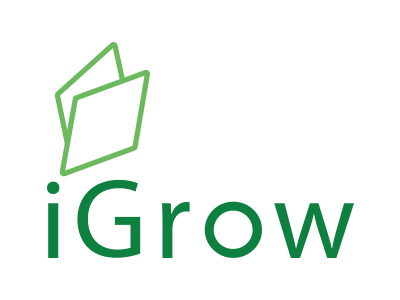
Welcome to iGrow News, Your Source for the World of Indoor Vertical Farming
Inside China's 'Smart Vegetable Farm': Autonomous Greenhouse Allows Plants To Grow Without Soil Or Sunlight
Inside China's 'Smart Vegetable Farm': Autonomous Greenhouse Allows Plants To Grow Without Soil Or Sunlight
- Futuristic farm maximizes the growth potential of plants and is 75 times more efficient than conventional farming
- 54,000 sq ft plant in Fujian, south-east China, can produce eight to 10 tonnes of vegetables every day
- The system automatically regulates temperature, water, humidity, nutrients and LEDs that replace sunlight
By KELSEY CHENG FOR MAIL ONLINE
PUBLISHED: 6 July 2018
These luscious leafy greens sprout from stackable trays in a confined room - without the need of a single drop of pesticide, natural sunlight or soil.
In what could be the future of agriculture in China, a company in Anxi, Fujian province, has been developing a smart farm that enables vegetables to grow efficiently in an automated environment.
The firm's latest expansion project - a 5,000-square-metre (53,819-square-foot) indoor farm - has been under development for the past two years and was finally unveiled last Friday.
Eight to 10 tonnes of vegetables are produced every day on the farm, which is almost the size of a football pitch. That amount of vegetables would be enough to feed nearly 36,000 people, according to Sanan Sino-Science, the company behind the project.
In what could be the future of agriculture in China, a company in Anxi, Fujian province, has been developing a smart farm factory that enables vegetables to grow efficiently in an automated environment
The firm's latest project - a 5,000-square-metre (53,819-square-foot) indoor farm - has been under development for the past two years and was finally unveiled last Friday. The new farm can produce between eight to 10 tonnes of veggies daily
The massive incubation room requires only four staff members to manage - compared with about 300 farmers required in conventional farmlands to produce the equivalent amount.
People in China consume an average of 276 grams (9.7 ounces) of vegetables every day, according to the National Institute for Nutrition and Health.
'Compared with our first generation smart farm, this new plant yields even more effective results while reducing labour and environmental costs,' Sanan Sino-Science CEO Zhan Zhuo told MailOnline.
The company was founded in 2015 by San'an Group and the Chinese Academy of Sciences' Institute of Botany.
Its first generation plant factory, which covers an area of 10,000 square meters (1 hectare), is claimed to be the world's largest vertical farming complex.
The smart farming method, which practices growing vegetables and herbs in multilevel cultivation beds of hydroponic solutions in a controlled environment, is equipped with highly advanced autonomous technology.
The smaller-sized varieties can be harvested in 18 days while larger vegetables take between 33 and 35 days
An automated converter belt was also seen transporting the plates of crisp green veggies for packaging
Scientists donning a full biohazard gear with goggles, face masks, rubber gloves and boots while examining the veggies
The confined indoor space has a strict system that regulates temperature, water source, humidity, nutrients and LEDs that replace sunlight.
'This maximizes the plant's growth potential while maintaining a sustainable and continuous growth cycle,' Mr. Zhan said.
In the factory, the smaller-sized varieties can be harvested in 18 days while larger vegetables take between 33 and 35 days, he added. Vegetables in a conventional farm need about 40 to 60 days to reach maturity, which is also highly dependable on weather conditions.
At full capacity, when the energy cost is neglected, the smart factory can produce 3,000 tonnes to 3,500 tonnes of leafy greens per year.
Video footage of the gigantic smart plant shows factory workers donning a full biohazard gear with goggles, faces masks, rubber gloves and boots while examining and patrolling rows of rainbow-colored LED-lit shelves.
Various plants including lettuce, basil, and bok choy are seen growing on large white trays in tiny allocated slots, submerged in nutrient solutions that are essentially free of soil.
Sanan Sino-Science's first generation plant factory is claimed to be the world's largest vertical farming complex
These vegetables taste less bitter and possess higher nutritional value compared with other conventionally grown plants
The incubation room requires only four staff members, compared with about 300 farmers required in conventional farmlands
An automated converter belt was also seen transporting the plates of crisp green veggies for packaging.
'These vegetables taste less bitter and possess higher nutritional value compared with other conventionally grown plants,' Mr. Zhan said.
More importantly, the new technology greatly saves on water, which is a scarce resource in the country.
'We are working hard to attain a 1:1 ratio between the water used and the vegetables harvested,' Mr. Zhan said, meaning that one tonne of water used can ideally produce one whole tonne of vegetables.
'Currently, 80 percent to 85 percent of the water used could be recycled back into the plant. We hope to reach the 1:1 ratio goal by 2020.'
The company also plans to install AI technology in the facility that can record and analyze growth data through sensors.
The self-learning model will automatically design a template that illustrates the optimal growing condition for each specific kind of vegetable, Mr. Zhan said.
This will also help the farm produce a precise, stable, year-round supply of leafy greens, which means that market prices vegetables could also be more predictable.
More importantly, the new technology greatly saves on water, which is a scarce resource in the country
The smart, GMO-free veggies are sold around 30 yuan (£3.4) to 36 (£4) yuan per kilogram in China
'This farming method is particularly beneficial in challenging environments such as deserts, mountainside towns, or in cities where labor come at a high cost,' Mr. Zhan said.
A tightly controlled environment not only speeds up the growth cycle but also allows researchers to create vegetables that suit specific needs, he added.
For example, scientists can lower the amount of potassium in the greens for patients with kidney problems or increase zinc in cabbages for children.
Right now, the vegetables produced are being shipped to the rest of Fujian province and Shanghai in supermarkets and high-class restaurants.
The brand new technology could help transform China's rapid green revolution amid growing concerns about food safety and nutrition.
The country is also the largest producer of vegetables in the world, harvesting 78.7 million tonnes of vegetables in 2016. The number is expected to rise continuously, according to the National Bureau of Statistics.
The farm can produce a precise, stable, year-round supply of leafy greens, meaning market prices will be more predictable
Through the system, scientists can lower the amount of potassium in the vegetables for patients with kidney problems
The smart, GMO-free veggies are sold around 30 yuan (£3.4) to 36 (£4) yuan per kilogramme in China, while regular vegetables are sold at a wholesale price of 2.85 yuan (£0.32) per kg, according to the latest statistics released by the Chinese Ministry of Agriculture and Rural Affairs.
While this may be an eye-watering price tag to many, a recent food and health survey conducted recently by China Youth Daily on 2,001 Chinese residents shows that more than 76 per cent of participants are willing to spend more money on healthier food choices.
Another 66 percent of those surveyed agreed that they would now pay more attention to the product's nutritional value than its flavor and taste.
The smart factory's relevant equipment and technologies have been shared with countries possessing advanced technological capabilities such as the US, Japan, and Singapore, Mr. Zhan said.
'We hope to bring the concept of "produce locally, sold locally" to different cities,' he said. 'We have ambitious plans to expand.'
Silicon Valley Executive Craig Elliott Joins Autogrow
Silicon Valley Executive Craig Elliott Joins Autogrow
July 3, 2018
Entrepreneur and technology expert Craig Elliott has joined global agtech company Autogrow as an Independent Director.
“We are incredibly excited to welcome Craig to the Autogrow family and our Board of Directors. His wealth of experience will be an asset to the company as we continue our global expansion,” says CEO Darryn Keiller.
Craig has spent over thirty years working in Silicon Valley, starting with ten years at Apple Computer where he worked for Steve Jobs in the mid-80’s. Before moving to California, he grew up working on a farm and received a degree in agriculture at Iowa State University.
He was founder and CEO of Packeteer, a startup that developed deep packet inspection and application-based networking, which he took public on the NASDAQ stock exchange. Craig also founded Pertino which built the first cloud-based, global business network and sold in 2015 to Cradlepoint.
“I was very impressed with Autogrow when Darryn first approached me. I’ve always had a passion for agriculture and watching how technology can truly change the way crops are grown is incredibly exciting. What Autogrow has achieved in the past two years has been disruptive for the industry and it’s just getting started,” says Craig.
Craig is currently a Director of Magic Memories based out of Queenstown and Enable Networks based out of Christchurch. Craig also independently consults with companies looking to develop their technical and global expansion strategies.
His corporate board and governance experience extends to the U.S. and New Zealand and he has just completed five years on the boards of Xero and San Francisco IT development hub, The Kiwi Landing Pad. He and his family have just received their permanent residency in New Zealand and live part time in Wanaka and part-time in California.
(w) www.autogrow.com www.lab.autogrow.com www.cropsonmars.com
Sales queries – Sales@autogrow.com
About Autogrow
Autogrow leverages the power of technology, data science, and plant biology to provide indoor growers affordable, accessible and easy-to-use innovation – 24/7, anywhere in the world.
Our hardware, software and data solutions support growers and resellers in over 40 countries producing over 100 different crop types.
We have a depth of experience and passionate, fun people creating original ideas and making them a reality for our growers.
Indoor Farm Hopes To Bring Locally Grown Produce, Technological Innovation To Las Vegas Food Market
A variety of microgreens and herbs on display at Oasis Biotech on Tuesday, July 10, 2018. The 215,000-square-foot indoor farm, located in southeast Las Vegas, will produce a variety of crops for the local market. (Jeff Scheid/The Nevada Independent)
Indoor Farm Hopes To Bring Locally Grown Produce, Technological Innovation To Las Vegas Food Market
By Jackie Valley
July 15th, 2018
In a brightly lit room, workers donning head-to-toe protective clothing — white jumpsuits, blue bouffant caps, surgical masks, booties, and gloves — huddle over tables lined with trays.
