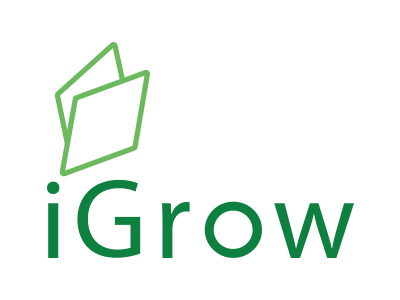
Welcome to iGrow News, Your Source for the World of Indoor Vertical Farming
Growing Quality Food and Meeting Nutritional Requirements
Can climate-controlled freight containers help in farming or can plants grow without any soil?
By Murali | May 23, 2020 | City Today
Can climate-controlled freight containers help in farming or can plants grow without any soil? The answers to these questions can be found in Urban farming. It involves indoor cultivation under controlled conditions with up to eight (8) harvests in a year. It offers an ideal solution for regional or community-specific food needs, for local crops that would not be economically viable for full-scale cultivation. It can also help cities become sufficient in their produce demand while getting fresh food year-round. Vertical urban farming whether with soil or hydroponics-based increases the space utilization by 3-4 fold with lower water and nutrient usage.
Therefore, it allows the farmer to have a 3-4 fold higher area with a 20 percent faster growth rate, leading to 3-4 fold higher harvests. Multiple harvests in a year would lead to higher profits compared to traditional farming. Indoor farms may use drip-irrigated pots, hydroponics, aeroponics, or hydrogel-based polymers for growing vegetables depending on the growth requirements of the plant.
To View the Full Article, please Click Here
IDTechEx: How to Succeed in Vertical Farming
Vertical farming is an emerging technique within agriculture that involves growing crops indoors under controlled environmental conditions
NEWS PROVIDED BY IDTechEx
May 26, 2020
BOSTON, May 26, 2020,/PRNewswire/ -- Vertical farming is an emerging technique within agriculture that involves growing crops indoors under controlled environmental conditions. By carefully tailoring the environment to the exact requirements of the crop, such as through using LED lighting to produce the exact light spectrum needed for optimal photosynthesis, it is possible to obtain yields hundreds of times higher than traditional agriculture.
Vertical farms can be set up almost anywhere, making it possible to grow crops in the middle of populous urban centers, meaning that it is possible for crops to reach consumers within minutes of harvest. This contrasts with traditional agriculture, where fresh produce can take weeks to reach consumers, losing the freshness, and increasing contamination risk along the way. The recent IDTechEx report, "Vertical Farming: 2020-2030" explores the technologies and markets around the fast-growing vertical farming industry.
Vertical farms use artificial lighting and carefully controlled climates to grow crops at far higher yields than conventional agriculture. Source: Intelligent Growth Solutions (PRNewsfoto/IDTechEx)
Vertical farming has been the subject of a lot of hype in recent years, with supporters claiming it could revolutionize food production. Industry advocates, such as Columbia University Professor Dickson Despommier, have presented visions of a future world where fresh food is grown inside skyscrapers to feed giant, high-tech metropolises (for further visions of the cities of the future, see the IDTechEx report, "Smart City Opportunities: Infrastructure, Systems, Materials 2019-2029"). Investors are also feeling the hype, with vertical farming start-ups raising over a billion dollars in investment in the last five years alone.
However, despite this optimism, the industry does face some major challenges and the sector has more than its fair share of bankruptcies. PodPonics, once the most well-funded vertical farming company in the world, and FarmedHere, which once operated what remains the largest vertical farm ever built, both went bankrupt. David Rosenberg, Chief Executive of New Jersey-based vertical farming outfit AeroFarms, recently said he wouldn't be surprised if 90% of the players in the industry went out of business within the next three years.
Broadly, many vertical farms struggle for the same reasons. As well as costing a lot of money to set up, vertical farms can be very expensive to run, largely because they require continuously running artificial lighting and climate controls. This is compounded by high labor costs and logistical difficulties that often get more difficult as the vertical farm gets larger. This all makes it very difficult to compete on price with produce grown on conventional farms, which typically have razor-thin profit margins.
Because of these challenges, vertical farmers generally only grow crops where the whole of the plant can be consumed, in order to maximize space efficiency and avoid wasting energy on growing inedible stems and leaves. Therefore, almost all vertical farmers are restricted to growing herbs and leafy greens. These are still a large market but fall somewhere short of the lofty claims made by some supporters of the industry.
It is certainly possible to run a successful vertical farming business, as fast-growing players such as Bowery Farming and InFarm will attest to, however, it requires a carefully planned out strategy and consideration of all the variables and trade-offs involved in vertical farming, in addition to a fair amount of investor capital.
The keys to success in vertical farming are outlined in the recent IDTechEx report, "Vertical Farming: 2020-2030". The report discusses several factors that can contribute to the success or failure of a vertical farm, including:
Whether or not to automate. Automation can significantly reduce labor costs while streamlining the logistical processes. However, investing in advanced automation equipment can lead to extremely high start-up costs.
Choice of crops. Should vertical farming try to branch out beyond leafy greens, or should it corner the market it has? What about higher-value crops inaccessible to conventional agriculture?
How large is too large? Larger centralized facilities could lead to economies of scale but could also face spiraling logistical difficulties. However, smaller localized facilities may face much higher start-up costs relative to the output capacity.
The importance of location: is a city center location really the best place to set up a vertical farm?
The need for experience in the food industry. Crops are living organisms and are not always predictable. Despite this, there is a relative lack of food and agriculture experience in the vertical farming sector.
For more information on this report, please visit www.IDTechEx.com/vertfarm or for the full portfolio of Food & AgTech research available from IDTechEx please visit www.IDTechEx.com/research/agtech.
IDTechEx guides your strategic business decisions through its Research, Consultancy and Event products, helping you profit from emerging technologies. For more information on IDTechEx Research and Consultancy, contact research@IDTechEx.com or visit www.IDTechEx.com.
Media Contact:
Jessica Abineri
Marketing Coordinator
press@IDTechEx.com
+44-(0)-1223-812300
SOURCE IDTechEx
What Is A Business Framework And Why Is It Needed For Vertical Farming?
Emiel Wubben is an associate professor of strategic management at Wageningen University and specializes in agrifood clusters & circular business. His prime interest is about: “strategizing business transitions towards a more sustainable bio-based and circular economy.”
Emiel Wubben is an associate professor of strategic management at Wageningen University and specializes in agrifood clusters & circular business. His prime interest is about: “strategizing business transitions towards a more sustainable bio-based and circular economy.”
The first time Michele Butturini heard about the work of Emiel Wubben was during VertiFarm2019, where he gave the presentation entitled “Where is the business? A study into the key variables of the Vertical Farm Business Framework.” The research paper in which that presentation was based on, will soon appear in the European Journal of Horticultural Science. Emiel allowed Michele to read the submitted version of the research paper, leading to this interview.
In the interview, Emiel also shares his vision of the future for vertical farming: "In countries that import a lot of foods, like Japan and Singapore, I think that they will have an incentive to continue the attempt of vertical farming successfully. I think that, in some countries, there's quite some pressure to get vertical farming working, while in Europe, I don't see that there is a lot of eagerness to get vertical farming done. In America, you typically often see the financial drive, motivating competition and selection. I expect more vertical farming expansion on the outskirts, such as on ships, but also on the north and south pole, in deserts, where these technologies can easily be brought and somebody can run it as a franchise. But I think it will become more like a chain or with someone who owns and runs a lot of them. I think that the container-farms may succeed and be the format that will work earlier since they are easily movable and easy to do data gathering and data sharing. I think that the technology is still too complicated for franchises to build. Large vertical farms for buildings are very investment intensive."
Read the full interview at Agritecture.
Publication date: Fri 22 May 2020
Are Vertical Farms Even Remotely Efficient? Putting A Figure On Plant Factories
Researchers in the Netherlands are calculating the feasibility of vertical farming in urban areas
Researchers in the Netherlands are calculating the feasibility of vertical farming in urban areas.
