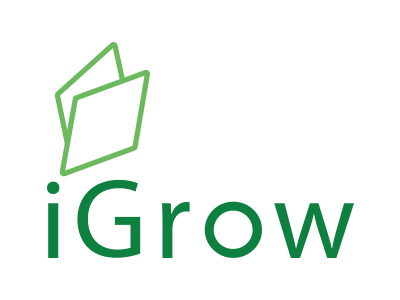
Welcome to iGrow News, Your Source for the World of Indoor Vertical Farming
Hydroponic Farms Become Produce Alternative For Local Businesses
By Desiree Montilla | September 20, 2018
CHARLOTTESVILLE, Va. (CBS19 NEWS) -- A couple of places around the city will soon be farming indoors when their hydroponic gardens from Babylon Micro-Farms are installed.
Babylon Micro-Farms is a company that focuses on bringing fresh produce to the table using hydroponic control technology.
The company said it will be installing hydroponic gardens at a couple of University of Virginia dining halls and the Trout House at Boar's Head Resort.
Three Notch'd Brewery already installed a hydroponic farm and has been using it for a month to help produce spices and herbs for dishes.
Patrick Carroll, executive chef at Three Notch'd Brewery, said the company reached out to them and offered this alternative indoor method to grow their produce.
"We use a lot of different microgreens for garnishing and also for soups," said Carroll.
Carroll said a representative from Babylon Micro-Farms approached him with the idea to bring their farming indoors.
"The great thing about hydroponic is that you can grow pretty much the same thing with no soil and 50 times faster than with soil," he said.
He also said the hydroponic farm is an important feature to show their guests the way they handle their food.
"It's a huge wild factor for guests because you don't see this anywhere. I think that it really draws people to the restaurant," Carroll said. "They see that we're really doing craft things here growing our own food and harvesting our own food."
The hydroponic farm also challenged Carroll to use new herbs in recipes.
"It kind of challenged me a little bit more to learn about what it tastes like and what would go well with it and then we would put that in our menu," he said. "Since we change our menu every week here at Three Notch'd, it's actually easier for us to do because we have new micro-greens and greens coming out for us."
Babylon Micro-Farms said it'll be installing hydroponic gardens at Newcomb and O-Hill Dining Halls at UVA on Friday.
The Trout House renovation is expected to be completed in late October.
NL: The Green East Opened A New Innovation Center
“We are proud that we have such a gem in the municipality of Raalte,” said mayor Martijn Dadema during the opening of The Green East on Friday 24 August.
Exactly a year ago, the presentation of the plans for a new innovation center with its focus on a circular economic future for the agri-food business was held. Now a large part of the innovation center was ready for use. During this festive day, The Green East, ABC Kroos and Energiefonds Overijssel also signed an agreement to jointly establish a pilot factory for the extraction of proteins out of duckweed.
Cultivation room
The new innovation center wants to be a 'home of green development', not only for Raalte and the Zwolle region, but it also has ambitions to be active nationally and internationally. Educational institutions, (research) companies and start-ups can head to The Green East to acquire knowledge and to exchange information with each other. For example, secondary education students will be able to complete a research project at the innovation center. Also for higher education institutions, there is the opportunity to gain knowledge about the latest developments in the field of circular economy. For example, students from Aeres Hogeschool Dronten will start their Entrepreneurship minor at The Green East in early September, as is explained by Geert Sol, board member of The Green East. “Knowledge valorisation and multifold value creation are two of our core values. We are very much looking for links with companies, governments and educational institutions to take steps together in the transition to a circular economy in the agri-food business.”
Water lentils the new gourmet food
Jeroen Willemsen, 'green protein crusader', was pleased with the cooperation agreement signed between The Green East, ABC Kroos and Energiefonds Overijssel in order to work towards energy efficiency in the meat industry. ABC Kroos is going to install a pilot factory on the site of The Green East where duckweed, also called water lentils, can be processed into ingredients that can be used in human food and food supplements, but also in raw materials for use in animal feed. In order to provide the world's population in the future with food, a food transition has to take place. "There will have to be a shift in the consumption from animal to vegetable proteins. A margarine manufacturer already advertises with the slogan 'plants are the new cows'. Soon water lentils will be the new gourmet food", according to Willemsen.
Laboratory
Martijn Dadema, mayor of Raalte, is also pleased with such an innovation center within his municipality, where companies and educational institutions are willing to contribute to the revolution in agribusiness. One of the other speakers, Menno ten Heggelen, program manager for circular economy at the Province of Overijssel, was also positive about the arrival of an innovation center that fits within his field of expertise. He already sees various initiatives in the province in the field of circular economy, but calls for a transition of, for and by the sector. "The Green East research center is already a great example of this."
For more information:
The Green East B.V.
Drosteweg 6 - 8
8101 NB Raalte
The Netherlands
info@thegreeneast.nl
www.thegreeneast.nl
Publication date: 9/13/2018
10 Great Plants To Grow With Hydroponics
Hydroponic growing is perfect to quickly grow vegetables, fruits, and herbs quickly. Having delicious crops all year around is simple through this soilless growing method.
Hydroponic growing is perfect to quickly grow vegetables, fruits, and herbs quickly. Having delicious crops all year around is simple through this soilless growing method. There are a few plants you can easily grow by providing a few basic necessities such as hydroponic nutrients, temperature, and pH levels
1. Strawberries
Growing strawberries all year around is simple and easy through hydroponics. This growing technique removes the worry of planting a seasonal fruit, allowing for an added ease of harvesting and growing. Whether with a deep water culture or an ebb and flood system, you’re sure to provide delicious strawberries. For quicker growth, it’s advised to plant strawberry runners instead of strawberry seeds.
pH Levels: 5.5 to 6.2.
Growing Time: Approximately 60 days.
Temperature: ℃ to ℃.
2. Lettuce
Lettuce is extremely easy, as these vegetables grow without needing any support due to their shallow root system and low vegetable height. It’s advisable to stagger lettuce planting to ensure a continuous supply, with regular nutrient solution changes for optimal growth.
pH Levels: 6.0 to 7.0.
Growing Time: Approximately 30 days.
Temperature: 7℃ to 21℃.
3. Peppers
A bit more advanced but a great vegetable to grow, peppers should be pruned at approximately eight inches tall to promote pepper growth. Either an ebb and flood or a deep water culture system are ideal for hydroponic growth. Peppers require around 18 hours of light per day, with lighting suspended at approximately six inches above the plants.
pH Levels: 5.5 to 6.0.
Growing Time: Approximately 90 days.
Temperature: Approximately 23℃ to 27℃.
4. Spinach
Ready to harvest from seedlings approximately 14 to 20 days, spinach does very well in hydroponics. Harvesting leaves weekly provides a good and steady supply, especially when planting plants close together. It’s advised to harvest leaves from the outside of the plant and not from the inner leaves.
pH Levels: 6.0 to 7.0.
Growing Time: Approximately 14 to 20 days.
Temperature: Approximately 18℃ to 20℃.
5. Tomatoes
Many different types of tomatoes can be easily grown hydroponically, however, some require approximately 18 hours of light to grow properly. They’re typically not advised for beginners but, if you have experience growing vegetables, you are very likely to succeed. Make sure to provide a two-part nutrient mix to achieve the level of nutrients that tomatoes need.
pH Levels: 5.5 to 6.5.
Growing Time: Approximately 10 to 14 days.
Temperature: 18℃ to 25℃.
6. Radishes
Radishes grow very easily in both soil and in hydroponic systems, being typically ready for harvesting in around a month. It’s advised to start growing radishes from seeds in cool temperatures. You don’t need to provide radishes with special lighting.
pH Levels: 6.0 to 7.0.
Growing Time: 3 to 7 days.
Temperature: 10℃ to 18℃.
7. Cucumbers
pH Levels: 5.5 to 6.0.
Growing Time:
Temperature: 22℃ to 24℃.
8. Beans
Both low maintenance and extremely productive, beans are great hydroponic crops. Whether you choose to grow pole beans, green beans, or lima beans, this vegetable germinates very quickly. Pole beans require vertical support when growing. Beans can be harvested approximately six to eight weeks after growth, with crops continuing for three to four months.
pH Levels: 6.0.
Growing Time: 5 to 7 days.
Temperature: Approximately 21℃ to 27℃.
9. Basil
As one of the most grown herbs in hydroponics, basil thrives with either a drip system or with a nutrient film technique (NFT) system. Make sure to weekly trim and harvest basil when it fully matures. Basil can be propagated from seed or from cuttings, the latter which form roots within approximately seven to ten days.
pH Levels: 5.8 to 6.5.
Growing Time: 7 to 10 days.
Temperature: Approximately 24℃.
10. Chives
Chives are easily grown from plants through hydroponics, requiring approximately 12 to 14 hours of light per day. It can take between six to eight weeks for chives to fully mature, and around three to four weeks of waiting between harvests.
pH Levels: 6.0 to 6.5.
Growing Time: 45 to 60 days.
Temperature: 18℃ to 21℃.
Choosing the ideal crops is the first step into your hydroponic growth journey. If you’re a beginner, fast growing crops are ideal for quick and delicious results, ensuring you get experience and results quickly.
VividGro® Launches GroNet™
Company Announces Indoor Precision Agriculture Platform, Enabling The Connected Indoor Farm
NEWS PROVIDED BY VividGro
CHICAGO, Sept. 12, 2018 /PRNewswire/
Building on its position as a market leader in horticultural lighting, VividGro announced today the release of its intelligent farm platform, GroNet, which enables growers to optimize crop yields and profitability. GroNet leverages sophisticated diagnostic and monitoring technology in a user-friendly format to reduce overhead and maximize crop health. "The keys to profitably operating a modern indoor farming business are data and analytics. GroNet offers commercial growers the real-time insights and recommendations they need to optimize every aspect of their growing environment in order to maximize yield at minimum cost," said Ted Vucurevich, VividGro's Chief Technology Officer.
