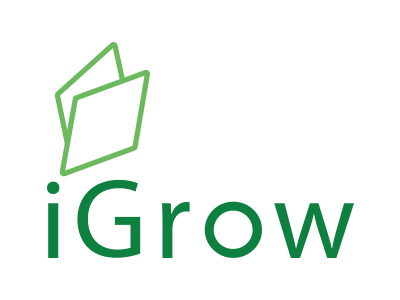
Welcome to iGrow News, Your Source for the World of Indoor Vertical Farming
CO2 GRO Trials
Matthew Bohlsen
November 20, 2018
There’s a lot of activity coming out of Canada with the recent legalization of cannabis, which has been very good for CO2 GRO. Following this the desire to produce better and faster crops and flowers looks like the next challenge for CO2 GRO to expand into new markets beyond cannabis.
CO2 GRO Inc. (TSXV: GROW | OTCQB: BLONF) (“GROW”) is a Canadian company with CO2 technologies that are dedicated to increasing the growth of all indoor and outdoor value plants. The technology works by transferring CO2 gas into water and foliage spray for use across the entire plant leaf surface area, which is a semi permeable membrane. The dissolved concentrated CO2 then penetrates the leaf’s surface area naturally, like concentrated nicotine dissolves through human skin into the bloodstream from a nicotine patch.
Previously CO2 GRO has had good success in the cannabis market. The Company previously announced a 45% increased commercial cannabis bud value growth in trials. More recently the Company announced trials on flowers and peppers proving it’s not only cannabis that can benefit.
CO2 GRO trials result in quicker growing flowers
On October 24, 2018 CO2 GRO announced a series of positive flower grow trials using dissolved CO2 spray versus no CO2 gassing at a commercial Michigan flower greenhouse. The first two trials were done in a large commercial greenhouse that does not use CO2 gassing. The dissolved CO2 sprayed flowers were healthier, showing more branching and side shoots with bigger, thicker leaves, and a more advanced root systems that delivers more water and nutrients up to the leaves. Importantly these flowers were commercially ready to ship 7-10 days faster at 32-35 days versus the control flowers requiring 42 days. The third and fourth trials resulted in bushier plants without additional stretching, with deeper more vibrant flower coloring. Propagation times were consistently reduced by one-third to 14 days versus the control flowers requiring 21 days.
John Archibald, CEO of GROW, stated: “We are really pleased with these Michigan flower results as the global flower market is a $200 billion a year retail business. Flowers are more valuable than food on a greenhouse per square foot basis.”
CO2 GRO trials on pepper yield great results
CO2 GRO have also been conducting pepper grow trials, with dissolved CO2 sprayed plants receiving a 30% greater fruit yield and a 20% faster growing rate.
CEO John Archibald stated: “Until legal cannabis, the top two greenhouse crops in Canada were tomatoes at 38% and peppers at 33%. We can add plant yield and speed to maturity value to any greenhouse or indoor grow facility that does not use CO2 gas, or to the 95% of the world’s plant food grown outdoors, where it has been impossible to add CO2 until now.”
GROW’s global target plant markets are retail food at $8 trillion per year, retail non-food plants at an estimated $1 trillion per year, and legal retail cannabis that may reach $50 billion per year by 2022.
The world has been discussing global warming and food shortages for years now. With almost a permanent drought in many continental climate type countries, the global food basket is under pressure.
With a mission to accelerate the growth of all value plants safely, economically, and naturally; using their patented advanced carbon dioxide technologies, GROW now have proof in trials that their concentrated CO2 foliage spray could well be a savior to the world’s food shortages and of course don’t forget the great results from cannabis trials.
GROW expect to continuously strengthen their patent portfolio as experience optimizing CO2 technologies for plant yields continues to evolve. Keep an eye on this company as they have something the planet definitely needs.
"Smart Lighting Makes Growing Easier And More Cost Effective"
After being in the LED market for years, ITC is now expanding in to horticulture with the Amplify and Amplify Plus product lines. Remarkable is how their smart LED lighting solution can be steered on the actual weather conditions at individual locations.
"Our research resulted in grow light products, specifically intended to reduce energy usage, increase yield, and enhance plant strength", the team with ITC explains while showing their new Amplify product line. "It offers multiple, scientifically proven spectrums and lamp configurations to provide a solution for greenhouse or controlled environment growers."
The LEDs used in the Amplify product line are optimized for light distribution and plant level light intensity. The spectrum options are focused on the light needs of different cultivars at different points of development. "These are key to consistent and even growth patterns, that produce better yields and quicker turns. While the finned heatsink design of the lamp dissipates the minimal heat and the whale tail feature provides an additional protective shield for water and dirt intrusion."
Extra attention is paid to the design of the fixtures. "The simple hang and plug single and double lamp options are great for narrower spaces or long runs. Both are available in 80 or 150 degree light spreads. The 5-Lamp fixture gives consistent light placement across larger areas while reducing the number of electrical drops needed. This feature reduces install labor and can comply with existing infrastructure of greenhouses."
Smart lamps
And then there's the smart technology. "Many experts continue to explore the complexities that climate change and environmental factors are having on our food growing capabilities. These factors are making the consistency within food production environments a necessity.
Nebula Controls modules
Nebula Controls, a technology company, is providing artificial intelligent wireless controls for ITC Horticulture’s Amplify Plus smart LED lighting. This partnership is enabling the ability to program and reprogram the cloud based lighting control operation from mobile devices for enhanced growth and energy savings.
"Based on weather conditions at individual locations or programmed zones the Nebula Control smart control system is able to maximize efficiencies and reduce energy usage with minimal human dependency", the team explains. "Both ITC Horticulture’s Amplify Plus smart LED lighting and Nebula Controls are working to elevate supplement and controlled environmental horticulture lighting to a new level by using a new state-of-the-art smart lighting control system that contribute to consistent high performing food production environments. This way we are working to make growing easier and more cost effective for today and tomorrow."
For more information:
Nebula Controls
519-749-3373
contact@nebulacontrols.ca
Publication date : 11/16/2018
What Do Investors Need To Know About The Future of LED Grow Light Technology?
NOVEMBER 16, 2018 PATRICK FLYNN
Editor’s Note: Patrick Flynn created Urbanvine.co in 2016 to help urban dwellers learn how to start urban farming without any previous experience. As the site grew, he discovered that “urban farming” was actually a general term that can include a wide variety of concepts, including grow lights and hydroponics, topics which the site now covers in depth.
The horticultural lighting market is growing, and growing rapidly. According to a September press release from Report Linker, a market research firm specializing in agribusiness, the horticultural lighting market is estimated grow from a $2.43 billion market this year to $6.21 billion in 2023.
One of the key factors driving current market sector growth is increased development of LED grow light technology. LEDs (light emitting diodes) were first developed in the 1950s as a smaller and longer-lasting source of light compared to the traditional incandescent light bulb invented by Thomas Edison in 1879.
LEDs last longer, give off less heat, and are more efficient converting energy to light compared to other types of lights, all features that can result in higher yields and profits for indoor growers.
But until recently, LEDs were only used to grow plants indoors experimentally, largely because the cost was still too high for commercial businesses. Many commercial growers still use HID (High Intensity Discharge) lights such as High Pressure Sodium, Metal Halide, and Ceramic Metal Halide; all lights that have a high power output but are less durable than LED lights, generate far more heat, and have less customizable light spectra.
Today, LEDs are fast becoming the dominant horticultural lighting solution. This is due primarily to the one-million fold decrease in fabrication cost of semiconductor chips used to make LED lights since 1954.
For investors more familiar with field-based agriculture, it can certainly be a minefield to know where LED lighting technology for horticulture is going in the future. Although it is no longer the “early days” of LED technology development, current trends are still shaping the future of LED technology.
So what does the intelligent agtech investor need to know about the current state and future of LED grow light technology?
I interviewed Jeff Mastin, director of R&D at Total Grow LED Lighting, to discuss what the future of LED grow light technology for agriculture looks like, and how investors can use current trends to their advantage in the future.
What is your background – how did you get involved in grow light technology at Total Grow?
The company behind TotalGrow is called Venntis Technologies. Venntis has, and still does, specialize in integrating touch-sensing semiconductor technologies into applications.
Most people don’t realize LEDs are semiconductors; you can also use them for touch-sensing technologies, so there’s a strong bridge to agricultural LED technology.
Some of the biggest technical challenges in utilizing LEDs effectively for agriculture include LED glaring, shadowing and color separation.
We have used our expertise in touch-sensing LEDs to expand into horticultural LEDs, and we have developed technology that addresses the above challenges better, giving better control over the spectrum that the LED makes and the directional output of the light in a way that a standard LED by itself can’t do.
My personal background is in biology. When TotalGrow started exploring the horticultural world, that’s where being a biologist was a natural fit to take a lead on the science and the research side of the development process for the product; that was about 7 years ago now.
If you were going to distill your technical focus into trends that you’re seeing in the horticultural lighting space, what are the main trends to keep an eye on?
The horticultural lighting industry is really becoming revolutionized because of LEDs. Less than 10 years ago, LEDs in the horticultural world were mainly a research tool and a novelty.
In the past, they were not efficient enough and they were definitely not affordable enough yet to really consider them an economical general commercial light source.
But that is very quickly changing. The efficiencies are going up and prices down and they are really right now hitting the tipping point where for a lot of applications, but definitely not all applications, the LED world is starting to take over horticulture and indoor agriculture.
How do you view the translation of those trends into actionable points? For investors or technology developers in the agriculture technology space, how do they make sure that the LED light technology they are investing in isn’t going to be obsolete in a year or two?
