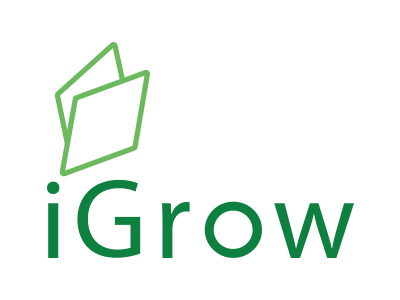
Welcome to iGrow News, Your Source for the World of Indoor Vertical Farming
BIG Reveals Miami Produce Center Raised On Stilts Above Former Warehouses
Eleanor Gibson | July 8, 2018
Architecture firm BIG has released plans to build a major complex in an industrial neighborhood of Miami, combining housing, offices, a school, and urban farming.
BIG's Miami Produce Center will be elevated on columns above a trio of warehouses in Allapattah – a district known for a large open-air produce and textile markets.
The 125,000-square-metre complex will comprise a stack of eight volumes, containing co-working offices, co-living apartments, and a hotel. The three existing buildings traversing the site will also be transformed as part of the scheme into restaurants, shops and cafes, and a school.
Newly released renderings show ground-level spaces around each structure will be landscaped into gardens. A street will run through the middle of the site, which will include an educational campus. Large expanses of glazing will be added to the front of the renovated low-rise warehouses to open up the interiors to the outdoor space.
"Between the warehouses, three public spaces will exhibit a variety of lush landscapes that create diverse microclimates and allow the buildings' programmes to extend outdoors," said a project description from BIG, which just completed a pair of skyscrapers in Shenzhen.
Related story
BIG completes
pair of twisting towers in Miami's Coconut Grove
Four long buildings will then be raised on slender stilts above the warehouses and arranged around the perimeter of the site.
Each will host a different function – one for offices, another for a hotel and two for residences – with outdoor space on the rooftops. The images show sports courts, parkland, and rows that suggest vegetable planting. BIG describes an aim of the project as to activate the site with "urban farming".
Another four residential blocks will then be built above, bridging the gaps between the lower volumes. These will also be raised on stilts and feature rooftop gardens.
"Large industrial floor plates" will make up the levels in each new building, allowing for plenty of flexibility inside.
Zigzagging walls between the plates will create outdoor nooks, while their offset arrangement will produce patterns across the facades. These walls will be colored pale pink, orange or blue, depending on their block.
An abundance of planting is planned for the development – from gardens and walkway canopies to the car park, where greenery will drape through gaps in the ceiling. A night-time rendering of the garage also shows it transformed into a nightclub.
BIG designed the Miami Produce Center for local real-estate company UIA Management, with American planning, engineering, and design consulting firm Kimley Horn.
It marks the firm's second major project in the city, joining the luxury housing development is completed in the Coconut Grove neighborhood in 2016.
The firm, founded by Danish architect Bjarke Ingels in 2005, is working on several projects across North America. In New York, where it has an office, these include a barrier system designed to protect Lower Manhattan from tidal surges and rising sea levels, and a pair of "dancing" towers beside the city's High Line park.
Related story
Pleated facades cover
pair of Shenzhen skyscrapers by BIG
Project credits:
Partners-in-charge: Bjarke Ingels, Agustin Perez Torres, Thomas Christoffersen
Project leader: Shane Dalke
Project team: Agne Rapkeviciute, Chris Tron, Emily Chen, Emine Halefoglu, Karolina Bourou, Kevin Pham, Kig Veerasunthorn, Manon Otto, Matthijs Engele, Phillip MacDougall, Siva Sepehry Nejad, Terrence Chew, Tracy Sodder, Veronica Acosta, Xander Shambaugh
Sustenir Sows The Seeds of Success
Company plows efforts into high-tech methods of farming to maximize land-use and yield while reducing wastage.
July 31, 2018
Sustenir is an urban farming company that uses controlled environment agriculture to grow non-native plants in Singapore. Seen here are regional sales manager Jack Moy (left) and co-founder Benjamin Swan. The company is also looking at using AI to monitor plant growth. BT PHOTO: LEE JIA WEN
GROWING cold-weather crops such as strawberries and kale in Singapore might seem impossible to many, but that is exactly what Sustenir Agriculture is doing.
Since 2014, Sustenir has been using high-tech methods such as controlled environment agriculture (CEA), vertical farming, and hydroponics to grow a variety of non-native plants indoors.
For co-founder Benjamin Swan, this unlikely agricultural venture is far from frivolous. He sees it as an important environmental move: "It was really my opportunity to do the right thing, to fight the good fight, you know. This was something that needed to happen."
Cultivating an idea
The idea first came to Mr. Swan when he read an article about vertical farming on his MRT ride home from work in 2012 - and felt that current methods were not efficient enough.
"The illustrations that I saw, they were wasting a lot of space. It may work in the United States where there is a lot of space, but in Singapore and Hong Kong, where land is scarce and rent is high. It just wouldn't work wasting space like that," he says.
That night, the then-engineer and project manager designed more compact versions.
Much of that early design work has translated to Sustenir's commercial farm in Admiralty today, which covers an area of 10,000 square feet (approximately 930 square metres).
While keeping his day job, the budding indoor farmer spent his weekends and after-office hours connecting with academics and farmers from all over the world to learn more about this industry.
"I took bites from what everyone was doing, because everyone was doing things so differently, and from that, I just formed my own hypothesis on how growing would happen."
With the knowledge gained, he focused on "growing impossible products at impossible places".
His first impossible place was the basement of a swimming facility in April 2013. There, he experimented with varying light wavelengths, nutrient solutions, carbon dioxide levels, and many other variables to find the optimum conditions for different species of plants to grow.
"I was growing kale by tricking the plant into thinking it was cold by chilling the water. It was there that I learned the power of a controlled environment. You just need to think outside the box."
After seeing the fruits of his labor, he decided to become a full-time farmer. The construction of Sustenir's facility in Admiralty started in October that year.
Mr. Swan wanted to use the budding technology of CEA to address the growing issue of environmental sustainability.
"If we keep going with farming the way it's being done right now, we're going to need farming land the size of Brazil by 2050 to feed the growing population. That means more deforestation, more pesticide run-off into rivers killing fish - it's not great.
"It's not to say that traditional farming is the devil, but we're saying that we need to fix it because it's not sustainable."
Through Sustenir's methods of vertical farming, land can be optimized to obtain more yield.
In an area of 54 square metres, Sustenir produces 1 tonne of kale or 3.2 tonnes of lettuce per month.
According to some reports, this can be 14 to 127 times more than the yield produced through traditional farming on the same area of land, depending on the climate.
Unlike traditional outdoor farming, vertical farming is not affected by seasonal changes. This allows for continuous production.
This form of farming also reduces water consumption, as the harvested crops do not need to be washed before they are consumed.
Sustenir keeps the plants clean by keeping external air pollutants out of the growing area and by having staff put on clean-room suits before they enter. This cleanliness is then maintained by packing the produce in airtight containers.
Producing non-native plants locally also reduces the ecological footprint from transport and food waste.
"Thirty-three percent of produce is wasted in the logistics alone before it even gets to the merchants," says Mr. Swan. "Then the merchants also have wastage as well. It's what they call shrinkage."
Sustenir further reduces wastage by using all of its yields. Physically imperfect specimens are made into juice instead of being thrown away.
"Sometimes during the harvesting process, we could be a bit rough and the leaves are not perfect, so we don't sell those to retail," says general manager Jack Moy. "What we do is find a way to repurpose this, because they taste equally good and they have the same nutrition."
To support Singapore's self-sustainability - at least where greens are concerned - Sustenir does not grow local produce. Instead, the firm aims to grow imported veggies which are popular among residents.
"We put our customers at the heart of all our decisions," says Mr. Swan.
For instance, after learning that many Singaporeans are fans of Japanese and Korean strawberries, Sustenir made that fruit its newest project.
Officially launched on June 20 this year, the strawberries have enjoyed substantial demand - so much so that Sustenir plans to allocate more space in its farm for growing the fruit.
Unfortunately, not all its products were equally well-received.
Upon the launch of its kale, the Sustenir team gave out samples at Cold Storage stores, only to find that many locals do not enjoy the vegetable's tough texture and bitter taste.
Mr Swan then went back to the "grow room" - as the growing area is dubbed - and altered the environment to reduce these unpopular attributes of kale, resulting in a softer-leaf, less bitter product.
The team also visits farmers' markets to study customer preferences. This feedback is used to modify produce, for instance by cultivating sweeter strawberries or milder arugula.
Mr. Swan hopes to apply the same CEA methods to maximize the nutrients in plants and grow them for medicinal purposes, too.
Sustenir is also working on developing local grapes and wine.
Leveraging technology
Apart from its own techniques, Sustenir taps external technologies for greater efficiency.
Through Spring Singapore - now Enterprise Singapore, after its merger with International Enterprise Singapore - Sustenir partnered PBA Systems to create robotic arms for seeding. One robotic arm does the work of three people.
Sustenir also works with educational institutions such as the National University of Singapore (NUS) and the Singapore Institute of Technology (SIT) to boost awareness of and interest in the industry.
After learning about vertical farming and CEA, students get the opportunity to develop projects and help the company in its green journey.
Says Mr. Moy: "It's kind of like an internship. We even bring NUS (students) onto the business side where they can help with the marketing."
Ideas which the firm finds feasible will be commercialized, he adds. "So it's really cool for the students. They can be proud to share that they worked with Sustenir to create a new innovation that customers love."
In line with its zero-waste policy, Sustenir is working with SIT to find the most suitable way to turn physically imperfect kale into kale powder.
The company is currently exploring different ways of drying the vegetable - from spray drying to vacuum drying - to find one that retains the most nutritional value.
Another technology Sustenir is looking at is artificial intelligence, which can be used to monitor plant growth and detect problems so they can be nipped in the bud.
Says Mr. Swan: "We're working with companies right now to work on our own in-house AI technology, to not only help us monitor and track plant growth, but to also help with the whole farming system. Everything from upstream with the resource materials to downstream with the ERP (enterprise resource planning) system." He declined to reveal the companies.
Sustenir also plans to create an online platform, Sustenir Life, to educate consumers on health, fitness, and vertical farming.
The company will work with health and fitness professionals, environmentalists and charities to share their stories and promote their causes on the blog-like platform.
