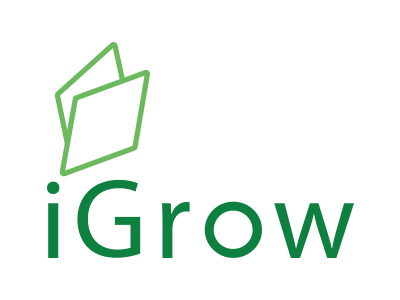
Welcome to iGrow News, Your Source for the World of Indoor Vertical Farming
5 Repurposed Warehouses Turned Indoor Farms That Need No Land Or Sun To Grow Crops
5 Repurposed Warehouses Turned Indoor Farms That Need No Land Or Sun To Grow Crops
June 15, 2017 Chuck Sudo, Bisnow, Chicago
Earth's population is expected to reach 8.5 billion people by 2030. That is 8.5 billion mouths to feed. With dwindling land resources and soaring farming costs across the country, vertical indoor farms may be a solution to feeding the world. Often repurposed from former warehouses, the indoor farms need no sunlight or pesticides and require less water to grow produce.
Following are five indoor farms leading the pack.
1. AeroFarms
AeroFarms, Newark, N.J.
Location: Newark, New Jersey
Produce Grown: Baby greens and herbs
Company/Owner: AeroFarms At 70K SF, the world's largest indoor vertical farm cost $39M to build, and uses LED lights and computer controls to tailor the lighting for each plant. A closed-loop aeroponic system mists the roots of the greens and reduces water usage by 95%. Constant monitoring of nutrients allows AeroFarms to grow a plant from seed to harvest in half the time of a traditional farm. AeroFarms produces 2 million pounds of produce a year.
2. Gotham Greens
Courtesy of Gotham Greens rooftop greenhouse in Chicago
Location: Gotham Greens operates greenhouses in Brookln, Queens and Chicago's Pullman neighborhood.
Produce Grown: Eight types of lettuce, tomatoes, arugula, basil and bok choy Company/Owner: Gotham Greens A pioneer in the indoor farming industry, Gotham Greens built its first rooftop greenhouse in Greenpoint, Brooklyn, and installed solar panels, LED lighting, thermal curtains and a recirculating irrigation system to offset electrical use and reduce water usage. Gotham Green's newest greenhouse in Chicago is located on top of the Method home products plant and cost $8M to build. At 75K SF (or two acres), it produces a crop yield equal to that of a 50-acre farm.
3. Green Sense Farms
Green Sense Farms, Portage, Indiana
Location: Portage, Indiana
Produce Grown: Micro and baby greens, lettuce and herbs Company/Owner: Green Sense Farms Green Sense's 30K SF farm is capable of growing produce for up to 20 million people within a 100-mile radius. The farm is equipped with customized LED lights from Dutch technology firm Royal Philips and grows its produce in automated carousels, while computerized controls provide perfect conditions for year-round farming. Green Sense CEO Robert Colangelo believes his model is scalable and last year raised over $400K in equity crowdfunding to help build a nationwide network of similar indoor farms.
4. Bowery Bowery
Bowery Farming, Kearny, N.J.
Location: Kearny, New Jersey
Produce Grown: Baby kale, arugula, butterhead lettuce and basil. Company/Owner: Bowery Dubbing itself the world's "first post-organic greens" grower, Bowery uses LED lights to mimic sunlight, grows its greens in nutrient-rich water trays stacked from floor to ceiling, uses data analysis to monitor plantings from seed to harvest and robotics to harvest the crops. Investors love what Bowery is doing so much that the company announced Wednesday that it raised $20M to expand its operations in the U.S. and overseas. Bowery raised $7.5M in February from a pool of investors including "Top Chef" judge and chef Tom Colicchio.
5. Local Roots Farms
A shipping container farm from Local Roots Farms
Location: Vernon, California
Produce Grown: Baby and micro greens Company/Owner: Local Roots Farms Local Roots Farms is innovating urban farming design and building indoor farms from 40-foot-long shipping containers. These portable indoor farms are capable of producing the equivalent of a five-acre farm. Local Roots believes this model will disrupt food deserts around the world by setting up the container farms where they are needed most.
Urban Farming Reaches New Heights At Levi’s Stadium
Urban Farming Reaches New Heights At Levi’s Stadium
Emily Saeger, full-time gardener at Faithful Farms, harvests produce to send downstairs to the Levi’s Stadium kitchens. (Courtesy Isha Salian)
By ISHA SALIAN | PUBLISHED: June 10, 2017 at 7:00 am | UPDATED: June 12, 2017 at 11:11 am
SANTA CLARA — Five varieties of kale. Fresh arugula, lettuces and herbs arranged in neat rows. It’s a typical Californian vegetable garden — except it’s nine stories off the ground. The patch of greens and morning sunlight are juxtaposed against the industrial metals, bright billboard display and giant corporate logo in the backdrop. Levi’s Stadium, the sign proclaims.
This well-manicured garden, planted last year, is the first to top an NFL stadium. The Atlanta Falcons are following suit with a raised-bed garden of their own, and baseball stadiums are already in on the game: Boston’s Fenway Park set up a rooftop garden in 2015, and San Francisco’s AT&T Park boasts a vegetable garden behind center field.
Taken together, the unexpected confluence of professional sports and organic gardening signals just how far the sustainability conversation reaches — but also accentuates the role corporate patronage plays in enabling green urban design. Authentic local food production and energy savings aside, these gourmet, microgreen-rich enterprises are a far cry from the gritty, empty lot urban farms that defined the urban agriculture movement for the last two generations.
Christened “Faithful Farm,” Levi’s Stadium’s rooftop garden opened in July 2016 as a subsection of the stadium’s 27,000-square-foot green roof. As spring planting season nears, Faithful Farm produces 500 pounds of produce per month, on average.
“Originally, this roof was designed just as an ornamental perennial space,” said Emily Saeger, Faithful Farm’s full-time gardener. “It was all grasses and succulents.”
This much lower-maintenance green roof was incorporated into the stadium’s design early on, said Jim Mercurio, vice president of operations and general manager at Levi’s Stadium. Green roofs save energy by keeping the stadium cooler, reducing air conditioning costs. It earned the stadium points for LEED certification (a third-party accreditation for green building design), allowed them to demonstrate a commitment to sustainability and also just looked good.
But then Danielle York, wife of San Francisco 49ers CEO Jed York, had an idea. She had hired urban farming venture Farmscape Gardens to landscape her backyard in Los Altos Hills, and asked Farmscape’s co-owner if she could develop a farm on the roof of Levi’s Stadium. The stadium’s operations team green-lighted the project on May 15, 2016. Just six weeks later, the garden was planted.
“When we looked at what we wanted at first, which was to have a natural garden of sorts, we didn’t take it to the next level,” Mercurio said, looking out over the greenery. “This is taking it to the next level.”
The garden has been expanded twice since it opened in July, and now occupies 6,500 square feet, about one and a half times the size of an NFL endzone—not counting pathways. Food grown in the garden (primarily leafy greens and herbs during the winter months) takes a short elevator ride each day down to the stadium kitchens, where it is used in dishes served at the stadium’s restaurants and private events. “It’s the whole farm-to-fork concept coming to life,” said Mercurio.
A rooftop lettuce supply is only the tip of the iceberg for Levi’s sustainability efforts. The stadium uses 85 percent recycled water, has a solar panel canopy and has received multiple sustainability awards. It’s the first stadium to open with LEED Gold certification, and last year achieved LEED Gold for operations and maintenance too. LEED recognition is a sustainability stamp of approval for the San Francisco 49ers, and can in turn attract more business for the stadium. A 2014 Nielsen survey found more than half of respondents were willing to spend more on products and services from eco-friendly companies. But Mercurio says the stadium’s owners have more in mind than positive publicity.
“Titles are great, being the first to do this or that it’s okay, it’s fine,” Mercurio said. “But it’s part of a greater movement. If someone does it bigger and better than us, we’d encourage that. If we had a role in making the environmental and the sustainability conversation bigger, that’s awesome.”
Farmscape also manages the garden at the San Francisco Giants’ AT&T Park. The company was started nine years ago in Los Angeles, and its Bay Area branch focuses primarily on gardens for corporate buildings and multifamily residences.
“We’d never gotten a project like this; it was so exciting,” Farmscape co-owner Lara Hermanson said. “They have a weather station down here for the roof. This place is the coolest.”
The funding and support from the stadium let Farmscape find its way in the relatively new space of rooftop gardening. “There are plenty of examples of people putting a planter on a roof,” said Hermanson. But gardens set directly onto a standard aluminum roof are much rarer — a 5-year-old East Coast urban farming company is the oldest she can think of. “Really no one has the expertise yet.”
Green roofs, whether or not they include edible plants, have several benefits. They reduce the cost of heating and cooling a building by decreasing the temperature of the roof. They also mitigate the urban heat island effect, which occurs when asphalt roads and concrete pavement and roofs soak up and reflect sunlight as heat, resulting in a higher air temperature in urban centers than suburban and rural areas. If the green roofs grow produce, they also diminish the cost of transporting fresh produce from rural areas to urban centers.
But can a rooftop farm actually grow enough produce to turn a profit? Finding an economically sustainable model for urban agriculture isn’t as easy as reaping the environmental benefits. Getting urban agriculture to support itself solely on the value of its produce is difficult, particularly in places like the Bay Area where land values are high.
