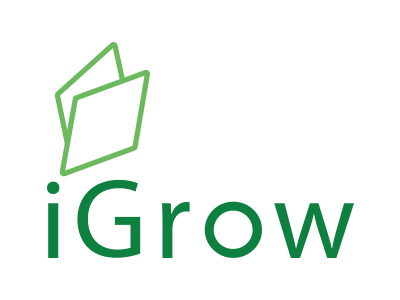
Welcome to iGrow News, Your Source for the World of Indoor Vertical Farming
Sugarmade Introduces New State-of-the-art iPower Cultivation Equipment on Amazon.com
Sugarmade, Inc. (OTCQB: SGMD) ("Sugarmade", "SGMD", or the "Company"), a leading supplier of hydroponics and cultivation equipment and resources, is excited to introduce its new line of "iPower" branded inline duct ventilation fans
PR Newswire September 10, 2019
LOS ANGELES, Sept. 10, 2019 /PRNewswire/ -- Sugarmade, Inc. (SGMD) ("Sugarmade", "SGMD", or the "Company"), a leading supplier of hydroponics and cultivation equipment and resources, is excited to introduce its new line of "iPower" branded inline duct ventilation fans. Designed for durability, high-performance, and affordability, this advanced equipment for indoor and hydroponic cultivators is now available for immediate purchase on the Company's website at zenhydro.com and on Amazon.com.
"Indoor and greenhouse cultivation is becoming increasingly sophisticated, helping both hobbyists and commercial cultivators maximize output regardless of seasonality or weather conditions," commented Jimmy Chan, CEO of Sugarmade. "This sophistication, along with expanding mainstream interest in products derived from hemp and hemp-related crops in North America, has driven increasing interest in both indoor and hydroponics cultivation, which has helped to foster booming demand for related equipment. We have positioned Sugarmade as a leading supplier of superior quality equipment catering to that boom. And our new line of iPower inline fans represents the latest example of our commitment to that standard and strategy."
Management notes that the global indoor farming market is valued at more than $106 billion, with steady growth anticipated over coming years due to projected declines in arable land and increasing demand to cultivate newly legalized cash crops in North America, suggesting upward demand pressure on the indoor and hydroponics cultivation equipment and supplies market. The Company also believes the 2018 US Farm Bill, with its positive implications for hemp-related cultivation, will drive further growth in expected demand forecasts for indoor and hydroponic cultivation equipment suppliers.
To meet that expanded demand, the Company sees ventilation as a core product category in the indoor and hydroponic cultivation market, on par with advanced lighting and nutrient resources. In addition to its new state-of-the-art iPower inline ventilation fans, the Company also offers an extensive grow light product portfolio.
The iPower inline fan has been designed to produce superior air flow while optimizing energy efficiency and minimizing noise production through its advanced composite fan blade and center hub design, which reduces noise and vibration. iPower inline fans are available in 4-inch, 6-inch, or 8-inch models, can be used with or without iPower carbon filters and duct ventilation, and come packaged in a unique lightweight yet durable housing.
Mr. Chan continued, "We are confident that the iPower line represents the superior choice in the marketplace. iPower inline fans provide strong flexibility in configurations and include intelligent programing capabilities. They make an excellent addition to our growing product portfolio as we continue to build a leadership role in catering to a very wide market footprint, from hobbyist cultivators all the way through the largest commercial cultivators."
About Sugarmade and iPower Brands
iPower is a leading manufacturer of grow light systems; supplying gardeners, worldwide, for over a decade. The product lines use the transformative power of light to make gardening more efficient and productive. In addition to HPS/MH and Ceramic MH technology, iPower product offer digital ballasts, fluorescent, and LED lighting systems. Sugarmade Inc. is a product and brand marketing company investing in products and brands with disruptive potential.
For more information, visit the company's website at www.Sugarmade.com.
FORWARD-LOOKING STATEMENTS: This release contains "forward-looking statements" within the meaning of the safe harbor provisions of the U.S. Private Securities Litigation Reform Act of 1995. Forward-looking statements also may be included in other publicly available documents issued by the Company and in oral statements made by our officers and representatives from time to time. These forward-looking statements are intended to provide management's current expectations or plans for our future operating and financial performance, based on assumptions currently believed to be valid. They can be identified by the use of words such as "anticipate," "intend," "plan," "goal," "seek," "believe," "project," "estimate," "expect," "strategy," "future," "likely," "may," "should," "would," "could," "will" and other words of similar meaning in connection with a discussion of future operating or financial performance. Examples of forward looking statements include, among others, statements relating to future sales, earnings, cash flows, results of operations, uses of cash and other measures of financial performance.
Because forward-looking statements relate to the future, they are subject to inherent risks, uncertainties and other factors that may cause the Company's actual results and financial condition to differ materially from those expressed or implied in the forward-looking statements. Such risks, uncertainties and other factors include, among others. such as, but not limited to economic conditions, changes in the laws or regulations, demand for products and services of the company, the effects of competition and other factors that could cause actual results to differ materially from those projected or represented in the forward looking statements.
Any forward-looking information provided in this release should be considered with these factors in mind. We assume no obligation to update any forward-looking statements contained in this report.
Contact:
Jimmy Chan
+1-(888)-982-1628
info@Sugarmade.com
Vertical Farming, A Sustainable Innovation
This new form of farming, within buildings located close to urban areas, is gaining momentum. Some believe it will become common place as the world’s population grows. According to the UN, the global population will hit 9.7 billion by 2050.
September 10, 2019
Could new innovative light recipes in indoor farms hold the key to feeding the world’s growing population?
Innovatus, a sustainable agricultural business in Fuji City, Japan, reached out to us. It had an interesting challenge it wanted help in solving. Namely, to produce high-quality, tasty, and pesticide-free lettuce in the most efficient way possible. In recent years, Japanese consumers have become increasingly concerned with food safety. People worry about pesticide-treated vegetables grown outdoors and the effects of fine particle pollutants that can be a serious health risk. To cater for the demand for clean, safe produce, Innovatus established a vertical farm with strict hygiene controls to produce truly safe vegetables.
We swung into action, responding with a mix of LED lighting expertise and technology. Our goal was simple: to increase the efficiency of one of the world’s largest closed-environment vertical farms - helping it to deliver 12,000 heads of lettuce every single day.
This new form of farming, within buildings located close to urban areas, is gaining momentum. Some believe it will become common place as the world’s population grows. According to the UN, the global population will hit 9.7 billion by 2050.
“We were really impressed by how well-suited the Philips LED modules are for vertical farming. They allow us to create consistent quality produce locally, using only a fraction of the water and electricity compared to open field lettuce or lettuce grown with the help of fluorescent lighting,” said cultivation management group team leader Shinichi Kitamura.
Consumers find the lettuce fresh and flavorful, especially compared to lettuce grown outside. Additionally, since the lettuce from Innovatus is grown and packaged in an extremely hygienic environment, there is no need for its consumers to wash it before eating and it lasts for two weeks.
“At Signify, we’re proud to be contributing to such projects because it reflects how we can solve social and environmental challenges using technologies that are more sustainable,” said Anton Brummelhuis, Senior Director Sustainability at Signify. “This project meets one of our eight sustainable focal areas. In this case, Basic Needs – in other words, how we contribute to the availability of fresh air, water, and food.
Vertical farming for smarter and more sustainable cities
More efficient food production will be needed to support an additional two billion people on the planet through to 2050. New and smarter agricultural methods other than rural farming will be required to deliver food – at scale – to meet demand.
And that’s why Signify develops special lighting for vertical farming and high tech horticulture – to help feed this growing population in a more sustainable way.
We help optimize growth systems with LED lighting for crop cultivation all year round. Our tailor-made light recipes contribute to predictable growth, bigger harvests and higher quality plants.
Our tailor-made light recipes contribute to predictable growth, bigger harvests, and higher quality plants."
Our GrowWise Center in Eindhoven, the Netherlands, is where much of the research into new light recipes takes place. There, scientists constantly look for improvements in crops such as taste, health benefits, texture and quality. By controlling parameters needed to grow plants, such as light, humidity, and irrigation, we help our customers get the most out of crops while saving space, energy and water.
“We use exactly the same photons as the sun, just optimized for the type of plant. We use water but we recycle it so use less. We keep out bugs and pests and optimize the plant for taste. We do this in a clean environment, all year-round. The result is reduced waste, food miles…and produce that is clean, healthy, and nutritious food, grown in a resource efficient way,” said Roel Janssen, Global Director City Farming
In Japan, a new large-scale vertical farm was built using the Philips GreenPower LED production module to grow high-quality lettuce varieties, spinach and coriander year-round.
Crops from the vertical farm don’t use pesticides and have a much lower bacterial count. The automated process from seeding to harvest takes only 39 days compared to 70 days in the open field, and production reaches up to 3,200 kg of lettuce a day. And the controlled environment gives the customer the opportunity to steer growth characteristics to improve shelf life, red coloration in lettuce, even vitamin C levels.
Vertical Farming and Sustainable Development
To help create a bright future for people and the planet, the UN established global goals for sustainable development. These interconnected goals aim to tackle the most pressing challenges we face as a global community including, but not limited to, climate, resource scarcity and poverty.
Vertical farming as a sustainable agricultural practice is important. Innovative solutions for urban agriculture, if scaled up, can be an answer for future food scarcity while developing sustainable food production patterns.
Sustainable agricultural practices are crucial if the world is to achieve the UN’s Sustainable Development Goals, such as goals 11 and 12, for sustainable and resilient cities and communities, and responsible production and consumption.
With our research, we develop climate-resilient technology and increase resource efficiency that contribute to the transition towards more sustainable and smarter cities, at the heart of SDG 11. And scaling up these solutions creates sustainable food production patterns, which in turn contribute to SDG12.
