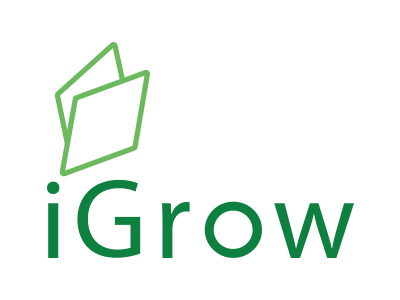
Welcome to iGrow News, Your Source for the World of Indoor Vertical Farming
Why A Peanut Farmer From South Carolina Created A Facebook For Farmers
Why A Peanut Farmer From South Carolina Created A Facebook For Farmers
OCTOBER 2, 2015 LAUREN MANNING
As a nasty nor’easter hammers the Southeast, hurricane Joaquin lingers just off the Atlantic coast guaranteeing many more days of torrential downpour. For Pat Rogers, a fifth-generation peanut farmer running a 550-acre operation in the small town of Blenheim, South Carolina, the rain is unwelcome.
Peanuts, which grow underneath the topsoil, have to be dug up and flipped over to lie on the soil for a week so they can dry out. The last thing any peanut farmer wants to happen after a “dig up” is rain—let alone the one-two punch of a massive storm and a hurricane.
In prior years, Rogers would have been short on opportunities to commiserate with his farming colleagues about the cruel hand Mother Nature doled out. Thanks to a spark of inspiration and a whole lot of hard work, however, Rogers is hoping to change that for himself and other farmers in the business—and he’s using technology to do it.
“I was at the InfoAg conference in St. Louis during 2014. It’s just a whole bunch of farm tech and I was sitting there in the earliest session, looking around, and thinking, ‘This is great!’” says Rogers tells AgFunderNews. “But, the thing about farming is that so much of it is very rural. It’s not like we can all get together and network very often.”
Rogers returned to Blenheim and quickly set to work creating a way to make invaluable coffee shop chatter, tailgate talk, and barnyard business exchanges a lot more accessible for farmers far and wide. What was one of the first sources Rogers tapped to shape his plan? Entrepreneur Eric Ries’ famous book, The Lean Startup.
Over the summer, Rogers and a team of web developers soft-launched a website called AgFuse, a social media platform dedicated to farmers, and designed to help professionals across the agriculture world connect, share tips, show off their crops, pitch products, and keep in touch. Operating in a similar way to Facebook, with a healthy dose of LinkedIn’s business networking savvy, users can create a profile page, join groups, post messages, and peruse their news feeds to see what’s happening with other farmers in their network.
Building AgFuse’s website from the ground up enabled Rogers and the web development team to create algorithms that help members see the information that’s most relevant to their interests, operations, and needs.
While farm-focused message boards provide a flood of information, AgFuse is calibrated so that users only see postings and information from other members with whom they’ve connected.
For now, the crew is satisfied with its current algorithms, perfecting them is a routine objective. “We have a pretty good system that we are rolling out over the next week or two,” says Rogers.
After observing the soft-launch site and getting feedback from initial users, Rogers, and the AgFuse team, officially launched the site on July 22, 2015. While the platform became an instant hit with Rogers’ local community in South Carolina, he quickly saw users join from around the country and engage with other members.
AgFuse, which Rogers has fully funded himself, has even caught the attention of some venture capital investors. “In the future, that’s hopefully not only a possibility but a reality. Right now we are just focused on building a good product and building our user base,” he says. He also hasn’t ruled out the possibility of monetizing the site to provide members with carefully curated advertisements.
Rogers’ current priorities include site enhancements and building up its user base. They also have some big projects in the works, including a mobile app that is in the final stages of development, and additional AgFuse platforms focused on consolidating farmers’ knowledge around the globe.
According to Rogers, AgFuse is the first farm-centric social media platform of its kind. Although there are a number of message boards dedicated to farming and agriculture topics, he felt they weren’t cutting it when it came to helping farmers make real connections.
“If I sign in from South Carolina and they are talking about crop conditions in Illinois, that doesn’t really pertain to me,” explains Rogers. “You can still learn a lot of general things, but AgFuse’s specific niche is helping farmers find a specific audience.”
Traditional social media platforms haven’t provided a good solution either, tending to involve more talk about play and less talk about business. AgFuse, according to Rogers, is strictly a business affair.
“The content can range anywhere from somebody wanting to show off a good series of coverage crops, to showing a scouting report or weather reports. Somebody just showed a picture of armyworms they found in their soybeans to let everyone know they’ve shown up,” says Rogers.
Although the rain may have dampened Rogers’ hopes for a timely peanut harvest, it’s given him time to work on AgFuse and check in with some of his connections on AgFuse. Today’s news feed was full of reports from other farmers in the region lamenting the weather, with one farmer posting a few pictures of cotton sprouts popping through his plants’ bright white cotton lint—a sure sign that the crop has become oversaturated. Although the news may be a downer, knowing you aren’t the only frustrated farmer in the region has its value.
While agtech is making incredible headway toward helping farmers produce food more efficiently and sustainably, AgFuse is a good reminder not only of the infinite possibilities for technology’s role in agriculture but of how technology can go a long way towards bringing people together.
A Brief History of Modern Farming
A Brief History of Modern Farming
While today it’s possible to grow crops indoors, without soil or sunlight — the way we do at Bowery — this wasn’t always the case. In this post we’re going to provide an overview of the evolution from traditional field farming to industrialized agriculture, explain the differences between greenhouse farming and vertical farming, and introduce you to some of the different techniques used in modern farms today.
From Subsistence to “Super Farms”
Around the time of the American Revolution, 90% of the population were farmers. Today, only 3% of the U.S. population is employed on a farm, and 2% of U.S. farms produce 70% of all domestic vegetables.(1) So how did we get here?
The first significant inflection point for the agrarian economy came with the Industrial Revolution in the 1850’s, which brought with it the use of machinery to increase productivity and reduce labor. Farmers began to use fertilizers, often in the form of natural organic material like animal waste and manure, and learned to rotate crops to achieve better soil productivity. The first use of chemical pesticides also coincided with this period.(2)
“Excavator on Mile 52 being pulled by traction-engine, plow side. August 8, 1904” by War Department Office of the Chief of Engineers, Chicago District. Image from the National Archives and Records Administration, CC-PD-Mark, PD-USGov.
Between the 1930’s and the late 1960’s, The Green Revolution accelerated new methods and technologies that increased agricultural production worldwide, including the transition from animal to mechanical power, the increased the use of chemical fertilizers, agro-chemicals and synthetic pesticides, and single cropping practices. The rapid industrialization of agriculture during this time period required farmers to become more efficient to remain competitive. It resulted in small farms, which had historically grown a wide variety of crops, being pushed out by large, corporate farms specializing in large-scale monocultures of single high-yielding crop varieties, like corn, soy, or wheat. These corporate farms were able to produce large quantities of food more efficiently to feed a growing population. Yet, this progress occurred at an environmental cost: the proliferation of synthetic pesticides, widespread soil depletion, and a heavy carbon footprint. As a result, many researchers and companies sought more efficient and environmentally friendly ways to feed a growing and increasingly urban population.
“Spraying pesticides” by John Messina for the EPA, May 1972. Image from the National Archives and Records Administration, PD-US-EPA.
Modern Farming
The idea of growing plants year-round by controlling environmental factors dates back as far as the Roman Empire. Emperor Tiberius Caesar had moveable plant beds built that could grow cucumbers year-round by being brought inside during cold or unfavorable weather. Over time, this evolved into the concept of greenhouses, which were used throughout Europe and Asia as early as the 13th century, and worked by trapping heat from the sun within an enclosed structure that insulated plants from cooler, ambient temperatures. These greenhouses, while innovative at the time, were all relatively low-tech compared to controlled-environment agriculture (CEA) today.
Today, CEA can be defined as “an advanced and intensive form of hydroponically-based agriculture,”(3) which uses technology to create and maintain optimal conditions for plant growth and minimize the use of resources including water, energy, and space. CEA works within an enclosed structure to provide a greater level of control over environmental factors which affect plant growth and quality like light, humidity, temperature, CO2, and nutrient levels.
In the 1970’s, greenhouses in the Netherlands were the first to use computer-assisted environmental control systems, but rising commodity prices quickly made the cost of heating and cooling prohibitive, and many of these were forced to shutter their operations.(4)
In the 1980’s and 1990’s, NASA used CEA to grow crops on a Martian Base prototype research facility at the Kennedy Space Center in Florida, providing evidence that the nutritive value of indoor-grown food crops could be as good or better than field grown crops.(5) And in 1999, Cornell University built an advanced, commercial-scale CEA greenhouse facility in Ithaca, NY, which grew over 1,000 heads of lettuce per day. Since then, and increasingly over the last 5 years, CEA has been adopted as a commercially-viable solution to urban food production, and companies like Bowery have used CEA to build farms closer to the point of consumption that can produce food efficiently for urban populations.
Modern Farming Techniques
While CEA is a broad term, there are actually a number of different approaches that can be used to grow indoors. These techniques differ in how they deliver a plant’s three primary needs: water, nutrients, and light.
Water: Hydroponics vs. aeroponics
“Hanging Gardens of Babylon” by Maarten van Heemskerck, CC-PD-Mark, PD-Art (PD-old-100)
For water, CEA relies on either hydroponics or aeroponics. Hydroponics is defined as the science of growing plants without soil, and has been used throughout history by the Babylonians, the Aztecs, and even the ancient Egyptians, among others. The commercial use of hydroponics spread after WWII (when it was used by the U.S. Air Force to provide fresh food to troops stationed on small, rocky islands in the Pacific), and continues to accelerate with the development of better accompanying technology and automation. Traditional hydroponic methods, which we use at Bowery, grow plants directly in nutrient-rich water.
Used with permission from San Diego Hydroponics
Aeroponics is technically a subset of hydroponics, and works by suspending plant roots in air and misting them with nutrient water. This method can provide a greater level of control over the amount of water that is used throughout the growing process, but may leave plant roots vulnerable to pathogens, if not carefully controlled.
Nutrients: Hydroponics vs. aquaponics
The second main difference in technique concerns the way nutrients are supplied to the plants. Hydroponics use mineral salts that mirror those naturally-occurring in soil, including minerals like calcium, magnesium, and iron. These mineral salts are combined in precise proportions and dissolved in water to provide nutrients directly to a plant’s roots, allowing for a balanced nutrient environment to achieve optimal plant growth.
Used with permission from Ecolife Conservation
Aquaponics, on the other hand, is a closed-loop system that relies on the symbiotic relationship between aquaculture (fish) and agriculture (plants) for fertilization. While fish waste accumulates in the water and provides the nutrients necessary for plant growth, the plants naturally clean the water. It provides a balanced, yet less regimented, environment.
Light: Greenhouses vs. Indoor vertical farms
Greenhouses vs. indoor vertical farms
Any growing environment requires energy to power photosynthesis. The biggest distinction in Controlled Environment Agriculture is in where this energy comes from, since it doesn’t come (entirely) from the sun, as it does in field farming.
Greenhouses often use a combination of natural and artificial lighting. Greenhouses grow crops indoors in a structure with walls and a roof made primarily of transparent material, like glass or polyethylene, in order to make use of naturally occurring sunlight. They use glass to filter out the UV rays, reducing the heat build-up inside the growing environment. Often, they supplement this sunlight with artificial light to counteract the times when the sun’s energy is either less intense or hidden by clouds.
Indoor vertical farms rely solely on artificial lighting. These farms grow crops entirely indoors inside of a warehouse or shipping container. In some of these farms, crops grow along vertical columns, and in others, they grow horizontally in stacked rows like the stories of a skyscraper (as they do at Bowery). One advantage to relying on LED lights, as we do at Bowery, is that they allow us to grow consistently and reliably 365 days of the year, regardless of weather or seasonality. Another advantage is that we can precisely control their spectrum, intensity, and duration, which allows us to adjust many variables including flavor profiles, and make our mustard greens spicier or our arugula more peppery, for example. We do this using BoweryOS, the software-based brains of our farm.
Inside a Bowery Farm
Until about 5–10 years ago, greenhouse production dominated, but in the last few years more indoor vertical farms have emerged, due in large part to falling LED prices. Both greenhouses and indoor vertical farms can be built in and around cities allowing modern farmers to cut thousands of miles out of the supply chain and deliver fresh produce within days rather than weeks of harvest.
The Future Looks Ripe
While urban farming is on the rise, it still comprises less than 20 percent of agricultural production worldwide today according to the U.N. Food and Agriculture Organization.(6) Yet, this next frontier of farming boasts some important advantages: it allows farmers to produce more output, use fewer resources, and reduce transportation by locating operations closer to the point of consumption. As the global population continues to rise, people continue to move to and around cities, and resources continue to dwindle, indoor vertical farming is going to continue to grow rapidly in both scale and importance. At Bowery, we’re excited to be at the forefront of this growth and are passionate about realizing the potential of indoor agriculture to grow food for a better future by revolutionizing agriculture.
Keep up-to-date with all the latest from Bowery by signing up for our email updates at boweryfarming.com and following us on Instagram, Facebook, and Twitter. We’re hiring!
SOURCES:
(1 & 2) Trautmann, Porter and Wagenet (2012): Modern Agriculture: Its Effects on the Environment Source via Cornell University Pesticide Safety Education Program (PSEP).
(3 & 5) Cornell University College of Agriculture and Life Sciences: Controlled Environment Agriculture.
(4) Rorabaugh, Patricia A. (2015): Introduction to Hydroponics and Controlled Environment — Chapter 1 via University of Arizon aControlled Environment Agriculture Center.
(6) Royte, Elizabeth (2015): Urban farms now produce 1/5 of the world’s foodvia GreenBiz.
Going Green - How Worcester, Central Mass Are Leading The Way
Solar Farm panels on the former Greenwood Street Landfill. Elizabeth Brooks photo.
The irony seeps through the ground – a vast wasteland on Greenwood Street that once held heaps of residential trash for more than a decade is now home to what city officials deem to be the largest municipally-owned solar farm in New England. With a ribbon-cutting ceremony expected to occur sometime this summer, the 25-acre site will have completed its transformation from an environmentally unfriendly dump to one that will be the greenest of the green in terms of energy saving measures.
The solar arrays over on the south side of Route 146 are impressive – 28,600 panels tilted at 25-degree angles, row after row, one after another. And then, just up ahead, with the hills in the distance on the northern side of 146, a lofty wind turbine spins at 262 feet high on the campus of Holy Name Central Catholic Junior/Senior High School. Separately, the two are just some of the many energy efficiency projects in the city; together, they serve as a beacon along the highway, a gateway to the city and the road map for the future. Driving down the highway and seeing both gives a feeling of “Welcome to Worcester,” says John Odell, Energy & Asset Management director for the city.
Welcome to Worcester, indeed. In a world of “going green,” the city has gone green enough that officials there consider Worcester to be a leader in such efforts.
“Yes,” says City Manager Edward M. Augustus Jr. “You might expect me to say that. I think you can prove that.”
In fact, “going green” is not a new concept for Worcester. Efforts date back to before the current administration, and other city institutions, such as Worcester Polytechnic Institute, have been practicing energy efficiency for more than a decade. Worcester was one of the first in the state to have a curbside recycling program and a climate plan, and it was also one of the first certified Green Communities. Even the Beaver Brook Farmers’ Market, which sets up Mondays and Fridays on Chandler Street, is the oldest in Worcester – its roots dating back to the ‘90s, when it was originally located near City Hall.
