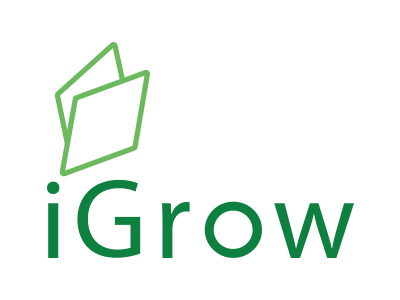
Welcome to iGrow News, Your Source for the World of Indoor Vertical Farming
This Brooklyn Farm Company Is Training A New Generation of Urban Farmers
In old shipping containers, the shoots of a new way of urban farming are starting to emerge, which could help meet the demand of a growing urban population
February 7, 2020, by World Economic Forum
(Credit: Unsplash)
This article is brought to you thanks to the collaboration of The European Sting with the World Economic Forum.
Author: Kate Whiting, Senior Writer, Formative Content
The average age of an American farmer is 57.5 years.
Just under 70% of the world’s population will live in urban areas by 2050.
Square Roots is teaching young city farmers how to grow food sustainably.
Among the high-rise buildings and concrete sidewalks of Brooklyn, there’s a quiet green revolution taking place.
In old shipping containers, the shoots of a new way of urban farming are starting to emerge, which could help meet the demand of a growing urban population.
Square Roots is an indoor urban farming company, which not only grows food sustainably without soil but is teaching a new generation of farmers how to do it too.
“We realized there were tens of thousands of young people who were as passionate about changing the food system as we were, but just didn’t know how to get started,” says Tobias Peggs, CEO of Square Roots.
Feeding the future
Square Roots is tackling several issues in one go: the need to use less water and other resources in agriculture, the aging of farmers, the global population rise and, in particular, the growing urban population.
Farmers in the US aren’t getting any younger, with an average age at 57.5, according to census data, up 1.2 years from 2012.
A new way of farming. Image: WWF/Netflix
And it’s a similar story in other places around the world. In Kenya, the average farmer is 60. In Japan, 67.
By 2050, 68% of the world’s population is expected to live in urban areas, so that’s where much of the focus of food growing will need to be.
“Younger generations are really interested in making sure we’re all eating healthy food that’s nutritious and grown in sustainable ways, but they’re less interested in living in the middle of the country,” says Peggs.
The future of farming
The Next-Gen Farmer Training Program teaches would-be farmers how to grow leafy greens in a high-tech hydroponic system that it says uses up to 95% less water than traditional farms.
They study plant science, to find out what’s happening at a molecular level as the plant grows, they learn about the business side and engage with the local community and agriculture ecosystems.
Food
What is the World Economic Forum doing to help ensure global food security?
Two billion people in the world currently suffer from malnutrition and according to some estimates, we need 60% more food to feed the global population by 2050. Yet the agricultural sector is ill-equipped to meet this demand: 700 million of its workers currently live in poverty, and it is already responsible for 70% of the world’s water consumption and 30% of global greenhouse gas emissions.
New technologies could help our food systems become more sustainable and efficient, but unfortunately, the agricultural sector has fallen behind other sectors in terms of technology adoption.
Launched in 2018, the Forum’s Innovation with a Purpose Platform is a large-scale partnership that facilitates the adoption of new technologies and other innovations to transform the way we produce, distribute and consume our food.
With research, increasing investments in new agriculture technologies and the integration of local and regional initiatives aimed at enhancing food security, the platform is working with over 50 partner institutions and 1,000 leaders around the world to leverage emerging technologies to make our food systems more sustainable, inclusive and efficient.
Learn more about Innovation with a Purpose’s impact and contact us to see how you can get involved.
Each shipping container at the company’s campus in Brooklyn’s Bed-Stuy neighborhood can produce up to 45kg of fresh basil, chive or mint leaves per week, which is grown without pesticides and uses data to optimize flavor and nutrition.
“Successful companies in the 21st century have to be doing well – and doing good at the same time,” says Peggs.
“We’re growing food and selling food, that’s how we make money. But we’re doing that in a sustainable way, which is better for the planet and we’re empowering the next generation of leaders in urban farming.”
8 Keys To Getting Funding Through Contain
Figuring out financing is one of the big challenges every new indoor farmer faces. Like death and taxes, it’s nearly inevitable. According to research from software provider Artemis, indoor farmers’ greatest challenge is finding funding
February 28, 2020
Figuring out financing is one of the big challenges every new indoor farmer faces. Like death and taxes, it’s nearly inevitable. According to research from software provider Artemis, indoor farmers’ greatest challenge is finding funding.
Contain’s mission is to change that, and in our work using tech to better connect growers to vendors and lenders, we always get the same question: how do you up your odds of securing equipment leases? Well, we’ve got answers.
We put together this guide to help anyone considering working with Contain up their odds of funding. We hope it helps demystify the funding process in general, too.
1. Where are you based?
We work with growers across the U.S. and Canada, but our best lender coverage is in the lower 48.
2. How long have you been farming?
We work with lots of startup farms. They’re great. But those with at least a two-year history of operations are more appealing to lenders. They’re viewed as a safer bet. Occasionally, lenders are willing to consider the track record of a different kind of business as you finance your farm.
3. Is your farm profitable?
Naturally, lenders prefer to work with profitable farms. That said, they also understand that increasing a farm’s scale will transform its economics, too. Don’t count yourself out if you’re still building towards the black.
4. What lease size are you looking for?
For a startup farm, we’ve found that it’s best to start small, sell out your produce and then scale to meet your customers’ demand. A common mistake we see is new growers trying to launch with a large setup, more than $1 million in equipment. Lenders rarely back farms like this at the get-go.
