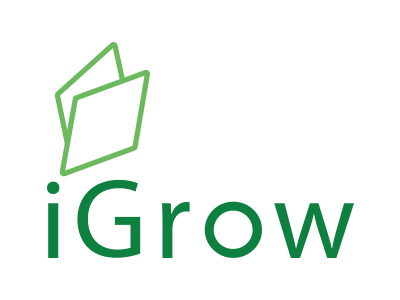
Welcome to iGrow News, Your Source for the World of Indoor Vertical Farming
New Downtown Restaurant to Grow its Own Produce at Indoor Urban Farm
New Downtown Restaurant to Grow its Own Produce at Indoor Urban Farm
Friday, October 13th 2017, 7:37 pm CDT | By WTOL Staff
New location for Balance Pan-Asian Grill (Source: WTOL)
TOLEDO, OH (WTOL)
Business continues to boom in downtown Toledo, especially when it comes to food.
Balance Pan-Asian Grille began construction on Friday on its new downtown Toledo location.
The restaurant will be at the corner of Summit and Jefferson.
It's not only a restaurant though.
They are also building an indoor 8,000 square foot urban farm that will grow seventy percent of the produce for their restaurants.
"This is location number four for the restaurant and our very first attempt at urban farming,” said co-founder Prakash Karamchandani.
The restaurant wanted to find ways to bring locally grown produce to their diners year-round.
"In the midwest, living somewhere like we live here with the inconsistency of the weather, we couldn't find a better idea to continue to grow local, fresh produce and be able to utilize it in our own restaurant,” said co-founder Hochan Jang.
Owners said they've loved working with the city to get the project going.
They are so excited that they're working hard to open the new restaurant before the new year.
https://balancegrille.com/ | eat@balancegrille.com
Largest Automated Farm to Open in Japan
GABRIELLE EASTER | @gab_produceplus
Tuesday 23rd May 2017, 08:19 Hong Kong
Largest Automated Farm to Open in Japan
Japanese group Spread has announced it’s opening the world’s largest automated vertical farm, Techno Farm Keihanna
Kyoto-based Spread has announced it will be opening the world’s largest automated vertical farm in Kizugawa, Japan.
Called Techno Farm Keihanna, the farm will produce 30,000 heads, or three tonnes, of lettuce each day once it’s fully operational by the beginning of 2018.
Techno Far Keihanna builds on Spread’s established indoor vertical farm, Kameoka Plant, which was built in 2007 and produces 21,000 heads, or two tonnes, of lettuce each day, all sold under the Vegetus brand.
At the new factory, the company will use automated cultivation to reduce labour costs by 50 per cent compared to the Kameoka Plant, and improve the recycling rate of water used for cultivation by 98 per cent. Using LED lighting developed by Spread itself, the company can reduces energy consumption by 30 per cent compared to existing LED lighting.
Spread aims to grow its share of the Japanese lettuce market to 10 per cent through expanding its production and establishing 20 facilities under a franchise model.
Kappa Farms to Open Loudoun Aquaponics Facility
Kappa Farms
Kappa Farms to Open Loudoun Aquaponics Facility
Urban farming company Kappa Farms will invest $865,000 and hire 21 people to open an aquaponics operation in Sterling.
According to the office of Governor Terry McAuliffe, the company will build a closed-loop nutrient cycle aquaponics facility which will produce certified organic baby lettuces and arugula using water and nutrients derived from fish waste. The company will produce more than $7 million worth Virginia-grown lettuces over the next three years, which it will then sell to customers and restaurants in the Washington, DC, metro area.
“It is an incredibly exciting time to be involved in agricultural technology,” stated Schuyler Milton, who co-founded Kappa Farms with Keith Born. “Environmental challenges, changes in economics, and advances in materials and technology have all come to a point at which supplying locally grown and organic produce is both more vital and more feasible than ever before. We’re very privileged to have been born and raised in Virginia, and we’re very happy to be able to help bring this new industry to Virginia, in no small part thanks to Governor McAuliffe and Loudoun County.”
The Virginia Department of Agriculture and Consumer Services worked with Loudoun County and Chrysalis Vineyards to land the business. McAuliffe approved a $40,000 grant from the Governor’s Agriculture and Forestry Industries Development Fund, which the Loudoun government will match.
“The success of Virginia’s agriculture industry is a testament to the diversity and quality of our products, as well as our outstanding reputation in the global economy,” McAuliffe stated. “… We will continue to support projects and products that diversify our agriculture industry, build the new Virginia economy and contribute to the Commonwealth’s reputation as the best place to do business around the world.”
Virginia is the nation’s third largest seafood producer and the largest on America’s Atlantic coast, according to the governor’s office. Virginia is ranked 10th nationally in aquaculture production. Virginia’s watermen harvest 50 commercially valuable species from 620,000 acres of water, including sea scallops, blue crabs, striped bass, summer flounder, croaker, spot, clams and oysters. The Virginia Institute of Marine Science reported the annual economic impact of Virginia’s seafood industry to be over half a billion dollars.
“Aquaculture production represents an opportunity for Virginia to capitalize on the need to feed a growing population with limited resources,” said Virginia Secretary of Agriculture and Forestry Basil Gooden. “We are lucky to have an innovative company like Kappa Farms as a member of the agriculture community in Virginia.”
“We’re proud to welcome Kappa’s expansion into Loudoun County,” said Loudoun Economic Development Executive Director Buddy Rizer. “Theirs is the type of unique, science-based innovation that sets Loudoun businesses apart.”
“I applaud Kappa Farms for their investment and expansion in Sterling,” said Sen. Jennifer Wexton (D-33). “Loudoun’s agricultural community will be elevated by Kappa’s innovative agricultural technology and I look forward to seeing their products in the homes and restaurants in the 33rd District and beyond.”
Future of the Prairie
FUTURE OF THE PRAIRIE
October 11, 2017 at 5:00 am | By DEVIN HEILMAN Staff Writer
LOREN BENOIT/Press From left, Coeur CEO Tom McNabb, Coeur Greens operations manager Kelly Lattin and Innovation Collective founder Nick Smoot pose for a photo in front of house at 1915 E. Mullan Ave in Coeur d’Alene. The house is a prototype for a future sustainable living community in Hayden.
A mixed-use sustainable village destined for Hayden is starting with a little old house in downtown Coeur d'Alene.
Coeur, a company that focuses on sustainable resources including power and food, recently purchased the house at 1915 E. Mullan Ave. to serve as a prototype for a sustainable living community and industrial campus in Hayden. Coeur purchased the 35 acres at the southeast corner of Hayden Avenue and Huetter Road in early 2016 and plans to start construction in the spring.
Coeur CEO Tom McNabb and Innovation Collective founder Nick Smoot, a partner in the project, are using the Mullan house as a demo site for the village.
"It's a simple model to see what we can do for starters," McNabb said Tuesday. "The word ‘sustainability,’ you never really know what it is, but we figure we’d try and figure it out."
Smoot said the community will be built on three core principles: outbound, sustainable and intellectual.
"Most people of this next generation want to live an outbound life in nature and having experiences in their community," Smoot said. "The idea of creating a whole village of people who have that mentality is something that's interesting as a housing development."
The "sustainable" principle is built upon dedication to low-cost, low-impact living where power sources such as wind and solar are maximized, gray water (mostly clean waste water from sinks, baths and kitchen appliances) is recycled, and native landscaping is used. Those involved in the project are researching and working on ways to expand even further into the sustainability aspect.
The third principle is "intellectual," meaning home owner associations and covenants, conditions and restrictions would encourage residents to read books, watch documentaries, help pay for educational guest speakers and otherwise maintain an intellectually stimulated community.
Smoot said he can imagine riding his bike into such a community, parking it at the community bike corral and walking to his house through a neighborhood where community fire pits generate conversation and serve as social gathering places. The houses are small (500 to 1,200 square feet), but provide enough space for their residents, and the community dining hall provides even more opportunities for people to meet and get to know each other.
"It makes me very happy," Smoot said. "That's the kind of place you want to live."
The solar-powered Coeur Technology Campus will be located just west of the village. It will house a solar farm to generate power for schools and public buildings, vertical farms to grow local produce, and a bottling plant to bottle local water at the source. It will also serve as a space where entrepreneurs and forward-thinkers can share ideas and put them into action.
"A lot of people don’t know it, but we have more sun hours per year than Florida,” McNabb said, “Solar, about five years ago, was 2 cents off because the rates for hydropower were cheap, but in the last five years the rates (for hydropower) are going up and the rates of hardware have gone down about 40 percent, so all of a sudden it makes sense.”
The 630-square-foot house on Mullan, built in 1930, would probably have been torn down if it had not been selected for this project. McNabb explained that the original structure will be kept as the inside is remodeled to be a studio-type dwelling that can be rented out on a short-term basis to give people an experience in sustainable living.
Tanks will be installed to recycle the gray water and help with temperature. The roof will be lined with solar panels, and energy-efficient appliances and products will be used, among other forward-thinking alterations that will boost the home's sustainability.
McNabb said a more precise estimate could be given near the house's completion date in the spring, but he believes the cost of giving the house a sustainable makeover will be somewhere around $50,000 or $60,000. About 20 people representing a wide variety of talent and expertise have already expressed interest in contributing to the project, he said.
The community is welcome to attend an open house from 11 a.m. to 1 p.m. Saturday to check it out prior to its sustainable makeover and exchange ideas with those leading the project.