“The main goal is to put a figure on vertical farming,” Wageningen Universit & Research’s Luuk Graamans tells FoodNavigator.
https://www.foodnavigator.com/Article/2019/05/15/Are-vertical-farms-even-remotely-efficient-Putting-a-figure-on-plant-factories?utm_source=copyright&utm_medium=OnSite&utm_campaign=copyright
By Flora Southey | Food Navigator | May 15, 2019
The Farm Of The Future Is Here, and It's Vertical
Green Sense Farms, in Portage, Indiana—the largest commercial indoor vertical farm in the US.
At first glance it looks like a scene out of Breaking Bad—a huge warehouse space with a few people wandering around in hazmat suits and blue gloves under glowing pink lights. But look closer and you’ll discover that it’s actually Green Sense Farms, in Portage, Indiana—the largest commercial indoor vertical farm in the US.
To grow produce indoors, Green Sense Farms collaborated with the lightbulb maker Philips to create sunlight-mimicking low-energy LEDs that can be programmed for hue, angle and time-of-day saturation to support around-the-clock growing of leafy lettuce, kale, arugula and more. Because of these lights, Green Sense farmers can harvest up to 26 times a year. And thanks to the vertical growing techniques, along with the basics of hydroponics—which provides direct nutrients, is soil free and water conserving––the savvy farm is using 0.1 percent of the water, land and fertilizer that the same crops would use outdoors.
The crops themselves grow in a medium made from coconut husks, instead of soil. The farmers germinate non-GMO seeds in the coconut material and when they’re done, it’s recycled. Whatever’s left is composted. This combination of vertical farming and LED-lights is paving the way for farmers to grow indoors in urban environments, which is what we’ll need if our population increases and arable land becomes even scarcer. But with just 30,000 square feet in Indiana, Green Source Farms can put out 3,000 cases of produce a week.
Right now Green Sense Farms is supplying only restaurants, commercial and retail, but one can imagine a future where we could go online, watch our lettuce grow and then double-click our way to salad heaven.
By Larissa Zimberoff | Food & Wine | January 7, 2020
Lead Photograph: Green Sense Farms
Growing Up In The Garden State: Vertical Farms Prove To Be Bright Spot on N.J.'s Agricultural Horizon
New Jersey’s numerous vertical farms represent a bright spot on the Garden State’s agricultural horizon
In Newark, AeroFarms converted a 75-year-old, 70,000-square-foot steel mill into the world’s largest indoor vertical farm in 2015, which is soon to become the world’s second–largest when AeroFarms completes construction of its new 150,000-square-foot vertical farm in Danville, Va. Photo courtesy of AeroFarms
While New Jersey is famously known as the ‘Garden State’ based on its bountiful produce, numerous forces here and abroad indicate that the delicate balance between food growers and consumers is reaching a dangerous tipping point. Among key concerns, the world population is currently growing faster than the food supply, agriculture accounts for nearly 25% of the greenhouse gases that contribute to global warming, and modern commercial farming practices have led to a rise in dangerous and costly food-borne and antibiotic-resistant illnesses. Closer to home, a recent report by the U.S. Department of Agriculture revealed that between 1982 and 2007, New Jersey lost a greater share of its agricultural land to development than any other state in America, putting further strain on a local industry already under pressure.
Proving that necessity is the mother of invention, however, a new crop of innovators is tackling these challenges head-on. Based on the benefits of “vertical farming” – a process by which crops are grown indoors in vertically stacked layers within highly controlled environments – New Jersey’s numerous vertical farms represent a bright spot on the Garden State’s agricultural horizon.
A Strategic Solution
“Vertical farms lead back to the need to build a world in which the current food system must support the needs of an expanded population with a rapidly dwindling set of resources,” said Irving Fain, founder, and CEO of Bowery Farming, a 5-year-old, Kearny-based indoor farming company that’s addressing the impending climate and food crisis by using the power of technology to grow fresh, high-quality produce closer to the point of consumption. With two commercial indoor farms located in Kearny and a third recently launched in the Baltimore/Washington, D.C. area, “Bowery’s model and proprietary technology, BoweryOS, enable the growth of high-quality crops year-round, regardless of whether or seasonality, using zero pesticides and over 95% less water,” Fain said.
“We’re re-appropriating industrial space to grow crops indoors at a rate that’s 100 times more productive per square foot of land than that of traditional agriculture,” noted Fain, who said that Bowery’s data-rich systems and ability to control the entire growing process enable it to trace every individual crop back to its original seed and deliver superior produce to restaurants and stores (including Whole Foods and Stop & Shop locations) within days of harvest.
Five miles away in Newark, AeroFarms converted a 75-year-old, 70,000-square-foot steel mill into the world’s largest indoor vertical farm in 2015 (soon to become the world’s second-largest when AeroFarms completes construction of its new 150,000-square-foot vertical farm in Danville, Va.). Growing a range of fruit, vegetables, and greens (under the “Dream Greens” label) without sun or soil in a fully controlled, indoor environment using a patented aeroponic growing system for faster harvest cycles, predictable results, superior food safety and less environmental impact, the company’s annual yields are reportedly 390-plus times higher per square foot than conventional farming. Harvesting up to two million pounds of highly nutritious, premium-quality produce per year, AeroFarms was recently named one of Time’s ‘Best Inventions of 2019.’
Farming 8,000 square feet of grow space within a historic greenhouse in Newark’s Branch Brook Park, Radicle Farm grows hydroponically using a nutrient film technique (NFT) and flooded tray system. Though not a vertical farm per se, “vertical growing makes sense within densely populated urban areas, and field farming and ground-level greenhouse growing will also continue to play a major role for quite some time,” said Radicle Farm Co-Founder Tony Gibbons.
Hackensack-based Greens Do Good is proving that vertical farms can not only be rooted in food delivery but in social responsibility as well. At the 3,600-square-foot facility, which opened in April 2019, all proceeds from the growth of its dozens of different microgreens, lettuce, and herbs – all grown without soil, pesticides or herbicides – go to REED Next, a nonprofit organization that provides continued education, life experience and work opportunities to adults with autism.
“We believe that growing healthy food with minimal impact to the environment is the future of farming, and Greens Do Good is transforming the way our local community sources healthy produce by providing the freshest ingredients in a sustainable and socially responsible way,” said Jennifer Faust, REED Foundation’s director of Communications. “In a state like New Jersey, where urban communities don’t have space, access or optimal year-round outdoor growing conditions to provide fresh produce, Greens Do Good is solving that problem by creating a sustainable social enterprise that not only helps individuals with autism but provides our community with produce that’s delivered hyper-locally on the same day it’s harvested, 365 days a year.” At its core, Faust said, “we’re a community partner providing sustainable produce to local businesses while supporting adults with autism, a greatly underserved population.”
With a similar desire to support its community, Bowery works closely with Table To Table, a food rescue program that delivers perishable food to organizations that serve the hungry in Bergen, Essex, Hudson and Passaic counties and also has developed lesson plans to aid local teachers and students in discussions about the modern agricultural landscape and its challenges.
Building A Better Future
Often located in urban settings in order to bring agriculture back to city centers, vertical farms incorporate the utmost in sustainable products and practices. At Bowery, for example, energy-efficient LED lighting mimics the spectrum of the sun for crops, while rooftop solar panels, a clean gas backup generator, and a battery energy storage system further reduce the company’s energy use and carbon emissions in New Jersey. “In addition, Bowery uses over 95% less water by recirculating it continuously and only replenishing the amount that’s used by the plants or lost during daily operations,” Fain said.
Part of a current network of 2,000 vertical farms in America within an industry that’s estimated to grow to over $3 billion by 2024, New Jersey’s vertical farms are proud of the contribution they’re making to meet the state’s food challenges while transforming agriculture around the world.
“Bowery was founded on the fundamental belief that technology applied at scale can solve difficult and important global problems, with agriculture sitting at the nexus of many of these issues, and our mission is to grow food for a better future,” said Fain, whose company was honored as one of Fast Company’s “2019 Most Innovative Companies in AI.” Based on its benefits and success, he said, “we see indoor farming becoming an even more meaningful and integral part of the farming and agriculture industries in the next 5 to 10 years and look forward to continuing to experience the positive impact of vertical farming on the environment.”
By Susan Bloom | For Jersey’s Best | April 21, 2020
How To Do Urban Vertical Farms Properly
Framlab, a creative agency, has proposed democratised vertical urban farming for lower socio-economic demographics in Brooklyn’s boroughs, entitled Glasir
11/02/2020
Sarah Buckley
Framlab, a creative agency, has proposed democratized vertical urban farming for lower socio-economic demographics in Brooklyn’s boroughs, entitled Glasir.