The environment could pass as a research lab or sterile-processing center deep inside a bustling hospital, but it’s neither. The trays contain the mission behind this quiet room: Seeds. And lots of them, in perfectly arranged rows.
This is the seeding room at Oasis Biotech, an indoor hydroponic farm in Las Vegas that’s gearing up to ship its crops to restaurants on the casino-dotted Strip. It’s the first step in a new-age farming process that doesn’t carry the traditional trappings of the industry. No soil, tractors or natural sunlight exist in this 215,000-square-foot-building-turned-farm.
And as far as Brock Leach, the facility’s chief operating officer, and general manager, is concerned, that’s a step in the right direction. He points to worldwide population growth, climate changes and land challenges as reasons why indoor farming is becoming increasingly important.
“This movement isn’t about rocket science,” he said. “This movement is really going to be about innovation and continuous improvement.”
That improvement is already underway. Several weeks ago, workers were assembling 145 seed-filled trays per day, Leach said. On this day, they’re poised to produce 1,045 that will birth crops such as baby arugula, microgreens, and red butterhead.
“That’s how quickly they are ramping up,” he said. “They are the rock stars of this organization.”
Technicians plant vegetable seeds at Oasis Biotech on Tuesday, July 10, 2018. The 215,000-square-foot indoor farm, located in southeast Las Vegas, will produce a variety of crops for the local market. (Jeff Scheid/The Nevada Independent)
A growing industry
As of last year, Nevada contained nearly 250 farms, which includes both indoor and outdoor operations. Most are small or medium-sized farms that pump out everything from potatoes and onions to watermelon and cantaloupe, said Jennifer Ott, plant industry division administrator for the Nevada Department of Agriculture.
“We actually have a pretty thriving melon industry in Nevada,” she said.
But to the Las Vegas resident or tourist who doesn’t venture too far beyond the suburban ring, it might not be very obvious. Many of the farms exist in Northern Nevada, in Churchill and Lyon counties, and others are clustered east of Las Vegas in the Moapa Valley.
State officials said the farming industry has grown in recent years. They expect that trend to continue, especially as indoor farming becomes more popular.
“The more farmers and the more agriculture that is in Nevada, the better,” Ott said. “As a community, when everyone is working together, it sort of lifts up everybody. The more locally available food in Nevada and the more Nevada growers that we have is better for the citizens of the state.”
It’s a belief echoed by Leach as Oasis Biotech prepares to enter the scene. The fledgling company’s roots are half a world away: San’an Optoelectronics Co., a Chinese company that is the world’s largest producer of LED chips, owns Oasis Biotech.
Founded in 2017, Oasis Biotech wants to help feed the world through its massive hydroponic, vertical-farming facility located in a warehouse district in southeast Las Vegas. The plants grow in a nutrient-rich solution, and the seed-to-harvest process all happens inside this massive building, which once served as home to a mail-order pharmaceutical company. Now, white hallways lead to temperature-controlled germination and growing rooms, where the seeds come to life.
As long as farming can be done outdoors, he thinks it will. But Leach considers indoor farming wise preparation for the future.
“It would be foolish for us not to invest and develop in this technology,” he said.
After all, roughly 124 million people in 51 countries endure food insecurity or worse, according to the 2018 Global Report on Food Crises, produced yearly by the Food Security Information Network with help from other global agencies. That’s a 15 percent increase over the prior year.
The report notes that long-lasting conflicts and climate disasters, such as droughts, have contributed to the problem.
The food produced in Oasis Biotech’s indoor farm won’t directly feed the hungry in the most food-insecure nations, but Leach said the operation can indirectly help by fine-tuning indoor farming, thus making it a more common practice.
“Our intent is to help other people engage in this industry by supplying our expertise,” he said.
Decreases in the cost of LED lights paired with an increased desire for locally grown food have spurred the expansion of the indoor farming industry, according to a 2017 report by Agrilyst, a software provider for indoor farmers. Of operation types, indoor vertical farms led the pack in growth last year. And many, like Oasis Biotech, are growing leafy greens and microgreens — crops that have a shorter grow cycle and higher profit margin.
Oasis Biotech has been quietly prepping for its entry into the Las Vegas market. The company, which will sell produce under the brand name Evercress, has been delivering produce to local charities as well as samples to restaurant chefs. Leach said the company plans to work with a local food distributor — he declined to name which one until it’s publicly announced— and provide customizable products to the city’s food-service industry. (For instance, if a chef desires a certain leaf size or a mix of greens, that can be accommodated, he said.)
The long-term plan: produce delivered to local grocery stores.
The company is hosting a grand opening Wednesday for invited guests, followed by a public event Saturday when community members can tour the facility and sample produce. The first distribution to paying customers will occur July 24, Leach said.
Oasis Biotech expects to produce 12,000 servings of salad a day during its initial operational phase, he said. Phase two would quadruple that output. Eventually, the company expects to grow strawberries, raspberries, beets and radishes, among other crops, in the same building. Vast, open rooms await the planned crops.
Former land farmer Dustin Wanders from Caldwell, Idaho, now works at Oasis Biotech The 215,000-square-foot indoor farm, located in southeast Las Vegas, will produce a variety of crops for the local market. (Jeff Scheid/The Nevada Independent)
A new kind of farmer
So far, Oasis Biotech has hired more than 100 people and plans to invest nearly $30 million in the Southern Nevada economy during its inaugural year. The workers include farm hands, data scientists, plant physiologists, salespeople and maintenance crews.
Among them is Dustin Wanders, a 34-year-old who grew up on his family’s potato farm in Caldwell, Idaho. He recently traded his outdoor farming lifestyle for a new gig as grow room supervisor at Oasis Biotech.
Wanders said his father and brother originally thought he just wanted to forgo the farming career. But that’s not the case. The new Las Vegas resident said he developed a fascination with indoor farming and began applying for jobs across the country.
His second day on the new job, Wanders already had identified a perk: “I don’t have to wear sunblock.”
Wanders has a leg up compared to many of the indoor farm workers. Leach said many don’t have prior farming experience, much less in an indoor hydroponic facility, so they’re learning a new skill set. The best way to teach them? “By putting them to work,” he said.
Educational partnerships could sprout in the future. A large group from UNLV recently toured the facility.
Brock Leach, chief operating officer and general manager at Oasis Biotech, displays microgreens and herbs on Tuesday, July 10, 2018. (Jeff Scheid/The Nevada Independent)
In the meantime, Leach said he hopes Oasis Biotech’s presence in Las Vegas at least educates the broader community about indoor farming and its benefits. The grow method and production process, he said, yield fresher produce in a recycled environment that uses less water.
“People don’t understand how much flavor is possible,” he said, motioning to an assortment of product on his desk, including parsley, cilantro, lemon basil and a custom salad mix. “Because of the supply chain and how we’re used to selling our food, we are completely ignorant.”
FROM THE EDITOR
The Nevada Independent is a 501c3 nonprofit. We have generous corporate donors, but we can’t survive on those alone. We need support from our readers. I know you have many commitments. But if you would support our work (or bump up your current donation), we would be forever grateful.
Best,
Jon Ralston
Turn-Key Vertical Farm Technology Available In Japan
Turn-Key Vertical Farm Technology Available In Japan
Netled has made an agreement with M2 Solution on a presence in the Japanese market. The agreement opens Asia's fast growing market to Finnish high-tech vertical farming technology.
Netled has been developing vertical farm technology with the brand name Vera for several years. Turn-key farming technology with intelligent automation has several benefits: it saves fresh water and energy, and with automated processing minimizes the need for manual work. Main automation is not only about steering the equipment, it also includes ready growing recipes, which enables successful growing operations wherever the farm is located.
“We have studied the Japanese market for some time now. These studies have shown, that there is a niche for our state-of-the-art technology and know-how. We have had successful co-operation with Mr. Tsuneo Tozawa, Company Executive of M2 Solution, already in previous projects. With their deep understanding and know-how on the Japanese market and actors we have strong support for our actions in Japan”, says Niko Kivioja, CEO, Netled Oy.
For more information:
netled.fi
Publication date: 6/28/2018
Open AgTech Announces New API Standard Enabling Growers To Use Technology To Its Fullest Within Greenhouses And Vertical Farms
Open AgTech Announces New API Standard Enabling Growers To Use Technology To Its Fullest Within Greenhouses And Vertical Farm
Technologists come together to form new standard for connecting hardware and software for the indoor agriculture industry.
NEW YORK (PRWEB) JUNE 18, 2018
Allowing hardware and software from many different companies to communicate and interact benefits the grower directly and is a leap forward for our industry.
Open AgTech today announced the first version of the AgTech API (ATA) Specification, a standard, programming language-agnostic interface description for REST APIs. The ATA Specification is the first standard to facilitate data transfer and collaboration efforts in the greenhouse and vertical farming industries.
A growing number of technologies common in vertical and greenhouse farming can now complement each other. This provides growers with greater abilities to control indoor growing operations and gain business insights concerning their farming practices.
To date, growers face significant challenges when trying to connect control systems, sensors, machinery, lighting, and software tools made by different companies. This disadvantages growers from gaining new means to manage and automate their operations. The ATA Specification serves to standardize the way technology companies build their APIs, making it possible to exchange data and operational control among different systems used in greenhouses and vertical farms. Growers can now purchase systems from many different manufacturers and have their data flow back and forth, so long as the systems follow the ATA protocol.
