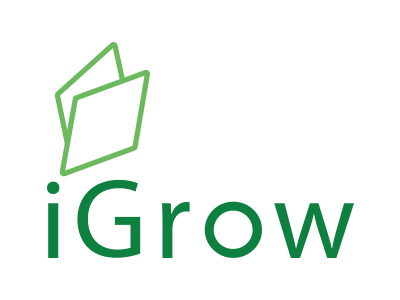
Welcome to iGrow News, Your Source for the World of Indoor Vertical Farming
How We Can Rethink Agriculture So It’s More Local
With a global population projected to exceed eight billion in 2023 and 10 billion by 2056, we can ill afford the inefficiencies and incremental gains of today’s industrial agriculture
SEP 21, 2020
Climate Week is a reminder of how susceptible global agriculture systems are to climate change risks. More than 800 million people went to bed hungry every night even before COVID-19 disrupted the global food supply chain, which put an additional 130 million at risk of food insecurity.
This unprecedented crisis comes as industrial agriculture already struggles to feed a growing global population under threats of declining resources and an increasingly inhospitable environment.
While we can still produce enough food to feed the world today, we are running out of time. Many experts believe that conventional farming techniques are becoming unsustainable because of the vast amounts of land, water, and energy required, as well as additional crop failures that will occur with the warming climate. To achieve sustainable food security, we must fundamentally disrupt the traditional forms of agriculture. We must pivot towards more cost-effective food production that is closer to home, more sustainable than factory farming, and less land-intensive.
Building more local capacity for agriculture
With a global population projected to exceed eight billion in 2023 and 10 billion by 2056, we can ill afford the inefficiencies and incremental gains of today’s industrial agriculture. Feeding 10 billion people will require an additional 109 million arable hectares, a landmass larger than Brazil. Given that 80 percent of arable land is already in use, the world faces even more acute food shortages if we can’t figure out how to grow more with less and get it where’s it’s most acutely needed.
The first step is to decentralize food production and distribute it more locally. When the 2017 famine in South Sudan took hold, it wasn’t because there wasn’t enough food to feed the five million people; it was because disruptions to the food supply prevented its distribution. Similarly, when food supply disruptions caused harrowing shortages on American supermarket shelves in the early months of the pandemic, we all witnessed how quickly panic and hoarding set in.
Urban agriculture is one way to build more local capacity. Building in cities, even on rooftops, can improve local food security and nutrition in food deserts where underserved communities suffer from access to fresh produce. Studies show that urban agriculture can meet 15 to 20 percent of global food demand today.
The next step is to bring food production indoors, when and where it makes sense. Technological innovation has helped bring food closer to local communities, enabling food to be grown more in places once thought impossible. However, we need to rethink our approach to indoor growing systems.
Today’s most advanced greenhouses and indoor vertical farms have significant shortcomings. Vertical farms, for instance, require massive amounts of energy due to the need for climate control systems and artificial lighting. Some argue that energy and environmental costs of vertical farms are offset by the reduced “food miles” of transporting food from afar. But as climate and environmental scientist, Dr. Jonathan Fole points out this argument turns out to be a red herring. Local food typically uses about the same energy per pound to transport as food grown away due to volume and method of transport.
And both indoor vertical farms and greenhouses suffer from a lack of the sun’s full light spectrum, compromising the robustness of indoor plant growth as well as the quality of the food.
The need for precise controls
Instead, a new model of agriculture is emerging that is nimbler than large-scale commercial farming, safer than outdoor farms, greener than greenhouses, more natural than vertical farms, and more efficient than almost any other growing technique in terms of water consumption, power usage, and CO2 production. It’s essentially a hybrid approach of all three growing modalities – outdoors, greenhouses, and indoor farms. This “fourth way” of agriculture integrates and continually refines entirely new approaches to crops, operations, facilities, systems, and the growing environment (COFSE). The model was developed to produce far higher yields per acre than outdoor farms, superior yields to greenhouses and up to 20 percent better yields than comparably sized indoor farming systems.
The new model has two key principles: first, bring the full sun indoors and, secondly, create and control an indoor ecosystem precisely tuned for each kind of crop.
Plants grow most robustly and flavorfully in full natural sunlight. While it may seem counter-intuitive to some, even the clearest of glass greenhouses inhibit the full light spectrum of the sun. But new cladding materials have emerged recently that enable the near-full-transmission of the sun’s RV and light spectrum.
Unlike plastic or glass, these new transparent membranes can help crops achieve their full genetic (and flavor) potential. Natural light also warms the microclimate when necessary, dramatically reducing heating energy requirements. And at times when the sun isn’t cooperating, advances in supplemental grow lighting can extend the plants’ photoperiod – even beyond natural daylight hours – to maximize crop growth and quality, and reduce time to harvest by up to 50 percent or better.
Greenhouses and vertical farms are also compromised by outdoor and human-introduced contamination. The new model relies on creating a tightly-sealed, cleanroom-like microclimate that keeps pests, pesticides, and other pollutants outside.
Thanks to artificial intelligence (AI), the Internet of Things, and similar advances, growers can create highly automated growing systems that reduce human intervention and its associated costs. Finely-tuned convective air circulation systems enable the microclimate to remain sealed and protective. Natural temperature regulation using sunlight and organic foam-based clouds can significantly reduce air-conditioning electricity requirements. And highly automated hydration, fertilization, and lighting are all continuously optimized by machine learning.
This new model, which has been designed over more than three years of research and development, is set to be put into large scale practice when the first of three new grow facilities completes construction on a 41-acre site in Coachella, Calif. Construction is set to commence within the next year. This unique approach, which included contributions from lighting experts who had previously worked at NASA sending plants into space, was developed to significantly affect local food security in an environmentally friendly way. It applies the best aspects of current growing methods – outdoors, greenhouse, and indoors – and, where possible, replaces their shortcomings with superior technology and processes, creating an overall improved approach. Yet as a result of the facility design and automated growing system, it is designed to and expected to consume up to 90 percent less energy than traditional indoor grow operations while producing up to 10 to 20 percent better yields than other comparably sized farming systems.
The world we live in now gives us the intelligence and technologies we need to change the outdated legacy of how farming is done today into tomorrow’s way of producing food, creating a robust, delicious, and nutritious food chain on a global level. Using these technologies, we can decentralize production, reducing our reliance on global supply chains, and move high-density growing systems closer to communities to ensure food security for all.
Image credit: Devi Puspita Amartha Yahya/Unsplash
AppHarvest, A Pioneering Developer and Operator of Sustainable, Large-Scale Controlled Environment Indoor Farms, To Become A Public AgTech Company
Operates a 60-acre controlled environment agriculture facility in Morehead, KY — one of the largest high-tech greenhouses in the world — and has an active and robust development pipeline for future large-scale controlled environment indoor farm projects
September 29, 2020 | Source: AppHarvest
AppHarvest has entered into a definitive business combination agreement with Novus Capital Corporation (Nasdaq: NOVS)
Transaction to provide $475 million of gross proceeds to the company, including $375 million fully committed common stock PIPE at $10.00 per share anchored by existing and new investors – including Fidelity Management & Research Company, LLC, Inclusive Capital, and Novus Capital Corporation
Pro forma equity value of the merger is approximately $1.0 billion, at the $10.00 per share PIPE price and assuming minimal Novus shareholder redemptions
Transaction advances AppHarvest’s mission to redefine American agriculture and to build America’s AgTech capital in the heart of Appalachia through the development of several large-scale controlled indoor farms
MOREHEAD, Ky., Sept. 29, 2020 (GLOBE NEWSWIRE) -- AppHarvest (“the Company”), a developer and operator of large-scale, high-tech controlled environment indoor farms, and Novus Capital Corp. (Nasdaq: NOVS) (“Novus Capital”), a publicly-traded special purpose acquisition company, announced today a definitive agreement for a business combination that would result in AppHarvest becoming a public company. Upon closing of the transaction, the combined company will be named AppHarvest and is expected to remain listed on Nasdaq under a new ticker symbol. The combined company will be led by Jonathan Webb, AppHarvest’s Founder & Chief Executive Officer.
Company Overview
AppHarvest is redefining American agriculture by developing modern, large-scale and efficient indoor farms in Central Appalachia, a water-rich region strategically located within a day’s drive of approximately 70% of the U.S. population. AppHarvest has strong relationships with the leading agricultural and construction firms and universities in the Netherlands, the world’s leader in high-tech controlled environment indoor farms. The Netherlands, despite a land mass similar in size to Eastern Kentucky, is the world’s second-largest agricultural exporter behind only the United States due to its extensive network of controlled environment agriculture facilities. These relationships allow the Company to utilize the most recent proven technologies in an effort to sustainably increase crop yields, improve access to nutritious, non-GMO food, build a consistent and safe U.S.-grown food supply for national grocers, and increase investment in Appalachia. The Company operates a 60-acre controlled environment agriculture facility in Morehead, KY — one of the largest high-tech greenhouses in the world — and has an active development pipeline for additional large-scale indoor controlled environment farm projects.
Upon the closing of the transaction, AppHarvest will retain its highly experienced management, a team of growers with over 140 years of agricultural experience, including 120 years of sustainable agriculture experience, a sustainability team with more than 40 years of experience; and construction managers who have successfully managed over $19 billion in projects.
In addition, AppHarvest announced that Peter C. Halt has joined the executive team as Chief Financial Officer. Mr. Halt is a seasoned finance professional with several years of experience as a publicly-traded company CFO, most recently having served as the CFO for TiVo Corporation, up until its announced acquisition by Xperi Corporation.
AppHarvest Investment Highlights
Operates a 60-acre controlled environment agriculture facility in Morehead, KY — one of the largest high-tech greenhouses in the world — and has an active and robust development pipeline for future large-scale controlled environment indoor farm projects
First produce scheduled to be harvested, in early 2021, will be tomatoes, a crop that has seen imports rise to 60% of all fresh tomatoes available in U.S. stores
Designed to reduce water usage by 90% compared to traditional open-field agriculture and eliminate agricultural runoff
Aims to improve access to fresh non-GMO fruits and vegetables, as approximately 70% of the U.S. population is within a one-day drive of the Morehead, KY facility, which AppHarvest estimates will lower transportation costs compared to existing growers by up to 80%
Positioned to capitalize on the secular shift to plant-based foods, creating increased demand for locally grown, high-quality produce
Experienced leadership team and board of directors with experience in sustainable investing
Promoting sustainable change in agriculture as a Public Benefit Corporation, registered with Delaware, and a B Corporation, independently certified by the non-profit B Lab
Long-term distribution agreement in place to reach top grocers in the United States
“We are excited to transition AppHarvest to a public company and raise nearly a half a billion dollars in the process,” said Jonathan Webb, Founder & Chief Executive Officer of AppHarvest. “This will allow us to pursue our mission of transforming agriculture. A mission that’s become even more important since the global pandemic exposed how a rapidly increasing reliance on imports jeopardizes food security. We now know that to build a more resilient food system that meets our growing population demands, we must immediately start building controlled environment agriculture facilities, as these farms use far fewer resources to grow far more produce. We believe that this partnership with Novus Capital is a transformative transaction which will allow us to both rapidly scale our agriculture facilities, in pursuit of our goal to redefine American agriculture and build the country’s AgTech capital within Appalachia. Together we can transform agriculture.”
Bob Laikin, Chairman of Novus Capital, commented, “AppHarvest is a unique and compelling investment opportunity that is redefining American agriculture by improving access for all to fresh non-GMO produce, growing more with fewer resources, and creating an AgTech hub from within Appalachia. With significant tailwinds from heightened investor focus on ESG initiatives and the secular shift to plant-based foods, we believe AppHarvest is well-positioned to execute on its strategy for rapid growth and value creation.”