With LEDs, the key question is still cost-efficiency, and there’s only so far the technology can improve.
Why? There are physical limitations. You can’t make a 100% efficient product that turns every bit of electricity into photons of light. At this point, the efficiency level of the top of line LEDs are up over 50%.
Can we ever get up to 70 or 80%? Probably not any time soon with an end-product, not one that’s going to be affordable and economical generally speaking.
So to answer your question, it’s not a category where you’re going to say, “well this is obsolete, I can get something three times better now.” The performance improvements will be more marginal in the future.
Ten years from now the cost will be cheaper. But that again doesn’t make current LED technologies obsolete. In terms of that fear, I don’t think people have to worry about current LED light technologies becoming obsolete.
In a large commercial vertical farming set up, what is the ballpark cost of horticultural LEDs currently?
To give just an order of magnitude sort of number, you’re probably going to be someplace in the $30 per square foot number for lights for a large facility. It can be half that or it can be double that.
That’s just talking within the realm of common vertical farming plants like greens and herbs, or other plants similar in size and lighting needs.
If you start talking about tomatoes or medicinal plants, then the ability to use higher light levels and have the plants make good use of it skyrockets. You can go four times higher with some of those other plants, and for good reason.
What type of horticultural lighting applications are LEDs still not the best solution for now and in the foreseeable future?
There are at least 3 areas where LEDs still may not make sense now and in the near future.
First, if the LED lights are not used often enough. The more hours per year the lights are used, the more quickly they return on their investment from power savings and reduced maintenance. Some applications only need a few weeks of lighting per year, which makes a cheaper solution appropriate.
Second, in some greenhouse applications, LED’s may not be the best choice for some time to come. Cheaper lights like high-pressure sodium have more of a role in greenhouses where hours of use are less and higher hang heights are possible. (Many greenhouses will still benefit strongly from LEDs, but the economics and other considerations make it important to consider both options in greenhouses.)
Lastly, some plants are not the best in vertical farming styles of growing where LEDs have their most drastic advantages. At least at this point it is not common to attempt to grow larger fruiting plants like tomatoes or cucumbers totally indoors, though when attempted that is still more practical with LEDs than legacy lights.
Thanks Jeff!
To learn more about Total Grow, visit www.totalgrowlight.com
How-To: Microgreen Growing
Are you interested in growing microgreens indoor year round, or for the winter months? Today’s blog will help you make the right decisions while growing healthy and nutritional microgreens. Microgreens are most commonly harvested from leafy greens such as kale, arugula, radish greens and herbs. The taste of microgreens depends on the original vegetable. Microgreens have a very strong and concentrated taste of the original vegetable. This means that cilantro microgreens will still taste of cilantro, but with a stronger taste and condensed format.
Here are your instructions:
Get a 10 x 20 tray or container. 10 x 20 trays are the best, but my personal favorite are those clear plastic salad containers with a lid. It’s a little harder to harvest, and you may not get ideal air flow, but the lids are nice for keeping the seeds moist while in the germination stage.
Get a growing medium such as bio strate, burlap or soil. Pre-moisten your growing medium by soaking in a 5 gallon bucket or a big bowl. Keep the medium soaking for a couple of hours.
Place the growing medium in the tray and make sure to flatten the medium with your hands.
Sprinkle seeds over the top of the medium. Don’t worry about spacing. You’ll be harvesting so soon that a nice little carpet is what you’re going for. For best results use a spice shaker to spread the seeds evenly.
Spray your seeds with a spray bottle or water lightly and then spray the inside of your humidity dome. Cover your tray with the humidity dome and place in a dark location. Covering the tray helps keeps in the moisture, and the darkness helps the seeds to germinate.
Remove cover after seeds sprout, which should take a few days. Remove the cover and place in front of a sunny window sill.
Carefully water your microgreens. The best option is to bottom water, which is setting your tray with drainage holes in a sink of water and letting the microgreens soak it up. If you top water, be careful not to flatten the tiny greens.
Cut your microgreens with a sharp knife, most are delicious after they develop their second set of leaves, and are about 2 inches tall.
Eat your microgreens! You can eat them on sandwiches, in stir fry, on pizza, in green smoothies, in salads, or as a garnish or other ingredient.
These are simple and easy instructions for growing microgreens year-round. Microgreens can be a refreshing addition to your food in winter months when fresh produce isn’t always as available as it might be in the summer. If you have any questions don’t hesitate to reach out.
Category: microgreens
Whole Foods Supplier Embraces Robotic Farming
By PYMNTS
2018
To supply retailers such as Whole Foods and U.S. Foods with greens, 80 Acres Farms is constructing a “fully automated indoor farm.” The project’s reported cost is in the range of $10 million to $15 million, CNBC reported.
“With the … facility, we will achieve the next-generation of indoor vertical farming,” 80 Acres Farms’ CEO and co-founder, Mike Zelkind said. “This project will deliver our proof of concept that indoor farming can be fully automated, commercially scalable, higher-yielding, and profitable.”
The first phase of construction will bring grow centers that can make products such as kale, culinary herbs and microgreens. Then, three more phases could follow. In all, the facility could grow to over 150,000 square feet — or roughly 3.5 acres.
Another vertical farming company, Smallhold, works sort of like a nursery to expedite the growing process. The company grows the produce — mushrooms, at the moment — three-quarters of the way. Then it delivers the almost-grown produce to their customers, who finish growing the fungi in their vertical growing units. The company also helps customers create the right growing conditions with WiFi enabled units that allow Smallhold to monitor and control them remotely. As a result, customers simply have to pick and serve the produce.
Smallhold’s farms also reduce the environmental impact of growing produce. Their farming units reportedly create 40 times the output per square foot compared to a traditional farm, and use 96 percent less water, according to the company.
Smallhold is not the only urban farming concept in the U.S. Boston-based agricultural tech company Freight Farms grows produce inside of shipping containers. One freight farm can grow approximately two acres worth of produce, according to the company, and that can either be sold direct to consumers (D2C) or through partnerships with local distributors, restaurants and grocery stores.
Nation’s First Fully Automated Vertical Farm Breaks Ground In Ohio
Posted by Laura Drotleff| September 25, 2018
Cincinnati-based 80 Acres Farms announced that it plans to build a large, fully automated indoor farm in Hamilton, OH, which will produce specialty greens to supply local independent retailers including Jungle Jim’s International Market and Dorothy Lane Markets, and national chain locations for Whole Foods and U.S. Foods.
The facility would be the first of its kind in the nation, according to 80 Acres. A groundbreaking was held for one of two facilities on Monday, Sept. 24. An MSNBC article stated the project would cost between $10 million and $15 million initially, and create 40 jobs would be created, which would average in the $40,000 to $50,000 range including benefits. The city discounted land in Hamilton Enterprise park for the project and is providing an Enterprise Zone property tax abatement of 75% for 10 years, MSNBC reported.
80 Acres Farms personnel will manage the facilities, which will feature robotics, artificial intelligence, data analytics, and around-the-clock monitoring sensors and control systems to optimize every aspect of growing produce indoors. The Cincinnati firm will work with its current technology partners, Signify, an LED horticultural lighting company, and Priva, which provides environmental controls and process management software, according to Tisha Livingston, President and Co-founder of 80 Acres.
The initial phase, which is to be completed later this year, will feature grow centers to produce microgreens, culinary herbs, leafy greens, and kale. Three additional phases are planned. When completed, the indoor farm is to encompass more than 150,000 square feet, which equates to nearly 3.5 acres.
The full-phase expansion of controlled environmental agriculture will enable 80 Acres Farms to provide more product to serve existing customers and new ones with fresh-picked, year-round produce. 80 Acres Farms now serves Cincinnati-area customers from its facility in Spring Grove, where it grows microgreens, culinary herbs, leafy lettuce, kale, and vine crops such as cherry tomatoes, cucumbers, and peppers.
“We already have demonstrated that we can provide to our customers the freshest, best-tasting and nutritious locally grown produce, while using renewable energy, very little water, and no pesticides,” said Mike Zelkind, CEO and co-founder of 80 Acres Farms in a September 21 release. “With the Hamilton facility, we will achieve the next-generation of indoor vertical farming. This project will deliver our proof of concept that indoor farming can be fully automated, commercially scalable, higher-yielding, and profitable. It will serve as a prototype for our ambitious plans to co-locate similar facilities with commercial customers in other parts of the country.”
Zelkind said 80 Acres Farms will work with partners such as JDL Warm Construction and Open Architecture Inc., both of downtown Cincinnati. Site Solutions Consulting of Loveland will do excavation site preparation work.
80 Acres Farms is headquartered in the Spring Grove community of Cincinnati, where the company was founded in 2015 by Zelkind and Livingston, both veteran food industry executives. It now employs more than 60 people in Cincinnati and other company research and development, engineering, and production facilities in three other states. In its mission to locally grow the best tasting, most nutritious fruits and vegetables, the company partners in research with many agrotechnology and academic research institutions.
Infarm Expands Its ‘In-Store Farming’ To Paris
Steve O'Hear@sohear / November 8, 2018
Infarm, the Berlin-based startup that has developed vertical farming tech for grocery stores, restaurants and local distribution centres to bring fresh and artisan produce much closer to the consumer, is expanding to Paris.
Once again, the company is partnering with Metro in a move that will see Infarm’s “in-store farming” platform installed in the retailer’s flagship store in the French capital city later this month. The 80 metre square “vertical farm” will produce approximately 4 tonnes of premium quality herbs, leafy greens, and microgreens annually, and means that Metro will become completely self-sufficient in its herb production with its own in-store farm.
