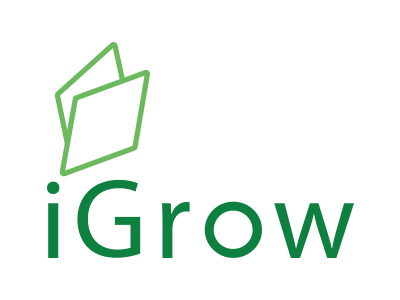
Welcome to iGrow News, Your Source for the World of Indoor Vertical Farming
Seeds&Chips Starts By Examining How Millennials are Changing The Food System
Seeds&Chips Starts By Examining How Millennials are Changing The Food System
The third annual Seeds&Chips Global Food Innovation Summit started off with a panel titled How Millennials Are Changing the Food System. Speakers discussed why young people are doing more than just taking pictures of their food. Their activity on social media platform indirectly spearheads change in the food industry. Brands have been forced to adapt by altering their marketing strategies and product lines to meet Millennials’ expectations.
According to Tobias Peggs, founder of Square Roots, Millennials are willing to pay more for local food, expect to know where their food comes from, want healthy snack options, and actively seek out nutritious recipes online. His company seeks to bring the farm to the city and coaches young farmers how to grow nutritious food in urban greenhouses. He hopes that his company can help feed a rapidly urbanizing population and allow consumers to know where their food came from and build a relationship with their local farmer.
Two of the ten speakers during the session were entrepreneurs: Danielle Gould, CEO of Food+Tech Connect, a food and innovation community, and Deepti Sharma Kapur, CEO and founder of FoodtoEat, an online ordering service focused on food trucks and corporate catering.
This panel commenced four days of panel discussions and meetings at Rho Fiera in Milan, Italy, with former U.S. President Barack Obama as the keynote speaker. Following his talk on May 9, Obama will also participate in a panel that includes Sam Kass, the former White House chef and current advisor to Obama. More than 200 international speakers are discussing various topics during the four-day event. Panel discussions are centered around strategies to feed more people with less land.
Marco Gualtieri, Seeds&Chips chairman, has put the focus on young people’s involvement this year. For each Seeds&Chips talk, there will be at least one speaker or panelist under thirty and a “teenovator” under 18 years old who presents their vision for the future of food.
This year, he has also gathered young people to participate in a Hackathon for food waste over the next few days. Gualtieri hopes that they can come up with an innovative solution that reduces waste in the food system. The Hackathon is put on in collaboration with the Ministry of Education, University and Research. There is also a space at the Summit called Give Me Five, where young entrepreneurs can meet a leader for five minutes, to whom they can pitch their ideas.
Click here to view the full schedule for Seeds&Chips. Organizers are urging attendees to use #SaC17 in social media posts relating to the Summit.
Affinor Growers Receives New Order and Provides UFV Growth Trial Update
Affinor Growers (CSE:AFI, OTC:RSSFF, Frankfurt:1AF)
Affinor Growers Receives New Order and Provides UFV Growth Trial Update
Vancouver (Canada), May 8, 2017 - Affinor Growers (CSE:AFI, OTC:RSSFF, Frankfurt:1AF) (“Affinor” or the “Corporation), is pleased to announce it has received its largest equipment order to date from the license holder in Abbotsford B.C. These 10 level growing towers will be installed during the next 6 months and be used to grow and produce strawberries and other produce.
The license holder has ordered 32 vertical growing towers capable of holding 20,480 strawberry plants in 10,000 square feet. Under the terms of the order, a single vertical tower will be manufactured and installed immediately to verify various installation design specifications with the remainder 31 growing towers to be delivered and installed over the summer.
Jarrett Malnarick, President and CEO comments, "We are excited to see our license holder and partner in Abbotsford B.C. progress with construction of the facility, as it will be a showcase to demonstrate Affinor's vertical technology on a large scale, as well as revenue from equipment sales and potential long term royalties."
Strawberry University of the Fraser Valley (“UFV”) Test Site Update:
Affinor is also pleased to update that the small 4 level, 8 arm tower, and the 4 level 16 arm tower are now producing strawberries. Affinor expects to start harvesting strawberries within the next several weeks. Affinor and UFV are testing various strains, crop inputs, lighting conditions and nutrients to maximize production, document protocol and prepare for commercial applications.
For More Information, please contact:
Jarrett Malnarick, President and CEO
contact@affinorgrowers.com
About Affinor Growers Inc.
Affinor Growers is a publicly traded company on the Canadian Securities Exchange under the symbol ("AFI"). Affinor is focused on growing high quality crops such as romaine lettuce, spinach, strawberries using its vertical farming techniques. Affinor is committed to becoming a pre-eminent supplier and grower, using exclusive vertical farming techniques.
On Behalf of the Board of Directors
AFFINOR GROWERS INC.
"Jarrett Malnarick"
President & CEO
The CSE has not reviewed and does not accept responsibility for the adequacy or accuracy of this release.
FORWARD LOOKING INFORMATION
This News Release contains forward-looking statements. The use of any of the words "anticipate", "continue", "estimate", "expect", "may", "will", "project", "should", "believe" and similar expressions are intended to identify forward-looking statements. Although the Company believes that the expectations and assumptions on which the forward-looking statements are based are reasonable, undue reliance should not be placed on the forward-looking statements because the Company can give no assurance that they will prove to be correct. Since forward-looking statements address future events and conditions, by their very nature they involve inherent risks and uncertainties. These statements speak only as of the date of this News Release. Actual results could differ materially from those currently anticipated due to a number of factors and risks including various risk factors discussed in the Company's disclosure documents which can be found under the Company's profile on www.sedar.com. This News Release contains "forward-looking statements" within the meaning of Section 27A of the Securities Act of 1933, as amended, and Section 21E the Securities Exchange Act of 1934, as amended and such forward-looking statements are made pursuant to the safe harbor provisions of the Private Securities Litigation Reform Act of 1995.
Urban Agriculture: Food, Jobs, and Lower Food Miles
Urban Agriculture: Food, Jobs, and Lower Food Miles
SUBMITTED BY VIVEK PRASAD ON TUE, 05/02/2017
CO-AUTHORS: IFTIKHAR MOSTAFA
Millions of urban dwellers cultivate vegetables and fruit trees in home gardens, both for their families and for sale. In Dakar, 7500 households “grow their own” in micro-gardens. In Malawi, 700 000 urban residents practice home gardening to meet their food needs and earn extra income. Low-income city gardeners in Zambia make US$230 a year from sales. In cities like Bamako, Accra and Kumasi, depending on crop and season, between 60 and 100 per cent of leafy vegetables consumed are produced within the respective cities with employment figures ranging from 1,000 to 15,000 jobs. Even megacities such as Shanghai, with about 15% population growth per year, one of the fastest growing cities on the planet, maintains its urban farming as an important part of its economic system.
Farm plots amidst apartment blocks in Chaozhou, China
Around 15 percent of the world’s food is now grown in urban areas. According to the U.N. Food and Agriculture Organization (FAO), urban farms already supply food to about 700 million residents of cities, representing about a quarter of the world’s urban population.
Most cities in developing countries are facing challenges to create formal job opportunities. Urban agriculture can play an important role not only in enhancing food security but also in contributing to the eco-system - improved nutrition, poverty alleviation, local economic development and job creation as well as productive reuse of urban wastes.
Cuba has a system of urban organic farms called Organopónicos, which provides a fresh supply of organic food to the community, neighborhood improvement, beautification of urban areas, as well as employment opportunities. Cuba has more than 7,000 organopónicos, with some 200 gardens in Havana alone, covering more than 35,000 hectares of land, which supply its citizens with 90% of their fruit and vegetables. In Havana, 117,000 jobs in Havana and income for 150,000 low income families were directly provided by urban and peri-urban agriculture.
