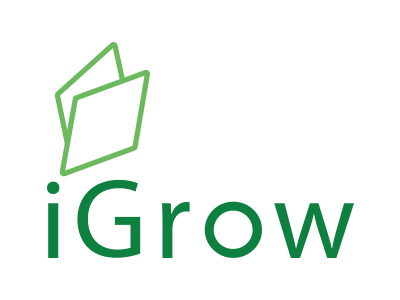
Welcome to iGrow News, Your Source for the World of Indoor Vertical Farming
AUSTRALIA - VIDEO: Shipping Container Farm Teaching TAFE Students More Than Just Agriculture
Nestled beside a building on a TAFE campus in Toowoomba is an ugly metal shipping container, but it's no ordinary storage shed
August 16, 2021
By Lucy Cooper
Nestled beside a building on a TAFE campus in Toowoomba is an ugly metal shipping container, but it's no ordinary storage shed.
Key points:
TAFE is using a shipping container farm to teach students about alternative farming
All features of the farm are controlled by an app
Agriculture, hospitality, and IT students are using the "grow pod" in their studies
Step inside and it's bursting with greenery.
Packed floor to ceiling with vegetables and herbs like basil, kale, mint and mustard, this state-of-the-art modular farm is changing the future of agriculture, all with the push of a button.
TAFE Queensland school manager Elaine Wallace said the "grow pod" aimed to change students' perspectives on traditional farming.
"Often when people think about agriculture, they think, 'Oh, I don't want to go stand in the sun all day picking vegetables, that's a bit too dirty for my liking," Ms. Wallace said.
"This is just one of those technologies that really enables students to get involved in something different and something up and coming."
Student Kallia Stebbins said when she first saw the vertical farm she was amazed by the technology.
"I didn't realise that you can grow crops like this, compared to just out in the middle of a field," she said.
"Now that I've seen this, it's very cool. I'm very interested to learn more about it."
A farm controlled from the palm of a hand
The container farm is controlled remotely with an app.
To switch the lights on inside, Ms Wallace simply whips out her phone.
"If we have a look at our monitors, it tells us that our irrigation cycle has started up, so we can set the cycle to however long or short we need it," she said.
"It's drip irrigation from the top filter through to the bottom and it's caught in the gutter that is at the bottom.
"We have pumps that will feed nutrients into the water and then, of course, we've got our lights, which are LED lights, and they are also set on a timer, so they are grow lights."
'Absolutely no limits'
It's not just agricultural students reaping the benefits of the multidisciplinary project.
Information technology students studied the app controlling the farm, while electrical students looked at how the farm kept running.
Hospitality and cookery teacher Nev Siebenhausen said his students also gained valuable first-hand experience in paddock to plate catering.
"For our students, it's a great opportunity to obviously shorten up the duration and travel on the product," he said.
"It's great for our guys to see different ways it can be grown."
Mr Siebenhausen said the walk up the hill from the grow pod to the hospitality school reduced carbon miles and cut waste by 70 percent for produce like basil, which had a short lifespan.
Any leftover produce is donated to the food relief charity, Oz Harvest.
Talks are also underway to trial sensory herbs for community service students to study the calming effects on people.
"The possibilities are endless," Ms. Wallace said.
USA - VIDEO: Could Hydroponic Farms In Shipping Containers Promote Water Conservation?
Dozens of red leaf lettuce heads grew without ever seeing the actual light of day with the help of Freight Farms "ag tech," a repurposed shipping container, and students from La Sierra University
JULY 21, 2021
RIVERSIDE, Calif. — Dozens of red leaf lettuce heads grew without ever seeing the actual light of day with the help of Freight Farms "ag tech," a repurposed shipping container and students from La Sierra University. One of the students was Max Proebstle, who never thought he would find a personal interest in hydroponic farming.
"As soon as you transplant them into the growth panels after about a week, they're already like a full head of lettuce; it's pretty amazing to see," the graduate student said.
What You Need To Know
More than 20 La Sierra students are working together to study hydroponic farming inside a repurposed shipping container
The Freight to Table program used Freight Farms "ag-tech" to grow leafy greens with the help of high-intensity lights, circulating water, and plant nutrients
The system uses at least 90% less water than traditional farming, according to La Sierra University project director Marvin Payne
The program will utilize harvested crops in the university dining halls and provide locally sourced produce for the surrounding area
Proebstle and about 20 other students have been volunteering their time inside the repurposed shipping container turned indoor hydroponic farm on campus. This method of growing crops replaces the need for soil with plant nutrients, artificial light, and recirculating water. After working with the new tech system, Proebstle believes it could be a game-changer for the future of farming.
"If you have a connection to a water system and electricity, you can basically grow produce sustainably and organically, anywhere and anytime," he said.
The Enactus team on campus recently harvested more than 500 heads of red leaf lettuce, with more on the way. The program is helping students get a hands-on approach in STEM and agriculture while also introducing them to a way to create their urban farms in the future.
Project Director Marvin Payne, who oversees the Freight to Table program on campus, explained that this model allows hydroponic farms to be placed just about anywhere for year-round harvesting.
"The entire footprint of this container is basically 320 square feet, and so with this, you can turn out thousands of plants in a fairly short period of time," he said.
The tech allows growers to monitor nutrient levels, production and light schedules remotely. Since it's inside a container, the amount of artificial daylight for the crops can be increased to about 16 hours each day. Doing so means more growth but also a higher electricity output.
As drought conditions worsen, at least 94% of California is considered to be in a severe drought. There will be more pressure on the farming industry for water conservation, and this model — according to Payne — uses at least 90% less water.
"You are using electricity, but we're getting creative in producing electricity these days, and it uses only a very small fraction of the water that any traditional farming is going to use," he said.
After plucking the leafy greens from growth panels inside the controlled agriculture environment, Proebstle and the team have brought their harvest from a hydroponic farm to the table with a new passion for farming.
"In my personal life, I can totally see this being a part of my life, something that I'll be interested in and involved in for the rest of my life," Proebstle said.
Until then, the Enactus team at La Sierra University will continue exploring how this growing method could bring sustainability and locally sourced produce where it's needed most.
Solar Firm To Convert Shipping Containers To Urban Greenhouses
CEO James DiPrima said: “We also felt that inner city urban areas also needed a way to get fresh fruits and vegetables grown right in their own neighborhood. Reimagining old shipping/cargo containers as the structural framework for our soar technology would greatly reduce the costs of building greenhouses
July 9, 2021
New York, New York, July 09, 2021 (GLOBE NEWSWIRE) — Green Stream Holdings Inc. (OTC PINK: GSFI) (“the Company”) (http://www.GreenRainSolar.com), an emerging leader in the solar utility and finance space, which had previously announced that it would be entering the rapidly growing urban gardening sector with solar greenhouses dedicated primarily to rooftop farming, today announced that it is also moving forward with its previously announced project to convert old shipping/cargo containers into inexpensive greenhouses for urban and inner city neighborhoods.
Last year, on October 6, 2020, the Company previously announced that it had entered into a non-binding agreement with Aoki Group Inc. (“Aoki”) and famed restauranter, Kevin Aoki, who wanted to ship his famous mushrooms to his various sites around the world. The mushrooms would grow inside the container while being shipped to their destination.
Blondie’s specializes in custom urban landscapes including roof decks, terraces, courtyards and entry gardens, and is now utilizing that expertise in designing the irrigation systems for our Cargo container Solar Greenhouses. Blondie’s transforms concept and vision into realized functional design.
Blondie’s is experienced in specifying, installing, renovating and maintaining green wall systems. They are famous for their interior and outside Green Walls.
For more information go to: https://blondiestreehouse.com.
CEO James DiPrima said: “We also felt that inner city urban areas also needed a way to get fresh fruits and vegetables grown right in their own neighborhood. Reimagining old shipping/cargo containers as the structural framework for our soar technology would greatly reduce the costs of building greenhouses. Less room, less labor and less panels was a marriage made in heaven for underserved communities. Communities can get one, ten or 100 containers… whatever amount of land is available… and since each container has a small footprint, there is a lot of flex flexibility for each situation.
Using solar energy has two main benefits: Solar energy systems do not produce air pollutants or carbon dioxide, and Solar energy systems on buildings have minimal effects on the environment… OUR Solar Greenhouses combine the two creating a physical structure that produce electricity, with the ability to capture the sun from many different angles.”
About Green Stream Finance, Inc.
Green Stream Finance, Inc., a solar utility and finance company with satellite offices in Malibu, CA and New York, NY, is focused on exploiting currently unmet markets in the solar energy space, and is currently licensed in California, Nevada, Arizona, Washington, New York, New Jersey, Massachusetts, New Mexico, Colorado, Hawaii, and Canada. The Company’s next-generation solar greenhouses constructed and managed by Green Rain Solar, LLC, a Nevada-based division, utilize proprietary greenhouse technology and trademarked design developed by world-renowned architect Mr. Antony Morali. The Company is currently targeting high-growth solar market segments for its advanced solar greenhouse and advanced solar battery products. The Company has a growing footprint in the significantly underserved solar market in New York City where it is targeting 50,000 to 100,000 square feet of rooftop space for the installation of its solar panels. Green Stream is looking to forge key partnership with major investment groups, brokers, and private investors in order to capitalize on a variety of unique investment opportunities in the commercial solar energy markets. The Company is dedicated to becoming a major player in this critical space. Through its innovative solar product offerings and industry partnerships, the Company is well-positioned to become a significant player in the solar space.
SOURCE: Green Stream Holdings Inc.
Tagged indoor farming
USA - Pennsylvania: Container Farm To Be Delivered To School In Oakmont
CEA Advisors announced today that they have delivered another custom-built 40’ Growtainer® Vertical Farm to the Riverview School District in Oakmont, PA. Unlike other school’s container farms that can only teach one method of production, this farm is specifically designed to teach the students about multiple growing methods
CEA Advisors announced today that they have delivered another custom-built 40’ Growtainer® Vertical Farm to the Riverview School District in Oakmont, PA. Unlike other school’s container farms that can only teach one method of production, this farm is specifically designed to teach the students about multiple growing methods.
