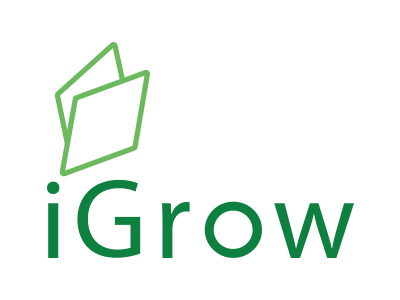
Welcome to iGrow News, Your Source for the World of Indoor Vertical Farming
‘AI Must Outperform Growers’ Green Fingers’
5 October 2018
Top executive David Wallerstein from the Chinese technology company, Tencent, has recently discovered horticulture. He believes combining Artificial Intelligence (AI) and food production will make it possible to unlock enormous potential.
The CEO of Tencent is Ma Huateng, better known as Pony Ma. But David Wallerstein, an American, is also a kind of CEO at the tech giant – Chief Exploration Officer. Officially, he is Senior Executive Vice President of the Chinese company.
With a stock exchange value of $ 523 billion (€ 429 billion), Tencent became one of the top 5 largest tech companies in the world in autumn last year, behind Apple, Google, Microsoft and Amazon, but just ahead of Facebook. Recently, Mr Wallerstein’s thirst for exploration has lighted upon agriculture and horticulture and in particular on the Autonomous Greenhouse.
Using AI to run a greenhouse autonomously
Mr Wallerstein believes that combining AI with a food production system that is as efficient as possible is “a moral imperative and simply good business”. “What we want for humanity is as many solutions as possible for the issue of food security. Our only option is to commit our brightest talents to creating a food production system that requires decreasing levels of input to achieve an ever-increasing output.”
Will Dutch growers become redundant if the Autonomous Greenhouse challenge is a success?
“Absolutely not. This competition to find the best autonomous cultivation system is intended as a learning opportunity for everyone who participates. Learning how the latest computer technology and AI technology can benefit horticulture and — in practical terms — the entire world population. Complementing the cultivation techniques that we already have. The only people who need to worry are the ones who want to keep using a particular method simply because they have always done it that way.”
‘The complexity of decision making in modern horticulture is growing with the amount of data that is becoming available to growers’
At what stage will this project be deemed a success?
“The winning team will have to overcome two hurdles: it must outperform the other teams with a higher production when compared to the input, and – ideally – it must also defeat traditional cultivation methods. Only then will this definitely be the most convincing business model. And why not?”
“The complexity of decision making in modern horticulture is growing with the amount of data that is becoming available to growers. What I’m hoping the outcome of this project will be is that the competing teams will find new types of patterns and ways of introducing variables to each other.”
Hacking the environment around the plant
According to Mr Wallerstein, what the teams who are looking for a self-governing and self-learning cultivation system are actually going to be doing is “hacking the environment around the plant.” Well-programmed computers may well be able to analyse and control the bigger picture of which raw materials and resources are required, and what conditions have to be influenced and how, to achieve the best possible cultivation results in a different and more effective way than growers are able to do using their green fingers and intuition.
David Wallerstein, American, is a kind of CEO – Chief Exploration Officer – at Tencent, a Chinese tech giant. Officially, he is Senior Executive Vice President. Recently, Wallerstein’s thirst for exploration has lighted upon agriculture and horticulture and in particular on the Autonomous Greenhouse. - Photo: Koen Verheijden
Droughts and soil erosion
“I foresee a big future for distributed agriculture; in other words, no more increasingly large companies that use a few central locations to produce the food for an entire country or continent. That is still how they do things in the US. Three-quarters or more of the fruit and vegetables eaten by Americans are grown in the Central Valley in California. But growers there are facing worsening droughts and soil erosion, and extreme weather caused by climate change is making this kind of cultivation more and more risky.”
So, each town would have its own autonomous greenhouse?
“Exactly. Food produced closer to consumers. Maybe even an autonomous greenhouse for each household. Just like the decentralised generation of energy from the sun with solar panels on residents’ roofs.”
‘Plenty of companies in Silicon Valley are involved in applying AI to marketing and advertising, but I couldn’t find any looking at AI in food production’
What role can Tencent play in developing this kind of new approach to cultivating vegetables?
“We aren’t planning to move everything to China. We are new in Europe, but we really want to come and do business here. So that even more companies want to work in our cloud and use our payment systems. We are looking forward to partnering in projects that help the world to move forwards, such as discovering more effective pharmaceutical products or better materials, or ways in which the cloud and AI can have a positive impact on the everyday lives of all the billions of people on our planet. Plenty of companies in Silicon Valley are involved in applying AI to marketing and advertising, but I couldn’t find any looking at AI in food production. So, I kept searching and found the Autonomous Greenhouse challenge at Wageningen.”
‘I also believe in applying the hacker mentality. Let’s get our hands dirty’
Why Wageningen? After all, there are so many Chinese and American universities to choose from.
“Wageningen is number one in the world. And the Netherlands already has plenty of companies working in horticulture around the world. I‘ve also visited greenhouses in Iceland, all of them using Dutch technology, I’m told. So, if there is anywhere that is a breeding ground for the idea of developing and designing a greenhouse that is largely self-governing, and is capable of utilising this reduced input to increase production, then that place is here.”
