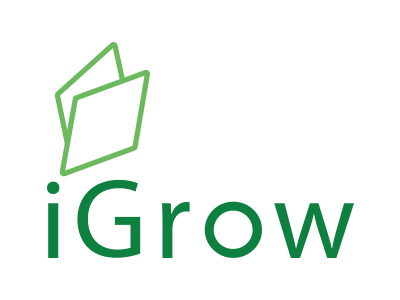
Welcome to iGrow News, Your Source for the World of Indoor Vertical Farming
Belgian Bio-Planet Now Sells Vertically-Farmed Coriander Too
For us, the story didn't end with sustainable basil.
Just under a year ago, Bio-Planet first introduced its basil to the market. This came from this Belgian store's self-developed vertical farm. "This cultivation method differs from conventional farming. It requires less water and space and fewer nutrients. That results in herbs with tiny ecological footprints. For us, the story didn't end with sustainable basil. We now have the technique down for coriander. We've been selling this second vertically-farmed herb since 19 February. That's in the Bio-Planet webshop and 31 stores", says a representative from this supermarket chain.
"Consistent, year-round quality"
"The Colruyt Group is the only retailer in Belgium with its a self-developed vertical farm. It grew basil plants for Bio-Planet last year. That was in a closed system, in two rows, one above the other. The group could, therefore, test out its vertical farm for a year. That was in all aspects, from production through logistics to sales. And the results are impressive. In a challenging year, we managed to guarantee a stable production of quality basil plants," says Jan Van Holsbeke, Bio-Planet's Manager.
"The global pandemic ensured it wasn't the easiest test year. We had to scale up our vertical farm. That's was due to the increased sales in our stores. At the same time, this demonstrates the power of indoor multilayer cultivation. We can create the perfect growing conditions, regardless of the weather. That means the herbs have consistent, year-round quality. And we can match production to demand." And demand there certainly was. More people bought fresh basil from Bio-Planet last year than the previous year.
"Coriander with a tiny environmental footprint"
Bio-Planet sees potential in this new farming method. They can grow herbs with a minimal ecological footprint. "Up to 20 times less space is needed the same number of plants. They also need 50% fewer nutrients and 90% less water. The herbs are 100% pure too because no pesticides are used," adds the company spokesperson.
"We integrated the farm into one of the group's distribution centres. So, transportation was cut five-fold. The farm uses purified rainwater that's collected on the DC's roof. It has self-developed, energy-efficient LED lighting and an innovative ventilation system. These make the farm very energy efficient. Moreover, the system runs on 100% green electricity. This is generated by wind turbines and solar panels."
“All these factors make the farm and its herbs very sustainable. That's crucial for Bio-Planet. We want to offer our shoppers sustainable, local, innovative products. We think other herbs and even leafy green vegetables can be vertically-farmed too. This, however, requires more research and investment. Also, the technology has to be further developed," concludes Jan.
IPO Planned To Improve Revenues Indoors
Light Science Technologies has gained the funding from Intuitive Investments Group plc (IIG), ahead of going public on the London Stock Exchange in the next six months.
8-01-2021| Business Live
“We believe that there is no better time to be involved in both agritech and medtech." A company which makes technology to improve indoor crop yields has received a £1 million investment ahead of a planned IPO.
Light Science Technologies has gained the funding from Intuitive Investments Group plc (IIG), ahead of going public on the London Stock Exchange in the next six months.
The business, based on the Hilton Business Park, Derby, provides lighting and plant growing and monitoring technology for agriculture in partnership with university research teams.
Its agricultural tech can be used in three main indoor settings – vertical farming (where crops such as tomatoes are grown in vertically stacked layers), greenhouses and medicinal plants.
Its patent-pending, sustainable light unit combines interchangeable LEDs, power and technology to help reduce costs and generate maximum yields over 25 years.
Its real-time monitoring and control technology can also be used to link technicians, farmers, and facility managers with their crops to provide instant production data.
Management said that with better light quality and energy savings, its light, science and technology products increase cycles.
It also supplies technology to clients in the electronics, audio, automotive, AI technology and pest control sectors.
The move to become a publicly listed company follows significant investment in its team and operations over the past few years which, the business said, has “brought to market a fully updateable, bespoke and intelligent lighting solution that provides optimal yield”.
The company is also due to launch its own in-house growth and laboratory service in the spring, focusing on plant growth and performance to help farmers with their crops.
Chief executive Simon Deacon said: “We believe that there is no better time to be involved in both agritech and medtech as two rapidly expanding sectors which are going to be responsible for spearheading some of the most significant global developments over the coming decade and beyond.
“IIG’s investment is not just a reflection of its commitment to LSTH as a fast-growing business backed by almost 30 years’ expertise in light technology but also of its awareness of the importance in achieving a better, more sustainable approach to agricultural production as well as pioneering potential life-saving solutions in digital health innovation.”
Light Science Technologies is IIG’s first investment following its own successful IPO and admission to AIM in December, as it seeks to attract investors with its life sciences portfolio.
IIG chairman David Evans said: “LSTH has the key ingredients for success; it has an excellent management team, a deep knowledge of the light spectrum and the application of that knowledge to areas where substantial growth can be obtained.
“I am personally excited about the potential diagnostic applications in the digital health sector, such as non-invasive haemoglobin measurement, as well as the developments in vertical farming technology that will underpin the long-term growth of LSTH.”
The investment follows recent funding for Light Science Technologies from Innovate UK which will see it work over the next six months with Nottingham Trent University to develop a growing sensor and transmission node for vertical farms.
Photo: Light Science Technologies designs lighting, science and plant monitoring technology.
Source and Photo Courtesy of BusinessLive
“We Are Developing A Sustainable Technology That Uses 75% Less LED Lighting”
Verde Compacto, a Mexican start-up, producer of container farms and indoor farming growing technologies, has seen significant demand for their growing systems during the pandemic
Verde Compacto, a Mexican start-up, producer of container farms and indoor farming growing technologies, has seen significant demand for their growing systems during the pandemic.
