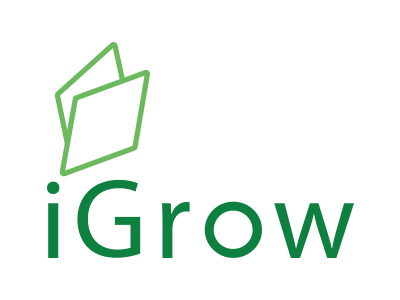
Welcome to iGrow News, Your Source for the World of Indoor Vertical Farming
Grodan Plugs Are A Key Factor In The Success of Smart Indoor Gardens
“The recent changes in the world such as urbanization and the COVID-19 pandemic have further spurred the grow-your-own food movement
Lynn Radford
Finland-based Plantui produces smart indoor gardens for sale to consumers. The company has doubled its sales volumes over the past year, driven by a number of macrotrends including sustainability, food safety, local sourcing, healthy eating, and home cooking. Besides the innovative LED technology and closed-loop irrigation system, the Grodan plugs in which the edible plants are grown are a key factor in the success of these miniature ‘vertical farms’ in the home.
Biotech company Plantui Oy is aiming to solve some of today’s and tomorrow’s food challenges by enabling consumers to grow edible plants in their own homes. Founded in 2012 in Turku – a major hub for agriculture, manufacturing, and the high-tech inudstry in the southwest of Finland (which, incidentally, has been ranked the happiest country in the world for the third consecutive year) – it has developed a range of indoor ‘smart gardens’ that combine Nordic design and functionality with cutting-edge technology. The plug-and-play devices come with simple instructions, making it easy for consumers to produce fresh, ready-to-pick herbs, lettuces, tomatoes, chilies, and edible flowers for use in home cooking.
“The recent changes in the world such as urbanization and the COVID-19 pandemic have further spurred the grow-your-own food movement. People are looking for safe and sustainable solutions, and hydroponic growing is a good fit with this because it requires no soil and no pesticides,” says Kari Vuorinen, CTO of Plantui. “We’ve put all our knowledge and research related to plant science, nutrients, light, and technology into creating a patented indoor hydroponic growing method, from seed to plant. Our unique artificial lighting solution is based on a special photon stream that replicates the light of Finnish Lapland and optimizes photosynthesis. This results in more green mass and better quality, meaning the plants are much tastier and more nutritious than the ones you can buy in supermarkets.”
Automatically regulated
The device is sold with everything included: horticultural LED lighting, a water bowl with an integrated pump system, seed capsules, and nutrients, which are adjusted by the integrated microcontroller in line with the growth phase algorithm recipe. “After extensively testing relevant light spectra, we’ve programmed the computer in the device to automatically regulate the wavelength and intensity of the light and the water-pumping rhythms as the seeds progress through the germination, seedling and growth phases,” explains Martina Angeleri, head of plant science at Plantui. “So all the customer needs to do is fit the device together, fill the water bowl, insert the capsules, plug the device in and then keep the water and nutrients topped up roughly once a month. At the end of the harvesting period, they simply clean the device – and everything is dishwasher-proof – and then they can buy new capsules and start all over again. This solution supports local year-round growing, irrespective of the season. An indoor garden can produce three to four harvests a year, depending on which types of plants people choose to grow.”
Besides the automated lighting and irrigation system, the substrate is equally important in ensuring that Plantui can deliver on its 100% guarantee of success. “If the seeds don’t germinate you won’t have any plants, so the growing medium has to be failsafe,” says Kari. “That’s why we tested lots of different solutions when we first started out in 2013, including peat, sphagnum moss, coconut fibre and stone wool. Sphagnum moss was very promising in the growth stage but it’s not easy to get hold of. When we tested it against Grodan’s plugs, we found that they were just as good in the growth stage and actually achieved better performance in the germination stage – plus they are readily available in large quantities, so we’d hit the bullseye!” Plantui initially sourced the plugs through the Grodan distributor in Finland, but later started working directly with the company in the Netherlands. “Grodan has played a big part in our success with the plants and the device. For example, the company has tailored the existing plugs specifically to our needs by creating a slightly bigger hole for the seeds in the capsule.”
No risk of contaminants
Grodan’s plugs offer other important benefits in the Plantui Smart Gardens, according to Martina. “Stone wool is a homogeneous inert substance. Unlike with an organic material such as peat, we know for sure that the plugs are clean and pure with no risk of contaminants such as insects, bacteria or fungi. Therefore, we can rely on uniform and reproducible support for plants. This allows us to make things as easy as possible for users, as they don’t need to check the pH before adding the nutrients,” she explains. “Additionally, the density of the stone wool helps to prevent light from penetrating into the root zone, thus protecting the roots and avoiding the formation of algae in the substrate. And last but not least, no organic fibres can leach into the water and clog the active pumping system.”
Sustainability
Sustainability is a top priority for Plantui; its devices are energy-efficient, produce 100%-natural food with no pesticides or other additives, and help to reduce the carbon footprint in terms of food miles and food waste. “Stone wool is a good fit with this because basalt is an inexhaustible resource. Additionally, Grodan is the only company of its kind that is EU-certified for environmental excellence. At the end of the harvesting phase, the stone wool plugs can be separated from the plastic holders and both parts can be recycled, which supports our ‘100% recyclable’ message,” states Kari.
Path to sales growth
The company is already selling tens of thousands of devices annually, both to high-end department stores across Europe – including in the UK and Italy – and through its own web shop. It is on track to double its sales this year, having received a major boost from an agreement between Plantui and a leading European producer of home appliances which has recently started marketing and distributing Plantui’s products under its own brand. Additionally, promising negotiations are underway with retailers in countries including Switzerland and the Netherlands.
Exciting future
The future not only looks very exciting for Plantui because of the increasing sales of its devices, but also because it has patented its technology and growing method globally. “We ourselves are focusing on consumer products for now, and there may be opportunities to branch out into other channels such as food service. For example, a couple of hotels and restaurants are already using our devices. We’ve even developed a specific lighting programme exclusively for a chef at a one-star Michelin restaurant who now grows his own unique-tasting dill!” exclaims Kari. “But the technology itself is ready for use on a larger scale and we’re now licensing it to other companies. In fact, we’ve recently sold licences to two small-scale vertical farms. We believe that networking is the key to success nowadays, so we are looking to build a good network of partners around the world – including in the USA and China – who can help us to further expand our market, and we are pleased that Grodan forms a part of that,” he concludes.
Martina Angeleri PhD from Plantui Oy examines a liquorice seedling in a Grodan plug from a Plantui Smart Garden.
No Soil. No Growing Seasons. Just Add Water And Technology
A New Breed of Hydroponic Farm, Huge And High-tech, is Popping Up in Indoor Spaces All Over America, Drawing Celebrity Investors And Critics
A New Breed of Hydroponic Farm, Huge And High-tech, is Popping Up in Indoor Spaces All Over America, Drawing Celebrity Investors And Critics.
By Kim Severson
July 6, 2021
MOREHEAD, Ky. — In this pretty town on the edge of coal country, a high-tech greenhouse so large it could cover 50 football fields glows with the pinks and yellows of 30,600 LED and high-pressure sodium lights.
Inside, without a teaspoon of soil, nearly 3 million pounds of beefsteak tomatoes grow on 45-feet-high vines whose roots are bathed in nutrient-enhanced rainwater. Other vines hold thousands of small, juicy snacking tomatoes with enough tang to impress Martha Stewart, who is on the board of AppHarvest, a start-up that harvested its first crop here in January and plans to open 11 more indoor farms in Appalachia by 2025.
In a much more industrial setting near the Hackensack River in Kearny, N.J., trays filled with sweet baby butterhead lettuce and sorrel that tastes of lemon and green apple are stacked high in a windowless warehouse — what is known as a vertical farm. Bowery, the largest vertical-farming company in the United States, manipulates light, humidity, temperature, and other conditions to grow produce, bankrolled by investors like Justin Timberlake, Natalie Portman, and the chefs José Andrés and Tom Colicchio.
“Once I tasted the arugula, I was sold,” said Mr. Colicchio, who for years rolled his eyes at people who claimed to grow delicious hydroponic produce. “It was so spicy and so vibrant, it just blew me away.”
The tomatoes at AppHarvest were delicious enough to attract an investment from Martha Stewart.Credit...Luke Sharrett for The New York Times
The two operations are part of a new generation of hydroponic farms that create precise growing conditions using technological advances like machine-learning algorithms, data analytics and proprietary software systems to coax customized flavors and textures from fruits and vegetables. And they can do it almost anywhere.
These farms arrive at a pivotal moment, as swaths of the country wither in the heat and drought of climate change, abetted in part by certain forms of agriculture. The demand for locally grown food has never been stronger, and the pandemic has shown many people that the food supply chain isn’t as resilient as they thought.
But not everyone is on board. These huge farms grow produce in nutrient-rich water, not the healthy soil that many people believe is at the heart of both deliciousness and nutrition. They can consume vast amounts of electricity. Their most ardent opponents say the claims being made for hydroponics are misleading and even dangerous.
“At the moment, I would say the bad guys are winning,” said Dave Chapman, a Vermont farmer and the executive director of the Real Organic Project. “Hydroponic production is not growing because it produces healthier food. It’s growing because of the money. Anyone who frames this as food for the people or the environment is just lying.”
The sprawling Kentucky farm is one of a dozen that AppHarvest hopes to open across Appalachia.Credit...Luke Sharrett for The New York Times
The technical term for hydroponic farming is controlled environmental agriculture, but people in the business refer to it as indoor farming. What used to be simply called farms are now referred to as land-based farms or open-field agriculture.
“We’ve perfected mother nature indoors through that perfect combination of science and technology married with farming,” said Daniel Malechuk, the chief executive of Kalera, a company that sells whole lettuces, with the roots intact, in plastic clamshells for about the same price as other prewashed lettuce.
In March, the company opened a 77,000-square-foot facility south of Atlanta that can produce more than 10 million heads of lettuce a year. Similar indoor farms are coming to Houston, Denver, Seattle, Honolulu, and St. Paul, Minn.
