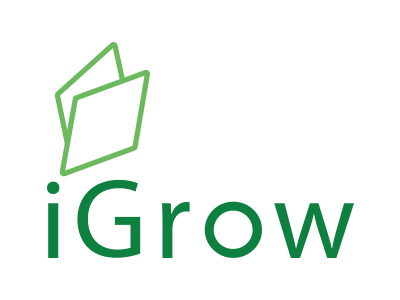
Welcome to iGrow News, Your Source for the World of Indoor Vertical Farming
Montreal-Based Start-Up Motorleaf Enables Greenhouse Farmers to More Accurately Forecast Their Future Harvests Using Artificial Intelligence
Montreal-Based Start-Up Motorleaf Enables Greenhouse Farmers to More Accurately Forecast Their Future Harvests Using Artificial Intelligence
It all started in 2016 in rural Sutton (Quebec) when Ramen Dutta, now CTO of Motorleaf, had trouble finding friends to water his plants while he was away on vacation.
With a US$2.85 million round of financing, artificial intelligence start-up Motorleaf can revolutionize greenhouse growers’ crop planning, achieving major productivity gains and reducing greenhouse gas (GHG) emissions. The financing round comprised notably Radicle Growth, Desjardins Capital, Real Ventures, Fluxunit and BDC Capital. With their support, Motorleaf can be a game changer in this agri-food sector niche in industrialized countries.
Motorleaf develops yield-predicting algorithms and indoor growth sensors. Using these advanced technologies that monitor plant growing conditions, greenhouse vegetable and tomato producers can make better business decisions and reduce costs, energy in particular, as well as water consumption, a critical factor in many regions around the world.
“We’re ready to distribute our technology so farmers can meet their fullest potential and acquire an innovative cost-cutting tool within the controlled-environment agriculture sector,” said Alastair Monk, co-founder, and CEO of Motorleaf.
Predicting the amount of vegetables from a harvest is currently a time-consuming process. Agronomists count samples of vegetables, leaves, and flowers in a small area and that sample then serves to estimate the expected yield of the entire grow operation. Often imprecise, farmers are unsure if they will produce enough vegetables to meet contract obligations or know how much labour they will need to package their produce. If they produce too much, farmers try to sell their perishable goods quickly at rock-bottom prices. Using Motorleaf’s artificial intelligence and machine-learning algorithms, the digital agronomist software can acquire data from indoor growing conditions. In turn, the algorithms learn growing patterns in the greenhouse, which then can predict the size of future harvests.
Cutting harvest prediction errors by half
Harvest yield-predicting algorithms are the latest technology born from Montreal’s booming artificial intelligence sector. With this financing round, Motorleaf aims to further develop its software and sensors so that its equipment can acquire additional data from common indoor climate control and irrigation systems. Farmers can now adopt this technology with a small addition of Motorleaf equipment but without the need for dramatic changes to their greenhouse infrastructure.
“Better yield prediction is only the beginning for Motorleaf’s added value to this sector,” says Alastair Monk. “We’re ultimately producing dynamic grower protocols, which help manage everything from light and nutrients to predicting greenhouse diseases before they happen, and optimized growing conditions that increase return on investment – all based on real-time data.”
Initial trials of the technology since October 2017 in a 70-acre California greenhouse cultivating tomatoes demonstrated its value to farming. Client SunSelect reduced its error in predicting weekly tomato yield by half, resulting in significant cost savings for the grower. As a result of the improved predictability using Motorleaf’s technology, SunSelect has since abandoned manual yield predictions in favour of Motorleaf’s algorithms. See the SunSelect case study at https://bit.ly/2IxxeF9.
The province of Quebec has 900 greenhouses, half of which have an area of under 999 square metres
Data compiled by the Ministère de l’Agriculture, des Pêcheries et de l’Alimentation (MAPAQ) shows 900 greenhouses in 2016, including 356 specialized in vegetables, 388 in flowers and 156 mixed greenhouses, for a total area of 297.2 hectares (ha). The same data shows that the three regions with the largest greenhouse areas were Montérégie (77.8 ha or 26%), Laurentians (54.3 ha or 18%) and Laval(34.8 or 12%). As for the number of farms, Montérégie had 226 (or 25%), Laurentians 117 (or 13%), Chaudière-Appalaches 72 (or 8%), Centre-du-Québec 59 (or 7%), Laval and Lanaudière with 55 each (or 6%) and the Eastern Townships 51 (or 6%).
Inspired by dead plants
The idea for Motorleaf stems from the heartbreak of returning home to find your prized plants dried out. Living in rural Sutton, Ramen Dutta, CTO of the Montreal start-up, had trouble finding friends that could drive to his home and water his indoor plants while he was away on vacation. Being an agricultural engineer, he built an automated, sensor-controlled irrigation system that would become the foundation of Motorleaf’s technology.
SOURCE Desjardins Capital
After Soilless Babyleaf, Here's Hand-Less Babyleaf
After Soilless Babyleaf, Here's Hand-Less Babyleaf
Little Leaf Farms, one of the largest growers of hydroponic baby greens in North America, has officially opened its expanded greenhouse in Devens, Mass this week. The expansion doubles the size of the greenhouse from 2.5 acres to 5 acres, and more than doubles its annual production of baby greens. Thanks to their innovative growing system the greens are grown fully automated, without any chemicals and without any human hand touching the produce. Little Leaf Farms also announced it has purchased adjacent land for a third expansion project set to begin in 2019, which will further increase the size of the greenhouse to approximately 10 acres.
Baby lettuce
Opened in 2016, Little Leaf Farms produces locally grown, fresh baby greens year-round that are delivered to New England consumers within hours of being harvested. Little Leaf Farms grows multiple varieties of baby lettuce at its greenhouse. “Our ability to deliver fresh, great tasting and safe baby greens to consumers that can be easily traced back to the Massachusetts greenhouse has led to our rapid growth and expansion”, said Paul Sellew, CEO and founder of Little Leaf Farms. “We are passionate about transforming the way food is grown. Our process is clean from the start, so consumers can be confident they’re purchasing a safe product, grown in an environment that employs the most advanced food safety practices.”
For doing so, Little Leaf Farms is using a fully automated growing system. The system is optimized for growing of baby leaf lettuce and makes it possible to grow leafy greens fully automated without any human hand touching the produce from medium filling and seeding to harvesting. The seeding is done directly into the gutters to avoid the need of transplanting. Germination takes place under the growing line. After germination the gutters are lifted up to the growing line. During the growing process the gutters are moved automatically through the greenhouse toward the harvesting area. As plants grow the distance between the gutters continuously is adjusted - giving each plant as much space as necessary, but as little as possible. Once ready for harvesting the gutters are transported per conveyor belt to the harvesting area and guided into the cutting machine for a fresh cut.
The system is developed by Green Automation and has recently been upgraded and updated. “The growing lines are now even more robust, offers more precise and easier operations resulting in reduced maintenance needs as well as noise levels”, Patrik Borenius of Green Automation explains. Making the system more durable with increased frame thickness and additional steel components also allows for longer greenhouse growing lines to be designed and for increased gutter capacity.”
Seeding directly into the narrow gutters – eliminating the need for transplantin
Electric lift moving the gutters from the germination level to the growing line in one smooth movement.
New generation harvesting end with more space efficient conveyor design
Sustainability
The system is an important part of the Little Leaf hydroponic growing process, using mineral nutrient solutions in water without soil. “We incorporate principles of sustainability in everything we do, all to provide consumers with delicious, local baby greens at a fair price”, Paul explains. “The growth is completely sustainable, utilizing natural sunlight, a computer-controlled growing environment and a rainwater-based irrigation system that uses 90 percent less water than field-grown lettuce companies”, Paul shows. “The system enables the baby greens to be seeded, grown, cut and packaged without ever being touched by human hands. The production system is free from chemical pesticides, herbicides and fungicides, ensuring that what customers purchase is safe.”
LED lighting
The greenhouse is to be lighted with LED and the company opted for Oreon Grown Light 2.1, water-cooled fixtures by Lemnis. The complete installation of both water and electricity was provided by PB Techniek, Sellew’s installation partner for many years.
Salad mixes
Little Leaf Farms grows multiple varieties of baby lettuce at its greenhouse that are blended into salad mixes and sold in more than 1,000 Northeast grocery stores and to many restaurants, Universities and institutional customers. “More than 98 percent of the lettuce we eat in this country is grown on the West Coast and shipped for days, which means customers in New England are not receiving the highest quality or freshest product,” said Andrew W. Kendall, executive director of the Henry P. Kendall Foundation, an organization focused on creating a resilient and healthy food system in New England to increase the production and consumption of local, sustainably produced food. “Little Leaf Farms has cracked the code on providing the region with fresh baby greens within hours of being harvested. It’s exciting to see that consumers appreciate the value of the product, which will drive the company’s growth for years to come.”
For more information:
Little Leaf Farms
Green Automation
Patrik Borenius
Publication date: 5/25/2018
Author: Arlette Sijmonsma
Copyright: www.hortidaily.com
Philips Lighting Is Now Signify
May 16, 2018
Philips Lighting Is Now Signify
Eindhoven, the Netherlands - Signify (Euronext: LIGHT), the world leader in lighting, has today launched its new company name, following the amendment of the company's articles of association changing its name from Philips Lighting N.V. to Signify N.V.