5. How much deposit will you put down?
Lenders generally want at least 20% down, and up to 50%. Of course, higher deposits often mean lower interest rates and, generally, better funding odds.
6. Do you have other collateral?
Lenders like to see other collateral for the lease, such as land or an existing property—especially if you’re a new grower. It’s not always necessary, but it definitely helps.
7. Do you have agreements with customers?
We know that most farmers sell produce without a prior written agreement but — at least where it makes sense for your business — lenders always appreciate letters of intent or even letters of support from customers. No bank has ever been mad because it got too many documents vouching for you.
8. How does your credit look?
A good credit rating with no recent bankruptcies usually translates into better leasing offers.
So that’s what you need to get started! Want to calculate your own odds of finding lease-funding? Take our quiz here.
Photo credit: Steve took it on VisualHunt.com / CC BY-NC-SA
Tags: Startup Funding Agriculture Sustainability Small Business
WRITTEN BY
Nicola Kerslake
We’re Contain Inc. We use data to improve access to capital for indoor growers, those farming in warehouses, containers & greenhouses.
Elon Musk's Brother Wants To Transform Farming
Vertical farming is an indoor farming method in which crops are grown in stacked layers, often without soil. The practice is becoming more popular and important as urban populations grow dramatically and available farmland decreases
February 28, 2020
New York (CNN Business)Plant-based foods are all the rage right now, and vertical farms are capitalizing on the trend.
Vertical farming is an indoor farming method in which crops are grown in stacked layers, often without soil. The practice is becoming more popular and important as urban populations grow dramatically and available farmland decreases.
While vertical farming isn't a new concept, these eco-friendly indoor farms are now rapidly expanding.
Elon Musk's younger brother, Kimbal Musk, who was named "Global Social Entrepreneur" of the year by the World Economic Forum in 2017, started Square Roots, an indoor urban farming company based in Brooklyn, in 2016. Square Roots' mission is to bring fresh, local food to cities around the world by empowering younger generations to participate in urban farming.
"When I was a kid, the only way I could get my family to sit down and connect was by cooking the meal," Musk, co-founder and executive chairman of Square Roots, told CNN Business in an email.
Kimbal Musk teaches students how to plant a vegetable garden in California.
"Getting involved with the internet, especially in the late '90s, was very exciting and I wouldn't change anything about those experiences, but my passion has always been food," Musk said. "The moment Elon and I sold Zip2, our first internet company, I knew I wanted to pursue food and become a trained chef." He moved to New York and enrolled at the International Culinary Center.
Musk said the company plans to open a Square Roots "Super Farm" — with 25 climate-controlled shipping containers, cold storage, biosecurity infrastructure and everything else needed to run a vertical farm at scale — in less than three months.
Since its inception, Square Roots has grown more than 120 varieties of crops, including greens, vegetables, and strawberries.
The company isn't the first of its kind. Startups like Silicon Valley's Plenty, which was founded in 2013 and is backed by Jeff Bezos, are also beginning to dominate the space.
"Environmentalists, urban farmers, architects, agronomists, and public health experts, among others, have been joining this mini-revolution as they partner to work out a way to salvage a food-scarce, ultra-urbanized future," Kheir Al-Kodmany, a professor of sustainable urban design at the University of Illinois at Chicago, said in a report.
It involves various techniques, such as hydroponics, which uses mineral nutrient solutions in a water solvent; aquaponics, which uses aquatic creatures -- such as fish and snails -- and cultivates plants in water; and aeroponics, which grows plants in the air.
As for job creation, rapid climate change will put millions of traditional farmers out of business, but vertical farmers won't be affected, according to microbiologist Dickson Despommier, an emeritus professor of public and environmental health at Columbia University.
Although vertical farming was first introduced in the early 1900s, it was recently popularized by Despommier. More than 20 years ago, he began teaching a class at Columbia called Medical Ecology.
Despommier spent a decade growing crops indoors with his students. "Ten years ago, there were no vertical farms," he said, noting that LED grow lights have vastly improved farming efficiency over the last five years, making indoor growing cheaper and more reliable.
Basil growing at the Square Roots farm in Brooklyn.
"People want local food because they've lost trust in the industrial food system that ships in high calorie, low nutrient food from thousands of miles away with little transparency as to who grew the food and how," said Peggs, the Square Roots CEO.
At the same time, the world population is growing and urbanizing rapidly. Peggs said climate change is threatening existing supplies of food, forcing the industry to figure out new ways to grow food quickly.
Peggs is optimistic about raising money for vertical farming. "A lot of smart money and capital is entering the space," he said. "The quality of food that can now be produced in these indoor systems is at least on par with the best organic field-grown food you can buy."
Despommier said that cities will eventually be able to grow "all they can eat" from indoor farms located within city limits. "If an outdoor farm fails, the farmer has to wait until next year to start again, he said. "Indoor farms fail too, but the indoor farmer can start again within weeks."
Containerized Vertical Farming Company Freight Farms Secures $15 Million
Freight Farms — a global innovation leader of containerized vertical farming — announced that it has raised $15 million in Series B funding
By Noah Long ● February 15, 2020
Freight Farms — a global innovation leader of containerized vertical farming — announced that it has raised $15 million in Series B funding
Freight Farms — a global innovation leader of containerized vertical farming — announced that it has raised $15 million in Series B funding led by Ospraie Ag Science. Spark Capital also participated in the round. Including this funding round, the company has raised over $28 million.
“It’s a big step forward for the industry when financial markets recognize and champion the value of creating a distributed food system,” said Freight Farms CEO Brad McNamara. “Aligned on mission-driven growth as a team, there is a massive opportunity before us to scale across global markets, propelling meaningful technology that’s already doing good.”
