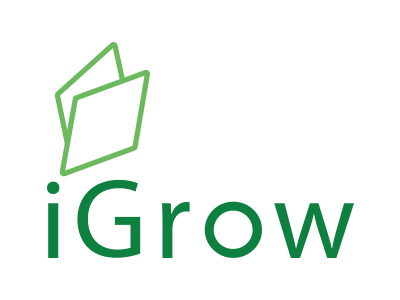
Welcome to iGrow News, Your Source for the World of Indoor Vertical Farming
Workshop Iberia 2018 Light, The Right Element - Grow Your Life
The horticultural and agricultural industry is undergoing a transformation in the way plants are grown. Behind these changes, there are innovations in the field of LED lighting that use new technologies to boost plant growth, maximize production and minimize energy consumption.
These LED lighting solutions are making it possible to have crops almost anywhere, from big cities to people's homes. Wherever we look, from vertical crops and hydroponic greenhouses to the cultivation of algae, green facades and small farming systems - LED solutions are increasingly present.
At the seminar of Osram Opto Semiconductors, "LEDs for horticulture - growing green", researchers from the CSIC ("Higher Council of Scientific Research"), Osram partners and specific experts of Osram Opto Semiconductors will present from a didactic and practical perspective the benefits and latest advances in LED technology in the field of horticulture.
We will also provide a vision of the market, as well as the opportunity to talk with our partners and exhibitors about real applications.
Do not miss the opportunity to benefit from the knowledge and experience of our experts. Interacting with them and with our partners, you can give added value and gain inspiration for your existing and future projects.
Come visit us, "and let's grow green together!"
Sign up for free!
The horticultural and agricultural industry is undergoing a transformation in the way plants are grown. Behind these changes, there are innovations in the field of LED lighting that use new technologies to boost plant growth, maximize production and minimize energy consumption.
These LED lighting solutions are making it possible to have crops almost anywhere, from big cities to people's homes. Wherever we look, from vertical crops and hydroponic greenhouses to the cultivation of algae, green facades and small farming systems - LED solutions are increasingly present.
At the seminar of Osram Opto Semiconductors, "LEDs for horticulture - growing green", researchers from the CSIC ("Higher Council of Scientific Research"), Osram partners and specific experts of Osram Opto Semiconductors will present from a didactic and practical perspective the benefits and latest advances in LED technology in the field of horticulture.
We will also provide a vision of the market, as well as the opportunity to talk with our partners and exhibitors about real applications.
Do not miss the opportunity to benefit from the knowledge and experience of our experts. Interacting with them and with our partners, you can give added value and gain inspiration for your existing and future projects.
Come visit us, "and let's grow green together!"
Sign up for free!
Partners that participate:
"Smart Lighting Makes Growing Easier And More Cost Effective"
After being in the LED market for years, ITC is now expanding in to horticulture with the Amplify and Amplify Plus product lines. Remarkable is how their smart LED lighting solution can be steered on the actual weather conditions at individual locations.
"Our research resulted in grow light products, specifically intended to reduce energy usage, increase yield, and enhance plant strength", the team with ITC explains while showing their new Amplify product line. "It offers multiple, scientifically proven spectrums and lamp configurations to provide a solution for greenhouse or controlled environment growers."
The LEDs used in the Amplify product line are optimized for light distribution and plant level light intensity. The spectrum options are focused on the light needs of different cultivars at different points of development. "These are key to consistent and even growth patterns, that produce better yields and quicker turns. While the finned heatsink design of the lamp dissipates the minimal heat and the whale tail feature provides an additional protective shield for water and dirt intrusion."
Extra attention is paid to the design of the fixtures. "The simple hang and plug single and double lamp options are great for narrower spaces or long runs. Both are available in 80 or 150 degree light spreads. The 5-Lamp fixture gives consistent light placement across larger areas while reducing the number of electrical drops needed. This feature reduces install labor and can comply with existing infrastructure of greenhouses."
Smart lamps
And then there's the smart technology. "Many experts continue to explore the complexities that climate change and environmental factors are having on our food growing capabilities. These factors are making the consistency within food production environments a necessity.
Nebula Controls modules
Nebula Controls, a technology company, is providing artificial intelligent wireless controls for ITC Horticulture’s Amplify Plus smart LED lighting. This partnership is enabling the ability to program and reprogram the cloud based lighting control operation from mobile devices for enhanced growth and energy savings.
"Based on weather conditions at individual locations or programmed zones the Nebula Control smart control system is able to maximize efficiencies and reduce energy usage with minimal human dependency", the team explains. "Both ITC Horticulture’s Amplify Plus smart LED lighting and Nebula Controls are working to elevate supplement and controlled environmental horticulture lighting to a new level by using a new state-of-the-art smart lighting control system that contribute to consistent high performing food production environments. This way we are working to make growing easier and more cost effective for today and tomorrow."
For more information:
Nebula Controls
519-749-3373
contact@nebulacontrols.ca
Publication date : 11/16/2018
The Cutting-Edge Technology That Will Change Farming
Thousands of young collard greens are growing vigorously under a glow of pink-purple lamps in a scene that seems to have come from a sci-fi movie, or at least a NASA experiment.
WASHINGTON POST
NOVEMBER 6, 2018
Mike Zelkind, chief executive of 80 Acres Farms, grows produce with artificial-light made possible with new LED technology.
Mike Zelkind stands at one end of what was once a shipping container and opens the door to the future.
Thousands of young collard greens are growing vigorously under a glow of pink-purple lamps in a scene that seems to have come from a sci-fi movie, or at least a NASA experiment. But Zelkind is at the helm of an earthbound enterprise. He is chief executive of 80 Acres Farms, with a plant factory in an uptown Cincinnati neighborhood where warehouses sit cheek by jowl with detached houses.
Since plants emerged on Earth, they have relied on the light of the sun to feed and grow through the process of photosynthesis.
But Zelkind is part of a radical shift in agriculture - decades in the making - in which plants can be grown commercially without a single sunbeam. A number of technological advances have made this possible, but none more so than innovations in LED lighting.
“What is sunlight from a plant’s perspective?” Zelkind asks. “It’s a bunch of photons.”
Diode lights, which work by passing a current between semiconductors, have come a long way since they showed up in calculator displays in the 1970s. Compared with other forms of electrical illumination, light-emitting diodes use less energy, give off little heat and can be manipulated to optimize plant growth.
In agricultural applications, LED lights are used in ways that seem to border on alchemy, changing how plants grow, when they flower, how they taste and even their levels of vitamins and antioxidants. The lights can also prolong their shelf life.
“People haven’t begun to think about the real impact of what we are doing,” says Zelkind, who is using light recipes to grow, for example, two types of basil from the same plant: sweeter ones for the grocery store and more piquant versions for chefs.
For Zelkind, a former food company executive, his indoor farm and its leading-edge lighting change not just the way plants are grown but also the entire convoluted system of food production, pricing and distribution in the United States.
High-tech plant factories are sprouting across the United States and around the world. Entrepreneurs are drawn to the idea of disrupting the status quo, confronting climate change and playing with a suite of high-tech systems, not least the LED lights. Indoor farming, in sum, is cool.
It has its critics, however, who see it as an agricultural sideshow unlikely to fulfill promises of feeding a growing urbanized population.
Zelkind agrees that some of the expectations are unrealistic, but he offers an energetic pitch: He says his stacked shelves of crops are fresh, raised without pesticides and consumed locally within a day or two of harvest. They require a fraction of the land, water and fertilizers of greens raised in conventional agriculture. He doesn’t need varieties bred for disease resistance over flavor or plants genetically modified to handle the stresses of the field. And his harvest isn’t shipped across the country in refrigerated trucks from farms vulnerable to the effects of climate change.
“We think climate change is making it much more difficult for a lot of farms around the country, around the world,” he says, speaking from his office overlooking a demonstration kitchen for visiting chefs and others.
In addition to shaping the plants, LEDs allow speedy, year-round crop cycles. This permits Zelkind and his team of growers and technicians to produce 200,000 pounds of leafy greens, vine crops, herbs and microgreens annually in a 12,000-square-foot warehouse, an amount that would require 80 acres of farmland (hence the company’s name).
Zelkind says he can grow spinach, for example, in a quarter of the time it takes in a field and half the time in a greenhouse. Growing year-round, no matter the weather outside, he can produce 15 or more crops a year. “Then multiply that by the number of levels and you can see the productivity,” he said.
Zelkind and his business partner, 80 Acres President Tisha Livingston, acquired the abandoned warehouse, added two shipping containers and converted the interior into several growing zones with sophisticated environmental systems that constantly monitor and regulate temperature, humidity, air flow, carbon dioxide levels and crop health. Grown hydroponically, the plant roots are bathed in nutrient-rich water. The moisture and unused nutrients exhaled by the plants are recycled.
But it is the LED lighting that has changed the game. Conventional greenhouses have relied on high-pressure sodium lamps to supplement sunlight, but HPS lights can be ill-suited to solar-free farms because they consume far more power to produce the same light levels. They also throw off too much heat to place near young greens or another favored factory farm crop, microgreens. Greenhouses, still the bulk of enclosed environment agriculture, are moving to a combination of HPS and LED lighting for supplemental lighting, though analysts see a time when they are lit by LEDs alone.
In the past three years, Zelkind says, LED lighting costs have halved, and their efficacy, or light energy, has more than doubled.
