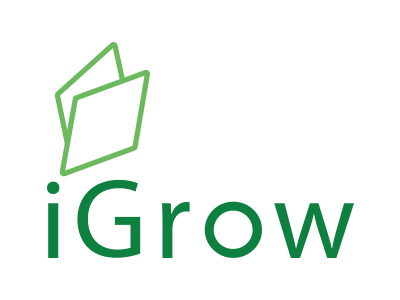
Welcome to iGrow News, Your Source for the World of Indoor Vertical Farming
Tech Connection Boosts NY Vertical Farmers
By AFP
24 February 2019
A Bowery Farming employee inspects some of their greens grown at the hydroponic farming company in Kearny, New Jersey
Workers at Bowery Farming's warehouse near New York have swapped out a farmer's hoe for a computer tablet that takes real-time readings of light and water conditions.
Launched in 2015, Bowery is part of the fast-growing vertical farming movement, which employs technology in a controlled, man-made setting to grow fresh vegetables indoors all year long.
Champions of the practice see vertical farming as a key tool to meet the world's food needs at a time when the population is rising and the climate is changing.
Irving Fain, CEO and co-founder of Bowery Farming, talks about his hydroponic grown greens
The company's chief executive and co-founder, Irving Fain, said his company's Kearny, New Jersey site uses fewer resources than traditional farms and does not employ pesticides.
"I have been a big believer my entire life in technology as being able to solve not only hard problems, but also important problems," said Fain, who previously ran a company that provides data analysis for big companies on their loyalty programs.
Bowery employs more programmers than agricultural scientists. The company says its use of algorithms enables it to be 100 times more productive per area compared with a traditional farm and to use 95 percent less water.
- Lower electricity costs -
Greens are grown at Bowery Farming, a vertical farming site founded in 2015
Vertical farming has long been practiced in Japan and some other places but it did not take off in the United States until recent technological leaps made it viable.
A key component has been LED bulbs, which have enabled indoor farmers to drastically cut electricity costs.
But Bowery is also making heavy use of robotics and artificial intelligence to keep prices under control.
Bowery makes heavy use of robotics and artificial intelligence to keep prices under control
The combination of these newer tools "is how we really rethink what agriculture will look like in the next century and beyond," Fain said.
The company has also benefited from more than $120 million in funding from tech titans including Google Ventures and Uber Chief Executive Dara Khosrowshahi.
The Silicon Valley connection has also boosted San Francisco-based Plenty, another prominent vertical farming company, which has garnered more than $200 million from Amazon Chief Executive Jeff Bezos, Softbank and others.
US-based Crop One and Emirates Flight Catering have launched a $40 million joint venture to build a giant vertical farming facility in Dubai.
- Profitable? -
AeroFarms co-founder and chief marketing officer Marc Oshima looks at baby kale
The world's biggest vertical farm is in Newark, New Jersey and operated by AeroFarms.
The company, founded in 2004 and considered a pioneer in the sector, remains privately-held and does not disclose financial data. But the company says it is now profitable after a series of fumbles.
David Chang, founder of the noodle restaurant brand Momofuku, is an investor.
AeroFarms exclusively uses company-made technology that has now made its way to China, the Middle East and Europe, said its co-founder Marc Oshima.
AeroFarms's vertical grow towers in Newark, New Jersey
In a warehouse that was once a steel mill with 40-foot (12-meter) ceilings, the company is growing kale and arugula leaves set in rows of 12 metal racks each. The roots are suspended in the air as they are intermittently irrigated while the leaves bask under LED lights.
AeroFarms experiments regularly with lighting and nutrients with an eye towards finding the optimal recipe for each plant and developing the best algorithm.
The company produces watercress that reminded a reporter of her grandmother's soup, kale as tender as spinach and arugula with a hint of spice.
Basil from Bowery Farming was tinged with the flavor of lemon.
But it can take a while for vertical farms to find solutions that are viable.
"The big, big vertical farms are having a difficult time being profitable because they are so capital-intensive at the beginning," said Henry Gordon-Smith, founder of Agritecture, a consultancy.
Large farms typically need seven or eight years before they are profitable, with smaller farms requiring perhaps half as long.
But entrepreneurs in the business are confident in their prospects as more young people in cities express worry about climate change and pesticides.
Baby kale is grown at AeroFarms
"Vertical farming is not THE solution to food security," said Gordon-Smith. "It is one out of the possible solutions."
Critics of vertical farming say it has a large carbon footprint due to heavy use of lighting and ventilation.
But defenders say that this negative impact is more than offset from the benefits of lower water use, the location near population centers and the non-use of pesticides.
A bigger issue may be the limitations of the output itself, at least in terms of nutrition.
"You can't feed the world with salad alone," said Princeton University plant researcher Paul Gauthier, who says vertical farmers will need to develop more protein-rich offerings.
Gauthier -- who grew spicier peppers in his own lab by subtly increasing potassium levels -- said vertical farming could supply fresh food to so-called food "deserts" where it is absent and could in the long-term meet growing food demand as the climate changes.
Does AI Hold the Key To A New And Improved “Green Revolution” In Agriculture?
Producing enough healthy food to feed the world—on a changing planet—is going to be a steep challenge. These researchers are giving farmers AI-driven techniques and tools to find solutions
Producing enough healthy food to feed the world—on a changing planet—is going to be a steep challenge. These researchers are giving farmers AI-driven techniques and tools to find solutions.