Top Leaf Farms, another rooftop farming venture on a residential complex in Berkeley, aims to produce as high a rooftop crop yield as possible, selling the produce grown to high-end restaurants in Berkeley and the building’s residents. These upscale restaurants pay a premium for the hyper-local produce, allowing Top Leaf to sell to locals at lower prices through their website — a pound of beet greens, for example, was priced at three dollars this week.
Co-owner Benjamin Fahrer points out that with Levi’s Stadium, the 49ers paid for the farm’s installation and continue to pay for its maintenance by Farmscape. As part of a much larger system, it doesn’t really matter whether Faithful Farm as an entity is profitable. He says there’s an opportunity cost to having walkways and flowers, as Faithful Farm does — something he must be conscious of as the owner of a for-profit farming company. “As soon as you want to make it look better, your costs go up,” he said.
Green infrastructure expert Elizabeth Fassman-Beck agreed, “If you’re looking for a cost-effective system, you don’t want to waste water on the roof for specific plants because they look good.”
Having less pressure to be turn a profit has perks beyond the ability to plant a row of flowers instead of edible greens. Nonprofit, community-based urbanfarms “are producing a yield of social equity, while we’re trying to get yield that is productively and financially viable,” Fahrer said. These socially productive farms engage the community, save energy and raise sustainability awareness even if they don’t actually net a profit for the owners.
“The environmental impact of urban development is enormous,” said Fassman-Beck, an associate professor at Stevens Institute of Technology, in Hoboken, New Jersey. “Anytime we can encourage leading by example and champion this sort of technology, that’s going to have widespread positive impacts.”
Whether the primary mission of a rooftop farm is to be profitable and environmental friendly, the sustainability benefits remain the same. And though Levi’s Stadium is the first NFL stadium to take this step, major construction projects from all kinds of industries seem certain to follow suit.
“It’s not a surprise to me that the team in Northern California was the first in the nation to be like ‘Let’s do an organic farm,’” Hermanson said. “It’s almost expected now that a world-class venue like this would have their own vegetable garden—their own herb production at least.”
FreshTEC Achievement Award for Peter Quiring
NatureFresh Farms' TOMZ Best New Vegetable Finalist
FreshTEC Achievement Award for Peter Quiring
Thousands of produce industry executives are arriving in Chicago this week to attend the United Fresh Produce Association’s Annual FreshMKT & FreshTEC Expos & Convention June 13-15. During the festivities on Tuesday, June 13, greenhouse vegetable grower and NatureFresh Farms owner & president Peter Quiring will be receiving the FreshTEC Achievement Award for his contributions to the produce industry over the last 20 years.
“Peter’s contributions to greenhouse technology have advanced the industry significantly,” said United Fresh President & CEO Tom Stenzel. “His competitive drive and commitment to invest in technology advancements in controlled growing environments are what set him apart. We’re proud to honor Peter with this FreshTEC Achievement Award.”
“It is a great honor to be recognized by your peers,” said Peter Quiring. “Innovation in the way we build our greenhouses and how we grow our vegetables is what has driven my companies for many years. Implementing the latest in technology has allowed us to be a more efficient operation from start to finish”, stated Quiring.
In addition to receiving the FreshTEC Award for Achievement, NatureFresh™ Farms has been named a Finalist for the Best New Vegetable Award for its TOMZ® Snacking Tomato Program.
“We saw a need in the market place to create a category wide program that would give consumers consistent quality, regardless of the season”, said Chris Veillon, Director of Marketing. The TOMZ® Program is unique in that it provides consumers up to 7 different types of specialty tomatoes under one brand: Red/Yellow/Orange Grape, Red Cherry, Mixed Snacking, Mixed Grape, and Sweet Red Cocktail Tomatoes. Grown in NatureFresh™’s new state of the art greenhouse in Delta, OH from October to July and in NatureFresh™’s high tech greenhouses in Leamington, ON March to November, the company is ensuring that locally grown snacking tomatoes are available year-round.
“Consumers want summer-like flavor in July, November, and February and the TOMZ® Program does just that!”, commented Veillon.
The TOMZ® Program is built on the following principles:
- TOMZ® is promoting the category as a whole, not just one item
- Driven by Flavor; 7 unique products under one brand
- Reduced food miles creates extended shelf life
- Creating a consumer connection with multiple flavors
- Same seed | same grower | same farms = consistency
- High impact packaging colors to brighten the produce aisle
- Geo-targeted consumer facing digital content to raise awareness
- Available year-round: Delta, OH & Leamington, ON
“We believe that the TOMZ® Program can strengthen the snacking category as a whole. It is not just about one tomato with flavor, it is a complete line of fresh tomatoes with flavor”, said Ray Wowryk, Director of Business Development.
NatureFresh™ Farms continues to sample its TOMZ® Tomatoes at all #GreenInTheCity tour stops this year with the company’s mobile Greenhouse Education Center.
NatureFresh™ Farms will have its complete line of greenhouse grown tomatoes, bell peppers, and cucumbers on display at the FreshMKT Trade show during the United Fresh Convention in Chicago, June 14-15. Attendees are invited to visit Booth 3231.
To learn more about NatureFresh™ Farms, visit naturefresh.ca.
The Next Big Thing: Hydroponic and Aquaponic Greenhouse Farming
Greenhouse farming is expanding at a rapid rate, using hydroponic and aquaponic methods to grow produce. Many believe it's the next big thing in farming.
Wednesday, June 14th 2017 - by Nathan Edwards
The Next Big Thing: Hydroponic and Aquaponic Greenhouse Farming
MIAMI VALLEY, Ohio (WKEF/WRGT) - Greenhouse farming is expanding at a rapid rate, using hydroponic and aquaponic methods to grow produce.
Many believe it's the next big thing in farming.
Endless rows of carefully grown tomatoes are nurtured at golden fresh farms in Wapakoneta.
"You can see the consistency with the quality and size," VP Paul Mastronardi points out.
99 percent of the tomatoes in this massive greenhouse make it to the grocery store. That's 16 million pounds, enough to give everyone in Ohio and Kentucky a package of tomatoes.
"We are maximizing our yield per square meter," Mastronardi said.
What's the secret? Mastronardi said hydroponic farming.
Water is coursing through the pipes, keeping plants alive
"With the greenhouse environment we have more control over outside factors which helps us," Mastronardi said.
Famers monitor bees living near the plants, use gas to heat the floor on cold days and create sun light when there isn't any.
"One of the major benefits of growing in a greenhouse structure is that the consistency week in and week out is there," Mastronardi said.
The industry is rapidly expanding. In Wilmington, Bright Farms is planning a 10-million-dollar greenhouse, adding 30 jobs.
The hydroponic farm will grow lettuce, tomatoes, herbs and more.
Clinton County Commissioner Kerry Steed said they'll be the source of fresh produce for a hundred-mile radius.
"We're talking Cincinnati, Dayton, Columbus regions in regard to fresh produce," Steed said.
A 2014 USDA study said Ohio already has more than 50 indoor farms. That number is growing.
On a much smaller scale at Oasis Aqua Farm in Beavercreek, Kimball Osborne and his wife Stephanie grow 20 different crops.
"The first thing that you'll see when you look around is there's no dirt," Osborne said.
This is considered aquaponic farming, where fish help the plants thrive.
"We feed the fish and the fish take care of the fertilizer and the plants in turn send the water back to the fish," Osborne said.
They create a sustainable ecosystem. In these tubs herbs and vegetables grow 30 percent faster than a traditional farm.
"I have everything in this greenhouse that I need other than the sun, so as long as the sun doesn't go away I should be good," Osborne said.
The Osborne’s plan to expand as the demand grows, selling both produce and fish directly to locals.
At Golden Fresh Farms, their tomatoes are already sold in most major grocery stores.
Now they're testing peppers, wanting to eventually add 80 acres to their facility.
"The future of the greenhouse industry in the United States is about to take off in the next 5 years," Mastronardi said.
He believes this will replace traditional farming, due to its efficiency, making it the next big thing.
Indoor Farming Plus Made In USA LED Grow Lights: Profile 1.3
Indoor Farming Plus Made In USA LED Grow Lights: Profile 1.3
GREENandSAVE Staff
This is one of the profiles in an ongoing series covering next generation agriculture. We are seeing an increased trend for indoor farming across the United States and around the world. This is a positive trend given that local farming reduces adverse CO2 emissions from moving food long distances. If you would like us to review and profile your company, just let us know! Contact Us.
Company Profile: Farmbox Greens
Farmbox Greens is Seattle's first indoor vertical farm.
Here is some of the “About Us” content: At Farmbox Greens we approach agriculture in an innovative way. We grow in square feet, not acres. We use energy efficient LEDs and a fully climate controlled environment to produce the freshest produce that can be on your plate within hours of harvest.
Since planting the first seeds of our urban farm in 2011 we’ve set out to change where and how great produce is grown. We’ve created a sustainable farm where the harvest cycle is days not months. Our farm uses 90 percent less water than traditional farming, is pesticide and herbicide free and is fresh year round.
Seattle’s first indoor vertical farm to grow produce, we make fresh local greens more accessible. We use a small amount of space (just a few hundred square feet) to grow thousands of pounds of greens annually. We work hard to grow local produce because we think it tastes better. Go ahead and taste it, we think you’ll agree!
Here is the link to learn more: http://www.farmboxgreens.com/.
