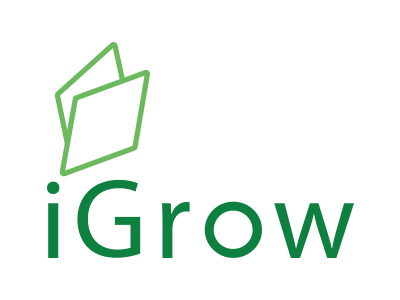
Welcome to iGrow News, Your Source for the World of Indoor Vertical Farming
BrightFarms Launches Multimillion-Dollar R&D Hub in Greater Cincinnati
BrightFarms, a New York-based grower of indoor leafy greens since 2013, is forming BrightLabs, a new innovation and research hub, at its Wilmington greenhouse. BrightLabs, overall, will represent a tenfold increase in the company’s research capabilities, while increasing profitability and delivering new product innovations.
By Liz Engel - Staff reporter
June 24, 2021
An indoor farming company is investing millions in Ohio with the debut of a new research and development hub.
BrightFarms, a New York-based grower of indoor leafy greens since 2013, is forming BrightLabs, a new innovation and research hub, at its Wilmington greenhouse. BrightLabs, overall, will represent a tenfold increase in the company’s research capabilities, while increasing profitability and delivering new product innovations.
Steve Platt is the CEO of BrightFarms. (Jenn Erickson)
CEO Steve Platt declined to disclose the exact investment but told me it’s in the multimillions. The project is being launched as part of the company’s $100 million Series E funding round in October led by media conglomerate Cox Enterprises.
“BrightFarms as a company has been growing very consistently, and the indoor farming industry is at an inflection point,” Platt said. “We’ve perfected how we grow – among competitors, we’ve developed the most profitable model for the production of indoor leafy greens – but now’s the time to invest behind R&D to secure an advantage for the future. It’s essential to stay ahead of the curve.”
Like others in the indoor farming space, BrightFarms lauds the fact that its lettuce is healthier, tastier, looks better, is more nutritious, and, particularly for customers in Ohio, fresher than field-grown produce hauled in from states like California and Arizona. Today the company’s five greenhouses in Ohio, Virginia, Illinois, Pennsylvania produce 9 million pounds of produce each year.
But unlike several outfits, particularly vertical farms that use purple-hued LED lighting, BrightFarms leverages natural sunshine. Its souped up, high-tech greenhouses grow spinach, romaine, arugula and more using a hydroponic system, or water instead of soil.
Wilmington, which celebrated its first harvest in 2018, isn’t the company’s largest greenhouse in terms of size or production, but Platt said it made a good host for the innovation hub because of its centralized location. It’s close to customers and easily accessible from its other farms. He also credited the workforce and level of academic talent available from universities nearby.
BrightFarms celebrated its first harvest in Wilmington in 2018. BrightLabs is investing millions to build out an innovation and research hub at the site. (Brian Mollenkopf)
Phase one for BrightLabs includes a new, approximately 1,350 square foot lab that has been built at the Wilmington greenhouse site. BrightFarms will also dedicate space on the farm for the BrightLabs team to work.
Platt said BrightLabs will focus on three key areas:
Biotech. BrightFarms wants to study the environments in which plants grow to increase yield, flavor, and texture.
Agtech. BrightOS, the company’s proprietary AI software system, acts as the company’s central nervous system, Platt said, collecting millions of data points from its fives farms to streamline operations. How can the company improve that technology?
Product innovation. BrightFarms recently launched NutriGreens, a new lettuce packed with antioxidants – double the amount, Platt said, found in a serving of blueberries. BrightFarms wants more advances like that.
BrightLabs itself will be led by Matt Lingard, a former Bayer plant scientist and Ph.D. with over 15 years of experience, who joined BrightFarms in May as its VP of agriculture and science. Platt said the BrightLabs team will include four employees to start.
“We’re the leading grower of indoor spinach – in the U.S. we grow 90% of the indoor spinach that’s sold – but we want to double our production on that. How do we come out with new types of spinach that can grow even better in a hydroponic system?” he said.
“We’re taking on a massive industry and a complicated, broken system – where greens are grown all in one location, shipped thousands of miles across the country, generally with pesticide reside, there’s a food-borne illness, and the product isn’t that good,” Platt added. “We have a simpler system and a better product, but we need to deliver that at a price point and at a volume that competes with what’s coming out of California. If we’re trying to unseat this big gorilla, we can’t be this niche that’s only affordable to people who drive Teslas.”
Overall, there’s billions being invested in the industry. New York City-based Bowery Farming, in late May, announced a $300 million funding round with a $2.3 billion valuation. Kentucky-based AppHarvest merged with a special purpose acquisition company in February, an IPO approach that’s gaining ground in 2021, and is now worth $1.5 billion.
BrightFarms, with its Series E, has raised more than $200 million in total. In addition to launching BrightLabs, it plans to use the funds to expand its network of regional indoor farms – new farms are currently under development in Massachusetts and Texas – and grow its retail footprint. Locally, BrightFarms is available at Sam’s Club, Walmart and Pipkin Produce as well as Food Lion and Kroger in other markets.
The company said by the end of 2021 its leafy greens will be available at over 3,500 stores.
“It’s amazing. Even when I joined the company two years ago, we were convincing people this was the future. Now customers are coming to us saying, ‘We want to replace field grown with indoor-grown,’” he said. “We think the future is here.”
Lead photo: BrightFarms grows leafy greens like spinach, romaine, and arugula in high-tech, computer-controlled greenhouses.
Nature Fresh Farms Releases NEW 100% Home Compostable Cucumber Wrap
An alternative to traditional polyethylene plastic, this film is an environmentally friendly compostable wrap that breaks down in a household compost without leaving behind microplastics
Leamington, ON (September 8, 2020) – Nature Fresh Farms continue their sustainable initiatives by releasing a new, 100% home compostable wrap for their Long English Cucumbers, a first in the North American market.
An alternative to traditional polyethylene plastic, this film is an environmentally friendly compostable wrap that breaks down in a household compost without leaving behind microplastics. The compostable film will prolong the shelf life of the product; however, it will do so without adding to long term landfill waste. Made from a starch-based PLA that is derived from plant-based resources including non-GMO corn starch, it is 100% compostable, breaking down naturally into CO2 and water.
Each cucumber wrap contains 0.00436 lbs of plastic; this translates to the equivalent of 23-million plastic straws saved from landfills for every 5-million Cucumbers wrapped in the compostable film. Cucumbers are packed in shrink wrap to significantly extend their life by minimizing evaporation. Through the compostable film, Nature Fresh Farms has found a packaging solution that can maintain the shelf life of the Cucumber, while meeting the demands of more sustainable packaging alternatives.
“The launch of the compostable wrap is a demonstration of our commitment to our consumer’s wants of reducing plastic usage. We are excited to be first to market with this initiative in North American and are hopeful this will start a trend with the industry while we continue to lead in sustainable packaging solutions.”
--Matt Quiring, Director of Sales
In addition, the wrap includes a PLU pre-printed on the film in compostable ink. This feature allows the entire wrap to be thrown in with backyard compost or in landfills without harming the environment. PLU stickers are commonly made of vinyl and plastic. This new wrap eliminates the need for the additional application.
“After two years of research & development and a lot of trial & error, it’s so exciting to see this film launch in the market. We are confident in this product’s ability to make a true difference
(in reducing harmful plastic waste)”
---Luci Faas, Product Development Specialist
At Nature Fresh Farms we are driven to accelerate innovation via evidence-informed sustainable packaging solutions that provide a better experience for our customers, while also helping to preserve the vitality of our planet.
-30-
About Nature Fresh Farms -
Continuously expanding, Nature Fresh Farms has become one of the largest independent, vertically integrated greenhouse vegetable farms in North America. As a year-round grower with farms in Leamington ON, Delta OH, and Mexico, Nature Fresh Farms prides itself on consistently delivering exceptional flavor and quality to key retailers throughout North America, while continuing to innovate and introduce more viable and sustainable growing and packaging solutions.
SOURCE: Nature Fresh Farms | info@naturefresh.ca T: 519 326 1111 | www.naturefresh.ca
Valoya And Citizen Electronics Enter A Licensing Agreement
Citizen Electronics will apply Valoya's spectrum technology know-how in order to strengthen its COB (chip on board) LED products intended for the horticulture industry
Citizen Electronics Co. Ltd., leading developer of electronic devices and applied products, and Valoya, the research-driven LED grow light manufacturer have entered a licensing agreement whereby Citizen Electronics will take Valoya’s LED spectrum portfolio into use.
Citizen Electronics will apply Valoya's spectrum technology know-how in order to strengthen its COB (chip on board) LED products intended for the horticulture industry.
Valoya has launched its patent licensing program in June this year. After more than a decade of persistent focus on R&D, the company has amassed one of the largest patent portfolios of the horticulture lighting industry.
‘The spectrum makes all the difference. High-quality light creates high-quality plants. We are excited and proud to have a company like Citizen recognize the value of our expertise and to choose to include it in their product portfolio. We look forward to seeing their COB LED products with Valoya spectrum reach the market and the growers who will greatly benefit from Valoya’s spectra which have been developed through meticulous plant R&D efforts spanning over a decade’ comments Mr. Lars Aikala, the CEO and Co-Founder of Valoya.
Access to the Valoya license program not only gives us a solid IP base, but also extends Valoya's experience, research, and know-how to our COB products and our customers.
Our higher power [300 Watt] COBs provide a wide spectrum light, in a very small package. It is a superior solution for greenhouses and other horticultural applications where high power light is needed", comments Mr. Kanetaka Sekiguchi, CEO of Citizen Electronics.
The patent portfolio accounts Valoya’s inventions in the field of light spectra for plant cultivation and lighting applications.
