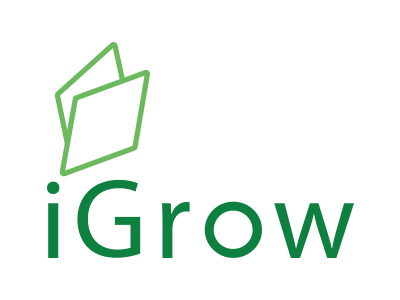
Welcome to iGrow News, Your Source for the World of Indoor Vertical Farming
US (PA): Hydroponic Farm Provides Hunger Relief
The pilot farm, which is now in production, is growing leafy greens, herbs, and microgreens
First Light Project announced the opening of their pilot for a hydroponic vertical farm located at the W. Berks Street warehouse location of the Delaware Valley’s largest hunger-relief organization, Philabundance.
The pilot farm, which is now in production, is growing leafy greens, herbs, and microgreens. These greens are grown using hydroponic technology in a 5-tier vertical racking system that supplies nutrient-rich water to the plant’s roots. High efficiency LED lights mimic optimal sunlight conditions up to 18 hours a day.
The 312 sq.ft. Pilot Farm is the precursor for First Light Project’s full-scale indoor hydroponic farm. The pilot farm is growing:
9 varieties of lettuce
2 varieties of Arugula
Varieties of Mustard Greens, Asian Greens, Kale and Swiss Chard
Genovese Basil
Mild & Spicy Microgreens
Crop cycles vary from 12-17 days for Microgreens, 31 days for lettuce and up to 45 days for Basil. Over the next 6 months, the pilot will grow continuous small batches of leafy greens, microgreens, and herbs to test for growth rate, yield, flavor and visual appeal. This testing enables First Light Project Farm to determine which optimal attributes of taste, size, and texture appeal to the customer base.
The host for the farm pilot is Philabundance who serves 90,000 people each week, 30 percent of whom are children and 16 percent of whom are seniors. A portion of the food grown by First Light Project Farm will be available to the community through Philabundance and its network of 400 member organizations. First Light Project Farm is one of a number of innovative community partners working with Philabundance to end hunger for good.
For more information:
First Light Project
Lois Davidson, Co-Managing Director
ldavidson@firstlightproject.org
www.firstlightproject.org
Publication date: Fri 24 Jan 2020
Why Vertical Farming Isn't A Miracle Solution To Food Security
Vertical farming is great for growing lots of food in a small space, but productivity comes at a cost: high energy use
Vertical farming is great for growing lots of food in a small space, but productivity comes at a cost: high energy use. We need to consider other, more sustainable, types of urban agriculture, says Andrew Jenkins
Friday 28 September 2018
A company in Scotland has unveiled what it claims is arguably the world’s most technically advanced indoor farm. Intelligent Growth Solutions’ vertical farm uses artificial intelligence and specially designed power and communication technologies. The firm says this reduces energy costs by 50 percent and labour costs by 80 percent when compared to other indoor growing environments, and can produce yields of up to 200 percent more than that of a traditional greenhouse.
Vertical farms like this aim to minimize water use and maximize productivity by growing crops “hydroponically” in small amounts of nutrient-rich water stacked in a climate-controlled building. But it’s important to recognize that the increased productivity of indoor vertical farming comes at the cost of much higher energy usage due to the need for artificial lighting and climate control systems.
By 2050, global food production will need to increase by an estimated 70 percent in developed countries and 100 percent in developing countries to match current trends in population growth (based on production information from 2005 to 2007). But in countries that already use the majority of their land for farming, this is easier said than done.
The UK, for example, uses 72 percent of its landmass for agricultural practices but imports nearly half of the food it consumes. To improve domestic food security and prevent natural habitats from being destroyed for new farmland, countries such as the UK need to consider new methods of food production.
Urban farming presents a unique opportunity to grow food on already developed land, increase domestic food production and minimize the distance food travels. Since the publication of Dickson Despommier’s 2010 book The Vertical Farm: Feeding the World in the 21st Century, vertical farming has become synonymous with urban farming. Although the agricultural skyscrapers illustrated in Despommier’s book are yet to be realized, the idea of growing food vertically has captured the minds of designers and engineers alike.
Aquaponic systems that grow food with the help of fish are a naturally lit option (Andrew Jenkins)
The energy demand associated with vertical farming, however, is much higher than other methods of food production. For example, lettuces grown in traditionally heated greenhouses in the UK need an estimated 250kWh of energy a year for every square metre of growing area. In comparison, lettuces grown in a purpose built vertical farm need an estimated 3,500kWh a year for each square metre of growing area. Notably, 98 percent of this energy use is due to artificial lighting and climate control.
Even with the reductions promised by Intelligent Growth Solutions, the energy demand associated with most vertical farms would still be very high, which positions vertical farming in a grey area. On the one hand, the world needs to produce more food, and on the other hand, it needs to reduce energy use and the production of greenhouse gases.
Urban alternatives
But indoor vertical farming isn’t the only way to grow food in cities. A plethora of naturally lit methods also exists, from raised beds in communal gardens to rooftop aquaponic systems that grow food with the help of fish. These methods all require less energy when compared to vertical farming because they don’t need artificial lighting.
Lufa Farms makes use of vacant roof space to grow food in naturally lit hydroponic greenhouses (Wikimedia Commons)
When viewing cities from above, it is clear to see just how many flat roofs are left vacant and the agricultural opportunities they represent. In the city of Manchester in the UK, unoccupied flat roofs account for an area of 136 hectares, representing one-third of the city’s inner urban area.
Gotham Greens in New York and Lufa Farms in Montreal, for example, are both commercial farms that use vacant roof space to grow food in naturally lit hydroponic greenhouses. Given the success of such projects and the area of roof space available, it seems strange that so many companies would skip ahead to methods of food production that still need a lot of costly development, as well as more energy to operate. Although they can’t grow as much food, rooftop greenhouses need at least 70 percent less energy for each square metre of growing area than artificially lit vertical farms.
Lead Photo: The method is a tempting solution for city designers low on space... but it’s not the only one out there ( Reuters )
3 Challenges of Growing In A Vertical Farm
As our world faces challenges associated with population growth, climate variability and the loss of arable land and freshwater, we humans need to find new and efficient ways to grow food
March 25, 2019
As our world faces challenges associated with population growth, climate variability and the loss of arable land and freshwater, we humans need to find new and efficient ways to grow food. Vertical farming has emerged in the past decade as one of the tools we can implement to face some of those challenges. In most cases, the vertical farm (VF) is characterized by an array of shelves stacked vertically and side-by-side, filling the volume of a warehouse-type space with lettuce greens and culinary herbs that are usually spaced tightly together. Under this configuration, a farm can grow upwards of 5 to 10 times the number of plants for a given footprint as compared to field-grown crops. Theoretically, the number of plants grown is only limited by the height of the building.
This unlimited growth potential is a lucrative proposition and has created a “sky is the limit” mentality for many prospective VF growers and developers who envision a space filled to the brim with plants. Unfortunately, this perspective has led many down an unrealistic path of ”packing them in,” considering only how much space is required between each vertical rack to fit the growing media, the lights, the full-height plant and sometimes even the arms of the automated harvesting machine. The space requirements for HVAC equipment and air circulation around the plants are often overlooked, resulting in the two most commonly identified difficulties when controlling the environment: humidity control and air movement.
Challenge No. 1:
Temperature and humidity
The first climate management challenge that vertical farmers must overcome is figuring out how much cooling, dehumidification, and heating is required to manage the temperature and humidity of the grow space. In a VF, lighting contributes the greatest source of heat, followed by motors used to operate fans, pumps, and automation. Because VFs are often well insulated and designed to operate day and night throughout the year, cooling is usually required 24/7 and year-round to remove the heat generated inside the space.