BY JACKIE SNOW | FEBRUARY 19, 2019 | NOVA NEXT
Automation in agriculture may soon make robots as common in greenhouses as they are on factory floors. Photo credit: Shutterstock
On a stretch of highway in the Netherlands not far outside of Amsterdam, a row of greenhouses at Wageningen University & Research (WUR) poke up like knuckles along the flat landscape. The Dutch university is known for its cutting-edge agricultural research, but some of these greenhouses recently ran an experiment that’s novel even for them: autonomous growing.
Stepping into a humid box from a brisk autumn day, you hear the noises of machines adjusting themselves mixing with the sounds of leaves rustling. The amount of light, water, fertilizers, and carbon dioxide—along with the temperature of the greenhouse—are all set by deep learning algorithms and executed by machines. Humans are still responsible for moving vines up the lattices as they grow, as well as pruning and harvesting.
But it’s pretty clear who—or rather, what—is calling the shots.
The Future of Farming?
By 2050, we’ll need to feed nine billion people with about a third less arable land than we had in the 1970s, experts estimate. Farmers will need all the help they can get, including insights gleaned from artificial intelligence, or AI. Developed carefully—and with the people who will be using it taken into account—AI can be part of the solution to feeding a growing world, according to the Refresh report, a document put together by researchers from Google, university professors, nonprofits, and farmers. And as an added bonus, some of the unsustainable practices developed over the past 70 years could be reversed with more efficient, AI-driven technology.
The Green Revolution was a set of advances that started in the 1950s in areas like high-yield crops, synthetic fertilizers, and irrigation technology that greatly increased food production, especially in developing countries—saving an estimated one billion people from starvation. But it left in its wake a culture of pesticides, reduced agricultural biodiversity, and overuse of chemical fertilizers that deplete the soil and poison waterways.
“It was never meant to be used in the long term,” says Danielle Nierenberg, the president of Food Tank, a non-profit working to build a better food system that also worked on the Refresh document. Farmers were supposed to transition back to organic, Nierenberg adds: It just never happened because increased yields generated by industrial-scale farming put pressure on smaller farms to follow suit.
One of the main ways AI could help agriculture transition out of practices forged in the Green Revolution and into a more sustainable future is with precision farming. Until now, there hasn’t been an easy way for farmers to learn from historical or real-time data. But AI-powered programs can combine data on weather patterns, crop yields, market prices, and more to guide farmers to planting at the right time, adding the appropriate level of fertilizers, and harvesting at peak ripeness.
In a greenhouse at Wageningen University & Research (WUR) in the Netherlands, cucumbers grow with the help of deep-learning algorithms and machines. Photo credit: Dr. Silke Hemming, WUR
WUR is one of the places where big data approaches to growing food are being tested. Last fall, five teams of AI researchers and biologists from around the world competed in growing cucumbers in separate 96-square-meter greenhouses, with a sixth grown manually as a reference. Each team trained its own algorithm, although the teams had the ability to decide how closely to follow the solutions that their AI models came up with. The teams kept an eye on their crops with sensors and cameras, and could feed the algorithms new data and tweak them as needed. To win, teams had to maximize total yield and net profits while minimizing the use of resources.
The winner was a team called Sonoma, made up of Microsoft Research employees and students from Danish and Dutch universities. According to Silke Hemming, head of the scientific research team for greenhouse technology at WUR, Sonoma’s plan used more artificial light earlier and kept carbon dioxide levels higher than a typical gardener might. But other teams also discovered counterintuitive ways to increase yield, such as pruning smaller cucumbers close to harvest or letting bigger ones have a chance to grow a little more.
Like all problems in AI, growing cucumbers and other crops by algorithm demands a food source of its own: data—and lots of it. The cucumber contest was a start at putting information together that other researchers can build on with future projects.
“You have a dataset you would never have,” Hemming says. “You can learn so much from that.”
The researchers organizing the competition chose cucumbers because they are a fast-growing crop cultivated worldwide, and problems like blight show up in them immediately. But this project could transform how other indoor crops are grown. It’s a first step in finding ways to combine humans and AI technology to produce more food, more efficiently.
“It’s not all about winning.” Hemming says. “It’s also about learning.”
FARMWAVE Founder and CEO Craig Ganssle uses its smartphone app with an automated kernel count feature to assess corn yield. Photo credit: FARMWAVE
AI on the Farm
“Farming is a lot more complicated than other industries,” says Joshua Woodard, an agricultural business and finance professor at Cornell and founder of the farming data company Ag-Analytics. “It’s a really complex system of environment and management practices."
Ag-Analytics’s wants to bridge that gap with easy-to-use data analysis tools to help farmers plan and monitor their fields. Their farm management platform takes data from sensors in John Deere farm equipment and combines it with other datasets, like satellite imagery and weather forecasts, to develop predictions for individual farms.
Algorithms working from afar could make a huge impact for less tech-heavy farms, too. Farmers in the developing world are working with minimal data and stand to make leaps in productivity with algorithms in the cloud instead of expensive machinery in their fields. According to the United Nations, 20 to 40 percent of crop yields are lost each year due to pests and diseases. AI tools like Plant Village and FARMWAVE allow farmers to take photos with their phones of sickly plants, bugs, and weeds, and then have computer vision-powered algorithms diagnose the problem from afar in seconds. FARMWAVE is already working with farmers in countries across the world, who, despite their distance, are all dealing with similar problems that AI can spot.
"Army worm in corn looks the same in Africa versus the U.S.,” says Craig Ganssle, the founder and CEO of FARMWAVE.
