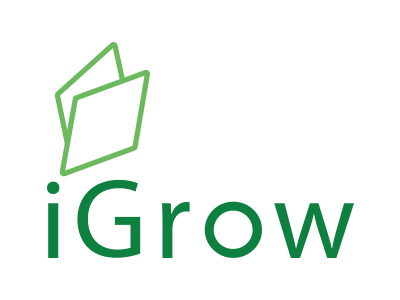
Welcome to iGrow News, Your Source for the World of Indoor Vertical Farming
5 Repurposed Warehouses Turned Indoor Farms That Need No Land Or Sun To Grow Crops
5 Repurposed Warehouses Turned Indoor Farms That Need No Land Or Sun To Grow Crops
December 2017
Earth's population is expected to reach 8.5 billion people by 2030. That is 8.5 billion mouths to feed. With dwindling land resources and soaring farming costs across the country, vertical indoor farms may be a solution to feeding the world. Often repurposed from former warehouses, the indoor farms need no sunlight or pesticides and require less water to grow produce.
Following are five indoor farms leading the pack.
Company/Owner: AeroFarms
At 70K SF, the world's largest indoor vertical farm cost $39M to build, and uses LED lights and computer controls to tailor the lighting for each plant. A closed-loop aeroponic system mists the roots of the greens and reduces water usage by 95%. Constant monitoring of nutrients allows AeroFarms to grow a plant from seed to harvest in half the time of a traditional farm. AeroFarms produces 2 million pounds of produce a year.
2. Gotham Greens
Company/Owner: Gotham Greens
A pioneer in the indoor farming industry, Gotham Greens built its first rooftop greenhouse in Greenpoint, Brooklyn, and installed solar panels, LED lighting, thermal curtains and a recirculating irrigation system to offset electrical use and reduce water usage. Gotham Green's newest greenhouse in Chicago is located on top of the Method home products plant and cost $8M to build. At 75K SF (or two acres), it produces a crop yield equal to that of a 50-acre farm.
3. Green Sense Farms
Company/Owner: Green Sense Farms
Green Sense's 30K SF farm is capable of growing produce for up to 20 million people within a 100-mile radius. The farm is equipped with customized LED lights from Dutch technology firm Royal Philips and grows its produce in automated carousels, while computerized controls provide perfect conditions for year-round farming. Green Sense CEO Robert Colangelo believes his model is scalable and last year raised over $400K in equity crowdfunding to help build a nationwide network of similar indoor farms.
4. Bowery
Company/Owner: Bowery
Dubbing itself the world's "first post-organic greens" grower, Bowery uses LED lights to mimic sunlight, grows its greens in nutrient-rich water trays stacked from floor to ceiling, uses data analysis to monitor plantings from seed to harvest and robotics to harvest the crops.
Investors love what Bowery is doing so much that the company announced Wednesday that it raised $20M to expand its operations in the U.S. and overseas. Bowery raised $7.5M in February from a pool of investors including "Top Chef" judge and chef Tom Colicchio.
5. Local Roots Farms
Local Roots Farms is innovating urban farming design and building indoor farms from 40-foot-long shipping containers. These portable indoor farms are capable of producing the equivalent of a five-acre farm. Local Roots believes this model will disrupt food deserts around the world by setting up the container farmswhere they are needed most.
Source: Forbes
Indoor/Vertical Farms Set to Boom, LEDs Leading The Transition, Says Yole
The 2016 horticultural lighting market (i.e. system level) represented a business of about US$3.1 billion, representing approximately US$3.8 billion in 2017. But according to a recent report from market research firm Yole Développement, this market is set to grow rapidly at a 17.8% CAGR between 2016 and 2022, possibly reaching more than US$17 billion by 2027.
Indoor/Vertical Farms Set to Boom, LEDs Leading The Transition, Says Yole
November 23, 2017 //By Julien Happich
The 2016 horticultural lighting market (i.e. system level) represented a business of about US$3.1 billion, representing approximately US$3.8 billion in 2017. But according to a recent report from market research firm Yole Développement, this market is set to grow rapidly at a 17.8% CAGR between 2016 and 2022, possibly reaching more than US$17 billion by 2027.
While Yole sees the current business mostly driven by greenhouse applications and incumbent technologies (92% and 79% in revenue, respectively) during 2017, the transition to LED technology and the emergence of new applications will expand the market’s size.
In its report "Horticultural LED Lighting: Market, Industry, and Technology Trends" Yoles sees this market reaching nearly US$8.6 billion in 2022.
Horticultural lighting market revenue ($B),
2017 vs. 2022 vs. 2017.
Source, Horticultural LED Lighting:
Market, Industry and Technology Trends,
Yole Développement.
than US$17 billion in 2027”, comments Pierrick Boulay, Technology & Market Analyst at Yole.
At the LED device level, market opportunity represents almost US$100 million in 2017 and should grow to about US$400 million in 2022, eventually reaching US$ 700 million in ten years' time.
The LED lighting industry sees horticultural lighting as a new opportunity for which to develop high added-value products with greater margin levels. In Q4/2017, Yole identified less than 50 players as offering dedicated LED-based systems. The industry is highly concentrated in North America with a 50% market share (number of companies involved), the result of medicinal cannabis’s legalization.
“Looking ahead, industry evolution will strongly depend on market dynamics,” explains Joel Thomé, PISEO’s CEO. “Indeed, industrial players’ marketing and communications are currently focused on two main applications including medicinal plants (mostly cannabis) production, which is today the main market driver and vegetable production, which is developing with a “low-end / high-volume products” focus.”
The 2016 horticultural lighting market (i.e. system level) represented a business of about US$3.1 billion, representing approximately US$3.8 billion in 2017. But according to a recent report from market research firm Yole Développement, this market is set to grow rapidly at a 17.8% CAGR between 2016 and 2022, possibly reaching more than US$17 billion by 2027.
Part of the established lighting system industry may never proceed with the medicinal plants application, in order to preserve brand reputation. Such a situation is likely to benefit new entrants that will generate revenue swiftly and rapidly increase their horticultural lighting market expertise.
At the device level, most LED manufacturers embrace a “technology push strategy”, taking advantage of their traditional LED portfolio (i.e. UV, visible, and NIR LEDs) to quickly offer some horticultural lighting solutions and related marketing tools, such as dedicated datasheets.
In the future, with a better understanding of LED light’s effect on plant growth, these players might start offering more dedicated solutions (i.e. fine-tuned wavelength package, multiple wavelength packages, etc.).
The missing block in the supply chain is mostly at the module level, with no real supplier in 2017 – reason being that the market is still emerging and the industry is still young, with no standards and regulations. In this context, each lighting system manufacturer design its own module with a specific wavelength mix/recipe.
Some companies are finally starting to position themselves as solution providers, offering not only lighting systems but global solutions integrating sensors (humidity, oxygen, etc.) and data management software. The objective of these smart lighting systems is to further increase the productivity of greenhouses and urban farms.
Yole Développement – www.yole.fr
Steven LaFerrière - laferriere@yole.fr
Horticultural lighting applications.
Source, Horticultural LED Lighting:
Market, Industry and Technology Trends,
Yole Développement.
BrightFarms Named to Inc. Magazine’s Top 10 Most Successful Startups in Food List
BrightFarms Named to Inc. Magazine’s Top 10 Most Successful Startups in Food List
Company aims to build local greenhouse farms in every major U.S. metro
New York (December 11, 2017) – BrightFarms has been named to Inc. Magazine’s list of the top 10 most successful startups in the food and beverage industry. Featured among brands such as Halo Top and Chef’s Cut Real Jerky, BrightFarms was the only fresh produce brand to make the list.
The company has grown by more than 1,800 percent in the last three years with the development of greenhouse farms for leading retailers like Ahold-Delhaize and Roundy’s (Kroger). Earlier this year, Inc. Magazine ranked BrightFarms number 235 on their list of the 500 fastest-growing private companies in America.
To support the growth, the company has recruited a number of key leaders from the food industry, including Vice President of Sales Dean Martel, former sales executive at Fresh Express; Vice President of Marketing Abby Prior and Vice President of Operations Josh Norbury, formerly with Bimbo Bakeries, among several others.
“Our rapid growth stems from the enormous consumer demand for locally grown produce” said BrightFarms CEO Paul Lightfoot. “We’re developing the next phase of growth for our company and plan to enter every major metropolitan market across the country.”
BrightFarms operates three commercial greenhouse farms in Rochelle, IL.; Culpeper, VA.; and Bucks County, PA., with another under construction in Wilmington, Ohio. The company plans to open another 10-15 greenhouses in the next three years.
For more information, visit www.brightfarms.com.
About BrightFarms
BrightFarms grows local produce, nationwide. BrightFarms finances, builds, and operates local greenhouse farms in partnership with supermarkets, cities, capital sources, and vendors, enabling it to quickly and efficiently eliminate time, distance, and costs from the food supply chain. BrightFarms’ growing methods, a model for the future of scalable, sustainable local farming, uses far less energy, land, and water than conventional agriculture. Fast Company recognizes BrightFarms as “One of World’s 50 Most Innovative Companies” and one of the “Top 10 Most Innovative Companies in Food” in the world. New York (December 11, 2017) – BrightFarms has been named to Inc. Magazine’s list of the top 10 most successful startups in the food and beverage industry. Featured among brands such as Halo Top and Chef’s Cut Real Jerky, BrightFarms was the only fresh produce brand to make the list.
Could Indoor Farming Help Address Future Food Shortages?
By 2050, Earth’s population is expected to rise to 10 billion, while the resources on the planet continue to shrink. Researchers in the Netherlands are experimenting with one way to feed more people with less: growing crops indoors.
