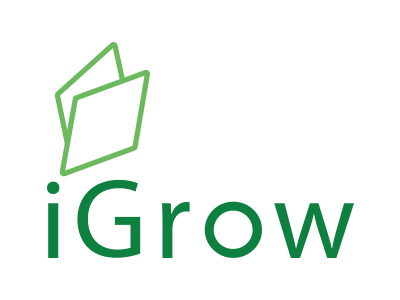
Welcome to iGrow News, Your Source for the World of Indoor Vertical Farming
Square Roots Opens New Indoor Farm, Produces First Harvest
The farm’s first locally grown harvest of herbs and greens that includes basils, arugula and radish microgreens will be available for consumers to purchase on e-commerce platforms, restaurants and grocery stores across the Great Lakes region in the coming weeks
April 15, 2021
New York-based Square Roots, an urban indoor farming company, opened a two-story indoor farm located at Gordon Food Service headquarters in Wyoming.
The farm’s first locally grown harvest of herbs and greens that includes basils, arugula and radish microgreens will be available for consumers to purchase on e-commerce platforms, restaurants and grocery stores across the Great Lakes region in the coming weeks.
Construction on the indoor farm began in December and the first seeds were planted in March. The farm is cloud-connected and is managed by Square Roots’ farmers and in-house software.
“COVID-19 exposed major weaknesses in the industrial food supply chain and accelerated the already fast-growing local farming movement,” said Kimbal Musk, co-founder and executive chair of Square Roots. “Square Roots can now deploy commercial-scale, controlled-climate farms, fast, in locations across America to meet the demand for local food, all year-round. My wider mission is to bring responsibly grown, local food to everyone in America.”
A farmer harvest basil. Courtesy Square Roots
The farm’s proprietary OS, otherwise known as The Square Roots Farmer Toolbelt, provides day-to-day guidance to farmers while capturing millions of data points throughout growing cycles. The data can then be analyzed to determine how changes in certain environmental parameters impact factors like yield, taste, and texture.
In addition to the technology that drives its operation, there also are cold storage, biosecurity, climate-controlled packaging space, and distributor loading docks, among other things in the farm that ensures food safety.
The new indoor farm is Square Roots’ third commercial facility.
Lead photo: Construction on Square Roots' indoor farm began in December and the first seeds were planted in March. Courtesy Square Roots
When We Started Freight Farms In 2010, There Was No Such Thing As An “Ag Tech” industry
Freight Farms has a passionate customer base of small businesses, entrepreneurs, traditional farmers, hotels, restaurants, corporate campuses, universities, and non-profits
We weren’t even sure how to explain what we were trying to do to our own friends and family! But we knew that there was a need for urban agriculture to emerge as a competitive industry in the food landscape. That’s why Freight Farms was born—to build the infrastructure and technology that would allow local food to thrive around the globe.
Less than a decade later, we are proud to be on the forefront of the fast-growing Agriculture Technology industry. Freight Farms has grown into a platform that anyone can use to supply their communities with fresh produce year-round, regardless of background or geographic location. We’ve had the pleasure of launching our container farming system in over 44 states in the US and 24 countries around the globe, creating the largest network of connected farmers.
Freight Farms has a passionate customer base of small businesses, entrepreneurs, traditional farmers, hotels, restaurants, corporate campuses, universities, and non-profits. We’d love to welcome you into our community of Freight Farmers, and our team is ready to help you get started.
Jon Friedman and Brad McNamara
Freight Farms Co-Founders
VIDEO: One Sure Way To Save Our Soil – Don’t Use Any
The advantage of container farming is the ability to create commercial-scale production within a small space the size of your standard 40-foot shipping container through vertical farming techniques
In the push for regenerative agriculture and soil rehabilitation, container farming has an important role to play.
The idea behind regenerative agriculture isn’t new, but this year it is front and center as one of the key initiatives of the official Earth Day 2021 campaign: Restore Our Earth™.
According to the Earth Day organization, overfarming has caused soil capacity in the U.S. to decline dramatically, losing soil 10 times faster than it can be replenished. The result is that in many places, the land has as few as 60 harvests left before it is completely depleted. Unfortunately, with ownership of farms increasingly concentrated in the hands of industrial or foreign producers, the promise of short-term profits wins out over long-term solutions that would prioritize soil health.
What is regenerative agriculture?
Regenerative farming takes an opposite position. As a school of thought, it is a method of farming that actively fights soil degradation by restoring carbon to the soil, which has a double benefit of renewing the viability of the land while simultaneously removing carbon dioxide from the atmosphere. There are many different types of regenerative agriculture, here’s a helpful video to explain the main three:
But between destroying the soil and saving the soil, there’s a third option: not using any soil at all. This is the premise behind container farming.
Container farming to save soil.
Container farming is a subset of the indoor farming industry, which includes everything from greenhouses and warehouses to at-home tabletop setups. The advantage of container farming is the ability to create commercial-scale production within a small space the size of your standard 40-foot shipping container through vertical farming techniques. Inside the container, plants are protected from the external elements and nurtured using nutrient-enriched water, powerful red and blue light, and optimal temperatures.
Notice anything missing? Oh yeah–soil!
Container farming with hydroponics completely eliminates the need for soil to grow food, which is great news for the whole regenerative agriculture movement. Since regenerative farming is based on the idea of protecting soil, container farming is able to take the whole idea to the logical extreme by not using any soil–period.
Not only does container farming prevent the further degradation of soil, but it actually frees up land to be actively regenerated. At Freight Farms, our containers (each capable of growing an average of 2 acres of food) have already saved 700 acres of land… which’s equal to about 530 football fields!
Additional sustainability benefits
Beyond regenerative agriculture, which is primarily focused on soil, container farming brings many additional sustainable benefits. The Greenery S is able to save:
Water: 99% less water than is used in conventional agriculture.
Food miles: we move the farms, not the food. Instead of trucking/shipping food from a centralized location, we put the farm as close to the final consumer as possible.
Carbon emissions: in addition to reducing food miles, we’ve partnered with Arcadia to make it easy and effective for our farmers to get onto the renewable energy grid and make their carbon footprint just one-quarter of what it would be if they were farming using industrial farming methods.
Regenerating communities
While regenerative agriculture may start with soil, the implications on climate change, food access, and food security are clear. In the same way, container farming is also more than just improving the sustainability of our agriculture system. In addition to saving soil, land, water and reducing food miles and carbon emissions, container farming unlocks many important social gains:
Independence: when we are not reliant on soil, land, and climate, we can make any place a farm. This makes it possible for us to create the distributed system we need to combat the harmful effects of industrial farming and centralized food systems.
Equality: independence from soil and land also creates more food equality, since individuals and communities need fewer resources (money & land) to create commercial-scale farms.
More farmers: Soil is complicated and nuanced, it takes huge amounts of experience and education to know how to do regenerative agriculture properly. With container farming, everyone can be a low-impact farmer.
More varieties: Conventional agriculture is beholden to monocropping, which improves the unit economics of growing food but also increases the risk of crop failure, blight, and soil degradation. Container farming makes it possible to grow hundreds of plant varieties, introducing people to new types of plants and growing public perception of the diversity you can have with fresh greens. This can have an overall positive effect on market demands and help move the whole system away from relying on mono-cropping.
Learn more about the Earth Day Restore Our Earth™ campaign and check out how Freight Farms is helping support the regenerative farming movement with container farming!
Freight Farms
Empowering anyone to grow food anywhere. Freight Farms makes local food accessible in any climate with the Greenery™ container farm.
April 23, 2014
Follow Earth Day Earth Day 2021 Sustainability Regenerative Agriculture Agriculture
US: NEBRASKA - The Bay, Beyond School Bells Launch Youth-Focused 'Freight Farm'
In partnership with Beyond School Bells, The Bay is launching The Greenery, a self-contained hydroponic farm housed in a repurposed shipping container
Apr 25, 2021
A 40-foot-long shipping container in the parking lot of The Bay will soon be filled with a whole lot of green.
In partnership with Beyond School Bells, The Bay is launching The Greenery, a self-contained hydroponic farm housed in a repurposed shipping container. Members of Beyond School Bells and The Bay gathered with local leaders Saturday to officially launch the program.
Much like The Bay’s other youth-focused programs, The Greenery is designed to allow students access to engaging, hands-on activities — in this case growing food.
“We are thrilled about the opportunity to be able to turn kids on to sustainable agriculture,” said Andrew Norman, executive director and co-founder of The Bay’s parent organization Rabble Mill. “A lot of the kids in our neighborhood have never seen anything like this; none of us have.”
The Greenery setup is designed by the Boston-based company Freight Farms. Beyond School Bells was able to purchase the unit through a partnership with the Ben Hormel Harris Foundation, said state Sen. Anna Wishart, the director of partnerships for Beyond School Bells. Several local companies and individuals donated their time to help get it up and running.
Through vertical planting that doesn’t require soil, the shipping container is able to house 13,000 plants at a time, or about as much food as a 2.5-acre farm. Throughout the container are thousands of red and blue LED lights that can be precisely controlled through the trailer’s high-tech programming to provide the perfect amount and color of light for each plant, said Doak Field, director of operations at Freight Farms.
The setup is also water-efficient, as the water that flows throughout the trailer is repumped through the cycle.
“Everything is just way more efficient than growing outside,” Field said. “You can get the exact science down to whatever you need to grow.”
Field said the team hopes to start planting the container within the next two weeks and is planning to start with greens such as lettuces and kale, as well as herbs.
The program leaders plan to sell the food grown at the Greenery at local farmers’ markets or through weekly community-supported agriculture projects. They'll also source produce to local restaurants.
While many of the similar freight farm projects that have popped up across the country have been for-profit and run by adults, Lincoln’s will be one of only a few that are not-for-profit and youth-focused, Wishart said.
Beyond School Bells works statewide to provide after-school opportunities for students like The Greenery, she said.