To date, the cost of man made lighting has been a barrier for indoor agriculture. A new generation of LED lighting provides cost effective opportunities for farmers to deliver local produce. Warehouses and greenhouses are both viable structures for next generation agriculture. Here is one example of next generation made in USA LED grow light technology to help farmers: Commercial LED Grow Lights.
Indoor Farming Plus Made In USA LED Grow Lights: Profile 1.1
Indoor Farming Plus Made In USA LED Grow Lights: Profile 1.1
GREENandSAVE Staff
Posted: Monday. 12th June 2017
This is one of the profiles in an ongoing series covering next generation agriculture. We are seeing an increased trend for indoor farming across the United States and around the world. This is a positive trend given that local farming reduces adverse CO2 emissions from moving food long distances. If you would like us to review and profile your company, just let us know! Contact Us.
Company Profile: Tiger Corner Farms Manufacturing
Here is a great example of a company specializing in aeroponics.
Here is some of the “About Us” content: We’re a team of builders, growers, geeks, problem solvers, foodies, parents, engineers and enthusiasts designing farm systems that transform the way we eat. Our aeroponic container farms were born from a dream that every individual deserves access to healthy food—and that dream starts right here at our home in South Carolina. Our mission is to create container farm systems that power healthier, sustainable communities. Housed in recycled shipping containers, the TCFM aeroponic farm system is customized with an innovative cloud-based control system that allows growers 24-hour, 365-day monitoring of each plant from seed to sale and the ability to adjust any farm system setting from any computer, tablet, or mobile device. A single farm can be grown in any climate, in any location, using 98% less water than traditional farming—a healthy, fresh, and sustainable approach to achieving bountiful harvests in a small space. Tiger Corner Farms Manufacturing is locally owned and operated in Summerville, SC.
Here is the link to learn more: http://tigercornerfarmsmfg.com/
To date, the cost of man made lighting has been a barrier for indoor agriculture. A new generation of LED lighting provides cost effective opportunities for farmers to deliver local produce. Warehouses and greenhouses are both viable structures for next generation agriculture. Here is one example of next generation made in USA led grow light technology to help farmers:
Plant Based Foods Association Launches New Research and Education Initiative
Plant Based Foods Association Launches New Research and Education Initiative
The Plant Based Foods Association is expanding its reach with an affiliated organization called the "PBFA Research and Education Fund" to determine best practices and conduct outreach to promote plant-based foods.
It’s an exciting time for the plant-based foods industry. This new initiative will allow us to apply best practices to support this growing food sector and reach more consumers.
SAN FRANCISCO, CALIFORNIA (PRWEB) JUNE 14, 2017
Today, the Plant Based Foods Association (PBFA), the trade association representing the plant-based foods sector, announced the launch of an affiliated organization called the PBFA Research and Education Fund.
The new non-profit will conduct outreach to retailers to expand shelf space for plant-based foods, as well as help food service directors offer more plant-based options.
“It’s an exciting time for the plant-based foods industry. This new initiative will allow us to apply best practices to support this growing sector and reach more consumers,” said Michele Simon, executive director of the Plant Based Foods Association, who will also lead the new organization.
Board members of the new entity include two board members from PBFA: Jaime Athos, CEO of The Tofurky Company, and Martin Kruger, COO of Follow Your Heart.
Joining them is Julie Mann, global protein program manager at Ingredion Incorporated. “Given my background in plant-based proteins, I am genuinely passionate to contribute my expertise to further the plant-based foods movement,” said Ms. Mann.
In the longer term, the group plans to conduct research projects to determine best practices for merchandising plant-based foods, and understand what drives consumers to purchase more plant-based foods.
"Because the new organization is organized as a 501(c)(3) non-profit, we can receive donations and grants from foundations, individuals, and others seeking to support the plant-based movement in an innovative way to help grow the market," Simon added.
The Plant Based Foods Association is a trade association representing 90 of the nation’s leading plant-based food companies. Launched in March 2016, the association engages in policy advocacy and outreach to promote the growing sector of plant-based foods.
USDA Announces Grants Designed to Increase Amount of Local Food Served in Schools
USDA Announces Grants Designed to Increase Amount of Local Food Served in Schools
June 13, 2017 | seedstock
News Release: WASHINGTON – The U.S. Department of Agriculture today announced the projects selected to receive the USDA’s annual farm to school grants designed to increase the amount of local foods served in schools. Sixty-five projects were chosen nationwide.
“Increasing the amount of local foods in America’s schools is a win-win for everyone,” said Cindy Long, Deputy Administrator for Child Nutrition Programs at USDA’s Food and Nutrition Service, which administers the Department’s school meals programs. “Farm to school projects foster healthy eating habits among America’s school-age children, and local economies are nourished, as well, when schools buy the food they provide from local producers.”
According to the 2015 USDA Farm to School Census, schools with strong farm to school programs report higher school meal participation, reduced food waste, and increased willingness of the students to try new foods, such as fruits and vegetables. In addition, in school year 2013-2014 alone, schools purchased more than $789 million in local food from farmers, ranchers, fishermen, and food processors and manufacturers. Nearly half (47 percent) of these districts plan to purchase even more local foods in future school years.
Grants range from $14,500 to $100,000, awarding a total of $5 million to schools, state agencies, tribal groups, and nonprofit organizations for farm to school planning, implementation, or training. Projects selected are located in urban, suburban and rural areas in 42 states and Puerto Rico, and they are estimated to serve more than 5,500 schools and 2 million students.
This money will support a wide range of activities from training, planning, and developing partnerships to creating new menu items, establishing supply chains for local foods, offering taste tests to children, buying equipment, planting school gardens and organizing field trips to agricultural operations, Long said. State and local agency interest and engagement in community food systems is growing. Having received 44 applications from state or local agencies, 17 state agencies will receive funding.
Grantees include the Nebraska Department of Education, which will refine and expand the “Nebraska Thursdays” program, which will focus on increasing locally sourced meals throughout Nebraska schools, and the Virginia Department of Education, which will focus on network building to ensure stakeholders from all different sectors are leveraged. Both the South Dakota Department of Education and the Arkansas Agriculture Department will use training grants to build capacity and knowledge about the relationship between Community Food Systems and Child Nutrition Programs. More information on individual projects can be found on the USDA Office of Community Food Systems’ website at www.fns.usda.gov/farmtoschool/grant-awards.
USDA’s Food and Nutrition Service administers 15 nutrition assistance programs that include the National School Lunch Program, School Breakfast Program, Supplemental Nutrition Assistance Program, Special Supplemental Nutrition Program for Women, Infants and Children (WIC), and the Summer Food Service Program. Together, these programs comprise America’s nutrition safety net. Farm to school is one of many ways USDA supports locally-produced food and the Local Food Compass Map showcases the federal investments in these efforts. For more information, visit www.fns.usda.gov.
Vertical Farming Startup Plenty Acquires Bright Agrotech to Scale
Vertical Farming Startup Plenty Acquires Bright Agrotech to Scale
California-based vertical farming company Plenty, previously See Jane Farm, has acquired Bright Agrotech in an effort to reach “field-scale.”
Bright Agrotech is an indoor ag hardware company that’s focused on building indoor growing systems for small farmers all over the world, in contrast to Plenty, which is aiming to become a large-scale indoor farming business and currently has a 52,000 sq. ft farm in South San Francisco.
“The need for local produce is not one that small farmers alone can satisfy, and I’m glad that with Plenty we can all work toward bringing people everywhere the freshest food,” said Nate Storey, founder and chairman of Bright Agrotech.
The move to acquire Bright Agrotech will give Plenty the breadth of expertise and intellectual property (IP) to scale with rapid speed, and is a natural move after a four-year relationship, according to Matt Barnard, cofounder and CEO.
“We have a great portfolio of system level IP. They have a great portfolio of component level IP,” he told AgFunderNews. “We’re getting a fire hose of demand from around the globe right now. This is an industry that is emergent, but the way to truly lift it off the ground is to do a whole set of things extraordinarily well.”
Bright Agrotech was founded in 2010 in Laramie, Wyoming, and sells a wide range of indoor farming equipment for indoor vertical farms as well as greenhouses along with smaller systems suitable for homes and business development tools – most of which are under the trademark brand “ZipGrow.”
The relationship between the two businesses started in 2013. Later Storey, the former CEO of Bright Agrotech, became chief science officer at Plenty in a part-time capacity in 2015 and went on to join the team full time earlier this year.
Barnard would not confirm to what extent Plenty already uses Bright Agrotech’s hardware in its farm, which consists of 20-foot high towers with vertical irrigation channels and facing LED lights. Leafy greens ready for picking end up looking similar to a solid wall of green.
Plenty claims to use 1 percent of the water and land of a conventional farm with no pesticides or synthetic fertilizers. Like other large soilless, hi-tech farms growing today, Plenty says it uses custom sensors feeding data-enabled systems resulting in finely-tuned environmental controls to produce greens with superior flavor.
Based on the West Coast, it plans to compete with the existing supply of greens from the salad bowl of California, by choosing premium seeds and catering growing conditions for optimal taste. Barnard says most greens growing in the field are bred to be hardy enough to last the 3,000 mile journey to the east coast and beyond.
He would not share specific growth goals for the near-term, but said that eventually they expect to be able to build two to six farms per month. The plan is to build these farms just outside major cities where retailers have distribution centers and real estate is more affordable. Barnard also said that an announcement about a major retail partnership is forthcoming.
