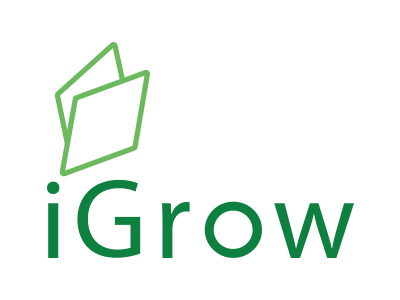
Welcome to iGrow News, Your Source for the World of Indoor Vertical Farming
China Focus: Factory Farms The future For Chinese Scientists
China Focus: Factory Farms The future For Chinese Scientists
Source: Xinhua| 2017-04-30 09:06:29|Editor: Yamei
XIAMEN, Fujian Province, April 30 (Xinhua) -- In a factory in eastern China, farming is becoming like scientific endeavor, with leafy vegetables embedded neatly on stacked layers, and workers in laboratory suits tending the plants in cleanrooms.
The factory, with an area of 10,000 square meters, is in Quanzhou, Fujian Province. Built in June 2016, the land is designed to be a "plant factory," where all environmental factors, including light, humidity, temperature and gases, can be controlled to produce quality vegetables.
The method is pursued by Sananbio, a joint venture between the Institute of Botany under the Chinese Academy of Sciences (IBCAS) and Sanan Group, a Chinese optoelectronics giant. The company is attempting to produce more crops in less space while minimizing environmental damage.
Sananbio said it would invest 7 billion yuan (about 1.02 billion U.S. dollars) to bring the new breed of agriculture to reality.
NEW FARMING
Plant factories, also known as a vertical farms, are part of a new global industry.
China now has about 80 plant factories, and Sananbio has touted its Quanzhou facility as the world's largest plant factory.
In the factory, leafy greens grow in six stacked layers with two lines of blue and red LED lights hung above each layer. The plants are grown using hydroponics, a method that uses mineral nutrient solutions in a water solvent instead of soil.
"Unlike traditional farming, we can control the duration of lighting and the component of mineral solutions to bring a higher yield," said Pei Kequan, a researcher with IBCAS and director of R&D in Sanabio. "The new method yields ten-times more crops per square meter than traditional farming."
From seedling to harvesting, vegetables in the farm usually take 35 days, about 10 days shorter than greenhouse plants.
To achieve a higher yield, scientists have developed an algorithm which automates the color and duration of light best for plant growth, as well as different mineral solutions suitable for different growth stages.
The plant factory produces 1.5 tonnes of vegetables every day, most of which are sold to supermarkets and restaurants in Quanzhou and nearby cities.
The world's population will bloat to 9.7 billion by 2050, when 70 percent of people will reside in urban areas, according to the World Health Organization.
Pei said he believes the plant factory can be part of a solution for potential future food crises.
In the factory, he has even brought vertical farming into a deserted shipping container.
"Even if we had to move underground someday, the plant factory could help ensure a steady supply of vegetables," he said.
HEALTHIER FUTURE
Before entering the factory, Sananbio staff have to go through strict cleanroom procedures: putting on face masks, gloves, boots, and overalls, taking air showers, and putting personal belongings through an ultraviolet sterilizer.
The company aims to prevent any external hazards that could threaten the plants, which receive no fertilizers or pesticides.
By adjusting the mineral solution, scientists are able to produce vegetables rich or low in certain nutrients.
The factory has already been churning out low-potassium lettuces, which are good for people with kidney problems.
Adding to the 20 types of leafy greens already grown in the factory, the scientists are experimenting on growing herbs used in traditional Chinese medicine and other healthcare products.
Zheng Yanhai, a researcher at Sananbio, studies anoectohilus formosanus, a rare herb in eastern China with many health benefits.
"In the plant factory, we can produce the plants with almost the same nutrients as wild anoectohilus," Zheng said. "We tested different light, humidity, temperature, gases and mineral solutions to form a perfect recipe for the plant."
The factory will start with rare herbs first and then focus on other health care products, Zheng said.
GROWING PAINS
Currently, most of the products in the plant factory are short-stemmed leafy greens.
"Work is in progress to bring more varieties to the factory," said Li Dongfang, an IBCAS researcher and Sananbio employee.
Some are concerned about the energy consumed with LED lights and air-conditioning.
"Currently, it takes about 10 kwh of electricity to produce one kilogram of vegetables," said Pei, who added that the number is expected to drop in three to five years, with higher LED luminous efficiency.
In a Yonghui superstore in neighboring Xiamen city, the vegetables from the plant factory have a specially designated area, and are sold at about a 30 percent premium, slightly higher than organic and locally produced food.
"Lettuce from the plant factory is a bit expensive, at least for now, there are many other healthy options," said Wang Yuefeng, a consumer browsing through the products, which are next to the counter for locally produced food.
Sananbio said it plans to expand the factory further to drive down the cost in the next six months. "The price will not be a problem in the future, with people's improving living standards," Li said
San'an Opto headquarters in Xiamen, China. (Photo courtesy of San'an Opto)
GrowNYC Throwing Open House For New Community Center Project Farmhouse
GrowNYC has an official home — and you’re invited inside.
GrowNYC Throwing Open House For New Community Center Project Farmhouse
By Meredith Deliso meredith.deliso@amny.com April 23, 2017
The organization, which runs greenmarkets and gardens throughout the city and hosts programs on environmental issues like recycling, will celebrate the opening of its new sustainability and education center with an open house on April 29.
Project Farmhouse opened its doors late last year, hosting private events and school programming. At the open house, visitors can get a sense of what kinds of public programming will be on offer down the line, with tours of the space and cooking demos by Peter Hoffman, Gaggenau’s Eric Morales and a chef from Brooklyn’s Olmsted, as well as composting demos, nutrition workshops, recycling games, take-home DIY planters and more.
“We really built this space to be a community center for people to come together around sustainability and healthy eating and all of the programs that GrowNYC is already involved in, in the community,” said Laura McDonald, events director at Project Farmhouse.
Much of GrowNYC’s existing programming focuses on teacher training and student education. The organization anticipates hosting 500 teachers and 2,000 children each academic year at Project Farmhouse. Hands-on programs for students include GrowNYC’s Healthy Food Healthy Bodies series, which features field trips to greenmarkets and discussions with chefs on nutrition and health, as well as programs on renewable energy and farming.
The state-of-the-art space is a lesson in sustainability itself, from a farm-inspired entry archway made using repurposed wood beams to sun tunnels to let in natural light and a kinetic hydroponic wall. A centerpiece is its induction kitchen, donated by kitchen design company Boffi Soho, for cooking demos.
McDonald looks to ramp up public events in the summer, with potential programming like lectures, movie nights and demos from cookbook authors. Having the Union Square Greenmarket just steps from Project Farmhouse is also an advantage.
“There are lots of tie-ins with the market,” McDonald said. “We’re trying to get the farmers in here, doing some demos or talking about what their lives are like. It’s awesome that it’s just a couple blocks away.”
IF YOU GO
Project Farmhouse will host an open house April 29 from 11 a.m.-4 p.m. | 76 E. 13th St., projectfarmhouse.org | FREE
Autogrow Announces Its Support Of A Global Indoor Agriculture Hub In Kennett Township, Pennsylvania
Autogrow Announces Its Support Of A Global Indoor Agriculture Hub In Kennett Township, Pennsylvania
AUCKLAND, NZ – Today Autogrow, a major supplier of automated control systems for indoor agriculture facilities, announced its support for a major public-private initiative to develop a global indoor agriculture production, research, training, and service hub on the US East Coast, to be located in Kennett Township, Pennsylvania.
According to Darryn Keiller, CEO of Autogrow, “Kennett is already the center of the US mushroom industry, producing about 1.5M lbs. of fresh product every day, all grown indoors and delivered within 48 hours of picking to markets across North America via Kennett’s extensive ‘cold-chain’ infrastructure of refrigerated packing, storage, and shipping facilities. Over the coming years, that unique infrastructure is likely to attract many new facilities growing other indoor crops, such as leafy greens. This alone makes Kennett a huge potential market for our control systems.”
“But that’s just the beginning of our interest in Kennett’s very innovative initiative,” continued Keiller. “Kennett is also working with a several of the region’s world-class agriculture, engineering and business schools to develop a joint indoor agriculture research, training, and innovation incubator center in Kennett, the first of its kind in a major indoor ag production area. This center will be a major asset to our rapidly evolving industry, and Autogrow very much wants to be a part of its development.”
Michael Guttman, who directs the initiative for Kennett Township, explained that “it is very important to our initiative to attract innovative ag tech companies like Autogrow to help us grow and diversify our regional indoor ag industry. But Autogrow offers a lot more than just its state-of-the-art control systems. Autogrow also has a very forward-thinking strategy that can help us adapt our extensive infrastructure to incorporate emerging trends like the Internet of Things (IOT) and ‘big data,’ which will have a huge impact on how indoor agriculture is done in the future. Working together with Autogrow and our other partners, we hope to develop a blueprint not only for Kennett, but also for a network of similar indoor agriculture hubs around the world.”
About Autogrow
Autogrow (www.autogrow.com) is a leading supplier of climate and automation control systems for indoor agriculture, building systems for everything from single compartment environments through to large-scale, fully-automated greenhouses. In the last few years, Autogrow, based in Auckland, NZ, has been at the forefront of new emerging developments from the US, Canada, UK and Asia in vertical growing, building conversion and shipping container based systems.
About Kennett Township, Pennsylvania
Kennett Township (www.kennett.pa.us) is a municipality in SE Pennsylvania, and historically the center of the 100+ year old US mushroom industry, with grows 500M pounds of fresh produce year-round exclusively in climate-controlled indoor facilities. Kennett Township is currently involved in a major initiative to diversify its economy by leveraging its already-extensive indoor agriculture infrastructure to create a world-class research, training and production hub for the whole indoor agriculture industry.
Metropolis Farms: Vertical Farming Designed to Grow Out, Not Up
Jack Griffin of Metropolis Farms. Credit: Tricia Burrough
Metropolis Farms: Vertical Farming Designed to Grow Out, Not Up
The Philadelphia-based startup is looking to change the thinking around the green-collar economy, building a sustainable, modular design around optimized indoor farming technologies.
By Matt Skoufalos | April 27, 2017
Photos by Tricia Burrough
Griffin holds a tray of microgreens grown at Metropolis Farms. Credit: Tricia Burrough.
While the first harvests of spring herald the upcoming farmers market season in South Jersey, across the river in South Philadelphia, Jack Griffin has been hauling in crops all winter long.
On the second floor of a warehouse in the 2400 block of Water Street, he’s just a few blocks away from the other shipping and receiving terminals that supply many area supermarket chains with fresh produce.
But in a fraction of the physical space—and at a fraction of the costs of growing and shipping those fruits and vegetables there from across the corners of the country—Griffin’s Metropolis Farms is quietly growing their organic, non-GMO, vegan-certified competition.
More to the point, Griffin is growing a business that he believes can close gaps in food insecurity, social justice, and sustainability.
“The transactional nature of food means that we have a lever to change the world,” he said. “Everybody eats. The conversations around food are so ingrained in our society [that] in between those transactions is an opportunity.”
Seedlings at the Metropolis Farms headquarters in Philadelphia. Credit: Tricia Burrough
Indoor vertical farming has been touted as “the next big thing” in the green-collar economy for about the past half-decade.