Freight Farms’ Greenery is able to produce over 500 varieties of crops like calendula at commercial scale year-round using 99.8% less water than traditional agriculture. Four rows of the company’s panels on a flexible moving rack system are able to house more than 8,000 living plants at once thus creating a dense canopy of fresh crops.
This round of funding will be used for advancing the Freight Farms’ platform through continued innovation with new services designed to benefit its growing global network of farmers and corporate partners. And this investment follows the announcement of Freight Farms’ strategic national partnership with Sodexo to grow food onsite at educational and corporate campuses nationwide and will support ongoing contributions to collaborative research projects and partnerships.
“Freight Farms has redefined vertical farming and made decentralizing the food system something that’s possible and meaningful right now, not in the ‘future of food,'” added Jason Mraz, President of Ospraie Ag Science. “Full traceability, high nutrition without herbicides and pesticides, year-round availability – these are elements that should be inherent to food sourcing. Freight Farms’ Greenery makes it possible to meet this burgeoning global demand from campuses, hospitals, municipal institutions and corporate businesses, while also enabling small business farmers to meet these needs for their customers.”
Launched in 2010 by McNamara and COO Jon Friedman, Freight Farms debuted the first vertical hydroponic farm built inside an intermodal shipping container called the Leafy Green Machine with the mission of democratizing and decentralizing the local production of fresh, healthy food. And this innovation, with integral IoT data platform farmhand, launched a new category of indoor farming and propelled Freight Farms into the largest network of IoT-connected farms in the world.
Freight Farm’s 2019 launch of the Greenery raised the industry bar, advancing the limits of containerized vertical farming to put the most progressive, accessible, and scalable vertical farming technology into the hands of people of diverse industry, age, and mission.
“With the Greenery and farmhand, we’ve created an infrastructure that lowers the barrier of entry into food production, an industry that’s historically been difficult to get into,” explained Friedman. “With this platform, we’re also able to harness and build upon a wider set of technologies including cloud IoT, automation, and machine learning, while enabling new developments in plant science for future generations.”
Freight Farms has been an integral part of scientific and academic research studies in collaboration with industry-leading organizations, including NASA (exploring self-sustaining crop production) and Cold Spring Harbor Laboratory (exploring the integration of CRISPR seed genetics and vertical farming to create commercial opportunity).
The company’s customers hail from education, hospitality, retail, corporate, and nonprofit sectors across 44 states and 25 countries, and include independent small business farmers — who distribute to restaurants, farmers’ markets, and businesses such as Central Market, Meijer, and Wendy’s
US: South Carolina - Vertical Roots Hits The Road In Their Lettuce Localmotive, Spreading The Good Word of Hydroponics
The hydroponic growing system is simple - nutrient-filled water replaces traditional soil in order to grow the plant, and for the first time since we started tilling land farmers can grow crops without the soil beneath their feet
The technology of planting crops has revolutionized over the years.
The hydroponic growing system is simple — nutrient-filled water replaces traditional soil in order to grow the plant, and for the first time since we started tilling land, farmers can grow crops without the soil beneath their feet.
Hydroponic container grower Vertical Roots is taking one of their shipping container farms on the road — they're hitting the streets with the Lettuce Localmotive, teaching people about the process of growing lettuce. They'll be making stops at Publix and Greenwise Markets across the country.
RELATED Tiger Corner Farms produces full-scale, aeroponic crops in recycled shipping containers: The Future of Farming
Unlike traditional farms, the Vertical Roots' containers grow plants vertically indoors without soil, with the plants obtaining all their nutrition from water and their light energy from powerful LED lights.
During tour stops, guests will get a hands-on experience with seeding lettuce, learn how technology manages the growing process, and get schooled about all the benefits of this alternative way of farming.
The first stop of the tour is at Vertical Root's home base — Charleston. Check them out at the Daniel Island Publix this Sat. Feb. 15 from 10 a.m.-4p.m.
A Belly Ache Can lead To A Trip To The Urgent Care. E. coli Poisoning Lands You In The Emergency Room
The FDA has called little attention to the surge in E. coli outbreaks from leafy green vegetables. It has been slow to investigate or publicize risks and did not disclose one outbreak to the public until the Globe contacted agency officials about reports of E. coli poisonings
Dietitian Determined To Save Salads!
February 12, 2020
Written by Dr. Jenna Bell, RD VP of Nutritional Science at Crop One
Crop One is the world’s largest scalable, completely controlled, vertical farming company. Our Greater Boston brand is FreshBox Farms.
Spend a few days bent over, writhing in abdominal pain and you’ll understand how serious foodborne illnesses can be. It may even require a trip to urgent care. Experience an outbreak of E. coli O157:H7 from salad greens and you may be among hundreds heading to the ER.
E. coli poisoning can be life-threatening.
What is E. coli, anyway?
Straight out of the Center for Disease Control (CDC):
“Escherichia coli (abbreviated as E. coli) are bacteria found in the environment, foods, and intestines of people and animals. E. coliare a large and diverse group of bacteria. Although most strains of E. coli are harmless, others can make you sick. Some kinds of E. coli can cause diarrhea, while others cause urinary tract infections, respiratory illness and pneumonia, and other illnesses.”
To be crystal clear — we’re talking about fecal contamination. Poo in food. Bird, cow, human, someone’s poop.
As a registered dietitian, I swear by colorful salads of leafy greens with favorite fruits, veggies, seeds, nuts and proteins atop. Making that recommendation sans lettuce feels blasphemous and unfulfilling. But given the pace at which the outdoor-grown romaine industry reports bacterial outbreaks, food safety threatens our salad fixings.
