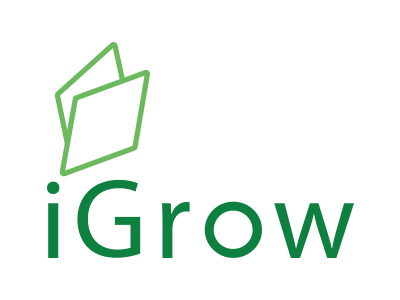
Welcome to iGrow News, Your Source for the World of Indoor Vertical Farming
21 Reasons To Start Container Farming In 2020
With container farming, you are not limited to the crops that grow naturally in a location or crops that are seasonal
January 3, 2020
The beginning of a new year is a great time to pick up new hobbies, interests and maybe even start a new career!
If you’ve been thinking about getting into container farming, there has never been a better time.
In this article, you’re going to learn 21 reasons why you should start container farming in 2020.
Let’s get started!
1. Be your own boss! One of the main benefits of container farming is that you make the rules. You decide what you grow, and how you grow it. Starting a container farm can be a side hustle to make a little more money or it can become a new career! It’s really all up to you.
2. Create your perfect lifestyle. Are you struggling with finding the right work/life balance? Starting a new career in container farming could be the perfect solution. You’ve probably heard the saying “If you love what you do, you’ll never work a day in your life.” With container farming, you can turn your passion into a real, sustainable business.
3. Stop sitting all day. It’s been said that “sitting is the new smoking.” Starting a container farm business will get you out from behind a desk. With container farming, you will be working in your container every day! Planting, harvesting, and monitoring your crops. Starting a container business is a great way to move away from a sedentary lifestyle towards a more active one!
4. Support your local community. Starting a container farm business is really starting a local food business. As a container farmer, you will be selling mostly to your local community at farmer’s markets, local restaurants, and even local grocery stores that want to add fresh local produce to their selections. Through this process, you will get to know your local community as you provide them with fresh, delicious nutritious food!
5. Help people eat healthier! Locally grown food is fresher, more nutritious, and safer! When you sell local produce, you grow in your container farm, you are improving the health of your community. Especially if you live in what’s known as a food desert. A food desert is an urban area where it can be difficult to buy affordable or good quality food. Food deserts happen for a variety of reasons from harsh climates that make it difficult to grow produce to communities not having good quality roads to allow in food trucks. With a container farm business, you can set up shop in a food desert and be the only supplier of quality affordable produce.
6. Save water. Container farms use less water than traditional farming techniques. Traditional farming is responsible for 80% of the entire US’s water usage! What you might not know is that growing a normal head of lettuce using traditional farming, uses a whopping 3.5 gallons of water! Now contrast that with a head of lettuce grown on a container farm which only uses about 1/10th of a gallon of water total! Every head of lettuce grown with a container farm saves more than 3 gallons of water! And as we all know water is a consumable resource, not a renewable one, so every gallon of water saved helps the planet in a big way!
7. Give people safer food. Remember when Chipotle had that E-coli outbreak in 2016? How about in November of 2019, when an E-coli outbreak got so bad that it lead to the recalling of Romaine lettuce in California? Just because the food comes from a supermarket or a fast-food chain doesn’t make it safe. In fact, a quick google search for “produce recalls” will show you exactly how unsafe some of the food you are being sold truly is. When you start container farming, you can be sure that you are providing safe food that won’t make people sick.
8. Save money on taxes. Starting a business is tax-deductible. That means that you can write off or depreciate a portion of all the money you spend on your container farm business.
9. Fill a missing niche in the market. Most produce is grown and sold seasonally, which is why cherries, for example, are only available for a very short time period. But when you use a container farm, you don’t have to worry about seasons or weather. That means that you can harvest crops that would normally be out of season, filling a niche in the existing food marketplace in your city.
10. Join the local food movement. According to Wikipedia “Local food movements aim to connect food producers and consumers in the same geographic region, to develop more self-reliant and resilient food networks; improve local economies; or to affect the health, environment, community, or society of a particular place. The term has also been extended to include not only the geographic location of supplier and consumer but can also be “defined in terms of social and supply chain characteristics.” For example, local food initiatives often promote sustainable and organic farming practices, although these are not explicitly related to the geographic proximity of producer and consumer.” By starting a container farm, you join with the local food movement in your city.
