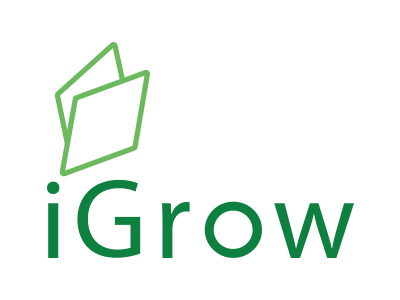
Welcome to iGrow News, Your Source for the World of Indoor Vertical Farming
The Future of Food: Why Farming Is Moving Indoors
Ten shipping containers dominate a corner of the Brooklyn parking area, each full of climate control tech, growing herbs that are distributed to local stores on bicycles. This is urban farming at its most literal
November 27, 2019 Staff Writer
A car park opposite the infamous New York City housing estate where rapper Jay-Z grew up seems an unlikely place for an agricultural revolution.
Ten shipping containers dominate a corner of the Brooklyn parking area, each full of climate control tech, growing herbs that are distributed to local stores on bicycles. This is urban farming at its most literal.
The containers are owned by Square Roots, part of America‘s fast-expanding vertical farming industry, a sector run by many tech entrepreneurs who believe food production is ripe for disruption.
The world‘s best basil reputedly comes from Genoa, Italy. Square Roots grows Genovese seeds in a container that recreates the city‘s daylight hours, humidity, Co2 levels – and all fed hydroponically in nutrient-rich water.
“Rather than ship food across the world, we ship the climate data and feed it into our operating system,” says co-founder Tobias Peggs.
High costs
An artificial intelligence expert, Mr. Peggs founded Square Roots with investor Kimball Musk (Elon‘s brother) two years ago. They‘ve signed a deal with one of America‘s big distribution companies, Gordon Food Service, to locate herb-growing containers at some its 200 warehouses.
He says the deal represents everything about indoor farming‘s potential: locally grown, quick-to-market, fresh produce that can be harvested year-round and is free of pesticides and harsh weather.
“Indoor farming can answer many of the questions being asked by today‘s consumers about the provenance, sustainability and health of the food they eat,” he says.
Jeffery Landau, director of business development at estimates the global value of the vertical farming market will rise to about $6.4bn by 2023, from $403m in 2013, with almost half that attributed to growth in the US.
Despite the sector‘s high costs and limited food range, the potential is not lost on investors. Recently, AeroFarms, a producer of lettuce and other leafy greens, raised $100m, including from Ingka Group, Ikea‘s parent company. Bowery Farming raised $90m in a funding round backed by Google Ventures and Uber boss Dara Khosrowshahi.
Plenty, another major US player, raised funds from Softbank chief executive Masayoshi Son and former Google head Eric Schmidt. The company has ambitions to build hundreds of vertical farms in China. In the UK, food delivery and robotics company Ocado is investing in indoor farming.
But there have also been failures. “Vertical farms are a highly intensive capital expenditure,” says Mr. Landau. “Your lighting system will be one of your highest capital costs.” And then there‘s ventilation, air conditioning, irrigation, and harvesting. “Make a mistake and you will have one costly upgrade on the horizon,” he adds.
Mr. Peggs chose a modular system based around shipping containers because he says it is quickly scalable according to demand. “We can put a herb farm in a new city for less than $500,000 and be growing within two months. We just press the ‘basil button‘ – or mint, or tarragon – and the box configures itself to grow in optimum climate conditions.”
In neighboring New Jersey, however, Bowery Farming takes a different approach. The five-year-old company runs industrial-sized farms. Outside one huge, grey windowless warehouse a heat haze shimmers off the concrete. It‘s a sharp contrast to the chilly interior where an aroma of fresh farm produce hits you immediately.
Robots
Produce is grown on trays stacked ceiling-high to maximize acreage. Everything from the automatic seeding machine to harvesting is run by Bowery‘s proprietary operating system (OS) which controls light, adjusts water nutrients and takes camera images of each plant to monitor its health.
“The OS is our central nervous system. There are millions of data points,” says founder Irving Fain. “The artificial intelligence is constantly learning and predicting how to produce the best quality product.”
Running the farm manually would be difficult, he says. Staff operates things from computer screens and iPads. In the cavernous farm room itself, the only sound is robots moving the shelves.
Growing food indoors has been around for decades, but the industry got a kick-start from advances in the performance of lower-cost LED lighting. Combine that with robotics, innovations, and AI, and you have an industry that Mr. Fain says is both viable and scalable.
“The big question was, how can we grow in large volumes at a consistently high quality? Suddenly, the economics changed,” he says. “We can grow 365 days a year – a major departure from thousands of years of agriculture. Unlike outdoor farming, our yield is virtually 100% guaranteed.”
Vertical farmers talk with a zeal you‘d expect of entrepreneurs with tech world backgrounds. With population growth and climate change putting pressure on food production, they think they may have answers.
But this highlights one of the industry‘s limitations. You can‘t feed the world on leafy greens. That said, for Mr. Fain, if Bowery only ever grew lettuce or kale, “it‘s still a win”. But his ambitions are greater. Bowery is growing radishes and turnips that he expects to come to market with two years.
Square Roots hopes to soon start commercial production of beetroots and strawberries and is experimenting with so-called heirloom produce from rare and long-forgotten seeds.
Carbon footprint
Mr. Peggs says: “It makes sense to grow perishable produce in the same neighborhood as the consumer – stuff that doesn‘t travel well. A lot of produce – tomatoes, strawberries – are grown for travel, not for taste. It doesn‘t make sense to vertically farm food with a long shelf life.”
But different produce presents different challenges, says Mr. Landau. Where plants are concerned, not all light is created equal. Fruiting and flowering crops such as tomatoes, strawberries, and peppers have different needs.
“Lights for these types of crops will generally be more expensive, require more electricity, and produce more heat, meaning additional cooling,” says Mr. Landau. “Harvesting these crops can be a significant operational cost.”
But it is being done. In the US, Oishii vertically farms the much-prized Japanese Omakase strawberry year-round. And Farm One produces more than 200 products, including 34 edible flowers. Plenty is experimenting with watermelons. As technology costs fall and R&D intensifies, the crop variety will expand.
That may also ease criticism of the industry‘s carbon footprint. In the artificial light versus sunlight debate, the latter often has the upper hand. But, then, indoor farmers point to the transportation costs and waste in traditional agriculture.
For the moment, Mr. Landau says, the carbon footprint concerns are valid, although he expects indoor farms to increasingly draw on renewable energy.
“And when you look at markets located in extreme climate environments or island nations where they import a majority of food, indoor farming could be a viable option,” he says.
Mr. Peggs stresses that the industry is still young and is trying to work out the right business models and direction. The entrepreneurs don‘t agree on everything, though they certainly agree on this: vertical farming has the potential to transform global food production as we know it.
High-Tech Farm In Shipping Container Cutting Growth Time In Half
A shipping container and a lot of ingenuity -- is changing the way produce is grown. "It's a 3.4-acre farm inside a 320 square foot shipping container," explained Dale Speetjens, CEO & Co-founder ShipShape Urban Farms.
To View The Video, Please Click Here
MOBILE, Ala. (WALA) -- A shipping container and a lot of ingenuity -- is changing the way produce is grown.
"It's a 3.4 acre farm inside a 320 square foot shipping container," explained Dale Speetjens, CEO & Co-founder ShipShape Urban Farms.
Calling it a "Business in a Box" -- Speetjens gave us a tour. Inside the container garden was several varieties of lettuce in various stages of growth.
"Inside here right now it's a balmy 70 degrees and it's this temperature whether it's 100 degrees outside or 30 degrees," said Speetjens.
Every variable is controlled by a computer system.
"This here is I would say the brain of the container... This is actually the control," said Carlos Augusto, VP of Marketing ShipShape Urban Farms.
From the temperature, PH levels, lighting, and right amount of water -- Augusto manages the day to day operations using hydroponic technology.
They're able to recycle the water - using only 10% of what a traditional farm uses and cutting down the growth time from 10 weeks to five weeks. The process all starts with employees planting seeds into individuals cells.
While they're seeding each cell by hand -- machines will eventually take over the process. The seedlings are then placed into the nursery section of the container.
Each container is designed for one person to work about 15 to 20 hours a week. The containers producing 1,200 heads of lettuce weekly.
INFORMATION BOOK
"So one of the steps we did to help is to make more efficient. We developed these lids and all the farmer needs to do to harvest is to pull the lid out and they harvest all the lettuce at once," Augusto demonstrated.
Each container costs $95,000 and upward. Debuting their prototype in New Orleans at the Louisiana Restaurant Association Expo in August -- ShipShape Urban Farms generated a lot of interest.
"Over 3,000 people walked through garden close to 300 to 400 people say they were interested in becoming a ShipShape Urban farmer," said Speetjens. "Eventually we'd like to create a network of urban farmers where all of us work together to produce food for our local communities.
Because it's all done on the computer and backed up every 15 minutes on a server -- ShipShape can monitor every stage of growth and share success stories with other farmers. There's also an app that allows the farmers to control settings from their phones.
"We will be able to monitor all the urban farms through the computer system -- not only to assist them but if we have a container that is producing more than average -- we can contact that farmer and share their experience with other farmers," explained Augusto.
The company hopes to build about 850 over the next five years. So far they have more than 30 orders and say while their focus is on the southern region of the U.S. -- they've had interest from as far away as the Galapagos Islands, India, Canada, and South America.
UAE: DUBAI - Regions’s First Instore Hydroponic Farms Open in Carrefour
The region’s first hydroponic in-store farms were inaugurated at Carrefour, operated by Majid Al Futtaim, in the capital on Sunday. Located at the hypermarket’s stores in Abu Dhabi’s My City Centre Masdar and Yas Mall, the hydroponic farms are part of the company’s Net Positive strategy that aims to overcompensate its water and carbon footprint by 2040
25kg of Fresh Herbs, Microgreens To be Produced Everyday
Published: November 24, 2019, Staff Report
Dubai: The region’s first hydroponic in-store farms were inaugurated at Carrefour, operated by Majid Al Futtaim, in the capital on Sunday.
Located at the hypermarket’s stores in Abu Dhabi’s My City Centre Masdar and Yas Mall, the hydroponic farms are part of the company’s Net Positive strategy that aims to overcompensate its water and carbon footprint by 2040. The farms were inaugurated by Dr. Thani bin Ahmed Al Zeyoudi, Minister of Climate Change and Environment.
Speaking on the occasion, Dr. Al Zeyoudi said: “The UAE spares no effort in leveraging new technologies and innovative solutions to reach high levels of sustainability across the board. In this context, MOCCAE supports technological development and innovative techniques in the agricultural sector, including vertical and hydroponic farming that reduces water consumption by at least 90% and increases the productivity of multiple agricultural products.”
Carrefour’s hydroponic farms are the result of a recently renewed memorandum of understanding (MoU) between MOCCAE and Majid Al Futtaim Retail to sell locally grown agricultural products across all Carrefour stores in the UAE and enhance the use of innovative farming methods. The two farms are the first of their kind to be installed in the region. They use 90 percent less water and less space than traditional farms to deliver around 25kg of fresh herbs and microgreens a day.
The isolated and temperature-controlled glass farming chambers were designed in line with the highest standards of hydroponics. While not accessible, the farms are visible to consumers at the stores, significantly enhancing their shopping experience. With virtually no food miles involved, customers are free to choose from a select range of herbs and microgreens, once fully grown, at the store.
