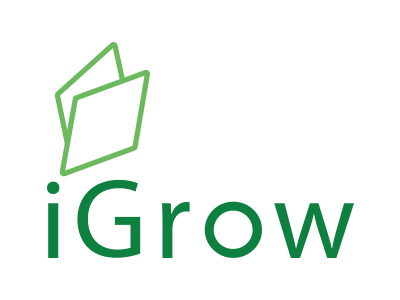
Welcome to iGrow News, Your Source for the World of Indoor Vertical Farming
$200M Invested For a Global Network of Indoor Farms? That’s Plenty
$200M Invested For a Global Network of Indoor Farms? That’s Plenty
Frank Vinluan | July 21st, 2017 | @frankvinluan | @xconomy | Email
Agtech startup Plenty has reeled in $200 million in financing as the company presses forward on its plans to build a global network of indoor vertical farms.
Softbank Vision Fund of Japan led the Series B funding round for South San Francisco, CA-based Plenty. The round included investments from affiliates of Louis Bacon, the founder of Moore Capital Management, as well earlier investors Innovation Endeavors, Bezos Expeditions, DCM, Data Collective, and Finistere Ventures.
The founders of Plenty say they aim to site their farms near major cities. By growing plants vertically, these farms can produce more food from a smaller footprint while also shortening the supply chain to reach consumers. The company also says these facilities will use sensors and software to optimize growing conditions, avoid the use of crop chemicals, and conserve water—savings that help keep the produce affordable. Plenty CEO Matt Barnard toldBloomberg News that the company’s goal is to provide food priced to fit everyone’s budget.
“That’s the thing that’s hardest to do,” Barnard said. “Now that we’ve accomplished those milestones, we’re looking to scale.”
Plenty has plenty of company in the indoor farming space. In June, New York-based Bowery raised $20 million in its Series A round, four months after announcing its seed round of financing. Bowery CEO Irving Fain hinted at ambitions to build its indoor farms around the world but in the near term, he said the funding will support the construction of at least one additional indoor farm in the New York area. Last year, New York-based BrightFarms raised $30.1 million in a Series C round to bankroll expansion of its indoor farms across the country.
Indoor farming investments have heated up in recent years; the category accounted for $247 million invested in 43 deals last year, according to a report from online investment marketplace AgFunder. But Plenty’s latest round appears to be the biggest agtech investment ever. The $200 million round tops the $100 million Series C round of Boston agricultural microbials startup Indigo a year ago in what AgFunder calculated was previously the largest-ever agtech investment.
Softbank has a lot of money to invest in agtech and elsewhere. In May, the fund announced it had closed on $93 billion in committed capital, a sum that it expected would reach $100 billion. At the time, Softbank said it would seek investments of $100 million or more as it builds a portfolio diversified across technology sectors and geographies. The fund said it is looking to invest in companies “that seek to enable the next age of innovation.”
Plenty has also been a dealmaker in the indoor farming space. Last month, the company acquired Laramie, WY-based Bright Agrotech, a maker of vertical farming equipment. No financial terms were disclosed for that deal but at the time it was announced, Bright Agrotech CEO Chris Michael wrote in a blog post that his company’s technology would help Plenty “build field-scale vertical indoor farms around the world.”
Among the technologies that Plenty gained in the Bright Agrotech deal is the ZipGrow Hydroponic Tower. These towers use gravity to feed nutrient-rich water to plants grown in a vertical plane. Barnard told Bloomberg that using gravity saves energy compared to the energy-consuming systems of other farms that pump nutrients to plants.
Plenty has not yet said where it plans to build its farms, nor has the company set a timeline for bringing produce to the market. Other than the Bright Agrotech facilities, Plenty’s only disclosed location is its 51,000-square-foot warehouse in South San Francisco.
ZipFarm photo by Plenty subsidiary Bright Agrotech.
Frank Vinluan is editor of Xconomy Raleigh-Durham, based in Research Triangle Park. You can reach him at fvinluan [at] xconomy.com Follow @frankvinluan
The Freshest Farm-to-Table Meal in New York City: Dinner at Edgemere Farm in Far Rockaway
At first glance, Far Rockaway may seem like a strange location for a small farm—the peninsula on which it resides is known more as a summer beach getawaythan a bastion of fresh produce. While Edgemere Farm is thriving several years after its 2013 opening, it took a great deal of effort to even make the land productive and arable.
The Freshest Farm-to-Table Meal in New York City: Dinner at Edgemere Farm in Far Rockaway
Most people don't think of New York City as a hotbed of urban farming, but there are a number of hidden pockets of agriculture scattered throughout the city’s five boroughs supplying local produce to everyone from neighborhood residents to Michelin-starred restaurants. Case in point: Edgemere Farm, a half-acre of land in Far Rockaway, Queens, that grows everything from potatoes to raspberries to peppers.
At first glance, Far Rockaway may seem like a strange location for a small farm—the peninsula on which it resides is known more as a summer beach getawaythan a bastion of fresh produce. While Edgemere Farm is thriving several years after its 2013 opening, it took a great deal of effort to even make the land productive and arable.
“Originally the space where the farm stands housed a few bungalows, but during the 1970s a lot of people left the Rockaways and the city condemned the buildings that remained,” says Edgemere Farm co-founder, Matt Sheehan. “Before we arrived, the lot had been used as a place to park cars or change tires. We had a lot of work to do to get the land in usable shape.”
Four years later, though, the four-person team at Edgemere Farms grows more than 40 varieties of plants on the property, along with playing home to weekly farm stand markets. Edgemere also provides produce to more than ten area restaurants—the team makes deliveries in their cars, blasting the AC to preserve freshness.
While the farm’s focus is growing great produce, Sheehan and his team also host dinners on the property, each run by a different visiting chef. Edgemere Farm continues to host dinners almost weekly throughout the summer and most recently they teamed up with Grindhaus’ Erin Norris and chef Kevin Speltz, along with noted baker, and Matt’s wife, Jessie Sheehan, for the Hooked On Edgemere Farm dinner. Here's a look at what it's like to eat the freshest farm-to-table dinner in the city.
— Max Bonem
For Farmers Without Land, a Long Island Lawn Will Do
For Farmers Without Land, a Long Island Lawn Will Do
By ARIELLE DOLLINGER | JULY 23, 2017
Jim and Rosette Adams, owners of Lawn Island Farms, at the home of Cassandra Trimarco in Bay Shore on Long Island. Ms. Trimarco volunteered to allow the couple to turn her front yard into a farm in exchange for a share of weekly produce. CreditJames Estrin/The New York Times
BAY SHORE, N.Y. — Jim Adams met his wife on a trip to Uganda a decade ago. Rosette Basiima Adams, 35, grew up in Kasese, a town, she said, where “everything we ate, we grew.”
“I went to see the gorillas in the Congo,” Mr. Adams, 42, recalled recently. But he left his tour group and ended up meeting Rosette, who was working at a hostel where he stayed.
Today, the couple are trying to grow a business cultivating crops on suburban lawns on Long Island. Their business, Lawn Island Farms, is the result of research and a desire to find a way to farm on the island.
“A lot of it was seeing America through Rosette’s eyes,” Mr. Adams said. In his wife’s hometown, he added, “all their food comes from within miles.”
With lots of ideas and little money, the Adamses began looking for land to farm. They started an online fund-raiser and posted fliers asking area residents to consider turning their lawns into small farms.
“There’s definitely an interest,” Mr. Adams said. “People say, like, ‘How do we replace the lawn and make it into a productive system?’”
The Adamses have received more inquiries than they can handle.
For now, the couple is farming at two locations in Bay Shore: one is a homeowner’s front lawn; the other is behind St. Peter’s by-the-Sea Episcopal Church.
They sent the additional inquiries they received to Pennie Schwartz, a home-farmer in Southold, farther east on Long Island.
Ms. Schwartz, 61, a retired chiropractor, said she wanted to help the Adamses turn each inquirer’s lawn into “an edible space.”
“It’s called foodscaping,” she said. “It’s really getting people to understand that lawns are really environmental energy suckers, for lack of a better word.”
Ms. Schwartz studies permaculture, a phenomenon that she said “combines landscape design with sustainability and environmental ecology” — and holds a certificate from Cornell.
“I don’t want to put the lawn guys out of business,” she said. But, “with all the chemicals that go into it, and all the watering we have to do to keep it green, there are better ways and better things to do.”
Ms. Schwartz wants to set up systems that landowners can maintain independently; each system should meet the landowner’s needs.
In other words, a family with children can still have a swing set.
On the two properties they farm, Mr. and Mrs. Adams are cultivating crops that grow quickly and that do not require much space, like salad greens and radishes.
One evening last month, the Adamses’ 9-year-old twins, Daisy and Curtis, ran through the front yard farm here on Hyman Street in pursuit of a rabbit.
Ms. Adams planting sunflowers in Ms. Trimarco’s lawn. Ms. Adams grew up in Kasese, Uganda, a town, she said, where “everything we ate, we grew.” CreditJames Estrin/The New York Times
Mr. and Mrs. Adams had just planted sunflowers when the homeowner, Cassandra Trimarco, drove up.
Ms. Trimarco, a physician assistant, contacted the Adamses after noticing their flier at a coffee shop.
“It’s me kind of donating in a way rather than controlling, because I don’t control anything, and it’s wonderful,” she said. “They think they’re lucky, but I think I’m lucky.”
Ms. Trimarco’s neighbors did not feel lucky, at first.
“We got yelled at,” Mr. Adams said. “One time, a lady pulled up on me and yelled at me for 10 minutes, like, ‘How could you do this? This is disgusting. You’re ruining the neighborhood.’”
Several neighbors declined to comment.
Ms. Trimarco originally volunteered her backyard, but there were too many trees, Ms. Adams said. So they asked about the front yard.
Ms. Trimarco gets $30 worth of produce each week. She also saves on landscaping costs because Mr. and Mrs. Adams do all of the work.
The couple are still working on their business plan. Currently, they sell the crops at two farmers markets and to one restaurant, Henley’s Village Tavern, in nearby Brightwaters.
“When you can deal with a farm directly, and watch it come from that farm, you know you’re getting the freshest product,” said Daniel Kitson, 41, who owns the tavern.
