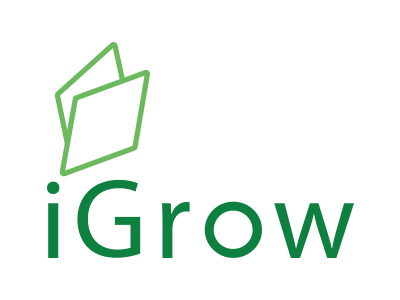
Welcome to iGrow News, Your Source for the World of Indoor Vertical Farming
Could Vertical Farming Meet The Food Needs of Tomorrow's Cities?
The majority of today’s global population lives in cities and by 2050, our population will have reached 9 billion people with 70% - 80% living in cities and urban areas
Five Takeaways
The majority of today’s global population lives in cities and by 2050, our population will have reached 9 billion people with 70% - 80% living in cities and urban areas.
Apart from large scale food security concerns, the world is also facing the loss of arable land and decreased access to fresh water fueled by global warming.
Vertical farming creates the future blueprint for securing the world’s food supply. It refers to growing crops in multiple vertical layers indoors, in controlled-environments, repurposed warehouses, growth chambers and even shipping containers.
Here are Heliospectra's five takeaways:
LED Grow Lights Make Vertical Farming Viable
LED grow lights have been the catalyst for growers looking to grow vertically. With recent developments in technology, growers can now maximize crop yields and standardize production 365 days a year.
The ability to alter light spectra and the quality of light that the crops are exposed to has huge implications on every aspect of production. Growers gain more control than ever by knowing that correct light can influence each variable—from how crops develop, when they bloom, how they taste, and even their chemical compositions.
Vertical Farms Use Less Water for Food Cultivation
Agriculture currently accounts for roughly 70% of our water usage and is also responsible for the vast majority of water runoff and contamination issues that are present today.
In contrast, vertical farming utilizes 70% - 95% less water compared to traditional farming. Some of the largest and most successful vertical farms also incorporate closed-loop water circulation systems to recirculate water to their crops, leading to an even greater reduction in water usage.
Vertical Farming is Less Labour Intensive
Vertical farming enables smart farming with precision technologies and controls to greatly reducing the crop input costs and intense labour of field farming.
The increasing development of Al, automation and robotics will also continue to increase revenue for growers and support even greater resource savings and operational efficiencies.
Vertical Farming Has the Ability to Conserve Land
Simply put, vertical farming produces more food per square meter, using up to 90% less land. This can help promote biodiversity as farmers drastically reduce their environmental footprint by growing more food on less land, encouraging an increase in livestock populations and natural enrichment of arable farmlands.
Arable land is also a valuable resource and as soil health decreases with use, so does the nutritional value of our food. The more we continue to farm through traditional methods, the more we reduce the bare mineral components and quality of soils. Vertical farming changes this by instead using aquaponic, hydroponic and aeroponic growing mediums instead of soil. By using these controlled media, vertical farming has also helped farmers move away from using pesticides in their production.
Vertical Farms Bring Local Food to Consumers and Neighbourhoods
Reducing emissions from transport is one of the most important measures to combat global warming from cars, trucks, aircraft and boats creating almost 20% of manmade carbon dioxide worldwide. Vertical farming addresses these issues by creating a sustainable model for locally grown produce. By growing local, food has to travel less distance and requires less artificial protection (i.e. refrigeration), resulting in produce that is not only fresher, but has a smaller environmental impact across the entire production chain.
All Pictures are Heliospectra’s SIERA Light Bar in different Vertical Farming environments.
For more information:
Heliospectra
info@heliospectra.com
www.heliospectra.com
Publication date: 8/19/2019
Signify Helps AppHarvest To Increase Yields In 25-Hectare Greenhouse
Eindhoven has partnered with AppHarvest to help the company increase efficiency and boost yields using significantly fewer resources in their 25 hectare greenhouse in Morehead, Ky., USA
AppHarvest Improves
Efficiency Through Combining LED And Conventional Lighting
Eindhoven has partnered with AppHarvest to help the company increase efficiency and boost yields using significantly fewer resources in their 25 hectare greenhouse in Morehead, Ky., USA. The greenhouse will be fitted with a hybrid LED lighting system, utilizing Signify’s Philips GreenPower LED toplighting compact and Agrolux high pressure sodium lighting. AppHarvest will grow tomatoes and cucumbers in its facility, which will be completed in the second half of 2020.
“This LED installation reinforces how we use proven technology to grow more fresh food with fewer resources,” said Jonathan Webb, Founder and CEO of AppHarvest. “With this cutting-edge hybrid system, we will dramatically reduce energy usage in the greenhouse. Working with Signify has given us the benefit of leveraging on a decade of growing knowledge and expertise.”
The facility uses a unique LED and High-pressure sodium (HPS) hybrid lighting system, to significantly reduce energy while increasing yield over the year. The LED lighting system is 40 percent more energy efficient than traditional greenhouse lighting, while it disseminates less radiant heat. During fall and spring, LED lighting will be used to grow more produce. HPS lamps will be used during colder months, in addition to the LED system. The heat from the HPS system will help warm the greenhouse and reduce natural gas usage.
AppHarvest is partnering with Equilibrium, a leading greenhouse investment firm. The LEDs will be installed by Dalsem Complete Greenhouse Projects, which is overseeing construction of the greenhouse.
“We’re very excited about our collaboration with AppHarvest and Equilibrium,” said Bill Bien, CEO of Signify Agriculture Lighting. “It’s great to work with partners just as committed to sustainable horticulture as we are, and we’re looking forward to helping them increase growth predictability, crop quality and yields, while improving their energy efficiency.”
The LED toplighting compact delivers high light output of 1,800 µmol/s and an efficacy of up to 3.0 µmol/J and helps growers effectively optimize crop growth, enhance crop quality and cut operational costs. Compared to a 1,000 W HPS fixture, the Philips GreenPower LED toplighting compact produces the same amount of light, has a similar light distribution, while consuming 40% less power and emitting considerably less radiant heat. By separating heat and light, this product gives growers independent control over their greenhouse climate.
Evesham Vale Growers and R & L Holt Increase Marketable Yield By 25% Using Signify’s Hybrid Lighting System
Signify (Euronext: LIGHT), the world leader in lighting, today announced that Evesham Vale Growers and R & L Holt, premium tomato growers in the UK, have once again chosen Philips LED and HPS lighting for a new greenhouse, based on the 25% increase in crop production that was achieved with its Philips hybrid lighting set-up which was installed by Philips Horti LED partner Certhon in 2015
Hybrid lighting enables year-round production of consistent, high quality tomatoes for supermarkets
Hybrid LED plus HPS toplighting make it possible to precisely control growth throughout the year
R & L Holt and Signify extend their partnership to maximize crop results in new greenhouse
Eindhoven, the Netherlands – Signify (Euronext: LIGHT), the world leader in lighting, today announced that Evesham Vale Growers and R & L Holt, premium tomato growers in the UK, have once again chosen Philips LED and HPS lighting for a new greenhouse, based on the 25% increase in crop production that was achieved with its Philips hybrid lighting set-up which was installed by Philips Horti LED partner Certhon in 2015.
In the new greenhouse, the company will install Philips GreenPower LED toplighting compact and Philips GreenPower LED interlighting, together with HPS lighting installed by the Philips Horti LED partner Certhon. The compact, passively cooled LED toplighting can be easily installed with the HPS lighting on the same trellis. This combination allows the company to use LEDs to extend lighting in the spring when it’s warmer, instead of the HPS lighting which produces more heat.
“I’m delighted to see that our customers are returning to us for new projects”, said Udo van Slooten, Business Leader Horticulture at Signify. “Our long-term partnerships enable us to learn from the improvements they have achieved and help them further improve the consistency and predictability of their crops. This move also confirms that our customers recognize the value that the LED toplighting compact offers in terms of combining LED with HPS lighting on the same trellis construction.”
Evesham Vale Growers and R & L Holt grow cherry, cocktail and large tomatoes on the vine, as well as loose classic tomatoes. All crops are grown for flavor, as supermarket premium ranges. Since all of the crops are grown in heated glasshouses, the season can stretch from February until November, but the company is always looking to further extend its season.
