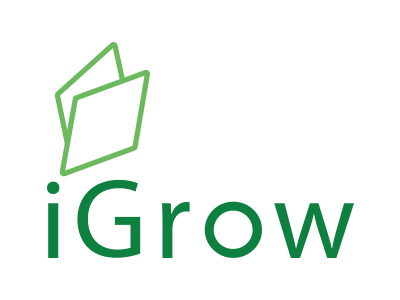
Welcome to iGrow News, Your Source for the World of Indoor Vertical Farming
‘Farm of The Future’ To Unlock Potential of Horticulture
Modular Farms Australia director James Pateras said the training farm would help unlock potential in the Australian farming landscape
Special report: EMILY BRADFIELD, Rural Weekly
February 19, 2020
THE Darling Downs is at the forefront of agricultural innovation and is now home to Australia’s first educational modular farm.
This month, TAFE Toowoomba welcomed its first cohort of students to the new Rural Centre of Excellence.
The $2.7 million facility includes a groundbreaking indoor vertical farm, allowing farmers of the future to get their hands on new technology and help shape the future of Australia’s food supply chain.
The vertical farm is the first educational facility of its kind in Australia and one of just two modular farms in the country.
Modular Farms Australia director James Pateras said the training farm would help unlock potential in the Australian farming landscape.
The LED growing lights inside the pod were designed specifically for the system to promote maximum growth .
INSIDE THE FARM
Mr. Pateras describes the farm as a “complete growing system” where plants are grown from seed to harvest inside the controlled growing environment.
The process of growing inside the pod starts with seeds planted in a host plug made from peat moss and allowed to germinate and grow into a seedling, which usually takes about two and a half weeks in most crops.
Plants are grown from seed, rather than seedling, to prevent pathogens or disease entering the pod.
From there the seedling is moved into a vertical tower on the growing wall, where it remains until ready for harvest.
Modular Farms pods are generally used to grow herbs and small leafy greens or even strawberries and blueberries.
The growing lights inside the pod were designed specifically for the system to promote maximum growth and are placed at an ideal distance from the plant canopy.
The farm is also much more water-efficient, using 95 percent less water than traditional crops, as well as the ability to recapture and recirculate water used inside the farm.
The pod is controlled by four indicators: lighting, climate, fertigation, and irrigation, and can be monitored and controlled remotely using an app.
“With a consistent environment, the plants mature much faster than those in a traditional crop.
“It allows us to create a very solid and clean environment for the plants to live in. There’s no cold one day, hot the next day, it’s a very steady environment inside,” Mr. Pateras said.
“A farm like ours can turn a basil seed into a harvestable crop in about five weeks, which is about half the time you’d see in a traditional greenhouse.”
The yield in the vertical farm is also significantly higher than that of a traditional crop.
Inside the 36sq m container farm, there are four growing walls with a surface area of about 65sq m. That 65sq m is able to produce the equivalent of 1000sq m in traditional crops, which equates to about one tonne of basil per year, or upwards of 45,000 lettuces.
Plants are grown in the vertical tower from seedling to harvest.
IN THE CLASSROOM
Dubbed by students as the “farm of the future”, Mr. Pateras said the farm would give students the opportunity to learn about indoor growing technology as the way of the future.
“To be able to do what we do and use as little water as we use is a great opportunity for the kids to realize how we can save on the environment and still consume and grow food,” he said.
The Modular Farms installation at the TAFE campus is one farm with two growing environments, allowing students to experience two different nutrient programs side by side.
“It’s got a dual irrigation system which allows (students) to run experiments side by side but then really focus on the plant biology as well. They can run tests a lot quicker and faster from that set-up,” Mr Pateras said.
Mr Pateras hopes hands-on experience in the growing pod will get the students thinking about the future of food production.
“What I think it will do is create a huge awareness about where plants are going and also allows the kids to learn a lot more about growing plants indoors, which is not new but growing plants on a commercial scale indoors is obviously becoming a bigger factor in the agricultural landscape.
“So it will definitely teach them a lot about what the future may hold about growing food in Australia,” he said.
“The idea of getting in a tractor and plowing up a paddock will maybe one day be a thing of the past, time will tell.
“The technology right now isn’t going to replace the farmer tomorrow but the farm of the future is here now.
“It’s just a matter of more and more people realizing the benefits of what this type of farming can bring to the environment, the community and the people consuming the food.”
A Modular Farms vertical farming operation.
THE FUTURE
Mr. Pateras believes the future of indoor farming is bright, with the potential to completely change the food supply chain and provide fresher, locally sourced produce to communities.
“I definitely think the indoor agriculture space is growing in steam,” he said.
“With the technology improvements over the course of the last few years, we’re seeing reduced entry costs in that controlled system’s space.
“We’re even seeing a lot of the traditional farmers supplementing their traditional greenhouses with growing lights to try to fast-track the speed of growth of their normal traditional greenhouse.”
The container farm has huge potential for isolated communities and city landscapes in delivering clean, fresh produce and eliminating food miles.
“As our cities begin to grow … the opportunity to grow in those areas is huge,” he said.
“It’s probably just scratching the surface in terms of where these types of systems can live, how they can change the food supply chain and improve the quality of food.
“We’re a very lucky country in Australia, where we can grow a lot of our food year-round. What our system allows people to do is create that microeconomy and sense of community farming.
“These things can live anywhere, so the ability to grow fresh leafy greens in Mt Isa or Birdsville is quite powerful in itself.”
The farms also have the potential to eliminate any unnecessary food miles. Australia’s first modular farm is located at Brisbane’s Eat Street Northshore, supplying vendors with fresh produce.
“We harvest our crop on a Thursday, we walk it down 50m to the vendors who buy our crops and by the next night, the produce is on the plate.
“You won’t be able to get in any fresher than that, and in terms of food miles we’re talking 50m,” Mr Pateras said.
“If you can grow food locally with one of our farms, I think it will be a far better injection into the local economy than bringing food in from interstate or overseas.”
Robot Farmers Are Changing The Future of Agriculture
80 Acres Farms doesn't just want to make fresh, local produce for Cincinnati and neighboring areas; it wants to completely overhaul the food system in the US
A robot named Sam rules over this atypical Ohio Farm.
Megan Wollerton February 9, 2020
It's a cloudy day in early October and I'm circling my rented Jeep Wrangler around a maze of industrial buildings in Hamilton, Ohio. Hamilton is a small city 30 miles north of Cincinnati with a population of just over 62,000 people. Like much of Ohio, farming is important here.
I'm on my way to a farm called 80 Acres, but it isn't the sprawling midwestern wheat field you're picturing in your mind. This tech-centric farm is indoors, housed entirely in a nondescript 10,000-square-foot warehouse.
You can't tell from the outside, but this is a bustling produce farm that has tested over 100 varieties of leafy greens. Megan Wollerton/CNET
Food and agriculture are the top contributors to Ohio's economy. There are about 78,000 farms in Ohio, putting it near the top of every list ranking US states by number of farms. Its biggest crops are soybeans, corn, and wheat.
But US farming is in trouble. There are roughly 2 million farms in the country spread across 900 million acres and they earned a total of $389 billion in sales in 2017, according to the 2017 Census of Agriculture, released in April 2019. All three of those numbers are lower than they were five years ago. There are fewer farms, there's less land dedicated to agriculture and the remaining farms are making less money.
There are a lot of reasons for these declines, from dropping commodity prices, to climate change and a trade war with China. There's also a growing trend of larger farms making the majority of the profits. Less than four percent of US farms made more than two-thirds of ]=agriculture sales in 2017.
80 Acres Farms doesn't just want to make fresh, local produce for Cincinnati and neighboring areas; it wants to completely overhaul the food system in the US.
"We decided that the [food] industry was really broken and that it had to be fixed from within. Farmers are struggling and they don't want their kids to be in farming," 80 Acres CEO Mike Zelkind explains as we watch a robot named "Sam" expertly maneuver containers of leafy greens around a series of stacked shipping containers inside the Hamilton warehouse.
I'm here to see how 80 Acres is changing farming for this corner of Ohio -- and how its sister company, Infinite Acres, is selling its sustainable technology to other farms with an ultimate goal of "feeding the world."
A plan to feed the world
Zelkind and Tisha Livingston, the president of 80 Acres and CEO of Infinite Acres, came up with the idea for their farm in 2015. Back then, "controlled-environment agriculture" -- more commonly known as indoor or vertical farming -- was a relatively new industry. Indoor farming is a type of climate-controlled agriculture that typically relies on artificial lights and other technology to grow crops indoors.
Zelkind has a lot of respect for early indoor farming pioneers, but he says there's one thing they don't have that sets 80 Acres Farms apart: He and Livingston have over 50 years of combined experience in the food industry.
Zelkind worked for General Mills from 1991-1996. He later transitioned to VP and SVP roles at ConAgra Foods, Bumble Bee Foods, and AdvancePierre Foods. He was the CEO of Sager Creek Vegetable Company before he and Livingston co-founded 80 Acres.
Livingston held various roles at Pierre Foods and AdvancePierre Foods from 1995-2014, before becoming a VP and then COO at Sager Creek Vegetable Company.
We're exhilarated and we're scared and we've gotten further than anybody else we know. And we're absolutely nowhere. We know that this won't cut it, and this is yesterday. We're working on tomorrow. Mike Zelkind
The duo witnessed firsthand the systemic problems with the food industry for decades. Zelkind says three things need to happen for any long-lasting, positive change to take place: We need to grow things differently, change the supply chain and distribution channels and merchandise differently.
For 80 Acres Farms, "growing things differently" translates to indoor farming.
Indoor farms can grow produce without pesticides, year-round. That immediately negates concerns about any of the synthetic or natural pesticides used in commercial and organic agricultural production and the inherent seasonality of traditional outdoor farming, as well as weather-related issues due to climate change such as droughts and floods.
Mike Zelkind and his business partner, Tisha Livingston, stand in front of Sam the robot inside their Hamilton, Ohio farm. | Tyler Lizenby/CNET
Even if you grow it differently, you can't stick it on some broken supply chain," Zelkind adds. Tomatoes and strawberries are bred for transportation -- and food in the US travels at least 2,000 miles on average to get from the farm to your grocery store shelf, he explains.
Tomatoes and strawberries are specifically bred to have thicker skins and they're picked from farms before they're ripe -- just so they will survive the 2,000 journeys to your town. When you factor in the travel time, the shelf life of produce is significantly lower than it would've been if it were picked at peak ripeness and sent to a local store.
80 Acres puts its farms near the stores it serves and currently has six fully operational facilities. There's one in Alabama, one in North Carolina, two in Arkansas and two in Ohio, including the one I'm visiting today.
The name 80 Acres comes from their other Ohio farm, which is located on a quarter acres of land and grows the equivalent of 80 acres worth of crops.
The Ohio farms supply local grocery stores including Kroger, Whole Foods, Jungle Jim's and Dorothy Lane Market (a Dayton, Ohio-based store that also happens to make the best brownies I've ever tasted).
80 Acres has a dedicated produce section in a downtown Cincinnati Kroger.Tyler Lizenby/CNET
80 Acres has a dedicated produce section in a downtown Cincinnati Kroger.
Tyler Lizenby/CNET
The final hurdle for 80 Acres is how to merchandise their food, which they package locally in-house. For this, they forget about the tech powering 80 Acres and lean on the taste. "We are sampling in the store aggressively because once you taste it, you know," says Rebecca Haders, vice president of creative and marketing at 80 Acres, who's tagging along with us today.
