botsile said the method proved a success after its trial at Taukome lands, adding that they realised that it had potential to assist those who had failed in their back yard gardens as a result of water shortages.
He noted that the water was mostly recycled and could yield 90 to 100 per cent harvest, as the farmer was able to monitor individual plants.
“Although the concept of growing plants without soil seems contrary to a plant’s nutritional needs, plants can actually grow exceedingly well in soilless growing systems.
To thrive, plants need water and nutrients, which are traditionally absorbed from the soil they are grown in. However, if these nutrients can be provided through a nutrient-rich solution applied directly to a plant’s root zone, it can be grown without any soil at all. This is what basically happens under hydroponics planting,” he said.
Mr Botsile noted that under hydroponic systems, they use dnutrient solutions to feed plants, and use other substrates to provide support for roots, adding that some hydroponic systems required no substrates at all.
“Our company supplies different methods and variations of hydroponic gardening, ranging from small, in-home systems to large, complex commercial systems, depending on our client’s need,” he said.
He indicated that hydroponic growing methods, in combination with vertical gardening, could aid in expanding the possibilities of urban gardening and indoor gardening, where there was insufficient space.
“Although the amount of hydroponically grown produce has not overtaken the amount of field-grown produce yet, it is quickly gaining a foothold,” he said.
Mr Botsile indicated that this was especially true as more and more consumers were becoming aware of where their food came from and how it was grown, as evident in the growing interest people had shown towards the system.
“In addition to using much less water, he noted that hydroponic farms did not require the same amount of upkeep as traditional farms, adding that it was ideal for people with less time on their hands and could be best used by even retired individuals.
“Hydroponic farms are much less labour intensive, hence less tiring, than traditional farms because they are in compact spaces, often at waist-high levels.
Therefore, harvesting and replanting is much easier with hydroponic systems.
In this system there is no digging or weeding required, making the overall upkeep of hydroponic systems minimal.
Source : BOPA
Author : Thuso Kgakatsi
Location : SEROWE
Event : Interview
Date : Aug 13 Mon,2018
MightyVine Tomatoes To Double Operations — Again — To Meet Growing Demand
Agricultural start-up MightyVine, the Rochelle-based hydroponic grower of tomatoes, plans to double its operation by building two more greenhouses. (Stacey Wescott / Chicago Tribune)
Greg TrotterContact Reporter Chicago Tribune
MightyVine, the Rochelle-based hydroponic grower of tomatoes, plans to double the size of its operation once again to help meet increasing demand from large retailers like Costco, Walmart, and Jewel-Osco, according to company executives.
Come September, construction will begin on two more 7.5-acre greenhouses in Rochelle, located about 80 miles west of Chicago, said MightyVine Chairman Jim Murphy. Once the $16 million project is complete,
MightyVine will have four adjacent greenhouses totaling 30 acres that will produce about 105 million tomatoes a year, Murphy said. That represents the second major expansion for MightyVine since launching in 2015 to offer fresh, locally grown tomatoes year-round in the Chicago area.
The agricultural startup has experienced some growing pains, too. In the summer’s hottest weeks, the greenhouses can get too hot, making it difficult to maintain the same size and quality of fruit, Murphy said.
Quantity has been the far greater challenge, though.
Deciding when to enroll in a Medicare prescription drug plan is a big decision and we can help. Check out helpful video tips on getting the most out of Medicare Part D at Walgreens.
“We can’t keep up with demand. … It’s hard to keep them in stores, so we have to build more,” Murphy said.
Much of the company’s recent growth has come through large retailers like Costco, Walmart and Jewel. MightyVine is poised to sell through a second Walmart distribution center, which will expand its reach throughout the state, said MightyVine CEO Gary Lazarski. And after a trial run in 10 Costco stores, MightyVine plans to expand to more than 50 stores by the end of the year. In true supersized Costco fashion, MightyVine tomatoes come packaged in a 3-pound box for $6.49.
Walmart and Costco did not respond to interview requests Monday.
At Jewel, one of MightyVine’s first retailers after Whole Foods Market, the tomatoes are typically available in all 187 stores — when they’re available, said Scott Bennett, produce sales manager for Jewel-Osco.
MightyVine, the Rochelle-based hydroponic tomato farm, plans to double its operation by building two more 7.5 acre greenhouses this fall.
Quality is never the problem with MightyVine, which leaves the tomatoes on the vine to ripen longer than most growers, Bennett said. After the tomatoes are harvested, they’re transported to Jewel’s distribution center in Melrose Park within a couple of hours, he said, and are in stores the next day.
“I’ve been doing produce for 35 years, and this is the best darn tomato I’ve ever had,” Bennett said. “They just don’t have enough product. They have enough to keep everyone hooked. It’s a great game they’re playing — we’re all hooked.”
Lazarski acknowledged there’s been tension with retailers as a result of supply shortages but said that ultimately, that’s a good problem to have. MightyVine has grown from being a “speculative venture” to an established brand, Lazarski said.
MightyVine is one of a handful of large-scale indoor commercial farms to enter the Chicago market in recent years. Others have also found a mix of successes and challenges. BrightFarms, a New York-based company that also has a hydroponic greenhouse in Rochelle, sells its leafy greens in Mariano’s stores. Gotham Greens, another New York-based grower of leafy greens, announced earlier this year that it would build a second greenhouse in the Pullman area on Chicago’s Far South Side.
They’re not all happy stories: FarmedHere, a pioneer of commercial hydroponic farming, closed its Bedford Park greenhouse last year, citing onerous costs and increased competition. Here Holdings, parent company of FarmedHere, instead shifted its focus to making food products — such as juices, salad dressings and spreads — under the Here brand at the company’s food processing plant in Carol Stream in DuPage County.
READ MORE: Coming to Englewood: Kimbal Musk's Square Roots urban farm in shipping containers »
When MightyVine began selling tomatoes in 2016, it almost immediately found high-profile allies among some of Chicago’s top chefs, including celebrity chef Rick Bayless who promoted the brand on social media. Today, MightyVine sells tomatoes to more than 200 restaurants in the Chicago area, including restaurants with the Lettuce Entertain You Enterprises and Four Corners restaurant groups.
MightyVine is backed by Grow Forward, Murphy’s investment and philanthropy firm. Local Foods, another of Murphy’s ventures, is the wholesaler that distributes the MightyVine tomatoes to restaurants. The Grow Forward portfolio also includes Handcut Foods, a food service company for schools and universities, and Carbon Green BioEnergy, a Michigan-based ethanol company.
Murphy, a longtime Chicago-area entrepreneur, called MightyVine his “baby.”
“Everyone in the business said we couldn’t brand a tomato,” Murphy said. “We’ve captured the marketplace.”
Twitter @GregTrotterTrib
UAE developer Seven Tides To Use Hydroponics To Supply Its Hotels
Seven Tides is planning to expand a hydroponic greenhouse on the World Islands to supply its portfolio of three Dubai hotels
UAE-based developer Seven Tides is planning to expand a hydroponic greenhouse on the World Islands to supply its portfolio of three Dubai hotels, according to CEO Abdulla bin Sulayem.
Hydroponics, a subset of hydroculture, allows one to grow plants without the need for soil, using mineral solutions in a water solvent. According to bin Sulayem, the process will allow the company to grow almost any plant at any time of the year, meaning that climate and season will no longer present any limitations.
According to bin Sulayem, collectively, Seven Tides’ hospitality portfolio – which includes Anantara, DUKES and the Mövenpick Ibn Battuta Gate hotel – “consume a large amount of fruit and vegetables on a daily basis.”
“We already have a large greenhouse located on the World Islands, but we are currently working to upgrade the facility, with the intention of supplying all of our hotels with the majority of the fruit and vegetables they require within the next few months,” he told Arabian Business.
Sulayem added that hydroponics is cleaner and more efficient than traditional agriculture techniques.
“It also produces better tasting produce with more nutritional value and can reduce water consumption by up to 90 percent,” he said.
In addition to its hospitality portfolio, Seven Tides has an upcoming project on the World Islands, where the company is creating an exclusive resort of 60 one-and two-bedroom villas, as well as SE7EN CITY JLT, a mixed-use development in Dubai’s Jumeirah Lakes Towers.
For all the latest travel news from the UAE and Gulf countries, follow us on Twitter and Linkedin, like us on Facebook and subscribe to our YouTube page, which is updated daily.
Last Updated: Tue 31 Jul 2018
You Can Farm Anywhere, Even Inside A Shopping Mall
You Can Farm Anywhere, Even Inside A Shopping Mall
BeGreen, a startup company in Belo Horizonte in Brazil, is producing fresh and organic produce inside the city’s main shopping center.
Giuliano Bittencourt and Pedro Graziano launched BeGreen with the goal of producing sustainable and healthy food for the urban community, while simultaneously reducing the amount of food wasted along the supply chain. The urban farm uses hydroponic methods to grow fresh and organic produce and sells it locally.
Food travels a long distance from farmer to consumer in Brazil, a major inefficiency in their food system. An estimated 80 percent of all agricultural production in Brazil is lost during transportation. Along with this tremendous quantity of wasted edible food, there are additional transportation costs resulting in increased greenhouse gas emissions. BeGreen is a response to these inefficiencies.
Bittencourt was first introduced to this type of urban farm when he visited the Agricultural Technology lab facility of MIT. It was after this visit that he was inspired to start BeGreen, which brings accessible and affordable technology to modernize the Brazilian food chain.
Ricardo Batistic, CTO of BeGreen, explains, “we want to change the general perspective that access to healthy food is only viable in rural areas, we want to impact as many people as we can with our vision and bring the best product we can to the market.”
Using aquaponic methods, the farm produces roughly 40,000-60,000 plants per month. Most of these are greens and microgreens including beet leaves, watercress, parsley, coriander, basil, thyme, sage, arugula, radish, mustard, cabbage, and a diverse range of lettuces.
The fish serve as a natural fertilizer for the farm, and they raise over 500 tilapia per month. There are biofilters, which metabolize the fish’s waste to enrich the water used throughout the whole system. The farm uses 90 percent less water than conventional farming and does not use pesticides, significantly lowering their environmental footprint.
BeGreen sells their produce to approximately 30 restaurants, four retail stores, and directly to visitors of the farm. Sustainability is at the heart of the business model. They keep sales as close to the farm as possible, with the farthest shipment located only 10 kilometers away.
Producing high-quality organic vegetables and minimizing waste are at the core of BeGreen’s mission. They have very strict quality control processes including daily production area checks for diseases, water shortages, leakages, or any other systems issues. They conduct daily pH and water temperature tests, and weekly tests of the macronutrients in the fish water. They are developing a new system to assess the growth conditions of the plants to optimize quality and productivity. BeGreen keeps a robust database tracking the number of seeds that fail to grow and the amount of full-grown produce lost during distribution. Currently, these failures are under 2 percent of their total production.