Recently, the Henley’s menu featured a crispy artichoke and chickpea salad with roasted peppers, capers, raspberry vinaigrette and Lawn Island Farms mixed greens.
Cars slowed as they passed the farm lawn. A woman in a truck waved; a man in a minivan said, “Nice!”
Robert Carpenter, administrative director of the Long Island Farm Bureau, said it was not too long ago that a farm in western Suffolk or Nassau Counties would not have looked so out of place.
“Farming was actually very prevalent in that area, going back as little as maybe 75 or 80 years ago,” Mr. Carpenter said.
According to 2012 agricultural census data, the most recent available, Suffolk County is the third-largest agricultural county in New York, Mr. Carpenter said. There remain 35,000 to 40,000 acres of farmland in production in Suffolk County, he said.
“There is agriculture taking place; it’s just not the way that it was 100 years ago or 50 years ago, when you had farms interspaced with houses,” he said. “The days of somebody growing 500 acres of a vegetable, and sending it into the city through the Hunts Point Market, those days are few and far between now.”
At the lawn farm, a Jeep stopped.
“Young man, I want you to know this is fantastic,” the passenger, Bruce F. Stelzer, 64, told Mr. Adams.
Mr. Stelzer said he grew up on a farm in Southold.
“This impressed the hell out of me,” he said. “Except I think a lot of people are going to be picking tomatoes from the street, though, when they walk their dogs.”
“That’s kind of the point,” Mr. Adams said.
A version of this article appears in print on July 24, 2017, on Page A16 of the New York edition with the headline: For Farmers Without Land, a Long Island Lawn Will Do Fine.
First of Its Kind ‘Food Sovereignty’ Law Just Legalized Local Food Trade Without Govt
Maine has taken a bold step toward freedom, becoming the first state in the U.S. to enact a ‘food sovereignty’ law giving communities power to regulate their local food economy
First of Its Kind ‘Food Sovereignty’ Law Just Legalized Local Food Trade Without Govt
Raw milk? Free Range Eggs? Organic Vegetables? No Problem. State's 'Food Sovereignty' Law just legalized their food trade once again.
By Justin Gardner | July 21, 2017
Maine has taken a bold step toward freedom, becoming the first state in the U.S. to enact a ‘food sovereignty’ law giving communities power to regulate their local food economy. The bill, titled An Act To Recognize Local Control Regarding Food and Water Systems, was passed unanimously by the state Senate and signed into law by Governor Paul LePage.
“LePage signed LD 725, An Act to Recognize Local Control Regarding Food Systems, Friday legitimizing the authority of towns and communities to enact ordinances regulating local food distribution free from state regulatory control…
Supporters of food sovereignty want local food producers to be exempt from state licensing and inspections governing the selling of food as long as the transactions are between the producers and the customers for home consumption or when the food is sold and consumed at community events such as church suppers.”
What this means is that neighbors can sell their eggs, milk, and other wholesome food to neighbors, without fear of state-level interference. This includes raw milk sales, a particular area where government has cracked down on those who dare engage in voluntary exchange.
Maine’s move is very welcome at a time when freedom is generally being chipped away by the police/surveillance state and the corporatocracy. Longstanding alliances between corporate food giants and government agencies have come to exert vast control over what we put in our bodies.
Almost every large food and beverage brand is controlled by 10 corporations, which pay off politicians to stifle smaller, more localized competitors. Regulatory burdens are created which do little or nothing to actually help the consumer or environment, but create enormous burdens that the little guy operating in a more localized area can’t handle.
The result is more unhealthy processed foods, massive factory farms poisoning humans and polluting the environment, more pesticide use from industrial monoculture which damages ecosystems, and loss of family farms.
The food and agriculture biotechnology Industry spent more than half a billion dollars over a decade to influence Congress for the privilege of feeding America. To politicians running DC, that kind of money makes the will of the people meaningless.
Betsy Garrold of Food for Maine’s Future summed up the simple, undeniable rationale behind food sovereignty.
“We believe face-to-face transactions with your neighbors is safe and beneficial to both parties,” said Garrold, “They know you, you know them and, frankly, poisoning your neighbors is a very bad business plan.”
Food freedom is certainly popular among the people, as 20 municipalities had already enacted food sovereignty ordinances prior to the bill being signed. Garrold said her phone “has been ringing off the hook” with townspeople who have every intention of using this freedom to build a thriving local, healthy food economy.
This demonstrates the hunger that likely exists all across the nation to take back control of our food supply, bringing a more localized, diverse approach which in turns provides health and environmental benefits.
“This is a great day for rural economic development and the environmental and social wealth of rural communities,” said Rep. Craig Hickman, D-Winthrop. “The Governor has signed into law a first-in-the-nation piece of landmark legislation [and] the state of Maine will [now] recognize, at last, the right of municipalities to regulate local food systems as they see fit.
“It’s been a long time coming,” Hickman said. “Food sovereignty means the improved health and well-being of the people of Maine by reducing hunger and increasing food self-sufficiency through improved access to wholesome, nutritious and locally produced foods.”
Maine’s move seems like an unusual and novel idea in these times, but food freedom has been around for most of humanity. Other states, including California, are considering similar food sovereignty measures.
Organics: Ferreting Out the Fraudulent Few, While Demanding Higher Standards, Better Enforcement
Organics: Ferreting Out the Fraudulent Few, While Demanding Higher Standards, Better Enforcement
July 18, 2017
Organic Consumers Association | by Katherine Paul and Ronnie Cummins
A recent series of articles by a Washington Post reporter could have some consumers questioning the value of the USDA organic seal. But are a few bad eggs representative of an entire industry?
Consumers are all for cracking down on the fraudulent few who, with the help of Big Food, big retail chains and questionable certifiers give organics a bad name. But they also want stronger standards, and better enforcement—not a plan to weaken standards to accommodate "Factory Farm Organic."
The Washington Post exposed a couple of companies, certified organic, that don’t strictly adhere to organic standards. The Post and othersalso recently reported on what one lawmaker, who serves on a key U.S. Department of Agriculture (USDA) committee, called “uncertainty and dysfunction” at the National Organic Standards Board (NOSB).
All these reports are troubling on multiple levels, especially to consumers who rely on the USDA organic seal to help them avoid pesticides, genetically modified organisms (GMOs), synthetic ingredients and foods produced using methods that degenerate soil health and pollute the environment. (It's important to note that none of these reports address the biggest marketing and labeling fraud of them all—products sold as "natural," "all natural" and "100% natural," a $90-billion industry that eclipses the $50-billion certified organic industry).
What can consumers do to ensure that the certified organic products they buy meet existing organic standards? And how do we, as consumers, fight back against efforts to weaken those standards?
The short answers: One, there are about 25,000 honest organic local and regional producers, vs. a handful of big brands, mostly national, who flout the rules. (Most "Factory Farm Organic" companies sell their products, and provide private-label products, for big retail chains like Costco, Walmart, Safeway, Albertson’s, Kroger’s and others).
Two, if consumers want stronger, not weaker organic standards, we need to demand them.
Bad actors hurt consumers and legitimate organic producers
Over the past several months, the Washington Post has reported the following:
• Eggland’s Best eggs, marketed as certified organic by Herbruck’s Poultry Ranch, come from hens that never go outside. (Even before the Post’s expose, OCA had called for a boycott of Eggland’s Best eggs).
• Aurora Organic Dairy, which supplies organic milk to Walmart, Costco and other major retailers, doesn’t adhere to organic standards that require cows to be outdoors daily during the growing season. (OCA, Cornucopia Institute and other groups have been demanding better policing of Aurora Dairy for more than a decade).
• Some “organic” soy and corn imports aren’t actually organic.
• Some “organic” foods contain a synthetic oil brewed in industrial vats of algae.
Stories like these erode consumer confidence in the organic seal. When consumers give up on organic, legitimate organic farmers and producers lose sales, too.
But that’s only the part of the problem. By cutting corners on organic standards, big producers can sell at lower prices—that puts the smaller, local and regional organic producers who don’t have big contracts with big retailers, and who must charge more because they actually follow organic standards to letter, at a competitive disadvantage in the market.
In some cases, it puts them out of business.
The Washington Post’s Peter Whoriskey recently interviewed Amish organic dairy farmers who are struggling to compete against companies like Aurora, which the farmers say, don’t deserve the organic label. The Post reported:
Over the past year, the price of wholesale organic milk sold by Kalona [Iowa] farms has dropped by more than 33 percent. Some of their milk — as much as 15 percent of it — is being sold at the same price as regular milk or just dumped onto the ground, according to a local processor. Organic milk from other small farmers across the United States is also being dumped at similar rates, according to industry figures.
After the Washington Post ran its April 30 exposé on Aurora, Liz Bawden, an organic dairy farmer in New York and president of the Northeast Organic Dairy Producers Alliance and member of the Northeast Organic Farmers Association (NOFA-NY) board wrote:
A consumer reads “Why Your Organic Milk May Not Be Organic” on the front page of their newspaper. That might be the end consumer for the milk from my farm. And that person is sitting in front of a bowl of cornflakes wondering if she has been scammed all this time. Just a little doubt that the organic seal may not mean what she thought it meant. That is real damage to my farm and family income.
Boycott the organic imposters
Consumers choose organic for many reasons. At the top of the list health. Consumers believe food that doesn’t contain pesticides, genetically modified organisms and synthetic/artificial ingredients, all of which are largely prohibited under USDA organic standards, is better for their own health.
That said, many consumers have an expanded list of reasons for buying organic, which include concern about the environment, animal welfare, fair trade and the desire to support local farms, and farmers committed to building healthy, rich soil capable of drawing down and sequestering carbon.
It’s naturally discouraging to read articles that sow doubt about whether a certified organic product meets your expectations. Fortunately, there are things you can do to minimize the chances of ending up with an organic carton of milk or eggs produced by an “organic imposter.”
• Boycott large, national brands. As demand grows for organics, Big Food is scooping up smaller organic brands. In most cases, nothing good comes this for consumers, as large corporations apply the “economies of scale” theory and ultimately skimp wherever they can on quality and production. As a general rule of thumb, the big players—like Aurora Dairy and Herbruck’s Farm (Eggland’s Best)—don’t play by the rules.
