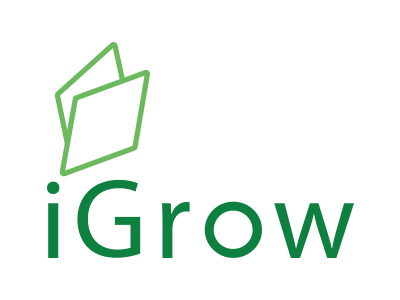
Welcome to iGrow News, Your Source for the World of Indoor Vertical Farming
Helping Small-Scale Operations Develop A Recipe For Horticultural Lighting Success
Helping Small-Scale Operations Develop A Recipe For Horticultural Lighting Success
December 19, 2017
By Jeff Mastin
Venntis Technologies LLC
During the Emerging Applications track at Strategies in Light (SIL), co-located with The LED Show and Lightspace California in Long Beach, CA, Venntis Technologies biologist Jeff Mastin will explore the landscape of modern farming on the smaller scale, with a presentation on the economics of equipping a small indoor/vertical farm and how such operations can leverage the qualities of LED-based horticultural lighting. Mastin explains the appeal of close-to-consumer growing operations, but notes that a smaller operation will naturally need a different approach than a mass commercial grower. In the presentation “Small-scale vertical farming success recipes: Horticultural lighting reports from the field,” he will address a Michigan-based grower as a case study for analyzing the horticultural lighting needs of localized vertical farms with specific crop and usage objectives. Here Mastin looks at the prospects and exciting opportunities for both the grower community and the solid-state lighting (SSL) industry in expanding this horticultural niche. — Carrie Meadows
Where does our food come from? Three generations ago, this question had much simpler and well-known answers. Most food was derived from family gardens and family farms. Organic, local, sustainable, hydroponic, aeroponic, vertical-farming, container farming, etc. — these terms were not in our vocabulary with the absence of a dozen ways to buy lettuce at the local grocery store. After recent decades of urbanization, population growth, climate care (or lack thereof), and both geographic and relational disconnect from our food sources, vertical farms are an exciting new approach to shorten these distances in fascinating new ways with the help of recent technological advancements. Most foundational to the ability to move some types of farming indoors into dense, highly productive spaces is the advancement of LED-based horticultural lighting technology to make it possible to grow without the Sun and have a chance at economic viability.
Lighting as a Platform Part I: What It Is and Why You Should Care
In the world of the smart building, smart has real meaning. Creating buildings whose performance is optimised with respect to a variety of goals and which meet the increasingly challenging demands of building and energy efficiency regulations is a tough job these days. Energy use must be minimised and operating costs kept low.
Brought To You By LED - Bluetooth Feed
Related: 10 Things to Love about Strategies in Light 2018
LEDs Magazine will continue its countdown to Strategies in Light with more industry insights here at ledsmagazine.com. You can find details on the conference program, speakers, exhibitors, and more at strategiesinlight.com.
Within the realm of vertical farming, besides both strong proponents and objectors, there is also a wide spectrum of approaches. Vertical farmers can grow in soil, hydroponically, or aeroponically; use pallet rack shelving or vertical towers with plants growing horizontally; invest in various levels of control of humidity, CO2, isolation from potential pests; establish operations in abandoned warehouses or new facilities; and focus on “simpler” crops like leafy greens and herbs or break metaphorical ground on potentially higher value crops. For the Feb. 14 Strategies in Light session, we will of course focus on the various options and opportunities related to the critical lighting component of vertical farms, with an emphasis on how the scale of the vertical farm may impact horticultural lighting choices.
Garden manager Christy Kaledas has established indoor vertical farming operations that utilize LED horticultural lighting for the Black Pearl restaurant in Ann Arbor, MI.
Understandably, the most press is given to the largest vertical farming entities such as Plenty, which has raised at least $260 million to date with visions of large vertical farms on the outskirts of every major city. However, your local news might also have shared a story recently about a garage, basement, classroom, or industrial space that is now growing microgreens, leafy greens, or herbs for local restaurants, groceries, and farmers’ markets. In many cases, these are self-funded and driven by conversations with local chefs regarding exactly what they’d like to be adding to their menu next. The specifics of how these grow operations are set up are dictated by budget, physical space constraints, and information sources. Many of these growers are coming out of non-horticultural career paths and are learning from blogs, books, university extension offices, equipment suppliers, and other sources.
Related: Strategies in Light tracks send strong signals about lighting prospects
For the largest-scale vertical farmers, lighting technology is often developed in-house to lower costs. Facilities are large enough to justify multiple lighting approaches where experience, curiosity, or a physical constraint makes it worthwhile. These can include lights of various intensities and spectra. However, for smaller-scale vertical farmers, developing their own horticultural lighting is not an option. Furthermore, changes in their operation as they grow, changing customers, and the completely unforeseen places a premium on versatility within their lighting source. At any scale, upfront costs and operating costs are extremely important as lighting can represent a very large proportion of both costs. Furthermore, lighting performance will have a drastic impact on growth quality and quantity.
An example to be discussed in detail at Strategies in Light will be Black Pearl Gardens. The Black Pearl restaurant recruited its garden manager, Christy Kaledas, to begin growing microgreens and other crops for the restaurant in 2014. The small vertical farm began in Christy’s basement until the restaurant basement was ready, and has since expanded to include a warehouse facility for increased production space. The aforementioned need for versatility resulted in early setups using soil-filled trays, simple and adjustable wire shelving, and TotalGrow Broad Grow Spectrum LED lamps on flexible socketed cords, which could be configured to match the various setups that fit in the basements. The modular, individual lights with an all-purpose growing spectrum also allow the ability to adjust lighting concentrations as needed for different crops and production schedules. Most of this equipment is still used in the new spaces, though not necessarily in the same configuration. Besides multiplying shelving quantities, Black Pearl Gardens has experimented with varying degrees of success with hydroponic systems, higher-powered lighting over more spacious grow ponds, and other variations on its base system.
Black Pearl Gardens’ operations have since expanded into the restaurant basement (shown) and an additional warehouse facility equipped with TotalGrow Broad Grow Spectrum LED lamps with flexible configurations for various crops and growing schedules.
The combination of entrepreneurial aptitude, a great culture for selling high-quality and high-value crops in Ann Arbor, MI, successful horticultural lighting, and other growing techniques are consistent with the stories of other successful small-scale vertical farmers who seek to bring the farm closer to the consumer.
JEFF MASTIN is chief biologist for Venntis Technologies, a specialist in custom spectra, volumetric LED lighting, and custom output pattern lighting, and a finalist in the 2017 LEDs Magazine Sapphire Awards.
Fluence Bioengineering Launches New Vertical Farming Lighting Solutions
Fluence Bioengineering Launches New Vertical Farming Lighting Solutions
Versatile, easy-to-deploy LED systems designed to increase plant density, yield, and quality while reducing installation and operating costs
Fluence RAZR4 LED Grow Light
The Fluence RAZR system not only creates an environment for improved growth and development of our microgreens, but allows us to run a commercial-scale vertical farm at a lower operating cost.
AUSTIN, TEXAS (PRWEB) NOVEMBER 30, 2017
Fluence Bioengineering, Inc. (“Fluence”) today launched three new horticulture lighting solutions designed for the world’s largest vertical farms. With a sleek form-factor, broad-spectrum, optimized light intensity, and world-class energy efficiency, the new Fluence RAZR Series is built for a wide range of vertical farming applications from full-cycle cultivation of leafy greens and microgreens, to young plant propagation of vegetable, ornamental and cannabis crops.
“The new Fluence RAZR solutions are purpose-built to address the unique challenges and opportunities associated with vertical farming,” said Randy Johnson, Co-Founder, and CTO at Fluence Bioengineering. “Every design consideration that went into the new RAZR Series, from the thin form-factor to modular daisy-chain configuration, is predicated on increasing our vertical farming customers’ outputs while reducing their inputs.”
Dense Vertical Farming
With a 1.5-inch thin form-factor, and a mounting height as close as five inches from the plant canopy, the Fluence RAZR Series delivers uniform photosynthetic photon flux density (PPFD) for maximum space-use efficiency and yield per square foot. With the ability to stack vertically in carts and shelving, or daisy-chain horizontally across racks and rolling tables, the new Fluence RAZR Series is built for quick and easy deployment to reduce installation time and material costs thanks to a one-to-many design which connects up to ten lighting modules to one power supply.
The RAZR4 Array is ideal for full-cycle leafy green, basil, strawberry and culinary herb production as well as early-stage vegetative growth for vegetables, ornamentals and cannabis cultivation with an average PPFD up to 375 µmol/m2/s over a 2-foot by 4-foot canopy with a 5-inch mounting height above the plant canopy. The RAZR4 Array includes five lighting modules, and covers 40 square-feet of the canopy.
The RAZR3 Array is ideal for full-cycle leafy green and microgreen production as well as
propagation of vegetable, ornamental and cannabis crops with an average PPFD up to 260 µmol/m2/s over a 2-foot by 4-foot area with an 8-inch mounting height above canopy. The RAZR3 Array includes seven lighting modules, and covers 56 square-feet of canopy.
The RAZR2 Array is ideal for tissue culture, seedlings and cutting/cloning propagation as well as ornamental plugs and starter pots with an average PPFD up to 160 µmol/m2/s over a 2-foot by 4-foot area with a 12-inch mounting height above canopy. The RAZR2 Array includes 10 lighting modules, and covers 80 square-feet of canopy.
Each RAZR lighting system is designed and built in Austin, Texas, USA with an anodized, extruded aluminum alloy chassis and integrated passive heatsink for natural convective thermal management (zero moving parts), and is ETL wet location rated to withstand the harshest of growing environments.
