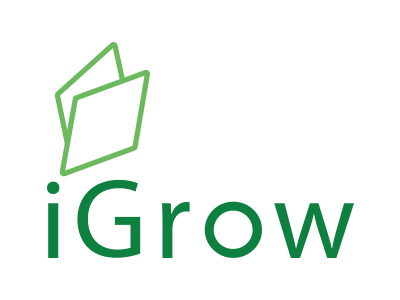
Welcome to iGrow News, Your Source for the World of Indoor Vertical Farming
New "Lego-Like" Vertical Growing System Offers Flexibility And Small Footprint
New "Lego-Like" Vertical Growing System Offers Flexibility And Small Footprint
16 June 2017, by Gavin McEwan, Be the first to comment
A German firm has launched the latest format in high-density soil-less urban growing.
Image: Aponix
The modular Aponix Vertical Barrel uses an NFT hydroponic system and is designed particularly for urban farming facilities operating on limited space.
"There are no fixed structures necessary for the set-up, like tables or racks, so the barrels can be positioned and moved easily to provide flexibility," explained its inventor Marco Tidona.
The units are constructed out of a single "Lego-like" part that forms 1/6th of a ring segment, any number of which can then be stacked vertically, topped with a lid that incorporates irrigation using a simple sprinkler or spray nozzle, he added.
The entire barrel can sit ona stand or even be hung from above, and rapidly dismantled after use for washing and re-planting.
"Many barrels can be connected in line and be powered by a central reservoir with organic or mineral liquid nutrient solution and a pump for irrigation," Tidona said, and suggested herbs, lettuce or strawberries as candidate crops.
He added: "Aponix is expanding and is currently looking for sales and manufacturing partners."
In 2002 Organics Alive Was Formed As A Sustainable Bio-Tech Company
In 2002 Organics Alive was formed as a sustainable Bio-tech companyto provide gardeners with another option from toxic chemical fertilizers and to advocate an all-natural, organic and sustainable method of gardening and agriculture.
Our roots began to grow in 1997 with a discovery of a diet fed to Eisinea Fetida Earthworms. Through intensive and costly research we have perfected our worm feed to produce a casting by-product with a high concentration of beneficial, diverse and balanced biology which includes patented levels of chitin and cellulose degraders. We feed our worms a diet that excludes any landscape trimmings, due to its herbicides and pesticides, also excluding any manure or animal waste because of their lack of bio-diversity and certain foods containing GMO or unsubstantial diets. The natural vegetable waste is broken down through a proprietary composting method and finished off with a vermi-composting process. The Earthworms consume tons of waste per hour and secrete a casting by-product (waste) that is rich in beneficial microbes, nutrients, minerals, growth hormones, beneficial enzymes and chitin and cellulose recyclers.
In 2002 Organics Alive was formed as a sustainable Bio-tech company to provide gardeners with another option from toxic chemical fertilizers and to advocate an all-natural, organic and sustainable method of gardening and agriculture. Our method of composting is truly revolutionary and is at the forefront of Green sustainable technology. Organics Alive’ core technology can help achieve solutions to several social, economic and environmental problems afflicting human society one being safe and sustainable food production.
Organics Alive focuses on four main concepts: Crop Nutrient management, Genetics, Crop Management, Crop energy Management. By addressing these four concepts your garden will be more bountiful, your crops immunity will increase, and fruits will be much richer in profile increasing financial and nutritious value.
The Organics Alive Product line is all natural and certified organic. We provide a variety of soil amendments to create a soil environment for your plants to thrive in. We also provide an in home Bio-Extractor and Mix Kits, which allows you to brew quality Microbial Rich Solution at your own convenience. Our fermentations provide building blocks such as minerals, Amino Acids, humic and Fulvic acids. We extract these elements from Grain, beans and seeds instead of animal byproduct or heavy mining operations that hurt the environment; and finally, our innovative fertilizers which are derived from microbial extracts avoiding animal byproducts, animal waste and contaminated plant sources. They contain no salts, and are made up of Nitrogen, Potassium, Phosphorus, minerals and contain high amounts of carbon; the basic building blocks of life. Organics Alive provides the most effective garden nutrients on the market today!
The team at Organics Alive is passionate and works hard to bring you quality products and real results. Results you can see and truly benefit from. Our group has been mentored by a leading Vermiculture engineer second to none. We have tested our product vigorously with much critique and have been awarded for our patented Bio-Extractor and the Microbial tea it produces.
Our design, construction, and assembly are made in the California. We manufacture and ship through the foundation, “The Arc of San Diego.” We work with locally owned small businesses which creates long lasting jobs in our community. We are proud of our work and the message we convey.
Protix Raises $50m in Largest Insect Farming Investment on Record
Protix Raises $50m in Largest Insect Farming Investment on Record
JUNE 14, 2017 LOUISA BURWOOD-TAYLOR
Protix, a Netherlands-based company, has raised €45 million ($50.5 million) in equity and debt funding to expand its insect farming business. This is the largest investment in the nascent insect farming industry to-date, according to Protix and its investors.
Dutch food and agriculture bank Rabobank invested in the round alongside Aqua-Spark, the sustainable aquaculture investment fund, Dutch government-backed Brabant Development Agency (BOM) and other private investors.
Protix farms insects predominantly for animal and aquaculture feed, with feed products in over 12 countries, ranging from pig and poultry to pet food specialties. It has four products — feed ingredients Protix Protein X, Protix Lipid X, Protix Chitin X, and a fertilizer Protix Flytilyzer X — which are all currently derived from Black Soldier Fly (BSF). It is also moving into the food sector.
Insects are increasingly seen as a viable and low-impact protein alternative, because they can be reared on waste and are much more resource efficient versus other sources of protein and feed such as soy, corn, forage fish and meat.
Aqua-Spark, which is investing in Protix for its potential to replace fishmeal with insects for aquaculture feed, had been looking deeply at insect production for a long time, surveying over 45 insect producers globally, according to Mike Velings, founder of the Dutch open-ended fund. Aquaculture feed demand is set to increase eight times before the end of the century, according to Aqua-Spark, in what some analysts value as a $100 billion industry, where neither wild forage fish nor soy are viable long-term solutions.
“We took the time to find the right partner and one that could take this to scale because we think insects have the potential to really become a mainstream ingredient in fish feed,” he said. “But the main problem for us in looking at the sector was the ability for these players to scale, because that’s really not easy.”
Insect farms are tough to scale because they are capital intensive; operators need a lot of capital to build the insect factories in what Velings calls a “chicken and egg situation” where you don’t have the offtake to get finance to pay for construction, but you need the finance to get the offtake.
Securing feedstock — the waste you feed the insects such as unsold fruits or grain byproducts — can also be tricky in the right quantities, he added.
Protix cofounder and CEO Kees Aarts, a former McKinsey & Co employee, says that Prolix has cracked the scalability challenge by optimizing the three consecutive processes of industrial insect production: breeding, rearing, and processing.
“Through advanced data monitoring and proprietary technology, we’ve been able to optimize these processes,” he told AgFunderNews. “The combination of highly talented people, data infrastructure, and automation have created modular designs that can scale quickly and produce at the highest standards.”
The technology that Prolix has developed over the past eight years is of key importance to the scalability and success of the business, according to Velings, who believes Protix is head and shoulders ahead of the rest in the industry.
“They are incomparable with other names in the sector, sometimes because they’re raising a different type of insect, but also because they’re at a very different stage of development,” Velings added.
Protix would not divulge much about the technology used in its farms, but it involves a completely controlled environment, monitored and automated with sensors, much like you might see in indoor vertical leafy greens farms.
“We started with a rigorous and well-designed trial and error phase along all stages of the insect growth. We stand out because of the combination of technologies, operations, and R&D,” said Aarts. “Our differentiation lies in that golden combination of a range of technologies, operating protocols and talented people, augmented by the sensor-data infrastructure.”
Also vital to its scalability and technological development going forward, is the company’s joint venture with Swiss food technology group Buhler.
Announced earlier this year, the JV, Buhler Insect Technology Solutions, will manufacture and sell equipment and provide know-how to any feed or ingredient producer in the industry in an effort to scale the industry overall.
The JV will leverage Buhler’s generations of engineering knowledge and Protix’s insect rearing operational expertise, which involves proprietary equipment and processes, including methods for separating and extracting proteins and lipids from insects.
“It’s all about the modularization of proprietary Protix and Buhler technologies and the development and supply of insect production technologies and equipment,” Aarts said of the JV. “Together, we can develop both sustainable and cost effective solutions for large-scale insect producers and processors that cover the whole value chain. Protix will play a supporting role in the long run by providing young larvae to customers of our joint venture and operational support services. This way the industry will accelerate vastly due to setting the dominant design, standards of operations and increase of total production capacity. We have seen a strong increase in demand over the last months since the nascence of our joint venture.”
Protix will use the funding from this latest round to expand its production capacity, especially for aquaculture, deepen its biological and technical R&D, and diversify to other markets like food. It is also on the lookout for potential M&A opportunities. The company wouldn’t disclose exactly what types of companies it was looking to acquire, but Aarts said it would make acquisitions that strengthened its position in the industry.
Protix has now raised €70 million to-date.
Other insect-for-feed farming businesses to raise funding in recent months include French startup Ynsect, which raised $15.2 million in Series B funding last December, and AgriProtein, a South Africa-based business, which raised $17.5 million in the same month.
Plantagon Announces its 40th Approved Patent
Plantagon Announces its 40th Approved Patent
News • Jun 16, 2017 10:18 GMT
Plantagon World Food Building in Linköping. Standard Patent Certificate for Australia. The uPot
Developing and expanding the Intellectual Property Portfolio is an important corporate strategy for the Sweden based innovation company Plantagon International, with recent patents granted in the US, China and Australia.
"R&D and the resulting technological innovations are the principal factors for Plantagon International’s business success. Plantagon International’s innovation strategy involves benefiting from technological innovations by using the full range of intellectual property rights in the development of urban agriculture”, says Owe Petersson, CEO of Plantagon.
The company’s most recent patents are: in the USA: Methods and arrangements for growing plants; in China: The uPot; and in Australia: Building for cultivating crops in trays. There are still 28 pending patents.
"It is with great pleasure I follow the progress of the Plantagon Intellectual Property Portfolio. Pending patents get granted without major objections from local patent authorities. This means our inventions have inventive step, novelty and usefulness", says Joakim Rytterborn, Research & Development Manager at Plantagon.
Four patent families
Plantagon currently has filed for patents within four patent families:
- Conveying system, tower structure with conveying system, and method for conveying containers with a conveying system
- Building for cultivating crops in trays, with conveying system for moving the trays
- Method and arrangement for growing plants
- Pot device and method related thereto
Asia
Last year Singapore, as the first country, granted a patent from Plantagon’s fourth patent family, the uPot, and this year this patent for the uPot was granted in China. The uPot solves the problem with spacing the plants during growth. This by an adjustable distance ring, which enables spacing in two dimensions and hence is about 20 percent more effective than other methods on the market.
