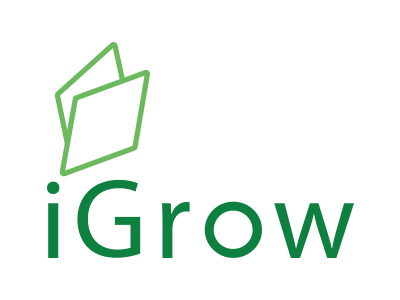
Welcome to iGrow News, Your Source for the World of Indoor Vertical Farming
Forums And Online Toolkit || Urban Edible Spaces: Growing Food And Happiness In Sustainable Community
HKU Edible Spaces (港大可食空間) has developed an Online Toolkit about urban farming and we hope that it would help those who are interested to start an urban community garden/farm
HKU Edible Spaces (港大可食空間) has developed an Online Toolkit about urban farming and we hope that it would help those who are interested to start an urban community garden/farm. In addition, two forums discussing the positive impacts of edible spaces are now put online (English and Chinese subtitles will be available soon)
Celeste Shai, Senior Programme Officer - General Education
CEDARS, The University of Hong Kong
For any enquiry, please feel free to contact me at cymshai@hku.hk.
USA: Wisconsin’s Largest Indoor Farm Soon Will Operate In Ripon
Ernessi Farms has come a long way since its 2013 origins as a small hydroponic garden in business owner Bryan Ernst’s basement
July 7, 2021
Ernessi Farms owner Bryan Ernst looks over some of the plants growing inside the farm’s new location at 111 East Fond du Lac St. Joe Schulz photo
Ernessi Farms has come a long way since its 2013 origins as a small hydroponic garden in business owner Bryan Ernst’s basement.
The business is continuing to blossom downtown and will be moving operations to a new location in the coming weeks, which, when fully operational, will be the biggest vertical farm in the state.
Ernessi Farms is finalizing the transformation of the former Market Fresh Foods building at 111 East Fond du Lac St. into an indoor farm in the heart of Ripon’s historic downtown.
In addition, the relocation will more than quadruple Ernessi Farms’ production capacity.
The move and building renovation were made possible by a Community Development Investment (CDI) Grant from the Wisconsin Economic Development Corp.
Ernst and his staff recently began transplanting seedlings into a new robotic system and are expecting their first harvest at the new location in about five weeks.
In approximately two weeks, Ernst says employees will work primarily in the facility on East Fond du Lac Street, rather than Ernessi Farms’ location in the basement of 325 Watson St., which eventually will be closed.
“As soon as we are able to be here full time, we’ll start a slow transition where we’re breaking the racks down and sterilizing everything before we bring it over here,” Ernst said. “Once everything’s out of that building, we will be done in that location; [111 East Fond du Lac St.] will just be our only location.”
Ernessi Farms combines hydroponics with vertical organic farming. Plants grow without soil on shelves, utilizing mineral nutrient solutions and lights.
Because the farm uses a controlled environment, it can change the level of nutrients and lighting that plants receive to enhance smell, taste and other characteristics.
Plants grow inside Ernessi Farms’ new facility at 111 East Fond du Lac St. Ernessi Farms utilizes a combination of hydroponics and vertical farming. Joe Schulz photo
For example, manipulating the wavelength of light basil plants receive enhances leaf size and reduces stem size, Ernst noted.
“We’re able to control every aspect down to levels of nitrogen, air movement, wavelengths of light to give the plant the optimum growing conditions possible,” he said. “That gives us larger yields and faster turnover of crops. And we guarantee that everything is delivered within 24 hours of harvest.”
Years before operating a farm in the heart of downtown Ripon, Ernst’s passion for hydroponic and vertical farming originated during his time in the Marines.
“When you’re deployed to a lot of impoverished areas around the world, you see how hard of a time people have getting access to clean water and food,” Ernst said. “That really got me thinking, ‘There’s got to be a better way to grow food closer to urban centers, where we’re not transporting it cross country, and you can grow year round.’”
Plants grow inside Ernessi Farms’ new facility at 111 East Fond du Lac St. Ernessi Farms utilizes a combination of hydroponics and vertical farming. Joe Schulz photo
Soon after, Ernst had the idea to start experimenting with hydroponics and vertical farming
As a geologist by trade, Ernst first had the idea to grow plants in his basement utilizing hydroponics. He worked with fellow geologist Tim Alessi to start Ernessi Farms in 2013.
“We designed water treatment systems for groundwater pollution and experimented with different types of wavelengths of light and varying levels of nutrients for plants,” Ernst said of the early days.
At the time, both men quit their jobs and started the company in Green Bay because Alessi lived in Door County and Ernst in Ripon.
About six months later, Ernst bought Alessi out of the company. Ripon Main Street Inc. Executive Director Craig Tebon connected Ernst with the owners of 325 Watson St., who were interested in renting the basement.
As a result, Ernessi Farms moved operations to Ripon, where it has been for roughly the last six and a half years.
In 2019, he caught wind that local entrepreneur John Maczuzak was interested in selling 111 East Fond du Lac St.
Ernessi Farms owner Bryan Ernst looks at the mushroom incubation area, which was once the grocery’s stores former meat area. Joe Schulz photo
As Ernessi Farms worked to research it’s financing options, Tebon informed Ernst that Ernessi could be eligible for the CDI grant, which ultimately helped fund renovation costs and asbestos remediation.
In applying for the grant, Ernst said the farm received help from Tebon, Envision Greater Fond du Lac, as well as Tom and Mary Avery of Ripon College.
“Had it not been for Ripon Main Street and Craig Tebon, there’s no way we would have gotten the CDI grant,” he said.
Ernessi Farms’ facility in the basement of 325 Watson St. has about 6,000 square feet, with fewer than 3,000 square feet for the grow area.
Meanwhile, the building on East Fond du Lac is about 21,000 square feet, enabling the shelving for plants to go from four to seven shelves high.
Ernst says the move quadruples production for plants and sextuples mushroom production.
The move comes at an opportune time as vertical farming is starting to boom with big money figures like Amazon founder Jeff Bezos and Goldman Sachs investing in the industry, Ernst noted.
He says Ernessi Farms’ latest expansion won’t be the last for the business. Ernst plans to build another location in western Wisconsin in the next year or two.
“The industry is definitely here to stay; the last report that I read said that by 2050 the industry should be worth over $30 billion,” he said. “We’re seeing a lot of growth in the industry, and you always have to stay one step ahead. That’s why we’re expanding.”
Ernessi Farms supplies products locally to Webster’s Marketplace and Crossroads Market. Its products also are in 27 Festival Foods and the Wisconsin Food Hub Cooperative.
Ernessi Farms recently began transplanting seedlings into a new robotic system and are expecting its first harvest at the new location in about five weeks. Joe Schulz photo
Ernst said the business is in talks with other grocery store chains, as well as with food distributors.
To help meet an increasing demand, he says the new facility will implement robotics and automation equipment that utilize machine learning.
“The more efficient we can make the system, the more competitive we can be with traditional agriculture,” Ernst said. “That’s why we’re really investing a lot of time and resources into automation and artificial intelligence.”
Lead photo: Ernessi Farms owner Bryan Ernst looks over some of the plants growing inside the farm’s new location at 111 East Fond du Lac St. Joe Schulz photo
Tags Bryan Ernst Ernessi Farms Company Economics Commerce Agriculture Industry Finance
Written By
Joe Schulz
Joe Schulz served as the reporter of the Green Laker in 2019 and 2020, before being hired as a reporter for the Commonwealth in October 2020. He is from Oshkosh and graduated from UW-Oshkosh in December with a bachelor's degree in journalism.
BrightFarms Launches “BrightLabs” Innovation Hub
BrightFarms, the leading grower of indoor leafy greens, today announced the formation of BrightLabs, a world-class innovation and research hub launching at its Ohio growing facility
BrightFarms Accelerates Indoor Farming Innovation Tenfold with the Formation of R&D Hub Led by Bayer Veteran and Greenhouse Expert “BrightLabs” will expand the company’s focus on the development of biotechnologies that increase the profitability of its indoor farming operations and deliver breakthrough product innovations
IRVINGTON, N.Y. – BrightFarms, the leading grower of indoor leafy greens, today announced the formation of BrightLabs, a world-class innovation and research hub launching at its Ohio growing facility. Matt Lingard, PhD, a former Bayer plant scientist with over 15 years of experience working at the intersection of biotechnology and greenhouse science, will lead the BrightLabs team as Vice President of Agriculture and Science.
