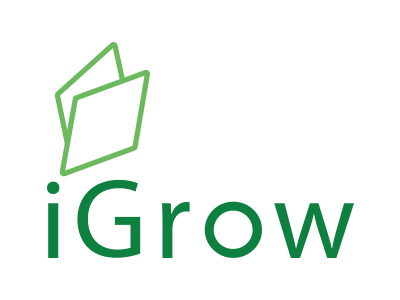
Welcome to iGrow News, Your Source for the World of Indoor Vertical Farming
AEssenseGrows Software Delivers 40% Faster Growth with Automated Sensor-Controlled Indoor Farming
AEssenseGrows Software Delivers 40% Faster Growth with Automated Sensor-Controlled Indoor Farming
The Guardian™ Grow Manager Makes It Easy to Manage Precision Control Through Any Device
NEWS PROVIDED BY AEssenseGrows, Inc.
SUNNYVALE, Calif., Feb. 5, 2018 /PRNewswire/ -- AEssenseGrows, a precision sensor and software technology company specializing in fully automated aeroponic platforms for consistent indoor high-yield plant production, announced the release of its Guardian Grow Manager intelligent software, now including a complete range of water, nutrient, air, and environmental controls that help customers achieve up to 40 percent faster growth with higher year-round yields.
AEssenseGrows Software Delivers 40% Faster Growth with Automated Sensor-Controlled Indoor Farming
AEssenseGrows produces modular aeroponic grow systems that are constantly aware of plant status through a blanket of precision sensors controlled by the Guardian Grow Manager software. Optimal delivery of nutrients to indoor plants is guaranteed with confidence from recipe through execution, with the constant attention to detail that automation provides. Every sensor reading is processed and mirrored to the AWS cloud, providing a perfect data record for any grow cycle and any plant variety. The company's AEtrium System produces top-shelf pesticide-free crops while reducing the requisite amount of water, nutrients and labor of traditional farming.
"The Guardian Grow Manager is what we rely on to generate a consistent, high-quality product," said Matthew Willinger, master grower at Fitchburg, in Oakland. "I can focus on plant health while the Guardian executes my orders perfectly. The reduction in time and labor is allowing us to be ultra-competitive."
The software provides fully automated intelligence to guarantee nutrient dosage is precise and consistently applied perfectly with every irrigation cycle. Wireless controlled sensors ensure that the Guardian constantly senses, doses, tracks, and analyzes an entire grow operation to specification.
In addition, AEssenseGrows has been licensed to integrate California's Metrc system into the software, meaning users will soon have "seed-to-sale" visibility end-to-end for their operations. The state selected Metrc as its track-and-trace system for tracking commercial cannabis activity and movement throughout the distribution chain.
"The Guardian software makes managing a large facility easy. With all the information of our entire grow at our fingertips we can see up-to-the-second sensor data from anywhere in our facility," said Andrew Lange, CEO of Black Diamond Biotech. "The software makes it easy to maintain the perfect nutrient and light levels and, by integrating the Guardian software into our climate control system, we can maintain the perfect environment for huge consistent yields."
The Guardian Grow Manager features:
- The ability to access, manage, and operate anywhere
- Full facility awareness and control
- Nutrient recipe control and automatic adjustments
- Predictable and repeatable grow results
- 24/7 real-time monitoring
- Complete data monitoring, AWS storage, and back-up in the cloud
- Easy system maintenance
The software delivers total control over photoperiod, nutrient concentration, nutrient dosing ratio, fertigation period (day and night), pH, hydrogen peroxide dosing, air temperature (day and night), humidity, carbon dioxide monitoring, carbon dioxide concentration, air movement, light intensity, water temperature, pump pressure and reservoir water level.
"Our customers have quickly recognized the benefits of having complete control of their grow environments at their fingertips," said Robert Chen, president and CEO of AEssenseGrows. "Advances like the Guardian Grow Manager have turned aeroponics from a theoretically effective method of indoor farming to a practical one. We help our customers compete with automated, low-cost manufacturing so they can be aggressive competitors."
AEssenseGrows will demonstrate its advanced aeroponics systems at the Global Forum for Innovations in AgricultureFeb. 5-6 in Dubai, United Arab Emirates, at CannaCon Feb 15-17 in Seattle, Wash., and at the World Agri-Tech Innovation Summit March 20-21 in San Francisco, Calif.
AEssenseGrows offers free webinars on key issues concerning indoor farming. The next, on integrated pest management, will be at 10 a.m. Pacific Time Feb. 14, and reservations can be made on the company's website.
The Sunnyvale, Calif.-startup was recently selected by Ackrell Capital as one of the firm's Top 100 Private Cannabis Companies for 2018.
AEssense, Inc. (pronounced "eh-sense") founded in 2015, is a new precision AgTech company based in Sunnyvale, CA. AEssenseGrows provides accelerated plant growth SmartFarm platforms and software automation delivering pure, zero pesticide, year-round, enriched growth to fresh produce and medicinal plant producers globally. With AEssenseGrows, you can precisely control your production operations at your fingertips from anywhere in the world.
For more information for AEssense, visit AEssenseGrows.com.
Phil Gibson
AEssenseGrows, Inc.
669.261.3086
pgibson@aessensegrows.com
SOURCE AEssenseGrows, Inc.
Related Links
Balderton Capital Leads $25M Series A In ‘Urban Farming’ Platform Infarm
Infarm, a startup that has developed vertical farming tech for grocery stores, restaurants, and local distribution centres to bring fresh and artisan produce much closer to the consumer, has raised $25 million in Series A funding.
Infarm, a startup that has developed vertical farming tech for grocery stores, restaurants, and local distribution centres to bring fresh and artisan produce much closer to the consumer, has raised $25 million in Series A funding.
February 5, 2018 | Steve O'Hear (@sohear)
Balderton Capital Leads $25M Series A In ‘Urban Farming’ Platform Infarm
Infarm, a startup that has developed vertical farming tech for grocery stores, restaurants, and local distribution centres to bring fresh and artisan produce much closer to the consumer, has raised $25 million in Series A funding.
The round is led by London-based VC firm Balderton Capital, with participation from TriplePoint Capital, Mons Investments, and previous investors Cherry Ventures, QUADIA and LocalGlobe.
It brings the total raised by the Berlin-based company to $35 million, including a $2.5 million grant from the European Commission as part of the Horizon 2020 program.
Related Articles
Infarm wants to put a farm in every grocery store
Infarm says the new capital will be used for international expansion and to further develop its 5,000 sqm R&D centre in Berlin. This will include bringing its vertical farming system to Paris, London, and Copenhagen, in addition to other German cities later this year. The startup is targeting 1,000 farms to be operational across Europe by the end of 2019.
Founded in 2013 by Osnat Michaeli, and brothers Erez and Guy Galonska, Infarm has developed an “indoor vertical farming” system capable of growing anything from herbs, lettuce and other vegetables, and even fruit. It then places these modular farms in a variety of customer-facing city locations, such as grocery stores, restaurants, shopping malls, and schools, thus enabling the end-customer to actually pick the produce themselves.
The distributed system is designed to be infinitely scalable — you simply add more modules, space permitting — whilst the whole thing is cloud-based, meaning the farms can be monitored and controlled from Infarm’s central control centre. The whole thing is incredibly data-driven, a combination of IoT, Big Data and cloud analytics akin to “Farming-as-a-Service”.
The idea, the founding team told me back in June last year when I profiled the nascent company, isn’t just to produce fresher and better-tasting produce and re-introduce forgotten or rare varieties, but to disrupt the supply chain as a whole, which remains inefficient and produces a lot of waste.
“Behind our farms is a robust hardware and software platform for precision farming,” explained Michaeli. “Each farming unit is its own individual ecosystem, creating the exact environment our plants need to flourish. We are able to develop growing recipes that tailor the light spectrums, temperature, pH, and nutrients to ensure the maximum natural expression of each plant in terms of flavor, colour, and nutritional quality”.
Two years since launch, Infarm says it is now operating more than 50 farms across Berlin in supermarket aisles, restaurants kitchens, and distribution warehouses. This includes introducing in-store farming into EDEKA and METRO locations, two of Germany’s largest food retailers, in which dozens of “quality herbs and leafy greens” are grown and sold at what the startup describes as affordable prices.
Noteworthy, with an output of up to 1,200 plants per month from a single farm unit, Infarm claims it has already enabled some locations to become completely self-sufficient in their herb production.
“This is the beginning of the urban farming (r)evolution: it will redefine what it means to eat well, reshape the landscape of cities, and re-empower the people to take ownership of their food,” says Erez Galonska in a statement. “Our ambition is to reach cities as far as Seattle in the United States or Seoul, South Korea with our urban farming network”.
Pegasus Food Futures Will be Showcasing Their Pioneering Hydroponic Farming Capability At The Global Forum For Innovations in Agriculture, in Abu Dhabi on February 5th and 6th.
ABU DHABI, United Arab Emirates, February 1, 2018 /PRNewswire/
Pegasus Food Futures Will be Showcasing Their Pioneering Hydroponic Farming Capability At The Global Forum For Innovations in Agriculture, in Abu Dhabi on February 5th and 6th.
With the world population set to grow from 7.3 billion to 8.5 billion by 2030 and 11.2 billion by 2100, an agricultural solution to the growing food needs of the population is essential.
- Hydroponic farming is an innovative, soil-less system that uses up to 90% less water than conventional farming, uses less land producing high yields of sustainably high quality, reasonably priced crops.
- Farms in arid areas such as the Gulf Cooperation Council (GCC) countries can make the most of the long hours of sunlight, providing the region with crops and reducing the need to rely on expensive imports.
- Visit the Pegasus Food Futures stand at the Abu Dhabi Exhibition Centre and hear farming, technology and business specialist James Yau give an expert talk on Combining Operations and Finance to Provide Best Fit Solutions: Bringing the Offline of Traditional Farming Online at the Controlled Environments and Indoor Farming conference session at 11.30am on 5th February.
