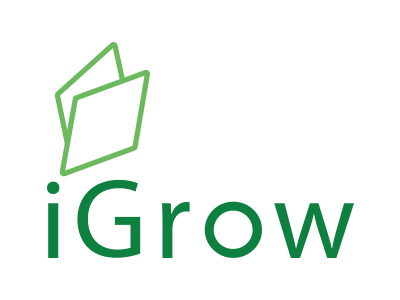
Welcome to iGrow News, Your Source for the World of Indoor Vertical Farming
Something Has Sprung Up Out of The Ground In Food Tech!
Something Has Sprung Up Out of The Ground Inf Food Tech!
US (WI): Superior Fresh Grows Salmon And Veggies At High-Tech Facility
US (WI): Superior Fresh Grows Salmon And Veggies At High-Tech Facility
Superior Fresh is the largest aquaponics facility in the world. Their state-of-the-art fish facility is coupled with a 3-acre glass greenhouse where they grow various leafy greens and herbs. They grow everything from seed in their greenhouse under LumiGrow grow lights and produce 1.8 million pounds of leafy greens each year. The leafy vegetables make their journey from the greenhouse to supermarket shelves within 48 hours.
Superior Fresh’s fish house and greenhouse have been meticulously designed and built using state-of-the-art technology to maximize profits with a superbly modern facility. For their greenhouse lighting, Superior Fresh is using LumiGrow LED grow lights paired with LumiGrow Light Sensor technology to ensure yield and quality goals are met consistently while reducing energy costs by 50% compared to traditional HPS lighting.
The light sensor technology allows Superior Fresh to monitor the exact light levels in the greenhouse and create programs that automatically adjust the fixtures to efficiently meet production goals year-round.
“Our biggest leap forward has been the LumiGrow smartPAR software,” says Adam Shinner, Head Grower at Superior Fresh. “…When we have enough sun, the lights turn off. When we don’t have enough sun, they turn back on. It allows for full integration of our lighting system [with the greenhouse zoning], which has truly not been possible up until this point.”
“Understanding that we are going to have 9 billion people on this planet in the next 30 years or so, we have to start thinking about how we’re going to efficiently grow food close to the marketplace,” says Brendan Gottsacker, CEO at Superior Fresh. “LumiGrow has allowed us to grow food right here in Wisconsin in the middle of the winter.”
For more information:
LumiGrow
800-514-0487
info@lumigrow.com
www.lumigrow.com
Publication date: 5/29/2018
Wendy's Makes Another First in Fresh with Innovative Tomato Supply Initiative
Wendy's Makes Another First in Fresh with Innovative Tomato Supply Initiative
First-in-QSR Commitment to Source Vine-Ripened, Greenhouse-Grown Fresh Tomatoes
DUBLIN, Ohio, June 5, 2018 /PRNewswire/ -- As part of its ongoing commitment to sourcing fresh, high-quality produce, today, Wendy's® is announcing an initiative to source vine-ripened tomatoes for its North American restaurants exclusively from greenhouse farms by early 2019.
Tomatoes for Wendy's will be grown in indoor greenhouse and hydroponic farms from approximately a dozen suppliers throughout North America, including the West Coast, Pacific Northwest, Southeast and Great Lakes regions of the United States; Eastern and Western Canada; and Mexico. Nearly all tomatoes will be sourced from the United States and Canada, giving Wendy's customers the benefit of fresh, great-tasting tomatoes from sources that match the brand's North American restaurant footprint.
"We've always been committed to providing customers with fresh, high-quality food. From our fresh never frozen beef, to creating the first salad bar in the QSR space, to hand-chopping produce in our restaurants daily, this newest initiative to source vine-ripened tomatoes from greenhouse farms is the latest way we're delivering on that commitment," said Liliana Esposito, chief communications officer for Wendy's.
"We're making this change for a variety of reasons that will benefit our customers, but taste and quality are the top factors and we are excited about the superior flavors we can achieve with this change," said Dennis Hecker, senior vice president of quality assurance for Wendy's. "Additionally, greenhouse farms provide supply predictability and quality assurance benefits—including continuity of supply; protection of crops from harsh weather; safe, indoor growing conditions; and a significant reduction of chemical pesticides used on the plants."
Wendy's also believes that greenhouse growing will support local economies by sustaining the agricultural workforce with fresh produce that can be grown year-round in comfortable, indoor environments. It will also bring economic opportunities to regions that previously have been unable to support year-round agriculture production due to geography and climate.
As Wendy's transitions to its new tomato supply, it expects to see social and environmental sustainability benefits about which it will communicate regularly. Expected benefits include the significant reduction of chemical pesticide use, including replacing pesticides with natural integrated pest management practices such as ladybugs; water and land use benefits; safe, indoor working conditions and economic benefits to regions where the greenhouses are located.
With the transition actively underway, vine-ripened, greenhouse-grown tomatoes will be available at Wendy's in the U.S. and Canada between now and early 2019.
About Wendy's
Wendy's® was founded in 1969 by Dave Thomas in Columbus, Ohio. Dave built his business on the premise, "Quality is our Recipe®," which remains the guidepost of the Wendy's system. Wendy's is best known for its made-to-order square hamburgers, using fresh, never frozen beef*, freshly-prepared salads with hand-chopped lettuce, and other signature items like chili, baked potatoes and the Frosty® dessert. The Wendy's Company (NASDAQ: WEN) is committed to doing the right thing and making a positive difference in the lives of others. This is most visible through the Company's support of the Dave Thomas Foundation for Adoption® and its signature Wendy's Wonderful Kids® program, which seeks to find every child in the North American foster care system a loving, forever home. Today, Wendy's and its franchisees employ hundreds of thousands of people across more than 6,600 restaurants worldwide with a vision of becoming the world's most thriving and beloved restaurant brand.
Please visit www.wendys.com and www.squaredealblog.com for more information and connect with us on Twitter and Instagram using @wendys, and on Facebook, www.facebook.com/wendys.
*Fresh beef available in the contiguous U.S., Alaska, and Canada.
SOURCE Wendy's
Current, Powered By GE And Jones Food Company Partner To Launch Europe’s Largest Indoor Farm
Current, Powered By GE And Jones Food Company Partner To Launch Europe’s Largest Indoor Farm
- Horticultural lighting solution enables environmental benefits including 90% less water, 50% less fertilizer, reduced energy and carbon footprint
- High-care operation creates opportunities to redefine the future of global food, pharma, and cosmetics with industrial-scale production
- Clean room automation enables “no touch” harvesting versus an average of 13 human contact stages
The impact of indoor farming with Current by GE Arize lighting solution (Graphic: Business Wire)
June 07, 2018
LONDON & AMSTERDAM--(BUSINESS WIRE)--Current, powered by GE (NYSE: GE) and Jones Food Company Ltd. (JFC), today announced that construction is underway toward building one of the world’s largest indoor farms. The intensive plant nursery, located in North Lincolnshire, England, will be the largest indoor farm in Europe, producing up to 420 tonnes of leafy greens per year across a growing area of 5120m2, arranged in racks rising to the height of 11m. To maximize the facility’s yield, Current by GE is installing more than 12Km of its new Arize* LED horticultural lighting solution, with a balanced light spectrum that catalyzes optimal growth in every plant and shortens the growth cycle for more intensive production.
