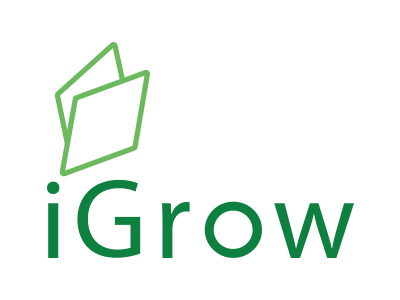
Welcome to iGrow News, Your Source for the World of Indoor Vertical Farming
Capturing The Spectral Composition of Light Sources
Light management is a critical factor in commercial greenhouse and growth chamber efficiency. "Growers can gain enhanced control of desired plant characteristics by accurately measuring and optimizing the composition of your supplemental light", Abby Brooke with LI-COR Biosciences explains. That's why the company has released a Spectrometer to capture the spectral composition of light sources. In addition, they also offer a light sensor package for use in greenhouses and growth chambers. The new spectrometer and light sensor will be shown at the Canadian Greenhouse Conference next month in Niagara Falls.
PAR
"Plant growth and reproduction is driven by photosynthetically-active radiation (PAR), which occurs at wavelengths between 400 and 700 nanometers. Not all light contains PAR, and PAR requirements vary between types and growth stages of plants", Abby Brooke with LI-COR Biosciences shows.
"As the intensity of natural light in your greenhouse changes throughout your photoperiod, so do your artificial light requirements. Understanding when and how to apply artificial light allows you to consistently hit your target daily light integral (DLI) for optimal growth without wasting energy. "
The team developed the LI-190R Quantum Sensor to solve this. The sensor measures the PAR inside greenhouses and growth chambers with the same precision in sun, artificial lighting, or both, without the need for calibration or correction factors. "Compatible artificial sources include incandescent and high-pressure sodium lamps, high-intensity fluorescent lights, and the rapidly emerging range of LED light systems."
Spectral composition
In addition, now there's also the LI-180 Spectrometer This one captures the spectral composition of light sources. "Not all light affects plant growth and reproduction the same way. As said photosynthetically-active radiation (PAR) occurs at wavelengths between 400 and 700 nanometers. This interval covers three distinct “color” bands of light, and modifying the intensity of these red, blue, green wavelengths, and additional near-UV (380-400 nm) and far-red (700-780 nm) bands can provide control over a variety of plant characteristics including growth rate, chemical composition, taste and nutrition, and more. The LI-180 spectrometer allows you to capture and optimize the spectral composition of your supplemental lighting which can add significant value to your greenhouse or growth chamber operation."
The measured parameters including color-specific photosynthetic photon flux density (PPFD), photon flux density (PFD) at 1-nm intervals between the entire 380 and 780 nm interval, irradiance (W/m2), and more, are all visible in the mobile application and desktop software.
The Spectrometer is to be introduced at the Canadian Greenhouse Conference. Met Li-Cor at booth 1015.
For more information:
Li-Cor Biosciences
402-467-0617
www.licor.com
abby.brooke@licor.com
Publication date : 9/25/2018
Author:
© HortiDaily.com
TotalGrow Turns Greenhouse Into Year-Round Operation
During the cold, dark months of January and February, the greenhouses of Mud Lake Farm were formerly dormant. Most of the staff was on temporary layoff awaiting a return to work when the longer daylight of spring made the farm bounce back to life.
TotalGrow Lighting
Thanks to an unexpected opportunity to test the TotalGrow light emitting diode (LED), the green houses now grow produce all year long and the staff is never without work. It’s an interesting story that is founded upon energy efficient lighting.
The Kent Garden Club recently heard the fascinating story of Mud Lake Farm in a presentation highlighting hydroponic gardening. The speaker was Kris Van Haitsma and I followed up with her to hear the rest of the story.
Kris is co-owner of Mud Lake Farm along with her husband Steve. The title of Kris’s presentation to the garden club was “Playing with Mud” and detailed the evolution of the farm from a muddy cow pasture to a highly productive hydroponic greenhouse operation.
The property on which the farm was built has been in Steve’s family for generations. It is primarily low lands and difficult to grow crops on. Kris wanted to do something different with the land which led her to purchase a used greenhouse. After many false starts Kris and Steve settled upon a hydroponic farming operation as the focal point of the farm.
At the point where Kris and Steve had four greenhouses operating during the usual short growing season they were asked to test TotalGrow LED lighting in one of their greenhouses. The goal was to extend the growing season and increase their productivity.
Hydroponics
With hydroponics no soil is needed and the plants float on nutrient rich water 4 to 12 inches deep. During the winter many types of lettuce thrive in a hydroponic garden if they can be kept from freezing and if supplemental light is provided.
In the past the Van Haitsmas had considered high pressure sodium lighting but could not justify the inefficiency of what is considered a typical greenhouse light. The bulb is expensive, uses lots of electricity, needs to be replaced fairly frequently and does not produce the optimum spectrum of light for good plant growth. Not a good combination when your goal is profitability.
An attempt at supplemental lighting with fluorescent bulbs led to less than desirable plant growth so when the test offer was presented, the Van Haitsma’s agreed to install the LED based TotalGrow system in one of their greenhouses.
Kris and Steve were amazed when they realized that the one greenhouse, using TotalGrow lights, was producing more than the other three greenhouses combined. That made adding TotalGrow lights to a second green house an easy decision. Ultimately they have plans to light the remaining houses with total grow as demand for their products rises.
Using a geothermal heating system to keep the air temperature above freezing, the Van Haitsmas expanded the variety of plants they could grow at the same time they developed new outlets for selling their fresh produce. Mud Lake Farms is now a vibrant year round operation!
According to Kris:
“We grow around 40 different varieties of lettuce, including red and green romaine, butterhead, batavia, and leaf lettuces. Since we grow lettuce year-round, we can provide produce to our customers even in winter.”
Kris’s customers include 80 – 100 families living in West Michigan that are enrolled in a type of buyers club. During the Farmer’s Market season they have a booth offering fresh picked products including custom made cordials (flavored syrups) that are made from ingredients grown on the farm.
Mud Lake Farm Cordials
Many local chef owned restaurants prefer the premium quality of Mud Lake Farm’s freshly picked produce. Relationships with those chefs are most often made by word of mouth and one came from a web search of LocalHarvest.org. Sadly, most chain restaurants do not seek out local growers, a situation that the restaurant chain Chipotle is making great strides at correcting.
Kris noted that a lot more infrastructure is in place for connecting locally grown products with local outlets. The sustainability and farm to table movements are helping drive those connections.
When a product like the energy efficient LED TotalGrow can improve the cost efficiency and productivity of a local grow operation, everyone wins as more products are brought to market and enjoyed by customers in many venues. The Van Haitsma’s Mud Lake Farm is a “shining” example of using energy efficiency to drive productivity as well as profitability!
The Energy Alliance Group of Michigan is a leader in clean energy PACE project development and financing.
UGA Researchers Receive $5 million To Help Reduce Energy Costs of Indoor Farming
By: Merritt Melancon University of Georgia College of Agricultural and Environmental Sciences
September 15, 2018
Photo courtesy of UGA CAESUGA College of Agricultural and Environmental Sciences Department of Horticulture’s Professor Marc van Iersel, right, is leading an interdisciplinary team which hopes to integrate new lighting technologies, big data and better growing practices to reduce energy costs in greenhouses and plant factories. Dorothy Kozlowski
One of the steepest barriers to profitable controlled-environment agriculture is the energy cost associated with providing the plants enough light, but new research being pioneered by University of Georgia could cut those costs by 50 percent.
With the support of a $5 million grant, a UGA-led team is working to develop strategies to increase the efficiency of lighting for controlled-environment agriculture: the practice of growing plants in greenhouses or plant factories.
Professor Marc van Iersel, of the UGA College of Agricultural and Environmental Sciences (CAES) Department of Horticulture, is leading the effort. The U.S. Department of Agriculture National Institute for Food and Agriculture Specialty Crop Research Initiative funded the project, called “LAMP: Lighting Approaches to Maximize Profits,” earlier this summer.
“When you are talking about a greenhouse or plant factory, up to 60 percent of their total costs can go to energy and about half of that goes to lighting,” said van Iersel, who has studied ways to reduce the lighting and irrigation costs in greenhouses for more than a decade. “So, if we can reduce those lighting costs, that would be a really big deal. The economic feasibility of plant factories is still questionable because it is so expensive to provide electric light to the plants.”
Currently, high costs and energy usage make it difficult for all but the most valuable crops to be grown profitably in controlled environments. Reducing the costs and carbon footprint of controlled-environment agriculture could open the door to more food being grown in arid, frigid or urban areas or for ornamental plants to be grown more efficiently.
U.S. growers spend about $600 million per year on electricity for lighting in their greenhouses and plant factories. Using informatics, engineering, high-efficiency LED lights and state-of-the-art greenhouse management practices, van Iersel hopes that they will be able to reduce the lighting energy costs by 50 percent.
“This will increase the narrow profit margins in the industry while reducing carbon dioxide emissions associated with energy production,” he said.
The team received the grant funds late this summer and has started work on its prototype lighting systems and strategies to optimize crop growth and quality.
“Having team members with such different areas of expertise is critical to the success of the project,” van Iersel said. “Together, we will be able to do things that none of us can do by ourselves.”