Leading owner and operator of hydroponic farming facilities in Europe, the Middle East and Africa, Pegasus Food Futures will be showcasing their pioneering hydroponic farming facilities at the Global Forum for Innovations in Agriculture (GFIA) Exhibition in Abu Dhabi on February 5th and 6th at the Abu Dhabi Exhibition Centre.
With the world population set to grow from current levels of 7.3 billion to 8.5 billion by 2030 and 11.2 billion by 2100, ensuring long-term food security has never been more important. Providing an affordable and reliable food source that is also environmentally sustainable is essential to meet the needs of the growing population. Pegasus Food Futures provides solutions for these global food supply challenges through its operations and innovations in farming, livestock, feedstock and food production.
Their primary goal is to provide security for our food and agricultural future. Through continued investment into hydroponic farming technology, techniques and innovation they aim to support food security by growing sustainable and consistent produce that offers consumers a high quality, reasonably priced and fresh harvest each and every time.
Hydroponics explained
The hydroponic system is a soil-less culture for crops in which water and nutrients are delivered directly to the roots of the plant, dispensing with the need for the plant to expend precious energy growing long roots through the soil to reach these vital ingredients. Produce is grown in advanced, environmentally- friendly greenhouses, equipped with technology that controls and monitors each plant's nutrient intake with optimum accuracy. The design of the hydroponic farming systems ensures that the system uses up to 90% less water than traditional agriculture. Not only does this preserve precious natural resources, it also helps to reduce costs. This is particularly important for farms located in arid regions like the GCC, where water is scarce. Hydroponic farms in such regions can make use of the long periods of natural sunlight and produce affordable crops that reduce the need for the region to rely on expensive imports. Moreover, the controlled conditions mean the crops require no pesticides and produce consistently high yields.
A hydroponic farm can continue functioning for more than 100 consecutive years, resulting in a secure, stable source of both food and employment for the local area.
The Global Forum for Innovations in Agriculture
Pegasus Food Futures will be exhibiting at GFIA on Feb 5th and 6th and the farming and business expert James Yau will be giving a talk on Combining Operations and Finance to Provide Best Fit Solutions: Bringing the Offline of Traditional Farming Online at the Controlled Environments and Indoor Farming conference session at 11.30am on 5th February.
James Yau has 20 years' experience in management consulting in North America and Asia. In early 2009, he established and operated more than 10 farms within Asia Pacific. In 2013, he founded a retail chain to sell safe, high quality food produce in Hong Kong. During 2016, he partnered with a well-established Hong Kong wholesale company and penetrated the south China region which now trades over 65 million kilos annually. With extensive knowledge of financing and operating farms combined with technological expertise, James offers a unique opportunity to learn about how to bring traditional farming online.
Exhibition attendees can visit the Pegasus Food Futures stand in B20 and attend James' talk in the Conference Theatre, with the session starting at 11:30 pm, Monday, 5 February.
Keep an eye on the Pegasus Food Futures social media channels from for updates, news and pictures from the show (Instagram @pegasusfoodfutures, Twitter @pegagsusff, Facebook @pegasusfoodfutures)
Currently, hydroponic farming comprises only 1% of world agriculture. There is huge room for expansion of this innovative, sustainable solution to the problem of the growing demand for food. Pegasus Food Futures are keen to expand their portfolio and will be on hand to talk to farmers and investors alike.
About hydroponic farming
The System
The Pegasus Food Futures System (PFFS) combines intellectual property, seed germination processes and bespoke nutrient formulas that produce superior crops compared to competitors. From 2013 this system has been refined and adapted with continued investment into innovation ensuring that Pegasus Food Futures remains the market leader in the Europe, Middle East and Africa.
With further farms under construction in Europe, the PFFS has been further modified through research and development, investing in people and recruiting new skills into the team. The system and team now have an impressive track record in hydroponic farming technology and the ability to produce a wide range of fresh salad items, soft fruits, herbs, and vegetables.
The PFFS needs to also incorporate other key elements which will ensure all of our farms work under a defined efficiency and produce a stable, sustainable, high quality produce each and every harvest.
The controlled environment
Having the right environment is essential for the hydroponic farm. Key elements to a proper environment include humidity, temperature, Carbon Dioxide (CO2), and air circulation/exchange. Most crops grow and bloom according to the amount of light they are given. Generally produce require 10-12 hours of sunlight per day. PFFS uses natural lighting (sunlight) and this is achieved by building our farms in locations where there is an abundance of natural sunlight throughout the year.
All living things need space in which to live, grow, and reproduce. Different crops have different spacing requirements so the growing frames are specifically designed for each crop that is grown.
The water that supplies the plants is tightly monitored and controlled, from the pH to the nutrient balance, which varies throughout the growing cycle. The PFFS uses a unique formula for nutrients, specific to each crop and stage of the growing cycle, enabling the ideal produce to be grown.
About Pegasus Food Futures
What's New?
In 2017 Pegasus Food Futures acquired farms in Abu Dhabi, Ras-Al-Khaimah and two sites in Portugal. For more highlights of 2017, visit: http://pegasusfoodfutures.com/highlights-of-2017/
Social media and web
Web: http://pegasusfoodfutures.com/
Investors: http://go.hydroponic-investment.com/invest
Instagram @pegasusfoodfutures, Twitter @pegagsusff, Facebook @pegasusfoodfutures
About GFIA
Cultivating Change.
Born with the belief that continuous innovation in agriculture is the only way to sustainably feed nine billion people by 2050, the Global Forum for Innovations in Agriculture has emerged as a global authority on sustainable food production, driving innovation through exhibitions and conferences across the Middle East, Europe and Africa. Since 2014, GFIA events have welcomed over 20,000 visitors and worked with over 50 globally significant partners committed to using the Forum as a catalyst for change.
Global Vision. Local Relevance.
Showcasing the latest game-changing innovations and technology, each GFIA exhibition and conference offers stakeholders a pioneering forum and marketplace to foster meaningful dialogue, collaboration, recognition and year-round action between regional food producers, buyers, innovators, policy makers and investors.
Abu Dhabi.
At the centre of the arid world and with a rapidly growing population, the MENA region's need to address food security is more urgent than almost anywhere else. Hosting a large exhibition and free conference programme, GFIA Abu Dhabi will present the latest innovations and technologies to regional food producers across six key areas: indoor farming and hydroponics; date palm production; aquatech; livestock and animal health; smart honey production; and sustainable crops.
Part of UAE Innovations Month, GFIA Abu Dhabi is held under the patronage of H.H. Sheikh Mansour bin Zayed Al Nahyan and enjoys strategic support from Abu Dhabi Food Control Authority and the UAE Ministry of Climate Change and Environment.
For more information, visit: http://innovationsinagriculture.com/
SOURCE Pegasus Food Futures
Living Greens Farm is Changing The Way Produce is Grown
Living Greens Farm is Changing The Way Produce is Grown
Living Greens Farm, located just south of the Twin Cities in Faribault, MN has developed its own patented aeroponic vertical growing system that, according to its own estimates, uses 200 times less land and 95 percent less water than traditional farming.
Launched in 2012, the company currently grows fresh lettuces, herbs and microgreens on vertical platforms indoors in its Faribault Industrial Park facility, without the use of herbicides or pesticides.
“We didn’t invent aeroponics,” said Dana Anderson, founder and president at Living Greens Farm. “But we invented how to commercialize it. We feel aeroponics is the fastest and most disease-resistant way to grow.”
Historically, farming has always been dependent upon the mercy of Mother Nature. But with this high-tech type of indoor farming, a computer controls all light, temperature, humidity and nutrients, thereby eliminating the uncertainties of day-to-day weather changes.
Plus, with aeroponics there is no growing medium like soil or water used; the plant roots are simply open to the air and regularly misted with a nutrient solution. Plants are initially grown outside of the machines before they are placed into the rows under the misting system technology, thus maximizing space and giving the plants the room they need to grow. The company has 10 patents for its traversing misting system, allowing it to grow more food in a much shorter amount of time.
“It’s proprietary technology that we invented here,” Anderson told The Product News. “We’ve invested five years of time and about $5 million into the research and development side of our business. Beyond the aeroponics piece, there was also the invention of the traversing misting system. There are many moving irrigation systems for field crops and it’s easy to understand when you see irrigation systems moving across a cornfield. But what we own is a moving irrigation system for roots and that allows for fewer nozzles and improved reliability. Instead of installing hundreds of thousands of nozzles in a full-scale facility, we just have to install hundreds.”
The company recently completed a major expansion project and added 30 more growing systems to its already existing 10 systems, so it will be producing substantially more produce. Normally, in 15 to 17 cycles per year, the farm harvests around 1,500 plants per cycle.
“We are building a rather large farm — one of the largest indoor farms in the world — in Faribault,” Anderson said. “It has four times more grow space, and larger expansion in terms of production because we are adding more grow lights, so we think it’s actually going to be more like a 10 times increase in total revenue and total sales and production. It’s 21,000-square-feet of grow space and that will produce about 1 million units, or heads of lettuce, per year. Aeroponics is very fast in germs of growing plants and it’s actually the fastest way to grow, according to NASA. That is a big deal for indoor farming because if you can grow four or five more cycles a year, that is of course more revenue per square foot — 40 percent more revenue per square foot of grow space — and that means the operation is more efficient.”
Living Greens Farm is definitely changing the way food is grown and it may eventually go worldwide, duplicating its Minnesota operation in other countries and producing additional types of crops. According to the company’s website, its goal is “to make the world a better place by growing healthy, sustainable, fresh produce.”
And Living Greens Farm Chief Executive Officer Dave Augustine said, “Things like this are totally necessary to feed the human population in the future.”
By Richard Lutes
Source: The Produce News
http://www.theproducenews.com/digital_editions/pn101617issue/index.html
Kitchen Farms and Cultivators: The “Urban Farm” is Shrinking… Right Down to Kitchen Size
By Barbara Langford, President HydroPro Sales Inc
Is a “Kitchen Farm” in your future? Would you jump at the chance to grow all of your leafy greens and herbs fresh, pesticide-free and healthy right in your own kitchen? The concept to provide fresh healthy food for your family right from your kitchen is hard to resist. Can you actually control what you eat, providing your family with healthy HYPER LOCAL greens, herbs and small vegetables and fruits, that you grow yourself? Yes, you can.