Africa
Recently Plantagon also was granted its first ARIPO Patent (African Regional Intellectual Property Organization). Regarding this Mats Lundberg CEO of Sweden’s oldest IP-firm Groth says:
“Plantagon is a company in the very forefront in terms of both innovation and IP. This recently granted patent is further evidence of this. Africa, for example, is a continent often overlooked when companies strive for global IP protection. But it is an emerging market important to consider. Also, thanks to the African Regional Intellectual Property Organization, ARIPO, foreign companies can now apply for a unified patent in a cost-efficient way in 19 African states.”
"Plantagon started with an idea from a Swedish gardener. If you have any great ideas that will make the world a better place, join Plantagon and develop them together with us,” says Joakim Rytterborn.
---
Plantagon International is a world-leading pioneer within the field agritechture and social entrepreneurship – combining urban agriculture, innovative technical solutions and architecture – to meet the demand for efficient food production within cities; adding a more democratic and inclusive governance model. We see global corporate governance, food security and sustainable food production as among the most critical areas for the future of our planet. Plantagon’s objective is to inspire a value change for survival and meet the rising demand for locally grown food in cities around the world, minimizing the use of transportation, land, energy and water. www.plantagon.com & www.plantagon.org
AgFuse’s Farmer Founder Is Dedicated To Building Social Network For Farmers Despite Challenges
AgFuse’s Farmer Founder Is Dedicated To Building Social Network For Farmers Despite Challenges
The farming community and Silicon Valley have built quite the relationship during the last few years as innovators and entrepreneurs continue to identify major opportunities for new technology to disrupt the agriculture sector. But for one South Carolina peanut farmer, simply getting acquainted wasn’t enough; he wanted to launch his own startup, too.
Pat Rogers, a fifth-generation peanut and cotton producer operating in Blenheim, SC, is the creator and visionary behind AgFuse, a social networking site created for farmers that features a variety of crop, geographic, and product-based groups. It operates similarly to Facebook, providing users with a news feed and allowing them to follow other users and groups that pique their interest.
Why AgFuse?
Launched in 2015, Rogers conceived the idea for his farmer-focused networking app while attending the InfoAg conference in St. Louis. Surrounded by many other producers and industry officials, he realized that the rural and dispersed geographic nature of farming made it hard for colleagues to connect, share information, and support one another.
Since launching, he has relied primarily on freelance support to develop and update the website and app, which has recently undergone a major update including a range of new features like group subscriptions, news feeds showing suggested and trending topics, and providing easier access to the info that users want most. Also, AgFuse now offers invitation-only “ghost” groups, which are ideal for companies or organizations seeking a central networking spot that isn’t public.
Why do farmers need a dedicated social media platform?
“There’s a lot of information on the internet and existing social media networks for farmers, but you have to hunt for it and you can’t always be sure that it’s good information,” Rogers recently told AgFunderNews. “Plus, sometimes those things can be more of a distraction than a tool. I want to build a digital Swiss army knife for farmers, a centralized location where all of the information on the internet is flowing to the user.”
Being able to customize the information to the specific crops or livestock that the farmer deals with is another added bonus to a farmer-focused outlet.
Challenges & Future Plans
Launching and growing AgFuse has not been without its challenges. He decided early on that an app-based platform would be ideal for farmers, who typically lack spare time to spend in front of a computer. Farmers need to consume essential information in the field when the issues arise, not later that day after they get home, he says.
One of the biggest obstacles Rogers faces is achieving a critical mass of users that will cultivate interaction and connectivity on the platform. He’s relied on fine-tuning the interface, a developed marketing strategy, an word-of-mouth to increase the platform’s membership, which now totals roughly 2,000 farmers across 63 countries.
“Many of the users from foreign countries are seeking production knowledge. They want to connect with US-based farmers and learn about their practices,” says Rogers. “Some of our earliest users are from Australia.”
And while this was to be expected, an unforeseen challenge he’s faced is getting a better feel for the production timeline and the amount of time it takes to create, revise, and promote a social networking site for farmers.
“When we make changes, it seems like it takes a lot longer to push out the finished product than we initially estimated. People want to know to expect the update and I have a hard time knowing exactly what to tell them,” he explains. “It’s kind of like farming; it’s a never ending job and there’s always work to be done!”
He has many plans for the future of AgFuse, including a platform for publishing articles that’s similar to Medium, to give industry experts a platform for sharing knowledge and connecting with farmers. He’s also considered doing live Q&A sessions with experts or agtech companies, providing them with opportunities to answer farmers’ questions about each technology.
Technology Perspective
While diving into the tech arena head first has given Rogers better insight into what it takes to launch and grow a startup, he’s also become a careful observer of trends in the space and how his farming colleagues perceive the plethora of new agtech tools on the market.
“I think in some areas there is over-saturation. There is so much new tech coming out that the average farm is overwhelmed and doesn’t know the best place to spend their money and attention,” he explains. “Farmers are aware of this issue because it happens to them very year in terms of chemicals and fertilizer programs. There is always some new, bigger and better thing.”
Surprisingly, for many farmers, money isn’t always the issue when considering adopting a new technology. It comes down to an arguably more precious resource: time. For farmers, finding spare time or achieving optimum time management is just as precious as a perfectly timed rain or a successful harvest.
“When I think about my own operation, there are a lot of things I want to try, but I have limited funds and more importantly limited time. And, any farmer who has done this long enough knows that the guys who thrive and survive are the ones who know how to allocate resources. A lot of times, that means sitting tight and watching your neighbor.”
This mentality is a common approach to agtech adoption based on Rogers’ observations. Farmers are keen to hear about other users’ experiences with a particular data management platform before they fork over their cash and commit to learning how to use the new tool.
Next to time, failing to recognize a clear value proposition is another common trend among farmers’ perceptions of agtech. He and many of his colleagues would like to see startups providing a clearer cost-benefit analysis on how the product will pay for itself and put more profits in their wallets.
And, as far as education goes, farmers find it lacking.
“It took me a year to figure out my current data management tool and then they changed it,” Rogers says, preferring not to name the company. “If it took me a year and I have been using the product for three years total, you better have a really doggone good product if you expect me to switch to something else and start all over again.”
He would like to see companies offer free trials or use periods in exchange for switching platforms, something to ease the hassle and headaches that will surely result. He also thinks many farmers would prefer to engage with many agtech tools in a service-based relationship as opposed to a purely product-based one.
“If somebody could ever figure out how to franchise a data management company that has local stores or offices that could go around and help farmers pull information off their equipment, run it through a program, and analyze the data, it would be gold.”
Time, once again, is the primary factor in this equation. Many farmers are thrilled about agtech’s potential, but don’t have enough time to master the technologies and glean their full potential. Having someone with serious savvy assist them with the process and confirm their conclusion would help underscore the value proposition while providing confidence that the tool is operation optimally.
“I think farmers have a voice in the agtech sector. And I often think about the famous Henry Ford quote: ‘If I had listened to my customers, then I would have built them a faster horse.’ Sometimes farmers don’t necessarily know what the newest thing is and they don’t know that they need it yet. When it comes to adoption, it’s really about communication of the benefits.”
FreshTEC Achievement Award for Peter Quiring
NatureFresh Farms' TOMZ Best New Vegetable Finalist
FreshTEC Achievement Award for Peter Quiring
Thousands of produce industry executives are arriving in Chicago this week to attend the United Fresh Produce Association’s Annual FreshMKT & FreshTEC Expos & Convention June 13-15. During the festivities on Tuesday, June 13, greenhouse vegetable grower and NatureFresh Farms owner & president Peter Quiring will be receiving the FreshTEC Achievement Award for his contributions to the produce industry over the last 20 years.
“Peter’s contributions to greenhouse technology have advanced the industry significantly,” said United Fresh President & CEO Tom Stenzel. “His competitive drive and commitment to invest in technology advancements in controlled growing environments are what set him apart. We’re proud to honor Peter with this FreshTEC Achievement Award.”
“It is a great honor to be recognized by your peers,” said Peter Quiring. “Innovation in the way we build our greenhouses and how we grow our vegetables is what has driven my companies for many years. Implementing the latest in technology has allowed us to be a more efficient operation from start to finish”, stated Quiring.
In addition to receiving the FreshTEC Award for Achievement, NatureFresh™ Farms has been named a Finalist for the Best New Vegetable Award for its TOMZ® Snacking Tomato Program.
“We saw a need in the market place to create a category wide program that would give consumers consistent quality, regardless of the season”, said Chris Veillon, Director of Marketing. The TOMZ® Program is unique in that it provides consumers up to 7 different types of specialty tomatoes under one brand: Red/Yellow/Orange Grape, Red Cherry, Mixed Snacking, Mixed Grape, and Sweet Red Cocktail Tomatoes. Grown in NatureFresh™’s new state of the art greenhouse in Delta, OH from October to July and in NatureFresh™’s high tech greenhouses in Leamington, ON March to November, the company is ensuring that locally grown snacking tomatoes are available year-round.
“Consumers want summer-like flavor in July, November, and February and the TOMZ® Program does just that!”, commented Veillon.
The TOMZ® Program is built on the following principles:
- TOMZ® is promoting the category as a whole, not just one item
- Driven by Flavor; 7 unique products under one brand
- Reduced food miles creates extended shelf life
- Creating a consumer connection with multiple flavors
- Same seed | same grower | same farms = consistency
- High impact packaging colors to brighten the produce aisle
- Geo-targeted consumer facing digital content to raise awareness
- Available year-round: Delta, OH & Leamington, ON
“We believe that the TOMZ® Program can strengthen the snacking category as a whole. It is not just about one tomato with flavor, it is a complete line of fresh tomatoes with flavor”, said Ray Wowryk, Director of Business Development.
NatureFresh™ Farms continues to sample its TOMZ® Tomatoes at all #GreenInTheCity tour stops this year with the company’s mobile Greenhouse Education Center.
NatureFresh™ Farms will have its complete line of greenhouse grown tomatoes, bell peppers, and cucumbers on display at the FreshMKT Trade show during the United Fresh Convention in Chicago, June 14-15. Attendees are invited to visit Booth 3231.
To learn more about NatureFresh™ Farms, visit naturefresh.ca.
The First Online Marketplace That Connects Buyers and Sellers
For The Fresh Produce Industry Worldwide
The First Online Marketplace That Connects Buyers and Sellers
"We are a new company that was founded six months ago and we already have more than 800 companies from all over the world involved in the fresh fruits and vegetables sector," said Elena Molinaro, from Fruitsapp.
Until now, the way to communicate with other sellers, buyers, and merchants had been through telephone calls, emails, and faxes. "This is costly and inefficient because there is no quick way to reach all the buyers and producers in the world to compare options," said Elena. "However, we can solve this problem. Through our platform, you can have access to a global market and get to know other companies around the world," she said.
This website also provides the possibility to sell the products more quickly through an innovative 'Hot Offer' service. FruitsApp, notifies other web users who may be interested in those products. Producers and buyers are connected through algorithms and Artificial Intelligence, which unite them according to their common interests.
For example, if you have avocados to sell, you register for free on the platform and once you are registered you can include your interests. The algorithms will then look for other companies that are interested or that are looking for avocados and an interactive map indicating that you have a match with a company will appear in your personal profile. Then, users can contact the company by clicking on it and entering their profile. If you are an avocado vendor, you can directly send your offer to all potential clients, such as wholesalers, importers, exporters, and supermarkets around the world that already use the platform.
