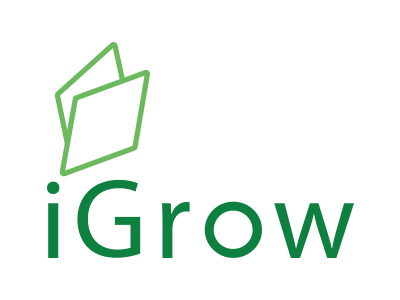
Welcome to iGrow News, Your Source for the World of Indoor Vertical Farming
UAE: Armela Farms Gears Up To Open 3 ha Automated Lettuce Farm
After launching in August 2016, the Armela team has spent more than two years in Research and Development regarding techniques, varieties of produce and optimum climate conditions, before celebrating their first harvest in August 2018
After launching in August 2016, the Armela team has spent more than two years in Research and Development regarding techniques, varieties of produce and optimum climate conditions, before celebrating their first harvest in August 2018. Since then, the team has advanced its process to achieve over 250% of an increase in production and is currently finalizing the opening of a new facility for Q1 2021, which will boast over 3 hectares of fully automated advanced lettuce farm, making it the largest facility of its kind in the GCC.
Armela Farms will also partner with several leaders in the Dutch agriculture sector to build the largest automated data-driven growing facility in the United Arab Emirates. Located in Abu Dhabi, the farm will be able to create over 9,000,000 lettuce heads per annum; that’s equivalent to 2,300 tonnes per annum.
Dutch tech
Armela Farms has chosen Van der Hoeven Horticultural Products to supply the project. In conjunction, Armela Farms will be using specialist technologies from a variety of suppliers like Hoogendoorn, Patron Agri Systems, Green Production Systems, Rijk Zwaan, Jiffy, Koppert, due to the expertise and experience by each company in their individual fields.
Mr. Avir Shah, CEO, and Founder of Armela Farms states, “Our aim is to produce products which exceed our community's expectation and reduce the reliance of imported highly-priced products by bridging the supply and demand gap with affordable price. We can achieve this vision by utilizing available resources and transforming it into a hi-tech, sustainable food production facility in accordance with the country’s vision of National Food Security and self-sustainability.”
Mr. Yazan Abu Jaish, General Manager of Armela Farms: “The new facility, for example, will enable us to monitor the evaporation of a single plant at any given time and many other advanced parameters required for optimum plant grown and output. Armela Farms is now moving from traditional hydroponic farming to data-driven farming.”
Mr. Gerard Oorthuys of Van der Hoeven Horticultural Projects: “I was very impressed by the sheer knowledge of the Armela farms team and wanted to show them one of our constructed greenhouses to show our capability. From our regional experience, we understand the climatic challenges more than any other company and we are confident we will deliver them a fantastic project.”
For more information:
Armela Farms
armelafarms.com
Publication date: Mon 9 Mar 2020
Democracy, Trust And The Virus
March 15, 2020
This Is A Moment To Be Sanguine.
Read This Letter With That in Mind.
For readers outside of the UK, please note the parochial focus of this particular missive touches on many issues that might be relevant in your country.
[T]he allocation criteria need to guarantee that those patients with the highest chance of therapeutic success will retain access to intensive care.
These are the new guidelines for the Italian College of Anesthesia, Analgesia, Resuscitation and Intensive Care, written an eon ago on Monday when Italy had 40% fewer cases of coronavirus than as I type these words. (There has been an update reported by the Daily Telegraph, “This is how it is in a war.”)
As COVID19 continues its exponential growth in most countries, the strategies which country select will have a massive impact on the severity outcome of this pandemic. Ignoring science at the top of government is unacceptable. However, science must not equally be a shield under which leaders absolve themselves of their political responsibility.
Writes my friend Nicolas Granatino, in a recent issue of his newsletter, Coronadaily reflecting on the British government’s approach to tackling the epidemic.
Boris Johnson and two senior science advisors delivered an impressive presentation. but their strategy for tackling the spread of the virus is controversial. As is becoming clear, the British government’s approach to handling the pandemic has been understood, in a nutshell, rightly or wrongly, as “let it roll through the population, avoiding tough containment measures because Brits will get bored, and protect the old until enough of us have herd immunity.”
It turns out it is more complicated than that.
Adam Kucharski, the epidemic modeler, author of The Rules of Contagion, and a member of one of the expert groups that comprise SAGE which advises the government, makes it very clear here.
A lot of modellers around the world are working flat out to find best way to minimise impact on population and healthcare. A side effect may end up being herd immunity, but this is merely a consequence of a very tough option - albeit one that may help prevent another outbreak.
Ian Donald, a psychology professor with expertise in anti-microbial resistance points out:
The govt strategy on #Coronavirus is more refined than those used in other countries and potentially very effective. But it is also riskier and based on a number of assumptions. They need to be correct, and the measures they introduce need to work when they are supposed to…
This is probably the best strategy, but they should explain it more clearly. It relies on a lot of assumptions, so it would be good to know what they are - especially behavioural. (emphasis mine.)
Models, even scientific ones, tell different stories, depending on the assumptions you put in. The assumptions are often uncertain and represent judgments & choices. The outputs of models have variances, based on the assumptions you make.
And an epidemiological model is a complex one with many inputs, variables, feedback loops and delays. (See this video here.)
These outputs become scenarios, which are based on your assumptions and judgments. Scenarios which you can navigate and use to explore future possibilities.
How you validate those assumptions is critical. How you select them is critical. How you make those judgments is also critical. It is also a human process that lends itself to argument and debate.
It is not sufficient to say “We are using the best science” and leave it at that. And certainly not in the era of open science, open data, and common tools to foster a healthy critical debate.
In the UK, the government gave us one choice, one approach, “from the science” as a fait-accompli.
But no model works like that. Science doesn't work like that.
Behavioral scientists have challenged one tenet of the British government’s plan: that of behavioral fatigue. Here a stampede of behavior scientists write: (I don’t know what the collective noun for behavioral scientists is. Stampede seemed a reasonable choice)
we are not convinced that enough is known about “behavioural fatigue” or to what extent these insights apply to the current exceptional circumstances. Such evidence is necessary if we are to base a high-risk public health strategy on it.
An abelian of mathematicians has also written to challenge the UK government’s approach.
Science doesn’t work the way Boris Johnson suggested it did.
Especially not in the context of health decisions. Readers will remember part of my tooth fell out a couple of weeks ago. Even my dentist offered me the choice of yet another filling or a crown. Science drove my dentist’s assessment, and I was still offered two choices.
There are discussions, arguments, challenges, disagreements, external trade-offs that went into the final recommendations. But with millions of lives at stake and an entire economy built with and enabling those lives, there needs to be a deeper debate, deeper scrutiny.
The doctors in Lombardy have had to become utilitarians, applying clear criteria of survivability on the decisions they make. I support them--on the front line they have few luxuries.
But the British government is making similar decisions with many more variables, without clearly explaining the choices they faced and the roads they took.
There is no doubt about the capabilities of the Chief Scientific Officer or Chief Medical Officer or the work of epidemiologists in various expert groups. Or the quality of their models. (Although no model is perfect, many are wrong and some may even have catastrophic mistakes in them. Think back to the models driving financial risk in the run-up to the global financial crisis. Remember David Viniar’s bullshit about “twenty-five standard deviation” events?)
It is that the modeling only throws light on a couple of aspects of the problem at hand. The model’s job is to also outline the possible paths of specific political choices.
It was a curious approach by the British government. One which has lost the trust. Yet, as I argued two weeks ago, public health emergencies require public trust.
the current British government, fought its electoral campaign with explicit attacks on the mechanisms of the state that stand outside politics, such as the judiciary and the Civil Service. At a moment when trust is most needed, to manage this burgeoning public health crisis, the government has been involved in a vicious attack on the very institutions that engender that trust.
How do you regain trust?
You can brief journalists and you can get your more articulate ministers to write an article in friendly newspapers. This is an industrial-age approach that might have worked with the poorly-educated, information-starved, under-networked, populace of the 1930s.
In the exponential age, your population is vastly more educated, resource-rich and networked. It has access to pretty much the same international research you do. It has, in many cases, better capabilities than the government can rely on.
And we can look on the Internet and read what is happening in South Korea, Taiwan, Singapore, Spain, Italy, Norway, Iceland, the Faroe Islands, China and you name it. We can see what they are doing. The temperature guns. The drive-through testing.
Italy looks like it can flatten the curve.
South Korea (below) is squishing new cases even as it tests vigorously. We can see this because the information is available from reliable sources.
We can hear Andy Slavitt, Obama’s healthcare majordomo, sound the alarm for the impending tsunami.
Nearly 30m of us have read Tomas Pueyo’s “Coronavirus: Why you must act now”. Some will have read the critique of whether “flattening the curve is a delusion.” You might have seen the Washington Post’s visualisations on how flattening the curve works.
Or perhaps you have been following the work of Yanner Bar-Yam and colleagues at the New England Complexity Science Institute whose models suggest “massive testing can stop the coronavirus outbreak” or their earlier work on Ebola contact tracing which has led them to suggest that even low compliance towards travel can stop outbreaks.
Many will wonder how quickly we could administer drugs to stop the cytokine storm that kills many who die of Covid-19. Or could we expand testing of and access to remdesivir, chloroquine or viagra, all of which seem to have some efficacy.
Some will ask whether acting aggressively now to slow the spread could buy time for health capacity to build up, even marginally. Or for Senegal to finish work on its 10-minute PCR test kit, or for us to validate Singapore’s serological tests.
In 2002, most Brits do not sit around doing the Daily Telegraph crossword, sipping tea, eating crumpets, waiting to lap-up the latest announcement from Downing Street on the wireless. So it’s truly bizarre to present a plan (perhaps it is the best??) that is such a massive outlier to the rest of the world and not expect pushback.