Could Indoor Farming Help Address Future Food Shortages?
November 11, 2017
By 2050, Earth’s population is expected to rise to 10 billion, while the resources on the planet continue to shrink. Researchers in the Netherlands are experimenting with one way to feed more people with less: growing crops indoors. NewsHour Weekend’s Ivette Feliciano takes a look at how indoor farming could shift our relationship with food.
Megan Thompson:
The United Nations estimates that by the year 2050, the world’s population will grow from today’s 7.5 billion people to nearly 10 billion. And as natural resources like farmland and water become scarce, feeding everyone will become an even greater challenge. In tonight’s Signature Segment, NewsHour Weekend’s Ivette Feliciano reports on how there might a solution well underway in the Netherlands. This story is part of our ongoing series, “Peril and Promise – the challenge of climate change.”
Ivette Feliciano:
Just south of The Hague, in the Westland region of the Netherlands, miles upon miles of greenhouses are spread across the landscape. They’ve been built by Dutch farmers as part of a 20-year movement by the country to pursue sustainable agriculture by growing indoors.
Dutch farmer Hans Zwinkel grows tomatoes in two greenhouses that cover 20 acres of land. His annual harvest of two-and-a-half million pounds of tomatoes is more than double the average yield of an outdoor farm.
Hans Zwinkel:
The plant started over there as a small plant, stands about five meters, six meters further.
Ivette Feliciano:
Zwinkel and growers like him achieve high yields by controlling the climate and water for their crops under glass. Filtration systems allow them to collect and recycle the plants’ water supply. Crops receive direct sunlight — supplemented as needed by artificial light — and are protected from unpredictable weather events and insects, which almost completely eliminates the use of chemical pesticides.
Hans Zwinkel:
It’s nice to see the plants grow. You–it gives you energy.
Ivette Feliciano:
These growing techniques have helped foster an indoor growing boom in the Netherlands. Greenhouses now produce 35 percent of the country’s vegetables–despite occupying less than one percent of its farmland.
The Netherlands’ Wageningen University has led much of the research on how to best grow crops indoors. Leo Marcelis–a professor at the university–says that in the era of climate change, the Dutch agricultural revolution needs to move beyond greenhouses, which still rely on some outside forces like sunlight.
Leo Marcelis:
We wanted to control the production process, that we can control the yield, the quality, that we can give guarantees towards the consumers. Although we can control a lot we’re still dependent on the outdoor conditions. So the next step would be to have a further control. So we can, in fact, guarantee how much produce we will have tomorrow or on any date of the — of the year, of a guaranteed quality.
Ivette Feliciano:
Marcelis is now experimenting with indoor vertical farming–growing plants stacked on shelves to maximize space–and completely cut-off from the outside. As in many greenhouses, water for the plants is drained, collected, and reused, reducing their dependence on an outside water source. And instead of sunlight, the researchers use LED's — light bulbs that can replicate solar light in a variety of colors and intensities.
Leo Marcelis:
Whether we are growing tomatoes, whether it’s about getting fruits, or whether it’s a lettuce or leafy vegetables. You can imagine that you want a different type of plant. And that may require therefore a different light. With LEDs, we can also put them in between the plants. And that’s very good. Because usually there is maybe too much light on the top, but insufficient at the bottom. So we can have a much better distribution of the light in the plant.
But growing indoors isn’t cheap. Marcelis says a quarter of the expenses for indoor growers in the Netherlands relate to construction–something farmers who grow in fields don’t have to worry about. Then there’s the energy costs of round-the-clock climate control and artificial lighting. But Marcelis says a key advantage to indoor farming is that by creating ideal growing conditions and maximizing space, it can produce much higher yields, in some cases, up to 350 times the yield of a conventional farm of the same size.
Leo Marcelis:
What really matters is if the income is larger than the cost. So if the investment costs are high, and also the other costs are high, well, if the income is then also very high, then it is about the balance.
Ivette Feliciano:
Marcelis says one important part of their work is developing techniques that can be replicated anywhere, even in arid climates like the Middle East or sub-Saharan Africa. The United Nations estimates as the world’s population grows, global food demand will rise 70 percent by 2050, even as the amount of water and farmable land shrinks due to the global warming.
The Netherlands is already doing its part to feed the world. Propelled by indoor farming, it’s become the second biggest food exporter in the world, accounting for nearly 90 billion dollars last year. This is all the more astounding given that the Netherlands is less than one-percent the size of the United States, the world’s number one food exporter, where indoor farming is also gaining a foothold.
Here in Kennett Township, Pennsylvania, mushroom growers have been practicing indoor farming for over a hundred years, and today produce half the U.S. mushroom crop.
An hour outside Philadelphia, this small community of eight thousand people harvests half a billion pounds of mushrooms every year — all of it indoors and at a low cost of about one dollar per pound.
Chris Alonzo:
We invested nine years ago into a Dutch-style farm.
Ivette Feliciano:
Chris Alonzo owns this indoor farm that uses the vertical farming methods seen in the Netherlands.
Chris Alonzo:
We put in aluminum shelving instead of wooden beds, we invested in equipment which made the job less labor intensive. We have heat in the room, air conditioning in the room, and air flow. And we use those tools to make sure that the room environment is specifically controlled for what the mushroom likes.
Ivette Feliciano:
Using these techniques, Alonzo’s facility alone is responsible for more than one percent of the nation’s mushroom crop — growing 11 million pounds of mushrooms a year — protected from potentially harsh outdoor conditions.
Chris Alonzo:
The only day we take off is Christmas. And the consumer wants fresh produce year-round. So we’re able to meet the needs to have locally grown produce all year-round. As opposed to some crops where they’re only grown seasonally.
This is our environmental control unit…
Ivette Feliciano:
Alonzo says the difficulty with indoor farming–as with outdoor farming–is finding the balance between your harvest’s revenue and its expenses.
Chris Alonzo:
Mushrooms has been sustainable for– for generations. However, land is – is — affordable, because Mother Nature provides rain, Mother Nature provides sun. Growing indoors is very capital intensive. You have the building, you have the infrastructure, you have energy costs. But if you can maximize productivity and having consistent quality year-round, yes, it’s economically viable, but the margins are still very tight.”
Ivette Feliciano:
Most indoor farmers can’t grow at the same scale as mushroom farmers in Kennett Township. But where they — and some venture capitalists — see the future of indoor agriculture lying is in small-scale urban production in areas with no farming industry of their own.
Matt Barnard:
The place where we’re stepping in now is to serve demand that is unmet.
Ivette Feliciano:
Three-thousand miles west of Alonzo’s farm, indoor farming pioneer Matt Barnard heads a major agriculture project in San Francisco called “plenty.” Its farm is a retrofitted former warehouse, now with walls of fresh vegetables that stretch for 100-thousand square feet.
Currently, it grows leafy greens like spinach and kale–the easiest and most affordable crops to grow indoors–but it will soon start growing tomatoes and strawberries as well. The plants grow directly out of vertical columns. Similar to Dutch researchers, the company also uses l-e-d lighting, water recycling, and climate control.
No genetically modified seeds or pesticides are used in production. Instead, it’s the environment that’s modified, carefully crafted around each type of plant to give them the ideal conditions for growing.
Matt Barnard:
The advantages that we find are because of that control– we, for example, don’t have to use pesticides. Instead of using 15 gallons of water to produce one head of lettuce, we use less than one-fifth of a gallon to produce that same head of lettuce. So we’re saving a significant amount of water. We can actually influence the way the food tastes by making sure it has exactly the right nutrient recipe, the right light recipe, the right water recipe.
Ivette Feliciano:
Plenty hopes to become an industry leader in indoor farming. The company recently received 200 million dollars of private funding, which it plans to spend on building farms in the ten most populous American cities and hundreds more worldwide.
But, as in the Netherlands, plenty has to overcome certain challenges — the upfront cost of building or retrofitting indoor spaces suitable for farming…and the energy costs of indoor lighting and climate control.
But Matt Barnard believes that the advances that have been made in indoor agriculture will make it a key player in feeding the world’s ever-growing population.
Matt Barnard:
We’ve added, you know, six billion people since the tractor came around, and so we believe this is one of the core innovations that’ll help us, you know, serve the next two to three billion people that we add to the planet.
Peril and Promise is an ongoing series of reports on the human impact of, and solutions for, Climate Change. Lead funding for Peril and Promise is provided by Dr. P. Roy Vagelos and Diana T. Vagelos. Major support is provided by Marc Haas Foundation.
Board Approves Conceptual Plans For Dutch Style Hydroponic Greenhouses, Main Street Market
Board Approves Conceptual Plans For Dutch Style Hydroponic Greenhouses
- December 4, 2017
- By TERRY FLORES tflores@kenoshanews.com
PLEASANT PRAIRIE — The Village Board on Monday night approved the master conceptual plans for a hydroponic greenhouse project east of Highway H and a proposed development that would include a 50,000-square-foot medical facility at Green Bay Road and 104th Street.
Prairie Produce Farm LLC is expected to break ground in the spring on its first greenhouse, a 15.3-acre building, on 54.5 acres of a 65-acre site in the Green Hill Farm neighborhood at 122nd Street east of 88th Avenue. The site is just to the northeast of the village’s recycling center.
The $3 million Dutch-style hydroponic greenhouse operation also includes plans for another 20-acre greenhouse that would be constructed in a second phase as early as 2020, depending upon market conditions, according to Jim Hershenbach who represents Prairie Produce, a sister company of DeFresco Produce and Sunrite Greenhouses in Ontario, Canada.
The Green Hill Farm neighborhood had originally been planned for eventual rezoning for residential units. Because of the greenhouse proposal, however, the agricultural zoning currently in place will remain intact, according to Jean Werbie-Harris, the village’s community development director.