Liberty Produce And Partners Are Transforming The Vertical Farming Landscape
Liberty Produce and Partners have launched their ambitious programme to coordinate the development of the technology needed to make Controlled Environment Agriculture (CEA) more effective, efficient and sustainable
2nd December 2019
London, UK
Liberty Produce and Partners have launched their ambitious programme to coordinate the development of the technology needed to make Controlled Environment Agriculture (CEA) more effective, efficient and sustainable.
The joint venture, co-funded by Innovate UK (the UK’s innovation agency), is supporting the creation of an integrated technology system focussed on reducing operational costs by 25%, improving crop yield by 30% and reducing necessary grower intervention through improved decision support and automation in lighting, nutrient and environmental control technologies.
The project involves several partners and experts in CEA, including Crop Health and Protection (CHAP). In work being carried out at CHAP’s Fine Phenotyping Lab, based at Rothamsted Research, experts are assessing ways in which plants react to light throughout the day, determining how to activate and make them most receptive to light, particularly through the manipulation of wavelength and light intensity. They have already found evidence that plants photosynthetic response to light levels off and reaches saturation. Within CEA systems, avoiding the unnecessary application of light is crucial in reducing operational cost and making systems more sustainable.
The data collected on how different crops respond to artificial LED lighting systems will inform the development of further technologies around sensing and automation - work packages being led by FOTENIX and Iceni Labs.
As the new technologies are developed, they will be evaluated at the IHCEA facilty, a vertical farming commercial demonstrator established by Liberty Produce in partnership with Crop Health and Protection (CHAP) and located at the James Hutton Institute, in Dundee, Scotland.
Zeina Chapman, Director of Liberty Produce commented, “Vertical farming is not yet sustainable - the capital and operational costs limit the adoption of these systems. This vital research and development will enable the build of innovative new technologies that will ensure CEA becomes an essential and sustainable element of crop production as the global population grows.”
Dr Ruth Bastow, Innovation Director of CHAP said, “CEA has great potential to be part of a global solution to produce food in more efficient, resilient and sustainable ways. However, there are still bottlenecks to be overcome for large-scale adoption, and this project will help accelerate the development of new technologies and approaches to improve the overall efficiency of CEA utilising capabilities across the CHAP network.”
Crops growing in the IHCEA facility. Credit: Liberty Produce 2019.
***Ends***
About Liberty Produce
Liberty Produce is a farming technology company, enabling the growth of local produce year-round, using a fully-controlled, industry-leading, indoor vertical farming system. With expertise in lighting and nutrient delivery technology, Liberty develops and builds systems that reduce operational costs and improve yields of crops grown in controlled-environment farms. Their vision is to drive innovations that will enable the UK to meet our crop requirements over the next century, without harming the planet.
https://www.liberty-produce.com/
For further information contact:
Benita Rajania
+44 20 3290 8801
About CHAP
Crop Health and Protection (CHAP), funded by Innovate UK, is one of four UK Agri-Tech Centres. CHAP’s vision is for the UK to be a global leader in the development of applied agri-technologies, to help secure our future by nourishing a growing population sustainably while delivering economic, environmental and health benefits to society.
CHAP acts as a unique, independent nexus between UK government, researchers and industry, building innovation networks to identify and accelerate the development of cutting-edge solutions to drive incremental, transformative and disruptive changes in sustainable crop productivity and to establish controlled environment agriculture (CEA) as a core competency.
www.chap-solutions.co.uk/
For further information contact:
Darren Hassall
Darren.hassall@chap-solutions.co.uk
+44 (0)1904 462062
About Innovate UK
Innovate UK drives productivity and economic growth by supporting businesses to develop and realise the potential of new ideas. We connect businesses to the partners, customers and investors that can help them turn ideas into commercially successful products and services and business growth. We fund business and research collaborations to accelerate innovation and drive business investment into R&D. Our support is available to businesses across all economic sectors, value chains and UK regions. Innovate UK is part of UK Research and Innovation.
7 Smart City Urban Planning Ideas Using IoT
Square Roots, another high-tech vertical farming startup that has raised $6.5 million for its shipping container farms. At the helm is a somewhat familiar name, Kimbal Musk, the brother of a more familiar CEO who favors Twitter and flame throwers
One of the things that you learn after being a digital nomad for a while is that some cities are much better designed than others. There is a certain aesthetic quality to a well-laid out urban center like New York City compared to, say, Boston, which one article on the topic of city grids said appears as if “a group of city planners decided to lay out the roads one day by taking turns pissing blindfolded onto a scroll of parchment – during an earthquake.” The idea of urban planning dates back to Egypt and its contemporaries, as archaeologists have found evidence of paved streets laid out at right angles in a grid pattern, all leading to the same slave brothel. Today, we have internet porn. And we have the Internet of Things (IoT), which is becoming increasingly integral to smart city urban planning.
The whole idea behind using IoT infrastructure – sensors, big data, and analytics that help manage everything from traffic and parking to buildings and baseball stadiums – is to make cities more efficient. The more efficient the city, the theory goes, the more sustainable it will be in a future where we’re harvesting methane-munching bacteria or growing bugs to feed 10 billion or more people by mid-century. Earlier this year, the big brains at data research firm CB Insights produced one of their iconic market maps on companies developing smart city solutions:
Credit: CB Insights
You’ll notice there’s a whole category devoted to smart city urban planning startups, which can tell us something about the possible breadth of this emerging industry to shape the way a city is developed – and how far an analyst can stretch the definition of urban planning to complete a market map.
For example, one of the startups on the list, Berlin-based Infarm, is one of many vertical farming startups that we’ve covered in the past. Infarm has since raised an additional $100 million since we profiled the company. CB Insights also lists Square Roots, another high-tech vertical farming startup that has raised $6.5 million for its shipping container farms. At the helm is a somewhat familiar name, Kimbal Musk, the brother of a more familiar CEO who favors Twitter and flame throwers. A QR code on the back of the Brooklyn-based company’s products will give you background info on how the herb was grown. While many of these vertical farms use sensors, big data, and analytics to optimize yield, it’s unclear how exactly Infarm, Square Roots or its cohort are directly involved in the activity of smart city urban planning. Maybe the smart city of tomorrow grows all its own food?
Smart City Urban Planning Acquisitions
In addition, a couple of companies have dropped off the startup scene through acquisitions. San Francisco-based PlanGrid had raised $69.1 million before being bought last year for $875 million by Autodesk (ADSK), the company behind the drafting and design software AutoCAD. PlanGrid provides a variety of products around cloud-based construction software.
Another San Francisco startup called Civic Insight helps cities make their data on buildings and homes – think permits and other zoning or construction information – easily accessible to the public. It’s sort of like Zillow for nosy neighbors. Yet another San Francisco company, Accela, took possession of Civic Insights more than four years ago. Accela offers various solutions for cities to digitize and automate processes like building permits and cannabis licensing. The 20-year-old company, which had raised about $215 million and absorbed 10 startups over that time, was itself acquired by Berkshire Partners in 2017. That now leaves us seven companies still to cover.
Street-Level Mapping
The most well-funded of the bunch is a Swedish startup called Mapillary that was founded in 2013 and has raised $24.5 million, including a $15 million Series B last year led by BMW and involved high-profile venture capital firms like Sequoia Capital and Atomico. Mapillary is one of a growing number of companies putting together high-definition maps for applications like self-driving cars and smart city traffic management. Its platform builds street-level map imagery using computer vision to automatically detect objects like bicycles and trash cans, while also automating the privacy aspect by blurring faces and license plates. It draws on a database of more than 900 million images along millions of miles of roads. Here’s the big-picture view of how the tech works:
Credit: Mapillary
In the case of a small town that needed to inventory its street signs, Mapillary’s cameras and machine vision system identified 5,000 traffic signs. The data could then be used to address repairs and fix obstructions, like your nosy neighbor’s unruly azalea bushes.
Sim City for Smart City Urban Planning
You know you have an urban planning problem if $100,000 qualifies you as low income. That’s the story in San Francisco, where housing costs can make a six-figure income nearly as worthless as Monopoly money. Enter UrbanFootprint, based in nearby Berkeley, that was founded in 2014 and has raised $6.5 million to date for its cloud-based software that helps cities “create sustainable, resilient communities.” That’s according to its founder, a well-known architect named Peter Calthorpe who is one of the leading figures behind New Urbanism, which promotes dense, mixed-use, walkable neighborhoods. In an interview last year, Calthorpe likened UrbanFootprint to Sim City because “it allows non-experts to model the impacts of different urban planning scenarios, such as zoning changes and road reconfigurations” in just a few minutes by leveraging an extensive database on environmental, social, and economic conditions.
An UrbanFootprint analysis of greenhouse gas emissions per household in Merced, California, helped planners understand the impact of land management use and smart city growth. Areas shaded in deep red indicate higher levels of emissions emitted. Credit: UrbanFootprint
The company has partnered with California to bring the smart city urban planning tool to more than 500 cities and government agencies free of charge.
Digital Bulletin Boards
For those who can’t get enough posts about lost cats in their neighborhood from Next Door, there’s Soofa, a Boston area startup that has raised $3.2 million for what amounts to a digital bulletin board that anyone with an app and an agenda a cause can post to. The 42-inch displays are solar-powered. There goes a million jobs in the flyposting industry.
Getting the Public Involved in Smart City Urban Planning
Another startup that is trying to get the public involved in smart city urban planning is Boulder-based Neighborland. And like Soofa, Neighborland is putting a digital spin on re-inventing the wheel. The company basically builds webpages and mobile platforms to support civic engagement on various projects. It claims to have worked with more than 200 city agencies, universities, foundations, and nonprofits across the United States, delivering more than $3 billion in social and economic impact.
For instance, it helped Mesa, Arizona build support for a $300 million bond to improve city facilities and services last year.
Automating Analysis for Smart City Urban Planning
Founded in 2016, UrbanLogiq is a British Columbia, Canada startup that has pulled together $150,000 in disclosed funding. The company offers two smart city urban planning solutions. The first is for traffic management, where the platform aggregates all historic and real-time data about traffic speed, accidents, etc., and then turns the machine-learning algorithms loose to predict traffic patterns days in advance and with a “high level of certainty.” The company also claims it can do the same for a city to forecast economic development using everything but the kitchen sink, from business licensing and building permits to employment and unemployment rates and housing statistics to less structured data like weather and public policy. It’s business intelligence for the public sector.
Geospatial Solutions for Smart City Urban Planning
We’ve written quite a bit over the last few years about the value that companies are getting from satellite imagery. Geospatial intelligence startups like San Francisco-based Planet apply machine-learning algorithms to space-based pictures to help farmers grow better crops or insurance companies spot fraud. In fact, there’s a long list of companies doing this sort of geospatial analytics. Philadelphia-based Azavea has been in the business since 2000 apparently, specializing in urban planning projects, especially in the hometown of Rocky Balboa.
One of the many products that use geospatial tools to help with smart city urban planning. Credit: Azavea
For instance, the company built an application (above) where non-residential building owners can sketch out ideas using up to five different stormwater tools such as green roofs or permeable basins that show how such improvements can help reduce monthly stormwater bills.
Location, Location, Location
Finally, Paris-based Cityzia, founded in 2017, is the Zillow version of online dating in that it helps people find their perfect home through an online Q&A that matches your preferences – quiet neighborhood or party central – against a database of properties. It’s French-centric and seems to imply that the cities of tomorrow will become a small collection of tribes, where each lifestyle flourishes among its own type. The bigger cities get, the more important it is for people to get along. A great example of this can be found in Hong Kong at the local dog park where you’ll see a dozen dogs playing together with hardly a bark to be heard. When you live in small cramped spaces where you can hear your neighbors cough, even the pets learn how to play well with others.
