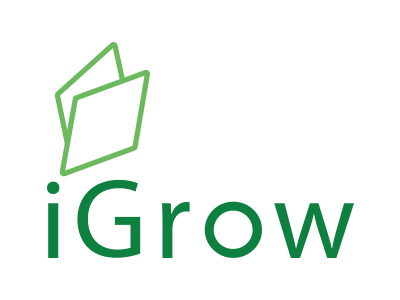
Welcome to iGrow News, Your Source for the World of Indoor Vertical Farming
Five-Day Introductory Training Course On Plant Factory With Artificial Lighting (PFAL)
Five-Day Introductory Training Course On Plant Factory With Artificial Lighting (PFAL)
By urbanagnews
July 18, 2018
In response to increasing global demands from indoor farmers, researchers and future entrepreneurs in the exciting emerging field of plant factory with artificial lighting (PFAL), also known as vertical farm, this coming October, Japan Plant Factory Association (JPFA) together with Chiba University will host an intensive five-day introductory training course in English on PFAL.
Since 2010, JPFA and Chiba University have been organizing various in-depth and practical sessions, including introductory to advanced courses. This five-day introductory session in English, held October 1st -5th, covers what you would need to know before or after starting PFAL business or research.
The sessions will be interactive academic and practical classes, covering topics such as structure and function of PFAL, environmental control, lighting, plant physiology, nutrient solutions, seedlings, recent new technology, and business case studies of commercial large-scale PFALs. In addition to lectures by academic professionals and PFAL representatives, optional excursions to some commercial PFALs on the last day of the course will be organized.
Objective and Goal
-To offer foundation for theory and experience-based practice, with a view to foster academic and industrial development toward next generation PFAL.
-To facilitate development and dissemination of technically and economically sustainable PFAL, through providing the firsthand technical and conceptual classes by broad-ranging professionals in practice from both academia and PFAL industry.
Who should attend?
Motivated current/potential indoor farmers who plan to start or just started PFAL business or research. They will gain understandings of elementary theory and practice of PFAL, basic knowledge of cultivation and operational management, and keys for business success, etc.
Lecturers
Scheduled Lecturers
Chiba University / JPFA: T. Kozai, Y. Shinohara, T. Maruo, S. Tsukagoshi, N. Lu, M. Takagaki, T. Yamaguchi, O. Nunomura and E. Hayashi
Lecturers from the PFAL industry: Representatives from 808 Factory and others
Guidelines for Applicants
Date: 2018. 10.1 Mon – 10.5 Fri
On the first day (2018.10.1), the reception and classes are scheduled to start in the morning.
On the last day (2018. 10.5), the optional excursion will be held in the greater Tokyo area and is scheduled to finish at approximately 15:00.
(Detail schedule will be announced once fixed.)
Location: 6-2-1 Kashiwanoha, Kashiwa, Chiba, Japan 277-0882
Center for Environment, Health, and Field Sciences, Chiba University
Japan Plant Factory Association (1F Meeting Room)
Kashiwanoha campus is located less than 1 hour from Tokyo by train.
There are several accommodations nearby. We will provide the information after you apply.
Fee: JPFA member JPY115,000/person
JPFA Non-member JPY145,000/person
Includes materials for lectures and the transportation fee on the excursion day.
Lunch is not provided, however, there are many options in walking distance including a shopping mall food court and grocery store.
How to apply
Click here for the application form!
Seats will be filled in the order that applications are received.
After applying, you will receive the invoice within 7 to 10 business days. After confirming your payment, your seat will be reserved and we will provide your confirmation booking number.
If your payment can not be made within 5 business days after receiving the invoice, your reservation may be canceled automatically.
Deadline for registration: The end of August or when capacity is filled.
Cancellation:
If participants cancel the training course on or before August 20th, 2018, we will return the fee except JPY 40,000 (a cancellation fee). If the cancellation occurs after August 21st, 2018, the fee shall be due in full.
In most cases, in lieu of canceling you may transfer your registration to another person without penalty.
Japan Plant Factory Association
Japan Plant Factory Association(NPO) is devoted to academic and business advancements in the global indoor farming/CEA industry. Our mission is to develop and disseminate sustainable systems that can address global food, energy and resource issues. We
manage around 20 R&D projects, monthly workshops, and training courses, etc. at Chiba University campus in Kashiwanoha, a smart city in Japan.
JAPAN PLANT FACTORY ASSOCIATION (JPFA)
6-2-1 Kashiwanoha, Kashiwa, Chiba 277-0882, JAPAN
Tel: 81-(0)-4-7137-8318 Fax: 81-(0)-4-7137-8312
http://npoplantfactory.org/e_trainingcourse.html
E-mail: training@npoplantfactory.org
Canadian Online Food Supplier Grow Vegetables on Rooftop With LED Lights of Current by GE
Lufa Farms, a Canadian food supplier based in Montreal, has collaborated with Hort Americas and Current by GE to install LED lights for maximizing the production efficiency of its hydroponic rooftop greenhouses.
Located in urban Montreal with long winter and limited sunlight and space, Lufa Farms has taken the challenge of growing food for local people in sustainable ways and with a modern approach. The company breeds more than 75 vegetables year-round in hydroponic rooftop greenhouses and delivers food directly to their customers through a subscription-based service. Lufa Farms had to increase its production to meet the needs of growing consumers and decided to introduce a new growing system.
(Image: Current by GE)
Current by GE, Hort Americas, and Lufa Farms worked together to develop a three-tier lighting system with the installation of roughly 430 GE Arize Lynk LED lights in a 650 square meters (7,000 square feet) space in the new greenhouse and facilitated seeding propagation. The solution helped Lufa Farms to increase the speed of seeding production by 15 percent as well as to scale the growth. Moreover, the Lufa team noticed greater consistency within each variety of vegetable, as they grew in optimized conditions during this pivotal period. All these benefits helped Lufa Farms to feed its over 10,000 customers and the founders of the company thus will consider to shift to LED lighting for more areas.
Lauren Rathmell, the co-founder of Lufa, said “The design we created means there’s a lot more uniformity across the board. At the same time, it’s quite unique that we have been able to grow many varieties at this volume—and at a faster rate.”
(Image: Current by GE)
Their success had attracted Justin Trudeau, Canadian Prime Minister to visit when the company launched the new greenhouse with a GE growing system.
- Keywords: horticulture lighting Current by GE
Jones Food Company (JFC) And Current By GE Collaborate On Enormous Indoor Farm
Jones Food Company (JFC) And Current By GE Collaborate On Enormous Indoor Farm
July 25, 2018
Current, powered by GE and Jones Food Company Ltd. (JFC) are in the process of constructing one of the largest vertical indoor farms in the world. The intensive plant nursery in North Lincolnshire, England, will be the largest indoor farm in Europe. It will produce up to 420 tons of leafy greens per year across a growing area of 5120m2. The growing area is arranged in racks rising to the height of 11m. In order to help the vertical farm maximize its yield, Current by GE is installing more than 12Km of its new Arize* LED horticultural lighting solution.
Baby watercress grown under Arize LED grow lights from Current by GE
According to Current, the Arize LED horticultural lighting solution features a balanced light spectrum that stimulates optimal growth in every plant and shortens the growth cycle for more intensive production.
“We knew that lighting would be the lifeblood that could bring high-care intensive food production to an industrial level that demonstrates real commercial viability.” JFC CEO James Lloyd-Jones said.
JFC worked with the Current team to develop a customized version of the Arize grow lights that emit a combination of red, blue and white wavelengths that could be flexible and efficient enough to grow a strong, balanced plant. The equipment is located within an intelligent cleanroom (or “high-care”) environment that lets crops grow in complete isolation from external contamination. Each growth area will have its own water and nutrient supply.
As part of being an intelligent high-care environment, the new facility will leverage Current by GE’s cloud-data system to monitor electricity usage from its LEDs and HVAC systems. JFC points out that such a growth environment is ideal for food production as well as growing high-quality cosmetic and pharmaceutical ingredients.
Production of First Crop Expected to Start in Autumn 2018
“Nobody has been able to scale indoor, high-care intensive food production to an industrial level that demonstrates real commercial viability,” explained James Lloyd-Jones, CEO, and co-founder of JFC. “We knew that lighting would be the lifeblood of the facility and we’d need a partner who could see the potential and work with us to develop the right lighting set-up and spectrum to make our vision a reality.”
JFC Claims Facility is Europe’s Largest Indoor Vertical Farm
With a growing area of 5120m2, the equivalent of 26 tennis courts, arranged across racks with a height of just over three stories, the JFC intends for the facility it owns and operates to set new crop production and environmental standards of the future. JFC plans to slash food miles and produce leafy greens, herbs and other crops with year-round local production. The company hopes that these crops, herbs, and greens can be delivered from harvest to plate in minimal time.