Even so, “It’s easy not to notice the strides the city has made in green issues,” says Steve Fischer, executive director of the Regional Environmental Council, an organization that started in 1972 with a mission to study clean air, clean water and open space issues. It has since expanded over the years to include other green initiatives, including urban farming.
Today, however, officials want residents to take note of Worcester’s many green efforts.
Saint Gobain Kiln.
Worcester Energy, a municipal initiative of the Executive Office of Economic Development and the Division of Energy & Asset Management, has an extensive website detailing the city’s green projects past and present. And both Augustus and Odell cited three ongoing projects – not only the solar farm, but also a street light replacement conversion and an energy aggregate plan – that have had or will have significant impact on the city. The three together, Odell says, are “near completion or far enough along that we can say we are in a leadership position. We’re in a great position to start spreading the word.”
Ten years ago, the city entered into a multiyear, multi-million energy efficiency and renewable energy project to assess all of its municipal facilities. Honeywell International was hired in 2009 as Worcester’s Energy Services Company to conduct energy audits of those buildings. Two years later, the city signed an Energy Savings Performance Contract for $26.6 million. As part of the ESPC, energy conservation work was to be done in 92 of the city’s largest facilities, out of 171 total. Some buildings have benefited from small changes, such as computer power management systems, while other, more aging facilities have received more extensive improvements – heating and cooling systems, insulation, air-sealing, lighting fixtures and water conservation equipment and solar panels.
The goal, according to Odell, was to save $1.3 million a year – an amount guaranteed by the ESCO. But a recently completed assessment of the ESPC revealed a $1.7-million savings per year.
“Energy efficiency has become a really good investment,” Odell says. “I think it’s important to note that the dollars are real. It costs money to do these things, but because of the benefits you get, it’s a savings.”
Mayor Joe Petty agrees, saying green energy is ever-important, not just for the environmental aspects, but for cost-savings as well.
“I know it’s a little more expensive sometimes, but that in itself is a positive,” he says, adding the city’s endeavors are going to save millions of dollars over the next several years.
A major contributor to those savings are the city’s numerous solar projects, including the Greenwood Street solar array. Although it cost approximately $28 million to construct, with a three-year payback, the 8.1-megawatt farm will produce about 10 million kilowatt hours of electricity each year once connected to National Grid’s distribution center. That’s enough to offset the electricity used by more than 1,300 homes in the city. In total, the city expects a return of about $50 million over the 20 years of the project, plus approximately $15 million more the following 10 years.
“It’s equivalent to 19 football fields of energy,” Augustus says. “That’s a big deal in terms of taxpayers’ dollars and in terms of shrinking our carbon footprint.”
Another major project completed this past fiscal year involved the installation of approximately 4,500 LED, high-efficiency street lights throughout the city, a measure expected to save $400,000 in electricity costs. Once all 14,000 planned street lights are switched over, city officials say they expect the savings to be more than $900,000 per year.
Beyond the cost savings are the additional benefits that come with the new street lights. Officials say the lights will cost less to maintain and have longer life cycles, reduce carbon emissions and light pollution at night, and improve lighting quality overall, plus give a sense of greater security. According to Augustus, Los Angeles County did a similar street light conversion and officials there credited the project with a 10-percent reduction in crime because the intensity of the lights was able to be calibrated at specified times.
“There are a lot of operational efficiencies that come from having this kind of technology,” Augustus says.
In addition to those projects, Worcester has upgraded lighting at four parking garages to LED, saving an additional $89,000 per year in electricity costs; completed a $1.7 million lighting upgrade project at the DCU Centre without using any taxpayer funds; and replaced a failing HVAC center at the senior center, among other initiatives, with more on the way. And when President Donald Trump announced the federal government would no longer participate in the Paris Climate Agreement, Petty made his own announcement: that the city would continue to battle climate change locally and invest in green technology.
“As our federal government retreats from its responsibility as steward of our environment, it is vitally important for state and municipal government to uphold our commitment to the future of our planet,” says Petty, who joined mayors across the country in signing the U.S. Climate Mayors statement. “If the president doesn’t want to do it, we will.”
Mary O’neill and Eva Elton display fresh produce at the Mobile Farmers Market Laurel St. location, in Plumley Village.
Green Schooled
Worcester Public Schools has gotten into the green zone as well. Over at 35 Nelson Place, a school dating back to 1927 is being demolished in preparation for a new building to serve Worcester students in pre-kindergarten through grade 6 starting this fall. But unlike the old Nelson Place School, the new 600-student facility will be twice the size – 110,000 square feet compared to the original’s 55,000 square feet – and will be the city’s first-ever, net-zero energy building, defined by the U.S. Department of Energy as, “an energy-efficient building where, on a source energy basis, the actual annual delivered energy is less than or equal to the on-site renewable exported energy.”
And even though “you could effectively pull that building off the grid,” Odell says, that doesn’t mean the new school is being built with highly-specialized technology and equipment. On the contrary, it’s all “off-the-shelf technology.”
According to Brian Allen, chief financial and operations officer for Worcester Public Schools, the roof’s solar panels will provide 100 percent of the building’s energy, and together with the high-efficiency windows and insulation, “natural gas for heating will be one-third of what we’re using.”
“You basically have one school taking care of itself,” Augustus says. “Imagine if I could have every city building take care of itself.” The school was designed as a green building from the start as part of the application process for the Massachusetts School Building Authority, which works with cities and town across the state to help build affordable, sustainable and energy-efficient schools. Because the state offers more reimbursement credits for green buildings, it made more sense to create the new Nelson Place School as net-zero energy, Allen explains.
The new Nelson Place School is just one of the many examples of how the city of Worcester and the educational system have collaborated on the ESCO contract, and in the near future, the hope is to do another energy partnership with the schools, Augustus says. Many of the schools have benefited from new doors and windows, with others slated for similar work soon.
“The city,” he says, “has been very aggressive over the years with window replacement, making them energy-efficient and more aesthetically pleasing in some of the older buildings.”
Other schools have been outfitted with new boilers and exterior LED lights, while converting interior lights is currently being explored, according to Allen. In addition, the school district as a whole also benefits from numerous solar panels at its buildings, about 3 million kilowatts of energy, Allen says. Two of the schools have parking lot canopies, and eight – including the new Nelson Place – have roof arrays. Four of those roofs, according to Odell, were nearing the end of their lifespan and were resealed with white roof coating application instead of black to make the arrays more effective.
“The net effect,” said Odell, “is we got the roofs for free.”
As a result, all of these green efforts are beneficial to the city and school district and the students. “Any way that we can be part of the initiatives and save money and be more environmentally aware, it seems to perfectly align with the mission of the school district,” Allen says, noting it also demonstrates to students that there are ways to be environmentally conscious and friendly.
The solar panels on the roof of the new Nelson Place School
Windfall
Holy Name’s wind turbine is another example of how the city has collaborated with schools. Although it is a private school and no city funds were expended to construct the turbine, regulations did not allow for such projects a decade ago. City officials, however, allocated staff resources to review the regulations, and as a result, in June 2007, adopted the Large Wind (Energy Conversion Facilities) Ordinance, allowing for wind turbines to be located in Worcester by special permit with provisions for height, abutting uses buffers and noise regulations.
The turbine has been largely successful. Holy Name, built in 1967 and heated electrically, was paying $180,000 in utility bills each year, according to a sustainability profile by Worcester Energy. In 2015, when the report was written, the turbine was producing an average of 74 percent of Holy Name’s yearly energy needs.
That’s one of the reasons why Worcester officials feel it is so important to partner with other schools and businesses on green technology.
“It allows us to be credible,” when businesses want to locate or relocate in the city, so that they don’t feel like they’re working on projects in isolation, says Odell.
City officials also believe it is important to help residents go green – and stay green. The Municipal Electric Aggregation program, which City Council recently approved, pools all of Worcester’s National Grid customers into one negotiating block as long as they are signed up for the Smart Grid program. By doing so, the city can offer residents and businesses various components of green energy to them.
“That’s the next big thing,” Odell says. “You can make your own portfolio greener.”
Saint Green
One such company that is no stranger to green issues is Saint-Gobain, a world leader in designing and building high-performance, innovative and sustainable building materials. Recently, the company announced a renewed commitment to the U.S. Department of Energy’s Better Plants Program, which works with manufacturers to improve energy efficiency to drive cost savings for the industrial sector. Eighty four of Saint-Gobain’s manufacturing plants in the country – Worcester included – are participating in the program, with a goal of achieving an energy savings of 20 percent over the next 10 years. Saint-Gobain joined the program in 2011, the same year it launched.
Michael Barnes, vice president of operations for Saint-Gobain Abrasives North America, says the company chose to focus on the Better Plants Program because it “really aligns with our own strategic direction. Saint-Gobain is committed to not only what we do every day with the products we make and sell, but in the communities as well.”
In Worcester, specifically, the plant is getting a lights makeover with the installation of LED lamps, plus a new kiln was installed. Many of the company’s products, Barnes says, are fired in high-temperature kilns, and the new one has provided the company with a significant reduction in natural gas consumption. In addition, Saint-Gobain in Worcester has its own powerhouse that generates steam, which in turn heats the buildings, so that the company not only procures energy but produces it as well.
It’s a “very smart move,” Barnes says, to look at the energy the company consumes and expels. Part of that as well is the company’s carbon monoxide emissions, which SaintGobain seeks to reduce by 20 percent.
With these strategic, long-term plans “heavily supported” by capital investment, a creative team and the continued financial support from the corporation, Barnes says, it shows Saint-Gobain’s commitment to remain in Worcester and to contribute to the city’s employment rate.
“It’s difficult to do business in New England. It’s a high-cost area. It’s very highly regulated environmentally. It’s easy for people to say, ‘Let’s do this elsewhere,’” Barnes says.
But, he adds, the company remains committed to its Worcester roots and helping the environment as well through its Better Plants Program participation.
“Energy is a very critical cost component. That’s why we take this initiative seriously,” he says, adding, “This isn’t just something we talk about. It’s something we’re committed to.”
While the company cites its efforts to become more environmentally friendly, it has not been without its missteps. Saint Gobain allegedly violated the Clean Water Act, reaching a settlement last December with the U.S. Environmental Protection Agency that required the company to pay a $131,000 penalty and to install new storm water treatment equipment.
Technically Green
If Worcester and its businesses have been in the green game for some time, WPI has, too. In fact, its very mission statement pledges the college will “demonstrate our commitment to the preservation of the planet and all its life through the incorporation of the principles of sustainability throughout the institution.”
WPI has a Sustainability Plan, an initiative put into motion during spring 2012 by the WPI Task Force on Sustainability, that outlines goals, objectives and tasks for academics, campus operations, research and scholarship, and community engagement. It offers 119 undergraduate and 30 graduate sustainability related courses, as well as a minor degree in sustainability engineering. And, back in 2004, five undergraduate students from the college were the ones to conduct the wind turbine study at Holy Name’s request.
Ten years ago, the Board of Trustees passed a resolution that all new buildings be designed to meet LEED (Leadership in Energy and Environmental Design) certification, a national rating system created by the U.S. Green Building Council. Today, WPI boasts four LEED buildings: Bartlett Center, LEED Certified in 2006; East Hall, LEED Gold in 2008; the Recreation Center, LEED Gold in 2012; and Faraday Hall, LEED Silver in 2013.
Although WPI has many sustainability programs, two have stood out, according to WPI Director of Sustainability John Orr, who is also a professor emeritus of electrical and computer engineering.
“The project with the greatest environmental impact has been our building energy and lighting retrofit program that saves energy and reduces greenhouse gas emissions,” Orr says. “This is largely invisible to the community, but has a great environmental impact. Our bike share program, Gompei’s Gears, is highly visible and has received great community feedback.”
Gompei’s Gears was originally an Interactive Qualifying Project (submitted for degree requirements) by two students, Kevin Ackerman and John Colfer, and the program has evolved from an idea in 2015 into a fullscale program. Gompei’s Gears, named after the WPI mascot, allows students, faculty and staff access to bikes from various locations on campus that they can ride anywhere on site or even off school grounds. It is available after spring break (weather depending) until the first snowfall.
For all its efforts, in June WPI earned a gold rating in the Sustainability, Tracking, Assessment and Rating System (STARS), awarded by the Association for the Advancement of Sustainability in Higher Education. Two years ago, the first time the school submitted a STARS application, it earned a silver rating and worked hard to improve upon that. This year, WPI was one of 117 schools out of 415 total that received a gold rating. Only one received platinum, 201 silver, 67 bronze and 29 reporter rating.
Orr says he believes the campus’ four LEED-certified buildings – with another under construction – Gompei’s Gears, the building energy upgrades and other programs make WPI a leader in the “going green” movement out of colleges in similar size.
“Also, very much in our educational programs – environmental engineering and environmental and sustainability studies – and our global project programs in developing nations,” Orr says. “Advanced technology is required to address the world’s environmental challenges, and we are showing leadership in our campus operations, our educational programs and our research (advanced batteries, biomass, advanced recycling, etc.).”
Leeding and Leading the Way
Other Worcester and Central Mass colleges are making an effort to go green as well.
At Assumption College, the new Tsotsis Family Academic Center, which will open this fall, and site lighting were all designed for LED lights, with the exception of specialized lighting in the performance hall, according to the school’s Office of Communications. Five interior space renovations are underway, where the lighting will be replaced with LEDs and reverse refrigerant systems will be installed in place of air-conditioning to control the temperature within those particular spaces. In addition, speed controllers were added to the HVAC units in the Fuller/IT buildings, and last summer, low flow shower heads and aerators were installed on the sink’s faucets in all the resident halls. Opened in 2015, it is the first building on the campus to be designated LEED certified and is the only Gold-certified building in southern Worcester County (a term sometimes used to define towns south, southwest and southeast of Worcester), according to college officials.
Over at Nichols College in Dudley, its newest academic building was awarded LEED Gold certification last year. Opened in 2015, it is the first building on the campus to be designated LEED certified and is the only Gold-certified building in southern Worcester County, according to college officials. The three-story building’s green components include locally-sourced and recycled materials; excellent indoor air quality; efficient water use systems; sensors that better control heating and lighting in individual rooms; and large windows for natural light, which reduces the need for interior lighting and minimizes the use of electricity during the daytime.
“Gold LEED certification for the new academic building is an exciting accomplishment and a statement to Nichols College’s commitment to environmental stewardship,” says Robert LaVigne, associate vice president for facilities management at Nichols. “Since opening its doors last fall, the building has served as a testament to the college’s dedication to innovation – not only in sustainable design, but also education.”
Other green programs at Nichols include its single-stream, campus-wide recycling program, food waste recycling at Lombard Dining Hall, geothermal heating and cooling systems at two residence halls and LED conversion of all exterior lights on campus. In addition, Fels Student Center received National Grid’s Advance Building Certification for energy efficiency.
Food for Thought
But “going green” doesn’t just refer to eco-friendly buildings, energy-efficient lights and solar panels – it can also mean the food we eat and how it is sourced. In cities, people don’t always have access to fresh food, but Worcester has been working to change that as well.
On Mondays and Fridays, from 9 a.m. to 1 p.m. at 306 Chandler St., the Beaver Brook Farmers’ Market sets up shop with local produce, plus bread and craft vendors. Originally the Worcester Hill Market, it is the oldest farmers’ market in the city, according to Fischer. It moved to Chandler Street when the front of City Hall closed for repairs, and the REC took over management in 2012.