BeGreen implements additional methods to avoid waste, such as preserving the roots on the plants at the point of sale, which extends their shelf life an additional week. They also donate unsold produce to a charity, Mesa Brasil.
BeGreen is currently seeking to expand their operations and is building their second urban farm in São Paulo. According to Batistic, the company “want[s] to have at least three working urban farms by the end of 2018. We intend to grow at a steady pace to cover as many cities in Brazil as possible, and we are also open to international possibilities if they present themselves.”
Edmond, Oklahoma - Native NBA Player Officially Launches Hydroponic Farm In Edmond
Edmond, Oklahoma Native NBA Player Officially Launches Hydroponic Farm In Edmond
JULY 22, 2018, BY SARAH STEWART
EDMOND, Okla. - This weekend, Edmond native and Utah Jazz Center Ekpe Udoh has officially launched his company, LGR Farms, in Edmond.
Oklahomans attended the Saturday night launch party, getting a hands-on tour, even planting some seeds that will eventually grow into crops.
“It’s been four years in the making,” Udoh said.
It’s a hydroponic farm that literally sits in a shipping container. The crops grow vertically with filtered water and nutrients instead of soil and blue and red LED lights instead of sunlight.
It’s herbicide- and pesticide-free for the leafy greens and herbs grown there. And, the “farmer” can control everything from a phone.
“I can turn on and off the lights with the touch of my phone, and it controls like literally everything,” said LGR Farms Vice President Erica Young. “We have in, our farm, approximately nine to 10 different crops being grown currently. We have four or five lettuces, herbs right now, different leafy greens that we’re growing.”
Udoh hopes his farm can make a difference in inner city communities.
“There’s higher rates of obesity and such in inner city, inner city areas. As you can see just going around, fast food’s on every corner in those neighborhoods, unfortunately. And, this is just something different, you know, be able to get them fresh produce and, then, try to educate them along the way,” Udoh said.
One of Udoh’s goals is to provide food for public schools, especially inner city schools.
“Growing up in Edmond, we had salad bars. I didn’t appreciate it back then, you know, being a knucklehead. But, now, I understand it. With all the pictures that have been going viral, Oklahoma City public schools, just want to give them a choice,” Udoh said.
Udoh plans to expand his Edmond operation and go into other states as well, eventually selling to chefs and grocery stores also.
He also announced he’s partnered with Magic Johnson’s food service company, Sedexo MAGIC, to provide produce to kids in inner city schools. And, he said he’s in talks with Oklahoma City public schools to provide food for them as well.
The Micro Revolution: Growing Hydroponic Microgreens
Succulent, slender but packing a powerful flavor punch, microgreens are increasing in popularity both on our plates and as a profitable hydroponic crop with just five days from seed to harvest for some species
Takeaway: Succulent, slender but packing a powerful flavor punch, microgreens are increasing in popularity both on our plates and as a profitable hydroponic crop with just five days from seed to harvest for some species.
Succulent, slender but packing a powerful flavor punch, microgreens are increasing in popularity both on our plates and as a profitable hydroponic crop. While they may seem tender and delicate, most microgreens are easy to germinate and with just five days from seed to harvest for many quick-growing species, even the most impatient grower will be satisfied with the results.
Microgreens are also ideal for those with a limited indoor growing space – as little as a few square inches can grow a crop packed with the distinctive flavor of the mature plant but in a small, compact and highly nutritious package.
On a slightly larger scale, microgreens make a profitable commercial crop, well-suited to soilless production methods, hydroponic nutrition and a protected growing environment to give a high-quality, clean and grit-free product.
What are Microgreens?
Microgreens originated in California, where innovative chefs started using them in new dishes to incorporate color, flavor, texture and interest, a trend that rapidly spread worldwide. Microgreens are used as toppings, garnishes, flavorings in salads and features in many up-market dishes and are sold as a high-value product in produce stores and supermarkets.
Microgreens are larger than a sprout but smaller than a baby salad leaf and will usually have produced at least two true leaves after expansion of the seedling leaves or cotyledons. Because they are harvested at such an immature stage, seed is sown at a high density to maximize yields from each crop.
This also allows the developing seedlings to grow tall and straight with a tender, almost blanched stem and bright, well-developed leaves. While a diverse range of plant species are grown as microgreens, some are produced specifically for their healthy compounds and properties and these have found a niche market within the health food industry as well as being popular with home gardeners.
The most well-known of these is wheatgrass, which has been grown for many years as a health supplement. Other species such as flax, chia, broccoli and varieties of red brassica also have health compounds of interest. The darkly colored purple and red varieties of radish microgreens, which produce intensely colored young leaves, contain high levels of antioxidants shown to have cancer-fighting properties.
Commonly Grown Microgreens
Microgreens fall into four main categories. Shoots and tendrils such as pea, sunflower and corn shoots, are often used as garnishes, although they all have their own mild and somewhat surprising flavor. Spicy greens include arugula, radish, cress and mustards.
Micro herbs include those used not only as garnishes, but also for their characteristic flavor such as parsley, fennel, edible chrysanthemums, cilantro, basil, French sorrel, mint, dill, chives, onion and shisho (perilla).
Tender greens are highly diverse in flavor, leaf size, shape and color, and include red cabbage, broccoli, spinach, beet (red), tatsoi, mitzuna, amaranth, chard, kale, corn salad, endive, chicory, celery, carrot and lettuce.
Hydroponic Production of Microgreens
Hydroponic microgreens have a distinct advantage over those grown in trays of substrates or soil mixes in that no granular growing medium needs to be used. The high sowing rate and density of microgreens means small particles of substrate can end up in the foliage and since microgreens are not usually washed after harvest, this poses a risk of crunchy grit ending up in the final dish.
For this reason, hydroponic microgreens are best produced on a thin mat or capillary pad that holds the seed in place and retains some moisture for germination. Paper towel, hessian/burlap sheets, rockwool cubes or sheets, thin kitchen cloth and hydroponic microgreen pads can all be used to grow a clean, high-quality crop with little expense.
Seeds that have been specifically produced and packaged for sprout or microgreen production should be obtained, which means the seed will have a low percentage of foreign matter, will not have been treated with fungicides or other chemicals and will have been well cleaned.
This is particularly important when buying seeds for pea, corn or spinach microgreens, as the seeds from these species are often coated with fungicide. Seed companies have also introduced a range of specific microgreen cultivars that are a great improvement on standard varieties.
Many of these feature intensely colored or modified first leaves, such as some of the radish microgreen species and those grown for pea shoots. Some microgreen varieties have seeds that are mucilaginous, meaning that once wetted, the seed forms a thick, gelatine-like layer that holds moisture.
Cress and basil are examples of mucilaginous seed and these seed types should not be pre-soaked before sowing. Larger seeds such as wheatgrass, corn and peas may be pre-soaked in warm water for 24 hours before sowing, although this step is not essential.
Hydroponic systems for microgreens can be as simple as a small, flat, hand-watered kitchen tray or as complex as an aeroponic or nutrient film technique system. Ideally, the growing system needs to have a flat, slightly sloping surface onto which the growing mat/pad paper or cloth can be laid out and wetted down.
The microgreen seed should then be weighed out and sown onto the wetted surface as evenly as possible. Use of seed shakers assists with this process. The correct seeding density depends somewhat on the species being grown.
As soon as the seeds germinate, microgreens require light and nutrients to produce the highest quality product. Artificial lighting doesn’t need to be intense and these young seedlings produce well under propagation lamps provided the lamps don’t produce too much heat, which may burn the tender young foliage.
Once the cotyledons (seedling leaves) are visible and are starting to develop chlorophyll, the seedling will have exhausted the reserves contained in the seed. At this stage, the young plant is starting to photosynthesize and produce its own assimilate and nutrient ions will be absorbed by the root system.
A general purpose vegetative or seedling nutrient formulation is usually sufficient for microgreen production, but wheatgrass has different nutritional requirements, including a higher EC level, for maximum harvest quality. EC levels are typically run at seedling strength for microgreens (0.5 – 1.0 mS cm -1), although they may be adjusted for season in a similar way to lettuce and herb crops.
There is some scope to manipulate growth of microgreens with use of EC – higher EC can be used to boost color development in red types during low winter light if necessary. Control of EC will also affect the shelf life of cut microgreens. Seedlings grown on dilute solutions or in media with a high water-holding capacity can develop softer tissue and a higher rate of water loss post-harvest than those that have received a higher EC and been slightly more hardened.
Nutrient solution needs to be applied regularly and carefully to developing microgreens to avoid flooding the microgreens and wetting the foliage, which encourages fungal diseases, and also to make sure fresh nutrient solution is flushed through the root zone, oxygenating and feeding the seedlings.
Most hydroponic systems used for microgreens don’t use a continual flow of nutrient solution, but intermittent application, followed by a period of drainage with the growing mat/pad or substrate holding sufficient moisture around the roots between waterings.
Food Safety and Hygiene Considerations
Just as with sprout production, there are food safety requirements for microgreen production. Various fungal pathogens can develop and grow on sprouting seeds, particularly under the humid conditions and high densities microgreens are grown at, and these can pose a contamination risk. Generally, high-quality, viable seed, sown into a clean system at the correct temperature for germination and optimal moisture levels, will germinate rapidly with few problems.
Disease outbreaks are more common when old seeds are used or when temperatures are either too hot or cold for rapid germination. Over-watering also poses a risk as seeds may begin to rot before germination can occur. The water supply needs to be high quality – water can carry human and plant pathogens that contaminate a crop, although the municipal water supply is treated to prevent this risk.
There is an increasing concern and more regulations these days relating to food safety so commercial growers of microgreens need to be aware of the guidelines they must follow for fresh salad crops.
Harvesting Microgreens
Cutting height is important, as high-quality microgreens need a good, clean portion of stem below the leaves, but should not be cut so low as to risk contamination with the growing media or material the seeds were sown into.
This becomes particularly important if a light, loose, granular media has been used for production, as particles can easily be picked up during the harvesting process and contaminate the product. Clean, sharp scissors are suitable for cutting microgreens on a small scale, while larger growers use mechanical harvesters.
During warm growing weather, microgreens, just as with herbs and lettuce, are best harvested early in the day when the foliage is coolest and most turgid. This will prolong the shelf life of the packaged product. Some microgreens are shipped out to customers while still growing in trays or cells, prolonging shelf life and allowing on site harvesting as required.
Problems with Microgreens
One of the most common problems seen in microgreen production is seedling rot and disease outbreaks caused by over-watering or high humidity levels, which create a saturated environment around the foliage.