All this is in the service of a larger, industry-level goal: changing the nature of outdoor farming, too.
"That's really the future of Sustenir," says Mr. Swan. "It's to take technology and help outdoor farmers - through our center of excellence in indoor farming - to apply smart technology into their farms, to optimize their farming programmes."
This is another reason Sustenir does not grow local produce. This ensures it does not compete with local farmers, instead of complementing their existing products.
Currently, Sustenir's cold-weather crops can be found at select Cold Storage outlets and online at Redmart. Sustenir also supplies food chains, restaurants and hotels such as SaladStop!, Les Amis and Shangri-La.
Mr Swan hopes to expand to other countries. "We're going to start with Asia-Pacific. In all heavily urbanized cities in Asia, we want to have Sustenir."
The company is building a 50,000 square foot facility in Hong Kong and is working with local farmers in Indonesia and Malaysia to integrate smart technology - such as the robotic seeding arm - into their traditional methods.
Outdoor farmers can also tap Sustenir's research findings for optimal growth, for instance by varying the pH levels of water in response to changes in climate and temperature.
Ultimately, Mr. Swan envisions Sustenir broadening its reach to the whole world: "It's time for a change in agriculture."
Brought to you by The Future Economy Council
How To Go From City Living To Urban Farming In Six Months
July 2018
Photos by Matthew Modoono/Northeastern University
Do you know where your leafy greens come from? If you’re dining at a restaurant in Boston, there’s a good chance the salad greens you’re eating have been grown by two friends inside a small apartment in the city’s South End neighborhood.
Oliver Homberg and Matt Alto, two recent graduates of Northeastern, founded Boston Microgreens six months ago with little farming experience. But now they’re selling tray upon tray of tender leafy greens to home cooks and chefs from 30 Boston restaurants, including Uni, O Ya, Ostra, and Sorellina.
“Basically we just started growing stuff for ourselves, and then we got obsessed,” said Homberg, who studied international affairs and sustainable development at Northeastern. “We learned everything we know from videos on YouTube.”
The young entrepreneurs keep two hobby gardens that are bursting with corn, kale, carrots, melons, edible Borage flowers, summer squash, Bibb lettuce, purple Kohlrabi, zucchini, pickling cucumbers, and raspberries, which Alto picked as a kid.
But it’s microgreens—which can be used to add depth to a salad, crunch to a sandwich, or flavor to a dish—that are their specialty.
As their name suggests, microgreens are the first small leafy shoots produced by vegetables such as radishes, peas, and kale. Alto and Homberg cut the shoots before the vegetable has time to mature, which makes them especially flavorful and nutrient-dense. Their purple Sango radish microgreen, for example, is a tiny purple sprout of leaves that has all the spicy bitterness of a full-grown radish.
Because the plants are so young and tender, it’s important to move the greens from the soil to the plate as soon as possible, said Homberg.
“Chefs love these because we’re local,” he said. “We cut and deliver the greens the same morning, so they know they’re getting super fresh ingredients that haven’t been in the back of a refrigerated truck for a week.”
Being a local farmer in Boston’s densely-developed, land-poor South End neighborhood is hard work.
Homberg and Alto have converted their apartment into a modern greenhouse, which includes one room dedicated to growing their greens. Three days a week, they sprinkle hundreds of partly-germinated seeds onto 10-inch by 20-inch trays filled with soil. They cover the seeds with more soil and then water them to start the growing process.
Once those seeds begin to sprout, they put the tray on a shelf outfitted with fluorescent lights and a watering system, leave the seeds to grow for anywhere from a few days to a few weeks, and then cut and package the greens for delivery.
“It can all be done in the middle of your living room,” said Alto, who studied mechanical engineering and material science at Northeastern.
Homberg and Alto, who graduated in May, say they have applied the lessons they learned in class to help them become successful urban farmers.
Alto credited his engineering coursework with helping him develop and build many of the irrigation and growing systems they use to farm, including a water-based growing unit. Homberg said his business courses primed him to—pardon the pun—grow a business from the ground up.
They plan to expand the business. They’re looking for a bigger space to grow microgreens and hope to partner with local elementary schools to bring kids into their outdoor gardens.
“Growing up, I was that kid who just ate whatever without thinking about it,” Alto said. “To have the opportunity now to be in control of the whole process—that’s something we want to share with as many people as possible.”
Society & Culture Boston Microgreens Farming gardening
hobby garden microgreens Restaurants urban farming
- Written by Molly Callahan
9 Most Profitable Plants To Grow Hydroponically
Simply put, hydroponics uses mineral nutrient solutions to feed plants that are growing in water, so no soil is used in the process. The practice is also pretty versatile because you can set it up in a big greenhouse space or in your living room using smaller systems or towers.
August 1, 2018
by MADISON MORGAN in Lists, News
If you have a green thumb and are looking for a side hustle, you need to read this list of the most profitable plants to grow hydroponically.
With the Whole Foods culture taking over — seriously, there’s a Whole Foods in the center of Harlem, New York City now — there’s a major push for freshly grown fruits, vegetables and anything else that can be grown locally. It seems many Americans are just starting to wake up and realize, “oh, maybe I should pay more attention to where my food is coming from.” I mean, I’m not organic everything, mainly because it’s expensive and I’m a millennial, but I do pay attention to the foods I eat and try to eat pretty “clean” foods. Honestly, if you still think it’s normal for a chicken breast to be the size of an adult baseball mitt, then you really have some research to do.
Anyway, if you are looking for healthy and locally grown options, thankfully many grocery stores and markets have a wide variety these days, or you can visit your local farmer’s market. If you really want to be serious about your food, you can take it up a level by growing your own produce. If you’re really good at it, you can even sell what you don’t eat, for a generous profit. So really, it’s a win-win situation.
If you’re a city dweller, like myself, that doesn’t mean learning to plant and growing things is out of reach for you. Thanks to technology there are now really cool ways to be able to grow plants indoors, using minimal space and that’s where hydroponics come in. Simply put, hydroponics uses mineral nutrient solutions to feed plants that are growing in water, so no soil is used in the process.
The practice is also pretty versatile because you can set it up in a big greenhouse space or in your living room using smaller systems or towers. If you’re not totally confined to the indoors and have a little yard space to work with, take a look at this article on the most profitable plants for aquaponics, small gardens, and backyard nurseries.
There are a variety of plants that can grow indoors, without needing too much sunlight, which you can learn more about with the easiest indoor plants to grow from seed and the easiest edible plants to grow indoors. While it’s great to be able to grow your own plants to eat, it’s even better to do that and to also make money. Depending on what kind of hydroponic system you’re interested in (and have the space for), you’ll want to research the hydroponic farm startup cost before you get in too deep. Costs can range anywhere from $50 for a small in-home system, to $100,000 for an indoor farm set up.
So, is hydroponic farming profitable? The answer is, yes. If you do your research on the most profitable plants to grow and sell, you should have no problem making money. You also want to take a look at growth time too. For example, hydroponic ginseng can take a few years to grow, but it sells for some crazy good prices (we’ll talk more about this in a bit).
We decided not to focus on the most profitable crops per acre since you would need to be a big deal farmer for that, but on smaller systems that you can grow in your home. Furthermore, we focused on price per pound of crop, since that’s more reasonable to grow in a smaller system. To figure out some of the most profitable plants to grow hydroponically we used the U.S. Department of Agriculture, Farmer’s Daughter Herbs, and Simply Hydroponics and Organics. Once we determined the price per pound for crops that can be grown hydroponically, we ranked them starting with those with lowest prices.
9. Cilantro
$6.00 per pound
We’ll start our list with a popular herb, and you will notice many more herbs on this list as they grow well in hydroponic systems, and sell for good prices, as well. Cilantro is popular in many Chinese and Thai dishes but can be used in a variety of different recipes. It can be harvested in about 3-4 weeks after planting, so you won’t have to practice patience with this herb.
8. Basil
$14.00 per pound
Who doesn’t like basil? You can use it for pizza, fresh pesto sauce (my personal favorite), or for a salad. Basil has tons of nutrients and vitamins and is considered to be one of the healthiest herbs.
Pixabay/Public Domain
7. Dill
$14.00 per pound
Number seven on our list of most profitable plants to grow hydroponically is dill that is kind of random, and you can only see it occasionally, but it’s actually part of the celery family. Dill takes very little work to grow, as all you need to do is plant the seeds and give it a little sunlight. So, if you’re just developing a green thumb (or not even there yet), this is a good option for you.
Pixabay/Public Domain
6. Mint
$14.00 per pound
You can never have enough mint leaves around in my opinion. Whether you put it in a glass of sweet tea or use it to make mojitos (my personal favorite), you can’t go wrong with having it near. It also sells really well, so that’s a plus too, which is why we have it on our list of most profitable plants to grow hydroponically.
Anna_Pustynnikova/Shutterstock.com
5. Chives
$14.00 per pound
We are continuing our list of most profitable plants to grow hydroponically with chives that are a natural insect repellant, so if you’re growing these in your living room or a crowded apartment building, this might benefit you in more ways than one. On the other hand, chives can be used for soups, fish, baked potatoes and much more. At $14 per pound as the average resale price, you will be glad you grew them.
Pixabay/Public Domain
4. Tarragon
$16.00 per pound
Next on our list of most profitable plants to grow hydroponically is Tarragon that goes well with meats like fish and chicken and is predominantly used in French cuisine. However, it also has and can be used to induce sleep, increase appetite, improve cardiovascular health, and even for pain relief.
Pixabay/Public Domain
3. Bay Leaves
$30.00 per pound
Many times, dried bay leaves are used to add to the aroma and taste of a dish, and they are also not cheap. There are multiple varieties of the herb, like the Indonesian bay leaf, California bay leaf, and the Mexican bay leaf.
Pixabay/Public Domain
2. Ginseng
$500-$600 per pound
We briefly mentioned this earlier, but ginseng sells for some really high prices, especially the wild one. It’s a “rooty” crop that looks like ginger, and it is used a lot in teas and energy drinks. For many centuries, it’s also been used for various health purposes.
Pixabay/Public Domain
1. Cannabis
$1,600 per pound
Last but not least, we have cannabis to top our list. There’s a reason why the marijuana business does so well, which is mainly because weed makes a ton of money for the people who grow it. Obviously, this one only applies to you if you live somewhere where it can be grown legally though. If you do, it can be grown hydroponically, and you can spend the rest of your days counting your cash as this tops the cake on the list of 9 most profitable plants to grow hydroponically.