The new RAZR Series is available now. To learn more, visit http://fluence.science/razr
Proven Results in Vertical Farms
Edenworks is moving leafy green and microgreen production closer to consumption with their Brooklyn-based aquaponics vertical farm. Edenworks conducted a trial of several LED vendors, ultimately installing the latest Fluence RAZR3 system which enables Edenworks to add more layers of production per square foot while increasing plant quality and decreasing operating costs. To learn more, visit http://fluence.science/edenworks
“Vertical farming allows us to deliver the highest quality product possible at the lowest cost possible,” said Ben Silverman, Co-Founder and Chief Design Officer at Edenworks. “The Fluence RAZR system not only creates an environment for improved growth and development of our microgreens, but allows us to run a commercial-scale vertical farm at a lower operating cost.”
Farm.One grows hundreds of rare crop varieties for New York City’s finest restaurants out of their downtown Manhattan vertical farm. With a continual focus on improving plant flavor, texture and color, Farm.One tested numerous LED lights culminating in their decision to deploy Fluence RAZR solutions after seeing higher quality and yields. To learn more, visit http://fluence.science/farm-one
“We are constantly evaluating new forms of ag-tech to improve the production and bottom-line of our vertical farm,” said Robert Laing, CEO at Farm.One. “The Fluence RAZR system achieves both with a thin, easy-to-install form-factor which allows us to grow more product per square inch, and optimal light intensity, uniformity and spectrum to cultivate a high-quality crop that exceeds our customers’ expectations.”
About Fluence Bioengineering
Fluence Bioengineering is a photobiology design company exploring physiological plant development under various levels of photosynthetically active radiation and custom spectra. The company partners with leading research institutions to engineer the most powerful and efficient horticulture lighting solutions for both science and commercial applications. All Fluence systems are designed and built in Austin, TX. https://fluence.science/
How To Build A Successful Vertical Farm
How To Build A Successful Vertical Farm
The interest in growing plants indoors in vertical farms keeps increasing. But many investors who thought they could simply buy an empty warehouse, plug in some grow lights and turn out perfect heads of lettuce to make money have been disappointed. Here are a few key lessons learned from city farming expert Roel Janssen on successful vertical farm projects.
Part 1: Getting the climate, lighting and spacing right
The most crucial part when starting an indoor farm is to have a grower that understands how to grow plants indoors. New (sensor) technologies and the internet of things offer great opportunities for indoor farming, but if you don’t have a grower you will not get out the most of your operation. You can have great packaging and attractive marketing tools, but the product itself will determine your success. That being said; these are some of the most important factors that can determine the success or failure of your vertical farm investment:
- Crop selection
- Lighting selection and design-in
- Airflow design and climate control
- Spacing strategies for plants
- Crop logistics and automation
- Irrigation and nutrition
- Data, sensors, control and software
- Substrate choice
- Target audience and sales channel
When we look at how to get the highest return on an investment for a vertical farm, we focus a lot of attention on creating a facility that allows you to produce the highest yield of crops (measured in grams) using the most ideal amount of light (measured in moles or mol). That’s because your LED grow lights are amongst the highest expenses in terms of the city farming infrastructure and operation. Keeping that in mind, here are a few of our most valuable tips for increasing your grams per mol. The information is gathered from research done at the Philips GrowWise Center as well as commercial projects ranging from US, Japan to Europe.
Step 1: Get the climate right
One aspect that many new vertical farm growers overlook when they are creating an indoor farming environment is maintaining the best climate conditions. If we assume 50% of the electrical input power is converted into light, the remaining 50% is converted directly into heat. A proper airflow can remove this direct heat, but also the light that will be absorbed by the crop will indirectly be converted into heat. Typically the crop evaporates water into the air to get rid of this heat, therefore this process will result in a higher humidity of the air. To keep increasing humidity and temperature under control, you must start with a good ventilation and air handling system in your vertical farm. Not installing a proper climate control and air handling system will decrease your yields, resulting in additional costs and hassle after installation to fix inefficiencies.
Step 2: Get the lighting right
Once you have a good climate, how can you get the highest yields from it? We have done hundreds of research projects on growing plants indoor focusing on yield and the most optimal light intensity for a certain crop or variety. Yield however is not always the most crucial and single most important part. Let’s take red oak lettuce as an example. When this lettuce is grown outside in a field, it turns red because it is stressed by the sun or large temperature changes and it typically yields less compared to its’ green version. When the same variety is grown indoors, it remains mostly green because there is no UV light, but it does develop fast and shows comparable or sometimes even better growth than a green version. At Philips Lighting’s GrowWise Center, we have four full-time plant specialists who develop so-called light and growth recipes for specific crops. Based on their research, we developed a coloration light recipe for red oak lettuce that turns a mostly green head of red oak lettuce into a dark red lettuce in just three days. Growers can grow a large head of lettuce in their regular growth cycle, apply this light recipe as a pre-harvest treatment, and get a great quality crop with much higher yields and the proper appearance. Together with breeding companies we screen and help them develop varieties that could support growers to help them differentiate even more based on taste, quality or color.
Step 3: Get the spacing right
The spacing strategy you use when growing plants indoors is another way to improve your grams/ mol. You want to space plants so that each one gets an optimal amount of light and you are lighting the plants instead of the shelves they are on. Knowing the ideal spacing strategy can avoid you having to invest in spacing robots because you can check the extra yield spacing plants delivers compared to the investment needed for automation of this strategy. For our vertical farm projects, we can contribute to your business calculations with advice on the best spacing and light recipe to use for each crop. Based on that information you can decide if manual spacing or spacing robots are the most cost-efficient choice for your facility. Next to that our cooperation with the leading breeders in the industry will enable you to pick the right variety for your crop specific requirements.
In the next blog, we will discuss more crucial starting points to boost your chance of success in a vertical farm.
Roel Janssen is the Global Director City Farming at Philips Lighting. With a background in business administration, Roel has 8 years of experience in vertical farming. Roel has led the implementation of two Philips City Farming facilities – GrowWise and BrightBox and currently oversees all activities in the City Farming group. Next to his work at Philips Lighting, Roel is a guest lecturer for courses on vertical farms and growing without daylight at universities and other organizations.
A Beginner’s Guide to Vertical Farming
Also known as indoor farming, vertical farming has in recent years gained recognition as a solid method of sustainability. The system was born out of the challenges affecting the 21st century, specifically issues like food shortage, resource depletion, and overpopulation.
A Beginner’s Guide to Vertical Farming
November 28, 2017
Written by Claudia Beck
Also known as indoor farming, vertical farming has in recent years gained recognition as a solid method of sustainability. The system was born out of the challenges affecting the 21st century, specifically issues like food shortage, resource depletion, and overpopulation.
Feeding the future: vertical farming
Vertical farming is the practice of food production that takes the form of vertically stacked layers and vertically inclined surfaces. The method is executed inside a controlled environment building, usually without soil or natural light.
The method of growing the crops in a vertical farm involves the following elements.
• Temperature control
• Humidity control
• Artificial lighting
• Control and monitoring of nutrients and fertiliser
When undertaking vertical agriculture as a small to medium business, planning is essential. You need to ensure that you can sell what you grow, and that your production costs are not too high. The first step to ensuring this, therefore, is picking the right crops.
The aspiring vertical farmer needs to conduct a feasibility study and come up with a profitable and sustainable plan. This is because each species you plan to grow will have a growing method tailored to its needs. Determining the daily nutrient and light uptake each crop requires is crucial.
Animated GIF credit: Lizzie Lomax
The indoor farm represents significant benefits to the consumer as it increases food accessibility. Because farms can be located anywhere, more people can start growing their own crops. Production then moves closer to the consumer, and farms are able to produce consistent value and volume year-wide. Currently, building-based and shipping container vertical farms are the most common.
How does indoor farming work?
There are several key factors that determine the viability of a vertical farm.
1. Physical layout
The objective of indoor farming is to maximise volume. This is achieved by maximising the output efficiency per square meter, which is where the vertical tower structure comes from.
2. Lighting
Image credit: Business Wire
Optimising light for crop growth in vertical agriculture usually involves a mixture of grow lights and natural light. Specialised technologies like rotating beds increase the efficiency of the light sources and can fulfil different crop requirements.
3. Growing medium
There are three different models for the indoor agriculture system.
A. Hydroponics
In hydroponics, crops grow in the nutrient-rich water basin and water is recirculated, creating better efficiency and lower water consumption. Scalable in size and cost, hydroponic farming is highly adaptable to its farmers’ production goals and needs. It includes methods like Drip Irrigation, Deep Water Culture, Ebb and Flow, Nutrient Film Technique, and the Wick System.
B. Aeroponics
Image credit: Foundation Far
Aeroponic farming involves frequently spraying crops with a nutrient-based mist, using a periodic timer (no soil, sunlight, or water). Aeroponics delivers nutrients directly to the plant roots to conserve water and reduce intensive labour. Scalability is another massive benefit with this method, and crops are easily harvested without soil.
C. Aquaponics
A closed-loop food production system, aquaponics is the practice of cultivating both fish and plants. The fish provide nutrients and beneficial bacteria to the plants,which in turn filter the water for the fish. Aquaponic farming creates a highly productive and balanced ecosystem with many benefits, including its water-conservative approach.
4. Sustainability features
Image credit: Cleanroom News
Many built-in sustainable features like rainwater tanks, wind turbines, and multipurpose spaces can offset energy costs in a vertical farm. Indoor farminguses less water than conventional farming practices and is not season-dependent for seed growth, which maximises revenue year-round.
What can you grow in your vertical farm?