And that is something that companies have been working on for years already. Can this competition suddenly accelerate that process?
“It’s down to us at Tencent and at Wageningen University & Research to make the world aware that we are looking for an autonomous greenhouse. I have the utmost confidence in what talent can achieve. If we can find the best talents and teams in the world, and if they can perfect their algorithms, then we can learn a huge amount from this process. Of course, it makes good business sense to want to develop new technology in-house, and to bring this to the market ourselves, but I also believe in applying the hacker mentality. Let’s get our hands dirty.”
Ton van der Scheer
Read more about:
At This High-Tech Farm, The Boss Is An AI-Powered Algorithm
Bowery Farming Says Its Proprietary Software Can Top The Intuition Of A Seasoned Farmer.
By Aki Ito
September 20, 2018
This High-Tech Farmer Grows Kale in a Factory
Each morning when she gets to work at Bowery Farming Inc., Katie Morich changes into a clean uniform, puts on a hairnet and cleans her hands with sanitizer. Then she consults a computer monitor displaying all the tasks she needs to accomplish that day. The to-do list’s author isn’t human; it’s a piece of proprietary software that uses reams of data collected at the indoor farm to make important decisions: how much to water each plant, the intensity of light required, when to harvest and so forth. In short, Morich and her fellow human farmers do what the computer tells them to do.
Morich, 25, doesn’t mind taking orders from a computer. “I guess I do kind of report to the Bowery Operating System,” she laughs, referring to the software her employer developed to run the so-called vertical farm in a New Jersey industrial park. Bowery says the machines are constantly learning how to grow crops more effectively and are more than a match for the intuition of a seasoned farmer. “We don’t really have to double-guess ourselves,” says Morich, who is the subject of the latest episode of Bloomberg’s mini-documentary series Next Jobs, which profiles people in careers that didn’t exist a generation ago.
Katie Morich, a farmer at indoor vertical farm startup Bowery Farming.
Photographer: David Williams/Bloomberg
Bowery is part of an emerging industry promising to bring new efficiencies to the millennia-old science of agriculture, focusing for now on greens such as lettuce, arugula and kale. The startup, based in New York and backed by leading Silicon Valley investors, including Alphabet Inc.’s venture arm, says automation, space-saving, vertically stacked crops and a year-round growing season make its operations 100-plus times more productive per square foot than traditional farms.
Morich and Bowery declined to disclose her salary, but the company says she earns more than the median $23,380 annual salary pulled down by a traditional American farm worker. This is how economists hope technology will help the economy: by raising workers’ productivity and bolstering their wages over time. It’s also worth noting that Morich’s job is far safer and less strenuous than tending the acreage of a conventional farm.
Trays of vegetables growing at Bowery Farming.
Photographer: David Williams/Bloomberg
Of course, artificial intelligence also has the potential to kill jobs, and Morich’s role, however new, is not immune. Bowery hasn’t yet figured out how to automate everything that needs to get done in the farm, but since she was hired less than two years ago, the company has made progress:
Such processes as seeding, once done by hand, are now completed by machines. Morich says she doesn’t worry about job security, but economist Erik Brynjolfsson is more skeptical. “If a task doesn’t draw on human creativity or other human strengths like interpersonal skills, then it’s a candidate for automation,” says Brynjolfsson, a professor at the MIT Sloan School of Management and co-author of “The Second Machine Age: Work, Progress and Prosperity in a Time of Brilliant Technologies.” “This could be profitable in the short and medium term,” he says, but as robots become more mobile and dexterous, “I would not count on having a job like that in 10 or 15 years.”
Nor should the rest of us. Machines and automated software may displace 75 million workers by 2022, the World Economic Forum forecast in a report this week. “Technology has always been destroying jobs, and it has always been creating jobs,” says Brynjolfsson. “The answer is not to freeze in any particular set of jobs or skills. It’s to be flexible and be ready for the new jobs, many of which haven’t been invented yet.”
Morich, for one, isn’t standing still: In May, she was promoted to lead a team of farmers, which left her confronting a whole new set of challenges. She’s been working long hours ahead of the opening of Bowery’s second facility. Once things settle down, she plans to read “Managing For Dummies.”
Nebullam Aims To Revolutionize Indoor Farming
Jul 16, 2018 | News
By leveraging artificial intelligence, Ames startup focused on introducing product-to-producer method of production
Founded in a region of the United States with, arguably, the richest soil on the planet, a young Ames-based startup is aiming to revolutionize farming – without any of that soil. Employing a combination of high pressure aeroponics and artificial intelligence (AI), Nebullam is making waves in an increasingly competitive indoor farming industry.
The company was founded in 2016 when two former community college classmates reconnected. Today, Nebullam is operating two model farms – simultaneously generating income to keep the lights on and providing proof of concept for their innovative approach to agriculture – and seeking investment from engaged venture capitalists across the country.
The Genesis of an Idea
The seed for Nebullam’s founding was planted almost a decade ago when Danen Pool, co-founder and Chief Technology Officer, made a trip to Africa.