In India, a team at the International Crops Research Institute for the Semi-Arid Tropics (ICRISAT) is working on providing real-time pest predictionsto help Indian farmers take specific actions to protect their crops. ICRISAT uses cloud computing, machine learning, and data from IoT (short for the “Internet of Things”) sensors to come up with personalized predictions about pest risks.
Dr Avijit Tarafdar of ICRISAT converses with chickpea farmer Mr Srinivasa Boreddy in Adilabad District, Telangana. Photo credit: D Chobe, ICRISAT
“Whenever [farmers] see the pests in the field, they simply go for pesticides,” says Dr. Mamta Sharma, a principal scientist at ICRISAT. “It will help them reduce the amount of sprays that farmers are applying."
ISCRISAT has offices in Africa that could eventually use the tool, with interest coming from South America as well. As these offices collect more data, Sharma says, it could be used to spot new risks due to climate change.
“It helps us recognize emerging threats,” she says.
Robot Green Thumbs
Indoor farming currently occupies around 2.3 million square feet worldwide. But based on information from growers, the analysis firm Agrilyst predictsthis number will balloon to 22 million square feet over the next five years. Despite the expense of setting up these spaces and the limited types of produce that can currently be profitably grown, much of AI research is being done in greenhouses and other indoor spaces because, with the reduction of arable land, these production methods will become more critical. Indoor farming can also produce up to 20 times as much fruit and vegetables per square foot as outdoor farming, while using up to 92 percent less water, according to one study, with one company claiming it needs 99 percent less water.
In San Carlos, California, two robots cruise within a hydroponic farm developed by the start-up Iron Ox. These robots, which plan, care for, and harvest produce, are overseen by a computer program affectionately nicknamed “the Brain.” Even before the advent of AI, hydroponic systems were known to use less water, need fewer pesticides, grow faster, and produce more plants in less space. However, hydroponics are notoriously labor-intensive, requiring plants to be moved to different vats throughout the growing phase. Training robots for this monotonous task could make razor-thin profit margins a little less tight.
“A lot of things that weren’t feasible outside of a lab five years ago are possible now,” says Brandon Alexander, the CEO of Iron OX.
In the end, improved agricultural processes lead to better food options. And making small indoor farms more efficient could open up the possibilities of food grown closer to city centers. Most produce travels an average of 2,000 miles from farm to shelf in the U.S., which forces farmers to plant fruits and vegetables that can handle being transported—not necessarily those that taste good.
“Fresh produce isn’t that fresh,” Alexander says.
After improving its robotic systems, Alexander says, Iron OX’s long-term plans include breeding plants using data currently being gathered on its farm. Algorithms crunching this data and other local information, like what sells best, could replace tasteless, homogenized tomatoes and lettuce with more varieties suited to different communities’ tastes.
“We could make delicious, extra healthy things that people want to eat,” Alexander says.
Meet The Farmers Of The Future: Robots
A robotic arm lifts plants being grown at Iron Ox. Iron Ox has been talking to San Francisco Bay area restaurants interested in buying its leafy vegetables and expects to begin selling to supermarkets next year. (AP photo)
By: The Associated Press 2018
Iron Ox CEO Brandon Alexander looks out at his robotic indoor farm in San Carlos, California. Alexander builds robot farmers that roll through a suburban warehouse, tending to rows of vegetables. (AP photo)
SAN CARLOS, Calif. (AP) — Brandon Alexander would like to introduce you to Angus, the farmer of the future. He’s heavyset, weighing in at nearly 1,000 pounds, not to mention a bit slow. But he’s strong enough to hoist 800-pound pallets of maturing vegetables and can move them from place to place on his own.
Sure, Angus is a robot. But don’t hold that against him, even if he looks more like a large tanning bed than C-3PO.
To Alexander, Angus and other robots are key to a new wave of local agriculture that aims to raise lettuce, basil and other produce in metropolitan areas while conserving water and sidestepping the high costs of human labor. It’s a big challenge, and some earlier efforts have flopped. Even Google’s “moonshot” laboratory, known as X, couldn’t figure out how to make the economics work.
After raising $6 million and tinkering with autonomous robots for two years, Alexander’s startup Iron Ox says it’s ready to start delivering crops of its robotically grown vegetables to people’s salad bowls. “And they are going to be the best salads you ever tasted,” says the 33-year-old Alexander, a one-time Oklahoma farmboy turned Google engineer turned startup CEO.
Iron Ox planted its first robot farm in an 8,000-square-foot warehouse in San Carlos, California, a suburb located 25 miles south of San Francisco. Although no deals have been struck yet, Alexander says Iron Ox has been talking to San Francisco Bay area restaurants interested in buying its leafy vegetables and expects to begin selling to supermarkets next year.
The San Carlos warehouse is only a proving ground for Iron Ox’s long-term goals. It plans to set up robot farms in greenhouses that will rely mostly on natural sunlight instead of high-powered indoor lighting that sucks up expensive electricity. Initially, though, the company will sell its produce at a loss in order to remain competitive.
During the next few years, Iron Ox wants to open robot farms near metropolitan areas across the U.S. to serve up fresher produce to restaurants and supermarkets. Most of the vegetables and fruit consumed in the U.S. is grown in California, Arizona, Mexico and other nations. That means many people in U.S. cities are eating lettuce that’s nearly a week old by the time it’s delivered.
There are bigger stakes as well. The world’s population is expected to swell to 10 billion by 2050 from about 7.5 billion now, making it important to find ways to feed more people without further environmental impact, according to a report from the World Resources Institute.
