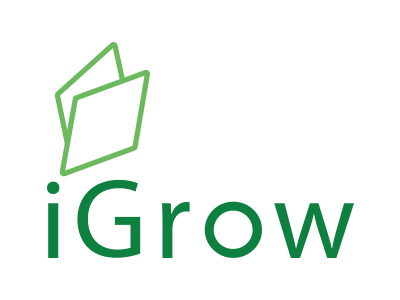
Welcome to iGrow News, Your Source for the World of Indoor Vertical Farming
Farm.One Launches Latest NYC Vertical Mini-Farm At Whole Foods Market, Manhattan West
Farm.One custom-designed the farm for the Manhattan West store and maintains the on-site mini-farm to supply the in-store prepared food and beverages with freshly grown and harvested Blue Spice Basil
Blog, News from Fluence by monique
Establishes A New Distributed Urban Agriculture Model To Support
Onsite Farms For Grocers, Restaurants,
And Other Businesses In The Greater
New York City Area
NEW YORK (September 9, 2020) — Farm.One, Manhattan’s only vertical farm, launched its latest mini-farm at the newly opened Whole Foods Market Manhattan West. Farm.One custom-designed the farm for the Manhattan West store and maintains the on-site mini-farm to supply the in-store prepared food and beverages with freshly grown and harvested Blue Spice Basil. The basil is used as an ingredient for a variety of delicious menu items, including freshly made pizza and the Whole Foods Mule, a specialty cocktail.
With a mission to surprise and delight with fresh, local, specialty ingredients grown at innovative farms in city centers, Farm.One’s mini-farm represents a major shift in urban food production and supply chains. With mini-farms, businesses have continual access to the highest quality, most flavorful, and consistent professional-grade ingredients. Further, the distance between production and consumption is now mere footsteps, eliminating any carbon emissions associated with the delivery of the produce.
“Every kitchen knows the difference that freshness and quality of ingredients can make to the food they serve,” said Rob Laing, founder and CEO of Farm.One. “When we started in 2016, it wasn’t financially feasible to build and operate small farms profitably in cities like New York. We’ve now been able to decrease the cost of building a farm and have developed a model where a larger farm, like our TriBeCa flagship, can support small farms for grocery stores, restaurants and the hospitality industry all over the greater New York City area. This marks a real inflection point for what people can expect in their meals and the economy of urban food production.”
Farm.One’s mini-farm at Whole Foods Market Manhattan West takes up just thirty two square feet and features a hundred and fifty plant sites on three growing levels. The hydroponic system was designed and built by Farm.One’s engineering and technology team to optimize crop productivity, minimize intrusiveness to the store experience, and require minimal maintenance. The facade of the mini-farm was customized to match the familiar brushed stainless steel aesthetic of Whole Foods Market. The mini-farm is capable of supplying at least 8 pounds of basil every month, including harvesting the fragrant basil flowers for use in the Whole Foods Mule.
“The first thing our customers notice when they enter the prepared food section of the store is the incredible fragrance of the basil,,” said Chris Manca, local forager, Whole Foods Market Northeast Region. “As soon as our chefs, and even our mixologist, had access to the basil they were inspired to create menu items that highlight the freshness and flavor of Farm.One’s blue spice basil. This collaboration with Farm.One has really impacted the way we think about fresh ingredients in our kitchens and we can’t wait for customers to come by and experience it.”
Farm.One’s Distributed Agriculture Model
Farm.One has taken a distributed approach to scaling indoor farming in cities, an alternative to the large, expensive warehouse farming models. By establishing a Farm.One flagship as a hub in a city, the company is able to centralize farming and business operations, engineering, training, and support, to build and maintain on-site ‘spoke’ farms throughout a city for its customers. This results in lower investment requirements, a faster path to profitability, and the flexibility to grow a diverse range of crops that meet a variety of customer needs.
“Our hub-and-spoke model of distributed agriculture proves that indoor agriculture doesn’t need tens or hundreds of millions of dollars to be viable and achieve scale,” added Laing. “Also, by putting farms in visible places around the city we’re ensuring openness and transparency never before achieved in the industry. Whether you visit a Farm.One flagship for a tour or class, when it’s safe to do so, or experience a mini-farm in the middle of a grocery store, you’ll see and learn about how your food is grown.”
The company has plans to build flagships and mini-farms in major cities around the United States and globally over the next twenty four months.
Farm costs are further reduced through its relationship with leading LED lighting company Fluence by OSRAM. The cost of lighting and electricity remains one of the highest cost centers for building and operating indoor farms. By collaborating with Fluence, Farm.One is leveraging innovative LED technology to ensure its growing environments are optimized by crop type and for operational efficiency.
“In a vertical farming environment, efficiency isn’t a perk, it is paramount to the farm’s success,” said David Cohen, CEO of Fluence. “Farm.One is tapping into the world’s most advanced cultivation technology to deliver beautiful, delectable plants in the heart of one of the busiest metropolitan areas in the world. Their ability to localize high-quality crop production illustrates how exploring the interaction between light and life will yield a healthier and more sustainable world.”
The mini-farm at Whole Foods Market Manhattan West adds to several mini-farms Farm.One has built out of its flagship farm in TriBeCa, including at OCTOBER, a restaurant in Nolita which features a 100% plant-based menu, Eataly NYC Flatiron, and at the Institute of Culinary Education (ICE), the site of Farm.One’s original prototype farm. Farm.One also maintains a farm at Project Farmhouse at Union Square.
For more information about purchasing a Farm.One mini-farm for restaurants, grocery stores, and other businesses in the greater New York City area, visit: https://www.farm.one/vertical-farms/custom-units.
For more information about bringing a Farm.One flagship to a city, visit https://www.farm.one/vertical-farms/flagship-farm.
Farm.One Press Inquiries:
Rob Laing
rob@farm.one
Running A For-Profit Business With A Not-For-Profit Mission
Vertical Harvest is using controlled environment agriculture to give people with disabilities the opportunity to improve their livelihoods along with the sustainability and economies of their communities
Vertical Harvest is using controlled environment agriculture to give people with disabilities the opportunity to improve their livelihoods along with the sustainability and economies of their communities.
Jackson, Wyo., might not be the first place you think of when it comes to innovation in controlled environment agriculture. Vertical Harvest, which began operating in 2016, produces leafy greens, tomatoes, and microgreens in a 13,500-square-foot vertical greenhouse.
“From the beginning, Vertical Harvest set out to create a model that could leverage the greatest impact in communities,” said Nona Yehia, co-founder and CEO. “We are a model that is setting forth to cultivate healthy people, communities, and economies. It is through that understanding that all those things are linked to create sustainable communities. We know that successful communities are sustainable communities.”
Yehia said Vertical Harvest was born out of two critical needs in her community.
Nona Yehia, co-founder and CEO at Vertical Harvest, said her company is a model that aims
to cultivate healthy people, communities, and economies. Photos courtesy of Vertical Harvest
“Number one was that we import the vast majority of food that we eat,” she said. “By the time it arrives, it’s not that great to eat. Number two is that Jackson is a burgeoning local community, but it has never been a place that has been known to build careers. People come here to ski and party and then they leave. Business owners were having a really hard time keeping consistent employees, making it really hard to run a business.”
Creating a diverse, inclusive, and profitable workplace
One of the things most unique and innovative about Vertical Harvest is the workforce it employs.
“What was really important to me and to company co-founder Caroline Croft Estay was that Vertical Harvest would provide a place where underemployed populations could feel that they were contributing in a profitable environment,” Yehia said. “By employing people with physical and intellectual disabilities we were exposing peoples’ abilities rather than focusing on their disabilities. We were creating an employment bank that was actually beneficial to the bottom line. This was a big part of why we wanted to be a for-profit organization as well.”
From the beginning, Vertical Harvest was set up as a L3C or a benefit corporate model.
By employing people with physical and intellectual disabilities, Vertical Harvest has developed a workforce that is beneficial to the company’s bottom line.
“We wanted Vertical Harvest to be a scalable, replicable model that doesn’t have to be supported by a charitable or philanthropic organization,” Yehia said. “We wanted it to be a model that could be a part of the civic infrastructure and could perpetuate its own growth. The scalability and replicability of Vertical Harvest was why we chose the L3C model.”
Croft Estay was an employment facilitator trying to find consistent, meaningful work for her clients with physical and intellectual disabilities.
“These were people who grew up in the community, who wanted to contribute to their community and wanted to find consistent meaningful work,” Yehia said. “This is where we put food and jobs together in this vertical capacity. From the beginning, we were targeting a common problem that businesses undergo in our community.
“Right from the outset, other business owners were saying they were having this problem and they saw that Vertical Harvest was not. They asked us to help them. There is not only support for the individuals with disabilities, but there is support for the whole employee team to create a diverse inclusive workplace. The most valuable thing that we have built out of this commitment is our culture. We all know that businesses live or die on the quality of the culture that they have built. It is one of the most amazing things that we have built through this commitment to diversity and inclusion.”
Vertical Harvest, which initially built a 13,500-square-foot vertical greenhouse (shown) to
produce leafy greens, tomatoes and microgreens, is planning to expand with a 50,000-square-
foot prototype.
Developing a premium brand
Arik Griffin, who is Vertical Harvest’s chief financial officer, said one of the things the company has discovered is that part of the power of Vertical Harvest’s brand is the humanitarian good it is doing.
“People want to support us and buy our products,” Griffin said. “The restaurants and grocery stores like us for our quality and for the humanitarian message that they can get behind as do the consumers in the market place. People love our quality and they love our message. That translates into a brand premium.”
Yehia said it also helps that more people want to know where their food is coming from.
“Everybody has someone they know or a family who has a disability and the struggles that person goes through,” she said. “The reason that I am so passionate about this project is because I have a brother with a disability. At a very young age I realized he wasn’t going to have the same opportunities that I was going to have to create a career. That really resonates with people.