"COVID is driving this market forward because people want to know what is behind their food and their diets. Logistic chains in countries like South Korea and Arab countries are really dependent on imports. They are trying to implement urban technologies to strengthen their supply chains. As we’re focusing on growing systems, we are trying to turn this into reality. We are growing food in a more sustainable way where everyone can benefit from it”, Juan Gabriel Succar, Co-Founder and CCO of Verde Compacto says.
The company has an R&D container farm, Huvster, with several labs and small scale systems. The company sells some of its crops locally to better understand the urban business model, as Verde Compacto is educating the future indoor growers.
The Huvster growing container
Succar continues: “We are providing the knowledge to any grower that wants to have an urban farm and we are helping them throughout the process by constructing a farm to their needs.” The company does not only build container farms, which is their standard model but also provides custom made projects such as warehouses or buildings. Or on a smaller scale like supermarkets and restaurants. “We provide the knowledge to install a farm at any size”.
Decreasing LED use
Verde Compacto is looking to improve the electricity use for its growing solutions. “We are developing a sustainable technology that uses 75% less LED lighting, which is part of a sustainable R&D project. The tests are still running but they have delivered positive results. In the end, our technology used for indoor farms allows us to rotate the lamps. Rather than using four lamps at one spot, Verde Compacto can use one light that is constantly rotating. That's why we can make such a big impact on light usage”, Succar affirms.
Lack of quality and water
“Every business model and location has different benefits. As we are one of the largest agricultural countries in the world, we can offer excellent fresh produce quality. The sad story is that all the good fruits and vegetables are exported, thus there is a lack of quality products here in Mexico”, Succar says.
Succar says that Verde Compacto’s technology can build a profitable business model to deliver excellent quality and healthy food to the Mexican society. He notes that the central Mexican region sees a big challenge: a large water shortage. “With our solution, companies still see an opportunity to grow food and maintain their quality by using fewer resources”, Succar notes.
Sustainability
“We always try to give the best options possible regarding our client’s budget, business model, and capabilities. Verde Compacto is cooperating with solar panels to give access to clients for installing these solutions. “Renewable energy, in the end, really depends on the client. Our goal is to make vertical farming as sustainable as we can”, Succar states. At the end of October this year the company will install the first urban farm in Salamanca, Mexico which will be run on 100% solar energy.
Price opportunities
Succar: “In Mexico, we provide our produce at a lower price level than supermarkets. This is done on purpose, to get people to know about vertical farming. Sometimes we are on the same price level.”
Olivier Kappetein, EU representative at Verde Compacto notes: “We have a financial stimulator and we found out that we can bring product prices down. Consumers would pay less compared to supermarket prices as they are unbelievably high. In the United Arab Emirates, locally grown products are unfindable. An iceberg lettuce costs around €7.60 (9 USD) or more. We could get that price down by at least 350% and still make a profit if we were to sell our produce there. We are aiming to sell high-quality food and that’s what they are looking for.”
Pre- and post COVID story
Verde Compacto has a pre- COVID story and a post-COVID story regarding any company expansions. The pre-COVID story was to expand to all Latin American countries, as a priority. They started several alliances and promoted the Verde Compacto technology in Latin America. However, the economy in Latin America was really affected during the pandemic.
“Thus, countries depending on imports saw a great opportunity in our technology for constant production. We didn’t get behind on the expansion actually. Right now, we are working with associations to open different commercial offices in several countries in Latin America. We will be expanding there at the beginning of next year. We are also exploring different options in different parts of the world, expanding globally. One of the regions is Northern Europe because we saw the need for farming technology in those countries. Especially in Luxemburg, where there’s limited fresh produce available.
“The most common problem in vertical farming is the unawareness of the consumer”, Kappetein adds. “They don’t know what it has to offer. It’s still an investment that needs to be made. There is still a greater focus on organic produce as they are aware of the great benefits that come along.”
The Verde Compacto team
Forage
Verde Compacto has been developing its own R&D department, generating knowledge that is also used for new product lines. Succar continues: “We are developing indoor farming systems that are not limited to leafy greens and herbs, but also for forage e.g.. Forage is eaten by grazing cattle mostly. With our hydro system, we can feed cows e.g. with using fewer resources in a more profitable way. The meat and milk industry is impacting the ecosystem significantly. Implementing this technology will help us to make this type of agriculture more sustainable.” The company is also exploring the opportunities of launching indoor strawberries, with the greatest focus on Europe.
For more information:
Verde Compacto
Juan Gabriel Succar, Co-founder, and CCO
juan.gabriel@verdecompacto.com
Olivier Kappetein, EU representative
olivier.kappetein@verdecompacto.com
Phone: +316 14 62 13 10.
www.verdecompacto.com
Publication date: Tue 8 Sep 2020
Author: Rebekka Boekhout
© HortiDaily.com
Four Storeys Up, A Commercial Vegetable Garden Thrives In A Converted Sears Warehouse
Growing food on roofs represents the future of farming, especially in these pandemic times, says Mohamed Hage, Lufa’s chief executive officer, who co-founded the company with his wife, Lauren Rathmell
DAVID ISRAELS
SPECIAL TO THE GLOBE AND MAIL
SEPTEMBER 1, 2020
The Lufa greenhouse sits atop a former Sears warehouse in Montreal's St-Laurent neighbourhood.
CHRISTINNE MUSCHI/THE GLOBE AND MAIL
In the industrial part of Montreal’s St-Laurent area, it can be hard to distinguish the bulky buildings from one another, except for one – the roof sticks out like a green thumb.
It’s a great glass greenhouse roof atop a former Sears warehouse – a giant vegetable garden, said by its creators to be the world’s biggest commercial rooftop greenhouse.
The 163,000-square-foot garden, which opened last week, is the equivalent of nearly three football fields worth of food. To date, it is the fourth and biggest commercial facility for Montreal-based Lufa Farms.
Lufa is already well known among local “Lufavores” – foodies, restaurants, and alterna-living people in the Montreal area, who value its fresh tomatoes, eggplants, and vegetables, as well as the produce it gathers from local farmers.
Growing food on roofs represents the future of farming, especially in these pandemic times, says Mohamed Hage, Lufa’s chief executive officer, who co-founded the company with his wife, Lauren Rathmell.“
When we looked at how to grow where people live, we realized that there was only one option – rooftops. It’s not sustainable to always be trucking food in from across the continent or shipping from all over the world,” Mr. Hage says.
