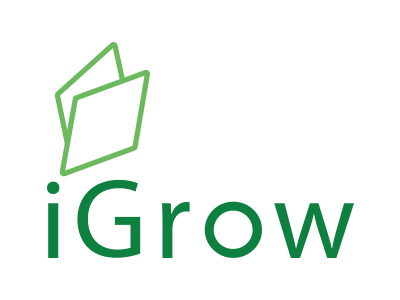
Welcome to iGrow News, Your Source for the World of Indoor Vertical Farming
Early History of Indoor Agriculture & Associated Technology Development
This month’s Indoor Ag Science Café was about the history and current technology status of indoor farming. The beginning seems to be in Syracuse, NY, where General Electric developed an indoor hydroponic farm funded by DoD in 1973
By urbanagnews
October 17, 2019
By Dr. Cary Mitchell (Purdue University)
This month’s Indoor Ag Science Café was about the history and current technology status of indoor farming. The beginning seems to be in Syracuse, NY, where General Electric developed an indoor hydroponic farm funded by DoD in 1973. Then there was a large commercial indoor farm for leafy greens in Dekalb, IL, owned by General Mills, which was closed in the 1990s. The longest survived may be the one in Japan (TS Farm by Kewpie Co.) where they use HID lamps and aeroponics since 1989. Most significant technological improvements are two ways – one in lighting and another in rack/shelving systems. Dr. Mitchell also introduced the contributions that NASA indoor farming studies made over the past 30+ years, as one of the contributors in the space.
Indoor Ag Science Café is supported by the USDA SCRI grant program and designed to create a precompetitive communication platform among scientists and indoor farming professionals. The Café presentations are available from YouTube channel. Contact Chieri Kubota at the Ohio State University (Kubota.10@osu.edu) to be a Café member to participate.
Green Automation Is Bringing Automation And Efficiency To New Greenhouse Operation In Texas
Green Automation Group is proud to announce the latest project realization in the North American market – hydroponic lettuce producer TrueHarvest Farms in Belton, Texas. The 50,000 square feet greenhouse is equipped with growing automation technology from Green Automation
October 24, 2019, Wellington, FL, USA
Green Automation Group is proud to announce the latest project realization in the North American market – hydroponic lettuce producer TrueHarvest Farms in Belton, Texas. The 50,000 square feet greenhouse is equipped with growing automation technology from Green Automation. Riding on the steadily increasing demand for locally grown produce, TrueHarvest Farms will grow fresh and pesticide-free head lettuce locally in the controlled environment of a greenhouse 365 days a year. The farm is strategically located in the “Texaplex Triangle”, which is formed between the cities, Dallas-Fort Worth, Houston, San Antonio, and Austin. With a population of around 20 million people and having 80% of the state’s population growth since 2000 as well as generating up to 70% of the Texas economy, this area is the ideal location for new, innovative and sustainable production of leafy greens.
“The climate here in Texas makes year-round field growing of leafy greens impossible and the area has so far, as the rest of the USA, relied heavily on having lettuce trucked into the state from California and Arizona for a substantial part of the year”, says Marshall McDaniel, Managing Member at TrueHarvest Farms. “We will be distributing truly fresh, nutritious, safe and locally grown lettuce to stores within a 250 miles radius of our operations. The lettuce will be available to the customer in less than 24 hours of harvesting”.
TrueHarvest Farms, rooted in Belton, TX, is ready to supply fresh, nutritious and safe leafy greens to the Texaplex Triangle.
Recent food safety scares in the lettuce industry has led to an increased interest in and call for safe and clean lettuce produced in a controlled environment. The greenhouse is a closed system, controlling what comes into the greenhouse, making it possible to not only keep the lettuce clean but also to grow them without using any chemical pesticides. The irrigation water, the air, and the growing medium are controlled, monitored and clean - keeping consumers safe and the environment protected.
“There is an enormous demand for locally grown and safe lettuce today”, confirms Jason Maks, Managing Member, and Grower at TrueHarvest Farms. “Our facility is in the final stage of obtaining PrimusGFS certification and we are dedicated to meeting the highest safety standards in the food industry. TrueHarvest Farms will be a reliable source for locally grown and safe produce for the Texas markets. We are ramping up our production right now and expect to reach full capacity in January 2020. At the moment we are growing Butterhead, Crisp and Romaine varieties”, explains Maks.
TrueHarvest Farms is using the automated growing system optimized for head lettuce production. “When growing leafy greens in tough climates it is imperative to operate the greenhouse with the highest efficiency and to generate the highest yields per square foot, therefore TrueHarvest Farms decided to use the automated growing system from Green Automation”, says Patrik Borenius, CEO, Green Automation Americas. “Throughout the entire growing process maximal space efficiency is achieved through automatic movement and adjustment of gutters, giving the plants as much space as needed, but as little as possible”.
In addition to maximizing yield through space efficiency, labor efficiency is an essential key component in a profitable operation. The system has a highly automated and versatile medium filling and seeding line arrangement using stackable trays and supporting both net pots as well as Ellepots. After seeding and germination, the plants are placed onto the automatic growing system, featuring adjustable and movable growing lines, where they will soak up the natural sunlight. As the plants grow, they are moved automatically through the greenhouse toward the harvesting station.
TrueHarvest Farms did multiple trips to reference operators in Europe, including to such remote locations as Joensuu, Finland, before making a decision. “It is a proven system and on par with our earth-conscious commitment. We are looking forward to growing and providing the Texas market with the highest quality lettuce”, says Marshall McDaniel. “This is only the beginning, we have room to grow and our head house as well as the irrigation system are designed for future expansions,” McDaniel explains.
Contact:
Patrik J. Borenius
Green Automation Americas LLC
13833 Wellington Trace, Suite #E4-203
Wellington, Florida 33414
About Green Automation Group
Green Automation Group Ltd, headquartered in Finland, and it’s subsidiary Green Automation Americas LLC, based in Florida, develop, manufacture and market the most advanced greenhouse automation systems for lettuce and herb production. The systems are designed for commercial greenhouse operations with a growing area of 1 acre / 0.4 hectares and above. www.greenautomation.com
About TrueHarvest Farms
TrueHarvest Farms, LLC is a controlled environment hydroponic farm specializing in leafy greens. Founded in 2017, the company is focused on rapid growth through the production and distribution of high-quality lettuce and other leafy greens. TrueHarvest Farms is the evolution of a family hay and pecan farm now 40 years old. So, whether it is the “family roots” or the “plant roots,” we are truly “Rooted in Belton, Texas”.
https://www.facebook.com/trueharvestfarms
Can Container Farming Help Meet The Rising Demand For Local Food?
With container farming, farmers can actually control the climate, along with soil, quality, heat and even light exposure. The containers use technology to be retrofitted with heating and water systems, and gas and electrics can also be installed to offer a whole host of benefits for crops and farmers alike.”
October 24, 201
© Andrii Zastrozhnov |
With the demand for local produce constantly rising due to environmental, economic and quality reasons, Johnathan Bulmer, MD at Cleveland Containers, has urged for more pick up on container farming
He suggests that, with Brexit also looming and causing uncertainty as to where the weekly food shop will come from, container farming can produce many of our favorite fresh produce in the UK. The fully contained structures allow for year-round growth no matter the weather or available land.
Bulmer said: “Most of us are eating produce that has traveled thousands of miles from its source. One of the reasons why UK supermarkets sell fruit and vegetables which aren’t often produced in the country is that farmers face the challenge of providing seasonal produce all year round – which isn’t possible with changing weather conditions.
“But with container farming, farmers can actually control the climate, along with soil, quality, heat and even light exposure. The containers use technology to be retrofitted with heating and water systems, and gas and electrics can also be installed to offer a whole host of benefits for crops and farmers alike.”
This modern twist has helped farmers to produce goods all year round, avoiding common restrictions such as extreme weather, pests, and seasonal struggles.
Bulmer estimates that container farms can produce up to 4,000 heads of lettuce every ten days, using no soil and 97% less water than a conventional farm.
“Crops are protected from nasty pests, eliminating the need for pesticides which can also cause health problems in those who consume them,” he continued.
One company, Freight Farms, has produced its ‘Leafy Green Machine’, which it claims to cut water demand by up to 98% using hydroponic container techniques, which could help to reduce demand on freshwater reserves.
Benefits of local produce
By cutting the distance that our food has to travel, greenhouse gas pollution from air freight is minimized, and the shorter distance means that it’s sold sooner after it’s grown and picked.
This benefits not only the taste due to it being fresher, but producers can also pick from a wider variety of fruit that has great flavor but doesn’t usually travel well so it isn’t sold.
He said: “There are a host of other benefits to container farming for local produce. It benefits the local economy, reduces the seasonality of foods, and also cuts down on plastic waste which is often multi-wrapped to protect it from travel.
“This boost in freshness can reduce food wastage and encourage more nutritional diets with simple, fresh ingredients. And you also don’t get the problem of land being in the wrong place or relocation restrictions, because container farms are so flexible. They can be easily stacked, which means farmers also won’t need to empty their pockets and pay for extra land to expand – you build up.
“We’re seeing a huge amount of farmers deciding to go down the container route in this country. The flexibility and option to mass-produce fruit and vegetables within such a short space of time, along with savings on waste usage means they can save costs, but produce seasonal fruit and veg all year, without being limited by space,” Bulmer said.
“There is a billion-dollar consumer demand for local food – let’s work together to achieve it.”
Cleveland Containers offers one of the largest nationwide stocks of new and used shipping containers, available throughout the UK.
Based in Middlesborough, its models for sale or hire come in all sizes to fit different needs. From 6 to 45ft, its specialized containers can be used for storage, office containers, site accommodation, farming, hospitality and more.
Why Indoor Ag Is Like 3D Printing
As a student, Maarten Vandecruys was looking for a way to scale his impact. After seeing the waste and inefficiency of the old food supply chain, he decided indoor agriculture was how he’d make his mark. He’s kept this focus on impact as Founder and Managing Director of Contain vendor Urban Crop Solutions
As a student, Maarten Vandecruys was looking for a way to scale his impact. After seeing the waste and inefficiency of the old food supply chain, he decided indoor agriculture was how he’d make his mark. He’s kept this focus on impact as Founder and Managing Director of Contain vendor Urban Crop Solutions, working with diverse partners on projects to reduce food waste at IKEA and simulate growing on Mars. We sat down with Maarten to hear what he’s learned in the process.