Production in the Cincinnati location began in December 2016. In September, the company broke ground on the first phase of a major expansion 30 miles away in Hamilton, Ohio, that will eventually have three fully automated indoor farms totaling 150,000 square feet and a fourth for 30,000 square feet of vine crops in a converted factory. (The company also has indoor growing operations in Alabama, North Carolina and Arkansas, which acted as proving grounds for the technology.)
“We feel the time is right for us to make the leap because the lighting efficiency is there,” Livingston says.
The visible spectrum is measured in minuscule wavelengths, shifting at one end from violet-blue light through green to red at the other. For decades, scientists have known that photosynthesis is optimized within the red band, but plants also need blue lightwaves to prevent stretching and enhance leaf color.
A barely visible range beyond red, known as far red, promotes larger leaves, branching and flowering. With advances in LED technology, light recipes - determining the number of hours illuminated, the intensity of photons directed at plants and the mix of colors - can be finely tuned to each crop and even to each stage in a crop’s life.
Given the evolving nature of the technology and its enormous commercial potential, light manufacturers and universities, often in collaboration, are actively involved in research and development.
“We have a completely new era of research,” says Leo Marcelis, a horticulture professor at Wageningen University in the Netherlands. Tweaking light recipes has allowed researchers to manipulate crops in a way never seen before. In the lab, chrysanthemums have been forced into bloom without the traditional practice of curtailing their daily exposure to daylight. This will allow growers to produce bigger plants in flower.
“It’s to do with playing around with the blue light at the right moment of the day,” Marcelis says. “Its internal clock is affected differently, so it doesn’t completely recognize it’s still day. There are so many amazing responses of the plant to the light.”
Lettuce, for example, likes as much as 18 hours of light per day, but basil prefers brighter light for 15 hours, says Celine Nicole, a researcher for Signify, formerly Philips Lighting. “Every plant has its own preference,” says Nicole, who conducts research at the company’s high-tech campus in Eindhoven, Netherlands. She has already tested 600 types of lettuce.
Although the permutations are still under study, the sun suddenly seems so analog. “The spectrum from sunlight isn’t necessarily the best or most desirable for plants,” says Erik Runkle, a plant scientist at Michigan State University. “I think we can produce a better plant” with LED lights, he says. “The question becomes: Can you do it in a way that is cost-effective considering the cost of plants indoors?”
The answer seems to be yes. LED light shipments to growers worldwide are expected to grow at an annual average rate of 32 percent until 2027, according to a market report by analysts with Navigant Research in Boulder, Colorado. Shipments of LED lights will overtake those of legacy lights starting next year, says Krystal Maxwell, who wrote the report with Courtney Marshall.
Most of the growth will be as supplemental lighting in greenhouses, but vertical farms are seen as an alternative production system that will develop alongside greenhouses, not displace them, Marcelis says.
Runkle estimates there are 40 or more vertical farms in the United States, and new ones are opening every year with the help of deep-pocketed investors. In some of the biggest deals, AeroFarms, headquartered in Newark, last year raised a reported $40 million. Plenty, a grower based in South San Francisco, raised $200 million in 2017 for a global network of vertical farms. (One of the backers is a venture capital firm created by Amazon founder Jeff Bezos, who also owns The Washington Post.)
Zelkind declined to reveal his capital costs, but for start-up entrepreneurs, LED-driven vertical farms can be one of the most lucrative forms of agriculture. “Based on manufacturers and growers I have talked to, that’s where the money is,” Marshall says.
Critics argue that a lot of the hype around indoor farming is unwarranted, saying it won’t fulfill promises of feeding an increasingly urbanized planet and reverse the environmental harm of industrialized agriculture, not least because most staples, such as corn, wheat and rice, cannot be grown viably indoors.
Also, to build enough indoor farms for millions, or billions, of people would be absurdly expensive.
Runkle says vertical farming “shouldn’t be considered as a way to solve most of our world’s food problems.” But it is a viable way of producing consistently high-quality, and high-value, greens and other plants year-round.
Zelkind says what he’s doing may be novel, but it’s just one component of how we feed ourselves in this century. “We shouldn’t overblow what we do. Eventually it’s going to become more important, but vertical farming alone isn’t the cure-all.”
He adds, however, that “there’s no reason today to ship leafy greens from California to Ohio.”
Livingston likens LED-raised food to the advent of smartphones. “Five years from now everyone is going to be living with indoor farming and wonder how we did without it,” she says.
What Do Investors Need To Know About The Future of LED Grow Light Technology?
NOVEMBER 16, 2018 PATRICK FLYNN
Editor’s Note: Patrick Flynn created Urbanvine.co in 2016 to help urban dwellers learn how to start urban farming without any previous experience. As the site grew, he discovered that “urban farming” was actually a general term that can include a wide variety of concepts, including grow lights and hydroponics, topics which the site now covers in depth.
The horticultural lighting market is growing, and growing rapidly. According to a September press release from Report Linker, a market research firm specializing in agribusiness, the horticultural lighting market is estimated grow from a $2.43 billion market this year to $6.21 billion in 2023.
One of the key factors driving current market sector growth is increased development of LED grow light technology. LEDs (light emitting diodes) were first developed in the 1950s as a smaller and longer-lasting source of light compared to the traditional incandescent light bulb invented by Thomas Edison in 1879.
LEDs last longer, give off less heat, and are more efficient converting energy to light compared to other types of lights, all features that can result in higher yields and profits for indoor growers.
But until recently, LEDs were only used to grow plants indoors experimentally, largely because the cost was still too high for commercial businesses. Many commercial growers still use HID (High Intensity Discharge) lights such as High Pressure Sodium, Metal Halide, and Ceramic Metal Halide; all lights that have a high power output but are less durable than LED lights, generate far more heat, and have less customizable light spectra.
Today, LEDs are fast becoming the dominant horticultural lighting solution. This is due primarily to the one-million fold decrease in fabrication cost of semiconductor chips used to make LED lights since 1954.
For investors more familiar with field-based agriculture, it can certainly be a minefield to know where LED lighting technology for horticulture is going in the future. Although it is no longer the “early days” of LED technology development, current trends are still shaping the future of LED technology.
So what does the intelligent agtech investor need to know about the current state and future of LED grow light technology?
I interviewed Jeff Mastin, director of R&D at Total Grow LED Lighting, to discuss what the future of LED grow light technology for agriculture looks like, and how investors can use current trends to their advantage in the future.
What is your background – how did you get involved in grow light technology at Total Grow?
The company behind TotalGrow is called Venntis Technologies. Venntis has, and still does, specialize in integrating touch-sensing semiconductor technologies into applications.
Most people don’t realize LEDs are semiconductors; you can also use them for touch-sensing technologies, so there’s a strong bridge to agricultural LED technology.
Some of the biggest technical challenges in utilizing LEDs effectively for agriculture include LED glaring, shadowing and color separation.
We have used our expertise in touch-sensing LEDs to expand into horticultural LEDs, and we have developed technology that addresses the above challenges better, giving better control over the spectrum that the LED makes and the directional output of the light in a way that a standard LED by itself can’t do.
My personal background is in biology. When TotalGrow started exploring the horticultural world, that’s where being a biologist was a natural fit to take a lead on the science and the research side of the development process for the product; that was about 7 years ago now.
If you were going to distill your technical focus into trends that you’re seeing in the horticultural lighting space, what are the main trends to keep an eye on?
The horticultural lighting industry is really becoming revolutionized because of LEDs. Less than 10 years ago, LEDs in the horticultural world were mainly a research tool and a novelty.
In the past, they were not efficient enough and they were definitely not affordable enough yet to really consider them an economical general commercial light source.
But that is very quickly changing. The efficiencies are going up and prices down and they are really right now hitting the tipping point where for a lot of applications, but definitely not all applications, the LED world is starting to take over horticulture and indoor agriculture.
How do you view the translation of those trends into actionable points? For investors or technology developers in the agriculture technology space, how do they make sure that the LED light technology they are investing in isn’t going to be obsolete in a year or two?
With LEDs, the key question is still cost-efficiency, and there’s only so far the technology can improve.
Why? There are physical limitations. You can’t make a 100% efficient product that turns every bit of electricity into photons of light. At this point, the efficiency level of the top of line LEDs are up over 50%.
Can we ever get up to 70 or 80%? Probably not any time soon with an end-product, not one that’s going to be affordable and economical generally speaking.
So to answer your question, it’s not a category where you’re going to say, “well this is obsolete, I can get something three times better now.” The performance improvements will be more marginal in the future.
Ten years from now the cost will be cheaper. But that again doesn’t make current LED technologies obsolete. In terms of that fear, I don’t think people have to worry about current LED light technologies becoming obsolete.
In a large commercial vertical farming set up, what is the ballpark cost of horticultural LEDs currently?
To give just an order of magnitude sort of number, you’re probably going to be someplace in the $30 per square foot number for lights for a large facility. It can be half that or it can be double that.
That’s just talking within the realm of common vertical farming plants like greens and herbs, or other plants similar in size and lighting needs.
If you start talking about tomatoes or medicinal plants, then the ability to use higher light levels and have the plants make good use of it skyrockets. You can go four times higher with some of those other plants, and for good reason.
What type of horticultural lighting applications are LEDs still not the best solution for now and in the foreseeable future?
There are at least 3 areas where LEDs still may not make sense now and in the near future.
First, if the LED lights are not used often enough. The more hours per year the lights are used, the more quickly they return on their investment from power savings and reduced maintenance. Some applications only need a few weeks of lighting per year, which makes a cheaper solution appropriate.