The new building was planned and construction began well before COVID-19 hit the world, but it offers a strong response to the pandemic, he explains.“
In March 2020, we saw a doubling of demand for our food. Growing food locally on rooftops and sourcing from local farming families allows us to swiftly adjust and respond to this demand,” he says.
An employee works inside the Lufa greenhouse. | HANDOUT
Co-founder Ms. Rathmell, who is also Lufa’s greenhouse director, says it took three months to build the St-Laurent facility and grow the site.“That would normally have taken years,” she says.
“In response to COVID-19, we enacted stringent safety protocols early on, launched seven-day service, tripled our home-delivery capacity, and launched new software tools,” she says. The company also brought in more than 200 new team members, 35 new local farmers and food makers, and 30,000 new Lufavores customers.
Lufa’s new staff includes two full-time nurses to take workers’ temperatures as well as “social-distancing police” to walk around and make sure workers aren’t too close to one another, Mr. Hage says. The company has also boosted the frequency of its air exchange in all of its facilities, including the new one.
Designing and building a rooftop greenhouse is challenging, Mr. Hage says. Although some of the preparation required is not much different than getting any equipment onto a roof, some of the prep work up there is more complicated, he says.“
We have to meet national building codes, and of course, everything for the greenhouse needs to be hauled up to the roof on a crane,” he says. “Yet once it’s there, you have to do a lot of stuff manually rather than mechanically. All of this is harder than it would be to do on the ground.”
It’s also expensive. “This greenhouse costs two times as much as a ground-based greenhouse,” he says. Lufa declines to give out the cost of this latest project but says the first of its four facilities, built 10 years ago, cost $2.2-million.
Using buildings for farming is catching on, says Mike Zelkind, co-founder of 80 Acres Farms in Cincinnati, Ohio, which also operates building-based facilities in Arkansas, North Carolina, and New York.
“A field can be the least efficient place to grow food,” he says. “An indoor farm can produce more than 300 times more food, with 100-per-cent renewable energy and 97 percent less water. That’s the beauty of growing in buildings.
Montreal-area foodies value Lufa's fresh tomatoes, eggplants and various other vegetables. HANDOUT
”Similarly, in Poughkeepsie, N.Y., up the Hudson River from New York City, restaurateur, food-truck owner, and chef John Lekic pivoted as the COVID-19 lockdowns spread to launch an indoor farming business called Farmers & Chefs.“
“We use technology from an Israeli company called Vertical Field that was being showcased at the Culinary Institute of America, which is nearby,” he says. The Israeli company supplies all the materials to grow some 200 different crops on roofs and in parking lots with minimal experience required.“
We planted and installed a container in March and our first harvest was in April, Mr. Lekic says. “We’re learning fast, but it’s an easy way to grow herbs and produce.”
”Mr. Hage agrees, adding that “rooftops are superior places for an urban farm.”
“When we started [in 2009], we considered leasing parking lots for growing, but no one wanted to give them up,” he recalls. “But for most commercial building owners, rooftops are unloved – they leak, they have to be maintained and, in a cold climate like ours, you have to clean off the snow. A commercial rooftop greenhouse is a solution.”
The new St-Laurent project gives Lufa a total of about 300,000 square feet of agricultural production, and the company plans to eventually expand into Southern Ontario and the U.S. northeast.
Mr. Hage points out that a rooftop greenhouse also makes great sense in terms of environmental sustainability and reducing energy and carbon emissions.“
“We don’t use pesticides and our greenhouses use half the energy that a greenhouse at ground level would consume because we use heating from the building that rises up to the roof,” he explains.
“The biggest challenge is not the greenhouse space – who doesn’t want to walk around in a warm sunny greenhouse when it’s 20 below outside? The challenge is maximizing the warehouse space below the greenhouse,” he says.
“We’re growing so many tomatoes that the warehouses never seem to be big enough to store them.”
Urban farming in Canada is still a niche in a nationwide food industry that is primarily export-based, and accounts for 12 percent, or $62.5-billion, of Canada’s total exports every year, says Claire Citeau, executive director of the Canadian Agri-Food Trade Alliance (CAFTA).
But in a post-COVID-19 world, every bit of food production counts, she says. “We continue to see the adoption of science, technology, and innovative ways to feed people and create new economic opportunities at home and abroad.”
And if that’s not enough, just look at the place, Mr. Hage says. “Boy, do I like driving by – it sticks out like a crystal,” he says. “And when you go inside, it’s like being in a spa.”
TOPICS AGRICULTURE CORONAVIRUS GREENHOUSE MONTREAL ORGANIC FOOD
Is Vertical Farming The Future of Herb Cultivation?
“With vertical farming, I can plant a herb, and can be sure it'll ready to sell in five weeks,” says Berjelle. “You also have certainty about your product’s quality. That’s because the product is optimally controlled. The plant grows evenly, thanks to the LED lighting, so it tastes better too."
Berjelle van Namen, Van Namen Specialties
Berjelle van Namen’s roots lie primarily in mushroom cultivation. His father, Johan, has a farm on the banks of the Maas river in the Netherlands. Yet, a few years ago, Berjelle decided to add herb cultivation. Not in a greenhouse or in full soil; in a converted mushroom cultivation cell.
The room is illuminated with violet-colored LED bulbs, and the containers holding the herbs are stacked, one atop the other. This can clearly be considered vertical farming. This concept is gaining increasing popularity among farmers - especially those who grow herbs, leafy and micro vegetables, and edible flowers.
There have even recently been trials with soft fruit. It’s been standard practice in the mushroom world for some time now. Hence the relationship between Van Namen mushrooms and the herbs of Van Namen Specialties.
For Berjelle, it started as an experiment. He encountered this cultivation method during his internship in Finland. There, at Robbe’s Little Garden, they grow lettuce, herbs, and micro vegetables in this way. According to Berjelle, vertical farming offers numerous advantages over traditional herb cultivation.
Vertical farming’s advantages
“With vertical farming, I can plant a herb, and can be sure it'll ready to sell in five weeks,” says Berjelle. “You also have certainty about your product’s quality. That’s because the product is optimally controlled. The plant grows evenly, thanks to the LED lighting, so it tastes better too."