• Steer clear of private-label organics. It’s easy to identify the bad actors when they market products under their own names. But when it comes to private-label organics (think Safeway’s O’ Organic, Costco’s Kirkland, Walmart’s Great Value), it’s not readily apparent who is producing those products for big retail chains. We know that Aurora, which doesn’t market any milk under its own name, supplies organic milk to Walmart, Costco and Safeway. But in general, lack of transparency in the organic private label arena is a “huge problem,” one industry consultant told us. Most big retailers are complicit in organic fraud. The best strategy is avoidance.
• Check the codes on your milk carton. In her response to the Post’s story on Aurora, Bawden told consumers how to avoid milk produced by Aurora Dairy by checking the code on the carton. If you find the number 08-29, you’ll know that the milk comes from a plant that processes milk from Aurora Dairy. You can look up all the milk carton codes on the “wheredoesmymilkcomefrom” website.
• Do your homework. It would be great if you could rely entirely on the USDA organic seal. But given what we know about the weak links in that otherwise valuable chain, it pays to research. Googling brand names is one way to find information—but don’t rely on company websites, which are often loaded with false claims. Visit the Cornucopia Institute’s website, where you’ll find organic dairy, eggsand other products “scored” according to various criteria.
• Pay attention to who certified your milk or eggs as organic. In addition to the USDA organic seal, certified organic products must list, on package, the name of the independent body that certified the product to organic standards. There’s an argument to be made that certifiers should be held accountable for certifying products that don’t adhere to organic standards. Until that happens, avoid certifiers like Quality Assurance International (QAI) and the Colorado Department of Agriculture, which certify Aurora Dairy. Some of the more reliable certifiers include Oregon Tilth, PCO (Pennsylvania Certified Organic) and California Certified Organic Farmers (CCOF). For a complete list of organic certifiers, consult this list.
• Buy local. There’s a lot to be said for getting to know, and for supporting, your local organic farmers. They are more likely to follow organic standards, partly out of dedication, and partly to protect their own reputation within their communities. Here’s some advice for identifying local authentic and ethical farmers.
• Report suspected fraud. If you think a brand is violating organic standards, or falsely advertising/labeling a product “natural,” “all natural” or “100% natural,” email us at fraud@organicconsumers.org.
Consumers will have to help protect organic standards
Organic Consumers Association was founded, in 1998, when the USDA was writing the very first set of organic standards, as required under the Organic Foods Production Act (OFPA). The policy writers wanted irradiation to be allowed in organic. And sewage sludge. And GMOs. We fought successfully to keep them out.
Since then we’ve had to go to battle with every administration since over the integrity and enforcement of organic standards. The Clinton Administration tried to get GMOs into organic. The Bush Administration made it easier to get synthetics into organic. The Obama Administration made it harder to get synthetics out of organic.
It didn’t help any that in 2005, Congress passed a law that made it a lot easier for the largest food companies to create “organic” versions of their factory farm and processed foods.
Now those companies are stepping up their game, threatening to make changes to the OFPA and NOSB that could weaken organic standards beyond recognition. Why now? Two reasons.
One, as consumer demand for organic products grows, Big Food is buying up organic brands. This gives them a seat at the organic policymaking table, where, naturally, they are hard at work to lower standards in order to raise profit margins.
And two, they smell opportunity. The Trump Administration has made its position on regulations clear: more industry involvement, more concern for corporate profits, and less concern for consumer rights, public health, the environment.
Congress needs to hear from consumers—often, and in large numbers—that we want stronger, not weaker organic standards. Standards that support small, authentic producers.
Putting it in perspective
Organic isn’t perfect. The standards aren’t perfect. The enforcement process isn’t perfect. And some of the players are downright crooked.
That said, consumers can by and large trust all organic produce. And if they’re willing to do a little homework, they can identify the producers in the organic processed food arena who abide by the rules.
To put things in perspective, compare the $50-billion organic industry with the $90-billion “natural” industry. No standards. No ethics. And the clear intention to increase sales by falsely claiming that products that contain all manner of “unnatural” substances, including pesticides, synthetic ingredients—even drugs —are the “healthy choice.”
So let’s keep policing the organic industry, exposing the fraud, working for stronger standards and better enforcement of those standards.
But let’s be just as vigilant about exposing the “Myth of Natural,” and cracking down on what is arguably the biggest food marketing scam in the history of advertising.
Katherine Paul is associate director of the Organic Consumers Association.
Ronnie Cummins is international director of the Organic Consumers Association.
Vertical Farming Tour Visits Delval Programs
Vertical Farming Tour Visits Delval Programs
Chris Filling, hydroponics greenhouse manager, leads a tour of DelVal's greenhouses during an educational tour conducted by the state Department of Agriculture. Delaware Valley University photo
DOYLESTOWN, Pa. — As interest in vertical farming continues to grow, the Pennsylvania Department of Agriculture has been conducting an educational tour for its urban agriculture partners featuring hydroponics and aquaponics programs in Pennsylvania.
Delaware Valley University was the first stop on the tour, which kicked off Tuesday in the Philadelphia area.
Guests toured the University’s hydroponics and aquaponics greenhouses to see how DelVal is preparing students for these industries.
In hydroponics, growers use soilless systems for more precise control of inputs. In aquaponics, fish provide nutrients for plants in a soilless system.
These systems allow growers to produce food in unconventional places, using less space and resources.
“The hydroponics and aquaponics industries have tremendous potential to help solve pressing challenges, such as how to feed a growing population with limited resources,” said Chris Tipping, DelVal’s interim dean of agriculture and environmental sciences.
“At DelVal, we’re educating our students about these industries, and we’re also reaching out into the larger community to partner with other educational programs,” Tipping said. “There’s a real sense of excitement about hydroponics and aquaponics in Pennsylvania.”
Scott Sheely, special assistant for workforce development for the state Department of Agriculture, was part of organizing the tour.
“As schools, government officials and businesses look at ways to apply the technology to grow food in cities, there has been a demand for education on urban agriculture,” Sheely said.
“The Pennsylvania Department of Agriculture invited its urban agriculture partners to join it in visiting sites across Pennsylvania to learn more about this technology and how it is being used in the region,” he said.
“DelVal was chosen as a stop because the university is investing in research and education in hydroponics and aquaponics,” Sheely said.
DelVal President Maria Gallo and Tipping addressed the group.
DelVal is currently building a new specialization in hydroponics and aquaponics within its established Department of Plant Science, thanks to the support of DelVal trustee Kate Littlefield.
“This support was used to renovate two greenhouses as well as to provide the opportunity to create the first endowed professorship in DelVal history,” Tipping said. “This professor will lead the program.”
The tour also visited sites in Lancaster on Wednesday and Harrisburg on Thursday. Other stops included W.B. Saul High School, Metropolis Farm, Aero Development, Garden Spot Village, Steelton-Highspire High School, Ladder & Vine and Messiah College.
For Additional Information, please click on the link below:
MSU Students Launch Local Food Business Made From Campus Grown Foods
MSU Students Launch Local Food Business Made From Campus Grown Foods
Look for Land Grant Goods products this summer on campus.
July 20, 2017 by Kendra Wills, Michigan State University Extension
Land Grant Good founders, Alex Marx (left) and Bethany Kogut (right). Photo credit: Land Grant Goods
For anyone who finds themselves around the Brody Halls at Michigan State University, whether they be an incoming resident, staff, family member, or simply someone in the neighborhood, it may be beneficial to know that this location site offers their own handmade goods straight from the Bailey GREENhousecommunity garden located next to Bailey Hall in the Brody Complex, west of the Kellogg Center. Stop by to help support this student-run organization.
Since Michigan State University opened its doors in 1855, it has always been dedicated to education and to agriculture. In fact, it was originally called “the Agriculture College of the State of Michigan.” Which is why, to this day, you will see various gardens, hoop houses, open fields, and an overall beautiful landscape when touring the campus. As the school continues to build on to this campus, as you can see in the future visions they have set for the year 2020, MSU will continue to embrace the university’s agricultural heritage.
With this in mind, various students studying agriculture, sustainability, and education have decided that the Brody Halls, which is secluded from much of campus, needed their own greenhouse. With MSU having such a large agriculture department, and Brody Halls being located several miles away from the MSU Student Organic Farm and other MSU agricultural production facilities, it created a barrier for students living in these halls to be exposed to the culture of farming. Luckily, the Bailey GREENhouse enables students living on campus to be involved in agriculture without having to travel far distances.
This idea was put in motion in 2012, joining with the Residential Initiative for the Study of the Environment (RISE). The Bailey GREENhouse produces a wide variety of greens, tomatoes, herbs, mushrooms and even an apiary they have created themselves. The amount of components being produced in such a small area between the dorm halls is impressive and is all student-grown.
Bailey GREENhouse crops were originally used only for the residential dining halls and the State Room restaurant in the Kellogg Center, but the students knew they could take their successes further. They launched Land Grant Goods in 2015, with a goal to promote locally-made products to the community.
Today, using a mobile certified kitchen inside of a trailer parked at the MSU Student Organic Farm, the students process their jams. They sell the honey made from the apiary, and make teas from GREENhouse herbs. Overall, they have shown that they can work to make their small space as productive as possible by thinking about various value-added products that can be created.
For anyone who finds themselves visiting this site, seek out the students running this operation. This group of passionate individuals welcome all those interested in learning more about how they run their business, and will talk with excitement about the work they do and the new projects they have lined up. This may only be the start for these students, but in order to achieve these goals they will need a support system to do it.
Michigan State University Extension supports commercial agricultural producers and food businesses. For more information about launching a food business or seeking business counseling services, please contact the MSU Product Center at (517) 432-8750.
This article was published by Michigan State University Extension. For more information, visit http://www.msue.msu.edu. To have a digest of information delivered straight to your email inbox, visit http://www.msue.msu.edu/newsletters. To contact an expert in your area, visit http://expert.msue.msu.edu, or call 888-MSUE4MI (888-678-3464).