Lighting is perhaps the killer app for vertical farming. Recent breakthroughs in LED technology may well lead to a golden age for urban farmers, improving plant consistency, quality and yield. Vertical farms that use fewer resources, located close to towns and cities will reduce the distance from farm to fork, reshaping the role of agriculture.”
Anton Brummelhuis
Senior Director Sustainability at Signify
“Lighting is perhaps the killer app for vertical farming. Recent breakthroughs in LED technology may well lead to a golden age for urban farmers, improving plant consistency, quality and yield. Vertical farms that use fewer resources, located close to towns and cities will reduce the distance from farm to fork, reshaping the role of agriculture,” said Anton Brummelhuis, Senior Director Sustainability at Signify.
About the author:
Thomas Marinelli
Head of Sustainable Design and Sustainable Products
Bejo Zaden And Signify Team Up To Accelerate Breeding of More Seed Varieties
Signify has partnered with Bejo Zaden to accelerate breeding of more seed varieties through a new vertical farm approach to cultivation. In the facility, a large climate-controlled room is equipped with Philips GrowWise Control System to automate control of Philips GreenPower LED dynamic modules
Signify has partnered with Bejo Zaden to accelerate breeding of more seed varieties through a new vertical farm approach to cultivation. In the facility, a large climate-controlled room is equipped with Philips GrowWise Control System to automate control of Philips GreenPower LED dynamic modules. The company can now produce multiple crop cycles per year to meet the high demand from growers, faster.
“We’ve actually doubled the number of growing hours per day. Normally our crops only flower once a year, but now with this dynamic LED lighting solution, our crops flower multiple times a year,” said Jan Kempen, Crop Specialist at Bejo Zaden. “Thanks to our dedicated light recipes from Signify, we can steer the light spectrum and intensity for each individual crop and growth phase. We’re able to force flowering or prevent plants from bolting. For asparagus, we are now getting stronger, more vigorous tissue culture plants.”
Bejo Zaden first used supplemental lighting and later LED lighting to speed up the breeding process for new varieties, which typically takes 10 to 15 years. After several trials in smaller climate-controlled rooms, set up by their long-term horticulture partner Lek Habo, Bejo Zaden reached out to Signify in 2017 to help them implement a larger climate-controlled room. Signify’s plant specialists helped the company develop a custom-made growing process in the right environment and created special light recipes to meet the company’s requirements.
“Bejo Zaden tries to accelerate breeding of more disease-resistant seed varieties, said Udo van Slooten, Business Leader Horticulture at Signify. “Our LED solutions give growers the control they need to move to new cultivation techniques that are both sustainable and profitable.”
Bejo Zaden will share the results during their Open Days September 24 – 28th.
For more information:
Publication date: 9/17/2019
Scientists Grow Tastier Vegetables Just By Changing Light Falling On Them, No Gene-Edit Needed
In order for farmers to make a decent profit on their crops, they need to have a reliable produce. Of course, they only have limited land to work with, so limited number of plants need to have enough weightage of output. Unfortunately, that can result in tasteless produce
Gwyn D'Mello April 16, 2019
In order for farmers to make a decent profit on their crops, they need to have a reliable produce.
Of course, they only have limited land to work with, so limited number of plants need to have enough weightage of output. Unfortunately, that can result in tasteless produce.
Think of a simple vegetable (fruit?) like tomato. You might see two different varieties of it in your local market, where one is much larger but the smaller ones are tastier. That's due to something scientists called the "dilution effect", where there's an overlap between the compounds a plant requires to produce more or produce tastier fruit.
That's why you're more likely to see this happen with a large scale farm as opposed to when you grow tomatoes in your garden. But apparently, it doesn't have to be that way, at least according to researchers at MIT.
Scientists at the University's OpenAG group have been researching basil plants in particular, led by principal researcher Caleb Harper. They've been trying to change the various stress factors acting on basil plants to see how it changes the flavour. "If you took the same basil seed and you put in 50 different countries, you would have started with the same genetics but you would get 50 different flavors," he told Digital Trends.
The process behind tastier vegetables
What these researchers, in partnership with the University of Texas, found is that exposing basil to light 24 hours a day made them the most flavourful. The constant light produced more secondary metabolites. These are organic compounds the plants don't necessarily need to survive, but can help them keep away animals that eat them. And the presence of these are affected by everything from drought to the presence of certain insects, ultimately changing how the plants taste.
The researchers had no reason to believe 24-hour light exposure would make the basil tastier, they instead went with 18 hours to begin with. It was a custom-developed AI algorithm, developed by MIT and Cognizant, that analysed all the factors and made the suggestion. In fact, that same AI was originally used by the startup that developed it (before being acquired by Cognizant) for hedge fund trading.
The basil was grown in hydroponic boxes, full of sensors and circuits, allowing the scientists to completely control everything from temperature, to humidity, to the light intensity and exposure.
But ultimately this experiment wasn't just about making industrial agriculture plants tastier. Using the AI, researchers can possibly even have the plants develop in other ways. For instance, Harper talks about his dream for "diabetes basil", grown in such a way that it's rich in proteins found to be helpful in treating the illness.
"That's kind of amazing that we could design flavor from climate," he said. "And now we're going to see can we design nutrition."
IMAGES COURTESY: MIT
How To Determine If LED Grow Lights Are A Good Investment
As LED grow lights continue to become more affordable, an increasing number of greenhouse growers and vertical farmers are considering whether the lights would benefit their production systems
Based on the benefits controlled environment growers are experiencing with LED grow lights, a return on investment (ROI) analysis could help you decide how quickly the payback would be for your operation.
As LED grow lights continue to become more affordable, an increasing number of greenhouse growers and vertical farmers are considering whether the lights would benefit their production systems. Add to this the testimonials of growers who have installed LEDs and the positive results they’ve gotten with commercial horticultural crops has caused more growers to look at the efficiencies these lights have to offer.
Comparing investment options
“The information on return on investment (ROI) for LED grow lights would have application to any type of equipment growers would be looking to purchase,” said Nathan Farner, president and CEO at North Ridge Solutions Inc. in Dallas, Texas, who is an adviser to Hort Americas. “Growers would be using a business case modeling approach to determine full project costs of various solutions and to understand what it takes to implement those solutions.
“Comparing the savings or increased revenue related to these investments would enable growers to say which option or scenario makes the most sense for their operations. Growers would compare their options and determine how long it would take to recoup their investment. Whether it is installing LED lights or some other capital infrastructure for a greenhouse, this ROI analysis would apply.”
Farner said one of the advantages of determining the benefits of LED lights with a specific crop is growers should have an opportunity to see whether the lights provide the results desired.
“Growers who are seeking to prove the benefits of LED technology have the ability to do a portion of their operation to become comfortable with it and to validate the results before making a large capital expenditure,” he said. “Growers can conduct a trial in a fairly small area of their greenhouses to prove LEDs deliver the results they desire. After this testing it should be a relatively easy decision for most growers.”
Improved crops
Farner said when doing a business case analysis growers can look at the revenue side and the expense side.
“Looking at the revenue side for LED grow lights, this would include increased yields whether this is reducing the time to crop maturity of a crop like leafy greens or increasing the amount of produce from a long term crop like tomatoes and cucumbers,” he said. “There could also be increases in quality including size and/or number of fruit, taste and color. An example of this is red lettuce grown under LEDs, not only are there improvements in yields, but there is also an enhancement of the red pigment in the leaves. Growers who are able to increase crop yields and quality are able to continue to sell a consistent product at a consistent price year round.”
Nathan Farner at North Ridge Solutions Inc. said looking at the benefits of LED grow lights from the revenue side would include increased yields whether this is reducing the time to crop maturity or increasing the amount of produce. Photos by Jessie Wood, State Fair of Texas
Farner said growers need to be sure they have a market for the increased product they are going to be able to produce by installing LEDs.
“In general that has not been an issue, especially considering the increased interest and demand for locally-grown food products,” he said. “LEDs are going to help improve the quality of the product and most customers are going to welcome that.
“If growers choose to quadruple the size of their greenhouse space carries a lot higher capital expenditure. In that case, the growers better be sure they have the market for the increased amount of product they are going to produce. Installing or replacing grow lights, that is less of a challenge to sell the additional amount of product based on my experience.”
Improved energy efficiency
Looking at the benefits of LEDs on the expense side Farner said this comes primarily from LEDs being more energy efficient than alternative lighting sources.
“On the expense side primarily what growers are looking at with LED lights is reducing their operating costs,” he said. “Comparing the electrical costs of other grow lights that aren’t as efficient, there should be a significant drop in electrical expenses by installing LEDs.
“When talking about the lighting model from an electrical perspective, it is more than just buying and installing the fixtures. Depending on the fixtures that are being installed, they may exceed the current power infrastructure for the electrical supply to the greenhouses. If this is the case, more electricity would be needed and would require an investment to increase the electrical infrastructure as well. Once growers understand their lighting plan and the electrical requirements for their facilities, they can determine their annual operating expenses.”
Identifying the best ROI
Farner said growers would need to work with commercial horticulture lighting suppliers like Hort Americas to develop a light plan for their operations. This plan would be based on a number of factors including the crops that will be grown, the light spectrum required for the plants, the amount of production space that will be lit, and the expected number of hours the lights would be operating.
Comparing the electrical costs of less efficient grow lights to LEDs, there should be a significant drop in electrical expenses by installing LEDs.
“Once growers know the number of fixtures it becomes fairly straight math to figure the cost of the fixtures along with the installation costs to determine the capital investment required up front,” he said. “Other components that would have to be considered include maintenance requirements and parts replacement.”