With the right hydroponic, aeroponic, or aquaponic farm set-up, you can grow almost anything. Just because you can do so, however, doesn’t mean you should. Consider the following aspects when choosing the best crops for your vertical farm.
1. Economic viability
Especially if you’re growing for profit, study the economics of the species you have shortlisted for your indoor farm.
A. Demand
What is the demand for this crop within your area or within the market you choose to serve? You may decide that your project will provide for your family as well as for your local community.
B. Growing technique
Though vertical farming methods mean lower overheads on average, the size and particular system you use dictates your short and long-term production costs. You’ll want to keep these figures as minimal as possible.
C. Climate
Different systems have climate requirements (heating, cooling, and lighting) that may necessitate another sectioned-off space. Consider if you have the room and operations budget for your chosen system design.
As a grower, striking a balance between these elements ensures maximum yield and value out of your indoor farm.
2. Timing and liability
All good things take time—patience is a necessary element of indoor agriculture. This truth is embodied in what is called in farming as a ‘turn.’ A turn is the total amount of time it takes to introduce a seed or seedling into the farm system, grow it, and harvest it as a mature plant, for sale at the market or serving on your plate.
There are two types of crops you can choose to grow: fast turn crops and slow turn crops. Dependent on your growing reason, needs, and requirements, you can pick either one or both for your vertical farm.
Image credit: Forbes
Fast turn crops include lettuce, cabbage, chard, collard greens, mustard greens, parsley, cilantro, mint, chives, basil, and various microgreens. They usually take up to six weeks to produce.
Slow turn crops are typically harder to grow, but have a higher revenue margin compared to leafy greens. This includes ‘woody’ herbs like oregano and rosemary, and fruiting crops like strawberry and tomato. A good guide to follow for a beginner grower is to plant 80 percent greens, and 20 percent herbs.
Vertical agriculture: from farm to fork, all under one roof
Vertical farming can be as small or as large in scale—it all depends on the farmer’s goals and requirements! A vertical farm can benefit both your home and business, providing your community with reliable access to fresh produce.
While the traditional block of land enabled families to grow their own food, block sizes have gotten increasingly smaller throughout the decades.
Luckily, indoor farming lets us grow crops with a fraction of the space, sun, soil, and water conventional farming uses. What’s more, vertical farms are protected from the harsh weather brought about by climate change. The result? Robust and resilient crops turning up whenever needed, grown in soil and water-conservative, stable crop systems.
Title image courtesy of Digital Trends
Why LED Lighting is Ideal For Indoor Farming
According to data from National Geographic, the sun radiates enough energy in 15 minutes to equal energy consumption of the entire world for ONE YEAR.
Why LED Lighting is Ideal For Indoor Farming
According to data from National Geographic, the sun radiates enough energy in 15 minutes to equal energy consumption of the entire world for ONE YEAR.
The sun is so powerful that it was worshiped by ancient cultures.
So how is it possible to have lighting for growing plants indoor that is actually more efficient than the sun?
And why is it often a shade of purple???
Why is LED lighting is ideal for indoor growing?
Ancient cultures worshiped the sun due to its life giving power (source)
The idea that plants need exposure to daylight for perfect growing conditions has persisted during the sustained growth of indoor farming in the past several decades.
But, as numerous researchers (and an increasingly large amount of growers) have realized, the concept of sunlight as a necessity is, in fact, a flat out myth.
Why?
Read on to find the step-by-step explanation for how LED lighting is revolutionizing indoor growing, and more!
In the rest of the article we will discuss:
1) Why Purple (a.k.a. blue-red LEDs?
2) LED Lighting vs Daylight
3) PROS and CONS of LED Grow Lights
Ready?
Let's get started!
Why Purple (a.k.a. blue-red) LEDs?
The technical answer, in a nutshell, is related to the spectrum of color present in different types of light. While good 'ol sunlight contains a variety of color spectra (think rainbows), it turns out that plants only need specific color spectra to grow properly.
What colors work best?
According to urban farming research on the way plants respond to light, the blue-red spectra is ideal for plant growth.
The reason for this is because chlorophyll, which plays a central role in plant growth and photosynthesis, responds primarily to "peak" spectra in the blue and red ranges, or 450 nanometer and 650 nanometer wave lengths respectively.
Some research has also experimented with using other forms of light in urban agriculture growing settings, often yellow LED spectra, to alter plant traits such as color, texture, and increased shelf life.
With a consumer base increasingly enamored by rare and interesting varieties of common fruits and vegetables, concepts such as red or yellow carrots can be marked up as exotic items or at the very least add some extra zest for small-scale urban farmer.
Plant growth does not require the full spectra present in daylight (via Illumitex)
LED Lighting vs Daylight
Sunlight, in fact, is inefficient in many ways when it comes to optimizing small-scale, urban agriculture.
For one, the heat generated by the sun can be damaging to plants and can have an adverse effect on shelf life immediately post harvest.
This "heat effect" caused by sunlight is even further amplified when the plants are closely packed, as is often the case in urban farming.
In contrast to sunlight, LED lights are known for transferring nearly undetectable amounts of heat onto plants, and the bulbs themselves are even often cool to the touch. The result?
Urban farms with LED lighting can have more closely packed arrangements for maximum efficiency. These arrangements would not be possible in normal agricultural environments without compromising the health of the plants.
Besides the decreased heat transfer, LED lighting is a cheaper alternative to traditional lighting sources that emulate daylight conditions.
Although there is often a higher upfront cost with LED lighting, the best way to view the cost-savings of LED lighting for urban farming is as a long-term investment.
This is because LED lighting has a much higher energy efficiency over time compared to other urban farming lighting technologies such as halogen or compact fluorescent (CFL).
As a quantitative example, average CFL lighting options on the market will have approximately 1/3 the lifespan of LED lighting options, with similar lighting strengths (Look for 12-16 W / 800-1000 Lumens)
Plants, due to the presence of chlorophyll necessary for photosynthesis, respond mainly to red and blue color spectra (via NPR)
Pros and Cons of LED Grow Lights
PROS
1) LED's use WAY less electricity:
Most LED grow lights use 40% - 50% of the wattage of other lighting sources, like high pressure sodium lights or fluorescent.
2) Less airflow needed
It is a simple fact that for indoor growing, proper ventilation is required.
According to this post from Epic Gardening, ventilation for indoor growing helps prevent at least:
- Excess Moisture
- Proliferation of Pests
- Weakening of Plant Stems
Now, can you guess the #1 cause of heat in an indoor growing environment?
That's right: Grow lights.
But here's the catch:
LEDs generate far less heat than all other types of grow lights. As a result, less ventilation is needed to prevent excess moisture, pest problems, and other ventilation related issues.
From an economic perspective, smaller fans cost less than larger fans, so your ventilation investment requirement with LED grow lights will typically be lower than with other types of grow lights.
Additionally, the on-going electricity cost of powering fans is also eliminated.
3) Less Heat
As we have already discussed above (#2), LEDs generate far less heat than other grow lights.
Now, the reason why LED's generate less heat is because they emit far less infrared heat as output.
Other types of grow lights like high pressure sodium and metal halide grow lights emit enormous amounts of infrared heat - over half of the wattage that powers an HPS or MH light is instantly lost as heat.
Bottom line?
LEDs are far more efficient and produce far less heat.
4) EXTREMELY long life
LED's grow lights are as close to immortal as grow lights get:
They typically have at least 50,000 hours of usable life, which is nearly 6 years of continuous use.
If you are utilizing the lights on a 50% on /50% off schedule (common benchmark), this is over 11 years of shelf life.
5) No need to purchase reflector equipment to improve efficiency
HPS/MH systems often require use reflectors to help re-capture light that was not directed toward plants and instead illuminates walls and ceiling.
LED's have superb directional focus and therefore reflectors are not necessary.
6) Stackability
Because LED's have so much lower heat emission, they can be placed closer to the plants.
The result of this is that the ability to "stack" plants in a growing space is possible.
This is potentially the most exciting benefit of using LEDs: the potential to double the production output (or triple, or 4x, etc) without changing the area of the growing space.
Now, one consideration to remember is that the height of the growing space is a factor.
However, this type of stacking functionality is just not doable with other types of grow lights.
Cons
1) Upfront Cost
LED's will commonly be at least 2x more expensive then many other types of grow lights.
The return on investment may pay off over time with less energy use, replacement cost, and less investment in other previously needed equipment like fans and reflectors.
See how the economics compare with the case study from Diffen above.
2) Heavy
The component of an LED grow light that makes it heavy is the heat sink, which helps absorb excess generated heat.
As a rule of thumb, a quality LED grow light will have 10 square inches of heat sink space per LED watt.
If you do the math, you will see that this heat sink space adds up VERY quickly and adds a lot of weight.
The result of this is that investment to support the weight of LED grow lights is often a good idea, *especially* if you are stacking layers into a vertical farming stylesystem.
3) Technology Still Developing
As far as commercial indoor growing, LED technologies have not been around for very long (less than 10 years).
Previously lighting methods have included High Pressure Sodium and Metal Halidelighting.
One risk with LED lights is that they are understood less thoroughly than other types of grow lights, which have been studied for several decades.
What does this mean?
Essentially, the support and knowledge base for LED grow lights is far more limited than other types of grow lights.
However, where there is a knowledge gap, there is also opportunity...
4) "Purple" Color
The purplish color that most LED grow lights will generate can be problematic beyond just being annoying:
How?
This color of lighting presents a couple real challenges that can become huge problems:
- Pest damage is harder to identify with LED grow lights
- Nutritional deficiencies, such as yellow under-nourishment and black rot, are more difficult to identify
- Potential danger to YOUR eyes without proper protection. As detailed in this article from Electronics Weekly, the potential to damage your vision with LED lights is very real, and protective eyeware is best practice
Solution: Inspecting plants being grown with LED grow lights is best done using an alternate source of light, such as a fluorescent bar. Most commercial LED operations will inspect plants with fluorescent lights at least once every 10 days.