Valoya and Citizen Electronics are happy with this partnership and are both looking to further contribute to support the development of the global horticulture industry.
To inquire further about Citizen’s COB LED products, please click here.
To learn more about Valoya's patent licensing program, please click here.
About Valoyarop
Valoya is a provider of high end, energy-efficient LED grow lights for use in crop science, vertical farming, and medicinal plants cultivation. Valoya LED grow lights have been developed using Valoya's proprietary LED technology and extensive plant photobiology research. Valoya's customer base includes numerous vertical farms, greenhouses, and research institutions all over the world (including 8 out of 10 world’s largest agricultural companies).
Additional information:
Valoya Ltd, Finland
Tel: +358 10 2350300
Email: sales@valoya.com
Web: www.valoya.com
Facebook: https://www.facebook.com/valoyafi/
Twitter: https://twitter.com/valoya
THAILAND: "We Are Lacking Research Here To Backup The Benefits of Indoor Growing"
Thai startup Wangree Fresh has been in the market for over two years now. Krisana Tamvimol, Founder and CEO has done research on more than 200 local vegetables
Thai startup Wangree Fresh has been in the market for over two years now. Krisana Tamvimol, Founder and CEO has done research on more than 200 local vegetables. Eventually, he decided to grow four different vegetables in his Wangree Fresh farm: kale, spinach, rockets and swiss chard. Wangree Fresh has had no problems with incoming orders during the pandemic.
He says: “We’ve had an increase in orders as people wanted more clean and home-delivered vegetables, in the comfort of their own house. Having reached our capacity, we haven’t been able to grow any further beyond that. Now with the pandemic, our company growth is put on hold as we cannot get into new investments and expand our business to meet the growing demand. Our supplies are still constant and we will keep producing at maximum capacity.”
Founder and CEO, Krisana Tamvimol
Under construction
The Siam Pun Sun factory, an 1800 m2 farm, will supply 50 tons of vegetables per month. The construction is about 80% completed and will be fully completed at the end of this year. The new farm is looking into giving educational courses as well. Wangree Fresh will provide educational courses on the new property as well. “I want to share my knowledge of vertical farming and my researches. So, I would love to train more people and teach them more about vertical farming so they can become engineers, scientists, or other”, Tamvimol adds.
The farm's end result
It is no coincidence that Tamvimol has established his new farm there. The farm will be located nearby the Wat Pra Baht Nam Phu temple, which is 120km north of Bangkok. The temple is run by monks who are treating people with medical needs and therefore many underprivileged people are relying on their help.
Tamvimol sees the new farm as a corporate social responsibility project because, once the construction has been completed and the net revenue has come in, all revenue will go directly to the temple. “This will help with the operations of the temple and its maintenance, so the temple won’t be in need of donors anymore. Essentially, the temple will return Siam Pun Suk’s fresh produce to its formal donors as a sign of gratitude.”
The 1800 m2 Siam Pun Sun factory
Supermarkets as a direct competitor
The company sells four different kinds of vegetables, namely kale, spinach, rockets and swiss chard. Simply because we have a pretty good calling price for them. Normally, vegetables of the same species are much more expensive in supermarkets than to what we offer. Our quality is even better. “We are competing with supermarkets in terms of price and quality. We are still researching and looking into strawberries and other fruits, but for now we haven’t gotten that far yet in terms of production”, Tamvimol says. Currently, Wangree Fresh consists of one farm and sells its products under two brands: Wangree Health, the organic wing and Wangree Fresh, using new technologies the company has been reversing over the years.
The farm currently produces at maximum capacity
Although supermarkets have been in the market for a longer time, they can’t produce in the high volume and quality like Wangree Fresh can. He continues: “Quality-wise, we are the best producers of these kinds of vegetables in Thailand. We haven’t been able to address demand in supermarkets yet”, Tamvimol confirms. He says that high-quality and clean food is mostly preferred in urban areas. However, supermarkets in the sub-urban areas do not sell this kind of high-value vegetables.
“We haven’t been able to address the demand in supermarkets so far. Simply, because we have a subscription model and we haven’t been able to address the demand of our subscribers just yet”, Tamvimol says. Since February, the company has gone from 1000 to 2000 subscriptions. Previously, we used to have 1000 subscribers and home-delivered vegetables to them on-time.”
Because the subscriptions doubled during the pandemic, the home-delivery time became longer as well. “We were at maximum capacity already, but we wanted to keep making our customers happy. A guarantee to deliver the fresh produce within 24h e.g., to maintain the freshness of the vegetables”, he adds.
Franchise model
In the future, Wangree Fresh might consider having a franchise. “As in, people signing up to use our system. However, at this point, I have my hands dirty on researching the entire growing system. There might come a franchise model where people can sign up for the consultation of our design and construction of the system. The system needs fine tuning all the time, so it’s not easy to sell it off as one package”, Tamvimol states.
Vertical farming system
“There are two main difficulties in vertical farming here. One is the adoption of new technologies. The Thai people and mostly farmers are not bold enough to try new things. They use their own systems that have been used for over decades” Tamvimol says. It’s hard for Tamvimol to get them involved and for them to try the new systems. “The second thing is that there aren’t many vertical farming systems available in Thailand. Next to that, most of the academic works are conducted by foreign researchers and we are lacking researches here to back up the benefits of indoor growing”, he says.
An impression of Tamvimol's growing system
Tamvimol has done a lot of research on technology, hardware and factors of finetuning his system. He grew up in Chiang Mai, where the main business is agriculture, and used to work in the computer hardware business. After an academic tour to Japan, he became involved with vertical farming. That’s when he decided to combine his experience in digital technology and agriculture. After spending the past few years on research: finding the right formula to grow any kind of vegetable and how many vegetables he needs to grow to generate a good return on investments.
For more information:
Wangree Fresh
Krisana Tamvimol, CEO
krisana@wangreefresh.com
www.wangreefresh.com
Publication date: Mon 24 Aug 2020
Author: Rebekka Boekhout
© HortiDaily.com
Pablo Bunster, Co-founder and CCO of AgroUrbana “In Our Next Farm, We Will Be Able To Use 100% Renewable Energy”
As Chile has been in a complete lockdown since mid-May, AgroUrbana is lucky to continue its operations. “It’s not easy, because you have to change the way of operating, the interactions, and in-farm activities, even when food safety was already key to the company culture
As Chile has been in a complete lockdown since mid-May, AgroUrbana is lucky to continue its operations. “It’s not easy, because you have to change the way of operating, the interactions, and in-farm activities, even when food safety was already key to the company culture. Our customers have been ordering through home delivery”, Cristián Sjögren, Co-founder and CEO of AgroUrbana says.
Renewable energy
Bunster notes: “It took us from the energy market, from renewable energy, to farming. We believe that this is the perfect testing round to see what vertical farming can do.” Chile has drought, cheap labor, we have competitive, available and abundant renewables. Which is always a discussion around vertical farming. We manage sunlight here as we use 100% renewable energy PPA. However, we cannot do this with our pilot because the overall consumption is too low, so we have to regulate it. In our next farm, we will be able to go 100% renewable. That puts a lot toward sustainability for vertical farming.” The urban population is growing fast in Latin America. AgroUrbana believes that vertical farming can accommodate that food demand.
“Our next stage is, going commercial to a scale where we can bring costs down”, Bunster continues. “First, we thought of a small community distributed model with a few small blocks around, such as container farms. But, we believe that scale is still required as you can become more competitive with higher efficiency.
“First, we’re farmers and technology comes to serve that purpose be the best farmers! We are developing some technologies internally to run our farms, but our focus now is how we can actually rate the curve of cutting costs to make our products increasingly competitive. We want to stay out of the commodity but still reach the masses. Our mantra is to deliver better quality food to everyone”, Sjögren adds.
Pablo Bunster harvesting some fresh lettuce
Pilot farm
Sjögren states: “We started with a pilot farm, because vertical farming is something completely new in Latin America.” Before launching a new category for Agriculture in Chile, Sjögren and Bunster wanted to understand the economics of vertical farming. They took an approach of technology-agnostic by building a 3000 sq. ft pilot farm, where different technologies are tested. The 18-month pilot phase will be completed by the end of this year.
“We are integrating our own recipe that combines the seeds nature provides us with its nutrition and environmental parameters. Next to that, we are constantly improving and optimizing our operations in order to drive down costs”, Bunster adds. These quantities are allocated in a 3000 sq. ft farm which is not a large production, Sjögren noted, but this is done to test the market, integrate and develop our technology and do R&D in new varieties. AgroUrbana is planning on scaling up throughout Chile in 2021 with an aim to further expand into the new markets, mainly large urban areas, in the region in the next years.
“Chile is a perfect testing ground to start, test and stress what vertical farming can do, due to the Mediterranean weather we have, favorable to open farming, but also abundant and competitive renewable energy. We both spent our last ten years in the wind- and solar energy industry. Renewables will help AgroUrbana close the gap between traditional agriculture and vertical farming”, Sjögren says.
The country has suffered from climate change, with a 10-year drought that highly affected Chilean agriculture. AgroUrbana has achieved surprising improvements in its yield. “We are planning to transfer all this knowledge to our next farm, a 30,000 sq. ft commercial-scale farm. In the upcoming months, we are doing funding rounds in order to help us realize this farm.
Sjögren says that AgroUrbana is going to pilot in the berry space as well, such as strawberries. “We are starting a pilot to test the different varieties of strawberries. Next to that, we are developing edible flowers and some microgreens”, Sjögren affirms. Most of the volume is lettuce, but we will be rolling out other leafy greens and we will see how it goes with the other crops.
