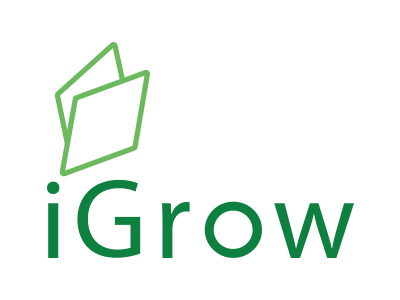
Welcome to iGrow News, Your Source for the World of Indoor Vertical Farming
Dachnik Aquaponics Completes Vertical Aquaponics Renovation of Commercial Facility in Copperton, Utah
Dachnik Aquaponics, an Aquaponics Technology company founded in Utah, spent the entire summer renovating their Vertical Growing Commercial Aquaponics Facility located in Copperton, Utah.
Their previous design, consisting of Bamboo vertical growing towers, created a lot of attention and buzz in the community; including videos by top YouTube Organic Food channel “Growing Your Greens” which has currently received over 273,000 views explaining the system and its unique design in detail.
Video Link
Dachnik Aquaponics was barely able to keep up with email inquiries and phone calls for months when the system went live and was revealed to the world.
However, the bamboo towers while looked gorgeous; were not viable for a large-scale commercial operation. They did not have the durability needed to last long-term and were extremely high maintenance.
With every new system Dachnik Aquaponics builds, new ideas come along that help solve potential problems and how to make it better. Their goal is to never idlily standby any design, but to always keep improving it for maximum efficiency in order to keep raising the bar in Aquaponics.
“Most of the media attention, buzz and money is currently flowing towards Hydroponics. However, we feel like Aquaponics provides the full spectrum needed for sustainable agriculture but has remained quite stagnant over the years without any substantial, disruptive developments in order to solve the problems all commercial Aquaponics farms face that make it unattractive to farmers and investors and hinder profitability. Our next generation design solves the issues plaguing Aquaponics by creating a one-of-a-kind biofilter, massively increased plant yield per SqFt, and effectively eliminating most labor requirements.”
Sean Burrows, Co-Founder, Dachnik Aquaponics
Fast forward to where we are now. We have built a complete proof of concept and working farm about a 1/6th scale of the commercial farms we envision our next projects to be. Our automated vertical Aquaponics systems are simpler to operate and provide the most grow holes per square foot of any other Aquaponics system to date. Thanks to our new patented vertical growing tower consisting of 48 grow holes per tower as well as our “stackable” float bed design.
We can produce as many plants in 10,000 square feet as 36 acres in California. Based on 15,000 plants per acre and 4 harvests per year. Attached to the Aquaponics greenhouse is the fish and production/storage building where we expect the five 18,000-gallon fish tanks to produce up to 100,000lbs of fish per year, as well as Australian Redclaw and other Crayfish. We are forming alliances with state-of-the-art greenhouse designs and solar to create completely off grid systems with a very attractive return on investment.
Our Aquaponics growing system is quite simply the ultimate bio filter. We set out to create a system that works in harmony with nature and yes, we kept the media and worms.
Looking five years down the road, Dachnik Aquaponics sees itself as the leader in Aquaponics technology with large fully automated commercial systems built worldwide. We want to be adding billions of dollars into the economies where our systems are built. Dachnik Aquaponics is also planning on selling smaller “residential” sized systems as well based off their commercial designs.
Here’s the latest video update from Dachnik Aquaponics showing their new and improved design after the renovation of their previous one:
Video Link
Their current model is now selling fresh produce within Salt Lake County to restaurants, markets, caterers along with a monthly membership direct to consumer model.
Dachnik Aquaponics is currently taking orders for commercial sized farms.
Here’s a link to their website to learn more
Urban Food From Vertical Farming
Urban Food From Vertical Farming
May 23, 2018, CORDIS
Credit: diephotodesigner.de
Your local supermarket and favourite restaurant could soon be growing their own food, thanks to an EU-funded project that has completely redesigned the food supply chain to develop the concept of in-store farming.
Our busy, modern lives demand that fresh produce be available 365 days a year, even though some varieties may only be seasonal and/or produced on the other side of the world. The result is a food system centred on quantity, low prices and efficiency rather than on quality, sustainability and traceability.
The EU-funded INFARM (The vertical farming revolution, urban Farming as a Service) project reflects a growing desire for highly nutritious locally grown food, which is free of herbicides and pesticides and addresses the lack of accountability in the current food system. "By growing produce directly where people eat and live, we can cut out the lengthy supply chain, significantly reduce food waste, offer nutrient-dense food without any chemical pesticides and improve the environmental 'foodprint' of our plants," says the INFARM's Chief Technical Officer and co-founder, Guy Galonska.
