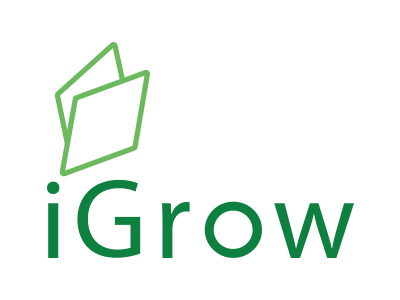
Welcome to iGrow News, Your Source for the World of Indoor Vertical Farming
Indoor Ag Sci Cafe Discusses Lighting Strategies for Energy Savings
Funded by NASA and USDA SCRI, Cary has a long research history focusing on energy savings while maximizing crop productivities
By urbanagnews
November 2, 2018
The second ‘Indoor Ag Science Café’ of this month had Dr. Cary Mitchell, as a speaker.
Funded by NASA and USDA SCRI, Cary has a long research history focusing on energy savings while maximizing crop productivities through his in-depth understanding of plant physiology under controlled environment.
In his presentation ‘Lighting Strategies for Energy Savings’ introduced his innovative approach to optimize the lighting environment.
Indoor Ag Science Café is a monthly online forum organized by three scientists (Chieri Kubota, Ohio State U; Erik Runkle, Michigan State U; and Cary Mitchell, Purdue U). Please contact kubota.10@osu.edu to join the café.
Bowery Farming Adding Microgrid With Solar, Natural Gas And Storage
Schneider Electric and Scale Microgrid Solutions have announced an agreement to design, engineer and build a new microgrid for modern-farming company Bowery Farming.
Posted by
November 15, 2018
Schneider Electric and Scale Microgrid Solutions have announced an agreement to design, engineer and build a new microgrid for modern-farming company Bowery Farming.
Under the terms of the agreement, Scale Microgrid Solutions will build, own and operate a proprietary hybrid microgrid system that leverages Schneider Electric EcoStruxure technology for Bowery’s newly commissioned facility in New Jersey.
The system will use distributed energy resources, including a rooftop solar array, a natural gas generator equipped with advanced emissions-control technologies and Schneider Electric’s lithium-ion battery energy storage system interconnected in a behind-the-meter configuration.
“Bowery has created a facility wherein crop production is already 100 times more efficient than traditional farmland, creating a greater need for reliable, efficient power,” says Ryan Goodman, CEO of Scale Microgrid Solutions. “Microgrids offer a compelling value proposition, but they’re inherently complex machines, and not many companies have the in-house expertise needed to make the investment. We’re excited to deploy an affordable microgrid solution in conjunction with Schneider Electric that will further reduce Bowery’s carbon footprint and provide critical resilience.”
Schneider Electric’s EcoStruxure Microgrid Advisor (EMA), a cloud-connected, demand-side energy management software platform, will be integrated to optimize the system’s performance. By leveraging predictive and learning algorithms, EMA will empower Scale Microgrid Solutions to better manage the production and consumption of its renewable energy and control energy spend. The system will also be equipped to operate in parallel with traditional utility electric services during normal operating conditions and in “island mode” to ensure that the farm remains powered during unexpected outages.
“Bowery is committed to growing food for a better future, and we are excited to have found partners in Schneider Electric and Scale Microgrid Solutions, who will help us achieve our mission,” says Brian Donato, senior vice president of operations at Bowery Farming. “We’re looking forward to continuing to provide consumers with access to local, high-quality produce and drive a more sustainable future.”
Commissioning of the Bowery microgrid project is scheduled for the first quarter of 2019.
Cover Crop Powers First Transatlantic Flight Using Sustainable Biojet
A United Airlines plane powered by biojet fuel made a landmark non-stop voyage from San Francisco to Zurich.
SEPTEMBER 24, 2018 LAUREN MANNING
On Monday, a United Airlines plane powered by biojet fuel made a landmark non-stop voyage from San Francisco to Zurich. Agrisoma Biosciences, a Canadian agtech company that develops Carinata seeds to produce aviation biojet fuel, partnered with United Airlines and French oil and proteins sector company Avril Group to accomplish the second international commercial flight using the company’s seed oil.
As with any startup, proof of concept is a key milestone.
“We are creating a new industry,” Hank Krakowski, Agrisoma’s Director of Sustainable Aviation, told AgFunderNews. “The question was whether the fuel is ready, and it is. Until we got through the approval process, we couldn’t talk to people about investing in contracts with us to create the feedstock for the biojet fuel.” Krakowski has deep ties to the aviation industry after working as a commercial pilot for United Airlines for 30 years. After hanging up his wings, he served as chief operating officer of the Federal Aviation Administration’s Air Traffic Organization for a few years before transitioning into aerospace investment banking. It was through this endeavor that biojet fuel and a sustainable future for aviation captured his focus.