“The purpose of the trip was to provide water chlorinators to people in Swaziland and Johannesburg, South Africa,” Pool says. “A lot of the areas we visited were in a very arid climate. There was not a lot of fertile soil and produce had to be shipped in from long distances. It got me thinking about how you could sustainably grow produce in an area like that and that led me to begin researching different types of non-traditional growing techniques.”
That was in 2010. For months, Pool spent his free time experimenting with various forms of hydroponics and drip irrigation. By chance, during his research, he stumbled upon a NASA article detailing high pressure aeroponics, a technology developed originally in the 1980s as a method to grow produce on space missions.
The deeper Pool got into the science, the more he believed this was the way forward.
“It took me about six years to get a few system up and running,” Pool says, looking back. “I did all of the initial work in my home and it was promising. I could get the system up and going, leave it for a couple weeks and come back to it running just fine. I could grow produce very quickly and that was the major thing. Just with this first very rudimentary system, I could shorten growth cycles considerably.”
Reaching Out
With the technology, even in a very early stage, developed and tested, Pool knew that he needed some help with the business aspects of bringing his system to market. Among those at the top of Pool’s list was Clayton Mooney, a former classmate at Indian Hills Community College who had spent time as a professional poker player among other things.
“We had kept in touch, and I had been following what he was up to on social media,” Pool says of Mooney. “I knew he had returned to Ames and was in the startup space. I contacted him and let him know what I was thinking, hoping we could figure out a way to move forward together.”
Mooney took a measured approach to Pool’s initial pitch.
“Initially, I told him I’d be happy to look at his business plan and help him make connections here in Ames,” Mooney says. “I wasn’t really looking to get into something like this because I had a commitment coming up at Startup Ireland in Dublin. I told him I would take the summer to think about it.”
The summer in Dublin offered Mooney the time and space to consider the potential in full. The more he thought about it, he says, the more intrigued he became. Upon returning to Iowa, he was ready to partner with Pool to move the business forward. Mooney became the Chief Executive Officer, they settled on the name AeroLands, and began the startup process in earnest.
Building the Business
Among the newly formed team’s first actions was to reach out to experts at Iowa State University for feedback on the concept. The initial business model called for them to be producers – “indoor farmers” – providing their product from a warehouse. The longer term play was to put production units right into grocery stores and sell consumers produce they could pick themselves in the aisles of Hy-Vee or Fareway.
“We heard from a lot of people that they loved our technology but weren’t sold on our business model,” Mooney says. “The cost of labor just didn’t pencil out. We could grow indoors, but we were still going to need space to do it and workers to plant, manage and harvest the crops. That was all going to eat into our margins. We needed to figure out a way to automate as much as we possibly could.”
In the search for help in solving the automation challenge, Pool and Mooney met Mahmoud Parto, who would eventually become the Chief Software Architect and final member of the founding team. Mooney met Parto within the CYstarters cohort in summer of 2016. After learning of his background in computer and software engineering, Mooney asked Parto if he’d been interested in learning more about the company.
Initially, Pool and Mooney were just looking for a little help.
“When I showed him what we were working with in terms of automation, I was most interested in whether he could help us to reduce the cost of the equipment we were using to measure things like temperature and humidity,” Mooney says. “He came out of that meeting and was able to build us a working prototype with the same functionality, plus Bluetooth capability, for next to nothing.”
It was then, Pool and Mooney knew that Parto could play a pivotal role.
“I remember calling Danen that night,” Mooney says. “I told him we had to get Mahmoud on the team. We decided that night to offer him equity as a co-founder.”
Parto couldn’t commit to the idea at first.
“He told us he’d rather just help us out in the short term,” Mooney recalls. “But I think the gears started turning and it wasn’t long before he saw the potential and reached back out to accept our offer.”
Growing and Learning
With a full founding team established, the trio began looking for opportunities to get bigger and better. In December of 2016, they were accepted into the second cohort of the ISU Startup Factory.
The Startup Factory schooled the group on best practices in building a business while pushing them into a formal customer discovery process. The year-long program proved invaluable in clarifying the vision, developing a plan for growth, completing a friends and family round of investment, and preparing the team for pitching to larger investors. They also settled on the name change to Nebullam during their participation.
“The Startup Factory was instrumental in helping us to maintain a structured approach to building the company and keeping the team accountable to the vision,” Mooney says.
“The accountability is huge,” Pool adds. “I think the first time you become your own boss, you see the freedom to it, but there is also some trepidation that you are the one making the decisions. The intro classes were a big help to me in knowing what to expect.”
As part of their participation in the Startup Factory, the team was provided office space in the Vermeer building in the Iowa State University Research Park. With a location so close to Iowa State, it offered more than a place for meetings and to sit down in front of a laptop. It offered access to top tier interns to move the company forward.
“It is such a supportive entrepreneurial ecosystem,” Mooney says.
The Next Steps
Now “graduates” of the Startup Factory and a series of other accelerators and business development programs, the team at Nebullam has swelled to 10. They have settled on a hardware + software model that will enable indoor growers to leverage AI to fully automate the growing and harvesting process.
“The vast majority of indoor grow operations currently employ a producer-to-product model,” Pool says. “That means that the staff has to go to the product to plant it, tend to it, and harvest it, a method that isn’t much different from traditional farming.”