“Our goal is to ensure that every kid, no matter where they grow up in Nebraska, has access to quality out-of-school programming and this freight farm is absolutely an example of that,” she said.
The project will offer an opportunity for students to learn a variety of skills, Wishart said, and University of Nebraska-Lincoln honor students will also play a role in mentoring younger students working on the project.
“This also creates an incredible platform for youth to learn entrepreneurship and about sustainable, high-tech agriculture and future careers in that space,” Wishart said.
The Greenery project is part of a series of environmental-focused projects across the state that Beyond School Bells is working on, the organization's network lead Jeff Cole said.
“This will be the crown jewel,” he said. “But we're already starting to do investments in rural Nebraska around outdoor classrooms, environmental education, and a series of other things across the state.”
Lincoln Mayor Leirion Gaylor Baird said she sees the project as an example of innovative, environmentally friendly solutions that can help move the city forward.
“This is such a wonderful demonstration of how we can take better care of the Earth, create greater value for everyone in our community and hand something on to the next generation, something that they can have a leadership role in,” Gaylor Baird said.
Lead Photo: Jeff Cole of Beyond School Bells talks to visitors about the Greenery, a 40-foot-long shipping container that will operate as a high-tech hydroponic farm at The Bay. The container has space to vertically grow over 13,000 plants — the equivalent of a 2.5-acre farm. FRANCIS GARDLER, Journal Star
USA: BALTIMORE - Hydroponic Operation Supplies High-End Restaurants
Growing vegetables in a shipping container have opened new marketing opportunities for a Baltimore County farm
Art Petrosemolo, Southeastern Pennsylvania Correspondent
Apr 23, 2021
Growing vegetables in a shipping container have opened new marketing opportunities for a Baltimore County farm.
The hydroponic growing system has allowed Karma Farm to sell fresh produce regardless of the season to high-end restaurants in Baltimore and Washington.
“Today we are delivering leafy greens and herbs year-round to a growing customer base,” said Jon Shaw, founder of the family operation.
The farm, which makes multiple weekly deliveries to 27 customers, has picked up clients through word of mouth and sampling visits arranged with chefs who find the farm on social media.
“Well-known chefs talk and move from restaurant to restaurant ... and they have brought us with them,” Shaw said.
The farm got its start just over a decade ago when Shaw was growing produce on 5 acres, both outside and in hoop houses, for retail sale as well as a nearly 100-member CSA.
Karma Farm purchased a freight container vertical hydroponics Leafy Green Machine from Freight Farms in Boston in 2017. Photo by Art Petrosemolo
Jon’s 28-year old son, Nat, learned the business from his dad as a teenager, and in the past few years he has helped Karma Farm pivot to the new customer base, embracing the new ag technologies.
Nat, now the farm’s hydroponic production manager, researched vertical growing in insulated shipping containers while he was studying entrepreneurship at the University of Baltimore and thought the year-round production method would be a good fit.
“Hydroponic container farming is still relatively new and is being introduced to farmers in parts of the country where short growing seasons, weather, and soil conditions make profitable, small family farming difficult,” he said.
With a feasibility study completed and a new focus for the business, the Shaws purchased a Leafy Green Machine container in 2017 from Freight Farms in Boston. The container is 40 feet long by 8 feet wide.
“These are the insulated type of refrigerated containers used to ship fresh produce across the country,” Nat said.
With delivery and setup, the container cost about $100,000.
Lead photo: Nat Shaw, left, and his dad, Karma Farm owner Jon Shaw, stand in their freight container.
This Is What The Future of Farming Looks Like
Vertical farming is nothing less than exactly what it sounds like. As opposed to spreading crops out along the ground, beds are effectively turned on their side, and grown on vertical panels
Why Grow Plants Horizontally When You Can Grow Them Vertically?
What do most people think of when imagining a farm? Typically: Acres upon acres of crops, fed by an extensive irrigation system, with tons of pesticides and heavy machinery— in other words, an image of modern farming that’s simply dated. Today’s most technically advanced farms don’t require nearly as much water or chemicals and take up just a fraction of the footprint. How? The answer is simple: Vertical farming. Specifically, the brand new Greenery S hydroponic system by Freight Farms.
Vertical farming is nothing less than exactly what it sounds like. As opposed to spreading crops out along the ground, beds are effectively turned on their side, and grown on vertical panels. This isn’t exactly new; some of the earliest indigenous farmers would plant crops on layered terraces to achieve similar results. But the modern form of vertical farming is barely two decades old. While it’s proven hyper-efficient, the technological cost of entry has also traditionally proven to be high, requiring expensive lights, temperature and irrigation control systems, and enormous amounts of electricity — to say nothing of capital. Until now.
Enter Freight Farms, a fully-functional farm in a 40-foot container. Launched in 2011, Freight Farms’ mission is to build accessible, modular vertical farming technology that empowers anyone to grow fresh, healthy food in their local communities — wherever that may be. While industrial farms tend to rely on GMO seeds, extensive pesticides, and centralized distribution systems, Freight Farms has worked tirelessly to cram 2.5 acres worth of farmable land into a 320-square-foot shipping container that can be placed almost anywhere and scaled up (or down) to meet your individual needs. Whether you’re a small restaurant looking to grow your own vegetables, an entrepreneur looking to bring fresh food to a food desert, or even just a homestead hobbyist, the Greenery S by Freight Farms is here to make your vertical farm aspirations a reality.
Freight Farms brings a decade of experience to the Greenery S. The Greenery S uses 99% less water than traditional industrial farm systems, mainly because you don’t need to worry about losing so much water to evaporation over acres and acres of land. Furthermore, the Greenery S has built-in temperature controls that make farming viable year-round, with a minimum temperature of -40 degrees Fahrenheit and a maximum of 120 degrees Fahrenheit. And with over five hundred supported crop varieties, you can throw out your hardiness zone map and grow pretty much whatever you want, wherever you want.
Besides being far more cost-effective than purchasing, tilling, planting, irrigating, and harvesting multiple acres of land, Freight Farms also uses data to help you get the most out of your yield. The proprietary farmhand® software integration gives operators complete automation and control over their grow operations. The software connects hundreds of farmers and is constantly compiling data from them to help you better manage your own crops based on learnings from the entire Freight Farms network.
The Greenery S is available now, to everyone. Whether you’re a seasoned farmer looking to scale out your operation or you’re simply looking for an exciting new business opportunity, Freight Farms’ intelligent automation and exceptional design can transform any small space into a commercial-scale farm. Head here to learn more and reserve yours now.
Lead Image: Image by Freight Farms
Futurism fans: This post was paid for by Freight Farms and was written by non-editorial staff. This content does not necessarily reflect the views or the endorsement of the Futurism.com editorial staff.
As a Futurism reader, we invite you to join the Singularity Global Community, our parent company’s forum to discuss futuristic science & technology with like-minded people from all over the world. It’s free to join, sign up now!
US: KENTUCKY - AppHarvest Continues To Expand Operations, Adds New Container Farm In Madison County
Some Central Kentucky high school students will soon be able to help grow food not only for themselves but the entire region
AppHarvest (WYMT)
By Brandon Robinson
Apr. 22, 2021
RICHMOND, Ky. (WYMT) - Some Central Kentucky high school students will soon be able to help grow food not only for themselves but the entire region.
On Thursday, officials with Morehead-based AppHarvest announced the expansion of their container farm program to Madison County High School in Richmond.
Watch Live Below:
Gov. Andy Beshear, who attended the event, appropriately held on Earth Day, said the move will not only provide food but help students prepare for possible careers in a field with growing demand.
“AppHarvest has been reimagining and reinventing sustainable food production at its state-of-the-art facility in Morehead. With the opening of the company’s container farm classroom at Madison Central High School, AppHarvest is showing its commitment to the Commonwealth runs both strong and deep,” said Gov. Andy Beshear. “This living, teaching lab will inspire and engage Kentucky students to learn about cutting-edge technology that will become the basis of the jobs of the future. Thank you to Founder & CEO Jonathan Webb and his team for making education and Kentucky students a priority in his plans for success.”
The container farm is 2,880 cubic feet, weighs 7.5 tons and includes space to grow up to 4,608 seedlings and 8,800 mature plants all at once using 440 vertical crop columns.
Each retrofitted shipping container serves as a hands-on agricultural classroom for students, allowing them to grow and provide fresh leafy greens to their classmates and those in need in their communities. The company has previously opened container farms in Eastern Kentucky at Breathitt High School in Jackson, Shelby Valley High School in Pikeville, and Rowan County Senior High School in Morehead, the site of the company’s flagship farm.
AppHarvest Founder & CEO Jonathan Webb said the latest expansion will not only help feed Kentuckians but will help Eastern Kentucky’s struggling economy.
“We knew long before opening our Morehead farm that we wanted to invest in the region to help grow our growers and build on the many outstanding community and education programs focused on creating a more resilient Appalachian economy,” Webb said. “The technology in each of these container farms is a good example of what AppHarvest’s modern farmers use daily on a larger scale.”
The Madison Central High School container program will be led by agriculture teacher and FFA adviser Derek Adams.
“Our students are looking forward to getting hands-on experience with state-of-the-art technology that will better prepare them for career opportunities in the agriculture industry,” Adams said. “They are especially eager to see the leafy greens come full circle from farm to table in their own school cafeteria.”
USA: This Colorado Company Is Building Farms In Shipping Containers To Help Feed People In Need
FarmBox Foods wants people to be able to farm anywhere, allowing them to access fresh food they otherwise wouldn't be able to
Author: Jeremy Moore
April 19, 2021
FarmBox Foods Wants People To Be Able To Farm
Anywhere, Allowing Them To Access Fresh Food
They Otherwise Wouldn't Be Able To
SEDALIA, Colo. — A three-year-old Colorado company has an ambitious goal: to bring food security, safety, and sustainability to communities in need around the world.
FarmBox Foods aims to achieve that goal by connecting those communities to sustainably sourced food that's grown locally inside one of their container farms.