Eliminating the guesswork
In the GroNet solution, hardware sensors and photometric equipment continuously measure the environmental conditions that are critical for growers to be able to optimize yields. Standard conditions that GroNet monitors include ambient temperature and humidity, CO2 levels and light exposure. Additional factors, such as nutrient dosing, fertigation management and power usage and consumption can be easily configured to each grower's specific preferences on a crop-by-crop. Integrated software proactively alerts the grower when conditions fall outside defined parameters, enabling quick action to eliminate or minimize adverse effects on the crops. GroNet creates algorithms to establish and automate predictive and corrective actions through direct communication with agricultural equipment. A streamlined, user-friendly dashboard offers at-a-glance data, detailed reporting and ongoing grower education.
Connects to existing systems
The GroNet sensors and software seamlessly interface with any compatible hardware, allowing for easy installation and integration. The system is already compatible with many existing lighting, HVAC, humidity control and nutrient delivery systems. Customized interfaces are available for systems that are not currently supported. OPIX Systems has signed a Master Integrator agreement with VividGro and will sell and integrate the GroNet system via its nationwide group of experienced systems integration professionals. OPIX and its affiliates have been working with the underlying control technology that GroNet is built upon for over a decade. "We are excited to be the premier partner selected to work with VividGro and the exciting new market for horticulture automation control systems," said Charlie Garcia, Managing Partner at OPIX Systems, LLC.
About VividGro
VividGro is a pioneer in the AgTech space. Tailored to the automation and efficiency needs of the indoor agriculture and horticultural markets, VividGro implements solutions that help growers maximize yields and reduce costs. Our state-of-the-art VividGro customized lighting product line delivers optimized PAR to maximize plant growth and PAR efficacy. Our control automation systems and data collection strategies are able to measure and modify growing to help growers learn how to use their resources more efficiently. It is not the lights you use it is how you use them. Learn more about VividGro at www.VividGro.com and join us on social media at Facebook, Twitter, and Instagram.
SOURCE VividGro
Related Links
Nebullam Aims To Revolutionize Indoor Farming
Jul 16, 2018 | News
By leveraging artificial intelligence, Ames startup focused on introducing product-to-producer method of production
Founded in a region of the United States with, arguably, the richest soil on the planet, a young Ames-based startup is aiming to revolutionize farming – without any of that soil. Employing a combination of high pressure aeroponics and artificial intelligence (AI), Nebullam is making waves in an increasingly competitive indoor farming industry.
The company was founded in 2016 when two former community college classmates reconnected. Today, Nebullam is operating two model farms – simultaneously generating income to keep the lights on and providing proof of concept for their innovative approach to agriculture – and seeking investment from engaged venture capitalists across the country.
The Genesis of an Idea
The seed for Nebullam’s founding was planted almost a decade ago when Danen Pool, co-founder and Chief Technology Officer, made a trip to Africa.
“The purpose of the trip was to provide water chlorinators to people in Swaziland and Johannesburg, South Africa,” Pool says. “A lot of the areas we visited were in a very arid climate. There was not a lot of fertile soil and produce had to be shipped in from long distances. It got me thinking about how you could sustainably grow produce in an area like that and that led me to begin researching different types of non-traditional growing techniques.”
That was in 2010. For months, Pool spent his free time experimenting with various forms of hydroponics and drip irrigation. By chance, during his research, he stumbled upon a NASA article detailing high pressure aeroponics, a technology developed originally in the 1980s as a method to grow produce on space missions.
The deeper Pool got into the science, the more he believed this was the way forward.
“It took me about six years to get a few system up and running,” Pool says, looking back. “I did all of the initial work in my home and it was promising. I could get the system up and going, leave it for a couple weeks and come back to it running just fine. I could grow produce very quickly and that was the major thing. Just with this first very rudimentary system, I could shorten growth cycles considerably.”
Reaching Out
With the technology, even in a very early stage, developed and tested, Pool knew that he needed some help with the business aspects of bringing his system to market. Among those at the top of Pool’s list was Clayton Mooney, a former classmate at Indian Hills Community College who had spent time as a professional poker player among other things.
“We had kept in touch, and I had been following what he was up to on social media,” Pool says of Mooney. “I knew he had returned to Ames and was in the startup space. I contacted him and let him know what I was thinking, hoping we could figure out a way to move forward together.”
Mooney took a measured approach to Pool’s initial pitch.
“Initially, I told him I’d be happy to look at his business plan and help him make connections here in Ames,” Mooney says. “I wasn’t really looking to get into something like this because I had a commitment coming up at Startup Ireland in Dublin. I told him I would take the summer to think about it.”
The summer in Dublin offered Mooney the time and space to consider the potential in full. The more he thought about it, he says, the more intrigued he became. Upon returning to Iowa, he was ready to partner with Pool to move the business forward. Mooney became the Chief Executive Officer, they settled on the name AeroLands, and began the startup process in earnest.
Building the Business
Among the newly formed team’s first actions was to reach out to experts at Iowa State University for feedback on the concept. The initial business model called for them to be producers – “indoor farmers” – providing their product from a warehouse. The longer term play was to put production units right into grocery stores and sell consumers produce they could pick themselves in the aisles of Hy-Vee or Fareway.
“We heard from a lot of people that they loved our technology but weren’t sold on our business model,” Mooney says. “The cost of labor just didn’t pencil out. We could grow indoors, but we were still going to need space to do it and workers to plant, manage and harvest the crops. That was all going to eat into our margins. We needed to figure out a way to automate as much as we possibly could.”
In the search for help in solving the automation challenge, Pool and Mooney met Mahmoud Parto, who would eventually become the Chief Software Architect and final member of the founding team. Mooney met Parto within the CYstarters cohort in summer of 2016. After learning of his background in computer and software engineering, Mooney asked Parto if he’d been interested in learning more about the company.
Initially, Pool and Mooney were just looking for a little help.
“When I showed him what we were working with in terms of automation, I was most interested in whether he could help us to reduce the cost of the equipment we were using to measure things like temperature and humidity,” Mooney says. “He came out of that meeting and was able to build us a working prototype with the same functionality, plus Bluetooth capability, for next to nothing.”
It was then, Pool and Mooney knew that Parto could play a pivotal role.
“I remember calling Danen that night,” Mooney says. “I told him we had to get Mahmoud on the team. We decided that night to offer him equity as a co-founder.”
Parto couldn’t commit to the idea at first.
“He told us he’d rather just help us out in the short term,” Mooney recalls. “But I think the gears started turning and it wasn’t long before he saw the potential and reached back out to accept our offer.”
Growing and Learning
With a full founding team established, the trio began looking for opportunities to get bigger and better. In December of 2016, they were accepted into the second cohort of the ISU Startup Factory.
The Startup Factory schooled the group on best practices in building a business while pushing them into a formal customer discovery process. The year-long program proved invaluable in clarifying the vision, developing a plan for growth, completing a friends and family round of investment, and preparing the team for pitching to larger investors. They also settled on the name change to Nebullam during their participation.
“The Startup Factory was instrumental in helping us to maintain a structured approach to building the company and keeping the team accountable to the vision,” Mooney says.
“The accountability is huge,” Pool adds. “I think the first time you become your own boss, you see the freedom to it, but there is also some trepidation that you are the one making the decisions. The intro classes were a big help to me in knowing what to expect.”
As part of their participation in the Startup Factory, the team was provided office space in the Vermeer building in the Iowa State University Research Park. With a location so close to Iowa State, it offered more than a place for meetings and to sit down in front of a laptop. It offered access to top tier interns to move the company forward.
“It is such a supportive entrepreneurial ecosystem,” Mooney says.
The Next Steps
Now “graduates” of the Startup Factory and a series of other accelerators and business development programs, the team at Nebullam has swelled to 10. They have settled on a hardware + software model that will enable indoor growers to leverage AI to fully automate the growing and harvesting process.
“The vast majority of indoor grow operations currently employ a producer-to-product model,” Pool says. “That means that the staff has to go to the product to plant it, tend to it, and harvest it, a method that isn’t much different from traditional farming.”
Nebullam, however, is developing proof of concept on a product-to-producer model. The plants would come to the producer, at a central transplanting and harvesting point. Using an elaborate network that learns with each crop cycle, everything is managed by AI – from what minerals are needed to spur growth, to when a given crop is ready for harvest.
This is a major differentiating factor for Nebullam when compared to others in the marketspace.
“There are a lot of startups on the hardware side, and a lot of others on the software side,” Pool says. “But running those varied systems together, there is a huge learning curve for the producer. We eliminate that. If you are powering your grow with Nebullam, we’ve eliminated any compatibility issues or learning curves.”
With Nebullam’s technology, when crops are ready to be picked, the system is automated to perform the entire process from harvesting and cleaning conveyor belts to planting the next crop.
“Everything will be monitored,” Pool says. “That monitoring will continually inform the network on what is working with a specific crop and help us to increase efficiencies and yields over time. The more we can automate, the more we can address the initial concerns that were raised in the infancy of our business about labor eating into our margins.”
The plan is being put into practice at the company’s second model farm, located in space at the ISU Research Park.
Nebullam’s vision – and the addition of Model Farm 2 – has been met with interest. The company was recently a top 3 finisher in the Young Entrepreneur Convention Pitch Competition, which is one of the largest single-day pitch competitions in the world. Through that, the team earned a coveted spot in angel investor Jason Calacanis’ intensive program for founders, Founder University. They have also reached the finals of a handful of other prestigious pitch and business plan competitions as they continue to identify individual accredited investors and venture capitalist firms to partner with in moving Nebullam along.
The team is confident they will find the right partner to bring Nebullam’s idea into practice on a large scale. And once that happens, the team is ready to shoot for the moon … or beyond.
“Our technology is applicable in zero gravity conditions,” Pool says with a smile.
“Seriously,” Mooney quickly adds, “we think we can complement a lot of the companies that are figuring out space travel. We might be nerding out a bit, but we are less than 1,500 days away from a spaceship landing on Mars. We are less than 2,500 days away from being a multi-planetary species. Who knows? Maybe our technology will be the one that makes it possible to nourish people as they explore space.”
While there is plenty to be done in those 2,500 days to make it happen, Mooney says the team is ready to do what it takes to make Nebullam a household name.
“The juice is always worth the squeeze,” he says.
VegBed Releases Update To Popular Bamboo Microgreens Mat
VegBed Increases Mat Weight And Introduces Their Growing Medium In Roll Form
The new Bamboo Fiber Microgreens Roll now offered in 10” x 400” (Photo: VegBed)
New York, NY - Sept 10, 2018
VegBed.com, the leader in innovative hydroponic growing medium, announced the released updated versions of their popular bamboo fiber microgreen mats. The company has been working closely with microgreens farmers to help design the new product.