These Joburg Offices Now Have Farms Inside Them — And Workers Get To Harvest Lunch
Timothy Rangongo, Business Insider SA
Jul 27, 2018
Office farms are gaining traction in SA, with more businesses signing up for veggie gardens.
- One service provider of commercial gardens has installed over 250 business gardens.
- These edible gardens are not only aesthetically pleasing but are saving some establishments money, and reducing employees' stress by exposing them to nature.
Some South African office workers are picking their own herbs and vegetables for lunch, without ever leaving the office.
An organic salad can be quickly put together from lettuce, garlic, tomatoes, cucumber, onion, and bell peppers for instance, and topped with lemon juice — all picked from 'office farms' as the installations are colloquially known.
Vertical gardens in SA offices with hardware and irrigation supplied by Vicinity. (Photos: Vicinity)
Edible business gardens are also taking over office rooftops, balconies and walls.
Urban Harvest, a company that sets up and maintains edible gardens, says it has already created 250 such gardens, and has many more potential customers thinking about urban farms.
Edible business gardens set up by Urban Harvest. (Photo: Urban Harvest)
Vicinity, a company that manufactures the structures for such gardens, confirms the trend.
Most of their installations are corporate-oriented. Vicinity just signed on one of the Radisson's Cape Town hotels to install a rooftop garden with edible plants.
Google South Africa's office has one such small vegetable garden on its rooftop, offering a quiet, environmentally-friendly retreat with various edible plants.
Google South Africa's rooftop garden provides on-site access to fresh herbs and vegetables. (Photos: Timothy Rangongo, Business Insider SA & @MzansiGirl, Twitter)
"A business is seen as more cutting edge and credible if it includes green practices or characteristics, such as offsetting its carbon footprint, in its work," says MD of Urban Harvest, Ben Getz.
Obtaining a favourable green-star rating is also an incentive to install an edible garden, Urban manager Timothy Kachiri tells Business Insider South Africa.
Payroll company Sage's building in the new Menlyn Maine development – which promises "to become Africa's first green city" – sports a 4-star green-star rating and features a functioning vegetable garden on the roof that provides the canteen with fresh herbs and veggies.
Sage VIP's new building in Pretoria sports a large rooftop vegetable garden. (Photos: Menlyn Maine)
Google South Africa also directs its fresh produce in-house restaurant Gogo's Shebeen.
Google SA's cool canteen, Gogo's shebeen, makes use of veggies harvested from their rooftop garden. (Photos: @Karabo_Mokgoko, Twitter)
According to a 2015 Human Spaces report, people who work in environments with natural elements report a 15% higher level of well-being, a 6% higher level of productivity, and a 15% higher level of creativity than those who work in environments devoid of nature.
Hotels and restaurants are also increasingly producing right on site.
The Westin hotel's rooftop garden in Cape Town, installed by Vertical Veg. (Photos: Vertical Veg)
A vegetable garden allows The Westin's chefs in Cape Town access to fresh, organically-grown herbs and vegetables for use in dishes promoted as having a minimal carbon footprint.
Dishes prepared by the Westin's chefs, using edible plants from the hotel's garden. (Photos: Vertical Veg)
Manager of The Culinary Table restaurant in Johannesburg, Warren Tshuma, says its garden is tied to a philosophy of "honest garden-to-table cuisine, made from scratch."
The Culinary Table's large kitchen garden and meals prepared from edible plants harvested from the garden. (Photos: Culinary Table)
The Culinary Table also saves money by sourcing ingredients from its own garden, according to Tshuma.
It takes about three days on average to install a big business garden or one for a small office space. Vertical gardens take about a day and half to erect, says Kachiri.
You Can Farm Anywhere, Even Inside A Shopping Mall
You Can Farm Anywhere, Even Inside A Shopping Mall
BeGreen, a startup company in Belo Horizonte in Brazil, is producing fresh and organic produce inside the city’s main shopping center.
Giuliano Bittencourt and Pedro Graziano launched BeGreen with the goal of producing sustainable and healthy food for the urban community, while simultaneously reducing the amount of food wasted along the supply chain. The urban farm uses hydroponic methods to grow fresh and organic produce and sells it locally.
Food travels a long distance from farmer to consumer in Brazil, a major inefficiency in their food system. An estimated 80 percent of all agricultural production in Brazil is lost during transportation. Along with this tremendous quantity of wasted edible food, there are additional transportation costs resulting in increased greenhouse gas emissions. BeGreen is a response to these inefficiencies.
Bittencourt was first introduced to this type of urban farm when he visited the Agricultural Technology lab facility of MIT. It was after this visit that he was inspired to start BeGreen, which brings accessible and affordable technology to modernize the Brazilian food chain.
Ricardo Batistic, CTO of BeGreen, explains, “we want to change the general perspective that access to healthy food is only viable in rural areas, we want to impact as many people as we can with our vision and bring the best product we can to the market.”
Using aquaponic methods, the farm produces roughly 40,000-60,000 plants per month. Most of these are greens and microgreens including beet leaves, watercress, parsley, coriander, basil, thyme, sage, arugula, radish, mustard, cabbage, and a diverse range of lettuces.
The fish serve as a natural fertilizer for the farm, and they raise over 500 tilapia per month. There are biofilters, which metabolize the fish’s waste to enrich the water used throughout the whole system. The farm uses 90 percent less water than conventional farming and does not use pesticides, significantly lowering their environmental footprint.
BeGreen sells their produce to approximately 30 restaurants, four retail stores, and directly to visitors of the farm. Sustainability is at the heart of the business model. They keep sales as close to the farm as possible, with the farthest shipment located only 10 kilometers away.
Producing high-quality organic vegetables and minimizing waste are at the core of BeGreen’s mission. They have very strict quality control processes including daily production area checks for diseases, water shortages, leakages, or any other systems issues. They conduct daily pH and water temperature tests, and weekly tests of the macronutrients in the fish water. They are developing a new system to assess the growth conditions of the plants to optimize quality and productivity. BeGreen keeps a robust database tracking the number of seeds that fail to grow and the amount of full-grown produce lost during distribution. Currently, these failures are under 2 percent of their total production.
BeGreen implements additional methods to avoid waste, such as preserving the roots on the plants at the point of sale, which extends their shelf life an additional week. They also donate unsold produce to a charity, Mesa Brasil.
BeGreen is currently seeking to expand their operations and is building their second urban farm in São Paulo. According to Batistic, the company “want[s] to have at least three working urban farms by the end of 2018. We intend to grow at a steady pace to cover as many cities in Brazil as possible, and we are also open to international possibilities if they present themselves.”
The Micro Revolution: Growing Hydroponic Microgreens
Succulent, slender but packing a powerful flavor punch, microgreens are increasing in popularity both on our plates and as a profitable hydroponic crop with just five days from seed to harvest for some species
Takeaway: Succulent, slender but packing a powerful flavor punch, microgreens are increasing in popularity both on our plates and as a profitable hydroponic crop with just five days from seed to harvest for some species.
Succulent, slender but packing a powerful flavor punch, microgreens are increasing in popularity both on our plates and as a profitable hydroponic crop. While they may seem tender and delicate, most microgreens are easy to germinate and with just five days from seed to harvest for many quick-growing species, even the most impatient grower will be satisfied with the results.
Microgreens are also ideal for those with a limited indoor growing space – as little as a few square inches can grow a crop packed with the distinctive flavor of the mature plant but in a small, compact and highly nutritious package.
On a slightly larger scale, microgreens make a profitable commercial crop, well-suited to soilless production methods, hydroponic nutrition and a protected growing environment to give a high-quality, clean and grit-free product.
What are Microgreens?
Microgreens originated in California, where innovative chefs started using them in new dishes to incorporate color, flavor, texture and interest, a trend that rapidly spread worldwide. Microgreens are used as toppings, garnishes, flavorings in salads and features in many up-market dishes and are sold as a high-value product in produce stores and supermarkets.
Microgreens are larger than a sprout but smaller than a baby salad leaf and will usually have produced at least two true leaves after expansion of the seedling leaves or cotyledons. Because they are harvested at such an immature stage, seed is sown at a high density to maximize yields from each crop.
This also allows the developing seedlings to grow tall and straight with a tender, almost blanched stem and bright, well-developed leaves. While a diverse range of plant species are grown as microgreens, some are produced specifically for their healthy compounds and properties and these have found a niche market within the health food industry as well as being popular with home gardeners.
The most well-known of these is wheatgrass, which has been grown for many years as a health supplement. Other species such as flax, chia, broccoli and varieties of red brassica also have health compounds of interest. The darkly colored purple and red varieties of radish microgreens, which produce intensely colored young leaves, contain high levels of antioxidants shown to have cancer-fighting properties.
Commonly Grown Microgreens
Microgreens fall into four main categories. Shoots and tendrils such as pea, sunflower and corn shoots, are often used as garnishes, although they all have their own mild and somewhat surprising flavor. Spicy greens include arugula, radish, cress and mustards.
Micro herbs include those used not only as garnishes, but also for their characteristic flavor such as parsley, fennel, edible chrysanthemums, cilantro, basil, French sorrel, mint, dill, chives, onion and shisho (perilla).
Tender greens are highly diverse in flavor, leaf size, shape and color, and include red cabbage, broccoli, spinach, beet (red), tatsoi, mitzuna, amaranth, chard, kale, corn salad, endive, chicory, celery, carrot and lettuce.
Hydroponic Production of Microgreens
Hydroponic microgreens have a distinct advantage over those grown in trays of substrates or soil mixes in that no granular growing medium needs to be used. The high sowing rate and density of microgreens means small particles of substrate can end up in the foliage and since microgreens are not usually washed after harvest, this poses a risk of crunchy grit ending up in the final dish.
For this reason, hydroponic microgreens are best produced on a thin mat or capillary pad that holds the seed in place and retains some moisture for germination. Paper towel, hessian/burlap sheets, rockwool cubes or sheets, thin kitchen cloth and hydroponic microgreen pads can all be used to grow a clean, high-quality crop with little expense.
Seeds that have been specifically produced and packaged for sprout or microgreen production should be obtained, which means the seed will have a low percentage of foreign matter, will not have been treated with fungicides or other chemicals and will have been well cleaned.