Good levels of air movement (such as portable fans in small areas) help prevent issues of root rot, fungal and bacterial pathogens taking hold in the dense canopy of succulent young leaves. Over-mature microgreens may become too tall and flop over, making harvesting extremely difficult, so this is a crop that must be cut at just the right stage.
For the small-scale indoor gardener, microgreens are an ideal crop – fast, productive and requiring just a few inches of well-lit space, they can be easily grown on a warm, sunny windowsill, or incorporated into a high-tech hydroponic system. Their short shelf life makes them a good prospect for local markets and restaurants, as they are best used fresh within two or three days of harvest.
Although there is a degree of skill required in growing these seedlings at high densities and maintaining post-harvest quality, the wide range of species, diversity of uses and growing popularity makes them a great proposition for hydroponic growers.
Written by Lynette Morgan
Dr. Lynette Morgan holds a B. Hort. Tech. degree and a PhD in hydroponic greenhouse production from Massey University, New Zealand. Lynette is a partner with Suntec International Hydroponic Consultants and has authored several hydroponic technical books. Visit suntec.co.nz for more information. Full Bio
New Farm Growing Fresh Greens Year-Round
New Farm Growing Fresh Greens Year-Round
Cutting-edge technology featured in hydroponic, vertical farm
Jun 22, 2018 by: Maija Hoggett
A new farm is growing a way to eat locally, year-round.
From the outside, the Borealis Fresh Farms’ modular building doesn’t look like anything special. It’s a white structure that’s 10 feet wide, 10 feet high and 40 feet long tucked away on top of a hill with a view of Porcupine Lake.
Inside is a hydroponic vertical farm equipped with cutting-edge technology. From the walls, parsley, basil, bok choy, and three varieties of kale are growing in strips.
“When we’re talking traditional farming, this is not that, at all,” said Marc Rodrigue, who co-founded the farm with Alex Cochrane.
Everything inside is controlled by technology — the lights, temperature, humidity levels and more can be monitored from anywhere.
“We’re growing clean, fresh, nutrient-dense food that hasn’t been exposed to pesticides, herbicides,” said Rodrigue.
Unlike traditional farms where the plants grow in soil, this produce thrives from nutrient-rich water.
Rodrigue likens it to eating at a buffet.
When you’re there and “hungry for something, you get up and you go get what you want. Well the plant acts like that as well. It has a smorgasboard of all the nutrients that it needs and then once it’s hungry, it goes and gets it.”
While the produce isn’t considered organic, it’s grown in a sterile environment and the partners are going to lengths to track all of the data.
“We can tell you exactly the day that it was seeded, what pack, what lot number from that seeding package that we got. We can tell you all of that information. That’s pretty powerful information,” he said.
The Borealis project has been in the works for about two years.
The modular building arrived at the end of January this year and a second farm should be on site by the end of August and will allow them to diversify the produce being grown. They also have plans to build a vestibule and micro-greens farm.
They weren’t planning on a third farm, but the way things are going, they see the potential for it.
Rodrigue and Cochrane have both had agricultural projects on their mind for a while.
They met through the entrepreneur centre at Northern College.
Rodrigue was an entrepreneur officer and Cochrane a client. They formed a friendship, which eventually budded into the business partnership.
“The number of times that we had talked about agricultural stuff back and forth was lots, the whole year before we were just bouncing ideas. Never complete ideas, because we were trying to keep our ideas to ourselves, but you could tell that it was getting closer and closer to the same thing,” recalled Cochrane.
Knowing they had similar aspirations, when Rodrigue was serious about getting started he went to see Cochrane.
The zip tower growing that was on Cochrane’s mind was what Rodrigue was envisioning as well.
There are a number of ways to buy local produce in the region.
With a short growing season in Northern Ontario, however, there is a limited time to access those foods.
Eating a plant-based diet, Rodrigue noted he couldn’t find fresh foods like what they are now growing.
“At the end of the day we’re just trying to take a little bit more control over our food chain that we have up here. Instead of buying it from Texas or California or Mexico or some other place that’s miles and miles away, we value a great eco system,” he said.
“Now we have nutrient-dense foods that you can actually have on your plate the morning that it’s cut.”
By tracking data and developing new technology along the way, they are hoping to grow a bigger movement.
“We want to build a business model based on this technology that will allow us to scale up to a level where you can finally have a sustainable food source in any region,” Rodrigue said.
Like any business venture, there are benefits and challenges.
The main selling point is being able to offer fresh, nutrient-dense produce year round.
“Also for the grocer, the price doesn’t change through the year,” said Cochrane.
The challenge with the modular set up is energy.
“There’s always inputs,” said Rodrigue. “Our largest input right now...is power. So electricity is a cause of concern, our high electricity rates.”
To combat the high prices, they work with the time of use rates.
With the growing lights giving the plants 18 hours of ‘daylight’, they’re turned on overnight when the cost for electricity dips.
The price point for the produce is the similar to other high-end options.
In Timmins, the greens are available in the Trussler's Pantry Box and Pick of the Crop.
They’ve also recently been talking to Holy Cow downtown Timmins and are growing mint for the Indian restaurant’s chutney.
They’ll be talking to other restaurants in town about their product soon as well.
“It’s really about building that local food culture as much as we can, getting it out there,” said Rodrigue.
You can keep in touch with where the produce is being sold and what the partners are up to on Facebook.
Inside China's 'Smart Vegetable Farm': Autonomous Greenhouse Allows Plants To Grow Without Soil Or Sunlight
Inside China's 'Smart Vegetable Farm': Autonomous Greenhouse Allows Plants To Grow Without Soil Or Sunlight
- Futuristic farm maximizes the growth potential of plants and is 75 times more efficient than conventional farming
- 54,000 sq ft plant in Fujian, south-east China, can produce eight to 10 tonnes of vegetables every day
- The system automatically regulates temperature, water, humidity, nutrients and LEDs that replace sunlight
By KELSEY CHENG FOR MAIL ONLINE
PUBLISHED: 6 July 2018
These luscious leafy greens sprout from stackable trays in a confined room - without the need of a single drop of pesticide, natural sunlight or soil.
In what could be the future of agriculture in China, a company in Anxi, Fujian province, has been developing a smart farm that enables vegetables to grow efficiently in an automated environment.
The firm's latest expansion project - a 5,000-square-metre (53,819-square-foot) indoor farm - has been under development for the past two years and was finally unveiled last Friday.
Eight to 10 tonnes of vegetables are produced every day on the farm, which is almost the size of a football pitch. That amount of vegetables would be enough to feed nearly 36,000 people, according to Sanan Sino-Science, the company behind the project.
In what could be the future of agriculture in China, a company in Anxi, Fujian province, has been developing a smart farm factory that enables vegetables to grow efficiently in an automated environment
The firm's latest project - a 5,000-square-metre (53,819-square-foot) indoor farm - has been under development for the past two years and was finally unveiled last Friday. The new farm can produce between eight to 10 tonnes of veggies daily
The massive incubation room requires only four staff members to manage - compared with about 300 farmers required in conventional farmlands to produce the equivalent amount.
People in China consume an average of 276 grams (9.7 ounces) of vegetables every day, according to the National Institute for Nutrition and Health.
'Compared with our first generation smart farm, this new plant yields even more effective results while reducing labour and environmental costs,' Sanan Sino-Science CEO Zhan Zhuo told MailOnline.
The company was founded in 2015 by San'an Group and the Chinese Academy of Sciences' Institute of Botany.
Its first generation plant factory, which covers an area of 10,000 square meters (1 hectare), is claimed to be the world's largest vertical farming complex.
The smart farming method, which practices growing vegetables and herbs in multilevel cultivation beds of hydroponic solutions in a controlled environment, is equipped with highly advanced autonomous technology.
The smaller-sized varieties can be harvested in 18 days while larger vegetables take between 33 and 35 days
An automated converter belt was also seen transporting the plates of crisp green veggies for packaging
Scientists donning a full biohazard gear with goggles, face masks, rubber gloves and boots while examining the veggies
The confined indoor space has a strict system that regulates temperature, water source, humidity, nutrients and LEDs that replace sunlight.
'This maximizes the plant's growth potential while maintaining a sustainable and continuous growth cycle,' Mr. Zhan said.
In the factory, the smaller-sized varieties can be harvested in 18 days while larger vegetables take between 33 and 35 days, he added. Vegetables in a conventional farm need about 40 to 60 days to reach maturity, which is also highly dependable on weather conditions.
At full capacity, when the energy cost is neglected, the smart factory can produce 3,000 tonnes to 3,500 tonnes of leafy greens per year.
Video footage of the gigantic smart plant shows factory workers donning a full biohazard gear with goggles, faces masks, rubber gloves and boots while examining and patrolling rows of rainbow-colored LED-lit shelves.
Various plants including lettuce, basil, and bok choy are seen growing on large white trays in tiny allocated slots, submerged in nutrient solutions that are essentially free of soil.
Sanan Sino-Science's first generation plant factory is claimed to be the world's largest vertical farming complex
These vegetables taste less bitter and possess higher nutritional value compared with other conventionally grown plants
The incubation room requires only four staff members, compared with about 300 farmers required in conventional farmlands
An automated converter belt was also seen transporting the plates of crisp green veggies for packaging.
'These vegetables taste less bitter and possess higher nutritional value compared with other conventionally grown plants,' Mr. Zhan said.
More importantly, the new technology greatly saves on water, which is a scarce resource in the country.
'We are working hard to attain a 1:1 ratio between the water used and the vegetables harvested,' Mr. Zhan said, meaning that one tonne of water used can ideally produce one whole tonne of vegetables.
'Currently, 80 percent to 85 percent of the water used could be recycled back into the plant. We hope to reach the 1:1 ratio goal by 2020.'
The company also plans to install AI technology in the facility that can record and analyze growth data through sensors.
The self-learning model will automatically design a template that illustrates the optimal growing condition for each specific kind of vegetable, Mr. Zhan said.
This will also help the farm produce a precise, stable, year-round supply of leafy greens, which means that market prices vegetables could also be more predictable.
More importantly, the new technology greatly saves on water, which is a scarce resource in the country
The smart, GMO-free veggies are sold around 30 yuan (£3.4) to 36 (£4) yuan per kilogram in China
'This farming method is particularly beneficial in challenging environments such as deserts, mountainside towns, or in cities where labor come at a high cost,' Mr. Zhan said.
A tightly controlled environment not only speeds up the growth cycle but also allows researchers to create vegetables that suit specific needs, he added.
For example, scientists can lower the amount of potassium in the greens for patients with kidney problems or increase zinc in cabbages for children.
Right now, the vegetables produced are being shipped to the rest of Fujian province and Shanghai in supermarkets and high-class restaurants.