The beauty of the process, Mr. Malechuk, and other executives say, is that it isn’t limited by seasons. The cost and growing period for a crop can be predicted precisely and farms can be built wherever people need fresh produce.
“We can grow in the Antarctic,” he said. “We can be on an island. We can be on the moon or in the space station.”
That’s easy to picture: The farms are staffed by a new breed of young farmers who wear lab coats instead of overalls and prefer computers to tractors.
Today, the more than 2,300 farms growing hydroponic crops in the United States make up only a sliver of the country’s $5.2 billion fruit and vegetable market. But investors enamored of smart agriculture are betting heavily on them.
Lettuces at a Kalera vertical farm destined for nutrient-filled water begin in small plugs of growing medium.
Credit...Courtesy of Kalera
In 2020, $929 million poured into U.S. indoor-farming ventures, more than double the investments in 2019, according to PitchBook data. Grocery chains and California’s biggest berry growers are partnering with vertical farms, too.
“There is no question we are reinventing farming, but what we are doing is reinventing the fresh-food supply chain,” said Irving Fain, the founder, and chief executive of Bowery, which is based in Manhattan and has the indoor farm in New Jersey and one in Maryland, another under construction in Pennsylvania, and two research farms in New Jersey.
Mr. Fain said his farms are 100 times as productive as traditional ones and use 95 percent less water. Other companies claim they can grow as much food on a single acre as a traditional farm can grow on 390.
Vertical farms can be built next to urban centers, so lettuce, for example, doesn’t have to sit inside a truck for days as it makes its way from California to the East Coast, losing both quality and nutritional value. Vegetables can be bred for flavor rather than storage and yield.
The new systems are designed to produce a sanitary crop, grown without pesticides in hygienic buildings monitored by computers, so there is little risk of contamination from bacteria like E. coli, which forced large recalls of romaine lettuce in 2019 and 2020.
Bowery, the largest vertical-farm company in the United States, is growing hydroponic vegetables that have attracted the attention of chefs. Credit...Brian Fraser for The New York Times
Still, many farmers and scientists remain unpersuaded. Mr. Chapman, of the Real Organic Project, served on a U.S. Department of Agriculture hydroponics task force five years ago, and is leading an effort to get the agency to stop allowing hydroponic farmers to certify their produce as organic. The very definition of organic farming, he and others say, rests on building healthy soil. In May, the Center for Food Safety, an environmental advocacy group, led an appeal of a federal court ruling that upheld the agency’s policy.
Although the nutritional profile of hydroponic produce continues to improve, no one yet knows what kind of long-term health impact fruits and vegetables grown without soil will have. No matter how many nutrients indoor farmers put into the water, critics insist that indoor farms can never match the taste and nutritional value, or provide the environmental advantages, that come from the marriage of sun, a healthy soil microbiome, and plant biology found on well-run organic farms.
“What will the health outcomes be in two generations?” Mr. Chapman asked. “It’s a huge live experiment, and we are the rats.”
The divide between soil loyalists and ag-tech futurists is playing out on a much more intimate scale between two influential brothers: Dan and David Barber, who founded and own the organic farm Blue Hill and its restaurants in Greenwich Village and at Stone Barns in Pocantico Hills, N.Y.
In 2018, David Barber created an investment fund to support new food tech companies, including Bowery. But Dan Barber, a chef whose 2014 book “The Third Plate: Field Notes on the Future of Food” devotes an entire section to soil, believes that truly delicious food can come only from the earth.
“I am not buying any of it,” Dan Barber said of the hydroponic fever.
The chef Dan Barber, a soil loyalist, is skeptical of the claims made for hydroponic farms.
Credit...James Estrin/The New York Times
Trying to enhance water with nutrients to mimic what soil does is virtually impossible, he said, in part because no one really knows how the soil microbiome works.
“We know more about the stars and the sky than we do about soil,” he said. “We don’t know a lot about nutrition, actually.”
There is a cultural cost, too. For centuries, cuisines have been developed based on what the land and the plants demanded, he said. Regional Mexican diets built on corn and beans came about because farmers realized that beans fixed nitrogen in soil, and corn used it to grow strong.
“The tech-farming revolution is turning this equation on its head,” Mr. Barber said. It aids efficiency in the name of feeding more people but divorces food from nature.
His brother, David, had long been skeptical of hydroponics, too. “Most of my career was about good soil leads to good agriculture and good systems and ultimately good flavor,” David Barber said.
But the environmental advantages of next-generation hydroponic food production can’t be ignored, he said. Nor can the improvements in taste over earlier hydroponic produce. “They are combining outdoor and indoor thinking, and science and history, to create something special,” he said. “There are not going to be many winners in this space, but it is going to be a part of our food system.”
At Bowery, “there is no question we are reinventing farming, but what we are doing is reinventing the fresh-food supply chain,” said Irving Fain, its founder, and chief executive. Credit...Brian Fraser for The New York Times
Indoor farm companies view their competition as the large, industrial growers that produce fruits and vegetables bred to withstand processing and shipping — not smaller farmers using more natural growing techniques. The battle, they say, is against monoculture, not farmers who maintain healthy soil and feed their communities. Hydroponic farms can help develop new and more diverse plants, and reduce overall pesticide use.
“The only thing we are trying to do is get as good as farmers were 100 years ago,” said Mr. Malechuk, the hydroponic lettuce grower.
Indoor farming is a bet on the nation's agriculture, said Jonathan Webb, the Kentucky-born founder and chief executive of AppHarvest.
“The American farmer is already obsolete,” he said, pointing out that the United States imports four billion pounds of tomatoes from Mexico every year. “Our hope is we can get farmers back on U.S. shelves.”
Even Mr. Colicchio, who led a campaign against genetically modified food and has long been a champion of small farmers, said the two styles of farming can coexist. “We’re going to need a lot of tools in the toolbox,” he said.
Ouita Michel, a chef in Kentucky, likes AppHarvest because the company is creating jobs and growing tomatoes she is happy to use in her restaurants.
But technology, she said, will never trump the magic of soil. “Nothing will ever replace my summer Kentucky tomatoes.”
Lead photo: AppHarvest, the nation’s largest hydroponic greenhouse, opened in January in Morehead, Ky. — one in a new breed of huge indoor produce farms that use technology to fine-tune flavor, texture, and other attributes. Credit...Luke Sharrett for The New York Times
Forums And Online Toolkit || Urban Edible Spaces: Growing Food And Happiness In Sustainable Community
HKU Edible Spaces (港大可食空間) has developed an Online Toolkit about urban farming and we hope that it would help those who are interested to start an urban community garden/farm
HKU Edible Spaces (港大可食空間) has developed an Online Toolkit about urban farming and we hope that it would help those who are interested to start an urban community garden/farm. In addition, two forums discussing the positive impacts of edible spaces are now put online (English and Chinese subtitles will be available soon)
Celeste Shai, Senior Programme Officer - General Education
CEDARS, The University of Hong Kong
For any enquiry, please feel free to contact me at cymshai@hku.hk.
USA: Wisconsin’s Largest Indoor Farm Soon Will Operate In Ripon
Ernessi Farms has come a long way since its 2013 origins as a small hydroponic garden in business owner Bryan Ernst’s basement
July 7, 2021
Ernessi Farms owner Bryan Ernst looks over some of the plants growing inside the farm’s new location at 111 East Fond du Lac St. Joe Schulz photo
Ernessi Farms has come a long way since its 2013 origins as a small hydroponic garden in business owner Bryan Ernst’s basement.
The business is continuing to blossom downtown and will be moving operations to a new location in the coming weeks, which, when fully operational, will be the biggest vertical farm in the state.
Ernessi Farms is finalizing the transformation of the former Market Fresh Foods building at 111 East Fond du Lac St. into an indoor farm in the heart of Ripon’s historic downtown.
In addition, the relocation will more than quadruple Ernessi Farms’ production capacity.
The move and building renovation were made possible by a Community Development Investment (CDI) Grant from the Wisconsin Economic Development Corp.
Ernst and his staff recently began transplanting seedlings into a new robotic system and are expecting their first harvest at the new location in about five weeks.
In approximately two weeks, Ernst says employees will work primarily in the facility on East Fond du Lac Street, rather than Ernessi Farms’ location in the basement of 325 Watson St., which eventually will be closed.
“As soon as we are able to be here full time, we’ll start a slow transition where we’re breaking the racks down and sterilizing everything before we bring it over here,” Ernst said. “Once everything’s out of that building, we will be done in that location; [111 East Fond du Lac St.] will just be our only location.”
Ernessi Farms combines hydroponics with vertical organic farming. Plants grow without soil on shelves, utilizing mineral nutrient solutions and lights.
Because the farm uses a controlled environment, it can change the level of nutrients and lighting that plants receive to enhance smell, taste and other characteristics.
Plants grow inside Ernessi Farms’ new facility at 111 East Fond du Lac St. Ernessi Farms utilizes a combination of hydroponics and vertical farming. Joe Schulz photo
For example, manipulating the wavelength of light basil plants receive enhances leaf size and reduces stem size, Ernst noted.
“We’re able to control every aspect down to levels of nitrogen, air movement, wavelengths of light to give the plant the optimum growing conditions possible,” he said. “That gives us larger yields and faster turnover of crops. And we guarantee that everything is delivered within 24 hours of harvest.”
Years before operating a farm in the heart of downtown Ripon, Ernst’s passion for hydroponic and vertical farming originated during his time in the Marines.
“When you’re deployed to a lot of impoverished areas around the world, you see how hard of a time people have getting access to clean water and food,” Ernst said. “That really got me thinking, ‘There’s got to be a better way to grow food closer to urban centers, where we’re not transporting it cross country, and you can grow year round.’”