We knew that lighting would be the lifeblood that could bring high-care intensive food production to an industrial level that demonstrates real commercial viability. - JFC CEO James Lloyd-Jones
The equipment is housed within a futuristic, intelligent cleanroom (or “high-care”) environment that allows crops to be grown in complete isolation from external contamination – ideal for food production as well as growing high-quality cosmetic and pharmaceutical ingredients. Production of the first crop from the Jones Food Company operation is due to start in autumn 2018.
“Nobody has been able to scale indoor, high-care intensive food production to an industrial level that demonstrates real commercial viability,” explained James Lloyd-Jones, CEO, and co-founder of JFC. “We knew that lighting would be the lifeblood of the facility and we’d need a partner who could see the potential and work with us to develop the right lighting set-up and spectrum to make our vision a reality.”
The world’s largest high-care indoor farm
With a growing area of 5120m2, the equivalent of 26 tennis courts, arranged across racks rising to a height of just over three storeys, the facility – owned and operated by JFC – will set new production and environmental standards for crop production of the future. With year-round local production JFC aims to slash food miles and produce leafy greens, herbs and other crops that can be delivered from harvest to plate in minimal time.
In addition, by designing the farm as a “high-care” facility, JFC will also be able to cater to the growing demands of cosmetics and pharmaceutical customers who require reliable supplies of the highest quality, natural ingredients. Every factor in the growth of the crops produced will be highly controlled; from the nutrient solution delivered to the roots of each and every plant, to the concentration of CO2 in the room, to the light wavelengths and duration of the growing “day” and subsequent rest period. Thanks to intelligent automation and advanced robotics, every plant can be grown in ideal, cleanroom conditions, untouched by human hand from planting to harvest. By comparison, conventional production cycles typically average 13 stages of human contact.
Lighting the future of horticulture with Arize
Malcolm Yare, Horticulture Business Development Manager for Current by GE commented, “We’ve spent years honing our technology in other industrial lighting sectors, and years more partnering with agricultural experts and researching the needs of horticultural applications. Our Arize LED solutions now lead the industry for efficiency and we continue to research new ways to improve performance through innovation. We look forward to working with Jones Food Company and our wider ecosystem of partners to find new ways to scale high-quality, global food production whilst reducing the energy and environmental costs of vertical farming.”
The Arize range of lighting solutions is low cost to install and maintain, with a market-leading 36K-hour lifetime (L90) and a five-year warranty to provide peace of mind and long-term reliability. An IP66, UL Wet rating also makes them ideal for high-care and cleanroom facilities as the luminaires can be easily washed and sanitized in-place.
Saving the environment whilst boosting the balance sheet
The JFC facility is designed to minimize the environmental impact of vertical farming, which will also offer a direct financial benefit to the company. For example, it will use up to 90 percent less water and 50 percent less fertilizer than conventional growing methods, saving on input costs. In addition, Current by GE’s Arize LED solutions are highly efficient, generating less heat than competitive products, reducing energy consumption and carbon footprint by 33 percent compared with vertical farming averages.
Notes to editors:
Jones Food Company production statistical visualization:
- The growing surface area is 5120m2 – close to 26 singles tennis courts
- 12.3Km of Arize lighting is the equivalent of laying nearly 38 Eiffel Towers end to end
- The growing racks reach a height of 11m, just over 3 storeys
- 420 tonnes of leafy greens are expected to be produced each year – roughly the same weight as 70 adult elephants
For more information regarding Current by GE’s Arize LED solutions for horticulture, visit www.currentbyge.com or visit us at our booth at GreenTech Amsterdam between 12th and 14th June 2018 (Hall 8, booth 105).
About Current, powered by GE
Current is the digital engine for intelligent environments. A first-of-its-kind startup within the walls of GE (NYSE: GE), Current blends advanced LED technology with networked sensors and software to make commercial buildings, retail stores and industrial facilities more energy efficient & digitally productive. Backed by the power of Predix*, GE’s platform for the Industrial Internet, and a broad ecosystem of technology partners, Current is helping businesses and cities unlock hidden value and realize the potential of their environments. www.currentbyge.com
About Jones Food Company
The nucleus of the Jones Food Company consists of three main protagonists: James Lloyd-Jones (CEO), Dr Paul Challinor (CTO) and Gary Thorneycroft (CFO). Together, they have consolidated initial ideas on improving the management of high-value crops in intensive growing conditions by constructing a world class plant production unit based in the UK.
The use of wide-ranging experience gained in the energy, horticultural research, and finance industries has been paramount in the solving of complex production issues, ahead of the first crop harvest. The combination of intensive hydroponics, energy-efficient LED lighting and sophisticated environmental control systems, coupled with the maintenance of a high-care production and harvesting process flow, takes growing to a new level in the UK fresh produce industry and is world-leading in its wider outlook.
*Trademark and/or Service Mark of General Electric Company
Contacts
Current, powered by GE
Karen O’Neil, +1 857-265-9113
karen.oneil@ge.com
or
Racepoint Global
Jenna Keighley, +44 208 811 2151
Jenna.keighley@racepointglobal.com
3rd Greenhouse and Hydroponic Technical Management Course for India
3rd Greenhouse and Hydroponic
Technical Management Course for India
"Delish Veggies, Graeme Smith Consulting and Future Farms are pleased to announce the 3rd Greenhouse and Hydroponic Training Program in Pune India after the grand successes of our two training courses in 2017.
We received a phenomenal response for both training programs due to the presence of renowned international trainers from Australia and practical farm tours whereby we hosted many international participants, multiple Indian states, and 60 participants and received “extremely satisfied” feedback from all the participants.
Delish Veggies had to decline many participants in these training programs due to limited seats, therefore due to popular demand we are organizing a 3rd course this June (4th to 8th) and have again included many interesting topics and commercial farm set up sessions."
The course will again be conducted by two highly experienced Australian industry presenters Graeme Smith and Rick Donnan.
Graeme is the proprietor of Graeme Smith Consulting, he consults throughout the world, runs regular study tours to Holland/EU and North America, and is the past Chairman of Protected Cropping Australia. Recent international greenhouse projects include Hyderabad, Abu Dhabi, China and Rajasthan.
Rick owns Growool Horticultural Systems and is the Q&A columnist in the world’s leading hydroponic industry publication- Practical Hydroponics and Greenhouses magazine and provides consultancy services.