“After our success with our first hybrid HPS and LED interlighting system, we knew we were on the right path,” says Roly Holt, co-owner of R & L Holt. “We did a trial in another greenhouse with LED toplighting, LED interlighting and HPS lighting, and that system allowed us to specifically target different parts of the canopy to control our products. That is why we’ve now chosen this three-component set-up. We think this will give us a really sustainable and consistent product.”
Introduced in June 2019, the Philips GreenPower LED toplighting compact delivers excellent performance. Its high light output of 1,800 µmol/s and efficacy of up to 3.0 µmol/J help growers effectively optimize crop growth, enhance crop quality and cut operational costs. Compared to a 1,000 W HPS fixture, the Philips GreenPower LED toplighting compact produces the same amount of light, has a similar light distribution, while consuming 40% less power and emitting considerably less radiant heat.
Illumitex, The Digital Horticulture Company, Announces Dennis Riling As New Head of Sales
“Dennis’s depth in horticultural knowledge combined with over a decade’s worth of business and leadership experience makes him the ideal individual to lead our commercial efforts.” said Jeff Bisberg, Illumitex CEO. “
Dennis Riling rises to top commercial role as LED and Digital Horticulture hit the tipping point in the horticulture adoption curve.
AUSTIN, TX August 1, 2019 – Illumitex, a leader in Digital Horticulture and LED lighting announced today that Dennis Riling has been promoted to Head of Sales and VP of Business Development.
“Dennis’s depth in horticultural knowledge combined with over a decade’s worth of business and leadership experience makes him the ideal individual to lead our commercial efforts.” said Jeff Bisberg, Illumitex CEO. “LED is at the tipping point for adoption and Dennis’ team is aligned to support this accelerating growth. It’s Exciting.”
“Helping farmers more profitably grow crops at scale is our continued focus.” said Dennis. “We are innovating to deliver value way beyond LED lighting with our services and integrated FarmVisionAI platform. FarmVisionAI uses cameras integrated into our lighting, powered by horticulturist guided AI to detect anomalies near real time, at scale. I am proud to step into this leadership role and to do nothing less than help transform agriculture with new powerful digital solutions.”
About Illumitex, Inc:
Founded in 2005 in Austin, Texas, Illumitex is the Digital Horticulture company. Illumitex leverages the granular position of LED lighting in the CEA farm to deploy digital cameras to collect and analyze imagery of every plant, in every corner, at every moment. We go beyond lighting to deliver greater value to help digitally transform indoor farming. Illumitex LED lighting systems are based on decades of technology and help the farmer by reducing energy costs, maintenance costs, and increase plant yield, taste, color, and smell. We believe the combination of digital and lighting will open up a new age of highly productive and profitable farming. Learn more at www.illumitex.com
###
Scientists Play With Light And Water To Speed Up Crop Breeding
A number of challenges face crop production around the world, including drought, diseases, pests and limited land. Scientists are tasked with breeding varieties that will produce higher yields but use less land and fewer resources
BY DTN Grains - Loren Lindler | July 27, 2019
OMAHA (DTN) — This twice-monthly column condenses the latest news in the field of crop technology, research and products. Researchers say that by 2050, there could be 10 billion people in the world. A number of challenges face crop production around the world, including drought, diseases, pests and limited land. Scientists are tasked with breeding varieties that will produce higher yields but use less land and fewer resources. To aid in this, some international researchers are experimenting with two new techniques to speed up the breeding process: LED technology and hydroponics.
PLEASE, SIR, CAN I HAVE SOME MORE LIGHT?
Lee Hickey, a plant geneticist at the University of Queensland in Australia, is combining breeding and light-emitting diode (LED) technology to produce a form of “speed breeding.”
Plant breeding can often take years. With speed breeding, researchers are able to use LED lights that are ideal for photosynthesis, which allows researchers to grow crops three times faster, creating more generations in a single year.
Botanists started growing plants under artificial light over 150 years ago. As the years passed, LED technology has vastly advanced, allowing scientists to be more precise by customizing light settings to individual crop species. The Australian researchers exposed their crops to 22 hours of continuous blue and red LED lights, under ideal temperatures, which essentially convinced the plants to flower early. A generation of crops can take months, or even a year, to breed with traditional methods. However, with the use of LED lights and speed breeding, scientists were able to grow six generations of wheat, barley, chickpeas and canola in a year.
A WATERY WONDER
To obtain the fastest breeding results in their greenhouses, scientists at the John Innes Centre in the U.K. are using hydroponics, the practice of growing crops without soil, usually with the use of a water-nutrient solution. Hydroponic techniques allow nutrients and oxygen to reach plant roots quicker.
Many researchers have found that hydroponic plants grow 30% to 50% faster than a plant grown in soil. The ample amount of oxygen in a hydroponics system allows the roots to absorb nutrients much faster, stimulating root growth. The U.K. researchers are taking advantage of this faster-growing time to speed up their evaluation of the genomes of wild relatives of modern crops, which can hold valuable disease-resistance genes.
You can learn more about the LED technology and plant breeding with hydroponics: https://www.nowscience.co.uk/…
NASA-Inspired Speed Breeding For Crop Improvement To Feed The Future
NASA experiments to grow wheat in space using continuous light on wheat which triggered early reproduction in the plants were the inspiration for University of Queensland scientists to develop the world’s first ‘speed breeding’ procedures here on planet Earth
June 20, 2019 . | . Ken Ecott
Crop improvements can help us to meet the challenge of feeding a population of 10 billion, but can we breed better varieties fast enough?
Farmers and plant breeders are in a race against time. The world population is growing rapidly, requiring ever more food, but the amount of cultivable land is limited. Warmer temperatures have extended growth seasons in some areas — and brought drought and pests to others.
While a host of fascinating innovations are primed to change the face of agriculture, there remains a stubborn limiting factor for plant breeding. This is the long generation times of crops that allow only one or two generations per year.
This roadblock to progress has been alleviated by speed breeding protocols developed by research teams at the John Innes Centre and the University of Queensland.
Fast-growing plants in the crop-speed breeding facility at The University of Queensland. The plants featured are barley plants. Credit: The University of Queensland
“We face a grand challenge in terms of feeding the world,” said Lee Hickey, a plant geneticist at the University of Queensland in Australia. “If you look at the stats, we’re going to have about 10 billion on the planet by 2050 and we’re going to need 60 to 80 percent more food to feed everybody. It’s an even greater challenge in the face of climate change and diseases that affect our crops that are also rapidly evolving.”
NASA experiments to grow wheat in space using continuous light on wheat which triggered early reproduction in the plants were the inspiration for University of Queensland scientists to develop the world’s first ‘speed breeding’ procedures here on planet Earth.
The team tricked the crops into flowering early by blasting blue and red LED lights for 22 hours a day and keeping temperatures between 62 and 72 degrees Fahrenheit. Last November, in a paper in Nature, they showed that they can grow up to six generations of wheat, barley, chickpeas and canola in a year, whereas traditional methods would only yield one or two.
Dr Lee Hickey in his speed breeding lab at University of Queensland, 20 June 2016.
Botanists first started growing plants under artificial light — carbon arc lamps — 150 years ago. Since then, advances in LED technology have vastly improved the precision with which scientists can adjust and customise light settings to individual crop species.
So far, the researchers have mainly experimented with one parameter, light, but they have plans to investigate several other method of increasing, growth and generation times.
The team highlight that speed breeding combines well with a range of other developing technologies. These include speed gene cloning a technique developed by Dr Wulff’s team at the John Innes Centre to rapidly scour the genomes of wild relatives of modern crops to identify disease resistance genes which can be bred into elite crops.
This involves using hydroponic culture which gives plant roots quicker access to nutrients and oxygen. A carbon dioxide-enriched atmosphere is also under investigation and one of the most productive areas of research is likely to be temperature.
“One technology alone is not going to solve our problems,” Dr. Hickey said. “We’re going to need all the tools in the shed.”
Dr Hickey believes the sky is the limit for the new technology and he is now investigating the integration of speed breeding with other modern crop breeding technologies.
“It could also have some great applications in future vertical farming systems, and some horticultural crops,” Dr Hickey said.
A review published in the journal Nature Biotechnology outlines continuing efforts to harness speed breeding to a raft of crop technology innovations required to meet the 2050 challenge.