Their first product was a vertical hydroponic farm, or VHF, built inside a shipping container.
The company has since developed a second product: a gourmet mushroom farm, or GMF.
So far, customers in Colorado include Centura Health, Vitamin Cottage Natural Food Markets, and the C Lazy U Ranch in Granby.
FarmBox CEO Rusty Walker and COO Jake Savageau joined 9NEWS to talk about how they hope to change the way the world thinks about farming.
9NEWS also spoke with a prospective customer of FarmBox, Cori Hunt of the Denver restaurant group Edible Beats.
(Editor’s note: Responses have been edited for context and clarity.)
As a mission-driven company, what is the mission of FarmBox Foods?
Walker: Our goal and our mission is to get our products out into the communities where we can help develop food security programs. We’re looking to get into food deserts, opportunities where folks in the world might not have access to good, clean nutritional food. And so we kind of strive as a company that’s driven to feed the world one container at a time. And we’re ready to go out and manufacture thousands of these if we can.
We’re able to decentralize growing food by being mobile – being able to deploy these by just having a semi come in. We can then lift it up on a flatbed and take it to anywhere in the world. We’ve got two containers going to islands. We’ve got our first container that took off for the island of Jamaica. It’s going to Montego Bay where it’s going to be used behind mega marts on the island. And then we have another container which is our gourmet mushroom farm that’s going to be going to Tahiti where they’re going to be using that to feed the island population which does not have access to that type of food.
One big area that we’re really focusing on is the urban areas throughout the U.S. where they don’t have a lot of land to grow. These farms can go right into the parking lots, behind a church for example. We’re working with a community church on the south side of Chicago that’s looking at placing two of these containers – a vertical hydroponic farm and a mushroom farm – right outside in the parking lot outside the church.
And we think we could bring an educational spin to this where we can have the community grow their own food and supply the community themselves with highly nutritional food that ordinarily they just would not be able to get their hands on. So, we’re thinking that if this pilot program goes well this would be an application that would apply to every inner city throughout the U.S.
Farmbox Foods grows vegetables in shipping containers. Credit: Jeremy Moore, KUSA
Savageau: The mission’s always been to create products that are for the decentralized food insecurity industry. So, we want to create a product that can be deployed anywhere in the world, can run off-grid, and can feed communities. So, we have two different products – the VHF and the GMF. Every product that we develop gets us one step closer to being able to feed a community with everything they need, because you can’t feed communities forever just on leafy greens.
So mushrooms, they’re more nutrient dense, that gets us one step closer. There’s other products that we’re going to develop to get us to that point. But, I think the mission for the company is to be able to deploy these farms into communities where they’re needed, whether that’s a rural area, a food desert in the U.S., an inner city, or somewhere in Africa like Ghana or the Sudan.
We want to align with big ag and we want to help the industry get better. So we want to get food to where it’s needed. We’re looking at doing stuff with food insecurity and food inequality. That’s big with what we’re doing. So, that kind of aligns with our mission. If you look at our food system – just take for instance – you know if you look at a SNAP program or food subsidy program – you’re taking food and giving it to somebody or they’re purchasing it.
But, a lot of that food that they’re purchasing is processed, sugar – I mean, it’s poison. And if you go on a military base anywhere in the U.S., there’s fast food on the base. It’s really what you see. So, there’s a lot of reasons why we’re doing this I think. We can help fix our food system. And we can help educate the youth on how they should eat. We’re doing some stuff with an Inuit community in Alaska. They don’t necessarily know how to fix this food or prepare it or use it. So, I think education is a big part of what we’re doing.
How do these container farms work?
Savageau: When people think of farms, they don’t think of agriculture like this. Vertical hydroponics and indoor ag and controlled environments – it’s been around for a long time. I think that the way that this one works is pretty simple. The water gets fed into a tube system and the water trickles down and goes back into the tank. And where you’re standing – the seedling tray area – the water goes into a tank, into the seedling trays, gets flooded, and then back into the tank.
There’s a software that we use called Agrotech that monitors the temperature, the humidity, the lights – basically, all automated. So, it’s fairly easy to run. You need about 15 to 20 hours a week to run one farm. The GMF farms takes about 25 hours a week. It’s a little bit more intensive. The VHF is the vertical hydroponic farm and that’s the farm that we’re standing in. The GMF is the gourmet mushroom farm, which is the one that you went through earlier. You want to just keep things as clean as possible. The cleaner that you keep it the better it’s going to run.
So, we have a standard SOP, you know, that we implement with our training. Cleaning the floors. Cleaning the tubes. You don’t clean them every time. But, usually, every couple harvests you’ll take the tubes out, wash them out. You’re cleaning the tanks about every 60 days.
But, on average it’s pretty easy to maintain if you’re doing the daily checklist. The seeds are going to be in the seedling tray for about two weeks. Then, they go into the wall. And then they get harvested about 60 days after they start in the seedling tray. So, on average you’re about 60 days from seedling to harvest depending on what you’re growing.
And this farm is really setup for vertical hydroponics. So, it’s leafy greens. You can do hundreds of different types of lettuce. You can do cherry tomatoes, strawberries and peppers. There’s a lot of different things that you can grow in here. Most of our clients are only growing a couple things at one time. You don’t have to worry about weather. You don’t have to worry about if this is in a cold climate like the arctic. You know, they can’t grow food. If it’s in a desert, they can’t grow food. If it’s on an island, they can’t grow food. So, these can be deployed anywhere. And they grow 365, all day, every day. Also, the yield is very high for the square footage. So, you can put these on top of a building, inside of a building. It only takes up 320-square feet. You don’t have any pesticides. So, you don’t have to worry about pests, bugs, mildew, stuff like that’s going to effect the plant as it’s growing. It’s also decentralizing the food system.
So, you’re not having to ship food hundreds of thousands of miles from point A to point B. So, the food is right there. And the nutrients that we use are organic plant-based nutrients. And there’s no pesticides. So, the nutrient density is extremely high compared to something that you would buy – even organic – in a store.
Walker: We grow a variety of vegetables and lettuces. I believe that we’re somewhere in the area of 30 to 40 different types of vegetables and lettuces that we can grow in our farms. And, then of course we’ve got our gourmet mushroom farm which we’re currently growing anywhere from eight to nine different varieties of mushrooms. We’re in the startup phase of running that farm ourselves. So, we’re exploring the different types of mushrooms that we can grow. But, we’re very proud of the folks that are actually running these farms – our staff, very knowledgeable and they do a great job. We’re going upwards to 300 to 400 pounds a week now. We’re not competing with traditional farming. We’re actually a compliment.
Who are your customers?
Walker: One of our first customers is Centura Health. They purchased their first container – which is now sitting at St. Mary’s in Pueblo. They ordered two more containers after seeing how the first container behind their hospital worked. We actually started up a pilot program with Centura Health where we’re now running them as the FarmBox family.
We’re working with Centura Health in identifying not only their hospitals and the patients who are going to be fed through our vertical farm – but then we’re also identifying where the food deserts are and Centura Health will then help us with what we’re going to be growing, and then the communities that we’re going to be serving from those, those particular crops.
We do have a couple that’s looking at doing some farming right here in Sedalia. They’re going to use it to supplement their traditional farming, which will be an interesting pilot program for us to work with them on. We’re working with C Lazy U Ranch out of Granby, Colorado. They’ve ordered a hydroponic farm and we’re going to be manufacturing that. And they’re going to place that at the ranch. They don’t really have access to a lot of good food as far as having it grown right there on the property. So, this will be a nice compliment to the services and the customer experience that they provide their customers by having one of our farms right on site.
Centura Health is one of FarmBox Foods' first customers. Credit: Jeremy Moore, KUSA
One big area that we’re really focusing on is the urban areas throughout the U.S. where they don’t have a lot of land to grow. These farms can go right into the parking lots, behind a church for example. We’re working with a community church in the south side of Chicago that’s looking at – we’re looking at placing two of these containers – a vertical hydroponic farm and a mushroom farm right outside in the parking lot outside the church.
We can have the community grow their own food and supply the community themselves with highly nutritional food that ordinarily they just would not be able to get their hands on. So, we’re thinking that if this pilot program goes well this would be an application that would apply to every inner city throughout the United States.
Savageau: We have a customer here in Lakewood that’s going to put one in their backyard. They run a small organic farm. We’re looking all the way up into federal government and military, and everything in between.
So, Rusty was talking about FEMA, the UN, UNICEF, those are the big customers that take a long time to build a relationship with. And then we have customers that are all the way down to just an individual that wants one for their property or maybe a couple of people are going to run one for a restaurant or a developer wants one for a small development that he’s doing.
We’re working with a group in New Mexico and they’re building a huge development of about 45,000 houses. So, we’re talking about 100 of these units that are going to be deployed in that area right outside Albuquerque to feed those communities within that area over the course of about two years. We work with a grocer that’s regional. And we work with some other customers that are kind of at a government, federal government level.
I think we’ve done a lot in the last three years. I mean we haven’t gone out and raised any capitol. So, we’ve self-funded it. And I think from that point of view you know we’ve done a lot. We’re kind of at the point right now where we’re just starting to scale. So, we’ve just started our social media. You know SEO (search engine optimization), SEM (search engine marketing). We have a sales team. And orders are starting to come in. We’ve partnered with RK which is manufacturing our units. That’s giving us the ability to scale. Because before that we were building these one or two at a time in Sedalia and now we can build 100 of them. So, that’s really been a huge part of us being able to scale is the manufacturing side.
How much does it cost to purchase and operate the farms?
Jake: This VHF farm – vertical hydroponic farm – starts at $140,000. The GMF starts at $150,000. Then, you have training and deploy, getting it there. So, usually, you’re over $150,000 for a farm. So, your ROI (return on investment) in this product is going to be about 12 months to 24 months depending on what you’re growing and where it is in the world.