Earlier this year, Agrisoma and Australia’s Qantas Airways partnered on a transpacific flight from Los Angeles to Melbourne that used biojet fuel produced from Carinata, which is a member of the mustard seed family.
“Qantas came to us over a year ago curious about whether we could be the source for their biofuel needs in Australia,” Krakowski explains. “Something happened that surprised us in a wonderful way: when the flight ended, over the next few months Australian farmers called us and Qantas to see how they could work with us.”
Since launching in 2001, Agrisoma has captured over $27 million in venture capital from Canadian investors, with its most recent Series C in March 2018 raising roughly $12 million. Its four investors – fund manager DesJardins Capital, impact investors Cycle Capital, Quebec-focused funders LuneRouge, and multi-stage investor BDC – all hail from Canada and seek out sustainable technologies. Krakowski hints at more financing activity for Agrisoma in the near future, but could not share more details at this time.
A Seed Company at Heart
While many might assume that Agrisoma brands itself as a biofuel company, it’s better categorized as a seed company. Agrisoma’s proprietary Carinata seed, currently being cultivated by growers in both the Americas and Australia, is a non-food, mustard-like oilseed that produces a grain that is roughly 50% oil and 50% protein. Carinata biojet fuel is made by harvesting tons of Carinata crop, crushing the grain to recover the oil, and refining that oil into jet fuel by the same process used for petroleum-derived jet fuel.
Agrisoma sells its Carinata seeds to farmers or agricultural cooperatives who then grow the seed as a cover crop and sell it back to Agrisoma. It has developed 20,000 lines of germplasm so that it can select the precise variation for different geographical locations and holds numerous patents for the germplasms.
“We have to go into different locations, do trials, sort out the right seed varieties and germplasms for that area, and then we put a two-to-five-year scale-up plan in place where we increase the acreage every year. We have to get farmers to plant and grow the seed and to harvest it correctly,” he explains. The company currently reports 50,000 acres of commercial crop growing across the Americas and Europe with the hope of doubling this acreage every year. It’s started the trial process for Carinata cultivation in Australia, New Zealand, and France.
While biojet fuel is a relatively new product in the jet fuel market, Agrisoma has found a way to slip into the existing supply chain: the company sells directly to existing refineries with biofuel production capabilities, aiming to avoid adding additional layers of complexity to the process and the existing supply chain, says Krakowski.
The biojet fuel typically replaces 10% to 30% of the petroleum jet fuel needed for a flight, making for a cleaner fuel blend that reduces greenhouse gas emissions, according to Agrisoma. Carinata is the first oilseed to be certified as sustainable by the Roundtable on Sustainable Biomaterials, an independent global standard, and certification program for sustainable biomaterials.
Competing with Conventional Jet Fuel
When it comes to industry acceptance, Agrisoma is banking on recent agreements from United Nations International Civil Aviation Organization (ICAO) encouraging airlines to achieve carbon neutral status by 2021 with the goal of claiming a 50% reduction of CO2 emissions by 2050. Carinata and the way in which the company goes about cultivating the crop offers certain environmental benefits that play directly into the ICAO’s aims.
“When you grow it, it sequesters carbon out of the atmosphere like any plant and puts it into the ground. Then, you harvest the plant, and you have a biomass that you leave behind on the ground that does a number of things: it prevents carbon from escaping and provides nutrients for the next crop growing.”
Farmers have been largely receptive to cultivating Carinata, which is used as a cover crop. This means that it doesn’t compete with traditional food growing cycles. And while other cover crops commonly don’t have a dollar value, Carinata cultivation offers farmers an additional stream of income during the off-season.
As an added bonus, Agrisoma sells the spent meal that’s leftover after the seed-crushing process for livestock feed. Because Carinata is a non-GMO seed, the meal sells at a premium to dairies producing organic products.
With some estimates suggesting that airline travel will double from current demand levels by 2040, Krakowski thinks that airlines will have no choice but to seek out sustainable fuel sources that allow them to keep pace with demand while satisfying the ICAO agreement. In fact, Agrisoma is in active discussions with a handful of oil companies about using its oil as a feedstock for biofuel production, says Krakowski.
The Sky’s the Limit
With a few successful flights under its belt, the company is focusing on increasing its acres of production and scaling up in the Americas and France, as well as Australia, New Zealand and perhaps Asia. Most startups keep a close eye on the competition, but for Agrisoma and Krakowski there is plenty of room in the biojet fuel space for additional players.
“If you look at the numbers the industry needs to meet a doubling of air commerce against biofuel availability, they will need every drop they can get from anybody who can produce biofuel regardless of where it comes from.”