Nebullam, however, is developing proof of concept on a product-to-producer model. The plants would come to the producer, at a central transplanting and harvesting point. Using an elaborate network that learns with each crop cycle, everything is managed by AI – from what minerals are needed to spur growth, to when a given crop is ready for harvest.
This is a major differentiating factor for Nebullam when compared to others in the marketspace.
“There are a lot of startups on the hardware side, and a lot of others on the software side,” Pool says. “But running those varied systems together, there is a huge learning curve for the producer. We eliminate that. If you are powering your grow with Nebullam, we’ve eliminated any compatibility issues or learning curves.”
With Nebullam’s technology, when crops are ready to be picked, the system is automated to perform the entire process from harvesting and cleaning conveyor belts to planting the next crop.
“Everything will be monitored,” Pool says. “That monitoring will continually inform the network on what is working with a specific crop and help us to increase efficiencies and yields over time. The more we can automate, the more we can address the initial concerns that were raised in the infancy of our business about labor eating into our margins.”
The plan is being put into practice at the company’s second model farm, located in space at the ISU Research Park.
Nebullam’s vision – and the addition of Model Farm 2 – has been met with interest. The company was recently a top 3 finisher in the Young Entrepreneur Convention Pitch Competition, which is one of the largest single-day pitch competitions in the world. Through that, the team earned a coveted spot in angel investor Jason Calacanis’ intensive program for founders, Founder University. They have also reached the finals of a handful of other prestigious pitch and business plan competitions as they continue to identify individual accredited investors and venture capitalist firms to partner with in moving Nebullam along.
The team is confident they will find the right partner to bring Nebullam’s idea into practice on a large scale. And once that happens, the team is ready to shoot for the moon … or beyond.
“Our technology is applicable in zero gravity conditions,” Pool says with a smile.
“Seriously,” Mooney quickly adds, “we think we can complement a lot of the companies that are figuring out space travel. We might be nerding out a bit, but we are less than 1,500 days away from a spaceship landing on Mars. We are less than 2,500 days away from being a multi-planetary species. Who knows? Maybe our technology will be the one that makes it possible to nourish people as they explore space.”
While there is plenty to be done in those 2,500 days to make it happen, Mooney says the team is ready to do what it takes to make Nebullam a household name.
“The juice is always worth the squeeze,” he says.
Technology Promises To Calculate "True" Shelf Life
One of the causes of food waste is produce that goes bad earlier than expected. Of course, shipping produce that is fresh is the goal of every grower. In what manner it arrives and how fresh it remains once in the store, however, is largely out of their control. Furthermore, it is also in the retailer's best interest for the produce to remain fresh and tasty for customer's enjoyment.
Zest Labs, a company based in San Jose, California, has come up with a solution called Zest Fresh that allows growers and shippers to know how long each pallet of their produce will remain fresh. Using IoT sensors placed in each pallet at the time of harvest and cloud-based analytics, Zest Fresh takes into consideration temperatures at time of harvest, cut-to-cool duration, as well as conditions at each point right up until the receiver, and based on this data, calculates what the "true" remaining shelf life is.
"IoT sensors in each pallet use predictive analytics, machine learning and other functions to calculate a freshness metric of the dynamic remaining shelf life for each pallet," said Kevin Payne of Zest Labs. "We have profiled produce from different regions to determine the maximum freshness duration. Consider us as a postharvest freshness management solution. The reason is that despite a batch of produce coming out of the same field on the same day, the conditions in which they were harvested and eventually placed in the cooler can vary significantly. A pallet of strawberries picked at 7:00am and placed in the cooler at 8:00am will have a different shelf life than the pallet picked at 2:00pm during the heat of the day and placed in the cooler at the end of the day. This causes the 'true' remaining shelf life to be different for each pallet."
Kevin Payne and Todd Clayton with Zest Labs
Sending the pallets to the optimal destinations
Data collection and analysis is great, but varying forms have been around for a long time. Zest Labs noted that the point of difference with their Zest Fresh technology is that something can be done about proactively solving the problem. "Many solutions out there tend to be reactive, meaning an action can only take place after the fact," Payne explained. "However, we believe we offer the only proactive solution, by using the predictions and allowing the shipper to make decisions based on insights and information."
Fundamentally, the idea is to utilize the information to send pallets to destinations most appropriate for the calculated freshness. Most obviously, the greater the shelf life remaining, the further the produce can be sent. "When the calculated shelf life of one pallet is, say, 3 days shorter than another, it can be sent to a receiver that is closer, in order to maximize the shelf life for the receiver," Payne added. "The data is collected continuously and is read at pre-determined waypoints, such as being placed in the cooler, in the truck, moving out of the warehouse, arrival at the receiver, etc. This produces a dynamic shelf life, updated at each interval to give the most accurate shelf life at any one time."
Payne further noted that growers can use the data to monitor their processes to ensure they're being adhered to, adjusting procedures accordingly. "Zest Fresh empowers workers to keep product on process with real-time tools that reflect each process step – such as received inventory, time and temperature of product staged for pre-cool, pre-cooling, and shipping," he said. "It also drives notifications when preset process parameters are exceeded, focusing workers on the most acute problems in real-time."