The brand new technology could help transform China's rapid green revolution amid growing concerns about food safety and nutrition.
The country is also the largest producer of vegetables in the world, harvesting 78.7 million tonnes of vegetables in 2016. The number is expected to rise continuously, according to the National Bureau of Statistics.
The farm can produce a precise, stable, year-round supply of leafy greens, meaning market prices will be more predictable
Through the system, scientists can lower the amount of potassium in the vegetables for patients with kidney problems
The smart, GMO-free veggies are sold around 30 yuan (£3.4) to 36 (£4) yuan per kilogramme in China, while regular vegetables are sold at a wholesale price of 2.85 yuan (£0.32) per kg, according to the latest statistics released by the Chinese Ministry of Agriculture and Rural Affairs.
While this may be an eye-watering price tag to many, a recent food and health survey conducted recently by China Youth Daily on 2,001 Chinese residents shows that more than 76 per cent of participants are willing to spend more money on healthier food choices.
Another 66 percent of those surveyed agreed that they would now pay more attention to the product's nutritional value than its flavor and taste.
The smart factory's relevant equipment and technologies have been shared with countries possessing advanced technological capabilities such as the US, Japan, and Singapore, Mr. Zhan said.
'We hope to bring the concept of "produce locally, sold locally" to different cities,' he said. 'We have ambitious plans to expand.'
One Of The Nation's Largest Indoor Farms Takes Root In Las Vegas
One Of The Nation's Largest Indoor Farms Takes Root In Las Vegas
June 29, 2018
A new era is underway in Southern Nevada as Oasis Biotech, now one of the nation’s largest indoor hydroponic vertical farming facilities of its kind, is proud to announce that it has officially taken root in Las Vegas, bringing hundreds of jobs, millions in local investment dollars and some of the most nutritious and flavorful produce in the world.
Founded in 2017, the company plans to leverage its 215,000-square-foot facility, proprietary state-of-the-art technology, precise growing methods and a highly qualified team of experts to fulfill their mission to “Feed the World. Better.”
“The crops grown at our facility will be some of the best tasting, most nutrient-rich and environmentally sustainable crops in the world,” says Brock Leach, Chief Operating Officer and General Manager at Oasis Biotech. “Completion of phase 1 of the new facility alone will allow us to provide Las Vegas restaurants and eventually grocers with over a million pounds of produce per year.”
According to Leach, produce can travel more than 1,500 miles before it ever reaches a consumer, which means a significant loss in nutrients and flavor.
“We want to redefine the meaning of fresh produce to Las Vegas,” says Leach. “We are now living in a world where the produce your family consumes will be grown in the same city in which they live and eaten almost immediately following harvest.”
Drawing on the expertise of a management team that includes some of the nation’s top experts in hydroponic crop production, Oasis Biotech’s indoor farm brought new life to a vacant industrial property that once housed a distribution facility and call center.
Now the company is gearing up for rapid growth.
It’s recruiting skilled agricultural professionals and technicians from across the nation to support its massive investment in the region.
In its current state, the company has brought over 100 jobs to Southern Nevada and plans to invest nearly $30 million into the region’s economy within its first year — all of it into a highly sustainable business model that further diversifies the region’s economy.
“Today, agriculture accounts for only a tiny portion of the employment in Clark County, roughly 0.15 percent of all the jobs in the area,” says Leach. “Our technology and ability to help feed the world with highly sustainable practices are attracting a highly motivated team of modern-day farmers from around the world.”
Founded in 2017 and located in Las Vegas, Nevada, Oasis Biotech is now one of the nation’s largest indoor hydroponic vertical farming facilities of its kind. Utilizing their proprietary state-of-the-art technology, precise growing methods, and a qualified team of experts, the company is dedicated to fulfilling their mission to “Feed the World. Better.,” by providing the world’s highest-quality, most nutritious and environmentally sustainable produce and non-traditional crops to local restaurants and grocery stores across the globe.
Tags Biotech Economics Commerce Agriculture Brock Leach Oasis
Why Hydroponics Could Be The Future Of Farming
Most people in India have grown up with the idea that good water, good soil and lots of sunlight translate into good farming. That may have been true for most farmers, for a great deal of time. But new research and practice have shown that what healthy plants really require are good seeds, good water, and nutrients.
Why Hydroponics Could Be The Future Of Farming
The word hydroponics comes from hydro meaning water, and ponos meaning labour. It is meant to represent the growing of plants in any medium -- sand, gravel, or liquid, with added nutrients, but without soil.
RN Bhaskar
Most people in India have grown up with the idea that good water, good soil and lots of sunlight translate into good farming. That may have been true for most farmers, for a great deal of time. But new research and practice have shown that what healthy plants really require are good seeds, good water, and nutrients. Plants do not really require soil. And plants need not sunlight, but spectrum. The entire process of photosynthesis is possible when the plant separates the sunlight to soak in the spectrum that it requires. Broadly, different types of plants use blue, red or yellow spectrum. Some use white spectrum as well.
What is hydroponics?
The word hydroponics comes from hydro meaning water, and ponos meaning labour. It is meant to represent the growing of plants in any medium -- sand, gravel, or liquid, with added nutrients, but without soil. It is also referred to as vertical farming, because this type of farming allows for crops to be grown in layers – in shelves or trays, one layer over another. These layers could be as many as you want – from 2 or 3 or even 20 – one on the top of another. A very good idea of the potential hydroponics can have can be viewed from ‘The rise of vertical farming – a VPRO documentary – 2017’, a 54 minute video of how it is practiced around the world.
What hydroponics does best is eliminating the need for soil, sunlight and rain. Since almost 90% of pests come from the soil, there is automatically a dramatic reduction in pests. Hence fewer pesticides, herbicides and insecticides are used. Aerial pests that may sneak in are often caught by the insect traps that are there in any hydroponics farm. The plant uses the water that runs below each tray, and this water is then re-circulated, preventing both evaporation and wastage. Nutrients that the plants need are carried through the water and caress only the roots of the plants -- each range of trays carries the nutrients specific to each type of plant, depending on its age and the and the special qualities it is meant to have when it is ready to be sold to customers.
The identification of nutrients that plants need has itself become a big booming industry.
Market size
Is hydroponics just a fringe movement, primarily found on the shelves of laboratories, or has it become commercially viable? The truth is that this industry is growing by leaps and bounds. The hydroponics industry has become huge during the past decade.
How big? Well, that is where the problem lies. There are varying estimates.
For instance, a news report put out by Reuters in August 2017, which quotes Stratistics MRC, expects the global hydroponics market to grow from $226.45 million in 2016 to reach $724.87 million by 2023. And it is reported to be growing at a furious pace of 18.1% CAGR (compounded average rate of growth).
But another estimate put out by Mordor Intelligence and which is often quoted by many industry experts, paints a picture that is positively glowing. This report puts the global hydroponics market at US$ 21,203.5 million in 2016. The market is expected to register a CAGR of 6.5% during 2018 to 2023. The percentage looks modest, but on a base of $21,203 million, it means that the industry grows by at least US$1.4 billion each year. That is heady growth indeed!
If one takes into account the types of plants grown using hydroponics, you will find products like tomato, cucurbits, lettuce, almost all varieties of leafy vegetables, peppers, and other food crops.
Tomato forms the largest market segment and it is likely to account for 30.4% share of the global market, by the end of this year.
As consumers become increasingly aware of the superior quality in greenhouse-grown vegetables, the demand for hydroponics has been growing in Europe and Asia-Pacific. Hydroponics crop production is expected to continue growing when it comes to tomatoes, lettuce, and other leafy vegetables. Experiments with creeper plants have also been quite promising, and it won’t be long before we have large-scale cultivation of fruit like grapes and plums using hydroponics.
The scale of operations for hydroponics-focused companies is actually astonishing. For instance, just one company in Holland produces and exports almost 100 million kilos of tomatoes (100,000 tonnes).
But if all types of crop are considered, it is the US which is the hydroponics center of the world (refer to timeline 20:45 in the video mentioned above). There, one company, Aero Farms, has begun picking up dilapidated and abandoned warehouses and reshaping them into hydroponic farms. As one of its managers puts in, “Today, we can produce more than 130 times what a person can conventionally produce in one acre.” This is done by multiplying the layers of farm shelves in our hydroponic farms, and also increasing output.” Thus, effectively, with a 130 x output, economies and technologies are brought into play making this one of the most incredible industries in the agriculture sector.
And when people tell hydroponics scientists that their way of farming is unnatural, they chuckle. They point out that organized farming is barely a thousand years old. Compared to the millions of years the earth and its natural evolution has been around, it is farming that is unnatural. Hydroponics is only one way of doing what nature does but in a better and more scientific manner.
As Aero Farms managers point out, once a crop is harvested, it begins to lose its nutritional value and its flavour very rapidly. Hydroponics allows a farmer to grow the crop next to consuming centres. Thus a hydroponics farm on the terrace of a building located in a business district can supply fresh crop to workers as well as to restaurants in this very district. There is less of transportation, hence hardly any transportation or refrigeration costs. Moreover, the crop is both safe and fresh, hygienic and nutritional.
Some of the key players in the world’s hydroponics market include AMCO Produce Inc., American Hydroponics, Inc., Argus Control Systems Ltd., BetterGrow Hydro, Eurofresh Farms, General Hydroponics, Inc., Greentech Agro, Llc, Heliospectra AB, Hydrodynamics International, Inc., Hydrofarm, Inc., HydroWholesale Inc, Koninklijke Philips NV, Logiqs B.V., Lumigrow, Inc., and Village Farms International.
Expect this list to grow longer as Asian companies have now begun to look at hydroponics as the next big market. Already, since South Korea is the hub for LED lights, almost half the leafy vegetables in that country are said to be through the hydroponics route. China has begun to embrace it, because it uses barely 10% of the water plants conventionally use. As the plant grows on shelves, and as the water gets recycled, there is little evaporation, little of water going into the earth, and hence you actually get more crop per drop than even drip irrigation. Even energy costs have tumbled as most hydroponics plants use solar power instead of the more expensive power through the power grids.
Media to nutrients
It is the nutrients market that got one Indian company – HiMedia – to begin looking at the hydroponics market very seriously. HiMedia is a group headquartered in Mumbai but with its main laboratories in Nasik and it is one of the largest players globally in the biological media industry. It produces media required by industries related to pathology, pharmaceuticals and food. HiMedia’s brochure proudly defines itself as one of the top 5 media companies in the world.
What started as a home enterprise by the Warke family, in 1973 gradually grew into a firm dealing with microbiology, animal cell culture and gradually to plant cell culture. The last phase was accidentally triggered by an incident when a consignment of HiMedia was rejected by Australia because that country was not comfortable with India’s quality standards especially when related to animal-based culture media. The Mad Cow disease was a dreaded word, and hence culture media from animal-origin were deemed suspicious especially if they originated in countries like India.