The course assists participants to improve their ability to understand the key principles in a commercial greenhouse and hydroponic production by:
• understanding the principles of controlled production systems
• using correct strategies and technologies to manage
greenhouse climates and irrigation
• understanding plant growing requirements and plant
production techniques
• developing new strategies for plant protection and integrated
pest & disease management
• understanding plant nutrition and fertigation programs
• identifying the risks and opportunities of climate change
Topics Include:
• Media types & characteristics • Plant structure
• Nutrition & nutrient management • EC & pH
• Water quality and treatment • Plant physiology
• Environmental management • Irrigation management
• Greenhouse business and marketing plan • Plant health
• Greenhouse design and layout • Pest and disease control
Greenhouse Technical Management Course Details
Greenhouse Technical Management Course Photos
Location: Pune, India
Dates: June 4th to 8th 2018 (5 days)
Course cost: Rs. 50,000 excluding 18% GST. (Lunch, as well as morning and afternoon tea, will be provided throughout the course)
To register your interest, please contact the course Coordinator, Uday Mathapati on +91 9130098714 or email: udaymathapati@gmail.com or visit www.delishveggies.com for further information
Greenhouse Training Online Courses Win National Award For The University of Florida
Greenhouse Training Online Courses Win National Award For The University of Florida
BY urbanagnews
May 15, 2018
The Greenhouse Training Online (GTO) program offered to growers by the University of Florida IFAS Extension is the winner of the 2018 Extension Division Education Materials Award from the American Society for Horticultural Science. Over 1300 growers have participated in GTO courses, with an 80% success rate.
Eight courses for greenhouse and nursery growers are offered this year last 4 weeks, and include streaming video lessons, readings and assignments (about 2 hours total commitment per week). Courses are in English and Spanish and can be accessed at any time of day. Click here to register (hort.ifas.ufl.edu/training/).
The first two courses begin on June 4, 2018: Greenhouse 101 and Costing & Profitability.
Greenhouse 101 teaches basic horticulture science and is designed to help staff with no formal training make better crop management decisions.
Costing and Profitability helps grower managers develop the skills to accurately estimate production cost and profit for your greenhouse or nursery business.
For more information, go to hort.ifas.ufl.edu/training/, or contact Greenhouse Training, Environmental Horticulture, University of Florida, USA,
Email: greenhousetraining@ifas.ufl.edu.
Little Leaf Farms Expands Its Indoor Baby Greens Production
Little Leaf Farms Expands Its Indoor Baby Greens Production
May 22, 2018, Posted By Brian Sparks | Email
Little Leaf Farms, one of the largest growers of hydroponic baby greens in North America, has officially opened its expanded greenhouse in Devens, MA. The expansion doubles the size of the greenhouse from 2½ acres to 5 acres and more than doubles its annual production of baby greens. The company has also purchased adjacent land for a third expansion project set to begin in 2019, which will further increase the size of the greenhouse to approximately 10 acres.
“We are passionate about transforming the way food is grown,” says Paul Sellew, CEO, and Founder of Little Leaf Farms. “We incorporate principles of sustainability in everything we do, all to provide consumers with delicious, local baby greens at a fair price. Our process is clean from the start, so consumers can be confident they’re purchasing a safe product, grown in an environment that employs the most advanced food safety practices.”
Opened in 2016, Little Leaf Farms produces locally grown, fresh baby greens year-round that are delivered to New England consumers within hours of being harvested. Little Leaf Farms grows multiple varieties of baby lettuce at its greenhouse that are blended into salad mixes and sold in more than 1,000 Northeast grocery stores and to many restaurant, university, and institutional customers. Little Leaf Farms’ ability to deliver fresh, great tasting and safe baby greens to consumers that can be easily traced back to its Massachusetts greenhouse has led to the company’s rapid growth and expansion.
Little Leaf Farms’ hydroponic growing process uses natural sunlight, a computer-controlled growing environment, and a rainwater-based irrigation system that uses 90% less water than field-grown lettuce. The company’s technologically advanced growing system enables the baby greens to be seeded, grown, cut, and packaged without ever being touched by human hands.
More information about Little Leaf Farms’ expanded greenhouse facility and where its baby greens can be purchased can be found on the company’s website.
TOPICS: Leafy Greens, Little Leaf Farms
How To Guarantee Your Greenhouse Success Story?
How To Guarantee Your Greenhouse Success Story?
Why a comprehensive project lifecycle methodology with a proven methodology and complete services package, delivered by the right partner is key to growing your greenhouse business profitably.
When planning a greenhouse project, farmers and investors alike face a long list of worries and concerns. How will I know if my project is financially viable? Will it be completed on time? Once construction is complete, will my team have the agronomic knowhow to create the optimal growing conditions for successful harvests?
To answer these questions and give you the confidence to initialize a greenhouse project, it helps to have a partner that combines deep agronomic expertise with a comprehensive and proven greenhouse project lifecycle methodology; one that addresses all stages of the project from feasibility assessment through planning and design to agronomic planning, operations, and maintenance services.
Managing your Greenhouse project: From start to success.
In the feasibility assessment stage, a preliminary evaluation of the project is conducted to determine its viability and financial viability. In certain cases, a full feasibility study is required to analyze a range of aspects, including preferred technology, workforce requirements, agronomical aspects and financial analysis.
Tailor-made solution
As every project inevitably brings a unique set of requirements, it is critical to plan and design a tailor-made solution that meets your climatic and agronomical challenges head-on. It begins with choosing the right structure, be it a glasshouse, polyhouse or nethouse, and fitting it with the right equipment and accessories to ensure an optimal growing environment.
Next, it is important to choose an execution model, turnkey or supply and supervision, that fits your needs and your desired level of peace of mind.
The operations and maintenance stage is often the most critical stage in the project. Services such as agronomical guidance and consultancy, technical support for the structure and equipment and marketing linkages to off-takers, will determine if your project will be successful and financially viable in the long term.
In summary: Managing a successful greenhouse operation can be complex and full of pitfalls. Choosing a greenhouse project partner with deep agronomy expertise who can accompany you throughout the entire lifecycle with a proven methodology can give extra peace of mind and ensure high-quality results and rapid return on your investment.
"At Netafim, we don’t just build your greenhouse, we help build your business. Want to know more? Come and meet us at GreenTech 2018, booth #12.323."
For more information:
Netafim
Contact a Netafim expert here.
Publication date: 5/30/201
Nature Meets Technology At Oakland Urban Growers
Nature Meets Technology At Oakland Urban Growers
MAY 16 2018
WATERFORD, Mich. (WJBK) - Oakland Urban Growers provides fresh, local produce to families and businesses across metro Detroit. It's also a perfect example of how technology and nature can come together.
Mike Skinner and Bruce Ellwanger turned a greenhouse that was about to be torn down in Oakland County into a high-tech agriculture company. Their different types of growing systems allow them to grow fresh produce all year long.
"Really, this is a 21st century way of growing produce," Skinner says. It's mostly done via a hydroponics operation -- which means, without dirt.
That means they're responsible for providing all the nutrients to the plants, which usually come from the soil. They figure out what nutrients the plants need through a small water sample that comes in from the gutter.
The nutrients are them pumped into all the different plants.
The shop opened up last year in conjunction with Oakland County. Skinner says they're the first ones to bring hydroponics growing to Oakland County.
Other growing takes place at the greenhouse the more conventional way, in the soil, but in an area that's completely, climate controlled. Specialty, baby crop versions of the vegetables are mostly grown here.
Skinner says they sell a lot of their products to top-notch country clubs and restaurants that are looking for high quality, local produce.
You can learn more about how the systems work by watching the report from Josh Landon in the video player above.