The Oakmont Growtainer has three distinct chambers to provide a real hands-on experience for the students, including a classroom/lab/germination area, an LED-lit multi-level soil chamber, and an LED-lit multi-level hydroponic system.
Glenn Behrman, President, and founder of CEA Advisors, a global controlled environment consulting firm and the manufacturer of Growtainers worked with the school’s staff to design a cost-effective system that could provide various levels of a learning experience as well as providing fresh leafy greens for the cafeteria for their students of all ages.
“Due to Corona virus supply chain issues, the school couldn’t wait for our Growracks to arrive from our manufacturing partner in Holland. So we designed and built a custom multi-level racking system for the ebb and flood hydroponic installation including automatic irrigation and water monitoring and dosing.”
The soil side is also a multi-level design with LED lighting and an irrigation system. The climate is independently controlled in each chamber including de-humidification. In the next month or so the entire campus, including the Growtainer will be powered by solar.
For more information:
CEA Advisors LLC
Glenn Behrman, Founder, and President
gb@cea-advisors.com
www.cea-advisors.com
23 June 2021
VIDEO: Sweden: Growing Food In Umeå In A Freight Farms Shipping Container
Ellen Bergström and Daniel Remes are growing food in Umeå, Sweden to create a resilient and sustainable local food system
Ellen Bergström And Daniel Remes Are Growing
Food in Umeå, Sweden To Create A Resilient
And Sustainable Local Food System.
Although they had little agriculture experience, the realization that their community needed a dependable food supply chain that offered fresh, quality produce even through the long, dark winter months, led them to start their Freight Farming business, MY Harvest.
Click on the video below to watch their story.
For more information:
Freight Farms
info@freightfarms.com
www.freightfarms.com
24 Jun 2021
CANADA: Thursday, July 8th, 2021 - 12:00 PM EST
Sit back and learn more about Growcer's beginnings, our farm's uses, and essential considerations for starting your own Growcer project. It will be an informal opportunity to ask our team questions and learn more!
Every first Thursday of the month, we'll be hosting a Meet and Eat that anyone can join; however, we're going to have it on the second Thursday in July to accommodate for the statutory holiday on Thursday, July 1st.
Register Now →
Sit back and learn more about Growcer's beginnings, our farm's uses, and essential considerations for starting your own Growcer project. It will be an informal opportunity to ask our team questions and learn more!
SIGN UP TODAY
Thursday, July 8th, 2021
12:00 PM EST
Brick Street Farms Expands Through Florida and East Coast
“We really wanted to bring food production to the point of consumption, so we’re focused on embedding our farms in urban areas,” says Shannon O’Malley, CEO, and co-founder of Florida-based container farming company, Brick Street Farms
"We Are As Much A
Technology Company
As We Are A Farm Operator”
“We really wanted to bring food production to the point of consumption, so we’re focused on embedding our farms in urban areas,” says Shannon O’Malley, CEO, and co-founder of Florida-based container farming company, Brick Street Farms.
The company was founded by Shannon and her husband Bradley, who combined her expertise in electrical engineering with his background in software development to design their own shipping container farms.
According to Shannon, a major differentiator of Brick Streets Farms is that the company manufactures and operates its own shipping container farms.
Brick Street Farms Hubs
Brick Street Farms has recently secured a significant investment from Lykes Brothers, which is reportedly one of the largest and longest-running private agricultural companies in the United States. During the official announcement last week, the financial investment will be used to aggressively expand Brick Street Farms hubs, which are the combination of container farms with a retail front in densely populated areas.
Click here to Zoom the photo. (Photo courtesy of Brick Street Farms)
According to Shannon, this expansion will begin in west-central Florida then expand to the east coast. From these hubs, Brick Street Farms will also introduce home delivery and will support restaurant partners located within 50-100 miles of the hubs. Already in 272 Publix supermarkets, Brick Street Farms will continue this partnership and plans to expand into additional product categories.
Building a resilient, multi-channel sales strategy
Brick Street Farms was first developed in 2015, and during its early years, the company predominantly sold its products to restaurants and directly to customers. However, the pandemic-induced shutdown in 2020 resulted in the loss of 70% of Brick Street Farms’ clients due to restaurant closures. As Shannon explains, Brick Street Farms was already selling its products in the GreenWise section at Publix supermarkets, which is reportedly the largest employee-owned supermarket chain in the US. This partnership allowed Brick Street Farms to quickly pivot following the mandated closure of restaurants.
“In the same month that Florida went into lockdown, grocery stores saw an incredible jump in demand so we were able to quickly pivot and provide our vegetables to grocery stores within a week. We are currently in 272 Publix stores and are working to expand into west-central Florida,” says Shannon. The state of Florida has since reopened and Brick Street Farms was able to bring back its previous accounts and sign new ones, according to Shannon.
Brick Street Farms also has its own gourmet market located at the farm that is open six days per week. Consumers can shop either on-site or online, with contactless delivery available. Shannon also explains that the company has adopted a unique twist to community-supported agriculture. By subscribing to a farm membership, consumers receive a discount and support the recently approved non-profit, Desert Farms Foundation.
“We established Desert Farms Foundation to help us bring container farms to food deserts within the United States. With a farm membership, 1% of the proceeds go to Desert Farms Foundation to really support community agriculture,” explains Shannon.
Thrive Containers
“Our containers are under the name Thrive Containers, which is wholly owned by Brick Street Farms. Our containers are the equivalent of 2-3 acres of traditional farmland. They use very little water, are energetically efficient, produce very little waste and use no chemicals. Since our products are wash-free, our customers get the benefits of long-lasting produce,” explains Shannon.
According to Shannon, Brick Street Farms is as much an agtech company as it is a farm operator. The company decided to establish Thrive Containers as its own entity within Brick Street Farms in order to differentiate between the food production and manufacturing aspect of the company. “When people see Brick Street Farms, we want them to think of butterhead lettuce, basil and our other vegetables,” notes Shannon.
Thrive Containers does not sell its container farms to third parties, but instead continuously improves the farm design for current and future installations. As Shannon explains, the company focuses on designing intelligent systems that can adjust to indoor and outdoor environmental conditions. Thrive containers have more than 120 sensors in and around the farm to monitor and respond to ambient temperature, humidity, carbon dioxide, vapor pressure deficit, etc.
Brick Street Farms and Thrive Containers work closely, with the engineers and designers having all undergone farmer training to ensure that the systems designed truly respond to the needs of Brick Street Farms’ growers.
Why Florida?
While warm and sunny Florida may seem ideal for outdoor agriculture, Shannon explains that soil conditions make soil-based agriculture somewhat difficult. She says that Florida soils are rather degraded and sandy, lack nutrients and lack natural bacteria, meaning farmers need to spend significant time and effort on rebuilding soils. Also, water sources are highly saline because of our position at level, near the coast, and with a low water table. Finally, the lack of winter makes it difficult to regulate pest cycles.
Lead photo: Co-founders Brad Doyle and Shannon O’Malley
For more information:
Madeline McNaughton, Head of Business Development
Brick Street Farms
madeline@brickstreetfarms.com
www.brickstreetfarms.com
Publication date: Thu 27 May 2021
Author: Rebekka Boekhout
© VerticalFarmDaily.com
Vertical Future And Crate To Plate Plot Fleet of Shipping Container Farms In London
Each of the 'container farms' will be able to produce up to five tonnes of leafy greens and veg each year with zero carbon footprint, the firms claim
Jessica Rawnsley
14 May 2021
Credit: Vertical Future
Each of The 'Container Farms' Will Be Able To produce Up To Five Tonnes of Leafy Greens And Veg Each Year With Zero Carbon Footprint, The Firms Claim
Urban farming specialists Vertical Future and Crate to Plate are together gearing up to rollout a fleet of indoor container farms in London, with each capable of producing zero carbon fresh salad and vegetables for swift delivery across the UK capital city, they announced yesterday.
Crate to Plate, an urban farming start-up, plans to use the 'container farms' designed by Vertical Future - a technology company focused on controlled-environment-agriculture (CEA) - across several new sites in London's Bermondsey and Stratford.
By using the container farms, Crate to Plate said it would be able to produce up to five tonnes of fresh produce - including lettuce, kale, and rocket - per year, and then deliver it to customers within 24 hours with a zero-carbon footprint, all without any use of pesticides or toxic chemicals. The firm counts Ollie Dabbous, chef-patron of Michelin-starred restaurant, HIDE, as well as independent grocers such as The Notting Hill Fish Shop and Artichoke in Hampstead among its customers.
Vertical Future's innovative farms, built within 40ft shipping containers, allow for highly-controlled indoor growing conditions, harnessing LED lighting, full climate control, and dual irrigation in order to create the optimal conditions for cultivating leafy salad and vegetables.
Proponents of vertical farming argue producing crops in such circumstances can reduce the amount of countryside land used for farming, better protect crops against the impacts of increasingly volatile outdoor climate conditions, and cut down on transport and logistics typically needed to ferry food from farms to urban centres. They also require far less water and zero pesticides.
"Our Container Labs create the optimal growth environment for growing fresh produce and can be deployed close to point of consumption, using minimal space," said Jamie Burrows, Vertical Future's CEO. "Using zero chemicals and growing crops in a controlled environment enables our partners to meet demand all-year-round, as opposed to regular food production systems which are reliant on seasonal limitations."
By shifting towards using Vertical Future's 'Container Labs', Crate to Plate's founder Sebastien Sainsbury said the firm would be able to scale up its systems across the UK while offering more efficient growing capabilities to improve both output and product quality.