Beaver Brook is just one of the city markets, which all opened in late June and run through Oct. 28. The University Park Farm Stand, a Main South staple since 2008, moved to its current location last year so that the REC could more closely partner with Clark University, the Main South Community Development Corporation and other area organizations to provide not only fresh food but family-friendly activities as well. It is open every Saturday, from 9 a.m. to 1 p.m., at 965 Main St. The REC also runs the Mobile Farmers’ Market, which makes 16 stops around the city Tuesdays through Fridays, bringing locally grown produce straight to residents who might not otherwise be able to travel to a farm stand. Fischer notes the city is home to many other farmers’ markets not run by the REC. “We’re seeing a demand in farmers’ markets,” he says. “We’re seeing a demand for local food.” Martha Assefa, manager of the Worcester Food Policy Council, agrees.
“There are so many amazing farmers’ markets happening in the city,” she says, recalling, “A while ago, it was a few folks at the table talking about this. Now local food and food access is becoming mainstream. I think folks are much more interested in buying local than they were 15 years ago.”
But is buying fresh and local more expensive? The Healthy Incentives Program makes sure people who receive SNAP (Supplemental Nutrition Assistance Program) assistance have just as much access to fresh food as others. Through March 31, 2020, the program will match any SNAP dollars spent at farmers’ markets or stands, mobile markets and Community Supported Agriculture (CSA) farm stand programs. Families of one to two people can have up to $40 instantly debited back to their EBT card each month, $60 for three to five people, and $80 for families with six or more people.
“I think many folks realize it makes sense to buy local,” Assefa says, adding it reduces the amount of food travel from producer to consumer, and it also reduces some of the packaging it comes in as well. Plus, it directly helps local farmers – and all that leads to a greener planet.
“A lot of the farming community knows how important it is to protect Mother Earth. A lot of the farmers are innovators. If they don’t protect it, they’re going to see it on their fields,” Assefa says. “That’s the forefront of it all,” she says. “Plus, local food tastes better.”
Urban Gardens
Just as farmers’ markets are not reserved for the suburbs, neither are gardens. In 1995, the REC started a network of urban farms and community gardens that has now grown to 64 in number. These farms have allowed citizens to contribute to the community, learn about growing their own food and beautify their neighborhoods. There are also 20 gardens at the public schools, as well as a youth program in Belmont Hill for ages 14 through 18 that has been in existence since 2003, Fischer says. Both programs, he says, are “transformative,” adding that, for many, this exposure to gardening is the first time students see “how a carrot comes to be, how lettuce comes to be, other than buying it in stores.”
And by working in the gardens, Fischer continues, “They can see the fruits of their labor. It has an amazing impact.”
That’s precisely why groups in the city are pushing for more urban farming – specifically to allow residents to grow and sell their own food. Although personal gardens are allowed, Fischer says, residents are not currently permitted to set up roadside stands or sell to farmers’ markets or stores.
The Urban Agriculture Zoning Ordinance seeks to change that.
“It’s a set of rules to make sure there are rules in place for growing and selling food in the city,” Fischer says. “Right now there’s a big hole in the regulations for growing food in the city.”
Currently in committee hearings, the ordinance has been three years in the making, after the mayor convened a working group with concerned citizens, those associated with urban farming, the Chamber of Commerce and other groups to look at the zoning regulations from environmental and social justice perspectives, Fischer says.
The Worcester Food Policy Council is also heavily involved with the proposal to make sure anyone in the city can farm their land and in turn sell their products. The ordinance has received some pushback, however, particularly among area beekeepers who worry it will infringe upon their efforts.
The ordinance would require beekeepers to notify abutters that they have bees, which the keepers find potentially prohibitive. Worcester Magazine wrote about their concerns earlier this month, in a story titled, “Beekeepers buzzing over proposed urban agriculture ordinance.”
Still, says Fischer, the ordinance and other work is an acknowledgment that urban agriculture is real.
“There is a growing interest as to how the food is produced and where it is grown and the quality of how it’s grown,” he says, noting that “it’s full circle, and essentially we need to rebuild the infrastructure that was dismantled over the last decade, and also to rebuild the biodiversity.”
Plus, says Fischer, “It’s exciting to have the city and local businesses and the residents taking an interest in these things and providing leadership in moving things forward.”
It is a project of which the mayor is particularly proud.
“I think it’s a great asset to the city,” Petty says of the ordinance. “We are taking what people are doing anyway and putting some rows around it.”
Plus, he adds, with that and the existing farmers’ markets, “It’s a driver for jobs. We’re taking locally grown food and selling it.”
Barking Up a New Tree
Amanda Barker knows much about urban agriculture. On a sunny day, she is planting scallions at Cotyledon Farm, her newest venture in nearby Leicester. She is the founder of Nuestro Huerto on Southgate Street in Worcester, which she watched grow from a small-scale community garden to a successful urban farm.
When she moved to Main South eight years ago for graduate school at Clark University, she didn’t know anyone but had a desire to “ultimately help create and become part of a community around food,” she recalls.
Barker started a garden in her back yard, but soon found the shady space and the lead in the soil made it unsuitable for growing anything. Faced with needing to take on an unpaid internship for her requirements at Clark, her “practical” gardening project ended up becoming long-term when she set up on land owned by Iglesia Casa de Oración (House of Prayer Church). Initially, she says, she started with 10 raised wooden garden beds, with the intent to give away the food for free. Eventually, it became a full-scale urban CSA.
“It demonstrated interest and demand for those projects. Certainly, we weren’t lacking for volunteers, depending on the day,” Barker says, recalling that there were always a “lot of young people showing interest in being outside and being in a non-city place. It was a respite and a green space.”
Today, after a largely successful run, Nuestro Huerto and the CSA are now closed to the public, but with good reason—the site is host to three farmers from Nepal who will use the opportunity to provide for themselves, their families and their communities. Barker still serves as a liaison for the project, she says, even though the farmers are mostly independent.
“You can produce incredible amounts of food, and they certainly are. Every inch is going to be packed with vegetables,” she says.
It is why she has “mixed thoughts” on the Urban Agriculture Zoning Ordinance.
“What I want is everything to be allowed by right in all zones,” Barker says. “We’re human beings; we eat food. What is there to have a conversation about?”
If the proposal is successful, it should address some of her questions and transform some of those blank spaces into only more green spaces for the city.
“We’re excited about the potential urban agriculture has in responding to how difficult it is for some people who are working hard but are unable to access fresh food,” Fischer says. “It also makes neighborhoods beautiful. That is a key strategy for beautifying the city.”
Not only that, but “people in the area grow to love those neighborhood farms, and they look out for it,” he says. Between the urban farms and solar farms, plus all the energy-efficiency programs, is there room for Worcester to improve? Augustus says,“Yes,” adding Worcester should “continue to set the pace of what can be done by a municipality … in terms of great and innovative ways to save the taxpayer money instead of being paid to a utility to produce.”
Worcester, Petty says, “is killing it” not only with green issues, but other aspects as well, such as the arts.
“I think we have a government that’s pretty interactive, and people are noticing. We’ve made all the right decisions so far.” When it comes to going green, he says, “This is good, cooperative effort between the government and the community.”
Harvest Dinner
Harvest Dinner
THE EVENT
Join us for a unique evening at the Indiana State Fair benefiting the Indiana State Fair Foundation!
Traditional harvest dinners bring together family and friends for celebration and fellowship at the end of a long planting season. They are the culmination of months of hard work, commitment and stewardship. They are the very essence of what it means to be a farmer in Indiana.
The Indiana State Fair is our state’s largest celebration of agriculture, so what better way to celebrate than with a Harvest Dinner to honor Indiana’s farmers.
This year’s event will take place on Wednesday, August 16, in the Indiana Farmers Coliseum.
HARVEST AWARD
Purdue University President Mitch Daniels Accepting the 2016 Harvest Award
The Harvest Award is given annually at the Harvest Dinner to an individual, organization or company that has made a significant contribution to the growth of our great Indiana State Fair with a focus on agriculture, youth and education.
Past Harvest Award Recipients:
DOW AgroSciences – 2015
Purdue University – 2016
FUNDRAISING
All proceeds from this event will benefit the Celebration of Champions which awards the hard working 4-H youth who rise to the top of their peers at the Indiana State Fair.
Click Here to learn about sponsorship opportunities and to reserve your table today!
Indoor Farming Plus Made In USA LED Grow Lights: Profile 1.8
Indoor Farming Plus Made In USA LED Grow Lights: Profile 1.8
GREENandSAVE Staff
Posted on Thursday 29th June 2017
This is one of the profiles in an ongoing series covering next generation agriculture. We are seeing an increased trend for indoor farming across the United States and around the world. This is a positive trend given that local farming reduces adverse CO2 emissions from moving food long distances. If you would like us to review and profile your company, just let us know! Contact Us.
Company Profile: Gotham Greens
Here is a great example of an urban farm with greenhouse locations on rooftops of New York City and Chicago.
Here is some of the “About Us” content: Gotham Greens’ pesticide-free produce is grown using ecologically sustainable methods in technologically-sophisticated, 100% clean energy powered, climate-controlled urban rooftop greenhouses. Gotham Greens provides its diverse retail, restaurant, and institutional customers with reliable, year-round, local supply of produce grown under the highest standards of food safety and environmental sustainability. The company has built and operates over 170,000 square feet of technologically advanced, urban rooftop greenhouses across 4 facilities in New York City and Chicago. Gotham Greens was founded in 2009 in Brooklyn, New York and is privately held.
Our flagship greenhouse, built in 2011, was the first ever commercial scale greenhouse facility of its kind built in the United States. The rooftop greenhouse, designed, built, owned and operated by Gotham Greens, measures over 15,000 square feet and annually produces over 100,000 pounds of fresh leafy greens. The greenhouse remains one of the most high profile contemporary urban agriculture projects worldwide.
Here is the link to learn more: http://gothamgreens.com/.
To date, the cost of man made lighting has been a barrier for indoor agriculture. A new generation of LED lighting provides cost effective opportunities for farmers to deliver local produce. Warehouses and greenhouses are both viable structures for next generation agriculture. Here is one example of next generation made in USA LED grow light technology to help farmers: Commercial LED Grow Lights.
13 Facts About "Organic" Foods That Will Shock You
image: http://mobile.wnd.com/files/2017/07/organic-fruits-vegetables-tw-600.jpg
No Testing, Mostly Imported, More Sickness, Higher Costs, More Subsidized
WASHINGTON – Do you choose “organic” produce because it’s healthier and locally grown?
Think again.
And that’s not the worst of it, says the report by the Capital Research Center.
Here are some shockers about how the “organic foods” phenomenon is costing you more, making foods less safe and costing real American organic farmers marketing share:
http://mobile.wnd.com/files/2017/07/USDAorganicbudget-386x1024.png
1. So-called “organic food” in America tests positive for synthetic pesticides four times out of 10.
2. Up to 80 percent of food labeled “organic” in American stores is imported. This increase has coincided with incidents of organic food-borne illness.
3. The USDA tripled its organic foods budget over the last eight years without requiring any field-testing of either domestically grown produce or imported.
4. During that time, tens of millions of dollars in subsidies were given to preserve the 0.7 percent of American farmland devoted to growing organic food.
5. The USDA has increased spending to $9.1 million on the organic bureaucracy, yet none of its 43 staffers are responsible for finding fraud, field-testing for safety, recalling unsafe food or encouraging domestic farming.
6. About 43 percent of the organic food sold in America tested positive for prohibited pesticide residue, according to two separate studies by two separate divisions of the USDA, conducted in 2010-2011 and 2015.
7. Organic groceries accounted for 7 percent of all food sales in America last year, but the U.S. government contracts out organic inspections to a total of 160 private individuals for the entire country. There are only 264 organic inspectors worldwide.
8. The USDA’s National Organic Program tests only finished product and only 5 percent of the time covering only pesticides, never looking for dangerous pathogens from manure. Yet synthetic pesticides show up 50 percent of the time. It took until 2010 before any field-testing at all was required by the USDA.
9. The USDA “certified” label for organic food is not based on any objective, scientific process that ensure authentic or safe produce. In fact, the program is regulated by the USDA’s Agricultural Marketing Service and not connected to the department’s food safety, research, inspection, nutrition or risk management services.
10. Many natural pesticides approved for organic use are more toxic than the synthetic ones used by conventional farmers.
11. Though the USDA insists on an annual onsite inspection of every organic farm and facility it certifies, the inspector (regardless of country) needs permission from the farmer or processor whose facilities he or she intends to inspect, and he or she makes an appointment weeks in advance. Individual inspectors can be refused contracts to perform inspections by any USDA-certified organic entity, with no reason required.
12. Many of the 79 certifying agencies that grant USDA organic certification to farmers and processors receive 1.5 to 3 percent of gross revenue from their clients – this “royalty” from an industry worth roughly $40 billion a year. As noted, certifiers collect these royalties only on shipments they approve.
13. Many farmers make use of manure, but usually not on crops for human consumption. Only in the organic industry is manure routinely applied to fields growing crops for humans, a practice which can be detrimental to human health – even deadly, especially when manure is not fully composted. Even so, the USDA does not require field testing for possible fecal contaminants on the organic crops it certifies, even though such testing costs less than $25 per episode.
As long as consumers believe organic food is worth more (that it is “wholesome,” “natural,” and “authentic,” so certified by the USDA) no one making money in the organic sector will be obligated to prove organic food is worth the extra cost. Meanwhile, the interests of non-organic consumers, conventional and biotech farmers, processors, and wholesalers recede as the organic movement, with its knee-jerk opposition to modern farming, dominates the debate and sets the rules.
When Walmart Leaves Rural America…
Many rural people still celebrate when Walmart comes to town. However, we now know the eventual consequences for new Walmart communities.
When Walmart Leaves
Rural America…
The town “still boasts imposing brick buildings as a memory of better times. But the glow of coal’s legacy has cooled, as the boarding up of many of the town’s shops and restaurants attests.” This description of a coal mining town in Appalachia might just as easily describe a typically farming town in Middle America. The description is from a recent article in US edition of The Guardian: “What happened when Walmart left?” The place abandoned by Walmart was McDowell County—an economically depressed county in rural West Virginia. If current trends are allowed to continue, this may also be the future of farming towns all across America.
Coal mining was the economic foundation of McDowell County. When coal miners were replaced by technology—giant digging and hauling machines—many local residents were left without jobs or any other economic means of making a living in the county. It wasn’t only the mining jobs that were lost, but all of the other jobs needed to meet the varied needs of the miners and their families. “McDowell County has seen a devastating and sustained erosion of its people, from almost 100,000 in 1950 when coal was king, to about 18,000 today. That depleted population is today scattered widely across small towns and in mountain hollows, accentuating the sense of sparseness and emptiness.”
Farming was the economic foundation of many rural counties in the Middle America. As farmers were replaced by agricultural technologies—machines, agri-chemicals, livestock confinements—many local residents were left without jobs or other economic means of making a living in the community. It wasn’t only the farmers who lost their livelihoods, but all of the others local residents who had met the various economic needs of the displaced farm families. Farming communities all across America have seen the devastation and have sustained the erosion of rural people caused by the industrialization of agriculture. The depleted rural populations today are scattered widely across small towns and the rural landscape, accentuating the sense of rural economic depression and social disintegration.