Info: www.coeurllc.com
AeroFarms: The Most Interesting Dell IoT Example
AeroFarms: The Most Interesting Dell IoT Example
Rob Enderle | UNFILTERED OPINION | POSTED 13 OCT, 2017
I was at Dell’s big IoT coming out party, which had many working examples, but one really stood out for me. You see, I grew up spending my winters on a ranch and my summers working on a farm. And I quickly concluded that farming sucked. Getting up at an ungodly hour in the morning to fight bugs that had no sense of a decent hour to be awake, set sprinklers, spread pesticides that were known carcinogens, and fight flies for horse crap (I was perfectly happy to let them have it) in hot weather just wasn’t any fun. Oh, and my grandfather had a view that work shouldn’t be fun so if I found a creative way to enjoy the job, like having paint wars while painting the fence, I got punished. So, for me to look at a farming application and think it was cool takes a lot. But AeroFarms was cool.
Making Farming Not Suck
Farms don’t just suck from my perspective. They consume massive amounts of water; they were highlighted as the primary cause for the massive California drought. They are highlighted as massive polluters because the pesticides they use can contaminate ground water and spread beyond the fields being treated (and are often classified as high-level carcinogens). Driving this home, my uncle, who ran the farm I hated working so much, died because of this and the type of cancer he had basically consumed his body. Trust me, it wasn’t a pleasant way to die.
What AeroFarms does is apply IoT technology to farming. It is closer to hydroponics in that they move the fields inside and the result looks more like a factory than a farm. Using below 10 percent of the water, no pesticides, and having yields that, due to optimized environmental conditions and the lack of pests that farmers would die to enjoy, they also don’t use farmers, they use techs.
Now I didn’t like being a farmer, but I’m perfectly fine being a tech.
Rethinking Farming
The advantage of this is that you can place farming inside cities and far closer to the people who consume the produce. This reduces transport cost massively, reduces storage cost massively, reduces spoilage massively, and it also results in a far higher quality product. According to AeroFarms, the cost for producing the product goes down but, due to far higher consistency and the lack of pesticides, the quality and thus the potential price of the produce could go up.
This means increasing margins and reduced risk. Much of what kills a farm is risk. The ranch I lived on grew oranges. California used to lead in orange production, but a disease called Quick Decline wiped out virtually all the orange ranches in the state and now that market belongs to Florida. The poor ranchers either had to change their entire business model or go bankrupt. Many failed. But in a contained environment, you can better isolate and prevent this kind of thing and reduce most act-of-god type risks. Granted, major problems that take out cities like earthquakes and hurricanes would still be issues, but you can harden against these. You generally don’t need or want windows (to better control light), so your structures can be more resistant naturally, and there is at least a reasonable chance that, in a disaster, these things could be functioning lifelines, helping avoid localized starvation, which is now a concern in areas like Puerto Rico.
Labor
One other area where farming is a problem is that that conventional farms tend to employ a high number of illegal aliens. This makes them attractive havens for those who enter the country illegally and allows excessive levels of employee abuse because these employees can’t complain to the police.
As noted above, AeroFarms uses techs, not unskilled labor, and far less of them. Lending itself to robotics and automation, the model directly addresses this problem as well.
Wrapping Up: Making the IoT Work
AeroFarms likely highlights best the kind of potential for the IoT effort that Dell Technologies is trying to roll out. Farming has massive problems in terms of resource usage, pollution, labor and risk. By using current generation IoT technology, AeroFarms has massively addressed each of these areas and created a solution that is far better for the world of tomorrow, with increasing weather risks and higher uses of robotics. I’m kind of wondering how long before someone who is tech forward like Amazon builds this right into a grocery store.
And, from a personal perspective, this could make farming fun. My younger self would have loved to work for AeroFarms and I’m sure I wouldn’t miss the bugs, heat and horse poop.
Rob Enderle is President and Principal Analyst of the Enderle Group, a forward-looking emerging technology advisory firm. With over 30 years’ experience in emerging technologies, he has provided regional and global companies with guidance in how to better target customer needs; create new business opportunities; anticipate technology changes; select vendors and products; and present their products in the best possible light. Rob covers the technology industry broadly. Before founding the Enderle Group, Rob was the Senior Research Fellow for Forrester Research and the Giga Information Group, and held senior positions at IBM and ROLM. Follow Rob on Twitter @enderle, on Facebook and on Google+
Illumitex Launches Major Upgrade to PowerHarvest® Series
Illumitex Launches Major Upgrade to PowerHarvest® Series
Illumitex’s PowerHarvest 14 delivers more output at higher efficiencies to meet the needs of the most demanding growing applications.
PowerHarvest 14
We are delivering the best light recipes to produce quality plants with high-quality cost-effective solutions.
AUSTIN, TEXAS (PRWEB) OCTOBER 13, 2017
Illumitex, Inc. is proud to announce the release of the PowerHarvest 14. This LED horticulture lighting solution, ideal for large-scale greenhouse operations, will provide the controlled horticulture environment with 30% increased output, 30% increase efficiency and up to 2.2 µmol/J. The next generation in the popular series will give growers a powerful solution that will improve quality and yield.
The PowerHarvest 14 will be utilized in supplemental or soul-source lighting facilities where growers are looking to achieve a PPF as high as 1300 µmol/second. The light will be offered in various configurations to match the need of each customer. The fixture will be offered in the F3 spectrum, as well wattage of either 556 or 640 and accommodate low and high voltage. These options were carefully selected to meet the needs of the constantly evolving controlled environment horticulture market.
“PowerHarvest 14 takes our field proven horticulture lighting platform to new levels of efficiency and output giving growers approximately 30% more light,” says Jeff Bisberg, CEO & President. “We are delivering the best light recipes to produce quality plants with high-quality cost-effective solutions. It is inevitable that LED will replace traditional lighting solutions in all horticulture applications and our PH14 brings us one step closer to realizing that goal.”
Versions of the PowerHarvest will meet or exceed requirements for utility rebates offering an opportunity to partner with growers and make switching from the traditional lighting to the more efficient LED solution a reality.
The release of the PowerHarvest 14 ushers in a new era of design and innovation from Illumitex as they continue to transform LED lighting for greenhouses, urban farms, and other controlled environments.
About Illumitex, Inc:
Founded in 2005 in Austin, Texas, Illumitex works diligently to create industry-shifting achievements in horticultural lighting. Our team of horticulture scientist and engineers have radically transformed LED lighting that influence plant benefits including yield, taste, color and smell. Illumitex is enthusiastically committed to scientific research, cutting-edge design, and innovative engineering. We are dedicated to work with our customer to deliver world class horticulture solutions while pushing lighting into the digital age with automated tools and services. http://illumitex.com.
These Cold-Weather Container Farms Let Produce Grow In The Arctic
In the subarctic town of Churchill, Manitoba–unreachable by paved roads and best known for its population of polar bears–a head of romaine lettuce can cost as much as $8 without subsidies. Shipments of produce can take weeks from distant farms, and when vegetables arrive, it’s an event. But the town will soon have another option: a shipping container farm growing greens on site.
- 10.12.17
- Fast Company | WORLD CHANGING IDEAS
These Cold-Weather Container Farms Let Produce Grow In The Arctic
As traditional Inuit diets change, they’re being replaced with processed food because it’s so difficult to stock markets with fresh produce. Now, they can grow it themselves, even in sub-zero temperatures.
“The impetus for the whole project was the high cost of food and lack of opportunities for employment in Inuit communities.” [Photo: Vertical Harvest Hydroponics/The Growcer]
In the subarctic town of Churchill, Manitoba–unreachable by paved roads and best known for its population of polar bears–a head of romaine lettuce can cost as much as $8 without subsidies. Shipments of produce can take weeks from distant farms, and when vegetables arrive, it’s an event. But the town will soon have another option: a shipping container farm growing greens on site.
A 40-foot shipping container was repurposed into a hydroponic greenhouse in Spokane, Washington, then shipped to Montreal, where a cargo ship has taken it through the St. Lawrence River, around the coast of Newfoundland, and is now traveling through the Hudson Bay. When the delivery arrives on October 19, Churchill will be the seventh community in the Far North to begin using this type of farm, called the Arctic Growing System.
“If you’re in a community in Northern Canada where it already takes a week for produce to get to an urban center, and another week or two for it to fly to three different communities . . . everything that was fresh is no longer really edible.” [Photo: Vertical Harvest Hydroponics/The Growcer]
“The impetus for the whole project was the high cost of food and lack of opportunities for employment in Inuit communities,” says Corey Ellis, cofounder and CEO of The Growcer, the startup that makes the shipping container farms and works with the small communities that operate the farms.
The company was born out of a project called the Northern Innovation Hub, which aims to find solutions to local problems like food security, housing, and employment. Ellis and others worked with remote communities to brainstorm potential solutions, and landed on local food production as a way both to spur economic development and improve health.
Right now, many people in the area struggle to afford food. Even when grocery stores get subsidies from the Canadian government to offset high produce prices, the cost of shipping extremely long distances and the rates of spoilage on the journey means fruits and vegetables are still quite expensive. That cost means that consumers are more likely to pick unhealthy packaged foods, which have pushed up the rate of diabetes.
And the fresh options that do make it often aren’t very appealing. “If you’re in a community in Northern Canada where it already takes a week for produce to get to an urban center, and another week or two for it to fly to three different communities and kind of bunny hop over to yours, everything that was fresh is no longer really edible,” Ellis says.
The container farms can also create new jobs. “I think they saw an opportunity: Hey, why are we spending money down south to buy food when we could keep it in our community and pay someone local to harvest it?” he says.
“Why are we spending money down south to buy food when we could keep it in our community and pay someone local to harvest it?” [Photo: Vertical Harvest Hydroponics/The Growcer]
Shipping container farms aren’t new, but the startup realized that current options–typically developed for cities in milder climates–wouldn’t work in the region. The farm they designed is insulated enough to withstand days at 60 degrees below zero and blizzards. By splurging on more expensive parts than a typical indoor farm kit, such as the highest-quality lights, the Arctic Growing System can actually be more productive than a similar farm in Boston or New York.