The security system checks all companies that are registered to avoid fraud, in addition, at the time of registration, they verify that the company is real, that it can guarantee its transactions, and that their products meet the minimum quality requirements through Global GAP or HACCP certificates.
Currently, the greatest difficulty is modernizing a traditional sector through new technologies. Fortunately, the new generations are helping this change a lot, as they are more used to using these types of innovative platforms and Applications.
The registration is totally free and the sellers only pay a small commission if they manage to make a sale through the platform. In addition, logistics are integrated and buyers can choose between the logistics proposed by Fruitsapp or the logistics that the seller proposes.
It also includes a section of advice and forecasts on demand, trends, and prices to help companies optimize their buying decisions.
For more information:
Elena Molinaro
Fruitsapp
T: +393275496390
elena.molinaro@fruitsapp.com
www.fruitsapp.com
Vertical Farming Startup Plenty Acquires Bright Agrotech to Scale
Vertical Farming Startup Plenty Acquires Bright Agrotech to Scale
California-based vertical farming company Plenty, previously See Jane Farm, has acquired Bright Agrotech in an effort to reach “field-scale.”
Bright Agrotech is an indoor ag hardware company that’s focused on building indoor growing systems for small farmers all over the world, in contrast to Plenty, which is aiming to become a large-scale indoor farming business and currently has a 52,000 sq. ft farm in South San Francisco.
“The need for local produce is not one that small farmers alone can satisfy, and I’m glad that with Plenty we can all work toward bringing people everywhere the freshest food,” said Nate Storey, founder and chairman of Bright Agrotech.
The move to acquire Bright Agrotech will give Plenty the breadth of expertise and intellectual property (IP) to scale with rapid speed, and is a natural move after a four-year relationship, according to Matt Barnard, cofounder and CEO.
“We have a great portfolio of system level IP. They have a great portfolio of component level IP,” he told AgFunderNews. “We’re getting a fire hose of demand from around the globe right now. This is an industry that is emergent, but the way to truly lift it off the ground is to do a whole set of things extraordinarily well.”
Bright Agrotech was founded in 2010 in Laramie, Wyoming, and sells a wide range of indoor farming equipment for indoor vertical farms as well as greenhouses along with smaller systems suitable for homes and business development tools – most of which are under the trademark brand “ZipGrow.”
The relationship between the two businesses started in 2013. Later Storey, the former CEO of Bright Agrotech, became chief science officer at Plenty in a part-time capacity in 2015 and went on to join the team full time earlier this year.
Barnard would not confirm to what extent Plenty already uses Bright Agrotech’s hardware in its farm, which consists of 20-foot high towers with vertical irrigation channels and facing LED lights. Leafy greens ready for picking end up looking similar to a solid wall of green.
Plenty claims to use 1 percent of the water and land of a conventional farm with no pesticides or synthetic fertilizers. Like other large soilless, hi-tech farms growing today, Plenty says it uses custom sensors feeding data-enabled systems resulting in finely-tuned environmental controls to produce greens with superior flavor.
Based on the West Coast, it plans to compete with the existing supply of greens from the salad bowl of California, by choosing premium seeds and catering growing conditions for optimal taste. Barnard says most greens growing in the field are bred to be hardy enough to last the 3,000 mile journey to the east coast and beyond.
He would not share specific growth goals for the near-term, but said that eventually they expect to be able to build two to six farms per month. The plan is to build these farms just outside major cities where retailers have distribution centers and real estate is more affordable. Barnard also said that an announcement about a major retail partnership is forthcoming.
Zack Bogue, an investor in Plenty through San Francisco venture capital fund Data Collective, agreed that the Bright Agrotech acquisition will help the startup scale. “By vertically integrating parts of their component supply chain, it will make the most efficient system out there more efficient,” he said.
Plenty claims to get 350 times the crop yield per year over an outdoor field farm. Or, as Barnard described, “It is the most efficient in terms of the amount of productive capacity per dollar spent, period.”
Plenty was the first indoor ag investment for big data-focused Data Collective, which participated in its $24.5m Series A in July 2016. “We’re pretty excited about that space because some of the hardest problems in agriculture are now lending themselves to an algorithmic or computational or applied machine-learning solution,” he said. But he added that the ability to scale was paramount, because scale is what allows data to be useful for machine-learning applications. “I came away feeling this was an endeavor that could truly achieve global scale pretty quickly,” he added.
Bogue said that though this match was a natural fit, he doesn’t expect more consolidation in the space.
Plenty has raised $26 million to date in a seed and Series A Round, both in 2016. The startup’s other investors are Innovation Endeavors , Bezos Expeditions , Finistere Ventures, Data Collective, Kirenaga Partners, DCM Ventures, and Western Technology Investment
High-Tech Farms Give A New Meaning To ‘Locally Grown’
High-Tech Farms Give A New Meaning To ‘Locally Grown’
Published: June 8, 2017 4:58 a.m. ET
This is the new urban farm
Bloomberg
Plants growing in a rotary light-tracking system inside a greenhouse at a high-tech indoor farm on the outskirts of Beijing. China is turning to technology to make its land productive again.
By Betsy McKay
Billions of people around the world live far from where their food is grown.
It’s a big disconnect in modern life. And it may be about to change.
The world’s population is expected to reach 9.7 billion by 2050, 33% more people than are on the planet today, according to projections from the United Nations. About two-thirds of them are expected to live in cities, continuing a migration that has been under way around the world for years.
That’s a lot of mouths to feed, particularly in urban areas. Getting food to people who live far from farms—sometimes hundreds or thousands of miles away—is costly and strains natural resources. And heavy rains, droughts and other extreme weather events can threaten supplies.
Now more startups and city authorities are finding ways to grow food closer to home. High-tech “vertical farms” are sprouting inside warehouses and shipping containers, where lettuce and other greens grow without soil, stacked in horizontal or vertical rows and fed by water and LED lights, which can be customized to control the size, texture or other characteristic of a plant.
Companies are also engineering new ways to grow vegetables in smaller spaces, such as walls, rooftops, balconies, abandoned lots — and kitchens. They’re out to take advantage of a city’s resources, composting food waste and capturing rainwater as it runs off buildings or parking lots.
“We’re currently seeing the biggest movement of humans in the history of the planet, with rural people moving into cities across the world,” says Brendan Condon, co-founder and director of Biofilta Ltd., an Australian environmental-engineering company marketing a “closed-loop” gardening system that aims to use compost and rainwater runoff. “We’ve got rooftops, car parks, walls, balconies. If we can turn these city spaces into farms, then we’re reducing food miles down to food meters.”
Moving beyond experiments
Urban farming isn’t easy. It can require significant investment, and there are bureaucratic hurdles to overcome. Many companies have yet to turn a profit, experts say. A few companies have already failed, and urban-farming experts say many more will be weeded out in the coming years.
Getty Images
In London, former air raid shelters are home to 'Growing Underground', the UK’s first underground farm, shown here in 2016. The farm grows pea shoots, rocket, wasabi mustard, red basil, red amaranth, pink stem radish, garlic chives, fennel and coriander, and supply to restaurants across London.
But commercial vertical farms are well beyond experimental. Companies such as AeroFarms, owned by Dream Holdings Inc., and Urban Produce LLC have designed and operate commercial vertical farms that aim to deliver supplies of greens on a mass scale more cheaply and reliably to cities, by growing food locally indoors year round.
At its headquarters in Irvine, Calif., Urban Produce grows baby kale, wheatgrass and other organic greens in neat rows on shelves stacked 25 high that rotate constantly, as if on a conveyor belt, around the floor of a windowless warehouse. Computer programs determine how much water and LED light the plants receive. Sixteen acres of food grow on a floor measuring an eighth of an acre.
Its “high-density vertical growing system,” which Urban Produce patented, can lower fuel and shipping costs for produce, uses 80% less fertilizer than conventional growing methods, and generates its own filtered water for its produce from humidity in the air, says Edwin Horton Jr., the company’s president and chief executive officer.
“Our ultimate goal is to be completely off the grid,” Horton says.
The company sells the greens to grocers, juice makers and food-service companies, and is in talks to license the growing system to groups in cities around the world, he says. “We want to build these in cities, and we want to employ local people,” he says.
AeroFarms has built a 70,000-square-foot vertical farm in a former steel plant in Newark, N.J., where it is growing leafy greens like arugula and kale aeroponically — a technique in which plant roots are suspended in the air and nourished by a nutrient mist and oxygen — in trays stacked 36 feet high.
The company, which supplies stores from Delaware to Connecticut, has more than $50 million in investment from Prudential, Goldman Sachs and other investors, and aims to install its systems in other cities globally, says David Rosenberg, its chief executive officer. “We envision a farm in cities all over the world,” he says.
AeroFarms says it is offering project management and other services to urban organizations as a partner in the 100 Resilient Cities network of cities that are working on preparing themselves better for 21st century challenges such as food and water shortages.
The bottom line
Still, these farms can’t supply a city’s entire food demand. So far, vertical farms grow mostly leafy greens, because the crops can be turned over quickly, generating cash flow easily in a business that requires extensive capital investment, says Henry Gordon-Smith, managing director of Blue Planet Consulting Services LLC, a Brooklyn, N.Y., company that specializes in the design, implementation and operation of urban agricultural projects globally.
The greens can also be marketed as locally grown to consumers who are seeking fresh produce.
Other types of vegetables require more space. Growing fruits like avocados under LED light might not make sense economically, says Gordon-Smith.
“Light costs money, so growing an avocado under LED lights to only get the fruit to sell is a challenge,” he says.
And the farms aren’t likely to grow wheat, rice or other commodities that provide much of a daily diet, because there is less of a need for them to be fresh, Gordon-Smith says. They can be stored and shipped efficiently, he says.
The farms are also costly to start and run. AeroFarms has yet to turn a profit, though Rosenberg says he expects the company to become profitable in a few months, as its new farm helps it reach a new scale of production. Urban Produce became profitable earlier this year partly by focusing on specialty crops such as microgreens—the first shoots of greens that come up from the seeds—that generally grow indoors in a very condensed space, says Horton, who started the company in 2014.
One of the first commercial vertical-farming companies in the U.S., FarmedHere LLC, closed a 90,000 square-foot farm in a Chicago suburb and merged with another company late last year. “We’ve learned a lot of lessons,” says co-founder Paul Hardej.
Among them: Operating in cities is expensive. The company should have built its first farm in a suburb rather than a Chicago neighborhood, Hardej says. Real estate would have been cheaper.
“We could have been 10 or 20 miles away and still be a local producer,” Hardej says.
The company also might have been able to work with a smaller local government to get permits and rework zoning and other regulations, because indoor farming was a new type of land use, Hardej says. While FarmedHere produced some crops profitably, it spent a lot on overhead for lawyers and accountants “to deal with the regulations,” he says.
Hardej is now co-founder and chief executive officer of Civic Farms LLC, a company that develops a “2.0” version of the vertical farm, he says—more efficient operations that take into account the lessons learned. Civic Farms is collaborating with the University of Arizona on a research and development center at Biosphere 2, the Earth science research facility in Oracle, Ariz., where it runs a vertical farm and develops new technologies.
Blossoming tech
New technology will improve the economic viability of vertical farms, says Gordon-Smith. New cameras, sensors and smartphone apps help monitor plant growth. One company is even developing augmented-reality glasses that can show workers which plants to pick, Gordon-Smith says.