Maarten Vandecruys, image courtesy of Urban Crop Solutions
What’s Urban Crop Solutions’ signature approach?
We’ve always looked at the industry rather holistically, not as an engineering company, building systems or technology, and not as purely biologists, looking at how to grow things. For us, it always starts with the customer and starts with the customer’s market. It’s the end-user that defines the needs of a producer.
Then we have our plant scientists find the most optimal conditions and then they optimize the yields our client can produce to maximize their profits. Based on that, we can maximize their system, using different lights, sizes, etc.
We see that our growers have enough challenges as it is. At the end of the day, they’re producing living things, so we want to take tech and biological challenges away from them.
You’ve collaborated on projects ranging from reducing waste and supplying greens to IKEA, to simulating life on Mars with Puratos. What did you learn from these diverse partnerships?
One thing that you always see, looking at the two — the Mars project, which is more of a fundamental research approach, while with IKEA, it’s a practical applied project — what you always see is there is still so much about the growth and production of crops that is learning, daily, about new methods and which process is happening inside the plant.
The potential is far from unlocked. In initial trials with Puratos, we are already increasing the yields of wheat fivefold, per square meter of growing surface, not accounting for multiple layers of growth, as in a vertical farm. Economically, it’s still not viable enough, that’s the downside, but we continue to focus on optimizing.
IKEA had a very strong focus on sustainability. We are trying to approach our clients’ projects as holistically as possible. That’s the essence of what we did with IKEA, where we’re producing food from food waste. All waste from their restaurants included in our project were brought to a biogas facility, which provided electricity for our containers, and CO2 for our plants. It’s a real circular system, which functions well as a business case, and also increased interest in IKEA’s dishes using our greens, once they started communicating with the public about where it came from. This is what I see as the start of something very big for the industry.
Image courtesy of Urban Crop Solutions
Some people say indoor farming has overstated its potential to the media and investors. What do you think?
There’s really a lot of similarities with the 3D printing industry. When it was new, it was this big thing attracting lots of investment, only for people to initially find out that it was all too expensive. However, as the tech improved, the costs have gone down, and now there are multiple niches that create huge and sustainable added value.
Indoor vertical farming is very similar in that regard. Will indoor vertical farming feed all of humanity in ten years? Let’s be honest, likely no. Will it offer huge benefits to specific industries and shorten the supply chain with better quality? Yes. This will happen in food, pharmaceuticals, the floriculture industry, and it’s already happening now. It’s not moving as fast as five years ago, but it’s for the best. You start walking before you can run.
What are some of the biggest challenges you see when new growers want to get into indoor ag, especially around financing?
Financing is very important. We always conduct a feasibility study with our clients. It’s mainly an industry of new entrants, people or companies with no experience in food production or distribution. They have a lot of challenges coming towards them. We look at who is their customers, what is the location, what to grow, how are they funded.
It’s a new industry, so traditional funders and lenders aren’t as interested in this. What’s important is that growers can improve their case by covering their risk, and one of the things to help with that is working with a tech provider with a proven track record and customer base. It’s still not as easy as it seems, which is why having an industry-specific provider, like Contain, which knows what the field looks like, benefits each side.
The larger companies are slowly moving into the field, like IKEA and some of the airlines, which creates more credibility towards the banks. Five years ago, that wasn’t happening. It’s only for the best, especially because they are successful.
What’s the common feature among the most successful indoor growers you see, and what can our readers learn from them?
Understand the complexity of the industry. In the end, you are producing a living organism. You’re getting way more output than input, which is pretty unique. In order to do that properly, you need tons of expertise: plant physiology, food safety, etc. It’s not easy to have all of that, especially as a small company. That’s why having the right team is so important, or to put yourself with the right partners. That’s the best way to succeed.
What industry trends are you most excited about?
What I’m most excited about is breeding for indoor ag. In the past, our plants have been bred for disease-resistance and yields. But right now we have more and more interest in collaborations to breed for indoor farms, which unlocks way more potential. We can drop the disease element and focus on quality. This will open us up to new perspectives on food, thinking about the functionality, putting new vitamins in food. If we can maximize the number of crops we grow, while reducing the necessary water, waste, and transport, the impact will be incredible. It’s happening already, whereas in the past it was too little. The impact will slowly drip to the market, and that’s what I’m really excited about.
This conversation transcript has been lightly edited for length and clarity.
Learn more about Contain and funding your indoor ag business at our website, and subscribe to Inside The Box, our weekly newsletter.
Abu Dhabi Prepares For The Future of Food
This is a historic year for Agriculture Technology (AgTech) in the UAE. This March the Abu Dhabi government approved an AED 1 billion package to support the AgTech sector
This is a historic year for Agriculture Technology (AgTech) in the UAE. This March the Abu Dhabi government approved an AED 1 billion package to support the AgTech sector. The package is part of Ghadan 21 (Tomorrow 21), which is a three-year AED 50 billion program designed to accelerate the capital’s economic growth and reduce dependency on oil revenues. It is led by the Abu Dhabi Investment Office (ADIO), which was created in 2018 with the mandate to increase foreign direct investment. In this article, we are going to take a deep dive into the initiative.
What is it?
The stimulus consists of cash and non-cash benefits, which include rebates of up to 75% of R&D costs subject to eligibility and commercialization criteria.
Who is eligible?
Local and international companies are eligible. The program is focused on three specific sectors in the AgTech industry that have been identified for their strategic significance: precision farming and agriculture robotics, indoor farming, and bioenergy (algae).
But why?
The government has taken this major decision primarily for three reasons.
Firstly, the government seeks to establish Abu Dhabi as a global center for innovation in agriculture, especially in desert environments. This is achievable because the AgTech industry is in its early stages globally. As such, there is an opportunity to become global leaders if we become knowledge exporters. R&D is underfunded globally, which is why the initiative targets R&D and seeks to attract the best talent from around the world.
Secondly, agriculture is a high-risk industry due to the sheer number of variables that cannot be controlled, which is why governments around the world provide various levels of assurances and support. AgTech promises to decrease these risks in the medium term. However, developing and localizing these solutions to the UAE’s environment adds a degree of complexity. This is why the government’s initiatives are crucial for the success of this industry as a whole.
Finally, the government recognizes the urgency of addressing food security and diversifying the economy. Currently the UAE imports over 90% of its food, and the country’s population is forecast to increase from today’s 9.4 million to 11.5 million by 2025. Demand for food, especially high-quality produce, is set to rise sharply. A booming AgTech industry should meaningfully reduce dependence on imports.
What is expected?
Like any investor, the government seeks the highest return for its investment. The government measures success by analyzing which initiative will have the largest GDP multiplier (i.e. where 1 AED will generate the biggest knock on effect). In addition to reducing dependency on food imports and oil revenues, the package is expected to generate a contribution of AED 1.65 billion to the GDP and create more than 2,900 jobs in Abu Dhabi by 2021.
Are there any other benefits?
In addition to funding R&D, the initiative allows it to be easy to setup in AD with world-class infrastructure etc. and attract global level talent here to make UAE a global center of excellence for this industry.
Additionally, …
Government funding alone does not ensure success. Regulations need to keep pace with technological and commercial innovation. The ADIO acts as a bridge for industry to discuss the regulatory environment. These discussions have played in a key role in recent regulatory changes for the agricultural industry.
The Abu Dhabi government consolidated regulation of the agriculture sector through the establishment of the Abu Dhabi Agriculture and Food Safety Authority (ADAFSA). This new organization has taken on the roles of the Abu Dhabi Food Control Authority, the Abu Dhabi Farmers’ Services Centre, and the Food Security Centre – Abu Dhabi. It is responsible for overseeing agriculture, food safety, food security, and biosecurity. The founding of ADAFSA is another step in accelerating the emirate’s efforts to drive scientific research and agricultural development while helping to build partnerships between the public and private sectors, according to Sheikh Mansour bin Zayed Al Nahyan, the deputy prime minister and minister of presidential affairs. He told local media:
“Food security continues to be a national and strategic priority that entails concerted actions between the government and private sectors in order to ensure a well-integrated food security strategy that is conducive to unlocking the value in the agriculture and food supply chains, and ensuring all segments of society have access to all food supplies”.
Like any new industry, businesses in the AgTech industry will inevitably discover that some aspects of the existing regulatory framework do not meet their commercial needs. This is natural as regulators cannot predict future industry requirements with 100% accuracy. However, it is encouraging to see that the government is proactive about increasing their understanding and are taking decisive actions. We are more optimistic than before about the AgTech industry’s prospects in the UAE.
For more information, please visit www.investinabudhabi.ae or follow them on Instagram, Twitter, LinkedIn and Facebook.
Digant Raj Kapoor
People Manager
Sources
Gulf News – 11 March 2019
The National – 11 March 2019
Arabian Business – 11 March 2019
ADIO Website – seen on 26 August 2019
Zawya – 15 May 2019
AgFunder News – 25 March 2019
World Future Energy Summit – 27 March 2019
Vertical Farming Reaches New Heights In Germany With Fraunhofer IME
The AVF was invited to visit its member Fraunhofer IME in Aachen, Germany, one of 72 institutes of the Fraunhofer-Gesellschaft, the leading organization for applied science in Europe with over 26,000 employees and various international branches around the world
OCTOBER 22, 2019 | KYLE BALDOCK | Indoor Vertical Farming - Association
Visit to the Fraunhofer IME in Aachen: On September 4th, the AVF was invited to visit its member IME and experience their groundbreaking, innovative vertical farming technologies live on the spot.
Aachen, 04. September 2019: The AVF was invited to visit its member Fraunhofer IME in Aachen, Germany, one of 72 institutes of the Fraunhofer-Gesellschaft, the leading organization for applied science in Europe with over 26,000 employees and various international branches around the world.
The Fraunhofer Institute for Molecular Biology and Applied Ecology IME has six different sites in Germany and conducts research in the field of applied life sciences from the molecular level to entire ecosystems. Its division “Molecular Biotechnology” is located in Aachen, Germany and conducts R&D in the field of biotechnology with a strong focus on plant-based applications.