The mat weight has been increased from 160gsm to 200gsm to allow for even more water absorption. The normal 10” x 20” mat will be able to hold about 10X’s its weight in water. The new roll option now offers the bamboo fiber with dimensions of 10” x 400”, great for large scale farms.
“I am very excited to announce Version 2 of our product as well as the option to purchase the bamboo fiber as a roll. A lot of farmers have channels and different sized trays, so we created the roll to help accommodate the custom sizing. Now, our bamboo fiber microgreens mat will be able to work with a variety of systems”, says VegBed founder Albert Lin.
VegBed has been researching and producing easy to use, clean and innovative growing mediums for the hydroponic market since 2018. The company ships worldwide
To learn more about VegBed growing mediums, future plans, or to book an interview, contact Albert Lin at (646)-247-1783 or email, info@vegbed.com, or visit the website at www.vegbed.com
About VegBed
VegBed provides the cleanest and easiest to use grow medium for hydroponic farms and other horticultural applications. We currently offer 3 products - foam grow cubes, bamboo fiber microgreen mats and a bamboo fiber microgreens roll.
VegBed can custom size their products for many application types - aeroponics, deep water culture, nutrient film technique, floating raft, vertical, flood & drain and many more. We work with commercial farms, hobby growers and are headquartered in New York, NY.
###
Local Charlottesville, VA Startup Is Changing The Vegetable-Growing Game
August 29, 2018
CHARLOTTESVILLE, Va. (WVIR)
A Charlottesville startup with big plans to change the way people get their vegetables is blossoming within the community.
By creating a system that allows the user to grow all their own produce quickly and efficiently, Babylon Microfarms is making it so people and restaurants are now enjoying fresher vegetables at lower costs.
Babylon Microfarms installed one of its hydroponic systems at Charlottesville's Three Notch'd Brewery two weeks ago and has a couple of other big projects in the works as well.
“It uses water and nutrients and plants are able to grow twice as quickly using up to 95 percent less water than conventional agriculture so we can grow a really high amount of produce in a small area,” said founder and CEO of Babylon Microfarms Alexander Olesen.
According to Olesen, they send everything pre-seeded to the user, so a restaurant’s chef wouldn’t have to worry about any farming or gardening. The only thing the user is responsible for his planting and harvesting the crops.
“It’s great to be out seeing these out with customers, seeing them enjoying the produce,” Olesen said.
The product is easy to use and provides places like Three Notch'd with Monticello bib lettuce for salads and many more leafy greens. The executive chef at Tree Notch’d Patrick Carroll said the system allows them to grow a lot of different microgreens, which are “great for flavors and garnishing.”
“It just really pulls a great ‘wow’ factor to the guests coming in,” Carroll said. “It’s a focal point of the restaurant. It’s just a wonderful product.”
This week, six of the restaurant’s menu items incorporate the produce grown in-house, and that number is expected to increase in the coming weeks.
Babylon Microfarms also has deals in place to install similar systems at UVA’s O-Hill Dining Hall as well as the Boar’s Head Resort. Olesen said he’s excited because Boar’s Head Resort’s recent renovation project allows them to make a larger commercial installation that will make their restaurant completely self sufficient in salad. According to Olesen, Boar’s Head would be the first in North American to have their own private hydroponic farm.
“It definitely sets you apart from everybody else,” Carroll said. “People come in and the first thing they see is that you’re really doing local seasonal even though you define the season with this because you can grow anything year-round.”
Babylon Microfarms is also working on a smaller-scale hydroponic unit that can be used in any home. The goal is for that unit to debut within the next year.
Signify Launches New Philips GreenPower LED Toplighting With Higher Output For Light-Loving Crops
Signify, the world leader in lighting, today announced the introduction of the new Philips GreenPower LED toplighting high output with a light efficacy up to 3.0 µmol/J and an output of 800 µmol/s. The new module will help greenhouse growers improve the growth of vegetables, fruits, flowers and other crops that require a lot of light. The new toplighting is available as of September 2018.
In addition to higher light levels and improved efficiency, the high output modules will have a lifetime of 35,000 hours and give growers greater control over their growing climate because of minimal heat radiation while accelerating the growth cycle and enabling more efficient use of grow space.
Best choice for increasing light or decreasing energy costs
“For many years, the use of LED toplighting for greenhouse vegetable cultivation has been steadily growing. Now we can offer an even more efficient solution for a variety of growing needs and light-loving crops,” said Udo van Slooten, Business Leader Horticulture at Signify. “Whether growers are looking to apply more light to leafy greens, roses, or bio-based crops, or are focused on reducing their energy costs, the new GreenPower LED toplighting can meet both requirements.”
Uniform light distribution and long lifetime
This 800 µmol/s version GreenPower LED toplighting module may be mounted on a trellis to deliver uniform light distribution, which gives growers flexibility with installation and adhere to light plans without the use of an additional C profile.
The high output version operates at an input voltage of 277V – 400V and will be available in three spectrums: deep red/blue low blue; deep red/white low blue; and deep red/white medium blue.
Signify became the new company name of Philips Lighting as of May 16, 2018.
Five-Day Introductory Training Course On Plant Factory With Artificial Lighting (PFAL)
Five-Day Introductory Training Course On Plant Factory With Artificial Lighting (PFAL)
By urbanagnews
July 18, 2018
In response to increasing global demands from indoor farmers, researchers and future entrepreneurs in the exciting emerging field of plant factory with artificial lighting (PFAL), also known as vertical farm, this coming October, Japan Plant Factory Association (JPFA) together with Chiba University will host an intensive five-day introductory training course in English on PFAL.
Since 2010, JPFA and Chiba University have been organizing various in-depth and practical sessions, including introductory to advanced courses. This five-day introductory session in English, held October 1st -5th, covers what you would need to know before or after starting PFAL business or research.
The sessions will be interactive academic and practical classes, covering topics such as structure and function of PFAL, environmental control, lighting, plant physiology, nutrient solutions, seedlings, recent new technology, and business case studies of commercial large-scale PFALs. In addition to lectures by academic professionals and PFAL representatives, optional excursions to some commercial PFALs on the last day of the course will be organized.
Objective and Goal
-To offer foundation for theory and experience-based practice, with a view to foster academic and industrial development toward next generation PFAL.
-To facilitate development and dissemination of technically and economically sustainable PFAL, through providing the firsthand technical and conceptual classes by broad-ranging professionals in practice from both academia and PFAL industry.
Who should attend?
Motivated current/potential indoor farmers who plan to start or just started PFAL business or research. They will gain understandings of elementary theory and practice of PFAL, basic knowledge of cultivation and operational management, and keys for business success, etc.
Lecturers
Scheduled Lecturers
Chiba University / JPFA: T. Kozai, Y. Shinohara, T. Maruo, S. Tsukagoshi, N. Lu, M. Takagaki, T. Yamaguchi, O. Nunomura and E. Hayashi
Lecturers from the PFAL industry: Representatives from 808 Factory and others
Guidelines for Applicants
Date: 2018. 10.1 Mon – 10.5 Fri
On the first day (2018.10.1), the reception and classes are scheduled to start in the morning.
On the last day (2018. 10.5), the optional excursion will be held in the greater Tokyo area and is scheduled to finish at approximately 15:00.
(Detail schedule will be announced once fixed.)
Location: 6-2-1 Kashiwanoha, Kashiwa, Chiba, Japan 277-0882
Center for Environment, Health, and Field Sciences, Chiba University
Japan Plant Factory Association (1F Meeting Room)
Kashiwanoha campus is located less than 1 hour from Tokyo by train.
There are several accommodations nearby. We will provide the information after you apply.
Fee: JPFA member JPY115,000/person
JPFA Non-member JPY145,000/person
Includes materials for lectures and the transportation fee on the excursion day.
Lunch is not provided, however, there are many options in walking distance including a shopping mall food court and grocery store.
How to apply
Click here for the application form!
Seats will be filled in the order that applications are received.
After applying, you will receive the invoice within 7 to 10 business days. After confirming your payment, your seat will be reserved and we will provide your confirmation booking number.
If your payment can not be made within 5 business days after receiving the invoice, your reservation may be canceled automatically.
Deadline for registration: The end of August or when capacity is filled.
Cancellation:
If participants cancel the training course on or before August 20th, 2018, we will return the fee except JPY 40,000 (a cancellation fee). If the cancellation occurs after August 21st, 2018, the fee shall be due in full.
In most cases, in lieu of canceling you may transfer your registration to another person without penalty.
Japan Plant Factory Association
Japan Plant Factory Association(NPO) is devoted to academic and business advancements in the global indoor farming/CEA industry. Our mission is to develop and disseminate sustainable systems that can address global food, energy and resource issues. We
manage around 20 R&D projects, monthly workshops, and training courses, etc. at Chiba University campus in Kashiwanoha, a smart city in Japan.
JAPAN PLANT FACTORY ASSOCIATION (JPFA)
6-2-1 Kashiwanoha, Kashiwa, Chiba 277-0882, JAPAN
Tel: 81-(0)-4-7137-8318 Fax: 81-(0)-4-7137-8312
http://npoplantfactory.org/e_trainingcourse.html
E-mail: training@npoplantfactory.org
Increasing Lettuce Coloration With LEDs
Using LED grow lights in plant production is a relatively new branch of science. In vertical farming where artificial light sources are used in a closed environment, it is important to collect data about the individual plant species to be able to produce the right spectrum and light intensity for vegetative and generative growth. Light spectrums can also be used to manipulate the plant's growth cycle for example in plant breeding (see blog post: Light Approaches To Speed Up The Generation Turnover) or secondary metabolite contents (anthocyanins, flavonoids, antioxidants, polyphenols etc.).
Why Does Lettuce Turn Red?
When cultivating red baby leaf lettuce in closed environments like vertical farms, without natural light conditions the artificial light quality and quantity plays a key role in the production of good quality vegetables. Of course, in the case of red leaf lettuce the deep red color that is caused by the higher anthocyanin content must be produced without affecting the other good qualities of the leafy green. Anthocyanin accumulation is generally linked to the abiotic stress the plant is experiencing or it’s a way for the plant to protect itself against herbivores and plant pathogens.