David Lee, Chief Financial Officer of Impossible Foods and AppHarvest Board Member, said, “AppHarvest is working to solve the critical need for a more resilient and sustainable food supply chain — both of which are fundamental to the future of farming, our food ecosystem, and our ability to ensure food security. I believe the company is building a scalable business that could revolutionize the business of food production in the United States.”
Dave Chen, CEO of Equilibrium Capital and AppHarvest Board Member, commented, “Jonathan Webb is exceptional at getting big complex projects done fast and with the highest precision. He is the right leader for AppHarvest’s disruptive mission. Furthermore, with his leadership, AppHarvest has drawn together some of the most talented individuals in the AgTech industry to drive the needed scale. I am extremely excited to see the fruits (or vegetables as the case may be!) of this team’s labors, as they execute on their plans to change food production in the United States.”
Martha Stewart, Founder of Martha Stewart Living Omnimedia and AppHarvest Board Member, said, “All Americans should believe in the AppHarvest mission to develop large-scale sustainable food production in the heart of Central Appalachia. Jonathan and his exceptional team are disrupting the food production ecosystem in the best way — to provide better, healthier food in a more sustainable manner.”
J.D. Vance, Narya Capital Partner, and AppHarvest Board Member, said, “AppHarvest is developing a world-class food production ecosystem to benefit a majority of consumers in the United States, right here from Central Appalachia. This region offers tremendous resources in terms of location, and in terms of the skilled hardworking people of the region who make this incredible mission possible.”
Jeffrey Ubben, Founder and Managing Partner of Inclusive Capital Partners and AppHarvest Board Member, said, “Our investment platform is about leveraging capitalism and governance in pursuit of a healthy planet and the health of its inhabitants — and AppHarvest is perfectly aligned with this mission.”
Transaction Overview
The business combination values AppHarvest at a $1.0 billion pro forma equity value, at the $10.00 per share PIPE price, and assuming minimal redemptions by Novus Capital shareholders. The transaction will provide $475 million of gross proceeds to the company, including $375 million fully committed common stock PIPE at $10.00 per share anchored by existing and new investors – including Fidelity Management & Research Company, LLC, Inclusive Capital and Novus Capital Corporation. Assuming minimal redemptions, it is anticipated that this transaction provides AppHarvest over $435 million of unrestricted cash at close, which will primarily be used to fund operations, including building additional high-tech controlled environment indoor farms, support growth, and for other general corporate purposes. In addition, AppHarvest issued a $30 million convertible note to Inclusive Capital which funded on September 28, 2020. The proceeds of the convertible note will primarily be used to fund operations, including the development of new high-tech controlled environment indoor farms, during the period prior to the close of this transaction. This note will convert to shares of AppHarvest’s common stock in connection with the close of this transaction.
The Boards of Directors of each of Novus Capital and AppHarvest have unanimously approved the transaction. The transaction will require the approval of the stockholders of both Novus Capital and AppHarvest, and is subject to other customary closing conditions, including the receipt of certain regulatory approvals. The transaction is expected to close late in the fourth quarter of 2020 or early in the first quarter of 2021.
Additional information about the proposed transaction, including a copy of the merger agreement and investor presentation, will be provided in a Current Report on Form 8-K to be filed by Novus Capital with the Securities and Exchange Commission and will be available at www.sec.gov.
Advisors
Cowen is serving as sole placement agent and capital markets advisor, and Blank Rome LLP is serving as legal advisor to Novus Capital. Cowen is serving as financial advisor and Cooley LLP is serving as legal advisor to AppHarvest.
Investor Conference Call Information
Novus Capital and AppHarvest will host a joint investor conference call to discuss the proposed transaction Tuesday, September 29, 2020, at 8:30, am ET.
Interested parties may listen to the prepared remarks call via telephone by dialing (877) 425-9470, or for international callers, (201) 389-0878. A telephone replay will be available until October 13, 2020, by dialing (844) 512-2921, or for international callers, (412) 317-6671, and entering the passcode: 13710943.
About AppHarvest
AppHarvest is an applied technology company building some of the world’s largest indoor farms in Appalachia. The Company combines conventional agricultural techniques with cutting-edge technology and is addressing key issues including improving access for all to nutritious food, farming more sustainably, building a home-grown food supply, and increasing investment in Appalachia. The Company’s 60-acre Morehead, KY facility is among the largest indoor farms in the U.S. For more information, visit https://www.appharvest.com/.
About Novus Capital Corporation
Novus Capital raised $100 million in May 2020 and its securities are listed on the Nasdaq under the ticker symbols “NOVS and “NOVSW.” Novus Capital is a blank check company organized for the purpose of effecting a merger, share exchange, asset acquisition, stock purchase, recapitalization, reorganization, or other similar business combination with one or more businesses or entities. Novus Capital is led by Robert J. Laikin and Larry Paulson, who have significant hands-on experience helping high-tech companies optimize their existing and new growth initiatives by exploiting insights from rich data assets and intellectual property that already exist within most high-tech companies. For more information please visit https://novuscapitalcorporation.com/.
Forward-Looking Statements
Certain statements included in this press release that are not historical facts are forward-looking statements for purposes of the safe harbor provisions under the United States Private Securities Litigation Reform Act of 1995. Forward-looking statements generally are accompanied by words such as “believe,” “may,” “will,” “estimate,” “continue,” “anticipate,” “intend,” “expect,” “should,” “would,” “plan,” “predict,” “potential,” “seem,” “seek,” “future,” “outlook,” and similar expressions that predict or indicate future events or trends or that are not statements of historical matters. All statements, other than statements of present or historical fact included in this presentation, regarding Novus Capital’s proposed acquisition of AppHarvest, Novus Capital’s ability to consummate the transaction, the benefits of the transaction, and the combined company’s future financial performance, as well as the combined company’s strategy, future operations, estimated financial position, estimated revenues and losses, projected costs, prospects, plans and objectives of management, are forward-looking statements. These statements are based on various assumptions, whether or not identified in this press release, and on the current expectations of the respective management of AppHarvest and Novus Capital and are not predictions of actual performance. These forward-looking statements are provided for illustrative purposes only and are not intended to serve as, and must not be relied on as, a guarantee, an assurance, a prediction, or a definitive statement of fact or probability. Actual events and circumstances are difficult or impossible to predict and will differ from assumptions. Many actual events and circumstances are beyond the control of AppHarvest and Novus Capital. These forward-looking statements are subject to a number of risks and uncertainties, including changes in domestic and foreign business, market, financial, political, and legal conditions; the inability of the parties to successfully or timely consummate the proposed transaction, including the risk that any regulatory approvals are not obtained, are delayed or are subject to unanticipated conditions that could adversely affect the combined company or the expected benefits of the proposed transaction or that the approval of the stockholders of Novus Capital or AppHarvest is not obtained; failure to realize the anticipated benefits of the proposed transaction; risks relating to the uncertainty of the projected financial information with respect to AppHarvest; risks related to the rollout of AppHarvest’s business and the timing of expected business milestones; the effects of competition on AppHarvest’s business; the amount of redemption requests made by Novus Capital’s stockholders; the ability of Novus Capital or AppHarvest to issue equity or equity-linked securities or obtain debt financing in connection with the proposed transaction or in the future, and those factors discussed in Novus Capital’s final prospectus dated May 15, 2020 under the heading “Risk Factors,” and other documents Novus Capital has filed, or will file, with the SEC. If any of these risks materialize or our assumptions prove incorrect, actual results could differ materially from the results implied by these forward-looking statements. There may be additional risks that neither Novus Capital nor AppHarvest presently know, or that Novus Capital nor AppHarvest currently believe are immaterial, that could also cause actual results to differ from those contained in the forward-looking statements. In addition, forward-looking statements reflect Novus Capital’ and AppHarvest’s expectations, plans, or forecasts of future events and views as of the date of this press release. Novus Capital and AppHarvest anticipate that subsequent events and developments will cause Novus Capital’s and AppHarvest’s assessments to change. However, while Novus Capital and AppHarvest may elect to update these forward-looking statements at some point in the future, Novus Capital and AppHarvest specifically disclaim any obligation to do so. These forward-looking statements should not be relied upon as representing Novus Capital’s and AppHarvest’s assessments of any date subsequent to the date of this press release. Accordingly, undue reliance should not be placed upon the forward-looking statements.
Important Information for Investors and Stockholders
In connection with the proposed transaction, Novus Capital will file a registration statement on Form S-4 (the “Registration Statement”) with the SEC, which will include a preliminary proxy statement to be distributed to holders of Novus Capital’s common stock in connection with Novus Capital’s solicitation of proxies for the vote by Novus Capital’s stockholders with respect to the proposed transaction and other matters as described in the Registration Statement, as well as the prospectus relating to the offer of securities to be issued to AppHarvest’s stockholders in connection with the proposed transaction. After the Registration Statement has been filed and declared effective, Novus Capital will mail a definitive proxy statement, when available, to its stockholders. Investors and security holders and other interested parties are urged to read the proxy statement/prospectus, any amendments thereto, and any other documents filed with the SEC carefully and in their entirety when they become available because they will contain important information about Novus Capital, AppHarvest, and the proposed transaction. Investors and security holders may obtain free copies of the preliminary proxy statement/prospectus and definitive proxy statement/prospectus (when available) and other documents filed with the SEC by Novus Capital through the website maintained by the SEC at http://www.sec.gov, or by directing a request to: Novus Capital Corporation, 8556 Oakmont Lane, Indianapolis, IN 46260. The information contained on, or that may be accessed through, the websites referenced in this press release is not incorporated by reference into, and is not a part of, this press release.
Participants in the Solicitation
Novus Capital and its directors and officers may be deemed participants in the solicitation of proxies of Novus Capital’s shareholders in connection with the proposed business combination. Security holders may obtain more detailed information regarding the names, affiliations and interests of certain of Novus Capital’s executive officers and directors in the solicitation by reading Novus Capital’s final prospectus filed with the SEC on May 15, 2020, the registration statement / proxy statement and other relevant materials filed with the SEC in connection with the business combination when they become available. Information concerning the interests of Novus Capital’s participants in the solicitation, which may, in some cases, be different than those of their stockholders generally, will be set forth in the registration statement / proxy statement relating to the business combination when it becomes available.
Contacts:
Novus Capital Corporation
Investors Relations
Robert Laikin, Chairman
RobertJLaikin@gmail.com
AppHarvest
Investor Relations
John Mills and Melissa Calandruccio, CFA
AppHarvestIR@icrinc.com
Media Relations
Cory Ziskind and Keil Decker
AppHarvestPR@icrinc.com
Matt Roney New Lumileds CEO
Roney most recently served as President of Lumileds’ Automotive Business Unit and succeeds Dr. Jonathan Rich who will continue with the company as Executive Chairman of the Board
Lumileds announced the appointment of Matt Roney as the company’s Chief Executive Officer, effective October 1, 2020. Roney most recently served as President of Lumileds’ Automotive Business Unit and succeeds Dr. Jonathan Rich who will continue with the company as Executive Chairman of the Board.
“Speaking on behalf of the Board of Directors, we are grateful for Jon’s contributions as CEO and believe Lumileds is well-positioned for success in this next phase under Matt’s leadership,” said Rob Seminara, Senior Partner at Apollo Global Management. “Matt has nearly 25 years’ experience in the automotive industry and his performance and leadership throughout his career have given us even greater confidence in his ability to drive long-term innovation and growth at Lumileds.”
“Lumileds has a long history of innovation in conventional automotive lighting and is a pioneer of leading-edge LED technology for the consumer electronics, automotive, and general illumination markets,” said Roney. “I am honored by the opportunity to lead this company and team in its next phase and excited by the opportunities ahead to bring new and innovative lighting solutions to market. I look forward to building on the foundation Dr. Rich has put in place to further advance our technologies and increase the value we deliver to customers across a broad set of industries.”