"It's been incredibly encouraging and exciting to align with other dynamic, innovative, and enterprising British business, which will help us to scale up our vision and execute our exciting opportunities both nationally and internationally," Sainsbury said.
Square Roots Expands Premium Herbs Range With Fresh And Aromatic Cilantro, Dill, And Parsley Grown In Climate Controlled Local Farms Across The Country
Indoor farming company takes the next step in bringing local, real food to cities using modular farm technology that empowers both farmers and consumers
Indoor farming company takes the next step in bringing local, real food to cities using modular farm technology that empowers both farmers and consumers
May 17, 2021 (New York, NY) — Square Roots, the technology leader in urban indoor farming, is expanding its herb range by introducing three premium fresh offerings - Cilantro, Dill, and Parsley - to complement its widely successful signature Basil. Co-founded by Kimbal Musk, Square Roots’ herbs are grown across the company’s network of cloud-connected and climate-controlled indoor farms in New York and Michigan and are now available in more than 200 retail stores - including Whole Foods Market, Fresh Thyme Market, SpartanNash, and FreshDirect.
“COVID-19 has accelerated the adoption of locally grown indoor produce”, said Raji Margolin, EVP of Sales and Marketing at Square Roots. “The habits of at-home cooking and using fresh, local produce are here to stay. Now more than ever, people care about the food they eat, and where it's grown - and our goal is to make sure that fresh and local food is available to consumers year-round. These herbs are just the beginning of our product offerings and we can’t wait to expand into additional categories.”
Square Roots has a strategic partnership with Gordon Food Service (GFS), one of the country’s leading food service providers, to deploy farms across the country together and provide fresh, high-quality, local food to consumers across cities, year-round. Square Roots broke ground on its latest indoor farm in Grand Rapids, Michigan in December 2020 and began planting seeds just three months later, in March 2021. This rapid deployment capability is enabled by the company’s modular farm-tech platform.
“We’re using technology a little differently at Square Roots farms”, said Tobias https://www.igrow.news/igrownews/indoor-ag-science-cafe-may-18th, Co-Founder, and CEO at Square Roots. “Food, farmers, and consumers are all connected at the center of our system. We surround our farmers with data, tools, and insights to help them grow more, better-tasting food with fewer resources. At the same time, with features like our unique Transparency Timeline, we help our consumers understand exactly where their food comes from and who grew it.”
The expanded herb range is available in both the New York City area and the Great Lakes Region.
About Square Roots
Square Roots is the technology leader in urban indoor farming. Its mission is to bring local, fresh, real food to people in cities around the world - setting new standards for transparency and responsibility while empowering the next generation of leaders in agriculture. Founded by serial entrepreneurs, Kimbal Musk and Tobias Peggs, its range of fresh produce is available in more than 200 retail locations around the country including Whole Foods Market, Fresh Thyme Market, SpartanNash, and FreshDirect. Square Roots’ strategic partnership with Gordon Food Service reinforces a larger shared ambition to build commercial scale, climate-controlled indoor farms together across the continent - enabling local food at a global scale, year-round.
For more information, please visit www.squarerootsgrow.com.
Raleigh Shipping Container Farm Using Hydroponic Technology
The technology that Nanue’s Farm uses was created by Boston-based company, Freight Farms. Each container has thousands of LED grow lights, temperature controls and uses between five and ten gallons of water each day
BY KYLEIGH PANETTA RALEIGH
MAY 10, 2021
RALEIGH, N.C. — Summer is one of the busiest and most profitable times for farmers across the state but what if they could grow produce year-round?
Nanue’s Farm in Raleigh is using some advanced technology to do just that.
What You Need To Know
Nanue's Farm is located in downtown Raleigh and uses hydroponic technology
The "container farm" is about 320-square feet and can hold 5,000 heads of lettuce
The technology is being used in dozens of countries and may help eliminate "food deserts"
Nanue’s Farm is on S. West Street, what some may say is a pretty strange place for a farm.
“This is in downtown Raleigh. You can see the great skyline we have here,” said Trevor Spear, the owner of Nanue’s Farm. “I walk to work when I can. I don’t have to drive.”
Spear admits that a seemingly empty parking lot with a shipping container is not what most people expect to see when they arrive at a farm.
“It’s funny because people don’t understand what it is. They think it’s just a shipping container and people are storing stuff inside it,” said Spear.
Nanue’s probably looks more like a science experiment than a farm.
“It’s 65 degrees, 60% humidity. Co2 runs at night, so we’re like 2,000 parts of Co2 in there. It’s optimal growing conditions for lettuce and that’s how we do it in seven weeks’ time,” said Spear.
Spear specializes in leafy, crunchy greens. Something else you can hear inside the farm, from time to time, is classical music.
“We play classical music at night and I think it makes a difference. They like it. Sometimes we play a little Van Halen but usually Bach or Beethoven,” said Spear who knows that a little TLC goes a long way and said every lettuce has a name.
It’s not your typical lettuce but Spear is also not your typical farmer. He named the farm after his grandmother, Lydie Cox.
"When I was a kid I would go have summers at Nanue’s house and she had a huge garden, an acre size garden. I would go up and down the rows with her as a kid. That’s where I probably got the bug because once it bites you, you live with the sting," said Spear.
Nanue’s Farm is getting a second container in June and hopefully a third by the end of the year. They currently offer home delivery to a few areas and are looking into creating a farm stand. The majority of the produce is sold to local restaurants in the area.
"When chefs come and tour the farm, they open the door and they’re like, 'Wow.' We can hold 5,000 heads of lettuce. We harvest 60 cases a week, so when they walk in and see that much lettuce growing and looking as good as it does, it’s a take-back," said Spear.
If you’re interested in trying some of their lettuce, you can also find a Nanue’s salad at Hummingbird, a restaurant in Raleigh.
The technology that Nanue’s Farm uses was created by Boston-based company, Freight Farms. Each container has thousands of LED grow lights, temperature controls and uses between five and ten gallons of water each day.
The containers also have cameras and connect to Wi-Fi so it can be monitored from an app or website. Freight Farms said the goal is to replicate an ideal farming environment so that more people have access to fresh produce.
“In the U.S., food moves 500 to 1,000 miles, predominantly from California. If you can move the farm then you can put a farm in a food desert and then you can grow the food and the hyperlocal food and the high nutritional values of that food. Either food deserts or even urban areas,” said James Woolard, the chief marketing officer for Freight Farms. “You might not think it’s a food desert but it is from a socio-economic point of view and an access point of view.”
USA: NEW YORK - When A Shipping Container Becomes A Farm
Compact, enclosed vertical farms are making their way to Hudson Valley's urban areas
Compact, Enclosed Vertical Farms Are Making Their
Way To Hudson Valley's Urban Areas
May 3, 2021
John Lekic is the chef and owner of Farmers & Chefs in Poughkeepsie and vertically grows his own produce for his restaurant in a shipping container on site. He came across the concept of shipping container farming at an exhibition at the Culinary Institute of America in 2019. Aaron Lacan
The Hudson Valley is quite familiar with what it means to be farm-to-table, but what if the farm is also practically right next to the table, even in the more urban and metro areas?
Vertical farming via high-tech shipping containers is emerging as a new solution for businesses seeking to grow their own produce in a way that shrinks the necessary agricultural footprint while maximizing yield and reducing produce travel time. Here in the Hudson Valley, a 20 by 20-foot shipping container is being used to grow up to 400 pounds of fresh produce a month at Farmers & Chefs restaurant in Poughkeepsie.
Last year, the restaurant partnered with an Israel-based agro-tech company Vertical Field to grow herbs and vegetables for its dishes in a new and innovative way. The startup, established in 2006, uses technology to create innovative growing methods to improve food supplies in urban areas around the world, working mostly in the Middle East and Europe but also recently in the United States — including right here in Dutchess County.
Poughkeepsie's Farmers & Chefs is one of the first businesses in the Hudson Valley to try shipping container farming. The restaurant's 20 by 20-foot climate-controlled container (pictured above) produces about 400 pounds of fresh produce a month. Aaron Lacan
John Lekic, chef and owner of Farmers & Chefs, grows everything from buttercrunch lettuce, kale and baby arugula to herbs like rosemary, sage and basil in his enclosed vertical farm. The container is divided into four growing fields and is set on the restaurant’s property for customers to see, which has drawn even more interest to Farmers & Chefs as of late.
So why vertical farming?
Vertical Field is just one manufacturer specializing in reimagining steel shipping containers into enclosed, climate-controlled farms that are powered by LED lights instead of the sun, essentially supercharging a growing environment. Freight Farms and Grow Pod Solutions, other manufacturers, also tout this farming approach for its lower burden on farm labor and land, and for the higher output per square foot.
Shipping container farming is climate-controlled, powered by LED lights instead of the sun, and can produce high yield in a small space. But humidity and start-up infrastructure costs can be challenges. Aaron Lacan
“It’s a dream come true for chefs to be involved from the seed to the plate,” said Lekic. “It’s a great experience when you grow your own ingredients.”
Lekic pursued vertical farming after coming across Vertical Field during an exhibition showcasing a number of Israeli-based companies involved in food and agriculture at the Culinary Institute of America in late 2019.
Before the shipping container arrived at the Poughkeepsie restaurant, Lekic sourced vegetables from nearby farms and grew herbs in small outdoor gardening beds on site. However, Lekic found that it wasn’t enough yield, especially in the summer, and he often collaborated with additional farms to fill the gap. With a shipping container for growing, the restaurant is able to produce enough of what they need and on site – a key benefit for Lekic.
“There is a huge importance of having urban farms where the demand is,” said Lekic. “The problem with today’s agriculture is that everything has to travel. Most people are not aware of it, but depletion of the nutrients in our food is a huge issue.”
If you harvest spinach, it would be full of vitamin C that same day, Lekic said. But that changes dramatically just 48 hours later, when that nutrient is mostly gone. (A 2013 study by the University of California showed that spinach could lose as much as 90 percent of vitamin C in a single day.)