Plenty Attracts Largest-Ever Agriculture Technology Investment Led by the SoftBank Vision Fund to Solve Global Fresh Produce Shortages
Plenty Attracts Largest-Ever Agriculture Technology Investment Led by the SoftBank Vision Fund to Solve Global Fresh Produce Shortages
Investment will drive deployment of global, large-scale indoor farm network to deliver radically fresher, affordable food to local communities everywhere
July 19, 2017 10:00 AM Eastern Daylight Time
SOUTH SAN FRANCISCO, Calif.--(BUSINESS WIRE)--Plenty, the leading field-scale indoor farming company remaking the global food system, announced today a $200 million Series B funding round led by the SoftBank Vision Fund, making it the largest agriculture technology investment in history. In connection with the investment in Plenty, the SoftBank Vision Fund’s Managing Director, Jeffrey Housenbold, will join the Plenty Board of Directors.
“Fruits and vegetables grown conventionally spend days, weeks, and thousands of miles on freeways and in storage, keeping us all from what we crave and deserve — food as irresistible and nutritious as what we used to eat out of our grandparents’ gardens”
Plenty is using proven plant science and patented technologies to build a new kind of indoor farm that uses cutting-edge LED lighting, micro-sensor technology, and big data processing to deliver higher-quality produce for pricing as good or better than what consumers pay today. The world has run out of economically viable, arable land for many fresh fruit and vegetable crops. This investment will support building out Plenty’s global, hyper-yield farm network and support its mission of solving the increasingly critical need to make fresh produce available and affordable for people everywhere.
“Fruits and vegetables grown conventionally spend days, weeks, and thousands of miles on freeways and in storage, keeping us all from what we crave and deserve — food as irresistible and nutritious as what we used to eat out of our grandparents’ gardens," said Matt Barnard, CEO and co-founder of Plenty. “The world is out of land in the places it’s most economical to grow these crops. After a decade of development driven by one of our founders, our technology is uniquely capable of growing hyper-organic food with no pesticides nor GMOs while cutting water consumption by 99 percent, making locally-grown produce possible anywhere. We’re now ready to build out our farm network and serve communities around the globe.”
"By combining technology with optimal agriculture methods, Plenty is working to make ultra-fresh, nutrient-rich food accessible to everyone in an always-local way that minimizes wastage from transport," said Masayoshi Son, Chairman & CEO of SoftBank Group Corp. "We believe that Plenty's team will remake the current food system to improve people's quality of life."
Plenty’s farms, which the Company plans to build near the world’s major population centers, will deliver industry-leading yields of the freshest, best-tasting local produce that’s completely GMO- and pesticide-free, all while transitioning agriculture to a predictable and perpetual model. Plenty farms maintain a perfect growing environment, use one percent of the water and a tiny fraction of the land of conventional agriculture, while delivering produce to local grocery shelves within hours of harvest.
The Series B funding round was led by the SoftBank Vision Fund, with participation from affiliates of Louis M. Bacon, the founder of Moore Capital Management, LP, and existing investors including Eric Schmidt’s Innovation Endeavors, Bezos Expeditions, DCM, Data Collective and Finistere.
About Plenty
Plenty is a new kind of farm for a new kind of world. We’re on a mission to bring local produce to people and communities everywhere by growing the freshest, best-tasting fruits and vegetables, while using one percent of the water, less than one percent of the land, and none of the pesticides, synthetic fertilizers, or GMOs of conventional agriculture. Our field-scale indoor farms combine the best in American agriculture and crop science with machine learning, IoT, big data, climate creation technology and the extraordinary flavor and nutritional profiles of heirloom seed stock, enabling us to grow the food nature intended — while minimizing our water and energy footprint. Based in San Francisco, Plenty is currently building out and scaling its operations to serve people around the world.
Indoor Farming Plus Made In USA LED Grow Lights: Profile 1.18
Indoor Farming Plus Made In USA LED Grow Lights: Profile 1.18
E-mailRSS
GREENandSAVE Staff | Posted on Thursday 20th July 2017
This is one of the profiles in an ongoing series covering next generation agriculture. We are seeing an increased trend for indoor farming across the United States and around the world. This is a positive trend given that local farming reduces adverse CO2 emissions from moving food long distances. If you would like us to review and profile your company, just let us know! Contact Us.
Company Profile: Metropolis Farms
Here is a great example of a large scale vertical indoor farm growing vegetables and herbs.
Here is some of the “About Us” content: We are urban-vertical farmers with over 15 years of indoor growing experience. We grow great tasting, wholesome herbs and vegetables, inside city buildings year-round. We grow the highest-quality food without pesticides, herbicides, or many of the other health risks that impact the food that reaches your table. We harvest and deliver our fresh produce the same day to local stores and restaurants. We can also make our fresh herbs and vegetables available by next-day air to restaurants and home gourmets nationwide. Our South Philadelphia Location is the first vertical farm in Philadelphia in addition to being the first vertical farm ever built on a second floor.
Our proprietary Revolution Vertical Farming Technology ™ is ultra-efficient, environmentally-responsible and commercially scalable. Our farms are highly-adaptive and virtually eliminate many of the health business and environmental risks that make conventional and greenhouse farming so expensive. Our farms can operate profitably for both smaller-artisan farms (Flash Farms) as well as large-scale operations (Super Farms). Our farming systems use 95 to 98 percent less water and 82 percent less energy than traditional farms. Our cost-effective technology allows us to grow more than an acre of produce in a 36 square feet of space, over 1,200 times the herbs and vegetables of an outdoor farm per square foot. We bring great food, good jobs and opportunities to local communities.
Instead of focusing on creating the world’s largest vertical farm. Our focus is on creating the world’s most efficient, cost effective and consequently productive local farms. It seems like every few months the media announces yet another proposed “World’s Largest Vertical Farm”. To date exactly none of these projects have ever fulfilled their promises. Our technology produces the most food, at the lowest cost, of both capital and operational expense, while maintaining the highest taste and nutritional values. Our goal is to grow both farms and farmers nationwide.
Here is the link to learn more: http://www.metropolisfarmsusa.com.
To date, the cost of man made lighting has been a barrier for indoor agriculture. A new generation of LED lighting provides cost effective opportunities for farmers to deliver local produce. Warehouses and greenhouses are both viable structures for next generation agriculture. Here is one example of next generation made in USA LED grow light technology to help farmers: Commercial LED Grow Lights.
Navy Yard Apartment Gives Residents Free Rooftop Produce Garden
Navy Yard Apartment Gives Residents Free Rooftop Produce Garden
By Jeff Clabaugh | @wtopclabaughJuly 13, 2017 12:25 pm
The Navy Yard apartment building has partnered with Up Top Acres to design and maintain a vegetable and herb garden on the roof, so residents can have access to a variety of produce through the summer and the fall.
WASHINGTON — F1RST Residences just upped the game for luxury apartment amenities in Washington, giving residents access to fresh, rooftop-grown produce.
The new 325-unit Navy Yard apartment building’s first tenants began moving in this spring.
The building has partnered with Up Top Acres to design and maintain a vegetable and herb garden on the roof, so residents can have access to a variety of produce through the summer and the fall.
There will be no cost for residents to participate in the garden program, and it will be entirely cared for by Up Top Acres.
The 470-square-foot garden will yield roughly 500 pounds of produce each year, including tomatoes, peppers, cilantro, parsley, thyme, rosemary, arugula, basil and zucchini.
“F1RST is giving its residents a community-supported agriculture program,” said Up Top Acres co-founder Kristof Grina. “This new farm will transform an underutilized part of the rooftop into a vibrant, productive living ecosystem — and bring ‘farm-to-table’ right in the same property.”
F1RST has already made extensive use of its rooftop.
The building, at First and N Streets in Southeast, includes a rooftop pool and hot tub, dog park, grills and D.C.’s only residential “stadium-style” seating with views into Nats Park.
The one- and two-bedroom apartments rent for $2,000 to $3,500 a month.
Pure Flavor®’s Growth Prompts Leadership Team Addition
Pure Flavor®’s Growth Prompts Leadership Team Addition
Leamington, ON (July 19th, 2017) – Building on consistent year over year growth, greenhouse grower & marketer Pure Flavor® announced the addition of Chris Veillon as Chief Marketing Officer to the company’s executive leadership team.
“As we continue to grow our retail & foodservice business, we needed to strategically evolve our marketing direction to support our premium line of greenhouse vegetables. In adding Chris to our executive team, we have added a seasoned strategic marketer who not only understands the industry but has been successful in building consumer facing brands over the last 20 years “, said Jamie Moracci, President.
Under the Pure Flavor® brand, the company grows & markets an extensive variety of greenhouse tomato, bell pepper, cucumber, eggplant, and living lettuce that is grown in Canada, USA, and Mexico. Founded in 2003, Pure Flavor® has experienced significant growth year over year with its expanding product offering.
“This is a fantastic career opportunity, I am very excited to join the leadership team at Pure Flavor®. The company culture and growth opportunity is unique which made it even more of a reason to join the Pure Flavor® team “, said Chris Veillon. “The product base is vast and expanding year after year to meet retail demand, I’m very excited to work with the team to strengthen the Pure Flavor® brand position “, commented Chris. As Chief Marketing Officer, Veillon will be responsible for all initiatives related to conceptualizing and implementing market strategy while providing strategic direction for promotion & advertising.
With the addition of Veillon as Chief Marketing Officer, the company also promoted Matt Mastronardi to Executive Vice-President. Mastronardi is one of the founding partners of Pure Flavor® and is part of the sales team.
“These are exciting times for our company. The strategic partnerships we have built with our growers, retail, and foodservice partners, is allowing us to continually extend our reach across North America”, said Matt Mastronardi. Mastronardi, Jamie Moracci, and Jeff Moracci, Pure Flavor’s CFO founded Pure Flavor® in 2003. With its corporate headquarters in Leamington, ON the company now operates in 3 countries with multiple distribution center locations providing year-round production.
Pure Flavor® will be exhibiting at the upcoming PMA Foodservice Trade Show in Monterrey, CA July 30. Stop by Booth #1106 to see Pure Flavor’s product line.
To learn more about Pure Flavor®, please visit Pure-Flavor.com
-30-
About Pure Flavor® - Pure Flavor® is a privately held greenhouse vegetable company providing year-round production of premium vegetables to retail & foodservice partners throughout North America.
SOURCE: Jamie Moracci | Jamie@pure-flavor.com
President | Pure Flavor®
T: 519 326 8444
Chris Veillon
Chief Marketing Officer
Pure Hothouse Foods Inc.