Openness, transparency about these types of decisions is a pillar of a democratic society. And it is foolish to think you can get away with a decision like this without someone asking difficult questions. Much more so when scientists are willing to state they disagree with you. And even more so in the era of the Internet. ( Paul Ginsparg demonstrated the value of open access when he launched Arxiv in 1991. Arguably Gutenberg did if even earlier.)
A better approach would be to open the model, to open the assumptions, for constructive discussion in the brief moments we have available, in a way that could catalyze improvements. You still have to lead, as Prime Minister, without question but you have to bring people with you. And we only at most a few weeks before the tsunami hits and our hospitals are, likely, overwhelmed.
Playing with one epidemic simulator, as it happens, helped me better understand Sir Patrick Vallance and Chris Witty, the UK government’s advisors rationale. Don’t get hung up on the model simulation I used. It is a toy simulator. Its conclusions are mostly useless. I don’t know what was under the hood. And it almost certainly ignores many of the more nuanced variables and relationships the real models used by SAGE have.
This toy simulator irrelevant except that:
It is clarifying for a citizen to play with a model like this, fiddle with assumptions, run simulations. It helped you understand the trade-offs that we face in tackling this epidemic—and it starts to outline what our personal responsibility and capacities may be.
The trade-offs are complex with non-linear effects of such a baffling nature I can only describe them as counter-intuitive. (Which more shows up the weaknesses in my expertise, more than anything else.)
I have no deep professional expertise on whether these epidemiological models. But I do understand the useful limits of models and can grok that the model is one input into an overall decision. That there are nuances. I do know there are assumptions on which decisions are made. The British government failed to give us their assumptions, the tools and democratic rigor to allow us to come to any kind of conclusion.
They still have a chance to do that. And early signs are that the British Government is demonstrating some pretty creative thinking (especially in enlisting the private sector and ramping up the NHS, our vehicle for universal, socialised medicine.)
But in being clearer and more inclusive in their communications, they might enlist creativity and talent and trust around the country in myriad other ways—not least in our willingness to step up and do the right thing.
What if we are more resilient and self-organizing and willing to clamp down on contact immediately? And will we do, as my community is, to support the vulnerable at a community level? What if we, the people, understand the horrific consequences of widespread promiscuous lunching at the local boozer?
Public health crises require public trust. A crisis like this, as we are learning from Italy, is more like a war. And it will be a long, grinding war, for which citizen trust, forbearance, and participation will be required.
As I went to bed on Saturday night, #boristhebutcher was, perhaps unfairly, trending on the socials. Such is the cost of forgetting about open, transparent, interactive communication that the internet enables.
This is the shape of democracy in the exponential age.
My friend from Shenzhen, six weeks into quarantine, sent me a WhatsApp. I know he won’t mind me sharing it with you: “Covid19 cases going up in Europe. Pls, take care.”
And let me add, keep your distance and WASH YOUR HANDS.
Azeem
P.S. On the point about the economy and its importance during a crisis… we’ll need a healthy economy of sorts to survive this marathon. The economy provides the goods and services that keep our population fed, nourished and healthy, and creates capacity in our health system. This isn’t so much an argument about GDP growth, but more than a healthy economy enables a healthy population and a functioning medical system.
Thanks to Nicolas Granatino, Vishal Gulati, Hampus Jakobsson, Paola Bonomo and many others for discussions that helped with this letter.
Thanks for subscribing to Exponential View.
This post is public, so feel free to share it. Share
Coalition for Sustainable Organics Disappointed in Latest Attempts Center for Food Safety to Restrict Supplies Organic Foods Through Lawsuit
Lee Frankel, the executive director of the CSO stated, “It is disappointing to see groups target pioneering organic farmers that use the most appropriate organic growing methods adapted to their site-specific conditions on their farms to meet the needs of consumers
SAN DIEGO, CALIFORNIA March 3, 2020 – The Coalition for Sustainable Organics (CSO) is saddened by the latest attempts by the Center for Food Safety and their allies to limit fair competition and organic supplies in the market through legal action.
Lee Frankel, the executive director of the CSO stated, “It is disappointing to see groups target pioneering organic farmers that use the most appropriate organic growing methods adapted to their site-specific conditions on their farms to meet the needs of consumers. The members of the CSO are strongly committed to the integrity of organic standards and the organic label. The groups behind the lawsuit failed to convince the members of the National Organic Standards Board (NOSB) to prohibit container and hydroponic production methods after significant industry debate and submission of public comments. Instead of unifying the industry after the decision made by representatives of the organic community at the NOSB, the CFS is seeking to eliminate public input to achieve their goals of restricting competition to drive up the price of organics for organic consumers to allow favored producers to increase their profit margins.”
Frankel continued, “Growers using containers adhere to the U.S. Department of Agriculture organic standards under the National Organic Program (NOP) and have been allowed to grow certified organic produce since the initiation of the NOP more than 25 years ago. After extensive study in 2010, the USDA through the NOP opted not to change these high standards for certifying organic produce – and affirmed that organic produce can be grown through containerized methods. After additional review in 2015-2017, the National Organic Standards Board voted to reject a proposed prohibition on container and hydroponic systems.”
Karen Archipley of Archi’s Acres of Escondido, California added “Our production systems are managed in accordance with the federal organic law. We chose to incorporate hydro-organic methods at our operations since it is the most appropriate way to promote ecological balance by drastically reducing our water use, conserve biological diversity by preserving valuable habitat while still incorporating the microbial processes described by organic pioneers to recycle nutrients to nourish our crops. Every choice we make and every input we use must be audited and approved by USDA-accredited certifying agents like any other Organic Farmer.”
Archipley continued “Changing the rules now would limit the amount of organic produce available to the public – just as the public is demanding more organic produce. This is not an issue that should be settled in the courts or politicized. If a grower meets USDA standards for organic certification, they should be able to market organic produce, whether they grow in soil or any other sustainable, certified organic growing media.”
#######
Stop Basil Downy Mildew With These Simple LED Strategies
Every basil grower’s worst nightmare is Basil Downy Mildew. You walk down the aisles, peer across the canopy, and then “Oh No!”. You see leaf yellowing and fuzzy purple growth. The once sweet smell of herbaceous goodness no longer smells so sweet knowing you have hours not days to react
"Every very basil grower’s worst nightmare is Basil Downy Mildew. You walk down the aisles, peer across the canopy, and then “Oh No!”. You see leaf yellowing and fuzzy purple growth. The once sweet smell of herbaceous goodness no longer smells so sweet knowing you have hours not days to react.
Image source: Cornell University
This awful gut feeling can be felt by any plant grower, and most know it too well. In cucumbers, it’s all about powdery mildew. In cannabis, white powdery mildew.
Traditional techniques call for using fungicides and adjusting your environment. These are still important methods given the severity of the situation, but there’s now a new promise of prevention strategies using light.
First, what is Basil Downy Mildew?
Basil that’s become infected with downy mildew will begin to turn yellow and may be mistaken for a problem with nutrition. This yellowing may be followed by dark brown or purple fuzz as sporulation continues to develop. Peronospora belbahrii is the Latin name for basil downy mildew.
The promise of using light to stop downy mildew in basil
Light has many effects on plants and other organisms’ physiology. In the case of downy mildew, disrupting the dark period with red light while managing temperature and humidity has been shown to prevent the production of spores in sweet basil.
Image source: Cohen Y, Vaknin M, Ben-Naim Y, Rubin AE (2013) Light Suppresses Sporulation and Epidemics of Peronospora belbahrii. PLoS ONE 8(11): e81282. https://doi.org/10.1371/journal.pone.0081282
Researchers at Bar-IIan University in Israel found that low-intensity red light inhibited sporulation of Peronospora belbahrii on sweet basil when applied during the dark period while maintaining moderate temperatures and low humidity.
Infected basil leaves were exposed to 5 or 10 micromoles of blue, green, red, or incandescent light. They were incubated at 20°C in moist conditions for 20 hours in a growth chamber.
Results showed that red light (at a peak of 625 nanometers) inhibited 99.7% sporulation regardless of the leaf surface exposed to light! Light strongly inhibited sporulation on leaves incubated at 15-27°C, but not on leaves incubated at 10°C.
What to do about powdery mildew in cucumbers
In the case of powdery mildew cucumber diseases, blue light has been shown to prevent the spread of disease by preventing the release of fungal spores.
Researchers at the Department of Chemical Biological Sciences in the Women’s University of Tokyo found that blue light can prevent the release of powdery mildew spores from developed fungal bodies and prevent the spread of disease melons.
Melon plants, inoculated with Podosphaera xanthii were grown in growth chambers under purple, blue, green, orange, red and broad-spectrum light, as well as in complete darkness and in a greenhouse under solar light. Light treatments were used on the powdery mildew for 14 days under continuous illumination of 59.5 micromoles of light.
Results showed that, while conidium fungal spores were still produced under all light treatments, spores were not released from conidiospores (or reproductive fungal spores) under blue light in the growth chamber. This research proves promising for preventing the spread of mildew in cucumbers, melons, and other cucurbits.
What this means for the future of Basil Downy and Powdery Mildew
These researchers have shown that light quality has the potential to stop the spread of fungal pathogens. It’s possible that in many cases, light spectrum must be readily controlled to inhibit the spread of mildew and other disease types.
In the case of fungal pathogens, light has been shown to suppress disease by disrupting the pathogen’s reproductive cycle and by exploiting natural adaptations in its circadian rhythm.
Depending on the fungi and plant species in question, this disruption can be a response to specific light wavelengths, the duration of the light period, duration of the dark period, total light intensity or a combination of these factors.
Light can also suppress disease by increasing the plant’s secondary metabolite production, which enhances the plant’s ability to defend against attack.
Using light to suppress disease in your operation
Research on light’s ability to suppress plant disease is in its early stages, but there are some important findings that can help guide growers when trialing light treatments for disease suppression.
Light treatments are plant and pathogen-specific, so it’s important to seek out information for light treatments specific to your particular crop and pathogen.