Conclusion
Speaking of CB Insights: The firm projects that within the next five years, the smart city market will be worth $1.4 trillion. You’ll notice that the market map is tilted heavily toward transportation. That’s not surprising, given that traffic congestion hit the U.S. economy for about $87 billion in losses last year, according to the World Economic Forum. Meanwhile, the digital road is being laid for the eventual arrival of self-driving cars and trucks. Smart city urban planning will be a key technology to integrate smart mobility with other smart infrastructure, especially as the 5G revolution helps connect it all together.
US: Texas - Vertical Farming Technique Growing At A&M
TAMU Urban Farm United is a concept organization with the intent of introducing vertical farming to A&M’s campus and the local community
By Luis Sanchez @LuisSanchezBatt
November 12, 2019
TAMU Urban Farm United is a concept organization with the intent of introducing vertical farming to A&M’s campus and the local community.
An Aggie Green Fund major grant project, TUFU is overseen by capstone students from various majors who grow the crops to provide food for locals. The group will be hosting an open house on Friday at 530 Floriculture Rd. from noon to 7 p.m.
TUFU was co-founded by Broch Saxton, plant and environmental soil science senior, and Lisette Templin, instructional assistant professor in health and kinesiology. Saxton, who serves as a student coordinator, said that it only made sense for A&M to develop methods of vertical farming, with such a historical background in agriculture; although originally Saxton envisioned using a hydroponic system, where the roots of plants would sit in water.
“In my interest, I see that it is not here, hydroponics isn’t here,” Saxton said. “So I was thinking to myself, ‘Why is it that this huge agriculture monster of an entity isn’t taking a step towards this specific agriculture field of interest?’”
Saxton said he and Templin both wanted to bring their respective expertise in order to help others in this innovative manner. It wasn’t until the two put their ideas together that they were able to commence with the building of the vertical farming towers.
“[Templin] had the tower garden idea,” Saxton said. “I came there thinking, ‘I want to get some help launching some sort of hydroponic system,’ and it turned into, ‘Okay, she has a similar idea that I do.’”
Saxton said he and Templi applied for a grant from the Aggie Green Fund. The application was submitted in 2018, but it wasn’t until the summer of 2019 that they could start working. According to the Aggie Green Fund website, the TUFU project was awarded $59,566 in the spring of 2019.
Templin said the project worked with The 12th Can, a food pantry for A&M students, faculty and staff, to provide a fresh and local food source with the first harvest on Nov. 7.
“This is the first time that The 12th Can has received fresh, locally grown, living food, that [has] not been sprayed with a chemical product,” Templin said.
Templin said the towers used for the vertical farming are based on an aeroponic system, an environment of air rather than soil for the plants. She said the tower system feeds the plants via mimic rain, and since each tower is isolated, contamination does not spread among them.
“The aeroponic system means that the roots are in a [cylindrical] tower base, where the roots are exposed to air,” Templin said. “There’s a pump that pumps the [mineral] water upward, and then the water trickles down like rain. And [that] feeds the roots with minerals and nutrients.”
Templin said the shape of the tower not only conserves space but is able to cycle the water as needed. Templin said the system also brings a 30 percent higher yield when compared to traditional alternatives.
“It uses 90 percent less water because there’s no evaporation,” Templin said “The only loss of water is through root absorption. It uses 90 percent less land because, per tower, we can grow forty-four heads of lettuce in about four square feet of space. [And] we don’t get earth-borne pests.”
Stephon Warren, plant breeding graduate student, is a member of TUFU and said the organization is trying to expand in any way possible. Warren said alongside forming business relationships, TUFU is looking to educate more students about the project.
Saxton said although he would be graduating soon, he was confident the project will grow and make connections in the academic and market settings. Saxton said too much effort has already been put into the project, and he only sees it growing in the future.
“We already have too much university involvement, student involvement and time invested from partners that we have accumulated,” Saxton said. “The interest is there and this is going to keep going when I’m gone.”
Plenty’s Plans To Shelve Its Seattle-Area Operation Raises More Questions About Vertical Farming
Indoor ag-tech startup Plenty is shelving its plans for a Seattle-area vertical farming operation, according to an article published over the weekend on GeekWire
Indoor ag-tech startup Plenty is shelving its plans for a Seattle-area vertical farming operation, according to an article published over the weekend on GeekWire.
Plenty, who also runs a facility in the San Francisco Bay Area, announced plans for a 100,000-square-foot vertical farm in Kent, Washington in 2017 — the same year the company nabbed a $200 million investment that included contributions from Softbank and Jeff Bezos. The Kent facility was supposed to grow 4.5 million pounds of greens annually using a combination of LEDs, sensors, and cameras inside a completely climate-controlled environment.
However, Christina Ra, Plenty’s senior director of integrated marketing, told GeekWire that the company’s farming facility, Tigris, was too tall to fit inside the Kent location and that Plenty had “ceased operations” there one year ago: “As a relatively lean company, we had to just make a decision about where we were going to put our focus and we felt like building Tigris, while also focusing on Seattle as a new and really important market, was something that we couldn’t do well,” Ra said.
Meanwhile, seven former Plenty employees recently spoke with Business Insider and highlighted problems inside the company that allegedly range from unsafe working conditions to the fact that “Plenty’s leadership had exaggerated the company’s capabilities on more than one occasion.”
Plenty will carry on with its planned location in the middle of Los Angeles, which the company recently announced, and it still operates a facility in the SF Bay Area. But as this news about the Seattle operation indicates, what Plenty (or any vertical farm startup) promises versus what it actually produces aren’t necessarily aligning right now.
Perhaps unsurprisingly, that refrain around expectation versus reality in vertical farming is one we’re going to hear more in the near future. As an industry, vertical farming has yet to prove itself as an environmentally and economically efficient piece of the agriculture system, and along with the hype are more and more stories about complications or outright closures of vertical farms. Already, a company called FarmedHere shut down in 2017, Plantagon went bankrupt in March of 2019, and just recently, MIT halted work on its controversial Open Agriculture Initiative project after reportedly exaggerating results of its vertical farming experiments.
While it’s bad news pretty much anytime a company goes under, for vertical farming, it’s also good information to have. As Paul P.G. Gauthier, who started the now-shelved Princeton Vertical Farming Project, told The Spoon this year, we need the stories about what isn’t working (e.g., operational costs, failure to break even, etc.) as much as we need the success stories.
And we need those stories not just to give lessons on how to employ vertical farming more effectively but how much effort (and money) we should even be investing in it as the agricultural industry continues to look for alternative forms of farming.
FILED UNDER:
Brownstein: Montreal's Lufa Farms Reaches New Heights
Airplanes are buzzing above. Gridlock has set in below. One couldn’t possibly imagine a more unlikely agricultural setting, yet on top of a non-descript office building in St-Laurent, within a tomato’s throw of the Place Vertu mall, construction is underway on the world’s largest urban rooftop farm
The fourth Lufa rooftop installation — this one the size of three football fields — is to open in March in St-Laurent.
BILL BROWNSTEIN, MONTREAL GAZETTE
November 21, 2019
Airplanes are buzzing above. Gridlock has set in below. One couldn’t possibly imagine a more unlikely agricultural setting, yet on top of a non-descript office building in St-Laurent, within a tomato’s throw of the Place Vertu mall, construction is underway on the world’s largest urban rooftop farm.
This will be the fourth Lufa Farm around Montreal, and when it opens in March, it will measure nearly 164,000 square feet, or roughly three football fields. That’s a whole lot of tomatoes and eggplants.
The Lufa mantra is: “We grow food where people live, and grow it more sustainably.” And that it does.
The plan is that this gi-normous greenhouse will double Lufa’s growing capacity and the four farms combined will allow it to feed two per cent of Montreal with fresh veggies. The St-Laurent farm is intended to meet the ultimate standard in energy-saving greenhouse technology. And like the other farms, it, too, will operate without use of synthetic pesticides.
In addition to the produce, St-Laurent borough mayor Alan DeSousa is also pumped about the rooftop farm’s ecological benefits: “It will make it possible to fight against heat islands in our district, where more than 70 per cent of the surface area is devoted to industrial and commercial activities.“
The bottom floor of the St-Laurent office building serves as a distribution centre, wherein individual boxes of vegetables, fruits, breads and cheeses, among other goodies, are prepared for Lufavores, Lufa’s member individuals and restaurants. About 17,000 boxes are shipped every week to Lufavores at hundreds of pickup points around the city. Lufa also provides home delivery by, natch, electric-powered autos.
“We like to think of the distribution centre as a giant online farmers market,” Lufa co-founder and greenhouse director Lauren Rathmell says.
Rathmell and her husband, Lufa co-founder and CEO Mohamed Hage, started germinating their business 10 years ago. Their first farm sprouted in Ahuntsic. Then came rooftop farms in Laval and Anjou. The company now has 327 employees — and counting.
While allowing that the Ahuntsic farm cost $2.2 million, Rathmell is tight-lipped about the budget for the St-Laurent greenhouse, which is five times the size of the former. She does, however, note that Lufa Farms has been profitable since 2016 and is not ruling out more expansion, in Montreal and elsewhere.
“Our goal is to be ecologically and economically sustainable,” says Rathmell, a Vermonter who moved here to study biochemistry at McGill and stayed on after meeting Hage.
“Our first site was the world’s first commercial rooftop greenhouse. There are ground-level greenhouses and farms, but this concept had never been done — taking an industrial space and repurposing it for food production. There’s still not many doing what we’re doing. We wanted to create a local food engine, and to do so by following tenets of responsible agriculture with hydroponic farms and reducing our footprint in the process.”
The trick was in finding rooftops around Montreal that would have enough room and that would be structurally able to support a greenhouse.
“We literally surveyed the entire island of Montreal on Google maps to find the rooftops.”
Lufa, incidentally, is a squash/cucumber-like vegetable indigenous to Lebanon, where Hage was born. While the Lufa farms grow almost every kind of veggie, they don’t yet produce a lufa. “We probably should soon.” Rathmell concedes. “It’s very practical. You can eat it. It’s hollow inside, and when you dry it, it turns into a sponge that grows on walls and rooftops.”
The hustle-bustle of St-Laurent’s distribution centre is in marked contrast to the laid-back vibe of Lufa’s Laval rooftop farm.
Of course, like Lufa’s other facilities, one might be hard-pressed to spot the Laval farm, situated atop another nondescript office building, off a fairly gridlocked highway.
But once inside the sprawling, 43,000-square-foot Laval greenhouse, one is transported from the grey and the cold and the snow to a near-tropical setting. There is a glow hanging over the place and with temperatures in the low 20s, cheery-faced farmers, mostly attired in T-shirts and one even in shorts, are planting and harvesting tomatoes and eggplants. A couple of them appear to be actually whistling while they work. It is almost surreal.
It’s more than just talk about reducing footprints. In touring the Laval greenhouse, Rathmell points out how all the water employed is re-circulated and reused. Rainwater is also collected off the roof. And considerable energy is saved simply by being on a rooftop.
“Being on a rooftop also means we’re not using new land, and also keeping us as close as possible to urban centres,” Rathmell says.
On the other hand, trying to convince prospective landlords on setting up rooftop farms was initially difficult.