In September 2016, AeroFarms of Newark drew national headlines for the massive scale of its 69,000-square-foot, $30-million operation.
The company converted a shuttered steel factory into a indoor greenhouse the company says is the largest indoor farm in the world, capable of producing 2 million pounds of crops per year, according to CNN.
But Griffin said the thinking that produced it is grandiose and wrongheaded: in his opinion, the key to vertical farming is actually horizontal growth.
“If I’m ever the world’s largest vertical farm any way other than by accident, shoot me,” he said. “We don’t need the world’s largest farm, we need a dense network of independent, smart farms.
“Everybody’s got the same idea; ‘I’m going to build 60 farms,’” Griffin said. “Who’s going to buy 60 farms at $26 million a farm? We can make a profitable farm with our stuff for $600,000.”
Griffin claims the technology behind Metropolis Farms is capable of growing 2 million pounds of produce in just 14,000 square-feet of real estate, and by using one-tenth the energy of a system like AeroFarm’s. Powered by a rooftop solar array on Swanson Street in Philadelphia—where Griffin says he also can recapture 2 million gallons of water annually—Metropolis Farms is made to be energy-independent and disaster-resistant.
It also doesn’t need prime real estate to operate, or even much of it at all. By licensing the technology behind his work, which includes the growing equipment and seedling optimization schedule, Griffin is optimistic that he’ll be able to create a distributed indoor farming culture, not just a farming network. His licensing agreements will include labor clauses about paid time off, living wages, and possibly an degree correspondence program to give inmates the chance of a stable career upon release.
“I think that social responsibility should be part of this,” Griffin said. “Equal pay for equal work, and no discrimination. Our goal is to get as many people as possible farming.”
Lee Weingrad, VP of Metropolis Farms. Credit: Tricia Burrough
“It’s the evolution of technology,” said Metropolis Farms vice-president Lee Weingrad, a U.S. Air Force veteran who co-developed the technology at the heart of the system with Griffin.
“Everything’s on a schedule,” Weingrad said. “We made it simple on purpose. Anyone with a high-school diploma can work here.”
The Metropolis Farms infrastructure is modular and able to be built from equipment available at a hardware store, which Griffin said cuts out the construction costs of retaining a design firm to build custom architecture.
It’s able to be dismantled for cleaning with quick-connect PVC systems, and features optimization algorithms that are designed to help crops flourish without the use of genetic modification.
The first-generation lights were based on a design of Nikola Tesla’s, but the ballast atop them retained too much heat and showed too much infrared light, Griffin said. Their replacements are high-intensity discharge (HID) lamps with a proprietary core, shielded with lightweight, reflective, and refractive German aluminum. They’re suspended from a motorized track, which carries the light across the plants on a timed sequence to simulate cloud cover.
At $25,000 per unit, each tower can produce 20,000 pounds of produce annually, Griffin said. He expects farms will consist of 15- to 50-tower implementations; each can yield 19 harvests per year versus two-and-a-half on conventional real estate.
Insectivorous plants keep the produce free of pests without chemical sprays. Credit: Tricia Burrough
Nearby carnivorous plants secrete nectar and resin, attracting and eliminating pests without chemical sprays.
The entire system can pivot from fruits and vegetables to things like pharmaceutical herbs, stevia leaf, or biodiesel jet fuel, all grown at a consistent grade and domestically.
“A lot of what we’ve done is fourth-grade math and freshman geometry,” Griffin said.
“We’re selling ubiquity: a simple system with architecture.”
Griffin isn’t lacking for interest in his model; as of a few months ago, he was sitting on more than $20 million in letters of intent from cities across the United States and Canada to bring his model there. He wants to start in the Philadelphia metro area first.
The challenge when you’re growing 2 million pounds of produce per year is generating enough institutional purchases—from hospitals, universities, prisons, and other governmental agencies—to generate local “velocity of capital” that creates sustainable economic change.
“How many schools do you have?” Griffin said. “They’ll buy locally if you can produce at scale. The key is to drive cities to understand that where they spend their money matters. If we spend that money on local food, we create velocity of capital; we create local jobs.
Sprouts are grown floating in an aqueous solution. Credit: Tricia Burrough
“When those people go and buy things because they’re making $18 an hour, they’re getting benefits, they’re having a life,” he said.
“If we can show them better food, and they buy it because it’s in their self-interest to buy the food, that’s enough.”
Griffin said his goal “is to have every city in the United States steal this idea” so that Metropolis Farms can manufacture the necessary equipment at its core in Philadelphia and ship it out to other markets, creating yet another level of employment. But he believes the model should take root locally first because it has the potential to be a key driver of regentrification and redevelopment with a critical difference: pushing out the poverty instead of the impoverished.
“In Fishtown, there’s 15,700 people,” Griffin said. “What if I could produce enough lettuce for the daily lettuce requirement of everyone in that community, enough tomatoes, and peppers, and so on? And surround that community with wings of prosperity?
“It’s a synergistic model instead of an exploitive one. It is the ultimate demand-based business.”
Indoor Farming Operations Still Unsure If They Are "Organic"
04/27/2017
Indoor Farming Operations Still Unsure If They Are "Organic"
Source: Specialty Food News
Categories: Industry Operations; Suppliers
Indoor farming operations will need to wait until the fall to find out whether the government considers their operations "organic," after the National Organic Standards Board delayed its ruling on the subject. In the meantime, operations can call themselves organic, but many in the industry are troubled by the uncertainty. Current guidelines are very specific on the type of soil that can be used by organic operations, but there is not a set rule on whether plants must be grown in soil.
“It's more about organic, certified farmers wanting to maintain their market share,” JP Martin of GROWx, an aeroponic farming system told Forbes. “The fertilizers are identical... so the argument that they use different nutrients breaks down." Full Story
How NASA LED Lighting Research Became A Hit Product: With Hedi Baxter Lauffer, Founder of LED Habitats
How NASA LED Lighting Research Became A Hit Product: With Hedi Baxter Lauffer, Founder of LED Habitats
For this interview, we sat down with Hedi Baxter Lauffer, Founder of LED Habitats, a company that has developed an indoor growing product was inspired by "fast" plant research developed by NASA and the University of Wisconsin-Madison. We discussed basic LED lighting tips, the future of LED lighting, and some of its history as well!
Introduction
UV: What's the background story and how LED Habitats got started?
Hedi: My husband and I have been working together in science education for a very longtime, decades now, primarily in that, our focus has been on getting plants into classrooms and informal science situations to try and help get more growing minds actively engaged with plants.
We are getting more and more removed from opportunities to grow plants and interact and understand the importance of plants. I taught high school for a while before I started really getting national and global outreach efforts and it always amazed me when we would do a unit on food, how many students had absolutely no clue where their food had come from.
So in our work, with getting plants into classrooms, both my husband and I were at University of Wisconsin Madison, working with "fast" plants.
They're really cool little plant that was (being studied) at UW Madison, as a research plant. It was just bred through traditional plant breeding to try and look for disease resistance in cabbage. Wisconsin used to be a really big cabbage growing state.
(Usually) cabbage has a two year life cycle, which makes it really hard to support farmers with disease resistance because it takes so long to look for it.
This little plant was bred because it cropped up when the scientist Paul Williams was looking for disease resistance. It went straight to flower instead of producing any fruit.
He bred for this super fast life cycle. It goes from seed to flower in just fourteen days, it goes through it's whole life cycle and produces viable seed in a month to forty-five days. So, it's really cool. And, it's used in classrooms a lot.
The thing is, because it's growing so fast, it needs twenty-four hour and very high quality light. So, we've all been developing light systems for indoor growing in classrooms and things like that, for a very long time. CFL's (compact fluorescent lighting) came out first, it was fluorescent, it was the compact fluorescent light bulb.
Then finally, LED's were kind of always in the background because actually that little fast plant was the first plant to successfully produce seed in micro-gravity, up in space.
UV: With NASA?
Hedi: Yeah with NASA. So, it gave us opportunities, especially my husband at the time, was working directly with UW Madison, with NASA and others, gave exposure to the idea of LED's.
Even before they were a viable option, because there weren't blue LED's until 2009, so you couldn't really use those successfully in growing plants, in horticulture.
UV: Which color were the earlier ones?
Hedi: They have advanced now, I think the very earliest ones were red. Well, that's areally good question. What the very first colors were and just know the blue was really hard to get. It won the Nobel prize, actually, for Physics in 2009.
When science figured out how to produce a blue LED. That opened them up for horticultural use.
So, anyway, we were trying to look at ways to get LED's into classroom study. and be able to switch to LED's, because we had a lot of concerns about a combination of things with non LED lighting options.
The heat that's put off by other light sources, the fact that there is mercury gas in fluorescent bulbs, It seemed like LED's was the way to to go.
But, every LED light that we tried out that was commercially available and, kind of, in our price range and size and scope for use in classrooms were not very high quality.
Because our plants are so sensitive to needing high intensity light, we could really be damaged easily when the intensity of the light declined.
UV: What do you specifically mean by quality in LEDs? Is it the intensity or are there other factors like spectrum?
Hedi: It's both. (intensity) and the spectrum that they're emitting, but I think for us, what we we're detecting most was the decline in intensity. In pretty short periods of time, like eight months to a year, we would notice changes.
Later, we learned that that was because when there's quality factors both in the LED chip itself and in the design of the match between the drivers that are pushing electricity, electrical energy into be converted into light energy. If the drivers are over pushing the LED chip, they burn them out.
(As a result), you do have a decline in quality over time. In a much faster time than what LED's are technically specified to last for.
My brother had been off the grid in New Mexico, I knew he'd done some stuff with LED's, I reached out to him and said, "Do you know anybody who's working with LED's, we're trying to find some people besides the scientists here that we've been working with at the University to help us come up with a low cost, relatively low cost solution for classroom?"
So, my brother introduced us to this German cabinet maker who is now our colleague and partner, he's been working with LED's for a long time in kitchen cabinetwork; and, he's a German craftsman, a cabinet maker, so, it was like this perfect triad of my husband and I with our plant backgrounds, I have a very strong agricultural background, I used to run a wholesale organic truck farm, many years ago.
All of these things converged and came up with this really clever design for being able to raise and lower the LEDs and how to house the LEDs, in a hood that is completely silent and self-cooling, and it worked beautifully. We tried it out, did prototypes, and got plants growing wonderfully and then we had them sitting around in our house.
As we were trying them out and everyone who walked in said where do I get one of those?
At that point we realized maybe this isn't just for school. Maybe this is actually a broader impact thing. And, that's how we came up with the company.
UV: The research and the inspiration is with that one cabbage plant that you mentioned, is that exclusively what you try to grow in the system now? Have you brought in the reach, to other types of micro greens or whatnot?
Hedi: Yes, we have definitely broadened, even in our prototype work we broadened. The advantage that we had in doing our initial work with the brassica, is the scientific (category) of the plant.
It's like a lab rat, in that it, its a good indicator for flowering plants, in general. And, because it does its whole life cycle in such a short time. We can group past prototypes to see how they effected the grooming, vegetative growth, seed production, stuff like that in really rapid cycles.
Once we've got to where we were really pleased with what we we're seeing, then we could start going out to longer growing crops.