In Summary
So, why does all of this information matter? In an urban farming environment where space and resources may be limited, optimizing lighting will often be a winning strategy for best urban farming results.
- Red and Blue light (purple when combined) are optimal for plant growth in tightly packed, urban farming style conditions
- LED lighting has several advantages over daylight or other lighting alternatives, such as cheaper pricing over time and reduced heat transferred onto plants
- Experimentation with other color spectra with LEDs such as Yellow LEDs can cause changes in urban farming crop flavor, color, and other aesthetic characteristics.
- There are many pros and cons to using LED grow lights. In general, LEDs are far more efficient than other types of grow lights in many aspects, however they are more expensive and still relatively new as far as large scale commercial use goes.
Questions, comments, feedback? Follow us @urbanvineco
Indoor/Vertical Farms Set to Boom, LEDs Leading The Transition, Says Yole
The 2016 horticultural lighting market (i.e. system level) represented a business of about US$3.1 billion, representing approximately US$3.8 billion in 2017. But according to a recent report from market research firm Yole Développement, this market is set to grow rapidly at a 17.8% CAGR between 2016 and 2022, possibly reaching more than US$17 billion by 2027.
Indoor/Vertical Farms Set to Boom, LEDs Leading The Transition, Says Yole
November 23, 2017 //By Julien Happich
The 2016 horticultural lighting market (i.e. system level) represented a business of about US$3.1 billion, representing approximately US$3.8 billion in 2017. But according to a recent report from market research firm Yole Développement, this market is set to grow rapidly at a 17.8% CAGR between 2016 and 2022, possibly reaching more than US$17 billion by 2027.
While Yole sees the current business mostly driven by greenhouse applications and incumbent technologies (92% and 79% in revenue, respectively) during 2017, the transition to LED technology and the emergence of new applications will expand the market’s size.
In its report "Horticultural LED Lighting: Market, Industry, and Technology Trends" Yoles sees this market reaching nearly US$8.6 billion in 2022.
Horticultural lighting market revenue ($B),
2017 vs. 2022 vs. 2017.
Source, Horticultural LED Lighting:
Market, Industry and Technology Trends,
Yole Développement.
than US$17 billion in 2027”, comments Pierrick Boulay, Technology & Market Analyst at Yole.
At the LED device level, market opportunity represents almost US$100 million in 2017 and should grow to about US$400 million in 2022, eventually reaching US$ 700 million in ten years' time.
The LED lighting industry sees horticultural lighting as a new opportunity for which to develop high added-value products with greater margin levels. In Q4/2017, Yole identified less than 50 players as offering dedicated LED-based systems. The industry is highly concentrated in North America with a 50% market share (number of companies involved), the result of medicinal cannabis’s legalization.
“Looking ahead, industry evolution will strongly depend on market dynamics,” explains Joel Thomé, PISEO’s CEO. “Indeed, industrial players’ marketing and communications are currently focused on two main applications including medicinal plants (mostly cannabis) production, which is today the main market driver and vegetable production, which is developing with a “low-end / high-volume products” focus.”
The 2016 horticultural lighting market (i.e. system level) represented a business of about US$3.1 billion, representing approximately US$3.8 billion in 2017. But according to a recent report from market research firm Yole Développement, this market is set to grow rapidly at a 17.8% CAGR between 2016 and 2022, possibly reaching more than US$17 billion by 2027.
Part of the established lighting system industry may never proceed with the medicinal plants application, in order to preserve brand reputation. Such a situation is likely to benefit new entrants that will generate revenue swiftly and rapidly increase their horticultural lighting market expertise.
At the device level, most LED manufacturers embrace a “technology push strategy”, taking advantage of their traditional LED portfolio (i.e. UV, visible, and NIR LEDs) to quickly offer some horticultural lighting solutions and related marketing tools, such as dedicated datasheets.
In the future, with a better understanding of LED light’s effect on plant growth, these players might start offering more dedicated solutions (i.e. fine-tuned wavelength package, multiple wavelength packages, etc.).
The missing block in the supply chain is mostly at the module level, with no real supplier in 2017 – reason being that the market is still emerging and the industry is still young, with no standards and regulations. In this context, each lighting system manufacturer design its own module with a specific wavelength mix/recipe.
Some companies are finally starting to position themselves as solution providers, offering not only lighting systems but global solutions integrating sensors (humidity, oxygen, etc.) and data management software. The objective of these smart lighting systems is to further increase the productivity of greenhouses and urban farms.
Yole Développement – www.yole.fr
Steven LaFerrière - laferriere@yole.fr
Horticultural lighting applications.
Source, Horticultural LED Lighting:
Market, Industry and Technology Trends,
Yole Développement.
Quick Guide On Grow Lights
Everyone agrees that knowing how to grow food indoors with grow lights is valuable. It improves your health, brightens your day, calms your nerves, and allows you to do more with your existence.
Introduction
Grow lights are the most important environmental element affecting plant growth and development because the selection of grow lights can have a remarkable effect on the costs, operational costs, and quality of plants in your indoor grow room. This blog describes the physical properties of grow lights. Light sources often used in indoor grow rooms are introduced with a simple clarification of the fundamentals necessary to understand the grow lights. Particular importance is placed on LEDs, which have received extraordinary awareness recently, and on fluorescent lights, which are still commonly used in indoor grow room.
Physical Properties
Light is electromagnetic energy, which is also explained as electromagnetic radiation comprise both visible and invisible wavelengths. The smaller the wavelength, the greater the energy. The wavelength of visible light ranges from 380 to 780 nm, which is what people eyes see.
Visible light is key to plants because it occurs simultaneously with photosynthetically active radiation (PAR, 400-700 nm). For solar radiation, 97% is inside the 280-2800 nm range. In this regard, 43% is visible light, which is practical for plant growth, 4% is ultraviolet, and 53% is infrared, which make heat.
Only electric lights are used in indoor grow rooms. Light has two opposed properties: it can be noticed as a wave phenomenon and it also acts as separate particles called photons. A photon is the smallest particle of light, or a single quantum of light. Light varies in at least three dimensions: quantity, quality, and duration.
When electric lights are used in a indoor grow room, the lighting cycle, which affects plant growth and development, can be willingly changed. Light effects plants in two ways: providing energy or a quantum source and acting as an information medium.
While an energy source, the photons of light, is caught by plants and a part (up to 10%) of photons caught by plants is converted to chemical energy (carbohydrates) through photosynthesis. Almost all of the light energy or photons caught by plants is converted into heat energy.
Light Sources
Till recently, most of the light sources used for indoor grow rooms were fluorescent lights and high-intensity discharge (HID) lights. Till just a decade ago, LEDs were used almost exclusively for research on plant cultivation, but are now being used as a light source for commercial plant cultivation in indoor grow rooms because of their fast price decline and quick improvement in luminous efficacy, which is a measure of how efficiently an electrical lamp produces visible light.
LEDs
LEDs offer advantages over fluorescent and HPS lights: they are strong; produce a stable output; are long lived, compact, and lightweight; turn on right away; and allow the light output to be easily controlled with a light source consist of several color types of LEDs. Benefit of using LEDs as a light source for indoor grow rooms is that LEDs offer great flexibilty for making various light environments compared to conventional lights. A light source having a few types of LEDs with different peak wavelengths can produce light of which the spectral radiant inconstancy can be varied with time. The biggest disadvantage of using LEDs for indoor grow rooms is the high beginning cost for a set of LED lights, compared to conventional lights.
Fluorescent Lights
Fluorescent lights offer no direct advantage over other lights including LEDs. Tubular fluorescent lights are the most suitable light source at present for indoor grow room when taking into account all the factors of bulb and luminaire prices, rated life, luminous efficacy, ready availability, and lighted bulb temperature. A tubular fluorescent light normally consists of a glass tube coated inside with a fluorescent material (phosphor), two tungsten electrodes at the two inside ends that are coated with an electron emissive material, a tiny amount of mercury, and low vapor pressure inert gas (mainly argon) enclosed in the glass.
High-Intensity Discharge (HID)
HIDs are a type of electrical gas discharge light, which generates light by means of an electric arc between tungsten electrodes sheltered inside a translucent or transparent fused quartz or fused alumina arc tube. HID lights make more visible light per unit of electric power adsorbed than fluorescent lights, since a larger proportion of their radiation is visible light in contrast to infrared. Yet, the lumen output of HID lighting can lower by up to 70% over 10,000 burning hours.
If you enjoyed this, you might also enjoy this blog on lighting:
Tags: quickguide growlights leds fluorescent highintensity discharge indoorgrowroom
Rensselaer Polytechnic Institute Study
Rensselaer Polytechnic Institute Study Demonstrates that Both High Yields and Nutritional Quality of Leafy Greens Can Be Achieved With LUXEON SunPlus Lime LEDs
In a comparison study, Rensselaer researchers determined that LUXEON SunPlus Lime + Purple and Green + Purple LEDs provided beneficial growth spectra, resulting in high crop yield and high levels of antioxidants important to human health.