Vertical Harvest has expanded its customer base for its leafy greens, tomatoes and microgreens from Wyoming to include Montana and Idaho.
“We are creating opportunities and we have created an employment model where we bring out the abilities and it changes perceptions of what people are able to do. That creates a foundation of trust and strength with the community that really resonates with people, especially right now. It is what businesses can do. There is a real reward in benefitting people outside of your own stakeholder groups. This is something that is going to become more attractive as we move into 2021 and beyond.”
Unlimited expansion
Yehia has no doubt that the model Vertical Harvest has created can be profitable.
“Our incubator farm in Jackson will achieve profitability next year,” she said. “Vertical Harvest’s position in the industry is unique. There are a lot of these farms that have not succeeded. We have created a group of stakeholders who are committed to seeing Vertical Harvest and its prototype achieve profitability.
“Our two biggest hurdles that we learned are the production facility was too small to start out with and our market is too small. Jackson is a seasonal market. It is a smaller market than what our production system can produce in order to be profitable. We’ve expanded our customer base to include Montana and Idaho.
Arik Griffin, chief financial officer at Vertical Harvest, said part of the power of the company’s brand is the humanitarian good it is doing, which has been supported by its customers and consumers.
“We have worked very hard to understand the right crop mix, the correct market size, and the correct farm size that can create a return that would be attractive to social impact investors. We have created a 50,000-square-foot prototype that when placed in the right markets will succeed and that will occur quickly. We knew that we could take what we’ve learned from our successes as well as our failures to create this model that fits within the objectives of social impact finance.”
Vertical Harvest is looking at building five new greenhouses in the next five years. Its next project will be built in Westbrook, Maine, in 2021 with crop production expected to begin the following year.
“We want to bring this model to every community that we possibly can within the country and internationally,” Griffin said. “We have as our mission providing good food and good jobs to local communities. Another piece of our mission is to spread that out, to bring it to as many people as possible. We’re in the first stage of our Series A capital raise. We are raising funds in order to provide the infrastructure at the corporate level so that we can expand.
“The other thing we need to achieve this is hearing from communities and finding local stakeholders who want to do impact investing and make a difference in their communities. Bringing together the people who want to make a difference. We also need to make sure we are constantly in touch with experts in the CEA industry trying to nurture our relationships with the very best people.”
For more:
Vertical Harvest, (307) 201 4452; info@verticalharvestfarms.com; https://verticalharvestfarms.com/
This article is the property of Urban Ag News and was written by David Kuack, a freelance technical writer in Fort Worth, Texas.
The Fifth Annual [Virtual] NYC AGTECH WEEK
Our 2-day virtual conference features farm tours, panels, workshops, and presentations highlighting the fast-growing and innovative AgTech sector in NYC, the US, and Internationally
THE FIFTH ANNUAL [VIRTUAL]
NYC AGTECH WEEK
OCTOBER 20-21, 2020
Produced by the NYC Ag Collective: a Non Profit organization dedicated to educating and sharing the opportunities and benefits of AgTech. NYC AGTECH WEEK is the only AgTech conference on the East coast run by the leaders of the industry themselves.
Our 2-day virtual conference features farm tours, panels, workshops, and presentations highlighting the fast-growing and innovative AgTech sector in NYC, the US, and Internationally. NYC AGTECH WEEK brings together industry Founders, Investors, CEOs, Startups, and Thought Leaders through curated networking events and opportunities.
GET YOUR TICKET HERE
Use the following Discount Code: iGrow10
20 October 2020 - 21 October 2020
20 October
Day 1: The Local View - Session I
Session I: Introduction to NYC Urban Agriculture - Oko Farms Tour - Farm.One Tour
[Virtual]
12:00 PM - 01:30 PM
Tickets
20 October
Day 1: The Local View - Session II
Session II: NYC Food Resilience During COVID-19 - Opening remarks and introduction
[Virtual]
02:00 PM - 03:15 PM
Tickets
20 October
Day 1: The Local View - Session III
Session III: NYC AgTech Startups: Where They’re At Now - Product/ tech demos
[Virtual]
03:30 PM - 04:00 PM
Tickets
20 October
Day 1: The Local View - Session IV
Session IV: Networking Breakout Rooms
[Virtual]
04:15 PM - 05:30 PM
Tickets
21 October
Day 2: The Global-View - Session I
Session I: Spotlights & Comparisons of Global Urban Agriculture Hotbeds - Region
[Virtual]
12:00 PM - 03:00 PM
Tickets
UA-CEAC Online Hydroponic Tomato Intensive Workshop
Are you interested in growing tomatoes hydroponically? Join the University of Arizona Controlled Environment Agriculture Center for the Hydroponic Online Intensive Workshop - November 16th& 17th via Zoom
The University of Arizona Controlled Environment
Agriculture Center Is hosting Its First-Ever
Hydroponic Tomato Online Intensive Workshop
On November 16th and 17th
Are you interested in growing tomatoes hydroponically? Join the University of Arizona Controlled Environment Agriculture Center for the Hydroponic Online Intensive Workshop - November 16th& 17th via Zoom.
Taught by Dr. Stacy Tollefson, this two-day event is perfect for novice growers and will be packed with tons of critical information and research discoveries that UA-CEAC has assembled into their courses and programs for over 20 years.
You will get access to numerous lecture materials, personal question follow-ups, certificate of completion, and tons of knowledge!
Click Here To Register!
Limited seats are available
For questions, please email arizona.ceac@gmail.com
Rooftop Greenhouses Take Urban Farming To New Heights In Quebec
Lufa claims this latest site, opened this summer, becomes the world's largest rooftop greenhouse
BY EMMA JACOBS (FREELANCE REPORTER/PRODUCER) , IN MONTREAL
Lauren Rathmell co-founded the company Lufa, whose latest rooftop greenhouse opened in Saint-Laurent, QC earlier this year. Photo courtesy: Lufa.
October 8, 2020 — Cherry tomato plants tower over Lauren Rathmell’s head in the latest greenhouse built by the company she co-founded, called Lufa.
"We train everything vertically so that we can keep these plants a lot longer than a typical garden tomato plant," she explains. "We're in the probably 15 to 20-foot-long plant range now. They're really high."
Emma Jacobs Rooftop greenhouses take urban farming to new heights in Quebec
Their height makes it hard to tell that the greenhouse encloses a space the size of three football fields — all dedicated to growing varieties of tomatoes and eggplants.
It’s also four stories off the ground, on the roof of a former Sears warehouse not far from Montreal’s Trudeau International Airport.
Greenhouse-grown produce is a relatively small but growing part of agriculture in the Canadian provinces of Ontario and Quebec.
Lufa claims this latest site, opened this summer, becomes the world's largest rooftop greenhouse.
The NCPR team has worked tirelessly to make sure you and your neighbors can depend on us for journalism like this story in this challenging time. And you’re essential to that work. If you’re able, please make a donation now to ensure our effort can continue to be everything you count on.
"Once everything's picked and ready, it's going to go down right to our warehouse below us and packed into tomorrow - early tomorrow morning, into the baskets for the day," says Rathmell. The baskets containing the items customers' order online get delivered around the Montreal area and as far away as Quebec City in the company's electric delivery vehicles.
"We forecast really accurately and we try to pick just what's needed for that day's baskets. It's better for taste, it's better for quality, and it means no waste in the end as well," she says.
Lufa's latest 163,000 square foot greenhouse is located on top of a former Sears warehouse in Saint-Laurent, QC. Photo courtesy: Lufa.
Rathmell, originally from Vermont, founded Lufa with her husband to try and eliminate the environmental footprint associated with shipping produce across the continent. Lufa is named for a Lebanese cucumber. Rathmell’s husband is Lebanese. They call their customers "lufavores."
While greenhouses use a lot of energy, especially up north, Rathmell says putting them on a rooftop cuts winter energy use in half.
"We benefit by just passively receiving the heat that's coming from that building below, rather than being on a cold ground level in wintertime," she said. The greenhouse also creates an insulating bubble over the building below. The former Sears building now also contains other offices and warehousing.
Lufa established what was then the world’s first commercial rooftop greenhouse back in 2011.
With its latest, the company now operates four sites in the greater Montreal area, which have year-round growing seasons. Building on a rooftop does come with extra costs but Rathmell says energy savings and proximity to consumers help to offset them.
At the start of the pandemic, those customers doubled virtually overnight. People looking to order groceries for delivery signed up at rates that took the company by surprise.
"Within a week or two we had gotten a waitlist in place, first time ever we've never had a waitlist before, but we couldn't keep up," Rathmell recalls.
The company had to reorganize its greenhouses and warehouses for safety while also increasing the density of plants in its greenhouses. But Rathmell says it was a useful test for their business, which she’d like to expand someday to other cities, potentially in the northeastern United States.
Eggplants grow in the Saint-Laurent rooftop greenhouse. Photo courtesy: Lufa.
She’s also interested in expanding the range of crops.
"We do have two banana trees at one of our greenhouses as well," she says. "You can basically grow anything in a greenhouse. Is it worth growing in a greenhouse? Maybe not. But yeah, the bananas, I think they took like a year and a half, but we did get bananas.
So Quebec’s probably not the next banana capital, but certainly, a good place to experiment with greenhouse farming in cold climes.
Related Topics
montreal · environment · quebec · canada · agriculture
BARBADOS: Agricultural Push
“To date, we have some 800 farmers signed up to be trained for the FEED program and in St George North I am prepared to come here and identify space, where Toni can have Freight Farms which is also a Hydroponic system on a lease-to-own basis to young people who are interested in getting involved in agriculture.”
10/10/2020
Agriculture Minister Indar Weir
The Ministry of Agriculture and Food Security is pressing ahead with plans to breathe new life into the sugar cane industry.
Speaking at the Barbados Labour Party (BLP) public meeting at Newbury, St. George on Thursday night, Minister Indar Weir reported that the strategy to revitalize this country’s oldest industry has already gone to Cabinet.