UV: Right. So, have you guys seen that with a really high quality LED light, you can quicken the flowering and general growth of any plant? Like, regardless, of it's life cycle. You mentioned that the quality of the LED light helped you speed up even the fast plant. What's the multiplier in terms of productivity and speed to the flowering or any point in growth, when you have really high quality lighting?
Hedi: There are (multiple) key elements in the environment that affect the rate of growth, temperature often is a big one. Nutrient content, volume of the soil, so there's other factors besides the light.
But, the quality of the light and the availability of the light, in terms of intensity, and spectrum. It's so cool to work with, because you're plant responds by really producing strong, vigorous plants.
So, while it might be, I could keep my plants in very cool growing conditions and it wouldn't be that the LEDs would speed them up, necessarily, if it affected the cold.
But, what I would see, because of the light, is these really stocky, sturdy plants with large mass. They're really thriving. You'll notice the difference if you side by side grow six tomatoes under the fluorescent and LEDs that are full spectrum because the fluorescent tend towards the blue, the plants elongate and much more left out and reaching for light.
And they are so vulnerable to that. When you put them under LEDs, it's so satisfying to see, wonderfully, stocky little seedlings.
It's really cool as a plant lover, it's really fun to grow under really high quality lighting.
UV: Can you talk about, I don't know how much interaction you have with people who are just getting started; maybe there are people who approach you tobuy but what do you see is the biggest mistakes that people make?
Or, biggest misconception about LED lighting?
Hedi: That is really something that we encounter a lot, actually. There's people who are trying to grow micro greens, there's people who are trying to grow herbs or medicines, or all kinds of things. And, I think there are three things that, kind of, continually repeat themselves.One is, the confusion about how to compare different lights, because in the past, when we use incandescent bulbs, we talk in sense of watts. And, then in terms of lumens.
But, actually watts don't matter with LEDs. That's not a good measure, because they beauty of the LEDs is that they hardly require any input of electricity, which is what watts are made of.
To have a really high output,so, you know, you can't compare an incandescent or a fluorescent wattage input with the output of the LED. It's just not a good measure. And lumens are a measure for human. So, shifting to where we're talking about the photosynthetic area of radiation that is emitted or hard value on things like that, that's a big challenge. And, the LED world does not adjust that well, we don't have a good standard for how we talk about light, lighting or label them. Although, that's coming, hopefully.
I want to make sure that I also touched on, there is a real big misconception among those who have been looking at LEDs, that they don't give off heat.
They actually do. A lot of the quality of the LED chip and it's mount, and the quality of the LED lamp itself, is how that heat is dealt with.
That's the critical thing with the LED.
So, there needs to be a really effective design to the way the LEDlamp is engineered so that the heat dissipates really quickly. And, that prolongs the life of the LED and the lives that it has good intensity.
So, I guess that is the third thing I would say is a big misconception. That an LED is an LED is an LED and that is not true.
There is high quality LEDs, that are really made by reputable manufacturers and there's cheap, crappy ones that come, trying to flood the market with something that looks much more affordable.
UV: If you wanted to set up a dead simple urban farming system, how would you do it?
Hedi: Well,I think the dead simple part is the hanging of the LEDs and determining what the footprint is going to be that you want to light up.
So, LEDs, the chips themselves, tend to be uni-directional, that's part of what makes them really efficient. They're not shooting light off out the back and sides, they're shooting it in the direction that you point them.
You can put lenses on them that broaden their footprint, their lighting, but whenever you do that,you're also then distributing their intensity over a greater area (and as a result, reducing intensity).
I think the key is, deciding how much space are you trying to light well. Then you want to be the one that rigs how the lights go up and down or do you want to get a system that already does that for you.
Because the beauty in the LED is that they're built well so they dissipate their heat well. You can have your plants, the canopy top over tops of your seedlings or whatever just a few centimeters from the LEDs themselves. That's where you're going to have the high intensity. That's the way that you want to give your plants maximum lighting. So, you need to either raise the plants up and down or lower the lights.
UV: Keeping the focus on the hanging mechanism, that's the key take away.
Hedi: That and then the quality of the LEDs that you're getting. So, if you're just getting a cheap one strip of LEDs, be aware that you can't put that down the middle of a big, wide tray and expect that it's going to light the outside edges.
UV: How do you make sure that you're on the right track (with LED quality)? Is there some kind of measure? On YouTube, you see people measure the intensity. What tools or what do you suggest for doing the quality assurance? Or, I guess coverage assurance?
Hedi: You can get a little PAR meter, its called. That would be your most accurate measure of how many photons are actually striking the leaf surface. And, those are fairly affordable, although it's more of an investment than I would call atypical do-it-yourself thing.
So, I guess I would advise that you either do some research and make sure that the company you're buying your LEDs from LED lamp is what they actually address how much output there is, in terms of the spectrum that the lights are giving.
The PAR value, and when they tell you what the output is, that they tell you how to measure that, how far away from the light that was. If it's a good, reputable company, they will tell you what the footprint is being lit beneath it.
I would just be leery if it seems like it's over stating what is possible with the LEDs, you know then I would just be leery. I've bought enough cheap ones in our prototyping work and before we started doing LED Habitats.
You end up investing more money than you wanted anyway on ones that you can't continue to use, if you've got really cheap ones. They just won't work.
UV: So, what are some of the, what are some of your favorite brands? What would you recommend? Obviously, besides your own system.
Hedi: We've been pretty impressed by some of the higher end lights. Like by kind. You know, I would have to actually give you a list of, the problem is that, the world that I work in because I've had the benefit of being in the University system. The lights that we've had really good luck with are very high end horticultural LEDs.
So, when we tried to go into the lower, more cost effective, like you'd bring into your home or something like that range, things like Aero Garden and stuff like that.
That's where we started running into problems and that was what drew us to do the LED Habitat (product creation).
I could try and come up with some responses for you. Mostly, I've had people send me pictures of other LED systems that they're trying to use and some other things.
Their little seedlings are all elongated and stretching and reaching for the light, I just haven't been very impressed yet.
UV: What do you see as the future, what is the next wave of technology that will downsize in (LED) cost so that they're more available to the average person?
Is there a new type of LED? Are there new blends? What do you see as the next big trend?
Hedi: Iwas really impressed at the first annual LED Light and Horticulture Conference that was in Chicago. I was really impressed by how much enthusiasm there was towards the place that LEDs will take in horticulture.
Certainly, high pressure sodium still is a big, important light source for indoor growing.
I think that it's clear that with this vertical farming movement, the fact that you can layer into tight spaces,the growing space and the lighting is just phenomenal. And, it's pretty exciting to look at some of the large scale projects that are taking place with vertical farming.
I'm sure that LED technology is going to continue to get better. I think already even, it's pretty affordable. I think that on a small scale, it's not that bad.
It'sworth it. I think that there are some really nice options for tabletop or counter top growing. Helping to supplement the freshness of what you're feeding your family and larger scale urban farming too.
UV: What is your favorite fruit or vegetable?
Hedi: My favorite fruit or vegetable? Wow. Okay, avocado.
UV: If you had to give just one sentence of advice to somebody starting urban or vertical farming or LEDs or not. What would that advice be just in one sentence?
Hedi: Start with greens. Doing like brassica family greens. They're super fast, easy to get to know and they're really rewarding and good for you.
UV: Okay What's the best advice you ever heard from maybe a mentor or somebody that you encountered in the academic setting?
Hedi: Soil matters. You know, we sometimes, especially in academia, but in general, get really arrogant. Thinking that we can deconstruct nature and understand it all.
So, having humility about things and learning from the natural world and recognizing that soil is part of the picture, and it matters.
Thanks Hedi!
Water-Smart Farming: How Hydroponics And Drip Irrigation Are Feeding Australia
Water-Smart Farming: How Hydroponics And Drip Irrigation Are Feeding Australia
How energy-smart technology is allowing fresh vegetables to be grown in arid, isolated communities. Our Future of farming series is looking at the people, places and innovations in sustainable agribusiness in Australia
Is hydroponic farming the way forward for arid Australia? Photograph: Paul Miller/AAP
Wednesday, 26 April 2017 20.01 EDT
Sydney Fresh, Organic Angels, Freshline, Box Fresh. It’s a wonder Australian supermarkets still stock vegetables, such is the explosion of veg-box delivery services. OK, they may be a bit on the pricey side, but the food is out-of-the-ground fresh, typically free of chemicals and refreshingly wonky.
But for a veg-box scheme to work, the vegetables have to be grown locally. That effectively ruled out the arid wheatbelt towns of Western Australia. Or, it did, before Wide Open Agriculture opened a huge greenhouse-like facility to grow fresh vegetables. Boxes destined for domestic doorsteps have been leaving the Wagin-based site loaded with cucumbers, capsicums, tomatoes and the like.
Because we don’t rely on soil, we can osition our farm closer to centres of population
Philipp Saumweber, Sundrop
“We’ve had a lot of anecdotal feedback that we have brought the taste back to vegetables, particularly our tomatoes,” says Ben Cole, executive director at Wide Open Agriculture, the startup behind the initiative. “But our key is selling fresh vegetables in a region that doesn’t have many other local growers.”
The venture is tapping into growing consumer demand for food that is fresh and that doesn’t (environmentally speaking) cost the earth. It uses drip-irrigation technology, for instance, that requires only 10% of the water needed for open-field agriculture. In addition, the 5,400 square metre facility is equipped with a retractable roof and walls that open and close automatically, thus reducing water loss to evaporation.
The water used at the high-tech farm is sourced from natural surface water runoff that is directed into a series of dams before being pumped via a solar-powered system for use in irrigation. By capturing water high in the landscape, Cole argues, the wheatbelt’s first major vegetable producer is able to make use of it before it becomes saline.
“The wheatbelt has seen reductions in rainfall up to 20% over the last 20 years, so water scarcity is an issue for traditional wheat and sheep farmers,” says Cole, who holds a doctorate in environmental engineering and recently exited a successful social enterprise in Vietnam.
Wide Open Agriculture believes its agroecological approach to farming could usher in a new age of vegetable production in the wheatbelt. With its first harvest only just completed, it is already looking to list on the Australian Securities Exchange to raise finance for a second large-scale unit.
Another new player in Australia driving supply of water-smart food is Sundrop Farms. The Adelaide-based firm is the first company in Australia to develop a commercial-scale operation using hydroponic technology.
Sundrop Farms’ 65-hectare facility near Port Augusta in South Australia. Photograph: Sundrop
Pioneered by companies such as BrightFarms and AeroFarms in the US, hydroponic farming requires no soil or natural sunlight. Instead, plants are grown in trays containing nutrient-rich water and encouraged to photosynthesise by low-energy LEDs.
“Hydroponics is a thriving industry right across the globe, with produce being grown in a huge variety of environments” says Philipp Saumweber, a former investment banker who heads up the company. As if to prove the point, Sundrop has located its 65-hectare facility in an area of virtual desert near Port Augusta in South Australia.
One of the criticisms of the technology is that it is energy-intensive, what with all those indoor lights and automated heating and cooling systems. Sundrop has successfully ducked that charge by installing a concentrated solar power plant with 23,000 flat mirrors to meet most of its energy needs.
Saumweber is quick to push the water-efficiency credentials of the indoor farm too. With precious little rain or subterranean water to draw on, Sundrop has opted to pump seawater from the ocean and desalinate it. Its renewably powered desalination plant generates around 1 million litres of fresh water every day. The company also uses the seawater as a natural disinfectant, reducing the need for pesticides.