“That is making the payback look a lot better,” he says. “The future is bright for vertical farming, but if you’re building a vertical farm today, be ready for a challenge.”
Some cities are trying to propagate more urban farms and ease the regulatory burden of setting them up. Atlanta Mayor Kasim Reed created the post of urban agriculture director in December 2015, with a goal of putting local healthy food within a half-mile of 75% of the city’s residents by 2020. The job includes attracting urban-farming projects to Atlanta and helping projects obtain funding and permits, says Mario Cambardella, who holds the director title.
“I want to be ahead of the curve; I don’t want to be behind,” he says.
Many groups are taking more low-tech or smaller-scale approaches. A program called BetterLife Growers Inc. in Atlanta plans to break ground this fall on a series of greenhouses in an underserved area of the city, where it will grow lettuce and herbs in 2,900 “tower gardens,” thick trunks that stand in large tubs. The plants will be propagated in rock wool, a growing medium consisting of cotton-candy-like fibers made of a melted combination of rock and sand, and then placed into pods in the columns, where they will be regularly watered with a nutrient solution pumped through the tower, says Ellen Macht, president of BetterLife Growers.
The produce will be sold to local educational and medical institutions. “What we wanted to do was create jobs and come up with a product that institutions could use,” she says.
The $12.5 million project is funded in part by a loan from the city of Atlanta, with Cambardella helping by educating grant managers on the growing system and its importance.
Change at home
Another company aims to bring vertical farming to the kitchen. Agrilution GmbH, based in Munich, Germany, plans to start selling a “plantCube” later this year that looks like a mini-refrigerator and grows greens using LED lights and an automatic watering system that can be controlled from a smartphone. “The idea is to really make it a commodity kitchen device,” says Max Loessl, Agrilution’s co-founder and chief executive officer, of the appliance, which will cost 2,000 euros—about $2,200—initially.
The goal is to sell enough to bring the price down, so that in five years the appliance is affordable enough for most people in the developed world, Loessl says.
Biofilta, the company Condon co-founded, is marketing the Foodwall, a modular system of connected containers, an approach that he calls “deliberately low tech” because it doesn’t require electricity or computers to operate. The tubs are filled with a soil-based mix and a “wicking garden-bed technology” that stores and sucks water up from the bottom of the tub to nourish the plants without the need for pumps. The plants need to be watered just once a week in summer, or every three to four weeks in the winter, says Chief Executive Marc Noyce. The tubs can be connected vertically or horizontally on rooftops, balconies or backyards. “We’ve made this gardening for dummies,” Noyce says.
Biofilta
Biofilta's Foodwall
The Foodwall can use composted food waste and harvested rainwater, helping to turn cities into “closed-loop food-production powerhouses,” Condon says.
He and Noyce were motivated to design the Foodwall by a projection from local experts that only 18% of the food consumed in their home city of Melbourne, Australia, will be grown locally by 2050, compared with 41% today, Noyce says.
“We were shocked,” says Noyce. “We’re going to be beholden to other states and other countries dictating our pricing for our own food.”
“Then we started to look at this trend around the world and found it was exactly the same,” he says.
Traditional, rural farming is far from being replaced by all of these new technologies, experts say. The need for food is simply too great. But urban projects can provide a steady supply of fresh produce, helping to improve diets and make a city’s food supply more secure, they say.
“While rural farmers will remain essential to feeding cities, cleverly designed urban farming can produce most of the vegetable requirements of a city,” Condon says.
Betsy McKay is a senior writer in The Wall Street Journal’s Atlanta bureau. She can be reached at betsy.mckay@wsj.com.
The article “A Farm Grows in the City” first appeared in The Wall Street Journal.
Food Revolution
Food Revolution
Applying innovation to agriculture, a student startup plans to use hydroponics to grow fruits and vegetables four times faster using 90 percent less water.
May 04, 2017 | Abigail Lague, avl8bj@virginia.edu
Those walking into the University of Virginia’s Clark Hall find themselves face-to-face with a state-of-the-art hydroponics system. A table full of growing plants and violet light is hard to miss.
As part of an undergraduate sustainability initiative, these systems have been installed in various locations on UVA’s Grounds, including Newcomb Hall and Observatory Hill Dining Hall.
An undergraduate-led company, Babylon Micro-Farms, is bringing these small hydroponic farm prototypes to Grounds as part of an effort to make fresh fruit and vegetables easily accessible for more people.
Hydroponic farming is the growing of plants in nutrient-rich solutions without the use of soil. Usually, hydroponic systems are large, costly and used in mass production – not readily available to the average consumer. However, the system created by Babylon Micro-Farms are less bulky and available for personal use in the home. Each structure is only 6 feet wide by 3 feet deep and about 6 feet tall. Above the plants are LED grow lights that emit light at the right wavelength for photosynthesis.
Plants grown in hydroponics systems, such as those used by Babylon Micro-Farms, are free of GMOs and pesticides. (Photo by Dan Addison, University Communications)
This high-tech farming method uses 90 percent less water and grows food up to four times more quickly. Additionally, hydroponics systems do not use genetically modified organisms, pesticides or inorganic fertilizers and help reduce “food miles,” the distance between where a food item is grown and where it is sold.
The Babylon team began testing prototypes around Grounds after building an early model through the student entrepreneurial clubhouse, HackCville, and winning $6,500 from Green Initiatives Funding Tomorrow. Student Council’s sustainability committee, with assistance from the Office of the Dean of Students, funds the annual GIFT grant.
“It’s been a massive hit,” company founder and fourth-year student Alexander Olesen said of the hydroponic systems’ reception in dining halls. “At first, they weren’t too sure about it, and then after a month when the plants grew, they said we could go ahead and pitch them a more finalized version.”
From left, Stefano Rumi, who handles the business expansion of Babylon Micro-Farms; founder Alexander Olesen; electrical engineer Patrick Mahan; and head engineer Graham Smith. (Photo by Dan Addison, University Communications)
The hydroponic systems in the dining halls have been growing a mixture of lettuces, arugula, kale and spinach. The yield from one table alone has been enough to feed the entire Babylon Micro-Farms team for about a week. Olesen, a foreign affairs major, and his business partner, third-year student Stefano Rumi, a sociology and social entrepreneurship double-major, hope to add their produce to the UVA Dining menu so that other students may enjoy the vegetables produced by their hydroponics systems.
To make the produce affordable, Babylon Micro-Farms plans to offer a comprehensive hydroponics system for less than $1,000 – something that cannot be found on the market today. Their system will be much smaller than other hydroponic structures and easier to have in the home.
“The existing systems you get are made out of the same materials as trash cans, and they’re still more expensive, which is crazy,” Olesen said. “It’s just a table, and it blends in. You can fit in around 100 plants. Unlike other systems, you have versatility.”
These LED grow lights emit light at a wavelength that facilitates photosynthesis so that the plants will grow faster. (Photo by Dan Addison, University Communications)
The system can be easily installed in the home and doesn’t require any special skills to set up, he said.
While the benefits of hydroponics are appealing to many, Olesen is aware that not everyone wants to have to do a “science experiment” at the end of a long day to grow lettuce. With this in mind, Babylon Micro-Farms plans to provide premeasured seeds, nutrients and an automated system to optimize the pH of the hydroponic system, making the process of growing one’s own food as easy as possible. All users have to do is pour in the mixture.
“Food is such a fundamental part of our lives,” Rumi said. “In a world where we’re innovating everything, the last thing we’ve innovated is how we grow our food. We essentially do it the same way we’ve been doing it for 10,000 years, except for pumping unhealthy pesticides that have these terrible environmental effects.”
Alexander Olesen, founder of Babylon Micro-Farms, hopes that his hydroponic systems will soon be put to use in UVA dining halls and low-income areas. (Photo by Dan Addison, University Communications)
Olesen and Rumi also see a possible educational aspect to of their hydroponics system.
“A lot of the early interest we’ve gotten has been in having these in schools, teaching children how to grow in the community garden, or having these in low-income neighborhoods so that there’s a public space where residents can grow their own food,” Rumi said. “Beyond having the perfect product that everyone can have in their home, we would like to give back to communities that are in need of things like this. I think this is a great step to solving food insecurity.”
“We are connecting people to where food comes from,” Olesen said.
Babylon Micro-Farms is now in beta testing with customers and currently taking preorders. The startup team also will participate in UVA’s 2017 i.Lab incubator summer cohort.
Media Contact
Katie McNally - University News Associate Office of University Communications
katiemcnally@virginia.edu 434-297-6784
EU Awards Greek Patent for Automated Indoor Farming
EU Awards Greek Patent for Automated Indoor Farming
By Philip Chrysopoulos | Jun 11, 2017
The European Commission on Wednesday awarded Christos Raftogiannis and Evriviadis Makridis for their invention of an Automated Indoor Farming device with which you can grow 40 different fruits and vegetables in your home.
CityCrop offers a fully automated indoor garden based on the technique of hydroponics. The two Greek men were awarded as best startup in the category “Smart Cities”.
The company was incorporated in 2015 and is based in London. CityCrop created the mobile device and application that allows users to grow fresh and healthy food all year-long as well as control and monitor their crops. Users can grow leafy green vegetables, herbs, fruits, edible flowers, and microgreens.
The device can take up to 40 glass cubes and the owner can grow spinach, cherry tomatoes, kale, radish, strawberries, basil, cilantro, lettuce and more. CityCrop can take 10 liters of water and its power consumption does not exceed five euros per month. Inside the glass cube the appropriate humidity, temperature and lighting conditions of plant growth are ensured. Furthermore, the device should be connected on the internet so that the grower can have constant contact with the plants to cater to their needs, such as add more water or adjust the temperature.
The cost of CityCrop is currently 1,000 euros, but could be reduced significantly if it is mass-produced.
The World's Largest Dedicated Showcase of Sustainable Agriculture Innovations
The World's Largest Dedicated Showcase of Sustainable Agriculture Innovations
In 2018 GFIA Europe will be co-located with VIV Europe and Future Food Manufacturing to bring over 29,000 key buyers and decisions makers concerned with smart food production from around the world to Utrecht, the Netherlands.
The world's largest dedicated showcase of sustainable agriculture innovations, GFIA is your platform to do business with thousands of buyers and procurement managers from food producers and growers, agribusinesses, governments and resellers & distributors.
WHO WILL BENEFIT FROM EXHIBITING AT GFIA EUROPE?
Any company that sells solutions for sustainable agriculture. Visitors that want to make their businesses smarter and more productive without damaging our environment or climate.
They want to save water and natural resources, improve soil quality, protect livestock health and increase yields in all areas of food production.
If you can help food producers and growers do that, you should book a stand at GFIA Europe..