For instance, in the case of high light conditions, the anthocyanins serve the plant as an optical filter, redirecting excess light away from the saturated photosynthetic electron transport chain (Gould 2004). This means that the anthocyanins are protecting the plant leaves from harmful structural damage to their photosystems. Raising light intensity is, therefore, an effective way to increase the leaves anthocyanin content but it’s not a very energy efficient way to do this.
Using UV-A to Grow Lettuce
Previously this has been studied by Li and Kubota (2009) and they concluded in their study that both spectrums with enhanced blue and UV-A light increased the anthocyanin content in the leaves of lettuce ‘Red Cross’, but the far-red and green light had the opposite effect decreasing the anthocyanin production. Hence, at the end of the cultivation cycle in indoors only enhancing the blue and/or UV-A light spectrum would lead the red baby leaf lettuce to produce anthocyanins which gives them the special red coloration.
Using LEDs is the easy and energy efficient way to get quick results in anthocyanin formation in closed environment conditions. This could be easily implemented into the existing indoor growth systems by merely switching on the right spectrum for enhancing the coloration at the end of the growth cycle.
Valoya made internal trials where two light spectrums were used to test this light quality effect with enhanced UV-A / blue spectrum light (S46) and our standard light for vegetative growth with leafy greens (AP673L). Light intensity levels were taken into consideration and tested in a pre-trial. The amount of anthocyanin was measured at the end of the trial with optical polyphenol measuring tool (Dualex, ForceA). The experiment was done with two red baby leaf lettuce varieties: ‘Sadawi’ and ‘Diablotin’, with very similar results.
The light treatments were done with the two spectrums and in the case of AP673L spectrum with three different intensities. The data was analyzed in SPSS with two-way Anova. The homogeneity of variances was analyzed with Levene’s test and the normality of the data with Shapiro-Wilks test.
The results for anthocyanin accumulation confirmed the hypothesis that the enhanced blue and UV-A spectrum will increase the production of anthocyanins in red baby leaf lettuces’ leaves leading to a similar amount as in that of the high intensity treatment. Increasing the AP673L light intensity from 200 µmolm-2s- to 400 µmolm-2s- had linearity trend with increasing intensity (Figure 2).
Figure 1 Red baby leaf lettuce anthocyanin trial with different spectrums. The anthocyanin amount was measured three times and three measurements were taken from one plant. Anthocyanin index = Log* (Near-infrared fluo. excited red / Near-infrared fluo. excited green).
Figure 1 Red baby leaf lettuce anthocyanin trial with different intensities (in micromoles). The anthocyanin amount was measured three times and three measurements were taken from one plant. Anthocyanin index = Log* (Near-infrared fluo. excited red / Near-infrared fluo. excited green).
This accumulation of anthocyanins could also be observed visually…Read the rest at valoya.com
Autogrow Unveils OpenMinderTM – An Open-Source Solution For Water Monitoring
29 August 2018: Global AgTech innovator Autogrow has unveiled an open-source root zone monitor as part of an ‘open-collaboration’ platform.
“OpenMinderTM is a product that someone can build themselves, but more than that it represents where this industry is going with open-collaboration, APIs and a focus on water sustainability,” explains CEO Darryn Keiller.
“Governments and local legislators around the world are tightening the rules for growers when it comes to water usage and run-off. Growers need to use any and all tools at their disposal to ensure they are not only growing sustainably but have the data to back it up.”
OpenMinderTM is an open-source DIY project from Autogrow targeted to technology developers and for application with small growers. Released under a Creative Commons BY-NC-SA license, OpenMinderTM provides an open-source API used in conjunction with a Raspberry Pi HAT.
“Essentially we are giving away water management technology. There are very few people who understand how to design and build these technologies and, for someone motivated enough, we are providing the hardware schematics and source code to do it.”
“OpenMinderTM is the perfect product for an NGO or government to fund and manufacture for countries whose farmers need a subsidized or free, water run-off or irrigation monitoring system. And from an education perspective, there are high schools all around the U.S. and in other countries introducing classes on hydroponic systems. OpenMinderTM gives them a practical build they can do.”
Autogrow sees OpenMinderTM and other products built with APIs as the future for the industry where tech-savvy growers will demand suppliers work together and provide tools that can integrate seamlessly and give them exactly what they want.
“When I first began shaping the new vision for Autogrow one key realization was to embrace the idea of open collaboration, and this was because the entire tech sector that supported indoor and controlled environment growing was built on closed and proprietary technologies,” says Mr. Keiller.
“Fundamentally, that behavior is a roadblock to accelerating growers and producers’ rapid adoption of new and beneficial technologies. Having polite discussions isn’t changing anything. Robert Stallman, GNU and Linus Torvalds with Linux changed the way that all commercial operating systems got developed by breaking the stranglehold of UNIX, which was dominated by Sun, DEC, and IBM. We are doing the same for agriculture.”
For more information:
OpenMinderTM Getting Started – https://lab.autogrow.com/docs/en/open-source.html
OpenMinderTM Blog post - https://medium.com/the-growroom/monitoring-your-rootzone-with-openminder-fba51b16913
Go to GitHub - https://github.com/autogrow
ENDS
MEDIA QUERIES
Kylie Horomia, Head of Communications
(e) Kylie.horomia@autogrow.com
(m) +6421 733 025
(w) www.autogrow.com https://lab.autogrow.com/ www.cropsonmars.com
Sales queries – Sales@autogrow.com
About Autogrow
Autogrow leverages the power of technology, data science and plant biology to provide indoor growers affordable, accessible and easy-to-use innovation – 24/7, anywhere in the world.
Our hardware, software and data solutions support growers and resellers in over 40 countries producing over 100 different crop types.
We have a depth of experience and passionate, fun people creating original ideas and making them a reality for our growers.
A ‘Fresh’ Look At Indoor AgTech
ndoor production of fresh fruits and vegetables leveraging aeroponic and hydroponic growing techniques has gained meaningful investor momentum in recent years.
Kenneth Scott Zuckerberg, AIF® AFA®, Wells Fargo Sector Manager, Agrifood Technology and Packaged Foods
Indoor production of fresh fruits and vegetables leveraging aeroponic and hydroponic growing techniques has gained meaningful investor momentum in recent years. The simplistic bull case for sector investment is that indoor farming operations provide direct exposure to a growing consumer demand for healthy, local, farm-fresh produce. Unfortunately, the defendable bear case is that indoor farms are expensive to build and operate, lack full automation, and do not command a pricing premium over outdoor-grown, organically produced crops.
In my opinion, the path to greater value creation lies in the partnership between indoor farms and food retailers. I think this can be accomplished by: 1) creating a branded ultra-premium offering; 2) creating private-labeled products leveraging the retailer’s brand name; and/or 3) installing living breathing vertical farms inside the produce section of the grocery store. Can anyone say craft produce?
I commenced a deep-dive into indoor farming prior to moderating a panel at the Indoor AgTech Innovation Summit sponsored by Rethink Events, Ltd., this past June. The event afforded me the opportunity to gain perspectives from the leading players in the space, including AeroFarms, Bowery, Bright Farms, 80 Acres Farms, Gotham Greens, Plenty, and Uriah’s Urban Farms, as well as greenhouse data service providers such as iUnu, and academic experts from Cornell University. The knowledge gained augments existing Wells Fargo Food and Ag Industry Advisor subject matter expertise.1
Defining indoor farming and Controlled Environment Agriculture
Indoor farming is actually a sub-segment of a much broader segment of farming called Controlled Environment Agriculture. The New York State Energy Research and Development Authority’s definition reads as follows:
Controlled Environment Agriculture (CEA) is the combination of engineering, plant science, and computer managed greenhouse control technologies used to optimize plant growing systems, plant quality, and production efficiency. CEA systems allow stable control of the plant environment, including temperature, light, and CO2, and provide separate control of the root-zone environment.
In simple terms, indoor farming can be seen as an innovative, conservation-oriented method of growing high-quality produce such as lettuces, microgreens, tomatoes, and other fruits and vegetables on a year-round basis in local communities. Currently, a large amount of the fresh produce consumed in the U.S. is grown on the West Coast and shipped cross country, or imported from other farming regions such as Mexico.
To be clear, CEA is not a new concept as evidenced by the fact that mushrooms have been grown indoors in the U.S. for approximately 100 years, and edible plants and decorative flowers have been grown in greenhouses and nurseries in Holland for approximately 50 years. Tomatoes are another important crop grown in greenhouses. Additionally, NASA has claimed to pioneer the process of growing plants utilizing LED lights as far back as the 1980s. What is new, however, is the combination of more powerful and energy efficient LED lights coupled with improved controls on temperature, humidity, and sensors, tied into a plant growing system on warehouse vertical racks, in shipping containers, or on rooftop farms.
Investor interest in indoor agriculture
In recent years, more than $500 million of capital has been deployed by investors in indoor AgTech startup companies based on the simple thesis of high-return potential resulting from the intersection of declining prices for LED lighting technologies and the growing consumer demand for fresh produce grown with limited use of traditional crop inputs. The capital has come from socially responsible funds and others seeking returns from companies that use clean technology and emphasize sustainable business practices.
The following table presents a snapshot of the competitive landscape for the indoor AgTech Industry. It should be noted that this snapshot excludes traditional nurseries and greenhouses along with certain technology robotics companies. (The latter happens to be a very interesting category, including startups such as AgriLyst, Arable, FoodLogic, Harvest Automation, and iUnu, that I’ll cover in a future blog.)
A theory on how indoor Ag retailers and consumers can all win
To recap several of the points above, produce grown in indoor farms provides an interesting alternative to outdoor-grown fruits and vegetables. That being said, I struggle with the notion that indoor farming will fully disrupt the existing outdoor growing regions and seasonal migration of growing operations between central, coastal, and desert valleys in the Western U.S. and Mexico. My reasoning is as follows:
- Many, not all, business models are capital intensive, and could be challenged to scale profitably in local regions.
- Local indoor farms typically offer high-quality produce delivered to grocers more quickly than many Californian or Mexican producers can, however the industry is not achieving additional compensation for this perceived competitive advantage.