11. Provide jobs to your local community. When you start a container farm business, you’re going to need some help. Which means you will be providing jobs to your community. But more than that you will be creating a sustainable, beneficial job that helps bring safe, nutritious, healthy food to your community. That’s what we call paying it forward.
12. There are therapeutic benefits to farming! Gardening has long been renowned for its relaxing qualities but there are tangible therapeutic benefits to farming as well. “A ten percent increase in nearby green space was found to decrease a person’s health complaints in an amount equivalent to a five-year reduction in that person’s age” according to the Gardening Matters nonprofit of Minneapolis’ page, “Multiple Benefits of Community Gardens.” Farming also reduces stress! An experiment published in the Journal of Health Psychology compared the relaxation benefits of reading and gardening and found that farming subjects experienced more relaxation than those that read.
13. Grow food across generations. With a container farm, you can spread your love for farming to your parents, kids, and even grandkids. A container farm business is perfect for anyone of any age who wants to learn more about growing food. Some container farm owners we know even set up camps to teach kids how to farm and earn a nice profit in the process! Plus, you can pass down your container farm to your kids just like any other business.
14. Container Farms can be set up and ready to go in a few hours. With most business opportunities you must wait a long time to get started. For example, if you were to buy a McDonald’s franchise, you would need to wait for the permits, construction, hiring, and delivery of equipment like fryers and soda machines. But with a container farm, you can have everything set up and ready to deploy in just a few hours. No muss, no fuss.
15. Manage your crops from your smartphone. With regular farming you need to get out there and see what’s going on with things like pests, watering and monitoring ph. levels. With a container farm, you can monitor everything from your smartphone with the growlink app.
16. Grow more food in less space. Another reason to start container farming in 2020 is that you can grow a lot of food in a little space. With an 8 X 40 container farm you can harvest up to 400lbs of herbs or leafy greens per month!
17. Save on water and energy. Container farming is WAY more energy efficient than traditional farming! A report by Urban Agnews showed a Swedish based company Spisa Smaker saved 48% more electricity than when compared with traditional farming! Additionally, using a closed-loop irrigation system like those found in most container farms saves around 50% more water than traditional farming as well. Container farming helps you save money and consume fewer resources while producing high-quality food.
18. Reduce your footprint by planting without soil. One of the main reasons traditional farming uses so much space, energy and water is because it requires soil. Every crop planted using traditional farming monopolizes the land that they are planted on at least for the growing season if not forever. Soil can also affect where and when you can and cannot plant crops. For instance, areas with limited soil, icy or snow-covered soil or even soil that has become contaminated can be difficult for crops to grow in. But with a container farm, you don’t have to worry about the soil at all! With a hydroponic system like the ones, we use here at Pure Greens AZ plants absorb nutrients directly from a water-based nutrient delivery system.
19. Grow pesticide and herbicide-free crops! With traditional farming, you’ll need to use pesticides or herbicides to protect your crops from a variety of pests. Most farmers do this with pesticides or herbicides. Now some of these pesticides are natural and not that harmful, while others like Roundup have been linked to cancer. With container farming, you can use all-natural pesticides like Neem leaves, salt sprays, and Eucalyptus oil. Growing crops without harsh pesticides and herbicides is a great way to produce safer food for your community.
20. You can grow a wide variety of crops. With container farming, you are not limited to the crops that grow naturally in a location or crops that are seasonal. Container farming allows you to grow a wide variety of crops based on what you want to grow, not other factors like soil conditions or weather patterns.
21. Experience fast and consistent growth. Container farms can grow crops incredibly quickly as you can see in this video of the Pure Greens team harvesting 14 lbs. of Kale in an hr.! But it’s not just speed, container farming also allows you to grow crops consistently in areas where otherwise you would not be able to like areas with heavy winters or food deserts!
There you have it 20 great reasons why you should start container farming in 2020!
And if you need some help or want to learn more about the state-of-the-art turnkey container farms, we build here at Pure Greens head over to our website or give us a call at 602–753–3469.