Carmelo platform
“There are many components such as climate control, irrigation, growing structures, and so on. We want to put all the pieces together and operate these very efficiently”, Sjögren states. The company is developing a technology ‘Carmelo’, a platform of sensors with hardware and software to monitor and control our operations. “We are at a level of precision, where we are able to handle the microclimates within the farm. Using Carmelo, we are collecting data already for over one year which is helping us to become even more precise and consistent.” All data gathered will be used for our first large scale commercial farm planned for 2021.
“We’re all about technology and data because that’s how you drive down the costs. We are combining genetics, giving the perfect climate, and the perfect environment. Carmelo is all about finetuning the recipe we’re creating, through managing a farm, and having consistent quality food, every day of the year”, Bunster adds.
Product pricing
“Our team is in good spirits as we have been keeping up production. The pandemic hit us hard, but we were able to relocate all production to different distribution channels, such as e-commerce, supermarkets and subscriptions”, Bunster states. We were planning on doing that already, but we accelerated our go-to-market because of the current situation. “There’s no going back on e-commerce because customers are getting used to it. If we can take our produce to e-commerce, keep our customers satisfied and easy about always getting the perfect product, they’ll always order it online. It’s something we already wanted to do and we are currently testing and proving it. So far, we’re doing okay”, Bunster adds.
AgroUrbana has two markets, one of them being retail with a fast pace opening of new distribution for their products, with 100% recyclable packaging. Furthermore, the company delivers its products to restaurants. Since one year, AgroUrbana has launched its own house mix of lettuce.
Cristián Sjögren and his colleague preparing the plugs for planting
Bunster mentioned that AgroUrbana is selling to restaurants that are price sensitive. Meaning that they care about food quality and the costs. “Here’s where food waste comes into play. We do not have any food waste. We’re coming to the point where most of what we grow, we’re able to process and sell. In restaurants only, we’re saving between 25-35% food of waste in leafy greens. We are very efficient in logistics as we don’t truck. We move food for a few miles from our farms to the kitchens of different clients. This helps us to make numbers for a competitive market.”
Focusing on the next generation
“It has been exciting to put our team together because nobody has a vertical farming degree on its resumé. We’re really excited to prepare the next generation of vertical farmers. We’re putting together different skills and attracting the next generation of farmers that want to move from the countryside to the city. It’s an attractive way to get a generation back to growing veggies in the city with a lot of interaction with technology”, Sjögren ends.
For more information:
AgroUrbana
Cristián Sjögren, Co-Founder and CEO
cristian.sjogren@agrourbana.ag
Pablo Bunster, Co-Founder and CCO
pablo.bunster@agrourbana.ag
www.agrourbana.ag
Publication date: Tue 25 Aug 2020
Author: Rebekka Boekhout
© HortiDaily.com
Smart Acres CEO on The launch of The UAE’s Latest Vertical Smart Farm
The launch of Smart Acres, the UAE’s latest addition to the hydroponic vertical farming industry, this week means that a line of the freshest, most nutrient-dense greens for UAE residents and businesses alike is now being produced in containers on the Armed Forces Officers Club in Abu Dhabi, with the aim to expand across the UAE
Smart Acres Is Here With Lettuce At The Helm. In An Exclusive Interview With Abu Dhabi World, Smart Acres CEO Abdulla al Kaabi Reveals What This Means To Abu Dhabi And The Farming Community On The Whole.
words Derek Issacs
If you love healthy produce, and who doesn’t, then this news is going to please you and your tastebuds no end. The only draw back at the moment is they’re not for sale in supermarkets just yet, but it won’t be long before they are.
The launch of Smart Acres, the UAE’s latest addition to the hydroponic vertical farming industry, this week means that a line of the freshest, most nutrient-dense greens for UAE residents and businesses alike is now being produced in containers on the Armed Forces Officers Club in Abu Dhabi, with the aim to expand across the UAE.
So we headed over to the St. Regis Abu Dhabi to meet Smart Acres CEO Abdulla al Kaabi to find out more.
Tell us about your background?
I am from tech and farm background. My father has a passion for farming and gardening; he’s very strict about anybody who messes around with his garden or farm. My father has a few farms across the UAE, where he grows crops and dates. When he heard that I was pursuing a project in the agriculture sector he got excited and actually gifted me a farm, which I am grateful for and will keep. However, Smart Acres, rather than the farm my father gifted me, is an urban farm.
How was Smart Acres first developed?
CEO Abdulla al Kaabi (centre)
Smart Acres was founded in 2017 and local testing began in July 2019. Smart Acres was developed by a team of experts, including myself, Director Sean Lee and Lead Project Manager, Aphisith Phongsavanh with the aim of improving food security within the United Arab Emirates and developing the country’s farming capabilities, providing a solution to potential socioeconomic threats such as pandemics and climate limitations the Middle East currently endures.
Tell us more
We planted lettuce and after a few harvests, we decided to expand from two containers to eight containers. From the two insulated containers the yield was 3.5 tons annually, which was our proof of concept. For the proof of concept, our target weight for each lettuce head was 140g. However, we have reached an average of 200g per head. I don’t think any other vertical farm here reached that quality or weight in terms of vegetables at this size.
How would you describe Smart Acres?
It is a one-of-a-kind agriculture system that is designed to produce some of the highest yields of crops within the UAE’s vertical farming industry, while introducing a new future for clean foods and allowing both business to business (B2B) and business to consymer (B2C ) sectors to locally source produce.
Tell us about the containers
We invested heavily in the containers, not just financially, and it took us a while to partner up with n.thing, a South Korean vertical farming technology company, to bring the best vertical farm here in the UAE. We had talks with other companies before and we decided to go with this one, in terms of risk, in terms of technology they are using. And the system we are using in the containers is hydroponics (growing plants without soil) which has been used by growers for hundreds of years. Techno advancements means we were able to implement the Internet of Things for operations, which helps us to monitor the entire farm in terms of humidity, temperature, and even the nutrients that goes inside the plants. Now we have our expansion plan from eight to 78 containers, which eventually will produce more than 140 tons of produce annually. We are currently in talks with private and public entities in terms of the expansion. We are also planning to have a research and development centre in order to start growing our own potato seeds in a controlled environment.
Will Smart Acres just be growing lettuce?
In our current eight containers, we grow four types of lettuce; Lolo rosso , green glace, oakleaf Batavia, but we are able to grow 30 types of lettuce. Currently we are testing new methods to improve quality and weight of the existing lettuce. The results of last month’s test resulted in lettuce whose individual heads weighed more than 200 grams on average. However, we aim to grow more than just lettuce. We have plans to eventually grow baby spinach, mature spinach, and baby arugula. Smart Acres’ vision is to expand to meet the demand of popular produce in the region such as strawberries, and, as I previously mentioned, a shift and emphasis on cultivating potato seeds.
Where can we buy your smart lettuces?
We are now supplying restaurants and hotels for free to get ourselves known, and we have had great feedback from them. We have also partnered with several restaurants and cafes around the country including Inked and Fae Cafe, and have plans to have our produce in the kitchen of dozens of other F&B outlets. The recent initiative by HH Sheikh Mansour bin Zayed, Deputy Prime Minister, Minister of Presidential Affairs, and Abu Dhabi Agriculture and Food Safety Authority (ADAFSA), stating that all major grocery stores in the capital must allocate space for local produce means we are perfectly poised to enter local supermarkets. We have had lots of offers from Abu Dhabi Holding and other government entities that are members in the food security committee to buy our whole produce. Currently we are focused on our actual produce itself, in terms of quality, weight.
Posted in Features, Food, Life, News
Tagged agriculture system Abu Dhabi, CEO Abdulla al Kaabi, Clean foods UAE, food security UAE, SMART ACRES Abu Dhabi, st regis abu dhabi, UAE Climate Change Risks and Resilience, UAE farms, UAE’s vertical farming industry, vertical farming Abu Dhabi
VIDEO: iFarm Raises $4 Million To Automate Urban Farming With AI And Drones
The Finnish startup has developed a vertical agricultural system called iFarm Growtune. By growing food closer to consumers and in spaces where conditions can be carefully controlled, iFarm promises to produce food that is fresher while reducing environmental impact
August 20, 2020
Image Credit: iFarm
iFarm has raised $4 million to expand its automated system that uses AI and drones to grow fruits and vegetables in enclosed spaces. Gagarin Capital led the round of funding, which included investment from Matrix Capital, Impulse VC, IMI.VC, and some business angels.
The Finnish startup has developed a vertical agricultural system called iFarm Growtune. By growing food closer to consumers and in spaces where conditions can be carefully controlled, iFarm promises to produce food that is fresher while reducing environmental impact.
As companies rethink logistics and the environment in the wake of the pandemic, self-contained urban farms hold growing appeal.
“The main advantage of indoor farms is that you can be growing all year round, wherever you are,” said iFarm co-founder and CEO Max Chizhov. “And you don’t need a special technologist or agronomist who knows how to use software or grow stuff.”Automation, AI, robotics, and farming are increasingly converging. Paris-based Agricool installs automated systems shipping container to grow strawberries in urban areas. Naïo Technologies builds autonomous farming robots, a Berkeley lab is developing AI systems for polyculture gardening, Burro makes an autonomous vehicle to transport grapes during the harvest, and Enko Chem uses machine learning to help farmers protect their crops without pesticides.
Meanwhile, iFarm is working with clients, typically businesses or farmers, to set up systems in warehouses, factories, basements, and other spaces.
The iFarm system places seedbeds in long racks that are stacked up to 5 meters high. An array of sensors monitors and adjusts the lighting and humidity. Drones are equipped with computer vision to track the crops’ growth and provide further data for the system’s algorithm.
The company developed the algorithm by feeding it scientific data about plant growth, along with data obtained from working farms. The company’s platform can measure the size and weight of plants to help farmers modulate growing conditions. It also uses computer vision to spot potential diseases, which helps growers avoid the use of chemical treatments. In some cases, the system adjusts the microclimate automatically, but it can also provide recommendations to staff.
iFarm currently helps customers create farms ranging from 3,000 square meters to 5,000 square meters. The company has helped develop 11 farms in Finland, Switzerland, the U.K., the Netherlands, Andorra, Russia, and Kazakhstan. Chizhov said iFarm will use the new funding to continue the development of Growtune and expand into new countries in Europe and the Middle East.