Dehumidification is also constantly required to remove the moisture added to the air via evapotranspiration (Et) from the plants and irrigation system. The rate and quantity of Et depends on several variables, including light intensity, air temperature and humidity (or vapor pressure deficit), air movement and the irrigation method. Although Et is greatest when plants are mature and the lights are on, Et does not stop when the lights go out. Plants continue to respire and give off moisture when the lights are off, and for continuously recirculating irrigation systems (e.g. NFT and aquaponics), evaporation from these systems can remain constant all day. Therefore, the size and operation of the dehumidification system should take into consideration both the maximum and minimum Et rates expected inside a VF.
Heating systems in the VF are rarely required, due to all the heat generated inside the space by lights. However, if the air conditioning (AC) system is used to both cool and dehumidify the space, then the AC system will create very cold air to remove (or condense) water out of the air. Typically, we don’t want to deliver that cold air (eg. 45° F) back to the plants, so we reheat it before sending it to the room. This is the most common use of heating in a VF.
Challenge No. 2:
Air circulation
The second biggest challenge is figuring out how to deliver the conditioned air everywhere within the vertical farm to create a (hopefully) uniform growing environment. When racks are spaced tightly together — both vertically and horizontally — it is difficult to create uniform conditions everywhere. In the horizontal direction, the plants and lights obstruct the flow of air from Point A to Point B, often resulting in temperature, humidity and airspeed differences from one end of the rack to the other. When the vertical height is very short (say 4 inches or less), this obstruction of air movement is magnified. On top of that, the air moving across the shelf is picking up heat (from lights) and moisture (from plants), causing it to become hotter and more humid along its path. Shorter vertical heights exacerbate this trend, as they limit the volume of air that can be squeezed between the rack levels, thereby restricting the amount of heat and moisture that can be absorbed and causing the air to heat up and humidify even more quickly as it travels from end to end. The result: large differences in temperature and humidity levels from Point A to Point B. And the longer the shelf, the longer the path of air and the greater the difference.
Several strategies can be applied to facilitate air movement in the VF. Many farmers employ the use of small circulating fans, installing them at incremental positions within the racking system and above the plants to help boost airflow from one end to the other. Air movement can also be enhanced by considering where conditioned air is introduced into the space and where it is then removed after loading up with heat and moisture. The type of air diffusers can also help distribute and push air into desired locations, as well as help mix cold air near the floor with warmer air near the ceiling to prevent the stack effect.
Cooling is usually required 24/7/365 in a vertical farm. Photo: Adobe Stock
Challenge No. 3:
HVAC equipment location
Space considerations aren’t limited to moving conditioned air through the racking system; they also include where to put HVAC equipment. Depending on the design, HVAC equipment can include air conditioners, dehumidifiers, circulation fans, ductwork, chillers, boilers, pumps, and pipes. Cooling and dehumidification equipment are best located outside the building, where heat and moisture can be rejected to the outdoor air. Some equipment (air conditioners, dehumidifiers, etc.) are ideally located on the roof of the building or on the ground outside and next to the room it is serving, helping to limit ductwork. Other equipment, such as chillers, need a designated area away from the building to accommodate the larger equipment. Inside the building and the VF itself, better air movement can be realized if adequate space is provided for ductwork, fans, and air delivery and mixing in general.
Conclusion
No matter what crop is grown, managing humidity control and air movement in a vertical farm is essential to plant productivity, harvesting schedules, quality control and, ultimately, profitability. Every developer, designer and dreamer would do well to include climate management as a foremost systems consideration — in line with lighting, racking, irrigation and automation — during the conceptual and facility planning stage. Only then can vertical farming rise to its full potential.
Nadia is the president and founder of Dr. Greenhouse, Inc., an agricultural and mechanical engineering firm that specializes in the design of HVAC systems for indoor plant environments.
Lead photo: Photos: Adobe Stock
Dr. Nadia Sabeh
Vertical farms Aquaponics Lettuce NFT Herbs Temperature Climate control
Malaysian Brothers Cultivate Indoor Farming
Agriculture technology firm Plant Cartridge Sdn Bhd has developed a growing kit to enable sustainable urban farming at home
Agriculture technology firm Plant Cartridge Sdn Bhd has developed a growing kit to enable sustainable urban farming at home. Now, it is utilising its knowledge for the growth of smart industry-scale farms in response to an insatiable demand for safe and sustainable food produce.
By collaborating with Cultiveat Group Sdn Bhd, another innovative agritech company, Liang and his team have been able to industrialise their humble growing kit. It is based on the simple science of hydroponics but refined and upgraded using a one-step soilless growing method.
The current venture with brothers John-Hans and John-Ian Oei of Cultiveat involves the extension of Plant Cartridge’s existing business and the former’s expertise in developing and managing industrial farms. Plant Cartridge provides the technology, which includes its highly successful growing kit — a 2ft-long covered rectangular ultraviolet-coated polyethylene tank that has holes to fit eight pods that contain select seeds and growing medium as well as a hole in the centre for irrigation purposes.
Meanwhile, Cultiveat worked on clearing the land it owns and is in the process of constructing greenhouses on a two-acre plot at the edge of Kapar, which is less than 3km from the coast of the Straits of Malacca. It already has a greenhouse on a plot of land in Klang, where it is growing 18 types of lettuce.
Read more at The Edge (Pathma Subramaniam)
Publication date: Mon 13 Jan 2020
Underground Farms Sprout in Seoul's Subway Stations
Subterranean vegetable farms are cropping up at subway stations in Seoul in a collaboration between Seoul Metro and an agricultural startup to utilize vacant spaces and diversify the subway operator's revenue sources
Consumers give thumbs up to less polluted air
KOTARO HOSOKAWA, Nikkei staff writerJ
ANUARY 14, 2020 JSTSeoul
Metro and startup Farm8 are exploring innovative methods of food production in urban areas. (Photo by Kotaro Hosokawa)
SEOUL -- Subterranean vegetable farms are cropping up at subway stations in Seoul in a collaboration between Seoul Metro and an agricultural startup to utilize vacant spaces and diversify the subway operator's revenue sources.
Seoul Metro is renting idle spaces to Farm8, a startup with about 300 employees which supplies vegetables grown indoors efficiently and safely to retailers and restaurants.Farm8 is also testing farm cafes in three stations and plans to open more outlets in the future, as well as to export longer-life vegetables, including paprika, to Japan.
Passing through a ticket gate at Sangdo Station on Line 7 of Seoul Metro in the central area of the city, passengers can see a glass-walled room filled with leafy vegetables in an underground space. Business people and families are seen relaxing at a cafe equipped with juicer-mixers and coffee machines next to Metro Farm, which opened in September last year.
As South Korea's subway stations contain large underground spaces, most transfer hubs and other big stations have commercial areas with restaurants and shops. However, locations further away from ticket gates are often left unused because they are unattractive to retailers.
Hydroponically grown vegetables at a Metro Farm in Seoul's Dongjak district.
(Photo by Kotaro Hosokawa)
Seoul Metro has been seeking tenants that will help improve the image of subway stations without additional costs as part of efforts to make use of unoccupied spaces, said Kim Seong-jin, a Seoul Metro manager. Farm8, which runs vegetable farms nationwide, grabbed Kim's attention.
Unlike with ordinary tenants, Seoul Metro signed a 10-year contract with Farm8 to cover rents and provide a fixed amount of profit. The store also provides a space next to the cafe in which children can learn about agriculture.
