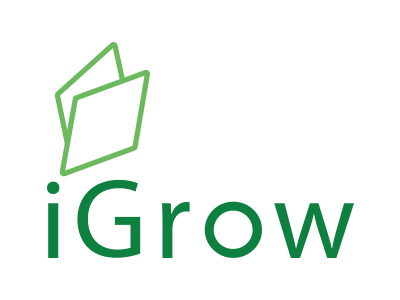
Welcome to iGrow News, Your Source for the World of Indoor Vertical Farming
Growtainers® Custom Build For A US Food Retailer And On-Site Production
Growtainers® Custom Build For A US Food Retailer And On-Site Production
CEA Advisors & Growtainers® promises even more global excitement in Indoor Farming and Controlled Environment Agriculture in 2017.
After more than a year of meetings with the Produce Marketing team at a major US food retailer, the first custom built for onsite production Growtainer® has been delivered and will begin production in Q1, 2017. “We spent over a year discussing the retailer’s concerns and objectives and when I was sure we were all on the same page we began the design and manufacturing process” said Glenn Behrman, founder of Greentech Agro LLC and CEA Advisors LLC.
Growtainers® have come a long way from those first two prototype models built about 4 years ago and recently donated to Texas A & M Agrilife Research Center in Dallas. Our understanding of the critical importance of the growing environment and the need for intuitive control systems has increased. “We’re collaborating with more industry experts in all areas that are critical to the development of a well-balanced successful production environment”.
“Increasing global awareness of indoor local vertical production has been the driver in our laser focused pursuit of new, modern and sustainable indoor farming practices”. On site production in the Growtainer® to produce the freshest, unique, gourmet leafy greens and herbs for their customers at the retail level is the objective of the project. Our retail partner is the first in the nation to train their team members in a food safety compliant, climate controlled, LED lit multi-layer vertical indoor production environment.
“CEA Advisors is proud to be working with a forward-thinking food retailer that is committed to innovation and focused on food safety, unique products and the customer experience” said Behrman. For this project, CEA collaborated with a McKinney Texas based water management firm, whose team assisted in the design and installation of a state of the art irrigation system. The container modifications were carried out by the largest and most experienced group in the USA. North America’s leading horticultural supplier of goods and services provides their expert and ongoing consultation to the project, as well.
This unique 53’ custom built Growtainer® has a separate utility area and provides 480 square feet of climate controlled vertical production space, specially designed for maximum efficiency and food safety compliance. Each Growrack® is equipped with energy efficient LED production modules, specifically designed for multilayer cultivation. The irrigation system is divided into separate zones to provide flexibility and allow a wide variety of production of crops at various growth stages. Behrman worked closely with the engineering team to design a sophisticated control system. The proprietary irrigation system is constantly monitored and any corrections to EC or PH are made immediately. Every irrigation event is perfect for the plants optimum growth.
For more information on this and other exciting innovations in Indoor Vertical Farming visit www.growtainers.com or email gb@cea-advisors.com
Vertical Farms: How To Feed Our Rapidly Growing Cities
Vertical Farms: How To Feed Our Rapidly Growing Cities
By Judith Dubin and Leeron Hoory
Jan 17, 2017 at 4:15 PM ET
“As long as there’s been life on earth, there have been parasites,” says Dickson Despommier, emeritus professor of Public Health and microbiology at Columbia University. And, he says, a lot of us live in one: Cities — which feed off the earth’s resources without replenishing them — basically function as giant parasites. “They take advantage of what’s there and use it for their purposes,” Despommier says.
And they’re growing rapidly. By 2050, nearly 80 percent of the world’s population will be living in cities, and we’ll need a sustainable way to grow enough food to feed everyone. To that end, Despommier proposes vertical farms. Basically greenhouses stacked on top of each other, vertical farming produces food more efficiently to “ease the parasitism of cities on food production.”
These farms in buildings already exist in the real world. Japan, South Korea, Singapore, China and Taiwan, have hundreds of vertical farms, as do several U.S states, including New Jersey and Illinois. And that’s a good thing, since already fully one-seventh of the earth’s land mass (or the entire continent of South America) is devoted to producing food for the 7.3 billion people who live here.
If we don’t keep working to implement sustainable ways to feed our cities, Despommier says, “The parasite will exceed its capacity and collapse under its own weight.”
Urban Farming Poised to Revolutionize Agri-Food Production, says Professor Dickson Despommier and Leaders in This Market Sector
David Stradling
Urban Farming Poised to Revolutionize Agri-Food Production, says Professor Dickson Despommier and Leaders in This Market Sector
David Stradling, Sales Director, Global Forum for Innovations in Agriculture, receives inspiration from a banana boat while getting to grips with the urban and vertical farming movement.
The sands that surround the shores of Koh Tao in Northern Thailand are the colour of golden demerara sugar, the surrounding sea is crystal clear, and the wildlife in the sea and on the land seems as plentiful as it is exotic.
But as I snorkel off the southern tip of this divers’ paradise, something is clearly amiss. The corals are often sun bleached, the diversity of fish has been shown to be in decline, and on the island itself, natural fresh water supplies have fallen to an all-time low.
This little corner of heaven has environmental problems that are as pressing to the local ecosystem, and to its three thousand local inhabitants who depend on tourism for their livelihood, as they are to the rest of the planet.
There is no escaping the blight caused by climate change. At 10.0955 degrees west and 99.84042 east, the challenges faced by this tropical paradise are ongoing. Failure to meet them will potentially have as serious an impact on the local environment and its population, as it’ has had on those who made a living from agriculture in what was one of the most fertile regions of the United States - and is now the American dust bowl.
On holiday in Koh Tao recently, I was working out the approach to take in an article exploring urban agriculture and, as a technology sub-set within that, the future of vertical farming. Then inspiration struck in the shape of a banana boat! I’d been chilling out on a mix of vitamin D-inducing sunshine and coconut and banana smoothies when to my dismay, the island’s stock of the fruit dried up. Suddenly, there was a tap on my shoulder, ‘’Bananas here now, the boat has arrived,’’ declared our friendly beach bar waitress.
I was delighted, but at the same time I pondered the fact the fruit was being shipped in, as I would guess was most of the island’s food. Therein lies one part of the challenge. Not only can agri-food production be a drain on the land and its resources, but shipping it from one destination to another is a contributory factor in climate change.
Enter the age of vertical farming! It’s this that some believe could be the key to many of the problems that come with industrial scale agriculture, and the use of farming methods which fail to show consideration for the environment.
Last week I talked at length with Dickson Despommier, Professor of Microbiology and Public Health at Columbia University, New York City, USA, and author of The Vertical Farm: Feeding the World in the 21st Century. Professor Despommier is widely considered a founder of the vertical farming movement, and is a long-term advocate of urban farming as a potential counterbalance to the negative impact of large scale traditional agri-production. We spoke about the future and he provided me with some useful insights into the positive returns, he, and increasing numbers of experts, foresee will be a direct result of continuing innovation and advancement in vertical food production technology.
Vertical farming; the dawn of a new age
WHILE THE MEDIA'S focus throughout the 1990s and the beginning of this century has been mainly on the role that heavy industry and fossil fuels have played in eroding the ozone layer, the role of agriculture in resource depletion and climate change, has gone relatively unnoticed. Traditional agricultural practices continue to take a major toll on planetary resources and are a key offender in climate change. Transporting produce from one place to another involves the emission of gases that damage the outer atmosphere, while over-farming has a disastrous impact on the soil and acts as the biggest drain on water reserves.
Professor Despommier believes that agri-crop growing in the traditional sense is often inefficient, citing the United States where the biggest crop is wheat, followed by corn and soya beans, as an example. He points out that soya beans are often grown as a means of putting nutrition back into the soil, a practice that is extremely inefficient, and is enthusiastic about the use of climate-smart agriculture in outdoor farming. However, all plant life requires water and if that is not available then the only option is to take growing indoors – and to do this locally where the crops which are grown are consumed, so reducing pollution caused by transportation. The Professor has a stark warning for us if we fail to take action. ‘California is in its sixth year of drought,’ he says. ‘Food prices are going crazy and it’s going to get worse.’ In his view, controlled environment agriculture (CEA) is the solution – and vertical farming is the method which could save our environment from disaster.
An efficient greenhouse hydroponics system uses five percent of the water required in the outdoors and can deliver multiple times the yield of farming outdoors. According to Professor Despommier, a vertical farm can deliver the same yield again, using a fraction of the water the greenhouse system requires. So if vertical farming, with all its obvious advantages, has such a role to play, where does that leave the land farmer? ‘’I have a great answer but it isn’t the one that many people want to hear,’’ he says. ‘’Dirt farmers and the big industrial scale producers are struggling to make a living and this will only get harder, given the climate change issues they face.’’ He believes the time is ripe for change in agricultural crop production on an unprecedented scale. The vertical farming industry is moving at an extraordinary pace and he estimates there are currently about 500 successful vertical farms operating globally. In the next few years the number will grow so fast he will lose count. Technology and innovation in this sector is thriving and there is no stopping the movement toward growing crops in the city – in our homes, at our place of work and within the vertical farms that are emerging as commercial enterprises.
It is an exciting prospect but the advantages of vertical and urban farming do not end here. There are huge social-economic-implications too. He refers to projects like the AeroFarms facility in Newark, New Jersey, USA - a project that is delivering prosperity to a part of the city that was formerly in decay, and which will revolutionise and revitalise that whole area.
AeroFarms hopes to develop 25 more farms in the USA and overseas in the next five years. The company says the new trend amongst consumers is for locally grown produce and it has no problem in meeting demand. It can grow plants within twelve to sixteen days, compared with thirty to forty-five days outdoors. A year round controlled environment ‘grow cycle’ allows it to operate at 75 times the production capacity of an outdoor farm.
Other farms that Professor Despommier is optimistic about, include a flag ship, model three- storey farm in Suwon, South Korea, the leading position taken by Sky Greens in Singapore, and a twelve-storey farm in Moscow – all excellent examples of where the sector is heading. He also cites the case of Pasona Group in Tokyo, Japan, which allocated 43,000 sq feet of office space for crop production that is used to feed employees, although this is more of an example of good urban agriculture production. As well as rice, the Pasona building features over 200 varieties of fruit and vegetables.
Another crucial factor in the advancement of urban agriculture and vertical farming is a preference for urban rather than rural dwelling. At present, the split is about 50/50 country to city dwelling, but by 2050 he believes this will change to 80/20 in favour of the city. ‘’All we need to see now is a shift in the mind-set of people who make policy within our cities. Once they understand the importance and benefits of this movement in urban agriculture then there will be no stopping its growth, nor that of vertical farming as a critical part of that.”
In a global context, the Professor believes that, together with the US, it is Japan and countries in the Far East that are driving the movement in take-up of new technologies and ideas. Factors which have influenced change in these regions have included incidents like the Kobe earthquake and the tsunami that hit Japan in 2011. For South East Asia, it has been the intensity of monsoons and the impact of adverse weather on farming that have forced city policy-makers to realise the importance of growing food in their own back yard. “This is a major food security issue,” he says. “When the logistical infrastructure for the delivery of produce is no longer there, or when crops are washed away, then you have a big problem.’’
A small leap for the imagination; a major step for mankind…
In fact, it does not take a major leap of the imagination to see how quickly vertical farming could develop as the dominant force in urban growing, provided innovators can deliver affordable technology solutions. According to the Food & Agriculture Organisation of the United Nations, about 30% of global food supply comes from urban farms. ‘’Most urban farms are small scale and on home plots or in the urban areas of cities,’’ explains Mr Henry Gordon-Smith, Vice Chair of the Association for Vertical Farming (AVF). AVF was set up to foster the growth and development of the movement and to galvanise the efforts of contributing innovators and leaders through collaboration and knowledge-sharing. He says vertical farms will allow urban agriculture to progress further, so cities are more independent than ever in their own food production. Vertical farms can be integrated with existing food systems and set up anywhere, including schools, institutions and government cafeterias. They can also be merged with food distribution hubs, making them more resilient.
Mr Gordon-Smith sees innovation as key to sector development and feels it is moving forward quickly. LED lighting technology and automation and sensor technology are helping to reduce operation costs. LEDS lower the energy consumption, and automation decreases labour costs. He believes that among the companies that stand out for their leadership in these areas are SPREAD Co of Japan and Urban Crops from Belgium. AVF expects there to be a vertical farm in almost every city within a decade.
Neither Professor Despommier nor Mr Gordon-Smith see any drawbacks to vertical farming if costs associated with operating grow-light can be overcome. Both are convinced the potential advantages are huge, and that with the advance of technology and greater political drive from city policy makers, we can look forward to seismic change. ‘’Vertical farms can be pest-free using strict food safety and bio-security protocols and strategic ventilation,’’ Mr Gordon-Smith explained. He concedes there are challenges ahead, but innovation in technological advancement and bypassing some areas (like lighting and robotics) will pave the way. Vertical farming will become more mainstream as we move to a stage ‘’’where water is no longer considered a ‘free’ resource and when climate change hardens its grip, and when costs for LEDs and robotics drop. ‘’
Among the other challenges he cites are zoning and code interpretation, which is delaying the development of vertical farms in many cities. They are also being hampered by a shortage in skilled labour to operate these facilities. Asked about his vision for urban and vertical farming in the next 10 – 15 years, Mr Gordon-Smith predicts:
- High-tech agriculture will become a central education tool in science, engineering, maths and technology.
- Kitchens will be designed with vertical farming systems embedded as appliances.
- City edges and waterways will become agricultural hubs.
- Restaurants, markets, hotels and office buildings will embed agriculture and it will be a part of a unique experience for tenants and the public .
- Large scale warehouse vertical farms like AeroFarms’ model will be common place on the outskirts of large cities.