30MHz And Asian Perlite Industries Partner To Bring Wireless Sensing Tech To Southeast Asian Agriculture
30MHz And Asian Perlite Industries Partner To Bring Wireless Sensing Tech To Southeast Asian Agriculture
May 29, 2018
Asian Perlite Industries, leading provider of greenhouse solutions in the Asia Pacific region, has partnered with agricultural technology provider 30MHz to become the first distributor of the company’s wireless smart sensing technology in Asia. With 30MHz wireless sensors and its intuitive analytics platform, the two companies will empower Asian growers in horticulture and floriculture to be more productive, sustainable and cost-effective by providing real-time insights on their crops and growing environment.
Agricultural intelligence made accessible
30MHz provides all the elements growers need to deploy a wireless sensor network and start capturing accurate, crop-level metrics in moments, without technical expertise. Customers select the combination of sensors that fit their needs (capturing metrics including vapor pressure deficit, dewpoint, soil moisture, EC/VMC, light intensity, CO2, temperature and humidity) and have the option to scale with more sensors, or new sensor types at any time. The user-friendly, customizable dashboard provides customers with full control over how data is displayed, with all metrics in one central location. For a greater overview of growing conditions, customers have the option to view sensor data alongside third-party data sources, like climate control systems.
A natural fit with Asian agriculture
The partnership will focus on the agricultural markets in Southeast Asia, with a special interest in Cameron Highlands, Malaysia, Dalat, Vietnam, and the Philippines. With deployments in 14 countries spanning five continents, including Malaysia, Vietnam, and Laos, increased focus on Asian agriculture is a natural progression for Dutch-founded 30MHz. “We see that growers in this region crave data and tools to innovate and make the most of their resources. They want technology that isn’t complicated and is quick to get started. This makes Asia a no-brainer for 30MHz. With 20 years of established trust in Southeast Asia, Asian Perlite Industries is perfectly positioned to bring the power of smart sensing to this market” says JP Papaioannou, Director Southeast Asia & China.
“30MHz provides an easy solution to show what is going on in the farms which takes away assumptions and guessing,” notes Luuk Runia, owner of Asian Perlite Industries. “The solution is affordable and farmers can easily expand and increase their sensors as the solution is highly scalable. Over my 20 years in the greenhouse space, I have seen many different systems. However, I really like 30MHz because the software interface is extremely user-friendly. 30MHz already works with leading customers in the Netherlands, such as Proeftuin Zwaagdijk, Kwekerij Moors, and Jan de Wit, and I’m excited to bring cutting-edge Dutch agricultural innovation to Southeast Asia.”
30MHz already counts tomato and cucumber growers Fresh Grow Holdings, in Cameron Highlands, as customers. Michael Rapattoni, CEO of Fresh Grow Holdings added: “We are very excited to work with 30MHz. Their sensor solution will allow us to better manage our production numbers and it will take away the guessing game. One of our goals is to be a high-tech leader in the Asian region and our relationship with 30MHz is key to accomplishing this.”
About Asian Perlite Industries
Asian Perlite Industries was established in 1997 in Cameron Highlands, Malaysia by owner and director Luuk Runia, and is a leading provider of greenhouse solutions in the Asia Pacific region. Amongst its products are irrigation and water storage solutions, soil steaming, cooling systems and harvesting, grading, labeling and packaging machines.
About 30MHz
30MHz is a rapidly accelerating provider of smart-sensing technology. The innovative 30MHz technology comprises a network of wireless sensors and an analytical software platform which gives growers real-time insights on their crops and environment. The company is headquartered in the Netherlands and has regional offices in the UK, Hong Kong and Australia.
Mucci Farms Now Officially "Ohio Grown"
Mucci Farms Now Officially "Ohio Grown"
MAY 31, 2018
Mucci Farms is now officially “Ohio Grown”
May 30th, 2018 Huron, Ohio — Mucci Farms announces that they are officially harvesting out of Phase 1 of their 60-acre greenhouse facility in Huron, Ohio. “After years of hard work and strategic planning, we’re excited to hit another milestone in the Mucci Farms story,” said Bert Mucci, CEO of Mucci Farms. “We’re very appreciative of the strong partnership we’ve developed with The City of Huron, Huron Township, and Erie County officials to get the first 24-acre project off the ground.”
The entire 60-acre facility will be growing primarily Tomatoes On-the-Vine with some snack sized specialty tomatoes. The company also announced that the entire 60-acres will be equipped with supplemental High Powered Sodium (HPS) lighting in order to grow through the winter months allowing them to harvest Ohio grown tomatoes 365 days per year. “We chose tomatoes on-the-vine because of its high demand year round, particularly in the winter months,” said Joe Spano, Vice President of Sales & Marketing. “With grow lights in the entire facility, it was important to have a product that was always in demand.”
Headquartered in Kingsville, Ontario, this is Mucci Farms’ first expansion into the United States, where the majority of their product is distributed. “Expanding into Ohio allows us to reduce the food miles for our US retailers and gives US consumers their own locally grown vegetables,” explained Danny Mucci, President of Mucci International Marketing. “With such a high volume of our product already being shipped to the US, expanding into Huron was strategically done to improve efficiencies with logistics and food safety. Our proximity to market and avoiding a border crossing improves our opportunity to offer consumers with fresh, flavourful products with maximum shelf.” In addition to the remaining 36-acres of greenhouses being built in two remaining phases, Mucci Farms Ohio will include a 272 000 square foot distribution facility that will be operational this summer. Harvesting from the final two phases will begin in the spring of 2019 and 2020.
Owning and Operating over 200-acres of tomato, pepper, cucumber, lettuce and strawberry greenhouses in Kingsville, Ontario, Mucci Farms also markets on behalf of 700-acres across the continent. An active community partner for initiatives focused on health, fitness, and education, the company plans to extend these commitments into Erie County. “We are looking forward to getting familiar with Huron and Erie County over the next several months to find ways that we can be effective members of the community,” said Emily Murracas, Director of Marketing. “Once we are fully operational, we’ll be setting up a grand opening week to welcome city officials, media members, educators and residents of Huron to tour our facility, learn about what we do, and share their ideas on ways we can be helpful to the local community.” The Company is confident that there are a number of inspiring things to come with this investment in Ohio and Mucci Farms looks forward to growing with the City of Huron, Huron Township, and Erie County.
Employment
Additional employment opportunities will become available as the company approaches completion of the distribution facility over the next few weeks. Resumes and cover letters for general warehouse positions are being accepted at CareersOhio@muccifarms.com. Alternatively, available jobs are posted at muccifarms.com/careers.
Brunei: Sultan’s Call Well-Answered, Youth Surge In Agribusiness
Brunei: Sultan’s Call Well-Answered, Youth Surge In Agribusiness
May 23, 2018
| Aziz Idris |
AN INCREASING number of young entrepreneurs in the Sultanate are venturing into agribusiness, thanks to His Majesty Sultan Haji Hassanal Bolkiah Mu’izzaddin Waddaulah ibni Al-Marhum Sultan Haji Omar ‘Ali Saifuddien Sa’adul Khairi Waddien, Sultan and Yang Di-Pertuan of Brunei Darussalam’s call for youth to get into agriculture.
Answering His Majesty’s call, four young Bruneians have embarked on an ambitious agriculture business to construct and supply hydroponic structures.
Their company, Agrometro, is located at the IBTE Agro-Technology Campus, formerly known as Wasan Vocational School.