GFIA EUROPE REVIEW
Including emerging markets of Egypt, Former Soviet Union, India, Kenya, Nigeria, Russia, Sri Lanka, Taiwan, UAE
COMPANIES ALREADY CONFIRMED TO EXHIBIT INCLUDE
THREE MAJOR NEW INITIATIVES FOR 2018
Co-located with VIV Europe: the European trade show for the international Feed to Meat industry
Co-located with Future Food Manufacturing Expo: Europe’s first major international trade fair dedicated to essential sustainable technologies in food processing and production
Smart Agri Mechanisation Zone: the latest in connected machinery and digital farm equipment revolutionising precision agriculture will be showcased
CONTACT:
David Stradling, Sales Director
E: d.stradling@turretme.com | T: +971 (0)2 234 8486 | www.GFIAEurope.com
Lake Stevens High Seniors Convert Fridge to Hydroponic Garden
Lake Stevens High School seniors Isabelle Eelnurme (left) and Elise Gooding converted an old refrigerator to a hydroponic garden for their engineering design class. Their award-winning device is for growing healthy, nutritious produce in food deserts. (Dan Bates / The Herald)
Lake Stevens High Seniors Convert Fridge to Hydroponic Garden
- KARI BRAY Sat Jun 10th, 2017 1:30am
LAKE STEVENS — Isabelle Eelnurme and Elise Gooding salvaged the small refrigerator from Eelnurme’s grandparents’ back yard.
It was a putrid shade of yellow. The brand label wore off long ago. They cleaned out bugs and grime.
Then the teens painted it turquoise and turned it into a hydroponic garden. It’s a contained produce-growing system that doesn’t require soil or much space. They picture it in apartments in neighborhoods where poverty is high and access to fresh fruit and vegetables is limited.
At the beginning of the school year, the 18-year-olds set out to find a solution for food deserts, which are areas where people lack healthy, affordable food. During their research, they noted a link to health issues such as diabetes. They also found that there are deserts close to home, with more than a dozen in Seattle.
The transformation of an old refrigerator into a hydroponic garden was a year-long project, part of the engineering and design course at Lake Stevens High School. The friends have been in engineering classes since they were in ninth grade. Both plan to continue with those studies.
Gooding is bound for California Polytechnic State University and Eelnurme for the University of Washington this fall. Both are interested in civil engineering, and Eelnurme also wants to focus on environmental engineering.
The engineering and design course has been at the high school for about 10 years, teacher Kit Shanholtzer said. Students from the program have gone on to find success. He recalls one phone call from the FBI to background a job candidate, one of the first students who had gone through the course.
Students are tasked with defining an issue, researching solutions and coming up with their own version of how to solve the problem. Some look at transportation projects such as trains and bridges, while others focus on safety, health and quality of life.
“It’s wonderful when I can just mentor and guide, and the students have the drive and passion to do the project,” Shanholtzer said.
Eelnurme and Gooding have that drive. They’re professional and dedicated to their work, he said.
Though a school year seems like a long time for one project, students just have an hour per day in class, Shanholtzer said. If the annual hours are converted into 40-hour work weeks, students have about a month.
They don’t need to come up with new inventions, but rather an innovative approach to an existing solution. Hydroponic gardens aren’t new. Recycling outdated appliances into an easy-to-use system is a creative approach. Next, Eelnurme and Gooding hope to make one with a full-size fridge.
The two talked over more than 60 ideas before settling, they said. They wanted to think outside the box, but keep their project realistic.
Neither knew what a food desert was prior to doing an essay for their college-level English class. They learned just how widespread and often invisible the problem is.
“We didn’t know people were going without fresh produce,” Eelnurme said. “All they have is maybe a convenience store or fast food because fresh produce is too far away, and they don’t have a car to get there. We need to bring the produce to them.”
Inside the fridge-turned-garden, the portion that once was a freezer is where seeds start to germinate in small, cubic pods. The pods then go into the main body of the fridge, with a water spout and aerator. A gutter downspout has been repurposed into a container and magnetically attached inside the fridge. Once a plant grows to edible size, the downspout can be pulled out, the pod removed and a new one slotted in. The system doesn’t work for root plants such as carrots, but it’s good for lettuce, spinach and other leafy greens.
The students took their work to several engineering fairs, winning accolades at the regional and state level. Most recently, they received an honorable mention at the Imagine Tomorrow engineering fair at Washington State University, where more than 100 teams competed.
The WSU competition was the same day as their prom, so they woke up at 6 a.m. on the other side of the state, spent most of the day at the fair and caught an hour-long flight home to dance in Seattle. They got home around 1 a.m., exhausted and accomplished.
They hope students in next year’s engineering and design program will find projects they’re passionate about, and have fun while they figure out ways to make a difference in the world.
Kari Bray: 425-339-3439; kbray@heraldnet.com.
With their refrigerator-turned-hydroponic garden, Isabelle Eelnurme and Elise Gooding received an honorable mention at the Imagine Tomorrow engineering fair at Washington State University, where more than 100 teams competed. (Dan Bates / The Herald)
These Food Computers Use AI To Make “Climate Recipes” For The Best-Tasting Crops
06.09.17
These Food Computers Use AI To Make “Climate Recipes” For The Best-Tasting Crops
The tech-filled greenhouses can adjust growing conditions over and over again until they find the combination of light, humidity, and other factors that make the most delicious vegetables.
When the researchers asked the algorithm to optimize for flavor, there was as much as a 895% increase in the plant’s production of one specific flavor molecule. [Photo: Open Agriculture Initiative/MIT Media Lab]
Inside a shipping container-sized box at MIT Media Lab, crops of basil are growing in micro-climates designed by artificial intelligence. The first experiments, with controlled levels and duration of UV light, aim to grow a tastier version. As the mini-greenhouse generates roughly 3 million data points for each growth cycle of a single plant, the AI uses machine learning to analyze it and create new and better “climate recipes”–which can then be shared with anyone trying to grow food indoors.
As climate change makes it more difficult to grow crops in outdoor farms because of heat waves, more frequent storms, and more pests and disease, the researchers envision that climate-controlled, tech-filled greenhouses (which they call “food computers”) could be an increasingly useful place to grow food. The technology could also eliminate food miles: Instead of shipping avocados from Mexico to China, a Chinese greenhouse could precisely recreate a Mexican climate in Beijing–or tweak it to create a climate even better for an avocado tree.
It definitely speeds up the timescale by which we can get interesting results.” [Photo: Open Agriculture Initiative/MIT Media Lab]
Researchers at the Media Lab first developed a prototype of what they call the OpenAg Personal Food Computer in 2015. The contained growing environment, packed with sensors, actuators, and machine vision, can study and then replicate optimal growing conditions for food, changing everything from the pattern and spectrum of light used to the salinity of water and the nutrients added. A larger version, the Food Server, is the size of a shipping container, with racks of plants that can each be grown with unique variables. Initially, the researchers analyzed the data themselves to improve their climate recipes. But in June 2016, the team began working with the AI company Sentient to use its software to optimize the growing environment more quickly.
“It definitely speeds up the timescale by which we can get interesting results,” says Arielle Johnson, one of the researchers at MIT Media Lab Open Agriculture Initiative, or OpenAg.
“When you talk to [Caleb Harper, the director of OpenAg], he’s like, ‘Yeah, basil is a fast-growing plant,’ but in his terminology, fast-growing is six to eight weeks,” says Babak Hodjat, CEO of Sentient, a company that also designs AI to help stock traders find patterns in the market and hospitals predict infections. “That’s a long time to wait just to get a data point. So we tried out this methodology where the AI itself decides what are the next set of data points to try out.”
The basil is grown in staggered batches, so the AI can use the data from each batch to suggest changes to the “climate recipe” for the next crop before the first crop is finished growing, increasing the experimental throughput.
When the researchers asked the algorithm to optimize for flavor–by creating an environment that would maximize the number of volatile molecules in the plant–they discovered that if the lights in the Food Computer stayed on continuously, there was as much as a 895% increase in the plant’s production of one specific flavor molecule, and a 674% increase in production of another. The AI also rediscovered a known trade-off between weight and flavor (the bigger the plant, the less delicious).
“We’re trying to provide the standard that is open for all of this data and optimization to be shared by anybody.” [Photo: Open Agriculture Initiative/MIT Media Lab]
Using AI, the team will be able to optimize its climate recipes for multiple factors, including taste, cost, and sustainability, and create recipes for growing a myriad of crops. All of the data is available open-source, along with instructions to build a food computer yourself. “It can be made by anyone with reasonable hacking skills,” says Johnson.
The fact that it’s open-source distinguishes it from related research happening at vertical farming companies (some of which are also using artificial intelligence) or places like Philips’ GrowWise research center for urban farming in the Netherlands.
“Most people doing this kind of research, it’s proprietary, and it’s to optimize their own setups,” says Johnson. “Where I think we’re really strong is, more than trying to optimize something for ourselves, we’re trying to provide the standard that is open for all of this data and optimization to be shared by anybody.”
For fledgling indoor farming companies, the open-source climate recipes could help farmers grow better tasting, more productive, more efficient crops. New indoor farming companies typically invest heavily in their own research. “What we’ve seen is massive capital expenditure to get something up and running using controlled environments,” says Hildreth England, assistant director of the Open Agriculture Initiative. “But what happens is they sort of have to iterate in isolation.” The team envisions creating a shared language for indoor farming, “like the Linux of agriculture,” she says. “If we’re all using the same baseline, then that just lifts everybody up in an industry that is still trying to figure out its place in the conventional ag world.”
The research could also lead to tastier, more sustainably grown food, created without the type of genetic modification that some consumers find objectionable. “Ultimately, this is non-GMO GMO,” says Hodjat. “You’re not messing with the plant’s DNA . . . you’re just allowing it exhibit behavior that it would in nature should that kind of environment exist.”
ABOUT THE AUTHOR
Adele Peters is a staff writer at Fast Company who focuses on solutions to some of the world's largest problems, from climate change to homelessness. Previously, she worked with GOOD, BioLite, and the Sustainable Products and Solutions program at UC Berkeley. More
Go Ahead and AVA Byte of Fresh Produce From This Countertop Garden
Go Ahead And AVA Byte of Fresh Produce From This Countertop Garden
Derek Markham (@derekmarkham)
Technology / Gadgets
June 14, 2017
This soil-free smart garden promises fresh greens and veggies that are grown as local as it gets.
When it comes to naming new indoor growing products, the puns and wordplay may be bad, but getting more people growing their own food is definitely not, so please forgive the title of this article and lettuce move on to the actual product itself.
If you'd like to grow some of your own produce, but you don't have a place outdoors for a garden, or you'd like to grow year-round, a countertop indoor garden can be the answer, especially in a small space. A low-tech solution, such as a plant pot or an Urban Leaf in a sunny window, can be effective until the short days of winter arrive, after which supplemental lighting is needed until spring arrives. That's one of the reasons that growing devices with integrated lighting and watering systems are a popular choice, because they can be set up virtually anywhere in the home, without regard to access to sunlight. With LED lighting that is automated and tuned for optimal plant growth, combined with a hydroponic or aeroponic growing system, even those who've never had a green thumb can successfully grow greens, herbs, and veggies indoors.
In today's edition of YAUGU (yet another urban grow unit), the AVA Byte promises to bring adaptive intelligence and machine learning to the countertop growing scene for a hassle-free experience that is "So Smart & Simple it Must be Magic."
This 5-pot growing unit is designed to accept the company's soil-free compostable grow pods, which are pre-seeded and contain a nutrient mix appropriate to the plant variety, and which are then watered automatically according to the growth of the plants. The lighting, which is supplied by LED bulbs (no other specs given), is monitored and controlled automatically by the device, and is said to be "plant-optimized." According to the company, the lighting and growing system offers up to triple the growth rates of conventional growing, and requires much less water (something which is a feature of hydroponics systems in general).