"It satisfies clients, who are increasingly demanding just-in-time delivery of products like herbs. Of course, we mustn’t forget the sustainable character of this cultivation method. Especially since farming like this uses very little gas and no pesticides. We’re looking for ways to be highly energy-efficient too.”
There was a demand for herbs
Berjelle now grows about 12 kinds of herbs and has added a second cell. “In this way, we can vary cultivation conditions like using different temperatures," explains van Namen. "Basil is our top seller. It’s a popular herb that sells well. It’s followed by herbs such as parsley and mint.”
Berjelles sells his herbs under the company’s own brand, Pika Surprisa, and Esperanto for ‘spicy surprises’. Still, Berjelle points out that it’s mainly enjoyable to cultivate and experiment with these herbs. “It’s not quite profitable yet. To achieve this, you’d have to seriously consider scaling up and adding rooms."
"You’d also have to see if you want to grow only one variety. We chose to grow herbs mainly because of the increasing demand for year-round delivery and consistent quality. Vertical farming guarantees this. You can also be relatively lazy with your purchases. You know what you’ll get on the day you want it."
"From the cultivation side, there aren’t as many operational issues either. Although you always have to deal with that. The only thing is, it doesn’t save labor; hands are still needed in that cell,” admits Berjelle.
Herb sales differ from those of mushrooms. “We’ve attracted many new clients who really only buy herbs, and we’ve noticed fewer clients buying both. We keep these two products separate. That’s why the herbs fall under Van Namen Specialties. For example, we export mushrooms to countries like Germany and the UK, but not yet our herbs. Perhaps we will in the future.”
For the coming months, Van Namen’s main goal is to make it through the corona crisis successfully. “The mushroom market was very volatile in these unusual times. It’s slowly recovering, but it still has a long way to go. There aren’t any major developments planned for the rest of the year, either. Now, it's mostly a matter of serving our clients well,” Berjelle concludes.
More information:
Van Namen Specialties
www.vannamenspecialties.nl
Berjelle van Namen
berjelle@vannamenspecialties.nl
Publication date: Thu 27 Aug 2020
Author: Thom Dobbelaar
© FreshPlaza.com
Kuwait JV Opens Large-Scale Indoor Vertical Farm
&Ever Middle East, a joint venture between Kuwait’s NOX Management and German company &ever, in partnership with German engineering companies SAP and Viessmann, has opened the first commercial indoor vertical farm in the Middle East
August 16, 2020
&Ever Middle East, a joint venture between Kuwait’s NOX Management and German company &ever, in partnership with German engineering companies SAP and Viessmann, has opened the first commercial indoor vertical farm in the Middle East.
Kuwait, a country that previously relied on European and overseas imports for most of their leafy greens and herbs, can now locally grow up to 250 varieties of greens and herbs using dryponics technology.
The facility, with approximately 3,000 sq m growing (or farming) space, has a daily output capacity of up to 550 kg of salad, and herbs. The products are available in all leading retailers and co-operatives under the brand name &ever Kuwait.
The farm produces high-quality and sustainable crops indoors, which increase the nutritional quality and decrease environmental impact. The cutting-edge vertical farming method uses 90 percent less water compared to traditional farming, 60 percent less fertilizer, and zero pesticides. Using a sustainable “farm to fork” model, the technology is able to preserve the plants’ nutritional value until the produce reaches the customer, said the statement.
“Previously, Kuwait’s restaurants imported all of our greens and herbs, mainly from Europe,” said Faisal AlMeshal, Director of Strategy and Business Development, NOX Management. “Our JV with &ever and the partnership with SAP and Viessmann on this indoor farm is enabling the local farming supply chain to save on costs and logistics, to minimize waste, and to make a better choice for the planet. Our customers have enhanced experiences with tastier and fresher produce.”
This knowledge exchange complements Germany and Kuwait’s trade ties. Bilateral trade is €1.3 billion, and Germany’s private sector invests €14.6 billion in Kuwait, according to Germany’s Federal Foreign Office.
Germany and Kuwait are strong partners not only in politics but also in business, said Stefan Möbs, German Ambassador to Kuwait, who recently participated in a virtual media roundtable about the farm’s success hosted by the German Business Council Kuwait.
“I welcome the innovative business idea of German company &ever specifically here in Kuwait. Both countries are seeking new ways in difficult times. Even better to work together!”
Climatized rooms
The farm has partnered with Viessmann Refrigeration Solutions to develop highly efficient climatized rooms which are used in its indoor vertical farm. The technology is 40% more energy-efficient than other indoor vertical farming systems when it comes to energy use for climatization, said the statement.
&ever built its operating system, &ever Cloud, using the SAP Business Technology Platform -- SAP HANA in-memory platform and SAP Cloud Platform. Farmers can monitor, analyze, and adjust hundreds of data points on plant health, airflow, light, carbon dioxide levels, humidity, and temperature in real-time.
“Technology is the foundation for transforming customer experiences in restaurants and agricultural production in Kuwait, and for fostering diversified economic growth and sustainable agriculture worldwide,” said Andy Froemmel, Managing Director, SAP Kuwait. “Digitally transforming Kuwait’s agricultural sector supports New Kuwait 2035 goals, and helps to foster the local innovation economy and job creation.”
&ever is ready for global roll-out
Building on the global deployment capabilities of its key partners, &ever will scale its operations quickly and globally. “Our vision is to bring better tasting greens with high nutritional value to more and more people,” says Mark Korzilius, Founder of &ever. “We have an interesting pipeline of opportunities around the globe,” adds Dr Henner Schwarz, CEO of &ever. “We hope to be able to travel internationally again soon to get our next farms live as quickly as possible.”
The German Business Council Kuwait is a non-profit organization and business platform, founded in 2005, in order to promote and cultivate relations between German-speaking individuals and companies with their counterparts from the host country and the region. - TradeArabia News Service
Are We Ready For Indoor Wheat Farms?
They Could Feed The World on a Fraction
of The Land Area, But at What Energy Cost?
By Emma Bryce
July 31, 2020
Bread made from high-rise farms may be a thing of the future. Researchers have found that if we started growing wheat in stacked vertical farms instead of the field, we could generate 600 times more of this grain than traditional farming methods do—all while freeing up huge amounts of land from agriculture.