“We ended up with a system that has probably twice the cost but very similar ROI to a unit like Freight Farms, because we were able to basically triple the yields that a Freight Farm unit would get,” says Ellis. (Beyond using more expensive parts, the yield was improved by a unique advantage of farming in the Arctic: The cold, dry air helps make it easier to expel humidity from the greenhouse, which helps plants grow faster.)
“Somebody has to make money for this to grow sustainably, so that’s at the root of everything we do.” [Photo: Vertical Harvest Hydroponics/The Growcer]
The system arrives with everything needed to start the farm, including 14 months’ worth of growing material, seeds, cleaning solution, and multiple spare parts for every major part in the system. The community plugs it in, connects it to water, and it’s ready. The farm managers don’t need prior experience farming; the startup works very closely with customers, helping develop custom business models and monitoring the greenhouses by satellite to help managers troubleshoot any issues. “Somebody has to make money for this to grow sustainably, so that’s at the root of everything we do,” he says.
Six communities in Alaska have started using the farms, some for as long as 18 months, and all have broken even. Even with the relatively high energy bills required to keep the farms warm, the system is far less expensive than shipping produce thousands of kilometers. In one community, for example, growing the produce is roughly 25% of its retail cost. The growers and the grocery store can add margins and customers still pay 30% less than they would have otherwise.
Notably, produce was not traditionally part of the diet of Inuit or other indigenous people. But, then again, neither was soda, candy, or other junk food that has become common. As diets evolve, Ellis says that there’s a growing interest in fresh produce. The startup is also working to develop plans for ready-made meals that combine traditional ingredients with produce, which greenhouse owners will be able to offer as another product.
“What we’re doing is basically creating an environment where the healthy alternative is just as convenient and affordable as the unhealthy one,” he says.
ABOUT THE AUTHOR
Adele Peters is a staff writer at Fast Company who focuses on solutions to some of the world's largest problems, from climate change to homelessness. Previously, she worked with GOOD, BioLite, and the Sustainable Products and Solutions program at UC Berkeley.
Major Green Technology Breakthrough! Metropolis Farms Unveils A New Device That Reduces Electric Cost by 60% and Disrupts The Entire Industry
On 10/16, President of Metropolis Farms Jack Griffin unveiled and demonstrated this new ballast technology at Indoor Ag Con alongside Pennsylvania's Secretary of Agriculture, Russel C. Redding. We are working on plans to manufacture these ballasts in Philadelphia and estimate they will be available in 2018.
Major Green Technology Breakthrough! Metropolis Farms Unveils A New Device That Reduces Electric Cost by 60% and Disrupts The Entire Industry
October 17, 2017
Do you know what a lighting ballast is? Chances are, if you're not involved in a trade that deals with lighting, you probably don't.
You're probably reading this because you saw a headline about a massively disruptive technology that reduces electric costs by 60%. This might be puzzling to some, since most folks don't even know about ballasts in the first place.
Well, we're here to tell you that lighting ballasts are one of the most important technological devices that very few people know about. And we have developed a ballast that can make a significant impact on the amount of energy the world uses.
There are two paths to travel to get the world to a more sustainable future:
1. Increase the percentage of power generated by renewable energy sources
and/or
2. Decrease the amount of energy consumed
We are attacking this problem on the consumption side of the equation. This new technology dramatically decreases the amount of energy that is needed to power most lights. (By the way, we are attacking this problem on the production side too, check out the world's first solar powered indoor farm we're building in South Philadelphia.)
But before we dive into this new breakthrough, since most folks don't know what a ballast is, let's start with the basics.
In the simplest of terms, a ballast's responsibility is to ensure lights work properly and don't burn out immediately.
In more defined terms, per the National Lighting Product Information Program, a "ballast regulates the current to lamps and provides sufficient voltage to start the lamps. Without a ballast to limit its current, a lamp connected directly to a high voltage power source would rapidly and uncontrollably increase its current draw. Within a second the lamp would overheat and burn out. During lamp starting, the ballast must briefly supply high voltage to establish an arc between the two lamp electrodes. Once the arc is established, the ballast quickly reduces the voltage and regulates the electric current to produce a steady light output."
Ballasts are connected to all fluorescent, compact fluorescent, HID, and many commercial LED lights. Regarding LEDs, ballasts are called drivers, but they are effectively the same thing. So whenever you're out and about, know that almost all of the lights you see in commercial or public spaces are connected to a ballast.
Lighting accounts for 53% of electric usage in U.S. retail buildings. And ballasts are the bridge that enables that power consumption.
In 2016, the U.S. Energy Information Administration estimates about 279 billion kilowatthours (kWh) of electricity were used for lighting by the residential sector and commercial sector in the United States. That's 279 million megawatts and does not account for public buildings or streetlamps.
So lighting is responsible for a massive amount of energy that is consumed.
Beyond the statistics that are directly related to powering the lights, more energy is used by HVAC systems to combat the excessive BTUs (heat) that lighting systems generate. This is a particularly sensitive issue when the temperature needs to be highly regulated, like in an indoor vertical farm.
Currently in our vertical farms, we are using 315W ceramic metal halide bulbs and we have 1 ballast for 1 bulb. For every bulb in our hydroponic farms, there's a ballast regulating the energy necessary for the light to work properly.
That's typical for most big lighting systems. For example, in another sector, each streetlamp you see illuminated at night is connected to a ballast.
All that said, you're now probably wondering: what's this development that will change the world?
Well, it's a new ballast. A more efficient ballast. One that brings unprecedented breakthroughs in ballast technology.
Here are two facts that will show why this is not hyperbole:
1) This new ballast will reduce total energy consumption in our indoor farms by 60%.
2) We will use 1 ballast to power 8 bulbs.
These results are being verified by a major university's lighting laboratory and certified by a CPA firm.
If you don't understand the game-changing ramifications of those statements, please keep reading!
The most common argument against indoor farming or vertical farming is that it requires too much energy to produce diverse crops. And in light of that argument (pun intended), we've already developed vertical farming systems that can grow diverse crops while still using less energy than other indoor farms that only grow leafy greens, and we have shown that these systems can produce profitable results for farmers.
Now with this new ballast, the energy argument can be totally put to bed. The equation has completely changed and by making these ballasts available to everyone, all indoor vertical farms will be able to reduce their energy consumption dramatically. All businesses and cities will be able to reduce their energy consumption dramatically.
We recently wrote a post on the topic of legal cannabis and how it's going to change the world. We said that due to the technologies being researched and developed to grow cannabis better, there will be emerging technologies that are backwards compatible and enable us to grow foodbetter.
But this technology takes it a step further. By focusing efforts on how to grow anything in a more energy efficient way, a technology was discovered that will enable every industry to operate using less energy.
With our old ballasts, the bulbs in our hydroponic systems required 3 amps and 315W to power them. With this new ballast, they only need 1 amp and 110W. That is far less energy used by the most efficient LED lights, and we still produce full spectrum light so our plants thrive.
This was me after being told how these ballasts work:
Below are a few other features of this new ballast breakthrough that changes the game:
There's a massive heat reduction at the bulb from 400 degrees to 150 degrees, which significantly reduces energy cooling loads.
Remember the Superbowl when the power went out and the lights couldn't be turned on for 34 minutes? That happened because the ballasts and bulbs needed time to cool down and recalibrate the energy flowing into the bulbs. With our new ballast, those lights could have been turned on right away.
Before, a ballast could only power a certain kind of light. For example, one type of ballast could power fluorescents, another could power HIDs, while another powers LEDs. This new ballast can power any kind of bulb, simultaneously.
As mentioned earlier, this one ballast can power multiple high usage lights.
And as nature goes, there are indirect consequences from a technological advancement. It just so happens that in this case, we are extremely excited about one consequence in particular.
Since 1 ballast will effectively replace 8, the economics work in such a way that we will be manufacturing these ballasts in the United States.
We are already working on plans to build a Philadelphia-based manufacturing facility that will provide a significant amount of living-wagejobs to local Philadelphians.
Beyond the manufacturing jobs, there will be a significant amount of work for electricians everywhere as we envision this new technology becoming the norm. Building owners will be able to retrofit their existing light systems with these new ballasts and immediately decrease the amount of energy they use.
To review, this technology can help decrease electric usage by 60%. Considering the 279 billion kWh used for just lighting in the residential and commercial sectors, and that the average residential price per kWh is 12.99 cents, saving over 167 billion kWh is the same as saving over $21.7 billion. Indoor farming for cannabis alone accounts for 1% of the entire country's energy usage, at $6 billion annually, and that number will continue to climb as more states legalize cannabis.
If these ballasts are installed everywhere, think of what $22+ billion could be spent on!
On 10/16, President of Metropolis Farms Jack Griffin unveiled and demonstrated this new ballast technology at Indoor Ag Con alongside Pennsylvania's Secretary of Agriculture, Russel C. Redding. We are working on plans to manufacture these ballasts in Philadelphia and estimate they will be available in 2018. From there, we believe this new ballast will become the new standard not only in indoor vertical farming, but in all commercial lighting. This will have an immense impact on the amount of energy that is used for lighting by decreasing the energy consumed immediately upon installation. This will help the world transition to a more sustainable future. And this will create living-wage jobs in the U.S.
We are incredibly excited about this new breakthrough and hope that you are on board as well. The times they are a changing and indoor agriculture is here to stay, here to create positive change, and here to revamp the broken food system. Join us for the journey.
Let's get lit.