Of course, the tech really doesn't matter if the produce doesn't taste good -- but Zelkind, Livingston, and Haders are unanimous: You really *can* taste the difference between typical grocery store produce and produce from 80 Acres Farms.
I bought a carton of their "Fireworks Tomatoes" at a Kroger in downtown Cincinnati and they were right; they were delicious. They tasted better than standard grocery store tomatoes, but on-par with the freshest, most flavorful produce at your local farmers market.
One drawback is the price. The 9-ounce carton of 80 Acres cherry tomatoes cost me $3.99. Kroger-brand conventional cherry tomatoes come in a 10-ounce carton and cost $2.49; Kroger's Simple-Truth-brand cherry tomatoes cost $2.99 for a 10-ounce carton. Even Whole Foods, a brand known for its higher pricing, sells packaged tomatoes for less than 80 Acres.
While 80 Acres' tomatoes were better, I wouldn't want to spend over $1 more on them each time I went to the store. I asked 80 Acres why budget-conscious customers -- or any customers, really -- should buy their produce when it costs more. Haders tells me the retailer sets the price, not 80 Acres.
"We know, based on consumer feedback, that the customer highly values our consistent flavor, truly pesticide-free, local, just picked-fresh tomatoes. Pricing is at par today with local, organic, but with efficiencies of scale, we intend to bring prices down without compromising product quality, freshness, or flavor," Haders adds.
Their focus may be on taste, but the truth is, Zelkind and the rest of the team care deeply about the tech. It's the crucial piece that has enabled 80 Acres Farms to grow so quickly. It's also the key component in solving the challenges associated with overhauling the food industry.
80 Acres "Fireworks Tomatoes" are described on the packaging as "an explosion of flavor."Megan Wollerton/CNET
A top-secret facility"
This facility is kind of top-secret," Zelkind says as we stand in front of ten stacked shipping containers. "Everything in here is proprietary." I'm the first reporter to see it, I learn, and Zelkind, Livingston and Haders talk about the technology here in hushed, excited tones. While other indoor farms rely on tech, 80 Acres says it has taken a more holistic commercial approach with fully-automated robots loading produce for shipping and computer systems to help monitor the crops and manage their lighting schedule.
The team has spent five years on intensive trial and error to build this farm. They've brought in tech from other companies and also experimented by building their own to get as close as they can to an "optimal" indoor farm.
Each new farm they build benefits from the things they learned the last time around -- and this facility in Hamilton is their newest and most high-tech farm."
We're exhilarated and we're scared and we've gotten further than anybody else we know. And we're absolutely nowhere. We know that this won't cut it, and this is yesterday. We're working on tomorrow," Zelkind explains.
80 Acres' Hamilton farm has 10 shipping containers that measure 40 feet long, eight feet wide and eight feet tall. Each shipping container has between four to six levels and can accommodate roughly 4,000 plants. If every shipping container is filled to capacity, that's 40,000 plants total. This facility focuses on lettuces and other leafy greens.
There's a reason why 80 Acres and other indoor farms focus on these types of crops, explains Erik Runkle, professor of horticulture at Michigan State University. Customers want them year-round, despite seasonal availability -- and leafy greens are typically transported long distances, despite being perishable. Their nutritional content can also decrease during shipping.
Then the question becomes: How economically viable is indoor farming really? In short, we don't exactly know yet, Runkle tells me. He and colleagues from Michigan State and other universities received a grant from the USDA (the US Department of Agriculture) to study this exact thing, but even after the four-year study, Runkle doesn't expect the answer to be a simple "yes" or "no."
Commercial indoor farming in the US got started about 8-10 years ago, Runkle explains. He estimates that less than 1% of US produce farming comes from indoor farming today. Most of the early companies have gone out of business. Some well-known pioneers, like New Jersey's AeroFarms, are still around.
"Indoor farming is always going to be much more expensive than anything grown in a field," Runkle adds. He doesn't expect indoor farming to replace traditional farming anytime soon -- or perhaps ever. But he does see it as a potential solution in places where water is a limitation and field irrigation is either unrealistic or impossible.
Fortunately, some technological advancements have reduced the cost of indoor farming, making at least a little more viable today than it would've been a decade ago.
Ten modular "grow zones" are stacked inside their warehouse. During my visit, the team was testing dozens of different varieties of leafy greens. Tyler Lizenby/CNET
LED lights have been one of the most significant technological advancements that made 80 Acres possible. Older lights cost more money, used more energy and made the environment too hot for plants. Now, with LEDs, 80 Acres has customizable, automated lighting systems in place to simulate daylight with different color temperatures. They use less energy, spend less money and the plants are happier too.
This farm also relies on two robots, Sam and Barney, to handle most of the heavy lifting. The bots load and unload pallets of plants from each shipping container on a set schedule -- or manually, as needed. Other companies still hire people to go up on scissor lifts and move these heavy plant containers, Zelkind explains.
There are cameras inside each container, too, so the team can check in on their plants whenever they want. And 80 Acres is developing machine learning to identify irregularities -- pests, color deficiencies, variations in plant sizes and much more -- so that growers don't have to watch the plants 24/7.
When the cameras find an irregularity, it can be shared across the 80 Acres team to more quickly identify the potential issue and work toward a solution.
"We use all of that [technology] to assist growers, not to replace growers," Zelkind says. The AI tech today isn't anywhere near where it would need to be to take over the job of a grower, but making room for technology has definitely changed how growers interact with plants. 80 Acres even offers its own training classes to teach employees how to use their technologies.
Controlled-environment agriculture is becoming an increasingly prevalent area of study in agriculture departments at the University of Arizona, Cornell University, University of Nebraska and many other schools.
Plant manager Tim Brobbeck is so dedicated to the work, he sometimes sleeps at the Hamilton farm.
Tyler Lizenby/CNET
Tim Brobbeck started out as a grower at 80 Acres three years ago. Now Brobbeck's the plant manager. Brobbeck says it can be tricky to gauge what's going on with a certain plant when you can't climb up and access it easily. The cameras help, but it can still be difficult sometimes to tell what exactly is happening. This tech learning curve is exactly what Livingston is focused on as the CEO of Infinite Acres.
To Infinite Acres -- and beyond
Infinite Acres is 80 Acres' tech company. As head of Infinite Acres, Livingston works to make the tech as smart as possible, in order to support the growers and the rest of the team here. But there's another goal that goes way beyond the Hamilton farm or even 80 Acres' five other farms: She wants to take what they've learned about indoor farming tech from 80 Acres and sell it to other farmers all over the world.
80 Acres is open to selling its technology to other farms and helping them run things or simply selling the tech, training the existing staff to use it and leaving them to it, Livingston explains. They're eager to share what they know about lighting, sensors, vision systems, robots and automation with other farmers -- and there's a big demand for it.
These are "R&D" crops, leafy greens they're testing out at the Hamilton farm. Tyler Lizenby/CNET
I ask the 80 Acres team what makes them special, how they managed to keep going. "Our pedigree is grit," Zelkind chimes in. Their failures, coupled with their existing knowledge of the food industry and genuine passion for the work keep them going.
"We say, 'fail fast and cheap with tremendous insights,'" Livingston adds. It's kind of their motto. They've made a lot of mistakes, they readily admit.
They've killed a lot of crops. They've had so much humidity in grow zones that it literally rained, and killed everything. "We were in the process at one point where we were just continuing to seed knowing that we were gonna kill all of the crops that we had," Zelkind says with a chuckle.
But they've come this far and they're determined to train a new generation of farmers, just like Tim Brobbeck, to make healthy produce more accessible than ever before. "I love the scalability of [80 Acres] and the idea that we can go out and maybe feed the world someday," says Brobbeck. That sounds pretty good to me.
Infarm’s Tech-Powered Micro Farms Deliver Fresh Produce On-Site In Urban Settings
Based in Berlin, Infarm has been pioneering a whole new wave of agricultural innovation with its product, a modular smart farm that operates on IoT and machine learning technologies to produce highly nutritious and flavorful greens that are grown fresh and sold in urban environments, such as local supermarkets and restaurants
By Liz Vaknin, NoCamels February 18, 2020
What started as a small initiative in 2013 by Israeli-born brothers Guy and Erez Galonska and Osnat Michaeli to cultivate greens in the dead of the German winter, grew into a multinational brand that, in just six short years, has managed to draw a decent amount of media attention and bring in an impressive $134.1 million to date from investors.
Based in Berlin, Infarm has been pioneering a whole new wave of agricultural innovation with its product, a modular smart farm that operates on IoT and machine learning technologies to produce highly nutritious and flavorful greens that are grown fresh and sold in urban environments, such as local supermarkets and restaurants.
In recent years, the field of urban farming has rapidly expanded on a global level and has been especially successful in places where the growing climate is seasonal and temperamental, like Canada or Saudia Arabia, or where the demands of a developing population can no longer be met solely by traditional farming practices due to spatial, financial and environmental concerns. Large, industrial-scale farms that produce food hundreds and thousands of miles away from the final destination are slowly proving their inability to provide a constant, safe supply of produce, especially leafy greens, and sometimes result in public safety horrors that damage consumer trust and company valuations.
Infarm’s model is based on hydroponics (a method of growing plants without soil), patented modular ‘growth trays’ and energy tech. The company puts a premium on nutrition, taste, and freshness while also emphasizing an environmentally conscious approach. The Galonska brothers told Friends of Friends, an interview-focused Berlin magazine, in 2014 that they were inspired in part by NASA’s biofarming methods and sustainable design.
“For us, there is an important combination between gardens, flowers, trees – which is nature – and this more futuristic side of things: LED, artificial light, hydroponic fogs, the more NASA-style elements. We combine these two sides through experience. Experience for Infarm means tasty food: herbs from the vertical garden, for tea, for salads, for fresh products of any kind,” according to Erez Galonska.
Infarm’s unique, cloud-based technology allows its operators to monitor a network of 678 micro farms (and growing) from its Berlin headquarters, gathering data to offer the highest quality products, and making it easy for their clients to sell the just-harvested greens. The systems produce enough still-living micro-greens, salad greens, and herbs to serve thousands of city dwellers which would not have ready access to that degree of freshness otherwise.
This approach also does away with food miles and has created an opportunity to provide the most nutritious versions of greens, even introducing plants that were previously unavailable because they do not transport well. According to Infarm, their system uses 95 percent less water and 75 percent less fertilizers to grow the produce. There are no chemical pesticides involved, and their product demands 90 percent less transportation and 99 percent less space than traditionally farmed lettuces and herbs.
Moreover, the cloud-based technologies utilized to monitor the growing processes of their micro-farms continuously feed data into their IoT and machine learning algorithms to maximize their growing methods according to criteria such as yield and nutrition. With 22 varieties of leafy greens and herbs, Infarm’s systems offer a range of flavors, shapes, and textures that truly embody the values of farm-to-table cuisine.
From trailer to brand
Erez Galonska told EU Startups in September that he and his co-founders “realized that our current food system’s biggest deficiency is that it is too far removed from the people it is trying to feed.”