Plants grow inside Ernessi Farms’ new facility at 111 East Fond du Lac St. Ernessi Farms utilizes a combination of hydroponics and vertical farming. Joe Schulz photo
Soon after, Ernst had the idea to start experimenting with hydroponics and vertical farming
As a geologist by trade, Ernst first had the idea to grow plants in his basement utilizing hydroponics. He worked with fellow geologist Tim Alessi to start Ernessi Farms in 2013.
“We designed water treatment systems for groundwater pollution and experimented with different types of wavelengths of light and varying levels of nutrients for plants,” Ernst said of the early days.
At the time, both men quit their jobs and started the company in Green Bay because Alessi lived in Door County and Ernst in Ripon.
About six months later, Ernst bought Alessi out of the company. Ripon Main Street Inc. Executive Director Craig Tebon connected Ernst with the owners of 325 Watson St., who were interested in renting the basement.
As a result, Ernessi Farms moved operations to Ripon, where it has been for roughly the last six and a half years.
In 2019, he caught wind that local entrepreneur John Maczuzak was interested in selling 111 East Fond du Lac St.
Ernessi Farms owner Bryan Ernst looks at the mushroom incubation area, which was once the grocery’s stores former meat area. Joe Schulz photo
As Ernessi Farms worked to research it’s financing options, Tebon informed Ernst that Ernessi could be eligible for the CDI grant, which ultimately helped fund renovation costs and asbestos remediation.
In applying for the grant, Ernst said the farm received help from Tebon, Envision Greater Fond du Lac, as well as Tom and Mary Avery of Ripon College.
“Had it not been for Ripon Main Street and Craig Tebon, there’s no way we would have gotten the CDI grant,” he said.
Ernessi Farms’ facility in the basement of 325 Watson St. has about 6,000 square feet, with fewer than 3,000 square feet for the grow area.
Meanwhile, the building on East Fond du Lac is about 21,000 square feet, enabling the shelving for plants to go from four to seven shelves high.
Ernst says the move quadruples production for plants and sextuples mushroom production.
The move comes at an opportune time as vertical farming is starting to boom with big money figures like Amazon founder Jeff Bezos and Goldman Sachs investing in the industry, Ernst noted.
He says Ernessi Farms’ latest expansion won’t be the last for the business. Ernst plans to build another location in western Wisconsin in the next year or two.
“The industry is definitely here to stay; the last report that I read said that by 2050 the industry should be worth over $30 billion,” he said. “We’re seeing a lot of growth in the industry, and you always have to stay one step ahead. That’s why we’re expanding.”
Ernessi Farms supplies products locally to Webster’s Marketplace and Crossroads Market. Its products also are in 27 Festival Foods and the Wisconsin Food Hub Cooperative.
Ernessi Farms recently began transplanting seedlings into a new robotic system and are expecting its first harvest at the new location in about five weeks. Joe Schulz photo
Ernst said the business is in talks with other grocery store chains, as well as with food distributors.
To help meet an increasing demand, he says the new facility will implement robotics and automation equipment that utilize machine learning.
“The more efficient we can make the system, the more competitive we can be with traditional agriculture,” Ernst said. “That’s why we’re really investing a lot of time and resources into automation and artificial intelligence.”
Lead photo: Ernessi Farms owner Bryan Ernst looks over some of the plants growing inside the farm’s new location at 111 East Fond du Lac St. Joe Schulz photo
Tags Bryan Ernst Ernessi Farms Company Economics Commerce Agriculture Industry Finance
Written By
Joe Schulz
Joe Schulz served as the reporter of the Green Laker in 2019 and 2020, before being hired as a reporter for the Commonwealth in October 2020. He is from Oshkosh and graduated from UW-Oshkosh in December with a bachelor's degree in journalism.
BrightFarms Launches “BrightLabs” Innovation Hub
BrightFarms, the leading grower of indoor leafy greens, today announced the formation of BrightLabs, a world-class innovation and research hub launching at its Ohio growing facility
BrightFarms Accelerates Indoor Farming Innovation Tenfold with the Formation of R&D Hub Led by Bayer Veteran and Greenhouse Expert “BrightLabs” will expand the company’s focus on the development of biotechnologies that increase the profitability of its indoor farming operations and deliver breakthrough product innovations
IRVINGTON, N.Y. – BrightFarms, the leading grower of indoor leafy greens, today announced the formation of BrightLabs, a world-class innovation and research hub launching at its Ohio growing facility. Matt Lingard, PhD, a former Bayer plant scientist with over 15 years of experience working at the intersection of biotechnology and greenhouse science, will lead the BrightLabs team as Vice President of Agriculture and Science.
“The indoor farming industry is at an inflection point as local, indoor-farmed produce becomes a priority for retailers and consumers. Among competitors, we’ve developed the most profitable model for the production of indoor leafy greens, but it’s essential that we maintain our market advantage to stay ahead of the curve,” said Steve Platt, BrightFarms CEO. “We’ve built up a team of the best minds in indoor agriculture to officially launch BrightLabs, where we’ll develop the next phase of game-changing products and technology solutions for our operations.”
BrightLabs is one of the most advanced biotechnology ventures in the indoor farming industry, with a key focus on developing proprietary & patented ecosystems for plants to thrive, increasing their flavor, yields and texture in the process. The team will be comprised of the strongest minds from the food and agriculture industry, bringing together experts in technology, microbiology and plant science to deliver breakthrough innovations in the salad category and beyond.
“No other indoor farming company is studying a plant’s microbiome, the naturally occurring bacteria that help determine its health, to the same degree that we are,” said Lingard. “Instead of pouring dollars into artificial lighting research, we’re developing cutting-edge biotechnology solutions to out-maneuver our competition with the most productive indoor farms in the industry. There’s no question that high-tech greenhouses that leverage natural sunshine have emerged as the most promising new generation of agriculture technologies, and optimizing the microbiome will allow us to unlock even more of a plant’s natural potential in our indoor farms.”
This multi-million dollar R&D investment is launching as part of the company’s $100MM Series E Fundraise led by Cox Enterprises, and represents a tenfold increase in the company’s research capabilities. Ten percent of the company is now dedicated to developing complex, patented growing solutions to be applied to BrightFarms’ burgeoning network of greenhouses.
Already known for proprietary research on growing spinach in a hydroponic system, BrightLabs aims to double its production of the crop, which is the industry’s best-selling tender leaf variety. BrightFarms will also build on the success of its best-selling Sunny Crunch variety with a new, industry-first antioxidant-rich lettuce, NutriGreens, set for release this June. BrightOS, the company’s award-winning proprietary data system, will help the BrightLabs team accelerate their research with machine learning and advanced data analysis.
BrightFarms’ five greenhouses – located in Ohio, Virginia, Illinois, Pennsylvania, and North Carolina – cover 1.2 million square feet and produce 9 million pounds of fresh lettuce annually. By the end of 2021, BrightFarms leafy greens will be available at over 3,500 stores, more than any indoor farming company in the industry.
To learn more about BrightFarms and their fresh produce offerings, visit www.brightfarms.com.
About BrightFarms
BrightFarms is the leading provider of locally grown packaged salads, serving the freshest, tastiest and most responsibly grown produce to consumers nationwide. BrightFarms operates hydroponic greenhouse farms in the communities it serves, enabling it to eliminate time, distance, and costs from the food supply chain. BrightFarms’ growing methods, a model for the future of scalable, sustainable local farming, use far less energy, land, and water than long-distance, field-grown agriculture. Forbes has recognized BrightFarms as one of the “100 Most Consumer-Centric Companies” and Fast Company has recognized BrightFarms as “One of World’s 50 Most Innovative Companies” and one of the “Top 10 Most Innovative Companies in Food.” BrightFarms is funded by leading investors Cox Enterprises, Catalyst Investors, WP Global Partners and NGEN Partners. For more information, please visit www.brightfarms.com.
High Hopes For Aquaponics System Inspired By Sewage Treatment
“Our work shows that this type of cultivation is not only more sustainable, but it is also capable of providing nutrients in a form that is easily accessible to plants
by The Fish Site
30 June 2021
A novel water purification system inspired by sewage plants has been shown to be effective at optimizing fish waste for use as fertilizer for plants in aquaponics facilities.
In a recent study, researchers demonstrated that the system could improve nutrient remineralization for the plants, while removing excess nitrogen and carbon from the system, creating a healthier environment for fish.
The study, published in Frontiers in Plant Science, was undertaken by researchers from the Department of Marine Sciences at the University of Gothenburg and involved the production of rainbow trout and lettuce.
As lead author, Victor Lobanov explained to Frontiers Science News: “Fish sludge is a waste product made up of uneaten food and fish feces and is normally broken down by bacteria in the water. In addition to physically harming fish gills, excess carbon in the solids leads to excessive bacterial growth – diminishing oxygen in the water and hampering the ability of the fish to breathe. We wanted to find out whether this waste could be used to fertilize plants in aquaponics systems by removing the excessive carbon, yet preserving the minerals needed for growing crops.”
The researchers investigated a potential solution inspired by sewage and wastewater treatment plants found around the world, called enhanced biological phosphorus removal (EBPR). They adapted it so that the risk of bacteria build-up in the water was reduced, but the minerals from the fish waste were soluble in the water and could therefore be biologically available for plants to take up.
They found that their solid treatment system was as effective at delivering nutrients from the fish waste to the aquaponic system as a commercial nutrient solution. Although the fertilizer did not meet plant needs entirely, as some nutrients such as manganese were missing, the researchers hope to optimize this system in future studies.
“Hopefully we can scale the system more efficiently in the future, not just for lettuce as used in this study but as well as for other plants, with the right number of fish corresponding to the size of the system. By further optimizing the breakdown of fish solids by the solid treatment system, we can also achieve a faster treatment rate and make the whole process more efficient,” explained Lobanov.