Break out bacteria
Over the past few years, romaine has been hit hard by outbreaks of bacterial contamination — especially from the strain, E. coli O157:H7. The most recent string of outbreaks is considered “under control” by the CDC and Food and Drug Administration (FDA), but the final count as of January 13, 2020, is 167 individuals reported in the US.
“Reported” is a key word here because how many times have you called the CDC or the FDA when you were sick?
Lettuce + E. coli is not a new thing
Several years ago (2013), a scientific investigation of a decade-worth of data on hospitalizations and deaths attributed to food commodities (including seafood, farm animals and plants) revealed that among the 17 commodities, more illnesses were associated with leafy vegetables (2.2 million [22%]). Illnesses associated with leafy vegetables were the second most frequent cause of hospitalizations (14%) and the fifth most frequent cause of death (6%).¹
A 2020 piece in the Boston Globe written by venerated reporter, Christine Haughney Dare-Bryan, traced the tracks of the recent outbreaks and illuminated the grimness with a family’s horrific experience with E. coli poisoning in their two-year-old son. In the article, Haughney Dare-Bryan reflects on the quick response from then commissioner of the FDA, Scott Gottlieb:
…[Gottlieb] tweeted to a startled nation that they should stop eating romaine lettuce just two days before Thanksgiving 2018.
E. coli fatigue
However the seriousness, history shows that someone hit the snooze button. Despite the number of updates and investigations, CDC and the FDA can’t seem to get ahead of it. Haughney explains:
Despite the growing number of outbreaks, the agency remains protective of the growers, taking little enforcement action and sometimes shielding growers suspected of causing outbreaks from bad publicity. Consider:
The FDA has called little attention to the surge in E. coli outbreaks from leafy green vegetables. It has been slow to investigate or publicize risks and did not disclose one outbreak to the public until the Globe contacted agency officials about reports of E. coli poisonings. FDA officials insist they planned to disclose the early fall 2019 outbreak all along.
The FDA has not punished any farm or distributor in connection with the seven outbreaks traced to lettuce since 2017 even though federal law prohibits the sale of contaminated foods. The agency concluded that three of the outbreaks were linked to a single California lettuce grower but declined to release the name.
The FDA staff monitoring lettuce production is just a small fraction of that detailed to the federal oversight of beef: There are 614 FDA field investigators responsible for leafy greens compared to 7,068 workers overseeing beef for the Department of Agriculture. Congress recently gave the FDA $8 million to better handle outbreaks, but the agency doesn’t want to talk about the state of its staffing. When the Globe tried to examine just how understaffed the agency is, officials redacted hundreds of pages of records discussing their internal problems.
The agency relies almost entirely on voluntary cooperation from the lettuce industry, an approach that has brought about some safety improvements. But FDA has asked relatively little of the industry and recently delayed implementing rules aimed at preventing E. coli contamination of irrigation water until 2022.
What do we do now?
From one salad enthusiast to another, or one mom to another, or one PhD/dietitian to consumer (take your pick): there is a safer way to grow your lettuce and eat it too.
We can grow indoors. Out of the soil and away from questionable water, weather disruption messes and “run-off” contaminants (think poop).
I found my safe salad environment when I met and started working for CROP ONE.
How do I know it’s safe?
Concealed, confined, enclosed, controlled, secured, safe, protected — all synonyms for Crop One’s modular growing rooms (“mods”). Mods are protected by double door entryways with fancy sliding doors like at the supermarket and a vestibule. Anyone who enters is fully gloved and covered in stylish lab wear (no, not stylish).
Pictured: The most stylish lab wear in Massachusetts
I should add here that because our plants are protected from the world, we don’t need or use any type of -cide (pesticides, herbicides or fungicides), nor do we deal with pests, insects, rain, contaminated water or other farm’s fertilizer or chemicals. We’re free from all that stuff you’re trying to stay free from.
Pure, clean, filtered — water and air. Each mod is carefully controlled for contaminants, chemicals, heavy metals, and other unwanted impurities through a multi-step, quality-controlled purification system.
FreshBox KVH Kosher Certified romaine lettuce.
Two words: Kosher. Certified.
If you’re not familiar with the process by which produce is certified Kosher, visualize microscopes, tweezers, fastidious inspectors, etc. KVH Kosher certification officers perform comprehensive inspections to ensure that Crop One/FreshBox Farms’ produce is free of all pests and insects.
The salad solution.
Crop One can keep your salad safe. Miraculously, along with safety, our modular enclosures are scalable and sustainable in any climate, on very little land, with barely any water compared to traditional farms (about 95–99% less water required), but we’ll save that for another conversation.
Jenna A. Bell, PhD, RD, joined the Crop One team in September 2019 as the VP of Nutritional Science to be part of the global food supply solution.
References:
Painter JA, Hoekstra RM, Ayers T, et al. Attribution of Foodborne Illnesses, Hospitalizations, and Deaths to Food Commodities by using Outbreak Data, United States, 1998–2008. Emerging Infectious Diseases. 2013;19(3):407–415. doi:10.3201/eid1903.111866.
Haughney Dare-Bryan C. Green Alert. Boston Globe. Last accessed January 30, 2020: https://edition.pagesuite.com/popovers/dynamic_article_popover.aspx?artguid=a497f64d-df30-4f48-b026-10aadc66901b&appid=1165
WRITTEN BY
Crop One Holdings
We grow the cleanest, healthiest greens for anyone, anywhere in the world. Our sustainable vertical farms are free from chemicals and climate-proof.