The economic demise of mining towns is just more visible and more easily understood. When flying over the mountaintop removal coal mines in Appalachia, the environmental devastation is clear and compelling. Looking down at the green center-pivot crop irrigation circles on the High Plains creates a very different image—a false image of vitality. Both enterprises are mining nonrenewable natural resources. Coal mining is simply more obvious than water mining. These industrial farming operations are also mining the natural fertility of the soil, the only sustainable source of productivity. The demand for coal is slowing, environmental restraints of coal fired power plants are growing, and alternative energy sources are on the horizon. Meanwhile, demand for agricultural production is growing, industrial farming is heavily subsidized and virtually unregulated, and there are no alternatives to soil, water, or food. The erosion, degradation, salinization, and desertification of farmland may be occurring at a rate even faster than the depletion of coal.
Another major difference is that Coal mining is unsustainable by nature, but farming is unsustainable by choice. The earth’s reserves of usable and economically recoverable coal are finite and eventually and inevitably will be depleted. Soil, water, and solar energy are renewable resources that are capable of sustaining a resourceful, resilient, and regenerative agriculture indefinitely into the future. Unlike coal mining, today’s extractive, exploitative industrial system of farming is a matter of choice, not necessity. Regardless, the economic and social consequences of coal mining and industrial farming are much the same for rural communities.
Walmart got its start in the 1960s by moving into farming towns that were in early stages of economic decline—also the early stages of agricultural industrialization. The prosperity brought to farming and farming towns by World War II was fading. Local merchants were offering lower quality products at higher prices in an attempt to maintain their profit margins. Sam Walton understood rural people and saw an opportunity for continuing expansion and growth of Walmart in the face of rural economic decline. Walmart would offer better quality products at lower prices to rural people.
Early on, Walmart would not locate a store in a town with more than 15,000 people or more than 500 miles from Bentonville, Arkansas. Obviously those days are long past. Walmart found there were people in urban areas who also thought prices in their communities were too high. Walmart’s expansion strategies obviously have changed but its philosophy remains virtually unchanged. Walmart prospers from serving those with declining economic opportunities. Lower prices are their key to better living—but only as long as prices and sales are high enough to maximize profits and growth for Walmart. When that’s no longer the case, Walmart closes stores and leaves town.
Many rural people still celebrate when Walmart comes to town. However, we now know the eventual consequences for new Walmart communities. Quoting from the Guardian article, “Much has been written about what happens when the corporate giant opens up in an area, with numerous studies recordinghow it sucks the energy out of a locality, overpowering the competition through sheer scale and forcing the closure of mom-and-pop stores for up to 20 miles around. A more pressing, and much less-well-understood, question is what are the consequences when Walmart screeches into reverse: when it ups and quits, leaving behind a trail of lost jobs and broken promises?” In the Guardian article, the people in McDowell County expressed a deep sense of betrayal, depression, and loss of hope for the future of their community.
Communities abandoned by Walmart obviously are left with few surviving local retailers to supply the basic needs of people in the community. By the time Walmart leaves, a community is no longer seen as a logical place to start a new business venture. Walmart only leaves when the “economic carcass” of a community is pretty well “picked clean.” However, the people are also left without the social connections and sense of community that becomes centered on shopping at Walmart, once other local retailers are gone. There is no common local place for people to see and visit with their neighbors as they drive off in different directions to find the nearest remaining Walmart-like store in the area. There are no local businesses left to replace Walmart’s PR-motivated contributions to the Girl Scouts, Little League, county fair, local food bank, or other charitable causes. The Guardian article focuses on the deep sense of personal or even spiritual loss by local residents, which few might have expected from the closing of a Walmart Supercenter.
The basic point of this post is that if we do not stop and reverse the ongoing industrialization of American agriculture—with its miles and miles of corn and soybeans and giant animal factories—rural communities all across America can expect their Walmart to leave town. They can expect the same deep sense of economic, personal, and spiritual loss the local folks felt in McDowell County, West Virginia. Walmart came to much of rural America because rural America had bought into the extractive, exploitative system of industrial agriculture. When Walmart leaves rural America, it will be because there is nothing of economic value left for industrial agriculture or Walmart to extract or exploit.
However, the people in rural American have a choice. There are better ways to farm and better ways to develop rural economies. They can choose to replace industrial agriculture with an ecologically sound, socially just, economically viable—socially responsible agriculture. Then, Walmart can leave town, along with industrial agriculture, and people in rural American will be glad to see them both gone.
John Ikerd
At The Innovation Apex of Agriculture
At The Innovation Apex of Agriculture
New crops, automation and big data fueled conversations at the 5th annual Indoor Ag-Con in Las Vegas.
July 27, 2017 | Patrick Williams
Photo: Patrick Williams; Logo courtesy of Indoor Ag-Con
Between the metallic dinosaur at the trade show’s entrance, vertical gardens exhibiting multicolored lettuce and leafy greens, and booths showing off the latest in lighting technology, the 5th annual Indoor Ag-Con in Las Vegas, May 3-4, provided attendees an all-encompassing tour of controlled environment agriculture (CEA) and the technology and innovation that surround it.
Produce Grower was proud to be a sponsor of the event, where sessions focused on everything from securing funding to managing lighting needs to ensuring food safety. To learn more about the keynotes and Produce Grower’s general takeaways from Indoor Ag-Con, listen to our event recap at bit.ly/2tJ0yB4. In these pages, we will look at sessions centered around new crops and the future of automation and big data in CEA.
New Crop Opportunities
From drastic flavor modification to growing crops with major health benefits, the Indoor Ag-Con session “Which crops will move indoors next?” spotlighted new crop opportunities in CEA.
By changing one ingredient in a hydroponic mix, Dr. Deane Falcone, SVP, plant sciences and product development at FreshBox Farms, says he and his colleagues have been able to modify the flavor intensity of arugula to create mild and spicy varieties. “[The spicy variety] is very, very spicy, and the mild is almost completely bland,” he says. “That means we have the opportunity to titrate that and ... make yet a third one.”
Additionally, scientists can adjust the phytonutrient content of specific crops to produce anticancer qualities, Falcone says. Studies over the past 10 to 15 years, for instance, have shown that broccoli possesses anticancer activity through compounds called sulforophanes, he says.
Ice plant (Mesembryanthemum crystallinum) and purslane are other crops that growers may want to consider adding to their existing offerings, Dr. Richard Fu, president of Agrivolution, discussed in the session. These crops will not only allow growers in the United States to differentiate their product lines and stick out from the crowd, he says, but they carry health benefits as well.
The inositol in ice plant helps reduce insulin resistance for people with prediabetic conditions or polycystic ovary syndrome (PCOS), and it contains beta-Carotene and Vitamin K. The Super Omega-3 and alpha-linolenic fatty acids in purslane, meanwhile, can help alleviate allergies. To learn more about ice plant and purslane, read Greenhouse Management’s Q&A with Fu at bit.ly/2uFT6EG
In the fruit realm, Driscoll’s, the largest berry marketer in the world, has recently begun growing blackberries in glasshouses and has seen promising results, says Ian Justus, senior manager, controlled environment production. Justus works in research and development and produces high quality and high yields growing the company’s new Victoria variety under glass.
The Victoria crops grow approximately 13 feet tall, which makes them difficult to harvest on foot but conducive to cart passes in the greenhouse, Justus says. Multiple supplemental lighting sources exist in the glasshouses. “We’ve got high-pressure sodium lights at the top, and we’ve got really intricate LED bars down at the bottom,” Justus says.
Clockwise from left: Dr. Deane Falcone, Dr. Richard Fu, Ian Justus, Alastair Monk, Darryn Keiller, Nate Storey
Photos courtesy of Nicola Kerslake
The future of Big Data and Automation
Many produce growers have some type of automation set up in their greenhouse or vertical farm, and all of them collect data in some way. But how can growers use automation and large data sets to improve their operations, and is there room in CEA for data sharing? These are questions that were addressed in the Indoor Ag-Con session “What impact can big data and automation have on indoor agriculture?”
Operations can track data that measures how fast crops have been growing compared to previous years, and which inputs those crops need at a given point, says Alastair Monk, co-founder and CEO of Motorleaf. Monk says he wants to see a future where every single grower can automatically use intelligent data to control their operations.
A question that came up at multiple points through Indoor Ag-Con and that Monk addressed is “Who owns the data?” He gave the example of a field farmer using a tractor that collects data. In his example, the farmer owns the raw data, but it is then put onto a server, mixed together with data from other farmers. Once the source of the data is no longer identifiable, the data is made accessible to third-party companies. “I think that’s probably the kind of model that indoor agriculture is going to have to follow,” he says.
Currently, automated systems control environments and crop dosing, but companies are beginning to look more at how to improve the productivity, quality and taste of a crop, says Darryn Keiller, CEO of Autogrow. And while much of this information is proprietary, he, too, would like companies to share data to make it “big.”
Keiller equates an improved system, at least in part, with predictive analytics. “Lighting strikes, stormfronts, record temperature drops, solar radiation, reduced cloud cover — all these things effect production practices,” Keiller says. “But what if you could predict those things?”
Rounding out the session was Nate Storey, founder and chairman of Bright Agrotech. He is also the chief science officer at Plenty, which recently acquired Bright Agrotech (Editor’s Note: Read about the acquisition at bit.ly/2sF5fbs). Storey spoke specifically about machine vision, which he explains as the process of using images to glean data such as size, color and changes over time.
In fact, Storey says, machine vision can tell changes over time better than a human can, as well as temperature, nutrient deficiencies, fruit ripeness and environmental conditions. This outlook may not rest easy with every grower, but Storey is confident in it. “Even [with] my eyes, my mind and all of my experience in growing plants, I’m not as sensitive to these issues as we can get with the right set of images and the right analysis,” he says.
Nine Tours Offered At The 20th Annual Detroit Tour of Urban Farms And Gardens
Nine Tours Offered At The 20th Annual Detroit Tour of Urban Farms And Gardens
MONDAY, JULY 24, 2017 | Plum Street Farm | MARVIN SHAOUNI
Detroit has an impressive number of urban farms -- over 1,500 according to Keep Growing Detroit -- a number that has grown significantly in recent years. But the the urban farm "movement" has been alive in the city for some time, as demonstrated by the fact that the 20th Annual Detroit Tour of Urban Gardens and Farms takes place August 2.
Presented by Keep Growing Detroit, patrons can take one of nine bus and bike tours organized by theme and location. For example, a west side bus tour, called "Making Institutional Change," will swing by D-Town Farm, Detroit Public School's Charles R. Drew Transition Center, and Knagg's Creek Farm to demonstrate "how farms are inspiring systemic changes in our community."
Other tours will highlight black-led farms, farms with a focus on youth development, the history of urban farming in Detroit, and more.
All the tours will begin in Eastern Market at 6:00 p.m. and last approximately two hours. Afterwards, there will be a reception with local produce cooked by local chefs.
Keep Growing Detroit, an urban agriculture organization dedicated to food sovereignty in Detroit, hopes to not only showcase these farms, but educate attendees about Detroit's food system.
"We demand healthy, green, affordable, fair, and culturally appropriate food that is grown and made by Detroiters for Detroiters," writes the organization in a press release. "Transforming our broken food system begins with ensuring there are places to grow food in every neighborhood in the city. Places where residents can dig their hands in the soil to cultivate a healthy relationship to food, learn healthy habits from family and neighbors, and nurture an economically viable city where residents are strong and thrive."
The 20th Annual Detroit Tour of Urban Gardens and Farms takes place August 2 at 6:00 p.m. Purchase tickets at the Eventbrite page.
Mahindra Automotive North America Announces Third Round Of Urban Agriculture Grants Totaling $100,000 To Six Non-Profits
Mahindra Automotive North America Announces Third Round Of Urban Agriculture Grants Totaling $100,000 To Six Non-Profits
NEWS PROVIDED BY Mahindra Automotive North America
TROY, Mich., July 28, 2017 /PRNewswire/ -- Now in its third year, the Mahindra Urban Agriculture Grant Program announced donations totaling $100,000 in funding or Mahindra farm equipment to six southeast Michigan non-profits on Thursday evening, July 27. The presentations took place at the second of three shows in the Mahindra Summer Concert Series at Lafayette Greens in downtown Detroit. These concerts build on the musical foundation laid by the Mahindra Group's Mahindra Blues Festival in Mumbai, India, which launched in 2011 and is the largest and finest presentation of legendary blues artists in Asia.
Marhindra Automotive North America executives with the Urban Agriculture Grant winners: Front row, from left: Kieran Neal (Neighbors Building Brightmoor); Lionel Bradford (The Greening of Detroit); Holly Glomski (Pingree Farms); Coleman Yoakum (Micah 6 Community) Seated on tractor: Rick Haas (President & CEO, Mahindra Automotive North America) Behind tractor: Ashley Atkinson (Keep Growing Detroit); Rich Ansell (VP, Marketing, Mahindra Automotive North America); Patti Allemon
By awarding these grants, Mahindra Automotive North America (MANA) renewed the company's commitment to this region's robust urban agriculture movement, as well as continued to fulfill its parent company, the Mahindra Group's global corporate social responsibility initiatives.
Since the program's inception in 2015, Mahindra has donated a combined total of $300,000 in cash and farm equipment to ten non-profits in support of sustainable farming and gardening in Detroit. In 2017, the Mahindra Urban Agriculture Grant Program expanded to accept applications from urban agriculture programs in Pontiac.
"The progress our urban agriculture partners are making, with assistance from Mahindra's grants, is very commendable," said Richard Haas, MANA's President and Chief Executive Officer. "I am amazed by the innovative ideas these groups present for funding. We couldn't be prouder of the impact the company's support is having on accessibility to fresh, nutritious produce at affordable prices to residents within each organization's service area."
This year's program also marks the second grant-making collaboration between MANA and Mahindra North America (MNA), which manufactures and markets the company's line of tractors and farm equipment in the United States and Canada.
Cleo Franklin, MNA's CMO/Vice President of Strategic Planning, said, "Through this urban agriculture grant we have the privilege of collaborating with our sister company in donating a tractor. The tractor will be put to good use in supporting a nonprofit organization's efforts to have a positive impact on the city through their urban farming program. Driving positive change is an inherent part of our company's culture and core values, and is reflected in the good works of these organizations."
This year's recipients and the programs the grants will support, including four that received Mahindra funding in 2015 and 2016, are listed below.
- Full Circle Foundation ($7,075): to fund a summer intern employment program for developmentally disabled teens and young adults (2015 & 2016 grant recipient)
- The Greening of Detroit ($20,000): to support the Build-A-Garden program that provides assistance to gardeners across the city. (2015 & 2016 grant recipient)
- Keep Growing Detroit ($20,000): to install technology that will enable low-income individuals and families to use government issued EBT bridge cards to buy produce and seedlings from the Grown in Detroit program. (2015 & 2016 grant recipient)
- Neighbors Building Brightmoor ($22,000): to partially fund, along with Mahindra North America, the purchase of a Mahindra tractor with attachments (2015 & 2016 grant recipient)
- Micah 6 Community ($8,000): to build a 2,000 square foot greenhouse at the Webster Community Center in Pontiac. (1st year recipient)
- Pingree Farms ($26,010): to purchase a Mahindra tractor for use at the 13-acre farm site. (1st year recipient)
"Mahindra is committed to lifting up and celebrating the communities in which we operate," said Anand Mahindra, Chairman of the Mahindra Group. "There are few better examples of our RISE philosophy in action than the work Mahindra Automotive North America is doing in Detroit. MANA's pioneering Urban Agriculture Grant Program continues to lift up Detroit residents by giving them access to fresh, sustainable produce and inspiring work opportunities for the underserved."