“We are modernizing our sugar industry to the extent that we are using a full value chain industry which goes from sugar for domestic consumption, molasses for our rum industry, and then the waste matter is being used to generate renewable energy.”
Minister Weir thereby explained the government’s foresight is to “bring the industry to profitability”.
“And all of you who are part of the labor force in farms and in the sugar industry would have an opportunity for the first time in our existence to own shares where you can get a return on the profits made through the sugar industry transitioning program.”
The Agriculture Minister also informed the people of St. George North that he will honor the BLP candidate Senator Toni Moore’s wish to introduce Hydroponics and Aquaponics into the constituency.
He said this will be achieved through the Farmers’ Empowerment and Enfranchisement Drive (FEED) program aimed at reducing agricultural imports into the island which will ensure national food and nutrition security. Currently, farmers are also being trained in Apiculture and Freight Farming.
“I say to you St. George North that you do not have the traditional jobs that you used to get – we do not have enough land space even. And so, we must embrace technology, where you can take a freight farm and with your mobile phone, laptop, tablet and you can operate that farm, get to production faster and get greater yields. Yet, you do not have to use pesticides and of course, it is a revolving system so, therefore, it is less water-intensive, and you do not have to worry about climate change and prolong droughts,” he explained.
“To date, we have some 800 farmers signed up to be trained for the FEED program and in St George North I am prepared to come here and identify space, where Toni can have Freight Farms which is also a Hydroponic system on a lease-to-own basis to young people who are interested in getting involved in agriculture.” (TL)
The Ministry of Agriculture and Food Security is pressing ahead with plans to breathe new life into the sugar cane industry.
Speaking at the Barbados Labour Party (BLP) public meeting at Newbury, St. George on Thursday night, Minister Indar Weir reported that the strategy to revitalize this country’s oldest industry has already gone to Cabinet.
“We are modernizing our sugar industry to the extent that we are using a full value chain industry which goes from sugar for domestic consumption, molasses for our rum industry, and then the waste matter is being used to generate renewable energy.”
Minister Weir thereby explained the government’s foresight is to “bring the industry to profitability”.
“And all of you who are part of the labor force in farms and in the sugar industry would have an opportunity for the first time in our existence to own shares where you can get a return on the profits made through the sugar industry transitioning program.”
The Agriculture Minister also informed the people of St. George North that he will honor the BLP candidate Senator Toni Moore’s wish to introduce Hydroponics and Aquaponics into the constituency.
He said this will be achieved through the Farmers’ Empowerment and Enfranchisement Drive (FEED) program aimed at reducing agricultural imports into the island which will ensure national food and nutrition security. Currently, farmers are also being trained in Apiculture and Freight Farming.
“I say to you St. George North that you do not have the traditional jobs that you used to get – we do not have enough land space even. And so, we must embrace technology, where you can take a freight farm and with your mobile phone, laptop, tablet and you can operate that farm, get to production faster and get greater yields. Yet, you do not have to use pesticides and of course, it is a revolving system so, therefore, it is less water-intensive, and you do not have to worry about climate change and prolong droughts,” he explained.
“To date, we have some 800 farmers signed up to be trained for the FEED program and in St George North I am prepared to come here and identify space, where Toni can have Freight Farms which is also a Hydroponic system on a lease-to-own basis to young people who are interested in getting involved in agriculture.” (TL)
VIDEO: Net Zero Festival: Vertical Farming - Food For Thought In A Net Zero World?
In the first of three Glimpses reports looking at potential net zero gamechangers, BusinessGreen looks at the role for vertical farming in delivering a more sustainable food system
To view the video, please click Here
VIDEO: In the first of three Glimpses reports looking at potential net-zero game-changers, BusinessGreen looks at the role for vertical farming in delivering a more sustainable food system
One of the most devastating and direct ways in which the climate crisis impacts on society is on our food and farming system: water scarcity, drought, and soil degradation are just a few of the problems that are being exacerbated by the planet's rising temperatures. Meanwhile, our unsustainable food production system is also a major contributor to climate change, accounting for around a quarter of humanity's greenhouse gas emissions.
But the demand for change from consumers, policymakers, and businesses is growing, as shoppers seek greater transparency over where their food comes from, and more and more people cut down on their meat and dairy intake.
As a result, businesses are being forced to respond in increasingly innovative ways. In the first of three of 'Glimpses' videos produced for the world's first Net Zero Festival last week, BusinessGreen takes a look at the challenges facing the food and farming system, and also visits Vertical Future, a company developing indoor farming technologies that could be set to play an increasingly integral role in the future net-zero economy.
All of the panel debates, keynote speeches, and presentations from the world's first Net Zero Festival - which took place over three days from 30 September featuring hundreds of top speakers from business, politics, and academia - are now available to watch again on demand through the Net Zero Festival website.
RELATED ARTICLES
Second Chances Farm Announces New Farm In Philadelphia
The farm will be part of the North Station redevelopment of several million sq. ft. of vacant buildings and land near the Temple University campus being led by Bailkin’s Arete Group
Second Chances Farm founder Ajit Mathew George recently announced that he has reached an agreement with Philadelphia developer Michael Bailkin, who will invest the capital needed to open a 30,000 square feet farm – roughly 10 times larger than Second Chances Farm’s current operation – with enough space to eventually expand to 100,000 square feet.
The farm will be part of the North Station redevelopment of several million sq. ft. of vacant buildings and land near the Temple University campus being led by Bailkin’s Arete Group.
Second Chances Farm will not be putting capital into the project but is considered a minority partner because staff from the Wilmington operation will be sent to Philadelphia to help get the new farm up and running. The new farm is slated to open in 2021. Michael said that he intends to use Philadelphia as a headquarters site, while opening satellite farms in “older industrial cities” throughout Pennsylvania.
Michael has been very interested in indoor vertical farming for a long time, and his wife, Billie, and son, Cole, were looking at a whole range of opportunities.
“And then we met Ajit about a year ago,” he says, who is active in Opportunity Zones, “and we became very intrigued by the technical approach that he had, setting up a vertical farm, and doing that in a way that was going to make a major social impact by bringing in returned citizens and providing a job base and other opportunities for them. It was the combination of those two things that made us focus on doing something with our budget and over the next year or so, we continued working with him.”
Michael and Second Chances Farm agreed to do a large project in Philadelphia, essentially as the headquarters, at least the regional, possibly national, headquarters for expansion. Starting off with a 30,000 sq. ft. facility with a potential to expand it up to a 100,000 sq. ft., they will open a series of smaller units, of 15 to 20,000 sq. ft. in Opportunity Zones in some of the older industrial cities in Pennsylvania like Scranton, Coatesville and Norristown, while also doing economic development in those cities. The most important consideration will be on creating opportunities for second chance citizens.
The second target of the partnership is to provide healthy food for areas that are food deserts, which most of these opportunities are. The third is economic development, which is what Michael brings to the table. “Second Chances Farm will be the anchor and catalyst for other economic development activities in each of these opportunities zones,” Bailkin says.
For more information:
Second Chances Farm
www.secondchancesfarm.com
Publication date: Wed 30 Sep 2020
Why Kroger And Publix Are Bringing The Farm To The Grocery Store
In March, Publix’s GreenWise market in Lakewood, Florida, added a 40-foot container hydroponic farm in the parking lot
October 8, 2020
By Jesse Klein
Just like every other retailer, grocery stores are focusing on the customer experience to get people back in store. Grocery delivery was already a rising trend, and the pandemic kicked it into the next gear. In May, U.S. online grocery sales had grown to 40 percent. So grocers including Kroger and Publix are looking at onsite vertical farms as one way to attract consumers.
"That experience of going into a grocer and picking something essentially off the vine is compelling from a customer experience standpoint," said Shireen Santosham, head of strategic initiatives at Plenty, a vertical farm company based in San Francisco.
According to Grant Vandenbusschet, chief category officer at Fifth Season, a robotic vertical farm company based in Pittsburgh, fresh produce is keeping a lot of traditional grocery stores alive. It’s the main category still driving traffic into stores, he said, so innovating and investing in this department has been a focus for most retailers.
On-site container farming is not a new idea for grocery stores, but as urban vertical farming has advanced to become a more mainstream part of the supply chain, the idea is becoming more feasible. Some big players have finished their strategic analysis and pilot programs, and are leaning into vertical farming in a bigger way.
That experience of going into a grocer and picking something essentially off the vine is compelling from a customer experience standpoint.
In two Seattle stores, for example, Kroger installed modular vertical farms from German startup Infarm. While the seedlings spend the first few days at Infarm’s centralized nursery, most of the growing happens on-site at the grocery stores.
In March, Publix’s GreenWise market in Lakewood, Florida, added a 40-foot container hydroponic farm in the parking lot. Customers can see the equivalent of three acres of traditional farmland through the container’s windows. It grows about 720 heads of lettuce each week, all sold in the store. But it’s still early days and the process has kinks to work out. At first, Publix wasn’t getting the yields it was expecting.
"It takes time to grow the product and offer consistent quality, flavor, and size," said Curt Epperson, business development director at Publix. "I believe over time, once hydroponic growers refine their processes, and scale-up, we’ll find more efficiencies."
According to Vandenbusschet, one of those efficiencies may be a focus on supporting vertical farms at a large-scale grocer’s distribution center instead of at every single retail location. To get significant business and sustainability impacts from vertical farming, companies will need to get large enough to take true advantage of economies of scale.
"We think a lot of retailers are looking at this format if they are going to have high enough volumes of product to start replacing [traditional] grown products inside of all of their stores," Vandenbusschet said.
Growing is a hard, finicky business. Retailers are experts at retailing, and it’s hard to be good at both retailing and growing, so expect to see key partnerships materialize. Along with the Infarm and Kroger partnership, Publix’s onsite farm is run and managed by Brick Street Farms.
"Finding systems that are not over-encumbering to their operations, things that they can plug-and-play well is really going to be critical," Vandenbusschet said.