In Cagayan de Oro City, the Philippines, 9 percent of the economically active population were employed in agriculture. There were 13,000 farmers in the peri-urban area; 40 per cent of all households maintained backyard gardens and 70 per cent of the city’s demand for fish was produced within the city.
In Mumbai India, a Vertical Farming Association has been formed to promote vertical farming and aeroponics, air-based plant growing that requires no soil, no sunlight (LEDs are used instead) and dramatically less water — roughly 95 percent — than conventional growing methods. The targeted groups for his mission are builders, real-estate people, food industry, green house owners, industrialists, and bankers, who own buildings with large roof space.
A sizable area of Bangladesh’s capital city Dhaka and its periphery are engaged in agricultural activities. For example, the business district of Tejgaon in the center of Dhaka has 38 per cent of the land available for agriculture. In addition, about 10 square kilometer of rooftops within the Dhaka City Corporation are vacant and potentially could be used for urban food production.
In developed countries urban agriculture can contribute to the reduction of 'food miles' - with local distribution via farmers' markets and specialized shops. In South London, United Kingdom, Growing Underground is a 7,000 square feet urban farm, which is housed in a network of dark and dingy tunnels originally built as air-raid shelters during World War II. Growing Underground limits the food miles by providing vegetables and salads to local wholesalers and restaurants in London. Similarly in Newark, New Jersey, USA, a 69,000 square-foot former steel factory has been converted into the world's largest urban farm.
Growing Underground, an urban farm in a tunnel.
Urban agriculture has potential for not only to provide fresh and nutritious food for urban consumers but also to create more and better jobs faster for growing youth population. For urban agriculture to play such an instrumental role, appropriate policy instruments must ensure that the sector functions well. Furthermore, strong institutional capacity at all levels of national economies will be needed to deal with challenges that arise from urban agriculture.
Build Your Personalised Vertical Farm With Altifarm
Build Your Personalised Vertical Farm With Altifarm
Sindhu Kashyap 6 MAY 2017
Mumbai-based Altifarm gives you the delight of home farms and gardens in an easy modular and plug-and-play format.
In 2014, 31-year-old Arun Raj, who then ran a boutique industrial design studio, Primus Design, was working on a large granite-based modular garden design project for a Swiss client. After several iterations of the design, Arun realised that there were hardly any home-garden shops or brands. That’s when Arun says he felt the need for an all-season modular home farm. And this led to the genesis of Altifarm, a home garden platform.
With designs centred around tight and busy urban spaces, Alitfarm sells vertical structures that comprise special trays that one call fill with soil and sow herbs and vegetables for their daily use.
The team at Altifarm.
The Mechanisms
The idea was to make the process of gardening easier and also enjoy the benefits of a homegrown farm, without the need for routine watering, electricity, or recurring subscriptions.
The trays come with a watering sprout and a water level indicator. The water in the sprouts can be filled once a week, and the rest is taken care of by a pressure mechanism which ensures the plants are watered through the holes in the platform situated in the tray. Explains Arun,
“The self-watering system works with the help of capillary action (and gravity). There is no electricity or motor/pump involved. It also helps with oxygenation of roots leading to healthier plants.”
The trays also come with a Growlight expansion pack, which is used for indoor plants so that they can work on their processes away from the sunlight. Arun adds that LEDs are chosen to impart certain specific wavelengths, which promote vegetative growth, flowering, and germination.
By providing the exact wavelength to plants, the system is rendered highly power-efficient with minimal operating costs and the included timer takes care of auto-shutoff functions. It has an IP65 rating and is custom manufactured to specs for optimal performance. For colder climates, there is also the Greenhouse pack for outdoor use.
Working on a Three-Year Pipeline
Altifarm allows for both outdoor and indoor use. It provides one sq. metre of gardening space from no more than the footprint of a chair and makes an unused corner of the house into a mini-food farm.
“We are confident that Altifarm lets you grow almost anything, as long as plants are not too tall, that tiers are height adjustable and removable to facilitate this,” adds Arun.
The journey started in 2014 with paper sketches and a proof of concept with acrylic sheets that were held on frames made from hardware pipes. This meant close to three years of trial and error tests. After the basic mould, they followed it with a CAD-based design and 3D printing for trials and moved on to mould making.
While the first product was ready by late 2014, for the next three years, the team kept working and re-working on the product.
“The product you see is Altifarm 2.0 and we believe this is our best yet. All the learning we had over the years at the design studio has been invested into Altifarm and it has helped us meet amazing people and take some huge risks,” says Arun.
Setting The Team
Since Arun had already founded Primus Design, getting initial help wasn’t difficult. His mentor and neighbour David Ghosh joined in as the co-founder. With decades of experience in the manufacturing space, David was able to bring the needed manufacturing know-how and in-house production capability for the metal frame, while the plastic part of the business is handled by a captive vendor nearby.
The core team is a mix of designers, engineers, tinkerers, and production specialists. The 12-member team works out of Mumbai with a manufacturing facility in Pune. The first sale was made to Switzerland, where the team shipped 80 units to their friend and mentor Jean. Currently, the units are priced at $199.
Revenue and Numbers
The team is focused just on building and selling the units. Individuals will need to buy their own soil, seed, and all other farming tools.
Their revenue model is only through (online) sales of Altifarm and expansion packs, of which barring customised grow lights, everything is mostly done in-house or in close vicinity. While the concept of vertical gardens is relatively new in India, the idea is thriving in Mexico, Europe, US, and New Zealand.
Some of the companies in a similar space include Mexico’s Vertical Green, which was a part of a kickstarter programme. There also is Delhi-based Green Walls, US-based Green Sense Farms, and other US-based company City Farm.
“We plan to develop Altifarm further as a product platform and are already working on variants and expansion packs. We look forward to feedback from users to improvise the product and add more features and functionality. We also invite those who would like to join us in our journey towards Urban Farming Movement, by partnering us in sales and distribution,” says Arun.
Hydroponic Farm In Lakewood, Colo., Takes Next Step
Hydroponic Farm In Lakewood, Colo., Takes Next Step
Photo courtesy Infinite Harvest |
The room Infinite Harvest grows food in look pink because only red and blue lights are used during photosynthesis.
Before 2002, Tommy Romano's life plans were not necessarily Earthly.
He was at the University of Colorado studing for his master's in aerospace engineering. His thesis was on ways to grow food in space.
But man still has yet to land on Mars, so Romano thought, why not tru this technology on Earth, first?
It took a lot of trial and error and growing food in his basement, including ears of corn. And in January 2015, Infinite Harvest began.
“The traditional ways aren’t fulfilling (the holes left by problems). If we held to the same traditions of farming ... we’d still be riding horses right now. We’re helping it take the next step.”
Infinite Harvest is an indoor hydroponic vertical farm. Currently the farm in Lakewood, Colo., grows 13 microgreens and lettuce. A week ago, when the Denver-metro area was hit with rain, hail and snow, the crops at Infinite Harvest weren't even touched by the elements.
TECHNOLOGY
That's the beauty of growing vegetables in an indoor hydroponic vertical farm — the weather is controlled by technology.
"We don't actively manage a lot," said Nathan Lorne, operations manager. "We really rely on her."
The "her" in this scenario isn't a human, but the greenhouse control system. A box containing machines and wires takes notes on everything that happens in the greenhouse.
The system controls how much water and nutrients the plants get, the temperature, humidity, carbon dioxide levels — anything that can and will affect the plants.
And, if something goes wrong, the control system will send a message to someone so they can come in to fix it.
The room doesn't have any natural lighting, only blue and red spectrum lights are used because that's all the plants need for photosynthesis. They go through day and night cycles.
One you leave the room, everything has a green hue to it because your eyes overcompensate after only seeing two hues of light.
The other lights just waste energy, which is against the goals of Infinite Harvest.