Depending on whether a disease is suppressed by enhancing the plant’s defense system or disrupting the pathogen’s physiological processes, light treatments may need to be applied throughout the plant’s entire growth cycle, limited to a short exposure or applied during a specific growth period in order to be effective.
Like all crop production processes, light treatment is only one part of the integrated strategy. Environmental factors like temperature and humidity, as well as production processes like irrigation and crop management, should be considered as part of an integrated pest management plan.
For more information:
LumiGrow
800-514-0487
info@lumigrow.com
www.lumigrow.com
Publication date: Mon 9 Mar 2020
Sobeys, Safeway, Thrifty Foods Adding In-Store Hydroponic Farms
The first stand-alone ecosystems will launch this spring at two Safeway stores in Vancouver, British Columbia, followed by additional stores in seven Canadian cities: Calgary, Edmonton, Halifax, Toronto, Vancouver, Victoria and Winnipeg
By Abby Kleckler - 03/09/2020
Empire's family of brands has partnered with in-store farming technology company Infarm to add vertical farming units to select Sobeys, Safeway and Thrifty Foods stores in Canada. The first stand-alone ecosystems will launch this spring at two Safeway stores in Vancouver, British Columbia, followed by additional stores in seven Canadian cities: Calgary, Edmonton, Halifax, Toronto, Vancouver, Victoria, and Winnipeg.
Shoppers in the United States can already find Infarm systems like this one at some Kroger-owned QFC banners in Washington state
"Our goal at Empire is to be the fastest-growing and most innovative retailer in Canada. As we strive to achieve that goal, we continuously seek out first-to-market opportunities," said Niluka Kottegoda, VP customer experience at Stellarton, Niva Scotia-based Sobeys Inc. "Our partnership with Infarm is unique in Canada and offers our customers a world-leading urban farming solution. The products we will offer in store are unique to customers in urban communities. We're excited to test and learn with our customers along the way."
The in-store farms use machine learning and AI technology to produce fresh, nutritious and flavorful produce year-round without the use of chemical pesticides. The vertical farms use 95% less water, 90% less transportation and 75% less fertilizer than industrial agriculture does.
Infarm currently operates in the United States — through its partnership with Kroger at some QFC banner stores in Washington — Denmark, France, Germany, Luxembourg, the United Kingdom and Switzerland.
"Our partnership with Empire builds upon our vision to grow a resilient ecosystem that can help feed people living in cities around the world by 2050, while improving the environmental footprint of our food," said Erez Galonska, co-founder and CEO of Berlin, Germany-based Infarm. "For example, through vertical farming, we can introduce plants to markets that were previously unavailable because they were too delicate to be transported. We're proud to partner with Empire to share the Infarm revolution with Canadians."
The Philadelphia Zoo Is Running A Farm Inside A Converted Shipping Container
Tua lives at the Philadelphia Zoo, the first zoo in the country with its own on-site vertical garden used to grow leafy greens for its animals. And she loves the produce they’re feeding her
by Brianna Baker, For The Inquirer, March 4, 2020
Kristen Waldren, director of strategic initiatives at The Philadelphia Zoo, walks through the zoo's new "Cropbox" — a vertical farm being used to grow plants that are harvested to feed animals. MARGO REED
If you’re a fan of homegrown arugula and mustard greens, you just may have the same taste as Tua, a 27-year-old Sumatran orangutan.
Tua lives at the Philadelphia Zoo, the first zoo in the country with its own on-site vertical garden used to grow leafy greens for its animals. And she loves the produce they’re feeding her.
The garden is located in a retrofitted shipping container in the Urban Green, the zoo’s open-air food marketplace. A mural, by Philly-based environmental artist and activist Eurhi Jones, transforms the front of the shipping container into a colorful collage of the animals who’ll chow down on the vegetation.
But the real beauty is inside, where stacked, tidy shelves hold rows of plants that are grown hydroponically, in nutrient-rich water instead of soil. LED lights, a substitute for sunlight, shine 18 hours a day. Farm operators use a mobile app to remotely control the container’s light, temperature, and humidity levels.
Kristen Lewis-Waldron, director of strategic initiatives at the zoo, said the vertical farm is far more sustainable than bringing in food from outside sources. It uses 70% to 90% less water than traditional farming, has no need for pesticides or herbicides, and cuts greenhouse gas emissions out of the equation since no motor-powered transportation is necessary to get the food to the zoo.
“It really kind of creates this farm-to-table [model] — in this case, shipping container-to-exhibit,” she said of the project, which is in a pilot phase.
Want to know what's going on in Philly? Find out about upcoming concerts, shows, and other events with our weekly newsletter.
Lewis-Waldron is short on farming experience but knows a thing or two about feeding animals. She landed her first role at the zoo 23 years ago as a nutrition intern. She went on to work for, and eventually lead, the zoo’s conservation department, before transitioning to her current position. Growing greens for the animals makes her feel like she’s come full circle, she said.
A peacock at the Philadelphia Zoo walks past the "Cropbox," a converted shipping container being used to grow plants being used to help feed the animals. MARGO REED
To launch the project, she enlisted the services of CropBox (which is also what the zoo calls the vertical farm), a North Carolina company that provides all the equipment customers need, including the shipping container, and helps set up the system.
Lewis-Waldron also consulted with industry experts, including those who operate their own vertical farms, to learn best practices and how to troubleshoot technical challenges. All in all, the preparation process took about a year.
In its nine months of operation, the CropBox has fed 20 animal species with its microgreens. It produces 275 pounds of leafy greens a month, which is only 10 percent of the zoo’s monthly requirement. But that number, Lewis-Waldron said, will grow once the pilot year concludes and the project is expanded.
“You can take over a vacant warehouse or vacant building and convert it,” she said. “You could take six of these and make a dent in the requirements of our collection.”
The CropBox also benefits the zoo economically by replacing a collection of food it would otherwise purchase.
But perhaps most importantly, the greens grown in the vertical farm are rich in nutrients. The zoo takes animals’ diets very seriously and even employs a full-time nutritionist. By feeding leafy greens to the animals, the zoo is keeping their health in shape.
Still, that doesn’t mean the greens are every species’ favorite snack. Just like humans, animals have unique palates. And the current variety growing in the CropBox — a stir-fry mix that includes arugula and mustard greens — isn’t always a crowd-pleaser.
“It’s got a little kick to it, a little bit of spice. Our emus were a little hesitant,” Lewis-Waldron said. “But our monkeys, langurs, apes, gorillas, orangutans, tortoises absolutely love it. So it’s interesting, and we’ll continue to test out different types of greens.”
Brianna Baker, For The Inquirer
High Hopes For UK Vertical Farming Startup
Vertical farming startup LettUs Grow is one of a number of UK firms developing technology that could help shore up the UK’s food security. Andrew Wade reports
By Andrew Wade 3rd March 2020
Vertical farming startup LettUs Grow is one of a number of UK firms developing technology that could help shore up the UK’s food security. Andrew Wade reports.
LettUs Grow co-founder Charlie Guy inspecting produce
Between the UK’s EU exit and the growing threat of climate change, food security has become a headline topic. The supply lines from farm to fork that many of us take for granted can be more fragile than we think, as illustrated by recent weather events in the UK.
“At the height of the heatwave that we had last summer, (the UK) was importing lettuce by plane from California, importing around 30,000 heads a week just to keep food on our shelves,” explained Charlie Guy, managing director and co-founder of agritech startup, LettUs Grow.
Set up in 2015 while Guy was still at Bristol University, LettUs Grow is one of several emerging UK businesses focused on vertical farming, where plants and crops are grown indoors in upright stacks, typically without soil, using LED lighting, climate control, and targeted nutrient delivery. Although still a relatively niche enterprise, it’s attracting plenty of attention, with grocery retailer Ocado recently announcing a £17m investment in the sector.
Green machines: sowing the seeds of farming 4.0
For its part, LettUs Grow has just secured £2.35 million in seed funding, which Guy says the company will use to scale up and invest in new products. Currently, the business has two major components: its aeroponic nutrient delivery system and an integrated farm management software platform called Ostara. According to LettUs Grow, its aeroponics equipment can boost growth rate by 70 percent across a range of crops compared to other vertical farming methods such as hydroponics, as well as reduce water usage by 95 percent versus traditional agriculture.
“At LettUs Grow we’ve developed two key technologies,” Guy explained. “The first is a new aeroponic method where we irrigate the crop roots with a very fine mist using a patent-pending method that we’ve developed over the last few years. It has massive benefits in terms of how scalable the technology is and controllable and optimizable it is.
“It’s all about the amount in the root zone that plants experience. Everyone knows that healthy soil has good pockets of oxygen and nutrients and is well aerated. So this is really what we’re maximizing. By having no soil and an air gap you’ve got bountiful oxygen and carbon dioxide for plants to perform at their biological optimum.”
Vertical farming sees trays of produce stacked under LED lights
Somewhat misleadingly, LettUs Grow is primarily a technology provider rather than an actual food grower, supplying its equipment and software to farmers and entrepreneurs seeking out new opportunities. According to Guy, the return on investment of aeroponics takes just two to three years, while the more widely used hydroponics takes between four and five.
But nutrient delivery is just one part of the vertical farming picture. Advances in LED lighting, coupled with a reduction in cost, have played a key role in the sector’s boom. Rather than simply replicating sunlight, LEDs can be finely tuned to different wavelengths for various crops. Combined with carefully controlled climate conditions, LEDs and aeroponics can enhance every aspect of growth, maximizing crop yields.
“All of these are effectively ways that we can optimize or tune the performance of a plant so that it’s most photosynthetically efficient and working at its optimum,” said Guy.
The second pillar of LettUs Grow is Ostara, a bespoke software platform that can monitor and control indoor growing in greenhouses as well as vertical farms. Sensors throughout the growing environment feedback to the software, which collates the data and provides crop growth analysis. On top of this, Ostara also incorporates tracing of crop history, something that Guy believes has become more important for retailers and consumers given events of recent years.