The greenhouse development would be the first of its kind in the state and would sell produce such as tomatoes, peppers, cucumbers and strawberries to area grocery outlets. Hershenbach said the high-tech hydroponic greenhouse operation is unique to the Dutch, who perfected such growing methods due to the destruction of soils. The massive hydroponic system will allow non-GMO plantings to grow vertically within maximum height limits of the greenhouses.
While there will be no retail sales to the public onsite, Hershenbach said the greenhouses would be open to visitors and schools for planned educational tours, and the company would partner with area schools and colleges for student internships.
The greenhouses would employ 30 to 40 full-time workers once fully operational, according to Prairie Produce.
The board also approved detailed conceptual plans for the Main Street Market development in the Highpoint Neighborhood, which will accommodate a four-story medical building for Froedtert South on a 22-acre parcel at Green Bay Road and 104th Street.
The development proposal also includes a convenience store, a grocery store and a mix of other retail and commercial services.
Froedtert’s medical building would be the first of six lots to be developed by Bear Development.
Trustee Michael Serpe expressed concerns about traffic safety at 104th Street at the south end of the development and whether there were other options, including the use of Jelly Belly Lane as another outlet. Werbie-Harris said a traffic impact analysis by the Wisconsin Department of Transportation is currently underway and is among several options being studied.
Werbie-Harris said Froedtert representatives will also be presenting more detailed building plans for the medical facility in January.
Construction is planned to begin early next year and be completed by the winter of 2018-19.
Village Farms: For The Good of The Earth
Village Farms: For The Good of The Earth
For the technology-driven growers of Village Farms, cutting-edge sustainable practices yield a bumper crop of success.
The bright red cherry tomato bursts with a pop as you sink your teeth into it, and for a few delightful seconds it’s still summertime—even though it’s winter. You take another bite to make sure you’re not imagining that freshness, and, sure enough, it’s just as bright, tart, and sweet as the first. The taste takes you back to your childhood, when you’d steal tomatoes from a neighbor’s garden, helping yourself to another, and another…
As summer fades and the air grows colder you’ve become accustomed to the average pinkish-orange globes posing as tomatoes that start filling the shelves of the produce department. Thankfully, Village Farms has no interest in growing average produce, and its environmentally-friendly growing methods allow for fresh, high-quality produce year-round. In fact, nothing that the North American-based company does is anywhere near average, and that’s not just great for veggie lovers—it’s great for the planet, too.
As the premier greenhouse grower of tomatoes, bell peppers, cucumbers, and other crops in North America, Village Farms’ dedication to sustainability, technology, and innovation shows with every pristine vegetable picked. Launched in Pennsylvania in 1988, Village Farms has grown from a single 10-acre greenhouse operation to a vertically-integrated agricultural enterprise.
“On day one it wasn’t the plan,” admitted Mike DeGiglio, Village Farms’ President and CEO. “Our first crop was half peppers, half tomatoes, and our focus was on being a grower.”
When that first crop was rejected by a surly Northeastern produce broker for being “no good,” DeGiglio ignored the slight.
“We hired a sales guy the next day and never looked back.”
New Day, New Business Model
When the company began, all the disciplines in traditional produce companies were separate.
“The grower is the grower, who went to a labor manager to pick the crop, then to a processor who graded and sorted it. Then that’s sent to a trucking company, then to a broker. That broker would send it to a retailer,” DeGiglio recounted. “We asked ourselves, ‘why can’t we do all of it?’”
The answer was, “We can.” Today, Village Farms is an end-to-end operation.
“Today we have 270 skus and 35 tomato varieties,” he noted. “We slowly added more salespeople, distribution centers, and transportation. We became a vertically integrated producer. We have our own engineering, even though there are plenty of companies that build greenhouses.”
The company built a sophisticated greenhouse in West Texas, in part of the Chihuahuan Desert.
“It’s not quite a biosphere but pretty close. It’s 110 degrees all summer and only 20 degrees in winter,” he chuckled, a trace of awe in his voice. “Nothing grows there but tumbleweeds and lizards. We’re like an oasis—it blows people away.”
Today, the company owns and operates seven facilities in British Columbia and Texas, and provides operational and technical support and logistics services for more than an additional 150 acres of greenhouse production throughout Canada and Mexico.
The Greenhouse Difference
Greenhouse growing is far superior to conventional land farming, producing better crops with markedly less waste and dramatically less environmental impact.
“It’s a combination of food safety, quality of the product, shelf life of the product, and taste—it’s consistent, available 365 days a year, and not just seasonal,” DeGiglio explained.
Indoor growing is the premier method of sustainable production and allows Village Farms to use integrated pest management as biological control, meaning they release good bugs to combat bad bugs instead of using chemical pesticides. “Of all agricultural products, proteins like beef and chicken, row crops, and fruits and vegetables, I think greenhouse growing is by far the most sustainable type of agriculture there is, even over organic growing methods,” he said.
“When you are in a controlled environment greenhouse, utilizing the same resources an outdoor farmer would use like sunlight and water, you can do it in an environment that is much more efficient and productive,” he added.
These carefully monitored environments offer protection against elements typical farmers have no control over like wind, rain, and extreme heat and cold.
“We can produce output that has 30 times more yield per acre than crops grown on farmland. A 100-acre greenhouse produces the equivalent of a 3,000-acre farm. And you can locate a greenhouse close to anywhere depending on the technology you use.”
Earth First
Village Farms’ approach to sustainability abides by a commitment to preserve the earth’s resources for future generations.
“The way Village Farms fits that definition of sustainability is: one, we don’t use soil, so it takes a lot less land for the same amount of crops. Two, we don’t take any nutrients out of the soil. Three, we don’t leachate any of our solutions into the ground,” DeGiglio enumerated.
“It took 500,000 years for the first one billion human beings to be on the planet. There are now seven-plus billion of us. The demographics say that by 2050, there will be a 30 percent increase of the population of the planet. That’s 2.5 billion people. Whether that number is up or down by twenty percent doesn’t matter,” he posited. “How is agriculture going to feed that amount of people with the same amount of water? It has to come from efficiency and sustainability.”
The company chose growing regions in British Columbia and Texas based on the climate conditions most favorable to producing consistently superior quality crops.
“You can’t move your farm to take advantage of a better climate,” he mused. “In Texas, we grow at the southernmost latitude at the highest elevation in the U.S. We are at a 5,000-foot elevation. We do that because of the warm days and cool nights.”
Natural gas is used to heat the greenhouse at night.
“The boilers designed for greenhouses over the past three decades are so efficient and clean, the carbon dioxide (CO2) that’s released is food grade. We capture all of it, and pump it into the greenhouse,” he revealed. “As you remember from ninth grade biology, plants take in CO2 and make oxygen. Not only do we not extract the CO2 into the atmosphere, we convert it into oxygen. That can’t be done outside.”
Village Farms produces only non-GMO crops, grown in an organic medium made of coconut husks. Crops are vine ripened and hand-picked at the exact right moment for the absolute best taste.
“A lot of field growers pick tomatoes when they’re green,” he said. “If a tomato doesn’t get to a certain level of maturity, then the ripening process never occurs. So they spray an ethylene gas on it so it turns an orangey pink. Bananas are shipped green, and when they’re ready to ship to the store they spray them with ethylene. Vine ripened taste is much better.”
The company’s agricultural engineers are working on extending product shelf life.
“There’s all kinds of good things happening that drives a better tasting, safer product, and people can trust that brand,” he added.
Committing to the Cannabis Crop
Canada approved the use of medical marijuana in 2001, and pending legislation is expected to legalize it for recreational use in mid-2018. Village Farms recently entered into a partnership with Emerald Health Therapeutics, a bio-pharma company focused on the use of cannabinoids to treat disease.
“We are currently in the process of converting our smallest greenhouse footprint of 1.1 million square feet to cannabis in British Columbia. It’s a very new crop, and a lot of the early folks that got into it weren’t farmers, they were just folks who saw an opportunity. We thought our ability to grow any crop was a good fit,” he stated.
“We’ve done modeling, we talked to Health Canada, and we saw a great opportunity in conversions of our Canadian high-tech greenhouses as a lower cost model rather than building new ones because we feel that it will eventually become commoditized out, and when it does, in the end it’s the low-cost producer that survives. That’s always a prudent thing in agriculture.”
While practicality is at the heart of everything Village Farms does as a business, the people of Village Farms are really what makes the difference and our planet—and palates—are much better for it.
New Affordable Bronx Development Will Feature a Rooftop Aquaponics Greenhouse
New Affordable Bronx Development Will Feature a Rooftop Aquaponics Greenhouse
Rendering of the Bedford Green House courtesy of Edelman Sultan Knox Wood/Architects LLP and Hollister Construction Services
NOVEMBER 15, 2017 DEVIN GANNON
The construction of a 13-story supportive housing development in the Bedford Park neighborhood of the Bronx will begin Thursday when federal, state and city officials join nonprofit Project Renewal in a groundbreaking ceremony at the site. Located at 2880 Jerome Avenue, the Bedford Green House will feature 118 units of affordable housing for families, seniors, and singles. To connect its residents to nature, the building will be covered in carbon sequestering plants and have an operational rooftop greenhouse where residents will be able to raise fresh fish and produce, partake in healthy cooking demos, and enjoy a community playground.
Rendering of the Bedford Green House courtesy of Edelman Sultan Knox Wood/Architects LLP and Hollister Construction Services
Designed by Edelman Sultan Knox Wood, with Hollister managing construction, the 83,000-square-foot building will pursue LEED Gold certification. Half of the greenhouse space will utilize aquaponics, with the other half focused on growing crops like kale, spinach, and arugula. In addition to the agricultural aspect, residents will have access to a workforce development office, laundry room, community area, warming pantry, and a playground. Plus, the building will feature custom artwork from locals.