In addition, by making the farm a “high-care” facility, JFC will also hopes to cater to the growing needs of cosmetics and pharmaceutical customers who require a reliable supply of natural ingredients of the highest quality. The facility will control every factor in the growth of the crops; Factors including everything from the nutrient solution delivered to the roots of every plant, to the concentration of CO2 in the room, to the light wavelengths and duration of the growing “day”and subsequent rest period will all be tightly controlled.
From planting to harvest, every plant will be untouched by human hands thanks to intelligent automation and advanced robotics. By comparison, conventional production cycles typically have 13 stages of human contact. In fact, JFC will use its own, self- driving forklift truck that can insert and remove trays. JFC says that this self-driving forklift will result in a 60% labor cut as only 3 humans will be permitted to enter the facility at a time.
Arize Lights the Future of Horticulture
Malcolm Yare, Horticulture Business Development Manager for Current by GE commented, “We’ve spent years honing our technology in other industrial lighting sectors, and years more partnering with agricultural experts and researching the needs of horticultural applications. Our Arize LED solutions now lead the industry for efficiency and we continue to research new ways to improve performance through innovation. We look forward to working with Jones Food Company and our wider ecosystem of partners to find new ways to scale high-quality, global food production whilst reducing the energy and environmental costs of vertical farming.”
The Arize range of lighting solutions are low cost to install and maintain, with a market-leading 36K-hour lifetime (L90) and a five-year warranty to provide peace of mind and long-term reliability. Arize also has an IP66 and UL Wet rating that also make them perfect for high-care and cleanroom facilities because the luminaires can be easily washed and sanitized while in-place.
The JFC facility is uniquely designed to minimize the environmental impact of vertical farming, which will also benefit JFC financially. For example, the facility will use up to 90 percent less water and 50 percent less fertilizer than conventional growing methods, saving on input costs. Additionally, Current by GE’s Arize LED horticultural lighting is highly efficient and generates less heat than competitive products, and it reduces energy consumption and carbon footprint by 33 percent compared with vertical farming averages.
JFC previously tested the LEDs on a mini-farm on Challinor’s property in order to identify best practices for efficiencies. Based on this testing, JFC has already created plans to pump pure CO2 into the facility, install roof solar panels and use GE’s cloud-data system to monitor energy use and controls integration.
The integration of sensors is reportedly still underway at the facility as there is a vision for Current to connect JFC’s sites into Current’s IoT Enterprise solution. Due to the phased nature of the project, Current is continuing research and development with the latest innovation for sensing and automation technology. JFC is reportedly working with a trusted Current ecosystem partner to ensure seamless integration of Current’s lighting systems into their site level building management system to limit the amount of work that needs to be done manually.
New LED Lighting Technology Brings The Power Of The Sun To Hydroponics
A high-tech lighting system that mimics the huge variety of sunlight — manufactured by Edmonton company G2V and developed in a University of Alberta lab by research scientist Michael Taschuk — is now being tested in four cannabis grow operations across Canada.
The G2V lighting system wasn’t developed to grow plants. Instead, it was built to test solar cells at the U of A’s National Institute of Nanotechnology. The goal with solar cells is to get even slight increases in efficiency. This makes it necessary to have extremely precise diagnostic tools for taking measurements, including lamps that mimic the sunlight as it’s experienced on the Earth’s surface in all its variety, hot and cold, bright and dim, and everything in between.
— David Staples
Italy: Tomato Grower Plans To Light 6 Hectares With LED
Italy: Tomato Grower Plans To Light 6 Hectares With LED
Prominent Italian tomato grower Gandini Antonio officially selected igrox srl as technological partner in LED supplemental lighting. Gandini is going to increase the LED lighted surface in their greenhouses with a new system, in order to improve yield and quality of crop. The first delivery of the LED systems is scheduled for week 39.
From HPS to LED
Gandini Antonio is the main tomato grower in the north of Italy; they currently have 16,000 m2 already lighted with HPS. Gandini wants to replace its 600W HPS with LED systems in order to increase PPFD (photosynthetic photon flux density) and improve the yield and quality of tomatoes, Alessandro Oliveri, CEO of igrox, tells us.
"In 2017 Gandini decided to test our a new LED fixture, a toplighting system of 300W and 2.35uMol/J efficiency with our HEx spectrum, specifically designed for supplemental lighting applications in greenhouses", Alessandro explains. "Our new system has been designed to get the best balance between efficiency and cost, ensuring high ROI and low investments per square meter."
In the test, Gandini compared different LED fixtures from other well known manufacturers. "Gandini selected our solution thanks to the best return on investment respect to the other tested LED fixtures. Our new systems produced the same yield but with 22% less power consumption respect to the other tested LED fixtures. In addition to this, the plants have a higher productivity and the fruits a superior quality if compared with the old HPS systems."
First phase: 7,500 square meters
The partnership with Gandini starts with a first order for substitution of HPS fixtures, getting a total LED lighted surface of 7,500 m2. Gandini aims to get to 60,000 m2 of LED lighted greenhouses in the next 2 years.
Cherry tomatoes during the test
igrox horticulture business
Horticulture is a relatively recent venture for the people behind igrox, but they have been around for a while, Alessandro says: "We have a history of 40 years in general lighting and, after 2 years spent in R&D, in 2017 we started the horticulture business with the new brand igrox.
"We develop LED lighting systems for plant growth in controlled environments, combining latest technologies and high quality LED chips to provide top class, cost-effective lighting solutions.
"Our team is composed of engineers, biologists and agronomists in order to optimize and integrate our solutions with the specific needs of controlled environments for plant growth."
For more information:
igrox
Via Vittorio Veneto 23b
20010 Bernate Ticino (MI)
Italy
info@igrox.com
www.igrox.com
For more information:
igrox
Via Vittorio Veneto 23b
20010 Bernate Ticino (MI)
Italy
info@igrox.com
www.igrox.com
For more information:
igrox
Via Vittorio Veneto 23b
20010 Bernate Ticino (MI)
Italy
info@igrox.com
www.igrox.com
For more information:
igrox
Via Vittorio Veneto 23b
20010 Bernate Ticino (MI)
Italy
info@igrox.com
www.igrox.com
For more information:
igrox
Via Vittorio Veneto 23b
20010 Bernate Ticino (MI)
Italy
info@igrox.com
www.igrox.com
For more information:
igrox
Via Vittorio Veneto 23b
20010 Bernate Ticino (MI)
Italy
info@igrox.com
www.igrox.com
For more information:
igrox
Via Vittorio Veneto 23b
20010 Bernate Ticino (MI)
Italy
info@igrox.com
www.igrox.com
For more information:
igrox
Via Vittorio Veneto 23b
20010 Bernate Ticino (MI)
Italy
info@igrox.com
www.igrox.com
For more information:
igrox
Via Vittorio Veneto 23b
20010 Bernate Ticino (MI)
Italy
info@igrox.com
www.igrox.com
For more information:
igrox
Via Vittorio Veneto 23b
20010 Bernate Ticino (MI)
Italy
info@igrox.com
www.igrox.com
For more information:
igrox
Via Vittorio Veneto 23b
20010 Bernate Ticino (MI)
Italy
info@igrox.com
www.igrox.com
For more information:
igrox
Via Vittorio Veneto 23b
20010 Bernate Ticino (MI)
Italy
info@igrox.com
www.igrox.com
For more information:
igrox
Via Vittorio Veneto 23b
20010 Bernate Ticino (MI)
Italy
info@igrox.com
www.igrox.com
For more information:
igrox
Via Vittorio Veneto 23b
20010 Bernate Ticino (MI)
Italy
info@igrox.com
www.igrox.com
For more information:
igrox
Via Vittorio Veneto 23b
20010 Bernate Ticino (MI)
Italy
info@igrox.com
www.igrox.com
For more information:
igrox
Via Vittorio Veneto 23b
20010 Bernate Ticino (MI)
Italy
info@igrox.com
www.igrox.com
For more information:
igrox
Via Vittorio Veneto 23b
20010 Bernate Ticino (MI)
Italy
info@igrox.com
www.igrox.com
For more information:
igrox
Via Vittorio Veneto 23b
20010 Bernate Ticino (MI)
Italy
info@igrox.com
www.igrox.com
For more information:
igrox
Via Vittorio Veneto 23b
20010 Bernate Ticino (MI)
Italy
info@igrox.com
www.igrox.com
For more information:
igrox
Via Vittorio Veneto 23b
20010 Bernate Ticino (MI)
Italy
info@igrox.com
www.igrox.com
For more information:
igrox
Via Vittorio Veneto 23b
20010 Bernate Ticino (MI)
Italy
info@igrox.com
www.igrox.com