"The choice of our new company name originates from the way light becomes an intelligent language, which connects and conveys meaning," said Eric Rondolat, CEO of Signify. "It is a clear expression of our strategic vision and purpose to unlock the extraordinary potential of light for brighter lives and a better world."
Signify will continue to use the Philips brand for its products, the most trusted lighting brand in the world, under the existing licensing agreement with Royal Philips. The company expects the name change to be implemented in all the countries where it is active by the beginning of 2019.
Founded as Philips in Eindhoven, the Netherlands, we've led the lighting industry with innovations that serve professional and consumer markets for more than 127 years. In 2016, we spun off from Philips, becoming a separate company, listed on Amsterdam's Euronext Stock Exchange. We were included in the benchmark AEX index in March 2018.
With operations in more than 70 countries and 32,000 people worldwide, Signify generated sales of EUR 7 billion and invested EUR 354 million in Research and Development in 2017.
"We are driven by the principle that light is essential," Eric Rondolat added. "And by connecting it to networks, software, sensors and IoT platforms, we open the door to a smarter world."
News from Signify is located at the Newsroom, Twitter and LinkedIn. Information for investors can be found on the Investor Relations page.
--- END ---
For further information, please contact:
Signify Investor Relations
Robin Jansen
Tel: +31 6 1594 4569
E-mail: robin.j.jansen@signify.com
Signify Corporate Communications
Elco van Groningen
Tel: +31 6 1086 5519
E-mail: elco.van.groningen@signify.com
About Signify
Signify (Euronext: LIGHT) is the world leader in lighting for professionals and consumers and lighting for the Internet of Things. Our Philips products, Interact connected lighting systems and data-enabled services, deliver business value and transform life in homes, buildings and public spaces. With 2017 sales of EUR 7.0 billion, approximately 32,000 employees and a presence in over 70 countries, we unlock the extraordinary potential of light for brighter lives and a better world. News from Signify is located at the Newsroom, Twitter and LinkedIn. Information for investors can be found on the Investor Relations page.
Growing Up - Why The UAE's First Vertical Farm Could Be A Regional Gamechanger
Growing Up - Why The UAE's First Vertical Farm Could Be A Regional Gamechanger
RABIYA JAFFERY
REUTERS
Abu Dhabi | Thu, May 10, 2018
Vertical farming is taking off elsewhere too: Europe's first commercial farm opened near Amsterdam last year, and Shanghai will next year start a 250-acre agricultural district with skyscrapers dedicated to growing fruit and vegetables. (Reuters/Mike Segar)
When people picture the United Arab Emirates, what likely comes to mind are desert sands, skyscrapers and a blue sea under a shimmering sun. Agriculture does not.
There are good reasons for this: the federation of seven emirates is hampered by high temperatures, a lack of arable land, salty soil and steep production costs. And that is without accounting for the occasional voracious locust swarm.
So it is hardly surprising that the UAE imports nearly 90 percent of its food needs, according to the Abu Dhabi Global Environmental Data Initiative, a data research organization.
This reliance on the global food trade brings opportunity, said Saudi Arabian entrepreneur Omar Al Jundi, who has built the Middle East's first commercial vertical farm in Dubai.
Badia Farm - the word means 'oasis' in Arabic - grows greens like radish, kale, mustard, basil and arugula in a controlled, indoor environment using hydroponic technology and LED lights.
"As a region that has struggled to grow crops due to largely hostile desert landscapes, our farm offers a viable solution to farming that produces harvests 365 days of the year," he said.
"The produce will not only be cheaper than imported goods but fresher too, as the farms will be producing all year round."
The farm, which began production late last year, is on an 800-square-meter plot of land in one of Dubai's main industrial areas and produces two hundred boxes of green vegetables a day.
Though this pales in comparison to the world's largest vertical farm - which operates on 6,500 square meters of a former steel factory in New Jersey in the United States - it marks a big step for alternative farming in this region.
Vertical farming is taking off elsewhere too: Europe's first commercial farm opened near Amsterdam last year, and Shanghai will next year start a 250-acre agricultural district with skyscrapers dedicated to growing fruit and vegetables.
Vertical farming brings some important benefits, said Al Jundi: because produce is grown in a controlled environment there is no need for pesticides or chemicals. And they use much less water - 90 percent less than open-field farming.
Growing food locally for the firm's 30 UAE clients - mainly restaurants and hotels - means a smaller carbon footprint, and saves on transport costs.
"It makes no sense to order produce that arrives in boxes in the back of a ship from as far tens of thousands of miles away when it can be grown at home," he said.
Food Security
Even though the UAE imports most of its food, the emirates are food secure, according to the United Nations Food and Agriculture Organization (FAO).
However, its food security is not without risk, said Hina Kamal, a research analyst at the UAE University's College of Food & Agriculture, as it is reliant on vulnerabilities in supplier countries and on the international food trade market.
Another concern is climate change, which is likely to increase food prices in the years ahead, said Majid Sultan Al Qassimi of the UAE's ministry of climate change and environment.
Although the UAE has strategic reserves in place to protect it from short-term disruptions, he said, "ensuring global food security will be challenging in the future due to impacts of climate change".
Part of the solution, he said, is to boost domestic production through sustainable means; another is "to diversify imports and investments to ensure that the country is food secure in the long-run".
Other solutions include setting up storage facilities abroad and acquiring farmland in Africa, Europe, and Asia. Emirates NBD, a large regional bank, says UAE investors were part of at least 28 deals in the past 50 years covering about 1 million hectares of farmland globally.
The Emirates' drive to secure land abroad to assure its food supply is not risk-free, Kamal said and could be undone by political conditions in those countries or by climate change.
"It is possible that some of (the countries) will be highly affected by climate change - both through more extreme weather events and reduced productivity over time."
Droughts or food shortages could, for example, see host governments impose export bans, she said, which is why boosting productivity at home is the lowest-risk way to ensure food security in the decades to come. It is also more sustainable.
Future-proofing
The UAE will need to improve its agricultural productivity in the coming decades to meet demand, said Qassimi, and to do so in the face of rising global temperatures that are expected to worsen extreme weather events.
"All of this has a direct impact on agricultural production, affecting both food producers and those who depend on them. The UAE is no exception," he said.
Nor, for that matter, is the Gulf region, noted a report last year from the Emirates Wildlife Society and World Wildlife Fund (EWS-WWF), which evaluated the likely effects of climate change on food security.
The UAE is a major regional hub for the re-export of food commodities, it pointed out, and the consequences of climate change, including hotter weather, could affect those facilities.
Any resultant food price spikes would hurt the poorest the most, and that could drive a long-term need for food subsidies.
There are other factors too, not least water. The UAE's agricultural sector accounts for just 1 percent of its economy, the EWS-WWF report noted, yet uses about one-third of its water - vastly disproportionate to its GDP contribution, said Fanack Water, a research group.
Given that water is more expensive than electricity in the UAE - and given that regular farmers benefit from subsidies for water - Al Jundi of Badia Farm said ending such breaks would make vertical farming a cheaper solution.
"The money spent on powering vertical farms is relatively much lower than of the cost of water used in open fields."
That said, Badia does use plenty of electricity: from pumping water to powering the artificial lighting and computers that monitor temperatures. But looking ahead, said Al Jundi, it is working with the government on a shift to renewable energy.
The impact one vertical farm can have, though, is limited, and will be felt only on the margins: it will not change the UAE's reliance on countries such as Brazil, India, Iran and South Africa for cereals, sugar and food oils, for example.
But what it represents - a better way of growing produce in a region that is facing significant challenges from climate change - is important, Al Jundi said.
"This technology will be a major contributor to agriculture sustainability, food diversity, and security as it enhances crop production and lowers their cost," he said.
Grow Closer With Light Polymers’ GrowBlade® Horticultural Lighting
Grow Closer With Light Polymers’ GrowBlade® Horticultural Lighting
Light Polymers - GrowBlade Test-Site, 2018 (Photo: Business Wire)
May 24, 2018
SAN FRANCISCO--(BUSINESS WIRE)--Light Polymers, a nanochemistry innovator specializing in lyotropic liquid crystals, is launching a Beta-test program for its innovative GrowBlade® horticultural lighting. GrowBlade flat-panels use Light Polymers’ Crystallin® remote phosphor films to let indoor farmers grow closer, delivering even, consistent lighting in a range of rich crop-specific spectra. GrowBlades have a long service life, running cooler with less spectrum shift and lumen drop over time than conventional LED grow lights. Better quality full-spectrum light in a thin, wide-area form factor is a key to higher farm productivity.
“Light Polymers has been busy starting production of our breakthrough Crystallin film, and developing specialty lighting designs that are eye-safe and comfortable, with extraordinarily rich spectra”
Tweet this
“As innovators in a range of specialty lighting markets, Light Polymers knows the importance of engaging potential customers as part of our product development process,” said Sandor Schoichet, VP of Grow Products at Light Polymers Lighting. “To this end, Light Polymers is opening up its GrowBlade Beta-test program to select vertical farm and controlled environment growers, to gain real world production experience and better understand the specific needs of our customers.”