Glasir is a project that intends to intervene with the current agriculture and water concerns, with its equally concerning economic ramifications.
“The borough of Brooklyn has seen an explosive economic growth throughout the last decade,” says Framlab.
Between 2001 and 2015, there has been an improved job creation rate, but with its development, it has seen both positive changes and a high degree of social stratification, with a correspondingly high degree of nutritional inequality.
As Brooklyn is largely understood as a ‘foodie’s paradise’, it conversely also has a 20 percent food insecurity rate.
Glasir is supposed to be deployed initially in the borough’s poorest and least food secure areas – neighborhoods such as East New York, East Flatbush, Canarsie, and Flatlands.
“With studies proving a direct correlation between food insecurity and health risk, Glasir’s proposition to offer affordable, locally-grown produce has the potential to not only boost the nutritional profile of the residents’ diet, but also plant the seed for societal and economic betterment in these neighborhoods.”
“By combining the flexibility of modularity with the efficiency of aeroponic growth systems, the projects offer self-regulating, vertical farming structures that can provide neighborhoods with affordable, local produce year-round.”
The trees are characterized by a monopodial trunk with rhythmic growth, developing tiers of branches, following Rauh’s model.
Additionally, the style of growing plants aeroponically, as was experimented with by NASA, proves a comparable crop to yield as opposed to traditional, geoponic cultivation.
The exclusion of soil leaves very little room for unexpected variables and makes aeroponics a highly flexible growth system.
The system is centered around a subscription service model for the periodic distribution of crops to households, businesses, and schools.
The structure is further designed to be physically explored/played upon and invite its community to harvest fruits and vegetables.
It also utilizes drone technology to deliver the greens to and from its destination, and with minimized waste material and decreased cost, alongside stored harvested energy that can be used to charge electrical bikes, mobile devices, and integrated lighting, these structures will act as an ecological and technological hub, guilt-free.
The African Association For Vertical Farming Joins The EBAFOSA
Established in mid-2015 and endorsed at the highest continental environment policy forum – the African Ministerial Conference on the Environment (AMCEN), EBAFOSA focus is on climate proofing and maximising productivity of Africa’s agro-value chains
The African Association for Vertical Farming (AAVF) has announced that it is joining the Ecosystem Based Adaptation for Food Security Assembly (EBAFOSA).
To expand the beneficial impacts of vertical farming, going beyond on-farm production to also integrate value addition is paramount. This is necessitated by the need to eliminate rising postharvest losses (PHLs) and leverage the process to unlock multiple enterprise opportunities along entire value chains. It is for this reason, and the urgent need to maximise agro-productivity while taking care of the environment that AAVF has joined the EBAFOSA.
Facilitated by the UN Environment, EBAFOSA is a countries-driven inclusive policy and implementation action framework that convenes multiple actors – state and non-state, individual and institutional – to forge complementary and mutually beneficial partnerships that connect the dots towards scaling climate action. But doing so from an enterprise paradigm that ensures market longevity.
Established in mid-2015 and endorsed at the highest continental environment policy forum – the African Ministerial Conference on the Environment (AMCEN), EBAFOSA focus is on climate proofing and maximising productivity of Africa’s agro-value chains. The end being to convert inefficiencies along Africa’s agro-systems that cost over $48 billion each year, into food secure homes, income and enterprise opportunities and macroeconomic expansion. The core strategy applied is enterprise partnerships that decentralise appropriate clean energy – a climate solution - to power value addition of produce sourced from ecological production – a climate solution as well. This as the core, is combined with innovative financing, market incentives and policy feedback to catalyse growth of diverse enterprises with climate action co-benefits along entire value chains.
Youth being the majority in the continent and hence the most significant nonstate actor constituency are key in driving this “connecting the dots” approach. They are structurally guided and inspired to leverage their skills, ongoing work and existing enabling policies, and work collaboratively with their peers of complementary skilling towards undertaking climate action enterprises. Such voluntary mutual & complementary collaborations to drive climate enterprise actions are the EBAFOSA modus operandi called Innovative Volunteerism.
In all these, the EBAFOSA logic is that challenges for actors along Africa’s agro-value chains present opportunities for complementary actors with solutions having climate co-benefits. But that these two polar opposites need to be brought together. EBAFOSA provides the inclusive framework where these two polar opposites are brought together for collaborative solutions and unlocking enterprises.
To date, EBAFOSA innovative volunteerism actions are ongoing in over 40 counties across Africa.
AAVF looks forward to working with EBAFOSA and the mentioned stakeholders towards ensuring vertical farming catalyses growth of multiple climate action enterprises in areas of AAVF operations through innovative volunteerism.
Publication date: 8/8/2019
Coventry, UK: Vertical Farming Training Instructor Needed
Funding is now in place for the VF training academy in Coventry. UK and we are looking for a suitable person who can take on the role of trainer
Funding is now in place for the VF training academy in Coventry and we are looking for a suitable person who can take on the role of trainer.
The academy is aimed at teaching the multitude of engineering technologies as well as the plant aspects that are integrated to produce a holistic system design.
The curriculum includes the following:
*Project and risk management *Process engineering design *Environment control
*Material handling & robotics *Ergonomics
*Phenome systems and AI *Plant physiology
* AR & Intelligent Vision systems
*Light & Nutrient recipes. *Pest and disease management
*Water treatment and renewable energy usage
The course is in collaboration with the Assoc for Vertical Farming and we are currently in the process to be a Lantra service provider.
We are looking for a quick start in September and the location is in Coventry. Anyone interested please contact me.
They must be able to work in the UK and be a good english speaker.
hashtag#agtech hashtag#verticalfarming hashtag#avf hashtag#trainingInstructor hashtag#jobvacancy hashtag#agritech hashtag#futurefarming
Please Contact:
Peter Lane: pl@vertical-farming.net
Tower Farm Training Class: Limited Space Available
You will be walked through every aspect of what is required to successfully start any sized Tower Farm
September 19th and 20th 2019
Don't Miss This Opportunity To Have
Hands On Training Led By Industry Experts!
You will be walked through every aspect of what is required to successfully start any sized Tower Farm. From a rooftop farm, a green house, hoop house, or any unused indoor or outdoor space, we are committed to providing the resources and knowledge that help make starting a farm affordable and accessible. We will be joined by the Tower Farm manufactuers and leaders to share this incredible technology and the many ways to apply them in Urban and Commercial Farming.
Register Today
Get Your Tickets Today!
In this in-depth Vertical Tower Farm Training:
You will be guided through the seeding, transplanting, and harvesting process.
Introduction to what crops you can grow and an overview of how to create and plan your crop schedule.
You will be walked through a business plan template, as well as, receive a spreadsheet of all the consumables based on the size of your farm. When you leave this class, you will be clear on what it costs to run a farm the size you are planning.
You will learn marketing plans and strategies for your produce and urban farm business model to give you an edge and help you succeed.
You will be introduced to resources available to you like the Green Food Solutions Farm Amenities, Farm Service and onsite trainings at your farm, as well as cutting edge automation experts to set your farm apart in a competitive market.
You will be given the free planning, design and layout for your Tower Farm location. (Bring your square footage or square meters)
A catered networking breakfast and seasonal farm fresh lunch will be included both days
Meet other Tower Farmers running successful businesses
Mix, mingle and network each day at breakfast and lunch
Get expert advice about placing farms and gardens on rooftops
Sign Up Now
Biomimicry Helps Urban Farmers Scale Up
The Biomimicry Institute sat down virtually with Felipe Hernandez Villa-Roel, CEO and founder of Hexagro Urban Farming, to ask him about his experience as an entrepreneur and Biomimicry Launchpad participant
The Biomimicry Institute sat down virtually with Felipe Hernandez Villa-Roel, CEO and founder of Hexagro Urban Farming, to ask him about his experience as an entrepreneur and Biomimicry Launchpad participant.
What motivated you to start HEXAGRO?
Hexagro started as a bachelor’s thesis in Product Design when I started to analyze the problems that organic farmers in Costa Rica are facing in terms of productivity, sustainability, and health. These challenges are related to the high amounts of pesticides used by adjacent traditional farms, soil degradation, and climate change, so I began researching methods that didn’t use soil as a growing medium.