Mr. Mahindra continued, "Also, MANA's new summer music series celebrates creative expression and community-building in the Motor City. To see these two initiatives working harmoniously is to truly know Mahindra."
An estimated 1.2 million pounds of fresh food have been grown and distributed to Detroit residents through the efforts of the groups that received Mahindra grants or equipment over the past two years. Among other outstanding results, the company's donations supported the opening of a Garden Resource hub in Southwest Detroit, and the purchase of a delivery vehicle to support the entrepreneurial efforts of the Full Circle Foundation's trainees at the Edible Garden.
About Mahindra Automotive North America
Mahindra Automotive North America (MANA) is Mahindra's North American automotive headquarters. In addition to leading all North American activity, MANA is a comprehensive automotive design, engineering, and vehicle development center. Established in 2013 and located in Troy, Michigan, MANA's team of veteran executives, engineers and designers, working with affiliate Mahindra automotive teams in India, Korea and Italy, is playing a key role in growing Mahindra's global automotive business. Visit: www.mahindranatc.com
About Mahindra
The Mahindra Group is a USD 19 billion federation of companies that enables people to rise through innovative mobility solutions, driving rural prosperity, enhancing urban living, nurturing new businesses and fostering communities. It has a leadership position in utility vehicles, information technology, financial services and vacation ownership in India and is the world's largest tractor company, by volume. It also enjoys a strong presence in agribusiness, components, commercial vehicles, consulting services, energy, industrial equipment, logistics, real estate, steel, aerospace, defense and two-wheelers. Headquartered in India, Mahindra employs over 200,000 people across 100 countries. Learn more about Mahindra on www.mahindra.com / Twitter and Facebook: @MahindraRise.
SOURCE Mahindra Automotive North America | Related Links http://www.mahindranatc.com
Job Layoff Kick Starts Vertical Farming Venture
Job Layoff Kick Starts Vertical Farming Venture
Landscape architect Jeffrey Orkin never planned to start his own vertical growing operation, but a job lay off and a passion for sustainability led to the launch of Greener Roots Farm.
After six years of college and landing a position with a large architecture and engineering firm in Nashville, Tenn., Jeffrey Orkin thought his career as a landscape architect was ready to take off. Then the recession hit. In 2009, after only 1½ years of employment, Orkin found himself jobless with limited prospects in his field.
Orkin partnered with his similarly unemployed friend Cliff Jones to start their own company called Landscape Solutions. The company is focused on design-build for residential and commercial outdoor spaces.
“We focus on how sustainable landscapes can contribute to the development of a healthier community,” Orkin said. “We are using native plants, rain gardens, bioswales and things other than typical high-demanding ornamental landscapes.”
Focus On Food
While Orkin’s main focus is on sustainable landscaping he also has a personal interest in extending his sustainability commitment to food production.
“I was living in a downtown fourth floor condominium trying to grow my own food,” Orkin said. “The only option at the time was to grow indoors on my windowsill using hydroponics. I started using a system developed by the Windowfarms Project, which got its start with a Kickstarter campaign.
In 2011 Orkin expanded from his windowsill plantings to a 4-foot wide by 12-foot long storage unit. He said that didn’t work real well because the unit lacked any kind of climate control.
The next move was to the roof of his 12-story condominium building.
“I discovered a 130-square-foot room on the roof of the building I was living in,” he said.” It was an unused utility room. I negotiated with the building management to rent me the room for a very reasonable rate. The room had a really tall ceiling which enabled me to grow using vertical farming with three different levels. That was in December 2012.”
In order to purchase the equipment he needed to set up his vertical farming facility, Orkin established the Urban Hydro Project.
“I did a Kickstarter campaign that helped to fund the build out and allowed me to test different crops and the other things necessary in a commercial hydroponic system. Urban Hydro Project was where the commercial business got its start. It was really the research and development arm of where I have transitioned to now.”
Expanding Again
Orkin has made a major production expansion by leasing a 6,000-square-foot warehouse that is about 5 miles outside of downtown Nashville. The new business venture is called Greener Roots Farm.
“I have divided the warehouse and curtained off a 3,000-square-foot grow room,” Orkin said. “I’m only about one-third of the way built out. Initially it was all I could afford. I am operating two vertical systems with space for two more. The warehouse production system is completely different than the one I was using in the condo building utility room.
“The warehouse has a completely new production design. It is a vertical set up with five levels of growing that maxes out at about 13 feet. I have a total of about 2,000 square feet of growing space that only occupies 224 square feet of floor space as it is currently built.”
Orkin is also renting 1,200 square feet of the warehouse space to Nashville Grown, a food hub that aggregates food from local growers and distributes it to area restaurants, grocery stores and schools.
Orkin said one of the biggest issues when moving to the larger facility was thinking through how to scale the system.
“This included everything from water volume and structural concerns with water weight,” he said. “We had to think through whether or not the warehouse’s existing HVAC system had the capabilities to do what we needed it to do. There were facilities considerations as far as the height, cooling, and where the water is coming from and where it is draining to.”
Everything from seed sowing to harvest takes place in the warehouse. Orkin is using 4-foot long Philips LED Production Modules in the production system.
Maximizing Crop Production
Orkin is producing a mix of herbs and leafy greens, including basil, cilantro, and parsley. He said he doesn’t have a major specific product.
“I signed a lease in April 2014 on the warehouse and we spent several months on build out,” he said. “The first seeds were planted on July 19. The crop mix allows me to provide some diversity and selection to the different restaurants that are purchasing from me. In the future there may be some direct to consumer sales at farmers markets. Right now I prefer being able to sell a larger volume in one delivery.”
Orkin said there are numerous farmers markets in the immediate Nashville area, including an “official” farmers market as well as several neighborhood markets.
“I don’t doubt that I eventually will carry many of my products to a farmers market on a regular basis,” he said. “Selling to restaurants I don’t harvest the plants unless they’re sold. It’s nice to be able to harvest for a restaurant customer and know that the crop was freshly harvested just an hour earlier.”
Orkin also said he shouldn’t have an issue with supplying local grocery stores year-round.
“I am really passionate about sustainability,” he said. “The one thing that kind of wears on me at retail is the amount of packaging that is required. Right now it’s nice to be able to put 4 pounds of product in one bag for a restaurant instead of placing that same 4 pounds in all of the 5-ounce clam shells that would have to be filled for grocery sales.
“I am trying to have the biggest impact on the local food scene that I can. I’m trying to produce and deliver the freshest local food that I can. Also, I have to figure out where I can be the most successful as a business.”
Excited About Future Opportunities
When Orkin started the Ultra Hydro Project he never expected the business to expand to the size it has.
“When my friend Cliff Jones and I started this business, we never planned to do it for as long as we have,” Orkin said. “It wasn’t necessarily our dream job. Although we have infused our passions into every aspect of the business, we can and do have a lot of fun with it. At the onset, however, it was something that we were able to do to make some money. It has just continued to grow.”
During the process of setting up the business Orkin went back to school for an MBA degree focusing on sustainability.
“A part of the degree program resulted in me going to California for a food security summit,” he said. “My mind was open to food security issues, the importance of local food and educating people about local food. Ultimately, I developed a passion for creative, innovative agriculture as it relates to augmenting the local food movement. I saw growing indoors as a way to remove seasonality when it comes to crops that in many instances are being shipped from thousands of miles away when there is this ability to grow it indoors.
“This concept of local food production presented a very interesting challenge. There is a lot of local food production going on, but not a lot of it necessarily makes money. For me the challenge is combining all of these factors. I want to be able to operate a farm with a business model that has the potential to make money and create jobs, while educating the community about how this can be done, and what it does for our food system. That gets me excited!”
For more: Greener Roots Farm, info@greenerroots.com; http://greenerroots.com.
David Kuack is a freelance technical writer in Fort Worth, Texas; dkuack@gmail.com.
Couple's 'Micro-Mini Farm' Venture Began As A Hobby
Couple's 'Micro-Mini Farm' Venture Began As A Hobby
Anne Schamberg, Special to the Journal SentinelPublished 6:00 a.m. CT July 16, 2017 | Updated 10:21 a.m. CT July 16, 2017
Photos: Aromatic Acres
(Photo: Courtesy of Carly Ledger)
During an end-of-June walk through the community garden space that Aromatic Acres calls home, rows of herbs, flowers and vegetables were showing promise. And some of the plants, like sharp-tasting radish seed pods, were ready to be harvested.
“Try this,” said Joseph Ledger, offering a few beanlike pods. “We eat them raw and they’re also good roasted.”
Since last summer, Joseph and wife Carly have been trying their luck at market gardening, digging in at the Firefly Ridge community gardens in Wauwatosa, which are rented from Milwaukee County University of Wisconsin-Extension.
The couple sell to a handful of area restaurants, but their their main outlet is Tosa Farmers Market, where they are first-time vendors. Last season, for their initial commercial foray, they were at Enderis Park Farmers Market.
They got their start as avid hobby gardeners. “We’re really self-taught,” said Carly.
Their “micro-mini farm,” as she calls it, adds up to about 1/6 of an acre, including three adjacent annual plots and, in a separate part of the gardens, a perennial plot where they plan to put a hoop house that will allow them to extend the growing season.
It was a brainstorming session that led to the name Aromatic Acres. And for the quibblers out there, she notes that “we personally aren’t farming on acres of land, but our garden is located on 11 acres of community garden space.”
The aromatics include more than 30 different herbs, for both culinary and medicinal use, that range from pineapple sage and anise hyssop to bronze fennel and epazote. They also grow cut flowers, many of which are edible, and a selection of veggies including heirloom tomatoes and oddballs like Mexican sour gherkins and those radish seed pods, an heirloom variety also known as rat’s tail radish.
“There are enough people out there selling your basic string beans,” he said. “I like growing some fun weird stuff that you don’t see.”
Joseph’s full-time gig is as an audio technician for Northern Lights Theater at Potawatomi Hotel and Casino, so he often spends mornings in the garden while she gardens later in the day. “We don’t sleep. We work nonstop,” she said. He quickly agreed.
“We do the farmers market together on Saturdays because we just love hanging out together — and we don’t have a lot of free time with each other,” said Carly, 32, whose day job is as office administrator for The Green Team, a Milwaukee-based landscaping service.
But the long hours are worth it.
Carly describes “the joy of working with the soil and being outside. I can’t put a price on it. I feel like my whole life has been bringing me here.”
With a degree in art and environmental studies from UW-La Crosse, she has been gardening since her college days and has had a series of outdoor jobs at parks around the country over the years.
Her “just-a-hired-hand” husband, as he dubs himself, has a degree in mathematics from Milwaukee’s Cardinal Stritch University — and he’s particularly enthusiastic about “growing chemical-free food and preserving the soil.”
Because it’s rented space, they are not moving toward organic certification, but they follow an organic-based system known as SPIN, or Small Plot INtensive, which helps them get the most from their limited urban space.
When it comes to peddling their produce, they find that people need to be sweet-talked into trying, say, electric blue borage flowers or honey melon sage.
“I hand someone some lemon basil and say see those strawberries over there? Sprinkle some lemon basil on them and you have a wonderful, simple dessert,” said Joseph, 40, who loves to cook.
They bring a different recipe each Saturday to the farmers market. In summer, it might be for a for a lemon balm mojito. And in fall, it’s perhaps a soup or stew with an accompanying “bouquet” of herbs.
And, somehow, this busy couple manages to cook at home on many evenings.
“This week we smoked two chickens and then had enough leftovers for sandwiches and to make stock,” he said. “We always make stock and a lot of soup. We just throw maybe some lentils in the pot and then add whatever vegetables and herbs we have. Once in a while we use a recipe.”
Leftovers make quick mealtimes possible.
“We cook, we freeze and we eat leftovers. I can’t get enough leftovers,” she said with a laugh.
They’ve just bought a house not too far from Aromatic Acres, so they’re dedicated to continuing their “urban farming” in Wauwatosa with an eye toward expanding their community garden space.
Possibilities for future projects keep cropping up, whether it’s mushroom growing, building a plant cloner for seedling starting, or setting up a portable kitchen for garden-side cooking demonstrations.
And they both dream about a day when they could do market gardening full time.
As Joseph wistfully puts it, “If we could make a living at this, we wouldn’t have a care in the world.”
To see the list of what they grow or for more information, go to aromaticacres.com.
Want your own garden plot?
Whether you’re a city slicker hoping to grow a few vegetables or an aspiring urban farmer, the University of Wisconsin-Extension in Milwaukee County is a good place to start.
According to the Extension website, the community garden program, which began in 1972, now rents to something like 500 families on 75 acres of land around the county.
There’s a wide range of plot sizes and rental prices. This summer, for example, a 20-by-20-foot plot at Firefly Ridge in Wauwatosa costs $45; and at Kohl Farm on West County Line Road in Milwaukee, a market gardener can rent a 120-by-90-foot “micro-farm” for $252.
If you need expert advice, the Extension has programs on urban agriculture or micro-farming, beekeeping and accessible gardening. For links to these programs and for more information on garden rental, go to http://milwaukee.uwex.edu/agriculture/.
'Grow Food On Mars': LA Startups Tackle Climate Change With Inventive Solutions
'Grow Food On Mars': LA Startups Tackle Climate Change With Inventive Solutions
Dozens of startups are inventing ways to keep LA cool with products and services that aim to avert environmental disaster – and yield profits
The entrance to Laci’s La Kretz Innovation Campus, which mentors local startups. Photograph: Los Angeles Cleantech Incubator
Rory Carroll in Los Angeles | @rorycarroll72
Tuesday 18 July 2017 07.00 EDT
Drought, floods, wildfires and heat waves – climate change and extreme weather events are wreaking havoc in California, especially in Los Angeles. The city has recently baked in record temperatures with a long, hot summer still stretching ahead.
It is the new normal: climate models predict the number of extreme heat days, defined as more than 95F, will triple by the middle of the century.
Little wonder Hollywood is churning out desert dystopias in films such as Mad Max: Fury Road and The Bad Batch.
Reality, however, has an overlooked subplot: geeks are inventing ways to keep LA cool – and possibly mint fortunes in the process.
Dozens of startups have turned the city and nearby regions into a laboratory for products and services which they hope will avert environmental disaster and yield business models replicable across the globe, even beyond.
“We would welcome opportunities for off-planet growing,” said Brandon Martin, vice president of business development of Local Roots, which turns shipping containers into hydroponic farms. “We’d love to be the first company to grow food on Mars.”
He was completely serious. Engineers from Elon Musk’s Space X have studied how the company uses sensors, algorithms and machine learning to transform 40ft containers into the equivalent of three to five acres of farmland while using 97% less water.
“We want to be a billion-dollar company as soon as possible,” said Kipp Stroden, another Local Roots executive. “We’d like to feed at least a billion people in the next 10 years.”
Time will tell if that is hubris but it reflects the confidence of startups which think solving some of LA’s environmental challenges will open other markets in a heating planet.
“LA is essentially a giant opportunity to demonstrate their technologies,” said Mike Swords, vice president of government relations for Los Angeles Cleantech Incubator (Laci), a public-private nonprofit which mentors startups. “If you can demonstrate that your company can help solve problems here there’s a good chance you will export it to other urban areas around the world.”