Some 30 types of vegetables, including varieties of lettuce, basil, and edible flowers, are grown in a cultivation room of about 200 sq. meters. The plan is to harvest 30 to 40 kg of vegetables a day on shelves of about 4 meters and sell them as ingredients for the cafe's salads, priced at 5,900 won ($5.04), and 3,000-won vegetable juice. Vegetables that are unsuitable for consumption at the cafes will be sold to outside restaurants.
Growing hydroponic vegetables under light-emitting diodes is 40 times more efficient per unit area than growing them outdoors, according to Yeo Chan-dong, assistant manager of Farm8. The company's hydroponic vegetables are gaining popularity among consumers, particularly parents, who are wary of vegetables grown outdoors because of air pollution caused by PM2.5 -- particulate matter that measures less than 2.5 micrometers in diameter -- which is seen as hazardous in South Korea.
The company will operate stores combining cultivation rooms and cafes depending on locations, including setting up salad box vending machines at subway stations in business districts. Farm8 has already started testing "smart farms" in which artificial intelligence-powered robots will plant and harvest vegetables as well as adjust water quality. It also plans to develop new types of stores so that it can reduce operation costs, and it will open two more outlets in early 2020.
There is still so much to do to improve the profitability of the subway station business, Yeo said, but Farm8 plans to open more Metro Farm stores, betting that opening "plant factories" at subway stations used by several million people per day will have a huge advertising impact. The effort is likely to draw attention as a new method of local food production for local consumption in urban areas.
New Dubai Vertical Farm Set To Start Operations In Q2 2020
Spanning an area of 50,000 sq ft, the facility will have the capacity to produce 3,500kg of high-quality fruits and vegetables on a daily basis
17 Dec 2019
Dubai Industrial City will host Badia Farms' upcoming new large-scale high-tech vertical farm
The Badia Farms facility in Dubai Industrial City is rare as it will combine fruits and vegetables on a commercial large-scale basis.
Dubai Industrial City has announced it will be home to Badia Farms’ upcoming new large-scale high-tech vertical farm.
Badia Farms, a regional AgTech leader, said the vertical farm is expected to start operations in the second quarter of 2020.
Saud Abu Al-Shawareb, managing director of Dubai Industrial City, and Omar Al Jundi, founder and CEO of Badia Farms, signed an agreement formalizing the partnership.
Spanning an area of 50,000 sq ft, the facility will have the capacity to produce 3,500kg of high-quality fruits and vegetables on a daily basis.
From Dubai Industrial City, Badia Farms will grow more than 30 varieties of fruits and vegetables sustainably, it said in a statement.
Vertical farming uses high-tech methods to produce crops in a controlled environment leveraging vertical space, without pesticides, and using fewer resources compared to traditional farming.
The Badia Farms facility in Dubai Industrial City is rare as it will combine fruits and vegetables on a commercial large-scale basis.
The signing ceremony was also attended by Dr. Thani bin Ahmed Al Zeyoudi, Minister of Climate Change and Environment, who said: “Badia Farms is an exceptional example of how the UAE’s agricultural industry can thrive while protecting our environment for future generations.
"This new high-tech vertical farm will contribute to the UAE’s commitment to becoming more sustainable. Hydroponic technology is a major contributor to agricultural sustainability and food diversity, as it improves crop production and lowers its cost. This is evident in the successful production achieved by Badia Farms in the very short time since its inception.”
Mariam bint Mohammed Saeed Hareb Almheiri, Minister of State for Food Security, added: “The UAE has set clear plans to enhance its food security, relying on an integrated ecosystem to produce and manage food – a system that employs advanced modern technologies to develop solutions to the challenges the UAE faces, most notably water scarcity and lack of arable land. Controlled-environment agriculture systems are an important solution for producing food in the UAE and the world. The UAE is now home to several vertical farms equipped with hydroponics and soilless farming technologies.”
Al Jundi said: “As founders of the first vertical farm in the region back in 2016, we are committed to innovation in the AgTech space to achieve our ultimate goal of elevating the UAE and the region from importers to exporters of fruits and vegetables.”
For all the latest tech news from the UAE and Gulf countries, follow us on Twitter and Linkedin, like us on Facebook and subscribe to our YouTube page, which is updated daily.
VERTICAL FARMING VERTICAL FARM IN DUBAI BADIA FARMS DR THANI BIN AHMED AL ZEYOUDI UAE'S MINISTER OF STATE FOR FOOD SECURITY FOOD SECURITY UAE DUBAI INDUSTRIAL CITY TECOM GROUP
SWITZERLAND: Migros Basel And Growcer Launch Joint Vertical Farming Project
Switzerland's first "Robotic Vertical Farm" is currently being built in a hall located on the Wolf site in Basel. From sowing to irrigation and harvesting, machines take over the work fully automatically
“Vertical Farming Meets The Demand
For More Sustainability And Regionality"
Together with the Migros Basel cooperative, Growcer is developing the first "Robotic Vertical Farm" in Switzerland, in order to grow regional foodstuffs there in the future, independent of weather conditions, pesticide-free and water-saving, and - thanks to the shortest transport routes - to deliver them quickly to the Migros branch. The start of production is imminent, and the first products are expected to be available exclusively in the MParc Dreispitz in the summer.
Switzerland's first "Robotic Vertical Farm" is currently being built in a hall located on the Wolf site in Basel. From sowing to irrigation and harvesting, machines take over the work fully automatically. The production chambers are sealed off from the environment, which means that production can take place all year round without soil, without any pesticides and with up to 90 percent less water.
In addition to all this, land consumption is, of course, minimal, as the cultivation beds can be stacked. This creates around 1,000m2 of cultivated area on a surface area of just 400m2. The farm can produce leafy vegetables and herbs all year round and, thanks to the immediate proximity of the sales point in the MParc Dreispitz, these can be delivered absolutely fresh within hours of being harvested.
Regionality and continuity
"Switzerland, like many countries, is dependent on imports. Via Growcer we bring regionality and continuity into it. In addition, pesticides are a problem for the population and nature, which we can solve by doing without them. With Migros Basel we have found a partner who supports our values and goals and is committed to the introduction of a new generation of sustainable products", says Marcel Florian, CEO of Growcer AG.
"Vertical farming is a trend that meets the demand for more sustainability and regionalism", says René Lori, Head of Supermarkets/Catering at Migros Basel. "The cooperation with Growcer gives us the opportunity to invest in an innovative and future-oriented project".
Year-round production
The production facility on the Wolf will be completed next spring, and the first products are expected to be available exclusively at Migros in the MParc Dreispitz in the summer. It is planned to produce further vegetables or fruit all year round at a later date and to supply other branches.
Migros Basel and Growcer are looking forward to the cooperation.