This is particularly important when buying seeds for pea, corn or spinach microgreens, as the seeds from these species are often coated with fungicide. Seed companies have also introduced a range of specific microgreen cultivars that are a great improvement on standard varieties.
Many of these feature intensely colored or modified first leaves, such as some of the radish microgreen species and those grown for pea shoots. Some microgreen varieties have seeds that are mucilaginous, meaning that once wetted, the seed forms a thick, gelatine-like layer that holds moisture.
Cress and basil are examples of mucilaginous seed and these seed types should not be pre-soaked before sowing. Larger seeds such as wheatgrass, corn and peas may be pre-soaked in warm water for 24 hours before sowing, although this step is not essential.
Hydroponic systems for microgreens can be as simple as a small, flat, hand-watered kitchen tray or as complex as an aeroponic or nutrient film technique system. Ideally, the growing system needs to have a flat, slightly sloping surface onto which the growing mat/pad paper or cloth can be laid out and wetted down.
The microgreen seed should then be weighed out and sown onto the wetted surface as evenly as possible. Use of seed shakers assists with this process. The correct seeding density depends somewhat on the species being grown.
As soon as the seeds germinate, microgreens require light and nutrients to produce the highest quality product. Artificial lighting doesn’t need to be intense and these young seedlings produce well under propagation lamps provided the lamps don’t produce too much heat, which may burn the tender young foliage.
Once the cotyledons (seedling leaves) are visible and are starting to develop chlorophyll, the seedling will have exhausted the reserves contained in the seed. At this stage, the young plant is starting to photosynthesize and produce its own assimilate and nutrient ions will be absorbed by the root system.
A general purpose vegetative or seedling nutrient formulation is usually sufficient for microgreen production, but wheatgrass has different nutritional requirements, including a higher EC level, for maximum harvest quality. EC levels are typically run at seedling strength for microgreens (0.5 – 1.0 mS cm -1), although they may be adjusted for season in a similar way to lettuce and herb crops.
There is some scope to manipulate growth of microgreens with use of EC – higher EC can be used to boost color development in red types during low winter light if necessary. Control of EC will also affect the shelf life of cut microgreens. Seedlings grown on dilute solutions or in media with a high water-holding capacity can develop softer tissue and a higher rate of water loss post-harvest than those that have received a higher EC and been slightly more hardened.
Nutrient solution needs to be applied regularly and carefully to developing microgreens to avoid flooding the microgreens and wetting the foliage, which encourages fungal diseases, and also to make sure fresh nutrient solution is flushed through the root zone, oxygenating and feeding the seedlings.
Most hydroponic systems used for microgreens don’t use a continual flow of nutrient solution, but intermittent application, followed by a period of drainage with the growing mat/pad or substrate holding sufficient moisture around the roots between waterings.
Food Safety and Hygiene Considerations
Just as with sprout production, there are food safety requirements for microgreen production. Various fungal pathogens can develop and grow on sprouting seeds, particularly under the humid conditions and high densities microgreens are grown at, and these can pose a contamination risk. Generally, high-quality, viable seed, sown into a clean system at the correct temperature for germination and optimal moisture levels, will germinate rapidly with few problems.
Disease outbreaks are more common when old seeds are used or when temperatures are either too hot or cold for rapid germination. Over-watering also poses a risk as seeds may begin to rot before germination can occur. The water supply needs to be high quality – water can carry human and plant pathogens that contaminate a crop, although the municipal water supply is treated to prevent this risk.
There is an increasing concern and more regulations these days relating to food safety so commercial growers of microgreens need to be aware of the guidelines they must follow for fresh salad crops.
Harvesting Microgreens
Cutting height is important, as high-quality microgreens need a good, clean portion of stem below the leaves, but should not be cut so low as to risk contamination with the growing media or material the seeds were sown into.
This becomes particularly important if a light, loose, granular media has been used for production, as particles can easily be picked up during the harvesting process and contaminate the product. Clean, sharp scissors are suitable for cutting microgreens on a small scale, while larger growers use mechanical harvesters.
During warm growing weather, microgreens, just as with herbs and lettuce, are best harvested early in the day when the foliage is coolest and most turgid. This will prolong the shelf life of the packaged product. Some microgreens are shipped out to customers while still growing in trays or cells, prolonging shelf life and allowing on site harvesting as required.
Problems with Microgreens
One of the most common problems seen in microgreen production is seedling rot and disease outbreaks caused by over-watering or high humidity levels, which create a saturated environment around the foliage.
Good levels of air movement (such as portable fans in small areas) help prevent issues of root rot, fungal and bacterial pathogens taking hold in the dense canopy of succulent young leaves. Over-mature microgreens may become too tall and flop over, making harvesting extremely difficult, so this is a crop that must be cut at just the right stage.
For the small-scale indoor gardener, microgreens are an ideal crop – fast, productive and requiring just a few inches of well-lit space, they can be easily grown on a warm, sunny windowsill, or incorporated into a high-tech hydroponic system. Their short shelf life makes them a good prospect for local markets and restaurants, as they are best used fresh within two or three days of harvest.
Although there is a degree of skill required in growing these seedlings at high densities and maintaining post-harvest quality, the wide range of species, diversity of uses and growing popularity makes them a great proposition for hydroponic growers.
Written by Lynette Morgan
Dr. Lynette Morgan holds a B. Hort. Tech. degree and a PhD in hydroponic greenhouse production from Massey University, New Zealand. Lynette is a partner with Suntec International Hydroponic Consultants and has authored several hydroponic technical books. Visit suntec.co.nz for more information. Full Bio
St. Cloud University Measures Eight-Fold Increase in CO2 Transfer To Plants Using CO2 GRO’s CO2 Foliar Spray Technology
TORONTO, ON – July 9, 2018 – CO2 GRO Inc. (“GROW” or the “Company”) (TSX-V: GROW) is pleased to announce further scientific proof validating its dissolved CO2 foliar spray technology accelerating plant growth. The second set of scientific trial results at St Cloud State University ("St. Cloud") measured over an eight-fold efficiency increase in the conductance (transfer availability) of CO2 from the dissolved CO2 enriched water sprayed on Romaine lettuce leaves over both unenriched water spray and no spray control plant treatments.
Conductance in plant leaf stomata (pores) is an estimate of the rate of CO2 gas entering and/or water vapor exiting a plant leaf. This further evidence was measured in three separate experiments using an SC-1 leaf porometer. With a series of previously announced scientific trials showing a fourfold sustained increase in Romaine leaf chlorophyll, GROW now has scientific proof why its dissolved CO2 Foliar Spray works better than indoor growers that gas with CO2 and outdoor growers that have no alternative to add CO2 outdoors to their plants.
According to Tridge Intelligence, the worldwide lettuce market of 26.8M tonnes/y is worth $30B/y wholesale with the US producing 15.2% or 4M tonnes/y, mostly in California. GROW believes that St Cloud's scientific CO2 gas transfer and chlorophyll experiments are confirming the potential of 1-2 more lettuce crops/year in California or $1-2B/y more wholesale California lettuce revenue with less water use per unit of lettuce yield.
St. Cloud's second plant science report for GROW excerpts: "This data continues to be encouraging and consistent with the hypothesis of significant plant growth enhancement with CO2 delivered via foliar spray" and that "NO significant difference existed between unenriched foliar spray and no spray plant treatments, strongly suggesting that CO2 availability was the factor increasing both chlorophyll A and CO2 gas conductance"
St Cloud State is now measuring: 1) CO2 foliar spraying plants versus gassing a control plant group at 1200 PPM, 2) a variety of bug, mould and mildew experiments to measure whether CO2 foliar spray has positive plant resistance impacts reducing the needs of herbicides, insecticides, pesticides and fungicides, 3) improved leaf stomata water vapor efficiency using dissolved CO2 reducing water needs per unit of plant yield and 4) completing ongoing grow trials started from lettuce and pepper seeds.
All patentable results from scientific discoveries at St Cloud are 100%-owned by GROW.
About CO2 GRO (GROW.TSXV) or "GROW"
GROW's mission is to accelerate all indoor and outdoor value plant growth naturally, safely, and economically using its patented advanced CO2 foliar technologies. GROW's global target plant markets are retail food at $8 trillion per year (Plunkett Mar 2017), retail non-food plants at an estimated $1 trillion per year and legal retail cannabis that may reach $50 billion per year by 2022 (Bay St Analyst estimates). GROW's sole focus is working with its plant grower and Agri-industrial partners in proving and adopting its CO2 technologies for specific growers’ plant yield needs.
The CO2 technologies work by transferring CO2 gas into water and foliar spraying across
the entire plant leaf surface area, which is a semi permeable membrane. The dissolved concentrated CO2 then penetrates a leaf's surface area naturally like nicotine naturally dissolves through human skin from a nicotine patch.
Foliar spraying natural nutrients and chemicals on plant leaves has been used for over 60 years by millions of indoor and outdoor plant growers. To date, outdoor growers have not had any way to enhance plant CO2-gas uptake for faster growth.
Indoor use of CO2 gassing has enhanced plant yields for over 60 years. However, over 50% of the CO2 gas is typically lost through ventilation. Current greenhouse CO2 gassing levels of up to 1500 PPM are also not ideal for worker health and safety. GROW's safer dissolved CO2 foliar spray can be used by indoor and outdoor plant growers with minimal CO2 gas lost.
GROW's CO2 technologies are commercially proven, scalable and easily adopted into existing irrigation systems. GROW's proven crop yield enhancements and revenue model is compelling for growers and Agri-industrial partners.
Forward-Looking Statements This news release may contain forward-looking statements that are based on GROW's expectations, estimates and projections regarding its business and the economic environment in which it operates. These statements are not guarantees of future performance and involve risks and uncertainties that are difficult to control or predict. Therefore, actual outcomes and results may differ materially from those expressed in these forward-looking statements and readers should not place undue reliance on such statements. Statements speak only as of the date on which they are made, and the Company undertakes no obligation to update them publicly to reflect new information or the occurrence of future events or circumstances, unless otherwise required to do so by law.
Neither the TSX Venture Exchange nor its Regulation Services Provider (as that term is defined in the policies of the TSX Venture Exchange) accepts responsibility for the adequacy or accuracy of this release.