Farmers & Chefs restaurant grows everything from buttercrunch lettuce, kale, and baby arugula to rosemary and sage in its on-site shipping container. Aaron Lacan
By growing the restaurant’s produce steps away from the kitchen, “it’s as fresh as it gets,” said Lekic.
Farmers & Chefs received its shipping container farm right around the same time that COVID-19 hit last year, which Lekic said actually worked out well, as it gave him a chance to learn the ins and outs of vertical farming during a period that was quiet for his restaurant. By April, he was harvesting the first crops.
“Overall, the goal of vertical farming is to reduce the cost of healthy and fresh food to the retailer and to the end buyer as well,” said Vertical Field marketing director Noa Winston. “Since vertical farming reduces transportation costs, food losses, inventory inconsistencies, and price fluctuations due to climate, natural disasters, and other crises that create shortages, the retailer with vertical farming can benefit from consistency, security, and ownership over the entire supply chain.”
In another regional example, Evergreen Market, a grocery store in Monsey in Rockland County, partnered with Vertical Field to grow vegetables that ultimately stocked the store’s produce aisles, while also inviting customers to view its micro-farm when they visit the store.
Cost and maintenance concerns
This farming approach isn’t for everyone and there are drawbacks. “While it does offer some solutions to things like land access — which is, frankly, a huge barrier to the farming we advocate for here in the Hudson Valley — there is a lot of infrastructure needed,” said Kathleen Finlay, president of Glynwood, a center for regional food and farming based in Cold Spring.
“That brings a whole other set of challenges — how to create enterprises with a high capital upfront cost, how to get sustainable systems. It’s a different suite of challenges than more land-based production.”
Indeed, the start-up costs for an on-site shipping container farms aren’t cheap, although businesses say savings can be realized downstream by the reduced costs of paying produce purveyors for food that a restaurant or business is now growing itself.
Freight Farms' 2021 Greenery S model costs $149,000, which doesn’t include the shipping fee. Additional start-up costs can vary depending on where its being shipped, training packages selected, and any extras. Vertical Field would not disclose the fees associated with its model.
Plus, there is a bit of a learning curve when farming in a shipment container. Lekic played around with different variables, like what was best to grow at the same time, to see what would produce the highest yield.
"It's as fresh as it gets," said John Lekic of Farmers & Chefs, pictured above, about the new way of farming. Aaron Lacan
“For my purposes, I learned to stick with only two to four items – mostly greens,” said Lekic about his growing. “It makes the most sense based on my demand.”
Maintenance is an ongoing effort with an enclosed growing system that requires constant electricity and temperature controls to assure optimal growing conditions. “It’s always work,” said Lekic.
Over the past year, Lekic had to work out some kinks and issues, like making sure the air conditioning and heat levels were favorable to growing produce year-round. Just like traditional farming, some seasons might require more work — a vertical farm in the summer, for example, would have increased humidity that could negatively affect plants if not properly controlled.
While some growers may need back-up plans for electricity outages, Lekic doesn't foresee issues there because he is connected to the main restaurant building, which runs on a hospital-grid electricity system. Just in case, he has two generators that he could connect to if needed.
These drawbacks are outweighed by the ability to grow such consistent produce yield himself on site, he said, and the built-in technology features like being able to water plants by pushing a button on his phone. Lekic said overall it’s pretty easy to operate and monitor, so much so that the restaurant is looking into upgrading its original container to the newer version of the same size, and purchasing a second container.
“I’m interested in doing a mushroom container,” said Lekic. “There is the possibility of that. It’s a completely different kind of experience, but we would be super excited.”
DIY shipping container farming
While the hefty price tag of some farming shipping containers might be too prohibitive for some, others are riffing off of elements of tech-first farming for their own DIY growing methods.
KC Sullivan, a New Jersey-based mushroom farmer, created his own vertical farming environment out of an abandoned 40-foot-length shipping container that was used for storage at the Whitechapel Projects in Long Branch. Sullivan, who often collaborates with Tivoli Mushrooms here in the Hudson Valley, decided to create his own container farm by spray foaming it, sealing the floors, putting in an HVAC system, adding lighting and installing a misting mechanism.
He estimated the costs to be between $15,000 and $20,000 — not insignificant but far cheaper than a new shipping container already turbo-charged for farming.
“It was challenging,” said Sullivan. “There is no real guidebook or instruction manual on how to create a container mushroom farm. It was all about brainstorming how we wanted it to be.”
While it’s only been a year since mushrooms have been grown out of this urban shipping container, Sullivan is happy with the high-yield results: he's growing around 400 to 500 pounds of mushrooms a week. Mushroom container farming is slightly different from growing vegetables or herbs; for example, Sullivan doesn’t grow compost mushrooms, so there is no dirt necessary.
“We grow hardwood varieties, so it’s exclusively on red oak saw dust that is supplemented with agricultural byproducts,” said Sullivan. “You mix the two together with water, pasteurize it to kill off any pathogens, inoculate it with the strain of mushroom you’re looking to grow. It goes through an incubation period in a separate room [outside of the container], and then it goes to the fruiting room, which is the container and where it will be harvested.”
Just like Lekic, Sullivan also has run into some maintenance hiccups. The waterlines froze during the winter, which was a “big challenge and setback,” leading to a starved off humidification system, costing him around 100 to 150 pounds of crop.
Despite that hurdle, Sullivan also says the container can stand up against storms because it’s “built like a tank,” while regular farmland could be vulnerable to severe thunderstorms and potential flooding.
“One tool in the toolbox”
While an exciting option for some, vertical farming is “one tool in the toolbox” and it’s important to not forget about the benefits of traditional farming, said Finlay of Glynwood.
Finlay applauds any effort to produce food “that aligns with environmental sustainability,” but doesn’t think vertical farming will ever replace traditional farming or even fix the lack of land available for production.
Still, any effort to grow fresh food for more people is a win overall.
“We need more healthy food, accessible and affordable to more people,” said Finlay. “As much as vertical farming can play a role to that, I think that’s wonderful.”
Written By
Cloey Callahan is a lifelong Hudson Valley resident who was born and raised in Brewster, lived in New Paltz for four years while she attended college, and now resides in Newburgh on Liberty Street. On a sunny day, she strolls through Newburgh enjoying the 19th-century architecture on her way to the Hudson River waterfront. You can reach her at cloey.callahan@hearst.com to say hi or with pitches.
USA: This Colorado Company Is Building Farms In Shipping Containers To Help Feed People In Need
FarmBox Foods wants people to be able to farm anywhere, allowing them to access fresh food they otherwise wouldn't be able to
Author: Jeremy Moore
April 19, 2021
FarmBox Foods Wants People To Be Able To Farm
Anywhere, Allowing Them To Access Fresh Food
They Otherwise Wouldn't Be Able To
SEDALIA, Colo. — A three-year-old Colorado company has an ambitious goal: to bring food security, safety, and sustainability to communities in need around the world.
FarmBox Foods aims to achieve that goal by connecting those communities to sustainably sourced food that's grown locally inside one of their container farms.
Their first product was a vertical hydroponic farm, or VHF, built inside a shipping container.
The company has since developed a second product: a gourmet mushroom farm, or GMF.
So far, customers in Colorado include Centura Health, Vitamin Cottage Natural Food Markets, and the C Lazy U Ranch in Granby.
FarmBox CEO Rusty Walker and COO Jake Savageau joined 9NEWS to talk about how they hope to change the way the world thinks about farming.
9NEWS also spoke with a prospective customer of FarmBox, Cori Hunt of the Denver restaurant group Edible Beats.
(Editor’s note: Responses have been edited for context and clarity.)
As a mission-driven company, what is the mission of FarmBox Foods?
Walker: Our goal and our mission is to get our products out into the communities where we can help develop food security programs. We’re looking to get into food deserts, opportunities where folks in the world might not have access to good, clean nutritional food. And so we kind of strive as a company that’s driven to feed the world one container at a time. And we’re ready to go out and manufacture thousands of these if we can.
We’re able to decentralize growing food by being mobile – being able to deploy these by just having a semi come in. We can then lift it up on a flatbed and take it to anywhere in the world. We’ve got two containers going to islands. We’ve got our first container that took off for the island of Jamaica. It’s going to Montego Bay where it’s going to be used behind mega marts on the island. And then we have another container which is our gourmet mushroom farm that’s going to be going to Tahiti where they’re going to be using that to feed the island population which does not have access to that type of food.
One big area that we’re really focusing on is the urban areas throughout the U.S. where they don’t have a lot of land to grow. These farms can go right into the parking lots, behind a church for example. We’re working with a community church on the south side of Chicago that’s looking at placing two of these containers – a vertical hydroponic farm and a mushroom farm – right outside in the parking lot outside the church.
And we think we could bring an educational spin to this where we can have the community grow their own food and supply the community themselves with highly nutritional food that ordinarily they just would not be able to get their hands on. So, we’re thinking that if this pilot program goes well this would be an application that would apply to every inner city throughout the U.S.
Farmbox Foods grows vegetables in shipping containers. Credit: Jeremy Moore, KUSA
Savageau: The mission’s always been to create products that are for the decentralized food insecurity industry. So, we want to create a product that can be deployed anywhere in the world, can run off-grid, and can feed communities. So, we have two different products – the VHF and the GMF. Every product that we develop gets us one step closer to being able to feed a community with everything they need, because you can’t feed communities forever just on leafy greens.
So mushrooms, they’re more nutrient dense, that gets us one step closer. There’s other products that we’re going to develop to get us to that point. But, I think the mission for the company is to be able to deploy these farms into communities where they’re needed, whether that’s a rural area, a food desert in the U.S., an inner city, or somewhere in Africa like Ghana or the Sudan.