“It’s become much easier with proof of concept,” Rathmell says. “When we approached the owners of that first building in Ahuntsic, in their minds it was cows and soil and tractors and whatever. We were able to convince them that wasn’t the case. Plus that the greenhouse would be fully contained and help insulate their building. And that we’d take care of the construction and electricity.”
And, oh yeah, the landlords would also be able to feast on the freshest produce around.
Tomatoes in lieu of cash for rent?
Quips Rathmell: “That’s the next deal.”
For more information about Lufa Farms or becoming a Lufavore, go to montreal.lufa.com.
RELATED
Indoor Farming: How Can You Ensure Success?
Any business can fail for any number of reasons, but indoor farming is an incredibly delicate organism that depends on many disparate factors being perfectly aligned and in balance
Any business can fail for any number of reasons, but indoor farming is an incredibly delicate organism that depends on many disparate factors being perfectly aligned and in balance. This increases the risk of failure for those unaware of the number of plates that need to be kept spinning in perfect time. This list is not definitive but gives you a good idea of the most common mistakes to avoid.
1. Avoid a Trial and Error Approach to Design
There are multitudes of factors that are naturally managed and balanced with indoor farming. The sun cannot be changed, irrigation to every plant is different as weather patterns can change from moment to moment and even the nutrition in the soil can vary across the area of the field. Planning your farm, therefore, gives you the ultimate control but also dramatically increases the variables that you can and must consider.
These variables start with the facility’s very layout, such as the size of growing space, plant distribution, airflow and more. Additionally, without having the right models in place to determine the exact light recipe and combination of CO₂, nutrients, and water required to grow a successful crop, growers can find themselves wasting time and money on testing phases to try to maximize yield and revenue. Once you have developed a model for your vertical farm, you should then put it through a testing phase on a smaller scale to ensure it is viable.
2. Pick the Right Crop
It’s far easier to develop a profitable and scalable facility if you know the needs of your crop inside and out. That ideally means specializing in one type of crop that you can design your facility around, electing the right growth spectrum and studying that particular plant’s biology to better understand how to optimize irrigation, nutrition, airflow, CO₂ concentration and propagation in order to maximize elements such as taste, nutritional content, visual appeal, potency or shelf life.
Too many growers have tried to hedge against perceived risk by trying to grow multiple crops. By default, it is extremely difficult to have one installation that is optimized for a wide variety of plants, and therefore the returns from each crop are lower than they could have been. The facility then may have to suffer through downtime as the technology is tweaked and optimized for the next crop-eating into profitability and adding unnecessary costs.
3. Location, Location, Location
The old adage that location is half the battle has never been more relevant than in vertical farming today. Vertical farms have a key advantage in their ability to be located close to their customers, whether they are selling to food processors, supermarkets or local shops. Removing the vast transport logistics associated with today’s food supply chain slashes costs and helps appeal to an increasingly conscientious customer. The lack of transport costs also helps counter the higher production costs resulting from higher energy and labor inputs.
At the city planning level, there are also many advantages of co-locating a vertical farm with other facilities such as office buildings, shops or residences — which could draw the vertical farm’s excess heat to reduce demands on other sources of energy.
4. Simplify Your Business Model
Proximity to customers and the ability to produce crops year-round at a sustainable rate is a strong advantage in the market, whether you’re growing for the food or pharmaceutical sectors. Therefore, consider the opportunities available through establishing exclusive contracts with customers at a fixed rate that will offer more financial security as you build your business.
5. Be Realistic About Operational Cost
Setup and fit-out costs represent a high initial outlay for any indoor farming entrepreneur, but the ongoing operational costs (energy, labor, inputs, maintenance, etc.) are also significant. Businesses not only need to find creative ways to mitigate these risks (e.g. growing through the night when energy tariffs are lower and the outdoor climate is cooler to assist HVAC systems’ efficiency), but also consider the cost-benefits of different configurations and process flow.
6. Set Prices Based on What Consumers Will Pay
At the 2017 inaugural AgLanta Conference11, PodPonics’ CEO admitted that the company missed out on higher potential margins as it priced its crops to compete with conventional growers, ignoring the price premium that food traceability, pesticide-free growing, and local production can increasingly attract from consumers in some markets.
7. The Skills Gap
In many cases, those who have embraced the promise of indoor farming have not been traditional growers but rather tech entrepreneurs, engineers or hobbyists. Vertical farming requires a unique mix of skills to be successful: big data scientists, systems integrators, project managers, engineers, growers and plant scientists all have a role to play in addition to the core functions that any business needs to be successful (financial strategists, marketing and business development, etc.). From the leadership perspective, experience at replicating and scaling a business is critical. Ignoring any one of these functions leaves a serious gap in business capability that could undermine the overall success of the operation.
8. Remember What You’re Selling
In a bid to capitalize on the new technology and growth models offered by vertical farming, some growers have forgotten that their primary focus should be on growing and selling the highest quality food. Instead, they have tried to recoup their investment by trying to commercialize their vertical farm’s technology, process, and methodology. Unfortunately, as we have seen, every vertical farm is different with potentially very different needs. The trick is not to try and do many different things at once, but instead, keep a clear focus on doing one thing as well as possible.
Source: www.currentbyge.com/ideas
UAE Minister Opens Carrefour’s Hydroponic Farms In Abu Dhabi
The UAE’s state-held news agency, Wam said that the farms are a part of the multi-billion dollar conglomerate’s Net Positive strategy that aims to ‘overcompensate’ its water and carbon footprint by 2040.
Two Farms Opened at Carrefour Stores In My City Centre Masdar, Yas
Mall, And Support Majid Al Futtaim's Net Positive Strategy
The farms were opened by UAE’s minister of climate change and environment (MOCCAE), Dr. Thani bin Ahmed Al Zeyoudi. [image: Wam]
25 Nov 2019
The UAE’s minister of climate change and environment (MOCCAE), Dr. Thani bin Ahmed Al Zeyoudi opened the region’s first hydroponic in-store farms at Majid Al Futtaim’s Carrefour stores in Abu Dhabi’s My City Centre Masdar and Yas Mall.
The UAE’s state-held news agency, Wam said that the farms are a part of the multi-billion dollar conglomerate’s Net Positive strategy that aims to ‘overcompensate’ its water and carbon footprint by 2040.
Careefour’s isolated and temperature-controlled glass farming chambers have been designed in line with the highest standards of hydroponics. Customers can choose from a select range of herbs and microgreens, once they are fully grown within the facility. The two farms, which are the first-of-their-kind to be installed in the region, use 90% less water and less space than traditional farms to deliver around 25kg of fresh herbs and microgreens each day.
The farms use 90% less water than traditional farms [image: Wam]
Speaking on the inauguration, Dr. Al Zeyoudi said: "MOCCAE supports technological development and innovative techniques in the agricultural sector, including vertical and hydroponic farming that reduces water consumption by at least 90% and increases the productivity of multiple agricultural products.
Meanwhile, chief operating officer of Carrefour UAE and head of operational excellence at Majid Al Futtaim Retail, Miguel Povedano, said: "As leaders in the retail industry, we should always be the pioneers in coming up with outstanding sustainable initiatives that leave a positive impact on our environment, economy, and society.
“As well as supplying our customers with fresh quality produce, the hydroponic farms will allow them to learn about the role of technology and innovation in the development of local agricultural production."
Indoor Farming Looks Like It Could Be The Answer To Feeding A Hot And Hungry Planet. It’s Not That Easy.
Viraj Puri, co-founder of one of the nation’s largest indoor farm companies, walks through the construction site, and even without the luminous frills of thousands of butter lettuces, it’s easy to see that the building going up where Bethlehem Steel once stood is something ambitious in the world of food
Viraj Puri, co-founder, and CEO of Gotham Greens, in the company's facility in Hollis, N.Y. Gotham Greens builds and operates ecologically sustainable greenhouses in cities across America. (Salwan Georges/The Washington Post)
By Laura Reiley
November 19, 2019
BALTIMORE — The next big thing is here, all girders and concrete pads, glass roofing and gravelly dirt. Viraj Puri, the co-founder of one of the nation’s largest indoor farm companies, walks through the construction site, and even without the luminous frills of thousands of butter lettuces, it’s easy to see that the building going up where Bethlehem Steel once stood is something ambitious in the world of food.
The Sparrows Point steelworks in Baltimore, once the largest steel-producing facility in the world, was shuttered in 2012, leaving no trace of what once supported 30,000 families with Bethlehem Steel wages. Now the vacated land is dominated by a FedEx distribution center, an Amazon fulfillment center, an Under Armour warehouse.
And by the beginning of December, Puri’s Gotham Greens farm will join them, part of a global craze for decentralized indoor food production.
Food and agriculture innovation have sucked up remarkable amounts of investor capital in recent years and could become a $700 billion market by 2030, according to a Union Bank of Switzerland report.
Millions are being invested globally in indoor urban farms because of their promise to produce more food with less impact, with two dozen large-scale projects launching in Dubai, Israel, the Netherlands, and other countries.
Gotham Greens' under-construction Baltimore facility in August. The company is transforming the old Bethlehem Steel site into a 100,000-square-foot hydroponic greenhouse, the largest it has built. (Salwan Georges/The Washington Post)
Still, the next big thing may be stymied in the United States by high start-up costs, high urban rents and lack of a safety net in a food system that is highly dependent on subsidies and bailouts for a few commodity crops. (An American Farm Bureau Federation report last month found that almost 40 percent of conventional farm income in 2019 will be provided by trade bailouts, disaster insurance, the farm bill, and insurance indemnities.)
And for indoor urban farms, especially those that rely solely on artificial light, there’s another concern: lightbulbs.
In September, the Trump administration announced it would roll back Obama-era energy efficiency standards that would have effectively phased out the standard pear-shaped incandescent variety. The step is expected to slow the demand for LED bulbs, which last longer and use less electricity than many other types but are more expensive.
The rollback, slated to take effect in January, is being fought by 15 states and a coalition of environmental and consumer groups that claim the changes will speed climate change and raise consumers’ energy bills.
For indoor urban agriculture, especially indoor vertical farms, the reversal represents a threat to an already narrow path to scalability and profitability, according to Irving Fain, chief executive of Bowery Farming. The indoor vertical farming company has raised $122.5 million from celebrity chefs Tom Colicchio, José Andrés and Carla Hall, Amazon worldwide consumer chief executive Jeff Wilke and Uber chief executive Dara Khosrowshahi.
“The Department of Energy recognized a lot of our energy was going to lights and that LEDs were a more efficient form of lighting, so they pushed from incandescent to LED in industrial spaces,” Fain said in a phone interview. “Those were the trends that got us here, and we were hoping cost could drop another 50 percent with more innovation and more volume."
Will indoor, vertical farming help us feed the planet — or hurt it?
Some indoor farms stack plants vertically nearly to the ceiling in repurposed shipping containers or enormous warehouses, all of the plants’ photosynthesis achieved via high-tech light-emitting diode (LED) bulbs. Others, such as Gotham Greens, are vast, glass-topped greenhouses, pulling their plants’ needs from the sun and giving a lightbulb assist in low-light times.
In addition to Gotham Greens, the Washington-Baltimore area will become home to an outpost of Bowery Farming in November. In the second half of 2020, a $100 million greenhouse tomato-and-cucumber project with the world’s largest LED installation for a single building will debut in Morehead, Ky., funded in part by “Hillbilly Elegy” writer J.D. Vance. And around the same time, California-based Plenty, with investors such as Amazon founder Jeff Bezos, will debut a Southern California indoor vertical farm about the size of a soccer field. (Bezos owns The Washington Post.)