Controlled Environment Agriculture or as the pros call it, CEA, is coming to a kitchen near you, perhaps your own. Controlled environment growing involves growing hydroponically in water or aeroponically, in mist, inside, in a building where factors like temperature, humidity, lighting, nutrient and water levels, CO2 levels and more, are constantly monitored and controlled. These facilities can be huge, housed in gigantic warehouses, or shrunk down to shipping container size. They can make a big impact on local food sources. CEA facilities are highly efficient when compared to traditional in-ground farming using a fraction of the water, and zero pesticides. Plus, they provide local fresh food, often in urban areas, reducing the carbon footprint of produce having to travel days to reach a market.
The “Cultivators” a Farm in Your Kitchen
Taking these methods, shrinking them down, even more, kitchen appliance makers are using the lessons learned by the big growers and are creating CEA appliances, known as “cultivators” for your home. Ranging in size from a dishwasher to a refrigerator, you now have the option of growing all your leafy greens, herbs and small vegetables and fruits right in your kitchen, living room or garage. It doesn’t matter if snow is falling or it’s 105 degrees outside, you can grow with minimum effort and automated success. OH.. and by the way? NO tilling, weeding or pests to deal with. You will grow clean and pure without backbreaking labor in a small space that will give you maximum results!
These units are being developed by companies everywhere and there are some beautiful examples of what your kitchen can look like with the addition of a kitchen farm cultivator. Some of these units are quite pricey but when you see them in designer kitchens, you’ll see why!
Tabletop Mini Farms
Kitchen farms can be as simple as a tabletop unit too, although, without the temperature, co2 and humidity control found in the self-contained closed units. The tabletop farms are experiencing great popularity as entry-level automated hydroponic growing systems that can provide leafy greens and herbs in an attractive home accessory way. Anyone who loves plants and gardening will enjoy seeing their fresh herbs and leafy greens growing inside, featured under high efficiency LED lights, even during a snowstorm! The winter “pent-up gardener” syndrome can be alleviated when one has a pretty crop of lettuce, spinach, bok choi or herbs, happily growing on the kitchen counter. No need to wait to peruse the Seed Catalogs! Buy now… Plant now.
The unit shown here is the Micro Farm by Keisue. Keisue specializes in LED lights, and for many years, studied how light spectrum effects plant growth. The LED lights in the Keisue unit have been specifically chosen to be the right frequency and intensity to provide exactly what leafy greens and herbs need to thrive. Watch out though, having these tabletop Micro Farms can become addictive! Once one is obtained, more may follow. Click the image to the left for more info and to purchase this affordable (and adorable) micro-farm.
Keisue is also involved in the production of enclosed, controlled environment kitchen farm cultivators, as seen above. These units can provide a continuous supply of fresh greens, up to 4 heads of lettuce or other greens per week! For more information, direct your inquiries here.
The video below is a great representation of how the kitchen cultivators work using crop rotation. Seeds and seedlings are cultivated in the bottom of the cultivator and, as they mature, moved to different levels to complete their growing cycle. There are always plants starting and always plants finishing under LED grow lights that provide the perfect light for maximum performance. Even microgreens, one of the most nutritious superfoods you can eat, can be grown in the cultivators. (or on your countertop) These fast crops finish in 8 to 10 days (!)
If controlling the quality of your food source is important to you, growing your own, right in your own kitchen may be your best bet! We have info on many systems that can start you off but not break the bank. Please contact us for more info.
Berlin Urban Farm-In-A-Box Raises $25 Million For European Expansion
The company, founded by three Israeli filmmakers-turned-entrepreneurs, plans to use the funds to roll out mini, in-store farms with Edeka, Germany’s largest supermarket chain. It is also working with Metro (B4B.DE), the country’s No.2 grocer.
Berlin Urban Farm-In-A-Box Raises $25 Million For European Expansion
February 5, 2018 Eric Auchard
FRANKFURT (Reuters) - Berlin-based urban farming start-up Infarm has raised $25 million to expand its indoor growing system - a soil-less technology better known for furtively growing marijuana - into major supermarket chains and restaurants across Europe.
The company, founded by three Israeli filmmakers-turned-entrepreneurs, plans to use the funds to roll out mini, in-store farms with Edeka, Germany’s largest supermarket chain. It is also working with Metro (B4B.DE), the country’s No.2 grocer.
Infarm wants to help cities become self-sufficient in food production, lowering farming’s environmental footprint.
A single, two-square-meter unit can be located in stores or dining rooms, or the same units can be chained together in central distribution centers to grow hundreds of different varieties of plants, each with its own micro-climate.
“We decided it would be more effective to distribute the farms themselves and farm directly where people live and eat,” Co-Founder and Chief Executive Erez Galonska said.
Industrial-scale U.S. rivals claim to be removing waste from long-distance agricultural supply chains, while Infarm is trying to break down the need for a supply chain itself, Osnat Michaeli, another co-founder, and Infarm’s chief marketing officer told Reuters.
Plenty Inc of South San Francisco, which operates vast indoor fields growing fruit, vegetables and herbs, raised $200 million in a 2017 round led by Softbank (9984.T) Vision Fund, marking the largest-ever agricultural tech venture funding.
Infarm said it will have 1,000 miniature urban farms operating across Europe by the middle of next year, starting with locations in Paris, London, Copenhagen and additional German cities by the end of 2018.
The compact plant growing system sits on stacked shelves, using hydroponics - a way of growing plants without soil - in a climate and LED-lighting controlled glass case. It grows everyday and exotic herbs like small-leaf Greek basil or Peruvian mint and leafy greens which customers are selling for prices at or below that of plastic-packaged herbs.
“We have replaced 15 grams of herbs in plastic boxes with living plants priced around 1.50 euros,” said Michaeli. “It’s the same type, similar price, but it’s alive.”
The new round of investment was led by Balderton Capital, one of Europe’s top early-stage venture investors, and joined by debt-financing firm Triple Point Capital and Mons Investments.
The company plans to invest further in its Berlin-based urban farm and research lab to expand its product catalog beyond some 200 herbs currently to include tomatoes, chillies, mushrooms, fruits and flowering vegetables, the company said.
Reporting by Eric Auchard; Editing by Kirsten Donovan
Our Standards:The Thomson Reuters Trust Principles.
What Does The Future of Conventional Agriculture Look Like? Does it Include Vertical Farming and Indoor AG?
Leading Japanese indoor ag tech companies to visit the heart of U.S. agricultural research and biotechnology community to attend controlled environment networking event.
What Does The Future of Conventional Agriculture Look Like? Does it Include Vertical Farming and Indoor AG?
Leading Japanese indoor ag tech companies to visit the heart of U.S. agricultural research and biotechnology community to attend controlled environment networking event.
If you are involved with the vertical farming or indoor agriculture industries, then you should plan on attending Ag Tech Worlds Collide. Scheduled for Feb. 21, 2018, at North Carolina State University, this event will tackle the big questions currently being addressed in the vertical farming and indoor agriculture industries worldwide.
Urban Ag News and the Japan Plant Factory Association in coordination with the Japanese Ministry of Economy, Trade and Industry are pleased to announce this joint networking event with U.S.-based agricultural organizations and operations. Participating Japanese organizations/companies include: Japan Plant Factory Association, Keystone Technology Inc., Shinnippou 808 Factory, Nihon Advanced Agri Corp., ESPEC MIC Corp. and MIRAI.
Presentations focus on CEA impact
Key presentations at this controlled environment agriculture (CEA) event will be made by Dr. Chieri Kubota, professor of controlled environment agriculture at The Ohio State University, and Dr. Ricardo Hernandez, assistant professor in the Department of Horticultural Sciences at North Carolina State University.
Dr. Kubota’s presentation will discuss “Optimizing input and output in controlled environment agriculture.” Dr. Kubota received a PhD. in horticultural engineering and M.S. in horticultural science from Chiba University in Japan. She worked for six years as a faculty member at Chiba University, 16 years in the School of Plant Sciences at the University of Arizona and recently joined the faculty at The Ohio State University. At Chiba University Dr. Kubota studied under and worked with Dr. Toyoki Kozai, one of the most published and greatest minds in indoor agriculture.
Dr. Kubota’s research program focuses on the development of science-based CEA technologies. She has been very active in interdisciplinary collaborations contributing to horticultural crop production under controlled environments. Her research includes value-added CEA crop production, vegetable grafting, hydroponic strawberry production and CEA LED lighting applications.
Dr. Hernandez will discuss “Using vertical farming/indoor ag to support traditional farming.” He is a faculty member in the Department of Horticultural Sciences in the area of horticultural energy at North Carolina State University. He has a B.S. in agronomy–crop consulting from New Mexico State University. His M.S. is in entomology–biological control from Texas A&M University. His PhD. is in plant sciences–plant physiology from the University of Arizona. He has a doctoral minor in entrepreneurship from the McGuire Center for Entrepreneurship, Eller School of Business and a minor in ag and biosystems engineering from the University of Arizona.
Dr. Hernandez’s research is focused on making CEA tools and techniques an integral part of sustainable agriculture and horticulture.
Event registration, location specifics
Ag Tech Worlds Collide will be held in the York Auditorium of the JC Raulston Arboretum in Raleigh, N.C. Entry to this event is $25 and includes morning coffee service and lunch. Attendance is limited and the event will sell out quickly. Click here to register.
Infarm Grows Produce In Supermarket Aisles
Infarm Grows Produce In Supermarket Aisles
There are more than 50 indoor vertical farms in Berlin alone
KEN SCHUCHTMANN
James Hurley
February 5, 2018, The Times
Retailers can earn brownie points with environmentally and ethically minded consumers already by boasting about selling local produce, but what if supermarkets could go one better and grow their own crops in-store?
It might sound fanciful, but some of Europe’s leading venture capitalists have invested $25 million in a start-up that produces vertical indoor “farms” that can be located in everything from supermarket aisles to restaurant kitchens, schools and distribution warehouses.