US: Minnesota - Shipping Container To Grow Year-Round Veggies At CLC
The project consists of an insulated shipping container outfitted with a complete hydroponic growing system able to provide numerous Minnesotans with fresh, leafy greens year-round. Partners include Todd-Wadena Electric Cooperative, Lakewood Health System, Great River Energy, the Electric Research Power Institute and CLC
By: Brainerd Dispatch | Jan 18th, 2020
A crane places a 'Sota Grown hydroponic growing system at its new home on the Central Lakes College Staples campus. The system will produce year-round leafy greens. Submitted photo
STAPLES — Central Lakes College’s Ag and Energy Center in Staples is the new home of ‘Sota Grown, a collaborative indoor agriculture container farm project.
The project consists of an insulated shipping container outfitted with a complete hydroponic growing system able to provide numerous Minnesotans with fresh, leafy greens year-round. Partners include Todd-Wadena Electric Cooperative, Lakewood Health System, Great River Energy, the Electric Research Power Institute and CLC.
Following the installation of the container farm, CLC students will receive hands-on training to plant, maintain and harvest the growing crops, the first of which will be kale, ready to be harvested 10 weeks from planting. The kale will then be delivered to Lakewood for its Food Farmacy program that feeds more than 600 people monthly.
Great River Energy, Todd-Wadena Electric Cooperative and Electric Research Power will collect data throughout the process for electricity load planning, technology evaluation, and beneficial rate design analysis.
“Efficiencies with indoor food production and hydroponics will be critical as we look to feeding a growing global population that will surpass 9 billion in a few decades,” Keith Olander, CLC dean of agriculture studies, said in a news release.
The ‘Sota Grown project is part of a national indoor crop production demonstration effort that looks at how using efficient electricity, technology, plant sciences, and control solutions to create microclimates can produce ideal conditions for plant growth, yield, quality, and consistency.
Growing produce locally for area communities will also reduce the distance to market — a significant factor for Todd and Wadena counties since they are impacted by food deserts — thereby reducing net greenhouse gas emissions. Leafy greens generally travel an average of 2,000 miles before reaching a store, according to the release.
A ribbon-cutting event where the public will be able to view and tour the container farm will be this spring.
Those interested in following the process from seedlings to the first harvest can do so on the ‘Sota Grown Facebook page.
US: Montgomery, AL - Local Restaurant Farms Out of Shipping Container For Fresher Produce
They say necessity is the mother of all invention. For a Montgomery restaurant group, a shipping container turned out to be the solution to their problem
Freight Farm Up And Running
In Midtown Montgomery
By Jennifer Horton | January 16, 2020
MONTGOMERY, Ala. (WSFA) - They say necessity is the mother of all invention. For a Montgomery restaurant group, a shipping container turned out to be the solution to their problem.
Eric Rivera is the executive chef for Vintage Hospitality, which runs Vintage Year and Vintage Café. He was struggling to find fresh, sustainable lettuce options for his restaurants.
“We found that importing all the stuff from California or from Florida, we would get these lettuces after they’ve been harvested for days and sometimes almost a week by the time we get to them,” Rivera explained. “The product goes bad really fast costs a lot of money to replace that product with other product, it’s just not that quality that we were looking for.”
Enter the Freight Farm, an unassuming shipping container housed in the heart of Old Cloverdale - only steps from his restaurants. The 320 square-foot farm is equipped to grow up to 4 tons of produce a year, according to the manufacturer. It runs on power and minimal water consumption, a stark contrast to the water needed to farm traditional row crops.
“We can control all the elements and control the growth cycles,” he explained. “No rain, no hail, we’re not exposed to any elements.”
Which means they can grow a variety of greens year-round while decreasing the carbon footprint of cross-country supply chains and the threat of lettuce recalls.
“We feel like that it’s our responsibility in the restaurant industry not only provide healthy, nutritious food; but that is done in a socially conscious way as well,” stated Rivera.
High-Tech Farm In Shipping Container Cutting Growth Time In Half
A shipping container and a lot of ingenuity -- is changing the way produce is grown. "It's a 3.4-acre farm inside a 320 square foot shipping container," explained Dale Speetjens, CEO & Co-founder ShipShape Urban Farms.
To View The Video, Please Click Here
MOBILE, Ala. (WALA) -- A shipping container and a lot of ingenuity -- is changing the way produce is grown.
"It's a 3.4 acre farm inside a 320 square foot shipping container," explained Dale Speetjens, CEO & Co-founder ShipShape Urban Farms.