Where new ideas are matched by contagious enthusiasm…
Other innovators who are embracing vertical and urban farming enthusiastically are equally ambitious, but their vision of how far the change will go and its relationship to traditional methods varies considerably. Marco Tidona, Managing Director of aponix.eu, based in Heidelberg, Germany (exhibiting in the Vertical Farm Zone at GFIA Europe 2017 in the Netherlands), says, ‘’Urban farming will not replace but will complement, the conventional methods of growing our food which will need to become more sustainable.’’ He believes urban production would become an element within a circular economy in the urban area. It would reduce waste and traffic for distribution and have positive social and nutritional effects. Like Professor Despommier and Mr Gordon-Smith, Mr Tidona believes this will have a positive effect on the fallout from transporting and shipping produce. Food miles would be reduced and commuters collect produce as they pass distribution hubs – perhaps set up inside train stations - so distribution in urban areas would become a part of day-to-day movement in the city ecosystem.
Mr Tidona is the designer and engineer behind Aponix Barrel, a unique system for use in vertical agriculture, which epitomises the kind of exciting innovative concepts that surround this emerging sector of agricultural technology. He explains that the barrel is used as a growing device in an existing nutrient cycle, either hydroponic, using liquid mineral fertilizer, or aquaponics, using fish organic fertilizer.
The aponix barrels are especially suited to growing herbs and lettuces in high density urban farming situations. The parts fit together like a Lego set and provide a means to assemble the barrel and do away with the need for complicated rack-structures. After harvesting, the ring segments can be easily cleaned and immediately replanted. Reflecting on the role of innovators like himself, Mr Tidona points to the nature of urban organic agriculture, an heterogeneous area of business with the challenges faced differing between sites. ‘’All the technologies are already here or developing rapidly, like LED lighting. Many innovators are coming to the market and they are a critical part of how the sector will develop.’’
As well as technological advancement and the political will to implement urban agriculture, he believes there are many areas that will need to change so that produce can find a place in the market. In Germany, there are labels such as ‘Öko’ and ‘Bio’, which cannot be used on labelling because they do not apply to crops grown in soilless environments. He suggests an internationally recognised coding system could be set up to help consumers evaluate the produce and compare it with that grown using more traditional means.
Another impressive example of creative thinking in urban agriculture comes from a Vancouver-based start-up company, AVA technologies. AVA has created a tech-enabled and climate-controlled micro farm called the AVA Smart Garden, a smart home gardening appliance that allows the user to produce fresh herbs, sprouts, mushrooms, fruits and vegetables from the comfort of their own home. It isn’t large scale like a vertical farm, but it is sustainable and reduces our personal ‘food print.’ The company has received a very positive response to the product and will be exhibiting in the Telus World of Science in Vancouver in March 2017.
Mr Mike Nasseri, Chief Systems Architect at AVA, says the distances which are travelled by crop vegetables are detrimental to the environment and to the nutritional value of the produce. ‘’By the time most leafy salad arrives with the consumer in Vancouver, it has travelled over 1500 kilometres. The plant enzyme content and nutritional value will have been devalued in that process.’’ With the coming (post-COP21) introduction of pricing for carbon emissions, the cost effectiveness of supply chains will be diminished. He points out that the new market conditions will place heavier demands on local production. This will have the dual effect of lower emissions and higher nutrient content when the product reaches the consumer.
One of the main purposes of the grow-box is to get people thinking about their own food security and to consider the environment, says Ms Valerie Song, joint founder and CEO at AVA. With the world population growing, Ms Song believes there are only a limited number of practical solutions that can address the food security challenge quickly. She says, ‘’There are two options which can be combined and implemented relatively fast and effectively – smart, vertical agriculture.”’ Her next comment harks back to Professor Despommier’s reference to the Pasona Group headquarters in Tokyo: ‘’What if your workplace cafeteria had a mini-farm full of luscious salad greens instead of a soda machine? What if your local restaurant had walls adorned with fresh heirloom tomatoes, instead of dull white paint?’’
Project4 Living Systems Ltd is another company out of Vancouver. Set up in 2013, the company uses permaculture principles and explores ways of enabling food, water and power independence. Mr Ben Newman, CTO at Project4 Living Systems Ltd, agrees with observations made by the other industry leaders, that limitations to development of urban agriculture and vertical farming are top-down. ‘’As we found in Canada, vertical farms are limited by a lack of general awareness and there is little information available due to the cutting-edge nature of technology and the ecosystems approach that we are used to, rather than the reductionism that science is able to offer. City officials often do not understand the concept. Lack of appropriate zoning and outdated regulations strangle projects attempting to create integrated vertical farms.”
Having had its first farming project rejected by the City of Vancouver in 2014, the company is currently awaiting a building permit for the city’s first ‘Food Hub’, comprising kitchen and dining area and a laboratory and innovation space. Mr Newman explains that, ‘’The purpose of the Food Hub is to draw attention to, and create a community of, food forward-thinkers, technologists and innovators to support the local food movements and enhance the possibilities of vertical urban farming in Vancouver and elsewhere.” His company is firmly behind vertical farming and he believes the changing political environment will be a driver in its development.
Evergreen Farm Oy of Finland (exhibiting in the Vertical Farm Zone at GFIA Europe 2017 in the Netherlands) is preparing to launch a 12,000 sq metre growing area with a major vertical farm in the city of Nokia in the South of Finland in May 2017. The company’s managing director and system designer, Mr Ali Amirlatifi, claims the growing system for integration into the Nokia site is safer than other hydroponic and aeroponic farming systems. The reason for this is that it is a closed loop, with modules that are self-sustaining and separate from one another. This eliminates the chances of disease spreading across an entire crop. The Evergreen Farm Oy system was developed with support from the Finnish Ministry of Natural Resources and University of Contemporary Technology, with a pilot scheme operated ahead of the full scale roll out.
Mr Amirlatifi says the company plans ten farms in Finland and will issue licenses to growers elsewhere in the world, beginning in Africa and the Middle East. As far as crops are concerned, the company has had major success with strawberries, blueberries, short vegetables and herbs, which can be produced all year round. The system has proved highly efficient at yield-delivery and as an example of this, the company believes that ten farms specialising in strawberry growing, have potential to outstrip the production capacity of even major growing regions like Huelva in Spain. Mr Amirlatifi says the company has also developed downscaled systems for less ambitious businesses that can be used domestically in restaurants, and by small and medium sized growers.
Evergreen Farm Oy is in the process of developing systems that will be capable of growing many other crops, such as wheat, oats and rice. In a single year there would be up to four harvests with a much higher yield than could ever be achieved in soil-based production.
It seems that with vertical farming there are no limits to the ideas reaching the marketplace, nor to the reserves of energy possessed by those making its development a part of their own futures. Provided the sector takes off in the manner our experts predict, then it will offer an as yet unrealised and hugely exciting potential.
Article written by David Stradling, Sales Director, Global Forum for Innovations in Agriculture (GFIA). David has 18 years experience in business to business trade fairs and exhibitions. He played a key role over an 11 year period in the launch and subsequent development of Automotive Testing Expo, one of the world’s leading automotive engineering events. He joined Turret Media in 2013, to head GFIA in Abu Dhabi from its launch and subsequent business development, with responsibility for the exhibition and event sponsorship. He is focussed now also on the inaugural European Edition of GFIA, to run in Utrecht, the Netherlands, 9-10th May, 2017. In his early career he worked as a journalist for several newspapers, consumer and business to business magazines. A UK citizen, he has lived and worked in Hongkong, Singapore and Thailand and currently resides in Dubai, UAE.
David welcomes comments and feedback on his article on urban farming and vertical agriculture. Companies wishing to book stand space at either edition of GFIA can contact him through Linkedin, by email at d.stradling@turretme.com or by calling +971 56 320 9377. GFIA Europe features a Vertical farming Zone specifically designed for suppliers in this sector.
The Best Crops For Vertical Farming
Vertical farming with ZipGrow is one of the most efficient type of growing in modern farms, but one question that people get hung up on is:
The Best Crops For Vertical Farming
Posted by Chris Michael on January 17, 201
A vital question: "What are the best crops for vertical farming?"
Vertical farming with ZipGrow is one of the most efficient type of growing in modern farms, but one question that people get hung up on is:
What can you actually grow on vertical planes?
It's a vital question! Anyone considering a vertical farm should be planning out their crops as part of the process. As a farmer, you have to make sure that you can actually sell what you grow and that your production costs won't be too high.
Part Of That Is Good Crop Choices.
Although choosing crops should be part of a whole feasibility study for your farm, we thought a guide on some of the best vertical crops for vertical farming would be helpful to people in the middle of the planning process.
What Can You Grow vs. What Should You Grow
With the right set-up, you can grow almost anything in a vertical farm.
Just because you can, however, doesn't mean that youshould. Here are several factors to choosing an appropriate crop for your vertical farm.
1) Economic viability
Even if a crop is biologically viable (you can grow it) it might not be economically viable (you can't make money on it!).
If you can't make money on a crop, there could be several reasons:
- Lack of demand (no profit)
- Inappropriate technique (high production costs)
- Climate (high heating, cooling, light costs)
Of course, each of those factors require a little balancing to master. "High" cost is relative to the margin that you're getting on the output.
Once you understand your demand, budget, and climate requirements, there are a few other factors to consider with your crops:
2) Timing and liability
A "turn" is the time it takes from the seedling going into the system to the mature plant coming out and going to market.
Focusing on crops with really fast turns (lettuce, mustard greens, collard greens, basil, mint) allows you to minimize your liability by never being more than six weeks or so away from production.
Slow-turn crops (like herbs and fruiting crops) are typically a bit trickier but can have higher margins than greens, depending on your local markets. We typically recommend a high greens-to-herbs ratio. For example, a new farmer could start with 80% of his space planted with greens and 20% planted with herbs.
(You can play with percentages and yield in our free Production Calculator.)
When you know what you do and don't want, you can start browsing through crop lists and seed catalogues! Here are some of ours and our farmers' favorites:
Lettuces (Romaine, Butterhead, Red Leaf, etc.)
Lettuces have fairly consistent demand across much of the world and throughout the year. There are dozens of varieties of lettuce, making it fun to grow and offer to customers. One of our favorites is Amish Deertongue Lettuce (pictured in the photo above).
Kales (Tuscan, Winterboar, and Dinosaur)
Kales are fairly easy to grow, although the crop requires extra care when harvesting if farmers are to get the highest yield. Each type of kale has its own variation on the rich taste and dark colors. The Tuscan kale above is one of the most popular varieties.
Chard & Collard Greens
Collard greens are like a thicker, deeper version of spinach. They can get quite large in the proper conditions; in the picture above, Sam gets ready to chomp down on a foot-wide collard green leaf!
The gentler version of collard greens, chard is a French green that cooks like spinach. Like kale or collard greens, chard can be harvested multiple times (taking only 30% of the plant each time) and grows back for larger yields later on.
Chives and Mint
Chives and mint are some of the best crops for beginners. Although categorized with herbs, both chives and mint have a quick turn and grow densely like a grass. It is also easy to harvest. Here, Dr. Nate prepares to harvest chives by cutting all the way down the face of the ZipGrow Tower.
Basil is possibly the most loved ZipGrow crop. It grows better in the ZipGrow Towers than any other technique in the world, and creates demand almost everywhere it goes. While a bit trickier to grow, harvest, and store, many farmers include basil in their crop offering. Some farmers even specialize in the popular crop.
Small woody herbs like rosemary and it's kin, thyme and oregano, represent a rather picky group of crops. As woody herbs, they prefer "dry feet", and have a relatively slow growing cycle. Since the shrubby herbs are so potent and unique, many farmers still find the traction to sell them in their markets.
Learn More About Crops
Want to learn more about individual crops? Learn more at Upstart University:
- Growing Basil in Hydroponics? Read This First
- How to Grow Mint in Hydroponics – All You Need to Know
- How to Grow Hydroponic Cabbage: The Beginner’s Guide
- Growing Oregano in Hydroponics? Read This First!
- Get the Scoop on How to Grow Fennel in Hydroponics
- How to Grow Classic Rosemary in Hydroponics
- Get the Tips & Guidelines on Growing Mustard Greens
- Here’s What You Need to Know About Growing Bok Choy in Hydroponics
- The Beginner’s Guide to Growing Kale in Hydroponics
- Best Conditions & Methods for Growing Parsley in Hydroponics
- Everything You Need to Know About Growing Chard Without Soil
- So You Want to Grow Chives? Read this first!
- Harvesting and Handling Lettuce for a Longer Shelf Life
- How to Grow Hydroponic Strawberries [PDF] [Video]
OR see which crops farmers like you are growing all over the world through their own pictures and posts.
Growing is only half of the equation
Farmers want to grow crops, but are often slowed down with the tasks of planning, selling, and marketing their crops. Now farmers can get back to growing by letting Able software do the planning for them. That's right - Able is your new virtual farm assistant!
FarmedHere, Indoor Farm In Bedford Park, Turning Off The Lights For Good
FarmedHere, Indoor Farm In Bedford Park, Turning Off The Lights For Good
Chicago Tribune
FarmedHere, a commercial-scale hydroponic farm in Bedford Park, had lofty goals of expanding to cities across the U.S. and beyond. The company was "on the precipice of international expansion," then-CEO Matt Matros said in July 2015.
Early last year, Matros announced a $23 million, 60,000-square-foot indoor farm that was to be the linchpin of a new development in a blighted area of Louisville, Ky.
But plans fell apart. Faced with onerous operational costs and increasing competition in the Chicago market, Nate Laurell, who took over as CEO last January, decided over the summer to pull the plug on the Louisville farm.
And as of Monday, FarmedHere, a pioneer of the new wave of commercial urban farms in the Chicago area, is closing its 90,000-square-foot Bedford Park facility for good.
"It was a difficult decision. This whole thing has been a hard decision to make. But we continue to be big believers in the (local food) space," Laurell said.
Though the farm is closing, it's not the end of the line. Here Holdings, parent company of FarmedHere, is shifting its focus and resources to making food products — such as juices, salad dressings and spreads — under the Here brand, which will be made at the company's food processing plant in Carol Stream. The goods will be made with produce from local farms, such as tomatoes from Rochelle-based MightyVine, in partnership with Local Foods, a Chicago produce distributor.