For more information on Metropolis Farms and to see where we plant our roots, read about us here.
AeroFarms - Job Offer
AeroFarms - Job Offer
On behalf of AeroFarms Green Career Consult is looking for a:
Commercial Head Grower
Vertically Controlled Environment Agriculture
AeroFarms is a change-the-world vertical farming company revolutionizing agriculture in the heart of Newark, NJ; just 8 short miles from New York City. AeroFarms mission is to transform agriculture by building and operating environmentally responsible farms throughout the world to enable local production at scale and nourish our communities with safe, nutritious, and delicious food. We use aeroponics to mist the roots of the greens with nutrients, water, and oxygen. AeroFarms’ aeroponic system is a closed loop system, using 95% less water than field farming and 40% less than hydroponics. Our engineered lighting allows tight control of size, shape, texture, color, flavor, and nutrition with razor-sharp precision and increased productivity. AeroFarms can take the exact same seed from the field and grow it in half the time as a traditional field farmer, leading to 390 times more productivity per square foot than a commercial field farm.
The past 12 months have been an exciting time for us. Our team has doubled during this period and we now need a special individual – an experienced and talented problem solver with two green thumbs to lead commercial growing operations in our new, state-of-the-art facility.
Your role:
You will be the onsite growing expert called upon for training, problem solving, and plant health monitoring, and will be responsible for yields and quality in collaboration with the Operations and R&D team. In this role, you will help provide leadership for the facility by working with cross-functional teams to ensure that long-range goals, strategies, plans, and policies are followed. You should be an experienced leader with a strong background in the growing of high quality produce. The ideal candidate will be able to demonstrate experience implementing new processes and facility start-up. You will be an energetic, forward-thinking and creative individual with high standards and good judgment. Our organization is fast-paced: we value individuals who can lead by example and keep focus in a team-centered environment.
Your tasks & responsibilities:
- Manage growing in a large-scale, commercial production facility.
- Ensure product quality, yields, sales volumes and deliveries are achieved.
- Oversee cleanliness, sanitation and organization of all equipment present within the facility.
- Implement and oversee water, media and nutrient solution management, sampling and testing procedures.
- Continue to develop an extensive knowledge base of successful Integrated Pest Management (IPM) strategies.
- Quantify and qualify data regularly, while following company policies and procedures.
- Lead by example and assist with seeding, scouting, irrigation, pest control, plant health, harvesting, etc.
- Contribute and improve upon already-existing operations and processes to improve work-flow, efficiency and provide constructive feedback and recommendations.
- Operate heavy and light horticultural equipment and machinery.
- Facility maintenance and trouble-shooting as necessary.
- Develop methods for reducing costs while optimizing production.
- Comply with all HR policies, including confidentiality and non-disclosure agreements.
- Communicate effectively with supervisors, contractors, and employees.
- Contribute to a fun, team-oriented and challenging work environment in an innovative and pioneering atmosphere.
- Other duties as assigned.
Your profile:
- Minimum five years of experience in a commercial greenhouse with a demonstrated history of success with progressive team management. Experience in hydroponic and aeroponic growing would be considered a plus.
- A four-year degree in Horticulture (BSc.) or closely related discipline; Masters preferred.
- Knowledge of large-scale commercial plant cultivation, including nutrient requirements and delivery systems, plant health, growing mediums, light requirements, temperature and humidity control, air flow, pH, EC and IPM etc.
- Knowledge of plant diseases, insects and fungi, as well as plant treatment options.
- Ability to perform routine equipment maintenance, management and minor repairs.
- Knowledge and experience with Horticulture automation and associated software with the ability to learn new technologies.
- The ability to use data to recommend and implement process improvements that enhance efficiency, yield, and quality.
- A commitment to compliance with Food Safety, HACCP, and Quality Control procedures.
- Experience developing and managing budgets.
- Ability to plan ahead, trouble-shoot, anticipate and solve problems and manage multiple tasks at a time.
- Ability to perform manual labor tasks required for the proper management of a large-scale grow greenhouse.
- Strong interpersonal skills and ability to lead and hold direct and non-direct personnel accountable for meeting daily, weekly and monthly goals.
- An eye for improvement: you will continuously work to improve operating efficiencies, increase learning and develop new skills.
- Leadership skills: you will recruit, train, mentor and motivate the farming team.
- Fluent in spoken and written English
- You are presently located, or willing to relocate to New York, USA
AeroFarms offers:
- An incredible ‘change-the-world’ company with the eyes of the world focused on our success.
- A team of motivated, intellectually curious individuals to support you.
- The backing of some seriously impressive firms including Goldman Sachs, Prudential and other leading venture funds.
- Be eligible to work in USA (Newark), AeroFarms will support you in this matter (working permit, etc.)
Contact: johan@greencareerconsult.nl
Johan Grootscholten (left) and Evert Verboom (right)
Indoor Farms of America Expands Key Corporate Staff
Indoor Farms of America Expands Key Corporate Staff
NEWS PROVIDED BY: Indoor Farms of America
LAS VEGAS, Oct. 18, 2017 /PRNewswire/ -- Indoor Farms of America is pleased to announce that it has recently filled several key roles at the company as the company client base expands into specific areas of need which its unique equipment can address.
Company CEO David Martin stated, "As 2017 has progressed, it was clear with the level of potential farm owners and operators we are working with that we needed to take our internal operations to a next level, and we are doing that by bringing on board some very solid folks."
Chef Georg Paulussen Director of Culinary Operations for Indoor Farms of America
Jake Arterbury Crop Scientest at Indoor Farms of America
Martin continued, "We are really focused on continued research into how we can push our equipment to grow plants to unlock the highest nutritional value possible, with the most purity. That, coupled with working on adjusting flavor profiles in crops we can grow, and continuing to increase the variety of crops we can grow at commercial scale, such as proteins, is where our interests are focused."
As such, the company has hired two key people: Jake Arterbury, who will work in the role of Crop Scientist and Staff Biologist. "Jake will work on all areas of testing crops grown in our patented aeroponic system, and we are delighted to have him on board. Jake is a graduate of Baylor University with a strong emphasis on field research and plant physiology, and he is a great addition to our team."
In addition, the company has hired a world class Five Star Executive Chef in Georg Paulussen, for the position of Global Director of Culinary Operations.
"Some folks wonder why would an indoor farming company need an Executive Chef? Well, when I met Georg, and I realized his passion for nutrition and he told me his vision for feeding people around the world healthier food which they can have immediate access to, I knew he was the perfect fit for Indoor Farms of America," stated Martin.
"Georg has worked literally around the globe for over 35 years as either the Executive Chef, or as the Director of Food and Beverage, for the leading five star resort companies of the world, the very best. His desire to be the best in his field took him to places where he witnessed countless people that are not nourished properly in day to day living."
Chef Georg Paulussen states it this way, "When I met with Dave initially, I thought, wow, this equipment is pretty cool stuff, as it grows so many plant varieties so beautifully, with such great taste. But when we connected on the level of nutrition and education, and how Indoor Farms of America has as a broader mission to reach people around the world who need it most, I knew this was a place I could have a positive impact and help the company achieve its goals."
"My working environments have always provided me with such passion, my work is my love as a chef, but now I want to focus on nutritional aspects for helping the most people, and this company has the correct plan for that," added Mr. Paulussen.
CEO Martin adds, "Both Jake and Georg will work on special projects alongside our Corporate Farm Manager, Anthony Randolph. Our initial sessions together have been incredible, and we are excited to have them on our team."
Chef Georg will also work directly with chefs and major hotels from around the world to educate them on how they can have an abundant and cost effective supply of fresh-harvested vegetables every day for their needs in restaurants anywhere they are. On the nutrition side, the focus is how hospitals and governments can bring immediate access to high quality foods, such as for patients in various levels of recovery.
Indoor Farms of America President Ron Evans sees it changing the landscape for access to fresh foods: "We have watched several companies make claims that are simply funny, in this growing area of indoor agriculture. One thing we know, if you are going to grow crops indoors, you simply must do it in far higher quantity to make it a success financially. If a growing system at the end of the day will not produce enough product to ensure it can be a financial model that will sustain, then it is a waste of time. That was our original vision, and now we can take our game even further beyond anyone in the industry with these new folks on our team."
Chef Georg will be available this week at the PMA Fresh Summit in New Orleans. "Stop by our booth for a visit if you are at the show, and let's talk fresh, and let's talk nutrition!" states Martin
Indoor Farms of America has a showroom with demonstration farms operating in Las Vegas, Nevada and in multiple locations in Canada, and in South Africa, where their patented vertical aeroponic equipment is on display.
CONTACT:
David W. Martin, CEO 181249@email4pr.com IndoorFarmsAmerica.com
4000 W. Ali Baba Lane, Ste. F Las Vegas, NV 89118
(702) 664-1236 or (702) 606-2691
SOURCE Indoor Farms of America
Also from this source
AUG 21, 2017, 10:56 ETIndoor Farms of America Receives Investment From Major U.S. Ag...
JUL 25, 2017, 12:40 ETIndoor Farms of America Bridges the Gap with Traditional U.S....
Start-up Furthers The Cause of Urban Farming From a Shipping Container
Start-up Furthers The Cause of Urban Farming From a Shipping Container
by Christina Anthony
Thursday, October 12th 2017
GRAND RAPIDS, Mich. (NEWSCHANNEL 3)
A farm on wheels is growing crops from a Grand Rapids parking lot.
Meteorologist Christina Anthony reports on a start-up company furthering the cause of urban farming.
When white-collar technology meets blue-collar labor it gives birth to the very interesting Green Collar Farms, where plants can grow without the help of soil or natural sunlight, and where size truly doesn't matter.