Views On Local Food, Not A Kumbaya Chorus
Everything is not rainbows and unicorns when it comes to feelings about local food demand.
Views On Local Food, Not A Kumbaya Chorus
July 18, 2018
Everything is not rainbows and unicorns when it comes to feelings about local food demand.
As I mentioned in a previous blog post, I asked the LinkedIn Fresh Produce Industry Discussion Group this question:
What do you think is the number one reason behind the consumer appeal of local produce? Will consumer preference for localincrease or decrease over the next five years? How should the supply chain respond?
While many see the enduring appeal of local food, others say it is not that simple.
Here are a few of the diverse comments on the question:
DL: Freshness and supporting local growers is important Pick your own fruits and veggies is a family experience to support healthier eating experience
JP: Part of the knee-jerk appeal is the consumer connection with a supposed environmental benefit, in this case, the discredited food miles campaigns. If we get back to the meaning behind the meaning, the benefits these consumers attribute to local are actually a cry for seasonal. Most things are always in season but some seasons are better than others. Eating an 11-month old apple is better than eating a 60-day old grape or a 30-day old blueberry. But sometimes an 11-month old apple from out of state, like I’m enjoying right now, is better than the 7-day old peach from the next county my grocer ruined by holding it at 42 degrees. Flavor trumps geography
VK; Just wait until the nonsense “vertical” farms implode
BB: Supporting “Locally Grown” is on the upswing. My wife and I do it ourselves and I haul produce. However, consumers have become used to having fruits and vegetables available year ‘round at their local grocery store and I wonder how many shoppers stop to ask where that plum they bought in December came from?
DV: It is good to support local. The path from farm to plate is also much shorter with a much smaller risk of contamination than the major retailers’ long supply chains.
JJ: In my opinion the preponderance of “local” produce is directly related to the environment and the myriad problems climate change presents. Educated consumers or “correct consumers” see their food choices from all angles including how it was grown, how far away it was grown and who grew it. Shipping a salad from a drought-plagued area 3000 miles away may not bother most customers now but going forward more and more consumers will use their wallets to demand a less environmentally damaging method of procuring things like salad greens that can be grown year round and shipped 90% fewer miles.
Great input and diverse thinking from the group as always.
Another item that caught my eye this morning:
On the importance of incentivizing healthy eating. From Rep. Jim McGovern, D-Mass. in the Congressional Record:
One shining example of a collaboration formed to tackle this terrible problem is Vitality. John Hancock, a leading life insurance company based in Boston, has partnered with the Friedman School at Tufts University on an innovative life insurance product that helps to encourage healthier behaviors.
John Hancock clients complete an online health review and engage in activities like preventative care, physical activity, smoking cessation, education, and improved nutrition to earn points that translate into discounts on insurance and other products. What is particularly impressive about the program is the discount it provides to participants who want to increase their purchases of fruits and vegetables. Those who sign up receive a 25 percent discount on healthy food at more than 14,000 grocery stores across the country.
The Vitality program is one example of the positive impact incentives can have on our collective public health when they motivate and reward individuals to take up healthy behaviors. We should learn from this innovative model and look at ways to expand upon its reach to greater segments of the population.
In 2011, the Commonwealth of Massachusetts worked with the U.S. Department of Agriculture to pilot a first in the Nation initiative to provide incentives for the purchase of healthy foods. The pilot enabled participants to increase their consumption of fruits and vegetables by 26 percent and led to the creation of USDA’s Food Insecurity and Nutrition Incentive, known as FINI.
FINI has provided States and localities across the country with Federal resources to expand incentive programs for SNAP beneficiaries. Massachusetts currently uses Federal FINI dollars in conjunction with private donations and State resources to increase the purchase of fruits and vegetables.
It is working. In our State, FINI has helped more than 63,000 SNAP recipients increase their fruit and vegetable intake in 1 year alone. Estimates suggest this increase can mean savings of more than $1.1 million in public health costs. So imagine the impact these sorts of programs and incentives could have if they were replicated and expanded on a larger scale.
New research from Tufts’ Friedman School shows that incorporating technology-based incentives for healthier eating into other Federal programs like Medicare and Medicaid would be highly cost-effective, saving millions of lives and billions of dollars in healthcare costs.
We should also look at how we can reach beyond Federal health and nutrition programs to encourage private worksite wellness programs.
TK: McGovern deserves more love as a strong advocate for industry interests. I’d like to hear more from him at fresh produce events.
Related Topics:
30MHz And Hort Americas Join Forces To Bring Smart Sensing To North American Growers
30MHz And Hort Americas Join Forces To Bring Smart Sensing To North American Growers
By urbanagnews
July 10, 2018
Photos by 30MHz
Leading commercial horticultural suppliers Hort Americas, and smart sensing technology providers 30MHz are pleased to announce that they’ve partnered to bring the power of real-time, crop-level monitoring to growers across Canada, the United States, the Caribbean, and Mexico. Hort Americas is the first North American distributor of 30MHz technology.
The data platform for Horti - and agriculture
30MHz provides agribusinesses with everything they need to start monitoring their crops and growing environment accurately and in real-time, with just minutes of setup. Customers choose from a variety of sensors sourced and developed with growers and agricultural research institutions (capturing metrics including VPD, dew point, temperature, humidity, soil moisture and airflow.) 30MHz also provides a private, scalable mesh network (with the option to easily add more sensors at any time) and an intuitive analytics platform with real-time alerts, visualizations, heatmaps, charts and graphs accessible on any device.
Photos by 30MHz
With 30MHz technology, customers can deploy a wireless sensor network themselves, without technical expertise. Sensors arrive preconfigured— customers simply connect their gateway to a power supply and ethernet and log into the platform to immediately start measuring.
Built to help agribusinesses of all sizes harness the full power of their environmental data, the 30MHz platform makes crop metrics accessible, shareable and actionable without the burden of juggling multiple interfaces. Real-time sensor data can be viewed alongside data from other sources, including climate control systems, shelf quality control and traceability monitoring and root zone monitoring software.
Empowering agribusinesses across the chain
The scalable and modular nature of 30MHz tech makes it a fit for growers of all sizes across agricultural verticals. With over 150 customers across five continents, 30MHz serves agribusinesses from farm to fork, in a greenhouse, vertical (hydroponic and aeroponic), arable, ornamental, cold store, processing, packing, transport, retail, and livestock. Based in Bedford, Texas, Hort Americas partners with leading suppliers of commercial horticultural products from around to world in order to serve the North American professional greenhouse and indoor ag grower community with the latest technologically advanced products from around the world. Hort Americas’ breadth of expertise across horticulture makes the company ideally positioned to bring the Dutch-founded 30MHz further into the North American market.
“We’ve seen the hunger for actionable data among North American growers— they’re constantly looking to innovate and make the most of their resources. But they don’t have time for overly complex systems that silo their data and take forever to get off the ground. Hort Americas understand the specific challenges and needs of North American agriculture, and how to translate Dutch agri-innovation into efficiency and productivity in local contexts” notes Director of Customer Affairs Cor Jan Holwerda. “Hort Americas continues to look for cutting-edge technology that solves problems and provides answers to the questions our grower partners are asking us. With believe that 30MHz’s product portfolio does just that,” adds founder and general manager, Chris Higgins.
More About 30MHz
30MHz helps agribusinesses of all sizes make the most of their resources with real-time data on their crops and environment, from farm to fork. Through an accessible data platform, scalable mesh network and a selection of wireless sensors, 30MHz provides all the elements growers need to start monitoring in moments, without technical expertise. All it takes is a few minutes and an internet connection.
More About Hort Americas
Based in Bedford, Texas, Hort Americas partners with leading suppliers of commercial horticultural products from around the world in order to serve the North American professional greenhouse and indoor ag grower community with the latest technologically advanced products. Learn more at www.hortamericas.com.
Urban Farming Social Enterprise Bears Fruit For Local Community
Urban Farming Social Enterprise Bears Fruit For Local Community
Edible Garden City has two aims: bring people together through farming and solve the sustainability problem in Singapore.
July 12, 2018
Bjorn Low, co-founder of Edible Garden City (back row, first from right), and the Citizen Farm team. Edible Garden City holds workshops at its production arm, Citizen Farm, and collaborates with local primary schools to teach farming to students.
Singapore
BECOMING a farmer in Singapore sounds risky enough, but former digital marketer Bjorn Low decided to take it a step further by starting his own urban farming social enterprise, Edible Garden City.
Established in 2012, the company aims to bring people together through farming, by building community farms and sharing its knowledge on urban farming.
"In every community, there is always a group of people who need help. So when we have the opportunity and capability to do so, we jump straight into it," said Mr Low.
After learning that many male elderly men tend to be reclusive and are at risk of social isolation, he worked with social workers to start a new project, Ah Gong Farm.
Located at Pearl Hill, Chinatown, the farm serves as an avenue for elderly men to learn about farming together and forge friendships. It also allows social workers to get to know them better and to cater to each elderly's individual needs.
Mr Low was deeply moved when he saw one withdrawn participant become more cheerful and talkative as the biweekly lessons progressed. The man even shared that he visited the garden on nights when he had difficulty sleeping.
"Boundaries are very blurred between gardening and therapy," said Mr. Low, who hopes that the elderly might become motivated to join Edible Garden City's team of part-time farmers.
"It is noble - something to be proud of - to grow food for the community. It is important to give our elderly this confidence," he added.
Recently, Ah Gong Farm also welcomed its first two female members.
Through collaborations with the Autism Resource Centre, Employment For People with Intellectual Disabilities, and the Singapore Prison Service, Edible Garden City also brings these farming lessons to people with autism, people with mental disabilities, and inmates as well, equipping them with the skills to pursue farming as a career.
Edible Garden City's other main objective is to solve the sustainability problem in Singapore.
"Mass-scale agriculture is causing land degradation. And Singapore, which imports 90 percent of its food products, is at the receiving end of it. So this is an urgent matter not for the sake of us today, but for our future generation," explained Mr. Low.
To tackle this, he is practicing closed loop agriculture, where food waste is made into compost to grow more food.
As an example, after three years of trial and error, Edible Garden City recently discovered a viable way of using grounded coffee waste to grow mushrooms, which are then sold to local restaurants.