Sign up for Funding Weekly to start your week with VB's top funding stories.
Canadian Space Agency Spends $450K on Latest Arctic Greenhouse
“The facility will be used to demonstrate plant production operations in a harsh environment and provide research opportunities while testing technology and operational procedures that may one day help astronauts grow food off Earth,” the Agency wrote
Postmedia News
August 14, 2020
Nunavut residents are being shown how to grow carrots by the Canadian Space Agency to the tune of $450,000.
The CSA described the effort as research on how to produce food during future space missions, according to Blacklock’s Reporter.
“The facility will be used to demonstrate plant production operations in a harsh environment and provide research opportunities while testing technology and operational procedures that may one day help astronauts grow food off Earth,” the Agency wrote.
The greenhouse, called the Nuarvik Food Production facility, is in Gjoa Haven — about 250 kilometres above the Arctic Circle, and is set to begin production in 2025.
“Developing capacity within the Gjoa Haven community for the long-term operation of the recently-installed facility is critical to its long-term success as both a local plant production facility and as a test bed for future space systems,” wrote staff.
The project is jointly funded with the Department of Agriculture and National Research Council, but the CSA didn’t reveal the total budget.
“The Agency has only recently commenced activities in the food production domain and is in the process of options analysis to explore how to help improve the accessibility of food across Canada including the North, with the aim of one day taking these lessons learned to help astronauts grow food off Earth,” wrote staff.
Past attempts at Arctic greenhouse operations have failed, according to research.
Sea cans are seen in Gjoa Haven, Nunavut in this undated handout photo. A pair of converted sea cans sitting on the rocky tundra are bringing fresh vegetables to the Arctic. The sea cans have been turned into greenhouses that are already producing lettuce and tomatoes for the residents of Gjoa Haven, well above the Arctic Circle. ARCTIC RESEARCH FOUNDATION / Via The Canadian Press
Vertical Farms Could Grow All The Wheat We Need
The global population eats a lot of wheat. It’s the most widely grown crop in the world, and it accounts for approximately 20% of the calories and proteins in the average human diet
05-08-2020 | Gizmodo
For years, vertical farming has captured headlines, including on this very website. A new study published in the Proceedings of the National Academy of Sciences on Monday shows the practice could revolutionize the world’s ability to grow wheat.
The global population eats a lot of wheat. It’s the most widely grown crop in the world, and it accounts for approximately 20% of the calories and proteins in the average human diet. As the global population grows, we’ll need more of it to sustain humanity. With arable land a premium, the new study looks at if vertical farming—a method of growing crops in vertically stacked layers—could help.
To find out, the authors created two growth simulation models of a 10-layer vertical farm set up with optimal artificial light, temperatures, and carbon dioxide levels. They found that the simulation could yield up to a whopping 1,940 metric tons of wheat per hectare of ground per year. For context, the current average wheat yield is just 3.2 metric tons per hectare of land.
It makes sense that the authors would be looking into this now. Globally, one in nine people already face hunger, and the problem could become more acute as the population increases. The world could have to produce more than 60% more wheat to account for population growth. That won’t be easy; rising temperatures and other changes in growing seasons driven by the climate crisis are lowering crop yields around the world.
The new study offers an insight into how to address some of these problems. But right now, scientists are only offering simulations. Actually bringing these massive wheat crop yields to fruition would come with massive challenges.
For one, vertical farming is wildly expensive. It requires massive amounts of energy to work, especially because unlike traditional farming, it requires artificial lighting systems. The authors say their simulated systems would provide a light intensity for the crops 30 to 50% greater than directly overhead sunlight. Watering systems and technology to ensure optimal temperature and air quality conditions in these indoor environments would also be costly—not to mention energy-intensive. Depending on how the systems are powered, that could be a problem for the climate. Previous research shows that powering these systems could require vastly more energy than our current high-emissions food system.
“No one has ever attempted to grow food crops under artificial lighting that’s as strong as sunlight, much less strong, for the simple reason that it would require too much energy,” Stan Cox, a scientist and plant breeder at the Land Institute in Salina, Kansas, said in an email.
The new study’s authors note that recent innovations in solar energy are lowering the costs of electricity and lighting is becoming more efficient, but note crops grown this way are still not likely to be economically competitive with current market prices of agriculture. Cox found that to be an understatement.
“A decade ago, given the amount of light wheat plants require to produce one pound of grain, I calculated that growing the entire U.S. wheat crop indoors would consume eight times the country’s entire annual electricity output,” he said. “That was before recent advances in lighting efficiency. So, hey, maybe it would now use up only four to five times our total electricity supply! For one crop!”
Innovations in automation, the authors note, could further lower the costs of vertical farming. That may be true, but in our current economic system, that could be a problem for farmworkers, who are already seeing their pay get cut. For these reasons and more, vertical farming has been a controversial topic in agricultural and environmental circles.
The new study’s authors note that there are also many unanswered questions about growing wheat in indoor facilities. It’s not clear, for instance, what the nutritional value and quality of indoor-farmed wheat would be, or what diseases could arise in such facilities.
Though their projected crop yields are exciting, even if vertical farming does work, it can’t be the only solution to our agricultural issues. Other systemic changes, including reducing food waste, moving away from meat-centric agricultural systems, diversifying crops, and improving soil health, should also play a role.
“Under specific circumstances, and if the energy cost and profitability issues can be resolved, indoor vertical wheat farming might be attractive,” the authors conclude. “Nonetheless, the outcomes described here may contribute only a relatively small fraction (yet to be determined) of the global grain production needed to achieve global food security in the near future.”
By Dharna Noor
Source: Gizmodo
Photo by Science in HD on Unsplash
Temasek Backs US $30m Firm For Vertical Farming Innovation to Boost Singapore's Food Supply
Called Unfold, it is a tie-up between Singapore state investment firm Temasek and a unit of German pharmaceutical and life sciences giant Bayer
Temasek Is Partnering With A Unit of Bayer To Form A US $30 Million
Company To Develop Breakthroughs In Vertical Farming.
August 12, 2020
SINGAPORE - A new US $30 million (S$41.2 million) company has been formed to develop breakthroughs in vertical farming, a move that will help to further reinforce Singapore's food supply.
Called Unfold, it is a tie-up between Singapore state investment firm Temasek and a unit of German pharmaceutical and life sciences giant Bayer.
The Straits Times understands that they will have an equal share of the company, which is incorporated in the United States.
Its primary focus is on improving the quality and variety of food as well as boosting the efficiency of its production, including that of popular vegetables such as lettuce and spinach.
In doing so, it will ensure the safe and reliable supply of food, something that is vital for countries with little arable land and in times of crisis like the Covid-19 pandemic, said Bayer on Wednesday (Aug 12), when announcing the union between its investment unit Leaps by Bayer and Temasek.
Temasek's head of agribusiness, Mr. John Vaske, noted that food security is a priority for Singapore, pointing to the country's "30 by 30" goal, which is to produce 30 percent of its nutritional needs locally by 2030.
He also told The Straits Times that Singapore has been formative in developing vertical farming. "So, we have insights and knowledge of the industry that Unfold can benefit from through the set-up of its commercial, research, and development operations here."
These operations will also be established in California, where Unfold will be headquartered in the city of Davis.
The focus on the genetic potential of vertical farming also sets the company apart from most vertical farming start-ups, which invariably concentrate on developing more efficient infrastructures, Bayer said.
The aim of the venture is to improve the quality and variety of food as well as boost the efficiency of its production. PHOTO: BAYER STOCK PHOTOS
Unfold has already entered into an agreement for specified rights to germplasm, or seed genetics, from Bayer's vegetable portfolio, a move that will enable it to develop new varieties of seeds. It also plans to come up with agronomic advice that is tailored for growing crops in the unique indoor environment of vertical farms.
These farms, also known as indoor farms, leverage on artificial light to grow crops, are less dependent on man-made chemicals, and optimize the use of water.
The company's chief executive officer is Dr. John Purcell, who was previously Bayer Crop Science's head of vegetable seeds research and development, said Bayer in its statement.
Dr. Purcell said that Unfold's investment in germplasm and crop growth models is timely as the two fields are "largely underserved"."
Some technology companies do not have access to germplasm resources. The power of Unfold is that we will combine the expertise and 100 percent focus on the genetics for vertical farming, with access to the best in class germplasm of the Bayer vegetable seed business," he added.
www.bayer.com
www.leaps.bayer.com
www.temasek.com.sg
unfold.ag
Lead Photo: PHOTO: BAYER STOCK PHOTO
CubicFarm Systems Corp. Announces The Appointment of Sandy Gerber As Head of Marketing
As Head of Marketing for CubicFarms, Ms. Gerber is responsible for creating and launching a global marketing strategy that successfully positions CubicFarms in the market and drives lead generations and sales
VANCOUVER, BC, AUGUST 4, 2020 – CubicFarm® Systems Corp. (TSXV:CUB) (“CubicFarms” or the “Company”) is pleased to announce the appointment of Sandy Gerber as Head of Marketing, effective immediately.
As Head of Marketing for CubicFarms, Ms. Gerber is responsible for creating and launching a global marketing strategy that successfully positions CubicFarms in the market and drives lead generations and sales.
Ms. Gerber, an award-winning marketer, and communications strategist, has revitalized marketing and communications programs for companies of all sizes for over 20 years, including some of Canada’s most beloved brands such as Molson Canada, Appleton Estate, BC Lottery Corp, the University of British Columbia, and St. John Ambulance. Her marketing and communications expertise includes differentiation strategy, brand development, customer experience, business development, and digital content marketing.