Over the last 10 years, the IME has developed and established two different vertical farming systems at the Aachen site in cooperation with the Fraunhofer IPT and IIS (à VertiPharm) as well as the Fraunhofer IML (à OrbiPlant™):
VertiPharm, a fully automated vertical farm with a strong focus on different research applications (e.g. plant cultivation, plant phenotyping, biopharmaceutical production) and OrbiPlant™, a novel and cost-efficient approach to vertical farming of food crops. These two vertical farming systems are complemented by LEDitGrow, an innovative multi-chamber system for the rapid development of plant growth protocols and the optimization of specific plant target values.
The design of the two IME vertical farming systems, their degree of automation, data management, efficiency and productivity, as well as their application and research possibilities go beyond the current state of the art of indoor farming technology. The systems provide an unprecedented basis to promote vertical farming, not only in Germany but worldwide. The different technology platforms are available for cooperation projects. Potential cooperation partners are encouraged to get in contact with IME (see below).
During a facility tour AVF had the opportunity to visit the different systems that are outlined below.
Fig.1: LEDitGROW plant cultivation unit for the accelerated multi-parameter development of plant growth protocols (© Ann-Katrin Beuel, IME).
LEDitGROW – Multi-parameter single plant cultivation system
A LEDitGROW unit comprises 24 single plant cultivation chambers, each equipped with various different LED-based light spectra including UVA. The unit has been designed to fit into a phytotron to run experiments at defined temperature, humidity and CO2 concentration. Each plant chamber can hold a single plant or several tissue culture petri dishes and can be individually supplied with nutrient solution.
The parallelization of cultivation conditions together with a statistical multi-parameter design of experiment (DoE) approach allows the rapid establishment of species-specific growth recipes as well as the optimization of specific target values such as biomass, secondary plant metabolites or morphology.
VertiPharm – Automated multifunctional research platform for vertical farming
Fig. 2: Top view on VertiPharm’s vertical farming unit (above, © AVF) and N. benthamiana plants under LED lighting in one layer of the vertical farm unit (below, © Andreas Reimann, IME).
The highlight of the IME in Aachen is the fully automated, pilot-scale vertical farming research platform featuring core functionalities such as multi-tier-based vertical farming, single plant handling, sensor-based in-process control, 2D/3D plant scanning, vacuum plant infiltration, downstream processing and central data management.
The impressive construction of the vertical farm unit consists of eight cultivation levels and provides ~550m2 of net cultivation area for the continuous or batch-wise cultivation of plants under highest reproducibility.
Different parameters such as temperature, humidity, CO2-concentration, LED-based lighting and composition of the plant nutrient solution can be defined and monitored in the central control system. Each plant receives a unique ID during seeding and is tracked individually throughout the entire cultivation time until harvest. Movement, sensor and measurement data are continuously recorded and can be used for in-process control or retrospective analysis of cultivation parameters and specific plant characteristics.
The fully automated facility can be used to produce food and non-food plants of different varieties and sizes. In addition to the vertical farming of plants a separate vacuum-infiltration unit connected to a fermentation suite allows the rapid production of recombinant biopharmaceuticals (e.g. vaccines, antibodies or enzymes) in plants by Agrobacterium-mediated gene transfer. Thanks to this multifunctionality the plant production research platform at Fraunhofer IME enables a broad spectrum of applications in different plant-based fields but also in the field of engineering, for instance:
Cultivation of food plants
Cultivation of medicinal/ specialty plants
Cultivation of ornamental plants
Production of recombinant biopharmaceuticals
Plant breeding and plant phenotyping
Software-based applications (e.g. digitization of production, artificial intelligence, augmented reality-assisted maintenance)
OrbiPlant™ – groundbreaking vertical farming system for the cost-efficient production of food crops
Fig. 3: OrbiPlantTM pilot-scale system with various leafy greens and herbs on a conveyor belt. The plant size gradually increases along the four conveyor belt loops (© Andreas Reimann, IME).
OrbiPlant™ represents an innovative approach to vertical farming of food crops that can truly make a difference to the spread and market penetration of vertical farming.
The major difference to classical tier-based approaches is a continuous conveyor belt system that is flexibly arranged in vertical loops allowing the easy placement of seeds or seedlings on one end of the conveyor system and the easy harvest on the other end. In between plants grow self-sufficiently under specific LED lighting conditions that can be adapted to the respective growth stage.
The conveyor belt movement can be specifically adjusted to a plant’s growth cycle and takes advantage of a growth-stimulating orbitropal effect on the plant, which is stemming from the changing gravitational orientation of the plant on the conveyor belt. The water-nutrient supply is ensured by aeroponic nozzles inside the belt loops. The innovative OrbiPlant system has several key improvements over current vertical farming systems:
High plant biomass yields and short growth cycles
Low production costs (e.g. <0.40 € per lettuce head)
Optimal cost-efficiency due to minimal hardware and personnel costs
Modular conveyor belt concept easily adaptable to different plants and growth cycles as well as to different building geometries
Improved vertical heat convection
Low LED lighting requirement
Flexible degree of automation depending on customer need
OrbiPlant is not only providing a cost-effective, optimized production platform for food crops with minimal space and resource requirements, but its unique design and flexibility has the potential to take vertical farming to a new level. It overcomes the shortcomings of today’s most commonly used horizontal rack systems, saves energy, utilizes intelligent automation, and enables easy handling and operation.
The AVF in cooperation with the Fraunhofer IME welcomes company and stakeholder inquiries on the presented systems.
Contacts:
Christine Zimmermann-Lössl, AVF Chairwoman
Email: czl@vertical-farming.net
Marvin Spence, AVF Project Manager
Email: ms@vertical-farming.net
Andreas Reimann, Senior Acquisition and Project Manager at Fraunhofer IME, Business Field Indoor Farming/Vertical farming
Email: andreas.reimann@ime.fraunhofer.de
Visit Fraunhofer IME’s website to learn more about them.
Lighting Research Consortium Brings CEA Community Industry-Ready Technologies
The goal of the consortium, an initiative between NYSERDA, Cornell University and Rensselaer Polytechnic Institute, with Rutgers University participating as a collaborator, is to reduce carbon emissions, Erico explains
Without light, plants can't grow. The continued advance of controlled environment agriculture means that sunlight is often supplemented and in some cases completely replaced by artificial lighting. It works well, but there's one caveat: artificial lighting can take a lot of energy. Reason enough for the New York State Energy Research and Development Authority (NYSERDA) to kickstart the Greenhouse Lighting and Systems Engineering (GLASE) consortium with $5 million in funding. That was in June 2017. What's happened since then? Erico Mattos, the consortium's Executive Director, tells us more.
The goal of the consortium, an initiative between NYSERDA, Cornell University and Rensselaer Polytechnic Institute, with Rutgers University participating as a collaborator, is to reduce carbon emissions, Erico explains. "NYSERDA saw the growth of the CEA industry, indoor farms and greenhouses, and with technologies evolving really fast, especially on greenhouse systems like lighting controls and LEDs, they realized that there's a lot of room for technology development that can help reduce the energy consumption of lighting and integrated systems in greenhouses. So NYSERDA sponsored this program with the objective to reduce the carbon emissions coming from greenhouses' electricity use by 70% from the levels of 2017."
Cornell University Greenhouse
To achieve this ambitious goal, a combination of engineering and plant physiology is used. “At Rensselaer Polytechnic Institute we work with the center for Lighting Enabled Systems & Applications (LESA). Led by Dr. Elsebeth Kolmos, LESA engineers are developing new LED research modules, new driver technologies, and spectroanalysis to optimize plant growth under LED lights. At Cornell University, a team of researchers led by Dr. Neil Mattson is developing integrated lighting control systems based on plant physiology responses to optimize crop production yield and reduce operational costs in commercial greenhouses".
Focus on food, but everyone benefits
The consortium focuses their research on food crops - they work with the following crop models:
Lettuce
Strawberry
Tomatoes
"Those are the crops we use to do research. But the outcomes of this research," Erico points out, "can be applied to any of the industries. And our outreach activities, which are not sponsored by the NYSERDA funds but paid for by membership fees, are open to the entire CEA industry. They're pretty much crop agnostic." That means cannabis or ornamental growers, for instance, can also benefit from the consortium's efforts.
And while the consortium was started in New York, that doesn't mean it's geographically limited. "We started in New York because all the founding members are here, but at this time we have members all across the US, we have 22 industry members today, including an international body of farms, in the Middle East. For now, we're establishing a base in the US, the next step is going international."
Diagram of GLASE work frame
Sharing knowledge and technology
The consortium focuses on the following types of industry members:
CEA growers
Lighting, sensing and control manufacturers
Basic manufacturers (companies that make the LEDs, drivers, etc. that go into lighting, sensing and control)
Retailers
Service providers
So what do those members actually get out of it? "Growers get all this knowledge that we are generating. With the GLASE consortium, we have more than 300 technical milestones, from the development of new LEDs to implemented systems in greenhouses."
For growers, GLASE offers knowledge and technology transfer. "The knowledge transfer happens through our outreach activities, like webinars, industry talks, industry advisory board meetings where growers come together with manufacturers and we discuss all the research that we're doing." In addition, grower members have access to the GLASE researchers at Cornell, RPI and Rutgers University.
When it comes to the technology transfer, members of the consortium have first-hand access to technology that's developed by those researchers. "If there's any IP, for example, it's disclosed to members first - they have the right of first refusal.”
GLASE Commercial pilot: SAF Produce, Berlin, NY
Practical results
According to Erico, these are exciting times for the consortium. After the start-up phase, now the time has come to start harvesting. For instance, the consortium has developed their own LED module for lighting research. They use these to research how growers can best use lighting in their cultivation. But there's also something in it for the manufacturers: "Everything we do in these research fixtures, they can take that information and use this to guide product development.”