Kipp Stroden at the entrance to one of Local Roots’s container farms. Photograph: Rory Carroll for the Guardian
LA’s biggest climate challenges were extreme heat and drought and increased fires, said Matt Petersen, who was the city’s first chief sustainability officer before recently taking over the reins at Laci. “Trees are job number one, and cool surfaced roofs and streets are key strategies as well,” he said.
LA’s mayor, Eric Garcetti, has set bold targets to reduce the so-called urban heat island effect, improve air quality and ease congestion. Voters approved two measures which will generate $150bn in the next decades – a sum exceeding Franklin Roosevelt’s New Deal, according to some estimates – to replace traffic gridlock, a major source of heat and pollution, with cleaner transport and shaded, pedestrian-friendly sidewalks.
“It’s a city that has taken the climate change challenge seriously,” said Adrienne Alvord, western states director of the Union of Concerned Scientists.
California’s governor, Jerry Brown, and the state legislature, meanwhile, champion a cap-and-trade programme and ever more ambitious renewable energy targets – big-spending rebuffs to the Trump administration’s environmental policies.
The result is an El Dorado of subsidies, favorable rules and fast growing markets for cleantech companies.
“It has the attributes of a gold rush,” said Mike Hopkins, CEO of Ice Energy, which makes air conditioning units that store energy and can cool homes without using electricity. “It’s a bit of a wild west, the rules are still being formed. Those who innovate and take risks, win.”
A potential big winner is GuardTop, an asphalt coating manufacturer which makes CoolSeal, a reflective street surface which can reduce temperatures by more than 10F. It is being piloted around LA.
You can see other green technology on display even before entering Laci’s La Kretz Innovation Campus, a 3.2-acre site in LA’s downtown arts district.
The car park boasts a canopy of solar panels which feed a microgrid supplying a third of the campus’s energy needs. A bioswale collects and recycles rainwater. Amid the Teslas and other vehicles sits a triple-function generator which can turn biomass, including banana peels and coconut shells, into electricity, heat or cool air. A “living wall” of 2,100 plants looms over the reception.
The incubator was founded in 2011 with money from the federal government, the city and the Los Angeles Department of Water and Power (DWP), and moved to this campus in 2015. It has outposts in Silicon Valley and Northridge and plans to open one in Mexico City.
“We want to bring the best cleantech companies from around the world, especially startups, and help them grow,” said Swords, the spokesman. “This level of coaching and mentoring is an incredible deal. Every single one of the companies plans to scale. They hope to sell their products all over the world.”
In return, he said, LA and its water and power utility will get the chance to acquire technology to combat climate change.
The DWP has a tradition of thinking big: a century ago it siphoned water from the Owens Valley to LA, a controversial rerouting fictionalized in Roman Polanski’s Chinatown.
Mike Swords, at the LA Cleantech Incubator’s ‘living wall’. Photograph: Rory Carroll for the Guardian
Laci will survive even if the Trump administration ends federal funding, which was important but not essential, said Swords.
The buzz on the Laci campus was unmistakable. Pick My Solar, which helps householders choose solar panels, has grown from five to 30 employees in a year. “With the heatwaves and brownouts people are thinking a lot about energy,” said Kyle Graycar, a company analyst.
Green Commuter, another company, says it is the US’s first all-electric vanpool. “We reduce the cost of commuting, the amount of traffic and CO2 emissions,” said Bart Sidles, as he drove one of the company’s Tesla SUVs up Alameda Street.
River LA, one of the incubator’s nonprofits, is also feeling emboldened: it has been tasked with helping to spend $100m in water bond money to transform the Los Angeles River, in places a sorry trickle, into a lush waterway.
Torrential winter rains ended California’s drought but Local Roots, the farming company, believes continued water shortages plus a growing population and pressure to reduce transport costs will make their container farms a common sight in parking lots across the US and beyond. One container can produce 4,000 heads of butterhead lettuce every 10 days using just 25 gallons of water daily, said Stroden, the executive.
Jonathan Parfrey, executive director of the nonprofit Climate Resolve, cautioned that LA will inevitably heat up. “We could all turn into vegans driving electric vehicles and we’d still see this.”
Low-income residents will suffer most – several studies have shown the inequitable impact. Poorer neighborhoods near the coast such as Compton will enjoy relative coolness but be vulnerable to gentrification, potentially pushing residents to the city’s hotter, eastern side, said Parfrey.
Even so, he was optimistic. Technologies were getting cheaper and smarter. “The antidote to climate despair is working on solutions.”
Bring On Next-Gen Urban Farming: Usher In A New Era Of Food Production in New York City
When New Yorkers go to their local grocer or supermarket, we often see produce imported from other states or countries. There is no reason why the majority of our natural food products cannot be grown and sold right here in the Big Apple. For an urban center as large as New York City, we must be prepared for the challenges of climate change, greenhouse gas emissions, a changing ecological system, and the need to supply healthy food to an ever-growing population.
Bring On Next-Gen Urban Farming: Usher In A New Era Of Food Production in New York City
We can do so much more
(MIKE DI PAOLA/BLOOMBERG)
BY ERIC ADAMSRAFAEL ESPINAL
NEW YORK DAILY NEWS | Wednesday, July 26, 2017, 5:36 PM
If a tree grows in Brooklyn, so too can a cherry or a cucumber. Now imagine a crop large enough to feed our entire city.
When New Yorkers go to their local grocer or supermarket, we often see produce imported from other states or countries. There is no reason why the majority of our natural food products cannot be grown and sold right here in the Big Apple. For an urban center as large as New York City, we must be prepared for the challenges of climate change, greenhouse gas emissions, a changing ecological system, and the need to supply healthy food to an ever-growing population.
At the same time, we face a crisis of diabetes, heart disease, and obesity of epidemic proportions. The growing urban agriculture movement around the world, estimated at between 15% and 20% of global agricultural output, has the substantial potential to revolutionize our city's food system and turn a page on protecting our health and environment while bolstering the economy.
We have the ingenuity at hand to take advantage of the plentiful space in the five boroughs, to make this 21st century dream a reality. New York City has rehabilitated unused space before, most famously with the High Line. Our city has 14,000 acres of unused rooftop space, and there are more than 45,000 square feet of publicly owned land in East New York alone. With the use of smart, cutting-edge technology, we would be able to grow enough to feed as many as 20 million people in the metropolitan area.
As New Yorkers, we need to think boldly about the many benefits of expanding urban agriculture. Cities contribute to 70% of the world's global greenhouse gases, and a City Hall analysis from last year found transportation accounts for nearly 30% of our own output.
Local food production means less trucking required to go in and out of our neighborhoods, reducing the amount of carbon emissions pumped into our city as well as relieving stress on our highways. Green roofs and gardens used to grow produce pump oxygen into the air and cool down our environment, while playing a major role in reducing the runoff and flooding that heavy downpours create. Our environmental future is at stake, and urban farming helps us grow a more sustainable and resilient city.
In Brooklyn, food insecurity and poverty are compounded to create an economic and health crisis. A 2016 report by FoodBankNYC showed Kings County has a food insecurity rate of 20 percent, the only borough with a rising trend since 2009. Lacking basic healthy food access contributes to high levels of preventable diseases such as diabetes, heart disease, and obesity. African-American and Latino communities across central and eastern Brooklyn are twice as likely to suffer from these debilitating and deadly diseases.
There's even a condition known as Flatbush diabetes; that says it all.
Urban farming is the key to solving this problem, creating mixed-use neighborhoods where this kind of horticultural industry could thrive. The aquaponics market alone is expected to expand over the next five years at an annual rate of 14.3%, generating a value of more than $900 million by 2021. Thinking beyond the traditional expansive farms of America's heartland, the technology exists to grow crops and careers on unused spaces in the heart of New York City.
Think of the broad potential. We can even establish high-yield farms on our many public housing developments, creating jobs in communities plagued with chronic unemployment, educating a new generation in healthy living, and providing access to fresh foods right at residents' doorsteps.
The buds of this revolution are growing, but commercial and industrial scale urban farming is tangled in the weeds of bureaucratic uncertainty, making implementation that much more difficult. While scientists and agro-experts have done their jobs of innovating, government has not caught up.
Sophisticated vertical farming operations can be more efficient and profitable, but our zoning laws leave open many questions as to where these businesses can operate. For example, current regulations prohibit growing and selling produce on the same lot regardless of what the lot is zoned. In fact, the zoning text only mentions the word "agriculture" on a handful of its nearly 4,000 pages, thereby making this practice permissive but vague at best. This uncertainty stifles growth.
That is why we are proud to introduce City Council legislation that would rationalize this industry through the creation of a comprehensive urban agriculture plan in New York City. Our legislation would catalogue existing and potential growing spaces, classify and prioritize uses, identify potential land use policies that would favor expanding agricultural uses, as well as expand the availability of healthy food in low-income neighborhoods by integrating this practice across the city's conservation and resiliency plans.
This plan is the seed to robust growth. Let's cultivate a multi-million dollar industry here in New York City with a harvest of economic, environmental, and health benefits that we can all share.
Adams currently serves as the Brooklyn borough president. Espinal is a member of the New York City Council for District 37, which includes the neighborhoods of Bushwick, Brownsville, Cypress Hills and East New York in Brooklyn.
Food Strategist & Brand Builder Joins FreshBox Farms Advisory Board
Food Strategist & Brand Builder Joins FreshBox Farms Advisory Board
Former Starbucks VP Recognized for Innovations and R&D Strategies
MILLIS, MA – June 26, 2017 – Food strategist and recognized brand builder Dr. Mary Wagner has joined FreshBox Farms’ advisory board.
Wagner, who has worked with brands including Starbucks, Mars, Taco Bell and General Mills, will be focusing on product/business development and strategy for one of the nation’s most profitable modular vertical farms.
“We are very pleased to have someone with Dr. Wagner’s experience and record of success among our advisors,” says FreshBox Farms CEO Sonia Lo. “As a Senior Vice President at Starbucks, Mary built a culture of innovation, and she is recognized for her work in food quality and safety as well as her ability to build brands and create successful strategies that foster innovation.”
FreshBox Farms uses sustainable growing enclosures that use no soil, very little water, a rigorously-tested nutrient mix and LED lighting to produce the freshest, cleanest, tastiest produce possible. FreshBox Farms’ non-GMO certified products go from harvest to the grocer’s produce section in hours, rather than days, and it is the only greens grower -- hydroponic or conventional -- in Massachusetts to be certified kosher.
“As one of only two commercial vertical farms in the US that are gross margin positive, FreshBox Farms continues to innovate and continues to be an industry leader, and we look forward to Mary’s wise counsel as we continue to be a success story in this advanced, technologically-sophisticated food industry,” says Lo.
“Indoor hydroponic farming in the US has amazing growth potential -- no pun intended,” says Wagner. “Forecasters believe that over the next 10 years, 50% of all greens will be harvested indoors through some form of hydroponic growing, and I am eager to work with Sonia and her team on research and innovation that will keep FreshBox Farms an industry leader.”
As Senior Vice President at Starbucks, Wagner was responsible for creating global food and beverage products and solutions for Starbucks and its Evolution Fresh and Teavana brands. She led the effort to create Global Centers of Excellence for R&D, Quality and Regulatory in US, Asia and Europe, with the aim of offering innovative locally relevant products in key markets outside the U.S.
She also created a “stage/gate” product development priority process that focused resources and energy on innovations that had the highest return. The result was improved time to market and an increase in more meaningful new product launches.
Wagner recently founded MK Wagner and Associates, a global food science management consulting firm that specializes in R&D strategic leadership.
About FreshBox Farms, The Thoughtful Choice
Each time consumers go shopping, they make a variety of decisions. “The Thoughtful Choice” is knowing that FreshBox Farms’ produce will always be the best option for their health, happiness, and the planet. Founded in 2013, FreshBox Farms is an entrepreneurial company with a mission of producing non-GMO certified, fresh, healthy, and pure produce for local markets through industry leading and sustainable vertical farming. Its technology and values have received global attention with interest from European, Middle Eastern and Asian markets. To learn more about FreshBox Farms, please visit www.freshboxfarms.com.
Urban Farming 2.0: From Plow Beams to Leafy Green Machines
Urban Farming 2.0: From Plow Beams to Leafy Green Machines
SEARCH FOR SOLUTIONS
A new generation of urban farmers is leaving dirt behind and turning shipping containers into tech-driven vertical farms.
Shane Witters Hicks/Staff
Shane Witters Hicks | Staff
JULY 26, 2017 BOSTON—Shawn Cooney swings open the door of 320-square-foot industrial shipping container to reveal a futuristic setting: hundreds of edible plants growing in vertical columns, fed by the energy from strings of neon red and blue LED lights. Nutrient-infused water cascades from ceiling spigots down through artificial root systems in the growing towers. The temperature inside feels like a comfortable spring day – about 70 degrees F., with a touch of humidity. There isn’t a speck of dirt anywhere.
Welcome to the new urban farm.
This shipping container is one of four that comprise Corner Stalk Farm run by Mr. Cooney and his wife in the heart of Boston. Once the cargo holds for exhaust-spewing 18-wheelers, these discarded freight vessels have been transformed into units known as Leafy Green Machines outfitted with state-of-the-art growing technology by a company called Freight Farms. Now they help farmers turn out crops of lettuce and herbs at a rapid pace.
In the past, urban farmers have eked a living from food grown in greenhouses, reclaimed brownfields, vacant lots, or rooftop farms. But with these new kinds of urban crops – grown using what’s known as controlled-environment agriculture, or CEA – farmers leverage technology to break free from the seasonal and climatic limitations that bind traditional crops. As a result, these farmers enjoy longer growing seasons and more plentiful harvests – a hopeful promise for urban communities looking to boost access to fresh produce.
“To think that you don’t have to worry about whether it’s going to rain, or whether the sun is too bright because you flick a switch and you know how much light you have, you know how much water is being supplied ... that would take a lot of the stress out of agriculture,” says Joel Gruver, associate professor and director of Western Illinois University's research and demonstration farm.
Getting fresh food into urban centers has proved to be a persistent and growing problem. By 2050, 66 percent of the world’s more than 9 billion people will live in cities, predicts the United Nations. While some cities offer farmers’ markets and have worked to open more grocery stores in so-called food deserts, these farmer-entrepreneurs are searching for solutions that will not only grow fresh food within city limits but also mitigate some of the environmental effects of traditional farming.
“People want real food. And increasingly people live in the city. So there has been – unsurprisingly – a lot of innovation and investment in urban farming in the last handful of years,” says Tobias Peggs, co-founder and chief executive officer of Square Roots Urban Growers in Brooklyn, N.Y. Upon launching, the company received more than 500 applicants for 10 farmer slots from those wanting to take up the challenge.
Easing An Environmental Burden
Small-scale sustainable farming and organic practices have long sought to lessen the environmental impacts of monocropping and pesticide reliance, but CEA has a significant advantage: the ability to scale up without significantly increasing its ecological footprint. The vertical farming market is expected to quadruple from its $1.5 billion market value in 2016 to $6.4 billion in 2023, according to a recent report by Allied Market Research.
In San Francisco, agrotech company Plenty boasts a 51,000-square-foot warehouse that leverages machine learning to optimize plant growth.
Nate Storey, Plenty’s co-founder and chief science officer, says the environmental benefits gained by fusing technology and food production make large-scale CEA a no-brainer.