GrowBlade Edge 300 and 600 panels (approximately 300x300 mm or 1’x1’, and 300x600 mm or 1’x2’) will be available to select early adopters starting in June 2018. Longer GrowBlade Edge 1200 and 1500 models (approximately 1’x4’ and 1’x5’) will be available in late 2018. Both models have a slender form-factor (just 12.5 mm thick - not including the remote, dimmable LED driver) and will be among the earliest products certified to the new UL-8800 horticultural lighting standard. Initial Beta-test lights are available in two custom spectra, with more tailored crop-specific spectra to come based on customer input. Introductory pricing for GrowBlade Edge 300 and 600 models is set at $119 and $219 respectively.
“Light Polymers has been busy starting production of our breakthrough Crystallin film, and developing specialty lighting designs that are eye-safe and comfortable, with extraordinarily rich spectra,” said Marc McConnaughey, Chairman of the Board of Light Polymers Lighting. “We are excited to begin production of the GrowBlade and our other specialty lighting products based on our Crystallin film technology.”
GrowBlades achieve a unique level of horticultural lighting performance by leveraging the unique capabilities of our Crystallin remote phosphor film, which eliminates ‘point-based’ lighting issues common to other LED lights. Instead of assembling a variety of specialized LEDs into a bar or a box, GrowBlades use sheets of Crystallin film to down-convert the output of a simple blue LED array into a smooth, fully diffused spectrum with even edge-to-edge distribution. GrowBlade spectra can easily extend into the red and far-red range critical to flowering and fruiting, while blocking problematic blue and UV wavelengths below 420 nm. Formulating spectrum with Crystallin technology lets us move beyond simple narrow-band spectra to explore synergies across the multiple wavelengths that affect crop quality.
With cool, evenly distributed, high quality light, GrowBlades can be mounted closer to your plants for greater vertical density, higher yields, and improved crop consistency, for higher overall productivity.
Contact us now for updates and early release notification.
About Light Polymers
Light Polymers is a nanochemistry company with deep domain knowledge and expertise in lyotropic liquid crystals, which have many applications including OLED displays, LED lighting and building materials. Light Polymers recently debuted a family of human-centric eye-safe task and study lighting. Founded in 2013 in San Francisco, Light Polymers has over 50 patents issued and pending for its water-based lyotropic liquid crystal nanochemistry. For more information, visit http://www.lightpolymers.com/.
Contacts
Write2Market for Light Polymers
Casey Stokes 404-428-2135
casey.stokes@write2market.com
Urban Food From Vertical Farming
Urban Food From Vertical Farming
May 23, 2018, CORDIS
Credit: diephotodesigner.de
Your local supermarket and favourite restaurant could soon be growing their own food, thanks to an EU-funded project that has completely redesigned the food supply chain to develop the concept of in-store farming.
Our busy, modern lives demand that fresh produce be available 365 days a year, even though some varieties may only be seasonal and/or produced on the other side of the world. The result is a food system centred on quantity, low prices and efficiency rather than on quality, sustainability and traceability.
The EU-funded INFARM (The vertical farming revolution, urban Farming as a Service) project reflects a growing desire for highly nutritious locally grown food, which is free of herbicides and pesticides and addresses the lack of accountability in the current food system. "By growing produce directly where people eat and live, we can cut out the lengthy supply chain, significantly reduce food waste, offer nutrient-dense food without any chemical pesticides and improve the environmental 'foodprint' of our plants," says the INFARM's Chief Technical Officer and co-founder, Guy Galonska.
The answer lies in vertical farming, which grows food in vertically stacked layers under carefully controlled conditions, using hydroponics and light-emitting diodes (LEDs) that mimic sunlight. INFARM takes the concept a step further by employing its smart modular farming units throughout the city "Rather than asking ourselves how to fix the deficiencies in the current supply chain, we wanted to redesign the entire chain from start to finish; Instead of building large-scale farms outside of the city, optimising on a specific yield, and then distributing the produce, we decided it would be more effective to distribute the farms themselves and farm directly where people live and eat," Galonska explains.
Use of technology
Each farming unit is its own individual ecosystem, creating the exact environment for plants to flourish. By developing the optimal light spectrum, temperature, pH, and nutrients researchers can ensure the best possible flavour, colour and nutritional quality for each plant, whether it be rocket from Provence, Mexican tarragon or Moroccan mint.
The distributed farms are connected by INFARM's central farming platform, creating a first of its kind farming network: "Each farm acts as a data pipeline, sending information on plant growth to our platform 24/7 allowing it to learn, adjust and optimise." A matrix of sensors collects and record data, enabling researchers to remotely optimise the growth of the plants in real-time. This information is also fed into the central farming platform, ensuring its continual development and improvement.
The design of the growing trays mimics the petal pattern of the sunflower, which represents the most efficient arrangement of space in nature. The tray moves plants from the centre to the outer perimeter according to their size and growth. Young seedlings are placed in the centre of the spiral and are harvested from the outside when matured. This design allows fresh produce to be harvested each day at a significantly higher output than comparable technologies.
Supply chain reduced
INFARM is now operating more than 50 farms across Berlin in supermarket aisles, restaurant kitchens and distribution warehouses. In addition to the in-store farms, INFARM has successfully installed and activated a large-scale seedling plant and logistical support system that allows the continued, successful operation of all farming units.
These results are the first step towards creating an urban farming network in Berlin that will ultimately make the city more self-sufficient in its food production. According to Galonska: "With our system, we have completely reduced the food supply chain, as our produce is grown in the heart of the city, often directly at points-of-sale. Thus, customers can purchase fresh produce, minutes after being picked, thereby retaining all its original nutritional qualities, which are lost when the produce is transported and refrigerated."
Those benefiting from the work of INFARM range from small grocers to global retail conglomerates and governments interested in water conservation, food security and reducing greenhouse gas emissions. Galonska concludes, "INFARM's innovative business model has attracted major interest and I believe that our success will serve as proof, to both aspiring entrepreneurs and established companies, that going 'green' can be profitable and sustainable."
Explore further: Computer-controlled 'greenhouses' in kitchens grow fresher, healthier produce
Provided by: CORDIS
Read more at: https://phys.org/news/2018-05-urban-food-vertical-farming.html#jCp
Princeton University’s Vertical Farming Project Partners With Hopewell Elementary
Princeton University’s Vertical Farming Project Partners With Hopewell Elementary
By MercerMe May 23, 2018
Vertical Farming at HES
Princeton University’s Vertical Farming Project announced they will partner with Hopewell Elementary School in Hopewell, New Jersey to develop their vertical farm-to-cafeteria program.
Fifth grade teacher at Hopewell Elementary, Helen Corveleyn, oversees the school’s outdoor garden beds, six indoor vertical hydroponics towers, and has been instrumental in their new vertical farming initiative partnership with Princeton. Corveleyn will work closely with Princeton University’s Dr. Paul Gauthier, founder and director of the Princeton Vertical Farming Project to develop the program at the elementary school. The on-site, indoor classroom will be fully functioning in September 2018 and will allow preschool through fifth grade kids to mirror Princeton’s program while providing kids with fresh, organic produce for lunch and an invaluable introduction to hands on, cutting edge scientific development.
The Princeton Vertical Farming Project focuses on the sustainability and energy efficiency of vertical farming as they study production rates of hydroponic engineering systems along with marketing and economic feasibility. Gauthier says, “Two of the main challenges that vertical farms are facing revolve around awareness and data sharing. Through establishing a resonant collaboration with the Hopewell Elementary School, the Princeton Vertical Farming Project hopes to educate new generations about the benefits of vertical farming, and to inspire them to expand their knowledge through the application of new, groundbreaking research and technologies, which the farm has been producing. Furthermore, this collaboration will create citizen science datasets, which will contribute to the improvement of the vertical farming field as a whole. By inspiring students today, we hope to shape the future of farming and reduce human impacts on the environment.”
Room to Grow–Princeton Vertical Farming Project Video:
Elementary students and teachers have embraced the homemade, nutritious lunch options infused with organic ingredients served in Hopewell Elementary’s cafeteria. Their community is excited for the new vertical farming initiative with the goal of featuring 100% of the lettuce in the cafeteria grown at the school. Additional vegetables and herbs will be grown, harvested and featured as well.
Principal David Friedrich’s passion for locally sourced, homemade, organic food for his students is evident in the Organic Menu offered at Hopewell. The menu is now in its third year and has seen a 50% increase in participation from the start.
Principal Friedrich said, “At Hopewell Elementary School, we are thrilled to expand the vertical farming initiative which reinforces our commitment to sustainability. As the first public school in New Jersey to offer an organic menu featuring homemade entrees, we will now be able to prepare more nutritious meals infused with our own vegetables and herbs grown and harvested by students. The project also supports hands-on, relevant and high-quality science instruction aligned to Next Generation Science Standards.”
Dr. Thomas Smith, Superintendent of Schools, said, “Lead by Mrs. Corveleyn and Principal David Friedrich, the Hopewell Elementary School has been a driving force in our district-wide sustainability efforts. The vertical farming project has captivated the interest of students and staff. By bridging the gap between science and nature, students can observe the real-life connection between farming and food by seeing what is necessary to grow and produce the food we eat. An important part of this project is that virtually all of the food grown in the vertical farm will be used in our school lunches.”
Children respond to living organisms in the classroom with excitement and passion. Typically in an elementary setting, animals and insects are a wonderful way to promote living organism studies, but at Hopewell Elementary School, they have captured a unique Next Generation Science Standards (NGSS)–aligned curriculum that is plant-based and integrates both life science and chemistry.