With support from Temasek Foundation, the company is also currently working on creating closed-loop self-contained farming units in the form of containers. It hopes to distribute these containers to housing areas across the island so that each community can grow their own food sustainably.
Similar to Edible Garden City's other farms, these container farms will also be semi-commercial, which means the yield will be sold to generate profit.
"For Singapore to be a fully closed loop is possible, but becoming fully self-sustainable will be a challenge. Growing rice and grains locally is still challenging, but if there is a need, we will find a way to do it," stated Mr. Low.
To achieve this goal, Edible Garden City also holds workshops at its production arm, Citizen Farm, and collaborates with local primary schools to teach farming to students.
"The industry is so young and so new, we want to encourage more people to join it. We even encourage our own staff to go out and create their own urban farming systems. Competitors can bring in new ideas and push for healthy growth in the industry," said Mr. Low.
However, competition does not hinder the business from growing rapidly. From an S$10,000 capital six years ago, Edible Garden City's revenue reached S$1.3 million last year. This was generated from building herb gardens for restaurants and hotels, teaching in schools, and selling harvested plants and urban farming tools. The company's team has also expanded to almost 40 individuals from various walks of life.
"Whenever we do a project, we always remind ourselves that we are a social enterprise, so we try to find areas where we can maximize our social impact."
This year, Mr. Low was nominated as a fellow of Ashoka, a non-profit organization which supports social entrepreneurship.
"It made me happy that the work done in the last five years is being recognized, but I'm also a little bit nervous because it means I have more responsibilities," shared Mr. Low, who hopes to exchange knowledge and ideas with the fellows from all around the globe.
- This article is part of a fortnightly series highlighting socially impactful companies. For more information, visit www.raise.sg
You Don’t Have To Live Near A Large Urban Area To Commercially Grow Hydroponic Leafy Greens
You Don’t Have To Live Near A Large Urban Area To Commercially Grow Hydroponic Leafy Greens
By urbanagnews
July 12, 2018
Tom Murphy, operator at mGardens, said everyone who has tried his company’s leafy greens have raved about the taste and freshness.
Photo courtesy of mGardens
mGardens is growing hydroponic leafy greens in rural Kansas and marketing them to local grocery stores, restaurants and a farmers market.
While much of the country’s indoor hydroponic food production is being done by growers located near large urban areas, mGardens in Gorham, Kan., is bucking the trend. Tom Murphy, who is the company’s operator, asked why should people living in or near large cities be the only ones able to enjoy the taste, freshness and nutrition associated with hydroponic leafy greens?
“My wife Jo and I first got interested in hydroponic food production when we talked to Ron Cramer,” Murphy said. “Ron and my wife are from the same home town, went through school together and continue a longtime friendship.
“When Ron retired from Sakata Seed he got interested in hydroponic food production with LED lights. He has been talking to me and my wife for about five years about growing leafy greens. He said more food production is moving in this direction. This is related to the loss of freshness and nutritional value during shipping of perishable crops.”
In 2015, Tom, Ron and their wives met with Chris Higgins at Hort Americas, a horticultural distributor in Bedford, Texas.
“While we were in Texas we visited a Central Market grocery store that is using a GrowRack to offer its customers fresh produce,” Murphy said. “The store was growing hydroponic lettuce in its produce department and marketing it to its shoppers. You can’t get any fresher and local than that.
“We came back home and purchased a three-level GrowRack hydroponic unit equipped with LED lights. We started operating it in March 2017 and were very impressed with the taste and quality of our first crops of lettuce, kale and arugula.”
When Murphy began growing the crops Cramer told him that he would end up producing more food than he knew what to do with. Murphy initially gave the produce to relatives and neighbors.
“The people to whom we gave the produce raved about the taste and the freshness,” Murphy said. “We started playing around with producing a greens mix.”
In September 2017, Murphy put on a salad-making demonstration with the greens mix at a meeting sponsored by the Russell County Economic Development & Convention and Visitors Bureau. At the meeting were local entrepreneurs and business people.
“I explained to the attendees where a lot of our food comes from, how much food is wasted and what we can do to offer fresher better-tasting food,” Murphy said. “I told them how this food could be grown locally and asked for feedback. Everybody loved the salad. At the meeting was the owner of the local grocery store, Klema’s Apple Market Grocery. He said the store would buy and sell the greens. A solid grocery market was what I felt was needed to start growing commercially.”
Getting serious about growing
After the response from the business community about the greens, Tom and his nephew Mike Murphy and Mike’s wife Tonya decided to set up a commercial operation.
“We prepared a business plan and met with Chris Higgins,” Murphy said. “Chris explained to us that the floating pond system is the most economical way to grow vegetables. So Mike and I converted the three-level GrowRack ebb-and-flow system into a three-level floating pond system.”
mGardens started growing leafy greens using a GrowRack equipped with an ebb-and-flood irrigation system and LED lights.
Photo by Alison Murphy
Tom ran the floating pond system from July 2017 until January 2018. He was looking for a system that didn’t require acres of land like Hort Americas’ demonstration greenhouse, which he had toured during his trip to Texas.
“I asked Chris how we could adapt a confined totally environmentally controlled area equipped with LED lights into a pond system,” he said. “We ended up designing the system on a napkin.”
The Murphys purchased two old stainless steel refrigeration rail cars that are 40-feet long by 8-feet wide by 9-feet tall. Tom and Mike began working on the system in November 2017.
“We gutted everything out of these stainless steel containers and poured concrete footings because we knew there would be a lot of weight from the pond system,” Murphy said. “We calculated that we could put in two rows of racks. We purchased the pond liners and 8-foot GE LED lights from Hort Americas. Mike did all of the electrical, plumbing and welding.”
mGardens expanded its production by retrofitting two stainless steel refrigeration rail cars. One of the cars was equipped with deep water pond racks and GE LED lights.
Photo by Alison Murphy
Prior to beginning the construction, Murphy said he contacted the USDA to inspect the production system that he and Mike were installing.
“I wanted the USDA to insure compliance with its guidelines,” he said. “USDA officials visited us three times before they did their final walk-through to give us a license to operate.
“We also wanted to be FSMA (Food Safety Modernization Act) certified. We had to install a three-basin commercial sink without a connector drain. It had to have an air drain on it. Before we started growing we wanted to make sure that we were compliant with FSMA, even though that law doesn’t go into effect until January 2019.”
Murphy said the company also was required to obtain a grower license as well as a processor license in order to bag the produce for grocery sales.
mGardens plants about 1,000 plants per week in its deep water pond rack system.Photo by Alison Murphy
“Just like a restaurant has to be inspected by USDA, so do we,” he said. “That fit right in with what we were doing in regards to meeting FSMA guidelines. Our main concern is food safety. We’re telling our customers we don’t grow in soil, we monitor for pests and diseases and no insecticides or fungicides are used. The facility is closed to the public.”
Expanding markets
The Murphys began growing in the new production facility in May 2018. Initially they thought grocery stores would take more of the leafy greens, but they are currently taking less than 25 percent of the crops produced.
mGardens packs 5 ounce bags of leafy greens for grocery store sales. The package label includes the pick date so consumers don’t have to guess about product freshness.
“The grocery stores have to develop their market,” Murphy said. “They don’t want to buy too much and then watch it go bad. Right now restaurants are buying more. Hickok’s Steakhouse in Hays, Kan., is a higher-end restaurant that was looking for locally-grown produce. It is now buying all of its greens from us and making some unbelievable specialty dishes with our products. North Central Kansas Technical College has a culinary arts program and a catering business and is buying from us.
“We believe our future is in the restaurant business because they tend to use more of our product on a consistent basis. Our goal is to grow 100-150 pounds of produce per week. We built the system so we could double our production capacity if needed.”
Trialing new crops
When Murphy was doing all of the production in the GrowRack, he tried various crops. While lettuce, kale, arugula, and basil are his core crops, he continues to try new species and varieties.
“We buy all of our seed from Johnny’s Selected Seeds,” he said. “After experimenting with these crops, if they are going to be grown commercially, it’s all based on turns per square foot. This is where growing in the GrowRack for a year really helped us. When we started growing in the pond system we were ready to go. We had already selected the crops that we were going to grow. We plant about 1,000 plants per week.”
For more: mGardens, (785) 637-5604; mGardens@gorhamtel.com.
This article is property of Urban Ag News and was written by David Kuack, a freelance technical writer from Fort Worth, TX.
Scientific Proof of CO2 GRO's Dissolved CO2 Foliar Spray Plant Benefits On Lettuce
Scientific Proof of CO2 GRO's Dissolved CO2 Foliar Spray Plant Benefits On Lettuce
TORONTO, ON – June 20, 2018 – Toronto based CO2 GRO Inc. (“GROW” or the “Company”) (TSX-V: GROW) is pleased to announce more scientific proof validating its dissolved CO2 foliar spray technology on lettuce.
The first trials at St Cloud State University in Minnesota ("St. Cloud") measured a fourfold sustained increase of chlorophyll concentration in Romaine lettuce leaves with dissolved CO2 foliar spray pulsed in 15-minute intervals for four hours. More chlorophyll lets plants grow faster and larger.
According to Tridge Intelligence, the worldwide lettuce market is 26.8M tonnes/y with the US producing 15.2% or 4M tonnes/y.
Over 90% of US lettuce grown is in California.
At the current $1.17/kg global wholesale lettuce price, the global wholesale lettuce market is worth $30B/y.
GROW believes that these initial chlorophyll trials with further replication of previous lettuce grow trials using its CO2 foliar spray technology will confirm the potential of 1-2 more lettuce crops/year in California or $1-2B/y more wholesale California lettuce revenue with less water use per unit of lettuce yield.
St. Cloud's first weekly plant science report states " Notable in these initial experiments is the rapidity of physiological response seen in CO2 exposed plants. This data is encouraging and consistent with the hypothesis of significant plant growth enhancement with CO2 delivered via foliar spray:"
In April 2018, GROW signed an ongoing Collaboration Agreement with St Cloud for scientific plant cultivation research services. Regular scientific documentation of CO2 foliar spray impacts on plant leaf stomata and now started grow trials in lettuce and peppers will be ongoing.
The primary objective of the started St. Cloud Romaine lettuce trial is to duplicate the excellent 100% incremental biomass results from an earlier lettuce trial conducted by the University of Guelph. That dissolved CO2 foliar spray lettuce biomass result was measured against lettuce grown with 800 PPM of CO2 gassing.