Brian Harris, Former President and CEO of H&H Metal Source, spent twenty years employing science against the elements of steel.
Now, he's using his scientific background to harvest crops for his new company, Green Collar Farms, all from the inside of a shipping container.
Harris said, "It's 350 square foot inside, but because we're growing hydroponically without soil in a vertical form factor, we're able to yield about an acre in a half to two acres of crop every seven weeks, 365 days a year."
By growing crops in a controlled environment, Harris can weed Mother Nature out of the equation.
He can adjust the temperature, humidity, lights, and carbon dioxide levels manually from within the container, or with an application on his iPhone.
Harris can even feed crops nutrients through a computer system wired to vertically stacked columns of greens.
He said, "The food all comes to them. Their root ball is about 10 percent the size of a normal root ball. So they taste really, really good."
Green Collar crops, like lettuce, kale, and arugula, are harvested alive with the tiny root attached, and distributed within 24 hours. No matter the season, which means the leafy greens have a longer shelf life than those trans-plants.
Harris said, "This container farm is simply the first expression of what indoor agriculture can be."
Harris's mission for Green Collar Farms runs deeper than his scientific roots.
He said, “Once we get down the road another twelve months or so, we will have an idea about how to bring in the whole 10,000 square foot facility in the urban core that provides stem education opportunities, employment, health, and wellness benefits, jobs. So that's the journey."
Harris hopes his container farm will grow on Grand Rapids, and kids interested in science.
If you want to learn more about his blossoming business head to http://www.greencollarfoods.com/
Your Next Head of Lettuce, Grown By A Robot
Your Next Head of Lettuce, Grown By A Robot
You could drive past and never see the only farm in San Carlos, California. The tiny city of 30,000 that sits between San Francisco and Silicon Valley has all the charms of suburbia—sprawling office parks and single-story homes—but doesn’t seem a likely suspect for agriculture.
The farm, run by startup Iron Ox, is nestled between three stonemasons and a plumber in a nondescript office park building; there’s no greenhouse, no rows of freshly-tilled soil, or tractor parked outside. Only peeking in the large bay door reveals the building’s tenants: a few hundred plants and two brightly-colored robot farmers.
Iron Ox looks a lot like a tech company. One of its co-founder is an ex-Google engineer and it raised $1.5 million in pre-seed venture capital from Y Combinator, Pathbreaker, and Cherubic Ventures in April 2016. Instead of fake food, or plant-based meat meals, or even a food delivery service tethered to an app, Iron Ox is reinventing farming, raising real, not faux, food. Think hydroponically raised lettuce and basil, like what you’d get at an ordinary farmers market.
Iron Ox plans to build a network of autonomous, robot-run greenhouses near major US cities, complete with a fleet of trucks to ensure same-day delivery. Traditional outdoor farms don’t mesh with suburban sprawl, but the planned square-acre greenhouses have a small footprint that can easily fit into dense urban or suburban areas. The robots plant, raise, and harvest the crops.
Iron Ox founders Jon Binney, left, and Brandon Alexander. (Iron Ox)
Pod lettuce
Co-founder and CEO Brandon Alexander, who worked on Google’s Project Wing, figuring out how to make multiple robots work together, says it takes just three or four months to set up one of its farms. Plants take six weeks to mature. One of these modular, square-acre farms could provide the same yearly yield as 30 acres of traditional farmland, Alexander says.
“We want to have the most efficient farm out there,” says Alexander. “In some ways this is just the natural evolution of [farming].” Growing up, Alexander spent summers working on his grandfather’s peanut, potato, and cotton farm that straddles Texas and Oklahoma. He’s seen his grandfather adopt self-guided tractors and other new technologies, giving the ability to scale the family farm from 40 to 5,000 acres in one generation.
While raising crops has evolved from the time of small family farms, it’s still inefficient, Alexander says. Vegetables waste a large portion of their shelf lives traveling 2000 miles to get from farm to store. In addition, the pool of labor for existing centralized farms is aging and diminishing. The average US farmer is 55 years old, and the average crop worker is 33. “There’s just not enough labor to go around,” Alexander says.
Iron Ox isn’t the only company trying to revolutionize food production. Plenty, another Bay area startup, recently received $200 million from the Softbank Vision fund with a similar mission of distributed farms near metropolitan areas. Plenty’s buzzword isn’t automation, but vertical farming: growing crops up walls to save space. AeroFarmswants to disrupt hydroponics with nutrient-filled mist. Freight Farmswill grow crops in shipping containers.
The robots
Iron Ox plans to use three robots powered by artificial intelligence to work each square-acre of greenhouse. Two robots, without official names but referred to as transporters, will lift and ferry trays of plants over to the third robot, a robotic arm. The robotic arm will plant seeds, cycle juvenile plants into larger growing plots, image the plants to check for disease, and harvest the crop. Iron Ox plans to grow leafy greens like the lettuce and basil varieties it is testing now. Large-field crops like corn aren’t on the roadmap.
Iron Ox is using a hydroponic system called deep water culture; the plants, seated in plastic cones, float on a raft in a tray of water, their roots submerged in nutrient-rich water.
These trays are the key to Iron Ox’s indoor farm; while many deep water culture systems are built around large, stationary pools of water, these trays allow the plants to be moved to and from the robotic arm. The company developing the three components—robotic arm movement, transporter robot, and automated hydroponic system—separately. Humans now do the work slated for the robots, but the pre-robot farming provides a valuable runway of data for Iron Ox about optimal growing conditions.
Half a dozen data points are collected from each water tray per second, plus air temperature and quality, ambient light, humidity. The brains of the system are in the robotic arm. If it knows certain plants need more space, the transporter can be summoned to collect them for transplanting. If it’s time for harvest, the trays come to the arm.
The arm, which stands between two trays, moves with serpentine ease only occasionally interrupted by a mechanical lurch. As I watch, it’s controlled by CTO Jon Binney, but can be set to autonomously shuffle plants around from tray to tray. The goal is to only have one robot arm per acre of greenhouse, able to switch out its end effector, or hand, for specialized tools based on the task. Universal Robots is the arm’s manufacturer, but it runs custom code for motion planning. The stereoscopic cameras used to image the produce are installed and integrated by Iron Ox, and the end effectors used to inject and transplant are built custom-built by the company as well.
The transporter’s job is to hulk over a tray of plants, tuck the tray into its belly, and carefully transport it to a space next to the arm. It glides around the warehouse with a precise, mechanical grace, seemingly able to drift in any direction on its Mecanum wheels. These specialized wheels mean the trays can be just inches apart on the entirety of the greenhouse floor, since the transporter doesn’t need space to turn.
The process
The plants start as seeds, which are injected by the robotic arm into small, foam-like cubes seated in a plastic cone. The plastic cone protects the base of the plant from the robotic arm’s grippers, which giving each plant a standardized place to grip the plant while moving it around.
When the seeds have sprouted and grown for about two weeks, they are brought to the arm by the transporter. The robotic arm then picks up the plants and transplants them to a tray with more room between each plant. Each tray is outfitted with augmented reality tags (that allow the arm to recognize which tray it’s working with, and the bounds of where it can and can’t put plants.)
Two weeks later, the transplant process occurs again, and then again two weeks after that. Each time a plant is moved, two cameras on the arm build a 3D model of it, which is analyzed to check for disease and to ensure it’s growing normally. After the plant is fully grown, the arm pulls it—roots and all—from its plastic cone, and places it in a plastic clamshell container to be shipped.
The company has yet to launch its first fully-functioning greenhouse, and it currently donates its hydroponically-grown produce at a local San Carlos food bank in addition to supplying the company salad bar. IronOx wants to build the first greenhouse by the end of 2017, sell to local chefs in the Bay Area, and then scale to grocery stores in early 2018.
Masayoshi Son’s Grand Plan for SoftBank’s $100 Billion Vision Fund
Masayoshi Son’s Grand Plan for SoftBank’s $100 Billion Vision Fund
By KATIE BENNER | OCT. 10, 2017
Eric Gundersen, chief executive of Mapbox, met in July with Masayoshi Son, who led a $164 million investment in Mapbox that was announced on Tuesday. CreditJason Henry for The New York Times
SAN FRANCISCO — When Eric Gundersen, the chief executive of a mapping start-up called Mapbox, met Masayoshi Son, the head of the Japanese conglomerate SoftBank, in late July, he expected to have to sell Mr. Son on what made Mapbox important.
Son recently told Matt Barnard, the chief executive of Plenty, that computers were ushering in a revolution in agriculture not seen since the invention of the plow.
But Mr. Son, 60, did not need to be convinced that Mapbox’s technology — which powers Lyft drivers and companies like Snap and Mastercard — had value. After a whirlwind courtship, Mr. Son’s nearly $100 billion Vision Fund, which SoftBank unveiled last October with money from Saudi Arabia and others, led a $164 million investment in Mapbox that was announced on Tuesday.
In the process, Mr. Son also explained his grand plan for deploying the Vision Fund to Mr. Gundersen. The Japanese billionaire said he believed robots would inexorably change the work force and machines would become more intelligent than people, an event referred to as the “Singularity.” As a result, Mr. Son told Mr. Gundersen, he is on a mission to own pieces of all the companies that may underpin the global shifts brought on by artificial intelligence to transportation, food, work, medicine and finance.
“For Masa, his vision is not just about predictions like the Singularity, which has gotten a lot of hype,” Mr. Gundersen said. “He understands that we’ll need a massive amount of data to get us to a future that’s more dependent on machines and robotics.”