Prior to joining Lumileds, Roney served as Chief Operating Officer for Stanley Infrastructure, a division of Stanley Black & Decker. Previously, Roney was the President of Paladin Attachments, which was acquired by Stanley Infrastructure. He also spent eight years at TRW Automotive, now known as ZF TRW, in roles of rising responsibility, including Vice President and General Manager of its $2.5 billion Global Steering Business. Roney has a BS in Electrical Engineering from Cornell University, an MSE in Mechanical Engineering from Purdue, and an MBA from Harvard Business School.
For more information:
Lumileds
www.lumileds.com
Publication date: Tue 22 Sep 2020
Hydroponics For Beginners 101: The Basics
When broken up into two words -hydro and -ponics, it translates to “water” and “labor.” The Greek definitions of these words essentially translates to “working water.”
Hydroponics is a growing method for beginners and experts alike. This innovative farming system provides users with more controlled environments to grow their crops all-year-round. In this article, you will learn about hydroponics for beginners, and we’ll cover the basics to get you started.
What is hydroponics anyways?
When broken up into two words -hydro and -ponics, it translates to “water” and “labor.” The Greek definitions of these words essentially translates to “working water.” The reason for this is because hydroponics is a method used to grow crops without using soil. Through hydroponic systems, plants can grow by using nutrients in water instead.
What are the benefits of hydroponics?
There are various reasons why farmers are starting to adopt hydroponics as a means of growing crops.
1. Crops grow at a faster rate
Hydroponic plants tend to grow at a faster rate ranging from 30 to 50% faster than plants grown in traditional soil methods. This happens because hydroponically grown plants do not have to spend time searching for nutrients in the soil since it is provided several times throughout the day using hydroponic systems. With its saved energy, these plants can focus on growing into healthier plants.
2. Greater Yields
Since hydroponic plants can get the nutrients they need at all times, the plants don’t need to have large roots. With smaller roots, these plants don’t require as much room as traditional soil-grown plants, so farmers can plant more of these plants side-by-side, thus producing greater yields.
3. Hygienic Way of Growing
Since hydroponic plants are grown indoors, they’re free from the pests that soil typically attracts. This helps prevent disease and promotes hygiene.
4. Can Grow All Year Round
Hydroponic systems allow users to grow plants all-year-round. These automated systems are controlled by timers and computers, which helps growers to grow food no matter the season.
How do hydroponic systems work?
Hydroponics was created to take out the uncertainty aligned with growing plants in traditional farming methods. Hydroponic systems give users more control over the plant’s environment and nutrient sources to ensure it can grow without being interfered with by natural disasters, lack of nutrients, or pests. Knowing this, it makes sense as to why hydroponic systems work to give a plant what it needs.
Even though the soil is not in the equation, a growing medium is still used in hydroponics. Some mediums include perlite, sand, and Rockwool. These mediums get nutrients in the water and provide oxygen for the plant’s roots.
Want to learn more about hydroponics for beginners?
Now that you have a basic understanding of hydroponic systems, it’s time for you to learn more about this modern way of farming. We at the Nick Greens Grow Team use our knowledge and expertise to inform our readers about the innovations in farming. Want to learn more about hydroponics for beginners? Make sure to subscribe to our blog and YouTube channel for weekly updates! We also are teaching a microgreen class where you can learn more about microgreens and hydroponics for beginners.
Sign up for our microgreens class here.
#hydroponicsforbeginners #hydroponicforbeginners #startinghydroponics #startinghydroponic #hydroponics #hydroponic #hydroponicsfarming #hydroponicsgrowing #hydroponicfarming #hydroponicgrowing #usinghydroponics #hydroponicssetup #hydroponicsetup #hydroponicssystem #hydroponicsystem #hydroponicsfarmer #hydroponicfarmer
Lef Farms Keeps The Fresh Coming With The Addition of Fresh New Production Manager
Mariana’s new position was created to provide more time for training, education, and coordination between different departments within the organization
(Loudon, NH) – Coming off a very eventful summer that resulted in expanding distribution by adding Stop & Shop stores throughout New England and supporting medical first-responders during the pandemic with donations of a quarter of a million dollars in baby greens, hydroponic lettuce grower, lef Farms continues its forward momentum by adding a new production manager to its mix.
“We’re so excited to add Mariana Robles to our management team”, smiles lef founder, Henry Huntington. “As a 2015 graduate from the University of Los Llanos Colombia, specializing in Agronomy, Mariana brings with her some fresh, out-of-the-box thinking that we can’t help but benefit from”, finishes Huntington.
lef Farms of Loudon, NH, welcomes its new production manager, Mariana Robles.
But Mariana isn’t a new face at lef Farms. With a passion for farming that brought her to the region in 2015, Mariana was eventually hired by lef in early 2018 to support its seeding line. Since then, Mariana developed into one of lef’s key team members, taking on additional responsibilities as food safety officer and cooler supervisor. As the company continued to grow, Mariana’s new position was created to provide more time for training, education, and coordination between different departments within the organization. As production manager, Mariana will be responsible for driving efficiencies, improving procedures and protocols, and increasing teamwork at Farm.
“With expansion in our near future, putting Mariana in the role of production manager allows the Farm to continue its maturation process prior to pulling that trigger”, concludes Huntington.
lēf Farms is a 1-acre hydroponic greenhouse growing facility located in Loudon, NH, producing nearly 1.5 million pounds annually of its Crisp, Smooth, Spice, and Fusion baby greens for New England.
Breakthroughs With Photonics: Growing Lettuce With Red And Blue Light
During Photonics Applications Week you can attend digital lectures and workshops on the applications of photonics, like those in agriculture and horticulture
During Photonics Applications Week you can attend digital lectures and workshops on the applications of photonics, like those in agriculture and horticulture.
1 October 2020
LUCETTE MASCINI - Innovation Origins
From October 5 to 9, the third edition of the Photonics Applications Week will take place. In this series, Innovation Origins highlights the breakthrough that the application of photonics has meant for three different fields: medical care, the gaming industry, and vertical farming. Today, Part 3: You can influence the shape and color of plants during their cultivation with special lighting in vertical farms.
“The market for vertical farming is growing,” says Sebastian Olschowski, a biologist at the bioengineering company Fluence, part of the Munich-based lamp manufacturer Osram. And this cannot be achieved without photonics. After all, plant growth is dependent on light due to the photosynthesis process it undergoes.
Vertical farming is gaining traction over the past five to ten years. Plant and flower growers set up farms within an enclosed space. The plants are then grown in multiple layers on top of each other.
Light influences shape and color of plants
The climate inside a vertical farm is regulated by nutrient supply, temperature, and lighting. Olschowski is an expert when it comes to lighting. The company he works for supplies the lamps. Olschowski is researching the effects of different light frequencies on plant growth. “We know that plants are able to perceive different frequencies of light. We also know how different types of light affect the plant’s metabolism, color, and shape.”
At the request of plant growers, vertical farms are set up on the basis of this science and the research that Olschowski is conducting in collaboration with universities and research institutes. A grower can, for example, ask the biologist how they can increase basil production so that they can sell more of it. Adjusting the lighting is one way of doing this.
A plant that needs to blossom quickly is subjected to a shorter night. The lighting is switched on earlier in the morning to provide more light. The lights are switched on later for plants that do not need to flower quickly.
Lighting formula is not a ‘one size fits all’ solution
However, these types of lighting formulas are not ‘one size fits all’ solutions, Olschowski notes. “Various light spectra and light intensities have a different effect on one group of plants than on another. A certain amount of extra infrared light when growing basil leads to longer stems. That doesn’t necessarily work like that with another plant.”
Several videos on YouTube present vertical farming as a possible solution for world population growth and to the lack of space for growing food crops such as grains. But Olschowski does not think this is very realistic. “Setting up a vertical farm is expensive and consumes a lot of electricity. In countries where the days are long, growing grain on fields is much more efficient. After all, the sun shines for free.”
Fewer pesticides
One advantage is that vertical farms that have good phytosanitary measures in place require fewer pesticides or even none at all. “At least if you know how to keep pests out. That’s definitely an advantage then.”
But if farming on land is just as good, why set up these expensive vertical farms? That’s because certain crops, such as leafy vegetables that do not last long, can be grown very close to their consumers like those in large cities, says Olschowksi. They can then be delivered to shops and the hospitality sector immediately after harvesting.
Moreover, there are plenty of vegetables that you want to eat in winter but can only grow outdoors in summer, like lettuce for example. “By growing them in a vertical farm, you are assured of quality all year round.”
REGISTER HERE FOR THE WORKSHOP ON
APPLICATIONS FOR PHOTONICS IN VERTICAL
FARMS TO BE HELD DURING THE PHOTONICS
APPLICATION WEEK FROM
2 PM TO 5.30 PM ON OCTOBER 8.
On Innovation Origins you can read the latest news about the world of innovation every day. We want to keep it that way, but we can't do it alone! Are you enjoying our articles and would you like to support independent journalism? Become a member and read our stories guaranteed ad-free.
Lead photo: Dr.-Ing. Grit Bürgow prüft Pflanzen an der vertikalen Farm © TU Berlin
VIDEO: It's A 2-Acre Farm, Packed Into A Shipping Container That Doubles As A Farm Building
The Farm From A Box system is designed to feed 150 people per year and includes drip irrigation, all of the tools, and its own renewable energy setup
The Farm From A Box system is designed to feed 150 people per year and includes drip irrigation, all of the tools, and its own renewable energy setup.
This plug-and-play farming system combines water-smart irrigation, renewable energy, and precision farming technology in a single shipping container that is said to be capable of supporting the cultivation of almost two and a half acres, using regenerative agriculture practices.
We've covered a few different approaches to the "farm in a box" concept, but all of them so far have been built around the idea of growing the crops inside a shipping container, using hydroponics or aeroponics, and artificial lighting. The Farm From A Box is quite a bit different in that the farming takes place outside of the box (or shipping container) and after the contents have been unpacked and deployed, the box itself becomes the hub of the farm infrastructure.
According to the company, this is a "turnkey farm kit" that can be used to build a stronger local food system, especially in food deserts and in the developing world, where infrastructure can be spotty and unreliable at best, and possibly even non-existent. The system is described as being “food sovereignty in a box" that can be a “Swiss Army Knife” for off-grid farming, and while there is a basic template, each unit can be customized to fit the particular situation."
We want to develop this as a rapid response transitional food production system. The box is really infrastructure for places that are struggling with a lack of infrastructure." - Brandi DeCarli, co-founder of Farm from a Box. While the units are designed to be complete systems with all of the core components (minus the land and water rights and labor, of course), the company doesn't just stop there, but also includes a training system to help "new farmers tackle the steep learning curve of permaculture technique." To me, this is one of the critical parts of the venture, because if you've ever tried to grow food on a larger scale than your own backyard, without having any formal training or guidelines to follow, it can be a humbling experience that is full of failures learning opportunities."
Based on extensive field research, we found that rural communities often lack the resources and infrastructure needed to access nutritious food. We developed a toolkit that contains all of the core components needed to grow your own food, on a two-acre plot of land, without the need for an existing grid. Imagine the good it can do by growing local, organic food for a school, or helping jumpstart food production after a disaster. ‘Farm from a Box’ enables and empowers communities to provide for themselves." - DeCarli
Currently, Farm In A Box has a prototype unit operating in Sonoma, California, and a second version is in the works for deployment in the Rift Valley of Ethiopia. Basic units will cost about $50,000, which includes a 3 kW solar PV array, a battery storage system, a drip irrigation system and water pump (which can be fitted to a well or to a municipal water supply), basic farm tools, a sensor package, a seedling house, and a WiFi connectivity package, all packaged into a single shipping container. Other options are available as well, including a water filtration system, an advanced sensor suite, remote monitoring capabilities, and more.