San Jose, CA – December 5, 2017 – The results of a controlled horticulture lighting study conducted by the NSF funded Center for Lighting Enabled Systems and Applications (LESA) at Rensselaer Polytechnic Institute (RPI, Troy, NY), have been released. The study, utilizing a variety of commercial LEDs, compared the effectiveness of different LEDs on the growth of red lettuce Rouxai. The best combined yield and antioxidant concentrations in the lettuce was observed using LUXEON SunPlus Series LEDs. “Comparing the growth results using different combinations of LEDs shows that the spectra that performed best for yield (fresh weight), anthocyanin and chlorophyll concentrations were the LUXEON SunPlus Lime + Purple and Green + Purple LEDs from Lumileds,” said LESA’s Dr. Tessa Pocock, a global expert on light and plant physiology. “Green light is necessary for crop growth and the specific wavelengths within the green region matters.” This work is also part of the Greenhouse Lighting and Systems Engineering (GLASE) Consortium operated by LESA and Cornell University and funded by the New York State Energy Research and Development Authority (NYSERDA) that is examining the most effective way to add green light to horticultural fixtures.
“Growers today are experimenting with various LEDs to arrive at the best color combinations for their crops. The LESA study indicates that such experimentation is paying off because a common, nutrient-rich crop can be produced with excellent yield,” said Jennifer Holland, Product Line Director of the LUXEON SunPlus Series. The study demonstrated that a light spectrum like the combination of LUXEON SunPlus Lime and Purple, which contains a certain ratio of royal blue, green, deep red and far red components, is beneficial to growth optimization.
For details of the study, see here: www.lumileds.com/uploads/702/WP34-pdf
To learn more about the LUXEON SunPlus Series including the new Far Red and Deep Red LEDs, see www.lumileds.com/horticulture
About Lumileds
For automotive, mobile, IoT and illumination companies who require innovative lighting solutions, Lumileds is a global leader employing more than 9,000 team members operating in over 30 countries. Lumileds partners with its customers to push the boundaries of light.
To learn more about our portfolio of lighting solutions, visit lumileds.com.
For further information, please contact:
Kevin Lucido
Senior Director of Global Marketing Communications
Lumileds
+1 650 576 3864
Kevin.Lucido@lumileds.com
Determining The Potential Benefits of LEDs on Plants
Determining The Potential Benefits of LEDs on Plants
NOVEMBER 20, 2017 | DAVID KUACK
Researchers at Wageningen University in the Netherlands are studying the effects of LED lights on the growth, flowering and fruiting of vegetable and ornamental plants in controlled environments.
Dutch growers who are building new greenhouses or adding new grow lights to their existing operations are comparing high-pressure sodium (HPS) and light emitting diodes (LEDs) when making their decision.
“At the moment there aren’t as many growers making the switch from HPS to LEDs,” said Leo Marcelis, head of the chair group horticulture and product physiology at Wageningen University in the Netherlands. “Most growers who have made the investment in HPS lamps, they’re not just going to replace HPS with LEDs. It’s growers who are starting with a new greenhouse or who are retrofitting an existing greenhouse without lamps who are looking to install LEDs.
“The other growers who are adding LEDs are the ones who already have installed HPS and want to increase the light intensity and are adding LED interlighting. They are combining HPS top lighting with LED interlighting. This is occurring especially with the tall greenhouse vegetable crops like tomatoes. The HPS lamps are installed over the top of the crop and the interlighting LEDs are installed within the canopy.”
Photos courtesy of Leo Marcelis, Wageningen University
Many unanswered questions
With the increased grower interest in LEDs, researchers at the university are focusing more of their studies on the effects of single and combined light wavebands on plant growth, flowering and fruiting.
“Most of the research we are doing on lighting is with LEDs,” Marcelis said. “High-pressure sodium lamps are still the standard for most growers so the lamps are still relevant. But for our research, there is not as much being done with HPS as with LEDs. We are focusing more on LEDs. The opportunities created by LEDs, there are so many questions still unanswered about using LEDs. As growers start to put in new lights they are making the switch to LEDs. We expect more of that to occur in the coming years.”
Focus on controlled environment crops
Marcelis said greenhouse tomatoes are the largest crop in the Netherlands, even bigger than cut flowers such as roses and potted ornamental crops such as orchids.
“Tomato is the most important crop in our research. In the Netherlands, there are about 1,700 hectares of tomatoes in glass houses. About 1/3 of that area is equipped with HPS lamps. There are about 1,200 hectares of sweet peppers in glass houses with only a few hectares equipped with HPS lights. The calculations are such that the economics are not that profitable for sweet pepper and cucumber. It is more economical and profitable to light tomatoes, not sweet peppers and cucumbers. There are more growers starting to grow strawberries in greenhouses who are using LEDs to control the day length. More growers are also using LEDs for assimilation lighting.”
Marcelis said lettuce is another crop that is being studied whether it’s grown in vertical farming setups in warehouse facilities or in greenhouse operations. Roses and phalaenopsis orchids are the most important ornamental crops being studied.
“We currently aren’t doing any projects with cucumbers or sweet peppers using LEDs,” he said. “Since there are not as many growers using lights on these two crops, we are not focusing our research on them, but this could easily change in the coming years.”
Focused on issues important to growers
Marcelis said most of the university’s lighting research projects are on greenhouse produce because that is the area of most economic activity in the Netherlands.
“Vertical farming is attracting a lot of attention,” he said. “We are also conducting research in climate chambers which can have application to vertical farming.
Breeding researchers at Wageningen University are working in cooperation with commercial breeding companies to screen different genotypes to determine any variation under LED lights.
“We are looking at different aspects of lighting, including light spectrum and energy savings. Energy savings is an important issue with the growers so we are doing a lot of research on that. If the light used is more efficient, then there can be energy savings. Talking to the growers, year-round production, fruit quality and energy savings are the issues they’re interested in. If growers can increase production with the same amount of light, then there is an energy savings.
“The majority of lights are used for assimilation. They are primarily used from September through April. The greenhouses are equipped with climate control and the growers are measuring outside radiation. If the outside radiation falls below a designated level, then the lamps are often turned on. The growers typically choose a time frame during the day. From September through April all of the lights are used. After April then the lights might be used during relatively dark days.”
Looking at plant processes
Marcelis said the researchers are doing a lot of studies on photosynthesis and the morphology or architecture of the plants.
“Affecting the morphology impacts the light absorption of plants and the light distribution,” he said. “We feel light distribution is a very important issue where improvements can be made. We also do work with three-dimensional assimilation models. From light absorption, it goes to total growth of the plant as a whole. Another area of research is the distribution of assimilates among the different plant organs.”
Most of Wageningen University’s lighting research is on greenhouse produce because that is the area of most economic activity in the Netherlands.
Marcelis said there is also some preliminary research that indicates plants can be made more resistant to diseases, particularly increasing the resistance of roses to powdery mildew.
“We have done experiments that have indicated that we can improve disease resistance. Flower induction is also very important. It can be done now with controlling photoperiod, but can it be done using different spectra?
“There is also some work being done on the quality of the plants. Is it possible to focus the light on the tomato fruit in order to increase the vitamin C content? Some of the same things can be done with lettuce. We are also starting to look at post-harvest qualities. So we are looking at not only what can be done during cultivation, but also can the post-harvest quality of the fruit be improved. This also includes lengthening the shelf life of lettuce and cut flowers.”
Marcelis said studies are also being conducted in cooperation with commercial breeding companies and breeding researchers at the university.
“One of the projects is screening 40 different genotypes, including commercial cultivars,” he said. “One study is looking at the variation between genotypes under LEDs. The breeders will look at the variation between genotypes and try to determine why the variation is occurring. What parts of the plant are affected? Can breeders predict if varieties will do well or not so well under certain wavebands?
“There are all of these different genotypes. Some do better under white light than a mixture of red and blue. Some genotypes are showing better results under the red and blue light. They all don’t respond similarly. For breeders, it means there is a lot of opportunity and room for improvement. Since the focus is on using LEDs with tomatoes that is where most of the breeding research is being done.”
For more: Leo Marcelis, Wageningen University, Horticulture and Product Physiology Group, Wageningen, The Netherlands; (31) 317-485-675;
leo.marcelis@wur.nl; http://www.hpp.wur.nl
David Kuack is a freelance technical writer in Fort Worth, Texas; dkuack@gmail.com.
Innovative Light Measurement Solutions for Indoor Horticulture; High Precision, Handheld PAR Meters from Gamma Scientific
Innovative Light Measurement Solutions for Indoor Horticulture; High Precision, Handheld PAR Meters from Gamma Scientific
San Diego, CA – Commercial success in indoor horticultural operations requires intricate knowledge and carefully managed growing conditions. Among them, a detailed understanding of your lighting parameters is key; including efficiency, spectral properties, aging affects, fixture spacing and optimal working distances.
The PG100N provides a robust and reliable solution for light measurement with fully NIST-traceable performance. Through an integrated, high-resolution color display, PPFD values can be viewed over the PAR range, or within specific wavelength bands from the UVA to the Near-Infrared. In addition to internal data logging, downloads via SD card, USB port or Wi-Fi mode allow data tracking and analysis over time, and downloads in Excel and JPG formats are standard.
The detector head can be removed for optimal positioning, and operating time is up to 5 hours on a full battery charge. Units are in stock in our warehouse and available for rapid delivery.
For over 50 years, Gamma Scientific has delivered highly unique, state-of-the-art measurement solutions for manufacturers and users of light sources, sensors, and displays. Products include high precision spectroradiometers, calibration light sources, goniophotometers, integrating spheres, thin film measurement systems, and LED testers and sorters. The company also operates an ISO 17025, NVLAP accredited laboratory (NVLAP Laboratory code 200823-0) for calibration and testing.
Philips Lighting To Install its First LED Grow Light Project in New Zealand at Gourmet Mokai
Philips Lighting To Install its First LED Grow Light Project in New Zealand at Gourmet Mokai
November 21, 2017
Eindhoven, The Netherlands - Philips Lighting (Euronext: LIGHT), the world leader in lighting, today announced it has signed its first LED grow light project in New Zealand with Gourmet Mokai Ltd to improve the quality and cost efficiency of growing its popular Campari cocktail tomatoes.