“The indoor farming industry is at an inflection point as local, indoor-farmed produce becomes a priority for retailers and consumers. Among competitors, we’ve developed the most profitable model for the production of indoor leafy greens, but it’s essential that we maintain our market advantage to stay ahead of the curve,” said Steve Platt, BrightFarms CEO. “We’ve built up a team of the best minds in indoor agriculture to officially launch BrightLabs, where we’ll develop the next phase of game-changing products and technology solutions for our operations.”
BrightLabs is one of the most advanced biotechnology ventures in the indoor farming industry, with a key focus on developing proprietary & patented ecosystems for plants to thrive, increasing their flavor, yields and texture in the process. The team will be comprised of the strongest minds from the food and agriculture industry, bringing together experts in technology, microbiology and plant science to deliver breakthrough innovations in the salad category and beyond.
“No other indoor farming company is studying a plant’s microbiome, the naturally occurring bacteria that help determine its health, to the same degree that we are,” said Lingard. “Instead of pouring dollars into artificial lighting research, we’re developing cutting-edge biotechnology solutions to out-maneuver our competition with the most productive indoor farms in the industry. There’s no question that high-tech greenhouses that leverage natural sunshine have emerged as the most promising new generation of agriculture technologies, and optimizing the microbiome will allow us to unlock even more of a plant’s natural potential in our indoor farms.”
This multi-million dollar R&D investment is launching as part of the company’s $100MM Series E Fundraise led by Cox Enterprises, and represents a tenfold increase in the company’s research capabilities. Ten percent of the company is now dedicated to developing complex, patented growing solutions to be applied to BrightFarms’ burgeoning network of greenhouses.
Already known for proprietary research on growing spinach in a hydroponic system, BrightLabs aims to double its production of the crop, which is the industry’s best-selling tender leaf variety. BrightFarms will also build on the success of its best-selling Sunny Crunch variety with a new, industry-first antioxidant-rich lettuce, NutriGreens, set for release this June. BrightOS, the company’s award-winning proprietary data system, will help the BrightLabs team accelerate their research with machine learning and advanced data analysis.
BrightFarms’ five greenhouses – located in Ohio, Virginia, Illinois, Pennsylvania, and North Carolina – cover 1.2 million square feet and produce 9 million pounds of fresh lettuce annually. By the end of 2021, BrightFarms leafy greens will be available at over 3,500 stores, more than any indoor farming company in the industry.
To learn more about BrightFarms and their fresh produce offerings, visit www.brightfarms.com.
About BrightFarms
BrightFarms is the leading provider of locally grown packaged salads, serving the freshest, tastiest and most responsibly grown produce to consumers nationwide. BrightFarms operates hydroponic greenhouse farms in the communities it serves, enabling it to eliminate time, distance, and costs from the food supply chain. BrightFarms’ growing methods, a model for the future of scalable, sustainable local farming, use far less energy, land, and water than long-distance, field-grown agriculture. Forbes has recognized BrightFarms as one of the “100 Most Consumer-Centric Companies” and Fast Company has recognized BrightFarms as “One of World’s 50 Most Innovative Companies” and one of the “Top 10 Most Innovative Companies in Food.” BrightFarms is funded by leading investors Cox Enterprises, Catalyst Investors, WP Global Partners and NGEN Partners. For more information, please visit www.brightfarms.com.
High Hopes For Aquaponics System Inspired By Sewage Treatment
“Our work shows that this type of cultivation is not only more sustainable, but it is also capable of providing nutrients in a form that is easily accessible to plants
by The Fish Site
30 June 2021
A novel water purification system inspired by sewage plants has been shown to be effective at optimizing fish waste for use as fertilizer for plants in aquaponics facilities.
In a recent study, researchers demonstrated that the system could improve nutrient remineralization for the plants, while removing excess nitrogen and carbon from the system, creating a healthier environment for fish.
The study, published in Frontiers in Plant Science, was undertaken by researchers from the Department of Marine Sciences at the University of Gothenburg and involved the production of rainbow trout and lettuce.
As lead author, Victor Lobanov explained to Frontiers Science News: “Fish sludge is a waste product made up of uneaten food and fish feces and is normally broken down by bacteria in the water. In addition to physically harming fish gills, excess carbon in the solids leads to excessive bacterial growth – diminishing oxygen in the water and hampering the ability of the fish to breathe. We wanted to find out whether this waste could be used to fertilize plants in aquaponics systems by removing the excessive carbon, yet preserving the minerals needed for growing crops.”
The researchers investigated a potential solution inspired by sewage and wastewater treatment plants found around the world, called enhanced biological phosphorus removal (EBPR). They adapted it so that the risk of bacteria build-up in the water was reduced, but the minerals from the fish waste were soluble in the water and could therefore be biologically available for plants to take up.
They found that their solid treatment system was as effective at delivering nutrients from the fish waste to the aquaponic system as a commercial nutrient solution. Although the fertilizer did not meet plant needs entirely, as some nutrients such as manganese were missing, the researchers hope to optimize this system in future studies.
“Hopefully we can scale the system more efficiently in the future, not just for lettuce as used in this study but as well as for other plants, with the right number of fish corresponding to the size of the system. By further optimizing the breakdown of fish solids by the solid treatment system, we can also achieve a faster treatment rate and make the whole process more efficient,” explained Lobanov.
Commercial fertilizer solutions often have very high levels of nitrogen, stimulating crops to swell and absorb large amounts of water and giving the appearance of improved growth but often decreasing the amounts of minerals in the plant. Despite the fertilizer created by the solids treatment system containing lower levels of nitrogen than commercially available chemical fertilizers, plants were not nutrient deficient. This suggests that the high nitrogen levels commonly used are in excess of what the plants need. The authors hope that this finding will stimulate further research into the connections between plant nutrients, health, and taste,
“Our work shows that this type of cultivation is not only more sustainable, but it is also capable of providing nutrients in a form that is easily accessible to plants. Farmers can take this system and optimize it for their specific crops and production volumes, potentially even supplementing with additional nutrients if required,” said Lobanov.
Lead photo: The aquaponics facility where the trial took place. © Victor Lobanov
Urban Crop Solutions SpaceBakery Project Wins First Place At Global Space Exploration Conference
The winning SpaceBakery project is an interdisciplinary cooperative research project between seven partners, of whom, Urban Crop Solutions is the lead vertical farming technology and research partner
The Global Space Exploration Conference (GLEX) took place in St. Petersburg in June 2021. The conference brought together several leaders and decision-makers in the international science and space exploration community. Urban Crop Solutions and partners were selected to present two projects of the 250 that were presented during the conference. The SpaceBakery project was awarded the first-place prize.
Organised by the International Astronautical Federation (IAF) and Roscosmos (the Russian space agency responsible for space flights and aerospace research), the conference gathered several international stakeholders from the science and space exploration community, on a year which marks the 60th anniversary of Yuri Gagarin’s spaceflight.
The winning SpaceBakery project is an interdisciplinary cooperative research project between seven partners, of whom, Urban Crop Solutions is the lead vertical farming technology and research partner. The objective of the consortium is to develop the next generation of bread products to support future space missions and aid the long-term survival of settlers on Mars, in addition to being applicable for modern agriculture. The overall goals and objectives of the consortium were presented by the Puratos Group (Belgium), the leading commercial partner of the SpaceBakery project.
Urban Crop Solutions also presented another joint project, the ‘variable climate biosphere’ that they have designed. The variable climate biosphere is a macro life support system that aims to create the best-suited environment for humans and plants to thrive together during extended periods of isolation, either on another planet – namely, the moon and Mars – or on earth in an underground shelter. The presentation showcased the 3D renderings, as well as the results that have so far been obtained.