For more information:
igrox
Via Vittorio Veneto 23b
20010 Bernate Ticino (MI)
Italy
info@igrox.com
www.igrox.com
For more information:
igrox
Via Vittorio Veneto 23b
20010 Bernate Ticino (MI)
Italy
info@igrox.com
www.igrox.com
For more information:
igrox
Via Vittorio Veneto 23b
20010 Bernate Ticino (MI)
Italy
info@igrox.com
www.igrox.com
For more information:
igrox
Via Vittorio Veneto 23b
20010 Bernate Ticino (MI)
Italy
info@igrox.com
www.igrox.com
For more information:
igrox
Via Vittorio Veneto 23b
20010 Bernate Ticino (MI)
Italy
info@igrox.com
www.igrox.com
For more information:
igrox
Via Vittorio Veneto 23b
20010 Bernate Ticino (MI)
Italy
info@igrox.com
www.igrox.com
For more information:
igrox
Via Vittorio Veneto 23b
20010 Bernate Ticino (MI)
Italy
info@igrox.com
www.igrox.com
For more information:
igrox
Via Vittorio Veneto 23b
20010 Bernate Ticino (MI)
Italy
info@igrox.com
www.igrox.com
For more information:
igrox
Via Vittorio Veneto 23b
20010 Bernate Ticino (MI)
Italy
info@igrox.com
www.igrox.com
For more information:
igrox
Via Vittorio Veneto 23b
20010 Bernate Ticino (MI)
Italy
info@igrox.com
www.igrox.com
For more information:
igrox
Via Vittorio Veneto 23b
20010 Bernate Ticino (MI)
Italy
info@igrox.com
www.igrox.com
For more information:
igrox
Via Vittorio Veneto 23b
20010 Bernate Ticino (MI)
Italy
info@igrox.com
www.igrox.com
For more information:
igrox
Via Vittorio Veneto 23b
20010 Bernate Ticino (MI)
Italy
info@igrox.com
www.igrox.com
For more information:
igrox
Via Vittorio Veneto 23b
20010 Bernate Ticino (MI)
Italy
info@igrox.com
www.igrox.com
For more information:
igrox
Via Vittorio Veneto 23b
20010 Bernate Ticino (MI)
Italy
info@igrox.com
www.igrox.com
For more information:
igrox
Via Vittorio Veneto 23b
20010 Bernate Ticino (MI)
Italy
info@igrox.com
www.igrox.com
For more information:
igrox
Via Vittorio Veneto 23b
20010 Bernate Ticino (MI)
Italy
info@igrox.com
www.igrox.com
For more information:
igrox
Via Vittorio Veneto 23b
20010 Bernate Ticino (MI)
Italy
info@igrox.com
www.igrox.com
For more information:
igrox
Via Vittorio Veneto 23b
20010 Bernate Ticino (MI)
Italy
info@igrox.com
www.igrox.com
For more information:
igrox
Via Vittorio Veneto 23b
20010 Bernate Ticino (MI)
Italy
info@igrox.com
www.igrox.com
For more information:
igrox
Via Vittorio Veneto 23b
20010 Bernate Ticino (MI)
Italy
info@igrox.com
www.igrox.com
For more information:
igrox
Via Vittorio Veneto 23b
20010 Bernate Ticino (MI)
Italy
info@igrox.com
www.igrox.com
For more information:
igrox
Via Vittorio Veneto 23b
20010 Bernate Ticino (MI)
Italy
info@igrox.com
www.igrox.com
For more information:
igrox
Via Vittorio Veneto 23b
20010 Bernate Ticino (MI)
Italy
info@igrox.com
www.igrox.com
For more information:
igrox
Via Vittorio Veneto 23b
20010 Bernate Ticino (MI)
Italy
info@igrox.com
www.igrox.com
For more information:
igrox
Via Vittorio Veneto 23b
20010 Bernate Ticino (MI)
Italy
info@igrox.com
www.igrox.com
For more information:
igrox
Via Vittorio Veneto 23b
20010 Bernate Ticino (MI)
Italy
info@igrox.com
www.igrox.com
Nichia Turns Vegetables Into Medicinal Plants With LED Lighting
Nichia Turns Vegetables Into Medicinal Plants With LED Lighting
LED applications have opened an explosive market in horticulture lighting. Nichia, the Japanese LED giant, set up a laboratorial plant factory in Shanghai to test how different LED light sources can alter the ingredients of plants to create medicinal effects.
By combining blue LED with various phosphors, Nichia managed to generate artificial LED light with sunlight spectrum to upgrade the quality of light, which not only enhances eye comfort for people but also improves vegetable growth. In Nichia’s plant factory in Shanghai, Chun Chia Tai, Chairman and President of Nichia’s Shanghai and Taiwan Offices, established an indoor farm to conduct experiments on plants with several LEDs.
(Image: Nichia; Chairman and President of Nichia’s Shanghai and Taiwan Offices)
According to Tai, Nichia aims to grow vegetables with intensified medicinal effects. The ingredients of vegetables could be modified by changing the spectrum of LEDs. For example, Nichia has bred vegetables containing lower sugar which would be beneficial for diabetic patients. With its unique technology of mixing phosphors with LEDs, the company is bringing horticulture lighting to a new level.
Nichia has connected with local supermarkets to sell its vegetables in Shanghai and shipped some products to the Netherlands. The wide range applications of LED have built up a bridge between cutting-edge technologies and farming, bringing more healthy options for people.
- Keywords: Nichia Horticulture lighting Plant factory
Adjusting Lighting Conditions To Grow NASA Salads
Adjusting Lighting Conditions To Grow NASA Salads
Osram is providing the National Aeronautics and Space Administration (NASA) with a customized version of its proprietary connected horticulture research lighting system, Phytofy RL. The smart lighting software, coupled with a unique setup of connected grow light fixtures, will supplement the lighting technology used in NASA’s Food Production. Research focused on production of salad-type crops for crews during space travel.
All software, hardware and LEDs in Phytofy were developed by Osram. Osram has developed a broad portfolio of horticulture LEDs that irradiate the specific wavelengths needed for optimum growth of a wide variety of plants and flowers, allowing the light to be adapted specifically for the needs of various crops.
“Osram is developing smart, innovative lighting technologies that can improve food production in a variety of environments, even unique environments like space,” said Steve Graves, Strategic Program Manager of Urban & Digital Farming, Osram Innovation, Americas Region. “Many of the world’s coolest and most beneficial inventions have come from scientists at NASA over the past several decades, and to play a role in empowering further innovation through the use of our technologies is an honor. We are excited about the possibilities Phytofy RL will bring to a wide variety of horticulture applications, and our teams are excited to continue learning and refining its setup before ultimately bringing this exclusive solution to market within the next year.”
NASA was introduced to Osram through Hort Americas, which works closely with leading manufacturers to provide North American greenhouse growers, vertical farmers and researchers with the most technically advanced and cost-effective products to help them reach their yield, quality and project goals. Members of NASA's food production research team presented Hort Americas with a list of features they wanted from a lighting fixture, Hort Americas then used its network to help NASA team up with Osram to learn more about the Phytofy RL horticulture lighting technology.
Phytofy’s unique features include:
- A UV channel which provides researchers with the ability to add a brief UV light to see how plants react and change.
- More LEDs, which means a higher Photosynthetic Photon Flux (PPF). PPF measures light emission by calculating how many photons are coming out of the light every second. This is an important metric for plant researchers so they can determine the most efficient and effective light recipes.
- An Irradiance Map – Researchers can see the irradiance using Osram software, so there is no need for them to measure irradiance separately before changing the light setting.
Osram’s smart horticulture lighting system is being piloted through a series of collaborations with universities and research labs around the world that are using the technologies and sharing insights. At NASA, Phytofy RL will allow researchers to easily adjust lighting conditions to optimize plant growth in various conditions and then replicate those settings in the Advanced Plant Habitat on the International Space Station, meeting the sophisticated needs of space food production. Installation of Phytofy RL within a growth chamber at Kennedy Space Center in Florida was completed recently, with plans to move the configuration to one or more of the Center’s walk-in plant grow rooms.
Via radiation with light of different wavelengths, the growth cycles of plants can be controlled and accelerated, allowing the plants to be harvested either more often or as required. Special light recipes optimize not only yield and growing time but also can increase the amount of vitamins and nutrients in the plant, and can enhance certain tastes and flavors. LEDs not only provide tailor-made bioactive lighting, but are also very efficient.
For more information:
Osram
www.osram.com/horticulture
Hein van der Sande Opens Certhon Innovation Centre
Hein van der Sande Opens Certhon Innovation Centre
"The Innovation Centre is going to teach us a lot"
On Thursday 31 May, the Certhon Innovation Centre was officially opened by Hans Hoogeveen, Ambassador at the UN organizations for Food and Agriculture (FAO, WFP and IFAD) in Rome. With this center, the greenhouse builder responds to the need to produce food worldwide, in every place on earth and 365 days a year. There are more and more mouths to feed. Hein van der Sande: "The main aim is to achieve a significant increase in production."