Zack Bogue, an investor in Plenty through San Francisco venture capital fund Data Collective, agreed that the Bright Agrotech acquisition will help the startup scale. “By vertically integrating parts of their component supply chain, it will make the most efficient system out there more efficient,” he said.
Plenty claims to get 350 times the crop yield per year over an outdoor field farm. Or, as Barnard described, “It is the most efficient in terms of the amount of productive capacity per dollar spent, period.”
Plenty was the first indoor ag investment for big data-focused Data Collective, which participated in its $24.5m Series A in July 2016. “We’re pretty excited about that space because some of the hardest problems in agriculture are now lending themselves to an algorithmic or computational or applied machine-learning solution,” he said. But he added that the ability to scale was paramount, because scale is what allows data to be useful for machine-learning applications. “I came away feeling this was an endeavor that could truly achieve global scale pretty quickly,” he added.
Bogue said that though this match was a natural fit, he doesn’t expect more consolidation in the space.
Plenty has raised $26 million to date in a seed and Series A Round, both in 2016. The startup’s other investors are Innovation Endeavors , Bezos Expeditions , Finistere Ventures, Data Collective, Kirenaga Partners, DCM Ventures, and Western Technology Investment
Plenty Acquires Bright Agrotech to Globally Scale Impact of Local Farmers
Plenty Acquires Bright Agrotech to Globally Scale Impact of Local Farmers
Industry-leading technology will play crucial role in Plenty farms
June 13, 2017 - 09:00 AM - Eastern Daylight Time
SOUTH SAN FRANCISCO, Calif.--(BUSINESS WIRE)--Plenty, the leading field-scale vertical farming company reshaping agriculture to bring fresh and locally grown produce to people everywhere, announced the acquisition of Bright Agrotech, the leader in vertical farming production system technology. Bright’s technology and industry leadership combined with Plenty’s own technology will help Plenty realize its plans to build field-scale indoor farms around the world, bringing the highest quality produce and healthy diets to everyone’s budget.
“Plenty grows food for people, not trucks. By making us all one team and formalizing our deep and close relationship, with a shared passion for bringing people healthy food through local farming, we’re positioned in a way no one else is today to meet the firehose of global demand for local, fresh, healthy food that fits in everyone’s budget,” said Matt Barnard, CEO and co-founder of Plenty. “Everyone wins — the small farmer, people everywhere and Plenty — as we all move forward delivering local food that’s better for people and better for the planet.”
Bright has partnered with small farmers for over seven years to start and grow indoor farms, providing high-tech growing systems and controls, workflow design, education and software. Bright will continue its work, expanding its base of hundreds of farmers around the world.
“We’re excited to join Plenty on their mission to bring the same exceptional quality local produce to families and communities around the world,” said Nate Storey, founder of Bright Agrotech. “The need for local produce and healthy food that fits in everyone’s budget is not one that small farmers alone can satisfy, and I’m glad that with Plenty, we can all work toward bringing people everywhere the freshest, pesticide-free food.”
About Plenty
Plenty is a new kind of farm for a new kind of world. We’re on a mission to bring local produce to people and communities everywhere by growing the freshest, best-tasting fruits and vegetables, while using 1% of the water, less than 1% of the land, and none of the pesticides, synthetic fertilizers, or GMOs of conventional agriculture. Our field-scale indoor vertical farms combine the best in American agriculture and crop science with machine learning, IoT, big data, sophisticated environmental controls and the exceptional flavor and nutritional profiles of heirloom seed stock, enabling us to grow the food nature intended — while minimizing our environmental footprint. Based in San Francisco, Plenty has received funding from leading investors including Eric Schmidt’s Innovation Endeavors, Bezos Expeditions, DCM, Data Collective, Finistere and WTI and is currently building out and scaling its operations to serve people around the world.
Contacts
Plenty
Christina Ra
christina.ra@plenty.ag
Food Revolution
Food Revolution
Applying innovation to agriculture, a student startup plans to use hydroponics to grow fruits and vegetables four times faster using 90 percent less water.
May 04, 2017 | Abigail Lague, avl8bj@virginia.edu
Those walking into the University of Virginia’s Clark Hall find themselves face-to-face with a state-of-the-art hydroponics system. A table full of growing plants and violet light is hard to miss.
As part of an undergraduate sustainability initiative, these systems have been installed in various locations on UVA’s Grounds, including Newcomb Hall and Observatory Hill Dining Hall.
An undergraduate-led company, Babylon Micro-Farms, is bringing these small hydroponic farm prototypes to Grounds as part of an effort to make fresh fruit and vegetables easily accessible for more people.
Hydroponic farming is the growing of plants in nutrient-rich solutions without the use of soil. Usually, hydroponic systems are large, costly and used in mass production – not readily available to the average consumer. However, the system created by Babylon Micro-Farms are less bulky and available for personal use in the home. Each structure is only 6 feet wide by 3 feet deep and about 6 feet tall. Above the plants are LED grow lights that emit light at the right wavelength for photosynthesis.
Plants grown in hydroponics systems, such as those used by Babylon Micro-Farms, are free of GMOs and pesticides. (Photo by Dan Addison, University Communications)
This high-tech farming method uses 90 percent less water and grows food up to four times more quickly. Additionally, hydroponics systems do not use genetically modified organisms, pesticides or inorganic fertilizers and help reduce “food miles,” the distance between where a food item is grown and where it is sold.
The Babylon team began testing prototypes around Grounds after building an early model through the student entrepreneurial clubhouse, HackCville, and winning $6,500 from Green Initiatives Funding Tomorrow. Student Council’s sustainability committee, with assistance from the Office of the Dean of Students, funds the annual GIFT grant.
“It’s been a massive hit,” company founder and fourth-year student Alexander Olesen said of the hydroponic systems’ reception in dining halls. “At first, they weren’t too sure about it, and then after a month when the plants grew, they said we could go ahead and pitch them a more finalized version.”
From left, Stefano Rumi, who handles the business expansion of Babylon Micro-Farms; founder Alexander Olesen; electrical engineer Patrick Mahan; and head engineer Graham Smith. (Photo by Dan Addison, University Communications)
The hydroponic systems in the dining halls have been growing a mixture of lettuces, arugula, kale and spinach. The yield from one table alone has been enough to feed the entire Babylon Micro-Farms team for about a week. Olesen, a foreign affairs major, and his business partner, third-year student Stefano Rumi, a sociology and social entrepreneurship double-major, hope to add their produce to the UVA Dining menu so that other students may enjoy the vegetables produced by their hydroponics systems.
To make the produce affordable, Babylon Micro-Farms plans to offer a comprehensive hydroponics system for less than $1,000 – something that cannot be found on the market today. Their system will be much smaller than other hydroponic structures and easier to have in the home.
“The existing systems you get are made out of the same materials as trash cans, and they’re still more expensive, which is crazy,” Olesen said. “It’s just a table, and it blends in. You can fit in around 100 plants. Unlike other systems, you have versatility.”
These LED grow lights emit light at a wavelength that facilitates photosynthesis so that the plants will grow faster. (Photo by Dan Addison, University Communications)
The system can be easily installed in the home and doesn’t require any special skills to set up, he said.
While the benefits of hydroponics are appealing to many, Olesen is aware that not everyone wants to have to do a “science experiment” at the end of a long day to grow lettuce. With this in mind, Babylon Micro-Farms plans to provide premeasured seeds, nutrients and an automated system to optimize the pH of the hydroponic system, making the process of growing one’s own food as easy as possible. All users have to do is pour in the mixture.
“Food is such a fundamental part of our lives,” Rumi said. “In a world where we’re innovating everything, the last thing we’ve innovated is how we grow our food. We essentially do it the same way we’ve been doing it for 10,000 years, except for pumping unhealthy pesticides that have these terrible environmental effects.”
Alexander Olesen, founder of Babylon Micro-Farms, hopes that his hydroponic systems will soon be put to use in UVA dining halls and low-income areas. (Photo by Dan Addison, University Communications)
Olesen and Rumi also see a possible educational aspect to of their hydroponics system.
“A lot of the early interest we’ve gotten has been in having these in schools, teaching children how to grow in the community garden, or having these in low-income neighborhoods so that there’s a public space where residents can grow their own food,” Rumi said. “Beyond having the perfect product that everyone can have in their home, we would like to give back to communities that are in need of things like this. I think this is a great step to solving food insecurity.”
“We are connecting people to where food comes from,” Olesen said.
Babylon Micro-Farms is now in beta testing with customers and currently taking preorders. The startup team also will participate in UVA’s 2017 i.Lab incubator summer cohort.
Media Contact
Katie McNally - University News Associate Office of University Communications
katiemcnally@virginia.edu 434-297-6784
Making A Life Out of Lettuce
Making A Life Out of Lettuce
Controlled environment hydroponic lettuce growing provides an honest living for Jeff Adams and the employees of Circle A Farms in Cumming, Ga.
Jeff Adams started growing lettuce after 20 years of working as a contractor. Photo courtesy of Jeff Adams
Like others with a strong work ethic and an affinity for the outdoors, Jeff Adams enjoys what he does for a living. It’s demanding work to simultaneously grow and sell multiple varieties of lettuce — a job that, for him, doesn’t let up any time of the year. However, it’s worth the time he gets to spend in greenhouses and in the community learning the intricacies of growing and selling hydroponic produce.