- Existing industry players are generally low-cost, high-efficiency operators with long-established relationships with food distributors and retailers. Without a large scale national player, the incumbent players will remain in control of the terms of trade.
- Indoor farming operations have not yet proven they can fully insulate themselves from a disease outbreak such as the recent outbreak of the E.coli virus in Romaine lettuce, even though growing in a controlled environment.
- Indoor-grown lettuces, microgreens, arugula, and tomatoes lose flavor and remain highly perishable once harvested, packaged, and shipped to product sellers.
Notwithstanding this backdrop of challenges, I remain intrigued by the idea that closer alignments and joint ventures between indoor farmers and food retailers can create and deliver significant value. How can this be accomplished? Here are a few tactical ideas:
- Creation of an ultra-premium line of produce – Working directly with retailers, indoor farming operations can better message key product attributes: high-quality consistent products, year-round availability, and local/sustainable production. Wendy’s recent announcement to eventually source 100% of its tomatoes from indoor greenhouses would seemingly provide a positive tailwind for marketing indoor-grown produce.
- Installation of vertical farms in or on top of the grocery store – The difference in quality is noticeable between produce harvested immediately prior to consumption as compared to packaged, post-harvest produce. Again, the taste and quality attributes need to be properly marketed to achieve better pricing, however, the idea of produce harvested on-demand should theoretically de-risk the stand alone indoor ag business model from the perspectives of efficiency and waste reduction.
Parting thoughts
Personally speaking, nothing makes me happier than starting a meal with a healthy salad filled with fresh, peppery arugula, leafy spinach, and flavorful, red tomatoes, and cucumbers. Based on ongoing sector research and visits to several indoor farming facilities, I believe that indoor AgTech offers a compelling method to extend the seasonality of domestically-grown produce to 12 months of the year. I look forward to further exploring the issues raised in this blog in a future webinar on indoor farming and Controlled Environment Agriculture.
1. Article input provided by David Branch, Wells Fargo Sector Manager, Specialty Crops, Matt Dusi, Wells Fargo Sector Manager, Fresh Produce, and Karol Aure-Flynn, Wells Fargo Senior Sector Analyst, AgriFood Technology and Packaged Foods
Emirates Is Creating a Massive New Farm for Fresh Airplane Food
Dubai is certainly well-known for being an over-the-top travel destination. But soon, it may become more famous for its farming.
Courtesy of Emirates
JULY 18, 2018
Dubai is certainly well-known for being an over-the-top travel destination, and with some of the most luxurious hotels, designer clothing stores, and world-class restaurants, it’s more than earned that descriptor. But soon, it may become more famous for its farming.
Emirates Flight Catering, a subsidiary of Emirates Group, announced in June a new partnership with Crop One Holdings. The pair of companies, Gulf News reported, will co-invest $40 million to create an absolutely massive indoor farm in Dubai that will break the vertical farming world record.
Courtesy of Emirates
The farm, which is set to open next year, will produce the equivalent of 900 acres of fresh food, Gulf News reported. That means it will produce three tons of “high-quality, herbicide-free and pesticide-free leafy greens daily.”
However, it will produce all this food using far less water than traditional farming, and will also grow produce without soil, sunlight, and chemicals. It will indeed mark a massive step for the United Arab Emirates towards becoming more self-sustainable. As Gulf News explained, a massive amount of the food consumed in the UAE comes from foreign markets. According to 2015 data, 85 percent of the UAE’s food was imported.
Courtesy of Emirates
“This investment to build and operate the world’s largest vertical farming facility aligns with the UAE’s drive for more agricultural self-sufficiency, a vision which began with the late His Highness Shaikh Zayed bin Sultan Al Nahyan, the UAE’s founding father,” Shaikh Ahmed bin Saeed Al Maktoum, chairman and chief executive of Emirates Airline and Group said in an announcement. “The introduction of ground-breaking technology at the facility also enhances Dubai’s position as a global innovation hub.”
According to the announcement, the two companies expect to be delivering their first batch of produce to their customers (which include their 105 airlines and 25 airport lounges) by December of 2019.
Indoor-Farming Tech Is Growing On Investors
TYLER HAMILTON
CONTRIBUTED TO THE GLOBE AND MAIL
fin AUGUST 15, 2018
Tyler Hamilton works with cleantech companies from across Canada as an adviser with the non-profit MaRS Discovery District in Toronto.
There’s plenty of buzz around the coming legalization of cannabis, but behind all the smoke, another type of grow-op is catching the attention of investors and budding entrepreneurs.
Indoor farming is taking root in Canada and around the world – in homes and businesses, cities and remote communities, in bone-dry deserts and in the frigidness of the Arctic Circle.
These aren’t just greenhouses. Most of the growth has been around a subcategory called vertical farming, which involves the cultivation of leafy greens and other produce using surfaces that are vertically stacked or vertically inclined. Often, the plants are grown without soil and in climate-controlled environments. Almost always, they use LED lighting systems to allow for precision, year-round growing, an approach pioneered by NASA in the 1980s for long-duration space travel.
An employee inspects a wall of kale and greens growing vertically inside a modular farming unit at Modular Farms Co. headquarters in Brampton, Ont., on Aug. 11, 2017. JAMES MACDONALD / BLOOMBERG
Leaders in the market include Canada’s Modular Farms, based in Toronto, and Nova Scotia’s TruLeaf, which are joined by competitors across the United States and Europe, including names such as Plenty, Infarms, AeroFarms, Oasis Biotech and Bowery Farms. As a group, they attracted $350-million in venture capital last year, a big increase over 2016.
Some harsh realities are driving investment. Rising world population means more mouths to feed, while the availability of arable land isn’t just capped, it’s shrinking. shrinking as a result of development and changing climate patterns. Vertical indoor farming allows nutritious food to be grown where it’s needed, regardless of land availability or climate. It also reduces, sometimes dramatically, the amount of water and energy that goes into agriculture production.
“Every hectare under vertical farming can potentially substitute nine hectares of conventional outdoor farmlands, and save up to 200 tonnes of water every day,” according to market-intelligence firm Frost & Sullivan.
Frost calculated that about 22,000 vertical farming patents were filed globally between 2014 and 2016 alone. Allied Market Research, another research firm, estimates the market will grow at a compound annual rate of 23.6 percent, to US$6.4-billion by 2023 from US$1.5-billion in 2016.
“A new container-farm company still probably pops up every month, but this is about more than just growing heads of lettuce,” says Aaron Spiro, president of Modular Farms, founded three years ago out of frustration with vertical indoor farming systems that overpromise and underdeliver.
He says anyone can grow herbs and leafy greens indoors. “But if the goal is to get the highest quality and yield, and be flexible enough to grow everything from kale and quinoa to raspberries and tomatoes, then achieving the perfect balance of temperature, air flow, water, light and nutrients is crucial.”
A tour of a Modular Farms system in an industrial parking lot in east Toronto demonstrates just how far vertical farming has come. Roughly the dimensions of a shipping container, the company’s core farming module is heavily insulated and designed with its own automated heating, air-conditioning and humidity-control systems.
Inside, two evenly divided rows accommodate four growing walls, each lit up by a retractable LED curtain emitting a spectrum of purple-hued light that’s ideal for growing. The walls themselves are lined with 240 vertical growing towers capable of supporting more than 3,500 plants at the same time.
No soil is used. Instead, seedlings take root inside grow plugs made of moss. Once the seedlings grow large enough, they are transplanted into a fibrous material housed within each tower. An automated closed-loop drip system makes sure the roots get just the right amount of nutrient-spiked water.
All key operations can be remotely monitored and its spacious layout makes for easy maintenance and harvesting. The company says this design allows a range of plants to be grown using 95 per cent less water and up to 30 per cent less energy than an outdoor soil-based farm with similar yields.
Time will tell if the system delivers as promised, but after only a year on the market more than 15 of these container farms have been sold with dozens more in the sales pipeline.
“We’ve been getting so much interest from people we never thought we’d be selling to initially,” Mr. Spiro says, explaining that urban and remote communities alike are drawn to the idea of growing their own food year round. Schools, mining and logging operations, commercial caterers and food distributors are among the customers Modular Farms is now targeting.
In September, for example, the company will deliver one of its farms to Dene High School in La Loche, Sask. The student-run farm will grow vegetables and fruit to support the school’s lunch program, and will double as a classroom where students can learn about biology, nutrition and entrepreneurship.
Over time, as more operational data is collected on different plant species, the company’s farms are expected to get smarter and more self-sufficient by incorporating advanced robotics, machine vision and artificial intelligence. Want to grow strawberries? Just press “strawberry” mode and the farm will make sure temperature, humidity, nutrients and lighting are balanced just right. Is tower five in Aisle 2 underperforming? A text alerts you and recommends corrective action.
Modular Farms is also taking a more holistic approach to its farms, developing a variety of connectible, plug-and-play modules with different capabilities and climate settings, including air-tight vestibules that allow seamless movement between modules – similar to the way the International Space Station is designed. One module, for example, would generate its own power using solar panels, while another would extract and store water from the outside air.
“It’s about pushing the boundaries of what and where people think it’s possible to grow,” Mr. Spiro says.
And yes, he adds wryly, growing cannabis is an option.
Microgreen Seed Density Charts
8/1/2018
Microgreens are becoming increasingly popular, allowing growers the opportunity to expand further into existing markets or to venture into new markets.
From farmers markets to local restaurants and chefs, microgreens are perfect for enhancing salads or using as a garnish.
By definition, microgreens are tiny plants with only their first leaves developed. Most varieties are harvested at 8-14 days and while they may be smaller and more delicate, they are also more robust and flavorful.
The CropKing microgreen growing system is a cost-effective and efficient way to maximize production while ensuring high quality.
The correct seed density is crucial to the success of growing microgreens. The chart below was put together to assist all microgreen growers in finding the correct information for growing over 20 different varieties.
Click here to download a printable chart.
Soaking Seeds (large seeds)
To soak the microgreen seeds, a plastic kitchen storage container works well
Use cold water (always pH balanced)
Refrigerate in warm weather
Soak for 8-12 hrs typically.
Fill the container with enough water to rise above the seeds ¾” to 1”. The seeds will swell as they absorb water, and you’ll want to be sure they stay below the water line.