The Agrometro team is led by Norisa ‘Azuma binti Mohd Norazmi, 29, as the Director. Siti Badariah binti Darius, 29, is serving as Nursery Plant Specialist, Nursalwana binti Kamidi, 20, as Marketing Manager and Norwardi bin Griffin, 22, as General Manager.
Founded in 2017, Agrometro was initially part of the IBTE Agro-Technology Campus module that needed to be implemented to get the school’s scoring system. The company participated actively during the Agriculture and Agrifood Expo and SME Day as well as in the government initiative, the Entrepreneurial Development, and Guidance (EDGE).
During these exposures, Agrometro’s hydroponic structures have received positive feedback from the public with over 30 structures sold and more orders still coming in. Apart from constructing the structures, the start-up sells other agricultural products such as Sekam, Kulit Padi, and Cocopeat.
(From left) Nursalwana binti Kamidi, Norisa ‘Azuma binti Mohd Norazmi, Siti Badariah binti Darius and Norwardi bin Griffin in a group photo
Raft Hydroponic and Mobile Hydroponic (background). – PHOTOS: AZIZ IDRIS
To date, Agrometro has developed three different structures – Mini Hydroponic System which has four tiers and can accommodate 44 plants; Vertical Hydroponic System which comes with 30 holes in the form of towers; and Raft Hydroponic System which stores 30-40 plants.
There are also more than 10 types of plants available such as Bayam, Kangkong, lettuce, mint leaves and more. However, the plants can be customised depending on customers’ needs, Norisa ‘Azuma said.
According to her, using hydroponics, the method of growing plants without soil, using mineral nutrient solutions in a water solvent, plants can be grown anywhere.
“It’s an example of organic gardening in which plants are grown in nutrient solution, instead of soil. By practising hydroponics, gardeners don’t have to worry about issues such as weeding, soil borne diseases, when to fertilise, spraying pesticides, tilling and soil texture.
“It is an easy way of growing fruits and vegetables that are healthier and have more nutritional value. With hydroponic gardening you can expect results in a very short span. “Hydroponic gardens are simple to maintain – both indoor and outdoor. You can relish fresh, home-grown fruits and vegetables that will bring you happiness and peace of mind while saving money,” she added.
Apart from responding to His Majesty’s call to further develop the agricultural sector in the Sultanate, the start-up’s goal is to create awareness on growing plants using the hydroponic system without spending a lot of money, she said, highlighting Agrometro’s motto, “We plant, We Grow, We Sell”.
Brooklyn Grange Announces A New Location — In A Former WWII Shipyard
Inhabitat is thrilled to announce that New York City urban farming group Brooklyn Grange is launching its first location outside the city — at Kearny Point in New Jersey.
Brooklyn Grange Announces A New Location — In A Former WWII Shipyard
- May 15, 2018
by Lacy Cooke
Inhabitat is thrilled to announce that New York City urban farming group Brooklyn Grange is launching its first location outside the city — at Kearny Point in New Jersey. The location holds its own storied past: a former World War I and World War II shipbuilding yard in an industrial area that’s spiraled downhill, Kearny Point is undergoing redevelopment under recycling corporation Hugo Neu. Inhabitat caught up with Brooklyn Grange COO and co-founder Gwen Schantz and Hugo Neu CEO Wendy Neu to learn about the project’s emphasis on not only economic revitalization but also the restoration of local ecology.
At Kearny Point in New Jersey, Brooklyn Grange will help with landscaping, converting just under three acres of sod into a native meadow. In addition, the group will help transform about an acre of former parking lot space into a demonstration garden, complete with a vegetable patch and children’s play area, as well as host plant sales and educational workshops. Although none of these gardens will be on rooftops, Brooklyn Grange does plan to host green roof workshops using a Kearny Point roof.
Related: 6 urban farms feeding the world
Schantz told Inhabitat, “We know what these industrial spaces can become and how they can be reinvented. We’ve seen the evolution of the Navy Yard. When we talked to the people at Hugo Neu about their vision about Kearny Point, we really got it. It resonated with us.”
Neu is one of the people behind that vision. She told Inhabitat that Kearny Point, which is between the Hackensack and Passaic Rivers, was once a main economic driver for the area as “one of the most productive shipbuilding facilities in the world.” During World War II, 35,000 people worked on the 130-acre site. But after the war, the shipbuilding industry died in the United States. Hugo Neu acquired Kearny Point in the 1960s and dismantled ships, but that operation shut down around 1985. Until recently, Kearny Point was an industrial warehouse distribution facility.
“Hurricane Sandy was a defining moment for us because we were approximately four feet underwater. We’d never had any kind of issue with flooding. My late husband and I know climate change is coming and the environment is changing dramatically, and we had to think about what we were going to do with this site,” Neu told Inhabitat.
After her husband passed away suddenly, Neu joined forces with Steve Nislick, former Edison Properties CEO, with the goal of doing “something transformative.” The new vision for Kearny Point includes offices for startups, coworking spaces, and a waterfront opened to the public.
“The opportunity to take a heavy industrial site like this and integrate all the new technology – wind, solar, stormwater – and be able to show we can have people growing businesses without having to harm the environment but also actually improve it at the same time is, to me, a very compelling opportunity,” Neu said. Brooklyn Grange is “an indication of just what the possibilities are.”
The project’s native meadow serves as a prime example. According to Schantz, when people try to convert land into meadows or gardens, they sometimes kill what’s growing there with pesticides. Brooklyn Grange is taking a more natural approach: they’re suffocating grass and enriching the soil with the help of recycled materials, such as leftover cardboard from a nearby shipping company and wood mulch from a local tree service, both of which the urban farming group inoculated with blue oyster mushrooms. Once this process is complete, they’ll plant native flowers and grasses.
“Our approach is, let’s take this strip of land which has had a rough history along a railroad track, it has not been loved the way it could be, and give it a new lease on life and make it a place where insects and birds can feed and nest, and restore it the way it might have looked before there was a shipyard here,” said Schantz.
How will Kearny Point handle natural disasters in the future? Neu said that not only are they raising the site up two feet, they’re creating at least 25 acres of open space and putting in bioswales to boost the site’s resiliency.
“We’ll have underground parking that will serve as reservoirs for water that comes onto the site. We’ll remove as many impervious surfaces as possible, which is huge in terms of the amount that gets discharged into the Hackensack, and we’re going to do everything to improve the quality of what gets discharged,” said Neu. “I want to minimize our impact as much as possible. We have to be able to figure out how to have people prosper without destroying the environment and further degrading it.”
Brooklyn Grange’s first plant sale will be Sunday, May 20, from 10 a.m.to 4 p.m. “We’re really excited to be reaching out to our neighbors across the river,” Schantz said. “We know there’s already a culture of gardening here in the Garden State, and so we’re excited to bring some of our urban farming techniques and our general mindset of sustainable, organic gardening to the local community and hopefully get people excited about growing their own food.”