“The real importance of this was seen in 2018 with the romaine lettuce scandal in the US, where contaminated produce was on shelves and nobody knew where it had come from,” he explained.
“One of the massive benefits of indoor and controlled-environment agriculture is that we can really know where our produce has gone and what it’s experienced after it was produced and grown.”
The elephant in the room remains cost. Swapping sunshine and soil for LEDs and aeroponics may deliver a host of benefits, but is also comes at a price. The energy inputs currently required for vertical farming make it difficult to turn a profit on anything but high-value herbs and leafy greens. Basil, parsley, and watercress grow quickly and sell at a premium, making them the perfect candidates for vertical farming in terms of competitiveness.
“To date, we’ve grown around 60 different crops in our facility,” said Guy. “We’re mainly focused on the high-value herbs or lettuce and leafy green crops, but we’ve also grown things like carrots, radishes strawberries and a whole host of things like tobacco and propagation for trees.”
Energy inputs make up the bulk of the crops’ final cost
Seasonal demand sees peaks and troughs in the price of things like cress and lettuce, and carefully choreographed growing at scale could allow vertical farms to be profitable in these types of markets. Whereas traditional agriculture has been pushed to the limits of its productivity, this nascent farming method has plenty of headroom to make leaps in efficiency as it scales up and technology improves. Urban farms that supply on-demand to high-end city restaurants is one business model that Guy thinks could work, but knowing your market is key.
“There’s no point growing crops that are fashionable but you don’t know where you’re going to sell them,” he said.
“We’ve been working with a company that supplies 20 or so of the best restaurants in Bristol – Michelin Star quality. So quality is definitely one of the biggest selling points.”
Ultimately, the produce also has to be able to match conventional agriculture on price.
“Food grown in these systems has to be competitive with traditional methods…and we’re building tools and features into our software that will enable efficiencies in labor and energy as well,” said Guy.
One of those features is integration with renewable energy. LettUs Grow recently partnered with Octopus Energy to optimize power usage throughout the day, avoiding times of peak demand. In a controlled indoor environment, day and night can be variable concepts that reflect the vagaries of the energy market rather than the rising and setting of the sun.
“We’ve already shown around a 15 percent reduction in energy through this,” said Guy. “And with energy being one of the biggest contributors to most crops in an indoor facility, this is pretty significant.”
As well as herbs and leafy greens, the company has identified a more niche area with potential for profit. Research sectors, including the pharmaceutical industry, often require exotic plants or novel strains of crops. The closely controlled environment of vertical farming can not only guarantee provenance, it can provide tweaks and adjustments in growing conditions to produce an abundance of different outcomes on demand.
“We’ve been working with a company testing crops that could be used for vaccine production,” Guy explained, “so there’s all sorts of novel uses where you really want that tight level of control.”
Despite the produce being endorsed by high-end restaurants and big pharma, the nature of the growing method has also brought some unexpected hurdles.
“At the moment we aren’t able to certify as organic, even though our sustainability credentials are arguably better than organic,” said Guy. “This is a bit of a sticking point because we don’t have any soil, and without any soil, it’s hard to certify that soil as organic.”
As much a philosophical problem as a technical one, the absence of soil is nonetheless preventing vertical farming from achieving the same certifications as traditionally grown food. It’s symptomatic of an industry still coming to terms with a new method and its impact. As the sector expands, these growing pains will no doubt be overcome, allowing vertical farming to play an important role in agriculture’s 21st-century tech revolution.
AeroFarms Reveals To California North Coast Food Producers Its High-Tech Controlled Environment Agriculture
Imagine a farming method so efficient that you could grow a variety of leafy greens in half the time it traditionally takes — without any pesticides, herbicides or fungicides — and where the sun has no role
NORTH BAY BUSINESS JOURNAL March 2, 2020
CHERYL SARFATY
Imagine a farming method so efficient that you could grow a variety of leafy greens in half the time it traditionally takes — without any pesticides, herbicides or fungicides — and where the sun has no role.
It’s all done indoors, and it’s a growing trend known as controlled environment agriculture (CEA). The biggest player in the space is AeroFarms, a Newark, New Jersey-based operation that was among the businesses that participated at the Feb. 25 North Coast Specialty Food & Beverage Conference.
“We track everything that happens to the plants, from its genetics all the way to harvest. And by measuring along the way, we can use that data to learn more about what makes plants grow,” said AeroFarms Chief Financial Officer Guy Blanchard. “The ability to do this is transformative, it’s brand new if you think of the difference with field farming, where you can’t control the temperature and you can’t control the weather. You’re really reacting and trying to respond to the things that Mother Nature is throwing at you.”
In addition to AeroFarms, which is privately held, there are a variety of CEA players in the marketplace, including Bright Farms, Little Leaf Farms, Bowery Farms, Revol Greens and Plenty, which is based in South San Francisco. The majority of these businesses are headquartered in the Midwest and further east, where bad weather makes it impossible to grow the greens outdoors.
There are a variety of growing methods within the CEA category, the two most common being hydroponics and aeroponics. With hydroponics, plants are grown with mineral nutrients in a water base rather than in soil. Aeroponics, which is AeroFarms’ method, also uses no soil, instead of planting seeds in fabric and misting them with mineral nutrients.
AeroFarms grows 800 varieties of edible greens, such as lettuce, arugula, and spinach. The plants require 95% less water than on farms and are completely grown in 12 to 14 days, rather than 30 to 45 days in the field. The company’s retail brand, Dream Greens, is sold in grocery stores in New Jersey and New York.
Blanchard declined to disclose the company’s financial metrics. According to ROI-NJ, a New Jersey business publication, AeroFarms raised $40 million in 2017.
The vertical farming market size was valued at $2.23 billion in 2018 and projected to hit $12.77 billion by 2026, according to Allied Marketing Research.
There’s going to be change, but I don’t want to lose our small farmers.
Pegi Ball, Santa Rosa Original Certified Farmers Market
Pegi Ball and Janet Ciel, who each run farmers markets in the North Bay, said at the conference they wonder how the CEA industry might someday impact the region’s farmers“.
There’s going to be change, but I don’t want to lose our small farmers,” said Ball, who manages the Santa Rosa Original Certified Farmers Market at the Luther Burbank Center for the Arts. “It’s more than just lettuce and that sort of thing. It’s the culture, it’s the tradition, it’s our community, so that’s what concerns me.”Ciel, who manages the Healdsburg Certified Farmers Market and also works with the Agricultural Institute of Marin’s Stonestown Farmers Market in San Francisco, came away impressed by Blanchard’s presentation, but also curious about how traditional farming and controlled environment agriculture could potentially coexist.
“I think the technology is brilliant,” Ciel said.
“I just think the small farmer is … dealing with the weather and pests and (various other factors), and they don’t have the funding or the education to pull something like this off. Is there something there that is for them?”
Blanchard views the growing CEA industry to be more comparable to — and therefore more competitive with — commercial food-processing operations than traditional farming because of the costs involved, from investing in capital equipment to staffing, of which AeroFarms employs about 160 people.
“If you’re going to have a farm manager, a safety manager, a shipping manager and a maintenance manager (among the staff), you may be up to like $600,000 a year in wages and benefits before you’ve even gotten to anything really related to the farm,” Blanchard said. “In many ways, even though the processes are different, this isn’t different than some other food-processing (businesses) necessarily, and you’ve got to manage it.”
I’m certain we’ll continue to see new and different commodities take advantage of innovative growing techniques of a controlled environment.
Mary Coppola, United Fresh Produce Association
Another reason CEA poses little to no threat to farmers, at least at this point in time, is because food grown in this vertical indoor environment is limited primarily to leafy greens. Greenhouses have more latitude.
“There are a number of companies who are growing greenhouse strawberries, peppers, cucumbers and tomatoes with much success,” said Mary Coppola, vice president for marketing and communications at United Fresh Produce Association. The Washington, D.C.-based organization was founded in 1904 and advocates for companies in the fresh produce supply chain. “I’m certain we’ll continue to see new and different commodities take advantage of innovative growing techniques of a controlled environment.”
And where agriculture industry experts laud controlled environment agriculture for its renewable and sustainable efforts, such as conserving land and water, there are other cost concerns.“
They rely a lot on artificial lighting, so obviously energy consumption is an issue,” said Humberto Izquierdo, agricultural commissioner, and sealer of weights and measures for Napa County. “I think the economics have to be there.”
Guy Blanchard, chief financial officer of AeroFarms, explains how the New Jersey-based startup gets dozens of turns of fresh produce annually through its vertical indoor farm, speaking at North Bay Business Journal’s North Coast Specialty Food and Beverage Industry Conference on Tuesday, Feb. 25, 2020, at Doubletree Hotel by Hilton Sonoma Wine Country in Rohnert Park. (Jeff Quackenbush / North Bay Business Journal)
Blanchard said he doesn’t view energy consumption as a challenge for AeroFarms.“I think when people think about energy or environmental footprint, it’s tough to see how much is really embedded in traditional agriculture when you have all the energy going to root watering, soil and soil degradation, and the energy that goes into fertilizers and harvesting a field,” Blanchard said, as well as transporting, cooling and washing.
Marc Oshima, AeroFarms co-founder, and chief marketing officer said the company and its competitors are focused on strengthening the overall agriculture industry, such as sharing their expertise about how to grow greens safely to avoid contamination. They also formed their own group, called the Controlled Environment Agriculture Food Safety Coalition.
“(It) was a critical step to establishing best practices and educating the FDA and customers on why indoor farming has so many more safeguards versus traditional field farming, and less exposure that often occurs with co-mingling at the major leafy greens processors, who are sourcing from multiple growing regions both domestically and internationally,” he said.
The coalition also has partnered with Foundation for Food and Agriculture Research on a $2 million, three-year program to identify stressors of leafy greens in order to optimize taste and nutrition, he said.