If retailers pursue this model, the customer experience might be more akin to going to a farmers’ market than going straight to the farm. But this model has a better chance of scaling well for businesses while also creating sustainability benefits such as cutting freight emissions, lowering water usage, and prolonging shelf life.
Lead photo: Publix is hoping to lure shoppers back to grocery stores with new onsite vertical farms.//Courtesy of Publix
World’s First Fully 3D-Printed Vertical Farm Debuts
The Banyan Eco Wall is a vertical farm with a seamless sculptural design. Unlike other 3D-printed structures, its functionality — the irrigation and drainage system — is embedded inside. The eco wall was printed with a BigRep One V3, which is considered one of the most advanced large-scale industrial 3D printers in the world
29-09-2020 | Yahoo/In The Know
The world’s first fully 3D-printed irrigated green wall made its debut in June 2019.
The Banyan Eco Wall is a vertical farm with a seamless sculptural design. Unlike other 3D-printed structures, its functionality — the irrigation and drainage system — is embedded inside. The eco wall was printed with a BigRep One V3, which is considered one of the most advanced large-scale industrial 3D printers in the world.
Mirek Claßen, Tobias Storz, and Lindsay Lawson of NowLab, BigRep’s research and innovation program, designed the project.
“Similar vertical farm structures have required channels to be manually embedded into the design in a complicated process after manufacturing with metal piping and a variety of other parts,” BigRep said in a statement. “The Banyan, on the other hand, is 3D-printed with internal channels included in the design.”
That means consumers won’t have to figure out how to create and install a plumbing system on their own once the vertical farm is installed. Thus, it’s cheaper and more user-friendly than its predecessors — which is also demonstrated by its irrigation system’s ability to self-regulate. The Banyan disperses water in the form of “micro-showers” at controlled intervals to meet each plant’s needs.
Not only is it functional, but it’s also aesthetically beautiful. The white wall consists of interlocking, organic shapes that resemble the curves of tree branches.
The Banyan is 6.5 x 6.5 x 2 feet and printed in four modular parts that snap together. It is printed with PETG, a form of plastic used in 3D printing that can be 100 percent recyclable.
“Systems such as this inspire interior designers and architects developing a greener future — from home or workspace plant walls and green facades to vertical gardens and other forms of urban farming,” the statement said.
Source: Yahoo/In The Know
Photo Courtesy of Bigrep
Vertical Farming: IDTechEx Research Asks How Big Is Too Big
An ongoing argument within the industry is a question of size – is it better to focus on building a large, highly automated plant factory to minimize production costs, or is a small, more flexible approach the best way to set up a vertical farm?
NEWS PROVIDED BY IDTechEx
Oct 05, 2020
BOSTON, Oct. 5, 2020,/PRNewswire/ -- Vertical farming is growing quickly. The concept of vertical farming, the idea that crops can be grown far more efficiently indoors under controlled environmental conditions than would be possible on conventional farmland, has captured the imagination of entrepreneurs and investors alike, with dozens of start-ups being founded across the world raising ever-increasing amounts of investor capital. The recent IDTechEx report, "Vertical Farming 2020-2030" explores the technologies and market factors that are shaping this rapidly expanding industry.
An ongoing argument within the industry is a question of size – is it better to focus on building a large, highly automated plant factory to minimize production costs, or is a small, more flexible approach the best way to set up a vertical farm?
This question stems from some of the challenges facing the vertical farming industry. Setting up and running a vertical farm is not cheap and many vertical farming companies have struggled to overcome spiraling labor and power costs, alongside unforeseen logistical complexities, and issues with maintaining an optimum growing environment.
A potential solution to some of these problems is to build a very large vertical farm, which allows the power costs to be averaged out over a large quantity of crops. Additionally, large vertical farms make it easier to justify using advanced automation systems that can help reduce labor costs, with the cost of the automated systems also being spread out over large quantities of crops. These sorts of economies of scale can help a vertical farm begin to reach price parity with a conventional farm, something which has long eluded smaller vertical farms, which are often forced to sell produce in premium categories. Large vertical farms producing large quantities of crops can also be more easily incorporated into existing food supply chain structures, for example, next to a supermarket's main distribution center.
One company attempting to use this scale-based approach is Jones Food Company, a British vertical farming start-up that currently operates Europe's largest vertical farm. The company believes that the only way that vertical farming will be successful in the long term is by reaching price parity with conventional farming, which it hopes to achieve through automation and by operating large scale facilities close to distribution centers.
The company takes its inspiration from car factories – it is far more cost-effective to produce cars in a large central facility than it would be to produce them in small facilities near the dealerships and Jones Food Company believes this same logic applies to vertical farming. Crops grown in distribution centers are still able to reach consumers rapidly, often within a day of harvest, and the company doesn't believe that the hyper-local model promoted by certain competitors is worth the inefficiencies and costs of many small facilities located in city centers.
Several other vertical farming companies are following this approach, with New Jersey start-up AeroFarms announcing in 2019 that it was investing $42 million to construct a 150,000 square foot facility in Danville, Virginia, which the company claims will be the largest in the world. Jeff Bezos-backed Plenty operates a 52,000 square foot facility in South San Francisco, with the company aiming to maximize production efficiency to improve the economics of vertical farming.
Not everyone agrees with this large-scale approach, however. Large facilities and automation are expensive, with large scale facilities costing tens of millions of dollars to set up. Whilst this approach might make sense for a factory producing cars or other high-margin products, for low margin products such as fresh produce, it can take decades to pay back this initial investment.
Additionally, supply and demand for fresh produce is not always consistent and pricing can change frequently, making it difficult to accurately predict returns on investment, which can be very problematic for a vertical farm that cost several million dollars to build. Furthermore, many of the processes required to grow crops cannot yet be addressed through off-the-shelf automation solutions, creating difficult engineering challenges that can make scale-up very complicated.
A further problem for very large-scale vertical farms is that operational complexity can increase vastly for larger farms. Plants are living organisms that can behave in unpredictable ways, making it difficult to grow them in a manner resembling a factory production line. Plants give out heat and water vapor as they grow, whilst also needing a supply of carbon dioxide and oxygen, in addition to nutrients. Keeping the crop inputs consistent across the whole vertical farm and managing waste heat and water vapor can also be very difficult in a high-density growing space. Careful consideration of the plant science, alongside planning the logistical workflow to maximize efficiency are needed to successfully operate a large-scale vertical farm.
Because of these challenges, some companies have chosen instead to focus on smaller vertical farming facilities, choosing to focus on flexibility instead of economies of scale. For example, Freight Farms, which manufactures turnkey modular vertical farms inside 40' containers, believes that smaller vertical farms enable a more flexible and targeted business model than large, centralized facilities. Small vertical farms can be tailored to certain markets with gaps, such as crops that can't be imported, transient falls in supply for high-demand crops, and restaurants or food suppliers that need a specific ingredient. These are all markets in which large, warehouse-like vertical farms cannot easily access.
Rather than focusing on mass-produced, wholesale crops, where vertical farms will always struggle to compete on price with traditional farms and greenhouses, it may make more sense for vertical farm operators to focus on high-value crops that command a price premium, perhaps within niche markets or specialized applications.
The debate over the best size for a vertical farm is still ongoing. There is no easy answer on which model is best, and a would-be vertical farm operator should carefully consider their options and target market before starting a business. For more information and discussion over business models in vertical farming, as well as industry evaluations and 10-year market forecasts, see the recent IDTechEx report "Vertical Farming 2020-2030".
For more information on this report, please visit www.IDTechEx.com/VertFarm or for the full portfolio of AgTech research available from IDTechEx please visit www.IDTechEx.com/Research/AgTech.
IDTechEx guides your strategic business decisions through its Research, Consultancy and Event products, helping you profit from emerging technologies. For more information on IDTechEx Research and Consultancy, contact research@IDTechEx.com or visit www.IDTechEx.com.
Media Contact:
Natalie Moreton
Digital Marketing Manager
press@IDTechEx.com
+44(0)1223 812300
SOURCE IDTechEx
I Grew Tomatoes With The Heat From My Crypto-Mining PC
Just before Covid-19 struck, I started a project to build the world’s most overengineered, high-tech garden.
Anything Worth Engineering Is Worth Overengineering
10-08-20
Images courtesy of the author.
If you spend time on Instagram in our post-pandemic world, you’re probably experiencing some gardening FOMO. Maybe your biggest lockdown goal was “pwn Candy Crush” or, if you’re like me, “limit your toddler’s screen time to a scant five hours per day.” Now that we’re months into the pandemic, though, your friends who channeled their early quarantine angst into planting seeds are likely starting to reap the benefits in terms of fresh herbs and handfuls of juicy, Insta-friendly heirloom tomatoes.
If you’re more comfortable with wires and while loops than bugs and compost, don’t despair. Gardening has become increasingly tech-enabled. There are now tons of ways that you can apply emerging technologies to the challenge of growing your own food.
Just before Covid-19 struck, I started a project to build the world’s most overengineered, high-tech garden. It ended up incorporating hydroponics, solar power, cryptocurrency mining, recycled water, sensors, the Internet of Things, infrared imaging, and much else. Here’s how I did it — and how you can build your own tech-enabled pandemic garden, too.
I should say this clearly from the get-go: I kill plants. Even succulents, which can go weeks with no care at all, are too much for me. People often give these to me as gifts, and I’ve managed to keep exactly three of them alive. This is surprising, as I come from a long line of gardeners — my father is an avid gardener, as was my maternal grandmother. But apparently this inclination — and the corresponding skill — skipped at least a few generations.
It was a dilemma, then, when I discovered that my three-year-old has a passion for gardening. We got him some plants last summer, and he diligently watered them every day, growing a handful of tomatoes and a lovely calla lily on our back patio. Mornings began with at least five minutes of “plant time,” spent checking his plants, fertilizing, pollinating flowers with a toothbrush, and performing other gardening functions that are alien to me. Obviously, we wanted to encourage that interest. But again, none of that is in my wheelhouse.