A tech-based farm might sound like it's just wasting energy, but the way the control system is set up, the farm actually pays about six times less than marijuana greenhouses pay in electricity costs each month. When it comes to energy comparisons, marijuana is the best comparison because both grow crops are grown indoors.
Another concern that Lorne said hydroponic farms raise is the amount of CO2 released.
But the system controls the amount of CO2 that is released at all times.
'BEYOND ORGANIC'
Lorne said one of the benefits of having an indoor farm is having complete control over what the plants are exposed to. Even more important for them, though, is what the plants aren't exposed to.
Before going into the farm, a person enters an air cleanser room. Air is circulating and that is where hair nets, hats, shoe covers or specific farm shoes are put on. This helps prevent some unwanted outside elements from getting in. There are traps that attract bugs to keep them from going in, too.
Because there aren't bugs or anything else in the farm, aside from what is planned, Infinite Harvest doesn't have to use genetically modified plants and there is no need to use pesticides.
Even organic farms use natural products to get rid of weeds or pests. Infinite Harvest doesn't have to.
Even with the organic trend, Romano said there aren't plans to apply to be organically certified because he thinks the "Colorado Proud" label means more.
And, "We're beyond organic," Romano said.
KEEP MOVING FORWARD
There are a number of worries and problems farmers face, and Infinite Harvest looks to find solutions for them, Lorne said.
"Everyone here loves the romance of traditional farming," he said.
Romano said the purpose of this farm is not to compete with traditional farming. In some ways, it is an ongoing science experiment. Because indoor hydroponic vertical farms are a fairly new, some of the technologies are on the expensive side.
But the energy saving measures the company is able to do even that out.
Romano said they're looking to expand, but they don't want it to be a big leap from what they're doing now. They want to take lessons learned and improve upon them a little at a time.
"There is no textbook," Lorne said.
That's something any farmer can relate to. As technology changes on farms, there's always an experimental phase before the technology becomes widely used.
That's why Romano doesn't see Infinite Harvest as a competing entity, but as the next forward step in the industry.
"The traditional ways aren't fulfilling (the holes left by problems)," Romano said. "If we held to the same traditions of farming … we'd still be riding horses right now. We're helping it take the next step."❖
— Fox is a reporter for The Fence Post. She can be reached at (970) 392-4410, sfox@thefencepost.com or on Twitter @FoxonaFarm.
The Startup That Will Change The Way China Feeds Its Cities
The Startup That Will Change The Way China Feeds Its Cities
Beijing-based startup Alesca Life is democratizing access to fresh food by creating solutions that enable anyone anywhere to grow the safest, healthiest, and freshest produce in the most efficient way possible. Their automated indoor food production system is currently growing nutrient-dense produce using no pesticides, no soil, no sunlight, 20-25 times less water, fertilizer, and land compared to traditional farming practices.
CEO Stuart Oda shares his thoughts on the necessity of evolving the modern agriculture framework to feed the globe’s ever-growing population.
What experiences inspired you to start this company?
I’ve traveled to over 40 countries and one of the most common challenges faced by emerging market countries was the access to highly nutritious, safe, fresh foods. The unpredictability of weather due to climate change and lack of access to critical resources and education makes food production and distribution and the stable supply of nutrition through fresh foods an enormous challenge.
Also, fresh food logistics is essentially the movement of water and nutrition in a perishable, damageable form: incredibly energy intense and wasteful with both food and packaging. Many of the problems of the agricultural supply chain can be overcome by removing the key variables of present day agriculture: weather, logistics, and land.
Finally, the environmental degradation associated with agriculture is quite alarming. When I was an investment banker in Tokyo, someone I greatly respected always reused printouts until the white on the paper was almost gone. Her explanation was simple, “I don’t want my grandchildren to have to visit a museum to see what a tree looks like.”
Agriculture must become a more environmentally friendly practice to ensure that future generations do not inherit a heavily polluted planet. Alesca Life was born out of the frustration of an archaic method of food production to create a more sustainable alternative to feed our current and future population.
Why solve the issues you’re trying to solve?
The world will face a number of significant challenges in the coming decades, including rapid population growth and urbanization, higher food distribution inequality and waste, environmental degradation, and natural resource depletion. In developing countries, there is the additional problem of poor food quality and safety.
Also, as the sharing economy and automation grows, the most basic of urban infrastructure and human capital will become idle or underutilized. A solution to these challenges will be critical for global social, economic, and environmental development.
Why is your solution unique?
Alesca Life designs and builds turn-key farming solutions that enable anyone in any environment to produce safe and healthy produce locally. We have several hardware form factors that enable pesticide-free food production at any scale, and we coupled it with a cloud-based operational management system that enables complete production data transparency and supply chain traceability.
The agricultural industry has traditionally been additive: more chemicals, more water, more logistics, more land. Alesca Life’s philosophy is the exact opposite: food production utilizing minimal inputs on virtually no land.
Also, our solution is looking to integrate an IT infrastructure that allows for supply chain transparency to end the production of “anonymous food” and by growing in a more consistent environment we want to end the concept of “ugly vegetables” which are some of the biggest contributors to poor food quality and high food waste.
What has been your company’s proudest moment been to date?
For the founders, completing our hand-built shipping container farm and commencing fresh vegetable production was a moment of incredible pride.
For the team, installing our first indoor food production system into Swire Hotels for the onsite production of fresh wheatgrass was one of our collective highlights.
My personal proudest moment was when, following a visit to our urban container farm, a young child told us that he wanted to be an urban farmer when he grew up.
What do you hope the world will look like as a result of your work?
Our team hopes that the integration of food production as one of the core functions of urban environments will help to create more resilient, sustainable, and beautiful cities for urban citizens. Also, if the extension of our technology can impact food production in space (outer space), it would be an incredibly exciting future.
Upping The Ante For Urban Growing
Upping The Ante For Urban Growing
4 May 2017, by Gavin McEwan, Be the first to comment
Europe is starting to catch up with the Far East and the USA with the opening of a major indoor lettuce-growing facility in the Netherlands, Gavin McEwan reports.
Lettuce: plants at Staay Food Group’s new facility in the Netherlands will be grown hydroponically in coir underneath LEDs - image: HW
With the imminent opening in the Netherlands of Staay Food Group’s €8m, 27,000sq m high-rise indoor lettuce-growing plant, Europe finally appears to be following the Far East and the United States down the route of large-scale commercial urban growing.
Located at its Fresh-Care Convenience processing plant in Dronten, central Netherlands, the facility will initially produce around 300,000kg of lettuce, a mixture of Lollo Biondo, Lollo Rosso, Rucola and Frisée forms, rising eventually to more than a one-million kilograms, for processing into salads.
The plants will be grown hydroponically on eight or nine levels in coir plugs underneath LEDs. "At this moment, we still source our lettuce in southern Europe during part of the year. The disadvantages are that the climate is erratic and the transport distances are great," says the company.
"Once the vertical farm supplies the lettuce, it will be fresher, there won’t be any pesticides involved, the quality will be stable, we will be able to plan production better and we will contribute to Staay Group’s sustainability goals."
Production times will also be considerably shorter than in conventional growing, it adds. Last year, in partnership with Philips Lighting and breeder Rijk Zwaan, it tested the format at Philips’ High Tech Campus in Eindhoven, with "positive results".
While the UK has yet to see anything on this scale, the wide exposure of a handful of pioneer projects on television and in national newspapers has brought the format to wider public attention. But suppliers tend not to think in purely national terms, according to Stephen Fry, senior business development executive at Midlands hydroponics equipment supplier HydroGarden.
"We have had a significant increase in business for our urban growing solutions," he says. "Most weeks I am drawing up plans for new systems, which could be in Lebanon, Kenya, New Zealand or the Far East as well as mainland Europe. People are looking at producing food where it’s required. For the UK, what is the carbon footprint of driving produce up from Spain?"