“Our approach to partner with ambitious global industrial groups and research institutions for controlled indoor farming solutions is finally paying off. We feel that we are at the cutting-edge with our technology, products and services in the fast-emerging urban farming industry – whether it is in space, in cities, on the surface or beneath it.” – Maarten Vandecruys, CTO and co-founder of Urban Crop Solutions
ABOUT UCS
Urban Crop Solutions is a Belgium-based pioneer in the fast-emerging technology of indoor vertical farming. It has developed over the past six years, 220+ plant growth recipes in its research centre in Waregem, Belgium. To date, UCS has delivered over 25 projects in multiple global locations. Their farms are being operated both for commercial and research purposes. Uses range from the production of leafy greens, microgreens, and herbs for food retail, service and industrial use, and scientific research across multiple institutions.
Website: www.urbancropsolutions.com
Facebook: www.facebook.com/urbancropsolutions
Twitter: www.twitter.com/U_C_Solutions
LinkedIn: www.linkedin.com/company/urbancropsolutions
For more information on this press release, on Urban Crop Solutions and their products and services, or the SpaceBakery project, you may contact Maarten Vandecruys, Serge Ameye or Lucie Beckers.
Maarten Vandecruys
Founder & CTO, UCS
maarten.vandecruys@urbancropsolutions.com
Serge Ameye,
Space, Tunnels & Special Projects, UCS
serge.ameye@marsbakingsociety.space
Lucie Beckers,
Research Manager Agronomy, Puratos Group
LBeckers@puratos.com
Is Vertical Farming Cost Effective?
The technological change caused a shift in farming from conventional to container farms. Currently, farming is turning to vertical farms
The technological change caused a shift in farming from conventional to container farms. Currently, farming is turning to vertical farms.
The more exciting part is that this time round, key economy participants such as Amazon, Google’s Eric Schmidt are pumping money into the trending farming method.
Since it is a new technology, many investors are still unsure about its profitability. They have several questions on vertical farming’s viability. That is to enable them to have a better understanding of the technology.
One of the most typical questions is whether vertical farming is cost-effective. The most straightforward answer is yes. Vertical farming is cost-effective if done on a large scale.
Here, you will find out differences among the core farming technologies in terms of
initial investment,
operating costs,
appreciation, and
profit margins.
You will find it easier to decide whether to continue your current farming methods or switch to vertical farming after reading this article. Find out more below.
What Is Vertical Farming?
Understanding vertical farming requires finding out milestones of farming.
The traditional form of farming is open field farming. Here, the crops grow under direct sunlight, temperature, and humidity. Also, it does not entail artificial fertilizers.
The second milestone of farming is conventional farming, mainly called greenhouse farming. Here, you design appropriate growth conditions for the crops. For example, you introduce artificial seeds, fertilizers and shield the plants from harsh weather conditions such as an extreme cold.
The increasing scarcity of farming lands and demand for more food has caused many farmers to implement container farming. In container farming, you grow crops in soils in vessels instead of letting them grow in the open fields.
The growing technology has resulted in vertical farming. Vertical farming entails packing and growing crops indoors with the help of vertical farming lighting.
Here, you incorporate energy efficiency and customizability of LED lights— to set color, temperature, and humidity conditions for plants to thrive.
Factors that Lead to Changing Farming Criteria
The core reason for farming evolution is market demand and supply. For example, most consumers need tasty and healthy food. The plants’ growth conditions should not hurt consumer health in the long run.
They should be assured of the availability of food whenever and wherever they need it. Most importantly, the supplier should provide competitive prices.
It is on the price that many farmers question the viability of vertical framing, bearing in mind the massive cost of material needed to operate vertical farms.
Here is a summary of recent findings on vertical farming costs.
Cost Determination
Research tells that vertical farming costs three times to implement than conventional farming. The prices inflate when you cater to initial investment and operating costs.
On the other hand, you can produce twice on a vertical farm than on a convention farm. For example, investing in 70000 feet vertical farm is likely to output 1 million kilograms of vegetables annually.
Depending on market location and pricing, you are likely to propel your profit margin when you sell than in the case of conventional farming.
The more exciting part is vertical farming value appreciates twice a year compared to greenhouse farming.
So, Is Vertical Farming Effective in the Long Run?
From the above figures, you can realize that vertical farming is more profitable on a large-scale application. The appreciating value proves that the market demands its products.
The best part is that it is becoming cheaper due to smart lighting technology that becomes less expensive. What do the above findings imply?
Key Takeaways
The best time to invest in vertical farming is now. Chief economic players are channeling a wealth of money into it.
For example, leading investors such as SoftBank Vision Bank, AeroFarms, and BrightFarms recently pumped more than $200 million into vertical farming.
Large-scale investment, crops’ quick turn, and increasing food demand for the growing population make vertical farming cost-effective.
Lead photo: Image by BrightAgrotech from Pixabay
VIDEO: What's In The Bag: Zoomin' Along
We're saying goodbye to gas for good with this all-electric car. With this new mode of transportation, we'll be able to expand our local delivery range and keep our zero-carbon footprint deliveries. We'll continue to deliver by bike, foot, and public transportation
Look Out For The Farm. One Electric Vehicle on NYC Streets!
We're sure you won't miss it. We're saying goodbye to gas for good with this all-electric car. With this new mode of transportation, we'll be able to expand our local delivery range and keep our zero-carbon footprint deliveries. We'll continue to deliver by bike, foot, and public transportation!
“We Are Just At The Beginning of Understanding Plants In These Environments”
OnePointOne (OPO) recently announced its partnership with Sakata Seeds to develop seeds for vertical farms.
OnePointOne Sees Many Opportunities In Seed Breeding Partnerships
OnePointOne (OPO) recently announced its partnership with Sakata Seeds to develop seeds for vertical farms. When being asked about the initial reason for the partnership, Sam Bertram, CEO and Co-Founder of OPO says, “Sakata is a world leader in hybrid and open-pollinated seeds for leafy greens and vegetables, with decades of research, IP on varieties, and access to new crops in development from around the world”.
Sam explains that putting these seeds through OPO’s vertical plane aeroponic system will push the quality and productivity limits of some of the highest quality seeds on earth. “OPO’s high-resolution and hyperspectral imaging capabilities will arm our plant scientists with new data sets to further push the boundaries of what’s possible. Sakata’s executive team see tremendous value in this space and are quickly becoming leaders in the CEA seed space,” Sam affirms.
OPO’s ability to reactivate varieties in Sakata’s seed bank is of great strategic interest to both parties. In the end, a business deal depends on great people doing great work. OPO has found working with Sakata to be positive and rewarding. The tremendous synergies in strategic outcomes and company culture have made this deal powerful.
Samuel Bertram
Sakata partnership
“Our intent behind this deal is to screen Sakata’s immense seed bank to find the most nutritious, best tasting, and most productive varieties. The most important outcome is to uncover these high-performance seeds and ensure that they are distributed to the entire vertical farming marketplace,” Sam states.
This partnership will ensure that high-quality, biodiverse products are available to more people, sooner. Some varieties like Savannah grow in limited locales outside, but exceptionally well inside; creating new opportunities for “lost varieties”. According to Sam, it will drive differentiation between outdoor and indoor products in the market, making it simpler for consumers to identify indoor-grown products. “Now that we have eliminated all pesticides and contaminants, many old and new cultivars become viable for the market. In the end, the consumer will win.”
Portfolio expansion
“As we have barely scratched the surface,” Sam says, “this is a new paradigm of cultivation that just achieved its Kittyhawk flight.” He continues, “we are just at the beginning of understanding plants in these environments.” Imagine the breadth of work to be done when surveying the 30,000 varieties of edible plants, 29,800 of which are not generally found on the market. The opportunity is vast, and the future is bright. “OnePointOne is exceptionally well suited to support the needs of seed research, climate modeling and novel seed breeding for data collection or production at scale.”