RELATED COVERAGE
SoftBank and Fund to Invest $4.4 Billion in WeWorkAUG. 24, 2017
SoftBank’s $100 Billion Investment Fund Starts to Take Shape JAN. 10, 2017
SoftBank and Saudi Arabia Partner to Form Giant Investment Fund OCT. 13, 2016
What Mr. Son laid out for Mr. Gundersen helps explain why SoftBank and its Vision Fund have invested billions of dollars in a seemingly random sample of more than two dozen companies since the fund was announced. The investments span robotics software start-ups like Brain Corporationand the indoor farming business Plenty, as well as more prominent companies like the business software maker Slack. The deals have run the gamut from smaller investments in start-ups to larger deals with public companies.
Mr. Son is deploying SoftBank’s nearly $100 billion Vision Fund by investing in a network of companies.CreditAlessandro Di Ciommo/NurPhoto, via Getty Images
Yet the companies all have something in common: They are involved in collecting enormous amounts of data, which are crucial to creating the brains for the machines that, in the future, will do more of our jobs and creating tools that allow people to better coexist.
Most recently, SoftBank has been involved in a plan to buy nearly a fifth of the existing stock of Uber, the world’s biggest ride-hailing company and one that has changed the transportation industry. SoftBank is aiming to accumulate Uber’s stock through a tender offer that could value the company at a discount to its current valuation of $68.5 billion, according to people briefed on the negotiations, who spoke on the condition of anonymity because the details were confidential. The tender offer could still fall apart, one of the people said.
If it ends up being completed, Mr. Son would own significant chunks of ride-hailing companies globally because SoftBank already owns stakes in Uber’s rivals like Didi Chuxing in China and Ola in India. Altogether, SoftBank would have a network of companies that gather valuable logistics data and operate large, connected fleets that could work well with self-driving car technology.
“Location data is central and mission critical to the development of the world’s most exciting technologies,” Rajeev Misra, who helps oversee SoftBank’s Vision Fund, said about Mapbox in a statement on Tuesday. He added that the investment was part of SoftBank’s plan to put money into “the foundational infrastructure for the next stage of the Information Revolution.”
SoftBank declined to comment further for this article.
For more than three decades, Mr. Son has consistently made over SoftBank with acquisitions and investments to keep it on the cutting edge. The company began in 1981 as a PC software distributor in Japan and expanded to the United States in 1994 with the acquisition of the PC trade show operator Comdex.
Mr. Son later became the largest shareholder of Yahoo, started Yahoo Japan and, in the last decade, invested in broadband and telecommunications companies — SoftBank agreed to buy the majority of Sprint for $21.6 billion in 2012 — anticipating the need for high-speed connectivity. He has also invested in e-commerce companies, including the Alibaba Group of China and Gilt Groupe, as well as video game businesses like Supercell and media like HuffPost and BuzzFeed.
A Mapbox office in San Francisco. The company makes mapping technology that powers fleets of Lyft drivers and companies like Snap.CreditJason Henry for The New York Times
In a speech last month in New York, Mr. Son declared that in 30 years, there would be as many sentient robots on Earth as humans and that those robots, which he called metal collar workers, would fundamentally change the labor market.
“Every industry that mankind ever defined and created, even agriculture, will be redefined,” Mr. Son said. “Because the tools that we created were inferior to mankind’s brain in the past. Now, the tools have become smarter than mankind ourselves.”
Mr. Son is having many of the same conversations with entrepreneurs these days as he looks to spread investments from the Vision Fund. Many entrepreneurs said Mr. Son’s conversations jumped from philosophical discussions about technology’s impact on humanity to the minutiae of a technical problem.
Mr. Son recently told Matt Barnard, the chief executive of Plenty, that computers were ushering in a revolution in agriculture not seen since the invention of the plow. Mr. Son led a $200 million investment in Plenty in July, part of an effort to make it a global leader in indoor farms. Plenty, which has no farms operating at scale, is now planning its first farm in South San Francisco that will open by the end of the year.
“I really do like to believe he likes us a lot,” Mr. Barnard said of Mr. Son. “I’d say the thing we have in common with his other investments is that they are all part of some of the largest systems on the planet: energy, transportation, the internet and food.”
Some entrepreneurs travel the globe to spend time with Mr. Son at his palatial home in Woodside., Calif., and his offices in India, San Francisco and Tokyo. The SoftBank chief is known for almost always smiling and speaking slowly. He rarely picks up phone calls and his email signature includes the whirring fan icon that shows a computer is booting up, or “thinking.”
Many of the entrepreneurs speak of Mr. Son with reverence.
“Only people close to him know how huge his vision is,” said Eugene Izhikevich, the chief executive of Brain Corp., a company based in San Diego that makes the software that controls autonomous robots.
Mr. Son’s engineers stumbled on Brain Corp. when they were looking for self-driving car technology. Mr. Izhikevich was soon seated across from Mr. Son, talking about robotics as well as how Britain operated 200 years ago when the landed gentry did not work, but came up with new inventions and business improvements.
Like many other entrepreneurs, Mr. Izhikevich said SoftBank moved “scary fast” to sew up its investment. Mr. Son’s team swarmed Brain Corp.’s businesses and spent hundreds of hours on due diligence, wrapping up in a few months.
Unlike other investors, Mr. Son, who is already talking about a second Vision Fund, does not insert himself into the day-to-day operations of most of the companies he has invested in. His Sprint deal has yet to pan out and may be dependent on merging with another company. When other investments have lagged, as did his investment in Snapdeal, an online retailer in India, he has invested in competitors, leading a $2.5 billion investment into Flipkart, a rival Indian e-commerce company.
Some entrepreneurs said Mr. Son’s breakneck investing pace with the Vision Fund was unlikely to slow.
“Masa is in a hurry,” said Vijay Sharma, the chief executive of Indian digital payments start-up Paytm, which SoftBank put $1.4 billion into in May. “He sees this once-in-a-lifetime opportunity where everything we touch can become a market, where we’re at the opening up of a new industrial revolution.”
Indoor Farming Grows In Greater Boston
Credit: Cristina Quinn/WGBH News
Indoor Farming Grows In Greater Boston
October 11, 2017
Indoor farming is an industry that continues to grow — and not just your greenhouse variety, either — but a close cousin that uses no sunlight or pesticides, little water, and a whole lot of technology.
Inside an old ginger ale factory in Millis, Freshbox Farms has 8-by-40 foot containers lined up, each connected to a water purification and air filtration system. Inside every container is a hydroponic farm growing an acre’s worth of leafy greens. But, before we can even enter one, the company’s senior vice-president of plant science and product development, Deane Falcone, and I suit up in lab coats and hair nets so we don’t bring in insects that can damage the plants.
Inside, rows of lustrous, leafy green romaine lettuce greet us from trays of water. Each section is in a different stage of growth ranging from two weeks to harvest time, which occurs at five weeks. The company also monitors the soil and air conditions, which is captured every 30 seconds with software created in-house
This romaine lettuce receives 16 hours of fake sunshine from LED lights and uses about 18,000 gallons of water in an entire year, a fraction of what traditional lettuce farms use. Hydroponic farming has long been regarded for its water efficiency but critics of indoor farming like this say the cost to power the LED lights is hard to justify. Falcone agrees that it’s costly but cites Haitz’s Law, which predicts the efficiency of LED lights to increase exponentially every decade.
“So we're paying for a lot of electricity to power up a lot of the LED lights,” he said. “The thing that we always point to is the fact that the efficiency of the LEDs is increasing every couple of years.”
The cost factor is something the founders of Freight Farms, a local startup, considered when they started turning shipping containers into pre-fabricated vertical farms that require only one layer of lighting on each side. They’re called Leafy Green Machines.
It was one of the draws for Bobby Zuker and Chris Mutty, who bought one of these containers. Together they launched Greenline Growers, right out of a former taxi depot in Coolidge Corner, Brookline.
“We started in December of 2015,” Zuker said. “That was when we got our first Freight Farm. And then by March we were actually selling to restaurants.”
Greenline Growers now has three vertical farms. Freight Farms sells these Leafy Green Machines to budding farmers like Zuker and Mutty for $85,000. They also provide training and now an app that allows users to control settings remotely.
“They've taken a lot of different technologies and aggregated it and made it fairly simple to automate it and then we just do the farming part.” Zuker said.
Tim Griffin of the Friedman School of Nutrition Science and Policy at Tufts, said this latest iteration of urban agriculture could diversify the food supply as weather becomes more erratic.
“I see it as being it's another way that we grow food and if it works really well with particular foods, then we should be thinking about how we should be thinking in a positive way,” he added. “And then [we should] also always [be] thinking about who has access to what and who does not.”
Even though we won’t be seeing corn or wheat grown in these things, that doesn’t rule out strawberries and even someday rice and grapes to go with the ever-growing varieties of lettuce.
Food Loves Tech Conference Will Explore Food’s Not-Too-Distant Future
The two-day expo is designed to give “attendees a chance to see, smell, touch, hear, and taste food’s not-too-distant future,” according toEdible Manhattan and Edible Brooklyn Editor-In-Chief Brian Halweil and Publisher Stephen Munshin.
Food Loves Tech Conference Will Explore Food’s Not-Too-Distant Future
Food and drink innovators and enthusiasts will gather in Brooklyn, New York, on November 3 and 4, 2017, to explore the developing relationship between modern technology and food systems at this year’s Food Loves Tech conference. Produced by Edible Manhattan and Edible Brooklyn, the event is described as an “education-by-entertainment innovation expo” and will be hosted at Industry City.
The two-day expo is designed to give “attendees a chance to see, smell, touch, hear, and taste food’s not-too-distant future,” according to Edible Manhattan and Edible Brooklyn Editor-In-Chief Brian Halweil and Publisher Stephen Munshin. They write that the event will be careful to not only highlight those novel technologies that solve what they call “#firstworldproblems,” like faster ways to order food online, but also those technologies and startups that are “compelled by a mission to fix our broken food system.”