Corveleyn remarked, “No child is too young to understand hydroponics. The bottom line is, kids love planting something they know they can eat! Creating an opportunity for sustainable gardening for the future at a young age makes hydroponics not just a buzzword, but a way of life.”
Hopewell Elementary secured several grants to sustain the vertical farming project (click links for articles):
First Lettuce Harvested In Bio4safe Biostimulant Project
First Lettuce Harvested In Bio4safe Biostimulant Project
The Bio4safe biostimulant pilot project started off in August 2017. It's a collaboration between various partners from Belgium, France and the United Kingdom and is coordinated by the Belgian Test Center for Horticulture (PCS). They are researching the effects of biostimulants on nutrient use, tolerance against abiotic stress and crop quality. The aim of the project is to reduce water and fertilizer use by applying biostimulants in combination with innovative sensors.
In order to measure the effects of the biostimulants, various tests are being conducted with different crops, including tomatoes, lettuce, strawberries, chrysanthemums, and tulips. The lettuce tests take place at Pôle Légumes Région Nord in France. The first lettuce was harvested last week and is currently being examined by Yncréa Hauts de France, établissement ISA Lille (France).
Chrysanthemum trials
In a few weeks, Proeftuin Zwaagdijk will finish the first trials with chrysanthemums, which are investigating the effects of four different seaweed products and a mycorrhizal fungus. In addition to measuring the branch length and the fresh and dry weight, they will also analyze nitrogen absorption. A certain amount of the nitrogen isotope 15N has been applied to the potting soil in which the chrysanthemums are grown. By measuring the amount of this isotope present in the plants at the end of the test, it can be determined whether the biostimulants increased nitrogen absorption.
Seaweed as a biostimulant?
In addition to carrying out these tests, Noordzeeboerderij has worked on mapping both the existing and the potential biostimulant market. The potential of this market appears to be very substantial. Moreover, further research will be done about using seaweed as a biostimulant. For example, which varieties are being cultivated, and are they suitable for use as biostimulants?
Source: Proeftuin Zwaagdijk
Publication date: 5/21/2018
Lettuce Abound Farms Serves Up First Harvest From New London Aeroponics Operation
Lettuce Abound Farms Serves Up First Harvest From New London Aeroponics Operation
By Carolyn Lange on May 4, 2018
NEW LONDON — With plates heaped high with at least five varieties of lettuce picked that morning at an aeroponics farm a couple miles away, restaurant owners and volunteers working to bring a food cooperative to New London were clearly enjoying their salads.
They were also talking with the farm's owners about getting the fresh greens on the menu and on the shelves.
"Absolutely," said Leah Michaelis, owner of Lake Affect Coffee in New London, when asked if she would consider purchasing the leafy greens from Lettuce Abound Farms. "It's good and nearby and fresh."
Mateo Mackbee and his partner Erin Lucas, who will be opening Model Citizen Restaurant this month in the Goat Ridge Brewery in New London, said the locally grown greens will fit perfectly with the farm-to-market emphasis of their menu.
That's exactly the kind of reaction Kevin Ortenblad and Brian Dengler were hoping for when they invited several business owners and business leaders on a tour last week to see how their aeroponics lettuce is grown and to serve up a meal featuring their first harvest.
When Ortenblad and Dengler, along with their wives Julie Ortenblad and Melody Dengler, started the process 16 months ago to build the region's first commercial-scale aeroponics lettuce farm, they asked local grocery stores and restaurateurs if they would be interested in buying lettuce grown year-round in rural New London.
"They told us, 'let us know when you have something to taste,'" said Dengler, who is Ortenblad's son-in-law.
That time has arrived.
To show people how the lettuce is raised, how it tastes and how much it costs, the family-owned farm is giving tours and giving potential customers a taste of the product.
While building up their wholesale commercial base, individuals can purchase the lettuce from 9 a.m. to 4:30 p.m. directly from the farm site, 3825 County Road 40 N.E. The price is $2.25 a head.
"You pray at the end that people want it," said Dengler, who is also setting up private meetings with local grocery stores. Their goal is to sell their product to local vendors.
"We're very optimistic," Dengler said.
They're hoping that once people taste the greens, they'll be hooked.
"My life was rocked when I found out what real lettuce can taste like," Dengler said.
Lettuce Abound is the first franchise operation of the Faribault-based Living Greens Farm, which developed this type of aeroponics system.
Ortenblad and Dengler modified the system and, despite some challenges that delayed the start-up, they said the system is working flawlessly and plants are growing faster than expected.
The facility is housed in a farm machine shed they turned into an immaculate indoor farm that meets federal vegetable production and packaging standards.
After suiting up in a white jacket and hairnet, washing one's hands and stepping in a shallow shoe wash before entering the indoor farm, visitors see vertical walls of lush green lettuce.
The quantity and vibrancy of the edible greens stops visitors in their tracks.
When the facility is eventually in full year-round production, the 102- by 50-foot building will produce the equivalent of a 180-acre farm.
But these plants are grown without one grain of soil.
Instead, seeds for the greens — including butter lettuce, red and green oak leaf lettuce, romaine, arugula and microgreens — are hand-seeded in a product called "rock wool" that Dengler describes as crushed volcanic rock "spun like cotton candy."
After the seeds germinate and plants are a couple inches high, the chunks of rock wool are placed into panels with cup-like plastic containers and attached to 12 stainless steel A-frame units that are eight feet high and 32 feet long.
Each unit holds 1,536 lettuce plants.
The roots of the plants dangle in the air underneath the frame and are spritzed every 12 minutes with a mist of reverse osmosis water and fertilizer delivered through mechanical sprayers run by a complex computer program.
The water does not touch the leaves of the lettuce, and there are no pesticides used.
Banks of intense lights — which are so strong sunglasses are needed to work among the plants — help fuel the plants' rapid growth. (The lights are turned down during tours.)
The carbon dioxide level is carefully measured, the temperature is kept at 70-72, the humidity is at 55-65 percent and a fan blows air to mimic the wind and makes the indoor farm "smell amazing," Dengler said.
"Schedule is king," Dengler said of the enclosed system and computer program that controls nearly every aspect of the growing process.
It takes about a month from when seeds are started to when plants are harvested. During peak capacity, they will harvest three units, or about 4,600 heads of lettuce, every week, Ortenblad said.
The plan is to harvest lettuce on Thursday, and get it packaged and cooled and delivered on Friday.
They are gradually increasing the number of varieties of lettuce and will grow specific types of greens requested by large-scale customers, Dengler said.
While they're growing just lettuce now, they have already laid the groundwork for a potential expansion in a couple years for a new building to grow aeroponics strawberries and small cherry tomatoes.
Ortenblad, a retired farmer who raised organic soybeans in traditional fields near Willmar, said he is "having a ball" with this new project, in part because he gets to work with his family, including grandchildren, who help plants the seeds.
During the April blizzard, he teased his farmer friends that he was already working in his fields in a perfect climate-controlled environment surrounded by sumptuous green leaves ready to eat while they were waiting out the storm.
Grow Closer With Light Polymers’ GrowBlade® Horticultural Lighting
Grow Closer With Light Polymers’ GrowBlade® Horticultural Lighting
SAN FRANCISCO--Light Polymers, a nanochemistry innovator specializing in lyotropic liquid crystals, is launching a Beta-test program for its innovative GrowBlade® horticultural lighting. GrowBlade flat-panels use Light Polymers’ Crystallin™ remote phosphor film technology to let indoor farmers grow closer, delivering even, consistent lighting in a customizable range of rich crop-specific spectra. The GrowBlade has a long service life, running cooler and experiencing less spectrum shift and lumen drop over time than conventional LED grow lights. Better quality light in a thin, wide-area form factor is one key to higher farm productivity.
“As innovators in a range of specialty lighting markets, Light Polymers knows the importance of engaging potential customers effectively as part of our product development process,” said Sandor Schoichet, VP of Grow Products at Light Polymers Lighting. “To this end, Light Polymers is opening up its GrowBlade Beta-testing program to select vertical farm and controlled environment growers, with the twin goals of gaining real world production experience while better understanding the evolving needs of participating growers.”
GrowBlade Edge 300 and 600 panels (approximately 300x300mm or 1’x1’, and 300x600mm or 1’x2’) will be available to select early adopters starting in late May 2018. Longer GrowBlade Edge 1200 and 1500 models will become available in late 2018. Initial Beta-test lights are available in two standard spectra, with new tailored spectra to be added based on customer input. Introductory pricing for GrowBlade Edge 300 and 600 models is set at $129 and $189 respectively.
“Light Polymers has been busy starting production of our Crystallin film, developing specialty lighting product designs that are eye-safe and comfortable, with extraordinarily rich spectra,” said Marc McConnaughey, Chairman of the Board of Light Polymers Lighting. “We are excited to begin production of the GrowBlade and our other specialty lighting product lines based on our Crystallin film technology.”
GrowBlade lighting achieves a unique level of performance by leveraging our breakthrough Crystallin remote phosphor film, which eliminates ‘point-based’ lighting issues common to other LED lights. Instead of converting blue LED light to specific frequencies on each LED diode and then assembling a variety of specialized LEDs, GrowBlades use sheets of Crystallin film to convert the output of a blue LED array into an evenly distributed, consistent, fully diffused spectrum, while blocking problematic blue and UV wavelengths below 420nm.