The answer lies in vertical farming, which grows food in vertically stacked layers under carefully controlled conditions, using hydroponics and light-emitting diodes (LEDs) that mimic sunlight. INFARM takes the concept a step further by employing its smart modular farming units throughout the city "Rather than asking ourselves how to fix the deficiencies in the current supply chain, we wanted to redesign the entire chain from start to finish; Instead of building large-scale farms outside of the city, optimising on a specific yield, and then distributing the produce, we decided it would be more effective to distribute the farms themselves and farm directly where people live and eat," Galonska explains.
Use of technology
Each farming unit is its own individual ecosystem, creating the exact environment for plants to flourish. By developing the optimal light spectrum, temperature, pH, and nutrients researchers can ensure the best possible flavour, colour and nutritional quality for each plant, whether it be rocket from Provence, Mexican tarragon or Moroccan mint.
The distributed farms are connected by INFARM's central farming platform, creating a first of its kind farming network: "Each farm acts as a data pipeline, sending information on plant growth to our platform 24/7 allowing it to learn, adjust and optimise." A matrix of sensors collects and record data, enabling researchers to remotely optimise the growth of the plants in real-time. This information is also fed into the central farming platform, ensuring its continual development and improvement.
The design of the growing trays mimics the petal pattern of the sunflower, which represents the most efficient arrangement of space in nature. The tray moves plants from the centre to the outer perimeter according to their size and growth. Young seedlings are placed in the centre of the spiral and are harvested from the outside when matured. This design allows fresh produce to be harvested each day at a significantly higher output than comparable technologies.
Supply chain reduced
INFARM is now operating more than 50 farms across Berlin in supermarket aisles, restaurant kitchens and distribution warehouses. In addition to the in-store farms, INFARM has successfully installed and activated a large-scale seedling plant and logistical support system that allows the continued, successful operation of all farming units.
These results are the first step towards creating an urban farming network in Berlin that will ultimately make the city more self-sufficient in its food production. According to Galonska: "With our system, we have completely reduced the food supply chain, as our produce is grown in the heart of the city, often directly at points-of-sale. Thus, customers can purchase fresh produce, minutes after being picked, thereby retaining all its original nutritional qualities, which are lost when the produce is transported and refrigerated."
Those benefiting from the work of INFARM range from small grocers to global retail conglomerates and governments interested in water conservation, food security and reducing greenhouse gas emissions. Galonska concludes, "INFARM's innovative business model has attracted major interest and I believe that our success will serve as proof, to both aspiring entrepreneurs and established companies, that going 'green' can be profitable and sustainable."
Explore further: Computer-controlled 'greenhouses' in kitchens grow fresher, healthier produce
Provided by: CORDIS
Read more at: https://phys.org/news/2018-05-urban-food-vertical-farming.html#jCp
RotoGro Inks Pivotal Ag-Tech Perishable Foods Deal
RotoGro Inks Pivotal Ag-Tech Perishable Foods Deal
Written by Zoe Gross, edited and authorised by Jonathan Jackson. Published at May 22, 2018, in Biotech
Cannabis tech company, RotoGro World Wide (ASX:RGI), has penned a binding letter of intent (LOI) with organic perishable foods grower, Gibio Inc.
The LOI enables RGI to subscribe for up to 49 percent equity participation in Gibio and includes a 20-year exclusive manufacturing, technology and service contract for all rotational garden systems required for Gibio’s perishable food production facilities.
Gibio is located and incorporated in St Apolinaire, Quebec, Canada. Its mission is to develop environmentally responsible local farms which defy traditional growing seasons, enabling sustainable, socially responsible and traceable organic produce all year round.
This LOI is the culmination of 12 months of collaboration — Gibio and RGI have been working together to trial, test and customize the RotoGro Rotary Hydroponic Garden System with Gibio’s growing know-how and bespoke substrate technology.
Building, owning and operating perishable farms led by the tech of both companies will ensure produce is grown with maximum efficiency, minimal water, and without pesticides or herbicides.
Gibio will proceed with the first 80,000 square foot flagship facility, aiming to roll out an additional 10 facilities over the next five years.
RGI’s equity interest in Gibio’s global growing facilities provides considerable depth to its second vertical of growing management and growing facility ownership.