Clinton Hill School Gets Millions In Greenhouse Funding
Urban Assembly Unison is one of seven schools slated to share $7 million from Adams' Growing Brooklyn's Future initiative, which will fund building rooftop gardens and greenhouses, the borough president announced Tuesday.
Clinton Hill School Gets Millions In Greenhouse Funding
The Urban Assembly Unison School is one of seven schools slated to receive greenhouse funding from Eric Adams' $7 million initiative.
By Kathleen Culliton, Patch Staff | Nov 29, 2017
CLINTON HILL, BROOKLYN — A Clinton Hill school can begin building its greenhouse after Brooklyn Borough President Eric Adams announced the expansion of his green school initiati
Urban Assembly Unison is one of seven schools slated to share $7 million from Adams' Growing Brooklyn's Future initiative, which will fund building rooftop gardens and greenhouses, the borough president announced Tuesday.
"This is about keeping Brooklyn's kids at the forefront of innovation and growing their futures," said Borough President Adams.
"Young people across the borough will now have the opportunity to learn about growing fruits, vegetables, herbs, and plants that will empower them to make healthy choices."
Urban Assembly — a profession-focused public school with an urban farming program — received $2 million from Growing Brooklyn's Future and an additional $1.05 million from City Councilwoman Laurie Cumbo's office.
The school plans to begin construction on its courtyard greenhouse — which is expected to produce about 25 thousand pounds of fresh fruits and vegetables per year — early in 2018 with an anticipated completion date set for 2020, school officials said.
The money will be divided between seven schools in Bedford-Stuyvesant, Bergen Beach, Brownsville, Clinton Hill, Gravesend and Sheepshead Bay, according to the Brooklyn borough president.
Adams first launched Growing Brooklyn's Future in 2015 when he channeled more than $2 million to create hydroponic classrooms to 12 Brooklyn schools in Bed-Stuy, Brownsville, Bushwick, Canarsie, Cypress Hills and East New York.
The Hydroponic, Robotic Future of Farming in Greenhouses
Here in 2017, the automation revolution in agriculture is poised to take on a whole new life—thanks to robots. In a nondescript office park in Silicon Valley, a startup called Iron Ox is taking the first steps toward roboticizing greenhouse farming, which has so far stubbornly resisted automation.
The Hydroponic, Robotic Future of Farming in Greenhouses
WHEN YOU THINK of automation, you probably think of the assembly line, a dramatic dance of robot arms with nary a human laborer in sight. But that’s child’s play. The grandest, most disruptive automation revolution has played out in agriculture. First with horses and plows, and eventually with burly combines—technologies that have made farming exponentially cheaper and more productive. Just consider that in 1790, farmers made up 90 percent of the US workforce. In 2012, it was 1.5 percent, yet America still eats.
Here in 2017, the automation revolution in agriculture is poised to take on a whole new life—thanks to robots. In a nondescript office park in Silicon Valley, a startup called Iron Ox is taking the first steps toward roboticizing greenhouse farming, which has so far stubbornly resisted automation. In the very near future, then, the salad on your table may come from the hand of a robot.
Unlike a lot of indoor farming operations, Iron Ox isn’t joining the booming movement of LED-powered grow houses. It’s still very much interested in harnessing the energy of the sun (free energy!). So it’s invading the greenhouse instead. “The problem up until today is that greenhouse production costs around twice as much to grow a head of lettuce as the outdoor farm,” says Brandon Alexander, CEO of Iron Ox. “And one reason is there's no tractors or anything indoors.”
Iron Ox doesn't have a tractor, but it also doesn't need one. Its solution begins with a custom hydroponics tray filled with nutrient-rich water. Over that is a cover with a grid of holes, in which the plants sit in little pods. This is all designed so a custom robot—essentially an intelligent rectangular frame—can come along and slide lifters under the tray, then cart it to a different part of the greenhouse.
Why bother with all the shuttling around? Because they can. Out in a field, farmers have no choice but to leave plants where they planted them—and because plants grow, farmers have to space out seeds to accommodate their fully-grown dimensions. But Iron Ox doesn't have to waste that extra space.
Here in the greenhouse, they’re using different trays with different spacing of their holes, some farther apart than others. Leafy greens, in particular, need more horizontal room to expand, so baby plants start off in a more densely packed tray, then graduate to trays with more room as they grow. “This, combined with the fact that we don't have to worry about seasonality—we can always be seeding, always be harvesting—allows us to grow over 30X per acre compared to an outdoor farm,” says Alexander.
The problem then becomes transplanting between trays. That’s where the robotic arm comes in. It sees with stereo cameras on its wrist and grabs the plants with a gripper custom-designed to fit the pods (which the plants never outgrow, by the way). The arm sits between two trays of different densities, eyeballing the plants and moving them from one tray and to another.
Because it’s equipped with a camera, it can simultaneously build a 3-D image of each plant. “Is it the size that we expect?" says Jon Binney, CTO of Iron Ox. "Is it the shape that we expect? If it's going to fall one way or the other, that could be a lighting problem. Brown spots on the edges of the leaves could be too much light and not enough air coming through.”
So Iron Ox’s system not only automates greenhouse growing but supercharges it. The company is developing machine learning algorithms that will automatically detect diseased plants and kick them out of the system before the sickness spreads. Underdeveloped plants would also get the boot. What you end up with is a system that does the repetitive tasks of greenhouse farming faster and more precisely than a human, and uses that data to make the process all the more efficient.
Whether in the greenhouse or the field, it’s this kind of automation that will be essential to the future of humanity. Our species has to figure out how to feed a rapidly growing population on a planet that refuses to grow bigger. So we’ll have to get smarter about how we use the land we’ve got, or we’re going to have trouble. That and climate change will monkey with water supplies around the world, so the inefficiencies of traditional outdoor farming are going to start looking more and more untenable. (Iron Ox claims its hydroponics system uses 90 percent less water than outdoor farming. Studies of hydroponics, in general, have found about the same efficiencies.)
But automation means humans lose jobs though, right? Not in this industry. “We've talked to dozens of commercial farmers, outdoor and indoor, and the biggest issue by far is labor scarcity,” says Alexander. “So the truth is today, it doesn't matter what country, newer generations are not taking up farming. And so there's a significant labor shortage especially here in California.” (He ain’t lying— between 2002 and 2014, the number of full-time farm workers in the US plummeted by 20 percent.)
The solution is to hand the future of our food supply to the machines. There’s simply no other way to go about it. So be careful not to bite the robotic hand that feeds you.
$30 Million Greenhouse Project Planned In Pleasant Prairie, Wisconsin
$30 Million Greenhouse Project Planned In Pleasant Prairie, Wisconsin
Would be first Dutch-style hydroponic greenhouse in Wisconsin
November 27, 2017
A $30 million greenhouse that could employ up to 40 people is planned on a vacant site in Pleasant Prairie.
The 35-acre Prairie Produce Farm will be the first Dutch-style hydroponic greenhouse in Wisconsin, according to plans submitted by Jim Hershenbach to the village.
The greenhouse will be affiliated with sister companies Del Fresco Produce and Sunrite Greenhouses in Kingsville and Leamington, Ontario, Canada.
Hershenbach is planning to purchase about 54.5 acres of a 65-acre site located west of 112nd Street and east of 88th Avenue for the development.
The first phase of the development includes a 15.3-acre greenhouse and a 30,000-square-foot support building that will house equipment, two loading docks, lab offices and a caretaker’s apartment.
The produce grown at the farm will be sold to local grocers, their distribution centers and institutional suppliers, according to documents submitted to the village. There will be no retail sales.
The greenhouse will employ 30 to 40 full time workers who will earn $12 to $48 per hour, depending on their responsibilities.
Construction is expected to begin in early 2018, pending village board approval.
The plan commission will review the proposal Monday.
Phase two includes an additional greenhouse on 18.5 acres that will be constructed “as soon as market conditions allow,” which is estimated to be in 2020.
Determining The Potential Benefits of LEDs on Plants
Determining The Potential Benefits of LEDs on Plants
NOVEMBER 20, 2017 | DAVID KUACK
Researchers at Wageningen University in the Netherlands are studying the effects of LED lights on the growth, flowering and fruiting of vegetable and ornamental plants in controlled environments.
Dutch growers who are building new greenhouses or adding new grow lights to their existing operations are comparing high-pressure sodium (HPS) and light emitting diodes (LEDs) when making their decision.
“At the moment there aren’t as many growers making the switch from HPS to LEDs,” said Leo Marcelis, head of the chair group horticulture and product physiology at Wageningen University in the Netherlands. “Most growers who have made the investment in HPS lamps, they’re not just going to replace HPS with LEDs. It’s growers who are starting with a new greenhouse or who are retrofitting an existing greenhouse without lamps who are looking to install LEDs.
“The other growers who are adding LEDs are the ones who already have installed HPS and want to increase the light intensity and are adding LED interlighting. They are combining HPS top lighting with LED interlighting. This is occurring especially with the tall greenhouse vegetable crops like tomatoes. The HPS lamps are installed over the top of the crop and the interlighting LEDs are installed within the canopy.”
Photos courtesy of Leo Marcelis, Wageningen University
Many unanswered questions
With the increased grower interest in LEDs, researchers at the university are focusing more of their studies on the effects of single and combined light wavebands on plant growth, flowering and fruiting.