None of this comes cheap, mind. Sundrop’s Port Augusta farm cost a reported A$200m. Yet Saumweber insists this high upfront investment will be offset in the long run by lower operational costs, thanks to the use of cheaper renewable energy.
What can’t be argued with is the net result: 15,000 tonnes of tomatoes a year from a patch of land that is barely habitable, let alone productive. The prospect of siting such facilities inside cities is also a very real possibility, Saumweber adds. “Because we don’t rely on soil, we can position our farms closer to centres of population to greatly increase the efficiency of our supply chain.”
For the most part, however, water-smart technologies such as hydroponics and aquaponics (a related system that uses fish waste as an organic food source for plants) remain the preserve of hobby producers in their backyards.
For Murray Hallam, a Queensland-based expert and lecturer on aquaponics, the sector struggles with being seen as “just for hippies and way-out vegans” – an image he insists is false. A cultural propensity to think “it’ll be all right, mate” also holds back people from taking the risk of water scarcity and climate change seriously with respect to future food production, he argues.
The country is missing a trick, he continues: “In a regular farm, it doesn’t matter how well you organise it, when you irrigate, about 70% of the water evaporates straight away. Then the water that does get into the soil usually ends up going down to the subsoil and leaking away … taking with it the nutrients and fertiliser.”
Two of Hallam’s students have gone on to create multimillion dollar aquaponic businesses: Mecca in South Korea, and WaterFarmers, which has farms in India, Canada and the Middle East. He fears it will take a food crisis for Australian consumers to step up en masse and demand similar innovative solutions from the country’s agricultural industry.
Back amid the wheat fields of Wagin, Cole is more optimistic. Wide Open Agriculture is now looking to break into the local hospitality and retail market. It has opted for the brand name, Food for Reasons. For once a product that says what it is on the tin – or box.
Will Vertical Farming Continue To Grow, Or Has It Hit The Greenhouse Ceiling?
Will Vertical Farming Continue To Grow, Or Has It Hit The Greenhouse Ceiling?
Agriculture has come a long way in the past century. We produce more food than ever before — but our current model is unsustainable, and as the world’s population rapidly approaches the 8 billion mark, modern food production methods will need a radical transformation if they’re going to keep up. But luckily, there’s a range of new technologies that might make it possible. In this series, we’ll explore some of the innovative new solutions that farmers, scientists, and entrepreneurs are working on to make sure that nobody goes hungry in our increasingly crowded world.
A pair of lab workers, dressed head to toe in bright white biohazard suits, patrol rows of LED-lit shelves of lettuce, quietly jotting down a series of numbers and readings. Stacked some 15 to 20 feet high, the shelves cover nearly every inch of a massive 25,000-square-foot facility. As the lab hands pass by each row of lettuce, some in the germination phase, some ripe for picking, a psychedelic pink glow wraps around them, painting an almost extraterrestrial setting.
This isn’t a scene plucked from Alfonso Cuarón’s latest blockbuster; it’s an everyday occurrence at a vertical farm in eastern Japan.
The farm was built in the wake of a devastating magnitude 9.1 earthquake that rocked Japan in 2011 and led to a temporary food crisis in the affected area. After seeing the chaos, Japanese plant physiologist Shigerharu Shimamura decided to develop a more consistent, reliable model for manufacturing lettuce. He ended up turning an old Sony-backed semiconductor facility into the planet’s largest vertical farm – a huge operation that now churns out an astounding 10,000 heads of lettuce per day.
“We’re talking coming in and supplying 10, 20, 30 percent of the food supply of an entire city.”
Recently, the facility (and others like it) has become a poster child for indoor farming. There’s now a rapidly expanding movement to bring this type of food production to urban centers all over the globe.
It’s easy to see the appeal. In theory, indoor farms could allow us to grow food 24 hours a day, protect crops from unpredictable weather, and even eliminate the use of pesticides, fertilizers, and herbicides. If these farms were built in cities, we could potentially mitigate crop loss due to shipping and storage, and cut down on fossil fuel usage because food wouldn’t need to be transported very far after harvest.
But of course, the idea of indoor farming isn’t without its detractors. Critics are quick to point out the method’s shortcomings when it comes to efficiency, effectiveness, and cost. In their eyes, vertical farming simply isn’t something that can be deployed on a large enough scale, and therefore isn’t a viable solution to our problems.
So, who’s right? Should we start building giant, garden-stuffed skyscrapers in our cities, or abandon the idea and devote our efforts to improving existing (horizontal) farms? Could vertical farming legitimately help us meet the world’s growing demand for food, or are we chasing the proverbial pie in the sky?
Upward trajectory: the benefits of growing vertically
In his seminal book, The Vertical Farm: Feeding the World in the 21st Century, Dr. Dickson Despommier puts forth the theory that vertical farming is a prime candidate to help solve the growing food, water, and energy crisis in the United States.
As populations continue to rise in urban centers around the globe, Despommier sees no other solution.
“As of this moment, the WHO (World Health Organization) and the Population Council estimate that about 50 percent of us live in cities and the other half, of course, live somewhere else,” Despommier said in a video. “Another thing we can learn, from NASA of all places, is how much land those 7 billion people — half urban, half rural — actually need to produce their food every year. It turns out to be the size of South America. So, the size of South America, in land mass, is used just to grow our crops that we plant and harvest. I’m not even talking about herbivores like cows, goats, or sheep.”
When the book was first published in 2011, the indoor farming industry essentially stood as a barren landscape, with few companies setting out to literally put vertical farms on the map. Now, with Despommier’s written blueprint in the wild, the concept has recently gained a good deal of popularity.
“It’s estimated that by around 2050, roughly 80 percent of the world’s population will reside in urban city centers.”
Aside from Despommier, a growing number of people strongly believe in a prominent future for vertical farms. Today, there exist throngs of vertical farming companies all geared toward making this innovative technology a reality. Unsurprisingly, it’s with Despommier and these upstart companies that the industry’s appeal rings the loudest.
Companies such as Bright AgroTech and AeroFarms have set out to educate and inform small farmers to grow locally in urban areas, while other firms like Freight Farms and Edenworks lean on unique and innovative growing concepts — such as shipping containers or rooftop aquaponics — to bring the idea to life. Thus far, there’s no real right or wrong way to go about it, and the recent influx of startups should only prove advantageous to the industry in the long run.
“I do believe there are a few players coming to the table that look poised to supplement local food supplies to a really significant degree,” aquaponics expert Dr. Nate Storey told Digital Trends. “We’re talking coming in and supplying 10, 20, 30 percent of the food supply of an entire city. So, you have this future where you have indoor growers taking on that task, and you have small guys that are kind of collaborating and cooperating to sell to niche markets, really high-value products. Then you have the big boys who are really kind of going head-to-head with some of your field producers, who are growing at much larger scales and interested in replacing that wholesale product.”
As Despommier states on his website, it’s estimated that by around 2050, roughly 80 percent of the world’s population will reside in urban city centers, with the population of the world ballooning by an additional 3 billion people over that time. To Storey’s point, the diversity of vertical farms should allow these urban areas to continue to function as they do today. That is, access to food should remain a basic function of society, as opposed to it serving as a luxury should food production dwindle in the future.
Like the Green Revolution from the 1930s to the 1960s, Storey believes the world sits poised for yet another research and development breakthrough regarding vertical farming.
“When you step back a bit, you begin to realize that we’re kind of on the verge of another Green Revolution,” he added. “I think that indoor agriculture plays a huge role in that. So, the 40,000 feet in the air perspective is it’s not just about supporting local demand for food, it’s about controlling the environment completely. This means eventually taking things out of the field entirely and putting them indoors.”
Bringing a high-flying idea back down to Earth
While the upstart vertical farming community largely agrees with Storey’s stance, there also exists a wing of detractors who point to indoor farming’s inefficiencies.
The loudest voice among these critics is former United States Department of Agriculture biologist Stan Cox. After serving for the USDA for 13 years as a wheat geneticist, Cox joined the Land Institute as a senior scientist in 2000, specifically focusing on plant breeding in greenhouses and fields. An author of several books looking at the past, present, and future of all things agriculture and food, Cox is an expert in the field — which is why his view of vertical farming as a scam is a perspective that should give anyone pause.
“This will never be able to supply any significant percentage of our food needs.”
Vertical farming’s largest hurdle — a concept Cox thinks should’ve “collapsed under its own weight of illogic” and that he says remains incredibly difficult to overcome — concerns its scale. Cox posits that to be truly effective, vertical farms would require an incredible amount of floorspace. Despommier envisions indoor farming as a means to avoid the degradation of soil, but turning currently cultivated land into soil-preserving indoor farms would require an almost unfathomable amount of space.
To get a true picture of this, Cox breaks down the floorspace requirement for growing just vegetables — which clocks in at roughly 1.6 percent of cultivated land in the U.S.
While that number may not sound like much, turning that 1.6 percent of cultivated land into a functioning indoor or vertical farming operation demands the relative floorspace of around 105,000 Empire State Buildings. As Cox also points out, even with that much dedicated space, 98 percent of U.S. crops would continue to grow at outdoor farms.
“A colleague and I originally did some back of the envelope calculations that show if we grew grain- or fruit-producing crops [in vertical farms], it would take half of the country’s electricity supply or tens of thousands of Empire State Buildings,” Cox told Digital Trends. “These huge numbers would show that this may be fine for growing, on the small side, fairly expensive leafy greens to be used in restaurants or local areas. But the two things we have to always keep in mind is the amount of energy and resources being put into each unit of food, and the second is the scale. This will never be able to supply any significant percentage of our food needs.”
Despite Cox’s calculations painting a grim picture for large-scale urban production of grain or vegetables, he did emphasize that he’s “all for” urban gardening, or growing food as close to a population center as possible. To Cox, it just “makes sense.” Unfortunately, small urban gardening operations won’t likely have any shot at replacing the more than 350 million acres of rural U.S. cropland that consistently churn out America’s food supply.
“We can only grow enough crops within cities to substitute for a very tiny portion of [our food supply],” Cox added. “We’re still going to depend on rural America for growing the bulk of our food. There’s no big problem with that, really. We certainly want for perishable food, like fresh produce, to grow as much as we can close to where we live. But for grains, dry beans, food legumes, oil seeds, quinoa, all of these dry, nutrient-dense foods with a lower moisture content that can be shipped with very little energy or cost (by rail), that’s still going to be grown around our rural areas.”
Plain and simple, Cox doesn’t see a way around the issue of energy as it pertains to vertical farms — at least for the sustained growth of something like grains or fruit. Because leafy greens require less light to grow sufficiently, it makes much more sense to operate vertical farms geared solely around these foods. Conversely, growing something like corn or wheat — which produce much more dry matter — just doesn’t seem like a feasible option if there’s an intention to keep energy, production, and food costs down.
Growing up: The future of vertical farming
With the vertical farming industry still very much in its infancy, its future remains somewhat murky. Despite the growing number of startups committed to nurturing the idea, its hindrances and drawbacks pointed out by critics like Stan Cox carry just as much clout. Because of this, it’s hard to confidently put stock in either its failure or success.
“The Achilles’ heel of vertical farming or gardening is that it just does not work out energetically.”