I analyzed the latest trends on soilless food production, starting from the indoor farming sector and through vertical farming, which proposes a more efficient way to grow food with less effort through new technologies like LED lighting and hydroponics in vertical configurations. I concluded that the main issue with these solutions was their scalability, since they followed a centralized model which is capital-intensive, requires infrastructure and expert personnel, and is difficult to set up and launch. The thesis made an analysis of nature’s strategies to reduce space while maximizing productivity with a modular structure that was then translated into the first version of Hexagro’s Living Farming Tree.
What was your experience in the Biomimicry Launchpad? What did you learn and how did you apply that to your business?
This project became a team and then a finalist in the Biomimicry Global Design Challenge, thanks to the inspiration taken from nature to develop the first product iteration. After that, we were invited to participate in the Launchpad program. From 2015-2016, we participated in many training sessions and had access to expert mentoring. This gave the team the tools to define a clear business model, which changed the approach of the first design iteration and led to a second design iteration that gave the basis for the current pre-industrial product. Today, the team continues to take inspiration from Nature’s Unifying Patterns to create solutions that follow the principles of biomimicry for every aspect, from product development to marketing and business development. Hexagro Urban Farming was incorporated as a for-benefit company in Milan, Italy, after the participation in the finals of the Launchpad in late 2016.
The Hexagro team
Tell us about your work to incorporate the Living Farming Tree in hotels and workplaces. What are you hoping to accomplish?
Our vision for Hexagro is a future in which anybody, anywhere, can access healthy food through urban farming. In order to get there, the team has determined a strategy to enter the market and launch its first product, the Living Farming Tree (LFT). Urbanization is booming, and at the same time we are spending around 90% of our time indoors where the conditions are not always meant for people’s well-being. This disconnection from nature within working spaces has direct consequences in employees’ health and psychology and can lead to lack of productivity and engagement, which could have direct consequences for companies. We are reconnecting employees to nature and their work through a “gamified” urban farming experience in which users follow the instructions from a digital interface to perform various maintenance tasks during the cultivation process, aiming to achieve a successful harvest of medicinal herbs for fresh infusions to improve well-being and productivity. Our LFT educates and increases the awareness of indoor farming technologies, while reducing the costs of office greenery maintenance. It engages people with their company and becomes a “gravitational center” for social gathering and relaxation.
The Living Farming Tree (LFT) utilizes a “gamification” strategy to engage employees in offices to become active participants in their own health.
What are the benefits to a modular, decentralized system?
Our team took inspiration from nature to create a system that could adapt to any space available and provide the maximum diversity with the lowest inventory. The Living Farming Tree has a standard configuration, but our plug-and-play components, along with our 3D-printed node and IoT automation systems, allow our system to adapt to any space available indoors (horizontally or vertically) to make it productive.
What is your ultimate hope for Hexagro?
We envision a new and regenerative food system based on the circular and sharing economy, helping people to grow plants and make a profit through a Smart Urban Farming Network. This nature-inspired model can increase accessibility to healthy food, decentralize indoor farming production, create new economic opportunities, and reconnect people to people through food.
For more information:
Biomimicry Institute
info@biomimicry.org
biomimicry.org
Publication date: 7/5/2019
Controlled Environmental Farming Inc - Provides True Urban Farming In Tucson, AZ
The facility of approximately 40,000 square feet will house a closed loop aquaponic method of production that uses patented technology to provide for vertical cultivation
07/07/19
Controlled Environmental Farming Inc (CEF) has released the initial Site Plan for an urban farm to be located inside the city limits of Tucson, AZ.
The proposed location, 4431 E 22nd Street, has received preliminary approval from the City of Tucson Planning Department. This location in the heart of Tucson will provide locally grown fruits, vegetables, herbs, shrimp and fish at an affordable price.
The facility of approximately 40,000 square feet will house a closed loop aquaponic method of production that uses patented technology to provide for vertical cultivation. This vertical integration allows CEF to reduce land and capital construction costs and provides operation cost reduction through production density. “Our philosophy is to make every cubic inch count in product production,” states Bruce Carman, Director of Technology / Owner of CEF.
CEF intends to use direct distribution to the consumer to ensure product quality, freshness and food safety.
The all-inclusive, highly efficient facility will provide cultivation, processing, packaging and distribution to all clientele which are modeled to be private individuals and restaurants. This model helps to keep consumer costs down.
According to a report released by the U.S. Department of Agriculture's Economic Research Service (ERS), for every consumer dollar spent on food, the farm-share average is approximately $0.15 cents meaning that $0.85 cents is spent toward distribution, marketing and retail of the product. “Our direct-to-consumer model, will allow CEF to maintain and control costs for our customers while also allowing us to provide the freshest quality produce. Consumers increasingly want to know where their food is coming from, how it’s being grown, and who their farmer is. Local urban farming responds to those questions,” said Kristen Osgood, CEF’s CEO.
The facility will provide direct sales through an on-line ordering system that can also arrange delivery if desired. Customers will be able to shop on site at the “Farm Market” or use the drive through to pick-up their orders, including complete meal-kits, salads, whole shrimp, fish and raw veggies.
In each area CEF locates, it intends to create local partnerships with other farmers and producers who share in the same food ethos as CEF. It is through these partnerships CEF hopes to integrate and promote local food economies. This will allow CEF customers to have the very best the local foodshed has to offer.
A Look At The History of Vertical Farming
Although vertical farms have only begun to appear on the agricultural scene in the last decade or so, the concept behind these innovative farming facilities is hardly new
Although vertical farms have only begun to appear on the agricultural scene in the last decade or so, the concept behind these innovative farming facilities is hardly new. Read on for a look at some of historical theories, discoveries, inventions, and prototypes that have led to the evolution of the modern vertical farm.
Pre-20th Century
600 BC — Perhaps the earliest example of a “vertical farm” is the legendary Hanging Gardens of Babylon, built by King Nebuchadnezzar II more than 2,500 years ago. According to some scholars, the gardens consisted of a series of vaulted terraces, stacked one on top of the other, and planted with many different types of trees and flowers. Reaching a height of 20 meters, the gardens were likely irrigated by an early engineering innovation known as a chain pump, which would have used a system of buckets and pulleys to bring water from the Euphrates River at the foot of the gardens to a pool at the top.
Hanging Gardens
1150 AD — Nearly a thousand years ago, Aztec people used a form of hydroponic farming known as “chinampas” to grow crops in marshy areas near lakes. Since the swampy soil in these areas was not suitable for agriculture, the Aztecs instead constructed rafts out of reeds, stalks, and roots; covered the rafts with mud and soil from the lake bottom; and then drifted them out into the lake. Due to the structural support provided by the rafts, crops could grow upwards while their roots grew downwards through the rafts and into the water. Often, many of these individual rafts were attached together to form expansive floating “fields.”
1627 — The first published theory of hydroponic gardening and farming methods appears in the book Sylva Sylvarum, by the English scientist and statesman Sir Francis Bacon. In this book, Bacon establishes and explores the possibility of growing terrestrial plants without soil.
1699 — English scientist John Woodward refines the idea of hydroponic gardening with a series of water culture experiments conducted with spearmint. Woodward finds that the plants grow better in water with impurities than they do in distilled water, leading him to conclude that the plants derive important nutrients from soil and other additives mixed into water solutions.
20th Century and Beyond
1909 — Life Magazine publishes the earliest drawing of a “modern” vertical farm. The sketch shows open-air layers of vertically stacked homes set in a farming landscape, all cultivating food for consumption.
1915 — The term “vertical farming” is coined by American geologist Gilbert Ellis Bailey in his book of the same name. Interestingly, Bailey focuses primarily on farming “down” rather than “up.” That is, he explores a type of underground farming in which farmers use explosives to be able to farm deeper, thus increasing their total available area and allowing for larger crops to be grown.
1929 — William F. Gericke, an agronomist at the University of California, Berkeley, is credited with developing modern hydroponics. In his article “Aquaculture: A means of Crop-production,” published in December 1929, Gericke outlines the process of growing plants in sand, gravel, or liquid, using added nutrients but no soil.