“Most of the research we are doing on lighting is with LEDs,” Marcelis said. “High-pressure sodium lamps are still the standard for most growers so the lamps are still relevant. But for our research, there is not as much being done with HPS as with LEDs. We are focusing more on LEDs. The opportunities created by LEDs, there are so many questions still unanswered about using LEDs. As growers start to put in new lights they are making the switch to LEDs. We expect more of that to occur in the coming years.”
Focus on controlled environment crops
Marcelis said greenhouse tomatoes are the largest crop in the Netherlands, even bigger than cut flowers such as roses and potted ornamental crops such as orchids.
“Tomato is the most important crop in our research. In the Netherlands, there are about 1,700 hectares of tomatoes in glass houses. About 1/3 of that area is equipped with HPS lamps. There are about 1,200 hectares of sweet peppers in glass houses with only a few hectares equipped with HPS lights. The calculations are such that the economics are not that profitable for sweet pepper and cucumber. It is more economical and profitable to light tomatoes, not sweet peppers and cucumbers. There are more growers starting to grow strawberries in greenhouses who are using LEDs to control the day length. More growers are also using LEDs for assimilation lighting.”
Marcelis said lettuce is another crop that is being studied whether it’s grown in vertical farming setups in warehouse facilities or in greenhouse operations. Roses and phalaenopsis orchids are the most important ornamental crops being studied.
“We currently aren’t doing any projects with cucumbers or sweet peppers using LEDs,” he said. “Since there are not as many growers using lights on these two crops, we are not focusing our research on them, but this could easily change in the coming years.”
Focused on issues important to growers
Marcelis said most of the university’s lighting research projects are on greenhouse produce because that is the area of most economic activity in the Netherlands.
“Vertical farming is attracting a lot of attention,” he said. “We are also conducting research in climate chambers which can have application to vertical farming.
Breeding researchers at Wageningen University are working in cooperation with commercial breeding companies to screen different genotypes to determine any variation under LED lights.
“We are looking at different aspects of lighting, including light spectrum and energy savings. Energy savings is an important issue with the growers so we are doing a lot of research on that. If the light used is more efficient, then there can be energy savings. Talking to the growers, year-round production, fruit quality and energy savings are the issues they’re interested in. If growers can increase production with the same amount of light, then there is an energy savings.
“The majority of lights are used for assimilation. They are primarily used from September through April. The greenhouses are equipped with climate control and the growers are measuring outside radiation. If the outside radiation falls below a designated level, then the lamps are often turned on. The growers typically choose a time frame during the day. From September through April all of the lights are used. After April then the lights might be used during relatively dark days.”
Looking at plant processes
Marcelis said the researchers are doing a lot of studies on photosynthesis and the morphology or architecture of the plants.
“Affecting the morphology impacts the light absorption of plants and the light distribution,” he said. “We feel light distribution is a very important issue where improvements can be made. We also do work with three-dimensional assimilation models. From light absorption, it goes to total growth of the plant as a whole. Another area of research is the distribution of assimilates among the different plant organs.”
Most of Wageningen University’s lighting research is on greenhouse produce because that is the area of most economic activity in the Netherlands.
Marcelis said there is also some preliminary research that indicates plants can be made more resistant to diseases, particularly increasing the resistance of roses to powdery mildew.
“We have done experiments that have indicated that we can improve disease resistance. Flower induction is also very important. It can be done now with controlling photoperiod, but can it be done using different spectra?
“There is also some work being done on the quality of the plants. Is it possible to focus the light on the tomato fruit in order to increase the vitamin C content? Some of the same things can be done with lettuce. We are also starting to look at post-harvest qualities. So we are looking at not only what can be done during cultivation, but also can the post-harvest quality of the fruit be improved. This also includes lengthening the shelf life of lettuce and cut flowers.”
Marcelis said studies are also being conducted in cooperation with commercial breeding companies and breeding researchers at the university.
“One of the projects is screening 40 different genotypes, including commercial cultivars,” he said. “One study is looking at the variation between genotypes under LEDs. The breeders will look at the variation between genotypes and try to determine why the variation is occurring. What parts of the plant are affected? Can breeders predict if varieties will do well or not so well under certain wavebands?
“There are all of these different genotypes. Some do better under white light than a mixture of red and blue. Some genotypes are showing better results under the red and blue light. They all don’t respond similarly. For breeders, it means there is a lot of opportunity and room for improvement. Since the focus is on using LEDs with tomatoes that is where most of the breeding research is being done.”
For more: Leo Marcelis, Wageningen University, Horticulture and Product Physiology Group, Wageningen, The Netherlands; (31) 317-485-675;
leo.marcelis@wur.nl; http://www.hpp.wur.nl
David Kuack is a freelance technical writer in Fort Worth, Texas; dkuack@gmail.com.
Is Organic Labeling Something The Hydroponic Industry Needs?
Is Organic Labeling Something The Hydroponic Industry Needs?
Conscientious shoppers are seeking out organically labeled food in their grocery stores and even at farmers markets.
November 28, 2017
CropKing
In an extremely close vote Nov. 1, the USDA’s National Organic Standards Board made a decision on a controversial issue: can hydroponically grown crops be certified organic? The answer, by an 8-7 margin, was yes. With the vote out of the way, the NOSB will now have to make recommendations on how the hydroponic industry can be governed under the organic label. However, as both organic and hydroponic agriculture adjust to the board’s decision, a simple question looms in the air, “Is organic the best path forward for hydroponically grown crops?”
Here’s the thing, there’s no arguing that organic is a hot niche. In April 2016, the Huffington Post wrote an article detailing Costco’s fast-selling organic produce section, entitled, “Costco Is Selling So Much Organic Produce, Farmers Can’t Keep Up”. In fact, while the USDA doesn’t keep hard numbers on total organic sales, the agency does have this chart showing the growth of sales. Even to the untrained eye, it’s clear organic sales have been steadily growing since 2005. That’s more than a decade of increasing sales.
Organic is having a sustained moment in the sun. Conscientious shoppers are seeking out organically labelled food in their grocery stores and even at farmers markets.
There are downsides to organic though. The market is already saturated with growers competing in the space. The Organic Authority says there are already 100 hydroponic growers certified to sell organic. And that’s just the hydroponic growers that got in before Nov. 1. Given the national attention on the NOSB decision, more applications for organic certification could be coming into USDA shortly.
There’s also growing confusion over organic versus competing labels, particularly the “local” identifier. Some consumers don’t know the two aren’t synonymous.
“What is a consumer looking for when they buy organic? Most buyers who purchase organic do so because organic, to them, equals safety, pesticide free, healthy food for my family,” said CropKing President Paul Brentlinger.
Plus, shoppers are increasingly heading to farmers markets to buy local crops, perhaps signaling a shift in priorities for heady produce buyers. In 2013, the USDA said there were 8,144 farmers markets, that’s up from 1,755 in 1994. That’s why more produce is carrying a “local” label.
It seems consumers are increasingly interested in where crops come from and how they’re grown. That’s why some industry vets have been wondering about a hydroponic-specific label, something that indicates growers are utilizing the best, most sustainable practices available in the CEA, hydroponic environment. Something the fast-growing industry can tout as its own and put marketing might behind. Something that can be added to the already impressive list of labels.
“Regardless of the debate surrounding salt based fertilizer or organic fertilizer I think the CEA industry can check those boxes for the consumer. Many CropKing growers market their product as "locally grown", "pesticide free" and are able to develop that relationship with the communities they support,” said Brentlinger.
After all, the organic labelled products totaled $47 billion in sales last year, according to Business Insider. Could a hydroponic-specific label push your sales to new heights?
Tell us what you think, would a hydroponic label benefit you? Let us know in the comments.
Photo: iStock
Urban Agriculture Production Act Could Help Eliminate Urban Food Deserts
Congresswoman Marcy Kaptur (OH-09) introduced the Urban Agriculture Production Act in September. This bipartisan bill aims to support nutritional and farmers’ market programs and help create the next generation of local, urban farmers and food producers.
Urban Agriculture Production Act Could Help Eliminate Urban Food Deserts
NOVEMBER 28, 2017 | DAVID KUACK
Urban Agriculture Production Act offers growers, retailers and consumers opportunity to produce, market and purchase locally-grown food.
Congresswoman Marcy Kaptur (OH-09) introduced the Urban Agriculture Production Act in September. This bipartisan bill aims to support nutritional and farmers’ market programs and help create the next generation of local, urban farmers and food producers.
Kaptur was joined by 11 original cosponsors: Rep. John Conyers (MI-13), Rep. Barbara Lee (CA-13), Rep. Eleanor Holmes-Norton (DC-AL), Rep. Gwen Moore (WI-04), Rep. Hakeem Jeffries (NY-08), Rep. Chellie Pingree (ME-01), Rep. Sanford Bishop (GA-02), Rep. Tim Ryan (OH-13), Rep. Dwight Evans (PA-02), Rep. Alma Adams (NC-12) and Rep. Don Young (AK-AL). The bill is supported by the National Sustainable Agriculture Coalition and Farmers Market Coalition.
Ohio Congresswoman Marcy Kaptur introduced the Urban Agriculture Production Act in September with the goal of supporting small farmers, helping to eliminate food deserts and promoting local agriculture.
Photos courtesy of Congresswoman Marcy Kaptur
Congresswoman Kaptur sat down with Urban Ag News to talk about the Urban Agriculture Production Act and the impact it could have on growers, local food retailers and urban communities.
UAN: What are the goals of the Urban Agriculture Production Act and why did you introduce the bill at this time?
Kaptur: The Urban Agriculture Production Act can serve as a marker for the next Farm Bill reauthorization. My key goals are to support small farmers and producers, work to eliminate food deserts and promote local agriculture in our nation’s metropolitan areas.