But the U.S. Department of Energy’s proposed reversal of energy efficiency standards could hamper this emerging agricultural sector, according to Fain.
Indoor vertical farming became economically viable when LEDs became plentiful, cheap and efficient. Before that, indoor growing lights produced enormous amounts of heat — heat mapping was frequently how police identified illegal marijuana growing houses — and thus cooling costs and electricity bills were astronomical.
Young greens are seen at the Gotham Greens facility in Hollis, N.Y. (Salwan Georges/The Washington Post)
With the passage of energy legislation in 2007, the Department of Energy required that most general-service lightbulbs emit at a minimum efficiency of 45 lumens per watt by the beginning of 2020. Halogen and incandescent bulbs don’t generally meet that efficiency standard. LEDs, which use a semiconductor to convert electricity into light, do.
Within just a few years, LEDs doubled inefficiency and prices fell 85 percent. Widespread adoption caused energy companies to throw money at research and development. Indoor urban farmers, especially those farming vertically, have built their profitability models on projections that LEDs will continue to get exponentially brighter and less expensive, will run cooler and will become more efficient.
Chris Granda, senior researcher/advocate at the Appliance Standards Awareness Project, says rolling back the efficiency standards will hamper the expansion of LEDs and their continued march toward greater efficiency.
“I think what the efficiency standards rollback will do is slow the rate of consumer uptake,” Granda said. “There’s a cohort of people who just don’t like to try new things. The standards would have nudged them along into LEDs. Even if it delays the adoption of LEDs for five years, that’s a huge loss of energy.”
Efficient bulbs are not the only challenge to indoor urban agriculture, Fain says. To take a small indoor farm and make it a big one requires innovations in robotics and artificial intelligence. There, too, prices have come down substantially for sensors, processing and data storage. Altogether, these make indoor farming viable but not easy.
Fain talks about Bowery’s operating system, “the brains and central nervous system of our farm, with a plant-monitoring system and proprietary deep-learning algorithms” that help predict what will happen to each crop. He says the operating system, one of the most expensive components of Bowery, runs everything at each farm, with real-time data to improve outcomes over a network of farms. The cost of that operating system has to be amortized over that network.
And because profitability is so elusive, some of the early promises of indoor agriculture are slow to be realized. Steep start-up costs mean farmers must grow crops that generate major cash: specialty items, such as flowers, or crops that have quick growth cycles, such as leafy greens. The five main indoor crops are leafy greens, microgreens, herbs, flowers and tomatoes, items that are a pull for those of high socioeconomic status but aren’t go-to products for low-income people.
There’s inherent elitism that is hard to avoid, even with school tours, food bank donations and other efforts toward democratizing access to good food.
Indoor urban farming is frequently touted as a mechanism for urban renewal and job creation in low-income neighborhoods. But farms kitted out with sensors and robots often require highly specialized and educated workers. They typically are not huge employers. Bethlehem Steel employed 30,000 at its peak; Gotham Greens’ largest farm yet will have only about 60 full-time employees.
Butterhead lettuce grows in Gotham Greens' facility in Hollis, N.Y. (Salwan Georges/The Washington Post)
For Puri, Fain, and others, the necessity to succeed with indoor urban agriculture is self-evident. More than 95 percent of head lettuce in the United States comes from two drought-prone states, California and Arizona, and according to the U.S. Department of Agriculture, traditional agriculture accounts for 80 percent of the country’s water consumption, as high as 90 percent in many Western states.
In 2018 alone, three food-borne illness outbreaks on traditional romaine farms killed six people, hospitalized 128 and infected 300, according to the federal Centers for Disease Control and Prevention. The safety challenges of outdoor farming are becoming more acute with climate change and unexpected shifts in pests and bird migrations.
After Hurricane Sandy in 2012, news stories reported that local Gotham Greens lettuces were some of the only leafy greens available in grocery stores in New Jersey and New York. Indoor farming gives cities “urban resiliency,” something planners are increasingly concerned about.
Cities are where most of us live, says Sabine O’Hara, dean of the College of Agriculture, Urban Sustainability and Environmental Sciences at the University of the District of Columbia. The conversation now, she says, is how to shrink the food footprint of cities, how to make cities more sustainable and their food systems robust when disaster strikes.
2018 saw the most multistate outbreaks of foodborne illness in more than a decade, CDC says
By the end of the year, Gotham will operate 500,000 square feet of greenhouses across five states.
Gotham Greens’ first indoor greenhouse farm debuted in 2011 in Brooklyn on the rooftop of an old bowling alley. The second was on the roof of a Whole Foods, also in Brooklyn, and the third was in Queens atop what once housed the Ideal Toy Co., which made the Betsy Wetsy doll after World War II and had its last big hit with the Rubik’s Cube. Another, in Chicago, sits on the second floor of an eco-friendly cleaning products company.
The fifth farm, in Baltimore, will be Gotham Greens’ biggest to date and has raised $45 million in equity capital.
A worker walks the construction site of Gotham Greens' new Baltimore facility. The farm’s first stage will be 100,000 square feet, but there’s space to go up to 400,000. (Salwan Georges/The Washington Post)
At Sparrows Point, Puri walks past what will be the packaging room, the break room, and the computer control room. He lists off some stats. One indoor acre at Gotham is as productive as 40 acres of conventional soil. Gotham Greens’ Baltimore farm will require 95 percent less water and 97 percent less land than a traditional dirt farm, and only about an eighth of the energy consumption of an indoor vertical farm.
Almost nothing will go to the landfill, the majority of its waste being compostable or recyclable. Gotham Greens lettuce can go from seed to full head in 35 days, about half the time it takes outdoors.
The farm’s first stage is 100,000 square feet, but there’s space to go up to 400,000. Puri talks about eliminating food waste, passing shelf life along to consumers, millennials’ desire to know where their food is from. He says Gotham’s first farm became profitable within the first year of operation.
“As the largest urban agriculture company in North America,” Puri said, “we’ve demonstrated that urban greenhouse agriculture can be a viable agribusiness that addresses a real need in the commercial supply chain of fresh produce.”
But with almost none of the agricultural subsidies and safety nets of traditional row crop agriculture, and with high operating costs and the trajectory of lightbulb research uncertain, some sectors of indoor urban agriculture may be on shaky ground.
Young greens sprout at the Gotham Greens facility in Hollis, N.Y. (Salwan Georges/The Washington Post)
Laura Reiley is the business of food reporter. She was previously a food critic at the Tampa Bay Times, San Francisco Chronicle and Baltimore Sun. She has authored four books, has cooked professionally and is a graduate of the California Culinary Academy. She is a two-time James Beard finalist and in 2017 was a Pulitzer finalist. Follow
Kroger Brings Farming To Its Stores In Push To Get Greener (And Sell More Kale)
Visitors to Seattle-area Kroger supermarkets next week will be able to walk out with fresh parsley, cilantro and other greens grown in the store, the latest example of grocers bringing the farm right to their aisles
The grocery-store giant makes a bet on farm-to-aisle, trying to win back shoppers.
By Deena Shanker and Matthew Boyle
November 19, 2019
Visitors to Seattle-area Kroger supermarkets next week will be able to walk out with fresh parsley, cilantro and other greens grown in the store, the latest example of grocers bringing the farm right to their aisles.
Kroger’s deal with German startup Infarm includes two stores with plans for 13 more to come online by March of next year. It’s part of a broader push by the nation’s biggest traditional supermarket chain to improve sluggish sales by amping up it’s fresh-food offering, while also enhancing its environmental cred. The greens—including crystal lettuce and Nero Di Toscana kale—only need tending once or twice a week and will sell for no more than Kroger’s existing store-brand organic produce, according to Suzy Monford, Kroger’s group vice president of fresh.
“We’re removing touches in the supply chain, which is more economical and allows us to pass those savings along to customers,” Monford said in an interview. “We know that fresh food drives shopping trips and it’s a real differentiator.”
Infarm offerings grown right in the store. | Photographer: Infarm
The industry could no doubt use some buzz. Consumers have been dialing back on traditional grocery shopping for years, sparking a slew of bankruptcies and consolidation. Blame meal kits and the ease of restaurant-ordering apps. A flood of retailers, like pharmacy chains and dollar stores, have expanded into food. And when many Americans do buy groceries, it’s often via online delivery. The industry needs to win back a cohort that has largely moved on from the grocery-store trip, and offering the farm could help.
While this is Infarm’s first stateside venture, the Berlin-based company is already well established, with more than 500 farms dispersed through partnerships at more than 25 major food retailers internationally, including Edeka and Amazon Fresh in Germany, Marks & Spencer in the U.K., and Metro in France. Its farms grow a variety of herbs and leafy greens including stalwarts like parsley and kale, as well as more specialized options like green mizuna and Peruvian mint.
Kroger’s tie-up with Infarm comes during a period of robust growth for this kind of produce. In the U.S., sales of fresh herbs and spices are up 6% for the year, and leafy greens are up 9%, according to data from Nielsen. That coincides with surging investments in innovative farming methods, too. In 2013, vertical farming startups received $4.5 million in venture funding, according to AgFunder, an investor in food and ag-tech companies with an active media and research arm. In just the first half of 2019, they raised $140 million. Infarm, for its part, raised $100 million in a Series B round in June.
As these new forms of farming gain steam, the companies behind them are looking for ways to appeal to major customers and, ultimately, the consumer at the store. Brooklyn-based Square Roots builds farms inside of refurbished shipping containers, and recently announced a new partnership in Grand Rapids, Michigan, putting the containers at the headquarters for food distributor Gordon Food Service. Gotham Greens, a Brooklyn-based greenhouse grower, has six locations in New York and Chicago, including on the rooftop of a Whole Foods. Indoor vertical farming company Plenty, which raised $200 million in a Series B round in 2017 from the likes of Jeff Bezos, recently announced a soccer-field sized farm planned for Compton, California.
While farming models differ, the basic pitch remains the same: Growing food closer to the urban shopper, in computer-controlled micro-climates, means less transport, less water usage and less pesticides, fertilizer or food safety concerns, if any at all, all while delivering more shelf life, more flavor, and overall, a better eating experience.
Infarm uses a “distributed farming” format, growing its plants in centralized nursery hubs for a few days, before placing the days-old seedlings in its hydroponic modular farms in stores in the nearby area. Once Infarm’s initial partnership in a given city is well settled, it spreads out, adding customers that can all be serviced from the same hub.
Smallhold, a Brooklyn-based mushroom farm company, uses a similar model in the New York area that includes the Standard Hotel in the East Village, the trendy Lower East Side’s Mission Chinese eatery and two Whole Foods locations, with more on the way.
Smallhold’s mushroom farm at a Whole Foods in New Jersey | Source: Whole Foods Market
“It’s about finding places where you can fill a niche,” says Chris Manca, a purchasing manager for Whole Foods in the northeast region, adding that he might expand beyond oyster mushrooms to rarer varieties like lion’s mane—popular in meat-replacement dishes—in the coming months.
Retailers pay Infarm for “farming as a service,” as co-founder Osnat Michaeli describes it, which includes not just the produce itself, but also its planting and preparation for sale. Consumers can see their food growing right before their very eyes, and then take their Italian Basil or green mint home, roots still intact, to allow for the most flavorful food. “The real harvest,” Michaeli says, “happens just before eating.”
“It’s about a ‘wow factor,’” says Henry Gordon-Smith, founder and managing director of Agritecture Consulting, a global adviser to vertical farming entrepreneurs. “This is a new way to think about herbs and cooking,” Gordon-Smith says, calling the model “compelling.”