Infarm already operates more than 50 farms across Berlin and says that 1,000 units will be operational by 2019, including about 200 farms in London.
Erez Galonska, co-founder and chief executive of Infarm, said: “Rather than asking ourselves how to fix the deficiencies in the current supply chain, we wanted to redesign the entire chain from start to finish. We decided it would be more effective to farm directly where people live and eat.”
Infarm installations can be found in Edeka and Metro stores in Germany, two of the country’s largest grocers, with herbs and leafy greens being cultivated.
The company says that a single farm unit of two square metres can produce 1,200 plants per month and that some stores have become self-sufficient in herb production.
The plants are fed and nurtured by an internet-controlled system that uses sensors to monitor light, temperature, acidity, and nutrients for each crop.
Guy Galonska, co-founder of Infarm, said: “We collect 50,000 data points throughout a plant’s lifetime. Each farm acts as a data pipeline, sending information on plant growth to our platform, allowing it to learn, adjust, and optimise.” Thus different varieties of crops can be adapted for different supermarket locations to suit customer tastes.
Infarm was founded in 2013 by the Galonska brothers and Osnat Michaeli. Its vertical farms use “hydroponics”, a system that grows plants in oxygen and nutrient-enriched water instead of soil.
Osnat Michaeli, Erez Galonska and Guy Galonska have big plans
Erez Galonska said: “Our ambition is to reach cities as far as Seattle in the United States or Seoul, South Korea.”
The funding round was led by Balderton Capital, the London-based venture capital firm. The investment will help to pay for the planned international expansion.
Daniel Waterhouse, a partner at Balderton, said: “Urban living is growing unrelentingly across the world and societies are at a point where they have to confront big existential questions, such as how to feed their growing populations sustainably.
“ Infarm is right at the forefront of a new wave of companies setting out to tackle the inefficiencies in the food supply chain by making it possible to grow fresh produce right in the heart of our communities.”
Two Companies Taking A Vertical Leap In Newark
Two Companies Taking A Vertical Leap In Newark
By Sarah Fensom
Salad may not be the first thing that springs to mind when thinking of Newark. With its long history of environmental pollution and food deserts, Brick City is not a paragon of health.
Yet in recent years, it has embarked on a quest for wellness. In 2015, a ShopRite opened in the Central Ward, where there had previously been a scarcity of supermarkets. The following year, Newark Beth Israel Medical Center established the Beth Greenhouse, a small hydroponic farm that sells affordable produce in the South Ward.
In 2017, the former Hahne's department store building on Broad Street became home to Newark's first Whole Foods. And even former Newark mayor and current New Jersey senator Cory Booker has gone green, sharing snaps of his plant-based meals on social media and talking publicly about his veganism.
Getting in on the act are AeroFarms and Radicle Farm, two relatively new companies that are growing farm-fresh salad greens not in fields but in the city itself. The larger of the two, AeroFarms, runs several facilities in the Newark area, including a sustainable 70,000-square-foot vertical farm in a former steel plant in the Ironbound section. There, 2 million pounds of greens and herbs are produced each year, using an aeroponic growing method.
The other, Radicle Farm, operates in an 8,000-square-foot greenhouse in Branch Brook Park and grows greens hydroponically in horizontally-oriented plots using a method called nutrient film technique (NFT).
Both methods cut down on the environmental costs of field farming by using less water, less energy, and less space. Growing indoors allows the two companies to bypass fickle weather patterns and maintain the ideal conditions for their crops year-round, increasing both the yield and the freshness of their greens. AeroFarms and Radicle are showcasing two models for efficient, sustainable food growth, all the while helping to place Newark at the forefront of urban farming -- as unlikely as that may seem.
AeroFarms is the vanguard of the vanguard. Based on annual growing capacity, its Ironbound facility on Rome Street houses the largest indoor vertical farm in the world. With projects in development in China, the United Arab Emirates, and Europe, the company has its sights on the world but is still very focused on Newark.
"We embody Mayor Baraka's initiative 'Hire. Buy. Live.,' " says Marc Oshima, the chief marketing officer and a co-founder of AeroFarms. "In Newark alone, we have four farming operations and employ over 120 people -- 40 percent of which live in Newark, with 80 percent within a 15-mile radius."
The company's roots have spread throughout the city, with a research and development farm in a former downtown nightclub on Market Street; a 30,000-square-foot farm on Ferry Street, in what was once Inferno Limits, the paintball and laser-tag arena; and a smaller, 50-square-foot vertical farm in the dining hall of Phillips Academy. The school farm, which has been up and running since 2011, was a catalyst for the company to move its headquarters from Utica, N.Y., to Newark several years ago.
Later this year, AeroFarms is set to open a 78,000-square-foot vertical farm -- its biggest yet -- in Camden.
AeroFarms worked with RBH Group, the developers behind Teachers Village, on its Rome Street facility, with substantial backing from Goldman Sachs and Prudential Investment. (While it has raised some $50 million from investors, AeroFarms has yet to make a profit.)
"We looked at just about every ward and every property, and then we found the opportunity with RBH in the Ironbound and we thought it was somewhere we could make an impact," says Oshima. "There's a food desert right there."
One way AeroFarms is trying to stamp out food deserts is by giving Newark residents immediate access to their products, Oshima says.
"Wherever our farms are, people can come in and get greens all year round."
Many of the supermarkets that sell AeroFarms's retail brand Dream Greens (a 4.5 oz. package retails for $3.99) are extremely close to the farm, as well, reducing the toll that transportation takes on both the environment and the quality of the food.
The distribution center for ShopRite, one of AeroFarms's key partners, is just minutes from the Rome Street farm. "ShopRite puts a lot of emphasis on sourcing produce from local farms in the communities where our stores operate, and AeroFarms offers fresh produce we can source right here in Newark for our local ShopRite store," says Derrick Jenkins, vice president of produce and floral for ShopRite. "AeroFarms is a local business making an investment in Newark, and ShopRite believes it's important to support our neighbors and the city."
AeroFarms was co-founded by Oshima (the only Jersey native of the bunch), David Rosenberg, the company's CEO, and Ed Harwood, the chief science officer. Oshima and Rosenberg, who met in business school, formed a company called Just Greens in 2004. Research into the latest sustainable agricultural methods led them to Harwood, a former professor at Cornell's School of Agriculture, who was perfecting methods of aeroponic farming.
AeroFarms' patented growth method uses neither sun nor soil. The seeds rest on a special reusable cloth, developed by Harwood, which is made of BPA-free recycled plastic. They're housed in mobile modules that can be stacked many stories, effectively creating high-rises for plants.
Unlike with hydroponic methods, the seeds don't sit in water but are instead misted with a solution of nutrients, water, and oxygen deployed by a special nozzle (also developed by Harwood). Because the system is closed, fertilizer isn't leached into the waterways.
The method uses 95 percent less water than traditional farming and 40 percent less than hydroponics. In lieu of sunlight, energy-efficient LED lights supply the exact spectrum, intensity, and frequency that each individual plant needs for photosynthesis. This light system also ensures tyrannical control over each plant's texture, color, flavor, nutrition, shape, and size.
The farms also employ big data, monitoring more than 130,000 data points every harvest. Computer-generated algorithms enable the 250 varieties of greens and herbs the company grows to grow fast, some reaching maturity in two weeks, about half the time as those in the field.
Radicle Farm, though a much smaller operation than AeroFarms, also represents the future of farming. Co-founders Tony Gibbons and Jim Livengood started the company in Newark in 2014 and expanded quickly, adding a 50,000-square-foot facility in Utica in 2015.
Radicle grows a variety of microgreens, such as spinach, kale, tatsoi, and Russian mizuna, which have gained a reputation for their extraordinary flavor. As a measure to ensure freshness and maintain a diminutive carbon footprint, it keeps things exclusive, limiting its delivery zone to a 300-mile radius.
Before Radicle, Gibbons, a native of Maplewood, was immersed in the fine dining world, serving as the maitre d' at the celebrated Manhattan restaurant Gramercy Tavern for nearly a decade. He'd also dipped a toe into sustainable agriculture, establishing Garden State Urban Farms with his mother, Lorraine, in 2008 (together they helped launch the Beth Greenhouse).
Livengood, who grew up in South Orange, was a grant writer at the Liberty Science Center in Jersey City before joining up with Gibbons. While working on an indoor growing exhibition, he became fascinated by traditional agriculture's concerns and hydroponic agriculture's benefits.
"In terms of conserving water and land," says Livengood, "hydroponics sounded like an elegant solution."
He began looking for companies that were using hydroponic and sustainable growing methods and eventually found Gibbons.
When Garden State Urban Farms received a grant to turn the Branch Brook Park greenhouse into a working farm, the space hadn't been used in 20 years and was in bad shape.
"It looked like Jumanji when I first went in there," says Gibbons. With an opportunity to transform the historic space, the duo didn't initially have business in mind.
"Our original goal was just to get it up and running," says Gibbons, "but then, because of how much room was available, we decided to launch Radicle and use the greenhouse as a commercial space."
Still, the operation is a relatively small one, with only five people -- most of whom come through training programs from halfway houses -- working in the space.
"It's important for us to work with the community and give our employees job skills," says Gibbons. "We hire a small number of people and train them to do a lot of things. Most of our employees can do 80 percent of what we do here."
The nutrient film technique that Gibbons and Livengood use in the greenhouse involves irrigating and fertilizing the plants with a recirculating solution that contains all of the nutrients necessary for proper growth. No soil is used; instead, the plants sit in long, pod-like channels with a shallow film of the solution lightly bathing their root systems. Because the fertilizer is contained within the growing system, it doesn't enter the local water table and harm the ecosystem.
The method uses only 10 percent of the water that field farming does. It also cuts down on the use of fossil fuels -- the minimal amount of machinery Radicle employs is powered electrically -- and space.
"It accounts for the needs of the plants, so they're not sprawling out, looking for water like they would in the field," says Livengood. "We can also grow more -- we get five times more yield per square foot because we're growing year-round, and the plants themselves grow two or three times as fast."