Gourmet Mokai Ltd is part of the New Zealand Gourmet group of companies and sells premium fruits and vegetables to local markets and in Australia, Japan and Southeast Asia. The new LED grow lighting will be installed in January 2018 in a 4,500 square meter greenhouse at the facility in Mokai on the North Island, known for its sophisticated eco-friendly growing practices.
"Over the years, our LED technologies have helped tomato growers across the globe produce better quality fruit and higher yields, with more control over their growing climate," said Udo van Slooten, Business Leader Horticulture at Philips Lighting. "We feel privileged to be participating with New Zealand Gourmet, a leader in its field, and look forward to showing other growers in the region what we are doing at this location."
Gourmet Mokai Ltd is a joint venture of New Zealand Gourmet and two New Zealand Maori trusts, and it uses naturally occurring underground geothermal steam for heating. The Campari tomatoes are grown under glass using a hydroponic type method. The LED system chosen combines Philips GreenPower LED toplighting with GreenPower LED interlighting.
"We expect several benefits from the LED grow lights. We are using an optimal spectrum for plant growth and crop management, based on the LED light recipe specified by Philips Lighting's horticultural team. We also hope to improve the taste, vitamin C content and shelf life of our product with the LED grow lights," said Roelf Schreuder, Production Director Protected Crops at New Zealand Gourmet. "At the same time, we expect to reduce our operating costs and gain more control over the growing climate as the LEDs produce hardly any heat."
According to Schreuder, Gourmet Mokai must first learn how to grow tomatoes under LED lights and evaluate how it affects their heating set-up, CO2 supply, irrigation management and pollination. "We release bumblebees to pollinate our crops. However, when there's no daylight and the lighting system is on, the beehives have to be closed and the bees can no longer pollinate the crops. The lights will be connected with the existing Hoogendoorn climate computer system which will also control the opening and closing of the bumblebee boxes and CO2 supply."
Several parties are collaborating to make this project a success, including Philips Lighting, RTF Climate, Agrolux, Zonda Beneficials and Hoogendoorn Automation with the iSii Next Generation System equipped with a special LED light module software package.
For further information, please contact:
Philips Lighting - Horticulture LED Solutions
Daniela Damoiseaux, Global Marcom Manager Horticulture
Tel: +31 6 31 65 29 69
E-mail: daniela.damoiseaux@philips.com
www.philips.com/horti
About Philips Lighting
Philips Lighting (Euronext: LIGHT), the world leader in lighting products, systems and services, delivers innovations that unlock business value, providing rich user experiences that help improve lives. Serving professional and consumer markets, we lead the industry in leveraging the Internet of Things to transform homes, buildings and urban spaces. With 2016 sales of EUR 7.1 billion, we have approximately 34,000 employees in over 70 countries. News from Philips Lighting is located at the Newsroom, Twitter and LinkedIn. Information for investors can be found on the Investor Relations page.
Valoya Launches a New Line of State-of-the-Art LED Grow Lights
Valoya Launches a New Line of State-of-the-Art LED Grow Lights
Since its entrance to the LED grow lights market in 2009 Valoya has been dedicated to producing the highest quality horticultural LED lights for its customers which include 8 out of 10 world’s largest agricultural companies. Countless crop science companies, research institutes, universities, vertical farms etc are equipped with Valoya’s existing series (L, C, B and R). The range is now complemented with a new a line that brings significant improvements and pushes the LED grow lights industry forward.
The BX-Series is the next evolution step of the existing B-Series, the high intensity bar shaped luminaires widely used in growth chambers and similar applications demanding high light intensity. With the intensity of up to 2,1 µmol/W and a dimming feature these luminaires can produce the micromole output for the widest range of plants. The spectra include Valoya’s already available, patented wide-spectra such as NS1 (sunlight spectrum widely used in research) and AP673L (vegetative growth spectrum, widely used by vertical farmers and other growers). These adhere to Valoya's Spectrum Quality Standards which define the permitted wavelength variations among production batches as well as over time of the fixtures' usable life. This is a quality guarantee for researchers and growers ensuring them that the spectrum will remain consistent with minimal variation over a long period of time as well as when they acquire luminaires produced in more recent batches. The BX-Series, like all Valoya products, has been designed with GMP compliant production facilities in mind.
Boasting an Ingress Protection rating of IP67 the BX-Series is entirely dust and humidity resistant and can even withstand water submersion. These fixtures are passively cooled without fins thus they do not accumulate dirt over time and can be easily cleaned and if needed sterilized with harsh chemicals like peroxide, alcohol etc. Another innovation that the BX-Series brings are the GORE-TEX components in its end-caps that push the hot air and moisture out of the luminaire preventing condensation and overheating. This means the luminaires can function in high temperatures (up to 40°C / 104°F) and thus the LED chips inside last longer than in a typical LED grow light. Furthermore, their high Impact Protection (IK) rating (IK08) makes them robust and allows them to keep functioning consistently even when getting dropped or hit. All of this comes in an only 2,6 kg / 5.7 lb heavy luminaire that consumes 132 Watts (model BX120).
These are heavy duty, research grade luminaires designed to produce high and uniform light output over a long period of time. Combined with Valoya’s patented spectra and the support of a team of photobiologists, BX-Series is a smart choice of LED grow lights.
To learn more about the BX-Series, please download the brochure.
About Valoya Oy
Valoya is a provider of high end, energy efficient LED grow lights for use in crop science, vertical farming and medicinal plants cultivation. Valoya LED grow lights have been developed using Valoya's proprietary LED technology and extensive plant photobiology research. Valoya's customer base includes numerous vertical farms, greenhouses and research institutions all over the world (including 8 out of 10 world’s largest agricultural companies).
Additional information:
Valoya Oy, Finland
Tel: +358 10 2350300
Email: sales@valoya.com
Web: www.valoya.com
Facebook: https://www.facebook.com/valoyafi/
Twitter: https://twitter.com/valoya
This $40 Million Robotic 'Plantscraper' Will Feed over 5,000 People Per Year
By 2050, the world's population is expected to swell to 9.6 billion, with around 66% living in urban areas. This projection is leaving many cities wondering how they will feed all those people.
This $40 Million Robotic 'Plantscraper' Will Feed over 5,000 People Per Year
- Leanna Garfield
- Nov. 18, 2017
Plantagon
By 2050, the world's population is expected to swell to 9.6 billion, with around 66% living in urban areas. This projection is leaving many cities wondering how they will feed all those people.
A Swedish food-tech company called Plantagon is proposing that cities consider building what it calls "plantscrapers" — office towers that contain giant indoor farms. Plantagon is constructing its first plantscraper in Linköping, Sweden.
Called The World Food Building, the tower will operate hydroponically, meaning vegetables (mostly greens) will grow without soil in a nutrient-rich, water-based solution. The farm will largely be automated, Plantagon CEO Hans Hassle told Business Insider.
Construction of the $40 million building began in 2012, and it's set to open by early 2020.
Check out the plans below.
The World Food Building will produce approximately 550 tons of vegetables annually — enough to feed around 5,500 people each year.
Plantagon
Source: Helgi Analytics
The front of the 16-story tower will include the farm, while the back will include the offices.
Plantagon
About two-thirds of the building will be devoted to offices, while the other third will include a huge indoor farm.
Plantagon
Companies are now signing leases to move in when it's complete.
The crops will grow using both natural sunlight and LEDs.
Plantagon
The LEDs will be calibrated to specific light frequencies to maximize production.
Plantagon
Robots will perform many of the farm's processes. This will keep operational costs down.
Plantagon
Compared to an outdoor farm of the same size, the plantscraper will generate more food while using less land and water, Hassle said. He estimates the tower will save 1,100 tons of CO2 emissions and 13 million gallons of water annually.
Plantagon
Some meeting rooms, like the one below, will have a view of the farm.
Plantagon
In other areas of the tower, there will be eateries for office employees and the public.
Plantagon
In addition, the building will include a market where people can purchase veggies. Local restaurants and other food retailers will be able to buy directly from Plantagon, which will operate the farm, Hassle said.
Plantagon
Plantagon has designed another similar indoor farm with offices, though it's in the shape of a globe. There are no plans to build it yet.
Plantagon
This plantscraper will include a spiraled food production line, which automatically moves the plants from the bottom to the top and back again while they grow. The length of the cycle would depend on the crop, but would normally take around 30 days, Hassle said.
Plantagon
The designers hope Linköping's plantscraper will encourage other cities around the world to build large-scale indoor farms that have multiple uses.
Plantagon
Plantagon is in conversations with other developers in Sweden, Singapore, the United States, Hong Kong, and Shanghai to build similar structures.
Hassle believes that more cities should grow food closer to urban centers. "This project demonstrates how to feed cities of the future when they lack land, water, and other resources," he said.
Anti-Bacterial LED Horticultural Lighting Solving Major Issues
Anti-Bacterial LED Horticultural Lighting Solving Major Issues
Granville, Ohio - November 3, 2017 - InCite Lighting, LLC is proud to announce the arrival of new anti-bacterial LED Lighting technology to the United State indoor horticultural market. Indoor horticultural operations have long battled mold, viruses, and other unwanted biological contaminants in their facilities.