Hein continued: "In addition, the water can be recirculated completely. Moreover, crop protection products are not needed if you cultivate in this manner. So this method of cultivation fits in perfectly with the policy of the supermarkets. Supermarkets are getting ever stricter requirements to the use of crop protection products. We have already learned a lot, but we're going to learn a lot more. We are going for it, and I look to the future with confidence."
The Innovation Centre is a 240 m2 greenhouse construction with insulation panels. Different cultivation methods and multi-layer cultivation are tested here. The cultivation is computer-controlled. And, last but not least, robots are going to be used. "Because that too is one of the aspects that makes progress worldwide: Technology will increasingly replace simple labor."
In the Certhon Innovation Centre, research is being done into crops in which Certhon has expectations in various climates, humidity, and light recipes. Hein van der Sande, CEO at Certhon: “With the knowledge, we gain from the Innovation Centre, we can give our customers and partners optimal advice for maximum results. The first studies we started in the facility with herbs, tomato, sweet pepper, strawberry and raspberry plants already gave promising results and a delicious harvest!”
Certhon did not devise this alone. Philips, Rijk Zwaan, Delphy, Wageningen UR and Koppert Biological Systems are part of this project. Hein van der Sande: "We see opportunities for the future of Dutch horticulture. We are faced with a new challenge, and we are keen to take it on. Certhon's innovative genes recognize opportunities."
Mr. Hoogeveen, ambassador and permanent representative at the UN organizations for Food and Agriculture (FAO, WFP, and IFAD) in Rome, addressed the audience: "It is a great honor to be standing here. We are proud of the Dutch horticulture sector. We notice that, everywhere in the world, Dutch horticulture is closely followed. Parties would like to cooperate with us on this level. We do not realize sufficiently the golden opportunities that this gives us. With the results of this center, everyone can produce good and nutrition-rich food thanks to conditioned cultivation. There is a need for that. After all, more and more people are going hungry. Growers have the need to be supported globally. Especially the growers in Africa are badly in need of our support."
After the speeches of Van der Sande and Hoogeveen, the guests were given the opportunity to head to the Innovation Centre. Explanations, questions, and admiration all over.
For more information:
Certhon
+31 (0)174-225080
www.certhon.com
info@certhon.com
Publication date: 6/5/2018
Author: Mark Mandemakers
Copyright: www.hortidaily.com
Herifi Introduces Advanced Led Grow Light Technology To Improve Interior Aquarium, Plant Growing Efficiency
Herifi Introduces Advanced Led Grow Light Technology To Improve Interior Aquarium, Plant Growing Efficiency
June 1, 2018
Shenzhen Herifi Technology Co., Ltd develops a wide range of LED grow light to increasing more efficient light energy applicability in aquarium, plant growth, flowering and art while reducing global energy cost.
Shenzhen Herifi Technology Co., Ltd, a high-tech enterprise in electronics manufacturing, introduces new innovative LED grow light with enhanced features and a wide range of other LED products to provide global customers with the ideal lighting condition for all phases of water solution culture and hydroponics, plant growth and flowering as well as soil culture, while saving cost on conventional light sources. Again, it is aimed at providing global architects, engineers and designers with the source and inspiration for creation.
Recently, LED lights have become very popular particularly due to the widespread indoor growing practices. Today, most global electronic companies have ventured into the production of LED grow lights, however, there is yet the need for standard and quality in addition to products with high durability to save cost. Shenzhen Herifi Technology Co., Ltd fills this space with their full spectrum lighting solution and other innovative products. One unique product amongst these is the LED grow light bar, which has been designed for large and extensive compartments.
The Apolo LED grow light is considered as one of the best effective replacements for the conventional High-Intensity Discharge (HID) lighting such as the Fluorescent Light Bulbs, High Sodium Bulbs, and Metal Halide. These products have also been designed in different aesthetic forms and varieties for better applications which include Apotop series, sky series, ladder series, star trek series, Diamond series, STM series, KING series and more. The company also offers special custom services to meet their clients’ specific needs.
One of the company’s LED light products is the dimmable grow light. Several forms of this product have found application in the smart plant factories. Together with moisture and appropriate quantities of nutrients, adjusting this unique LED lighting provides a conducive growing environment for plants in the interior. The LED lighting also increases the growth rate of crops as well as the nutritional value while limiting, as much as possible, any interference from the immediate environmental factors. This provides good advantage particularly for countries in the polar and land-lock regions, with poor climatic conditions and land constraint for effective crop cultivation.
Clients who are interested in purchasing their new collections or wish to know more about Shenzhen Herifi Technology Co., Ltd and their other services are urged to visit their website on http://www.herifi.com
About Shenzhen Herifi Technology Co., Ltd
Founded in 2012, Shenzhen Herifi Technology Co., Ltd specializes in the manufacture of the plant led grow lights and aquarium led lightings. The company has a staff strength of 200 present in their 5000 square meters factory, in addition to high-tech equipment such as reflow soldering machine, automatic SMT machine, all sorts of electric test, production and R&D equipment, and large integrating sphere. Herifi has earned a high reputation throughout Europe and America in grow led lamps and aquarium led lights fields.
Website: http://www.herifi.com
Top-Shelf Growing With LEDs
Top-Shelf Growing With LEDs
Mike Zelkind’s vertical farming company, 80 Acres Farms, relies on technology and expertise for its success.
May 30, 2018
GIE Media Horticulture Group
Mike Zelkind worked in the food industry for more than 25 years before co-founding and becoming CEO of 80 Acres, an indoor farming company producing pesticide-free crops. He spent time in operations, marketing and sales at leading food companies such as General Mills, Conagra Foods, Bumble Bee Foods, Advance Pierre, and as the president and later CEO of Sager Creek Vegetable Company, a division of DelMonte Foods.
In that time, Zelkind came to believe that technology could help improve what was available to consumers while offering them local food. As a result, he co-founded 80 Acres Farms with Tisha Livingston in 2015. Its products are available at retailers such as Dorothy Lane Markets, Rouses, Whole Foods and Jungle Jim’s International Market, and through broadline foodservice distributors like USFoods.
“There’s an opportunity to grow it much more efficiently, to grow it without any pesticides — to grow a clean, nutritious product,” he says.
He said over the past few years when looking at the broader food industry, he came to believe that a core problem for food production is that field farmers are unable to control their environments. Since he does not come from a growing or horticulture background, Zelkind traveled the world with his business partner to understand different greenhouse types, growing methods, and technology, including the LEDs that he uses in all of 80 Acres’ facilities.
“I’ve been watching farmers struggle for years,” he says. “I felt like there was a real need. The food that we eat is not the same quality as what we ate 20 or 30 years ago.”
A better way
Using the best possible technology available, including LEDs from Philips Lighting, is a key part of Zelkind’s business philosophy. Unlike some indoor farms that are focused on building a new growing system altogether, Zelkind sees 80 Acres finding success by using the best technology available for each part of the business. With that technology in place, the idea is to grow a variety of different crops consumers want. That includes vine crops and herbs in addition to greens and microgreens.
“We’re not just doing lettuce or microgreens,” he says.
Zelkind adds that technology is advancing to a point where it helps improve what 80 Acres does. For lighting, for instance, he says a number of different LED spectrums and fixture types were trialed for the different crops grown at 80 Acres before he and his team decided that the best option was to grow each type of crop with specific fixtures and light spectrums. So, in the 80 Acres systems, a vine crop like tomatoes will be grown under a different fixture and spectrum than leafy greens or herbs, to meet each crop’s individual needs.
The operation uses LED bulbs with fixed spectrums from Philips Lighting, as well as a few different fixtures types from Philips Lighting, depending on the crop. Zelkind says he knows he’s getting a dependable light source from Philips and knows he can trust their advice. He also says Philips’ variety of available light fixtures and spectrums make them the best fit for his business and a partner in his success.
“[They] have the deepest grow knowledge,” he says. “It’s a phenomenal company with tremendous experience and a great set of lights.”
In addition to growing technology, Zelkind says 80 Acres is staffed with experienced industry people. He says having people who are well-versed in all parts of the business — everything from growing, engineering, food safety and plant science to marketing, sales, operations and data science — with 10 or 20 years’ experience in food, is what it takes to be successful in this new industry. It also sets the 80 Acres Farms apart.
“We think that cracks the code of how to build a commercially viable farm,” he says.
Potential for growth
Currently, 80 Acres has farms in four different locations — Daphne, Alabama; Springdale, Arkansas; Granite Falls, North Carolina; and Cincinnati, Ohio — with plans for more facilities in the works. A lot of the company’s effort right now is expanding what crops it can grow well. Zelkind says 80 Acres has already successfully grown strawberries and hops in its facilities.
“The plan is to go way beyond lettuce,” he says.
Zelkind, though, does admit that there is still much to figure out before indoor farming becomes commercially viable. However, he does know that buying the right products – including the various LEDs he gets from Philips – are part of any realistic solution.