Signify Supports Bryte For Its New Greenhouse Equipment With Hybrid Philips LED Lighting System
Signify (Euronext: LIGHT), the world leader in lighting, announces today that it will start an extensive horti project in cooperation with Stolze at Bryte, one of the largest tomato growers in the Netherlands
Signify Supports Bryte, One of The Largest Dutch Tomato
Growers, For Its New Greenhouse Equipment (83,000 m²)
With A Hybrid Philips LED Lighting System
Eindhoven, the Netherlands - Signify (Euronext: LIGHT), the world leader in lighting, announces today that it will start an extensive horti project in cooperation with Stolze at Bryte, one of the largest tomato growers in the Netherlands. For the location in 's-Gravenzande, an 8.3 hectare greenhouse will be equipped with a combination of Philips GreenPower LED top lighting compact and HPS lighting. This solution allows greenhouses to benefit from the advantages of LED top lighting: higher predictability, better quality and an improved yield, as well as lower energy costs.
Bryte was founded in early 2019 as a combination of two renowned growers in the Westland and Voorne Putten areas: Kwekerij Dukker and Zwinkels Tomaten. Two different family businesses, but with a shared DNA. Identical in size, comparable in the way of working and thinking about cooperation in horticulture. For years, these companies have been growing tomatoes that are only known for one thing: their taste.
The introduction of the Philips GreenPower LED top lighting compact as a one-to-one replacement for the existing HPS lighting was the time for Bryte to think about a partial implementation of LED as a hybrid lighting solution for one of the company's seven locations. Compared to a 1,000 W HPS lamp, the Philips GreenPower LED top lighting compact produces the same amount of light using 40% less electricity. The lamp also produces very little radiant heat. Compared to a 600 W HPS lamp, the new energy-efficient LED top lighting compact produces 80% more light with the same amount of electricity.
A total of 180 μmol/m²/s will be realized over a total area of over 8.3 ha of glass, of which 90 μmol/m²/s will come from the HPS lighting and 90 μmol/m²/s from the LED top lighting. The heat and light in the greenhouses can be controlled independently, allowing for a very specific response to the natural lighting conditions. This creates the right balance between the amount of growing light and heat in the greenhouse, resulting in an increased yield and lower energy costs.
"It's good to see one of the largest Dutch greenhouse vegetable growers expressing confidence in LED," says Udo van Slooten, Business Leader Horticulture at Signify. "Bryte recognizes that the Philips GreenPower LED top lighting compact is not only an ideal replacement, but also the ideal addition to the existing HPS lighting in tomato cultivation."
Bryte's starting point is a more efficient growth too: "Our locations must meet the requirements of today and tomorrow in terms of efficiency, food safety, and sustainability. Together, we produce tomatoes on an area of 40 hectares. In summer and in winter, because a large part of the production area is lighted. Our customers are thus assured of a continuous supply, even when outdoor conditions produce poor lighting. We expect that the new hybrid LED installation will enable us to grow more efficiently, while reducing our energy and maintenance costs. A better balance in the greenhouse will result in higher profits," says Tom Zwinkels, Bryte's owner and director.
The whole project will be implemented in close cooperation with Philips horti LED partner Stolze.
Not All LEDs Are Equal: How Greener Roots Farm Is Growing Faster With Horticulture Lighting From Current
From a small window sill to an empty storage closet, to a rooftop utility room and, finally, to a spacious warehouse and greenhouse, Founder and President Jeffrey Orkin has been growing Greener Roots Farm one harvest at a time since 2012
Meet the light bars behind “the best damn lettuce you’ve ever tried.”
From a small window sill to an empty storage closet, to a rooftop utility room and, finally, to a spacious warehouse and greenhouse, Founder and President Jeffrey Orkin has been growing Greener Roots Farm one harvest at a time since 2012. As the first commercial-scale hydroponic vertical farm in Nashville, Tennessee, Greener Roots supplies herbs and leafy greens to local establishments year-round, including fresh lettuce and flavorful pea shoots, sunflower sprouts, sorrel and more that are picked and delivered within two days, never traveling more than 50 miles.
For Orkin, consistency is the key to Greener Roots’ steady success, measured in predictable crop yields and high-quality, nutrient-dense produce with no seasonal fluctuations. It’s what keeps local grocery stores and restaurant owners racing back to fill new orders, and it’s why Orkin relies heavily on LED lighting to help his business thrive. However, when a big investment in a new system started to go bad, Current, powered by GE, stepped in with a brighter solution.
Rising Above the Rest
Greener Roots cultivates over 14 tons of produce a year, with most of the greens being raised in racked hydroponic beds stacked high to the ceiling. Between its warehouse and greenhouse, the indoor operation totals nearly 7,000 square feet of grow space, requiring more than 300 LED light bars to provide optimal illumination for plant health. According to Orkin, it’s all part of producing “the best damn lettuce you’ve ever tried.”
“Some chefs are adamant about soil, but we’re showing them you can grow very flavorful things without soil, and having extremely high and uniform light levels is critical to that,” he says.
Greener Roots was growing fast, and new and better lighting technology was hitting the market. With help from Hort Americas, a leading commercial greenhouse and hydroponics supplier, he started to test an array of new LED options including horticulture lighting from Current. Immediately, Orkin gravitated to Current’s Arize™ LED growing system for its ease of installation, long life and proven results in improving production yields.
“The new lights from Current are very reliable and are producing faster growth, and now we can get red leaf varieties to turn red, where we couldn’t do that before,” Orkin said.
“The new lights from Current are very reliable and are producing faster growth, and now we can get red leaf varieties to turn red, where we couldn’t do that before.”
– Jeffrey Orkin, Founder and President, Greener Roots Farm)
“The Arize system also puts off less heat, so we can add more layers to our vertical beds if we choose. And what’s convenient is how you can daisy-chain the product end-to-end to make installation much simpler, which we really liked, having done all the work ourselves.”
Growing the Future
By isolating and combining different light wavelengths to replicate and accelerate natural photosynthesis, Arize LEDs can shorten growth cycles and enable different growth patterns, allowing urban farmers to tailor the light to the specific needs of every crop. Including LED tubes, light bars, suspended fixtures and lamps, the full Arize product family features everything needed for indoor vertical and greenhouse farming.
“Overall, we’re getting more biomass from every harvest,” says Orkin. “It’s all about ensuring the correct light intensity throughout the day, and how many photons we’re ‘feeding’ to the plants essentially. Current’s LEDs help us create the ideal condition for each crop.”
“Overall, we’re getting more biomass from every harvest.”
Orkin notes that Greener Roots is now pulling over 2,500 heads of lettuce a week from its greenhouse as more local customers discover the soil-free urban farm flourishing in their city. In fact, the new greenhouse―located on the outskirts of Nashville in nearby Franklin, Tennessee―is part of a large agritourism destination dubbed Southall Farms. This farm-to-table rural retreat will feature an inn, guest cottages, an event center and an agricultural barn, adding up to over 160,000 square feet of relaxed destination space where people will be able to savor experiences that celebrate culture, community and craft.
“There’s been an undercurrent for urban farming for some time, whether that’s someone raising a garden at home or a small farm making more fresh food options available to people,” Orkin says.
Rooted in Results
Orkin still drives the delivery truck that drops off freshly picked foods to his customers each day because to this entrepreneur, relationships are the seeds of success. It’s an approach that has taken the landscape-architect-turned-urban-farmer from a single planter in a kitchen window to a sprawling production system that ensures sustainable produce is always in stock.
“Having Current and Hort Americas there to support us, to answer our questions and try new things, it’s been huge,” says Orkin. “We’re trying to have the biggest impact on the local food scene we can, and that takes partners who understand the importance of durable and reliable technologies, such as LED.”
Learn more about how Current, with its deep expertise in LED technology, is helping indoor farmers reach new heights.
Are you ready to talk about
the right growth spectrum for your business?
START THE CONVERSATION
Luminaires Manufacturer Industria Lighting Is Back
Richard Schmidt and Ferry Breeuwer started developing a new light fixture in May of 2018. Now, one year later, that fixture is already being installed in several Canadian, Australian and Dutch greenhouses
“Even In The Horticultural Industry, The One-Stop Shop Is A Trend”
Richard Schmidt and Ferry Breeuwer started developing a new light fixture in May of 2018. Now, one year later, that fixture is already being installed in several Canadian, Australian and Dutch greenhouses. Notable about the new strategy used by Industria is the exclusive collaboration with the installers PB Tech and Stolze. Ferry: “As OEM-suppliers (Original equipment manufacturer), we can focus on production and product development.”