MAURITIUS: Promotion of Entrepreneurship In Green And Sustainable Agri-Business Activities
A training course in Hydroponics Crop Production and Greenhouse Management, aimed at encouraging entrepreneurship in green and sustainable agri-business activities among co-operative planters, was launched
Date: August 20, 2020
Domain: Agriculture and Food Security
Persona: Business; Citizen; Non-Citizen; Government
GIS – 20 August 2020: A training course in Hydroponics Crop Production and Greenhouse Management, aimed at encouraging entrepreneurship in green and sustainable agri-business activities among co-operative planters, was launched, today, at the National Cooperative College (NCC), in Terre Rouge. Some 75 co-operative planters and unemployed persons are participating.
The course, which covers both theoretical and practical aspects of hydroponics, is being offered jointly by the NCC, the University of Mauritius (UoM), and the Food and Agricultural Research and Extension Institute (FAREI).
In his address, the Minister of Industrial Development, SMEs, and Cooperatives, Soomilduth Bholah, recalled that the course is in line with Government’s policy to drive agricultural innovation and promote sustainable agriculture and food production. The training, he said, focuses on providing essential basic knowledge and practical skills pertaining to crop production.
The Minister also lauded the benefits of hydroponics farming which are namely: water conservation, use of fewer chemicals, space-saving, faster growth, nutrient control, bigger yields, no soil erosion, and healthier plants.
This emerging sector, Mr. Bholah indicated, is aligned with initiatives promoting the protection of the environment and of public health, food safety, and entrepreneurship. He also highlighted that hydroponics farming requires less pesticides and herbicides, resulting therefore in healthier food for consumption.
The Hydroponics course
This part-time course is of a 30-hour duration and will be conducted once weekly at the NCC. Practical sessions will be held at the Mapou Model Farm and the UoM Labs.
The topics being covered include: introduction to agriculture and hydroponics, greenhouse models and structures, fertigation and nutrient solution preparation, management of greenhouse environment, pre/post-cyclone management practices, troubleshooting, choice of varieties of crop, seedling production, cultural practices, pest and disease management, and harvest and post-harvest practices.
It is recalled that financing plans for hydroponics are available at FAREI and the Development Bank of Mauritius.
Government Information Service, Prime Minister’s Office, Level 6, New Government Centre, Port Louis, Mauritius. Email: gis@govmu.org Website: http://gis.govmu.org Mobile App: Search Gov
Farming Goes Vertical
Vertical farming works by growing vegetables in stacked layers that takes place in a controlled environment, often without the use of soil and instead the use of light energy
06-08-2020 | This is money
Top of the agenda for many big firms across Britain and the world in recent years is to find ways to help reduce their environmental footprint and become more sustainable. This has been driven by consumer demand for change and warnings over irreversible damage by large companies, who can make small improvements to help that add up. One such way is vertical farming and it has seen one middle-class supermarket favourite get involved in some stores.
· Vertical farming works by growing fruits and veg in vertically stacked layers
· Claims it can significantly reduce environmental damage
· M&S Simply Food is one of the latest UK retailers to introduce vertical farming
Marks and Spencer is the latest UK retailer to adopt vertical farming into its stores, with a selection of herbs now freshly grown and harvested in stores across London for shoppers to buy.
Vertical farming works by growing fruits and vegetables in vertically stacked layers inside
It has partnered with Infarm, a fast-growing vertical farming firm based in Berlin, that also now operates in other supermarket chains across Europe.
Ocado has also invested £17million in vertical farming while John Lewis plans to grow salads in store in the future in a partnership with LettUs Grow.
Aside from Marks and Spencer, Infarm has recently partnered with the online sustainable supermarket Farmdrop, which stocks a selection of herbs and salad leaves.
It added it will be announcing some new retailers it has teamed up with in the next few months.
Inform also works with a number of chefs in Europe, some of whom have installed farms into their restaurants so they can access the herbs at the freshest point, whenever they want.
In the UK, it supplies produce to Zala Grill in Camden Lock, but it doesn't have a farm in the restaurant.
Meanwhile, in Germany, Infarm currently has eight restaurants with farms including the Michelin starred Sky Kitchen at Vienna House Andel's.
How does it work?
Vertical farming works by growing vegetables in stacked layers that takes place in a controlled environment, often without the use of soil and instead the use of light energy.
Emmanuel Evita, global communications director at Infarm, said: 'Our approach allows us to be climate independent and grow under any conditions, despite changing climate, extreme weather, or disasters which normally interfere with food production and distribution.
'Our vertical farms can be installed directly in any urban space, which is where the majority of the global population will live in the next few decades.'
Compared to conventional farming methods, Infarm argues that vertical farming uses less space, less water, and less transportation.
Its plants are also all locally-grown and free of chemical pesticides, making them better for both consumers and the planet.
When the food comes to harvest, it's just one person in store, moving the produce about a meter from the growing with no machinery, storage or long-distance haulage.
Infarm's hubs are used to initiate the growth seeds.
Once these seeds have developed to a certain maturity, they are delivered to the in-store farms at retailers, to complete their growth cycle and be offered to the consumer.
The hubs grow seeds across more than 65 combinations of herbs, microgreens and leafy greens and also deliver special varieties, like Peruvian Mint or Wasabi Rucola, directly to chefs for use that day.
The fruit and vegetables growing in vertical farming takes place in a controlled environment
One reason vertical farming can help reduce the ecological waste associated with traditional industrial farming, according to Infarm, is that it uses 95 percent less water and 75 percent less fertiliser.
It also uses no chemical pesticides, no genetically modified seeds and says it is able to save 14 litres of water per kilogram of produce.
Evita said: 'Growing fresh produce creates a huge environmental burden on our planet.
'People want to eat the same foods at all times of the year, and this, combined with lengthy transportation routes, and overtaxed soil take a heavy toll not just on the environment but also on the taste and nutrition of what we eat.'
He believes that more retailers are now interested in vertical farming due to the current climate uncertainty.
However, vertical farming is not the cheapest resource out there and has been predicted by some agriculture experts to be three to five times more expensive than traditional farming.
But Infarm says that the product they provide is worth the extra money, especially with the benefits it brings to the environment.
Retailers set the price for the produce Infarm provides in-store with M&S currently charging £1.20 for herbs.
It said the price does not tend to be significantly higher than their other produce offerings.
Vertical farming helps reduce the ecological waste associated with industrial farming
Evita added: 'We find that in recent years, investors from around the globe have been drawn to innovation that addresses the need for sustainable solutions to the challenges that affect our planet.
'Certainly, these are challenges that many countries and regions are dealing with now, and they are becoming increasingly urgent for all of us.'
Coronavirus has also posed many problems to the vertical farming industry, including the need to implement social distancing measures at hubs, although Infarm said it has been able to keep growing during this period.
It added that the global pandemic has seen increased interest from both investors and consumers in the industry with Infarm clients experiencing a 222 percent sales growth in the second quarter of this year.
This means the business has more than doubled its employees since June last year.
The future of vertical farming definitely looks bright. Infarm started just under a decade ago and since then, it has grown to more than 900 farms in supermarkets and distribution centres all around the world, allowing it to harvest over 250,000 plants a month and growing.
It is now expanding from just Europe to the United States with Kroger and Canada with Sobeys as well as recently announcing plans to enter Japan and build the first vertical farming network in Asia through a new partnership with Konikuniya.
Source: This is money
Photo Courtesy of Infarm
Urban Crop Solutions Launches New "Modulex Plant Factory" on Sept. 9th, 2020
Launch Webinar hosted by Henry Gordon-Smith, CEO of Agritecture, on Sept 9th, 2020 (9 am EDT, 3 pm CEST, 9 pm SGT - 45 minutes)
Register And Get A Sneak Preview on The
New www.urbancropsolutions.com Website
Launch Webinar hosted by Henry Gordon-Smith, CEO of Agritecture,
on Sept 9th, 2020 (9 am EDT, 3 pm CEST, 9 pm SGT - 45 minutes)
Indoor Vertical Farming is a fast-emerging agriculture technology that provides compelling solutions to the United Nation’s Sustainable Development Goals: waste less food and support local farmers (Goal 2), avoid wasting water (Goal 6), and provide decent work (Goal 8).
However, few early adopters are making a profit.
Urban Crop Solutions has worked tirelessly to find a sensible solution to the open issues many investors and growers still face today. The initial Capex or investment cost is high and creates the need for a scalable solution. The unique freshness, taste, and shelf life of the crops go to niche markets with ever-changing needs, which requires a Plant Factory to be extremely adaptable. Also, high labor costs push Indoor Farms to implement more automation and become more efficient.
Based on the experiences and feedback of the customers on the 1st generation products, a new generation Plant Factory was designed from the ground up. The company believes it developed a concept that ‘simply makes sense’.
The ModuleX, the “Sensible Plant Factory” is Scalable, Adaptable, and Efficient.
The ModuleX can be configured between 2 to 64 Grow Modules, which means that the Plant Factory is scalable. One Grow Module contains 86 m² (925 sq.ft) of growing surface, yielding about 6.000 kg/year (13.228 lbs/year) of fresh vegetables. Each separate module features an independent climate and nutrient system, allowing the mix of crops to be adaptable to customers’ needs.
The base price is an industry-low Capex of 1.800 EUR per m² growing surface ex-works (199 USD/sq.ft). The labor costs are reduced by the automated crop-to-person ‘BenchCarousel’. For example, the ModuleX-8 has 8 Grow Modules for a total of 688 m² (7.403 sq.ft). The base price is 1.238.400 EUR (approx. 1.47 mm USD) for an output of 44 ton/year of romaine lettuce (97.000 lbs/year). For mid-sized solutions under 5500 m² growing surface, this is probably the most efficient solution on the market today.
To help people in the long and confusing journey into indoor vertical farming, the company also initiates an end-to-end support program, with a free feasibility calculator, technical support, biological consulting, and contract research. Urban Crop Solutions also developed a Corona-proof support system for training, set-up, startup, and first harvest support of any ModuleX Grow Module, which all can now happen remotely.
Tom Debusschere, CEO of Urban Crop Solutions: “We’ve been listening closely to the feedback of our customers and we found improvements just about everywhere. But the breakthrough invention is the automated BenchCarousel. This new crop-to-person carousel brings any bench of your choice to you within 90 seconds. It also allows us to fit a growing surface of 86m² (925sq.ft) within a 40ft insulated freight container, which we believe is an industry record.
What you really pay for is growing surface, labor, and electricity, and the ModuleX Plant Factory offers a step-change improvement in each. We invite you to take a look at our new website, with the investment cost in full transparency, so you can quickly see which solution is the best fit for you.”
Urban Crop Solutions is an agtech pioneer in the fast-emerging world of ‘Indoor Vertical Farming’. Throughout years of research, 220+ ‘plant growth recipes’ were developed for efficient indoor growing. All drivers for healthy plant growth, such as optimal LED spectrum and intensity, nutrient mix, irrigation strategy, and climate settings are tested and validated daily in the company’s own Indoor Biology Research Center.
To date, Urban Crop Solutions has manufactured container Farms and a Plant Factory for clients throughout Europe, North America, and Asia. Urban Crop Solutions’ commercial farms are being operated for vegetables, herbs, and micro-greens for food retail, foodservice, and industrial applications. Research institutions operate the growing infrastructure of Urban Crop Solutions for scientific research on banana seedlings, flowers, hemp, and many more.
Visit www.urbancropsolutions.com for a full virtual tour.