1937 — The term “hydroponics” is coined in an article published in Science magazine. Derived from the Greek words “hydro,” or water, and “ponos,” or labor, the term was suggested to Gericke as an alternative to “aquaculture” (which was already in use to describe fish-breeding techniques) by his University of California associate, botanist William Albert Setchell.
1940 — World War II sees hydroponic growing systems used on a large scale for the first time in modern history. More than 8,000 tons of fresh vegetables are produced hydroponically on South Pacific Islands to feed the Allied forces stationed there.
1964 — At the Vienna International Horticulture Exhibition, a vertical farm in the form of a tall glass tower is displayed.
1989 — Architect and ecologist Kenneth Yeang created a vision of mixed-use buildings that are seamlessly integrated with green spaces, allowing plant life to be cultivated in buildings in the open air. Yeang described this as “vegetated architecture.” Unlike many other approaches to vertical farming, this vision is based on personal and community use rather than large-scale production and distribution.
1999 — The concept of the modern vertical farm is developed in a class led by Columbia University environmental health sciences professor Dr. Dickson Despommier. In an effort to figure out an effective way to feed the population of New York using only urban rooftop agriculture, Despommier and his students developed the idea of a multi-story building in which layers of crops could be grown on each floor: in other words, a contemporary vertical farming tower. (Despommier has since gone on to become the world’s foremost expert on and proponent of vertical farms.)
2006 — The Japanese company Nuvege develops one of the essential ingredients for indoor vertical farms: a proprietary light network that balances light emissions in order to increase the return rate of vegetables.
2009 — The first modern vertical farm is built. Sky Green Farms’ Singapore facility consists of more than 100 towers, each of which is 9 meters tall, that grow green vegetables using sunlight and captured rainwater.
WRITTEN BY
Mark Crumpacker
Mark Crumpacker is a passionate marketing specialist with years of creative storytelling experience.
Want Chemical-Free Vegetables? Vertical Farming Might Be The Answer
These vertical farming towers developed by the Telangana State Centre of Excellence may be the answer to the increasing demand for chemical-free leafy green vegetables
JULY 01, 2019
The Telangana State Centre of Excellence (TSCoE) in Jeedimetla feels like an oasis, in contrast to the barren highway that leads to the area and the humble residential colony in its vicinity. The 10.35-acre facility managed by the department of horticulture is a hub of experiments for cultivation of vegetables and flowers.
In one of the poly houses covered by a UV-stabilising film, more than 800 PVC pipes have been converted into vertical farming towers. Each of these pipes have been filled with a mix of coco peat, red soil, neem cake, vermicompost and micronutrients that help plant growth. Each pipe has more than 20 slots from which small branch-like extensions emanate, it is in these that green leafy vegetables are grown.
The CoE designed and tested such prototypes in December 2018, approved by the department of horticulture authorities and a technical committee of agriculture experts; it has so far grown coriander, amaranthus, bacchali (Malabar spinach) and palak (spinach). At the moment, the 800-plus towers grow spinach, some of them ready to harvest.
A retail counter near the entrance of the premises sells fresh greens and vegetables grown at the centre and it’s a big hit with the neighbourhood. Palak is sold at ₹40 per kg, double the price of wholesale market, but there are many takers since these greens are free of chemical pesticides. There have been days when the centre sold 400 to 600 bunches of leafy greens.
Around the world
Singapore: The vertical urban farm called Sky Greens, located in Lim Chu Kang, harvests 500kg of green leafy produce every day. According to a Straits Times report, the yield in this farm is 10 times that of traditional farms, as it uses tiered metal towers up to nine metres tall. The rotation of these towers in glass buildings allows all the plants to get uniform sunlight.
San Francisco: Tigris, a hydroponic vertical farm in San Francisco, is a futuristic project focusing on growing leafy greens. The new farm reportedly can grow one million plants at a given time.
While vertical ornamental gardens add aesthetics to premises, vertical farming is more utilitarian. CoE intends to encourage residential colonies in urban areas and farmers at the district and zilla parishad levels to grow more greens using vertical farming.
The CoE feels that having several small crop colonies in urban pockets and rural areas might help meet some of the growing demand for vegetables in the state. Leafy greens, tomatoes, brinjals, chillies and okra, for instance, can be cultivated in balconies and terrace gardens to meet individual home needs.
In addition, enterprising farmers in both urban and rural areas can do vertical farming to grow greens that meet the needs of their neighbourhoods, believes the CoE. “Green vegetables are the need of the hour. They perish easily and don’t withstand long-distance transport. A lot of greens available in the market are also laced with chemical pesticides. There’s an increasing awareness today about safe food. Growing your own greens will ensure safe food and reduce food miles,” says K Latha, assistant director of horticulture, CoE.
Traditional farmers can use vertical farming towers to step up the yield. “In flat-surface farms, it’s tough to harvest green leaves during monsoon. Leafy vegetables can be harvested every 25 to 30 days, so ideally you can aim for 12 harvests a year. In flat cultivation farmers only manage eight or nine harvests. Using these towers and a poly film roof, greens can be grown all round the year,” she says.
K Latha, additional director of horticulture, COE, with agriculture engineering students at the vertical farming polyhouse | Photo Credit: K V S Giri
The coco peat and nutrient mixture in these towers can be replenished after three or four harvests to get quality produce. To counter weeding, the CoE uses a weeding mat on the ground. Small outflow pipes from each of the towers drain excess water.
To make vertical farming economical, the CoE uses non-ISI mark PVC pipes that cost ₹400 to 500 each, as opposed to ISI-certified ones that cost around ₹5000. However, the non-ISI pipes stand the risk of damage when exposed to prolonged heat. The UV-stabilising poly film roof counters this problem.
Latha points out that there are several smart vertical farming methods worldwide, including those that use hydroponics and aeroponics. “There are various designs of vertical farming towers too, across the world. The indigenous technology we developed is one of the methods,” she says, signing off.
Planet Healers celebrates eco-conscious initiatives. If you know an eco warrrior, write in to hydmetroplus@thehindu.co.in
Vertical Farming ‘Not Feasible’ In Soft Fruit
BY FRED SEA
April 4, 2019
James Hutton Institute dissuades berry producers from growing vertically but says certain technologies can be beneficial in conventional systems
Rob Hancock spoke at the Global Berry Congress 2019
Vertical farming in soft fruit is a sure-fire way to lose money, one of the UK’s foremost fresh produce research organisations has warned.
Delivering a presentation at the Global Berry Congress in Rotterdam last week, Rob Hancock of the James Hutton institute told delegates emphatically that berry production is not feasible in a vertical farm.
“If you want to lose money, start growing your fruit in an indoor farm,” he said.
Following vertical farming trials by the institute, Hancock said that, crucially, growing soft fruit hydroponically using LEDs does not provide enough light intensity, with a negative impact on yields, quality and sugars in the fruit.
Furthermore, the architecture of soft fruit plants is unsuited to vertical growing, and crucially the high cost of installing and running a vertical farm makes it extremely difficult to generate a profit.
“Vertical farming is becoming more commonplace – particularly these indoor vertical farms,” he said. “The number of new openings has increased in recent years, however if you look at whether these guys are making profit, many of them are not.
“The advantages [of vertical production] are optimising nutrition, temperature, humidity, CO2. But you’ll also get many of these benefits in conventional protected cropping.
“The one thing you can control in an indoor farm that you absolutely cannot in an external farm is the light. By messing around with the light spectrum, you can have impacts on the colour and quality of the strawberry. By manipulating the light spectrum, you can massively enhance the concentration of anthocyanins present in the crop.
“The disadvantage is the light intensity. In an indoor farm you’re lucky if you’re getting 200 micromoles of light, so with a product like strawberries or raspberries you’re operating at nowhere near maximal photosynthetic rate – that’s going to impact yields, quality and sugars.
“Another disadvantage is clearly that the architecture of something like a blueberry or raspberry cane is not very well suited to vertical growing.”
Despite these important limiting factors, Hancock stressed that a lot of the individual technologies associated with vertical farming can be “really useful” for advancing berry production using conventional systems.
As such, the James Hutton Institute is trialling some of these technologies at its Advanced Plant Growth Centre in Invergowrie near Dundee – a £27 million project funded by the Scottish and UK governments to enable research, development and innovation in crops grown under cover.
He said vertical production can be “very useful” to propagate soft fruit plants before then planting them in conventional tunnels, and that a lot of the technologies associated with vertical farming can be used to accelerate breeding.