Informatics will be used to schedule lighting around peak power-use times, reduce light use to compensate for natural sunlight and further refine lighting efficiency. Horticulture researchers and engineers will look at the possibility of growing plants with limited-spectrum lighting, which could reduce energy use and be used to manipulate crop growth and quality.
“We want to help producers answer a few simple questions,” van Iersel said. “One: Is lighting cost-effective in their specific situation? Two: If lighting is cost-effective, are high-pressure sodium or LED lamps the better option? And three: What is the most cost-effective way to use those lamps?”
They’ll also be calculating the carbon footprint of each scenario to see if growing indoors makes environmental sense.
Answering these questions could help growers decide when it may be feasible to grow crops in a harsh environment and when it makes better sense to ship food to a location. Their findings could also have substantial impact on the way military deployments provide fresh food to troops or how fresh produce is supplied to desert or arctic locales.
CAES team members dedicated to the project include van Iersel, horticulture professor Paul Thomas, agricultural economist Ben Campbell and impact evaluation expert Kay Kelsey.
UGA faculty Mark Haidekker, WenZhan Song, Javad Mohammadpour Velni and Tom Lawrence, all of the College of Engineering, will contribute to the project, as will UGA Terry College of Business energy informatics experts Rick Watson and Maric Boudreau.
Collaborators from other institutions include Jennifer Boldt at the USDA Agricultural Research Service in Toledo, Ohio; Neil Mattson and Kale Harbick at Cornell University; A.J. Both at Rutgers University; Bruce Bugbee at Utah State University; and Tessa Pocock at the Rensselaer Polytechnic Institute.
For more information about the project, visit http://www.facebook.com/HortLAMP/.
US (MD): South Mountain MicroFARM Increases Lettuce Yield By 60% And Microgreens Yield By 10%
South Mountain MicroFARM is a 100% LED-lit, aquaponic leafy greens cultivator in Maryland. The 7,500 square foot greenhouse is situated on the Sellers family’s 22-acre Christmas tree farm. Two-thirds of the greenhouse contains media beds, hydroponic channels and vertical racks that grow a wide range of lettuces, herbs, and microgreens. The remaining one-third houses tanks of tilapia. For Levi Sellers, South Mountain’s Head Grower, building the greenhouse was a homecoming in multiple ways. Levi has lived many lives - he’s worked in a hydroponics supply shop, as a mountaineering guide, and an EMT. But he felt agriculture calling him back to the family farm.
Building an energy-efficient greenhouse
One of the biggest challenges to growing year-round in Maryland is the summer heat and humidity. As a result, the greenhouse was designed with the west-facing wall open for ventilation, so that the winds that blow from west to east can passively cool the greenhouse. Levi installed shade cloths to further soften the relentless heat and light of Maryland summers. Vertical fans help control humidity levels. The lower heat output of the LumiGrow fixtures made them the practical choice for Maryland’s climate.
“When it’s 80% humidity and 100 degrees outside, there’s not a thing you can do. If it’s a cloudy day, you still need to run your lights so that you don’t lose production," explains Levi, "If we were using HIDs, we’d just be increasing our heat more. It’s much harder to control. We really like that we’re able to run our lights on cloudy days and not worry so much about the heat.”
Choosing LumiGrow has also allowed South Mountain to save on upfront infrastructure costs. Installing HID fixtures would have required them to install an additional electrical service panel and purchase a larger backup generator. When the power goes out for extended periods of time during the summer, the lower power draw of the LumiGrow fixtures makes it possible to run both the fish tanks and the lights on the farm’s existing generators. South Mountain MicroFARM also received a 40% utility rebate for purchasing energy-efficient lights, which made the price competitive with HID.
For South Mountain, the benefits of choosing LEDs over HPS were clear. LumiGrow’s high standard of customer service made the choice a no-brainer.
“We looked at several of your competitors, but they weren’t offering the same spectrum adjustability and their customer service wasn’t as good as what I experienced with [our Account Manager] Mike," recalls Levi.
Picture-perfect lettuce
According to Levi, South Mountain’s heads of lettuce are a lot bigger and denser than their hydroponically grown competitors at the grocery store. South Mountain’s lettuce fills the package better, making them more attractive to the end-consumer.
“When I compare photos of our greens grown under LEDs to others' grown with the same aquaponics system who went with the manufacturer’s recommendation to use HID, our LED-grown lettuce looks so perfect and pristine that it almost looks fake,” says Levi.
Levi runs his fixtures year-round to maintain the specific DLI that produces the uniform, picture-perfect plants that consumers are looking for. He tries to maintain about 18 hours of light per day, so the energy savings from his LumiGrow fixtures make a big difference. DLI and photoperiod are both key factors in biomass generation - the higher the DLI, the more biomass produced per plant lifecycle.
Levi’s LumiGrow fixtures have had a huge impact on his lettuce crop - they reach harvest size in 40-50 days, shaving up to 33% off the crop production cycle. This allows Levi to fit in more turns. Levi has also had great results with his microgreens - his LumiGrow-lit trials were ready to harvest 2-3 days earlier than his unlit microgreens. The LumiGrow-lit trays also produced approximately 10% more material per tray.
Levi has also experimented with allowing the heads of lettuce to grow for the full 55-60 days. He found that the LumiGrow-lit lettuce was 40-60% heavier. Restaurants buy lettuce by the tote, so heavier heads of lettuce allow South Mountain to reach the tote weight that restaurants expect with fewer heads of lettuce. All of this means more revenue for South Mountain MicroFARM.
In addition to producing a better-looking, more marketable product, South Mountain MicroFARM uses 75% less energy than their friend’s similar-sized greenhouse.
A pink beacon of sustainability
Initially, Levi had some concerns about what the locals would think about the greenhouse’s vivid hue illuminating the side of the mountain. His fears were unfounded. While the locals often jokingly ask if the farm is having a rave without inviting them, the truth is that they love the pink glow. Their kids adore how it stands out at night and proudly use it as a landmark when telling their friends where they live.
“It acts as a form of advertisement for us, and it’s really sped up the word of mouth advertising about our business and what we’re doing,” says Levi, “We’ve built our brand around being very sustainable and eco-friendly. We focus on every detail, down to the fish feed to make sure it’s locally sourced and sustainably grown. And what better way to show people that than an uncommon glow of pink from our greenhouse? The pink glow means we’re doing something different.”
For more information:
LumiGrow
800-514-0487
info@lumigrow.com
www.lumigrow.com
Publication date : 9/24/2018
Researching The Impact of LED Lighting on Leafy Greens
A multinational light manufacturer and Michigan State University (MSU) have combined to create the ultimate vertical farm test lab for light emitting diode (LED) lights and their impact on indoor crop growing.
Cam Maxwell | September 11, 2018
Takeaway: With urban and vertical growing becoming more of a necessity than a trend, better information is being sought to provide a baseline on how LED grow lights affect indoor crops. To do that, Michigan State University’s Department of Horticulture and lighting manufacturer OSRAM are teaming up to perform cutting-edge research in a state-of-the-art facility.
A multinational light manufacturer and Michigan State University (MSU) have combined to create the ultimate vertical farm test lab for light emitting diode (LED) lights and their impact on indoor crop growing.
MSU's vertical farm test lab
The university’s Department of Horticulture built a state-of-the-art controlled environment lighting laboratory (CELL) that enables indoor vertical farming using a light system developed by lighting manufacturer OSRAM. The idea is to use the facility to research the impact of various LED light spectrums and combinations on growing crops in hydroponic solution. Specifically, researchers are looking into how LED lighting effects various traits exhibited by certain crops.
“We think we can manipulate (how plants grow) to a certain point,” says Erik Runkle, a professor in MSU’s Department of Horticulture. “So, we’re looking at a couple different things. One is floriculture crops that are high-value crops with seasonal demand, and leafy greens. You can really have a big effect on things like the leaf unfolding, the size of the leaf, the shape of the leaf, the texture of the leaf, how dense it is. You can influence nutritional content—that’s pretty clear. We also think to some extent you can influence the taste. Those are the areas of research that we’re investigating right now.”
The CELL is a research-first lab for Runkle and MSU’s Department of Horticulture to study exactly how the different color spectrums of LED lights (along with light duration and other factors) impact all aspects of crop growing, including taste.
Runkle is working with PhD candidate Qingwu (William) Meng, who is leading the research on lighting to produce those leafy greens with desired attributes, which could have a huge impact on vertical farming in the future. Once concluded, their research should pinpoint an optimized lighting blueprint to maximize crop growth that will eliminate much of the guesswork when it comes to LED lights and indoor horticulture.
As the crops are tested, several controls are in place to ensure the environment changes as little as possible, while the recirculating hydroponic system ensures constant nutrition is provided to crop roots. The CELL is actually two independently controlled and refrigerated growrooms, each with 12 deep-flow hydroponic shelves.
But it’s the lights that are the true workhorse at MSU.
The lights at MSU
The complex LED system was designed and implemented by OSRAM, a multinational lighting manufacturer headquartered in Munich, Germany. Lights in the CELL use seven different light channels (colors) ranging from UV to the far red, along with two different white channels. The entire light system is calibrated, and customized software enables digital light control of individual shelves, allowing for temporal alternations of light quality and intensity.
“We wanted to reduce the variability of the light output from one canopy to another, so we know what each of the fixtures puts out in terms of light and is uniform across all fixtures,” says Rodrigo Pereyra, a research and development manager at OSRAM. “That way, within a margin of error, we’ll still have the same results.”