+ Brooklyn Grange + Hugo Neu + Kearny Point
Images courtesy of Valery Rizzo
under Gardening and Plants, New Jersey, News, Recycled Materials, Urban Farming
Gotham Greens Grows Into Metro Baltimore
STATE-OF-URBAN-AG: This is an artist concept of Gotham Greens rooftop greenhouse facility in the Queens, N.Y. The Baltimore system won’t be a rooftop design. Gotham Greens
Gotham Greens Grows Into Metro Baltimore
Brooklyn, N.Y., ag tech startup expands its urban greenhouse system to Maryland.
John Vogel | May 15, 2018
If your mental image of urban agriculture is of a food plot or garden between city buildings, you won’t recognize Gotham Greens, the high-tech agribusiness model now coming to metro Baltimore, Md. This rapidly growing ag tech startup, headquartered in Brooklyn, N.Y., will open its fifth state-of-the-art hydroponic greenhouse at an old steel mill site at Sparrows Point in southeast Baltimore.
The initial 100,000-square-foot greenhouse facility is expected to bring fresh branded competition to produce growers serving the Mid-Atlantic region by early 2019. The deal was announced recently by Tradepoint Atlantic, which operates the port logistical center. Maryland Gov. Larry Hogan noted that Tradepoint's location provides a competitive advantage for fresh food businesses to reach a significant Mid-Atlantic customer base.
Gotham Greens’ expansion to Baltimore makes it the third city in its network of high-tech urban greenhouses, after New York and Chicago. The facility will create more than 60 full-time jobs and bring a reliable, year-round, local supply of fresh produce to serve retail, restaurant and foodservice customers throughout the Mid-Atlantic, says Viraj Puri, the company’s CEO, and co-founder. The company, reportedly, has an additional 500,000 square feet of greenhouse under development in four U.S. states.
The system
Up to this point, Gotham Greens main production menu has been lettuce varieties, arugula, basil and vine-ripened cherry tomatoes. The climate-controlled farm will be powered by 100% renewable electricity and recycled irrigation water.
Puri says that the proprietary methods yield more than 30 times that of conventional farms, with higher levels of food safety and environmental sustainability. Gotham’s other greenhouses feature solar photovoltaic panels, LED lighting, passive ventilation and thermal curtains.
Gotham’s flagship greenhouse, built in Brooklyn in 2011, was the first commercial-scale urban greenhouse of its kind in the country. After opening new locations in New York, the company expanded to Chicago in 2015 by building the world’s largest rooftop farm. Once the Baltimore facility opens, Gotham Greens will own and operate 500,000 square-feet of advanced greenhouses across eight facilities in five states.
“We’re honored and humbled to join the rich heritage of Maryland farmers, growers and food producers,” Puri says. “Urban agriculture, at its core, is about reconnecting with the community through food, jobs, and economic development. To that end, we’ve found a great partner and are proud to be part of the American industrial turnaround story taking place at Tradepoint Atlantic.”
Dutch Restaurant Has Rooftop Greenhouse With LED-Lighting
Dutch Restaurant Has Rooftop Greenhouse With LED-Lighting
APR 23, 2018
CONTENT SOURCED FROM HORTIDAILY
In the center of Utrecht, within a stone's throw from the Central Station - a new restaurant has opened. 'The Green House' proclaimed in large letters above the entrance. The restaurant, opening to the public on April 9, did not get that name for nothing. A greenhouse of 85 m2 has been built on top of the restaurant, in which various vegetables and herbs are grown to be processed in a number of delicious dishes.



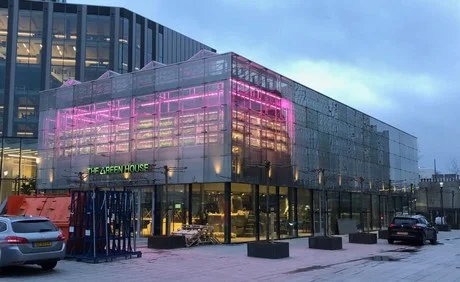


Always fresh
The vegetables and herbs are delivered in half cultivated state and grow further in the greenhouse. After harvest, new trays of herbs are delivered by the Amsterdam company Hrbs, which invented the concept.
The used trays are returned to the open garden of nursery Lindenhoff where they are turned into compost, to be used for growing crops. Tessa Duste from Hrbs: "The carts with the plants have been specially converted for this project. The boxes are placed in trays full of water. The part in between is filled with capillary fibers which suck up the water in the substrate."
LED lighting
Parus Europe supplied the carts and lighting for the greenhouse. Sandro van Kouteren: "We supplied two different types of lighting. The carts are lighted by light which is to the eye white, sufficient for growing crops but not powerful enough for proper cultivation. And we are not lighting up the entire center of Utrecht."
"In the top layers, we have installed color adjustable, dimmable lighting, so that they have a bit of control over the length and blossoming of the crop."
Circular
Tessa: "We always clean the trays when the plants are harvested. The trays are made of recycled plastic, which we can use at least a 100 times and probably more. When they break eventually, we use them in the production of new trays."
In this way, Hrbs has done its utmost to make The Green House circular. "There are always ways to improve. For other customers, we are currently engaged in processing herbs which have not been used to make new products, such as syrup."
For more information:
Hrbs
Tessa Duste
tessa@hrbs.com
www.hrbs.com
Mill Creek, NJ Urban Farm Expands Greenhouses, Community Spirit
Mill Creek, NJ Urban Farm Expands Greenhouses, Community Spirit
May 24, 2018
Gateway Community Action Partnership Director of Agriculture and Food Initiatives Marcus Weaver, at left, with Bridgeton Mayor Albert B. Kelly, in front of two new greenhouses at Mill Creek Urban Farm Wednesday, May 23, 2018. The greenhouses were built with a $250,000 grant from the TD Charitable Foundation.
BRIDGETON — Two new greenhouses at the nonprofit Mill Creek Urban Farm will soon be filled with towering tomato and cucumber plants, grown hydroponically to provide year-round produce to food pantries, senior centers, restaurants and schools.
Built with a $250,000 grant from the TD Charitable Foundation, they were open for a tour and ribbon-cutting Wednesday. The farm is on the five-acre site of a former public housing project on Ronald Bowman Way, which used to be called Mill Street.
“I grew up here. My father and grandfather grew up on this street,” said Bridgeton Mayor Albert B. Kelly, president and CEO of the Gateway Community Action Partnership that runs the farm, now in its ninth season. “It’s a personal triumph to me to be able to utilize the street I once played on and lived on for something positive and productive for our community.”
Gateway CAP runs daycare, housing, family support and other programs for much of South Jersey and Philadelphia.
The farm started as a way to address food insecurity in the area, Kelly said. About 30 percent of the 24,505 people who live in Bridgeton live in poverty, according to the U.S. Census Bureau. That means they live on less than about $25,000 per year for a family of four.
Bridgeton's median household income was $35,417 in 2016.
The U.S. Department of Agriculture lists Bridgeton as a food desert, in spite of being located in a rural county with many farms. Being a food desert means at least 33 percent of the population has low access to a supermarket or large grocery store.
Some of what the farm grows is donated to CAP's emergency food pantry, senior centers, and soup kitchens, and some are sold to support the farm, said Marcus Weaver, Gateway CAP director of agriculture and food initiatives. The farm sells to the Bridgeton School District, local farm markets, and others.