“We have no runoff, we have no erosion, we have few, if any, pests, we don’t need to use many of the pesticides, we don’t have any soil to sterilize, we don’t have any intensive irrigation, we use a fraction of the water,” he explains. “There are just not a whole lot of reasons not to do this.”
Unlike other large-scale food producers who must optimize their goods for long truck rides and shelf lives, indoor growers located closer to customers can instead prioritize food quality, such as flavor and “mouth feel,” as Dr. Storey puts it.
For independent CEA farmers, starting up a controlled environment for indoor growing doesn’t come cheap. A Freight Farms unit costs $85,000 and the annual operating costs range between $8,000 and $16,500. But Cooney of Corner Stalk Farm, who bases the size of his crop on customer demand, explains that similarly sized outdoor farms are pressured to overproduce during short growing seasons.
“Their losses are much higher. So that’s why it comes out to be about the same,” he says. Moreover, other farms may spend a fortune on transportation and land. Taking up about 1/34th of an acre, Cooney’s lettuce farm can have a marketable yield that’s about the equivalent of 8 acres of traditional farmland yield, according to Freight Farms. And the indoor environment allows for a continual harvest.
But without the government subsidies that larger farms receive, greens grown within shipping containers will inevitably cost more than most supermarket greens.
“A bag of our Square Roots greens costs about as much as a Starbucks [coffee],” admits Mr. Peggs. He is quick to add that the enhanced sense of community fostered through farmer-customer relationships makes the price worthwhile.
“Customers come to the farm and hangout – we have a big window on the farm, so everyone can see what’s going on. It’s all about total transparency in the food-supply chain,” Peggs says.
But is High-Tech Food ‘Natural’?
The benefits of CEA may be tantalizing, but Dr. Gruver of Western Illinois University foresees potential difficulties for the burgeoning industry. Controlled-environment agriculture depends upon those who can operate and fix the technology. In other words, finding someone who can troubleshoot a malfunctioning LED system may prove more difficult than finding someone who can repair a tractor, for example.
And while local food and connections to the farmers who grow it have proven to be profitable in urban markets, not everyone embraces the idea of food grown exclusively in an artificial environment.
“I think with any high-tech approach, there is a general concern that it’s not natural,” says Gruver. “There’s more potential for unforeseen, unintended consequences.”
Urban tech growers are well aware of this perception.
“We’re sensitive to that,” responds Storey of Plenty. “We’re really focused on how do we show people that this new growing environment is something that is important for our food supply.”
Before indoor farmers can dominate the urban food arena, however, they’ll need to grow more than lettuce and herbs. The larger the plant, the more energy it costs to grow it, and this energy is currently expensive.
But based on the rapid pace of innovation and technology, Peggs predicts large, affordable produce may not be far off. He thinks his Square Roots entrepreneurs will figure out how to grow sustainable strawberries within 18 months.
“Imagine a farmer traipsing through 2 feet of snow to deliver you a box of freshly harvested, locally grown strawberries in the middle of a New York winter,” he says. “In the near future everyone will have local food and they will know your farmer.”
How Urban Agriculture Swept Through Greater Cleveland
How Urban Agriculture Swept Through Greater Cleveland
Posted on July 17, 2017 at 7:00 AM | By Patrick Cooley, cleveland.com | pcooley@cleveland.com
CLEVELAND, Ohio -- Kinsman Farm, marked by crop-filled fields and surrounded by tall trees and grass filled lots, would seem at home in a rural Ohio county.
But the pasture of leafy greens sits in the heart of Cleveland, Ohio's second most populous city.
And Kinsman Farm isn't the only field of fruits and vegetables within Cleveland's city limits. It's part of a trend that picked up steam in recent years: urban farming. That practice began 25 to 30 years ago, said Kareem Usher, an assistant professor of city and regional planning at the Ohio State University. But a push by restaurateurs for local ingredients and the desire of city officials to fill empty and unused lots helped fuel the rise of urban agriculture in recent years.
The city leases land to Kinsman Farm, which in turn leases quarter acre plots to local farmers looking to advance from gardening or backyard farming to full-scale urban farming.
"I've been farming on a plot in North Royalton for the past two and a half years and I just moved (to Kinsman Farm) this season," said farmer Halle Kirsch. She plans to grow lettuce, microgreens and kale and manages a beehive that produces honey.
Kirsch said her time in North Royalton was her first foray into urban agriculture. Fellow farmer David Horvath, who also has a plot at Kinsman Farm, said he had an urban garden before he decided to grow crops for sale.
"I'm using Kinsman as an opportunity to scale up and learn as I go," Horvath said.
He grows tomatoes, peppers, herbs and mouse melons (a small cucumber) on his plot in Kinsman.
Both Kirsch and Horvath said they hope to sell their crops to Cleveland area restaurants.
"This past fall I went to a variety of restaurants (from small-scale family owned restaurants to trendy, upscale restaurants) and gave them samples and they were receptive," Kirsch said. "They were so happy to have local, fresh produce. The demand is way bigger than the push that's happening right now."
Urban farms are taking up root in formerly vacant lots all over the East Side, encouraged by local laws intended to convert unused land into green space.
Most are much smaller than Kinsman Farm and Rid-All, containing a single hoop house or a small field (Bay Branch Farm, a Lakewood farm run by a Cleveland couple, is a half acre).
Erich Hooper is one Northeast Ohio's first urban farmers. He grows fruits and vegetables in his backyard and sells food (mostly vegan and vegetarian) at festivals. He took up the pastime in 1994 and now proudly refers to his farm -- which he calls Hooper Farm -- as the oldest urban farm in the city of Cleveland.
Hooper grows Swiss chard in a small greenhouse. Further down the gentle slope of the hill that his house sits on, he keeps a pasture surrounded by a four-foot-high fence that's filled with asparagus, squash, beets and other assorted fruits and vegetables.
An elaborate system of barrels captures rainwater.
"We collect about 1,000 gallons of water a summer," Hooper said. "It saves us on water costs."
A strategically placed set of traps capture animals like groundhogs that burrow under the garden and endanger his crops.
Hooper sells much of his crops to local restaurants, a common theme among urban farmers. Shortly before speaking with a cleveland.com reporter on a recent Wednesday, he had just sold Fahrenheit -- an Ohio City restaurant -- a shipment of ghost peppers.
What follows is a look at urban farms, and how and why they have proliferated.
You can read about specific urban farms in Greater Cleveland here.
How many urban farms are there in Greater Cleveland?
It is difficult to come up with an exact number because there's no commonly accepted definition of an urban farm that separates it from an urban garden. But by some estimates, Cleveland is the second largest urban farming city in the United States.
Justin Husher, a horticulture specialist for the Cuyahoga County Soil and Water Conservation District, said the county has between 30 and 40 urban farmers.
Do they benefit the community?
By putting empty lots to use and creating jobs in impoverished neighborhoods, urban farms appear to provide many benefits to the communities they inhabit.
"It's putting that land to some use, particularly in cities that are shrinking," said Usher, the assistant professor at the Ohio State. "And I think it can build community pride and social capital."
Cleveland has more than 14,000 parcels of vacant land, and although it will likely experience population growth, said Michael Cosgrove, director of community development for the city of Cleveland, the city probably won't grow enough to fill all of its empty space.
Although they are still few and far between, urban farms could help make up some of the difference.
But experts said more research is necessary to determine whether or not urban agriculture helps a community in other ways.
While urban farmers tout the advantages of their trade, the practice hasn't been scrutinized enough to conclusively say how it impacts a neighborhood, said Zoe Plakias, an assistant professor of agriculture at the Ohio State University.
"Urban ag is very exciting and promising, and we've seen a lot of positive impacts," she said. But "there's definitely a need for more research to better understand" those impacts.
For example: an urban farm can absorb carbon and reduce the greenhouse gases that contribute to climate change. However it's unclear if urban farms absorbs carbon better than urban forests.
And as urban farms become more prevalent, they may begin to clash with traditional farms, Usher said.
"What happens to food producers who exist outside of the city?" he asked. "When we help local growers, are we going to be competing with family-owned farms? There's a long of entanglement. It can work well, but we don't have a sustainable model as of yet."
A 2016 report from the Johns Hopkins Center for a Livable Future found that urban farming and urban gardens can raise property values, but said that higher property rates can push poor people out of their neighborhoods. Farms create jobs in impoverished areas, the report said, but few of the jobs pay a living wage.
Indeed, Cleveland Area urban farmers interviewed for this story said they pay workers between minimum wage and $10 an hour. Their goal, they said, isn't solving joblessness, but giving young people valuable experience.
"This year I'm expecting 20 kids," Ka La Healing Garden Founder and CEO Tanya Holmes said. "I teach them how to do landscaping and urban farming."
In 2015 "I had 32 kids and only two of them knew how to cut grass," Holmes said.
But she said the most important lesson she teaches is community stewardship.
"We generally have three to four people here," said Mansfield Frazier, executive director of Neighborhood Solutions, which manages Chateau Hough in the rugged and Hough neighborhood on Cleveland's East Side.
His farm -- which grows grapes used to make wine -- was built by workers from Oriana House, which provides rehabilitation for alcoholics and drug addicts. But Frazier said he mostly hires teenagers now.
How do they get started?
Cleveland's city government, along with state and federal agencies, offer financial help to aspiring urban farmers. Available assistance includes grants from the U.S. Department of Agriculture, the Ohio State University Extension Office and the National Resources Conservation Service.
The NRCS, for example, invested in more than 80 hoop houses throughout Cuyahoga County in 2011 and 2012, said Husher, the horticulture specialist.
Holmes, of the Ka La Healing Garden, secured loans from Farm Credit of Mid America -- with help from Cleveland Congresswoman Marcia Fudge -- to repair the garden's gate and feed her workers.
Legal changes made the city more amenable to urban agriculture in the 2000s, when zoning laws changed to accommodate hoop houses and other buildings urban farmers rely on.
Cleveland has programs for both urban farmers looking to sell their crops for profit and community gardeners who grow mostly for themselves.
"Community gardens are, at most, a few parcels large," said Cosgrove, the Cleveland community development director. "They're usually in the sort of area that is accessible to the community. They're small scale, more built around the neighborhood.
The city leases land to farmers -- and occasionally sells them plots at a hefty discount. Cleveland also partners with Cuyahoga County's Ohio State University Extension office to fund community gardens through a Summer Sprout program, which provides grants that extension officials use to train gardeners and provide them with seeds, starter plants and services like soil tilling.
Eric and Annabelle Stoffer of Bay Branch Farm in Lakewood said they took a master gardener training program through the OSU extension.
In 2008, Cleveland amended its Neighborhood Retail Assistance Program to create the Gardening for Greenbacks program, which provides $3,000 grants to farmers who pledge to stay in urban agriculture for at least two years and sell their crops for profit.
"Some of them sell at local farm stands in neighborhoods that could be a food desert," said Kevin Kevin Schmotzer, executive for small business development for the Cleveland Department of Economic Development.
Others sell to local restaurants, he said.
In 2012, Cleveland got the attention of CoBank, which is part of the U.S. Farm Credit system, which helped Cleveland increase the value of its grants to $5,000. The city awarded $40,000 to eight community farms in 2015 and 2016.
Technical help is also available. Husher's duties include connecting farmers with the services they require.
"Sometimes people are really good growers but they need an insurance agent," he said. "Other times it's people trying to build a hoop house and they have really bad soil and they need to bring it up to speed."
What are the challenges?
Starting an urban farm requires an upfront investment that can reach tens of thousands of dollars. Eric Stoffer of Bay Branch Farm said he and his wife spent thousands on equipment alone
And while most urban farms are self-sustaining, many don't provide their operators with a living wage. Most urban farmers have a job off the farm. Eric Stoffer tends to his farm full time, but his wife still works part-time.
And farmers taking up root in a city have to deal with limited space and soil that is not always conducive to agriculture.
"One of the webpages I'm developing is literally just pictures of rocks to show what farmers have to contend with in terms of soil quality," said Husher, the horticulture specialist. Much of Cleveland's vacant land was once industrial, making its tainted soil of little interest to farmers, Cosgrove said.
Once they've established their farm, he said, some struggle to find places to sell their crops.
Farmers who work on the Kinsman Farm said they've spoken to local restaurateurs who are eager to use locally grown fruits and vegetables in their kitchens. But Husher said Cleveland's lack of a central farmer's market can hinder an urban farmer's ability to sell their crops to everyday customers.
Cities like Portland, Oregon and Ithaca, New York have large, central farmer's markets, whereas Cleveland and its suburbs have many small ones, which Husher said dilutes the customer base.
"Farmer's market sales are down across the board," he said. "There are just too many."
Even as restaurants increasingly seek out local fruits and vegetables, smaller farmers say they must with large-scale farms that can provide larger volumes of food. Eric Stoffer said only a small portion of his crops are sold to restaurants.
"There are restaurants that want to do local, but I've worked in the food-service business, and I understand you have a menu" and you can't take items off of it because suppliers aren't able to provide certain ingredients that week, he said.
What are they growing?
Most urban farmers grow specialty crops like tomatoes, kale, chard, beets and peppers.
Limited space means that most urban farmers can rule out the volume crops -- such as corn and soybeans -- that rural farmers depend on.
The Hough Chateau grows grapes for wine and the Rid-All Green Partnership has, among other things, peach trees and raspberry bushes.
Tanya Holmes of the Ka La Healing Garden sold vegetables at farmer's markets before upgrading to a full scale urban farm complete with a greenhouse on Cleveland's East Side in 2010.
Her garden grows tomatoes, collard greens, squash, peppers, zucchini, cantaloupe, cucumbers, and Swiss chard.
Eric Stoffer of the Bay Branch farm in Lakewood said he grows leafy greens and root vegetables, which he sells at farmers markets and to local restaurants, most notably the Root Cafe on Lakewood's Detroit Avenue.
"That's our main customer," Stoffer said. "But we're still looking for other relationships."
What does the future hold?
Husher said urban agriculture is entering it's "2.0" phase. Farms are starting to mature and flourish, rather than simply subsist, and he said he hopes to see new and exciting crops grown here in Cleveland in the coming years.
Usher, the Ohio State University professor, said he's visited urban farms in cities as far away as Portland, and believes the industry is here to stay.
"People do this because they believe in something," he said. "They believe in doing the work."
This Vertical Farm Wants To Be An Agriculture Company, Not A Tech Company
- 07.12.17 | Updated: 07-26-17
This Vertical Farm Wants To Be An Agriculture Company, Not A Tech Company
The FreshBox model centers around shipping containers. [Photos: courtesy FreshBox Farms]
FreshBox Farms is going big by focusing on harvests, not proprietary growing systems.
As the indoor farming industry has taken off in the last several years–over the next 10 years, indoor farming is expected to account for 50% of leafy green production, and grow to a $42 billion industry–it’s become apparent that it’s as much about technology as it is about agriculture. Bowery, a new startup operating out of an old warehouse building in Kearney, New Jersey, developed a sensor-based proprietary technology, called BoweryOS, specifically to support the venture by determining necessary nutrient levels, as well as when crops are ready for harvesting. And in South San Francisco, Plenty is growing produce via a tech-supported vertical farming model that has already received $26 million from tech investors like Bezos Expeditions and Innovation Endeavors.