Iron Ox, Alexander reasons, can be part of the solution if its system can make the leap from its small, laboratory-like setting to much larger greenhouses.
The startup relies on a hydroponic system that conserves water and automation in place of humans who seem increasingly less interested in U.S. farming jobs that pay an average of $13.32 per hour, according to the U.S. Department of Agriculture. Nearly half of U.S. farmworkers planting and picking crops aren’t in the U.S. legally, based on a survey by the U.S. Department of Labor.
The heavy lifting on Iron Ox’s indoor farm is done by Angus, which rolls about the indoor farm on omnidirectional wheels. Its main job is to shuttle maturing produce to another, as-yet unnamed robot, which transfers plants from smaller growing pods to larger ones, using a mechanical arm whose joints are lubricated with “food-safe” grease.
It’s a tedious process to gently pick up each of the roughly 250 plants on each pallet and transfer them to their bigger pods, but the robot doesn’t seem to mind the work. Iron Ox still relies on people to clip its vegetables when they are ready for harvest, but Alexander says it is working on another robot that will eventually handle that job too.
Alexander formerly worked on robotics at Google X, but worked on drones, not indoor farms. While there, he met Jon Binney, Iron Ox’s co-founder and chief technology offer. The two men became friends and began to brainstorm about ways they might be able to use their engineering skills for the greater good.
“If we can feed people using robots, what could be more impactful than that?” Alexander says.
Take A Look At America’s First Robotic Farm
December 30, 2018
America’s first robotic farm claims to use less energy than other modern forms of farming. The hydroponics system uses 90% less water than traditional farming and this is while producing 30 times more crops/ac.
The farm, which is just 8,000ft² in size, is said to take a human-led, robotics first approach. This, it says, allows plants to be grown at their best from seed to harvest.
By using the hydroponics system, the farm provides the same products all year round; which are not affected by seasonality.
What is hydroponics?
Instead of soil, plants are grown using a mineral nutrient solution and misting methods. LED lights are often used as the light source.
However, hydroponic farms require a lot of labour, such as transferring individual plants at different growth stages.
To see the robots in action, take a look at the video below.
Quality Produce
Iron Ox – the company behind the robotic farm – states on its website that: “Quality shouldn’t be a luxury or compromise.”
The company claims that it is “using robotics and intelligence to grow better food for less. In a way that uses less; less of what we can’t get back or can’t afford to waste.”
The farm plans to provide a secure food supply and access to premium produce for everyone.
According to reports, the farm plans to grow 26,000 heads of lettuce, greens and herbs. Restaurants will be the first port of call for the produce, which is set to hit the market soon.
Canadian Automated Vertical Farm Systems Developer Inno-3B Raises C$6m Seed Funding
Canadian vertical farming systems developer Inno-3B has completed its first seed round of financing at nearly C$6 million ($4.45m).
Located in Quebec and Ontario, the company provides turnkey vertical farming systems for a variety of customers, from researchers, biotechnologists, and small-scale farmers, to regional and multinational producers.
Inno-3B provides fully automated, controlled, scalable, and remotely monitored robotic growing systems with real-time support to help customers grow organic produce, berries, and herbs locally.
This week, the business benefitted from a seed investment round led by the Ecofuel Fund, with the participation of Desjardins Capital, the Fonds de Solidarité FTQ, Premier Tech, the Fonds de Solidarité FTQ Bas Saint-Laurent, Investissement Québec and the Ministère de l’Économie et de l’Innovation.
Inno-3B said that the C$6m will enable the business to implement a demonstration of its technology in the context of real-time operations, a move which is designed to accelerate product marketing and ensure constant support for customers. This will include creating 10 new jobs to advance the company’s design and manufacturing processes; the company already has 15 employees across its two locations.
“We are enthusiastic to start this new phase of development with such strategic investors dedicated to our success,” said Martin Brault, President and CEO of INNO-3B, adding that the Ecofuel Fund, Desjardins Capital and the Fonds de solidarité FTQ were, in particular, actively supporting the company’s growth.
Richard Cloutier, president and CEO of the Ecofuel Accelerator and managing partner of the Ecofuel Fund, said that Inno-3B’s innovative technology had the capacity to enable customers to produce vegetables with low production costs, high yields and low energy consumption, and to do so all in a small space.
“Innovation makes it possible for the company to respond to the growing needs of consumers for fresh quality products while also reducing greenhouse gases significantly,” he said.
In addition to accelerating Inno-3B’s marketing push, the new funding will also be used help to intensify R&D activities within the business.
“Thanks to the technological advances made in recent years, we have managed to position ourselves among the leaders in automated vertical farming,” said Brault, revealing that the company was also exploring certain ‘interesting synergies’ relating to artificial intelligence (AI) as part of its future development planning.
The Ecofuel Fund is a C$30m venture capital investment fund and accelerator offering customized training programs for clean technology companies. Powered by Cycle Capital, Ecofuel works with entrepreneurs to assist them in starting businesses to breakthrough internationally.
Ecofuel is funded by Investissement Québec, BDC Capital, Fondaction, the Fonds de solidarité FTQ and the Centre québécois de valorisation des biotechnologies (CQVB).
Desjardins Capital, working with a background of nearly 45 years expertise, is committed to the promotion and support of small and medium-sized businesses in Quebec, having assets under management of C$2 billion. The fund contributes to the sustainability of 460 businesses, cooperatives and funds operating in various sectors of activity and from all regions of Quebec.