We want to align with big ag and we want to help the industry get better. So we want to get food to where it’s needed. We’re looking at doing stuff with food insecurity and food inequality. That’s big with what we’re doing. So, that kind of aligns with our mission. If you look at our food system – just take for instance – you know if you look at a SNAP program or food subsidy program – you’re taking food and giving it to somebody or they’re purchasing it.
But, a lot of that food that they’re purchasing is processed, sugar – I mean, it’s poison. And if you go on a military base anywhere in the U.S., there’s fast food on the base. It’s really what you see. So, there’s a lot of reasons why we’re doing this I think. We can help fix our food system. And we can help educate the youth on how they should eat. We’re doing some stuff with an Inuit community in Alaska. They don’t necessarily know how to fix this food or prepare it or use it. So, I think education is a big part of what we’re doing.
How do these container farms work?
Savageau: When people think of farms, they don’t think of agriculture like this. Vertical hydroponics and indoor ag and controlled environments – it’s been around for a long time. I think that the way that this one works is pretty simple. The water gets fed into a tube system and the water trickles down and goes back into the tank. And where you’re standing – the seedling tray area – the water goes into a tank, into the seedling trays, gets flooded, and then back into the tank.
There’s a software that we use called Agrotech that monitors the temperature, the humidity, the lights – basically, all automated. So, it’s fairly easy to run. You need about 15 to 20 hours a week to run one farm. The GMF farms takes about 25 hours a week. It’s a little bit more intensive. The VHF is the vertical hydroponic farm and that’s the farm that we’re standing in. The GMF is the gourmet mushroom farm, which is the one that you went through earlier. You want to just keep things as clean as possible. The cleaner that you keep it the better it’s going to run.
So, we have a standard SOP, you know, that we implement with our training. Cleaning the floors. Cleaning the tubes. You don’t clean them every time. But, usually, every couple harvests you’ll take the tubes out, wash them out. You’re cleaning the tanks about every 60 days.
But, on average it’s pretty easy to maintain if you’re doing the daily checklist. The seeds are going to be in the seedling tray for about two weeks. Then, they go into the wall. And then they get harvested about 60 days after they start in the seedling tray. So, on average you’re about 60 days from seedling to harvest depending on what you’re growing.
And this farm is really setup for vertical hydroponics. So, it’s leafy greens. You can do hundreds of different types of lettuce. You can do cherry tomatoes, strawberries and peppers. There’s a lot of different things that you can grow in here. Most of our clients are only growing a couple things at one time. You don’t have to worry about weather. You don’t have to worry about if this is in a cold climate like the arctic. You know, they can’t grow food. If it’s in a desert, they can’t grow food. If it’s on an island, they can’t grow food. So, these can be deployed anywhere. And they grow 365, all day, every day. Also, the yield is very high for the square footage. So, you can put these on top of a building, inside of a building. It only takes up 320-square feet. You don’t have any pesticides. So, you don’t have to worry about pests, bugs, mildew, stuff like that’s going to effect the plant as it’s growing. It’s also decentralizing the food system.
So, you’re not having to ship food hundreds of thousands of miles from point A to point B. So, the food is right there. And the nutrients that we use are organic plant-based nutrients. And there’s no pesticides. So, the nutrient density is extremely high compared to something that you would buy – even organic – in a store.
Walker: We grow a variety of vegetables and lettuces. I believe that we’re somewhere in the area of 30 to 40 different types of vegetables and lettuces that we can grow in our farms. And, then of course we’ve got our gourmet mushroom farm which we’re currently growing anywhere from eight to nine different varieties of mushrooms. We’re in the startup phase of running that farm ourselves. So, we’re exploring the different types of mushrooms that we can grow. But, we’re very proud of the folks that are actually running these farms – our staff, very knowledgeable and they do a great job. We’re going upwards to 300 to 400 pounds a week now. We’re not competing with traditional farming. We’re actually a compliment.
Who are your customers?
Walker: One of our first customers is Centura Health. They purchased their first container – which is now sitting at St. Mary’s in Pueblo. They ordered two more containers after seeing how the first container behind their hospital worked. We actually started up a pilot program with Centura Health where we’re now running them as the FarmBox family.
We’re working with Centura Health in identifying not only their hospitals and the patients who are going to be fed through our vertical farm – but then we’re also identifying where the food deserts are and Centura Health will then help us with what we’re going to be growing, and then the communities that we’re going to be serving from those, those particular crops.
We do have a couple that’s looking at doing some farming right here in Sedalia. They’re going to use it to supplement their traditional farming, which will be an interesting pilot program for us to work with them on. We’re working with C Lazy U Ranch out of Granby, Colorado. They’ve ordered a hydroponic farm and we’re going to be manufacturing that. And they’re going to place that at the ranch. They don’t really have access to a lot of good food as far as having it grown right there on the property. So, this will be a nice compliment to the services and the customer experience that they provide their customers by having one of our farms right on site.
Centura Health is one of FarmBox Foods' first customers. Credit: Jeremy Moore, KUSA
One big area that we’re really focusing on is the urban areas throughout the U.S. where they don’t have a lot of land to grow. These farms can go right into the parking lots, behind a church for example. We’re working with a community church in the south side of Chicago that’s looking at – we’re looking at placing two of these containers – a vertical hydroponic farm and a mushroom farm right outside in the parking lot outside the church.
We can have the community grow their own food and supply the community themselves with highly nutritional food that ordinarily they just would not be able to get their hands on. So, we’re thinking that if this pilot program goes well this would be an application that would apply to every inner city throughout the United States.
Savageau: We have a customer here in Lakewood that’s going to put one in their backyard. They run a small organic farm. We’re looking all the way up into federal government and military, and everything in between.
So, Rusty was talking about FEMA, the UN, UNICEF, those are the big customers that take a long time to build a relationship with. And then we have customers that are all the way down to just an individual that wants one for their property or maybe a couple of people are going to run one for a restaurant or a developer wants one for a small development that he’s doing.
We’re working with a group in New Mexico and they’re building a huge development of about 45,000 houses. So, we’re talking about 100 of these units that are going to be deployed in that area right outside Albuquerque to feed those communities within that area over the course of about two years. We work with a grocer that’s regional. And we work with some other customers that are kind of at a government, federal government level.
I think we’ve done a lot in the last three years. I mean we haven’t gone out and raised any capitol. So, we’ve self-funded it. And I think from that point of view you know we’ve done a lot. We’re kind of at the point right now where we’re just starting to scale. So, we’ve just started our social media. You know SEO (search engine optimization), SEM (search engine marketing). We have a sales team. And orders are starting to come in. We’ve partnered with RK which is manufacturing our units. That’s giving us the ability to scale. Because before that we were building these one or two at a time in Sedalia and now we can build 100 of them. So, that’s really been a huge part of us being able to scale is the manufacturing side.
How much does it cost to purchase and operate the farms?
Jake: This VHF farm – vertical hydroponic farm – starts at $140,000. The GMF starts at $150,000. Then, you have training and deploy, getting it there. So, usually, you’re over $150,000 for a farm. So, your ROI (return on investment) in this product is going to be about 12 months to 24 months depending on what you’re growing and where it is in the world.
The GMF is going to be closer to 12 months because mushrooms tend to be more expensive – again – depending on where it’s going. We have a unit that’s going to Tahiti for example. That ROI is going to be extremely fast because they ship everything in. If there’s a market for mushrooms there, which there is with a grocer, it’s going to be quick. So, the cost of running it with labor and everything you need to grow the plants, usually around $20,000 to $40,000 a year. We’re a mission-driven company. So, money isn’t the first thing that’s important. We want to build a certain amount of these and then every x amount that we build, we build one for free and we send it to a community that maybe our social media has engaged with or given us an idea that ‘hey, this would be a good community.’ And then, we send it there. We pay for it. We train people. And that’s something that we want to do. We can’t do it yet. But, I think that’s coming in the next year.
Why is Edible Beats interested in working with FarmBox?
Hunt: We try to be as local and organic as possible and that’s what brought us here to FarmBox. We can put a box behind a restaurant and have lettuces cut and washed and put on the plate the next day.
Just to have that connection with our food and know exactly where it’s coming from and how it was produced. It’s going to be better quality because it’s not traveling. It’s not ripening in a truck coming from Mexico. Economically, what we can do to not pay the mileage on the vehicles and the gas, the inputs, the emissions, the extra packaging, the plastics.
That’s one of the best things about FarmBox – that what we can do is – if we produce food for our restaurant group – I’m not going to have to buy packaging that’s going to go into a landfill or even need to be recycled. It’ll go directly into the vessels that we’re going to store them in the cooler. We don’t have to worry about marketing and labeling and you know stickers and plastics and all this extra stuff – this hoopla that we don’t need – because FarmBox is a possibility now.
The Farmbox Foods containers allow leafy greens to grow vertically, maximizing space.
Credit: Jeremy Moore, KUSA
We are looking at lettuces and herbs, leafy greens. So yeah, like basils, sage, leaf lettuces, butter lettuces, arugula – these kinds of things that we use that could greatly help our impact. Essentially it’s a self-contained box that you can grow fruits and vegetables in – most likely leafy greens – and it’s a soilless or near soilless medium.
So, essentially you plant your seed in a very small amount of coconut core or soil or peat moss – something to hold the root structure – and that, according to with FarmBox, they’re system is a vertical farming.
So, they have vertical towers and then they put the lettuces in the towers in their small soil medium and then they drip water with enhanced nutrients mixed into the water specifically built for those vegetables. It doesn’t have a lot of soil waste.
For the amount of the surface area you can get way more production out of it and the water that goes through is recycled. Per plant, it uses far less water than any other type of growing system.