The GMF is going to be closer to 12 months because mushrooms tend to be more expensive – again – depending on where it’s going. We have a unit that’s going to Tahiti for example. That ROI is going to be extremely fast because they ship everything in. If there’s a market for mushrooms there, which there is with a grocer, it’s going to be quick. So, the cost of running it with labor and everything you need to grow the plants, usually around $20,000 to $40,000 a year. We’re a mission-driven company. So, money isn’t the first thing that’s important. We want to build a certain amount of these and then every x amount that we build, we build one for free and we send it to a community that maybe our social media has engaged with or given us an idea that ‘hey, this would be a good community.’ And then, we send it there. We pay for it. We train people. And that’s something that we want to do. We can’t do it yet. But, I think that’s coming in the next year.
Why is Edible Beats interested in working with FarmBox?
Hunt: We try to be as local and organic as possible and that’s what brought us here to FarmBox. We can put a box behind a restaurant and have lettuces cut and washed and put on the plate the next day.
Just to have that connection with our food and know exactly where it’s coming from and how it was produced. It’s going to be better quality because it’s not traveling. It’s not ripening in a truck coming from Mexico. Economically, what we can do to not pay the mileage on the vehicles and the gas, the inputs, the emissions, the extra packaging, the plastics.
That’s one of the best things about FarmBox – that what we can do is – if we produce food for our restaurant group – I’m not going to have to buy packaging that’s going to go into a landfill or even need to be recycled. It’ll go directly into the vessels that we’re going to store them in the cooler. We don’t have to worry about marketing and labeling and you know stickers and plastics and all this extra stuff – this hoopla that we don’t need – because FarmBox is a possibility now.
The Farmbox Foods containers allow leafy greens to grow vertically, maximizing space.
Credit: Jeremy Moore, KUSA
We are looking at lettuces and herbs, leafy greens. So yeah, like basils, sage, leaf lettuces, butter lettuces, arugula – these kinds of things that we use that could greatly help our impact. Essentially it’s a self-contained box that you can grow fruits and vegetables in – most likely leafy greens – and it’s a soilless or near soilless medium.
So, essentially you plant your seed in a very small amount of coconut core or soil or peat moss – something to hold the root structure – and that, according to with FarmBox, they’re system is a vertical farming.
So, they have vertical towers and then they put the lettuces in the towers in their small soil medium and then they drip water with enhanced nutrients mixed into the water specifically built for those vegetables. It doesn’t have a lot of soil waste.
For the amount of the surface area you can get way more production out of it and the water that goes through is recycled. Per plant, it uses far less water than any other type of growing system.
RELATED: Why Colorado agriculture groups oppose Initiative 16, an animal cruelty proposal
Foundation Farms Corp., Announces Vertical Farm Out For Delivery
The turnkey farm package has left the ZipGrow manufacturing facility for arrival at the Red Deer area site this week
April 20, 2021
NEW YORK, NY / ACCESSWIRE / April 20, 2021 / Foundation Farms, Corp., ("Foundation Farms") a subsidiary of GME Innotainment, Inc. (OTC PINK:GMEV) today announced confirmation of delivery and installation dates for the first of its many vertical farms. The turnkey farm package has left the ZipGrow manufacturing facility for arrival at the Red Deer area site this week. The installation crew is scheduled to arrive on-site next Monday and assembly and commissioning will be completed next week. Production of the first crop will begin on May 1.
Management is also excited to report that each of the company's vertical farms will become local community food hubs known as E-ROOTS CENTRES. In addition to selling its own vertical farm produce, each E-ROOTS CENTRE will buy other locally grown food products from farmers wholesale and then package, market, and distribute the locally grown food products to corporations, families, schools, restaurants, caterers, sports teams, and stores, maintaining economic growth in the community. These E-ROOTS CENTRES will develop health food brands utilizing local produce to promote nutritious diets. Mechanisms for dispatch and delivery logistics are included.
Ed Kroeker, CEO of Foundation Farms stated, "The installation and startup of our first E-ROOTS CENTRE is a wonderful milestone achievement but what I am even more excited about is the interest we are getting throughout North America from prospective joint venture partners and host communities. Demand is even greater than we anticipated. Projects are aggressively underway in Minneapolis-our important entry point for the United States as well as Regina, the Greater Vancouver Region, and the Greater Toronto Area, with the list of projects growing weekly."
Yves R. Michel, GMEV CEO applauded the milestone achievement this week and further added, "Food sustainability and reliability have become two of the most important goals within North American communities today. Foundation Farms has developed a business strategy that provides the components as well as the assembly, packaging, and distribution systems to achieve those goals in every community serviced by E-ROOTS CENTRES."
Yves R. Michel
Chief Executive Officer and Director
208 East 51st St., Suite 170
New York, NY 10022
Source: GME Innotainment, Inc. ("GMEV")
www.srcorpgroup.com/
Released April 20, 2021
OTCPink:GMEV
This press release may include certain statements that are forward-looking in nature and that involve a number of uncertainties and risks. Such forward-looking statements are within the meaning of that term in Section 27A of the Securities Act of 1933, as amended, and Section 21E of the Securities Exchange Act of 1934, as amended. The forward-looking statements in this press release are based on GME Innotainment, Inc., current expectations and projections regarding future events, which are based on currently available information. The forward-looking statements in this press release may also include statements relating to GME Innotainment, Inc.'s anticipated new developments, business prospects, financial performance, strategies and similar matters. GME Innotainment, Inc. disclaims any obligation to update any of its forward-looking statements, except as may be required by law.
SOURCE: GME Innotainment, Inc.
GME Innotainment, Inc.
POLAND: The Only Way Is Up! Puławy Vertical Farm First In Europe To Supply Beauty And Health Industries With Plant Extract From Herbs
Vertigo Farms, located in the Puławy Science and Technology Park in the east of Poland grows 11, 000 plants on an area of 300 square metres using 4 metres high metal constructions resembling shelving units, a capacity which would require an area 100 times larger if using a traditional farm
BLANKA KONOPKA
APRIL 20, 2021
Established by the husband and wife team Anna and Dawid Drzewiecki after their observations of where different plant extracts came from in cosmetics and natural supplements, the company’s innovation is based on their unique form of production, combining the growth of plants and the production of extracts in one place.
An ‘experimental’ start-up has become the first in Europe to utilize a vertical farm to both grow herbs and produce plant extracts for the beauty, health, and pharmaceutical industries.
Vertigo Farms, located in the Puławy Science and Technology Park in the east of Poland grows 11, 000 plants on an area of 300 square metres using 4 metres high metal constructions resembling shelving units, a capacity which would require an area 100 times larger if using a traditional farm.
Vertigo Farms grows 11, 000 plants on an area of 300 square metres using 4 metres high metal constructions resembling shelving units, a capacity which would require an area 100 times larger if using a traditional farm. CC BY 4.0
Established by husband and wife team Anna and Dawid Drzewiecki after their observations of where different plant extracts came from in cosmetics and natural supplements, the company’s innovation is based on their focus on vertical farming for the cosmetics and pharmaceutical industry as well as their unique form of production, combining the growth of plants and the production of extracts in one place.
The two-processes of growth and production have hitherto been separate in other companies in the same field, with sites often large distances apart.
Dawid Drzewiecki told Puls Biznesu: “Our idea was to shorten the supply chain and make it independent of logistics.
The process starts from seeds which are first kept under lamps and with constant access to water before they sprout.Vertigo Farms/Facebook
“These needs were strongly highlighted by the pandemic. Last year, there were delays in production due to difficulties in transport due to closed borders.
“More importantly, climate change is more often disrupting the production of plants, which our method of cultivation enables us to avoid.”
The farm, which is the only vertical farm in Poland focusing on delivery to the cosmetics and pharmaceutical industry, currently produces three plant types: basil, coriander and bakuchi, the latter being a herb from Asia often used as a substitute of retinol, a popular ingredient used in anti-ageing and acne creams.
Plants are grown under violet lamps with the continual monitoring of various indicators.Vertigo Farms/Facebook
The process starts from seeds which are first kept under lamps and with constant access to water before they sprout when they are transferred to the 4m units whose shelves are comprised of gutters with peat plant pots where plants are grown under violet lamps with the continual monitoring of various indicators.
The plants are then picked, dried, and passed through a machine to extract extracts from them for use in creams, oils, and dietary supplements. The whole process requires the service of just four people.
The ambitious company, which sees themselves as filling a niche due to the small number of companies producing plant extracts for the cosmetics, health, and pharma sectors, has big expansion plans.
The oil from plants grown on vertical farms.Vertigo Farms/Facebook
Earlier this year, it signed an important deal for innovative vertical farming technology with a leading Finnish company specialising in the building of vertical farms.
The technology will enable the company to experiment with tropical plants and to grow a wider variety of herbs.
Their aim is to expand to 10-20 plant types by 2022-2023.
TAGS: TECHNOLOGY, START-UP, STARTUP, HERBS, PHARMACY, PLANTS, FARM, VERTICAL FARM, VERTIGO FARMS, DAWID DRZEWIECKI, ANNA DRZEWIECKA
CANADA (YT): Tackling Food Insecurity Above The 60th Parallel
ColdAcre Food Systems is based in Whitehorse, Yukon, one of the northernmost provinces in Canada. The company was incorporated in August 2019 and specializes in controlled environment agriculture.
In the northernmost territories of Canada, agricultural development is underway but must contend with the cold climate, variable photoperiod and other environmental challenges. It comes as little surprise, then, that interest in controlled environment agriculture is on the rise. ColdAcre Food Systems is one of the companies that supports this endeavor and has installed multiple growing systems in northwestern Canada.
ColdAcre Food Systems is based in Whitehorse, Yukon, one of the northernmost provinces in Canada. The company was incorporated in August 2019 and specializes in controlled environment agriculture. Prior to its incorporation, ColdAcre primarily sold retrofitted shipping containers and also operated its own container farm to supply the Whitehorse market with fresh greens and herbs.