As with aeroponics, this hydroponic system can be used to grow any plant, but it is particularly efficient with greens. "Focusing on greens allowed us to start quickly," says Livengood.
Ensuring that their greens taste good is a priority for the Radicle crew, who are always experimenting with what they grow and with various blends in which their products can be sold.
"Selling mixes allows us to be creative with what we send our customers," says Gibbons. Their "Chef's Selection" blend, for example, combines red and green romaine lettuce with bitter mustard greens, as well as peppery arugula and mizunas. The result is a fiery mixture of piquant flavors.
The "Petal Power" adds a visual pop, with edible flowers joining beet greens, baby chard, and romaine.
This attention to look and flavor has helped Radicle develop a niche fan base among fine restaurants in New York and Jersey City.
"In the very beginning," says Gibbons, "we had success with restaurants in New Jersey that were Italian in an authentic way, which makes sense because Italian cooking is defined by going to the market and getting fresh food."
Arturo's, an osteria and pizzeria in Maplewood, was one of Radicle's first clients. "When they first started, their production was limited to primarily delivering to us and Gramercy Tavern," says Fred Shandler, the owner
of Arturo's. "To see how far they've grown and leveraged that experience into Radicle Farm is pretty impressive. Their product and overall operation are really solid. We'll regularly receive awesome basil or a micro green (that's delivered while still in its root system) and literally use it the same day."
Radicle sells its blends straight from the farm to consumers through Fresh Direct and several grocery stores across New Jersey, such as Whole Foods. A 4-ounce package sells at the same price point as AeroFarms's Dream Greens, $3.99.
Global Expansion Tipped For ‘Breakthrough’ Indoor Farming Venture
80 Acres Farms regards itself as a supply chain disruptor; choosing to focus on delivering high quality produce without the food miles by converting indoor urban spaces into ultra-efficient controlled environment agriculture (CEA) farms.
Global Expansion Tipped For ‘Breakthrough’ Indoor Farming Venture
by Gill McShane
30 January 2018
Samantha Bergman shows 80 Acres Farms' freshly picked lettuce at high-end U.S. retailer Dorothy Lane Market in Dayton, Ohio.
80 Acres Farms' shelf space at Clifton Market in Cincinnati, Ohio, which is just 2.4 miles from the company's farm.
Setting its sights on going global in the future, progressive indoor farming business 80 Acres Farms is about to launch on the mainstream U.S. market with a 12-month offer of locally-grown micro-greens, culinary herbs, leafy greens, tomatoes, cucumbers and peppers that have been bred, grown and harvested for nutrition and taste, rather than transportation. PBUK speaks with co-founders Mike Zelkind and Tisha Livingston, and their first major investor, Shawn Harris from start-up facilitator Orange Wings in the Netherlands.
80 Acres Farms regards itself as a supply chain disruptor; choosing to focus on delivering high quality produce without the food miles by converting indoor urban spaces into ultra-efficient controlled environment agriculture (CEA) farms.
Since its creation in late 2015, the company has worked tirelessly with major U.S. universities and Dutch technology company Priva to fine-tune its hydroponic growing systems. At a time when they saw other indoor growers facing challenges, 80 Acres Farms believes it has made phenomenal progress and is approaching a major breakthrough.
“This is the first real proven indoor farming business that is on the verge of getting the process completely right,” claims Harris. “We can now confidently say that we will be part of this game-changing trend to deliver fresh, healthy produce from around the corner.”
Harris invested in 80 Acres Farms in 2016 and sits on the board of directors. She set up her start-up accelerator Orange Wings after stepping down late last year as chief executive of another firm she founded – Nature’s Pride, Europe’s biggest exotic fruit and vegetable importer.
Having developed four urban indoor production sites with experienced growers in Ohio, Alabama, Arkansas and North Carolina, 80 Acres Farms has been selling its produce commercially for almost a year. In the last few months, Harris says the business has secured early commitments from some highly respected retailers and one of the biggest foodservice companies in the United States.
Using local depots, each production site will pick its produce at the peak stage of ripeness to deliver daily to local restaurants and various regional and national retailers located within 100 miles. Further details have yet to be disclosed.
Ultimately, 80 Acres Farms aims to deliver its accessible, nutritious, tasty and affordable local food concept to other parts of the world, particularly areas that are unable to either produce outdoors or in conventional greenhouses for 12 months of the year.
Disrupting the supply chain
According to company CEO Zelkind, the key factor that sets the business apart from others is the indoor status of its farms and its product mix, added to the fact that the team not only has food industry experience but has run food companies on a commercial scale.
Importantly, Zelkind says 80 Acres has built an indoor system that grows affordable produce all year round under a completely controlled environment.
“It’s the next generation of controlled environment agriculture,” he claims. “80 Acres grows products much faster than in the traditional outdoor environment or even in a greenhouse environment. We can control all the factors, like CO2 levels, and when and how much to deliberately stress the plant to get the right level of nutrition and flavour.”
Co-founders Zelkind and Livingston have spent decades running companies in the food industry. Before 80 Acres Farms, Zelkind was president and chief executive officer of Sager Creek Vegetable Company when it was a division of Del Monte Foods Inc., San Francisco, while Livingston was chief operating officer at the same firm.
In establishing 80 Acres Farms, the duo says they are bringing back the “backyard fresh taste” of produce to many communities around the United States all year-round.
Livingston points out that currently fresh produce often travels long distances.
“Because of these distances traveled, our food is now being bred, grown and harvested for transportation rather than nutrition and taste,” adds Zelkind. “80 Acres Farms drastically disrupts current produce supply chains.”
Indeed, being local to its customers in four U.S. states means 80 Acres Farms can pick produce when it’s ripe, and plant varieties that are bred for flavor and yield, rather than transportation and survival in an unpredictable environment.
“This is a huge differentiating point,” Livingston says. “We can deliver ‘just-picked’ quality produce to a retailer or restaurant year-round. We have partnered with and continue to partner with commercial and research institutions to gather nutritional information and to grow produce that has much more nutritional value.”
Thanks to the proximity to customers, Zelkind claims the products offered by 80 Acres Farms are also “more nutritious than most organics”. “We view ourselves as the next generation of organics,” he explains. “We don’t use pesticides – organic does.
“We are considering getting an organic certification but at this point, we are better than organic. We abide by most organic practices but we go way beyond what organic does. We are closer to the customer and we offer fresher products.”
Already, Zelkind explains that the first chef and consumer feedback is about how the produce offered by 80 Acres Farms is much tastier and fresh.
“I have visited stores with Mike and Tisha and I have heard customers talk about their experience with the products and the taste difference, which is why they keep coming back – it just makes you feel good,” Harris explains.
As such, Zelkind and Livingston believe the company’s target consumer market is wide open to anyone who likes high quality, fresh, tasty and pesticide-free produce, whether that be millennials or baby boomers.
Expansion plans
From its headquarters in Cincinnati, Ohio, 80 Acres Farms now plans to build many more sites across the US, while aiming to expand globally. Each individual farm will deliver a product mix driven by the needs of local customers. On top of that, the company is building its biggest farm that will use 100% renewable energy when completed.
“80 Acres has very ambitious goals, but there is a lot to prove before that kind of expansion is warranted,” Zelkind notes. “We believe in keeping our heads in the clouds and feet firmly planted in the mud!”
For now, that means scaling with its customer base and striving to delight its growing consumer base. To that end, 80 Acres Farms has an exciting R&D product portfolio in the pipeline that includes root crops, which will complement its current range of micro-greens, culinary herbs, leafy greens and vine crops such as tomatoes, cucumbers, peppers, and hops.
“No one has yet figured out how to grow vine crops profitably indoors, in a completely controlled environment,” Zelkind comments. “We are the first and only ones in the world doing it so far but we can do it better. That’s the most exciting part. That’s the challenge for the next few years.”
Of course, one of the drawbacks of indoor farming is that it isn’t possible yet to economically grow all fruits and vegetables. “You won’t be able to do so for a long time to come,” admits Zelkind. “But there is no intention to replace traditional farmers. 80 Acres wants to work with these farmers and supplement what they can grow locally.”
Getting the process right
While the concept of indoor agriculture is logical and straightforward when broken into its subunits, Zelkind says bringing together all the components is not simple.
Firstly, to achieve the optimal growing environment you need multi-disciplined engineering, an understanding of plant science, and good farming experience. Then to grow crops profitably you must be able to understand manufacturing practices, automation and how to scale production.
Once you have that, you need the ability to brand and sell your products in a crowded marketplace. Plus, to run and build the business, you need the right people with the right experience. To set up the farms in the first place also requires a great deal of capital investment.
So, starting in late 2015 with a small R&D facility, 80 Acres Farms teamed up with international academics and scientists to figure out how to grow high quality plants with the right nutrition and flavour levels in the most effective way.
Since then, the company has developed a strong in-house engineering team and a large pool of data analysts who manage a production system guided by various sensors and other technologies to understand and optimise plant growth and development.
Following much trial and error, 80 Acres Farms is now on the fourth iteration of its production systems, which are installed across its current production sites in four states of the US. From here on, the company remains committed to driving the industry forward.
“This is a new industry and we all have so much to learn,” concludes Zelkind.
What is Controlled Environment Agriculture?
Controlled Environment Agriculture (CEA) is designed to optimise the growing conditions for food and aquatic production in an enclosed area, such as a greenhouse or building.
By controlling variables, such as: light, carbon dioxide, temperature, humidity, water, nutrients and pH levels, plants receive the correct amounts of water and nutrients, which often results in greater yields, all year-round. Production technologies include: hydroponics, aquaculture and aquaponics.
CEA operations can vary from fully-automated glasshouses with computer controls for watering, lighting and ventilation, to low-tech facilities that use cloches or plastic film to cover rows of field-grown crops, or basic plastic-covered tunnels.
CEA focuses on raising efficiency and maximising resources, including: space, water, energy, labour and capital. Given its nature, CEA also reduces the incidences of pest and disease, and allows the grower to recycle inputs like water or nutrients.