Second Greenhouse Heated by Cryptocurrency Mining
UnitedCorp's technology uses the heat from cryptocurrency mining to support greenhouse agricultural operations
Miami-based United American Corp announces the completion of its second BlockchainDome and the full commissioning of 1,500 additional miners for a total of 2,500 miners (3.8 megawatts) now in service in two BlockchainDomes. Pre-installation of 1.5 megawatts of electrical service for adjacent greenhouses heated by the BlockchainDomes is now also complete.
The latest BlockchainDome incorporates a number of improvements in construction and deployment from the first dome which includes mass pre-fabrication of a number of dome components and in-house CNC manufacturing of the mining rig docking stations. Construction logistics have also been refined to include pre-installation of foundations and utilities for future domes resulting in overall lower construction costs and shorter construction timelines.
"We have taken everything we have learned from the construction of the first BlockchainDome and used this knowledge to make the implementation of this subsequent BlockchainDomes faster, cheaper and of better quality," stated UnitedCorp CEO Benoit Laliberte. "Along with the generation of heat from the BlockchainDomes for agricultural purposes, our goal remains to be the low cost and environmentally sustainable standard for the industry."
UnitedCorp's technology uses the heat from cryptocurrency mining to support greenhouse agricultural operations through the BlockchainDome Heat Station system which keeps greenhouses at 20oC year-round. This represents a simple design solution compared to various alternatives whereby the cost of generating this heat from a single source is shared between multiple use cases.
Commercial greenhouses in cooler climates like in the Province of Quebec typically require a significant amount of thermal energy to supplement daytime solar energy, particularly during the period of September to May, and many older greenhouses utilize inefficient heating systems for this purpose. The dry heat produced by the BlockchainDome Heat Station is also used in the summer to reduce greenhouse mold and fungus caused by condensation thereby reducing or eliminating the need for chemicals to treat this problem and creating a more organic growth environment.
UnitedCorp believes this "Heat Campus" approach for heat generation and utilization is the future for agriculture and any other industry that can make use of low-cost heat with the ultimate goal being to get as close zero waste as possible. This is not only good economically but allows businesses to "green" their operations by significantly reducing the amount of electricity the combined operations require from the grid.
For more information:
UnitedCorp
5201 Blue Lagoon Drive, 8th floor,
Miami FL 33126
www.unitedcorp.com
Study Shows How Badly Smog Can Cripple Solar Farms
New research finds that severe air pollution can eliminate all profits from solar panel installations.
Aug 30, 2018
A lot can keep solar panels from generating electricity, from cloud cover blocking the sun to simply being nighttime. But according to recent research, one of the biggest obstacles facing solar farms is smog and haze from air pollution.
It’s not surprising that air pollution can make solar panels less effective since it can cut down on visibility and reduce the amount of sunlight reaching the ground. In the past, researchers have found that air pollution can lead to dust buildup on solar panels that can dramatically reduce their effectiveness.
This new research, from scientists at MIT and Singapore, calculates how much solar energy is lost due to smog in many of the world’s biggest cities. In the city of Delhi, one of the world’s most polluted cities, electricity generation is reduced by more than 10 percent the study finds, which translates to a cost of more than $20 million.
The problem is more than just inefficiency. A loss of this size could spell doom for many urban solar farms by seriously inhibiting their ability to turn a profit. Pollution can turn a money-making solar farm into a money sink.
Even worse, the lack of a solar alternative naturally just increases reliance on smog-generating fossil fuels and could serve to lock entire regions into a vicious cycle. This gives us another reason to keep our air clean, just in case we didn’t have enough.
Source: Energy and Environmental Science
Investors Should Look At Naturally Lit Rather Than Energy Hungry Vertical Farming, Says Researcher
The energy required for artificial lighting and climate control makes "vertical farming" much less sustainable than its alternatives for local city-grown produce, according to an expert in urban sustainability.
19 September 2018
by Gavin McEwan
The energy required for artificial lighting and climate control makes "vertical farming" much less sustainable than its alternatives for local city-grown produce, according to an expert in urban sustainability.
Writing in response to the recent opening of "the world's most technically advanced indoor farm" near Dundee, Andrew Jenkins, a research fellow at Queen's University Belfast's School of Natural and Built Environment, said: "Vertical farming currently requires a lot of energy, which will hopefully decrease over time as companies like Intelligent Growth Solutions make technical advances.
"But for the time being, the practice of vertical farming is still a long way from being a sustainable method of agriculture."
This is because the energy required for vertical farming "is much higher than other methods of food production", he said.
"For example, lettuces grown in traditionally heated greenhouses in the UK need an estimated 250kWh of energy a year for every square metre of growing area. In comparison, lettuces grown in a purpose-built vertical farm need an estimated 3,500kWh a year for each square metre of growing area."
Other urban growing formats using natural light currently offer a less energy-intensive alternative, he said, adding: "I am surprised that more companies are not considering and maximising the opportunities presented by naturally-lit urban environments.
"Although they can’t grow as much food, rooftop greenhouses need at least 70% less energy for each square metre of growing area than artificially lit vertical farms."