InCite Lighting, LLC is the master distributor for Full Spectrum Technologies Group (FST). FST's illumiGrow (featuring illumiPure technology) LED Grow Lights 405nm spectral peak model of lights can destroy those unwanted items, while still providing superior grow light technology. The illumiPure technology has been proven to kill several known strains of bacteria and fungus. Beginning in January 2018, FST Grow Lights will be manufactured in Houston, Texas. Patented Proprietary Technology, Fully Customizable, Controllable, with Great Warranties. Large customers can visit the factory to observe their orders being manufactured
InCite Lighting LLC has worked to bring exciting new LED Grow Light technology to the indoor horticulture market, including the exclusive anti-bacterial 405nm spectral peak model. This cost-effective highly productive technology allows growers to grow products in more environmentally conscious methods and organically.
InCite Lighting is dedicated in helping our client partners find the perfect combination of technology, efficiency, and economical solutions to serve their needs (both present and future). We are a master distributor for several manufacturers, specializing in horticultural lighting.
# # #
Illumitex Launches Major Upgrade to PowerHarvest® Series
Illumitex Launches Major Upgrade to PowerHarvest® Series
Illumitex’s PowerHarvest 14 delivers more output at higher efficiencies to meet the needs of the most demanding growing applications.
PowerHarvest 14
We are delivering the best light recipes to produce quality plants with high-quality cost-effective solutions.
AUSTIN, TEXAS (PRWEB) OCTOBER 13, 2017
Illumitex, Inc. is proud to announce the release of the PowerHarvest 14. This LED horticulture lighting solution, ideal for large-scale greenhouse operations, will provide the controlled horticulture environment with 30% increased output, 30% increase efficiency and up to 2.2 µmol/J. The next generation in the popular series will give growers a powerful solution that will improve quality and yield.
The PowerHarvest 14 will be utilized in supplemental or soul-source lighting facilities where growers are looking to achieve a PPF as high as 1300 µmol/second. The light will be offered in various configurations to match the need of each customer. The fixture will be offered in the F3 spectrum, as well wattage of either 556 or 640 and accommodate low and high voltage. These options were carefully selected to meet the needs of the constantly evolving controlled environment horticulture market.
“PowerHarvest 14 takes our field proven horticulture lighting platform to new levels of efficiency and output giving growers approximately 30% more light,” says Jeff Bisberg, CEO & President. “We are delivering the best light recipes to produce quality plants with high-quality cost-effective solutions. It is inevitable that LED will replace traditional lighting solutions in all horticulture applications and our PH14 brings us one step closer to realizing that goal.”
Versions of the PowerHarvest will meet or exceed requirements for utility rebates offering an opportunity to partner with growers and make switching from the traditional lighting to the more efficient LED solution a reality.
The release of the PowerHarvest 14 ushers in a new era of design and innovation from Illumitex as they continue to transform LED lighting for greenhouses, urban farms, and other controlled environments.
About Illumitex, Inc:
Founded in 2005 in Austin, Texas, Illumitex works diligently to create industry-shifting achievements in horticultural lighting. Our team of horticulture scientist and engineers have radically transformed LED lighting that influence plant benefits including yield, taste, color and smell. Illumitex is enthusiastically committed to scientific research, cutting-edge design, and innovative engineering. We are dedicated to work with our customer to deliver world class horticulture solutions while pushing lighting into the digital age with automated tools and services. http://illumitex.com.
Lumileds Adds New Deep Red, Far Red As Well As CoB Offerings To Its Leading Portfolio of LEDs For Horticulture Lighting
Lumileds Adds New Deep Red, Far Red As Well As CoB Offerings To Its Leading Portfolio of LEDs For Horticulture Lighting
September 26, 2017
The new LUXEON SunPlus 35 Deep Red and Far Red LEDs combine with Royal Blue to enable spectrum customization, while the new LUXEON SunPlus CoB Purple ramps Photosynthetic Photon Flux (PPF) for greenhouse productivity.
San Jose, CA – Lumileds today introduced three new products in its LUXEON SunPlus Series of award winning LEDs for horticulture lighting. The LUXEON SunPlus Series is the only line of LEDs on the market to be tested and binned by photosynthetic photon flux (PPF). The portfolio of colors enables wavelength tuning for maximum crop yield in both greenhouse and vertical farming applications. The addition to the LUXEON SunPlus 35 Line of Far Red and Deep Red will enable designers of vertical farm and interweaving fixtures to tune the spectrum specifically for the crop being grown. The new LUXEON SunPlus CoB Line, available in Purple, is designed for greenhouse applications where attaining high PPF and fast time to market are top priorities.
The LUXEON SunPlus 35 Line is optimized for vertical farming in shallow tiers so uniformity is optimized at very short distances. The Deep Red (650-670 nm) and Far Red (720-740 nm) wavelengths join the existing Royal Blue (445-455 nm), Lime (broad spectrum) and three shades of Purple with varying contributions of blue (2.5%, 12.5% and 25%) in a 3.5 x 3.5 mm format. “These essential red wavelengths are combined with blue to give the exact spectra needed for each crop. Our Horticulture Lighting Calculator is especially helpful in this context because lighting manufacturers can experiment with LED ratios and spectral power distributions before building the fixtures,” said Jennifer Holland, Product Line Director of the LUXEON SunPlus Series.
Customer success and market adoption of the LUXEON SunPlus 35 Purple and the need for even greater PPF in a single device led to the development of the LUXEON SunPlus CoB Purple (12.5% blue) product. In contrast to vertical farming where lighting is positioned a short distance from plants, greenhouse lighting requires deep penetration into the plant canopy, which is achieved with a directional CoB. The CoB portfolio complements the LUXEON SunPlus 20 and 35 Lines, which offer a variety of colors to optimize the spectrum for greenhouse applications. The CoB form factor also means that standard optics, holders and drivers are available to help manufacturers accelerate time to market of their fixtures. “The chip on board approach allows us to maximize PPF to as high as 350 µmol/s from a single source,” said Holland. The LUXEON SunPlus CoB Purple is available with 15, 19 and 32mm light emitting surfaces.
For more information on the LUXEON SunPlus Series, see www.lumileds.com/horticulture/products
For further information, please contact:
Kevin Lucido
Senior Director of Global Marketing Communications
Lumileds
+1 650 576 3864
Kevin.Lucido@lumileds.com
About Lumileds
For automotive, mobile, IoT and illumination companies who require innovative lighting solutions, Lumileds is a global leader employing more than 9,000 team members operating in over 30 countries. Lumileds partners with its customers to push the boundaries of light.
To learn more about our portfolio of lighting solutions, visit lumileds.com
Philips Lighting Supports MiniCrops’ First Vertical Farm With GreenPower LED Lighting
MiniCrops is the flagship initiative of Vertical Future, a technology start-up aiming to improve health in cities. The MiniCrops initiative provides households, farm shops, catering companies and restaurants with locally distributed boxes of fresh produce, focusing on nutrition, price and sustainability.
October 9, 2017
Philips Lighting Supports MiniCrops’ First Vertical Farm With GreenPower LED Lighting
Eindhoven, The Netherlands – Philips Lighting (Euronext Amsterdam ticker: LIGHT), the global leader in lighting, today announced that it supported MiniCrops, an agriculture technology initiative in the UK, using 200GreenPower LED production modules for its first vertical farm in the center of London. The MiniCrops farm has 65 m2 of production capacity, and triples its growing surface to 195 m2 by rotating crops every 8 hours.
MiniCrops is the flagship initiative of Vertical Future, a technology start-up aiming to improve health in cities. The MiniCrops initiative provides households, farm shops, catering companies and restaurants with locally distributed boxes of fresh produce, focusing on nutrition, price and sustainability. Household customers currently have the choice between boxes totaling either 150 or 300 grams, with each box containing between 6 and 9 different microgreen varieties, such as Rioja Radish, Red Kale, Sorrel, Sweet Genovese Basil and Broccoli. MiniCrops offers fair pricing and free delivery to customers across Greater London, and also recently invested in an electric vehicle fleet, further reducing food miles and environmental impact.
“We see a need for local fresh food with premium quality,” said Udo van Slooten, business leader for Philips Lighting’s horticultural lighting business. “On top of enhancing growth, we now have the ability to influence taste, flavor, nutritional value and shelf life by applying the right growth recipe. This enables our customers to meet the growing demand for fresh consistent quality produce year-round.”
Jamie Burrows, founder of Vertical Future and MiniCrops, realized that with over 70% of people expected to be living in cities by 2050, food sustainability and food security will become bigger and more relevant risk factors. He foresees a significant amount of volatility in food pricing, changes across the farming industry, and temperature variations in food exporting countries. “Consumers expect fresh, locally-sourced, sustainable food – all at the touch of a button. To meet future demands we need to use technology to our benefit, maximizing food production in our own market, close to consumers,” Burrows said, adding that he also thinks that projects like MiniCrops will create local jobs in a new industry.
MiniCrops closely collaborates with Philips Lighting’s horticultural LED lighting partner Cambridge HOK, which supported with the design and build process, resulting in a controlled, uniform, high-quality, maximum yield production facility – minutes from the center of London. MiniCrops is currently in discussions with various parties to develop its second site in London.
For further information, please contact:
Philips Lighting, The Netherlands
Daniela Damoiseaux, Global Marcom Manager Horticulture
LumiGrow Partners With Nectar Farms to Light 40 Hectares of Greenhouse in Australia
LumiGrow Partners With Nectar Farms to Light 40 Hectares of Greenhouse in Australia
Sydney, Australia – Nectar Farms Headquarters – October 4, 2017
Nectar Farms, an Australian agri-business, has selected LumiGrow as their lighting partner for its first 40 hectares of greenhouse developments, representing the largest greenhouse installation in the southern hemisphere. LumiGrow will be the exclusive provider of LED lighting systems comprised of both LED hardware and software for the facility growing vine crops and other vegetables in Victoria, Australia.