So the Warke family began experimenting with plants to source cell cultures from there. The HiMedia management believes that when it comes to plant based culture, their group could be the world’s largest player.
A chance meeting with the legendary Jim Rogers in China in 2006 brought them global attention and an association with VWR Inc, one of the biggest players in this line of business. That brought HiMedia more credibility and today it exports its products to almost all major markets in the world, including EU, USA, Japan and Korea. Today, even though 35% of its product is still sold under the brand names of some of the biggest players in the world, the remaining 65% sells under the HiMedia brand.
Working on plant cultures brought the company close to identifying the molecules that plants need to grow healthily. Today, HiMedia has protocols for over 50 different plants relating to nutrition and growth. That in turn has got the Warke family into hydroponics. Today the management is looking at this business segment a lot more seriously than most people do in India. The Warke family has decided to call this division Higronics.
The case for India
But why should India look at hydroponics?
There could be several reasons why India may have no option but to embrace this method of farming.
The first is that it is economically viable (see chart). The figures are indicative, from just one vendor. But as more vendors start entering this field, prices could drop. What is needed is a sound government policy on the one hand and active handholding of the farmer on the other.
Second, this is the closest one can get to fresh food, uncontaminated by pesticides and insecticides.
Third, at a time when agriculture itself is being buffeted by climate change including unseasonal rain and hail storms, hydroponics is a way of managing to grow plants under controlled conditions. Thus, you could recreate the atmosphere of say Gangtok in the middle of Maharashtra and actually focus on growing medicinal plants that normally found in the North East parts of India.
You could control all the variables, including the strength of active ingredients which have tended to degenerate and deteriorate over a period of time.
Fourth, it could be the best solution for the Indian government when it comes to land acquisition. The government could offer farmers land for land, and work out ways whereby the hydroponics company would handhold the farmer to teach him how to master the technologies involved. That was the strategy Narendra Modi used when he was chief minister of Gujarat. He allowed micro-irrigation companies to get the subsidy amounts only after another specified government agency certified that they had handheld customer farmers. That way, farmers would be able to stick to farming even if the landholding was very small (you can grow as much as 130 times the conventional amount on any plot of land).
Fifth, with controlled supply of nutrients and with hardly any pesticides being used, the cost for crop management begins to diminish.
Sixth, since consuming markets are close to producing centres, the transport miles shrink, leading to a further reduction in costs. As farmers learn to strike deals directly with consumers, and as they learn to space out crop production so that a limited supply is available every day, they can move away from rapacious middlemen as well.
And lastly, this is one way to reduce farmer distress. These new technologies have the power to reduce the germination life of plants from around 30 days (the conventional time span for plants) to just around 11 days. Thus the farmer can rotate his crop more often. That allows him to keep pace with changing tastes. A higher crop intensity also helps him to better his earnings. It is also one way to bring farming closer to food processing centres and embrace the cold chain system that agriculture so sorely needs.
There is also one more factor that would endear urban investors to this opportunity. The sale proceeds from the agricultural produce got through hydroponics invites zero taxes. That could add another dimension to urban incomes altogether.
Hopefully, weather vagaries and farmer distress with soon compel the government to sit up and embrace and promote this method of farming.
(The author is consulting editor with Moneycontrol.com)
EU: Ten-Year Reprieve For Organic Hydroponic Growers
EU: Ten-Year Reprieve For Organic Hydroponic Growers
The European Union has published its new organic regulation, which will enter into force on January 1, 2021. For organic hydroponic growers, the following passage is of interest, which states that operations certified as organic before June 28, 2017, may continue growing on their production surfaces for another ten years following the date of application of the Regulation.
"As organic plant production is based on nourishing the plants primarily through the soil ecosystem, plants should be produced on and in living soil in connection with the subsoil and bedrock. Consequently, hydroponic production should not be allowed, nor growing plants in containers, bags or beds where the roots are not in contact with the living soil.
"However, certain cultivation practices which are not soil-related, such as the production of sprouted seeds or chicory heads and the production of ornamentals and herbs in pots that are sold in pots to the consumers, for which the principle of soil-related crop cultivation is not adapted or for which no risk exists that the consumer is misled regarding the production method, should be allowed. In order to facilitate organic production at an earlier growing stage of plants, growing seedlings or transplants in containers for further transplanting should also be permitted.
"The principle of land-related crop cultivation and the nourishing of plants primarily through the soil ecosystem was established by Regulation (EC) No 834/2007. Some operators have, however, developed an economic activity by growing plants in ‘demarcated beds’ and have been certified as organic under Regulation (EC) No 834/2007 by their national authorities. An agreement has been reached within the ordinary legislative procedure on 28 June 2017 that the organic production should be based on nourishing the plants primarily through the soil ecosystem and be soil-related, and that growing plants in demarcated beds should not be allowed anymore from that date.
In order to give the operators who have developed such economic activity until that date the possibility to adapt, they should be allowed to maintain their production surfaces, if they were certified as organic under Regulation (EC) No 834/2007 before that date by their national authorities, for further 10 years after the date of application of this Regulation. On the basis of the information provided by Member States to the Commission, such activity had only been authorised in the Union before 28 June 2017 in Finland, Sweden, and Denmark. The use of demarcated beds in organic agriculture should be subject to a report of the Commission which is to be published five years after the date of application of this Regulation."
Click here to read the full Regulation.
Publication date: 6/22/2018
COMMENT- Why Hydroponics Could Be The Future of Farming
The word hydroponics comes from hydro meaning water, and ponos meaning labour. It is meant to represent the growing of plants in any medium -- sand, gravel, or liquid, with added nutrients, but without soil.
Jun 25, 2018 | Source: Moneycontrol.com
COMMENT- Why Hydroponics Could Be The Future of Farming
The word hydroponics comes from hydro meaning water, and ponos meaning labour. It is meant to represent the growing of plants in any medium -- sand, gravel, or liquid, with added nutrients, but without soil.
RN Bhaskar
Most people in India have grown up on the idea that good water, good soil and lots of sunlight translate into good farming. That may have been true for most farmers, for a great deal of time. But new research and practice have shown that what healthy plants really require are good seeds, good water, and nutrients. Plants do not really require soil. And plants need not sunlight, but spectrum. The entire process of photosynthesis is possible when the plant separates the sunlight to soak in the spectrum that it requires. Broadly, different types of plants use blue, red or yellow spectrum. Some use white spectrum as well.
What is hydroponics?
The word hydroponics comes from hydro meaning water, and ponos meaning labour. It is meant to represent the growth of plants in any medium -- sand, gravel, or liquid, with added nutrients, but without soil. It is also referred to as vertical farming because this type of farming allows for crops to be grown in layers – in shelves or trays, one layer over another. These layers could be as many as you want – from 2 or 3 or even 20 – one on the top of another. A very good idea of the potential hydroponics can have can be viewed from ‘The rise of vertical farming – a VPRO documentary – 2017’, a 54-minute video of how it is practiced around the world.
What hydroponics does best is eliminating the need for soil, sunlight, and rain. Since almost 90% of pests come from the soil, there is automatically a dramatic reduction in pests. Hence fewer pesticides, herbicides, and insecticides are used. Aerial pests that may sneak in are often caught by the insect traps that are there in any hydroponics farm. The plant uses the water that runs below each tray, and this water is then re-circulated, preventing both evaporation and wastage. Nutrients that the plants need are carried through the water and caress only the roots of the plants -- each range of trays carries the nutrients specific to each type of plant, depending on its age and the special qualities it is meant to have when it is ready to be sold to customers.
The identification of nutrients that plants need has itself become a big booming industry.
Market size
Is hydroponics just a fringe movement, primarily found on the shelves of laboratories, or has it become commercially viable? The truth is that this industry is growing by leaps and bounds. The hydroponics industry has become huge during the past decade.
How big? Well, that is where the problem lies. There are varying estimates.
For instance, a news report put out by Reuters in August 2017, which quotes Statistics MRC, expects the global hydroponics market to grow from $226.45 million in 2016 to reach $724.87 million by 2023. And it is reported to be growing at a furious pace of 18.1% CAGR (compounded average rate of growth).
But another estimate put out by Mordor Intelligence and which is often quoted by many industry experts, paints a picture that is positively glowing. This report puts the global hydroponics market at US$ 21,203.5 million in 2016. The market is expected to register a CAGR of 6.5% during 2018 to 2023. The percentage looks modest, but on a base of $21,203 million, it means that the industry grows by at least US$1.4 billion each year. That is heady growth indeed!
If one takes into account the types of plants grown using hydroponics, you will find products like tomato, cucurbits, lettuce, almost all varieties of leafy vegetables, peppers, and other food crops.
Tomato forms the largest market segment and it is likely to account for 30.4% share of the global market, by the end of this year.
As consumers become increasingly aware of the superior quality in greenhouse-grown vegetables, the demand for hydroponics has been growing in Europe and Asia-Pacific. Hydroponics crop production is expected to continue growing when it comes to tomatoes, lettuce and other leafy vegetables. Experiments with creeper plants has also been quite promising, and it won’t be long before we have large scale cultivation of fruit like grapes and plums using hydroponics.
The scale of operations for hydroponics-focused companies is actually astonishing. For instance, just one company in Holland produces and exports almost 100 million kilos of tomatoes (100,000 tonnes).
But if all types of crop are considered, it is the US which is the hydroponics centre of the world (refer to timeline 20:45 in the video mentioned above). There, one company, Aero Farms, has begun picking up dilapidated and abandoned warehouses and reshaping them into hydroponic farms. As one of its managers puts in, “Today, we can produce more than 130 times what a person can conventionally produce in one acre.” This is done by multiplying the layers of farm shelves in our hydroponic farms, and also increasing output.” Thus, effectively, with a 130 x output, economies and technologies are brought into play making this one of the most incredible industries in the agriculture sector.
And when people tell hydroponics scientists that their way of farming is unnatural, they chuckle. They point out that organized farming is barely a thousand years old. Compared to the millions of years the earth and its natural evolution has been around, it is farming that is unnatural. Hydroponics is only one way to doing what nature does, but in a better and more scientific manner.
As Aero Farms managers point out, once a crop is harvested, it begins to lose its nutritional value and its flavour very rapidly. Hydroponics allows a farmer to grow the crop next to consuming centres. Thus a hydroponics farm on the terrace of a building located in a business district can supply fresh crop to workers as well as to restaurants in this very district. There is less of transportation, hence hardly any transportation or refrigeration costs. Moreover, the crop is both safe and fresh, hygienic and nutritional.