Growth for 80 Acres also involves scaling up farms over time at the right pace and in the right markets. In Ohio, for instance, a second facility near Cincinnati is being built to establish a regional hub. And when a new location is added, one or two modular farms are built to see how the location fares before a large amount of capital is invested.
“We’re in the first inning of the game,” he says.
As that happens, and the business grows, the goal remains the same.
“We want to provide, healthy, nutritious, local food,” he says. “And do so in a very sustainable way.”
Photo courtesy of Mike Zelkind
Understanding Greenhouse Lighting
Understanding Greenhouse Lighting
There’s a lot more to greenhouse lighting than meets the eye. Growers in search of the appropriate lighting for their greenhouse should consider the following three factors: the type of crop being grown, what time of year it is and how much sunlight is available.
Greenhouses generally require six hours of direct or full spectrum light each day. If this can’t be done naturally, supplemental lighting must be incorporated. Supplemental lighting is the use of multiple, high-intensity artificial lights to promote crop growth and yield. Hobbyists like to use them to maintain growth and extend the growing season, whereas commercial growers use them to boost yields and profits.
Equally important as supplemental lighting is photoperiod control lighting. A photoperiod of light is the number of hours that a plant receives light in a 24-hour time span. For example, if the sun rises at 6 in the morning and sets at 8 in the evening, a 14-hour photoperiod has lapsed. Photoperiod control lights are used to simulate long days, triggering early flowering or promoting delayed flowering, depending on the plant’s needs.
Growers have a wide array of lighting options to pick from, so it’s important to understand the nuances of different lighting styles. Let’s examine the uses and advantages of four different lighting types.
High-pressure sodium fixtures
High-pressure sodium fixtures provide more orange and red spectrum light and have a golden-white appearance to the human eye. Since they promote budding and flowering, they are generally used later in the growth cycle of the plant. These fixtures are approximately 7 times more efficient than incandescent bulbs and work best when used in conjunction with natural daylight, making them a great option for greenhouses. High-pressure sodium lights also offer the potential for a 10% increase in intensity and photosynthetically active radiation (PAR.)
Give high-pressure sodium lights about 4 to 5 minutes to warm up and one minute to cool down. It is for this reason that they aren’t good for locations where the lights turn on and off frequently. It’s also important to be cognizant of placement; high-pressure sodium lights should be mounted 30 to 36 inches above the plant for optimal results.
Fixed and programmable spectrum LED fixtures
LED (light emitting diode) fixtures are the longest lasting option offered by Growers Supply, with a typical lifespan of 50,000 hours. The diode of an LED won’t burn out as fast as standard light bulbs, which gives it such an incredibly long lifespan. LED lighting fixtures have a higher efficiency than standard lighting because more of the power input goes to light than heat. For instance, incandescent bulbs are only about 20% efficient, as most of their input power goes to producing heat.
Perhaps one of the biggest advantages of LED lighting is the massive energy savings. They are easily integrated into any operation and offer up to 70% savings when compared to high-intensity discharge (HID) lighting.
There is no warm-up time required with an LED fixture and they are also free of mercury, making disposal much easier than other bulbs. LED’s provide superior functionality when used as a sole source of lighting, making them an attractive option for many growers.
Ceramic metal halide
Ceramic metal halide lamps are used for their blue light, although they appear bright-white to the human eye. They can easily function as a primary light source, with an average lifespan between 8,000 to 15,000 hours. Since metal halides are 3 to 5 times more efficient than incandescent bulbs, they make an excellent option for areas that don’t receive natural sun.
Important to note is that metal halides have to warm up for about 5 minutes or less before they can give out full light. They also need a cool down period of about 5 to 10 minutes before restarting. For this reason, they are not recommended for locations where the lights will turn on and off frequently.
Ceramic metal halide lights should be hung 30 to 36 inches over plants and can result in darkened leaves and overall healthy-looking greenery. Growers Supply PARLucent Ceramic Metal Halide Lights are ideal for greenhouse and hydroponic applications. Growers often use them in the early phase of a plant’s life when seeds are in the vegetative growth phase. The dimmable ballast allows growers to obtain the perfect lighting for their operation. They are completely silent too, so there are no bothersome humming, buzzing or high-pitched noises to deal with.
T5 fixtures
T5 fixtures are the most efficient and most popular fluorescent greenhouse lighting option for growing. They use less energy than traditional lamps and can last up to 50,000 hours. These environmentally-friendly lights sometimes feature aluminum reflectors for maximum efficiency. They are ideal for use in hydroponics, greenhouses, warehouses, barns and more. They can be used from the initial phase of seed starting to full term growth.
The letter “T” denotes the tubular shape of the lamp and the number 5 indicates its diameter in eighths of an inch. T5 lamps are slim, only 5/8” of an inch in diameter, which makes T5 fluorescent tubes more efficient than standard fluorescent tubes.
GrowSpan’s High-Performance 45” T5 Fluorescent Lamp features extremely high lumen output and full spectrum lighting that is excellent for plants from the seedling stage up to full term growth. Its minimal heat output means that it can safely be placed very close to plants, within 6 to 12 inches to be precise. While there’s technically no such thing as too much light, it’s important not to use too powerful a light in a small space, which can result in overheating of the leaf surface area.
For more information:
GrowSpan Greenhouse Structures
1395 John Fitch Blvd
South Windsor, Connecticut 06074
Toll-free USA: (800) 476 9715
International: +1 860 528 9550
info@growspan.com
www.growspan.com
Signify And New Horti LED Partner Hortilife Boost Yields at Latvian Grower "Getlini EKO" Through Philips Greenpower LEDs
June 11, 2018
Signify And New Horti LED Partner Hortilife Boost Yields at Latvian Grower "Getlini EKO" Through Philips Greenpower LEDs
- Getlini EKO, Ltd. increased production of IMEA cucumbers
- Successful start of new Horti LED partnership between Signify and Hortilife B.V.
Eindhoven, the Netherlands – Signify (Euronext: LIGHT), the world leader in lighting, today announced that its new partnership with Hortilife B.V. has boosted the yields at Getlini EKO, a Latvian grower of tomatoes, cucumbers and hanging plants. Results of the first commercial full-LED horticultural lighting project for IMEA cucumbers at Getlini EKO mirror those achieved in an earlier trial.
From September 2017 to early January 2018, Getlini EKO harvested 146 fruits per square meter in its 3,000 square meter cucumber greenhouse, in line with Signify yield estimates. Hortilife assisted with the installation of Philips GreenPower LED toplighting and Philips GreenPower LED interlighting at the Getlini EKO greenhouse.
“Our participation in projects like Getlini EKO and the full-LED trial at Warsaw University of Life Sciences (SGGW), proves that companies can successfully grow IMEA cucumbers year-round using our LED technologies,” says Udo van Slooten, Business Leader Horticulture at Signify. “Furthermore, it showcases our leadership in LED lighting for horticulture.”
Jointly established and managed by the Riga and Stopini Municipalities, Getlini EKO greenhouses are located on the site of the largest municipal solid waste landfill in the Baltic States. The facility was opened in 2015 and uses heat from the waste recycling process. It installed the energy-efficient Philips LEDs in spring 2017.
“We wanted to start growing IMEA cucumbers year-round,” says Guntars Strauts, agronomist at Getlini EKO. “We needed to install lights with little heat radiation as the recycling process already produces a lot of heat. LED lighting offered that in the most economical and ecologically friendly way.”
LED lighting generates significantly less heat than high-pressure sodium (HPS) lighting, allowing Getlini EKO to independently control light and heat in the greenhouse. “Signify had demonstrated its strong know-how in growing with Philips LED lighting,” Strauts adds. “We were convinced after seeing the results of the full-LED trial at the SGGW, Poland. The first trial period at the SGGW produced cucumbers with 60% less energy usage and 1.4 liters less water per kilo and achieved 24.8% higher yields.”
The Netherlands-based Hortilife and its export companies specialize in the engineering, installation and supplying of greenhouses and agro-storage equipment, installations and construction. It is active across
many crop segments, including tomato, cucumber, lettuce, roses and pot roses, among others. Hortilife has successfully overseen installations of greenhouses throughout Russia, Ukraine, and the Baltic States.
Signify N.V. became the new company name of Philips Lighting N.V., the ultimate parent company of the worldwide group of Philips Lighting companies. The name of Philips Lighting Eurasia LLC will be changed at the beginning of 2019.
--- END ---
For further information, please contact:
Signify Corporate Communications
Daniela Damoiseaux, Global Marcom Manager Horticulture at Signify
Tel: +31 6 31 65 29 69
E-mail: daniela.damoiseaux@signify.com
About Signify
Signify (Euronext: LIGHT) is the world leader in lighting for professionals and consumers and lighting for the Internet of Things. Our Philips products, Interact connected lighting systems and data-enabled services, deliver business value and transform life in homes, buildings and public spaces. With 2017 sales of EUR 7.0 billion, approximately 32,000 employees and a presence in over 70 countries, we unlock the extraordinary potential of light for brighter lives and a better world. News from Signify is located at the Newsroom, Twitter and LinkedIn. Information for investors can be found on the Investor Relations page.