Second, in some greenhouse applications, LED’s may not be the best choice for some time to come. Cheaper lights like high-pressure sodium have more of a role in greenhouses where hours of use are less and higher hang heights are possible. (Many greenhouses will still benefit strongly from LEDs, but the economics and other considerations make it important to consider both options in greenhouses.)
Lastly, some plants are not the best in vertical farming styles of growing where LEDs have their most drastic advantages. At least at this point it is not common to attempt to grow larger fruiting plants like tomatoes or cucumbers totally indoors, though when attempted that is still more practical with LEDs than legacy lights.
Thanks Jeff!
To learn more about Total Grow, visit www.totalgrowlight.com
AEssenseGrows Introduces ‘The Perfect Grow Light’ For Cannabis
AErix Line Brings Broad Spectrum and High Photon Efficacy
that Help Plants Grow Superior Buds
SUNNYVALE, Calif., Nov. 12, 2018 -- AEssenseGrows, an AgTech company specializing in automated precision aeroponic platforms for consistent high-yield plant production, today introduced a unique new line of grow lights optimized for premium value plants like cannabis. The AErix LBR003 grow light delivers the specifications required to improve the quality of buds grown indoors along with all of the automation features large cultivation facilities desire.
AErix lights offer a balanced broad spectrum coupled with high photon efficacy, making them ideal for premium leafy plants. The lights will be showcased Wednesday through Friday at MJBizCon in Las Vegas at the AEssenseGrows booth, #2473.
“Science has come a long way in pinpointing the role lighting plays in plant growth, and our new AErix line is built around these findings,” said Phil Gibson, AEssenseGrows’ vice president of marketing. “The best quality buds grow under balanced broad-spectrum light--light that contains sufficient amounts of blue, green, yellow, and red—and that’s what AErix lights deliver. That’s why we call them the perfect grow light.”
AErix lights (dimensions: 40”x50”) provide intense output with wide wavelength coverage and full light spectrum with an average PPFD of 1,000 µmol/s/m2 when placed 6 to 12 inches above the plant canopy—optimal for cannabis. With a maximum power usage of 700W, the lights are less than 3 inches thick including the power supply with no fan required. All AErix lights include an IP65 water repellant rating covering everything you want in a high humidity-intensive grow room.
The AErix lights drew praise from Joel Cuello, professor of Agricultural and Biosystems Engineering at the University of Arizona and a global expert in indoor farming.
“The AErix LBR003 indoor grow light spans the wavelength range of the photosynthetically active radiation with a spectral output distribution that remarkably conforms with the significant portions of the average plant's photosynthetic response curve to light,” Cuello said. “Its excellent spectral quality distribution combined with its high photon flux output makes it a superior indoor grow light.”
The new networked lights include many automation features and are optimized for the AEssenseGrows AEtrium-4 Bloom System. Fully controlled by the Guardian Grow Manager central control system software, the AErix lights include 0-100% dimming through an integrated AES link for complete scheduling and intensity automation. When connected, the lights automatically daisy chain to the network and can be sequenced in massive grow rooms to soft-start, one row at a time, without complex relays or programming.
Also included is a wide range 100-277V universal input power connection so the light is ideal for all power grids and geographies. The AErix lights will deliver as much as 16-24 pounds of dry trimmed bud per light per year, at below $150 per pound at scale. The complete AEssenseGrows system will be on display this week at MJBizCon Las Vegas.
The lights are automated to enable scheduling at various intensity levels. They are built for longevity and require little to no maintenance. The AErix light is verified by the Electrical Testing Laboratories (ETL) safety certification, exceeding or surpassing all Standards for Safety published by UL and other standards bodies.
For more information about the AErix lights, including a data sheet and user manual, visit the AEssenseGrows website or contact Gibson at pgibson@aessensegrows.com or 669.261.3086.
Ackrell Capital listed AEssenseGrows as one of the firm's Top 100 Private Cannabis Companies for 2018.
AEssenseGrows (pronounced "essence grows"), founded in 2014, is a precision AgTech company based in Sunnyvale, CA. AEssenseGrows provides accelerated plant growth SmartFarm platforms and software automation delivering pure, zero pesticide, year-round, enriched growth to fresh produce and medicinal plant producers globally. With AEssenseGrows, you can precisely control your production operations at your fingertips from anywhere in the world.
CAM Led Lighting, A Division of CAM Mfg., A California Company, Announces It’s Agreement To Market And Distribute The Wand.
Latest Product News for InDoor Growers, Farmers and Commercial Horticulture Operators
Los Angeles, CA, October 16, 2018:
CAM Led Lighting, a Division of CAM Mfg., located in Murrieta, CA is proud to announce their partnership with BioRadiance Grow Science, a cutting- edge Science & Technology Company based in the UK. BioRadiance offers cost-effective straight forward solutions to urgent, destructive, very costly and sometimes life-threatening sickness problems caused by harmful pathogens.
The “Wand” delivering BRe3, is a Patented Light Energy Science that prevents Pathogen infection and cures infected plants, vegetables, cannabis & seeds & extends the lives of flowers, cut vegetables/plants by organically destroying fungi and bacteria. The non-visible WaveLength light is safe for use from Seed 2 Sale, has no residues or toxins to leave behind and is safe for all humans, animals and plants. Growers can maximize crop potential and eliminate the use of pesticides and chemicals allowing them to grow clean and healtheir produce/plants and cannabis.
The Wand is a LED Emitter Light Bar, approximately 48” L x 1- 1/ 2” W, installs along side current grow lights, or can be used as a stand-alone LED Grow Light + Pathogen Control. The Light source uses the non-visible spectrum of light and delivers natural occuring wavelengths, covering up to a 6’ x 4’ area at a distance of 24” away from the plant(s), or as close as 6” away from the plant(s) covering a smaller footprint of 4’ x 2’ for quicker results. The Bar has an IP65 rating and can be also be installed in outside grows under cover with structural support for attachment.
Several Certified Lab Tests have been conducted in commercial grow rooms and results are available upon request. Please email Director of Marketing, Judi Randall, @ info@camledlighting.com, for more information on Test Results.
“We are excited and thrilled to be offering such an amazing product to the Indoor Grower’s Industry, particularly here in California where regulations on Pesticides are on the forefront and may detour good quality growers from entering into the market. We believe this product and it’s science is the answer to grow/production issues relating to the quality, control and the safety of plants, vegetables, fruit, flowers, insects and related products to the Public.” States, Judi Randall.
Judi can be contacted @ their CA company headquarters, 1-951-837-4776 or by email info@camledlighting.com for additional information, pricing or ordering.
## END ##
ASABE Announces The Publication Of A New Lighting Standard For Horticulture
November 1, 2018
ST JOSEPH, MICHIGAN— The American Society of Agricultural and Biological Engineers (ASABE) has published the second in a three-part series of standards relating to LED radiation measurements for plant growth and development.
ANSI/ASABE S642, Recommended Methods for Measurement and Testing of LED Products for Plant Growth and Development, describes the methods used for measurement and testing of LED packages, arrays, and modules; LED lamps; and any other LED optical radiation devices.
This standard was preceded by the first document in the series, S640, Quantities and Units of Electromagnetic Radiation for Plants (Photosynthetic Organisms), which presented definitions and descriptions of metrics for plant growth and development. The final standard in the series will focus on performance criteria for LED systems used in horticulture.
ASABE members with standards access and those with site-license privileges can access the full-text of the standard by electronic download within the next few weeks. Location for the download is on the ASABE online Technical Library at: elibrary.asabe.org. Others can obtain a copy for a fee directly from the library or by contacting ASABE headquarters at OrderStandard@asabe.org.
ASABE is recognized worldwide as a standards developing organization for food, agricultural, and biological systems, with more than 260 standards currently in publication. Conformance to ASABE standards is voluntary, except where required by state, provincial, or other governmental requirements, and the documents are developed by consensus in accordance with procedures approved by the American National Standards Institute.
For information on this or any other ASABE standard, contact Scott Cedarquist at 269-932-7031, cedarq@asabe.org.
A current listing of all ASABE standards projects can be found on the ASABE web site at www.asabe.org/projects.
ASABE is an international scientific and educational organization dedicated to the advancement of engineering applicable to agricultural, food, and biological systems.
Further information on the Society can be obtained by contacting ASABE at (269) 429-0300, emailing hq@asabe.org or visiting www.asabe.org/.
Bell Pepper Year Round With LED or Hybrid Lighting
Sander Hogewoning (Plant Lighting) about lighting test Bell peppers are hardly grown year round in The Netherlands. Growing year round has advantages for the market, but also a number of challenges. In the past results of tests with lighted bell pepper growth were mixed, with sometimes difficult fructification and insufficient stretching of the bud. By combining cultivation knowledge (Delphi and growers), plant physiological support (Plant Lighting) and light knowledge (Signify), we hope to realize successful year round cultivation.
The basis of the research is that the quantity of assimilates are being produced by the variety in balance with the demand for assimilates by the developing fruits. In a regular unlighted cultivation, daylight and plant taxation increase simultaneously. In the lighted test the results are exactly reversed: shortly after planting there is lots of daylight and little need for assimilates.
The plant tends to produce lots of fruits. Then the plant taxation will increase, and also the demand for assimilates, but daylight is diminishing. The hypothesis is that a too large plant taxation in the beginning will lead to imbalance-related problems later on.