New CEO Matt Matros sees FarmedHere close to international expansion
Laurell and other investors believe the new direction will be success. But the rise and fall of FarmedHere, founded in 2011 and considered a national leader in indoor farming, provides a sobering example of how difficult the urban farming business can be.
Last year, FarmedHere arrived at a crossroads: Grow large enough to offset the considerable labor and energy costs — or instead focus the business on making branded products, Laurell said. Ultimately, the company decided return on investment looked significantly better by giving up the farm.
"The more I learned about the reality of farming, it led to a change of strategy," Laurell said.
Some of the 30 or so FarmedHere workers will find employment at the Carol Stream facility; others will be laid off, said Laurell, who said he couldn't provide exact numbers at this point.
FarmedHere's salad dressings, basil and microgreens are sold at stores throughout the Chicago area, including Whole Foods, Mariano's and Pete's Fresh Market. Here Holdings is in conversations with retailers now about selling the new Here-branded products that will be rolling out in the first and second quarters of the year, Laurell said.
"They really grew some fantastic products. They did a beautiful job," said Steven Jarzombek, vice president of produce for Mariano's, adding he expected Mariano's would continue to partner with Here Holdings going forward.
FarmedHere: Mark Thomann's drive to be 'a vehicle for greater good'
Despite the challenges, urban farming continues to grow. In recent years, competitors like Gotham Greens, BrightFarms and MightyVine have opened indoor farming facilities in the Chicago area — part of the "local food" movement that's enthralled consumers and chefs across the U.S.
Such companies also can provide a source of jobs and economic development, which was the hope for the planned West Louisville FoodPort. FarmedHere agreed to occupy more than half of the development, said Stephen Reily, the Louisville developer who formed the nonprofit Seed Capital Kentucky for the project.
The project, touted by the Louisville mayor and Kentucky governor, was approved for up to $400,000 in tax credits.
Once FarmedHere pulled out, Seed Capital couldn't find a feasible way to move forward with the project, Reily said. More generally, he said, the setback reflected the gap between the excitement surrounding indoor farming and the much harsher current reality for the still-budding industry.
"There are not a lot of success stories yet," Reily said.
Reached by phone, Matros mostly declined to comment, referring questions to Laurell. Founder of the Protein Bar fast casual chain, Matros has moved on and is preparing to launch a new coffee company called Limitless High Definition Coffee & Tea in Chicago's Fulton Market district.
Organic, local, sustainable. But can startups make sure food is safe?
"I don't know that it didn't work," said Matros, of FarmedHere. "We just changed entities. ... I know all this stuff is positive."
In July, FarmedHere merged with 87P, a food processing plant in Carol Stream that makes juices, to form Here Holdings, a Delaware entity, Laurell said.
Prior to the failed Louisville expansion, Mark Thomann led FarmedHere as CEO, from April 2014 to July 2015. Thomann, an entrepreneur known for restoring old brands through his River West Brands firm, said he was drawn to the mission of FarmedHere after being diagnosed with cancer.
"I got sick and really wanted to fix a broken food system," Thomann said.
The end of the farm is bittersweet for Thomann, who, like Matros, is an investor in Here Holdings. He believes it will be a greater success financially in its new iteration. But he also still feels personal ties to FarmedHere and believes in the future of indoor farming.
"There's a lot of good that FarmedHere did for indoor farming and hopefully lessons learned will prove beneficial for businesses that come after," Thomann said.
For Steve Rodriguez, the change in business model will mean a shift in his life direction. A graduate of the Chicago Botanic Garden's Windy City Harvest urban farming program, Rodriguez has worked for FarmedHere since 2012, working his way up from washer to crop manager.
Rodriguez described working at FarmedHere as an overwhelmingly positive experience and lamented parting ways with some of his co-workers.
"For us to get shut down like that, to me, it kind of broke my heart," Rodriguez said.
Next, the 29-year-old father of four young children will go to work at the Carol Stream facility — doing what exactly, he's not sure. But he's ready to work his way up again, if he has to. For the forseeable future, he's done with urban farming.
"I have to find another way. I'm not going to go through this again," Rodriguez said. "As much as I love farming, my family comes first."
Twitter @GregTrotterTrib
Nothing Is Harvested On This St. Thomas Farm Until You Order It
Nothing Is Harvested On This St. Thomas Farm Until You Order It
By Jennifer Bieman, St. Thomas Times-Journal
Saturday, January 14, 2017 | 10:02:01 EST AM
Where some saw an empty warehouse space, Ruth and Harvey Easton saw a fresh new business idea.
The couple has built an indoor hydroponic farm from the ground up in a 6,000 sq. ft. Burwell Rd. building. St. Thomas' Urban Farm is getting ready for its grand opening on Feb. 1.
“We can control the environment in here. There's no pests, there's no excessive humidity... It's a very contained system, we can monitor it,” said Ruth Easton, co-owner of The Urban Farm.
The former medical lab technician and cytologist lost her job in March 2015 and, not wanting to retire just yet, decided to embark on a new career path.
“We've always gardened, we have a garden in our backyard,” said Easton. “I knew something about hydroponics, but not a lot, so I went online.”
Easton and her husband Harvey researched hydroponic technology and decided to build a business together. The husband and wife team got to work on the ambitious indoor farm in August 2016 and began growing their first plants shortly after. The pair, who hail from Port Stanley, have been spending 10 hours each day tending to the plants, sprouting seedlings and planning for an ambitious expansion.
“Eventually... I'll be able to grow peppers, beans, tomatoes, strawberries. I'm planning on growing those off-season,” said Easton. “Hopefully this time next year I'll be selling strawberries.”
The plants are grown on towering vertical racks, not horizontally like most hydroponic farms, with coloured LED lights and no soil. Water is circulated automatically through the system with special pumps and computers to measure nutrient and fertilizer levels. It takes about six weeks for most of Easton's crops to go from seeds to harvest-ready plants.
Though The Urban Farm boasts some high-tech infrastructure, building the business didn't take millions of dollars in capital costs. They built their own racks for $3,500 and are running the lights through the evening hours to avoid peak electricity costs. The couple is trying to keep their expenses manageable, their carbon footprint low and their business growing.
Right now, the Eastons have dozens of different plants on the go, from bok choy to kale, spinach, several varieties of leaf lettuce and herbs. Though they haven't begun selling their harvest yet, The Urban Farm's produce will soon be hitting the market. Easton said there's been some early interest from local restaurants, bars and caterers. The public will also be able to pick up produce of their own at the Burwell St. location.
“They can come in, say 'I want green loose leaf lettuce' for example. There will be no coolers out there... Someone will come to the rack, cut it off, bag it, weigh it and sell it,” said Easton. “It's called live sales. Nothing is harvested until you order it.”
The Eastons are hosting an official grand opening for The Urban Farm on Wednesday Feb. 1 beginning at 9 a.m. They will be giving tours of their facility and helping the public learn a little more about hydroponic farming.
The Urban Farm Grand Opening
When: Wednesday Feb. 1 starting at 9 a.m.
Where: 150 Burwell Rd. St. Thomas
More Information: 519- 914-016
Green Sense Farms Builds Bridges By Exporting Know-How
Green Sense Farms Builds Bridges By Exporting Know-How
Tony V. Martin
A Portage company has brought new meaning to the phrase, east meets west, by exporting its indoor food-growing technology to China.
Green Sense Farms, of Portage, last year partnered with Star Global Holdings, of the People's Republic of China, to begin building a network of indoor vertical farms that use Phillips LED grow lights to grow produce.
The first farm was built in August in the city of Shenzhen in southern China's Guangdong Province and will serve the Shenzhen area.
Future plans call for building a network of some 20 farms in Bejing, Shanghai and Chengdu to provide fresh, chemical-free produce to major cities in China, said Green Sense Farms CEO Robert Colangelo.
"We're exporting our technology. Food is a bridge-builder. When feeding people, you rise above the political," Colangelo said.
Being able to grow food indoors is something that is new to China but very much needed, given that 80 percent of the aquifer in that country is affected by industrial output from factories.
"So even getting clean water is a challenge," Colangelo said.
By growing a variety of greens and herbs geared to the palate of the Chinese, Green Sense Farms can increase food security and help feed the Chinese people in an environmentally friendly way, Colangelo said.
"It's fun to be part of it. Rarely do you get to be part of something like this," Colangelo said.
Green start
Green Sense Farms started its first indoor growing operation in AmeriPlex at the Port business park in Portage in March 2014. Arugula, cilantro, kale, peas, lettuce and other crops are grown for markets within an average distance of 75 miles, guaranteeing freshness.
The 20,000-square-foot facility — hailed by Popular Science magazine as one of the year's 100 Greatest Inventions in 2014 — produces a large volume of crops year-round in a small footprint, a fraction of the size of a field farm and using much less land, water and fertilizer.
Most of its customers are restaurants, grocers and produce sellers, including Whole Foods, Strack & VanTil and Meijer.
Green Sense Farms is one of just a couple of commercial indoor vertical farms in the state, said Lyndsay Ploehn, a Purdue Extension educator for agriculture and natural resources based in Porter County.
"And Green Sense Farms is one of the first to take their technology to another country," Ploehn said. "They're not traditional farmers. They are kind of thinking out of the box."
Indoor vertical farms are a supplement to traditional outdoor farming, both Ploehn and Colangelo agree.
"It's not going to replace traditional farming. They're not taking away farmland, but are using abandoned buildings to grow food, and land is expensive to produce what they are producing," Ploehn said.
And there have been traditional greenhouse-type businesses in the past that have grown a variety of vegetables and other produce.
"It (vertical farming) isn't new. What's new is the scale they're doing it in," Ploehn said.
The first China farm is expected to produce 750,000 to 1 million heads of lettuce and about 1.5 million leafy greens per year. It's a production level slightly less than the Portage facility, but it's still the start of making a beneficial change in China's food production, Colangelo said.
First there's the population the farm can potentially serve.
Green Sense is starting out in an area of China that has about 50 million people in a 50-mile radius. And after the first farm, there are plans for many more in the area.
"The expansion possibilities are unlimited in China," Colangelo said.
And there's also the quality of product the farm will be growing. China's dense population and large industrial climate has taken away farmland and highly polluted the air, water and soil. By growing produce in vertical towers, Green Sense needs little space compared to a traditional farm, Colangelo said.
Expansion plans
Green Sense is expanding elsewhere, too. Green Sense is partnering with Ivy Tech Community College on a $3 million, 20,000-square-foot farm to be built at 250 E. Sample St. in South Bend.
"We like to be innovative and do things to improve the community and make it more sustainable," Colangelo said.
Green Sense will oversee the farm, but Ivy Tech students will work there in an earn-to-learn setup. Students also will earn credit toward related degrees from the college.
Colangelo's future goals include expanding operations in the United States, Scandinavia and Canada.
Another long-term goal is to spin off a biopharmaceutical business that grows plant proteins using non-GMO seeds that can be synthesized into vaccines and medicine.
Colangelo is a Chicago-area native who has authored books on the environment.
The idea for the indoor urban garden went through many iterations. Colangelo worked with Phillips as a technology partner on lighting and conducted research with Purdue University.
People have been experimenting with vertical farms since the 1980s, Colangelo said. In the case of Green Sense Farms, Colangelo and others integrated and modified an existing system and arrived at a successful product.
"It's ours," Colangelo said.
Colangelo received both his master’s and bachelor’s degrees in earth science from Northeastern Illinois University.
Colangelo spent much of his career in the environmental field, including working with the National Brownfield Association to come up with ideas to clean up the environment.
During his work and research in large cities such as Chicago and New York, the topics of producing food and vertical farming continued to surface.
"We came up with the methodology, and the rest is history," Colangelo said.
The Green Miracle of the Bronx to Deliver Aglanta’s Keynote
The Green Miracle of the Bronx to Deliver Aglanta’s Keynote
Hearing Stephen Ritz of Green Bronx Machine speak is a sensational experience. Stephen’s energetic style fully engages by binding the listener on a journey of wide ranging emotions. There will bemoments of intense sorrow and despair where the world seems hopelessly broken. Rest assured though, Stephen guides us to emerge from rock bottom with a powerful realization: a movement to grow away our problems is achievable and gaining more momentum every day.
Stephen Ritz is a South Bronx educator / administrator who believes that students shouldn’t have to leave their community to live, learn, and earn in a better one. Moving generations of students into spheres of personal and academic successes which they had never imagined — while reclaiming and rebuilding the Bronx — Stephen’s extended student and community family have grown more than 40,000 pounds of vegetables in the Bronx while generating extraordinary academic performance. Recently named a 2015 Top Ten Finalist for the $1m Global Teacher Prize, Stephen’s accolades include a 2016 Project Based Learning Champion Award, 2016 Health Champion Award, 2016 Dr. Oz Award, 2015 BAMMY Laureate – Elementary Educator of the Year Award, 2014 Greenius Award, 2014 Green Difference Award, 2013 Latin Trends Award, ABC Above and Beyond Award, Chevrolet / General Motors National Green Educator Award, USS Intrepid Hometown Hero Award, NYC Chancellor’s Award and various others.
Do all those awards get you excited to try Stephen’s flavorfully compelling speaking style? Taste it yourself straight from the source by listening to Stephen’s TED Talk, which has over one million views. During his talk, Stephen discusses how he began his journey as a teacher working at a school in a tough neighborhood. He knew nothing about growing produce, yet he was able to learn alongside his students and eventually shape his organization into an influential thought leader for youth food justice.
Did you just watch the TED talk? If so, we understand that your chest may be bumping like a dryer with shoes in it. By all means, take a deep breath and let that feeling sink in.
Now that we’re on the same page with what Stephen Ritz and Green Bronx Machine are capable of, we at Agritecture are thrilled to announce that Stephen will deliver the keynote at our upcoming Aglanta conference on Feb 19th. Although it feels like we’re stating the obvious at this point, we must say we are filled with honest-to-goodness jubilation about this development.