Some of the key players in the world’s hydroponics market include AMCO Produce Inc., American Hydroponics, Inc., Argus Control Systems Ltd., BetterGrow Hydro, Eurofresh Farms, General Hydroponics, Inc., Greentech Agro, Llc, Heliospectra AB, Hydrodynamics International, Inc., Hydrofarm, Inc., HydroWholesale Inc, Koninklijke Philips NV, Logiqs B.V., Lumigrow, Inc., and Village Farms International.
Expect this list to grow longer as Asian companies have now begun to look at hydroponics as the next big market. Already, since South Korea is the hub for LED lights, almost half the leafy vegetables in that country are said to be through the hydroponics route. China has begun to embrace it, because it uses barely 10% of the water plants conventionally use. As the plant grows on shelves, and as the water gets recycled, there is little evaporation, little of water going into the earth, and hence you actually get more crop per drop than even drip irrigation. Even energy costs have tumbled as most hydroponics plants use solar power instead of the more expensive power through the power grids.
Media to nutrients
It is the nutrients market that got one Indian company – HiMedia – to begin looking at the hydroponics market very seriously. HiMedia is a group headquartered in Mumbai but with its main laboratories in Nasik and it is one of the largest players globally in the biological media industry. It produces media required by industries related to pathology, pharmaceuticals and food. HiMedia’s brochure proudly defines itself as one of the top 5 media companies in the world.
What started as a home enterprise by the Warke family, in 1973 gradually grew into a firm dealing with microbiology, animal cell culture and gradually to plant cell culture. The last phase was accidentally triggered by an incident when a consignment of HiMedia was rejected by Australia because that country was not comfortable with India’s quality standards especially when related to animal cell cultures. The Mad Cow disease was a dreaded word, and hence cell cultures from animals were deemed suspicious especially if they originated in countries like India.
So the Warke family began experimenting with plants to source cell cultures from there. The HiMedia management believes that when it comes to plant based culture, their group could be the world’s largest player.
A chance meeting with the legendary Jim Rogers in China in 2006 brought them global attention and an association with VWR Inc, one of the biggest players in this line of business. That brought HiMedia more credibility and today it exports its products to almost all major markets in the world, including EU, USA, Japan and Korea. Today, even though 35% of its product is still sold under the brand names of some of the biggest players in the world, the remaining 65% sells under the HiMedia brand.
Working on plant cultures brought the company close to identifying the molecules that plants need to grow healthily. Today, HiMedia has protocols for over 50 different plants relating to nutrition and growth. That in turn has got the Warke family into hydroponics. Today the management is looking at this business segment a lot more seriously than most people do in India. The Warke family has decided to call this division Higronics.
The case for India
But why should India look at hydroponics?
There could be several reasons why India may have no option but to embrace this method of farming.
The first is that it is economically viable (see chart). The figures are indicative, from just one vendor. But as more vendors start entering this field, prices could drop. What is needed is a sound government policy on the one hand, and active handholding of the farmer on the other.
Second, this is the closest one can get to fresh food, uncontaminated by pesticides and insecticides.
Third, at a time when agriculture itself is being buffeted by climate change including unseasonal rain and hail storms, hydroponics is a way of managing to grow plants under controlled conditions. Thus, you could recreate the atmosphere of say Gangtok in the middle of Maharashtra and actually focus on growing medicinal plants that normally found in the North East parts of India.
You could control all the variables, including the strength of active ingredients which have tended to degenerate and deteriorate over a period of time.
Fourth, it could be the best solution for the Indian government when it comes to land acquisition. The government could offer farmers land for land, and work out ways whereby the hydroponics company would handhold the farmer to teach him how to master the technologies involved. That was the strategy Narendra Modi used when he was chief minister of Gujarat. He allowed micro-irrigation companies to get the subsidy amounts only after another specified government agency certified that they had handheld customer farmers. That way, farmers would be able to stick to farming even if the landholding was very small (you can grow as much as 130 times the conventional amount on any plot of land).
Fifth, with a controlled supply of nutrients and with hardly any pesticides being used, the cost for crop management begins to diminish.
Sixth, since consuming markets are close to producing centres, the transport miles shrink, leading to a further reduction in costs. As farmers learn to strike deals directly with consumers, and as they learn to space out crop production so that a limited supply is available every day, they can move away from rapacious middlemen as well.
And lastly, this is one way to reduce farmer distress. These new technologies have the power to reduce the germination life of plants from around 30 days (the conventional time span for plants) to just around 11 days. Thus the farmer can rotate his crop more often. That allows him to keep pace with changing tastes. A higher crop intensity also helps him to better his earnings. It is also one way to bring farming closer to food processing centres and embrace the cold chain system that agriculture so sorely needs.
There is also one more factor that would endear urban investors to this opportunity. The sale proceeds from the agricultural produce got through hydroponics invites zero taxes. That could add another dimension to urban incomes altogether.
Hopefully, weather vagaries and farmer distress with soon compel the government to sit up and embrace and promote this method of farming.
(The author is consulting editor with Moneycontrol.com)
First Published on Jun 25, 2018
Growers From Around The World Travel To Eureka, CA To Learn Hydroponic Growing And Business Techniques.
Growers From Around The World Travel To Eureka, CA To Learn Hydroponic Growing And Business Techniques.
“Hands-on learning is the ONLY way to build a hydroponic business.”
Recently, potential and current hydroponic growers converged on Eureka California to engage in the latest AmHydro “Introduction to Commercial Hydroponics” seminar.
AmHydro holds several 2-day seminars each year in various locations across the US, featuring classroom, lecture, and “hands-on” knowledge provided by successful commercial growers and industry leaders. In addition to hydroponic growing techniques, attendees also were immersed in classes on building a CEA business, managing operations, and food safety protocols.
A highly diverse group attended, which included representatives from the Ministry of Agriculture and Climate Change from the African country of Burkina Faso (traveling over 7,000 miles!), a large-scale grain farmer from Kansas, fruit plantation owners from Jamaica, and the owner of a West Virginia hydroponic farming business.
After leaving the classroom setting, the group ventured to a nearby commercial hydroponic greenhouse where they participated in seeding, transplanting, harvesting, and biological pest control practices.
Joe Swartz, VP of Amhydro explains, “the goal here is to provide participants with a well-rounded understanding of building and operating a controlled environment agriculture business.” He adds, “understanding proper horticultural practices, ag-related business management, and food safety/regulatory issues are all critically important to the success of your operation. We strive to provide sound, time-tested systems, and procedures based on our successful experience as commercial growers ourselves.”
AmHydro’s next seminar is planned for October 11th and 12th.
An Agricultural Revolution
An Agricultural Revolution
JUNE 16TH, 2018 CATHERINE MORRIS0
Ino-Gro Inc. uses high-density vertical farming techniques coupled with automation and remote monitoring software to create a climate-smart food production system.
How GreenTech is transforming the agricultural industry in Saint Lucia and beyond
In the past, successful farmers relied on the land, the weather, their instincts and a little bit of luck. Thanks to a boom in ‘green technology’ there are now a lot more tools at their disposal. The uptake of GreenTech among agricultural pioneers is helping to modernise the industry and streamline farming, as well as aiding the Caribbean in achieving its goal of food security.
CREATIVE TECH
More than US$800m was invested in agricultural technology (‘agtech’) globally between 2012 and 2016, according to research group CB Insights.
“Technology has been the main driver of change in most industries, and agriculture is no different,” says Warren Kellman, Managing Director of Ino-Gro Inc, a hydroponic farm in Barbados. “New technologies are being created every single day around the world and people are coming up with creative solutions [to environmental challenges].”
Ino-Gro Inc is one of those creative solutions. Launched in 2016 by Kellman and a friend, the farm is the first of its kind in Barbados and consists of a 40ft shipping container stacked with walls of leafy greens and operated through a fully automated, online system. Kellman and his team can monitor and control the environment – temperature, humidity, LED lighting – within the container through an app downloaded to their smartphones. Sensors, timers and alerts feed them information in real-time, with all data available via the cloud.
The vertical farming model allows Ino-Gro Inc to practise high-density farming in a relatively small area. Kellman says the container is equivalent to one acre of farmland and produces around 40kg of produce a week, including three different types of lettuce, mint, basil and edible flowers. Demand is high and the produce sells out every week, with hotels, restaurants, chefs and the general public eager to buy local.
Ino-Gro Inc’s success, however, was not guaranteed. There were challenges along the way but Kellman says he was not just motivated by turning a profit. “When we started, we wanted to find a way to make money but also do something good. We import too much. The population of the Caribbean is only going to grow, we need to find more sustainable ways to produce enough food.”
PRECISION FARMING
One of the biggest obstacles for Ino-Gro Inc was the initial expense. “These are high tech systems; the main challenge is the cost associated with them. It is one thing to buy them in the United States, but then you have to get them to the Caribbean,” says Kellman.
Ino-Gro Inc’s computerised container was developed by US firm Freight Farms but Kellman would like to see the Caribbean develop its own agtech industry. He is working as a consultant with Saint Lucia’s TeleCarib Labs, Inc to help develop a model, climate-controlled, indoor farm. “We are working on being the first to create, design and build this type of model farm. We want to find a more affordable solution so we can overcome the challenges of cost and, from there, we can approach other countries who are interested. Our aim is to manufacture in the Caribbean, reduce the cost of these systems and enable a lot more people to grow their own food.”
A prototype for the farm will be established before the end of the year at the TeleCarib Labs’ campus, and will be “data-centred”, according to Kellman who says sensors will collect information that can be analysed to maximise productivity. “It allows for more accurate farming. We can analyse the data and make calculated decisions.”
VIRTUAL HUB
When the TeleCarib Labs farm becomes operational, it aims to sell directly to consumers through a virtual platform created by Tri Farms Ltd, a Saint Lucia company founded by local entrepreneur Garvin Francis.
Tri Farms’ eCrop is the region’s first virtual agricultural hub where producers and buyers can connect online. Producers simply log on, create a profile for their farm and let potential buyers know what they are selling and when it will be available. This direct service allows farmers to pre-sell their goods and gives buyers certainty so they can plan their purchases and minimise supply chain risks.
The system, which went live in January 2017, is used by the Saint Lucia Hotel and Tourism Association to host its Virtual Agricultural Clearing House (VACH) which encourages hotels, restaurants and food and beverage distributors to buy local. Francis says that helping Saint Lucia limit its food import bill was the impetus for Tri Farms Ltd when he first began brainstorming the idea over a decade ago. “Agriculture has been lagging in Saint Lucia and tourism provides an opportunity for local producers,” he says. “It sounds simple on paper but it’s not that easy – the market is so fragmented. There was a disconnect in terms of information; you could have a glut of one item one week and the next you might not find it on the island.”