But before this could become a reality, we’d need some serious technological innovation to offset the controversially high energy costs of vertical farms.
Wheat currently supplies 20% of calories and protein for the world’s population, which is projected to grow to 11 billion people by 2100. With that expanding population, we’ll need a 60% increase in the worldwide production of grain. The researchers on the new study wanted to investigate how vertical farming—the production of crops across multiple floors in enclosed buildings—could help to plug that gap.
To find out, they used a crop simulation tool called DSSAT-NWheat, which projects yield based on the simulated field conditions, incorporating inputs like temperature, light, and water. This simulation showed that if wheat were grown inside a 10-floor vertical farm, covering one hectare of ground land, and under optimal conditions, the crop could generate almost 2000 metric tons of grain per hectare. That’s about 600 times more than the current annual world average of 3.2 metrics tons per hectare. Ramping things up to simulate a 100-floor farm, the researchers showed that the vertical farm could generate 19,400 metric tons of grain per hectare —6000 times more than the average hectare of farmland produces every year.
In some countries, vertical farming is already used to produce foods like lettuce and herbs where plenty can be grown at more confined scales. But crops like wheat—which require more space and typically need a lot of sunshine—haven’t yet been commercially produced in this environment. Showing that we could grow staple crops in this way, instead of only niche foods like salad greens, is an important step.
This massively efficient production approach would generate enough food to feed an expanding world population. By growing food vertically on smaller plots of land, it could also drastically curtail farmland expansion, an enormous source of emissions, and a driver of biodiversity decline. Growing food indoors, under perfectly controlled conditions, would shield crops from the vagaries of climate change and therefore bolster food security. It would also reduce pesticide use, and limit the chances that they’d get into soil and water.
But as the researchers caution, we shouldn’t get too swept up by these possibilities: farming wheat in high-rises—such a tantalizing idea—nevertheless comes with one considerable caveat. The cost, both financially and energy-wise, of artificially lighting up the interior of a vertical farm so that crops can photosynthesize, is enormous, enough to draw a question mark around the viability of this farming method. This is a problem that already haunts vertical farming in general: considering that its image depends partly on the idea that it’s better for the environment, the high energy usage—and consequent emissions contribution—makes it somewhat controversial. The researchers also point out that most field-based cereal farming around the world is heavily subsidized to make it financially viable, so the elevated costs of vertical wheat farming would make it difficult to compete with traditional modes of production.
Innovation in energy production could go some way to closing this gap. The researchers highlight the growing potential of renewable energy to provide all the light needed to keep crops growing artificially indoors. But even so, if vertical wheat farming does take off, it’s likely to form only a tiny part of the market at first, until we figure out how to make it less costly. And in the meantime, the researchers acknowledge that there are more urgent agricultural challenges to tackle, and which we already know can improve food security and ease the pressures on our planet—such as reducing food waste, and diversifying our food sources so that we’re perhaps not so reliant on single monocrops.
Yet, it may also be the case that entirely separate forces speed up energy innovation and make vertical wheat farming a reality one day. For example, the association between wheat prices and food riots we’ve seen in the past “could be reason enough to develop and install some indoor wheat production facilities,” the researchers suggest. Climate change in regions already beset by food insecurity might also hasten the arrival of bold new farming approaches like this one.
So, while we might not quite be ready for vertical wheat farming, options like these are likely to become more important in our changing world. “Although it is unlikely that indoor wheat farming will be economically competitive with current market prices in the near future,” the researchers say, “it could play an essential role in hedging against future climate or other unexpected disruptions to the food system.”
Source: Asseng et. al. “Wheat yield potential in controlled-environment vertical farms.” Proceedings of the National Academy of Sciences. 2020.
GERMANY: "Dry-Fog is The Next Generation of Aeroponics"
Lite+Fog can replace heavy steel racks with unique fabric, which separates the root zone from the growing zone and allows farmers to grow with any substrate
Lite+Fog, a Berlin-based company, started focusing on dry-fog systems as they noticed many benefits from it. "Dry-fog is the next generation of aeroponics. I started working on indoor farms for more than ten years. Because I did a lot of mushroom farming, I began to work with dry-fog and realized that it is a great way to feed plants. So we are now able to ultimately reduce the typical costs of Vertical Farming by around 80% and even triple the energy efficiency", states Martin Peter, Co-founder, and CEO of Lite+Fog.
Lite+Fog can replace heavy steel racks with unique fabric, which separates the root zone from the growing zone and allows farmers to grow with any substrate. "The system is a realization of work that originally started with urban farming projects, where I built many prototypes and tested a lot of approaches, especially vertical column-based farming technologies. The system as we plan it right now, however, has been developed over the last year."
Efficiency There is a lot of interest from farmers based in Israel, India, and the UK, all with different purposes. Compared to other systems, the Lite+Fog system dramatically reduces the costs in production, maintenance, and labour. The company is planning to have a pilot farm constructed by next year. "We are still on the lookout for potential pilot partners, strategic investors, and research institutes which are interested in joining this new generation of Vertical Farming. Bringing the efficiency up and lowering the costs is the most important thing to transform this vital technology into the mass-market application it has to be", says Martin.
Standardized farms
"We want to become a core technology supplier for indoor farms. As the technique has proven to be successful, we are now upscaling, and engineering the larger versions of our prototype farms. So we're connecting with suppliers and core industries in Germany and elsewhere, to create an important industrial network, able to satisfy the demand we expect in the future.
We plan on delivering at least 60 bigger farms per year during the next five years. Very simply put, we create a big box where seeds enter at one end and plants come out at the other. Eventually, we want to focus on standardizing these farms, as this would significantly improve cost efficiency and comparability. These are both essential factors for research and marketability", Martin states.
The concept design of Lite+Fog's 1000m2 footprint farm creating more than 45.000 m2 of growing surface for greens and berries
Benefits
"Dry-fog enables plants to be better nourished and improves growth by up to 20%. This way of growing is also practically weightless, so you can completely reimagine the architecture of farms - which we make great use of. Improving the efficiency of indoor farms is about how many square meters of growing space you generate in a given volume. Our approach is focusing on that primarily.