Our goals in organizing the Aglanta conference are further highlighted here, but in one sentence the target is: to connect the opportunities of urban agriculture to the community of Atlanta. One way we aim to achieve that goal is with an education workshop, which will help Atlanta educators learn to implement a Farm in School model in their city. We view Stephen’s work with Green Bronx Machine as an ideal node in the advocacy for the farm in school model. Stephen’s experience offers ‘been there done that’ insights as a role model in our movement to grow hope, which is a significant part of what Aglanta is all about.
Green Bronx Machine began as a way to engage at-risk youth, to make cultivating food as exciting as an iPad or Snapchat. But Green Bronx Machine isn’t a technology; it’s a way of life that has since expanded to reach many more children. Students at Ritz’s school have grown over 30,000 pounds of vegetables inside their fourth floor classroom using 90% less water than conventional agriculture. “My kids are all losing weight,” Stephen was quoted saying in this article. “They’re eating things that they’ve never eaten before. They’re getting critical nutrition where they need it most: in school. It affects their academic health, their social health and their physical health.”
Stephen recognizes that the best way to really help a child, though, is to have an adult who supports and cares about them. So with Green Bronx Machine’s Health, Wellness and Learning Centervegetables are grown so that parents can come in after school and cook the freshly harvested produce with their children. It has become an adult workforce development program where parents and children have the opportunity to eat, learn, and cook together.
Stephen’s vision has now gone global, taking him and his students from the Bronx to as far away as Dubai. Earlier this year, Stephen was campaigning his green education vision at the White House’s South by South Lawn event. President Obama described South by South Lawn as an event that seeks to tackle the task of “building a future that’s more inclusive, tolerant, and full of opportunity for everybody.” We can’t think of a more perfect fit for what Green Bronx Machine does.
Agritecture is proud to have Stephen Ritz delivering the keynote at Aglanta. We invite you to meet Stephen at the event, and to support Green Bronx Machine by donating or by volunteering.
As Stephen AKA El Capitan would say, “Si Se Puede!”
By Andrew Blume
@ablumetweets
andrew@agritecture.com
Original Source on Agritecture Here
We hope to see you at Aglanta on February 19, 2017
at The Georgia Freight Depot in downtown Atlanta
Register for Tickets here.
Early bird Ticket sales end Jan. 18th, 2017
Or contact Jeff Landau for Sponsorship Information
Jeffrey@blueplanet.consulting
Hospital Farms Grow To Heal
In a recent New York City Food Policy Center newsletter Dr. Robert Graham, founder of FRESH MED NYC, an integrative health practice that emphasizes nutrition along with conventional medicine, said, “During the past four years of the Healthy Hospital Food Initiative, we can applaud some hospitals for thinking differently about the food they offer patients and visitors. Hospitals are beginning to appreciate the old adage of ‘food is medicine.’”
Hospital Farms Grow To Heal
Published on January 13, 2017
Jim Pantaleo
Director of Business Development at Urban Ag News
By Jim Pantaleo (The below is an excerpt from the January 2017, Issue 16 of Urban Ag News. For the full article please go to: http://urbanagnews.com/emagazine/issue-16/)
Su·per·food, ˈso͞opər fo͞od/
Plural: Superfoods - A nutrient-rich food considered to be especially beneficial for health and well-being.
In my six decades on planet Earth, I’ve never spent a single night in a hospital…with the exception of when I slept on cold linoleum after the birth of my first child back in 1997. So I can credibly say I’ve never been subjected to hospital food, much maligned what with all of its high sodium and sugar (Jell-O!). Given that a hospital should be a place of healing and recovery, it’s no secret that most in the United States are woefully deficient when it comes to the food they serve their patients.
Of course I’m not referring to those patients requiring a special diet or relegated to certain and specific food types. For the majority of “regular eaters” or those who don’t require a specialized diet, one would think hospital dieticians, physicians and administrative policy makers would know better in terms of what’s being put on the menu. They do know better, and there is no question; dietitians and healthcare professionals are dedicating their lives to making a positive difference in providing healing and wellness options to patients.
In a recent New York City Food Policy Center newsletter Dr. Robert Graham, founder of FRESH MED NYC, an integrative health practice that emphasizes nutrition along with conventional medicine, said, “During the past four years of the Healthy Hospital Food Initiative, we can applaud some hospitals for thinking differently about the food they offer patients and visitors. Hospitals are beginning to appreciate the old adage of ‘food is medicine.’”
There is however another (not so) little secret in today’s health care world – cost. Food which is not generally considered healing or restorative is inexpensive. Food that heals? Not so much. Just imagine being a patient recovering from any general ailment and being served a breakfast which includes a fresh wheat grass-apple-carrot smoothie and an egg white omelet with fresh spinach instead of a “fruit cup” and watered down eggs.
Hospital farms are a unique albeit scarce answer to address the challenge of providing healing and wellness through food. Before I dig deep, let’s consider for a moment the proven healing properties of food which can be grown for that which ails us; foods like garlic, turmeric, mushrooms, culinary herbs, micro greens, wheat grass, carrots, sweet potatoes and leafy greens and lettuces. Many of these foods are being successfully grown on available hospital land, within onsite greenhouses or even indoors with the use of LED lighting.
A 2015 study published in Preventative Medicine Reports found that hospital gardens are not only associated with lower rates of obesity in communities they serve, “they may hold potential to complement other strategies to reduce public health disparities through providing nutrition education, promoting lifestyle physical activity among patients and hospital employees, accelerating healing from injury and disease, and growing food for medically underserved populations.”
Still, it’s hard to believe that some 42 U.S. hospitals actually host either a McDonald’s, Wendy’s or Chick-fil-A onsite. This recently prompted the Physicians Committee for Responsible Medicine to enact the petition “Make Hospital Patient Rooms Fast Food-Free.” (source)
In Ypsilanti, Michigan the St. Joseph Mercy Ann Arbor Hospital is leading the way and in just 6 years following the first crop planting in 2010 on 10 onsite and available acres, the farm has grown to 25 acres, three hoop houses and four beehives. The Farm at St. Joe’s, as it is known, grows fresh basil, collard greens, spinach, garlic and strawberries all on hospital grounds.
“The farm helps us support a culture of wellness in the hospital,” says director of nutrition and wellness Lisa McDowell. “We can’t grow enough to meet the needs of all of our patients and staff, but we can make an educational statement about the importance of eating a healthy diet.”
As of the writing of this article in Mid December, the weather in Ypsilanti will hit a high of 19 degrees Fahrenheit. This not-so-balmy temperature begs for growing in a controlled, indoor environment not only to supplement greenhouse-grown produce but also to continue to provide jobs and employment for hospital “farm staff” year round.
The Farm at St. Joe’s Video
There is no doubt that engaging in such Ag undertakings represent an investment and hospital budgets are beastly enough; to the point where I was disappointed when doing my research to find there are not a lot of onsite hospital farms in the United States. In fact, I discovered only about a dozen with actual onsite operations. Many hospitals, especially those with significant food and beverage budgets, rely on large food distribution companies (think SYSCO) to feed patients, staff and hospital visitors (cafeteria). Canned, boxed, processed or ready-to-eat meals are ubiquitous and cost-effective. Fresh, local and possibly even USDA-certified organic options are simply not available or feasible for many hospitals despite the obvious short and long-term benefits.
St. Luke’s University Health Network in Bethlehem, Pennsylvania opened a 10-acre farm in 2015 (onsite at the Anderson campus) which provides over 44,000 pounds of produce per year, all going to patients, cafeterias and farmers markets (source). In partnering with the Rodale Institute, pioneers in organic farming through research and outreach, the Hospital’s Auxiliary raised $125,000 used for farm start-up costs. The result is the St. Luke’s Rodale Institute Organic Farm. The farm’s success also begat a 1,200 square foot hoop house to help extend the growing season, an additional 1.5 acres added in 2016, and a renewed Food Revolution movement at the hospital.
Jim Pantaleo, Director of Business Development at Urban Ag News.
jim@urbanagnews.com
Greenhouse Grows Inspired Young People
Greenhouse Grows Inspired Young People
By Anne Hillman, Alaska Public Media
January 13, 2017
A new Anchorage greenhouse is sprouting more than seeds – it’s helping young people develop life skills and improve their mental health. Anchorage Community Mental Health Services recently began the new program Seeds of Change
Nineteen-year-old Quavon Bracken walked through the facility’s rows and rows of tall, dangling racks of hydroponic growing towers. Green vegetables and herbs were just starting to poke out through slits the sides.
“My favorite over here is the Jericho Romaine,” he said, pointing to small heads of lettuce. “They’re really green right now.”
Their growth is spurred by powerful LED lights that sway back and forth in front of the plants. When the lights switch on with a loud click, it’s so bright, you gotta wear shades.
Bracken started working with Seeds of Change a few weeks ago. Most of the time he’s a peer outreach worker with Alaska Youth Advocates. Their teen center is now located in the same building as the greenhouse in midtown Anchorage, and the youth workers are helping get the project up and running.
Bracken said he’s been interested in agriculture for a while, and he hopes to work on a farm in Israel sometime soon. In the meantime, working with Seeds of Change is giving him the chance to learn about tending plants – what nutrients they need, how much light. Soon he’ll be helping sell the produce at local farmers’ markets and to restaurants. But the experience is having a deeper impact, too.
“I feel like kind of at peace. Like I can plant some seeds and then you know, think about something that challenges me in life,then just go along planting the seeds. I just feel like I can think a little more around it. Probably all the oxygen that’s being emitted from them,” he said, chuckling.
Those are some of the ideas behind the new nearly $3 million-dollar project.
“That sense of being responsible for life and nurturing it is a really powerful thing,” said Mike Sobocinski, the Chief Operating Officer at Anchorage Community Mental Health Services and one of the founders of the program.
Seeds of Change is primarily targeting young people who have been involved with foster care, juvenile justice, and mental health programs.
“We tend to look at these youth as ‘at-risk’ and what we’re doing here is looking at them as ‘at-promise,’” he said. “You give them the opportunity and you have expectations that they’re going to be responsible and you support them along the way. It really does a lot for your mental health.”
The program supplements on-the-job training with life skills lessons, like apartment hunting and resume building. It will employ up to 20 youth at a time for about 6-9 months each. It’s a transitional program to help the young people get started.
Seeds of Change was 15 years in the making. Sobocinski began developing the project well before starting his current post, but he said it was hard to find the money and the space to actually pull it off.
“I like to tell everybody that every community mental health center should own a 10,000 foot greenhouse,” but they don’t, he said.
The greenhouse can produce up to 50 tons of fresh produce per year. Most will be sold to fund the project, which should be self-sustaining by the end of the year. A portion of the food will be donated to people in need.
Quavan Bracken said he’s excited to see the first harvest. “I really wanna like go and slice them down. And I want to see them all piled up in one area and see the massive amount we’re gonna have. Especially for my favorite right there, though, Romaine Jericho.”
The plants should be ready to pick in four to five weeks.
Top 5 Books For Vertical Farming
Top 5 Books For Vertical Farming
Posted on January 12, 2017
Many of you have asked me how I started learning about vertical farming. Well, today I’m sharing five books that cover everything from entrepreneurship and the potential of vertical farming to space efficiency and nutrient management that will help you get started. Without a doubt, the knowledge in these books will put you on your way to owning your own vertical farm.
Recommended Books:
The Vertical Farm: Feeding the World in the 21st Century, Dickson Despommier: Despommier is considered the father of vertical farming and this is the book that got many people started in this movement. After reading this, you’ll fantasize about skyscrapers feeding cities and know where to look for further research.
The E-Myth Revisited, Michael Gerber: This is a general business book that demonstrates the importance of implementing replicable systems – something most small farmers avoid that leads to wasting their own labor and often money on bad hiring decisions and inefficient work flow.
The Urban Farmer: Growing Food for Profit on Leased and Borrowed Land, Curtis Stone: While not focused on hydroponic or vertical production, learning how Stone thinks through his farming decisions in terms of maximizing profit and space is beneficial for any farmer.
Vertical Gardening: Grow Up, Not Out, for More Vegetables and Flowers in Much Less Space, Derek Fell: Though this book is meant for gardeners, its principles are easily transferable and people love it. Fell teaches you how to look at intensifying a given space while minimizing effort – the foundation of vertical farming.
Teaming With Nutrients, Jeff Lowenfels: This book makes cellular biology not only readable, but super engaging too. While also written for gardeners, the science Lowenfels explains is absolutely necessary for people working with hydroponics or reliant on nutrient (whether from things like compost tea or synthetics).
There are others out there that I’ve read, and I’m sure some that I’m missing out on some, but I’ve found most other books on vertical farming to be either too ponderous/impracticable for starting out, or filled with useless minutiae.
So, instead of having you wade through that unknown, this list was selected by myself and the other vertical farming panelists at Future Harvest’s Cultivate the Chesapeake Foodshed for their quality and accessibility. While I’ve been working with vertical farms and helping others set up their own for about 3 years, I’ve only just started selling produce commercially. So don’t just take my word for it! Niraj Ray and Mary Ackley have demonstrated their chops and are doing great things here in DC. Check out their sites while you’re at it!
Thanks for checking out our blog and website. I will note that the links are affiliate links, meaning amazon will give me a portion of the sale if you make the purchase on that page. That would really help me out (more LEDs!) and if you’d like to say thank you for giving you some helpful information, buying there is a good way to do it.
CT Agri-Tech Maker Lands Product Deal
JANUARY 12, 2017 | CT GREEN GUIDE
CT Agri-Tech Maker Lands Product Deal
A South Windsor company that began as a member of UConn's startup incubator program said it will supply its LED technology to a Las Vegas manufacturer of vertical aeroponic farming systems.
Agrivolution, founded in 2012 by Richard Fu, said Indoor Farms of America recently selected it as a horticultural LED provider for leafy greens and other crops such as heirloom tomatoes, squash and cucumber.
Terms of the agreement were not disclosed, but the companies said the selection came after approximately one year of testing Agrivolution's Triple-Band LED bars against a dozen other lights.
