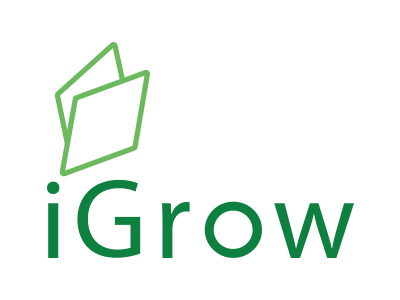
Welcome to iGrow News, Your Source for the World of Indoor Vertical Farming
Vertical Farming Comes to Edinburgh
Scotland’s Rural College is to be the first higher education institute in Scotland to open its own vertical farm for research and education.
By Gordon Davidson
August 10, 2021
Scotland’s Rural College is to be the first higher education institute in Scotland to open its own vertical farm for research and education.
The half million-pound facility is to be built at the SRUC's King’s Buildings campus in Edinburgh next year, with the backing of a £200,000 grant from the Scottish Government. It will enable key research into plant and crop science, growing nutrient-dense fruit and vegetables with specific human health qualities, while analysing crop yield and growth rates – with all inputs recorded in the closed environment – to compare their carbon footprint to other production systems.
SRUC's vertical farm will operate on renewable energy sources from the national grid, supported by battery technology to manage peaks in energy demand.
With only a handful of commercial vertical farms in Scotland so far, it is envisaged that the facility will be important for demonstration and knowledge exchange with farmers, growers and small businesses. It will also be used by SRUC students as part of their educational activities, looking to a future when such systems will be far more common places of work.
Cabinet Secretary for Rural Affairs and Islands, Mairi Gougeon, said: “As we look to produce more fruits and vegetables locally, vertical farming could provide us with a way to make better use of our land. It’s an exciting and innovative field that could bring us real benefits and it is important that we have the skills in Scotland to take advantage of this technology.
“By supporting the industry at an early stage, we can assess these benefits and help to focus our long-term strategy. We will also be reaching out to the wider industry to explore in further detail the opportunities low-carbon vertical farming offers. We will work together to establish the future of vertical farming in Scotland.”
Principal and chief executive of SRUC, Professor Wayne Powell, said: “One of the most critical challenges we face is how to feed a growing global population. We have been teaching farmers for generations but, as the population increases, it is important that we look at growing different, more nutritious crops to support healthy diets and local access to food.
“Not only will this vertical farming unit be a valuable asset to our students, but it will also provide us with important data to help optimise and promote innovation into this expanding industry.”
Lead Photo: A new vertical farm at SRUC will be used for education and research.
Women in AI: How Does the Future of Horticulture Will Look?
But what skills are needed to work in AI tech? And what does the future of working with AI look like? Britta Meixner, Saheli De and Gosia Piekarska of Blue Radix answer these questions, and suggest how we can encourage more women to aim for tech jobs in AI or IT
August 11, 2021
Getting the best from your crop and greenhouse will increasingly become a computer responsibility. We need to make better decisions, to get better results and fix the global food problems and expertise shortages. Artificial Intelligence can help us with this. But what skills are needed to work in AI tech? And what does the future of working with AI look like? Britta Meixner, Saheli De and Gosia Piekarska of Blue Radix answer these questions, and suggest how we can encourage more women to aim for tech jobs in AI or IT.
What’s your job at Blue Radix?
Britta: “My name is Britta Meixner, and I’m a Scientific Data Engineer. I advise the Blue Radix management team on technical implementations. I keep track of new technologies enabling us to introduce innovative products to customers. I also design, build and maintain a scalable and future-proof IT environment. Other tasks include implementing proof of concepts for new technologies and setups; I design and realize solutions when we start using these new technologies. One of these is the Azure IoT Hub, which lets us send results from the Data Science Team to greenhouses, steering installations autonomously.”
“A day in a data scientist’s life entails a range of tasks,” explains Saheli De, who works as a Data Scientist at Blue Radix. “Developing new functionalities for our customers involves preparing, cleaning and analyzing the data that comes from the climate computers and other data platforms. In this phase we work closely with our product development team to understand the dynamics and strategies involved in the greenhouse. Then there’s extensive discussion of strategies to solve the business requirement, leading to building models using cutting-edge AI technologies like machine learning. The essence of the job lies in translating the horticulture industry’s business requirements into data science solutions.”
Gosia Piekarska works as a Blue Radix Test Engineer and is responsible for implementing testing procedures, shaping the testing process, and software testing. “My job is to check the quality of the infrastructure and components in both Crop Controller and the energy domain. My work is my hobby; I’m always trying to improve my software testing knowledge in my spare time. I’m particularly interested in Test Automation, Data Analysis and DevOps.”
What do you like about working with new AI tech solutions for horticulture?
Britta: “There’s often no standard way of doing something when creating new AI solutions. Every new project requires new skills and technology knowledge. I can never stop learning in my job. Staying up to speed on new developments and technologies is the key to success. This makes my job demanding, but at the same time it never gets boring.”
Adds Saheli: “The tech industry is growing rapidly, and being the flag-bearer of AI in horticulture lets you design unique and sustainable solutions. Imagine walking into a supermarket picking up a tomato that was produced with the help of your algorithms! That’s powerful!”
“I always love working on the cutting-edge technology solutions, because they introduce the innovations which are so desperately needed in our world,” says Gosia. “I think that sustainable technology in the food-growing industry is critical for people’s well-being.”
What skills are needed to work in the AI tech-field?
“You need a broad spectrum of knowledge to make our solutions work in the greenhouse, from network protocols and operating systems, databases and APIs, to data pipelines. It’s only the combination of these which enables us to steer a greenhouse autonomously,” explains Britta. “Because the IT infrastructure differs in every greenhouse, we must be able to create solutions that quickly adjust to a wide range of situations. So alongside a very broad technical knowledge, you also need to be flexible, and to understand new situations and requirements quickly.”
Saheli adds: “Data Science in particular is a mix of mathematics, statistics, and computer science skills. Horticulture-related skills are a benefit, but not mandatory in my role.”
Gosia: “Constant learning of both broad technologies and tools.. On top of that, don’t forget soft skills.”
How do you think the future of working with AI will look?
Britta: “Data Scientists now focus mainly on a deep understanding of algorithms and data sets to be able to get the most accurate results for steering the greenhouse. This is often done in controlled offline setups. But there’s still a large gap before these algorithms are ready to be integrated into production environments to produce real-world data for the greenhouse. Data science and data engineering have to work together early in the development process to close this gap. That lets us deliver new features and improvements to existing functionalities faster.”
Saheli: “As we say at Blue Radix: ‘Algorithms can feed the world’. We believe that algorithm-based solutions, like our Crop Controller, offer growers worldwide a digital brain for their greenhouse. The dream is to work towards a symbiotic utopia of growers and AI-driven solutions.”
Gosia adds: “The key will be the AI-human interaction and how to deliver AI solutions to customers who don’t necessarily have a deep technical understanding of AI systems. This is important in horticulture, because advanced controlled systems are relatively new in this industry.”
How can we generate enthusiasm among women for tech jobs in AI or IT?
Britta: “Women have different styles of working, thinking and communicating than men. While that might cause confusion here and there, it can really help a team to reach their goals faster, and to find better solutions. If we are to encourage more women to take up AI or IT jobs, it’s important to reach true equality in opportunities and pay in every job out there. We need to remove gender stereotypes in daily work, while also avoiding them in early childhood and at schools.”
Saheli: “I completely agree with Britta,; we need to generate opportunities for both genders to be able to access and experience meaningful interaction with technology from a very young age. I strongly believe that curiosity is the key to science. Stay curious and keep asking questions!”
Gosia: “We can’t shape our world if we’re not involved. Working in IT offers enormous opportunities for women to make their mark. I also believe there are great career prospects if you choose a future working in AI, IT and sustainability. There are so many great challenges, and you can really contribute to a better world. The best would be to provide successful examples and stories of women working in AI, to encourage young girls to join the field.”
"Using Variable Spectrum Luminaries Allows us to Grow a Wide Range of Plants"
Bringing food closer to consumers is no longer an option but rather a necessity, given the strain traditional agriculture and transportation place on the environment.
August 11, 2021
Bringing food closer to consumers is no longer an option but rather a necessity, given the strain traditional agriculture and transportation place on the environment. Czech grow tech company GreeenTech teamed up with Hungary’s Tungsram to provide vertical farming solutions that pave the way for sustainable crop production.
Prague-based GreeenTech was born out of this realization. The company specializes in the research and development of hydroponic technologies to be used in container farms and vertical farms set up in buildings. Established in 2000, the business aims to enable people to grow agricultural crops anytime and anywhere in the world.
They are involved in developing innovative solutions for the local production of leafy vegetables, herbs, and small fruits through their own hydroponic cultivation technology complete with an IOT control system created in cooperation with Siemens. The uniqueness of the solution provided by GreeenTech lies in the development of tailor-made hydroponic farming technology.
Finding the perfect lighting solution
"Hydroponic systems are soil-less, water-based farming processes. The technology is based on growing plants in a controlled environment where crops are fed nutrient-rich water. Crop cultivation takes place in an enclosed growing space, where sensors control conditions such as humidity, temperature, or light cycle. The result is quality crops that have not been subjected to treatment with pesticides and herbicides and the farm uses about 90% less water than conventional agriculture," the GreeenTech team explains.
Given that crops are not exposed to natural light, selecting the right lighting solution in these farms is of utmost importance. GreeenTech’s quest for the best lighting solution provider-led them to Tungsram, whose variable spectrum LED luminaries proved to be the perfect match as the light sources have been designed and created only for the purposes of a growing container.
“We were searching for a lighting solution and we realized that Tungsram’s luminaries and the automation solutions provided by them are ideal for our needs because they are well suited for research purpose. Using variable spectrum luminaries allows us to grow a wide range of plants. In addition, customers have a high degree of flexibility in deciding what kind of plants they want to grow or in switching from one crop to the other,” said Karolína Pumprová, CGO at GreeenTech.
LED lights
"Our four-channel LED lights offer the highest performance in their category and are extremely easy to install," the Tungsram team says. "The luminaries are controlled remotely and allow users to adjust the color spectrum and light intensity independently for each growing rack, which is a game-changer for large-scale urban farms."
In addition to the lights, Tungsram also provided a tailor-made lighting design with the help of the company’s engineers and designers. "Variable spectrum luminaries are a powerful tool for growers in terms of adopting a “dynamic light recipe approach,” which is a rather unique offering in the market."
Compatible with software
“Another factor that weighed heavily in favor of Tunsgram was the fact that the lighting solution developed together with them was compatible with the software and system we already had in place,” said Milan Souček, CTO at GreeenTech.
GreeenTech will use the Tungsram luminaries at the expo in Dubai, which will run from September through March. The cultivation container will be set up in a restaurant and the plants will be used in the restaurant. As part of a cooperation with the Technical University in Prague, Tungsram lights will be installed at a small hydroponic farm set up by GreeenTech where students will be conducting research and testing.
For more information:
Tungsram
Keith Thomas, Commercial Leader
keith.thomas2@tungsram.com
agritech.tungsram.com
Kalera AS to Acquire &ever GmbH to Form a Global Leader in the Vertical Farming Industry
Kalera AS (Euronext Growth Oslo: KAL, Bloomberg: KSLLF), one of the fastest-growing and largest vertical farming companies in the world, announces today that it has entered into a share purchase agreement for the acquisition of all shares in &ever GmbH, a global leader in baby leaf indoor farming, for a total consideration reflecting an enterprise value for &ever GmbH of EUR 130 million on a cash and debt free basis as of 1 July 2021. T
August 11, 2021
&ever has been represented on the global market since 2015 and operates a large vertical farming facility in Kuwait, in addition to in-store grow-towers in Germany. It is also currently constructing a mega-facility in Singapore.
Kalera will become the only company with capabilities to serve every segment within the leafy green industry solidifying Kalera’s position as the overall indoor farming market leader.
Through the combination with &ever’s existing portfolio of vertical farms, Kalera will own the largest portfolio of farming systems from small in-store or on-property farms to megafarms.
ORLANDO, Fla., (GLOBE NEWSWIRE) -- Kalera AS (Euronext Growth Oslo: KAL, Bloomberg: KSLLF), one of the fastest-growing and largest vertical farming companies in the world, announces today that it has entered into a share purchase agreement for the acquisition of all shares in &ever GmbH, a global leader in baby leaf indoor farming, for a total consideration reflecting an enterprise value for &ever GmbH of EUR 130 million on a cash and debt free basis as of 1 July 2021. The consideration will consist of a combination of cash and Kalera shares. Under the terms of the agreement, &ever GmbH shareholders will receive EUR 21.6 million in cash and 27,856,081 Kalera shares at a subscription price of NOK 36.68.
The cash consideration will be financed through a debt facility provided by DNB or by other financing sources available to Kalera. Kalera shareholders will own an 87% stake in the combined company, while current &ever GmbH shareholders will own 13%, on a fully-diluted basis.
&ever is a vertical farm company headquartered in Germany with operations in the Middle East, Asia and Europe. The acquisition will transform Kalera into a global vertical farming leader, accelerating its plans for international growth and broadening its product line to include several cut leaf baby greens in high demand.
The company will be wholly owned by Kalera AS upon closing of the transaction. &ever GmbH will be renamed to Kalera GmbH.