This design also results in a slender form-factor just 15mm thick (not including the remote, dimmable LED driver). With evenly distributed light, efficient operation, and a low-profile, GrowBlade light can be placed closer to your plants to improve yields and crop consistency for greater productivity.
Contact us now for updates and early release notification.
About Light Polymers
Light Polymers is a nanochemistry company with deep domain knowledge and expertise in lyotropic liquid crystals, which have many applications including OLED displays, LED lighting and building materials. Light Polymers recently debuted a family of human-centric eye-safe task and study lighting. Founded in 2013 in San Francisco, Light Polymers has over 50 patents issued and pending for its water-based lyotropic liquid crystal nanochemistry. For more information, visit http://www.lightpolymers.com/.
Photo Report: 6th Annual Indoor Ag-Con
Photo Report: 6th Annual Indoor Ag-Con
Networking opportunities, interesting speakers and exploring new technologies. On the sixth edition of the Indoor Ag-Con it was al present and we will inform you completely on it. But first get ready for some photos!
Organizer Newbean Capital every year unites the indoor farming industry in the Las Vegas Convention Center and on May 3rd & 4th this year it was no different. Networking opportunities were the main reason for many visitors to come to the event, but also the talks of the big players in the industry were visited very well.
The emerging indoor growing market attracts also many opportunists and it becomes clear during the event a lot is still to explore in the indoor farming market. From financing to closing the chain and from special bred varieties to focussing on the market, the indoor farming industry is developing rapidly but offers many opportunities for further growth.
An important topic in the industry is the rise of new crops. After the leafy greens of course, cannabis is also a settled crop by now, but what else is on the horizon? Strawberries for sure, but also other medical plants and growing opportunities are talk of town.
Over the next couple of weeks, we'll update you completely on the opportunities in this growing industry. Let's take a look at some photos first!
Check out the photo report here.
Publication date: 5/7/2018
Author: Arlette Sijmonsma
Copyright: www.hortidaily.com
People, Power Costs Keep Indoor Farming Down To Earth
In this Jan. 18, 2018 photo, production manager Emy Kelty, left, and senior grower Molly Kreykes scan and monitor plants growing on towers in the grow room at the Plenty, Inc. office in South San Francisco, Calif. More than 30 high-tech companies from the U.S. to Singapore hoping to turn indoor farming into a major future food source, if only they can clear a stubborn hurdle: high costs. Jeff Chiu AP Photo
People, Power Costs Keep Indoor Farming Down To Earth
BY RYAN NAKASHIMAAP, Technology Writer May 10, 2018
South San Francisco, California
There's a budding industry that's trying to solve the problem of the limp lettuce and tasteless tomatoes in America's supermarkets.
It's full of technologists who grow crops in buildings instead of outdoors, short-cutting the need to prematurely harvest produce for a bumpy ride often thousands of miles to consumers in colder climes.
More than 30 high-tech companies from the U.S. to Singapore hoping to turn indoor farming into a major future food source, if only they can clear a stubborn hurdle: high costs.
These companies stack plants inside climate-controlled rooms, parse out nutrients and water and bathe them with a specialized light. It's all so consumers can enjoy tasty vegetables year-round using a fraction of the water and land that traditional farming requires. Farmers can even brag the produce is locally grown.
Thanks for subscribing; you should start to receive your newsletter shortly.
But real estate around cities is pricey. Electricity and labor don't come cheap. And unlike specialty crops like newly legal marijuana, veggies rarely command premium prices. (It's tough to compete with plants grown in dirt with free sunlight, after all.)
Even the best-funded indoor farming company on the planet — Plenty, which has raised nearly $230 million so far — has embraced a longtime farmers' crutch: government handouts. It hasn't found any takers yet.
"We believe society should consider investing in this new form of agriculture in the way it invested in agriculture in the 1940s," said Plenty CEO Matt Barnard in a recent interview.
Barnard says public aid — in the form of cheaper power — is one way to turn a good but elusive idea into a sustainable venture.
Last year, the U.S. paid farmers $9.3 billion in direct support, and subsidized weather-related crop insurance to the tune of $5.1 billion. In a nutshell, Barnard argues that some of that money could be diverted to crops that grow in rain or shine.
Plenty grows kale, mixed greens, basil and natural sweetener stevia in a grey, low-rise warehouse complex in the industrial suburb of South San Francisco.
Visitors arriving via the back door must don full-body overalls and rubber boots dipped in disinfecting shoe baths before entering the air-tight workspace.
Seedlings are grown on flatbeds and bathed in purple light that gives them the look of a 3D movie watched without glasses. Maturing plants are stuffed into columns where they grow sideways, fed by drip irrigation, and irradiated by columns of light-emitting diodes.
The plants will be clipped and packaged before heading to stores later this year.
But there are some noticeable gaps in the menu. There are no carrots or tomatoes, because long roots that grow down and vines that require human pruning don't do well on walls.
For indoor farms, making money has largely meant shipping in bulk to grocery stores, a conundrum if costs aren't in line.
Investment in indoor farming soared to $271 million last year, up from just $36 million in 2016, according to market research firm Cleantech Group.
"The question is, how are they going to scale?" asks Pawel Hardej, CEO of Civic Farms, a vertical farming consultancy in Austin, Texas.
There have been plenty of indoor farming failures already.
FarmedHere shuttered its operations in Louisville, Kentucky, and Bedford Park, Illinois, in January last year due to cost overruns.
Georgia-based PodPonics, which filed for bankruptcy in 2016, cited labor costs as its biggest drag.
Google's X, the search giant's secretive "moonshot factory," killed its indoor farming efforts because it couldn't grow food staples like grains and rice.
Even fans of the technology aren't sure it can beat another sheltered alternative: greenhouses.
"Vertical farming to a lot of (investors) is an 'if' and a 'maybe' versus a 'when,'" says Cleantech adviser Yoachim Haynes. "The question that needs to be answered is, 'Can they do it with cheaper electricity and cheaper labor?' This is not a question that many have been able to answer."
Barnard says Plenty can prosper if it spends 3 to 5 cents per kilowatt hour on power — well below the 10.4 cents that is the average price nationwide, according to the U.S. Energy Information Administration.
While Plenty announced plans to build a 100,000 square-foot facility in the Seattle suburb of Kent in November, it said it isn't in talks about power breaks with any U.S. city now.
Most public support has so far been in rebates for energy-efficient lighting, not running costs.
Seattle City Light provided $10,000 worth of energy-efficient lighting to an indoor growing facility that helped feed the city's homeless. But it already offers the lowest power rate of the top 25 cities in America. "That's the deal that's on the table," says spokesman Scott Thomsen.
Chicago provided some $344,000 in construction grants since 2008 to The Plant , a former pork processing plant that is home to multiple indoor farms.
While that helped with structural improvements, it didn't help with operations, says John Edel, the president of Bubbly Dynamics LLC, which owns The Plant.
Supplying grocery stores in large volumes is "harder than it sounds," he says. And other ways of obtaining cheap power — like The Plant's plan to install a bio-gas guzzling turbine — have faced obstacles that make it uneconomical.
"There isn't a whole lot in the way of incentives for farms here," Edel says. "There needs to be."
UK: Will EDEN ISS Plant Cultivation Technologies Deliver Terrestrial Applications?
UK: Will EDEN ISS Plant Cultivation Technologies Deliver Terrestrial Applications?
The EDEN ISS research project in Antarctica is designed to help astronauts grow food in space and on other planets. It has produced its first crop: 3.6kg of lettuce, 70 radishes and 18 cucumbers. But will the new technologies the project aims to develop be useful on Earth?
Evolution and Design of Environmentally-closed Nutrition Sources (EDEN)
The ISS EDEN plant cultivation project is led by the Institute for Space Systems (ISS), a consortium of experts in human spaceflight and controlled environment agriculture from academia and industry.
The ISS also aims to identify possible developments of closed or nearly closed-loop plant cultivation systems that would enable terrestrial agriculture to be conducted in regions that are currently unsuitable.
It’s not the first research project to attempt to grow food in conditions similar to those in space – and astronauts are already growing individual plants on the International Space Station - but the consortium is researching key technologies that it hopes will be relevant to large-scale food production in space and on Earth. These technologies include:
- Nutrient delivery systems
- Bio-detection and decontamination systems
- Food quality and safety
- High-performance LED lighting systems
- New UK research into LED lighting
Dr Jim Monaghan, Director of the Fresh Produce Research Centre at Harper Adams University, is working with Cambs Farm Growers (part of the G’s group) to develop the use of LED lighting in the commercial propagation of young vegetable transplants and production of leafy crops.
LED lighting could enable optimised transplant production for field crops and allow year round production of leafy crops in vertical or indoor production systems.
Normally, transplants of lettuce and celery are grown under protection (such as glass) in the UK but seasonal light and temperature changes influence the production time. By manipulating the light environment it is possible to control the duration of propagation as well as characteristics of the transplant that may be beneficial when planted on into the field.
Currently, baby leaf crops are mainly field-grown in the UK in spring and summer then imported in winter. Using indoor growing technologies may enable UK growers to supply a year-round crop with potentially enhanced nutritional status.