Manchester alone has 136 hectares of unoccupied flat roofs, accounting for one-third of the city’s inner urban area, he pointed out.
Food Security: Vertical Farming Sounds Fantastic Until You Consider Its Energy Use
Intelligent Growth Solutions
September 10, 2018
Author
Research Fellow, School of Natural and Built Environment, Queen's University Belfast
Andrew Jenkins does not work for, consult, own shares in or receive funding from any company or organization that would benefit from this article, and has disclosed no relevant affiliations beyond their academic appointment.
Partners Queen's University Belfast provides funding as a founding partner of The Conversation UK.
A company in Scotland has unveiled what it claims is arguably the world’s most technically advanced indoor farm. Intelligent Growth Solutions’ vertical farm uses artificial intelligence and specially designed power and communication technologies. The firm says this reduces energy costs by 50% and labour costs by 80% when compared to other indoor growing environments, and can produce yields of up to 200% more than that of a traditional greenhouse.
Vertical farms like this aim to minimize water use and maximize productivity by growing crops “hydroponically” in small amounts of nutrient-rich water stacked in a climate-controlled building. But it’s important to recognize that the increased productivity of indoor vertical farming comes at the cost of much higher energy usage due to the need for artificial lighting and climate control systems.
By 2050, global food production will need to increase by an estimated 70% in developed countries and 100% in developing countries to match current trends in population growth (based on production information from 2005-2007). But in countries that already use the majority of their land for farming, this is easier said than done.
The UK, for example, uses 72% of its landmass for agricultural practices but imports nearly half of the food it consumes. To improve domestic food security and prevent natural habitats from being destroyed for new farmland, countries such as the UK need to consider new methods of food production.
Farms don’t need fields. Andrew Jenkins, Author provided
Urban farming presents a unique opportunity to grow food on already developed land, increase domestic food production and minimize the distance food travels. Since the publication of Dickson Despommier’s 2010 book The Vertical Farm: Feeding the World in the 21st Century, vertical farming has become synonymous with urban farming. Although the agricultural skyscrapers illustrated in Despommier’s book are yet to be realized, the idea of growing food vertically has captured the minds of designers and engineers alike.
The energy demand associated with vertical farming, however, is much higher than other methods of food production. For example, lettuces grown in traditionally heated greenhouses in the UK need an estimated 250kWh of energy a year for every square meter of growing area. In comparison, lettuces grown in a purpose-built vertical farm need an estimated 3,500kWh a year for each square metre of growing area. Notably, 98% of this energy use is due to artificial lighting and climate control.
Rooftop farm in Salford, UK. Andrew Jenkins, Author provided
Even with the reductions promised by Intelligent Growth Solutions, the energy demand associated with most vertical farms would still be very high, which positions vertical farming in a grey area. On the one hand, the world needs to produce more food, and on the other hand, it needs to reduce energy use and the production of greenhouse gases.
Urban alternatives
But indoor vertical farming isn’t the only way to grow food in cities. A plethora of naturally lit methods also exist, from raised beds in communal gardens to rooftop aquaponic systems that grow food with the help of fish. These methods all require less energy when compared to vertical farming because they don’t need artificial lighting.
Naturally lit aquaponic farm. Andrew Jenkins, Author provided
When viewing cities from above, it is clear to see just how many flat roofs are left vacant and the agricultural opportunities they represent. In the city of Manchester in the UK, unoccupied flat roofs account for an area of 136 hectares, representing one-third of the city’s inner urban area.
Gotham Greens in New York and Lufa Farms in Montreal, for example, are both commercial farms that use vacant roof space to grow food in naturally lit hydroponic greenhouses. Given the success of such projects and the area of roof space available, it seems strange that so many companies would skip ahead to methods of food production that still need a lot of costly development, as well as more energy to operate. Although they can’t grow as much food, rooftop greenhouses need at least 70% less energy for each square metre of growing area than artificially lit vertical farms.
Lufa Farms rooftop greenhouse. Fadi Hage/Wikimedia Commons, CC BY-SA
Having designed and built a rooftop aquaponic system myself in an ex-industrial building in Salford in the UK, I am surprised that more companies are not considering and maximizing the opportunities presented by naturally-lit urban environments. If nothing else, I believe we should be exploring the potential of naturally lit environments before we delve into dimly lit buildings where special technologies, artificial lighting and air handling units are needed to produce food.
There is little question that vertical farms will play a big role in urban farming and agriculture in the future. But when considering any method of food production, we need to understand the impact and energy use of the practice to ensure it is a sustainable and comprehensive response to global food demands. Vertical farming currently requires a lot of energy, which will hopefully decrease over time as companies like Intelligent Growth Solutions make technical advances. But for the time being, the practice of vertical farming is still a long way from being a sustainable method of agriculture.