Leading Technology and Capabilities for Baby Leaf Production
Founded in 2015 to grow select baby leaf produce and herbs including spinach, kale, endive, arugula, watercress, cilantro and bok choy, &ever has developed a proprietary approach for seeding, germination, propagation, harvesting, and delivery of fresh baby leaf products that optimize the entire production cycle through unique growing methods and technologies.
&ever has operations in Europe, Asia, and the Middle East and has designed production facilities of various sizes, ranging from small scale installations to mega-farms. Large-scale installations or mega-farms allow for mass scale production of baby leaf greens in facilities that can be built in less than 10-months and that can produce up to 1,500 MT of produce per year.
&ever has a large-scale farm in Kuwait that is currently in ramp-up phase, built in partnership with NOX Management. A second mega-farm is under construction in Singapore with support from a major competitive government grant and is expected to start operations during Q1 2022.
Small scale production facilities include an on-site Grow Box® for small retail stores and an on-site Grow Tower® for larger retail stores allowing the company to grow on-site in a local grocery store.
In addition, the company has unique growth solutions that include Dryponics® and Bestponics®, which are exclusive to &ever and expand the existing alternatives for growing leafy greens. Additional capabilities include advanced climate cells for perfect climate conditions for each product and an automated intra-farm bench movement system that significantly reduces operating expenses for high volume/short cycle growing methods, developed in partnership with German engineering firms Viessmann and Kardex Mlog, and Italy-based Modula.
Transformational Acquisition Creating a World Leader in Vertical Farming
"With Kalera’s farms in North America and &ever’s operations in Asia, the Middle East and Europe, we will jointly revolutionize the global vegetable production industry and further expand our market leadership in vertical farming,” says Daniel Malechuk, CEO of Kalera. “In addition, we see &ever's climate cell technology and their high degree of automation as excellent additions to our advanced nutrient management system, which will further increase the productivity of our production facilities."
“From the beginning, our vision has been to offer communities worldwide hyperlocal high-quality salads and herbs year-round. Together with Kalera, we have now come a big step closer to this goal,” says Dr. Henner Schwarz, CEO of &ever who will serve as Managing Director of EMEA and Asia for the combined entity. "We share very similar visions, core values, and goals and are eager to immediately begin the integration of the companies together."
“The merger is an important milestone for the global future of vertical farming. We are very much looking forward to the next steps with &ever as a new, stronger Kalera,” says Daniel Malechuk who will serve as CEO of the combined company. “This acquisition, combined with our previous acquisition of Vindara, the only seed company dedicated specifically for controlled environment agriculture, continues to complement and accelerate Kalera’s now global industry-leading position.”
The Largest Portfolio of Indoor Farming Systems
Through the combination with &ever’s existing portfolio of vertical farms, Kalera will own the largest portfolio of farming systems from small in-store or on-property farms to mega-farms, allowing Kalera to serve all market segments through a full spectrum of indoor farming systems that require low CAPEX and can deliver all products ranging from baby leaf, full head, cut leaf, or teen leaf to serve all segments and customer preferences.
Ability to Produce the Full Array of Leafy Green Products from Whole-Head to Baby Leaf
The indoor farming industry has been highly fragmented into different product segments between microgreens, baby leaf, cut leaf, teen leaf, and full head. Kalera will become the only company with capabilities to serve every segment within the leafy green industry solidifying Kalera’s position as the overall indoor farming market leader. This will provide retailers and foodservice customers with a single source to serve all their leafy green needs, a value proposition in the marketplace that no other company has been able to offer until now.
Accelerate Global Expansion
Kalera will accelerate its international rollout plan with the addition of two international facilities and a strong pipeline of opportunities especially in the Middle East and Asia. The &ever facility in Kuwait is a partnership with NOX Management, an investment arm of IFA Group, an owner of food markets, restaurant chains, retail chains, and food distributors. The &ever farm in Singapore is under construction and will launch operations by the end of Q1 2022. These two farms will become Kalera’s first international operations accelerating Kalera’s rollout schedule. Additional rapid international expansion at strategic locations throughout Asia, Middle East, and Europe, will be driven by Kalera’s and &ever’s combined business plan with an ability to offer the widest product portfolio to customers.
World-class Management Team to Join Kalera
&ever’s management team will join Kalera to strengthen Kalera’s international business development initiatives and operational capabilities. In addition, one member of &ever’s Board will join Kalera’s Board, adding to a team of world-class professionals that will help to drive the company’s future.
Technology and Partnerships are Highly Complementary
With &ever, Kalera adds grow technologies and strong German engineering partnerships. Kalera’s best-in-class hydroponic grow systems have been used to-date for growing whole-head lettuce and microgreens, whereas Dryponics® and Bestponics® technology is more flexible and productive for growing baby leaf including certain product varieties such as spinach and arugula. &ever’s technology also allow for a more effective offering of smaller in-store growing systems. These technologies can be combined to produce a wider variety of products with maximum efficiency. &ever’s partnerships with Viessmann and Kardex Mlog, and Modula add outstanding expertise in climate control and in-farm bench movement systems, respectively.
Transaction Terms
Under the terms of the agreement, &ever GmbH shareholders will receive EUR 21.6 million in cash and 27,856,081 Kalera shares at a subscription price of NOK 36.68. The consideration shares will be subject to a twelve-month lock-up after closing except for management who will be subject to a three-year lock-up.
The cash consideration will be financed through a debt facility provided by DNB or by other financing sources available to Kalera.
Kalera shareholders will own an 87% stake in the combined company, while current &ever GmbH shareholders will own 13%, on a fully-diluted basis.
By continuing to own shares of the combined company, &ever GmbH shareholders will have the opportunity to participate in the enlarged Kalera’s long-term value creation potential.
The current &ever shareholders will propose Faisal Al-Meshal as a new Kalera Board member and Dr. Klaus Bader as an observer to the Kalera Board, both to be proposed for election at a Kalera general meeting. The election is expected to take effect upon completion of the contemplated merger between Kalera and the new Luxembourg parent for the group, which has previously been announced. In the period between completion of the &ever acquisition and such merger, Faisal Al-Meshal and Dr. Klaus Bader will be invited to participate in Kalera Board meetings.
Up to 2.2 million Kalera share options will be granted to &ever management in connection with the transaction. The options will have a strike price of NOK 36 and will vest over four years with the following schedule: 0% at the end of year one, 25% at the end of year two, 25% at the end of year three, and 50% at the end of year four.
The transaction is subject to customary closing conditions, including a resolution of the Kalera general meeting to issue the consideration shares to the &ever shareholders.
It is expected that the transaction will be completed by the end of September 2021.
A presentation about the acquisition is attached here and is also available at the Kalera's website, www.kalera.com/investor.
About &ever:
&ever is a German indoor vertical farming company that combines technologies from the fields of software, mechanical engineering and agriculture. &ever has been represented on the global market since 2015 and operates a large vertical farming facility in Kuwait, in addition to in-store grow-towers in Germany. It is also currently constructing a mega-facility in Singapore. The company's focus is on building sustainable farms in cities around the world to provide more and more people with better tasting lettuce with higher nutrient content at the same time. The patented cultivation systems from &ever are easily scalable in shape and size so that indoor vertical farms of various sizes can be operated anywhere in the world, regardless of local climatic conditions. More information is available at www.and-ever.com.
About Kalera:
Kalera is an American vertical farming company based in Orlando, Florida. The company uses technology to ensure that more people around the world have access to the freshest, most nutritious, and cleanest products possible. It has spent several years optimizing plant nutrient formulas and developing an advanced automation and data acquisition system with Internet of Things, cloud, big data analytics and artificial intelligence. Kalera currently operates farms in Orlando, Florida, and Atlanta, Georgia. Kalera’s Houston, Texas farm will open soon, and the company has plans to open more farms in the US and also in both the Middle-East and Asia in the coming months. More information is available at www.kalera.com.
For more information, please contact:
Molly Antos
Phone: +1 847 848 2090
Email: kalerapr@dadascope.com
Important notice:
Matters discussed in this announcement may constitute forward-looking statements. Forward-looking statements are statements that are not historical facts and may be identified by words such as "believe", "expect", "anticipate", "strategy", "intends", "estimate", "will", "may", "continue", "should" and similar expressions. The forward-looking statements in this release are based upon various assumptions, many of which are based, in turn, upon further assumptions. Although the Company believes that these assumptions were reasonable when made, these assumptions are inherently subject to significant known and unknown risks, uncertainties, contingencies and other important factors which are difficult or impossible to predict, and are beyond their control. Actual events may differ significantly from any anticipated development due to a number of factors, including without limitation, changes in public sector investment levels, changes in the general economic, political and market conditions in the markets in which the Company operates, the Company's ability to attract, retain and motivate qualified personnel, changes in the Company's ability to engage in commercially acceptable acquisitions and strategic investments, and changes in laws and regulation and the potential impact of legal proceedings and actions. Such risks, uncertainties, contingencies and other important factors could cause actual events to differ materially from the expectations expressed or implied in this release by such forward-looking statements. The Company does not make any guarantee that the assumptions underlying the forward-looking statements in this announcement are free from errors nor does it accept any responsibility for the future accuracy of the opinions expressed in this announcement or any obligation to update or revise the statements in this announcement to reflect subsequent events. You should not place undue reliance on the forward-looking statements in this announcement.
The information, opinions and forward-looking statements contained in this announcement speak only as at its date, and are subject to change without notice. The Company does not undertake any obligation to review, update, confirm, or to release publicly any revisions to any forward-looking statements to reflect events that occur or circumstances that arise in relation to the content of this announcement.
Lead Photo: &ever is a German indoor vertical farming company that combines technologies from the fields of software, mechanical engineering and agriculture
Kalera CEO Makes an Impact on the Future of Farming
When he enrolled in North Carolina State University’s College of Management, Daniel Malechuk (’03) didn’t picture himself working in the food industry, but he couldn’t be more proud today of his role in the future of sustainable farming
By Lea Hart
August 10, 2021
When he enrolled in North Carolina State University’s College of Management, Daniel Malechuk (’03) didn’t picture himself working in the food industry, but he couldn’t be more proud today of his role in the future of sustainable farming.
Malechuk was named CEO of Kalera in 2019. Based in Orlando, Florida, Kalera grows leaf plants – mainly lettuce – in a vertical farming system inside clean room facilities. That means no pesticides or genetic modification, and the process uses five percent of the water that traditional farms use.
A video on Kalera’s website notes that 80 percent of land suitable for farming in the U.S. is already in use. Due to the growing population, it’s expected that the U.S. will need to produce 70 percent more food by 2050.
What’s more, the video goes on to point out that 95 percent of U.S. produce is grown in Arizona and California, and can take weeks to reach the consumer. That depletes vitamins, increases the risk of spoiling and the risk of contamination. Kalera’s approach localizes farming, bringing the product closer to the community.
From dreams of working in the sky to a career working for the planet
Malechuk enrolled at NC State with dreams of being an aviator. He was the recipient of a prestigious Park Scholarship and began a major in aerospace engineering. However, he enrolled prior to the Sept. 11, 2001, terrorist attacks and felt, post 9-11, that an aviation career didn’t look as promising.
At the same time, a mentor of his in the College of Management (now Poole College of Management), Professor Art Padilla, regularly encouraged him to consider a business degree instead. When he made the switch, Malechuk said he knew he’d made the right choice.
“I fell in love with the business degree,” he said.
Upon graduation, he went to work for Aldi USA as a district manager and quickly climbed the ladder to become director of corporate buying. While Malechuk didn’t plan to work in the food industry, he said he was excited by the management profile and career opportunities that it presented to him at such a young age.
His next role took him around the globe as vice president at Keysource Foods, a seafood company. He saw shrimp harvested in Vietnam and traveled on mussel boats off the coast of Ireland.
What’s so unique about a business degree and what I love about it is, it can open so many doors; it is one of the broader degrees
“What’s so unique about a business degree and what I love about it is, it can open so many doors; it is one of the broader degrees,” Malechuk said. “I don’t think I could have appreciated how true that is.”
During that time, Malechuk and his family had the opportunity to live in Apex, NC and he never forgot the Wolfpack, enjoying season tickets to athletic events.
He was recruited from there to run the retail division for Shamrock Foods, and his family moved to Arizona. During his time there, Malechuk pursued his executive MBA from the University of Arizona.
When the opportunity at Kalera presented itself, Malechuk admits he had never heard of vertical farming before, but he jumped at the opportunity for many reasons.
“This was a really exciting opportunity to, one, do something so cutting-edge, and two, to have that first opportunity to be CEO,” he said.
While his title is CEO, Malechuk calls himself something else most days.
“Right now, I call myself a farmer,” he says with a laugh.
But it’s fine with Malechuk, who ties it back to NC State’s roots as an agriculture school.
“I’m excited about feeding people,” he said. “It’s a noble cause and a great reason to get up in the morning.”
Demand and growth mean opportunity at Kalera
It’s also a great time to be leading Kalera. The company has a fascinating history. Its founders had initially worked on several different projects, including being a part of a sustainable city located in Florida, before pivoting to focus on indoor farming.
Daniel Malechuk in the Kalera facilities
“Historically, produce is farmed outside,” Malechuk said. “It’s susceptible to weather, fires, contaminants and more – it’s been a challenge.”
As sophisticated as the supply chain has become, he points out that there is also the issue of transporting and delivering it.
By growing produce locally, Kalera changes that business model. The company is currently expanding rapidly with facilities up and running in Orlando, FL and Atlanta, GA , where they have produced 12 times more leafy greens than the entire state of Georgia produced a year earlier. They’re expanding to Houston, Seattle and Honolulu to name just a few other locations, and recently took the company public on the European stock exchange, with plans for a NASDAQ IPO in the U.S. in the future.
I can’t imagine not having exposure and access to culture, people, learning and new experiences. I don’t know that I could have appreciated how much a business degree could give me those opportunities.
It’s been an opportunity for Malechuk professionally in more ways than one. The company was very small when he joined, and he’s had the opportunity to build a team and a culture from the ground up.
“It really has challenged me in a lot of ways,” he said. “It’s been a lot of neat and unique opportunities.”
Though it’s a very different path than the one he envisioned as a high school graduate enrolling at NC State, it fits Malechuk’s personality. As someone who has always had a sense of wanderlust, his various roles have taken him through all 50 states and 67 countries. While it’s not as a pilot, it still provides the same sense of satisfaction.
“I can’t imagine not having exposure and access to culture, people, learning and new experiences,” he said. “I don’t know that I could have appreciated how much a business degree could give me those opportunities.”
Tying it all back to NC State
Malechuk says his degree from NC State has been critical to his current success. He concentrated in marketing in his undergraduate, and said he’s applied everything he learned at NC State at some point during his career. And that includes experiences outside his degree framework as well.
“I don’t know that there was anybody that enjoyed their time at NC State more than I did,” he said.
He took extra Physical Education courses just because he enjoyed them, including scuba diving, and even put that to use during a business trip.
Malechuk was active with the Park Scholars. He calls that experience life-changing, noting the doors it opened and the opportunities it provided for mentorship and relationship-building. He’s hired and hopes to continue to hire NC State students and Park Scholars at Kalera as well.
He was president of the Bragaw Hall Council, served as a resident advisor, was active in the Catholic Campus Ministry, and participated in intramural sports, to name a few other activities.
“Through all of those things, the friendships that you develop and the maturing that you go through – that’s equally as important as the degree,” he said. “It helped me understand how to multi-task and become a dynamic leader in multiple different avenues.”
Malechuk and his wife of 15 years live in Florida currently with their four children, three girls and a boy.
While he is clearly invested in his career, Malechuk is also a big believer in balance and works as a team with his wife in that respect. He strives for balance among what he calls “the five F’s:” faith, family, friends, fitness and finances, saying he always tries to be cognizant that putting too much into one takes away from the others.
He and his family are active in their Catholic Church, and Malechuk enjoys fishing and boating. He got certified in Scuba Diving through NC State, still loves to travel and loves being active.
And, though he didn’t become a career aviator, he has his pilot’s license and enjoys flying.
While he’s committed to Kalera right now, Malechuk hopes things may come full circle one day in the future.
“I would love, perhaps someday, to become a professor in the business school at NC State,” he said. “I’d like to have that same experience of mentoring and leading students that I received, and to replicate what I had from some of the great professors there.”
Lead Photo: Daniel Malechuk, class of '03 graduate from Poole College
Genie Scissors Assist ‘Europe’s Largest’ Vertical Farm
Farming company Nordic Harvest has purchased a range of electric scissor lifts from Genie, for the construction and daily operations of its new vertical farming facility in Denmark.
By Leila Steed
August 10, 2021
Farming company Nordic Harvest has purchased a range of electric scissor lifts from Genie, for the construction and daily operations of its new vertical farming facility in Denmark.
A specialist in hydroponic cultivation, the company grows a variety of vegetables and herbs for wholesale in a 14-storey vertical farm near Copenhagen.
It added nine Genie scissors to its operations, specifically the GS-2632 and GS-2646. Flemming Dyring, Nordic Harvest’s sales director, said, “The scissor lifts had to provide a high level of stability for safe work. In addition, their handling had to be as easy as possible, including intuitive controls and the possibility of instant troubleshooting, all of which met our requirements.”
Five Genie GS-2632 electric scissor lifts helped build and set up the internal structures of its facility, which provides an area of 4,950m2 of growing space, and is said to be the largest indoor of its kind in Europe.
With a maximum working height of 9.8m and a platform capacity of 227kg, the GS-2632 slab scissors were used to install the farm’s cultivation trays at heights of up to 9m.
Genie GS-2646 electric scissor lift has a maximum working height of 9m and platform capacity of 454kg.
Due to the vertical nature of the sustainable farming technique, Nordic Harvest then added four Genie GS-2646 electric scissor lifts with platform capacities of 454kg.
The 9m models are now being used by the company’s staff to access all 14 storeys of cultivation trays, enabling employees to check the healthy growth of the plants and herbs before harvesting.
Nordic Harvest purchased the new scissor lifts through Genie’s authorised distributor Jøma Lift Teknik.
“For our work, a minimum working height of 8.80m (28ft 9in), a comfortable working space and high manoeuvrability in small spaces were imperatives”, said Dyring.
“Before making our decision, we took the opinion of our Taiwanese partners who recommended Genie scissor lifts to us for their design quality and proven reliability to effectively complete our assigned tasks: construction of the cultivation structures and control of the seedings and harvest.”
Lead Photo: Genie GS-2646 electric scissor lift at the Nordic Harvest vertical farm in Denmark.
Vertical Farming and the Future of Automation in Agriculture
Vertical farming is by no means a new idea. However, recent supply chain disruptions coupled with the falling price of produce, is opening new doors for a farming method previously deemed unviable by many.
August 10, 2021
Vertical farming is by no means a new idea. However, recent supply chain disruptions coupled with the falling price of produce, is opening new doors for a farming method previously deemed unviable by many. Here, John Young, APAC country manager at automation parts supplier EU Automation, highlights the renewed interest in vertical farming among a new generation of farmers, and explores the advantages it offers in tackling some of the biggest challenges facing the sector.
Turn the clock back approximately 1000 years, and less than four per cent of the world's habitable land was used for farming — that is the equivalent of four million square kilometres. Today, farmland takes up more than half of the world's habitable land, which equates to a landmass larger than South America.
Our World in Data reports the alarming facts associated with industrialized livestock farming, involving climate change, extinction of species, widespread destruction of habitat, and 80 per cent of cropland grown to feed livestock. With the population of the Asia Pacific region expected to reach 5 billion by 2050, the responsibility to supply food to an ever-growing population is becoming difficult.
A new generation of farmers are rising to the sustainability challenge. This agricultural revolution presents the transition from traditional farming to futuristic high-tech artificial intelligence (AI) and robotics. Whether it's weed-killing robots, harvesting and picking robots, or autonomous tractors, the farming landscape is evolving. In this age of robotic farming, producers believe incorporating automation and data will enable farmers to produce more, while damaging the environment less.
One major process change that is currently on the rise is the shift to vertical farming. Currently, 16.55 million square feet (sq ft) of indoor farms operate across the globe. However, the State of Indoor Farming report suggests this figure will increase to 22 million sq ft by 2022. The demand is high, and the AI journey is only getting started.
Why are farmers suddenly interested in vertical farming?
Vertical farming is the practice of producing food in vertically stacked layers. The climate-controlled indoor farms contain rows of plants situated next to each other, growing vertically, and hanging from the ceiling. Robotics help manoeuvre the products around, and AI can monitor the different parameters that are required for the crops to grow, such as the levels of water, temperature, and light.
Indoor agriculture is at an exciting point in its development. Key technologies used in farming systems today range from perception technologies which use cameras and sensors to detect and monitor various factors of the lifecycle. AI processes the data from sensors and provides solutions, while automated and autonomous mechatronics that use robotics and automated machines collect products when ready to dispatch to the market and recover the crops from ailments during the growing cycle.
Right now, the focus is to take vertical farming to the next level by developing smart robots which can increase precision and productivity, while minimizing environmental impact and risk. Agriculture, one of humankind’s oldest inventions, is merging with the latest technology, and farmers will soon be looking to pair with a reliable automation parts supplier to make the step up to vertical farming.
Vertical farming offers a unique set of advantages. Farmers understand there are many urgent and practical reasons to grow upwards rather than outwards. This farming method has huge potential for sustainability and food security, while protecting the environment, economy, and ecosystems.
In addition, the inclusion of AI and robotics ensures high-quality growth of products all year round, while preserving water, nutrients, and land consumption by 95 per cent. The controlled process of indoor farming with the help of AI and robotics also protects crops against pest invasions, and ensures they are well insulated — this is an aspect field farming cannot guarantee since it requires amenable weather conditions and labour.
Vertical farms can operate anywhere with no geographical constraints and are not subject to the limitations presented in outdoor farming, such as extreme conditions. This not only protects the crops, but also provides a safer working environment for labourers. What’s more, labour costs can be significantly reduced due to the automated indoor growing systems; thus, there is no longer a need for manual labour all year long.
In addition, energy consumption can be drastically reduced in vertical farming by implementing LED lighting to mimic the sun as a light source. A minor change like this can limit heat waste while increasing energy efficiency and cutting energy costs. Not only can LED lighting be used as an alternative, but renewable energy generated from wind turbines can be paired with vertical farming to ensure 100 per cent of its energy is produced from renewable sources. It is a win-win situation.
How will it boost the economy?
This sector is expecting a huge boom in investment and interest and manufacturers, suppliers and retailers are therefore preparing for this shift through early adoption. In the past, vertical farming was viewed as theoretical, but now the vertical farming market in the APAC region is expected to grow at a compound annual growth rate (CAGR) of 29 percent, rising from its current value of $0.78 billion to $2.77 billion by 2026. This is largely due to the advancement in technology such as sensors and smart energy systems that have improved the efficiency of growing products.
Although vertical farms will not replace traditional ways of farming, they hold great potential to revamp the future of agriculture in the APAC region by pushing towards a sustainable, environmentally conscious, tech savvy, economically rational, and health-sensitive world.
Source and Photo Courtesy of Agritech Tomorrow
Vertical Farming: Turning Deserts Into Fresh Food Hubs
Deserts and arid lands are commonly perceived as worthless. Because of this image of the world’s drylands, agricultural investments and development initiatives pass these regions by. Moreover, with the new NASA food challenge, it seems like AgriTech enthusiasts would rather attempt to cultivate plants in space than in desert environments on their native planet.
August 10, 2021
Vertical farming technologies allow for collecting the humidity produced by plants. With recirculating and recycling techniques, hydroponic and aquaponic systems can reuse 98% of water, which makes vertical farms feasible in deserts.
Deserts and arid lands are commonly perceived as worthless. Because of this image of the world’s drylands, agricultural investments and development initiatives pass these regions by. Moreover, with the new NASA food challenge, it seems like AgriTech enthusiasts would rather attempt to cultivate plants in space than in desert environments on their native planet.
Taking up 41% of our planet’s landmass, arid zones have always been seen as marginal for agriculture. But thanks to technological advancements, they can produce fresh food and compete on the global market. How? By adopting next-generation technologies like vertical farming.
How vertical farming enables agriculture in deserts
The most fascinating thing about vertical farming technology is that it brings food production to regions with no arable land. Crops grow indoors, stacked in layers under LED lights. Most vertical farms rely on hydroponic, aeroponic, or aquaponic methods, as they don’t require soil. Anything “hydro” and “aqua” may seem inappropriate for arid lands, but these methods are extremely water efficient.
And here’s what thrills me a lot: While most barren lands suffer from aridity, agriculturally developed regions waste tons of water. Even though modern smart irrigation systems do help reduce water use on traditional farms, water is still lost because of wind and evaporation. On the contrary, vertical farming technologies allow for collecting the humidity produced by plants. With recirculating and recycling techniques, hydroponic and aquaponic systems can reuse 98% of water, which makes vertical farms feasible in deserts.
Vertical farms ensure plants have exactly what they need
The ultimate goal of vertical farming technology is to get the highest possible yield by precisely meeting plants’ needs. One can believe me or not, but it works like magic.
After the vertical farming facility is built and all equipment is installed, a complex network of IoT and analog sensors comes to life. They measure gases and nutrients, humidity, light, and temperature inside and outside the farm. Additionally, the monitoring system takes photos and videos of plant growth. Then, all this data is transferred to secure cloud storage via edge gateways.
This provides a huge volume of raw data that can be integrated into AI-based software and analytics platforms. Built-in machine learning algorithms can match plant images against a huge database and learn to recognize plant types as well as deviations in their growth. The analytical algorithms can process plants’ growth data and correlate it with microclimate measurements to find the perfect combination of environmental factors for particular crops.
The final flourish is data visualization. User-friendly dashboards present calculations, analytics, and prediction results in meaningful histograms and neat reports. Having vertical farming software installed on any device, owners can get real-time insights into farm health and make data-driven decisions.
Basically, a vertical farm is a premium luxury ultra-all-inclusive spa resort for plants.
The vertical farming market has huge potential
An ever-changing climate along with the depletion of soil nutrients and groundwater have accelerated the adoption of vertical farming technology. The coronavirus pandemic has also contributed. The risk of supply chain disruptions has underscored the need to locate vertical farms near distribution routes and intended markets.
With many drivers igniting the industry, the global vertical farming market will reach USD 11.71 billion by 2027, growing at a CAGR of 20.1% according to Emergen Research. But we’re only at the advent of vertical farming in terms of technology. Innovative advancements are expected to reduce costs and improve the efficiency of plant growth in vertical farms, giving us high hopes for the future.
Desert reality: vertical farming or nothing
Some skeptics may consider vertical farming advantages controversial. But with temperatures reaching +40 degrees Celsius (over 100 degrees Fahrenheit), just a few days of rain a year, and barren sands, deserts don’t seem like suitable places for any other agricultural practices. In addition, climate change promises to make these lands even drier, hotter, and less valuable. Being land-agnostic and capable of conserving water, vertical farming is a reasonable option for arid lands. This ingenious method of producing food in deserts might be a springboard to economic development of arid regions.
Boosts the local economy
Local economies have attracted a lot of attention recently. And guess what I consider to be a remarkable contribution to developing local economies? Right, vertical farms near desert cities. The more often and the faster a dollar circulates in a region, the more income it creates. Studies also show that the most prosperous communities gain and sustain their wealth because they have the highest percentage of jobs in local businesses. Such communities still engage in global trade, but they import only things they can’t supply themselves.
Reinforces food security
The coronavirus pandemic has spotlighted local food production, making it more of a necessity than a luxury. Countries that heavily rely on food imports are now striving to achieve food security and resilience more than ever. And the risk of food supply chain disruptions is less imminent with several vertical farms near megalopolises. Because indoor environments are independent of outside weather conditions, vertical farms ensure reliable harvests to meet delivery schedules and supply contracts.
Decreases prices for fresh food
Besides ending dependence on imported food, vertical farming in close proximity to cities lowers the cost of products. Since food prices are linked to oil prices, delivery distance is an influential factor in food costs. The shorter the distance food travels, the less it costs. Additionally, local produce is fresher, as it isn’t stored in fridges for long during delivery. On top of that, vertically farmed crops are healthier than field-grown crops and are naturally flavorful, as strict biosecurity procedures in indoor farms eliminate plant diseases and the need for pesticides.
Creates new jobs
Among other vertical farming advantages are the job opportunities the technology provides. Yes, an indoor farm doesn’t require much manual labor due to automated growing systems and robotics. Nevertheless, it creates a lot of new jobs in farm construction and management, plant cultivation, technology development and support, distribution control, and personnel management.
Uses energy sustainably
Although a 30-story vertical farm needs 26 million kWh of electricity, it can generate 56 million kWh through biogas digesters and solar panels. The excess energy can be transferred back to the grid and bring additional income.
Given the technical opportunities, market potential, and benefits for communities, I struggle to find a rational explanation as to why large desert areas still lie unused. Fortunately, some early adopters have already recognized the potential of arid lands.
The challengers who have already succeeded
However challenging the idea of growing crops in hostile climates may seem, some daring companies are already leveraging high-tech techniques of vertical agriculture and running successful businesses, boosting food production in their countries.
The Al-Badia market garden farm is among these pioneers. The daily harvest of the Middle East’s first commercial vertical farm is two hundred boxes of greens, including radishes, kale, mustard, basil, and arugula. The multi-story setup is on an 800-square-meter plot of land in one of Dubai’s main industrial areas. Al-Badia serves nearly 70 local caterers and restaurants, providing fresh and pesticide-free products that wouldn’t be available otherwise.
The driest state in the USA, Nevada, has become home to a 20,000-square-meter hydroponic vertical farm built by Oasis Biotech. Besides catering to the needs of the Las Vegas restaurant industry, the company has created its first consumer-facing brand, which is currently sold through a local distributor. While most US produce travels between 1,500 and 2,500 miles before reaching the consumer, Oasis Biotech ensures its goods are delivered within an average of four miles and go from harvest to plate within 36 hours.
In Australia — a country that is 53% deserts and drylands by landmass —vertical farming technology is also being adopted. Stacked Farm’s two locations (200 and 4000 square meters) focus on salad greens, leafy vegetables, and livestock feed. But what’s more exciting about these farms is that they’re fully automated, from planting the seeds to harvesting and packaging the produce. Nevertheless, Stacked Farm doesn’t intend to take work away from farmers but rather to support farming communities that are suffering through drought or during off seasons.
Deserts are no longer deadlands
Vertical farming technology is certainly a game changer for regions with severely hot climates. Once a dryland gets a vertical farm, it stops being a deadland and becomes an advanced hub of fresh food. Vertical farming pioneers will be remembered as the kick-starters of thriving desert economies. The first to build a vertical farm in a desert will most likely be the first to start getting profits from desert farming and eventually become a frontrunner in the industry.
Source: Agritech Tomorrow
A Manufacturer and a Food Caterer Among New Players Feeding Singapore’s Urban Farming Boom
In a small room tucked away on the second floor of a precision engineering factory in Tuas, pots of kale and lettuce stacked in vertical racks grow under the glow of pink-purple lights.
August 10, 2021
SINGAPORE: In a small room tucked away on the second floor of a precision engineering factory in Tuas, pots of kale and lettuce stacked in vertical racks grow under the glow of pink-purple lights.
These light-emitting diode (LED) lights have been designed to shine at a customised spectrum that will help crops grow better. Smart sensors also keep tabs on temperature and humidity in the room, while a special water treatment system reduces bacteria growth.
In here, the goal is to find the best way to farm vegetables indoors, all with the use of technology.
“You can control everything, even how much nutrients or water is being used for each plant,” said Mr Nelson Lim, co-founder of I.F.F.I, which stands for Indoor Farm Factory Innovation.
“We want to bring indoor farming into something more precise, where you calculate the least input for the best output. That is precision farming,” he told CNA.
Mr Lim is also the chief executive of precision engineering firm TranZplus Engineering, which is the parent company of I.F.F.I. TranZplus’ two-storey office in Tuas now houses both a manufacturing facility for semiconductor components and a farming showroom.
“A lot of people ask me: ‘Nelson, are you crazy? You’re in engineering, why suddenly do farming?’ Actually, the two are not unrelated. We can put our engineering skills to good use in indoor farming,” Mr Lim said, while demonstrating the farming racks that can be adjusted according to height and size.
Robotics is another expertise that the company has incorporated into its farming solutions to not just improve the yield and quality of crops, but also workflow efficiencies.
For instance, automated machines that can perform seeding, transplanting, potting and harvesting tasks will be put to work at I.F.F.I’s mega indoor farm when ready at the end of this year.
(Left to right) I.F.F.I's general manager Veronica Lee, chief operating officer Kelvin Ng and co-founder Nelson Lim. (Photo: Tang See Kit)
SEEDING A DIVERSIFICATION
TranZplus’ venture into agriculture was first seeded in 2016 when it became one of the vendors for Panasonic’s indoor farm in Singapore.
“Initially, they just wanted to have a rack. Then we thought why not have racks that can be customised, why not put in an irrigation system and other types of automation?” Mr Lim recalled. “We worked out a prototype and they were impressed.”
The company kept on with research and development after that, while being involved in setting up three other small-scale farms. In 2019, it decided it had gained enough experience to give it a shot.
Mr Lim said the decision to venture into indoor farming was driven by “strong business potential”, partly on the back of Singapore’s “30 by 30” goal to produce 30 per cent of the country's nutritional needs locally by 2030.
The COVID-19 pandemic has accentuated the potential, with global disruptions to the harvesting, shipping and sale of food making it even more important for the country to have its own resources. Indoor farms can be the solution, he added.
Last September, I.F.F.I. became one of the nine urban farms to secure grants totalling S$39.4 million from the Singapore Food Agency.
Its 38,000 sq ft indoor farm, which remains under development at the JTC Space @ Tuas, will be using a soil-based cultivation method that allows more vegetable varieties to be planted.
When operational, the mega farm will be able to produce 800 to 1,000kg of vegetables, like nai bai and spinach, per day, said Mr Lim.
Another new player on the field is food caterer Kitchen Haus, which co-founded “farm-to-table” concept brand Frux Earth a few months ago.
With its core business facing a slow recovery amid the pandemic, the company has been diversifying actively in search of new opportunities over the past year.
Agriculture is “not unrelated territory”, chief executive Patrick Chan said. “It’s still part of the food ecosystem so when the opportunity came, I agreed instantly.”
It teamed up with home-grown urban farming company Metro Farm for the new venture. With the latter’s expertise, the farms under Frux Earth – three sites spanning 60,000 sq ft – are powered by an aquaponics system that converts fish waste into nutrients for the vegetables.
For instance, its 12,000 sq ft rooftop farm atop an industrial building in Bendemeer has eight fish tanks with red tilapia and jade perch. These fishes were chosen for their hardiness and ability “to produce more waste”, said Metro Farm’s director Chris Toh.
“We have a filter to separate the fish waste, which is then broken down by bacteria. Our system will then keep the nutrients flowing to the vegetables 24/7,” said the farm’s other director Brandon Toh, who added that the system is “self-sustainable” and keeps costs low.
The Bendemeer farm, with its 720 vertical plant towers, can harvest more than 30,000 stalks of vegetables, including purple lettuce and kale, a month. The fish will also be sold once they reach table size.
Mr Chan said: “This is a breath of fresh air for us and we pivoted because we want to jump on the trend of food sustainability.
“I think Metro Farm sees the value in us having the know-how of food preparing, catering and retail. And we partner them because it’s not easy to set up a farm and they are the experts.”
Metro Farm’s director Chris Toh (left) and Kitchen Haus' chief executive officer Patrick Chan (right) joined hands to form a new urban farming company Frux Earth. (Photo: Tang See Kit)
OPPORTUNITIES AND CHALLENGES
Metro Farm, which started its first farm in Kranji almost nine years ago, noted that the local agriculture sector has become “much more vibrant”.
While the presence of new and bigger players means greater competition, the increased attention has also made it easier for businesses to secure farming sites in land-scarce Singapore, including vacant rooftops on both public and private buildings.
“In the past, we have to explain what is a rooftop farm and what we are doing but now, more landlords are opening up to the idea,” said Mr Brandon Toh, although he noted that not all rooftops are suitable given the need to take into consideration the additional loads of farming.
Frux Earth has plans to open three more urban farms over the next few months.
Its “farm-to-table” menu is in the works as it ramps up its crop production, while it is also gauging the interest for a weekly vegetable subscription service, said Mr Chan.
These “culture boxes”, as they are called, will be filled with 1 to 2kg worth of freshly harvested organic vegetables and delivered to the doorsteps of customers every week. For now, it has started supplying a few restaurants located near its farm at the Marina Country Club.
Frux Earth is planning to launch a weekly vegetable box subscription service. (Photo: Frux Earth)
Over at I.F.F.I, the protracted pandemic and its impact on labour and supplies of raw materials have caused some delays at its mega indoor farm which was initially scheduled to open in the middle of this year.
“We are catching up and hopefully we can have everything ready soon,” said Mr Lim. “Certainly, costs have also gone up with the increase in raw material prices, but we are managing that."
Meanwhile, the company is working on opening an “indoor farm pro-shop”.
“There will be a mini-farm set up for visitors to understand and raise awareness about indoor farming,” said I.F.F.I chief operating officer Kelvin Ng.
“If they like what they see and want to start their home cultivation system, they will also be able to purchase everything they need at the shop. We will even have consultants ready to guide you. It will be a one-stop shop about indoor farming.”
I.F.F.I. also sees opportunities beyond Singapore where they can serve as consultants or designers to those looking to set up indoor farms. For instance, in Russia where crop production is a challenge due to the cold climate.
Its technologies can also be deployed in “bite sizes” even in traditional food-producing countries as solutions to specific problems, such as water pollution.
Mr Ng said: “There are many opportunities emerging in the space of indoor farming, and we want to be bold and seize them.”
Lead Photo: I.F.F.I, an affiliate of precision engineering firm TranZplus Engineering, is looking to open its mega indoor farm in Tuas by the end of this year. (Photo: Tang See Kit)
US (CO): Container Farm at Historic Ranch to Grow Restaurant's Produce
A historic ranch in the mountains of Colorado is using a high-tech container farm to broaden its focus on farm-to-table options for guests.
August 10, 2021
A historic ranch in the mountains of Colorado is using a high-tech container farm to broaden its focus on farm-to-table options for guests.
Having been in business for 102 years, C Lazy U Ranch in Granby has a storied reputation as a luxurious, year-round mountain getaway with 8,500 acres of land for a multitude of activities. The ranch’s culinary program will soon be complemented by fresh leafy greens and herbs. The produce will be grown on-site in an automated container farm, built by Colorado-based FarmBox Foods.
“We saw an opportunity with FarmBox Foods to essentially have a year-round farm-to-table option,” said Paul Klees, assistant general manager of C Lazy U Ranch. The container farm is scheduled for delivery in mid-August.
Container purposes
Guests and members will have the opportunity to tour the farm. C Lazy U Ranch is planning to grow lettuce and culinary herbs inside the 320-square-foot farm. The sensor-based technology and insulation in the container farm are superior to greenhouses, which are susceptible to the bitter cold of the Colorado Rockies, Klees said.
The container farm is slated to be the next hands-on attraction at the ranch, where guests and members could have the opportunity to harvest their own veggies and prepare meals with a chef. “It’s interactive, it’s educational, and it builds into our vision and mission statement of having a sustainable model,” Klees said.
Purchasing a container farm is “just another step in the ranch’s continuing effort to create authentic farm-to-table dining,” Klees said.
“There are economic aspects to it because we’re shipping in all of the food, including produce,” he said. “When guests eat at our restaurants, we want the meals to resonate with them, and what people are looking for is healthy organic fresh produce.”
Horses get their share
The 200 horses on the property already benefit from C Lazy U’s sustainable approach to food sourcing; most of the hay they eat is grown on the ranch. C Lazy U is also supplied with water by its own spring and operates its own wastewater facilities.
The exterior of the container farm will be finished with a rustic scheme so it will easily blend in with its natural surroundings, which include a creek and historic structures.
For more information:
FarmBox Foods
www.farmboxfoods.com
$160 Million Funding Round Secured To Expand Operations
80 Acres Farms, a vertical farming producer, has secured $160 million in additional funding in a round led by General Atlantic and joined by Siemens Financial Services, the U.S. financing arm of tech company Siemens.
August 10, 2021
80 Acres Farms, a vertical farming producer, has secured $160 million in additional funding in a round led by General Atlantic and joined by Siemens Financial Services, the U.S. financing arm of tech company Siemens.
The company intends to use the capital for continued expansion and product development, building from its current footprint of vertical farms that yield a diverse offering of high-quality produce.
Thriving for impact
Mike Zelkind, CEO of 80 Acres Farms, said: "We are proud of what our team has been able to accomplish and enthusiastic about the road ahead. We are also honored to be supported by such a high-caliber group of strategic investors who are enabling us to continue to lead this evolving and fast-growing industry." Mike said the investment is a quantum leap for the business to build more farms both nationally and globally.
"80 Acres Farms is building an incredibly exciting vertical farming business that provides high-quality produce through innovative practices," noted Shaw Joseph, Managing Director of General Atlantic.
Shaw said that with global food consumption increasing and growing threats impacting supply chains and food security, there is a pressing need for healthy, fresh and local foods that are grown in more sustainable and cost-effective ways. He added, "We look forward to working closely with Mike, Tisha and the broader 80 Acres Farms' team as they scale."
"The new investment positions the company as the leading proven and profitable technology provider prepared for rapid
expansion," said Tisha Livingston, CEO of Infinite Acres, and Co-founder of 80 Acres Farms. "In addition, this enables 80 Acres to focus on their operational expertise and deep research and development capabilities beyond leafy greens."
Combining capital and tech know-how
Jason Thompson, Vice President of Sustainability and Growth Equity at Siemens Financial Services, said, "We are committed to helping scale sustainable vertical farming technology. 80 Acres has demonstrated their ability to build and operate profitable farms."
According to Jason, Siemens is enthusiastic about the opportunity to support its global expansion with both its capital and technical know-how. Including, their recently established Center of Competence dedicated to supporting companies in realizing their digital transformation.
"We are excited to be partnering with General Atlantic and Siemens to provide growth capital and support to Mike, Tisha and the entire 80 Acres team to help scale their operations within existing and new markets," said Kayode Akinola, Head of Private Equity Directs at Blue Earth Capital.
New board member
As part of this funding round, Shaw Joseph will join the 80 Acres Farms board. Eli Aheto, former 80 Acres Farms board member, led BeyondNetZero's contributions to this round. He noted, "I am pleased to be able to continue and grow my support of 80 Acres with this contribution from the BeyondNetZero team. 80 Acres has proven a farm design that is poised to reduce food miles, food waste and the
resulting in negative carbon emissions that exist within our food supply chain."
For more information:
80 Acres Farms
Rebecca Haders, VP Marketing
rebecca.haders@eafarms.com
www.80acresfarms.com
Lead Photo: Mike Zelkind and Tisha Livingston
Vertical Farm Specified Seeds With Open-Source Licensing
When thinking of vertical farming, we usually think of rows of lettuce or herbs all neatly placed under purple LED lights. However, if it were to Rosario Iacono, founder of Kasveista, vertical farming should be all but limited to leafy greens. Kasveista’s mission is to expand vertical farms with all other crops through extensive research.
By Rebekka Boekhout
August 10, 2021
When thinking of vertical farming, we usually think of rows of lettuce or herbs all neatly placed under purple LED lights. However, if it were to Rosario Iacono, founder of Kasveista, vertical farming should be all but limited to leafy greens. Kasveista’s mission is to expand vertical farms with all other crops through extensive research.
“For me as an agronomist, seeds have always been the most fascinating stage of a plant’s life. Without seeds there is no agriculture,” Rosario explains. “When I became interested in vertical farming, I was shocked to find out that the whole sector relies on seeds developed for open-field or greenhouse environments. Developing seeds specifically for the vertical farming sector can strongly increase the sector’s profitability. After all, the range of benefits for vertical farming will be obtained only if it produces the same range of food that is now produced in traditional agriculture.”
Read the rest of the article here
Things Are Looking Up For New Vertical Farming Students
Building work on the £500,000 facility is expected to begin next year with the £200,000 grant from the Scottish Government helping key research to be carried out in this growing area of plant and crop science – and being the first such facility to be directly connected with an educational establishment, it will also give students hands-on experience of this new field of technology.
By The Newsroom
August 10, 2021
Building work on the £500,000 facility is expected to begin next year with the £200,000 grant from the Scottish Government helping key research to be carried out in this growing area of plant and crop science – and being the first such facility to be directly connected with an educational establishment, it will also give students hands-on experience of this new field of technology.
The new building and associated technologies will focus on growing nutrient-dense fruit and vegetables with a specific focus on human health qualities. The site will also analyse crop yield and growth rates along with all resource inputs - allowing the true overall carbon footprint of the latest in growing techniques to be compared with more traditional production systems.
Vertical farming systems focus on controlling all inputs into the growing system, with light levels and frequencies carefully controlled along with temperature and CO2 levels on top of water provision and all other nutrients and substrates.
The SRUC said the facility would operate on renewable energy sources from the national grid, with new battery technology being used to help manage peaks in energy demand.
“With only a handful of commercial vertical farms in Scotland, the facility will be important for demonstration and knowledge exchange with farmers, growers and small businesses, giving vital support and promoting innovation,” said Professor Wayne Powell, Principal and Chief Executive of SRUC.
“One of the most critical challenges we face is how to feed a growing global population,” he continued.
“We have been teaching farmers for generations but, as the population increases, it is important that we look at growing different, more nutritious crops to support healthy diets and local access to food.”
But he said that the vertical farming unit would also be a valuable asset to students studying at the site, while also providing important data which would help optimise and promote innovation into what was becoming a fast-expanding area of the industry.
The Scottish Government’s cabinet secretary for Rural Affairs and Islands, Mairi Gougeon said:
“As we look to produce more fruits and vegetables locally, vertical farming could provide us with a way to make better use of our land. It’s an exciting and innovative field that could bring us real benefits and it is important that we have the skills in Scotland to take advantage of this technology.
She said that by supporting the industry at an early stage, policy makers would be better able to assess the benefits and help to focus on long-term strategy.
“We will also be reaching out to the wider industry to explore in further detail the opportunities low-carbon vertical farming offers. We will work together to establish the future of vertical farming in Scotland.”
The project will be going out to tender in the coming weeks.
AeroFarms Is Trying To Cultivate The Future of Vertical Farming
2021 is turning out to be quite the year for Newark, New Jersey-based vertical farming pioneer AeroFarms.
By Jesse Klein
August 10, 2021
2021 is turning out to be quite the year for Newark, New Jersey-based vertical farming pioneer AeroFarms.
The biggest news is that the company is going public. In March, it announced a merger with a blank-check firm, Spring Valley Acquisition Corp., that will see the company traded publicly later this year under the ticker ARFM. Also in March, AeroFarms announced a research and development partnership with Hortifrut to push vertical farming technology into the lucrative $39.8 billion berry market, reducing its dependency on revenue from leafy greens. And in July, AeroFarms rebranded its Dream Greens produce line to AeroFarms to capitalize on its name recognition. At the same time, it expanded into five new leafy green products: Baby Bok Choy, The New Spinach, Micro Arugula, Micro Broccoli, Micro Kale and Micro Rainbow Mix. And in August, AeroFarms announced another partnership with Nokia Bell Labs, the New Jersey-based historic scientific research firm, to take its technology to the next level with increased networking, advanced autonomous systems, machine vision and machine learning technologies.
The company is obviously picking up steam. The public market offering and the capital gained during the process will be crucial for AeroFarms to reach the next level of its growth and to achieve several strategic expansions, including improving operational and energy efficiency, adding into new products (right now it’s focusing on berries), and maintaining its social impact.
"We told investors, we view this as a long-term industry," CEO David Rosenberg said. "It is going to be massive. We feel we have a strong leadership position in the industry from a technology standpoint. So how do we build upon that and really double down on the tech producing [capital expenditures], reducing [operating expenses] and improving quality as well as new varieties of plants on this platform."
AeroFarms was founded in 2004, and its products are sold in 200 grocery stores across the Northeast including Whole Foods. It operates one vertical farm in New Jersey, with more on the way. AeroFarms is breaking ground on a facility in Abu Dhabi, pitched as the world’s largest vertical farm, as well as one in Danville, Virginia. Along with the publicly announced farms in Abu Dhabi and Danville, AeroFarms plans to build 16 more farms with the capital it’s raising, using a slightly different strategy than the company’s previous build locations.
"It’s not where the mouths are, but where the produce distribution centers are," Rosenberg said. "So we can sell to a surrounding number of cities. We’ve gone from a lens of hyper local to a more looser definition of local."
AeroFarms uses aeroponics, a soilless way of growing produce that uses mist to cut down on water usage by 95 percent; it plants seeds in cloth made from recycled plastic bottles. Using LED lights, the vertical farms draw on specific wavelengths to maximize efficiency of the plants’ photosynthesis.
The vertical farming industry, already an important part of the food supply chain, is poised to explode. According to a 2020 report by the World Wildlife Fund, indoor farming is projected to have a combined annual growth rate of more than 24 percent between 2018 and 2024, hitting $3 billion in revenues worldwide in 2024. The challenges and opportunities faced by AeroFarms over the next few years will inform the vertical farming playbook for its followers.
Energy is the next big hurdle
The SPAC merger is expected to bring AeroFarms $317 million in cash, on top of the $80 million the company already has, to scale and expand into new geographies. According to Rosenberg, the company focused most of the last 15 years on innovating its technology, seeds and plants. He is confident its technology can support a massive jump in demand and commercialization.
Energy stands out as one of the bigger hurdles facing the [vertical farming] industry.
But the process of scaling up vertical farming isn’t without controversy. A World Wildlife study that compared the life cycle assessment of lettuce grown traditionally in California and transported to St. Louis against indoor farming solutions based in St. Louis — including greenhouse hydroponically grown lettuce, greenhouse aquaponically grown lettuce, indoor vertically farmed lettuce, hydroponically grown lettuce and indoor vertically farmed, aquaponically grown lettuce — found that the energy required to run the lights, irrigation and automation for all the indoor solutions resulted in an overall higher climate impact than the traditional farming method.
"Energy stands out as one of the bigger hurdles facing the [vertical farming] industry," said Julia Kurnik, director of innovation startups at WWF and author of the study. "Because it already is making great gains around things like water use, pesticide use, food loss and food waste. So it’s doing wonderful things there."
According to Kurnik, hydroponics and aeroponic farming use less water and don’t degrade soil like traditional farming, but for vertical farming to become environmentally sustainable on a carbon emissions level, these systems need to source electricity from renewables such as solar, wind or hydro.
But simply hooking up a vertical farm to solar or wind power won't solve the problem. Manufacturing solar panels is also an environmental strain due to the materials mined and energy used to make the solar panels. Like Kurnik said, everything that produces energy has to be built. And on the business side, AeroFarms said it’s very difficult for the company to find locations that have access to 100 percent renewable energy.
According to Rosenberg, access to a greener grid is part of AeroFarms’ weighting process for picking new locations for farms, but it can’t be a dealbreaker. For example, Danville relies heavily on nuclear and natural gas for energy, which is one reason AeroFarms decided to build there. Rosenberg also hopes AeroFarms will start to focus on places and cities that have access to hydropower.
But both Kurnik and AeroFarms CTO Roger Buelow agreed that one of the main goals for both the industry and AeroFarms specifically should be reducing the energy intensity of vertical farm growing.
"Let’s be more efficient," Buelow said. "Let’s make sure we are getting the most pounds per square meter per photon we can get. So that we’re really being good stewards with that energy. And we’re making sure that every photon gets to do its job."
One way AeroFarms does this, according to Buelow, is to put a lot of effort into making sure it uses the most efficient LED lights. But Rosenberg emphasizes that there is more to the environmental picture than just energy usage. He notes that aeroponic farming doesn’t use pesticides, herbicides or fungicides, which all have embodied energy in their production and produce degradation effects on the environment.
"There’s the environmental picture. There’s the energy side. There’s the pollution side. There’s the soil degradation side. There’s the water usage side. The water contamination side. There’s the food waste side," he said. "It’s part of a much broader narrative in assessing what’s good or what’s not as smart for the environment."
Working on expanding crop offerings
According to the WWF study, energy represents about 25 percent of the operating costs for vertical farms, and those costs have limited what is profitable to grow in contained-environment agriculture.
"I’ve seen pretty much anything, even fruit trees growing in these systems," Kurnik said. "But it isn’t cost-effective or energy-effective. You would spend so much energy growing them, it would bring a large environmental footprint, and it would become too expensive for the farms to sell that produce. So to see the entire industry scale and be able to grow a much greater variety of things and therefore capture all the benefits that these farms do bring, we need to figure out how to lower and/or green that energy footprint."
Berries are a high-value crop that could make the investment on the vertical farming side worthwhile for businesses such as AeroFarms.
AeroFarms is working on breaking out of the leafy green market and making some of those more energy-intensive crops profitable. The company has grown 550 varieties of plants in at least the research phase and is participating in a trial of growing a pharmaceutical ingredient for a drug. But the most likely success story will be the berries it hopes to cultivate working alongside Hortifrut.
"[The partnership] is a great example of how we really think of ourselves as a platform," Rosenberg said. "And how we work on this platform to solve broader problems in agriculture."
Berries are a fickle fruit in the agriculture world. Berries are part of the Dirty Dozen, a list of 12 produce types created by nonprofit The Environmental Working Group that use a lot of pesticides. They are also a high-demand product that people want year-round but that only grow best in summer months, leading to massive transportation costs (both financially and environmentally) as the industry ships berries from farther away places to meet this demand. With that in mind, berries are a high-value crop that could make the investment on the vertical farming side worthwhile for businesses such as AeroFarms.
"It’s local. It’s perishable. There’s a reliable demand. There’s a need for consistency. There’s a need for pesticide-free, herbicide-free," said AeroFarms CFO Guy Blanchard. "There’s many, many markets that look like they could very well make sense [for vertical farming]. We’re at the forefront of looking for those types of crops and markets and finding ways to deploy the technology to address those markets."
One example of that initiative: AeroFarms is also a founding member of Precision Indoor Plants (PIP), a joint venture between The Foundation for Food and Agriculture Research and other participants including BASF, Benson Hill, FFAR, Fluence, GreenVenus and Priva. The consortium is working on genetically adapting seeds for optimized indoor growing, improving light recipes, advancing speed breeding technology and altering the chemical makeup of plants to improve flavor, nutrition and medical efficacy.
"The broader world of vertical farming will have access to all those genetics, and we’ll all be able to grow stronger plants that really make the best use of the features of vertical farms," Buelow said.
PIP and AeroFarms plan to share their findings and innovations with the broader vertical farming community so every business in the industry can operate as efficiently as possible.
"I do think there is a lack of knowledge sharing and best practices across the industry," Kurnik said. "Because it is a bunch of startups. It is very nascent. I think the entire industry could benefit from sharing and establishing metrics and a baseline to figure out how to improve."
Balancing automation alongside social goals
The sustainability of farming and food are huge social issues as much as they are environmental ones. According to Rosenberg, one reason AeroFarms chose to locate a farm in Danville was because of the social impact it could make there. The city is 51 percent African American and has a relatively higher poverty rate than its neighbors.
By entering an economically depressed city, AeroFarms can address food deserts and help alleviate them by providing locally sourced food and creating jobs. The Danville operation will employ about 100 people from the community, according to Rosenberg. "We want to go into those communities and inspire those communities," he said.
AeroFarms also supports a past offenders program that started in 2016 and provides employment for 15 formerly incarcerated people so far.
Automation is coming, and it is one way AeroFarms will decrease costs. But that could undermine the jobs added by the company in the future. Right now, the company automates the seeding process, but the seedlings are placed in trays manually. The loading, unloading, harvesting and packaging is automated but pockets of manual work are needed as well. AeroFarms wants to use the best technology while still providing jobs, according to executives.
Vertical farms are often a collision of education levels; highly educated engineers working alongside farm labor.
"Obviously, our next farms are going to be more automated, much more automated and that innovation is something we are proud of," said Diego Rivera, Aerofarms’ master grower. "But even with automation, nothing is going to replace the human eye. Some key positions are going to be still there."
So it’s going to be about retraining. According to Rivera, Aerofarms has programs in place that create conditions for people to stay at the company by promoting people from within.
"Our approach is going to innovate and continue to work to bring our workforce along with us," Rosenberg added. "How do we train for those next skills? How do we get them to understand how to use those controls so they could apply their contribution in a higher level way? We’re constantly training them to be ready for the next challenges."
To provide employees with the opportunity for upward mobility, AeroFarms offers computer literacy programs and financial literacy workshops. According to Rosenberg, vertical farms are often a collision of education levels; highly educated engineers working alongside farm labor.
"So how can we get the highly educated workforce to work with our frontline workers to teach them these skills and help form that sense of community," Rosenberg added.
It’s clear vertical farming sits right in the middle of many of the largest issues facing our economy and our planet. AeroFarms is trying to tackle a lot of them; everything from food insecurity to energy usage to job sustainability. Succeeding could create a path leading others towards a sustainable and equitable economy of the future for others to follow, while failing will offer a parable of trying to be all things to all people and biting off more than you can chew.
Opening Large Vertical Farming Facilities in Europe
Infarm has signed a contract for a new Growing Centre in Bedford which will measure 9,760 sqm in size, offering more than 5500 sqm of growing space in Infarm’s cloud-connected farming units.
August 9, 2021
Infarm has signed a contract for a new Growing Centre in Bedford which will measure 9,760 sqm in size, offering more than 5500 sqm of growing space in Infarm’s cloud-connected farming units.
Jeremy Byfleet, UK Country Director at Infarm, said: “Infarm has a clear goal to expand in the UK market. Our second UK Growing Centre located in the “golden triangle” allows us to significantly increase the amount of fresh produce grown year-round in the UK.
When fully equipped, the units - each occupying 25 sqm of ground space and 10 metres in height - are able to produce up to 18 million plants per year and generate the crop equivalent of 360,000 sqm of farmland. The Growing Centre is currently in construction and on track for a first harvest in Q4 of 2021.
Each Infarm Growing Centre can save up to ten million liters of water per year, reducing water consumption by 95% versus traditional agricultural methods. Pentadel, appointed by Infarm to select a site as well as design and manage the construction of the new Growing Centre, has also integrated rainwater harvesting into the design of Infarm's new facility. Implementing rainwater harvesting is expected to capture a further 2.5 million litres of water per year, which will be used for conditioning plants.
Infarm will continue to operate its existing Growing Centre in Edmonton, North London and is currently hiring. “We have already opened up new positions for our locations in London and Bedford and will continue to do so as we expand our Bedford operation,” said Byfleet. To establish this large vertical farming facility, Infarm has partnered with Pentadel Project Management.
The location of the facility enables us to serve 90% of the UK population within four hours, bringing the freshest plants just on time to our clients. Consequently, food mileage is substantially reduced. One of the largest indoor vertical farming facilities in Europe to date is going to deliver millions of plants and provide fresh and locally grown produce to even more consumers via our retail partners, restaurants and online food retailers.”
James Kemp, Managing Director of Pentadel, said: “We are thrilled to be supporting Infarm with the delivery of this innovative facility that we believe represents the future of sustainable, scalable and resilient farming. We are passionate about delivering projects just like this – projects that place the future of people and the planet at their heart – and I know the whole team is proud to play a part in Infarm's revolutionary story.” Pentadel has identified a suitable UK site, negotiated terms and is now designing and managing the construction of the facility.
In the UK, Infarm’s herbs and leafy greens are currently found at Whole Foods Market, Selfridges, Marks & Spencer, Fortnum & Mason and Budgens as well at online retailers Weezy and Farmdrop. The new Growing Centre will join Infarm’s expanding global network of vertical farms that all connect to a central farming brain that gathers data constantly to improve plant yield, taste, and nutritional value, while further reducing the use of natural resources. By the end of 2025, Infarm plans to expand to 100 locations worldwide.
For more information:
Infarm
press@infarm.com
www.infarm.com
80 Acres Farms Secures $160 Million In Series B Led by General Atlantic To Accelerate Global Farm Expansion & Product Development
80 Acres Farms' vertical farm systems grow the widest variety of produce commercially sold at scale by any vertical farm to-date, including leafy greens, herbs, tomatoes, cucumbers, and microgreens
August 9, 2021
HAMILTON, OH / ACCESSWIRE / 80 Acres Farms, the industry-leading vertical farming company, has secured $160 million in additional funding in a round led by General Atlantic and joined by Siemens Financial Services, Inc. (the U.S. financing arm of global technology company Siemens). The company intends to utilize the capital for continued expansion and product development, building from its current footprint of vertical farms that yield a diverse offering of high-quality produce.
The funding round also included Blue Earth (formerly PG Impact Investments) and General Atlantic's Beyond Net Zero team, in addition to participation from existing investors including Barclays and Taurus.
80 Acres Farms' vertical farm systems grow the widest variety of produce commercially sold at scale by any vertical farm to-date, including leafy greens, herbs, tomatoes, cucumbers, and microgreens. The company's breakthrough growing technologies and advanced data analytics capabilities have enabled this industry-leading product breadth, driving over 450% revenue growth since the end of 2020. 80 Acres Farms now services over 600 retail and food service locations, including its recent expansion with Kroger, announced earlier this year to 316 stores in the U.S. Midwest and to the e-commerce channel powered by Kroger - Ocado Solutions' partnership. With farms co-located near customers, 80 Acres Farms' produce travels significantly fewer food miles, shortening the farm-to-table footprint and reducing overall food waste. Growing methods at 80 Acres Farms use 97% less water than traditional farming practices and are powered by renewable energy.
- ADVERTISEMENT -
To date, 80 Acres Farms operates eight indoor farms and is committed to supporting and building high-tech production facilities close to regions where fresh produce is consumed. The company has transformed a former factory in Hamilton, Ohio, to a world-class tomato indoor farm, and in 2020, 80 Acres Farms completed construction on a new, 64,000-square-foot, state-of-the art farm with 10 levels of cultivating space. 80 Acres Farms is currently engaged in identifying new farm locations for additional commercial farms to operate at similar scale.
Shaw Joseph, Managing Director of General Atlantic, said: "80 Acres Farms is building an incredibly exciting vertical farming business that provides high-quality produce through innovative practices. With global food consumption increasing and growing threats impacting supply chains and food security, there is a pressing need for healthy, fresh and local foods that are grown in more sustainable and cost-effective ways. We look forward to working closely with Mike, Tisha and the broader 80 Acres Farms' team as they scale."
Jason Thompson, Vice President of Sustainability and Growth Equity at Siemens Financial Services, said, "We are committed to help scale sustainable vertical farming technology. 80 Acres has demonstrated their ability to build and operate profitable farms, and Siemens is enthusiastic about the opportunity to support its global expansion with both our capital and technical know-how, including our recently established Center of Competence dedicated to supporting companies in realizing their digital transformation."
Kayode Akinola, Head of Private Equity Directs at Blue Earth Capital, said, "We are excited to be partnering with General Atlantic and Siemens to provide growth capital and support to Mike, Tisha and the entire 80 Acres team to help scale their operations within existing and new markets."
Mike Zelkind, CEO of 80 Acres Farms, said: "We are proud of what our team has been able to accomplish and enthusiastic about the road ahead. We are also honored to be supported by such a high caliber group of strategic investors who are enabling us to continue to lead this evolving and fast-growing industry. The investment is a quantum leap for the business to build more farms both nationally and globally.
Tisha Livingston, CEO of Infinite Acres, and Co-founder of 80 Acres Farms, said: "The new investment positions the company as the leading proven and profitable technology provider prepared for rapid expansion. In addition, this enables 80 Acres to focus on their operational expertise and deep research and development capabilities beyond leafy greens."
As part of this funding round, Shaw Joseph will join the 80 Acres Farms board. Eli Aheto, former 80 Acres Farms board member, led BeyondNetZero's contributions to this round. "I am pleased to be able to continue and grow my support of 80 Acres with this contribution from the BeyondNetZero team. 80 Acres has proven a farm design that is poised to reduce food miles, food waste and the resulting negative carbon emissions that exist within our food supply chain," said Eli Aheto.
Barclays acted as sole placement agent to 80 Acres on the capital raise.
About 80 Acres Farms
80 Acres Farms is a vertical farming leader providing customers with the freshest, and most nutritious fruits and vegetables at affordable prices. Utilizing world-class technology and analytics, the Company offers customers a wide variety of pesticide-free food with a longer shelf-life that exceeds the highest standards in food safety. Consumers can find 80 Acres' products of just-picked salads, tomatoes, cucumbers, herbs, and microgreens at Kroger, Whole Foods, The Fresh Market, Dorothy Lane Markets, Jungle Jim's Markets, and key National Foodservice Distributors including Sysco and US Foods.
Media Contact
Rebecca Haders / rebecca.haders@eafarms.com / +1 513-910-9089
About General Atlantic
General Atlantic is a leading global growth equity firm with more than four decades of experience providing capital and strategic support for over 400 growth companies throughout its history. Established in 1980 to partner with visionary entrepreneurs and deliver lasting impact, the firm combines a collaborative global approach, sector specific expertise, a long-term investment horizon and a deep understanding of growth drivers to partner with great entrepreneurs and management teams to scale innovative businesses around the world. General Atlantic currently has over $65 billion in assets under management and more than 175 investment professionals based in New York, Amsterdam, Beijing, Hong Kong, Jakarta, London, Mexico City, Mumbai, Munich, Palo Alto, São Paulo, Shanghai, Singapore and Stamford. For more information on General Atlantic, please visit the website: www.generalatlantic.com
General Atlantic also recently formed its BeyondNetZero (BnZ) team to seek out growth companies delivering innovative climate solutions. BnZ looks to identify entrepreneurs with technologies that enable companies to meet and exceed Net Zero emissions targets, with a focus on de-carbonization, energy efficiency, resource conservation and emissions management.
Media Contacts
Mary Armstrong & Emily Japlon / General Atlantic media@generalatlantic.com
Faustine Rohr-Lacoste / Spendesk faustine@spendesk.com
About Siemens Financial Services
Siemens Financial Services (SFS) - the financing arm of Siemens - provides business-to-business financial solutions. A unique combination of financial expertise, risk management and industry know-how enable SFS to create tailored innovative financial solutions. With these, SFS facilitates growth, creates value, enhances competitiveness and helps customers access new technologies. SFS supports investments with equipment and technology financing and leasing, corporate lending, equity investments and project and structured financing. Trade and receivable financing solutions complete the SFS portfolio. With an international network, SFS is well adapted to country-specific legal requirements and able to provide financial solutions globally. Within Siemens, SFS is an expert adviser for financial risks. Siemens Financial Services has its global headquarters in Munich, Germany, and has around 2,800 employees worldwide. www.siemens.com/finance.
About Blue Earth Capital
Blue Earth Capital is a global investment firm focused on sustainability and impact investing. Headquartered in Zug, Switzerland, with operations in New York, London, Singapore, Luxembourg and Guernsey, Blue Earth Capital seeks to invest in businesses that address pressing environmental and social challenges, whilst generating market-rate financial returns. Initiated in 2015 by Urs Wietlisbach, one of the founders of Partners Group, and backed by the Wietlisbach Foundation, Blue Earth Capital was incubated and built up with the support of Partners Group.
Media Contacts
Urs Baumann / CEO Blue Earth Capital urs.baumann@blueearth.capital
80 Acres CEO Reflects on Vertical Farming Post $160m Raise: ‘There Will Be Losers With Very Big Names’
For Mike Zelkind, CEO at Ohio-based vertical ag operation 80 Acres Farms, not everyone will make it to the finish line.
By Lauren Manning
August 11, 2021
The indoor farming sector is dazzling investors and attracting its fair share of nine-figure deals. But as the space grows more crowded and competitive, questions are sprouting up regarding market saturation, the right business models, and whether indoor mega-farms like the one Minnesota’s Revol Greens is planning are the way to go.
For Mike Zelkind, CEO at Ohio-based vertical ag operation 80 Acres Farms, not everyone will make it to the finish line.
“This is the way the market works. There will be winners and losers and there will be losers with very big names,” he tells AFN.
“But the world needs this and even the losers [will have been] very well-intentioned. My heart will go out to everyone who does not win because I know they fought the good fight.”
80 Acres just announced the close of a $160 million Series B round led by US growth equity firm General Atlantic.
Other investors in the round included Siemens Financial Services — the US financing arm of German tech giant Siemens — as well as Barclays, Blue Earth, Taurus Investment Holdings, and General Atlantic’s impact-focused BeyondNetZero team.
Although Zelkind views the indoor farming space as big enough for many players to do well, he thinks some recent valuations are exaggerated.
In his opinion, 80 Acres sets itself apart through its partnerships, like its joint venture with e-grocer Ocado and tech provider Priva. The trio formed the venture, Infinite Acres, in 2019 to help growers enter the tech-enabled indoor farming space.
Staying close to the consumer
80 Acres takes a decentralized approach to getting its produce on consumers’ tables, building its farms close to areas where its customers are located. The startup runs eight farms, and sells its products in around 600 retail and foodservice locations. Without sharing specific figures, it claims to have posted 450% growth in revenue since the end of last year.
Building close to its customer base has also been a foundational aspect of 80 Acres’ business model, Zelkind suggests.
“I don’t think there are any other farming operations today that have built a farm as close to the distribution center of their customer,” he says. “Just getting a little closer to the customer is not good enough.”
Zelkind claims that 80 Acres had a lot of options when it came to choosing investors for its Series B round but that funders with strategic angles were the winning choice. General Atlantic focuses on world-changing technologies, including foodtech, while Siemens can assist with continued industrialization of the startup’s capabilities, he adds.
80 Acres will use the new funding to expand its footprint while supporting product development. Based on his own observations of rival startups’ activities and claims, Zelkind argues that his company offers the widest variety of produce in the vertical farming industry, selling leafy greens, herbs, tomatoes, cucumbers, and microgreens, among others.
“I’m not aware of anybody even making a claim that they are commercially growing these items, and we’ve had the product in the marketplace for the last four years,” he says. “It’s not a claim – it’s a fact.”
Lead Photo: Mike Zelkind, CEO, 80 Acres Farms. Photo credit: 80 Acres Farms Facebook page.
Urban Crop Solutions Awarded As Best-In-Class Vertical Farming Solution Provider
Urban Crop Solutions has been awarded a ‘Best-in-Class’ award for their production systems by the Center of Excellence for Indoor Agriculture. They were selected as the winners for the category of ‘systems starting between $250k-$500k’.
August 2021
Urban Crop Solutions has been awarded a ‘Best-in-Class’ award for their production systems by the Center of Excellence for Indoor Agriculture. They were selected as the winners for the category of ‘systems starting between $250k-$500k’. Each finalist went through a rigorous review process and was evaluated according to several criteria. Emphasis was given to sustainable farms and equipment manufacturers that efficiently use resources such as land, energy, labour and water to produce the highest yields at an affordable price in indoor farm settings.
“The award is definitely a recognition for our team that is continuously working on state-of-the art growing solutions which optimise the sustainability of our industry, whether this is in an existing building or for a greenfield project.” says Maarten Vandecruys, Founder and CTO, Urban Crop Solutions.
“Today we are rewarded with a prize for our approach, but to be successful for our customers, the knowledge of the plant science is as equally important as the engineering part. We keep on striving for a more sustainable impact, not just on the consumption of our natural resources, but also the yield, which positively impacts the financial sustainability” he adds.
"We are enormously proud of the entire team! A team that works together for the future. A team that is there for each other, to give the best of themselves. Looking at our latest realisations, the ModuleX and the FarmLab, and our 24/7 support both technically and biologically, as a team leader you can look forward with a broad smile!" says Jean-Pierre Coene, CEO, Urban Crop Solutions.
Jean-Pierre Coene operating the ModuleX
ABOUT UCS
Urban Crop Solutions is a Belgium based pioneer in the fast-emerging technology of indoor vertical farming. It has developed over the past six years, 220+ plant growth recipes in its research centre in Waregem, Belgium. To date, UCS has delivered over 25 projects in multiple global locations. Their farms are being operated both for commercial and research purposes. Uses range from the production of leafy greens, microgreens and herbs for food retail, service and industrial use, and scientific research across multiple institutions.
Website: www.urbancropsolutions.com
Facebook: www.facebook.com/urbancropsolutions
Twitter: www.twitter.com/U_C_Solutions
LinkedIn: www.linkedin.com/company/urbancropsolutions
CONTACT
Filip Meeuws – Sales Director, Urban Crop Solutions
fime@urbancropsolutions.com
Maarten Vandecruys – Co-founder & CTO, Urban Crop Solutions
maarten.vandecruys@urbancropsolutions.com
Jean-Pierre Coene – CEO, Urban Crop Solutions
jpco@urbancropsolutions.com
Lead Photo: Maarten Vandecruys in the UCS Research Centre
Growing Up: The Next Frontier In Farming Is Vertical And It Could Cut Canada's Reliance on Imported Food
The spicy mustard micro green begins its short life in a plastic tray of mud, filed away in a germination warehouse at an industrial park on the outskirts of Guelph, Ont. It spends several days in hot and humid darkness, using all its energy to open itself, push through the top layer of soil and unfurl its first two tender leaves
By Jake Edmiston
July 30, 2021
The spicy mustard micro green begins its short life in a plastic tray of mud, filed away in a germination warehouse at an industrial park on the outskirts of Guelph, Ont. It spends several days in hot and humid darkness, using all its energy to open itself, push through the top layer of soil and unfurl its first two tender leaves.
In the germination room, trays of mustard greens all sit on shelves the size of ping pong tables, stacked in rows up to the roof. The plants are ready after about two days and the automated growing system comes to retrieve them, pulling the shelf from its stack and ejecting it through a slot in the warehouse wall.
Soaring crop prices will catch up to consumers
Next, they enter another, larger warehouse, with more shelves stacked up three to four storeys high. Here, the spicy mustard greens feel light for the first time. More than 14,000 LED lamps shine for 14 to 20 hours a day, using only the part of the light spectrum that the plants will need: red and blue. So the warehouse is always a thick, glowing magenta.
After spending two days in the darkness of the germination room, a large flat of spicy mustard greens is moved into the 45,000 square foot vertical farming grow room. PHOTO BY GLENN LOWSON FOR NATIONAL POST
“It’s always a beautiful, spring day,” says Juanita Moore, the executive director of operations at GoodLeaf Farms, which owns this indoor farm in Guelph.
It is incredibly important that these mustard greens survive, not just for GoodLeaf — the company uses them for its Spicy Mustard Medley and Ontario Spring Mix — but also for the long-term stability of the Canadian food system.
Canadian agriculture scholars are warning that the country’s dependence on California and other southern growing regions for fresh produce through the winter has become a national security risk.
“We have to really ask the question, ‘How secure are we?'” said Evan Fraser, director of the University of Guelph’s Arrell Food Institute. “On fruits and vegetables, we are not secure at all.”
On fruits and vegetables, we are not secure at all
EVAN FRASER
The pandemic has given companies and consumers a glimpse at how a global crisis can stymie supply chains and push trading partners to hold back exports. And the extreme drought and wildfires that have threatened California’s vast crop production this summer are just the latest example of a glaring vulnerability in the Canadian food chain, which relied on $11.2-billion worth of imported vegetables, fruits and nuts last year. Farmers in the United States supplied $5.4 billion of that produce — $3.1 billion of which came from California.
“Suddenly this idea that California might not be able to provide food is not that farfetched at all — to the point I’m actively kind of worried about it,” said Lenore Newman, director of the Food and Agriculture Institute at the University of the Fraser Valley. “My worry is, we’re going to start having shortages, because California’s production is going to fall. They don’t have the water.”
Fraser and Newman are part of a growing chorus of professors and industry leaders calling for Canada to stop relying on imports from the U.S. and Mexico and start feeding itself, fast. The best hope to do that, in a country with only five or six good growing months, is to farm indoors.
Juanita Moore, the executive director of operations at GoodLeaf Farm, in Guelph, Ont. PHOTO BY GLENN LOWSON FOR NATIONAL POST
“If the trends continue, we’re in real trouble in North America,” Newman said. “Growing all of this food intensively in one location and moving it all over the continent is not going to work. So we may as well start now. I mean, we should have started five years ago but now is good too.”
This ambition for Canada to grow its own supply of fresh produce in the dead of winter isn’t as implausible as it might sound. The country actually isn’t bad at growing things indoors. Canada’s greenhouse industry is already proficient at growing tomatoes, cucumbers and peppers — to the point that 81.2 per cent of the domestically grown supply of cucumbers come from a greenhouse, according to Statistics Canada.
Historically, the problem with greenhouses has been that they rely on the sun, which means production dips in the darker, winter months. They’re also expensive to heat. Even in summer, the sun can be confounding, as Newman put it. It’s bright one day, obscured by clouds the next. It hits the plants unevenly, making it tougher to produce the sort of uniform crops that the market demands.
The new frontier in farming, Newman said, is to sideline the sun. Advancements in more efficient LED light technology have reduced the cost of growing plants indoors, allowing greenhouses to add lights to augment the sun and effectively extend their growing season.
Cheaper LED technology has also made it possible to farm without any sun at all, in the sort of windowless warehouses “you’d put a Costco in,” Newman said.
LED lights are calibrated to only emit the red and blue of the light spectrum. PHOTO BY GLENN LOWSON FOR NATIONAL POST
This new generation of indoor crop factory can pump out more production per acre because the farmer doesn’t have to worry about sun exposure, droughts or pests. In vertical farming — a common method in the rapidly changing world of closed environment agriculture — the plants are stacked one on top of another, in soil trays or in hydroponic fluid, with LED lights in between.
“You can take a 100-acre farm, compress it into a one-acre farm, and put the rest back into wilderness,” Newman said.
Vertical farms can recycle much of the water they use, and often cost little to heat through winter thanks to warmth from the LED lamps and the plants themselves. But possibly the most important perk, she said, is that “everything will taste better.”
The general vision, for Newman and others, is to have vertical farming operations supplying produce to every region in the country. That would drastically reduce the distance between farm and market, so producers would be able to focus on making varieties that taste good instead of the “wooden” varieties preferred in California because they travel thousands of kilometres without bruising.
Major food and technology companies have been funnelling capital into the indoor farming sector, including French fry giant McCain Foods Ltd.’s roughly $65-million investment to become the single largest shareholder in GoodLeaf.
A sampling of three of the six varieties of leafy greens GoodLeaf cultivates in it’s indoor 45,000 square foot vertical farming operation in Guelph, Ont. PHOTO BY GLENN LOWSON FOR NATIONAL POST
But vertical farming hasn’t quite proven itself to be a profitable option yet, according to one analyst who follows the sector. The building costs for new vertical farms and other large-scale indoor models can range as high as $30 million to $50 million per site. Even when the facilities are built, high energy bills and labour costs make it difficult for the farms to make consistent profits. So most operations focus on crops that grow quickly, can be packed into tight spaces and sell at a premium.
“A lot of these groups are still losing money,” said Steve Hansen, managing director at Raymond James Ltd. “The big challenge is, ultimately, getting to profitability.”
And the goal isn’t just to reach profitability by competing with organic farms on expensive niche products like spicy mustard greens. If the true purpose is to replace Canada’s $11.2-billion reliance on imported produce, indoor operations need to be able to reach the sort of scale that will allow them to compete in the broader fruit and vegetable market. More advancement in LED lighting and automation inside the farms are expected to keep tamping down energy and labour costs.
“The vertical industry is still not quite yet on par with field-grown product,” Hansen said. “They’re getting down there and they’re getting closer but they’re still not there.”
Hansen estimated that globally, capital investments into vertical farms and next-generation indoor farming technology are now in the “billions of dollars” globally.
“It’s become a large sector very quickly,” he said, adding that some established operations are finally starting to reach a scale where they’re able to make a profit. “The development we’ve seen on the indoor space has really happened in the last five years.”
Samples of the latest daily crop of leafy greens are taken for testing before shipping to customers at GoodLeaf. PHOTO BY GLENN LOWSON FOR NATIONAL POST
Still, vertical farms are mostly confined to growing salad greens, which grow within a matter of days and allow the farms to constantly be turning over product.
Branching out to other crops will be a challenge, Hansen said. Tomatoes and cucumbers, for example, can be too tall for vertical farming, which means the farm has to pack fewer rows into the space before hitting the ceiling. (Interestingly, greenhouses actually benefit from the height of cucumbers and tomatoes because they’re essentially vertical farms in and of themselves, Newman said.)
Other vegetables that take months to reach market size mean months’ worth of energy costs have to be included in the price — which Newman suggested could lead to potatoes that cost $20 per pound.
Seed companies, however, have started to turn their attention to breeding varieties of crops that will work well indoors, though the developments are still in the early stages, Hansen said. “Very little effort has been done on short, stubby plants that can produce really high volume, because why would you have ever wanted that?”
Fully grown spicy mustard greens await packaging at GoodLeaf. PHOTO BY GLENN LOWSON FOR NATIONAL POST
The GoodLeaf vertical farm in Guelph is currently able to produce more than 800,000 pounds of micro greens and baby greens annually, though it’s currently producing less than half that. Hospitality and restaurants were intended to make up half the business, so the pandemic-related shutdown in that sector has significantly impacted sales. But the business is able to break even at an output of around 400,000 to 500,000 pounds, selling boxes at $3.99 for micro greens and $4.99 for baby greens in major Ontario supermarkets , including Whole Foods Market Inc., Metro Inc., Loblaw Cos. Ltd.
But even a top capacity of 800,000 pounds of greens is considered light. A new GoodLeaf facility in development in Montreal is expected to reach up to 1.4 million pounds, with an expansion option that would double that output.
“We won’t build farms as small as this one going forward,” GoodLeaf’s Juanita Moore said during a tour of the Guelph plant last week. “Every generation of farm will have kind of perfected it a little bit more.”
Fully grown spicy mustard greens grown at GoodLeaf in Guelph, Ont. PHOTO BY GLENN LOWSON FOR NATIONAL POST
In Guelph, the spicy mustard greens spend about six days in the glowing purple growing room. In that time, they extend themselves to half a finger long. There are hundreds of them per tray, a mix of vibrant greens and purples, all of them never knowing the sun or a bug or a breeze.
The automated lifts move the shelves of plants from one end of the growing warehouse to the other end, a little bit at a time, gradually pushing the mustard greens through the stages of their lives. At the end of it all, there is what appears to be a blue garage door.
When the greens are ready, the blue door cranks open and white light shines in. A worker in an overcoat and hardhat pulls them out of the growing warehouse and into a cold, sterile room with a conveyor belt in the centre.
Here, the greens meet the man who made them. As the move along the conveyor, Cesar Cappa, the head grower at the Guelph plant, stands over them and stares.
Agronomist and head grower Cesar Cappa inspects spicy mustard greens at GoodLeaf Farms in Guelph, Ont. PHOTO BY GLENN LOWSON FOR NATIONAL POST
He calls them by their technical name, cotyledons — the first little leaves to sprout from a seed. He watches for deviations in the cotyledons, aware that any problem means the micro mustard greens could rot and spoil the lettuce when they’re together in the spring mix.
“It can be something small,” he says, dressed in a lab coat.
After the inspection, the mustard greens continue along the conveyor belt toward a vibrating blade at the end of the line. It saws back and forth at high speed, aimed at the necks of the mustard greens. The trays move closer and closer in a slow, inevitable march. Each stem meets the knife and it severs them, clean and quick. From there, the greens are packaged, and the trays of roots and dirt are sent for compost.
Afterward, in an open-concept office connected to the vertical farm, Moore passed around paper plates of micro greens and lettuces grown at the facility. Everything tasted of the outdoors.
“It takes me right back to my grandpa’s farm,” she said.
Lead Photo: A tray of spicy mustard greens grown at GoodLeaf’s vertical farm in Guelph, Ont. PHOTO BY GLENN LOWSON FOR NATIONAL POST
Smart Farms: Getting To the Heart of The Matter
Labour costs account for up to 50% of the market price of vegetables, berries, and herbs. However, just like the tractor that once transformed agriculture, the new technological revolution greatly reduces the need for manual, skilled and specialist labour
August 3, 2021
Take a look behind the scenes of vertical plant automation and find out what it takes to bring a smart farm to life with exciting exploded-view diagrams.
Labour costs account for up to 50% of the market price of vegetables, berries, and herbs. However, just like the tractor that once transformed agriculture, the new technological revolution greatly reduces the need for manual, skilled and specialist labour. Today, the work is done by a team of robots, sensors, artificial intelligence, and a core team of highly skilled professionals who manage hundreds of farms at once using special software. As a result, we witness the “battle for the harvest” moving into the IT domain.
A vertical farm functions as an organism, and its equipment can be compared to human organ systems. Its sensors and senders are the nervous system, its air conditioners and dehumidifiers act as the respiratory system, while the solution supply pipeline represents the circulatory system. We can compare the nutrient mixing unit to the endocrine system, tray conveyors and lifts to muscles. Naturally, this organism has a “brain” — the Growtune IT platform.
The degree to which the brain can accurately and confidently “take control” determines how ready various systems, nodes, and technologies are to operate without human intervention. Below, we describe all of the tech that lies inside a vertical farm. How, where, and at what production stages does the automation work? For this purpose, we’ll leverage the somewhat forgotten “exploded-view diagram” style. This way, we'll be able to show all the devices the farm uses to take care of the plants.
1. Breathing: ventilation and air conditioning
Let’s remember biology classes. Plants use photosynthesis to turn light, water and CO2 into oxygen and energy. By doing so, they can consume far more CO2 than is normally present in the air. Since the farm, like a space station, uses a closed-loop air exchange system, with no air inflow from the street, creating an optimal environment and climate for plants is purely an engineering challenge. This includes purifying, conditioning, and adding some CO2 to the room to allow plants breathe freely and grow intensively.
“People who walk into a vertical farm for the first time notice how nice and clean the air is. That’s no surprise because it doesn’t contain any dust — there’s nowhere dust can appear from in the closed-loop circuit of the farm.
Alexey Novokreshchenko, Head of Automation at iFarm
The farm has multiple air conditioning units. It’s not just a matter of maintaining a certain temperature and humidity. We need to make sure that the climate is as homogeneous as possible throughout the entire arm, including at different heights. So, instead of one super-powerful unit, we install several medium-sized devices. This provides the right air circulation and creates a failure-proof system.
Hydroponic technologies tend to create a lot of moisture, and the farm air typically needs to be dehumidified (iFarm has developed and patented a dehumidification system that allows you to reuse this water to feed your plants). There are times, though, when you need to do the opposite: for example, you may need to humidify the air, especially at the initial stage of starting a farm when you don’t have a lot of plants.
2. Energy: grow lights
Photosynthesis, that is the conversion of light energy into chemical energy, only occurs when there is light. Agronomists call artificial lighting of plants “supplemental lighting”. It may vary from one area of the farm to another, depending on the crop and its cultivation phase. The light control unit creates “day” and “night” conditions for plants. The most frequent setup resembles a nice summer day: 14–16 hours of light and 8–10 hours of darkness. Darkness is crucial: the night is when cellular respiration occurs and other important processes take place.
“The plant depends on the day-and-night schedule. Its structure and maturation phases vary depending on the light cycle. Keep the microgreen sprouts in the dark a little longer, and they'll stretch out but will become coarser. By changing the lighting, you can experiment with taste. For example, if you keep sunflower microgreens in the dark for 10 days and then expose them to the light for a full day, you’ll get long and very sweet sprouts.”
Nikolai Podvigin, Head of the Agrolaboratory at iFarm
Agronomists at pilot farms refine cultivation flow charts. For example, they are currently experimenting with variable brightness to grow pine strawberries: the lamps are equipped with a dimmer so you can gradually add brightness. It seems that the agronomists’ hypothesis holds true — the berry evidently "enjoys" long dawns. Through smooth, incremental changes in lighting, the osmotic pressure in the stem and leaves grows gradually, whereas its surge upon sudden light exposure can have a tissue-damaging effect.
Sometimes you have to focus not only on what the plants need but also on organisational or purely economic factors. For example, the cost of electricity. True, the lamps we manufacture and install in racks are highly energy-efficient: they convert every watt of electricity into 0.6 watts of photosynthetically active radiation (FAR). Still, energy costs make up a large portion of the costs of growing herbs indoors. Automation can (and should) be leveraged to ensure optimal load distribution. If the farm can use a night rate, we change “days” with “nights” and reschedule the supplemental lighting for the nighttime to minimise operating costs.
3. Nutrition: irrigation and nutrient solution supply
The nutrient solution is made from several components stored in individual containers which can easily be replaced. The solution is prepared in the mixing unit, a sophisticated automated system capable of mixing dozens of litres of stock solutions with high precision and in the right proportions.
The nutrient solution is delivered to the roots of the plants through a tube system. Since the specific recipe depends on the type of the plant and its cultivation stage, the system continuously monitors (and sometimes adjusts) the composition of the solution.
“Plants eat and plants drink. We provide them with both by mixing nutrition with water. This water continuously runs through the rack. To create an individual “menu” for each plant type, we divide the farm into different watering areas and install an additional storage tank in each of them. Each area is equipped with an additional set of sensors that dynamically monitor the changes in the solution. In fact, these sensors control whether the plant “ate well” today and whether they have everything they need.”
Alexey Novokreshchenko, Head of Automation at iFarm
The water used for preparing the solution is added to the system after it is properly treated with a reverse osmosis filter. This removes contaminants, such as minerals, heavy metals, bacteria and viruses, leaving the water virtually pure.
4. Well-being: IoT sensors
The purity of the source water, the ratio of nutrients in the solution, its acidity, the brightness of the light, the amount of carbon dioxide in the air, temperature, and humidity — you need to control all these things with precision. A large farm can have hundreds of sensors.
Based on sensor measurements, the farm's central processing unit controls the equipment and hardware in real-time, always keeping climatic and biochemical parameters within the limits set by the cultivation flow chart.
If these limits are exceeded, it triggers an alarm and remote technicians are alerted. The algorithm helps identify potential human errors, among other things. For example, it will immediately alert you if a technician incorrectly replaces the cans with the source materials for the solution.
“Plants can be extremely sensitive, some may “dislike” even a one-degree deviation from the usual temperature. We covered the racks with sensors and cameras so we could understand what a crop is sensitive to during cultivation. Now we’ve stabilised the process by defining the optimal number of devices to ensure accurate environment control.
Nikolai Podvigin, Head of the Agrolaboratory at iFarm
5. Analytics: computer processing of Big Data
The “head” of the system is a cloud server. It collates and computes data indirectly from the array of actual measurements collected. For example, it calculates the efficiency of air circulation across the farm based on the data from all of the climatic sensors. What’s even more important is the ability of Growtune, the farm management software platform, to process all of the Big Data collected on the farm.
“The algorithms we use to prepare nutrient solutions are based both on recipes and on the processing of collected data. The outcomes of plant nutrition in previous cycles affect future mixing. The controller monitors the plants’ reaction to “dinner” on the previous day and adjusts the solution accordingly. And, after reviewing the combined data from different farms, we gradually optimise the flow charts.”
Alexey Novokreshchenko, Head of Automation at iFarm
Farms are increasingly using machine vision in their “nervous system”. Images from the cameras installed on the racks are analysed by a neural network trained to determine if the plants are healthy. Technicians can also use this neural network by uploading a picture of plants through a chatbot to gain critical information about its health. Another neural network calculates the dynamics of herbage mass accumulation using the same stationary video cameras or drone cameras.
6. Movement: automation of tray movements
Problems usually dealt with by rare and expensive specialists, agronomists, biochemists, and phytopathologists can be solved using artificial intelligence, special equipment, or remote consultants. But, until recently, there hasn’t been a fully automatic farm where electronics also handle routine manual work, such as moving trays.
In February 2021, iFarm engineers implemented and tested a design prototype of a fully automated vertical farm. It features a conveyor belt that moves trays with pots through the planting, germination, growth, ripening, and cutting areas. The farm can also be equipped with individual robot modules for packaging products and preparing trays for the next cycle.
7. A human helping hand
As with any sophisticated modern equipment, an automated farm has special service message protocols. Naturally, these protocols are intended for a person, such as an employee of a certified service provider. Automatic warnings about errors, worn-out nodes, or the need for consumables to be replaced translate into assignments for replenishment or troubleshooting.
The reports of deviations in the growth of herbs are handled by an iFarm agronomist. The first thing this expert does is double-check that the actual conditions match the ones in the flow chart. They then go through a list of tasks almost identical to the sections of this article. So, what’s happening with the air, climate, energy, and nutrition of the plants on the farm? Do the sensors provide correct data? When suspecting a technical failure, the agronomist connects a service employee to the diagnostic interface with one click. They can also connect to the technician’s camera or AR glasses if the employee is already on site.
“We have several continuous operation circuits, millions of second-by-second measurements, sensors, robots, conveyors, drones, cameras, and neural networks. It seems we’ve automated almost everything we can. The only thing you can’t automate is the R&D process itself. This is why people in the company focus on this process. And this is exactly why we are fighting for strategic investments.”