Source: Migros Basel
Publication date: Fri 17 Jan 2020
The Planty Cube is A Vertical Farming System Assembled Like LEGO Bricks
Agriculture IoT startup n.thing has developed ‘planty cube,’ an automated vertical farming system that allows users to maintain crops at any time and from anywhere. the system connects like LEGO bricks with a modular design made up of multiple capsules called pickcells that contain the seeds of each plant
jan 14, 2020
Agriculture IoT startup n.thing has developed ‘planty cube,’ an automated vertical farming system that allows users to maintain crops at any time and from anywhere. the system connects like LEGO bricks with a modular design made up of multiple capsules called pickcells that contain the seeds of each plant.
images courtesy of n.thing
to demonstrate its potential, n.thing has developed a smart hydroponic farm that uses the planty cube design. shaped like a shipping container, it is made of stacked rows and shelves of planters on each wall with each pickcell roughly two inches in width, length, and depth. after seeds are sown through their smart seed capsules, a computerized system controls the environment by monitoring plant health and adjusting the LEDs, temperature, and humidity, accordingly. the planty cube system, which uses sensors to collect data on the plants, can also be controlled via a smartphone, presenting the unique opportunity to farm remotely.
the grow system can work in a number of different settings, from an apartment to a cafeteria, and is automated enough that plants can thrive without constant human attention. the ease of use also makes it simpler for clients who want to start vertical farming businesses, to increase the size of their farm at low-costs, over longer periods of time, and in line with their individual business growth.
a number of companies are developing vertical farming concepts including LG who launched its own indoor vertical farm at CES 2020. unlike glasshouse production, which relies on sunlight, vertical farming makes use of led lighting to provide different wavelengths of light, according to crop and growth stage need. these high-tech units are being presented as the solution to many of the challenges facing traditional production methods, such as pollution and water use.
Farmshelf Takes Growers From Seed to Plate
Kitchen gardens are going high-tech as the development of smart, efficient hydroponic grow systems helps both novice and experienced growers from seed to plate
Farmshelf is A Smart, Automated Farm For Hotels,
Restaurants And Corporate Cafes
BY CORRIS LITTLE ON JANUARY 15, 2020
BROOKLYN, NY—Kitchen gardens are going high-tech as the development of smart, efficient hydroponic grow systems helps both novice and experienced growers from seed to plate. One such company is Farmshelf, based here, which builds smart indoor farms that enable people to grow leafy greens, herbs and flowering crops where they live, work and eat.
“Our bookcase-sized smart, indoor farms are small enough to fit into a restaurant and powerful enough to provide pounds of fresh produce every week. Farmshelf brings the outdoors inside and grows food two to three times faster than conventional farming,” said J.P. Kyrillos, co-founder, Farmshelf.
Farmshelf’s bookcase-style growing system was invented by Andrew Shearer, Farmshelf co-founder, and CEO. He found inspiration through his passion for food, technology, engineering, and community.
“He married his years of volunteering experience to fund education in agriculture in Nicaragua’s food-insecure communities, and professional tech experience in Silicon Valley to build a tool that allows people to grow healthful, flavorful food anywhere, any time and know its source,” said Kyrillos.
As a result, the hospitality industry has taken notice. At HX: The Hotel Experience Powered by AAHOA, Farmshelf was the winner of the Best of Show award. Farmshelf has also captured the attention of hotel chefs and high-profile New York restaurateurs like Marcus Samuelsson of Red Rooster and Jose Andres of Mercado Little Spain, who have entered into partnerships with the company.
“They find as much value in the five to six pounds of leafy greens and herbs the units produce weekly as they do the organic marketing value,” Kyrillos said. “Our partners in the hospitality space share with us that the units add beauty to whatever space they are in. We designed Farmshelf to be eye-catching, and we often see hotel guests and diners in the restaurants that house Farmshelf taking time to really look at the unit, discover what it is and admire what it provides.”
Kyrillos also noted that the chefs at the hotels where Farmshelf is stationed regularly praise the accessibility and freshness of the produce.
“We aim to shorten the distance between farm to plate—a journey that’s often hundreds or thousands of miles—and having fresh herbs and greens right at your fingertips not only allows for speedy and easy access, it provides superior freshness,” he said.
Sustainability is a key facet of the Farmshelf business.
“Farmshelf helps minimize food waste because you know exactly how much produce you are able to harvest at any time, and no food expires in transit,” he said. “Nearly 40% or more of the food we grow in the U.S. ends up in a landfill. That equates to millions of dollars and pounds of food that could have otherwise been used. It’s a solvable problem, and we’re working to lay the building blocks to address it in a scalable way. In addition, Farmshelf uses 90% less water in comparison to traditional soil growing. By enabling you to harvest just what’s needed, Farmshelf also eliminates packaging, environmental impacts from transportation, and food waste.”
Kyrillos noted that the Farmshelf leadership team has seen firsthand the devastation that a lack of access to food causes.
“At Farmshelf, we are passionate about ensuring people have access to fresh, healthful food, anywhere and anytime,” he said. “And, while we are still a young company, we are working to scale our technology so that more people can have access to food.”
Andrew Shearer Farmshelf food waste garden Gardening HX: The Hotel Experience Hydroponic J.P. Kyrillos Sustainability
Wasabi Japonica Grown Under GE LED Grow Lights
Contact Hort Americas if you are looking to learn more about using the Current LED grow lights to produce crops grown in tissue culture and micropropagation facilities
The “Hardest to Grow” Plant in the World
The Opportunity
Wasabi Japonica is widely accredited as the “hardest to grow” plant in the world. The plants are native to Japan and require a very specific set of environmental conditions to successfully produce healthy plants.
Wasabi is most commonly associated with Japanese food, where it is used as a unique spice and as a condiment on sushi, but many are now learning of its secondary metabolites that possess distinct health benefits including significant anti-cancer and antimicrobial properties. Unfortunately, few growers outside of Japan have successfully grown Wasabi Japonica commercially. This has led not only to a high global demand for fresh grown product, but also to an increasing amount of interest from commercial growers trying to tap into a market that now pays an estimated $325/£250 per kilo of rhizome.
The Possibilities and the Challenges
Successful field cultivation is difficult because of the specific parameters required for growth over a relatively long harvest period of up to 2 years. Wasabi is also highly susceptible to pests and disease. Although resistant strains are available in Asia, the West is restricted to two main varieties: Mazuma and Daruma. Vegetative propagation can be successful for F1 generations, but thereafter, endogenous fungal infection leads to poor yields and major crop loss. Therefore, it is important to grow from clean stock produced under controlled environmental conditions.
A small startup in Scotland called The Functional Plant Company is currently working with LED grow lights from GE Current, a Daintree company to grow wasabi. The Functional Plant Company is using a variety of hydroponic and micropropagation techniques to produce plantlets from tissue culture through to acclimation and eventually full maturity. They are proving that light intensity and spectrum are equally important factors in establishing new cuticle and stomatal development. Their aim to prove this can become more efficient and faster by using GE LED battens as compared to natural daylight.
Finding Success with LED Grow Lights
Trials show the plants have established good root production using the Arize Lynk LED Grow Lights at 60umols/m2/s, although they noted the leaf canopy growth is slower and darker than when using TLEDs at equal intensity. The Functional Plant Company added that interesting results also arose when trying other spectrums of the Arize LED grow lights. They have noted a darker callus at higher light levels with high percentage of red light, while lower intensity prevents leaf burn and dehydration during early acclimation.
They concluded by noting that the Arize LED grow lights are very energy efficient, generating little heat—which is perfect for Wasabi as even a small temperature increase can cause wilt and plant loss.
Contact Hort Americas if you are looking to learn more about using the Current LED grow lights to produce crops grown in tissue culture and micropropagation facilities.
US: Lynchburg, Virginia - Lynchburg Hospital Offers Unique Experience With Home-Grown Lettuce
Centra in Lynchburg is offering fresh lettuce that’s grown in the building at its salad bar. Centra partnered with a Charlottesville company to grow four different kinds of lettuce, including romaine. Nutrition service officials said they can control the plant’s environment and receive alerts on their phone if something is wrong
Lettuce takes two to four weeks to grow before served to patients, families
LYNCHBURG, Va. – Feedback has been good for one hospital that’s taking dining to another level.
Centra in Lynchburg is offering fresh lettuce that’s grown in the building at its salad bar.
Centra partnered with a Charlottesville company to grow four different kinds of lettuce, including romaine.