The key in terms of the research is learning how specific LED light colors impact plant development with all other factors being equal.
“The real value right now is to develop some understanding around these individual colors for plant development and plant health,” says OSRAM’s David Hamby, project lead of the lighting setup for CELL. “It allows for some independent study of the impact of the lights.”
By helping out with light design and providing the LEDs for the CELL, OSRAM is in a win-win position in terms of being able to take the research and use the findings to better help its commercial clients properly get their lights set up, calibrated, and dialed in for maximum yields.
“We know of other researchers who are working on similar subjects, but we know the flexibility of our lighting system and our ability to deliver literally an infinite combination of different lights, colors, and intensities,” Pereya says.
The plan is to publish the findings in both scientific journals and trade magazines, but no timetable has been established, though Runkle says some results could be unveiled later this year or early in 2019.
Written by Cam Maxwell
VividGro® Announces Happy Sprouts Farm Partnership
August 22, 2018
CHICAGO
Brian Turner’s cancer diagnosis ignited the flame for Happy Sprouts Farm. Passionate about health and fitness, the former personal trainer focused on improving his nutrition to speed his recovery. While conducting intense research, Brian discovered the healing powers of microgreens, a nutrient-dense food that previously had been considered just a simple garnish.
Given their scarce supply, to meet his personal consumption needs, Brian began growing his own greens in his basement. After gaining experience as a grower, he was ready to branch out and did so by founding Happy Sprouts Farm, delivering samples to local restaurants and soon earning his first accounts. Located just outside Louisville, Kentucky, a food Mecca, Brian found a ready market in innovative chefs eager for fresh, locally grown produce.
But Brian’s primary challenge to achieving financial success became the expense of lighting. True to form, Brian began researching lighting products, and he settled on two brands that were generally considered the best available at the time. Not satisfied with his farm’s large energy consumption, further research brought Brian to VividGro® and their GroBar™ fixtures. Brian was wary that he would obtain the same yields from bulbs that required only 30 watts (versus his existing 108 watt bulbs) but impressed with VividGro’s industry-leading three-year warranty and supportive customer service, Brian decided to try the GroBars.
The test results were immediate. Based on these positive results, Brian decided to completely convert his entire grow space to GroBar lighting. Throughout the process, VividGro customer service team was incredibly easy to work with at every step. “The customer service has been amazing,” Brian said. “They are always there to answer my questions. They have made it so easy. I really appreciate that.
As his business and passion continue to flourish, Brian is preparing to expand his operations, adding more grow space and cultivating new crops, including edible flowers and mushrooms. And of course, VividGro products are prominently included in his design. Brian is now perfectly positioned to make a lasting impact as a grower of healthy, nutrition-filled, locally sourced products and to generate financial success for his family and workers.
About VividGro
VividGro®, the groundbreaking horticultural LED division of Lighting Science, is a pioneer in the AgTech space. Tailored to the automation and efficiency within indoor agriculture and horticultural markets, VividGro® implements solutions that help Growers grow in the most efficient way possible. Our state-of-the-art VividGro® lighting product line delivers optimized PAR to maximize plant growth and PAR efficacy, while also providing light suitable for the human visual system and excellent color penetration. In addition, unlike other LED grow lights, VividGro distinguishes itself from its industry peers by helping growers learn how to use their resources. It’s not the lights you use it is how you use them. Learn more about VividGro on our website at www.VividGro.com and join us on social media at Facebook, Twitter, and Instagram.
About Happy Sprouts Farms
Happy Sprouts Farms, located in Taylorsville, KY, offers delicious nutrient-packed microgreens and shoots to restaurants and chefs in Louisville, Lexington, and the surrounding areas. Happy Sprouts Farms is a member of Kentucky Proud, an organization that supports and promotes Kentuckian “foods, nursery items, crafts, agritourism sites, farmers’ markets, state parks, and many other products and destinations with roots in Kentucky soil.”
Filed Under: VividGro Tagged With: LED, LED Lights, Press Release
Does It Make Economic Sense For You To Install Grow Lights?
Posted on 09/27/2018
Written by David Kuack, HortAmericas.com
The Lighting Approaches to Maximize Profits (LAMP) project aims to determine how growers can maximize their return on investment when considering installing grow lights.
As light emitting diodes (LEDs) become more efficient and more affordable, an increasing number of greenhouse and plant factory growers will consider installing LED luminaires to light their crops. In the case of greenhouse growers, these luminaires would provide light to supplement natural sunlight. For plant factory growers, production depends entirely on the light provided by an artificial light source including LEDs, high pressure sodium or metal halide luminaires.
According to University of Georgia horticulture professor Marc van Iersel, the electricity for supplemental lighting in a greenhouse accounts for 20-30 percent of variable costs. In the case of plant factories which rely solely on artificial light, the electricity cost accounts for 50-60 percent of the variable costs.
van Iersel is heading up a $5 million, four-year research project that will focus on enabling growers to maximize the return on their lighting investment. Funding for the Lighting Approaches to Maximize Profits (LAMP) project is being provided by the USDA National Institute for Food and Agriculture Specialty Crop Research Initiative. The team that has been assembled to work on the project includes 15 university researchers, an advisory panel of greenhouse and plant factory growers and industry consultants.
“The job of the advisory grower panel is to make sure that the research that we do is actually what they need,” van Iersel said. “These are growers who will directly benefit from the research. We are also working with consultants who represent a big section of the industry. We are looking to them to help disseminate the information generated by the research to the industry.
“The research is looking to determine how growers can maximize their return on investment. There has been a lot of research done on how to grow plants with LED lights. We know growers can produce plants with lights. But what we don’t really know is how can growers make the most money doing it.”
Focused on LEDs
van Iersel said most of the project’s research will focus on the use of LEDs with some economic comparison to high pressure sodium (HPS) lamps.
“LEDs are clearly the lights of choice for the future,” he said. “Where we are interested in comparing LEDs and HPS is in regards to the economics. LEDs are more efficient, but they are also more expensive. Is the extra cost of LEDs worth it or are some growers actually better off paying less in capital expense for HPS lamps and more for the electricity to operate them? That is not a simple question to answer.
“There really hasn’t been a big price drop in LEDs. What LED manufacturers have done is rather than lowering the price, they have focused on making the LEDs better. Newer LED lights have hundreds of individual diodes in them. That is one way to help make the lights more efficient. But obviously they are putting more hardware in the lights. In older LED lights there were fewer individual diodes that went into a single light. The diodes were expensive. Now that the diodes are relatively cheap the manufacturers are putting in more of them so that the lights are more efficient. There seems to be a race among manufacturers to try to make the most efficient LED light possible. Right now it seems like the focus is more on creating a more efficient light than on creating a cheaper light.”
van Iersel said LED light manufacturers can easily match the light intensity of HPS lamps.
“What the LED manufacturers typically do with more diodes is run the diodes at only a fraction of their full power,” he said. “That makes the diodes more efficient. If an LED operates at 50 percent of its maximum power, it is substantially more efficient than running it at full power.”
Using supplemental light efficiently
One area that van Iersel is particularly interested in studying is making sure that growers provide supplemental light when plants are best able to efficiently use the light.
“LEDs are fully dimmable and can be dimmed instantaneously,” he said. “LEDs can very easily be programmed to respond to ambient light levels. One of the things that we are working on is designing systems that dim automatically as the sunlight level increases.
“With LEDs it’s more than turning them off and on, it’s dimming them. We have a system where we are calculating every second how much light to provide and how much to dim or brighten the LEDs. That is not possible to do with HPS.”
van Iersel said most LEDs are already dimmable.
“Every LED light is dimmable, it’s just a matter of using the right driver, which provides the power to the LEDs,” he said. It is very easy to incorporate into the lights. What I would hope is going to ultimately happen is growers are going to demand this kind of technology when they look at LEDs and the manufacturers have no choice than to provide it.”
van Iersel said another area of interest with the research is using the light spectrum as a way to manipulate quality.
“This could be accomplished with either the red:blue ratio or the amount of far red that is incorporated into the spectrum,” he said. “We also want to look at how the light is actually delivered to the plants. Right now, at least with ornamentals, growers look at the daily light integral (DLI) that is required to grow a particular crop. There are some clear indications that if the DLI is spread out over a longer photoperiod, for example, 20 hours instead of 14 hours, with the same amount of light over the entire day that more growth occurs with the longer photoperiod. This would be a lower instantaneous light level, but the same amount of light over the course of the entire day. This would allow growers to purchase fewer lights.”
Simplifying growers’ choices
van Iersel said one of outcomes of the research project is to be able to provide growers with a simple to use calculator that allows them to figure out if supplemental lighting will actually pay back in their particular production situation.
“If we can prevent growers from buying lights if they are not going to realize a return on investment that is going to be a good thing,” he said. “If they do decide that they want to use supplemental light, what makes more sense? Is it better to purchase HPS or LEDs? Which lights are going to offer a better return on investment? We hope to develop spreadsheets and some of this information will be incorporated into the Virtual Grower software program that is available free to growers.”
Current, powered by GE, Arize Lynk LED grow lights are being used by mGardens in its vertical farm in Gorham, Kan.
van Iersel also said some of the information that has been incorporated into the proposed horticultural lighting label is going to be required for the calculations.