According to Sam, plants are the basis of human health. OPO’s mission is to unleash the power of plants on human health. Moreover, consumer interest in a variety of tastes and flavors is no surprise, nor should it come at the cost of global sustainability. “Right now, consumers are fed the illusion of choice, but are beholden to a supply chain that makes the choice for them.” He continues, “providing new environments for the development and production of sustainable produce should be seen as an integral piece of the food supply chain.”
Difficulties
Seeds bred for outdoor settings are bred for climate and supply-chain hardiness. Sam says, “When you control the environment and eliminate the supply chain, your breeding objectives change. Therefore, the seedbanks we are drawing from have not been built for vertical farms.” According to him, breeding indoors is a far simpler and faster exercise than breeding outdoors, especially if the process and data analytics are automated. As Sam likes to put it, “Some plants just grow exceptionally better in controlled conditions.” They open new opportunities to change the flavor or biofortify nutrients just by changing the precision environment it is grown in.
As Sam explains, there’s currently no difference between vertical farming and greenhouse seeds. “In the future, there will be. Numerous early-stage organizations are dedicated to developing seeds for indoor vertical farms. Since we have tighter control over temperature, humidity, and illumination than greenhouses, we can work with the most delicate seeds and provide the precise environment they need to thrive.”
Demand
Sam sees demand coming from consumers that have been disillusioned with the false narrative of “Organic”. Consumers that know Organic cultivation practices still use pesticides and result in products laden with heavy metals. Next to that, demand comes from consumers that are willing to pay a premium for the guarantee of safety and consistent quality.
“I hope to see a greater number of people having access to higher quality, safer, pesticide-free, tasty fruits and vegetables with a much greater choice and control. This is only the beginning of the proliferation of vertical farming,” Sam notes.
Potential partnerships
“Rijk Zwaan is another great seed company,” Sam notes, “which we hope to work with to better understand how their seed libraries and crop IP could support indoor farmers with new products.” Seed breeding is a decade-long endeavor in almost every case. Being able to reproduce and vary environmental factors on demand means a dramatically faster breeding program is possible.
Currently, OPO is developing a production system that doubles as a high-throughput phenotyping system. This volume and quality of (especially imagery) data will allow AI to discover things humans cannot possibly discover. This is a clear, key differentiator.
For more information:
OnePointOne
info@onepointone.com
www.onepointone.com
24 June 2021
Author: Rebekka Boekhout
© VerticalFarmDaily.com
August 20th - 2nd Annual OptimIA Research Collaborative Update
Plan to join our annual stakeholder meeting online to learn our collaborative research update
Registration is now open!
2021 OptimIA Research Collaborative Update
August 20th, 2021
10 AM - 3 PM Eastern
Plan to join our annual
stakeholder meeting online to
learn our collaborative research update!
Meeting Information & Agenda
OptimIA (Optimizing Indoor Agriculture) is a USDA-funded Specialty Crop Research Initiative project to support indoor farming industry through critical research and extension activities.
Register
How Much Are You Willing To Pay For The Perfect Strawberry?
One of Japan's most coveted strawberry varietals is now being grown in a high-tech farm in Newark. And you can get a taste for a cool $50
One of Japan's most coveted strawberry varietals is now being grown in a high-tech farm in Newark. And you can get a taste for a cool $50.
BY LEENA KIM
JULY 2, 2021
MICHAEL STILLWELL
Of the reasons for which Newark is famous—namely its reputation as a former murder capital of America—there is a high likelihood that it will soon be known for something a little more savory: as the epicenter of the agricultural revolution, 2.0.
Over the past few years, New Jersey's gritty port city has become ground zero for a burgeoning vertical farm movement. First, what is a vertical farm? It's basically an indoor farm that uses aeroponics (or hydroponics) systems, artificial intelligence, robots, LED lights, and other forms of technology to grow produce in a controlled environment sans sun, soil, and pesticides. Newark is currently home to the world's largest vertical farm, the 70,000-square-foot AeroFarms, which has 8 others in this city alone (plus facilities in Virginia and Abu Dhabi) and is slated to IPO this month at a $1.2 billion valuation.
Nearly all of the vertical farms that have sprung up around the country specialize in leafy greens (kale, watercress, spinach, arugula, etc.). Why? It's the easiest crop to grow—and the cheapest ticket into the business. But Hiroki Koga, co-founder and CEO of Oishii, a 4-year-old vertical farm near Newark, had far grander ambitions. He didn't want to open yet another outfit for lettuce and spinach that, to be honest, can't taste so radically different from lettuce and spinach shipped in from California. He was going to go straight for Goliath on the first try: the strawberry.
Most vertical farms specialize in leafy greens because they are the easiest to grow. Not Oishii, which went straight for the holy grail in vertical farming: strawberries. OISHII
"They are one of the most sophisticated crops with an extremely complicated plant physiology, and one of hardest to grow in a vertical farm," says Koga, whose former life in Tokyo as a consultant to large corporations making headway in this agricultural category provided an early education in the business. (Not surprisingly, Japan has been way ahead of the curve on this trend, mastering the tech long before the term even entered the modern lexicon—today, many vertical farms use machines made by Japanese corporations like Sony and Panasonic.) "So while other companies started with something easy, we decided to invest all of the money we raised into something that was harder and might take longer to succeed, but that once we cracked the code to it, it would let us unlock other crops, like tomatoes, melons, and grapes, much more easily."
Hiroki Koga, co-founder and CEO of Oishii.
OISHII
Another key reason that deters vertical farms from graduating beyond leafy produce: the bees. Or rather, the lack of them. Greens don't need pollination but fruits do. The problem is, though, bees are sensitive. Put them in an artificial environment and they'll soon realize it's a setup and stop functioning properly. Koga has cracked this, too. "We were the first in the world to figure out how to trick the bees into believing they are in Mother Nature," he says.
Mind you, Koga certainly hasn't gone through this much trouble for just any kind of strawberries. His are a replica of Japan's Omakase berries, a unique, highly prized, and rare varietal grown in greenhouses in the foothills of the Japanese Alps only during wintertime (from January to March). They are characterized by an intensely fragrant, almost floral, bouquet, and a flavor profile that is juicy and creamy, soft and buttery, and, above all, super sweet. In other words, like nothing that is found in America. Oishii's Omakase berries tick all of these boxes, plus one more: they are perfect every time. Because even Japan's most meticulous strawberry growers can't control sun and temperature. "In our vertical farm, we can control for temperature, humidity, even levels of carbon dioxide, to optimize for this specific variety to thrive every single day," Koga says.
The strawberries grown in Oishii’s vertical farm in New Jersey. ZI JIAN/OISHII
So, about that price tag. Oishii's Omakase berries—at first only supplied to Michelin-starred restaurants, they are now available for delivery in Manhattan, Brooklyn, and Jersey City, and at select purveyors like Eli's on the Upper East Side and Carissa's in East Hampton—are $50 for a box of 11 medium-sized strawberries (or 8 large). While these are exponentially more expensive than your average Driscoll's, even traditionally grown Omakases command a similar cost back in Japan, where they are considered treasured gifts for special occasions and celebrations.
But they are hardly Japan's most expensive strawberry. That distinction is held by the Bijin-hime varietal, grown exclusively by a veteran farmer named Nichio Okuda, who spent 15 years perfecting the berry and produces only 500 a year. A single Bijin-hime strawberry retails for 50,000 yen, or $448. (It ought to be noted that the Japanese are unrivaled in the realm of status produce: in 2019, for example, two Hokkaido melons sold at auction for $5 million yen, aka $45,000.)
Of course there are far more reasonably-priced Japanese varietals as well—the country has 250 different strawberry cultivars, which account for more than half of the global supply—and Koga plans to introduce them to the U.S. market, and eventually, the rest of the world. Thanks to a recent $50 million infusion of investor capital, Oishii has begun its expansion, first with the construction of a second vertical farm the size of a football field. "We're not just a small strawberry farm in New York selling fancy strawberries. We're offering a new way to grow, experience, and access food," he says. "We hope to bring a really big paradigm shift to the agriculture industry. Vertical farming is the way forward."
LEENA KIM Associate EditorLeena Kim is an associate editor at Town & Country, where she writes about travel, weddings, arts, and culture.