Founded in 2013 by Osnat Michaeli, and brothers Erez and Guy Galonska, Infarm has developed an “indoor vertical farming” system capable of growing anything from herbs, lettuce and other vegetables, and even fruit. It then places these modular farms in a variety of customer-facing city locations, such as grocery stores, restaurants, shopping malls, and schools, thus enabling the end-customer to actually pick the produce themselves.
The distributed system is designed to be infinitely scalable — you simply add more modules, space permitting — whilst the whole thing is cloud-based, meaning the farms can be monitored and controlled from Infarm’s central control centre. It’s data-driven: a combination of IoT, Big Data and cloud analytics akin to “Farming-as-a-Service”.
The idea isn’t just to produce fresher and better tasting produce and re-introduce forgotten or rare varieties, but to disrupt the supply chain as a whole, which remains inefficient and produces a lot of waste.
“Many before have tried to solve the deficiencies in the current supply chain, we wanted to redesign the entire chain from start to finish; Instead of building large-scale farms outside of the city, optimising on a specific yield and then distributing the produce, we decided it would be more effective to distribute the farms themselves and farm directly where people live and eat,” explains Erez Galonska, co-founder and CEO of Infarm, in a statement.
Meanwhile, the move into France follows $25 million in Series A funding raised by Infarm at the start of the year and is part of an expansion plan that has already seen one hundred farms powered by the Infarm platform launch. Other recent installations include Edeka locations in Düsseldorf, Frankfurt, Stuttgart, and Hannover. Further expansion into Zurich, Amsterdam, and London is said to be planned over the coming months.
“One thousand in-store farms are being rolled out in Germany alone,” adds Infarm’s Osnat Michaeli. “We are expanding to other European markets each and every day, partnering with leading supermarket chains and planning our North America expansion program for 2019. Recognising the requirements of our customers we have recently launched a new product; DC farm – a ‘Seed to Package’ production facility tailored to the needs of retail chains’ distribution centres. We’ve just installed our very first ‘DC farm’ in EDEKA’s distribution center”.
Geothermal Energy May Make Indoor Farming Work in The Future
The farms of the future may be possible even in an urban setting with the right alternative energy.
September 27, 2018 By JULIE CAMPBELL
The farms of the future may be possible even in an urban setting with the right alternative energy.
Technology and geothermal energy advances are sending farming indoors on an increasing basis. This is the case both with urban greenhouses on a smaller scale or larger scale greenhouses.
The primary challenge with these types of greenhouse have to do with the energy they need.
Greenhouse operation is energy intensive, with high demands for electricity because of lighting, but, more importantly, heating. It is in the area of heating that geothermal energy presents a significant opportunity.
As populations rise and the demand for local food production increases, indoor farming may become much more important even in urban settings, according to a recent World Economic Forum article. That said, in order to make that financially feasible, producers need to look to affordable alternative energy options.
These urban operations rely on using every square inch to its greatest potential, as space is much more limited. Moreover, everything must operate on less water. That said, as these indoor farms – small or large in size – have the same heating and lighting requirements as a traditional farm. This requires affordable sources of energy.
Many in the industry believe geothermal energy will be among the leading solutions for indoor farming.
Among the reasons that many will look to geothermal energy is that there are already many success stories with this technology. It is not only receiving increasing attention from those in the industry, but it has also already proven itself in many examples.
For example, one of the largest flower producers in Kenya, called Oserien, uses geothermal power for heating as well as small-scale electricity production. In the Netherlands, energy is becoming increasingly expensive, so geothermal wells are being drilled for many greenhouse operators that need heat. Iceland has widespread geothermal energy heating in its greenhouses to make it possible to grow vegetables throughout the year.
Germany is home to several geothermal power projects being developed to use this resource for their greenhouse operator heating. A new effort has also been underway in Pagoda Springs, Colorado, where it is being used for vegetable production on top of broadening economic development.
Indoor Farm Celebrates Groundbreaking in Welland
A new indoor farm is coming to Welland, phase 1 of the 20,000 sq. ft. industrial facility is about to get underway.
June 26, 2018 | Posted by: Erie Media
A new indoor farm is coming to Welland, phase 1 of the 20,000 sq. ft. industrial facility is about to get underway.
Niagara Holdings Canada announced Monday June 25/2018 that construction is about to get underway. They celebrated the start of this phase with a ground breaking ceremony at the Enterprise Industrial Subdivision at Hwy. 140 and Ridge Rd.
” Well connected infrastructure, ready access to markets, business friendly incentive programs like the Gateway Community Improvement Plan and the proactive and dynamic attitude of officials from the City of Welland and Niagara Foreign Trade Zone, are the main reasons we chose Welland”, said Clarence D’Souza, President of Niagara Holdings in a press release.
Local and federal dignitaries attended the celebration.
Niagara Holdings held it’s groundbreaking ceremony Monday at the location of its new facility in Welland. Photo submitted
Niagara Centre M.P. Vance Badawey congratulated all those involved in bringing the project to Welland.
“Great work by all partners to bring this all together,” Badawey said.
”This project exhibits investor confidence in South Niagara,” he said. “This confidence is a reflection of our current designations as a Gateway Economic Centre and Foreign Trade Zone and our overall proximity to markets. Our ability to work together continues to strengthen our economic performance, globally.
The “purpose built” facility will be the housing for “sophisticated and automated indoor farms in the world,” the press release said.
It is the first on this scale in Canada.
The design is for high volume production of leafy green vegetables. Romaine, Arugula, Kale and Basil are the primary products to be produced at this facility.
The operators for the facility are going to be Intravision Greens (Canada).
“lntravision Greens (Canada), together with lntravision Group Norway (http:/ /www.intravisiongroup.com/), is a leading provider of technology featuring broad spectrum lighting and full system integration. Backed by technology perfected at the University of Guelph’s Controlled Environment Systems Research Facility, the company’s focus is on multi-band and spectrum variable LED lights, enabling biological control and optimization of plant responses to specific wavelengths between UV A and IR light,” the press release said.
“The location in Welland, with its ability to scale up rapidly, it’s green and clean environment and close proximity to several key markets, is of considerable strategic value”, said Amin Jadavji, President of lntravision Greens (Canada) in the release.
The building contract has been award to Timbro, “one of Welland’ s best known engineering firms, with over l 00 years of experience in Ontario,” the release said.
Operations are targeted to begin in the first quarter of 2019.
Leafy Greens are Grown by Machines at New, Automated Silicon Valley Farm
Called Iron Ox, the farm aims to produce leafy greens — romaine, butterhead, and kale, alongside various herbs
Luke Dormehl POSTED ON 10.13.18 - 1:00PM
Did you hear the one about the Google software engineer who packed it all in to start a farm? No, it’s not the setup for a joke. Nor is it the premise for some quirky Sundance comedy, probably telling the story of a stressed-out programmer who rediscovers their happiness by moving to the country. It’s a real, honest-to-goodness farm, which just opened in San Carlos, around 20 miles outside San Francisco. Called Iron Ox, the farm aims to produce leafy greens — romaine, butterhead, and kale, alongside various herbs — at a rate of roughly 26,000 heads per year. Oh yes, and it’s staffed almost exclusively by robots.
“This is a fundamentally different way of approaching farming,” CEO and co-founder Brandon Alexander, 33, told Digital Trends. “Traditionally, the farming process means that you seed, you wait a few months, you come back, you harvest, and you distribute. That hasn’t changed a whole lot in hundreds, if not thousands, of years.” Until now, at least.
Iron Ox’s indoor farm measures around 8,000-square-feet. That makes it paltry compared to the thousands of acres occupied by many traditional farms, but, through the use of some smart technology, it promises a production output that’s more in line with an outdoor farm five times its size. To achieve this, it has a few tricks up its sleeve. For starters, Iron Ox is a hydroponics farm, a method of growing plants without soil, using mineral nutrient solutions in a water solvent. Unlike a regular farm, hydroponic farms grow their produce in vertical and horizontal stacks; every element minutely controlled through the use of glowing LED lights and jets of water to affect the crops’ size, texture, and other characteristics.
In place of a farmer, Iron Ox employs a giant, 1,000 pound robot called Angus. It’s Angus’ job to move the heavy 800 pound, water-filled tubs of fresh produce without spilling them. A robot arm is used to tend the crops, making this the agricultural equivalent of Elon Musk’s automated Tesla factory in Fremont, CA.
“We’ve taken a robotics-first approach to the growing,” Alexander continued, in what can only be described as an understatement. “Everything is designed with that in mind.”
DISRUPTING THE FAMILY BUSINESS
When he was a kid, Alexander was shipped off each summer to his grandfather’s family farm in the Texas and Oklahoma area. Looking back at it today, it’s a cherished memory. At the time, not so much.
Iron Ox
“I’ll be honest: I hated it,” he said. “All my friends were going on vacation and I was the one who was stuck on a farm.” When his buddies were sleeping in, he was getting up at the crack of dawn. When they were on the beach, he was on a tractor. Years later, when he and his co-founder and CTO Jonathan Binney, 34, were busy planning out Iron Ox, he called his grandfather. Now 83 and still running a farm, Alexander told him about his plans for roboticizing the work that his family had done by hand for generations.
But this isn’t a story about a guy who decided to take revenge for summers of hard labor by disrupting the industry. Far from it. Alexander has a deep respect for farming, evident from the reverent way that he speaks about a profession that has looked after his family for years.