Soaking the Burlap Grow Mat
Plan to put the mat in the day before you plant. Once you know how many total channels/trays of microgreens you’ll be planting.
Fold and place burlap mat in a soaking tub.
Fill the tub with water until it completely covers mats.
Cover and soak overnight.
EASIEST TO GROW
Arugula
Seeding Rate: 0.7 oz
Pre-Soak: No
Blackout Time: 1-3 Days
Estimated Time to Harvest: 8-14 Days
Broccoli
Seeding Rate: 1.0 oz
Pre-Soak: No
Blackout Time: 2-3 Days
Estimated Time to Harvest: 10-14 Days
Buckwheat
Seeding Rate: 12 oz
Pre-Soak: Yes
Blackout Time: 3-4 Days
Estimated Time to Harvest: 8-12 Days
Cabbage
Seeding Rate: 1.0 oz
Pre-Soak: No
Blackout Time: 2-4 Days
Estimated Time to Harvest: 8-12 Days
Chia
Seeding Rate: 1.0 oz
Pre-Soak: No
Blackout Time: 2-3 Days
Estimated Time to Harvest: 8-12 Days
Kale
Seeding Rate: 1.0 oz
Pre-Soak: No
Blackout Time: 2-4 Days
Estimated Time to Harvest: 8-14 Days
Kohlrabi
Seeding Rate: 0.7 oz
Pre-Soak: No
Blackout Time: 2-4 Days
Estimated Time to Harvest: 8-14 Days
Mustard
Seeding Rate: 0.7 oz
Pre-Soak: No
Blackout Time: 2-4 Days
Estimated Time to Harvest: 8-12 Days
Sunflower
Seeding Rate: 9.0 oz
Pre-Soak: Yes
Blackout Time: 2-4 Days
Estimated Time to Harvest: 8-14 Days
Wheatgrass
Seeding Rate: 16.0 oz
Pre-Soak: Yes
Blackout Time: 2 Days
Estimated Time to Harvest: 8-10 Days
AVERAGE DIFFICULTY
Celery Leaf
Seeding Rate: 0.75 oz
Pre-Soak: No
Blackout Time: 6-8 Days
Estimated Time to Harvest: 18-21 Days
*Slow to germinate and emerge
Popcorn
Seeding Rate: 8.0 oz
Pre-Soak: Yes
Blackout Time: 6-10 Days
Estimated Time to Harvest: 6-10 Days
*Keep in the dark for full 6-10 days to harvest
Fennel
Seeding Rate: 1.0 oz
Pre-Soak: No
Blackout Time: 3-5 Days
Estimated Time to Harvest: 14+ Days
Leek
Seeding Rate: 2.0 oz
Pre-Soak: No
Blackout Time: 3-5 Days
Estimated Time to Harvest: 12-14 Days
*Seed heavy
Peas
Seeding Rate: 12.0 oz
Pre-Soak: Yes
Blackout Time: 3-5 Days
Estimated Time to Harvest: 8-14 Days
*Use plenty of water when soaking seed, they are extremely absorbent
Sorrel
Seeding Rate: 1.0 oz
Pre-Soak: No
Blackout Time: 3-5 Days
Estimated Time to Harvest: 12-16 Days
*Keep seeds in freezer to help with germination rates
HARDEST DIFFICULTY
Amaranth
Seeding Rate: 1.0 oz
Pre-Soak: No
Blackout Time: 3-6 Days
Estimated Time to Harvest: 8-14 Days
*Prefers warmer environment, sensitive to direct light
Basil
Seeding Rate: 1.0 oz
Pre-Soak: No
Blackout Time: 4-7 Days
Estimated Time to Harvest: 14-18 Days
*Spray through to establish root
Beets
Seeding Rate: 2.0 oz
Pre-Soak: Yes
Blackout Time: 6-8 Days
Estimated Time to Harvest: 10-14 Days
Chard
Seeding Rate: 2.0 oz
Pre-Soak: Yes
Blackout Time: 4-7 Days
Estimated Time to Harvest: 10-14 Days
Cilantro (Coriander)
Seeding Rate: 2.0 oz
Pre-Soak: No
Blackout Time: 6-7 Days
Estimated Time to Harvest: 21-28 Days
*Keep medium moist throughout blackout period, prefers cooler temperatures
Download a printable chart below!
File: SeedingCharts.pdf
Indoor Farmers Are “Way Too Complacent” About Food Safety
“If you mess up indoors, everything is magnified,” says Sarah Taber.
Taber is an independent food safety consultant specializing in indoor farming. Previously she served as director of food safety for The Aquaponics Association after earning a Doctorate of Plant Medicine. At the association, she saw startups pitch to investors a risk-free way of farming, and that’s where the worrying began, says Taber.
Since then she has worked with half a dozen hydroponic indoor farming operations of various sizes, funding sources, and technologies and her early worries are now full-blown concerns about the safety of the food grown on indoor farming for consumers. And with food safety scandals increasingly hitting the headlines — just last month thousands of pounds of romaine lettuce were recalled when 200 people became ill and five died — it’s time some indoor ag players stopped being “way too complacent” and woke up to the dangers, says Taber. (She chose not to name the farms due to non-disclosure agreements.)
Often called controlled environment agriculture (CEA), indoor farming is not new. Commercial greenhouses have been around since the 1920s, but in the last few years, CEA startups have started to raise large amounts of funding for high tech farming operations, often in urban areas. The basic formula is a controlled environment — where the temperature and ventilation can be controlled — soilless growing, using some form of hydroponics system, and in some cases, artificial light from specially designed LEDs. The promises of these farms are many: decrease the distance food must travel from farm to table, use less water and fewer agrochemicals, grow seasonal items all year round and in climates where it otherwise would not be possible.
Controlling every variable from temperature to humidity to plant nutrition while using artificial light perfectly calibrated for each plant is a pitch that has obviously sparked the imagination of the public and investors when you look at the more than $300 million invested in the space last year. And it can be very good business. Just ask the Netherlands, which is second only to the US in food exports despite having 270 times less landmass thanks to its prolific CEA industry.
But a controlled environment does not automatically mean produce is exempt from food safety issues. And with investor appetite for big-ticket, high-tech indoor farms growing, particularly in the US, the sector is full of relatively new players growing plants and businesses very quickly — many spreading the idea that indoor farms are plant factories where the outcome is as assured as a Detroit auto assembly line.
The proclaimed dominance of technology over biology by this category of entrepreneurs has left some food safety experts concerned that consumers could be getting the wrong idea and startups may be drinking their own kool-aid.
“As a consultant, a lot of my time is spent grief counseling people over the loss of the innocence they had when they thought that food safety wasn’t a problem [indoors],” says Taber. “When you’re outside you have air circulation and sunlight that can brush back some of your mistakes. Temperature and humidity can get out of control indoors in a way it can’t outdoors and that can grow bacteria,” she continues.
What’s the risk? People and a lack of vigilance
It’s true; growing indoors inside a building or other structure can protect plants from contamination from above, like bird droppings and chemical drift. Isolated from other farming operations also means that the plants are safe from the inadvertent spreading of agrochemicals or animal waste — major causes of salmonella and e.coli contamination in outdoor farming.
But, based on currently available CEA technology, indoor farmers are not immune to other food safety challenges, says Jeff Brandenburg. Vigilance is still very much needed.
Brandenburg is president of the JSB Group, a Massachusetts-based consultancy for every link in the produce supply chain. He has a masters degree in food safety and teaches good agricultural practices at various universities including UC Davis. He says that local farming, no matter the growing method, is often perceived as safer, not just by the public, but by the growers.
“You get these greenhouses and high tech operations that don’t have a fundamental understanding of food safety and how it works, and they think that it’s not their problem because of how their farms are built; that’s a problem,” says Brandenburg. “It might be slightly safer because you’re in a more controlled environment, but if that controlled environment gets out of control, then you’ve got a big problem. Bacteria is not biased. It doesn’t grow more on the west coast than it does on the east coast,” he adds.
All of the experts consulted for this report emphasized that people are the number one source of food safety problems in indoor farming. People bring in bacteria on clothes, shoes, and skin. With proper controls such as hairnets, face masks, foot baths, single-use or clean suits, the risk can be mitigated, but there is still plenty of room for error and these practices are not commonplace all over the industry.
Though eventual automation is part of the promise of the major indoor farming technology companies, it hasn’t become a reality in any meaningful way yet, so there are still a lot of people involved.
“Everybody’s talking about automation, but nobody is actually doing it, so there’s a huge amount of contact from workers. That’s the same as outdoor farming,” says Taber.
How is all this monitored?
The food safety of most commercial farms, indoor or outdoor, is monitored through audits and certifications where an outside body verifies that food safety practices and preventative measures are being carried out over varying lengths of time — sometimes several hours, sometimes several days.
The government body that oversees foods safety in the US is the Food and Drug Administration (FDA), but historically they have played a larger role in the aftermath of an outbreak than in its prevention.
The real pressure to keep up standards (other than the honest and genuine desire not to hurt people) comes from retailers that often require audits before they take on a new vendor and increasingly send their own auditors directly to farms.
The most stringent and widely-recognized family of audits are under the umbrella of the Global Food Safety Initiative (GFSI), which was established by the industry in 2000 to reduce food safety risks and streamline the audit process in an effort to lower costs for operators while improving overall food safety. GFSI certifications include Primus GFS Food Safety Management Systems, Global Good Agricultural Practices (GAP), Canada GAP, and Hazard Analysis Critical Control Points — HACCP, and SQF – considered to be the most stringent audit of the group.
The USDA also offers a Good Agricultural Practices audit, which experts say is less stringent than the GFSI certifications, but is accepted by some retailers.
Venture-backed certifications
We asked some of the major venture-backed US indoor farms what certifications they had achieved. https://www.brightfarms.com/ and Bowery Farming both have SQF certifications. Plenty and Gotham Greens are both GFSI GAP certified (Gotham Greens manufacturing facilities for pesto and other products are comparably certified) and AeroFarms is USDA GAP certified.
A lack of advanced certifications does not necessarily mean that the practices required to pass such an audit are not in place, say several farmers consulted for this report. Farms often build their food safety capacity over time and only go through the time and expense of an audit when processes are finalized and unlikely to change.