At Infarm, “rather than asking ourselves how to fix these deficiencies in the current supply chain, we looked to redefining the entire chain from start to finish; Instead of building large-scale farms outside of the city, optimizing on a specific yield, and then distributing the produce, we decided it would be more effective to distribute the farms themselves throughout the city,” he explained.
The founders, he went on, came around the idea that “being close to the land and particularly its produce is vital to our health and creativity as a society. And from the beginning, we began to explore – through travel, growing and experimentation – ways to bring natural vitality of the local farm into the city and the freshness and flavor back into our lives.”
They began by building a hydroponic system in their home in Neukölln, creating a space for over 100 plants. “It was snowing outside and we had fresh vegetables inside,” Galonska recalled in the Friends of Friends interview, telling the magazine that from that moment “we knew that we had something.” The founders then moved to a studio and eventually bought a 1955 Airstream trailer, converting it into a mobile vertical farm and setting up shop in a popular urban farm space in the city.
“This trailer became a hub for our early experimentation, where visitors could harvest herbs and microgreens and we could welcome a vibrant community of urban planners, designers, food activists, bio-dynamic farmers, architects, chefs, biologists, and hackers to explore the diverse challenges behind making urban farming a reality. This research station and lab would form the beginnings of what we today call Infarm,” Galonska told EU startups.
Infarm’s urban farming system in Germany. Photo via Kroger
Infarm’s urban farming system at M&S. Photo: Samuel Cane / Marks & Spencer
The company scaled in Berlin, earning a grant from Horizon 2020 in 2017 and later partnering with Metro Group, one of Europe’s biggest wholesalers. In 2018, Infarm expanded and secured partnerships with two large German grocery chains and a number of restaurants. It also raised significant funding ($25 million from Balderon Capital) and launched its first Infarm system in France that same year.
By 2019, Infarm expanded to two other European cities, London and most recently Copenhagen. In London, where the company has a partnership with Marks and Spencer, Paul Willgoss, Director of Food and Technology for the British chain, said in a press release that the collaboration is a “fantastic example of what can happen when passionate agricultural, food and technology experts work together. We operate as part of a complex global food supply chain and want to understand the emerging technologies that could help provide more sustainable solutions, whilst also delivering fantastic products with exceptional taste, quality, and freshness for our customers”.
Following a recent $100 million Series B round and a partnership deal with Kroger, the highest-grossing American supermarket chain, Infarm is also poised to rapidly expand in the American market.
Launching in Seattle, a city notorious for the amount of rain it receives annually, Infarm is set to prove how valuable its product is when the local climate is not conducive to growing anything, let alone delicate greens, in the depths of winter.
In a televised interview with Bloomberg, when asked how Infarm plans to spend the new investment, Erez Galonska responded by saying that “a big part of this round is really to start thinking about how we can build Infarm into a global company, expanding into the US and Asia, and building those relationships.”
SEE ALSO: Israel’s Unique Successes in AgTech May Help Stem Looming World Food Crisis
With partners like Kroger Group, Infarm is on the right track. “Kroger believes that everyone deserves access to fresh, affordable and delicious food, no matter who you are, how you shop or how you like to eat,” said Suzy Munford, Kroger Group’s VP of Fresh, at the first Infarm harvest in the QFC Kirkland store in Seattle in early December 2019. “Our partnership with Infarm allows us to innovate by combining ground-breaking in-store farming technology with our passion for fresh, local produce and ecological sourcing. Kroger is excited to be first to market and offer the best of the season, and we’re proud to lead the US on this journey.”
According to the Seattle Times, after the second location in Bellevue has opened, there are plans to open up in fifteen more QFC supermarkets in Washington and Oregon by April of 2020.
With an average of three new locations per month, Infarm is expanding at a rapid pace that isn’t uncommon for tech startups that reach the west coast. Hopefully, the cofounders have learned from the mistakes of other west coast based agricultural technology startups, and are prepared with data-backed solutions to tackle significant logistical, infrastructural and marketing issues that frequently arise in this niche vertical.
Lead Photo: Infarm's urban farming system in Germany. Photo via Kroger
Hamilton’s 80 Acres Farms To Grow Tons of Tomatoes On New York City’s Fifth Avenue
Hamilton-based 80 Acres Farms will grow tomatoes on one of the busiest streets in New York outside the Solomon R. Guggenheim Museum. The grow is part of “Countryside, The Future,” the Guggenheim’s new exhibition in collaboration with Rem Koolhaas, which opens to the public Feb. 20, and runs through Aug. 14
February 21, 2020
By Eric Schwartzberg, Staff Writer
HAMILTON —
80 Acres Farms will grow tomatoes on one of the busiest streets in New York outside the Solomon R. Guggenheim Museum.
The grow is part of “Countryside, The Future,” the Guggenheim’s new exhibition in collaboration with Rem Koolhaas, which opens to the public today and runs through Aug. 14.
Along with its commercial partner’s Infinite Acres and Priva Holding BV, 80 Acres Farms will grow cherry tomatoes in an indoor grow area right outside the museum on Fifth Avenue.
80 Acres Farms is a leader in indoor growing for retailers such as Kroger, Jungle Jim’s International Market, Whole Foods, Dorothy Lane Markets, and Giant Eagle.
MORE: ‘The perfect home’: Why 80 Acres chose Hamilton to move its headquarters and create 125 jobs
People in New York will be able to look through a large window in the indoor farm to view a crop of fresh tomatoes being grown continuously during the next six months. The first tomatoes grown will be ready for harvesting and consumption by late March.
The “Countryside, The Future” exhibition will examine political forces, social issues, and environmental factors altering landscapes across the world, including traditional farmlands.
“We believe that what we are doing is about the future of food,” said Mike Zelkind, chief executive officer of 80 Acres Farms. “We are changing the way fruits and vegetables are grown and harvested locally then delivered to grocers the very next day. There is an enormous market and consumer appetite around the world for produce that our crop scientists and other food experts have been perfecting during the past five years.”
MORE: Dilapidated Hamilton building transforms into an industry-changing grow facility
Zelkind said 80 Acres’ participation in the “Countryside, The Future” exhibition will allow New York residents and visitors to experience how “the freshest, tastiest locally-grown tomatoes” can be grown year-round indoors in one of the busiest cities in the world.
For the Guggenheim exhibition, 80 Acres Farms, Infinite Acres, and its Priva partners have collaborated on the 700-square-foot grow center, which is expected to grow 50,000 tomatoes in six months. Additional tomatoes will be donated to City Harvest, a New York City food rescue organization that recovers excess food and distributes it to people in need.
MORE: Hamilton’s large indoor growing operation is so advanced they want it around the world
Last year saw a massive year of growth for 80 Acres. It opened its automated facility on Enterprise Drive, a facility that grows leafy vegetables, herbs and strawberries, then a downtown Hamilton location on South 2nd St. that grows vine crops, including tomatoes, cucumbers, and peppers.
The company also launched Infinite Acres, an independent joint venture aimed at providing large-scale indoor farming facilities worldwide. The venture also includes UK-based Ocado Group, one of the world’s largest dedicated online grocery retailers, and Netherlands-based Priva Holding BV, a leading provider of technology solutions, services, and automation systems to horticultural and other industries.
That partnership is now building large-scale, fully automated indoor farms in the United States, Asia and Europe.
It also inked a deal to moved its headquarters from Cincinnati to Hamilton and was granted a tax credit for committing to create 125 new jobs and investing at least $26.9 million.
MORE: Innovative Hamilton indoor growing company part of a worldwide deal to supply food
Interview With Thomas Hausmaninger
Indoor farming allows for precise control of growing conditions such as light, water, temperature and nutrition
The award-winning junior researcher on his love for experimental projects, communicating bold ideas to the public and how universities can foster creativity
February 6, 2020
Thomas Hausmaninger is a researcher in optical spectroscopy, the study of how matter interacts with electromagnetic radiation, at the Centre for Metrology at VTT Technical Research Centre of Finland. In November, he was awarded €100,000 (£85,000) for winning a global research pitching competition for postdoctoral researchers. The contest was organized by Slush and Skolar, a Finnish community of academics, research funders, and science communications professionals.
Where and when were you born? Salzburg, Austria in 1987.
How has this shaped who you are? My parents often took us out for mountain hikes. I loved to look down from a mountaintop and see the city from this perspective. I was fascinated by seeing how all the places were connected by streets and how tiny everything seemed from up there. Maybe, therefore, I also want to see the bigger picture and understand how things connect after diving into the details of a research question.
What kind of undergraduate were you?
I was fascinated by the world of theoretical physics and enjoyed seeing how one could suddenly understand complex natural phenomena after getting used to a certain formalism or concept. However, I didn’t have the patience to go deep into theoretical physics unless I really needed it. On the other hand, when it came to experimental physics and experimental projects, I could never let it be “good enough” and always wanted to improve things and try yet another idea to further optimize an experimental setup, a code, or a measurement procedure.
Your winning research idea is to create a breathalyzer to understand plants better. Why is this important?
Plants are an essential and versatile source of food for humans. The climate crisis is reducing resources like water and, at the same time, the world population is growing. This implies that the food crisis is becoming more and more severe. One solution is to grow plants indoors in vertical farms that can save orders of magnitude in water and valuable land. Indoor farming allows for precise control of growing conditions such as light, water, temperature, and nutrition. However, the condition of the plants is still controlled manually. With the plant breathalyzer, one can automatically monitor the plants and grow more food with fewer resources. For example, it will be possible to avoid crop failure by early pest detection and save resources by optimizing the nutrition supply.
What do you think will be the biggest challenge in bringing this project to fruition?
Understanding how the gases emitted by the plants are connected to their metabolism and their needs is certainly a challenge; learning a new language takes time. Furthermore, in the vertical farms, the signals are diluted by convection. Therefore, sensitive detectors are required to measure them. We are facing the challenge of identifying suitable biomarkers in the gas around the plants and developing the sensitive measurement techniques needed to measure them in real-time in indoor farms. The combination of these two challenges also makes this project fun, since they require a lot of interdisciplinary work between engineering and biology.
What other interesting projects are you working on?
Currently, I’m part of the environmental metrology team at VTT where we develop laser spectrometry-based trace-gas sensors for various applications. This includes real-time monitoring of beer brewing that reveals how complex this biological process is and how strongly it gets affected by slight changes of the starting parameters. Furthermore, we are also developing monitoring instruments to make nuclear power plant decommissioning safer. Such applications require sensitive field-deployable detectors. I’m currently applying for funding for the development of a field-deployable trace-gas detector with unprecedented sensitivity that can detect gases present at concentrations below parts-per-quadrillion levels.
What is the biggest misconception about your field of study?
That it is impossible for outsiders to understand what we are working on and that we are doing research on things that are not useful for any practical purposes. I think one reason for this is that it is often difficult to predict the outcome of fundamental research. It is challenging for scientists to communicate science because it is their job to be critical and avoid drawing conclusions that are not sound. However, I think scientists should be less afraid of having bold ideas about future applications of their research and telling people about these visions.
What have you found to be the hardest part about being an early career researcher?
Workplaces that offer freedom in research and at the same time good working conditions are difficult to find. In addition, many world-leading institutes have a reputation for strong internal competition instead of strong teamwork. That is why I left the track of pure fundamental research towards more applied research. In this area, I found more options for doing excellent research combined with good working conditions. It is tough to make these decisions since they can strongly affect both your future career as well as your private life.