80 Acres Farms has developed a CEA system for urban indoor buildings where it claims the growing environment is completely controlled and guided by sophisticated technology. The company uses hydroponic technology to locally produce year-round and pesticide-free commercial volumes of micro-greens, culinary herbs and leafy greens, as well as vine crops, such as tomatoes, cucumbers, peppers and hops.
World Vegetable Map 2018: More Than Just a Local Affair by Rabobank
World Vegetable Map 2018: More Than Just a Local Affair by Rabobank
FEBRUARY 1, 2018 URBAN AG NEWS
The 2018 World Vegetable Map shows essential vegetable trade flows and highlights some key global trends in the sector, such as the growing importance of production in greenhouses and vertical farms, as well as the popularity of organic vegetables.
Download
> Click here to download the World Vegetable Map
Poster versions of the World Floriculture Map are exclusively available to Rabobank clients. To receive one, please contact your relationship manager.
Map summary: more than just a local affair
The global vegetable market is still predominantly a local market. Only 5% of the vegetables grown are traded internationally. But that share is increasing. Easy market access is vital for export-focused vegetable-producing countries like Mexico, Spain, and the Netherlands. Over the last decade, Mexico has further expanded its prominent position on the North American market, and internal EU trade has continued to grow.
Market for fresh (prepared) vegetables up, demand for canned vegetables down
An estimated 70% of all vegetables grown in the world are sold as whole fresh vegetables. This market is still on the increase, mainly outside of the US and the EU. Processing of vegetables (freezing, preserving, and drying) is a good way to prevent wastage, but global consumption of preserved (canned) vegetables has decreased over the last decade. At the same time, demand for frozen vegetables has increased by an average of 1% per year. Demand trends seem most favourable for vegetables that are convenient to eat and prepare and/or do well on (social) media because of considered health effects or their visual appeal. Examples are all kinds of (prepared) salads as well as sweet potatoes. EU imports of sweet potatoes (mainly from the US) have tripled in just four years’ time.
Organic vegetables most popular in wealthy nations
Organic foods are gaining market share around the world. The share of organic fruit & vegetable sales (in total fresh fruit & vegetable sales) has already passed 10% in wealthy countries such as Switzerland, Sweden, Austria, and Denmark (see Figure 1). In the US, this share is 9% and quickly growing. Income is not the only determinant for organic vegetable consumption. In the Netherlands, where the average income per capita is similar to that of Sweden and Austria, the market share of organic vegetables is only 5%. The reasons behind this are not clear, but it is likely related to supermarkets’ decisions on the category, price, availability, and quality of conventional vegetables, as well as cultural factors.
Sources: UN-Comtrade, Eurostat 2017
Figure 1: Share of organic fresh fruit and vegetable sales vs. income, 2016
Free trade agreements vital
As most fresh vegetables are highly perishable, easy market access is essential. In Latin America and Africa, vegetables are mainly sold regionally. Growing circumstances (climate, water availability), production costs, exchange rates, and trade agreements can trigger vegetable trade flows. Distortions in NAFTA or EU trade agreements (such as Brexit) will negatively affect vegetable trade. In the last decade, Mexico has further extended its very prominent position as North America’s vegetable garden. Spain and the Netherlands are key vegetable exporters within the EU (see Figure 2). Morocco has emerged as an up-and-coming vegetable supplier for the European market.
Figure 2: Intra-EU trade
Source: UN-Comtrade, Eurostat 2017
Up-and-coming import markets
A significant change in the world of vegetables is the rise of new vegetable-importing nations. Vegetable imports used to be concentrated in North America, western Europe and Japan. But gradually, countries like India, China, and the United Arab Emirates have upped their vegetable imports. Russia has also shown an increase in trade, despite the 2014 import sanctions for vegetables from the EU, the US, and a number of other countries. Currently, Belarus, Morocco, China, Armenia, and Azerbaijan are important vegetable suppliers to Russia.
The rise of controlled production in greenhouses and vertical farms
Globally there is a growing need for vegetables that are available year-round, produced in a safe and resource-efficient manner, and are of a consistently high quality. Consequently, vegetable production in greenhouses and vertical farms is rising. The area of greenhouses is estimated at 500,000 hectares, including roughly 40,000 hectares of glasshouses. Recently, we have seen vertical farms popping up in various places around the world, mainly in the Northern Hemisphere close to large consumer concentrations.
Vertical farming entails growing crops (often leafy vegetables) in a controlled environment using artificial lighting. As investments and electricity costs are relatively high, it is (still) challenging to run an economically viable vertical farming business. That said, discerning customers are willing to pay a premium for locally grown vegetables grown in a contained environment.
For more: https://research.rabobank.com/far/en/sectors/regional-food-agri/world_vegetable_map_2018.html
Restaurants Are Installing Their Own Mini Indoor Farms To Grow Mushrooms
Restaurants Are Installing Their Own Mini Indoor Farms To Grow Mushrooms
BY AIMEE LUTKIN
January 29, 2018
A company called Smallhold is changing how restaurants procure produce. They've developed a hydroponic system that can be installed to suit most kitchen spaces, or even as an aesthetic addition to the dining room. Inside these glowing blue shelves are mushrooms, whose health and growth is monitored by technology at Smallhold's headquarters. Vogue interviewed the company's founders, Andrew Carter and Adam DeMartino.
Carter and DeMartino are based in Brooklyn, in a deliberately urban environment. They're interested in changing the supply chain for cities and believe they can start a movement towards sustainable food production that eliminates some of the issues associated with transport. After meeting as roommates in college, they went their separate ways. Carter started experimenting with growing mushrooms in basements and other spaces he could find in the city. He started building out a shipping container as a larger mushroom farm; after showing his work to DeMartino, they decided to go into business together.
The "hardware" of the mushroom grow boxes, or "fruit chambers," are just one part of the equation. Temperature, humidity, carbon dioxide levels, airflow, and light exposure are all monitored with sensors and tiny cameras inside. Smallhold can check in to see how their shrooms are doing from their laptop anywhere, which makes it easier on the restaurants where they're installed. No one has to become a champion mushroom farmer overnight.
Even the material the mushrooms grow in is sustainable. It's a substrate made from recycled materials, like sawdust, coffee grounds, or wheat berries. The mushrooms mature in a Smallhold facility before being brought to their new home in a restaurant's fruit chamber. A few days later, the guys come by and help with the harvest. Mushrooms have a relatively short shelf life after they're harvested, so making their transport part of their growth cycle means having the freshest product possible at hand.
Danny Bowien is the chef and owner of Mission Chinese Food, which proudly features a fruit chamber. Having so many fresh mushrooms to hand has even changed his menu. He now has a mushroom jerky option to top fried rice—before it was beef. That probably makes local vegans happy, and the fruit chamber itself has become part of the restaurant's look.
“A lot of people think it is art,” said Bowien. “It doesn’t look like anything you’d see in any other Chinese restaurant.”
Smallhold is a great example of how hydroponic growing can be incorporated into every meal; according to their website, they've also started to offer fresh greens and herbs as part of their mini-farms. Soon, indoor farms could be adding flavor to every dish.
‘Amazon’ Has Put The Food Retail Market On Notice, Is This The Beginning Of A Trend?
‘Amazon’ Has Put The Food Retail Market On Notice, Is This The Beginning Of A Trend?
2/1/2018
Prepared by: Gregory Smith | ColdPICK / Chill Produce
Amazon is responding to a market trend; Social Media is creating a new market paradigm. The Boomers through the Millennials have gone from reacting to ads in newspapers delivered daily, to news flashes and tweets delivered on a second to second basis.
Amazon acquired ‘Whole Foods’ and will create an online provider of food and services. Whole Foods, as a result, of the Amazon acquisition will create a new age of grocery shopping characterized by an ‘on-line’ scheduled pick-up and delivery.
This will change, fresh produce supply dramatically. The Grower / Shipper / Marketing Company needs to recalculate the road ahead to ‘supply the new end user’.
In the future this will occur; less at the retail store and more directly to the individual buyer; through purchasing via Amazon and/or the National Supermarket / Big Box retailer’s offering ‘On-Line’ programs for pick up and home delivery.
The Effect on the Fresh Fruit and Vegetable Grower / Packer / Shipper and Marketing Company;
1. Packaging will change to deliver fruit and vegetable in “family style” units.
a. Package weights may increase.
b. Designs need to hold up to the material handling associated with ‘mail order’ deliveries;
i. Nesting feature to accommodate automation through the delivery process.
ii. Venting that will provide ‘freshness’.
iii. An insulated ‘master shipper’ and ‘pallet system’ to accommodate multiple products.
2. Field Pick and Packing will be replaced by Line Packing to accommodate
“Family Style” packaging units.
3. Methods of Post-Harvest Pre-Cooling will need to change to accommodate Line Packing.
a. A packaging change is not an easy step for a grower/ packer/shipper and it should be noted that the material handling in the existing packing- houses will not support the ‘new’ direction of the market.
4. Change is a Positive Step. The Fruit and Vegetable Grower / Packer Shipper / Marketing Company has not changed material handling procedures in decades; dating back from wood boxes to corrugated. Pick and Pack at the grow site will be adversely affected by the different packaging required to serve the new market direction.
What needs to happen;
5. Automate Material Handling in the Cold Chain to accommodate Line Packing versus Field Packing;
i. Pre-Cool individual family oriented cartons, not pallets – this will significantly Reduce Dwell Time
1. Energy Cost Reduction
2. Improved Quality – Shelf Life
3. Improved Productivity
ii. Automation will Eliminate LABOR
iii. Cost of Automation; OFFSET by Energy and Labor Reduction 2:1
iv. Package design needs to accommodate automated material handling and a change from ‘stacking tabs to nesting’
1. NESTING design adds an extra layer of trays per pallet level – Increasing Pallet Revenue – Decrease Shipping Cost resulting in (19th truckload is free).
‘Vertical / Greenhouse’ Urban Grow Sites
“Urban Grow Sites” will locate near defined Market Destinations;
a. The “Economy of Scale” associated with ‘Packing House Throughput’ will be modified to suit the new Fresh Market Paradigm.
i. Each produce unit (head of leaf lettuce, sprout, berry) has a per acre measurement.
ii. Each of these measurements can be calculated into a truckload of production.