“Why are we so fascinated by this?,” they write. “At best, this data-flooded food culture will mean more traceability, less waste, increased crop diversity, less overeating. Hopefully.”
In addition to the experiential component of the conference, 10 scheduled panels will explore various questions: How can tech help save our oceans? How can technology help mitigate food waste? How will we buy groceries in 2050? Can vertical agriculture help us produce more food, more sustainably? Food Tank President Danielle Nierenberg will be both speaking on and moderating panels at the event.
For tickets to Food Loves Tech 2017, click here.
A $140 Million Prototype Of A Mars Colony Is Being Planned For A Desert Near Dubai — Here's What It Looks Like
A $140 Million Prototype Of A Mars Colony Is Being Planned For A Desert Near Dubai — Here's What It Looks Like
- Leanna Garfield
- Oct. 4, 2017
BIG's design for the Mars Science City near Dubai, UAE.Dubai Media Office
What might it be like to live on Mars?
Bjarke Ingels Group — the architects behind the designs for Two World Trade Center in Manhattan and the Hyperloop One — has an idea.
The firm is designing a city in the desert of the United Arab Emirates meant to simulate a Mars colony. The $140 million development near Dubai is slated to be "a viable and realistic model to simulate living on the surface of Mars," according to the local government.
The design for the Mars Science City, as it's called, spans 1.9 million square feet — which would make it the largest of its kind in the world. The plan calls for a team of astronauts to spend a year living in the simulated city after it's completed. However, there's no timeline for construction yet.
A team of Emirati scientists and engineers from the Mohammed bin Rashid Space Centre plan to conduct research about colonizing the red planet at the Mars Science City.
Dubai Media Office
Source: The Government of Dubai
The city is expected to include a giant greenhouse to test agricultural techniques, as well as laboratories designed to explore how to store food, generate energy, and get water.
Dubai Media Office
The greenhouse plan calls for the use of an agricultural technique called vertical farming. Instead of natural sunlight, crops would grow under LEDs on stacked trays in a climate-controlled environment.
Dubai Media Office
The ceiling would be made of materials that can block solar radiation (which is stronger on Mars than on Earth, due to its lack of protective atmosphere). The walls would be 3D-printed.
Dubai Media Office
A portion of the development includes a museum where visitors could learn about achievements in space exploration.
Mars Science City is part of the United Arab Emirates' larger mission to create a viable community on the red planet within the next century.
Dubai Media Office
"The UAE seeks to establish international efforts to develop technologies that benefit humankind ... and that establish the foundation of a better future for more generations to come," UAE's prime minister, Sheikh Mohammed bin Rashid, said at a recent meeting of government officials.
Dubai Media Office
Viability of Indoor Urban Agriculture is Focus of Research Grant
Viability of Indoor Urban Agriculture is Focus of Research Grant
By Krishna Ramanujan | October 12, 2017
A commercial CEA greenhouse operation producing leafy greens in eastern New York. Chris Kitchen/University Photography
Neil Mattson, associate professor in the Horticulture Section of the School of Integrative Plant Science.
Growing crops in controlled environments – in greenhouses, plant factories and in vertical farms – provides alternatives to conventional farming by producing food year-round near metropolitan areas, reducing transportation costs and water use, and improving land-use efficiency. Such local systems also offer valuable educational and psychological benefits by connecting urban people to the food they consume.
At the same time, there is little concrete evidence to show how so-called controlled-environment agriculture (CEA) compares to conventional field agriculture in terms of energy, carbon and water footprints, profitability, workforce development and scalability.
Cornell will lead a project to answer these questions, thanks to a three-year, $2.4 million grant from the National Science Foundation, through its new funding initiative called Innovations at the Nexus of Food, Energy and Water Systems.
“By putting all these pieces together – including energy, water, workforce development and economic viability – we hope to discover if CEAs make sense for producing food for the masses,” said Neil Mattson, the grant’s principal investigator and associate professor in the Horticulture Section of the School of Integrative Plant Science.
Six projects included in the grant will look at:
Case studies: Food system analysis of case studies in metropolitan areas will examine where vegetables are currently sourced and the market channels they go through to reach consumers, such as supermarkets, retailers or restaurants. Researchers will model whether urban CEAs could replace a large fraction of this produce, and whether it makes sense for CEA produce to go through the same market channels or other ones that may suit them better. This project is led by Miguel Gómez, associate professor, and Charles Nicholson, adjunct associate professor, both in Cornell’s Dyson School of Applied Economics and Management.
Computer modeling of energy and water use: Computer models of energy and water use for different crops in greenhouses, vertical farms and plant factories (indoor environments with artificial lighting and racks of plants) will be developed. The models will be calibrated with real-world data from greenhouse growth trials at Cornell and the Rensselaer Polytechnic Institute (RPI). A 2008 study by Lou Albright at Cornell found that based on that year’s technologies, the carbon footprint to produce lettuce in a greenhouse in New York state was twice that of growing it in a field in Arizona or California. Other researchers have reported that CEAs use 20 times less water than field agriculture, since water can be recycled indoors. Mattson leads this effort with research associate Kale Harbick, also in the Horticulture Section of the School of Integrative Plant Science.
Networking: The project will foster industry-to-research networks for facilitating the acceptance, adoption and improvement of metropolitan CEA systems. Anusuya Rangarajan, senior extension associate, will lead this project.
Nutritional value: Researchers will examine the nutritional value of produce from greenhouses and plant factories and comparing those values with CEA systems where lighting might be optimized for more healthful produce. Project leaders include Marianne Nyman, associate professor of civil and environmental engineering, and Tessa Pocock, a senior research scientist, both at RPI.
Workforce needs: Cornell researchers are collaborating with the Association for Vertical Farming to assess the workforce needs of the urban CEA industry and develop programs to meet those needs and test if requirements are being met. Researchers will examine if, for example, all the tomatoes consumed in New York City were to be grown indoors, how many jobs at what education levels and training would be needed. Rangarajan leads this effort.
Training opportunities: Rangarajan and the Association for Vertical Farming will also create workforce training opportunities. They will spearhead outreach through conferences and events to share information. A forthcoming website will house a toolkit to assess the viability and resource availability of proposed urban agriculture projects.
“Urban agriculture is an increasingly touted way to connect producers with consumers, and this grant will help guide full development of this industry and do better to figure out where the best opportunities might be, as well as cases where it doesn’t make sense,” Mattson said.
STORY CONTACTS
Krishna Ramanujan
MPA ESP Student to Transform Urban Farming
MPA ESP Student to Transform Urban Farming
BY LAURA PIRAINO | October 6, 2017
MPA-ESP student Alexander Rudnicki is a civil engineer (Columbia University ’10), who comes to SIPA from AeroFarms, an urban farming pioneer. Rudnicki speaks to MPA ESP intern Shagorika Ghosh about the urban farming industry, the enriching experiences of the ESP program, and his plans for the future.
How did your background working with innovative and transformative urban farms lead you to pursuing theMPA-ESP program?
I was the first engineer working at AeroFarms, where being the plant manager for over three years allowed me to experience the entire spectrum of working in the industry. For example, there was a day in particular that I remember, when I spent all day working in the plant training people, supervising operations, as well as having to present our work to the Duke of Westminster, who is one of our largest funders. Working at AeroFarms allowed me to experience the reality of working in the sector–how slowly things can move in real life, how implementation of projects needs teamwork and lots of capital.
AeroFarms was a vehicle for agricultural companies to engage in urban farming. People are excited and enthusiastic about urban farming, but it is a nascent industry with respect to policy and technology, so it’s kind of like the Wild West right now. There isn’t much incentive for farming companies to move into urban areas at this point. I wanted to explore the confluence of urban farming technology and traditional farming techniques, and studying environmental policy seemed to be the way forward.
What specifically motivated you to choose the MPA-ESP program at Columbia University?
I want to shape what the future industry looks like, and how the industry can be developed. The MPA-ESP program really equips me to do that. There is a focus on the environment, but it also takes into account social perspectives. The length of the program and its rigor is definitely another factor. It is a shorter, more intensive program, and the course structure and hands-on experience is great for mid-career professionals because it doesn’t feel like a full step back into school, but more like a half step back. At the same time, it’s great to be at SIPA, which allows you to be flexible, branch out and take different electives. Being at Columbia has also broadened my horizons, and it’s possible to keep abreast of everything that is happening in the industry. A lot of avenues then open up–working in policy or with companies in different areas of the urban farming industry.
What are your favorite classes and why?
One of my favorite classes has been Leadership and Urban Transformation, taught by Professor Michael Nutter, the former mayor of Philadelphia. He brings his long time public service perspective, and incredible insights into the actual implementation of policies, and the challenges of politics involved in policy implementation. I am also enjoying Sustainable Finance with Professor Bruce Kahn, which covers components of corporate finance, sustainability accounting, and sustainability metrics.
How has living and studying in NYC contributed to your experience in this program?
New York City is taking efforts to be at the forefront of sustainability, and this is being supported through high level executive action as well. OneNYC (formerly the Bloomberg Administration’s PlanNYC) is the sustainability plan for the City of New York. I am very interested in their Zero Waste initiative, and I intend to volunteer for the city in the future.
What has been your experience with your Environmental Science and Policy cohort been like?
In the MPA-ESP cohort, we work collaboratively for workshop presentations and other group projects. After multiple projects, we all have worked and interacted with at least half of the entire class. Our cohort is a very close-knit one, and I make it a point to interact with my fellow classmates. It has been very interesting to know their backgrounds, their interests and what they want to pursue. In my role as the ESP Treasurer, I also work to understand what the needs of the cohort are, what events and speakers they would be interested in.