Nutrition service officials said they can control the plant’s environment and receive alerts on their phone if something is wrong.
“We have chefs who serve things. We want the food to be nutritious. We want the food to be good tasting. So, things like this are innovative. We are the first ones to have this in the U.S. This does not exist in any other hospital,” Timothy Schoonmaker, executive chef of Centra Nutrition Services, said.
Schoonmaker said it takes about two to four weeks for the lettuce to be ready and served to patients and families.
ABOUT THE AUTHOR:
Magdala Louissaint
Magdala Louissaint is an award-winning journalist who joined WSLS 10 in July 2017 as the Lynchburg bureau reporter.
A First International Project For Inno-3B
Using Inno-3B Technology, Madar Farms plans to triple its current production of microgreens. Inno-3B’s vertical farming towers enable high yields while producing plants at low cost and with little energy, in a limited space
Saint-Pacôme, Quebec, Canada, January 14, 2020
This document is to announce that Inno-3B, a company specializing in the development of automated vertical farming technology, has recently entered into an agreement for the design, construction, and delivery of an automated production tower with a major customer in Dubai ̧ in the United Arab Emirates. The delivery is scheduled for the summer of 2020.
Using Inno-3B Technology, Madar Farms plans to triple its current production of microgreens. Inno-3B’s vertical farming towers enable high yields while producing plants at low cost and with little energy, in a limited space. Madar Farms also plans to produce tomatoes exclusively under LED lighting in this same facility, which will be located halfway between Dubai and Abu Dhabi, a world-first according to the company.
"We are very proud and enthusiastic to export our know-how from here to the international market. This agreement marks the deployment of our sales efforts on a global scale," says Martin Brault, President, and co-founder of the Canadian company.
About Inno-3B:
Inno-3B is a young innovative company based in Saint-Pacôme, Québec, Canada. The company designs and manufactures vertical farming towers with controlled environment for growing high-density plants. The technology developed aims to offer sustainable solutions to global food production issues while reducing greenhouse gas emissions related to agriculture.
About Madar Farms:
Madar Farms is a company that uses advanced methods to grow high-quality fresh produce, with a mission to help solve the food and water security problems in the region.
Madar Farms aims to provide a holistic approach to sustainability by supporting sustainability education in schools through learning content, resources, and practical experiences, working with governments to inform policy, ensuring that the crop is sustainable and always provides an excellent product, developing future solutions for food sustainability.
Headquartered in Dubai and with a research and development center in Abu Dhabi, Madar Farms also operates Sustainable Futures, a program for schools to give the next generation the awareness, knowledge, skills, and behaviors needed to create a sustainable future for us all.
An Urban Farm Is In The Works For Milwaukee's Near West Side
Planet2Plate's plans include a building at 817 N. 27th St. and a lot at 2734 W. Wells St. that will be used for growing, processing and serving the produce grown on-site
Sarah Hauer Milwaukee Journal Sentinel
Dec 30, 2019
Building at 817 N. 27th Street in Milwaukee, site of proposed urban farm.
Michael Sears / Milwaukee Journal Sentinel
An urban farm is in the works for Milwaukee's near west side.
Planet2Plate Inc. has filed applications to develop a building and lot off Wells Street west of downtown into an urban farming site. The Brooklyn-based company that designs edible learning spaces and hands-on education programming is planning to launch its first project in Milwaukee.
Planet2Plate's plans include a building at 817 N. 27th St. and a lot at 2734 W. Wells St. that will be used for growing, processing and serving the produce grown on-site.
At 817 N. 27th St., Planet2Plate applied to use the first and second floors as a commercial farming enterprise with food processing, a sit-down restaurant, a retail area, an assembly hall and space for personal instruction. Planet2Plate plans to use the lot at 2734 W. Wells St. to grow plants with plans to build a new greenhouse.
Building at 817 N. 27th Street in Milwaukee, site of proposed urban farm.
Michael Sears / Milwaukee Journal Sentinel
The building on 27th Street is owned by Cecelia Building LLC, which is led by Rick Wiegand, the owner of the Ambassador Hotel. He said earlier this year he was considering plans to redevelop buildings at 801-813 and 817-831 N. 27th St.
Planet2Plate says that it revitalizes existing urban spaces with green infrastructure for hands-on learning opportunities. It said in December 2018 that it was looking for a space in Milwaukee to develop its new project.
Sarah Hauer can be reached at shauer@journalsentinel.com or on Instagram @HauerSarah and Twitter @SarahHauer. Subscribe to her weekly newsletter Be MKE at jsonline.com/bemke.
Wageningen Researches Efficiency of Vertical Farming
Researchers of Wageningen University & Research are looking at how vertical farming can be more efficient
14 Jan 2020
Researchers of Wageningen University & Research are looking at how vertical farming can be more efficient.
“In a high-rise building – on a surface area about the size of a soccer field – you can grow enough vegetables for 100,000 people who each eat 250 grams of vegetables a day. You have complete control over the production process, so you are not dependent on the weather, the temperature, the daylight and the season. This makes vertical farming possible everywhere – also in infertile areas, in the desert or on Mars”, says Leo Marcelis, professor of Horticulture, in his blog on the website of Wageningen University & Research.
Vertical farming 1 of the solutions to the global food issue
“Vertical farming will not solve food shortages. It does not lend itself to rice and cereal production, but it is good for healthy, fresh vegetables, packed with fiber and vitamin C, and grown without contamination by pesticides or harmful microorganisms. That makes vertical farming one of the solutions to the global food issue”, says Marcelis.
Vertical farming takes place in buildings – the crops are grown on top of each other in several layers. - Photo: AFP
2 to 4 litres of water to grow a kilo of tomatoes
Vertically grown vegetables can make do with much less water. “We can recycle all the water and recover most of the water that the plants evaporate. As a result, we only need 2 to 4 litres of water to grow a kilo of tomatoes, whereas we use 17 litres of water in a Dutch greenhouse and in theory at least 60 litres for soil cultivation in for example southern Europe, and in practice often 200 litres,” says Marcelis.
In the closed cultivation system, nutrients such as nitrates and phosphates are also retained, while outside cultivation they end up in the soil, groundwater and surface water.
Pesticides a thing of the past
The use of pesticides is also a thing of the past, the professor emphasises. “By ensuring high hygiene levels, we can prevent insects and diseases from entering the building with employees, materials, seeds or air.”
Marcelis says the fact that the vegetables are not sprayed is good for our health, the environment and the preservation of plant and animal species. Moreover, thanks to local production, no shipping over long distances is required, which means that the CO2 footprint for transport is a lot smaller.
LED light healthy for plants?
The vegetables are grown on multiple floors of a high-rise building without daylight using special LED lamps, which often emit purple or bright pink light. Is LED light healthy for plants? “If we adjust the amount, colour and duration of the light, the amount of water and the temperature and composition of the air very precisely, we can give the crops much more nutritional value. I am absolutely convinced of that; there is already evidence that these factors influence nutritional value. In addition, we can also improve taste and shelf life.”
High energy consumption
Even though LED lamps are economical, a quarter of the costs goes to energy consumption says Marcelis in his blog. “If you can make substantial savings on this, the investment will become more affordable,” he says. Together with colleagues, he is studying options for reducing energy consumption. “We want to ensure that the light is used more efficiently by the plant. If we can optimize the temperature, humidity, the concentration of carbon dioxide and availability of water and fertilizers and can determine the optimum intensity and color of the light for every moment of the day, we can produce much more per unit of light,” says Marcelis. He also wants to improve the efficiency of climate control technologies.