“[My grandad is] technophobic; he doesn’t know how to use an iPhone [or about machine learning or computer vision],” Alexander said. “But when I explained what I was doing, he said, ‘This is inevitable.’ That kind of surprised me, but it shouldn’t. When he was a kid, and his dad was farming, they managed 40 acres. Now him and his crew are managing 6,000 acres. He’s seen the progression.”
JUST-IN-TIME FARMING
Farming isn’t an industry that’s at the forefront of many people’s minds in Silicon Valley. It probably should be, though, because the emphasis on farm-to-table produce is only growing. When Alexander and Binney speak to chefs, they regularly hear stories about customers wanting to know exactly where a particular bit of produce has been sourced from, or how old it is.
That typically gets an unsatisfactory answer in the U.S., where the average distance travelled by fresh fruit and vegetables is around 2,000 miles. “There are relatively few places that have the right conditions for growing,” Alexander explained. “Everyone else gets week-old produce.”
Iron Ox
Iron Ox aims to change that by building farms within easy reach of cities. Using its autonomous technology, customers can get fresh greens grown in their neighborhood. Better yet, they can get it year round, since an indoor farm isn’t subject to the same seasonal conditions as traditional farms are.
“We call this just-in-time farming,” Alexander said. He is using terminology that is usually applied to manufacturing, pioneered by automaker Toyota in Japan during the 1960s and 70s. What makes just-in-time manufacturing special is that it focuses on making items to meet demand, rather than creating surplus in advance of need. It means less waste with overproduction, less waiting, and less excess inventory. That works well for cars, computers, or smartphones. The Iron Ox team hope it will work great for crops, too.
“In a traditional greenhouse, you’re committed to growing a thousand or tens of thousands of a particular varietal,” Alexander said. “Our systems gives us the ability to fine-tune the nutrients for each crop. We’re only committed to growing a hundred of something at a time. That’s important. Previously you would committed to, for example, kale. ‘Kale’s going great,’ you say. ‘Let’s go all-in on kale.’ But trends change. If we suddenly notice a big demand for purple bok choy or Italian basil, our system can adapt to that consumer demand very quickly.”
Overseeing the farm, like a green-fingered HAL 9000 from 2001: A Space Odyssey, is what Alexander calls “The Brain.” This is a cloud-based, A.I. which constantly monitors information relating to nitrogen levels, temperature, and the location of robots. Over time, it will expand this to take into account data pertaining to food orders, or more general information about food-based trends.
Weighing up all this data, it can then make decisions about exactly what should be growing — and in what quantities — in each of the modular tanks.
THE ROAD FROM HERE
Right now, Iron Ox is starting to take chef’s orders for the two dozen-plus varieties of leafy greens that it is growing from the start. It aims to be in full production by the end of the year. This is still the beginning of the journey, but it’s one that Alexander and his co-founder are happy to be on.
“We had some pretty good, cushy jobs at Google and whatnot,” Alexander said. “We wanted to make sure that, when we took the next step, it was something we were passionate about. It’s not about staying passionate for one year; it’s about whether or not this was something we could put decades of our life into? That’s a different metric, for sure.”
How does he feel about the impact of automation on jobs in the farming community as a whole?
“I think farming is a fairly unique space in this regard,” he said. “Agriculture is one of the few industries right now where they can’t get enough help. That was something that surprised Jon and myself when we first started. When we quit our jobs, we spent four months roadtripping California, talking to farmers. We talked to dozens of outdoor and indoor farmers. One of the questions we asked was ‘what’s your biggest pain point?’ 100 percent of them said that it was labor scarcity. They could not get enough help for their farms.”
Added to this is the fact that, in the United States, the average age of a farmer is 58. “It’s a bell curve distribution, and it keeps shifting over to older and older,” he said.
Those jobs are not being replaced in equal numbers by the younger generation. “There simply aren’t enough people wanting to do this,” he continued. “And I don’t blame them. It’s hard, back-breaking work. It’s just where it’s going.”
Iron Ox isn’t the only startup applying the latest technology to farming. Other companies and researchers are building self-driving tractors for farms, using CRISPR gene editing to improve the efficacy of crops, and building robots that are capable of picking a variety of fresh produce without damaging it. But Iron Ox’s business model nevertheless represents an enormous step potential forward in U.S. agriculture and the way that it works.
In 1820, more than half of the United States population lived and worked on farms. Today, this is fewer than 2 percent of the population, with the overwhelming majority having moved to the city. Thanks to companies such Iron Ox, people may no longer have to choose between farm and city. If people won’t leave the city for farms, then the farms will just have to come to them.
Could the Future of Farming be Vertical?
Vertical farming is greener and more efficient than traditional agriculture, writes Natalie Mouyal
Photo: BrightAgrotech, Pixabay
Vertical farming promises a more sustainable future for growing fruit and vegetables. Instead of planting a single layer of crops over a large land area, stacks of crops grow without soil or sunlight.
The nascent technology enables farmers to grow more food on less land. Among the benefits, it reduces the environmental impact of transportation by moving production from the countryside to the cities, where most people live.
Dilapidated warehouses and factories around the globe are being transformed into urban farms to grow salads and other leafy greens at a rate that surpasses traditional farming techniques. LEDs provide the lighting plants need to grow, while sensors measure temperature and humidity levels. Robots harvest and package produce.
At one vertical farm in Japan, lettuce can be harvested within 40 days of seed being sown. And within two towers measuring 900 m2 each (actual cultivation area of 10 800 m2 and 14 400 m2), the factory can produce 21 000 heads of lettuce each day.
Indoor farming is not a new concept, as greenhouses have long demonstrated. It has existed since Roman times and can be found in various parts of the world.
Greenhouses are described in a historic Korean text on husbandry dating from the 15th century and were popular in Europe during the 17th century. In modern times they have enabled the Netherlands to become the world’s second largest food exporter.
Vertical farming offers a new take on indoor farming. Popularized by the academic Dickson Despommier, its proponents believe that vertical farming can feed millions of people while reducing some of the negative aspects associated with current agricultural practices: carbon-emitting transportation, deforestation and an over-reliance on chemical fertilizers.
Vertical farming is defined as the production of food in vertically stacked layers within a building, such as a skyscraper or warehouse in a city, without using any natural light or soil. Produce is grown in a controlled environment where elements including light, humidity, and temperature are carefully monitored.
The result provides urban dwellers with year-round access to fresh vegetables since they can be grown regardless of weather conditions, without the need for pesticides and have only a short distance to cover, from farm to plate.
Initially conceived by Despommier with his graduate students as a solution to the challenge of feeding the residents of New York City, vertical farming has since taken off around the world, most notably in the United States and Japan. According to the research company Statista, the vertical farming market is expected to be worth USD 6,4 billion by 2023.
High-tech farming
According to the UN Food and Agriculture Organization, food production worldwide will need to increase by 70% by 2050 to feed a projected global population of 9,1 billion. Vertical farming seeks to address the dual challenges of feeding a growing population that, increasingly, will live in urban centres.
By repurposing warehouses and skyscrapers, these ‘high-tech’ greenhouses reuse existing infrastructure to maximize plant density and production. One vertical farm in the United States claims that it can achieve yields up to 350 times greater than from open fields but using just one percent of the water traditional techniques require.
In general, two methods for vertical farming are used: aeroponics and hydroponics.
Both are water-based with plants either sprayed with water and nutrients (aeroponics) or grown in a nutrient-rich basin of water (hydroponics). Both exhibit a reliance on advanced technology to ensure that growing conditions are ideal for maximizing production.
So as to produce a harvest every month, vertical farms need to control the elements that affect plant growth. These include temperature, requisite nutrients, humidity, oxygen levels, airflow and water.
The intensity and frequency of the LED lights can be adjusted according to the needs of the plant. A network of sensors and cameras collects data with detailed information about the plants at specific points in their lifecycle as well as the environment in which they grow.
This data is not only monitored but also analyzed to enable decisions to be taken that will improve plant health, growth and yield. Data sets sent to scientists in charge of the growing environment enable decisions to be made in real-time, whether they are onsite or at a remote location.
Automation can take care of tasks such as raising seedlings, replanting and harvesting. It can also be used to provide real-time adjustments to plant care. One factory plans to automate its analytical process with machine learning algorithms so that real-time quality control can take into account a diverse range of data sets.
While each of these farms will implement varying levels of technology, it can be expected that as these technologies become more widespread, their adoption will increase. The use of artificial intelligence and cloud computing is not yet extensive but is likely to become increasingly important to ensure production yields remain high.
Growing pains
Despite the enthusiasm for vertical farming, its business model is not yet proven. The initial investment needed to launch a vertical farm and the electricity required to power the 24-hour lights, sensors and other technologies can be costly.
Depending on the source of the electricity used to run the equipment, it may not necessarily prove environmentally cleaner than traditional farming techniques. For this reason, a shift towards renewable energy sources could support the claim that these farms have a positive environmental impact.
At this stage, vertical farms are used primarily for growing crops that attract high market prices, such as herbs, medicinal plants and baby greens. They have not been used to grow the wheat, beans, corn or rice which feed much of the world. Its scale is not yet sufficient to meet food demands.
Vertical farming is still in its infancy. No large scale studies have yet been completed to allow a full comparison with traditional farming techniques. Despite this, it has generated much enthusiasm and, more recently, significant financial support, which may enable vertical farming to create a niche market for the supply of fresh produce to city dwellers.
Kimbal Musk Is Reinventing Food One Shipping Container At A Time
Interesting dresser, marketing pro, rich dude, brother to the most famous man in tech: Musk is changing food production, one shipping container at a time. And it's starting to work.