Indoor Farms began selling its vertical aeroponic farming systems in late 2015 and last year announced it had secured a product distributor in South Africa. Aeroponics
Growing Power Vertical Farm
Growing Power Vertical Far
LOCATION: Milwaukee, Wisconsin
SIZE: 27,000 square feet
STATUS: In Progress
PROGRAM: Highly sustainable urban five-story vertical farm including greenhouses, conference / training and retail spaces
Growing Power, Inc. is an internationally-recognized non-profit organization and land trust supporting people from diverse backgrounds and the environment in which they live by helping to provide equal access to healthy, high-quality, safe and affordable food. This mission is implemented by providing hands-on training, on-the-ground demonstration, outreach, and technical assistance through the development of Community Food Systems that help people grow, process, market and distribute food in a sustainable manner.
Growing Power currently operates six greenhouses on a historic two-acre site that is the last remaining farm and greenhouse operation within the City of Milwaukee. As the organization has expanded, the need for additional space to support production, classes, meetings, meal preparation, offices, and on-site warehousing has grown exponentially. Growing Power and TKWA have worked together to develop plans for an ambitious new facility, the world’s first working urban Vertical Farm.
Five stories of south-facing greenhouse areas will allow production of plants, vegetables, and herbs year-round. Expanded educational classrooms, conference spaces, a demonstration kitchen, food processing and storage, freezers, and loading docks will further support Growing Power’s expanding mission as a local and national resource for learning about sustainable urban food production.
Growing Power was founded by Will Allen, one of the world’s leading authorities in the expanding field of urban agriculture. In 2008 he was named a MacArthur Foundation Fellow and he is a member of the Clinton Global Initiative. In May, 2010 Time Magazine named him one of the Time 100 World’s Most Influential People.
Indoor Vertical Farm Hosts Farm Foundation’s Round Table
Indoor Vertical Farm Hosts Farm Foundation’s Round Table
Urban Produce, Orange County’s organic, indoor vertical farm, hosted members of the Farm Foundation’s Round Table for a tour at their state-of-the-art facility in Irvine, California on Wednesday, January 4th. Urban Produce’s patented growing technology has placed them at the forefront of sustainable agriculture; making them an ideal destination for The Farm Foundation’s bi-annual Round Table tour.
A program of Farm Foundation, NFP, the Round Table is an invitational discussion forum comprised of agricultural leaders from across North America. The Farm Foundation® Round Table meets twice yearly to provide a forum for discussion and interaction among select members and invited government, academic, agribusiness and other interest group leaders.
“We’re proud to welcome esteemed members of the Farm Foundation’s Round Table into our facility,” commented Ed Horton, who was named one of Agriculture’s Leading Innovators by USA Today. “To be able to share our advancements in agricultural technology and our global vision with some of the nation’s leading stakeholders in our field is a catalyst for even more discussion, innovation, and partnership opportunities.”
The Round Table program is designed to create an exchange of ideas and to foster understanding of different approaches to issues and challenges facing agriculture, the food system and rural regions.
Ed Horton, President and CEO of Urban Produce led the group through their state-of-the-art facility which houses their patented High Density Vertical Growing System. He showed members how Urban Produce can successfully grow 16 acres of organic produce using just 1/8 an acre. Urban Produce continues to push the envelope of sustainability by creating its own water for its crops through Atmospheric Water Generation; ultimately using 93% less water than traditional farms producing similar yields. Members learned how vertical farming offers a sustainable solution to climate change, the rapidly growing population, and increase in food deserts.
For more information: Talia Samuels | Outshine PR | Tel: 949.690.1531
Publication date: 1/11/2017
Blue Planet Consulting 2016 Annual Report
visit blueplanet.consulting in your browser today and learn more
Blue Planet Consulting 2016 Annual Report
- Published on January 11, 2017
Henry Gordon-Smith
Urban Agriculture Consultant
2016 was a year of notable growth for Blue Planet Consulting. For one, we successfully acquired over 15 new client projects, many of which have already been fulfilled to completion. Servicing these clients has strengthened our core team with relevant skills and experience to keep Blue Planet Consulting (BPC) on the forefront of building a thriving urban agriculture industry.
Further keeping our team in the catbird seat of the industry is our continued management of both Sky Vegetables and Stonebridge Farms. Managing these commercial farms for our partners has supplied BPC with more of the relevant knowledge and experience to be able to provide our clients with data-driven and first-hand operator insights. Our involvement with these facilities proved highly useful in multiple client engagements in 2016. Typical urban agriculture problems surrounding waste, labor, energy, sales, and marketing are being overcome by our growing team every day.
Related: Blue Planet Consulting 2015 Annual Report
Another major 2016 development for BPC is that my blog, the Agritecture platform has signed an agreement to be added into the Blue Planet family. This move has diversified BPC’s capabilities, giving the company access to quickly communicate to a growing community of urban agriculture professionals. Agritecture’s strong audience growth in 2016 gives me confidence that BPC will continue to develop its ability to influence the industry. This partnership also allows us to grow the amount and quality of knowledge we share through the platform as we have now hired our first employee: Community Manager Andrew Blume.
2016 was a year where BPC sharpened the methodology we use to help our clients overcome the challenges of developing urban agriculture businesses. Whether those challenges are zoning complexity, site and crop selection issues, recruiting strategies, yields and waste calculations, or implementing a new sales strategy for your product – BPC has likely serviced clients with similar issues facing your team.
In the report below, we showcase some of our work in 2016, from client engagements to industry events and partnerships we have supported. These activities depict how we have helped entrepreneurs and large companies navigate the uncharted waters of planning, implementing, and operating their urban agriculture business.
Thank you for your time and interest in our company’s 2016 endeavors. On behalf of my whole team, I wish you a warm, healthy, productive, 2017!
Sincerely,
Our 2016 Client Engagements
We conducted a feasibility study for Rob Laing, CEO of Farm.one and helped turn his brilliant idea of growing rare culinary herbs in Manhattan into a reality. We assisted Farm.one with crop selection, site selection, design, and economic analysis. We even assisted with the installation of Farm.one. We also helped Rob recruit his head grower, the talented David Goldstein. We are happy to hear that Farm.one is expanding its operations to another facility in 2017!
The Child Development Services Corporation (CDSC) is one of the only food banks with a vertical farm within it, providing fresh and clean produce to Clinton Hill residents in need. The farm was originally installed by Boswyck Farms 5 years ago and was in need of a retrofit. We assisted CDSC with a retrofit of the lighting, plumbing, and nutrient dosing systems. We also made the vertical farm more ergonomic for its users. CDSC benefitted from an updated management manual of the farm we developed as well as a training we conducted for their volunteers.
A large Chinese manufacturer wanted to explore how converting some of its facilities into a “green campus” could improve worker health and wellbeing. We provided a rapid concept development service including sketching out four interventions to their existing facilities that would improve oxygen within the factories, provide some produce for consumption, and improve overall well being. The final results were a set of renderings which we pitched to some of the companies executive team who continue to discuss the possibility of developing the green campus in 2017.
Our storefront office in Brooklyn certainly catches the eyes of pedestrians passing by. Josh Smith is a local resident and world-renowned artist that saw the +FARM in our window and ask us to design a custom system for his basement. We consulted with Josh what he wanted to grow and designed a system that fit his space and budget. Now Josh and his wife can enjoy leafy greens and microgreens year-round from their home.
Another community group in Brooklyn that has a system originally set up by Boswyck Farms requested our services to update the system. We advised them on means to improve their management of the farm and also recommended certain equipment upgrades.
This organization serves special needs students and families in New Jersey. We conducted a feasibility study on the costs and benefits of converting an unused ~3,000 sf warehouse into a commercial vertical farm for the purposes of generating additional revenue for the school. Our team completed design of the farm and even conducted focus groups with local residents to determine crop selection and packaging choices. The Reed leadership and board are considering funding options and partnerships to develop the vertical farm in the near future.
Global LED Company
We were hired by a global LED manufacturer to conduct market research and analysis to understand the potential for a new product they were considering developing. Our team developed a thorough document reviewing the potential for the product, target customers, pricing, and marketing strategy recommendations.
We assisted Brooklyn’s newest urban farmers and its only urban agriculture accelerator Square Roots launch their first campus. Our primary contributions were on recruiting, curriculum development, and horticulture planning. Now, many of our team serve as mentors to the 10 entrepreneurs that are growing real food in shipping containers in Brooklyn. Read more about Square Roots here.
Grownex USA chose us to help them launch their brand and new product Salad Wall at NYC AgTech Week. We were happy to assist them by building their first US website, social media accounts, and marketing strategy. We also displayed their system in our office getting them their first customer as a result of the exposure we provided them. Grownex is growing its sales to the US market in 2017 and Blue Planet Consulting is excited to continue to help them share their unique product Salad Wall with the US market.
Phillips Programs (Phase II)
Two years after helping our first client Phillips Programs in Maryland install a hydroponics learning lab (pictured), we were able to help them design their next phase: an additional six vertical microgreens systems. For this project we partnered with our local contacts at Modernature and co-designed cultivation systems that were appropriate for the Programs’ special needs students. Phase II of the Phillips’ Growing Futures Program is set to launch in Spring 2017.
BMoreAg
Also in Maryland, this client is interested in making a big impact on jobs and food security in Baltimore. We are assisting this client with concept development for now and eventually a full feasibility study. The plan is to convert a large vacant lot into a productive mix of vertical farming and greenhouse operation with an on-site market.
We are very excited to be working with Goler CDC, one of Winston-Salem, North Carolina’s well known community groups. Our role in their latest project is to provide a comprehensive feasibility study on converting a vacant lot into a series of greenhouses. This project is currently in progress with the site visit complete and crop selection underway. We will be providing Goler CDC with everything they need to get the project moving forward including equipment selection, economic analysis, management planning, and recruiting. The project is set to break ground in 2017.
Global Investor
We provide a benchmarking and case study report to a global investor interested in understanding the ins and outs of vertical farming. The list was comprehensive and included both case study data and analysis from our team of consultants and the investment climate of the emerging vertical farming industry.
Entrepreneur in Dubai
CJ is a young Dubai-based Indian entrepreneur looking to launch a model for vertical farming in Mumbai, India. We are developing a vertical farming concept for CJ that considers the opportunities and challenges of the local market and climate. Crop selection, pre-sqf costs, and a pitch deck are in progress to help CJ raise money for his unique vertical farming idea.
2016 Agritecture Workshops
In 2016 we conducted three Agritecture workshops:
· Fresno, CA (Feb)
· London, UK (June)
· Boston, MA (Dec)
These three 2016 workshops have brought the total number of Agritecture workshops to seven (7). Agritecture workshops match interdisciplinary teams of architects, growers, entrepreneurs, engineers, marketers, designers, and sustainability managers together for a shared mission: to develop a viable “agritecture” concept for the host city.
The Agritecture Design Workshops comprise of three teams, each matched with the goal of demonstrating creativity, sustainability, and feasibility when integrating agriculture into cities. On-site mentors from Blue Planet Consulting guide participants through urban agriculture project planning, hydroponic agriculture, and sustainability.
In the past, Agritecture Workshops were typically planned in partnership with the Association for Vertical Farming. For the Boston Agritecture Workshop, and for future workshops, this will no longer be the case. The AVF has indicated they will seek to develop their own proprietary workshop series, although they may still occasionally promote future Agritecture workshops.
We would like to thank our main sponsors for the three 2016 workshops included the following companies:
Agritecture also began offering sponsored content packages in 2016. These packages helped innovative companies showcase their products or services to our audience of 30,000+ vertical and urban farming enthusiasts. Contact Andrew@agritecture.com for more information on how you can reach our primarily millennial and gen-X audience.
2016 Milestones
January
- Hired new Engineer Jeffrey Landau
- Acquired new client Farm.one
- Visited the first installed Growtainer in NYC
- Completed DIY vertical farming kits for 2016 client Bergen Academies
February
- Hosted Agritecture Workshop in Fresno, California
- Attended GFIA conference in Abu Dhabi
- Attended FarmTek CEA Workshop
- Acquired new client CDSC
- Acquired new client Foxconn
- Became an Autodesk Entrepreneur Impact Partner
March
- Attended U of A CEAC Short Course
- Attended and Spoke at Thought For Food Summit in Zurich, Switzerland
April
- Attended Indoor Ag Con
- Participated in Urban Agriculture Roundtable with Brooklyn Borough President’s Office
- Acquired new client Los Surres
- Acquired new client Reed Academy
- Initiated the California Urban Agriculture Collective
- Attended Food + Future CoLab event @ IDEO in Boston
- Acquired new client Josh Smith
May
- Attended Silicon Valley AgTech Conference
- Spoke at first AgroHack conference in Puerto Rico
- Acquired new client Global LED Manufacturer
- Hired West Coast Representative David Ceaser
June
- Sponsored AVF Summit 2016
- Conducted first international Agritecture Workshop in London, England
July
- Acquired new client Square Roots Urban Growers
August
- Acquired new client Grownex USA
- Hired Djavid Abraham as our new Lead Systems Designer
September
- Participated in 2nd annual NYC AgTech Week
- Acquired new client Global Investor
- Started phase II for client Phillips Programs
- Hired MIT CityFarm veteran Elaine Kung to join our team as a designer
October
- Spoke at the Canadian Greenhouse Conference, offering the first talk on Vertical Farming to ever be featured at the event.
- Attended Chicago LED Magazine Event
- Attended and spoke at Fluence Bioengineering PhotoX event in Austin, TX
- Attended LARTA Institute Urban Agriculture event in Los Angeles
- Whitehouse announces our DIY vertical farming system +FARM on its website
November
- Hired Andrew Blume to join our team as our Community Manager for Agritecture.com
- Spoke at Building Success event sponsored by Microdesk in San Francisco
- Acquired new client Goler CDC
- Attended Seedstock Grow Local OC event
December
- Acquired new client based in Dubai
- Launched Aglanta: the South’s first CEA conference together with the Mayor’s Office of Atlanta and with platinum level sponsor, Southern Company
Our 2017 Strategy & Outlook
2016 was a big year for proving that Blue Planet Consulting’s methodology and team are capable of meeting industry challenges. Our acquisition of high-profile customers such as Foxconn, Square Roots, and Southern Company are evidence that as urban agriculture becomes more mainstream in 2017, BPC will play a role in assisting more high-profile organizations to enter the space successfully.