For more information: www.urbancropsolutions.com
Brecht Stubbe, Sales Director brst@urbancropsolutions.com
Maarten Vandecruys, CTO mava@urbancropsolutions.com
Tom Debusschere, CEO tode@urbancropsolutions.com
European headquarters: Regional headquarters:
Grote Heerweg 67 800 Brickell Avenue, 1100 Suite
8791 Beveren-Leie (Waregem) Miami (FL 33131)
Belgium Florida
(+32) 56 96 03 06 +1 (727) 601 7158
Facebook: www.facebook.com/urbancropsolutions
Twitter: www.twitter.com/U_C_Solutions
LinkedIn: www.linkedin.com/company/urbancropsolutions
YouTube channel: http://www.youtube.com/c/UrbanCropSolutions
Instagram: https://www.instagram.com/urbancropsolutions/?hl=en
2nd Annual Global CEA Census Announced: CEA Amidst COVID-19
AgTech leaders Autogrow and Agritecture Consulting have launched their 2nd Annual Global CEA Census, focusing on understanding the impact of the COVID-19 pandemic on controlled environment agriculture (CEA) operations around the world
The 2020 Global Census will run from July 7 2020 until August 10 2020.
8/14/20 UPDATE:
The Global Census has been extended
& will run thru this Weekend
7 July 2020
AgTech leaders Autogrow and Agritecture Consulting have launched their 2nd Annual Global CEA Census, focusing on understanding the impact of the COVID-19 pandemic on controlled environment agriculture (CEA) operations around the world.
“We’re all operating in a unique situation right now and what’s required is a reality check. All of us, including growers, suppliers, distributors, government and financial institutions, need a clear view of what should be implemented, ensuring farm operators address a raft of challenges to continue to feed communities,” explains Autogrow CEO, Darryn Keiller.
“In every major market, media coverage of farms has made clear the high COVID-19 infection rate amongst farm workers, coupled with major challenges in getting their traditional immigration sourced labor across closed borders. Infection rates in food processing plants are another example.”
“It will take accelerated engagement between industry stakeholders to get us through the next 12 months and on into the future. Some farm operators have adapted well, whereas others will require additional financial intervention and modernize their approach to farming. We hope this Census will highlight the true impact of what’s happening and where the priorities lie.”
Last year, the 2019 Census reported on several areas including growth plans, agricultural experience, and profitability. This year, the Census will focus specifically on COVID-19 and whether decisions indicated last year have been affected.
“In 2019, we found 90% of respondents planned to increase their production area. We’re curious as to whether that is still the case, and if not, what other business changes are being implemented due to COVID-19,” says Agritecture Founder and CEO, Henry Gordon-Smith.
“The future is going to be about maintaining the health of workers, alongside the health of the business. Consumers will be looking for transparency around food sourcing, sustainable and local producers, and this is an opportunity for the CEA industry to take a lead in what will be our new normal.”
Recent figures released by the World Health Organization show the rapid spread of COVID-19 that has resulted in countries implementing various lockdown measures. This, in turn, has had a major impact on the entire food supply chain, including CEA farms that are key food producers around the world.
The 2020 Global Census will run from July 7 2020 until August 10 2020.
All completed submissions will go in the draw to win multiple prizes, including tickets to Agritecture Xchange, a speaking spot in the conference, a feature on Agritecture’s blog, and a discount off an annual Folium subscription with every purchase of a Folium Sensor Starter Pack.
TAKE THE SURVEY HERE
READ TERMS & CONDITIONS HERE
MEDIA INQUIRIES
Kylie Horomia, Autogrow Head of Communications
(e) Kylie.horomia@autogrow.com
(m) +6421 733 025
(w) https://autogrow.com/ | www.farmroad.io
Briana Zagami, Agritecture Media Strategist
(e) briana@agritecture.com
About Autogrow
Autogrow leverages the power of technology, data science, and plant biology to provide indoor growers affordable, accessible, and easy-to-use innovation – 24/7, anywhere in the world.
Our solutions support growers and resellers in over 40 countries producing over 100 different crop types.
We are the experts in Controlled Environment Agriculture (CEA) and continue to stay ahead of a rapidly evolving landscape.
About Agritecture Consulting
Agritecture Consulting provides a comprehensive approach to CEA project development.
In operation since 2014, Agritecture has helped more than 100 organizations determine the feasibility of their ideas, validate their business strategies, recruit talent for their projects, and manage operational challenges.
Our job is to jumpstart your knowledge of CEA, help you navigate barriers to entry, make industry connections, and mitigate risk. Our consulting services are backed by several years of operations data and a team of experienced growers, engineers, and sustainability managers.
Farming In The Desert: Are Vertical Farms The Solution To Saving Water?
"When I told people I was going to grow tomatoes in the desert, they thought I was crazy," Sky Kurtz, founder of Pure Harvest Smart Farms, told DW
With high temperatures and water scarcity, the Emirates might seem an unlikely place for a farm. Yet, as coronavirus and climate change heightens the desire for food security, could vertical farms be the solution?
"When I told people I was going to grow tomatoes in the desert, they thought I was crazy," Sky Kurtz, founder of Pure Harvest Smart Farms, told DW.
With just an average 12 days of rain a year, less than 1% arable land, a desert location, and an 80% import rate for food, the United Arab Emirates (UAE) seems an unfavorable place to set up a farm.
Read more: World needs 7 planets to eat like a G20 nation, food report finds
Kurtz is one of several entrepreneurs using high-tech farming techniques to boost crop production in the Emirates. Pure Harvest built the first climate-controlled greenhouse in Abu Dhabi in 2017.
Prompted by arid conditions and a desire for greater food security, the country is investing millions in technologies — such as vertical farming — that could make it an unlikely agricultural pioneer.
Read more: Goodbye to fields: What food production may look like tomorrow
Sky Kurtz says people thought he was crazy when he said he would grow tomatoes in the desert
Vertical farms can grow a rich variety of different crops by stacking them in layers under LED lighting in climate-controlled greenhouses and watering them with mist or drip systems. The process is tailored to each crop's specific needs, resulting in high-yield, year-round harvests.
"It takes 30 to 40 days to grow leafy greens out in the field. We can grow that same crop in 10 to 12 days," says Marc Oshima, co-founder of Aerofarms. The company received funding from the Abu Dhabi Investment Office to build the capital's largest indoor vertical farm, with 800 different crops, by 2021.
With vertical farming, crops can flourish year-round, far from traditional regions of production
Water scarcity and fossil-fuel reliance
The technology uses minimal land and up to 95% less water than conventional agriculture.
The hydroponics system places the plants' roots directly into a water-based and nutrient-rich solution instead of soil. This "closed-loop" system captures and recirculates all the water, rather than allowing it to drain away — useful for a country like the UAE suffering from extremely high water stress.
Read more: Blue Gold: The dwindling resource of water
Globally, agriculture accounts for 70% of freshwater withdrawals, and UAE is extracting groundwater faster than it can be replenished, according to the International Center for Biosaline Agriculture (ICBA).
"Water is very expensive over in the UAE, but energy is cheap as it is subsidized," says Jan Westra, a strategic business developer at Priva, a company providing technology to vertical farms.
The artificially controlled environment is energy-intensive because the air conditioning and LED lights need a constant source of electricity.
This bringing forth of life in the desert could come at a high environmental cost. Most of that energy comes from carbon-emitting fossil fuels, even as the Middle Eastern country feel the effects of climate change.
By 2050 Abu Dhabi's average temperature is predicted to increase by around 2.5°C in a business-as-usual scenario. Over the next 70 years, patterns of rainfall are also expected to change.
Aerofarms has received funding from the Abu Dhabi Investment Office to build the capital's largest indoor vertical farm, with 800 different crops, by 2021
Integrating renewable energy
Although Pure Harvest is building a solar-powered farm in neighboring Saudi Arabia, its UAE operations get electricity from the carbon-intensive national grid.
Investing more in renewables "is a goal of ours," Kurtz told DW. He said the company has not set a clean energy target but is working on various green power projects, including a plan to integrate solar power generated in UAE into its operations.
However, Willem van der Schans, a researcher specializing in short supply chains at Wageningen University in the Netherlands, says sustainability and clean energy should be "inherent in the technology and included in plans when starting a vertical farm."
He argues that many vertical farming companies are not sustainable in terms of energy as they still view clean power as an optional "add-on."
Read more: Innovative clean water technologies
Ismahane Elouafi, director-general of the government-funded ICBA in Abu Dhabi, acknowledges that vertical farming has some way to go before achieving "real sustainability," but she believes the innovations are "promising."
Improved battery storage, increasingly efficient LED lights and cheaper solar panels will help, she adds.
Local solutions
By 2050, the UAE government wants to generate almost half its energy from renewable sources.
Fred Ruijgt, a vertical farming specialist at Priva, argues that it's important to factor transport and refrigeration into the energy equation. Vertical farming uses more energy to grow crops than traditional agriculture, but because crops are grown locally, they do not have to be transported by air, sea or truck over long distances.
Vertical farming installations come in all shapes and sizes, meaning food can grow where land and water are scarce
"The energy-saving is difficult to calculate exactly, but the advantages of locally grown crops are huge," he says, adding that those grown in vertical farms not only use less water and pesticides but that they also have a longer shelf life due to minimal transportation time.
Read more: Dubai: Can the city of black gold go green?
Food security and coronavirus
In 2018, the UAE set out its vision to become a hub for high-tech local food production.
Companies and investors have flocked to the region, attracted by the 0% corporate tax rate, low labor costs, and cheap energy. With their help, UAE aims to reduce its reliance on imports and make its food system more resilient to shocks like climate change and pandemics.
Oshima from Aerofarms says the coronavirus pandemic has brought "greater appreciation of how fragile the supply chain is and raised questions about food safety and security."
When the UAE went into lockdown in April, imported supplies of perishable goods like vegetables fell and business boomed for local suppliers.
ICBA's Elouafi said they have helped keep the UAE well-stocked during the pandemic.
"With the help of local food production and adequate imports, there has been absolutely no shortage of food in the UAE," Elouafi told DW.
Climate change, however, poses an altogether more complex threat to the country in the long-term. Given climate change's likely impact on food production, she says vertical farming has shown it is "an economically viable proposition even with harsh climatic conditions."
VIDEO: New Documentary ‘Heart of Glass’ Features Urban Farm That Hires People With Disabilities
“Heart of Glass” follows the creation and story of Vertical Harvest — an urban farm in Jackson, Wyoming, that hires individuals with intellectual and developmental disabilities. A state-of-art indoor vertical farm, Vertical Harvest not only can harvest fresh tomatoes all year round, they pay all their employees a competitive wage
July 12, 2020
What happened: After nearly a year on the film festival circuit, “Heart of Glass” is headed to the silver screen. The disability-centric documentary will begin airing on more than 200 television stations later this month, and the broadcasts are slated to coincide with the 30th anniversary of the Americans with Disabilities Act on July 26.
“Heart of Glass” follows the creation and story of Vertical Harvest — an urban farm in Jackson, Wyoming, that hires individuals with intellectual and developmental disabilities. A state-of-art indoor vertical farm, Vertical Harvest not only can harvest fresh tomatoes all year round, they pay all their employees a competitive wage.
The film has been many years in the making. In 2019, director Jennifer Tennican told The Mighty developing a feature-length independent documentary was “a marathon, not a sprint” but she pushed on because the heart of the film was (and is) its people and their stories.
The Frontlines: Vertical Harvest isn’t the only organization that employs members of the disability community. These organizations can be critical because people with disabilities are significantly more likely to be unemployed compared to their typical counterparts. Here are a few other businesses working to change this:
Bitty & Beau’s, a coffee chain in North Carolina, South Carolina and Georgia, is run by individuals with Down syndrome.