As the founder of an A.I. company and the owner of a DIY-tech YouTube channel, though, gadgets, green tech, sensing, and the like most definitely are. In late 2019, I hatched an idea of creating an indoor sustainable garden by applying as many technologies and gadgets as I could think of. I wrote up my musings about the idea in January of this year. Then I figured what the hell, dove in, and actually built it.
Right from the start, I knew I didn’t want to mess around with soil. For one thing, it’s yucky. It’s also mysterious. As The Atlantic shares in a detailed article about soil, the stuff is teeming with bacteria, archaea, microbes, and fungi — as well as bugs, earthworms, and other beneficial creatures — that work together in a complex synergy to keep plants healthy. As The Atlantic reports, a single teaspoon of good soil can contain 10,000 to 50,000 different species of “protozoa, nematodes, mites, and microarthropods” and “more microbes than there are people on the earth.”
That felt way too complex to me. Wanting to abstract much of that away, I turned to a technology that has existed for thousands of years and is enjoying a tech-enabled resurgence: hydroponics. Hydroponics is the science of growing plants in water. Instead of placing them in soil, you bathe your plants’ roots in flowing water. You then add the basic nutrients they need to that water, instead of providing them via soil.
The benefits are numerous. Compared to traditional gardening, hydroponics can allow for up to a 90% reduction in water use, much higher yields, and up to two times faster growth rates. Because the water in a hydroponic system continually recirculates, there’s also no need to worry about watering plants consistently, you can control and eliminate fertilizer runoff, and you can grow plants indoors, in a tiny space.
This last part was important to me, as I wanted to set up my high-tech garden in my garage. The San Francisco Bay Area, where I live, enjoys long outdoor growing seasons and little danger of frost, but I wanted to demonstrate that one can create a viable high-tech garden in any space: a basement, an unfinished room or shed, the balcony of a rented apartment, etc. Hydroponics allows you to grow meaningful amounts of produce in small spaces — including indoor spaces with little to no natural light — so it felt like a fit for that reason, too.
When I first started my project, I expected to have to build a small hydroponics system from scratch. But I quickly discovered that someone had done that for me. AeroGarden — a division of the well-known garden supply company Miracle-Gro — sells a variety of premade hydroponic gardens. These range in size from the diminutive Sprout (which retails for $76.99 and grows a handful of herbs table-side) to the $895 Farm 24XL, which grows 24 plants and includes advanced features like a programmable day/night cycle and Alexa voice control.
Choosing a new type of plant to grow feels a bit like importing a Python module or installing a new graphics card.
All AeroGarden models (and, fundamentally, all hydroponic systems) include a few basic components. There’s a water-filled tray to hold your plants, a small pump to circulate water over their roots, and a set of LED grow lights that provide the illumination your plants need to thrive, even in an otherwise dark room.
AeroGarden sells its plants as “pods,” which include seeds and a porous support material inside a plastic tube that you snap into your garden. Larger garden models accommodate more pods. You can mix and match many pods within a single garden, allowing you to grow several kinds of plants at once. AeroGarden offers a dizzying array of premade pods, from spring flowers to ghost peppers. It also offers a grow-anything kit, which allows you to create your own pods and grow nearly anything in your AeroGarden. (To preempt an obvious question, yes, you can grow pot in it.)
I love the modular aspect of AeroGarden’s pods. For someone used to the conventions of the tech world, it’s very familiar. Choosing a new type of plant to grow feels a bit like importing a Python module or installing a new graphics card. You browse through a list of options, make a choice based on a set of capabilities or features that you want to access, and then plug the new module into your project.
I bought two AeroGarden Harvests — a midrange model that costs around $110 and accommodates six pods each. I also picked up a set of heirloom cherry tomato pods and a set of pods for assorted herbs. My son and I set up the AeroGardens in the garage and installed the pods. By the time we got them up and running, it was mid-February.
AeroGardens are primarily designed for indoor use in a climate-controlled room. My garage isn’t climate controlled. California has mild weather, but it still gets chilly at night. In February, daytime temperatures are usually around 60 degrees Fahrenheit and dip into the 40s after sundown. Tomatoes grow best with a daytime temperature of 70 to 85 and a nighttime temperature above 60, so this didn’t seem optimal. I knew we would need some kind of heat.
We started by getting an Educational Insights tabletop greenhouse ($43 on Amazon) to hold the AeroGardens. This helped a bit with temperature—and kept the tomatoes nice and humid—but it still wasn’t ideal. To bump up the temperature and our tomato yield, I had an idea: Why not heat the greenhouse with the waste heat from a cryptocurrency-mining computer?
Cryptocurrency has exploded in prominence and impact over the past several years. According to industry publication Coin Telegraph, the market for mining hardware (used to create new cryptocurrency coins) is set to grow by $2.8 billion between 2020 and 2024. All this growth comes at a very real cost. The mining of bitcoin alone is estimated to consume up to half of all the electricity used by all data centers worldwide. The bitcoin network currently uses as much electricity as the country of Colombia.
All this electricity ultimately turns into heat. Most of the time, that heat is wasted. But some cryptocurrency miners, seeing an opportunity, are putting waste heat to productive use. Ukrainian company Hotmine is developing crypto-powered hot-water heaters and furnaces for home use. Heatmine, a Canadian company, has experimented with using crypto waste heat in homes in Quebec, which has frigid winters. And as of 2018, a Czech company was experimenting with “cryptomatoes” using heat from bitcoin mining to heat tomato greenhouses.
I’ve experimented with heating my home using cryptocurrency-mining waste heat on a small scale, with a good deal of success. For that project (and a photo series on the cryptocurrency industry), I built my own mining rig. It uses a custom PC, a super-high-efficiency EVGA power supply, and an NVIDIA GeForce 1070 graphics card — a staple of cryptocurrency miners — to mine a variety of crypto coins using the automated software NiceHash.
Running at full blast, the PC also gets quite toasty. For my heating experiment, I calculated that my rig draws about 220 watts of electricity, putting out 716 BTUs of heat per hour. That’s about the output of a small space heater or one of those overhead heaters you see on restaurant patios. The rig, which cost around $600 to build, generates up to $0.76 in mining revenue per day — not remarkable, but enough to offset some of my heating costs when I used it indoors in the winter.
Piping 716 BTUs per hour directly into my tiny greenhouse, I calculated, would be way too much heat. My greenhouse is 24 cubic feet, so putting in all the heat from the cryptocurrency-mining computer would increase its temperature by around 40 degrees. Even in the dead of winter — with a nighttime temperature of 45 degrees — that would still push my tomatoes to their 85-degree limit. On warmer nights, it would risk roasting them on the vine.
Instead, I opened the side panel on the computer and connected it to the side of the greenhouse. Using a FLIR One infrared thermal camera, I determined that the NVIDIA 1070 heats up to around 110 degrees when mining. This radiates a nice amount of heat into the greenhouse, moderating its internal temperature without overdoing it.
The glowing green logo of the NVIDIA GeForce is visible inside my greenhouse.
I also found that just running the computer near the greenhouse kept my garage a bit warmer than normal. It’s like a high-tech version of the tried-and-true gardening practice of placing water bottles near your plants. The bottles heat up in the sun during the day and then radiate heat at night, protecting your plants from frost and helping them grow just a bit better.
With all the supplemental heat from my mining computer, I felt like I needed some kind of monitoring system for my garden. At first, I thought about building a DIY temperature monitor with a RaspberryPi. But in keeping with the modular concept of the project, I decided to use another solution: an industrial sensing system from Monnit.
Monnit sells a variety of sensor gateways, which you install in your facility and connect to the internet. Once you have a gateway installed, you can buy up to several hundred tiny sensors, which allow you to monitor everything from temperature to vibrations to whether someone is sitting in a chair.
Each sensor uses a coin cell battery that lasts about six months and transmits over a short-range wireless radio to the gateway. That means you can place the sensors anywhere you want in the space you’re trying to monitor. The gateway forwards the sensors’ data along to Monnit’s cloud, where you can log into a web interface and get a real-time read on conditions in your facility.
This is a system intended for commercial or industrial applications, so it’s not cheap. Monnit’s ethernet gateways run about $220, and each sensor costs around $50 to $80. But the system has rock-solid reliability and accuracy, and Monnit’s data storage and charting functions are top-notch. I also liked how the system could potentially scale to a commercial-size greenhouse. I don’t plan to scale up my tomato project to a commercial facility, but it’s good to know that the technologies I’m demonstrating in my tiny greenhouse could potentially be used in a real, full-sized indoor farm.
I’ve experimented with heating my home using cryptocurrency-mining waste heat on a small scale, with a good deal of success.
The final step for my garden was to add water. Hydroponic systems use dramatically less water than traditional planting methods; according to the National Park Service, they can use up to 1,000% less. But because the plants are immersed 24/7, water is a crucial part of the process of growing plants hydroponically.
AeroGarden recommends using distilled water with its gardens. This felt like a big hassle — and a potential generator of a ton of plastic waste. So I looked for another solution. Ideally, I wanted to use recycled water. On a trip to Israel in 2012, I saw tomatoes grown using recycled water in the Negev Desert. And closer to home, I did a photo series at CoCo San Sustainable Farm in the Bay Area, which uses recycled water from sanitation provider Central San to grow food for local schools. So I knew it could be done.
But I didn’t want to have to drive to a recycled-water pickup point every time I wanted to water my tomatoes, and the water provided there wouldn’t be distilled. Doing some research, I came up with a solution: I could use the condensation generated by my home air-conditioning system to irrigate my garden.
If you have central air and you’ve walked around outside your home in the summer, you may have seen a little tube or hose dribbling out a stream of water. You probably thought, “I hope that isn’t a problem,” and then went about your day. It’s not a problem — air-conditioning systems work in part by removing water vapor from the air in your home. All the water has to go somewhere. Most air-conditioning systems jettison it through a little tube into the ground in your backyard or, in some cases, directly into the sewer.