Vertical farming’s best shot at a lasting legacy may be to simply pump the brakes on continued advancement. As it stands today, the startups that currently run operations geared toward producing heaps of leafy greens might want to think long and hard about introducing anything capable of completely shutting down momentum — i.e., fruits, grains, etc. In this case, energy usage is the bane of vertical farming’s existence.
“The Achilles’ heel of vertical farming or gardening is that it just does not work out energetically,” Cox points out. “The amount of energy put into [vertical farming] per unit of food you get out of it is very tiny. That’s why almost everything you see being grown this way is some type of leafy green that doesn’t require as much light to produce.”
Now, this isn’t to say vertical farming won’t continue to exist, or even that any of the startups dedicated to its advancement won’t try to introduce fruit or grain to their production. Perhaps there comes a time when someone finds a solution to the energy dependence issue, but for now, leafy greens are the vertical farming industry’s ceiling.
Dr. Nate Storey is the founder of BrightAgrotech — a company that designs and develops vertical farming technologies, such as the ZipGrow hydroponic system pictured above. (Credit: Bright Agrotech)
First Large Scale Commercial Vertical Farm in Europe To Be Set Up in The Netherlands
First Large Scale Commercial Vertical Farm in Europe To Be Set Up in The Netherlands
Farm to serve one of Europe’s biggest supermarket chains with fresh-cut lettuce grown using LED horticultural lighting
Eindhoven, the Netherlands – Philips Lighting (Euronext Amsterdam ticker: LIGHT), a global leader in lighting, today announced that Staay Food Group, a leading fresh fruit and vegetables company, is building the first of its kind vertical farm in Europe, in Dronten, the Netherlands, which will use Philips GreenPower LED horticultural lighting. The facility will serve one of Europe’s biggest supermarket chains and will be used for testing, and optimizing processes for future, large vertical farms.
Ahead of new legislation
The 900m2 indoor vertical farm will have over 3,000m2 of growing space and produce pesticide-free lettuce. With upcoming stricter regulations on the residual pesticide levels in a bag or bowl of lettuce, retailers will need to provide exceedingly high quality, pesticide-free lettuce.
Defining growth recipes
Staay, Philips Lighting and vegetable breeder Rijk Zwaan collaborated and undertook intensive research over the past three years to determine the best combination of lettuce varieties and growth recipes to improve crop quality and yields. Having the right growth recipe prior to the start of operations at the vertical farm will help Staay achieve a faster return on investment.
“Our plant specialists at our Philips GrowWise research center in Eindhoven are testing seeds from a selection of the most suitable lettuce varieties, to define the best growth recipes and to optimize crop growth even before the farm is running,” said Udo van Slooten, Managing Director of Philips Lighting Horticulture LED Solutions.
Sustainable growth
“Producing lettuce for the fresh-cut segment indoors not only means avoiding all pesticides, it also means a much lower bacterial count and therefore longer shelf life at the retailers. With the lettuce being packaged at the same spot as where it is grown, we save on transport before distribution to retailers,” says Rien Panneman, CEO of Staay Food Group. “Also, by avoiding weather fluctuations, we maintain an optimized and stable production environment to guarantee consistent and optimal product quality.”
Looking for the best varieties
Wim Grootscholten, Marketing and Business Development Manager of Rijk Zwaan, worldwide market leader in lettuce seeds said: “The tests we are conducting within this project are enabling us to identify which varieties are optimal for growing in a vertical farm, and also which varieties offer the best taste and texture. It will help us with our continuous challenge to offer solutions for the growing world population. We believe that vertical farms will become increasingly important, because in the future we see more economic and environmental pressure to produce fruit and vegetables, such as lettuce, closer to where end-customers are located.”
First of its kind
The vertical farms in Europe, using LED-based lighting have so far been research centers or specialist producers serving restaurants. The new Staay facility in Dronten will be the first in Europe to operate commercially, serving large-scale retail. The facility will start operations in the second half of 2017.
About Philips GrowWise
Philips GrowWise Center in Eindhoven, the Netherlands, is the largest research facility of its kind with a total growing surface of 234m2. Here, Philips Lighting’s researchers trial a variety of crops under different LED lighting and climate conditions to help determine their economic potential. Vertical farming investors and operators can visit the facility to see demonstrations of different vertical farm technologies, taste crops grown under LED lighting and discuss the economic viability of the technology used.
For further information, please contact:
Philips Lighting Global Media Relations
Bengi Silan Genc
Tel: +31 6 25441798
E-mail: bengi.genc@philips.com
Philips Lighting; Horticulture LED Solutions
Daniela Damoiseaux, Global Marcom Manager Horticulture
Tel: +31 6 31 65 29 69
E-mail: daniela.damoiseaux@philips.com
Fresh-Care Convenience (member: Staay Food Group)
Marco Kleijn, Managing director Fresh-Care Convenience
Tel: +31 321 382 308
E-mail: marco.kleijn@fresh-care.nl
www.staayfoodgroup.com
Rijk Zwaan
Ton van Leeuwen, Communication Specialist
Tel: +31 174 532 487
E-mail: t.van.leeuwen@rijkzwaan.nl
www.rijkzwaan.com
About Philips Lighting
Philips Lighting (Euronext Amsterdam ticker: LIGHT), a global leader in lighting products, systems and services, delivers innovations that unlock business value, providing rich user experiences that help improve lives. Serving professional and consumer markets, we lead the industry in leveraging the Internet of Things to transform homes, buildings and urban spaces. With 2016 sales of EUR 7.1 billion, we have approximately 34,000 employees in over 70 countries. News from Philips Lighting is located at http://www.newsroom.lighting.philips.com
About Staay Food Group
Staay Food Group is the fresh fruit and vegetables company in which centralized policy, marketing and sourcing control is supplemented by local expertise in growing and sales. Since 1946, we have delivered a wide range of excellent quality fresh fruit and vegetables worldwide. In response to supply chain integration, Staay Food Group positions itself closer to the growing process by cooperation and participation. Our regional offices closely monitor the growing process and the direct deliveries to customers.
About Rijk Zwaan
Rijk Zwaan develops vegetable varieties and produces seeds, which it sells in more than 100 countries. The family-owned company is amongst the top five in the global vegetable seed market and is characterized by a people-focused approach. More than 2,600 employees in over 30 countries work enthusiastically to provide products and services that add value for the market. The company has its headquarters in De Lier, The Netherlands.
Vertical Farming Grows Up And Comes Of Age
Vertical Farming Grows Up And Comes Of Age
Growing food without sunlight or soil is now a reality, but the economics leave little room for error
By Jennifer Blair Reporter
Published: April 25, 2017
Partners Wayne Lohr and Ulf Geerds have turned their extensive experience in agriculture and horticulture into a growing vertical farming venture near Olds. Photo: Jennifer Blair
Olds-area greenhouse operator Wayne Lohr and business partner Ulf Geerds are dreaming big — they want to grow an acre of strawberries.
That may not sound like a big deal until you consider that acre will take up just 360 square feet and produce strawberries year round. And even though they’re grown in racks on a shed, these berries will, the duo says, taste just as good as ones picked fresh in the field on a nice summer day.
“They taste like they’re from the field because they actually get the same treatment as from the field. We mimicked the environment that’s outside,” said Geerds.
“At the end, you’ll end up with a crop that has the same taste as from the field, but you can have it year round.”
The duo is talking about vertical farming, a relatively new industry birthed by the advent of LED lights and ‘aeroponics’ — rather than soil and sunlight — to produce fruit and vegetable crops in a small indoor area.
What was, until fairly recently, the stuff of science fiction is now a reality. Sales of produce grown via this method topped US$1 billion in 2015, and with production increasing by nearly 30 per cent annually, sales are forecast to surpass $15 billion by 2025.
And although it’s touted as a way to grow food in cities (as well as in countries where land is in short supply), vertical farming has also arrived in Alberta. And it’s winning over traditional growers such as Lohr and wife Carolyn, who have been in the greenhouse business (mostly growing ornamentals) since 1982. They got into vertical farming a year and a half ago, forming Lohr-A-Lee Indoor Gardens with Geerds and his wife, Sangeetha Varghese.
They started small, with two integrated upright systems purchased from Indoor Farms of America. The vertical panels take up a floor area of about 16 square feet in one of Lohr’s outbuildings, and have 650 plants in total. That’s an incredibly dense 40 plants per square foot of floor space — normally strawberries need one square foot per plant. At that density, their plan to scale up to 360 square feet will give them the equivalent of an acre of strawberries. (Aeroponics means there is no growing medium and roots are kept moist by misting.)
Lohr-A-Lee Indoor Gardens started small with its system, with plans to scale up with an additional 24 panels in the next few months.photo: Jennifer Blair
The pair has tried their hand at lettuce, basil, kale, arugula, Swiss chard, and bok choy, but so far, strawberries are the real star. There are no weather, disease, weed, or insect pressures, and with “total control of the environment,” the strawberry plants will grow for up to 14 months before needing to be replaced. Normally, the growing season for strawberries is two months, so the potential yield per plant is much higher.
“Effectively, you create an environment that’s consistent, so as far as this plant’s concerned, it’s July 15 every day,” said Lohr. “The target is to get four pounds per plant per year. We feel that that’s more than achievable. That’s the target. The goal is to beat it.
“We don’t need to import this stuff. We can grow it here.”
‘Lots of unknowns’
Despite their belief in vertical farming’s future, both men warn that this is not a way to make a quick buck.
That view is echoed by horticulture consultant Cees VandenEnden, owner of HortiSource Consulting in Mountain View County.
“I truly believe that 50 per cent — or maybe even more — of the startups will not see their fifth anniversary,” VandenEnden said at a workshop last month. “There are plenty of opportunities. I’ll be the last one to say this is not working. But there are some big question marks.”
But VandenEnden is being “optimistic,” said Lohr, who expects 80 to 90 per cent of startups will fail in their first year.
While vertical farming has many attributes — including a reduced carbon footprint, zero pesticide use, high nutritional value, good water-use efficiency, and local production — anyone taking a “romanticized” view will be in for a rude awakening, said Geerds.
VandenEnden agrees.
“There’s a lot going on, and I think it has a lot of potential — it’s ‘sexy,’” said VandenEnden. “In the public mind, local produce and knowing your producer is good.
“(But) this piece of the industry is attracting people who have no agricultural background and no growing knowledge. Your learning curve is tremendous and very costly. There are hyped-up expectations, and your startup cost is high. Making an income is not easy.”
In addition to the typical challenges associated with agriculture, such as labour and marketing, vertical farming comes with its own set of problems, including picking the right growing system, climate controls, light sources, watering systems, and product mixes.
“There’s a lot of thinking and problems to solve,” said VandenEnden.
“At this point in time, it’s new, so we do not know what works and what doesn’t,” added Geerds.
Ready for takeoff
Figuring out the market is even trickier. Geerds points to lettuce, which is an “easy” crop to grow.
“Lettuce grows very well in here. In 26 days, we have a crop that we can sell, but the demand is not there,” said Geerds. “We want to grow what the market wants. Strawberries make a lot of sense to us because there’s a high demand and the quality is very poor from the imports.”
Lohr and Geerds have partnered with a retailer for “significant volumes of strawberries weekly” for a small price premium.
“We’re getting a reasonable premium over what they’re paying wholesalers, but it’s not huge,” said Lohr. “Economics will ultimately take the premium away, so it comes down to production efficiencies and cost efficiencies.”