But while consumers are likely to be excited about the environmentally-positive, foodie-friendly marketing around vertical farming, the reality is not that simple. Though the aforementioned benefits, like lower water use and pesticides, are real, the energy required to power these farms can counteract some of that.
“If you had a balance sheet, the carbon footprint from energy would be a significant dirty part of vertical farming overall,” Gordon-Smith says, depending on the energy source.
Renewable energy options are sometimes available—Infarm’s Berlin hub uses 100% green energy, for example—but the requirements are about 10 times that of conventional agriculture. Infarm's model uses similar amounts of energy to produce a pound of lettuce as other indoor farming methods, like using shipping containers or large-scale plant factories, according to calculations by Agritecture, which periodically benchmarks operators to each other to analyze the environmental impacts. But there are still enough other variables to consider—plant transport, for example—that it could actually be significantly higher.
Kroger’s Monford admits that the company still has “a lot to learn” about in-store farming, but says the venture’s environmental footprint is pretty minimal. “It’s just water and light.”
Second Chances Farm Launches In Wilmington With New Trainees And A Hemp License
Ajit George and his team had a lot to announce at the launch of social impact startup Second Chances Farm, where it celebrated the official opening of its 47,500-square-foot facility in Wilmington with a “ladybug dedication.”
The 47,500-square-foot facility in Riverside is bringing on 17 returning citizens to help run the indoor urban farm.
By Holly Quinn / STAFF
Ajit George speaks next to one of the hydroponic towers that will soon fill the warehouse space in Riverside. (Photo by Holly Quinn)
Ajit George and his team had a lot to announce at the launch of social impact startup Second Chances Farm, where it celebrated the official opening of its 47,500-square-foot facility in Wilmington with a “ladybug dedication.”
That’s like a ribbon-cutting, but instead of wielding oversized scissors, the governor, New Castle County executive, mayor and City Council president (among others) released tiny bags of live ladybugs into a floor-to-ceiling vertical “fields” of hydroponic lettuce and herbs.
The urban farm in Riverside will soon also be growing hemp, which is processed into CBD oil, after receiving approval for a license to grow it. (Hemp, a strain of cannabis that has an extremely low level of THC — the substance that gets you high — was made legal in all 50 states with the passage of the 2018 Federal Farm Bill.)
The farm will also offer a few free services to people who live in the neighborhood, including a Crossfit gym and wireless WhyFly service via a connection on the top of the building.
Seventeen returning citizens who have completed their sentences of incarceration have been selected as the first trainee cohort and will receive 16 weeks of paid training.
“We believe those nearest to the solution have also been affected nearest to the problem,” said Saad Soliman, executive director of Peace by Piece, the organization that assists with the reentry program at Second Chances Farm. “Borrowing from my own experience having served 15 years in prison and overcoming boundaries, overcoming barriers, overcoming obstacles, I believe in the leadership of every single man and woman that we’re bringing in here. Let’s humanize the components of who these men and women really are.”
In addition to Second Chances Farm launch, George is also celebrating the launch of his new book, “The Magic of the Red Carpet,” which follows his journey from the founding of TEDxDelaware to Second Chances Farm. All proceeds of the book will go to Peace by Piece.
Watch Soliman introduce the new team members here:
Vertical Farming, A Growing Industry?
Vertical farming is at root a simple concept – instead of spreading out, you spread up. Where previous agricultural innovations have tended to focus on intensity, vertical farming solves for density
MOIRA BENIGSON
6 APRIL 2018
Vertical farming is at root a simple concept – instead of spreading out, you spread up. Where previous agricultural innovations have tended to focus on intensity, vertical farming solves for density. And it needs to – while the number of malnourished people in the world has fallen from one in four in 1970 to one in ten today, the global population is set to reach nearly 10 billion by 2050.
Moreover, industrial development and urbanization mean that even as the human population grows ever larger, there is less arable land today than there was yesterday, and there will be less tomorrow than there is today. The earth has in fact lost 40% of its farmland since 1970.
There have so far in human history been three major agricultural revolutions. The first, around 12,500 years ago, was the shift from the hunter-gatherer lifestyle of our forebears to the sedentary, agrarian system that enabled mass societies to grow. The second, which began in Britain in the 18th century, gave the industrial revolution the workforce it needed to transform the world. The third, in the 1950s and 60s, saw the development of high-yield disease-resistant crop varieties that massively increased the world’s agricultural output and has been credited with saving more than a billion lives. Could vertical farming be the fourth?
Growing crops and plants in stacked layers indoors, vertical farming uses far less water than its conventional counterpart (some estimates put it at one-twentieth) and, theoretically, produces a radically greater yield. By using aeroponic (spraying the roots of plants with a nutrient-rich solution) or hydroponics (growing the plants in a shallow bath of water containing their nutrients) methods, vertical farming reduces the reliance on the soil. It is in short a way to maximize the productive capacity of every square foot while minimizing waste and ecological damage.
Investors have taken note of the method’s potential value. Plenty, a San Francisco-based vertical farming startup that aims to build a large-scale indoor vertical farm outside of every major city in the world last year secured the largest agro-tech investment in history, a $200m funding round involving Softbank, Jeff Bezos, and Eric Schmidt among others. In 2017 the company announced plans to build a 100,000-sq. ft. facility just south of Seattle.
But mass vertical farming may not be the most important change to be brought about by this technology in the near future. For that, we must look to Berlin, where a startup called InFarm is creating modular vertical farming units that can be scaled easily and effectively.
The idea is to have a farm in every store. Imagine going into your local supermarket and instead of aisle after aisle of carefully packaged herbs and fresh-ish vegetables that have travelled hundreds if not thousands of miles, there’s a vertical farm where you can pick your own. It doesn’t get much more ‘experiential retail’ than that.
It’s not just effective marketing or something pretty to look at – InFarm’s clever use of data and monitoring means that yields per square foot can be multiples higher than from conventional farming. Importantly, the proximity of the farm to the consumer allowed by InFarm’s modules means that a different set of incentives can govern the growing process – taste and flavour can be prioritised over shelf life and durability.
When a new plant is added to the system, the company’s team of data scientists and engineers write a new algorithm designed to ensure that the module is perfectly calibrated to every plant. Each of their units is, in essence, an individual ecosystem. A world in miniature that uses machine learning and data to mirror the perfect growing environment of a plant in its natural environment. All modules are monitored and operated using the cloud from a central control centre. As they call it, it’s ‘farming as a service’.
This model of vertical farming might also be the ultimate form of vertical integration, offering grocers the chance to simplify their supply chains, reduce cost and increase yield while at the same time bringing food to shelves that is fresher than ever before. InFarm has already signed deals to place its units in the stores of two of Germany’s largest retailers, Metro and EDEKA.
Not incidentally, InFarm’s system, and vertical farming in general, avoids the use of pesticides. A clear selling point as more and more consumers turn to products which tout their environmentally friendly credentials, minimal waste and chemical-free production processes.
“Rather than asking ourselves how to fix the deficiencies in the current supply chain, we wanted to redesign the entire chain from start to finish; Instead of building large -scale farms outside of the city, optimising on a specific yield, and then distributing the produce, we decided it would be more effective to distribute the farms themselves and farm directly where people live and eat,” Erez Galonska, co-founder & CEO of InFarm
Vertical farming businesses are also budding up in the direct-to-consumer market. Several, such as neoFarms, offer in-home farming modules with built-in ease-of-use technology. neoFarms’ model is about the size of a fridge and can handily fit into a kitchen. CityCrop has already brought a mini-unit to market.
Vertical farming still has a way to go yet. While the industry is predicted to be worth $5.8bn by 2022, that pales in comparison to the $300bn value of the indoor farming market in general, or the estimated $3.1trn global agricultural industry. For the vast majority of producers, distributors and retailers vertical farming will for the time being at least be an attractive addition, rather than a sufficient replacement, to the conventional supply chain.
In the developed world, we have largely been freed from the need to think about where our food has come from, how it was grown, and who grew it. But, perhaps counterintuitively, the increasing urbanisation of much of the world’s landmass may also involve the farmification of our cities. Urban spaces may be eating into our farmland, but farms have already started to eat into our urban space.
The grocers and retailers of the future may become our farmers as well. Combining the technologies of firms like InFarm with their own customer data they’ll be able to produce the food that customers want in the places they want it at a higher quality and with lower impact. Previously farm-to-table has been about bringing the table closer to the farm. Now it’s about putting the farm right next to the table.
Why Do Vertical Farms Fail In India? Stop Copying The West
In this series starting today, we will share with you a few insights (specific to Indian context) that we have gained over time. These insights are based on our understanding and the inferences we have drawn. These may not be directly applicable in your specific set of circumstances
During our journey in CityGreens, we have met many Consultants, Competitors, Collaborators, Govt. Dignitaries, Investors, Entrepreneurs, Aspirants, and so forth. These encounters have helped us develop deep insights into the industry. It will not be an understatement to say that the Vertical Farming industry in India is still in its infancy. The way this industry shapes up will depend upon a lot of factors, primarily being the establishment of a few successful commercial models at a scale that can help the fence-sitters to make an informed leap of faith.
In this series starting today, we will share with you a few insights (specific to Indian context) that we have gained over time. These insights are based on our understanding and the inferences we have drawn. These may not be directly applicable in your specific set of circumstances. However, we do hope that these will help you think more in-depth about the issues that you may face in your journey of Urban Growing.
The first insight that we will cover today is the one that we have observed most commonly and has the potential to inflict the maximum damage on the success potential of a farm.
Aping the West
Agriculture in India, per se, is way behind the western world, when it comes to using technological advancements. One such technology that was promoted and supported by various Governments and vehemently abused by some unscrupulous Farmers (to misuse the subsidy system and make undue financial gains) was that of Greenhouse.
The reason for failure – aping the west. If you consider polyhouse or greenhouse technologies, their roots are in Europe. The primary reason these were created was to protect the crops from cold weather. The climate/weather profile in India is very different. Blindly copying the technology to tropical parts of the country resulted in disastrous consequences in many states. (the technology does work well in the colder climatic regions of the country)
When it comes to Vertical Farming, one can observe a similar phenomenon is taking place. Most of the vertical farming aspirants we talked to had two things in common:
1. They wanted to use LEDs
2. They wanted to grow Lettuce
The reason? Because that is what they have seen everyone doing the world over. Let us evaluate both of these in the Indian context, one by one.
1. Use of LEDs:
Take a step back and look at the problem that LEDs solve, they help you grow indoors. And why do you want to grow indoors?
a. the land cost is too high.
b. The temperature outdoors is not conducive of growing (its either sub-freezing or too hot).
c. one wants to grow in multiple vertical layers (say 10 – 15 levels at least).
In the Indian context, the first two will not hold. What LEDs will result in, in such a scenario, will be a manifold increase in the Cap-Ex and the Op-Ex, thus pushing away the break-even period further, or increasing the input cost so much that the output product becomes uncompetitive in the market.
The third reason may still be the right reason for someone to set-up an LED-based farm in India. But it is cap-ex heavy and should be pursued if one is willing to wait for a long gestation period to break-even.
2. Growing Lettuce:
It is surprising that we rarely come across any Urban Farming aspirant who does not want to grow Lettuce. The questions we like to ask is, after all, how much lettuce can Indian’s consume? People in the west grow lettuce because they eat lettuce day in and day out (as a part of salads, or sandwiches which form their staple diet). Indian’s just don’t.