That’s a major wasted opportunity. While the water from an AC condensate drain isn’t safe to drink untreated, it tends — like distilled water — to be very low in mineral content. It’s also free, readily available, and otherwise wasted. Many big institutions take advantage of this source of eco-friendly water on a grand scale — Rice University, for example, captures 14 million gallons of water per year from its AC systems. I decided to try doing so at home.
In a series of experiments, I determined that my home AC system dumps about one gallon of condensate water per hour. That’s a lot of water. At first, I thought about building a complex device to catch water from my AC unit using a marine bilge pump, external power supply, and tubing to pipe the water into my AeroGardens.
Instead, I settled for a clear plastic bucket, which I placed under the condensate drain in my backyard. AC condensate can contain Legionella bacteria, so ideally you should boil it or treat it with UV light, chlorine tablets, or ozone before using it and avoid using it in applications that create aerosols, like a sprinkler system. I settled for letting my buckets fill up, then placing them in the sun for several days before pouring the water into my AeroGardens. I can’t vouch for the safety of that technique, but I’ve been okay so far.
With all the pieces put together, I now had a system that used hydroponics and LED grow lights to nurture modular plant pods. The whole thing was contained in a tabletop greenhouse, kept at optimal growing temperatures 24/7 by cryptocurrency waste heat, monitored by industrial IoT sensors, and irrigated with recycled water. It was an ideal way to experiment with some of today’s most compelling green technologies.
Oh, and it produces tons of tasty tomatoes. With AeroGardens, your only real responsibility as a gardener is to keep each garden filled with water and add some liquid fertilizer every two weeks when a light on the garden turns red. You can also do some light pruning to increase the yield on your plants — if you don’t, they’ll grow so large that they overshoot the AeroGarden’s grow lights, and your tomato production will drop. My son and I watched as our tomatoes germinated and began to sprout right on schedule, about five days after we “planted” the tomato pods.
Our herbs started to shoot up even faster, with little sprouts emerging about two days after planting. Over the next several months, our plants grew aggressively. We got to experience the excitement of seeing our tiny tomato seedlings grow into a giant, leggy plants with little yellow flowers, and ultimately green tomatoes, which rapidly turned red — and were perfect for plucking by tiny hands.
The tech aspects of the project have worked out surprisingly well. The Monnit sensor system beams in temperature readings every two hours, which I can access as a series of charts in a web interface. The cryptocurrency computer has done an admirable job of keeping things balmy. On a recent chilly night in September, when nighttime temperatures dropped into the 50s, our garden stayed at a comfortable 74 degrees. In the heat of the day, it got a few degrees above the ideal maximum temperature of 85 degrees, but the tomatoes seem fine.
Chart of temperatures in the greenhouse during a day and night in mid-September.
From our limited experiment, I’ve seen that hydroponics really do appear to deliver on its promise of faster-growing times and bigger yields. Last summer, we labored for months to grow about 10 tomatoes and a handful of herbs in the backyard. With our high-tech garden, we got to watch as our herbs—the basil especially—started out by producing enough leaves to flavor a tomato sauce, then enough for pesto, and finally so many that I had to cut them back almost daily, drying them or using them in infused olive oils to stop them from going to waste.
AeroGarden plants last about six months; during that time, you can harvest from them continually. Our herbs died back after their six-month growth window was over, but the tomatoes are still going strong. At times, we’ve been able to harvest tomatoes by the handful and have used them in everything from sandwiches to Caprese salads to soups.
At the beginning of the project, I struggled with deciding what to grow. It takes about an acre of land to grow enough food to feed one person, so feeding our whole family with a hydroponic garden wasn’t realistic. What, I wondered, would have the most impact? Should I grow plants that perform other functions, like filtering the air? Should I look toward something like blue spirulina, which several readers of my first Medium piece on the project emailed me to suggest as a space-efficient superfood?
As you do a bit more gardening, you might also be surprised how similar gardeners are to coders and other technologists.
When the pandemic hit, that question rapidly answered itself. The absolute best use for a Covid-19 garden, I found, is to grow ingredients that enliven and add interest to other foods.
I can’t even begin to describe the mental health benefits — at the height of the pandemic lockdowns, when going to the grocery store literally felt like a life-and-death endeavor — of taking some boring, pandemic-friendly canned food or store-brand boiled pasta and topping it with fresh basil, crushed sprigs of thyme, and sliced cherry tomatoes, picked a few minutes earlier in our garage.
One of the hardest parts of weathering a lockdown is fatigue. Sticking with the same routine day in and day out for months — with limited trips outside your home — is mentally and emotionally draining. So is eating the same foods for months on end. In the early days, we ate whatever shelf-stable staples weren’t sold out at Target or bought strange brands of pasta or canned goods by the box for absurd prices on Amazon.
Gardening itself has been shown to reduce stress. But the little handfuls of fresh ingredients that we harvested each week from our AeroGardens served their own, extremely important function: They allowed us to add color, freshness, and variety to the bland, generic things we were otherwise eating. That, in turn, lent a bit of variety, excitement, and connection with the natural world to the drab, monotonous process of quarantine.
Having that little bit of freshness in our diet made the lockdowns a tiny bit easier to tolerate — and gave us one fewer reason to go to the store. When the world is falling apart outside your door, don’t underestimate the power of a handful of Thai basil or a drink topped with mint you grew yourself to make things just a bit better. It’s an effect that’s been around since the victory gardens of World War 1, and it’s something that thousands of us are rediscovering today.
Even if you’re more familiar with the silicon variety of random trees than the ones found in a real forest — or if your historical track record with plants isn’t stellar — now might be the perfect time to try out gardening. Gadgets like the AeroGarden make the process simple—and especially with more complex models that allow you to track and tweak light levels and feeding schedules, downright geeky.
As you do a bit more gardening, you might also be surprised how similar gardeners are to coders and other technologists. Take one look at an experienced gardener’s charts of hardiness zones and little grid-based garden maps drawn on graphing paper or mapped in Excel, and you might feel a sense of familiarity. If you want to take a stab at growing your own plants, you could do what I’ve done and make your garden extremely automated and tech-intensive. I’m still planning to work solar power from my private microgrid and a self-watering system into mine. My garden is, of course, more a platform for experimentation than an economical way to grow produce — accounting for the mining PC and Monnit sensor system, I estimate that it cost about $1,200 to build. But even if you just buy an AeroGarden and put in on your kitchen counter — or borrow a few of the ideas I’ve demonstrated and create your own DIY versions — that’s a great start.
I’m still reluctant to call myself a full gardener. That title goes to the people who effortlessly call up plants from the soil or, like my son, have a passion for the watering and pruning that managing a full garden often requires. But I’m comfortable calling myself a technologist who dabbles — or perhaps as Wired suggests, a “domestic terraformer.” And I’m proud to say that I now have the tomatoes to back up that title.
WRITTEN BY
Thomas Smith
Co-Founder & CEO of Gado Images.
I write, speak and consult about tech, privacy, AI, and photography.
Subscribe: https://bit.ly/33xx752 Email: tom@gadoimages.com
"Vertical Farming Won’t Replace All Greenhouse Production, But It’s More A Combination of All of Them"
“We have been studying the vertical farming market for a couple of years now. Today, we haven’t seen any new, exciting things I must say, but vertical farms continue to improve
“We have been studying the vertical farming market for a couple of years now. Today, we haven’t seen any new, exciting things I must say, but vertical farms continue to improve. More production systems become high-tech, from greenhouse growers to other farmers. It’s also more about looking at what is applicable per location, whether it’s an indoor farm in an urban area or a high-tech greenhouse more suitable for the area it’s based,” Cindy van Rijswick, Expert Fresh Produce at Rabobank Research Food & Agribusiness, says.
Cindy van Rijswick
Not at its peak yet
Vertical farming in the Netherlands isn’t very thrilling production-wise, but many great techniques are developed here, she notes. “The USA e.g. is not very familiar with glass greenhouses. They switched to vertical farming at some point and often skipped the glasshouse concept. The only disadvantage a greenhouse has, compared to vertical farming, is that it needs more space and it is less easy to control because still sunlight is used.”
In the indoor farming market, there are a lot of small-scale companies. In comparison to the Dutch greenhouses, it’s not as profitable as it could be. When stacking multiple layers vertically it will increase production. “However, it's not large-scale enough. Now there is a limited range of products, such as luxury lettuces and herbs, for which there is only a narrow market.”
Uniformity
“The market is currently in a development phase. Before it will become mature, mistakes are being made. There are still many steps to be taken before we’ll get there. One being, increasing efficiency. In addition to that, there are too many different systems being used and instead, more uniformity is needed.
"All kinds of systems are developed while there are companies that have existing well-working systems. However, large sums of money are put into the sector while very little working proof comes out of it. In the future, there will be more vertical farm suppliers that will operate effectively. The sector needs to collaborate and compare more. In this way, steps can be taken. Although even then, it will not replace all greenhouse production, it’s more a combination of all of them,” Van Rijswick explains.
Costs per m2
The investment costs for a vertical farm are more or less starting at € 2000 per m2 in comparison to a greenhouse which is about € 200-500 per m2. There is a huge difference between investment costs which is a major disadvantage for farmers looking for funding. Efficient herb plant factories could possibly compete with a greenhouse at the same cost price. Unfortunately, there’s so little transparency in the industry that not much is known about it.
Suitable location?
Van Rijswick affirmed that in some cases it’s better to be located inside the city. However, there are also many disadvantages to it. The land price is very high-priced in large cities, which causes it to be competing with for example office space. “There are many logistic problems as it's very complicated to get around within the city. The location has to be looked at in a more efficient way. As a large-scale farm, when being located next to a distribution center it’s much easier to distribute products to retail stores.”