This research is conducted in the context of the milestones set by NYSERDA, but the GLASE researchers do get feedback from industry members during quarterly meetings (two of them by phone, two of them in-person meetings) on how this knowledge can be applied practically. "For example," Erico says, "they can make recommendations on what to research next, or on how to better implement the technology we're developing into commercial facilities." Using this feedback, the researchers tweak or adjust their research to end up with a practically implementable solution. “We are working to de-risk the technology development process by validating new technics in the lab and in commercial pilot greenhouses to provide the CEA community industry ready technologies.”
GLASE Commercial pilot: Wheatfield Gardens, Buffalo, NY
For the practical implementation, GLASE is working with two commercial lettuce greenhouses in New York State: SAF Produce in Berlin, and Wheatfield Gardens in Buffalo. Both greenhouses were retrofitted with LEDs. "It is our goal to implement all the technologies that were developed by GLASE in each of those greenhouses, establishing a baseline on the energy consumption and then compare the results before and after." This is an ongoing process, and GLASE will publish the results at a later stage.
For more information:
Greenhouse Lighting and Systems Engineering
glase.org
Publication date: 9/18/2019
Author: Jan Jacob Mekes
© HortiDaily.com
Early History of Indoor Agriculture & Associated Technology Development
This month’s Indoor Ag Science Café was about the history and current technology status of indoor farming. The beginning seems to be in Syracuse, NY, where General Electric developed an indoor hydroponic farm funded by DoD in 1973
By urbanagnews
October 17, 2019
By Dr. Cary Mitchell (Purdue University)
This month’s Indoor Ag Science Café was about the history and current technology status of indoor farming. The beginning seems to be in Syracuse, NY, where General Electric developed an indoor hydroponic farm funded by DoD in 1973. Then there was a large commercial indoor farm for leafy greens in Dekalb, IL, owned by General Mills, which was closed in the 1990s. The longest survived may be the one in Japan (TS Farm by Kewpie Co.) where they use HID lamps and aeroponics since 1989. Most significant technological improvements are two ways – one in lighting and another in rack/shelving systems. Dr. Mitchell also introduced the contributions that NASA indoor farming studies made over the past 30+ years, as one of the contributors in the space.
Indoor Ag Science Café is supported by the USDA SCRI grant program and designed to create a precompetitive communication platform among scientists and indoor farming professionals. The Café presentations are available from the YouTube channel. Contact Chieri Kubota at the Ohio State University (Kubota.10@osu.edu) to be a Café member to participate.
Indoor AgTech Landscape: 1,000+ Companies Innovating Inside
AgFunderNews created an image keeping track of the indoor growing landscape featuring 1000+ companies that take part in the industry, from greenhouse growers to suppliers of environmental controls
AgFunderNews created an image keeping track of the indoor growing landscape featuring 1000+ companies that take part in the industry, from greenhouse growers to suppliers of environmental controls.
The first thing to note is that they include greenhouses in the discussion as an indoor growing approach. At times, the conversation seems to be just limited to growing in buildings or containers with artificial lights, what we call “Sunless” or others broadly refer to as indoor, vertical, or urban farming.
Secondly, while there has been a great deal of activity around cannabis and alternative proteins such as insects, for the purpose of this landscape AgFunderNews kept to traditional food crop production.
The map focuses on the technology used in that production, from seeding to immediate post-harvest activities. We segment the landscape into the specific categories of component technologies, different types of growing systems and growers.
Read the full article, including the image of the landscape, at AFN (Louisa Burwood Taylor)
Adapter To Fool-Proof Irrigation In Vertical Farming System
Aponix’ Vertical Barrel systems have been on the market for a while now, and since their conception, they have offered an alternative to rack systems as a way of making use of three-dimensional growing spaces. Aponix is releasing some new additions to make the system even more easy to use
Marco Tidona from Aponix talks about new accessories for the Aponix vertical barrels
Aponix’ Vertical Barrel systems have been on the market for a while now, and since their conception, they have offered an alternative to rack systems as a way of making use of three-dimensional growing spaces. Aponix is releasing some new additions to make the system even more easy to use. A new adapter to simplify irrigation with the Barrel, and a new larger and soil-based XL Vertical Barrel. Marco Tidona with Aponix: “We wanted to come with a solution that would make irrigation foolproof, so we built an adapter.”
Water Adapter
Irrigation in the cylinders requires a different approach than growers are used to. “To irrigate with the barrel all you have to do is put liquid on the inside surface at the highest point, gravity will pull it down and the wing system inside will make sure is an even spread,” says Marco. “We have been testing with different kinds of irrigation methods. One simple method is to just attach an inverted sprinkler, but these additions and sprinklers needed to be used with caution, but some users didn’t. Most of the users had irrigation cycles that lasted for too long and so there was too much liquid and they drowned their plants.”
In order to come up with a solution “We wanted to come with a solution that would make irrigation foolproof, so we built an adapter. The adapter can be integrated with all Netafim spraying mechanisms. It allows us to fix the drip stop to the lid of the barrel, and then the grower can define the flowrate using the Netafim equipment.”
Lego pieces
The Vertical Barrel system is a cylindrical alternative to the typical vertical farming solution of racks. “The Barrel is constructed of individual pieces, each ring consists of 6 pieces that click into each other like Lego pieces,” says Marco, emphasizing the ease of use of the system. “The rings can be stacked on top of each other to create the barrel, this way you can define the height of the barrel yourself. We have several different pieces that are suited for different types of produce so you can configure for different types of plants to optimize the cultivation area. The cultivation area is the outside of the cylinders, and with the variable height and the possibility to chain multiple of these units, the idea is to have an alternative for a rack system in vertical farming.”
So what are the benefits of growing with the cylindrical surface of the Barrel? “When you build racks, you cannot use natural sunlight,” says Marco. “On top of that you also get microclimate issues – plus when you go very high you need these scissor lifts or climbing equipment. The Barrel is an alternative that allows you to grow vertically in a greenhouse and use natural light.”
Though the system is already quite complete, a lot of additions are being planned in order to get it technologically up to par with other vertical farming solutions. “We are also expanding the system to have plant trellis holders left and right of the grow spaces,” says Marco. “Also we are working on ways to manage the microclimate, there will be an area where you can attach an airhole next to the grow spaces which can finetune the humidity and could also fertigate CO2. These things are necessary to compete with all the high-tech solutions that are already out there.”
Credibility
It can be quite difficult to get your foot in the door with a new product in the horticultural industry. “It took a lot of time to get slight credibility,” says Marco. “I remember the first year I was presenting this new technique at GreenTech, people thought it was just a gadget for your living room – they didn’t take it seriously. They didn’t see it as serious growing equipment, because it wasn’t what they knew – it wasn’t gutters and tables. So I am now trying to get this credibility by integrating and getting a lot of help from Gakon.”
According to Marco, Gakon are a very important partner for Aponix. “Gakon are helping me to add all these gadgets and functions that they know from the standard equipment they are using for large scale production. We are collecting ideas from them for the practical side, and we are translating them for vertical barrels. Gakon have been a major help for getting taken seriously. They have their partner companies, with whom they discuss our products. One such partner company is Hortilux, for lighting. With the help of Gakon, Hortilux are creating lighting plans for use with our barrels.”
The future
Marco believes that there is still a lot of future potential for the Vertical Barrels, and these new accessories are a step forward. “All the processes that are normally part of larger commercial operations are missing,” he says. “This product has the potential, but I need to find strategic partners who actually have the experience in the market and want to have a future alternative to racks. More and more big players in the industry are understanding the value of my product and inviting me to talk to them.”
Marco continues: “I had an interesting conversation with a company from the UK. They are building this robot that you can put over your raised beds and it functions like an agricultural printer: it irrigates, plants seeds, it takes care of your plants, and it’s fully automatic. This company is thinking about putting one of these robots, but with a circular arm, on top of my barrels. So it’s not using a flat surface like you have in a raised bed, but the round surface coming from the top and circling around. The future is looking exciting, but I am still looking for more people that believe in my product and want to support it in ways that I alone cannot.”
For more information:
Marco Tidona
Aponix
Publication date: Tue, 08 Oct 2019
Author: Brian de Lint
© HortiDaily.com
Netled To Supply SweGreen With Production Units
Netled has signed a distribution agreement with Swedish technology company SweGreen. They will start providing Vera Compact Production Units for SweGreen’s urban farming destinations in Sweden. SweGreen is an innovation and technology urban farming company based in Stockholm. The company provides circular solutions for controlled-environment urban farming
Netled has signed a distribution agreement with Swedish technology company SweGreen. They will start providing Vera Compact Production Units for SweGreen’s urban farming destinations in Sweden.
SweGreen is an innovation and technology urban farming company based in Stockholm. The company provides circular solutions for controlled-environment urban farming. By integrating smart vertical farming solutions into real estate properties SweGreen provides circular energy-waste-water and carbon-absorbing systems, which enable locally grown, quality greens and help minimize the environmental footprint of facilities. Under the brand Stadsbondens, SweGreen’s CityFarm in Stockholm produces herbs for ecological-minded citizens all year round in a sustainable way.
Netled´s Vera Compact Production Units are especially well-suited for limited scale production of salads, herbs, seedlings and pot plants, and will complement SweGreen’s efforts perfectly.
For more information:
Netled
netled.fi
Publication date: Tue, 08 Oct 2019
US: Indiana - High-Tech Aeroponic Farming Company Bringing Greenhouse To Electric Works
A northeast Indiana native and Purdue graduate, Clint Crowe, with an extensive background in health technology, is bringing his innovative and high-tech urban-farming concept to Electric Works
September 18, 2019
A northeast Indiana native and Purdue graduate, Clint Crowe, with an extensive background in health technology, is bringing his innovative and high-tech urban-farming concept to Electric Works.
Sweetwater Urban Farms, an Atlanta-based company founded in 2017 that uses aeroponic technology, helped by with proven Internet of Things — no human interaction to transfer data — to produce nutrient-rich greens and herbs, will open a greenhouse in the food hall at the planned Electric Works, according to a statement from a spokesman for the developer, RTM Ventures.
The greenhouse uses a “zero-mile delivery” system, so food is available closer to where it is consumed. It will also offer retail sales of its produce at Electric Works, a mixed-use project that reuses the former General Electric complex on Broadway. As of Aug. 29, the project had up to 15 leases or letters of intent for leases on between 200,000 and 225,000 square feet at Electric Works.