Dr Monaghan said: “We have seen how we can manipulate plant growth rates and morphology through using different LED light spectra. These effects may have significant benefits when the plants are moved into the field. One challenge is the cost of LED systems and it will be interesting to see the LED developments produced by EDEN ISS and how much energy is required to power them.
In addition to his work at Harper Adams University, Dr Monaghan also teaches fresh produce courses offered through the Agrifood Training Partnership. Topics include post-harvest quality and advanced agronomy. Last year Dr Monaghan was involved in a series of training workshops for growers focussed on managing food safety risks in the production of fresh produce crops.
Training opportunities with the Agrifood Training Partnership
The range of crops that make up fresh produce is wide, covering root crops, leafy vegetables, bush fruit and tree fruit. The fresh produce sector of agriculture is fast moving, innovative and high value. The constant pressure to improve efficiency and come up with new crops has led to significant innovations and refinements in growing methods.
The Agrifood Training Partnership offers a range of short and full-time courses on crops and fresh produce including production, quality management, plant pathogens, sustainability and agricultural drones.
Short courses starting soon
- Applied Precision Crop Production starts 27 May
- Advanced Agronomy for Fresh Produce starts 3 June
- Fresh Produce Postharvest Quality Management starts 4 June
Winter courses
- Advanced Sugar Beet Production Management starts 31 October
- Potato Production and Management starts 21 November
For more information about our short courses, contact us on 0330 333 4530.
For more information:
AgriFood Training Partnership
The University of Reading
PO Box 226, Whiteknights
Reading RG6 6AP
T. +44 (0)330 333 4530
www.aftp.co.uk
Publication date: 5/7/2018
Italy: ENEA Patents Field Simulator To Grow Plants Indoor
Italy: ENEA Patents Field Simulator To Grow Plants Indoor
Science and technological innovation are advancing day by day and often change our lifestyles. First and foremost, they benefit producers, although the concept of cultivation is no longer strictly connected to open fields. What used to be a simple veggie plot could potentially turn into a super-Hi Tech micro-plot that can be kept in the house.
Microcosm cultivation
ENEA patented and developed the first microcosm for the indoor and extreme-environment cultivation of plants with a root and an aerial part (fruit-bearing trees, lettuce, basil, tomatoes, potatoes). It's a true Hi Tech field simulator that makes it possible to grow plants in environments that would usually be unsuitable for plant growth such as airports, undergrounds and shopping malls as well as in extreme environments such as the Poles, desert areas or within space missions. It replicates the growth pattern, production of beneficial properties and biomass that occurs in nature.
Created in collaboration with private entrepreneur Gruppo FOS, this innovative smart-agriculture system differs from greenhouses and traditional growth chambers for a series of elements, starting from architecture, the network of sensors that monitor environmental control, plant growth and reproduction to the LED precision lighting system employing selected wavelengths.
Luigi d'Aquino from ENEA's Nanomaterial and Device Laboratory
"The main innovation is the double independent chambers. One is a subterranean chamber destined to the growth of the root system and rhizosphere (i.e. organisms that live in the soil where roots grow) and the other is an above-ground chamber destined to the cultivation of the aerial part of plants and the phyllosphere (i.e. organisms living in the air)," explains Luigi d'Aquino from ENEA's Nanomaterial and Device Laboratory.
Although the chambers are independent and can be managed separately, they are actually interconnected - just like it happens in nature - thanks to the geseous exchanges through the root growth substrate (soil, compost or peat).
"We're currently experimenting the effectiveness of the microcosm paired with precision lighting. We have sowed and cultivated a field of basil plants of the same variety in a pot in our lab (a typically inhospitable environment for plants), in a microcosm under white light (they grew much more) and in a microcosm under precision lighting (plants developed a biomass dozens of times higher, with higher chlorophyll levels and even started the reproductive phase)."
Ecosystems that can replicate nature
Microcosms are true ecosystems that can faithfully replicate what happens in open fields. Specific environmental conditions are set and there are organisms that interact with vegetable functions such as pathogens or parasites.
Microcosms have been developed within the TRIPODE public private laboratory and are currently being developed further within the ISAAC Project, co-financed with over €4.7 million by Horizon 2020 and PON Imprese & Competitività 2014-2020 (ENEA, FOS and BECAR, a subsidiary of Beghelli, are part of it).
"Over the next three years, the ISAAC Project also aims at developing an innovative lighting system to effectively grow, develop and reproduce plants indoor and in extreme environments as well as supporting the well-being of human beings. We will go from a TRL 4 (Technology Readiness Level) to a TRL 7, i.e. from lab prototypes to practical application prototypes."
Practical applications
"Our patent could be the base to develop prototypes for research labs studying plant physiology, pathology and parasites, ecophysiology, ecotoxicology and soil ecology but could also be useful to develop prototypes to promote plant cultivation in unconventional environments with excellent market and commercial potential."
Publication date: 5/7/2018
Copy of Growtainers Expands With Central Market, Looks to New Crops
For just about a year now, Central Market in Dallas has tested out offering produce that was grown on-site in a Growtainer. Evidently, that partnership has gone so well that Central Market is making the relationship more permanent and expanding it with the addition of another Growtainer.
Growtainers Expands With Central Market, Looks to New Crops
By Chris Albrecht | The Spoon
February 17, 2018
For just about a year now, Central Market in Dallas has tested out offering produce that was grown on-site in a Growtainer. Evidently, that partnership has gone so well that Central Market is making the relationship more permanent and expanding it with the addition of another Growtainer.
Growtainers are modified shipping containers that provide a food-safe indoor growing environment. Each one contains a vertical rack system for holding crops, crop-specific LED lighting fixtures, and a proprietary irrigation system. Growtainers come in 40, 45 and 53-foot sizes and are customized for each customer, costing anywhere from $75,000 – $125,000 a piece. The amount a Growtainer can produce depends on the crop.
The Growtainer at Central Market offers leafy greens and herbs grown on-site in a 53-foot container. While he couldn’t provide specific numbers, Growtainer Founder and President Glenn Behrman told me by phone that “demand outpaces supply” for the market’s store-grown produce. “We’ve proven the concept,” he said.
Central Market expanding its relationship with Growtainer helps push the idea of produce grown on-site more into the mainstream. Other players in this sector include Inafarm, which has been installing indoor vertical farming systems at food wholesalers in Berlin. And here at home, indoor farming startup Plenty raised $200 million last year from investors including Jeff Bezos (who happens to run Amazon, which owns Whole Foods).
As on-site farming technology improves and gets cheaper and easier to use, it’s not hard to imagine more stores opting to grow their own fresh produce in-house instead of having it transported across the country.
Behrman says that there are Growtainers all over the world for a variety of agricultural and pharmaceutical customers. He built two Growtainers for the Community Foodbank of Eastern Oklahoma so they could grow their own produce, and he’s talked with both the military and the United Nations about installing Growatiners for them in more remote (and volatile) areas.
One group Behrman hasn’t chatted with is venture capitalists. He laughed when I asked him about funding. “We have no investors, and we’re profitable,” said Behrman. But in the next breath, he said he realizes that his current go-it-alone approach won’t scale. “I think once this Central Market project expands and becomes more mainstream, I will have to look for some funding.”
Until that time, Behrman wants to have Growtainers produce more high value crops. “Lettuce and leafy greens are not that challenging,” he said. Behrman, who’s been in horticulture since 1971, believes Growtainers could be excellent for growing exotic mushrooms that have short shelf lives, or fungi that historically could only grow in particular seasons.
Perhaps after another year or so you’ll see truffles and porcinis grown on-site and offered at Central Market (and elsewhere).
Vertical Farm In Jackson Wyoming Offers Fresh Produce And Jobs For The Disabled
Vertical Farm In Jackson Wyoming Offers Fresh Produce And Jobs For The Disabled
The idea for Vertical Harvest first blossomed about 10 years ago, when three women from different backgrounds came together to solve a problem.
“Our growing season is only about four months long, so we shipped a lot of our produce in from other places,” said Vertical Harvest CEO Nona Yehia. “A friend of mine said she got some lettuce from the grocery and by the time she got it home, it was brown.”
Yehia said Jackson is also known for having a high unemployment rate for people with disabilities, something the three women believed they could cure with their business model.
Vertical Harvest uses a growing method called hydroponic farming.
“It means that you feed the plant through water so we don’t need soil in the greenhouse,” said Yehia. “So basically we have a growing medium that holds the roots for the plants and is basically a delivery device for the nutrients.”
Each of the three floors has a different micro-climate, allowing a variety of produce – from tomatoes to micro-greens – to thrive year round.
Sam Bartels: “If we have a hail storm outside if we have snow our plants are smugly watching from their high rise apartments,” said Vertical Harvest Director of Business Development Sam Bartels. “So there are a lot of benefits to growing indoors.”
On Tuesday, the temperature in Jackson was a cool 34 degrees, which is less than optimal for most growing.
But on the third floor of vertical harvest, they grow tomato plants that will be served on dinner plates in Jackson restaurants in just a few weeks time.
“When you go out and see your produce on a gorgeous plate and others enjoying it and commenting on the quality of the produce, it’s incredibly rewarding,” said Barels.
It’s a feeling shared not only by the company’s three female co-owners, but Vertical Harvest’s 15 employees, who now have an opportunity like never before.