Farner said regardless of the type of equipment purchased, growers should be able to earn back their investment in three to five years.
“The shorter that timeframe the decision becomes much easier,” he said. “Just like with other businesses, growers making capital investments should be looking at the ones that offer the best payback. Growers should always be looking for new equipment, systems or efficiencies that increase yield, drive revenue faster or lower costs so that margins are higher. Growers working to find different ways to build efficiencies and reduce costs for their overall operation should be looking for those that have the fastest payback. Based on my experiences of working with growers, LED lighting is one of those investments where they can get those types of returns more quickly.”
For more: Nathan Farner, North Ridge Solutions Inc., (214) 507-8594; nfarner@northridgesolutions.com.
This article is property of Hort Americas and was written by David Kuack, a freelance technical writer in Fort Worth, TX.
US: Utah - World’s First Commercial, Indoor Strawberry Farm Coming To Murray
It could be the world’s first private, commercial, vertical, indoor strawberry farm, and the Murray City Council approved it during their June 18 meeting. In a first for an urban Utah city, the City Council amended the Murray City Municipal Code to allow for indoor, vertical farming
August 29, 2019 ● By Shaun Delliskave
By Shaun Delliskave s.delliskave@mycityjournals.com
It could be the world’s first private, commercial, vertical, indoor strawberry farm, and the Murray City Council approved it during their June 18 meeting. In a first for an urban Utah city, the City Council amended the Murray City Municipal Code to allow for indoor, vertical farming.
This clears the way for Chihan Kim, a businessman whose holdings include a Sandy coffee shop, to develop what would be Utah’s first large-scale commercial, indoor, hydroponic farm in a vacant warehouse building located at 158 E. 4500 South.
“(I) will collect all the material to build the facility and…grow vegetables and some fruits, like strawberries, that will benefit from the omittance of herbicides,” Kim told the Murray City Planning Commission on May 2.
Vertical farming has become a buzzword in agriculture. The process includes producing food in vertically stacked layers, such as in a skyscraper, unused warehouse, or stacked shipping containers, with controlled-environment agriculture technology, where all environmental factors can be controlled. Such facilities utilize artificial light control, environmental control (humidity, temperature and gases) and fertigation. Some vertical farms use techniques similar to greenhouses, where natural sunlight can be augmented with artificial lighting and metal reflectors.
One of the most successful vertical farming operations is in Jackson, Wyoming. There, Vertical Harvest produces 100,000 pounds of vegetables a year on a plot 30 feet high by 150 feet long. Their 1/10th-of-an-acre site grows an annual amount of produce equivalent to 10 acres of traditional farmland. However, other ventures have failed.
Vertical farms are expensive to set up and take a long time to expand. Technology is changing at such a rapid pace that a newly opened competitor in the field could offer produce at a lower rate than an established producer. Still, indoor farming is appealing as a sustainable solution to growing food with little need for pesticides, water and land.
Before the code change, “Indoor Farming” was not listed as an allowable use in any zone in Murray City. For Kim to move forward with his zoning request, he needed to go through the extreme measure of having Murray change its code to allow for such a business.
This won’t be the first vertical, indoor farm in Utah, as an 11,000-square-foot facility sits on farmland in Charleston. Strong Vertical Garden supplies produce from that building to Smith’s grocery stores and microgreens to several chefs and restaurants in Utah.
The building that Kim intends to transform into an indoor farm is the former Electrical Wholesale Supply building. That building will allow Kim’s company, City Farm, to have 40,609 square feet for operations. LED lighting will be the primary source of light for the plants.
Murray City planning staff noted in their recommendation to the City Council that the indoor farm, “…will create the best opportunities to adaptively re-use and potentially revitalize older buildings and vacant spaces… (and) have the potential to place year-round access to fresh food closest to populations with limited transportation options, creating a positive impact on public health.”
“The main crops that we are considering at this moment are strawberries,” Kim said. Strawberries, he said, are one of the most contaminated fruits because of outdoor pesticides. This process will save them from harmful chemicals that get trapped in their seeds and pores and don’t all wash out with water.
“The farm operations will be maximum automation. Pollination—I am going to use drones. Drones will produce wind that will promote pollination. The farm will be open to the public with large windows. Strawberries will be supplied to grocery stores, but we will also make strawberry smoothies and food like that,” Kim said.
Councilwoman Diane Turner stated, “I think it is a great idea. I am really pleased you are doing this in Murray.”
Lead photo: An example of vertical farming shows stacks of crops growing in an indoor building. (Photo courtesy Murray City)
Sustainable Living: Hydroponic Mobile Farms To Let Anyone Grow Vegetables In Hong Kong, Slashing Carbon Footprints
Shops, restaurants, schools, and households could grow their own fresh produce, reducing need for imports, if mobile farming trial is successful. Technology is the latest brainchild of team of University of Hong Kong MBAs behind urban farm that supplies restaurants vegetables and herbs grown without soil
Shops, restaurants, schools, and households could grow their own fresh produce, reducing need for imports, if mobile farming trial is successful
Technology is the latest brainchild of team of University of Hong Kong MBAs behind urban farm that supplies restaurants vegetables and herbs grown without soil
13 Aug, 2019
Farmacy grows vegetables and herbs hydroponically in Causeway Bay, and is trialling mobile farms. Co-founder Raymond Mak talks about cutting Hong Kong’s carbon footprint and delivering fresh produce. Photo: Jonathan Wong
As a social movement gathers pace on the city streets this summer, there’s another growing revolution – a green movement.
This one is all about groundbreaking farming technology that cuts lengthy supply chains to allow easy access to fresh produce rich in nutrients and bursting with flavour.
Farmacy (farmacyhk.com), an urban farming technology company launched in January 2018, has been offering herbs, micro greens, and edible flowers to restaurants, hotels and home cooks. It will take things to the next level in a couple of weeks with the launch of its first “mobile farm”.
“That’s a farm that is so mobile it can be stored in your home, restaurant, school or supermarket. In the future, supermarkets won’t need to import vegetables, you can grow the vegetables fresh – lettuce, pak choi, choi sum, whatever,” says Raymond Mak, Farmacy’s CEO and co-founder.
Farmacy grows vegetables and herbs hydroponically. Photo: Jonathan Wong
Using hydroponic technology, the greens will grow in-store so that consumers know exactly where their food is coming from – they can actually see their vegetables as they grow. The pilot mobile farm will be launched in mid-August at the organic convenience store JustGreen in Sai Kung.
“They want to first roll it out at the Sai Kung store because there’s more room and they have a good relationship with clients who are open to trying new things and are more demanding about sustainability and freshness,” says Mak.
Customers will be able to order vegetables that can be harvested and delivered within minutes or hours, instead of the usual four-day minimum for imported goods. Photo: Jonathan Wong
We are in the firm’s hydroponics farm in Fashion Walk, Causeway Bay, a 200 sq ft space with two glass walls that allow the curious a peek at the herbs, micro greens, and edible flowers growing in their shallow blue tubs. There’s no air-conditioning in here – the plants like it warm – and just a fan to cool things down a bit if necessary. At 11am it’s time to turn on the lights and “wake up” the greens. “They need eight hours sleep, just like humans,” says Mak.
Hydroponic basically refers to the way that the plants absorb nutrients, which is through water instead of soil. Farmacy uses organic nutrients bought from the United States which has US Federal Drug Administration approval, and adds it to water. An advantage of indoor farming is that it’s very “clean” – there are none of the pesky insects and pests you get with soil and outdoors – and it also saves water.
“Compared with soil-based farming, where a lot of water is lost, goes underground, hydroponic farming saves 90 per cent more water,” says Mak.
Tastes like chicken? Why maggots might be the future of food
Hong Kong imports an astounding 98.3 per cent of its vegetables, with 70 per cent of the imports coming from China and 28 per cent flown in from around the world. All the emissions involved in getting our greens into Hong Kong is a massive black mark in terms of sustainability – and it’s also bad for our health. As soon as produce is harvested, the roots stop supplying water to the leaves and stem and the plant starts leaking goodness, with much of the nutrition going as the plant’s water evaporates.
“University of California studies show that vegetables can lose 15 to 55 per cent of vitamin C within a week and some spinach can lose 90 per cent of vitamin C within the first 24 hours after harvest,” says Mak, one of five University of Hong Kong MBA graduates who teamed up to found Farmacy.
The beauty of a mobile farm is the ability to buy your greens with the roots still intact, take the produce home and cut it up and cook it while it’s still super fresh and packed with goodness.
Raymond Mak co-founded Farmacy with four other HKU MBA graduates. Photo: Jonathan Wong
He notes the irony of consumers forking out high prices at high-end supermarkets for organic goods from Italy and France when the long travel time seriously affects its nutritional value. The four days minimum it takes to get from farm to supermarket represents a huge loss of nutrients. Even produce from Yunnan in southwest China – where much of Hong Kong’s vegetables are grown – takes one to two days to reach Hong Kong, Mak says.
The longer it takes to transport produce, the more flavour it loses. Mak proposes an impromptu tasting session.
First, we try a purple flower, oxalis, which is super sour, then a yellow cucumber flower, followed by lime basil, and a nasturtium (known as Empress of India) which knocks our socks off with a powerful wasabi hit. Harvested just moments before we ingested them, the flavours are full of zing, so it’s easy to understand why Michelin-starred chefs want to get their hands on them. French restaurant Le Salon de Thé de Joël Robuchon was an early adopter.
University of California studies show that vegetables can lose 15 to 55 per cent of vitamin C within a week and some spinach can lose 90 per cent of vitamin C within the first 24 hours after harvestRaymond Mak, Farmacy’s CEO and co-founder
But Farmacy isn’t about just catering to celebrity chefs – it’s got a bigger mission in mind.