"Growing your own food is a vote against the way the food system is today. Being food-lovers, we wanted to start a food revolution. Unfortunately, unlike houses with large backyards, a condo-dweller like myself is restricted by lack of space and access to sunlight. My kitchen herbs kept dying because Vancouver gets really dark and dry at certain times of the year." - Valerie Song, co-founder and CEO of AVA Technologies
The unit measures 18" x 4.75" x 7.5" (45.75 x 12 x 19cm) and weighs 4 pounds (1.8 kg) empty, and the lighting bar telescopes up to 21" high to adjust for plant growth. According to the company, the device is "intelligent, connected, and self-improving" and can connect with Alexa, Google Home or Apple Homekit.
Plug it in, place your pods, connect to Wi-Fi using the app, and fill the water reservoir. AVA notifies you when it's time to refill the reservoir and when your plants are ready to harvest! - AVA Byte
One unique feature of the AVA Byte is the inclusion of an HD camera pointed at the plants, which allows it to track plant health and growth, as well as letting users make time-lapse videos of their herbs and veggies. I'm not totally sure there's a huge need for more time-lapse indoor gardening videos, but it could be fun, right? There's also a mention of using the camera for something called Plant Vision, which I imagined to be something that could diagnose plant issues via an image, but nothing more is said about it, so perhaps it's a future feature. And of course, there's an app for the device, which allows users to monitor the light, water, and growth of the unit, as well as to manually customize the device's growing settings if desired.
Another intriguing element, also only mentioned briefly, was that the units could not only grow herbs, greens, and veggies, but could also be used to grow mushrooms. There's no other information about how the AVA Byte system would work for growing mushrooms, but perhaps that's another feature coming in the future, which could be a way for it to stand out among other similar countertop growing systems.
The company is currently running a crowdfunding campaign for the AVA Byte, which has already surpassed its initial goal, and backers at the $189 level will receive a unit and 5 growing pods (said to be $320 MSRP) in March of 2018. Find out more at the website.
EAT-Lancet Commission On Their Way To Transform The Food System
EAT-Lancet Commission On Their Way To Transform The Food System
Food Planet Health was recently launched to showcase news, case studies, data tools, and ongoing research updates from the EAT-Lancet Commission for Food, Planet and Health. The website focuses on the need to transform the food system in order to improve human health and health of the planet.
The EAT-Lancet Commission, a partnership between the EAT Foundation and the Lancet, is delivering the first full scientific review of what constitutes a healthy diet from a sustainable food system, and which actions can support and speed up food system transformation. The results will be presented in The Lancet in Spring 2018. There are 20 EAT-Lancet Commissioners, each of which are experts in the fields of food, health, agriculture, environment, and policy.
The Commission’s areas of expertise are sustainable food, healthy diets, and dietary trends, modelling food systems and developing supporting policies. These working groups are led by prominent researchers, practitioners, academicians, and policymakers from across the world, such as Walter-Willet, Anna Lartey, Lindiwe Majele Sibanda, Johan Rockström, Srinath Reddy, Christopher Murray, Jessica Fanzo, Tara Garnett, and Sunita Narain.
The launch of the website comes just prior to the EAT Food Forum 2017. Last year, Dr. Gunhild A. Stordalen, President of EAT Foundation, acknowledged the challenges of the current agricultural system with respect to the environment, health, and nutrition. Similarly, Johan Rockström, Co-founder of the EAT Foundation reiterated the goal of feeding a population of more than 9 billion in 2050 through sustainable means.
Follow the Commission’s updates and related news on their website, Facebook, and Twitter.
'Plant Factories' Churn Out Clean Food in China’s Dirty Cities
'Plant Factories' Churn Out Clean Food in China’s Dirty Cities
Researchers build urban farms, crop labs to combat contamination
Bloomberg News | May 25, 2017, 4:00 PM CDT
Yang Qichang walks through his “plant factory” atop the Chinese Academy of Agricultural Sciences in Beijing, inspecting trays of tomato vines that may help farmers slip the stranglehold that toxins have on China’s food supply.
The containers are stacked like bunk beds, with each vine wrapped in red and blue LED lights that evoke tiny Christmas trees. Yang is testing which parts of the visible-light spectrum are optimal for photosynthesis and plant growth while using minimal energy.
He’s having some success. With rows 10 feet high, Yang’s indoor patches of tomatoes, lettuce, celery and bok choy yield between 40 and 100 times more produce than a typical open field of the same size. There’s another advantage for using the self-contained, vertical system: outside, choking air pollution measures about five times the level the World Health Organization considers safe.
Rows of tomato seedlings are monitored in an experimental greenhouse at the Chinese Academy of Agricultural Sciences. Photographer: Qilai Shen/Bloomberg
“Using vertical agriculture, we don’t need to use pesticides and we can use less chemical fertilizers—and produce safe food,” said Yang, director of the Institute of Environment and Sustainable Development in Agriculture.
Yang’s government-funded research on vertical farming reflects the changing mindset of China’s leaders, who for decades preoccupied themselves with raising incomes for 1 billion-plus people. Runaway growth created the world’s second-biggest economy, yet the catalyzing coal mines and smokestacks filled the environment with poisons and ate up valuable farmland.
That stew inhibits the nation’s ability to feed itself, and is one reason why China increasingly relies on international markets to secure enough food. For example, it imported about $31.2 billion of soybeans in 2015, an increase of 43 percent since 2008, according to the National Bureau of Statistics. About a third of that came from the U.S.
Given the fluctuating state of trade relations with U.S. President Donald Trump’s administration and the increasing global competition for resources, China is turning to technology to make its land productive again.
“We will undertake rigorous investigations on soil pollution, and develop and implement category-based measures to tackle this problem,” Premier Li Keqiang told the National People’s Congress in March.
The silver bullet would be to eliminate emissions and industrial waste, an unrealistic option for a developing $11 trillion economy. Yet inventors and investors believe there are enough promising technologies to help China circumvent—and restore—lost agricultural productivity.
Government money backs a variety of efforts to modernize farming and improve growers’ livelihoods. The state-run Agricultural Development Bank of China pledges 3 trillion yuan ($437 billion) in loans through 2020 to finance key projects promoted by the Ministry of Agriculture.
By comparison, the value of U.S. agricultural production last year is forecast to be $405.2 billion.
Favorable terms will be offered to projects trying to improve efficiency, increase the harvest, modernize farming operations and develop the seed industry to ensure grain supplies, the bank said.
The loan program also intends to stimulate overseas investment in agriculture by Chinese companies. The biggest example would be state-owned China National Chemical Corp.’s planned acquisition of Switzerland’s Syngenta AG for $43 billion. That will give ChemChina access to the intellectual property, including seed technology, of one of the largest agri-businesses.
Yet China is reluctant to unleash genetically modified foods into its grocery stores. The government doesn’t allow planting of most GMO crops, including pest-resistant rice and herbicide-resistant soybeans, especially as an October survey in the northern breadbasket of Heilongjiang province showed that 90 percent of respondents oppose GMOs. China will carry out a nationwide poll on the technology next month.
“China’s past food-safety problems have caused the public to distrust the government when it comes to new food technologies,” said Sam Geall, an associate fellow at Chatham House in London.
A researcher transplants rice seedlings in a greenhouse of the Chinese Academy of Agricultural Sciences. Photographer: Qilai Shen/Bloomberg
About a fifth of China's arable land contains levels of toxins exceeding national standards, the government said in 2014. That's more than half the size of California.
About 14 percent of domestic grain is laced with such heavy metals as cadmium, arsenic and lead, scientists at government-affiliated universities wrote in 2015. The danger is most evident in industrial coastal provinces, where many of the world’s iPhones and Nikes are manufactured.
The government of Guangdong province, adjacent to Hong Kong, said in 2013 that 44 percent of the rice sampled locally was laced with excessive cadmium, which can damage organs and weaken bones if consumed regularly in high quantities.
That’s where Yang’s “plant factories” would come in. For now, the greenhouse-like structures are mostly demonstrations as he tries to improve their energy efficiency and make their produce more affordable to consumers—and a better investment for the government. Yang’s work is supported by an $8 million government grant.
“With the challenges our agriculture is facing, including China’s rapid urbanization and the increasing need for safe food, plant factories and vertical agriculture will undergo a big development in China,” he said. “There will be many ways to farm in big cities.”
He isn’t alone in hunting for techniques to grow untainted food in the concrete jungle. A Beijing startup called Alesca Life Technologies is using retrofitted shipping containers to farm leafy greens.
Roots of a kelp plant grow through a sponge under artificial light at an Alesca Life shipping-container farm in Beijing. Photographer: Qilai Shen/Bloomberg
A demonstration model is parked atop metal stilts in an alley between a Japanese restaurant and a block of office buildings in Beijing.
Inside, co-founder Stuart Oda, a former investment banker for Bank of America Merrill Lynch in the U.S. and Japan, checks on rows of planters sprouting peas, mustard, kale and arugula under LED bulbs. Alesca Life’s smartphone app allows growers to monitor air and water conditions remotely.
“Agriculture has not really innovated materially in the past 10,000 years,” Oda said. “The future of farming—to us—is urban.”
The containers can sell for $45,000 to $65,000 each, depending on the specifications, Oda said. Alesca Life sold portable, cabinet-sized units to a division of the Swire Group, which manages luxury hotels in Beijing, and the royal family of Dubai. The startup hasn’t publicly disclosed its fundraising.
Shunwei Capital Partners, a Beijing-based fund backed by Xiaomi Corp. founder Lei Jun, has invested in 15 rural and agriculture-related startups in China, including one that makes sensors for tracking soil and air quality.
Shunwei manages more than $1.75 billion and 2 billion yuan across five funds.
“For agriculture technology to be adopted on a wider scale, it needs to be efficient and cost-effective,” said Tuck Lye Koh, the founding partner.
That’s one reason why Shunwei is backing agricultural drones, which more precisely spray fertilizers and the chemicals that ward off crop-destroying pests and diseases.
Clockwise from top: Trays of wheat grass grow in one of Alesca Life's converted containers; Kelp seedlings are cultivated in a foam mat at the urban farm; An employee carefully places each seed.
Photographer: Qilai Shen/Bloomberg
As China’s farmland dwindled because of urbanization, the remaining growers attempted to boost yields by soaking fields with fertilizers and pesticides, degrading the soil and contaminating the crops.
Farmers in China use four-and-a-half times more fertilizer per hectare (2.4 acres) of arable land than farmers in North America, according to the World Bank.
“There’s overuse of fertilizers in every country, but especially China,” said Jeremy Rifkin, whose books include “The Third Industrial Revolution.” “The crops can’t even absorb the amount of fertilizers that are being dumped.”
As dawn squints over cornfields on Hainan island, a pastel-blue truck rumbles down the gravel road and stops. Workers emerge with a pair of drones made by Shenzhen-based DJI and a cluster of batteries.
Zhang Yourong, the farmer managing 270 mu (44 acres), arrives in a pickup loaded with pesticide bottles. The crew adds water and pours the milky concoction into 10-liter plastic canisters suspended under the drones.
The stalks part like the wake of a boat as the drones fly over. Every 10 minutes, the eight-armed machines return, and the crew refills canisters and changes batteries.