“The lighting companies typically provide this information already, specifically the efficacy of the lights. Every reputable lighting manufacturer will be able provide this information. After the LAMP research is completed, growers should be able to look at the label information from different lighting companies and run some scenarios to tell them which lights are the most cost effective for them. It is really difficult right now for growers to decide whether or not to light and what kind of lighting is cost effective. It depends on a number of factors including where they’re located, their electricity prices, the crops they’re producing and how well those crops respond to supplemental light. Unfortunately, currently there is a lot of information that needs to go into doing these calculations. This has hampered the adoption of LED lights because growers can’t determine if they can pay for them.
“Once the research is done, the only numbers growers should need to plug in are basically the profit margins on their crops. Hopefully we will be able to provide them with the rest of the information they need to determine whether installing lights makes sense financially.”
For more: Marc van Iersel, University of Georgia, Department of Horticulture, Athens, GA 30602; (706) 583-0284; mvanier@uga.edu; http://hortphys.uga.edu/personnel/van-iersel.html; https://www.facebook.com/HortLAMP.
This article is property of Hort Americas and was written by David Kuack, a freelance technical writer in Fort Worth, TX.
Posted in News
Tagged Ag Tech, Indoor Ag, LED, LED grow light research, LED Grow Lights
Merida Capital Funds VividGro
August 17, 2018
By Iris Dorbian - NEW YORK–(BUSINESS WIRE)
VividGro, a spin-out from Lighting Science Group Corporation, which is backed by Pegasus Capital Advisors, has secured an undisclosed amount of funding. The investors are Merida Capital and LSG. Based in West Warwick, Rhode Island, VividGro is a provider of controlled environment agriculture LED lighting solutions and services for the indoor horticultural and cannabis industries.
VividGro, LLC, a portfolio company of private equity firm Pegasus Capital Advisors (Pegasus), today announced it has tapped investment firm Merida Capital Partners (Merida) as its strategic partner. VividGro, a spinout from Pegasus-funded Lighting Science Group Corporation (LSG), offers products based on LSG’s origins in developing lighting for NASA and the International Space Station and currently focuses on distributing controlled environment agriculture (CEA) LED lighting solutions and services to the indoor horticultural and cannabis industries.
The Company will initially be funded by investments from LSG and Merida Capital. Merida Managing Partner Mitchell Baruchowitz will join the VividGro Board and work with VividGro CEO David Friedman, former CEO of MJIC, as well as Board Chairman and Pegasus Operating Advisor Abraham Morris, to aggressively grow VividGro, including through acquisition of innovative CEA technology and service providers.
VividGro CEO David Friedman commented, “With the rapid growth of indoor cultivation in both the indoor horticultural and cannabis industries, the need for energy efficient and ‘smart’ lighting products has multiplied. We are excited to partner with leading cannabis investor Merida Capital, and their sophisticated portfolio of ancillary companies, to help drive VividGro’s strategy of creating a world-class suite of CEA technologies and services.”
Mitchell Baruchowitz, Managing Partner of Merida, remarked, “Merida is humbled by the opportunity to partner with a seasoned investment firm such as Pegasus and top technology provider, VividGro, which has a great management team in David Friedman and Abe Morris, to execute on our shared vision of creating a connected ecosystem of leading companies to drive the indoor horticultural and cannabis industries forward.”
Addressing the partnership with Merida, Joel Haney, a Principal at Pegasus said: “With its focus on responsible investing and governance, Merida is the perfect partner for Pegasus to rely on to assist VividGro in navigating the emerging investment landscape in its core areas of growth.”
About VividGro
VividGro is a pioneer in the AgTech space. Tailored to the automation and efficiency needs of the indoor agriculture and horticultural markets, VividGro implements solutions that help growers maximize yields and reduce costs. Our state-of-the-art VividGro lighting product line delivers optimized PAR to maximize plant growth and PAR efficacy. VividGro distinguishes itself from its industry peers by helping growers learn how to use their resources more efficiently. It is not the lights you use it is how you use them.
Learn more about VividGro at www.VividGro.com and join us on social media at Facebook, Twitter, and Instagram.
About Merida Capital Partners
Merida Capital Partners is a private equity fund targeting fundamental growth drivers which accelerate the rapid development of the cannabis industry. Our motto is Responsible Investing in the Emerging Cannabis Industry. For more information, please visit www.meridacap.com or follow us on Twitter @meridacap.
About Pegasus Capital Advisors, L.P.
Pegasus Capital Advisors, L.P. is a private equity firm founded and led by Craig Cogut. Since inception in 1996, Pegasus has invested across five private equity funds and currently manages approximately $1.9 billion in assets. The Firm invests in companies within the sustainability and wellness sectors that are seeking strategic growth capital.
A Light Salad: LEDs Revolutionize The Horticulture Industry
By Len Williams
Wednesday, September 12, 2018
With their low energy usage, reduced heat output and the ability to control the light colour they emit, LEDs are poised to revolutionize the horticulture industry.
“It’s a real luxury to eat locally grown, leafy greens in the middle of a Chicago winter,” declares Robert Colangelo, founder and CEO of Green Sense Farms. Before he launched his business in 2012, the only truly feasible way to provide fresh salads and herbs during the cold Illinois winter was to truck them thousands of miles from farms in the warmer southern US states.
However, Colangelo has no ordinary farm. Inside a warehouse a few miles east of Chicago, his ‘vertical farm’ contains rows of tightly packed plants, stacked from floor to ceiling. Bathed in a bluey-pink LED light, the vertical farm principally grows salads, herbs and starter crops, while also constantly experimenting with new plants. Green Sense Farms, which is in the process of building new installations and selling its technology worldwide, mostly supplies a local Whole Foods Market distribution plant, as well as nearby restaurants.
Colangelo’s farm offers benefits beyond producing basil in winter. He is able to intensively grow his crops within 30-35 days and constantly send these to his customers – far more regularly and dependably than growing the same crops in a field. The warehouse attracts few pests and, because the environment is entirely controlled, the company uses significantly less water than traditional farming, while avoiding the need for pesticides.
Farms like Colangelo’s offer a tantalising vision for the future of farming. They allow for faster, more efficient growing, significantly less waste and the ability to produce crops near or even within cities – where most plants are now consumed. This potential revolution is, above all, powered by LEDs.
Plants need light to provide the energy that lets them create their own food: they capture this through chlorophyll, a pigment in their leaves. Until relatively recently, there have only been two commercially viable ways to provide plants with this light: using the Sun, or via high-pressure sodium lamps (HPS) installed in greenhouses.
The Sun is, of course, undependable – cloud cover can limit the light available to plants, meaning crops grow more slowly. Growing outdoors also introduces many risks – from too much or too little water, pests, and the requirement to use pesticides. You can also only grow on one level, meaning farms require a huge footprint.
HPS lamps have advantages over the Sun. When installed in a greenhouse they can provide a constant source of light – even when the Sun is behind clouds or when days are shorter. However, Simon Thaler, press officer at Osram, the German lighting manufacturer, explains their drawbacks: “HPS lamps produce over 100lm/W [lumens per watt] but over a wide wavelength range, which is not necessarily optimised to plant growth. The high power consumption and the heat radiated from HPS luminaires also require a significant distance between the light source and the plants, leaving them primarily suitable for top-lighting systems in greenhouses. To compensate for the heat development, they also often require additional hydration of the plants.”
SCIENCE
Effects of colour on plants
Light is a kind of electromagnetic radiation. It is visible to the human eye at wavelengths between approximately 400 and 700nm, with different wavelengths perceived as being different colours. The human retina is most effective at picking up blue, red and green light, with different cells being sensitive to each.
Plants absorb light via pigments called chlorophyll a and chlorophyll b, which reflect green light but are effective at absorbing ‘deep blue’ light (450nm) and ‘hyper red’ light (660nm) as well as ‘deep red’ (730nm). Exposure to different amounts of these wavelengths can affect how the plant grows.
Blue light provides plants with a lot of energy and is used to regulate the opening of stomata – tiny openings on the surface of leaves that control water loss and uptake of carbon dioxide. Providing more blue light results in plants with smaller, thicker and darker green leaves. Hyper red light is especially effective at triggering photosynthesis, and makes plants grow tall and fast. And deep red light impacts on when a plant begins to flower. By combining different colour light in different quantities, you can change the final plant’s qualities.
For instance, a plant mainly exposed to red light will grow tall and thin. But add around 10 per cent of blue light into the ‘recipe’ and it will grow shorter and more densely. Exposing the plant to more of one type of light or another at different stages of its growth can also affect its development.
LEDs offer many advantages over these traditional light sources. They do not warm up the surrounding air in the same way as HPS luminaires do, meaning they can be placed much closer to plants in stacks – allowing for ‘vertical farms’ like Colangelo’s. Thaler notes that LEDs last significantly longer than HPS lamps and use less electricity. They can also be turned on and off in seconds – which is more effective than HPS lamps that require up to 30 minutes to reach capacity.
However, perhaps the most exciting thing about LED is that it gives growers control over the kind of light that the plant is exposed to. As it turns out, plant growth is especially benefited by light in the blue or red part of the spectrum. LEDs can be designed to specifically generate more of this kind of light, which is especially useful for growing plants.
Professor Neil Mattson, a horticulture researcher at Cornell University in New York, describes his lab’s research into LEDs and light. “We look at plant performance when the plant is exposed to different spectra of light, and how this affects the plant’s qualities. For instance, if you expose the plant to more blue light, this produces a plant with thicker leaves. It can also turn on the pathways for secondary benefits such as a plant which contains more antioxidants.”