Ferry Breeuwer
Although Richard and Ferry had the plan in mind already, it was the demand from the market that led them to take this step. “The commitment from both sides convinced us to go for it. Our services are fully tailored to our distributors.”
Installers become the contact person
Ferry thinks that the work method is characteristic of the current market. “A change is going on with horticultural installation companies. They are becoming ‘system integrators’ more and more. Their role is changing. Where they used to mainly offer installation parts for horticultural technology, they now offer a complete package. They bring a variety of subsystems to one system to ensure all of the subsystems functioning together as one system. For the growers, this means there is only one contact person for all of the parts, which is very practical. Even in the horticultural industry, the one-stop shop is a trend.”
Patijnenburg
The light fixture is developed in cooperation with the Odacon firm, with the same engineers as the ‘old’ Industria. “We were done in December. The CSA and CE certification was handled quickly, and the production started.”
This happens in the Patijnenburg production warehouse. A conscious decision, says Ferry. “At first, we wanted to start our own production line, but due to the knowledge already available here, the short lines in the Westland and, last but not least, the fact that it fits nicely within our CSR -plan, we decided to have our production line at Patijnenburg.”
Production
Lean is a business strategy, and most of all, a way of working in which everyone and everything in the company aims at creating value for the customer in all of our processes, Ferry explains. “To do this, wastage is being limited, and the customer becomes the central focus point. In doing so, the quality improves, lead times are shortened and costs are reduced.”
For Industria, this strategy leads to:
Traceability. It is one of the keywords in the production space. Both the lamps and the drivers, as well as the reflectors, are equipped with a QR-code.
Electronics are very sensitive to electrostatic discharge. The discharge causes invisible damage and Industria does everything in its power to prevent this. An antistatic ESD-floor has been placed in the production space, and everything is grounded. Of course, every light fixture gets tested. This is not done by using a real lamp, but with a dummy. Ferry: “This is safer and faster than the conventional testing method. Also testing with a real lamp isn’t good for the lamp itself.”
Poka Yoke is Japanese for Mistake Proofing. Poka Yoke is about countermeasures that prevent mistakes from being made and because of that is used a lot in companies that work Lean. “The fun thing about Poka Yoke is that the solution is often simple. For Industria this means minimalizing the risk of assembly errors. The different colored wires, as shown in the picture above, are a good example of this.”
The lamp heater in the reflector lengthens the life span of the lamp and the reflector. The critical components of the lamps are heated by it, which is especially important during the start-up phase. The heater could be removed after around 7,000 hours of being used.
"Huge market for HPS"
The HPS luminaires are a proven product. The technology of HPS has been developed to now create a problem-free light fixture. Ferry: “Although the set-up is different, at its core it’s the same. After all, this light fixture has proven itself. What works, works. You shouldn’t want to change that too much,” Ferry says. “For HPS fixtures, there is still a large market. LED is coming up, but is still not quite there yet. Although the stretch is gone, as far as innovation is concerned, HPS still has a couple of years to go.”
For more information:
Industria Lighting
Ferry Breeuwer
Zuid-Hollandlaan 7
2596 AL Den Haag
0611 264 557
ferry.breeuwer@industria-lighting.com
www.industria-lighting.com
Publication date: 7/18/2019
© HortiDaily.com
LED Success Story
Owner, Rick OUdling, talks about his Success with Phillips LED toplighting
Kalamazoo Specialty Plants Roots Cuttings More Quickly And More
Uniformly With Philips LEDs
After trialing different brands of horticulture LEDs, Kalamazoo Specialty Plants (KSP) installed a small Philips toplighting trial in 2016 and then proceeded with a significant expansion in 2018. Owner, Rick Ouding, talks about his success with Philips LED toplighting.
Micro-Naps For Plants: Flicking The Lights On And Off Can Save Energy Without Hurting Indoor Agriculture Harvests
Growing crops under artificial light is gaining momentum , particularly in regions where produce prices can be high during seasons when sunlight is sparse
7/22/2019
Author: Kevin M. Folta
(MENAFN - The Conversation) A nighttime arrival at Amsterdam's Schiphol Airport flies you over the bright pink glow of vegetable production greenhouses. Growing crops under artificial light is gaining momentum , particularly in regions where produce prices can be high during seasons when sunlight is sparse.
The Netherlands is just one country that has rapidly adopted controlled-environment agriculture , where high-value specialty crops like herbs, fancy lettuces and tomatoes are produced in year-round illuminated greenhouses.Advocates suggest these completely enclosed buildings – or plant factories– could be a way to repurpose urban space, decrease food miles and provide local produce to city dwellers.
One of the central problems of this process is the high monetary cost of providing artificial light , usually via a combination of red and blue light-emitting diodes.Energy costs sometimes exceed 25% of the operational outlay. How can growers, particularly in the developing world,compete when the sun is free ? Higher energy use also translates to more carbon emissions, rather than the decreased carbon footprint sustainably farmed plants can provide.
I'vestudied how light affects plant growth and development for over 30 years. I recently found myself wondering: Rather than growing plants under a repeating cycle of one day of light and one night of darkness, what if the same daylight was split into pulses lasting only hours, minutes or seconds?
Indoor plants need plenty of artificial light. josefkubes/Shutterstock.com
Short bursts of light and dark
So my colleagues and I designed an experiment . We'd apply the normal amount of light in total, just break it up over different chunks of time.
Of course plants depend on light for photosynthesis, the process that in nature uses the sun's energy to merge carbon dioxide and water into sugars that fuel plant metabolism. Light also directs growth and development through its signals about day and night, and monkeying with that information stream might have disastrous results.
That's because breaking something good into smaller bits sometimes creates new problems. Imagine how happy you'd be to receive a US$100 bill – but not as thrilled with the equivalent 10,000 pennies. We suspected a plant's internal clock wouldn't accept the same luminous currency when broken into smaller denominations.
And that's exactly what we demonstrated in our experiments . Kale, turnip or beet seedlings exposed to cycles of 12 hours of light, 12 hours dark for four days grew normally, accumulating pigments and growing larger. When we decreased the frequency of light-dark cycles to 6 hours, 3 hours, 1 hour or 30 minutes, the plants revolted. We delivered the same amount of light, just applied in different-sized chunks, and the seedlings did not appreciate the treatment.
The same amount of light applied in shorter intervals over the day caused plants to grow more like they were in darkness. We suspect the light pulses conflicted with aplant's internal clock , and the seedlings had no idea what time of day it was. Stems stretched taller in an attempt to find more light, and processes like pigment production were put on hold.
But when we applied light in much, much shorter bursts, something remarkable happened. Plants grown under five-second on/off cycles appeared to be almost identical to those grown under the normal light/dark period. It's almost like the internal clock can't get started properly when sunrise comes every five seconds, so the plants don't seem to mind a day that is a few seconds long.
Just as we prepared to publish, undergraduate collaborator Paul Kusuma found that our discovery was not so novel. We soon realized we'd actually rediscovered something already known for 88 years. Scientists at the U.S. Department of Agriculture saw this same phenomenon in 1931 when they grew plants under light pulses of various durations. Their work in mature plants matches what we observed in seedlings with remarkable similarity.
A 1931 study by Garner and Allard tracked the growth of Yellow Cosmos flowers under light pulses of various durations.
J. Agri. Res. 42: National Agricultural Library, Agricultural Research Service, U.S. Department of Agriculture.,CC BY
Not only was all of this a retread of an old idea, but pulses of light do not save any energy. Five seconds on and off uses the same amount of energy as the lights being on for 12 hours; the lights are still on for half the day.
But what would happen if we extended the dark period? Five seconds on. Six seconds off. Or 10 seconds off. Or 20 seconds off. Maybe 80 seconds off? They didn't try that in 1931.
Building in extra downtime
It turns out that the plants don't mind a little downtime. After applying light for five seconds to activate photosynthesis and biological processes like pigment accumulation, we turned the light off for 10, or sometimes 20 seconds. Under these extended dark periods, the seedlings grew just as well as they had when the light and dark periods were equal. If this could be done on the scale of an indoor farm, it might translate to a significant energy savings, at least 30% and maybe more.