According to chief executive officer Carl Burgess, “the original intent was to sell and provide growing systems but we immediately identified an opportunity and a need to demonstrate commercial production north of the 60th parallel year-round.”
With its incorporation in 2019, ColdAcre thus based itself on four pillars:
Growing produce for the Whitehorse market and beyond
Selling prefabricated and custom growing systems for its clients
Providing consultation and pathfinding services
Active learning and engagement in various projects.
Growing produce for the Whitehorse market
When ColdAcre first began producing greens and herbs, the company started with three dozen products but have since narrowed its product line in order to have a robust supply and client demand. ColdAcre has also recently begun producing mushrooms. Explaining the Yukon’s consumer base, Carl says that the territory is the size of Spain yet is home to only 40,000 people. Whitehorse is the territory’s capital and its businesses service much of the territory, as well as southern Alaska, northern British Columbia and the western Northwest Territories.
As such, Whitehorse acts as an important hub for northern residents and has a relatively robust food demand. According to Carl, “some people drive 1,000 km to buy goods and groceries in Whitehorse a few times a year. That said, the Yukon only produces 1% of the food that is purchased and consumed in the territory.”
Importing most of its consumables carries the double burden of a heavy carbon footprint and limited nutritional quality. “When comparing the quality of fresh produce between Vancouver and Whitehorse, there is a significantly lower quality in the Yukon, which is only heightened when you go further north. Producing locally also virtually eliminates waste and the carbon footprint of production,” says Carl.
Selling growing systems
ColdAcre also continues to sell prefabricated and custom growing systems for clients through Canada’s northwestern region. While the company began with CropBox and has had success doing so, ColdAcre has found that its clients typically require more customization. Moreover, working with an American company has subjected ColdAcre to a higher degree of volatility with respect to changes in the dollar and availability of equipment, according to Carl.
With respect to its technology, Carl also explained that ColdAcre’s technology “is not necessarily unique, but that the skillset and assembly is. In the Yukon, we face the challenge of growing lettuce when it’s 40°C outside in the summer or down to -53°C. We address these extremes using high-tech and smart-tech solutions. We customize the whole management and contingency for potential crises specific to a client or area.”
Consultation and active learning
ColdAcre has also committed to providing consultation and pathfinding services to growers regardless of whether the grower is using a ColdAcre system or not. As Carl explains, “we think that our growing challenge are everyone’s challenges so if we can solve ours, we’d like to share.”
ColdAcre also has multiple research partners throughout northern Canada and while the projects are generally northern-based, the results have applications in various settings.
2020 and 2021 at a glance
In all four pillars, ColdAcre has reported increased interest in the past year. The fragility of Yukon’s food system was heightened by the COVID-19 pandemic and ensuing supply chain disruptions. As such, the interest in local food production and stabilized food system has surged in the territory. ColdAcre’s production has been sold out since October 2019 and the company will be tripling its production in the coming months. According to Carl, ColdAcre’s proximity to market channels allows the company to compete with imported commodities from California and Mexico and demand a reasonable premium. Similarly, the company is reportedly experiencing an increased demand for its systems for residential, office, and educational purposes.
Most recently, ColdAcre shipped a 53-foot container farm to Inuvik, a community in the Arctic Circle and whose community greenhouse will use the shipping container to produce fresh produce year-round.
For more information:
Carl Burgess, CEO
ColdAcre
carl@coldacre.ca
www.coldacre.ca
Publication date: Fri 9 Apr 2021
Author: Rebekka Boekhout
© VerticalFarmDaily.com
USA: Local Farm Brings Hope To Food Desert
A hydroponic produce farm in Indianapolis is filling a need in food deserts around the city. Food deserts are areas where grocery stores aren’t easily accessible. More than 200,000 people live in food deserts in Indy, according to a study published by SAVI
Q&A: Mario Vitalis
April 13, 2021
Mario Vitalis, farmer, owner, and founder of New Age Provisions, holds plants grown on his farm.
INDIANAPOLIS — A hydroponic produce farm in Indianapolis is filling a need in food deserts around the city.
Food deserts are areas where grocery stores aren’t easily accessible. More than 200,000 people live in food deserts in Indy, according to a study published by SAVI.
Mario Vitalis, farmer, owner, and founder of New Age Provisions farm, uses advanced hydroponics and vertical planting to grow year-round.
It all starts inside a shipping container on an old car lot on East 10th Street. A step inside transports visitors to a lush, green garden of produce. A variety of herbs, leafy greens, microgreens, and hemp are grown inside.
The location allows Vitalis to provide fresh produce to the community, one of the city’s many food deserts. The farm also provides produce to restaurants in Indianapolis.
“I’ve always known the city life — but there is a nagging desire to get back to my roots,” Vitalis said. “As an African American, my roots made it from slaves in the field, to sharecroppers in the South, to farming in the city.
“As a descendent of slaves, this farm enables me to get back to the type of living where our people once lived off the land. Having an urban farm allows me to connect to a long history of farming that has been forgotten.”
Vitalis shared his story with AgriNews.
Tell me a little bit about your farm.
“We are a hydroponic commercial farm. We officially started farming in August 2020.”
What was your inspiration to grow things?
“I wanted to be involved in agriculture, to be able to provide fresh food to the community independent of the supply chain, and independent of herbicides, pesticides, and contaminants.”
Indiana has several food deserts. Did that inspire you to fill a need in the community?
“Yes, it did. It provides us with the equipment to do so, as well. We’re the first company in Indiana to own this piece of equipment, the Freight Farms Greenery. We’re currently the only African American owner of the equipment. We want to be able to provide food and also provide a new way of farming. We want people to see it and have access to it.”
How does the farming system work?
“It’s called a Greenery and it’s built by Freight Farms, based in Boston. It’s essentially a hydroponic farming system in a 40-foot shipping container. If you can imagine those shipping containers that go up and down the highway, you go inside of one of these and grow vegetables. It has everything you need to do that. It has a seedling table and growth tower with different types of hydroponic methods.”
Basil grows at a hydroponic produce farm in Indianapolis.
What are some of the features of the technology?
“It has its own dosing system to control nutrients. You can control humidity, temperature and pH levels. You can check your settings and programming on a computer. There’s an app that goes with it, as well. So, you can control your farm from your phone. The technology is state of the art.”
What are some of the challenges you’ve faced as a new farmer?
“I think the biggest challenge is developing a market and getting our name out there. There’s also a learning curve to farming. I didn’t have any experience. So, I had to learn what to do and how to operate.”
What do you enjoy most about growing things?
“Seeing the plant life cycle from seed to seedling into a full plant. I also enjoy the environment. Since we’re in an enclosed environment, we can grow year-round and it’s always 65 degrees.”
Do you have any advice for minorities interested in farming?
“Right now there are so few minority farmers in general. For African American farmers, the best thing they can do is get land and find ways to cultivate the land or make use of it. Good land is becoming a scarce resource. If they’re interested in farming, there’s funding available from USDA for Black and minority farmers. There are different avenues out there. But it all starts with land and a business plan. After that you just have to have motivation and knowledge to do it.”
Anything else you’d like to share about your farm?
“Our farm is local on the east side of Indianapolis. We grow hydroponically without herbicides, pesticides or contaminants.”
How can people purchase your products?
“They can go online to our website www.newageprovisions.com. We deliver. Or, you can purchase through Market Wagon or Hoosier Harvest Market.”
ZipGrow Expands To New Facility, Inks Deal With Sodexo
ZipGrow has expanded its footprint, moving from leased premises to its own building at the corner of Cumberland and Seventh Street
April 9, 2021
By Bob Peters
Cornwall Ontario – ZipGrow has expanded its footprint, moving from leased premises to its own building at the corner of Cumberland and Seventh Street.
The new building more than doubles the amount of space available to the manufacturer of the world’s most installed vertical hydroponic equipment.
“Demand for our products continues to soar,” says Eric Lang, President of ZipGrow. “The new building allows us to be more efficient while at the same time giving us room to grow in the future.”
Growth is on the menu at ZipGrow, with the company launching an innovative partnership with Sodexo to introduce sustainable growing systems to facilities throughout Canada and the United States.
“Having been installed throughout the world over the past decade, our system enables growers, both big and small, to access fresh produce no matter where they are located”, explains Mr. Lang. “We are excited to move ahead with this new partnership with Sodexo. Together we will be able to introduce sustainable food to Sodexo locations throughout North America.”
ZipGrow technology is a patented system that utilizes both hydroponic growing systems and vertical planes to maximize production volume within a small footprint. Primarily growing leafy greens such as lettuce and kale, along with herbs and small fruiting crops such as strawberries, ZipGrow systems will be installed in Sodexo locations including educational institutions, conference facilities, and corporate food service centers.
“This new partnership with ZipGrow not only enables us to reduce our carbon emissions of distance traveled for food source, onsite food waste, and packaging requirements, but also to introduce innovative technology to our facilities and team members”, said Normand St-Gelais, Director of Corporate Responsibility, Sodexo Canada.
About ZipGrow
ZipGrow is an international leader in indoor, vertical farming technology. The company’s flagship product, the ZipGrow Tower, is a core component of many of the world’s most innovative farms; from indoor hydroponic warehouses to vertical aquaponic greenhouses and high-density container farms.
Categorized in: Business, Community, Environment, General, News
CHINA: $500 Billion To Bring All World Crop Farming Indoors
China will build 2 Million hectares (20 billion square meters) of controlled environment greenhouses by 2025 and this will produce half of their vegetables and crop needs
Brian Wang | April 3, 2021
China will build 2 Million hectares (20 billion square meters) of controlled environment greenhouses by 2025 and this will produce half of their vegetables and crop needs. Temperature, humidity, lighting would all be under controlled conditions. It would not matter if there were new extreme temperature swings outside or if there was drought. The needed food and water would be immune to any projected climate change over the next 500-1000 years.