While we are ecstatic to have worked with these influential customers, we are also proud that we continued our practice of servicing school and institutional clients at a reduced rate. We’re excited to continue working for these small niche customers and adding more value to their installations with the introduction of the +FARM in 2017. We work with these clients because corporate social responsibility is a major motivating factor for our team. Thus, we fully intend to continue devoting resources to communities and clients of all shapes and sizes in 2017.
I can’t think of a more perfect example of how we will engage with big and small, business and education, industry and community, then the Aglanta Conference on February 19th, 2017. Aglanta will be organized by BPC, the Mayor’s Office of Atlanta, and by the conference’s platinum level sponsor, Southern Company. Alongside these entities will be Aglanta’s keynote speaker, Stephen Ritz, who is the undisputed champion of growing in schools.
I encourage you to purchase tickets to Aglanta here or contact me to get your company involved. There are still some exciting opportunities to exhibit or sponsor the event!
Only a crystal ball with tell us exactly how urban agriculture will manifest in 2017. While there are challenges and risks, we are confident that this is the year lucrative and impactful businesses will emerge. If you intend to pioneer and develop alongside the industry, we encourage you to contact us to see how we can work together to turn your growing aspirations into growing operations.
Request your urban agriculture, greenhouse, or vertical farming feasibility study here.
Vertical Farming May Not Feed The World, But Could Empower Cities
Vertical Farming May Not Feed The World, But Could Empower Cities
BY LISA NIKOLAU ON 11 JANUARY 2017
Aware of population growth’s growing impact on global food security, many agricultural experts are debating the use of vertical farming – and its ability to feed the world – but don’t deny its potential in urban agriculture.
Vertical farming is a relatively new term that, at its core, simply means growing more food in smaller spaces. Instead of having a single layer of crops over a large land area, for example, stacks of crops climb upward, typically in highly controlled indoor environments.
The method usually grows crops without soil or natural light. It’s dramatically different from how humans grew food just a few decades ago, but has the potential to produce drastically higher yields with significantly less space.
For humanitarians, the idea is tantalizing. The world’s population is exploding at an exponential rate, stressing the need to find ways to feed people without further destroying the planet. Proponents say vertical farming uses less water and fossil fuel than outdoor farming and eliminate agricultural runoff, all while providing fresh and local food.
As the concept garners both attention and legitimacy, vertical farms are already popping up in Seattle, Houston, New York and Milwaukee, as well as Linköping, Sweden. Some enthusiasts have even considered the rise in vertical farming the “third green revolution.”
Whether the model can be used among the rural poor – where the bulk of the world’s food is grown, in countries with highest food insecurity – is still up for debate.
“Can vertical farming feed the world? I’ll tell you right now: No it can’t,” said Erik Cutter, founder of California-based urban farm company Alegría Fresh, in an interview with Humanosphere. “It’s too expensive to feed the world.”
According to Cutter, the price tag on the type of vertical farm tower conceptualized by Dickson Despommier – the ecologist credited for modernized the idea of vertical farming – can be upward of $1 billion.
He said such a model might intrigue the elite, but is irrelevant to the majority of the world’s farmers. For them, many agriculturalists say building food security would rely on the adoption of regenerative agriculture – a range of techniques with the aim of restoring soil fertility and sequestering carbon.
In Irvine, Calif., Cutter uses a hydroponic vertical farming system – utilizing coconut fiber instead of soil, and powered by the sun – but is quick to describe its shortcomings. Vertical farms generally have a limited range of crop species, such as leafy greens or herbs, and its energy requirements are debated among critics who say lighting and other necessary equipment have a heavy impact on the climate.
But the biggest problem with vertical farming, Cutter adds, is that there isn’t an economic model to sustain it.
“Really, we have to train thousands of thousands of farmers in this country to farm differently, plus source capital, plus develop a market for that food,” he said. For this reason, he says one of his goals is to create decent-paying jobs in urban agriculture.
Even if it can’t feed the planet, proponents of vertical farming say it could at least work for the world’s cities. One of the largest, AeroFarms in Newark, N.J., appears to have created a sustainable economic model. An in-depth look at the company by the New Yorker explained that its main crop is baby salad greens because its premium price makes the enterprise attractive – and because it’s easy to grow.
If sustainable, such enterprises could help prevent cities from what urban agriculturalists warn is the inevitable: intolerable overcrowding with overwhelmed sanitation systems, housing, water and, of course, food. If the bulk of food production could happen close to these highly concentrated centers, the hope is that urban populations could harbor some control of their food supply.
Agrivolution’s Agri LED Light Picked for New Vertical Farming Panels From Indoor Farms of America
Agrivolution’s Agri LED Light Picked for New Vertical Farming Panels From Indoor Farms of America
January 11, 2017 | 07:38 PM Eastern Standard Time
SOUTH WINDSOR, Conn.--(BUSINESS WIRE)--Light-emitting diode (LED) lighting from agri-technology company Agrivolution LLC has been selected for integration into a patented aeroponic vertical farming system developed by Indoor Farms of America, LLC after Agrivolution won a year-long performance review against other LED products that provide artificial light for agricultural uses.
The new relationship brings together Indoor Farms of America, a U.S. market leader in affordable, economically viable, high-yield vertical aeroponic crop growing equipment that can grow pesticide-free local fruits and vegetables year round, and Agrivolution that supplies advanced horticultural LEDs that are popular in Asia and elsewhere around the globe.
The announcement comes as Las Vegas, NV-based Indoor Farms of America has steadily increased its market share as the company expands across North America and into key markets globally.
"Indoor Farms of America tested the Agrivolution ultra-thin and lightweight bar type Triple-Band LED against a dozen competing products for over a year and determined its superior performance to grow plants indoors," said Agrivolution President Richard Fu. "Based on the trial results, Indoor Farms of America decided on Agrivolution as its standard LED equipment provider for leafy greens and other select crops."
The global vertical farming industry is forecasted to grow to $6.81 Billion by 2022 according to a report issued by international research group Research and Markets called "Global Vertical Farming Market Analysis & Forecast, 2016-2022." Agrivolution expects to supply approximately 10,000 units of the Triple-Band LEDs across North America in 2017.
"We are very happy with the steady performance of the Triple-Band LED bars from Agrivolution," states David Martin, CEO of Indoor Farms of America. "We have grown about 20 different leafy green products, as well as flowering and fruiting plants, and they (Agrivolution LEDs) do a great job in helping us reach our targeted harvest times for what we grow."
Indoor Farms of America will integrate the Agrivolution LEDs into its enhanced aeroponics system to grow larger plants such as heirloom tomatoes, squash, and cucumber. The company has already been successful testing its growing techniques that produce a variety of leafy green products, as well as cherry tomatoes, chili peppers, and strawberries.
Aeroponics is a technique that mists nutrient solutions and supplies ample oxygen to plant and vegetable roots directly. It promotes root growth which reduces root rot and results in healthier plants. Artificial light from LEDs enables plants, vegetables and fruits to photosynthesize ― the process by which plants use ― to convert energy of light into chemical energy as its fuel.
Agrivolution’s UL certified Triple-Band LED being used by Indoor Farms of America is based on a patented single-chip design that emits RED-, BLUE-, and GREEN-bands that covers full Photosynthetically Active Radiation (PAR) between 400 nm and 700 nm. Because of the unique single-chip architecture, the Agrivolution LEDs are able to output a balanced full-spectrum light while reducing energy usage.
Interest in horticultural LED lighting and weather agnostic indoor plant factories that can support steady food production in North America has been on the rise year after year as traditional growers struggle with unpredictable weather patterns in recent years and the extreme, long-term drought in agricultural rich California as well as drought conditions in various parts of the nation including the Northeast.
A separate research report issued last year forecasts the LED grow light module market currently at $395 million in 2014 to reach $1.8 billion by 2021 according to LED Agricultural Grow Lights: Market Shares, Strategies, and Forecasts, Worldwide, 2015 to 2021 by WinterGreen Research.
South Windsor, Connecticut-based Agrivolution is developing innovative products for the indoor vertical farming industry that support sustainable farming solutions.
Agrivolution is a multiple winner of the State of Connecticut's CT Innovation Summit "Tech Companies to Watch."
For more information visit www.agrivolution.co.
Contacts
AGRIVOLUTION CONTACT:
TrahanPR
Michael Trahan, 860-256-1698
trahanm@comcast.net
or
INDOOR FARMS AMERICA CONTACT:
David W. Martin, 702-664-1236
CEO
davem@ifoamerica.com
Alaskan Containerized Hydroponics Win Prestigious Farming Award
Alaskan Containerized Hydroponics Win Prestigious Farming Award
The brains behind an “Arctic ready” hydroponic, mobile system for producing fresh vegetables have won the American Farm Bureau Federation’s (AFBF) Entrepreneur of the Year Award.
Linda Janes and Dan Perpich of Alaska-based Vertical Harvest Hydroponics took home US$30,000 to support their business, which uses LED lighting in containers to produce fresh produce in the most remote of locations.
In a video briefing (below), the group explains 95% of Alaska’s fresh produce has to be imported from the continental U.S. or elsewhere, and often takes two weeks before reaching store shelves plus an extra three or four days to reach rural zones.
As it stands, the company estimates around 25% of the fresh produce that comes into Alaska is wasted, and that the lack of fresh produce availability is contributing to health problems in the state.
But through Vertical Harvest Hydroponics’ manufactured containerized growing systems, producers or interested parties can grow 450 heads of lettuce a week, wherever they may be.
“Innovation and entrepreneurship have always been essential ingredients in the success of America’s farmers and ranchers,” said AFBF president Zippy Duvall.
“From the adoption of new business models and the development of new tools and services, to unique adaptations of technology in agriculture, our industry is driven by people with vision who are willing to step forward with fresh ideas.”
Janes described the experience of winning the award as “surreal”.
“We entered into the Strong Rural American Entrepreneurship Challenge last year and certainly didn’t expect to win. However, we were notified a few months later that we were in the top four out of 356 applicants,” she said.
“This weekend, they flew all the four teams into Phoenix to compete for either the Entrepreneur of the Year (decided by the four judges) or the People’s choice award (via online voting). This competition also coincided with the American Farm Bureau Annual Convention and IDEAg Trade Show, which was held at the Phoenix convention Center.
“In fact, our pitches to the judges and full house audience took place on the convention stage, while the convention was in full swing.”
She said her competitors were “exceptional” with great business models and teams.
“It was an unbelievable moment to hear our name called as the winners. We are humbled and thankful. This was a great opportunity and privilege to be in the company of fantastic and brilliant people,” she said.
“It is wonderful to know that so many great entrepreneurs and farmers are working hard to make our country better. This has been a challenging and rewarding experience. We want to thank everyone who has supported us over the last two years.
“We would like to extend a huge thank you to the American Farm Bureau for their entrepreneurial nature in realizing and following through on the important mission of encouraging innovation and supporting our rural communities and our farmers. This win is overwhelmingly for Alaska.”
Indoor Harvest Corp Announces Vertical Farm Development Financing Across North America
Indoor Harvest Corp Announces Vertical Farm Development Financing Across North America
January 10, 2017
Source: Indoor Harvest Corp
HOUSTON, Jan. 10, 2017 (GLOBE NEWSWIRE) -- Indoor Harvest Corp (OTCQB:INQD), through its brand name Indoor Harvest®, is a solutions provider to the vertical farming and indoor agriculture industry. Indoor Harvest is pleased to announce an alliance with OneWorld Business Finance through its division US Energy Capital (OneWorld) to assist with financing for its customers and projects. The new relationship will allow OneWorld to expand their business offering in this new and exciting industry and will allow clients expanded options for financing.
“After conducting a search for a company that combined the experience we were looking for with the flexibility our clients need, we chose OneWorld. A centrally planned indoor farm facility is a cost intensive project. This partnership gives the operators in the industry a strong option to reduce their initial costs and efficiently manage their cash flow while they focus on growing crops and revenue," stated John Choo, CEO of Indoor Harvest. "With the pedigree of US Energy Capital and OneWorld Business Finance, we are excited to bring their options to the Vertical Farming space across North America," further stated Mr. Choo.
“US Energy Capital, recently acquired by OneWorld Business Finance, has been offering attractive vendor finance programs for over 30 years,” stated Jim Borland, Team Leader of the US Energy Division. Jim also stated that they are now excited to work very closely with Indoor Harvest and their clients. “Attractive financing offered by US Energy Capital will make the acquisition of cultivation hardware and facility build outs through Indoor Harvest much easier and quicker.” US Energy Capital will be offering no payments during implementation and installation for qualified companies.
About Indoor Harvest Corp
Indoor Harvest Corp, through its brand name Indoor Harvest®, is a full service design-build engineering firm for the indoor agriculture industry. Providing production platforms and complete custom-designed build-outs for both greenhouse and building integrated agriculture (BIA) grows, tailored to the specific needs of virtually any plant crop, it leads development and implementation in this new and growing industry. Visit our website at http://www.indoorharvest.com for more information about our Company.
About OneWorld and US Energy Capital
OneWorld is an Austin, Texas-based independent business finance company founded in 1995 that provides various forms of commercial finance to companies throughout the United States. Although focused on equipment finance and working capital, OneWorld also works with service companies, manufacturers, healthcare providers and municipalities to help its customers plan for and acquire funding for capital acquisitions, refinancing and operational expansion. Its US Energy Capital division focuses on lighting, energy saving and production assets. More can be found at www.usenergycapital.com or www.oneworldbusinessfinance.com.