The Fonds de solidarité FTQ is a capital development investment fund that is financed with Quebec savings. With net assets of C$13.7 billion as at November 30, 2017, the fund contributes to the creation and maintenance of 186,440 jobs, partnering with more than 2,700 companies and with more than 645,000 shareholders.
Related Stories
AeroFarms ‘Always in Capital Raising Mode’ as Vertical Farming Group Raises $20m
How Canadian Vertical Farming Company TruLeaf Aims to Prevent Disease Through Nutrition
Circular Economy and True Sustainability: the Next Phase for Vertical Farming
Association for Vertical Farming to Reveal Sustainability Certification Scheme at Summit
4 Things Every Investor Should Know About Vertical Farming: Lessons Learned From AVF Summit
What Do Investors Need to Know About the Future of LED Grow Light Technology?
Ag Industry Brief: FBN Makes Moves in Canada, Bayer Sells Digital to BASF, more
No Tractors Required! Britain's First 'Vertical Farm' Is About To Produce Its First Crop With The Help Of A Robot Named Frank Working In A Warehouse In Scunthorpe
And It Could Change Agriculture Forever
A 'vertical farm' in Scunthorpe has the potential to change agriculture forever
Only four human beings work at the vast warehouse, bathed in eerie pink light
It is designed to produce 500 tonnes of plants annually starting with fresh herbs
A single robot — called Frank — is responsible for gathering trays of plants
By GUY WALTERS FOR THE DAILY MAIL
PUBLISHED: 18 November 2018
Normally, November is not the month for the herb harvest in the British Isles, nor is an industrial estate in Scunthorpe the type of place you’d expect to find people gathering in crops.
Yet that is exactly what will be happening next Monday at a radically new farm — and it may just herald a sea-change in the way we grow our food.
Forget all those traditional images you have of agriculture: rolling fields, combine harvesters and lumbering tractors, even greenhouses and polytunnels.
Instead, picture something straight off a sci-fi movie set — a vast warehouse bathed in an eerie pinkish glow, filled with racks of plants stacked 40ft high and tended by a robot that glides about the floor.
It looks like a scene from a sci-fi movie. In fact, this Scunthorpe warehouse is the world’s most advanced ‘vertical farm’ — and its first harvest could change agriculture for ever
The few humans present on this farm look nothing like farmers. Instead of sporting favourite old pullovers or check shirts, they wear overalls, high-vis jackets and hairnets.
In short, this is less the Darling Buds Of May, more a laboratory from the distant future. Welcome, then, to the world’s most advanced commercial ‘vertical farm’.
It’s run by a new firm called Jones Food Company, and is designed to produce 500 tonnes of plants annually starting with coriander, basil, dill and chives to feed the growing appetite for fresh herbs all year.
The first crop was sown as recently as the middle of last month, and by next week, the initial batch will already have been harvested. Everything here is geared towards growing plants as quickly and efficiently as possible. And all without a single handful of soil.
At the heart of the operation is a technique known as hydroponics, whereby plants are grown under artificial light with their roots resting in a ‘hydroponic solution’ made up of water and essential nutrients such as potassium, calcium, nitrogen, nitrate and magnesium, instead of soil.
In the pink: Hydroponic herbs being grown under artificial light at the country's first vertical farm
During the growing process, the water is also periodically drained away ensuring the plants’ roots are able to ‘breathe in’ enough oxygen.
Almost the entire procedure is automated. A single robot — called Frank — is responsible for gathering up the trays of plants and taking them around the various parts of the farm, including the seeding and germination areas, and ultimately, the harvesting room.
In fact, only four human beings work in the vast warehouse. In order to avoid the plants being contaminated by micro-organisms that can cause diseases such as blight, they have to follow a strict handwashing procedure, after which they must don protective overalls. They then have to pass through an ‘air shower’ which blows off any remaining rogue particles.
All this is despite the fact that at no stage do any humans actually touch the plants themselves.
Pure carbon dioxide is pumped into the room, which enables the plants to absorb 50 per cent more than they would in a traditional greenhouse, causing them to grow faster than normal.
All the air that enters passes through medical-grade filters, and the pressure inside the warehouse is kept higher than the air pressure outdoors to stop insects getting in.
Rather than a brand new concept, Scunthorpe’s vertical farm is the latest step in the long-running attempt to find a way of factory farming plants indoors.
There are already a number of hydroponic farms in Britain. Thanet Earth, for example, south of Gatwick, has been operating for nearly a decade. In 2013, this facility alone produced 225 million tomatoes — around 12 per cent of the UK’s total crop.
In Clapham, South London, hydroponics and artificial lights are used to grow salad crops in former air raid shelters — an indicator of how valuable this technique could be in cities.
What makes the project in Scunthorpe so revolutionary — and so exciting — is the use of so many layers of plants and the high levels of automation which make managing them possible. The other great development from which the vertical farm has benefited has been the source of the artificial light.
At the heart of the operation is a technique known as hydroponics, whereby plants are grown under artificial light with their roots resting in a ‘hydroponic solution' made up of water and essential nutrients such as potassium, calcium, nitrogen, nitrate and magnesium, instead of soil.
Previously, sodium bulbs have been used which require enormous amounts of energy. This didn’t just negate many of the environmental benefits but also made operating the farms hugely expensive.
Back in 2010, one estimate put the electricity bill for growing the amount of wheat required for a just single loaf of bread via hydroponics at around £12.