Staff Writer Cheryl Sarfaty covers tourism, hospitality, health care, and education. Reach her at cheryl.sarfaty@busjrnl.com or 707-521-4259.
Signify Expands Collaboration With Planet Farms
Thanks to the latest agreement, Europe’s largest vertical farm will boost the quality and yield of the crops using the Philips GreenPower LED production module managed by the Philips GrowWise Control System
Signify is expanding its collaboration with Planet Farms, a European operator of vertical farms based in Italy. Thanks to the latest agreement, Europe’s largest vertical farm will boost the quality and yield of the crops using the Philips GreenPower LED production module managed by the Philips GrowWise Control System.
Signify has also reached an agreement to provide horticultural LED grow lights to an additional five vertical farms that Planet Farms is planning to build in different European countries in the coming years, including Switzerland and the UK.
The Philips Greenpower LED production module, Signify’s latest horticultural LED innovation for vertical farming, helps growers optimize multilayer crop cultivation. By managing the lights with Philips GrowWise Control System, growers can easily create and run custom light recipes on dimmable and color-controllable modules to meet the needs of different crops and growth phases. This gives growers the ability and flexibility to create and control their own time-based light recipes and improve crop results and operational efficiency in closed, climate-controlled cultivation facilities.
“We started working with Signify five years ago because of the company’s knowledge and expertise of horticultural LEDs and light recipes,” said Luca Travaglini, co-founder and co-CEO of Planet Farms. “Thanks to the collaboration we’re able to grow high-quality crops all year round and that’s why we’re now expanding our collaboration. The GrowWise Contol System helps us easily adjust light recipes and continuously enhance the taste of our crops, which is crucial for us.”
This year, Planet Farms will finish construction of Europe’s largest vertical farm in Cavenago, just north of Milan. The vertical farm will cover more than 9,000 m2, which is the equivalent size of 45 tennis courts. Planet Farms operates an innovative integrated growth process that starts with the seeds and ends with packaged products. The production process is entirely automated meaning that consumers are the first to touch the crops.
“We’re proud to provide Europe’s largest vertical farm with our innovative lighting products and knowledge and expertise of light recipes. This next step in our collaboration shows that we can really help vertical farmers around the globe to improve the quality, yield and taste of their produce,” said Udo van Slooten, Business Leader Horticulture lighting at Signify. “The plans to build another five farms across Europe shows that vertical farming is rapidly growing and evolving. It’s a thrilling time to be involved in vertical farming, and we’re excited to help shape its future.”
Signify and Planet Farms formalized their collaboration in 2018 when Planet Farms announced the construction of Italy’s first vertical farm research lab in Milan. This lab opened in 2019. Signify supported Planet Farms with its lighting expertise for vertical farming and by providing its Philips GreenPower LED production module Dynamic grow lights.
For more information:
Signify: www.philips.com/horti
Gotham Greens Greenhouse Replaces Bethlehem Steel Mill
Like other Gotham Greens facilities, the greenhouse uses hydroponic systems and is 100 percent powered by renewable energy
March 3, 2020
By Anca Gagiuc
All images courtesy of Gotham Greens and Julie McMahon
Like other Gotham Greens facilities, the greenhouse uses hydroponic systems and is 100 percent powered by renewable energy.
A portion of the former Bethlehem Steel Mill in Sparrows Point, Md., has sprouted as a hydroponic greenhouse. The 100,000-square-foot facility is located just outside of Baltimore, Md., and is Gotham Greens’ seventh facility of its kind nationwide.
Like the other Gotham Greens facilities, this greenhouse uses hydroponic systems and is 100 percent powered by renewable energy. The company claims that it uses 95 percent less water and 97 percent less land than conventional farming. In addition, the new greenhouse is served by proprietary data-driven tools that enable the producer to run one of the highest-yielding, most energy-efficient indoor farming systems available on the market.
The greenhouse will be the first to provide a year-round supply of fresh lettuce to retail, restaurant and foodservice customers across 10 states in the Mid-Atlantic and Southeast regions. The current project opens 60 full-time green jobs in Baltimore. The firm has partnered with the Baltimore County Department of Economic and Workforce Development and the Center for Urban Families to find the best candidates for the positions.
Bethlehem Steel Mill has its origins in the 1880s and was acquired by Bethlehem Steel in 1916 when Sparrows Point became the world’s largest steel-producing center, where girders for the Golden Gate, George Washington and Bay bridges, as well as steel for shipbuilding during the World Wars, was produced. The facility gradually deteriorated until its bankruptcy in 2012.
Grocery Micro-Farms Take Off
Kroger has teamed up with Infarm, a six-year-old startup based in Germany, to install modular vertical farms. In these mini-farms, which use a hydroponic farming method, nine varieties of lettuce and herbs are stacked in rows and grown in nutrient-rich water until they are mature enough to be sold to customers
Kroger And Infarm Install Vertical Farms In Stores
By Phil Lempert on Feb. 24, 2020
In our annual trend report three years ago we correctly predicted that the time has come for supermarkets to install their own indoor farms, in which shoppers could pick their own produce right from the farm—the ultimate in freshness, taste and local. Kroger is leading the way by adding these mini-farms to two of its Quality Food Centers (QFC) stores in the state of Washington.
Kroger has teamed up with Infarm, a six-year-old startup based in Germany, to install modular vertical farms. In these mini-farms, which use a hydroponic farming method, nine varieties of lettuce and herbs are stacked in rows and grown in nutrient-rich water until they are mature enough to be sold to customers.
Infarm has more than 500 such installations in stores and distribution centers in other parts of the world, but this is its first installations in U.S. grocery stores. The growing process at the two pilot stores involves LEDs and an irrigation system with recycled water.
Infarm uses a cloud-based technology system to remotely control the temperature and lighting for each of its farms.“
Customers today want transparency; they want to know exactly where their product is from, the provenance where it was grown,” said Suzy Monford, Kroger’s group VP of fresh foods.
The program has already been deemed a success by Kroger. Monford said the stores have been selling everything from kale to cilantro as fast as the plants have been able to mature. Kroger has announced plans to expand vertical farming to 13 more QFCs in Washington and Oregon by April.
Infarm’s the ultimate goal is to make local food production mainstream. “For the bulk of the last century, food has been produced far from where it is consumed, generating a supply chain that is environmentally unsustainable,” said Osnat Michaeli, the company’s co-founder and chief brand officer. “Our modular farms offer the potential of turning the supply chain on its head by building the world’s first global farming network.”
Fireside Chat With Square Roots CEO & Co-Founder Tobias Peggs: Scaling Indoor Farming At Speed
Indoor Ag-Con is excited to announce that Square Roots Co-Founder & CEO Tobias Peggs has joined our conference line-up for the May 18-20, 2020 edition! Tobias will join Nicola Kerslake, Indoor Ag-Con Founder and Co-Founder, Contain, for the afternoon Fireside Chat: Scaling Indoor Farming At Speed
Square Roots Co-Founders Tobias Peggs and Kimbal Musk Empowering Next-Gen Farmers
Indoor Ag-Con is excited to announce that Square Roots Co-Founder & CEO Tobias Peggs has joined our conference line-up for the May 18-20, 2020 edition! Tobias will join Nicola Kerslake, Indoor Ag-Con Founder and Co-Founder, Contain, for the afternoon Fireside Chat: Scaling Indoor Farming At Speed. If our industry is to bring high-quality, local produce to customers all year round, we must collectively understand how to scale farming at speed to reach as many people as possible. Using a unique and scalable ‘farmer-first’ technology platform, Square Roots is doing just that. Tobias will share how this tech-enabled urban farming company is training and empowering the next generation of leaders in urban agriculture to grow local food that is delicious, responsible, nutritious, and profitable. And, be sure to check out the story further down in this issue highlighting our special guest blog post from Square Roots Co-Founder Kimbal Musk, too!
CHECK OUT FULL CONFERENCE SCHEDULE >>>
During Indoor Ag-Con, we’ll be featuring the panel presentation, What Is the Next Technical Frontier for LED Lighting” on Monday, May 18 from 10 – 10:45 am. Moderated by Dr. Morgan Pattison, SSLS, Inc., the panel will include Blake Lange, Signify, formerly Philips Lighting – City Farming; Brandon Newkirk, LumiGrow; and Xander Yang, Sananbio.
Ahead of the session, we reached out to our participants to find out, from an LED perspective, what is the next hot thing in lighting?
WHAT'S THE NEXT HOT THING IN LED LIGHTING? >>>
KIMBAL MUSK: 10 WAYS SQUARE ROOTS' FARM-TECH PLATFORM EMPOWERS THE NEXT GENERATION OF FARMERS
Ahead of Square Roots CEO & Co-Founder Tobias Peggs' Fireside Chat at Indoor Ag-Con, Co-Founder & Exec Chairman Kimbal Musk has shared a guest blog post with us.
"There are a lot of smart people in this industry, many with different visions for the optimum architecture and model for indoor farming (e.g. plant factories)," says Musk. "But all working hard to bring better food to market — which, given our wider vision to bring real food to everyone, is wonderful to see. The more of us working on the real food revolution the better — and we want all of these systems to flourish. But here are 10 reasons why we think container farming rocks.....”
10 WAYS SQUARE ROOTS' FARM-TECH PLATFORM EMPOWERS NEXT-GEN FARMERS>>>
YOU COULD WIN 2 TICKETS TO BIOSPHERE 2!
When you arrive at Indoor Ag-Con, be sure to enter for your chance to win two general admission tickets to Biosphere 2 and an overnight stay at B2 cabanas!
The winners will get to tour one of the world’s most unique facilities dedicated to the research and understanding of global scientific issues. The Biosphere 2 facility serves as a laboratory for controlled scientific studies, an arena for scientific discovery and discussion, and a far-reaching provider of public education.
What’s more, as part of the package, the University of Arizona Controlled Environment Agriculture Center (UA-CEAC) would like to also extend an invitation for the recipients to its vertical farm research and educational facility (UAgFarm) at UA-CEAC and other UA-CEAC projects/facilities as an additional welcome!