BrightFarms Launches Multimillion-Dollar R&D Hub in Greater Cincinnati
BrightFarms, a New York-based grower of indoor leafy greens since 2013, is forming BrightLabs, a new innovation and research hub, at its Wilmington greenhouse. BrightLabs, overall, will represent a tenfold increase in the company’s research capabilities, while increasing profitability and delivering new product innovations.
By Liz Engel - Staff reporter
June 24, 2021
An indoor farming company is investing millions in Ohio with the debut of a new research and development hub.
BrightFarms, a New York-based grower of indoor leafy greens since 2013, is forming BrightLabs, a new innovation and research hub, at its Wilmington greenhouse. BrightLabs, overall, will represent a tenfold increase in the company’s research capabilities, while increasing profitability and delivering new product innovations.
Steve Platt is the CEO of BrightFarms. (Jenn Erickson)
CEO Steve Platt declined to disclose the exact investment but told me it’s in the multimillions. The project is being launched as part of the company’s $100 million Series E funding round in October led by media conglomerate Cox Enterprises.
“BrightFarms as a company has been growing very consistently, and the indoor farming industry is at an inflection point,” Platt said. “We’ve perfected how we grow – among competitors, we’ve developed the most profitable model for the production of indoor leafy greens – but now’s the time to invest behind R&D to secure an advantage for the future. It’s essential to stay ahead of the curve.”
Like others in the indoor farming space, BrightFarms lauds the fact that its lettuce is healthier, tastier, looks better, is more nutritious, and, particularly for customers in Ohio, fresher than field-grown produce hauled in from states like California and Arizona. Today the company’s five greenhouses in Ohio, Virginia, Illinois, Pennsylvania produce 9 million pounds of produce each year.
But unlike several outfits, particularly vertical farms that use purple-hued LED lighting, BrightFarms leverages natural sunshine. Its souped up, high-tech greenhouses grow spinach, romaine, arugula and more using a hydroponic system, or water instead of soil.
Wilmington, which celebrated its first harvest in 2018, isn’t the company’s largest greenhouse in terms of size or production, but Platt said it made a good host for the innovation hub because of its centralized location. It’s close to customers and easily accessible from its other farms. He also credited the workforce and level of academic talent available from universities nearby.
BrightFarms celebrated its first harvest in Wilmington in 2018. BrightLabs is investing millions to build out an innovation and research hub at the site. (Brian Mollenkopf)
Phase one for BrightLabs includes a new, approximately 1,350 square foot lab that has been built at the Wilmington greenhouse site. BrightFarms will also dedicate space on the farm for the BrightLabs team to work.
Platt said BrightLabs will focus on three key areas:
Biotech. BrightFarms wants to study the environments in which plants grow to increase yield, flavor, and texture.
Agtech. BrightOS, the company’s proprietary AI software system, acts as the company’s central nervous system, Platt said, collecting millions of data points from its fives farms to streamline operations. How can the company improve that technology?
Product innovation. BrightFarms recently launched NutriGreens, a new lettuce packed with antioxidants – double the amount, Platt said, found in a serving of blueberries. BrightFarms wants more advances like that.
BrightLabs itself will be led by Matt Lingard, a former Bayer plant scientist and Ph.D. with over 15 years of experience, who joined BrightFarms in May as its VP of agriculture and science. Platt said the BrightLabs team will include four employees to start.
“We’re the leading grower of indoor spinach – in the U.S. we grow 90% of the indoor spinach that’s sold – but we want to double our production on that. How do we come out with new types of spinach that can grow even better in a hydroponic system?” he said.
“We’re taking on a massive industry and a complicated, broken system – where greens are grown all in one location, shipped thousands of miles across the country, generally with pesticide reside, there’s a food-borne illness, and the product isn’t that good,” Platt added. “We have a simpler system and a better product, but we need to deliver that at a price point and at a volume that competes with what’s coming out of California. If we’re trying to unseat this big gorilla, we can’t be this niche that’s only affordable to people who drive Teslas.”
Overall, there’s billions being invested in the industry. New York City-based Bowery Farming, in late May, announced a $300 million funding round with a $2.3 billion valuation. Kentucky-based AppHarvest merged with a special purpose acquisition company in February, an IPO approach that’s gaining ground in 2021, and is now worth $1.5 billion.
BrightFarms, with its Series E, has raised more than $200 million in total. In addition to launching BrightLabs, it plans to use the funds to expand its network of regional indoor farms – new farms are currently under development in Massachusetts and Texas – and grow its retail footprint. Locally, BrightFarms is available at Sam’s Club, Walmart and Pipkin Produce as well as Food Lion and Kroger in other markets.
The company said by the end of 2021 its leafy greens will be available at over 3,500 stores.
“It’s amazing. Even when I joined the company two years ago, we were convincing people this was the future. Now customers are coming to us saying, ‘We want to replace field grown with indoor-grown,’” he said. “We think the future is here.”
Lead photo: BrightFarms grows leafy greens like spinach, romaine, and arugula in high-tech, computer-controlled greenhouses.
Signify Announces New Philips Horticulture LED Partner Hortipar
“We are excited to be a partner of Signify and offer the range of Philips GreenPower LED grow lights to our customers”, said Aad van Ruijven, director at Hortipar
June 28, 2021
Eindhoven, the Netherlands – Signify (Euronext: LIGHT), the world leader in lighting, has signed a partnership agreement with Hortipar, an expert in realizing lighting projects for the horticultural sector worldwide. Hortipar is based in ‘s Gravenzande, the Netherlands, and operates mainly in North America, Canada, Eastern Europe, and the Netherlands.
Hortipar will now add Philips GreenPower LED grow lights to their global portfolio. Focussing on quality, flexibility, knowledge, and expertise, Hortipar offers their customers a complete solution for their greenhouse from the beginning till the end of a lighting project. With their independent advisors and team of dedicated experts, Signify is proud to add Hortipar to the global partnership network of Philips Horticulture LED.
“We are excited to be a partner of Signify and offer the range of Philips GreenPower LED grow lights to our customers”, said Aad van Ruijven, director at Hortipar. “Sustainability and innovation are of great value to us and to our network. Our customers expect the highest quality, and that we offer them the full package for their lighting installation, together with high-end advice and project management. The expertise of the team at Signify and their Philips GreenPower LED grow lights fit perfectly within these expectations and in our ambitions for the future.”
“Adding Hortipar to our global network of certified Philips Horticulture LED partners is something we are proud of”, said Udo van Slooten, Business Leader Horticulture at Signify. “According to our estimates, about 30% of the world’s greenhouse surface will be lit by 2025, and LED technology will light more than half of that surface. Therefore, we are continuously pursuing further development of our Horti LED partnerships worldwide, and Hortipar is a valuable addition.”
Signify continues to expand its Horticulture partner network, further demonstrating its commitment to lead the horticulture industry as the innovative LED lighting systems provider for greenhouses and indoor farming.
--- END ---
For further information, please contact:
Global Marcom Manager Horticulture at Signify
Daniela Damoiseaux
Tel: +31 6 31 65 29 69
E-mail: daniela.damoiseaux@signify.com
www.philips.com/horti
About Signify
Signify (Euronext: LIGHT) is the world leader in lighting for professionals and consumers and lighting for the Internet of Things. Our Philips products, Interact connected lighting systems and data-enabled services, deliver business value and transform life in homes, buildings and public spaces. With 2020 sales of EUR 6.5 billion, we have approximately 37,000 employees and are present in over 70 countries. We unlock the extraordinary potential of light for brighter lives and a better world. We achieved carbon neutrality in 2020, have been in the Dow Jones Sustainability World Index since our IPO for four consecutive years and were named Industry Leader in 2017, 2018 and 2019. News from Signify is located at the Newsroom, Twitter, LinkedIn and Instagram. Information for investors can be found on the Investor Relations page.
VIDEO: Is Hydroponic Produce Organic?