In addition to that, with no clogging nozzles, less maintenance, and easier central production, dry-fog is the next step of indoor farming. And that's why we are so much more cost-efficient than other approaches which are not vertical but multilayer horizontal farms anyway. We develop a true vertical "food-reactor".
The state-of-the-art spray nozzles typically used in vertical farms, which directly spray water on the plant roots, are bound to clog up as they are using a salty solution. These now outdated systems need to be cleaned and maintained all the time - and are reliably unreliable in the long run. However, dry-fog does barely weigh anything, doesn't need nozzles, and is therefore much cheaper and easy to use. "
Challenges
However, "fogponics" also has its challenges. As there is no growing medium, you have to be extra aware of the temperature of the root zone and on the complex system delivering the fog to the roots. Also, the droplet size has to be adjusted for bigger nutrients that are essential for some crops. But "these 'difficulties' can easily be mitigated if you adapt a bit - and that's what we are researching currently," says Martin.
For more information:
Lite+Fog GmbH
Martin Peter, Co-Founder, and CEO
Marienburger Str. 8
10405 Berlin
martin.peter@liteandfog.com
www.liteandfog.com
Publication date: Fri 17 Jul 2020
Author: Rebekka Boekhout
© HortiDaily.com
VIDEO: Vertical Farming Offers Solutions
Vertical farming has long been seen as a solution to rising populations and increasing urbanisation, but its efficiency may make it key to sustainability in general
BY TOM JOYCE
23rd June 2020
Vertical farming has long been seen as a solution to rising populations and increasing urbanization, but its efficiency may make it key to sustainability in general
Finland-based Novarbo, part of the Biolan Group, is helping growers to adapt to the concept of vertical farming and all the benefits that come with it, according to project engineer Arttu Lammensalo.
A specialist in greenhouse technology, Novarbo’s Vertical Farming Concept is able to solve the challenges of various operations, he said.
According to Lammensalo, a facility equipped with climate control and heat re-use systems is an extremely energy-efficient way of cultivating high-quality plants indoors.
Any surplus heat energy is stored for reuse, while food transportation is decreased by moving production closer to the consumer, reducing the carbon footprint. A large amount of transpiration from the crop is captured from the air and returned to the irrigation system.
In addition, with Novarbo Growisor software, the grower is able to optimise the plant growth factors of the fully automated facility, Lammensalo said, enabling long-term production planning and wireless tracking.
“Our first vertical farm serves as our laboratory for climate control experiments,” he explained. “We want to help people to adapt to vertical farming. We have collected data for over a year and a half, working on more than ten products, determining the effect of LED lights at different times and for different periods of time. The climate control system allows us to improve irrigation efficiency by 90 per cent.”
According to Lammensalo, vertical farming is quite expensive initially, but after five years, you can expect to get your investment back. “Some are a little afraid of this technology,” he said. “If there is a power cut, for example, you need a backup energy source. Herbs and salads can be quite expensive in the winter, though, so the costs can sometimes balance out.”
Vertical farming is also gaining considerable attention as a solution to feeding the large numbers currently crowded into the world’s cities.
“Vertical farming will be useful anywhere there isn’t much growing area,” Lammensalo stated. “In Singapore, they import most of their herbs and vegetables from abroad, so they are very keen on vertical farming to avoid any supply issues. It also significantly reduces the carbon footprint, as well as the water footprint, so it’s a good solution in countries that suffer from water shortages.”
Future of Indoor Vertical Farming With Microgrids
Schneider Electric’s Don Wingate discusses how microgrids can help the indoor vertical farming movement realize its full potential
09-07-2020 | Microgrid Knowledge
Schneider Electric’s Don Wingate discusses how microgrids can help the indoor vertical farming movement realize its full potential.
While indoor agriculture has steadily gained traction in recent years as the world seeks alternative ways to feed growing populations, the uncertainty of today’s global pandemic has accelerated a rethinking of the way we obtain our food. In the last few months, modern supply chains experienced volatility like never before and it wasn’t long before we started to see the impact beyond medical gear and personal protective equipment and began to affect food production. According to the Institute of Supply Chain Management, 75% of companies reported some kind of supply chain disruption due to COVID-19.
Indoor vertical farming is emerging as an alternative to conventional farming because it both requires lower land-use and introduces the opportunity to bring agricultural production closer to consumers — shortening supply chains and increasing footprint productivity. This is especially important during times of turmoil, which is broader than the current pandemic as weather events and changing climate patterns continue to put constant strain on traditional farming practices. In addition to shortening supply chains, indoor farming has many other advantages in comparison to traditional agriculture such as using zero pesticides, employing 95% less water, and reducing food waste. Health benefits also include fresher food, increased urban availability, and pollution reduction.
Despite the major advantages, there is one looming barrier to mainstream adoption: the process is very energy-intensive.
Solving for the energy intensity problem
Vertical farming presents a unique opportunity to grow food on already developed land and increase domestic food production, but the energy demand required to power these facilities is much higher than other methods of food production. In fact, we’ve identified indoor agriculture as one of the four major drivers that will increase electricity consumption in the next decade, along with electric vehicles, data centers, and the electrification of heat. This is why more of today’s modern farming companies are turning to microgrids as a possible solution to ease their energy challenges.
Although most of today’s facilities are not equipped to meet the electricity needs of an indoor agriculture operation, microgrids can provide dynamic energy management and the resources required to support maximum productivity, sustainability, and energy efficiency. They can provide localized power generation and utilize renewable distributed energy resources to help deliver power and reach clean energy goals, while also allowing users more control and reliability. Additionally, microgrids can capture and repurpose CO2 emissions to help in crop production.
Moreover, microgrids provide resilience from unexpected outages that could result in a loss in production. A key advantage of vertical farms is their ability to allow crops to grow year-round, and communities rely on their ability to deliver on this promise. Microgrids not only have several clean energy benefits, but they also increase business continuity that maximizes output. Given their ability to operate either in conjunction with or as an island from the utility grid, they can keep the farm producing even when the grid goes down.
The case for investment: Securing an affordable solution
Building and operating a vertical farm requires various technologies that can translate to high startup cost and design complex processes. At the same time, it is more expensive to maintain a vertical farming operation than traditional field farming. Microgrids offer a compelling value proposition, but they’re inherently complex machines and not many companies have the upfront capital or in-house expertise needed to make the investment. Fortunately, innovative business models such as energy-as-a-service (EaaS) help provide price certainty and make the investment attainable.