Responding to trends
"It’s still very niche," Fry admits. "We aren’t going to save the planet from starvation on our own, but a 50% increase in world food production has to come from somewhere. What we are doing is responding to trends in food. You only have to go to a half-decent restaurant or even pub to see the emphasis on freshness."
The VydroFarm tiered indoor growing system developed by HydroGarden took the innovation prize in the Future Manufacturing Awards presented by EEF, formerly the Engineering Employers Federation, earlier this year. Now rebranded as V-Farm, the system currently leads the company’s push into world markets.
It is also launching a new flood-and-drain vertical system at international trade events this month, says Fry.
On a smaller scale it has also developed a compact format for coffee shops, small supermarkets and high-end restaurants to grow their own micro-leaves and other crops. Its own range of LEDs "are giving very good results — they have needed to have a different spectrum for micro-greens, which are popular in the Far East", Fry explains.
"We also do a lot of work on the nutritional element. With our new product lines we can affect the nutritional content of things like micro-greens. Kale is hailed as a superfood but, if you compare the vitamin and mineral content, these are super-duper foods."
HydroGarden has also installed a trial 12-rack growing room at its Coventry headquarters, while a specially commissioned hybrid version of V-Farm combined with a FishPlant aquaponics system is also due to open at Pershore College in Worcestershire later this month.
This will be used to educate post-16 and degree-level students on a variety of courses including horticulture and animal care about hydroponics and aquaponics as sustainable alternatives to traditional farming methods.
HydroGarden’s V-Farm unit combined with FishPlant aquaponics system
Water quality and health
The college’s project manager John King explains: "In the first instance, our animal-care students will carry out testing to monitor and manage the water quality and subsequent health of the fish and plants.
These readings will be shared with our horticulture students whose focus will be the produce, grown from seed in separate propagators before being transplanted into the hydroponics part.
"If the plants are less than healthy, the students will have a real-life scenario to determine what is going wrong and what factors need to be altered such as lighting, nutrient flow and temperature." Animal-care students will then feed the finished produce to rabbits and other small herbivores in the department.
"We also plan to invest in a larger vertical-farming unit in the future so any students who are particularly interested in hydroponics will be able to take their knowledge and learning to the next level by working on a larger scale," says King.
Fry adds: "We are working with Pershore on growing protocols. Having a system without protocols on how to use it is like giving a car to someone who can’t drive."
The understanding of plants’ response to LEDs in controlled growing environments has so far been driven in the UK by AHDB Horticulture-funded work at Stockbridge Technology Centre’s LED4Crops facility. But while this three-year programme finishes at the end of this month, there is still much more in this area that the North Yorkshire research station is keen to investigate.
The facility’s manager, photobiologist Dr Phillip Davis, says: "We have a lot of data on the effect of different light on crops. We can control everything from how tall the plant grows to when it flowers. We have looked a lot of different crops — lettuce, tomatoes, peppers, cucumbers and many ornamentals — mainly from the point of view of propagation, but for lettuce and leafy herbs through to harvest. For
a crop like basil you can control the intensity of the flavour, for example, whether you want it mild for salads or stronger for sauces."
This response is already being harnessed by salad and herb grower Vitacress, which has recently installed Heliospectra programmable LED grow lights at its West Sussex site to increase shelf life and chill tolerance of basil plants during the final growth stage.
"There isn’t a vast acreage of indoor farming in the UK yet, though there are rumblings of big things taking off," Davis notes.
"And in research we are really just touching the surface. The more we look at it in total, the more we discover is possible in things like flavour and shelf life."
Urban growing economics
While the LED4Crops facility continues with research including private commissions, Stockbridge Technology Centre is now taking on a new project to look specifically at the economics of urban growing, and hence the barriers to commercial uptake, as part of the Innovate UK-funded Centre for Crop Health & Protection.
"There are a lot of questions in people’s minds as to whether it makes economic sense," says Davis. "It’s certainly not a low bar to start with." The new facility will have three growing areas, each producing "large volumes" of a single crop "and will be flexible enough to allow us to test what’s out there.".
He continues: "LED lighting is coming down in price — though not as quickly as some had hoped. But they are getting more efficient so you need fewer and your payback is quicker."
Viewpoint: Professor Tim Benton
"Urban agriculture, including vertical farming, is a potentially useful way to provide some high-value produce locally, and helps to connect people and food. However, it is unlikely it will underpin food security in the sense of access to a healthy diet as the amount of land necessary to provide nutritional needs is likely to be difficult to find within a purely urban setting.
"There is a clear role for it in some circumstances and for some markets, perhaps most obviously for things like lettuce, herbs and some fruit and veg. The degree to which it may emerge depends on a host of factors like access to food from other places, local access to land and water, infrastructure and so on.
"The space in most cities is very expensive relative to peri-urban and rural areas, so it might be more likely to emerge strongly in very large cities where ‘local fresh’ food might be highly valued, and where there is a market to support it, or in cities like Singapore, where access to land is absolutely difficult. Where land is cheap and available near cities, and it is easy for fresh produce to find its way into the centre, it may not play a huge role."
Number of U.S. Indoor Warehouse Farms On The Rise
Number of U.S. Indoor Warehouse Farms On The Rise
The number of urban, indoor and warehouse agricultural operations in the U.S. has grown significantly over the last two years. According to a new white paper that was presented on the first day of the 5th Indoor Ag-Con in Las Vegas this Wednesday, there are currently 56 warehouse farms, plant factories and rooftop greenhouses across the US, compared to only 15 in a previous report of March 2015.
This growth was also reflected in the atmosphere of the first day of the 5th annual Indoor Ag-Con that is being held this week on Wednesday and Thursday at the Las Vegas Convention Centre. While not very crowded, the event has grown this year and brings together the industry's best suppliers, researchers, growers, investors and other professionals from the food industry.
And while it remains a cliché to say that this industry is still young, it is growing up fast and is clearly looking more at the overall business management side of growing indoors. Therefore the first day of the event covered a number of business related topics such as real estate development, planning, management and funding. As well as this, several expert speakers shared their vision on how automation and crop selection can increase the efficiency of indoor farming and make businesses profitable.
While the first day also covered a few technical topics, the speaker program on the second day will provide more emphasis into technical aspects of indoor growing.
We will be back with more reports on the event and the presentations over the coming days. On Monday we will publish a complete photo report of the conference and exhibition.
The white paper will be available for download shortly.
Publication date: 5/4/2017
Author: Boy de Nijs
Copyright: www.hortidaily.com
Shanghai's 100-Hectare Vertical Farm to Feed 24 Million
Shanghai's 100-Hectare Vertical Farm to Feed 24 Million
More Urban dDevelopment Plans
By Flora Burles | Tue, May 2, 2017 02:47 PM
Plans have just been unveiled by international architecture firm Sasaaki for a spectacular 100-hectare urban farm growing fruit and vegetables in Shangahai.
News comes to us from Inhabitat that a new 250-acre farming district, “Sunqiao Shanghai”,set amidst the skyscrapers of the city, will meet the food needs of almost 24 million people using both hydroponic and aquaponics farming systems.
The farm also will also serve as a center for innovation, interaction and education within the world of urban agriculture, as visitors will be able to tour the interactive greenhouses, a science museum and an aquaponics system. There will even be family-friendly events to educate children about modern agricultural techniques and sustainability.
Given its urban setting, the Sunqiao Urban Agricultural District’s layout will have to utilise vertical space as efficiently as possible, so will include multiple growing platforms such as algae farms, floating greenhouses, vertical walls and seed libraries. Some of the crops will even be grown indoors, under LEDs and in nutrient-rich water. The farms will primarily grow leafy greens, like kale, bok choi, and spinach, which will be sold to restaurants, grocers, or be exported.
It is part of a larger plan to turn part of the city into an ag-tech hub, according to Michael Grove, a principal at Sasaki. Grove estimates that building work on the project will commence by 2018.