FORWARD LOOKING STATEMENTS
This release contains certain “forward-looking statements” relating to the business of Indoor Harvest and its subsidiary companies, which can be identified by the use of forward-looking terminology such as “estimates,” “believes,” “anticipates,” “intends,” "expects” and similar expressions. Such forward-looking statements involve known and unknown risks and uncertainties that may cause actual results to be materially different from those described herein as anticipated, believed, estimated or expected. Certain of these risks and uncertainties are or will be described in greater detail in our filings with the Securities and Exchange Commission. These forward-looking statements are based on Indoor Harvest’s current expectations and beliefs concerning future developments and their potential effects on Indoor Harvest. There can be no assurance that future developments affecting Indoor Harvest will be those anticipated by Indoor Harvest. These forward-looking statements involve a number of risks, uncertainties (some of which are beyond the control of the Company) or other assumptions that may cause actual results or performance to be materially different from those expressed or implied by such forward-looking statements. Indoor Harvest undertakes no obligation to publicly update or revise any forward-looking statements, whether as a result of new information, future events or otherwise, except as may be required under applicable securities laws.
Contacts: Indoor Harvest Corp CEO, Mr. John Choo jchoo@indoorharvest.com
The VERTICAL FARM: Growing Crops in The City, Without Soil or Natural Light
Vertical farming can allow former cropland to go back to nature and reverse the plundering of the earth.Illustration
JANUARY 9, 2017 ISSUE
THE VERTICAL FARM
Growing crops in the city, without soil or natural light
By Ian Frazier
Vertical farming can allow former cropland to go back to nature and reverse the plundering of the earth.Illustration by Bruce McCall
No. 212 Rome Street, in Newark, New Jersey, used to be the address of Grammer, Dempsey & Hudson, a steel-supply company. It was like a lumberyard for steel, which it bought in bulk from distant mills and distributed in smaller amounts, mostly to customers within a hundred-mile radius of Newark. It sold off its assets in 2008 and later shut down. In 2015, a new indoor-agriculture company called AeroFarms leased the property. It had the rusting corrugated-steel exterior torn down and a new building erected on the old frame. Then it filled nearly seventy thousand square feet of floor space with what is called a vertical farm. The building’s ceiling allowed for grow tables to be stacked twelve layers tall, to a height of thirty-six feet, in rows eighty feet long. The vertical farm grows kale, bok choi, watercress, arugula, red-leaf lettuce, mizuna, and other baby salad greens.
Grammer, Dempsey & Hudson was founded in 1929. Its workers were members of the Teamsters Union, whose stance could be aggressive. Once, somebody fired shots into the company’s office, but didn’t hit anyone. Despite the union, the company and its employees got along amicably, and many of them worked there all their lives. Men moved steel plate and I-beams with cranes that ran on tracks in the floor. Trucks pulled up to the loading bays and loaded or unloaded, coming and going through the streets of Newark, past the scrap-metal yards and chemical plants and breweries. In an average year, Grammer, Dempsey & Hudson shipped about twenty thousand tons of steel. When the vertical farm is in full operation, as it expects to be soon, it hopes to ship, annually, more than a thousand tons of greens.
Ingrid Williams, AeroFarms’ director of human resources, lives in Orange but knows Newark well. She has degrees in labor studies and sociology from Rutgers, and she visited many of the city’s public-housing apartment buildings in her previous job as a social-services coördinator. She is a slim, widely smiling woman with shoulder-length dreads who dresses in Michelle Obama blues, blacks, and whites. For a while, she had her own show, “The Wow Mom Show,” on local-access TV. Through it she met many people, including a woman who is a financial expert and helps local residents with their budgets. The two became friends, and last year when this woman was giving a speech at a Newark nonprofit Williams showed up to support her.
One of the other speakers that day was David Rosenberg, the C.E.O. and co-founder of AeroFarms. “A light went on in my head when I heard AeroFarms,” Williams told me. “There’s an AeroFarms mini-farm growing salad greens in the cafeteria of my daughter’s school, Philip’s Academy Charter School, on Central Avenue. I volunteer there all the time as part of parents’ stewardship, and I know the kids love growing their own lettuce for the salad bar.” After the speeches, she stayed to congratulate her friend and also introduced herself to Rosenberg. He asked her if she was looking for a job. She started as H.R. director at AeroFarms nine days later.
The mini-farm in the cafeteria at Philip’s Academy is a significant piece of technology. In fact, it is a key to the story, and it figures in the larger picture of vertical farming worldwide and of indoor agriculture in general. If the current movement to grow more food locally, in urban settings, and by high-tech indoor methods follows the path that some predict for it, the mini-farm in the school cafeteria may one day have its own historical plaque.
The mini-farm’s inventor, Ed Harwood, of Ithaca, New York, sold it to the school in 2010. Harwood is a sixty-six-year-old man of medium stature who speaks with the kind of rural accent that sometimes drops the last letters of words. He has been an associate professor at Cornell’s famous school of agriculture, and he began his career as an inventor by coming up with revolutionary improvements in the computer management of dairy cows, an animal he loves. His joyous enthusiasm for what he does has an almost messianic quality.
After spending part of his youth and young adulthood working on his uncle’s dairy farm, he got degrees in microbiology, animal science, dairy science, and artificial intelligence, and applied his knowledge to the dairy industry. One of the first inventions he worked on was a method to determine when a cow is in estrus. Research showed that cows move around more when they’re ready to breed. Harwood helped develop a cow ankle bracelet that transmitted data on how active the cow was each day; the farmer could then consult the data on his computer and know when it was time for the artificial inseminator. To check the accuracy of the bracelet, Harwood spent days walking around the pasture beside a cow with his hand on her back while he counted her steps. He enjoyed the companionship during this rather tedious exercise in ground-truthing and thinks the cow did, too.
He first became interested in growing crops indoors in the two-thousand-aughts. Around 2003, his notebooks and diaries began to converge on ideas about how he could raise crops without soil, sunlight, or large amounts of water. That last goal pointed toward aeroponic farming, which provides water and nutrients to plants by the spraying of a mist, like the freshening automatic sprays over the vegetables in a grocery’s produce department. Aeroponic farming uses about seventy percent less water than hydroponic farming, which grows plants in water; hydroponic farming uses seventy percent less water than regular farming. If crops can be raised without soil and with a much-reduced weight of water, you can move their beds more easily and stack them high.
Harwood solved the problem of the crop-growing medium by substituting cloth for soil. He tried every type of cloth he could think of—“They got to know me well at the Jo-Ann Fabric store in Ithaca,” he said. Finally, he settled on an artificial fabric that he created himself out of fibres from recycled plastic water bottles, and he patented it. The fabric is a thin white fleece that holds the seeds as they germinate, then keeps the plants upright as they mature. The roots extend below the cloth, where they are available to the water-and-nutrients spray.
Devising a nozzle for the aeroponic sprayer proved a tougher problem. The knock-on aeroponics had always been that the nozzles clogged. How he solved this Harwood won’t say. He has no patent for his new nozzle. “It’s more of a stream than a spray,” he said, “but we’re keeping the design proprietary. I have no fear of anyone copying it. You could look at it all day and never figure out how it works.”
He rented an empty canoe factory in Ithaca and set up a two-level grow tower a hundred feet long and five feet wide to employ his new discoveries, along with a light system that eventually consisted of L.E.D. lights modified to his needs. He had decided to grow commercial crops and chose baby salad greens. “My ‘Aha’ moment came when I was in the Wegmans supermarket in Ithaca,” he said. “My engineer, Travis Martin, and I looked at the greens for sale and saw that a pound of lettuce cost one dollar, while a pound of baby greens cost eight dollars. That was enough of a premium that we figured I could make my system profitable with baby greens, so I started a company I called GreatVeggies, and soon I was selling baby greens in several supermarkets in Ithaca.”
When that didn’t bring in enough money, he shut the company down. His financial situation, never robust, then took an upturn when an investor offered funding on the condition that he concentrate on selling the grow towers themselves, rather than the greens. Switching to that business model, Harwood formed a new company called Aero Farm Systems. He leased a number of his grow towers and sold a few. One of them went to Jeddah, Saudi Arabia, and he has no idea what happened to it. Another went to Philip’s Academy, where it’s the mini-farm in the cafeteria. The new company did not earn much, either, but he kept it going in a smaller part of the canoe factory.
The term “vertical farming” has not been around long. It refers to a method of growing crops, usually without soil or natural light, in beds stacked vertically inside a controlled-environment building. The credit for coining the term seems to belong to Dickson D. Despommier, Ph.D., a professor (now emeritus) of parasitology and environmental science at Columbia University Medical School and the author of “The Vertical Farm: Feeding the World in the 21st Century.”
Hearing that Despommier would be addressing an audience of high-school science teachers at Columbia on a recent morning, I arranged to sit in. During the question period, one of the teachers asked a basic question that had also been puzzling me: What are the plants in a soil-free farm made of? Aren’t plants mostly the soil that they grew in? Despommier explained that plants consist of water, mineral nutrients like potassium and magnesium taken from the soil (or, in the case of a vertical farm, from the nutrients added to the water their roots are sprayed with), and carbon, an element plants get from the CO2 in the air and then convert by photosynthesis into sucrose, which feeds the plant, and cellulose, which provides its structure.
In other words, plants create themselves partly out of thin air. Salad greens are about ninety percent water. About half of the remaining ten percent is carbon. If AeroFarms’ vertical farm grows a thousand tons of greens a year, about fifty tons of that will be carbon taken from the air.
Despommier lives in Fort Lee, New Jersey, and not long after his lecture I visited him at his apartment, in a high-rise with a skyline view of New York. He is a cheerful, demonstrative man, seventy-six years old, with a short gray beard and a mobile face. The concept of vertical farming came from a class he taught in medical ecology, he said. “It was in 2000, and the students that year were bored with what I was teaching, so I asked them a question: ‘What will the world be like in 2050?’ and a followup, ‘What would you like the world to be like in 2050?’ They thought about this and decided that by 2050 the planet will be really crowded, with eight or nine billion people, and they wanted New York City to be able to feed its population entirely on crops grown within its own geographic limit.
“So they turned to the idea of rooftop gardening,” he continued. “They measured every square foot of rooftop space in the city—I admired how they went to the map room of the public library on Forty-second Street and found aerial surveys and got their rulers out—and then they calculated what the city’s population will be in 2050, and the amount of calories that many people will need, and what kind of crops can best provide those calories, and how much space will be necessary to grow those crops. Finally, they determined that by farming every square foot of rooftop space in the city you could provide enough calories to feed only about two per cent of the 2050 population of New York. They were terribly disappointed by this result.”
At the time, Despommier’s wife, Marlene, who is a hospital administrator, was working in midtown Manhattan. As the couple drove back and forth along the West Side Highway, Despommier considered the light-filled glass-and-steel structures, and that got him thinking about the thousands of abandoned buildings throughout the city. He began to wonder why plants couldn’t live on multiple levels, as human beings do. For his next year’s class, he carried over the previous year’s project, and this time had the students calculate what kind of structure a multilevel urban farm would need and how many people you could feed that way.
Despommier taught the class for nine more years, always asking his students to build on what previous classes had done. He began using the term “vertical farming” in the second year. For methods of indoor agriculture, he referred to technology pioneered by nasa and to the work that a scientist named Richard Stoner did decades ago on how to grow crops in non-Earth environments. By the class’s final year, Despommier and his students had determined that a complex of two hundred buildings, each twenty stories high and measuring eighty feet by fifty feet at its base, situated in some wide-open outlying spot—say, Floyd Bennett Field, the airport-turned-park on Jamaica Bay in Brooklyn—could grow enough vegetables and rice to feed everybody who will be living in New York City in the year 2050. These vertical farms could also provide medicinal plants, and all the herbs and spices required for five different traditional cuisines.
The possibilities that opened up put stars in his eyes. Agricultural runoff is the main cause of pollution in the oceans; vertical farms produce no runoff. Outdoor farming consumes seventy percent of the planet’s freshwater; a vertical farm uses only a small amount of water compared with a regular farm. All over the world, croplands have been degraded or are disappearing. Vertical farming can allow former cropland to go back to nature and reverse the plundering of the earth. Despommier began to give talks and get noticed. He became the original vertical-farming proselytizer. Maybe the world’s mood was somehow moving in that direction because ideas that he suggested other people soon created in reality.
“When my book came out, in 2010, there were no functioning vertical farms that I was aware of,” Despommier said. “By the time I published a revised edition, in 2011, vertical farms had been built in England, Holland, Japan, and Korea. Two more were in the planning stages in the U.S. I gave a talk in Korea in 2009, and they invited me back two years later. Fifty reporters were waiting for me. My hosts led me to a new building, where they had ‘Welcome Dr. Despommier’ in neon lights. I saw that, and I cried! The ideas that I had described in my ’09 talk they had used as the basis for building a prototype vertical farm, and here it was. When I’m lying in my coffin and they pull back the lid, the smile on my face will be from that day in Korea.”
Today in the U.S., vertical farms of various designs and sizes exist in Seattle, Detroit, Houston, Brooklyn, Queens, and near Chicago, among other places. AeroFarms is one of the largest. Usually, the main crop is baby salad greens, whose premium price, as Ed Harwood realized, makes the enterprise attractive. The willingness of a certain kind of customer to pay a lot for salad justifies the investment, and after the greens get the business up and running its technology will be adapted for other crops, eventually feeding the world or a major fraction of it. That is the vision.
AeroFarms occupies three other buildings in Newark aside from the main vertical farm, on Rome Street. At 400 Ferry Street, it has a thirty-thousand-square-foot space whose most recent previous use was as a paintball and laser-tag entertainment center called Inferno Limits. The graffiti-type spray-painted murals and stylized paintball splatters of that incarnation still cover the walls. AeroFarms’ headquarters—sometimes referred to as its “world headquarters”—are in this building, some of which is taken up by a multiple-row, eight-level vertical farm that glows and hums. Technicians in white coats who wear white sanitary mobcaps on their heads walk around quietly. Some of these workers are young guys who also have mobcaps on their beards. The salad greens, when you put on coat and mobcap yourself and get close enough to peer into the trays, stand in orderly ranks by the thousands, whole vast armies of little watercresses, arugulas, and kales waiting to be harvested and sold. For more than a year, all the company’s commercial greens came from this vertical farm.