Improve the crops
Current crops have been bred for outdoor cultivation and greenhouse cultivation. “We can also breed crops for these indoor circumstances, but that is a long-term task. Plant breeding projects easily take ten years.” And finally, the buildings can also be made more energy-efficient, for example by using the heat generated by the light for the heating of houses and offices.”
5 million euros for research into vertical farming
The Netherlands Organization for Scientific Research (NWO) has awarded 5 million euros to Wageningen research into vertical farming. “Our greenhouse horticulture sector is leading and has a lot of technology and knowledge that the Netherlands exports worldwide, also in the field of vertical farming. That is why it is important that we stay ahead,” says professor Marcelis.
Greenhouse cultivation is very efficient in the Netherlands and therefore much cheaper than vertical farming. In many places in the world, however, it is too cold in the winter or too hot in the summer to keep growing vegetables all year round. And sometimes there is simply not enough land available, for example in the city-state of Singapore. Singapore, but also the US, countries from the Middle East and Japan, are interested in vertical farming, according to the professor. “In Japan, food safety has become very important since the Fukushima nuclear disaster, and vertical farming is very safe,” explains Marcelis.
The Humble Veggie Patch Just Went Hi-Tech
Growing vegetables and herbs is set to get a whole lot easier with big tech companies creating indoor 'vertical farms'
Forget battling insects and having to remember to water your veggie patch, growing herbs and vegetables at home is set to become hi-tech with new indoor farms.
by Tanya French
9th Jan 2020
Growing vegetables and herbs is set to get a whole lot easier with big tech companies creating indoor 'vertical farms'.
Samsung and LG have both spruiked their answer to the humble vegetable patch - creating indoor gardening appliances that enable people to have their own veggie garden, even if they don't have a backyard.
Samsung's Chef Garden technology integrates with its next-generation Family Hub refrigerator and automatically regulates light wavelengths to enable users to grow and enjoy fresh, pesticide-free fruit and vegetables all year round.
Samsung's vertical farm.
"There is a growing interest in healthy food," said Samsung LED technology centre's Chohui Kim.
"Horticulture LED is playing a key role in vertical farming and indoor crop cultivation, and we are looking to expand its applications in various fields."
The indoor farm integrates with the Family Hub fridge.
While Samsung's offering can easily fit into an existing kitchen, LG's version needs to be in-built into new or renovated kitchens.
The LG vertical farm consists of 24 pods which all have seeds and fertiliser in-built.
The machine recognises the amount of light and water it requires for optimum growth.
The farm - which takes 4-6 weeks to grow - will produce enough leafy vegetables to feed a family of four.
LG’s vertical farm solution. Photo: Tanya French
There's no word yet on when the technology will be available in Australia or what it will cost but an LG spokeswoman said it was 'very high end and part of a bigger kitchen solution'.
Vertical Farming Startup Expands Through New Retail Deals With Whole Foods, Safeway
A South San Francisco farming startup is quickly growing its retail roots after landing new distribution deals with two of the area's largest grocers
Vertical farming startup Plenty is ramping up its retail distribution through two new deals with Whole Foods Market and Safeway.
South San Francisco, CA
By Katie Burke – Staff Reporter, San Francisco Business Times
A South San Francisco farming startup is quickly growing its retail roots after landing new distribution deals with two of the area's largest grocers.
Vertical agriculture company Plenty will soon stock the produce shelves at a handful of Whole Foods Market and Safeway locations across the Bay Area to mark the beginning of what the startup is hoping will be a widespread push into new retailers and restaurants. Plenty's vegetables first began selling in retail outlets last year and are now available through Good Eggs, Berkeley Bowl, Bi-Rite Market and the robotic burger restaurant, Creator.
Plenty grows its produce hydroponically, meaning it feeds the plant without having it rooted in soil. By cutting water consumption, shortening the supply chain and shrinking the amount of space needed to grow produce, Plenty will be able to deliver more produce at a faster rate, Plenty CEO Matt Barnard previously told the San Francisco Business Times.
Matt Barnard, CEO and CoFounder, Plenty Inc.
Since it was founded in 2013, Plenty has raised more than $400 million, $175 million of which was raised as part of a Series C round the company closed last June. The round pushed the company's valuation to its current $1.05 billion.
The latest infusion of capital has helped fund the company's expansion to Los Angeles, where it's in the process of opening a new 95,000-square-foot farm in Compton. The new facility is expected to begin supplying produce like bok choy, mizuna, fennel, and kale to retail partners by the end of this year.
The company's South San Francisco farm, which launched last summer, is on track to hit full capacity before the end of the year. At that point, it will be able to supply more than 100 grocery partners throughout the Bay Area. Plenty also operates a test farm in Wyoming, where it experiments with different seeds and varietals.
Plenty is ultimately aiming to have as many as 500 vertical farms stationed in highly populated, urban areas around the world.
"We are able to deliver a product that’s both better than and at a price that is less than anything that’s in the market," Barnard previously said. "You are going to see us on more and more shelves. You going to be able to find us, have us delivered to your home. We want our product in more people’s hands and mouths."
Europe Can Be At The Heart of Tech With Purpose
“Some say China has all the data, and the US has all the money. But in Europe, we have purpose.”
09 Jan 2020
Tom Wehmeier Partner and Head of Research, Atomico
This article is part of the World Economic Forum Annual Meeting
• Venture-backed, purpose-driven companies represented 12% of all capital invested in Europe in 2019.
• Talent and consumers are both demanding start-ups display social commitment.
• Only 1 in 5 start-up founders actually measure environmental and social impact.
“Some say China has all the data, and the US has all the money. But in Europe, we have purpose.”
Thus observed EU commissioner for competition Margrethe Vestager when she outlined her priorities for the next five years in October.
Her words could not be timelier. This year, the number of purpose-driven European founders who have pitched to us at Atomico has been overwhelming. Tech leaders have the most powerful tech toolkit in history available to them, and European companies are stepping up to help solve some of the world's most pressing challenges such as the climate crisis and healthcare.
We quantified this trend in our annual State of European Tech report, released in November. With Dealroom, we created a framework to assess venture-backed European tech companies based on their alignment with the United Nations Sustainable Development Goals (SDGs). The analysis focused on a subset of seven of the 17 SDGs. Only companies where the purpose-driven impact was considered core to the business model were included in the final dataset and analysis.
In total, the analysis identified 528 unique venture-backed, purpose-driven tech companies. They raised a total of $4.4 billion in capital investment in 2019, up from less than $1 billion in 2015. That $4.4 billion represents 12% of the total capital in Europe invested in 2019. It also represents the third largest “industry” in European tech by capital invested, behind fintech and enterprise SaaS.
These companies span Europe and include Infarm in Germany, which is building advanced vertical farms, telemedicine firm Kry in Sweden, and insect farming start-up Ÿnsect from France.
From an investor's point of view, it is obvious that the world’s biggest challenges also represent some of the world’s biggest markets and opportunities. But the rise of purpose-driven tech in Europe is also a response to the changing priorities of talent and consumers in Europe.
More debate and visibility over the impact and unintended consequences of digital technology on our society have made talent think more about working for companies that align with their values. Kate Hilyard, COO at Healx in the UK who we partnered with this year, expressed this trend very well in the report.
“At Healx, we believe every rare disease patient deserves a treatment. It's this belief that drives us to achieve our mission of taking 100 new treatments towards the clinic by 2025. Having such a clear mission also helps with recruiting and retaining the best and brightest talent. For the team here, there's no bigger motivator than knowing you're applying your skills to improving the lives of patients, their careers and their families. This is especially the case for the many team members who count either themselves or a relative amongst the 400 million people worldwide living with a rare disease.”