Alibaba sells greenhouses for as little as 70 cents per square meter. The bulk, high volume cost to the manufacturer is about 50 cents per square meter. If installation labor costs are 50% of the 2 million hectare project then it would cost about $20 billion for the 2 million hectare project. $40 billion would be sufficient for China to make 40 billion square meters of climate-controlled greenhouses which could produce all vegetables and crops. It would cost $260 billion to make greenhouses for the food production of the entire world.
Indoor climate-controlled agriculture has almost no need for pesticides and uses 7% of the water. This would take up 3-5% of the total land area of open-air farming.
Additional funds could be provided for higher demand from population growth and for some level of automation, sensors and other systems.
There is an economic analysis of smaller scale greenhouse and vertical farming. The all-in delivered cost of a pound of greens grown in a commercial greenhouse is estimated to be $2.33 per pound. It cost $18.3 million to build 280,000 square feet (2.6 hectares) of commercial greenhouse in the USA. The total cost to grow would be just over $3.0 million per year for 2 million pounds of greens or $1.52 per pound. BrightFarms employs 165 people for the three greenhouses. $1.10 per pound consists of employee costs.
The cost estimates for greenhouses could be brought down to $1 per pound or less with large-scale construction. Below are costs for 2.8 hectare systems in the USA.
There is value to having national food security and not having to depend on imported food. Ten billion to twenty billion dollars per year in indoor farm subsidies closes the cost gap with open-air farming.
China’s controlled environment system will have a lot of automation and lower construction costs because of the massive scale and lower costs in China.
PNAS – Wheat yield potential in controlled-environment vertical farms
Wheat growing is vastly more land and water-efficient but costs are not yet competitive with open-air farming.
Wheat is the most important food crop worldwide, grown across millions of hectares. Wheat yields in the field are usually low and vary with weather, soil, and crop management practices. We show that yields for wheat grown in indoor vertical farms under optimized growing conditions would be several hundred times higher than yields in the field due to higher yields, several harvests per year, and vertically stacked layers. Wheat grown indoors would use less land than field-grown wheat, be independent of climate, reuse most water, exclude pests and diseases, and have no nutrient losses to the environment. However, given the high energy costs for artificial lighting and capital costs, it is unlikely to be economically competitive with current market prices. Wheat grown on a single hectare of land in a 10-layer indoor vertical facility could produce from 700 ± 40 t/ha (measured) to a maximum of 1,940 ± 230 t/ha (estimated) of grain annually under optimized temperature, intensive artificial light, high CO2 levels, and a maximum attainable harvest index. Such yields would be 220 to 600 times the current world average annual wheat yield of 3.2 t/ha. Independent of climate, season, and region, indoor wheat farming could be environmentally superior, as less land area is needed along with reuse of most water, minimal use of pesticides and herbicides, and no nutrient losses.
Meat production could also be brought under climate control. The feed for cows, pigs, chicken and fish could be either brought into greenhouses or converted to insects. Insect feed can be twenty to one hundred times more space and water-efficient.
Meat can be converted into cell-based production in large vats. This would be similar to the industrial production of beer.
There would be zero risk of mass starvation caused by temperature or drought-induced crop failure.
There may not be a need to bring all crops indoors. But if China brings half of all of their crops indoors in five years it clearly shows that civilization can bring all crops and farming indoors at any time. The cost as I have shown is less than 0.5% of global GDP for the crops and a few percent to deal with the meat and feed as well.
It is likely only truly economical (even with China’s mass production) to bring vegetable and fruit farming indoors. If China has indoor vegetable and fruit production at $1 per pound then other countries could follow at different levels based upon how cost-competitive indoor farming is against open-air farming for a particular crop. There is also the question if people will pay more for greenhouse crops. Greenhouses allow for year-round crop production. This means consistent prices and availability for fruits and vegetable year round. It also means indoor farms can be inside of cities for fruit and vegetables that are fresh from the tree and vine. The greenhouse crops would also be mostly or completely free of pesticides. Indoor farming share will grow as efficiency and costs are improved.
I think 20-60% of all crops (mainly higher-value fruits and vegetables) globally will go indoors by 2030 and gradually more as indoor becomes a lower cost and superior product to outdoor farming. Greenhouse farmed fruits and vegetables can have a higher quality versus outdoor grown fruits and vegetables.
Some of the advantages of protected culture greenhouse crops are:
Season extension is just one of the advantages gained from greenhouse growing. Protected crops are less apt to be damaged by wind, rain, and hail so the percentage of marketable products is higher. Yield is often higher as well, if you can provide optimum growing conditions for each crop. Greenhouses protect crops from many diseases, particularly those that are soilborne and splash onto plants in the rain. And greenhouse crops may be protected from common field pests. Of course, greenhouse crops have their own particular problems such as foliar disease, aphids, and whiteflies, so vigilance is still required.
SOURCES- Alibaba, PNAS, agfunder news
How Square Roots Is Meeting Unprecedented Post-Pandemic Demand For Fresh, Healthy, Locally-Grown Food
Square Roots is expanding fast—deploying its latest indoor farm in Michigan in just three months
Square Roots Is Expanding Fast—Deploying Its Latest
Indoor Farm In Michigan In just Three Months.
To meet rapidly increasing demand for our locally-grown produce, today we’re announcing our newest indoor farm in Grand Rapids, Michigan. We broke ground in late December and planted the first seeds in March—just three months later. Now we're preparing for the first harvest, and our delicious, fresh produce will be available at grocery stores, eCommerce platforms, and restaurants across the Great Lakes region in the coming weeks.
Kimbal Musk, our Co-founder and Executive Chairman, says: “COVID-19 exposed major weaknesses in the industrial food supply chain, and accelerated the already fast-growing local farming movement. Square Roots can now deploy commercial-scale, controlled-climate farms, fast, in locations across America to meet the demand for local food, all year round. My wider mission is to bring responsibly-grown, local food to everyone in America. With Square Roots, we’re going to do it fast.”
From shovels-in-the-ground to first-seeds-planted, we built our new farm in just three months.
Growing Reliable, Fresh Produce Throughout the COVID-19 Pandemic
While COVID-19 wreaked havoc across the industrial food system, consumers increasingly valued local food, which in turn accelerated the adoption of indoor-grown produce. Consumers, forced to stay at home and cook, were able to experience the consistent peak-season flavor of our locally-grown greens. Meanwhile, retailers appreciated the reliability, longer shelf life, and complete traceability of all Square Roots’ products. As a result, we’ve seen a big increase in retail demand this year, and we’re now available in more than 200 stores (including Fresh Thyme Market, D&W Fresh Market, Whole Foods Market, FreshDirect, and more!).
In parallel, working hand-in-hand with our strategic partner Gordon Food Service—one of the largest food distributors in North America—we've been supporting and supplying restaurants throughout the pandemic. We’re as excited as anyone to see diners begin to venture out once more, and the restaurant industry bounce back strong.
Square Roots' new Michigan farm
This new farm in Michigan, our third commercial facility, is co-located with Gordon Food Service and represents another step towards a larger shared ambition to build indoor farms together across the continent—enabling local food at a national scale.
Our produce can be found at more than 200 stores across the Midwest and New York City area.
Square Roots’ Modular Farm-Tech Platform
Central to our ability to move fast and meet demand is our modular farm-tech platform. Capital-efficient and pre-fabricated inside upcycled shipping containers, ready-to-go farms can be shipped and deployed just-in-time to any site in the world, immediately creating the perfect conditions for growing the highest quality food, regardless of local climate conditions or time of year. The overall growing capacity of any Square Roots farm can seamlessly scale up or down depending on demand in the local market.
Our new two-story farm in Michigan also includes all of the necessary infrastructures to run a state-of-the-art, food-safe, and people-safe commercial operation. This includes cold storage, biosecurity, climate-controlled packaging space, distributor loading docks, and more. Meanwhile, all of our farms are Harmonized Good Agricultural Practices (GAP) certified, in line with the USDA’s standards, and operate to strict COVID-19 safety protocols to keep farmers and the local community safe.
Our farms are also cloud-connected and managed by a combination of skilled Square Roots farmers and sophisticated in-house software. Known as The Square Roots Farmer Toolbelt, our proprietary OS provides day-to-day guidance to farmers while capturing millions of data points throughout growing cycles across our network. This data can then be analyzed to determine how changes in certain environmental parameters impact factors like yield, taste, and texture. Our system learns faster as we deploy more farms and our network gets larger, all while helping farmers determine how to grow more, better-tasting food with fewer resources. Training new farmers—and empowering the next generation of leaders in indoor agriculture—has always been core to our mission, and the Farmer Toolbelt is a key enabler in our ability to offer accessible pathways for young people to enter the high-tech farming industry.
Farmers are guided through day-to-day operations by The Square Roots Farmer Toolbelt.
Responsibly-Grown, Local Food, Available Everywhere
We’ve always designed our farms to provide responsibly-grown food in areas close to the end consumer. Our hydroponic system uses 95% less water than conventional agriculture, our farms require zero pesticides, and the location of our facilities cuts down dramatically on food miles and food waste by enabling delivery of fresh produce within 24 hours of harvest, all year round. Meanwhile, our latest farm design is easily configured for both vertical and horizontal-stacked growing formats—a new and unique capability that means we can grow a wide range of crops to meet a variety of local market needs. To date, we've grown over 200 different varieties of herbs, microgreens, leafy greens, fruits, and even root vegetables—and we’re just getting started!
Keep an eye on this blog for announcements about more new farms soon. For more information about Square Roots check out our website, squarerootsgrow.com. And for daily updates, follow us on social media @squarerootsgrow.
How Square Roots Is Training Next-Gen Farmers During A Pandemic
The average age of the American farmer is 58 years old. If we're going to change the food system, we need to create more pathways for young people to launch successful careers in agriculture
Square Roots
10.08.20
The average age of the American farmer is 58 years old. If we're going to change the food system, we need to create more pathways for young people to launch successful careers in agriculture.