‘Farm of The Future’ To Unlock Potential of Horticulture
Modular Farms Australia director James Pateras said the training farm would help unlock potential in the Australian farming landscape
Special report: EMILY BRADFIELD, Rural Weekly
February 19, 2020
THE Darling Downs is at the forefront of agricultural innovation and is now home to Australia’s first educational modular farm.
This month, TAFE Toowoomba welcomed its first cohort of students to the new Rural Centre of Excellence.
The $2.7 million facility includes a groundbreaking indoor vertical farm, allowing farmers of the future to get their hands on new technology and help shape the future of Australia’s food supply chain.
The vertical farm is the first educational facility of its kind in Australia and one of just two modular farms in the country.
Modular Farms Australia director James Pateras said the training farm would help unlock potential in the Australian farming landscape.
The LED growing lights inside the pod were designed specifically for the system to promote maximum growth .
INSIDE THE FARM
Mr. Pateras describes the farm as a “complete growing system” where plants are grown from seed to harvest inside the controlled growing environment.
The process of growing inside the pod starts with seeds planted in a host plug made from peat moss and allowed to germinate and grow into a seedling, which usually takes about two and a half weeks in most crops.
Plants are grown from seed, rather than seedling, to prevent pathogens or disease entering the pod.
From there the seedling is moved into a vertical tower on the growing wall, where it remains until ready for harvest.
Modular Farms pods are generally used to grow herbs and small leafy greens or even strawberries and blueberries.
The growing lights inside the pod were designed specifically for the system to promote maximum growth and are placed at an ideal distance from the plant canopy.
The farm is also much more water-efficient, using 95 percent less water than traditional crops, as well as the ability to recapture and recirculate water used inside the farm.
The pod is controlled by four indicators: lighting, climate, fertigation, and irrigation, and can be monitored and controlled remotely using an app.
“With a consistent environment, the plants mature much faster than those in a traditional crop.
“It allows us to create a very solid and clean environment for the plants to live in. There’s no cold one day, hot the next day, it’s a very steady environment inside,” Mr. Pateras said.
“A farm like ours can turn a basil seed into a harvestable crop in about five weeks, which is about half the time you’d see in a traditional greenhouse.”
The yield in the vertical farm is also significantly higher than that of a traditional crop.
Inside the 36sq m container farm, there are four growing walls with a surface area of about 65sq m. That 65sq m is able to produce the equivalent of 1000sq m in traditional crops, which equates to about one tonne of basil per year, or upwards of 45,000 lettuces.
Plants are grown in the vertical tower from seedling to harvest.
IN THE CLASSROOM
Dubbed by students as the “farm of the future”, Mr. Pateras said the farm would give students the opportunity to learn about indoor growing technology as the way of the future.
“To be able to do what we do and use as little water as we use is a great opportunity for the kids to realize how we can save on the environment and still consume and grow food,” he said.
The Modular Farms installation at the TAFE campus is one farm with two growing environments, allowing students to experience two different nutrient programs side by side.
“It’s got a dual irrigation system which allows (students) to run experiments side by side but then really focus on the plant biology as well. They can run tests a lot quicker and faster from that set-up,” Mr Pateras said.
Mr Pateras hopes hands-on experience in the growing pod will get the students thinking about the future of food production.
“What I think it will do is create a huge awareness about where plants are going and also allows the kids to learn a lot more about growing plants indoors, which is not new but growing plants on a commercial scale indoors is obviously becoming a bigger factor in the agricultural landscape.
“So it will definitely teach them a lot about what the future may hold about growing food in Australia,” he said.
“The idea of getting in a tractor and plowing up a paddock will maybe one day be a thing of the past, time will tell.
“The technology right now isn’t going to replace the farmer tomorrow but the farm of the future is here now.
“It’s just a matter of more and more people realizing the benefits of what this type of farming can bring to the environment, the community and the people consuming the food.”
A Modular Farms vertical farming operation.
THE FUTURE
Mr. Pateras believes the future of indoor farming is bright, with the potential to completely change the food supply chain and provide fresher, locally sourced produce to communities.
“I definitely think the indoor agriculture space is growing in steam,” he said.
“With the technology improvements over the course of the last few years, we’re seeing reduced entry costs in that controlled system’s space.
“We’re even seeing a lot of the traditional farmers supplementing their traditional greenhouses with growing lights to try to fast-track the speed of growth of their normal traditional greenhouse.”
The container farm has huge potential for isolated communities and city landscapes in delivering clean, fresh produce and eliminating food miles.
“As our cities begin to grow … the opportunity to grow in those areas is huge,” he said.
“It’s probably just scratching the surface in terms of where these types of systems can live, how they can change the food supply chain and improve the quality of food.
“We’re a very lucky country in Australia, where we can grow a lot of our food year-round. What our system allows people to do is create that microeconomy and sense of community farming.
“These things can live anywhere, so the ability to grow fresh leafy greens in Mt Isa or Birdsville is quite powerful in itself.”
The farms also have the potential to eliminate any unnecessary food miles. Australia’s first modular farm is located at Brisbane’s Eat Street Northshore, supplying vendors with fresh produce.
“We harvest our crop on a Thursday, we walk it down 50m to the vendors who buy our crops and by the next night, the produce is on the plate.
“You won’t be able to get in any fresher than that, and in terms of food miles we’re talking 50m,” Mr Pateras said.
“If you can grow food locally with one of our farms, I think it will be a far better injection into the local economy than bringing food in from interstate or overseas.”