It’s worth noting here that this is an early stage play and investors should seek professional financial advice if considering this company for their portfolio.
Some market peers in the vertical farming perishable foods space
Small-scale indoor farms have demonstrated the benefits of compact vertical farming for many years. In response to increasing real estate prices, energy and transportation costs, scarcity of fertile land, and the limitations of seasonal growing, the agricultural community has made a concerted effort to utilise urban spaces for the efficient growing of perishable foods.
Research has shown indoor vertical farming systems have the capacity to produce up to 350 times the volume of produce compared with a conventional farm occupying the same footprint, while using significantly less water and providing consistent quality year-round.
These hermetically sealed, climate-controlled indoor growing facilities provide shelter from the elements, weeds, insects and pests which eliminates the need for harmful herbicides and pesticides, while at the same time providing safe, dependable and nutritious food.
Two companies leading the charge for sustainable indoor vertical farming are New Jersey-based AeroFarms LLC and Silicon Valley-based Plenty Unlimited Inc. — Gibio aspires to the achievements of both.
AeroFarms recently completed construction of its ninth indoor vertical farm — a state-of-the-art 69,000 square foot flagship production facility in Newark, New Jersey. AeroFarms’ original investors, Goldman Sachs and Prudential Financial, have been recently joined by the Ikea Group and Meraas (the investment vehicle of Sheikh Mohammed bin Rashid).
Plenty, on the other hand, recently opened its first 50,000 square foot indoor vertical farming operation in California and is currently opening its second indoor vertical farming facility in the greater Seattle area, Washington. This second facility occupies 100,000 square feet of growing area and has the potential to cultivate enough produce to feed some 180,000 Americans annually.
Plenty has been well-supported with an investor base that includes SoftBank Vision, DCM Ventures, Bezos Expeditions (Amazon’s Jeff Bezos) and Innovation Endeavors (Google’s Eric Schmidt).
A critical transaction
Gibio president, Gino Poirier, said: “We are very excited to partner with RotoGro in our aspirations to be the global leader in organic perishable foods. Our relationship over the past 12 months has highlighted the strength of RotoGro’s innovation, engineering and solutions-based approach to our design requests.”
“We look forward to moving to the design and construction phase of our first 80,000 square foot flagship facility after which we aim to roll out a further 10 facilities over the next five years,” added Poirier.
RGI managing director, Michael Carli, commented: “Our investment in Gibio is a testament to the vision of both companies aligning to embark on the exciting space of large scale indoor perishable food growing facilities. Gibio’s first facility will rival that of both AeroFarms and Plenty, whilst moving the needle for more efficient solutions to indoor farming.”
“Our equity interest in Gibio’s global growing facilities provides depth to our second vertical of growing management and growing facility ownership. This is a company making investment and sets RotoGro apart from its peers in both the technology and agriculture space.”
This latest development comes hot on the heels of more good news for RGI. Last week, the company revealed it is acquiring the fertigation assets, intellectual property, ongoing contacts, key personnel, industry know-how and business goodwill of Hanson’s Water Treatment Inc.
This acquisition gives RGI leverage to Hanson’s specialised fertigation business line for water treatment and nutrient management in the viticulture, perishable foods and legalised cannabis space.
TAGS
Market For Distributed Farms That Grow Popular Fungi ‘Mushrooms’ In New York
Market For Distributed Farms That Grow Popular Fungi ‘Mushrooms’ In New York
ByPYMNTS
March 6, 2018
In the Big Apple, where space is at a premium, it’s not easy to grow farm fresh produce. As a result, most produce that ends up on a diner’s plate there comes in refrigerated trucks from a farm far away.
It’s an ecological nightmare with all the energy needed to fuel the trucks — and the produce doesn’t always arrive in grocery stores or city restaurants all that fresh, after all.
But one startup hopes to change that paradigm by bringing a more compact concept of a farm into New York City. Smallhold provides a vertical farming system that allows produce to be grown in dining rooms, basements – or even in the grocery store.
“You can put [it] literally anywhere,” Smallhold’s Co-Founder and COO Adam DeMartino told PYMNTS in an interview. “When you make it super easy to farm something, it becomes a whole new business opportunity for a community. There’s a million things you can do with it.”
The Business Model
To expedite the growing process, Smallhold also works sort of like a nursery. The company grows the produce — mushrooms, at the moment — three-quarters of the way. Then it delivers the almost-grown produce to their customers, who finish growing the fungi in their vertical growing units.