Francis, who has previously worked in both the tourism and agricultural sectors, teamed up with Melvin Felicien whose background is in IT. Together they developed Tri Farms’ forecasting tool which is primarily aimed at buyers in the tourism industry. “Availability and consistency are very important in the tourism sector. Those buyers needed a tool that could predict what was coming on the market,” says Francis. “There is no reason why the hotels should be importing any produce that can be grown locally.”
There are now around 80 farmers registered with Tri Farms’ eCrop service. The company is looking to acquire more capital so it can scale up operations to make the system more intuitive and offer users an app. Francis says: “As with any tech company, capital is our biggest restriction, but this product has so much potential. There is quite a bit of focus now on building these platforms to create linkages. That is the future of agriculture – the availability of information through the use of technology. I anticipate a huge buzz and some creativity coming out of the Caribbean.”
THE NEXT GENERATION
If the agricultural industry is to reach its potential, however, the next wave of entrepreneurs has to be engaged. “The awareness is there but it’s not where it needs to be, especially when it comes to the younger generation,” says Kellman who wants to see more technology in schools and regularly invites kids to Ino-Gro Inc to show them how the system operates and spark their interest. “They come to our farm so they can get introduced to this new technology and become familiar with the way farming will be in the future. That is part of our mission – to not only grow and supply food, but also to educate people and let them know the importance of food security.”
It’s also the goal of TeleCarib Labs, which aims to launch its Future Farmers Entrepreneurship Programme next year. This initiative will give students the opportunity for hands-on experience at the model indoor farm, as well as skill development workshops and online learning.
“TeleCarib Labs will transform farming by linking innovation with education,” says Kellman. “There is plenty of opportunity in the agricultural industry. I would encourage young entrepreneurs to never settle, never give up and keep up to date with the technology that’s out there, not just in their own country but all over the world.”
To learn more, visit:
Hydroponics Farm In Downtown Shreveport Progressing
Hydroponics Farm In Downtown Shreveport Progressing
- Jun 15, 2018
Michael Billings
TownNews.com Content Exchange
A farm in downtown Shreveport. Not something you would expect to hear about or see.
Well, you probably never will see this particular farm. It's behind an old brick wall in downtown Shreveport.
"We're at 406 Cotton Street. This used to be the old, originally Alltel and then Verizon's networking building. We're in the process right now of removing the old wires and networking equipment and retrofitting it to be an indoor hydroponics farm," said Michael Billings of Cotton Street Farms.
Hydroponics farm (File photo).
For those of you not familiar with hydroponics, Billings explains: "Hydroponics separates/removes the plant from the dirt. We use a medium, with a mixture of water and nutrients. We have computers that monitor everything so we can provide the exact nutrient level for that plant."
"It's kind of a futuristic ... perhaps ... look at growing food. But it's also local food. So it's food grown locally in Shreveport, which is kind of a great thing," said Carl E. Motsenbocker, LSU AgCenter horticulture professor.
Cotton Street Farms plans on producing lettuce, kale, spinach, herbs, micro greens, mushrooms and some hops for local beer makers. Billings says he can produce about a million dollars worth of produce in this space per year.
Construction continues in the interior of Cotton Street Farms.
"We'll be setting up rows, vertical growing rows. It will look something similar to a library. Tall stacks about 8 feet tall with power and water going to all of them," said Billings.
He says the vegetables will cost about the same as what you would expect to pay at Whole Foods, but they will be freshly picked within hours and stay good much longer. Motsenbocker agrees with that assessment based on his experience.
"We have a small hydroponics system at LSU. We harvest with the roots on and it'll stay in your refrigerator for four to six weeks, I mean it lasts a long time," Motsenbocker said.
Ordering and delivery of these vegetables will be quite futuristic as well. Customers will use an app called Waitr. Many of you probably already use it to get Chinese food or pizza delivered. This Caddo Magnet graduate hopes to have his products on your doorstep this fall.
"We're not just growing plants, we're growing Shreveport and we're very excited about it," Billings said.
Equipment that will be used in the hydroponic process at Cotton Street Farms.
Cotton Street Farms made it to the top 5 of the Louisiana Startup Prize presented by EAP -- Entrepreneurial Accelerator Program -- last year. Billings says what he learned through that was invaluable, and he's competing again this year for the top prize.
RELATED STORY: EAP producing results with new startup companies
This article originally ran on ktbs.com.Tags
- Agriculture Cotton Street Farms Hydroponics Michael Billings Lsu Agcenter
- Carl E. Motsenbocker Shreveport Waitr Louisiana Startup Prize
- Entrepreneurial Accelerator Program Farm Economics Food Botany
- Vegetable Cotton
Locations
BrightFarms Doubles Funding with $55m Series D
BrightFarms Doubles Funding with $55m Series D
BrightFarms, the controlled environment agriculture (CEA) company, has raised a $55 million Series D round, bringing the greenhouse grower’s total funding to more than $100 million.
BrightFarms grows salad greens and herbs in hydroponic greenhouses in Illinois, Pennsylvania, Virginia, and Ohio. The new funds will largely go toward building more greenhouse facilities and expanding the company’s geographical footprint. A new farm in Ohio will open this summer, followed by a Texas facility in early 2019, according to a statement.
This latest round was led by communications, media, and automotive services companyCox Enterprises, with existing investors Catalyst Investors, WP Global Partners and NGEN Partners also participating.
Like other indoor farming operations, BrightFarms produces locally-grown fresh food to densely populated urban communities. But, BrightFarms has historically been more focused on business model innovation that technological innovation, especially compared to its set of high-tech indoor competitors like AeroFarms, Bowery, and Plenty. BrightFarmsCEO Paul Lightfoot said at the recent Indoor AgTech Summit in Brooklyn, NY, that using sunlight is a more sustainable choice than artificial light (as vertical, warehouse farms do).
Though Bright Farms’ funding hasn’t quite caught up to its higher raising counterparts in AeroFarms and Plenty, the company appears to be the closest US venture-backed CEA startup to being a national brand. The Texas farm will also bring BrightFarms closer to the center of salad green agriculture in the US, Salinas, CA and Yuma, Arizona.
“We have always competed directly with West Coast field grown products at the shelf. When we enter new retailers, we are replacing the shelf space of West Coast distributors. Our program drives incremental category growth while attracting our retailers’ most valuable consumers. We will deliver that growth in Texas and throughout the US as we expand. This is a huge category and we are just getting started,” Lightfoot told AgFunderNews.
It has made this progress by insisting on forward purchase agreements with clients, meaning retailers must commit to purchasing a certain quality of BrightFarms product over a period of time in order to sell it at all, which is not usual practice for most retailers, especially when buying produce.
“Our [forward purchasing] model has enabled deep and meaningful partnerships with retailers. We will continue to leverage that model as we scale,” Lightfoot said.
Neal Parikh, former vice president of finance at BrightFarms told AgFunderNews in 2016 that the upfront legal costs of drafting these contracts and convincing supermarket retailers to deviate from their usual buying patterns can prove difficult, especially when it comes to securing a long-term purchasing commitment. But, CEA means that prices and supply should be consistent and BrightFarms was able to convince some of grocery’s largest players. Current clients include Kroger, Wegmans, Walmart, ShopRite, and Jet.com among others.
Lead investor Cox Enterprises is a 120-year-old company with $18 billion in revenue. The company launched a national sustainability initiative in 2007 and has since invested more than $100 million toward environmental goals, according to a statement. The company is also an investor in FarmCrowdy, a digital agriculture platform focused on connecting farm sponsors with real farmers, based in Nigeria.
Cox Enterprise’s David Blau, vice president of strategy & corporate development and Lacey Lewis, senior vice president of finance, have joined the BrightFarms board of directors.
Kids Grow Salad Greens On An Urban Concrete Schoolyard
Kids Grow Salad Greens On An Urban Concrete Schoolyard
Hydroponic hothouse program introduces disadvantaged girls to organic, sustainable veggies and herbs for eating and selling.
By Abigail Klein Leichman JUNE 19, 2018
Fresh greens are grown hydroponically at a Jerusalem girls’ school. Photo courtesy of StartUpRoots
Photos of smiling kids planting, picking and eating vegetables line the hallways of a school for girls in an impoverished Jerusalem neighborhood. The pictures were taken in the hydroponic hothouse the girls have tended for the past three years on their concrete playground.
Many of their families can’t afford veggies or haven’t been taught about their essential nutritional value, leaving children undernourished and unaware of the miraculous journey from seed to salad, says Shulamit, the teacher in charge of the project.
The nonprofit StartUpRoots provides the funds, equipment, and expertise for the hothouse, which nurtures some 1,400 greens and herbs each month. The students eat them, cook with them and even make creams and soaps from them.
“I think this is a project that belongs in every school. I love it so much,” Shulamit tells ISRAEL21c.
A student tends the leafy greens growing in the hydroponic hothouse. Photo courtesy of StartUpRoots
Lawyer, entrepreneur and former teacher Robin Katz founded StartUpRoots after investigating how Israeli produce could be grown locally without pesticides and while educating and empowering students in “poverty pockets” — including the ultra-Orthodox (Haredi) population characterized by large families and small incomes.
“The kids are at a disadvantage academically when they don’t have proper nutrition. And a lot of health problems occur when you don’t know what foods to choose or just choose what is cheap,” says Katz, who moved to Ra’anana from Chicago in 2007.
She didn’t want children only to eat more veggies but to take a hand in growing them organically and sustainably. Katz found the model she was seeking when she visited a hydroponic farm in northern Israel
“They had the cleanest, best-tasting vegetables I’ve ever had, and I’ve traveled extensively,” she tells ISRAEL21c.
Katz found the opportunity to put her idea into action when she was asked to help raise money for a school lunch program at the girls’ school in the Bukharim neighborhood of Jerusalem. She proposed building a small hydroponic facility in a corner of the schoolyard for the girls to grow their own vegetables.
“I was worried about taking space from the playground but the principal said, ‘No, take the back 100 meters.’ That was enough to grow 1,400 plants a month, and we’re working on ways to increase the yield exponentially,” says Katz.
Hothouse on a concrete schoolyard. Photo courtesy of StartUpRoots
The kids grow by growing
Supported by private donors, StartUpRoots provides the equipment, the services of professional agronomists and nutritionists, and a chef who comes after the first harvest to cook with the kids.
Katz and a team of expert volunteers developed a holistic curriculum for teachers like Shulamit to get ideas for lesson plans covering topics from healthy eating to the environmental impact of food production.
“I sat down with Israeli educators to talk about the objectives and goals of the program and they said, ‘Relax, Robin, the kids will grow by growing. They’ll see the direct relationship between their effort and the outcome.’ The life lessons they learn include personal responsibility and understanding that progress is gradual.”