The organic farming standards were created by the USDA in the 1990s when there was increased public awareness of the health and safety of our food. However, at that time, hydroponic farming wasn't as widespread as it is today
Aaron Fields, Eden Green Technology's Head of Horticulture
Photo from Eden Green Technology
The organic farming standards were created by the USDA in the 1990s when there was increased public awareness of the health and safety of our food. However, at that time, hydroponic farming wasn't as widespread as it is today. That leads us to question: is hydroponic produce organic?
Check out this great video from Eden Green Technology, a hydroponic farm based in Texas. Aaron Fields, their Head of Horticulture, explains what organic really means and how hydroponic growing can be sometimes cleaner and safer. (Did you know? I hate to burst the organic bubble, but produce that is grown organically can still have some level of pesticides.)
Affordable, Image-Based Crop Monitoring Using Smartphones and Microcontrollers
Dr. Krishna Nemali and his research group at Purdue University are tackling crop-monitoring challenges facing hydroponic and flower growers. Of the group’s many research foci, image-based crop monitoring using smartphones and microcontrollers has been at the forefront of Purdue’s technological advancements for the CEA industry.
Smart Sensors From Purdue University
With a mission to deliver easy-to-use, rapid and affordable technologies to the controlled environment agriculture (CEA) industry, Dr. Krishna Nemali and his research group at Purdue University are tackling crop-monitoring challenges facing hydroponic and flower growers. Of the group’s many research foci, image-based crop monitoring using smartphones and microcontrollers has been at the forefront of Purdue’s technological advancements for the CEA industry.
Image-based crop monitoring made practical and affordable
Image analysis is being used for monitoring plants in conventional, field-based agriculture through satellites, drones, and camera-mounted vehicles. However, these technologies are not practical for greenhouses and indoor farms due to the architecture of these facilities, which limits the movement of drones or camera-mounted vehicles over plants. Dr. Nemali and his research group are working to bring image-based crop monitoring on smartphones as handheld sensors. For installations where using cameras fixed to the growing systems is preferred (e.g. vertical farms with multi-tiered racking) or applications where continuous monitoring is useful, the research team is also building a system with a Raspberry Pi microcontroller and high-resolution camera, which sends the images to a central computer for processing and interpretation.
Left: Dr. Krishna Nemali. Right: smartphone sensor
Compared image-based monitoring to human evaluation
To test the efficacy of image-based crop monitoring, the research team grew lettuce and tomatoes under optimal and suboptimal conditions. In a blind trial, crop growth was visually evaluated daily by people (using a rating system) and by image-based sensors. As Dr. Nemali explains, the image-based system recorded statistically significant differences in crop growth between optimal and sub-optimal conditions 3-4 days before the human eye could detect differences.
“When you regularly take these photos and develop growth curves, you can monitor how your crop is measuring up against expected optimal growth. If these images indicate an issue, growers can resolve this before it is too late,” says Dr. Nemali.
The images can also be used to assess nitrogen status, germination percentage, and rate, and color progression, allowing the grower to monitor crop health, planting material, and estimate the time to harvest. Plant nitrogen status is usually measured in a laboratory, which is expensive and time-consuming or using expensive chlorophyll meters. Dr. Nemali’s research developed accurate algorithms using images captured by smartphones and microcontrollers to rapidly estimate plant nitrogen status.
Different plant measurements can be measured using images collected by a smartphone or microcontroller
Instantaneously assessing plant nitrogen
“Imaging the benefits of instantaneously assessing plant nitrogen status in CEA industry. Growers can supply fertilizers based on plant needs and avoid over or under application rates,” says Dr. Nemali
As these technologies are being developed at Purdue University, they will be made available to growers at a low cost, with any generated funds being poured back into further research and development. The smartphone app should be available in the spring of 2022, with a low purchase price and yearly license.
With photo-quality varying according to the camera, ambient light conditions, and distance from the crop, normalization processes have been incorporated into algorithms to ensure high-quality analyses. To account for differences in distance from the crop between imaging sessions, each photo is taken with a standard, measured object in the frame.
“Let’s say we have a red square with a known area of 25 cm2 and we place it beside the crop in each image. The computer will recognize that object, uses its area to determine the right pixel-area conversion and apply it to the plant. This creates a relative scale and eliminates height/distance altogether,” says Dr. Nemali.
To normalize for different light conditions, the technology considers different reflected wavelengths, both of which are affected by light intensity. By taking the ratio of two wavelengths, the setup can eliminate the effects of light intensity on the images altogether.
A demonstration of smartphone-based image technology can be viewed on Dr. Nemali’s website at this link.
Additional areas of research
Aside from image-based crop monitoring, Dr. Nemali’s research group is conducting extensive research on nitrogen management in hydroponically grown organic lettuce production.
“The yields of organic lettuce is usually lower compared to conventional production, because of challenges with nitrogen availability to plants in organic production. While organic lettuce does command a higher price, we still need to increase these yields to make it sustainable and organic produce more available to consumers,” explains Dr. Nemali.
Other areas of research include the use of ultraviolet radiation and ozone to reduce the risk of E. coli contamination in lettuce, and the optimization of production techniques to improve the nutritional density of leafy greens.
For more information on ongoing research in Dr. Nemali’s research group:
Dr. Krishna Nemali
Assistant Professor in Controlled Environment Agriculture
Purdue University
https://www.purdue.edu/hla/sites/cea/
24 June 2021
Author: Rose Seguin
© HortiDaily.com
New Innovations – Lettuce Wall at Newtown College
The eye-catching addition of the lettuce tower in the Newtown College foyer is part of the Crop Cycle project, a Farm Urban system to cultivate lettuce and other greens using a soilless system of vertical towers. This project is funded by the Welsh Government to introduce indoor growing CEA of food crops into communities.
NPTC Group of Colleges
23 June 2021
Newtown College (Part of @NPTCGroup of Colleges) is going all green-fingered as it introduces a new Horticulture course. This exciting new addition has brought with it a new collaboration with Cultivate, and a new initiative with the introduction of a lettuce wall to the Newtown College Foyer.
The new Level 1 & 2 Horticulture courses will be available from September. The course will utilize the fantastic facilities of Cultivate to do practical work, including accessing polytunnels, allotments, and projects within their grounds include growing via CEA (Controlled Environment Agriculture).
The eye-catching addition of the lettuce tower in the Newtown College foyer is part of the Crop Cycle project, a Farm Urban system to cultivate lettuce and other greens using a soilless system of vertical towers. This project is funded by the Welsh Government to introduce indoor growing CEA of food crops into communities. Whilst we live in a rural environment, new ways of nurturing plants, using what is known as hydroponics, is revolutionary and is growing in popularity.
Cultivate are piloting a number of different controlled environment vertical farming systems to grow hyper-local nutritious crops to offer within the community. Local, sustainably grown food is absolutely key in tackling important issues surrounding our food system, climate change and biodiversity. This will allow Cultivate food business to increase the amount of local foods produced and in turn, consumed, ensuring that growing models become more sustainable and that our population can eat more locally grown, sustainable, healthier produce.
Richard Edwards Cultivate Crop Cycles project manager said:
“They taste great, are highly nutritious and are super fresh, visit our Deli in Newtown to try them for yourself!”
NPTC Group of Colleges Head of Agriculture, Catering, Hospitality and Horticulture, Sue Lloyd-Jones said:
“We are very excited about introducing the Horticulture Courses to Newtown College. These courses are already popular in our Brecon Beacons, Neath College and Black Mountains Colleges. With this fantastic collaboration with Cultivate, it gives us extensive facilities and involvement with initiatives such as the CEA. The lettuce wall provides a point of education for students to learn about potential food sustainability and the subtle shift toward urban or hyper-local cultivation. It demonstrates how to grow plants without soil but in nutrient-rich water with oxygen and light. It also serves as a local edible wall producing greens for our catering department’.
AeroFarms Commences Construction On AgX Research Center
AgX will bring innovative research and development to the UAE and the Middle East to advance sustainable controlled environment agriculture (CEA) and vertical farming and help address broader global agriculture supply chain issues
AeroFarms Wholly-Owned Subsidiary AeroFarms AgX LTD Has Started
Construction Focused On Some Recent Developments
03 Jul 2021
AeroFarms, a certified B Corporation, and specialist in indoor vertical farming announced that AeroFarms AgX LTD, its wholly-owned subsidiary in the UAE, has started construction in Abu Dhabi on the company’s Research Center focused on the latest developments for indoor vertical farming, innovation, and AgTech.