VandenEnden predicts the fledging industry will quickly scale up.
“It took over 100 years for the greenhouses to go from small entities to the big greenhouses you see nowadays,” he said. “But (vertical farming) will not take 100 years to get to that point. It’s probably closer to five years or maybe even faster.
“When that volume comes on the market, your premium prices are gone. You’ll have to produce for regular market prices.”
Competition is already growing in Alberta, he added.
“I was surprised to learn how many people are already doing this in Alberta. That will only increase,” said VandenEnden. “Big producers will develop fairly soon, and they will basically drive the prices.”
When that happens, production will be “the least of your problems” when compared with marketing, he said.
“It takes time to grow, but it takes a lot of time to market as well,” he said. “I’ve seen very few people who are excellent at growing and do a good job of marketing, too. Most of the time, one of the two is mediocre.”
But ultimately, marketing vertically farmed produce is much the same as marketing any other crop, said Lohr.
“Know what it costs you to produce it, know what kind of returns you want, and that tells you what price you need to make money.”
A costly venture
Production costs will vary based on the crop and the system used to grow it.
“If a traditional crop costs $1 to produce, the closed environment systems are costing between $1.40 and $2,” said VandenEnden. “That’s something we have to work on because that is not sustainable.”
Generally, the cost of equipment is related to the size of the system, he added, and there will be power and labour costs on top of that.
“With the right setup, there are good prospects, but what is the right setup? You need to go over that in your mind to make the right decision,” said VandenEnden.
Geerds agrees.
“You can pretty quickly sink a lot of money into the system, and if you don’t do it right, you will definitely lose.”
Producers should look at the price per square foot of growing area rather than simply the price per square foot when costing out a system, said VandenEnden. Because vertical panels do more with less space, the growing area square footage is typically about double the actual square footage. The panels at Lohr-A-Lee Indoor Gardens cost $8,800 each, and Lohr and Geerds are in the process of scaling up with an additional 24 panels.
“It’s not cheap, and it does scare the financial world. The big system that would go in the whole building is about the same dollars as a new combine today,” said Lohr.
Each vertical panel, which costs $8,800 each, can accommodate around 325 plants, or 40 plants per square foot.photo: Jennifer Blair
“We’ve done some pretty elaborate cash flow projecting but again, you’ve got to look at this on a per-plant basis. They’re still big numbers and the bill still has to be paid, but on a per-unit basis, it’s not near as scary.
“The ROI is definitely there. You’ve just got to make it produce.”
The test unit they’ve been running for the past year has helped them verify their cost of production — data that isn’t available for this new type of farming.
“Because it’s the first commercial system that we’ll have, the next system will tell us, do we make money or don’t we?” said Geerds, adding they have a few other ideas of crops they can try if strawberries don’t pan out.
“We’ve talked to a lot of people who want to grow very big very fast. I don’t think that’s the right way to approach it. You have to find the sweet spot. You don’t want to be too small but because the science is just developing, we have to really see where the sweet spot is. We’re not sure what that is yet.”
Lohr’s advice is to “start small and learn as you go.”
“Do your homework. Otherwise, there’s going to be a lot of roadkill.”
Alumnus Goes Organic With Entrepreneurial Hydroponic Venture
Alumnus Goes Organic With Entrepreneurial Hydroponic Venture
25 Apr 2017
by Emily Reise
University of Wisconsin Oshkosh alumnus Bryan Ernst ‘12, of Ripon, is an entrepreneur who started Ernessi Organics, an original hydroponics system that grows herbs and vegetables.
Hydroponics is the growing of produce without the use of soil. Plant roots are suspended into a nutrient liquid mixture, which provides just the right amount of nutrients that the soil will accept. Ernest can control the specific mixture that certain plants receive to maximize growth and yield.
This venture is something the geology graduate has always been interested in pursuing.
“Prior to going to UW Oshkosh, I was a marine and had been to many barren areas, so I’ve seen first hand how hard it is for people to find food,” Ernst said. “I’ve always wondered how we can grow food efficiently in dense urban areas.”
Ernessi Organics grows all sorts of herbs and more than 100 types of micro-greens like kale, cabbage, basil, chives, cilantro and sage in Ripon’s urban downtown area.
“Basil is by far our highest selling item. We have done 2,100 pounds of basil in the first quarter here in our little grow operation,” he said.
Ernessi’s organic produce can be found in 17 Festival Food stores across the state as well as in local grocery stores and restaurants like the Roxy Supper Club.
He said supplying local people with local food that isn’t transported from overseas is gratifying.
“We come in at the same price as a producer from Mexico. By doing this we ensure that we don’t price certain people out of the market for our healthy and fresh food.“
The hydroponics system used in the operation is unique because Ernst designed it over years of experiments and research.
He also designed and had his own LED lights specially manufactured. Through research, he learned that most plants only need red and blue wavelengths. This saves energy costs and helps the plants grow more efficiently.
In addition, Ernst programmed an app that assists with the seeding and harvesting processes.
“The app was something I taught myself to design. It is a bunch of algorithms that indicates what plants need to be seeded and harvested weekly so we always have a constant turnover of product,” Ernst said.
Aside from growing plants ,the entrepreneur also grows mantis bugs. Since he doesn’t use pesticides, he controls pests by releasing carnivorous mantis bugs into the plants to find and eat the bugs that would otherwise damage the plants.
As Ernessi Organics keeps growing, Ernst said the next step will be expansion.
“We are looking to either franchise in other areas of the state or other states so we can provide food locally to other areas with intense farming seasons or areas of food desert,” he said.
Ernst said being an entrepreneur isn’t easy in the beginning, but it is rewarding once you get your feet on the ground.
“There is never a good time to start a business and you are never going to have enough money, so if you have a good idea you have to just jump into it,” he said.
Link to: Ernessi Farms
Learn more:
Vertical Farming: A Better Option
Vertical Farming: A Better Option
By Emily Williams, Columnist | Apr 25, 2017 | Opinion, Opinion Columns |
We need to rethink industrialized factory farming and quick. The agricultural revolution boomed back in the 18th Century which allowed the industrial revolution to change the world we lived in. So, this is a good thing with more access to food, food produced on higher levels and a decline in world hunger, right?
Wrong.
The agricultural revolution not only ruined the society humans had been living in for thousands of years, but it took our environment into a downward spiral that we may not fix in time. The agricultural revolution sparked war between mankind on drastic levels since it was one of the first times we as a species started assigning ownership to land.
If we weren’t killing each other, the diseases spread by factory farming were. The domestication of animals was needed for living purposes, but on the massive levels we’ve allowed to be perceived as appropriate have caused an influx of diseases carried by our animal friends.
Influenza, TB, smallpox, Measles and even the common cold are all linked back to the domestication and farming of livestock. But let’s argue for a second, the domestication and cultivation of animals in small populations allowed the human population to grow. That’s great, we’re living and able to reproduce at rates higher than we were dying.
But we were still dying. Hunter and gatherers shifted camps quickly and effectively. The quick rise in populations allowed us to establish villages and cities which ended up doing more harm than good. We created perfect living petri-dishes for microbes and diseases to spread. We may have been reproducing at large rates due to the advancements made with farming and domestication of meat, but death was occurring at the same rate. Our life-span declined drastically for a long time.
Sounds great.
We’ve moved on from disease altering life-spans and have outsmarted microbes like the common cold and smallpox for the most part. What has factory farming done to the environment? Not only did we introduce foreign species of plants and grasses but we allowed our carbon footprint skyrocket with meat production worldwide having quadrupled in the last 50 years.
Globalagriculture.org breaks it down for us easily: in 2014 meat production reached a high of around 315 million tons. An estimation of 450 million tons will be produced by 2050 yearly. Cows, pigs and chickens, the top three livestock handled in factory farming, have increased by over 50% percent in population for each animal, chicken an upward of 114%.
In 2016, 164 million metric tons of CO2 and methane gasses were produced by livestock in the world, and meat makes up 47.6% of greenhouse gasses from average food consumption based on the factsheet produced by the University of Michigan in August 2016 for U.S. households.
So, what is the future of farming if we want to somehow protect our environment that is deteriorating away? The future of farming is: well… not any kind of farming we’ve become comfortable with. Farms are businesses, and ones that are becoming less and less valuable unless you’re at the head of a factory farm rolling in the bundles of money you make. It’s also clear that as a society we are obsessed with technology.
Our world is crying out for help in the way we’ve destroyed it, and our global size is demanding a new revolution in our agricultural system. The technology is here, we just need to stand behind it and support it. Companies like AeroFarms, FreightFarms, and BoweryFarming have the right idea.
They’ve taken farming on land and put it inside. Vertical farming is what we need, and it works. It allows produce to be aligned in a systematic way for the purest and cleanest forms to be grown. Conditions can be manipulated for produce to be grown all year long and without the use of pesticides and fertilizer since variables can be changed and controlled easily.
These farms are able to exist in any urban environment, unlike the agricultural system we have now that takes up hundreds of acres. Not only is it using less space, farming like this uses less resources too. Bowery states they use 95% less water than traditional agricultural farming and produce 100x more on the same footprint of land.
Less CO2 emissions, less harm with fertilizers and pesticides and a more effective urban setting with farming is what we need to help the environment. There would be less demand for deforestation, and species affected by pesticides like the bees and butterflies would be able heal.
Let’s take a stance against factory farming and look at what we can do to change the way we’re treating the world. Start buying from your local farmer’s market, Oxford is a fantastic place to start. Findley Market isn’t a far drive either! Decreasing your meat intake by even one day a week and combining it with buying produce at a local market and these steps with help us heal the environment we’ve … well, trashed.
taylo193@miamioh.edu
This Incredible Vertical Farm Skyscraper Could Feed An Entire Town
Every year, the design magazine eVolo holds a competition for the most ground-breaking skyscraper concepts.
This year's first place winner is the Mashambas skyscraper, a vertical farm tower that would be able to feed an entire town in sub-Saharan Africa. The conceptual skyscraper could also be disassembled, and moved to different locations where communities need it.
This Incredible Vertical Farm Skyscraper Could Feed An Entire Town
- Leanna Garfield
- Apr. 25, 2017, 10:58 AM
Pawel Lipiński and Mateusz Frankowski
Every year, the design magazine eVolo holds a competition for the most ground-breaking skyscraper concepts.
This year's first place winner is the Mashambas skyscraper, a vertical farm tower that would be able to feed an entire town in sub-Saharan Africa. The conceptual skyscraper could also be disassembled, and moved to different locations where communities need it.
Designed by Polish architects Pawel Lipiński and Mateusz Frankowski, the tower would grow produce on the upper floors and would come with fertilizer and seeds. The other floors would feature kindergarten classrooms, a doctor's office, and even a docking port for drones that would deliver food to hard-to-reach areas. The ground floor would include an open-air market, where farmers could sell their crops.
Part of the tower would be made of modular pieces, which would allow it to be taken apart and transported somewhere else. (Though, the designers do not say how long that process would take.)
Pawel Lipiński and Mateusz Frankowski
"The main objective of the project is to bring this green revolution to the poorest people," Lipiński and Frankowski write. "Giving training, fertilizer, and seeds to the small farmers can give them an opportunity to produce as much produce per acre as huge modern farms."