All that has changed thanks to the widespread adoption of LED lights, which use far less power.
The farm in Scunthorpe boasts no less than 7.6 miles of LED lights, the equivalent of 38 Eiffel Towers laid end-to-end. Their pink glow illuminates a total growing surface area of 5,120 square metres — the size of 26 tennis courts.
The company’s co-founder and chief technology officer, Dr Paul Challinor, who has a doctorate in hydroponics and who did much of the testing of the lights at his own home, explains why his warehouse is lit in that eerie shade of pink.
‘The reason is because the plants grow best under red-and-blue light,’ he says, ‘although we also have white lights so that we can see what we are doing.’
The different-coloured lights have different roles to play during the plants’ life cycles. Red light helps to promote leaf coverage, whereas blue light promotes plant structure and leaf mass.
Dr Challinor says an order for his plants has already been placed by a customer who wants a ‘fresh product’, although he is tight-lipped about who it is. The plants are reputedly just as flavoursome as those grown in traditional soil, and it seems unlikely that any commercial customer would order several tonnes of herbs from the farm if they tasted bland.
Forget all those traditional images you have of agriculture (stock image)
In 1999, an American former professor of microbiology called Dickson Despommier claimed that a 30-floor skyscraper farm could one day feed 50,000 people.
By 2050 it is estimated around 86 per cent of people in the developed world will be living in cities and the world’s population is projected to have swollen from 7.7 billion today, to nearly ten billion.
Proponents of vertical farms have argued that as the food could be grown in the heart of cities, food miles — the distance it travels from traditional farms to consumers — could be all but eliminated, cutting greenhouse gas emissions and leaving us with fresher, tastier food.
The use of vertical farms also slashes the amount of land required to feed a growing population and saves us from having to use damaging pesticides and fertiliser.
Even better, because the inside of the warehouse is so closely controlled, vertical farms can grow crops all year, rather than following seasonal cycles. This also protects the crops from the frosts or droughts that can lay waste to traditional farms.
All this hinges on whether new technology has solved the problem of cheap and reliable artificial light.
It is too early to say whether the use of LEDs is, as the Agriculture and Horticulture Development Board claims, a ‘seismic shift that is set to change fundamentally how we grow plants’. For his part, Dr Challinor is nothing if not ambitious. ‘We have already looked at other sites in the Midlands and the South and hope to be running a number of units,’ he says, and claims the farm is taking ‘British horticulture to another level’.
At present, it is growing herbs because of their high retail value, and plans to diversify into growing salad leaves as well as high-value plants needed by cosmetic and pharmaceutical companies (that principle at least has been proved to work: many illegal cannabis operations grow the drug using hydroponics and artificial lights).
In future, it is hoped that other crops such as wheat and barley could be grown in warehouses rather than in open fields.
If Dr Challinor can manage that, then the sky really is the limit.
Robots, Hydroponics, 'Hands In The Dirt': A Look At Who — Or What — Will Feed Us In The Future
Play
November 19, 2018
This is the first in our series "Lab to Table: The Future of Our Food" exploring the future of food. Stories will publish every Monday from now until Dec. 17. In the spring, the series will continue with another week of stories.
Lettuce grows vertically in a controlled environment using LED lights and a hydroponic growth system in the Freight Farm Leafy Green Machine. (Jesse Costa/WBUR)
When you picture a dinner plate 20 or 30 years from now, what do you see? Lab-grown meat? Gene-edited crops? Superfoods? Or, something like Soylent?
Will fresh produce be part of that imagined future, or could agriculture end up forgotten, like in the movie "WALL-E" where a human character in 2805 thinks farmers once grew crops of pizza in the ground?
That scenario might not seem like science fiction if you consider the growing body of research on the threats of climate change. A recent U.N. report predicts temperature increases will cause extreme flooding, fires and drought that would impair our global food systems. Innovators across the food industry, including here in Massachusetts, are working hard on high and low tech solutions for feeding the planet.
Robot Farming
“We are building robots that care for crops and harvest their fruits,” Joshua Lessing, founder of Root AI, explains as he buzzes us through a set of doors at Greentown Labs in Somerville. It’s a “clean tech” incubator — the largest in the U.S. — that supports entrepreneurs focused on solving environmental problems.
“People are predicting CO2 levels are going to rise faster than we ever thought, ice melt is going to happen faster than we ever imagined,” Lessing says, echoing studies and conversations happening across the food industry. “The needs for food are larger than we ever conceived.”
There will be a lot of mouths to feed in the future. The world’s population is expected to reach 9.8 billion by 2050.
“I think a lot about what we can do here in Boston with all the talent we have,” Lessing says, “looking outward into the world: 'Are these problems that I myself can sit in my lab and fix?' ”
He hopes so, and he thinks his robots can help.
Lessing shows me a video of a Root AI prototype “bot” in action. It’s a buzzing, mobile, white metal box with a 3D-mapping camera and a unique arm. It’s got a gripper designed to delicately pluck fruits and veggies — like cherry tomatoes and strawberries — off vines without damaging their delicate flesh. The bot’s robust artificial intelligence can collect and analyze crop data to determine ripeness and reduce waste.
“Its nutrition, its disease, its yield forecasting, its harvesting,” he says. “Instead of having artificial intelligence figure out if there's an adorable cat in your friend's photo, it can see food that you want to eat.”