And the customers also can have the help of the company in creating the right growing conditions. The units come with wifi and allow Smallhold to monitor and control them remotely. As a result, customers simply have to pick and serve the produce.
Smallhold’s farms also reduce the environmental impact of growing produce. Their farming units reportedly create 40 times the output per square foot than the traditional farm — and use 96 percent less water, according to the company.
But Smallhold is not the only urban farming concept coming to a U.S. city. Boston-based agricultural tech company Freight Farms, for example, grows produce inside of shipping containers.
One freight farm can grow approximately two acres worth of produce, according to the company, and that can be sold either direct to consumers (D2C) or through partnerships with local distributors, restaurants and grocery stores.
And talk about local. Food production hubs — like those used by Freight Farms or Smallhold — were designed for urban settings where it can be difficult to access truly fresh food.
No farm? No problem. DeMartino said Smallhold develops mushrooms that are already fully grown, too, to help introduce new customers to its growing system.
The Mushroom Market
Smallhold chose to grow mushrooms because of strong demand. “The market for mushrooms is just so strong, especially local mushrooms,” DeMartino said, adding that beautiful exotic fungi have good margins.
The company grow all sorts of mushrooms — about 10 different species. And the mushrooms grow well in their high-tech environment: One Smallhold customer, for example, was able to grow a mushroom that weighed in at two pounds.
And the mushrooms also appeal to consumers who might want an alternative to meat, especially if they want a vegan or vegetarian option.
“A lot of people are looking to other protein sources,” DeMartino said. “Mushrooms make an actually great main if you’re at a restaurant.”
Overall, consumers are demanding healthier food when they are dining out — and are looking for vegan and other health-conscious options. According to an NPD study, health and wellness-related activity is leading to healthier restaurants that Smallhold could serve.
“It’s hard to miss all the vegan eateries, gluten-free bakeries and juice shops popping up across the map these days, hoping to grab a piece of the health pie (or rather, gluten-free, vegan rhubarb pie),” according to the study.
The New Produce Section
In the future, DeMartino wants to change the way consumers buy their produce — especially in the grocery store.
“The idea is — over the course of the next coming to years — to replace the produce aisle,” DeMartino said.
And, of course, he wants to grow more items than just mushrooms. Other produce is on the Smallhold roadmap as well.
“There’s many, many different crops that we can grow on site,” DeMartino said.
But he isn’t quite ready to expand to residential customers yet. An individual or family is just not going to purchase the same quantities that a restaurant would, after all.
“Our goal isn’t to have a novelty item that you keep in your kitchen to grow produce,” DeMartino said. “The goal is to make something that’s a utility.”
While DeMartino might not be looking to place Smallhold farms in consumer kitchens quite yet, he is looking to change consumer shopping behavior. By introducing the farms in grocery stores, he hopes that he can change consumer buying habits — and encourage people to buy farm-fresh produce.
In all, he’s trying to make people closer to the food — harkening back to the days of backyard gardens.
“[Smallhold is] also going to reconnect people to how produce is grown,” DeMartino said. “We’re reconnecting people back to their food in a busy society.”
Microfarm Startup Wins Pitch Competition
Microfarm Startup Wins Pitch Competition
Mike Platania February 22, 2018
Two food-based startups won a total of $11,000 Tuesday night at Randolph-Macon College. (Mike Platania)
A UVA-born startup focused on water-based gardening is set to sow more seeds after taking home $10,000 in a pitch competition this week.
Charlottesville-based Babylon Micro-Farms, which makes a Keurig-like appliance for growing produce, won Dominion Energy Innovation Center’s 2018 Pitch Competition, held Tuesday at Randolph Macon College.
Startups pitched to a panel of judges that included Virginia BioTechnology Research Park president and CEO Carrie Roth and Startup Virginia executive director Bryan Bostic. The $10,000 prize was provided by the center, an Ashland-based office and coworking space for startups.
Founded in 2017, Babylon makes a “micro-farm,” which grows produce through hydroponics, a gardening method using nutrient-rich water instead of soil as a base to grow plants. Babylon has set up micro-farms in some Charlottesville eateries and UVA dining halls.
Other finalists were TMI Consulting, a Richmond-based firm focused on diversity in workplaces, and AnswersNow, an online service connecting parents of autistic children with therapists. AnswersNow was part of Richmond-based accelerator Lighthouse Labs’ 2017 class.
In addition to the startup competition, three R-MC students also pitched for a $1,000 prize, provided by the college’s The Edge Career Center.