The ZIPR Code
To help with the monitoring process, Zest Fresh collects, stores and displays all the data in a unique, automatically-generated code, called the "ZIPR Code" which stands for Zest Intelligent Pallet Routing, the industry’s first freshness metric. The ZIPR Code references the dynamic remaining shelf-life of individual pallets and then users can view and manage that pallet's information.
"Once Zest Fresh combines the data and applies a score, it creates the ZIPR Code for each pallet," Payne explained. "This ZIPR Code is then matched to pending orders to ensure each pallet has sufficient remaining freshness to meet the retailer’s needs. The ZIPR Code ensures that customer shipments are loaded correctly, and that quality is tracked through actual delivery – providing the grower with visibility of delivered quality."
"The ZIPR Code can be integrated into a warehousing management solution, providing alerts and updates on whether the pallet is still in a suitable condition and routing," he added. "It is designed to be autonomous and wireless."
Practicalities
The company said the sensors themselves are small and easy to handle. They can be inserted into pallets at any time, depending on whether the grower wishes to monitor the entire supply chain, or just certain sections.
"The IoT sensors are about the same size as a deck of cards and are placed in the pallet in the field or at any point along the way," Payne described. "They are reusable and can also be used for certain segments. The software to view information is cloud-based, with the desktop and mobile tags operated by access points. A technician will install these and all that is required is power and a network connection."
The Zest Fresh "dashboard"
Zest Labs is aiming to be at the forefront of technology, so Payne shared that Zest Fresh has Blockchain capability for those that desire it. "Blockchain, which is basically a secure way to exchange and share information, is one of the aspects that I get asked about often," he said. "We do have the support for it although it is not required."
What types of produce and where?
According to Payne, the most common produce type that growers use Zest Fresh for are highly perishable fruits like berries. This is no surprise as these fruits are the ones that feel every effect of temperature changes and inadequate cooling times, for example. Currently, the company is working with growers in North America, and has also worked with suppliers in Central and South America.
"Zest Fresh can be used for any produce type, however most growers and retailers start by using them for the highly perishable produce items like berries, closely followed by leafy greens," Payne said. "We have also seen interest in grapes, cherries and stone fruit. Right now, our technology is used across North America, and we have also worked with growers in Central and South America, particularly in the northern winter. We are aiming to be at the forefront of technology and modernize the supply chain for the fresh produce industry."
For more information:
Kevin Payne
Zest Labs
Tel: +1 (408) 200-6527
Publication date: 7/10/2018
Author: Dennis M. Rettke
Copyright: www.freshplaza.com
Growlink Announces Beta Program for Exciting New AI Solution
Growlink Announces Beta Program for Exciting New AI Solution
Innovative Technology Collects 200 Million Monthly Data Points to Understand and Maximize Grow Operations
NEWS PROVIDED BY Growlink
DENVER, July 10, 2018 /PRNewswire/ --
Growlink, a leading agriculture technology company, is excited to announce a beta program for its new AI solution for greenhouse and indoor farming. More information on the Growlink Plant Health AI beta program, including online sign-up for Growlink customers, is available at http://growlink.com/ai.
The use of artificial intelligence is the next big innovation in agricultural technology. Growlink Plant Health AI uses cloud machine learning, computer vision, sensor data, and AI to track and predict plant health. Growlink currently collects over 200 million monthly data points from 2,200 active devices (environment, irrigation, and fertigation controllers). This massive amount of data is then combined with high-definition and infrared camera images to provide a comprehensive understanding of what's going on.
Powered by Microsoft Azure, including Computer Vision, Machine Learning and Speech, Growlink Plant Health AI is easily accessed on any internet-connected device through native mobile applications or a desktop browser. Other features of the application include:
- Data-powered agronomy: Growlink helps producers grow healthier, higher-quality crops. It continuously monitors, enforces, and optimizes climate, irrigation, and feed systems. It also helps agronomists plan with greater precision and allows growers to benefit from the collective knowledge and experiences of others.
- Predictable, optimized yields: With yield predictions that are up to 95 percent accurate, Growlink provides sales and purchasing teams with accurate supply forecasts to closely match demand dynamics. It maximizes farm output through optimal variety allocation, planting, and harvest planning.
- Early disease and pest detection: In greenhouse cultivation, disease occurrence is influenced by the basic parameters of temperature and humidity, along with the quantity of sunlight, leaf wetness, the growing environment, and the outside weather. Growlink uses AI to analyze these factors that affect crop development, along with computer vision to predict disease and provide early detection of pests.
- Voice-enabled system management: By using Microsoft Cognitive Services and raw voice files, including captured time stamps and location data, users can improve productivity and workflow management, increase documentation accuracy, and gain valuable insights to optimize the use of resources in crop production.
Current Growlink customers can sign up to be notified when the Growlink Plant Health AI beta program is available at http://growlink.com/ai. As members of the program, users can help shape Growlink software by test-driving pre-release versions and giving their feedback.