Our global brands are
Signify Signs New Partnership Agreement With Eiffage Energie Systèmes To Serve French Horticulture Market
Signify Signs New Partnership Agreement With Eiffage Energie Systèmes To Serve French Horticulture Market
- Signify now has a dedicated Horti LED partner in France to meet increasing demand for horticultural LED lighting
- Eiffage Energie Systèmes will sell Philips GreenPower LED lighting to the French horticulture market
Signify, the world leader in lighting, today announced it has signed an official Philips Horti LED partnership agreement with Eiffage Energie Systèmes. As of May 28, Eiffage Energie Systèmes will be a certified supplier of Philips GreenPower LED lighting for all horticulture applications, such as greenhouses as well as innovative vertical farming facilities.
Growing demand for year-round production
“Eiffage Energie Systèmes is a perfect addition to our partner network because of its location and knowledge of the sector. It has delivered and installed co-gens in greenhouses in France for many years and is well acquainted with the market,” said Udo van Slooten, Business Leader Horticulture at Signify. “We see a trend amongst French growers looking for ways to serve the market all year-round. Because of the French climate, growers need to increase the amount of light in the greenhouse, without further raising the plant temperature. LED lighting produces far less heat than HPS lighting, making it a smart choice on the path towards year-round uniform production,” Van Slooten added.
Quality cultivation solutions for French customers
“Eiffage Energie Systèmes and Signify are both companies that stand for quality, certainty, and knowledge,” said Jean Jacques Pince, Managing Director of Eiffage Energie Systèmes Nouvelle Aquitaine. “We are honored to work with Signify and to include Philips LED products in our portfolio because it fits our current way of working. We have expertise in greenhouse building and already do this type of installation work. LED lighting is a valuable addition to our portfolio because we can couple the quality of the Signify product offering with our strong presence in France.”
Signify and Eiffage Energie Systèmes are already working on three commercial projects to be installed later this year. The ongoing expansion of the Philips Horti LED partner network demonstrates Signify’s commitment to extend its leadership in the horticulture industry as an innovative LED lighting provider and partner for the greenhouse industry.
PS Signify became the new company name of Philips Lighting as of May 16, 2018.
Thrive Agritech Secures $2 Million Capital Injection
The latest investment round, led by New York-based Rose Capital, accelerates the LED lighting company's unique lighting technology into the global horticulture market.
May 22, 2018
Thrive Agritech, Inc., a technology company focused on leading innovations in LED horticulture lighting, has announced that it has received an additional $2 million in equity capital to accelerate the development and deployment of its LED technology in controlled environment agriculture. The investment round was led by Rose Capital, a New York-based institutional investor. In conjunction with the investment round, Rose Capital has also joined Thrive’s Board of Directors.
The financing round–and new partnership with Rose Capital–follows an exceptional year for Thrive Agritech, which saw a rapidly expanding customer base with lighting installations in greenhouses, vertical farms and cannabis production facilities across North America.
Rose Capital noted, “We are excited about this investment based on the extraordinary customer adoption that Thrive has experienced since its first product launch in 2015. Thrive has established a successful track record of commercializing best-in-class LED lighting products–having launched a new product every year since the company’s inception. We look forward to partnering with Thrive to continue to break down traditional industry barriers and commercialize some of the most innovative products in the global horticultural market.”
The United Nations Food and Agriculture Organization estimates that food production must increase by 70 percent over the next forty years to satisfy increasing demand. The total market in North America for LED lighting solutions for greenhouses is expected to grow from 2.5 million square feet in 2015 to more than 50 million square feet in 2021. In response to these trends, companies like Thrive are introducing high output lighting solutions to change the efficiency dynamic for global growers.
“Our biggest challenge today is responding to the overwhelming number of opportunities with which we are being confronted,” said Thrive Agritech CEO Brian Bennett. “As we close this investment round, we will be aggressively hiring sales, marketing and operations support and leveraging Rose Capital’s expertise, to exceed the expectations of our customers and further develop our product portfolio and core technologies. Additionally, we will be expanding operations into Europe to capture growth in the emerging greenhouse supplemental lighting market.”
Thrive Agritech was founded at the Y Combinator accelerator in Silicon Valley, with a mission to enhance sustainability for controlled environment agriculture. The company’s industry-leading energy efficient lighting products have already made significant reductions in the carbon footprint from older lighting technologies. Further, all Thrive Agritech products have an optimized horticulture light spectrum, high reliability, and most importantly improve efficiency and longevity of horticultural crop growth.
Current, Powered By GE And Jones Food Company Partner To Launch Europe’s Largest Indoor Farm
Current, Powered By GE And Jones Food Company Partner To Launch Europe’s Largest Indoor Farm
- Horticultural lighting solution enables environmental benefits including 90% less water, 50% less fertilizer, reduced energy and carbon footprint
- High-care operation creates opportunities to redefine the future of global food, pharma, and cosmetics with industrial-scale production
- Clean room automation enables “no touch” harvesting versus an average of 13 human contact stages
The impact of indoor farming with Current by GE Arize lighting solution (Graphic: Business Wire)
June 07, 2018
LONDON & AMSTERDAM--(BUSINESS WIRE)--Current, powered by GE (NYSE: GE) and Jones Food Company Ltd. (JFC), today announced that construction is underway toward building one of the world’s largest indoor farms. The intensive plant nursery, located in North Lincolnshire, England, will be the largest indoor farm in Europe, producing up to 420 tonnes of leafy greens per year across a growing area of 5120m2, arranged in racks rising to the height of 11m. To maximize the facility’s yield, Current by GE is installing more than 12Km of its new Arize* LED horticultural lighting solution, with a balanced light spectrum that catalyzes optimal growth in every plant and shortens the growth cycle for more intensive production.
We knew that lighting would be the lifeblood that could bring high-care intensive food production to an industrial level that demonstrates real commercial viability. - JFC CEO James Lloyd-Jones
The equipment is housed within a futuristic, intelligent cleanroom (or “high-care”) environment that allows crops to be grown in complete isolation from external contamination – ideal for food production as well as growing high-quality cosmetic and pharmaceutical ingredients. Production of the first crop from the Jones Food Company operation is due to start in autumn 2018.
“Nobody has been able to scale indoor, high-care intensive food production to an industrial level that demonstrates real commercial viability,” explained James Lloyd-Jones, CEO, and co-founder of JFC. “We knew that lighting would be the lifeblood of the facility and we’d need a partner who could see the potential and work with us to develop the right lighting set-up and spectrum to make our vision a reality.”
The world’s largest high-care indoor farm
With a growing area of 5120m2, the equivalent of 26 tennis courts, arranged across racks rising to a height of just over three storeys, the facility – owned and operated by JFC – will set new production and environmental standards for crop production of the future. With year-round local production JFC aims to slash food miles and produce leafy greens, herbs and other crops that can be delivered from harvest to plate in minimal time.
In addition, by designing the farm as a “high-care” facility, JFC will also be able to cater to the growing demands of cosmetics and pharmaceutical customers who require reliable supplies of the highest quality, natural ingredients. Every factor in the growth of the crops produced will be highly controlled; from the nutrient solution delivered to the roots of each and every plant, to the concentration of CO2 in the room, to the light wavelengths and duration of the growing “day” and subsequent rest period. Thanks to intelligent automation and advanced robotics, every plant can be grown in ideal, cleanroom conditions, untouched by human hand from planting to harvest. By comparison, conventional production cycles typically average 13 stages of human contact.
Lighting the future of horticulture with Arize
Malcolm Yare, Horticulture Business Development Manager for Current by GE commented, “We’ve spent years honing our technology in other industrial lighting sectors, and years more partnering with agricultural experts and researching the needs of horticultural applications. Our Arize LED solutions now lead the industry for efficiency and we continue to research new ways to improve performance through innovation. We look forward to working with Jones Food Company and our wider ecosystem of partners to find new ways to scale high-quality, global food production whilst reducing the energy and environmental costs of vertical farming.”
The Arize range of lighting solutions is low cost to install and maintain, with a market-leading 36K-hour lifetime (L90) and a five-year warranty to provide peace of mind and long-term reliability. An IP66, UL Wet rating also makes them ideal for high-care and cleanroom facilities as the luminaires can be easily washed and sanitized in-place.
Saving the environment whilst boosting the balance sheet
The JFC facility is designed to minimize the environmental impact of vertical farming, which will also offer a direct financial benefit to the company. For example, it will use up to 90 percent less water and 50 percent less fertilizer than conventional growing methods, saving on input costs. In addition, Current by GE’s Arize LED solutions are highly efficient, generating less heat than competitive products, reducing energy consumption and carbon footprint by 33 percent compared with vertical farming averages.