For example, a modern farming company, Bowery Farming, created a facility wherein crop production is 100 times more efficient than traditional farmland. This generated a need for a greater need for reliable, efficient power. Thus, the company made the decision to integrate a hybrid microgrid system that would feature a rooftop solar array, natural gas generator, and a lithium-ion battery energy storage system through an EaaS business model. Through EaaS, Bowery Farming saved upfront capital that can be used toward additional operational investments.
By 2050, the world’s population is expected to grow by another 2 billion people, and feeding it will be a major challenge. According to the projections of the Food and Agriculture Organization, we have to increase overall food production by 70% by this timeline. Coupled with new concerns that have surfaced as a result of today’s global pandemic and unstable weather, vertical farming will play a key role in future food production and institutions will take notice. However, the technology that will help ease some of the industry’s ongoing energy challenges will be just as important to aid the transition.
Don Wingate is the VP of utility and microgrid solutions at Schneider Electric.
Source: Microgrids Knowledge
Photo Courtesy of Microsoft News
VIRTUAL SUMMIT: Connecting Technology & Business To Create Healthy, Resilient Food Systems - July 23, 2020
By sharing best practice from around the globe, and facilitating new connections and collaborations, the summit offers an invaluable platform to develop new business and accelerate projects across the Indoor AgTech ecosystem
The Indoor AgTech Innovation Summit is going virtual! This year’s summit will be live online on July 23, 2020, providing an essential opportunity for the industry to meet, network, https://indooragtechnyc.com/, and exchange ideas at this critical time for our industry.
The world’s leading farm operators, food retailers, and investors will present live, before hosting virtual discussion groups on the emerging trends and technologies that will shape your business as we emerge from the current crisis into a redesigned food system:
Key Themes:
· Finding Growth in Crisis: Responding to a Rapidly Changing Food Landscape
· Scaling Up: Co-locating Food Production and Distribution Centers
· Enhancing Nutritional Value: Towards a Perfect Plant Recipe
· Optimizing Seeds for Indoor Agriculture: Breeding a Competitive Advantage
· Analytics and the Cloud: Digital Integration to Optimize Indoor Agriculture
· Robotics: Developing a Contactless Food System
· Energy Consumption: Driving Efficiency and Economic Viability
· Financing Growth: Can Capital Keep Pace with Industry Demand?
· Consumer Awareness: How to Build a “Holistic” Indoor Brand
All participants can schedule video 1-1 meetings with potential partners and clients throughout the summit, and for an extended period before and after the sessions.
By sharing best practice from around the globe, and facilitating new connections and collaborations, the summit offers an invaluable platform to develop new business and accelerate projects across the Indoor AgTech ecosystem.
Summit website: https://indooragtechnyc.com/
Registration:
- One summit pass Indoor AgTech: $195.00
- Start-Up pass: $95.00 / Please contact jamie.alexander@rethinkevents.com to enquire about the criteria to qualify for special rates.
Indoor Agtech Virtual Innovation Summit July 23, 2020
By sharing best practice from around the globe, and facilitating new connections and collaborations, the summit offers an invaluable platform to develop new business and accelerate projects across the Indoor AgTech ecosystem
We Are Proud To Be A Marketing Partner
Save 10% With Discount Code iGROW10
Major names join speaker line-up for virtual summit
We are thrilled to announce the first speakers confirmed for the 2020 virtual Indoor AgTech Innovation Summit on July 23.
They'll share critical intelligence on how the indoor farming industry is shaping the agri-food landscape, and redesigning food systems to meet consumer demand for fresh produce.
VIEW SPEAKER LINE-UP
Hear from and connect with international thought leaders including:
WHAT ARE OUR EXPERTS SAYING?
"Instead of shutting down, we implemented South Korean-style measures for our warehouse, farm, and office. Then, we launched a new nationally distributed product that allows folks to grow mushrooms at home rather than travel to the grocery store."
Andrew Carter, CEO, SMALLHOLD
"COVID-19 has raised awareness about the prospects for automation such as machines working in packing houses and indoor environments. I think it’s fair to say that humans can be relieved of those tasks."
Elyse Lipman, Director of Strategy, LIPMAN FAMILY FARMS
"Given current pressures on the U.S. food system, one thing is clear: the importance of strengthening our country’s food supply chain through decentralized, regional supply chains."
Viraj Puri, CEO and Co-Founder, GOTHAM GREENS
READ MORE INSIGHTS FROM OUR SPEAKERS>>
Secure your place at Indoor AgTech and save 10% with discount code iGROW10
and connect with the world’s leading farm operators, food retailers, and investors for a jam-packed day full of 1-1 video meetings, live panel sessions, and interactive roundtable discussion groups.
BOOK NOW WITH CODE iGROW10
We look forward to welcoming you online.
Best wishes,
Oscar Brennecke
Conference Producer
Indoor AgTech Innovation Summit
+44 (0)1273 789 989
oscar.brennecke@rethinkevents.com
THANKS TO OUR PARTNERS
Platinum Partner:
Marketing and Media Partners:
ONLINE WORKSHOP - The Ohio State University Empowerment Plant Workshop, July 9-10, 2020
The goal of this Workshop is for growers to empower crop production through a balanced growing method, through an integrated approach based on physics and plant physiology, for high yields, quality, saving energy, and profitability in greenhouse controlled environments
— Live Education —
The Ohio State University, in partnership with Gotham Greens and Hort Americas, will be organizing the Plant Empowerment Workshop Online on July 9-10, 2020 (10 am – 2:30 pm EDT).