Paul Lightfoot, CEO of Bright Farms, a hydroponic grower with four farms in four different US states, said that his company only underwent an SQF audit for each of its farms when the design of their farm was finalized and ready to be replicated in all new locations without alteration.
As many of the venture-backed farms are still iterating their technology, advanced certifications may be less likely, but food safety experts pointed out that one thing that makes high food safety standards much easier to achieve is ample funding.
“I don’t think the type of capital matters. I do think an insufficient amount of it might make a difference. Food safety requires investment. It changes the design of your facility. It changes how you staff your facility” says Lightfoot.
But funding is also no guarantee according to Brandenburg, “I’ve worked with a couple of startup operations that were venture capital-backed and the people had wonderful intentions, but knew nothing about the agricultural world. There’s a feeling of how hard can it be?”
On top of audits, farms are also subject to Food and Drug Administration regulation, most importantly the Food Safety Modernization Act (FSMA) — a newly enacted policy that is intended to give the administration better tools for preventing outbreaks rather than simply responding to them.
The first compliance date for the FSMA Produce Rule was January 26, 2018, and farms with annual sales over $500,000 are affected.
The new rule establishes protocols for how produce farmers harvest, wash, package, and store fruits and vegetables usually consumed raw. Standards for microbial water quality, biological soil amendments, managing livestock and wild animals, health and hygiene, and equipment, tools and building make up the majority of the law.
Some experts doubt whether the rule will reduce instances of food-borne illness in a meaningful way, and many small-scale farmers worry about the costs of coming into compliance.
“In the past, it could be a dusty binder sitting on a shelf and when you think you’re going up for an audit you just backfill in information, which is really problematic,” says Allison Kopf, CEO of Agrilyst, a farm management software platform and app for indoor growers. She says that though many farms were ready for FSMA, some used it as on opportunity to digitize some very analog systems of food safety control.
She adds that farmers have a real fear of hurting people and they want regulation that will actually help with that. What they don’t want is regulation that will add to their workload without helping with that.
The CEA Food Safety Coalition
Indoor farming executives speak about the possibility of a foodborne illness stemming from the industry with palpable fear. In order to allay that fear, they’re teaming up – a big deal for an industry laser-focused on proving and registering unique intellectual property.
Next week a group of indoor farming companies will meet at the United Fresh FreshTEC trade show in Chicago to hash out details of a new organization: the Controlled Environment Agriculture Food Safety Coalition.
The group is the brainchild of Lightfoot and counts AeroFarms and Massachusetts hydroponic farm Little Leaf Farms as founding members. Eleven other indoor farms have expressed interest.
Lightfoot said the idea was inspired by the recent romaine lettuce scandal. Bright Farms went through its own scare in the Fall of 2017 when it voluntarily recalled all of its products from four midwest supermarket chains for potential e. coli risk. No illnesses were reported.
Now the former software executive is working to spread the idea that food safety best practices should never be proprietary, with the knowledge that if one farm has a major food safety incident, all players in this young industry could feel the pain.
The goals of the coalition, according to Lightfoot, are to develop guidelines on food safety and protocols specific to indoor farming; to create a list of resources for coalition members; to establish a board of advisors to help members navigate food safety incidents; to build website to educate growers and address the public when needed.
But a lot is still yet to be decided before the work can even begin. At the conference in Chicago, the farms that have so far shown interest will meet to elect a steering committee. Eventually there may be a certain food safety certification requirement to join, but currently its open to all comers.
And while the industry is hoping and working to never see a major outbreak, Taber says that the outbreaks are the best teachers despite their sometimes tragic results.
“When you get down to it, the way people learn about fallibility, and that you can fail even if you didn’t mean to, is by seeing it happen. folks in the ag industry may not have had an outbreak on their farm, but they know someone its happened to. For them it is real.”
The Best Temperatures For An Indoor Grow Room
Finding the ideal operating temperature is one-way growers can help ensure growth rates and bountiful harvests. But as Goldilocks found out, determining ideal temperatures can sometimes take some experimentation.
Takeaway: Finding the ideal operating temperature is one-way growers can help ensure growth rates and bountiful harvests. But as Goldilocks found out, determining ideal temperatures can sometimes take some experimentation.
The atmospheric conditions in an indoor garden have a tremendous impact on the quality and quantity of the finished crop. Growers of all skill levels are continuously trying to master the subtle environmental factors that can make a significant difference in growth and yield over the course of a plant’s life cycle.
When discussing the atmospheric conditions of an indoor garden, people are often referring to humidity and temperature. Although humidity is an important aspect, this article will focus on temperature, which plays a vital role in the way a plant is able to process light and intake water and nutrients.
Temperature affects a plant’s ability to photosynthesize, and it also plays a key role in seed germination and fruit and flower development. If temperatures fall outside the desired range, the garden becomes less efficient. Over time, these inefficiencies can lead to smaller, lower-quality yields.
Maintaining a Consistent Temperature Inside Your Grow Room
One of the most important things a grower can do is maintain a uniform and consistent temperature. A uniform temperature means the growroom’s temperature is the same in all areas, from one end to the other.
Most growers use high-intensity lighting equipment in their growrooms, which produces excess heat from one focal point. If this is not addressed, the temperature around the light source will be much warmer than in the other areas.
Maintaining a uniform temperature can normally be achieved by creating adequate air flow within the room. Oscillating fans will continuously move the air around the room so the heated air underneath the light fixtures will mix with the cooler air in the room.
Consistency is also important when it comes to growroom temperatures. Plants love consistency and respond well to it. The better growers can maintain a consistent temperature range, the better their yields will be.
To achieve a high level of consistency, a grower will usually invest in a climate controller with ventilation fans or an air conditioner.
For ultimate control, air conditioners are the way to go. Mini-split air conditioners allow growers to maximize control over temperature consistency. Those who choose to invest in a properly sized mini-split air-conditioning system will not regret it—nothing is better than being able to simply push a button and have absolute control.
The Ideal Temperature Range for Indoor Gardens
To maximize efficiency, try to determine the garden’s ideal temperature range, which is the temperature at which plant growth is maximized. The ideal temperature is crop-dependent because plants differ greatly in their responses to temperature.
For most fast-growing annuals, a good initial range at which to operate a garden is 70-80°F (21.1-26.6°C). Most varieties will prefer the upper end of this range. This temperature range can be used for both the vegetative stage and the fruiting/flowering stage.
Growers with climate-controlled rooms can use the temperature range as a starting point when trying to figure out the room’s best operating temperature.
When experimenting, consider the way the air temperature will affect the root mass of the plant. In most indoor gardens, plants are grown in hydroponic systems or planting containers, and these plants are more affected by changes in the air temperature than plants that are planted directly into the ground.
For this reason, growers must always be aware that higher air temperatures can lead to higher temperatures around the plant’s root mass.
Growers with climate-controlled rooms can set up an experiment to find the ideal temperature by slowly increasing the temperature and monitoring vegetative growth. By using this method, a grower can measure plant growth as it correlates to temperature and then determine the optimal temperature for the vegetative growth of that plant variety.
Remember that different varieties of the same plant will have different optimal temperatures. For that reason, growers with multiple plant varieties will have to shoot for a happy medium to keep all plant varieties as content as possible.
For most plants, the ideal temperature range for vegetative growth will also be the ideal temperature range for the fruiting stage, although some varieties prefer slightly cooler temperatures for flowering.
Many plant varieties I have grown performed best at 78°F (25.5°C), although I have had a few varieties that liked it a bit warmer (80-84°F). For novice growers or those without an air-conditioning system, a thermostat controller and fan can still get the garden close to the 70-80°F (21.1-26.6°C) range.
"In a semi-enclosed environment, a significant drop in temperature can lead to condensation and moisture issues in the growroom and on the plants themselves."
Unfortunately, temperature control is only as good as the equipment, but don’t get frustrated if the ventilation system isn’t perfect to begin with. Instead, do your best to maintain consistent and uniform temperatures with the equipment that is on hand and work towards maximizing climate control in the future.
Temperature Differential
The temperature differential, or the temperature change between the lights-on (daytime) and lights-off (nighttime) periods, is an important aspect of controlling temperature that often gets overlooked. Once growers determine the temperature of the lights-on stage in the garden, they can start to determine what temperature is needed for the lights-off period.
The best lights-off operating temperature is generally about 10-15°F (5-7°C) cooler than the lights-on operating temperature. This temperature drop is significant enough to allow a plant to go through its normal process of rest and transpiration, but is not so great that problems are caused.
Keeping the lights-off temperature within 10-15°F of the lights-on operating temperature serves as a safeguard against pathogens, especially molds and fungi. In a semi-enclosed environment, a significant drop in temperature can lead to condensation and moisture issues in the growroom and on the plants themselves.
Over time, this will result in a perfect environment for molds, fungi, and other plant pathogens. For most indoor gardens, the ideal temperature for the lights-off period is 55-70°F (12.8-21.1°C). Adding an electric heater to warm up the garden at night goes a long way towards preventing problems and maintaining healthy growth rates. (Read More: Tips for Avoiding Mold Growth in the Grow Room)
CO2 Enrichment and Temperature Inside a Sealed Grow Room
Growth rates can be increased by enriching the garden’s environment with carbon dioxide, but to gain maximum benefits, growers need to increase the room’s operating temperature.
The increase in temperature enables plants to properly process the additional CO2 in the atmosphere and increase the rate of photosynthesis, which increases plant growth.
When operating a garden with CO2 levels of 1,200-1,500 parts per million (ppm), it is a good idea to increase the temperature range to 80-90°F (26.6-32.2°C). From there, slowly increase the temperature and monitor plant growth to find the ideal operating temperature.
Best Temperatures for Clones and Seeds
Just like fully established plants, clones and seedlings thrive on consistency. In fact, most seed varieties will only germinate once the temperature is consistently over the seed’s threshold temperature for sprouting.
For many plants, this is a temperature range of 60-70°F (15.5-21.1°C). In indoor gardens, a good temperature range for the seedling and cloning stage is usually around 72-82°F (22.2-27.8°C). Seedling heat mats or small electric heaters are great ways to maintain a consistent temperature warm enough to promote germination and early root development.