Its name, Mashambas, is a Swahili word that means cultivated land, Lipiński and Frankowski write. The goal of the tower would be to bolster agricultural opportunities and fight hunger in impoverished towns in African countries.
Pawel Lipiński and Mateusz Frankowski
"When farmers improve their harvests, they pull themselves out of poverty. They also start producing surplus food for their neighbors. When farmers prosper, they eradicate poverty and hunger in their communities," the designers write.
Though he share of Africans living in poverty declined from 56% to 43% from 1990 to 2012, many more African people are poor today due to population growth, according to a recent World Bank report.
"Today hunger and poverty may be only African matter, but the world’s population will likely reach nine billion by 2050. Scientists warn that this would result in global food shortage," the designers write. "Africa’s fertile farmland could not only feed its own growing population, it could also feed the whole world."
Pawel Lipiński and Mateusz Frankowski
Announced April 10, the tower was chosen from a pool of over 400 entries. Though the designers did not name an exact site for a Mashambas skyscraper, they said the first one could be in a town south of the Sahara desert. The design is merely a concept right now, and there are no plans to actually build one.
Though the design is certainly far-fetched, the vision behind it explores what rural farms of the future could look like.
Indoor Farmers Face Uncertainty Over Organic Labeling
The National Organic Standards Board have kicked the can down the road on hydroponic and aquaponic farming. The group was supposed to decide on April 21 if the systems can be considered organic. The only decision they made was to learn more about the farming process and have pushed their decision until the fall.
APR 24, 2017 @ 06:03 PM
Indoor Farmers Face Uncertainty Over Organic Labeling
Debra Borchardt , CONTRIBUTOR
Opinions expressed by Forbes Contributors are their own.
Indoor farms can stack plants vertically and grow more crops than a traditional outdoor farmer. (Photo by Shutterstock)
The National Organic Standards Board have kicked the can down the road on hydroponic and aquaponic farming. The group was supposed to decide on April 21 if the systems can be considered organic. The only decision they made was to learn more about the farming process and have pushed their decision until the fall.
This has left current hydroponic and aquaponic farmers that consider themselves organic in limbo. They can continue to call themselves organic until a decision is reached, but in the meantime the uncertainty is troubling.
“It's more about organic, certified farmers wanting to maintain their market share,” said JP Martin of GrowX, an aeroponic farming system. “The fertilizers are identical,” he said, “So the argument that they use different nutrients breaks down.”
Terra Tech is an indoor farming company that grows leafy greens and its crop that has some soil exposure has been certified organic. Chief Executive Officer Derek Peterson said, "If they came back and had some sort of ruling that disallowed organic, it would be tremendously hurtful. We would lose shelf space." He noted that the demand for non-organic produce continues to drop because the price premium is down for organic. "It's more affordable so the demand has increased," he said.
He's right. The market has grown tremendously. The USDA said that there was a 13% increase between the end of 2015 and 2016 of organic farms. This is the highest growth since 2008.
The point of contention is whether food grown without soil can be considered organic. The USDA admits that obtaining organic certification for crops is challenging and the guide is over 60 pages long. There is a lot of detail regarding the soil, but there isn't a hard and fast rule that the food must be grown in soil.
“It's really about where the nutrients are coming from and less about the methodology,” said Martin. He said it just boils down to money and market share because hydroponic farming has been around for years. If anything, the indoor farming is much more organic than outdoor farming according to Martin.
5 Control System Questions With Darryn Keiller of Autogrow
5 Control System Questions With Darryn Keiller of Autogrow
Darryn Keiller, CEO of control company Autogrow, came to the company from a consulting background, and has led the New Zealand-based company to a sub $3mn equity raise since taking the helm. Ahead of his presentation at Indoor Ag-Con on May 3-4, we caught up with Darryn to ask him about big data and the future of controls in controlled environment agriculture.
1. Autogrow has created a dedicated system – RoomBoss – for controlled environment applications. What drove you to do that?
Market need. Urban and vertical systems are on the rise; from a control and automation perspective innovators in this space have either a) been sourcing from industry vendors existing technology created for Greenhouse production or b) building their own. What is needed is a technology approach that is purpose designed for systems using LED / HPS grow lights, CO2 management and integrates dosing control and all other automation requirements. The Room Boss is a Beta product that also anticipates controlling automated harvesting and robotics. It’s an Internet of Things based platform, not just a device.
2. How much of the hoopla over the application of big data in the industry is well-founded and how much is just hype?
Certainly, there is no shortage of hype. Along with machine learning, deep learning, etc. in every other sentence. The opportunity to apply these data methodologies and techniques to solve real world problems in agriculture is real. The time-line to make these effective and beneficial on a prolific basis is a lot longer than everyone would like. Part of this is due to the slow rate of market adoption and part of it is the technology development itself. Its potential is well-founded.
3. What’s the most common mistake you see beginning farmers make when picking a control system?
The first thing is considering the control and automation side of things last – this happens all the time. And it then leaves the farmer trying to find a solution with what’s left of their budget. Automating your production is key to consistently great crops and profitability through using less labour and managing inputs like water, energy and nutrients. The second part is thinking ahead – if you purchase a limited system now, then what happens when you decide to scale your operations? Sometimes spending a little more now is better than having to “rip and replace” technology later. The approach is to obtain technology that is flexible and modular, that grows as you grow.
4. What do you expect control systems to look like in five years’ time?
I expect most indoor growing environments will be fully automated with no human component except pre-planting and post-harvest. All automation and control to be cloud delivered and all physical automation will be carried out through a variety IoT devices and multi-functions sensors. This will include automated robotic harvesting – it’s already here when you look at examples like Urban Crop Solutions of Belgium or integration of machine vision solutions for crop monitoring, pest and pathogen detection as examples.
5. What’s the biggest advantage that being a Kiwi gives you?
We’re a nation of innovators, inventors and entrepreneurs – it’s how Autogrow began 24 years ago. As a nation, we have a deep history in horticulture, agriculture and pastoral production including R&D in genomics, biologics and technology. We even have our own Rocket company which despite the name was founded and is based in New Zealand. A nation of 4.5m we feed 40m people, exporting 95% of what we produce to 100 countries, every month, including beef, wool, seafood, dairy products and fruit. Because of our location, we travel the World and we embrace the idea of boundarylessness – no limits! Autogrow now exports to 30 countries around the globe.
SEE DARRYN SPEAK AT THE 5TH ANNUAL INDOOR AG-CON ON MAY 3-4, 2017
Indoor Ag-Con Features Container Farm Tours From Indoor Farms of America & Modular Farms
Indoor Ag-Con Features Container Farm Tours From Indoor Farms of America & Modular Farms
Indoor agriculture's premier conference now features tours of live vertical farming operations on site, as well as 50+ exhibition booths & 40+ speakers
We’re excited to have our participants experience these farms on site”
— Nicola Kerslake, Founder, Newbean Capital
LAS VEGAS, NEVADA, USA, April 24, 2017 /EINPresswire.com/ -- Farm tours are a popular feature of agriculture trade shows, but Indoor Ag-Con – the indoor agriculture industry’s premier conference – likes to do things a little differently. It will instead be featuring two container farm tours at its next event, at the Las Vegas Convention Center on May 3-4, 2017.
The tours will be operated by two leading container farming equipment suppliers, Indoor Farms of America and Modular Farms. Their staff will be on hand from 8.30am to 5.30pm on each of May 3 and May 4 to walk participants through the farms and answer questions about their equipment. Their farming approaches are quite different from one another, and will allow participants to identify the best fit for their vertical farming needs. “We’re excited to have our participants experience these farms on site” commented Nicola Kerslake, founder of Newbean Capital, the event’s host.
Indoor Farms of America is based in Las Vegas, NV, and utilizes vertical aeroponic technologies in its container farm products, which range from the truck-mounted farm that it will be showcasing at Indoor Ag-Con to a farm specially adapted to meet the needs of disabled veterans. The farms offer 40 plants/ft2 of grow area, are designed to be used in both controlled environment and greenhouse settings and use just 3% of the water of a traditional farm. It recommends that customers grow leafy greens, herbs, chili & sweet peppers, peas, strawberries, cherry tomatoes and beans in its systems, and is continually adding more crops to the list. The Company’s website is at www.indoorfarmsamerica.com.
Canadian Modular Farms has developed a series of modular units, such as, ones for refrigerated storage and for growing microgreens, that work with its primary unit, a specially designed 40’x10’x10’ composite steel box. The eight unit options can be combined to create the optimal farm for each customer. Its units are based on hydroponic growing and include ZipGrow towers, with over 300 towers packed into its production-only macro farm unit. The Company’s website is at www.modularfarms.co.
The farms will be displayed at Indoor Ag-Con, a two-day event held at the Las Vegas Convention Center, and tailored toward corporate executives from the technology, investment, vertical farming, greenhouse growing, and food and beverage industries, along with hydroponic, aquaponic and aeroponic startups and urban farmers. The event is unique in being crop-agnostic, covering crops from leafy greens and mushrooms to alternate proteins and legal cannabis.
The farms will join industry majors such as Argus Controls, Autogrow, BrightFarms, Certhon, Dosatron, DRAMM, Hort Americas, Philips Lighting, Priva, and Transcend Lighting in a 50+ booth exhibition hall. The event includes two full days of speakers, including executives from CropKing, Driscoll’s, Fresh Box Farms, Grobo, Helical Holdings, Intravision, Kalyx Development, MedMen, Plenty, Shenandoah Farms and Village Farms among a 40+ strong speaking faculty.
Indoor Ag-Con has also hosted events in Singapore, SG and New York, NY in the past year, and is currently planning its first event in Dubai. Since it was founded in 2013, Indoor Ag-Con has captured an international audience and attracted some of the top names in the business. Events have welcomed nearly 2,000 participants from more than 20 countries.
Newbean Capital, the host of the conference, is a registered investment advisor; some of its clients or potential clients may participate in the conference. The Company is ably assisted in the event’s production by Rachelle Razon, Sarah Smith and Michael Nelson of Origin Event Planning, and by Michele Premone of Brede Allied.
5th Annual Indoor Ag-Con
Date – May 3-4, 2017
Place – South Hall, Las Vegas Convention Center, Las Vegas, NV
Exhibition Booths – available from $1,499 at indoor.ag
Registration – available from $399 at indoor.ag
Features – Two-day seminar, an exhibition hall, and after-party
For more information, please visit www.indoor.ag/lasvegas or call 775.623.7116
Nicola Kerslake
Newbean Capital
775.623.7116
email us here
Philips Lighting Results Show LED Growth
Philips Lighting Results Show LED Growth
24 April 2017, by Matthew Appleby, Be the first to comment
LEDs now represent 61% of Philips Lighting sales, with first quarter sales at 1,690 million euros.
Philips Lighting announced the company’s 2017 first quarter results.
"Our comparable sales growth improved in comparison to previous quarters, driven by double-digit growth in our business groups LED and Home and a return to growth in Europe and the Rest of the World, despite ongoing challenging conditions in some markets," said CEO Eric Rondolat.
"We continued to increase our operational profitability and free cash flow compared to the first quarter of last year, demonstrating the rigorous implementation of our strategy.
"These results reinforce our confidence that the company is well positioned to achieve its 2017 outlook and medium term goals," Rondolat added.
On a comparable basis, the decline in sales slowed to -0.8%, an improvement compared to previous quarters. Europe and the Rest of the World delivered growth, while the Americas was impacted by an accelerated decline in conventional lighting and softer market conditions.