AgX will bring innovative research and development to the UAE and the Middle East to advance sustainable controlled environment agriculture (CEA) and vertical farming and help address broader global agriculture supply chain issues.
Last year, ADIO announced that it is providing $150m in incentives to bring global AgTech pioneers to Abu Dhabi, including its partnership with AeroFarms to build a vertical farming facility dedicated to developing next-generation agriculture in arid and desert climates.
The transformational R&D conducted at AeroFarms AgX is expected to enable new business lines, technologies, and growth of the AeroFarms platform while serving as a hub for regional expansion. AeroFarms AgX is expected to be completed and operational in the first quarter of 2022.
HE Dr Tariq Bin Hendi, Director General of ADIO, said: “This important milestone for AeroFarms AgX is another step in the realization of Abu Dhabi’s mission to ‘turn the desert green’. In line with this goal, ADIO is supporting innovative technology that has the potential to impact farming practices across the globe and improve the food production value chain worldwide. AeroFarms AgX will add to the growing capabilities of Abu Dhabi’s agriculture ecosystem while benefiting from the emirate’s plentiful land, natural heat, competitive energy prices, access to research universities, and skilled talent.”
AeroFarms AgX will be the largest indoor vertical farm of its kind for research and development in the world, leading the way in breakthrough innovation to solve some of the world’s most pressing agriculture challenges.
AeroFarms AgX will employ a projected 60 highly skilled engineers, horticulturists, and scientists and will have high-tech laboratories conducting organoleptic research and precision phenotyping, phytochemical analysis, advanced speed breeding, as well as next-generation machine vision, machine learning, robotics, and automation. AeroFarms AgX will also play a key role in Abu Dhabi’s AgTech ecosystem by working with local universities on research projects to tackle problems of agriculture within desert and arid climates.
David Rosenberg, Co-Founder, and CEO of AeroFarms commented: “This is an important development for AeroFarms as we expand globally and leverage our R&D and growing expertise. AeroFarms has been the global leader for controlled environment agriculture since 2004, and we will utilize this cutting-edge R&D Center to conduct the latest research in plant science, vertical farming, and automation, accelerating innovation cycles and commercializing products.
Our vision has always been to leverage our expertise in plant biology and build on our successful history of collaborating with government, universities, industry and major international companies. We are pleased to take this step forward and proud to be a catalyst for helping to establish the Emirate of Abu Dhabi as a global hub for AgTech innovation.”
Lead photo: AeroFarms to build world's largest indoor vertical farm in Abu Dhabi. AeroFarms
Vertical Farms Hold Promise For Local, Sustainable Produce
Vertical farming uses controlled environmental agriculture techniques, like hydroponics or aquaponics, to grow crops in vertically stacked rows with 90% less water than traditional soil-based farming
Technique Uses Small Footprint,
Less Water To Provide Year-Round Crops
Beth Edwards
June 30, 2021
A former grocery store or an empty strip mall might not be the first images that come to mind when thinking of places to grow food. But around Indiana, many of these spaces are being turned into vertical farms to help alleviate farmland shortages and greenhouse gas emissions linked to traditional farming practices.
Vertical farming uses controlled environmental agriculture techniques, like hydroponics or aquaponics, to grow crops in vertically stacked rows with 90% less water than traditional soil-based farming. It also uses 75-90% less land than traditional farms and is able to be conducted in industrial areas. It allows the grower to have total control over the grow cycle of the crop.
Courtesy of Green Sense Farms
The technique allows for year-round income for farmers and fresh, healthy, local produce for consumers regardless of climate.
With the world’s population expected to grow to 9.7 billion people by 2050, agricultural production will need to increase by 70%. Vertical farming offers an alternative to scarce farmland and to traditional farming techniques, which cause 22% of the world's greenhouse gas emissions.
A controlled environment
Krishna Nemali, assistant professor of controlled agriculture at Purdue University, said controlled environmental agriculture is driven by both plant science and engineering, with the purpose of growing crops in managed environments year-round.
In Indiana, farmers can do little outdoors between fall and spring because of low light levels and temperatures, he said.
“But with controlled environmental agriculture, you can produce year-round because you artificially manage the ideal environmental conditions for plants,” he said.
The farmer controls the lighting, temperature, nutrients, water and sometimes even carbon dioxide, but needs to understand plant science to know what is best for the plant being grown, as well as the engineering behind how best to deliver those resources without waste.
Professor Krishna Nemali at a workshop held by Purdue Extension to show participants how researchers use hydroponics to grow crops. Photo by Tom Campbell
“Our research shows that we use about one-third of the water used to grow the same crop in the same acreage outdoors. That’s because we recycle the water; we don’t just add water on top of the plants. In controlled environmental agriculture, the water is recirculated and is delivered to plants in a closed-loop system, where there is no runoff or leaching,” said Nemali.
While such systems do require a large amount of energy use, Nemali said research has enabled farmers to optimize energy use and lower consumption.
But there are limits to what can be grown using these methods.
“Because your investment is high, your return should also be high in order to make profits. There is a technology piece and usually, there is high-intensity cultivation that happens; therefore, growers want to grow high-value crops like vegetables and those that have direct impact to consumers,” said Nemali.
The time for harvesting the vegetables is more condensed as well. For instance, it will take about a month to grow leafy greens, around six to eight weeks for tomatoes and eight weeks for strawberries, instead of an entire season like in traditional farming.
The industry is growing rapidly and creating new jobs in many urban areas because it doesn’t require soil to produce fresh produce.
“A grower can purchase an old warehouse, let’s say 10,000 square feet or a quarter of an acre. But then they can grow 10 or 11 levels vertically, and in doing so, that’s a quarter of an acre times 10. So they are actually producing crops that would normally require two-and-a-half acres of land on this quarter of an acre simply by going vertically,” said Nemali.
Nemali said there is a huge amount of interest in vertical farming in Indiana. Indiana currently imports around 95% of its vegetables from outside the state. That means there is potential for large profits in vertical growing.
For example, USDA estimates that each person in the US consumes around 11-13 pounds of lettuce each year, which would roughly equal a salad each week. Nemali estimates Hoosiers consume about $60 million in lettuce each year, but Indiana farmers grow only a fraction of that amount.
Courtesy of Green Sense Farms
“We probably won’t produce $1 million worth of lettuce this year. So there’s a huge demand for local production,” Nemali said. “I’m just giving you one crop; imagine all those vegetables we are importing from outside. If it’s grown locally, that money stays with our growers and our farmers, and that will improve their livelihoods. That is why there is a huge interest in this industry.”
A pioneer in northwest Indiana
One company that has been a leader in the vertical farming industry for a while is Green Sense Farms in Portage.
Before he founded Green Sense, Robert Colangelo spent many years working on a wide variety of environmental issues, from research at Argonne National Laboratories to cleaning and repurposing brownfields. He said he was looking for something new when a friend approached him with an idea to start a vertical farm.
“I became very passionate about it, and I thought this would be a next great step in my environmental career, getting involved in agriculture,” he said.
He said he wished he had gotten involved in agriculture earlier in his career.
“We are not here to put field farms or greenhouses out of business,” he said. “I think as the population grows, we really have to look at what crops grow best outdoors and what crops grow best indoors and just rethink agriculture based on water and soil conservation. When we approach it that way, everyone feels comfortable with vertical farming.”
Robert Colangelo, head farmer of Green Sense Farms. Courtesy of Green Sense Farms
Green Sense began as an owner-operated farm. Colangelo grew leafy greens and herbs, which he mainly sold in the Chicago and Northwest Indiana markets. However, he now helps other companies or growers develop and build their farms.
Colangelo said while the business side of Green Sense was harder to learn than the growing itself. Knowing where to locate the farm and find the right talent, having the right operating procedures in place, and finding the right customer base took longer to learn, but now Green Sense helps others with exactly those issues.