Lessing foresees robots like his working 24/7 — year-round — rolling along tracks in huge, indoor farms made of glass and polycarbonate. He points to vast greenhouse complexes in the Netherlands as models for the future. Dutch innovators have been wildly successful in carrying forward that country’s commitment to increasing agricultural production with advanced, sustainable growing systems.
Co-founder and CEO of Root AI Joshua Lessing holds his robot’s gripper. (Andrea Shea/WBUR)
Indoor farms are scattered throughout Canada and the U.S., too. Lessing thinks all metro areas should have versions of them.
They're climate-controlled and impervious to weather, AI would make them smarter, and they’d supply regional distribution centers that he says would help reduce CO2 emissions on a massive scale.
But talk of robots raises the inevitable question: Will robots replace humans?
Lessing says no, they'll help alleviate agricultural labor shortages. He cites the worker crisis California farms have been experiencing because of immigration policy. Lessing’s robots have been tested in that state, and he says Root AI will deploy its first wave of full-time AI workers next year.
It’s not the only Boston-area company bringing high tech to farming.
Hydroponic Farming
Two Freight Farms Leafy Green Machines sit stacked in a parking lot near their headquarters in the South End of Boston. (Jesse/CostaWBUR)
As you drive on Route 93 adjacent to Boston's South End you can spot two white and green shipping containers in a parking lot, one stacked on the other. The top box has the words, “THIS IS A FARM,” in capital letters painted on its exterior. Brad McNamara, CEO of Freight Farms, acknowledges it makes a novel, 40-foot-long billboard for his South End operation.
As he pulls open the door we are met with a chilly blast of ventilated air.
“This is a Leafy Green Machine,” McNamara says, “you step through the door and all of a sudden you smell it, you feel it, you taste it — you're in a farm growing acres’ worth of produce.”
The hydroponic farm is filled with rows of vertical columns packed with vibrant, edible greens – kale, arugula, Swiss chard. McNamara and his partner launched Freight Farms in 2010 to connect more people with farming on a micro-level, year-round.
“What we saw was an opportunity to allow more people to grow food locally, and reinvent or recreate the food system for the future,” McNamara recalls.
Everything can be managed within the turn-key farm’s four walls — from seeding to harvesting to feeding.
Leafy greens grow vertically in a controlled environment using LED lights and a hydroponic system in the Freight Farm Leafy Green Machine. (Jesse Costa/WBUR)
Containers of colorful, liquid nutrients flow through tubes to plants growing in polymer mesh, not soil. Energy-efficient LED light strips hang from the ceiling and water is recirculated through a drip irrigation system that can feed up to 5,000 plants with less than 5 gallons of water a day.
And there are growing “recipes” that Freight Farms COO Jon Friedman says can be custom-designed to perfection.
“Say you wanted a more purple color in your lettuce, you would have the blue lights on for longer. If you wanted them to grow faster you might put the red lights on for longer,” he says. “There's a lot of tuning you can do to get a desired effect.”
Then Friedman opens an app on his phone called “farmhand.” It controls the system remotely.
“Right away you'll see cameras that are placed in certain spots of the farm,” he points out. “So if you wanted to just see a quick view of how the lettuce is doing you could just pop in and see, ‘Do I need to transplant today or could I wait ‘til tomorrow?' ”
The "farmhand" app allows farmers to monitor and manage their farm from their phone. (Jesse Costa/WBUR)
So you could monitor crops from, say, the couch on a snowy day. With the app, farmers — be they citizens or professionals — can adjust settings and crunch data. It even offers a Spotify playlist with nature sounds and stimulating music.
The founders say their mission is to educate and get people excited about farming. But it’s also to help small, commercial farmers evolve into the future by adding hydroponic greens to their existing soil-based operations — like Karma Farms did in Maryland.
More than 210 Leafy Green Machines can be found around the world in 14 countries — in places like a farm in Guam that sells its greens to a couple of Wendy’s on the island; a pioneering urban farm in Brooklyn; Google’s campus in California; and at schools in Boston, Salem and elsewhere in Massachusetts. And this year, the company launched a program called "Grown By Freight Farms" that even adds a farmer to help with daily maintenance 20 hours a week.
Watercress seedlings sprout beneath LED lights inside the Leafy Green Machine. (Jesse Costa/WBUR)
The cost of the shipping containers, like other farming equipment, is tax-deductible, but you’d need about $85,000 to buy one. Even so, Friedman sees a future where every workplace, urban neighborhood and farm could have one.
“In our earlier phase of agriculture, as a society, we built everything around it, but now we've gotten so distant from it at the same time,” he muses. “It’s going to be interesting to see how technology helps bring it closer to us and make that more of our experience.”
But technology is only part of the solution for Jennifer Hashley.
“To what end are we going to have all this great technology if we don't have people that can afford to start these businesses?” she asks.
Soil Farming
Jennifer Hashley, director of the New Entry Sustainable Farming Project, grabs a handful of peppers for farm share orders in Lowell. (Jesse Costa/WBUR)
Hashley runs the New Entry Sustainable Farming Project at Tufts University where future farmers learn all aspects of the business of local agriculture.
“We still need people to have their hands in the dirt," she says. "As much as we want to rely on technology for advances in productivity and knowledge and data and efficiencies and to save labor — all those things are wonderful — but we're still going to need people to understand natural ecosystems."
Standing in a warehouse on the outskirts of Lowell, some of the students in the program, alongside volunteers, box up all kinds of fresh veggies, from carrots to jalapeños. They were grown on incubator farms the students manage. Some are for CSAs (Community Supported Agriculture farm shares) and others are being packed to go to homes for the elderly and other partner institutions.