“We don’t want this to be a small, niche thing, we want it to be accessible to the public, to all citizens, we want to make it a movement,” says Mak.
The movement is taking hold elsewhere. In Germany, the Berlin-based Infarm (infarm.com), founded in 2013 by two brothers, has partnered with 25 major food retailers and deployed more than 200 in-store farms, and is harvesting 150,000-plus plants monthly. Farmshelf (farmshelf.com), started by Andrew Shearer in a San Francisco garage in 2015, is now leading the urban farming pack in the US.
Closer to home, the idea has taken root in Singapore. Earlier this year the city state announced its intention to have all the island state’s needs home-grown by 2030, including vegetables cultivated in climate-controlled greenhouses under special LED lighting to maximise yields.
“Singapore has quite aggressive targets. Hong Kong needs to catch up and we want to play a role in it,” says Mak.
The Farmacy team – nine staff, including the five founders – have been using the Causeway Bay operation for research and development and a base in Cyberport to develop the mobile farm technology. Beyond the hydroponic technology, Mak says the team is developing even more sustainable and efficient farming technology, but they’ve taken it slow the first year to develop their green thumbs.
“You have to understand the plants before moving to the technology, or else it has no soul,” he says.
This article appeared in the South China Morning Post print edition as: green movement to turn city slickers into farmers
Sustainable Living Health and wellness Veganism Food and agriculture Singapore Environment
US, OHIO: Great Lakes Ag Tech Summit - September 23, 2019
Join Urban Ag News, Hort Americas and Current, powered by GE, for the inaugural Great Lakes Ag Tech Summit on September 23. The summit will be held at at the historic Nela Park campus in Cleveland, Ohio
By urbanagnews
August 14, 2019
Join Urban Ag News, Hort Americas and Current, powered by GE, for the inaugural Great Lakes Ag Tech Summit on September 23. The summit will be held at at the historic Nela Park campus in Cleveland, Ohio.
The one-day event features keynote presentations and panel discussions from leading researchers and innovative growers in the Great Lakes region. Attendees will be able to connect with growers, scientists, researchers and entrepreneurs as we shape the future of food and move controlled environment agriculture forward.
Keynotes
Optimizing Plant Production Under a Controlled Environment – Research and Education Programs at the Ohio State University
Dr. Chieri Kubota – The Ohio State University
Dr. Kubota’s research mission is to serve in the development of science and technology in the area of controlled environment agriculture (CEA). Her projects are in an interdisciplinary area that encompasses plant physiology and horticultural engineering to enhance understanding and efficiency of CEA plant production systems such as greenhouses, warehouses (vertical farms), and growth chambers.
Are Consumers and Growers Putting Dollars in the Local Food Industry? Insights on Technologies and Preferences
Dr. Ariana Torres – Purdue University
Dr. Torres’ background combines field experience in agriculture with theoretical and applied research on agricultural economics. She has worked on projects looking at the impact of marketing choices on technology adoption for fruit and vegetable growers; the economic implications of social capital on entrepreneurship; and the role of community support on the resilience of small business after disasters.
Dr. Torres uses economic analysis to support the economic viability of the horticulture industry. Her research focuses on the intersection between the horticulture industry and marketing decisions. Her goal is to conduct innovative outreach and applied research in specialty crops marketing, with the end of promoting economic sustainability for horticultural businesses.
Dr. Torres is currently working on a project evaluating the market, economics, and potential barriers to produce export-quality dried apricots from smallholders of southern Tajikistan. She is also working on evaluating the adoption of a solar dehydrator for selected dried specialty crops in Indiana and Georgia. Lastly, she is collecting foundational data and establishing long-term pricing reports for Indiana farmers markets.
Vertical Farm Production of Young Plants, From Hemp to Tomatoes
John Jackson – Sustainable Indoor Growing Systems, Inc.
John is the CEO of Sustainable Indoor Growing Systems, Inc. (SIGS) born from an USDA funded industry-academic partnership with Grafted Growers, the University of Arizona, and North Carolina State University. John is an award-winning entrepreneur and University of Arizona alum with an MBA from the Eller College of Management. John has successfully launched investor and grant funded businesses and operated tech based companies to early stage revenue. Born in Compton, California, John continues his grandfather’s legacy as a sharecropper of tomatoes in rural Texas.
SIGS gives plants what they need to express the features that the market wants.
Sustainable Indoor Growing Systems, Inc. (SIGS) is a clean agricultural technology company that uses controlled environment agriculture to induce young generic plants to express enhanced physiological traits customers want – while increasing the economics of propagation. This is made possible by scientific discovery and development of unique growing recipes which are learned and enabled only by the SIGS multi-layered growing platform and architecture.
Click Here to Register Now! Seats Are Limited!
Location
1975 Noble Rd. Cleveland, OH 44112
Date & Time
Monday, September 23, 2019
9 am to 4pm
Registration
Early bird admission price is $30 if registration occurs before Sept. 16.
Regular admission: $50
Hotel
Hyatt Legacy Village
24665 Cedar Rd
Lyndhurst, OH 44124
The rate is $129 for the night of 9/22/19.
• Call the toll-free number at 1-888-492-8847 for Hyatt Place Reservations and ask for the “Great Lakes Ag Tech Summit” or code G-GLGT
• OR use this link https://www.hyatt.com/en-US/hotel/ohio/hyatt-place-cleveland-lyndhurst-legacy-village/clezl?corp_id=G-GLGT
Click Here to Register Now!
About Urban Ag News
The mission of Urban Ag News is to be the leading science communicator for the commercial hydroponics, greenhouse vegetable, vertical farming and urban agriculture industries. Urban Ag News educates readers and provide an understanding of the industry’s latest technologies and luminaries.
About Current, powered by GE
Current, powered by GE, offers cutting-edge innovations in horticultural lighting. We’ve spent years perfecting our lighting technology and working with growers, systems integrators and plant scientists to establish the specific needs of the horticulture industry. The result? LED grow systems that maximize the potential of greenhouses and indoor farms by enabling efficient growth at an industrial scale.
TAGS Ariana Torres Chieri Kubota Conference GE Lighting Greenhouse Greenhouse Technology Hort Americas Indoor Ag Technology LED Grow Lights Ohio State University
US: How LED Lights Help Grow The Microgreens In Philadelphia
Adam Green was pursuing a career in filmmaking when he realized his real passion was raising the finest microgreens for the world’s top chefs. Now, the 25-year-old directs AGreen Farms, an indoor hydroponic farm in Philadelphia that specializes in selling garnishes to restaurants and hospitality establishments
Adam Green was pursuing a career in filmmaking when he realized his real passion was raising the finest microgreens for the world’s top chefs. Now, the 25-year-old directs AGreen Farms, an indoor hydroponic farm in Philadelphia that specializes in selling garnishes to restaurants and hospitality establishments. Of course, it’s not easy to make a mint while growing mint in the city, and that’s why Green is investing in LED horticulture lighting from Current, powered by GE, to produce herbs and edible flowers that make culinary pros go wild.
Seeds of Inspiration
At Drexel University, Green dabbled in business, cinema and screenwriting before finding that his true calling was not behind a camera but in a kitchen, sharing locally grown food with those who can appreciate the finer points of pea shoots.
“I realized the thing that made me happiest was food―eating the highest-quality food, stopping at farmers markets, making connections with the farmers―it was really exciting to me,” he says. “Growing my own food and knowing where it came from attracted me to agriculture, and I felt I could put a sound business case behind it.”
Green soon found himself in New York City, working as a sales intern for Farm.One. The technology-powered urban vertical farm grows a diversity of special crops for local chefs and gave Green the confidence he needed to step out on his own.
“My job was to find customers and sell them the best products,” he recalls. “I developed a rapport with chefs, and it was incredible to see the emotional impact when you bring them an excellent product they can’t get elsewhere. It’s about more than garnishing a plate; these ingredients are what make a great pesto or add layers of flavor to a dish. That’s when I knew I wanted to bring the same experience to chefs in Philadelphia.”
Sprouting Upward
Green launched AGreen Farms in 2018 in a mixed-use building in Philadelphia’s Germantown neighborhood. The 5,000-square-foot operation includes 3,500 square feet of grow space dedicated to microgreens and edible flowers of all kinds, many of them rare to the region. Helping Green get his indoor farm off the ground was Hort Americas, a leading horticulture supply company. As the operation came together, the conversation turned to lighting arrangements that could allow the fledgling farm to flourish.
“Hort Americas and specifically our rep Kyle Barnett were just very passionate about what we were doing and helped us source all the equipment we needed,” says Green. “Not only selling us the right products but educating us on making the best decisions is what Kyle and his team brought to the table, and that made it easy for us to work with them.”
After hearing Green’s goals for the farm, Barnett created unique light plans for the operation and found that the Arize™ Lynk light was the perfect fit. The system provides different light spectrums to promote all stages of plant growth. Importantly, Current’s varied light recipes offer the ideal spectrum for the unique needs of AGreen’s crops.
“Most of our farm is growing microgreens under pink light that helps them thrive, and then we have flowers that respond well to a reproductive purple light,” Green says. “We are currently in the middle of testing our first round of crops, and I will definitely say that the lighting is my last concern right now. I recently delivered some product to a very discerning chef, and he looked at the clamshells and said, ‘These are beautiful.’ Our opinion is that LED was the right answer, absolutely.”
More than 1,400 Arize Lynk LED lamps were installed at AGreen Farms to cultivate everything from Swiss chard to celosia to cilantro. As Green explains, microgreens demand more care than most crops to produce consistently amazing results.