Mattson describes cutting-edge research which looks at how different light wavelengths mean you can get taller or shorter plants, earlier flowering, or impact nutritional value. His current research has found that “lighting treatments can double the amount of vitamin C found in a tomato”, for instance.
Brandon Newkirk, marketing director at smart lighting company LumiGrow, explains how his company’s LEDs provide growers with this kind of cutting-edge control today. The Californian company has developed cloud-based software that connects to its lighting hardware. This allows growers to constantly monitor light levels in their greenhouses and then ‘tell’ the LEDs what to do according to their own automated growing strategy –whether that’s exposing the plant to more LED light or reducing it on sunny days to bring down electricity costs.
He describes custom-designed treatments, or ‘recipes’, that expose plants to either more red or blue light. These kinds of treatments can, for example, “make for a sweeter or spicier basil leaf”. LumiGrow’s customers can effectively design the ideal produce that end consumers might want by exposing the plant to different light spectrums at different stages of its growth. Newkirk explains how, for example, lettuce plants could be exposed to more blue light towards the end of their growth cycle in order to give a more vibrant colour to the final product.
For the end grower, LEDs have the added benefit of giving them much more predictability – and this can save them money. Professor Marc van Iersel from the University of Georgia reports that in the US alone, around $600m is spent every year on energy used in horticultural lighting. If growers can cut that cost by using more energy-efficient LEDs, then they can boost their profit margins. What’s more, he explains that “in the US, by the time a grower plants a crop in a greenhouse, it’s already been sold”. LED lighting means growers can confidently provide the plant with the right amount of light to ensure it will grow in time – because when growers miss deadlines they are often hit by financial penalties.
LEDs clearly have enormous potential. However, Mattson notes that only around 2 per cent of US greenhouses currently use LED technology, according to a recent Department of Energy study. What’s stopping uptake?
Put simply, LEDs are more expensive to buy than HPS lamps or sunlight. Prices will go down – van Iersel expects the technology to keep improving while costs drop over the coming decade. And companies like Osram and LumiGrow point to the longer lifespan of their products and reduced electricity bills.
Then there’s the question of return on investment (ROI). Mattson explains that for certain crops, it may take up to 10 years to achieve payback, although lighting firms assure ROI is normally achieved in less than five. Either way, growers expect ROI fast, meaning that many still have doubts about whether the investment is right for them.
And there’s the final price for the plants themselves. LED lights can, in theory, be used to grow any plant. However, at present the economics doesn’t make sense for anything but the highest value crops such as salads, herbs, flowers and marijuana. From apples to potatoes to wheat, many cheaper crops are already pretty much perfectly farmed in the great outdoors, meaning LEDs would offer limited value. Van Iersel describes a colleague’s calculation, which estimated that, should wheat be grown under LEDs in the US, a simple loaf of bread would cost an extortionate $11.
He explains that “it’s frustrating for people like us working in the field, because there are various ‘visionaries’ who claim that in future all produce will be grown in warehouses. But, as the example with the loaf of bread shows, that’s not going to happen any time soon.”
Besides the cost aspect of LEDs, Colangelo of Green Sense Farms also highlights other practical industry challenges, especially for vertical farms. There’s a general lack of workers in the agricultural industry, and even fewer who know how to build and rig up LED farms. “There’s no standard textbook on building a vertical farm yet.”
Despite these challenges, rapid advances in LED technology suggest we will reach a tipping point soon – Mattson estimates this will be reached within 5-10 years. At this point, LEDs will be more attractive and cost-effective than HPS, and this could really revolutionise the horticultural industry.
Colangelo expects to see farming become more stratified, with different types of crop being grown in the most appropriate environment. Some plants will always be best grown under the Sun, some in greenhouses and others in vertical farms.
He adds: “People get very excited to see plants growing indoors in a very sanitary environment.”
If he’s right, the future’s bright for the sector.
ECONOMICS
Urban Farming
Move over allotments: industrial vertical farms with plants grown under LED arrays might be the future of urban farming. By growing produce close to where it’s eaten, growers and supermarkets could cut their transport costs, while giving environmentally conscious consumers produce with a lower carbon footprint.
Professor Neil Mattson of Cornell University has been working with economists on a project to study the scalability of controlled urban agriculture. The research looks at the energy costs, as well as carbon and water footprint of a hypothetical urban greenhouse or warehouse farm in New York City, compared to growing and shipping the same food 3,000 miles from California.
Right now, it seems urban farming remains more expensive than traditional agriculture, with production costs roughly twice as high. Nonetheless, high-value and highly perishable plants do have the potential to be more valuable when grown close to where they’re eaten, because more of the product can be consumed before it goes bad. City slickers may soon be eating Waldorf salad grown down the road.
LIGHTING FOOD LIGHTING SUSTAINABILITY FOOD LED SUSTAINABILITY
Signify Launches New Philips GreenPower LED Toplighting With Higher Output For Light-Loving Crops
Signify, the world leader in lighting, today announced the introduction of the new Philips GreenPower LED toplighting high output with a light efficacy up to 3.0 µmol/J and an output of 800 µmol/s. The new module will help greenhouse growers improve the growth of vegetables, fruits, flowers and other crops that require a lot of light. The new toplighting is available as of September 2018.
In addition to higher light levels and improved efficiency, the high output modules will have a lifetime of 35,000 hours and give growers greater control over their growing climate because of minimal heat radiation while accelerating the growth cycle and enabling more efficient use of grow space.
Best choice for increasing light or decreasing energy costs
“For many years, the use of LED toplighting for greenhouse vegetable cultivation has been steadily growing. Now we can offer an even more efficient solution for a variety of growing needs and light-loving crops,” said Udo van Slooten, Business Leader Horticulture at Signify. “Whether growers are looking to apply more light to leafy greens, roses, or bio-based crops, or are focused on reducing their energy costs, the new GreenPower LED toplighting can meet both requirements.”
Uniform light distribution and long lifetime
This 800 µmol/s version GreenPower LED toplighting module may be mounted on a trellis to deliver uniform light distribution, which gives growers flexibility with installation and adhere to light plans without the use of an additional C profile.
The high output version operates at an input voltage of 277V – 400V and will be available in three spectrums: deep red/blue low blue; deep red/white low blue; and deep red/white medium blue.
Signify became the new company name of Philips Lighting as of May 16, 2018.
Five-Day Introductory Training Course On Plant Factory With Artificial Lighting (PFAL)
Five-Day Introductory Training Course On Plant Factory With Artificial Lighting (PFAL)
By urbanagnews
July 18, 2018
In response to increasing global demands from indoor farmers, researchers and future entrepreneurs in the exciting emerging field of plant factory with artificial lighting (PFAL), also known as vertical farm, this coming October, Japan Plant Factory Association (JPFA) together with Chiba University will host an intensive five-day introductory training course in English on PFAL.
Since 2010, JPFA and Chiba University have been organizing various in-depth and practical sessions, including introductory to advanced courses. This five-day introductory session in English, held October 1st -5th, covers what you would need to know before or after starting PFAL business or research.
The sessions will be interactive academic and practical classes, covering topics such as structure and function of PFAL, environmental control, lighting, plant physiology, nutrient solutions, seedlings, recent new technology, and business case studies of commercial large-scale PFALs. In addition to lectures by academic professionals and PFAL representatives, optional excursions to some commercial PFALs on the last day of the course will be organized.
Objective and Goal
-To offer foundation for theory and experience-based practice, with a view to foster academic and industrial development toward next generation PFAL.
-To facilitate development and dissemination of technically and economically sustainable PFAL, through providing the firsthand technical and conceptual classes by broad-ranging professionals in practice from both academia and PFAL industry.
Who should attend?
Motivated current/potential indoor farmers who plan to start or just started PFAL business or research. They will gain understandings of elementary theory and practice of PFAL, basic knowledge of cultivation and operational management, and keys for business success, etc.
Lecturers
Scheduled Lecturers
Chiba University / JPFA: T. Kozai, Y. Shinohara, T. Maruo, S. Tsukagoshi, N. Lu, M. Takagaki, T. Yamaguchi, O. Nunomura and E. Hayashi
Lecturers from the PFAL industry: Representatives from 808 Factory and others
Guidelines for Applicants
Date: 2018. 10.1 Mon – 10.5 Fri
On the first day (2018.10.1), the reception and classes are scheduled to start in the morning.
On the last day (2018. 10.5), the optional excursion will be held in the greater Tokyo area and is scheduled to finish at approximately 15:00.
(Detail schedule will be announced once fixed.)
Location: 6-2-1 Kashiwanoha, Kashiwa, Chiba, Japan 277-0882
Center for Environment, Health, and Field Sciences, Chiba University
Japan Plant Factory Association (1F Meeting Room)
Kashiwanoha campus is located less than 1 hour from Tokyo by train.
There are several accommodations nearby. We will provide the information after you apply.
Fee: JPFA member JPY115,000/person
JPFA Non-member JPY145,000/person
Includes materials for lectures and the transportation fee on the excursion day.
Lunch is not provided, however, there are many options in walking distance including a shopping mall food court and grocery store.
How to apply
Click here for the application form!
Seats will be filled in the order that applications are received.
After applying, you will receive the invoice within 7 to 10 business days. After confirming your payment, your seat will be reserved and we will provide your confirmation booking number.