Breaking Grounds Cafe in Peabody, Massachusetts, offers paid opportunities and food service training to people with disabilities.
And several large corporations have received recognition for their inclusiveness, including Adobe, Allstate, Capital One, Cigna, HP, Intel and Delta.
Get more on disability: Sign up for our weekly disability newsletter.
A Mighty Voice: Our contributor, Erin Noon-Kay, shared why opportunities like these are so important. “At 20% of the population, people with disabilities are one of the nation’s largest minority groups. Yet the most recent U.S. disability employment statistics show that only 20 percent of people with disabilities are participating in the workforce, compared to 69 percent of people without disabilities.” You can submit your first person story, too.
Temperature is The Biggest Challenge For Cultivation in The Maldives
They currently import 95% of their food. Fruit and vegetables are brought in from afar to provide food for the many tourists as well as the local
A pearly white beach and a vast blue ocean. This is the picturesque location for which many tourists travel to the Maldives every year. However, these islands in the Indian Ocean are tiny and are highly dependent on imports for fresh produce. They currently import 95% of their food. Fruit and vegetables are brought in from afar to provide food for the many tourists as well as the locals.
That could be done more efficiently, according to a group of university students from TU Delft. As part of an assignment, they designed a modern self-sufficient greenhouse in order to produce food locally. And where most study assignments remain a plan on paper, this greenhouse actually might be realized on one of the islands in the near future.
Biggest challenge is temperature
The plans of the Maldives Matter Project are already very advanced, says Carmen Jansen op de Haar of Resilient Island. "It will be a semi-closed greenhouse of one hectare in size. Two-thirds of it will be used to grow lettuce, there will be tomatoes in one-third and possibly strawberries at a later stage. There will be a hydroponic system for lettuce cultivation, for which we collaborate with Van der Hoeven. There is plenty of sunlight and an occasional shower. The biggest challenge for growing in the Maldives is the temperature and the high humidity. On the islands it is between 25 and 30 degrees Celsius all year round, both during the day and at night. Because this temperature difference is so small, many fruits and vegetables cannot grow in that climate, so that the Maldives become highly dependent on imports."
"In order to keep the temperature in the greenhouse at the right level, we need cooling technology. We are also looking at Deep Water Source Cooling, where you use the temperature differences in the water. A new technique that we certainly will not apply immediately, but that is worth investigating.”
Test greenhouse
To investigate the feasibility of the thought out plans, the group will first set up a miniature version of the greenhouse. “We have already done a test with tomatoes. The cultivation results in those circumstances were very positive. With a mini greenhouse, we mainly want to test the techniques.”
Growers from the Netherlands
According to Carmen, so far there is little horticulture to be found on the sun-drenched islands. “There is some cultivation in simple plastic tunnels without cooling or other techniques. The products on the field are sprayed a lot. Agricultural training is available, but currently only six people have completed the university horticultural training. Because there is little work to be found in it, that number will not grow anytime soon."
At the end of last year, Resilient Island made an appeal to find a Dutch grower who, once the greenhouse is completed, will start the cultivation. “We have found two growers who are currently helping us to answer technical cultivation questions and who also give advice on setting up an education program. Eventually, a Dutch grower will head over there to train the Maldivian growers. We are also going to bring local growers to the Netherlands to show them our horticulture here. Ultimately, they will have to manage cultivation independently, with the help of Hoogendoorn climate computers and some advice from the Netherlands.”
Supply to resorts
The choice of crops will be tailored to the demand of resorts. “Our market research showed that there was a great need for lettuce, however, if we would produce only lettuce then it would be too much. Lettuce and strawberries are fragile in transport and therefore very suitable for local cultivation. The intention is to supply various resorts with fresh produce packages."
The exact location for the greenhouse has not yet been determined. “We have selected three islands, each of which has potential in a different way. All three are local islands, which ensures that the local population can easily work in the greenhouse later on. "Although the Maldives have many luxury resorts, not every resort will be supplied." We are looking for resorts that share our vision. Some say that they strive for sustainability, but in practice, nothing much is achieved. It is important that the resorts with which we work support our principles."
Chain reaction
Further in the future, the Resilient Island team hopes to broaden the project. “Our goal is to make the Maldives less dependent on the rest of the world. We are hoping for a chain reaction to other Small Island Developing States, as these countries are called that are highly dependent on the mainland. The corona crisis once again made it very clear that it is important that countries and islands can meet their own needs. Air traffic almost came to a standstill, making it even more evident why it is so important that these kinds of countries can be self-sufficient."
For more information:
Carmen Jansen op de Haar
Resilient Island Foundation / Resilient Island B.V.
info@resilientisland.com
www.resilientisland.com
Publication date: Mon 6 Jul 2020
© HortiDaily.com
How Advanced Nutrients pH Perfect Technology Makes Growing Hydroponically Brain-Dead Simple!
If you are a new hydroponics grower … or even if you have years of experience under your belt … one thing that’s very important for all indoor growers to understand is the importance of pH in hydroponics.
If you are a new hydroponics grower … or even if you have years of experience under your belt … one thing that’s very important for all indoor growers to understand is the importance of pH in hydroponics.
In short, if you don’t understand how to monitor and achieve the best pH level for hydroponics, then you can seriously hurt your results and even drastically reduce your harvests.
What is pH and why is it so important?
pH is the measure of the level of acidity or alkalinity of your entire garden which consists of your nutrient solution and growing medium. It ‘s a scale that’s represented by figure 1 showing pH values from most alkaline to most acidic using common materials.)
To achieve optimal growing conditions, you want to achieve and maintain the best pH level for plants.
Here is why it’s so important to get the perfect ph balance …
Living, growing organisms such as your high-value plants are essentially chemical machines. One of your most important jobs as a grower is to keep those chemicals in balance. This means avoiding a shift in the pH toward either pH extreme: excessive acidity or excessive alkalinity.
The pH level makes the difference between having a grow room full of nutrient-healthy, thriving plants and seeing your time, effort, and money end up as little more than a compost waste pile!
Here’s what happens when pH gets out of balance
When the pH of your hydroponic system gets out of balance—which can happen quickly if some kind of stabilizing agent or mechanism is not put in place—the ability of your plants to absorb macro, secondary, and micronutrients, as well as vitamins, carbohydrates, and other beneficial sources, is limited.
For example, when the nutrient solution has a high (alkaline) pH, iron and manganese are locked out. That’s because they form poorly soluble chemical compounds. Adding chelators to compounds helps to keep them in bio-available form. However, chelation itself is a pH-dependent process.
Another reason why pH is so important for the absorption of nutrients is biochemistry. Nutrients cannot enter the plant roots on their own because plant cells are protected by membranes that are difficult for water soluble ions to penetrate. To overcome this barrier, nutrients are carried inside the plant by special transporters. These transporters are big protein molecules in the cell membranes. They recognize nutrient ions and let them enter the plant cells. Since proteins are rich in ionizable chemical compounds, their function is dependent on pH. Thus, every transporter protein has an optimal pH range where it works best.
In addition, the beneficial bacteria and fungi included in sophisticated hydroponic supplements need a consistent pH. These microorganisms thrive at pH 5.5–7.0 (Perry, 2003). A more acidic pH can foster an environment that allows the growth of pathogenic microorganisms, which may pose a risk to plant health.
Here’s what happens when pH gets out of balance
When the pH of your hydroponic system gets out of balance—which can happen quickly if some kind of stabilizing agent or mechanism is not put in place—the ability of your plants to absorb macro, secondary, and micronutrients, as well as vitamins, carbohydrates, and other beneficial sources, is limited.
For example, when the nutrient solution has a high (alkaline) pH, iron and manganese are locked out. That’s because they form poorly soluble chemical compounds. Adding chelators to compounds helps to keep them in bio-available form. However, chelation itself is a pH-dependent process.
Another reason why pH is so important for the absorption of nutrients is biochemistry. Nutrients cannot enter the plant roots on their own because plant cells are protected by membranes that are difficult for water soluble ions to penetrate. To overcome this barrier, nutrients are carried inside the plant by special transporters. These transporters are big protein molecules in the cell membranes. They recognize nutrient ions and let them enter the plant cells. Since proteins are rich in ionizable chemical compounds, their function is dependent on pH. Thus, every transporter protein has an optimal pH range where it works best.
In addition, the beneficial bacteria and fungi included in sophisticated hydroponic supplements need a consistent pH. These microorganisms thrive at pH 5.5–7.0 (Perry, 2003). A more acidic pH can foster an environment that allows the growth of pathogenic microorganisms, which may pose a risk to plant health.
In fact, pH affects every function of the root zone
For example, carbohydrate transporters in the roots require the right pH in order to perform their job of absorbing carbohydrates. These carbs are assimilated from decaying organic matter or carbohydrate supplements, which the plant uses as food.
Maintaining the normal pH of the nutrient solution and growing medium as close as possible to your plant species’ unique pH “sweet spot” is critical to obtaining a rich harvest.
The sweet spot is the optimal pH range where all the plant essential nutrients are readily available for absorption. For high value plants, the sweet spot is pH 5.5–6.3.
Why is maintaining a stable, consistent pH so difficult?
Three major factors tend to disrupt the pH balance for plants. Learning to control these influences is essential for a successful harvest.
* pH Problem #1: Your Water.
The truth is that there’s no such thing as pH perfect water. Here’s why …
Freshly distilled or deionized water has a pH of 7. However, the pH of the water may fall to as low as 5.5 within hours of preparation because water absorbs carbon dioxide (CO2) from the air.
The behavior of tap water is even more complex. It contains dissolved and slightly alkaline calcium and/or magnesium salts. In this case, absorption of CO2 from the air makes predicting the pH even more challenging.
Because the calcium and magnesium salts in most tap waters (not to mention even more chemically complex well and spring waters) create such serious problems, many hydroponic growers, from hobbyists to huge commercial greenhouses, prefer using treated water.
Although a number of water treatment systems exist, reverse-osmosis (RO) is considered the most economical. Water obtained from an RO system is almost as good as expensive distilled water.
Another option is to adjust the pH of tap water before using it. This can be done with so-called pH up or pH down additives. However, this task is demanding and often done incorrectly—and what’s worse, the acidic and alkaline chemicals used in these products, and the resulting sudden fluctuations in pH when they are added to the reservoir, can be hard on your plants.
* pH Problem #2: Your Nutrients.
Many pH changes are caused by the nutrients themselves. Many growers don’t realize there is a relationship between pH and ppm. Here’s what that means …
The more compounds in the water— measured in parts per million (ppm) or by the nutrient solution’s electroconductivity (EC)—the greater their influence on pH.
For example, the urea used in many fertilizers is broken down by enzymes into one molecule of CO2 (a slightly acidic compound) and two molecules of ammonia (a slightly alkaline compound). This can cause erratic changes in pH.
In addition to urea, any compound containing an amide chemical bond
(e.g., the proteinates used in many fertilizers) can, when broken down, affect the pH in unpredictable ways.
Nutrient absorption also leads to changes in pH. When a plant absorbs a lot of potassium ions, it gives out hydrogen ions in return. The result is a net decrease in pH. The situation reverses when the plant absorbs a lot of nitrate ions and gives out hydroxyl ions to compensate, thus increasing the pH (Bar-Yosef, Ganmore- Neumann, Imas, and Kafkafi, 1997; Ryan, P.R. and Delhaize, E., 2001).
In short, the higher the rate of nutrient absorption, the more dramatic the change in pH.
* pH Problem #3: Your Growing Medium.
The growing medium (also called the substrate) affects pH as well.
For example, coco-based growing media undergo subtle changes during your crop’s life cycle that affect the pH of the nutrient solution.