Veg Head Foods, a vegan food truck concept by R-MC senior Sheridan Skurupey, won the student competition, beating out tutoring service Meta Language and Northern Virginia United FC, a semi-professional soccer team.
The competition was the second startup pitch contest in the region in recent months.
In November, Capital One held a competition for Lighthouse Labs’ latest class at its West Creek campus. RoundTrip, a non-emergency medical transportation company, won the $5,000 prize. A few weeks later, RoundTrip went live in the Richmond market.
The Future of Automated Urban Farming by Babylon Micro-Farms
Alexander Olesen is Founder and CEO of Babylon Micro-Farms, developing automated hydroponic systems for the restaurant and hospitality industries that grow fresh, sustainable and organic food on-site.
The Future of Automated Urban Farming by Babylon Micro-Farms
February 17, 2018 AT 12:54 PM / BY ADMIN
Podcast: Play in new window | Download (Duration: 16:00 — 22.2MB) | Embed
Subscribe: Apple Podcasts | Android | Email | RSS | More
Alexander Olesen, Founder, and CEO of Babylon Micro-Farms joins Enterprise Radio to talk about his company and why technology and hydroponics will revolutionize the way we grow food.
Listen to host Eric Dye & guest Alexander Olesen discuss the following:
- What inspired you to start Babylon?
- How do you think hydroponics will change the way we consume food?
- Why should people be paying more attention to hydroponics in 2018?
- You are working on a new product, the Micro-Farm. What can you tell me about that?
- What are you most excited about for where Babylon is headed?
Alexander Olesen is Founder and CEO of Babylon Micro-Farms, developing automated hydroponic systems for the restaurant and hospitality industries that grow fresh, sustainable and organic food on-site. The idea was conceived in a Social Entrepreneurship class at the University of Virginia in 2015. Ever since then Babylon’s mission has been to make urban farming accessible to everyone and ensure a healthier and sustainable future.
Website: www.babylonmicrofarms.com
Social Media Links:
Facebook: www.facebook.com/BabylonMicroFarms
Twitter: www.twitter.com/BabylonMF
Pythium Root Rot on Hydroponically Grown Basil And Spinach
Pythium Root Rot on Hydroponically Grown Basil And Spinach
FEBRUARY 12, 2018 URBAN AG NEWS
by Neil Mattson for eGro (https://e-gro.org/pdf/E301.pdf)
Waterborne diseases that infect roots are a common production issue in hydroponic production. Several species of the water mold, Pythium, attack greenhouse crops. Basil and spinach are susceptible to economically devastating levels of Pythium root infection in hydroponics. In this article, we will present symptoms of Pythium infection and management strategies.
Many Pythium species, are generalists, meaning they can attack a wide range of plant species. Pythium aphanidermatum and Pythium dissotocum are two species commonly reported in hydroponics. Both species can produce zoospores, a mobile propagule that can propel itself through water.
Figure 1. Roots from basil growing in hydroponic rafts (deep water culture) exhibiting root discoloration from Pythium root rot. Photo: Neil Mattson, Cornell University
Symptoms of Pythium Root Rot
As Pythium infects and colonizes roots it can lead to a visible discoloration (browning) and decay of the root system (Figures 1 and 2). Overall root system development may be poor with few lateral roots or root hairs (Figure 1). Often the outer portion of the root (cortex) sloughs away leaving behind the inner part of the root (steele). This leads to the characteristic “rat tail” appearance of Pythium infected roots. The root system can eventually turn slimy and black.
Figure 2. Roots of baby leaf spinach growing in a Speedling tray in raft hydroponics infected with Pythium root rot. Notice discolored roots with poor branching. Photo: David de Villiers, Cornell University
Figure 3. Baby leaf spinach infected with low levels of Pythium root rot. Notice slightly discolored roots. No shoot symptoms are evident but overall plant size may be somewhat reduced. Photo: David de Villiers, Cornell University
Shoots of affected plants may not initially show symptoms of Pythium infection, however, the plants may be reduced in overall size (Figure 3). As the disease progresses, plants may become severely stunted and leaves may be chlorotic (yellow) which is often mistaken for a nutrient deficiency when it is really caused by poor root system development (Figures 4 -6). Plants may also wilt due to the inability of the root system to support plant water needs. At first, wilting may take place during only the hottest, brightest time of the day, but eventually wilting may become permanent.