Containerized Vertical Farming Company Freight Farms Secures $15 Million
Freight Farms — a global innovation leader of containerized vertical farming — announced that it has raised $15 million in Series B funding
By Noah Long ● February 15, 2020
Freight Farms — a global innovation leader of containerized vertical farming — announced that it has raised $15 million in Series B funding
Freight Farms — a global innovation leader of containerized vertical farming — announced that it has raised $15 million in Series B funding led by Ospraie Ag Science. Spark Capital also participated in the round. Including this funding round, the company has raised over $28 million.
“It’s a big step forward for the industry when financial markets recognize and champion the value of creating a distributed food system,” said Freight Farms CEO Brad McNamara. “Aligned on mission-driven growth as a team, there is a massive opportunity before us to scale across global markets, propelling meaningful technology that’s already doing good.”
Freight Farms’ Greenery is able to produce over 500 varieties of crops like calendula at commercial scale year-round using 99.8% less water than traditional agriculture. Four rows of the company’s panels on a flexible moving rack system are able to house more than 8,000 living plants at once thus creating a dense canopy of fresh crops.
This round of funding will be used for advancing the Freight Farms’ platform through continued innovation with new services designed to benefit its growing global network of farmers and corporate partners. And this investment follows the announcement of Freight Farms’ strategic national partnership with Sodexo to grow food onsite at educational and corporate campuses nationwide and will support ongoing contributions to collaborative research projects and partnerships.
“Freight Farms has redefined vertical farming and made decentralizing the food system something that’s possible and meaningful right now, not in the ‘future of food,'” added Jason Mraz, President of Ospraie Ag Science. “Full traceability, high nutrition without herbicides and pesticides, year-round availability – these are elements that should be inherent to food sourcing. Freight Farms’ Greenery makes it possible to meet this burgeoning global demand from campuses, hospitals, municipal institutions, and corporate businesses, while also enabling small business farmers to meet these needs for their customers.”
Launched in 2010 by McNamara and COO Jon Friedman, Freight Farms debuted the first vertical hydroponic farm built inside an intermodal shipping container called the Leafy Green Machine with the mission of democratizing and decentralizing the local production of fresh, healthy food. And this innovation, with integral IoT data platform farmhand, launched a new category of indoor farming and propelled Freight Farms into the largest network of IoT-connected farms in the world.
Freight Farm’s 2019 launch of the Greenery raised the industry bar, advancing the limits of containerized vertical farming to put the most progressive, accessible, and scalable vertical farming technology into the hands of people of diverse industry, age, and mission.
“With the Greenery and farmhand, we’ve created an infrastructure that lowers the barrier of entry into food production, an industry that’s historically been difficult to get into,” explained Friedman. “With this platform, we’re also able to harness and build upon a wider set of technologies including cloud IoT, automation, and machine learning, while enabling new developments in plant science for future generations.”
Freight Farms has been an integral part of scientific and academic research studies in collaboration with industry-leading organizations, including NASA (exploring self-sustaining crop production) and Cold Spring Harbor Laboratory (exploring the integration of CRISPR seed genetics and vertical farming to create commercial opportunity).
The company’s customers hail from education, hospitality, retail, corporate, and nonprofit sectors across 44 states and 25 countries, and include independent small business farmers — who distribute to restaurants, farmers’ markets, and businesses such as Central Market, Meijer, and Wendy’s.
US: Georgia State University - Freight Farms - Leafy Green Machine
Just yards behind Piedmont North, the Leafy Green Machine is a fully functional hydroponic farm built inside a shipping container. Configured for the immediate growth of a variety of crops such as lettuce, kale, spinach and other herbs, its innovative climate technology and growing equipment allow for the perfect environment 365 days a year
Freight Farms
Just yards behind Piedmont North, the Leafy Green Machine is a fully functional hydroponic farm built inside a shipping container. Configured for the immediate growth of a variety of crops such as lettuce, kale, spinach and other herbs, its innovative climate technology and growing equipment allow for the perfect environment 365 days a year.
LEAFY GREEN MACHINE
Ready, set, grow. Want to try our freshly-grown produce? Stop by Miss Demeanor’s or Centennial Café to try some on your salad or sandwich.
About Our Leafy Green Machine:
Seeds begin in the nursery area, where they germinate and grow into little seedlings.
In this area, plants grow in a shallow trough that periodically floods and drains with the nutrient-rich water solution.
This area holds up to 3,600 plants at one time.
After three weeks in the seedling station, the sprouts will grow into a sturdier leafy green. The plants are transplanted into vertical growing towers that hang from the ceiling.
This method creates a high-density growing environment and maximizes the cubic footage in the container.
Emitters drip nutrient-rich water down the vertical grow tower using only 10 gallons of water daily to grow more than 4,500 plants.
The water that isn’t consumed by the plant flows out the bottom of the tower and is then recirculated right back to the water tank.
As sunlight is important during photosynthesis, the windowless farm is equipped with LED lighting that mimics the sun’s natural light via growth-optimized blue and red hues.
There are 128 lighting strips running about 18 hours per day to maximize the growth cycle, with the lights turned off to give plants time to rest and during peak hours.
US: Florida - Making Microgreens A Household Word
In The Box, which is a completely retrofitted shipping container, Rodriguez sustainably grows an assorted variety of herbs and microgreens, using a minimal amount of water, energy, and soil
January 30, 2020
These broccoli microgreens are 40 to 50 times higher in nutritional value than the conventional form of broccoli. LOIS KINDLE PHOTOS
Farmer Seeks To Make Microgreens
A Household Word
By LOIS KINDLE
Eco-farmer Dario Rodriguez shows the container he uses to sell a variety of microgreens he sustainably grows at The Box Eco-Farm in Ruskin.