If one observes carefully, one will see that the palate preferences that get developed over time, do so based on the demographic dividends. In semi-arid and desert regions of western India, when our ancestors had to travel long distances they needed the food that can stay edible for long periods in the hot environment. And you see a lot of gram flour based snacks in those cuisines (think Gujarati / Rajasthani cuisines). Similarly, in the economically lesser developed eastern parts of the country, potato served as one of the cheapest sources of quick energy, and you can see that influence even today (think Bengali Chicken biryani) in most of the eastern cuisines. Similarly, when it comes to greens, Indian palate prefers the one that can be grown in tropical regions. Lettuce is definitely not the one.
Unless India transforms into a salad eating nation or lettuce becomes a part of mainstream Indian cuisines, (think lettuce paneer instead of Palak Paneer), the market for lettuce will remain limited. In such a scenario, if all the vertical farms start producing lettuce, it will flood the market and lead to price erosion.
In order to grow lettuce or other exotics not native to Indian weather, one needs to make a significant investment in temperature control infrastructure which makes the cost excessive. You can save on those investments and keep both your Cap-Ex as well as Op-Ex considerably lower if you grow the Indian greens like spinach. (You can still grow lettuce in the winter season and command market price). Having said that, In case, you do have an assured market for the supply of lettuce that comes out of your farm (through B2B rate contracts or otherwise), please go ahead and set-up a lettuce factory. But if you are doing it just based on the assumption that you will find the market later, better go small and test the hypothesis first.
This brings us to our second observation which we will cover in the next part of this series.
Till then,
Happy Growing!
Gaurav is an entrepreneur whose first Start-up was focused on providing services to patients suffering from Chronic Diseases. While researching about the causes of lifestyle diseases and the ways to reduce their incidence, he chanced upon the idea of growing healthy and nutritious food using advanced farming techniques.
He founded CityGreens with a mission to enable City Dwellers to access Safe, Healthy and Fresh food.
US: Alabama - Container Will Grow Food For Montgomery Restaurants
The future of Montgomery fine dining scene is growing inside a freight container in a parking lot off Decatur Street. Dropped into place by a crane earlier this week, the Freight Farm container is full of vertical hydroponics farming equipment and environmental controls
Brad Harper, Nov. 20, 2019
Vintage Year owner Jud Blount, left, and Executive Chef Eric Rivera show their new hydroponic container garden that is being set up to grow fresh vegetables for the Vintage Year restaurants in Montgomery, Ala., on Tuesday, November 19, 2019. (Photo: Mickey Welsh)
The future of Montgomery fine dining scene is growing inside a freight container in a parking lot off Decatur Street.
Dropped into place by a crane earlier this week, the Freight Farm container is full of vertical hydroponics farming equipment and environmental controls — everything you need to grow produce inside. Another crate is on the way and will be stacked on top of the current one.
“We’ll have two different climates, one primarily to (grow) our lettuce and some of our greens, and another climate that’ll be more conducive to growing all of our fresh herbs,” Vintage Year Executive Chef Eric Rivera said. “We should be able to come out and harvest that day for the produce we need that night.”
Everything can be controlled via a phone app.
Workers lower a Freight Farm container into place on South Decatur Street in Montgomery. (Photo: Contributed)
They’ll be up and running in a few weeks, with the first harvest around the end of the year. The team behind Cloverdale’s Vintage Year plans to use the crates as the source for food at its Cloverdale restaurant, the neighboring Vintage Café, and, eventually, at the Ravello Italian restaurant that’s now under construction downtown.
The production capacity in each crate is “huge,” Rivera said. A single crate can produce 700 heads of lettuce a week, for example. They plan to send some of the food to local farmers’ markets and sell more to other restaurants here.
Jud Blount, one of the people behind Vintage Hospitality, said he was sold on the idea after talking about the problems of outdoor gardening with Auburn University Horticulture Dean Desmond Layne. It was a way to work around issues like extreme weather and pests. “This is something where 365 days a year we’ll be growing,” Blount said.
Vintage Year owner Jud Blount, left, and Executive Chef Eric Rivera show their new hydroponic container garden that is being set up to grow fresh vegetables for the Vintage Year restaurants in Montgomery, Ala., on Tuesday, November 19, 2019. (Photo: Mickey Welsh)
Launching the container farming business, called MGM Greens, will give them the chance to work with interns and graduate students from the Auburn horticulture department. Those students, in turn, will have “an opportunity to use a full, functioning facility, which they don’t currently have,” Rivera said.
It also opens new menu options for Rivera. He said they’ll be able to grow herbs that are entirely new to Montgomery, and they can start growing something in the container just a few weeks before it pops up on the menu at one of the restaurants.
Vintage Hospitality announced this fall that they’re opening an upscale Italian eatery in the former City Federal Savings & Loan Building at 36 Commerce Street downtown. The 1925 structure is still being redesigned and restored. Plans call for marble floors, an event space, a ballroom, a courtyard, and a wine cellar.
That opening is still more than a year away.
Vintage Year's new hydroponic container garden that is being set up to grow fresh vegetables for the Vintage Year restaurants in Montgomery, Ala., on Tuesday, November 19, 2019. (Photo: Mickey Welsh)
Contact Montgomery Advertiser reporter Brad Harper at bharper1@gannett.com.
Workers Grow Food And Develop Skills At Arnold Center’s Plant Factory
Arnold Center President Craig Varterian, who began this hydroponic business, called Arnold Farms after growing plants in his basement, likens the facility to a ‘plant factory’.
CHERYL WADE | NOVEMBER 07, 2019
Agencies serving people with disabilities often have piecework projects with workers packaging materials in large quantities. Locally, the Arnold Center is in their second year of a new effort to grow plants in a process that combines recycled water and gravity.
Arnold Center President Craig Varterian, who began this hydroponic business, called Arnold Farms after growing plants in his basement, likens the facility to a ‘plant factory’.
Craig Varterian, Arnold Center President.
For several years before starting Arnold Farms, Varterian read plant journals, consulted experts and grew plants in his basement, often using simple equipment and bins to hold the soil and greens. By the time Arnold Farms launched in 2018, he had done enough background research to design the hydroponic system with help from a couple of other staff members.
“We brought in parts from all over the world – China, Korea,” Varterian says, noting the necessary LED bulbs give off very intense amounts of heat and light. “With some of the parts, you can’t buy in the U.S.”
Walk down the hall toward the large indoor growing area and one quickly breathes air with notes of basil, including a sweet variety that has a little whiff of licorice. There is Genovese, an Italian basil that’s excellent for pesto, and a spicy variety from Thailand that has red stems. Arnold Farms also grows varieties of lettuce and kale, plus edible flowers such as Mexican mint.
Multiple varieties and sizes of plants means the prospect for growth and a diversity of crops that Arnold Farms can produce.
The indoor farm has approximately 6,000 square feet of space and capacity for 26,000 plants. Varterian believes the farm is one of the most advanced, high-tech facilities in Michigan. Unlike many other plant farms with much higher startup costs, Arnold Farms was built for about $500,000, primarily from grants but also from private gifts in order to provide training in a specified field for workers.
Arnold Farms also produces microgreen whicg grow just 10 to 12 days before being harvested. These plant varieties carry many more nutrients than full-grown plants, says Chandra Jewel, the intake coordinator at Arnold Center. Some of the more unusual products include amaranth, green and purple shiso – an Asian member of the mint family -- and a spicy green mix for salads. More common herbs grown include wasabi, cilantro and mint.
The indoor farm has approximately 6,000 square feet of space and capacity for 26,000 plants.
Jewel has found at least one use for the corn shoots the farms grows. She mixes the wispy, grass-like plants with taco seasoning, salsa and sour cream. “They are great to add to Mexican dishes, because they provide the corn taste,” she says.
Jewel remembers when the fledgling hydroponics business began in a room about 14 feet square, a brick-walled space that was a classroom. There were just a few trays for plants and a couple of employees. “Now we can do so much more.”
Varterian explains this experimentation with multiple varieties and sizes of plants has meant the prospect for growth and a diversity of crops that Arnold Farms can produce.
Arnold Farms also produces microgreen whicg grow just 10 to 12 days before being harvested
“We have a great opportunity to explore agricultural sustainability and we’ve got a great opportunity to create jobs for people with disabilities,” Varterian says.
Varterian didn’t get his start in the disability field. First, he owned a factory. Then, he was president of Reclaim Detroit, a blight remediation program that started with 77,000 abandoned houses. The program trained people to make furniture from the recycled wood of houses that had been torn down.
Workers wear protective suits at Arnold Farms.
“I’d been thinking of doing some version of hydroponic farms,” he says, contrasting his new profession with the old. “Life as we did it (working with demolished houses and used wood) was unsustainable.”
Varterian spent years working to employ people, but knew nothing about running a disability-related organization. Still, he says, he’s always been up to a challenge. Recycling practices, which had been a practice for decades, would provide the renewable resource of plants and possibilities for expansion.
“How many times in your life do you get the chance to take over an organization where you could do something meaningful and make something exciting happen?” he says.
Microgreens are harvested after 10-12 days.
Facilities that traditionally provided supported employment or ‘sheltered workshops’ as they are sometimes described are moving away from piecework for large companies and toward providing people with jobs that pay at least minimum wage and give them training that also prepares them to eventually work outside the facility.
As employment needs change, sometimes the amount and type of work changes for people whose work is confined to a rehabilitation facility, leading to a drop in the amount of work contracted. Varterian said 60 to 70 percent of Arnold Center workers are working at jobs outside the center, and that also means their employers are required to pay them minimum wage.
Racks of produce inside Arnold Farms.
Another 12 to 14 full- and part-time employees work at the indoor farm. They monitor the pumps, which dispense nutrients as they are needed. They transfer plants from germination to seedling stage and later to the area where plants grow to their desired size and are harvested.
Plants are then packed into bags or clam shell containers for delivery to stores and restaurants that will use them. Local restaurant customers include Midland Country Club, Gratzi, Pizza Baker and Whine. Stores include Jack’s Fruit and Meat Market and LaLonde’s Market as well as several Bay City businesses.
“Arnold Farms staffers have sold their products at the Midland Area Farmers Market but now have ceased for the season”, Varterian says.
12 to 14 full- and part-time employees work at the indoor farm.
Although he’s aware that individuals might want to buy produce throughout the year, this is a farm and it’s not set up for individual orders.
“We’re focused mainly on training rather than commercialization,” he says.
At some point, the farm might have its own market day apart from the Midland Area Farmers Market, when staff could sell the products.
Joe Allen, who used to work on the Arnold Center’s floor, says he loves his job at the farms. Not only does he harvest and plant, but he helps with accounting tasks.
“They gave me employment and a safe, secure environment,” he says. “I like working with something that grows, something that’s planted, something to watch. And we’re always learning.”
Arnold farms supplies many area restaurants and stores as well as the farmers market.
Robert Goulette has worked at the farm for 10 months. Although he can use just one hand due to his cerebral palsy, Goulette says his disability doesn’t hold him back and he does everything he can. Varterian calls him “one of our rock stars” because he works hard and fast.
Workers need to keep close eyes on the plants, transferring them as they grow and making sure trays and other equipment are washed. Plants are stacked in trays up to five or six levels high. Gravity takes water down through the stacks; then it’s pumped back up to begin the process again.
“I’d like to see people with disabilities as leaders around the country in this type of farming."
Arnold Farms uses no pesticides, and Varterian likes to call the facilities plants ‘purer than organic’. Plants are germinated in a something called a clean room, which requires workers to use gowns so germs don’t come into the facility on their clothes.