“As cities continue to expand, we must continue to challenge the dichotomy between what is urban and what is rural. Sunqiao seeks to prove that you can have your kale and eat it too.”
Urban Farming Flourishes In New York
01:06 PM, May 02, 2017 / LAST MODIFIED: 01:37 PM, May 02, 2017
Urban Farming Flourishes In New York
Tobias Peggs, CEO of Square Roots Urban Growers, speaks about urban farming outside one of the Square Roots containers on April 25, 2017 in New York. The urban farm craze is finding fertile ground in New York, where 10 young entrepreneurs are learning to grow greens and herbs without soil, bathed in an indoor, psychedelic light. Photo: Don Emmert/ AFP
AFP Relaxnews
The urban farm craze is finding fertile ground in New York, where 10 young entrepreneurs are learning to grow greens and herbs without soil, bathed in an indoor, psychedelic light.
In a "hothouse" of invention in a Brooklyn car park, each farms a container, growing plants and vying for local clients in the heady atmosphere of a start-up, fighting against industrially grown food, shipped over thousands of miles.
Meet the farmer-entrepreneurs at Square Roots, a young company with a sharp eye for the kind of marketing that helps make Brooklyn a center of innovation well-equipped to ride the wave of new trends.
"It is not just another Brooklyn hipster thing. There is no doubt the local real food movement is a mega-trend," says Tobias Peggs, one of the co-founders, a 45-year-old from Britain who previously worked in software.
"If you are 20 today, food is bigger than the internet was 20 years ago when we got on it," he adds. "Consumers want trust, they want to know their farmers."
He set up Square Roots with Kimbal Musk, brother of Tesla Motors billionaire Elon, and they have been training 10 recruits since November.
Already well-established in parts of Europe -- the Netherlands in particular -- the technology is still being pioneered in the United States.
The greens are reared in an entirely closed and artificial environment that can be completely controlled, grown vertically and irrigated by a hydroponic system that feeds them water mixed with minerals and nutrients.
Wylie Goodman, a graduate student finishing a dissertation on urban farming at Cornell University, says the US financial capital was a captive market for the innovations.
"It makes total sense," she said. "You've got a well-educated and wealthy population willing to pay a lot for good local food" -- in this case $7 per single pack of fresh greens delivered to your door.
New York and its environs have seen constant innovation in urban agriculture from rooftop gardens to the huge AeroFarm complex in neighboring Newark and Gotham Greens, which grows greens and herbs in ultra-modern rooftop greenhouses that can be harvested before breakfast and on a New York plate for lunch.
Glowing Environment
Halfway through his year-long apprenticeship, Peggs says the 10 young entrepreneurs have already learned how to grow food customers want to buy.
The next stage will begin within a year, he says, with the creation of "campuses" capable of producing greens -- similar to the one in Brooklyn -- in other large US cities before the initiative rolls out "everywhere."
His enthusiasm is contagious. Around 100 people who took part in a guided tour of the farm this week, were for the most part not only willing to shop the greens but also appeared to be mulling over setting up something similar.
But there are downsides to the business model.
If indoor farms can be adapted to grow strawberries and blueberries, "no one with a background in agriculture" thinks they will replace traditional, soil-based farms, Goodman says.
Moreover, products with a denser biomass, such as cereals or beets, are out of reach for the moment. "If I grew beets, I would have to sell it for $50 a head," Peggs joked.
The working conditions are also an issue.
"Do you really want to work in an enclosed, glowing environment?" Goodman asks.
Besides, the lighting is too expensive and cultivation spaces at reasonable cost too few, at least for now.
Those questions are already being addressed by some apprentice entrepreneur-farmers at Square Roots.
Electra Jarvis, 27, joined program after earning a masters degree in environmental sustainability despite having "never grown a plant before."
In just a few months, she mastered the process and already has 20 clients for her bags of salad leaves, tagged "Grown with love by Electra Jarvis."
But if she's happy to learn how to turn "dead space" into "a productive green space," she's not sure it's really for her.
"I miss the nature," she said. "I prefer to be able to grow outdoors."
AeroFarms: The Farm of the Future
“Doesn’t it feel like we’re walking into the first scene of a sci-fi thriller?” I whispered to the woman in the white lab coat and hairnet (the same getup I was required to wear) as we approached the glowing towers in the distance. I made sure that one chick was way out in front, see her? It’s the same tactic I use in the ocean. Farthest one out gets devoured and gives you time to swim to shore. Take notes, kids.
Anyway, thankfully we weren’t headed into any crazy, sci-fi danger. (Sorry to put you out there, chick in the front.) We were actually taking part in a tour of AeroFarms’ temporary facility located in an abandoned indoor paintball arena in Newark. They left behind the really cool wall art which made the whole experience feel like the weirdest party I’d ever been to.
The aforementioned glowing towers were actually the vertical LED illuminated stacks of baby leafy greens thriving under perfect conditions, getting ready to be harvested and sent off to local grocery stores.
AeroFarms’ noble and awe-inspiring mission is to combat our global food crisis and bring farming and fresh, nutritious, leafy greens into our world’s food deserts. I’m pretty sure we can all get behind that.
The facility we toured was soon to be shut down and all growing moved to their new facility which is an abandoned steel mill on Rome Street in Newark, where their estimated annual output will be up to 2 million pounds. Currently, the Newark location employs a staff of 126, 60% from the surrounding area, 40% from Newark. Growing food and jobs: well played my friends. Well played.
AeroFarms has projects in development on four continents, with plans to open sustainable vertical farms all over the world in the coming years. The Garden State got lucky when the company chose New Jersey as the site for its beta farms in 2004.
The company claims to use “95% less water than field-farmed food, with yields of 130 times higher per square foot annually.” Those are some pretty impressive stats. And they take out the middle distribution man by growing right where the population for consumption is. It’s crazy clever.
The latest development under the AeroFarms brand is the new line of fresh greens “Dream Greens,” for retail. We were lucky enough to enjoy a brief chew-through of the varying taste profiles of a few of the more than 250 varieties of baby greens and herbs. On the menu for the day was their baby kale, baby arugula, baby ruby streaks (which had a surprising baked potato flavor), baby watercress, and baby bok choy.
Our guide for the day, Alina Zolotareva, explained the flavors we were discovering and talked about how AeroFarms greens are bred to be more flavorful and more nutritious than your typical fresh greens at the supermarket, which are raised with one goal in mind: shelf life.
With the AeroFarms model, pests are not an issue. Climate is not an issue. Lack of water is not an issue. The seeds are sewn on clothes made out of recycled plastic bottles and are used over and over again for germinating seeds. Plants grow faster in this environment which means the farm can yield more harvests per year than the traditional farm. I told you, it’s the farm of the future. There’s so much more I could go into, but it’s all on the website for if you’re looking for a deeper dive.
If you are looking to buy Dream Greens, which I highly recommend, check out the store locator here. AeroFarms currently supplies the NY-Metro area via brick-and-mortar retail partners including Whole Foods and ShopRite, as well as via FreshDirect to Connecticut, Washington, D.C., and Philadelphia.
I plan on keeping a close eye on this company and the company’s progress. Rumor alert: Next stop, Camden!
Engineer-Turned-Farmer Brings Vertical Farm Concept Back To Earth
Engineer-Turned-Farmer Brings Vertical Farm Concept Back To Earth
KATE TRACY MAY 2, 2017
Infinite Harvest founder Tommy Romano grows lettuce and other greens in his Lakewood vertical farm. (Kate Tracy)
The origin of Tony Romano’s startup sounds plucked from the pages of a sci-fi screenplay.
As an aerospace engineering master’s student at CU Boulder in 2002, Romano was working on a project for how to feed 200 humans on Mars for two years. The solution: hydroponics and vertical farming. The problem: a lack of humans on Mars.
“There is no one there yet,” Romano said. “Why aren’t we doing this down here?”
That’s when the plot veered from fantasy to reality.