“When you’re growing garnishes, it’s all about the taste, texture and aesthetics to produce the high-quality products that these incredible chefs deserve. The lights have a positive impact on making things crunch more or turn a darker green, for instance, and that’s what you need to walk into a kitchen with confidence and show someone something they haven’t seen before.”
Sage Advice
Bill Green, a self-admitted serial entrepreneur, is Adam’s father and author of the book All In. In it, he offers practical advice for cracking the code of success in the business world, including to approach every challenge with genuine enthusiasm.
“Adam enjoys talking to chefs, and sales is clearly his sweet spot,” says Bill Green, who brings 40 years of executive counsel and guidance to AGreen Farms. “I thought the plan he set forth really made sense, because he’s not trying to build a giant to compete against the biggest names―he knows his niche and what certain chefs are looking for, and his passion to customize that experience is what will shape his business.”
For Adam Green, perfect pentas blooms are a mark he will never stop aiming for, but with help from Current and Hort Americas, this young grower has already hit the mark with LED lighting for his budding operation. Beyond vibrant, leafy crops, AGreen Farms will also benefit from the significant energy savings LED can deliver compared to conventional light sources. It all adds up to a tasty finishing touch at the finest restaurants in Philadelphia.
“Giving chefs the best tools in their arsenal is what we’re all about,” he says. “Based on our first year in business, I don’t expect a shortage of customers anytime soon.”
For more information:
Current by GE
Publication date: 8/6/2019
Could Vertical Farming Meet The Food Needs of Tomorrow's Cities?
The majority of today’s global population lives in cities and by 2050, our population will have reached 9 billion people with 70% - 80% living in cities and urban areas
Five Takeaways
The majority of today’s global population lives in cities and by 2050, our population will have reached 9 billion people with 70% - 80% living in cities and urban areas.
Apart from large scale food security concerns, the world is also facing the loss of arable land and decreased access to fresh water fueled by global warming.
Vertical farming creates the future blueprint for securing the world’s food supply. It refers to growing crops in multiple vertical layers indoors, in controlled-environments, repurposed warehouses, growth chambers and even shipping containers.
Here are Heliospectra's five takeaways:
LED Grow Lights Make Vertical Farming Viable
LED grow lights have been the catalyst for growers looking to grow vertically. With recent developments in technology, growers can now maximize crop yields and standardize production 365 days a year.
The ability to alter light spectra and the quality of light that the crops are exposed to has huge implications on every aspect of production. Growers gain more control than ever by knowing that correct light can influence each variable—from how crops develop, when they bloom, how they taste, and even their chemical compositions.
Vertical Farms Use Less Water for Food Cultivation
Agriculture currently accounts for roughly 70% of our water usage and is also responsible for the vast majority of water runoff and contamination issues that are present today.
In contrast, vertical farming utilizes 70% - 95% less water compared to traditional farming. Some of the largest and most successful vertical farms also incorporate closed-loop water circulation systems to recirculate water to their crops, leading to an even greater reduction in water usage.
Vertical Farming is Less Labour Intensive
Vertical farming enables smart farming with precision technologies and controls to greatly reducing the crop input costs and intense labour of field farming.
The increasing development of Al, automation and robotics will also continue to increase revenue for growers and support even greater resource savings and operational efficiencies.
Vertical Farming Has the Ability to Conserve Land
Simply put, vertical farming produces more food per square meter, using up to 90% less land. This can help promote biodiversity as farmers drastically reduce their environmental footprint by growing more food on less land, encouraging an increase in livestock populations and natural enrichment of arable farmlands.
Arable land is also a valuable resource and as soil health decreases with use, so does the nutritional value of our food. The more we continue to farm through traditional methods, the more we reduce the bare mineral components and quality of soils. Vertical farming changes this by instead using aquaponic, hydroponic and aeroponic growing mediums instead of soil. By using these controlled media, vertical farming has also helped farmers move away from using pesticides in their production.
Vertical Farms Bring Local Food to Consumers and Neighbourhoods
Reducing emissions from transport is one of the most important measures to combat global warming from cars, trucks, aircraft and boats creating almost 20% of manmade carbon dioxide worldwide. Vertical farming addresses these issues by creating a sustainable model for locally grown produce. By growing local, food has to travel less distance and requires less artificial protection (i.e. refrigeration), resulting in produce that is not only fresher, but has a smaller environmental impact across the entire production chain.
All Pictures are Heliospectra’s SIERA Light Bar in different Vertical Farming environments.
For more information:
Heliospectra
info@heliospectra.com
www.heliospectra.com
Publication date: 8/19/2019
Signify Helps AppHarvest To Increase Yields In 25-Hectare Greenhouse
Eindhoven has partnered with AppHarvest to help the company increase efficiency and boost yields using significantly fewer resources in their 25 hectare greenhouse in Morehead, Ky., USA
AppHarvest Improves
Efficiency Through Combining LED And Conventional Lighting
Eindhoven has partnered with AppHarvest to help the company increase efficiency and boost yields using significantly fewer resources in their 25 hectare greenhouse in Morehead, Ky., USA. The greenhouse will be fitted with a hybrid LED lighting system, utilizing Signify’s Philips GreenPower LED toplighting compact and Agrolux high pressure sodium lighting. AppHarvest will grow tomatoes and cucumbers in its facility, which will be completed in the second half of 2020.
“This LED installation reinforces how we use proven technology to grow more fresh food with fewer resources,” said Jonathan Webb, Founder and CEO of AppHarvest. “With this cutting-edge hybrid system, we will dramatically reduce energy usage in the greenhouse. Working with Signify has given us the benefit of leveraging on a decade of growing knowledge and expertise.”
The facility uses a unique LED and High-pressure sodium (HPS) hybrid lighting system, to significantly reduce energy while increasing yield over the year. The LED lighting system is 40 percent more energy efficient than traditional greenhouse lighting, while it disseminates less radiant heat. During fall and spring, LED lighting will be used to grow more produce. HPS lamps will be used during colder months, in addition to the LED system. The heat from the HPS system will help warm the greenhouse and reduce natural gas usage.
AppHarvest is partnering with Equilibrium, a leading greenhouse investment firm. The LEDs will be installed by Dalsem Complete Greenhouse Projects, which is overseeing construction of the greenhouse.
“We’re very excited about our collaboration with AppHarvest and Equilibrium,” said Bill Bien, CEO of Signify Agriculture Lighting. “It’s great to work with partners just as committed to sustainable horticulture as we are, and we’re looking forward to helping them increase growth predictability, crop quality and yields, while improving their energy efficiency.”
The LED toplighting compact delivers high light output of 1,800 µmol/s and an efficacy of up to 3.0 µmol/J and helps growers effectively optimize crop growth, enhance crop quality and cut operational costs. Compared to a 1,000 W HPS fixture, the Philips GreenPower LED toplighting compact produces the same amount of light, has a similar light distribution, while consuming 40% less power and emitting considerably less radiant heat. By separating heat and light, this product gives growers independent control over their greenhouse climate.
Evesham Vale Growers and R & L Holt Increase Marketable Yield By 25% Using Signify’s Hybrid Lighting System
Signify (Euronext: LIGHT), the world leader in lighting, today announced that Evesham Vale Growers and R & L Holt, premium tomato growers in the UK, have once again chosen Philips LED and HPS lighting for a new greenhouse, based on the 25% increase in crop production that was achieved with its Philips hybrid lighting set-up which was installed by Philips Horti LED partner Certhon in 2015
Hybrid lighting enables year-round production of consistent, high quality tomatoes for supermarkets
Hybrid LED plus HPS toplighting make it possible to precisely control growth throughout the year
R & L Holt and Signify extend their partnership to maximize crop results in new greenhouse
Eindhoven, the Netherlands – Signify (Euronext: LIGHT), the world leader in lighting, today announced that Evesham Vale Growers and R & L Holt, premium tomato growers in the UK, have once again chosen Philips LED and HPS lighting for a new greenhouse, based on the 25% increase in crop production that was achieved with its Philips hybrid lighting set-up which was installed by Philips Horti LED partner Certhon in 2015.
In the new greenhouse, the company will install Philips GreenPower LED toplighting compact and Philips GreenPower LED interlighting, together with HPS lighting installed by the Philips Horti LED partner Certhon. The compact, passively cooled LED toplighting can be easily installed with the HPS lighting on the same trellis. This combination allows the company to use LEDs to extend lighting in the spring when it’s warmer, instead of the HPS lighting which produces more heat.
“I’m delighted to see that our customers are returning to us for new projects”, said Udo van Slooten, Business Leader Horticulture at Signify. “Our long-term partnerships enable us to learn from the improvements they have achieved and help them further improve the consistency and predictability of their crops. This move also confirms that our customers recognize the value that the LED toplighting compact offers in terms of combining LED with HPS lighting on the same trellis construction.”
Evesham Vale Growers and R & L Holt grow cherry, cocktail and large tomatoes on the vine, as well as loose classic tomatoes. All crops are grown for flavor, as supermarket premium ranges. Since all of the crops are grown in heated glasshouses, the season can stretch from February until November, but the company is always looking to further extend its season.
“After our success with our first hybrid HPS and LED interlighting system, we knew we were on the right path,” says Roly Holt, co-owner of R & L Holt. “We did a trial in another greenhouse with LED toplighting, LED interlighting and HPS lighting, and that system allowed us to specifically target different parts of the canopy to control our products. That is why we’ve now chosen this three-component set-up. We think this will give us a really sustainable and consistent product.”
Introduced in June 2019, the Philips GreenPower LED toplighting compact delivers excellent performance. Its high light output of 1,800 µmol/s and efficacy of up to 3.0 µmol/J help growers effectively optimize crop growth, enhance crop quality and cut operational costs. Compared to a 1,000 W HPS fixture, the Philips GreenPower LED toplighting compact produces the same amount of light, has a similar light distribution, while consuming 40% less power and emitting considerably less radiant heat.