By Kevin Dupzyk
Oct 24, 2018
DAVID SCOTT HOLLOWAY
The low-slung building on Evans Avenue with the greenhouse roof blends into the surroundings in an uninspiring stretch of Denver, all nondescript retail and pockets of ranch homes. It’s a hydroponic farm, run by partners Jake Olson and Lauren Brettschneider. The produce is all on tables at waist height, and the plumbing is subtle and minimalist. There is no soil anywhere. From the street it’s easy to miss Rebel Farm; inside, it looks like an Apple Store hosting a farmer’s market.
One afternoon this summer, Kimbal Musk, a tall, lanky man in a cowboy hat, ducked in through the front door. He was here to see about the produce for his Denver-area restaurants. Unlike, perhaps, the average restaurateur, he’d brought a couple of assistants, who used smartphones to photograph his entrance, and his greeting with Olson and Brettschneider, and the huge smile he put on when he surveyed the farm. He’d never been to Rebel Farm before, but the operation was already providing him gem lettuce, a trendy green, and now he wanted to see what else it might offer. Olson and Brettschneider start walking him up and down the aisles. The building’s southern exposure is a heat-exchanging wall, and they start there, in the cool-climate crops.
“We just can’t get spinach to grow,” the Rebel guys say.
“Really?” Musk asks. “What about kale?”
Arugula’s easy. “The gateway green,” they all agree.
Musk surveys the farm and talks hydroponic technology in the manner you expect his older brother, Elon Musk, might approach a tour of NASA’s Jet Propulsion Laboratory. Like his brother, Musk is a billionaire entrepreneur, but since 2004 he’s made his living in food.
Musk tastes hydroponically-grown greens at Rebel Farm, an urban farm in Denver, CO.
DAVID SCOTT HOLLOWAY
At each new crop, Olson and Brettschneider tear off a few leaves for Musk to try, and he takes each bouquet, contemplates it, smells it deeply, eyes closed, takes a bite, and stares off into the middle distance. For a moment it’s like he is absorbing the simple life of the leaf, just sun, soil, and water, the way cannibals eat the hearts of others to imbibe their essence.
Of course, this also makes for good photos. And Instagram Live opportunities. He asks Olson and Brettschneider to do a short live video with him, and they oblige him behind a planting of sunflower sprouts on a sheet of geometric growing foam called Horticubes. An assistant gets in position with her smartphone, and as soon as they start recording, Musk comes to life, a perfect host, asking leading questions and making sure that the brands’ audience gets to know Olson and Brettschneider and their strange urban farm of delicious hydroponic crops.
Video over, tour back on, and Musk quickly turns to logistics. “Do you know how much production you do?” he asks.
Musk has a particular interest in this farm that goes beyond his restaurant chains, The Kitchen and Next Door. Musk also cofounded an urban farming startup based in Brooklyn, called Square Roots. Square Roots develops hydroponic farms housed in shipping containers that use high-tech lighting systems and offer precise, scientific control of light and every other relevant variable, like water and nutrients. Then it teaches a new breed of farmer—think Brooklyn hipster with a back-to-the-land mentality—to use them.
“Well, this is 15,000 square feet,” says Olson.
“Right, so that’s about one third of an acre,” Musk says. “At Square Roots we’re able to take a shipping container and get two acres of productivity out of it.”
“That’s some big shipping container,” Brettschneider says, not quite getting what Musk’s driving at. Musk is speaking entrepreneur, but Olson and Brettschneider are just two people who left pretty good day jobs to work the land. (As it were.)
Sprouts on a low-water growth medium. DAVID SCOTT HOLLOWAY
Musk’s goal isn’t just to produce food, or just to produce food that’s good. It’s to produce what he calls “real food”—“food you can trust to nourish your body, trust to nourish the farm, and trust to nourish the planet”—as efficiently as possible. The way he sees it, the last few decades have seen two food movements, opposites, both misguided. There’s the precious food movement, which aims to set the table only with food grown in the immediate community. The problem with that is that it’s pretty much restricted to wealthy people in fertile places.
Then there’s the feed-the-world movement, which produces more food than we need, most of it processed, unhealthy, and untasty, leading to health problems like diabetes and obesity. Musk is trying to shoot the gap, and unlike the cornucopia of restaurateurs in most midsize or larger cities these days offering local kale, he has the background and resources to implement a grander vision. Kimbal opened The Kitchen, a fine-dining restaurant, in 2004 before conceiving of Next Door, which sources ingredients with the same principles but offers food with a tad less pretention and a bit more fun, at prices—generally under $15 an entrée—that most Americans can afford. And Musk has ancillary enterprises that lay the groundwork. He founded a nonprofit, Big Green, that installs learning gardens in schools to educate kids about real food. Then there’s Square Roots. Musk points out that with shipping-container farms, which lock out all the traditional encumbrances of farming—drought, locusts, 24-hour cycles of day and night—optimization of food is possible. Unlike a traditional farmer, who may work his land for 50 years and in that time get only 50 growing seasons to experiment with, a Square Roots farmer can iterate endlessly until: spinach.
As we’re getting ready to leave, Olson and Brettschneider ask if they can show off some of their more specialized crops, and we make our way to the hot north end of the farm. They take us to a rack covered with huge serrated leaves and tangles of thick stalks. Brettschneider pulls some of the tangle away and points at a smooth purple ball from which the stalks emanate.
“What is that?!” Musk asks.
“Kohlrabi!” Olson says, uprooting one and handing it to Musk, who holds it in one of his big hands and examines it from every side. Olson launches a disquisition on all the ways you can cook up kohlrabi, and while Brettschneider says it isn’t exactly her favorite veggie, even she’s clearly pleased to be showing off their crop. Musk smiles, pondering all the uses of this strange orb, and his assistants fire up the smartphones to catch him mugging with the vegetable.
“It’s a pretty good job I have,” Musk told me earlier that day, on the way into a shopping center in a neighborhood in South Denver. “I get to go drop off food at children’s hospitals.”
Just across the street is a branch of Children’s Hospital Colorado, and we’ll be heading there soon—just as soon as we finish at this shopping center, where we’re checking out what will soon be the newest Next Door. So far it’s a plywood husk. The whole time Musk walks around the interior, he’s being photographed. He throws on a hard hat and walks slowly from room to room, exaggerating looks of surprise. The check-in is as much photo op as inspection, part of the constant hard work of building a business.
I ask him if he ever gets tired of being photographed. “Oh, with Instagram, it’s all the time,” he says, in a way that might be wistful if one could be wistful through such a radiant smile. “Not just journalists.”
DAVID SCOTT HOLLOWAY
When every conceivable angle has been captured for social, he says—cheerfully—“Let’s go meet the neighbors!” When Musk opens a new location, he likes to scout the other businesses nearby. The shopping center is a quad, with rows of stores around each of four sides. We skip the eyelash store next door to Next Door, which isn’t open yet, and go into a clothing boutique one storefront down.
Musk asks the woman behind the counter at the boutique how long they’ve been open, and how things have been going, and which tenants are in already. You know—small talk. This is the thing about Musk: Everything he does has a purpose.
The woman mentions the parking situation, which is that there isn’t enough of it. “Yes,” Musk says. “I did notice that it seems like not quite enough spaces for the businesses here.” He looks out the glass walls of the boutique, a little troubled. We proceed to the Orangetheory Fitness on the adjacent side of the quad. Musk mentions the parking, and the young man and woman working agree that, yes, it really does seem like there are a lot of cars here. Musk peeks into the last two stores on that side of the lot and then works his way back to a Starbucks on the far corner, popping his head into more shops along the way. He eyes the full lot suspiciously as he walks, first on the way into the Starbucks, and again on the way back out, cup in hand.
When we finally climb through gull-wing doors into the backseat of a white Tesla Model X, Musk looks around for a moment before pushing a button on the back of the center console to release two cup holders.
“Have you given your input into the design of the cars?” I ask. (Musk serves on Tesla’s board of directors.)
“Oh yes, I’ve been quite involved,” he says. “Once there was a design with no consideration of cup holders. That was a terrible idea.”
In 1999 Kimbal and Elon sold Zip2, the company they cofounded, to Compaq for $307 million. Elon took his and became Tony Stark; Kimbal took his and moved to New York, where he enrolled at the French Culinary Institute. He was living blocks from the World Trade Center on 9/11—close enough that he had a security pass to get into the zone around the Twin Towers that shut down for rescue and cleanup. That’s the first of the foundational stories about Musk and food: that he used that pass and the good suggestion of a Culinary Institute colleague to spend weeks feeding firefighters at Ground Zero. He opened The Kitchen in Boulder three years later. The second foundational story about Musk and food happened in 2010. At the time, Musk was still working for tech companies in addition to working in food. He was tubing in the snow with his family when his tube flipped and he broke his neck. He was paralyzed for three days, and found himself contemplating all the big things one contemplates in such circumstances. It was time to get out of tech, he realized. Food was his passion.
As we pull out of our parking space, he asks his assistant, who’s driving, to exit the shopping center between a Shake Shack and a Torchy’s Tacos, a different way than we came in. He doesn’t know Torchy’s but he’s heard it’s popular. He gets a call as we’re leaving. “The problem with this place is going to be the parking,” he says into the phone. He bobs his head down to look at the patios of the Shake Shack and the Torchy’s, which are both full of customers, and registers approval.
Musk’s finishing up the call when we pull into the parking lot at the children’s hospital. On the way in, he shakes a few hands and takes more pictures. We wind our way back to a conference room, where Hal Reynolds, Next Door’s regional operations manager, and Brad DeFurio, development chef, are rotating in fresh trays of roasted veggie quinoa bowls, ancho chile chicken bowls, curry chicken sliders, and chips and guac and hummus for hospital staff. Musk greets Colin Ness, director of operations: Parking is going to be a problem, he tells him. Musk does more photos and a TV spot and grabs some food. I ask him what he recommends. He assures me that it’s all good.