StartUpRoots installed another hydroponic garden at a girls’ school in the Jerusalem neighborhood of Neve Ya’akov. “They didn’t have room outside, so we built an indoor farm with LED lighting, which we are currently expanding in a former library, utilizing a state-of-the-art vertical design,” says Katz.
A StartUpRoots staffer shows schoolgirls in Neve Ya’akov how to start a hydroponic garden. Photo: courtesy
The program requires that students spend at least 20 minutes every day tending the system and the plants, starting with dropping single seeds in a growing medium and making sure that the plants in the closed water system have the right levels of acidity, nutrients, and oxygen.
“The hydroponic method uses 90 percent less water than in-ground farming because nothing is getting absorbed in the soil and the water is recycled,” Katz explains. “The roots get nutrition directly from water and therefore grow faster. There are also few insects because it’s the dirt that attracts pests.”
“It’s a lot fresher and healthier,” adds Ronny Avidan, an Israeli agronomist who joined StartUpRoots in 2015 after completing agricultural projects in Africa. “I want to help promote the ideology of urban organic, pest-free agriculture and sustainability,” he tells ISRAEL21c.
Leafy veggies growing in a schoolyard hothouse in Jerusalem. Photo courtesy of StartUpRoots
Creating a sense of value
The hothouse has become part of Shulamit’s science curriculum for grades 1-7. The girls record their activities and observations after performing their assigned tasks.
The leafy greens grow so abundantly that the school began selling them for a token amount to the girls’ families. “When you charge a bit of money, you create a sense of value,” Shulamit explains.
She says the excitement created by the project has led directly to higher enrollment as children share their enthusiasm with parents and friends.
The girls also planted a conventional garden in another corner of the schoolyard along with a compost pile. Among the produce growing, there are sunflowers, the seeds of which are a favorite Israeli snack.
“When they buy sunflower seeds in a package in the store, they think they appeared from nowhere. Now they understand that these are natural seeds that God created,” says Shulamit.
Katz says some of the aspects of StartUpRoots are found in American programs like Virginia-based Edible Education.
“But we go beyond those programs. In Israel, we don’t have water and land to waste, and we have increasing populations. And yet if we can come out of those challenges shining it should inspire others to do the same.”
The program is not meant only for disadvantaged children. Katz is working with her hometown and partners Matan and Leket (Israel’s national food bank) to transform an unused area into a hydroponic community garden that she hopes will blossom into a farmers market.
Katz is in discussions with additional schools to join StartUpRoots. The no-carbon-footprint hothouses could be put on school rooftops or basements.
“To change dietary habits you first have to change consumer demand and the best way to do that is to start with children,” she says.
For more information, click here
Hydroponic Baby Greens Are ‘Clean From The Start’
Hydroponic Baby Greens Are ‘Clean From The Start’
Hydroponic Baby Greens Are ‘Clean From The Start’
By Cindy Cantrell GLOBE CORRESPONDENT JUNE 02, 2018
As founder of Backyard Farms, Paul Sellew of Carlisle brought flavorful, greenhouse-grown tomatoes to the East Coast market. His next company, Harvest Power, became a major processor of organic materials in North America. As founder and chief executive of Little Leaf Farms in Devens, he oversees the growing of hydroponic baby greens that are sold to grocery stores, food service institutions, and restaurants, as well as donated to food banks and other organizations.
Q. What is hydroponics?
A. It means growing plants using mineral nutrient solutions in water, without soil. This method is completely sustainable and 20 to 25 times more productive than soil-grown horticulture. In Massachusetts, where we have fierce winters, it’s also more efficient. The plants grow year-round in a controlled environment utilizing natural sunlight and a rainwater-based irrigation system that uses 90 percent less water than field-grown lettuce companies.
Q. Why is that advantageous to the consumer?
A. We seed and harvest seven days a week, so our produce is in the market the next day. We’re delivering unparalleled freshness and quality, which translates into better flavor and more nutrition.
Q. What does your motto ‘Clean From the Start’ mean?
A. Our lettuce is seeded, grown, cut, and packaged without ever being touched by human hands. We have never, and we never will use chemical pesticides, herbicides, or fungicides. Instead, we vigilantly practice biological control so if an insect attacks our lettuce, we introduce another insect to attack that one. Consumers can be confident they’re purchasing a safe product, grown in an environment that employs the most advanced food safety practices.
Q. What led to your recent greenhouse expansion?
A. It’s a consumer-driven expansion. In trying to keep up with demand, we concluded that we need to more than double production. We just added 2 1/2 acres, for a total of 5 acres under glass. We also got approval to build on 5 contiguous acres, which will give us 10 acres total when we expand the greenhouse again in 2019.
Q. What is your goal for the business?
A. We want to build a sustainable food production model that will be the dominant supplier to local markets. We’ve gone up against gigantic West Coast companies, and we’re honored that we’ve been able to build traction and a loyal customer following. We’re doing it a better way at Little Leaf Farms.
For more information, visit littleleaffarms.com.
Cindy Cantrell may be reached at cindycantrell20@gmail.com.
The Quality Standards For Hydroponic Lettuce
The Quality Standards For Hydroponic Lettuce
By Tyler Baras June 6, 2018
Living Butterhead Lettuce in Retail Clamshell
“Voluntary U.S. grade standards are issued under the authority of the Agricultural Marketing Act of 1946, which provides for the development of official U.S. grades to designate different levels of quality. These grade standards are available for use by producers, suppliers, buyers, and consumers. As in the case of other standards for grades of fresh and processed fruits, vegetables, and specialty crops these standards are designed to facilitate orderly marketing by providing a convenient basis for buying and selling, for establishing quality control programs, and for determining loan values.” (From the United States Standards for Grades of Greenhouse Leaf Lettuce)
Voluntary USDA grade standards designate different levels of quality in agricultural products. The USDA has official standards used to grade a lot of different crops including leafy greens like Greenhouse Leaf Lettuce, Field Grown Leaf Lettuce, Kale, Beet Greens, Collard Greens, Dandelion Greens and Mustard Greens. The standards for butterhead lettuce currently fall under the same standards used for Iceberg lettuce. Although the U.S. Standards for Grades of Lettuce do acknowledge the significant differences between the two types of lettuce, they are still grouped under the same standards. And there is no mention of living lettuce in the U.S. Standards for Grades of Lettuce, while living lettuce is one of the primary crops grown by hydroponic leafy greens growers. If the hydroponic lettuce industry is to grow beyond the premium product niche and enter the ‘real world’ of lettuce production, it would be helpful if hydroponic growers decided upon grading standards appropriate for hydroponically grown lettuce.
When hydroponic lettuce growers try to compete against field growers they almost never win in the battle for price per pound. Field growers can sell heads of lettuce wholesale under $0.75. Large hydroponic lettuce growers (3+ acres) can get their price per head close to $0.90. Field lettuce is generally packed in a 24 count box that will weigh 50+ pounds. The heads are easily 1 to 2 pounds. Hydroponic lettuce is often packed in a 6 or 12 count box and the heads rarely weigh over 10 ounces (0.625 pounds).
While hydroponic crops have a lot of external benefits like water savings and food safety, those benefits are not shown when a hydroponic butterhead is graded with the U.S. Standards for Grades of Lettuce. To preserve the narrative around hydroponic lettuce, it may be necessary to have USDA grading standards specifically for hydroponic lettuce so the crop does not lose some of its value when it enters the larger lettuce market that puts it ‘head-to-head’ with field grown crops.
USDA grade standards are helpful in international trade. The U.S. has one of the biggest lettuce importers on the northern border… Canada! (See Stats). Currently most hydroponic lettuce growers sell to local markets or if they are one of the larger hydroponic lettuce growers they might sell to a grocery store chain or produce broker that distributes their product in multiple states. I have seen living butterhead lettuce from Canada in the U.S. but I’m not aware of any U.S. hydroponic leafy greens growers shipping internationally. I would think that the increased shelf-life of living lettuce would be an advantage in international trade since lettuce is highly perishable.
The Standards for Butterhead Lettuce Quality
What should a USDA Grade A butterhead lettuce look like? How big should it be?
I’ve seen a wide range of targets from growers across the US and internationally. The majority of US hydroponic butterhead growers target a head that is between 5 oz. and 8 oz. (with roots attached). Many aquaponic and indoor vertical farms sell heads closer to 5 ounces. Many of the larger hydroponic lettuce growers (1+ acre greenhouses) target heads between 6-8 ounces. I’ve seen some greenhouse lettuce growers target 10 ounce heads. In Europe, it is common to see butterhead lettuce over 1 pound. In Japan, it is common to see living lettuce sold at less than 5 ounces. The market standards for hydroponic butterhead lettuce minimum weight vary but generally the bottom line is the head should not bobble around when packaged in a clamshell. Most living lettuce labels do not even state a minimum weight, instead the label might have “1 Count” or “1 Head”. Beyond weight there’s the more qualitative traits like leaf texture, leaf color and head formation. Check out these unofficial visual aids provided by the USDA to help grade romaine and lettuce. What would a visual aid for hydroponic butterhead lettuce look like?
Here are some of my favorite butterhead lettuces I’ve grown over the years, which do you think looks most like a ‘standard’ butterhead?
Learn more about Farmer Tyler and see his latest books/videos at www.FarmerTyler.com
The Farmhouse Launches UAE-Grown Pesticide-Free Produce
The Farmhouse Launches UAE-Grown Pesticide-Free Produce
The food producer has signed its first deal with Barakat Group to supply multiple product varieties
jobtphotography Tomato crops at The Farmhouse
Devina Divecha May 27, 2018
A new UAE fresh food producer, The Farmhouse, has launched its inaugural line of locally grown, pesticide-free vegetables.
The Farmhouse has since signed its first major sales contract, partnering with Barakat Group to supply multiple product varieties. The produce will also be sold in supermarkets across the UAE. The Farmhouse is currently selling cucumbers, capsicums, tomatoes, cherry tomatoes and zucchinis and has plans to expand its offering over time.
All crops are being grown in the controlled environment of its 430,000-square-foot greenhouse hydroponic farm in Ras Al Khaimah. The first phase of the facility was completed and produced its first harvest in March. When all crops are in harvest, The Farmhouse will supply more than 25 tonnes per week for local consumers.
The pesticide-free produce is grown using fully enclosed growbags and an advanced water runoff recovery system, resulting in 80% less water usage and significantly higher crop yields.
The Farmhouse offers customers a 'Grow to Suit' model, growing precise volumes required, providing options for various size and shape specifications, and delivering orders to a pre-agreed schedule.
A second phase expansion to over one million square feet will commence later this year.