The engineer-turned-farmer ran with his idea, writing his business plan for a vertical hydroponics farm in 2009. The next year, he launched his first operation out of a wind- and solar-powered shipping container in a field in Golden.
“That was the proof of concept that we used to raise our first capital raise in 2014,” Romano said. With those funds, Romano opened his first facility in Lakewood.
Now, Infinite Harvest has 18 employees and produces 100,000 heads of lettuce per month. And Romano raised $60,000, according to a March SEC filing.
“It’s all for getting this facility to increase its own production,” Romano said. “We’re not at 100 percent production yet.”
Romano, 45, uses peat as the medium and filtrated city water to grow his plants, which are stacked vertically and in columns on 10 tiers that are 16 feet high. In the 5,400-square-foot grow area, Romano can plant an acre’s worth of produce in one-tenth of the space, he said. Infinite Harvest controls the air and water temperature, light and other factors that create ideal growth environments.
Unlike aquaponics, Infinite Harvest does not use fish to fertilize plants, as it simplifies the system and lowers the risk of contamination, Romano said.
Even on Christmas Eve with 3 feet of snow outside, Infinite Harvest is planting.
“We grow every single month of the year,” Romano said. “It is farming on the manufacturing level.”
Romano plans to use the capital from his recent raise to buy more seeds, nutrients and greenhouse equipment to provide more leafy greens for Infinite Harvest’s main clients, Shamrock Foods and FreshPoint. Both distributors sell Romano’s produce to a variety of businesses in Denver, from casual joints like Tokyo Joe’s to fine-dining restaurants like Jax Fish House and Ocean Prime. Infinite Harvest also sells directly to a few local Denver businesses, including The Way Back, Serendipity Catering and Nooch Vegan Market.
Romano looks to hire two employees to keep up with the increase in production, and also is eyeing a bigger facility.
“We have a very solid confidence that we’ll be profitable this year,” Romano said.
Right now, Infinite Harvest grows three types of lettuce and 13 kinds of micro-greens, including baby arugula, baby kale and micro curly cress.
“We stay with leafy greens because they are very easy to grow,” Romano said, adding that they are a quick harvest and require the same nutrients and other environmental conditions. He hopes to expand to tomatoes and other produce that will require a different grow room.
Denver has other indoor growing operations. The GrowHaus, a nonprofit in the Elyria-Swansea neighborhood, also has a hydroponics farm, which sells produce to neighborhood residents and restaurants. Circle Fresh Institute in Wheat Ridge teaches classes to students interested in greenhouse farming.
But Romano says Infinite Harvest’s nearest competitor is Green Sense Farms in New Jersey. Japan, Belgium and Singapore also have vertical farms of similar scale.
Vertical Farming in Amsterdam
Vertical Farming in Amsterdam
GROWx Labs Opens in April 2017
Amsterdam, The Netherlands, Friday 24 March 2017 – GROWx is the leading innovator in vertical farming in the Netherlands will open GROWx Labs in Amsterdam Zuid Oost.
It is amazing that so much food arrives into cities every day, but it is not without problems. Farmers are far away from their market, there are negative ecological effects caused by modern farming, and collectively farms are the single largest users of land in the economy. Faced with limited fresh water resources and limited land to farm, we have to pioneer new ways to farm.
Today, local for local farming producing clean food is the new organic. People desire to know where their food is coming from and if it is clean of undesired chemicals. Urban farms are rising in cities around the world on roof tops and community space. Vertical farming, pioneered in the USA and Japan, is a new way to grow food year round for daily fresh products.
Jens Ruijg, engineer, and John Apesos, entrepreneur, founded GROWx in April of 2016 to build Netherland´s first production vertical farm. The project is focused on serving Amsterdam´s Chef community fresh greens. The GROWx Labs facilities opens in April for Amsterdam´s Chefs to taste interesting varieties of fresh greens and salads.
The Netherlands is a leader in horticulture technology. The GROWx Amsterdam project capitalizes on local expertise, suppliers and university eco-system to build next generation greenhouse technology in the form of vertical farming. Amsterdam has an opportunity to lead the revolution for a fresher urban food future.
GROWx:
GROWx BV is on a mission to accelerate the advent of sustainable urban agriculture. GROWx BV works in co-designing, implementing and operating sustainable vertical farming solutions for city scale food production. We are innovating in indoor food production technology involving multiple layers, controlled plant climates and LEDs.
See more on https://www.instagram.com/grow_x/
Press Contact:
Name: John Apesos
Mobile: +31 06 38 313 515
Email: john@growx.co
China Focus: Factory Farms The future For Chinese Scientists
China Focus: Factory Farms The future For Chinese Scientists
Source: Xinhua| 2017-04-30 09:06:29|Editor: Yamei
XIAMEN, Fujian Province, April 30 (Xinhua) -- In a factory in eastern China, farming is becoming like scientific endeavor, with leafy vegetables embedded neatly on stacked layers, and workers in laboratory suits tending the plants in cleanrooms.
The factory, with an area of 10,000 square meters, is in Quanzhou, Fujian Province. Built in June 2016, the land is designed to be a "plant factory," where all environmental factors, including light, humidity, temperature and gases, can be controlled to produce quality vegetables.
The method is pursued by Sananbio, a joint venture between the Institute of Botany under the Chinese Academy of Sciences (IBCAS) and Sanan Group, a Chinese optoelectronics giant. The company is attempting to produce more crops in less space while minimizing environmental damage.
Sananbio said it would invest 7 billion yuan (about 1.02 billion U.S. dollars) to bring the new breed of agriculture to reality.
NEW FARMING
Plant factories, also known as a vertical farms, are part of a new global industry.
China now has about 80 plant factories, and Sananbio has touted its Quanzhou facility as the world's largest plant factory.
In the factory, leafy greens grow in six stacked layers with two lines of blue and red LED lights hung above each layer. The plants are grown using hydroponics, a method that uses mineral nutrient solutions in a water solvent instead of soil.
"Unlike traditional farming, we can control the duration of lighting and the component of mineral solutions to bring a higher yield," said Pei Kequan, a researcher with IBCAS and director of R&D in Sanabio. "The new method yields ten-times more crops per square meter than traditional farming."
From seedling to harvesting, vegetables in the farm usually take 35 days, about 10 days shorter than greenhouse plants.
To achieve a higher yield, scientists have developed an algorithm which automates the color and duration of light best for plant growth, as well as different mineral solutions suitable for different growth stages.
The plant factory produces 1.5 tonnes of vegetables every day, most of which are sold to supermarkets and restaurants in Quanzhou and nearby cities.
The world's population will bloat to 9.7 billion by 2050, when 70 percent of people will reside in urban areas, according to the World Health Organization.
Pei said he believes the plant factory can be part of a solution for potential future food crises.
In the factory, he has even brought vertical farming into a deserted shipping container.
"Even if we had to move underground someday, the plant factory could help ensure a steady supply of vegetables," he said.
HEALTHIER FUTURE
Before entering the factory, Sananbio staff have to go through strict cleanroom procedures: putting on face masks, gloves, boots, and overalls, taking air showers, and putting personal belongings through an ultraviolet sterilizer.
The company aims to prevent any external hazards that could threaten the plants, which receive no fertilizers or pesticides.
By adjusting the mineral solution, scientists are able to produce vegetables rich or low in certain nutrients.
The factory has already been churning out low-potassium lettuces, which are good for people with kidney problems.
Adding to the 20 types of leafy greens already grown in the factory, the scientists are experimenting on growing herbs used in traditional Chinese medicine and other healthcare products.
Zheng Yanhai, a researcher at Sananbio, studies anoectohilus formosanus, a rare herb in eastern China with many health benefits.
"In the plant factory, we can produce the plants with almost the same nutrients as wild anoectohilus," Zheng said. "We tested different light, humidity, temperature, gases and mineral solutions to form a perfect recipe for the plant."