Commercial fertilizer solutions often have very high levels of nitrogen, stimulating crops to swell and absorb large amounts of water and giving the appearance of improved growth but often decreasing the amounts of minerals in the plant. Despite the fertilizer created by the solids treatment system containing lower levels of nitrogen than commercially available chemical fertilizers, plants were not nutrient deficient. This suggests that the high nitrogen levels commonly used are in excess of what the plants need. The authors hope that this finding will stimulate further research into the connections between plant nutrients, health, and taste,
“Our work shows that this type of cultivation is not only more sustainable, but it is also capable of providing nutrients in a form that is easily accessible to plants. Farmers can take this system and optimize it for their specific crops and production volumes, potentially even supplementing with additional nutrients if required,” said Lobanov.
Lead photo: The aquaponics facility where the trial took place. © Victor Lobanov
Urban Crop Solutions SpaceBakery Project Wins First Place At Global Space Exploration Conference
The winning SpaceBakery project is an interdisciplinary cooperative research project between seven partners, of whom, Urban Crop Solutions is the lead vertical farming technology and research partner
The Global Space Exploration Conference (GLEX) took place in St. Petersburg in June 2021. The conference brought together several leaders and decision-makers in the international science and space exploration community. Urban Crop Solutions and partners were selected to present two projects of the 250 that were presented during the conference. The SpaceBakery project was awarded the first-place prize.
Organised by the International Astronautical Federation (IAF) and Roscosmos (the Russian space agency responsible for space flights and aerospace research), the conference gathered several international stakeholders from the science and space exploration community, on a year which marks the 60th anniversary of Yuri Gagarin’s spaceflight.
The winning SpaceBakery project is an interdisciplinary cooperative research project between seven partners, of whom, Urban Crop Solutions is the lead vertical farming technology and research partner. The objective of the consortium is to develop the next generation of bread products to support future space missions and aid the long-term survival of settlers on Mars, in addition to being applicable for modern agriculture. The overall goals and objectives of the consortium were presented by the Puratos Group (Belgium), the leading commercial partner of the SpaceBakery project.
Urban Crop Solutions also presented another joint project, the ‘variable climate biosphere’ that they have designed. The variable climate biosphere is a macro life support system that aims to create the best-suited environment for humans and plants to thrive together during extended periods of isolation, either on another planet – namely, the moon and Mars – or on earth in an underground shelter. The presentation showcased the 3D renderings, as well as the results that have so far been obtained.
“Our approach to partner with ambitious global industrial groups and research institutions for controlled indoor farming solutions is finally paying off. We feel that we are at the cutting-edge with our technology, products and services in the fast-emerging urban farming industry – whether it is in space, in cities, on the surface or beneath it.” – Maarten Vandecruys, CTO and co-founder of Urban Crop Solutions
ABOUT UCS
Urban Crop Solutions is a Belgium-based pioneer in the fast-emerging technology of indoor vertical farming. It has developed over the past six years, 220+ plant growth recipes in its research centre in Waregem, Belgium. To date, UCS has delivered over 25 projects in multiple global locations. Their farms are being operated both for commercial and research purposes. Uses range from the production of leafy greens, microgreens, and herbs for food retail, service and industrial use, and scientific research across multiple institutions.
Website: www.urbancropsolutions.com
Facebook: www.facebook.com/urbancropsolutions
Twitter: www.twitter.com/U_C_Solutions
LinkedIn: www.linkedin.com/company/urbancropsolutions
For more information on this press release, on Urban Crop Solutions and their products and services, or the SpaceBakery project, you may contact Maarten Vandecruys, Serge Ameye or Lucie Beckers.
Maarten Vandecruys
Founder & CTO, UCS
maarten.vandecruys@urbancropsolutions.com
Serge Ameye,
Space, Tunnels & Special Projects, UCS
serge.ameye@marsbakingsociety.space
Lucie Beckers,
Research Manager Agronomy, Puratos Group
LBeckers@puratos.com
Is Vertical Farming Cost Effective?
The technological change caused a shift in farming from conventional to container farms. Currently, farming is turning to vertical farms
The technological change caused a shift in farming from conventional to container farms. Currently, farming is turning to vertical farms.
The more exciting part is that this time round, key economy participants such as Amazon, Google’s Eric Schmidt are pumping money into the trending farming method.
Since it is a new technology, many investors are still unsure about its profitability. They have several questions on vertical farming’s viability. That is to enable them to have a better understanding of the technology.
One of the most typical questions is whether vertical farming is cost-effective. The most straightforward answer is yes. Vertical farming is cost-effective if done on a large scale.
Here, you will find out differences among the core farming technologies in terms of
initial investment,
operating costs,
appreciation, and
profit margins.
You will find it easier to decide whether to continue your current farming methods or switch to vertical farming after reading this article. Find out more below.
What Is Vertical Farming?
Understanding vertical farming requires finding out milestones of farming.
The traditional form of farming is open field farming. Here, the crops grow under direct sunlight, temperature, and humidity. Also, it does not entail artificial fertilizers.
The second milestone of farming is conventional farming, mainly called greenhouse farming. Here, you design appropriate growth conditions for the crops. For example, you introduce artificial seeds, fertilizers and shield the plants from harsh weather conditions such as an extreme cold.
The increasing scarcity of farming lands and demand for more food has caused many farmers to implement container farming. In container farming, you grow crops in soils in vessels instead of letting them grow in the open fields.
The growing technology has resulted in vertical farming. Vertical farming entails packing and growing crops indoors with the help of vertical farming lighting.
Here, you incorporate energy efficiency and customizability of LED lights— to set color, temperature, and humidity conditions for plants to thrive.
Factors that Lead to Changing Farming Criteria
The core reason for farming evolution is market demand and supply. For example, most consumers need tasty and healthy food. The plants’ growth conditions should not hurt consumer health in the long run.
They should be assured of the availability of food whenever and wherever they need it. Most importantly, the supplier should provide competitive prices.
It is on the price that many farmers question the viability of vertical framing, bearing in mind the massive cost of material needed to operate vertical farms.
Here is a summary of recent findings on vertical farming costs.
Cost Determination
Research tells that vertical farming costs three times to implement than conventional farming. The prices inflate when you cater to initial investment and operating costs.
On the other hand, you can produce twice on a vertical farm than on a convention farm. For example, investing in 70000 feet vertical farm is likely to output 1 million kilograms of vegetables annually.
Depending on market location and pricing, you are likely to propel your profit margin when you sell than in the case of conventional farming.
The more exciting part is vertical farming value appreciates twice a year compared to greenhouse farming.
So, Is Vertical Farming Effective in the Long Run?
From the above figures, you can realize that vertical farming is more profitable on a large-scale application. The appreciating value proves that the market demands its products.
The best part is that it is becoming cheaper due to smart lighting technology that becomes less expensive. What do the above findings imply?
Key Takeaways
The best time to invest in vertical farming is now. Chief economic players are channeling a wealth of money into it.
For example, leading investors such as SoftBank Vision Bank, AeroFarms, and BrightFarms recently pumped more than $200 million into vertical farming.
Large-scale investment, crops’ quick turn, and increasing food demand for the growing population make vertical farming cost-effective.
Lead photo: Image by BrightAgrotech from Pixabay
August 20th - 2nd Annual OptimIA Research Collaborative Update
Plan to join our annual stakeholder meeting online to learn our collaborative research update
Registration is now open!
2021 OptimIA Research Collaborative Update
August 20th, 2021
10 AM - 3 PM Eastern
Plan to join our annual
stakeholder meeting online to
learn our collaborative research update!
Meeting Information & Agenda
OptimIA (Optimizing Indoor Agriculture) is a USDA-funded Specialty Crop Research Initiative project to support indoor farming industry through critical research and extension activities.
Register
How Much Are You Willing To Pay For The Perfect Strawberry?
One of Japan's most coveted strawberry varietals is now being grown in a high-tech farm in Newark. And you can get a taste for a cool $50
One of Japan's most coveted strawberry varietals is now being grown in a high-tech farm in Newark. And you can get a taste for a cool $50.
BY LEENA KIM
JULY 2, 2021
MICHAEL STILLWELL
Of the reasons for which Newark is famous—namely its reputation as a former murder capital of America—there is a high likelihood that it will soon be known for something a little more savory: as the epicenter of the agricultural revolution, 2.0.
Over the past few years, New Jersey's gritty port city has become ground zero for a burgeoning vertical farm movement. First, what is a vertical farm? It's basically an indoor farm that uses aeroponics (or hydroponics) systems, artificial intelligence, robots, LED lights, and other forms of technology to grow produce in a controlled environment sans sun, soil, and pesticides. Newark is currently home to the world's largest vertical farm, the 70,000-square-foot AeroFarms, which has 8 others in this city alone (plus facilities in Virginia and Abu Dhabi) and is slated to IPO this month at a $1.2 billion valuation.
Nearly all of the vertical farms that have sprung up around the country specialize in leafy greens (kale, watercress, spinach, arugula, etc.). Why? It's the easiest crop to grow—and the cheapest ticket into the business. But Hiroki Koga, co-founder and CEO of Oishii, a 4-year-old vertical farm near Newark, had far grander ambitions. He didn't want to open yet another outfit for lettuce and spinach that, to be honest, can't taste so radically different from lettuce and spinach shipped in from California. He was going to go straight for Goliath on the first try: the strawberry.
Most vertical farms specialize in leafy greens because they are the easiest to grow. Not Oishii, which went straight for the holy grail in vertical farming: strawberries. OISHII
"They are one of the most sophisticated crops with an extremely complicated plant physiology, and one of hardest to grow in a vertical farm," says Koga, whose former life in Tokyo as a consultant to large corporations making headway in this agricultural category provided an early education in the business. (Not surprisingly, Japan has been way ahead of the curve on this trend, mastering the tech long before the term even entered the modern lexicon—today, many vertical farms use machines made by Japanese corporations like Sony and Panasonic.) "So while other companies started with something easy, we decided to invest all of the money we raised into something that was harder and might take longer to succeed, but that once we cracked the code to it, it would let us unlock other crops, like tomatoes, melons, and grapes, much more easily."
Hiroki Koga, co-founder and CEO of Oishii.