One of the many ways Square Roots invests in the future of farming is through our Next-Gen Farmer Training Program—aimed at new farmers or those at early stages in their careers. Farmers initially join Square Roots as Apprentice Growers. Through our proprietary training methodology—supported by our intuitive technology platform—Apprentice Growers rapidly learn the essential farm skills needed to move into permanent roles on the farm team and accelerate their careers.
We continuously evolve our training program to zero in on the skills and experiences that help employees become the best indoor farmers they can be. Throughout COVID-19, we have been committed to prioritizing people safety and plant safety which has led to changes in our day-to-day farming operations, as well as rewiring our in-flight farmer training programs in May and adapting how we run the Square Roots Next-Gen Farmer Training Program going forward. Also, after several years of training farmers, we’ve listened and learned to what farmers value from their experience at Square Roots and have incorporated that into our program going forward. Read more about what it’s like to be a grower at Square Roots and how the program has evolved:
Individual Pathways
Based on the needs of our farm production teams, apprentices are hired and onboarded, either individually or in pairs, on a rolling basis. By spacing out onboarding and training, our team is able to provide more attention and support to apprentices, allowing them to move more quickly through the training program and into permanent positions on our team. We expect most apprentices will complete their training in three to six months, but each will advance at their own pace.
Foundational Remote Learning
We have moved our training materials onto a virtual learning platform, which houses videos, interactive presentations, animated diagrams, virtual tours, and other types of content that can be brought to life beyond a typical presentation. Since COVID-19 restricts our ability to hold classroom-style learning, online learning can be self-serve, supporting different types of learning styles. It also drives consistency in training and terminology, reducing the burden on managers responsible for administering it.
Intensive ‘Boot-Camp’ Style Farm Immersion
Training for Apprentice Growers is laser focused on the skills required for new farmers to quickly become the best indoor farmers they can be. After the initial foundational onboarding, apprentices will jump into production, and, in parallel, will be equipped with the necessary context and complementary training to support expanded learning and competency much sooner. Apprentices will be supported by our software operating system the Farmer Toolbelt, empowering them to get up to speed much faster, engaging with data, and ultimately helping them become better growers. Throughout the training process, farmers will receive direct supervision by one of our experienced farm team members who will act as their training guide and provide professional and moral support.
Pathway to Permanent Employment at Square Roots
Central to Square Roots is our mission to empower Next-Gen leaders in urban farming, and the Next-Gen Farmer Training Program is one of the most direct ways we do that. The program is designed to bring young people with little or no experience up to speed in our proprietary indoor farms as quickly as possible and on to their careers in indoor farming—acting as an internal training program for permanent full-time employees on the Square Roots farm team.
The Apprentice Grower role is the first step in a career path to indoor farming at Square Roots. To start, apprentices will earn an hourly rate indexed to the area’s living wage, and receive 100% covered health benefits and equity in Square Roots. Once they’ve successfully mastered indoor growing fundamentals (we expect this to take three to six months), apprentices will be eligible to move into Associate Grower positions.
For more information and to learn about new open positions on our farm teams, follow us on social media and sign up for our newsletter for updates.
Tags: Next-Gen Farm / Farmer Training / COVID-19 Response / Updates
Vertical Growing Solutions That Are Easily Multiplied Increasing The Management Scale of Each Grower
GrowSpec offers three main products, each with numerous product lines contained therein. These three products include LED grow lights, vertical grow systems, and container farms
GrowSpec is an indoor farming equipment supplier established in 2015. GrowSpec offers three main products, each with numerous product lines contained therein. These three products include LED grow lights, vertical grow systems, and container farms. According to GrowSpec CEO Alvis Ma, these products can be used to produce a variety of crops indoors.
LED Grow Lights
GrowSpec offers six different types of LED lighting: AgriSpec, AgriBar, Sun Ray, Panel, SlimSpec, and Quantum. According to the company’s website, AgriSpec is a high-performance top-lighting solution with dimmable capabilities to allow growers to transition from vegetative to regenerative growth (i.e., flowering). The lights’ slim configuration enables installation in low rooms, racking systems, etc. While AgriBar and Sun Ray are both advertised as applicable for greenhouses as well as indoor farms, Panel is more specifically designed for indoor growing as the wide panels are somewhat wide for greenhouse use yet provide high light uniformity for indoor environments.
Vertical Grow Systems
GrowSpec also designs a number of vertical grow systems, all consisting of racks with integrated power supply, control system, and PVC trays so that each 4’x 8’ tray can be managed independently. Among these product lines in VertiDrip, a modular rack consisting of GrowSpec’s lighting, drip irrigation, airflow system, power supply, and touchscreen controls. The company’s VertiGro follows similar principles. GrowSpec’s main grow system, which was previously featured in IGrow (Combining Hydroponic And Aeroponic In Vertical Farming — iGrow) is VertiAero, which uses aeroponic technology. According to Alvis, VertiAero is patent pending in both the United States and Europe and offers various savings to growers.
“VertiAero reduces operational costs by 40%. In terms of electricity, we use 30% less. With nutrients, we save 85% because we use aeroponics rather than soil, so the root area is sealed and water losses are reduced. Our vertical grow systems are designed to optimize farm’s operation, they can match up with different irrigation systems so as to meet growers’ different preferred cultivation skills, and easily multiplied increasing the management scale of each grower,” explains Alvis.
Moreover, Alvis explained that having an integrated ventilation system in every rack of GrowSpec’s vertical grow systems helps to decrease plant disease.
“With inadequate ventilation, some plants will have diseases like powdery mildew or botrytis. But if you have full ventilation and every leaf can be blown with air, you will seldom have those diseases,” says Alvis.
Alvis also explained that the racks are space-efficient by both having an adjustable height and by being horizontally mobile using a mechanical assist. This, according to Alvis, allows growers to fit more racks into a grow room.
Container Farms
GrowSpec’s third product offering is container farms, which are equipped with GrowSpec’s vertical grow systems. According to Alvis, GrowSpec’s container farms are ideal both for production and for research as the conditions are highly modifiable and allow growers to test various things.
“If people want to do research, they can use this container to do so. They can set up irrigation, lighting, temperature of the root zone, temperature of the canopy, light intensity, etc. It is the perfect toy for them.”
Efficiency and scalability as priorities
Across GrowSpec’s three product types (LEDs, vertical grow systems and container farms), the company has emphasized improved resource use efficiency and scalability so that growers can easily increase production over time.
“For installation, we design our systems in modules so that they are very easy to install. It is a complex system yet easy to install. And it is scalable. It is easy to design the grow room because every rack is independent. The rack height is also customizable, and the power is integrated so that there is one main cable per rack, this allows requires the systems to be easy to maintenance ” explains Alvis.
GrowSpec also reports increased crop productivity by allowing growers to produce seven crops per year rather than four crops in traditional farming systems.
For more information:
USA: ILLINOIS - Glenview's Wiseacre Farm To Be Featured On History Channel
"We were connected to this opportunity through Freight Farms, a hydroponic farming container company in Boston. Our farm was built and distributed by Freight Farms," said Yael Sheinfeld, whose father, Aviad, founded Wiseacre Farm
This Sunday's Episode of "Modern Marvels"
Will Highlight Innovative Hydroponic Techniques
March 23, 2021
The Wiseacre Farm crew (left to right): Sam Sheinfeld, Yael Sheinfeld and Aviad Sheinfeld. (Photo by Wiseacre Farm)
GLENVIEW, IL — Back in December of last year, a television production crew from the History Channel made a special visit to Glenview. Wiseacre Farm, a family-owned hydroponic farm, will be featured this Sunday as part of the network's "Modern Marvels" program.
Yael Sheinfeld, who handles marketing for the farm at 1975 N Lake Terrace, said the team at Wiseacre hasn't seen the episode titled, "Future of Food," yet. It is set to air at 9 p.m.
"We were connected to this opportunity through Freight Farms, a hydroponic farming container company in Boston. Our farm was built and distributed by Freight Farms," said Yael Sheinfeld, whose father, Aviad, founded Wiseacre Farm. "We're so grateful for the experience, and are very excited for the episode to air."
Aviad Sheinfeld shows off Wiseacre Farm during an episode of "Modern Marvels" on The History Channel. (Courtesy of Wiseacre Farm)
Sunday's episode of "Modern Marvels," hosted by food author and culinary entrepreneur Adam Richman, showcases Wiseacre's innovative hydroponic farming process as the future of food, highlighting the farm's mission to grow clean, fresh produce within the community that it serves.
"It was exciting for the film crew to visit the farm. Our farming team (Aviad Sheinfeld and his dad, Sam Sheinfeld) talked through each step of the plant life cycle and delivery process while the crew filmed," Yael Sheinfeld said. "[We also] participated in sit-down interviews where we discussed the concept behind the farm, how we started it, etc."
Yael Sheinfeld said that due to COVID-19 restrictions, the entire film crew for the episode was local.
Founder Aviad Sheinfeld talks about Wiseacre Farm during the episode of "Modern Marvels" titled, "Future of Food." (Photo by Wiseacre Farm)
Wiseacre Farm works to shorten the path from farm to table, promote and practice environmental sustainability, and educate consumers about the origins of their food.
"We're a family-owned hydroponic farm in Glenview that provides fresh, hyperlocal greens to the community," Yael Sheinfeld said. "We currently offer home delivery and farmside pickup options."
Wiseacre greens are available through home delivery subscriptions and weekly farmside pickup. Wiseacre Farm also makes frequent donations to local food pantries, working to ensure that fresh greens are accessible to all.
More information about Wiseacre Farm can be found here: https://www.wiseacre.farm/.