PO Box 607, Leamington, ON N8H 3X4
p: 519.326.8444 | p: 866.326.8444 | m: 519.878.1905 | f: 519.326.7960
Square Roots Is Looking For Its Next Class of Urban Farmers
Square Roots doesn’t just offer a crash course in the mechanics of urban farming. After the farms yield their first harvests a few weeks into the program, participants are expected to begin making sales. They receive guidance from program mentors in creating sustainable business plans.
Jul. 19, 2017 9:55 am
One of Square Roots' vertical hydroponic farms. | (Photo courtesy of Square Roots)
Square Roots Is Looking For Its Next Class of Urban Farmers
The program equips participants to launch their own food businesses in a matter of months.
By April Joyner / CONTRIBUTOR
Square Roots, the urban farming accelerator based in the Pfizer Building, is taking applications for its second cohort of resident entrepreneurs. The next round of the program will begin in October.
The 13-month program includes access to the distinctive shipping-container farms, made by Boston-based Freight Farms, that participants use to grow food. Participants pay a $5,000 deposit to cover operating expenses for the first three months, but those funds are returned to them at the end of the program. To help front those costs, participants can apply for microloans through the Department of Agriculture, with which Square Roots has partnered.
Square Roots doesn’t just offer a crash course in the mechanics of urban farming. After the farms yield their first harvests a few weeks into the program, participants are expected to begin making sales. They receive guidance from program mentors in creating sustainable business plans. Members of Square Roots’ first class, for instance, have devised a variety of sales strategies for their products, from setting up shop in greenmarkets to courting the CrossFit crowd. The accelerator does not take equity in the participants’ resultant businesses, though it does take a percentage of their sales.
Applications for Square Roots’ second program are due July 31.
SoftBank Vision Fund Leads $200 Million Bet on Indoor Farms
SoftBank Vision Fund Leads $200 Million Bet on Indoor Farms
By Selina Wang
July 19, 2017, 8:00 AM CDT July 19, 2017, 9:02 AM CDT
Masayoshi Son is betting on San Francisco startup Plenty
The investment will help Plenty expand around the world
Masayoshi Son has discovered a green thumb.
The SoftBank Group Corp. chief’s Vision Fund is leading a $200 million investment in Silicon Valley startup Plenty, which says it has cracked the code on growing crops indoors super efficiently. Other participants in the round include Moore Capital Management founder Louis Bacon as well as existing backers such as DCM Ventures and funds that invest on behalf of Alphabet’s Eric Schmidt and Amazon’s Jeff Bezos.
Plenty vertical farming | Source: Plenty
This is Son’s first big bet on agricultural disruption and something of a departure from his recent investments in giant startups like office-space startup WeWork Cos. and Chinese ride-hailing provider Didi Chuxing, but he was attracted by Plenty’s potential to help boost food production near big cities.
“We believe Plenty’s team will remake the current food system to improve people’s quality of life,” Son said in an emailed statement.
Matt Barnard, Plenty’s co-founder, is scheduled to appear Thursday in Tokyo at SoftBank World, the company’s annual two-day event aimed for customers and suppliers. In previous years, Son has shared the stage with Alibaba Group Holding Ltd. co-founder Jack Ma and the company’s Pepper robot.
Son’s backing could give a big boost to vertical farming, a much-hyped concept that so far has failed to revolutionize crop production. In recent years several companies including Atlanta-based Podponics, Vancouver’s LocalGarden and Chicago-area FarmedHere have shut down indoor farms because they weren’t economically viable.
’Plant Factories’ Churn Out Clean Food in China’s Dirty Cities
Barnard, who grew up on a commercial farm in Wisconsin, founded Plenty in 2014 with Nate Storey, a crop scientist who previously started another indoor farm. Plenty does things differently from its rivals. Where most grow plants on shelves like a tall dresser, Plenty uses 20-foot-tall columns from which the plants jut horizontally; picture poles lined up in rows, carpeted in plants from top to bottom. Nutrients and water drip down the columns. Plenty scientists also figured out how to more cheaply remove excess heat emitted by the LED grow lights–a problem Barnard says tripped up other operations.
The company says it can cultivate many more crops per square foot than competitors and uses less energy because the plant food is mostly gravity-fed rather than pumped. “Because we work with physics, not against it, we save a lot of money,” Barnard says. An internet-connected system delivers specific types of light, air composition, humidity and nutrition, depending on which crop is being grown. Plenty says it can yield up to 350 times more produce in a given area than conventional farms -- with 1 percent of the water.
During a recent visit to the company’s facility in San Francisco, the columns are covered in heirloom varietals of purple Siberian kale, red leaf lettuce, sorrel and special species of basil and chives. Barnard says these are more nutritious and flavorful varieties than the mass-produced seeds that were bred to survive the vagaries of commercial production. The company selects which plants to grow based on taste tests with consumers and professional chefs. (A sampling during the tour confirms that the produce is tastier than store-bought.)
“We select stuff that people love because we have the freedom to do that because our supply chain is so short and simple,” Barnard says. “The field doesn’t have that option. It has to grow things that can survive 3,000 miles in a truck. That’s why the field grows iceberg lettuce.”
Skeptics of vertical farms note that they are best suited to growing leafy produce. “Rooting and fruiting” vegetables like carrots, beets, tomatoes, peppers, eggplants and cucumbers are harder to grow under such circumstances and hence more costly. Barnard says Plenty is working on growing cucumbers. So far, most of the startup’s plants are donated to food banks or used for consumer tests, including at a Google campus kitchen. Plenty will start distribution in the San Francisco Bay Area this year. International expansion is the next step and that’s where Son comes in.
A few months ago DCM Ventures co-founder David Chao introduced Barnard to the SoftBank chairman and CEO in California. The meeting was supposed to take 15 minutes but ended up lasting 45 because Son was excited about Plenty’s vision. Two weeks later, Barnard and Chao flew to Tokyo for another meeting with Son, who was skeptical at first, Chao says, but ended up sold on Plenty’s prospects.
“Ever since the Egyptian period, farming has been done one way: flat on the ground, outdoors,” Chao says. “But with indoor farming Masa realizes it’s revolutionary.”
Masayoshi Son | Photographer: Akio Kon/Bloomberg
Son is particularly interested in how Plenty can help nations grow sufficient food to support the population. His Vision Fund backers include sovereign wealth funds from the Middle East, where drought, population growth and a lack of arable land are fueling concerns about food shortages and political instability. Japan, Son’s home country, imports much of its own food and lost farmland after the nuclear power accident six years ago. Sonny Ramaswamy, director of the National Institute of Food and Agriculture at the U.S. Department of Agriculture, says indoor farming will play a significant role in easing shortages of green vegetables.
Chao says the $200 million Vision Fund investment will be used mostly to help Plenty expand domestically and internationally. Eventually, the company hopes to erect pre-fabricated farms outside major cities around the world. SoftBank has extensive connections around the world, Chao says, and wants “to help Plenty expand very quickly, particularly in China, Japan and the Middle East.”
Dickson Despommier, a Columbia professor who wrote “The Vertical Farm: Feeding the World in the 21st Century,” says indoor farming will never completely replace conventional outdoor agriculture but will supplement a growing portion of certain kinds of produce.
“In places where there is no ready access to what they’re growing, then they can corner the market,” he says. “If they do it where the price is right and the demand is right, there’s no reason why they couldn’t go wander into the sunset laughing as they go.”
Kimbal Musk — Elon's Brother — Is Running A Shipping-Container Farm Compound In New York City
Kimbal Musk — Elon's Brother — Is Running A Shipping-Container Farm Compound In New York City
Cofounder Tobias Peggs outside the Square Roots shipping container farms in Brooklyn, New York. Sarah Jacobs
Kimbal Musk, the brother of Tesla CEO Elon Musk, is trying to change the way we eat by creating what he calls a "real-food revolution."
For over a decade, Kimbal Musk has run two restaurant chains, The Kitchen and Next Door, which serve dishes strictly made with locally sourced meat and veggies. Since 2011, his nonprofit program has installed so-called Learning Gardens in over 300 schools to teach kids about agriculture.
Musk's latest food venture delves into the world of local urban farming.
In early November, he and fellow entrepreneur Tobias Peggs launched Square Roots, an urban-farming incubator program in Brooklyn, New York. The setup consists of 10 steel shipping-container farms where young entrepreneurs work to develop vertical-farming startups. Unlike traditional outdoor farms, vertical farms grow soil-free crops indoors and under LED lights.
On Tuesday, Square Roots opened applications for its second season, which will start in October and last 13 months.
"Graduates are uniquely positioned to embark on a lifetime of real food entrepreneurship — with the know-how to build a thriving, responsible business," Musk wrote on Medium. "The opportunities in front of them will be endless."
Six weeks into the first season, just after the entrepreneurs completed their first harvests, Business Insider got a tour of the farms. Take a look:
The Square Roots farms in Brooklyn sit between an old Pfizer factory and the apartment building where Jay-Z grew up. Sarah Jacobs
Everything grows inside 320-square-foot steel shipping containers. Each container can produce about 50,000 mini-heads of lettuce a year. Sarah Jacobs
The US Department of Agriculture gave the Square Roots entrepreneurs small loans to cover preliminary operating expenses. Other investors include Powerplant Ventures, GroundUp, Lightbank, and FoodTech Angels.
On four parallel walls, leafy greens and herbs sprout from soil-free growing beds filled with nutrient-rich water. Instead of sunlight, they rely on hanging blue and pink LED rope lights. Sarah Jacobs
About the size of the standard one-car garage, each shipping container can produce the same amount in crops as two acres of outdoor farmland.
Musk and Peggs chose Square Roots’ first class of 10 entrepreneurs from over 500 applications. Peggs said they represented the next generation of farmers — though not all had previous farming experience.
Sarah Jacobs
In early 2016, while Aliber was recovering from a concussion, he learned about urban farming from a podcast. He started researching it from his bed and found out about the Square Roots program.
Sarah Jacobs
Before Josh Aliber, 24, moved from Boston to Brooklyn to join Square Roots, he had never farmed. Now he's starting up a specialty herb business and running a vertical farm. Sarah Jacobs
His shipping container farm runs on 10 gallons of recycled water a day, which is less than an average shower's worth.
Sarah Jacobs
Aliber can monitor everything from the oxygen level to the humidity — which affects the plants' taste and texture — using the "computer panel" near the door and sensors in the growing beds. If he wants a tropical or northeastern climate, he can control that, too.