RELATED: Why Colorado agriculture groups oppose Initiative 16, an animal cruelty proposal
USA: New Farm Brings Sustainable Farming To Northern Michigan
There's a new farm in northern Michigan that provides fresh and local produce all-year-round using environmentally friendly practices and high-tech resources. The container is home to Pine Hill Farms, a farm that uses a controlled environment agriculture system to grow produce
by Miya Ingle
April 16, 2021
To View The Video, Please Click Here:
Pine Hill Farms uses a controlled environment agriculture system to grow produce. (Miya Ingle/ WPBN)
KALKASKA COUNTY, Mich., (WPBN/WGTU) -- There's a new farm in northern Michigan that provides fresh and local produce all-year-round using environmentally friendly practices and high-tech resources.
If you're driving down Tower Road in Kalkaska, you might notice a big container.
The container is home to Pine Hill Farms, a farm that uses a controlled environment agriculture system to grow produce.
The produce is grown hydroponically instead of in the ground.
Staff at Pine Hill Farms say this growing method uses 95% fewer resources than traditional farming.
"Some of the biggest benefits to growing hydroponically versus in a traditional manner is number one; we can grow year-round, 365 days a year," Pine Hill Farms Founder Jeff Bickley said. "Number two, we're hyperlocal. Local is a really big deal. People want to support local businesses. They also benefit from the difference in freshness."
Pine Hill Farms is currently growing nine different kinds of lettuce but plans to expand its products in the future.
The farm is connecting with local restaurants to sell its produce to.
How Square Roots Is Meeting Unprecedented Post-Pandemic Demand For Fresh, Healthy, Locally-Grown Food
Square Roots is expanding fast—deploying its latest indoor farm in Michigan in just three months
Square Roots Is Expanding Fast—Deploying Its Latest
Indoor Farm In Michigan In just Three Months.
To meet rapidly increasing demand for our locally-grown produce, today we’re announcing our newest indoor farm in Grand Rapids, Michigan. We broke ground in late December and planted the first seeds in March—just three months later. Now we're preparing for the first harvest, and our delicious, fresh produce will be available at grocery stores, eCommerce platforms, and restaurants across the Great Lakes region in the coming weeks.
Kimbal Musk, our Co-founder and Executive Chairman, says: “COVID-19 exposed major weaknesses in the industrial food supply chain, and accelerated the already fast-growing local farming movement. Square Roots can now deploy commercial-scale, controlled-climate farms, fast, in locations across America to meet the demand for local food, all year round. My wider mission is to bring responsibly-grown, local food to everyone in America. With Square Roots, we’re going to do it fast.”
From shovels-in-the-ground to first-seeds-planted, we built our new farm in just three months.
Growing Reliable, Fresh Produce Throughout the COVID-19 Pandemic
While COVID-19 wreaked havoc across the industrial food system, consumers increasingly valued local food, which in turn accelerated the adoption of indoor-grown produce. Consumers, forced to stay at home and cook, were able to experience the consistent peak-season flavor of our locally-grown greens. Meanwhile, retailers appreciated the reliability, longer shelf life, and complete traceability of all Square Roots’ products. As a result, we’ve seen a big increase in retail demand this year, and we’re now available in more than 200 stores (including Fresh Thyme Market, D&W Fresh Market, Whole Foods Market, FreshDirect, and more!).
In parallel, working hand-in-hand with our strategic partner Gordon Food Service—one of the largest food distributors in North America—we've been supporting and supplying restaurants throughout the pandemic. We’re as excited as anyone to see diners begin to venture out once more, and the restaurant industry bounce back strong.
Square Roots' new Michigan farm
This new farm in Michigan, our third commercial facility, is co-located with Gordon Food Service and represents another step towards a larger shared ambition to build indoor farms together across the continent—enabling local food at a national scale.
Our produce can be found at more than 200 stores across the Midwest and New York City area.
Square Roots’ Modular Farm-Tech Platform
Central to our ability to move fast and meet demand is our modular farm-tech platform. Capital-efficient and pre-fabricated inside upcycled shipping containers, ready-to-go farms can be shipped and deployed just-in-time to any site in the world, immediately creating the perfect conditions for growing the highest quality food, regardless of local climate conditions or time of year. The overall growing capacity of any Square Roots farm can seamlessly scale up or down depending on demand in the local market.
Our new two-story farm in Michigan also includes all of the necessary infrastructures to run a state-of-the-art, food-safe, and people-safe commercial operation. This includes cold storage, biosecurity, climate-controlled packaging space, distributor loading docks, and more. Meanwhile, all of our farms are Harmonized Good Agricultural Practices (GAP) certified, in line with the USDA’s standards, and operate to strict COVID-19 safety protocols to keep farmers and the local community safe.
Our farms are also cloud-connected and managed by a combination of skilled Square Roots farmers and sophisticated in-house software. Known as The Square Roots Farmer Toolbelt, our proprietary OS provides day-to-day guidance to farmers while capturing millions of data points throughout growing cycles across our network. This data can then be analyzed to determine how changes in certain environmental parameters impact factors like yield, taste, and texture. Our system learns faster as we deploy more farms and our network gets larger, all while helping farmers determine how to grow more, better-tasting food with fewer resources. Training new farmers—and empowering the next generation of leaders in indoor agriculture—has always been core to our mission, and the Farmer Toolbelt is a key enabler in our ability to offer accessible pathways for young people to enter the high-tech farming industry.
Farmers are guided through day-to-day operations by The Square Roots Farmer Toolbelt.
Responsibly-Grown, Local Food, Available Everywhere
We’ve always designed our farms to provide responsibly-grown food in areas close to the end consumer. Our hydroponic system uses 95% less water than conventional agriculture, our farms require zero pesticides, and the location of our facilities cuts down dramatically on food miles and food waste by enabling delivery of fresh produce within 24 hours of harvest, all year round. Meanwhile, our latest farm design is easily configured for both vertical and horizontal-stacked growing formats—a new and unique capability that means we can grow a wide range of crops to meet a variety of local market needs. To date, we've grown over 200 different varieties of herbs, microgreens, leafy greens, fruits, and even root vegetables—and we’re just getting started!
Keep an eye on this blog for announcements about more new farms soon. For more information about Square Roots check out our website, squarerootsgrow.com. And for daily updates, follow us on social media @squarerootsgrow.
LONDON: New Vertical Farm Offers Eco-Friendly Greens Picked And Delivered Within 24 Hours
London’s first delivery service for vertically-farmed, eco-friendly greens has launched from its base in the Docklands. Vertical farming is a fast-growing trend, with the global market size that was valued at $2.23 billion in 2018, projected to reach $12.77 billion by 2026
Lettuces growing vertically at Crate to Plate, a new farm in London's docklands | CRATE TO PLATE
London’s first delivery service for vertically-farmed, eco-friendly greens has launched from its base in the Docklands. Vertical farming is a fast-growing trend, with the global market size that was valued at $2.23 billion in 2018, projected to reach $12.77 billion by 2026. Crate to Plate is a clever new vertical farming venture founded by Sebastien Sainsbury who is a firm advocate of the concept of "15-minute cities" where everyone has access to fresh produce within a 15-minute walk of home. Crate to Plate offers consumers a wide range of super fresh organic lettuces, leafy greens and herbs, all picked within 24 hours, available by home delivery or at select greengrocers throughout London.
Recycled shipping containers house Crate to Plate, a vertical farm in London | ALISTAIR CARMAN
The eco-friendly farm is located in a parking lot owned by international property company Lendlease on the Isle of Dogs (Canary Wharf) inside three recycled shipping containers kitted out with LED lighting and an automated nutrient delivery system. Each 40-foot container achieves the same production as over an acre of farmland, with the site projecting to produce around six tonnes of greens each year. Not only does the urban farm use far less land but the pesticide-free produce is grown using hydroponic technology that uses 96% less water than traditional farming.
Crate to Plate, a new vertical farming initiative |. CRATE TO PLATE
Scientists and farmers at Crate to Plate carefully control the environment inside the shipping containers. Meticulously monitored vertical farming ensures that greens can be grown locally in urban environments, all year round, using minimal water, allowing produce to be delivered to consumers within 24 hours of harvest, with zero carbon footprint in transporting from farm to customer. As a result, the produce is as fresh as possible and has the highest possible nutrient value, completely free of pesticides and toxic chemicals. Lettuce, rocket, kale, pak choi, herbs, microgreens and more are harvested and delivered twice a week. The difference in taste between Crate to Plate’s greens and those you can buy from a supermarket is astonishing and delicious. And dynamite options like wasabi rocket and basil Genovese are already proving to be customer favorites.
Basil growing vertically at Crate to Plate | JOANNE SHURVELL
Produce from Crate to Plate is available in select greengrocers like Artichoke in North London and direct to consumers via their website. A £15 mixed box includes three types of lettuce, three bags of greens, and three herbs. Crate to Plate also sells to restaurants and have recently become Chef Ollie Dabbous's exclusive distributor of greens for his Michelin-starred Mayfair restaurant Hide. Crate to Plate has an ambitious UK expansion plan. A second site will open near Elephant and Castle this month, followed by other London sites and farms in other cities (Manchester, Birmingham, etc). And further ahead will be expansion to the United States.
Seedlings before they are transferred to the walls of the farm | CRATE TO PLATE
Crate to Plate’s new site in Elephant Park is part of a £2.5 billion regeneration project headed by the local council and Lendlease. One of the key aims of the development is to create a local, community-oriented ecosystem, with businesses from the area supplying residents and other retailers in the nearby community. Crate to Plate slots nicely into this concept, aiming to sell direct to local residents and to the new food businesses that are opening. Crate to Plate’s next London site is already in the works: the International Quarter London development near the 2012 Olympic Park in Stratford, east London.
With the global covid-19 pandemic fueling home deliveries and such a high-quality product on offer, it’s no surprise that Crate to Plate’s greens have sold-out every week since launching. Founder Sebastien Sainsbury says he wants “everyone to be able to get fresh leafy greens no more than a mile away from where they live.” It appears he’s off to a good start at achieving that goal and it will be fascinating to follow the progress of this sustainable new business.