Dario Rodriguez wants the whole world to know about the nutritive value of microgreens, but for now, he’ll settle for South Shore and surrounding areas. LOIS KINDLE PHOTOS
The owner of Sustainable Eco-System LLC began his quest to make organic microgreens more mainstream by establishing The Box Eco-Urban Farm and setting it up at the Circle Pond Tiny Home Community in Ruskin last December.
In The Box, which is a completely retrofitted shipping container, Rodriguez sustainably grows an assorted variety of herbs and microgreens, using a minimal amount of water, energy, and soil.
“(The Box) allows for the maximum production of highly nutritional food in the smallest amount of space,” he said. “That’s what makes us eco-farmers.”
As part of his sustainability mission, Rodriguez sells only locally to individuals, restaurants, nutritionists, and chefs. His service area is South Shore, Brandon and some parts of south Tampa.
“To avoid the use of fossil fuels, I would rather place another box in Wesley Chapel, for example, rather than make deliveries there,” said Rodriguez, 49. “We do not ship what we grow.”
Microgreens are green, tiny vegetables with high concentrations of flavor and nutritional value. For example, broccoli microgreens are 40 to 50 times higher in nutritional value than the conventional form of broccoli, Rodriguez said.
Rodriguez’s wife, Iliana, helps him sell microgreens at the Firehouse Cultural Center in Ruskin.
Currently, he is growing broccoli, basil, red cabbage, peas, cilantro, arugula, parsley, kale, radish, sunflower, wheatgrass, and fennel Greek and mustard kohlrabi – all as microgreens. About 48 veggies can be grown as microgreens, Rodriguez said.
“When you buy microgreens from us, I like to tell you about their nutrients and health benefits, which have been acknowledged by the FDA,” he said.
The farmer also likes to tell you about their uses.
“Microgreens can be used in salads, sandwiches and as a topping for soups, pasta, eggs, and rice,” he said. “You don’t cook them; they’re tender without heat.”
Although Rodriguez and The Box are new to the area, he already has many satisfied customers.
“I bought four boxes last week: salad mix, broccoli, arugula, and radish,” said Dee Hood of Ruskin. “I use them on salads, and they’re so good, I just cut and eat them on their own.
“My teenage granddaughter and her boyfriend had some for lunch and loved them,” Hood continued. “I knew they were good for you, but I had no idea they would taste so good.”
Wheat grass, foreground is one of many microgreens Rodriguez currently grows in The Box.
Rodriguez uses high-density seeds in an organic growing medium like jute. In The Box, he’s able to control all of the production parameters: temperature, airflow and the humidity content of the air. The urban farm has a capacity of 720 10-inch by 20-inch trays of microgreens.
Rodriguez and his family moved to Ruskin from Argentina in 2016, when one of his three daughters began studying international business at the University of Tampa.
“We came as a two-year adventure,” said Rodriguez, who earned a master’s degree in global sustainability in 2018 from the University of South Florida. “But we’ve been here almost four years now, so we’ve decided to stay.”
He has invested $124,000 thus far between the Ruskin location and another at Fat Beet Farm in Oldsmar, where he grows mushrooms.
This is the completely retrofitted shipping container Rodriguez located at the Circle Pond Tiny Home Community in Ruskin to grow his microgreens. The Box allows him to produce the maximum amount of highly nutritional food in the smallest amount of space.
Rodriguez sells his microgreens for $3 per box, which is well below what you’d pay at a commercial establishment, and because they’re grown in an organic medium you can harvest as needed and they last longer.
Every Friday, you can find him set up at the Firehouse Cultural Center from 11 a.m. to 2 p.m. Microgreens can be preordered, paid for and picked up there.
To do so, call 813-416-5444, email sustainableecosystems@gmail.com or visit www.sustainablemicrogreens.net.
Facebook Twitter Share
For In-Store Farms To Succeed, Finding The Right Balance Is Key
High-tech growing operations promise to efficiently supply retailers with greens. But the bigger payoff may be in offering shoppers a bit of food theatre
High-tech growing operations promise to efficiently supply retailers with greens. But the bigger payoff may be in offering shoppers a bit of food theater.
Credit: Jeff Wells
AUTHOR: Lauren Stine
Feb. 6, 2020
To appeal to consumers' growing desire for transparency and to know where their food came from, retailers across the country have brought local products into their aisles. They've also created informational web pages, integrated with nutrition apps and encouraged suppliers to tell their story to customers.
With 95% of consumers saying they'll pay more for locally grown products and 21% saying they eat local at least twice a week, though, companies are feeling the pressure to up the ante. Some, like Kroger and Whole Foods, have taken that step by bringing high-tech produce farms into their aisles — a budding movement that's made possible by advancements in growing technology.
Discover how to improve engagement among hourly employees by providing predictability and flexibility.
“Across the indoor farming industry, there have been dramatic decreases in cost when it comes to the physical hardware, advanced LED lighting and technology platforms automating a lot of the growth cycle,” Alexander Olsen, founder of automated mini-farm purveyor Babylon Micro-Farms, told Grocery Dive.
As more and more retailers discuss shifting center store operations online and accentuating the store perimeter, miniature produce farms promise to offer a supply line as well as a touch of food theater.
“We are also seeing a lot of traditional goods that grocers stock being purchased online and it’s freeing up a lot of space in-store,” Olsen said.
Retailers have been bringing cultivation to their stores for several years now. As early as 2012, Rouses sought to dazzle shoppers with an aeroponic garden on the rooftop of one of its New Orleans store locations. Hy-Vee and H-E-B's Central Market stores have also experimented with growing operations, with the latter adding a 53-foot modified shipping container full of greens to one of its Dallas stores.