Tight schedule
That is the reason why plant taxation is built up according to a tight schedule, and any overage of fruits is immediate cut away. The lighting is geared as much as possible to the shortage of daylight to meet the assimilate demand. Aided by photosynthesis measurements and crop models the assimilation of the crop is calculated as precise as possible. Furthermore, part of the crops are being used for experiments with directional light to measure the effect on stretching in the bud.
The crop is looking healthy now, and the first fruits have set. The goal is to end up with around 40 kg production. It will be exciting how the growth will proceed around the shortest day and in the following period.
The program Kas als Energiebron, Signify, and crop cooperation Paprika financed the research.
Source: Kas als Energiebron
Publication date : 10/16/2018
Current, Powered by GE and Stockbridge Technology Centre Partner to Research the Farm of the Future
Stockbridge Technology Centre’s Vertical Farming Development Facility to enable growers to test and model their individual urban farm setup prior to investment
Aims to propel the success of the vertical farming industry, projected to be worth $13.9 billion USD in 20241 and generate more “farmable land” to address future global food production pressures
Current by GE’s Arize LED horticulture solution will help researchers test growth of crops such as leafy greens and herbs in different conditions
Stockbridge Technology Centre's Vertical Farming Development Facility (Photo: Business Wire)
October 16, 2018
LONDON--(BUSINESS WIRE)--Current, powered by GE (NYSE: GE) today celebrated the opening of CHAP’s new Vertical Farming Development Facility, supported by Innovate UK and based at Stockbridge Technology Centre (STC), which leverages the company’s Arize horticultural lighting solution to propel commercial urban farming success in the UK. The state-of-the-art research facility, located in Selby, North Yorkshire, is designed to help entrepreneurs, growers and investors gain deeper insight into the technology and environmental parameters needed to optimise crop yields before breaking ground on their own vertical farming operations.
We can help growers create more farmable space in industrial and urban areas in a way that is commercially and environmentally sustainable - Malcolm Yare, Current by GE
Modelling the Farm of the Future
In its 2017 report, Global Market Insights, Inc. predicted that the vertical farming industry (both indoor and outdoor applications) will grow from revenue of $2.5 billion USD in 2017 to $13.9 billion USD in 20241 and the new facility is designed to support this trend. By testing the latest technology and approaches relevant to this production model, the STC will improve the industry’s understanding of ideal indoor farming crop light requirements and growing conditions.
Potential investors and vertical farmers can work with STC’s plant scientists and vertical farming experts to identify and test the perfect vertical farm setup to maximise their planned harvest’s size, nutritional value and visual appeal. In a controlled environment, they are able to monitor and tweak parameters such as the length of the growing day, C02 concentration, humidity, nutrients and temperature, to ensure that their proposed farm will be commercially sustainable prior to construction. The resulting data supports business planning activity and minimises risks previously associated with vertical farming.
This “farm of the future”, built by systems integrator GrowStack working in conjunction with TCE Electrical Ltd., is the latest research initiative to be led by CHAP and Stockbridge Technology Centre (STC), a pioneer in experimental and applied horticulture research since the 1950s. Since its inception, STC has acted as a bridge between academia and commerce, sharing valuable research and insight that has helped to revolutionise farming practice in the UK.
The installation contains two identical grow rooms - a total growing area of 228m2 - with full climate control and a recirculating hydroponics system as well as futuristic propagation and germination rooms. Four tiers of cropping racks are lit by 780m of Arize LED lighting, delivering a balanced spectrum of red and blue wavelengths that will help boost the development of a broad range of plants.
“As cities’ populations grow at an exponential rate, the demand for fresh produce grows as well,” states Dr Rhydian Beynon-Davies, head of novel growing systems at STC. “We have the potential to grow more produce at an industrial scale within our cities and the focus of this new facility is to support the growers who are taking this bold step into the future of farming. By developing controlled environment grow systems integrated with LED lighting, we can demonstrate how, through technology, urban farming can improve the supply and nutritional value of food in a way that is commercially viable.”
Shining a Light on the Potential of Urban Farming with Arize
“Over the years, Stockbridge Technology Centre has been at the forefront of innovation, devoted to one of the most fundamental industries in the UK – that of feeding the population,” comments Malcolm Yare, Horticulture Business Development Manager for Current by GE. “Light is critical to the success of any crop and by focusing on combining the most effective wavelengths with the optimal environmental conditions, we can help growers outpace traditional methods by creating more “farmable space” in industrial and urban areas, increasing global harvests in a way that is both commercially and environmentally sustainable.”
The Arize range of horticulture solutions has been developed based on Current by GE’s experience in intelligent, connected industrial lighting, combined with extensive research and collaboration with horticulture and agriculture experts. The lights have been designed for easy, plug-and-play installation and are also fully sealed and IP66 UL Wet rated for easy cleaning in high-care, cleanroom environments. Arize lighting is one of the most energy-efficient solutions on the market, using less energy to power the LEDs and generating less heat to tax the facility’s cooling systems. With a 36K-hour lifetime (L90) and five-year warranty, the horticulture lighting solutions allow growers to amortise their capital expenditure over a longer period for greater return on investment.
Notes to editors:
The Vertical Farming Development Facility has been developed in partnership between the Crop Health and Protection Centre (CHAP) and Stockbridge Technology Centre and is supported by Innovate UK.
About Current, powered by GE
Current is the digital engine for intelligent environments. A first-of-its-kind start-up within the walls of GE (NYSE: GE), Current blends advanced LED technology with networked sensors and software to make commercial buildings, retail stores and industrial facilities more energy efficient & digitally productive. Backed by the power of Predix*, GE’s platform for the Industrial Internet, and a broad ecosystem of technology partners, Current is helping businesses and cities unlock hidden value and realize the potential of their environments. www.currentbyge.com
For more information about Stockbridge Technology Centre
www.stockbridgetechnology.co.uk
1 Global Market Insights, Inc. Insights Report 2017, “Vertical Farming Market Size by Product, Fruits, Vegetables & Herbs, Aquatic Species, By Technology, By Application, Industry Analysis Report, Regional Outlook, Growth Potential, Price Trends, Competitive Market Share & Forecast, 2018 – 2024” www.gminsights.com/industry-analysis/vertical-farming-market
Contacts
Current, powered by GE
Karen O’Neil, +1 857-265-9113
karen.oneil@ge.com
or
Racepoint Global
Jenna Keighley, +44 208 811 2151
CurrentEU@racepointglobal.com
Valoya Canna+, Ultra-Wide LED Spectrum For Superior Chemical Expression in Cannabis
The research into the interaction of the cannabis plant and light is growing but is yet not abundant due to bans which still exist in most places around the world. One thing we do know for sure is that high quality light will result in a high quality plant, one with a good chemical expression.
Valoya, the manufacturer of LED grow lights, known for their research based approach, has been testing and developing a variety of plant spectra over the past ten years. In the last three years, Valoya has conducted research on light interaction on cannabis, independently as well as in collaboration with research institutes and customers. The result is a new line of LED grow lights, designed to help growers achieve high quality cannabis plants, consistently, cycle after cycle. Valoya has placed emphasis on finding the right wavelengths for particular growth phases to achieve optimal growth. After having tested more than 60 LED spectra, Valoya has commercialized 5, earning it customers in 51 countries so far including 8 out of 10 world’s largest agricultural companies. Valoya Canna+TM is Valoya’s latest innovation which is a line of luminaires with a spectrum optimized for professional cannabis cultivation.
The spectrum is a wide (also known as full, broad or continuous) spectrum extending outside the commonly used PAR area. The range encompasses radiation between 380 and 780 nanometers which means the entire PAR area plus the far-red and the UV-A wavelengths. The benefit of these additional wavelengths is that the spectrum that is wider and fuller, contains more information and thus stimulates the plants more than a simpler spectrum would. The far red radiation is important for quick development of healthy plant biomass that can then later support large flower formations where most of the valuable secondary metabolites are. The UV-A creates a small amount of stress for the plant. The plant responds by strengthening its defense mechanisms i.e. creating more secondary metabolites. In addition to that, small pathogens cannot withstand the UV-A radiation thus the growing environment becomes less prone to outbreaks of powdery mildew and other such problems.
Valoya Canna+TM comes in two form factors:
- A 135 W bar LED grow light for indoor (single or multitier) cultivation and
- A 392 W box LED grow light for greenhouse (sea of green) cultivation
Valoya Canna+ 120
Valoya Canna+ 120 is a 4’ (120 cm) long, high intensity bar that reaches 2,4 µmol/W (PPF 320 µmol/m2/s). It is sealed shut, has no deep fins or fans that collect pathogens so it can be easily cleaned even with harsh chemicals. This makes it suitable even for the most demanding, GACP/GMP compliant grows. On both of its ends are pressure and temperature stabilizing vents thanks to which the luminaire will work even longer than the industry standard 50000 hours.
Valoya Canna+ 400
Valoya Canna+ 400 is a 13.7” x 15” (35 cm X 38 cm) high intensity light that reaches 2,3 µmol/m (PPF 880 µmol/m2/s). It is compact and robust thus suitable for greenhouse and sea of green cultivation. With excellent thermal dissipation properties this luminaire will last at least 50000 hours.