Sarah Jacobs
All of the Square Roots' farmers sold their first harvests at a local farmers market.
Aliber is selling his specialty herbs and basil primarily to upscale Italian and pizza restaurants in NYC.
Sarah Jacobs
All of the Square Roots' farmers sold their first harvests at a local farmers market.
Through the program, Aliber has had the opportunity to work with numerous mentors — Square Roots has 120 so far.
Sarah Jacobs
"Yes, I have the ability to make money," Aliber said, "But yes, I also have the ability to change the world."
Sarah Jacobs
Electra Jarvis, another 27-year-old farmer, usually comes to Square Roots three days a week. On Wednesdays, she spends four hours meticulously placing 800 seeds inside small troughs.
Mary Wetherill
Two weeks later, she transplants them to the walls. "We should be growing closer to us in cities," she said.
Mary Wetherill
Aliber, Jarvis, and the other eight entrepreneurs are not just learning how to grow plants, but also how to grow their businesses. A large part of the program is learning about branding and "how to tell our stories," Jarvis said.
In the late '90s, after the tech boom, the Musk brothers moved from South Africa to Silicon Valley. They invested in X.com, which later merged with PayPal and was acquired by eBay.
Sarah Jacobs
Kimbal Musk has known Peggs, who had worked for a decade on tech startups that eventually sold to Walmart and Adobe. Before Square Roots, they worked together at The Kitchen, where Peggs served as the "president of impact" and helped expand the chain to new cities.
When asked how his experience in tech translated to running a vertical-farming accelerator, Peggs said the two fields shared the same motivation. "You learn how to execute impossible dreams," he said. "This was all just a PowerPoint presentation six months ago."
Sarah Jacobs
Square Roots hopes to expand to 20 cities by 2020. "Today's consumer wants to know they are supporting companies that are doing something good for the world," Peggs said. "This not just a Brooklyn foodie trend."
Sarah Jacobs
The world's largest vertical farm, AeroFarms, launched last year in Newark, New Jersey. In late 2015, the urban-farming company Gotham Greens opened the world's largest rooftop farm in Chicago.
Vertical farms can grow crops all year, using significantly less water and space than outdoor farms.
Sarah Jacobs
Critics of vertical farms say that the LED lights drain a lot of electricity. Peggs said Square Roots was exploring how the farmers could switch to solar power in the future, since electricity is the program's biggest cost.
Sarah Jacobs
Square Roots' lights are on only in the evening and night, although other vertical farms run theirs 24/7.
Square Roots recently built offices inside the Pfizer factory. In its past life, the building produced ammonia, a chemical sprayed on plants that became vital to the industrial food system after World War I.
The building is populated by sustainable-food startups. "It's an act of poetic justice," Peggs said.
Sarah Jacobs
Urban Farming, Bolstered by Zoning Law Changes, Blossoms in NYC
Eagle Street Rooftop Farm in Greenpoint is one of several farms that has sprouted on rooftops around the city.(Credit: Annie Novak)
Urban Farming, Bolstered by Zoning Law Changes, Blossoms in NYC
By Ivan Pereira ivan.pereira@amny.com July 17, 2017
The seeds of New York’s rooftop farming industry, planted over the past decade, have yielded a harvest in recent years.
It has grown from a niche industry to a large-scale phenomenon, according to experts, thanks to a change in city regulations and a subsequent spur of investment.
And there’s potential for expansion in the years ahead, especially in Brooklyn and Queens.
“These large-scale greenhouses are advanced and expensive, but more and more consumers and businesses are supporting them,” said Nicole Baum, spokeswoman for Gotham Greens, a rooftop farm operator in Brooklyn.
The city changed its zoning laws in 2012 to allow rooftop greenhouses certain exemptions from limits on height and floor size on commercial and industrial properties. As a consequence, landlords have come to view them as a potential amenity and opportunity for profit.
“The landlords now see a way to use their space wisely,” said Annie Novak, a farmer who helped create the Eagle Street Rooftop Farm in Greenpoint in 2009. “Now there is a positive shift from the community who want to see these spaces.”
While the latest data on the number of urban farms comes from the U.S. Census — which said the city saw 11 new farms between 2007 and 2012 — agricultural experts point to a boom in the facilities on rooftops as evidence of the industry’s growth.
Sales from rooftop farms’ most common produce — collards, spinach, kale and other greens — have netted hundreds of thousands of dollars for farmers, with the average Brooklyn farm (on a rooftop or the ground) seeing $199,302 in sales in 2012, according to the Census.
For years, the biggest obstacle to rooftop farming was the cost.
An ideal space for a major harvest yield takes up 44,000 square feet, roughly an acre, according to an urban farming study released by Columbia University’s Earth Institute in 2013.
The space doesn’t come cheap; Brooklyn Grange’s 40,000-square-foot rooftop farm in Long Island City, for example, required $200,000 in startup capital in 2010.
After opening a successful 15,000-square-foot greenhouse on a rooftop in Greenpoint in 2011, Gotham Greens capitalized on the attention it was getting to grow its business.
“That was really a proof of concept,” Baum said of the initial facility.
The company reached various partnerships, including a deal with Whole Foods, that allowed it to build a 20,000-square-foot rooftop greenhouse on top of the Gowanus store in 2013.
Two years later, it opened a 60,000-square-foot facility on a Hollis, Queens, building and expanded to Chicago.
The city offers plenty of ready-made locations to allow for the industry’s further expansion, according to the Columbia University analysis.
It concluded that there were more than 5,701 private and public roofs in 2013 that, combined, were capable of holding 3,000 acres of rooftop farms. That’s nearly three and a half times the size of Central Park. Neighborhoods with the most rooftop space were Maspeth, Long Island City, Greenpoint and Sunset Park, according to the report.
Gabby Warshawer, the director of research for the real estate listing site CityRealty, said she’s hopeful building owners will use that potential as a selling point.
This Shipping-Container Farm Could Someday Solve The Food Desert Problem
This Shipping-Container Farm Could Someday Solve The Food Desert Problem
By Maura Judkis July 7, 2017
The inside of one of Local Roots’ shipping container farms. (Courtesy of Local Roots)
There’s a farm opening soon in Laurel, Md., that can grow strawberries in January. It could grow rare tropical fruits from Asia and Central America on our native soil. It could produce custom-designed lettuce, more peppery or sweet. It’s a hydroponic farm in a shipping container, and its owners hope it could eventually put an end to food deserts, including our biggest one: outer space.
Local Roots, a California company, has created an indoor farm that can turn any produce into local produce, anywhere. They grow fruits and vegetables in shipping containers that are stacked in old warehouses or parking lots, which can either be connected to the grid or, eventually, powered by solar energy. Local Roots has designed the custom growing technology and hardware, and it owns and operates the farms, selling its produce to restaurants and food distributors under its own brand. The fact that the company is vertically integrated differentiates it from other container farming systems, like Freight Farm, which sells their containers to others, including novice farmers.
[Want to get more people to eat their veggies? Make them sound like they’re bad for you.]
“You can start to bring that farm into communities that historically had to import their food due to geography, climate, weather, soil or light.” chief executive Eric Ellestad said.
Every 40-foot shipping container can yield the annual equivalent of three to five acres of farmland. Ellestad says his company can grow plants twice as fast as a conventional farm while using 97 percent less water.
Here’s how they do it: Every farm is hydroponic, meaning the plants are grown in nutrient-rich water instead of soil. Leftover water is recirculated, so each container only uses between 5 to 20 gallons each day. They also use sensors to keep tabs on how the plants are growing, and can give them exactly the nutrients they need at that phase in the growing cycle, speeding it up. It’s “almost a growing algorithm in some ways,” Ellestad said. “You can use that software platform to drive that farm as efficiently as possible.”
Included in that are LED lamps that give the plants exactly the right wavelengths of light they need to grow and which can bring out certain qualities in their appearance and flavor. Chlorophyll, the molecule that causes photosynthesis in plants, absorbs red and blue light, so the farms usually look pink or purple. With its rows of lights and repetition, a container farm that was on display at the South by Southwest conference in March felt a bit like stepping into a Yayoi Kusama infinity room.
A Local Roots farm at South by Southwest (Maura Judkis/TWP)
When they tool around with different growing conditions, they can bring out certain qualities in their produce — the same way that terroir gives grapes grown in California a different taste than ones grown in France.
[“Souping," birch water and Gochujang: 9 up-and-coming food trends]
“You can sit down and say, ‘What do you want your lettuce to taste like? Do you want it to be more peppery?’ ” Ellestad said. “Especially with basil, you can really accentuate some of those flavors. You can really sit down and co-design a product with a chef.”
All of the produce is grown organically, and there’s little risk of the types of E. coli scares that pop-up in conventional farming. “Occasionally a fly will get in, and that’s as serious as it gets,” Ellestad said.
Another key fact: Local Roots has figured out how to make the farm efficient enough that it can sell produce at a comparable cost to conventionally-grown fruits and veggies.
A Local Roots container farm on the move. (Courtesy of Local Roots)
“If you can only sell produce to affluent customers in the Northeast, then that’s a fantastic business but you’re not really going to change how the food system functions for most Americans,” Ellestad said.
They already have a farm of several dozen containers up and running in Los Angeles, and later this year, they’re bringing one to D.C. It will be located in Laurel because it’s adjacent to Coastal Sunbelt Produce, a major food distributor in the area that has partnered with Local Roots. Co-locating the farms means that they won’t have to worry about transportation time or costs — which also means the produce will be selected for its flavor, rather than its hardiness, as many vegetables that must travel long distances are.
“We’re pretty excited about the freshness, just having it grown about as local as it can get,” said Jason Lambros, vice president of purchasing for Coastal Sunbelt. “We can be a neat place for them to experiment and grow anything we can dream of, because we have the customers for it.”
The flexibility and scalability of the farms has huge implications for food deserts, a term for communities that have many fast food restaurants, but few places to purchase fresh, nutritious food. Once Local Roots has scouted a location and set up a farm, its first harvest can take place only four weeks later. The company could drop a farm in the middle of Alaska, where a bag of lettuce can cost nearly $6, or in famine-stricken South Sudan, or here in Anacostia, where there are only three full-service grocery stores in Ward 3.