Open AgTech is a collaborative community of technology professionals dedicated to improving technology in agriculture. “The AgTech API Specification is the first step toward broad implementation of connected systems for greenhouses and vertical farms,” said the Open AgTech Technical Steering Committee. “Allowing hardware and software from many different companies to communicate and interact benefits the grower directly and is a leap forward for our industry.”
Any organization can adopt the ATA Specification for their products and contribute to further development of the standard. Open AgTech calls on all companies with a product offering in the greenhouse or vertical farming industry to implement and test the standard. Open AgTech holds monthly working sessions that are open to the community and encourages participation from individuals and companies alike. To participate and view Version 1.0 of the ATA Specification, you can go to: https://github.com/open-ag-tech/api-spec.
Many industry leading companies have endorsed and commit to complying with the ATA Specification, including Agrilyst, Argus Controls, Autogrow, Illumitex, Link4, Lumigrow, Motorleaf, and Osram.
About Open AgTech
Open AgTech is a collaborative community of technology professionals dedicated to improving technology in agriculture.
About the AgTech API Specification
The AgTech API Specification is a community-driven open specification within Open AgTech. ATA defines a standard, programming language-agnostic interface description for REST APIs, which allows both humans and computers to discover and understand the capabilities of a service without requiring access to source code or inspection of network traffic.
Can Vertical Farms Reap Their Harvest? It’s Anyone’s Bet
Indoor-grown produce is available in more than 20 supermarket chains nationwide. But despite massive investment, questions remain about efficiency and costs.
Can Vertical Farms Reap Their Harvest? It’s Anyone’s Bet
Indoor-grown produce is available in more than 20 supermarket chains nationwide. But despite massive investment, questions remain about efficiency and costs.
BY STEVE HOLT | FARMING, Technology, Urban Agriculture
07.02.18
By now, the images of shelves full of perfect greens in hulking warehouses, stacked floor to ceiling in sterile environs and illuminated by high-powered LED lights, have become familiar. Food futurists and industry leaders say these high-tech vertical farming operations are the future of agriculture—able to operate anywhere, virtually invincible against pests, pathogens, and poor weather, and producing local, fresh, high-quality, lower-carbon food year-round.
That future seemed one step closer to reality last year when San Francisco-based indoor farming startup Plenty, which grows a variety of salad and leafy greens hydroponically (without soil) and uses artificial lighting in facilities in three locations, announced that it had raised a whopping $200 million in funding from the SoftBank Vision Fund, whose investors include Amazon founder Jeff Bezos.
Flush with cash, Plenty quickly opened a 100,000-square-foot indoor farm outside Seattle that promised to produce 4.5 million pounds of greens annually—including some varieties not yet grown for the masses at scale, such as hydroponic peaches, carrots, and watermelon. To Plenty’s leadership and many observers, the cash influx signaled the economic promise of growing food indoors without sunlight and with less soil and water than field farming.
Photo courtesy of Plenty.
“My reaction [to the $200 million round] was both that of validation, excitement,” said Matt Barnard, Plenty’s co-founder, and CEO, over a manner of farming he says yields 350 times the produce per acre on one percent of the water used by dirt farming. “Now we must move with speed and efficiency if we’re to accomplish our mission of bringing people worldwide an experience that’s healthier for them and the planet.”
Not everyone is in agreement.
“My first thought was, ‘we could build a lot of greenhouses for $200 million,’” recalls Neil Mattson, a professor of plant science at Cornell and one of the country’s leading academic voices on indoor agriculture, who’s found that high-tech greenhouses that harness sunlight are more cost- and carbon-friendly than vertical farms that use artificial light.
Most vertical farmers are only hoping to claim a percentage of the conventional produce market, not replace it. To these founders and their investors, the market for lettuce and greens, especially—grown primarily in California and Arizona and shipped worldwide—is ripe for disruption. E. colioutbreaks like the one that hit Arizona-grown romaine lettuce earlier this year, killing a handful of people and sickening hundreds, only further their case.
But behind futurists’ fervent predictions about indoor agriculture, claims about product quality, and sexy technology lies a reality known by industry insiders but too often missing from media coverage: The future success of this nascent industry is still very much an open question.
The astronomical capital costs associated with starting a large hydroponic farm (compared to field and greenhouse farming), its reliance on investor capital and yet-to-be-developed technology, and challenges around energy efficiency and environmental impact make vertical farming anything but a sure bet. And even if vertical farms do scale, there’s no clear sense of whether brand-loyal consumers, en masse, will make the switch from field-grown produce to foods grown indoors.
Tricky Economics
Walking into any supermarket will reveal a small mountain of salad greens, carrying a price tag of between $9 and $12 per pound. They may be locally grown or organic, which will add $0.50 or $1 to the price tag. Meanwhile, a 4.5-ounce carton of Massachusetts-based FreshBox Farms’ spring mix—grown in the company’s hydroponic farm in Massachusetts—costs $3.99 for a 4-ounce box or $15.96 per pound. Or kale: the conventional variety will run you $1.33 per pound at Walmart; organic kale costs around $4.99 per pound at Whole Foods; and vertically farmed kale grown at Newark, New Jersey-based AeroFarms will cost you a whopping $14.18 per pound.
That dramatic price gap is due to the millions of dollars currently needed to build one large indoor vertical farm—and that price is not going to drop until the industry scales up. Agritecture Consulting, whose clients include current and prospective indoor farms, estimates that a 30,000-square-foot vertical farm growing leafy greens and herbs in the tri-state area around New York City requires nearly $4 million in startup capital—not including labor.
They should know: In 2016, Agritecture built farm.one in Manhattan’s TriBeCa neighborhood, which supplies hydroponic greens and edible flowers to a number of the city’s top restaurants. Chefs have been quick to catch onto the value of consistent, year-round, locally grown produce.
A farm.one indoor farming operation. (Photo courtesy of farm.one.)
In 2016, AeroFarms, now considered an industry leader, spent $30 million on its flagship aeroponic farm in Newark. The majority of these costs lie in the equipment needed to grow greens without soil or sunlight—heating and cooling systems, ventilation, shading, environmental controls, and lights.
All of these costs add up to a hefty electricity bill: According to models compiled for Civil Eats by Agritecture, a 30,000-square-foot vertical farm in metro New York City should budget upwards of $216,000 annually for lighting and power, and another $120,000 on HVAC systems; costs will vary region to region depending on what each state charges for electricity.
Energy and equipment costs are, by far, the largest drivers of expenses that can bring the price of operating a vertical farm close to $27 per square foot. By contrast, Agritecture’s models show that the cost to run a 100,000-square-foot smart greenhouse is roughly a third as expensive, thanks to the use of natural sunlight and more advanced automation.
Vertical farms’ energy usage carries a significant carbon footprint. While vertical farm companies promise more-sustainable produce by growing it closer to consumers and using renewable energy to power their operations, the industry still has a long row to hoe.
Industry leaders acknowledge the energy challenges in the short term, yet tout continually improving lighting technology that has brought down costs. But Mattson, whose Cornell team studies the way plants respond to different lighting, predicts a plateau coming for improvements to LED technology.
LEDs lighting an indoor farming operation. (Photo courtesy of Agritecture.)
“The best LEDs are 40 percent more energy efficient than in 2014,” Mattson says. “There continue to be improvements; however, those improvements will start to slow down over time. There’s only a finite amount of light you can generate at a given wavelength, and in 2022, I’m not expecting new lights to be 40 percent more efficient than the current lights now.”
FreshBox Farms began shipping greens from its 40,000-square-foot hydroponic facility in Millis, Massachusetts, in 2015. The warehouse farm, located 30 miles outside of Boston, runs on a combination of renewable energy and non-renewables, and CFO Dave Vosburg admits his company is “not doing any better” than field-grown greens when it comes to carbon usage.
When it eventually expands outside of Massachusetts, Vosberg says that by introducing a cogeneration system—technology that recycles otherwise wasted heat into new energy—FreshBox Farms will eventually keep costs and carbon emissions down in expensive markets like Connecticut, where commercial users pay an average of more than 14 cents per kilowatt-hour. But Vosburg says the company’s priority is to use contextually appropriate renewable energy sources to power the farms, such as wind energy in the Midwest, hydro in the Northwest, and solar in the Southwest.
“Yes, it sounds crazy to take the sun and turn it into electricity and turn that electricity back into light. It sounds ridiculous, but that’s what we’ll be doing,” Vosburg says. “It’ll be really efficient and clean and create a better product, and it won’t have the same carbon impact that we’re having today.”
And energy isn’t even a vertical farm’s top ongoing expense. The companies Civil Eats spoke to say labor is actually their largest budget item. Vertical farms typically pay workers higher, more metropolitan pay rates than both dirt farms—many of which rely heavily on migrant labor—and the more automated smart greenhouses. The fast-food chain Wendy’s announced in June that it plans to source vine-ripened tomatoes exclusively from greenhouse farms by early 2019.
Moreover, no matter how automated the indoor growing system is, vertical farmers are discovering the constant need for a human eye—or several—on the process. In fact, some estimate that if indoor agriculture continues to grow at the pace it has in recent years, vertical farms will have to hire 100,000 workers over the next decade.
That continued growth is not a given, however. Because of the high cost to launch, operate, and scale up a vertical farming operation, the industry is highly leveraged, with each new farm requiring tens of millions of dollars in investor capital before it can grow a single plant. Between 2016 and 2017, investments in vertical farming skyrocketed 653 percent, from $36 million to $271 million. The lion’s share of that investment went to Plenty, but Newark-based AeroFarms has raised $80 million in recent years and Brooklyn’s Bowery Farming added another $27 million.