OISHII
Another key reason that deters vertical farms from graduating beyond leafy produce: the bees. Or rather, the lack of them. Greens don't need pollination but fruits do. The problem is, though, bees are sensitive. Put them in an artificial environment and they'll soon realize it's a setup and stop functioning properly. Koga has cracked this, too. "We were the first in the world to figure out how to trick the bees into believing they are in Mother Nature," he says.
Mind you, Koga certainly hasn't gone through this much trouble for just any kind of strawberries. His are a replica of Japan's Omakase berries, a unique, highly prized, and rare varietal grown in greenhouses in the foothills of the Japanese Alps only during wintertime (from January to March). They are characterized by an intensely fragrant, almost floral, bouquet, and a flavor profile that is juicy and creamy, soft and buttery, and, above all, super sweet. In other words, like nothing that is found in America. Oishii's Omakase berries tick all of these boxes, plus one more: they are perfect every time. Because even Japan's most meticulous strawberry growers can't control sun and temperature. "In our vertical farm, we can control for temperature, humidity, even levels of carbon dioxide, to optimize for this specific variety to thrive every single day," Koga says.
The strawberries grown in Oishii’s vertical farm in New Jersey. ZI JIAN/OISHII
So, about that price tag. Oishii's Omakase berries—at first only supplied to Michelin-starred restaurants, they are now available for delivery in Manhattan, Brooklyn, and Jersey City, and at select purveyors like Eli's on the Upper East Side and Carissa's in East Hampton—are $50 for a box of 11 medium-sized strawberries (or 8 large). While these are exponentially more expensive than your average Driscoll's, even traditionally grown Omakases command a similar cost back in Japan, where they are considered treasured gifts for special occasions and celebrations.
But they are hardly Japan's most expensive strawberry. That distinction is held by the Bijin-hime varietal, grown exclusively by a veteran farmer named Nichio Okuda, who spent 15 years perfecting the berry and produces only 500 a year. A single Bijin-hime strawberry retails for 50,000 yen, or $448. (It ought to be noted that the Japanese are unrivaled in the realm of status produce: in 2019, for example, two Hokkaido melons sold at auction for $5 million yen, aka $45,000.)
Of course there are far more reasonably-priced Japanese varietals as well—the country has 250 different strawberry cultivars, which account for more than half of the global supply—and Koga plans to introduce them to the U.S. market, and eventually, the rest of the world. Thanks to a recent $50 million infusion of investor capital, Oishii has begun its expansion, first with the construction of a second vertical farm the size of a football field. "We're not just a small strawberry farm in New York selling fancy strawberries. We're offering a new way to grow, experience, and access food," he says. "We hope to bring a really big paradigm shift to the agriculture industry. Vertical farming is the way forward."
LEENA KIM Associate EditorLeena Kim is an associate editor at Town & Country, where she writes about travel, weddings, arts, and culture.
BrightFarms Launches Multimillion-Dollar R&D Hub in Greater Cincinnati
BrightFarms, a New York-based grower of indoor leafy greens since 2013, is forming BrightLabs, a new innovation and research hub, at its Wilmington greenhouse. BrightLabs, overall, will represent a tenfold increase in the company’s research capabilities, while increasing profitability and delivering new product innovations.
By Liz Engel - Staff reporter
June 24, 2021
An indoor farming company is investing millions in Ohio with the debut of a new research and development hub.
BrightFarms, a New York-based grower of indoor leafy greens since 2013, is forming BrightLabs, a new innovation and research hub, at its Wilmington greenhouse. BrightLabs, overall, will represent a tenfold increase in the company’s research capabilities, while increasing profitability and delivering new product innovations.
Steve Platt is the CEO of BrightFarms. (Jenn Erickson)
CEO Steve Platt declined to disclose the exact investment but told me it’s in the multimillions. The project is being launched as part of the company’s $100 million Series E funding round in October led by media conglomerate Cox Enterprises.
“BrightFarms as a company has been growing very consistently, and the indoor farming industry is at an inflection point,” Platt said. “We’ve perfected how we grow – among competitors, we’ve developed the most profitable model for the production of indoor leafy greens – but now’s the time to invest behind R&D to secure an advantage for the future. It’s essential to stay ahead of the curve.”
Like others in the indoor farming space, BrightFarms lauds the fact that its lettuce is healthier, tastier, looks better, is more nutritious, and, particularly for customers in Ohio, fresher than field-grown produce hauled in from states like California and Arizona. Today the company’s five greenhouses in Ohio, Virginia, Illinois, Pennsylvania produce 9 million pounds of produce each year.
But unlike several outfits, particularly vertical farms that use purple-hued LED lighting, BrightFarms leverages natural sunshine. Its souped up, high-tech greenhouses grow spinach, romaine, arugula and more using a hydroponic system, or water instead of soil.
Wilmington, which celebrated its first harvest in 2018, isn’t the company’s largest greenhouse in terms of size or production, but Platt said it made a good host for the innovation hub because of its centralized location. It’s close to customers and easily accessible from its other farms. He also credited the workforce and level of academic talent available from universities nearby.
BrightFarms celebrated its first harvest in Wilmington in 2018. BrightLabs is investing millions to build out an innovation and research hub at the site. (Brian Mollenkopf)
Phase one for BrightLabs includes a new, approximately 1,350 square foot lab that has been built at the Wilmington greenhouse site. BrightFarms will also dedicate space on the farm for the BrightLabs team to work.
Platt said BrightLabs will focus on three key areas:
Biotech. BrightFarms wants to study the environments in which plants grow to increase yield, flavor, and texture.
Agtech. BrightOS, the company’s proprietary AI software system, acts as the company’s central nervous system, Platt said, collecting millions of data points from its fives farms to streamline operations. How can the company improve that technology?
Product innovation. BrightFarms recently launched NutriGreens, a new lettuce packed with antioxidants – double the amount, Platt said, found in a serving of blueberries. BrightFarms wants more advances like that.
BrightLabs itself will be led by Matt Lingard, a former Bayer plant scientist and Ph.D. with over 15 years of experience, who joined BrightFarms in May as its VP of agriculture and science. Platt said the BrightLabs team will include four employees to start.
“We’re the leading grower of indoor spinach – in the U.S. we grow 90% of the indoor spinach that’s sold – but we want to double our production on that. How do we come out with new types of spinach that can grow even better in a hydroponic system?” he said.
“We’re taking on a massive industry and a complicated, broken system – where greens are grown all in one location, shipped thousands of miles across the country, generally with pesticide reside, there’s a food-borne illness, and the product isn’t that good,” Platt added. “We have a simpler system and a better product, but we need to deliver that at a price point and at a volume that competes with what’s coming out of California. If we’re trying to unseat this big gorilla, we can’t be this niche that’s only affordable to people who drive Teslas.”
Overall, there’s billions being invested in the industry. New York City-based Bowery Farming, in late May, announced a $300 million funding round with a $2.3 billion valuation. Kentucky-based AppHarvest merged with a special purpose acquisition company in February, an IPO approach that’s gaining ground in 2021, and is now worth $1.5 billion.
BrightFarms, with its Series E, has raised more than $200 million in total. In addition to launching BrightLabs, it plans to use the funds to expand its network of regional indoor farms – new farms are currently under development in Massachusetts and Texas – and grow its retail footprint. Locally, BrightFarms is available at Sam’s Club, Walmart and Pipkin Produce as well as Food Lion and Kroger in other markets.
The company said by the end of 2021 its leafy greens will be available at over 3,500 stores.
“It’s amazing. Even when I joined the company two years ago, we were convincing people this was the future. Now customers are coming to us saying, ‘We want to replace field grown with indoor-grown,’” he said. “We think the future is here.”
Lead photo: BrightFarms grows leafy greens like spinach, romaine, and arugula in high-tech, computer-controlled greenhouses.
VIDEO: Is Hydroponic Produce Organic?
The organic farming standards were created by the USDA in the 1990s when there was increased public awareness of the health and safety of our food. However, at that time, hydroponic farming wasn't as widespread as it is today
Aaron Fields, Eden Green Technology's Head of Horticulture
Photo from Eden Green Technology
The organic farming standards were created by the USDA in the 1990s when there was increased public awareness of the health and safety of our food. However, at that time, hydroponic farming wasn't as widespread as it is today. That leads us to question: is hydroponic produce organic?
Check out this great video from Eden Green Technology, a hydroponic farm based in Texas. Aaron Fields, their Head of Horticulture, explains what organic really means and how hydroponic growing can be sometimes cleaner and safer. (Did you know? I hate to burst the organic bubble, but produce that is grown organically can still have some level of pesticides.)
New Innovations – Lettuce Wall at Newtown College
The eye-catching addition of the lettuce tower in the Newtown College foyer is part of the Crop Cycle project, a Farm Urban system to cultivate lettuce and other greens using a soilless system of vertical towers. This project is funded by the Welsh Government to introduce indoor growing CEA of food crops into communities.
NPTC Group of Colleges
23 June 2021
Newtown College (Part of @NPTCGroup of Colleges) is going all green-fingered as it introduces a new Horticulture course. This exciting new addition has brought with it a new collaboration with Cultivate, and a new initiative with the introduction of a lettuce wall to the Newtown College Foyer.
The new Level 1 & 2 Horticulture courses will be available from September. The course will utilize the fantastic facilities of Cultivate to do practical work, including accessing polytunnels, allotments, and projects within their grounds include growing via CEA (Controlled Environment Agriculture).
The eye-catching addition of the lettuce tower in the Newtown College foyer is part of the Crop Cycle project, a Farm Urban system to cultivate lettuce and other greens using a soilless system of vertical towers. This project is funded by the Welsh Government to introduce indoor growing CEA of food crops into communities. Whilst we live in a rural environment, new ways of nurturing plants, using what is known as hydroponics, is revolutionary and is growing in popularity.
Cultivate are piloting a number of different controlled environment vertical farming systems to grow hyper-local nutritious crops to offer within the community. Local, sustainably grown food is absolutely key in tackling important issues surrounding our food system, climate change and biodiversity. This will allow Cultivate food business to increase the amount of local foods produced and in turn, consumed, ensuring that growing models become more sustainable and that our population can eat more locally grown, sustainable, healthier produce.