How can universities create an environment that enables creativity?
Freedom, trust, and safety enable researchers to unfold their full potential. The necessary challenges should come from scientific discussions with colleagues and not from career pressure. Universities should trust that the vast majority of researchers are eager to have the best ideas and to do the best research. Universities should also support researchers at all stages to make the right decisions and find their way to success. To be creative, scientists should get the time to do what they do best – that is to focus on their research.
If you weren’t an academic, what do you think you would be doing?
I would build my own home laboratory to do fun experiments and to be astonished by nature.
ellie.bothwell@timeshighereducation.com
Lead Photo: Kirstin Vonderstein
The Inside Scoop On Indoor Farming
Food retailers from coast to coast are increasingly turning to indoor, vertical and greenhouse farming to meet the demand for locally grown produce, reduce food miles and offer the freshest product possible
Grocers look to indoor farming to
source a steady stream of local greens
Feb. 03, 2020
Food retailers from coast to coast are increasingly turning to indoor, vertical and greenhouse farming to meet the demand for locally grown produce, reduce food miles and offer the freshest product possible. Some, such as Tops Friendly Markets in Williamsville, N.Y., are partnering with greenhouse operators off-site, while others, such as Whole Foods Market and The Kroger Co., work with greenhouse and indoor farming experts to grow on-site and in-store.“As our climate continues to change in primary growing regions, Mother Nature continues to add challenges that are very hard for growers to overcome.
Customers are demanding we have product regardless of that,” says Jeff Cady, director of produce and floral for Tops. “Greenhouses give us an opportunity to meet our customers’ needs day in and day out.”
Tops has partnered with greenhouse builder and operator BrightFarms of Irvington, N.Y., to offer shoppers lettuce, arugula, and spinach grown closer to home—specifically in a Wilmington, Ohio, greenhouse about 400 miles from Tops’ distribution center. “The idea was to try and take miles out of the supply chain and ultimately get as fresh a product as we can for our customers,” Cady says.
Photograph courtesy of BrightFarms
Cady, who estimates Tops sells 25% to 35% more greenhouse-grown produce than it did five years ago, sees continued potential for growth.“We will expand as products come online. Greenhouse-grown strawberries were not available five years ago. We have been bringing them in and have had very good results,” he says. “Perception is reality. Add in the perceived food safety and environmentally friendly components, and greenhouses will continue to thrive.
”In-Store Farming
The Kroger Co. recently partnered with Infarm, an indoor farming company based in Berlin, to bring high-tech modular farms inside its U.S. stores. The program, which began with 15 QFC stores in Bellevue and Kirkland, Wash., grows leafy greens inside glass tanks located in the produce department.
“Kroger believes that everyone deserves to have access to fresh, affordable and delicious food, no matter who you are, how you shop or what you like to eat,” Suzy Monford, Kroger’s group VP of fresh, said in November when announcing the Infarm partnership, which she said enables the Cincinnati-based chain “to innovate by combining groundbreaking in-store farming technology with our passion for fresh, local produce and ecological sourcing.
”The alliance with Kroger marks the first U.S. rollout for Infarm, which was founded in 2013 and has more than 500 farms in food stores and distribution centers in Germany, Switzerland, France, Luxembourg, and the U.K. Infarm remotely controls growing conditions at its units through a cloud-based farming platform that adjusts to the specific needs of each plant. The company says it can re-create growing conditions from around the world, bringing plants that were previously too delicate, rare or expensive to stores.“
The grocery retailer landscape is facing increased competition and demand for fresh herbs and leafy greens,” says Jeffrey Landau, director of business development for Agritecture Consulting in New York. “Vertical-farming companies such as Square Roots, Infarm and Dream Harvest Farming Co. are providing grocery stores with a fresher product that has a longer shelf life due in part to being grown within a few miles, if not feet from the store.”
Agritecture consults across the board, from controlled-environment agriculture (CEA) operations (both greenhouse and indoor vertical) to soil-based farms. Clients such as New York-based Square Roots, which grows all of its produce in modified shipping containers using 100% artificial light, sells throughout New York City to Whole Foods, the Greene Grape, C-Town and more.
Vertical vs. Greenhouse
The vertical-farming market is anticipated to reach $9.96 billion by 2025, according to a recent report by San Francisco-based Grand View Research, which points to increased use of internet of things sensors for producing crops, as well as the growth in agriculture automation and the use of big data to maximize yields as market drivers.
In the vertical-farming industry, there have been several high-profile capital funding deals within the past few years, says Landau. AeroFarms of Newark, N.J., raised $100 million in Series E funding and announced it will invest $42 million to build its largest facility to date, in Danville, Va. Investors have also backed Infarm, which raised $100 million in Series B funding in June 2019, and San Francisco’s Plenty, which raised an industry record of $200 million in Series B funding in 2017.“
All in all, the vertical-farming industry is on pace for substantial growth,” Landau says. “As it compares to the greenhouse industry, vertical farming is still a relatively new industry and profitability is not guaranteed. Most large-scale vertical farms take at least six years to return on their investment. However, greenhouse operations, if done correctly, can be profitable within the first two to three years of operation.”
As a result, the greenhouse industry has also experienced considerable growth in recent years. Both New York-based Gotham Greens and BrightFarms received substantial equity funding ($29 million and $55 million, respectively) in June 2018, while Little Leaf Farms of Devens, Mass., received $18 million in financing from Bank of America in December 2019, to be followed by an additional $20 million.“It’s difficult to say which one is growing faster, but it is clear from the numbers that both industries are experiencing strong growth,” Landau says.
Little Leaf Farms produces more than 1 million boxes of fresh greenhouse-grown baby green lettuce a month. Its greens are delivered to every major supermarket chain in New England in 24 hours, year-round
.When the company expands from five acres to 10 acres with the opening of a new Devens greenhouse in May 2020, its production of sustainably grown lettuce will double to 2 million boxes delivered to New York and New Jersey’s major supermarket chains, said Little Leaf.
Two-Mile-Farm to Fork
Denver-based Altius Farms is redefining the meaning of local for area restaurants and retailers. The vertical farm, which can be seen through tall glass windows above a popular downtown Denver restaurant, sells to 40 area restaurants and five local grocers, including Leevers Locavore, Choice Market and Marczyk Fine Foods.
All of Altius Farms’ highly perishable salad greens, herbs, and edible flowers are sold within a 10-mile radius, with the majority sold within a 2-mile radius. “We want to reduce our food miles and change the way we grow food. [Vertical farming] also reduces waste and depreciation of flavor content,” says Sally Herbert, Altius Farms co-founder, and CEO.
Increased production that uses fewer resources within a smaller footprint is another benefit of vertical farming. “We can grow 10 times the amount of produce than conventional farming,” says Herbert, former president and CEO of GS1, the largest supply-chain standards organization in the world.
Photograph courtesy of Altius Farms
Altius Farms cultivates 12 to 14 harvests on a series of 8-foot towers each year, producing 37,000 pounds of greens annually. “It’s a lot of bang for your buck,” she says. But the labor costs associated with vertical farming can be steep. “Labor is responsible for 40% to 50% of the cost of sale, and in some cases even higher.”
The higher price point for some indoor-grown greens means that consumer education is critical to category success.“
The consumer has to make a choice. We’ve got to get them to see the value of local. Small-format grocers are wonderful to work with and are really our partners in this,” says Herbert, whose Altius Farms leads in-store samplings to educate and inform consumers. “Whenever we do a Saturday demo at the grocery, we see an uptick in sales.
”Promoting local is also key. Choice Market uses little flags in its cold cases to alert shoppers that Altius Farms’ greens are a local product grown up the road.“Social media is also pretty important these days,” says Herbert, who points to grocery partners who have touted recipes featuring Altius local greens on their websites and digital communications. “It brings the product to the customer in a more personal way.”
For Herbert, who has worked for many years as a supply-chain executive, Altius Farms offers a solution in providing responsibly grown fresher food. “This is one way to grow. Mass-produced in a warehouse is also a way to grow, as is farming outdoors,” she says. “It’s not about a right way or a wrong way—it’s about giving movement to growing closer to consumption so we can start to see the impact on the climate and quality of product.”
Local Year-Round
U.S. consumers will place increased pressure on manufacturers to produce locally in 2020 and beyond, according to new research from New York-based Nielsen, which finds that local ingredients and food sourced and produced close to home are important to nearly half (48%) of consumers.
As locally grown, fresher produce continues to top the list of consumer demands, Steve Platt, CEO of BrightFarms, sees continued growth in greenhouse cultivation. Since 2016, BrightFarms has partnered with Ahold Delhaize USA’s Giant Food Stores and its supermarkets under the Giant and Martin’s banners, as well as Kroger’s Roundy’s.
“They chose to work with us early on because they saw the enormous potential of a year-round local program in the salad category,” says Platt. “These partnerships continue to play a major role in the growth of our company and are our primary focus. As early believers in fresh and local food, our retail partners have seen category growth beyond their competitors.” At press time in January, BrightFarms was on track to open a new Selinsgrove, Pa., greenhouse, which will service customers in the New York and New Jersey metro areas. The greenhouse grower’s operations have expanded by about 420,000 square feet to 740,000 square feet in the past several years.
“This growth is a direct result of the growing demand from new and existing retail partners,” says Platt, citing SPINS data that “shows that when retailers introduce our products, their salad category grows.
”Concerns around food safety are also driving demand for produce grown indoors, Platt says. “Leafy greens grown in controlled, indoor environments, like a greenhouse, deliver a structurally safer supply chain for retailers and consumers,” he says. “By growing indoors, we eliminate many of the risk factors associated with field-grown produce like agricultural water and proximity to animals.”
BrightFarms grows, packs and distributes its greens from one farm labeled clearly on the package. This “avoids co-mingled processing facilities that make it extremely difficult to trace pathogens back to a single contamination source,” says Platt.
Lead Photo: Photograph: Shutterstock
US: The Secret To Singapore Airlines' Delicious Meals Is An Indoor, Vertical Farm In New Jersey
Inside a nondescript warehouse, sprouts are thriving under banks of LED lamps: kale, bok choy, arugula, tiny little plants only a horticulturalist could identify
BY PAUL BRADY
FEBRUARY 14, 2020
Photo: COURTESY OF SINGAPORE AIRLINES
On an industrial block in Newark, New Jersey, behind the cement and brick Ironbound Recreation Center, there’s some magic happening. Inside a nondescript warehouse, sprouts are thriving under banks of LED lamps: kale, bok choy, arugula, tiny little plants only a horticulturalist could identify. Rows and rows and towers and towers of plants — like a scene from a super-sanitized version of "The Matrix" — are quickly becoming salad greens at AeroFarms. This 70,000-square-foot vertical farm, which the company says is the largest of its kind in the world, is hidden in plain sight — as planes roar overhead, on final approach for Newark Liberty International Airport.