Sky Vegetables’ rooftop hydroponic farming operation in New York City. (Photo courtesy of Agritecture.)
Just last week, Manhattan-based BrightFarms announced it had raised $55 million. Shoppers can now find produce grown indoors by more than 23 large vertical farms in more than 20 supermarket chains in nearly every major metropolitan area in the country, according to Agritecture.
While industry leaders say scaling offers the best hope for profitability in this business, many vertical farms have encountered problems when they began planning to add additional production facilities. Before Atlanta-based PodPonics closed its doors in 2016, executives from the five-year-old hydroponic farm startup met with executives from supermarket chain Kroger.
Kroger indicated that it was ready to purchase 25 million pounds of produce from PodPonics annually if it would build the facilities to support that kind of production, founder Matt Liotta told a crowd at the 2017 Aglanta Conference. According to Liotta, who said PodPonics had lowered the cost to produce a pound of lettuce to $1.36, Whole Foods and Fresh Market also expressed interest in bringing PodPonics greens into their stores nationally.
“This was our wildest dream,” Liotta said. “Then we realized how much capital that was going to require, how many people we were going to have to hire. Every retailer told us the same thing: ‘We will buy it if you will build it.’ We realized we were incapable of building everything that they wanted.”
Unproven Demand for Food Grown Indoors
In early 2016, researchers from the University of Illinois-Urbana set out to determine whether consumers would spring for produce grown indoors. They asked a panel of 117 participants a series of questions about their perceptions of and willingness to pay for lettuce grown in fields, greenhouses, and in vertical farms. While vertical farming ranked fairly high in terms of produce quality and safety, the tech-heavy production method was rated less “natural” than both field farming and greenhouse and ranked last in participants’ willingness to purchase it.
For the vertical agriculture industry to eat into the profits of field-grown products—a roughly $140 billion industry—Agritecture Consulting founder and managing director Henry Gordon-Smith says it will first need to prove consumers are demanding produce grown indoors. He points out that because of a lack of demand, many vertical farming operations are not yet at full production year-round—despite touting the 12-month growing season as a main benefit of the industry.
His sense is that indoor farms that have achieved the sales to produce continually—such as Gotham Greens has with its New York City greenhouses, for example—have a customer base that’s responding to strong “local” branding rather than the technology behind the food. That may include vertical farms selling their produce using the USDA Certified Organic label, which the National Organic Board reaffirmed in January, much to the dismay of many organic dirt farmers.
“I think the automation and economics are all improving,” Gordon-Smith says, adding that the question of “whether consumers are going to pay more or whether the products coming out of vertical farms are going to align with their values” is still an open question.
But while many of the East Coast vertical farms built their business models around replacing greens being shipped cross-country from California and Arizona, Matt Barnard of Plenty hopes to add to the global population consuming fresh produce. A 2015 report found that where USDA guidelines suggest each of us in the U.S. should eat up to three cups of vegetables daily, current U.S. production is only providing enough for 1.7 cups per person. Barnard extends that supply gap to the rest of the world, especially the Middle East and Asia, where a lack of water and high pollution have hampered agriculture.
Plenty CEO Matt Barnard. (Photo courtesy of Plenty.)
“We believe the industry will be five times larger when there is supply to meet the demand,” Barnard says. “With the field unable to deliver consistent supply, new forms of agricultural capacity like Plenty must be added to the global food system.”
But as vertical farming companies like Plenty go city by city attempting to dominate local markets, it may be that small farmers get hurt the most. Barnard drew the ire of Washington State dirt farmers last year when he told GeekWire that Plenty expanded to Seattle, in part, because it was the West Coast’s “best example of a large community of people who really don’t have much access to any fresh fruits and vegetables grown locally.”
Not so, according to Sofia Gidlund, Farm Programs Manager at Tilth Alliance, which advocates for and supports local agriculture systems in Greater Seattle.
“We work with many hardworking local farmers who supply Seattle with high-quality, delicious, and nutritious food while caring deeply for our land. These farmers use sustainable farming practices, nurse the soil, create beautiful open green space and provide wildlife habitat,” says Gidlund, who adds that she does not speak for all area farmers on the issue of vertical farming. “Many consumers in Seattle choose to support local farmers, both urban or rural, because of this deep connection to the land. Providing that support is a point of pride for many Seattleites.”
Actual Data Is Coming
Peer-reviewed research into the business of vertical farming has been sparse, partly because the industry is so new. That’s set to change, however, when Mattson and a team of researchers at Cornell University finish a comprehensive study into the viability of this approach.
A three-year, $2.4 million research grant, which is funded by the National Science Foundation and kicked off in January, will compare the vertical farming industry to field agriculture in a slew of categories, including energy, carbon, and water footprints, profitability, workforce development, and scalability. The study will include one of the first nutritional analyses of food grown indoors, as well as comparing the price-per-pound to deliver strawberries, lettuce, and tomatoes grown vertically and outdoors to five U.S. metropolitan areas: New York City, Chicago, Seattle, Los Angeles, and Atlanta.
A 2016 study conducted by a few of Mattson’s colleagues at Cornell found that the energy consumption and carbon footprint associated with a vertical farm (the study calls it a “plant factory”) is significantly higher than that of a greenhouse. Vertical farming leaders counter that they use significantly less water than field farms, are more space-efficient, and do not produce emissions from trucking produce across the country. Mattson says these factors were not considered in Cornell’s previous research but will be included in the current grant.
“[Vertical farming] is not a fad,” says Mattson, who wants to use data to help the industry become more sustainable over time. “I’m not sure to what degree it’s going to scale up, but this is happening. So we need to understand the economic and environmental implications—both the good and the bad.”
Cheers To That! IOT And DIY Solutions At The Smart Kitchen Summit
Cheers To That! IOT And DIY Solutions At The Smart Kitchen Summit
The international food community is full of passionate and enthusiastic people who love talking about and tasting new foods. However, not all of us are natural born chefs, and even the most experienced among us could always use a helping hand in the kitchen. Luckily, the Smart Kitchen Summit is filled with the latest technology to make better kitchens and better food, and Foodfoward made sure not to miss it.
Michael Wolf created the Smart Kitchen Summit in 2015 to bring people from culinary, production, retail, and tech backgrounds together for a conversation about the future. In just a few years, the SKS has become one of the leading events to find how where cooking is headed, what our kitchens will look like, and what they’ll be able to do for us.
The SKS travels through the US, Japan, and Europe, and Foodforward attended the European leg, held in Dublin in June. The gathering started in typical Irish fashion at the beautiful Guinness Storehouse, the museum that recounts the history of the famous beer. This was a perfect opportunity for attendees to meet ahead of the pitches that were scheduled for the following day. As people gathered among pints they discussed their ideas in the relaxed and friendly atmosphere for which Ireland is so well known.
The Smart Kitchen Summit is an important opportunity to better understand how technology can create a bridge between kitchen equipment and the solutions for creating an integrated and ‘smarter’ digital workshop both professionally and in the home. For the next generation of smart kitchens, applications employing IoT and DIY solutions are the main drivers of innovation. Consumers are getting more savvy, and the enormous range of emerging producers means that getting them all to communicate is even more important to get the most out of your kitchen.
DIY projects allow consumers to build their own smart devices and are a natural complement to IoT concepts for those of us who want to update our tools without breaking the bank. Developing these links is fast becoming one of the hottest sectors in food tech right now, and smart solutions from around the world are changing the way we think about our dinner.
Even large companies like Deliveroo are looking with interest at these trends as ‘dark kitchens’, which exist solely to provide for the food delivery market, could greatly benefit by integrating and connecting food production sites. As large-scale production changes to adapt to shifting consumer preferences and a surge in the home delivery market, technologies that bridge the gap between products and the market are more in demand than ever.
Foodforward is very interested in projects working on this sector and wants to know more about how innovation can transform our kitchens. If you’re working on a smart solution that can bring products or brands to consumers, apply now to be a part of the Foodforward accelerator at https://www.food-forward.it/en/ . We can’t wait to hear from you!
The 'Internet of Farming' Is Disrupting Traditional Agriculture
The 'Internet of Farming' Is Disrupting Traditional Agriculture
BY KAREN GRAHAM June 17, 2018 TECHNOLOGY
LISTEN
Generations of farmers have relied on knowledge and family expertise to grow food, but the sector is set for a surge of disruption at the hands of made-in-Canada artificial intelligence-powered systems.
Investment in artificial intelligence is growing in Canada. In 2017, venture capital investment in AI nearly doubled - to $12 billion. And looking at the agriculture sector, AI is helping farmers to increase crop yields, save costs and reduce environmental damages.How is this possible? For generations - farmers have relied on their own knowledge of the land and past experience to get the most profit from their farms, regardless of if they had a dairy or raised food crops. With the new technologies available today, farmers can now target their use of fertilizers or herbicides, saving money and minimizing environmental damage.
Growing vegetables using robotics. Bowery Farms
With AI, dairy farmers now have the option of getting accurate information on the levels of progesterone in milk, providing them with reliable data on when a cow is in heat and the optimum time to inseminate. The technology can enhance farming practices, manage mastitis, reduce unnecessary antibiotic usage, and virtually eliminate the addition of low-quality, low-fat milk into bulk storage tanks.
SomaDetect - Technology for the dairy industry Fredericton, New Brunswick, Canada-based SomaDetect, Inc. was founded in 2016 by Bethany Deshpande and her husband and business partner, Nicholas Clermont. In October 2017, the fledgling company was the $1 million grand prize winner of the fourth annual 43North competition, held in Buffalo, New York.