Recent yet-to-be published work in our lab has shown that the same concept works in leaf lettuces; they also don't mind an extended dark time between pulses. In some cases, the lettuces are green instead of purple and have larger leaves. That means a grower can produce a diversity of products, and with higher marketable product weight, by turning the lights off.
One variety of lettuce grew purple when given a 10-second dark period. They look similar to those grown with a five-second dark period, yet use 33% less energy. Extending the dark period to 20 seconds yielded green plants with more biomass.
J. Feng, K. Folta
Learning that plants can be grown under bursts of light rather than continuous illumination provides a way to potentially trim the expensive energy budget of indoor agriculture. More fresh vegetables could be grown with less energy, making the process more sustainable. My colleagues and I think this innovation could ultimately help drive new business and feed more people – and do so with less environmental impact.
GLASE - Free Webinar Series - July 25, 2019 - Supplemental Greenhouse Lighting During Propagation
Find out how to properly manage supplemental greenhouse lighting during propagation with Erik Runkle and Roberto Lopez from Michigan State University.
Date: July 25, 2019
Time: 2-3 p.m. EST
Presented by: Erik Runkle and Roberto Lopez
Light is the driving energy source for photosynthesis and carbohydrate accumulation in plants. During propagation cuttings and seedlings require a minimum quantity of light to provide the energy for root initiation and development. Light intensities below this minimum result in little or no root development, leading to a delayed crop or rooting failure. Conversely, too much light can bleach leaves and reduce root formation due to excessive stress on the cuttings.
Find out how to properly manage supplemental greenhouse lighting during propagation with Erik Runkle and Roberto Lopez from Michigan State University.
Register Here
Roberto Lopez
Assistant Professor @Michigan State University
Roberto Lopez earned his master’s degree in 2003 and PhD in 2007 from Michigan State. From 2008 until 2016, he was assistant and then associate professor in horticulture and landscape architecture at Purdue University.
His research focuses on energy-efficient propagation and production of floriculture crops with an emphasis on lighting and temperature management. By controlling environmental factors such as light, temperature, and carbon dioxide, Roberto has been able to influence crop timing, quality, flavor, nutrition, and color in many crops.
His lab is especially focused on light-emitting diodes (LEDs) and recently developed best-practice strategies for LED implementation in greenhouse and indoor sole-source lighting situations.
Erik Runkle
Professor @Michigan State University
Erik Runkle Ph.D, is a professor and extension specialist in the Department of Horticulture at Michigan State University. Erik obtained a B.S. in ornamental horticulture from the University of Illinois and an M.S. and Ph.D. in horticulture at Michigan State University.
Since he joining the Michigan State faculty in 2001, Erik and his graduate research team have performed numerous practical experiments in controlled environments to determine the effects of light, temperature, and other environmental factors on plant growth and development. Experiments have been performed on a wide range of herbaceous specialty crops including leafy greens and ornamentals. Erik recently developed the Controlled-Environment Lighting Laboratory to better understand how the light spectrum can be manipulated to produce crops with desired attributes.
To date, Erik has co-edited six books and authored 14 book chapters, nearly 100 papers in scientific journals, and over 250 articles in trade magazines.
The GLASE Consortium Webinar Series features the latest technological innovations and
best practices in the CEA field providing the audience with the opportunity to
discover new solutions and to connect with field experts.
Glase Uses Outreach Activities To Inform And Educate Growers, Manufacturers And Suppliers
The goal of the Greenhouse Lighting and Systems Engineering (GLASE) consortium is to create a more sustainable and profitable greenhouse industry
Greenhouse Lighting and Systems Engineering (GLASE) consortium is using outreach activities to provide controlled-environment growers, lighting manufacturers and service companies with pertinent information to increase energy efficiency and improve their products and operating procedures.
By David Kuack
The goal of the Greenhouse Lighting and Systems Engineering (GLASE) consortium is to create a more sustainable and profitable greenhouse industry. The consortium is a partnership between Cornell University in Ithaca, N.Y., and Rensselaer Polytechnic Institute (RPI) in Albany, N.Y. GLASE is supported by the New York State Energy Research and Development Authority (NYSERDA) and by industry partners.
The consortium is conducting research to improve controlled environment agriculture (CEA) operations. Research activities include improving lighting fixtures and systems that synergistically control lighting and developing plant lighting and carbon dioxide control strategies. These strategies would ultimately reduce energy consumption to create a more sustainable and profitable greenhouse industry. Although the focus of GLASE research is on greenhouse production, the findings are expected to have application to other controlled-environment production systems including vertical farms and warehouses.
Information for the CEA industry
In addition to the research being conducted by GLASE, the consortium is also offering a variety of outreach activities to provide growers, lighting manufacturers and service suppliers with information that can assist them in improving their business operations. These activities include webinars, technical meetings and trade journal articles.
“The webinar series is the one activity that GLASE has been doing the longest,” said Neil Mattson, horticulture professor and greenhouse extension specialist at Cornell University and GLASE principal investigator. “The webinars are open to the entire industry. Some have been more oriented towards growers. Others have more application to the supply side, including manufacturers and service providers.”
Improving energy efficiency through benchmarking
“One of the webinar topics we covered is our energy efficiency benchmarking platform, Mattson said. “GLASE worked with sustainability solutions service supplier EnSave Inc.. The company does farm energy audits and also helps farms to apply for grants to make energy efficiency improvements. What the company found working with other agricultural commodities, including dairy farms and poultry producers, is there are more solid benchmarks on how much energy those industries use. The greenhouse industry is highly fragmented in regards to the crops grown and the numerous geographic locations of growing operations. What’s lacking is a unified data bank or benchmarks of typical energy usage numbers for heating and lighting relative to the crops that are grown.”
Neil Mattson at Cornell University said GLASE is using a variety of outreach activities to provide CEA industry members with information that can assist them in improving their business operations.Photo courtesy of Neil Mattson, Cornell Univ.
Because of the diversification of the horticulture industry, Mattson said it has been more difficult to collect energy-use data.
“Through this collaboration with EnSave we are hoping that growers will use this benchmarking database,” he said. “We’ve tested it and we’re trying not to make it too onerous for the growers so it’s as easy as inputting their monthly utility bills. The growers would also input their productivity units, which could be heads of lettuce, pounds of tomatoes or number of 6-inch ornamental plants. We are looking to collect information from both greenhouse vegetable and ornamental plant growers. The data base could accommodate both types of crops.”
“The real strength of this data base would lie in having a critical mass of users. For the individual users of the data base, they would be able to see how their operations compare to other industry benchmarks. Growers would be able to compare their businesses to an anonymous group of similar operations. If growers find they are using more energy per output, they could try to determine why they are using more energy. Nationally this could be useful to growers who are trying to obtain federal funds from grant programs for adopting energy-efficient systems. We would also like to be able to share with the industry some of this anonymous benchmark data that is collected.”
Horticultural lighting label
Another GLASE webinar topic was on a horticultural lighting label. The webinar was presented by A.J. Both, a professor and extension specialist at Rutgers University and member of the GLASE research team.
One of the GLASE webinar topics was the horticultural lighting label which has helped to educate growers about lighting fixtures. Photo courtesy of A.J. Both, Rutgers Univ.
“This webinar was oriented toward greenhouse growers, educating them as to what to look for and what questions to ask lighting manufacturers when they are considering adding lights or looking to make changes to their lighting systems,” Mattson said. “The webinar was also aimed at the lighting manufacturers that potentially would adopt the label.”
Mattson said the lighting label has helped educate growers about lighting fixtures.
“Growers are learning the lighting units to use when comparing lighting fixtures,” he said. “Although lighting manufacturers haven’t adopted the entire label yet, they have incorporated elements of it. Lighting manufacturers have become much better at providing technical specifications. They are talking about lighting units in terms of plant lighting not human lighting. They are talking about micromoles of light instead of lumens of light. Rarely are footcandles used anymore by growers and lighting manufacturers.”
Lighting fixture analysis
Another one of GLASE’s outreach activities is to drive adoption of the horticultural lighting label. GLASE has partnered with Intertek, a total quality assurance provider, to work with its lighting company members.