“I think it’s also very important, if vertical farming and berry production are ever going to come to together, that we start thinking about breeding varieties for indoor farms,” he added.
“Crop monitoring and quality are other things that can be impacted using some of these technologies in conventional farming systems.”
[Going Green 1] Introducing Healthy Vertical Farming
April 23, 2019
Agricultural innovations are essential for feeding our ever-growing global population. Especially these days, as industrialization and global warming continue to negatively affect soil fertility and reduce the amount of arable land.
According to the United Nations, the world’s population is set to reach 9.8 billion by 2050. Such a large population would require approximately 1.7 times more food than is available now.
One potential solution for addressing the world’s need for more healthy and abundant food production is vertical farming – a process that’s growing increasingly popular in places like Europe, the U.S. and Japan, and involves food being grown indoors in vertically stacked layers.
Stable Food Production
What makes vertical farming such an efficient and viable means to produce food are the facts that it (1) saves space, and (2) allows farmers to grow crops all year round, regardless of climate or season.
Interest in vertical farming has been rapidly growing in recent years. Market research firm MarketsandMarkets predicts that the global market for vertical farming will be worth $18.4 billion by 2022, which is twice as much as the market was valued in 2016 ($9 billion).
Innovating for a Greener Future
The movement for healthy, sustainable food production is spreading across the world, and Samsung is committed to driving innovation in this area.
Last spring, Samsung announced the launch of a wide range of horticulture LED offerings that produce a broad spectrum of light to support healthy plant growth. On April 23, Samsung introduced an update to the LM301H, which features the highest photon efficacy among today’s mid-power white LED packages. The company has also revealed a number of exciting innovations designed to make it easy for consumers to grow and enjoy fresh, healthy vegetables from the comfort of their home.
Samsung also made waves at this year’s Kitchen & Bath Industry Show in Las Vegas with its all-new Chef Garden technology, which offers a simple, environmentally friendly way to grow food at home. Chef Garden integrates seamlessly with Samsung’s next-generation Family Hub refrigerator, and automatically regulates light wavelengths to enable users to grow and enjoy fresh, pesticide-free fruit and vegetables all year round.
“There is a growing interest in healthy food,” said Chohui Kim of Samsung Electronics’ LED Technology Center. “Horticulture LED is playing a key role in vertical farming and indoor crop cultivation, and we are looking to expand its applications in various fields.”
The second part of Samsung Electronics’ “Going Green” series will highlight technology trends and the company’s efforts regarding eco-friendly crop cultivation in detail.
Chef Garden Going Green horticulture LEDLM301H PLANTBOX vertical farming
Products > Home Appliances
Products > Semiconductors
RELATED ARTICLES
Urban Leaf x Farm.One
Urban Leaf is excited to announce our new collaboration with Farm.One, a vertical farming company that grows hundreds of specialty crops right here in New York City. Using hydroponics and LED lighting, Farm.One grows hard-to-find produce such as purple basil and marigold flowers for top end chefs around the city.
Like us, Farm.One believes in the importance of fresh and local food, using innovative techniques to grow food indoors in urban settings, and using practices that benefit the health of the planet.
We’re thrilled to share that starting this month, we will be working with Farm.One to provide a gift to everyone who visits the Farm.One site in TriBeCa. Through this collaboration, we hope to help more people discover the magic and ease of urban farming by giving them a chance to experience it at home.
Of course, you don’t have to wait to visit Farm.One to try some of the exotic flavors that top chefs use in their own dishes. You can grow some of these rare plants in your own indoor garden today. All you need is one of our kits, a dark glass bottle, and a sunny windowsill to get started. Or alternatively if you’re in New York save 10% on any Farm.One tour with code ‘URBANLEAF’.
Simple Secrets To Start A Vertical Farm
Talking to people just like you, it’s clear that the first step is always the hardest on the road to building a vertical farm. The plunge into the unknown where your own time, capital, and dreams are at risk stops a lot of entrepreneurs from fulfilling their ambition. Fortunately, Matt Farrell took that step for you and tells all in this exclusive interview on the Urban Vertical Project. Keep reading because Matt talks about:
Location, location, location (where to put your vertical farm)
The honest truth about Zip Grow Towers
How much money can you actually make when you start a vertical farm (what restaurants will pay you)
The simple secret of getting customers who pay
I know why taking that first step to start your farm is scary; it means taking a big chance with your time and money to do something that doesn’t really have a standard set of procedures.
I am right there with you. Chances are, if you’ve found this article, you’ve thought about what it takes to make one of these bad boys a reality. Maybe you’ve done some daydreaming or vision boarding, or maybe you’ve even built a small system. In the end, we’ve all probably come across or conjured within our own imaginations an idea for a vertical farm that works, but that’s a far cry from actually making it a reality.
How do you go about doing that? For me, I’m going to follow the process for starting a vertical farm I modeled off another entrepreneur in an earlier article:
Set up a proof of concept
Secure a buyer
Execute
Even knowing a structure like that one exists, transforming that to reality is a different story. But, as my favorite (and legendary, if you can believe such a thing) street performer says “It’s better to go out and do something than to stay home and plan something.”
So, I went out and did something. I helped my father buy a bunch of IKEA products and convert them into a hydroponic system for less than $100. It was a start.
Now I’m working on another prototype, and I hope to actually maintain this one. My goal with this next system is to collect and analyze a bunch of data to project future results like yields, energy costs, and calories/square foot. Maybe that will turn into an open source project that people can turn to for up-to-date information, or perhaps it will evolve into a farm in its own right. In addition to that prototype, I’ve been doing tons of research for different people that’s helped them to think about their own, personal businesses and projects.
Even so, if all of my work turns out perfectly, it still exists in a vacuum. Simply put, there isn’t enough information out there to for people to make realistic comparisons or projections for their own farm. Other websites and news articles have featured fantastic farms, ideas, and projects, but there aren’t a lot of actionable numbers. That partly comes from being in an industry that’s too scared to share (something we’ve mentioned before and that projects like MIT CityFarm is working to overcome). That’s why we work so hard to bring you these exclusive interviews and why we get down and geeky – getting the nitty gritty numbers. I want you to have a successful urban vertical farm.
All of that is to say, I’m working on my first step and outlining that process for you. But this article isn’t about just the first step; it’s about revealing the simple truths real farmers know that can help you think more realistically abut your project.
And that’s where Matt Farrell comes in. Matt has been into hydroponics for awhile, but he doesn’t come from any sort of traditionally agricultural background.
He was studying in the School of International Service at American University where he got hit with the idea to help the school build a small hydroponic system. Though the school has taken it down since, his dedication to the idea of local, high efficiency farming has persevered. Now, he’s out on his own running Stag’s Leap Produce. Their tagline:
“Always Fresh. Never From A Shelf.”
The site goes on to explain their goals a bit more: “We want to connect the community to a local source of fresh, organic produce at an affordable price. Come try the freshest, healthiest produce around.”
I’ve known Matt personally for awhile now and he was generous enough to take time out of his busiest growing season to give me some exceptionally candid answers about his experience getting his farm up and running.
Location
In this section, we’re going to take a quick look at why the location of Matt’s farm is so important and why it means you might have more flexibility than you thought in where to put your vertical farm.
Matt is the owner operator of Stag’s Leap Produce in Mullica Hill, New Jersey. Another New Jersey Farm, huh? Just like Freshwater Greens (from an earlier interview), Stag’s Leap produce illustrates a perfect lesson for aspiring vertical farmers to internalize; take advantage of local market access. In addition to supplying local restaurants and businesses (see below for a list Matt shouts out in addition to a local farmers market and customers that come to him directly), being in New Jersey means they potentially have access to the much denser populations in New York and the surrounding cities.
I talk a little bit more about the importance of these population centers combined with available space in the Rust Belt Hypothesis (you guys remember that, right? Probably not, I wouldn’t either, so here’s a link), but Stag’s Leap might demonstrate an alternative, or even start to unravel that hypothesis. Remember, the Rust Belt Hypothesis is the idea is that declining industrial cities are perfect environments for vertical farms because of the inherent socioeconomic conditions there. Those conditions include: population density, existing infrastructure (usually in the form of abandoned warehouses from the manufacturing golden age), cheap energy, local community support (jobs!), and legislative support to revitalize a struggling economy.