Both are dimmable and project light at a 120° angle making it possible to install them close to the canopy (Valoya Canna+ 120 only 4” / 10 cm and Valoya Canna+ 400 only 25” / 50 cm from the canopy). Instead of a silicone coating which expands and contracts in heat and deteriorates quickly, these luminaires’ LED chips are protected by tempered glass. AR (anti-reflection) coated glass is used which increases light transmission efficiency to about 98%.
As this emerging industry is rapidly growing, a need arises for high quality lighting solutions with which growers will be able to create consistent yields and cannabinoid expressions year after year. This is particularly so for the pharmaceutical grade cannabis and all large scale cannabis cultivation operations. Valoya provides a solution to this challenge with its new line of products. Valoya has published a spectrum quality guide which outlines the small permitted variations within the spectrum across production batches and generations of products. For growers this means that when they acquire Valoya luminaires for cannabis they can rest assure that all their future purchases, or replacements of products will be with the same spectrum, thus resulting in consistent yields.
The Valoya Canna+TM is available immediately, globaly. It will be introduced at the upcoming Marijuana Business Conference and Expo in Las Vegas in November (14-16). Valoya will be exhibiting at booth 3468.
For the North American customers, Valoya Canna+TM line is available through Innovative Growers Equipment, Valoya’s distributor
sales@innovativegrowersequipment.com
(815) 991 – 5010
About Valoya Oy
Valoya is a provider of high end, energy efficient LED grow lights for use in crop science, vertical farming and medicinal plants cultivation. Valoya LED grow lights have been developed using Valoya's proprietary LED technology and extensive plant photobiology research. Valoya's customer base includes numerous vertical farms, greenhouses and research institutions all over the world (including 8 out of 10 world’s largest agricultural companies).
Additional information:
Valoya Oy, Finland
Tel: +358 10 2350300
Email: sales@valoya.com
Web: www.valoya.com
Facebook: https://www.facebook.com/valoyafi/
Twitter: https://twitter.com/valoya
Alabama Power Looks Into Economic Feasibility of Indoor Agriculture
October 16, 2018
Alabama Power an electric utility company, has taken on a research project that is virtually unprecedented among utility companies. The power company is looking into the use of LED lighting to grow crops. A refurbished Freight Farm shipping container outside the Technology Applications Center at the General Services Complex in Calera is the location of the project.
Alabama Power engineer Blair Farley and Cheryl McFarland, commercial and industrial marketing support manager
In a specially customized, insulated and climate controlled shipping container, employees grow lettuce and other vegetables, as well as herbs and edible flowers. The goal of the project is to see if the cost of using electricity for indoor agriculture is economically feasible compared to traditional agriculture.
Exploring the container farm concept at Alabama Power originated from an increasing interest in indoor agriculture and the need to fully understand the benefits of using electricity to enhance the process.
Potential Advantages of Indoor Agriculture
It is thought that indoor agriculture could be a revolutionary for farmers, stores, restaurants, consumers. Alabama Power asserts that crop could be grown year-round in a controlled environment with nutrients in circulated water. Soil would not be necessary and few or no pesticides would be needed.
Furthermore, crops could be grown in urban settings and areas categorized as food deserts (locations where fresh food is not easily accessible). Also, transportation costs could be dramatically reduced or eliminated with food possibly grown near consumers and stores.
Alabama Power says for example that indoor farming can produce 12 more lettuce harvests a year, and needs up to 90 percent less water, than a traditional outdoor farm.
One way of saving on electricity, according to the company, is to use energy efficient LED lighting and other components which can be programmed to operate during off-peak hours to take advantage of cheaper electric rates. Alabama Power speculates that with the electricity needed to operate the lighting and climate control systems, indoor farming could present a new range of opportunities for the company.
Indoor Farming Could be Done in Repurposed Buildings and Warehouses
In theory, Repurposed vacant warehouses or buildings, including those with existing utilities, could be utilized for controlled-environment agriculture, providing jobs for Alabamians. Other potential advantages include growing crops during periods ofdrought or excessive rainfall; producing fruits and vegetables not native to a geographic area; and having uninterrupted growing seasons.
“Indoor agriculture can be a great addition to the already thriving agriculture industry in our state,” said Cheryl McFarland, commercial and industrial marketing support manager.
But there are challenges. Like any new, fast-growing concept, scarce data is available to determine long-term pros and cons. High start-up costs and unavailable labor may make it a financial risk. Additionally, vague or unfavorable city laws could pose a barrier to an indoor agriculture operation.
Shipping Container Farming Operation
In January 2017, Alabama Power employees installed a 40-foot hydroponic container and began producing lettuce one month later. The container has a seed germination table and 256 vertical towers holding up to 17 small heads of lettuce each. However, the food production is not limited to lettuce and includes basil, arugula, carrots, dill, and radishes.
With the help of automation, the APC container is relatively self-sufficient. However, one to two employees with other work responsibilities spend a little of their time each week planting, harvesting and performing routine maintenance in the container.Alabama Power plans to assess produce production and water and electricity usage, then compare findings with similar projects.
“We feel the interest in indoor agriculture is continuing to grow as consumers demand more fresh, local and healthy food options in stores and restaurants,” McFarland said.
“Interest in indoor agriculture or controlled environment agriculture is growing either in completely enclosed settings, such as our container, augmented greenhouses or empty buildings, like a vacant mall or Walmart,” McFarland added. “It’s a great way to provide access to fresh foods and jobs in rural communities and urban settings, particularly in areas of food deserts.”
New Vertical Farming Light Bar/Panel Hybrid Designed To Maximize Yields With Less Space
The team of lighting experts at TotalGrow have announced the launch of the new TotalGrow Stratum. The features and benefits of this new light include:
Thin profile to maximize space under 4” from canopy to shelf
Full spectrum and modular design for extra versatility
Broad panel/bar hybrid for improved uniformity and penetration in tight spaces
Simple mounting and electrical installation to save time and costs; up to 80 lights per plug
Cost effectiveness, waterproofing and warranty for economic sustainability
The 40W TotalGrow Stratum is designed and refined to maximize yields, space and versatility while minimizing costs. The spectrum and size are ideal for low/no-sunlight growing in virtually any vertical farm, growth chamber, propagation system, tower garden and more. Exceptional efficiencies and light delivery potential, along with long, low maintenance lifespans provide long-term sustainability.
Custom wiring harnesses create the cleanest, simplest power distribution for your operation. An example is shown for a typical 250 µmol*m-2*s-1 setup over several 4’x8’ shelves.
Spectrum customization available
For more information:
TotalGrow
Jeff Mastin – Biologist
315.373.9716
jeffm@venntis.com
totalgrowlight.com
Climate Cell On Wheels Helps Dutch Growers With LED Dilemma
"Everybody wants to do 'something' with LED and has the feeling something has to be done with it, but what? There's so much going on and being offered - how to get started and what to do?" That's why the Hortilux & Green Simplicity teams created a research solution for the industry. Currently they're on the road with it: for two weeks, a climate cell on wheels is shown at various companies. This Thursday it will be shown at Hortilux themselves.
The roadshow is fully booked, and every day two or three companies are visited: breeders, seed growers, research institutes and growers of course. For example De Ruiter and Syngenta are being visited. The climate cell on wheels drives there, and the possibilities of LED in horticulture, places without daylight, research and vertical farming are discussed. There's a lot of interest and many colleagues are visiting the climate cell. "We're not getting bored", the Hortilux / Green Simplicity teams agree.
"For example the roadshow offers an insight on the possibilities in research, but also how to translate it to a solution for production: going hybrid with SON-T or LED only, in a greenhouse or a vertical farm. With Hortilux & Green Simplicity we can have a fair amount of knowledge and can help with this."
This Thursday the roadshow will be at Hortilux, (Vlotlaan 412) and their employees can take a peek. Between 10:00 - 13:00 everybody is welcome to enter, also other people / companies with interest. Just send a message to Martin Moes or leave a voicemail (+31(0)6-22981504) in advance.
For more information:
LED'S RESEARCH
www.leds-research.com
US (MA): Horticultural Lighting On Show At Tech Festival
October 8-14 Boston
OSRAM will bring its technology to Boston’s City Hall Plaza in early October as the Gold Sponsor of HUBweek, a weeklong festival and civic initiative that explores the intersections of art, science and technology.
OSRAM will showcase smart horticulture lighting solutions, Human Centric Lighting (HCL) glasses and an HCL light ceiling in its shipping container; and will include pop-up experiences and exhibit participation with collaborative partners such as Workbar, Dan’s Power Plant, Corner Stalk Farm and FreshBox Farms. OSRAM technology experts also will take part in panel discussions and other events throughout the week. OSRAM will be centrally located at The HUB, across from the Hall of the Future, during HUBweek, held Oct. 8-14, 2018, on Boston’s City Hall Plaza.
“HUBweek has proven to be a hot spot for innovators. This year OSRAM is showing how some of its coolest technologies are at the heart of it all, including smart horticultural lighting for urban farms and human centric lighting glasses, which have been used by BMW M Motorsports race car drivers and the German ski team during the 2018 Winter Games,” said Lori Brock, OSRAM Head of Innovation, Americas Region. “Ten years ago, nobody could have predicted the impact of such technologies. Today, Urban Farming and HCL are increasingly making their way into the mainstream, providing a critical first step in fundamentally changing how we live our lives and build a healthier, more sustainable future.”
Brock will take part in a curated panel focusing on the impact of technology on health, along with other notable experts. The panel discussion will take place at Center Stage at The HUB at 2:30 p.m. Wednesday, Oct. 10, 2018.