“Intertek has the specialized equipment for quantifying light output and light distribution,” Mattson said. “Each lighting company that is a GLASE member can submit one lamp a year for testing by Intertek. Intertek conducts a series of measurements with each lamp. GLASE then takes the raw data generated by Intertek and we provide the lighting companies with a lighting label for each lamp that is analyzed.
“There are currently six lighting companies that are GLASE members. This spring we had the first companies take advantage of the lamp analysis. The companies decide whether they want to share the lighting label GLASE provides them. This is a good way to introduce the GLASE lighting company members into the process of what it takes to generate the information that is needed to prepare a lighting label.”
Informational conference calls
GLASE has been offering its members periodic informal conversations on industry-related topics.
“These industry talks enable GLASE members to learn in a more informal setting where there is not a large audience,” Mattson said. “This provides GLASE members more time to have their questions answered by the speakers which could directly help them with their business.”
The first industry talk was a video conference call with lighting researchers Kevin Folta at the University of Florida and Bruce Bugbee at Utah State University who discussed the potential benefits of green light in plants.
“The green light conference call was geared more towards the growers, but GLASE manufacturer and supplier members were also able to participate,” Mattson said. “The informal format for these calls has been conducive to discussion between members and the speakers. There are 20 minutes during which the thought leaders talk about the topic and then that evolves into a question and answer period with the members. The program format enables the participants to have their questions answered.”
One of the informal industry talks offered by GLASE to its members discussed the potential benefits of green light on plants. Photo courtesy of Kevin Folta, Univ. of Fla.
Another industry talk covered power supply and power distribution options for CEA. This call was geared more to the lighting manufacturers. The speakers included Bahram Barzideh, principal engineer of LED lighting components at Underwriters Laboratories (UL), and Frank Cirolia, systems and application engineer at Artesyn Embedded Technologies.
“For LED lights some of the energy is used by the diode,” Mattson said. “This is the energy used to produce the light. Some of the energy is used by the power supply as well as the driver. There have numerous developments in power supplies, which have helped to improve the energy efficiency of the new generation of lights. Regarding power distribution, there are opportunities for improving energy efficiency related to the way power is delivered to the fixtures.”
Articles on research findings
Technical articles about GLASE research results are the newest outreach activity.
“GLASE will be rolling out these articles this summer,” Mattson said. “Some of these articles will be geared more to the growers. Other articles will have application to suppliers and lighting manufacturers.
“Topics will include the plant research and the lighting control studies that we have conducted at Cornell. There will also be articles on designing more energy-efficient lights, which is what researchers at RPI are working on.”
The following articles will appear in CEA-related magazines in the coming months.
July: Multi-spectrum research LED lights
August: Greenhouse light and shade system implementation controls
September: Light distribution measurements in tall canopies
October: Spectral acquisition systems for greenhouses
November: Plant responses to integrated light and CO2 controls
December: Horticultural lighting fixtures analyses
For more: Neil Mattson, Cornell University, School of Integrative Plant Science, Horticulture Section, Ithaca, (607) 255-0621; NY 14853; nsm47@cornell.edu; http://www.cornellcea.com; http://www.greenhouse.cornell.edu
Editor’s note: Neil Mattson will be doing three educational presentations at this year’s Cultivate’19, July 13-16, in Columbus, Ohio
Biostimulants: Another Tool for the Grower’s Toolbox
Sunday, July 14, 2:45 p.m.-3:45 p.m.
Greenhouse Light and Carbon Dioxide Management to Enhance Crop Yield
This educational session will include information related to GLASE research.
Monday, July 15, 11:30 a.m.-12 p.m.
Lighting Approaches to Maximize Profits (LAMP)
Tuesday, July 16, 9:30 a.m.-10:30 a.m.
David Kuack is a freelance technical writer in Fort Worth, Texas; dkuack@gmail.com
Posted in Interviews
Heliospectra Continues Global Expansion With Tokyo Office
General Manager Yasuhiro Suzuki to Lead Installations of Heliospectra’s integrated LED and helioCORE™ Light Control Solutions for Japan’s Plant Factories and Vertical Farms
July 09, 2019
General Manager Yasuhiro Suzuki to Lead Installations of Heliospectra’s integrated LED and helioCORE™ Light Control Solutions for Japan’s Plant Factories and Vertical Farms
(GOTHENBURG, Sweden / SAN FRANCISCO, CA, 9 July, 2019) – Heliospectra AB (publ) (OTCQB: HLSPY, FIRSTNORTH: HELIO), a world leader in intelligent lighting technology for greenhouse and controlled plant growth environments, announces the formation of Heliospectra Japan Co., Ltd. and the opening of a new Tokyo, Japan office in July 2019 under the leadership of General Manager Yasuhiro Suzuki.
“With Yano Research Group forecasting indoor grown vegetable sales from Japan’s vertical farms to reach 27.8 billion yen by 2022, Japan has established itself as the global role model in demonstrating the seamless integration of automation and control systems. Using Heliospectra’s most advanced LED lighting technologies and light controls, these businesses will consistently deliver fresh, locally grown and nutritious produce to retail markets, urban food service and quality-conscious consumers,” said Ali Ahmadian, CEO, Heliospectra.
Over the years, Heliospectra has rapidly expanded their product portfolio to focus on the benefits spectra-controlled LEDs, real-time sensor feedback and dynamic, automated light response bring to growers and commercial food producers. The company has also established strong local market presence and collaborations directly with customers in Europe, Canada, the United States, South America and Oceania.
As Japan’s plant factories and controlled environment farms create new demand for the robust helioCORE™ light control and horticultural LED lighting integrations as well as the complete helioCARE™ plant science and technical services expertise that Heliospectra offers, the company will focus on building customer relationships and strategic partnerships with the Tokyo office and a local Japanese team.
“Heliospectra has created intelligent and highly advanced LED lighting and light controls that provide growers and businesses with a comprehensive, flexible and fully connected system,” said Yasuhiro Suzuki, General Manager for Heliospectra Japan. “I look forward to working with Japan’s highly sophisticated growers and large-scale facilities to improve their profitability through standardizing crop performance and yields with Heliospectra’s customizable business solutions.”
Mr. Suzuki previously served in senior leadership positions with Tetra Pak for 25 years developing strategic partnerships and an extensive business network in Japan and across Asia. He holds a bachelor’s degree in Sociology from Rikkyo University in addition to associated graduate degrees in Marketing, Management and Organizational Leadership from IMD and Ashridge Business Schools.
Investor Relations:
Ali Ahmadian, CEO of Heliospectra | +46 (0)72 203 6344 | ir@heliospectra.com
Redeye is Heliospectra Certified Advisor for Nasdaq First North - www.redeye.se
Certifiedadviser@redeye.se | +46 (0)8 121 576 90
Heliospectra AB (publ) (OTCQB: HLS, FIRST NORTH: HELIO) is the global leader in intelligent lighting technology, light control systems and related services for greenhouse and controlled plant growth environments. With the vision to make commercial crop production more connected and resource-efficient, Heliospectra integrates customized LED spectral strategies with real-time response and artificial intelligence to create predictable and reliable business forecasts and harvest results. Founded in 2006, Heliospectra is committed to helping growers and commercial producers across six continents consistently increase yields and produce crops with quality appearance, superior nutritional or medicinal value and longer shelf life, harvest after harvest. Heliospectra is the recipient of multiple international awards and recognitions. For more information, please visit https://www.heliospectra.com.
Forward-Looking Statements
The statements in this press release constitute forward-looking statements within the meaning of federal securities laws. Such statements are based on our current beliefs and expectations and are inherently subject to significant business, economic and competitive uncertainties and contingencies, many of which are beyond our control. In addition, such forward-looking statements are subject to assumptions with respect to future business strategies and decisions that are subject to change. Potential risks and uncertainties include, but are not limited to, technical advances in the industry as well as political and economic conditions present within the industry. We do not take any obligation to update any forward-looking statement to reflect events or developments after a forward-looking statement was made.
This information was submitted for publication, through the agency of the contact person set out above, at 14:00 CEST / 7.00 AM CDT on July 9th 2019.