Photo: COURTESY OF AEROFARMS
During a recent visit to the farm, Travel + Leisure got an up-close look at how aeroponic farming works: A variety of greens are grown from seed to harvest, planted not in soil but rather in reusable cloth that’s woven from recycled plastic water bottles. Lettuces and other leafy greens are constantly monitored, and environmental sensors throughout the facility make frequent adjustments. AeroFarms co-founder and chief marketing officer Marc Oshima says they’re even able to alter the taste of their crops — say, making arugula that much more peppery — by manipulating water levels, lighting, and other factors. (They don’t, he’s quick to point out, use any pesticides or herbicides.)
Despite the energy-intensive technology powering the operation, AeroFarms says its food is significantly better for the environment compared to traditional farming. A single square foot of vertical farm — like the one in Newark — can yield 390 times the produce as one outdoors, Oshima says. Water use is limited, as the plants are grown aeroponically and only misted when necessary. All this helps reduce the carbon footprint of the food, both by greatly reducing the resources it takes to grow the greens in the first place and by putting the harvested crop closer to market.
The Top 10 International Airports
That’s where Singapore Airlines comes in. The carrier, which operates the longest flight in the world between Newark and Singapore, has been working for years to reduce its carbon footprint, an airline rep says. One way to do that? Reduce the impact of on-board meals by sourcing greens from right down the road. AeroFarms, which is just a few miles from Singapore Airlines’ catering facility at Newark, is now supplying hyper-local produce for the nearly 19-hour Singapore Airlines Flight 21.
“Passengers understand that we’re trying to limit carbon footprint,” says Singapore Airlines food and beverage director Antony McNeil. Beyond that, high-tech vertical farming gives a level of control not found anywhere else, he says. “The beautiful thing is that we can work together to design, say, do we want more pepper in the arugula?” he says. “It’s like Star Trek!” Singapore Airlines will start serving AeroFarms produce on their flights from JFK International Airport, starting next month, and they may soon have sustainably sourced cuisine on all flights from the six U.S. cities the airline serves.
“The goal is, in the coming months, to have ‘farm-to-plane’ at every one of our U.S. gateways,” said James Bradbury-Boyd, a spokesman for Singapore Airlines. That could mean sustainably fished seafood for Seattle flights or thoughtfully made cheeses from Oregon aboard West Coast routes, McNeil said, in addition to vertically farmed greens.
For now, passengers will find AeroFarms produce in both business class and premium economy on flights from Newark, in these selections: Soy Poached Chicken, a riff on the classic Singaporean dish chicken rice; The Garden Green, a hot-smoked salmon salad; and Heirloom Tomato Ceviche, a sort-of caprese salad with burrata and arugula.
It’s possible that the partnership could grow in the future: AeroFarms has started an expansion of its Newark headquarters, which will give them even more space for indoor farming. And if they scale up, who knows? We may all soon be eating Star Trek–style salad in the air, no matter our destination.
Podcast - Future of Agriculture - Jim Pantaleo
This show explores the people, companies, and ideas shaping the future of agribusiness
Welcome to the Future of Agriculture Podcast with Tim Hammerich.
This show explores the people, companies, and ideas shaping the future of agribusiness. If you are curious about innovations in AgTech, rural entrepreneurship, agricultural sustainability, and food security, this is the show for you!
For more details on the guests featured on this show, visit the blog at www.FutureOfAg.com. Or, to learn more about career opportunities in agriculture, visit www.AgGrad.com
Triple Threat
Vertical Harvest takes a new approach to CEA by focusing on the three bottom lines of people, profit and the planet, employing a staff of workers with different abilities
Vertical Harvest takes a new approach to CEA by focusing on the three bottom lines of people, profit and the planet, employing a staff of workers with different abilities.
Patrick Williams | Photos by Allison Krieg
When visitors walk into Vertical Harvest’s luminous three-story glass building for tours, they’re stepping into the architectural brainchild of Nona Yehia.
The singular combination vertical farm and greenhouse grows specialty greens, leafy greens, microgreens, and tomatoes using LED lights, robots and moving hydroponic carousels.
An eclectic mix of workers, many of whom have intellectual and physical disabilities, take care of the futuristic farm and its many technologies, growing some of the freshest produce around.
The Jackson, Wyoming, grower aims to provide those with disabilities opportunities for upward mobility, says Yehia, who is co-founder and CEO. The operation, she says, provides an example of how farms can change the perception of the abilities of workers with disabilities. Workers who often only have opportunities in entry-level jobs thrive here in an environment where they can help solve some of the world’s most pressing problems, including land and water shortages and other environmental issues.
“It’s the way Vertical Harvest is a team that’s conceived of the company that’s really different, saying that you can do well by doing good and that it actually benefits the bottom line of the business to do so,” Yehia says.
She says Vertical Harvest would never open a farm without helping an underserved population, whether that be people with disabilities or other underserved groups, such as refugees or veterans. And Vertical Harvest aims to expand; for example, it is developing a vertical farm project in Lancaster, Pennsylvania.
Vertical Harvest maintains high standards for its produce, too. Daily, it regulates three separate growing environments that, with the glass walls, are influenced by the outside environment. It follows integrated pest management protocols and offers a varied product mix — including 30 different microgreens varieties — catering to chefs, high-end restaurants and grocery stores.
“I like to say that people come to us because of our mission, but they come back because of the quality of our produce,” Yehia says.
Vertical Harvest in Jackson, Wyoming
The mission
From the outset, passions about social issues and the environment influenced Yehia, Caroline Croft Estay and Penny McBride to found Vertical Harvest in 2010.
When she met McBride at a party in 2008, Yehia was well established as an architect, with 13 years under her belt at E/Ye Design, where she was partner with Jefferson Ellinger. While her architectural knowledge and experience helped her design a distinctive greenhouse-vertical-farm, she also wanted to address some of the social problems in America.
“I have a brother with developmental disabilities. … This country’s done a very good job of nurturing and including this population during education, but when it comes to employment, you’re on your own,” she says. Her focus on nurturing and inclusion would prove essential to Vertical Harvest’s mission.
McBride, a sustainability consultant, was looking for unique ways to sustainably and efficiently grow produce, Yehia says. Jackson imports most of its food, but a foodie scene in the short summers illustrated a need for local, fresh food. Many consumers were not satisfied with produce that was shipped in and sold in local grocery stores.
While the demand for better product was there, it proved a challenge to find land where they could build a controlled-environment farm. The surrounding public lands minimize areas that can be used for construction. “Ninety-five percent of the land that is developable is already developed,” Yehia says. “So, locating a greenhouse that might serve our downtown community was actually kind of a difficult proposition.” They settled on a tenth of an acre next to a parking garage and looked to the skies for more real estate.
To build up Vertical Harvest’s social mission, Croft Estay, a longtime employment facilitator, looked to the Employment First model, which the U.S. Department of Labor says is based on the idea that everyone, including people with disabilities, should be able to work well-paying jobs in integrated workplaces that offer benefits and opportunities for advancement. Croft Estay also followed an approach called customized employment, which involves a personalized relationship between employer and employee that helps both parties.
From there, Croft Estay developed Vertical Harvest’s “Grow Well Employment Model,” which Yehia says involves spreading customized employment and Employment First throughout the company’s culture. (Croft Estay is now director of diversity and inclusion at Vertical Harvest; McBride is a shareholder.)
In addition, Yehia and her colleagues were inspired by Arthur & Friends, a hydroponic greenhouse in New Jersey that Wendie Blanchard founded to employ people with disabilities. Blanchard named the operation after her nephew Arthur Blanchard, who has Down syndrome and enjoys growing produce with workers both with and without disabilities, according to New Jersey Monthly.
“She’s been consulting around the country for people who want to be more inclusive in their growing practices and employment practices, so that was really an inspiration from the very beginning,” Yehia says.
People with disabilities are the largest minority group in the United States, Yehia notes, and more of them need opportunities to excel in the economy. “It’s an important thing to be able to bring together all the research and understand, being that this is surrounded around this effort into corporate cultures,” she says.
Some of Vertical Harvest’s team
Offering empowerment
Vertical Harvest opened its 13,500-square-foot facility in 2016 to meet the needs of its rare mountain town. Nestled in the Jackson Hole valley, Jackson lays about 5 miles from Grand Teton National Park and about 80 miles from Yellowstone National Park. It’s a ski town and many people come and go, Yehia says. Some move there after college, then eventually leave for other opportunities.
“There’s a very transient employee base,” she says. “On the other hand, there’s a group of people who live and work here, or want to find consistent employment here, but experience very high unemployment.” She says among people with physical and intellectual disabilities, there’s about a 78% unemployment rate.
Nineteen of Vertical Harvest’s 34 employees have disabilities. That level of inclusion provides a healthy balance of different perspectives, Yehia says.
“What happens sometimes is that you might employ one or two people with a form of a disability, and then in the end they feel more segregated because they are almost separated out from the rest of the culture,” she says.
In addition, Vertical Harvest uses language that is meant to be empowering. Rather than saying people have “disabilities,” they prefer to say they have “different abilities.” “It’s not like we’re scared of the word ‘disability,’” Yehia says. “But we prefer the word[s] ‘different ability’ because we work toward bringing out people’s ability.”
Every day, Emily Churchill, director of production, visits the departments of tomatoes, lettuce, microgreens and integrated pest management. Throughout the process, she works with people with various abilities.
“My senior grower for lettuce [Michelle Dennis] is one of our employees with a different ability, and I talk to her probably five times a day, making sure the harvest is on track and the transplanting and all of that stuff — whereas some of our other employees who work in microgreens have their routine down and they are less social and they just like to put their headphones in and seed,” Churchill says.
Decision-making at Vertical Harvest follows a triple bottom line of profit, people and the planet, Churchill says. “Maybe one of our managers will take 30 minutes out of her day to sit down and have a one-on-one meeting with her employee to check in or to ask what they need help with and what they’re enjoying,” she says. “On paper, that looks like we’re losing 30 minutes of work that day, but actually, that’s 30 minutes that is going to one of our triple bottom lines.”
The energy in the greenhouse reflects the resourceful collaboration among its team, Churchill says. “I’m reminded of how revolutionary it is when new people come into the greenhouse and they’re kind of blown away by what we’re doing,” she says.
Vertical Harvest’s greens grown under LED lights
Glass-box transparency
Vertical Harvest’s glass-walled design allows it to use the external environment to its advantage as much as it can, Yehia says. Borrowing ventilation, heating, air conditioning and lighting from the outside saves energy. But these clear walls also reflect the business’ openness.
“We’re in a glass box, so the transparency with which we run our company is key to every element of Vertical Harvest,” she says.
The farm quickly makes its produce available at retail and consumers are noticing, Churchill says. “For us to be able to provide food that was harvested the day that someone buys it or the day before you buy it, is so different compared to anything else you can get in a grocery store,” she says. “And I think you can really taste it when you eat the product.”
Vertical Harvest started working with the Teton County School District on a program called “Fancy Food Fridays.” Every Friday for two months, the students tried a different microgreen. Then, if their parents would bring them to the farm, they would already be familiar with the product.
“When parents would come to the greenhouse with their kids, their kids were like, ‘Hey, Mom, this is my favorite microgreen,’ which, if you can imagine that, it’s pretty exciting, being able to introduce kids to this very, very new and important crop,” Yehia says.
Vertical Harvest also hosts a hospital market with St. John’s Hospital every week and it’s working with the University of Wyoming on a nutritional study to explore the health benefits of local produce. Consumers not only value that Vertical Harvest provides local produce but that it conducts education and outreach, Yehia says.