In fact, every chemical or biochemical process that goes on in the growing medium changes the pH of the nutrient solution. Each additional factor drives it further from the sweet spot.
In nature, the volume of surrounding soil—teeming with microbes, humates, and other pH stabilizing agents—does a good job of offsetting pH changes. Natural soils act as natural pH buffers. That’s why, in outdoor gardens, where the soil itself contributes to a more stable, consistent pH, changes in pH are more gradual than in hydroponic gardens.
In hydroponics, however, pH stability is a challenge. It is an intense gardening method where the concentration of nutrients and their absorption rate by plants are much higher than in soil. As a result, chemical and biochemical processes influence the pH to a much higher degree than in natural soils or traditional agriculture. The natural stabilizers and buffers in the nutrient solution, mainly phosphates, are weak, so indoor gardeners have to constantly be adjusting pH in hydroponics and adjust it when it goes below or above the sweet spot.
What a hassle!
Enter Advanced Nutrients pH Perfect® Technology – Automatically Balances Your pH For You.
The fact is that Advanced Nutrients has spent many thousands of man-hours developing a technology that automatically balances your pH for you — putting it in the “sweet spot” and holds it there for weeks.
And the technology is so “smart” it can account for many of the aforementioned variables in your grow room.
For example, they wanted to find pH stabilizers and buffers that would allow growers to use any source of low-mineralized water. The resulting proprietary pH buffering agents and stabilizing mechanisms became the foundation of a new system aptly called pH Perfect® Technology.
But developing a groundbreaking pH buffer and stabilizer wasn’t the whole answer. It required many years of field testing to determine the proper concentration for pH Perfect base nutrients.
How Does pH Perfect Technology Work?
The general answer is that pH Perfect Technology is a proprietary system, so the exact details cannot be shared with the public at this time.
However, Michael Straumietis, the founder and CEO of Advanced Nutrients has graciously shared detailed information about how the technology works …
First, the technology uses its proprietary and primary mechanism to quickly bring the nutrient solution into the “sweet spot” for growing–which is 5.5 to 6.3 pH (usually holding it at a rock-solid 5.6 pH). And it is able to do this across a wide range of pH ranges.
In addition to this main mechanism that quickly brings your pH into range, you have three chemicals that work synergistically to make sure the pH stays in that “sweet spot”. In lab experiments, Advanced Nutrients scientists have had pH Perfect Technology lock down the pH in this “sweet spot” for 10-14 days.
Then, there are a number of chelates used …
In particular, there is a type of chelate called “Zwitterionic” used — which simply means that this chelate can swing both towards more acidic or more base. That reinforces that stability of the pH column because it can go either way as needed to maintain the proper pH.
Then, heavy ‘cation’ elements are used that–after the plant takes them in–helps the plant to exude acid. This produces a more acidic growing medium.
So now your plants are working for you, not against you … But that’s still not enough …
Because the technology has a built-in “safety net” in the form of the chelates that are used. That’s because the extensive matrix of chelates that are utilized have a theoretical absorption range from pH 1 to pH 10.
Now, at pH 2.5 the plant’s roots are burning back faster than they can produce, and at pH 9.5 your plants are dying too. But the point is that … even if … the entire pH Perfect mechanism were to completely fail …we have this built-in “safety net” with the extensive amount of chelates used to protect the plant and make sure it feeds and stays healthy.
But Does Advanced Nutrients pH Perfect Work?
But the question is “Does it actually work?”
And the answer is a resounding yes!
Check out the YouTube video below for a demonstration of the pH Perfect Technology in action:
pH Perfect Technology VS The Competition
You can also visit the website pHShootout.com to see proof of the technology’s effectiveness. In short, they put pH Perfect Base Nutrients and supplements head-to-head against all the other top hydroponics brands and filmed it live for you.
They set up three diverse pH ranges of 4.5, 6.5, and 8.5 – then tested all the top brands against Advanced Nutrients to answer the ultimate question …
Does pH Perfect Technology really work? And how does it stack up against the competition? You can visit pHShootout.com to see the video results.
What’s the bottom line?
If you use any pH Perfect base nutrient as directed, you will never again have to monitor and adjust your pH. The pH Perfect Technology automatically brings the pH of the nutrient solution into the sweet spot for optimal growth and flowering—and keeps it there for at least one week.
You no longer have to hassle with pH meters and pens. Relax and rest assured that the pH of the nutrient solution and growing medium is right on target, providing optimal growing conditions and nutrient absorption for your plants. pH Perfect lives up to its name, making hydroponics easier and safer for any type of grower.
Here Are The Advanced Nutrients pH Perfect Nutrients lines
There are three main lines of Advanced Nutrients pH Perfect Base Nutrients.
* For 3-Part base nutrients, growers can use pH Perfect® Grow, Micro, Bloom.
* For 2-part base nutrients, growers can choose between The Sensi Series (pH Perfect® Sensi Grow Parts A & B and pH Perfect® Sensi Bloom Parts A & B) …
* Or Advanced Nutrients flagship 2-part base nutrient formulation pH Perfect® Connoisseur Grow Parts A & B and pH Perfect® Connoisseur Bloom Parts A & B.
* And for coco coir growers, Advanced Nutrients has separate Coco Base Nutrients formulations of their 2-part base nutrients made specifically for the challenges of growing with coco.
In short, it’s up to the individual grower as to whether they want to use a 2-part or 3-part base nutrient.
Many times, these days, it comes down to personal preference of the grower and making a fully informed choice is beyoned the scope of this article. Either way, choosing pH Perfect Base Nutrients ensures that you won’t have to worry about balancing and adjusting your pH throughout the process!
The Advanced Nutrients ph Perfect Feeding Chart
It’s important when using any 2 or 3-part base nutrient to follow the correct feeding chart.
If you are looking for the pH Perfect feeding chart then you are in luck because it can be found on this page here:
https://www.advancednutrients.com/nutrient-calculator/
On that page, you’ll find the official Advanced Nutrients ph Perfect Calculator and the official Advanced Nutrients ph Perfect Feeding Schedule can be found on every bottle of pH Perfect Nutrients.
References
Bar-Yosef, B., Ganmore-Neumann, R., Imas, P., and Kafkafi, U., 1997. Release of carboxylic anions and protons by tomato roots in response to ammonium nitrate ratio and pH in nutrient solution. Plant and Soil, 191 (1), pp. 27–34.
Nye, P.H., 1981. Changes of pH across the rhizosphere induced by roots. Plant and Soil,
61 (1–2), pp. 7–26.
Olsen, C., 1958. Iron uptake in different plant species as a function of the pH value of the nutrient solution. Physiologia Plantarum, 11 (4), pp. 889–905.
Perry, L., 2003. pH for the garden. University of Vermont Extension, Department of Plant and Soil Science, [online] available at: http://www.uvm.edu/pss/ppp/pubs/ oh34.htm [accessed 12 January 2012].
Ryan, P.R., and Delhaize, E., 2001. Function and mechanism of organic anion exudation from plant roots. Annual Review of Plant Physiology and Plant Molecular Biology, 52, pp. 527–560.
By Advanced Nutrients | December 2, 2016
Calculating Optimal Equipment And a Settings, Before The Greenhouse is Built
“Our software calculates the best configuration of a closed greenhouse for any crop all over the world,” says Vincent Stauffer, director of Hortinergy, a French technology company
“Our software calculates the best configuration of a closed greenhouse for any crop all over the world,” says Vincent Stauffer, director of Hortinergy, a French technology company. It’s mostly used before the construction of a closed greenhouse to select and size the equipment. It helps to make sure that the right choices for energy-efficient equipment are made to reach the optimal climate with the lowest energy expenditures.
The greenhouse simulation software calculates energy consumption and expenditures (cooling, dehumidification, heating, and lighting). It models the inner climate like a virtual greenhouse, with specific parameters, and allows users to compare different technical solutions. Growers, consultants, and greenhouse designers use the software to know what the best settings and equipment are.
Orange Climate
Orange Climate, a Dutch supplier of climate technique, uses Hortinergy software to calculate the demands for the installation. Jeroen Verhagen, Business Unit Manager at the company talks about how the product works for them. “We have to know how many kiloWatts of heating and cooling we need, to have the requested greenhouse conditions, and we can calculate that with Hortinergy.”
When the company first started using the software, there were some issues and questions. “Vincent really cooperated with us on this, we discussed via Teams. He is very involved in the process.” Sustainable climate solutions for greenhouses and special concepts can be a big save in energy. “With Hortinergy, we can calculate what can be saved.”
For more information:
Hortinergy
contact@hortinergy.com
www.hortinergy.com
Publication date: Fri 3 Jul 2020
Author: Marlies Guiljam
© HortiDaily.com
Tech-Driven Vertical Farming Company Kalera Announces New CFO Fernando Cornejo
Fernando held similar roles at Argo Group (NYSE: ARGO), where he was Segment CFO and subsequently CFO for EXIN Group, a financial services company
Mr. Cornejo’s extensive background in corporate finance, strategic planning, technology, and investment banking will help Kalera rapidly and sustainably expand.
July 20, 2020
Cornejo brings with him an extensive background in corporate finance, strategic planning, technology, and investment banking.
ORLANDO, Fla., July 20, 2020 (GLOBE NEWSWIRE) -- Today, technology-driven vertical farming company Kalera announced the appointment of Fernando Cornejo as Chief Financial Officer. Cornejo brings with him an extensive background in corporate finance, strategic planning, technology, and investment banking. He will be based out of Kalera’s Orlando, Florida headquarters.
Fernando held similar roles at Argo Group (NYSE: ARGO), where he was Segment CFO and subsequently CFO for EXIN Group, a financial services company. Mr. Cornejo oversaw corporate finance, cost management, financial planning and analysis, capital structure optimization, M&A, risk management, accounting, and corporate strategy.
Prior to his role as CFO, Mr. Cornejo was an investment banker for companies such as Citibank, Credit Suisse, and Bear Stearns where he executed several transactions including financings, mergers and acquisitions, and capital raisings including Initial Public Offerings. Mr. Cornejo has a B.S. in Industrial Engineering from ITESM and a Master of Business Administration from Georgetown University.
“I couldn’t be more thrilled to welcome Fernando to Kalera, where he will create value immediately as we continue to expand our operations,” said Daniel Malechuk, Chief Executive Officer of Kalera. “Fernando brings more than 20 years of experience in diverse organizations with core expertise leading finance and accounting operations while enabling companies to achieve fast and sustainable growth.”
Mr. Cornejo stated, “I look forward to joining Kalera’s leadership team and leading its finance operations to contribute to Kalera’s future success as the company accelerates growth and progresses to the next phase of its strategy.”
Mr. Cornejo will lead Kalera’s financial operations, accounting, and investor relations. He will report directly to Mr. Malechuk.
Kalera has experienced significant growth in recent months, with plans of its new growing facility in Atlanta announced only months after opening its facility in Orlando. Kalera also announced last week that it will open a vertical farm in Houston in Spring of 2021. Its Orlando facility is currently the single largest indoor vertical farm in the Southeastern United States, and the Atlanta facility will be even larger. The Houston vertical farming facility will be the largest in Texas.
Central to Kalera’s business is good science. The company is planting non-GMO seed, and over the past several years has perfected plant and data science-driven methods to naturally optimize the factors that make plants thrive. Kalera manages these natural factors in a way that makes plants reach their maximum potential, resulting in the highest quality produce, grown locally with consistent high yields year-round.
By using a closed-loop irrigation system, Kalera’s plants grow while consuming 95% less water compared to field farming. While a head of lettuce grown in a field may use as much as 60 gallons of water, Kalera’s systems result in a healthier plant with less than five gallons.