A photo of a cow being milked on a dairy farm in Girgarre, Victoria. JH
The technology allows dairy farmers to measure major indicators of milk quality and herd health, directly in the milking line. SomaDetect's technology does not require added chores or the use of chemicals, cartridges, or lost milk - It's all automatic.SomaDetect sensors are installed at each milking stall and will identify each cow, test their milk and quickly provide farmers an array of metrics such as protein and fat counts, indicators of disease, hormones (progesterone) that manage reproduction and antibiotic residuals.The company is now preparing to deliver commercial systems this fall that will test milk and use AI to maximize a dairy farmer's profitability through the "Internet of Cows."
SomaDetect
"We are in a fourth revolution in agriculture and AI is absolutely critical," said co-founder Bethany Deshpande. Deshpande points out that the technology is at an early stage - and farmers are just beginning to understand the power and full potential of AI."A lot of farmers have been demanding better technology, demanding better products for a long time and I think AI is a huge part of how they're going to get that."Motorleaf - AI for greenhouse and indoor operatorsFounded in 2015 by Alastair Monk and Ramen Dutta, Montreal, Quebec, Canada-based Motorleaf, Inc. has developed a system that acquires data from indoor growing operations and applies artificial intelligence and machine-learning algorithms to identify growing patterns.
Motorleaf Inc.
The Motorleaf system helps growers produce more, and a better quality product; by automatically adjusting to the needs of the crop. The company builds separate components, each of which has a specific set of functions. They can operate separately, or if you add onto the MotorLeaf HEART - operate as a larger whole. The technology has already been proven in vegetable production operations. California greenhouse SunSelect used Motorleaf’s technology in a trial that led to a 50-percent reduction in yield prediction error in tomatoes. These results were enough for SunSelect to adopt Motorleaf’s algorithms after a short trial. According to the Motorleaf website, "The Heart is the center of Motorleaf’s monitoring and automation system. It can operate separately to monitor air temperature, relative humidity, and light levels and it can connect to the Powerleaf, Droplet, Driplet, Space Sensor and Space Sensor Plus to monitor and control what’s important."
More about agriculture, technology, dairy, greenhouse crops, artificial intelligence
Read more: http://www.digitaljournal.com/tech-and-science/technology/the-internet-of-farming-is-disrupting-traditional-agriculture/article/524885#ixzz5IiyxouUd
Autogrow Welcomes Technology Focused CFO
Autogrow Welcomes Technology Focused CFO
Rod Britton has been named Chief Financial Officer at global AgTech company Autogrow to help drive its ambitious growth plans.
Rod has worked for over 30 years in technology-led businesses in the United Kingdom, Europe and the U.S. His experience spans operational, strategic and corporate finance as well as partnerships with private equity, venture capital and other external finance providers.
“I believe in a strong customer focus and understanding what they will experience. This includes how we price something, the value proposition, how support is handled, and generally how the customer is handled through their time with us,” Rod explains.
“Autogrow has growers of every size, in multiple countries, growing different crops in a variety of different growing environments (greenhouse, protected cropping, indoors), and all of them have different challenges. The common language amongst them all is ‘financial’.”
“In the end, we are solving the challenge of increasing the financial returns to growers, which could be through higher yields, better quality, reduction in waste, reduction in operating costs, reduction in natural resources or increasing the predictability of harvest. By improving these drivers of improved grower performance, the customer benefits and there is more food to go around when people want it.”
For more information: www.autogrow.com
Publication date: 6/18/2018
African Smallholder Farmers Embrace GPS-Based Digital Solution
Techno Brain
African Smallholder Farmers Embrace GPS-Based Digital Solution
Smallholder farmers are the most vulnerable to impacts of climate change, with rain-fed agriculture accounting for more than 90% of farmed land in sub-Saharan Africa. These farmers face many risks, including drought, disease and pest epidemics. But a new GPS-based digital technology may help many African smallholders improve their crop yields and income.
The new technology solution was initially deployed in India and is now being pushed across the African continent in countries like Malawi and Tanzania. This solution is the fruit of a partnership between Techno Brain (Microsoft) and the National Smallholder Farmers Association of Malawi (NASFAM) and ETG Farmers Foundation in Tanzania, respectively.
The technology solution will collate data, starting with the farm’s location using Global Positioning System (GPS) coordinates, expected rainfall and weather patterns, land type and soil nutrition. The collated data will be processed via intelligent cloud to create insights that help farmers in Africa make better farming decisions.
Farmers will receive tips on their mobile via SMS and voice platforms. These insights will include: best crops to plant, optimal sowing week, pest growth alerts, adverse weather notices, preferred harvesting time, market information and general farming tips. According to cp-africa.com, Microsoft says that the implementation of this solution will also enable development of new agribusiness models and make agriculture a viable livelihood for many farmers across the continent.
Publication date: 6/18/2018
"Indoor Farms Could Fine-Tune The Flavours of Our Food"
"Indoor Farms Could Fine-Tune The Flavours of Our Food"
A new way to farm indoors using different wavelengths of light could boost the taste of fruits, salads, and herbs, while also increasing food supply and nutritional value.
Growing food inside brings many benefits to farmers by reducing the amount of land, fertilizers, energy, and water needed to cultivate the plants.
But it can come with a major drawback – produce grown indoors sometimes lacks the depth of flavor it would have if it was allowed to flourish and ripen outside.
And it is the controlled environment of indoor farming itself that seems to be at least partly responsible.
‘A plant that grows outside is stressed,’ said Alexander Penzias, co-founder of Ponix Systems, an agriculture company specializing in indoor farming based in Vienna, Austria.
Extreme temperatures, hailstones, torrential rain or too much shade all produce stress that affects the growth rate of food. But these trying moments also force plants to produce phytochemicals, the active compounds that give fruit and vegetables their distinctive flavors.
In the future, produce could be grown directly in supermarkets or restaurants. Image credit - infarm
Despite increasing yield, the carefully controlled climates used in indoor farming do not stress the plants enough for them to produce these flavorsome phytochemicals.
This is bad news for taste. But it is also a weakness that could prevent this form of sustainable food production ever achieving widespread acceptance by consumers.
Indoor farming techniques like greenhouses and hydroponics systems, a soil-free system that uses artificial sunlight, also produce fewer greenhouse gas emissions than traditional agriculture. But if consumers are not willing to buy food produced in this way, the environmental benefits will be impossible to realize.
‘If you have plants that come out of a hydroponic system, it is not a case of them tasting good or bad, it is that they don’t have a taste at all,’ added Penzias.
His team, however, have focused on tuning light emitting diodes (LEDs) to produce specific wavelengths of light that encourage indoor plants to release phytochemicals.
They have developed this into a series of light recipes for specific plants that not only enhance flavor but allow it to be tuned. Amber light, for example, can increase the flavor of basil, while ultraviolet light can boost the taste of tomatoes flavor and also make salad leaves thicker and therefore more palatable.
Subjecting plants to different wavelengths of light can induce the production of phytochemicals and help develop flavors. Image credit - Ponix Systems
On top of that, it can also boost the health benefits of the food.
‘If it tastes better, it means it has a higher nutritional content,’ said Penzias. Many phytochemicals can be classified as antioxidants, which are good for heart health and the immune system, he added.
Ponix Systems are currently conducting a feasibility study of their LED technology as part of the flexiLED project. Once it is completed, they hope to team up with researchers and farmers to develop a commercial product.
Currently, the indoor farming company specializes in a hydroponic system called Herbert, which are stackable modules that can be installed on walls in homes or larger premises like offices or restaurants. They have already installed some of these modules in a school and a hospitality academy in Austria.
‘At first, the cooks were skeptical of the system,’ said Penzias. ‘But as soon as the cooks started harvesting the food, the flavors were more intense than what they expected.’
Commercialisation
Ponix Systems are planning to introduce their new light recipe technology at the school within the next few months and at the hospitality academy soon after that. The chefs there are already eager to tune the flavors of their indoor-farmed food.
This is a significant achievement, Penzias believes, because overcoming the skepticism of notoriously picky chefs is a good insight into the challenge of convincing the public.
‘When consumers hear the term hydroponics they are immediately scared,’ said Penzias. He said the term can often sound too technical or chemical to appeal to environmentally conscious shoppers.
But one indoor farming business based in Berlin, Germany, may have found the secret to successfully addressing the taste issue on a large scale in Europe.
Infarm offers supermarkets monthly subscriptions to rent an indoor farming system alongside their optimizing growing services, such as algorithms that determine the most efficient use of light, water and nutrients. They also use specific wavelengths to enhance the flavour of the plants they grow.
Martin Weber, chief financial officer at Infarm said: ‘We are really able to show that people are buying our produce and prefer it over existing stuff that is out there.’
Infarm produce has already been used by Michelin star chefs in Germany, while their indoor systems have been installed in other restaurants and a Berlin supermarket, which allows the retailer to sell the produce grown directly to its customers.
‘Normally, they are buying at a specific margin for a lot of produce, but they throw away a big amount of it,’ said Weber.
At the same time, it eliminates the costs of importing salads or herbs from other parts of the world, greatly reducing the environmental impact.
Infarm’s technology is now being used in over 50 Berlin supermarkets and they are planning to expand to Paris, France, in August and then to London, UK, soon after. Their first farm in a French supermarket will also be their biggest one yet. Covering 100m2, it will produce five tonnes of herbs, allowing the retailer to become self-sufficient for this commodity.
‘The food we are consuming is traveling too far and its carbon footprint is devastating for the world,’ added Weber. ‘(In the future) we will be growing a lot of food in cities, or closer to the cities.’