Across America, too many of our urban neighborhoods are absent of stores where community members can purchase fresh, healthy foods. There are more than 23 million individuals residing in these so-called “food desert” neighborhoods, where there are no stores within one mile in which they can buy healthy food. Without healthy options, people are forced to eat unhealthy, processed, junk food, because that is all that is available and affordable. This bill is a step to correct this unacceptable trend.
UAN: The term “urban agriculture” includes urban farms, hoop houses, aqua-culture, hydroponic and aquaponics facilities and rooftop, vertical and indoor farms. Would this also include new or existing commercial greenhouse growers who may be looking to set up production facilities in urban areas?
Kaptur: Certainly. But it is important to also note that new approaches to greenhouse growing should be re-imagined in order to manage energy and water systems through more efficient and renewable means. In urban communities like those I represent, resources are available and are waiting to be utilized. Vacant and blighted properties can be repurposed into productive sites with the installation of energy- and water-efficient commercial greenhouses. Waste heat from manufacturing operations can also be rechanneled to allow for an entirely new class of four-season growing.
Embracing such opportunities can empower new people through agriculture. Residents in urban areas could benefit from not only the jobs created, but also from the unique skills gained in food production and distribution processing.
UAN: How is the production of the food and its sales going to be coordinated? In other words, how are growers going to know that they have markets ready to handle their produce even before they grow the crops and retailers are going to be sure they have an adequate amount of produce to sell?
Kaptur: That is up to the growers, but ideally, we will have at least some venues, think farmers’ markets that are also empowered by the investments we’re making in this bill. From there, growers and producers can get a foot in the door to compete and succeed.
UAN: The Act directs the Secretary of Agriculture to establish an urban agriculture outreach program. Part of this program enables the Secretary to award grants. Would growers be eligible for these grants and what type of production and marketing activities/projects could these funds be used to finance?
Kaptur: That is one of the most exciting pieces of the legislation. Growers would be eligible for these grants. And the grants are for the following types of activities in urban or in and around urban areas:
- Infrastructure, land acquisition and land conversation.
- Education and training to enhance agricultural production.
- The aggregation of farmer products and supplies for purposes of transportation to market.
- Other activities that support urban agricultural production as determined by the Secretary of Agriclture.
Congresswoman Marcy Kaptur hopes the Urban Agriculture Production Act will encourage growers to look at new approaches to greenhouse growing that will enable them to manage energy and water systems through more efficient and renewable means.
UAN: Where would the money come from to operate the urban agriculture outreach program and who would oversee it?
Kaptur: Our bill authorizes Congress to allocate $50 million each year to the Department of Agriculture for the urban agriculture outreach program. It also creates an Urban Agricultural Liaison who would administer the program.
UAN: How much money will be available to initiate the urban agriculture outreach program and for how long would this funding be available? Does this amount of funding change from year to year and does it have to be appropriated annually?
Kaptur: $50 million is the amount authorized in our bill, starting in 2018 and each fiscal year thereafter. This authorizing amount does not change from year to year. We hope this money will eventually inspire other investment from businesses, nonprofits, churches and even local and state governments.
In my hometown of Toledo, for example, a local restaurant, Balance Pan-Asian Grille, is building an urban indoor aquaponics farm next door to their new location to grow the food that will be served every day. It is very exciting and ideally, our bill would help create more opportunities and the expertise for this to happen a lot more across the country.
UAN: Who will decide as to which production and marketing projects receive funding?
Kaptur: The Secretary of Agriculture will determine how the production and marketing funding is awarded based on the criteria set out the bill.
UAN: Some of these projects are eligible for grants and others are eligible for loans. Who will make the decision as to which projects receive which type of funding?
Kaptur: The Secretary of Agriculture, either as acting through the Administrator of the Farm Service Agency or any other USDA agent who he deems appropriate, will make the determination.
UAN: With the mentality of the current administration and some legislators in Washington to cut spending, what do you think are the chances of this bill passing even though it has received bipartisan support?
Kaptur: That is why we are focused on incorporating as much of our urban agriculture bill into the upcoming Farm Bill. Though it won’t be easy, this legislation is a must-pass bill, and historically has always crossed the finish line.
UAN: Will the Urban Agriculture Production Act have any connection with the upcoming 2018 Farm Bill? If so, would funding the urban agriculture outreach program and its projects have any impact on funding other programs in the upcoming 2018 Farm Bill?
Kaptur: Well, we hope so. And I am confident that other Members of Congress from both rural and urban areas alike will see the value in spurring innovation and investing in our urban agriculture infrastructure.
For more: Congresswoman Marcy Kaptur (OH-09), 2186 Rayburn House Office Building, Washington, DC 20515; (202) 225-4146; https://kaptur.house.gov.
Multi-Million Dollar Greenhouse Development Planned
Multi-Million Dollar Greenhouse Development Planned
- By TERRY FLORES tflores@kenoshanews.com
-
- 11-28-17
PLEASANT PRAIRIE - Tomatoes, peppers, cucumbers, and strawberries could soon be grown in hydroponic greenhouses that operate year-round in the village.
The Pleasant Prairie Plan Commission voted 6-0 Monday night to approve plans from Prairie Produce Farm LLC to build two high-tech hydroponic greenhouses.
They will be built in multiple phases, on about 54.5 acres of a 65-acre site in the Green Hill Farm neighborhood at 122nd Street east of 88th Avenue. The property is to the northeast of the village’s recycling center.
The proposed $31 million development would be developed in an agricultural area that would not need rezoning. The commission acknowledged about 67 residential units originally part of the master plan for the area would be eliminated.
If approved by the Village Board next week, the Dutch-style hydroponic greenhouse operation would start with a 15.3-acre, 28-foot high building and would be the first state-of-the-art hydroponic operation of its kind in the state of Wisconsin, according to Jean Werbie-Harris, the village’s community development director.
Prairie Produce Farm is a sister company of DeL Fresco Produce and Sunrite Greenhouses, which have established greenhouse growing operations in Kingsville and Leamington, Ontario, Canada.
Second phase by 2020
A second 20-acre greenhouse for Phase II of the project is proposed to be built as early as 2020, according to the proposal.
Jim Hershenbac of Prairie Produce indicated the first phase would be completed early next year.
“This type of greenhouse —to give you an idea of the amount of technology — costs almost a million dollars per acre to build,” he said. The technology is found in more than 40,000 greenhouses in European countries, with more than half in Holland,” he said.
In Canada, where Del Fresco and Sunrite are located, there are 4,000 acres of the hydroponic greenhouse systems growing.
According to Hershenbach, plants are established from non-genetically modified cuttings and each can grow about the height of the building yielding 40 to 60 pounds of tomatoes, for example.
The facility would be operating on water and minimal nutrients in a “closed-loop system,” meaning there would be no runoff and natural gas would be used for night heating. Carbon dioxide exhaust would feed the plants and the operation would compost plant trimmings.
According to the plans, the facility would employ 30 to 40 full-time employees with a payroll of just over $1.3 million.
Retail buildings, hotel
The Plan Commission also approved plans for a commercial property development for a corporate campus, multi-tenant retail buildings, a hotel. future restaurants, a gasoline station, convenience store and car wash north of Highway 165 at 120th Avenue on two parcels totaling about 34 acres for The Gateway at LakeView Corporate Park.
In approving the plans, the commission voted in favor on the condition that issues over a future assessment and traffic be addressed.
According to Werbie-Harris, the commission approved amending the comprehensive plan to accommodate the cluster of proposed mixed retail and business area, master conceptual plan, and zoning.
She said possible tenants for the proposed development have not yet been identified.
Jerry Franke, the retiring president of WisPark LLC, which represented the development, said he had concerns about some of the conditions, including the assessment for a sewer lift station that will be built to support developing the site and a future roundabout planned for the area.
Franke said he was unaware of the assessment for the lift station. A meeting with the developer and staff has been planned for Thursday. The plans are expected to be brought before the Village Board on Dec. 18.
Startup Iron Ox Mixes Robotics and Hydroponics to Futurize Farming
Silicon Valley-based startup Iron Ox is utilizing autonomous robotics to fundamentally change the nature of greenhouse-based agriculture. While the exterior of the Iron Ox greenhouse in San Carlos, California is far from remarkable, the cost-cutting integration of hydroponics, solar energy, robotics, and space-conscious farming is more than noteworthy.
Startup Iron Ox Mixes Robotics and Hydroponics to Futurize Farming
Photo Credit: Jirakan Jiherb/123RF
Silicon Valley-based startup Iron Ox is utilizing autonomous robotics to fundamentally change the nature of greenhouse-based agriculture. While the exterior of the Iron Ox greenhouse in San Carlos, California is far from remarkable, the cost-cutting integration of hydroponics, solar energy, robotics, and space-conscious farming is more than noteworthy.
Iron Ox
By using autonomous robots to plant, seed, water, and even harvest their hydroponically grown crops, Iron Ox’s system provides uniformity and rapidity which conventional, human-centric farming methods can’t match. Iron Ox greenhouses’ daily harvesting and proximity to urban centers, grocery stores and produce suppliers diminishes the nutrient loss and often bland taste which results from produce being shipped hundreds or thousands of miles from farm to store.
Founders Brandon Alexander, a former Google X engineer and John Binney, who holds a PhD in robotics, check all the boxes when it comes to consumer demand for non-GMO, pesticide-free produce. Alexander, Iron Ox’s CEO, is uniquely qualified as the leader of this farming revolution. His work on Google’s Project Wing included exploring and implementing ways for autonomous robots to work in combination. With the proper technology in place, Alexander estimates that set-up of one of Iron Ox’s urban greenhouses takes only three to four months, on average.