Richard Edwards Cultivate Crop Cycles project manager said:
“They taste great, are highly nutritious and are super fresh, visit our Deli in Newtown to try them for yourself!”
NPTC Group of Colleges Head of Agriculture, Catering, Hospitality and Horticulture, Sue Lloyd-Jones said:
“We are very excited about introducing the Horticulture Courses to Newtown College. These courses are already popular in our Brecon Beacons, Neath College and Black Mountains Colleges. With this fantastic collaboration with Cultivate, it gives us extensive facilities and involvement with initiatives such as the CEA. The lettuce wall provides a point of education for students to learn about potential food sustainability and the subtle shift toward urban or hyper-local cultivation. It demonstrates how to grow plants without soil but in nutrient-rich water with oxygen and light. It also serves as a local edible wall producing greens for our catering department’.
AeroFarms Commences Construction On AgX Research Center
AgX will bring innovative research and development to the UAE and the Middle East to advance sustainable controlled environment agriculture (CEA) and vertical farming and help address broader global agriculture supply chain issues
AeroFarms Wholly-Owned Subsidiary AeroFarms AgX LTD Has Started
Construction Focused On Some Recent Developments
03 Jul 2021
AeroFarms, a certified B Corporation, and specialist in indoor vertical farming announced that AeroFarms AgX LTD, its wholly-owned subsidiary in the UAE, has started construction in Abu Dhabi on the company’s Research Center focused on the latest developments for indoor vertical farming, innovation, and AgTech.
AgX will bring innovative research and development to the UAE and the Middle East to advance sustainable controlled environment agriculture (CEA) and vertical farming and help address broader global agriculture supply chain issues.
Last year, ADIO announced that it is providing $150m in incentives to bring global AgTech pioneers to Abu Dhabi, including its partnership with AeroFarms to build a vertical farming facility dedicated to developing next-generation agriculture in arid and desert climates.
The transformational R&D conducted at AeroFarms AgX is expected to enable new business lines, technologies, and growth of the AeroFarms platform while serving as a hub for regional expansion. AeroFarms AgX is expected to be completed and operational in the first quarter of 2022.
HE Dr Tariq Bin Hendi, Director General of ADIO, said: “This important milestone for AeroFarms AgX is another step in the realization of Abu Dhabi’s mission to ‘turn the desert green’. In line with this goal, ADIO is supporting innovative technology that has the potential to impact farming practices across the globe and improve the food production value chain worldwide. AeroFarms AgX will add to the growing capabilities of Abu Dhabi’s agriculture ecosystem while benefiting from the emirate’s plentiful land, natural heat, competitive energy prices, access to research universities, and skilled talent.”
AeroFarms AgX will be the largest indoor vertical farm of its kind for research and development in the world, leading the way in breakthrough innovation to solve some of the world’s most pressing agriculture challenges.
AeroFarms AgX will employ a projected 60 highly skilled engineers, horticulturists, and scientists and will have high-tech laboratories conducting organoleptic research and precision phenotyping, phytochemical analysis, advanced speed breeding, as well as next-generation machine vision, machine learning, robotics, and automation. AeroFarms AgX will also play a key role in Abu Dhabi’s AgTech ecosystem by working with local universities on research projects to tackle problems of agriculture within desert and arid climates.
David Rosenberg, Co-Founder, and CEO of AeroFarms commented: “This is an important development for AeroFarms as we expand globally and leverage our R&D and growing expertise. AeroFarms has been the global leader for controlled environment agriculture since 2004, and we will utilize this cutting-edge R&D Center to conduct the latest research in plant science, vertical farming, and automation, accelerating innovation cycles and commercializing products.
Our vision has always been to leverage our expertise in plant biology and build on our successful history of collaborating with government, universities, industry and major international companies. We are pleased to take this step forward and proud to be a catalyst for helping to establish the Emirate of Abu Dhabi as a global hub for AgTech innovation.”
Lead photo: AeroFarms to build world's largest indoor vertical farm in Abu Dhabi. AeroFarms
Vertical Farms Hold Promise For Local, Sustainable Produce
Vertical farming uses controlled environmental agriculture techniques, like hydroponics or aquaponics, to grow crops in vertically stacked rows with 90% less water than traditional soil-based farming
Technique Uses Small Footprint,
Less Water To Provide Year-Round Crops
Beth Edwards
June 30, 2021
A former grocery store or an empty strip mall might not be the first images that come to mind when thinking of places to grow food. But around Indiana, many of these spaces are being turned into vertical farms to help alleviate farmland shortages and greenhouse gas emissions linked to traditional farming practices.
Vertical farming uses controlled environmental agriculture techniques, like hydroponics or aquaponics, to grow crops in vertically stacked rows with 90% less water than traditional soil-based farming. It also uses 75-90% less land than traditional farms and is able to be conducted in industrial areas. It allows the grower to have total control over the grow cycle of the crop.
Courtesy of Green Sense Farms
The technique allows for year-round income for farmers and fresh, healthy, local produce for consumers regardless of climate.
With the world’s population expected to grow to 9.7 billion people by 2050, agricultural production will need to increase by 70%. Vertical farming offers an alternative to scarce farmland and to traditional farming techniques, which cause 22% of the world's greenhouse gas emissions.
A controlled environment
Krishna Nemali, assistant professor of controlled agriculture at Purdue University, said controlled environmental agriculture is driven by both plant science and engineering, with the purpose of growing crops in managed environments year-round.
In Indiana, farmers can do little outdoors between fall and spring because of low light levels and temperatures, he said.
“But with controlled environmental agriculture, you can produce year-round because you artificially manage the ideal environmental conditions for plants,” he said.
The farmer controls the lighting, temperature, nutrients, water and sometimes even carbon dioxide, but needs to understand plant science to know what is best for the plant being grown, as well as the engineering behind how best to deliver those resources without waste.
Professor Krishna Nemali at a workshop held by Purdue Extension to show participants how researchers use hydroponics to grow crops. Photo by Tom Campbell
“Our research shows that we use about one-third of the water used to grow the same crop in the same acreage outdoors. That’s because we recycle the water; we don’t just add water on top of the plants. In controlled environmental agriculture, the water is recirculated and is delivered to plants in a closed-loop system, where there is no runoff or leaching,” said Nemali.
While such systems do require a large amount of energy use, Nemali said research has enabled farmers to optimize energy use and lower consumption.
But there are limits to what can be grown using these methods.
“Because your investment is high, your return should also be high in order to make profits. There is a technology piece and usually, there is high-intensity cultivation that happens; therefore, growers want to grow high-value crops like vegetables and those that have direct impact to consumers,” said Nemali.
The time for harvesting the vegetables is more condensed as well. For instance, it will take about a month to grow leafy greens, around six to eight weeks for tomatoes and eight weeks for strawberries, instead of an entire season like in traditional farming.
The industry is growing rapidly and creating new jobs in many urban areas because it doesn’t require soil to produce fresh produce.
“A grower can purchase an old warehouse, let’s say 10,000 square feet or a quarter of an acre. But then they can grow 10 or 11 levels vertically, and in doing so, that’s a quarter of an acre times 10. So they are actually producing crops that would normally require two-and-a-half acres of land on this quarter of an acre simply by going vertically,” said Nemali.
Nemali said there is a huge amount of interest in vertical farming in Indiana. Indiana currently imports around 95% of its vegetables from outside the state. That means there is potential for large profits in vertical growing.
For example, USDA estimates that each person in the US consumes around 11-13 pounds of lettuce each year, which would roughly equal a salad each week. Nemali estimates Hoosiers consume about $60 million in lettuce each year, but Indiana farmers grow only a fraction of that amount.
Courtesy of Green Sense Farms
“We probably won’t produce $1 million worth of lettuce this year. So there’s a huge demand for local production,” Nemali said. “I’m just giving you one crop; imagine all those vegetables we are importing from outside. If it’s grown locally, that money stays with our growers and our farmers, and that will improve their livelihoods. That is why there is a huge interest in this industry.”
A pioneer in northwest Indiana
One company that has been a leader in the vertical farming industry for a while is Green Sense Farms in Portage.
Before he founded Green Sense, Robert Colangelo spent many years working on a wide variety of environmental issues, from research at Argonne National Laboratories to cleaning and repurposing brownfields. He said he was looking for something new when a friend approached him with an idea to start a vertical farm.
“I became very passionate about it, and I thought this would be a next great step in my environmental career, getting involved in agriculture,” he said.
He said he wished he had gotten involved in agriculture earlier in his career.
“We are not here to put field farms or greenhouses out of business,” he said. “I think as the population grows, we really have to look at what crops grow best outdoors and what crops grow best indoors and just rethink agriculture based on water and soil conservation. When we approach it that way, everyone feels comfortable with vertical farming.”
Robert Colangelo, head farmer of Green Sense Farms. Courtesy of Green Sense Farms
Green Sense began as an owner-operated farm. Colangelo grew leafy greens and herbs, which he mainly sold in the Chicago and Northwest Indiana markets. However, he now helps other companies or growers develop and build their farms.
Colangelo said while the business side of Green Sense was harder to learn than the growing itself. Knowing where to locate the farm and find the right talent, having the right operating procedures in place, and finding the right customer base took longer to learn, but now Green Sense helps others with exactly those issues.
It also designs farms specifically for the crop that the company or individual wants to grow, customizing growing techniques and economic data.
Vertical farming extends to other industries
Green Sense is currently working on several projects, including a casino in Las Vegas that would showcase a vertical farm in its restaurant so the diners could see the food they are eating. It has partnered with a company in Spain to offer combination greenhouses and vertical farms, and it also is considering a project that would turn old grain silos into a combination vertical farm, restaurant, and market.
“We’ve learned a lot about what doesn’t work, and we keep striving each day to figure out what works better,” said Colangelo.
Vertical farming isn’t limited to growing food. Green Sense has worked on projects for many different industries, including pharmaceutical companies, tree growing and many others that may seem surprising.