Source: European Commission (Steve Gillman)
Publication date: 6/14/2018
Maintaining Optimum Growth Conditions in Vertical Farms
Maintaining Optimum Growth Conditions in Vertical Farms
Sponsored by Edinburgh Sensors Jun 15 2018
Shutterstock | CC7
The global population is growing rapidly, and new technologies are required to meet the rising food demands. Vertical farming provides a secure supply of food all through the year while using lesser amounts of water, space, and energy. Creating the ideal environment, and particularly the perfect CO2 atmosphere, in vertical farms is vital for enhancing crop yields and farm economics. Edinburgh Sensors’ GasBoxNG is a ready-to-use gas sensor that allows conditions of ideal plant growth to be ensured.
By 2050, it is projected that the population worldwide will increase to nine billion, resulting in a 59-98% increase in food demand. Regardless of constant improvements in farming practices, present crop yields are growing very slowly to meet the anticipated increase in food demand. Furthermore, in the coming decades, the agricultural industries must start to adapt to changing conditions brought on by climate change. Researchers around the world are examining new and improved technologies that can transform food production and help keep up with the food demand.
Out of the nine billion people that will live on the earth by 2050, it is projected that 80% will dwell in cities. Vertical farms erected in small urban spaces such as sky-scrappers, warehouses, or even shipping containers, can provide a steady supply of local food in cities without the need for large areas of farming land.
Precision farming and environmental control technologies have allowed the progress of vertical farms that have been stated to use 95% less water, no pesticides, no soil, and 50% less fertilizer compared to traditional farms while creating 75% more crops per square foot.
Countries Around the World Are Investing in Vertical Farms
A number of projects have shown the benefits of vertical farms in prototypes, pilot projects, and at commercial production levels. A vertical farm was erected in Japan after the 2011 Fukushima nuclear disaster resulted in a food shortage.
Commercial vertical farms have also cropped up in empty industrial spaces in countries including the Netherlands, Singapore, and the USA. The vertical farming market is predicted to increase to $13 billion by 2024, with indoor growing in urban structures predicted to signify 70% of the market.
Environmental Control for Successful Vertical Farming
Engineering the ideal environment for crop growth has been the subject of a surplus of research over the last 10 years. It is vital to understand the impacts of environmental factors on plant growth to realize the best crop yields and resource efficiency in vertical farms.
Related Stories
- Simulating the Effect of Climate Change on Agriculture
- Studying the Effect of Global Warming on Tropical Crops
- Monitoring Stored Food and Grain using Carbon Dioxide Measurement
Temperature, water supply, humidity, nutrient content, light, and atmosphere must all be cautiously controlled to guarantee optimal crop yields and least resource use.
The effects of CO2 concentration on crop growth have been researched intensely in the last few years. Small variations in atmospheric CO2concentrations can greatly affect plant growth and photosynthesis rates, so CO2 levels in vertical farms must be carefully tracked and controlled.
The CO2 levels in vertical farms can be customized to the crop being grown, and the particular growth stage of the crops. A number of studies have revealed that increased CO2 levels can provide increased water efficiency and better plant growth rates. The specific effect of CO2 levels on plant growth is reliant on the crop species and the plant’s growth stage. For instance, yields of tomato plants cultivated in CO2-enriched conditions grew by 17%, while yields of lettuce cultivated in CO2-enriched conditions grew by 68%.
In order to preserve ideal growth conditions, CO2 levels must be checked and managed using gas sensing systems.
CO2 Sensors Are Essential for Vertical Farms
CO2 sensors are important equipment for tracking and controlling conditions in vertical farms. Sensors may be added to automated control systems to continually monitor and maintain CO2 levels, offering ideal plant growth conditions without the need for human involvement.
The most common solutions for monitoring indoor CO2 levels are non-dispersive infrared (NDIR) CO2 sensors. In an NDIR CO2 sensor, infrared light is conveyed through a tube of air to an infrared detector. The detector takes into account the light that was not absorbed by the CO2 present in the tube, and the concentration of atmospheric CO2 is measured. The NDIR CO2 sensors are mainly popular as they deliver accurate CO2measurements, are comparatively inexpensive, easy to operate, and easy for non-experts to set up.
The new GasBoxNG from Edinburgh Sensors is a ready-to-use NDIR CO2 sensor that is perfect for vertical farming applications. It employs a pseudo dual beam NDIR measurement system to provide better stability and reduced long-term drift, with least optical complexity. Therefore, the GasBoxNG provides fast and reliable CO2measurements. The useful CO2 data provided by the GasBoxNG can be transferred to atmospheric control systems using an optional RS232 communication interface.
To know more about this new NDIR CO2 sensor that is very successful in vertical farming, customers can visit the stall set up by Edinburgh Sensors to showcase the GasBoxNG at the SENSOR+TEST Measurement Fair in Nürnburg, Germany between 26th and 28th June. Customers can meet experts to discuss their specific application requirements.
References and Further Reading
- ‘Growing a better future: Summary’ –https://www.oxfam.org/sites/www.oxfam.org/files/file_attachments/cr-growing-better-future-170611-summ-en_0.pdf
- ‘Can vertical farming feed the world and change the agriculture industry?’ –https://inhabitat.com/can-vertical-farming-feed-the-world-and-change-the-agriculture-industry/
- ‘Future food-production systems: vertical farming and controlled-environment agriculture’– Benke K, Tomkins B, Sustainability: Science, Practice and Policy, 2017.
- ‘Vertical Farming: Key to Mitigating World’s Hunger’ – Pandey S, Science Reporter, 2017.
- ‘Vertical Farming Market to exceed $13bn by 2024: Global Market Insights, Inc.’ –https://globenewswire.com/news-release/2017/05/17/986832/0/en/Vertical-Farming-Market-to-exceed-13bn-by-2024-Global-Market-Insights-Inc.html
- ‘Plant Factory: An Indoor Vertical Farming System for Efficient Quality Food Production’ – Kozai T, Niu G, Takagai M, Elsevier, 2015.
- ‘A Novel Approach for Automating & Analysing Hydroponic farms Using Internet of Things’ –Paulchamy B, Balaji N, Pravatha SD, Kumar PH, Frederick TJ, International Journal of Scientific Research in Computer Science, Engineering and Information Technology, 2018.
- ‘GasBoxNG’ – https://edinburghsensors.com/products/oem/gasbox-ng/
- ‘Edinburgh Sensors to attend Sensor and Test 2018’ – https://edinburghsensors.com/news-and-events/sensor-and-test-2018/
This information has been sourced, reviewed and adapted from materials provided by Edinburgh Sensors.
For more information on this source, please visit Edinburgh Sensors.
New Type of Photosynthesis Discovered
The discovery of a new type of photosynthesis changes our understanding of the basic mechanism of photosynthesis and should rewrite the textbooks.
New Type of Photosynthesis Discovered
The discovery of a new type of photosynthesis changes our understanding of the basic mechanism of photosynthesis and should rewrite the textbooks. It will also tailor the way we hunt for alien life and provide insights into how we could engineer more efficient crops that take advantage of longer wavelengths of light.
The discovery, published in Science, was led by Imperial College London, supported by BBSRC, and involved groups from the ANU in Canberra, the CNRS in Paris and Saclay and the CNR in Milan.
The vast majority of life on Earth uses visible red light in the process of photosynthesis, but the new type uses near-infrared light instead. It was detected in a wide range of cyanobacteria (blue-green algae) when they grow in near-infrared light, found in shaded conditions like bacterial mats in Yellowstone and in beach rock in Australia.
As scientists have now discovered, it also occurs in a cupboard fitted with infrared LEDs in Imperial College London.
Photosynthesis beyond the red limit
The standard, near-universal type of photosynthesis uses the green pigment, chlorophyll-a, both to collect light and use its energy to make useful biochemicals and oxygen. The way chlorophyll-a absorbs light means only the energy from red light can be used for photosynthesis.
Colony of Chroococcidiopsis-like cells where the different colours represent photosynthesis driven by chlorophyll-a (magenta) and chlorophyll-f (yellow). Credit: Imperial College London
Since chlorophyll-a is present in all plants, algae and cyanobacteria that we know of, it was considered that the energy of red light set the ‘red limit’ for photosynthesis; that is, the minimum amount of energy needed to do the demanding chemistry that produces oxygen. The red limit is used in astrobiology to judge whether complex life could have evolved on planets in other solar systems.
However, when some cyanobacteria are grown under near-infrared light, the standard chlorophyll-a-containing systems shut down and different systems containing a different kind of chlorophyll, chlorophyll-f, takes over.
Until now, it was thought that chlorophyll-f just harvested the light. The new research shows that instead chlorophyll-f plays the key role in photosynthesis under shaded conditions, using lower-energy infrared light to do the complex chemistry. This is photosynthesis ‘beyond the red limit’.
Lead researcher Professor Bill Rutherford, from the Department of Life Sciences at Imperial, said: “The new form of photosynthesis made us rethink what we thought was possible. It also changes how we understand the key events at the heart of standard photosynthesis. This is textbook changing stuff.”
Peter Burlinson, lead for frontier bioscience at BBSRC-UKRI says, “This is an important discovery in photosynthesis, a process that plays a crucial role in the biology of the crops that feed the world. Discoveries like this push the boundaries of our understanding of life and Professor Bill Rutherford and the team at Imperial should be congratulated for revealing a new perspective on such a fundamental process.”
Preventing damage by light
Another cyanobacterium, Acaryochloris, is already known to do photosynthesis beyond the red limit. However, because it occurs in just this one species, with a very specific habitat, it had been considered a ‘one-off’. Acaryochloris lives underneath a green sea-squirt that shades out most of the visible light leaving just the near-infrared.