Daniela Marzuca, left, and Dalia Rosas of Whitemars Farm in Dracut weigh 1 lb bags of carrots at the New Entry Sustainable Farming Project in Lowell. (Jesse Costa/WBUR)
The 20-year-old New Entry program teaches students — many of them immigrants — about the realities of a career in sustainable farming. They also learn about soil management and being stewards of the earth’s fragile ecosystem.
Hashley says there's a long list of barriers to getting into farming – everything from high estate taxes that prevent farming families from passing down land, to over-development, to a lack of agricultural policy. She points to the stat that about 1 percent of workers in the U.S. are involved in agriculture. Hashley believes people have lost reverence for where our food comes from.
New Entry student Jorge Marzuca feels farming is one of the noblest professions.
“We think the future of farming is small farms, CSAs,” he says, adding that farmers should diversify their crops and rotate their fields.
As Marzuca sorts and weighs peppers, he explains that he and his wife, Daniela, moved to the U.S. from Mexico where they worked on a 200-acre broccoli farm.
“Mexican farmers are used to just doing one crop,” he says, speaking of the practice that’s known as monoculture. “You stick with broccoli, you stick with strawberries. And now we're seeing the side effects of that. More erosion, less products and you have to put more fertilizer in.”
Jorge Marzuca is eligible to lease land on a training farm in Dracut through the New Entry program. (Jesse Costa/WBUR)
Now Marzuca wants to farm differently by growing a wide variety of crops and selling them locally and directly to people in his community. This, he says, will help open more people’s eyes to the benefits of sustainable agriculture. Still, the 34-year-old farmer sees tech in his future.
“We have to combine and find the balance between labor and technology because a lot of people need jobs,” Marzuca says, “but we also need technology to be better farmers.”
Industrial agriculture is one of the world's largest polluters. Everyone interviewed for this story agrees: The more sustainable farming there is — in fields, shipping containers, greenhouses, backyards and even on balconies — the better off we, and the planet, will be.
(Jesse Costa/WBUR)
Correction: A previous version of this article misstated the number of Leafy Green Machines that exist in the world. The story has been updated. We regret the error.
This segment aired on November 20, 2018.
Andrea Shea Senior Arts Reporter
Andrea Shea is WBUR's arts reporter.
Agbotic Expands With Five New Robotic Greenhouses
SEPTEMBER 30, 2018
SYDNEY SCHAEFER / WATERTOWN DAILY TIMES
Construction is underway on Thursday on a major expansion to the robotic produce grower Agbotic in Sackets Harbor.
SACKETS HARBOR, NEW YORK — John P. Gaus plans to grow his automation-driven farm Agbotic Inc. fivefold with larger, more advanced greenhouses all in operation by early 2019.
Workers began building Mr. Gaus’s five new 18,000-square-foot greenhouses in July and have already constructed three of them at its County Route 75 farm where the company grows organic root vegetables and hemp. The foundation has also been laid for the other two, he said.
“Actually, the project is going very well. We’re on schedule,” said Mark W. Manns, president and COO of Agbotic.
The greenhouses will include the company’s signature robotic gantries, or self-navigating tilling, watering and harvesting machines, but will also feature more advanced automated technology to help gather and use more data, Mr. Gaus said.
Mr. Manns said acquiring more data with the upgraded technology will allow Agbotic to implement more optimal climate settings for produce growth, which the team can control in the greenhouses.
The expansion also includes a food washing and packing building, a cogeneration facility to power the greenhouses and plans to retrofit the first greenhouse with new technology.
“To the extent you think about an automated greenhouse as a machine, we’ll be driving that machine to machine learning and artificial intelligence,” Mr. Gaus said.
Mr. Gaus launched Agbotic in 2014 with his first 15,000-square-foot robotic greenhouse equipped with the gantry, climate controls and organic soil.
The prototype greenhouse has produced 40,000 to 60,000 pounds of food annually, but adding five larger facilities could increase the company’s annual yield to 240,000 or 320,000 pounds of food, if not more. Mr. Manns said the company could ship more product to its existing service markets in New York City, Watertown, Alexandria Bay, Syracuse, Utica, Rochester and Buffalo.
“The current greenhouse has the capability of growing year round. However, the new greenhouses will be more capable of doing it through better control measures,” Mr. Manns said.
The growth at Agbotic also comes with a growth in staff, with Mr. Gaus saying he wants to hire 10 or 11 more full-time workers.
“We’re particularly focusing on veterans leaving the military,” he said about hiring.
Despite multiplying the footprint of his operation, Mr. Gaus considers the advancement only the beginning of what he aims to accomplish with Agbotic.
The engineer and entrepreneur said he wants to replicate the success experienced by producers in the Netherlands, who also use controlled environmental agriculture. The European country generates $15 billion from agricultural product sales, Mr. Gaus said, while New York, which is about three times larger, brings in $5 billion from agriculture.
“The first greenhouse was very much a prototype to prove out the concept, and the next six greenhouses are just a small step in where we want to be,” Mr. Gaus said. “New York State is our initial focus area, but our investors are very interested in building a very big company with clusters (of greenhouses) throughout the United States.”
Agbotic also recently bolstered its operation by adding hemp to its product line. The state welcomed the company into the Industrial Hemp Agricultural Research Pilot Program, which permits farmers, businesses and institutions to research large-scale hemp production, in November. After initial testing, the firm dedicated an entire 300-foot soil bed in its greenhouse to growing hemp.