[The next big march in Washington should be for food, celebrity chefs say]
So why don’t they? It’s about having the infrastructure to distribute the food properly, Ellestad said.
“I think simply helicoptering a farm into a food desert could be part of the solution,” Ellestad said. “We would want to partner with the groups that are already working in that community … we can’t operate in isolation. The food system is far too complex and localized.”
For example, they could put a container farm in a neighborhood with few amenities and sell their produce to corner stores, but if the corner stores don’t have refrigerated cases for produce, it would rot. They are currently seeking partners that work in food deserts, as well as literal ones — “In the Middle East, there’s obviously huge food-supply-chain issues in those areas,” he said. Container farms could be a solution for disaster relief after earthquakes, floods or humanitarian crises.
But they’re also looking a bit further. The company is talking to aerospace manufacturer Space X because these types of growing systems could one day be used to feed astronauts on long-term missions to other planets. “The opportunities are global and intergalactic at the same time,” said Ellestad.
For now, they’re going to begin growing lettuce, herbs and microgreens in the area, while expanding to other cities in the United States. And as efficient as indoor growing is, Ellestad doesn’t think it will replace good, old-fashioned rain, sun and soil.
Ivy Tech, Green Sense Partner On Vertical Farm In South Bend
Ivy Tech, Green Sense Partner On Vertical Farm In South Bend
Ivy Tech to partner on vertical farm
Photos/BECKY MALEWITZ
SOUTH BEND — Ivy Tech Community College and Green Sense Farms have entered into a partnership to build a 20,000-square-foot “vertical farm” on land transferred by the college to the Portage-based grower on Sample Street in South Bend.
The announcement ends two years of speculation about the project, which also involves the city of South Bend. A ceremonial ground-breaking is set for Wednesday.
According to a press release, the state-of-the-art, $3 million to $4 million facility will be utilized for workforce training so that students better understand future opportunities in farming.
Courses will begin as non-credit or “through” courses complementing other programs while the school develops a curriculum for the program, and students will receive training in transferable skills for areas such as food service, retail and industrial maintenance.
Ivy Tech, for its part, will gain access to the vertical farming labs without the large-scale investment needed to acquire equipment, the release states.
“It's a working commercial farm, meaning we will be providing produce every day to the community, and it's a hands-on training center,” said Robert Colangelo, founder and CEO of Green Sense.
Items such as micro-greens, baby greens, lettuces and herbs will be grown at the facility to support local markets, restaurants and colleges, Colangelo said, including Martin's Super Market, the University of Notre Dame, the Morris Inn, Café Navarre, Four Winds Casino and Sodexo, the food service provider for Memorial Hospital and Saint Mary's College.
The facility will employ 10 students every six months in “earn to learn” roles, Colangelo said, plus five full-time employees who will earn $30,000 to $50,000 per year. The students will work 20 hours per week and gain hands-on experience in all aspects of the business.
Students who are interested in the retail or food service sides of the industry will train with the partner organizations as well, Colangelo said, with opportunities to work for those organizations afterward.
“The plan is that they graduate job-ready so that they've got real hands-on skills,” he said. “And more importantly, the much-needed soft skills that employers are looking for.”
Colangelo said he is working with Mike Keen, director of the Center for a Sustainable Future at Indiana University South Bend, to develop a curriculum for the course so students can earn credit for it and professional certification.
They're also working to develop some sort of criteria for the selection of the students, he said, likely to include an interview. “It's not just education,” he said. “Some of it will come down to personality, drive and interest.”
Founded in 2014, Green Sense Farms grows leafy greens in stacking, vertical towers, 365 days a year. The company uses automated computer controls to provide the precise amount of light, nutrients, water, temperature and humidity for the plants so they can be harvested year-round.
The process provides greater yield per unit of space than traditional farming because it allows for growing and harvesting year-round. A typical facility allows for 20 to 30 harvests per year depending on the crop, Colangelo said.
The company opened its first farm in Portage in 2014. It also designed and built a farm in Shenzhen, China, for its operating partner StarGlobal A. And it is preparing to break ground on a third facility in Las Vegas.
“We have about 10 farms in the pipeline being developed in the next six months,” Colangelo said. “And I think once news hits that we're doing this training center, we'll see a lot of colleges and universities want to emulate this.”
The facility here, financed, in part, with a $700,000, low-interest Industrial Revolving Loan from the city, will be at 250 E. Sample St., on the south side of the street, directly west of Ivy Tech's Sample Street location.
It will consist of space to germinate the seeds and grow, package, store and ship the plants, plus office space and an enclosed corridor for students and tour groups to observe the operation, Colangelo said.
Design-wise, the structure will be a steel-frame building with a front-facing brick facade made to match the adjacent Ivy Tech building in look and color, he said.
“It will be the nicest thing on the block,” he said.
Once up and running, the facility will provide fresh, organic produce to local stores, restaurants and food-service providers on a daily basis, Colangelo said. “Most of the stuff from the farm takes days to get from the farm to the table,” he said. “We're going to be able to do that in hours, so it's fresh.”
He said they're also hoping to deliver produce “live” with the roots still on the plant, “because as soon as you cut a plant and harvest it, it starts to decay and lose nutritional value.”
According to Ivy Tech South Bend Chancellor Thomas Coley, the school is approved to offer agricultural courses but never has, “and this seemed to be a very promising way to provide training for a market that seems to be growing fairly well.”
“And it could tie into other related programs in biotechnology or hospitality or even hospitality,” Coley said. “Or even, because it's technologically driven, industrial maintenance and other related areas.”
Colangelo said he hopes to break ground on the project in the coming weeks or months, with a completion date of next June.
He said, “I feel like we're setting a model here for how government, academia and business can work together to train the new, modern workforce.”
574-235-6187
@ErinBlasko
An Alaskan Wants To Put A Lettuce Tower In Every Elementary School In America
An Alaskan Wants To Put A Lettuce Tower In Every Elementary School In America
- Author: Erica Martinson
Lettuce flourishes in a hydroponic grow tower in Sen. Lisa Murkowski’s office recently in Washington, D.C. (Erica Martinson / Alaska Dispatch News)
WASHINGTON — Last month, Bernie Karl flew down to Washington, D.C., and installed a hydroponic grow tower in Sen. Lisa Murkowski's office. Next, he wants to hit every public school in Alaska.
Karl, who owns Chena Hot Springs northeast of Fairbanks, has a mission: He wants to teach kids how to feed their families using cheap, easily obtained materials.
Karl's daughter has a tower at her house — hers grows strawberries and cherry tomatoes, he said. In Murkowski's office, the tower grows only lettuce — enough to feed a family of six.
And for a few weeks now, the senator's staffers have been picking their own salad greens off the tower of orange Home Depot buckets in the corner of her office lobby in the Hart Senate Office Building.
Karl is well known to Murkowski as well as to other political bigwigs in Alaska. Murkowski, Sen. Dan Sullivan and Gov. Bill Walker routinely show up at his renewable-energy fair each August.
So it's not entirely surprising to see the tower appear in Murkowski's office, after he touted its earliest iteration at last summer's Chena Hot Springs energy fair.
"Our goal is to get one in every school in Alaska and every school in America by the end of next year — to teach third- and fourth-graders that everyone can be responsible for growing their own food," Karl said in an interview.
More than 98,000 public schools operated in the United States in the 2013-14 school year, according to the National Center for Education Statistics. More than 67,000 of them were elementary schools.
"The problem is that things are so expensive. But they don't need to be. So we decided that we would come up with something that you could go to any Home Depot and buy," Karl said.
The tower in Murkowski's office is the 3.0 version of Karl's efforts, along with others at his employee-owned Chena Hot Springs Resort, where they grow food for the staff and guests.
That tower is getting its own upgrades. On June 27, Murkowski's husband, Verne Martell, arrived in her office with a wax plumbing ring and set about tweaking a previous fix. Martell was working on quieting the sound of running water that plagued the two employees who sit at desks in the lobby, greeting visitors and answering phones.
Karl said Friday he had just sent an extra light to Martell, an upgrade for a side of the tower that wasn't growing as well as the rest.
Karl is a boisterous man — the kind of guy who has big ideas and even bigger plans. Currently, he's hoping to get a meeting with the top brass at Home Depot — he said Murkowski had kindly put in a call for him.
He's hoping to convince them to offer Saturday classes on building the tower at stores nationwide. And he wants the company to sponsor "one for every school in America."
Karl is in the process of patenting his invention — called "Lettuce Grow for Free" — but he doesn't plan to make money off it. He wants to give the plans away. And he encourages others to improve upon them.
"We're building a fourth prototype right now … that uses a little less material, gets it down a few more dollars."
Karl also hopes that school programs run by Future Farmers of America and 4-H will start programs in schools.
"I want them to help replant the world," he said of the youth agricultural organizations.
This fall, an elementary school in Fort Yukon will get Alaska's first school-based grow tower, Karl said. They were the first to ask for one, he said.
See the plans here: The Chena Grow Tower Project
About this Author
Erica Martinson is Alaska Dispatch News' Washington, DC reporter, and she covers the legislation, regulation and litigation that impact the Last Frontier. Erica came to ADN after years as a reporter covering energy at POLITICO. Before that, she covered environmental policy at a DC trade publication and worked at several New York dailies
LumiGrow Brings Smart Horticultural Lighting to Cultivate'17
Cultivate ’17, North America’s largest horticultural tradeshow is set to use the entirety of the newly expanded and renovated Greater Columbus Convention Center (GCCC). AmericanHort’s Cultivate’17, July 15-18 in Columbus, OH, is the horticulture industry’s renowned professional development event with the largest all-industry trade show. AmericanHort estimates about 10,000 attendees, more than 125 educational sessions and close to 700 exhibitors.
LumiGrow Brings Smart Horticultural Lighting to Cultivate'17
LumiGrow Lights Up Farming at Cultivate ’17 Tradeshow
Greater Columbus Convention Center, Ohio – July 14, 2017 – Cultivate ’17, North America’s largest horticultural tradeshow is set to use the entirety of the newly expanded and renovated Greater Columbus Convention Center (GCCC). AmericanHort’s Cultivate’17, July 15-18 in Columbus, OH, is the horticulture industry’s renowned professional development event with the largest all-industry trade show. AmericanHort estimates about 10,000 attendees, more than 125 educational sessions and close to 700 exhibitors.