“A consumer can really come and see all of Emily’s good work in her growing her lettuce, and then when they go to a grocery store, see us on the menu, they know exactly where that head of lettuce comes from,” Yehia says. “I think that’s a really important shift and why interest in our brand is growing — because it is really important that it is located in the heart of the community, not only for employees to be able to access it but also our anchor institutions.”
Product cards for Vertical Harvest’s microgreens
Expanding the model
The management and operational cultures at Vertical Harvest are laying the groundwork for expansion to other cities, Yehia says.
“Everything that we build there, we always say, ‘Could we do this in Lancaster?’” she says. “’Could we do this in any other greenhouse that we’re going to?’ and ‘How would we share this procedure or this practice or policy with other greenhouses?’”
Many CEA growers build their farms around intellectual property or growing technologies, but Vertical Harvest takes a different approach, she says.
“We are operators; we are farmers, so we build our intellectual property on our standard operating procedures and in our employment model,” Yehia says. “And so that is really what we are always looking at — how do we communicate with each other, how do we track data, how do we make something more efficient?”
At Vertical Harvest, the workers who grow microgreens are among the first people in the industry learning how to grow it, Yehia says, providing an example of how the farm empowers its community. Underserved populations, she says, will be leaders in the communities where the operation plans to expand.
“In our town, that was about people with different abilities,” Yehia says. “In another town, it might be refugees or veterans.”
The project in Lancaster could start as early as 2020, Yehia says. Then, Vertical Harvest could bring its model to other cities in the United States and beyond.
“If you invest in the people and the materials of your community, then you really strengthen not only the local economy, but the ethos, and you really empower a community,” Yehia says. “And I think that is worthy of being part of every urban community, to be another kind of civic building that we look at, like a community center or a library even.”
Little Leaf Farms’ CEO Paul Sellew Advances Hydroponics As Company Expands
As agriculture strives for sustainability, growers need to tackle the duel problem of food waste and the inefficiency of transporting fresh produce thousands of miles across the country
DEVENS, MASS. – As agriculture strives for sustainability, growers need to tackle the duel problem of food waste and the inefficiency of transporting fresh produce thousands of miles across the country.
Food waste is estimated at between 30-40 percent of the food supply, and 98 percent of the nation’s lettuce is trucked from California and Arizona, contributing to the problem of spoiled produce. These shipments generate over 10,000 lbs. of CO2 per truckload, and hundreds of hours are being spent planning the logistics of food distribution. Furthermore, California continuously faces major droughts, and soil erosion is a problem plaguing farmers nationwide. As a result, traditional farming is increasingly unsustainable.
With mounting concerns about climate change and growing population demands, Paul Sellew, the founder and CEO of Little Leaf Farms, has a model growing method that brings year-round sustainable farming to New England and the East Coast with a smaller carbon footprint.
With its expansion to 10 acres in Devens, Mass. and new greenhouses planned in Pennsylvania and North Carolina, Sellew and the company’s head grower and manager, Pieter Slaman, a Dutch master of growing produce, have designed the most technologically advanced greenhouses in the world to grow lettuce with nearly 100 percent natural sunlight and recycled rain water without pesticides, herbicides, or insecticides.
They are growing crisp, baby green lettuce, incorporating principles of sustainability and state-of-the-art climate control technology. Key features include:
Hydroponic production – growing without soil – naturally protects increasingly stressed topsoil that is vulnerable to soil erosion, an increasing problem in agriculture today. This precise, soil-less method utilizes up to 90 percent less water than field-grown greens to grow crunchy, flavorful lettuce.
Little Leaf Farms uses the best glass, which diffuses light throughout the greenhouse resulting in greatest possible distribution of natural sunlight. The greenhouse is designed with the most efficient LED lights that target the specific wavelength ranges to maximize photosynthesis in the plants.
Little Leaf Farms’ Nutrient Film Technique (NFT) mobile gutter system is the most advanced in the world, delivering an approximately 20x yield increase per acre compared to traditional West Coast field agriculture and higher yields compared to other hydroponic systems. The main advantage of this technique over other hydroponic growing systems is the plant roots are exposed to adequate supplies or water, oxygen and nutrients all at the same time. This better and more efficient use of inputs also leads to lower production costs.
At Little Leaf Farms, lettuce is grown with 100 percent captured rainwater and almost 95 percent natural sunlight through special high-light transmission glass windows. The average annual rainfall is 46 inches in New England, and Little Leaf Farms uses about 23 inches a year.
To heat the greenhouse, Little Leaf Farms burns clean natural gas and captures the CO2 and releases it back into the greenhouse – making the process net neutral. Solar panels also generate about 20-30 percent of electricity.
Hydroponic growing is also safer because the lettuce does not come into contact with contaminates that field-grown lettuce is subjected to from livestock. The lettuce is not handled by human hands. It is also grown free of chlorine, other chemical washing agents and harmful chemical residues.
Elevate Farms Inc.: Tech-Based Vertical Farming Company Completes Capital Funding to Scale Operations and Secure IP
A tech-based vertical farming company focused on cost-effectively growing leafy green vegetables at mass scale, Elevate Farms Inc. (“Elevate Farms”) is pleased to announce the closing of a $1.8M funding led by Brightspark Ventures
By urbanagnews
February 14, 2020
PRESS RELEASE – Toronto, CANADA / A tech-based vertical farming company focused on cost-effectively growing leafy green vegetables at mass scale, Elevate Farms Inc. (“Elevate Farms”) is pleased to announce the closing of a $1.8M funding led by Brightspark Ventures.
Elevate Farm’s unique solution uses hydroponics and a proprietary automation system, paired with photobiology, to grow high-quality leafy greens (such as arugula, kale, and basil) in a climate-controlled environment.
Elevate Farms’ system aims to deliver a product that is larger, tastes better and has higher nutritional content than traditionally-grown leafy greens – all at a lower cost. The produce grown by Elevate Farms also has the benefit of being local, completely non-GMO, as well as pesticide and chemical free.
“Elevate Farms represents the next generation of indoor farming: their system solves some of the biggest problems the first wave of vertical farms experienced,” says Mark Skapinker, Managing Partner at Brightspark Ventures. He continued, “their edge is their ability to cost-effectively create a tasty and nutritious product – and grow it at a mass-market scale. We invested because we saw meaningful potential, being a team of world-leading experts that can execute, proven technology, and true science being applied into a massive marketplace.”
Elevate Farms is the first to commercially implement an automated climate-controlled environment for plant-production that utilizes far less labor than other indoor farms.
Amin Jadavji, Elevate Farm’s CEO stated: “With the new funding, the company is now ready to scale significantly. This financing will allow us to execute on our currently secured flagship facilities in New Jersey and Niagara, each projected to produce in excess of one-million pounds of leafy greens annually.” Mr. Jadavji continued: “The funding will also fuel our plans to scale the business, grow our team, build and secure new and existing IP, prepare for business partnership opportunities, as well as finalize initial major orders and operational financing.”
Travis Kanellos, Elevate Farm’s Chief Strategy Officer added: “This is a major milestone for our North American operations. It also allows us to forge ahead on our global partnerships, as well as execute our global plan to build out facilities internationally over the next 12-months.”
ABOUT ELEVATE FARMS
Elevate Farms Inc., previously operating corporately as Intravision Greens Inc., is a technology-driven vertically-stacked indoor farming enterprise focused on a mass scale and cost-effective operations with patent secured and patent-pending technology as well as over a decade of advanced photobiology research deployed.
ABOUT BRIGHTSPARK VENTURES
Brightspark is one of Canada’s top-performing venture capital firms, actively investing in exceptional entrepreneurs since 1999. We provide growth capital and expertise to disruptive, market-transforming Canadian tech companies in seed to growth stages. Since inception, Brightspark has invested across traditional VC Funds, and more recently under an investment model open to individual and non-institutional investors.
Dissertation On Indoor Vertical Farming - Survey
I looked into several aspects of vertical farming including its advantages and disadvantages over conventional farming, energy requirements, perceptions of the industry and the challenges and opportunities that are currently facing the industry
My name is Caleb Owen and I am currently in my final year at Harper Adams University studying BSc (Hons) Agriculture. As part of my course, I am required to complete a dissertation. With the wide range of sectors within agriculture to choose from, I opted to look into urban agriculture and more specifically vertical farming. This field has become of growing interest to me due to it being a relatively young sector within agriculture. It offers exciting new opportunities for the industry as well as individuals who are interested in going into urban agriculture.
As it is a young industry I was intrigued to better understand the opinions that various stakeholders within vertical farming have towards the growth and especially the sustainability of their industry. I, therefore, decided to construct a questionnaire in order to understand the opinions and views of various stakeholders and try to determine any similarities as such.
Once my aims were established I underwent a literature review on the subject. I focused mainly on published peer-reviewed articles where I picked out their strengths and weaknesses. I discovered unsurprisingly that there was not much-published literature on vertical farming as it is such a young sector. However, I was surprised to find out that the concept was first mentioned over 100 years ago in a 1915 book by Gilbert Ellis Bailey where he described it as a utopian concept with the system similarly describing that of underground vertical farming in the Netherlands.
I looked into several aspects of vertical farming including its advantages and disadvantages over conventional farming, energy requirements, perceptions of the industry and the challenges and opportunities that are currently facing the industry. Although these were the topics that were mostly covered by the literature, there was still a lack of research. For example, there is a significant lack of information about the perceptions of vertical farming and more specifically the public perception of the industry. From looking at these various topics I drew out possible research gaps that can be looked into in the future. This included conducting more primary research into the sustainability and perceptions of vertical farming.
After conducting the literature review I was better informed in constructing a questionnaire that would help me achieve my targets. I then went to it to construct a short questionnaire that would provide me with as much information as possible about the views and opinions of vertical farming stakeholders. I chose to do this by using an online survey as it was easy to edit as well as being easy to distribute to as many people as possible. I understood from the start that there would not be many vertical farmers within the United Kingdom and therefore I have chosen to contact as many vertical farmers globally in order to make my results as statistically significant as possible. I hope that the results are drawn from my questionnaire highlight the knowledge that the stakeholders have on the sector as well as their concerns about any possible challenges.
Over the past few months, I have conducted a literature review on the topic and made a short questionnaire in order to better gain an understanding of vertical farmers perceptions on their industry
I would be very grateful if you are able to distribute the questionnaire link that is provided below to your members. The questionnaire should take 5-10 minutes to complete and will close on the 6th of March at 18:00 GMT.
Questionnaire link: https://harper-adams.onlinesurveys.ac.uk/vertical-farmers-perceptions-of-vertical-farming-copy
How Madar Farms Is Changing Agriculture
Countries such as the United Arab Emirates are increasingly facing problems growing food due to limited space, growing demand and decreasing resources.
FEBRUARY 1, 2020
SEATTLE, Washington — Countries such as the United Arab Emirates are increasingly facing problems growing food due to limited space, growing demand and decreasing resources. The creators of Madar Farms saw this need and put together a team and a process. This process includes vertical farming in combination with hydroponics to grow food using much fewer resources than traditional means. The benefits of this new style of farming are plentiful. In a world with a growing need for food security, it provides a promising solution.