THIS IS THE THING ABOUT MUSK: EVERYTHING HE DOES HAS A PURPOSE.
“This is really great for us,” he says, pausing to chew. I expect something about what fighters the kids are, and how pleased he is to have such an admirable neighbor. Instead: “Because we’re trying to add catering, and this is a good test.”
Musk never lost the skills he honed at Zip2 and the other tech companies he worked for. At Zip2, he was director of product marketing, and he tells me he’s still a product guy at heart. He figures out what he’s selling and how to position it. He makes himself an embodiment of the brand, which these days is about food and connection. When Kimbal Musk wants to reconnoiter a shopping center, he says, “Let’s go meet the neighbors!” When he needs a test run for catering, he finds a children’s hospital.
That night Musk works the open-air upper level at Next Door Glendale, a location in another corner of suburban Denver. Next Door hosts a school fundraiser series called 504U: On certain nights, when a school brings in business to the restaurant, they get to keep 50 percent of the profit. Tonight is the pre-school-year event to rev up the educators for another season of philanthropy. Musk goes from group to group of buzzed teachers and gorged administrators and expertly makes conversation and offers hugs.
Then Ness comes over and speaks to him semiprivately, voice a hush. Musk’s eyes grow wide with amusement, and he puts his hands over his mouth. From the looks of things, some part of tonight’s itinerary has gone wrong. Musk and Ness whisper, and then Musk shrugs, and Ness dashes off to fix it. Musk goes back to work. He greets everyone like he knows them. He’s mixing and greeting and good-humoring—even when a guest, like the fanboy wearing a ball cap emblazoned with “The Boring Company,” the name of one of the many projects of Musk’s brother, doesn’t seem so interested in the fundraising as in a real-life audience with a Musk.
Soon Reynolds comes walking slowly and carefully through the crowd, gingerly carrying a bucket and some kind of cloth-covered implement, which radiates heat. Ness follows, and he gets Musk’s attention. Musk jumps up on a chair and draws in the crowd. “We call this a branding party,” he says. “And we’re going to take an actual brand, like you’d use on an animal, and put a brand on the restaurant.”
“The catch is,” he says, “the handles burned off.”
MUSK GOES FROM GROUP TO GROUP OF BUZZED TEACHERS AND GORGED ADMINISTRATORS AND EXPERTLY MAKES CONVERSATION.
Musk hops down from the chair and walks over to the bucket. The charred remnants of the brand’s dual wooden handles have been wrapped in a few layers of towel and tied fast with string. What wouldn’t Elon give to fix a problem so easily? It’s not a bad gig Kimbal’s got, having expressed the Musk curiosity and faith in technology through a product that still has the most visceral, tangible kind of accountability—Does it taste good?—and now he’s got these restaurants and he’s teaching children to eat well and he’s pursuing his own dream of a previously unimaginable future, one in which a trendy city kid says “Welcome to my farm!” and cranks open the door of a shipping container in some gritty, hollowed-out urban district and runs his hands through hanging fields of chard.
Musk grabs the towel handles with both hands and presses the brand hard into the wood frame of a large chalkboard menu hanging on the restaurant’s wall. He splays his great long legs wide to form a base of support and pushes hard. At first, nothing seems to be happening, and Musk is straining, long arms taut. Then you start to smell it. Wood. Wood burning. Musk’s body quivers with the effort. It’s been a long day. Smoke starts to rise from the brand and the smell intensifies, that burning wood smell of chips in charcoal. Musk holds the brand in place a second longer, then pulls back. A perfect “ND” is burned into the wood. “Ha!!” he shouts. He lets loose a primal scream. He smiles a big, toothy smile. He’s made his mark.
Musk has made his mark.
DAVID SCOTT HOLLOWAY
The next morning, Kimbal invited me and David Scott Holloway, a photographer, to hike his commute: from his home in a Boulder neighborhood, up the side of Mount Sanitas, and back down to the original Kitchen and Next Door in downtown Boulder.
Looking east from just above the treetops of Kimbal’s neighborhood.
Kevin Dupzyk: So Square Roots attacks the farming problem with technology. Do you think of Square Roots as more of a technology company or a food company?Kimbal Musk: I think it’s not a meaningful distinction. In order to do anything great today, you have to be a technology company. But on the food side, you’ve got to grow something that tastes great and is super-nourishing. That people trust. If they don’t like it, they don’t like it. You can’t solve a product-quality problem by talking about the technology.
KD: You said yesterday that even when you were doing tech stuff, the marketing thing was what you were really good at. Where did that come from?
KM: I’d say product, marketing, and sales are what I was better at. I don’t know where it came from. I had a painting business in university, so that taught me a lot about sales. I don’t know. There’s this thing I learned from Steve Jobs—I didn’t know him, but I learned from reading about him—if you do what you love, success generally comes from that. And I just love product.
KD: You have chalkboards in your restaurants that list the sources of your ingredients. A lot of places do that now, but I’ve heard speculation that you were the first.
KM: I believe so, yeah. We actually designed those chalkboards for the menu. And our menu changes every day, and we didn’t quite get to the operational challenge of that—erasing a menu and writing it out every day. And so we had the idea to put our farmers on there because it would still change, but it wouldn’t change every day. And that really sort of hit a nerve.
We descend back down to the streets of Boulder, and we’re walking through a residential neighborhood just a few blocks from downtown.
KD: Because this is a food you’ve mentioned a couple times over the last two days . . . I have to confess I really don’t like tomatoes. KM:Well you’re probably eating bad tomatoes. Most tomatoes are pretty bad.
KD: That’s what the tomato people are always trying to tell me.
David Scott Holloway: Kimbal, are there any foods you don’t like?
KM: Um . . . I don’t like things that are too processed. And that’s more of, like, an aversion.
KD: Come on—there’s not one vegetable you don’t like?
KM: Let me think . . . I don’t think so, because I know how to cook pretty much any vegetable to make it taste good. But if I eat vegetables other people cook, I often don’t like them.
DSH: My family was definitely part of that convenience generation. If my mom could get it out of a can, or if it could go into a microwave, she was feeding it to me.
KM: Yeah, they idolized convenience for so long. And people still want convenience. But it got to such a point of convenience where you’re just sitting by yourself all alone in front of a TV eating a TV dinner, and that’s kind of where our life ended up.
KD: I still kind of feel like it’s a treat when I eat a TV dinner.
KM: Really?! Oh my God! That grosses me out!
KD: It’s just because when I was a kid, it was like—we’re going to watch TV while we eat, and there’s a brownie in there!
KM: Well, I admit, I don’t think I’ve ever had a TV dinner.
KD: You’ve got to try it.
KM: You eat a tomato, I’ll eat a TV dinner.
KD: I’m fascinated by this thing that Square Roots hints at, where our idea of what a farmer is really changes. Do you think the mix of factory farms and these other models is going to shift significantly by, say, 2050?
KM: I’m already seeing in Colorado a lot of family farms are coming back. These are farms that might have a top line of $500,000 in revenue. They’ll sell to restaurants, farmers’ markets, and they’ll live on the farm with a cash flow of maybe $100K after all expenses are paid. That’s a pretty good lifestyle. Not everyone wants that lifestyle, but it is a pretty good lifestyle. But if you want to live in the city, like New York, the family farm doesn’t really exist.
[Smiles broadly with a realization.] Actually—I take that back. Rebel Farm was a family farm! That was a couple, with their kids, running that farm in downtown Denver. So it can be done. It’s just, I think, a little more unusual.
Musk stops walking. We’re in the bustling center of downtown Boulder, right in front of The Kitchen and Next Door.
KM: So here’s Next Door. This is where I end up. That’s my commute.
Kimbal Musk on his commute to work. DAVID SCOTT HOLLOWAY
iGrow News Is Proud To Announce Our New Partnership With Lyle A. Bogorad
Lyle is an attorney from NY with a J.D. and LL.M. in intellectual property. He has recently left the legal arena to enter the cannabis industry.
We are proud to announce our new partnership with Lyle A. Bogorad, the Owner of Cannabis Canopy by Chromatic Clouds and Founder of Chromatic Clouds.
Lyle is an attorney from NY with a J.D. and LL.M. in intellectual property. He has recently left the legal arena to enter the cannabis industry.
We look forward to his contribution to iGrow and welcome him to the Family.
The cannabis revolution is here to stay.
The cannabis industry is expanding rapidly gaining worldwide interest. With growing scientific validation, cannabis is being integrated into the mainstream around the globe as sales for consumer wellness products have continued to grow steadily. Hemp and CBD oil are making headlines. From Pharmaceutical Companies and Big Tobacco to beer, soda and alcohol, Fortune 500 companies are focused on cannabis as it is becoming a billion-dollar industry in the United States.
The folks here at iGrow have recognized the growing interest society has for cannabis. We also acknowledge that much of the early advances in indoor and urban farming were made because of the technology introduced to us by indoor cannabis growers. As a “Wikipedia” for all your indoor vertical and urban farming news, we would be amiss if we didn’t begin to cover cannabis in our reporting,
Many of you probably already noticed the addition of a “New Ag Tech” category. We have linked this new tab to the “Cannabis Canopy by Chromatic Clouds” LinkedIn group. Please check out our new addition and join the group. Also, I would love to hear your thoughts on our plan to include the world of cannabis in our coverage to you. Please reach out to me with any thoughts and suggestions.