The company utilizes cleanroom technology and processes to eliminate the use of chemicals and remove exposure to pathogens. With indoor facilities situated right where the demand is, Kalera is able to supply an abundance of produce locally, eliminating the need to travel long distances when shipping perishable products and ensuring the highest quality and freshness.
About Kalera
Kalera is a technology-driven vertical farming company with unique growing methods combining optimized nutrients and light recipes, precise environmental controls, and cleanroom standards to produce safe, highly nutritious, pesticide-free, non-GMO vegetables with consistent high quality and longer shelf life year-round. The company’s high-yield, automated, data-driven hydroponic production facilities have been designed for rapid rollout with industry-leading payback times to grow vegetables faster, cleaner, at a lower cost, and with less environmental impact.
Elka Karl
Phone: 510-508-7328
Email: elka@dadascope.com
US (MI): Detroit Indoor Farm Will Deliver 1000 Ready-To-Eat Salads A Day
Planted Detroit is a controlled environment vertical farm, run by five enthusiastic entrepreneurial growers. “As a team, we’re trying to make the best decisions for the plants, the company, and our community,” Meg Burritt, managing partner of business development, says
Planted Detroit is a controlled environment vertical farm, run by five enthusiastic entrepreneurial growers. “As a team, we’re trying to make the best decisions for the plants, the company, and our community,” Meg Burritt, managing partner of business development, says.
“Planted Detroit’s salads are a unique product, including our own baby greens, microgreens, and herbs. It basically takes salads to another level”, Simon Yevzelman, managing partner of biosecurity, says. The indoor farm produces all kinds of baby greens. “We’re not doing head lettuces just yet. We are in R&D with edible flowers, so hopefully, in a few months we’ll be growing those, too,” said Burritt. The company is aiming to differentiate baby greens from fully grown produce of the same species, through an analysis of the nutritional makeup of the greens Planted Detroit has grown. “We want to differentiate ourselves from the competition, large scale soil growers.”
Planted Detroit’s ‘power lunch salad’
Scaling up
“Our CEO, Tom, started this farm for a number of reasons, one being he saw the lack of variety in fresh produce available in grocery stores and the poor quality of what was available. [Tom] knew that he would be able to deliver better greens, grown in a way that is additive to the food system – not extractive. Soon, we will figure out to scale that effectively,” Burritt says. Planted Detroit is currently constructing new grow rooms in their facility, in part utilizing technology from a long-term partner, AmHydro. “Joe Schwartz, CEO of AmHydro, has been a great help to us.” The company is getting a new automated cultivation system that will be fully automating the production area. “Now is the time to invest in our systems and infrastructure. The new construction will deliver 1000 ready-to-eat salads a day. We’ve taken a pro-active approach since the beginning of the pandemic,” Yevzelman notes.
A full view of the farm
“We are excited about the upcoming months because construction will come to a close. We built a firm consumer base over the past few years, so when launching direct-to-consumer salads we had a good starting market share. The farm is small-scale right now and we sell out everything we grow. Ultimately, there will be more greens to sell and we can satisfy more customers. However, we know the current risks and we’re fully anticipating a second wave [of Covid-19]. Now, we are definitely strategizing, trying to stay sustainable through this time, through direct customer engagement and social media sharing,” Burritt states.
Increase of local demand
There is noticeably more demand for fresh produce in South East Michigan and throughout the state. “The pandemic shut everything down and showed how we are really interdependent on others. Local produce supply keeps us safer and is a more secure food supply. We hope to see more of this demand as our produce is way fresher and more delicious. The great thing is that individual consumers are becoming more aware of that,” Burritt notes. Yevzelman shares, ”we maintained our production capacity throughout the pandemic, so we could continue to sell direct to local Detroit consumers without pause.”
Racks stacked with microgreens
Ups and downs
The past few months have been a rollercoaster for Planted Detroit. Before COVID-19 the company sold its produce to restaurant partners, but when restaurants were shut down they had to make some changes. “All the [Covid-19 cases] going on the East Coast back then, made us pivot the business the model. Thankfully, we had a backup plan in our back pocket as we anticipated on all changes happening,” Burritt says. The company already had strict food safety measures in place, which also work against the virus. “We built the company around food safety and our employees have always been more conscious of hygiene,” Yevzelman says. Production was not scaled back as a result of the pandemic and safety procedures were followed up tightly. The company obtained certifications to sell their fresh produce directly to consumers. A well-known partner of the company, Skidmore Studio, launched a fresh food e-commerce website, MichiganFields.com, during the peak of COVID-19 shutdowns in March. Planted Detroit has been selling the platform ever since.
Back on track
“The sales had been relatively steady, but they really popped up during the pandemic”, Burritt adds. So far, Planted Detroit still sells through MichiganFields.com and directly to consumers, including home delivery. Next to that, their greens are sold at Detroit’s Eastern Market at the Tuesday market and through fresh produce boxes, in combination with other fresh produce, for people who don’t want to be exposed to the virus while grocery shopping. This month, the company is back to normal production. “It’s business as usual for us again. Just this week restaurants started calling us for produce again. [Adding in restaurants again] will be a perfect customer mix for us, especially after the construction,” Burritt notes.
For more information:
Planted Detroit
Megan Burritt, Managing Partner of Business Development
Simon Yevzelman, Managing Partner of Biosecurity
admin@planteddetroit.com
www.planteddetroit.com
Publication date: Wed 22 Jul 2020
Author: Rebekka Boekhout
© HortiDaily.com
"We Want To Raise Awareness On Vertical Farming In Italy"
“As we’re located in Italy, a country with great farming traditions, some people would think that we don’t need indoor farming. But, especially today, this is wrong
“As we’re located in Italy, a country with great farming traditions, some people would think that we don’t need indoor farming. But, especially today, this is wrong. In fact, we import a great part of our food, and while adverse climate events are always more frequent, the fertility of the soil is decreasing rapidly and water scarcity is becoming a real problem in more and more areas”. Guido Medici says. “So, indoor and vertical farming can be a great solution to produce high-quality food close to the market. These are the cases of our friends of Agricola Moderna and Planet Farms, both vertical farms which are located outside of Milan”, Guido states.
Lorenzo Franchini adds, “There is a generational shift taking place in the agricultural sector, as more people are open to innovation. The challenge is to find the right set up to get started. Hopefully, more European governments are going to direct public investments in the sustainable farming sector, so this will definitely become easier-going in the future. Speaking of crops, although they are quite unknown in Italy, microgreens are the most interesting to grow here. We think that people will be immediately convinced by their delicious taste and high nutritional power.”
Sananbio's growing system
Scalable farms
Guido and Lorenzo have worked together as intermediaries, since 2017. They founded the project Vertical Farming Consulting to help customers finding the right set up to start their own farm. “We’re cooperating with SananBio (vertical farming racks), Monti & C (climate rooms), and with Ferriplastic (irrigation and installation). Through these partnerships, we are able to stand by the customer through all the project phases, from the initial idea to the active production.
Together with our partners, we have designed a layout that is easily scalable. Clients seem to like that idea as it allows for expansion. They can start with a small part of the farm, like 60 sq. m., and then increase production once the demand will grow. The aim of VFC is to offer a turnkey vertical farm…”, Franchini adds,“…while our future goal is to create an association for vertical farming in Italy, to bring all indoor farmers together in the country, to obtain a more powerful voice”, Medici states.
The fixed layout of a VFC’s farm
How it all started
“We originally started with a vertical farming blog, visiting farms, and attending important events in the sector. More and more people were requesting information on vertical farming, so we started our own consultancy project” says Franchini. “Together with our partners, we are currently finalizing a vertical farm in Southern Italy for the production of microgreens.”, adds excitedly Guido, “The new facility will be opening its doors at the end of this summer.”
The Vertical Farming Education’s team: (F.l.t.r.) Guido Medici, Alessandro Russo Montecchio, and Lorenzo Franchini
Educating kids through hydroponics Vertical Farming Education (VFE) is an environmental education laboratory. The laboratory was designed in 2019 by Guido and Lorenzo, in collaboration with Alessandro, a psychologist who is extremely passionate about nature and plants. “The goal of VFE is to increase awareness of the water footprint of food among young students. We’ll start with primary and secondary schools, and eventually, we will scale up the project for older students,” Lorenzo states. “We developed a four-week workshop, divided into five lessons. The practical part is carried out by the installation of a small in-class vertical farm rack. This allows students to grow small salad portions by themselves.
The in-class vertical rack
The theoretical part is carried out by providing schools all supporting teaching material, such as exercises, theory, and questionnaires”, Guido adds. The VFE’s Team is now working on the realization of 20 workshops in 10 different schools which will be held at the beginning of 2021.
For more information:
Vertical Farming Consulting
Guido Medici, Co-founder
Lorenzo Franchini, Co-founder
info@vfitaly.com
www.verticalfarmingconsulting.com
Vertical Farming Education
Alessandro Russo Montecchio, Co-founder
Guido Medici, Co-founder
Lorenzo Franchini, Co-founder
info@vfeducation.com
Publication date: Tue 21 Jul 2020
Author: Rebekka Boekhout
© HortiDaily.com
New Pieces of The 3D-NFT Vertical Barrels
The Aponix vertical barrel system is an alternative vertical NFT solution from Germany that can be used instead of rack systems to use vertical space more efficiently in hydroponic setups and at the same time be able to use natural sunlight better
07-07-2020 | Goedemorgen
GERMANY- The Aponix vertical barrel system is an alternative vertical NFT solution from Germany that can be used instead of rack systems to use vertical space more efficiently in hydroponic setups and at the same time be able to use natural sunlight better. The aim was to enable edible plant production also in smaller farming plots or community spaces and allow for more decentralized urban micro-farming.
The whole concept is based on lego-like ring segment pieces that serve either as spacers or provide differently organized inserts for standard 2-inch netpots. Assembling multiple of these ring segment pieces will result in stackable ring segments or barrel levels to assemble one or multiple such vertical cylinders or ‘barrels’. With more ring segments stacked, the height and the number of grow spaces are increased.
With regard to irrigation, there are multiple options with a pressure line or without pressure. Please visit www.aponix.eu/barrel-irrigation for more details. Apart from configuring for crop size and shape, users also need to plan how they integrate the barrel units. They can be operated as independent single units with their own reservoir in the base or be chained into a larger production context with externally managed liquid nutrients.
Aponix' mission is to facilitate the setup of high density grow spaces for soil-less cultivation by taking the existing 2D NFT concept to the 3rd dimension in a very flexible, simple, and also robust way. It is especially designed for urban farming facilities operating on limited space. The range of available pieces with different functions has been extended continually during the last 2 years of development. In the meantime, many new users started testing or are actively using vertical barrels worldwide in a wide variety of applications.
As of 2020, Aponix changed their market strategy from looking for distributors to working more extensively with product partners who bring in their own engineering and create more specific and distinguishable products from their barrel components. This is based on the definition of the Aponix components as being mere infrastructure parts that always need to be integrated into a greater individual context. Product partners are required to create their own unique solutions based on Aponix pieces adding other external even competitive pieces and/or service and market them independently under their own brand and own product name. As a result of this co-operative type of relation, some new interesting components have been designed that in turn can be used by other existing product partners too. One nice example is the new lid-base that can be used to put a unit on a rotation table or stationary with a standard 40mm PVC pipe to drain the liquid underneath. That way Aponix managed to move the focus from unproductive competition on just commodity pieces and open the door for all sorts of bad copies to the best possible solutions and product creation for the product partners.
For more details please visit www.aponix.eu/product-partners.
For more information on the Aponix vertical barrel please visit http://www.aponix.eu or follow Aponix.eu on https://www.facebook.com/aponix.eu.
Contact: Marco Tidona - hello@aponix.eu.