Colangelo believes the future of vertical farming will be highly automated.
“They will still require smart people to run them, but (with) a lot of the menial, repetitive tasks being done by machines. I think the future for farming is bright, and this is a great opportunity for young, smart people to get involved with,” he said.
Piper Halpin agrees. She worked with Colangelo for four years at Green Sense, starting out harvesting and seeding crops before becoming an operations manager. She now is involved in vertical farming in Boston.
“It’s exciting to be a part of and addicting because it is so technology forward, innovative and new,” she said. “Also, you don’t have to live in a rural area in order to be successful.”
Courtesy of Green Sense Farms
Colangelo and Halpin agree the technology aspect is attractive to younger people and helps to engage their interest in the field.
“It’s a great way to get young people reinvolved in agriculture,” Halpin said. “It’s been a cool bridge between old agriculture and new agriculture. I think it’s going to jumpstart a whole new interest level in ag that was kind of dying off before.”
Nemali said younger people are also interested because vertical farming is environmentally sustainable.
“They also see the importance of this industry in terms of feeding millions with fresh food, making sure it’s safe and done in a responsible way,” he said.
Nemali would like to see an increase in the variety of crops that can be grown in controlled environmental agriculture, technological improvements that lower energy consumption, and more university programs to train workers and researchers for these farms.
“This area is growing, and I want people to see, admire and provide support for it,” Nemali said.
Support from scientists, policymakers, marketers, and the government will enable a new workforce to develop the industry in the next 10 to 15 years
Polygreens Podcast Episode: 32 - Mark Thomas - Garfield Produce
Mark's background in operations and finance, mixed with his entrepreneurial spirit, makes him a dynamic leader. He always takes the time to get to know both his employees and customers, adding a personal touch to the company
Mark's background in operations and finance, mixed with his entrepreneurial spirit, makes him a dynamic leader. He always takes the time to get to know both his employees and customers, adding a personal touch to the company.
Latest Episode
Why Does Energy Efficiency Matter When Selecting LED Grow Lights?
Learn the 3 things to consider when choosing energy-efficient lighting in your greenhouse or vertical farm.
Before we get started, let’s set some ground rules for this article.
1. I want to believe that everyone wants to do what’s right for the planet as long as they think their business can afford it, so we will not focus on energy efficiency and its impact on sustainability.
2. In this article I will not post the name of suppliers or the price of the lights. The price of the light will definitely impact people’s decisions and will vary widely based on the volume of lights being purchased and the supplier providing it.
3. This article is not about light quality or light spectrum. To look for information on spectrum please read this article: Why I Still Believe in Red/Blue LED Grow Lights
4. This article is written with commercial greenhouse produce growers in mind, but we do include a model which shows high output led grow lights running for long hours per day which could imply a greenhouse cannabis crop.
5. We are fully aware that when you change the amount of energy going into the light as well as the type of electric light (HPS vs LED) one is using, it will have an impact on the climate in the growing/production area. Factors like heat and relative humidity would need to be taken into consideration if one was taking a holistic approach to energy savings on the farm.
6. All lights have different output (measured in PPF.) In this article we are going to make the assumption that a grower is using the same amount of fixtures per acre regardless of output. For simplicity we are also going to assume that the grower is running the lights for the same amount of time. We are fully aware that this will have an impact on the potential yield of the crop.
7. All greenhouses can require a different amount of lights per acre to achieve the target light intensities. I am using an average of the amount of lights per acre. Height of the greenhouse, width of the bays, placement of walkways, crop layout, crop density, as well as many other variables will impact the exact number of lights per acre.
__________
There is a growing amount of discussion around the environmental sustainability of a greenhouse or a vertical farm. Much of this discussion is being driven by two or three big energy hogs inside these production facilities. This includes the grow lights and climate management equipment like heaters and cooling units.
We all know that LED grow lights are more efficient than the older HPS lights that growers have used for decades, but do we know just exactly how to measure that? And do we understand how that will have a direct impact on not only energy savings but the operational cost at the farm? For those growing in a greenhouse, understanding these numbers during dark winter months can have a huge impact on electricity bills.
3 FOCUS POINTS
1. Start by understanding the amount of light you need.
Urban Ag News recommends going to websites like Suntracker or the ESRI DLI maps site. These websites allow anyone to determine the historical DLI monthly averages for their individual locations. For this example I am going to use the area where my grandparents farm is located in southwestern Michigan. As one can see this is an area of the United States that has very dark winters.
2. Work with a trusted advisor or extension specialist to determine the amount of hours your crop needs to grow consistently year round. Remember not all crops have the same light requirements and some crops have very specific photoperiods which can determine the amount of hours one can light their crops. Use all of this information to see when you will need supplemental light and how much light you will need to supplement with.
For this example I am going to use 1 acre of greenhouse tomatoes in a glass greenhouse located in southwestern Michigan.
3. Now let’s calculate how much it’s going to cost you to run the grow lights for the estimated hours you and your advisor determined were needed per year to get the desired yields.
a) To provide a baseline, we started with traditional 1000w HPS lights which are highlighted in yellow.
b) Then we chose six different LED grow light fixtures. Because the light spectrum has an impact on how efficiently the lights run, we chose three broad spectrum fixtures and three that are red and blue only.
c) Since HPS is the baseline, the final column labeled “savings” shows how much the total savings per year one would achieve when replacing traditional HPS with the latest LED grow light technology.
d) We made a few important assumptions in this example. First, the cost per kwh is around the USA national average of $0.09/kwh. Second, the same amount of grow lights would be used even though there would be some relative differences in umols/m2/s measurements for two of the samples. We decided not to change them because that would have an impact on uniformity (the even spread of the light over one’s entire crop) and associated capital cost not addressed in this article.
IMPORTANT NOTES!
It’s important to remember the 7 assumptions made at the beginning of this article and that lights are not equal. This chart only compares ppf (output) and w (watts). We elected to account for the difference in output by changing the amount of hours we estimated you would need to run the lights. Another way to look at this would be to remember the Golden Rule of Light in which 1% increase in light is equal to 1% increase in yield.
Running these simple calculations will show you why you need to look at energy efficient lighting and in general the importance of researching energy efficient equipment in general. What these calculations do not show is the quality of some fixtures over others. Buyers must always be aware of the value of warranties, ease of returns, durability and quality of product plus accuracy of your vendor to create detailed information on the best way to use and install fixtures. We understand that this topic is intimidating for most, but this is a major purchase for your farm. Make sure to take the time to learn the math and do your homework before purchasing.
Diving into these calculations will also highlight how much energy will be required to grow a wide variety of crops consistently with uniformed yields year round in climates with low light. Hopefully in articles to come we can discuss what this means for our environment and how we might develop additional ways to lower that ecological footprint.
For help in calculating the energy efficiency of grow lights you are considering, please email us and we will connect you with professionals capable of helping you make an informed decision.
Chris Higgins is the founder of Urban Ag News, as well as General Manager and co-Owner of Hort Americas, LLC a wholesale supply company focused on all aspects of the horticultural industries. With over 20 years of commercial horticulture industry experience, Chris is dedicated to the horticulture and niche agriculture industries and is inspired by the current opportunities for continued innovation in the field of controlled environment agriculture. Message him here.
Tagged GreenhouseGreenhouse TechnologyIndoor Ag TechnologyTechnologyVertical Farming
USA - GEORGIA - Giant Photovoltaic Canopy Tops Net-Positive Kendeda Building In Atlanta
US firms Miller Hull Partnership and Lord Aeck Sargent have designed a highly sustainable building at Georgia Tech university that generates more electricity and recycles more water than it uses.
US firms Miller Hull Partnership and Lord Aeck Sargent have designed a highly sustainable building at Georgia Tech university that generates more electricity and recycles more water than it uses.
The project – officially called The Kendeda Building for Innovative Sustainable Design – is located at the Georgia Institute of Technology, a public research university in central Atlanta.
The Kendeda Building for Innovative Sustainable Design is in Georgia
The educational building was designed by Seattle's Miller Hull Partnership in collaboration with local firm Lord Aeck Sargent, which was purchased by tech startup Katerra in 2018.
The project was backed by the Kendeda Fund, a private family foundation that supports a range of social and environmental initiatives. Skanska served as the general contractor.
The project is a highly sustainable building
The facility recently earned certification from the Seattle-based International Living Future Institute under its Living Building Challenge – one of the most rigorous green-building certification programmes in the world. The facility is considered to be a "regenerative building."
"Regenerative buildings create more resources than they use, including energy and water," the team said.
Classrooms and a design studio are included in the design
"The project's goal is to support the educational mission of Georgia Tech while transforming the architecture, engineering and construction industry in the Southeast US by advancing regenerative building and innovation."
The facility – which totals 47,000 square feet (4,366 square metres) – holds a range of spaces for students and faculty.
These include a design studio, two large classrooms, several laboratories, a seminar room, an auditorium and office space. There also is a rooftop garden with an apiary and pollinator garden.
The building's rooftop garden
Certain areas of the building are open to the public for special events.
While designing the facility, the team took inspiration from vernacular architecture – in particular, large porches that are commonly found on Southern homes.
"The project reimagines this regionally ubiquitous architectural device for the civic scale of the campus," said Miller Hull.
Rectangular in plan, the building is topped with a giant white canopy supported by steel columns. On the west elevation, the roof extends 40 feet (12 metres) to form a large, shaded area below with steps and seating.
A white canopy tops the building
In addition to providing shade, the canopy generates electricity. Its 900-plus solar panels form a 330-kilowatt array that produces enough power to exceed the building's energy needs.
For the exterior cladding, the team incorporated a mix of accoya wood, metal, glass and recycled masonry. The foundation walls are made of concrete.
Materials such as metal form the exterior cladding
Mass timber was used for the structural system due to it having a smaller embodied carbon footprint compared to concrete and steel, the team said.
In large-span areas of the building, the team used glue-laminated trusses with steel bottom chords.