If your payment can not be made within 5 business days after receiving the invoice, your reservation may be canceled automatically.
Deadline for registration: The end of August or when capacity is filled.
Cancellation:
If participants cancel the training course on or before August 20th, 2018, we will return the fee except JPY 40,000 (a cancellation fee). If the cancellation occurs after August 21st, 2018, the fee shall be due in full.
In most cases, in lieu of canceling you may transfer your registration to another person without penalty.
Japan Plant Factory Association
Japan Plant Factory Association(NPO) is devoted to academic and business advancements in the global indoor farming/CEA industry. Our mission is to develop and disseminate sustainable systems that can address global food, energy and resource issues. We
manage around 20 R&D projects, monthly workshops, and training courses, etc. at Chiba University campus in Kashiwanoha, a smart city in Japan.
JAPAN PLANT FACTORY ASSOCIATION (JPFA)
6-2-1 Kashiwanoha, Kashiwa, Chiba 277-0882, JAPAN
Tel: 81-(0)-4-7137-8318 Fax: 81-(0)-4-7137-8312
http://npoplantfactory.org/e_trainingcourse.html
E-mail: training@npoplantfactory.org
Is Warehouse Farming The Future Of Agriculture?
No matter what industry you’re in, you need to be looking ahead for technological changes, the cost-effectiveness of your competition, changing customer behavior, and potential government regulation.
One threat to the status quo I would like to explore is the potential for large-scale warehouse or vertical farming. Could it reduce the need for row-crop production?
If so, what kinds of crops will be first to face competition? And, what kinds of crops may never be grown indoors?
Because of shortages of arable land in some places, like Asia, indoor vegetable production has been in play for years. Alibaba.com, a Chinese internet retailer, advertises that it offers 2,466 vegetable warehouse products, including pre-fabricated buildings.
Companies like Philips are developing red and blue spectrum LED lights specifically for growing plants, while others are building sensors that detect optimal lighting levels for various crops.
Some companies on the West Coast are growing fruit and vegetables in 20-foot-tall towers inside of climate-controlled facilities with LED lights.
They claim to use no pesticides, herbicides, synthetic fertilizers, or GMOs. They do use thousands of infrared cameras and sensors to collect data in order to optimize lighting, water supply, and temperatures. Some warehouse type growers claim that this technology can achieve yields that are many multiples of traditional farming.
However, vertical farming still has one inefficient component: electricity usage. Without sunlight, plants require intense artificial lighting for 16 or more hours a day. That adds up to sky-high energy bills. Improvements in lighting efficiency may bring the overall cost of warehouse-grown crops into competition with outdoor crops, but that tech is still in the works.
You may not have heard of it, but there is an Association for Vertical Farming. On the group’s website, it states that they expect crop productivity for indoor farms to double every five years in the near future.
You can find many articles about the following crops being grown indoors: lettuce, kale, herbs, tomatoes, green beans, and peppers.
One company is growing greens on the roof of a Whole Foods in Brooklyn, New York. Another company claims to be growing 2 million pounds a year of greens in a 70,000-square-foot warehouse in Newark, New Jersey. There is also a 215,000-square-foot indoor ag facility in Las Vegas growing 16 types of greens and 11 types of herbs.
One company is even putting hydroponic farming systems inside of 40-foot shipping containers. They claim you can grow about 3 tons of herbs and greens out of it in one year.
On the flip side, you can find examples of vertical farms shutting down.
In the Chicago area there was a company called FarmedHere that was maintaining a 90,000 sq ft indoor farming operation and selling to about 100 grocery stores. It shut down a couple of years ago due to lack of profitability. Like any business, some operators figure out how to make it work, and others don't.
With labor shortages in some vegetable producing states, like California, it’s easy to envision warehouse production of vegetables becoming cost-effective eventually due to reduced labor requirements – plants covering fewer square feet, harvests happening year-round, and stationary robot vegetable pickers.
However, could warehouse production ever supplant the traditional row-crop production of corn, soybeans, or wheat? Answer: Probably not any time soon. I haven’t found any examples of commercially viable indoor grain production.
One executive with a vertical farm tech company suggested the optimal indoor crop mix as 80% greens and 20% herbs. Why? They need crops that turn fast and grow year-round. They need crops with high per-pound values in order to cover the labor, power, building, and equipment costs.
Waiting four to five months for an ear of corn is a big cash flow problem for a warehouse farm.
September Webinar: A Proposed Horticultural Lighting Label
We just announced our September Webinar: A proposed horticultural lighting label.
Registration link: https://cornell.zoom.us/meeting/register/ae44e0bcd76f57ddcde7dc3c8da9331e
The Webinar description:
Recent advances in light-emitting diode (LED) technology now provide the horticultural industry with multiple lighting options. However, growers are often unable to compare technologies and LED options due to insufficient data on lamp performance metrics.
As a result, researchers are now proposing a standardized product label that facilitates the comparison of lamps across manufacturers. Dr. A.J. Both from Rutgers University and Ryan Siddon from Intertek will talk about the importance of horticultural lighting standards, the proposed horticultural lighting label and the unique requirements for horticultural luminaires.
In the Rutgers Lab, Dr. AJ Both and his team conduct performance measurements on a variety of lamps used for horticultural applications. Their equipment is able to measure total light output as well as electric power consumption so that the efficiency (efficacy) of individual lamps can be determined.
Intertek’s Horticultural Lighting Certification Program addresses the unique requirements for horticultural luminaires, offering manufacturers an efficient path to launch products into this growing market.
The
Date: September 7th, 2018
Time: 2-3pm EST
Presented by: Rutgers University and Intertek
In the Rutgers Lab, Dr. AJ Both and his team conduct performance measurements on a variety of lamps used for horticultural applications. Their equipment is able to measure total light output as well as electric power consumption so that the efficiency (efficacy) of individual lamps can determined.
Intertek’s Horticultural Lighting Certification Program addresses the unique requirements for horticultural luminaires, offering manufacturers an efficient path to launch products into this growing market.
The GLASE Consortium Webinar Series features the latest technological innovations and best practices in the CEA field providing the audience the opportunity to discover new solutions and to connect with field experts.
Date: September 7th, 2018
Time: 2-3pm EST
Presented by: Rutgers University and Intertek
Intertek’s Horticultural Lighting Certification Program addresses the unique requirements for horticultural luminaires, offering manufacturers an efficient path to launch products into this growing market.
The GLASE Consortium Webinar Series features the latest technological innovations and best practices in the CEA field providing the audience the opportunity to discover new solutions and to connect with field experts.
Date: September 7th, 2018
Time: 2-3pm EST
Presented by: Rutgers University and Intertek
Increasing Lettuce Coloration With LEDs
Using LED grow lights in plant production is a relatively new branch of science. In vertical farming where artificial light sources are used in a closed environment, it is important to collect data about the individual plant species to be able to produce the right spectrum and light intensity for vegetative and generative growth. Light spectrums can also be used to manipulate the plant's growth cycle for example in plant breeding (see blog post: Light Approaches To Speed Up The Generation Turnover) or secondary metabolite contents (anthocyanins, flavonoids, antioxidants, polyphenols etc.).
Why Does Lettuce Turn Red?
When cultivating red baby leaf lettuce in closed environments like vertical farms, without natural light conditions the artificial light quality and quantity plays a key role in the production of good quality vegetables. Of course, in the case of red leaf lettuce the deep red color that is caused by the higher anthocyanin content must be produced without affecting the other good qualities of the leafy green. Anthocyanin accumulation is generally linked to the abiotic stress the plant is experiencing or it’s a way for the plant to protect itself against herbivores and plant pathogens.
For instance, in the case of high light conditions, the anthocyanins serve the plant as an optical filter, redirecting excess light away from the saturated photosynthetic electron transport chain (Gould 2004). This means that the anthocyanins are protecting the plant leaves from harmful structural damage to their photosystems. Raising light intensity is, therefore, an effective way to increase the leaves anthocyanin content but it’s not a very energy efficient way to do this.
Using UV-A to Grow Lettuce
Previously this has been studied by Li and Kubota (2009) and they concluded in their study that both spectrums with enhanced blue and UV-A light increased the anthocyanin content in the leaves of lettuce ‘Red Cross’, but the far-red and green light had the opposite effect decreasing the anthocyanin production. Hence, at the end of the cultivation cycle in indoors only enhancing the blue and/or UV-A light spectrum would lead the red baby leaf lettuce to produce anthocyanins which gives them the special red coloration.
Using LEDs is the easy and energy efficient way to get quick results in anthocyanin formation in closed environment conditions. This could be easily implemented into the existing indoor growth systems by merely switching on the right spectrum for enhancing the coloration at the end of the growth cycle.
Valoya made internal trials where two light spectrums were used to test this light quality effect with enhanced UV-A / blue spectrum light (S46) and our standard light for vegetative growth with leafy greens (AP673L). Light intensity levels were taken into consideration and tested in a pre-trial. The amount of anthocyanin was measured at the end of the trial with optical polyphenol measuring tool (Dualex, ForceA). The experiment was done with two red baby leaf lettuce varieties: ‘Sadawi’ and ‘Diablotin’, with very similar results.
The light treatments were done with the two spectrums and in the case of AP673L spectrum with three different intensities. The data was analyzed in SPSS with two-way Anova. The homogeneity of variances was analyzed with Levene’s test and the normality of the data with Shapiro-Wilks test.