A contractor by trade for 20 years, Adams didn’t have any experience with controlled environment agriculture (CEA) before he constructed his first two CropKing greenhouses in 2011 (He has since built two more). He did, however, have a passion for farming. He owned about 30 heads of cattle and grew lettuce in the backyard of his 13-acre Cumming, Ga., home.
Adams became interested in CEA and CropKing’s computer-controlled, hydroponic greenhouses when he read about R & G Farm, a lettuce grower based out of Dublin, Ga., in Hobby Farms magazine (Editor’s note: Read Produce Grower’s story on R & G Farm at bit.ly/2lsRZDe). “I started researching it for about two years, and went and took some classes through CropKing on it and just decided, ‘What the heck?’,” he says. “I think it might fit what we want to do in our passion for farming and growing. And we pulled the trigger. It’s been five years now.”
With a total of eight employees, a growing customer base and fresh, quality lettuce, Adams’ business, Circle A Farms, continues to grow.
Edible Education
Once Adams began growing produce in a greenhouse, it didn’t take long for him to realize that growing hydroponically is much different than growing in the ground.
Through its training materials and information, CropKing has helped Adams make his operation a success. “They have such a wealth of knowledge, and they’ve done it for so long, that, to me, they’re just a viable source that I’d hate to be without,” he says.
Adams' greenhouses control the environment — heating, cooling, air movement, nutrient supplies and carbon dioxide — through computers, he says. Adams has adjusted growth spacing by drilling small holes to accommodate growing baby lettuce.
Using nutrient film technique (NFT) trays, Circle A Farms grows nine varieties of lettuce, Adams says. “We grow bibb, romaine, spring mix, kale, arugula, basil and we do microgreens,” he says. “And there’s a couple other varieties. We do tropicana, frisee. All just leafy greens.”
Selling to local markets and consumers
Most of Circle A Farms’ customer base, which consists of stores and restaurants, are within about a 15-mile radius of the growing operation, Adams says.
Like many other CEA growers, Circle A Farms often markets directly to consumers through avenues such as local farmers markets. In January, it began delivering directly to customers’ homes through its new Farm to Porch program.
To participate in Farm to Porch, area customers find their location listed as a “zone” on circlealettuce.com and place a lettuce order, Adams says. “You either put a cooler out or we can sell you a cooler bag that you leave out, and then it’s delivered right to your porch,” he says.
I think a lot of people come into [CEA] like they’re going to make a lot of money — a get rich quick kind of deal — and that’s not the case, but there is some profitability. — Jeff Adams, Circle A Farms
Because Circle A Lettuce is grown in ideal conditions with computer-controlled nutrition levels, and sold to local markets, it has an approximately three-week shelf life, compared to lettuce that is shipped long distances, which often has a shelf life of only four to five days, Adams says. “It’s a great, wonderful product,” he says. “You just have to educate the consumer why they’re paying a little bit more for the product.”
When it comes to revenue streams for Circle A Farms, enough money comes in to provide Adams and his employees with a steady income, but that’s because of the hard work they put into the operation. “I think a lot of people come into [CEA] like they’re going to make a lot of money — a get rich quick kind of deal — and that’s not the case,” he says. “But there is some profitability.”
Growing Pains
It is often difficult to predict what will happen from one day to the next, Adams says. Tip burn and other problems have arisen that have taught Adams and his employees how to best care for the lettuce.
When production hiccups take a toll on a crop, customers still have the same expectations as when production is going flawlessly, Adams says. “They get used to your consistency and they start thinking you can produce it like a widget, that you can just turn out as many as you can, when still, you have issues and you have problems, and you might lose a crop of bibb or a crop of something here and there,” he says.
Many factors, such as lettuce variety and time of year, determine production cycles, Adams says. Circle A Farms doesn’t track how many cycles it produces in a year because they are constantly changing and rotating. Some lettuces have rotations of 30 days, while others have rotations of 45 to more than 50 days.
“It never stops growing, so you can’t just shut it down and leave,” Adams says. “It’s kind of like having chickens, except with chickens you get a break every six or so many weeks. With this, you never get a break.”
Still, Adams says he finds his work affords him an honest living. He doesn’t mind the extra hours he puts in throughout the week. “If you don’t mind hard work, weekends, nights, whatever — things happen, problems happen, you’ve got to be around — it can be rewarding because the product we’re able to turn out is superior to anything that’s out there
Engineers Use Shipping Containers For New Spin on Ancient Practice, Hydroponics
Engineers Use Shipping Containers For New Spin on Ancient Practice, Hydroponics
By Staff Reports - 6/8/17 6:27 PM
INDIANAPOLIS — Hydroponics — growing crops in water only, without soil — dates back to the first century, in the Roman Empire.
But four millennials working out of a barn just east of Indianapolis are putting a new spin on the old farming technique. And they’re using a surprising space for it.
During an educational outreach mission that took him through South Africa, Chris Moorman came up with a novel idea for refrigerated shipping containers.
Produce — and lots of it — could be grown in them, he surmised after a casual conversation with a local resident that somehow turned to the topic of uses for discarded shipping containers.
After concluding his overseas mission and a five-year tour as a Wall Street stock broker, Moorman decided to build a business on the unusual idea.
An acre’s worth of produce can be harvested from a 40-foot shipping container outfitted with his company’s high-tech system, according to the 30-year-old Bedford native.
These days, hydroponics is most often conducted in a greenhouse, but that involves high construction costs and building permits.
Moorman’s company, Greenfield-based Rubicon Agriculture, offers a self-contained, fully enclosed hydroponics unit, called an AgroBox, for $75,000. A higher-yield model costs $82,000.
Heads of lettuce in Rubicon’s AgroBox mature in less than half the time as those grown outside in a field.
“I’ve seen a lot of hydroponics operations, but I’ve never seen or heard of one using a shipping container,” said Robert Rode, lab manager of Purdue University’s AquaCulture Research Lab.
Rubicon’s founders’ backgrounds are as unique as their ideas. None of them have farmed.
Moorman, who graduated from Purdue University with an economics degree and is Rubicon’s CEO, spent his early career as a commodities trader before discovering his passion for sustainable agriculture during a year-long sojourn through several developing countries.
Moorman’s younger brother, Erik, 26, served as a nuclear engineer in the U.S. Navy. Serving on the USN Newport News, he learned about closed-circuit water systems in agriculture.
Jesse Robbins, 26, who, like the Moorman brothers, is from Bedford, and Pat Burton, 28, a Greenfield native, previously worked with automation technology in manufacturing that they now apply to the growing process. Both graduated from Purdue with electrical engineering degrees.
“We’re an eclectic group, but we all have vital skills we bring to the table,” Moorman said.
Initially, they had difficulty finding financing.
“We were a bunch of guys who never grew anything,” looking for funding to start an agricultural company, Moorman said with a laugh.
Eventually, the founders started the firm with $60,000 from their own pockets.
The company, which launched in July 2015, is approaching profitability, Moorman said.
Built-in Advantages
Rubicon’s system has several advantages, he said. It’s “easily movable with a semitruck and a winch. You can put it anywhere.”Also, because the containers are refrigerated, “they have a great insulation rating,” Moorman said, making temperature control — critical for maximum hydroponics production — easier and more efficient.
An added plus for Rubicon is that it can buy the containers — after they’ve made myriad trips across the globe — for pennies on the dollar.
About 2,500 plants can be placed on each unit’s floor-to-ceiling tiered shelving and, with only a water and electrical hookup, growers can control conditions inside a Rubicon unit with “pinpoint precision,” Moorman said. The key, he added, is a data-collection system that allows growers to monitor conditions for optimal growth.
“If I can’t act on the data, the data is just noise,” Moorman said. “Having our system is all about actionable data.”
Driven by Mitsubishi control components, the system is akin to those used in advanced manufacturing, he said.
Rubicon’s units are outfitted with LED lights and a system that controls light spectrum and wavelength, a climate control unit that tightly monitors and controls oxygen and carbon dioxide levels, and a hydration system that recirculates water with a precise mix of nutrients and a carefully set pH balance. Moorman boasts that Rubicon’s system uses only 10 percent as much water as traditional farming.
“One of the best parts of our system is, it doesn’t require pesticides or herbicides,” Moorman said. “It’s completely organic.”
But hydroponics comes with serious challenges, said Darin Kelly, who operates Good Life Farms in Eminence.
The technique “is technical and not simple,” said Kelly, who grows crops traditionally and through hydroponics. “You’ve got to worry about plumbing, slope, pressure and measuring nutrients. You become a plumber; you become an electrician.”
With Rubicon’s system, zoning can be a concern, too, Moorman admitted. Since this is a new concept, local zoning officials are still working out the regulations.
Rubicon’s system is best suited for predictably growing plants that don’t stretch upward too much or have lots of inedible biomass, like corn. Plants like snap peas, kale, basil, oregano, spinach, cilantro and lettuce are ideal.
Moorman said a head of lettuce grown in the field takes more than 60 days to mature — but only 24 in Rubicon’s unit. By using phased growing, Moorman said, farmers using Rubicon’s system can produce 500 heads of lettuce weekly year-round from a single 320-square-foot container unit.
“For a space that small, that type of production is really super,” Purdue’s Rode said. “It may even be optimistic. But if they can achieve that, it’s very, very good.”