Luiz Ribeiro Ribeiro/123RF
The master plan is to expand Iron Ox greenhouses manned by autonomous robot-farmers to as many American cities as possible, providing a fresher, potentially cheaper source of produce that traditional farms located far from these cities would be hard-pressed to compete with. Consider that, according to Alexander, a single square-acre Iron Ox greenhouse can match the annual yield of 30 acres of traditional farmland. It also stands to reason that the products created in these robotic greenhouses are less vulnerable to insects and parasites, eliminating the need to use harmful chemicals used to protect outdoor-grown crops.
Like so many industries that have long been a staple of the American and world economies, the application of robotic technology in agriculture will likely mean a drastic shift away from dependence on human labor. The proliferation of companies like Iron Ox carries clear benefits, but it will almost certainly mean structural unemployment for those who depend on traditional means of agriculture as a livelihood. That said, it’s not a matter of if, but a matter of when we see this shift toward autonomous greenhouse farming on a mass scale.
Rooftop Pioneer: Gotham Greens Takes Farming to a New Level
Rooftop Pioneer: Gotham Greens Takes Farming to a New Level
ENTREPRENEURSHIP, FOOD TECHNOLOGY, FOODPRENEURS
By Lindsey Greenberger, Marketing and Content Specialist
Eric Haley
Sensing urbanites’ hunger for locally grown produce, Gotham Greens seized an opportunity to turn cities’ abundant rooftops into farms. Here, Co-Founder and CFO Eric Haley shares how the company got its start and landed on the shelves (and roof!) of Whole Foods Market.
WHERE DID THE IDEA FOR GOTHAM GREENS COME FROM?
It was winter in NYC and my business partner and I came to the realization that most of the produce we were finding in the supermarkets was coming from places like Mexico, California, and Israel. We realized that by the time the produce made its way here, it was at least a week old and had changed hands multiple times. We also began to notice that consumer preferences were shifting toward more local and sustainably produced food and we realized there was an opportunity to disrupt the conventional model of agriculture. Overall we were inspired by innovation and technology, and driven by a sense of duty to address ecological issues facing our agricultural system.
HOW DID YOU GET STARTED?
Back in 2011 we built our first project on a 15,000 square foot rooftop in Greenpoint, Brooklyn. This state of the art, climate controlled rooftop greenhouse represented the first commercial scale facility of its kind in the U.S. We feel it represented a shift in the concept of urban farming from a seasonal community gardening resource, to a year-round, viable, commercial scale farming enterprise. Six years later, we have four greenhouses across two cities and over 150 full time employees.
WHY DID YOU CHOOSE TO LAUNCH IN NYC AND THEN CHICAGO?
NYC and Chicago are two of the largest cities in the U.S. and they both lack fresh, local produce year-round. Both cities have strong food scenes and we were seeing the proliferation of farmer’s markets and chefs becoming household names. Once we proved that our concept was successful and commercially viable in NYC, we started looking to other cities and Chicago was an easy choice.
HOW HAS THE PARTNERSHIP WITH WHOLE FOODS IMPACTED YOUR BUSINESS? ARE THERE OTHER CUSTOMERS THAT HAVE MADE A PARTICULARLY SIGNIFICANT IMPACT?
Shortly after launching our first greenhouse, we had attracted retail customers such as Whole Foods Market and notable restaurants such as Gramercy Tavern, so we knew that we were on to something. Whole Foods Market has been one of our early supporters and customers since day one. Our companies share a lot of the same ideals and commitment to sustainability so Whole Foods was a natural partner for our second greenhouse, which we built on top of their flagship Brooklyn store in Gowanus. The 20,000 square foot rooftop greenhouse produces over 200,000 pounds of fresh greensand herbs each year, much of which are sold direct to customers in the store downstairs. This project represents the first commercial scale greenhouse farm integrated into a supermarket. Both our relationship with Whole Foods Market and Danny Meyer’s Union Square Hospitality Group helped us establish credibility early on.
HOW DO YOU THINK AMAZON’S PURCHASE OF WHOLE FOODS WILL IMPACT YOUR BUSINESS?
Whole Foods Market was an early supporter of Gotham Greens and we share many of the same ethos around sustainability and community involvement. We’ve also been working with Amazon for the last few years and they’ve championed our brand so we have every reason to expect that they’ll continue to support our products and unique partnership!
HOW HAS YOUR VISION FOR THE COMPANY EVOLVED?
When we first started Gotham Greens we were looking to prove that it was possible to grow premium quality, hyper local produce year round right in NYC. Now that we’ve grown into a midsize company with four commercial scale facilities across two major U.S. cities, we’re looking to bring the concept to additional cities across the country.
WHERE DID YOU GET THE FINANCING?
When my co-founder and I came up with our concept back in 2009, we did what any sage business owners would do and wrote a business plan. We entered it into the New York Green Business Competition and won the grand prize which gave us a nice initial boost. We also pooled together money from friends and family. Since inception we’ve raised $30 million to date and are in the midst of doing our Series C.
WHAT HAVE BEEN THE BIGGEST CHALLENGES?
The greatest challenges have come from not having a prototype for what we’re doing. As a pioneer in the urban agriculture space we’ve had to learn on our feet and stay flexible.
HOW DO YOU DO MARKETING? WHAT HAVE YOU FOUND TO BE MOST EFFECTIVE?
We do all of our marketing in-house. We’re really committed to being part of our communities and do things like host weekly tours on our Gowanus observation deck and donate product to community organized events. We also partner with local community gardening programs, food rescue organizations and public schools to increase environmental education and healthy food access to our neighbors in need.
WHERE DO YOU WANT THE COMPANY TO BE IN 5 YEARS?
I’d like to see Gotham Greens be a local brand on a national level. Now that we’ve proven that urban farming can be done on a commercial scale, year-round and across multiple cities, the sky is the limit!
Vertical Farm Under Construction At New RiNo Development
Construction is underway on the company’s first greenhouse, a 7,000-square-foot structure at the new S’park development on the corner of 25th and Lawrence streets.
Vertical Farm Under Construction At New RiNo Development
KATE TRACY NOVEMBER 16, 2017
Altius Farms will have 340 tower gardens in its greenhouse. (Altius Farms)
Sally Herbert is looking for higher ground in RiNo.
Instead of a penthouse with mountain views or a rooftop bar, the Air Force veteran and GS1 executive plans to grow lettuce. And this farm requires some vertical.
Dissatisfied with Denver’s urban agriculture and farming, Herbert founded Altius Farms with the goal of growing produce on a footprint that spreads up, not out.
Construction is underway on the company’s first greenhouse, a 7,000-square-foot structure at the new S’park development on the corner of 25th and Lawrence streets.
Herbert said the greenhouse, with 340 aeroponic garden towers, could produce 75,000 pounds of lettuce, herbs or other leafy greens annually at full capacity. Aeroponics is the process of growing plants without soil.
“We will produce over 10 times the yield of conventional farming,” she said. “We use 10 percent of the water and 10 percent of the space.”
The greenhouse is set to open in spring 2018.
Herbert said she hopes nearby restaurants will account for most of sales. The produce prices will be comparable to other locally sourced products, and Herbert thinks restaurant owners would pay more for the freshness.
“If I can deliver every day or every other day to a restaurateur, they’re really happy,” she said.
Sally Herbert in front of the under-construction S’Park development. (Kate Tracy)
Plans call for the remainder of produce to be sold through CSAs – community support agriculture – to nearby residents.
Lettuce and arugula will be the greenhouse’s main crops, but the company also plans to grow celery, edible flowers and bok choy, and can grow custom produce by request.
Unlike Infinite Harvest, another local Denver vertical farm, Altius will not use LED lighting or a shared water system.
“We’re not sharing water from tower to tower,” Herbert said, adding that will reduce the number of waterborne pathogens to the produce.
Herbert, a graduate of the University of Colorado and Colorado State University, was an executive of barcode company GS1 until four years ago, when she moved back to Colorado.
She served on the board of nonprofit Veterans to Farmers, where she first learned about vertical farm technology.
Herbert said more than $500,000 has been invested in the project, a mix of her own capital, a bank loan and money from other backers. She plans to hire six veterans to run the greenhouse.
Altius looked at two other sites, near the Stanley Marketplace and in Westminster, before settling on the property at 25th and Lawrence.
It is leasing the greenhouse, above the future site of sushi restaurant Uchi, from S’Park developer Westfield. It’s next door to 99 condos and townhomes priced between $300,000 and $900,000.
Rendering of Altius Farms, bottom left, in the under-construction S’Park development. (Altrius Farms)
About the author: Kate TracyView all posts by Kate Tracy
Kate Tracy is a BusinessDen reporter who covers nonprofits, startups and the outdoors industry. She is a graduate of Corban University. Email her at kate@BusinessDen.com.
Cornell Group Explores Future of Indoor Farming
Known as controlled environment agriculture (CEA), the systems combine greenhouse environmental controls such as heating and lighting with hydroponic and soilless production, enabling year-round production of fresh vegetables.
R.J. Anderson/Cornell Cooperative Extension
Doctoral student Jonathan Allred, center, leads a tour of Cornell greenhouses in November.
Cornell Group Explores Future of Indoor Farming
By Jill Monti | November 21, 2017
R.J. Anderson/Cornell Cooperative Extension
Hydroponic tomatoes growing in a Cornell greenhouse.
Indoor farming entrepreneurs and experts came to Cornell in early November with a goal: leverage the innovation at the College of Agriculture and Life Sciences to create viable businesses for local vegetables and produce grown indoors.
Known as controlled environment agriculture (CEA), the systems combine greenhouse environmental controls such as heating and lighting with hydroponic and soilless production, enabling year-round production of fresh vegetables. The process extends the growing season through a range of low-tech solutions – such as row covers and plastic-covered tunnels – to such high-tech solutions as fully automated glass greenhouses with computer controls and LED lights.