Illumitex, The Digital Horticulture Company, Announces Dennis Riling As New Head of Sales
“Dennis’s depth in horticultural knowledge combined with over a decade’s worth of business and leadership experience makes him the ideal individual to lead our commercial efforts.” said Jeff Bisberg, Illumitex CEO. “
Dennis Riling rises to top commercial role as LED and Digital Horticulture hit the tipping point in the horticulture adoption curve.
AUSTIN, TX August 1, 2019 – Illumitex, a leader in Digital Horticulture and LED lighting announced today that Dennis Riling has been promoted to Head of Sales and VP of Business Development.
“Dennis’s depth in horticultural knowledge combined with over a decade’s worth of business and leadership experience makes him the ideal individual to lead our commercial efforts.” said Jeff Bisberg, Illumitex CEO. “LED is at the tipping point for adoption and Dennis’ team is aligned to support this accelerating growth. It’s Exciting.”
“Helping farmers more profitably grow crops at scale is our continued focus.” said Dennis. “We are innovating to deliver value way beyond LED lighting with our services and integrated FarmVisionAI platform. FarmVisionAI uses cameras integrated into our lighting, powered by horticulturist guided AI to detect anomalies near real time, at scale. I am proud to step into this leadership role and to do nothing less than help transform agriculture with new powerful digital solutions.”
About Illumitex, Inc:
Founded in 2005 in Austin, Texas, Illumitex is the Digital Horticulture company. Illumitex leverages the granular position of LED lighting in the CEA farm to deploy digital cameras to collect and analyze imagery of every plant, in every corner, at every moment. We go beyond lighting to deliver greater value to help digitally transform indoor farming. Illumitex LED lighting systems are based on decades of technology and help the farmer by reducing energy costs, maintenance costs, and increase plant yield, taste, color, and smell. We believe the combination of digital and lighting will open up a new age of highly productive and profitable farming. Learn more at www.illumitex.com
###
Scientists Play With Light And Water To Speed Up Crop Breeding
A number of challenges face crop production around the world, including drought, diseases, pests and limited land. Scientists are tasked with breeding varieties that will produce higher yields but use less land and fewer resources
BY DTN Grains - Loren Lindler | July 27, 2019
OMAHA (DTN) — This twice-monthly column condenses the latest news in the field of crop technology, research and products. Researchers say that by 2050, there could be 10 billion people in the world. A number of challenges face crop production around the world, including drought, diseases, pests and limited land. Scientists are tasked with breeding varieties that will produce higher yields but use less land and fewer resources. To aid in this, some international researchers are experimenting with two new techniques to speed up the breeding process: LED technology and hydroponics.
PLEASE, SIR, CAN I HAVE SOME MORE LIGHT?
Lee Hickey, a plant geneticist at the University of Queensland in Australia, is combining breeding and light-emitting diode (LED) technology to produce a form of “speed breeding.”
Plant breeding can often take years. With speed breeding, researchers are able to use LED lights that are ideal for photosynthesis, which allows researchers to grow crops three times faster, creating more generations in a single year.
Botanists started growing plants under artificial light over 150 years ago. As the years passed, LED technology has vastly advanced, allowing scientists to be more precise by customizing light settings to individual crop species. The Australian researchers exposed their crops to 22 hours of continuous blue and red LED lights, under ideal temperatures, which essentially convinced the plants to flower early. A generation of crops can take months, or even a year, to breed with traditional methods. However, with the use of LED lights and speed breeding, scientists were able to grow six generations of wheat, barley, chickpeas and canola in a year.
A WATERY WONDER
To obtain the fastest breeding results in their greenhouses, scientists at the John Innes Centre in the U.K. are using hydroponics, the practice of growing crops without soil, usually with the use of a water-nutrient solution. Hydroponic techniques allow nutrients and oxygen to reach plant roots quicker.
Many researchers have found that hydroponic plants grow 30% to 50% faster than a plant grown in soil. The ample amount of oxygen in a hydroponics system allows the roots to absorb nutrients much faster, stimulating root growth. The U.K. researchers are taking advantage of this faster-growing time to speed up their evaluation of the genomes of wild relatives of modern crops, which can hold valuable disease-resistance genes.
You can learn more about the LED technology and plant breeding with hydroponics: https://www.nowscience.co.uk/…
NASA-Inspired Speed Breeding For Crop Improvement To Feed The Future
NASA experiments to grow wheat in space using continuous light on wheat which triggered early reproduction in the plants were the inspiration for University of Queensland scientists to develop the world’s first ‘speed breeding’ procedures here on planet Earth
June 20, 2019 . | . Ken Ecott
Crop improvements can help us to meet the challenge of feeding a population of 10 billion, but can we breed better varieties fast enough?
Farmers and plant breeders are in a race against time. The world population is growing rapidly, requiring ever more food, but the amount of cultivable land is limited. Warmer temperatures have extended growth seasons in some areas — and brought drought and pests to others.
While a host of fascinating innovations are primed to change the face of agriculture, there remains a stubborn limiting factor for plant breeding. This is the long generation times of crops that allow only one or two generations per year.
This roadblock to progress has been alleviated by speed breeding protocols developed by research teams at the John Innes Centre and the University of Queensland.
Fast-growing plants in the crop-speed breeding facility at The University of Queensland. The plants featured are barley plants. Credit: The University of Queensland
“We face a grand challenge in terms of feeding the world,” said Lee Hickey, a plant geneticist at the University of Queensland in Australia. “If you look at the stats, we’re going to have about 10 billion on the planet by 2050 and we’re going to need 60 to 80 percent more food to feed everybody. It’s an even greater challenge in the face of climate change and diseases that affect our crops that are also rapidly evolving.”
NASA experiments to grow wheat in space using continuous light on wheat which triggered early reproduction in the plants were the inspiration for University of Queensland scientists to develop the world’s first ‘speed breeding’ procedures here on planet Earth.
The team tricked the crops into flowering early by blasting blue and red LED lights for 22 hours a day and keeping temperatures between 62 and 72 degrees Fahrenheit. Last November, in a paper in Nature, they showed that they can grow up to six generations of wheat, barley, chickpeas and canola in a year, whereas traditional methods would only yield one or two.
Dr Lee Hickey in his speed breeding lab at University of Queensland, 20 June 2016.
Botanists first started growing plants under artificial light — carbon arc lamps — 150 years ago. Since then, advances in LED technology have vastly improved the precision with which scientists can adjust and customise light settings to individual crop species.
So far, the researchers have mainly experimented with one parameter, light, but they have plans to investigate several other method of increasing, growth and generation times.
The team highlight that speed breeding combines well with a range of other developing technologies. These include speed gene cloning a technique developed by Dr Wulff’s team at the John Innes Centre to rapidly scour the genomes of wild relatives of modern crops to identify disease resistance genes which can be bred into elite crops.
This involves using hydroponic culture which gives plant roots quicker access to nutrients and oxygen. A carbon dioxide-enriched atmosphere is also under investigation and one of the most productive areas of research is likely to be temperature.
“One technology alone is not going to solve our problems,” Dr. Hickey said. “We’re going to need all the tools in the shed.”
Dr Hickey believes the sky is the limit for the new technology and he is now investigating the integration of speed breeding with other modern crop breeding technologies.
“It could also have some great applications in future vertical farming systems, and some horticultural crops,” Dr Hickey said.
A review published in the journal Nature Biotechnology outlines continuing efforts to harness speed breeding to a raft of crop technology innovations required to meet the 2050 challenge.
Signify Supports Bryte For Its New Greenhouse Equipment With Hybrid Philips LED Lighting System
Signify (Euronext: LIGHT), the world leader in lighting, announces today that it will start an extensive horti project in cooperation with Stolze at Bryte, one of the largest tomato growers in the Netherlands
Signify Supports Bryte, One of The Largest Dutch Tomato
Growers, For Its New Greenhouse Equipment (83,000 m²)
With A Hybrid Philips LED Lighting System
Eindhoven, the Netherlands - Signify (Euronext: LIGHT), the world leader in lighting, announces today that it will start an extensive horti project in cooperation with Stolze at Bryte, one of the largest tomato growers in the Netherlands. For the location in 's-Gravenzande, an 8.3 hectare greenhouse will be equipped with a combination of Philips GreenPower LED top lighting compact and HPS lighting. This solution allows greenhouses to benefit from the advantages of LED top lighting: higher predictability, better quality and an improved yield, as well as lower energy costs.
Bryte was founded in early 2019 as a combination of two renowned growers in the Westland and Voorne Putten areas: Kwekerij Dukker and Zwinkels Tomaten. Two different family businesses, but with a shared DNA. Identical in size, comparable in the way of working and thinking about cooperation in horticulture. For years, these companies have been growing tomatoes that are only known for one thing: their taste.
The introduction of the Philips GreenPower LED top lighting compact as a one-to-one replacement for the existing HPS lighting was the time for Bryte to think about a partial implementation of LED as a hybrid lighting solution for one of the company's seven locations. Compared to a 1,000 W HPS lamp, the Philips GreenPower LED top lighting compact produces the same amount of light using 40% less electricity. The lamp also produces very little radiant heat. Compared to a 600 W HPS lamp, the new energy-efficient LED top lighting compact produces 80% more light with the same amount of electricity.
A total of 180 μmol/m²/s will be realized over a total area of over 8.3 ha of glass, of which 90 μmol/m²/s will come from the HPS lighting and 90 μmol/m²/s from the LED top lighting. The heat and light in the greenhouses can be controlled independently, allowing for a very specific response to the natural lighting conditions. This creates the right balance between the amount of growing light and heat in the greenhouse, resulting in an increased yield and lower energy costs.