The factory will start with rare herbs first and then focus on other health care products, Zheng said.
GROWING PAINS
Currently, most of the products in the plant factory are short-stemmed leafy greens.
"Work is in progress to bring more varieties to the factory," said Li Dongfang, an IBCAS researcher and Sananbio employee.
Some are concerned about the energy consumed with LED lights and air-conditioning.
"Currently, it takes about 10 kwh of electricity to produce one kilogram of vegetables," said Pei, who added that the number is expected to drop in three to five years, with higher LED luminous efficiency.
In a Yonghui superstore in neighboring Xiamen city, the vegetables from the plant factory have a specially designated area, and are sold at about a 30 percent premium, slightly higher than organic and locally produced food.
"Lettuce from the plant factory is a bit expensive, at least for now, there are many other healthy options," said Wang Yuefeng, a consumer browsing through the products, which are next to the counter for locally produced food.
Sananbio said it plans to expand the factory further to drive down the cost in the next six months. "The price will not be a problem in the future, with people's improving living standards," Li said
San'an Opto headquarters in Xiamen, China. (Photo courtesy of San'an Opto)
GrowNYC Throwing Open House For New Community Center Project Farmhouse
GrowNYC has an official home — and you’re invited inside.
GrowNYC Throwing Open House For New Community Center Project Farmhouse
By Meredith Deliso meredith.deliso@amny.com April 23, 2017
The organization, which runs greenmarkets and gardens throughout the city and hosts programs on environmental issues like recycling, will celebrate the opening of its new sustainability and education center with an open house on April 29.
Project Farmhouse opened its doors late last year, hosting private events and school programming. At the open house, visitors can get a sense of what kinds of public programming will be on offer down the line, with tours of the space and cooking demos by Peter Hoffman, Gaggenau’s Eric Morales and a chef from Brooklyn’s Olmsted, as well as composting demos, nutrition workshops, recycling games, take-home DIY planters and more.
“We really built this space to be a community center for people to come together around sustainability and healthy eating and all of the programs that GrowNYC is already involved in, in the community,” said Laura McDonald, events director at Project Farmhouse.
Much of GrowNYC’s existing programming focuses on teacher training and student education. The organization anticipates hosting 500 teachers and 2,000 children each academic year at Project Farmhouse. Hands-on programs for students include GrowNYC’s Healthy Food Healthy Bodies series, which features field trips to greenmarkets and discussions with chefs on nutrition and health, as well as programs on renewable energy and farming.
The state-of-the-art space is a lesson in sustainability itself, from a farm-inspired entry archway made using repurposed wood beams to sun tunnels to let in natural light and a kinetic hydroponic wall. A centerpiece is its induction kitchen, donated by kitchen design company Boffi Soho, for cooking demos.
McDonald looks to ramp up public events in the summer, with potential programming like lectures, movie nights and demos from cookbook authors. Having the Union Square Greenmarket just steps from Project Farmhouse is also an advantage.
“There are lots of tie-ins with the market,” McDonald said. “We’re trying to get the farmers in here, doing some demos or talking about what their lives are like. It’s awesome that it’s just a couple blocks away.”
IF YOU GO
Project Farmhouse will host an open house April 29 from 11 a.m.-4 p.m. | 76 E. 13th St., projectfarmhouse.org | FREE
Metropolis Farms: Vertical Farming Designed to Grow Out, Not Up
Jack Griffin of Metropolis Farms. Credit: Tricia Burrough
Metropolis Farms: Vertical Farming Designed to Grow Out, Not Up
The Philadelphia-based startup is looking to change the thinking around the green-collar economy, building a sustainable, modular design around optimized indoor farming technologies.
By Matt Skoufalos | April 27, 2017
Photos by Tricia Burrough
Griffin holds a tray of microgreens grown at Metropolis Farms. Credit: Tricia Burrough.
While the first harvests of spring herald the upcoming farmers market season in South Jersey, across the river in South Philadelphia, Jack Griffin has been hauling in crops all winter long.
On the second floor of a warehouse in the 2400 block of Water Street, he’s just a few blocks away from the other shipping and receiving terminals that supply many area supermarket chains with fresh produce.
But in a fraction of the physical space—and at a fraction of the costs of growing and shipping those fruits and vegetables there from across the corners of the country—Griffin’s Metropolis Farms is quietly growing their organic, non-GMO, vegan-certified competition.
More to the point, Griffin is growing a business that he believes can close gaps in food insecurity, social justice, and sustainability.
“The transactional nature of food means that we have a lever to change the world,” he said. “Everybody eats. The conversations around food are so ingrained in our society [that] in between those transactions is an opportunity.”
Seedlings at the Metropolis Farms headquarters in Philadelphia. Credit: Tricia Burrough
Indoor vertical farming has been touted as “the next big thing” in the green-collar economy for about the past half-decade.
In September 2016, AeroFarms of Newark drew national headlines for the massive scale of its 69,000-square-foot, $30-million operation.
The company converted a shuttered steel factory into a indoor greenhouse the company says is the largest indoor farm in the world, capable of producing 2 million pounds of crops per year, according to CNN.
But Griffin said the thinking that produced it is grandiose and wrongheaded: in his opinion, the key to vertical farming is actually horizontal growth.
“If I’m ever the world’s largest vertical farm any way other than by accident, shoot me,” he said. “We don’t need the world’s largest farm, we need a dense network of independent, smart farms.
“Everybody’s got the same idea; ‘I’m going to build 60 farms,’” Griffin said. “Who’s going to buy 60 farms at $26 million a farm? We can make a profitable farm with our stuff for $600,000.”
Griffin claims the technology behind Metropolis Farms is capable of growing 2 million pounds of produce in just 14,000 square-feet of real estate, and by using one-tenth the energy of a system like AeroFarm’s. Powered by a rooftop solar array on Swanson Street in Philadelphia—where Griffin says he also can recapture 2 million gallons of water annually—Metropolis Farms is made to be energy-independent and disaster-resistant.
It also doesn’t need prime real estate to operate, or even much of it at all. By licensing the technology behind his work, which includes the growing equipment and seedling optimization schedule, Griffin is optimistic that he’ll be able to create a distributed indoor farming culture, not just a farming network. His licensing agreements will include labor clauses about paid time off, living wages, and possibly an degree correspondence program to give inmates the chance of a stable career upon release.
“I think that social responsibility should be part of this,” Griffin said. “Equal pay for equal work, and no discrimination. Our goal is to get as many people as possible farming.”
Lee Weingrad, VP of Metropolis Farms. Credit: Tricia Burrough
“It’s the evolution of technology,” said Metropolis Farms vice-president Lee Weingrad, a U.S. Air Force veteran who co-developed the technology at the heart of the system with Griffin.
“Everything’s on a schedule,” Weingrad said. “We made it simple on purpose. Anyone with a high-school diploma can work here.”
The Metropolis Farms infrastructure is modular and able to be built from equipment available at a hardware store, which Griffin said cuts out the construction costs of retaining a design firm to build custom architecture.
It’s able to be dismantled for cleaning with quick-connect PVC systems, and features optimization algorithms that are designed to help crops flourish without the use of genetic modification.
The first-generation lights were based on a design of Nikola Tesla’s, but the ballast atop them retained too much heat and showed too much infrared light, Griffin said. Their replacements are high-intensity discharge (HID) lamps with a proprietary core, shielded with lightweight, reflective, and refractive German aluminum. They’re suspended from a motorized track, which carries the light across the plants on a timed sequence to simulate cloud cover.
At $25,000 per unit, each tower can produce 20,000 pounds of produce annually, Griffin said. He expects farms will consist of 15- to 50-tower implementations; each can yield 19 harvests per year versus two-and-a-half on conventional real estate.
Insectivorous plants keep the produce free of pests without chemical sprays. Credit: Tricia Burrough
Nearby carnivorous plants secrete nectar and resin, attracting and eliminating pests without chemical sprays.