What are your plans once you graduate? What are some skills and tools you have developed over the last year that you can use?
I would love to work with city planning offices to integrate urban farming into city planning and layouts. It’s encouraging to see cities like Detroit that have outlined an urban farming policy. It’s a great start and I want to be involved in such urban initiatives after I graduate.
I came to SIPA to learn how to create policy that would shape the future of urban farming. Through my classes, I am developing skills to be able to do that. I am learning to adopt a systems thinking approach towards earth systems through classes such as Climatology and Hydrology, that allows for a broader perspective when looking at the sustainability industry as a whole. Through my Sustainable Finance class, I am learning not just how to evaluate sustainability quantitatively, but also learn and analyze trends in the industry that are attractive to investors. All of these will equip me to further develop the urban farming industry and integrate traditional techniques and new technologies.
Heading Off To The Eternal Ice
Heading Off To The Eternal Ice
EDEN ISS Greenhouse En Route to Antarctica
10 October 2017 | Credit: DLR (CC-BY 3.0).
The loading at the port of Hamburg begins
- DLR scientist Paul Zabel moves to the Antarctic for one year with the EDEN ISS greenhouse
- Test run in Bremen produces more than 40 kilograms of fresh vegetables
- Plant cultivation without soil, with optimised light, carbon dioxide content and closed water cycle
- Focus: Space, biosystems
The venture to cultivate plants in the Antarctic is gathering momentum: on 8 October 2017 the special EDEN ISS greenhouse container, packed safely away on a cargo ship, left the Port of Hamburg en route to the Ekström ice shelf in the Antarctic. The journey will last approximately 11 weeks. The EDEN ISS team is expected to receive the high-tech greenhouse at the German Neumayer Station III of the Alfred Wegener Institute (AWI) shortly before Christmas. In this project, the German Aerospace Center (Deutsches Zentrum für Luft- und Raumfahrt; DLR) is collaborating with international partners to investigate the fully self-sufficient cultivation of vegetables to supply food in harsh climatic environments and for future manned missions to the Moon and Mars.
Rich harvest in the trial run
Cucumbers, tomatoes, radishes, peppers, lettuce and herbs flourished in the 12-metre container greenhouse during the trial run from late June until August 2017. "The trial run at the DLR site in Bremen yielded a rich harvest," says Project Coordinator Daniel Schubert from the DLR Institute of Space Systems. "We are confident that everything will proceed smoothly in the harsh environment of the Antarctic as well."
In total, the researchers produced over 40 kilograms of fresh vegetables over the course of the test phase. What makes it so fascinating? There is no loss of water. The only water that leaves the self-sufficient greenhouse system is in the harvested fruits. The rest is recycled and reintroduced into the plants. Under special artificial light, in a temperature-controlled environment without soil and supplied with selected nutrient solutions, the plants can grow faster and more productively than in their natural environment.
Vegetables #MadeinAntarctica
The actual crop cultivation experiment in Antarctica will begin at the end of December 2017. DLR scientist Paul Zabel will move to the Antarctic, where he will live for one year at the Neumayer III research station and work at the EDEN ISS greenhouse. He will be part of the winter crew staffing the Neumayer III Antarctic station operated by the Alfred Wegener Institute (AWI). "Scientists live and working all year round in the research station, despite the harsh Antarctic. During the summer, there are up to 50 people at the station. In the winter, however, only nine people remain there: one cook, three engineers, one doctor and four scientists," says the long-time Station Manager Eberhard Kohlberg. This is the winter team that Zabel will join as the tenth member.
Team colleagues from the EDEN ISS project will help Zabel with the construction and commissioning of the greenhouse, before leaving him in charge of running the greenhouse and cultivating the crops. The harvest during the months of darkness will enrich the diet of the people at the Neumayer III station. At the same time, the project will imitate the supply scenario for a manned mission to Mars.
"The preparations for the winter sojourn are exciting and already account for much of my day's work," says Zabel. “It gives you an idea of just how painstaking the preparations for a space mission are, when every eventuality has to be considered and one must be prepared for everything." Zabel has already completed survival training in the Alps as a member of the Neumayer III winter team. He has also attended a number of seminars on the technical systems at the station and a one-week fire-fighting training course. And there is still a lot of preparatory work ahead before his departure in December.
Food production of the future
Global food production is among the key societal challenges of the 21st century. The world's rising population, coupled with the simultaneous upheaval associated with climate change, demand new methods to cultivate crops, even in climatically inhospitable regions. A closed greenhouse system will enable crop growth independent of the weather, Sun and season in deserts and low-temperature regions – as well as for future manned missions to the Moon and Mars – while also reducing water consumption and eliminating the need for pesticides and insecticides. The EDEN ISS project will put this model for a future greenhouse through its paces for one year during a long-term trial in the extreme conditions of the Antarctic. System assembly is planned for late December 2017 to February 2018. Research operations will follow and are scheduled to run through the Antarctic winter and until December 2018.
International cooperation in EDEN ISS
The EDEN ISS project will be conducted during an overwintering mission at the German Antarctic station Neumayer III, in collaboration with the Alfred Wegener Institute, Helmholtz Center for Polar and Marine Research (AWI). A large number of other international partners are contributing to a research consortium under the auspices of DLR, ensuring that the greenhouse will work smoothly in the Antarctic: Wageningen University and Research (Netherlands), Airbus Defence and Space (Germany), LIQUIFER (Austria), the National Research Council (Italy), the University of Guelph (Canada), Enginsoft (Italy), Thales Alenia Space (Italy), Arescosmo (Italy), Heliospectra (Sweden), the Limerick Institute of Technology (Ireland) and Telespazio (Italy) all form part of the consortium of the EDEN ISS project. The project is financed with funds from the EU Framework Programme for Research and Innovation under project number 636501.
Last modified:
10/10/2017 13:28:37
Contacts
Falk Dambowsky
German Aerospace Centre (DLR)
Media Relations, Aeronautics
Tel.: +49 2203 601-3959
Daniel Schubert
German Aerospace Center (DLR)
DLR Institute of Space Systems
Tel.: +49 421 24420-1136
Paul Zabel
German Aerospace Center (DLR)
DLR Institute of Space Systems
Tel.: +49 421 24420-1273
Dr. Eberhard Kohlberg
Alfred Wegener Institut (AWI)
Tel.: +49 471 4831-1422
Lumileds Adds New Deep Red, Far Red As Well As CoB Offerings To Its Leading Portfolio of LEDs For Horticulture Lighting
Lumileds Adds New Deep Red, Far Red As Well As CoB Offerings To Its Leading Portfolio of LEDs For Horticulture Lighting
September 26, 2017
The new LUXEON SunPlus 35 Deep Red and Far Red LEDs combine with Royal Blue to enable spectrum customization, while the new LUXEON SunPlus CoB Purple ramps Photosynthetic Photon Flux (PPF) for greenhouse productivity.
San Jose, CA – Lumileds today introduced three new products in its LUXEON SunPlus Series of award winning LEDs for horticulture lighting. The LUXEON SunPlus Series is the only line of LEDs on the market to be tested and binned by photosynthetic photon flux (PPF). The portfolio of colors enables wavelength tuning for maximum crop yield in both greenhouse and vertical farming applications. The addition to the LUXEON SunPlus 35 Line of Far Red and Deep Red will enable designers of vertical farm and interweaving fixtures to tune the spectrum specifically for the crop being grown. The new LUXEON SunPlus CoB Line, available in Purple, is designed for greenhouse applications where attaining high PPF and fast time to market are top priorities.
The LUXEON SunPlus 35 Line is optimized for vertical farming in shallow tiers so uniformity is optimized at very short distances. The Deep Red (650-670 nm) and Far Red (720-740 nm) wavelengths join the existing Royal Blue (445-455 nm), Lime (broad spectrum) and three shades of Purple with varying contributions of blue (2.5%, 12.5% and 25%) in a 3.5 x 3.5 mm format. “These essential red wavelengths are combined with blue to give the exact spectra needed for each crop. Our Horticulture Lighting Calculator is especially helpful in this context because lighting manufacturers can experiment with LED ratios and spectral power distributions before building the fixtures,” said Jennifer Holland, Product Line Director of the LUXEON SunPlus Series.
Customer success and market adoption of the LUXEON SunPlus 35 Purple and the need for even greater PPF in a single device led to the development of the LUXEON SunPlus CoB Purple (12.5% blue) product. In contrast to vertical farming where lighting is positioned a short distance from plants, greenhouse lighting requires deep penetration into the plant canopy, which is achieved with a directional CoB. The CoB portfolio complements the LUXEON SunPlus 20 and 35 Lines, which offer a variety of colors to optimize the spectrum for greenhouse applications. The CoB form factor also means that standard optics, holders and drivers are available to help manufacturers accelerate time to market of their fixtures. “The chip on board approach allows us to maximize PPF to as high as 350 µmol/s from a single source,” said Holland. The LUXEON SunPlus CoB Purple is available with 15, 19 and 32mm light emitting surfaces.
For more information on the LUXEON SunPlus Series, see www.lumileds.com/horticulture/products
For further information, please contact:
Kevin Lucido
Senior Director of Global Marketing Communications
Lumileds
+1 650 576 3864
Kevin.Lucido@lumileds.com
About Lumileds
For automotive, mobile, IoT and illumination companies who require innovative lighting solutions, Lumileds is a global leader employing more than 9,000 team members operating in over 30 countries. Lumileds partners with its customers to push the boundaries of light.
To learn more about our portfolio of lighting solutions, visit lumileds.com