"It's good to see one of the largest Dutch greenhouse vegetable growers expressing confidence in LED," says Udo van Slooten, Business Leader Horticulture at Signify. "Bryte recognizes that the Philips GreenPower LED top lighting compact is not only an ideal replacement, but also the ideal addition to the existing HPS lighting in tomato cultivation."
Bryte's starting point is a more efficient growth too: "Our locations must meet the requirements of today and tomorrow in terms of efficiency, food safety, and sustainability. Together, we produce tomatoes on an area of 40 hectares. In summer and in winter, because a large part of the production area is lighted. Our customers are thus assured of a continuous supply, even when outdoor conditions produce poor lighting. We expect that the new hybrid LED installation will enable us to grow more efficiently, while reducing our energy and maintenance costs. A better balance in the greenhouse will result in higher profits," says Tom Zwinkels, Bryte's owner and director.
The whole project will be implemented in close cooperation with Philips horti LED partner Stolze.
Not All LEDs Are Equal: How Greener Roots Farm Is Growing Faster With Horticulture Lighting From Current
From a small window sill to an empty storage closet, to a rooftop utility room and, finally, to a spacious warehouse and greenhouse, Founder and President Jeffrey Orkin has been growing Greener Roots Farm one harvest at a time since 2012
Meet the light bars behind “the best damn lettuce you’ve ever tried.”
From a small window sill to an empty storage closet, to a rooftop utility room and, finally, to a spacious warehouse and greenhouse, Founder and President Jeffrey Orkin has been growing Greener Roots Farm one harvest at a time since 2012. As the first commercial-scale hydroponic vertical farm in Nashville, Tennessee, Greener Roots supplies herbs and leafy greens to local establishments year-round, including fresh lettuce and flavorful pea shoots, sunflower sprouts, sorrel and more that are picked and delivered within two days, never traveling more than 50 miles.
For Orkin, consistency is the key to Greener Roots’ steady success, measured in predictable crop yields and high-quality, nutrient-dense produce with no seasonal fluctuations. It’s what keeps local grocery stores and restaurant owners racing back to fill new orders, and it’s why Orkin relies heavily on LED lighting to help his business thrive. However, when a big investment in a new system started to go bad, Current, powered by GE, stepped in with a brighter solution.
Rising Above the Rest
Greener Roots cultivates over 14 tons of produce a year, with most of the greens being raised in racked hydroponic beds stacked high to the ceiling. Between its warehouse and greenhouse, the indoor operation totals nearly 7,000 square feet of grow space, requiring more than 300 LED light bars to provide optimal illumination for plant health. According to Orkin, it’s all part of producing “the best damn lettuce you’ve ever tried.”
“Some chefs are adamant about soil, but we’re showing them you can grow very flavorful things without soil, and having extremely high and uniform light levels is critical to that,” he says.
Greener Roots was growing fast, and new and better lighting technology was hitting the market. With help from Hort Americas, a leading commercial greenhouse and hydroponics supplier, he started to test an array of new LED options including horticulture lighting from Current. Immediately, Orkin gravitated to Current’s Arize™ LED growing system for its ease of installation, long life and proven results in improving production yields.
“The new lights from Current are very reliable and are producing faster growth, and now we can get red leaf varieties to turn red, where we couldn’t do that before,” Orkin said.
“The new lights from Current are very reliable and are producing faster growth, and now we can get red leaf varieties to turn red, where we couldn’t do that before.”
– Jeffrey Orkin, Founder and President, Greener Roots Farm)
“The Arize system also puts off less heat, so we can add more layers to our vertical beds if we choose. And what’s convenient is how you can daisy-chain the product end-to-end to make installation much simpler, which we really liked, having done all the work ourselves.”
Growing the Future
By isolating and combining different light wavelengths to replicate and accelerate natural photosynthesis, Arize LEDs can shorten growth cycles and enable different growth patterns, allowing urban farmers to tailor the light to the specific needs of every crop. Including LED tubes, light bars, suspended fixtures and lamps, the full Arize product family features everything needed for indoor vertical and greenhouse farming.
“Overall, we’re getting more biomass from every harvest,” says Orkin. “It’s all about ensuring the correct light intensity throughout the day, and how many photons we’re ‘feeding’ to the plants essentially. Current’s LEDs help us create the ideal condition for each crop.”
“Overall, we’re getting more biomass from every harvest.”
Orkin notes that Greener Roots is now pulling over 2,500 heads of lettuce a week from its greenhouse as more local customers discover the soil-free urban farm flourishing in their city. In fact, the new greenhouse―located on the outskirts of Nashville in nearby Franklin, Tennessee―is part of a large agritourism destination dubbed Southall Farms. This farm-to-table rural retreat will feature an inn, guest cottages, an event center and an agricultural barn, adding up to over 160,000 square feet of relaxed destination space where people will be able to savor experiences that celebrate culture, community and craft.
“There’s been an undercurrent for urban farming for some time, whether that’s someone raising a garden at home or a small farm making more fresh food options available to people,” Orkin says.
Rooted in Results
Orkin still drives the delivery truck that drops off freshly picked foods to his customers each day because to this entrepreneur, relationships are the seeds of success. It’s an approach that has taken the landscape-architect-turned-urban-farmer from a single planter in a kitchen window to a sprawling production system that ensures sustainable produce is always in stock.
“Having Current and Hort Americas there to support us, to answer our questions and try new things, it’s been huge,” says Orkin. “We’re trying to have the biggest impact on the local food scene we can, and that takes partners who understand the importance of durable and reliable technologies, such as LED.”
Learn more about how Current, with its deep expertise in LED technology, is helping indoor farmers reach new heights.
Are you ready to talk about
the right growth spectrum for your business?
START THE CONVERSATION
Luminaires Manufacturer Industria Lighting Is Back
Richard Schmidt and Ferry Breeuwer started developing a new light fixture in May of 2018. Now, one year later, that fixture is already being installed in several Canadian, Australian and Dutch greenhouses
“Even In The Horticultural Industry, The One-Stop Shop Is A Trend”
Richard Schmidt and Ferry Breeuwer started developing a new light fixture in May of 2018. Now, one year later, that fixture is already being installed in several Canadian, Australian and Dutch greenhouses. Notable about the new strategy used by Industria is the exclusive collaboration with the installers PB Tech and Stolze. Ferry: “As OEM-suppliers (Original equipment manufacturer), we can focus on production and product development.”
Ferry Breeuwer
Although Richard and Ferry had the plan in mind already, it was the demand from the market that led them to take this step. “The commitment from both sides convinced us to go for it. Our services are fully tailored to our distributors.”
Installers become the contact person
Ferry thinks that the work method is characteristic of the current market. “A change is going on with horticultural installation companies. They are becoming ‘system integrators’ more and more. Their role is changing. Where they used to mainly offer installation parts for horticultural technology, they now offer a complete package. They bring a variety of subsystems to one system to ensure all of the subsystems functioning together as one system. For the growers, this means there is only one contact person for all of the parts, which is very practical. Even in the horticultural industry, the one-stop shop is a trend.”
Patijnenburg
The light fixture is developed in cooperation with the Odacon firm, with the same engineers as the ‘old’ Industria. “We were done in December. The CSA and CE certification was handled quickly, and the production started.”
This happens in the Patijnenburg production warehouse. A conscious decision, says Ferry. “At first, we wanted to start our own production line, but due to the knowledge already available here, the short lines in the Westland and, last but not least, the fact that it fits nicely within our CSR -plan, we decided to have our production line at Patijnenburg.”
Production
Lean is a business strategy, and most of all, a way of working in which everyone and everything in the company aims at creating value for the customer in all of our processes, Ferry explains. “To do this, wastage is being limited, and the customer becomes the central focus point. In doing so, the quality improves, lead times are shortened and costs are reduced.”
For Industria, this strategy leads to:
Traceability. It is one of the keywords in the production space. Both the lamps and the drivers, as well as the reflectors, are equipped with a QR-code.
Electronics are very sensitive to electrostatic discharge. The discharge causes invisible damage and Industria does everything in its power to prevent this. An antistatic ESD-floor has been placed in the production space, and everything is grounded. Of course, every light fixture gets tested. This is not done by using a real lamp, but with a dummy. Ferry: “This is safer and faster than the conventional testing method. Also testing with a real lamp isn’t good for the lamp itself.”
Poka Yoke is Japanese for Mistake Proofing. Poka Yoke is about countermeasures that prevent mistakes from being made and because of that is used a lot in companies that work Lean. “The fun thing about Poka Yoke is that the solution is often simple. For Industria this means minimalizing the risk of assembly errors. The different colored wires, as shown in the picture above, are a good example of this.”
The lamp heater in the reflector lengthens the life span of the lamp and the reflector. The critical components of the lamps are heated by it, which is especially important during the start-up phase. The heater could be removed after around 7,000 hours of being used.
"Huge market for HPS"
The HPS luminaires are a proven product. The technology of HPS has been developed to now create a problem-free light fixture. Ferry: “Although the set-up is different, at its core it’s the same. After all, this light fixture has proven itself. What works, works. You shouldn’t want to change that too much,” Ferry says. “For HPS fixtures, there is still a large market. LED is coming up, but is still not quite there yet. Although the stretch is gone, as far as innovation is concerned, HPS still has a couple of years to go.”