What’s Varterian’s dream for the future of Arnold Farms? He’d like to employ this kind of farming around the country, especially in ‘food deserts’ where food isn’t easily accessible.
“I’d like to see people with disabilities as leaders around the country in this type of farming,” he adds.
The Cube Root of Farming - Freeport Company Grows Crops In Containers
Homegrown, totally organic crops is the vision Freeport-based Cube Root has for transforming TT’s agricultural sector by using technology to develop indoor farms. Cube Root recently held an exposition for investors and customers at its headquarters, where it introduced the concept of a specially constructed container featuring an enclosed, climate-controlled environment
Thursday 7 November 2019
Homegrown, totally organic crops is the vision Freeport-based Cube Root has for transforming TT’s agricultural sector by using technology to develop indoor farms.
Cube Root recently held an exposition for investors and customers at its headquarters, where it introduced the concept of a specially constructed container featuring an enclosed, climate-controlled environment.
Managing director Hamlyn Holder said each farm container is capable of producing kale, strawberries, lettuce or 100 different types of crops.
The investment required is an estimated $350,000, which can be paid off in instalments as a farmer simultaneously produces crops for sale.“A $350,000 investment is a high capital investment, but if you look at the operational expenditure and the returns you will get once you sell the produce, it becomes an economical model at that point,” he said. “If you look at the engineering, there is a consistency in growth, and if you compare the economics package to that of imported technologies, ours is very economical.”
Cube Root Farms’ managing director Hamlyn Holder checks on crops in the Cube Root container farm in Freeport. - MARVIN HAMILTON
Financing, he said, is available from institutions such as the Agricultural Development Bank.
In an interview with Business Day, Holder said there are many benefits to using this type of technology, including its being in an environment where farmers can control the impact of the elements and theft.
“In an open farm there are things like pests, weather, praedial larceny and other...factors. But here it is totally enclosed and controlled and you are able to see how your plants are growing remotely – also over the net, through an app on the phone.
“This type of technology offers a much more controlled environment to avoid any uncertainty when it comes to diseases and pests that may wreak havoc on your plants or fields."
The interior of a Cube Root container. According to the company, each farm, which is enclosed and can be controlled, is capable of producing a variety of crop, even those not usually grown in the region. - MARVIN HAMILTON
It also allows farmers to grow crops that are not local to the region.
“Technically there aren’t many indoor farms in 100-per-cent closed-environment agriculture. We are probably, in the Caribbean, the only manufacturer to manufacture from scratch our own container farm. We can grow from kale to strawberries to cherry tomatoes.
"We have done many trials throughout the last year, so we are comfortable at this point that the technology can give that consistency, so it’s basically limitless.
"The only thing we can’t grow is big trees at this point – but seasonings, flowers, fruits: we can do that.”
According to Cube Root managing director Hamlyn Holder, the farm container can produce kale and lettuce among as well as many other crops. - MARVIN HAMILTON
Holder said one of the company's goals for 2020 is the manufacture of seven container farms for new investors. He said it would also work alongside customers to ensure that events such as a glut of the produce do not take place.
“We also market the product so there is no glut on the market. We are trying to work with customers so that everybody grows and it is sustainable for the business model.”
He said a single farm can produce over 2,000 heads of lettuce twice monthly or once a month depending on demand.
Holder said the technology also ensures that no pesticides are used in the farming process, which instead uses an organic-based nutrient called Azomite and LED lighting systems.
Azomite, according to online sources, is a natural mineral substance that is mined from the desert in Utah and can be used as an agricultural fertilizer and/or soil amendment product.“We are striving for zero pesticides. Our technology is offering the option of zero pesticides (and) protection against bacteria, aphids, and fungus.”
Thursday 7 November 2019 Richardson Dhalai
Bowery CEO: Building Tech Is Expensive, Takes Time But Has Direct Impact On Economics of Vertical Farming
Bowery Farming, the New York-based vertical farming startup that counts Google, First Round Capital, and famous chef Tom Collichio as investors, has just raised an extra $50 million as an extension to its Series B. Temasek, Singapore’s state fund, led the extension with participation from Henry Kravis, the founder of private equity giant KKR
November 12, 2019
Bowery Farming, the New York-based vertical farming startup that counts Google, First Round Capital, and famous chef Tom Collichio as investors, has just raised an extra $50 million as an extension to its Series B. Temasek, Singapore’s state fund, led the extension with participation from Henry Kravis, the founder of private equity giant KKR.
Temasek invested in the first tranche of the Series B and was taking advantage of its seat at the table to preemptively invest more into the company on the back of Bowery’s growing commercial success, said CEO Irving Fain, adding that he wasn’t looking for more funding; the company has raised $172.5 million to date. “To their credit, they are phenomenal partners and this deal closed at a nice place from a valuation perspective for us. They have a very strong conviction about this space, both because of the macro trends but also after spending a lot of time looking at [vertical farming] before choosing to invest in us.”
The big piece of news coming with the funding announcement was the launch of Bowery’s third farm, a facility in Baltimore that is 3.5 times larger than its last in New Jersey. The farm is already operational and will be selling greens in the New Year, Fain told AFN.
Why Baltimore? From a population perspective, it can serve 26 million people within a 150-mile radius from its location, which is a transportation hub. And the company will be able to hire a workforce from within the community, which Fain says has always been important to them.
Fun fact: the exact location, White Marsh, used to have a farm many moons ago, so Fain likes the idea that Bowery is bringing the area back to its agricultural roots but in a modern way.
This round also coincides with a step-change in Bowery’s commercial activities, which Fain said have been less of a focus until now in favor of the company’s technology platform. As part of this, the company has hired Carmela Cugini as EVP of sales. Cugini comes from Walmart where she led its online grocery business after it acquired Jet.com, and also spent time leading sales divisions at Pepsi. “She’s been both a seller and a buyer at some point and that’s a unique set of skills to find,” said Fain.
Having said that, Bowery has still managed to expand its retail footprint to Whole Foods Markets, Ahold, Amazon Fresh, Jet, Westside Market, among others and recently significantly increased its deal with Whole Foods, Fain told AFN. Bowery’s greens will now appear in Whole Foods stores in all of Manhattan, Westchester, and Connecticut. Fain puts the growth in demand for Bowery produce down to two critical consumer trends that are gathering pace rapidly: the demand for local food and food grown with sustainable farming practices.
Tell us about the tech!
Meeting the growing demand for indoor-grown food has been a challenge for many in the vertical farming industry; the high costs associated with building new facilities and the struggles to find the right talent have been some of the key challenges in scaling this industry. For Bowery, building its internal technology platform has been key to its strategy of “thoughtful scaling,” said Fain.
“With each new farm we’ve opened, we’ve made meaningful improvements and steps forward in the technology, taking time to learn and understand what’s working well and what needs to improve,” he said.
Dubbed BoweryOS, the firm’s technology platform combines sensors, control systems, computer vision, robotics, and machine learning to optimize many of the processes around the farm, making the overall operation more efficient in terms of labor and costs. Not only can it do some of the tasks humans would have previously done such as monitoring and altering the environment or moving plants around the facility, but its machine learning and software platform can also guide workers on what to do and when such as identifying plants ready for harvest and harvesting.
“This means the workforce can look and resemble an Amazon fulfillment center; they don’t need to have grown a crop or have familiarity with farming,” said Fain. The company recently hired Caralyn Cooley as chief people officer, who was also previously with Jet.com, Amazon, and Pepsi. Cooley has deep experience working with an hourly workforce and the types of workers Bowery will be looking for in its farms in terms of experience and salary, said Fain.
Bowery wouldn’t disclose how much of the $170 million-odd raised has been spent on its technology platform — although we know it to be significant — but Fain said its a critical part of the company’s success.
“Building technology is hard, it’s expensive, and it takes time, but the tech you use in indoor ag has a direct and clear impact on the economics of the business you’re creating, the varieties you can grow, and the efficiencies you can generate and we realized this early on,” he said.
As Boaz Toledano recently wrote in a very popular AFN post, this type of second-generation indoor ag technology can enable vertical farms to yield 55 times more than first-generation vertical farms where tasks such as controlling lighting, heat and Co2 were automated to some extent but not optimized with data analysis.
Asked why they decided to build it in-house instead of deploying third-party technology that would have been cheaper, Fain said the ability to control and own the technology meant they could iterate on it and optimize at a very fast rate, unreliant on other vendors to make changes and updates. “The ability to create tech specifically for our system and ecosystem provides enormous efficiencies from farm to farm,” he said of the benefits of internal tech in scaling the company to multiple farms.
But Bowery emphasized that technology is still just one piece of the business; “scaling for Bowery is more than just evolving technology or rapidly opening new farms in new cities – it also means investing in agricultural science and R&D, and hiring top talent across the organization to support this continued growth. All of these factors (and more) ensure the brand can continue expanding their farm network and distribution footprint in 2020, and beyond,” the company said in a statement.
The agricultural science team, under Susan McIsaac, a plant biology Ph.D., is looking at optimizing and improving the varieties of vegetables the company grows today and researching new ones including new species across root vegetables, vine crops, and fruiting crops. Using BoweryOS data, it also suggests detailed tweaks to how to grow different crops and is looking at “how to push the boundaries in conjunction with the farm design team.” It’s not considering gene editing at this stage though, unlike some others in the space that recently created the Precision Indoor Plants (PIP) Consortium.
From Bomb Shelter To farm: The Latest Food Revolution
When you think of growing anything ‘underground’, the first thing you may envisage is some kind of criminal activity. But, there’s a food innovation gaining traction around the world, specially in London, and while it might be coming from beneath the streets, it’s all above board
14 Nov 2019
Sponsored by KETTO
Food for thought
When you think of growing anything ‘underground’, the first thing you may envisage is some kind of criminal activity. But, there’s a food innovation gaining traction around the world, specially in London, and while it might be coming from beneath the streets, it’s all above board.
Here's what you need to know about the latest underground food revolution...
Growing Underground
The fully-working Growing Underground farm is located 33 metres beneath the busy streets of Clapham, in the abandoned tunnels of a former World War II air-raid shelter.
The urban farm covering 65,000 square feet lie 120 feet under Clapham High street and are home to 'Growing Underground', the UK’s first underground farm. The farms produce includes pea shoots, rocket, wasabi mustard, red basil and red amaranth, pink stem radish, garlic chives, fennel and coriander, and supply to restaurants across London.
Salad without soil?
Urban farmers, Richard Ballard and Steven Dring are using the latest hydroponic systems and LED technology to grow fresh microgreens and salad leaves, in a stable, sustainable and pesticide-free environment.
A spigot supplies nutrients and water to the roots of the plants and artificial light and warmth is provided by LED lighting. The site is powered with renewable energy.
Instead of using soil, seeds are planted into mats made out of old carpet offcuts. Once the seeds germinate, they are put under lights to mimic sunlight.
Science behind the sprouts
So what is hydroponics? According to the Royal Horticultural Society, it is “the science of growing plants without using soil, by feeding them on mineral nutrient salts dissolved in water.”
Hydroponics does not use soil, instead, the root system is supported using an inert medium such as perlite, Rockwool, clay pellets, peat moss, or vermiculite.
Location, location, location
Its central London location is convenient to distribute the vegetables to hotels, restaurants and shops, reducing the food miles for businesses and consumers. The farm also boasts using 77% less water than conventional agricultural methods.
The system is completely unaffected by the weather and seasonal changes, which means they can be grown 356 days a year.
All photos: Getty Images