Tags:
Heliospectra , LED Lighting Strategies , Heliospectra AB , HLSPY , HELIO , OTCQB , Ali Ahmadian
About Us
Heliospectra AB is the industry’s most proven intelligent lighting technology for greenhouse and controlled plant growth environments. With the vision to make commercial crop production more connected and resource-efficient, growers and commercial producers across six continents use Heliospectra’s holistic and flexible solutions to consistently increase yields while producing crops that achieve quality appearance, superior nutritional or medicinal value and longer shelf life, harvest after harvest. Founded in 2006 and winner of multiple international awards and recognitions, Heliospectra has raised more than $32 million in capital to date. As a publicly traded company, the majority ownership remains with some of Heliospectra earliest investors Weland Steel, Midroc New Technology and Swedish Industrial Fund. For more information, please visit https://www.heliospectra.com.
2019 Five-Day Introductory Training Course on Plant Factory With Artificial Lighting (PFAL)
By urbanagnews - July 8, 2019
September 23rd – 27th, 2019
In response to increasing global demands from indoor farmers, researchers and future entrepreneurs in the exciting emerging field of plant factory with artificial lighting (PFAL), also known as vertical farm, this coming September, Japan Plant Factory Association (JPFA) together with Chiba University will host again an intensive five-day introductory training course in English on PFAL.
Since 2010, JPFA and Chiba University have been organizing various in-depth and practical sessions, including introductory to advanced courses. This five-day introductory session in English, held September 23rd – September 27th, covers what you would need to know before or after starting PFAL business or research.
The sessions will be interactive academic and practical classes, covering topics such as structure and function of PFAL, environmental control, lighting, plant physiology, nutrient solutions, seedlings, recent new technologies toward next generation PFALs, and business case studies of commercial large-scale PFALs. In addition to lectures by academic professionals and PFAL representatives, optional excursions to some commercial PFALs on the last day of the course will be organized.
*The curriculm would be the same as the introductory course last year.
1. Objective and Goal
-To offer foundation for theory and experience-based practice, with a view to foster academic and industrial development toward next generation PFAL.
-To facilitate development and dissemination of technically and economically sustainable PFAL, through providing the firsthand technical and conceptual classes by broad-ranging professionals in practice from both academia and PFAL industry.
2. Target group: Who would attend?
Motivated current/potential indoor farmers who plan to start or just started PFAL business or research. They will gain understandings of elementary theory and practice of PFAL, basic knowledge of cultivation and operational management, and keys for business success, etc.
3. Lecturers and program
■Scheduled Lectures: Chiba University / JPFA:
T. Kozai, Y. Shinohara, T. Maruo, S. Tsukagoshi, N. Lu, M. Takagaki, T. Yamaguchi, O. Nunomura and E. Hayashi
Lecturers from the PFAL industry: Representatives from 808 Factory and others(K. Kai and K.Uraisami)
Read the complete article here.
Great Lakes Growers
An early LED adopter, Bonner began trialing LEDs in 2015, and after seeing the success in a small area, expanded his Philips LED toplighting installation in 2016, again in 2017, and will install Philips grow lights with his greenhouse expansion
John Bonner, owner of Great Lakes Growers, discusses how he considered qualitative and quantitative benefits when evaluating LED lighting.
An early LED adopter, Bonner began trialing LEDs in 2015, and after seeing the success in a small area, expanded his Philips LED toplighting installation in 2016, again in 2017, and will install Philips grow lights with his greenhouse expansion.
U.S. Vertical Farms Are Racing Against The Sun
Leafy salad greens grown under banks of LED lights, with mist or drips of water are having their day in the sun. Several top U.S. indoor farms, stacked with plants from floor to ceiling, tell Reuters they are boosting production to a level where they can now supply hundreds of grocery stores
JULY 5, 2019
(Reuters) - Leafy salad greens grown under banks of LED lights, with mist or drips of water are having their day in the sun. Several top U.S. indoor farms, stacked with plants from floor to ceiling, tell Reuters they are boosting production to a level where they can now supply hundreds of grocery stores.
TO VIEW VIDEO, PLEASE CLICK HERE
Plenty, Bowery, Aerofarms and 80 Acres Farms are among young companies that see a future in salad greens and other produce grown in what are called vertical farms that rely on robotics and artificial intelligence, along with LED lights. While the first versions of modern vertical farms sprouted about a decade ago, in recent years the introduction of automation and the tracking of data to regulate light and water has allowed them to get out of lab mode and into stores. Now they are trying to scale up.
Plenty and others say their customized, controlled lighting - some more blue light here, some more red light there - makes for tastier plants compared to sun-grown leaves and that they use 95% less water than conventional farms, require very little land, and use no pesticides, making them competitive with organic farms. And because vertical farms exist in windowless buildings that can be located in the heart of urban areas, produce does not have to travel far by fossil-fuel-guzzling trucks to reach stores.
The companies’ expansion comes as plant-based burger makers Beyond Meat Inc and Impossible Foods captivate investors and make inroads in high-end restaurants and fast-food chains.
But whether the sunless farms can compete financially with their field-grown brethren, given big upfront investments and electric bills, remains a question.
“We’re competitive with organic today and we’re working very hard to continue to make more and more crops grocery store competitive,” said Matt Barnard, chief executive and co-founder of Plenty, which is based in Silicon Valley.
Chef and Plenty advisory board member Nancy Silverton prepares a salad during a demonstration in San Francisco, California, U.S., June 11, 2019. Picture taken June 11, 2019. REUTERS/Jane Lanhee Lee
Plenty’s salads sell on organic grocery delivery site Good Eggs for 99 cents an ounce, while a leading brand, Organic Girl, on grocery chain Safeway’s online site was priced at 80 cents an ounce.
Plenty said its new farm, dubbed “Tigris,” can produce enough leafy greens to supply over 100 stores, compared with its previous farm that could only supply three stores and some restaurants.
The technology world is paying attention. In its last round in 2017 Plenty raised about $200 million from investors including Japan’s Softbank, Amazon founder and CEO Jeff Bezos and former Alphabet Chairman Eric Schmidt. New York City-based Bowery raised $95 million in a fund-raising round led by Google Ventures and Temasek last year.
Bowery said its third farm coming online soon will help it supply hundreds of stores from dozens today, and Aerofarms, in New Jersey, said it is doubling its space to meet demand.
None of the three companies would give details about costs.
Former Vertical Farm CEO Matt Matros is skeptical that sunless farms can make economic sense. He invested in and ran Chicago-based FarmedHere in 2015, but changed its business into food processing.
“The issue with indoor farming was that you could really only grow a couple things efficiently — namely basil and micro greens. But the problem is the world just doesn’t need that much basil and micro greens,” Matros said.
80 Acres Farms in Cincinnati says it already grows and sells tomatoes and cucumbers, and Plenty is testing cherry tomatoes and strawberries in the lab.
Plenty CEO and co-founder Matt Barnard tastes a salad prepared by chef and Plenty advisory board member Nancy Silverton during a demonstration in San Francisco, California, U.S., June 11, 2019. Picture taken June 11, 2019. REUTERS/Jane Lanhee Lee
Agriculture technology investor Michael Rose says vertical sunless farms are more expensive to run than modern greenhouses that rely on sunlight, supplemented by LED lights. He sees limited areas where it makes sense, such as the Middle East, where much of the food is imported, or China’s mega-cities where pollution and urban sprawl limit the availability of premium fresh food.
At Plenty’s new farm, robots put seedlings in tall, vertically hung planters. The planters move along a wall of LED lights for 10 days, and are then put through a harvesting machine that shaves off the leafy greens.
The machines minimize labor needs, and Plenty says the speed of production also helps control pests.
“We use no pesticides,” said Nate Storey, co-founder and chief scientist at Plenty. “We don’t even have to use things like ladybugs, because we go so fast in our production that we out-race the pests themselves.”
Reporting by Jane Lanhee Lee; editing by Peter Henderson and Leslie Adler
Our Standards:The Thomson Reuters Trust Principles.
Recently, FOX Business Aired A Segment About Full Spectrum LED Grow Lights And Spectrum King LED
Spectrum King LED, the pioneer of full spectrum LED Grow Lights (patent No.10238043), specializes in designing, manufacturing and selling professional-grade LED grow lights for indoor grows and greenhouse applications.
Spectrum King LED, the pioneer of full spectrum LED Grow Lights (patent No.10238043), specializes in designing, manufacturing and selling professional-grade LED grow lights for indoor grows and greenhouse applications.