Again, each plant variety is different. When starting from seeds, check the seed packet for instructions. Some cold-weather plants can be germinated in relatively cold conditions, whereas some summer plant varieties may require much warmer temperatures for germination.
Experiment to Find the Ideal Temperature
Every indoor garden is different and there are many variables that can affect the way a crop performs. Although growers can use the general operating temperature range of 70-80°F ((21.1-26.6°C) as a starting point, finding the ideal temperature for an indoor garden is something that can only be done through experimentation.
As with most horticultural experiments, finding the ideal operating temperature will take time. It is hard to determine how a small change in the garden will affect the overall results until the garden’s harvest can be measured.
For that reason, it may take multiple garden cycles before a grower is able to collect enough data to make a solid conclusion about the ideal operating temperature.
Although the process can be a bit tedious, committed indoor gardeners should have no problem documenting temperatures and how they relate to the growth of the garden. After all, growers are always in search of ways that will increase their return on investment.
Finding the ideal operating temperature for an indoor garden is just one-way growers can help ensure their gardens have consistent growth rates and repetitive, bountiful harvests.
Written by Eric Hopper
Eric Hopper’s past experiences within the indoor gardening industry include being a hydroponic retail store manager and owner. Currently, he works as a writer, consultant and product tester for various indoor horticulture companies. His inquisitive nature keeps him busy seeking new technologies and methods that could help maximize a garden’s performance.
Fluence Appoints Chief Operating Officer to Further Accelerate Business Growth
David Cohen joins as COO to direct operational growth and business consistency globally, in addition to improving the overall customer experience
Austin, Texas – August 16, 2018, Fluence Bioengineering Inc. today announced David Cohen has joined Fluence as chief operating officer. Cohen will lead the Fluence Marketing, Sales and Operations teams, and he will focus on the creation and execution of the global growth strategy along with defining and executing the digitization strategy for Fluence.
“David will be an integral part of Fluence’s growth trajectory as the company expands to become the global leader of the horticultural lighting industry,” said Nick Klase, CEO, and co-founder, Fluence Bioengineering. “David’s experience in directing high-growth products in the LED lighting industry will ensure Fluence anticipates and addresses developing trends in food and cannabis production around the world.”
Cohen has extensive leadership experience in the lighting industry and has held roles as CEO, general manager, COO, executive vice president and managing director while living in China, Italy, the Netherlands, and the U.K. His most recent position was general manager and CEO of Schréder Lighting U.S.A. Prior to that position, David was the general manager of Future Electronics’ lighting business in Europe, the Middle East and Africa, while based in London.
“The Fluence Bioengineering acquisition by Osram pairs best in class technology with a global lighting leader. I am excited to be joining Fluence at this critical time to drive global expansion,” said David Cohen, COO, “As Fluence refines its expertise in plant photobiology to address the escalating demand for natural food and medicine, I will be making sure we reach as many customers as possible around the world.”
About Fluence Bioengineering
Fluence Bioengineering Inc., a wholly-owned subsidiary of OSRAM, creates the most powerful and energy-efficient LED lighting solutions for commercial crop production and research applications. Fluence is the leading LED lighting supplier in the global cannabis market and is committed to solving the looming food crisis by enabling more efficient crop production with the world’s top vertical farming and greenhouse produce growers. All Fluence lighting solutions are designed and built at the company’s headquarters in Austin, Texas, U.S.A., with European sales and support based in Amsterdam, Netherlands. https://fluence.science
The Bay Area Company Building World's Largest Vertical Farm In Dubai
A small San Mateo company is building what is billed as the world’s largest vertical farm next year in Dubai, right on the runway that serves Emiratesairline.
Tara Duggan July 20, 2018
Crop One of San Mateo grows leafy greens without soil or sunlight in hydroponic facilities using LED lights.
Photo: Crop One
A small San Mateo company is building what is billed as the world’s largest vertical farm next year in Dubai, right on the runway that serves Emirates airline. The 50-foot-high sealed warehouse will produce 3 tons of leafy greens a day, without using a drop of what Sonia Lo calls “free energy” — otherwise known as sunlight — or soil, essentially recreating an optimized version of Central California in the Middle East.
“I love the fact that you’re redistributing the means of feeding back to where people actually are,” said Lo, CEO of Crop One Holdings in San Mateo, which since 2015 has provided fresh-cut lettuce and basil through Boston’s snowy winters from the company’s first vertical farm in Massachusetts. “The implications for what agriculture can do in terms of feeding more people are also incredibly exciting.”
Large-scale vertical farming, sometimes called indoor farming, uses LED lights and small doses of water and nutrients to grow leafy greens and herbs — and soon strawberries — year-round in otherwise unsuitable climates. Since the farming method can protect plants from the ravages of climate change and may have the potential to recreate terroir for wine grapes or coffee, it’s attracting big investors. In the Bay Area, Crop One’s just-announced partnership with Emirates Flight Catering amounted to $40 million just to build the Dubai farm, and Plenty in South San Francisco, which will open a farm in the Seattle area this year, raised $200 million in funding last July.
Both companies are exporting two things the region is known for: technology and fresh-cut greens. Yet they both plan to also open facilities in Northern California as the Salinas Valley, known as America’s Salad Bowl, copes with labor shortages, drought and high land prices.
Matt Barnard, CEO of Plenty, which will sell the greens to Bay Area customers in a few months from its South San Francisco farm, points out that the majority of the world’s fruits and vegetables grow best in Mediterranean climates, of which there are just a handful around the world, including Salinas Valley.
“We’ve tapped out Salinas. There’s not a way to add capacity,” he said.
Barnard prefers to use the term indoor farming, not to be confused with growing in greenhouses, which use natural sunlight and dirt. In vertical farms, vegetables grow hydroponically — in a “soil-less medium” of water and nutrients. They sit on actual vertical walls, in the case of Plenty, or on stacked shelves with LED lighting overhead. The temperature- and humidity-controlled environment can be as simple as a shipping container within a larger warehouse.
Vertical doesn’t necessarily mean towering high, though; it does mean the plants are stacked closely and efficiently. The Dubai farm will be only about four or five stories tall, but at 130,000 square feet, it is large enough to produce greens for the 225,000 meals Emirates caterers produce daily for in-flight meals. Lo said she can produce the same amount on a single acre indoors that would normally require 400 acres of land, and that her company landed the deal because it has shown it can make vertical farming profitable.
Sonia Lo, founder of Crop One in San Mateo says, “The implications for what agriculture can do in terms of feeding more people are also incredibly exciting.”
Photo: Crop One
But using LED lighting instead of “free energy” comes with high costs and a carbon footprint that can be comparable to shipping greens across the country. Running a 30,000-square-foot indoor farm in the New York City area would cost about $340,000 per year for power, lighting, heating and cooling, according to a recent report by Civil Eats. Because water can be filtered and reused in vertical farms, water use is only an estimated 1 percent of conventional farming.
Lo estimates that vertical farms cost one and a half times as much as traditional farms to operate, but that the cost to Emirates will be the same as what it currently pays for the vegetables shipped or flown from Spain, Italy or California. Plus, the greens will be available within 24 hours of harvest, she said, instead of the usual six weeks.
When it comes to the carbon footprint, a farm producing 1 ton of vegetables a day uses 3 megawatts of energy a year, Lo said, or enough to power roughly 2,200 homes. Greens produced by the Boston area farm, which sells under the FreshBox label, are carbon neutral when compared with greens transported from California, Lo said; they haven’t done a carbon analysis for Dubai yet. The company is planning to open three new farms in Connecticut and Texas soon and is eyeing sites in Northern and Southern California as well as the Midwest, Georgia, and Oklahoma.
One big advantage of vertical farming is that the sealed environment means no pesticides or herbicides are required, and the bacteria levels on the vegetables are much lower, which makes them safer as well as longer-lasting, reducing spoilage.
Then again, the same factors pushing vertical farming forward are also improving technology for traditional agriculture, such as remote sensors, software, and drones that help farmers make irrigation more precise and improve soil health.
In November, the U.S. Department of Agriculture reaffirmed that hydroponic farms may use the USDA organic label, even though traditional organic farms and greenhouse growers fumed over that decision, arguing that soil is inherent to organic farming.
Teeny Greenie Farming: Local Farmer Producing Nutrient-filled Microgreens
She grows "microgreens". Research shows that the first leaves of a plant have up to 40 times the nutrients of a full grown vegetable.
by Kathryn Daniel
July 21, 2018
ALLENTOWN, Fla. (WEAR) — Virginia Bates raises about a dozen crops. She listed off just a few for us, "Radish, broccoli, kale, bok choy, arugula."
Her dozen or so varieties aren't grown in fields or even a greenhouse, but in a small, insulated "grow" shed.
Bates laughed, "This is the type of farming that anybody can do. I think that's what appealed to me, you can farm in heels if you want."
Bates plants and harvests every week and loves her work.
"My goal is to get people to think about what they put in their bodies," she explained.
She grows "microgreens". Research shows that the first leaves of a plant have up to 40 times the nutrients of a full grown vegetable.
She elaborated, "A handful of broccoli microgreens is like eating a pound and a half of mature broccoli. That's crazy."
Once a vegetable reaches "adult" status, its nutrients are spread throughout the entire item. Bates said with micro greens, all of that goodness is condensed into the first, tender shoots.
Bates calls her product "Super Teenie Greenies." She harvests between every seven to ten days to get the maximum nutritional punch.
Bates detailed that anytime a crop is grown without soil, it's done so hydroponically. The medium she grows in only looks like dirt.
"It is organic ground coconut husks," she revealed.
Bates supplies several local restaurants and Ever'man Cooperative Grocery weekly. She and her assistant, Jewel Owens, set up shop at the Palafox Market every Saturday.
Jewel's favorite variety is the kale and spicy mustard combo.
The teenager grinned, "I really like the taste. I like how nutritious they are for you. Normally things that are super nutritious don't taste as good, but these are really, really good."
Bates said many parents buy the Super Tennie Greenies and "sneak" them into smoothies, in sauces and on pizza for their children to get a ton of vitamins and minerals.
She sells a "grow kit" and is shipping them all over the country, which makes this fifth generation farmer feel proud of her healthy fare.
She said, "To hear that my product is able to impact their daily life and make them feel better in a real way that's backed by science."