Ms. Gerber previously held executive and senior marketing leadership positions in a wide range of industries including advertising, consumer goods, heavy equipment, and non-profit.
Her innovative marketing strategies include Molson Canada’s online community, “iam.ca”; Canada’s first e-gaming platform, “PlayNow”; the revitalization of St. John Ambulance’s iconic 900-year-old brand; and Wesgroup Equipment’s successful “G.R.I.T.” customer service program.
She is the author of two books and the founder of three successful companies. As the CEO of NEXT Marketing Agency, Ms. Gerber set a new standard for B2C and B2B innovative marketing, growing the agency into one of British Columbia’s Top 100 Fastest-Growing Companies.
CubicFarms CEO Dave Dinesen commented: “I’m excited that Sandy has joined our team. Her ability to define and refine a company’s message to better connect with customers is exactly what we’re looking for. I’m looking forward to Sandy’s help in telling the CubicFarms story – that we’re leading an industry and we are passionate in helping our grower customers be successful in both the fresh produce and livestock feed sectors.”
Sandy Gerber, Head of Marketing, commented: “I am excited to create a global brand presence and differentiated marketing strategy for CubicFarms to grow exponentially. CubicFarms possesses a winning combination of industry-leading technology and growing expertise, fast-paced culture of innovation, and vision to improve food production efficiencies and food security – to ultimately help farmers feed the world sustainably and profitably.”
Neither the TSX Venture Exchange nor it’s Regulation Services Provider (as that term is defined in the policies of the TSX Venture Exchange) accepts responsibility for the adequacy or accuracy of this release.
About CubicFarm® Systems Corp.
CubicFarm Systems Corp. (“CubicFarms”) is a technology company that is developing and deploying technology to feed a changing world. Its proprietary technologies enable growers around the world to produce high-quality, predictable crop yields. CubicFarms has two distinct technologies that address two distinct markets. The first technology is its patented CubicFarm™ System, which contains patented technology for growing leafy greens and other crops. Using its unique, undulating-path growing system, the Company addresses the main challenges within the indoor farming industry by significantly reducing the need for physical labour and energy, and maximizing yield per cubic foot. CubicFarms leverages its patented technology by operating its own R&D facility in Pitt Meadows, British Columbia, selling the System to growers, licensing its technology and providing vertical farming expertise to its customers.
The second technology is CubicFarms’ HydroGreen System for growing nutritious livestock feed. This system utilizes a unique process to sprout grains, such as barley and wheat, in a controlled environment with minimal use of land, labour, and water. The HydroGreen System is fully automated and performs all growing functions including seeding, watering, lighting, harvesting, and re-seeding – all with the push of a button – to deliver nutritious livestock feed without the typical investment in fertilizer, chemicals, fuel, field equipment, and transportation. The HydroGreen System not only provides superior nutritious feed to benefit the animal but also enables significant environmental benefits to the farm.
Information contact:
cubicfarms.com
Kimberly Lim
VP, Corporate Communications & Investor Relations
Mobile: 236.858.6491
Office: 1.888.280.9076
Email: kimberly@cubicfarms.com
Our mailing address is:
CubicFarm Systems Corp.353 – 19951 80A AveLangley, BC V2Y 0E2Canada
How Can Crop Production Data Advance The Controlled Environment Agriculture Industry?
The Controlled Environment Agriculture Open Data project aims to advance controlled environment research, machine learning, and artificial intelligence through the collection and dissemination of crop production data
The Controlled Environment Agriculture Open Data project aims to advance controlled environment research, machine learning, and artificial intelligence through the collection and dissemination of crop production data.
by By David Kuack
There is a considerable amount of data being generated by both private companies and university researchers when it comes to controlled environment crop production. This data is being generated for ornamentals, food crops, and cannabis. One of the questions about all this data is whether it is being used to its maximum potential to benefit the horticulture industry.
“Data has become a big topic in the horticulture industry with university researchers and private companies,” said Erico Mattos, executive director of the Greenhouse Lighting and Systems Engineering (GLASE) consortium. “People can identify with the challenges and opportunities with the amount of data that is being generated. However, we don’t yet have a centralized repository and a standard methodology for storage to allow us to explore and exploit this data.”
The formation of the Controlled Environment Agriculture Open Data (CEAOD) project aims to promote crop production data sharing from universities and private companies to accelerate CEA research.
Addressing the data proliferation
In 2018 during the North Central Extension & Research Activity–101 (NCERA-101) meeting members of this USDA-organized committee discussed what should be done with the extensive amount of data being generated by controlled environment researchers. Ohio State University professor Chieri Kubota proposed the formation of a sub-committee to address the need to develop guidelines for sharing data generated by controlled environment agriculture researchers.
“Dr. Kubota initiated the discussion about the need for a centralized platform to store data collected from controlled environment research,” Mattos said. “A task force was formed that included Chieri, Kale Harbick at USDA-ARS, Purdue University professor Yang Yang, Melanie Yelton at Plenty and myself. Since the task force was formed Ken Tran at Koidra and Timothy Shelford at Cornell University have also become members of the task force.
“We started discussing how we could make use of all this data. Researchers in the United States collect a huge amount of data. All of the environmental data such as temperature, relative humidity and carbon dioxide and light levels in controlled environment research is collected. There is also a biological set of data which includes plant biomass and fruit yield.”
Mattos said there is also a great deal of research data generated and collected by private companies that is not shared with the horticulture industry.
“With the advancement in sensors and environmental controls, the capability now exists that this data can be collected,” he said. “With the advancements in computing power, this data can be used to start new applications and new tools that haven’t been available before. However, in order to do this, we have to have access to a large amount of data. That’s why the task force thought it would be good to create a repository where researchers and private companies could share the data following a specific format. This data could then be used in the advancement of machine learning and artificial intelligence applications to optimize crop yields in commercial CEA operations.”
An increasing number of funding agencies and organizations, including USDA, are requiring researchers include information about their data management plans in their grant proposals.
Need for collecting and organizing data
Mattos said university researchers see the value in creating a centralized database.
“There are probably millions of data points when you consider how many researchers are doing research in the U.S.,” he said. “Historically these researchers have not been required to share their data. However, an increasing number of funding agencies and organizations, including USDA, are requiring that researchers share their data. If researchers apply for a grant from USDA, they are required to include information about their data management plans in their grant proposals.
“Researchers see the value of sharing this data, but this is not a common practice which involves allocating time and resources. This means someone on their research team would have to organize and share the data. There are probably millions of data points (big data) when you consider how many horticulture researchers there are in the U.S.”
Creating a central database
Based on the need for collecting and organizing the controlled environment research data that is being generated, the task force established the Controlled Environment Agriculture Open Data (CEAOD) project [https://ceaod.github.io/]. The project aims to promote data sharing to accelerate CEA research.
The CEAOD website provides guidelines on how to upload the data. The task force developed the guidelines, which include three sets of data that can be uploaded to the website.
“One set is environmental data, including environmental controlled parameters such as temperature, carbon dioxide, relative humidity, and ventilation,” he said. “These data points are usually collected automatically by sensors. Another set of data is biological data, which is usually collected by humans. These biomass production yield parameters include shoot and root biomass and plant height and weight. The final document is the metadata which are descriptions of the experimental setups and data sets. It is a file that explains the experiments. It describes how the experiments were done.
“There is a certain format that is recommended to be followed to upload the data on the CEAOD website. The step-by-step process is listed on the website. There are no restrictions on which crops the data can be submitted. Our goal is to establish a platform to host a large number of crop production data sets to allow for the development of machine learning and artificial intelligence algorithms aimed at improving crop production efficiency.”
Leading by example
This winter GLASE will have a student collecting and organizing environmental and biological research data.
“The data will be uploaded to the CEAOD database and we will be documenting these activities,” Mattos said. “We will create a guideline of recommendations. We also plan to work with researchers from other institutions to demonstrate how the data can be organized and uploaded to create awareness and how to use the database.
“We hope this initial GLASE contribution will incentivize other researchers to share their data and will facilitate the uploading process. Access to the CEAOD database is free. It is an open platform and anyone can contribute to the development of this database tool.”
Once research data is collected and available for dissemination, the equipment used to produce controlled environment crops will be able to optimize the environmental conditions for a wide variety of crops, including lettuce, tomatoes, and cannabis.
Benefits to the horticulture industry
Mattos said private companies would also benefit from the collection of data and creating a centralized database.
“These companies need more data because it would allow them to analyze the data to develop new products and identify new markets,” he said. “Unfortunately, many of these companies don’t want to share their data. They are very proprietary about their data. They see that collecting and analyzing this data can put them ahead of their competition.
“Many private companies see the need for more data and how it can be valuable but are unwilling to share their own data. But like in other industries there are early adopters. I believe there will be companies that step up and will share their data with the horticulture industry. Hopefully, industry people will be willing to contribute and work on this database as well.”
Mattos said one of the big applications with this project is related to machine learning and artificial intelligence.
“With these applications, large sets of data are needed in order to create baselines,” he said. “Using the data, machines can be taught. Currently, growers’ production knowledge and opinion are more accurate for growing crops than artificial intelligence predictions. Growers are still more reliable, but it is just a matter of time before the use of big data and artificial intelligence will be able to match the growers in regards to optimizing growth.
“We are trying to develop this platform between the growers and controlled environment researchers and the machine learning/data computer scientists. I’m not sure the controlled environment researchers have grasped the potential that is available. We are not using this technology. Establishing this platform, as we collect and disseminate the data, there is real potential to help the advancement of the horticulture industry.”
For more: Erico Mattos, Greenhouse Lighting and Systems Engineering (GLASE), (302) 290-1560; em796@cornell.edu.