Vacant buildings are hardly suitable for a vertical farm because of the following:
Often the floors aren’t able to carry heavy racks and installations
There are risks involved using a lot of electricity and water and it is sometimes difficult to insure these
The building will have a different use which is not always accepted by the municipality
Van Rijswick adds: “In most cases, it is better to acquire a new building where a new farm can be built rather than in existing offices. People think about it too easily. The most commonly used argument is that the building is then utilized beneficially, but this is not always the case.”
‘Japan as a frontrunner’
The country that has been out there the longest is Japan. Although the cost price is higher than in the Netherlands, people are willing to pay more for their greens. Van Rijswick continues: “Many young people would like to start their own farm, having great technique and a proper business plan. However, they can't put into words what their market is. China has had many food scandals, so there’s more demand for fresh produce with guaranteed safety. They’d rather pay more for clean food, produced in a safe growing environment. In Europe, this is less of an issue and competition is high, which makes it difficult to sell produce at a premium.”
‘More suitable for leafy greens’
“In the end, I think that indoor farming is most suitable for leafy greens, such as lettuce and herbs. Young plants and starting materials are also very suitable for this kind of growing environment. These greens are well suited for this type of cultivation, in terms of hygiene requirements and product quality. The crops can easily be stacked in multiple layers. This results in a higher value per kilogram, which is great looking at the cost price of these farming techniques.”
Large farms can process this type of production better than a small farm growing plants. These farms can pack and deliver the products immediately because only then it becomes logistically efficient. “For ‘fresh-cut companies’ it could be useful if they could grow some of their raw materials within their factory, such as expensive types of lettuce. In small businesses, I see more potential for local markets and the hospitality industry. But in the future, there certainly will be more large professional farms that will be growing large scale,” Van Rijswick explains.
For more information:
Rabobank
Cindy Rijswick, Expert Fresh Produce at Rabobank Research Food & Agribusiness
Cindy.Rijswick@rabobank.com
www.rabobank.com
Publication date: Tue 22 Sep 2020
Author: Rebekka Boekhout
© HortiDaily.com
RSVP - Indoor Ag Science Cafe October 20th 11 AM Eastern Time
Learning critical control point for hydroponic food safety
October Indoor Science Cafe
October 20th Tuesday 11 AM Eastern
Please Sign Up!
Learning critical control point
for hydroponic food safety
"Hydroponic Crops --
How can you produce safe vegetables?"
By
Dr. Sanja Ilic (The Ohio State University)
Please sign up so that you will receive Zoom link info.
Indoor Ag Science Cafe is an open discussion forum, organized by Chieri Kubota (OSU), Erik Runkle (MSU), and Cary Mitchell (Purdue U.) supported by USDA SCRI grants.
Sign up here
Tri-State, EPRI Team To Officially Bring ‘Farm In A Box’ Program To Moffat County School District
Tri-State will install one of EPRI’s cutting-edge indoor agriculture facilities on the grounds of Moffat County High School later this year, according to a press release from Tri-State
09-23-20 | Joshua Carney | Follow
Tri-State Generation and Transmission Association’s decades-long relationship with the Electric Power Research Institute is about to bear fruit for Moffat County School District students and the Craig community as a whole as the “Farm in a Box” project moves forward.
Tri-State will install one of EPRI’s cutting-edge indoor agriculture facilities on the grounds of Moffat County High School later this year, according to a press release from Tri-State.
The “Farm in a Box” is valued at $250,000 – which is covered as part of Tri-State’s EPRI membership – and will provide a new source for fresh produce in the region and educational opportunities for MCSD students. Moffat County High School Business Teacher Krista Schenck presented the project to City Council in early September. The project has the capability to produce various crops, such as lettuce, kale, arugula herbs, flowers, carrots, and radishes, year-round inside the shipping container.
“Tri-State invests in its EPRI membership and is keen to find immediately applicable uses for the remarkable technologies that emerge to benefit the electric sector and society at large,” said Tri-State CEO Duane Highley in a press release. “We also recognize that the transition brought on by our Responsible Energy Plan will have a major impact on coal-dependent communities, so if we can leverage a program to bring new educational, economic, and lifestyle benefits to support Moffat County schools, we are proud and eager to do so.”
An EPRI-led team is constructing the facility – a 40-foot long shipping container equipped with efficient lighting, temperature control, and plumbing infrastructure needed to grow crops inside the container on a year-round basis.
Since 2015, EPRI has been examining the operational, technological, sustainability, and environmental characteristics for indoor agriculture, by installing container farms across the United States and assessing their performance with local electricity providers, academic institutions, and other community organizations.“
As an emerging industry in urban and rural areas throughout the United States, indoor farming can help us use our energy and water resources more efficiently,” said EPRI President Arshad Mansoor. “EPRI’s indoor food production research aims to help electric utilities better understand, plan for, and engage with this novel enterprise while also offering educational opportunities for project collaborators, the local community, and the next generation of farmers to address food availability challenges.”
According to Tri-State, EPRI staff will monitor the container to evaluate nutrient quality of the produce, utility program compatibility, community impacts, sustainability performance, technology trends, market drivers, electricity load profiles, and other broader environmental and economic aspects of indoor food production for the first two years following installation. EPRI will conduct research on the container and MCSD will be the sole owner and operator of the equipment.
“Moffat County School District is excited about the learning potential this program affords its career and technical education students in our community,” said Principal Sarah Hepworth of Moffat County High School.“
Through the collaboration between agricultural, business, marketing, and culinary programs, the opportunities to learn about horticulture, conservation, food regulations, business, and project management, marketing, sales, and food preparation are endless for MCSD students,” said Schenck. “Students and faculty look forward to utilizing this partnership and the technology of ‘Farm in a Box’ to grow crops from microgreens to lettuce and carrots.”
Preparing the container farm will take several weeks and involve manufacturing and a customized graphic treatment of its exterior. School officials are targeting early to mid-November for its arrival in Craig. The EPRI team will consult with the school district on installation and operation.“
This is a true team effort,” added Highley. “One of the seven cooperative principles under which we operate is ‘Concern for Community,’ so we’re excited to see the school district adopt this project and turn it into a real asset for community betterment.”In January, Tri-State announced its Responsible Energy Plan, which will transition the company to more renewable energy production for its members to address changes in the industry and to support new state requirements for clean energy. The effort will result in the closure of the Craig Generation Station by 2030, and Tri-State has been working with state and local officials to support transition efforts in the community.jcarney@craigdailypress.com
Dr. Peter Quinn Appointed As New Chair of CHAP
Peter holds an MBA and BSc(Hons) & Ph.D. in Epigenetics & Microbiology and has published on the importance of nutrition to improve health and wellness in society
Crop Health and Protection (CHAP) one of the four UK Agri-Tech Centres of Innovation, has appointed Dr. Peter Quinn, CEO of Genius Foods, to be its new Non-Executive Chairman, following the retirement, earlier this year, of John Chinn.
Peter brings extensive business leadership experience to the CHAP Board, having held Chief Executive, Managing Director, and Non-Executive Director roles. He has a background in creating enterprise value across a range of complex FMCG brand and private label markets in food and drink, manufacturing and retail, biotech, and agri-tech.
He is currently CEO of Genius Foods and was previously divisional MD of Samworth Brothers. In addition, he holds several NED positions in the Agri-Tech/Produce sector. He is an expert in transformational turnarounds and the creation of growth and value strategies through organizational alignment and ingenuity.
He is also passionate about building business cultures committed to people and has served on the Boards of BITC Charities, dedicated to creating opportunities for disadvantaged young people through education and personal development.
Peter holds an MBA and BSc(Hons) & Ph.D. in Epigenetics & Microbiology and has published on the importance of nutrition to improve health and wellness in society.
As Chairman of CHAP, he is committed to the vital function of science, technology and collaborative innovation to transform UK agriculture and sustainable food production.
CHAP CEO Fraser Black said: “CHAP is experiencing an exciting period of growth and development and Peter is well-placed to help us cement our position at the centre of the UK agritech innovation sector. His commercial, non-profit, and academic experience are a perfect fit for CHAP. I look forward to working with him to ensure CHAP continues to act as a catalyst for innovation in UK agribusiness. This will enable us to achieve our vision of making the UK a global leader in the development of applied agri-technologies, to help secure our future by nourishing a growing population sustainably while delivering economic, environmental and health benefits to society.”
Peter Quinn said: “I am delighted to be appointed to the Board of CHAP as Non-Executive Chairman. There has never been a more critical time to invest in the future of UK agriculture and sustainable food production. CHAP plays a pivotal role in creating world-class innovations through collaborations between scientists, farmers, and industry to transform the productivity of UK agriculture. CHAP is the nexus for new ideas and ingenuity that will deliver agricultural solutions for tomorrow’s world.”
About Crop Health and Protection (CHAP)
Crop Health and Protection (CHAP), funded by Innovate UK, is one of four UK Agri-Tech Centres. CHAP’s vision is for the UK to be a global leader in the development of applied Agri-Technologies, to help secure our future by nourishing a growing population sustainably while delivering economic, environmental and health benefits to society. CHAP acts as a unique, independent nexus between the UK government, researchers, and industry, building innovation networks to identify and accelerate the development of cutting-edge solutions to drive incremental, transformative, and disruptive changes in sustainable crop productivity.
Website: www.chap-solutions.co.uk Twitter: @CHAP_Enquiries
For further information contact:
Darren Hassall (Marketing Manager): darren.hassall@chap-solutions.co.uk
Tel: +44 (0)7866 799152
Sodexo Partners With Container Farming Startup Freight Farms To Bring Indoor Ag To College Campuses
The goal of the partnership is to bring fresh, traceable produce to college foodservice year-round that’s pesticide- and insecticide-free with low food miles
January 29, 2020
When a major foodservice player like Sodexo calls up your relatively young startup to ask whether you’d be interested in providing indoor ag services for their university clients, it’s safe to say you’ve arrived.