SEE WHO'S SPEAKING | SEE WHO'S EXHIBITING
INSIDE INDOOR AG | INDUSTRY NEWS HARVEST
PRODUCE GROWER: Elevate Farms Closes on $1.8 Million In Round Of Funding
GREENHOUSE GROWER: Gotham Greens Opens Another Massive Greenhouse
NEW YORK POST: I Tasted A Bug Diet, the Sustainable Protein That Could Save The WorldIGROW NEWS --CubicFarm Systems Announces Largest Sale To Date
SPECIAL THANKS TO OUR GROWING ROSTER OF
SPONSORS, MEDIA ALLIES & INDUSTRY PARTNERS
In addition, Indoor Ag-Con is proud to be a member of the Hemp Industries Association.
Indoor Farming And Qualified Opportunity Funds
In a recent interview with OpportunityDB’s Jimmy Atkinson, Local Grown Salads Founder Zale Tabakman explained that Opportunity Zones and indoor vertical farming are a good combination because these operations can be set up in “food deserts,”
2020
Qualified Opportunity Funds have been set up to fund Qualified Opportunity Zones and Qualified Opportunity Zone Businesses. One such QOF, the LGS Opportunity Zone fund, focuses on the development and maintenance of indoor vertical urban neighborhood farms, grown and distributed by Local Grown Salads. The “farms” are being developed in older buildings, situated in Baltimore, MD Opportunity Zones. According to the company’s website, four properties have been identified, to date, with the farms set up in 15,000-square-foot increments.
The product coming out of these businesses are packaged salads consisting of lettuce, cucumbers, chard, kale, and others, which are sold to local restaurants and the community.
In a recent interview with OpportunityDB’s Jimmy Atkinson, Local Grown Salads Founder Zale Tabakman explained that Opportunity Zones and indoor vertical farming are a good combination because these operations can be set up in “food deserts,” lower-income areas where people have to drive or take a bus long distances to get food to eat. Additionally, they are environmentally sound because the food grown isn’t using pesticides or fungicide, and little runoff. Tabakman also cited a carbon footprint reduction, pointing out that the locally grown food has less distance to travel than, say, produce from California to the East Coast.
Finally, these farms are set up to create local jobs. Tabakman indicated that each farm can create 25 jobs, with pay averaging around $15 per hour. Additionally, the company is working with the bank to ensure financial literacy for employees.
From Tabakman’s point of view, LSG’s vertical farms tick off the many boxes of Opportunity Zone investments, being located in the federally-designated areas, and providing a positive impact on the community. “Indoor vertical farming, because it’s food, is great . . . but any other product being produced locally really makes sense in an Opportunity Zone . . . especially when you need to be close to your customers,” he told Atkinson.
CONNECT WITH LOCAL GROWN SALADS
US: New Jersey - Hope Cahill Starts As Coordinator At Hydroponic Farm
A hydroponic farm, in the middle of a municipal center? Well, it all started in 2016, when Robbinsville Mayor Dave Fried found out about hydroponic farming in freight containers
By Lois Levine
March 1, 2020
A hydroponic farm, in the middle of a municipal center? Well, it all started in 2016, when Robbinsville Mayor Dave Fried found out about hydroponic farming in freight containers.
“He loved the idea and thought it would be beneficial to the township in terms of feeding programs and education on how to grow greens and learn more about nutrition,” said Kevin Holt, recreation manager for the Robbinsville Township.
Hope Cahill, the new coordinator of Robbinsville’s hydroponic farm, holds some of the farm’s yield.
Now, the farm has a new coordinator—Hope Cahill, who took over for original caretaker Kyle Clement in January.
“We can grow anything that is a leafy green,” Cahill said. “Here we are growing butterhead, oak leaf, and lollo lettuce, as well as spring mix.”
The farm also grows some herbs, basil, and cilantro. Cahill, 25, is certified in aquaponics, an off-breed of hydroponics.
After graduating high school, she got certified in a variety of different areas of agriculture, and before taking this position working as a naturalist at various garden centers, as well as with the Monmouth County Park system. Born and raised in Tinton Falls, Cahill will be soon moving to Freehold.
Hydroponic farming is farming done without soil. Plants typically get all their nutrients from the soil. In hydroponic farming, however, nutrient-rich water takes the place of the soil, enriching the seedlings as they grow into fully mature plants and watering them at precise times through a computerized system.
With the system that the Robbinsville Township purchased, known as the Leafy Green Machine, lettuces and herbs are grown in a vertical hydroponic farm that lives within a recycled, refrigerated, insulated, custom-built shipping container.
Between the nutrient-rich water and light energy from powerful LEDs, greens can be independent of the need for land, climate and season, growing in a modular design that is also mobile and can theoretically live anywhere.
The container consists of insulation, where it maintains an average internal temperature of 70 degrees Fahrenheit in extreme climates; climate control, built with an integrated “economizer” that saves energy by drawing in cool outside air when appropriate and also doubling as an intake fan; a dehumidifier to maintain optimal humidity levels and decreasing the farms overall water consumption; airflow ducts, consisting of two fans that distribute cool carbon dioxide enriched air evenly; and a carbon dioxide regulator with a safety shut-off feature, providing plants with exactly the right amount of carbon dioxide needed for photosynthesis.
In addition, the greenery’s LED lights provide the plants with the best quality light at its most efficient point. The LED boards are designed to emit only particular wavelengths of red and blue light, which are the colors that plants are able to absorb most easily for photosynthesis (red light is essential for stem and leaf growth, while blue light helps develop thick stems and dark green foliage).
Just as it is in nature, Cahill and her team start with the seeds, which begin in a flowing hydroponic system and are placed into compressed peat moss, known as grow plugs. The peat-moss plugs act as a sponge for absorbing nutrient-rich water. The seeds soak for 10 minutes, are covered with a humidity dome and sit under grow lights for about a week.
At that point, the seeds have become sprouts, with small roots, short stems, and a few young leaves. They then move up to the next level, a flow troth, where the roots “get completely soaked,” Cahill said. Now actual seedlings, taller and sturdier than they had been, with a secure root system, the plants sit in that troth for another two weeks, getting consistent water and light to develop strong stems needed to support the plant’s weight later in its life cycle.
After this time period, the seedlings are harvested and transplanted into the main cultivation area, where they are now in the towers, growing vertically for the first time. The roots, which are still in the peat-moss grow plugs, are wedged into stiff foam panels, which provide firm support, with the plant facing outward towards the LED light, encouraging the leaves to grow. Here, in this final destination, they spend from two to five weeks until they are ready for their harvest..
A view of the produce inside of the shipping container that houses Robbinsville’s hydroponic farm
“It is a continual cycle of putting new lettuce and herbs in, taking grown ones out,” Cahill said.
Every week, the team has something to harvest.
“What is nice about the system is that it is computerized so that plants get exactly the nutrients it needs at the right time,” Cahill said. “Sensors on the computer know when they might need nitrates or some other nutrient.”
Freight Farm, the company that built the hydroponic farm equipment, also developed an app that can be used via a person’s iPhone or desktop computer to keep an eye on all sensor data.
Holt admits he did not know much about hydroponic farming until Fried asked him to look into purchasing a machine.
“I did a ton of research on what hydroponic farming is, to educate myself, and then looked into what companies are out there to make these container farms,” he said. “We talked to a lot of companies, and decided on Freight Farm, out of Boston. At the time, they told us we were the only municipality they had ever sold a freight farm container to.”
Once Cahill and Holt have the finished products, the lettuce and herbs get donated back to the Robbinsville Senior Center.
“We also give some of the produce to Meals on Wheels, and also Mercer Street Friends, who disperse it to schools,” Cahill said. “They distribute it to about a dozen schools in the Trenton area.”
And how does the finished product taste?
“It is honestly the best lettuce you can ever eat,” Holt said. “You really can see and taste the difference between this produce and the produce you buy in a supermarket.”
It looks good and feels good, too, Cahill said.
“Before we distribute it, we take care to remove any brown or damaged leaves,” she said. “There are, of course, no pesticides, no chemicals that the greens were treated with, so it is very safe and very clean.”
Both Cahill and Holt rave about how green and fresh the lettuce is, “with so much more taste to it than what you get in the stores, which by comparison, tastes so bland,” Holt said.
Since starting the farm at the municipal center in 2017, companies have come through to see the set-up, expressing interest in buying machines for themselves. Holt said the township has also hosted schools and colleges, as well as field trips and local education programs.
“Our mission is to grow, educate and unite: we grow the lettuce, give it away, educate the community about how hydroponic farming works, and unite people by asking them to volunteer or hold events, which is a catalyst for bringing people together,” Holt said. “This has been a huge win-win for the community.”
Cahill said she is always seeking volunteers and visitors, as well.
To schedule a tour or for more information, visit robbinsville.net/recreation or send an email to hcahill@robbinsville.net.
Bowery Farming Appoints Newton Kalengamaliro To Role of Senior Agricultural Scientist
Kalengamaliro boasts over two decades of experience in plant breeding, physiology, biochemistry and product development, with a specific focus on the produce market
New York, NY – Bowery Farming (Bowery), the leader in sustainable indoor farming, announced today the appointment of Newton Kalengamaliro to the role of Senior Agricultural Scientist. Kalengamaliro boasts over two decades of experience in plant breeding, physiology, biochemistry and product development, with a specific focus on the produce market. He joins Bowery as a senior leader on the Agricultural Science Team and will be tasked with optimizing yield and quality.
“As we look ahead to the future of Bowery, we are confident that Newton will play a pivotal role in optimizing yield and quality,” said Susan MacIsaac, Bowery Farming’s Head of AgScience. “We welcome him to the team and look forward to leveraging his decades-long research and industry expertise.”