Notes to editors:
Jones Food Company production statistical visualization:
- The growing surface area is 5120m2 – close to 26 singles tennis courts
- 12.3Km of Arize lighting is the equivalent of laying nearly 38 Eiffel Towers end to end
- The growing racks reach a height of 11m, just over 3 storeys
- 420 tonnes of leafy greens are expected to be produced each year – roughly the same weight as 70 adult elephants
For more information regarding Current by GE’s Arize LED solutions for horticulture, visit www.currentbyge.com or visit us at our booth at GreenTech Amsterdam between 12th and 14th June 2018 (Hall 8, booth 105).
About Current, powered by GE
Current is the digital engine for intelligent environments. A first-of-its-kind startup within the walls of GE (NYSE: GE), Current blends advanced LED technology with networked sensors and software to make commercial buildings, retail stores and industrial facilities more energy efficient & digitally productive. Backed by the power of Predix*, GE’s platform for the Industrial Internet, and a broad ecosystem of technology partners, Current is helping businesses and cities unlock hidden value and realize the potential of their environments. www.currentbyge.com
About Jones Food Company
The nucleus of the Jones Food Company consists of three main protagonists: James Lloyd-Jones (CEO), Dr Paul Challinor (CTO) and Gary Thorneycroft (CFO). Together, they have consolidated initial ideas on improving the management of high-value crops in intensive growing conditions by constructing a world class plant production unit based in the UK.
The use of wide-ranging experience gained in the energy, horticultural research, and finance industries has been paramount in the solving of complex production issues, ahead of the first crop harvest. The combination of intensive hydroponics, energy-efficient LED lighting and sophisticated environmental control systems, coupled with the maintenance of a high-care production and harvesting process flow, takes growing to a new level in the UK fresh produce industry and is world-leading in its wider outlook.
*Trademark and/or Service Mark of General Electric Company
Contacts
Current, powered by GE
Karen O’Neil, +1 857-265-9113
karen.oneil@ge.com
or
Racepoint Global
Jenna Keighley, +44 208 811 2151
Jenna.keighley@racepointglobal.com
Signify Signs Deal With Agro-Inwest To More Than Double The Size of The world’s Largest LED Horticultural Lighting Project To 68.5 Hectares
Signify Signs Deal With Agro-Inwest To More Than Double The Size of The World's Largest LED Horticultural Lighting Project To 68.5 Hectares
Improvements in tomato production, quality and predictability lead Agro-Inwest to expand its LED installation from 25 to 68.5 hectares – an area equivalent to 100 soccer pitches
- First look inside the world’s largest LED horticulture lighting project in new video
Eindhoven, the Netherlands – Signify (Euronext: LIGHT), the world leader in lighting, today announced that Agro-Inwest, one of Russia’s most modern and rapidly growing companies cultivating fresh vegetables will expand its use of Philips LED lighting for growing tomatoes from its current 25 hectares to 68.5 hectares – an area of greenhouses equivalent to 100 soccer pitches. In 2017, Signify and Agro-Inwest introduced the largest LED horticulture lighting project in the world. The quick payoff and the clearly visible improvements in the crop yield, has led to the company expanding its investment in Philips GreenPower LED toplighting and Philips GreenPower LED interlighting system for its tomato production. The scale of the project illustrates Signify’s leadership in horticultural lighting.
“Demand in Russia for locally grown vegetables and fruits is increasing and Agro-Inwest has responded by scaling production using LED lighting,” said Udo van Slooten, Business Leader Horticulture at Signify. “Our partnership with them has been a big success and we are pleased to continue to help the company to expand its ability to improve crop quality and predictability while reducing its costs.”
Agro-Inwest has already achieved excellent results in the 25 hectares of tomato greenhouses that use Philips LED horticultural lighting. “The Philips LED lighting has reduced energy usage by almost 50% and improved growth predictability, crop appearance, and yield,” said Irina Meshkova, Deputy CEO and General Director, Agro- Inwest. “We are on track to recoup our costs on that project in two to four years, a very attractive return on investment. In addition, Signify has been very accurate in projecting our yields which gives us great confidence in future results. We know LED is the future and Signify has proved a reliable and knowledgeable partner.”
Signify N.V. became the new company name of Philips Lighting N.V., the ultimate parent company of the worldwide group of Philips Lighting companies. The legal name of Philips Eurasia LLC will be changed in the beginning of 2019
“The 2020’s Will Be The Decade of The Vertical Agriculture Revolution”- Ray Kurzweil, Director of Engineering at Google
“The 2020’s Will Be The Decade of The Vertical Agriculture Revolution”
- Ray Kurzweil, Director of Engineering at Google
MAY 30, 2018, BY SCOTT MASSEY
Indoor agriculture has gained an explosive amount of traction in past few years as it has been recognized as a viable solution to solve food and sustainability issues by offering the potential to grow and distribute produce near areas of demand.
For a planet with declining resources, indoor agriculture is a key component to improving food safety while reducing waste and growing more nutritious food in highly controlled environments that utilize electric lighting, thermal, and sensing controls. These include a 90% reduction in water usage, reduced transportation pollution and elimination of soil and additives. With the rising population and the decreasing costs of LED energy, there’s never been a better time to explore electrification of the indoor agriculture industry, which has the potential to fuel the future of sustainability.
However, there were still a number of technical hurdles that must be overcome for this technology to have a meaningful impact in yields of food production. The largest of which is astronomical energy costs due to indoor lighting preventing indoor agriculture from being a financially viable enterprise without dependence on government subsidies. In this industry glance, we met electrical and software engineering representatives to hear about their methods to reduce the operational cost and increase the profitability of CEA (controlled environment agriculture).
The Electric Power Research Institute (EPRI) conducts research and development relating to the generation, delivery, and use of electricity for the benefit of the public. An independent, nonprofit organization, EPRI brings together its scientists and engineers as well as experts from academia and industry to help address challenges in electricity, including reliability, efficiency, health, safety and the environment. EPRI's members represent more than 90 percent of the electricity generated and delivered in the United States, and international participation extends to 40 countries.
Q&A: Frank Sharp, Senior Technical Leader, Energy Utilization, EPRI.
What is the best form factor in this industry?
EPRI is researching CEA because of its potential to address issues related to population growth, food security, food safety, water access, water use, sustainability, grid load, local job creation, land usage, and smart city integration, all for community benefit. That said, we see three primary emerging forms and each has benefits:
1. The converted warehouse, vertical farm, custom building
This provides an opportunity to use underutilized or underperforming real estate in areas that often have limited economic potential. These facilities offer the ability to yield high quality produce in large volumes near population centers via their use of technologies to maintain ideal growing conditions.
2. Converted shipping containers or pods
This approach is highly mobile, is often modular, and utilize modern technologies to maintain growing conditions. These facilities offer the ability to reliability deliver fresh produce to targeted communities and applications and use minimal resources.
3. Augmented greenhouses where heat and lighting are added to keep the greenhouse operating year-round.
- This format has a lower operational cost per square foot since it’s lighting load is only utilized when sunlight is not available
These facilities have the ability to deliver crops in large scale and deliver fresh produce year-round to markets. We found a lot of unanswered questions about each of these types of controlled environment agriculture and they all warrant significantly more research as we move forward. We are working with utilities and CEA groups to better leverage current technology to forward each of these formats for the public benefit.
In addition to these three forms, there are other forms developing like aquaculture, indoor shrimp production, and insects for protein.
Note, established industries like traditional greenhouses and floriculture operations are also very common and will continue to expand and be utilized. These operations are typically not researched by EPRI since their operations and technologies are well established. EPRI does follow work in these areas and will engage to evaluate new process and technologies in these operations if they emerge.
With major e Coli and other pathogen outbreak concerns plaguing the food landscape, CEA is a viable solution if implemented correctly. What measures are you implementing now to reduce the likelihood of a pathogen outbreak, or warn a consumer that the food is not safe?
Controlled environment agriculture can reduce the likelihood of the spread of foodborne pathogens due to its ability to control the environment and limit exposure to outside factors. But there is still a risk and all agriculture facilities (indoor or out) should remain vigilant to maintain food safety and security in the future. Continued research into efficacies and future technologies will help reduce this risk further.
Energy is one of the most expensive components for an indoor growing operation. What is your number of grams that can be grown on the farm in a given month, then divide this by the number of KWH consumed per month? Please give more configuration details, pictures, and growth trial data from these trials.
While energy is one of the more significant costs of growing indoors, this industry has great potential to expand. This expansion will be driven by the need for fresh produce by expanding the population, but the CEA industry must focus on improving its operational efficiency where it can be a vital part of a further efficiently electrified economy.