The agri-business aims to transform the Australian farming model by using smart lighting techniques and other advanced technologies. “When considering an effective lighting solution there are a number of variables,” says Stephen Sasse, Managing Director and CEO of Nectar Farms. “Having completed a structured technology and vendor selection process we have chosen to partner with LumiGrow. We believe that their systems and technology are leading-edge.”
Nectar Farms’ lighting strategy promises to go well beyond traditional techniques. The greenhouses will be equipped with adjustable LEDs, controlled through the LumiGrow smartPAR cloud-based software. The spectrum, intensity, and photoperiod of the LEDs will be managed dynamically along with plant growth stages, to elicit beneficial plant characteristics and respond to plant stress. Additionally, the smartPAR software will be integrated with LumiGrow smartPAR Light Sensor Modules, to maximize utilization of the sun’s energy and reduce energy costs.
“After encountering soaring prices for grid-based electricity and gas, electrical efficiency became particularly important for us,” says Stephen. To bolster the glasshouses’ sustainability and to save on electrical costs, Nectar Farms has partnered with French renewable energy company Neoen in the Bulgana Green Power Hub. The partnership comprises a 196MW wind farm and a 20MW/34MWh battery storage facility to ensure uninterrupted supply, which will make Nectar Farms one of the largest sustainably-operated greenhouses in the world.
Smart horticultural lighting will be an integral component of Nectar Farms’ smart farming initiative, beyond simply energy savings from the LEDs. Their high-tech and sustainable model will use light’s characteristics to maximize exportable produce and reduce inefficiencies of supply and pricing to meet growing global demand. Nectar Farms and LumiGrow will be working in close partnership with Costa Group who will provide an off-take marketing alliance for the sales, marketing, and distribution of the produce.
“We know that LED light can profoundly improve our crop production and be used to increase efficiency,” says Stephen. “With smart horticultural LEDs, we also have a tool to direct our crops’ growth and meet our quality and production goals. The partnership with LumiGrow is working effectively already, and we particularly value the support from their in-house research department.”
LumiGrow, a smart horticultural lighting company, will work with Nectar Farms as their lighting partner, a level of designation traditionally reserved for development, design, construction, and distribution entities.
“The future of horticultural lighting is here, and it’s through smart lighting technology deployed by our qualified spectral scientists that growers are going to see exceptional value,” says Shami Patel, CEO of LumiGrow. “As our company drives the industry’s understanding of how plants interact with light, we continue to apply the latest research to our lighting solution. With the release of our newest sensor technology, Nectar Farms will be able to gather and respond to solar data for a largely automated lighting solution. We feel inspired to be working with Nectar Farms. Finding partners who value the impact that technology can make on crop production is key. It’s truly smart farming meets smart lighting, and we’re thrilled to see LED lighting come this far.”
Learn more about LumiGrow smart horticultural lighting technology here: https://www.lumigrow.com/technology/
Check out LumiGrow's newest light sensor product, the smartPAR Light Sensor Module: https://www.lumigrow.com/technology/smartPAR-light-sensor-module/
About LumiGrow Inc.
LumiGrow, Inc., the leader in smart horticultural lighting, empowers growers with the ability to improve plant quality, boost crop yields, and achieve cost-saving operational efficiencies. LumiGrow offers a range of proven grow light solutions for use in greenhouses, controlled environment agriculture and research chambers. LumiGrow solutions are eligible for energy-efficiency subsidies from utilities across North America.
LumiGrow has the largest horticultural LED install-base in the United States, with installations in over 30 countries. Our customers range from top global agribusinesses, many of the world’s top 100 produce and flower growers, enterprise cannabis cultivators, leading universities, and the USDA. Headquartered in Emeryville, California, LumiGrow is privately owned and operated. For more information, call (800) 514-0487 or visit www.lumigrow.com.
IKEA’s Indoor Farm Is Trying To Alter How We Grow Food
IKEA’s Indoor Farm Is Trying To Alter How We Grow Food
The prototype designed by SPACE10 can grow greens three times faster than traditional methods
- 5 OCTOBER 2017
Multinational furniture manufacturer IKEA has introduced an indoor farm with the hopes of giving people the ability to grow their own food at home. The prototype, or Lokal as it’s called, was designed by SPACE10, IKEA’s lab for innovation.
Lokal is the most recent prototype to come from The Farm, a SPACE10 lab seeking to change how we view traditional farming while implementing new food production methods into our cities.
By experimenting with hydroponics, which is the growing of food without soil, SPACE10 says that it’s able to grow food up to three times faster and with 90% less water than traditional methods, according to a blog post with Medium. In addition to being soilless and faster than traditional methods, Lokal is also able to grow greens without any sunlight at all. Instead, the plants survive solely off of LED lighting and mineral nutrient rich water, simulating what Lokal refers to as “The perfect spring day, every day”.
SPACE10 points out that the current global food system is problematic for a few reasons. For starters, our current method of food production is contributing to the changing climate and is also wasteful of resources that we are already running low on, like fresh water. Furthermore, current methods lend themselves to wasting food. The hope is that the benefits of hydroponic farming courtesy of Lokal will go a long way in remedying some of these problems.
People should understand that the benefits of Lokal are not exclusive to the planet. According to its post with Medium, the food also “tastes good, is more nutritious, pesticide-free and fresh all year round”.
While this is all very interesting, simply creating a hydroponic growing apparatus is not even the end goal for Lokal. The Farm seeks to take things further by meshing the agrarian and tech worlds in the future. As it posted in Medium, the lab has hopes of “Introducing sensors and machine learning to the vertical stacks and connecting the data with Google Home — to enable people to ‘talk’ to plants, in effect, and hear how they’re doing, as well as to teach children and adults alike about sustainable food”.
It will be interesting to see just how much of a change Lokal will be able to make on the food growth industry’s ecological footprint, but for now it’s still a prototype.
Philips Lighting Signs Deal With Glinwell PLC For First 100% LED Installation in The UK to Grow High-Wire Cucumbers
October 3, 2017
Philips Lighting Signs Deal With Glinwell PLC For First 100% LED Installation in The UK to Grow High-Wire Cucumbers
Eindhoven, The Netherlands – Philips Lighting (Euronext: LIGHT), the world leader in lighting, today announced that Glinwell PLC, a leading UK producer of tomatoes, cucumbers, peppers and eggplants, is installing the UK’s first 100% LED grow light system for cultivating high-wire cucumbers. In recent years, high-wire growers have been rapidly adopting LEDs as supplemental lighting systems for their crops and have experienced higher yields, more consistent quality and the ability to move to continuous production. These results convinced Glinwell PLC that a 100% LED system was the best way for them to produce high-quality, British-grown cucumbers all year long to meet growing demand from UK retailers.
The only way is up
“For years, we have seen growers reap the benefits of using our LEDs in the cultivation of high-wire tomatoes. These range from higher yields and better quality fruit to more control over the growing climate and energy costs,” said Udo van Slooten, Business Leader Horticulture at Philips Lighting. “Now we see these benefits also being achieved by high-wire cucumber growers. We expect that the only way is up for LED in high-wire cultivation.”
Shaping the future
“We’re proud to be participating in this ‘first’ for the UK high-wire cucumber market,” said Joe Colletti, Director of Glinwell PLC. “During the winter months, we produce our cucumbers at our own overseas nurseries. We expect that this move will enable us to start growing cucumbers also on British soil, every month of the year. Not only does this greatly reduce our food miles, it allows us to meet the demands of some of Britain’s largest retailers, who want to offer consumers fresh, tasty products that are locally sourced.”
Sam Cannatella and Joe Colletti
Philips Horticulture Partner Cambridge HOK will be installing the 100% LED system which consists of two lines of Philips GreenPower LED interlighting and one line of Philips GreenPower LED toplighting. The project will be undertaken jointly by Eduard Udyanskyy, Growing Manager at Glinwell PLC, and Erik Stappers, Plant Specialist at Philips Lighting.
For further information, please contact:
Philips Lighting, The Netherlands
Daniela Damoiseaux, Global Marcom Manager Horticulture
Tel: +31 6 31 65 29 69
E-mail: daniela.damoiseaux@philips.com
www.philips.com/horti
About Philips Lighting
Philips Lighting (Euronext: LIGHT), the world leader in lighting products, systems and services, delivers innovations that unlock business value, providing rich user experiences that help improve lives. Serving professional and consumer markets, we lead the industry in leveraging the Internet of Things to transform homes, buildings and urban spaces. With 2016 sales of EUR 7.1 billion, we have approximately 34,000 employees in over 70 countries. News from Philips Lighting is located at the Newsroom, Twitter and LinkedIn. Information for investors can be found on the Investor Relations page.
About Glinwell PLC
Glinwell PLC is a second-generation family run business, produce and marketing company growing cucumber, tomato, pepper and eggplants. The company is accredited to BRC, Soil Association and the Farm Assurance Fresh Produce Scheme. Because Glinwell PLC is involved at board level in the Pepper Technology Group, Cucumber Association and Tomato Growers Association – as well as being involved in the Lea Valley Growers Association and Soil Association Working Party – it is part of the voice of the industry. Glinwell PLC is helping to shape the future. Its growing methods keep it as natural as possible from the purchase of high grade seeds, the attention to detail with the growing of the plants and the care taken in harvesting the produce. More information can be found on its website: www.glinwellplc.com
About CambridgeHOK
CambridgeHOK is the UK’s leading Glasshouse, Heating and LED lighting specialist (certified Philips Horticulture LED Partner) with expertise managed by its own inhouse design engineers. It specialises in bespoke turnkey design and installation, adapting every solution to the client’s needs using the very latest in technology. More information can be found on their website: www.cambridgehok.co.uk