1. Time, energy, labor, depreciation, material handling, break bulk, weight, et.al. is associated with the Truck Load Cost.
b. The building of ‘Urban Farms’ to serve fresh produce to the differentiated end user markets is characterized by a single ‘Urban Farm’ unit that will increase production from 7% to 20% / acre of production grown on a conventional farm*Bright Agrotech
i. The cost of the ‘Urban Farm’ acre compared to the conventional cost per acre can be calculated and consideration can be given to partnerships to provide fresh produce to a ‘Client’ who grows and packs for a defined market end use.
ii. Defined Client;
1. Retailer (Big Box, National Supermarket Brand, Independent) for a defined geographic area.
2. Third party supplier; Sysco
3. Defined End User; University and Corporate Campuses.
4. Recreation Areas – Resorts – Destination Sites
The new Fresh Market Paradigm will promote the growth of the VERTICAL and GREENHOUSE grower. This growth will not be in competition with conventional fruit and vegetable farming. It will be in partnership. A partnership that will be forged by start-ups that promote the new Fresh Paradigm.
i. Instacart (www.instacart.com)
ii. Grocerkey (www.GrocerKey.com)
iii. Deliv (www.deliv.co)
iv. 84-51 (www.8451.com)
v. Boxed (www.boxed.com)
CHILL PRODUCE - CPC 'Skid Mounted' Small Footprint Vacuum Cooler
How a Mushroom Farm Grows in a Manhattan Restaurant
Lion's Mane Mushrooms | Photographed by Caroline Tompkins
Walking into Mission Chinese Food on Manhattan’s Lower East Side, a mix of textures provide plenty to look at. The pink chairs and robin’s egg-blue tabletops contrast with the stark reds, whites, and blacks of the walls and wainscoting. A chandelier glitters above, sparkling against the stock of bottles behind the bar, itself electric with aqua-hued lights.
But the most alluring sight is an overhead box at the entrance that glows neon blue. Clear plastic bags tied at the top and stretched taut sit inside. Abstract and intricate forms protrude from them—some pink, others bright yellow, a third variety bluish in hue, they look as though they have been pulled from the ocean deep.
Mission Chinese Food's mini-farm | Photographed by Caroline Tompkins
“A lot of people think it is art,” says Danny Bowien, the chef, and owner ofMission Chinese Food. “It doesn’t look like anything you’d see in any other Chinese restaurant.” Though intentionally futuristic in design, the installation is more than aesthetic—it’s a miniature mushroom farm. A far cry from the tired and bruised portobello, cremini, and shitake that frequent grocery store shelves, the fungi here radiate life.
Andrew Carter and Adam DiMartino installed the miniature mushroom farm at Mission Chinese Food in late 2017. College roommates-turned-business partners, they propose a different approach to urban farming— rather than grow and distribute produce, they design, build, and install small-scale indoor farms outfitted to provide a rolling supply of fresh mushrooms. Equal parts urban farm and tech startup, their company, Smallhold, deploys hardware and software not only to grow a bounty of fungi but to carve out alternative routes from farm to table.
By the bar at Mission Chinese Food | Photographed by Caroline Tompkins
There are few signs of life surrounding the Smallhold office in Bushwick, Brooklyn. The landscape alternates between garages, warehouses, and empty lots. The bunker-like workshop and office space look out over a gravel courtyard decorated with shipping containers; cranes swing overhead, at work on a new development. But for Carter and DiMartino, this was the place to start a farm. Taking advantage of unused urban space—no matter the size—is integral to how Carter and DiMartino want to redesign the supply chain for cities. “If we can do it here,” Carter says, “we can do it anywhere.”
Mushrooms at Mission Chinese | Photographed by Caroline Tompkins
Carter dove headlong into urban mushroom farming two years ago—he wanted to use the skill-set he’d developed working in hydroponics systems design to develop a semi-automatic indoor mushroom farm. He wanted to explore how to use technology to enable more sustainable food production and bring agriculture to urban environments—he and DiMartino see Smallhold as part of a larger movement towards a more conscious way of eating.
After a year doing research and development (it involved a lot of growing mushrooms in basements), Carter bought a shipping container to turn into a commercial facility. Just as he was building it out, DiMartino returned from a motorcycle trip across the country. The friends decided to go into business together—but not wanting to be constrained by the limitations of a single space like a rooftop, backyard, or greenhouse farm, they devised a network of miniature farms they can monitor from anywhere.
Andrew Carter and Adam DiMartino, cofounders of Smallhold
Photographed by Caroline Tompkins
The mini-farms, also called “fruiting chambers” are largely automated. Sensors and cameras monitor temperature, humidity, CO2 levels, airflow, and light exposure. Carter and DiMartino can keep an eye on any unit from a laptop anywhere. Before the mushrooms are ready for restaurants, they spend between four and six weeks maturing in a warehouse. The mushrooms grow in a substrate made of recycled materials—mostly sawdust mixed with organic matter like wheat berries and coffee grounds.
Every week, Smallhold delivers fresh bags of mushrooms to the restaurants they work with. They mature for a few days, then Carter and DiMartino come by to harvest. Freshness matters a lot for mushrooms, confirms Dr. John Pecchia, a professor of mushroom science at Penn State University. They have a short shelf life—once they’re harvested, the quality depreciates rapidly. “We’re not fighting decomposition because [the mushroom] is still living the entire time. It’s as fresh as possible,” Carter says. Smallhold grows ten varieties of mushrooms, many of which are unfamiliar to the American market, where the white button still dominates. DiMartino likes the Lion’s Mane best—furry and oblong, it could be mistaken for an oversized hamster. Pink, yellow, and blue oyster mushrooms curl out of the bags, their delicate, bubbly forms like something from Dr. Seuss.
Oyster Mushrooms | Photographed by Caroline Tompkins
An ample supply of fresh, exotic mushrooms pushed Bowien to rethink his menu. He uses a portion of the weekly harvest to make mushroom jerky that tops fried rice. Before Mission Chinese started working with Smallhold, Bowien used beef—now the dish is vegan. “I like that the mini-farm grows mushrooms,” he says. “It feels very democratic.”
Back in Bushwick, chef Tara Novell runs the food program at Honey’s, around the corner from the Smallhold offices. She always sought out wild foraged varieties of mushrooms, but Smallhold provides her with a predictable supply—indoor farming is more efficient, and consistent. She whips a variety of powdered mushrooms into chocolate cake, and makes tempura out of the Lion’s Mane. Battered and deep-fried, it tastes like chicken nuggets.
The technology remains unfamiliar—like encountering virtual reality in the 1980s, chefs and consumers aren’t used to seeing automated, indoor forms of growing. But the potential is great. “Imagine that instead of the walk-in, it’s just your own mini-farm,” Novell says. “It’s just like the Jetsons. There is no limit, you can just keep growing in these little spaces.”
Indoor Ag Isn’t Here to Replace Traditional Farms — it’s About More Than That
Vertical farming has been getting a lot of attention lately. It is being called everything from the “future of agriculture,” to the next driver of ag investment, to the solution to a warming planet. It’s almost as if it’s going to solve all of our future farming needs.
Image courtesy of NutraPonics
Indoor Ag Isn’t Here to Replace Traditional Farms — it’s About More Than That
By Allison Kopf, Agrilyst Published: January 30, 2018
Vertical farming has been getting a lot of attention lately. It is being called everything from the “future of agriculture,” to the next driver of ag investment, to the solution to a warming planet. It’s almost as if it’s going to solve all of our future farming needs.
But that’s not the truth.
Vertical farming, and indoor farming more generally, isn’t the be-all and end-all solution to everything facing the industry. It’s true that it can be capital intensive, rent dependent, and not suitable for all types of crops. But indoor farming is about more than that. It is a component of an agricultural system that’s becoming more innovative and more technology-focused every day.
At its most basic level, agriculture is a system that needs to feed a lot of people very efficiently. Right now, we have a pretty efficient system, if you look at just calories produced.
However, not all calories are equal. A large portion of corn is grown to create biofuels, we see massive challenges with food waste, and inaccessibility leads to hunger around the world. So we need to think about where we can increase efficiencies throughout the food system. Can we start relying less and less on water and land in the production of our food? Second, we need our food to be healthier, safer, and all-around better for the consumer. We know that we can grow things that are calorie-intensive, but can we also make sure they are good for us? What’s more, can we grow things in a more food-safe and secure way?
For example, can we grow lettuce in a way such as we don’t have to worry about listeria and E. coli contamination? Can we become less dependent on fertilizers? Can we do things in a more climate-independent way? Can we take a lot of the risk out of the operating side, that conventional farmers are subject to, in order to focus less on seasonality and unpredictability and more on producing healthy, tasty food at scale?
Part of the solution
This is where indoor agriculture and vertical farming can play a really interesting role in the system.
These technologies are never going to entirely replace traditional farms, but there are certain crops that grow really, really well indoors and are well-suited to these growing methods. These are things that have shorter growth cycles and are highly perishable, so you can grow closer to the point of consumption and cut out the inefficiencies on the logistics and delivery side. I’m talking about crops like tomatoes, peppers, cucumbers, traditionally grown in greenhouses, and lettuces, herbs, microgreens, and berries, which are being grown more and more in vertical applications.
It’s true we’re relatively limited in terms of what can be produced indoors right now, but the implications even of just these few crops could be significant. Moving to indoor production for the crops I mentioned would free up hundreds of thousands of acres of land for crops that do better outdoors, such as wheat and other cereals, while simultaneously saving water and other resources for those products. We just need to convince more farmers of the value of these technologies.
We know this will work because we’ve already seen it happen. With tomatoes.
A question of efficiency
Two things that farmers are focused on are profitability and efficiency.