"The world must produce more food using fewer resources, and we are certain AI supported by advanced technology platforms will truly benefit farmers," says Ted Tanner, CEO and Co-Founder of Growlink. "From commercial greenhouses to vertical farming, the comprehensive data AI gathers and the real-time actions made from this data will lead to greater, predictable yields and reduced crop loss. Our new Growlink Plant Health AI will take this bold step into the future, and we are thrilled to announce this beta program to give our users the first opportunity to use this incredible new technology."
To learn more about Growlink's innovative farming solutions, visit www.growlink.com.
About Growlink
Growlink's mission is to create smart farms that maximize production by leveraging the power of big data, the cloud, and IoT devices. The Growlink Platform controls and automates lighting, climate, and fertigation and irrigation systems. For more information, visit www.growlink.com.
SOURCE Growlink
Related Links
MotorLeaf: The Farming AI Which Helps Boost Modern Indoor Farms
MotorLeaf: The Farming AI Which Helps Boost Modern Indoor Farms
from RESET
Published on 23 May 2018
MotorLeaf introduces a green-fingered AI which can help indoor farms match the growing food demands of the future.
The Agronomist AI uses a range of wirelessly connected devices to monitor crops.
The recent expansion of agricultural tech, combined with emerging food security concerns, has led to the development of modern agricultural practices which seem a million miles away from the rolling green fields and romanticised ideas of farming yore.
For example, we recently reported on AeroFarms, a US-based company exploring the concept of urban vertical farming, while elsewhere, technological greenhouses can utilize new systems to greatly reduce water consumption without compromising on yield. Indeed, in many cases, the yield is drastically increased.
MotorLeaf is the latest company to find a role in this new market. The artificial intelligence developer has created a new AI which can help urban and indoor growers to monitor their crops, and predict issues in real time.
Their Agronomist AI uses data-driven machine-based learning to provide indoor farms with a comprehensive suite of insights, whether relating to potential yield or even predicting disease. Put all together, this data can help reduce waste and crop failure - something which will only become more important as more stress is put on the agricultural sector by population growth and climate change induced weather patterns.
Many of Agronomist’s services can be used individually or combined together with the MotorLeaf HEART system to operate as a larger AI manager of an indoor farm or greenhouse. Every four seconds, MotorLeaf’s AI collects data from a collection of wirelessly connected devices which can provide information on factors such as light spectrum, light intensity, CO2, humidity, air temperature, water usage and chemical makeup.
Recent trials conducted in California led to a fifty percent reduction in yield prediction errors of tomatoes, and with recently secured funding, they are seeking to expand the product to different crops and scales.
Can AI Be Environmental?
Currently, the system is mostly being used in hi-tech, comparatively low-yield indoor farms in developed nations - and is it likely to remain that way for some time. Furthermore, the current goal of MotorLeaf appears to be making these ventures more profitable and cost-effective, and less concerned with environmental protection - although the two are not mutually exclusive.
Despite this, technology such as the Agromost.ai or similar could also have major implications for farms and greenhouses in developing nations. Although the current expense and technical know-how required to operate such software may be beyond most farmers in the Global South, the ability to predict disaster and better monitor the conditions of your crops could become an invaluable tool in the fight against famines, crop failure, and poor weather conditions.
If AI is to become a tool of future, it should also be used broadly to help those most in need of its utility. AI that remains the sole possession of developed nations is likely only to exacerbate inequalities and economic gulfs between states. However, as AI becomes more widespread, and the tech it relies on cheaper and more available, it could be an important player in supporting an agricultural sector that can feed the entire world. Additionally, much else remains to be debated about AI from a social standpoint, including its potential impact on employment, not only in manufacturing but in a range of sectors and roles.
10 Key Learnings From Indoor Ag-Con Asia
10 Key Learnings From Indoor Ag-Con Asia
JANUARY 24, 2018 URBAN AG NEWS
By Jacob Eisenberg, Editor of Agri-Futures
Marina Bay Sands in Singapore — venue for Indoor Ag-Con Asia
This year’s Indoor Ag-Con Asia, hosted in Singapore, was filled with idea’s, innovators and enthusiasts alike — all eager to hear new promises and perils of indoor farms and vertical farming from around the world. For a fairly nascent industry, there was a strange aura that made it difficult to separate the inspiring success stories and potential from the soul-crushing, science-based reality this sector faces as it continues to grow. While financial and operational challenges are clear, there were also a number of interesting patterns throughout the two-day event — all likely to shape the industry in 2018 and beyond.
1. There is no silver bullet system… yet
As most enthusiasts and operators in the industry would expect, there was no grand showing of a fully viable, scalable and profitable solution for a vertical farm this year at Indoor Ag-Con Asia. With so many different growing systems, ranging from high performing hydroponics to scaleable aquaponics, the silver bullet still remains elusive for the best performing and most versatile crop cultivation system.
While many of the notable presentations covered the pros and cons of certain growing systems, none were clearly comparable in the cultivation of the same crops or products. And further industry comparisons become even more difficult as many of the turn-key solution companies keep proprietary aspects of their system, well, proprietary.
As disappointing as that may seem for the event, there was a diverse range of applications for new crop varieties grown indoors. Companies and research groups continue to push the frontier of plant recipes and techniques in their growing system using new lights, better controls, and more meaningful data.