The chlorophyll-f based photosynthesis reported today represents a third type of photosynthesis that is widespread. However, it is only used in special infrared-rich shaded conditions; in normal light conditions, the standard red form of photosynthesis is used.
It was thought that light damage would be more severe beyond the red limit, but the new study shows that it is not a problem in stable, shaded environments.
Co-author Dr Andrea Fantuzzi, from the Department of Life Sciences at Imperial, said: “Finding a type of photosynthesis that works beyond the red limit changes our understanding of the energy requirements of photosynthesis. This provides insights into light energy use and into mechanisms that protect the systems against damage by light.”
These insights could be useful for researchers trying to engineer crops to perform more efficient photosynthesis by using a wider range of light. How these cyanobacteria protect themselves from damage caused by variations in the brightness of light could help researchers discover what is feasible to engineer into crop plants.
Textbook-changing insights
More detail could be seen in the new systems than has ever been seen before in the standard chlorophyll-a systems. The chlorophylls often termed ‘accessory’ chlorophylls were actually performing the crucial chemical step, rather than the textbook ‘special pair’ of chlorophylls in the centre of the complex.
This indicates that this pattern holds for the other types of photosynthesis, which would change the textbook view of how the dominant form of photosynthesis works.
Dr Dennis Nürnberg, the first author and initiator of the study, said: “I did not expect that my interest in cyanobacteria and their diverse lifestyles would snow-ball into a major change in how we understand photosynthesis. It is amazing what is still out there in nature waiting to be discovered.”
Source: BBSRC
Publication date: 6/21/2018
Indoor Urban Agriculture Is Growing Up Thanks to These Cities
At this point, the benefits of indoor urban farming are common knowledge: fresher food, fewer transportation emissions, and less spoilage thanks to shorter transit distances.
NYC’s Gotham Greens highlighted those and other benefits this week with the announcement that it had closed a $29 million Series C equity funding round led by Silverman Group and Creadiv. This latest round brings the company’s total funding to $45 million and will help them “finance the expansion trajectory,” which covers 500,000 square feet currently under development in five different states.
Gotham is one of several major success stories for NYC-based urban indoor farming companies, many of which we’ve covered extensively at The Spoon. But the Big Apple’s not the only city making indoor urban farming widely available and, in the process, changing the way we think about farming.
In fact, today marks the opening of the Farm on Ogden in Chicago, a massive facility and project aimed at providing fresh, local food to an undernourished (literally and figuratively) part of the Windy City.
With those two pieces of news in mind, here’s a brief look at a few other cities and companies where the indoor farming movement is thriving:
The Farm on Ogden
Chicago
Though the enormous vertical farming operation FarmedHere shuttered in 2017, Chicago is still seeing plenty of developments from other urban agriculture players. Gotham Greens operates a facility in the Pullman area. And generating quite a bit of buzz of late is the aforementioned Farm on Ogden, a partnership between the Lawndale Christian Health Center and Chicago Botanic Garden. The $3.5 million year-round project will provide both jobs and local, sustainably produced food to the struggling North Lawndale area, where unemployment soars, over 14 percent of the population has diabetes, and one in four adults suffers from PTSD. The multi-use facility will offer year-round food production, teaching kitchens, and job training for everyone from teenagers to those with criminal backgrounds. The project is also in the midst of building a 50,000-gallon aquaponic system that will raise lettuce and tilapia.
Grove
Boston
Like Chicago, Boston’s urban landscape and often-grim weather make it a prime candidate for the indoor urban farming movement.
Dorm-room project turned full-fledged business Grove takes a slightly different approach, trading enormous warehouses for compact pieces of furniture in which to place its “farms.” As my colleague Catherine noted recently, Grove has teamed up with furniture and appliance companies to create custom hardware, while it supplies seed pods and ag software to cultivate the crops.
If, on the other hand, you’re after a more utilitarian means of growing your produce, Freight Farms can provide you with one of its vertical farms housed in 40-square-foot shipping containers. Each Leafy Green Machine container is a fully climate controlled environment with vertical crop columns, LEDs, and a closed-loop hydroponic irrigations system. The accompanying farmhand platform, meanwhile, lets users automate many of the growing tasks, and generates real-time data for crop analysis. Freight Farms counts multiple universities, as well as big names like Google, among its customers.
Detroit
Of course, if any city stands poised to benefit from the urban agriculture revolution, it’s Detroit; it's 78,000 empty/abandoned spaces are prime real estate for potential farming endeavors.
Artesian Farms is a great example: the company’s current warehouse facility sat abandoned from the late ’90s to when the company moved in around 2014. Now, thanks to a collaboration with Green Spirit Farms, Artesian has turned the warehouse’s 7,500 square feet of traditional space into one gigantic vertical farm. The company is also a community builder: 100 percent of current employees are from the surrounding Brightmoor neighborhood, which also benefits from access to the food produced.
RecoveryPark Farms, meanwhile, is another effort to transform urban blight via indoor and urban farming practices. The project grows produce, root vegetables, and herbs in hydroponic greenhouses that’s then shipped out to restaurants within a 300-mile radius.
Like many other companies listed here, RecoverPark provides as much community outreach and employment as it does homegrown food. Which, at the end of the day, is really what “eating local” should be all about.
Indoor AgTech Innovation Summit Taking Place At New Lab Innovation Hub In Brooklyn
- 3 WEEKS TO GO until @IndoorAgTech Innovation Summit! Full event details here: https://bit.ly/2FI1ubU New York, June 20-21, 2018
iGrow News readers can use the discount code IGR300 when you register to receive $300 off a delegate pass!
With resident space, on-site Product Realization, specialized programming, and access to a network that includes city agencies, venture capitalists, domain experts, and leading corporations, New Lab makes innovation move faster.
New Lab’s reputation as a center for innovation and technology makes it the ideal venue for the Indoor AgTech Innovation summit.
The inaugural Indoor AgTech Innovation Summit will focus on building and investing in more sustainable, profitable and healthy food systems and the role that vertical and indoor farming can have in serving local, regional and national food systems.
To find out more about the Indoor AgTech Innovation Summit, visit: https://indooragtechnyc.com/
iGrow is proud to be a marketing partner of the Indoor AgTech Innovation Summit in New York.
Use partner code IGR300 to save $300 on a delegate pass.
With 3 weeks to go until his keynote session at Indoor AgTech in New York, we spoke to Nate Storey, Co-Founder and Chief Science Officer at Plenty to discuss the company's meteoric rise and its ongoing mission to make affordable fresh produce accessible to everyone.
Q&A with Nate Storey, Plenty
What changes are needed to the current distribution model for this to happen, and what are the new technologies and approaches that will support the growth of indoor farming?
Follow them on Twitter: @IndoorAgTech #IndoorAgTech
"A Heated Greenhouse All Year Round By Using Flexible Residual Heat Computer Servers"
Jeroen Burks, Block Heating
"A Heated Greenhouse All Year Round By Using Flexible Residual Heat Computer Servers"
The greenhouse horticulture has an enormous need for heat, and residual heat as a renewable energy source is considered more often. Computer servers generate a lot of heat which is largely left unused. The start-up Block Heating wants to deploy that heat to heat greenhouses. Not by building data centers near greenhouse complexes, but by bringing servers by mobile containers to growers.
The idea for deploying residual heat arose about three years ago. Jeroen Burks, the man behind BlockHeating: "I supplied hardware for data centers and noticed that many customers wanted to make their residual heat useful. Most residual heat is still being routed outside. Together with the customer, we tried to find out if we could use residual heat to heat a building. A building of about 400 to 500 square meters is being heated successfully, and the building stays warm even on cold winter days.
Heat for a year
Fact is there are few buildings with a large need for heat in the summer, but greenhouse horticulture offered a solution. Jeroen: "If you know how much heat runs through a greenhouse each year, the deployment of residual heat by computer servers is a good match."
Because growers do not want a data center in their greenhouse, Block Heating aims at servers in mobile containers. Jeroen: "A 13-meter container can fit about 800 servers, worth a capacity of one megawatt per year. Depending on isolation and the sort of crop used, the residual heat of only one of those containers can heat a greenhouse of up to 10 hectare all year round."
Hot water
The focus is on supplying heat through warm water. The heat from the servers can be used to supply water of 60 degrees Celsius. This is considerably lower than residual heat supplied by the industry but more than sufficient to heat a greenhouse. It is important though to keep the distance between heat source and greenhouse as small as possible. Jeroen: "Another reason why containers are ideal because the water of 60 degrees can be supplied directly to the growers' buffer tank, which can then be used as desired."
The grower doesn't need to fear having his greenhouse full of servers, or extra tubing and wiring. Jeroen "With minimal adjustments, we provide energy saving and an opportunity to makes steps towards growing without gas."
Short investment horizon
The building of a data center easily has an investment time of five to ten years, but the investment horizon for the deployment of server containers is significantly shorter. We are going to test a version with 80 servers soon, and at the beginning of winter a container with 800 servers should be ready."
In the coming period BlockHeating hopes to get feedback from multiple growers, so the containers can be developed further. "We are fairly selective for the first versions, but interested growers are always welcome."
For more information:
BlockHeating
Jeroen Burks
jeroen@blockheating.com
+31 6 470 41000
Priva Knowledge Sessions During The GreenTech
Priva Knowledge Sessions During The GreenTech
How can Artificial Intelligence help growers with complex decision-making processes? In what way can knowledge sharing and applying become a major success factor for your company? And how can we improve controlling crop growth in greenhouses with smart technologies? Priva experts will give you answers to these questions. Visit eight sessions during the GreenTech and learn more about important themes within horticulture, including Vertical Farming, Human Capital Development, Crop management and more. An overview of the complete program, time, location can be found below.