Calling it a "Business in a Box" -- Speetjens gave us a tour. Inside the container garden was several varieties of lettuce in various stages of growth.
"Inside here right now it's a balmy 70 degrees and it's this temperature whether it's 100 degrees outside or 30 degrees," said Speetjens.
Every variable is controlled by a computer system.
"This here is I would say the brain of the container... This is actually the control," said Carlos Augusto, VP of Marketing ShipShape Urban Farms.
From the temperature, PH levels, lighting, and right amount of water -- Augusto manages the day to day operations using hydroponic technology.
They're able to recycle the water - using only 10% of what a traditional farm uses and cutting down the growth time from 10 weeks to five weeks. The process all starts with employees planting seeds into individuals cells.
While they're seeding each cell by hand -- machines will eventually take over the process. The seedlings are then placed into the nursery section of the container.
Each container is designed for one person to work about 15 to 20 hours a week. The containers producing 1,200 heads of lettuce weekly.
INFORMATION BOOK
"So one of the steps we did to help is to make more efficient. We developed these lids and all the farmer needs to do to harvest is to pull the lid out and they harvest all the lettuce at once," Augusto demonstrated.
Each container costs $95,000 and upward. Debuting their prototype in New Orleans at the Louisiana Restaurant Association Expo in August -- ShipShape Urban Farms generated a lot of interest.
"Over 3,000 people walked through garden close to 300 to 400 people say they were interested in becoming a ShipShape Urban farmer," said Speetjens. "Eventually we'd like to create a network of urban farmers where all of us work together to produce food for our local communities.
Because it's all done on the computer and backed up every 15 minutes on a server -- ShipShape can monitor every stage of growth and share success stories with other farmers. There's also an app that allows the farmers to control settings from their phones.
"We will be able to monitor all the urban farms through the computer system -- not only to assist them but if we have a container that is producing more than average -- we can contact that farmer and share their experience with other farmers," explained Augusto.
The company hopes to build about 850 over the next five years. So far they have more than 30 orders and say while their focus is on the southern region of the U.S. -- they've had interest from as far away as the Galapagos Islands, India, Canada, and South America.
VIDEO: The Indoor Farming Revolution
Growing crops in shipping containers could drastically reduce the economic and environmental costs of farming
Growing crops in shipping containers could drastically reduce the economic and environmental costs of farming.
Source: CNN
US: Colorado - Students At Mountain Vista High School Were Ready To Start The Year By Getting Their Hands Dirty Via The Agricultural Business Course
For the past two years classes and interns have operated the Mountain Vista Farm, which utilizes a hydroponic growing system called the Leafy Green Machine
By James Conlan / Ag Journal
October 16, 2019
Students at Mountain Vista High School were ready to start the year by getting their hands dirty via the Agricultural Business course taught by David Larsen.
“As part of the program, students are responsible for all aspects of the Mountain View Farms business,” Larsen said.
After being introduced to the different business principles, students are tasked with integrating them into running a successful business. Some of these tasks include marketing, social media/website, communications, graphic design, printed literature, handling of money/accounting, customer service, food safety, and business plan development.
“Agriculturally, they have to figure out all of the elements including environment, nutrient, tech, engineering, and automation to keep the plants alive and healthy for sale,” he said.
For the past two years classes and interns have operated the Mountain Vista Farm, which utilizes a hydroponic growing system called the Leafy Green Machine.
“I think hydroponics is far more sustainable and reliable than traditional farming for the crops we can grow,” he added. “This technology produces absolutely delicious products that are fresh and last multiple times longer than what is sold in stores.”
He said utilizing this machine involves more people in the local production of food, potentially builds community and is a great educational tool for life skills. For students of his Agricultural Business class he said they gain soft skills in terms of being a good employee including punctuality, engagement, responsibility, as well as a good representation of the business to the public.
Another added element to the Leafy Green Machine is the ability of students to use the app Farmhand App.
“When we first started Freight Farms, we considered ourselves a hardware platform – but our views quickly expanded for two reasons,” Freight Farms CEO, Brad McNamara said.
The first reason was when he and co-founder Jon Freidman realized their clients needed a way to stay in contact with their farms remotely. The second reason was that they wanted to address a historical challenge in the farming world. Which they said was the lack of reliable and transferable data between farms to increase overall agricultural efficiencies.