As a whole-plant physiologist/ecologist, Kalengamaliro has dedicated much of his career to studying how plants adapt to stress and developing strategies and tools that enhance plant resilience. Prior to joining Bowery, Kalengamaliro held positions at Philip Morris USA and British Petroleum. Most recently, he was Director of Driscoll’s on its Breeding and Variety Development team. Kalengamaliro is a graduate of Purdue University where he earned an MSc and Ph.D. in crop physiology and later studied at Virginia Commonwealth University where he earned an MBA.
“My sustained interest in business development, specifically, linking crop research findings to new business opportunities in the produce industry, perfectly aligns with Bowery’s current operations,” said Kalengamaliro. “I look forward to working alongside the Bowery team to stay at the forefront of research and development as it relates to produce and agtech.”
For more information about Bowery, please visit www.boweryfarming.com.
ABOUT BOWERY FARMING
Bowery is growing food for a better future by revolutionizing agriculture. Its modern farming company combines the benefits of the best local farms with advances made possible by technology to grow produce consumers can feel good about eating. BoweryOS, its proprietary software system, uses vision systems, automation technology, and machine learning to monitor plants and all the variables that drive their growth 24/7. Because Bowery controls the entire process from seed to store, its farms use zero pesticides, 95% less water, and are 100+ times more productive on the same footprint of land than traditional agriculture.
Bowery produce is currently available at select Whole Foods and Foragers stores in the Tristate area and featured on the menus of Tom Colicchio’s New York restaurants Craft and Temple Court. Based in New York City, the company has raised over $170 million from leading investors including GV, General Catalyst, GGV Capital, First Round Capital, Temasek, and Almanac.
This Ain’t Your Grandfather’s Lettuce: Meet The Farm Of The Future
The vegetable farming of the future looks very different from the fields of lettuce and other crops you’ll find in places like California’s Salinas Valley today, according to Daniel Malechuk, the 38-year-old CEO of Kalera, a vertical farming company based in Orlando, Florida
Daniel D'Ambrosio Senior Contributor
entrepreneurs I write about entrepreneurship and intriguing startups across the U.S.
The vegetable farming of the future looks very different from the fields of lettuce and other crops you’ll find in places like California’s Salinas Valley today, according to Daniel Malechuk, the 38-year-old CEO of Kalera, a vertical farming company based in Orlando, Florida.
Daniel Malechuk, CEO of Kalera, a vertical farming company, with a head of lettuce. KALERA
Kalera’s lettuce, including Bibb, Oakleaf, Frisee, Crystal, Gem, Batavia and mini-Romaine, is grown indoors in white towers of trays with carefully controlled temperature, light, and humidity.
Kalera claims to have adopted cleanroom technology from the semiconductor industry, ensuring that the plants in the growing rooms, bathed in a surreal pink-purple light, are never exposed to animal or human pathogens. As a result, pesticides are never used. Not an unimportant claim considering the travails Romaine lettuce has suffered in recent months as a result of contamination.
Kalera’s vertical indoor farms also utilize a closed-loop irrigation system that cuts water use by 95% compared to those fields in California, according to Malechuk. Kalera is scheduled to open a 33,000-square-foot facility in Orlando in February, which Malechuk describes as the largest indoor growing center in the southeastern United States.
Kalera builds towers with racks of lettuce. No soil or pesticides needed. KALERA
“When you walk in it’s racking from floor to ceiling with multiple layers of plants,” Malechuk said. “We’re 100 times more efficient than traditional farming, and we use five percent of the water.”
Kalera also claims the advantage of being close to its markets, drastically cutting transportation costs, along with the carbon footprint of its harvest. Malechuk points out that lettuce starts to die the second you cut it; and that it can take 10 days for a head of lettuce to travel the nearly 3,000 miles from California to the East Coast.
“Our vision is to quickly and rapidly bring food to people exactly where they are in a much more healthy, sustainable manner,” Malechuk said.
There is no soil involved in Kalera’s growing process. The roots of the lettuce grow directly in free flowing water, with nutrients added. The totally closed system eliminates the possibility of contamination from E. coli, according to Malechuk.
Malechuk has what he describes as “massive expansion plans” for Kalera, not only in the United States but also around the world. The key, he says, will be a franchise model that will make indoor farming as easy as “copy and paste.”
The new look of farming, as Kalera sees it. KALERA
Malechuk envisions Kalera moving into “food deserts” in cities like Detroit, where his parents grew up.
“After we decide to go somewhere we can produce millions of heads of lettuce, not taking up any land,” Malechuk said.
There are plenty of empty warehouses in Detroit where Kalera could build a vertical farm, he said.
Malechuk believes indoor vertical farming’s time has arrived.
“A whole lot of smart people spent years researching how to make this happen,” he said. “Not just Kalera, but key partners driving lighting costs down, figuring out the right seeds and right varieties to grow; countless hours of analyzing the right mix of water and nutrients.”
“I like to think we’re on the cusp of one of the most incredible evolutions we’ve ever gone through.”
Follow me on Twitter.
I am a business reporter based in Burlington, Vermont. In the last eight years, I have covered everything from IBM's "sale" of its semiconductor fab in Essex Junction
Whole Foods Charity, Teens To Grow Tons of Produce For NYC
A group of New York City teens grew enough food in an indoor hydroponic farm to feed more than 2,000 students at lunch, with the help of a Whole Kids Foundation partnership with Teens for Food Justice
Students of Martin Luther King, Jr. Educational Campus in Manhattan are feeding thousands at school lunches from what they grow at an indoor hydroponic farm. ( Photo courtesy The Parkside Group )
March 3, 2020
A group of New York City teens grew enough food in an indoor hydroponic farm to feed more than 2,000 students at lunch, with the help of a Whole Kids Foundation partnership with Teens for Food Justice.
Industry leaders and local elected officials attended a press conference Feb. 28, at the Martin Luther King Jr. Educational Campus where students, along with staff and community members, have built a hydroponic farm, according to a news release.
In January, the students harvested more than 700 pounds of fresh produce including kale and lettuce, which were used in school lunches. They are on track to grow more than 10,000 pounds of produce for the school and community this year, according to the release.
The students had help from Hunter College and funding from Whole Foods Market. Also participating were Manhattan borough president Gale Brewer, city council member Helen Rosenthal and United Way of New York City.
“The MLK farm will provide real-world opportunities for students to apply the concepts they learn in classes like biology and chemistry, and it also creates an indelible understanding of how food grows,” Nona Evans, president and executive director of Whole Kids Foundation, said in the release. “ ... We know from years of experience and stacks of research, that when students understand and participate in growing food — they make healthier choices for a lifetime.”The foundation’s goal is to support schools and inspire families to improve children’s nutrition and wellness.
One of the goals of this farm is to encourage students to transform their relationship with food, instilling a lifelong understanding of healthy eating habits and sustainability, according to the release.
The nonprofit Teens for Food Justice has a mission to ensure that all New Yorkers have access to healthy, affordable food through youth-led, community-based solutions. The organization runs four farms serving 14 schools in the Bronx, Brooklyn, and Manhattan.
These farms are expected to grow more than 30,000 pounds of produce annually that feed students daily at lunch and their local communities, according to the release.
Related Topics: Schools Northeast (U.S.) New York New York City New York ProduceNutrition Sustainability
US: Texas - Personal Growth As Well As Leafy Greens Thrive in San Antonio Nonprofit’s New Hydroponic Farm
A group of people crowded around a shipping container in the parking lot of the San Antonio Clubhouse, a community and resource center for adults with mental illness. Inside the 40-foot long container is a hydroponic farm, which produces as many crops as a three-acre farm, simply with water and lights
March 7, 2020
A group of people crowded around a shipping container in the parking lot of the San Antonio Clubhouse, a community and resource center for adults with mental illness.
Inside the 40-foot long container is a hydroponic farm, which produces as many crops as a three-acre farm, simply with water and lights.
But the best part of Clubhouse Grows — the new indoor water-based, high-tech farm — isn’t that it sprouts an abundance of leafy greens. It’s that it also serves as a recovery-oriented volunteer opportunity for the people the nonprofit serves.
“We are working together as a Clubhouse community on this farm,” said Mark Stoeltje, the executive director of San Antonio Clubhouse. “It is providing meaningful work for our members, but it is also providing a product.”
Clubhouse Grows, which was unveiled Friday, was made possible with a $100,000 grant from Impact San Antonio, a women’s philanthropic non-profit that awards grants to local organizations.
Jennifer Bennett, president of Impact SA, said one of the reasons the group chose to award Clubhouse a grant was “because of the multilayered benefits that it delivers to the community.”
“A lot of our citizens who have mental health challenges do not get the degree of support that they need to help them live lives that feel good to them,” Bennett said. “Clubhouse is really unique to doing that in our community.”
The plants in the 320-square-foot freight container do not rely on soil. Instead, they grow on 88 black foam and metal panels, which have water pumped through them. Powerful LED red and blue lights that emulate the sun are on 18 hours a day. And the climate-controlled space remains stable between 65 and 68 degrees.
“The extra sunlight, combined with the fact that it’s never cloudy and we don’t have to worry about different seasons, really helps accelerate the plants’ growth,” said Brandon Wagner, a staff member and project lead for Clubhouse Grows.
On ExpressNews.com: South San Antonio elementary students growing food with a larger goal in mind
Crops planted include five types of lettuce, kale, beets, arugula, basil, oregano, and even some flowers.
Wagner, who has been prepping the new farm and working with it for around a month, said he has found it to be very therapeutic.
“You zone out and just concentrate on the work,” he said. “You are planting 300, 400 or up to 500 seeds at a time, so there is a very meditative workflow.”
While the farm only uses about 25 gallons of water a month, Wagner said, it can grow 550 small and crisp heads of lettuce alone each week.
“I love lettuce, but that is more lettuce than we can eat,” Stoeltje said.
So, in addition to using the produce at the Clubhouse facility, the organization plans to donate some to local non-profits.
Stoeltje said while healthy eating is important, the farming process — seeding, maintaining, relocating and harvesting crops — is also a chance for Clubhouse members to work hard, work together, hone new skills, reach goals and ultimately feel a sense of accomplishment.