Sweetwater Urban Farms plans to make produce available for delivery to local restaurants, hotels, health care institutions, and schools.
The greenhouse is expected to house up to 400 patented commercial Tower Gardens and produce an estimated 47,000 pounds of produce a year, according to the statement. Tower Garden aeroponic technology re-circulates valuable water, requiring only 10% of the land and water of traditional growing methods.
Crowe, a Decatur native with nearly 18 years of experience in healthcare technology, founded the company with his wife, Sheree.
“When we visited the Electric Works site, we immediately saw the unique potential it offered our company and the community,” Crowe said in the statement. “Being from the region, it’s exciting to come back and see the momentum in the city. Food security is at the heart of any community’s long-term plan, and we see Sweetwater Urban Farms and Electric Works as a strategic starting point and will play a key role in ensuring this community’s future food security.”
Crowe expects to partner with area healthcare and educational institutions, and fellow agricultural-business entities to support increased awareness and education of the value of locally sourced food and its impact on health and wellness. The company may also support a planned agriculture-technology program that Fort Wayne Community Schools is exploring for its planned STEAM — Science, Technology, Engineering, Arts and Mathematics school at Electric Works.
“At the intersection of agriculture and technology, Sweetwater Urban Farms is the kind of innovative company that we want to bring to Electric Works and Northeast Indiana,” said Jeff Kingsbury of the Electric Works development team in the statement. “Clint’s unique background — both in health care technology and as a regional native — makes the company a perfect fit for Electric Works. The food hall and public market are important to building community within the Electric Works district. But, it’s also about enhancing access to healthy food to address this neighborhood’s long-standing status as a food desert – Clint and his team will play an important role in that from the beginning.”
Solar Foods Receives World's Most Prestigious Design Award
Solar Foods is a foodtech company developing globally revolutionary solutions for food production. The bioprocess and technology developed by Solar Foods enable food production without agriculture. In the future, harvesting can comprise of an entirely new harvest grown in a clean environment, while complementing existing protein sources with new natural protein
06/09/2019
Solar Foods, the Finnish company producing protein by using carbon dioxide and electricity, has been presented with the Index Award supported by the state of Denmark. The 100,000 euro award is given for the most impactful solution significant to the environment and improving people’s lives.
The Index Award is a biennial award supported by the state of Denmark. The total award fund is €500,000 divided between the winners in five award categories. Index Award has existed since 2005 and is the biggest money prize in its class. This recognition, also called the “Nobel prize for design”, acknowledges actors solving global problems in areas such as equality, food production, and plastic pollution.
Participants include projects from all over the world, with the finalists and winners judged by an international jury. Other winners of this year’s prize include Microsoft and Xbox, with previous winners including Elon Musk. The award is under the patronage of Crown Prince Frederik and Crown Princess Mary of Denmark.
Denmark has the ambitious goal of being a carbon-neutral country by 2050. Therefore, many Danish companies have set themselves the target of becoming the most responsible company before anyone else in their business.
“It is a magnificent feeling to know you are taking part in global responsibility. Researchers must turn the inventions and technologies incubated in laboratories into reality and commercialise them faster to benefit humankind. The Solein® protein is an excellent example of an innovation urgently needed by humans and the entire globe,” says Pasi Vainikka, CEO, Solar Foods.
Solar Foods is a food tech company developing globally revolutionary solutions for food production. The bioprocess and technology developed by Solar Foods enable food production without agriculture. In the future, harvesting can comprise of an entirely new harvest grown in a clean environment, while complementing existing protein sources with new natural protein.
At the core of the company’s operation is a sense of enormous responsibility: using renewable energy for producing food in a way that has the lowest possible environmental burden.
“The report by the Intergovernmental Panel on Climate Change and the rainforest wildfires in Amazonia are recent examples of the dire news we are witnessing about the state of the globe and its food system. At Solar Foods we develop solutions that disconnect natural resources from economic growth and food production. That’s how we are contributing to a solution in the crisis of global food supply,” Vainikka says.
Cleanest natural protein
Solar Foods is introducing a globally revolutionary protein for foodstuffs for consumers made in its bioprocess developed in-house. The Solein protein, suitable to be added to a variety of products, is produced mainly from air and electricity. In the future, Solein protein can be grown and harvested anywhere: in the middle of a desert, or even in space.
Solein is natural protein at its cleanest. Its production minimises harmful environmental impact, thereby providing transparent support for sustainable development. Revolutionary on a global scale, Solein is a protein for solving problems in managing the global food crisis and the overexploitation of natural resources. Solein is the product of natural evolution over hundreds of millions of years by using the diversity of nature.
At present, Solar Foods is studying the applicability of the Solein protein to different diets and consumer preferences. The protein includes no additives, instead, consumers will know it as an example of an ethical, clean source of protein. Solein’s amino acid composition is like that of soya and algae, therefore optimal for human needs.
Solar Foods aims at starting the first stage of commercial production of the protein during 2021.
Download Solar Foods Presentation
More information:
Pasi Vainikka, DSc (Tech), CEO, Solar Foods Oy, tel. +358 40 5825 987, pasi@solarfoods.fi
Solar Foods is a food-tech company that develops revolutionary innovations for food production at a global level. Solar Foods is an active player in solving the global food crisis and securing sustainable use of natural resources by disconnecting food production from agriculture. Solein® is a registered trademark of Solar Foods. www.solarfoods.fi
CANADA: NatureFresh Farms Celebrates Strong Start To Season For Newly-Developed 32-Acre Greenhouse In Leamington, ON
After nine months of construction, the fully completed facility measures 32 acres in total area and, to the gutter, is 7.3 meters tall. With ample space to grow hundreds of thousands of pounds of Tomato varieties for every season to come
NatureFresh Farms is celebrating a 20-year growing milestone with a strong start to the first season at their newly-developed 32-acre greenhouse in Leamington, ON.
After nine months of construction, the fully completed facility measures 32 acres in total area and, to the gutter, is 7.3 meters tall. With ample space to grow hundreds of thousands of pounds of Tomato varieties for every season to come, NatureFresh Farms is growing just over 15 acres of Tomatoes-on-the-Vine and over 15 acres of a diverse range of Specialty Tomato varieties, including Red Cherry, Red Grape, and Cocktail Tomatoes.
For their first crop, NatureFresh Farms successfully planted 235,000 Tomato plants in May 2019. With it only taking 8-9 weeks from planting to reach the first harvest of Tomatoes, their team started picking Tomatoes in June 2019 and will continue until late next Spring. A crew of 80 team members will be working every day to pick, pack, and ship their Tomato products, with the Growers, Scouts, and Crop workers attending the plants, offering their expertise for a seamless growing season.
Matt Quiring
Executive Retail Sales Accounts Manager Matt Quiring isn’t surprised by the great success of this new facility to meet demands for fresh local produce that is available year-round: “NatureFresh Farms made a major commitment to year-round consistency in supply, quality, and flavor five years ago when we built our greenhouse in Ohio for winter production. This allowed us to offset the typical growing season for Canada and it has been a tremendous success for our retail partners – and consumers have shown support for the USA-grown program from the start,” said Matt. “That demand continues to grow each year. We are excited to be able to offer retailers and consumers in Ontario and Canada that same consistency in supply, quality, and flavor that local products offer!”
This state-of-the-art greenhouse is also equipped with innovative technology, creating the best growing environment possible. The use of self-driving cart systems, High-Pressure Sodium supplemental lighting fixtures, and Vertical Circulation Fans are just a few examples of the innovative technology being used in this cutting-edge facility – all of which will help the NatureFresh Farms Tomato crop grow during the winter months and produce high-quality food on a consistent basis.
The completion of this greenhouse brings NatureFresh Farms to over 200 acres of family-owned facilities. With 20 years of providing quality greenhouse-grown vegetables all year-round, NatureFresh Farms looks forward to the future – with continued advancements in sustainable technology and product innovation on the horizon.
Indoor Farming Technology Leader, SANANBIO®, Debuts UPLIFT Vertical Farming System
SANANBIO firmly believes that agriculture technology should be based on science paired with input from farmers. Michael Yates, SANANBIO's VP of Sales said, "Advanced knowledge of plant physiology and photobiology are fundamental to success in the vertical farming industry
The System Offers Customers A Fully
Automated Indoor Growing Process
LAS VEGAS, NEVADA (September 25, 2019) – SANANBIO®, a leading provider in LED horticulture lighting and vertical farm equipment and technology, announces the commercial release of its fully automated vertical farming system, UPLIFT (Unmanned Platform of Lean and Intelligent Farming Technology). Decades of manufacturing and automation experience, combined with successful multi-year vertical farm operations through parent company Sanan Optoelectronics has given SANANBIO the expertise in designing and operating the UPLIFT system to offer its customers a proven, fully automated indoor growing process.
SANANBIO firmly believes that agriculture technology should be based on science paired with input from farmers. Michael Yates, SANANBIO's VP of Sales said, "Advanced knowledge of plant physiology and photobiology are fundamental to success in the vertical farming industry. Through employing one of the world's largest teams focused on advancing vertical farming technology, UPLIFT is the solution born from the efforts of over 100 plant scientists and engineers."
The UPLIFT automated solution is based on SANANBIO's highly successful manual vertical farming grow system being used in farms today, RADIX. "With over 1M square feet of commercial vertical farms currently using RADIX, farmers and investors in more than 10 countries believe in our company's highly engineered grow technology. The proof is in the plants as our customers like to say," said Yates.
SANANBIO designed and installed the first pilot UPLIFT farm in April 2018 at its facility in Xiamen, China. After 18 months of operation and optimization, the UPLIFT system is now available for commercial deployment globally.
UPLIFT offers a full suite of automation for growing vertically. From seeding and germination to transplanting and harvesting, the high-stack, high-cube configuration offers the latest advancements in vertical farming solutions that reduce labor while achieving higher yields. The UPLIFT farming platform also benefits from an industry-standard production and inventory management system facilitating crop management, farm production planning, and crop traceability.
"Labor costs continue to be a major challenge for vertical farm operators while also maintaining profitability," stated Dr. Charlie Wang, SANANBIO CEO. "The UPLIFT system will help operators significantly reduce labor costs so they can sell more fresh and healthy produce, and therefore receive better returns on their investment. The system also provides an open platform to integrate technology that enables farms with more intelligence and controls allowing for maximized yields and profitability," said Wang.