All patentable results from scientific discoveries at St Cloud will be 100% owned by GROW.
About CO2GRO (GROW.TSXV) or "GROW"
GROW's mission is to accelerate all indoor and outdoor value plant growth naturally, safely, and economically using its patented advanced CO2 foliar technologies. CO2 GRO's global target plant markets are retail food at $8 trillion per year (Plunkett Mar 2017), retail non-food plants at an estimated $1 trillion per year and legal retail cannabis that may reach $50 billion per year by 2022 (Bay St Analyst estimates). GROW's sole focus is working with its plant grower and Agri-industrial partners in proving and adopting its CO2 technologies for specific growers’ plant yield needs.
The CO2 technologies work by transferring CO2 gas into water and foliar spraying across the entire plant leaf surface area, which is a semi-permeable membrane. The dissolved concentrated CO2 then penetrates a leaf's surface area naturally like nicotine naturally dissolves through human skin from a nicotine patch.
Foliar spraying natural nutrients and chemicals on plant leaves have been used for over 60 years by millions of indoor and outdoor plant growers. To date, outdoor growers have not had any way to enhance plant CO2 gas uptake for faster growth.
Indoor use of CO2 gassing has enhanced plant yields for over 60 years. However, over 50% of the CO2 gas is typically lost through ventilation. Current greenhouse CO2 gassing levels of up to 1500 PPM are also not ideal for worker health and safety. GROW's safer dissolved CO2 foliar spray can be used by indoor and outdoor plant growers with minimal CO2 gas lost.
GROW's CO2 technologies are commercially proven, scalable and easily adapted into existing irrigation systems. GROW's proven crop yield enhancements and revenue model is compelling for growers and Agri-industrial partners.
Forward-Looking Statements This news release may contain forward-looking statements that are based on CO2GRO's expectations, estimates, and projections regarding its business and the economic environment in which it operates. These statements are not guarantees of future performance and involve risks and uncertainties that are difficult to control or predict. Therefore, actual outcomes and results may differ materially from those expressed in these forward-looking statements and readers should not place undue reliance on such statements. Statements speak only as of the date on which they are made, and the Company undertakes no obligation to update them publicly to reflect new information or the occurrence of future events or circumstances unless otherwise required to do so by law.
Neither the TSX Venture Exchange nor its Regulation Services Provider (as that term is defined in the policies of the TSX Venture Exchange) accept responsibility for the adequacy or accuracy of this release.
Startup Farmshelf Aims To Let Restaurants, Homeowners Grow Their Own Veggies
Nicole Zelniker, Special to USA TODAY
Published: July 3, 2018
In Singapore, several groups hope to transform the urban jungle into productive farmland by growing crops on rooftops. USA Today's Elizabeth Weise visited one.
(Photo: The Associated Press)
NEW YORK – When Andrew Shearer started Farmshelf in a San Francisco garage about two years ago, he created a business that set him on the path to the forefront of urban farming.
Farmshelf sells hydroponic growing systems, bookshelf-like units that come complete with everything needed to grow herbs and vegetables indoors, from seeds and nutrients to the LED lights that provide artificial sunlight.
Because Farmshelf's concept is hydroponic – employing science to grow food indoors – it says its veggies grow much faster than they would in fields.
Shearer founded Farmshelf on the belief that everyone should be able to grow their own food. For now, the systems are being pitched to restaurants and hotels, but individual consumers and home chefs may be next.
"At the end of the day, it all comes down to empowering people to grow the best-tasting food and the most nutritious food possible," said Shearer, also the CEO.
Current customers include Beefsteak, a restaurant with three locations in Washington, D.C., that specializes in vegetable-based dishes; and the Great Northern Food Hall, a Nordic-inspired restaurant in New York's Grand Central Station.
Shearer's background isn't in farming. Most recently, it's in technology.
Shearer worked at ideas-sharing site Pinterest in the San Francisco Bay Area, where he was a partner manager. At Pinterest, he said he began looking at ways to make his own food by searching for tips on Pinterest's message boards. He left to found Farmshelf in October 2015.
Now, Shearer has an office at the Brooklyn Navy Yard, where he can grow food and experiment with new technology.
"We drove across the country and relocated the company to New York," Shearer said. "The restaurant scene and the community are just amazing."
The effects of food insecurity on children. (Photo: Jerry Mosemak)
At Great Northern, Farmshelf's growing units are on display. Customers can see the origin of at least some of the ingredients in their meals. Chefs snip herbs and other greens from the shelves to prepare the day's meals.
"The Farmshelf team monitors our plants for us," said Jenny Pura, senior communications manager at Meyers USA, which oversees the Great Northern Food Hall. "They're great to work with because they see this as a science."
A favorite for Meyers' customers is micro-basil, which the chefs use in flatbread and some of the drinks at the Great Northern Food Hall. Pura said she often sees customers taking pictures of the Farmshelf units.
For Pura, Farmshelf matched the company's priorities when it came to sourcing food.
"We care immensely about where we get our food from," she said. "Not just sustainable, but as local as possible."
The idea of urban farming is not new. In the 1800s, Germans used urban gardens to fight food insecurity. During World War II, Americans were urged to plant Victory Gardens to supplement short supplies at home as farm production was diverted to feed soldiers, sailors and Marines.
As a startup, Farmshelf made a lot of sense, according to Barry Moltz, author and speaker on entrepreneurship. Small businesses such as Farmshelf have the advantage of low production costs and the ability to know what is happening in the community.
“People start businesses because they see a problem” they can fix, Moltz said. “They see a hole they can fill.”
The United Nations estimates that food production will need to at least double by 2050, according to a 2015 report. Plus, many households today need new sources of fresh food.
In New York City, about 15 percent of the population is what is termed as "food insecure," living in fear of running out of food or lacking access to nutritional food, according to a 2017 report. Many people who are food insecure have limited options, such as fast food, since it is cheap relative to other options, such as most organic produce.
Armed with the knowledge of how to lessen hunger with high-quality food, Farmshelf allows food to travel mere feet instead of miles on the path to consumption.
"Getting food into a city and providing high-quality food is difficult now," Shearer said.
Helping to solve an urban problem attracted investment from Urban-X, a collaboration between an automaker, BMW's Mini, and a venture capital firm interested in improving city life, Urban Us.
Farmshelf is one of seven small businesses that received support from Urban-X in 2016.
"Startups have an inherent advantage around speed and being really close to their customers," said Micah Kotch, managing director for Mini. "They're able to bring new thinking to the table."
LettUs Grow Wins "Best Elevator Pitch" At Tech-Xpo Event
Charlie Guy (right) with VWV’s Nathan Guest
LettUs Grow scooped the top prize of ‘Best Elevator Pitch’ last night at SETsquared Bristol’s annual Tech-Xpo event, which was held at Circomedia Bristol.
The start-up, which designs irrigation and control technology for vertical farms, was one of six tech start-ups to pitch at the event, with the audience using a digital voting system to crown the winner.
17 companies, including AutonoMe, Interactive Scientific, and YellowDog, exhibited to a crowd of investors, academics, and business leaders.
The six pitching companies were filmed as they presented their 60-second speed session, with the aim of winning over delegates, and winning the ‘Best Elevator Pitch’ award.
Charlie Guy, Managing Director of LettUs Grow who delivered their winning pitch, collected the prize for their patent-pending aeroponic technology, which delivers consistently high yields for vertical farms.
Aeroponics is a methodology of growing plants without soil, which allows greater oxygenation to the roots, delivering better flavour and faster growth, and using 95% less water than traditional agriculture.
Charlie Guy comments: “We’re absolutely over the moon to have won the ‘Best Elevator Pitch’ at SETsquared’s Tech-Xpo 2018. This is a really exciting time for us as a business, the team is growing, and building Europe’s first vertical farm, and we’re really excited to see what comes next.”
Oasis Biotech Brings Indoor Farming To Las Vegas
Oasis Biotech has opened an indoor farm in the Las Vegas valley and they will soon be growing produce for local restaurants. Parker Collins reporting.
LAS VEGAS (KTNV) - Seeing the building at 6225 Annie Oakley Drive you might not believe there's an entire farm inside.
They're growing a lot of things and they'll start delivering to their first customers July 24.
To go inside you have to wear a mask, gloves, and a full body suit. It looks like workers are gearing up for surgery, but it's actually a very scientific farm called Oasis Biotech. There's a reason for all the layers.
"Nobody wants to get sick from what they eat and quite literally there's cases of it being fatal," said Brock Leach, the general manager of Oasis Biotech.
Workers plant one seed at a time with tweezers. Crops are harvested in air conditioned rooms. In between, they grow crops in rooms right out of a sci-fi thriller. The germination room is kept at 85 degrees Fahrenheit and 85% humidity.
Right now, they're growing baby lettuce and micro-greens. You can't go buy it, but you could see it when you eat out. In fact, that's why the company came from China: because of all the high end restaurants in Las Vegas.
The plain-looking building down the block could give your next dish a kick.
"It's really not the meat and the potatoes of the dinner for say, but the things that add a lot of flavor and a little pizazz," said Leach.
They want to start growing berries and show up in local grocery stores next year.
Mucci Farms Takes Home Best New Packaging Award from United Fresh
Mucci Farms Takes Home Best New Packaging Award from United Fresh
June 29, 2018
by Lillie Apostolos
CHICAGO, IL - With so many people looking for inspiration in produce aisles, Mucci Farms is stepping up as a company wanting to lasso in consumers’ interest in new and interesting ways. Mucci's very own CuteCucumber Poppers won the Best New Packaging for this year’s United Fresh Produce Innovation Award at 2018’s Chicago-based FreshMkt Expo. The awarded company was selected after exhibitors and attendees voted on their favorite from a list of seven nominated packages in the category.
Emily Murracas, Director of Marketing, Mucci Farms
“We are delighted to win the packaging award for CuteCumber Poppers because we really feel like we’re bringing something new to the greenhouse produce category by including a tasty dip inside each container,” Director of Marketing Emily Murracas said. “In addition, our focus was to create multiple convenient packages to accommodate a variety of customers in the rapidly growing snacking category.”