San Antonio Clubhouse, which was founded in 2003, operates under a national model that's based on the belief that everyone deserves to be part of a caring community and has talents to share.
The non-profit helps its more than 2,000 members gain work experience through volunteering at the center, job training, résumé building, job-search assistance and advocating to potential employers.
“This is the perfect project for us because we are founded on two principles,” Stoeltje said, “meaningful relationships and rewarding work.”
sara.cline@express-news.net
Sara Cline
Follow Sara on: https://www.facebook.com/sara.cline.5494SaraLCline
Sara Cline is a staff writer for the San Antonio Express-News through the Hearst Fellowship Program.
She previously worked at the Times Union under the program. She also worked at the Brockton Enterprise, in Massachusetts, as a general assignment reporter. She has also contributed to newspapers and magazines in Arizona, Massachusetts and Rhode Island.
Sara graduated from the University of Arizona in 2016 with a B.A. in journalism.
Past Articles from this Author:
4 Things Indoor Farms Have To Do To Survive
As a large-scale controlled ag farming company who is essentially in the business of electrifying agriculture — sustainability is a constant consideration for Crop One
Future of farming? Only if you’re sustainable.
March 5, 2020
Written by Jenna A. Bell, PhD, RD VP of Nutritional Science at Crop One
The future of farming does not require tractors, rototillers, or pesticides.
“Sustainability” is a broad concept with ambiguous measures.
As a large-scale controlled ag farming company who is essentially in the business of electrifying agriculture — sustainability is a constant consideration for Crop One. We subscribe to several definitions for what it means to be sustainable:
Sustainability cares about the future. The United Nation’s World Commission on Environment and Development says, “sustainable development is development that meets the needs of the present without compromising the ability of future generations to meet their own needs.”
Sustainability needs to make money. To economists, it is the fine balance between economic growth and environmental, social, and cultural protection. An industry cannot be sustainable if it compromises only community and the planet, nor can it thrive without financial security.
Sustainability protects our resources and the environment. The U.S. Environmental Protection Agency (EPA) describes sustainability like it was by environmentalist and diplomat, G.P. Marsh in 1864, “Everything that humans require for their survival and well-being depends, directly or indirectly, on the natural environment.” Furthermore, the EPA attests that our health, well-being, economy and security rely on a high-quality environment.
As difficult as it may seem, we have developed a foundation for sustainable indoor farming. Our entire organization has adopted the 2030 Sustainable Development Goals (SDGs) put forth by the United Nations General Assembly.
The United Nation’s 17 Sustainable Development Goals are all interconnected and address some of the most pressing global challenges of our time.
In all facets of the farm, we work to align with these goals and achieve sustainability. In the simplest terms, we have to:
Achieve carbon neutrality
Grow more with less
Deliver long-lasting, safe produce
Build communities around farming…indoors
Crop One’s technology and infrastructure is built to achieve economic growth with fewer resources, less land and the pursuit of energy neutrality. Our plant and nutritional science depend on thoughtful control of air and water and are motivated by food resilience and human health. Crop One’s executive decisions focus on innovation and training for the future to develop global employment opportunities in diverse communities.
We recognize that the following four things must be done for us (and our colleagues) to survive:
1. Achieve carbon neutrality
To start, we put our farm in a box. We grow food in modular growing units that (to make us sound cool) we refer to as “Mods”. They are the same size and shape, and are totally controllable, scalable and separate. We have our finger on the pulse for airflow, temperature, humidity and carbon dioxide. We know how it will impact plant growth across the room, and we have optimized and digitized each Mod — precisely — so that resources are not wasted. But there’s more…
In these Mods, we can leverage the plant’s natural ability to “sink” or take up carbon dioxide, which is one natural way carbon compounds are interconverted in the environment. With all the control we have, we schedule and modify the level of carbon dioxide gas that is then taken up by the plants.
For the plant scientists, read here: by studying the ratio of water content to dry biomass for each cultivar grown in the Mods, we can adjust the environmental conditions and determine the average relative amount of reduced-carbon or oxidized carbon dioxide produced by the plants in a given area of growth. Our team is delineating the calculations necessary to achieve carbon neutrality by comparing total carbon produced by the farm, the carbon dioxide supplied to the plants, and the reduced-carbon found in the plants. With this, we can adjust the environmental variables to tip the scale towards carbon negativity.
For other smart people, read here: our plants can recycle carbon and lower our carbon contribution and reduce the overall level of carbon emitted. We call this nearing-negative.
2. Grow more with less
Controlled environment agriculture (CEA) uses less water (95–99% less than traditional farming), and less land (we can grow 400X more than outdoor farms in an acre). In addition to using less, Crop One reuses and recycles. We have built a proprietary system that modulates the carbon dioxide and heat injections (such as from the HVAC exhaust) to improve efficiency for each Mod. Condensate water from the HVAC can be reused as greywater.
By the way, land use is super important — the International Panel on Climate Change’s special report, “Climate Change and Land,” characterized how vulnerable the land ecosystems and biodiversity are to ongoing climate change and extreme weather. As the arable land space has declined, the number of people living in urban areas has exceeded those in rural regions around the world. Thus, reducing the amount of land required to grow food is a global priority.
3. Long-lasting, safe produce
Globally, crop production via conventional agriculture leads to approximately 30% of all crops being lost due to waste from spoilage or uncertainties in weather. With little handling and delivering, our produce lasts longer. Our greens can be found on retailer shelves in less than 24 hours from leaving the farm. So, when you buy it, there’s still a lot of life left (3–4 weeks even).
Our fully enclosed Mods and handling processes keep our greens so clean that there is no need to triple-wash. In fact, more washing means more opportunity to introduce a contaminant and the current industry standard for ready-to-eat greens requires millions of gallons of water treated with salt and chlorine.
Triple-washing is not 100% effective against certain pathogens in certain leafy greens, such as spinach.
4. Build communities around farming… indoors
CEA will never replace outdoor farming. We’re here to complement it. And part of that means that we need to help sustain the local economy and communities. For each farm we build, we will hire locally in order to maintain the promise of truly local food production. We are able to bring in people with diverse backgrounds to learn on the job — in plant science, digital sensors, networking and monitoring, and food growing and handling. The roles at the farm require a varying level of skill and experience, but oftentimes offer opportunity to learn transferrable skills. You can’t outsource local, so the jobs are sustainable
WRITTEN BY Crop One Holdings
We grow the cleanest, healthiest greens for anyone, anywhere in the world. Our sustainable vertical farms are free from chemicals and climate-proof.
Europe's Largest, Turkey's First Plant Factory Enters Production in Antalya
The factory grows plants in a closed area without soil or sun while using 95% less water than conventional farming. In the first stage, it will produce green leafy plants like lettuce, arugula, cress, spinach, thyme, and basil
BY DAILY SABAH WITH DHA
FEB 02, 2020
An Antalya-based firm has established Europe's largest and Turkey's first plant factory with an estimated investment of 2.5 million euros ($2.77 million), as part of its 5-million-euro research and development (R&D) activities.
The factory grows plants in a closed area without soil or sun while using 95% less water than conventional farming. In the first stage, it will produce green leafy plants like lettuce, arugula, cress, spinach, thyme, and basil.
The factory, Farminova is run by Cantek Group that has operated in the food storage, processing and refrigeration technologies business at the Antalya Organized Industrial Zone for many years.
Company Chairman Can Hakan Karaca said they have launched an innovative initiative, establishing the largest active plant factory in Europe.
Talking to Demirören News Agency (DHA) Sunday, Karaca said providing healthy, continuous and fixed-price food today is critical because the world's population is rapidly growing and agricultural areas are gradually shrinking.
He added that the factory produces plants in a closed area without soil and sun and uses 95% less water. It produces plants without harming nature and living creatures, 24/7 all round the year needing any agrochemicals.
Karaca said the factory uses artificial intelligence (AI) and uses 100% Turkish products. He noted that they will start producing green leafy plants like lettuce, arugula, cress, spinach, thyme and basil in the first phase and strawberry and mushrooms in the second phase. This will be followed by the production of vegetables like tomatoes, peppers and eggplants.
Karaca added that seedsmen should also develop low-stature plants now. Pointing out that Japan and the U.S. have carried out experiments in plant factories, he said that they are the only Turkish company to participate in the training program run by Professor Kozai, an industry pioneer.
"We have developed the plant factories project step by step, establishing the largest plant factory operating in Europe. What makes the difference here is that we have built this factory using our own products only," he told.
He said the factory in Antalya is an exemplary model. "We aim to establish, expand and share with global investors this innovative development in the world of agriculture, which is a 100% Turkish product from design to software."
Karaca said they are working on establishing factories in seven or eight countries, particularly in Africa. "Our goal is to open two to five factories this year and 100 factories in the next five years, 90% of which will be abroad."
Factory consultants Glenn Behrman and Christine Zimmerman Loessl, who have been working around the world in this area, also elaborated on the factory.
Loessl said the world and its inhabitants have changed. "However, if we continue to treat the world this way, the world is not going to end up anywhere good. We see every day that agriculture has had a huge and dramatic impact on this change.
This project will prevent the conversion of natural lands into agricultural lands. We can produce plants completely independent of the weather, the sun, and the conditions outside. It provides a healthy and fixed-price guarantee. Vertical farming practices will completely change their perspective. It's not going to happen in a tick, but it is going to happen eventually."
Behrman, on the other hand, said he has set up similar facilities in many countries around the world. "This is the most innovative and largest facility in Europe. It can produce healthy products that are harmless and chemical-free. It is possible to produce essential foods and products, not just edible foods. It is highly effective in seedling production and seed cracking.
It can also make healthy and high-quality contributions to the cosmetics industry. Healthy and nutritious products can be produced in shorter harvest time. It is a hyper-efficient system. Production is possible anywhere in the world with minimum energy and labor," he added.