Trays of kelp, a vitamin and mineral-rich seaweed, are ready to be transplanted to bigger growing spaces at Alesca Life's demonstration farm. Photographer: Qilai Shen/Bloomberg
Zhang used to hire four or five workers to walk the fields with backpack sprayers for five days. Now, the drones cover his crops in a morning and use 30 percent less chemicals, he said.
That’s what the government needs to hear as it tries to make China’s food supply safer.
“This is much easier and much faster than before,” Zhang said. “This is the future. Many farmers are switching.”
Urban Farming Insider: Jeff Mastin, R&D Specialist at Total Grow Horticultural Lighting
Urban Farming Insider: Jeff Mastin, R&D Specialist at Total Grow Horticultural Lighting
We sat down with Jeff Mastin, R&D Specialist at Total Grow Horticultural Lighting, to discuss the future of horticultural lighting, from small scale kitchen counter systems to mega-sized vertical farms.
___
Introduction
UV: A lot of people who come across Total Grow probably aren't too familiar with it. Could you talk about the background of it and your involvement, and maybe your personal story and how you got involved in the biology side of it. I'm sure people are curious why a biologist might be working with horticultural lighting.
Jeff: That could be a half hour story right there, a lot of pieces. Trying to not get too spread out on it all. The company behind total grow is called Ventis Technologies.
We had been, and still do, specialize in integrating semiconductor technologies into applications. So that was really in the realm of touch-sensing technology before we got into lighting.
But LEDs are semiconductors you use for touch-sensing technologies, so there's a strong bridge there. The lighting path started because we were working with a group of optical physicists that had a concept that they wanted to commercialize and put to the test.
Because of our skill set we were able to take this optical technology they were developing, help them build it, help them commercialize it, test it, refine it.
And really what that was based around was improving LEDs in some of the main weaknesses of them in terms of glaring and shadowing and color separation.
Some of the limitations that were really plaguing the LED industry. The end result of it is basically we had this technology that gave us great control over the spectrum that the light made and the directional output of the light in a way that a typical LED by itself couldn't do.
Because of the uniqueness of the horticultural lighting world in terms of what you need to do with a light to do it well, where you need to send it and what the spectrum should be, it actually made a lot of sense to start there with that optic. As opposed to the really crowded white lighting world.
So it fit really well into the horticultural lighting world. I was already with the company because of work that we'd been doing with, among other things, environmental technology of different sorts. Bioenergy systems, tree plantation projects in Indonesia. We do a lot of community development things.
So, without going too far in depth on the rabbit hole, when we started exploring the horticultural world where we could apply the technology, that's where being a biologist was a natural fit to really take a lead on the science and the research and that side of th edevelopment process for the product. And that was, I think, about 6 years ago now. So, we've come a long way since then.
UV: If you were going to distill that technical focus into trends that you're generally seeing, broad brush in the horticultural lighting space, what are you seeing?
Jeff: Yeah, so the horticultural lighting industry is really becoming revolutionized because of LEDs. Even though ten years ago and arguably five years ago, LEDs in the horticultural world were a research tool or a novelty.
They were not efficient enough yet and they were definitely not affordable enough yet to really consider them an economical general commercial sense.
But that is very quickly changing. The efficiencies are going up and prices down and they are really right now hitting the tipping point wherefore at least a lot of application, definitely not all applications, the LED world is taking over horticulture.
So, and there's a little bit of what I'd say is a positive feedback route loop, in the sense that as the prices go down and efficiencies go up and more people are buying them, there's, it's easier for the market to continue that process.
Plus LED's already were a research tool, but now the interest and the funding to do better research and the tools to do better research are also exploding. So the knowledge base is very rapidly improving.
There are still a lot of unknown questions and a lot of things to learn but at least the basics and the starting points, in terms of how do you grow a plant from a lighting perspective.
The improvement in how well we understand that has gone up quite a lot in the last, really, five years there's been a lot learned.
UV: How do you view the translation of those trends into actionable points? For people who are looking for action and looking to improve their current system or looking into systems to buy and their saying, "well if I'm going to spend a couple hundred bucks on a LED lighting system, how do I make sure that what I'm buying isn't going to be obsolete in a year or two?"
Jeff: Yeah, and that's certainly a very real question. I would say that with the boom with the LEDs, there's only so far the technology can improve.
There's physical limitations. You can't make 100% efficient product that turns every bit o felectricity into photons of light. At this point the efficiency level of the LEDs are good one's are up over 50%.
So can we ever get up to 70 or 80%? Probably not with an end-product, not one that's going to be affordable.
Maybe in a lab you can. So the room for improvement is still there but it's not in the category where you're going to say, well this is obsolete, I can get something three times better now.
Ten years from now the cost will be cheaper. But that again doesn't make it obsolete. So in terms of that fear, I don't think people have to worry about (current LED light technologies) being obsolete.
The biggest challenge with LEDs really comes down to the cost. Because it's not the cheapest option and so that's where the economics and the business model and really running the numbers of the economics of it all has to be done.
Because there are cases where LEDs are not the best solution.
If you're not using your lights enough the power saving doesn't add up quickly. If the quality of lighting isn't top-notch, some of the quality benefits you can achieve might not be worth the investment.
UV: So that leads me into the next topic that I think would have an interesting perspective on, when you start talking about giving into the heavy-hitting area of maybe investing six figures into a commercial enterprise lighting system, what are the questions that need to be answered (before buying)?
Is the cost driver for those heavy-duty lighting systems strictly a efficiency rating? Will a 48% efficiency lighting system be cheaper always than a 49% efficiency lighting LED system for horticultural commercial operations? How do you look at that macro, for-profit analysis?
Jeff: Yeah. So first and foremost there's got to be questions on what is trying to be accomplished. So, of course, I think in the six figure lighting installation, we're probably talking more the full source vertical lighting indoor environment.
So in those places, first of all it's got to make sense to do it. So you've got to have a market that wants (produce) that customers can buy at a high enough price that you can afford to do at all.
For one, what crop are you growing? One of the one's that can be tougher for people to answer is, is it better to airing on the side of economic and low upfront cost? Or airing on the side maximizing the growth o fthe yield per square foot.
Because you can have two people with essentially the exact same setup and crop but for different reasons it's going to make sense for one to use twice as much light intensity as the other.
It's going to be a different business model: the person using twice as much light is going to have a higher yield, for sure. But obviously they invested more and they have a higher operating expense because there's more lights to run.
So where that all shakes out is, that's one of the things that I think the industry is still figuring out.
And individuals have to figure out is where makes sense for them. And there's people doing it successfully on both sides of that.
Do you want your lights to be as tight on the plants as possible to stack yourshelves, as many shelves as you can, in a small vertical space?
Or do you want your lights to be two feet above the plants so you have plenty of room for your workers to be working right in there without having to move the plants around?
Are you going to provide reflectivity around the grow areas? Or is that going to be restricting air flow and access too much?
Because reflectivity will help improve uniformity and cut down at least a little on the amount of lights you need.
So some of those general things. How do you envision your system? How do you, on a day-by-day basis, want to be working? And then the business model side of things that really determine airing on the side of extra light or less light.
UV: How much can setting up a reflectivity system...Have you done any work onlooking at how much you can recover, as far as efficiency from using your addition like that?
Jeff: That's going to vary pretty widely depending on what your setup looks like. The two big factors are: how big is the grow area? So if you've got a two by four table or you've got a five foot by thirty foot shelf, the bigger the shelf, the less proportionately, the less lights are on the edge, which means, proportionately, light lost overall.
The other big factor is the height. If you are doing something where you've got your lights really tight onto the plant, there's not a lot of opportunity for light to escape out the sides.
If you're trying to do one of those setups where you've got lights two feet above the plant, then there's a lot of space for light to be lost outside of the grow area. So when all is said and done the number there could range anywhere from, probably, on the smaller side, you're probably talking 5% recovery that you could possibly achieve.
Maybe a little less. In a typical situation, you're probably more inthe 10-15% range. And in the cases where you have a smaller setup with higherlighting, it could be 20-50%, depending on more extreme cases.
UV: Is that just added on to the base lighting system efficiency?
Jeff: Yeah, that'd be the gist of it. Because if you've got 50% efficient and you've lost 20% of your light and now you're 40% efficient. And really, so when you're picking out how many lights you're going to need and this an industry person working with customers, there's a big range of who you're working with too.
In terms of whether someone can walk up and say, I want a 17 mole per meter squared per day DLI and I'm running it 18 hours, what do you recommend?
Or whether somebody's just saying, I'm growing lettuce on a shelf what should I do?
In terms of the technical savviness of laying out the light target or really having no idea. Light is a complicated topic. It's a lot more complex than it sounds. When you might talk from the point of, my plant is lit, should it be growing?
Obviously a lot more complex than that. Ultimately from a lighting standpoint, you're trying to make a light plan to hit lighting targets of a certain intensity. A technically savvy grower that's going to know what intensity they need to aiming for.
Someone who's less familiar with it is not going to know that and it's going to be up to the lighting provider to provide a good recommendation. That's where the efficiencies and everything really calculate out.
UV: Where you would suggest going to find the suggested intensity, would you go to the (lighting) provider? It seems like they might have an incentive to tell you that you need more so that you buy more. Is that accurate? Essentially where do you think is the most reliable source of figuring out your intensity? For somebody who is less geared toward that information.
Jeff: The safest thing is to ask a few different places for sure. You definitely want to ask the lighting provider, because they're going to have familiarity with their own light.
So for example, obviously there's bias and all that in terms of what I'll say here but, with the testing we've done and our spectrum. That's a big part of our claim to fame is part of spectrum control is, we've experienced that it had efficiency advantages over other light spectra.
So the same amount of photons is going to accomplish more. So when I give somebody a recommendation I might, depending on who I'm talking to and what's behind their light intensity recommendation, whether they understand these things or not, I might adjust what my target is a little higher or a littler lower based on what they have in their mind.
If they're thinking of a fluorescent or legacy light spectrum ability to grow at a certain light level, we're going to be able to accomplish that at a lower light level.
So there's nuances to it all. Other great people to talk to, if you can find somebody already doing what you're trying to do, that's a great resource. There are an increasing amount of university extension programs, places like that where you might be able to talk to somebody with a good understanding from an academia point of view.
Which sometimes that can be even more idealistic than the industry person, but it's still good input. Then the risky but potentially really good one is searching around online. You can find some good resources out there in terms of light targets.
Find a handful of them an average them out. Because there is going to be some people that are coming from different points of views and are too high or too low for different reasons compared to what you want to do.
UV: So we touched on this a little bit, but when you talk about the levels of price, can you provide an escalator of different stages of price? Would you say there's kind of a personal enthusiast cutoff? Then maybe you have your small, selling stuff to restaurants size growing system.
You may have the system where maybe you're dealing with it on an everyday basis where it's a premium system. How do you organize that out and what's the 30,000 foot view there?
Jeff: So to give just a order of magnitude sort of number, you probably going to be someplace in the fifty dollar per square foot sort of number. It can be half that it can be double that.
But that's sort of a general ballpark of what your up against. So the major factors that are going to drive that up or down: for one,and this is talking LEDs, if you're using something like a cheaper fluorescent light you're going to be able to get yourself setup for less.