More info on CEAOD
Want to learn more about the Controlled Environment Agriculture Open Data project? Then check out these two upcoming events.
Aug. 4, 2-3 p.m. EDT
GLASE webinar: Controlled Environment Agriculture Open Data project. Presented by Erico Mattos, executive director of GLASE, and Kenneth Tran, founder of Koidra LLC.
Aug. 13, 10:30 a.m.-12 p.m. EDT
American Society for Horticultural Science presentation: The Promise of Big Data and New Technologies in Controlled Environment Agriculture. Presented by Erico Mattos.
David Kuack is a freelance technical writer in Fort Worth, Texas; dkuack@gmail.com.
How Leafy Greens Growers Have Turned Food Safety Challenges Into Opportunities
Growing lettuce and other leafy greens in a controlled environment presents its own set of challenges and opportunities
July 30, 2020
Editor’s Note: This article is the second of a three-part series on food safety concerns in the production of leafy greens in a controlled environment.
Click here to check out Part One of the series, which covered the formation of the CEA Food Safety Coalition.
Growing lettuce and other leafy greens in a controlled environment presents its own set of challenges and opportunities. During United Fresh Live in June, Marni Karlin, Executive Director of the CEA Food Safety Coalition, moderated a discussion that outlined how indoor growers who make food safety a priority, rather than dismissing it as a problem unique to field-grown crops, can inadvertently create market opportunities for themselves. The panel featured growers of all types (greenhouses, vertical farms, and warehouses) and sizes. Here are a few insights from the discussion.
Don’t Overlook Irrigation and Growing Media
Jackie Hawkins, Senior Manager of Food Safety at BrightFarms, says irrigation water is likely potable if it comes from municipalities or wells. However, it can still be contaminated, so don’t assume it’s clean and forsake the necessary testing.“Test your incoming water, treat it if necessary, and test it again,” Hawkins says.
Growing media, as well, may not seem like a concern because many leafy greens producers are not growing in soil. “But the seeds might have been grown in media, so it’s important to do routine monitoring of your media as it comes into the greenhouse,” Hawkins says.
From Data Comes Solutions
Michael DeChellis, Co-Founder of Livingston Greens, a small indoor farm in Montana, says it’s critical for greenhouse producers to compile the data they’re able to collect from growing in a controlled environment to create a plan for developing a safer product.“
For small farms, working with other growers in the CEA Food Safety Coalition is a great opportunity,” DeChellis says. “Our members share data, and this culture of collaboration can help us identify ways to overcome challenges.”
For example, DeChellis cites a mold issue at Livingston Greens, which he addressed by using temperature and humidity data to highlight the problem area and the conditions that caused the problem.
Consider Design Upgrades
Simon Yevzelman, Managing Partner and Leader of Biosecurity at Planted Detroit, a vertical farm in the Motor City, says his company saw the concerns of food safety looming, so it opted to temporarily suspend production so it could enhance its production systems with food safety as a guiding principle.“
Thanks to those efforts, we are now in an expansion mode,” Yevzelman says.
Full Company Responsibility
Oscar Camacho, President of Superior Food Safety, a California-based consulting company, says any greenhouse production system should be designed to optimize best food safety practices.“
The system needs to work across the entire company,” Camacho says. “This means communication from one end of the production line to the other is critical.
Retailers and Consumers Care
Chris Livingston, General Counsel at Bowery Farming, a vertical farming company in New York, says the CEA Food Safety Coalition is currently developing a standard specific to controlled-environment production that addresses unique challenges such as water management and infrastructure.“
Our goal is to have a seal that members can use to show their customers they are complying with standards unique to our industry,” Livingston says. “We are also developing a research agenda based on food safety topics.”
Stay tuned for Part 3 of this series, which will focus on how the coronavirus pandemic added value to CEA-grown leafy greens.
Blue Nalu, Aero Farms Highlight Sustainable Food Technology
Entrepreneurs are utilizing new technologies to bridge the gap between where food is grown and where it is consumed
Photo: AeroFarms
08.03.2020
By Sam Danley
NEW YORK — Entrepreneurs are utilizing new technologies to bridge the gap between where food is grown and where it is consumed.
San Diego-based BlueNalu, Inc. is pioneering cellular aquaculture, a process by which living cells are taken from fish and grown using culture media to create seafood.“
(Seafood) is one of the most vulnerable supply chains on the planet,” said Lou Cooperhouse, co-founder and chief executive officer at BlueNalu, during a virtual Town Hall hosted by accounting and consulting group Mazars. “Global demand for seafood is at an all-time high. The problem is that our supply is increasingly diminishing.”
Lou Cooperhouse, co-founder and chief executive officer of BlueNalu, Inc.
A variety of overlapping factors, including illegal fishing and overfishing, warming oceans, plastic pollution, habitat damage, toxins, contaminants, and inconsistent quality of freshness have contributed to the diminishing supply, Mr. Cooperhouse said. Other issues like mislabeling, occupational hazards, and price volatility add to an already stressed system.“
Prices are going higher over time and are anticipated to grow increasingly higher in the years to come,” Mr. Cooperhouse said, adding that BlueNalu has been working to bring down the cost of its formulation to reach price parity with conventional seafood products.
As it scales, the company could potentially offer a price discount, he said.BlueNalu recently expanded its production and R&D capabilities with a new, 38,000-square-foot manufacturing facility in San Diego that includes a pilot-scale production plant. Eventually, it aims to build similar plants around the world, each with the capacity to produce enough cell-based seafood to feed millions of residents.“
Today we might be importing seafood 7,000 miles, 9,000 miles from Southeast Asia to New Jersey, and that's a 30% bycatch with a 60% yield at the foodservice operator level,” Mr. Cooperhouse said. “In our case, we're making a product with no head, no tail, no bones, and no skin. It’s just the filet.”
The pilot plant will help BlueNalu bring its first products to test markets within the next 12 to 18 months. The company currently is focused on several species that typically are imported, overfished or difficult to farm-raise, including mahi-mahi, tuna, red snapper, and yellowtail amberjack
The idea is to complement or supplement rather than disrupt the current supply, Mr. Cooperhouse said.“
Why would we disrupt an industry that’s doing well or focus on a species that currently isn’t an issue?” he said.
A similar mindset is behind Aero Farms, a Newark, NJ-based sustainable indoor agriculture company.“
Seafood is traveling thousands of miles, and it’s the same for produce,” said Marc Oshima, co-founder, and chief marketing officer at AeroFarms. “How can we bring farms closer to where people are and bypass what is a very complex supply chain?”
The company repurposes unused industrial spaces into indoor farms that use 95% less water than conventional agriculture and a fraction of the land space.
Marc Oshima, co-founder and chief marketing officer at AeroFarms“
We're misting the roots with the right amount of water and nutrients in a very targeted way,” Mr. Oshima said. “It leads to a faster-growing process and is much more efficient.”
AeroFarms’ main focus is baby greens, which are supplied to foodservice operators and sold to retailers under the Dream Greens brand.
Because they are grown independent of season and weather, the products offer more consistent quality, price, and year-round availability, Mr. Oshima said.
The company also is collecting data to optimize crops for taste and nutrition.“
We’re thinking about what the consumer is looking for and delivering on a lot of those benefits,” Mr. Oshima said.
Along with keeping transportation to a minimum, increasing yield, and offering more nutritious produce, indoor farming may complement traditional agriculture by accelerating seed development.“
Typical seed breeding is about a seven-year process,” Mr. Oshima said. “With our growing process, we can have up to 30 harvests in a year. Each one is a learning opportunity.”
Vertical Farms Could Grow All The Wheat We Need - But At A Cost
For years, vertical farming has captured headlines, including on this very website. A new study published in the Proceedings of the National Academy of Sciences on Monday shows the practice could revolutionize the world’s ability to grow wheat
July 27, 2020
For years, vertical farming has captured headlines, including on this very website. A new study published in the Proceedings of the National Academy of Sciences on Monday shows the practice could revolutionize the world’s ability to grow wheat.
The global population eats a lot of wheat. It’s the most widely grown crop in the world, and it accounts for approximately 20% of the calories and proteins in the average human diet. As the global population grows, we’ll need more of it to sustain humanity. With arable land a premium, the new study looks at if vertical farming—a method of growing crops in vertically stacked layers—could help.
To find out, the authors created two growth simulation models of a 10-layer vertical farm set up with optimal artificial light, temperatures, and carbon dioxide levels. They found that the simulation could yield up to a whopping 1,940 metric tons of wheat per hectare of ground per year. For context, the current average wheat yield is just 3.2 metric tons per hectare of land.
It makes sense that the authors would be looking into this now. Globally, one in nine people already face hunger, and the problem could become more acute as the population increases. The world could have to produce more than 60% more wheat to account for population growth. That won’t be easy; rising temperatures and other changes in growing seasons driven by the climate crisis are lowering crop yields around the world.
The new study offers an insight into how to address some of these problems. But right now, scientists are only offering simulations. Actually bringing these massive wheat crop yields to fruition would come with massive challenges.
For one, vertical farming is wildly expensive. It requires massive amounts of energy to work, especially because unlike traditional farming, it requires artificial lighting systems. The authors say their simulated systems would provide a light intensity for the crops 30 to 50% greater than directly overhead sunlight. Watering systems and technology to ensure optimal temperature and air quality conditions in these indoor environments would also be costly—not to mention energy-intensive. Depending on how the systems are powered, that could be a problem for the climate. Previous research shows that powering these systems could require vastly more energy than our current high-emissions food system.
“No one has ever attempted to grow food crops under artificial lighting that’s as strong as sunlight, much less stronger, for the simple reason that it would require too much energy,” Stan Cox, a scientist and plant breeder at the Land Institute in Salina, Kansas, said in an email.