Educational Component
Moorman has been working to get his system in the hands of several Hoosier high schools, including Shortridge High School in Indianapolis, another in southern Indiana, and one in Omaha, Nebraska. He said it’s a great teaching tool.“We’re going to have a generation of farmers that don’t live on farms,” Moorman said.
But the technology can go beyond farming.
It’s the same as that used “to make an intake manifold,” he said. “There’s a real workforce-development part of this.”
He predicted Rubicon’s portable system will also be key in furthering the farm-to-table movement and could help solve the problem of food deserts — neighborhoods, often low-income, that are more than a mile from a grocery store.
“The average American meal travels more than 1,500 miles from farm to plate,” Moorman said. “Of all the produce consumed in the U.S., 50 percent of it is grown in California, where there is a major water shortage. Those aren’t sustainable trends.
“We’re taking something — a shipping container — that has been bringing food to you in a more traditional sense and putting it back to work growing food right in your local neighborhood.”
No Aquaponics
One field Moorman has no interest in is aquaponics, a system not quite as old as hydroponics, but nevertheless one that has been around several centuries. In aquaponics, Rode said, producers have to balance two ecosystems that aren’t always compatible.Aquaponics operations use controlled ponds — often indoors — to raise fish, usually a hardy species like tilapia. The plants draw from the bionutrients in the fish ponds. The upside to aquaponics: Operators can sell both fish and crops. But Rode said establishing conditions that both the fish and crops can thrive in is tough.
“The fish and plants often prefer different pH levels and water temperatures,” he said.
Moorman said there’s plenty to harvest with the more manageable hydroponics. The U.S. hydroponics industry is projected to hit $9 billion by 2020, according to multiple sources. Moorman said Indiana can nab $2 billion of that, pointing out that Indiana and the four surrounding states spend $20 billion on produce annually.
“We think there’s an opportunity for Indiana to be a powerhouse of produce,” Moorman said. “But that opportunity comes with a lot of education. ”
These #4 Start-ups Are Promoting Hydroponics in India
These #4 Start-ups Are Promoting Hydroponics in India
Hydroponics or growing plants in water or sand, rather than soil, is done using mineral nutrient solutions in a water solvent
Image credit: Pixabay
Feature Writer, Entrepreneur.com
JUNE 8, 2017
You're reading Entrepreneur India, an international franchise of Entrepreneur Media.
Only an expert gardener knows how difficult it can be to grow plants and how much extra care it takes with special attention to soil, fertilizer and light. One can’t get the process right and expect good yields without getting his/her hands dirty. But, to make their work a lot easy and convenient, many start-ups in India are working on hydroponics farming.
Hydroponics or growing plants in water or sand, rather than soil, is done using mineral nutrient solutions in a water solvent.Additionally, this indoor farming technique induces plant growth, making the process 50 per cent faster than growth in soil and the method is cost-effective. Mineral nutrient solutions are used to feed plants in water.
Here’s a list of four start-ups in India that are innovating agriculture methods and leading the way in indoor farming.
Letcetra Agritech
Letcetra Agritech is Goa’s first, indoor hydroponics farm, growing good quality, pesticide-free vegetables. The farm in Goa’s Mapusa is an unused shed and currently, produces over 1.5 to 2 tons of leafy vegetables like various varieties of lettuce and herbs in its 150 sq metre area. The start-up is founded by Ajay Naik, a software engineer-turned-hydroponics farmer. He gave up his IT job to help farmers in the country.
BitMantis Innovations
Bengaluru-based Iot and data analytics start-up BitMantis Innovation with its IoT solution GreenSAGE enables individuals and commercial growers to conveniently grow fresh herbs throughout the year. The GreenSAGE is a micro-edition kit that uses hydroponics methods for efficient use of water and nutrients. It is equipped with two trays to grow micro-greens at one’s own convenience.
Junga FreshnGreen
Agri-tech start-up Junga FreshnGreen has joined hands with InfraCo Asia Development Pte. Ltd. (IAD) this year to develop hydroponics farming methods in India. The project started with the development of a 9.3-hectare hydroponics-based agricultural facility at Junga in Himachal Pradesh’s Shimla district.
Junga FreshnGreen is a joint venture with a leading Netherlands-based Agricultural technology company – Westlandse Project Combinatie BV (WPC) — to set up high-technology farms in India. Their goal is to create a Hydroponics model cultivating farm fresh vegetables that have a predictable quality, having little or no pesticides and unaffected by weather or soil conditions. They will be grown in a protected, greenhouse environment.
Future Farms
Chennai-based Future Farms develops effective and accessible farming kits to facilitate Hydroponics that preserve environment while growing cleaner, fresher and healthier produce. It focuses on being environment friendly through rooftop farming and precision agriculture. The company develops indigenous systems and solutions, made from premium, food grade materials that are efficient and affordable.
Ideas We Should Steal: Urban Food Forest
Ideas We Should Steal: Urban Food Forest
Seattle’s Beacon Forest provides free native edibles to anyone in the city. Could the soda tax make it possible for a Philly group to do the same here?
JUN. 05, 2017
Imagine this: On a two-acre plot of land, at the edge of Fairmount Park, sits a forest hearkening back to the days when nature—not people—ruled the planet. Fruit trees tower over berry shrubs, fruit-bearing vines creep upwards. Insects, birds, animals fill the spaces in between. And every day, scores of Philadelphians wander through, filling their arms with fresh produce to take home—all for free.
This is the vision of a group of Philadelphia food access advocates—and it’s not as crazy as it seems. In fact, there’s precedent in Seattle.
Beacon Food Forest, in Seattle’s Beacon Hill, will be the largest food forest on public land in the country when it is complete. So far, it occupies two acres of a seven-acre plot sitting above a covered reservoir in South Seattle; this summer, the mostly volunteers who maintain the forest will plant another two acres. The garden contains 420 different species of edibles, some native to Seattle, like rasberries, huckleberries and walnuts, and some a reflection of the surrounding communities of Chinese, Vietnamese, Somalians, Latinos and African Americans, like Chinese pepper trees, persimmons and figs. Everything grown at Beacon Forest is free to anyone and everyone who wants to pick it at anytime.
Muehlbauer says he is hopeful that the city will grant his group a couple of acres in Fairmount Park to launch a food forest. And it is conceivable that the city could help to fund Fair Amount Food Forest with revenue from the tax on sugary beverages, a portion of which is slated for public park improvement.
“The goal is to create community and awareness around a local food supply, what you can grow that you don’t get in grocery stores,” says Glenn Herlihy, the forest’s co-founder. “It’s social healing and land healing at the same time.”
Beacon Forest is an example of permaculture, which means it is self-sustaining and perennial. The idea came out of a permaculture workshop Herlihy took in 2009, when for his final project, he decided to design a dream farm on an undeveloped piece of land next to a large park in his neighborhood of Beacon Hill. He passed the class, and then took his idea to the community, where he found a willing group of residents who decided to make his dream a reality. In 2012, after securing permission from Seattle Public Utilities and $140,000, mostly from the city’s Department of Neighborhoods, Beacon Forest broke ground.
Five years later, Beacon has become a model of urban forestry that holds two principles steadfast: Remaining true to the land, and to the community it serves. “In a food forest, you’re looking for collaboration between the community, what you can grow and what’s available,” Herlihy says. The plantings utilize what ecoloigsts call the seven layers of a food forest—trees at the top, ground cover at the bottom with shrubs, pollinators, vines in between. Those plants then propagate naturally, and shift—where berry bushes used to be most prominent, the trees have now blocked the sun, and have started providing more of the fruit. The land is also becoming what Herlihy calls a “genetic food bank” for edible plants that are dying around the globe.
All of it—the planting, the upkeep, the harvesting—depends on the community. Only a few workers, like construction managers and teachers, receive occasional stipends. The rest of the 80 or so regular planters are volunteers from all over the city. Meanwhile, the food grown is picked regularly by neighbors, and anyone else who travels to South Seattle. How many people have eaten from the garden is unclear since it is unmonitored, on public land, and free.
“There are people in the city who don’t know how to use a shovel, never planted a tree, but really want to,” Herlihy says. “They haven’t had that experience of being able to forage in a public area, and the joy of finding a bunch of berries that they’ve never had before, like a goji berry. It’s an amazing experience.”
Like so many projects of its kind, Beacon was made possible by several different factors: A dedicated group of volunteers; a city willing to work with them; and available public funding, partly as a result of a levy approved by voters to make improvements to Seattle’s many parks.
That’s what makes this such an optimal time for a group of Philly volunteers working to develop what they call Fair Amount Food Forest, a publicly accessible food forest in Fairmount Park. Formed a little over a year ago by Michael Muehlbauer, a landscaper, farmer, and builder who was a core Beacon Forest member when he lived in Seattle, the initiative is in the very early planning stages—talking to the city, forming partnerships with like-minded organizations, reaching out to neighborhoods that abut Fairmount Park to see who, if anyone, would want something like the Beacon Food Forest in their community.
Muehlbauer, a Wisconsin native who had an edible landscaping business in Seattle, says he realized about six months after moving to Philly that this city—vastly different from that on the west coast—could be ready for this. “The people I’ve met and consistent, random conversations made me think, ‘We needed you at Beacon,’” Muehlbauer says. Those people now form the core of his planning group. “I realized we could do this really well here, maybe even better than in Seattle.”