The Mucci Farms team posing with their award. The company won this year’s United Fresh Produce Innovation Award
The one-bite variety used in CuteCucumber Poppers are on a roll, having recently won the People’s Choice Award at the Leamington Greenhouse Competition. Offering incredible flavor paired with an irresistible crunchy texture, the product will be available in three pack styles to stay in tune with club stores, retailers, and foodservice.
Fernanda Albuquerque, New Product Development Manager, Mucci Farms
“With this product, we decided to create a lineup of new packages to give our partners multiple options based on their demographics and value proposition,” Fernanda Albuquerque, New Product Development Manager, shared in a press release. “The 1.5 lbs and 5 oz top-seal packages are custom thermoformed trays that securely hold the dip container in place. The 9 oz tray is a 3 x 3 oz format with EZ Snap convenience, allowing consumers to tear off each container for 3 individual snack size packs.”
Mucci Farms' award-winning Cutecumber Poppers packaging
Attendees had the opportunity to check in with the company at their booth. The greenhouse grower also co-sponsored the breakfast session, which announced recipients of the 2018 Retail Produce Manager Awards. This segment of the show celebrated produce and foodservice industry professionals from across the continent.
Joe Spano, Vice President of Sales and Marketing, Mucci Farms
“Sponsoring this event is important to us as it recognizes the front-line staff that bring our products to life through merchandising and recipes,” Vice President of Mucci International Marketing Joe Spano shared. “We’d like to congratulate all the award recipients and thank them for all they do to raise the profile of healthy eating.”
Congratulations to the Mucci Farms team! We look forward to seeing how your award-winning packaging pushes the category forward and inspires more consumers to fall in love with produce and the cute offerings our industry provides.
Mucci Farms
Cucumbers Cucumber Mucci Farms New packaging CutecumberTM Poppers Award United Fresh Best New Packaging CuteCumbers
Mucci Farms grows a variety of standard and specialty tomatoes, peppers, cucumbers, and eggplant. Fresh and delicious,...
"A Good Growing Recipe For Every Crop"
Light4Food inovates with smart indoor growing system
"A Good Growing Recipe For Every Crop"
It all starts ten years ago with a shipping container in which LED lights were installed in layers. Leafy vegetables can be harvested year-round in these layers as is the idea. Led technology isn’t as efficient as we might want but entrepreneurs Peter Christiaens, René van Haeff and Michel la Crois see its potential. Experiments are being done with crops like spinach and other types of lettuce in association with partners like Van Dijck Groenteproducties who are members of growers association Fossa Eugenia.
In doing so Light4Food can gather the necessary experience for growing in an indoor environment. Light, climate, and air are being kept in the optimum balance in a computer-controlled environment. The first indoor growing facility is born.
Mobile climate chamber for rent
The innovation gets a lot of interest mainly from companies in seed breeding. The initial investment for a fixed installation, however, is quite high which still holds companies back on buying them. For this the entrepreneurs thought up a solution; they are developing a Mobile Climate Chamber to rent out for plant related research looking at possibilities of indoor growing.
In the following years, renting will soon change into buying. Mainly seed breeders both national and international are interested in these Mobile Climate Chambers for their own research. The most notable renter might just be Ciris in Norway, where they use the Mobile Climate Chamber for the International Space Station (ISS).
Growing vegetables on Mars: is also possible.
First green thumbs
Light4Food might be a technology company but it is starting to get green thumbs. This is the reason for their success tells Van Haeff. “Many companies start in technique. But technique is not good if you don’t know what the plant needs. That’s why we have botanists in our company that, together with our clients, look at the specific trades and needs of certain crops. Having this information allows us to change the lighting, climate, and nourishment to increase efficiency.”
Own research and engineering
Light4Food invests in their own botanist research besides the production of their installations. Van Haeff tells us why. “Every crop requires a different spectrum of light, climate needs, air flow and nourishment. For every crop, we go look for the right botanist growing recipe and in which installation this recipe will work the best. The technical growing recipe. By researching this ourselves we can develop better products.” The botanists are also researching the ideal growing recipe for high wire crops like cucumbers and tomatoes.
Christiaens explains: “A tomato plant is obviously much larger than a lettuce and produces more moisture. This, for instance, requires a different division of light and air flow. All of our research leads to a new type of installation.”
The first test installation for indoor growing of high wire crops is built in what used to be a spraying booth. Soon more advanced installations can be built.
Extreme climate is an opportunity
Advantages of the new solutions mainly are in regards to efficiency. Van Haeff: "The time of the breeding cycle can be greatly reduced by this. The growth quality is more stable due to optimal growing conditions and the growing itself becomes much more sustainable because of recirculation and regeneration of warmth and water. These are important components when it comes to costs in horticulture.” At first, Light4Food will serve the seed breeding companies in the Netherlands. Later even countries with extreme climate conditions for growers like Russia and Saudi Arabia will come into the picture. The reputation of the Netherlands will make it so that the market will be able to find them.
Christiaens: "You can imagine how important it is in desert areas to absorb sunlight and water to re-use. In countries with extreme cold, you want to be able to heath in an energy efficient way. By growing in one controlled environment you take away a lot of uncertainties and give sustainability.”
Indoor growing, not everywhere and all the time
Yet, the partners realise that indoor growing is not always the best solution. Van Haeff: "For the more generic crops like potatoes and grain outdoor growing remains a great way of doing things, especially in Western Europe. This is also something we look at with our partners and clients: when will indoor growing get interesting and how do we get there?” Producing more efficiently and wasting less they see as a theme that is applicable to all agri-food.
Christaens: "Here lies the solution to the worlds food problem. There is still so much being wasted in all phases from farm to table that there is still a world to win over.”
Free thinking and implementation
When talking with Van Haeff and Christiaens: it becomes clear: innovation is in their blood. They both believe you can not learn how to be innovative. Christians: "You must be sort of a hippie and dare to think freely. If you only see bears on the road you won't get anywhere.” At the same time though they believe you can stimulate innovation within a company. Van Haeff: "We have weekly meetings with all of our employees in which we look back at projects and discuss things we can still improve upon. This is how we create a company culture that keeps on evolving.”
By now they know that only innovating won't work. “if you only want to think of new ideas and not about implementation you cant build a good company. The art is in finding the balance.”
Innovation tips
The entrepreneurs have tree tips for innovation-seeking companies in the agri-food sector.
- Combining young talent with people who have been in the business for a long time. “We have a couple nearly retired employees with years of experience in things like lighting and growing, air treatment or engineering. This can be very useful if you want to be able to test out a new idea and eventually make a real product. The younger generation, on the other hand, is super-fast with computer technology.”
- Find suitable partners and allow each other to do things. “don’t try to do everything by yourself, together you can figure things out much faster. But you have to allow each other this and share your knowledge freely amongst each other. You will know rather quickly if this is possible. The give and take must be in balance.”
- Innovate from a demand or need. “Innovation without demand has no use, then it becomes just a gimmick. Do some research on the market. Talk to people and discover what it is they want.”
Source: Kiempunt-Limburg
Nichia Turns Vegetables Into Medicinal Plants With LED Lighting
Nichia Turns Vegetables Into Medicinal Plants With LED Lighting
LED applications have opened an explosive market in horticulture lighting. Nichia, the Japanese LED giant, set up a laboratorial plant factory in Shanghai to test how different LED light sources can alter the ingredients of plants to create medicinal effects.
By combining blue LED with various phosphors, Nichia managed to generate artificial LED light with sunlight spectrum to upgrade the quality of light, which not only enhances eye comfort for people but also improves vegetable growth. In Nichia’s plant factory in Shanghai, Chun Chia Tai, Chairman and President of Nichia’s Shanghai and Taiwan Offices, established an indoor farm to conduct experiments on plants with several LEDs.
(Image: Nichia; Chairman and President of Nichia’s Shanghai and Taiwan Offices)
According to Tai, Nichia aims to grow vegetables with intensified medicinal effects. The ingredients of vegetables could be modified by changing the spectrum of LEDs. For example, Nichia has bred vegetables containing lower sugar which would be beneficial for diabetic patients. With its unique technology of mixing phosphors with LEDs, the company is bringing horticulture lighting to a new level.
Nichia has connected with local supermarkets to sell its vegetables in Shanghai and shipped some products to the Netherlands. The wide range applications of LED have built up a bridge between cutting-edge technologies and farming, bringing more healthy options for people.
- Keywords: Nichia Horticulture lighting Plant factory
Mexico: New DTS Plug-In Tray For Stone Wool Plugs
Production started
Mexico: New DTS Plug-In Tray For Stone Wool Plugs
INA Plastics designed a new tray for stone wool plugs based on the Double Tray Invention, the DTS Plug-In tray on the 60X40 cm footprint holding 240 stone wool plugs of 27 mm.
The cell design of the DTS Plug-In offers ideal air pruning and allows the fingers of robotic transplanters to pick up the plants, thus the tray works well in advanced automatic production lines and offers all the benefits of the Double Tray System: economy, hygiene, productivity, plant quality and environmental protection.
Although the cost of the DTS Plug-In tray allows it to be considered as a one-use tray, with all the benefits of this procedure, it can be reusable by reusing the bottom tray for at least three or four years, replace only the top tray in order to take all the advantages of the one-use tray at half the cost of any other alternative e.g. light EPS tray.
The new DTS Plug-In tray will be available before the end of this year and its presentation coincides with the decision of the company to start producing the DTS locally, close to the big markets. This became necessary in order to be able to cover the demand, to minimize transportation costs and to ensure the growers for the availability of the trays even in unforeseen circumstances and periods of extreme demand.
Following this commitment, the company will establish production facilities in the Guanajuato area, to service customers in Mexico, via its affiliate company, INA Insumos Agricolas SA de CV, for the sales, technical support and distribution of its products. The first stage of production operations will be the set-up with an automatic line, especially developed by Conic System, for the assembly of the DTS Plug-In tray with stone wool plugs. Conic System is in close cooperation with INA Plastics over the years and has already in the market a special automation, the Double De-stacker, for the assembly of DTS.
The aim is to establish, as of March 2019, production of the DTS Plug-In tray and other configurations DTS trays, for the Mexican and the US market.
For more information
INA Plastics SA
Jacob Tsonakis
117, Megaridos street
19300 Aspropyrgos
P.O. Box 64
Tel: +30 210 5580126
Fax: +30 210 5574731
jacob@ina-plastics.com
info@ina-plastics.com
www.ina-plastics.com
Publication date: 6/14/2018