The new study’s authors note that recent innovations in solar energy are lowering the costs of electricity and lighting is becoming more efficient, but note crops grown this way are still not likely to be economically competitive with current market prices of agriculture. Cox found that to be an understatement.
“A decade ago, given the amount of light wheat plants require to produce one pound of grain, I calculated that growing the entire U.S. wheat crop indoors would consume eight times the country’s entire annual electricity output,” he said. “That was before recent advances in lighting efficiency. So, hey, maybe it would now use up only four to five times our total electricity supply! For one crop!”
Innovations in automation, the authors note, could further lower the costs of vertical farming. That may be true, but in our current economic system, that could be a problem for farmworkers, who are already seeing their pay get cut. For these reasons and more, vertical farming has been a controversial topic in agricultural and environmental circles.
The new study’s authors note that there are also many unanswered questions about growing wheat in indoor facilities. It’s not clear, for instance, what the nutritional value and quality of indoor-farmed wheat would be, or what diseases could arise in such facilities.
Though their projected crop yields are exciting, even if vertical farming does work, it can’t be the only solution to our agricultural issues. Other systemic changes, including reducing food waste, moving away from meat-centric agricultural systems, diversifying crops, and improving soil health, should also play a role.
“Under specific circumstances, and if the energy cost and profitability issues can be resolved, indoor vertical wheat farming might be attractive,” the authors conclude. “Nonetheless, the outcomes described here may contribute only a relatively small fraction (yet to be determined) of the global grain production needed to achieve global food security in the near future.”
Staff writer, Earther
Lead photo: Wheat being harvested in an open field. It could be a thing of the past someday. By, Christopher Furlong (Getty Images)
GERMANY: "Dry-Fog is The Next Generation of Aeroponics"
Lite+Fog can replace heavy steel racks with unique fabric, which separates the root zone from the growing zone and allows farmers to grow with any substrate
Lite+Fog, a Berlin-based company, started focusing on dry-fog systems as they noticed many benefits from it. "Dry-fog is the next generation of aeroponics. I started working on indoor farms for more than ten years. Because I did a lot of mushroom farming, I began to work with dry-fog and realized that it is a great way to feed plants. So we are now able to ultimately reduce the typical costs of Vertical Farming by around 80% and even triple the energy efficiency", states Martin Peter, Co-founder, and CEO of Lite+Fog.
Lite+Fog can replace heavy steel racks with unique fabric, which separates the root zone from the growing zone and allows farmers to grow with any substrate. "The system is a realization of work that originally started with urban farming projects, where I built many prototypes and tested a lot of approaches, especially vertical column-based farming technologies. The system as we plan it right now, however, has been developed over the last year."
Efficiency There is a lot of interest from farmers based in Israel, India, and the UK, all with different purposes. Compared to other systems, the Lite+Fog system dramatically reduces the costs in production, maintenance, and labour. The company is planning to have a pilot farm constructed by next year. "We are still on the lookout for potential pilot partners, strategic investors, and research institutes which are interested in joining this new generation of Vertical Farming. Bringing the efficiency up and lowering the costs is the most important thing to transform this vital technology into the mass-market application it has to be", says Martin.
Standardized farms
"We want to become a core technology supplier for indoor farms. As the technique has proven to be successful, we are now upscaling, and engineering the larger versions of our prototype farms. So we're connecting with suppliers and core industries in Germany and elsewhere, to create an important industrial network, able to satisfy the demand we expect in the future.
We plan on delivering at least 60 bigger farms per year during the next five years. Very simply put, we create a big box where seeds enter at one end and plants come out at the other. Eventually, we want to focus on standardizing these farms, as this would significantly improve cost efficiency and comparability. These are both essential factors for research and marketability", Martin states.
The concept design of Lite+Fog's 1000m2 footprint farm creating more than 45.000 m2 of growing surface for greens and berries
Benefits
"Dry-fog enables plants to be better nourished and improves growth by up to 20%. This way of growing is also practically weightless, so you can completely reimagine the architecture of farms - which we make great use of. Improving the efficiency of indoor farms is about how many square meters of growing space you generate in a given volume. Our approach is focusing on that primarily.
In addition to that, with no clogging nozzles, less maintenance, and easier central production, dry-fog is the next step of indoor farming. And that's why we are so much more cost-efficient than other approaches which are not vertical but multilayer horizontal farms anyway. We develop a true vertical "food-reactor".
The state-of-the-art spray nozzles typically used in vertical farms, which directly spray water on the plant roots, are bound to clog up as they are using a salty solution. These now outdated systems need to be cleaned and maintained all the time - and are reliably unreliable in the long run. However, dry-fog does barely weigh anything, doesn't need nozzles, and is therefore much cheaper and easy to use. "
Challenges
However, "fogponics" also has its challenges. As there is no growing medium, you have to be extra aware of the temperature of the root zone and on the complex system delivering the fog to the roots. Also, the droplet size has to be adjusted for bigger nutrients that are essential for some crops. But "these 'difficulties' can easily be mitigated if you adapt a bit - and that's what we are researching currently," says Martin.
For more information:
Lite+Fog GmbH
Martin Peter, Co-Founder, and CEO
Marienburger Str. 8
10405 Berlin
martin.peter@liteandfog.com
www.liteandfog.com
Publication date: Fri 17 Jul 2020
Author: Rebekka Boekhout
© HortiDaily.com
Bejing National Agricultural Science And Technology Innovation Park To Be Expanded
AgriGarden International is a Chinese provider of services covering the entire industry chain of horticulture
AgriGarden International: To Build a Platform of Innovation For global horticultural Industry
The Covid-19 pandemic that has been ongoing for months has affected China's horticulture industry to varying degrees, and many projects under construction had to be suspended. AgriGarden International is a Chinese provider of services covering the entire industry chain of horticulture. Liu, Manager of International Cooperation, said, “Since the outbreak of Covid-19 at the end of January this year, the construction of all of our ongoing projects has been forced to stop. Currently, projects in other provinces and cities have been able to resume, but due to the second wave of cases occurred in Beijing in mid-June, the construction of National Agricultural Science and Technology Innovation Park here had to be once again put on hold and is awaiting approval for the resumption of work.”
National Agricultural Science and Technology Innovation Park
Liu, Manager of the company’s marketing department, said, “The National Agricultural Science and Technology Innovation Park and the International Facility Horticulture Innovation Center that is to be expanded will serve as an exchange platform for the horticulture industry. By working with internationally renowned horticultural research institutions and companies, they will showcase the latest results of horticultural scientific research, and new technologies and equipment for facility horticulture to visitors at home and abroad, and promote exchanges, cooperation, and joint innovation among enterprises. The Innovation Park will also function as an investor and incubator. Since the establishment of the park, it has received nearly 40 heads of state and leading politicians.
Interior of the National Agricultural Science and Technology Innovation Park
About the Innovation Center
When talking about the International Facility Horticulture Innovation Center, Liu said, “AgriGarden International is an agricultural high-tech enterprise affiliated with the Chinese Academy of Agricultural Sciences. It is a benchmark enterprise for transforming scientific and technological achievements via in-depth integration of production, education, and research handpicked by the Ministry of Agriculture and Rural Affairs. We often receive domestic and foreign leaders with investment intentions. In the future, our Innovation Center can provide office space for domestic and foreign horticultural technology companies, and more importantly, provide a communication platform for these companies and help them open the Chinese market and bring more potential customers. We also hope to facilitate joint innovation of the horticulture industry in this center to create more innovative products for the Chinese market.”
In recent years, more and more companies have transitioned from traditional agriculture to facility horticulture, which shows the huge potential of the Chinese market. However, foreign companies have to face a series of challenges such as the lack of customers and ignorance of local policies, even though they have advanced technologies and concepts. The Innovation Center will provide these companies with localized information and help them expand the Chinese market.
International Facility Horticulture Innovation Center
AgriGarden International
AgriGarden International is an agricultural high-tech enterprise affiliated with the Chinese Academy of Agricultural Sciences. It is a benchmark enterprise for transforming scientific and technological achievements via in-depth integration of production, education, and research handpicked by the Ministry of Agriculture and Rural Affairs. “We welcome companies in the industry that are interested in joining the International Facility Horticulture Innovation Center (Alliance) to contact us." Manager Liu said.
Lead photo: The core part of the National Agricultural Science and Technology Innovation Park
For more information:
Contact: JING (Laurie) LIU
Company: AgriGarden International BD
Tel.: 00491791229249
Email: laurie.liu@agri-garden.com
Publication date: Thu 23 Jul 2020
© HortiDaily.com
How Vertical Farms Could Be Ready To Take-Off
A new interdisciplinary study combining biology and engineering sets down steps towards accelerating the growth of vertical farming, including the use of aeroponics which uses nutrient-enriched aerosols in place of soil, reports Science Daily
24 Jul 2020
Study identifies future research areas needed to accelerate growth of vertical farming using aeroponics.
A new interdisciplinary study combining biology and engineering sets down steps towards accelerating the growth of vertical farming, including the use of aeroponics which uses nutrient-enriched aerosols in place of soil, reports Science Daily.
Accelerate sustainable growth of vertical farming
The study was carried out by the John Innes Centre, the University of Bristol, and the aeroponic technology provider LettUs Grow. It identifies future research areas needed to accelerate the sustainable growth of vertical farming using aeroponic systems.
Dr. Antony Dodd, a group leader at the John Innes Centre and senior author of the study, says: “By bringing fundamental biological insights into the context of the physics of growing plants in an aerosol, we can help the vertical farming business become more productive more quickly while producing healthier food with less environmental impact.”
Vertical farming is a type of indoor agriculture where crops are cultivated in stacked systems with water, lighting, and nutrient sources carefully controlled.
Seven areas of future research
The study, which appears in the journal New Phytologist and is called Getting to the Roots of Aeroponic Indoor Farming, lays out seven steps – strategic areas of future research needed to underpin increased productivity and sustainability of aeroponic vertical farms.