Led by Neil Mattson, director of Cornell CEA and associate professor in theSchool of Integrative Plant Science, Cornell has become a world leader in CEA research. In early November, the Cornell CEA Advisory Council, which was formed in 2015 to expand the retail and food service markets for products grown using CEA, hosted on campus more than 80 entrepreneurs and stakeholders from across the Northeast to discuss the state of the indoor farming industry, urban agriculture, supermarket trends and new technology.
At the conference the group announced the formation of the Controlled Environment Agriculture Global Association, an organization to foster growth, understanding and sharing ideas related to controlled environment agriculture and associated industries.
Erico Mattos, executive director of the newly formed Greenhouse Lighting and Systems Engineering (GLASE) consortium, presented his vision to advance CEA by bringing together expertise from industry and academia to create solutions.
“The CEA Advisory Council meeting provided a great opportunity to connect with key players from the different segments of the CEA supply chain in New York. I was impressed with the quality and quantity of the ongoing initiatives in this area supported by Cornell University professors and staff members and the level of engagement from the industry members,” Mattos said.
Mattos said private companies and public research from Cornell offer collaborative opportunities that can advance the CEA industry.
Cornell graduates from the CEA program have been in high demand from companies who wish to leverage their skills and knowledge. Little Leaf Farms, a leader in indoor lettuce production founded by Paul Sellew ’79 and based in Devens, Massachusetts, has hired numerous graduates.
“These talented individuals have provided immediate contributions to our business,” said Tim Cunniff, Little Leaf Farms executive vice president of sales and marketing. “It is exciting to see how Cornell is expanding its commitment in controlled environment agriculture to include the business of running a CEA operation. Cornell is in an excellent position to advance a scalable local food movement, and all of us at Little Leaf Farms are excited to be part of the process.”
Paul Brentlinger, who served on the grower panel and is the second-generation owner of CropKing, said his business and Cornell “have similar outlooks on the future generations of farmers, and we support Cornell as much as we can with their goal of educating the next generation of CEA operators.”
Laura Biasillo, agricultural economic development specialist at Cornell Cooperative Extension (CCE) of Broome County, said: “CCE is the ‘boots on the ground,’ providing everything from technical assistance to the business planning, cost analysis and financing needed by startups and business that are expanding.”
The conference attracted participants from traditional agricultural businesses interested in adding CEA to existing operations, to individuals with significant business experience, to those not yet in agriculture.
“The diverse perspectives made the conversations highly engaging, and building a network for this emerging New York ag sector was one of the key benefits of the conference,” said Aileen Randolph, outreach and communications manager of the New York Farm Viability Institute. “Now it’s up to the participants to do the hard work of utilizing this information for their specific business planning process.”
Jill Monti is technical lead at the Cornell Institute for Food Systems Industry Partnership Program.
STORY CONTACTS
George Lowery
Solar Greenhouses Generate electricity and Grow Crops at The Same time, UC Santa Cruz Study Reveals
Electricity-generating solar greenhouses are outfitted with transparent roof panels embedded with magenta luminescent dye that absorbs light and transfers energy to narrow photovoltaic strips, where electricity is produced. A new study shows that this novel technology, which has the potential to take greenhouses offline, didn't interfere with plant growth or production.
Plants grown in this "smart" greenhouse fared as well or better than plants grown in conventional greenhouses. (Photo by Nick Gonzales)
The first crops of tomatoes and cucumbers grown inside electricity-generating solar greenhouses were as healthy as those raised in conventional greenhouses, signaling that "smart" greenhouses hold great promise for dual-use farming and renewable electricity production.
"Plants are sensitive not just to the intensity of light but also to color," says Michael Loik. "But it turns out the plants grow just as well."(Photo by Nick Gonzales)
"We have demonstrated that 'smart greenhouses' can capture solar energy for electricity without reducing plant growth, which is pretty exciting," said Michael Loik, professor of environmental studies at the University of California, Santa Cruz, and lead author on a paper that appears in the current issue of the American Geophysical Union's journal Earth's Future.
Electricity-generating solar greenhouses utilize Wavelength-Selective Photovoltaic Systems (WSPVs), a novel technology that generates electricity more efficiently and at less cost than traditional photovoltaic systems. These greenhouses are outfitted with transparent roof panels embedded with a bright magenta luminescent dye that absorbs light and transfers energy to narrow photovoltaic strips, where electricity is produced. WSPVs absorb some of the blue and green wavelengths of light but let the rest through, allowing the plants to grow. WSPV technology was developed by coauthors Sue Carter and Glenn Alers, both professors of physics at UC Santa Cruz, who founded Soliculture in 2012 to bring the technology to market.
Loik's team monitored photosynthesis and fruit production across 20 varieties of tomatoes, cucumbers, lemons, limes, peppers, strawberries, and basil grown in magenta glasshouses at two locations on campus and one in Watsonville, California.
"Eighty percent of the plants weren’t affected, while 20 percent actually grew better under the magenta windows," said Loik. Tomatoes and cucumbers are among the top greenhouse-produced crops worldwide, he said.
In additional experiments, small water savings were associated with tomato photosynthesis inside the magenta glasshouses. "Plants required 5 percent less water to grow the same amount as in more conventional glasshouses," he said.
"I thought the plants would grow more slowly, because it's darker under these pink panels. The color of the light makes it like being on the Red Planet," said Loik. "Plants are sensitive not just to the intensity of light but also to color. But it turns out the plants grow just as well."
Reducing the energy consumed by greenhouses has become a priority as the global use of greenhouses for food production has increased six-fold over the past 20 years to more than 9 million acres today—roughly twice the size of New Jersey, according to Loik. "It's big and getting bigger," he said. "Canada relies heavily on greenhouses for vegetable production, and their use is growing in China, too." Plastic greenhouses are becoming popular for small-scale commercial farming, as well as for household food production, he added.
Greenhouses use electricity to control temperature and power fans, lights, and other monitoring systems. "This technology has the potential to take greenhouses offline," said Loik, who specializes in climate change, plant physiology, water resources, and sustainable technologies. Cost per panel of WSPV technology is 65 cents per watt—about 40 percent less than the per-watt cost of traditional silicon-based photovoltaic cells.
"If greenhouses generate electricity on site, that reduces the need for an outside source, which helps lower greenhouse gas emissions even more," said Loik. "We're moving toward self-sustaining greenhouses."
Additional coauthors include Catherine Wade, who participated as a graduate student, Carley Corrado, who participated as a postdoctoral researcher, and undergraduates David Shugar and Devin Jokerst, all of UC Santa Cruz; and Carol Kitayama, senior grower at Kitayama Brothers Growers.
Renewable Energy: Smart Greenhouses Generate Solar Power and Grow Crops At The Same Time
Renewable Energy: Smart Greenhouses Generate Solar Power and Grow Crops At The Same Time
BY SYDNEY PEREIRA ON 11/6/17
Tomatoes and cucumbers appear to grow just fine—and just as healthily—in smart, solar-powered greenhouses that capture solar energy for electricity.
Scientists from the University of California, Santa Cruz, have shown how crops can grow as healthily in these new greenhouses as they do in conventional greenhouses.
"Plants are sensitive not just to the intensity of light but also to color," says Michael Loik. "But it turns out the plants grow just as well."(Photo by Nick Gonzales)
"We have demonstrated that 'smart greenhouses' can capture solar energy for electricity without reducing plant growth, which is pretty exciting," Michael Loik, professor of environmental studies at UCSC, said in a press release. Loik is the lead author for the paper, published in the American Geophysical Union's journal Earth's Future.
Solar Power Trapped by a Red Roof
Bright magenta panels cover the tops of the greenhouses, soaking up sunlight and transferring the energy to photovoltaic strips. From there, electricity is produced.
The greenhouses are able to take sunlight for energy and leave the rest, allowing plants to grow using a technology called Wavelength-Selective Photovoltaic Systems (WSPVs). The technology, developed by co-authors Sue Carter and Glenn Alers, is less expensive and more efficient than traditional photovoltaic systems.
The team tested the growth and fruit production across 20 varieties of tomatoes, cucumbers, lemons, limes, peppers, strawberries and basil at two locations at the Santa Cruz campus and one in Watsonville, California. Scientists reported that 80 percent of the plants were unaffected by the slightly darker lighting from the magenta panels, and 20 percent of the crops grew better. Tomato plants needed 5 percent less water under the magenta panels.
Reducing the energy used in greenhouses is crucial since the use of greenhouses to grow food has increased by sixfold in the past 20 years, according to Loik.
Solar-powered greenhouses are one of several developments for new ways of farming in recent years.
Plants grown in the smart greenhouse were just as good as plants grown in conventional greenhouses.NICK GONZALES
Smart Greenhouse Detects Infestations
Another company, NatureSweet, has outfitted its greenhouses in Arizona with artificial intelligence, reported CNN. The plants are monitored with 10 cameras installed in the greenhouse ceilings which continuously take photographs to detect insect infestations or dying plants.
The software, developed by a company called Prospera, recognizes those problem spots and sends feedback 24/7. Previously, reported CNN, NatureSweet's employees walked through the greenhouse in order to spot issues with the plants.
Green roofs are another method of growing food in an attempt to utilize space and close gaps in access to foods in urban areas.
In Washington, D.C., Up Top Acres has opened five urban farms on the rooftops of buildings since 2015, reported Washington City Paper. Green roofs improve storm-water collection, habitat protection and energy preservation, in addition to providing food. The company's co-founder, Kathleen O'Keefe, told the paper that the company may not produce enough food for the city, but green roofs can change the way people think about food, in addition to utilizing unused space.