If you look at tomatoes, 20 to 30 years ago almost all production was done via soil farming. But then, by the turn of the century, attitudes started to change and almost overnight we started to see a lot of new greenhouse producers start offering tomatoes, and it just took off. Today, 37 percent of all fresh tomatoes sold in U.S. retail stores are now hothouse (or greenhouse) production, up from almost zero in the early 1990s.
What happened? Farmers noticed that indoor tomato production was simply more efficient than outdoor and made the switch. Need proof? According to the USDA, the average yield of conventionally grown tomatoes in 2016 was 1.85 pounds per square foot. Greenhouse hydroponic tomato growers, on the other hand, reported an average yield of 10.59 pounds per square foot. Similarly, the average yield of the conventionally grown head, leaf, and romaine lettuce is 0.69 pounds per square foot, compared with 8.71 pounds per square foot for leafy greens grown in a greenhouse.
Almost everything in our agricultural system is about efficiency, and indoor farming is nothing more than a tool in the farmer’s toolbox that will help them in their search for new efficiencies.
Looking ahead
The population is becoming more urbanized and we’re going to have a lot more mouths to feed over the next few decades; that much we know for sure. The indoor farming industry has been predominantly dominated by greenhouse crop production in the past but now, due to decreases in technology costs and an increase in local demand for food, we’re seeing an increase in alternate growing systems, particularly fully enclosed vertical systems. With that in mind, I expect to see a lot of crop production where efficiency gains can be had — such as herbs, lettuces, and berries — start to switch to indoor production in the near term.
But I really think that vertical farming, and indoor farming in general, are simply going to be tools that help farmers do more with less. This isn’t the first step into some sort of dystopian society where all of our food is grown in laboratories. It’s a new and exciting component to the food system that will help the industry scale for the future.
Allison Kopf is the Founder and CEO of Agrilyst, an intelligence platform for indoor farms and winner of Techcrunch Disrupt 2015.
Melbourne’s Latest Cafe Innovation Brings farm-To-Table Closer Than Ever
A new Melbourne-based start-up, Farmwall, has started building vertical, edible farms that grow fresh produce inside some of Melbourne’s iconic cafes and restaurants, as part of a mission to transform cities into food-producing ecosystems
Melbourne’s Latest Cafe Innovation Brings farm-To-Table Closer Than Ever
A new Melbourne-based start-up, Farmwall, has started building vertical, edible farms that grow fresh produce inside some of Melbourne’s iconic cafes and restaurants, as part of a mission to transform cities into food-producing ecosystems. The three co-founders Geert Hendrix, Serena Lee and Dr. Wilson Lennard hope to show you that cities can live more closely to nature, and give cafes and restaurants a better – fresher – food experience.
Farmwall is hoping to revolutionise cafes in Melbourne. Image by Farmwall
As a starting point, the Farmwall team created a scaled down version of an indoor farm. “If we have to start small, how can we achieve the largest reach?” was their thinking. In the size of a bookshelf, these vertical farms provide a consistent supply of fresh herbs and microgreens, at the fingertips of the chef. By growing produce on-site, Farmwalls reduce packaging waste and high food miles while introducing quality, freshness and variety into Melbourne’s hospitality scene.
A farmwall in action. Image by Farmwall
The small-scale farms have custom-designed facades and use aquaponic principles — meaning a beautifully-designed fish tank recirculates nutrient-rich water to each growing layer, topped with LED lights, bringing “farm-to-plate in under a minute.” Weekly visits are made bringing trays of sprouted seeds from the local, aquaponic farm. Chefs do the harvesting, urban farmers take care of the rest, building connections between patrons and the origins of their food.
The founders are hoping to change cities into food-producing eco-systems. Image by Farmwall
The team is installing the first two Farmwalls into Higher Ground and Top Paddock, two award-winning cafes owned by high-profile venue owner Nathan Toleman. There is a growing waiting list of venues that are eagerly waiting to be signed up next. Grappling with population growth but finite farming land, sustainable food practices and urban farming is a growing trend across major cities all over the world. Watch this space.
Living Greens Farm is Hooked on Aeroponics
Living Greens Farm is Hooked on Aeroponics
The Faribault company produces lettuce year-round, 21 days from seed to salad.
JANUARY 23, 2018
KATE LERETTE
What do popcorn and lettuce have in common? Nothing, really. It’s how Dana Anderson describes how produce is grown at Living Greens Farm: “It’s like pushing the popcorn button on the microwave,” he says.
Based in Faribault, Living Greens Farm is one of the largest indoor farms in the world, according to Anderson, who is the founder, president, and chairman. The company uses a computer system to control elements such as light, temperature, humidity, and CO2, combined with aeroponics—a method of growing plants by suspending their roots in the air—to grow lettuce, herbs, and microgreens. Rather than using soil, plants are sprayed with a nutrient-rich solution.
“Aeroponics is the fastest way to grow plants,” says Anderson. “Harvest is less than 21 days for a head of lettuce. It’s about two times faster than traditional farming.”
While Living Greens Farm didn’t invent aeroponics, it did develop its own vertical growing and traversing misting systems. The patented systems use 200 times less land and 95 percent less water than a traditional farm, says Anderson, which is huge, given that “70 percent of the world’s fresh water is used for agriculture.”
Anderson launched Living Greens Farm in 2012 after working out of his garage for three years. He and his team raised $8 million from friends and family to help get the company off the ground.
In October, Living Greens Farm completed its first expansion, increasing growing space from 5,000 square feet to 21,000. With the additional space, the company added 32 growing units to its existing 10, increasing its production to 1 million heads of lettuce per year.
Living Greens still has plenty of room to grow; right now it’s using only about 35 percent of its space. Once the company reaches max capacity, it will have 60,000 square feet of growing space. “When all is said and done,” says Anderson, “we will be able to produce a head of lettuce for every person in the entire MSP metroplex.”
The company currently sells greens at Lunds & Byerlys, a handful of Cub Foods and Hy-Vee stores, Fresh Thyme and other major co-ops. A few stores in Iowa will begin carrying its products this year. In addition to growing its grocery-store base, Living Greens Farm is working on adding accounts with food services at local colleges and corporate offices. Anderson also is exploring licensing opportunities worldwide and expanding its operations in other markets.
“There are hundreds of people who do this type of farming as a hobby, but in terms of large commercial companies, we only have three or four major [U.S.] competitors,” says Anderson. “What makes us different is our patented systems and our impact on the economy; we keep more dollars in the state.”
Italy: Innovative Systems to Increase Productivity
"The rise and fall system makes it possible to cultivate 12 plants per square metre. We set up a greenhouse with a hydroponic strawberry crop and LED lights, but the system could also be applied to other crops," explains Cesare Ghezzi.
Italy: Innovative Systems to Increase Productivity
At Orticoltura tecnica in campo (24th-26th January 2018), Idromeccanica Lucchini presented two innovative protected crop cultivation systems. The purpose is to increase productivity per surface unit.
"The rise and fall system makes it possible to cultivate 12 plants per square metre. We set up a greenhouse with a hydroponic strawberry crop and LED lights, but the system could also be applied to other crops," explains Cesare Ghezzi.
Visitors were also interested in the intensive hydroponic vertical crop. Idromeccanica Lucchini is the distributor of an innovative system patented in the UK "Yields are 20 times those of traditional crops," adds Mattia Battistello.
There are cultivation columns containing inert material. The system automatically releases water according to temperature and humidity conditions. Nothing is wasted as everything recirculates. Operators only need to top up water if it drops below the limit.
"The system can be used in cold greenhouses too, but it works better if they are heated. Thanks to vertical cultivation, harvesting is easier and yields are higher."
"A mulching film is placed on the ground to prevent agents from climbing up. Of course the produce harvested is extremely clean."
Contacts:
Idromeccanica Lucchini S.p.a.
Via Cavriana 4B
46040 Guidizzolo (MN)
Tel.: (+39) 0376 818433
Fax: (+39) 0376 819498
Email: info@lucchiniidromeccanica.it
Web: www.lucchiniidromeccanica.it
Publication date: 1/29/2018
Ecobain Gardens Announces New Name
Ecobain Gardens Announces New Name
Saskatoon, SK, January 8, 2018
Ecobain Gardens, a major producer of natural herbs from its vertical hydroponic urban farm in Saskatoon, SK, has announced a name change to better reflect its business.
In the making of the announcement, Brian Bain, Cofounder and CEO said, “we have rebranded to become “Ecobain Naturals.” Bain continued, “Our new name better describes what we do, selling live natural, tasty and aromatic herbs to consumers through more than 450 retail locations in western Canada. These include Sobeys/Safeway & Federated Co-op locations.”
The Ecobain Natural herbs are sold in live potted, living clamshell, and bare root forms in bags to allow retailers a unique natural aromatic herb product catered to their specific demographics. Bain said, “Selling live natural herbs grown in Canada enables us to supply a fresher, more nutritional product. As well, this has the advantage of a longer shelf-life for retailers, who now do not have to rely on imported products to stock their retail shelves.
Bain continued, “Our technologically-advanced hydroponic buildings use 98% less water, which is good for the environment, and our LED lighting allows us to offer the most aromatic, tasty live herbs to the consumers, 365 days per year.”
Presently, Ecobain Naturals grows four herbs for their live herb market, including basil, mint, dill, and chives that are available in nine differing packages. Brian Bain said, “Since our business began in 2014, we have found our nine differing SKU packages including, four potted herbs, three root-attached smaller herb bags, and the larger clamshell basil are the most consistent sellers in the market.
In concluding the announcement on the rebranding to Ecobain Naturals, Brian Bain said, “Our goal is to continue to grow our business by supplying the best live natural and aromatic herbs to the consumer market while providing a very cost competitive product for retailers. Our new name, EcoBain Naturals reflects what we offer for the future.”
Ecobain Natural produces 80,000 units of live herb products each month from its 6,000-square foot facility located in northern Saskatoon. It is the hydroponic system that accommodates this, and like its vertical hydroponic buildings, with Ecobain Naturals, the only way for the business is “up.”
For more information on EcoBain Naturals, please go to the company’s website at
www.ecobainnaturals.ca or check them out on Twitter (@ecobainnaturals), Instagram and Facebook.
-- 30 --