Johnny Fifles, like most of his co-workers, has a developmental disability. It’s something that limited his employment options for years.
“I used to work at the Elk Country Inn,” said Fifles. “I had to fold laundry and carry bags of dirty laundry.”
But at Vertical Harvest, Fifles and Sean Stone find purpose. “It’s a great job,” said Stone. “It’s good for the environment and it’s healthy for people that buy this stuff from us.”
“It’s really shifted the perception of what this population is able to do and I think that story brings people to vertical harvest first and then they keep coming back because of the quality of the produce,” said Yehia.
Customers return for both the quality and the quantity, because Vertical Harvest produces 10 acres worth of fruits, vegetables and herbs on just a tenth of an acre.
Vertical Harvest distributes produce to multiple restaurants in Jackson and soon, it will be able to distribute to grocery chains like Albertson’s following its recent Good Agricultural Practices (GAP) certification.
While the idea clearly works today, skeptics had their doubts. “It’s a pretty far out thing to say to someone, we’re going to grow this 3-story high greenhouse in Jackson when it’s minus 20 degrees out and we’re going to employ these different growing methods that have never been done before and employ all these people with disabilities and people might be inclined to think that’s a bit much to bite off,” said Bartels. “But I think anyone with doubts has not only become a believer but has become an advocate.”
It’s a system of support the team at Vertical Harvest hopes to achieve in the five other communities they’ve pegged for future development.
“It’s all about pairing innovation with an under-served community and in Jackson that’s people with disabilities,” said Bartels. “But in other towns that might be veterans or ex-felons or the homeless so we’re excited to go do good elsewhere.”
The greenhouse is open to tours.
Source: KTVH
Publication date: 5/4/2018
Can A Nozzle Provide The Breakthrough Indoor Farming Has Been Waiting For?
Can A Nozzle Provide The Breakthrough Indoor Farming Has Been Waiting For?
3 May 2018, by Gavin McEwan
A British company says it can greatly extend the range of crops grown in indoor growing formats beyond the established leafy greens and herbs.
Images: Airponix
Discussions on the potential of urban and indoor farming invariably mention the need to feed a growing global population, forecast to reach 10 billion by the middle of the century, against a backdrop of climate change and depleted land and other resources.
But so far, for technical and economic reasons, the movement has largely targeted leafy greens and herbs — relatively high-value but low-mass, low-calorie crops. Indeed, one successful London grower specialises in "micro-salads" sought by higher-end retailers and restaurants that, for all their merits, are unlikely to displace much conventional farming or address food supply in the developing world.
This may be about to change though, thanks to a technological breakthrough by a British company. West London-based Airponix says it has overcome an obstacle to growing more high-calorie crops, thanks to spray nozzles adapted from printers.
Aeroponics is a variant of hydroponic growing in which plants’ roots are exposed to a nutrient-rich mist within a chamber, rather than sitting in a circulating water-and-nutrient solution. Like other indoor growing technologies, aeroponics has so far found a market in hobby growing more readily than in commercial horticulture, with several UK suppliers offering variants on the format on a range of scales.
That said, aeroponics is also the basis of what is claimed to be the world's largest commercial indoor growing facility, run by AeroFarms in a former steel mill in New Jersey, USA, and employing its own multi-tiered variant of the technology in combination with LED lighting to produce up to 900 tonnes of fresh produce a year.
But this too grows only salads. What has so far restricted aeroponic growing to such crops, Airponix explains, is that the size of the droplets in the chamber causes them to coalesce, precipitate out of the air and form larger droplets on the roots, inhibiting the uptake of nutrients and encouraging the growth of wastefully long roots.
Nutrient-rich 'fogs'
To address this, Airponix has worked with a developer of piezoelectric inkjet technology to engineer print heads that can emit nutrient-rich "fogs" — a term that Airponix contrasts with the "mists" of conventional aeroponics — comprising droplets that can be greatly reduced in size to below 20 microns, and indeed optimised to the needs of the particular crop.
These print heads also require less energy than other fog-making methods, are highly reliable and easy to install or replace under field conditions, says Airponix.
This allows the technology to extend into growing soft fruits, grapes, brassicas, root crops and even the cereal staples of rice, wheat and maize. Airponix says its own small-scale potato-growing trials show typical yields are around 50 times greater per hectare per year than from conventional farming, without the expense of heavy machinery, diesel or crop-protection products. Rather than capital-intensive glasshouses, or tech-heavy enclosed controlled growing environments, the growing system can be housed in simple polytunnels.
Airponix chief executive Michael Ruggier says: "Trials of our breakthrough technology show that we can produce crops such as potatoes with lower production costs and higher quality, competing strongly against conventionally grown new baby potatoes."
He adds: "The potential cost of the system is very low and requires little energy to operate. Manual labour is also greatly reduced because harvesting is a simple, clean process and root crops don't need washing."
Ruggier co-founded the company in 2016 with John Prewer, now its technical director, who developed and patented an early form of aeroponic growing more than 40 years ago, while its horticulturist and operations manager Barry Robertson was previously head of controlled environment horticulture at the John Innes Centre.
The technology has already garnered awards, including being named the overall winner in the Rushlight Awards for novel, clean technologies in January.
A-frame units
Airponix has now equipped a 1,000sq m glasshouse in Norfolk with its A-framed potato-growing units for development, testing and demonstration, thanks to a half-million-pound loan from Centrica Innovations. The glasshouse incorporates further growth-enhancement techniques such as imparting an electrostatic charge on the droplets for better adherence to and absorbption by the plants’ leaves and roots. A smart, fully automated system, operated by a mobile phone app, is also being developed.
The aim initially is "to demonstrate the yield quantities and the costs associated so that next year Airponix will be in a position to licence the technology", says a company representative, adding that it will also provide samples of the first crop, due next month, to supermarket retailers for evaluation.
"The type of potatoes that Airponix can grow and harvest are unlike anything currently being sold anywhere and has huge potential in both the fresh-produce and snacks categories," he points out. The company also hopes that selling this year’s remaining crop will provide revenue to enable it to extend its own glasshouse space and growing facilities next year.
Controlled Environments: The Future of Small-Scale Agriculture
Controlled Environments: The Future of Small-Scale Agriculture
April 25, 2018 | By Ted Tanner, CEO and Co-Founder | Agriculture, Technology
Many experts believe small-scale agriculture is the future of growing. For those who choose that path, success may be closely tied to controlled environments and the use of agricultural technologies.
To understand how ag-tech drives success in small-scale farming, it's important to first take a closer look at small-scale agriculture: what it is, how it works, and why some envision it as the logical next step for the agricultural industry..
Thinking Small
For decades, agriculture has been dominated by a push toward larger farms with bigger grow operations that leverage various means to produce massive yields at low costs. But this kind of farming, sometimes called “factory farming,” has come with a price.
This mode of agriculture is devouring resources such as land and water. In the U.S. alone, agriculture accounts for 80 percent of ground and surface water usage, according to the United States Department of Agriculture's (USDA) Economic Research Service. In many Western states, that number is as high as 90 percent. Big farms require a lot of labor, at a time when available farm labor is shrinking. Big farms also tend to be geographically removed from consumers, which increases food costs and the level of greenhouse gases produced because goods are trucked long distances to consumers.
Small-scale farms offer an attractive alternative.
With smaller farms, there are more options available. Farming can happen all over the world—even in more densely populated areas. With small-scale farming, food is fresh and grown locally year-round. Smaller agricultural systems are also more flexible, adapting to changing climate conditions and showing a greater resilience than large farms, according to small-scale farmers like California farmer Nikiko Masumoto.
A smaller grow enterprise can bring a new economic dimension into play, making agriculture a more commercially viable endeavor.
“Since small scale farmers tend to sell their products directly to consumers, they manage to avoid the middlemen. This means they can offer locally-grown, affordable, fresh, and sustainable food anywhere year-round,” according to Farming Solutions, a site that champions sustainable farming solutions for the future
How Ag-Tech Helps
Although big farms generate vast quantities of agricultural goods, small farms are making inroads. Globally, the Food and Agriculture Organization of the United Nations reports that farms of less than one hectare account for 72 percent of all farms. The USDA National Agricultural Statistics Service Census of Agriculture, which occurs every five years, revealed in 2012 that small-scale family farms account for 88 percent of all U.S. farms.
Technological innovation can be a key driver of success for the small-scale farm, because a smaller grow space is inherently more controllable than a vast span of acreage. By applying agricultural controls, the grower can drive bigger yields with less effort at a lower cost.
A controlled environment allows for a small-scale farmer to manage a range of variables that might otherwise prove a detriment to productivity. Nutrients and irrigation, soil quality, and pest control all can be managed effectively using sensors for environmental monitoring and app-based smartphone systems for automation and 24/7 remote access.
Using the latest ag-tech, a grower can keep a watchful eye on variables such as heat, light, humidity, and soil conditions—without being present on-site. The grower can adjust conditions remotely and program automated routines to maximize efficiency and predictability in agricultural activities.
Smart systems take advantage of the small-scale farm’s inherent advantages: its smallness and self-contained nature. The small-scale farm is by design a manageable space, and growers who implement ag-tech solutions to manage the land can drive dramatically enhanced results.