Horticultural lighting solutions
Due to limited natural resources, indoor farming soon will become more prevalent, providing fresh produce closer to urban environments like Boston. Visitors of the OSRAM showcase at HUBweek will learn how growing plants indoors with smart LED-based lighting technology can save water and energy.
The horticultural lighting solutions also can help growers improve flavor and nutrition profiles, better manage the growth cycle, and increase yield – either on-site or remotely. LED technology and advanced sensors ensure plant growth 365 days a year and supports local food production while helping to significantly reduce the environmental footprint.
OSRAM will be located across from the Hall of the Future in The HUB during HUBweek, held Oct. 8-14, 2018, on Boston’s City Hall Plaza. For more information about OSRAM, visit www.osram.us, and for more information about HUBweek 2018 and to purchase one of three pass types to unlock all types of experiences during HUBweek, visit hubweek.org.
Publication date : 10/1/2018
Capturing The Spectral Composition of Light Sources
Light management is a critical factor in commercial greenhouse and growth chamber efficiency. "Growers can gain enhanced control of desired plant characteristics by accurately measuring and optimizing the composition of your supplemental light", Abby Brooke with LI-COR Biosciences explains. That's why the company has released a Spectrometer to capture the spectral composition of light sources. In addition, they also offer a light sensor package for use in greenhouses and growth chambers. The new spectrometer and light sensor will be shown at the Canadian Greenhouse Conference next month in Niagara Falls.
PAR
"Plant growth and reproduction is driven by photosynthetically-active radiation (PAR), which occurs at wavelengths between 400 and 700 nanometers. Not all light contains PAR, and PAR requirements vary between types and growth stages of plants", Abby Brooke with LI-COR Biosciences shows.
"As the intensity of natural light in your greenhouse changes throughout your photoperiod, so do your artificial light requirements. Understanding when and how to apply artificial light allows you to consistently hit your target daily light integral (DLI) for optimal growth without wasting energy. "
The team developed the LI-190R Quantum Sensor to solve this. The sensor measures the PAR inside greenhouses and growth chambers with the same precision in sun, artificial lighting, or both, without the need for calibration or correction factors. "Compatible artificial sources include incandescent and high-pressure sodium lamps, high-intensity fluorescent lights, and the rapidly emerging range of LED light systems."
Spectral composition
In addition, now there's also the LI-180 Spectrometer This one captures the spectral composition of light sources. "Not all light affects plant growth and reproduction the same way. As said photosynthetically-active radiation (PAR) occurs at wavelengths between 400 and 700 nanometers. This interval covers three distinct “color” bands of light, and modifying the intensity of these red, blue, green wavelengths, and additional near-UV (380-400 nm) and far-red (700-780 nm) bands can provide control over a variety of plant characteristics including growth rate, chemical composition, taste and nutrition, and more. The LI-180 spectrometer allows you to capture and optimize the spectral composition of your supplemental lighting which can add significant value to your greenhouse or growth chamber operation."
The measured parameters including color-specific photosynthetic photon flux density (PPFD), photon flux density (PFD) at 1-nm intervals between the entire 380 and 780 nm interval, irradiance (W/m2), and more, are all visible in the mobile application and desktop software.
The Spectrometer is to be introduced at the Canadian Greenhouse Conference. Met Li-Cor at booth 1015.
For more information:
Li-Cor Biosciences
402-467-0617
www.licor.com
abby.brooke@licor.com
Publication date : 9/25/2018
Author:
© HortiDaily.com
TotalGrow Turns Greenhouse Into Year-Round Operation
During the cold, dark months of January and February, the greenhouses of Mud Lake Farm were formerly dormant. Most of the staff was on temporary layoff awaiting a return to work when the longer daylight of spring made the farm bounce back to life.
TotalGrow Lighting
Thanks to an unexpected opportunity to test the TotalGrow light emitting diode (LED), the green houses now grow produce all year long and the staff is never without work. It’s an interesting story that is founded upon energy efficient lighting.
The Kent Garden Club recently heard the fascinating story of Mud Lake Farm in a presentation highlighting hydroponic gardening. The speaker was Kris Van Haitsma and I followed up with her to hear the rest of the story.
Kris is co-owner of Mud Lake Farm along with her husband Steve. The title of Kris’s presentation to the garden club was “Playing with Mud” and detailed the evolution of the farm from a muddy cow pasture to a highly productive hydroponic greenhouse operation.
The property on which the farm was built has been in Steve’s family for generations. It is primarily low lands and difficult to grow crops on. Kris wanted to do something different with the land which led her to purchase a used greenhouse. After many false starts Kris and Steve settled upon a hydroponic farming operation as the focal point of the farm.
At the point where Kris and Steve had four greenhouses operating during the usual short growing season they were asked to test TotalGrow LED lighting in one of their greenhouses. The goal was to extend the growing season and increase their productivity.
Hydroponics
With hydroponics no soil is needed and the plants float on nutrient rich water 4 to 12 inches deep. During the winter many types of lettuce thrive in a hydroponic garden if they can be kept from freezing and if supplemental light is provided.
In the past the Van Haitsmas had considered high pressure sodium lighting but could not justify the inefficiency of what is considered a typical greenhouse light. The bulb is expensive, uses lots of electricity, needs to be replaced fairly frequently and does not produce the optimum spectrum of light for good plant growth. Not a good combination when your goal is profitability.
An attempt at supplemental lighting with fluorescent bulbs led to less than desirable plant growth so when the test offer was presented, the Van Haitsma’s agreed to install the LED based TotalGrow system in one of their greenhouses.
Kris and Steve were amazed when they realized that the one greenhouse, using TotalGrow lights, was producing more than the other three greenhouses combined. That made adding TotalGrow lights to a second green house an easy decision. Ultimately they have plans to light the remaining houses with total grow as demand for their products rises.
Using a geothermal heating system to keep the air temperature above freezing, the Van Haitsmas expanded the variety of plants they could grow at the same time they developed new outlets for selling their fresh produce. Mud Lake Farms is now a vibrant year round operation!
According to Kris:
“We grow around 40 different varieties of lettuce, including red and green romaine, butterhead, batavia, and leaf lettuces. Since we grow lettuce year-round, we can provide produce to our customers even in winter.”
Kris’s customers include 80 – 100 families living in West Michigan that are enrolled in a type of buyers club. During the Farmer’s Market season they have a booth offering fresh picked products including custom made cordials (flavored syrups) that are made from ingredients grown on the farm.
Mud Lake Farm Cordials
Many local chef owned restaurants prefer the premium quality of Mud Lake Farm’s freshly picked produce. Relationships with those chefs are most often made by word of mouth and one came from a web search of LocalHarvest.org. Sadly, most chain restaurants do not seek out local growers, a situation that the restaurant chain Chipotle is making great strides at correcting.
Kris noted that a lot more infrastructure is in place for connecting locally grown products with local outlets. The sustainability and farm to table movements are helping drive those connections.
When a product like the energy efficient LED TotalGrow can improve the cost efficiency and productivity of a local grow operation, everyone wins as more products are brought to market and enjoyed by customers in many venues. The Van Haitsma’s Mud Lake Farm is a “shining” example of using energy efficiency to drive productivity as well as profitability!
The Energy Alliance Group of Michigan is a leader in clean energy PACE project development and financing.
US (MD): South Mountain MicroFARM Increases Lettuce Yield By 60% And Microgreens Yield By 10%
South Mountain MicroFARM is a 100% LED-lit, aquaponic leafy greens cultivator in Maryland. The 7,500 square foot greenhouse is situated on the Sellers family’s 22-acre Christmas tree farm. Two-thirds of the greenhouse contains media beds, hydroponic channels and vertical racks that grow a wide range of lettuces, herbs, and microgreens. The remaining one-third houses tanks of tilapia. For Levi Sellers, South Mountain’s Head Grower, building the greenhouse was a homecoming in multiple ways. Levi has lived many lives - he’s worked in a hydroponics supply shop, as a mountaineering guide, and an EMT. But he felt agriculture calling him back to the family farm.
Building an energy-efficient greenhouse
One of the biggest challenges to growing year-round in Maryland is the summer heat and humidity. As a result, the greenhouse was designed with the west-facing wall open for ventilation, so that the winds that blow from west to east can passively cool the greenhouse. Levi installed shade cloths to further soften the relentless heat and light of Maryland summers. Vertical fans help control humidity levels. The lower heat output of the LumiGrow fixtures made them the practical choice for Maryland’s climate.
“When it’s 80% humidity and 100 degrees outside, there’s not a thing you can do. If it’s a cloudy day, you still need to run your lights so that you don’t lose production," explains Levi, "If we were using HIDs, we’d just be increasing our heat more. It’s much harder to control. We really like that we’re able to run our lights on cloudy days and not worry so much about the heat.”
Choosing LumiGrow has also allowed South Mountain to save on upfront infrastructure costs. Installing HID fixtures would have required them to install an additional electrical service panel and purchase a larger backup generator. When the power goes out for extended periods of time during the summer, the lower power draw of the LumiGrow fixtures makes it possible to run both the fish tanks and the lights on the farm’s existing generators. South Mountain MicroFARM also received a 40% utility rebate for purchasing energy-efficient lights, which made the price competitive with HID.
For South Mountain, the benefits of choosing LEDs over HPS were clear. LumiGrow’s high standard of customer service made the choice a no-brainer.
“We looked at several of your competitors, but they weren’t offering the same spectrum adjustability and their customer service wasn’t as good as what I experienced with [our Account Manager] Mike," recalls Levi.