Crate to Plate London home delivery boxes range from £6 to £28 depending on the selection and quantity, with no delivery charge on orders of £20 or more.
I've been writing on travel, food, fashion and culture for the past decade or so for a variety of publications. I co-founded PayneShurvell, a contemporary art gallery in London which is now an art consultancy in London and Suffolk. My photographer partner Paul Allen supplies photos for my features that often include a music or art event and our travels have taken us to under the radar music and art festivals in France, Italy, Portugal and Spain. I am the co-author of the Citysketch series of books that includes London, Paris and New York, published by Race Point and I'm the author of Fantastic Forgeries: Paint Like Van Gogh. Follow our adventures on Twitter at @jshurvell and on Instagram at @joshurvell and @andfotography
VIDEO: Kentucky Greenhouse Company AppHarvest Goes Public On Nasdaq As It Prepares To Grow
AppHarvest has estimated it will generate net revenue of $21 million in 2021. The company is expected to produce 45 million pounds of tomatoes annually. AppHarvest employs 300 Eastern Kentuckians
FEBRUARY 03, 2021
AppHarvest has estimated it will generate net revenue of $21 million in 2021.
The company is expected to produce 45 million pounds of tomatoes annually. AppHarvest employs 300 Eastern Kentuckians.
David Wicks, Nasdaq’s vice president of new listings, said he was “incredibly proud to be your partner and look forward to supporting your innovation as a NASDAQ listing company” in a video message Monday.
Founder and CEO Jonathan Webb eats an AppHarvest tomato in a video message displayed in Times Square on Monday.
Two weeks ago, AppHarvest shipped its first bundle of tomatoes from its flagship location in Morehead.
“All this noise that is happening around us — listing on the Nasdaq and being shown in Times Square, selling our tomatoes to the largest grocers in the U.S. — all that is resonating back on the ground inside of our facility where our employees are feeling the positive impact of the work we’re all doing together,” Webb said.
The beefsteak tomatoes are selling out at grocers around the country.
“We can’t grow fast enough,” he said. “Our tomatoes are hitting store shelves and flying off the store shelves. It’s not just Kentucky, it’s everywhere from Indiana, all the way down to Florida.”
Webb said the company’s job now is to build faster and grow more vegetables to get on store shelves.
The company continues to look throughout Eastern Kentucky for building sites, Webb said, but there are challenges.
“We just have to find a place to build,” he said. “We have the capital. We want to build there, but building on these reclaimed coal mine sites are incredibly challenging and very expensive to try to make work. We would love to be there.”
The first greenhouse was originally planned for Pikeville, but AppHarvest said the site, a reclaimed strip mine, was not feasible for construction. After about two years of delays, AppHarvest announced its decision to relocate to a 350-acre parcel about two miles off I-64 near the Sharkey community of Rowan County.
Webb said they continue to invest in Pike County with a container farm at Shelby Valley High School. AppHarvest has two other farms at schools in Rowan and Breathitt counties.
The company aims to have 12 facilities growing and supplying fruits and vegetables by 2025. AppHarvest already announced a Berea facility to grow leafy greens and a Richmond facility to grow vine crops.
“One massive impact of 12 facilities is we’re going to have hundreds of millions of pounds of fresh fruits and vegetables pouring out of our region,” Webb said. “Not only the economic benefits of that, but the health benefits are tremendous. We’re in a situation where not many companies can say they feel incredibly proud of the product they produce and we do that.”
The first AppHarvest tomatoes will be in grocery stores by Wednesday, Jan. 20, 2021.
Photos: COURTESY OF APPHARVEST
Liz Moomey is a Reporter for America Corps member covering Eastern Kentucky for the Lexington Herald-Leader. She is based in Pikeville.
Indoor Ag Fintech Startup Contain Raises Investment Round, Adds Industry Veteran To Team
We have plans to introduce new ways to support the burgeoning indoor agriculture industry in 2021, and this funding round will allow us to do just that.”— Nicola Kerslake, Founder, Contain Inc
NEWS PROVIDED BY Newbean Capital
January 04, 2021
Image from Contain Inc
A Techstars graduate, Contain Inc works with industry vendors and more than 20 lenders to facilitate access to capital for North American indoor growers.
We have plans to introduce new ways to support the burgeoning indoor agriculture industry in 2021, and this funding round will allow us to do just that.”— Nicola Kerslake, Founder, Contain Inc
Image from Rooted Global
RENO, NV, UNITED STATES, January 4, 2021 /EINPresswire.com/ -- Contain Inc, a fintech platform dedicated to indoor agriculture, today announced that it has closed a round of funding from investors in the US and Europe. They represent investments from indoor agriculture, food and beverage, entertainment, and financial industries. The funds will enable further technology development as well as new initiatives that support indoor agriculture. The industry has become ever more relevant in the time of COVID as consumers and produce buyers alike recognize the benefits of local secure produce supply.
Image from Contain Inc
A Techstars graduate, Contain Inc works with industry vendors and a pool of more than 20 lenders to facilitate access to capital for North American indoor growers of all sizes. In 2020, Contain collaborated with Singapore family office ID Capital to introduce a microlearning platform, Rooted Global, that enables corporate employees to grow a little of their own food at home. Its clients include tech and food majors, such as Danone and Dole. Nicola Kerslake, founder of Contain Inc, added: “We have plans to introduce new ways to support the burgeoning indoor agriculture industry in 2021, and this funding round will allow us to do just that.”
In addition, Chris Alonzo, President, and CEO of Pietro Mushrooms, will join Contain Inc to provide consulting services to future leasing clients. Chris brings a wealth of experience in planning, constructing and managing indoor farms across two continents. He is a third-generation mushroom farmer in Kennett Township, PA, an area that supplies half of the US’s mushroom supply. Nicola Kerslake said: “we’re frequently approached by indoor farmers planning large new projects and are delighted to be able to offer the services of such an experienced grower to those looking to bolster their plans before seeking financing.” Chris Alonzo added: “I’m excited to bring my expertise to Contain Inc’s fast-growing team and to engage with a startup that has long supported indoor farmers”.
The Company will also be expanding its team in business development, marketing and product development over the coming weeks, and encourages those seeking roles in this exciting space to visit its website at contain.ag for more details.
About Contain, Inc.
Contain Inc is a US-based fintech platform dedicated to indoor agriculture, growing crops in warehouses, greenhouses, and container farms. The Company works with leading equipment vendors and with an expanding pool of lenders to aid indoor growers in finding funding for their farms. It is also home to microlearning platform Rooted Global, which works with majors such as Danone and Dole to enable employees to grow a little of their own food at home. The Company graduated from the 2019 Techstars Farm to Fork program, backed by Cargill and Ecolab.
More information: https://contain.ag, https://rooted.global
Nicola Kerslake
Contain Inc.
+1 7756237116
email us here
Visit us on social media:
Twitter
LinkedIn
Food Will Be Grown Hydroponically In Shipping Containers In Cardiff's Bute Park
Starting with one trial shipping container in Bute Park, the plan is to expand across the city to grow much more food locally and with much less water. Growing food locally is seen as a key way to reduce carbon emissions, rather than shipping food from across the world
New Technology Means One Shipping Container
Could Grow The Same As 3.5 Acres Worth of Land
A hydroponics unit growing strawberry plants
Local democracy reporter
23 DEC 2020
Food will be grown hydroponically in shipping containers as part of Cardiff council’s plan to become a carbon-neutral city by 2030.
Starting with one trial shipping container in Bute Park, the plan is to expand across the city to grow much more food locally and with much less water. Growing food locally is seen as a key way to reduce carbon emissions, rather than shipping food from across the world.
Cardiff council has been consulting the public on its plan to cut the city’s carbon emissions to net zero in a decade. The draft One Planet strategy includes several schemes to reduce emissions and mitigate the effects of the climate crisis and rising global temperatures.
Food is a big part of that strategy, with the shipping container in Bute Park; plans to revamp Cardiff Market; letting community groups grow food on council-owned land, and making space on new housing developments for growing food.
Councillor Michael Michael, cabinet member for the environment, said one shipping container could grow the same amount of food as 3.5 acres of land. He said: “I’m a great believer in this technology,” as he revealed details of the plans.
The shipping container used to be in Bristol, growing herbs and vegetables for local restaurants. The council will pilot the technology in Bute Park, before potentially rolling it out further, working with community groups and possibly growing food to feed schoolchildren.
The technology works by growing food on racks without soil, using much less water, and controlling the heat and light inside the container to grow all throughout the year.
Cllr Michael said: “You can grow in that one container equivalent to three and half acres, because it’s 24 hours a day. This is becoming much more prevalent. Private companies are putting more and more money into hydroponics. If you can grow basil hydroponically in Scunthorpe, then why would you fly it in from Kenya?
“We do well with allotments in this city, but mostly at this time of year, they’re dormant. What if we work with people with these types of units? Unfortunately because of Covid, we haven’t been able to use it yet — but we will. This is an experiment. I’m a great believer in this technology.”
Several Marks and Spencer stores in London are also trialing the new technology, growing herbs in their shops. Cllr Michael said in the future Cardiff could see “giant greenhouses” above supermarkets growing food to be sold in the shops below.
He added the One Planet strategy will explore how food is bought for schools, and whether more of that food could be grown locally. Fruit trees could also be planted across the city for people to pick and help themselves.
Councillor Michael Michael, cabinet member for the environment (Image: South Wales Echo)
The draft carbon-neutral plan was welcomed by the Conservative and Liberal Democrat groups in Cardiff council, who both pointed out where they thought were gaps in the strategy.
Cllr Emma Sandrey, the Liberal Democrat’s spokesperson on the environment, said the council needs to focus more on reducing how much meat people eat. As well as transporting, a lot of emissions from food come from eating meat, especially beef.