There is a trend to break away from industrial agriculture. Consumers have grown skeptical of the factory farm, with its weighty environmental impacts and commoditization of the agricultural process. There is a call for something more authentic, something simpler and closer to home.
Growers who tap into that trend can find a valuable niche among consumers. By going small and using technology to maximize profitability, savvy growers can establish a unique position for themselves in an increasingly competitive marketplace.
Osram Advances to Become a Leader in Digital Farming Solutions with Acquisition of Texas-Based Fluence Bioengineering
Osram Advances to Become a Leader in Digital Farming Solutions with Acquisition of Texas-Based Fluence Bioengineering
Businesswire
May. 3, 2018
Osram is taking the next step in its quest to become the leading provider of intelligent plant growth solutions by acquiring Fluence Bioengineering, Inc. of Austin, Texas. Fluence was founded in 2013, has approximately 95 employees and its 2017 sales were in the mid-double-digit millions of dollars (USD). The company specializes in LED-based horticultural systems, using OSRAM LED chips, for a wide variety of applications including vertical farming, especially in urban areas. Potential crops range from salad greens and herbs to medicinal plants. Osram and Fluence have agreed not to disclose the purchase price.
"Fluence is opening the floodgates to a huge future market,” said Stefan Kampmann, CTO of OSRAM Licht AG. "Its extensive knowledge of the horticulture market and possible applications, combined with Osram’s expertise in lighting technologies, sensors and connectivity, will position us as a leading horticultural solutions provider.” Associated smart farming software can be integrated into Osram’s Internet of Things (IoT) platform Lightelligence, which brings the digitalization of lighting control to a new level. By combining and analyzing sensor data, Lightelligence enables significant progress in automation and intelligent applications far beyond lighting.
Increasing population and continued urbanization are intensifying the demand for fresh food, especially in densely populated cities around the world. To meet the needs of these areas, growers must tap the potential of greenhouses and vertical cultivation systems, utilizing smart lighting, sensor systems and artificial intelligence. In addition to growing healthy and flavorful food, vertical farms reduce the need for long-distance transportation routes. They also lessen the need for pesticides, fertilizers and excessive water use, and ultimately reduce spoilage. These technologies, which also can be used for growers of medicinal plants, contribute to the goal of sustainable agriculture.
LED-based solutions from Fluence help growers meet their yield and sustainability goals by increasing harvests up to 25 percent, reducing energy costs by as much as 50 percent and, through the targeted use of light, improving the quality and nutritional content of plants. Considering also that approximately 40 percent of food is spoiled between the producer and the supermarket shelf, there is an additional ecological aspect to benefit the smart farming approach.
"In the future, self-learning software algorithms will create and optimize digital plant models in order to cultivate tailor-made salads and herbs for platform partners such as supermarkets, online grocery shops and pharmaceutical companies,” Kampmann said.
Osram has increased its involvement in the horticulture sector over the last several years. The company has developed research and specialty luminaires that enable tailor-made light recipes to be controlled for specific plant types. In 2017, Osram invested in the Munich-based startup Agrilution which develops grow boxes with LED lighting for home use.
Fluence Bioengineering, upon closing, will be positioned within Osram’s Professional and Industrial Applications segment in the Specialty Lighting business unit. "We are excited to be teaming up with Osram to drive forward this global expansion and expand our digital product portfolio. Our new and existing customers will benefit from our partnership with Osram in all matters relating to light and sensors”, said Fluence CEO Nick Klase.
ABOUT OSRAM
OSRAM, based in Munich, is a leading global high-tech company with a history dating back more than 110 years. Primarily focused on semiconductor-based technologies, our products are used in highly diverse applications ranging from virtual reality to autonomous driving and from smartphones to smart and connected lighting solutions in buildings and cities. OSRAM uses the endless possibilities of light to improve the quality of life for individuals and communities. OSRAM’s innovations enable people all over the world not only to see better, but also to communicate, travel, work and live better. OSRAM has approximately 26,400 employees worldwide as of end of fiscal 2017 (September 30) and generated revenue of more than €4.1 billion. The company is listed on the stock exchanges in Frankfurt and Munich (ISIN: DE000LED4000; WKN: LED 400; trading symbol: OSR). Further information can be found at www.osram.com.
ABOUT FLUENCE
Fluence specializes in LED-based horticultural systems for a wide variety of applications including vertical farming. Its customers are agricultural producers in indoor locations such as high-rise buildings. Potential applications range from salad vegetables and herbs to medicinal plants. For more information go to https://fluence.science/.
Disclaimer
This document contains forward-looking statements and information, i.e. statements about events that lie in the future rather than the past. These forward-looking statements can be identified by words such as 'expect', 'want', 'anticipate', 'intend', 'plan', 'believe', 'seek', 'estimate', 'will', and 'predict'. Such statements are based on current expectations and certain assumptions made by OSRAM's management, so they are subject to various risks and uncertainties. A wide range of factors, many of which are beyond OSRAM's control, have an influence on the business activities, success, business strategy, and results of OSRAM. These factors may cause the actual results, success, and performance of OSRAM to differ significantly from those expressly or implicitly communicated in the forward-looking statements or from those that are expected on the basis of past trends. In particular, these factors include, but are not limited to, the circumstances described in the report on risks and opportunities contained in the annual report of the OSRAM Licht Group. If one or more of these risks or uncertainties materializes, or should the underlying assumptions prove incorrect, the actual results, performance, and success of OSRAM may differ significantly from those described in forward-looking statements as being expected, anticipated, intended, planned, believed, sought, estimated, or projected. OSRAM assumes no obligation, nor does it intend, to update these forward-looking statements above and beyond the legal requirements or to adjust them in light of unexpected developments. Due to rounding, numbers presented in this and other reports may not add up precisely to the totals provided and percentages may not precisely reflect the absolute figures to which they relate.
This Former Steel Mill Will Soon Be A Tech-Filled Greenhouse
- 05.07.18
This Former Steel Mill Will Soon Be A Tech-Filled Greenhouse
The next Gotham Greens location will convert old industry in Baltimore into a hydroponic farm, to provide local produce (and jobs).
1/8 [Photo: Gotham Greens]
For decades, a sprawling steel mill in Baltimore, Maryland was a key site for American industry, making steel for World War II battleships and the Golden Gate Bridge. By the year 2000, however, the industry was failing, and site owner Bethlehem Steel declared bankruptcy. Now, one corner of vacant land at the former mill will become an indoor farm growing pesticide-free lettuce in a sensor-filled greenhouse.
“I think what we’re doing is sort of representing 21st-century manufacturing,” says Viraj Puri, co-founder, and CEO of Gotham Greens, the Brooklyn-based urban agriculture company building the new greenhouse. “This, at one point, was the largest steel-producing facility in the world. It employed tens of thousands of people. Those jobs disappeared when the global steel industry changed . . . we’re coming in and helping to revitalize [the economy] and produce jobs that represent this innovative, technologically advanced way to produce food.”
In New York City, the company pioneered using large rooftop greenhouses to grow greens with no soil, no pesticides, and far less space and water than traditional farming in fields. Most lettuce, grown in areas with limited water like Arizona and California, is shipped thousands of miles to consumers on the East Coast. Gotham Greens, like other startups in the urban farming space, wanted to offer consumers fresher produce that used fewer resources.
After opening its first Brooklyn greenhouse in 2011, the company built another on top of a local Whole Foods. A third greenhouse, in Chicago, sits on top of a sustainably designed factory on a former brownfield. A second Chicago location, next to the first, will be complete by the end of this year.
Gotham Greens Chicago [Photo: Julie McMahon/Gotham Greens]
In Baltimore, as in the other cities, the company will provide both low-skill farming and packing jobs and high-skill jobs in horticulture and engineering. The site, now run by a company Tradepoint Atlantic, will now include a mix of occupants rather than a single industry (Tradepoint Atlantic is the fifth owner since the steel mill closed in 2000; the first four tried to revive steel manufacturing there and failed.) UnderArmour and FedEx will use the site for distribution, and others are using it for vehicle importing. But Gotham Greens represents a different type of industry.
It won’t be the first indoor farm at a former steel industry site. In Newark, New Jersey, the vertical farming company AeroFarms grows baby greens where a former steel factory once operated. Because the farms use hydroponic systems–growing without soil, indoors–it’s possible to grow anywhere, including on the ruins of heavy industry.
The new greenhouse in Baltimore will create 60 jobs. That’s far fewer than the 30,000 jobs the former steel plant provided at its height in the middle of the 20th century (though steel mills now use only a tiny fraction of the labor they once did). Puri says that the operation in Baltimore could triple over time.
The company also plans to continue expanding to other cities, albeit slowly. “We are producing a lot of lettuce,” says Puri. “We’re doing about 20 million heads a year. So we’re definitely large-scale at this point. But in order to maintain product quality, consistency, and food safety, which is incredibly important, we didn’t want to rush into opening more facilities than we thought we could effectively, efficiently manage. It’s a measured, step by step approach. We’re assessing sites in other cities as well. Our vision is certainly to have a network of urban greenhouse farms in cities throughout the country.”
ABOUT THE AUTHOR
Adele Peters is a staff writer at Fast Company who focuses on solutions to some of the world's largest problems, from climate change to homelessness. Previously, she worked with GOOD, BioLite, and the Sustainable Products and Solutions program at UC Berkeley.