Whole Foods has established a few different store growing operations. In 2018, it added an in-store mushroom growing display inside its Bridgewater, New Jersey store. The system was provided by Smallhold, a Brooklyn-based indoor farming company that also sells its mushrooms to local restaurants. A few years earlier, the chain partnered with urban greenhouse operator Gotham Greens to open a growing facility on top of a Brooklyn store location.
Credit: Kroger
The trend has gained momentum in Europe and Japan. Founded in 2013, Berlin-based InFarm has placed its in-store farms, which grow leafy greens, herbs, and vegetables, in hundreds of European stores, while Amazon Fresh sells its produce in Germany, France, and Switzerland. Last year, the company raised $100 million in Series B funding.
InFarm recently made its U.S. debut with two Kroger-owned QFC stores in Seattle and will bring its sprigs of kale, mint, cilantro, and dill to 13 more banner locations this year. The greens are initially planted at a nearby distribution center before being transferred to the store, where each plant's growth is monitored remotely by the company. The price points for the greens are competitive at $2.99 per bunch.
Grocery Dive reached out to Kroger and Whole Foods for comment but did not hear back by press time.
InFarm has lofty ambitions for its in-store farms, hoping to significantly impact grocery and restaurant supply chains, according to co-founder and CMO Osnat Michaeli.
“By growing produce on-demand and as close to possible to where it’s consumed, retailers are able to reduce food waste and sunk costs typically linked to industrial farming,” Michaeli wrote in an email to Grocery Dive. “We find that when retailers are able to understand the value, quality and flexibility of our business model they are more than enthusiastic to enter into conversations to explore our farms.”
Retail attraction or real action?
Although in-store farm displays and gardens are attractive additions, farming is no small feat even at a micro-scale.
“I think this trend is going to be closer to food theater and closer to a niche that engages the public and excites them about fresh produce,” Neil Mattson, associate professor at Cornell’s School of Integrative Plant Science, told Grocery Dive. Through his research, Mattson specializes in controlled environment agriculture systems such as hydroponics.
Operating an in-store farm is not for the novice beginner, he adds, noting that a retailer or its farming partner will have to allocate employees to monitoring the in-store farm to ensure it’s working properly. This requires intensive training, adds labor hours and could take the employee away from other tasks that still need doing.
If an in-store farm is not operating properly, the plants could fall victim to unsightly mold, disease and other issues that would make the display unappetizing to shoppers. Should a situation like this arise, the plants must be stripped out immediately and all surfaces must be sanitized, leaving an empty display, said Mattson.
Even for high-tech farming systems that are remotely monitored, Mattson has concerns about long-term success.
"Plants are biological systems so sometimes they don’t grow as fast as you think they should or some other factor becomes limiting and you have to adjust," he explained.
Credit: Pixabay
Mattson also questions whether an in-store farm could supply enough produce to be more than just an interesting display for consumers. Produce sales in the U.S. totaled $60.8 billion during 2018, representing a 1.7% increase over the prior year. The input costs for indoor farming systems, namely water, and around-the-clock electricity to power LED lights, are also substantial barriers even for large-scale indoor growing operations.
“It’s hard to foresee this producing the quantities of produce at the price points needed to become the widespread way that most Americans would buy their lettuce," Mattson said. "I think it is an expensive way to grow produce in a supermarket.”
High-tech farming operations have struggled to overcome high costs in the past, but the new crop of companies like InFarm and Babylon claim their systems are much more cost-effective and scalable.
To the extent that a retailer could overcome these challenges, benefits to having an in-store farm would include cutting out distributors and other middlemen, who often hike up the price of produce, and increasing store traffic, Mattson said. He believes the success of in-store farms may depend on balancing production needs and efficiency with the desire to amuse consumers.
Mattson said a larger-scale operation like Whole Foods' rooftop farm in Brooklyn offers the benefits of a customer draw with a more viable supply line. In recent years, retailers have also turned to large greenhouse and vertical farming operations to supply stores. Gotham Greens operates greenhouses in five states while BrightFarms operates greenhouses in four states and supplies to retailers like Giant Food, Acme and Food Lion.
Finding the middle ground
For Brooklyn-based grower and Whole Foods partner Smallhold, providing mushrooms first and in-store farms second has been a recipe for success. The duo behind the operation started out in a shipping container offering locally grown mushrooms to restaurants. They began asking their buyers whether they could fit a mini mushroom farm on-site and were encouraged enough to start modeling a prototype.
Whole Foods Local Forager Elly Truesdell ate lunch at a Vietnamese restaurant where one of Smallhold’s mushroom farms is located and promptly contacted the company to see about locating one at a Whole Foods store, according to co-founder Adam DeMartino.
“We didn’t intend to start a produce brand, it just sort of happened and a lot of that was because of Whole Foods,” DeMartino told Grocery Dive.
Today, Smallhold maintains mini mushroom farms in restaurants and retail locations, including two Whole Foods stores. It also sells mushrooms under a branded label.
Smallhold visits retail locations where its mini-farms are located once a week to swap out materials and harvest mushrooms. To achieve the volume that a retailer like Whole Foods demands, the company breaks up the growth process, completing the final stages, or fruiting, in-store. Mushrooms have an advantage over other crops grown indoors because of the high weight per square foot that mushrooms usually yield, according to DeMartino.
“Is it right for everyone? I’m not sure. That’s why it’s not the only thing we do,” co-founder Andrew Carter added. “How we look at it is we are offering a bunch of different tools to accomplish the task of getting mushrooms into the hands of everyone in the U.S. and hopefully the world. One of these tools is increasing the visibility of farming by growing on-site.”