Beacon contains 420 different species of edibles, some native to Seattle, and some a reflection of the surrounding communities of Chinese, Vietnamese, Somalians, Latinos and African Americans. Everything grown at Beacon Forest is free to anyone and everyone who wants to pick it at anytime.
Muehlbauer says he is hopeful that the city will grant his group a couple of acres in Fairmount Park to launch a food forest. And it is conceivable that the city could help to fund it with revenue from the tax on sugary beverages, a portion of which is slated for public park improvement. Like Beacon in Seattle, though, the city has first asked them to find other community partners and to get neighborhood buy-in for the project. Fair Amount is spending the next few months talking to residents who would be most affected by a public forest. “We don’t want to create this somewhere if no one wants it,” Muehlbauer says.
If Fair Amount gets off (into) the ground it would take Philly’s urban gardening movement to a whole new level. First there were community gardens, often built on empty lots across the city. Then urban farming took off, led by Fishtown’s Greensgrow Farms, which opened in 1997. The Philly Orchard Project launched 10 years later, and has now planted nearly 60 tree and berry farms on empty lots throughout town, harvesting some 3,000 pounds of fruit a year. A public food forest would go even further: Native plants set on to grounds that are, always, open to the public, for anyone to reap as they see fit.
And unlike Seattle, a relatively wealthy city with little unused land, Philly is ripe for a food farming revolution: The city has some 40,000 vacant lots, acres of land that are mostly eyesores. It also, despite incredible efforts on the parts of several groups, still is home to several food deserts, neighborhoods in which it is difficult and expensive for residents to access fresh produce. And many of those residents are the ones most in need: The 26 percent in poverty, with the host of ailments that go along with the city’s worst and most unshakeable problem. Fair Amount would not solve all of these problems But it could be part of an environmental, social and nutritional answer to many of the issues the city faces.
Herlihy says that when they first proposed the idea of Beacon Forest, they were asked about how to handle people who might want to take, for example, every blueberry in the garden. But Herlihy says it hasn’t been an issue. Plants are scattered throughout the forest, so grabbing any of one species would be more complicated than simply walking in with a big box to fill. And, anyway, it wouldn’t be an issue.
“If they’re coming in and taking it all, that means there’s a demand,” Herlihy says. “It means there are people who are hungry and need it, and that we should be doing more. We need more abundance to serve the need. We’re here for everyone.”
Correction: An earlier version of this story misstated that Beacon is the largest sustainable farm on public land in the country. It will be the largest food forest when it covers the full seven acres; right now, it occupies two acres.
Header photo: Volunteer planters at Beacon Food Forest. Courtesy of Beacon.
Urban Agriculture
Urban Agriculture
Image credit: Douglas Gayeton
Urban agriculture pioneers are taking action in their communities, growing not only fresh, healthy produce, but also providing jobs, beautifying their neighborhoods, and offering access to fresh, healthy food in areas where grocery stores are sparse.
As American agriculture continues to grow in new directions, NRCS conservation assistance is growing along with it. NRCS provides technical and financial assistance for assistance for urban growers in areas such as:
- Soil Health
- Irrigation and Water Conservation
- Weeds and Pests
- High Tunnels – NRCS can provide financial assistance for high tunnels, used to extend the growing season and to protect plants from harsh weather, air pollution and pests. By making local produce available for more months in the year, fewer resources are used to transport food to plates. Visit the NRCS High Tunnels website.
Resources:
- USDA Urban Agriculture Toolkit
- Fact Sheet: NRCS and Urban Agriculture (PDF, 4 MG)
- AMS Urban Agriculture Website
- Success Stories
Get Started
Starting an urban farm comes with a unique set of challenges and opportunities. NRCS can help with the challenges of conservation, and support urban farmers in their efforts to achieve local, healthy, sustainable food for their communities.
Start by contacting your local NRCS Service Center.
Success Stories in Urban Agriculture
Learn about urban farmers who have worked with NRCS. Read our stories.
Mastronardi Produce Acquires Backyard Farms
Mastronardi Produce Acquires Backyard Farms
Mastronardi Produce announced that it has acquired Backyard Farms, a large grower of year-round greenhouse-grown tomatoes in New England. The Backyard Farms brand name will be retained and continue to represent high-quality locally grown produce, and greenhouse operations in Madison, Maine will continue uninterrupted, as they have over the past decade.
"Together, Mastronardi and Backyard Farms will supply flavorful world-class, non-GMO verified tomatoes, peppers and cucumbers to the top food retailers in North America. The combined company will be better positioned to serve the underrepresented Northeastern region of the United States, where retailers focus on meeting consumer demand for locally grown, fresh produce", the company said in a news release.
The addition of Backyard Farms will increase Mastronardi’s internal greenhouse network to six locations across North America, and will increase the combined company’s headcount to approximately 3,000 employees. In total, Mastronardi produces and delivers fresh, locally grown produce to retailers from more than 4,000 productive acres of growing capacity.
“We have long been impressed with Backyard Farms’ commitment to fresh, high-quality tomatoes,” said Paul Mastronardi, President and CEO and the fourth generation family member to lead Mastronardi Produce. “Backyard Farms not only is a growing, customer-focused tomato grower with a strong and well-known presence in the Northeastern United States, but it also shares the same community-centric ethos that drives Mastronardi. Being a family-operated business, we have long prioritized our local communities and a ‘fresh from the farm’ commitment to our customers that we believe are critically important to our success.”
Mr. Mastronardi continued, “With Backyard Farms’ complementary capabilities, loyal and passionate customer base, growing footprint and enthusiasm for premium, vine-ripe tomatoes, we are excited for what our future holds together. We look forward to working alongside Stuart Jablon and his talented team as we continue serving customers the great produce they have come to expect from the familiar SUNSET® and Backyard Farms brands.”
Founded 10 years ago, Backyard Farms operates two greenhouses totaling 42-acres in Madison, Maine, from which it produces and delivers delicious, fresh tomatoes to the Northeastern United States year-round. Backyard Farms’ high-quality produce – tomatoes on the vine, cocktail tomatoes and beefsteak tomatoes – appears on the shelves of grocery stores from Maine to Maryland. Backyard Farms values freshness and quality, and is a strong advocate of supporting local communities.
“We are excited to be taking our business to its next level of operations,” said Stuart Jablon, who will continue to lead Backyard Farms, which is now an operating, wholly-owned affiliate of Mastronardi. “Joining the Mastronardi team allows us to continue expanding our business to reach more customers while remaining committed to growing the freshest, best-tasting fruit possible and deepening our community relationships. We look forward to being a part of a market leader and making sure that customers continue to receive fresh and high-quality produce throughout every season.”
US Food Price Inflation Continues To Outpace Overall Inflation
US Food Price Inflation Continues To Outpace Overall Inflation
6/8/2017
From 2012 to 2016, the Consumer Price Index (CPI) for all food (grocery store and restaurant food) rose by 6.1 percent—a larger increase than the 4.5-percent rise in the all-items CPI. When the CPI for a specific category, such as food, rises faster than the all-items CPI, it indicates that prices for the category are rising faster than prices for consumer goods and services as a whole.
Livestock and crop diseases, major weather events, and shocks to global food markets have caused price inflation for food to outpace many other consumer spending categories. Only prices for medical care and housing rose faster than food prices during 2012-16.
Food prices experienced larger increases than prices for recreation and education and communication, and apparel and transportation prices fell over 2012 to 2016. The 10.3-percent decline in transportation prices—a result of falling gasoline prices in 2015 and 2016—helped hold down economy-wide inflation. Food-price inflation outpacing economy-wide inflation is not a recent phenomenon. Over the last decade, food-price inflation averaged 2.4 percent per year and overall inflation averaged 1.8 percent per year.
This chart appears in ERS’s data product, Ag and Food Statistics: Charting the Essentials.
With Shipping Container, Fidelis Greens Fuses Technology, Farming
With Shipping Container, Fidelis Greens Fuses Technology, Farming
Credit: Josh Mandell, Charlottesville Tomorrow
Fidelis Greens aims to sell its fresh and sustainably produced microgreens to farm-to-table restaurants in Central Virginia year-round. From left: Kyle McCrory, Andre Ortiz, Joel Shindeldecker
Fidelis Greens, an agricultural startup near Crozet, is located on a picturesque 154-acre farm. But most of its work is confined to a much smaller space.
The company grows tiny, flavorful microgreens inside a repurposed steel shipping container, including arugula, amaranth, mustard greens and a "spicy mix" of several varieties.
The business aims to sell its fresh and sustainably produced microgreens to farm-to-table restaurants in Central Virginia year-round, giving chefs a local alternative to greens shipped from California and Mexico during the winter.
Joel Shindeldecker, who leads the company's marketing and sales, said the shipping container's hydroponic growing system can equal the output of a 2.5-acre plot of land, but requires much less water and allows for more consistent quality.
Fidelis Greens harvested its first microgreens earlier this year and has plans to share its open-source approach to indoor, "vertical" farming. They will be joined in the Charlottesville-area market by Freight Farms, a Boston-based startup that is bringing shipping container growing units to the Barracks Road and 29th Place shopping centers.
Fidelis Greens co-founder Randy Caldejon said his company has designed a simple, low-cost model for shipping container farms, while using computer technology to perfect the growing process.
"I'm fascinated by ways that farmers can optimize productivity and sustainability with software and machine learning," he said.