Advanced learning and discussion for growers towards “an integrated approach based on physics and plant physiology, leading to a balanced growing method for high yields, quality, saving energy, and profitability in greenhouse controlled environments
Instructor: Dr. Peter van Weel
Author of ‘Plant Empowerment’
Expert in greenhouse climate control
Former PI at Wageningen UR, The Netherlands
Host: Dr. Chieri Kubota
The Ohio State University
Ohio CEA Center
The goal of this Workshop is for growers to empower crop production through a balanced growing method, through an integrated approach based on physics and plant physiology, for high yields, quality, saving energy, and profitability in greenhouse controlled environments
Textbook (optional): ‘Plant Empowerment’ available at www.plantempowerment.com
Plant Empowerment Workshop Online
10 a.m. to 2:30 p.m. (EDT), July 9-10, 2020
Thursday, July 9, 2020 | 10 a.m. to 2:30 p.m. (EDT)
Part 1: Introduction to Plant Empowerment, The Theories
Basic knowledge about physics and physiology that play an important role in a greenhouse and for plantsPlant empowerment, from experience-based control to sensor-based control
Friday, July 10, 2020 | 10 a.m. to 2:30 p.m. (EDT)
Part 2: The Practical Applications of Plant Empowerment
Introduction to the sensors, the software tools and the value of data analysis
Registration is open through July 1.
Workshop fee is $20 per person.
Register now!
For more information, contact Dr. Chieri Kubota, kubota.10@osu.edu
Sustaining The Future of Indoor Vertical Farming With Microgrids
While indoor agriculture has steadily gained traction in recent years as the world seeks alternative ways to feed growing populations, the uncertainty of today’s global pandemic has accelerated a rethinking of the way we obtain our food
June 15, 2020, By Guest Post
Schneider Electric’s Don Wingate discusses how microgrids can help the indoor vertical farming movement realize its full potential.
Don Wingate, vice president of utility and microgrid solutions at Schneider Electric
While indoor agriculture has steadily gained traction in recent years as the world seeks alternative ways to feed growing populations, the uncertainty of today’s global pandemic has accelerated a rethinking of the way we obtain our food. In the last few months, modern supply chains experienced volatility like never before and it wasn’t long before we started to see the impact beyond medical gear and personal protective equipment and began to affect food production. According to the Institute of Supply Chain Management, 75% of companies reported some kind of supply chain disruption due to COVID-19.
Indoor vertical farming is emerging as an alternative to conventional farming because it both requires lower land-use and introduces the opportunity to bring agricultural production closer to consumers — shortening supply chains and increasing footprint productivity. This is especially important during times of turmoil, which is broader than the current pandemic as weather events and changing climate patterns continue to put constant strain on traditional farming practices. In addition to shortening supply chains, indoor farming has many other advantages in comparison to traditional agriculture such as using zero pesticides, employing 95% less water, and reducing food waste. Health benefits also include fresher food, increased urban availability, and pollution reduction.
Despite the major advantages, there is one looming barrier to mainstream adoption: the process is very energy-intensive.
Solving for the energy intensity problem
Vertical farming presents a unique opportunity to grow food on already developed land and increase domestic food production, but the energy demand required to power these facilities is much higher than other methods of food production. In fact, we’ve identified indoor agriculture as one of the four major drivers that will increase electricity consumption in the next decade, along with electric vehicles, data centers and the electrification of heat. This is why more of today’s modern farming companies are turning to microgrids as a possible solution to ease their energy challenges.
Although most of today’s facilities are not equipped to meet the electricity needs of an indoor agriculture operation, microgrids can provide dynamic energy management and the resources required to support maximum productivity, sustainability, and energy efficiency. They can provide localized power generation and utilize renewable distributed energy resources to help deliver power and reach clean energy goals, while also allowing users more control and reliability. Additionally, microgrids can capture and repurpose CO2 emissions to help in crop production.
Moreover, microgrids provide resilience from unexpected outages that could result in a loss in production. A key advantage of vertical farms is their ability to allow crops to grow year-round, and communities rely on their ability to deliver on this promise. Microgrids not only have several clean energy benefits, but they also increase business continuity that maximizes output. Given their ability to operate either in conjunction with or as an island from the utility grid, they can keep the farm producing even when the grid goes down.
The case for investment: Securing an affordable solution
Building and operating a vertical farm requires various technologies that can translate to high startup cost and design complex processes. At the same time, it is more expensive to maintain a vertical farming operation than traditional field farming. Microgrids offer a compelling value proposition, but they’re inherently complex machines and not many companies have the upfront capital or in-house expertise needed to make the investment. Fortunately, innovative business models such as energy-as-a-service (EaaS) help provide price certainty and make the investment attainable.
For example, a modern farming company, Bowery Farming, created a facility wherein crop production is 100 times more efficient than traditional farmland. This generated a need for a greater need for reliable, efficient power. Thus, the company made the decision to integrate a hybrid microgrid system that would feature a rooftop solar array, natural gas generator, and a lithium-ion battery energy storage system through an EaaS business model. Through EaaS, Bowery Farming saved upfront capital that can be used toward additional operational investments.
By 2050, the world’s population is expected to grow by another 2 billion people, and feeding it will be a major challenge. According to the projections of the Food and Agriculture Organization, we have to increase overall food production by 70% by this timeline. Coupled with new concerns that have surfaced as a result of today’s global pandemic and unstable weather, vertical farming will play a key role in future food production and institutions will take notice. However, the technology that will help ease some of the industry’s ongoing energy challenges will be just as important to aid the transition.
Don Wingate is the VP of utility and microgrid solutions at Schneider Electric.
Researchers Aim To Cut The Energy Footprint Of Indoor Farms
Indoor farms can grow vegetables close to cities, where there are lots of people to feed. Farming indoors can also extend the growing season in cold climates and protect crops from damage during extreme weather.
But growing food indoors is energy intensive, so it can produce a lot of carbon pollution.
“Lighting is a big factor,” says Erico Mattos of the Greenhouse Lighting and Systems Engineering Consortium. “You have the heating and cooling systems, ventilation systems, all the systems that you have to control. So it’s really important for us to reduce this energy demand.”
Mattos’s group is working to reduce the energy used in indoor farms and greenhouses.
“The challenge is, how can we still provide all these inputs that the plants require, the crops require to grow, but using energy with the most efficient way as possible?” he says.
Researchers are tackling the problem from multiple angles. For example, they’re designing high-efficiency LED lights and they’re experimenting with ways to optimize specific crops’ growth with customized lighting, ventilation, and humidity controls.
Mattos says these technologies and systems will help make greenhouses and indoor farms more cost-effective and better for the climate.
Lead Photo Credit: Terry Rice