“At the time, there wasn’t a turnkey hub for industrial-scale IoT, few if any climate-control apps for hydroponic indoor growers, nor a sophisticated way to bridge the gap between emerging IoT technology and old programming control language,” he said.
So building from the ground up, he said that they developed an integrated software platform called Farmhand. Which would enable its users to monitor and manage farm components remotely, automate tasks and analyze growing data.
“As IoT technology has evolved over the years, we’ve continuously integrated new updates and advancements to help our customers operate increasingly efficient farms with the touch of a button,” he said.
Consumers of Freight Farms products don’t just include schools, according to McNamara their tech has been used at restaurants, nonprofits, retail establishments, hospitality organizations and corporate employee benefit programs.
“We’ve been focused on taking the most advanced hydroponic technology and making it approachable. Enabling people of varying ages, experience levels, and industries to become successful food growers,” he said.
Farming Food In A Freight Container
An old shipping container arrived on campus last fall. From the outside, it was an innocuous-looking, beige structure that might have fallen out of the sky. The inside, however, contains one of the most innovative farming systems in the world
An old shipping container arrived on campus last fall. From the outside, it was an innocuous-looking, beige structure that might have fallen out of the sky. The inside, however, contains one of the most innovative farming systems in the world.
The shipping container is what is called a freight farm. Produced by Freight Farms, a company founded in 2010 and headquartered in Boston, the container is 320 square feet and contains an advanced hydroponic growing system, meaning that its plants are grown in a mineral nutrient mix instead of soil. The King’s freight farm was installed behind Atair House in November and subsequently painted by students from the Middle School.
The goal of the freight farm is to maximize food production while minimizing water use and the distance between the farm and the site of consumption. At capacity, the freight farm can grow 3,000-5,000 maturing plants simultaneously — the same amount of food that could be grown on two acres of farmland. Yet the farm uses fewer than 10 gallons of water per day, a reduction of about 90 percent, according to Freight Farms Client Services Director David Harris.
Called the Leafy Green Machine by Freight Farms, the unit produces greens for the Dining Hall. “Right now, it’s producing spinach, kale, chard, and romaine,” says Director of Operations Ola Bseiso. While capable of growing other types of vegetables, the Leafy Green Machine is designed specifically to produce greens. And thanks to a staggered schedule, the farm will yield fresh greens every day.
Seeds are first placed under light for two weeks until they become sprouts. Then, during the seedling stage, the plants grow deep roots and begin to show leaves, taking three weeks to fully mature.
When mature, the vegetables are harvested in the morning and placed in the Dining Hall for consumption in the afternoon.
The freight farm’s lettuce will pair nicely with the surrounding crops. “On one side of the freight farm, there is a large fruit tree section — apples, peaches, and other fruits,” says Bseiso. “And to the left are around 25 soil beds with various plants. And the best part is: it’s all organic!”
Beyond its beneficial nutritional and environmental effects, the freight farm offers ample opportunities for learning.
“You can see the entire process of plant growth happening, from the seedling all the way to harvest,” says Harris.
Dima Kayed, head of the Physical and Life Sciences, says that teachers of chemistry and biology intend to incorporate the freight farm into their classes, including looking at the dynamics of plant growth, types of plants, lighting, testing water quality, and other elements.
In addition, the trajectory of Freight Farms offers a case study for entrepreneurial students: eight years ago, the freight farm was only an idea, and now it is a full-fledged, successful product with a presence in nearly 20 countries.
Harris is hopeful that King’s students will gravitate to the freight farm. “You should care where your food comes from, as it doesn’t just appear on your table or plate,” he says. “There’s an entire industry built around it. Students can now understand the food system from a sheltered, air-conditioned box.”
But it’s not just about looking at the food; it’s about eating it. So if you find yourself in the Dining Hall, grab some lettuce from the salad bar, because odds are it’s the freshest salad you will ever eat.
Thinking Outside The Box: RIT Hydroponic Farm Changes The Dining Experience
The lettuce is tasting fresher at RIT’s main campus since the university installed a hydroponic farm-in-a-box behind the Student Alumni Union
September 23, 2019
A. Sue Weisler
Inside the 40-foot-long farm-in-a-box, farm manager Dave Brault harvests some leafy greens. By using a vertical hydroponic system, Brault is able to maximize the farms growing space.