In Need of a Solution
Despite the United Arab Emirates (UAE) being a relatively rich country, they still have unsolved issues with food security. As a desert country, there is not a large agricultural industry. This mostly stems from the lack of available fertile soil and freshwater supply. In fact, only 5 percent of the land in the UAE is even able to be farmed. Therefore, traditional methods would only be able to provide a small amount of the countries needs.
Beyond this, between 70 and 80 percent of the water consumption in the area is designated towards agriculture. Without a solution, it is not a sustainable practice. Furthermore, UAE imports between 80 and 90 percent of their entire food supply. This leaves them without a reliable domestic supply of food as well as a lack of fresh nutritious food. Concerns over political unrest in the region could potentially prevent full food shipments from entering the country. In order to ensure that the people of the UAE have access to food and water for years to come, it is necessary to think outside the box.
Starting Up
Abdulaziz Al Mulla co-founded Madar Farms in 2017 after realizing the stark issues that the UAE and many Arabian countries faced regarding food security. While working at his previous job, he encountered a project that exposed him to the numbers involved. He knew he could find a better way to produce food, so he resigned from his job and started working on Madar Farms. Using his background and passion for food security, he started Madar Farms and committed to developing solutions since then.
The team that makes up Madar Farms is a mix of people with business backgrounds, engineers and agricultural specialists. Together they have created a model that not only has created innovative ways to grow food but also has created a business model that can keep the farms running into the future. These innovative methods are proving to be a potentially revolutionary way for countries that suffer from poor agricultural climates to begin to secure a source of food.
Madar Farms is Changing Agriculture
Madar Farms uses advanced farming techniques to create an efficient farm in the desert. They used shipping containers as the exterior of their building and have the entire environment contained within. From here, they use a combination of vertical farming and hydroponics to maximize their output. Mader Farms regulates the temperature to keep the crops out of the blistering heat. They also utilize blue lights, used to replace sunlight. The design focus of the entire system is to be a better version of farming due to the extreme control and science that goes into the process.
The hydroponic system brings many benefits. The first of these is the lack of pesticides that are used in the crops. These crops, grown in water, do not require pesticides due to the fact that most pests live in the soil. Along with this, hydroponics allows for much less water to be used in the farming process. In fact, Madar Farms process uses 95 percent less water than traditional methods. By saving so much water, they are able to protect an important and scarce resource. Another added benefit of Madar Farms’ methods is year-long growth. Because they have control over every aspect, including water, nutrients, and sunlight, they are able to grow crops continuously.
They also do not have to worry about rotating crops or giving fields time to regain lost nutrients, as they control the nutrient levels in the water. These innovative methods are just one of the many ways Madar Farms is changing agriculture. Madar Farms will be able to provide fresh crops year-round. Further, these locally grown crops are pesticide- and GMO-free and help preserve precious resources.
Going Forward
The government of the UAE has identified food security as a top priority for the continued growth of the country. In 2018, the Minister of Food Security in UAE launched a national food security strategy that outlines the necessity of improved food security. The government’s interest in their project provides support and an opportunity to help Madar Farms; the farms could potentially become an established part of the food industry in the UAE.
Furthermore, experts estimate the vertical farming industry will become a multi-billion dollar industry in the 2020s. As the world’s need for food continues to increase with population growth, vertical farming such as Madar Farms will be in higher demand as countries look to secure their food and water supply. The world will have to put out more food with fewer resources. Madar Farms has developed a solution that could be a potential long-term solution.
A combination of innovative thinking and new technology make up how Madar Farms is changing agriculture in UAE. Madar Farms is using vertical farming and hydroponics to provide food using less water and never-ending growing cycles. This new way of farming could provide the UAE with a future of food security.
– Josh Fritzjunker
KyleTalksAgTech: Small Scale Indoor Farming Systems - The Future of How And Where We Grow w/ Alexander Olesen
On this episode of the CropTalk series, #KyleTalksAgTech, Kyle Barnett sits down with Alexander Olesen of Babylon Micro-Farms, to understand the ins and outs of small scale indoor farming systems
Feb 4, 2020
On this episode of the CropTalk series, #KyleTalksAgTech, Kyle Barnett sits down with Alexander Olesen of Babylon Micro-Farms, to understand the ins and outs of small scale indoor farming systems.
Alexander shares some unique perspective and what makes Babylon's growing system and service for their clients, special.
Why Growing Leafy Greens Indoors Is Trending
A group of horticulturists, engineers, and agricultural economists have been given the green light to study indoor production of leafy greens, thanks to a four-year, $2.7 million grant from USDA. But wait, there’s more
Posted by Paul Rusnak
February 6, 2020
A group of horticulturists, engineers, and agricultural economists have been given the green light to study indoor production of leafy greens, thanks to a four-year, $2.7 million grant from USDA. But wait, there’s more. Industry partners also recognize the value in the project and matched that funding, bringing the total to $5.4 million.
The multi-university team led by Michigan State University (MSU) Professor Erik Runkle knows production challenges outdoors with leafy greens, including food safety issues, have led to an interest in growing these specialty crops hydroponically in controlled environments. At this point though, there is little information on whether this is economically viable.ADVERTISEMENTCapital and operating costs can be significant for startups, especially as it relates to LEDs and cooling systems, Runkle points out.
“Indoor farming using LEDs has a lot of advantages,” he says.
“It takes much less space, there is a more efficient use of water and nutrients, production is year-round, and there are virtually no pesticides. But there is little science-based information about best-growing practices and very little economic data around indoor farming.”
To find some answers, Runkle is collaborating on the project with fellow MSU researchers Roberto Lopez and Simone Valle de Souza, as well as Chieri Kubota at Ohio State University, Cary Mitchell at Purdue University, and Murat Kacira at the University of Arizona.
The team has three major goals:
1. Define optimal profitability based on yield and other high-value attributes of the plants, such as nutrition content
2. Optimize indoor environmental conditions, such as humidity, air movement, temperature, light and carbon dioxide concentration, to increase yield and high-value attributes
3. Encourage indoor farming stakeholders to collaborate with academic and industry groups that are working in controlled-environment agriculture.“
It might not seem obvious, but energy prices are extremely important to growers looking at indoor farming,” Runkle says. “These costs can vary significantly across the country, so it’s something growers need to be aware of. There are other considerations as well, such as proximity to markets.”
According to the team, much of the work will be conducted in Runkle’s Controlled-Environment Lighting Laboratory, which opened in 2017 and is used to study how plants grow under various environmental conditions. The findings will be tested at partner locations.
For more information about the project and its progress, visit scri-optimia.org.
Paul Rusnak is Senior Managing Online Editor for the U.S. Horticulture Group at Meister Media Worldwide, which includes Florida Grower, American Vegetable Grower, American Fruit Grower, and Greenhouse Grower brand titles. See all author stories here.
CANADA: Let-Us Grow Hydroponics One Year in Hudson Bay’s Former School
Fresh produce in Hudson Bay
(Facebook/Let-Us Grow)
By Mat Barrett
Feb 06, 2020
FRESH PRODUCE IN HUDSON BAY
The old Stewart Hawke School in Hudson Bay is getting some good use.
The town asked for bids for the building in late 2018, and in early 2019, they awarded it to ‘Let-Us Grow Hydroponics’. The company is run by Jan and June Nel who grow fresh lettuce, herbs, and radishes under LED lights with no pesticides or herbicides. Jan said when the town was looking for bids, he and his wife started to think.
“We started looking for ideas, and we went and proposed doing this,” Jan said. “And they loved it.”
At the time, Jan was – and still is – working full-time with Nutrien, while June was working at the Pharmasave. June said they took their family and started preparing the building in January, with the hope of helping Hudson Bay.
“And do something that can add to the community,” she said. “So, hopefully in the future, create jobs, expand and maybe do a few other things within the school. There’s a thousand ideas we have.”
By late February, Let-Us Grow Hydroponics was planting its first seeds. Currently, there are two rooms being used, and the gymnasium as well but Jan hopes that can be used for something else later on.
Jan said through their year of growing fresh produce in Hudson Bay, it’s been a huge learning curve.
“We learned lots,” he said. “Things we thought were going to be easy, were challenging. Things we thought were going to be challenging were simple.”
He said while working at Nutrien, he’s had to adjust how he thinks when it comes to growing now compared to how he’d think at his full-time job.
“Growing in an environment where there’s no soil, there’s no buffering capacity,” Jan told northeast now. “The plants react so much quicker to any deficiencies, and getting those recipes and formulas worked out took a bit of trial and error. And we’re still working on it, it’s not perfect, but it’s way better than it was.”
Let-Us Grow Hydroponics grows lettuce, herbs, and radish with no pesticides or herbicides, all under LED lights. (Facebook/Let-Us Grow)
With Hudson Bay being so far off the beaten path, it can be hard to find fresh produce, or local produce. June said one thing with theirs is it is local.
“It’s not two weeks old, it hasn’t traveled across the country or across the world,” she said. “It actually tastes like lettuce. Lots of people have commented on our herbs, it actually still tastes fresh when you get it, and there’s nothing sprayed on it.”
Jan added the carbon footprint on the regular produce bought at the store is massive compared to this.
As for the future of Let-Us-Grow Hydroponics, they’ve got a lot of building to work with and the Nel’s said soon they hope to be producing enough to provide fresh produce for Hudson Bay. Then in a few years, they hope to expand and grow enough where all of northeast Saskatchewan can have this fresh produce.
Right now, Let-Us Grow is only selling out of the school right now, but they hope to expand the retail side a little bit more soon. June said for anyone who wants to get in touch with them to get some produce, they can contact via phone, or their Facebook page.
Both June and Jan praised community support of Hudson Bay, as well as the help and support they have received from the town itself.
–
mat.barrett@jpbg.ca
On Twitter: @matbarrett6
Brick Street Farms Will Open A Pop-Up Market In A St.Pete Warehouse Next Month
Brick Street Farms, a St. Pete-based urban farming and produce company, comes into 2020 ablaze in change now its “cultivation hub” is set to debut at the end of this year
C/O BRICK STREET FARMS
A temporary spot to cop your fresh kale and spinach.
FEB 6, 2020
Brick Street Farms, a St. Pete-based urban farming and produce company, comes into 2020 ablaze in change now its “cultivation hub” is set to debut at the end of this year. Renovations to Brick Streets' market location—located at 2001 Second Ave. S. in St. Petersburg—have shut it down its market temporarily, so a Brick Street pop-up market will soon open in its production warehouse in St. Petersburg’s Grand Central District (at the corner of 3rd Avenue S. and 22nd Street, to be exact.)A press release says that the warehouse pop-up market hopes to open in March and will sell Brick Street's prized fresh produce as soon as doors are open.
This cultivation hub, which is still in the beginning stages of construction, will allow Brick Street Farms to increase production in order to satisfy high-demand. St. Pete’s Urban Canning Co. will also rebrand itself into the “Brick Street Canning Company” and sell canned and pickled goods out of the Brick Street Farms complex when it opens at the end of 2020. Until the cultivation hub opens, this warehouse space will be home to the Thrive Program—which allows consumers to buy or lease the shipping container farms that the Brick Street team manufactures.
Keep your eyes peeled for the opening of this warehouse pop-up market in the Grand Central Warehouse district by following Brick Street Farms on Instagram.
Want to know everything going on with Tampa Bay's food and drink scene? Sign up for our Bites newsletter.