Figure 4. Leaves of baby leaf spinach infected with Pythium aphanidermatum (A) are chlorotic and greatly reduced in size compared to uninfected control plants (B). Photo: Ted Alhanti , Cornell University
Figure 5. Hydroponic basil infected with Pythium root rot demonstrating chlorosis (yellowing) of leaves as well as stunted plants. Photo: Neil Mattson, Cornell University
Figure 6. Hydroponic basil showing varying degrees of plant stunting and chlorosis due to infection from Pythium root. Photo: Neil Mattson, Cornell University
Management
Once plants are infected, Pythium can be very difficult to control. Therefore the best approach to Pythium management is adopting a suite of practices that reduce or eliminate exposure to the disease organism, restrict its spread, and promoting environmental conditions that reduce disease proliferation.
Exclusion and Sanitation
There are several ways Pythium can enter greenhouse operations, including from: water (especially surface water sources), soil and plant residue from workers’ shoes, air-borne dust, greenhouse tools, previously infected plants/seedlings, and some container media. Follow good hygiene practices to limit entry such as: foot baths to sanitize shoots and boots, sanitization of tools, and inspection of new plant material prior to transplanting. If the water source is found to harbor waterborne disease a treatment system should be installed. Container media with organic matter (such as peat, coir, compost, etc.) can occasionally contain Pythium. Source materials from a reputable supplier with quality control procedures in place.
Because of the prevalence of Pythium it will be difficult (or impossible!) to completely restrict Pythium from hydroponic operations. Therefore, it is important to periodically sanitize surfaces that come into contact with plants or the hydroponic nutrient solution, such as: pond or NFT channel surfaces, irrigation tubing, tools, and carts or other receptacles used to hold plants or move them around. Sanitize containers or seedling trays before reusing. When sanitizing surfaces be sure to remove debris/organic matter first. Be sure to include inspection of plant roots in your routine IPM scouting practices. Toss infected plants at the first sign of Pythium. Don’t reuse growing media.
Environment
Environmental conditions that favor Pythium include excessively high fertility, waterlogged substrates (for example, in the seedling stage), low dissolved oxygen, and extreme temperatures. Injury to roots such as through mechanical damage, allowing roots to dry out, or extreme temperatures can provide an entry point to Pythium. Maintain a target root zone temperature of 68 to 75 °F (20 to 24 °C). Lower temperatures favor establishment of Pythium dissotocum and higher temperatures favor development of Pythium aphanidermatum. At Cornell University, we have found that use of a water chiller to reduce hydroponic pond temperatures to about 68 °F is an effective way to reduce, but not completely eliminate, Pythium aphanidermatum from ponds with baby leaf spinach. Low dissolved oxygen levels in hydroponics have also been reported to increase Pythium infection. Therefore it is important to ensure adequate aeration so as to achieve greater than 6 ppm dissolved oxygen and ideally saturated dissolved oxygen (about 8- 9 ppm O2) in nutrient hydroponic solutions.
Biofungicides
Biofungicides are microbial-based products that act to prevent disease development. Several commercially available products are labeled for control of root-disease of greenhouse vegetable crops, see the excellent e-Gro article on this topic here. Some of these materials are primarily suited for use in substrates (such as seedlings or larger plants growing in container media) while some are also meant for use in hydroponic nutrient solutions. Biofungicides should be used as a preventative control strategy before a problem arises (rather than as a curative). Always follow the product label, and be sure to check if a given material is registered for use in your state.
In summary, if you are growing hydroponic basil or spinach you will almost certainly come across Pythium. However, careful attention to your growing practices and sanitation procedures can limit this disease to an occasional annoyance rather than an annihilating nemesis.
References
- Penn State Extension. 2017. Pythium, online factsheet. Retrieved on January 23, 2018 from https://extension.psu.edu/pythium
- Raudales, R.E. and McGehee, C. 2016. Pythium root rot on hydroponic lettuce. e -Gro Edible Alert. Volume 1, Number 4. Retrieved on January 23, 2018 from https://e -gro.org/pdf/E104.pdf
- Raudales, R.E. and McGehee, C. 2017. Biofungicides for control of root diseases on greenhouse- grown vegetables. e- Gro Edible Alert. Volume 2, Number 7. Retrieved on January 23, 2018 from https://e -gro.org/pdf/E207.pdf
- Sutton, J.C., Sopher , C.R., Owen -Going, T.N., Liu, W., Grodzinski, B., Hall, J.C. and Benchimol, R.L., 2006. Etiology and epidemiology of Pythium root rot in hydroponic crops: current knowledge and perspectives. Summa Phytopathologica , 32 (4), pp.307 -321.
Publication date: 1/31/2018