Business groups LED and Home achieved double-digit growth, driving total LED-based sales growth of 19% and total LED based-sales now representing 61% of total sales.
Rice U. Team Cultivates Ideas For Indoor Farming
Rice U. Team Cultivates Ideas For Indoor Farming
APRIL 12, 2017POSTED IN: NEWS RELEASES
David Ruth - 713-348-6327
david@rice.edu
Mike Williams - 713-348-6728
mikewilliams@rice.edu
Rice U. team cultivates ideas for indoor farming
Hydroponic garden graces university’s Oshman Engineering Design Kitchen
HOUSTON – (April 12, 2017) – Some engineering design projects click, hum or make no sound at all. Lettuce Turnip the Beet may be the first at Rice University to gurgle.
“The pumps are always going,” said design team member Dominique Schaefer Pipps. “The water never stops moving, keeping the plants alive.” The punningly named Team Lettuce Turnip the Beet has designed and built what is known technically as a “produce cultivation machine,” which resembles an oasis of greenery at Rice’s Oshman Engineering Design Kitchen (OEDK).
Sprouting from tiers of PVC pipes are lettuce, garlic and other vegetables, grown hydroponically — that is, without soil — and kept fresh by a pump circulating 55 gallons of water. The project was commissioned by a “zero-resource house” on the campus of Chalmers University of Technology in Gothenburg, Sweden. Previously, Chalmers partnered with another Rice team to create BioBlend, a variation on the in-sink garbage disposal that separates food waste from water and simplifies the composting process.
“The emphasis is on using as few resources as possible, using little energy and wasting nothing,” said Sanjiv Gopalkrishnan. He and Schaefer Pipps, along with team members Jared Broadman and George Dawson, are all seniors in mechanical engineering at Rice.
Dominique Schaefer Pipps tends to her team’s hydroponic experiment, a capstone design project required of most senior engineering students at Rice. Photo by Jeff Fitlow
The team achieved its goal to produce sufficient food to make one salad per week for one year, all in an apartment environment. The original prototype was built last November after two months of brainstorming. It’s a much bulkier, space-consuming model and has been moved outdoors to a fenced-in area behind the OEDK. It remains overgrown with sprawling tomato plants, broccoli and Swiss chard.
“We wanted to minimize power consumption and environmental impact, but maximize nutritional content and yield,” Dawson said. “The machine should coexist with humans in a rather small living environment. Noises, lights and smells shouldn’t interfere with the sleep cycle or life in general, and basic maintenance should be kept simple.”
According to the team, the device consumes about 900 watts, about as much power as a microwave or medium window air conditioner, and runs off one outlet even after replacing fluorescent lights with LED growing lights to improve the health of plants farther away from the fixtures.
The new prototype stands 8 feet tall, but its wooden frame and six levels of vinyl pipes are nearly flush with the wall. The biggest change is using square rather than round plastic pipes, which have a larger internal surface area and move more water. The frame is held together with pegs and friction and uses no glue or nails; the entire device weighs around 70 pounds.
George Dawson, a member of Lettuce Turnip the Beat, a senior engineering design team at Rice, works on its hydroponic garden. The team’s initial goal was to produce sufficient food to make one salad per week for one year in an apartment environment. Photo by Jeff Fitlow
“That makes transporting it easy. We have to get it to Sweden. This is like Ikea for toddlers, with really big parts,” Broadman said.
The team will install sensors to automatically monitor pH levels, nutrients, temperature and other factors before the device is installed in Sweden. The current setup uses one reservoir but the students expect a multiple-reservoir system, each with varying levels of nutrients, could permit fine-tuning the nutrient requirements of various plants.
The team is advised by Matthew Elliott, a lecturer in mechanical engineering, who said, “My job is easy. We meet once a week for updates. The students have taken care of everything.”
Team Lettuce Turnip the Beet will compete in the annual George R. Brown School of Engineering Design Showcase at Rice University’s Tudor Fieldhouse April 13. The showcase opens to the public at 4:30 p.m.
-30-
See the team’s web page at http://oedk.rice.edu/Sys/PublicProfile/34366121/4029765
Follow Rice News and Media Relations via Twitter @RiceUNews
Video:
Video produced by Brandon Martin/Rice University
Related materials:
Oshman Engineering Design Kitchen: http://oedk.rice.edu
George R. Brown School of Engineering: https://engineering.rice.edu
Images for download:
http://news.rice.edu/files/2017/04/0417_LETTUCE-1-web-1knd3s0.jpg
Rice University engineering students created a produce cultivation machine at the Oshman Engineering Design Kitchen on campus. From left: Jared Broadman, George Dawson, Dominique Schaefer Pipps and Sanjiv Gopalkrishnan. (Credit: Jeff Fitlow/Rice University)
http://news.rice.edu/files/2017/04/0417_LETTUCE-2-web-19ebcxm.jpg
Rice University engineering students expect to bring their hydroponic experiment to a “zero-resource house” on the campus of Chalmers University of Technology in Gothenburg, Sweden. (Credit: Jeff Fitlow/Rice University)
http://news.rice.edu/files/2017/04/0417_LETTUCE-3-web-1ep5mws.jpg
Dominique Schaefer Pipps tends to her team’s hydroponic experiment, a capstone design project required of most senior engineering students at Rice University. (Credit: Jeff Fitlow/Rice University)
http://news.rice.edu/files/2017/04/0417_LETTUCE-4-web-14oa51u.jpg
George Dawson, a member of Lettuce Turnip the Beat, a senior engineering design team at Rice University, works on its hydroponic garden. The team’s initial goal was to produce sufficient food to make one salad per week for one year in an apartment environment. (Credit: Jeff Fitlow/Rice University)
Located on a 300-acre forested campus in Houston, Rice University is consistently ranked among the nation’s top 20 universities by U.S. News & World Report. Rice has highly respected schools of Architecture, Business, Continuing Studies, Engineering, Humanities, Music, Natural Sciences and Social Sciences and is home to the Baker Institute for Public Policy. With 3,879 undergraduates and 2,861 graduate students, Rice’s undergraduate student-to-faculty ratio is 6-to-1. Its residential college system builds close-knit communities and lifelong friendships, just one reason why Rice is ranked No. 1 for happiest students and for lots of race/class interaction by the Princeton Review. Rice is also rated as a best value among private universities by Kiplinger’s Personal Finance. To read “What they’re saying about Rice,” go to http://tinyurl.com/RiceUniversityoverview.
- See more at: http://news.rice.edu/2017/04/12/rice-u-team-cultivates-ideas-for-indoor-farming/#sthash.yBzLqW2o.dpuf
Civic Farms To Break Ground On 20,000 sq.ft. Vertical Farm At Biosphere 2
Civic Farms To Break Ground On 20,000 Sq. ft. Vertical Farm At Biosphere 2
Vegetables can soon be reaped again from the Biosphere 2 complex of the University or Arizona. Tomorrow, on Earth Day, Civic Farms will break ground for anew 20,000 sq. ft. vertical farm inside Biosphere 2’s West Lung.
Civic Farms has come to an agreement with the University of Arizona to lease the cavernous space for a nominal fee of $15,000 a year. The new vertical farming operation has announced that it will invest more than $1 million in the facility and dedicate $250,000 over five years to hire student researchers in conjunction with the UA’s Controlled Environment Agriculture Center.
The brain behind the project is Paul Hardej, Illumitex' VP of Turnkey Horticulture Lighting Solutions and former co-founder of the recently dissolved indoor grow op FarmedHere. Hardej unraveled his new plans this week in an article on Tucson.com. "Half the 20,000-square-foot space to be devoted to production, with areas given over to research and scientific education. A variety of leafy greens and herbs such as kale, arugula, lettuce and basil will be packaged and sold to customers in Tucson and Phoenix"
In the article on Tucson.com, Hardej furthermore said that he recognizes the irony of growing food in artificial light at the giant Biosphere 2 greenhouse. He is convinced, however, that growing plants with artificial lighting can become as economical as growing them in sunlight. "[Indoor] Farming is much more productive and much more predictable than in a greenhouse [...] A vertical farm can be 20 to 100 times more productive. The overall direction globally is indoors".
The Civic Farms groundbreaking ceremony will take place tomorrow the special Earth Day event at Biosphere 2.
Click here for the complete article on Tucson.com, which also features CEAC's Gene Giacomelli and Murat Kacira.
Publication date: 4/21/2017
This Japanese Smart Farm is Getting Even Smarter
This Japanese Smart Farm is Getting Even Smarter
By John Hopton
April 21, 2017
Perfect lettuce is grown with help from robots and the Internet of Things
For all Japan’s advancements, it is still common to see older people in the country bending over awkwardly in fields, picking crops by hand – a vision of the past. Twenty miles west of Kyoto, though, stands a smart farm that’s very much a vision of the future.
SPREAD‘s Kameoka Plant grows 21,000 heads of lettuce a day using multistage hydroponics and artificial lighting.
A network of connected devices, the Internet of Things at work under the roof of one slick indoor farm, ensures full control and data analysis of variables like lighting, temperature and humidity, as well as the flow of liquid nutrients.
But, if this smart farming is not smart enough, it will soon get considerably smarter. Before the end of 2017, SPREAD will open the Techno Farm™.
The world’s first robot farm
The company envisages that its super high-tech farm will reduce running costs by around 30 percent. Most impressively, though, it will be run almost entirely by robots.
The new plant in Kizugawa, Kyoto prefecture, will produce 30,000 heads of lettuce per day, which will be tended to by robots that have been brought lettuce seedlings by stacker cranes.
The robots will take care of tasks like trimming and watering, before making sure that fully grown lettuce is harvested and delivered to the factory’s packaging line.
Several countries now have smart farms, but this will be the world’s first robot farm.
A vision of the future? Source: Wide Open Country/Twitter
SPREAD says it has, “developed the most advanced vegetable production system created by
taking advantage of the cultivation techniques and accumulated know-how with the cooperation of technology equipment manufacturers.”
The company showcased that production system at CeBIT 2017 in Hanover, Germany, last month. The opening of the plant is scheduled for winter 2017.
Is a smart farm an ethical farm?
Despite the obvious cost to jobs in the local area, SPREAD believes its methods will contribute to humanity, as well as, to technological advancement (and not just by giving us more lettuce).
SPREAD claims its mission is to “create a sustainable society where future generations can have peace of mind.”
“By developing a system that can produce high quality food, rich in nutritional value anywhere in the world in a stable way, we will build an infrastructure that can supply food to all people equally and fairly around the globe,” says the company site.
Spread says lettuce costs will be the same as regular produce. Source: Spread
Japan probably has more of a need to develop an automated labor force than most other countries do, given that its population is actually declining. Japanese people famously live long, and a future in which there are not enough younger workers to support older, retired people looms large.
Nevertheless, Spread’s global marketing manager, JJ Price, told the Guardian: “Our new farm could become a model for other farms, but our aim is not to replace human farmers, but to develop a system where humans and machines work together. We want to generate interest in farming, particularly among young people.”
The company hopes eventually to take its technology around the world. Meanwhile, Japanese shoppers can rest assured that even lettuce produced by such a futuristic smart farm will cost the same as lettuce always has.
[See More: How Agriculture Technology Has Helped Feed Our Growing Population]