Details on the building's exterior
"This hybrid approach reduces the quantity of wood required while making routing of building services more efficient," the team said.
For the structural decking, nail-laminated timber panels were made off-site and craned into place. A local nonprofit organisation, Lifecycle Building Center, sourced the lumber from discarded movie sets in Georgia.
Large windows flood spaces with natural light
Structural elements, along with mechanical systems, were left exposed so they could serve as a teaching tool.
Salvaged and recycled materials are found throughout the facility. For instance, stairs in the building's atrium are made of lumber off-cuts, and countertops and benches are made of storm-felled trees.
Mechanical systems were left exposed
Water recycling is also part of the building's sustainable design. Rainwater is captured, treated and used in sinks, showers and drinking fountains. In turn, that greywater is channelled to a constructed wetland, where it is treated and used to support vegetation.
The facility is also fitted with composting toilets, which nearly eliminate the use of potable water. The human waste is turned into fertilizer that is used off-site.
The rooftop has a pollinator garden
The building recently earned its Living Building Challenge (LBC) certification following a year-long assessment, in which it needed to prove it is net-positive for energy and water usage.
"It generates more energy from onsite renewable sources than it uses," the team said. "The building also collects and treats more rainwater onsite than it uses for all purposes, including for drinking."
The LBC programme evaluates buildings in seven categories – place, water, energy, health and happiness, materials, equity and beauty.
The Kendeda Building is the 28th building in the world to achieve LBC certification and the first in Georgia. The state's warm and humid climate poses a particular challenge when it comes to energy efficiency, the team said.
A large classroom
A communal workspace
"In spite of this, over the performance period the building generated 225 per cent of the energy needed to power all of its electrical systems from solar panels on its roof," the team said.
"It also collected, treated, and infiltrated 15 times the amount of water needed for building functions."
Students gather under the canopy outside
Other American projects that are designed to meet the LBC standards include the wood-clad Frick Environmental Center in Pittsburgh, designed by Bohlin Cywinski Jackson. It achieved certification in 2018.
Photography is by Jonathan Hillyer and Gregg Willett.
Project credits:
Design architect: The Miller Hull Partnership, LLP
Collaborating and prime architect: Lord Aeck Sargent, a Katerra Company
Contractor: Skanska USA
Landscape architect: Andropogon
Civil engineer: Long Engineering
Mechanical, electrical and plumbing engineer: PAE and Newcomb & Boyd
Structural engineer: Uzun & Case
Greywater systems: Biohabitatssolar panels
INDIA: Gourmet Garden Raises Over USD 3 Million Funding
Gourmet Garden, the first full-range zero-contamination F&V brand in the country, has announced its latest round of funding of Rs 25 Crores led by Beyond Next Ventures, M Venture Partners, and existing investors Incubate India & Whiteboard Capital among others
Gourmet Garden aims to expand their zero-contamination farming operations, broaden their portfolio with additional fresh categories, boost customer experience by deploying India’s first end-to-end B2C tech-enabled cold-chain, and improve ease of ordering with a mobile app and refreshed website.
01 July, 2021
Arjun Balaji Co-founder and Director Gourmet Garden and Vishal Narayanaswamy Co-founder Gourmet Garden.png
Gourmet Garden, the first full-range zero-contamination F&V brand in the country, has announced its latest round of funding of Rs 25 Crores led by Beyond Next Ventures, M Venture Partners, and existing investors Incubate India & Whiteboard Capital among others.
Established in early 2019, Gourmet Garden is known for offering the widest range of zero-contamination vegetables and fruits and other curated essential offerings. They stand out on quality and safety owing to their patented naturoponic farming operations, certified organic farming extensions, and a lean 1-day & 2-touch supply chain. Already a leading brand in Bengaluru and Chennai, the start-up is founded by Arjun Balaji, erstwhile a Partner at McKinsey and Company, and Vishal Narayanaswamy who launched among the first hydroponic farms in India.
With this funding, Gourmet Garden aims to expand their zero-contamination farming operations, broaden their portfolio with additional fresh categories, boost customer experience by deploying India’s first end-to-end B2C tech-enabled cold-chain, and improve ease of ordering with a mobile app and refreshed website.
Arjun Balaji, Co-founder, and Director, Gourmet Garden said, "We are fulfilling the consumer need-gap for a brand offering wholesome, distinctly fresh and safe food essentials for everyday consumption. Most other offerings are aggregating commodity supply, however, our focus has been to operate end-to-end and focus disproportionately on source quality and safety, which is at the core of overall customer experience and differentiation.”
"We wish to be the favoured brand destination for all things wholesome, fresh and curated. Our patented Naturoponic farming yields the highest quality vegetables and is our customers’ most loved offering. Essentials grown in certified organic farms along with an assortment of imported fruits make up our extended safe F&V range. In addition, we also offer a selection of authentic spices and dry fruits, and will soon be launching wholesome breads and organic sauces & dips for a wider range in fresh” said Vishal Narayanaswamy, Co-founder, Gourmet Garden.
The company now spans 60,000 customers in Bengaluru and Chennai alone. Over 75% orders, every month come from repeat customers, a testimony to their loyalty-building quality.
Tsuyoshi Ito, CEO, and Akito Arima, Agri/FoodTech Lead Capitalist, Beyond Next Ventures said, “We are delighted to see that their sustainable cultivation techniques and quality of succulent vegetables are comparable to those in Japan. The focus on affordable, high-quality and safe fruits and vegetables is rising in urban India. Gourmet Garden possesses a full basket of high-quality produce, delivered in shortest time keeping their loyal customers happy.”
“Simply put, we partner with great founder entrepreneurs,” commented Mayank Parekh, Founder - M Venture Partners, a Singapore-based venture capitalist. “The distinctive talent combination of Arjun and Vishal is the perfect formula to scale this incredible offering for consumers”
The existing investors are very excited by the progress thus far and have extended their commitments further. Nao Murakami, Founder - Incubate Fund India, said, “Since our initial investment in the start-up a few months ago, the founders and the team have shown a very strong execution capability. Even under COVID-19 pandemic and the series of lockdowns, the team managed to operate with full intensity despite a leaner covid-impacted team, showing agility to solve challenges. This is clearly backed by their passion and conviction”
"We continue to be very excited by the organic growth and customer love that has become the cornerstone of Gourmet Garden's promise. The offering has scaled well and is all set to become the largest clean and contamination-free fresh essentials D2C brand in India and we are looking forward to the journey ahead with Arjun, Vishal, and our co-investors" said Anshu Prasher, General Partner at Whiteboard Capital.
Tags assigned to this article:
Gourmet Garden fundraising fund investment investment investors Covid 19 zero-contamination vegetables Organic Farming
Q&A, Expert Source: Viraj Puri, Co-Founder And CEO of Gotham Greens, An Indoor Farming Company With Hydroponic Greenhouses Located In Cities Across America
Gotham Greens is focused on building a more sustainable food system and we are drawn to adaptive reuse projects in cities across America
A Q&A with Viraj Puri, Co-Founder, and CEO of Gotham Greens
For those that do not know Gotham Greens, please tell us a little bit about the company and when the company was formed?
Viraj Puri, Co-Founder, and CEO of Gotham Greens
Viraj: We are on a mission to transform how and where fresh food is grown. Gotham Greens is a pioneer in indoor greenhouse agriculture and a leading producer of fresh and sustainably- grown salad greens, herbs, dressings, dips, and cooking sauces. By using hydroponic systems in 100% renewable energy-powered greenhouses, our farms use 95% less water and 97% less land than conventional farming. Since our launch in 2011, Gotham Greens has grown from a single urban rooftop greenhouse in Brooklyn, N.Y., to a multi-state greenhouse operator and one of the largest hydroponic leafy green producers in North America.
How many farms do you operate? And where are those farms located? What do you grow?
Viraj: Gotham Greens currently operates 500,000 square feet of greenhouses across five U.S. states (and growing), including locations in New York City, Chicago, Providence, R.I., Baltimore, and Denver. Through our national network of high-tech, hydroponic greenhouses, Gotham Greens produces fresh, long-lasting, and tasty leafy greens and herbs along with a line of plant-based salad dressings, dips, and sauces, available in more than 2,000 retailers in 40 states, restaurants in select cities, and foodservice customers all year-round.
Why did you choose a greenhouse over a vertical farm?
Viraj: Gotham Greens is focused on building a more sustainable food system and we are drawn to adaptive reuse projects in cities across America. Gotham Greens has a track record of established, robust and proven operations and technology compared to vertical farming, which is still a relatively young industry. Our hydroponic greenhouse technology uses less energy than vertical farming. While vertical farming is an innovative extension of modern greenhouse farming with overlapping principles that has garnered quite a bit of interest, there are still questions surrounding the technology and financial viability of this farming method. In theory, fully indoor environments that rely on artificial light and HVAC systems can offer very high yields and levels of climate control, pest management, and food safety, but these benefits can be outweighed by significantly higher capital and operating costs than our hydroponic greenhouses.
What are your predictions for the future of controlled environment agriculture?
Viraj: For many parts of the country, it’s difficult to get fresh, locally-grown produce all year round. Since more than 95% of lettuce grown in the United States comes from California and Arizona, by the time it reaches other markets, it loses its quality, taste, and nutritional value – and has a much shorter shelf life. Gotham Greens, and controlled environment agriculture at large, provide an opportunity to transform our food system for the better by growing more fresh foods closer to where consumers live — all while using fewer natural resources.
Consumers, retailers and foodservice operators are increasingly recognizing the reliability, consistency and high quality of greenhouse-grown produce that’s grown in close proximity to large portions of the population and we only expect this model to continue to grow as consumers pay greater attention to the food they eat and its impact on the planet. While indoor farming may not represent the future of all fresh produce production, for certain types of crops, it will become much more prevalent in the coming years.
You can hear Viraj Puri speak at the virtual Indoor AgTech Innovation Summit June 24-25, 2021.
Register Now!
Learn more: @gothamgreens or gothamgreens.com