You're going to pay more as you run those lights - pay maintenance and then electricity costs. then the results, depending on what you're doing, you may or may not still be happy with them with other styles of lights and same goes with LEDs.
There's good LEDs and there's bad LEDs. Just because you're using an LED light doesn't guarantee you're going to love your results.
So, some of the major factors: volume obviously matters. If you're somebody doing ten thousand square foot facility you're going to be getting thousands of lights and getting a great price on it compared to somebody setting up fifty square feet.
What I was describing before in terms of the light intensity targets, people could be growing with double the intensity for one style of lighting compared to half for another.
That's just talking within the realm of common plants of green, the lettuce, the micro greens, herbs, berries can be in the same sort of target.
If you start talking about tomatoes or medicinal plants, then the ability to use higher light levels and have the plants make good use of it kind of skyrockets. You can go four times higher with some of those other plants, and for good reason.
UV: You said an example of those may be tomatoes or maybe, what are some other examples, cucumbers or stuff like that?
Jeff: Yes. For the most part at this point, the larger fruiting plants in general, like tomatoes or cucumbers, there's not a significant amount of people doing that totally indoors.
That's still really a greenhouse plant and for the foreseeable future that's probably going to remain true outside of really special situations. But one of the big opportunities in the indoor world is finding high value crops. And that can be more specialty herbs that are difficult to grow.
That can be medicinal crops. When you start getting into those realms of higher value product, you can better justify on airing on the side of maximizing your yield as opposed to minimizing your investment.
So there's that plus just the size of the plant. If you're talking micro greens or lettuce and something that's probably not getting bigger than nine inches tall, there's the plant itself doesn't need to have a huge biomass to support - lettuce is more of a winter crop then a summer crop in terms of the light levels. Whereas a tomato plant you can keep throwing more light at it and it'll keep producing higher yields for a very long time.
Lettuce you're going to start having tip burn and some negative effects like that if you over do it.
UV: One thing I always like to ask is what your favorite fruit or vegetable is.
Jeff: Favorite fruit or vegetable. In general my favorite fruit is something I haven't tried yet. So, I'll go with that in general. Otherwise favorite fruit would be different berries and favorite vegetable is anything sauteed with salt and butter.
UV: If you had to distill down to one single sentence, lighting advice for a beginner, what would it be just one sentence?
Jeff: In general, like I've reiterated, know what you're trying to accomplish, who that market is and what the opportunity really is, what's going to let you be successful.
Can't answer what you're perfect lighting solution is until you know what you're trying to accomplish.
UV: What's the best advice you heard as you were learning about lighting and kind of flip the last question on it's head?
Jeff: I would say, and I don't know if this is something somebody told me or not, but I think just getting information from a lot of different sources. There's a lot of different angles that people can have or a lot of biases and a lot of misinformation out there. So, fishing around and finding reliable sources that you can trust, that's a big deal.
Thanks Jeff!
Total Grow Horticultural Lighting
Indoor Farms of America Sales Growth Escalates
Indoor Farms of America Sales Growth Escalates
By News Release May 24, 2017 | 8:24 am EDT
Indoor Farms of America is pleased to announce that sales through the first four months of 2017 have exceeded the entire year of 2016, when the company first sold its patented vertical aeroponic indoor farm equipment.
According to company CEO David Martin, "During 2016, our first year selling our equipment, we enjoyed what we consider a very solid year for launching our unique vertical farming equipment, and 2017 has already eclipsed that in dollar volume and diversity of farms being sold, built and delivered."
Indoor Farms of America two story display at 2017 Indoor AgCon Las Vegas
GrowTruck Container Farm Display at 2017 Indoor AgCon Las Vegas
The company sold numerous smaller farm packages and container farms during 2016, many of which were considered "pilot farms," to allow potentially large warehouse farm operators to get a feel for this amazing vertical equipment, prior to making larger commitments.
"We knew when we introduced the equipment throughout the previous year, it would somewhat be a year of "tire kickers," and we were overwhelmed at the positive response to our total farm solutions. Those tire kickers are now converting into sold larger farms, as we continue to see positive crop growing results by folks across the U.S. and in key international markets."
Indoor Farms of America spent several years designing and developing its patented ultra high yield vertical aeroponic equipment. The firm manufactures a robust line of aeroponic products, including the world's most productive containerized farms, for deployment in any area of the world that has real need for such a unique small farm platform that produces commercial quantities of fresh produce in an manner superior to any other container farm manufacturer.
Other "turn-key" complete farm packages were specifically developed for fully scalable indoor farm applications to drive down initial capital costs as well as the ongoing operational costs. This focus combines to provide the operator with the single most cost-effective indoor agriculture equipment available in the world.
Ron Evans, company President, stated it this way: "We received numerous affirmations throughout 2016 from third party growers using our farm technology that it delivers on what we promise in overall farm performance. We are committed to the concept that if you are going to own and operate an indoor farm, it should provide you a very sound financial return."
"So many farm platforms that Ron and I analyzed in the early R&D phase back in 2013 and 2014, we believed were doomed to financial failure due to poor design with off the shelf 30 year old growing technology that was not innovative. We recognized that if those marginally profitable operators made errors in execution, they would not survive. It was our mandate internally to develop a complete farming solution that would transcend anything on the market, and we achieved that", stated Martin.
New sales by the company for 2017 to date include numerous locations around the U.S., as well as other countries, as the company continues on a path of rolling out the products in key markets that will benefit dramatically from truly locally grown fresh produce.
"We have sold our first farm for Alaska, destined for Juneau in the next couple months. As well, we have sold our first farm for the GCC region, destined for Dubai. This farm will change the landscape for food production in the Middle East." stated Martin. "Further developments include complete farms sold for multiple regions of Canada, including Alberta, Manitoba and Ontario provinces, and that region is about to explode with growth in the use of our farm solution."
Martin added, "We have sold our first large scale farm for Africa, destined for the country of Botswana. We have had a farm in operation in Johannesburg for many months, and our distributor there reports how amazed potential customers are with the robust growing they experience with our vertical aeroponics platform."
The company has spent thousands of hours developing new crops beyond leafy greens. Evans stated: "Leafy greens were the easy part, and ours does that better than anything else. We have proven out growing of certain varieties of cherry tomatoes, strawberries, peppers, peas and beans for proteins, and we are now working on specialty root crops like heirloom carrots and baby potatoes. We know a well-rounded garden approach is what many folks want to see, not just leafy greens, and we are rapidly developing those for commercial scale."
Indoor Farms of America has a showroom with demonstration farms operating in Las Vegas, Nevada and in multiple locations in Canada, and in South Africa, where their patented vertical aeroponic equipment is on display and receiving amazing reviews by industry leaders.
The Future of British Farming: Accentuate The Technology and Eliminate The Subsidy
The Future of British Farming: Accentuate The Technology and Eliminate the Subsidy
Editor’s Note: Richard Ferguson is founder of Ferguson Cardo, an agribusiness consultancy and research group in the UK. With several years experience in the industry working for groups such as PwC and Renaissance Capital, Ferguson recently wrote a new report on the future of UK agriculture in the wake of Brexit. Here he offers some key insights from that report.
Richard Ferguson
The future of British agriculture lies not in an annual £3 billion infusion of inefficient subsidies and misallocated capital via the Common Agricultural Policy, the European Union’s farm subsidy programme. Rather, the UK has the potential to re-pivot, refocus and redeploy its capital and energies towards the nation’s value-added agricultural technologies and cutting-edge science capabilities. This transformation will allocate capital efficiently and bring wide-ranging social and economic benefits across the UK economy. It may also redefine the country’s objectives in trade, aid and economic diplomacy.
To feed a world of some 10 billion people, according to the United Nations’ Food and Agriculture Organization (FAO), almost 77% of the additional output from farming will come from intensification and higher yields; only 20% will come from increased farming area. In other words, farming output growth in the future depends critically on the greater use of agricultural technologies, ranging from equipment to genetics.
The possibility of a Brexit-driven reconfiguration of the UK’s food and agricultural sector suggests that a period of significant transformation and structural adjustment lies ahead. Set against an industry already in the midst of rapid technological displacement, value-chain disruption and regulatory change, a transformative event such as Brexit appears to add to existing uncertainty.
However, while the potential institutional, financial and operating frameworks that will arise from Brexit suggest a wide range of possible outcomes, the process, if mapped successfully, can be a positive one. The UK’s current position is not unique. In the 1980s, the government of New Zealand instigated a reform programme to transform the country’s food and agriculture sector, the results of which were immediate and painful as well as long-term and beneficial.
At the core of the transformation that shook New Zealand’s agriculture sector in the 1980s and 1990s was a pressing need to access new markets in the face of external economic shocks and structural adjustments, such as the UK’s decision to join the then European Economic Community (EEC) in 1973. While there are obvious direct parallels between the New Zealand case study and Brexit, both situations remain distinct and unique. However, we would contend that an agenda focused on long-term goals can deliver significant economic and social benefits even if they come with considerable short-term costs. The battle about to commence is set to be as brutal, complex and ideological as that which determined the direction of the British economy in the late-1970s and early 1980s.
The UK must also consider to what extent environmental considerations should influence the policy-making agenda. What is the role of government in terms of regulation, environmental compliance, bio-security and food trust? Alternatively, can a free-market, liberalisation agenda deliver wider social, political and environmental objectives as well as economic goals? Can the UK use its fledgling – and flourishing – agtech knowhow to raise productivity, build exports and deliver added value to the British economy?
The British government, budget pressures notwithstanding, has to ask whether a pound spent subsidising a marginal farm in the Pennines is better spent on developing world-class facilities across the technology and biosciences sectors. How many UK startups and early-stage companies fail to thrive because they lacked capital at a vital stage of their evolution?
There are other strategic considerations for the UK if it wishes its food and agriculture sector to prosper. A global imperative is: how do we feed a world of 10 billion people within a generation when its current needs are delivered by an army of unsophisticated and undercapitalised smallholders? We contend that the Department for the Environment, Food & Rural Affairs (DEFRA) and the Department for International Development (DFID) need to shift their respective – and parallel – focuses on agriculture subsidies and development aid to collude with the Department for International Trade (DIT) and the Foreign & Commonwealth Office (FCO) to bring much of the UK’s technological, commercial, developmental and diplomatic ambitions in food and agriculture under a joint strategy.
This is relevant for the domestic landscape too. Britain has a large food deficit. The country needs to build its export capabilities and this is best done in commercial sectors where capital delivers the highest returns and creates the most economic value added. Subsidising agriculture may no longer make sense. The country needs to consider what are its best resources – whether technological, scientific or financial – and how best these can be combined. Such an assessment is hindered by many factors: the food and agriculture sector – excluding inputs, trading houses and the consumer end of the value chain – is notoriously fragmented. The most promising opportunities lie in the most awkward places to invest capital. An agricultural technology full of promise struggles to get funding, let alone access challenging new markets. In short, how do you get a world-beating piece of agtech into the likes of Africa or Asia ahead of your competitors?
The triggering of Article 50 by the British government on 29 March 2017 offers a strategic opportunity for the UK to eliminate agricultural subsidies after 2020 and refocus efforts on the promotion of value-added agricultural technologies. Make agricultural subsidies a thing of the past.