Then there are consumers who also want to support companies that align with their values and beliefs. According to a survey of 30,000 global consumers by Accenture Strategy, 62% of consumers want companies to “take a stand on current and broadly relevant issues like sustainability, transparency or fair employment practices”.
It also makes sense that European tech start-ups are differentiating themselves on purpose, as compared to their US or Asian peers. Many western European countries are leaders on sustainability from energy to transportation. According to RobecoSAM and Robeco’s Country Sustainability Ranking, a comprehensive framework for analyzing countries’ ESG performance based on governance, societal and environmental considerations, seven of the top 10 countries are in Europe.
Despite this rise in purpose-driven companies, only one in five founders told us in our State of European Tech survey that they are already measuring their firm’s environmental or social impact – something potentially important for all tech companies regardless of their business model. Given that the majority of founders say they are considering measuring this, and only 14% say they don’t think it’s important, measurement seems to be one way that investors could support all founders to consider the impact of their business on society.
In the early 20th century, technologies from electrification, to the washing machine to the jet engine improved the day-to-day lives of millions and opened up new frontiers for humanity. Technology drove economic growth and boosted prosperity, but it also left deep scars on the environment and failed to solve big problems such as global food security.
Though we are only two decades into this century, the work of purpose-driven European founders suggests that the legacy of technology in the 21st century might have a more beneficial and transformational impact on our society, one in which purpose and profit are mutually reinforcing.
Lead Photo: An employee of the urban farming start-up Infarm checks an indoor growing system.
Image: REUTERS/Hannibal Hanschke
US: Massachusetts - Alum Introduces Brookline To New Farming Techniques
Levine's startup Town to Table utilizes several different hydroponic technologies such as those made by Freight Farms, which allows plants to be grown in winter. Each 40-foot container can produce the equivalent of an acre of conventionally grown crops
GRAPHIC BY NICK CLONEY
Nick Cloney, News Managing Editor
January 14, 2020
Levine's startup Town to Table utilizes several different hydroponic technologies such as those made by Freight Farms, which allows plants to be grown in water. Each 40-foot container can produce the equivalent of an acre of conventionally grown crops.
Massachusetts isn’t exactly known for its farming capabilities. Between its varied terrain, harsh winters, and short growing seasons, many obstacles stand in the way of the state producing much agriculturally. But Jack Levine ‘16 is working to change that.
Levine felt that his experience in high school lacked real-world relevance. Now, his work to introduce innovative and sustainable agricultural techniques to the Brookline community through his startup Town to Table allows him to offer real-world experience to students at the high school.
Starting after Thanksgiving, Town to Table plans to take on up to 10 high school students as interns for the second semester. Student volunteers in the program would gain hands-on experience working in Town to Table’s hydroponic Freight Farm, a shipping crate modified to grow crops in a water-based medium, as opposed to a planting bed made of dirt.
Social Studies teacher and Food Justice Club adviser Roger Grande explained how the key feature of hydroponics – the delivery of nutrients through the water – is beneficial for the growing process.
“The key thing is that no matter how nutrients are being delivered to the plant, as long as they’re getting there, the plant is going to grow. If they are being delivered via water, then it cuts down on the lack of mobility and lack of flexibility that you have to deal with when everything is buried in dirt,” Grande said.
Levine said that the cross-country transportation that most vegetables in Massachusetts undergo reduces their quality, a problem solved by localized agriculture.
“In Massachusetts, 98 percent of our leafy greens come from California or Arizona, so pretty much every time I eat a salad, I think of it being jet-lagged, like how you feel when you get off that plane in California,” Levine said. “We’re offering districts farm-to-plate food. Within 24 hours of when we harvest it, students will be eating it.”
Grande said that one of Levine’s goals is to give students an opportunity to gain hands-on experience in an environment unlike any they have encountered before.
“I think he would also like to see this programming be integrated to the Brookline public school system, and for kids to have really interesting opportunities related to learning by doing. That’s authentic learning – it’s not just learning about something, it’s learning by doing that thing,” Grande said.
Levine said he was often a difficult student to teach during his time at the high school due to his lack of engagement with traditional high school subjects.
“Funny enough, I met with Brittany Stevens recently to talk about introducing this program to some of her classes. She asked me if I remember how I used to say every single day, ‘we have to fix the school,’” Levine said. “‘School doesn’t work’ was kind of one of my things since it especially didn’t work for me. I was off the walls. I was a pain in the butt for teachers, I was crazy.”
English teacher Elon Fischer, who taught Levine’s English for Entrepreneurs class during his senior year, said that he showcased an interest in business and charting his own path while still in high school.
“He was a goofball, but he was also very interested in entrepreneurship. By the time he was a senior, he was kind of fed up with school, and was looking to do something a bit more interesting than what BHS offered,” Fischer said. “Jack felt like school was just a big game and he wasn’t very interested in playing it. Great sense of humor, really a smart kid, but he was looking for something different to do.”
Grande said he was impressed with Levine’s vision to expand his business and involve food justice.
Levine said that the goal of any partnership would be to provide students with hands-on experiences that are relevant to their future career paths.
“That’s what we want, to take this and show other students that something like this can capture their attention in a classroom. You know, there’s no right or wrong answer when you’re growing a plant. It’s just a process and it’s a process in which you’re constantly learning. To us, that’s what we should be preparing students to do,” Levine said.
Grande explained that one of the biggest benefits of Town to Table’s services is the autonomy and decision-making power that sustainable, localized agriculture offers.
“At its core, it’s about empowerment: it’s about having more control over our health, our nutrition, and our values. It’s about seeing your place in the world and taking back some of your power from people who are making choices for you,” Grande said. “People should be more focused on being thoughtful about the choices they’re making, or the choices that are being made for them. There are many powerful forces that try to shape those things and steer us into buying what they’re marketing.”
Fischer said that Levine is a great role model for how students can take things they’re passionate about and transform them into careers.
“This is just a great example of what kids can do when they find something that they care about. And I think that the more that we as a school can make these opportunities available to kids, and work hard to spark their interests in things that aren’t directly academic, the better,” Fischer said.
ALASKA: Indoor Produce Sprouts In Anchorage
Anchorage Greens is an expansion of Juneau Greens, a similar business in the state’s capital, said Trevor Kirchhoff, who co-owns the businesses with John Krapek. In the back of Anchorage Greens’ warehouse, a vivid green garden grows in a hydroponic system. Racks of plants sit in nutrient-filled water under LED lights
Author: Alex DeMarban
Anchorage Greens: This new indoor farm at 1207 E. 73rd Ave. in South Anchorage is building a devoted clientele eager for tasty lettuce, herbs, and other greens, especially in winter when grocery stores can run low on quality produce.“
This is amazing produce," said customer John Schoen, buying a tub of butter lettuce and other leafy veggies on Friday. “Nothing at the grocery stores comes anywhere near this.”
“Our family doesn’t drive much," said Meghan Holton, another customer grabbing an order. "But we drive here every week to get fresh greens because it tastes like summer.”
Anchorage Greens is an expansion of Juneau Greens, a similar business in the state’s capital, said Trevor Kirchhoff, who co-owns the businesses with John Krapek.In the back of Anchorage Greens’ warehouse, a vivid green garden grows in a hydroponic system.
Racks of plants sit in nutrient-filled water under LED lights.
The first plants were harvested in November. Customers can subscribe to the Greens Bag program, a weekly rotating menu of lettuces and herbs including basil, cilantro, and red-veined sorrel. Kirchhoff said customers can also buy items individually.
The store features hard-to-find veggies such as purple-leafed basil, a colorful take on the herb.