AUSTRALIA: VIDEO - Shipping Container Farms: Check Out This Craze In Modified Containers
Greenhouses, hydroponics, and mushroom farms – converted shipping containers can produce protein and vegetables for all your needs
Greenhouses, hydroponics, and mushroom farms – converted shipping containers can produce protein and vegetables for all your needs. Even if you’re not an environmentalist, there are business opportunities to be had in delivering extremely fresh food to people in urban environments like Brisbane. Given the changing climate and topsoil loss we are facing, shipping container farms could well be an answer to these issues.
Over the years in the Gateway Gazette, we have published a number of stories that look at producing food in converted shipping containers. Reflecting on what we have published and looking at the detail of what can be done, let’s consider the possibilities that come with shipping container farms.
Open Top Container Greenhouse
One of the most cost-effective ways of using a shipping container as a food-producing unit is by attaching a glass top to an open-top shipping container.
In this video, Urban Farm Units looked at the concept of a greenhouse-container. An open-top 20-foot container would have a greenhouse attached to the top with shelving units directly under the glass. This allows photosynthesis to take place in the normal way.
Seedlings can be started in the lower part of the unit, which is warmed by the light and heat from the outside.
One step down from slapping a greenhouse on top of an open-top container would be to use a flat rack container and to have the greenhouse on the base (Gateway Containers can supply both open-top and flat rack containers).
The concept is an improvement on the one in the video, as long as you keep the greenhouse within the dimensions of a 20ft standard or high-cube container, it would be possible to lift and move the container farm from place to place.
This might be useful where you have an agreement with property developers or a council to use vacant plots of land in a city for agriculture. When the site is ready to be developed you can stick it all on a truck and move it to the next plot.
The concept of a shipping container greenhouse is:
Cheap to buy
Mobile
And often won’t need planning permission for a permanent site
Could this be something you’d consider? Contact us at Gateway Containers to discuss your needs!
Mushie Container Farm!
Image source: King Oyster Mushrooms Facebook
In 2019 we reported how Belgrave, Vic-based John Ford has developed a shipping container mushroom farm. This could produce protein for people as an alternative to meat or for anyone who loves the taste of freshly cut shrooms.
Mushrooms of any kind don’t store well and are best eaten as soon as possible after cutting. This is why having a mushroom farm close to restaurants could be a money-spinner.
This requires no modification from a basic shipping container, you could even install the racking inside the container yourself.
In their lifecycle, mushroom mycelium live out of sight of the world until they are stressed and get the impression that they are facing death. When stressed they flower to produce spores – those flowers are the mushrooms that many of us love to eat.
A shipping container is perfect to take advantage of such a lifecycle. Logs or other media are infected with the mycelium and left to rot for a certain time. By altering the environmental conditions, so you deliberately stress the fungi and they flower.
In our article, we reported how John Ford is producing mushroom species that are famed for their delicate taste but don’t travel well at all – shiitake and oyster mushrooms. As a sideline to his main income as a marine biologist restoring seagrass habitats near Belgrave, he produces freshly cut shrooms for local people and restaurants.
For you as an entrepreneur, mushroom growing would require buying a used shipping container and setting it up as a mushroom farm. If you are planning an urban mushroom container farm, you can take advantage of the fact that you can treat the container as a mobile unit and not as a permanent base. Shipping containers are also pretty inexpensive to buy and convert.
Hydroponics – The Rolls Royce of Shipping Container Farms
Image source: ABC
The hydroponics concept is highly developed for the use of fresh food and can be set up for high density vegetable farming in shipping containers. This requires a fair bit more modification than the two systems we describe above.
Unlike the Urban Farm Units company, several companies have managed to survive over the years selling their hydroponic container farm businesses to entrepreneurs and restaurants around the world.
Modular Farms is a company we featured in our blog originally based in Canada, but who recently set up shop over here in Australia. According to their website, they “design and manufacture container farm systems that can be used to grow food in most locations on earth.”
These systems strive to get around some of the issues we face here. Cities like Brisbane get far too much water sometimes and then face droughts for years on end. The Australian Food Services News reported, “With a focus on sustainability, Modular Farms’s hydroponic, closed-loop system uses 95% less water than a typical outdoor farm.”
Topsoil erosion is a problem, especially in prolonged droughts when it gets blown away as dust. Hydroponics use media like rock wool and even used mattresses to house the plants’ root systems and feed them nutrients via a watering system.
With our ever more extreme climate, food often has to be imported into cities from hundreds or thousands of miles away. A hydroponic container farm can enable you to grow many vegs very close to markets and restaurants.
This has been observed by global homewares retail giant IKEA, which in 2019 announced it was piloting growing vegetables in its stores for use at its restaurants. We reported, “While selling hydroponic indoor growing equipment to customers, IKEA is feeding its staff with lettuce and other vegetables grown in a container outside its Malmö and Helsingborg stores.”
Image source: ABC
There are a few downsides to hydroponics. Firstly, while some types of plants are happy enough growing in hydroponics – the simpler ones producing leaves and flowers (like broccoli!) – others aren’t so happy, such as cassava, wheat, and potatoes.
The next big issue is that for a high-intensity farm, not unlike factory farming chickens, you need to be ultra-clean in your production as the arrival of a destructive disease or fungus could wipe you out very quickly.
Container Fish Farm Too?
In theory, it is possible to run a fish farm connected to the hydroponics container farm, with you largely feeding the fish and collecting their feces and other waste to feed the plants. The plants would clean the fishes’ water and make it habitable for them as reed beds do in nature. This a concept that is in development but hasn’t caught on commercially yet.
How Can Gateway Containers Help?
We can provide and convert an insulated container for you to get started with and advise you how to best make further additions without compromising the overall structure.
If any or all of these ideas have caught your interest – or you just know about these concepts and need a shipping container to make it possible – then get in touch with us today to discuss your needs!
Posted on February 22, 2021
By Mark FinneganOtherShipping ContainerModified Shipping ContainersLeave a comment
UAE: “Hydroponic Farming Is Not Yet Deployed At A Meaningful Scale”
Greener Crop was founded in September last year with the goal of enabling hydroponic farming in the Middle East and Africa
“While hydroponic farming is extremely relevant to the water-poor Middle East, and incentives for agriculture such as energy and water subsidies have been put in place, the technology has not been deployed at a meaningful scale yet,” Alexander Kappes, founder of Greener Crop states.
Greener Crop was founded in September last year with the goal of enabling hydroponic farming in the Middle East and Africa. Alexander was working at an investment office prior to Greener Crop which brought his attention to the long-existing problem: the country is too dependent on food imports. “We wanted to enable local sustainable farming here as well.” Greener Crop offers farm management solutions, removing entry barriers.
The company offers four key solutions for existing or aspiring farmers: development of crop strategy, input management, physical farm management, and crop marketing. From Container farms to greenhouses and indoor vertical farms, Greener Crop supports their clients from finding the right supplier and setup, to selling the crops in the market. “It’s a great solution if you’re looking for an experienced partner to get your farm up and running, whether it’s short or long term,” says Alexander.
Alexander Kappes
There has been a strong push from local governments to develop alternative farming methods. The government in the UAE has invested over $200 million to support the development of growing facilities. This is a highly valuable approach, however, it is important to keep in mind that even a $40m indoor vertical farm can only contribute 0.03% of the local annual fruit & vegetable consumption. Farming is a highly democratized industry and requires not only a handful of a large farm but thousands of small and medium-sized farms that enable a country to be self-sufficient,” Alexander claims.
Removing barriers
Whether farmers want to expand or convert their farm into a hydroponic farm or an outsider investor, Greener Crop is here to help. The company connects farmers to suppliers and manufacturers, they can either run the farm, handle the supply chain and in some cases, handle the sales. “Clients no longer have to figure out everything on their own – we are here to support them with the operations and even sale of their crops. In many cases, clients are self-consumers such as hotels and restaurants,” Alexander explains.
The company sits together with their clients, comes up with a plan, ticks off the boxes, and starts setting things up, given the customer budget. Based on the expected yield, an approximate selling price per kg can be provided to clients. “We can always predict with a certain degree of accuracy. In this way, we can sketch revenue, utility costs, including labor, etc., which eventually leaves us to the expected profits. After the preliminary proposal is given, we reach out to potential suppliers as we understand what they offer in terms of yield, cycles, crop analyses, costs, and input.”
Green Crop has the ability to run a farm completely independently, however, the client can decide how hands-on they want the company to be. Clients can set foot on the farm at any time. “We can also operate certain parts of the operation such as maintenance for instance. Our benefit is that we come in, with trained staff, they do the work and go out.
Finding a suitable market
Alexander says, “The difficulty is not in selling all of the produce, but whether you are able to sell it at the right price. The smaller the farm, the higher the production costs. Being able to sell something at the price where it covers all costs is the main goal.” The challenge this therefore to gauge the available client-base for your produce, as well as the competition and their prices. Similarly, a thorough crop strategy must account for seasonal price fluctuations and ensure that we seed to harvest at the right time.
Often, the biggest challenge, according to Alexander, for smaller individual farmers is sourcing the right seeds and nutrients. Finding suppliers of quality products is often a challenge, and in most cases, they require you to buy large quantities that exceed the farms' annual consumption. “There are large differences in quality between suppliers and often when farmers choose the most affordable solution, this results in high costs for maintenance and replacements. For many new manufacturers, hydroponic farming looks like an easy enough industry to get into, but they underestimate the complexity of fine-tuning an indoor farm for efficient farming, and it’s often the farmers that pay the price for this,” Alexander notes.
Greener Crop started operations in the UAE and is now expanding into Saudi Arabia and Qatar, with the rest of the Middle East and all of Africa in their sights. Alexander adds: “As the region in the world most under threat from water stress and shortages, conventional farming is often not a sustainable option. It is for that reason that we chose to focus on enabling hydroponic farming in this area.”
For more information:
Alexander Kappes, Founder and CEO
Greener Crop
alexander@greenercrop.com
www.greenercrop.com
Publication date: Mon 22 Mar 2021
Author: Rebekka Boekhout
© VerticalFarmDaily.com