The results for anthocyanin accumulation confirmed the hypothesis that the enhanced blue and UV-A spectrum will increase the production of anthocyanins in red baby leaf lettuces’ leaves leading to a similar amount as in that of the high intensity treatment. Increasing the AP673L light intensity from 200 µmolm-2s- to 400 µmolm-2s- had linearity trend with increasing intensity (Figure 2).
Figure 1 Red baby leaf lettuce anthocyanin trial with different spectrums. The anthocyanin amount was measured three times and three measurements were taken from one plant. Anthocyanin index = Log* (Near-infrared fluo. excited red / Near-infrared fluo. excited green).
Figure 1 Red baby leaf lettuce anthocyanin trial with different intensities (in micromoles). The anthocyanin amount was measured three times and three measurements were taken from one plant. Anthocyanin index = Log* (Near-infrared fluo. excited red / Near-infrared fluo. excited green).
This accumulation of anthocyanins could also be observed visually…Read the rest at valoya.com
Arctic Agricultural Technologies: 'Smart' Greenhouses And Light On Demand
August 13, 2018
© Viktor Drachev/TASS
TASS, August 13. Scientists of the Tomsk Polytechnic University designed "smart" greenhouses for the Arctic regions, where growing vegetables does not depend on climate conditions or sunlight. The scientists told TASS about how the Arctic regions may grow vegetables for own needs and what other technologies may be used there.
Hydroponic vegetables
The "smart" greenhouses for the Arctic have automatic processes and do not depend on the climate or any other outside conditions, Director of the University’s Engineering School Alexei Yakovlev told TASS. The Tomsk project will use for lighting vegetables, which in regular conditions are short of light, polycrystalline LED materials - thus giving to vegetables the light of a necessary spectrum.
"Plants are sensitive to the spectrum, which is different for human eyes," the scientist said. "Our task is to offer to vegetables a comfortable spectrum." The equipment is programmed so that it will offer automatically more light for example on overcast days, he added.
The vegetables will grow not in the soil, but hydroponically. "We are using hydroponic systems," the expert said.
The scientists are beginning tests - they will try growing cucumbers in the greenhouse. Besides, they will study how plants react to various lights.
Supply and demand
People, living in the Yamalo-Nenets Region, consume every year 11,000 tonnes of cucumbers and tomatoes, while the local greenhouses produce only 18 tonnes a year, the regional governor’s press service told TASS. The gap is filled by supplies from the Krasnodar, Stavropol, Tyumen, Kirov, Moscow regions, and from the CIS countries.
A new greenhouse complex, which will open in Salekhard in 2020, will take an area of one hectare.
"This project, a public-private partnership, continues, and the complex will produce about 1,000 tonnes of vegetables a year," the press service said, adding the local authorities are interested in new agricultural technologies, in automatic "smart" greenhouses.
In the Arkhangelsk Region, two companies grow vegetables. The regional agricultural ministry told TASS the annual production there is 1-1.2 thousand tonnes of vegetables. The vegetables and herbs are sold in Severodvinsk, Arkhangelsk and Novodvinsk.
The Nenets Agricultural Company (in the Yamalo-Nenets Region) produces 70 tonnes of cucumbers, tomatoes and herbs. "The locally produced vegetables are supplied mostly to Naryan-Mar," the regional Department of Natural Resources, Ecology and Agriculture told TASS. "As we have nomadic population, the locally produced vegetables make only 12% of the demand, and the rest is brought from outside the region."
Komi’s Vorkuta, which is north of the Polar Circle, develops the project on hydroponic vegetables.
"We produce about 200 kg of herbs a month - lettuce, salad, basil, mint," the project’s head Elena Smirnova told TASS. "We supply them to cafes and restaurants, to some shops; the trade chains are only watching us yet."
"Anyway, we see the demand and plan to expand the production," she added.
New formats
Russian regions have other projects related to growing in the Far North of plants, which are not typical for those regions. Director General of the iFarm Company, working in Novosibirsk, Alexander Lyskovsky said his company, which produces greenhouses, eyes making vertical greenhouses, where every garden bed is above another. They are installed in absolutely dark spaces.
"Probably, it may be more correct to install the vertical farms using fully artificial light - anyway, there is so little sunlight in those regions," he said. "Vertical farms are organized in basements, hangars, to where the sunlight would not come, and there you install garden beds one above another."
"It is more complicated to grow there cucumbers or tomatoes, as they require much space, but it is quite possible to grow herbs and strawberry there," he added. iFarm’s specialists plan to test the technology and materials in Norilsk, where the authorities have expressed interest in greenhouses.
"Smart" greenhouses for the Arctic regions are also designed in St. Petersburg. The Defense Ministry is interested in portable complexes for growing any amounts of vegetables, the project’s head Gayane Panova told TASS.
"At the request from the Defense Ministry, we have initiated a waste-free energy-effective technology for growing greengrocery (parsley, dill, lettuce, other herbs, tomatoes, and cucumbers)," she said. "We were allowed to state tests in the Arctic." However, due to problems with an investor, the Arctic tests did not happen and the scientists are looking for new investors.
More:
http://tass.com/economy/1017011
Fluence Appoints Chief Operating Officer to Further Accelerate Business Growth
David Cohen joins as COO to direct operational growth and business consistency globally, in addition to improving the overall customer experience
Austin, Texas – August 16, 2018, Fluence Bioengineering Inc. today announced David Cohen has joined Fluence as chief operating officer. Cohen will lead the Fluence Marketing, Sales and Operations teams, and he will focus on the creation and execution of the global growth strategy along with defining and executing the digitization strategy for Fluence.
“David will be an integral part of Fluence’s growth trajectory as the company expands to become the global leader of the horticultural lighting industry,” said Nick Klase, CEO, and co-founder, Fluence Bioengineering. “David’s experience in directing high-growth products in the LED lighting industry will ensure Fluence anticipates and addresses developing trends in food and cannabis production around the world.”
Cohen has extensive leadership experience in the lighting industry and has held roles as CEO, general manager, COO, executive vice president and managing director while living in China, Italy, the Netherlands, and the U.K. His most recent position was general manager and CEO of Schréder Lighting U.S.A. Prior to that position, David was the general manager of Future Electronics’ lighting business in Europe, the Middle East and Africa, while based in London.
“The Fluence Bioengineering acquisition by Osram pairs best in class technology with a global lighting leader. I am excited to be joining Fluence at this critical time to drive global expansion,” said David Cohen, COO, “As Fluence refines its expertise in plant photobiology to address the escalating demand for natural food and medicine, I will be making sure we reach as many customers as possible around the world.”
About Fluence Bioengineering
Fluence Bioengineering Inc., a wholly-owned subsidiary of OSRAM, creates the most powerful and energy-efficient LED lighting solutions for commercial crop production and research applications. Fluence is the leading LED lighting supplier in the global cannabis market and is committed to solving the looming food crisis by enabling more efficient crop production with the world’s top vertical farming and greenhouse produce growers. All Fluence lighting solutions are designed and built at the company’s headquarters in Austin, Texas, U.S.A., with European sales and support based in Amsterdam, Netherlands. https://fluence.science
The Bay Area Company Building World's Largest Vertical Farm In Dubai
A small San Mateo company is building what is billed as the world’s largest vertical farm next year in Dubai, right on the runway that serves Emiratesairline.
Tara Duggan July 20, 2018
Crop One of San Mateo grows leafy greens without soil or sunlight in hydroponic facilities using LED lights.
Photo: Crop One
A small San Mateo company is building what is billed as the world’s largest vertical farm next year in Dubai, right on the runway that serves Emirates airline. The 50-foot-high sealed warehouse will produce 3 tons of leafy greens a day, without using a drop of what Sonia Lo calls “free energy” — otherwise known as sunlight — or soil, essentially recreating an optimized version of Central California in the Middle East.
“I love the fact that you’re redistributing the means of feeding back to where people actually are,” said Lo, CEO of Crop One Holdings in San Mateo, which since 2015 has provided fresh-cut lettuce and basil through Boston’s snowy winters from the company’s first vertical farm in Massachusetts. “The implications for what agriculture can do in terms of feeding more people are also incredibly exciting.”
Large-scale vertical farming, sometimes called indoor farming, uses LED lights and small doses of water and nutrients to grow leafy greens and herbs — and soon strawberries — year-round in otherwise unsuitable climates. Since the farming method can protect plants from the ravages of climate change and may have the potential to recreate terroir for wine grapes or coffee, it’s attracting big investors. In the Bay Area, Crop One’s just-announced partnership with Emirates Flight Catering amounted to $40 million just to build the Dubai farm, and Plenty in South San Francisco, which will open a farm in the Seattle area this year, raised $200 million in funding last July.
Both companies are exporting two things the region is known for: technology and fresh-cut greens. Yet they both plan to also open facilities in Northern California as the Salinas Valley, known as America’s Salad Bowl, copes with labor shortages, drought and high land prices.
Matt Barnard, CEO of Plenty, which will sell the greens to Bay Area customers in a few months from its South San Francisco farm, points out that the majority of the world’s fruits and vegetables grow best in Mediterranean climates, of which there are just a handful around the world, including Salinas Valley.
“We’ve tapped out Salinas. There’s not a way to add capacity,” he said.