The company started after the founder Rami Vardi, was looking for a more efficient solution for indoor growing. He wanted a light that would produce high-quality yields like the “old school” lamps, but with a much lower electric bill.
Now, Spectrum King LED has customers and fans all over the world, in both the cannabis and the food production industries.
If you grow indoor, contact Spectrum King LED at +1 (888) 654-0737 or email sales@spectrumkingled
Wageningen University Proves Viability of Fluence by OSRAM LEDs
Five-month growing trial on high-wire tomatoes conducted by Wageningen and Vortus demonstrates full-spectrum LEDs from Fluence by OSRAM are a viable solution to replace legacy HPS fixtures
June 11, 2019
ROTTERDAM, Netherlands & AUSTIN, Texas--(BUSINESS WIRE)--Wageningen University and Research (WUR), in cooperation with Fluence by OSRAM and Vortus, has released initial results of a cultivation trial analyzing the viability of full-spectrum LED lighting solutions, using Fluence PhysioSpec Greenhouse™ spectrum, in comparison to legacy high-pressure sodium (HPS) greenhouse lighting fixtures. Preliminary data shows PhysioSpec Greenhouse is up to 11% more effective than HPS in yield for certain tomato cultivars, with the added benefit of being more energy efficient than HPS fixtures.
“The initial results of this trial show growers can cultivate tomatoes as effectively with PhysioSpec Greenhouse as you can under HPS, possibly with a better yield, and with shorter stems,” said Dr. Ep Heuvelink, associate professor, WUR. “Of the tomatoes grown under PhysioSpec Greenhouse, when compared to the HPS control environment, the WUR team saw the crop developed well and fruits had similar dry matter content. In fact, fruit yield is a bit higher in the LED sections for the Tomagino cultivar, which is a welcome benefit when considering the energy reduction LEDs naturally exhibit over HPS technology.”
Dr. Heuvelink, and his team at WUR, tested PhysioSpec Greenhouse in comparison to HPS lighting from a recognized vendor. The research was conducted on Tomagino and Merlice tomato cultivars. WUR will publish the full data set later this year.
“Current practices use HPS technology as the sole source for supplemental lighting in greenhouses and the WUR trial proves this should not be the case,” said Barend Lobker, director and owner, Vortus. “Growers have been reluctant to transition to LEDs because they are uncertain if LEDs can be as effective for cultivation and the WUR trial eliminates any doubts around the capabilities of full spectrum LEDs.”
“This is a very exciting result for the application of full-spectrum LED technology in greenhouse tomato production. It demonstrates that even without any other environment optimization for LED solutions, LEDs can match, or even out-perform legacy lighting fixtures for commercial growers,” said Haris Ouzounis, horticulture service specialist and senior photobiologist, Fluence by OSRAM. “Upcoming studies from Fluence into the influences of light quality, distribution, and intensity, as well as optimizations to the rest of the environment should demonstrate improvements in productivity compared to legacy production practices.”
Further Collaborations in Science and Research
Cooperating with recognized thought leaders around the world is a top priority for Fluence by OSRAM. This initial trial with WUR is the first in a series of results Fluence will release over the coming months. Additionally, Fluence is advancing several other initiatives with research centers, universities, and organizations around the world to further develop best practices and forward-looking applications for the industry.
“Basing our solutions on research and science are fundamental differentiators which sets Fluence apart,” said David Cohen, chief executive officer, Fluence by OSRAM. “We are proud to be working with Wageningen University and to join the WUR Club of 100, to further extend the world’s understanding of critical and fundamental horticultural research. Greenhouses are a significant source of nutritious fruits and vegetables and WUR’s ground-breaking research will empower more countries to cultivate high-quality crops in an energy-efficient way.”
To learn more about the preliminary results, meet with the Fluence team at Green Tech in Amsterdam, or visit https://fluence.science/wageningen for more information.
About Fluence by OSRAM
Fluence Bioengineering, Inc., a wholly-owned subsidiary of OSRAM, creates the most powerful and energy-efficient LED lighting solutions for commercial crop production and research applications. Fluence is the leading LED lighting supplier in the global cannabis market and is committed to enabling more efficient crop production with the world’s top vertical farms and greenhouse produce growers. Fluence global headquarters are based in Austin, Texas, U.S.A., and its EMEA HQ in Rotterdam, Netherlands. https://fluence.science
About Wageningen University and Research
The mission of Wageningen University and Research is “To explore the potential of nature to improve the quality of life.” Under the banner Wageningen University & Research, Wageningen University and the specialized research institutes of the Wageningen Research Foundation have joined forces in contributing to finding solutions to important questions in the domain of healthy food and living environment. With its roughly 30 branches, 5,000 employees and 10,000 students, Wageningen University & Research is one of the leading organizations in its domain. The unique Wageningen approach lies in its integrated approach to issues and the collaboration between different disciplines.
About Vortus bv
Established in 1982, Vortus bv is an independent greenhouse consulting firm which services clients from around the world. The team is comprised of ten consultants, which specializes in providing technical advice regarding climate, irrigation, nutrition, energy management, and labor management for greenhouse environments. The Vortus bv office is based in Honselersdijk, The Netherlands. For more information on Vortus bv services, visit www.vortus.eu.
June 12, 2019 - LED Conference During GreenTech
The application of the LED technology can propel a cultivation business or a plant research project forward but can also pose challenges. Firstly, the LED offer on the market is vast, complex and confusing and secondly, LED is only one of the available lighting technologies.
The best way to understand how to advance properly onto LEDs is by hearing the stories of those who have done it before. Experts from the fields of crop science, vertical farming and medical plants cultivation will gather in the LEDs & Innovators Conference 2019 to discuss the application of the LED technology and more. The conference will be held during GreenTech at the RAI premises and is free of charge for the GreenTech participants but with a very limited number of seats available.
The 3-part event consists of a Crop Science and Light session, a Hard Science Talk on Cannabis session and a Vertical Farming Innovators Panel. Participants can choose which one to participate in and thus hear first-hand experiences from those who have ventured into the world of LEDs already. The scope will expand beyond just lighting and additionally participants will have a chance to ask their own questions.
In the Crop Science and Light session, we will try to show what kind of light is most useful for researchers and how to successfully transition from trialed and tested protocols made with fluorescent and other, more traditional technologies onto LEDs. In the Hard Science Talk on Cannabis, Dr. Grassi, one of Europe’s most prominent Cannabis sativa researchers, with two decades in the field will discuss terpenes.
The scent molecules of the cannabis plant are sought after almost as much as the cannabinoid compounds and our understanding of their value is still scarce. Finally, the Vertical Farming Innovators Panel will gather vertical farmers as well as industry specialists who will discuss not only lighting for vertical farming, but the ins and outs of this field which is on the exponential rise. You have a chance to propose a topic you wish to be discussed by the panelists. You will have an opportunity to do so in the registration form for the event.
The participation in the event is FREE of charge, however the number of seats is very limited so it is best to register right away.
To learn more about the event and register, please click here.
Conference Program
10:15 – 11:15 Crop Science and Light
Stefanie Linzer, Biologist, Valoya
High Quality White LED Light for Crop Science Applications
11:30 – 12:30 Hard Science Talk on Cannabis
Dr. Gianpaolo Grassi, Head Researcher, CREA-CI, Italy
How Does the Light Spectrum Affect the Terpene Profile of Cannabis?
13:00 – 14:30 Vertical Farming Innovators Panel
Mark Korzilius, Co-Founder & CEO, Farmers Cut, Germany
Rasmus Jakobsen, Manager, Greenlandic Greenhouse
Gus van der Feltz, Chairman, Farm Tech Society
Henry Gordon-Smith, Managing Director, Agritecture
Lars Aikala, CEO, Valoya
About Valoya
Valoya is a provider of high end, energy efficient LED grow lights for use in crop science, vertical farming and medical plants cultivation. Valoya LED grow lights have been developed using Valoya's proprietary LED technology and extensive plant photobiology research. Valoya's customer base includes numerous vertical farms, greenhouses and research institutions all over the world (including 8 out of 10 world’s largest agricultural companies).
Additional information:
Valoya Oy, Finland
Tel: +358 10 2350300
Email: sales@valoya.com
Web: www.valoya.com
Facebook: https://www.facebook.com/valoyafi/
Twitter: https://twitter.com/valoya