The mission of Cannabis Canopy is to provide a “canopy” of sorts for cannabis business enthusiasts to have a dedicated forum to explore the cannabis universe.
New Hydroponics Approach Draws £500k Seed Funding for Welsh Startup Phytoponics
A new deep-water approach to hydroponics has earned Welsh agtech startup, Phytoponics, £500,000 ($650k) of seed funding support over the last two years, lining the company up for major Series A investment push in mid-2019.
The first round in 2017, which closed on £200k, was backed by five new angel investors led by Smart Anchor Capital based in London and Cardiff. This year’s second round, which raised £300k and was also led by Smart Anchor Capital, consisted of follow-on funding by four of the first round investors, alongside eight new people.
The Aberystwyth-based company was co-founded by Adam Dixon and Luke Parkin in October 2016 with the aim of delivering hydroponic systems designed to produce better crop yields than are possible through conventional greenhouse-based methods. The company’s patented Hydrosac technology is now deemed to be ready for high volume commercial output, having proven itself by producing high-quality tomatoes through a pilot project run in conjunction with Aberystwyth University in Wales.
“The primary difference of Hydrosac is its use of more water than existing hydroponic systems, giving plants a wider buffer range of nutrients, temperature and dissolved oxygen,” said Dixon. “This results in less fluctuation in root zone conditions, which makes production more predictable and programmable than has been possible in the past.”
“Our system is particularly designed for large vine crops such as tomatoes, peppers, and cucumbers, as opposed to many others who concentrate more on salad crops.”
For tomato production, the Phytoponics system provides about 10 liters of water per plant, which the company says depletes the available nutrients at a much-reduced rate compared to when less water is used.
“I’ve been with working with hydroponics for more than 10 years, including leading up to starting preparations for the launch of Phytoponics about three years ago,” said Dixon. “Our first two years in business, since our official launch, has been focused on development and initial trials with a little bit of funding being sourced in year one, followed by the £500,000 we’ve raised this year.
“This new money allowed us to progress to the pilot trial at Aberystwyth University and the bringing in of high-level horticulture sector expertise to help us make our system fully commercial and ready to go.
“It was hard finding investors during the period we were developing the technology, especially in a sector like horticulture where trials, which are greenhouse-based, can only be run on an annual basis.
“Our big technology breakthrough came through running the pilot at Aberystwyth University and then winning the United Nation’s Young Champion of the Earth award in 2017. That gave us a major boost of recognition, enabling us to take our plans to a London investor in December last year, which led to our first round of seed funding.”
Despite gaining a $15,000 prize as part of the UN award and a number of other relatively small competition prizes over the last two years, Dixon doesn’t believe start-ups should concentrate too much on competitions and awards.
“It’s important to focus primarily on building the proof points of your business, relating to potential customers and developing the necessary specialist expertise to allow you to progress,” he said. “Awards are good if you can’t get sales, which we couldn’t in the early stage of our development, but not so much after that point.”
The next big change for the business was Smart Anchor Capital’s founder partner, Mark Hindmarsh, recently joining Phytoponics as chairman.
“Mark has really helped us refine and develop our business model, work on our proof points for fundraising and generally commercialize our operation,” said Dixon, whose initial contact with Mark came via a shared LinkedIn friend.
Hindmarsh is also upbeat about the relationship he has with Phytoponics and the company’s potential.
“The team at Phytoponics have achieved an amazing amount in the last 12 months, often with little resource,” said Hindmarsh. “Despite that, they have attracted the attention of potential partners and customers in the US, India, UAE, Africa, Canada, and many other countries.
“As new shareholders ourselves, we are excited to see what the future holds for the company considering the opportunities that lie ahead. As their recently appointed Chairman, I am personally looking forward to playing my part in helping the company achieve its next milestones in advance of a larger fund-raise within the next 12 months.”
Hindmarsh added that with this year’s round ending up 3x over-subscribed, the team is now considering opening up another £400,000 or so for funding early in 2019. This would be done via a convertible loan note instrument to give investors an opportunity to participate prior to the Series A round in late summer 2019.
Funding aside, the next physical step for Phytoponics involves the launch of a farm-scale trial with a major commercial grower (still secret at present) who will use the company’s technology to grow tomatoes for two major UK supermarkets early in 2019.
Beyond that, the company is planning to hire new employees to help with both technical and commercial developments.
“I believe our technology is globally significant,” said Dixon. “Initially, therefore, we’re looking to make a big impact on horticultural production in the UK, with the potential to scale our operation internationally through our own technology platform and business partnerships.”
'The Next Evolution of Farming Has Already Begun'
By Austin Stankus - Wednesday, October 10, 2018
The world population continues to grow with ever-increasing urbanization predicted to reach 80 percent by 2050. The U.N. predicts that human population will reach nearly 10 billion by 2050. This increasing population is also growing richer — and hungrier.
To feed this population using traditional farming practices, much more land would need to be brought under cultivation. But, already much farmland around the world has been degraded from poor management practices, and lands remaining available for food production are decreasing from the effects of erosion, salt buildup and pollution.
As you read this today, tens of millions of children are going to bed hungry, with the Food and Agriculture Organization of the United Nations estimating the number of hungry in 2018 at 812 million or approximately one out of 9 people.
Something needs to change. Food production needs to get more efficient, more equitable and more environmentally minded. Moreover, food production should follow the population to the cities, or as Dickson Despommier, a forerunner of this movement, simply states: “Put the food where the people live.”
Indoor farming through controlled-environment agriculture (CEA) will be an important component towards establishing local food systems that can address this pending crisis in global food insecurity. CEA, simply put, is using smart, sustainable farming practices inside of high-tech greenhouses. This is nothing new, and these modern greenhouses are an established technology and can be found around the world. In fact, much of the lettuce, tomatoes, peppers and cucumbers in the EU come from CEA in the Netherlands and Spain.
These greenhouses have incredible benefits compared to traditional farming: They use less water because they are protected from the sun and wind, they use fewer pesticides because insects and disease can be kept outside, and there is less waste because production can be matched exactly to consumer demands.
If hydroponics or other soil-less practices are used, the farmer does not need to use tractors for tilling, plowing and reaping, so the oil bills and energy consumption are lower. In addition, the fertilizer usage is reduced, and all the fertilizer the farmer uses is consumed by the plants, thereby reducing nutrient-rich runoff that can pollute watersheds.
Known as eutrophication, this nutrient pollution is a huge problem for coastal communities in the Chesapeake Bay and Gulf of Mexico and has impacted fisheries, recreational activities and livelihoods around the world.
However, CEA greenhouses can occupy a lot of space. So, the next logical evolution is stacking these modern greenhouses, one atop the other.
Vertical farming, as greenhouses stacking is called, has additional benefits. Reducing the footprint means that more food can be grown in a smaller area and therefore can be brought closer to the people eating that food. As populations move toward the cities, it makes sense for the food to follow.
Part of the vision of vertical farms is the reconnection of the producer and the consumer plus the restructuring of food value chains to become more transparent and responsive to the needs and wants of the people.
An added benefit of farming inside of skyscrapers is the option of having mixed-use buildings. When combined with a wholesale market, the skyscraper can not only produce the food but get it to the consumer faster. Less time in storage, less transportation and less handling means fresher produce and reduced need for postharvest treatments like irradiation and chemical fumigation.
There are still some daunting challenges as well as some encouraging recent developments.
Unleashing the innovative power of American small businesses has jump-started the transition to modern farming, and the public desire for local, healthy food is an economic engine driving the industry toward change. In fact, there are currently so many vertical farm startups that a shortage of qualified workers is now the main hurdle to accelerating the establishment of new indoor farms. On one hand this is a challenge to the industry, but on the other it presents an enormous opportunity for job creation in urban areas if an inclusive, enabling environment is codeveloped with the vertical farms to provide vocational training and career advancement prospects.
On a technical level, there is a significant energy demand needed for pumping water, maintaining good environmental conditions like temperature and humidity, and powering the grow lights to keep producing year-round. However, with smart buildings wired on intelligent platforms, the energy consumption can be monitored and controlled to maximize efficiency — and by tying into other green enterprises like photovoltaic and biogas generation, this energy demand is decreasing day by day. In fact, with the new innovations in LED lighting technology, the power demand has been reduced tenfold in the last few years.
The next evolution of farming has already begun, and big players are already involved. In fact, the National Grange wrote a letter to Congress with their support to public-private funding mechanisms to accelerate the modernization of agriculture, specifically highlighting the potential of vertical farming.
With this type of buy-in from large agribusinesses, national and international agricultural organizations, funded with innovative financial mechanisms, and driven by the innovative spirit and technological power only found in the U.S., vertical farming will feed tomorrow’s children with healthy, safe food; protect the environment while being resistant to environmental shocks; and spur economic growth in the process.
For a detailed look at one such startup, see the centerfold story on Skyscraper Farm.
• Austin Stankus, an integrated farming specialist, is chief science officer at Skyscraper Farm LLC.
Bell Pepper Year Round With LED or Hybrid Lighting
Sander Hogewoning (Plant Lighting) about lighting test Bell peppers are hardly grown year round in The Netherlands. Growing year round has advantages for the market, but also a number of challenges. In the past results of tests with lighted bell pepper growth were mixed, with sometimes difficult fructification and insufficient stretching of the bud. By combining cultivation knowledge (Delphi and growers), plant physiological support (Plant Lighting) and light knowledge (Signify), we hope to realize successful year round cultivation.