Top 7 Vertical Farming Companies
Vertical farming refers to the practice of producing fruits and vegetables or cannabis vertically, in stacked layers, perhaps on many floors inside a building, using artificial lights instead of the sun, and a whole range of relatively new technologies
Written by: GP Solutions
Vertical farming refers to the practice of producing fruits and vegetables or cannabis vertically, in stacked layers, perhaps on many floors inside a building, using artificial lights instead of the sun, and a whole range of relatively new technologies.
The three main reasons why it’s a much-discussed topic now is because:
There are a number of startup companies emerging in the sector and attracting tens of millions of dollars in investment; and more people live in cities than do in rural areas, a global trend which seems irreversible, and this means that the demand for fresh produce will increase in urban areas, and bringing the production closer to the consumer would make sense.
Vertical farming provides a low-cost, turnkey method to start farming. This is especially useful in the cannabis industry where traditional greenhouses require land that could cost many millions of dollars.
Some of these technologies have been available for some time, decades even, but they were probably too expensive in the past to make vertical farming a viable business proposition.
The key technologies in vertical farming include:
Perception Technologies – cameras and other sensors which can monitor for colour and other factors, such as disease;
Artificial Intelligence – which can process the data from the sensors and formulate solutions;
Automated and Even Autonomous Mechatronics – robots and other automated machines which pick the produce when it is ready for market, or apply cures to ailments during their growing.
The above list is a very simple breakdown of the fundamental technologies that will be required to, basically, reduce to a minimum or even eliminate the need for human involvement.
If vertical farms are run like traditional greenhouses, there would be too much human input required and it probably would not be profitable.
It’s the new automation technologies that will make it work.
Carnegie Mellon University is among a number of organizations which have developed integrated systems for vertical farming. CMU’s version is called ACESys, short for Automation, Culture, Environment, and Systems Model for Vertical Farming.
An academic paper probably worth checking out is called Advances in greenhouse automation and controlled environment agriculture: A transition to plant factories and urban agriculture.
In their introduction to the paper, the authors note: “Greenhouse cultivation has evolved from simple covered rows of open-fields crops to highly sophisticated controlled environment agriculture facilities that projected the image of plant factories for urban farming.
“The advances and improvements in CEA have promoted the scientific solutions for the efficient production of plants in populated cities and multi-story buildings.”
So the interest in the field is strong and most people seem to think it’s a viable business proposition.
And to underline the positivity about the sector, Research and Marketsforecasts the vertical farming market will grow to a value of $3 billion by 2024, from virtually nothing now.
In some sectors, such as marijuana production, indoor farming is providing a strong foundation for healthy profits.
COMPANIES FOCUS ON VERTICAL FARMING
It’s a very new business sector, so this list is subject to change:
1. AEROFARMS
This company has won many plaudits for its operation and uses its own patented “aeroponic technology… to take indoor vertical farming to a new level of precision and productivity with minimal environmental impact and virtually zero risks”.
The company has raised at least $138 million in funding since launch in 2004, according to CrunchBase. Some of its backers are quite impressive, as this article in Ag Funder News reports.
The term “aeroponic farming” refers to the process of growing plants in an air or mist environment without the use of soil or any earth-like material, which is known as “geoponics.”
Aeroponic systems enable the production of plants using 95 percent less water, which is what AeroFarms says it does.
2. GP SOLUTIONS
GP Solutions developed “GrowPods” – finely tuned, automated, transportable and scalable micro-farms that have been shown to grow all types of crops, including cannabis, at a faster rate than conventional means of agriculture.
GrowPods allow cultivation to take place year-round, which maximizes ROI. The systems are sealed from outside pathogens, contaminants, pesticides, and chemicals, and produce clean and robust crops.
The company has licensed its technology to Micro Lab Farms for the cannabis market only. The Pods from Micro Lab Farms differ slightly from the regular GrowPods from GP Solutions in that they have been specifically tuned for the production of cannabis.
Micro Lab Farms recently announced the development of a cannabis complex in Southern California that will hold many of the aforementioned GrowPods – some of which are being made available to farmers, businesses, and entrepreneurs looking to quickly enter the California cannabis market (the largest in the world).
GP Solutions also has a line of remarkable new proprietary soil mixtures, which contain no animal products. This is critical because many other soils and additives can contain harmful pathogens and contaminants that can cause crops to become tainted or fail rigorous testing.
The company is traded on the OTC stock exchange (ticker: GWPD) and is growing at a rapid pace (pardon the pun).
3. PLENTY
Like the other big vertical farming companies on this list, Plenty is another one that retails its produce, which includes kale and other greens, as well as some exotic herbs.
Plenty is probably the biggest company in terms of the amount of money it has raised in funding – approximately $226 million, according to CrunchBase.
4. BOWERY FARMING
You’d think any farming startup of any kind would steer clear of everything that’s genetically modified, but the fact that Bowery makes a point of saying it uses “zero pesticides and non-GMO” seeds might suggest that some vertical farming companies don’t have the same ideas.
Having raised more than $140 million in investment since inception in 2015, Bowery has carefully developed a distribution network in the US. Its leafy greens are available to buy in Whole Foods Market and Foragers. It also supplies a number of restaurants and sells online.
It doesn’t look like Bowery supplies its platform to other companies, even though some might be interested in its claims, such as: 95 percent less water usage than traditional agriculture; 100 times more productive on the same amount of land; and from harvest to shelf “within a few days”.
5. BRIGHTFARMS
Another of the big-money startups, BrightFarms has so far raised more than $112 million since its establishment in 2010, according to CrunchBase.
But unlike some of the other big companies, it isn’t into aeroponics as much. It seems more interested in hydroponics, which refers to growing plants with water, or, to be more accurate, mineral nutrient solutions in a water solvent.
6. GOTHAM GREENS
This company is one of many which have started up in the New York area. Strange to say it about such a new sector, but the market for vertical farming produce may be saturated – in that city at least.
Gotham Greens has so fair raised at least $45 million since its launch in 2011. It has four production-scale facilities, in New York City and in Chicago, and plans for more in several other states.
And, like BrightFarms, it’s more of a proponent for the hydroponic growing method, although it may well eventually mix it all up and try different approaches in different facilities.
7. IRON OX
This company appears to use robotics perhaps more than the others, in the picking process at least, and claims to operate fully autonomous indoor farmings. It too is a proponent of hydroponics, and is a retail-oriented company.
Its products are similar to the others’ – leafy greens such as lettuce and kale or things like that. It’s one of the newer startups on the list so a lot might change.
Iron Ox has only recently started supplying its products to local markets in California. The company has so far raised over $6 million in funding, according to CrunchBase.
US: Georgia State University - Freight Farms - Leafy Green Machine
Just yards behind Piedmont North, the Leafy Green Machine is a fully functional hydroponic farm built inside a shipping container. Configured for the immediate growth of a variety of crops such as lettuce, kale, spinach and other herbs, its innovative climate technology and growing equipment allow for the perfect environment 365 days a year
Freight Farms
Just yards behind Piedmont North, the Leafy Green Machine is a fully functional hydroponic farm built inside a shipping container. Configured for the immediate growth of a variety of crops such as lettuce, kale, spinach and other herbs, its innovative climate technology and growing equipment allow for the perfect environment 365 days a year.
LEAFY GREEN MACHINE
Ready, set, grow. Want to try our freshly-grown produce? Stop by Miss Demeanor’s or Centennial Café to try some on your salad or sandwich.
About Our Leafy Green Machine:
Seeds begin in the nursery area, where they germinate and grow into little seedlings.
In this area, plants grow in a shallow trough that periodically floods and drains with the nutrient-rich water solution.
This area holds up to 3,600 plants at one time.
After three weeks in the seedling station, the sprouts will grow into a sturdier leafy green. The plants are transplanted into vertical growing towers that hang from the ceiling.
This method creates a high-density growing environment and maximizes the cubic footage in the container.
Emitters drip nutrient-rich water down the vertical grow tower using only 10 gallons of water daily to grow more than 4,500 plants.
The water that isn’t consumed by the plant flows out the bottom of the tower and is then recirculated right back to the water tank.
As sunlight is important during photosynthesis, the windowless farm is equipped with LED lighting that mimics the sun’s natural light via growth-optimized blue and red hues.
There are 128 lighting strips running about 18 hours per day to maximize the growth cycle, with the lights turned off to give plants time to rest and during peak hours.
Container Farms Bring Fresh Vegetables To Remote Canadian Community
Over 1,000 kilometres northeast of Yellowknife sit two steel shipping containers that are changing how we understand and respond to food production challenges in Canada’s North, and in other harsh and isolated locations
Over 1,000 kilometers northeast of Yellowknife sit two steel shipping containers that are changing how we understand and respond to food production challenges in Canada’s North, and in other harsh and isolated locations.
These containers have been retrofitted into a research station in Gjoa Haven, Nunavut, where the local community is working with government researchers and a non-profit organization to understand what is needed to create local food sources, clean energy generation, resilient building materials, scalability and adaptability to local needs, and even job opportunities and training.
The local community of Gjoa Haven has named the initiative Naurvik, which means “growing place.” It is a first-of-its-kind venture in Canada’s North, being built and adapted on-site.
Listening closely to Gjoa Haven Elders and community members, the Arctic Research Foundation, Agriculture and Agri-Food Canada, the National Research Council of Canada, and the Canadian Space Agency are actively collaborating on the design and testing of this green energy-powered controlled environment production unit for growing plants in Canada’s North. The community is deciding what plants they want to grow. It’s then up to the research partners to figure out how to adapt the research to their needs, and to train community partners to operate and maintain the system in the harsh and remote location.
“When I first heard of [the project] I thought it would never work up here. No. Not in this 40 below zero. Now I know anything is possible if you have the right idea... I had a taste of the vegetation. It was fresh”, said Peter Akkikungnaq, Gjoa Haven Elder.
By actively working with the local community, and tailoring solutions to their needs, Naurvik is creating a roadmap of how to deliver effective programs, infrastructure, and research in Canada’s North. By integrating resilience and adaptability into the design, the goal is that the model will be able to respond to needs in other harsh and isolated locations, not only in Canada’s North but also on space missions.
“The Canadian Space Agency is looking at innovative solutions to food production challenges that are common to astronauts on deep-space missions and people on Earth living in remote or extreme environments, such as the northern community of Gjoa Haven. While working towards to help with the development of advanced, robust designs for a terrestrial food production system, we are hoping to find strategies that could help astronauts grow food in space”, said Christian Lange, Head of Exploration Strategic Planning, Canadian Space Agency.
While the project is in its early stages, it’s hoped that by 2025 a community-led, renewable energy-powered plant food production system will be fully operational in Gjoa Haven. It will serve as a scalable blueprint for collaborative partnerships and co-designed projects in the Arctic and will be a focal point for innovative research and educational opportunities.
“This is an effective, novel approach to community-driven collaboration with science institutions in Canada’s North, and that’s the reason why it has been so successful. It will generate research for the benefit of all Canadians while also producing tangible benefits for Gjoa Haven and, eventually, other communities throughout the Arctic”, Adrian Schimnowski, CEO, Arctic Research Foundation, comments.
For more information:
Arctic Research Foundation
www.arcticfocus.org
Publication date: Mon 10 Feb 2020