SANANBIO's engineers and sales teams are prepared to work with leading farmers and investors in the industry who share the same passion to build ground-breaking projects in controlled environment agriculture using this cutting-edge technology.
SANANBIO® is a trademark carried and backed by Sanan Sino-science Photobiotech, a company invested in by Sanan Optoelectronics, one of the world’s largest LED chip manufacturers. Supported by an elite R&D team comprised of plant scientists, researchers, and engineers; SANANBIO utilizes state-of-the-art technology that enables growers worldwide in the horticulture industry to increase the quality and quantity of their yields. Years of extensive research and real-world deployment and operations allow SANANBIO to offer its customers proven, scalable, efficient and cost-effective solutions in LED horticulture lighting and Controlled Environment Agriculture (CEA) vertical farming grow systems. SANANBIO empowers growers with the technology and knowledge to achieve unprecedented results in farming operations.
To learn more visit: https://sananbious.com/
###
Ahold Delhaize's 150-Square-Foot Store Packed With Big Tech
Ahold Delhaize is piloting a fully digital, 150-square-foot AH to go store, packed with technological innovations that make it possible for customers to buy something as if they were taking it out of their refrigerators, with no checkout or self-scan
September 05, 2019
Ahold Delhaize is piloting a fully digital, 150-square-foot AH to go store, packed with technological innovations that make it possible for customers to buy something as if they were taking it out of their refrigerators, with no checkout or self-scan. The store is located in front of a support office and will be tested with associates in the coming two months.
Under the roof of the small AH to go is an enormous amount of technology. This is how it works: the door opens automatically with a debit or credit card. In the store, customers grab the products they want. Cameras determine the position of customers (without facial recognition) and associate product items to their virtual baskets.
In addition, in-store sensors keep track of products that are taken off or put back on the shelves. When the shopping is done, customers walk to the exit where the payment takes place automatically and the door opens. Customers do not have to register in advance or download an app, which makes the payment system innovative and very accessible.
The store has been developed together with AiFi, a U.S.-based start-up. Dutch bank ING has developed the payment solution and takes care of payment processing.
Marit van Egmond, brand president of Albert Heijn, said, “This latest concept not only makes shopping very easy; due to its autonomous nature, this ‘plug and play’ store can be placed at locations where there is a (temporary) need for a small store, from offices or university campuses to residential areas under construction that do not yet have shopping facilities. A second advantage is that the store can always be open, which is useful for people who are on the road very early or very late.”
This initiative is the latest example of how Ahold Delhaize brands are experimenting with new payment solutions to help customers save time at the checkout. Albert Heijn last year opened its first checkout-free stores, where customers can pay right at the shelf with a “tap to go” card or using a mobile app. Delhaize Belgium earlier this year launched a mobile payment application, called YesWeScan, which allows customers to scan product barcodes with their smartphone, add the items to an electronic shopping basket, and then pay. And in the U.S., Stop & Shop is offering frictionless checkout using the SCAN IT! mobile app.
Intelligent Growth Solutions Attracts Further US AgriTech Investment To Scotland
Intelligent Growth Solutions Ltd (IGS), the Scottish-based indoor AgriTech and Commercial Lighting business, announced today a further raise of £1.6 million in the second and final close of its Series A funding
Edinburgh, Scotland – 26 September 2019 - Intelligent Growth Solutions Ltd (IGS), the Scottish-based indoor AgriTech and Commercial Lighting business, announced today a further raise of £1.6 million in the second and final close of its Series A funding. The £1.5 million received from globally established agri-investor Ospraie Ag Science (OAS), coupled with an additional £100k from Agfunder, brings IGS’ total Series A fundraise to £7 million.
Ospraie Ag Science (New York City) joins existing Series A investors S2G Ventures (Chicago), the most active agri-foodtech investor globally in 2018; online venture capital firm AgFunder (San Francisco); and the Scottish Investment Bank in the investment round.
Ospraie brings 25 years of agriculture investing experience to IGS, and its investment in the company is its first step towards building a global platform in the indoor AgriTech market.
Dwight Anderson, Chief Investment Officer at Ospraie Ag Science commented: “IGS has tremendous potential to transform the way food is produced and supplied, and our investment – Ospraie’s first in the indoor agriculture market and in Scotland – is a testament to our strong belief in the success of IGS’ technology. The benefits of IGS’s Vertical Farming align well with our mission of helping farmers do more with less. We look forward to leveraging our significant agriculture network to help IGS grow its business to meet the market’s demand for sustainable solutions.”
This latest raise allows IGS to further expand its market presence through global sales operations for both AgriTech and Commercial Lighting. Demands for its systems are high with the first deployments expected in early 2020.
IGS Chief Executive Officer David Farquhar said: “The further investment of £1.6 million is a hugely exciting one, not only for our business but also for the Scottish economy. Ospraie has chosen IGS as its initial investment target in the indoor agriculture market, and also as its first investment in Scotland, which is a substantial endorsement of our technology and approach to date. Working alongside our other investors in this Series A funding we are in a really strong position to take our offering to a global market and meet the demand that is growing almost daily.
“The pressures of climate change are real and clear and our technology and systems have the ability to play a part in addressing how we produce and supply food sustainably and productively all over the world. Our customers in the commercial property world are equally keen to adopt IOT-enabled smart lighting to create better indoor climates for their tenants and visitors alike.”
IGS has designed all its products to be highly pragmatic, flexible, modular and scalable in line with market expectations.
Sanjeev Krishnan, Managing Director of S2G Ventures said: “We are excited to partner again with Dwight and the Ospraie team. IGS will benefit greatly from the Ospraie insights, networks and entrepreneurial vision in building scaled businesses in the outdoor sector. Indoor Ag is set up to grow considerably and we are excited about IGS’ role in that effort.”
Michael Dean, founding partner at AgFunder commented: “We are delighted to see our friends at Ospraie join us as investors in IGS. We look forward to working with the Ospraie team to ensure that the game-changing IGS technology is rolled out to Controlled Environment Agriculture project developers globally.”
Kerry Sharp, Director, Scottish Investment Bank, said: “Intelligent Growth Solutions has made good progress recently. This latest investment is a testament to the hard work and vision of the management team and will help the company as it takes its technology to the global marketplace. A company like IGS securing three international investors in Ospraie, S2G, and AgFunder goes a long way to highlight the strength of opportunities available for Investors outside Scotland looking to invest in innovative Scottish companies. We look forward to continuing the journey with the company through our investment and our Scottish Enterprise account management service.”
The Scottish-led R&D team at IGS has developed, patented and productised a breakthrough, IoT-enabled power and communications platform consisting of patented electrical, electronic and mechanical technologies as well as the world’s most sophisticated ventilation system. All this is managed by a SaaS and data platform using AI to deliver economic and operational benefits to indoor environments across the globe.
About IGS:
IGS was formed in 2013. Its purpose was to bring indoor horticulture to commercial reality by combining efficient internet-enabled smart lighting with automation and power management. The founders’ experience combined extensive knowledge of horticulture, industrial automation, and big data.
IGS launched its first vertical demonstration facility in August 2018 and is now selling a revolutionary controlled-environment growth system. The location of IGS’ facility at the James Hutton Institute, a world-leading crop research facility, was deliberately chosen to enhance collaboration opportunities for the benefit of customers. Scientists and researchers at the Institute are working with the team at IGS to better understand how growing indoors can impact different varieties of crop growth, as well as driving increased productivity.
For more information visit www.intelligentgrowthsolutions.com or connect with us on Twitter and LinkedIn.
About Ospraie Ag Science:
Ospraie Ag Science LLC (OAS) identifies solutions to help farmers "Do More With Less". By increasing profitability, improving quality-adjusted yield, and reducing environmental impact, OAS’s companies not only benefit producers, but generate smarter, healthier, and more efficient food for consumers globally. Utilizing its extensive network and 25 years of experience investing in agriculture, OAS is positioned to help farmers achieve a sustainable future.
About S2G Ventures:
S2G Ventures (Seed to Growth) is a multi-stage venture fund investing in food and agriculture. The fund’s mission is to catalyze innovation to meet consumer demands for healthy and sustainable food. S2G has identified sectors across the food system that are ripe for change and is building a multi-stage portfolio including seed, venture, and growth-stage investments. Core areas of interest for S2G are agriculture, ingredients, infrastructure and logistics, IT and hardware, food safety and technology, retail and restaurants, and consumer brands. For more information about S2G, visit www.s2gventures.com or connect with us on Twitter and LinkedIn.
About AgFunder
AgFunder is an online Venture Capital Platform investing in the bold and exceptional entrepreneurs transforming our food and agriculture system. Our in-house technology enables us to invest globally and at scale, make better investment decisions, and support our portfolio companies. Through media and research, AgFunder has built a community of over 60,000 members and subscribers, giving us the largest and most powerful network in the industry.
Stay up-to-date with Food Tech and AgTech startup news, and other reports, by signing up to our newsletter here.
About the Scottish Investment Bank
The Scottish Investment Bank (SIB) is the investment arm of Scotland’s national economic development agency, Scottish Enterprise, operating Scotland-wide in partnership with Highlands and Islands Enterprise (HIE). SIB’s activities support Scotland’s SME funding market to ensure businesses with growth and export potential have adequate access to growth capital and loan funding.
SIB manages a suite of co-investment funds including the Scottish Co-investment Fund, the Scottish Venture Fund and the Energy Investment Fund on behalf of the Scottish Government. SIB is also an investor in Epidarex Capital’s Life Sciences Fund and is a participant in the Scottish-European Growth Co-Investment Programme with funding secured from the Scottish Government’s Scottish Growth Scheme alongside the European Investment Fund.
SIB also provides funding into LendingCrowd, Scotland’s marketplace lender providing loans to SMEs, and Maven's UK Regional Buy-Out Fund (MBO) that offers financial support for management buyouts (MBOs) and helps existing management teams acquire their businesses from their owners so they can continue to flourish. SIB’s team of financial readiness specialists help companies to prepare for new investment and access appropriate finance.