The basis of the research is that the quantity of assimilates are being produced by the variety in balance with the demand for assimilates by the developing fruits. In a regular unlighted cultivation, daylight and plant taxation increase simultaneously. In the lighted test the results are exactly reversed: shortly after planting there is lots of daylight and little need for assimilates.
The plant tends to produce lots of fruits. Then the plant taxation will increase, and also the demand for assimilates, but daylight is diminishing. The hypothesis is that a too large plant taxation in the beginning will lead to imbalance-related problems later on.
Tight schedule
That is the reason why plant taxation is built up according to a tight schedule, and any overage of fruits is immediate cut away. The lighting is geared as much as possible to the shortage of daylight to meet the assimilate demand. Aided by photosynthesis measurements and crop models the assimilation of the crop is calculated as precise as possible. Furthermore, part of the crops are being used for experiments with directional light to measure the effect on stretching in the bud.
The crop is looking healthy now, and the first fruits have set. The goal is to end up with around 40 kg production. It will be exciting how the growth will proceed around the shortest day and in the following period.
The program Kas als Energiebron, Signify, and crop cooperation Paprika financed the research.
Source: Kas als Energiebron
Publication date : 10/16/2018
Cotton Wool Mats Used To Grow Microgreens
Did you grow cress on cotton wool on your window ledge when you were at school? That is exactly the principle that Simon Macaulay followed when he first talked to Chris Moncrieff of Van Heineken Brothers (VHB) in Angmering, (now a housing development) Sussex in the late 1990s. Chris and Peter Walls, who ran the herbs business at VHB, were innovators. Simon takes up the story:
“I had recently taken over from my dad at Anglo and an old contact at M&S had told me that VHB used felt to grow cress. I took the 6 hour drive down to VHB and the lady I was due to see had forgotten I was coming. Luckily Chris is a very kind man and he took pity on me and had a chat. He was indeed growing cress on a felt but it was made from virgin materials and he liked the idea of maybe using a blend of virgin fibre offcuts - using cotton/wool and polypropylene. Growfelt was born.”
“For the first 6 years we supplied exclusively to VHB. In return they helped us to bring our factory up to food grade standard and to set in place a testing regime for Salmonella E-Coli and Listeria.”
"However in recent years we have broadened out our customer base and now offer a core of three products to meet the different needs of customers across Europe, the Middle East and the Far East for Growfelt, be it for retail presentation and appearance or water holding. We can offer rolls cut to your bench width or small pads to fit your punnet requirement."
"We are the largest manufacturer of mats for microgreens in Europe and we are never standing still."
Over to Managing Director Andy Hall: “As we expand our customer base we are constantly getting sent new challenges. A customer in the Philippines wanted a mat 10mm thick as the ambient temperature demands increased water availability for the herbs. I am regularly talking to my customer in the Middle East as he is expanding rapidly as the demand for fresh salads grown in the area.
Also we are undertaking trials to find a fully biodegradable product that meets micro and growth challenges but allows my customers to reduce their landfill costs. Not an easy one to solve but we are confident we will. We stay close to our customers, developing variants for their bespoke requirements. They are mainly small businesses like us and we try and help each other.”
For more information:
Anglo Recycling Technology
Tong Lane
Whitworth
Rochdale
Lancashire OL12 8BG
U.K.
Sandra Burdekin
+ 44 (0)1706-853513
sandra.burdekin@anglorecycling.com
http://www.growfelt.com/growing-media/
Publication date : 10/16/2018
Author:
© HortiDaily.com
Ag Software Provider Launches Survey
October 13, 2018
Written by Agrilyst (edited)
Software solutions provider Agrilyst has launched their third annual State of Indoor Farming Survey.
This survey will give Agrilyst and growers insight on emerging trends and challenges in the greenhouse and vertical farming industries.
Last year, Agrilyst received over 150 responses from indoor farmers in the US. The 2017 report shared insight on the benefits and challenges for growers. According to the report, 25 per cent of growers said that their biggest challenge was capital - from access to working capital and expansion capital to cost of production. Even though they faced these challenges, 51 per cent of growers reported operating profitably.
Allison Kopf, CEO of Agrilyst said, "this year we are digging even further into the costs of operating an indoor farm. We hope that the report will give everyone insight on the industry and help new growers get up and running faster." The company aims to expand their survey participants to growers in Canada.
More data collected means better insights for growers. Growers can participate in the 2018 State of Indoor Farming survey here. The survey takes approximately 25 minutes to complete.
Agrilyst provides software solutions to greenhouse and vertical farming operations, enabling them to track and analyze farm data in one place. They have customers in more than 10 countries.
Urban Farming Projects Attracting Greater Interest, Investments
By The Washington Times Special Sections Department - Wednesday, October 10, 2018
International interest in sustainable urban ecosystems — especially vertical farming — is exploding, according to numerous market forecasts.
Valued around $2 billion in 2015, the global vertical farming market is projected to reach anywhere from $6 billion in 2022 to $10 billion by 2025, according to forecasting firms such as Research and Markets and Grand View Research.
The impetus to scale up vertical farming worldwide stems from two U.N. projections on population and urbanization: The world’s population is expected to grow to 9.6 billion people by 2050, and most of these people — 68 percent, according to the U.N.’s revised 2018 urbanization report — will live in cities.
Governments, urban planners and architects, researchers, investors and the entire world of agriculture are now exploring ways to make sure there will be abundant, high-quality, nutritious foods to feed such a growing population — while also conserving energy and water and reducing environmental damage.
To many observers, the future is bright, thanks to advances in greenhouse technologies such as hydroponics, aeroponics and aquaponics.
“These high-tech systems represent a paradigm shift in farming and food products and offer suitable and efficient methods for city farming,” Dr. Kheir Al-Kodmany, an urban planning scholar, wrote in the Buildings journal in February 2018.
Dr. Al-Kodmany and his colleagues at the University of Illinois at Chicago reviewed more than 100 sources about vertical farming research since 2010 and examined 15 vertical farming projects worldwide — including two rooftop farms in New York; four “low rise” farms in Michigan, Illinois and Tennessee; and six proposed “high rise” farms in Sweden, France, Canada and the Philippines.
“Hypothetically”, if vertical farms were integrated in the city, they will be able to supply food for the entire population,” Dr. Al-Kodmany concluded. However, there are many challenges to address, including finding funding to build and sustain such projects; finding less costly ways to power facilities; and quickly assembling interdisciplinary research and collaborations on urban agriculture, he wrote in the Buildings article.
In the U.S., the U.S. Department of Agriculture is already supporting research funding on vertical farming through its National Institute for Food and Agriculture.
Also, on June 27-28, the USDA and the Department of Energy co-hosted a stakeholder workshop on vertical agriculture and sustainable urban ecosystems. A report on the two-day event, which was open to the public, will be issued later this year, a USDA spokesman said.
In its workshop, several USDA officials spoke, including Dr. Dionne Toombs, director of the USDA Office of the Chief Scientist; Dr. Chavonda Jacobs-Young, acting USDA chief scientist and acting deputy under secretary for research, education and economics; Dr. David Babson, senior advisor in the USDA Office of the Chief Scientist; Dr. John Hartung, research plant pathologist at the USDA’s Agricultural Research Center in Beltsville, Maryland; and Dr. Sarah Federman, AAAS Science and Technology Policy Fellow in the USDA Office of the Chief Scientist.
Additional featured speakers at the workshop included:
— Dr. Sabine O’Hara, dean of the College of Agriculture, Urban Sustainability and Environmental Sciences at the University of the District of Columbia, on envisioning ways to incentivize sustainable urban ecosystems.
— Dr. Dickson Despommier, microbiology and public health professor emeritus at Columbia University and author of the 2010 book, “The Vertical Farm: Feeding the World in the 21st Century,” on envisioning vertical agriculture.
— Dr. Nate Storey, co-founder and chief science officer at Plenty, Inc., a San Francisco-based indoor farming startup, on vertical agriculture in practice.
— Dr. Raymond Wheeler, NASA plant physiologist, on expanding applications for controlled agriculture.
— Nick Starling, U.S. Army Ranger and founder of Skyscraper Farm, LLC, on the economics and scalability of vertical farms.
— Dr. Weslynne Ashton, associated professor of environmental management and sustainability at Stuart School of Business at Illinois Institute of Technology, on industrial ecology for sustainable urban ecosystems.
The two-day workshop featured breakout sessions on pest and pathogen management, plant selection and breeding, systems engineering, community services, ecosystems services and economics.
New Vertical Farming Light Bar/Panel Hybrid Designed To Maximize Yields With Less Space
The team of lighting experts at TotalGrow have announced the launch of the new TotalGrow Stratum. The features and benefits of this new light include:
Thin profile to maximize space under 4” from canopy to shelf
Full spectrum and modular design for extra versatility
Broad panel/bar hybrid for improved uniformity and penetration in tight spaces
Simple mounting and electrical installation to save time and costs; up to 80 lights per plug
Cost effectiveness, waterproofing and warranty for economic sustainability
The 40W TotalGrow Stratum is designed and refined to maximize yields, space and versatility while minimizing costs. The spectrum and size are ideal for low/no-sunlight growing in virtually any vertical farm, growth chamber, propagation system, tower garden and more. Exceptional efficiencies and light delivery potential, along with long, low maintenance lifespans provide long-term sustainability.
Custom wiring harnesses create the cleanest, simplest power distribution for your operation. An example is shown for a typical 250 µmol*m-2*s-1 setup over several 4’x8’ shelves.
Spectrum customization available
For more information:
TotalGrow
Jeff Mastin – Biologist
315.373.9716
jeffm@venntis.com
totalgrowlight.com