“Their partnership team reached out to us and said this is a huge problem we are trying to solve and we have been watching you guys from corporate headquarters and we saw you have proven adoption on all these different university campuses,” Brad McNamara, Freight Farms CEO, told AFN. “It’s a surreal moment when the 800-pound gorilla calls you and says we’ve been talking about you internally for six months. Can we work with you?”
The Boston-based container farming company announced today a new partnership to bring Freight Farms’ Greenery container farm setups to the campuses that Sodexo services throughout the US. The goal of the partnership is to bring fresh, traceable produce to college foodservice year-round that’s pesticide- and insecticide-free with low food miles. Sodexo is engaging the company as part of its Better Tomorrow Commitments, developed according to the UN Sustainable Development Goals.
Sodexo is one of the world’s largest multinational corporations serving 80 countries with nearly $17 billion in annual revenue, which means the partnership could go a long way towards demonstrating whether indoor ag systems can provide fresh produce at large-scale. The first Greenery system will be deployed at a college campus this Spring, according to McNamara.
As part of the deal, Sodexo’s campus clients will come under Freight Farms’ ‘farming-as-a-service’ program like any other Greenery user. Freight Farms provides turnkey farming software, training, monitoring, refillables, and support. The number of Greenery machines deployed to each campus will depend on the goal that the university has, which could involve providing as much produce as possible to its foodservice outlets. McNamara describes the units as being able to operate on a commercial scale and to scale up or down quickly depending on the ultimate need.
Invest with Impact. Click here.
More than local lettuce
In 2012, Freight Farms launched a farming system built inside a shipping container dubbed the Leafy Green Machine. Last year, it launched a new model, Greenery, in the same 320-square foot space but with 70% more growing space. It also packs new IoT-driven technology to improve yield, efficiency, and automation, according to the startup.
Today, it claims to have the largest network of connected farms in the world with customers in 25 countries and 44 US states that range from small business farmers to corporate, hospitality, retail, and education entities. So far, 35 educational and corporate campuses are using Freight Farms’ Greenery machine and technology to grow food onsight. The University of Georgia has already purchased two Greenery containers. A group called WhyNot Farm also made a purchase.
What Freight Farms is really trying to achieve is more than just growing lettuce in a shipping container, however. Last time we interviewed the outfit, the goal was to achieve a distributed food system that addresses many of the issues that the conventional produce industry has created: food waste, ugly produce being discarded, and a focus solely on yield maximization to the detriment of ecosystems.
“Schools are a good fit because of the value add that is placed on food and the variety and the quality of food served in cafeterias. There’s not just one customer that schools have to attract. They’re also selling to parents. They have to really be able to give comfort to mom and dad that the student has access to high-quality food and food programming,” McNamara explains.
Students are also hungry for this type of offering, as consumers at large search for ways to get closer to the roots of the food that they consume any way they can. At McNamara’s alma mater, Northeastern, for example, one of its educational programs includes a food co-op where students can work on real-world applications of local food systems.
The indoor ag space is seeing some renewed attention recently, with three of AFN’s top 10 best-read stories in 2019 focusing on the sector.
“I think what’s really exciting now versus just a few years ago is the recognition that this opportunity a lot of us have been talking about is, in fact, big and that there are various markets for us to go after,” McNamara says.
With a freshly inked Sodexo partnership under his belt, it’s hard to say he’s wrong.
Gardyn Aims To Make At-Home Vertical Farming Small, Simple, And Stylish
Thanks to disruptions in the food supply chain, panic-buying sprees, and the general uncertainty of the times, growing food at home seems like a pretty good idea of late
SEPTEMBER 28, 2020
Thanks to disruptions in the food supply chain, panic-buying sprees, and the general uncertainty of the times, growing food at home seems like a pretty good idea of late. Trouble is, many consumers don’t have the know-how to cultivate their own leafy greens and other produce in the backyard. Even those who do often lack adequate space.
A company called Gardyn is addressing both of those issues with an at-home vertical farming system that requires minimal input from the user and can easily fit inside a small apartment if need be. The idea, as Gardyn founder and CEO FX Rouxel explained to me over the phone last week, is to make growing food in one’s own home as simple and straightforward as possible. To do that, the company has built a farm that relies on AI to do much of the heavy lifting in terms of monitoring and maintaining an edible crop of food. Or as Rouxel said, “The system is managing everything for you.”
Gardyn’s system is made up of two parts: a compact vertical tower, which can grow as many as 30 plants, and an accompanying app powered by an AI assistant named “Kelby.” Users only have to order seeds and “plug” the seed pods into the vertical towers. The system automatically circulates water and nutrients to the plants, while Kelby monitors plant growth and sends reminders when it’s time to add water to the garden or harvest the plants.
Right now, available crops from Gardyn’s site include mostly leafy greens and herbs, some flowers, cherry tomatoes, and jalapeños. Customers can also use their own seeds if preferred.
The system uses what Rouxel calls “a hybrid of different hydroponic technologies,” including the deep water method and aeroponics. (The company brands its approach as “hybriponics.”) By themselves, these different methods have certain limitations in the at-home setting. Deep water, where plant roots are fully submerged in nutrient-enriched water, requires a lot of space. Aeroponics is a great setup for outdoors, but once indoors it requires lighting, which gets expensive very quickly. Gardyn pulled elements from both to create a system that takes up only two square feet of space and doesn’t require any extra hardware. “Within just two square feet, you can produce a lot of food,” says Rouxel, adding that Gardyn’s units have produced “over 25,000 pounds of produce” during the last few months.
That quest to grow a lot of leafy greens in a small amount of space is an area with plenty of competition these days. Farmshelf recently unveiled its first-ever farm for the home, and companies like Rise Gardens and Agrilution (the latter recently bought by Miele) also offer promising solutions for the consumer space.
And while historically, investment in vertical farming has mainly gone towards the industrial-scale indoor farms (think AeroFarms), at-home farms are fast becoming a lucrative area. Investors, Rouxel explained to me, see traditional agriculture as a risky business that’s less insurable because its success is in part dependent on the weather outside. With climate change triggering more extreme weather, investors will look more and more to alternative solutions in controlled-environment agriculture.
“I am absolutely convinced we are going to see in the coming two years a total disruption in the way we grow things,” he says. Chiefly, that will be growing the food in much closer proximity to consumers, whether through at-home systems like Gardyn’s, in-store farms at grocery retailers, rooftop gardens, and high-tech greenhouses. “In future we’re going to have a spectrum of solutions,” Rouxel noted.
Getting these vertical farms closer to consumers and in their own homes will require bringing the price of the machines down. At the moment, Gardyn’s system is roughly on par pricewise with other systems out there that can realistically feed a family of four: $799 for the base model all the way up to $1485 for the “Plus” model.
Rouxel is aware that the cost is still too high for many consumers. “We don’t want this to be only for well-off people,” he told me. “It’s important that we find ways that anyone can afford this.”
Many companies, including Gardyn, offer financing options on their farms now. And more investment dollars going into the space in the future could mean companies have the time and space to innovate on ways to make their system cheaper for the average consumer.
While pricing remains a question, one thing that’s certain is that at-home vertical farming is on the path to becoming a regular part of the kitchen, rather than just a trend. “What we want is to develop solutions that will quickly change the way people access food,” said Rouxel. “We won’t solve everything, that’s for sure, but we want to be part of the solution for how we shape food.”
Hydroponic System Promises Cost Savings For Low To Mid-Tech Vegetable Growers
Plantlogic is focused on designing solutions for substrate production that will increase the health of plants and enable growers to adequately fertigate their crops
Plantlogic is focused on designing solutions for substrate production that will increase the health of plants and enable growers to adequately fertigate their crops. With these goals in mind, Plantlogic presents its newest, innovative product for hydroponic production of vegetables. The "Kratos" is aimed at offering low to mid-tech vegetable growers substantial purchase cost savings, reducing labor costs, and improving root health.
Kratos channels all drainage water into a narrow gutter below the center of the spacer. The open space between the slab and the gutter provides aeration and prevents the roots from growing out of the slab and coming into contact with drainage water.
Advantages of using Kratos:
Better drainage: V-shape improves drainage from slab by reducing the saturated zone.
Easy to use: Quick and simple installation. Easy to wash and disinfect.
Stackable: Reduce transportation costs by increasing packing efficiency.
Clean: Narrow gutter keeps ground free of water by containing all drainage below the slab, avoiding the dirt buildup and algae formation common in wide gutters. No concern of fruit touching dirty, wide gutter.
Airflow and oxygenation: Keeps roots off the ground and out of the gutter, preventing contact with pathogens.
Cost effective: More economical than wide gutter.
Durable: UV stabilized plastic is inexpensive and durable.
Plantlogic is committed to reducing the negative impact that substrate production runoff can have on the environment. Substrate production can produce great quality and yields of vegetables, but the run-off of irrigation water can also cause harm to the natural environment. Their drainage collection systems addresses this problem by collecting 100% of drained fertigation.
For more information:
Plantlogic
sales@getplantlogic.com
www.getplantlogic.com
Publication date: Fri 28 Aug 2020
VIDEO: Geothermal Energy For Greenhouse Application
Mariska Dreschler with GreenTech did an interview with Marit Brommer, passionate about geothermal energy and the Executive Director of the International Geothermal Association
Mariska Dreschler with GreenTech did an interview with Marit Brommer, passionate about geothermal energy and the Executive Director of the International Geothermal Association. In the interview, they talked about:
Why is geothermal energy a logical source for greenhouses
The sustainability factors of sustainable energies such as geothermal usage
What are the goals and missions of the IGA
The misconceptions about geothermal energy
The consequences of energy transition from gas and oil to sustainable energies
What are the basic necessities to implement and apply geothermal energy?
Examples of best practices of geothermal energy in greenhouses
For more information:
GreenTech
www.greentech.nl
Publication date: Fri 25 Sep 2020