Picture-perfect lettuce
According to Levi, South Mountain’s heads of lettuce are a lot bigger and denser than their hydroponically grown competitors at the grocery store. South Mountain’s lettuce fills the package better, making them more attractive to the end-consumer.
“When I compare photos of our greens grown under LEDs to others' grown with the same aquaponics system who went with the manufacturer’s recommendation to use HID, our LED-grown lettuce looks so perfect and pristine that it almost looks fake,” says Levi.
Levi runs his fixtures year-round to maintain the specific DLI that produces the uniform, picture-perfect plants that consumers are looking for. He tries to maintain about 18 hours of light per day, so the energy savings from his LumiGrow fixtures make a big difference. DLI and photoperiod are both key factors in biomass generation - the higher the DLI, the more biomass produced per plant lifecycle.
Levi’s LumiGrow fixtures have had a huge impact on his lettuce crop - they reach harvest size in 40-50 days, shaving up to 33% off the crop production cycle. This allows Levi to fit in more turns. Levi has also had great results with his microgreens - his LumiGrow-lit trials were ready to harvest 2-3 days earlier than his unlit microgreens. The LumiGrow-lit trays also produced approximately 10% more material per tray.
Levi has also experimented with allowing the heads of lettuce to grow for the full 55-60 days. He found that the LumiGrow-lit lettuce was 40-60% heavier. Restaurants buy lettuce by the tote, so heavier heads of lettuce allow South Mountain to reach the tote weight that restaurants expect with fewer heads of lettuce. All of this means more revenue for South Mountain MicroFARM.
In addition to producing a better-looking, more marketable product, South Mountain MicroFARM uses 75% less energy than their friend’s similar-sized greenhouse.
A pink beacon of sustainability
Initially, Levi had some concerns about what the locals would think about the greenhouse’s vivid hue illuminating the side of the mountain. His fears were unfounded. While the locals often jokingly ask if the farm is having a rave without inviting them, the truth is that they love the pink glow. Their kids adore how it stands out at night and proudly use it as a landmark when telling their friends where they live.
“It acts as a form of advertisement for us, and it’s really sped up the word of mouth advertising about our business and what we’re doing,” says Levi, “We’ve built our brand around being very sustainable and eco-friendly. We focus on every detail, down to the fish feed to make sure it’s locally sourced and sustainably grown. And what better way to show people that than an uncommon glow of pink from our greenhouse? The pink glow means we’re doing something different.”
For more information:
LumiGrow
800-514-0487
info@lumigrow.com
www.lumigrow.com
Publication date : 9/24/2018
Does It Make Economic Sense For You To Install Grow Lights?
Posted on 09/27/2018
Written by David Kuack, HortAmericas.com
The Lighting Approaches to Maximize Profits (LAMP) project aims to determine how growers can maximize their return on investment when considering installing grow lights.
As light emitting diodes (LEDs) become more efficient and more affordable, an increasing number of greenhouse and plant factory growers will consider installing LED luminaires to light their crops. In the case of greenhouse growers, these luminaires would provide light to supplement natural sunlight. For plant factory growers, production depends entirely on the light provided by an artificial light source including LEDs, high pressure sodium or metal halide luminaires.
According to University of Georgia horticulture professor Marc van Iersel, the electricity for supplemental lighting in a greenhouse accounts for 20-30 percent of variable costs. In the case of plant factories which rely solely on artificial light, the electricity cost accounts for 50-60 percent of the variable costs.
van Iersel is heading up a $5 million, four-year research project that will focus on enabling growers to maximize the return on their lighting investment. Funding for the Lighting Approaches to Maximize Profits (LAMP) project is being provided by the USDA National Institute for Food and Agriculture Specialty Crop Research Initiative. The team that has been assembled to work on the project includes 15 university researchers, an advisory panel of greenhouse and plant factory growers and industry consultants.
“The job of the advisory grower panel is to make sure that the research that we do is actually what they need,” van Iersel said. “These are growers who will directly benefit from the research. We are also working with consultants who represent a big section of the industry. We are looking to them to help disseminate the information generated by the research to the industry.
“The research is looking to determine how growers can maximize their return on investment. There has been a lot of research done on how to grow plants with LED lights. We know growers can produce plants with lights. But what we don’t really know is how can growers make the most money doing it.”
Focused on LEDs
van Iersel said most of the project’s research will focus on the use of LEDs with some economic comparison to high pressure sodium (HPS) lamps.
“LEDs are clearly the lights of choice for the future,” he said. “Where we are interested in comparing LEDs and HPS is in regards to the economics. LEDs are more efficient, but they are also more expensive. Is the extra cost of LEDs worth it or are some growers actually better off paying less in capital expense for HPS lamps and more for the electricity to operate them? That is not a simple question to answer.
“There really hasn’t been a big price drop in LEDs. What LED manufacturers have done is rather than lowering the price, they have focused on making the LEDs better. Newer LED lights have hundreds of individual diodes in them. That is one way to help make the lights more efficient. But obviously they are putting more hardware in the lights. In older LED lights there were fewer individual diodes that went into a single light. The diodes were expensive. Now that the diodes are relatively cheap the manufacturers are putting in more of them so that the lights are more efficient. There seems to be a race among manufacturers to try to make the most efficient LED light possible. Right now it seems like the focus is more on creating a more efficient light than on creating a cheaper light.”
van Iersel said LED light manufacturers can easily match the light intensity of HPS lamps.
“What the LED manufacturers typically do with more diodes is run the diodes at only a fraction of their full power,” he said. “That makes the diodes more efficient. If an LED operates at 50 percent of its maximum power, it is substantially more efficient than running it at full power.”
Using supplemental light efficiently
One area that van Iersel is particularly interested in studying is making sure that growers provide supplemental light when plants are best able to efficiently use the light.
“LEDs are fully dimmable and can be dimmed instantaneously,” he said. “LEDs can very easily be programmed to respond to ambient light levels. One of the things that we are working on is designing systems that dim automatically as the sunlight level increases.
“With LEDs it’s more than turning them off and on, it’s dimming them. We have a system where we are calculating every second how much light to provide and how much to dim or brighten the LEDs. That is not possible to do with HPS.”
van Iersel said most LEDs are already dimmable.
“Every LED light is dimmable, it’s just a matter of using the right driver, which provides the power to the LEDs,” he said. It is very easy to incorporate into the lights. What I would hope is going to ultimately happen is growers are going to demand this kind of technology when they look at LEDs and the manufacturers have no choice than to provide it.”
van Iersel said another area of interest with the research is using the light spectrum as a way to manipulate quality.
“This could be accomplished with either the red:blue ratio or the amount of far red that is incorporated into the spectrum,” he said. “We also want to look at how the light is actually delivered to the plants. Right now, at least with ornamentals, growers look at the daily light integral (DLI) that is required to grow a particular crop. There are some clear indications that if the DLI is spread out over a longer photoperiod, for example, 20 hours instead of 14 hours, with the same amount of light over the entire day that more growth occurs with the longer photoperiod. This would be a lower instantaneous light level, but the same amount of light over the course of the entire day. This would allow growers to purchase fewer lights.”
Simplifying growers’ choices
van Iersel said one of outcomes of the research project is to be able to provide growers with a simple to use calculator that allows them to figure out if supplemental lighting will actually pay back in their particular production situation.
“If we can prevent growers from buying lights if they are not going to realize a return on investment that is going to be a good thing,” he said. “If they do decide that they want to use supplemental light, what makes more sense? Is it better to purchase HPS or LEDs? Which lights are going to offer a better return on investment? We hope to develop spreadsheets and some of this information will be incorporated into the Virtual Grower software program that is available free to growers.”
Current, powered by GE, Arize Lynk LED grow lights are being used by mGardens in its vertical farm in Gorham, Kan.
van Iersel also said some of the information that has been incorporated into the proposed horticultural lighting label is going to be required for the calculations.
“The lighting companies typically provide this information already, specifically the efficacy of the lights. Every reputable lighting manufacturer will be able provide this information. After the LAMP research is completed, growers should be able to look at the label information from different lighting companies and run some scenarios to tell them which lights are the most cost effective for them. It is really difficult right now for growers to decide whether or not to light and what kind of lighting is cost effective. It depends on a number of factors including where they’re located, their electricity prices, the crops they’re producing and how well those crops respond to supplemental light. Unfortunately, currently there is a lot of information that needs to go into doing these calculations. This has hampered the adoption of LED lights because growers can’t determine if they can pay for them.
“Once the research is done, the only numbers growers should need to plug in are basically the profit margins on their crops. Hopefully we will be able to provide them with the rest of the information they need to determine whether installing lights makes sense financially.”
For more: Marc van Iersel, University of Georgia, Department of Horticulture, Athens, GA 30602; (706) 583-0284; mvanier@uga.edu; http://hortphys.uga.edu/personnel/van-iersel.html; https://www.facebook.com/HortLAMP.
This article is property of Hort Americas and was written by David Kuack, a freelance technical writer in Fort Worth, TX.
Posted in News
Tagged Ag Tech, Indoor Ag, LED, LED grow light research, LED Grow Lights
A Light Salad: LEDs Revolutionize The Horticulture Industry
By Len Williams
Wednesday, September 12, 2018
With their low energy usage, reduced heat output and the ability to control the light colour they emit, LEDs are poised to revolutionize the horticulture industry.