The lettuce is tasting fresher at RIT’s main campus since the university installed a hydroponic farm-in-a-box behind the Student Alumni Union.
Made from an upcycled freight container, the new RIT Hydroponic Farm will provide fresh produce for the chefs who serve nearly 14,000 meals on campus every day. So far, the farm has produced roughly 40 pounds of greens since farm manager Dave Brault started harvesting in early August. Once Brault establishes a consistent growth cycle, he hopes to harvest roughly four times per month.
A. Sue Weisler
Produce from the farm is already being used in Brick City Café and by RIT Catering. In the future, the produce will be used at all dining areas on the main RIT campus.
Rather than using soil to grow plants and provide them nutrients, plants on a hydroponic farm get everything they need from water. Using a vertical hydroponic system for RIT’s farm, Brault anchors the seedlings in a breathable mesh that allows for water flow, and he hangs them from the ceiling in long containers to maximize space.
RIT is one of few universities in the United States that has implemented a hydroponic garden to help sustain its dining needs. Stony Brook University, the University of Arkansas and Clark University have also had success using the same hydroponic set-up RIT adopted, purchased from Freight Farms.
“It helps us stand apart from other universities. This is how we keep RIT and RIT Dining at the forefront of innovation,” said Denishea Ortiz, director of strategic marketing and retail product management for Auxiliary Services. “It is one of many steps that we have taken to highlight the fact that RIT has an innovative campus beyond the classroom.”
Right now, Brault is focusing on growing smaller, leafy greens like basil, cilantro, kale, arugula and different varieties of lettuce. Going forward, he will get feedback from RIT chefs to see what types of produce are in high demand.
“This is square one and from here we have a huge opportunity to turn this farm into something lasting and impactful,” said Brault. “Hopefully, other universities will see that it can be done and that the logistical challenges in implementing something like this are not insurmountable.”
Gabrielle Plucknette-DeVito
Emma Junga, a third-year mechanical engineering student with a concentration in energy and the environment, works at the farm a few days a week. After taking a tour of the farm, Junga was interested in the process and asked Dave Brault for a job. Now, she helps care for the plants, including planting and harvesting, and helps give tours to help share information about the new farm.
Ortiz explained that the goal is to provide produce for all dining facilities on campus. Before they can roll things out on a larger scale, Brault and RIT Dining are experimenting with the growth cycles and outputs to learn what the farm is capable of.
The greens from the hydroponic farm are currently supplying produce for Brick City Café and are being used by RIT Catering.
“Brick City Café is known for its salad bar, thus the proximity of the farm is a chance to provide a literal farm-to-table experience,” Ortiz said. “The produce is fresher and contains more nutrients.”
Before coming to RIT, Brault built and established his own hydroponic farm in the Finger Lakes region of New York. Brault said he looks forward to the unique opportunities the university can provide with its plentiful resources of man-power, brain-power and technological innovations.
“Farming is not something that most people would think involves a lot of technology, but the industry needs these advances to address the challenges that are coming our way,” he said. “I think RIT will continue to find ways to innovate and use technology to help farmers move forward.”
Indoor Farming, Crop Monitoring, Pathogen testing Showcased
Six of the nine companies have been featured in recent editions of Agri-View. This article features the final three companies – Alesca Life, Farm X, and ProteoSense
Lynn Grooms lgrooms@madison.com
September 23, 2019
A container-farming system developed by China's Alesca Life features monitoring, automation and climate control. It was developed for food processors and food retailers.
Nine startup companies were chosen to participate in the 2019 SVG Ventures-Thrive Accelerator Program. Silicon Valley Global Ventures, known as SVG Ventures, is a venture capital, innovation, and investment firm. The Thrive Accelerator program invests in mentors and connects startups with investors and businesses for partnerships.
Six of the nine companies have been featured in recent editions of Agri-View. This article features the final three companies – Alesca Life, Farm X, and ProteoSense.
Alesca Life of Beijing has developed various indoor-farming systems. Its container-farming system features monitoring, automation, and climate control. It was developed for food processors and food retailers.
The company also has developed a small cabinet farm for on-site food production in restaurants and schools. The compact system is suitable for growing micro-greens and other leafy vegetables.