Barnard prefers to use the term indoor farming, not to be confused with growing in greenhouses, which use natural sunlight and dirt. In vertical farms, vegetables grow hydroponically — in a “soil-less medium” of water and nutrients. They sit on actual vertical walls, in the case of Plenty, or on stacked shelves with LED lighting overhead. The temperature- and humidity-controlled environment can be as simple as a shipping container within a larger warehouse.
Vertical doesn’t necessarily mean towering high, though; it does mean the plants are stacked closely and efficiently. The Dubai farm will be only about four or five stories tall, but at 130,000 square feet, it is large enough to produce greens for the 225,000 meals Emirates caterers produce daily for in-flight meals. Lo said she can produce the same amount on a single acre indoors that would normally require 400 acres of land, and that her company landed the deal because it has shown it can make vertical farming profitable.
Sonia Lo, founder of Crop One in San Mateo says, “The implications for what agriculture can do in terms of feeding more people are also incredibly exciting.”
Photo: Crop One
But using LED lighting instead of “free energy” comes with high costs and a carbon footprint that can be comparable to shipping greens across the country. Running a 30,000-square-foot indoor farm in the New York City area would cost about $340,000 per year for power, lighting, heating and cooling, according to a recent report by Civil Eats. Because water can be filtered and reused in vertical farms, water use is only an estimated 1 percent of conventional farming.
Lo estimates that vertical farms cost one and a half times as much as traditional farms to operate, but that the cost to Emirates will be the same as what it currently pays for the vegetables shipped or flown from Spain, Italy or California. Plus, the greens will be available within 24 hours of harvest, she said, instead of the usual six weeks.
When it comes to the carbon footprint, a farm producing 1 ton of vegetables a day uses 3 megawatts of energy a year, Lo said, or enough to power roughly 2,200 homes. Greens produced by the Boston area farm, which sells under the FreshBox label, are carbon neutral when compared with greens transported from California, Lo said; they haven’t done a carbon analysis for Dubai yet. The company is planning to open three new farms in Connecticut and Texas soon and is eyeing sites in Northern and Southern California as well as the Midwest, Georgia, and Oklahoma.
One big advantage of vertical farming is that the sealed environment means no pesticides or herbicides are required, and the bacteria levels on the vegetables are much lower, which makes them safer as well as longer-lasting, reducing spoilage.
Then again, the same factors pushing vertical farming forward are also improving technology for traditional agriculture, such as remote sensors, software, and drones that help farmers make irrigation more precise and improve soil health.
In November, the U.S. Department of Agriculture reaffirmed that hydroponic farms may use the USDA organic label, even though traditional organic farms and greenhouse growers fumed over that decision, arguing that soil is inherent to organic farming.
Canadian Online Food Supplier Grow Vegetables on Rooftop With LED Lights of Current by GE
Lufa Farms, a Canadian food supplier based in Montreal, has collaborated with Hort Americas and Current by GE to install LED lights for maximizing the production efficiency of its hydroponic rooftop greenhouses.
Located in urban Montreal with long winter and limited sunlight and space, Lufa Farms has taken the challenge of growing food for local people in sustainable ways and with a modern approach. The company breeds more than 75 vegetables year-round in hydroponic rooftop greenhouses and delivers food directly to their customers through a subscription-based service. Lufa Farms had to increase its production to meet the needs of growing consumers and decided to introduce a new growing system.
(Image: Current by GE)
Current by GE, Hort Americas, and Lufa Farms worked together to develop a three-tier lighting system with the installation of roughly 430 GE Arize Lynk LED lights in a 650 square meters (7,000 square feet) space in the new greenhouse and facilitated seeding propagation. The solution helped Lufa Farms to increase the speed of seeding production by 15 percent as well as to scale the growth. Moreover, the Lufa team noticed greater consistency within each variety of vegetable, as they grew in optimized conditions during this pivotal period. All these benefits helped Lufa Farms to feed its over 10,000 customers and the founders of the company thus will consider to shift to LED lighting for more areas.
Lauren Rathmell, the co-founder of Lufa, said “The design we created means there’s a lot more uniformity across the board. At the same time, it’s quite unique that we have been able to grow many varieties at this volume—and at a faster rate.”
(Image: Current by GE)
Their success had attracted Justin Trudeau, Canadian Prime Minister to visit when the company launched the new greenhouse with a GE growing system.
- Keywords: horticulture lighting Current by GE
Jones Food Company (JFC) And Current By GE Collaborate On Enormous Indoor Farm
Jones Food Company (JFC) And Current By GE Collaborate On Enormous Indoor Farm
July 25, 2018
Current, powered by GE and Jones Food Company Ltd. (JFC) are in the process of constructing one of the largest vertical indoor farms in the world. The intensive plant nursery in North Lincolnshire, England, will be the largest indoor farm in Europe. It will produce up to 420 tons of leafy greens per year across a growing area of 5120m2. The growing area is arranged in racks rising to the height of 11m. In order to help the vertical farm maximize its yield, Current by GE is installing more than 12Km of its new Arize* LED horticultural lighting solution.
Baby watercress grown under Arize LED grow lights from Current by GE
According to Current, the Arize LED horticultural lighting solution features a balanced light spectrum that stimulates optimal growth in every plant and shortens the growth cycle for more intensive production.
“We knew that lighting would be the lifeblood that could bring high-care intensive food production to an industrial level that demonstrates real commercial viability.” JFC CEO James Lloyd-Jones said.
JFC worked with the Current team to develop a customized version of the Arize grow lights that emit a combination of red, blue and white wavelengths that could be flexible and efficient enough to grow a strong, balanced plant. The equipment is located within an intelligent cleanroom (or “high-care”) environment that lets crops grow in complete isolation from external contamination. Each growth area will have its own water and nutrient supply.
As part of being an intelligent high-care environment, the new facility will leverage Current by GE’s cloud-data system to monitor electricity usage from its LEDs and HVAC systems. JFC points out that such a growth environment is ideal for food production as well as growing high-quality cosmetic and pharmaceutical ingredients.
Production of First Crop Expected to Start in Autumn 2018
“Nobody has been able to scale indoor, high-care intensive food production to an industrial level that demonstrates real commercial viability,” explained James Lloyd-Jones, CEO, and co-founder of JFC. “We knew that lighting would be the lifeblood of the facility and we’d need a partner who could see the potential and work with us to develop the right lighting set-up and spectrum to make our vision a reality.”
JFC Claims Facility is Europe’s Largest Indoor Vertical Farm
With a growing area of 5120m2, the equivalent of 26 tennis courts, arranged across racks with a height of just over three stories, the JFC intends for the facility it owns and operates to set new crop production and environmental standards of the future. JFC plans to slash food miles and produce leafy greens, herbs and other crops with year-round local production. The company hopes that these crops, herbs, and greens can be delivered from harvest to plate in minimal time.
In addition, by making the farm a “high-care” facility, JFC will also hopes to cater to the growing needs of cosmetics and pharmaceutical customers who require a reliable supply of natural ingredients of the highest quality. The facility will control every factor in the growth of the crops; Factors including everything from the nutrient solution delivered to the roots of every plant, to the concentration of CO2 in the room, to the light wavelengths and duration of the growing “day”and subsequent rest period will all be tightly controlled.
From planting to harvest, every plant will be untouched by human hands thanks to intelligent automation and advanced robotics. By comparison, conventional production cycles typically have 13 stages of human contact. In fact, JFC will use its own, self- driving forklift truck that can insert and remove trays. JFC says that this self-driving forklift will result in a 60% labor cut as only 3 humans will be permitted to enter the facility at a time.
Arize Lights the Future of Horticulture
Malcolm Yare, Horticulture Business Development Manager for Current by GE commented, “We’ve spent years honing our technology in other industrial lighting sectors, and years more partnering with agricultural experts and researching the needs of horticultural applications. Our Arize LED solutions now lead the industry for efficiency and we continue to research new ways to improve performance through innovation. We look forward to working with Jones Food Company and our wider ecosystem of partners to find new ways to scale high-quality, global food production whilst reducing the energy and environmental costs of vertical farming.”
The Arize range of lighting solutions are low cost to install and maintain, with a market-leading 36K-hour lifetime (L90) and a five-year warranty to provide peace of mind and long-term reliability. Arize also has an IP66 and UL Wet rating that also make them perfect for high-care and cleanroom facilities because the luminaires can be easily washed and sanitized while in-place.
The JFC facility is uniquely designed to minimize the environmental impact of vertical farming, which will also benefit JFC financially. For example, the facility will use up to 90 percent less water and 50 percent less fertilizer than conventional growing methods, saving on input costs. Additionally, Current by GE’s Arize LED horticultural lighting is highly efficient and generates less heat than competitive products, and it reduces energy consumption and carbon footprint by 33 percent compared with vertical farming averages.
JFC previously tested the LEDs on a mini-farm on Challinor’s property in order to identify best practices for efficiencies. Based on this testing, JFC has already created plans to pump pure CO2 into the facility, install roof solar panels and use GE’s cloud-data system to monitor energy use and controls integration.
The integration of sensors is reportedly still underway at the facility as there is a vision for Current to connect JFC’s sites into Current’s IoT Enterprise solution. Due to the phased nature of the project, Current is continuing research and development with the latest innovation for sensing and automation technology. JFC is reportedly working with a trusted Current ecosystem partner to ensure seamless integration of Current’s lighting systems into their site level building management system to limit the amount of work that needs to be done manually.