“Our biggest customer is a broker supplying the North Jersey restaurant market,” Weaver said. “The farm is not set up as a farm stand or for retail. But a few people show up at the farm and ask, ‘What do you have today?’ We are happy to sell them whatever we have.”
The new greenhouses add 5,376 square feet of new growing space, Weaver said.
The farm previously had just three greenhouses, where it has grown lettuces and other salad greens, shiitake mushrooms, tomatoes, eggplants, broccoli, squash, green beans and melons. It also grows in about 1,300 EarthBoxes, an outdoor container gardening system that increases yield over conventional methods.
Weaver said produce grown hydroponically develop roots in a medium that includes ground-up coconut hulls. But the plants take all their nutrients from a solution in water.
Compared to traditional growing methods, hydroponic growing produces 8 to 15 times more product and takes one-tenth of the water, Weaver said. And it produces all year, rather than in a compact growing season.
The housing project was torn down about 30 years ago because the houses were sinking, Kelly said.
“(The land) laid vacant for 20 years, until we developed a relationship with the housing authority, started a container garden that’s now grown to greenhouses,” Kelly said.
Three-quarters of the new space will be used to produce tomatoes, and the rest will produce seedless cucumbers, Weaver said.
Warren DeShields, director of food services for Bridgeton Public Schools, said the district prepares 4,000 meals a day and buys produce from the farm.
Weaver said the farm is about more than just growing food.
“This work provides an opportunity for education, to be able to demonstrate how food grows,” he said, for visiting students and the general public.
The new production capacity will allow the farm to hire three new full-time workers, Kelly said.
“No previous farming experience necessary,” Kelly said. Applications are available on the website at www.gatewaycap.org.
Contact: 609-272-7219
Twitter @MichelleBPost
In my first job after college got paid to read the New York Times and summarize articles for an early online database. First reporting job was with The Daily Record in Parsippany. I have also worked in nonprofits, and have been with The Press since 1990.
Office Car Parks Turning Into Farms
Office Car Parks Turning Into Farms
By Carolyn Cummins
19 May 2018
The future-proofing of buildings has led landlords to trial a range of new ideas, with pop-up farms the latest way to utilize basements and potentially redundant car spaces when driverless cars arrive.
Industrial, retail, and offices assets are now being inspected by owners for their potential to offer green''living'' walls, community gardens and greenhouses.
Pat Barrett, the director of investment analyst at the UBS Property Securities Fund, said ''green walls" or vertical gardens are quite a common sight, as seen at Broadway's One Central Park, Sydney, but the next step in green developments could be "produce walls" or vertical farms.
Mirvac’s amateur farmers Linette Salbashian and Krishna Mohan learning about farming from Farmwall’s Serena Lee
Mr. Barrett said retailers could take their fresh food campaign to another level, literally, by growing fresh produce on their roof, perhaps greenhouses alongside the solar panels.
And carparks could be converted to massive urban greenhouses.
''Vertical gardens are quite a common sight, but could the next step be vertical farming? Growing produce vertically is not a new concept, with the Hanging Gardens of Babylon one of the first examples,'' Mr. Barrett said.
''Could we see produce walls rather than green walls? Could shopping centres take the fresh concept all the way with produce grown on their roof space? Industrial facilities could have farmers' markets inside or at the very least, be used as urban farms.''
In Japan, a firm called Spread has developed a farming system called "Techno Farm". Using hydroponics their facility produces about 21,000 heads of lettuce a day using floor-to-ceiling shelves where the produce is grown.
The seed planting is done by people, but the rest of the process, including harvesting, is done by industrial robots. This has reduced personnel costs by about half and reduced energy expenses by nearly one third.
Mirvac is one landlord that has sought to look at adaptive re-use of properties, with a pop-up arm in the basement of its EY property at 200 George Street, Sydney. If successful it will look to roll out the concept nationally.
GPT trialed a community garden at one mall in Melbourne.
Campbell Hanan, Mirvac’s head of office and industrial said it was about challenging the business to come up with ideas for re-using car parking spaces when driverless cars became common and didn't need parking bays.
''It is also about giving people reason to get together and seeing things grow.'' Mr Hanan said.
''Our staff go down to the basement at 200 George and enjoy planting and working in the garden and getting to know their fellow employees.''
Mr. Hanan said landlords must keep experimenting with ideas to find practical solutions for office towers of the future.
Mirvac has transformed the basement of the EY Centre into an urban farm under its Cultivate pilot program.
The Australian-first pop up urban farm is a partnership between Mirvac and Farmwall, a startup that creates natural, food-producing ecosystems in urban spaces.
Mr. Hanan said it was the brainchild of Mirvac’s innovation team Hatch and was born out of a project that set out to explore how urban spaces such as car parks, rooftops, basements and community areas can be better utilized.
''With over $10 billion of assets currently under management in our office & industrial portfolio, Mirvac is one of Australia’s largest asset managers and is always looking for ways to add value and enhance the experience for its customers,'' Mr. Hanan said.
''We wanted to think more creatively about how we can use these spaces to extract greater value for our clients through a unique offering.''
Geert Hendrix, Farmwall’s chief executive said the farm has started supplying some produce to nearby cafes, including Avenue On George cafe, and it can basically get from ''farm to plate in about seven minutes''.
The farm hosts veggie patches, a hydroponic vertical farm and a vertical ‘Farmwall’, each growing their own varieties of herbs and leafy greens. It also produces mushrooms, grown in coffee ground waste saved from landfill.
While this is its first office farm, Mirvac has incorporated a number of kitchen gardens into its residential communities, including community gardens at The Moreton in Bondi in Sydney and Harcrest in Victoria.
After Soilless Babyleaf, Here's Hand-Less Babyleaf
After Soilless Babyleaf, Here's Hand-Less Babyleaf
Little Leaf Farms, one of the largest growers of hydroponic baby greens in North America, has officially opened its expanded greenhouse in Devens, Mass this week. The expansion doubles the size of the greenhouse from 2.5 acres to 5 acres, and more than doubles its annual production of baby greens. Thanks to their innovative growing system the greens are grown fully automated, without any chemicals and without any human hand touching the produce. Little Leaf Farms also announced it has purchased adjacent land for a third expansion project set to begin in 2019, which will further increase the size of the greenhouse to approximately 10 acres.
Baby lettuce
Opened in 2016, Little Leaf Farms produces locally grown, fresh baby greens year-round that are delivered to New England consumers within hours of being harvested. Little Leaf Farms grows multiple varieties of baby lettuce at its greenhouse. “Our ability to deliver fresh, great tasting and safe baby greens to consumers that can be easily traced back to the Massachusetts greenhouse has led to our rapid growth and expansion”, said Paul Sellew, CEO and founder of Little Leaf Farms. “We are passionate about transforming the way food is grown. Our process is clean from the start, so consumers can be confident they’re purchasing a safe product, grown in an environment that employs the most advanced food safety practices.”