But check this out!
Mullica Hills New Jersey is definitely not a Rust Belt City. So, if Stag’s Leap demonstrates that a vertical farm can work in less dense populations like there, that means the demand for these products (fresh, local vegetables available year round) and the expertise required to produce them is even higher than we expected. It means that if farms like Stag’s Leap become the norm, or even just more common, vertical farms will have demonstrated that they can fill needs beyond urban centers. That opens up huge swaths of the country that would otherwise wouldn’t have been considered; well beyond what’s normally considered the Rust Belt as seen below.
And according to Matt, that fits in perfectly with their mission: “We believe you should have the ability to purchase fresh, healthy, produce straight from its source. Without harmful chemicals or pesticides, at an affordable price.”
How is Matt growing food?
But how exactly is Matt meeting this demand? “I grow lettuce, basil, kale and arugula. I have two types of growing systems, Bright Agrotech’s Zip Grow Towers and custom made shallow water floating rafts.”
Image from Bright Agrotech
Essentially, he is using two types of growing systems inside of one 3000 sq ft greenhouse. Zip Grow towers utilize a wicking medium to deliver water and nutrients to plants.
Here’s a video directly from Bright Agrotech that explains in more detail how the Zip Grows work.
The floating rafts Matt describes to me seem like a conventional deep water culture (DWC) setup, though he’s modified this idea a bit by making the reservoirs shallower. I’ll let the folks at Boswyck Farms in New York City describe what that is as they have one of the few hydroponic certifications around and are really knowledgeable growers in general.
[DEEP] WATER CULTURE
Water culture systems are the simplest form of active hydroponics. Plant roots grow directly in the water reservoir and are supplied oxygen with an air pump. Water culture systems can be built from repurposed glass mason jars, plastic buckets, or tubs as the reservoir container, with the plant suspended from the lid in a net pot, letting the roots grow through the holes into the water below.
In larger, commercial scale designs, several plants are placed in a sheet of buoyant material that floats on nutrient solution like a raft. Water is generally held in a separate, larger reservoir and pumped up to the floating grow bed and then drained back down to the reservoir in a constant cycle.
Deep Water Culture Example From Epic Gardening
The combination of the Zip Grow towers and his tables allows Matt to maximize the efficiency of all the space in his 3000 sq ft greenhouse. That efficiency comes from incorporating the principles of vertical farming we talk about in this blog.
Remember, the definition of vertical farming is growing on multiple levels. The Zip Grows achieve this by having multiple plant sites on a vertical access hanging down from supports running above the ground. Additionally, Matt stacks his DWC beds to double his production/sq ft when compared to a set up like the one in the photo above. Below is a photo of Matt’s stacked system, which, even in its simple form, doubles his production/sq foot! That’s the power of vertical farming!
I was immediately intrigued about Matt using Zip Grow Towers. Bright Agrotech seems like a great company, but I’d struggled to find an account of using their product that wasn’t tied to their marketing material. I didn’t, and don’t, have any suspicions, but I just wanted to check things out. I’d even flirted with buying a few towers myself to test them out, but Matt’s review of the Zip Grow Towers based off his experience running a real business is even more helpful.
“In the zip grow towers I can plant 6-7 heads of lettuce. But lettuce heads grow much better in raft systems than NTF systems, so we grow our heads in our raft beds now. Each bed is around 4’ by 8’ and we grow 50 lettuce heads in each bed, we also stack our beds twice.“ But, as you can see in the video below (no making fun of the flipped video), those Zip Grows are not wasted.
“Basil, kale and arugula grow well in our Zip Grow towers. We plant 7-8 basil and arugula per tower and 6 kale. In a 10′ by 10′ space we can house about 30 towers. We get around half pound of basil and arugula per tower and we count kale by the leaves so we get around 12 or more mature leaves per tower. We pick our towers continuously so that we are always harvesting from our plants and doing little replanting. With Zip Grow towers the majority of the work is in planting and hanging the towers.“
That breaks down along these lines:
Harvest/Tower (Lettuce)Harvest/Tower (Basil)Harvest/Tower (Kale)7 plants½ pound12 leaves
So Matt is growing through a combination of Zip Grow towers and vertically stacked deep water cultures. We’ve looked at a few different ways to grow produce on this site, but what it really comes down to is how much money you can make off of what you grow. Remember, the incentive to go vertical is to produce more calories/square foot at a lower cost. To quote from our introduction to LEDs:
“In vertical farming, it comes down to producing calories people want to buy (assuming your product is food of course). To make money, you need to produce those calories efficiently.”
How much money can you actually make when you start a vertical farm?
Let’s assume you are producing those calories efficiently.
I asked Matt how he set his price points for the different restaurants he sold to. “So originally we followed bright agro’s models for crop pricing. They host a number of blogs and videos talking about how to price your basil and how to sell you produce and offer very large price points for their crops.” Off the top of his head, he cites “$2.00 an oz for their herbs and I think $3/pound for vegetables.”
Bright Agrotech Farm Wall (more info here)
If you remember when I talked about actual restaurant pricing here, you’d understand that I had some doubts that these price points were attainable. Matt agreed. “They like to highlight how restaurants will be happy to pay that price in the winter but all of the restaurants I went to were really turned off by these type of high prices.”
This is the main problem I have with purchasing ready-made systems from companies like Bright Agrotech or Freight Farms. This is not to disparage the actual products; not only have I never grown with them commercially myself, all testimony and evidence points to the fact that they work as intended and are examples of superior craftsmanship. However, it is completely fair to challenge the financial information they provide. They are incentivized by increasing sales of their product to use higher-than-realistic prices when they provide which gives the impression that you can pay off the initial investment in their product faster than is actually possible.
Here’s the table from above with Matt’s harvest per tower again.
Harvest/Tower (Lettuce)Harvest/Tower (Basil)Harvest/Tower (Kale)7 plants½ pound12 leaves
Let’s compare those numbers with those that Freight Farms shares. Real quickly, Freight Farms is a buy and farm as-is shipping container modification that also uses Zip Grows. I will note that I reached out to Freight Farms some time ago when I was originally considering investing in one of these and not for the purposes of an article. They were extremely helpful, but I ultimately decided the product was not for me at a $75,000 price point.
Image from Freight Farms
Here is the nice spreadsheet that they initially sent along for help with financial and crop planning. For full sized lettuce, they are saying that you can fit slightly more than what Matt was able to fit into one tower, but that may just be attributable to variety. They are also saying you can get 35 lbs/week of basil from a single tower. That doesn’t quite seem to stack up, though it could be the difference between a continual harvest like Matt uses, and harvesting a whole tower at once.
Anyways, as I said before, the company is super helpful and if you have any concerns, I’m sure they would be happy to address them. We’re going to look a little more at their financial models in a second too, so stick around.
I’m sure that there are examples of farmers getting the price that they advertise or even higher. However, in the interest of giving you an appraisal of the actual options out there for starting your farm, it’s fair to point out that it might always be the case. I definitely do not intend to disparage these companies or their products, and I’m happy to open up a space for them to respond to anything I’ve written.
As my research shows and Matt confirms “At these prices you’re [or a restaurant is] paying $30 a pound for herbs and twice or three times the industry standard for vegetables. Most restaurants simply can’t do those kinds of numbers. For example, most restaurants will pay around $8-12 dollars a pound for basil that they get from Cisco or other big food providers and while their willing to pay a small mark up for basil, the highest I got was $20, it is hard to get business owners to dish out to much money on basil and lettuce if it is breaking the bank.“
Based on that information, you’d be able to pay of the $75,000 investment in a Freight farm in just 2 years. Not only does that seem a little too good to be true, but if we plug in Matt’s numbers, we get a very different picture. Here are the price points Matt actually advertises when he sells direct to consumers:
Of course, neither Freight Farms nor any other supplier can be expected to anticipate market variance for the entire country. However, I want this information to be out there so you can more accurately make the decision on whether or not these products are right for you to start your business with.
Getting Customers Who Pay
Remember, the three steps to starting your vertical farm are
Proof of concept
2. Secure a buyer
3. Execute
I outline them in more detail here, but I wanted to include them here again to point out getting people who will pay you happens before most of the physical farming at a commercial level begins. Matt didn’t blink when I asked him how he did that and his unflinching attitude is probably one of the reasons Stag’s Leap is still chugging along.