Caldejon previously co-founded nPulse Technologies, a network security firm that was acquired by FireEye in 2014 for more than $60 million.
Caldejon now supervises Fidelis Farm & Technologies, an incubator for agricultural startups at his Albemarle County estate. Fidelis Greens is the incubator's first venture and the startup has five team members who serve the company in multiple roles.
Kyle McCrory, an Albemarle native, brought expertise in industrial design and horticulture to the company. After graduating from Virginia Tech in 2010, McCrory started his career at Gotham Greens, which operates several large greenhouses in New York City and Chicago.
Credit: Josh Mandell, Charlottesville Tomorrow
Fidelis Greens currently specializes in four kinds of microgreens: arugula, amaranth, mustard greens and a “spicy mix” of several varieties.
"It was a great experience to be part of one of the pioneers in this field," he said. "I wanted to bring what I learned back home."
Fidelis Greens' shipping container farm became fully operational in mid-March, when many traditional farmers in Virginia feared a late winter storm could jeopardize the upcoming growing season.
Andre Ortiz said Fidelis Greens spent a few thousand dollars on a shipping container that had only gone through one voyage, even though heavily used containers can be purchased for much less.
The team insulated the container with spray foam, and built a hydroponic growing system out of materials that can be found at most hardware stores.
The container currently has six shelves installed on one side of the container that fit a total of 216 standard gardening trays. Shindeldecker said the company hopes to add six more shelves to the other wall.
Once seeds sprout into microgreens in seven to 10 days, Fidelis Greens delivers trays of live greens to restaurants that chefs can clip and serve as needed. The reusable trays avoid the waste generated by plastic clamshell packaging.
Shindeldecker said one of Fidelis Greens' strengths is the shipping container's automated climate control system, which combines open-source computer hardware and software with additional programming by Caldejon.
Caldejon's software automatically adjusts the container's air conditioning unit and fans to keep the temperature in the container constant at 77 degrees during the day, and 65 at night. It reads data from sensors placed throughout the container to regulate humidity, vapor pressure deficit and carbon dioxide levels.
Fidelis Greens staffers usually spend no more than two hours tending to the greens each day. They can monitor and adjust the growing conditions online when they are away from the farm.
McCrory said the company is in a "fast-paced learning mode," finding new ways to improve the quality of the product and distributing samples to restaurants in Crozet and Charlottesville.
Six restaurants have committed to regular deliveries from Fidelis Greens this summer, Shindeldecker said.
Kardinal Hall, a restaurant and beer garden in Charlottesville, uses Fidelis Greens' arugula as a garnish for salads and sausages.
"Putting a little arugula in everything is so 'in' right now," said Allison Hurt, Kardinal Hall's marketing manager. "We are all about trying new things, especially when they are locally made."
Kardinal Hall chef Jeffery Burgess said he has been using one or two trays of the arugula each week. "I think it's a great product," he said.
Caldejon said he will keep the design of Fidelis Greens' shipping container farm in the public domain, and hopes to publish a construction manual later this year so other organizations and individuals can replicate it.
Caldejon said military veterans, especially those suffering from post-traumatic stress disorder, could benefit from the opportunity to start their own shipping container farm.
Caldejon, Ortiz and fellow co-founder James Edward King are veterans of the U.S. Marine Corps. The Marines motto, "Semper Fidelis," inspired the name of their company.
"It opens up an opportunity [for veterans] to be gainfully self-employed in an environment with relatively low stress," Caldejon said.
"High-tech can be intimidating, but we are incorporating technology in a way that makes it more approachable," McCrory said.
The Fidelis Greens team includes three veterans of the U.S. Marine Corps, whose flag flies above the shipping container farm. Credit: Josh Mandell, Charlottesville Tomorrow.
Lakewood Hydroponic Farm Looks To The Future of Farming
Samantha Fox sfox@swiftcom.com June 7, 2017
Joshua Polson/jpolson@greeleytribune.com | The Greeley Tribune
Tommy Romano stands alongside some of lettuce being grown at Infinite Harvest, 5825 West 6th Ave. Frontage Road in Lakewood. The farm is a hydroponic vertical farm that produces year-round.
Lakewood Hydroponic Farm Looks To The Future of Farming
FARM TO SCHOOL
For the crops grown at Infinite Harvest, there’s a push to make them more available for those who might want them or simply those who haven’t heard of microgreens before.
Microgreens are mainly seen at fine dining restaurants, but like we saw with kale, it’s becoming more popular, even at the school level. Infinite Harvest is working with Natalie Leffler, who works with Greeley-Evans School District 6’s Farm to School program to get some of their products into schools.
In the early 2000s, Tommy Romano started to grow plants in his basement. He wanted to experiment with ways to efficiently grow food inside through vertical farming rather than the traditional way.
He experimented with different vegetables, such as corn. He would grow them indoors and stacked crops atop of other crops. For vertical farming, the point is to use less horizontal space, which can allow for farming in the middle of urban areas.
It took a lot of trial and error to find a way to efficiently farm indoors, but Romano was used to the scientific process, as he has a master's in aerospace engineering from the University of Colorado. He studied his process as a way to grow crops in space before realizing they would work on Earth, too. Once he felt his techniques were ready, he started Infinite Harvest, which opened January 2015 in Lakewood.
The farm grows 13 microgreens and lettuce. Microgreens are young vegetables greens. They're harvested before baby greens but later than sprouts. They can come from corn, celery, arugula and other vegetables and greens. They're not always the easiest to find, but microgreens might be an option for schools in Colorado soon. Romano is working with Natalie Leffler, head of Greeley-Evans School District 6's Farm to Schools program, to possibly start supplying schools with Infinite Harvest crops.
Microgreens are ideal for Infinite Harvest because the plants don't need to grow very high before they're harvested, which means more rows can be used. The way those at Infinite Harvest put it, the ceiling is the limit.
But that ceiling comes in handy, too. This past month, when Colorado was hit with rain, hail and snow, the microgreens and lettuce weren't touched by the elements.
That's the benefit of an indoor hydroponic vertical farm — the weather is controlled by technology.
"We don't actively manage a lot," said Nathan Lorne, operations manager. "We really rely on her."
The "her" in this scenario isn't a human, but the greenhouse control system. The system, run by software, controls how much water and nutrients the plants get, the temperature, humidity, carbon dioxide levels — anything that will affect the plants. The system is contained in a box filled with machines and wires that take notes on absolutely everything that happens in the greenhouse. In case something goes wrong, the control system will send a message to someone to come fix it.
'BEYOND ORGANIC'
Joshua Polson/jpolson@greeleytribune.com | The Greeley Tribune
Red and blue lights shine around Lacy Saenz as she works on packaging a head of lettuce Wednesday at Infinite Harvest, 5825 West 6th Ave. Frontage Road in Lakewood. The farm was inspired by Tommy Romano's work on a thesis at CU that involved growing crops on Mars.
Lorne said one of the benefits of having an indoor farm is the complete control over what the plants are exposed to. Even with the lighting the farm uses. They want to save as much energy as they can, so they use only blue and red spectrum lights — those are what the plants need for photosynthesis.
The farm pays about six times less than marijuana greenhouses pay in electricity costs each month. Pot is a good comparison because it is also grown in greenhouses.
Even more important for them, though, is what the plants aren't exposed to.
Before even going into the farm, you enter an air cleanser room. Air is circulating and it's where visitors put on hair nets, hats, shoe covers or the specific farm shoes. This helps prevent some unwanted outside elements from getting in. There are traps that attract bugs to keep them from going in, too.
Because there aren't bugs or anything else in the farm aside from what is planned, Infinite Harvest doesn't use genetically modified plants, and there isn't a need for pesticides, either.
Even organic farms will use some sort of organic pesticide or spray to get rid of weeds or pests. Infinite Harvest doesn't have to.
Even with the organic trend, Romano said there aren't plans to apply to be organically certified. On one hand, the "Colorado Proud" label means more.
And on the other hand, "We're beyond organic," Romano said.
KEEP MOVING FORWARD
Joshua Polson/jpolson@greeleytribune.com | The Greeley Tribune
The rows and stacks of crops rise above Tommy Romano as he stands on the floor of the hydroponic-vertical farm Wednesday at Infinite Harvest, 5825 West 6th Ave. Frontage Road in Lakewood.
Romano made clear the purpose of this farm isn't to outdo farming. It's an ongoing science experiment in some ways. This isn't something that has been done before, and some of the technologies are relatively expensive.
There are a number of worries and problems farmers face, and Infinite Harvest looks to find solutions for them, Lorne said.
"Everyone here loves the romance of traditional farming," he said.
With the use of technology and indoor operations, Infinite Harvest has only 18 employees for their operation. They're not harvesting mass amounts of food at a time, but they're able to harvest food year-round.
But one of the most important roles is one most farms don't really need: a software engineer.
Romano said they're looking to expand, but they don't want it to be a big leap from what they're doing now. They want to take lessons learned and improve upon them a little at a time.
"There is no textbook," Lorne said.
And that's why Romano doesn't see Infinite Harvest as a competing entity, but as the next forward step in the industry.
"The traditional ways aren't fulfilling (the holes left by problems)," Romano said. "If we held to the same traditions of farming. … We'd still be riding horses right now. We're helping it take the next step."
Samantha Fox is a reporter for The Fence Post. She can be reached at sfox@thefencepost.com, (970) 392-4410 or on Twitter @FoxonaFarm.