Trade show attendees interested in learning about lighting strategies, LED applications and spectral science research are invited to visit the Discovery Café Smartfarm, attend the LumiGrow Cultivate Live session and stop by the LumiGrow exhibit booth.
As part of the $140 million conference center expansion and renovation, the GCCC will showcase a new onsite indoor vertical farm. The newly constructed indoor Smartfarm at the center’s Discovery Café is lit with LumiGrow LEDs and utilizes a hydroponic farming system built by Bright Agrotech, a vertical farming company. Restaurant chef’s will exercise their culinary creativity with hyperlocal ingredients grown from the Smartfarm.
Tradeshow attendees looking for a grower’s perspective on LED lighting strategies are invited to attend the LumiGrow Cultivate Live session on Monday July 17 between 1:45 PM – 2:15 PM. Steve Stasko, Orangeline Farms, and Marco de Leonardis, Freeman Herbs, will discuss how they use adjustable spectrum technology to apply advanced LED lighting strategies to positively impact profits for their greenhouse operations.
Growers, operators and industry professionals looking for a deeper conversation about smart horticultural lighting strategies are invited to visit LumiGrow at exhibit booth 2326.
Cultivate ’17 is set to define the green industry’s upcoming trends, technology and business best practices in horticulture.
About LumiGrow Inc.
LumiGrow, Inc., the leader in smart horticultural lighting, empowers growers and scientists with the ability to improve plant growth, boost crop yields, and achieve cost-saving operational efficiencies. LumiGrow offers a range of proven grow light solutions for use in greenhouses, controlled environment agriculture and research chambers. LumiGrow solutions are eligible for energy-efficiency subsidies from utilities across North America.
LumiGrow has the largest horticultural LED install-base in the United States, with installations in over 30 countries. Our customers range from top global agribusinesses, many of the world’s top 100 produce and flower growers, enterprise cannabis cultivators, leading universities, and the USDA. Headquartered in Emeryville, California, LumiGrow is privately owned and operated. For more information, call (800) 514-0487 or visit www.lumigrow.com.
Media Contact
Brandon Newkirk
bnewkirk@lumigrow.com
510-709-4437
INTERVIEW: Architect Thomas Kosbau On The Exciting Future Of Sustainable Design In NYC
INTERVIEW: Architect Thomas Kosbau On The Exciting Future Of Sustainable Design In NYC
POSTED ON MON, JUNE 26, 2017BY EMILY NONKO
Since Thomas Kosbau began working for a New York consultancy firm running its sustainable development group, in 2008, much has changed in the city’s attitude toward green design. Kosbau has gone from “selling” the idea of LEED certification to building developers, to designing some of the most innovative sustainable projects in New York to meet demand. He founded his firm, ORE Design, in 2010. Soon after, he picked up two big commissions that went on to embody the firm’s priority toward projects that marry great design alongside sustainability. At one commission, the Dekalb Market, ORE transformed 86 salvaged shipping containers into an incubator farm, community kitchen, event space, community garden, 14 restaurants and 82 retail spaces. At another, Riverpark Farm, he worked with Riverpark restaurant owners Tom Colicchio, Sisha Ortuzar and Jeffrey Zurofsky to build a temporary farm at a stalled development site to provide their kitchen with fresh produce.
From there, ORE has tackled everything from the outdoor dining area at the popular Brooklyn restaurant Pok Pok to the combination of two Madison Avenue studios. Last November, ORE launched designs for miniature indoor growhouses at the Brooklyn headquarters of Square Roots, an urban farming accelerator.
ORE’s latest project—and the one Kosbau feels best embodies his design philosophy—is Farmhouse, a sustainably-designed, minimalist community venue and kitchen for the city organization GrowNYC. The Union Square building features a live indoor growing area, fully-functioning kitchen, and a design inspired by the traditional geometry of the American barn. Kosbau and GrowNYC have continued their partnership to design a massive Bronx agricultural distribution center for the organization, to be called FoodHub. When it opens, the building will employ the city’s first closed-loop, entirely organic energy system that utilizes self-purifying algae blooms generated by rainwater. The system, of course, was designed by Kosbau.
With 6sqft, Kosbau discusses how his early projects set the tone for ORE Design, what’s unique about sustainable work in New York City, and how designers have to step up to the plate to offer great design that also happens to be environmentally friendly.
So you came to New York from Oregon.
Thomas: Yes, born and raised in Portland, Oregon. When I moved to New York, it wasn’t at the forefront of my mind for what kind of designer I was. But I think inevitably it’s influenced a lot of my design work.
What factors led you to start a firm in 2010?
Thomas: A combination of many different elements, which has resulted in some of our best projects. Part of it was the recession. I worked five years for another architect as a sustainability consultant in real estate. After a year, the recession hit, and the firm came to a cataclysmic halt. It made me question what would come next, and I already started receiving queries from my network to pick up small projects. I gravitated toward design work, small residential projects, then a store.
But the real culminating event was that I submitted an entry for the IIDA green idea competition hosted in Korea, in 2010. My design was a replacement for asphalt—an ubiquitous material in the world. I put together a proposal for replacing the world’s asphalt with organically-grown sandstone, as way to offset numerous health concerns associated with it.
I won that competition around the same time I received two major commissions from relationships I started years before. One was the Dekalb Market, the shipping container market in Downtown Brooklyn, and the other was Riverpark Farm, the first portable rooftop farm in an urban environment. There, we used milk crates to create a temporary farm on a stalled building site. Both were products of the economic downturn—they were stalled building sites that needed activation for various reasons.
Dekalb Market, courtesy ORE Design
Tell me more about Riverpark Farm.
Thomas: It was a site located right next to Riverpark, the restaurant owned by Tom Colicchio. The team was pretty forward thinking about doing something with this empty land. So they reached out to GrowNYC to think of a solution for a farm that would potentially be moved within a year. GrowNYC tapped our shoulder to do that.
Riverpark, courtesy ORE Design
It seems like these early projects set a tone for your firm, and how it thinks about sustainability.
Thomas: I think the gene that was inside of me from Oregon—mostly from my mother, who founded a community gardening program in Portland—was dormant. But as soon as the need became a higher-level issue, and designers became tasked with thinking about these things, the influence ingrained in who I am came out. The environment revealed this direction and ultimate design brand.
What makes NYC an interesting or challenging place to experiment with sustainable design?
Thomas: You can debate whether this is the most urban place in the world; it’s certainly the most urban environment in the United States. It’s also one of the most concentrated and most interesting environments in terms of diversity. There are so many ideas from around the globe that find a home here and are placed in a small dense environment.
Land is so critically valuable, as well, so people consider it precious. To see food, community gardens, and urban agriculture become such a priority is a litmus for how important it is to the world. We’re seeing rapid urbanization across the globe, and there’s been an influx of residents to New York making the land more precious.
It’s an exciting environment. There are so many different factors on how to use land, what’s considered valuable in green design, and thinking about design that’s equally productive as it is attractive.
Since founding your firm, have you seen a rise in awareness in sustainable design?
Thomas: I have witnessed a shift in priorities. It’s more accepted as a norm to be sustainable, and less of a selling point. LEED was an early vehicle to sell sustainability—we really had to sell developers on how these features could bring a return of value, even if it’s just from a branding standpoint. LEED has become so ubiquitous that’s not the case anymore, and I don’t think that’s a bad thing. The real revolution is that it made material sustainability an absolute must for projects. LEED created a market for sustainable materials to outperform other materials in sales. That’s the real shift. It’s that the choice is easier, and sustainable materials have become as performative, in terms of longevity, have much less of a cost premium, and there’s more variety.
The next step is good design. Making green design interesting, without being tagged green design.
What projects of yours really embody that idea?
Thomas: Farmhouse was our first project to unify our core values with our design aesthetic. It’s our first embodiment of “this is who we are.” It has the nonprofit roots, as a community space with an educational component for GrowNYC. Then there’s the green technology with the hydroponic walls, and food production on site. We did research into recycled materials that solve design issues, evidenced in the acoustic panels we chose. That became our major design move—to use acoustic panels we had pre-manufactured in our geometry, and unite the space with one design feature. It’s not only aesthetic, it balances the acoustics of the space and it’s a placemaker.
Inside farmhouse, courtesy ORE Design
We also used solar tubes to bring natural light into the darkest spaces, and we sourced hardwood from a forest that was drowned in the 1960s. That feature is then awash in natural light.
Farmhouse, courtesy ADG – Amanda Gentile Photography
We didn’t pursue the LEED designation for Farmhouse, though it could easily be Gold if not higher. We offered the option for the client, but LEED is no longer an identifier as an interesting, sustainable space. We pushed the design to make it a unique space. That’s on the shoulder of designers now, we have to be better to make these spaces speak for themselves.
So what’s next for the firm?
Thomas: GrowNYC is working on a really cool project up in the Bronx, a regional food hub. GrowNYC supplies the food for the city’s green markets, and it’s a huge task. The president of GrowNYC and his staff feel they’ve mastered the logistics for moving food in small quantities, and want now build a larger distribution center for farm fresh produce they can bring into the Bronx to distribute to various programs. It would be tenfold of what they’re able to provide now. They’ve tapped us to look at how to make a highly-performative building, with offset carbon emissions and localized power production. We also designed an “anthropomorphic stomach” for the building—a “bio digester” that would take food waste to provide energy for the electricity and heat of the facility.
275 South rooftop forest, courtesy ORE Design
L&M Development also tapped us to create a roof amenity for one of their buildings [275 South, in the Lower East Side]. The building is a 1970s, poured-in-place concrete bunker. It has a huge, bearing capacity. We looked at what it would take to allow large groups on roof—we needed to put a certain amount of steel to get to that level. We also wanted to maximize the view, so we elevated the steel above the existing concrete parapet. With the bearing weight, and 40 inches of room from the new roof to the existing roof, we realized we could plant a forest up here. That’s what we decided to do. We’re planting 80 mature aspen trees, and conceptually carving into the forest floor so the benches are situated within the forest, and trees frame different views toward Brooklyn.
If it’s done in time it will be the location of my wedding in September. The client didn’t have a problem allowing me to do that because they knew it’d get done quickly.
RELATED: