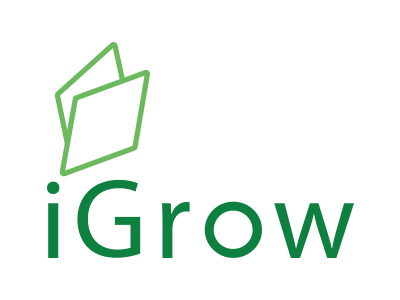
Welcome to iGrow News, Your Source for the World of Indoor Vertical Farming
US: South Dakota - Farm-In-A-Box Means Local Greens Year-Round
Missouri River Energy Services, the Electric Power Research Institute, South Dakota State University and the Children’s Museum of South Dakota are collaborating on a high-tech “farm-in-a-box” built entirely inside a specialized 40-foot container
Courtesy photos: Above, a specialized 40-foot container arrives on the South Dakota State University campus Friday. Food grown in the farm-in-a-box will be donated to the Children’s Museum of South Dakota to be used in Café Coteau. Below, the food pod is set into place on the SDSU campus Jan. 10.
By: Missouri River Energy Services Jan 15, 2020
Produce grown in a container on campus to be used at Children’s Museum of South Dakota
BROOKINGS – Missouri River Energy Services, the Electric Power Research Institute, South Dakota State University and the Children’s Museum of South Dakota are collaborating on a high-tech “farm-in-a-box” built entirely inside a specialized 40-foot container.
The container was delivered and installed Friday, Jan. 10, on the SDSU campus in Brookings. It will be operated by graduate students from SDSU’s Department of Agronomy, Horticulture and Plant Science. Production is anticipated to start in the spring.
Unlike traditional farms, plants in the container are grown vertically indoors without soil, getting their nutrition from water and light energy from powerful LEDs. The result is a system that operates independently from land, climate and season. That means fresh greens can be produced locally year-round.
The first crop to be grown in the container will be Red Rosie Romaine lettuce, a variety that is both disease-resistant and tasty. The container is expected to produce up to 110 pounds of produce a week.
Food produced in the container will be donated to the museum’s Cafe Coteau, which focuses on serving locally sourced and healthy foods. Produce that is beyond the capacity of the café will be donated to local organizations with missions to reduce food insecurity in the region.
“This project aligns well with our museum values to promote sustainability and to give back to the community,” said Kate Treiber, executive director of the Children’s Museum of South Dakota. “The research could potentially provide some unique opportunities for us to share information related to sustainable agriculture to our guests as well.”
“Local indoor agriculture has the potential to significantly reduce emissions because less transportation is required,” said Joni Livingston, MRES vice president of member services and communications. Leafy greens, like those that will be growing inside the container, currently travel an average of 2,000 miles before reaching a store, added Livingston. Indoor food production also requires significantly less water and chemicals than traditional agriculture.
“As an agency serving public power utilities, such as Brookings Municipal Utilities, we are excited to be a part of an emerging market that has so many potential benefits for local communities and for society as a whole,” Livingston said.
“We are particularly excited about the opportunity this Food Pod is providing to students for research connected with the long agricultural heritage at SDSU, as well as our recent efforts in the field of precision agriculture,” said Dr. John Killefer, South Dakota Corn Endowed Dean of the SDSU College of Agriculture, Food and Environmental Sciences. “The inclusion of the Food Pod on our campus and our collaboration with the research partners means the SDSU College of Agriculture, Food and Environmental Sciences now has the ability to share agriculture in a learning environment all the way from a highly integrated production system represented by this Food Pod, to our Local Food Education Center which utilizes high tunnels, to multi-thousand-acre food-production systems that utilize no-till and conventional tillage systems in all areas of the land-grant system from teaching, to research, to outreach. Our students are having a chance to experience agriculture throughout the spectrum of these varied production systems.”
The project is co-funded by MRES and a grant from the American Public Power Association’s Demonstration of Energy & Efficiency Development program. It is part of a larger, collaborative EPRI effort involving several other indoor agriculture facilities across the country.
MRES is a not-for-profit joint-action agency that provides wholesale electricity and energy services to 61 member municipalities in the states of Iowa, Minnesota, North Dakota and South Dakota. All MRES members own and operate local electric distribution systems. For more information, go to mrenergy.com.
The Children’s Museum of South Dakota, located in Brookings, promotes learning for children of all ages and abilities through interactive, informal, hands-on exhibits and demonstrations. The museum has welcomed more than 750,000 guests from around the world who make memories while learning through play. More information is available at prairieplay.org.
Café Coteau, located in the museum, serves fresh, healthy food with a focus on local fare, and is open to the public Tuesday through Saturday, 8 a.m. to 5 p.m., and Sunday, 10 a.m. to 5 p.m.
One of The Decades 10 Best Climate Innovations - Indoor Farming Technology
Alternative farming methods have been around for centuries — but over the past decade, the field has really grown thanks to technological innovation. Namely, new technology such as LED lights, temperature-controlled shipping container farms
SOURCE: COURTESY OF PONIX
Alternative farming methods have been around for centuries — but over the past decade, the field has really grown thanks to technological innovation. Namely, new technology such as LED lights, temperature-controlled shipping container farms, and indoor vertical farms have allowed for so many advancements in improving the way we grow produce — namely, by making it more accessible and by lowering agriculture's environmental impact.
Compared to conventional farming, indoor farming, and vertical farming take up less land, there is no risk of pests (or need for pesticides), they yield more crops, and they bring locally-grown produce to communities that cannot grow a variety of produce year-round (which is more nutritious and has less of an environmental impact, since it isn’t traveling across the world).
FarmBox Foods
December 27, 2019
Freight Farms Is Rearchitecting The Concept of Vertical Farming
Freight Farms helped invent the now-thriving farm-in-a-container market, where companies build vertical farms inside old shipping containers to grow pesticide-free produce throughout the year
Freight Farms helped invent the now-thriving farm-in-a-container market, where companies build vertical farms inside old shipping containers to grow pesticide-free produce throughout the year. But now that vertical farming companies are sprouting up almost as fast as the leafy greens they grow, the Boston, MA-based startup wants to completely rebuild the shipping container concept.
Its new product, The Greenery, which the company just announced today, isn’t a reiteration of its existing Leafy Green Machine (LGM). Instead, it’s a complete re-imagining of the shipping container concept that enables just about anyone to farm a large variety of crops. Or in the words of Freight Farms cofounder Brad McNamara, they’re “rearchitecting the whole vertical farm concept.”
To do that, McNamara and fellow cofounder Jon Friedman kept the foundational basics in play: farming still takes place inside a 40-foot shipping container and still involves the usual mix of hydroponics, LEDs, and software to control things like plant nutrients, temperature, and light levels. But inside the walls of that 40-foot container, Freight Farms has introduced some major changes.
One of the biggest tweaks is also one of the simplest: the inclusion of a racking system that’s actually movable. Since its founding in 2010, Freight Farms has used stainless steel vertical towers arranged in rows inside the shipping containers for growing. (SF-based Plenty employs a similar structure to its farms.) While this allows for much more growing space than in most vertical farms — which actually use horizontal rows of shelves — McNamara and Friedman saw a way to make the space inside the container even more productive by enabling customization.
With The Greenery, both the grow racks and the panels that hold the LEDs are now movable, so farmers can customize the layout inside the container based on the type and number of plants they grow. “In order to accommodate a larger variety of crops, rows can expand and contract,” Friedman explains of these mobile racks. For example, some plants are rooted, some grow on vines, and some simply need more space (e.g., tomatoes). Rather than having to grow plants according to what the space inside a container dictates, Greenery allows farmers to change the space based on what they need to grow.
A big impact on growth and yield is lights — that is, LEDs. But more LED power equals more electricity, which is financially constraining on companies and just all-around bad for sustainability. “Indoor agriculture has always struggled because you’re replacing the free resource of sun with lighting,” McNamara explains.
With The Greenery, Freight Farms addressed the lighting issue by redesigning the ropes of LEDs into panels that, according to the company, triples access to light and keep light energy from being wasted. McNamara and Friedman explained to me that the new lighting design produces a light intensity that’s 3x more powerful than its predecessor (the LGM) but doesn’t incur a 3x energy increase.
Arguably, though, the biggest improvement Freight Farms has made with The Greenery isn’t any one piece of technology, but the decision to bring all the tech in-house and build it themselves.
The typical vertical farm takes various off-the-shelf technologies, such as sensors, lighting, and hydroponics, and strings them together. The result is a farm that runs off fairly siloed elements that weren’t necessarily built to “talk” to one another, which can lead to interoperability issues, higher costs, and more time spent making sure these various systems work together. By contrast, the pieces at work in The Greenery were built with interoperability in mind, which in theory at least means a more reliable system and better control over the whole operation. Freight Farms also says it’s easier to automate the farming process with all the tech in-house, thereby making it simpler for anyone to use.
“It’s a turnkey offering in that no matter where you are in the world you can just pick up the instructions and go,” says Friedman. And because of that ease and lower costs, more populations can reap the benefits of vertical farming, including underserved ones most in need of easier access to fresh food. “This platform allows us the opportunity to not only feed a demographic and teach them how to farm,” says McNamara.
And while this vertically integrated vertical farm is a fairly new concept, Freight Farms isn’t the only one trying its hand at the idea. Over in the UK, the Future Farming Hub is attempting a similar one-stop-shop indoor farm, though their project doesn’t officially kick off until April of 2019. Even so, I expect we’ll see more companies in future exploring and offering vertically integrated systems.
Freight Farms currently operates in over 15 countries, including the Everlane factory in Vietnam and a Wendy’s location in Guam. According to Friedman, The Greenery will sell initially for $104,000. The company, meanwhile, plans to expand into new markets, particularly around the non-profit sector in order to help individuals and companies give back to their communities by making it easier and faster to get healthy, locally grown food.
Freight Farms Aced 2019 – Here's Our Report Card
2019 was a year for the books! We released the Greenery and showed you how it works. We hosted a record number of webinars featuring customers from all backgrounds and levels of experience
December 23, 2019
As we enter a new decade, we look back at all our 2019 accomplishments.
2019 was a year for the books! We released the Greenery and showed you how it works. We hosted a record number of webinars featuring customers from all backgrounds and levels of experience. We also invited you to a record number of open houses, where you were able to meet the team, tour the farm, and ask a local Freight Farmer all your questions. And, as with every year, we expanded our world map with new customers from the United Kingdom, Spain, Germany, and Australia!
2019 was also a banner year for our farm-to-school customers. As an increasing number of K-12 schools and universities add container farms to their campuses, we see the Greenery become more than just a means of food production. Instead, the Greenery can function as a classroom, research lab, after-school club, center for student jobs, and so much more!
Want to keep up with Freight Farms in 2020?
Follow us on Facebook, Twitter, Instagram, Youtube, and LinkedIn!
We also make emails! If you want to hear firsthand about 2020 events, webinars, and company news, make sure to sign up for our emails.
The Evolution of The Vertical Hydroponic Container Farm
On April 11th we hosted our most popular webinar ever: The Evolution of the Vertical Hydroponic Container Farm! We explored how the Greenery has reimagined controlled environment agriculture to bring farmers increased yields, customization, and control.
Don’t have a full hour? No worries! We went ahead and summarized our conversation in this blog post. We’re going to follow along with the webinar’s structure with an overview of CEA and an introduction to hydroponics, followed by a look at the evolution of the container farm: how we got started, where we’ve been, where we’re going with our new Greenery farm!Don’t have a full hour? No worries! We went ahead and summarized our conversation in this blog post. We’re going to follow along with the webinar’s structure with an overview of CEA and an introduction to hydroponics, followed by a look at the evolution of the container farm: how we got started, where we’ve been, where we’re going with our new Greenery farm!
OUR SPEAKERS
CAROLINE KATSIROUBAS
Director of Marketing & Community Engagement
DEREK BAKER
Industrial Designer
WHAT IS CONTROLLED ENVIRONMENT AGRICULTURE (CEA)?
CEA uses an enclosed space (in our case, a container) to bring farmers control over components such as lights, heating, ventilation, AC, pumps, etc. to create the perfect growing environment in any climate, 365 days a year. Hydroponics, specifically, uses nutrient enriched water to replace soil. Here at Freight Farms we use hydroponic techniques because they’re extremely water-efficient and can be adapted to many environments and crop varieties.
In our farms, we use:
A vertical drip system: This system pumps water up to the top of the vertical channel, and gravity allows it to drip down that channel so the roots can access it. Any excess water runs out the bottom and is returned in the reservoir where it is recycled.
An ebb & flow system: This is a horizontal system where nutrient rich water floods a shallow trough to saturate the plants’ roots, then drains back into the reservoir to be recycled.
Read about other systems in Hydroponics 101.
THE EVOLUTION OF THE CONTAINER FARM
The container farm’s story begins in 2009 when Freight Farms co-founders Jon and Brad set out to bring farming into urban centers in an effort to decrease the distance food travels to the people that are eating it. Although they were always certain CEA was the way to do it, their initial focus was in rooftop hydroponic farming.
Rooftop hydroponic farming had several pros, such as activating abundant yet unused space, and taking advantage of sunlight. However, they quickly ran into several cons. For one, they were constantly dealing with red tape and difficult zoning boards. There was also too much customization involved: Each new rooftop setup needed to be created with unique specifications, which led to extreme upfront costs.
Jon and Brad decided to pursue a method of CEA that was easier to standardize while still allowing people to activate unused space in their cities. That’s when the aha moment happened: What about shipping containers?
It was clear from the start that containers could be the perfect modular vessel for the farms. Plus, there was an abundance of decommissioned containers sitting around waiting to be used. The question then was, can you grow in them?
In 2012, Jon and Brad got a container and built the first prototype by hand. After months of testing and refinement, the world’s first container farm–the Leafy Green Machine–came on the market in 2013.
The next five years were spent iterating on the Leafy Green Machine as we learned more and more from our expanding customer base. We made subtle but important changes, resulting in 8 total versions of the Leafy Green Machine. Today, we have 200 farms operating in 39 states and 15 countries. Each has their own unique story, whether it’s a school uses their farms as learning labs, or operating in tandem with a traditional farm to extend their growing season and create revenue year round. All of them are positively impacting their communities 365 days a year.
The Greenery
“We knew that we had to develop a farm that could not only be a leader in production, but could be flexible in suiting the needs of all it’s users”
— Derek Baker
GREENERY EXTERIOR
In the past, we sourced used containers and modified them. Now we’re building new containers to our specifications, giving us unmatched control over weather-proofing and R-28 U.S. Department of Energy insulation rating. The R value is the capacity of an insulating material to resist heat flow. The higher the number, the better the insulative properties. This high value lets us operate in all kinds of harsh weather conditions by maintaining the perfect indoor temperatures.
The new Greenery design features an in-set rear so that all the components fit within the ‘standard’ 40 ft x 8 ft container boundaries. This makes is as easy to ship as possible.
At the back, you can find a 100-amp main breaker to accommodate any additional power draws, and a 36,000 BTU climate control unit with a built in dehumidifier and economizer. The economizer is a simple feature that helps the energy efficiency of the farm. Senses outdoor air and–if it’s below the set temperature in the farm–pulls it in instead of running the A/C (therefore conserving energy).
Audience Q&A with Derek
What’s the maximum temperatures that the Greenery can withstand?
DB: We haven’t seen anything yet that it can’t withstand! We have our previous generation farms operating in 120ºF in Dubai and various negative temperatures in places like Halifax, Colorado, Alaska…and that’s just with the Leafy Green Machine’s R-16 insulation.
How can you protect and secure the Greenery in aversive weather conditions, like hurricanes?
DB: The good thing about shipping containers is that we’re very familiar with them–we know how to secure them down, be it on a ship, on a truck, or on the ground. There is lots of standardized equipment available to lock the container in place as long as you put it on the right foundation. Plus, they weigh a lot–each container is about 8 tons–so they’re not typically going anywhere.
GREENERY SEEDLING AREA
The seedling area features a seedling station that doubles as a worktable. Mounted on the wall above it are dosers and reservoirs that monitor the seedling tank and the main tanks with smart, IoT connected sensors that tell the dosers to pull nutrient and pH solutions from their respective reservoirs to maintain the right water nutrient conditions. The seedling tank is arranged vertically on the right side of the station to make it easy to access and clean.
The seedling table itself is built of food-grade stainless steel and consists of two independently controlled ebb and flow troughs that, combined, hold up to 4,608 plant sites. The troughs were built independently so you can use one for seedlings and one for microgreens, or not use it at all, in which case you don’t end up wasting energy or water.
Audience Q&A with Derek
There is a lot of moisture inside these containers… is there any risk of rusting?
DB: We have chosen specific materials–stainless steel and aluminum–that don’t oxidize the same way as regular steel to avoid rust in the farm.
Can you reuse the water?
DB: Hydroponics in general is a super a water-efficient system. Compared to traditional agriculture we’re using about 95% less water. On a daily basis, you’re using 5-10 gallons. But, when the weather is hot and humid, we’re able to actually generate water. So, yes, the system is built to save and reuse water.
Is the seedling tank easy to move?
DB: The reason we put the tank where it is and made it vertical is so you don’t have to move it. We have all the hookups on the side of the tank along with an app-connected water level sensor. The lid is very accessible if you do have to get in there to clean it… the idea is that you don’t have to move it to perform any of your regular farming activities.
GREENERY MAIN GROWING AREA
The main growing area in the farm is where you can see the most innovative design improvements in the Greenery. Below we’ll first explain the features themselves, and then we’ll dive into the thought process behind the changes.
For one, individual hanging string lights have been replaced with 112 Freight-Farms-developed LED arrays that line the walls and hang between the growing rows and emit directional red and blue light onto the plants.
Our legacy 256 crop columns have been replaced with 88 plant panels that are designed to adapt to multiple crop types and maximize growing space. Combined, the panels have 7,480 potential growing sites.
Finally, both the LED arrays and the plant panels hang on a sliding rack system that allows you to configure the farms layout to best suit your harvesting and maintenance workflow.
Audience Q&A with Derek
Do you only use red and blue lights?
DB: Yes–This is a big debate in the hydroponic and general indoor ag world but we’ve done extensive research and...had great success with the 5:1 red-to-blue ratio lights. In the Greenery, you also have the opportunity to isolate the red and blue lights to create different light environments for different crops.
Can you remove the plant panels to clean them, and how does the hanging/removing process work?
DB: Yes, they are removable. And, to make them easier to hang, they include ribbing on the back that acts as a haptic feedback guide for when you go to hook them onto the racks.
How do you protect plants while you’re moving the rows?
DB: There are a few ways to do that. First is to come up with a compatible planting schedule where you have seedlings and mature plants on opposite walls of the farm so you have space to shift the rows. Then, there’s also spacers built into the racks themselves to maintain a minimum distance that protects most standard sized plants.
THE DESIGN PROCESS
“This design is really the culmination of two years of research, testing, and general gleanings. The Greenery takes the feedback that we’ve received from our customers and combines it with the most recent technology to build a farm that’s focused on creating greater yields, allowing more crop variety, and reducing labor.”
— Derek Baker
Achieving greater yields
THE PLANT PANEL
We upgraded to the plant panel to take advantage of unused space that was going to waste with the individual crop columns. This way, we’ve reduced the number of growing fixtures while drastically increasing the amount of food you can grow.
By planting in channels 1, 3, and 5 (option 1), you’re able to mimic the same row cropping techniques used with the crop columns. This is a great option for large head plants, like lettuce, Swiss chard, and kale. From there, you can also activate channels 2, 4 (option 2) for mixing in small crops, like turnips or radishes, between the larger ones growing in channels 1,3, and 5.
A different planting method involves using all five channels for one plant. This is called linear cropping, and it is very effective for smaller greens and herbs and allows you take advantage of the entire panel.
“I’m very excited to see how each farmer takes advantage of the plant panels and the different cropping techniques they develop in their own farms.”
— Derek Baker
THE LED ARRAY
Our new rigid LED board is specifically designed to create a powerful and uniform lighting environment to accelerate the rate of photosynthesis, the result of which are heavier, fuller, and richer plants.
To understand the value of the new LEDs, we first need to understand PPFD!
PPFD (Photosynthetic Photon Flux Density… say that five times fast) measures the amount of light energy that reaches the canopy. It’s important to understand that it refers to the amount of photons in the visible light spectrum that flow over a square meter in one second. That means that this value does not measure the power of the light fixture itself, but the amount of light that actually reaches the intended surface (in this case, your plants). For that reason, PPFD measurements always need to be paired with a distance measurement.
So, the Greenery’s lights generate 200 PPFD at a distance of 18 inches from the canopy, compared to the LGM, which generate 100 PPFD at 9 inches. This means that the Greenery has double the PPFD at double the distance!
This graph shows that increasing the PPFD in this way results in more than double the rate of photosynthesis. Doubling the PPFD results in more than double the rate of photosynthesis.
We specifically identified 200 PPFD as our preferred light intensity for the Greenery because, as you can see on the graph, anything over 200 PPFD results in a plateau in the rate of photosynthesis. What we wanted to avoid was putting unnecessary energy into our lights that would not be directly translated into a dramatic difference in growth.
More Variety, Simpler Workflow
The moving racks allow you to transform the space based on your needs. This can mean growing exciting new crops that require more space to grow. By moving the grow rows and center LED fixture you have the flexibility to organize the space for any crop type.
Default Position
Harvesting Position
Position 2 - Inner plants receive more intense light, outer plants have more room.
Position 3 - Inner plants have more room, outer plants receive more intense light.
You can space it evenly to allow small to medium crops or move them to any other position to allow for a combination of crop types and sizes (as seen in positions 2 and 3).
Mobile rows also lets you create walkways where you need them. This lets you harvest, transplants, and maintain directly in the rows.
“We wanted to create a space that suits everyone’s needs and could be configured to adapt to each individual’s workflow preference.”
— Derek Baker
There you have it!
For more details about the Greenery, Freight Farms, and our entire 30 minute live Q&A session, check out the complete webinar recording. You can also view more webinars in our portal!
Want information relating to a specific project? Contact our team!
Freight Farms Takes Container Growing To The Next Level
This Boston company has opened its new “Greenery” below an overpass
Oasis Springs Runs A CSA In Every Season
Sarah and Chris Ward got their start in urban farming in 2016 when they purchased a Leafy Green Machine (the predecessor of the Greenery
7 QUESTIONS WITH SARAH
WARD OF OASIS SPRINGS FARMS
Sarah and Chris Ward got their start in urban farming in 2016 when they purchased a Leafy Green Machine (the predecessor of the Greenery). Although neither Sarah nor her husband Chris had experience in commercial farming, Sarah had over 17 years experience in marketing, public relations, and project management, and Chris had a background in information technology and engineering, so they decided to leverage their professional abilities and mutual love for local food by launching Oasis Springs Farm. Their mission? To provide fresh, healthy, local produce year-round to their community in southern New Hampshire through environmentally friendly practices and high tech resources. We recently spoke with Sarah about operating her container farm and her tricks for maintaining a loyal customer base.
Freight Farms (FF): What, if any was your experience with farming before becoming a Freight Farmer?
Sarah Ward (SW): We did a little hydroponic growing in our home the winter before to have fresh herbs and lettuce throughout the winter months. It was during all the research we did for our home operation that we came across the opportunity to scale up large enough to not only feed ourselves but our community as well.
Sarah's husband Chris learning how to harvest crops during Freight Farms' training camp for new farmers
FF: How did you find customers to buy your produce?
SW: This was one of the scariest parts of the business, trying to find interested people to buy it. We connected with local groups and businesses that have like-minded missions to bring good food to people. And we are always rewarding people with free lettuce and greens when they connect us with new businesses or CSA members. Over time we grew our membership to 50-60 shares a week, and usually have a waitlist too!
“ It amazes me every week how much we can grow. ”
FF: Who do you sell to and how do you do it?
Most of our greens go towards the CSA, although we do still have a few chef customers as well. Our customer base it varied: families, senior citizens, health-conscious shoppers, and locavores. We found this customer base by partnering with local businesses as pick-up points and using them as opportunities for co-marketing.
FF: What kinds of crops do you grow?
SW: At first we did a lot of experimentation, but ultimately found that we gave customers the best value when we provided them with everyday staples. Today we grow about five lettuce varieties, kale, some herbs, and microgreens.
FF: What’s the best piece of advice you can give to people interested in becoming Freight Farmers?
SW: Be flexible and patient! When we first started we wanted everything handed to us with the perfect formula for success, but we quickly learned that things change and you can’t always count on what you planned for. Be adaptable and open to new ideas.
FF: What was the most challenging part of becoming a Freight Farmer and how were you able to overcome it?
SW: Even with a Freight Farms unit, farming, in general, requires a lot of time. There have been many exhausting early mornings and late nights. Managing a full-time business and raising a family certainly has its challenges. We have worked hard over the last year to find the right work-life balance by trying to create a schedule that works for our family.
FF: What are your plans for the future?
SW: We plan to grow and continue to find new ways that this resource can benefit both us and the community that we live in. Most people are amazed that we do this from our backyard. The support has been amazing. I get called Lettuce Lady a lot.
Want to learn more about how Oasis Springs is operating a successful CSA? Register for our webinar with
Sarah on December 12th, 2019 from 12-12:30 PM EST.
In the meantime, follow Oasis Springs on Facebook and Instagram for updates from the farm!
Colorado School Taps Container Farm for Classroom, Food Stand
A Douglas County High School is using a refrigerated freight container converted into a hydroponic farm as an extension of the classroom. At Mountain Vista High School in Highlands Ranch, students learn how to grow leafy greens and other vegetables
Freight Farms’ hydroponic vertical container farms use nearly 99% less water than a traditional farm, running with as little as zero to five gallons per day, less than the average dishwasher. (Pixabay)
December 9, 2019
HIGHLANDS RANCH, Colo. — A Douglas County High School is using a refrigerated freight container converted into a hydroponic farm as an extension of the classroom.
At Mountain Vista High School in Highlands Ranch, students learn how to grow leafy greens and other vegetables. And David Larsen, who teaches business agriculture at the school, said other learning opportunities branch out from there.
“Then you take all the different aspects of it, like the business side, marketing, branding all those things that we want kids to have practical experience on,” Larsen said. “If you have kids that are interested in the engineering technology side of it, there's a control system and automation in there."
Students package and sell their harvests to local restaurants, students' families and staff, and any extra produce goes to retirement homes and food pantries. Larsen said students also gain soft skills such as how to be a good employee, punctuality, engagement, responsibility, and how to be the public face of a business.
Because the climate is controlled inside the container, food can be grown all school year long with a predictable commercial-scale output. A greenery unit can support 13,000 plants at a time, producing harvests of up to 900 heads of lettuce per week. Larsen said the indoor farm also is resistant to shocks such as extreme weather patterns or drought.
"The taste is incredible. When people eat our lettuces, they're like, 'Oh, wow, I didn't know lettuce could taste like that,’” he said. “There's some very interesting varieties of herbs as well. We do a lot of different arugulas. I think the freshness just really sets it apart."
The high-tech containers are the brainchild of the Massachusetts-based company Freight Farms and are well suited for Colorado. They require a considerable amount of electricity, but use nearly 99% less water than a traditional farm, running with as little as five gallons per day - less than the average dishwasher.
Eric Galatas, Public News Service - CO
Watch: 5 Acres of Greens In 55m²? No Imports…Hyper-Local Food
Two re-purposed shipping containers, fitted with a ‘Farmony’ – 55m² in size, can produce 55,000 heads of lettuce per year or 408 trays of micro greens per week
November 20, 2019
Two re-purposed shipping containers, fitted with a ‘Farmony’ – 55m² in size, can produce 55,000 heads of lettuce per year or 408 trays of microgreens per week.
John Paul Prior sees these “5ac farms” as a way to compliment an existing farming enterprise.
His vision is to have as many Farmony models across the country as possible, complementing an existing beef enterprise for example and providing another income, all while replacing food imports into this country.
These salads, herbs and microgreens will be grown using hydroponic technology – no soil involved – and will be highly nutritious and free of pesticides.
That IT input into the farm provides a controlled environment.
Anyone who owns a Farmony solution can control it from anywhere in the world with a mobile device. The controlled environment means no pesticides are used and growth cycles are efficient.
Salads and microgreens are grown inside this controlled environment
“The growing season in Ireland is obviously from May to September. In a Farmony, a producer can grow all year round – 365 days a year,” John Paul explained.
This provides a whole new window of opportunity for Irish growers to have a continuous supply of fresh and local produce.
The business model allows for crops to be grown in small spaces. Restaurants could have their own source of salads and herbs all year round for example.
A restaurant’s beef supplier could provide the beef, the herbs to season it and the salad to accompany it.
“With microgreens your grow cycle is just six-to-seven days, so in terms of output one module can grow 24 trays of micro-greens per week and multiply that by 17 and you’re at 408 trays of micro-greens every week, so it’s an impressive output.”
Replacing Imports
At present, Ireland is heavily dependent on imports in this sector, which can be clearly seen on the supermarket shelves.
“We’re encouraging people to apply for the horticultural grant in 2020,” John Paul noted.
“The country imports about €300 million worth of produce, so we’re trying to basically offer a solution for producers to replace those imports.
You’re talking about hyper-local produce. These farms could be placed in urban centres or farmyards.
John Paul noted that while there are some farming sectors struggling at the minute, one of his company’s solutions could fit into a current farm business.
John Paul estimates a total workload of 25-30 hours/week and noted that there is a 40% grant available to set up the farm.
The system can also be used in an existing farm building. Mushroom houses, which are no longer in use for example, are ideal for these modules.
How Does It Work?
John Paul explained a small bit about how the farm works. The modules – which from the outside look like shelves – are basically flat-packs and can each be assembled in 45 minutes.
Water and nutrients flow through these modules feeding the plants. The gallery below shows the root structures of some of the plants and the water in the trays which is filled with artificial fertilisers.
“We use hydroponic technology so there’s a constant water flow throughout the module.
First of all the process is you seed sow. Then you transplant and the roots take the nutrients from the water solution that’s ebbing and flowing throughout the module.
Once the initial work of sowing and transplanting is carried out, the remainder of the work can be completed from a mobile device until harvest.
Lighting and temperature, as well as electrical conductivity and pH levels in the water, are all monitored and used to decide on the different “plant recipes”. The information is all sent to the master controller and sends nutrients to the plants accordingly.
Lights go on and off automatically, nutrients go in and out.
The irrigation system and lighting can all be changed from anywhere in the world. The amount of light hours can be changed for example, depending on the different plants.
Some plants like basil might require more white lights, while mustard or chard will have more blue lights.
As well as plant recipes, John Paul thinks he has the recipe to “supplement and compliment” current farming businesses, which he thinks can be made more sustainable and profitable by building a Farmony on site.
High-Tech Farm In Shipping Container Cutting Growth Time In Half
A shipping container and a lot of ingenuity -- is changing the way produce is grown. "It's a 3.4-acre farm inside a 320 square foot shipping container," explained Dale Speetjens, CEO & Co-founder ShipShape Urban Farms.
To View The Video, Please Click Here
MOBILE, Ala. (WALA) -- A shipping container and a lot of ingenuity -- is changing the way produce is grown.
"It's a 3.4 acre farm inside a 320 square foot shipping container," explained Dale Speetjens, CEO & Co-founder ShipShape Urban Farms.
Calling it a "Business in a Box" -- Speetjens gave us a tour. Inside the container garden was several varieties of lettuce in various stages of growth.
"Inside here right now it's a balmy 70 degrees and it's this temperature whether it's 100 degrees outside or 30 degrees," said Speetjens.
Every variable is controlled by a computer system.
"This here is I would say the brain of the container... This is actually the control," said Carlos Augusto, VP of Marketing ShipShape Urban Farms.
From the temperature, PH levels, lighting, and right amount of water -- Augusto manages the day to day operations using hydroponic technology.
They're able to recycle the water - using only 10% of what a traditional farm uses and cutting down the growth time from 10 weeks to five weeks. The process all starts with employees planting seeds into individuals cells.
While they're seeding each cell by hand -- machines will eventually take over the process. The seedlings are then placed into the nursery section of the container.
Each container is designed for one person to work about 15 to 20 hours a week. The containers producing 1,200 heads of lettuce weekly.
INFORMATION BOOK
"So one of the steps we did to help is to make more efficient. We developed these lids and all the farmer needs to do to harvest is to pull the lid out and they harvest all the lettuce at once," Augusto demonstrated.
Each container costs $95,000 and upward. Debuting their prototype in New Orleans at the Louisiana Restaurant Association Expo in August -- ShipShape Urban Farms generated a lot of interest.
"Over 3,000 people walked through garden close to 300 to 400 people say they were interested in becoming a ShipShape Urban farmer," said Speetjens. "Eventually we'd like to create a network of urban farmers where all of us work together to produce food for our local communities.
Because it's all done on the computer and backed up every 15 minutes on a server -- ShipShape can monitor every stage of growth and share success stories with other farmers. There's also an app that allows the farmers to control settings from their phones.
"We will be able to monitor all the urban farms through the computer system -- not only to assist them but if we have a container that is producing more than average -- we can contact that farmer and share their experience with other farmers," explained Augusto.
The company hopes to build about 850 over the next five years. So far they have more than 30 orders and say while their focus is on the southern region of the U.S. -- they've had interest from as far away as the Galapagos Islands, India, Canada, and South America.
US (MA): Container Farm Helps Provide Necessary Greens For College Lunch
HCC has been growing leafy greens inside the Freight Farms containers since October 2018. The project is a partnership with the city of Holyoke and MassDevelopment, who supplied the funding to purchase the two containers
In the early morning, Claire McGale, manager of HCC's Freight Farms urban agriculture program, received an urgent email message from Christopher Robert, chef supervisor for HCC dining services, which is managed by Aramark. They were in a bind. A national recall on Romaine lettuce from Salinas, California, issued over the weekend had left Aramark short of salad greens for the start of the week.
"He said, we'll take whatever you have," said McGale, a 2019 HCC graduate. Fortunately, they had a lot.
Over the course of the morning, McGale and her co-workers harvested close to 70 pounds of lettuce from the two repurposed shipping containers on Race Street managed by Holyoke Community College behind the HCC MGM Culinary Arts Institute.
"We were going to harvest today anyway," McGale said Monday morning, "but we're doing much more than we would have."
HCC has been growing leafy greens inside the Freight Farms containers since October 2018. The project is a partnership with the city of Holyoke and MassDevelopment, who supplied the funding to purchase the two containers.
Each container is a fully operational hydroponic farm equipped with 256 grow towers and the capacity to grow as much produce in a year as an acre of farmland, but without any soil.
The lettuce "picked" Monday – that is, pulled from the grow towers – included Romaine, two kinds of butterhead and sweet green crisp salanova.
"Unlike most places today, we have Romaine – thanks to Freight Farms," Robert said Monday.
The lettuce was used in the salad bar in HCC's cafeteria, for grab and go packaged salads, as well as toppings for sandwiches. Freight Farms "bailed us out," said Mark Pronovost, director of HCC dining services. "They helped us out big time."
Pronovost said he received an alert over the weekend about the recall on contaminated California lettuce and took immediate action.
"We threw out all our product," he said. "We don't take any chances. I don't know what other schools are doing, but reaching out to Freight Farms was easy for us."
Aramark has been buying Holyoke-grown Freight Farms lettuce and incorporating it into its salad blends since February, but never before as much as Monday.
"Today, because of what happened, it's pretty much all from Freight Farms," he said. "It's beautiful stuff. Tasty. Flavorful. Fresh. It's all hydroponic so it's nice and clean. They do a really nice job."
Monday was an auspicious day for Freight Farms in another way as well. They set a weight record for individual heads, recording 4.3 pounds for a container of 15 heads of salanova.
Freight Farms also supplies produce to the HCC culinary arts institute, Holyoke Medical Center and the HCC Food Pantry.
"That's encouraging," McGale said. "That's how I keep track of our success rate."
With more experience, McGale said, Freight Farms produce has become more robust. This batch of lettuce took five weeks to grow from seed to harvest.
She seemed especially impressed by two large heads of salanova she balanced in both hands.
Source: Holyoke Community College
Publication date: Wed 27 Nov 2019
A Tale of Two Crops
We applaud two current initiatives in agriculture that show how farming can be sustainable and can also build on unique local characteristics to gain a competitive edge
Business Day editorial
November 14, 2019 | Melanie Waithe
A variety of black, white and pink sorrel, which is grown by farmers Sharon Rosella Roopsingh and her husband, Renison. - ROGER JACOB
We applaud two current initiatives in agriculture that show how farming can be sustainable and can also build on unique local characteristics to gain a competitive edge.
What’s notable about the Cube Root farming model, which was featured in last week’s edition of Business Day, is how it repurposes an object that is traditionally not associated with agriculture and turns it into a means of farming without extensive acreage. Literally taking us out of the box, Cube Root proposes the use of containers as indoor farms. These containers can be carefully controlled to widen the range of products under cultivation, giving farmers a degree of flexibility they would not have if they took to the land. In light of the ongoing debate on land use, particularly with agricultural land being often diverted to meet other pressing needs such as housing, it’s an approach that is worth considering on a large scale.
A balance may be possible with container farming and similar initiatives which do not require expansive acres of often deforested land, with the run-on problems of chemical use, seepage into groundwater sources and the domino effect on local flora and fauna, especially in Nariva, the current food basket centre of the nation.
If there is anything Cube Root has achieved it is to remind us that creative thinking can help us get around some of the challenges we face when it comes to bolstering our food production, reducing our food import bill and securing our ability to sustain our population. Their product should be viewed as an important litmus test for the appetite for novel thinking within agriculture, the kind of thinking that will draw new, more diverse segments of society to this sector.
Meanwhile, there is an urgent need to generate income and foreign exchange, a matter which agricultural initiatives could assist in addressing. Being able to grow crops that might otherwise only grow in temperate climates not only helps us rely less on food from these zones but opens the door to newer export territories, spreading risk. It’s a process, however, that must be strategic of our exports are to have any chance of standing out in the crowded international market where other countries have long advanced their techniques of agricultural production.
Which is where Sharon Rosella Roopsingh and her husband Renison are in the pink. Their foray into sorrel production is inspiring, finding new tones and re-igniting interest in a seasonal favourite. As noted in last week’s edition as well, while sorrel is usually red, dark red or black – varieties all of which Roopsingh grows – she also grows a pink version which as attracted the attention of many people.
“We found it unusual and exotic and we went with it,” she says. It’s an example of turning something fortuitous to one’s advantage. Which is the perfect embodiment of what the sector as a whole needs to do if agriculture is to reap even bigger rewards.
The Cube Root of Farming - Freeport Company Grows Crops In Containers
Homegrown, totally organic crops is the vision Freeport-based Cube Root has for transforming TT’s agricultural sector by using technology to develop indoor farms. Cube Root recently held an exposition for investors and customers at its headquarters, where it introduced the concept of a specially constructed container featuring an enclosed, climate-controlled environment
Thursday 7 November 2019
Homegrown, totally organic crops is the vision Freeport-based Cube Root has for transforming TT’s agricultural sector by using technology to develop indoor farms.
Cube Root recently held an exposition for investors and customers at its headquarters, where it introduced the concept of a specially constructed container featuring an enclosed, climate-controlled environment.
Managing director Hamlyn Holder said each farm container is capable of producing kale, strawberries, lettuce or 100 different types of crops.
The investment required is an estimated $350,000, which can be paid off in instalments as a farmer simultaneously produces crops for sale.“A $350,000 investment is a high capital investment, but if you look at the operational expenditure and the returns you will get once you sell the produce, it becomes an economical model at that point,” he said. “If you look at the engineering, there is a consistency in growth, and if you compare the economics package to that of imported technologies, ours is very economical.”
Cube Root Farms’ managing director Hamlyn Holder checks on crops in the Cube Root container farm in Freeport. - MARVIN HAMILTON
Financing, he said, is available from institutions such as the Agricultural Development Bank.
In an interview with Business Day, Holder said there are many benefits to using this type of technology, including its being in an environment where farmers can control the impact of the elements and theft.
“In an open farm there are things like pests, weather, praedial larceny and other...factors. But here it is totally enclosed and controlled and you are able to see how your plants are growing remotely – also over the net, through an app on the phone.
“This type of technology offers a much more controlled environment to avoid any uncertainty when it comes to diseases and pests that may wreak havoc on your plants or fields."
The interior of a Cube Root container. According to the company, each farm, which is enclosed and can be controlled, is capable of producing a variety of crop, even those not usually grown in the region. - MARVIN HAMILTON
It also allows farmers to grow crops that are not local to the region.
“Technically there aren’t many indoor farms in 100-per-cent closed-environment agriculture. We are probably, in the Caribbean, the only manufacturer to manufacture from scratch our own container farm. We can grow from kale to strawberries to cherry tomatoes.
"We have done many trials throughout the last year, so we are comfortable at this point that the technology can give that consistency, so it’s basically limitless.
"The only thing we can’t grow is big trees at this point – but seasonings, flowers, fruits: we can do that.”
According to Cube Root managing director Hamlyn Holder, the farm container can produce kale and lettuce among as well as many other crops. - MARVIN HAMILTON
Holder said one of the company's goals for 2020 is the manufacture of seven container farms for new investors. He said it would also work alongside customers to ensure that events such as a glut of the produce do not take place.
“We also market the product so there is no glut on the market. We are trying to work with customers so that everybody grows and it is sustainable for the business model.”
He said a single farm can produce over 2,000 heads of lettuce twice monthly or once a month depending on demand.
Holder said the technology also ensures that no pesticides are used in the farming process, which instead uses an organic-based nutrient called Azomite and LED lighting systems.
Azomite, according to online sources, is a natural mineral substance that is mined from the desert in Utah and can be used as an agricultural fertilizer and/or soil amendment product.“We are striving for zero pesticides. Our technology is offering the option of zero pesticides (and) protection against bacteria, aphids, and fungus.”
Thursday 7 November 2019 Richardson Dhalai
Hydroponic Farms To Reduce Food Imports
In a 40-foot container situated in a warehouse in Central Trinidad, lies an amazing freight farm with the capacity of producing over 1,200 heads of lettuce, chive, and even strawberries
November 5, 2019
Lead Engineer at Cube Root Farms, Hamlyn Holder stands in a 40-foot container which was converted into at hydroponic farm at Preysal Crown Trace, Freeport. by: Kristian De Silva
Radhica De Silva
Lead Engineer at Cube Root Farms Hamlyn Holder stands in a 40-foot container which was converted into a hydroponic farm at Preysal Crown Trace, Freeport. © KRISTIAN DE SILVA
In a 40-foot container situated in a warehouse in Central Trinidad, lies an amazing freight farm with the capacity of producing over 1,200 heads of lettuce, chive and even strawberries.
Developed by Cuberoot Farms, the farm comprises of a state-of-the-art hydroponic farming system retrofitted inside a freight container.
Engineered by local agri-scientists and engineers, the farm is geared at producing enough crops to reduce T&T’s staggering food import bill.
During an interview with Guardian Media, Cuberoot Farm’s lead engineer Hamlyn Holder said they were hoping to share their technology with interested persons.
“We will provide training and our aim is to set up this entire system for 20 farmers,” he explained.
Using a stacky system with a fully-automated nutrient flow, one section of the farm produces four varieties of lettuce and chive. The other portion has a drip to waste system using cocopeat where other types of leafy vegetables could be grown.
“Everything is constructed in house. We utilise grow lights and this provides optimal temperatures for optimal growth. We use energy-efficient units to keep down operational costs while keeping plant performance high,” Holder said.
He said Agri scientists Jessica Churarian, chief executive officer Andrew Bridgemohansingh and Agri scientist Nkosi Felix were instrumental in establishing the farm.
“The Dexion shelving came from Massy, even the automation we put together. We have Alexa integration, CCTV cameras and we used local resources to put it all together,” Holder said.
He explained that everything grown on the farm is totally organic.
“We are aiming at using zero pesticides. Our systems are built so pests are mitigated against from bacteria to aphids or fungus. This type of technology offers a controlled environment when it comes to disease,” he explained.
After two years of trials, Holder said they were happy to report that more than 100 varieties of different crops could be grown in the farm.
Saying this was T&T’s only indoor farm, Holder said using the climate-controlled environment the farm can imitate the ideal conditions for crops to generate bountiful yields.
“We have grown strawberries, cherry tomatoes. We did many trials and technology gives that consistency. It is limitless and definitely can be used to grow any leafy vegetables as well as some flowers,” he added. Anthuriums were seen growing in the farm along with parsley, kale, baby spinach and cilantro.
Holder said the Ministry of Agriculture was very supportive of the project and so was the Agricultural Development Bank.
“We want to show this technology to the show this new technology to Minister of Health and the Minister of Education so they can incorporate technology into agriculture and reduce health issues as well as the food import bill,” he added.
Kennedy Charran of Greengold T&T Limited said the farm was innovative and had great potential. He said interested persons will see a return in investment adding that once the farm is bought it could last for decades.
Tagged in:
The Economics of Container Farming In Nauru
You might be excused for not knowing much about the country of Nauru. It’s a small island in the Pacific Ocean that’s only ten times larger than Microsoft’s campus in Redmond with one-fifth the people. The 11,000 citizens of Nauru occupy a footprint of about 8.1 square miles (21.98 sq. kilometers) out in the middle of absolutely nowhere where the waters are so deep they never have to worry about tsunamis
People from countries we refer to as frontier markets must roll their eyes when some people in America talk about how “oppressed” they are. The same people complaining about how bad it is in the States probably think Africa is a country when in fact it’s 54 countries. A lot of Africans actually are oppressed because about half of the continent’s countries are run by dictators. If you can go into your local store and buy some fresh lettuce at any hour of the day, 365 days a year, you’re not oppressed. Most people around the world don’t have access to a large selection of fresh vegetables or the means to purchase them. Take Nauru for instance.
You might be excused for not knowing much about the country of Nauru. It’s a small island in the Pacific Ocean that’s only ten times larger than Microsoft’s campus in Redmond with one-fifth the people. The 11,000 citizens of Nauru occupy a footprint of about 8.1 square miles (21.98 sq. kilometers) out in the middle of absolutely nowhere where the waters are so deep they never have to worry about tsunamis. About once a month, a ship will cruise into the harbor dropping off loads of food and supplies. Vegetables are all flown in by air. With its pleasant island breezes, Nauru is a hidden gem that happens to be the least visited place in the world. As a result of not having to deal with obnoxious tourists, the citizens are some of the kindest people you’ll ever meet. They’re also the world’s most portly. You would be too if you had to pay these prices for vegetables.
Produce prices in a Nauru supermarket in AUD – Credit: Nanalyze
We did the math for you on those numbers. If you want to buy a head of lettuce in Nauru, you can’t. They don’t have any right now. If they did, you would pay $3.29 a pound or $7.25 a kilo in greenbacks. That’s more than three times the retail price of lettuce in the United States which sits at around $1.09 a pound. In order to solve the obesity problem which commonly afflicts island nations like Nauru, we need to make healthy food more affordable. Maybe we can use something Nauru has a whole lot of already – shipping containers.
In a previous article, we wrote about the newly sprouted industry of “vertical farming.” Also called indoor farming, the eleven startups we looked at have collectively raised more than $900 million in venture capital so far. The appeal is in the delicious numbers. Indoor farming uses 95% less water and yields 400 times more output than the same land footprint when compared to traditional farming methods. That’s what it says on the tin, but the experts are skeptical when it comes to indoor farming using shipping containers like the one seen below.
The Greenery from Freight Farms – Credit: Freight Farms
Container Farming Economics
We’re not interested in the “farm to table” marketing spin being put on container farming, we’re solely interested in the economics. For that we can turn to Peter Tasgal, a man who used to work as an investment banker before he managed to turn his life around and became the CFO of a $100 million consumer packaged goods company. Today, he’s an agriculture consultant, and this past February he penned a piece on “What is the Future of Container Farming?” in which he talks about how it’s largely a niche business applicable to applications like “restaurants, traditional farmers seeking to maintain year-round customers, clean rooms, and areas of extreme climate.” This table pulled from his article compares various methods of farming:
Source: Agfunder News
Container farming has the “highest cost per delivered pound” with Mr. Tasgal stating that it’s “at best four times as expensive per pound to grow in a container farm and more likely over 10.0x as expensive as compared to traditional farming methods.” He proposed that either technology can be used to reduce the cost per pound (nothing on the horizon yet) or people can pay a price premium for “better quality produce.” Since the people of Nauru already pay a price premium, this isn’t exactly a showstopper.
Some Initial Concerns
We shipped one of our MBAs over to Nauru to visit with Mathew Batsiua, former Health Minister of Nauru, and someone who has spent the last 4 years of his life fighting his own version of an African dictatorship with the local government. He thinks that container farming might be able to provide the Nauruan people with an alternative to purchasing over-priced greens at the supermarket. Aside from being able to offer cheaper and fresher greens, container farming could be used as part of a school program to get the country’s youth eating healthier. An additional benefit would be creating some local jobs. If the initial implementation works out, Nauru could act as a model for other Pacific Island countries that all have a similar obesity problem for all the same reasons.
Some initial concerns he raised around container farming:
Support and training
Durability of the components in the unique climate of Nauru
Consumption of electricity
The need for solar integration
Availability of consumables required to operate the farm
In order to gauge the suitability of container farming for the country of Nauru, we’re turning to “the world’s leading manufacturer of container farming technology,” a startup called Freight Farms.
Freight Farms
Founded in 2013, aptly named startup Freight Farms hails out of Bahstun Massachusetts and has raised $11.4 million in funding so far to develop “high-volume crop production units made from upcycled shipping containers to support farming in any climate.” Their container farming solution can produce over 500 types of lettuces, herbs, leafy greens, and small root vegetables at a commercial scale. As of January 2019, their hydroponic container farms can be found in 38 U.S. states and 15 countries. Their latest growing platform, The Greenery, costs $104,000.
Credit: Freight Farms
It’s a significant price increase over their previous container solution, The Leafy Green Machine, which ran just $76,000. That’s because The Greenery has over 70% more growing space than the Leafy Green Machine.
If we’re going to deploy The Greenery on Nauru, we need to get it there first. Let’s say that’s an additional $8,000 in shipping costs. With an initial capital outlay of $112,000, we can begin to crunch some numbers. Firstly, let’s look at the operational requirements:
Credit: Freight Farms
Nothing too alarming here. Water is clearly in short supply for Nauru but 5 gallons a day is manageable. One gigabyte of data a month is affordable. We need to consider that electricity in this part of the world is more costly as well. Consumables like peat moss plugs, seeds, and nutrient solutions will all need to be imported by ship. Let’s do some back-of-the-napkin math and see how much time it might take to recoup our initial investment.
Container Farming Yields
According to an article by the University of Saskatchewan on hydroponic lettuce, “all it takes to grow one lettuce is 1 g of fertilizer, 1 L water, 1 seed, and 1 Jiffy-7 peat pellet, at a cost of as little as 10 cents per plant.” Now we have an estimated cost per head of lettuce. “With an average plant success rate of 95%, you can plan on harvesting about 940 plants a week,” says Freight Farms. They’re talking about harvesting lettuce at a 4-week maturity and we’re estimating the weight of each lettuce head to be 4 ounces based on an estimate given from Bright Agrotech in their article on How Much Can Container Farms Really Grow? That gives us 235 pounds of lettuce a week or 12,220 pounds of lettuce a year (just over 6 tons). If we sold that lettuce at $1.64 a pound – about half the price of lettuce on Nauru today – that gives us about $20,040 in revenues a year. For consumables, let’s assume ten cents per plant (48,880 plants = $4,888). For electricity, the company states that power consumption for a Greenery ranges from 150-165 kWh per day. Here’s an idea of electricity rates on Nauru in AUD.
Credit: Nauru Utilities Corporation
Unless we can convince the government to cut us a break, the math works out to $21,900 a year AUD which is $15,064 a year USD in electricity costs. Subtracting our costs ($15,064 + $4,888) from our revenues ($20,040) we get a meager profit of $88 and we haven’t even considered labor or the cost of support. Barring any serious errors in our assumptions, it doesn’t look like container farming would be very economically viable for the country of Nauru. Even with electricity subsidized at the lowest domestic rate, we’re still looking at 10 years before we can receive a return on our initial capital outlay and that’s without considering the time value of money.
Conclusion
Container farming shouldn’t just be about producing better tasting “farm to table” produce for over-priced restaurants to sell at a premium to well-off diners, it should do something better than that for mankind. Our back of the napkin calculations don’t quite add up. Sure, we might be able to negotiate down the price a bit, or the Government of Nauru might subsidize the operation, but as we’ve said before, subsidizing the world’s problems won’t scale. The operation needs to be self-sustaining, generate a profit, and provide an ROI in a reasonable amount of time. If you think your container farming startup can provide a solution to Nauru’s obesity problem, Mr. Batsiua would like to have a chat with you. Just drop us a line and we’ll put you in touch with him. Stay tuned for our next article on container farming where we look at all the players in this space in addition to Freight Farms.
Health Check Kids: Leafy Green Machine Planted At West Warwick High School
With permission and funding from the school district, a 40-foot climate-controlled container was planted just outside the cafeteria doors more than a year ago. And that's when the science department got on board
by BARBARA MORSE, NBC 10 NEWS
Thursday, October 31, 2019
A Leafy Green Machine planted at West Warwick High School. (WJAR)
To View The Video, Please Click Here
Sodexo — the school district’s food service company — seeing it in action at a University in Massachusetts.
"And we figured, gee, what a great idea. Local food, right on site. Why don't we just bring it in," said Donna Walker, general manager of Sodexo food services for the West Warwick School District.
With permission and funding from the school district, a 40-foot climate-controlled container was planted just outside the cafeteria doors more than a year ago. And that's when the science department got on board.
"We learned how to run the machine, how to seed and transplant and harvest the lettuce," said Gina Poulos, a science teacher at the high school.
Then they got students involved -- forming the leafy green club.
"I'm super interested in plants and all type of agriculture and it's a nice, relaxing thing to do after school or even in the middle of school when we have advisory and I can kind of just plant stuff and get to learn and talk to other people," said Joshua Dick, a junior at the high school.
"I love salads and I always thought plants were so cool. I always love going to botanical gardens and just thought it was so cool and was like why not," said Gabrielle Dascoli, a senior.
The plants, most leafy green lettuce, are grown -- chock full of nutrients -- vertically, which is a space saver. Special lights are programmed remotely. And the process uses minimal water and electricity.
Harvested and turned into salads within hours.
"I think it tastes amazing. you can taste the nutrients. You can tell it's really thought out. It's great," said Gascoli.
"We're trying different things,” said Walker. "We've done tomatoes, we've done some herbs, we've done kale for soups and stuff."
The leafy green machine can produce up to two acres' worth of greens. The modified shipping containers are re-purposed into green machines by Freight Farms in Boston.
Can Container Farming Help Meet The Rising Demand For Local Food?
With container farming, farmers can actually control the climate, along with soil, quality, heat and even light exposure. The containers use technology to be retrofitted with heating and water systems, and gas and electrics can also be installed to offer a whole host of benefits for crops and farmers alike.”
October 24, 201
© Andrii Zastrozhnov |
With the demand for local produce constantly rising due to environmental, economic and quality reasons, Johnathan Bulmer, MD at Cleveland Containers, has urged for more pick up on container farming
He suggests that, with Brexit also looming and causing uncertainty as to where the weekly food shop will come from, container farming can produce many of our favorite fresh produce in the UK. The fully contained structures allow for year-round growth no matter the weather or available land.
Bulmer said: “Most of us are eating produce that has traveled thousands of miles from its source. One of the reasons why UK supermarkets sell fruit and vegetables which aren’t often produced in the country is that farmers face the challenge of providing seasonal produce all year round – which isn’t possible with changing weather conditions.
“But with container farming, farmers can actually control the climate, along with soil, quality, heat and even light exposure. The containers use technology to be retrofitted with heating and water systems, and gas and electrics can also be installed to offer a whole host of benefits for crops and farmers alike.”
This modern twist has helped farmers to produce goods all year round, avoiding common restrictions such as extreme weather, pests, and seasonal struggles.
Bulmer estimates that container farms can produce up to 4,000 heads of lettuce every ten days, using no soil and 97% less water than a conventional farm.
“Crops are protected from nasty pests, eliminating the need for pesticides which can also cause health problems in those who consume them,” he continued.
One company, Freight Farms, has produced its ‘Leafy Green Machine’, which it claims to cut water demand by up to 98% using hydroponic container techniques, which could help to reduce demand on freshwater reserves.
Benefits of local produce
By cutting the distance that our food has to travel, greenhouse gas pollution from air freight is minimized, and the shorter distance means that it’s sold sooner after it’s grown and picked.
This benefits not only the taste due to it being fresher, but producers can also pick from a wider variety of fruit that has great flavor but doesn’t usually travel well so it isn’t sold.
He said: “There are a host of other benefits to container farming for local produce. It benefits the local economy, reduces the seasonality of foods, and also cuts down on plastic waste which is often multi-wrapped to protect it from travel.
“This boost in freshness can reduce food wastage and encourage more nutritional diets with simple, fresh ingredients. And you also don’t get the problem of land being in the wrong place or relocation restrictions, because container farms are so flexible. They can be easily stacked, which means farmers also won’t need to empty their pockets and pay for extra land to expand – you build up.
“We’re seeing a huge amount of farmers deciding to go down the container route in this country. The flexibility and option to mass-produce fruit and vegetables within such a short space of time, along with savings on waste usage means they can save costs, but produce seasonal fruit and veg all year, without being limited by space,” Bulmer said.
“There is a billion-dollar consumer demand for local food – let’s work together to achieve it.”
Cleveland Containers offers one of the largest nationwide stocks of new and used shipping containers, available throughout the UK.
Based in Middlesborough, its models for sale or hire come in all sizes to fit different needs. From 6 to 45ft, its specialized containers can be used for storage, office containers, site accommodation, farming, hospitality and more.
US: Colorado - Students At Mountain Vista High School Were Ready To Start The Year By Getting Their Hands Dirty Via The Agricultural Business Course
For the past two years classes and interns have operated the Mountain Vista Farm, which utilizes a hydroponic growing system called the Leafy Green Machine
By James Conlan / Ag Journal
October 16, 2019
Students at Mountain Vista High School were ready to start the year by getting their hands dirty via the Agricultural Business course taught by David Larsen.
“As part of the program, students are responsible for all aspects of the Mountain View Farms business,” Larsen said.
After being introduced to the different business principles, students are tasked with integrating them into running a successful business. Some of these tasks include marketing, social media/website, communications, graphic design, printed literature, handling of money/accounting, customer service, food safety, and business plan development.
“Agriculturally, they have to figure out all of the elements including environment, nutrient, tech, engineering, and automation to keep the plants alive and healthy for sale,” he said.
For the past two years classes and interns have operated the Mountain Vista Farm, which utilizes a hydroponic growing system called the Leafy Green Machine.
“I think hydroponics is far more sustainable and reliable than traditional farming for the crops we can grow,” he added. “This technology produces absolutely delicious products that are fresh and last multiple times longer than what is sold in stores.”
He said utilizing this machine involves more people in the local production of food, potentially builds community and is a great educational tool for life skills. For students of his Agricultural Business class he said they gain soft skills in terms of being a good employee including punctuality, engagement, responsibility, as well as a good representation of the business to the public.
Another added element to the Leafy Green Machine is the ability of students to use the app Farmhand App.
“When we first started Freight Farms, we considered ourselves a hardware platform – but our views quickly expanded for two reasons,” Freight Farms CEO, Brad McNamara said.
The first reason was when he and co-founder Jon Freidman realized their clients needed a way to stay in contact with their farms remotely. The second reason was that they wanted to address a historical challenge in the farming world. Which they said was the lack of reliable and transferable data between farms to increase overall agricultural efficiencies.
“At the time, there wasn’t a turnkey hub for industrial-scale IoT, few if any climate-control apps for hydroponic indoor growers, nor a sophisticated way to bridge the gap between emerging IoT technology and old programming control language,” he said.
So building from the ground up, he said that they developed an integrated software platform called Farmhand. Which would enable its users to monitor and manage farm components remotely, automate tasks and analyze growing data.
“As IoT technology has evolved over the years, we’ve continuously integrated new updates and advancements to help our customers operate increasingly efficient farms with the touch of a button,” he said.
Consumers of Freight Farms products don’t just include schools, according to McNamara their tech has been used at restaurants, nonprofits, retail establishments, hospitality organizations and corporate employee benefit programs.
“We’ve been focused on taking the most advanced hydroponic technology and making it approachable. Enabling people of varying ages, experience levels, and industries to become successful food growers,” he said.
Container Farming In The City
Modern industrial agriculture is a resource-intensive endeavor, requiring massive amounts of land, water, and energy. Some urban farmers are thinking outside the box by bringing their farms inside the box in the form of shipping containers
Corner Stalk Farm grows an acre’s worth of lettuce in a shipping container that only takes up 320 square feet. (Photo: Jay Feinstein)
Modern industrial agriculture is a resource-intensive endeavor, requiring massive amounts of land, water, and energy. Some urban farmers are thinking outside the box by bringing their farms inside the box in the form of shipping containers. Living on Earth's Jay Feinstein and Aynsley O'Neill took a trip to Corner Stalk Farms, in East Boston, Massachusetts to find out more.
Transcript
CURWOOD: Industrial agriculture today is a resource-intensive endeavor, requiring big machines, plenty of land, water, and energy to produce much of the food on a typical American dinner table. And as the public trends more toward plant-based foods, some are thinking outside the box by bringing farms inside the box. By retrofitting old shipping containers with grow lights and hydroponic gear, what would take about an acre of land to grow vegetables such as lettuce can be fit into just 8 by 40 feet. Living on Earth's Jay Feinstein and Aynsley O'Neill took a trip to Corner Stalk Farms in East Boston, Massachusetts to find out more.
GPS: Your destination is on the right.
O’NEILL: The only other time I've been to East Boston was to go to the airport. So I'm a little surprised at how busy it is. And I see these shipping containers. I mean, right in the middle of these houses and behind the auto body shop...but, here we are!
FEINSTEIN: You know, the funny thing is a farm like this would not have even been legal until 2013, when Boston revamped its zoning code.
O'NEILL: I didn't even know that someone would make a farm illegal.
FEINSTEIN: Yeah, I know, right?
O'NEILL: Do you think that's the guy upfront?
FEINSTEIN: Yeah, I think so.
O'NEILL: He's a little less sunburned than most farmers.
COONEY: My name is Shawn Cooney. And I'm the partner and owner of Corner Stalk farm in East Boston, Massachusetts, and we started in 2014. So this is it. So we...there's not too much to it. I mean, it's basically you've seen the whole of the farm by walking the 120 feet or so.
FEINSTEIN: That's amazing.
COONEY: And we've got four units that are you know, basically growing lettuce year-round. And, you know, that's it. Do you wanna go inside?
O'NEILL: Yeah!
FEINSTEIN: We'd love to.
COONEY: Cool.
O’NEILL: Well, it's definitely a few degrees cooler in here.
FEINSTEIN: And these lights are blinding. I mean, these red and blue lights, LEDs, it’s something like out of a sci-fi movie.
O'NEILL: Are those the plants in those columns all up and down?
COONEY: Right. You really need just an industrial area, you need a, you know, a place where you can basically bring as many plants as possible into as little amount of square footage as possible. So we kind of look at it as cubic feet. In a real farm, you're talking about square footage and acreage. Here, it's really cubic feet. We've got so many feet on the floor, but we plant plants up to ten high.
FEINSTEIN: So, show us around.
COONEY: Okay, so basically, you walk in and we're in a complete self-contained farm. We've got a climate control system, and a lot of fans keep the air moving so that everything's happy. And the plants get a little bit of stress. If you just leave them without any movement, the plants actually get weak.
O'NEILL: Wait, so they need exercise? They're lifting weights, they're jumping jacks, they're?
The shipping container uses a combination of red and blue LED grow lights and hanging hydroponics to grow their plants. (Photo: Jay Feinstein)
COONEY: Uh, pretty much yeah, it's stressing the plants is what it's really called in the industry, but they do need to be moved around for them to have a good texture to them, so that the cell walls are thick enough, so that it's not just eating a piece of water.
O'NEILL: And you can maintain it all using a box on the side of the container.
COONEY: Yeah, there's a tiny little antique style computer that's, that's very industrial. And you can log into it from the outside world. If you want to fiddle around with settings, or just check on everything, you can do that from home, you can do it from from vacation, you can do it, whatever.
FEINSTEIN: So how did you get into this?
COONEY: I started three software companies and sold them. And I started doing business plans, looking for the next thing, and one was the ag tech farming. This kept coming up is something that was interesting. Dug a little further, did a little more business planning, and it won. My wife and I self funded it, and we have loans and the loans are from the US Department of Agriculture, like a regular farmer would get his loans.
FEINSTEIN: So what are you growing in here?
COONEY: Well, mainly we grow lettuce. That's our business. And we've grown tomatoes, we've grown lots of flowers, we've grown all kinds of herbs, and God knows what else. But it turns out that as a business, you have to sell what people buy every day. And what people buy every day is our greens, even our restaurants, that's what they want.
O’NEILL: Well, so you sell to individuals and you sell to restaurants.
COONEY: We sell, we sell to both, we sell probably 50/50. We sell to a bunch of nice restaurants in the Boston, downtown Boston area. We deliver to them. And we sell to regular consumers.
FEINSTEIN: But still most of your customers, are they still in Boston? Because that's hyper local, when you think about it. You growing in Boston, you're selling in Boston?
COONEY: Oh, yeah. Yeah, no, they're all in the metro Boston area. A lot of Cambridge customers. But it is, you know, it is basically a hyper local thing. The reason we keep the customers is it's a better product than what you can by at, you know, pretty much anywhere. Basically what it comes down to is it looks better. It tastes better, and it's got more nutrients, and it feels better. It's got better texture. So that's kind of what people are buying.
FEINSTEIN: Tell us more about hyper local, it's sort of a buzzword nowadays. People say it's better for your health; it's better for the environment. Is that true?
COONEY: Pretty much, yeah, it's true. And it's got a downside. The downside is it's probably a little more expensive also. But it is - any vegetable, once you harvest it, loses some somewhere around 7% of its nutrient value every day from the day they're harvested, up to a point. And they lose a lot of their texture, and their attractive qualities. What we sell is still alive, we sell the lettuces with the roots on them. You get a much better life cycle lot of them that way. So they're, they're basically not losing any nutrients. And they maintain their freshness. If you ever had the experience of buying a nice box of brand name, cut lettuce in a plastic bin, that looks great, and you get home and then two days later, it smells funny and you've got black sludge on the bottom. That won't happen with what we're selling.
O'NEILL: I was wondering because there are times when I have bought, like you said, cut lettuce from the grocery store. And it's a race against the clock.
COONEY
I mean, that's one of our biggest customer satisfaction points, and our selling points was that you get to use it all. It's not like you're buying a $10 package of lettuce and using $3 worth. You know, with us you buy a $10 package of lettuce and you get to eat $10 worth of lettuce. But you can go on vacation, you can go on a business trip, and you can come back and still have something in there that's perfectly palatable.
FEINSTEIN: What type of environmental cost are you saving?
COONEY: Regular farming is a "grow as much as you possibly can and sell it when it's ready, as fast as you can". We’re an on-demand business, because we don't grow extra. We’re growing pretty much what we're selling, give or take a little bit. You know, and one of the things we definitely don't do is waste any water. No matter how good you are at growing outside, you could never grow with the kind of water use we have. We use, say 1000 plants we can grow in one unit, we probably use 25 gallons of water a week. So you couldn't water your patio plants for a week with 25 gallons and keep them alive.
Shawn Cooney and his wife Connie (not pictured) own Corner Stalk Farm, in East Boston, Massachusetts. (Photo: Jay Feinstein)
O’NEILL: So what was the inspiration behind deciding to build a farm inside? And I don't mean in a greenhouse. And I don't mean in a window box or anything like that? What was the shipping container idea?
COONEY: Part of it is, it's a durable, clean environment that can put up with the stresses that farming puts on a space. And basically there's all kinds of stuff that goes on in here that would basically bring down a building. You know, it would ruin the walls, you couldn't clean it. If something ever happened in here, we had some kind of a mold infestation or something. You could shut everything off. And you can sanitize this place just like you would the clean room in a restaurant or a food processing center.
FEINSTEIN: To what extent do you use chemicals in here?
COONEY
We do use them once in a great while. We can't be organic because we don't grow in dirt, it’s a water based environment, but we adhere to the organic principles. Generally, the way we control any kind of a pest in here is kind of preemptive. We basically use ladybugs. We ship them in once a month or so, and sprinkle them around, and they pretty much do the policing of any kind of bugs in here. And when we have had to use something it's called chrysanthemum oil.
O’NEILL: May I ask? May I try some of the lettuce?
COONEY: Sure. Okay, well we harvested some
FEINSTEIN: What is it?
COONEY: This is the Salanova Red Butter. There's not many people who actually have favorites, but if they do, this is the one that they want. So go ahead, have a taste.
O'NEILL: Sure looks like normal lettuce...
[SFX CHEWING]
O’NEILL: I don't mean to sound incredulous, but I'm a little incredulous. Might I have another one?
COONEY: Sure.
O'NEILL: Alright.
COONEY: Finish them all.
FEINSTEIN: It's very green.
O'NEILL: It's very green.
FEINSTEIN: I’m gonna try this too.
[SFX CHEWING]
FEINSTEIN: Wow, you can taste like it was grown right here. It was.
O'NEILL: It's definitely fresh. I mean, you literally just clipped it right in front of us. But it's... that's... I've never had lettuce like this. This I would eat. on its own, I don't even feel like I need to be you know, putting salad dressing on it. Or, oh, I need a crouton or something.
FEINSTEIN: And this is a weird thing to say too. But it kind of feels alive.
COONEY: You guys want to try something a little, little further on the edge? This is called wasabi arugula. And I grow it for a couple of restaurants. And they use it instead of wasabi on their crudo and their raw fish and their raw meats. So here, take a leaf of that and be prepared.
Jay Feinstein (left) and Aynsley O’Neill (right) prepare their notes and audio equipment outside Corner Stalk Farms. (Photo: Steve Curwood)
FEINSTEIN: All right, I'm prepared. I don't know what to expect here.
[SFX CHEWING]
FEINSTEIN: It does taste like wasabi. But it it's a little milder, but I love it actually.
O'NEILL: I myself am a little terrified. I have an all time low tolerance for wasabi.
[SFX CHEWING]
O’NEILL: Well, it is a bit much for me, but it is really good. And I'm a little astonished that it's not coming in those tiny little balls of green mush.
COONEY: It's actually a real arugula, and it just happens to have that flavor profile. It's not related to wasabi at all. It's the same as the arugula you buy in the plastic package, family wise.
O'NEILL: Well, I know that some people will call arugula "rocket". And that was certainly, you know, a blast off of flavor.
COONEY: Yeah, this is much closer to the rocket family part of arugula than the general arugula you buy in the store.
O'NEILL: So what do we owe you now? 10 bucks for the lettuce, and how much for the arugula?
COONEY:10 bucks for the lettuce, and the arugula is free.
O'NEILL: Well, I think we're all ready to head out. Thank you again for showing us around.
COONEY: Oh, you're welcome.
FEINSTEIN: Thank you so much.
COONEY: Thanks for coming. I appreciate everyone's time.
CURWOOD: That’s Living on Earth’s Aynsley O’Neill and Jay Feinstein with farmer Shawn Cooney at the shipping container called Corner Stalk Farms. And by the way, we ran some numbers, and found that the shipping container farm is using 99 percent less water than a traditional farm would use to grow the same amount of produce. The farm is also saving on the order of 5 metric tons of carbon dioxide in shipping for each crop, which is roughly what would be emitted to truck the same amount of lettuce from California to Boston. Around 300 of these types of shipping container farms have been sold as of now. This story is part of our series, Cool Fix for a Hot Planet. For pictures and more visit our website, LOE.org.
US - Massachusetts: Hydroponic Farm Grows At Framingham High School
Via a mobile app, staff can monitor the crops, adjust the pink ultraviolet light, and prompt a light rain without setting foot inside the farm. A webcam even snaps a photo every three minutes, so they can see changes as they happen. If any crop’s reading falls outside of the target range, the app will send a notification
By Zane Razzaq
Daily News staff
October 11, 2019
Via a mobile app, staff can monitor the crops, adjust the pink ultraviolet light, and prompt a light rain without setting foot inside the farm. A webcam even snaps a photo every three minutes, so they can see changes as they happen. If any crop’s reading falls outside of the target range, the app will send a notification.
FRAMINGHAM – In an old shipping container behind the high school, towers of lettuce enjoy springtime.
Walls of kale and other greens stretch down an aisle the length of the trailer, fed by ropes of LED lights that mimic sunlight. A wall-mounted keyboard that serves as the 320-square-foot hydroponic farm’s brain keeps the temperature at a steady 70 degrees. Every hour, a fan clicks on to distribute a spurt of carbon dioxide for a minute, helping the plants grow.
Later in the day, members of the Food Service Department will pluck leafy greens such as red romaine or wasabi arugula from about 35 grow towers. Then, produce is packed in crates and distributed to city schools to feed thousands of students.
“They might never see lettuce like this in their lifetime,” said Brendan Ryan, the foodservice department administrator for Framingham schools, holding up a particularly delicate lettuce. “You would be hard-pressed to buy this lettuce on the open market because it’s so hard to maintain.”
This will be the department’s first full year using the $104,000 product, which was first installed in April. It can grow the equivalent of two acres worth of vegetables inside without soil year-round.
Purchased from Boston-based Freight Farms with money from the department, it’s an example of the urban farming trend that the schools are now embracing. The indoor farm uses the technology of hydroponics: a technique where plants are grown with a nutrient solution and the same water recirculates repeatedly. Soil is not used.
For Ryan and his staff, it’s the latest “marketing tool” to promote the department, which previously started an outdoor garden to grow sunflowers, potatoes, corn and more.
“We’re trying to be as cutting-edge as we can and make sure that we’re serving these kids the best freshest product possible,” said Ryan. “This is one way for parents to see we’re making the lettuce right outside.”
Via a mobile app, staff can monitor the crops, adjust the pink ultraviolet light, and prompt a light rain without setting foot inside the farm. A webcam even snaps a photo every three minutes, so they can see changes as they happen. If any crop’s reading falls outside of the target range, the app will send a notification.
Containers of nutrient-infused water – chock-full of minerals found in healthy soil such as nitrogen, potassium, phosphorous – pump through tubes to the crops growing in polymer mesh.
Getting the hang of the technology posed some learning curves, said Raquel Vazquez, director of foodservice operations. For example, it takes more than an hour to calibrate the water tank filters to make sure every nutrient is properly dispensed into seedlings.
“If we don’t, then it improperly imbalanced and then our crops won’t yield as well,” said Vazquez.
The inside of the freight container also needs to be kept extremely clean to avoid problems like algae growth.
Ryan likened the “new endeavor” to going from “being a butcher to a brain surgeon.”
A head of lettuce that would normally take 14 to 16 weeks to grow in a field takes about eight weeks inside the trailer, 365 days a year. Another advantage: Crops are not exposed to any contaminants and are “beyond 100% organic,” said Ryan.
And it produces lettuce and other vegetables that would be too expensive for the district to buy from vendors, like the delicate lettuce that outside vendors would likely not risk shipping.
“They’re not going to be taking packed very well, they don’t take the exposure to extreme temperatures very well,” said Ryan, of the fine leaves. “You pack these in a shipping truck, stacked 30, 40 cases high – they flatten. Here, this crate goes right to the school.”
Vazquez said it also poses a learning opportunity for students, saying some have already toured the unit. Eventually, the biology department hopes to incorporate it into the curriculum.
“While our staff serves pizza on Fridays, they’re really teaching them about what hydroponic greens are, where this came from, all the way down to kindergarten. They’re starting to eat it and try it and taste it,” said Vazquez.
Ryan and Vasquez hope the high-tech aspect of the farm will get teens interested in farming as a career.
“A lot of kids think of agriculture as some lone farmer covered in mud in the middle of a field with a tractor. And it’s not anymore,” said Ryan.
Zane Razzaq writes about education. Reach her at 508-626-3919 or zrazzaq@wickedlocal.com. Follow her on Twitter @zanerazz.