2. Governments are finally taking notice
Singapore’s Minister of State, Koh Poh Koon, browsing the exhibition hall
It seems fitting that Singapore was chosen to be the venue for this year's Indoor Ag Con Asia event. Since 2015, the Singaporean government has publicly pursued a new smart agriculture future’ with significant policy and private sector activity as a result. New small-scale ventures as well as large corporate forays into the world of indoor Ag are receiving both support and increased scrutiny to produce food efficiently without compromising its quality and safety.
“We are committed to creating a robust food and agricultural sector of the future”.
This year, Singapore’s Minister of State, Koh Poh Koon, gave the opening keynote to the event. He described the Singapore government’s stance as
“Committed to creating a robust food and agricultural sector of the future”. Singapore is a clear example of a country with fast-moving policies intended to accommodate and possibly foster indoor agriculture.
However, the Netherlands also had a large presence at the event, sharing their respective successes and challenges in the first morning of presentations. Additionally, other government representatives were in attendance, ranging from countries around the world like Israel and Malaysia. Many of them hoping to learn about new technologies to better upgrade the efficiency of their respective countries traditional agricultural sectors.
But for urban planners and zoning commissions, big questions remain in how to fit the binary of classifying these farms as industrial or truly agricultural if marketed as ‘organic’.
3. Consistency is key
Among all aspects of indoor agriculture, consistency remains a critical benefit and continued challenge in using these systems. The quality of plants produced in indoor agricultural operations was one aspect, almost religiously touted throughout the event. Advancements in better environmental controls for air, light, water and plant nutrition are helping farmers ensure a more reliable look and taste for growing a variety of produce.
However, quantity and price continue to be clear challenges for systems that operationally still have many hiccups. Though most presenters shared success in better forecasts and reliability for the quantity of crops produced in their system, there were shared concerns in the difficulty to scale quickly and meet consumer or wholesale demands in time. Setting up new precision growing systems take some time to test and fine tune, complicating a clear picture of quantity and price.
4. Microbiome and nanotechnologies are making new headway
Aside from the core operating technologies of indoor farms like LEDs, sensors and growing beds, new technologies also made an appearance. Like many technologies in this sector, the benefits focused on growing more with less, in an attempt to reduce crop loss from disease, minimize the water required, and improve crop quality and health.
Presentations highlighting recent advancements in genomic extraction offer new opportunities for farms. Microbiome analysis is one example of one method to better cultivate healthy plant ecosystems from the molecular and bacterial level. Instead of introducing synthetic solutions, companies like Metabiome, highlighted their success in optimizing natural mycorrhizae ecosystems.
Other technologies, like nanotechnologies, were showcased in one successful application to inoculate fish with the equivalent of ‘flu shots’, to prevent the spread of bacterial and fungal diseases common in aquaponic systems. And this seems to be just the start in use cases for nanotech among these indoor systems.
5. Artificial Intelligence comes big and small
One feature that was alluded to in almost all presentations throughout the event were new opportunities for automation and the insinuation of artificial intelligence (AI). While many indoor farms have started to build systems to reduce labor costs, there is still a critical need for farming operators in quality and process management of the plants.
Yet Improvements in one technique of AI, called computer vision, are bolstering new applications for anomaly detection and harvest quality in indoor systems. However, there is still a steep learning curve for computers to successfully utilize AI in practice.
While manual automation is one goal for indoor farms, Blackbox automation (e.g. where to plant and when) offers another incredible opportunity to reduce the complexity farmers face mixing and matching different systems, lights and crop varieties. With so many variables involved in operating an indoor farm, computational assistance and automated planning will likely reduce many farmer headaches — and create shared opportunities — in the very near future.
6. Growing lettuce and big data
ZipTower System showcased in exhibition hall
While most presentations focused on the quality of production inside indoor growing facilities, there was also a great deal of interest in a fairly new byproduct of these farms — data. Big data.
Much of the focus in the industry has centered around basic viability of growing certain crops like leafy greens and tomatoes. But new improvements in sensor and IoT tech is shifting focus toward actionable insights from the farm data collected. Ramy Sanad from the sensor and controls company Autogrow, described in his presentation how having data isn’t enough, it needs to a priority to “make data meaningful” for the farmer. And for some in the industry, these data could be a priceless byproduct.
Some presentations did disclose “plant recipes” or the specific environmental factors required to grow healthy lettuce and leafy greens. But conversations primarily stayed away from any data or metrics to more profitable commercial plants like strawberries.
While many indoor facilities struggle to profitably sell their product in the market, it is possible that their crop data could be even more valuable for other farmers and companies alike — that is, if they are willing to sell it for the right price.
7. The new frontier of online delivery
Aside from the long list of technical difficulties involved in indoor growing systems, reaching a reliable market also remains elusive for many small to medium scale indoor growers.
Despite the high quality output of indoor farms, meeting demand at scale and in time seems to deter many wholesalers and 3rd party distributors from long-term partnerships. However, online food delivery services in countries like the United States, Singapore and China seem to offer a new frontier of opportunities connecting farmer directly to the consumer.