He kept his answer short, too. “I literally just went around to everywhere I could find with a business card and told them I was doing locally grown high value crops. Some people didn’t call me back and others did.“ I can shorten it even more. How do you get people to pay? “Elbow grease.”
Original Photo of Mirai in Japan
A google search is going to blast your screen with thousands of marketing books, articles, blog posts, and everything else that’s going to tell you about building a brand, marketing, and sales tactics. Trust me, I’ve read most of them. But what they all really boil down to is just putting in the work, it’s as simple as that.
Hydroponics versus Soil-based Produce
That work is made a lot easier when you have a quality product to back it up. I still can’t believe how closed minded people still are to hydroponic products. They insist that the best produce comes from soil because it’s natural. Honestly, I just think they have a preconceived picturesque notion of farming in their mind that they are too stubborn to get rid of.
Look, my uncles have owned a restaurant my whole life, and that’s impressive considering most restaurants close within 90% of restaurants close in their first 12 months of opening. I started working there when I was 6 years old and didn’t stop until I went to college. I’ve been cooking my own meals since then (shoutouts to the ginger scallion sauce in the Momofuku cookbook) and gardening for almost that long too. I know what good produce tastes like. I know that it even smells and feels different. And I know that you can get good produce with hydroponic crops because I eat them all the time.
Yet…just try and bring up the idea of vertical hydroponic farming with an organic or permaculture extremist. Even though the ideas are super compatible, it’s still awful.
Click for the article
And frankly, people don’t agree with them. As Matt says “I haven’t come across anyone that has said we can’t grow superior produce with hydroponics, and if I were, I would probably refer them to a number of studies that suggest hydroponics can grow healthier, more flavor produce. [I’d] also give them some of our lettuce to try.”
That’s not just regular Joe-schmoes vouching for Matt’s product either. “The chefs that we work with really like our produce and would probably pay a lot more for our produce if they ran their restaurants. We constantly get great remarks about the lettuce we produce and the quality and flavor of our basil. We have a number of repeat customers that come for our salads and lettuce heads that say we have the freshest and best tasting lettuce around. And that definitely has to do with the fact that we are growing inside and with hydroponics. It really makes the whole production a lot easier and since we are selling locally this allows us to grow lettuce for flavor instead of shipping and shelf life.”
Since Matt is focusing on local food, his produce is so much fresher than anything consumers would be able to buy in a grocery store.
Obviously I’m a fan of holistic farming and permaculture techniques. I’m also a general fan of the USDA Organic Label, even if I think it could be improved. I just think that people need to really think about the type of farming Matt is doing beyond writing him off for trying something new, even if he’s using a manufactured product or, “heaven forbid;” PLASTIC. Especially in comparison to USDA Organic, something as simple as plastic doesn’t have as bad of an environmental impact as the pesticides already in use– natural or not.
Matt and I talked about this as well: “So I think its interesting when people like to contrast holistic farming with vertical farming, or holistic farming with hydroponic farming. When I think about what does holistic mean, I think about what is healthy for the consumer and what is healthy or sustainable for the planet. I think that vertical and hydroponic farming are great in both of those ways. Vertical farming really saves on land, which, as we are having a serious land crisis in terms of farming and are losing a lot of farm land to urban sprawl, is a really sustainable and positive for the future of farming. Hydroponics also allows us to recycle about 70-80 percent of the water we use, reduce the fertilizer we use, and eliminate any runoff from fertilizer. We can also do a lot of traditional holistic methods like companion planting and natural pest control using beneficial insects.”
Those are just a few of the ways to merge ideas that both philosophies espouse.
Conclusion
We wandered through a few different areas in this post. We touched on why vertical farms, if Matt’s is any example, might not be so limited in location than I was writing earlier. We also looked at how Matt is growing his food. He is using a combination of Zip Grow Towers and a custom built, stacked water culture system that allows him to maximize his production in the space.
Then, and perhaps a little controversially, we looked at pricing produce. While Matt is able to get a premium for his product’s freshness and sustainability, he still has the feeling that he’s not hitting the marks companies set for their pre-fabricated products. Not all of the numbers we included were exactly comparable, but they still make the point that you need to do your own market research before basing any business plan on those figures.
Next, we looked briefly into how Matt got customers for his produce before wrapping up by focusing on one of my pet-peeves; the rejection of hydroponic growing techniques by soil fanatics. I think this, along with location planning, is a significant challenge to the adoption of vertical farming technology. Though by no means the most important, it would be great to start doing taste studies along those lines.
This post was jam packed, and I hope you enjoyed it. Besides the great discussion about some of the challenges in vertical farming, I think the biggest take away is the detailed look at potential pricing. “Trust, but verify” as the saying goes.
Edeka and Metro are Joining the Growers
In the farm, seedlings of various plants are being used. They are not growing in soil, but have been dipped in a thin layer of liquid that provides the necessary nutrients.
Vertical farming is a way to put an end to the climate-compromising import of vegetables from all parts of the world. Fruits and vegetables can also be grown in the supermarket, some manufacturers promise. But we are not there yet.
There is a large black box with Plexiglas windows, standing in the middle of the vegetable department of the Edeka market in Oberhausen. This is the "greenhouse of the future," explains Pascal Gerdes. In fact, it is a digitally networked herbal farm in which plants are to grow under optimal conditions.
After a critical appraisal of the plants and a smell test, a customer decides to buy some of the coriander, which she places in her almost empty shopping basket. Price: 1,29 Euro. The Gerdes family is not pleased with the customer's choice. This lady is the first buyer of the plants that are grown in the supermarket.
Only a few weeks ago, the futuristic-looking farm was set up in the store of the Gerdes family. It came from Berlin start-up Infarm, which is one of the major suppliers in the field of vertical farming. Infarm also cooperates with other retailers. The 'farm' is to be tested in the Edeka market for a whole year. If the mint, Greek basil, mountain coriander and the like prove to be worthwhile, the farm may remain there. It is, however, still too early to do away with the entire vegetable counter - that would be relying too much on this nascent technology.
Digital farms in Oberhausen, London and Paris
In the farm, seedlings of various plants are being used. They are not growing in soil, but have been dipped in a thin layer of liquid that provides the necessary nutrients. From above, LED lamps provide continuous lighting. Everything can be individually adjusted so that the optimal climate conditions can be created for every plant. Vertical farming promises efficient and, above all, rapid growth.
"Temperature and light intensity are adjusted completely autonomously," explains Martin Weber from Infarm. "We control the state and the growth of the plants via infrared cameras." An employee from Infarm will go to the Edeka stores to harvest. He or she will set the plants that are ready for sale apart, immediately inserting new ones in their place. Supermarket operators like the Gerdes family do not have to worry about anything. But that should change over time. With more experience, sowing and harvesting can be taken over by the supermarket operators.
Until now, Vertical Farming is limited to herbs, as in the Edeka store in Oberhausen. But one can grow any kind of fruit and vegetables, promises Infarms CFO Weber: "We would like to offer everything, without exception."
This optimism has apparently convinced some retailers: The incubators of Infarm are there at numerous German Edeka markets, including stores in the Swiss supermarket chain Migros and in metro markets - including a metro market in the suburb of Nanterre, Paris. And the internationalization is to go on: "In Paris and Zurich, we have already inaugurated the first farms outside Germany. And in early 2019, London will follow," said Weber. In the USA there is potential for the Berlin start-up as well.
Source: Wiwo.de
Publication date : 1/4/2019
Vertical Farming Conference Takes Place on June 26, 2019 in Venlo, The Netherlands.
Vertical Farming Conference
Focus topics:
Available technologies
LED lighting, sensors ,AI - Plant condition issues like:
CO2, Nutrients, Irrigation, Climate, Lighting | Food safety / HACCP | Robotics | Improved resource-use efficiency | Sustainable Buildings (design, green roof, energy) | Smart Cities / Architecture / Urban Design | From traditional farmer to vertical farmer
The conference is part of the two-day global Agri Food Innovation Event that includes a two-day expo, four conferences - 3D Food Printing Conference, Healthy Nutrition Conference, Vertical Farming Conference and Smart Farming Conference and more activities such as lab tours, demo corners.