It also designs farms specifically for the crop that the company or individual wants to grow, customizing growing techniques and economic data.
Vertical farming extends to other industries
Green Sense is currently working on several projects, including a casino in Las Vegas that would showcase a vertical farm in its restaurant so the diners could see the food they are eating. It has partnered with a company in Spain to offer combination greenhouses and vertical farms, and it also is considering a project that would turn old grain silos into a combination vertical farm, restaurant, and market.
“We’ve learned a lot about what doesn’t work, and we keep striving each day to figure out what works better,” said Colangelo.
Vertical farming isn’t limited to growing food. Green Sense has worked on projects for many different industries, including pharmaceutical companies, tree growing and many others that may seem surprising.
Colangelo believes the future of vertical farming will be highly automated.
“They will still require smart people to run them, but (with) a lot of the menial, repetitive tasks being done by machines. I think the future for farming is bright, and this is a great opportunity for young, smart people to get involved with,” he said.
Piper Halpin agrees. She worked with Colangelo for four years at Green Sense, starting out harvesting and seeding crops before becoming an operations manager. She now is involved in vertical farming in Boston.
“It’s exciting to be a part of and addicting because it is so technology forward, innovative and new,” she said. “Also, you don’t have to live in a rural area in order to be successful.”
Courtesy of Green Sense Farms
Colangelo and Halpin agree the technology aspect is attractive to younger people and helps to engage their interest in the field.
“It’s a great way to get young people reinvolved in agriculture,” Halpin said. “It’s been a cool bridge between old agriculture and new agriculture. I think it’s going to jumpstart a whole new interest level in ag that was kind of dying off before.”
Nemali said younger people are also interested because vertical farming is environmentally sustainable.
“They also see the importance of this industry in terms of feeding millions with fresh food, making sure it’s safe and done in a responsible way,” he said.
Nemali would like to see an increase in the variety of crops that can be grown in controlled environmental agriculture, technological improvements that lower energy consumption, and more university programs to train workers and researchers for these farms.
“This area is growing, and I want people to see, admire and provide support for it,” Nemali said.
Support from scientists, policymakers, marketers, and the government will enable a new workforce to develop the industry in the next 10 to 15 years
Polygreens Podcast Episode: 32 - Mark Thomas - Garfield Produce
Mark's background in operations and finance, mixed with his entrepreneurial spirit, makes him a dynamic leader. He always takes the time to get to know both his employees and customers, adding a personal touch to the company
Mark's background in operations and finance, mixed with his entrepreneurial spirit, makes him a dynamic leader. He always takes the time to get to know both his employees and customers, adding a personal touch to the company.
Latest Episode
Why Does Energy Efficiency Matter When Selecting LED Grow Lights?
Learn the 3 things to consider when choosing energy-efficient lighting in your greenhouse or vertical farm.
Before we get started, let’s set some ground rules for this article.
1. I want to believe that everyone wants to do what’s right for the planet as long as they think their business can afford it, so we will not focus on energy efficiency and its impact on sustainability.
2. In this article I will not post the name of suppliers or the price of the lights. The price of the light will definitely impact people’s decisions and will vary widely based on the volume of lights being purchased and the supplier providing it.
3. This article is not about light quality or light spectrum. To look for information on spectrum please read this article: Why I Still Believe in Red/Blue LED Grow Lights
4. This article is written with commercial greenhouse produce growers in mind, but we do include a model which shows high output led grow lights running for long hours per day which could imply a greenhouse cannabis crop.
5. We are fully aware that when you change the amount of energy going into the light as well as the type of electric light (HPS vs LED) one is using, it will have an impact on the climate in the growing/production area. Factors like heat and relative humidity would need to be taken into consideration if one was taking a holistic approach to energy savings on the farm.
6. All lights have different output (measured in PPF.) In this article we are going to make the assumption that a grower is using the same amount of fixtures per acre regardless of output. For simplicity we are also going to assume that the grower is running the lights for the same amount of time. We are fully aware that this will have an impact on the potential yield of the crop.
7. All greenhouses can require a different amount of lights per acre to achieve the target light intensities. I am using an average of the amount of lights per acre. Height of the greenhouse, width of the bays, placement of walkways, crop layout, crop density, as well as many other variables will impact the exact number of lights per acre.
__________
There is a growing amount of discussion around the environmental sustainability of a greenhouse or a vertical farm. Much of this discussion is being driven by two or three big energy hogs inside these production facilities. This includes the grow lights and climate management equipment like heaters and cooling units.
We all know that LED grow lights are more efficient than the older HPS lights that growers have used for decades, but do we know just exactly how to measure that? And do we understand how that will have a direct impact on not only energy savings but the operational cost at the farm? For those growing in a greenhouse, understanding these numbers during dark winter months can have a huge impact on electricity bills.
3 FOCUS POINTS
1. Start by understanding the amount of light you need.
Urban Ag News recommends going to websites like Suntracker or the ESRI DLI maps site. These websites allow anyone to determine the historical DLI monthly averages for their individual locations. For this example I am going to use the area where my grandparents farm is located in southwestern Michigan. As one can see this is an area of the United States that has very dark winters.
2. Work with a trusted advisor or extension specialist to determine the amount of hours your crop needs to grow consistently year round. Remember not all crops have the same light requirements and some crops have very specific photoperiods which can determine the amount of hours one can light their crops. Use all of this information to see when you will need supplemental light and how much light you will need to supplement with.
For this example I am going to use 1 acre of greenhouse tomatoes in a glass greenhouse located in southwestern Michigan.
3. Now let’s calculate how much it’s going to cost you to run the grow lights for the estimated hours you and your advisor determined were needed per year to get the desired yields.
a) To provide a baseline, we started with traditional 1000w HPS lights which are highlighted in yellow.
b) Then we chose six different LED grow light fixtures. Because the light spectrum has an impact on how efficiently the lights run, we chose three broad spectrum fixtures and three that are red and blue only.
c) Since HPS is the baseline, the final column labeled “savings” shows how much the total savings per year one would achieve when replacing traditional HPS with the latest LED grow light technology.
d) We made a few important assumptions in this example. First, the cost per kwh is around the USA national average of $0.09/kwh. Second, the same amount of grow lights would be used even though there would be some relative differences in umols/m2/s measurements for two of the samples. We decided not to change them because that would have an impact on uniformity (the even spread of the light over one’s entire crop) and associated capital cost not addressed in this article.
IMPORTANT NOTES!
It’s important to remember the 7 assumptions made at the beginning of this article and that lights are not equal. This chart only compares ppf (output) and w (watts). We elected to account for the difference in output by changing the amount of hours we estimated you would need to run the lights. Another way to look at this would be to remember the Golden Rule of Light in which 1% increase in light is equal to 1% increase in yield.
Running these simple calculations will show you why you need to look at energy efficient lighting and in general the importance of researching energy efficient equipment in general. What these calculations do not show is the quality of some fixtures over others. Buyers must always be aware of the value of warranties, ease of returns, durability and quality of product plus accuracy of your vendor to create detailed information on the best way to use and install fixtures. We understand that this topic is intimidating for most, but this is a major purchase for your farm. Make sure to take the time to learn the math and do your homework before purchasing.
Diving into these calculations will also highlight how much energy will be required to grow a wide variety of crops consistently with uniformed yields year round in climates with low light. Hopefully in articles to come we can discuss what this means for our environment and how we might develop additional ways to lower that ecological footprint.
For help in calculating the energy efficiency of grow lights you are considering, please email us and we will connect you with professionals capable of helping you make an informed decision.
Chris Higgins is the founder of Urban Ag News, as well as General Manager and co-Owner of Hort Americas, LLC a wholesale supply company focused on all aspects of the horticultural industries. With over 20 years of commercial horticulture industry experience, Chris is dedicated to the horticulture and niche agriculture industries and is inspired by the current opportunities for continued innovation in the field of controlled environment agriculture. Message him here.
Tagged GreenhouseGreenhouse TechnologyIndoor Ag TechnologyTechnologyVertical Farming