Anchorage Greens has done no advertising, Kirchhoff said. Clients are learning about it through word of mouth.
Business owner Trevor Kirchhoff closes the cooler door at Anchorage Greens, Jan. 3, 2020. (Anne Raup / ADN)
Lead Photo: Plants grow at Anchorage Greens, Jan. 3, 2020. (Anne Raup / ADN)
Brick Street Farms To Construct Cultivation Hub, Increase Production In St. Pete
Backed by proprietary technology developed by Brad and Shannon, Brick Street Farms is now able to produce the equivalent of 2-3 acres of agriculture per shipping container
OWNERS OF BRICK STREET FARMS, BRAD DOYLE AND SHANNON O’MALLEY
For some reason, I can never keep plants alive. Maybe I don’t water them enough. Or perhaps I water them too much! Could it be the amount of light I expose them to? You know what, it’s probably due to my cats eating the leaves off every plant I’ve ever owned. Either way, I’ve never been able to provide the perfect environment for green life to thrive. And back in 2015, Shannon O’Malley and Brad Doyle were having similar troubles. But for them, the problem was the Florida heat.
Luckily, the couple found a solution to their woes. When they took their plants inside and put lights on them, the plants flourished. Brad and Shannon didn’t know it yet, but this revelation would end up being the seed that would sprout into an agricultural movement in Downtown St. Pete. After extensive research, the duo realized they could use their backgrounds in computer engineering and IT skills to build indoor hydroponic farms.
HUMBLE BEGINNINGS: BRICK STREET FARMS FIRST THREE CONTAINER FARMS
And so in January 2016, the duo purchased an overrun junkyard at 2001 2nd Avenue South in the Warehouse Arts District for $125,000 to house their new venture — Brick Street Farms. After months of environmental inspections, permitting and zoning obstacles, and electrical and plumbing issues, Brick Street Farms kicked off their first grow cycle inside three 320 square-foot shipping containers in October 2016.
Backed by proprietary technology developed by Brad and Shannon, Brick Street Farms is now able to produce the equivalent of 2-3 acres of agriculture per shipping container. The farm cultivates a variety of leafy greens including heads of bibb, butterhead and romaine lettuce, kale, basil, and rainbow chard.
Best of all, the growing process uses no dirt, no pesticides and much less water than traditional farming. Needless to say, their concept caught the attention of many local residents, and restaurants, such as the Vinoy, Oak & Ola, Oxford Exchange, and Pacific Counter.
For the past three years, Brick Street Farms has been feverishly trying to keep up with production. “When we started, we really just thought we’d be a wholesale production facility to grow and sell to restaurants, and maybe grocery stores,” says O’Malley. "But the level of interest and inquiries we get from everyone from chefs to elementary schools, we realized we couldn’t be closed off to the public.”
INSIDE ONE OF BRICK STREET’S HYDROPONIC SHIPPING CONTAINER FARMS
This year will be Brick Street Farm’s biggest yet. After bringing on a few investment partners in late 2019, the hydroponic farm will begin construction on a community-focused grow facility and will also dramatically ramp up production to satisfy demand from a new Publix partnership.
The current farm, located at 2001 2nd Avenue South, will be transformed into the Brick Street Cultivation Hub, which will include an expanded market, more container farms, a commissary kitchen, a beautiful courtyard, and pop-up event space.
RENDERING OF THE BRICK STREET CULTIVATION HUB AT 2001 2ND AVENUE SOUTH IN THE WAREHOUSE ARTS DISTRICT OF ST. PETERSBURG
Right now there are four container farms on site, but once the Cultivation Hub is complete, there will be a total of ten, stacked two high. Not only will Brick Street continue to grow lettuces, kales, and herbs, but they’ll be expanding into other products, such as tomatoes and strawberries.
“People always laugh at us, but one product we can grow exceptionally well in the containers is strawberries,” says O’Malley. “We haven’t sold them because we live in the strawberry capital of the world, but ours are phenomenal so we are going to give them a try and see if people want them.”
The largest addition to the property will be a new 6,500 square foot mixed-use building. The first floor will contain a 1,800 square foot farm-to-table market featuring greens grown on-site, as well as items from other local farms, like dairy, fruits, and vegetables, which cannot be grown in Brick Street’s shipping containers.
Additionally, the market will carry sustainable products from other local businesses, such as baked goods, health and beauty items, apothecary products, grab-and-go meals, beer and wine, and much more. Well-known local companies like St Pete Ferments, Nightshift Wax Company, Mother Kombucha, and Sunny Culture will also be available at the market.
A coffee concept will be located in the center of the Cultivation Hub. “It’ll be a full-time community space serving coffee, beer and wine,” says O’Malley. “Customers can relax in the beautifully landscaped courtyard, connect to the wifi and just hang out.” Two local coffee companies are currently in negotiations to lease the space.
An existing 416 square foot building will be converted into a commissary kitchen. This will be the new home of Brick Street Canning Company, helmed by Illene Sofranko, founder of The Urban Canning Company, which recently closed up shop. “We will be revising all of her core products and introducing an all-new line of products as well,” says O’Malley.
When Sofranko isn’t using the space, it’ll be rented out to local food makers. A few local restaurants will be hosting pop-up events at Brick Street, including Greenstock, Pete’s General, and Top Chef alum Jeffrey Jew, whose new St. Pete restaurant, Lingr on 6th St, opens this Spring.
“The Cultivation Hub will be dog-friendly and kid-friendly,” says O’Malley. “It’s just going to be a multi-functional property centered on food.” Construction begins in February and is tentatively scheduled to open in November.
If the Cultivation Hub wasn’t exciting enough, Brick Street Farms has also leased a warehouse on 22nd Avenue South that will serve as a manufacturing facility as well as house all farming operations while the Cultivation Hub is under construction.
BRICK STREET FARMS RECENTLY STARTING SELLING AT A PUBLIX SUPERMARKET IN LAKELAND, FL. AS PRODUCTION INCREASES, BRICK STREET PRODUCE WILL BE AVAILABLE IN ST. PETE & TAMPA
Brick Street Farms recently started selling their greens at a Publix Supermarket in Lakeland, the grocery chain’s test market. Feedback has been stellar and Publix is interested in expanding the partnership. “We have been selling 12 times their projected volume,” says O’Malley. “As our production grows, we will begin expanding to more cities.” Brick Street Farms is slated to hit St. Pete Publix stores in early March followed by Tampa and Central Florida thereafter.
With interest from Publix and a growing list of wholesale partners, the 22nd Avenue South warehouse will serve as a farming container assembly line. “It’ll be like a car plant,” says O’Malley. “We have an entire construction crew ready to begin building the farm containers.”
The goal is to build 60 containers in 2020 and an additional 100 in 2021. So if Brick Street’s goal is met, they’ll be operating around 170 container farms or the equivalent of 340 to 510 acres of agriculture by the end of 2021.
BRICK STREET FARMS RED LEAF LETTUCE
So, where will all of these container farms live? Everywhere! One of the core tenants of Brick Street Farms is to decentralize farming. In other words, the Tampa market will be served by Brick Street farm containers in Tampa, and Orlando produce will come from farm containers in Orlando.
“We have been overwhelmed by the response from the community, both from individual households as well as our restaurant accounts,” says O’Malley.
At St. Pete Rising, we couldn’t be more excited for Shannon O’Malley, Brad Doyle and the future of Brick Street Farms, a true homegrown local business. Be sure to follow them on Facebook and Instagram to stay up to date on well their produce will hit St. Pete shelves and for the debut of the Brick Street Cultivation Hub at 2001 2nd Avenue South.