“It’s a real luxury to eat locally grown, leafy greens in the middle of a Chicago winter,” declares Robert Colangelo, founder and CEO of Green Sense Farms. Before he launched his business in 2012, the only truly feasible way to provide fresh salads and herbs during the cold Illinois winter was to truck them thousands of miles from farms in the warmer southern US states.
However, Colangelo has no ordinary farm. Inside a warehouse a few miles east of Chicago, his ‘vertical farm’ contains rows of tightly packed plants, stacked from floor to ceiling. Bathed in a bluey-pink LED light, the vertical farm principally grows salads, herbs and starter crops, while also constantly experimenting with new plants. Green Sense Farms, which is in the process of building new installations and selling its technology worldwide, mostly supplies a local Whole Foods Market distribution plant, as well as nearby restaurants.
Colangelo’s farm offers benefits beyond producing basil in winter. He is able to intensively grow his crops within 30-35 days and constantly send these to his customers – far more regularly and dependably than growing the same crops in a field. The warehouse attracts few pests and, because the environment is entirely controlled, the company uses significantly less water than traditional farming, while avoiding the need for pesticides.
Farms like Colangelo’s offer a tantalising vision for the future of farming. They allow for faster, more efficient growing, significantly less waste and the ability to produce crops near or even within cities – where most plants are now consumed. This potential revolution is, above all, powered by LEDs.
Plants need light to provide the energy that lets them create their own food: they capture this through chlorophyll, a pigment in their leaves. Until relatively recently, there have only been two commercially viable ways to provide plants with this light: using the Sun, or via high-pressure sodium lamps (HPS) installed in greenhouses.
The Sun is, of course, undependable – cloud cover can limit the light available to plants, meaning crops grow more slowly. Growing outdoors also introduces many risks – from too much or too little water, pests, and the requirement to use pesticides. You can also only grow on one level, meaning farms require a huge footprint.
HPS lamps have advantages over the Sun. When installed in a greenhouse they can provide a constant source of light – even when the Sun is behind clouds or when days are shorter. However, Simon Thaler, press officer at Osram, the German lighting manufacturer, explains their drawbacks: “HPS lamps produce over 100lm/W [lumens per watt] but over a wide wavelength range, which is not necessarily optimised to plant growth. The high power consumption and the heat radiated from HPS luminaires also require a significant distance between the light source and the plants, leaving them primarily suitable for top-lighting systems in greenhouses. To compensate for the heat development, they also often require additional hydration of the plants.”
SCIENCE
Effects of colour on plants
Light is a kind of electromagnetic radiation. It is visible to the human eye at wavelengths between approximately 400 and 700nm, with different wavelengths perceived as being different colours. The human retina is most effective at picking up blue, red and green light, with different cells being sensitive to each.
Plants absorb light via pigments called chlorophyll a and chlorophyll b, which reflect green light but are effective at absorbing ‘deep blue’ light (450nm) and ‘hyper red’ light (660nm) as well as ‘deep red’ (730nm). Exposure to different amounts of these wavelengths can affect how the plant grows.
Blue light provides plants with a lot of energy and is used to regulate the opening of stomata – tiny openings on the surface of leaves that control water loss and uptake of carbon dioxide. Providing more blue light results in plants with smaller, thicker and darker green leaves. Hyper red light is especially effective at triggering photosynthesis, and makes plants grow tall and fast. And deep red light impacts on when a plant begins to flower. By combining different colour light in different quantities, you can change the final plant’s qualities.
For instance, a plant mainly exposed to red light will grow tall and thin. But add around 10 per cent of blue light into the ‘recipe’ and it will grow shorter and more densely. Exposing the plant to more of one type of light or another at different stages of its growth can also affect its development.
LEDs offer many advantages over these traditional light sources. They do not warm up the surrounding air in the same way as HPS luminaires do, meaning they can be placed much closer to plants in stacks – allowing for ‘vertical farms’ like Colangelo’s. Thaler notes that LEDs last significantly longer than HPS lamps and use less electricity. They can also be turned on and off in seconds – which is more effective than HPS lamps that require up to 30 minutes to reach capacity.
However, perhaps the most exciting thing about LED is that it gives growers control over the kind of light that the plant is exposed to. As it turns out, plant growth is especially benefited by light in the blue or red part of the spectrum. LEDs can be designed to specifically generate more of this kind of light, which is especially useful for growing plants.
Professor Neil Mattson, a horticulture researcher at Cornell University in New York, describes his lab’s research into LEDs and light. “We look at plant performance when the plant is exposed to different spectra of light, and how this affects the plant’s qualities. For instance, if you expose the plant to more blue light, this produces a plant with thicker leaves. It can also turn on the pathways for secondary benefits such as a plant which contains more antioxidants.”
Mattson describes cutting-edge research which looks at how different light wavelengths mean you can get taller or shorter plants, earlier flowering, or impact nutritional value. His current research has found that “lighting treatments can double the amount of vitamin C found in a tomato”, for instance.
Brandon Newkirk, marketing director at smart lighting company LumiGrow, explains how his company’s LEDs provide growers with this kind of cutting-edge control today. The Californian company has developed cloud-based software that connects to its lighting hardware. This allows growers to constantly monitor light levels in their greenhouses and then ‘tell’ the LEDs what to do according to their own automated growing strategy –whether that’s exposing the plant to more LED light or reducing it on sunny days to bring down electricity costs.
He describes custom-designed treatments, or ‘recipes’, that expose plants to either more red or blue light. These kinds of treatments can, for example, “make for a sweeter or spicier basil leaf”. LumiGrow’s customers can effectively design the ideal produce that end consumers might want by exposing the plant to different light spectrums at different stages of its growth. Newkirk explains how, for example, lettuce plants could be exposed to more blue light towards the end of their growth cycle in order to give a more vibrant colour to the final product.
For the end grower, LEDs have the added benefit of giving them much more predictability – and this can save them money. Professor Marc van Iersel from the University of Georgia reports that in the US alone, around $600m is spent every year on energy used in horticultural lighting. If growers can cut that cost by using more energy-efficient LEDs, then they can boost their profit margins. What’s more, he explains that “in the US, by the time a grower plants a crop in a greenhouse, it’s already been sold”. LED lighting means growers can confidently provide the plant with the right amount of light to ensure it will grow in time – because when growers miss deadlines they are often hit by financial penalties.
LEDs clearly have enormous potential. However, Mattson notes that only around 2 per cent of US greenhouses currently use LED technology, according to a recent Department of Energy study. What’s stopping uptake?
Put simply, LEDs are more expensive to buy than HPS lamps or sunlight. Prices will go down – van Iersel expects the technology to keep improving while costs drop over the coming decade. And companies like Osram and LumiGrow point to the longer lifespan of their products and reduced electricity bills.
Then there’s the question of return on investment (ROI). Mattson explains that for certain crops, it may take up to 10 years to achieve payback, although lighting firms assure ROI is normally achieved in less than five. Either way, growers expect ROI fast, meaning that many still have doubts about whether the investment is right for them.
And there’s the final price for the plants themselves. LED lights can, in theory, be used to grow any plant. However, at present the economics doesn’t make sense for anything but the highest value crops such as salads, herbs, flowers and marijuana. From apples to potatoes to wheat, many cheaper crops are already pretty much perfectly farmed in the great outdoors, meaning LEDs would offer limited value. Van Iersel describes a colleague’s calculation, which estimated that, should wheat be grown under LEDs in the US, a simple loaf of bread would cost an extortionate $11.
He explains that “it’s frustrating for people like us working in the field, because there are various ‘visionaries’ who claim that in future all produce will be grown in warehouses. But, as the example with the loaf of bread shows, that’s not going to happen any time soon.”
Besides the cost aspect of LEDs, Colangelo of Green Sense Farms also highlights other practical industry challenges, especially for vertical farms. There’s a general lack of workers in the agricultural industry, and even fewer who know how to build and rig up LED farms. “There’s no standard textbook on building a vertical farm yet.”
Despite these challenges, rapid advances in LED technology suggest we will reach a tipping point soon – Mattson estimates this will be reached within 5-10 years. At this point, LEDs will be more attractive and cost-effective than HPS, and this could really revolutionise the horticultural industry.
Colangelo expects to see farming become more stratified, with different types of crop being grown in the most appropriate environment. Some plants will always be best grown under the Sun, some in greenhouses and others in vertical farms.
He adds: “People get very excited to see plants growing indoors in a very sanitary environment.”
If he’s right, the future’s bright for the sector.
ECONOMICS
Urban Farming
Move over allotments: industrial vertical farms with plants grown under LED arrays might be the future of urban farming. By growing produce close to where it’s eaten, growers and supermarkets could cut their transport costs, while giving environmentally conscious consumers produce with a lower carbon footprint.
Professor Neil Mattson of Cornell University has been working with economists on a project to study the scalability of controlled urban agriculture. The research looks at the energy costs, as well as carbon and water footprint of a hypothetical urban greenhouse or warehouse farm in New York City, compared to growing and shipping the same food 3,000 miles from California.
Right now, it seems urban farming remains more expensive than traditional agriculture, with production costs roughly twice as high. Nonetheless, high-value and highly perishable plants do have the potential to be more valuable when grown close to where they’re eaten, because more of the product can be consumed before it goes bad. City slickers may soon be eating Waldorf salad grown down the road.
LIGHTING FOOD LIGHTING SUSTAINABILITY FOOD LED SUSTAINABILITY