For FreshBox Farms, an indoor farm operational since 2015 at an old factory site in Millis, Massachusetts, around 30 miles outside of Boston, the technology is important–it is, after all, what enables the greens to grow–but it’s not sacred. “We’re equipment agnostic,” Sonia Lo, the CEO of Crop One Holdings, FreshBox’s parent company, tells Fast Company. “There are people out there doing great work to perfect lights, trays, control systems, nutrient dosing systems–we focus on growing as much as possible.” This almost brusque approach, Lo says, has enabled FreshBox Farms to become one of just two commercial indoor farming ventures in the U.S. that is gross-margin positive. The other is the Newark, New Jersey-based AeroFarms, which grows up to 2 million pounds of produce per year.
Earlier this year, Matt Barnard, CEO of Plenty, told Fast Company that “small-scale growing in 2017 is not a profitable enterprise.” He was referring to the fact that indoor farming startups, which, since the boom began within the last five years, have a track record of failure. FarmedHere, a Chicago-based venture, intended to expand nationally but instead went bankrupt earlier this year, citing the difficulty of maintaining financial equilibrium. PodPonics and LocalGarden, ventures based respectively in Atlanta and Vancouver, similarly failed; the business tensions derived from the high cost of technology, and the relatively small return on investment from output and distribution. Given the hefty price tag of developing proprietary growing technologies, not to mention renting pricey urban land, underwhelming harvests (which are common among startups still tinkering with their growing systems) can be financially devastating.
But with the cost of technology (for instance, LED lights, sensor technology, and smartphones, all of which are necessary for indoor farming) falling, and interest in local produce continuing to increase, Lo believes FreshBox Farms has hit on a sweet spot with its growing strategy. The company spends less money growing more product than any other indoor farm in the country, and Lo attributes that to FreshBox’s approach to technology, and easily scalable farm setup.
The FreshBox model centers around shipping containers (hence the name of the farm). At the farm in Massachusetts, which currently serves 37 supermarkets in the Boston region, each of FreshBox’s 12 commercial products, whether it be kale, arugula, or chard, is grown with hydroponics in its own shipping container; the farm currently houses 15, along with one “Mod”–a modular unit equivalent to nine containers. Conditions inside each container are optimized for each product, but the network as a whole is governed and monitored by the same technology system. By growing crops in separate containers, Lo says, FreshBox can focus on optimizing yield for each product.
The modular system, Lo says, is really what has enabled FreshBox to become profitable just 23 months after launching two years ago. “Because we’re modular, we’re not waiting for a whole farm to be built out to create revenue,” Lo says. “Once we have a box or two on the ground, we’re growing.” FreshBox can have a farm up and running, and selling, within 12 weeks.
The current FreshBox Farm configuration in Massachusetts produces a quarter ton of produce per day, but Lo emphasizes that as the company continues to iterate on the technology it uses and the size of the containers themselves, that number will likely increase. Currently, FreshBox is growing the equivalent of as much as 19 acres of produce in 320 square feet; as FreshBox verticalizes further, that efficiency will grow. “Real estate is a square-foot venture,” Lo says, “But we’re dealing in cubic feet.” Meaning that once FreshBox secures a plot of land on which to operate, they can continue stacking shipping containers higher and higher, and maximizing output. The containers on the farm are not yet stacked, but that’s a next step, Lo says.
Even as other indoor farming companies struggle with expansion, Crop One Holdings has locked in nine new locations for the next generation of FreshBox Farms. The majority will be in the northeast, and, like the Millis farm, located outside the urban center to cut down on property rental costs. And the focus, Lo says, will remain on productivity and profit–not necessarily for profits sake, but to ensure that fresh produce can become more available. “There are a ton of urban farmers out there who are talking about how they’re on the cutting edge of technology and measuring 20,000 data points,” Lo says. “But we’ve never fallen in love with the science. We’re all about: What is the yield? Are we actually growing things? Are we selling every leaf?”
Over the next five years, FreshBox is aiming to reach 25 farms across the U.S., each of which will produce between one and three tons of produce per day. The company will continue to iterate and switch out technology as it grows, and as more efficient systems become available. “I don’t think you should be in this industry unless you’re planning to be big,” Lo says.
Indoor Farms of America Bridges the Gap with Traditional U.S. Agriculture in Landmark Farm Sales
"With the sale of these farms, which will be up and running in the great state of Indiana in about 90 days from today, our company has achieved the first stage of the plans to have large scale indoor farming adopted by the very folks who have kept us fed in this country since its inception, and that is the traditional farmer," stated David Martin, CEO of Indoor Farms of America.
Indoor Farms of America Bridges the Gap with Traditional U.S. Agriculture in Landmark Farm Sales
NEWS PROVIDED BY | Indoor Farms of America
Indoor Farms of America corporate Farm Manager Anthony Randolph grows beautiful greens in the vertical aeroponics from IFOA.
LAS VEGAS, July 25, 2017 /PRNewswire/ -- In what is a watershed transaction and a continuance of plans to integrate world-class indoor agriculture equipment into traditional farming, Indoor Farms of America announces that it has sold the first two "warehouse" style farms to Co-Alliance, LLP one of the largest, oldest and most respected major locally owned Farmer Cooperatives in the United States.
Unlike all other commercial scale Indoor Farm equipment, Indoor Farms of America patented equipment does not require ladders or skylifts to operate, and grows 40 plant sites per square foot in just 8 feet of ceiling height.
"With the sale of these farms, which will be up and running in the great state of Indiana in about 90 days from today, our company has achieved the first stage of the plans to have large scale indoor farming adopted by the very folks who have kept us fed in this country since its inception, and that is the traditional farmer," stated David Martin, CEO of Indoor Farms of America.
"Co-Alliance has been investigating several companies and the equipment available for the indoor agriculture space for some time," states Darren Radde, Business Development Manager at Co-Alliance. "Our team understands quality equipment, and after reviewing numerous growing platforms, we believe the equipment developed and manufactured by Indoor Farms of America will provide our Farmer Members with a viable means of supplementing their income, allowing them to farm new crops all year long, and be within 30 minutes to 2 hours delivery time to any major market they can serve from their existing farm."
John Graham, CFO of Co-Alliance, said: "When we visited with the team at Indoor Farms of America, they expressed to us that while their indoor growing equipment was designed to be superior in performance to anything else in the world, which makes them very 'disruptive' in that space, Ron and Dave have a real desire to see existing traditional farmers embrace the technology."
Graham went on to say, "This means our farmers can take advantage of all our existing channels to market, our inherent ability to be close to those markets, which means our farmers can deliver fresh produce every day of the year from their farms. When the fields are covered in snow, they can produce income for their families. We like that."
The first of the two farms will be owned and operated by a long-time family farming operation, who have an existing building as part of their farming operation in central Indiana, that will be converted to state-of-the-art indoor growing facility at pretty minimal expense.
Phil Brewer, VP of Marketing at Co-Alliance, sees new opportunities for member farmers to have a major impact on the "locally grown" food movement, never seen before. "By bringing scale production of a variety of crops such as premium herbs, for example, to within a very short distance of the actual consumption of those products, we are able to deliver on two fronts. First, the consumer wins by having truly fresh, locally grown and high quality products available to them from local farmers they know and trust. Second, our farmers win, as they are now able to operate during the cold winter season when the fields are out of operation. This creates meaningful additional income for themselves."
After seeing a solid first year in sales of its game-changing vertical aeroponic farm equipment, Indoor Farms of America is on a path to more than quadruple first year sales in 2017, which is year two.
"The largest food-related companies in the world are working with us at this point. They have compared every aspect of every available indoor platform and come back to us. We designed, patented with multiple patents, and now build a fundamentally and economically sound indoor farming product that scales to as large as may be required, anywhere in the world. Nothing grows in quantities that are even close to our equipment, in terms of robust, healthy, clean and nutritious produce," states Martin.
According to company President Ron Evans, "We have seen traditional farmers who purchased our equipment last year respond with praise for our equipment and how it performs. This year we are seeing them buy larger farms. When you get compliments from a farmer that operates 5,000 acres for a living, yet understands the real need and place for this in his own operation, the light bulb goes on for him and those around him."
2 East Bay Companies Redefine Urban Farming
2 East Bay Companies Redefine Urban Farming
By Alix WallApril 4, 2017, 1 p.m. - Up Dated: July 25, 2017
Benjamin Fahrer at work at the Top Leaf Farms location on the roof of 2201 Dwight Way in Berkeley. Photo: Alix Wall
One hundred miles, give or take, from farm to table, is the ideal maximum distance for produce to be considered local. But there are some companies that are greatly improving on that goal — instead of triple-digit mileage, they’re offering produce that’s grown within just a few miles. Even better, when there’s a short distance involved, delivery happens by bicycle or on foot, eliminating any reliance on fossil fuels.
Traditionally, this type of urban farming takes place in abandoned lots, backyards or parks. But two new East Bay companies are changing up that paradigm.
Read more about Berkeley’s Garden Village building.
The larger of the two operations is Top Leaf Farms, a rooftop garden at 2201 Dwight Way in Berkeley. The building, which was built by the Oakland-based Nautilus Group, Inc., is called Garden Village and functions as student housing for UC Berkeley. It was completed in January 2016 and Top Leaf began installing its garden in August 2016. By October it was up and running, growing produce in 10,000 of its 12,000 square feet of space.
Top Leaf Farms is in contract for another rooftop garden at Telegraph and 51st Street in Oakland, where the garden will be grown across 30,000 square feet of roof space. The mixed-use building will include apartments, as well as a Whole Foods’ 365 store. In fact Top Leaf is already gardening in the vacant lot on which the building will be constructed; that garden will be dug up once construction begins. While Top Leaf Farms is in discussion to sell produce to the new 365 store headed to the building, nothing has been confirmed yet.
Benjamin Fahrer uses a Quick Greens Harvester (made by Farmer’s Friend LLC) at Top Leaf Farms. Photo: Alix Wall
Top Leaf has just two full-time employees. Benjamin Fahrer is the co-owner, principal designer and farm manager, and he is a 20-year veteran of organic farming in such places as Ocean Song Farm and Wilderness Center in Sonoma, as well as Esalen in Big Sur.
No doubt he would still be farming in a more rural locale had he not fallen in love with his wife, whose career requires her to be in an urban environment — she is a physician at UCSF and performs in a band.
There’s been a bit of a learning curve when taking his farming skills to the roof of a building. For one, much less soil can be used because of weight restrictions.
“Agriculture is a contrived system where we impose a production system on nature to serve our needs to extract product,” Fahrer explained. “On a roof, it’s even more contrived in that it’s separated from the earth. On the ground, you’re working with nature, and here you’re working with concrete, steel and metal. Fabricated materials have a certain rigidity you can’t be flexible with.”
The rooftop farm created by Top Leaf Farms at 2201 Dwight Way in Berkeley. Photo: Alix Wall
Whatever challenges a rooftop presents, though, are not apparent to a farming novice visiting the roof on Dwight. One can walk through numerous terraces and see neat rows of crops growing; it looks no different than a regular farm, except for the fact that you can also see the tops of nearby office buildings and past those, the Bay Bridge in the distance.
They may call the arugula they grow “arufula” or “aroofula”
Right now Fahrer is growing numerous varieties of kale and lettuces, arugula, pea shoots, herbs, flowers and more. Fahrer said he’s already determined which variety of arugula grows best on the roof — they may call it “arufula,” or “aroofula.”
Top Leaf sells produce to the students in the building in limited quantities, but makes most of its income with its “RSA,” or restaurant-supported agriculture, as Fahrer likes to call it. It currently supplies six restaurants with produce and all are within a three-mile radius. These include all three of Charlie Hallowell’s restaurants (Pizzaiolo, Boot & Shoe Service and Penrose), Juhu Beach Club, Chez Panisse, Ramen Shop, Benchmark Pizzeria and Gather.
“Ideally the [building’s] residents would take the majority of food that’s grown above them,” Fahrer said. “But right now the restaurants provide a constant revenue stream.”
Top Leaf Farms has an advisory board that includes author and sustainability expert Raj Patel and former Oakland Food Policy Council director Esperanza Pallana, and is in contract to design a handful of other projects, but Fahrer said they are very particular about their clients. The company has had a few experiences where a developer asks for a rooftop garden with the latest green technology, but after entering into a discussion, “at a certain point we realize we don’t agree with the ethics of that development,” said Fahrer. “We’ve declined because of gentrification and the way in which they’re developing because they’re evicting people from their homes.”
The hope for the Temescal farm, which Fahrer expects will be finished in 2019, is for it to be “a worker-owned cooperative, where we can train and employ local people to become part owners, and create more of a livelihood from urban agriculture,” he said.
Oaktown Farms: The only way is up
John Wichmann of Oaktown Farms (left) sells lettuce to Paul Bosky at the Temescal farmers market. Photo: Alix Wall
Meanwhile, another Oakland farm has taken shape, albeit on a much smaller scale. If you’ve shopped at the Temescal farmers market these past few weeks, you will likely have seen a white tower, attached to a bike trailer, with various types of greens growing in it.
This is Oaktown Farms.
While vertical towers are a new fad in urban agriculture, Oakland engineer John Wichmann has built one of his own design that he believes is better than any on the market.
“There’s one person making a tower system similar to mine but you’re only able to grow plants on one side of a four-sided box. Why not utilize all the real estate you have?” he asks.
Noting that this other system grows nine plants in the same amount of space in which he can grow 40, Wichmann said his tower grows 1,000 plants in 100 square feet of space.
Then there’s the portability factor. He can disconnect a piece of his farm, attach it to his bike, and ride it approximately three-quarters of a mile to the market. Wichmann doesn’t give out the exact address of the farm, but it is on a friend’s lot somewhere within a one mile radius of the Claremont Department of Motor Vehicles.
“The tower allows me to grow, transport and sell from one device, which is unique,” Wichmann said.
Oaktown Farms grows all of its produce in a vertical system. Photo: Alix Wall
Wichmann’s day job is as an engineer at Nauto, a company that’s competing with Google and Uber in the self-driving car space. His interest in gardening has been lifelong; growing up in Southern California, his father was a food technologist and his mother a dietician.
“My dad had a compost pile in the 1970s when I was a kid,” he said. “I always thought that was normal.”
His high school had a Future Farmers of America organization, and also offered advanced courses in wood and metal shop, all of which Wichmann took advantage of.
But while farming had always been a hobby, Wichmann was especially inspired when learning about aquaponics systems. “I got really excited about that because you can get fish and greens in the same system,” he said.
Like Fahrer, Wichmann was also inspired by the fact that more and more people are living in an urban environment. He thinks that new food systems should be feeding them.
And then, of course, there’s the issue of California’s drought.
While it’s hard to quantify, Wichmann believes his system uses 90% less water than conventional farming.
“When you water plants, a lot of it runs off and some evaporates,” he said. With his vertical-farming methods, called a close-looped system, “the water is in a reservoir if it’s not being sprayed onto the roots, and the only water that’s taken up [goes to] the roots.”
The Oaktown Farms stand at the Temescal farmers market. Photo: Alix Wall
Wichmann’s system also prevents waste, as customers only cut the plants when they buy them; whatever isn’t sold remains planted until the next market.
Wichmann also argues that his produce has better health benefits than traditionally farmed vegetables. He said that once you cut a plant, it slowly starts to lose its nutritional value. His are as close to living as you can get.
He’s been bringing to market a mix of Asian greens like tatsoi and mizuna, as well as heirloom varieties of lettuce and mustard greens. People have been puzzled so far, and they sometimes inquire about buying the tower rather than the greens from it.
This last request may become a reality: Wichmann has some big ideas about how a tower like his could alleviate hunger in certain parts of the world, and he is busy pitching it around.