For doing so, Little Leaf Farms is using a fully automated growing system. The system is optimized for growing of baby leaf lettuce and makes it possible to grow leafy greens fully automated without any human hand touching the produce from medium filling and seeding to harvesting. The seeding is done directly into the gutters to avoid the need of transplanting. Germination takes place under the growing line. After germination the gutters are lifted up to the growing line. During the growing process the gutters are moved automatically through the greenhouse toward the harvesting area. As plants grow the distance between the gutters continuously is adjusted - giving each plant as much space as necessary, but as little as possible. Once ready for harvesting the gutters are transported per conveyor belt to the harvesting area and guided into the cutting machine for a fresh cut.
The system is developed by Green Automation and has recently been upgraded and updated. “The growing lines are now even more robust, offers more precise and easier operations resulting in reduced maintenance needs as well as noise levels”, Patrik Borenius of Green Automation explains. Making the system more durable with increased frame thickness and additional steel components also allows for longer greenhouse growing lines to be designed and for increased gutter capacity.”
Seeding directly into the narrow gutters – eliminating the need for transplantin
Electric lift moving the gutters from the germination level to the growing line in one smooth movement.
New generation harvesting end with more space efficient conveyor design
Sustainability
The system is an important part of the Little Leaf hydroponic growing process, using mineral nutrient solutions in water without soil. “We incorporate principles of sustainability in everything we do, all to provide consumers with delicious, local baby greens at a fair price”, Paul explains. “The growth is completely sustainable, utilizing natural sunlight, a computer-controlled growing environment and a rainwater-based irrigation system that uses 90 percent less water than field-grown lettuce companies”, Paul shows. “The system enables the baby greens to be seeded, grown, cut and packaged without ever being touched by human hands. The production system is free from chemical pesticides, herbicides and fungicides, ensuring that what customers purchase is safe.”
LED lighting
The greenhouse is to be lighted with LED and the company opted for Oreon Grown Light 2.1, water-cooled fixtures by Lemnis. The complete installation of both water and electricity was provided by PB Techniek, Sellew’s installation partner for many years.
Salad mixes
Little Leaf Farms grows multiple varieties of baby lettuce at its greenhouse that are blended into salad mixes and sold in more than 1,000 Northeast grocery stores and to many restaurants, Universities and institutional customers. “More than 98 percent of the lettuce we eat in this country is grown on the West Coast and shipped for days, which means customers in New England are not receiving the highest quality or freshest product,” said Andrew W. Kendall, executive director of the Henry P. Kendall Foundation, an organization focused on creating a resilient and healthy food system in New England to increase the production and consumption of local, sustainably produced food. “Little Leaf Farms has cracked the code on providing the region with fresh baby greens within hours of being harvested. It’s exciting to see that consumers appreciate the value of the product, which will drive the company’s growth for years to come.”
For more information:
Little Leaf Farms
Green Automation
Patrik Borenius
Publication date: 5/25/2018
Author: Arlette Sijmonsma
Copyright: www.hortidaily.com
The Future of Hydroponics In Indonesia
The Future of Hydroponics In Indonesia
Nudira Fresh Farm: growing high-tech in the tropics
"I believe since 20 years ago that hydroponic and greenhouse technology is one of the answers to provide solutions to the constraints faced by vegetable agriculture in Indonesia." Speaking is Edi Sugiyanto. He is a commercial hydroponic grower, well experienced in Indonesia, Bahrain and Saudi Arabia and currently part of the team operating a high tech farm in Indonesia: Nudira Fresh.
Edi believes in the future, the role of hydroponic farmers in Indonesia would be better with the construction of modern Greenhouse agriculture and Hydroponics technology. "There are many obstacles faced by farmers in the field, to maintain the vegetables production remains high and stable, whether it is damage caused by rain water and the diseases. Elsewhere, rainy season is highly anticipated by most farmers especially in rainfed field."
The greenhouse project Edi participates in is the greenhouse built in Indonesia with full automatic control of temperature regulation, humidity and irrigation system. "The first stage we plant cherry tomatoes and for the next greenhouse we will plant lettuce, seed from Rijk Zwaan and growing media rockwool from Grodan."
Edi Sugiyanto, Nudira Fresh Farm, and Agrifam PT, in cooperation with iGrow investors, will continue to build the expansion of modern greenhouses in Indonesia, with hydroponics technology, as a commercial farm but also as a place to train the generation of modern agriculture in Indonesia. "Hydroponics are the future. Any plant, anywhere and anytime."
For more information:
Edi Sugiyanto
Publication date: 5/11/2018
TAPKIT: 500m2 Self-Assembly Hydroponic Greenhouse
TAPKIT: 500m2 Self-Assembly Hydroponic Greenhouse
After many years of specializing in large commercial-size hydroponic systems worldwide, TAP is launching the TAPKIT. The TAPKIT is a 500 m2 hydroponic unit, which can produce 6-12 tons of leafy vegetables and fresh herbs per year. "The idea is to enable small farmers to have their own hydroponic business, where they can grow and market their production to the neighbors, neighbor restaurants, and their own consumption", Teshuva Agricultural Projects CEO Avner Shohet explains.
The TAPKIT greenhouse will be presented at ’Agri-Tech Israel 2018’, in May. The hydroponic, self-assembly kit was designed as a cheap solution, while keeping a high standard. "The idea is 'from seeds to packages", Avner explains. "With an investment of 50,000 euros, the client will have a unit that also includes small plant nursery and packing equipment."
The unit can be operated by 2 people. The target audience are farmers, resorts, educational organizations, farmers shops, retired people, hospitals and many others.
NFT techniques on the rise
NFT uses a recirculating water system that carefully manages water usage and fertilizer volumes required to support healthy, consistent plant growth. This delivers multiple, proven advantages, including: very high production yields; significantly lower operating costs, more efficient production facilities; major savings in water and fertilizers; longer equipment lifecycles and increased profitability.
“NFT techniques are on the increase globally due to growing consumption of high-value and exotic crops and the increasing need for global food security by increasing yield in smaller spaces. Hydroponic crops are generally high-value, and every production refinement that can be made pays higher dividends to farmers. The industry is very focused on techniques that can improve yield and quality to give them a market advantage.”
Stabilizing temperature
The TAPKIT is developed in such a way that it can be adjusted to local circumstances and needs of the grower. The greenhouse currently built in Israel is provided with a monitoring and controlling operation system for optimization of the root zone temperature, developed and patented by Roots Sustainable Agricultural Technologies. This is one of the options the TAPKIT can be extended with.
According to ROOTS CEO Sharon Devir, stabilizing the nutrient temperature year-round will help farmers produce better quality crops, maximize production volume and minimize costs. “With this collaboration we can now address a major problem NFT farmers face in stabilizing nutrient temperatures and maintaining them at an optimal range year-round. This is a game-changer for Roots as it allows us to tap into an existing, rapidly growing global advanced-hydroponics market."
Agri-Tech Israel
The TAPKIT is to be presented at the Agri-Tech Israel 2018. The exhibition will be held May 8 – 10, 2018 at the Israel Trade Fairs and Convention Center in Tel Aviv. During and after the exhibition, visits can be made to the first TAPKIT greenhouse project.
For more information:
Teshuva Agricultural Projects
60 Nof Harim St., Olesh, 42855 Israel
+972-9-8940507
+972-50-7922579
+1-201-5803003
office@taprojects.com
www.taprojects.com
Publication date: 4/24/2018