As Robert Chen, President and CEO of AEssense, noted in his presentation, growing food close to online food distribution centers can help cut costs in storage and delivery. This allows the grower and the distributor to pass savings down to consumers — making their products more competitive in the market.
8. Diversifying factory farms to the niche
Presenters repeatedly recognized the need for farms to better define their value proposition as cleaner, better, more nutritious products, etc. However, some speakers at Indoor Ag-Con suggested widening the scope of indoor ag products to secondary and even non-edible crops.
Cannabis is an example, but rarely mentioned throughout the entire event in Singapore for obvious legal reasons. But it isn’t the only high value, non-edible crop that can be grown well inside. Nishida Shin, of Japan’s Nihon Advanced Agri highlighted recent success in organic food coloring from plants cultivated inside a plant factory.
The rising demand for specialized ‘organic’ products used in or around food production seems to also provide new opportunities for profitability in the sector. While the same benefits for growing food inside apply, these secondary commercial products, like natural food coloring, can be better controlled for their quality, while sold at an even higher premium in these niche markets — speeding up ROI for the facility capex costs.
9. Pain Point obscurity
In addition to unclear comparisons between systems growing similar crops, it was also challenging to ascertain specific pain points. Product feedback is critical for these systems, especially the turnkey solutions. While most of these companies work closely with their customer/farmers to improve systems, their proprietary nature prevents startups from building novel solutions, sharing feedback from customers or focus groups, or collectively improving system optimizations based on shared experiences.
Indoor Ag is an industry still early in its development, yet it remains riddled with gaps in efficiency and operational pain points. Also, obscurity helps to protect the existing IP of turnkey product systems and companies, it prevents tinkering improvements and solutions for the industry as a whole.
Though each system is different in requirements for operation and management, seeding and harvesting both remain major labor hurdles for indoor agriculture operations with fairly apparent pain points.
10. ROI is still a curse word
For many indoor farmers starting to operate facilities in this space, the term ROI still seems to conjure speculation and deep anxiety for farmers and investor alike. On the one hand, these numbers are critical to truly assess the viability of indoor agricultural operations. On the other hand, ROI forecasts are subject to change drastically (for better or worse) based on crop health, facility size, development of disruptive and scalable technologies, and market demand.
At the conference presenters of larger facilities seemed to suggest an ROI ranging between 3 to 5 years, while others in the industry continue to suggest a more conservative range of 5 – 7 years. Again, both of these estimates continue to depend on the size of the facility and the market they are growing for (and actively selling to). To date, there is still no highly profitable large scale prototype.
Hate The Taste of Kale? Artificial Intelligence Could Help
Farmers are using technology to tweak the color and flavor of vegetables, including algorithms that can suggest changes in factors like the amount of water vegetables receive and what temperature they’re grown in.
Hate The Taste of Kale? Artificial Intelligence Could Help
Jan 10, 2018
One company is using AI to grow beautiful lettuce without chemicals
Holger Hollemann/AFP/Getty Images
Some farmers are turning to high tech solutions to improve the taste of kale.
By MARIA LAMAGNA | REPORTER
Don’t like the taste of kale? Maybe you will soon.
Kale’s distinctive flavor has been compared to a “dusty bitter blanket,” but now there’s hope for those haters from an unlikely ally: artificial intelligence.
Farmers are using technology to tweak the color and flavor of vegetables, including algorithms that can suggest changes in factors like the amount of water vegetables receive and what temperature they’re grown in.
Can AI improve the taste of kale?
One such company, Bowery, which bills itself as “the modern farming company” and was founded in 2015, has an indoor farm based in New Jersey where scientists are adjusting the taste of vegetables including kale.
“Our system is able to say, ‘Do we like what we’re seeing, do we not like it?’” said Irving Fain, Bowery’s co-founder, and CEO. The company’s algorithms analyze everything from the nutrients in the plants’ water to the type of light they are grown under. Bowery said he’s able to grow vegetables without “blemishes,” even though they use no chemicals in their growing process.
See also: Why you may want to avoid eating romaine lettuce
Besides potentially improving taste, that could have another benefit: cutting down on waste. About 6 billion pounds of fresh produce go unharvested or unsold every year, according to an estimate by Feeding America, a nonprofit based in Chicago. Some of those losses happen because of pests, disease, whether or labor shortage, but another portion gets thrown away because it has physical imperfections, which grocery-store shoppers find to be a turnoff. The produce that is misshapen or blemished goes unsold.
As far as improving the taste of kale, Fain might have a tough battle to fight. Although it is trendy, and restaurants have increased their menu items that contain the leafy green, Americans still much prefer lettuces like iceberg. The U.S. either produces or imports approximately 13.5 pounds of iceberg per capita, compared to just 0.6 pounds of kale, according to the latest government data available.
Nutritional content also varies, depending on the lettuce. In one cup of chopped raw kale, there are about 2.2 grams of protein (4% of daily value), 1.3 grams of fiber (5% daily value) and vitamins including Vitamin A (206% daily value) and Vitamin C (134%.) A similar serving size of spinach has about 2% of daily value for protein, 3% of daily value for fiber, 56% of Vitamin A and 14% of Vitamin C. Romaine and iceberg, while they are low in calories, contain very little protein or calcium.