For more information:
Industria Lighting
Ferry Breeuwer
Zuid-Hollandlaan 7
2596 AL Den Haag
0611 264 557
ferry.breeuwer@industria-lighting.com
www.industria-lighting.com
Publication date: 7/18/2019
© HortiDaily.com
Grow Lights Are Major Focus of Cultivate’19 Educational Sessions
If you are contemplating installing supplemental grow lights in your controlled environment production facility, then Cultivate’19 was the place to learn how the lights are being used. Both growers and university researchers presented information on the results they have gotten with grow lights, particularly light-emitting diodes (LEDs)
Growers and researchers discuss the benefits of using grow lights when it comes to growing controlled environment crops.
If you are contemplating installing supplemental grow lights in your controlled environment production facility, then Cultivate’19 was the place to learn how the lights are being used. Both growers and university researchers presented information on the results they have gotten with grow lights, particularly light-emitting diodes (LEDs).
Grow lights a must for producing greenhouse strawberries
Sarah Gunn, head grower at De Jong Greenhouses in Pella, Iowa, discussed how she has been using LEDs to produce greenhouse strawberries from November through January. The company, which grows primarily ornamental plants, has been trialing greenhouse strawberries for eight years. For the last three years the company has been selling its strawberries through a produce distributor to local grocery stores. Gunn said the price point during the months the company produces the berries has been good enough to justify the costs associated with growing the crop.
Gunn said the strawberries which are grown in 12-inch containers can hold three to four plants. She advised growers to start with certified bare root plants. Greenhouse strawberries are a labor intensive crop requiring removal of runners (stolons), old leaves and harvesting fruit every two to three days.
Gunn said that two-thirds of the United States doesn’t have sufficient light levels during the winter months to grow greenhouse strawberries. The optimum daily light integral (DLI) for strawberries is 15-25 moles per square meter per day (mol·m-2·d-1). Gunn is using LEDs to deliver a DLI of 12 mol·m-2·d-1. Extending the day length to 13-16 hours can help boost fruit yields. Plants should not be lit for longer than 16 hours.
The company purchases bumblebees to pollinate the strawberry plants. Because different light spectrum can affect bumblebees, Gunn advises growers to find out how grow lights can impact the bees behavior.
Growers in two-thirds of the United States don’t have sufficient light levels during the winter months to produce greenhouse strawberries.
Photo courtesy of Chieri Kubota, Ohio St. Univ.
De Jong uses a template for berry size and color to determine when the berries are ready to harvest. Since strawberries were the first food crop the company had grown, a consultant was hired to implement food safety protocols.
Gunn said cultural practices and biocontrols are being used for greenhouse pests and diseases. Pests include two-spotted spider mite, aphids and thrips. Prior to growing greenhouse strawberries Gunn said she never had to deal with lygus bugs, commonly referred to tarnished plant bugs. Diseases issues include powdery mildew, Botrytis and leather rot (Phytophthora cactorum).
Multiple crops grow well under LEDs
A panel of growers and a university researcher discussed the experiences they have had growing under LEDs.
John Bonner, owner and CEO at Great Lakes Growers in Burton, Ohio, has been hydroponically growing leafy greens and herbs since 2011 when he started with 300 square feet of greenhouse production. His operation has expanded to 160,000 square feet. Bonner who started with high pressure sodium (HPS) lamps has replaced most of those fixtures with LEDs. Once the company’s current expansion is completed Bonner expects to be able to annually produce 6 million heads of lettuce.
James Darrow, general manager at Jolly Farmer in New Brunswick, Canada, began research with LEDs in 2012. He said Jolly Farmer provides at least 25 moles of light per day by LEDs during the winter. After installing LEDs Darrow said adjustments had to be made in how often crops were irrigated, fertilizer applications and crop timing. Many of the bedding crops, especially begonias, needed to be fertilized more often when grown under LEDs.
The economics of using grow lights
Horticultural researchers Neil Mattson from Cornell University and Marc van Iersel from the University of Georgia discussed the Lighting Approaches to Maximize Profits (LAMP) project. Funded by the USDA National Institute for Food and Agriculture Specialty Crop Research Initiative, LAMP aims to determine how growers can maximize their return on investment when considering installing grow lights.
Researchers involved with the Lighting Approaches to Maximize Profits (LAMP) project are working to help growers maximize their return on investment in grow lights while optimizing plant growth.
Photo courtesy of Marc van Iersel, Univ. of Georgia
The team of researchers involved in this $5 million, four-year project is studying the best way to optimize crop growth and quality in cost-effective ways. The research includes simulation of different lighting scenarios and the use of sensors to monitor crop growth and physiology. Researchers are studying how much light crops require and assessing supplemental lighting needs and options.
This article is property of Hort Americas and was written by David Kuack, a freelance technical writer in Fort Worth, TX.
Micro-Naps For Plants: Flicking The Lights On And Off Can Save Energy Without Hurting Indoor Agriculture Harvests
Growing crops under artificial light is gaining momentum , particularly in regions where produce prices can be high during seasons when sunlight is sparse
7/22/2019
Author: Kevin M. Folta
(MENAFN - The Conversation) A nighttime arrival at Amsterdam's Schiphol Airport flies you over the bright pink glow of vegetable production greenhouses. Growing crops under artificial light is gaining momentum , particularly in regions where produce prices can be high during seasons when sunlight is sparse.
The Netherlands is just one country that has rapidly adopted controlled-environment agriculture , where high-value specialty crops like herbs, fancy lettuces and tomatoes are produced in year-round illuminated greenhouses.Advocates suggest these completely enclosed buildings – or plant factories– could be a way to repurpose urban space, decrease food miles and provide local produce to city dwellers.
One of the central problems of this process is the high monetary cost of providing artificial light , usually via a combination of red and blue light-emitting diodes.Energy costs sometimes exceed 25% of the operational outlay. How can growers, particularly in the developing world,compete when the sun is free ? Higher energy use also translates to more carbon emissions, rather than the decreased carbon footprint sustainably farmed plants can provide.
I'vestudied how light affects plant growth and development for over 30 years. I recently found myself wondering: Rather than growing plants under a repeating cycle of one day of light and one night of darkness, what if the same daylight was split into pulses lasting only hours, minutes or seconds?
Indoor plants need plenty of artificial light. josefkubes/Shutterstock.com
Short bursts of light and dark
So my colleagues and I designed an experiment . We'd apply the normal amount of light in total, just break it up over different chunks of time.
Of course plants depend on light for photosynthesis, the process that in nature uses the sun's energy to merge carbon dioxide and water into sugars that fuel plant metabolism. Light also directs growth and development through its signals about day and night, and monkeying with that information stream might have disastrous results.
That's because breaking something good into smaller bits sometimes creates new problems. Imagine how happy you'd be to receive a US$100 bill – but not as thrilled with the equivalent 10,000 pennies. We suspected a plant's internal clock wouldn't accept the same luminous currency when broken into smaller denominations.
And that's exactly what we demonstrated in our experiments . Kale, turnip or beet seedlings exposed to cycles of 12 hours of light, 12 hours dark for four days grew normally, accumulating pigments and growing larger. When we decreased the frequency of light-dark cycles to 6 hours, 3 hours, 1 hour or 30 minutes, the plants revolted. We delivered the same amount of light, just applied in different-sized chunks, and the seedlings did not appreciate the treatment.
The same amount of light applied in shorter intervals over the day caused plants to grow more like they were in darkness. We suspect the light pulses conflicted with aplant's internal clock , and the seedlings had no idea what time of day it was. Stems stretched taller in an attempt to find more light, and processes like pigment production were put on hold.
But when we applied light in much, much shorter bursts, something remarkable happened. Plants grown under five-second on/off cycles appeared to be almost identical to those grown under the normal light/dark period. It's almost like the internal clock can't get started properly when sunrise comes every five seconds, so the plants don't seem to mind a day that is a few seconds long.
Just as we prepared to publish, undergraduate collaborator Paul Kusuma found that our discovery was not so novel. We soon realized we'd actually rediscovered something already known for 88 years. Scientists at the U.S. Department of Agriculture saw this same phenomenon in 1931 when they grew plants under light pulses of various durations. Their work in mature plants matches what we observed in seedlings with remarkable similarity.
A 1931 study by Garner and Allard tracked the growth of Yellow Cosmos flowers under light pulses of various durations.
J. Agri. Res. 42: National Agricultural Library, Agricultural Research Service, U.S. Department of Agriculture.,CC BY
Not only was all of this a retread of an old idea, but pulses of light do not save any energy. Five seconds on and off uses the same amount of energy as the lights being on for 12 hours; the lights are still on for half the day.
But what would happen if we extended the dark period? Five seconds on. Six seconds off. Or 10 seconds off. Or 20 seconds off. Maybe 80 seconds off? They didn't try that in 1931.
Building in extra downtime
It turns out that the plants don't mind a little downtime. After applying light for five seconds to activate photosynthesis and biological processes like pigment accumulation, we turned the light off for 10, or sometimes 20 seconds. Under these extended dark periods, the seedlings grew just as well as they had when the light and dark periods were equal. If this could be done on the scale of an indoor farm, it might translate to a significant energy savings, at least 30% and maybe more.
Recent yet-to-be published work in our lab has shown that the same concept works in leaf lettuces; they also don't mind an extended dark time between pulses. In some cases, the lettuces are green instead of purple and have larger leaves. That means a grower can produce a diversity of products, and with higher marketable product weight, by turning the lights off.
One variety of lettuce grew purple when given a 10-second dark period. They look similar to those grown with a five-second dark period, yet use 33% less energy. Extending the dark period to 20 seconds yielded green plants with more biomass.
J. Feng, K. Folta
Learning that plants can be grown under bursts of light rather than continuous illumination provides a way to potentially trim the expensive energy budget of indoor agriculture. More fresh vegetables could be grown with less energy, making the process more sustainable. My colleagues and I think this innovation could ultimately help drive new business and feed more people – and do so with less environmental impact.