Why Technology May Make Animals Obsolete
The world is about to change very quickly. As venture capitalists, our job is to identify technologies that will be embraced by the future and then bet on that future
Published on September 24, 2019
Rob Leclerc, PhD
Founding Partner at AgFunder, Forbes Contributor
Cars replaced horses, petroleum replaced whales, tractors replaced oxen, telecommunications replaced carrier pigeons, fermentation replaced cows and pigs for insulin production. And despite its many shortcomings, plastic continues to take market share from leather. Wherever we look, humans have consistently built technologies that surpass their animal predecessors. Food may be next.
The world is about to change very quickly. As venture capitalists, our job is to identify technologies that will be embraced by the future and then bet on that future.
All over the world, entrepreneurs are reinventing how we make products we’ve traditionally derived from animals. Applying the latest technologies from biotech, tissue engineering, artificial intelligence, and food science, entrepreneurs are trying to create new animal-free products that are cheaper, healthier, tastier, and more sustainable. Even if they’re moderately successful, they’ll have an opportunity to capture a meaningful portion of the $1.5 trillion dollar animal protein market [1]. Opportunities don’t come much bigger than that. As venture capitalists, this is hard to ignore.
The world is about to change very quickly. As venture capitalists, our job is to identify technologies that will be embraced by the future and then bet on that future.
Today we’re announcing AgFunder’s upcoming alternative protein fund. This fund will invest in animal protein alternatives, including plant-based alternatives, cellular agriculture, and the picks and shovels technologies required to enable this emerging industry.
The key insight driving our investment thesis is that for thousands of years animals have been employed as a technology to provide valuable products and services including transportation, communications, energy, labor, clothing, medicine, and of course food. But history has shown animals are not necessarily the best means for these end products and services. The market demands them, but it shows little allegiance to their mode of production. And so when new technologies come along that are better and cheaper, markets tend to switch. And switch fast. Just as chicken replaced beef as a staple protein because it was cheaper and perceived as a healthier alternative, large swaths of the commodity meat industry are similarly at risk of substitution. The history of technology teaches us that this outcome is rarely escapable.
We anticipate that many consumers will shift to animal-free food products if those products begin to meet or exceed their animal-based alternatives on key areas like cost, taste, functionality, convenience, and health. Factor in a more conscious consumer concerned about the impact of animal agriculture on our environment and sustainability and that switch may happen even faster.
Why now?
Plant-based products have been around for a long time, so why is this happening now? We believe it traces back to four key trends.
First is the emergence of social media, which led to the formation of new food tribes and trends including organic, gluten-free, vegan, keto, flexitarian and reducetarian. These new digital distribution channels are permissionless and they allow indie brands to take their message directly to customers long underserved by large food companies focused on the mass market. These customers embrace brands that reflect their own values.
Second is the emergence of a more conscious consumer concerned about health, climate change, the environment, and animal welfare. Particularly among millennials, Gen Z, and parents.
We anticipate that many consumers will shift to animal-free food products if those products begin to meet or exceed their animal-based alternatives on key areas like cost, taste, functionality, convenience, and health.
Third is the emergence of new technologies such as gene editing, recombinant proteins, and artificial intelligence as well as major advances in tissue engineering, DNA sequencing, and mass spectrometry. Not only can food companies now create new products like never before, but these new technologies can be protected with intellectual property, which ultimately makes these opportunities venture-backable.
Fourth is the recent emergence of a small group of passionate and mission-driven entrepreneurs who want to effect change in our food system. They recognize that to achieve their goals, they need to create products that taste as good as products derived from animals; products that even a carnivore would love.
Importantly, many of these early pioneers didn’t choose to become mere protein ingredient companies. Rather, they chose to be consumer-facing companies that could control their narrative and they took their message directly to the market. With savvy PR and the help of social media, a single article in the Wall Street Journal could launch dozens of blog posts and make the internet buzz. This early success has subsequently attracted a whole new generation of entrepreneurs and venture capitalists who can more rapidly execute on these successful playbooks. This is the beginning of the second wave.
Disruption can happen fast
In 2008, Blockbuster’s CEO declared that ‘Netflix wasn’t even on the radar’ in terms of competition. Eighteen months later they declared bankruptcy. The paradox of disruption is the proverbial frog in boiling water; not much happens from one moment to the next. You acclimate to the new environment without realizing you’re sealing your fate by not reacting.
Once alternative protein companies get the taste, texture and cost right, how fast do they need to scale to see a complete flip in the market? Let’s unpack this by using plant-based meat company Impossible Foods as an example and start with the assumption that they’re able to migrate to alternative pork, poultry, and fish products.
Technologies are emerging that are poised to capture large portions of the traditional animal ag market, not because they are being forced on the market but because consumers are making the switch.
To supply the world population with alternative meat at current animal-meat consumption levels (94 pounds/person), Impossible Foods would need to achieve a global annual production of 700 billion pounds. Today, they reportedly have an annual production capacity of just 24 million pounds from a single facility in Oakland; just 0.003% of their total addressable market. They’re not even making a dent. But what if they could double their production capacity every year? In just 15 years and with 30,000 production plants, they could match the global demand for meat.
Assuming a capital cost of $50m/plant, this would bring total CAPEX to $1.5 trillion. While we know of facilities producing eight million pounds monthly with similar CAPEX, this should serve as a high watermark. As a sanity check, Samsung spent $41 billion on CAPEX in 2017 and 2018 [2] so while CAPEX and scaleup challenges make it unlikely that any one company could corner the market, the sheer size of the opportunity suggests that there could be dozens of multi-billion dollar companies globally.
But what about the inputs? Given that one pound of soybeans has roughly 35% more protein than beef, we will make the conservative assumption that each pound of soy–or another equivalent protein-rich plant–could produce one pound of plant-based meat with equivalent protein content. At current average production of 50 bushels/acre, this would require 235 million acres of farmland to produce 700 billion pounds of protein-rich plants. On a land-equivalent basis, this could already be met with acreage from today’s global soy production alone.
However, if these products become better and cheaper, we’ll need to account for the ensuing rapid increase in global per capita consumption. Revising our calculation above, we can ask what would it take to supply the world at US consumption levels of 222lbs/year? As it turns out, we’d only need two years of doubling annual production to meet that additional demand and 550 million acres of soybean-equivalent acres. To put this in context, that would require about a third of the world’s arable land, which is the amount currently used to grow feed for livestock [3].
Here there be Dragons
Whether or not you support animal agriculture, there are major scale-up challenges in meeting the protein demands of another 2.5 billion consumers by 2050. This will require new ideas, not higher density animal confinement, deforestation, and further strip-mining of our oceans. Our thesis is that new technologies are emerging that are poised to capture large portions of the traditional animal agriculture market and advance pieces of the protein puzzle. Not because these technologies are forced on the market, but because consumers are making the switch.
Still, there are many questions that need to be answered around scalability, health, nutrition, price, regulations, and, of course, public acceptance. And so despite the size of the opportunity, investment in this sector comes with significant risks and challenges.
Health: Many consumers are growing increasingly wary of processed foods, and just because something is plant-based doesn’t necessarily mean it’s healthier. Margarine was invented in 1869 in France as a butter substitute made from rendered beef fat for the armed forces and lower class. Shortages in beef fat combined with advances in hydrogenation of plant materials eventually led to the production of pure plant-based margarine by the end of World War II [4]. At its peak, margarine captured nearly 75% of the butter market, but with growing health concerns around trans fats, margarine ceded its market dominance and today holds about 40% market share [5]. As highly processed foods, plant-based products are going to have to place a major focus on health as well as taste and cost to displace meat or compete against cellular agriculture. Furthermore, cellular agriculture and animal-based products may have other factors that contribute to nutrition that plant-based products need to contend with.
Environmental: Plant-based products are also going to have trouble escaping problems and criticism faced by conventional agriculture, which include monocropping, chemical and fertilizer use, and top-soil depletion. And if these products require ingredients like palm oil, critics will readily point out the hypocrisy given that industry’s record on human rights and sustainability. If startups choose to take a moral high ground, they’re also going to be held to a higher standard.
Cost: Fermentation-based startups like Perfect Day, Clara Foods, and New Culture, which brew genetically-modified microbes that express animal proteins, will also have their challenges. These techniques have been used successfully in the biopharma industry, but these tend to be extremely high-value proteins and it remains to be seen whether these companies can produce their proteins economically and at-scale to compete with commodity ingredients.
Scale: Cellular agriculture, which may be the holy grail, also has many challenges. Well known names in the space in different categories include Memphis Meats (Beef), Finless Foods (Fish), SuperMeat (Chicken), and Shiok Meats (Shrimp). A few years ago, critics pointed out that cellular agriculture relied on the blood of fetal calves (Fetal Bovine Serum), but that’s generally a thing of the past and several biotech companies are now offering plant-based, serum-free media. However, cell culture media still costs about $500/L and today you need between 10L – 40L of growth media to produce just 1kg of meat. These costs will need to come down significantly to compete with both conventional meat products and even plant-based alternatives. But costs are coming down quickly, and we’ve seen companies claiming media costs as low as $40/L on top of using dialysis technologies to recycle their media. In fact, what amazes us most about the cell-ag industry is just how fast it is moving.
Plant-based products will have trouble escaping problems and criticism faced by conventional agriculture, which include monocropping, chemical and fertilizer use, and top-soil depletion.
Capex: At scale, the cell-ag industry will also have to come up with bioreactor technologies that are more robust than food-grade fermentation equipment, but which are far less costly than pharmaceutical-grade bioreactors. Lessons from cleantech remind us that CAPEX can kill businesses producing commodity products. However, the first versions of these products will likely not be complex meat products. Instead, they will likely be high-value ingredients that improve the taste and texture of plant-based products, even at low quantities.
Consumer acceptance: But the ultimate test for cell-ag will be customer acceptance. To get taste and texture just right, startups may need to incorporate additional constituents like fats, myoglobin, and vasculature, making the process more complex. Even then, the thought of eating cultured meat may be off-putting to many consumers and it’ll be a challenge to create a product that can compete with a whole muscle bone-in ribeye steak. Still, there seem to be many opportunities in food ingredients and processed products like dumplings, meatballs, hotdogs and hybrid plant/cell ag burgers. This may not be the meat our fathers will eat, but with no antibiotics, chemicals, or ethical objections, it may be the meat our children will eat.