Small cabinet farms for on-site food production in restaurants and schools are offered by Alesca Life.
Contributed
“Our target is that customers will see a return on their initial investment within four years,” said Stuart Oda, co-founder, and CEO of Alesca Life.
Stuart Oda is the co-founder and CEO of Alesca Life, which has developed various indoor-farming systems.
Contributed
Another of the company’s indoor-farming systems is “Alesca Sprout.” Developed for hydroponic farms its sensor-based system automates irrigation and other farm electrical equipment.
The Alesca Cloud is a smartphone-based supply-chain-management system. It aggregates operational tasks, farm capacity and production data, operational inventory, environmental sensor data, and other data points.
“Indoor farming is one of many ways to produce food in a hyper-efficient and localized way,” Oda said. “Just as there are different modes of transportation for different types of travel needs, indoor farming is a mode of food production optimized for certain geographies and crop types. As indoor vertical farms become more productive and efficient they’ll be able to produce larger volumes and varieties of vegetables.”
Alesca Life’s turnkey food-production systems enable even inexperienced growers to produce vegetables. The company wants to ensure its customers have positive experiences with indoor farming so it provides troubleshooting for the mechanical and electrical aspects of its systems, Oda said.
Farm X of Mountain View, California, provides growers monitoring and analysis to improve crop productivity. Bill Jennings, chief technical officer for Farm X, discussed the company’s tiers of service in June at the Forbes AgTech Summit.
Bill Jennings
A basic service that Farm X offers involves weather monitoring. The company collects data from the National Oceanic and Atmospheric Administration, the California Irrigation Management Information System, IBM’s Weather Underground and other third-party sources. The company combines the data with imagery from satellites and unmanned aerial vehicles to help growers monitor crop health and performance.
The next tier of service involves the use of in-ground sensors placed every 5 acres to monitor crop health as well as irrigation performance. Farm X combines that information with its models to help growers ensure uniform distribution of irrigation water and reduce electrical costs associated with irrigation pumps.
The third tier of service is a yield-management program. Farm X forecasts crop conditions about three to four months in advance of harvest. That enables growers to improve harvest planning such as how many workers will be needed for harvest. Growers also can use the forecasts to inform their supply-chain partners about future sales, Jennings said. The company’s focus to date has been in California’s vegetable-production areas.
ProteoSense of Columbus, Ohio, has developed a portable biosensor that detects foodborne pathogens such as Escherichia coli and Listeria monocytogenes. Mark Byrne, president and CEO of ProteoSense, has several years of experience working in the medical-device industry. But he saw the need for rapid detection of pathogens in food production and processing.
A portable biosensor developed by ProteoSense detects foodborne pathogens.
Contributed
ProteoSense’s biosensor has been in testing at Taylor Farms of Salinas, California, a large producer of fresh-cut vegetables. The biosensor was first tested in a food-packing house where Listeria monocytogenes can live on countertops, floor drains, coolers, and other equipment.
Food producers have traditionally taken swabs of suspect areas to send samples for laboratory testing. Food producers often need to wait for three days to a week before receiving test results. The ProteoSense biosensor can be used on-site to provide immediate results, Byrne said. Using the biosensor a food producer would take swabs mixed with a buffer. The buffer is placed into the biosensor. The device then displays results and transmits them for storage in the “cloud.”
Mark Byrne
There could be several uses for the biosensor. In addition to being used to detect pathogens on vegetables the biosensor could be used to test irrigation water and ponds for E. coli, Byrne said.
“We’re working with the Pork Checkoff to learn if the biosensor could help pork producers,” Byrne said. “We want to talk with more farmers about how they could use pathogen testing.”
Visit alescalife.com or farmx.co or proteosense.com or thriveagrifood.com or www.forbes.com/series/forbes-agtech-summit -- and search for "agtech summit" -- for more information.
Lynn Grooms writes about the diversity of agriculture, including the industry’s newest ideas, research and technologies as a staff reporter for Agri-View based in Wisconsin.