These seek to understand:
Why aeroponic cultivation can be more productive than hydroponic or soil cultivation.
The relationship between aeroponic cultivation and 24-hour circadian rhythms of plants.
Root development of a range of crops in aeroponic conditions.
The relationship between aerosol droplet size and deposition and plant performance.
How we can establish frameworks for comparing vertical farming technologies for a range of crops.
How aeroponic methods affect microbial interactions with plant roots.
The nature of recycling of root exudates (fluids secreted by the roots of plants) within the nutrient solutions of closed aeroponic systems.
The report argues that a driver of technological innovation in vertical farms is minimizing operation costs whilst maximizing productivity – and that investment in fundamental biological research has a significant role.
Genetically tune crops to grow in vertical farms
John Innes Centre researchers have bred a line of broccoli adapted to grow indoors for a major supermarket and one of the aims of research will be to test how we can genetically tune more crops to grow in the controlled space of vertical farms.
Bethany Eldridge, a researcher at the University of Bristol studying root-environment interactions and first author of the study adds: “Given that 80% of agricultural land worldwide is reported to have moderate or severe erosion, the ability to grow crops in a soilless system with minimal fertilizers and pesticides is advantageous because it provides an opportunity to grow crops in areas facing soil erosion or other environmental issues such as algal blooms in local water bodies that may have been driven by traditional, soil-based, agriculture.”
Aeroponics is associated with very little water, automation, and high tech systems. But what is the current potential of aeroponics technology to grow food or cannabis crops economically?
Hugo Claver
Web editor for Future Farming
Lead Photo: - Photo: ThisIsEngineering
CubicFarms Attracts $1.16 Million Investment From Leading Dairy Entrepreneur Harry DeWit and Company Insiders
Harry DeWit is CEO and President of Blue Sky Farms, a Texas and Ohio-based dairy and farming business producing 1.2 million pounds of quality milk per day
NEWS PROVIDED BY
Jul 15, 2020
VANCOUVER, BC, July 15, 2020, /CNW/ - CubicFarm® Systems Corp. (TSXV: CUB) ("CubicFarms" or the "Company") is pleased to announce a non-brokered private placement with Harry DeWit and company insiders, involving the issuance of 1,659,600 common shares of CubicFarms at a price of C$0.70 per share for gross proceeds of up to C$1,161,720 (the "Offering"). Insiders participating in the Offering include Jeff Booth, Chairman; Rodrigo Santana, Chief Operating Officer; and Tim Fernback, Chief Financial Officer.
Harry DeWit is CEO and President of Blue Sky Farms, a Texas and Ohio-based dairy and farming business producing 1.2 million pounds of quality milk per day. He has been lauded as a forward-thinking dairy entrepreneur, having been awarded the International Dairy Foods Association's "Innovative Dairy Farmer of the Year", which recognizes the valuable contributions of progressive dairy producers. His soil conservation efforts were recognized by the USDA's National Resources Conservation Service.
Mr. DeWit commented: "Sustainability, efficiency, and automation have always been at the core of my business endeavors. I have looked to technology to conserve water, reduce labor, and generally improve the efficiency of my daily operations. When CubicFarms' board member John de Jonge introduced me to CubicFarms' HydroGreen system that automates the growth of livestock feed, I had to learn more about the company.
"CubicFarms' HydroGreen technology enables a more sustainable farming operation in that one system displaces thirty acres of land used for livestock forage production, not to mention the cost savings in labor, water, energy, and fertilizers. Providing fresh HydroGreen feed on a daily basis to a herd of cows should bring the herd to a higher production level with health benefits."
CubicFarms CEO Dave Dinesen commented: "Top tier ag-tech investor Ospraie Ag Science has added tremendous value to CubicFarms from day one of becoming a strategic investor just two months ago. We have benefitted from Ospraie's vast network, sector expertise, and vision in our company-building efforts. We are now pleased to welcome Harry to the roster of company supporters. An investment from an industry stalwart such as Harry is a big vote of confidence in CubicFarms and our HydroGreen livestock feed division."
The net proceeds from the Offering are expected to be used for research and development to expand machine capabilities and crop varieties, and working capital.
The Offering is scheduled to close on or about July 28, 2020, and is subject to certain conditions, including, but not limited to, the execution of definitive documentation and receipt of all necessary approvals, including the approval of the TSX Venture Exchange. All securities issued pursuant to the Offering will be subject to a hold period under applicable securities laws, which will expire four months plus one day from the closing date of the Offering.
This press release does not constitute an offer to sell or the solicitation of an offer to buy, nor shall there be any sale of these securities, in any jurisdiction in which such offer, solicitation or sale would be unlawful prior to registration or qualification under the securities laws of such jurisdiction. The securities have not been and will not be registered under the United States Securities Act of 1933, as amended (the "U.S. Securities Act"), or any state securities laws, and may not be offered or sold within the United States unless an exemption from such registration is available.
Neither the TSX Venture Exchange nor it’s Regulation Services Provider (as that term is defined in the policies of the TSX Venture Exchange) accepts responsibility for the adequacy or accuracy of this release.
About CubicFarm® Systems Corp.
CubicFarm Systems Corp. ("CubicFarms") is a technology company that is developing and deploying technology to feed a changing world. Its proprietary technologies enable growers around the world to produce high-quality, predictable crop yields. CubicFarms has two distinct technologies that address two distinct markets. The first technology is its patented CubicFarm™ System, which contains patented technology for growing leafy greens and other crops. Using its unique, undulating-path growing system, the Company addresses the main challenges within the indoor farming industry by significantly reducing the need for physical labor and energy, and maximizing yield per cubic foot. CubicFarms leverages its patented technology by operating its own R&D facility in Pitt Meadows, British Columbia, selling the System to growers, licensing its technology, and providing vertical farming expertise to its customers. The second technology is CubicFarms' HydroGreen System for growing nutritious livestock feed. This system utilizes a unique process to sprout grains, such as barley and wheat, in a controlled environment with minimal use of land, labor, and water. The HydroGreen System is fully automated and performs all growing functions including seeding, watering, lighting, harvesting, and re-seeding – all with the push of a button – to deliver nutritious livestock feed without the typical investment in fertilizer, chemicals, fuel, field equipment, and transportation. The HydroGreen System not only provides superior nutritious feed to benefit the animal but also enables significant environmental benefits to the farm.
Cautionary statement on forward-looking information
Certain statements in this release constitute "forward-looking statements" or "forward-looking information" within the meaning of applicable securities laws, including, without limitation, statements with respect to the use of proceeds of the Offering and the potential benefits of Harry DeWit's investment to the Company. Such statements involve known and unknown risks, uncertainties, and other factors including evolving market conditions, which may cause the actual results, performance, or achievements of CubicFarm Systems Corp., or industry results, to be materially different from any future results, performance, or achievements expressed or implied by such forward-looking statements or information including the Company obtaining the approval of the Offering from the TSX Venture Exchange. Such statements can be identified by the use of words such as "may", "would", "could", "will", "intend", "expect", "believe", "plan", "anticipate", "estimate", "scheduled", "forecast", "predict", and other similar terminology, or state that certain actions, events, or results "may", "could", "would", "might", or "will" be taken, occur, or be achieved.
These statements reflect the Company's current expectations regarding future events, performance, and results and speak only as of the date of this news release. Consequently, there can be no assurances that such statements will prove to be accurate and actual results and future events could differ materially from those anticipated in such statements. Except as required by securities disclosure laws and regulations applicable to the Company, the Company undertakes no obligation to update these forward-looking statements if the Company's expectations regarding future events, performance, or results change.
SOURCE CubicFarm Systems Corp.
For further information: Kimberly Lim, kimberly@cubicfarms.com, Phone: +1-236-858-6491, www.cubicfarms.com
US - ILLINOIS - Vertical Farm Adaptive Reuse Headed To Former Target location In Calumet City
Wilder Fields will begin construction this fall, repurposing a former Target location located at 1717 W. East Road in Calumet City, Illinois. Once completed, the 135,000-square-foot former big box store will serve as a vertical farm
JULY 21, 2020
Wilder Fields will begin construction this fall, repurposing a former Target location located at 1717 W. East Road in Calumet City, Illinois. Once completed, the 135,000-square-foot former big box store will serve as a vertical farm.
“When I learned about the possibility of acquiring a Super Target store in Calumet City, I knew it would be the perfect choice for building Wilder Fields’ first full-scale commercial vertical farm,” said Jake Counne, founder of Wilder Fields. “From the very beginning, we have developed our system to be flexible enough to fit existing buildings, including anchor retail spaces like this one.”
The majority of space will house 24 separate cleanrooms for growing dozens of varieties of greens. The site will also include a retail store and education center, a research laboratory, and a large loading dock which will serve as a hub for distributing produce to supermarkets and select restaurants within 100 miles of this next-generation vertical farm.
“To my knowledge, converting a big-box space to a farm has never been done before,” Counne said. “We are creating the blueprint for this transformation.”
Construction is planned for two phases. Phase one, to be completed in early 2021, includes building critical infrastructure and an initial group of cleanrooms. Each 105,000-cubic-foot cleanroom will house eight levels of growing space along with the proprietary technology created by Wilder Fields’ experts to provide a safe and efficient growing environment. The second phase will be completed in early 2023.
The enterprise is funded by Counne and a group of strategic private investors. The total cost for the Wilder Farms’ first facility is estimated at $40 million.
“We made vertical farming profitable by looking at industries outside of farming for inspiration to reduce the costs of labor and energy. We have improved the ways plants are grown, harvested, and shipped,” said Counne. “By negotiating mutually beneficial relationships with city leaders, we can convert abandoned big box stores—currently blighting commercial real estate markets—into profitable, tax-paying businesses.”