Nobody in the building appears to have an actual office. Employees are distributed in more or less open spaces here and there. In a dim corner of the area with the vertical farm, where the fresh, florist-shop aroma of chlorophyll is strong, young graduates of prestigious colleges confab around laptop screens that show photos of currently germinating seeds and growing leaves. Folding tables burgeon with cables, clipboards, and fast-food impedimenta. David Rosenberg, the C.E.O., who hired Ingrid Williams last year, is the boss. This distinction is hard to notice because he looks more or less like anybody else.
I first met Rosenberg at an international conference on indoor agriculture held at a theatre in Manhattan. He wore dark jeans, a blue-and-white plaid shirt with the AeroFarms logo on the breast pocket, and running shoes. In past years, he used to fence competitively and win championships. He is forty-four, tall, and still fit, with close-shaved black hair and dark, soulful eyes. The quietness and patience with which he speaks can be disconcerting. He grew up in the Bronx, went to U.N.C. at Chapel Hill, and got an M.B.A. from Columbia in 2002. AeroFarms is not his first company. When his grandfather Michael Rhodes, a chemist, died, in 2002, a relative told Rosenberg about a molecule that his grandfather had created that could be used to make a weatherizing treatment for concrete. Rosenberg used his grandfather’s invention to start a business called Hycrete, which he later sold, though not for a sum so great that he has chosen to fund AeroFarms himself. In recent years, his new start-up has raised more than fifty million dollars in investment, about twice as much as has any other vertical farm, or indoor farm of any kind, in the U.S.
After Hycrete, he wanted to create a for-profit company that would do good for the environment and for society. With his fellow business-school alumnus and fellow-fencer Marc Oshima, he set about researching the latest indoor agricultural technology. When they learned about the work of Ed Harwood, they immediately got in touch with him. “David and Marc called me, and they kept calling back and asking better and better questions,” Harwood remembered. “They said they wanted their first farm and their world headquarters to be in Newark, and I told them, ‘I’ve got a grow tower in a school cafeteria in Newark!’ That’s when I knew this was going to work out.”
Rosenberg and Oshima had set up an indoor-agriculture company called Just Greens, which existed primarily in name. Harwood had the trademark on the name Aero Farm Systems. They proposed to him that the two companies merge and do business under the name of AeroFarms. Rosenberg would be the chief executive officer, Oshima the chief marketing officer, and Harwood the chief science officer. Like the original Aero Farms Systems, this company would base itself on Harwood’s patented cloth for growing the plants and on his nozzle for watering and feeding them. It would build the vertical-farm systems but not sell them, grow baby greens commercially, and scale the operation up gigantically. This change in fortunes left Harwood thunderstruck. “I couldn’t believe it,” he said. “How many inventors have inventions sitting around, waiting for a break, and then something like this happens?”
Most of America’s baby greens are grown in irrigated fields in the Salinas Valley, in California. During the winter months, some production moves to similar fields in Arizona or goes even farther south, into Mexico. If you look at the shelves of baby greens in a store, you may find plastic clamshells holding five ounces of greens for $3.99 (organicgirl, from Salinas), or for $3.29 (Earthbound Farm, from near Salinas), or for $2.99 (Fresh Attitude, from Quebec and Florida). Harwood’s magic number of eight dollars a pound would be on the cheap side today. Four dollars for five ounces comes to about thirteen dollars a pound.
AeroFarms supplies greens to the dining rooms at the Times, Goldman Sachs, and several other corporate accounts in New York. At the moment, the greens can be purchased retail only at two ShopRite supermarkets, one on Springfield Avenue in Newark and the other on Broad Street in Bloomfield. The AeroFarms clamshell package (clear plastic, No. 1 recyclable) appears to be the same size as its competition’s but it holds slightly less—4.5 ounces instead of five. It is priced at the highest end, at $3.99. The company plans to have its greens on the shelves soon at Whole Foods stores and Kings, also in the local area. Greens that come from California ride in trucks for days. The driving time from AeroFarms’ farm to the Newark ShopRite is about eleven minutes. The company’s bigger plan is to put similar vertical farms in metro areas all over the country and eventually around the world, so that its distribution will always be local, thereby saving transportation costs and fuel and riding the enthusiasm for the locally grown.
At the Bloomfield ShopRite, I watched a woman pick up a clamshell of AeroFarms arugula, look at it, and put it back. Then she picked up a clamshell of Fresh Attitude arugula and dropped it in her cart. I asked her if she knew that AeroFarms was grown in Newark. She said, “I thought it was only distributed from Newark.” I told her the arugula was indeed Newark-grown and explained about the vertical farm. She put the out-of-state arugula back, picked up the Newark arugula, and thanked me for telling her. I think AeroFarms does not play up Newark enough on the packaging. They should call their product Newark Greens.
The reason they don’t is probably the obvious one—the negative ideas that salad buyers may have about Newark, its poverty and history of environmental disaster, including the presence of Superfund toxic-waste sites contaminated by dioxins and pesticides. That’s not the aura you want for a healthy-greens company. AeroFarms chose Newark because of its convenient location and the relative cheapness of its real estate. City and state development agencies encouraged the decision, and the company has hired about sixty blue-collar workers from Newark, some of them from a program for past offenders. At least geographically, the company so far is exclusively a Newark production.
But in another sense it could be anywhere. The technology it uses derives partly from systems designed to grow crops on the moon. The interior space is its own sealed-off world; nothing inside the vertical-farm buildings is uncontrolled. Countless algorithm-driven computer commands combine to induce the greens to grow, night and day, so that a crop can go from seed to shoot to harvest in eighteen days. Every known influence on the plant’s wellbeing is measured, adjusted, remeasured. Tens of thousands of sensing devices monitor what’s going on. The ambient air is Newark’s, but filtered, ventilated, heated, and cooled. Like all air today, it has an average CO2 content of about four hundred parts per million (we exceeded the three-fifty-p.p.m. threshold a while ago), but an even higher content is better for the plants, so tanks of CO2 enrich the concentration inside the building to a thousand p.p.m.
The L.E.D. grow lights are in plastic tubing above each level of the grow tower. Their radiance has been stripped of the heat-producing part of the spectrum, the most expensive part of it from an energy point of view. The plants don’t need it, preferring cooler reds and blues. In row after row, the L.E.D.s shining these colors call to mind strings of Christmas lights. At different growth stages, the plants require light in different intensities, and algorithms controlling the L.E.D. arrays adjust for that.
In short, each plant grows at the pinnacle of a trembling heap of tightly focussed and hypersensitive data. The temperature, humidity, and CO2 content of the air; the nutrient solution, pH, and electro-conductivity of the water; the plant growth rate, the shape and size, and complexion of the leaves—all these factors and many others are tracked on a second-by-second basis. AeroFarms’ micro-, macro-, and molecular biologists and other plant scientists overseeing the operation receive alerts on their phones if anything goes awry. A few even have phone apps through which they can adjust the functioning of the vertical farm remotely.
Though many of the hundred-plus employees seem to be diffused throughout the enterprise and most vividly present in cyberspace, everybody gathers sometimes in the headquarters building for a buffet-style lunch, at which Rosenberg makes a short speech. Talking quietly, he repeats a theme: “To succeed, we need to be the best at four things. We need to be the best at plant biology, the best at maintaining our plants’ environment, the best at running our operational system, and the best at getting the farm to function well mechanically. We have to be the best total farmers. And to do all this we need the best data. If the data is not current and completely reliable, we will fail. We must always keep paying close attention to the data.”
Ed Harwood’s original prototype mini-farm, the one he sold to Philip’s Academy in 2010, still produces crops six or seven times every school year. The invention sits in a corner of the cafeteria by the round lunch tables and the molded black plastic cafeteria chairs, an improbable-looking teaching tool. Examining it, you feel a mystified wonder, and perhaps a slight misgiving about the inventor’s soundness of mind, remembering what happened to Wile E. Coyote. For concentrated ingenuity and handcrafted uniqueness, its closest simile, I think, is the Wright brothers’ first biplane, the Flyer, now on display in the National Air and Space Museum, in Washington. Like the Flyer, and like many other great inventions, Harwood’s prototype is also an objet d’art.
Its dimensions are five feet wide by twelve feet long by six and a half feet high. Essentially, it consists of two horizontal trays of thick plastic, both about ten inches deep, one above the other, suspended in a strong but minimal framework of aluminum. Below the trays, at floor level, a plastic tank holds two hundred and fifty gallons of water. Frames like those used for window screens fit on top of the plastic trays. Each frame holds a rectangle of Harwood’s grow cloth, about two and a half feet by five feet in size. The cloth is attached to the frame by snaps. On small pipes running along the inside bottom of the tray, Harwood’s special nozzles emit a constant, sputtering spray of water at a downward angle. The spray hits the bottom of the tray and bounces up, and some of it becomes the mist that nourishes the roots growing through the cloths. Eventually, most of the water drains down and returns to the tank to be reused.
Seeds speckle the white surface of the cloth. The L.E.D. lights above the trays shine on the seeds. They germinate, and soon the roots descend. Seedlings grow. In about three weeks, the plants are ready for harvesting. The trays are taken out and the leaves are cut off and given to the cafeteria staff, who put them in the salad bar. The cloths are scraped of residues, which are composted for the school’s rooftop garden, and then the cloths go into the washing machine to be laundered for reseeding.
Throughout the mini-farm, PVC pipes and wires run here and there, connecting to clamps and switches. The pumps hum, the water gurgles, and the whole thing makes the sound of a courtyard fountain.
The teacher who keeps all this machinery in good order is Catkin Flowers. That is her real given name. A tall auburn-haired woman in her forties, she starts her science students working with the farm when they’re in kindergarten. “We use the farm to teach chemistry, math, biology,” she explained to me one morning between classes. “The students learn with it all the way through eighth grade. I think the farm is the reason our science scores are so competitive in the state. We get the kids involved in running the grow cycles and then solving the problems that inevitably come up. That’s how kids really learn, not from sitting back and watching the grownups do everything.”
“We’re also teaching food literacy,” put in Frank Mentesana, the director of EcoSpaces, the school’s environmental-science program, who joined us. “Some of our kids have never seen vegetables growing. They may live in a part of the city that’s a food desert, and their families get food at McDonald’s or at bodegas. They may never have seen fresh greens in a store.”
“Kids love to grow things,” Flowers said. “It teaches them about nutrients, the minerals we put in the water, and why the water’s pH affects how the plants absorb them, and about the light spectrum, and how photosynthesis works. The kids monitor the same kind of data as AeroFarms does, but less of it, of course.”
“Ed Harwood is still a huge help,” Mentesana said. “If we have a problem with the farm that we can’t solve, Ed will make time to stop by and fix it.”
“When we’re ready to harvest, the kids can’t wait to eat what they’ve grown,” Flowers said. “They’ll start eating the plants while they’re harvesting, and we actually have to tell them to wait because these are for the salad bar. They want to find out how they taste. And they’re excited when the plants they’ve grown become part of a meal for the whole school. Because of this farm, our school’s consumption of leafy greens is probably not met by any other school in the country.”
On another morning, I stayed for lunch. First, Mentesana took me, along with Marion Nestle (not Nestlé; she’s no relation), the nutrition expert, and N.Y.U. professor, on a tour of the school. A Clinton campaign e-mail released by WikiLeaks the day before had referred to harassment of Nestle by the beverage industry because of her book “Big Soda: Taking on the Soda Industry (and Winning),” and she was in a great mood, proud to have been mentioned. Robert Wallauer, the school’s young chef, introduced himself. He has worked for famous restaurants but decided he could contribute more to the public good by running school kitchens. The entrée was a Chinese-style dish of pasta with chopped vegetables. I told him it was so delicious that if this were a restaurant I would come back and bring my friends.
Zara Hawkins, a fifth grader, stopped by our table. Her mother is Ingrid Williams, the H.R. director at AeroFarms. Zara has a quiet manner, and she sometimes looks thoughtfully into the near distance as she talks. She noted the greens we’d just been served, supplied by AeroFarms. “We eat a lot of this salad at home,” she said. “My mom brings the bags of lettuce from work. I didn’t use to like it, but now I do. I have the baby kales in omelettes, with cheese. You can also put them in smoothies. They are O.K. In fact, they can be pretty good.”
Wallauer got up and brought us back glasses of a kale-pineapple-and-yogurt smoothie whose color had the bright seaside green of a lime treat. “It takes a while for kids to start eating certain foods if they’re not used to them,” Wallauer said. “We made some of these smoothies yesterday, and we handed them out as dessert. One little girl took a sip and said it was pretty good. Then she took another and looked at me suspiciously and said, ‘Did you put salad in this?’ ”
A few weeks before the vertical farm at 212 Rome Street was to harvest its first official crop, I walked through the building with David Rosenberg. After the usual hand washing, putting on of mobcaps and coats, and wiping our feet on mats for disinfecting, we stepped into the high-ceilinged room where the vertical farm was humming away. If Harwood’s prototype at the school was the Wright brothers’ first biplane, this immense scaled-up elaboration of it was a spaceship in drydock.
I thought of the tenderness of the greens this device produces—a natural simplicity elicited mainly from water and air by high-tech artifice of the most complicated and concentrated kind. It seemed a long way to go for salad. But if it works, as it indeed appears to, who knows what might come of it when we’re nine billion humans on a baking, thirsting globe? Rosenberg and I stood looking at the vertical farm in silence. On his face was a mixture of pride and love; he might have been seven years old. “We are so far above everybody else in this technology,” he said, after a minute or two. “It will take years for the rest of the world to catch up to where we already are now.” ♦
Ian Frazier is a staff writer at The New Yorker.
This article appears in other versions of the January 9, 2017, issue, with the headline “High-Rise Greens.”