Videos: Freight Farms - Container Farming
To learn more about how to get started with your own Freight Farm go to Freight Farms, or to inquire about a pre-owned Freight Farm Container go to iGrow News
FREIGHT FARMER SPOTLIGHT: PATRICK STOFFER
In a lot of ways, Patrick Stoffer isn't your average 28-year old. To start with, he is a hydroponic farmer, but perhaps even more unusual, he is roommates with a 90-year old, Harrie, just one of the members of his community he is passionate about serving. Patrick lives at Humanitas Independent Senior Living Facility in Deventer, The Netherlands. In exchange for room and board, Patrick spends time with the residents, who help him grow, harvest and prepare the fresh produce from his Freight Farms operation, Grow Local. To learn more about how to get started with your own Freight Farm go to Freight Farms, or to learn more about pre-owned Freight Farm LGM container, got to iGrow News.
GROW FOOD HERE: SPRINGDALE, ARKANSAS | VET VEGGIES
4 STEPS TO GROWING IN OUR CONTAINER FARM
FREIGHT FARMER SUPPORT
MEET THE FARMERS AT AGORA GREENS
2015 LEAFY GREEN MACHINE BY FREIGHT FARMS
INSIDE A SHIPPING CONTAINER VERTICAL HYDROPONIC FARM
INTRODUCTION TO THE LEAFY GREEN MACHINE
FREIGHT FARMS X KARMA FARM
THE STORY BEHIND FREIGHT FARMS
INSIDE THE LEAFY GREEN MACHINE
Farm Stores To Open New Locations Constructed From Old Shipping Containers
05/07/2019
Farm Stores rendering
MIAMI — Farm Stores will introduce its latest drive-thru convenience store in Scott, La., next month that will be made from two repurposed shipping containers.
Made from the two repurposed shipping containers melded together and painted to look like a red and white bar, the 640-square-foot store is the first franchised Farm Stores location in the state, CNN reported.
"When I moved to Louisiana, there was a drive-thru everything. To me, a drive-thru store is so convenient, especially when you have kids in the car," commented owner Robert Pressler.
Florida-based Farm Stores opened its first location in Miami in 1957 with a 350-square-foot drive-thru that sold fresh food like milk, butter, bread, eggs and ice cream. Customers would order at the window and an employee would then walk out to their car and deliver the items.
"In the 1950s, Americans were already going to drive-in theatres and drive-in diners. The idea emerged to replicate this model in convenience stores," explained Maurice Bared, Farm Stores owner and CEO, who noted the drive-thru concept was inspired by the pop culture of the time.
Today, the convenience store chain has 65 locations in the Sunshine State and its stores' footprint has nearly doubled over time to maintain its mission to cater to the needs of busy parents by providing dairy goods sourced from local farms, household cleaning products, detergents, pet food, baked goods that are made on-site and freshly squeezed juices.
"This is mom's neighborhood convenience store and we stock it with her in mind. … Speed and freshness is key," Bared said. "From the time a car pulls up and a customer orders bread, it takes less than two minutes to bake it and deliver it to them. Same thing with freshly squeezed orange juices."
Farm Stores was turned into a franchise in 2015, with 28 of the 65 Florida locations franchised. Inspired by his experience in construction, Bared came up with the idea to expand the concept nationwide in a low-cost, environmentally friendly manner by building all new stores in repurposed shipping containers.
"I had this vision of a Farm Store in a container for two reasons. First, the shoebox layout of a container is the same exact size as our stores," he said. "I also grew up in the construction industry with my father having his own business. It's where I saw the foremen had converted shipping containers into their offices."
Over the next seven years, he hopes to have as many as 600 new Farm Stores under development. More than half of those are already underway in New York, New Jersey and Connecticut, according to CNN.
"The majority of new stores are being built in shipping containers, but the local building codes and ordinances won't allow it in some places,” the CEO noted.
Farm Stores outsources the construction to shipping container manufacturers regionally to reduce transportation costs. According to Bared, recycling shipping containers this way is about 40 percent cheaper than building a store from the ground up.
The repurposed store is manufactured using two containers and features tiled floors, sliding glass doors and a canopy over the roof. The inside includes a baking station and employee bathroom.
Once the containers are delivered, the store is welded into place on a concrete foundation.
"The containers are very strong and made to withstand inclement weather, even hurricane force winds," said Bared, adding that the sustainable and eco-friendly building concept is also easy to maintain.
Pressler's Louisiana store will be the first to debut the shipping container model. The owner, who is an area representative for Farm Stores, hopes to open as many as 50 stores over the next few years, CNN reported.