Benefits derived from improved operational efficiency and higher yield can also help CEA facilities minimize labor costs, which are typically the highest costs. The combination of improved technologies, operational efficiency improvements, and maximized labor costs can help assure CEA facilities that their products are competitive.
CEA integration with an electrified economy will also make CEA a key part of future smart cities.
The smart city integration of CEA will be further enhanced by the use of grid-integrated renewable energy and other distributed energy. As these resources come online, access to affordable and clean energy resources will help shift the energy costs of CEA facilities. We will be exploring this aspect of CEA in great detail during our 2018 Electrification conference in Long Beach this summer.
With further electrification and demand on the grid, additional research is critical to learning how to support grid stability and reliability as more CEA operations come online.
We are working with utilities and CEA operations around the world to learn more about emerging technologies and identifying proper placement of these operations on the existing grid.
Philips Lighting Is Now Signify
May 16, 2018
Philips Lighting Is Now Signify
Eindhoven, the Netherlands - Signify (Euronext: LIGHT), the world leader in lighting, has today launched its new company name, following the amendment of the company's articles of association changing its name from Philips Lighting N.V. to Signify N.V.
"The choice of our new company name originates from the way light becomes an intelligent language, which connects and conveys meaning," said Eric Rondolat, CEO of Signify. "It is a clear expression of our strategic vision and purpose to unlock the extraordinary potential of light for brighter lives and a better world."
Signify will continue to use the Philips brand for its products, the most trusted lighting brand in the world, under the existing licensing agreement with Royal Philips. The company expects the name change to be implemented in all the countries where it is active by the beginning of 2019.
Founded as Philips in Eindhoven, the Netherlands, we've led the lighting industry with innovations that serve professional and consumer markets for more than 127 years. In 2016, we spun off from Philips, becoming a separate company, listed on Amsterdam's Euronext Stock Exchange. We were included in the benchmark AEX index in March 2018.
With operations in more than 70 countries and 32,000 people worldwide, Signify generated sales of EUR 7 billion and invested EUR 354 million in Research and Development in 2017.
"We are driven by the principle that light is essential," Eric Rondolat added. "And by connecting it to networks, software, sensors and IoT platforms, we open the door to a smarter world."
News from Signify is located at the Newsroom, Twitter and LinkedIn. Information for investors can be found on the Investor Relations page.
--- END ---
For further information, please contact:
Signify Investor Relations
Robin Jansen
Tel: +31 6 1594 4569
E-mail: robin.j.jansen@signify.com
Signify Corporate Communications
Elco van Groningen
Tel: +31 6 1086 5519
E-mail: elco.van.groningen@signify.com
About Signify
Signify (Euronext: LIGHT) is the world leader in lighting for professionals and consumers and lighting for the Internet of Things. Our Philips products, Interact connected lighting systems and data-enabled services, deliver business value and transform life in homes, buildings and public spaces. With 2017 sales of EUR 7.0 billion, approximately 32,000 employees and a presence in over 70 countries, we unlock the extraordinary potential of light for brighter lives and a better world. News from Signify is located at the Newsroom, Twitter and LinkedIn. Information for investors can be found on the Investor Relations page.
Grow Closer With Light Polymers’ GrowBlade® Horticultural Lighting
Grow Closer With Light Polymers’ GrowBlade® Horticultural Lighting
Light Polymers - GrowBlade Test-Site, 2018 (Photo: Business Wire)
May 24, 2018
SAN FRANCISCO--(BUSINESS WIRE)--Light Polymers, a nanochemistry innovator specializing in lyotropic liquid crystals, is launching a Beta-test program for its innovative GrowBlade® horticultural lighting. GrowBlade flat-panels use Light Polymers’ Crystallin® remote phosphor films to let indoor farmers grow closer, delivering even, consistent lighting in a range of rich crop-specific spectra. GrowBlades have a long service life, running cooler with less spectrum shift and lumen drop over time than conventional LED grow lights. Better quality full-spectrum light in a thin, wide-area form factor is a key to higher farm productivity.
“Light Polymers has been busy starting production of our breakthrough Crystallin film, and developing specialty lighting designs that are eye-safe and comfortable, with extraordinarily rich spectra”
Tweet this
“As innovators in a range of specialty lighting markets, Light Polymers knows the importance of engaging potential customers as part of our product development process,” said Sandor Schoichet, VP of Grow Products at Light Polymers Lighting. “To this end, Light Polymers is opening up its GrowBlade Beta-test program to select vertical farm and controlled environment growers, to gain real world production experience and better understand the specific needs of our customers.”
GrowBlade Edge 300 and 600 panels (approximately 300x300 mm or 1’x1’, and 300x600 mm or 1’x2’) will be available to select early adopters starting in June 2018. Longer GrowBlade Edge 1200 and 1500 models (approximately 1’x4’ and 1’x5’) will be available in late 2018. Both models have a slender form-factor (just 12.5 mm thick - not including the remote, dimmable LED driver) and will be among the earliest products certified to the new UL-8800 horticultural lighting standard. Initial Beta-test lights are available in two custom spectra, with more tailored crop-specific spectra to come based on customer input. Introductory pricing for GrowBlade Edge 300 and 600 models is set at $119 and $219 respectively.
“Light Polymers has been busy starting production of our breakthrough Crystallin film, and developing specialty lighting designs that are eye-safe and comfortable, with extraordinarily rich spectra,” said Marc McConnaughey, Chairman of the Board of Light Polymers Lighting. “We are excited to begin production of the GrowBlade and our other specialty lighting products based on our Crystallin film technology.”
GrowBlades achieve a unique level of horticultural lighting performance by leveraging the unique capabilities of our Crystallin remote phosphor film, which eliminates ‘point-based’ lighting issues common to other LED lights. Instead of assembling a variety of specialized LEDs into a bar or a box, GrowBlades use sheets of Crystallin film to down-convert the output of a simple blue LED array into a smooth, fully diffused spectrum with even edge-to-edge distribution. GrowBlade spectra can easily extend into the red and far-red range critical to flowering and fruiting, while blocking problematic blue and UV wavelengths below 420 nm. Formulating spectrum with Crystallin technology lets us move beyond simple narrow-band spectra to explore synergies across the multiple wavelengths that affect crop quality.
With cool, evenly distributed, high quality light, GrowBlades can be mounted closer to your plants for greater vertical density, higher yields, and improved crop consistency, for higher overall productivity.
Contact us now for updates and early release notification.
About Light Polymers
Light Polymers is a nanochemistry company with deep domain knowledge and expertise in lyotropic liquid crystals, which have many applications including OLED displays, LED lighting and building materials. Light Polymers recently debuted a family of human-centric eye-safe task and study lighting. Founded in 2013 in San Francisco, Light Polymers has over 50 patents issued and pending for its water-based lyotropic liquid crystal nanochemistry. For more information, visit http://www.lightpolymers.com/.
Contacts
Write2Market for Light Polymers
Casey Stokes 404-428-2135
casey.stokes@write2market.com
Osram Acquires US ‘Smart Grow’ Lighting Firm
Lighting giant Osram is acquiring Fluence Bioengineering, Inc. of Austin, Texas. The company specialises in LED-based horticultural systems, using Osram LED chips, for a wide variety of applications including vertical farming, especially in urban area
Osram Acquires US ‘Smart Grow’ Lighting Firm
MAY 21, 2018 BY ANNA
Lighting giant Osram is acquiring Fluence Bioengineering, Inc. of Austin, Texas. The company specializes in LED-based horticultural systems, using Osram LED chips, for a wide variety of applications including vertical farming, especially in urban areas.
Potential crops range from salad greens and herbs to medicinal plants. Fluence was founded in 2013, has approximately 95 employees and its 2017 sales were in the mid-double-digit millions of dollars (USD).
LED-based solutions from Fluence can increase harvests up to 25 percent, reducing energy costs by as much as 50 percent and, through the targeted use of light, improving the quality and nutritional content of plants.
Increasing population and continued urbanisation are intensifying the demand for fresh food, especially in densely populated cities around the world.
In addition to growing healthy and tasty food, vertical farms reduce the need for long-distance transportation routes. They also lessen the need for pesticides, fertilisers and excessive water use, and ultimately reduce spoilage.
“Fluence is opening the floodgates to a huge future market,” said Stefan Kampmann, CTO of OSRAM Licht AG. “Its extensive knowledge of the horticulture market and possible applications, combined with Osram’s expertise in lighting technologies, sensors and connectivity, will position us as a leading horticultural solutions provider.”
Osram has increased its involvement in the horticulture sector over the last several years. The company has developed research and specialty luminaires that enable tailor-made light recipes to be controlled for specific plant types.
In 2017, Osram invested in the Munich-based startup Agrilution which develops grow boxes with LED lighting for home use.
Fluence Bioengineering, upon closing, will be positioned within Osram’s Professional and Industrial Applications segment in the Specialty Lighting business unit.