Social: And let’s not forget the farmers in this equation. Many farming families have been proudly operating for six or more generations. Row crop farmers may see a welcome boom from plant and cell-ag based protein, especially if this demands higher grade–less commoditized crops–but farmers whose livelihood depends on animal farming will naturally feel threatened. Look no further than Missouri, which recently became the first State to prohibit the use of the word “meat” to refer to anything other than animal flesh [6]. However, since protein alternatives will likely compete with commodity meat, there should still be a long-lasting market for producers focused on high-quality, more sustainable meat production.
Competition: On the business front, startups will face fierce competition from the incumbents. On the plant-based meat front, Tyson recently announced their Raised & Rooted plant-based meat brand, Nestlé announced their Incredible Burger, Kellogg’s announced Incogmeato, Kroger’s announced Simple Foods. As they say, if you can’t beat them, join them. And you can bet companies like this are willing to spend billions of dollars on R&D to defend billions of dollars of market share. Plant-based protein companies will need to find defensible strategies beyond brand to remain durable but they are disadvantaged because Big Food is unable to take the same risks of the younger and more agile startups with much less to lose.
AgFunder’s Alt Protein Fund
The world is about to change very quickly. As venture capitalists, our job is to identify technologies that will be embraced by the future and then bet on that future. These bets are informed by consumer demands that drive markets and technology triggers that suddenly make the impossible possible.
All over the world, entrepreneurs are working to create new technologies to replace the need for animal farming. These are PhDs and food scientists from leading research labs around the world who are bringing the latest science and engineering to bear on this problem. With two biology PhDs from Yale and Stanford on our investment team, this is a language we also know how to speak. The passion and talent we see in this industry is second to none and it makes innovation in this space move so much faster. These are mission-driven founders who are out to make a big dent in the universe, and we’ve been inspired to join them on their journey.
The passion and talent we see in this industry is second to none and it makes innovation in this space move so much faster.
We believe this is an important mission, and that this is one of those rare moments in history where a technology comes along that could genuinely make the world a better place. In the short-term, we recognize that new technologies often lead to new problems. The invention of the car came with urban sprawl, pollution, and over 1.25 million fatalities each year. But cars are also getting cleaner, safer, and more efficient and few of us are willing to go back to the horse carriage. Disruption doesn’t occur because a technology is pushed on unwelcoming consumers. Instead, disruption occurs when it suddenly fills a vacuum in consumer demand. The arrow of technological progress always points toward a better future and we trust in the wisdom of the markets to get us there.
Over the next few weeks, we will be releasing a white paper followed by an announcement of the new fund with a tentative target size of $20 million. The fund will invest globally and will seek to invest in the best of breed companies from pre-seed to pre-IPO in addition to some secondary transactions.
The fund will be open to both individual accredited investors and institutional investors. Investors investing less than $1 million will have an opportunity to participate in the first close period ending on December 15. If you would like to get notifications and early access to the fund, you can signup here.
For others who are interested in getting involved, we’re also doing a call for mentors. We’re particularly looking for individuals who have distinguished careers or unique talents that will be relevant to the founders of these companies. If you’d like to be considered for a mentorship role you can apply here.
Questions or comments, email us at funds@agfunder.com
References
[1] Dr. Carsten Gerhardt, Gerrit Suhlmann, Fabio Ziemßen, Dave Donnan, Dr. Mirko Warschun, and Dr. Hans-Jochen Kühnle, How Will Cultured Meat and Meat Alternatives Disrupt the Agricultural and Food Industry? AT Kearney (URL)
[2] David Manners, Samsung Spends $46.8 Billion On Capex In 2017 and 2018, ElectronicsWeekly.com, 2018
[3] FAO
[4] Margarine, Wikipedia
[5] David McCowan, I can believe it’s not butter: The rise and fall of margarine, The Takeout, 2018
[6] Zlati Meyer, Missouri becomes first state to regulate use of the word ‘meat’, USA Today, 2018
Published by Rob Leclerc, Ph.D. Founding Partner at AgFunder, Forbes Contributor
Wherever we look, humans have consistently built technologies that surpass their animal predecessors. Food may be next.
hashtag#AlternativeProtein hashtag#VentureCapital hashtag#CellularAgriculture hashtag#PlantBasedProtein
RoBotany Builds 60,000-Square-Foot Vertical Farm In Braddock, Plans Nationwide Expansion As Fifth Season
The company's first urban farm, incubated at Carnegie Mellon University, uses proprietary robotics technology to grow affordable fresh produce for Pittsburgh-area grocery stores and restaurants
The company's first urban farm, incubated at Carnegie Mellon University, uses proprietary robotics technology to grow affordable fresh produce for Pittsburgh-area grocery stores and restaurants
NEWS PROVIDED BY Fifth Season
September 24, 2019
PITTSBURGH, Sept. 24, 2019,/PRNewswire/
Fifth Season, an indoor farming pioneer, announced plans for its first highly efficient, commercial-scale indoor vertical farm, which will open in early 2020 in Braddock, a historic steel town near Pittsburgh.
Fifth Season, originally founded as RoBotany Ltd., is a consumer-focused technology company that was incubated at Carnegie Mellon University's (CMU) Swartz Center for Entrepreneurship—an alliance of CMU's business, robotics, and other schools focused on fostering innovation. The company has raised over $35 million to date led by Drive Capital and other private investors with close ties to CMU. Its leadership team has deep expertise in plant science, robotics, AI and systems engineering.
Austin Webb, Fifth Season's co-founder, and CEO
Austin Webb, Fifth Season's co-founder, and CEO said the company's 60,000-square-foot Braddock farm will set a new vertical agriculture standard for efficient, safe and sustainable production of pesticide-free leafy greens and herbs in urban communities.
Fifth Season developed and perfected its technology with two R&D vertical farms in Pittsburgh's South Side neighborhood. Their leafy greens have been sold at local retailers, such as Giant Eagle and Whole Foods Market, along with popular Pittsburgh restaurants Superior Motors, honeygrow and Kahuna.
Produce from the flagship production farm coming to Braddock will also be available in Pittsburgh-area grocery stores and restaurants.
"The goal through our first three years of development was to prove we could bring fresh food to urban customers at prices competitive with conventionally grown produce," Webb said.
"We have developed fully integrated, proprietary technology to completely control the hydroponic growing process and optimize key factors such as energy, labor usage and crop output," Webb added. "The result is a vertical farm design that has over twice the efficiency and grow capacity of traditional vertical farms. Our unprecedented low costs set a new standard for the future of the industry."
Webb said the Braddock farm's ideal growing environment will deliver perfect, pure produce, in any season. It will produce over 500,000 pounds of lettuce, spinach, kale, arugula and herbs from its 25,000-square-foot grow room during the first full year of operation. The facility is partially solar-powered and requires 95 percent less water compared to traditional growing operations.
Webb said the company is planning a staged expansion in additional, similar-sized cities across the U.S.
Photos and graphics to accompany this announcement can be downloaded at this link: https://www.dropbox.com/sh/8ucvpnvlln10o7x/AADzxmH2iA3rr9LGNO_BrMc1a?dl=0
Contact:
Grant Vandenbussche, Fifth Season (248) 240-4694, grant@robotany.ag
or
Michele Wells, Wells Communications (303) 417-0696 or mwells@wellscommunications.net
SOURCE Fifth Season
COLORADO: Precision Farming With The Help of Technology - By The Numbers
Steve and Soozie Arnold used to run cattle on 30,000 acres in the San Juans. Now, they grow butter lettuce and other delicious greens on three acres just north of Spring Creek Road near Montrose
By Michael Cox Special to the Montrose Daily Press
August 22, 2019
Soozie and Steve Arnold pose with part of their hydroponic Garden at the Eatin’ Greens farm. The system they use is considered precision farming. (Michael Cox/ Special to the Montrose Daily Press)
Steve and Soozie Arnold used to run cattle on 30,000 acres in the San Juans. Now, they grow butter lettuce and other delicious greens on three acres just north of Spring Creek Road near Montrose.
They do it hydroponically. Steve can irrigate his crops from his smart phone. Soozie sells greens and things at the farmers' markets, Gold's Gym, several restaurants, and to other customers, taking plastic payment and processing it with The Square on her phone. She counts the beans on QuickBooks. Steve reads the Wall Street Journal online, which is where he found out about the growing system they use.
Without the internet, broadband or otherwise, life would not be the same for small and large ag operations alike. The Arnolds are part of the precision farming movement. It’s farming and ranching with much less guess work and fewer surprises. Growers with a few acres, like the Arnolds, and cattle outfits, like the one Steve used to run, are getting more yield, using less water and taking fewer chances because they have the internet and tools like phoning in your irrigation.
Soozie Arnold helps a Farmers Market customer “pick” her own greens from their hydroponic “farm field.”
(Michael Cox/ Special to the montrose Daily Press)
No more root cellars
When the refrigerator replaced the root cellar and the icebox back in the 1930s, everything from the way farmers finished crops to the way consumers bought them changed for the better. That came about when the Rural Electrification Act set the stage for energy being delivered to rural farms and ranches.
“A similar shift is upon us with the advent of digital technology and next generation precision agriculture, resulting in increasing productivity with fewer inputs, better market access and healthier rural communities,” said Megan Nelson of the American Farm Bureau Federation.
Nelson is all about pushing the idea of broadband for everybody. But what is broadband?
The dictionary definition is, “A high-capacity transmission technique using a wide range of frequencies, which enables a large number of messages to be communicated simultaneously.” In terms more of us can understand, it's like having a digital party line where everyone can talk at once and still get the message straight. In the unseen operations, the data — words, pictures, numbers, etc. — move at light speed in computer-assigned packets. The problem is the network that does this magic is not in place everywhere.
“Just recently the Federal Communications Commission admitted that the maps they have are wrong,” Nelson said, “We really donít know who has broadband available and who doesn’t.”
The FCC has promised to get the maps up-to-date as quickly as possible. In bureau speak that could be next year or the third June of 2021.