She said: “We believe the council should implement ‘meat-free Mondays’ or a similar scheme across local authority canteens, to educate and inform people about the alternatives to meat, and the benefits of reducing meat consumption for the environment and for individual health.”
She added tackling food waste should be another priority. Currently, apps like Too Good to Go help link up restaurants with surplus food at the end of the day to customers who can buy that food at a discount, to save it from going to waste.
Cllr John Lancaster, the Conservative’s spokesperson on the environment, said the strategy failed to mention the docks or Cardiff airport. Shipping and flying both emit a lot of carbon and are currently difficult to fuel with electricity.
He added the council only has one ecologist and one tree officer, despite promises to address the biodiversity crisis and plant thousands of trees. He said: “There’s a disparity between the words in this One Planet strategy and how they go about it.”
Monitoring emissions needs to be another priority, Cllr Lancaster said: “There’s no plan for committed monitoring or achieving targets. That’s a big concern. How do we know how well the council is doing, how do we know if their targets are on course?”
The latest available data, from 2018, showed that Cardiff emits about 1,647 kilotonnes of carbon dioxide annually — down from 2,679 in 2005. The plan is to get this number to zero by 2030.
The public consultation on the draft One Planet strategy has now ended, and the council is considering the responses, with a full strategy and delivery plan due in the spring.
All the details can be found on www.oneplanetcardiff.co.uk.
BARBADOS: Agricultural Push
“To date, we have some 800 farmers signed up to be trained for the FEED program and in St George North I am prepared to come here and identify space, where Toni can have Freight Farms which is also a Hydroponic system on a lease-to-own basis to young people who are interested in getting involved in agriculture.”
10/10/2020
Agriculture Minister Indar Weir
The Ministry of Agriculture and Food Security is pressing ahead with plans to breathe new life into the sugar cane industry.
Speaking at the Barbados Labour Party (BLP) public meeting at Newbury, St. George on Thursday night, Minister Indar Weir reported that the strategy to revitalize this country’s oldest industry has already gone to Cabinet.
“We are modernizing our sugar industry to the extent that we are using a full value chain industry which goes from sugar for domestic consumption, molasses for our rum industry, and then the waste matter is being used to generate renewable energy.”
Minister Weir thereby explained the government’s foresight is to “bring the industry to profitability”.
“And all of you who are part of the labor force in farms and in the sugar industry would have an opportunity for the first time in our existence to own shares where you can get a return on the profits made through the sugar industry transitioning program.”
The Agriculture Minister also informed the people of St. George North that he will honor the BLP candidate Senator Toni Moore’s wish to introduce Hydroponics and Aquaponics into the constituency.
He said this will be achieved through the Farmers’ Empowerment and Enfranchisement Drive (FEED) program aimed at reducing agricultural imports into the island which will ensure national food and nutrition security. Currently, farmers are also being trained in Apiculture and Freight Farming.
“I say to you St. George North that you do not have the traditional jobs that you used to get – we do not have enough land space even. And so, we must embrace technology, where you can take a freight farm and with your mobile phone, laptop, tablet and you can operate that farm, get to production faster and get greater yields. Yet, you do not have to use pesticides and of course, it is a revolving system so, therefore, it is less water-intensive, and you do not have to worry about climate change and prolong droughts,” he explained.
“To date, we have some 800 farmers signed up to be trained for the FEED program and in St George North I am prepared to come here and identify space, where Toni can have Freight Farms which is also a Hydroponic system on a lease-to-own basis to young people who are interested in getting involved in agriculture.” (TL)
The Ministry of Agriculture and Food Security is pressing ahead with plans to breathe new life into the sugar cane industry.
Speaking at the Barbados Labour Party (BLP) public meeting at Newbury, St. George on Thursday night, Minister Indar Weir reported that the strategy to revitalize this country’s oldest industry has already gone to Cabinet.
“We are modernizing our sugar industry to the extent that we are using a full value chain industry which goes from sugar for domestic consumption, molasses for our rum industry, and then the waste matter is being used to generate renewable energy.”
Minister Weir thereby explained the government’s foresight is to “bring the industry to profitability”.
“And all of you who are part of the labor force in farms and in the sugar industry would have an opportunity for the first time in our existence to own shares where you can get a return on the profits made through the sugar industry transitioning program.”
The Agriculture Minister also informed the people of St. George North that he will honor the BLP candidate Senator Toni Moore’s wish to introduce Hydroponics and Aquaponics into the constituency.
He said this will be achieved through the Farmers’ Empowerment and Enfranchisement Drive (FEED) program aimed at reducing agricultural imports into the island which will ensure national food and nutrition security. Currently, farmers are also being trained in Apiculture and Freight Farming.
“I say to you St. George North that you do not have the traditional jobs that you used to get – we do not have enough land space even. And so, we must embrace technology, where you can take a freight farm and with your mobile phone, laptop, tablet and you can operate that farm, get to production faster and get greater yields. Yet, you do not have to use pesticides and of course, it is a revolving system so, therefore, it is less water-intensive, and you do not have to worry about climate change and prolong droughts,” he explained.
“To date, we have some 800 farmers signed up to be trained for the FEED program and in St George North I am prepared to come here and identify space, where Toni can have Freight Farms which is also a Hydroponic system on a lease-to-own basis to young people who are interested in getting involved in agriculture.” (TL)
USA - MARYLAND - Father, Daughter Launch Hydroponic Farming Operation In Montgomery County
With lettuce regularly being in the news related to an outbreak of disease, father and daughter Rod Kelly and Alex Armstrong concluded that there has to be a better way to purchase fresh produce
By Sondra Hernandez, Staff writer
September. 28, 2020
With lettuce regularly being in the news related to an outbreak of disease, father and daughter Rod Kelly and Alex Armstrong concluded that there has to be a better way to purchase fresh produce.
“It’s really hard to get fresh produce,” Armstrong said. “About 80 percent of lettuce comes from California. It’s hard to find locally grown produce.”
It was also concerning to her that consumers don’t quite know what they are getting with lettuce brought in from another area. Is it pesticide-free? Was there any contamination from livestock waste runoff?
“People are more aware of what’s in their food and they are more concerned about it,” she said.
To offer a fresh, locally grown option, the two have turned to a climate-controlled, vertical, hydroponic farming operation set up in a shipping container on property in South Montgomery County.“It’s an amazing technology,” Kelly said. “It’s a perfect climate-controlled environment for growing leafy greens.”
Kelly is a petroleum engineer and Armstrong has a marketing background. Kelly also owns several businesses and was looking for a project that he and his daughter could work on together.
They found the technology behind hydroponic farming fascinating.
The farm is contained in a custom-built, insulated shipping container. Kelly and Armstrong worked with Freight Farms in Boston for their operation.
The shipping container came from Boston by 18-wheeler and was delivered in late June. They planted their first crop in late July.
The message of Freight Farms is that fresh produce can be grown anywhere regardless of the climate.
Seedlings begin growth in trays under red and blue LED lights. Once the seedling grows larger, it’s transferred to a vertical tower for growing until its ready to harvest.
Water flows from the top of the container down through the roots and is collected at the bottom of the tower before being recycled to use again. These methods use about 90 percent less water than conventional farming. A panel of red and blue LED lights help the plants to grow into nutrient-rich food.“It’s cool technology and as an engineer, I appreciate that” Kelly said.
Fare House Farms grows a variety of lettuce and herbs.
They offer a wide array of lettuce like butterhead, bibb, romaine, Summer Crisp, and Oakleaf just to name a few. They offer leafy vegetables like arugula, cabbage, collards, kale, mustard greens, spinach, and chard. They also offer a variety of herbs like basil, cilantro, chives, dill, and more.
See their website at farehousefarms.com for a full menu.
Before this experience, Armstrong said she never knew what truly fresh lettuce and herbs tasted like.
She said the hydroponically grown lettuce was sweeter and crunchier. Kelly added the lettuce was prettier too.
The lettuce is sold with the peat moss plug still on so it will stay fresh for longer.
Kelly said they will spend the rest of 2020 experimenting with what grows best and studying the produce preferences of local buyers.
They plan to participate in local farmer’s markets to get their start.
They harvest on Fridays before the Saturday farmer’s markets.“You’re getting the freshest crop that you can get,” Kelly said.
Visit the Fare House Farms page on Facebook for more information and to see the farmer’s markets that they’ll be at.shernandez@hcnonline.com
Photos:
Alex Armstrong left, shares a laugh with Jane Pope after handing her a bag of freshly harvested lettuce at Fare House Farms, a hydroponic farming operation, Wednesday, Sept. 23, 2020, in Oak Ridge. Hydroponic farming is a type of horticulture where indoor crops are grown without soil by using a nutrient-rich and climate-controlled
Photo: Jason Fochtman, Houston Chronicle / Staff photographer
Rod Kelly and Alex Armstrong run Fare House Farms, a hydroponic farming operation in Oak Ridge. Hydroponic farming is a type of horticulture where indoor crops are grown without soil by using a nutrient-rich and climate-controlled environment.
Photo: Jason Fochtman, Houston Chronicle / Staff photographer9of10Alex Armstrong, and Rod Kelly are lit with panels of red and blue lights Alex Armstrong and Rod Kelly at Fare House Farms, a hydroponic farming operation, Wednesday, Sept. 23, 2020, in Oak Ridge. Hydroponic farming is a type of horticulture where indoor crops are grown without soil by using a nutrient-rich and climate-controlled environment.
Alex Armstrong and Rod Kelly make their way past pannels of red and blue lights, which encourage strong plant health and production, at Fare House Farms, a hydroponic farming operation, Wednesday, Sept. 23, 2020, in Oak Ridge. Hydroponic farming is a type of horticulture where indoor crops are grown without soil by using a nutrient-rich and Photo: Jason Fochtman, Houston Chronicle / Staff photographer