Wednesday, 13 June
- 13:30 – 14:00 > Trends & Innovations Theatre
- ‘Artificial Intelligence and machine learning will change your horticultural business, for sure!’
- Greenhouses of the future by Theo Rieswijk, Innovator at Priva
What is artificial intelligence and machine learning? Concepts where each of us has his own image. But, one thing is certain. It touches our areas of work, but yours too. It offers enormous opportunities in the field of optimization and complex decision-making processes. Priva is active in this field and will give a number of examples with regard to energy savings and productivity. Theo Rieswijk explains how algorithms in a building environment already provide considerable energy savings in combination with excellent comfort for people. In the same way a foundation can be laid for horticultural greenhouses and plants.
- 15:30 – 16:00 > Food & Flowers Crops Theatre
- ‘Understand your business inside and out’
- Operational GreenHouse Management by André de Raadt, PMT manager at Priva
Companies are becoming larger and more complex. To deal with the horticulture challenges and to be able to manage a (part of the) company, managers need information to help them to make the right decisions. Operational, tactical and strategical decisions. Information about growing conditions, labour, costs, planning and progress are key. Without information managers are ‘driving blind’. It’s important that information is available for all ‘layers’ and managers within the company. By sharing, all departments are looking at the same information, they know from each other what they are doing and what they can expect from each other. Internal processes can be optimized and make the whole organization more efficient. FS Performance is a horticultural management information system which is designed to help the greenhouse operations managers. With practical examples and cases Priva will show the value of FS Performance for the greenhouse manager.
Thursday, 14 June
- 12:30 – 13:00 > Trends & Innovations Theatre
- ‘Precision Growing: Priva Moisture Balance Module’
- Precision horticulture by Dirk Prins, Business Developer at Priva
The precise control of water and fertilizers is essential in the production to lift the product quality throughout the chain at a higher level. The Priva Moisture Balance Module is an optimal irrigation start solution for substrate growing that determines every irrigation cycle fully automatically based on three important influences: water evaporation, plant water use and substrate water content. The result; increased fruit production by precise and timely dosing of water and fertilizers.
Moisture Balance Module: increased production by optimal water dosing
- 13:00 -13:30 > Trends & Innovations Theatre
- ‘How does sharing knowledge improve your business?’
- Human Capital Development by Rob Schoones, PMT manager at Priva
In a world where everything is digitized at a rapid pace, where technological developments follow each other ever faster, where boundaries fade and the interests of the individual become more and more central; flexibility, scalability and speed are important characteristics of a modern enterprise. Where the first, second and third industrial revolution mainly concerned the automation of traditional work, digitization now mainly affects the knowledge domain. The way in which knowledge is shared and the way in which knowledge is applied are important success factors for your company in the future. Are you curious how Priva has applied this? You are more than welcome to come and listen to the story about the Priva Academy.
For more information:
Priva
Zijlweg 3
2678 LC De Lier
Netherlands
T: +31 (0)174 522 600
F: +31 (0)174 522 700
contact.priva@priva.nl
www.priva.nl
Publication date: 6/11/2018
OLEDs Could Boost Vertical Farm Efficiency By 20 Percent
The energy efficiency of vertical farms could soon be boosted by as much as 20 percent, thanks to a new system developed by a student from Brunel University London.
vFarm, by design student Jonny Reader, 21, uses OLEDs – organic light-emitting diodes – and smart automation to significantly reduce the amount of power used in vertical farming.
The new system, which has already attracted significant interest from industry, will be unveiled at Made in Brunel in June.
A render of how a full-sized vFarm unit may look
“Current agriculture uses 70 per cent of the world’s pumped water, and accounts for 70 per cent of water contamination and 33 per cent of global warming,” said Jonny, from High Wycombe. “It also causes all kinds of toxic effects from the pesticides used.
“Vertical farming is a way of taking it inside – you use five per cent of the water traditional farming uses and don’t need pesticides, because you’re in an enclosed environment.”
Popular in Asia and gaining momentum elsewhere, vertical farming is the practice of producing crops in stacked layers, allowing for better use of space and resources. Already a billion-dollar industry, its popularity is expected to soar over the coming years as costs come down.
Where current vertical farms use traditional LEDs, vFarm uses OLEDs, which produce less heat and have a higher energy efficiency. Importantly, OLED panels are also significantly thinner than their LED equivalents, meaning greater yields can be achieved at shorter heights.
Whilst the price of OLEDs is currently prohibitive in most circumstances, Jonny predicts costs will fall heavily as the technology gains traction.
OLED's significantly thinner profile makes larger yields possible
vFarm also aims to increase efficiency and yield through the use of automation, using a series of sensors to help control factors such as temperature and humidity.
“It can read the current temperature, how much water there is in the reservoir, light intensity and how much power it’s drawing,” said Jonny. “Everything is automatic.”
“Though you can also do things like manually turn the lights on or off, or the fans on or off if you like.”
The working prototype will be on display at Made in Brunel
Whilst currently only in its prototype stage, vFarm has been turning heads within the industry, with commercial outfit Hydrogarden so impressed by Jonny’s work that they’ve invited him in to take part in an official Knowledge Transfer Partnership with them..
“Right at the start of the project I went up to Hydrogarden to do some general research and find out about their gardens,” said Jonny.
“When I finished I took it back up to show them, and they said they’d been trying to do something similar with small control units
“If it all goes through, I’ll be working with them for the next three years, developing this kind of technology.”
vFarm, along with a host of other innovative new devices designed by final-year design students from Brunel, will be on display at Made in Brunel, which runs at the Bargehouse, Oxo Tower Wharf, London, from 15–17 June.
Reported by:
Tim Pilgrim, Media Relations
+44 (0)1895 268965
tim.pilgrim@brunel.ac.uk
Autogrow’s API And Amazon’s Alexa Leads To World's First Talking AgTech System
Autogrow’s API And Amazon’s Alexa Leads To World's First Talking AgTech System
June 8, 2018
Global AgTech company Autogrow has utilized Amazon’s virtual assistant ‘Alexa’, and their IntelliGrow API (Application Programming Interface) to create the first ever talking automated growing system.
Their breakthrough technology demonstrates the versatility of their API and proves Autogrow’s commitment to crack the code of future crop production.
“We think this is the best use-case of AI (Artificial Intelligence) today. We’ve basically turned a vocal sound into a machine command and proven integration of different systems is possible,” says CEO Darryn Keiller.
“We have done it with Alexa, but we can also integrate with a growers HVAC or lighting system. The possibilities are limitless.”
Autogrow has been considering voice activation technology for a while, but it was a recent conversation with one of their growers that spurred them to accelerate development.
“One of our growers noted how modern apps like Apple’s Siri allows you to interact and how great it would be if he could ask his controller to update him on his crop environment but also instruct it to take action if required,” explains CTO Jeffrey Law.
“Our Solutions Architect, Lee Dunn, relished the challenge and chose Amazon’s Alexa Voice Service (AVS) due to their commitment to enable developers to voice-enable connected products.”
By connecting with Autogrow’s API, Alexa can answer a variety of questions related to readings from Autogrow’s Intelli Range of products including EC, pH, humidity, temperature, and light as well as force a nutrient dose.
“This is a new tool we can build on to give our growers more flexibility and control in their business and from here, the possibilities are limitless,” says Mr Keiller.
“At the heart of it, our burning drive is to help producers of crops grown in non-outdoor environments produce more yield, better quality crops, all year round. They can then generate more profit, enabling them to produce crops that the consumer wants, and when they want it,” says Mr. Keiller.
Lee Dunn, Solutions Engineer
About Autogrow
Autogrow leverages the power of technology, data science, and plant biology to provide indoor growers affordable, accessible and easy-to-use innovation – 24/7, anywhere in the world.
Our hardware, software and data solutions support growers and resellers in over 40 countries producing over 100 different crop types.
We have over two decades of experience and passionate, fun people creating original ideas and making them a reality for our growers.
US (WI): Superior Fresh Grows Salmon And Veggies At High-Tech Facility
US (WI): Superior Fresh Grows Salmon And Veggies At High-Tech Facility
Superior Fresh is the largest aquaponics facility in the world. Their state-of-the-art fish facility is coupled with a 3-acre glass greenhouse where they grow various leafy greens and herbs. They grow everything from seed in their greenhouse under LumiGrow grow lights and produce 1.8 million pounds of leafy greens each year. The leafy vegetables make their journey from the greenhouse to supermarket shelves within 48 hours.
Superior Fresh’s fish house and greenhouse have been meticulously designed and built using state-of-the-art technology to maximize profits with a superbly modern facility. For their greenhouse lighting, Superior Fresh is using LumiGrow LED grow lights paired with LumiGrow Light Sensor technology to ensure yield and quality goals are met consistently while reducing energy costs by 50% compared to traditional HPS lighting.
The light sensor technology allows Superior Fresh to monitor the exact light levels in the greenhouse and create programs that automatically adjust the fixtures to efficiently meet production goals year-round.
“Our biggest leap forward has been the LumiGrow smartPAR software,” says Adam Shinner, Head Grower at Superior Fresh. “…When we have enough sun, the lights turn off. When we don’t have enough sun, they turn back on. It allows for full integration of our lighting system [with the greenhouse zoning], which has truly not been possible up until this point.”
“Understanding that we are going to have 9 billion people on this planet in the next 30 years or so, we have to start thinking about how we’re going to efficiently grow food close to the marketplace,” says Brendan Gottsacker, CEO at Superior Fresh. “LumiGrow has allowed us to grow food right here in Wisconsin in the middle of the winter.”
For more information:
LumiGrow
800-514-0487
info@lumigrow.com
www.lumigrow.com
Publication date: 5/29/2018