The entire system can pivot from fruits and vegetables to things like pharmaceutical herbs, stevia leaf, or biodiesel jet fuel, all grown at a consistent grade and domestically.
“A lot of what we’ve done is fourth-grade math and freshman geometry,” Griffin said.
“We’re selling ubiquity: a simple system with architecture.”
Griffin isn’t lacking for interest in his model; as of a few months ago, he was sitting on more than $20 million in letters of intent from cities across the United States and Canada to bring his model there. He wants to start in the Philadelphia metro area first.
The challenge when you’re growing 2 million pounds of produce per year is generating enough institutional purchases—from hospitals, universities, prisons, and other governmental agencies—to generate local “velocity of capital” that creates sustainable economic change.
“How many schools do you have?” Griffin said. “They’ll buy locally if you can produce at scale. The key is to drive cities to understand that where they spend their money matters. If we spend that money on local food, we create velocity of capital; we create local jobs.
Sprouts are grown floating in an aqueous solution. Credit: Tricia Burrough
“When those people go and buy things because they’re making $18 an hour, they’re getting benefits, they’re having a life,” he said.
“If we can show them better food, and they buy it because it’s in their self-interest to buy the food, that’s enough.”
Griffin said his goal “is to have every city in the United States steal this idea” so that Metropolis Farms can manufacture the necessary equipment at its core in Philadelphia and ship it out to other markets, creating yet another level of employment. But he believes the model should take root locally first because it has the potential to be a key driver of regentrification and redevelopment with a critical difference: pushing out the poverty instead of the impoverished.
“In Fishtown, there’s 15,700 people,” Griffin said. “What if I could produce enough lettuce for the daily lettuce requirement of everyone in that community, enough tomatoes, and peppers, and so on? And surround that community with wings of prosperity?
“It’s a synergistic model instead of an exploitive one. It is the ultimate demand-based business.”
How NASA LED Lighting Research Became A Hit Product: With Hedi Baxter Lauffer, Founder of LED Habitats
How NASA LED Lighting Research Became A Hit Product: With Hedi Baxter Lauffer, Founder of LED Habitats
For this interview, we sat down with Hedi Baxter Lauffer, Founder of LED Habitats, a company that has developed an indoor growing product was inspired by "fast" plant research developed by NASA and the University of Wisconsin-Madison. We discussed basic LED lighting tips, the future of LED lighting, and some of its history as well!
Introduction
UV: What's the background story and how LED Habitats got started?
Hedi: My husband and I have been working together in science education for a very longtime, decades now, primarily in that, our focus has been on getting plants into classrooms and informal science situations to try and help get more growing minds actively engaged with plants.
We are getting more and more removed from opportunities to grow plants and interact and understand the importance of plants. I taught high school for a while before I started really getting national and global outreach efforts and it always amazed me when we would do a unit on food, how many students had absolutely no clue where their food had come from.
So in our work, with getting plants into classrooms, both my husband and I were at University of Wisconsin Madison, working with "fast" plants.
They're really cool little plant that was (being studied) at UW Madison, as a research plant. It was just bred through traditional plant breeding to try and look for disease resistance in cabbage. Wisconsin used to be a really big cabbage growing state.
(Usually) cabbage has a two year life cycle, which makes it really hard to support farmers with disease resistance because it takes so long to look for it.
This little plant was bred because it cropped up when the scientist Paul Williams was looking for disease resistance. It went straight to flower instead of producing any fruit.
He bred for this super fast life cycle. It goes from seed to flower in just fourteen days, it goes through it's whole life cycle and produces viable seed in a month to forty-five days. So, it's really cool. And, it's used in classrooms a lot.
The thing is, because it's growing so fast, it needs twenty-four hour and very high quality light. So, we've all been developing light systems for indoor growing in classrooms and things like that, for a very long time. CFL's (compact fluorescent lighting) came out first, it was fluorescent, it was the compact fluorescent light bulb.
Then finally, LED's were kind of always in the background because actually that little fast plant was the first plant to successfully produce seed in micro-gravity, up in space.
UV: With NASA?
Hedi: Yeah with NASA. So, it gave us opportunities, especially my husband at the time, was working directly with UW Madison, with NASA and others, gave exposure to the idea of LED's.
Even before they were a viable option, because there weren't blue LED's until 2009, so you couldn't really use those successfully in growing plants, in horticulture.
UV: Which color were the earlier ones?
Hedi: They have advanced now, I think the very earliest ones were red. Well, that's areally good question. What the very first colors were and just know the blue was really hard to get. It won the Nobel prize, actually, for Physics in 2009.
When science figured out how to produce a blue LED. That opened them up for horticultural use.
So, anyway, we were trying to look at ways to get LED's into classroom study. and be able to switch to LED's, because we had a lot of concerns about a combination of things with non LED lighting options.
The heat that's put off by other light sources, the fact that there is mercury gas in fluorescent bulbs, It seemed like LED's was the way to to go.
But, every LED light that we tried out that was commercially available and, kind of, in our price range and size and scope for use in classrooms were not very high quality.
Because our plants are so sensitive to needing high intensity light, we could really be damaged easily when the intensity of the light declined.
UV: What do you specifically mean by quality in LEDs? Is it the intensity or are there other factors like spectrum?
Hedi: It's both. (intensity) and the spectrum that they're emitting, but I think for us, what we we're detecting most was the decline in intensity. In pretty short periods of time, like eight months to a year, we would notice changes.
Later, we learned that that was because when there's quality factors both in the LED chip itself and in the design of the match between the drivers that are pushing electricity, electrical energy into be converted into light energy. If the drivers are over pushing the LED chip, they burn them out.
(As a result), you do have a decline in quality over time. In a much faster time than what LED's are technically specified to last for.
My brother had been off the grid in New Mexico, I knew he'd done some stuff with LED's, I reached out to him and said, "Do you know anybody who's working with LED's, we're trying to find some people besides the scientists here that we've been working with at the University to help us come up with a low cost, relatively low cost solution for classroom?"
So, my brother introduced us to this German cabinet maker who is now our colleague and partner, he's been working with LED's for a long time in kitchen cabinetwork; and, he's a German craftsman, a cabinet maker, so, it was like this perfect triad of my husband and I with our plant backgrounds, I have a very strong agricultural background, I used to run a wholesale organic truck farm, many years ago.
All of these things converged and came up with this really clever design for being able to raise and lower the LEDs and how to house the LEDs, in a hood that is completely silent and self-cooling, and it worked beautifully. We tried it out, did prototypes, and got plants growing wonderfully and then we had them sitting around in our house.
As we were trying them out and everyone who walked in said where do I get one of those?
At that point we realized maybe this isn't just for school. Maybe this is actually a broader impact thing. And, that's how we came up with the company.
UV: The research and the inspiration is with that one cabbage plant that you mentioned, is that exclusively what you try to grow in the system now? Have you brought in the reach, to other types of micro greens or whatnot?
Hedi: Yes, we have definitely broadened, even in our prototype work we broadened. The advantage that we had in doing our initial work with the brassica, is the scientific (category) of the plant.
It's like a lab rat, in that it, its a good indicator for flowering plants, in general. And, because it does its whole life cycle in such a short time. We can group past prototypes to see how they effected the grooming, vegetative growth, seed production, stuff like that in really rapid cycles.
Once we've got to where we were really pleased with what we we're seeing, then we could start going out to longer growing crops.
UV: Right. So, have you guys seen that with a really high quality LED light, you can quicken the flowering and general growth of any plant? Like, regardless, of it's life cycle. You mentioned that the quality of the LED light helped you speed up even the fast plant. What's the multiplier in terms of productivity and speed to the flowering or any point in growth, when you have really high quality lighting?
Hedi: There are (multiple) key elements in the environment that affect the rate of growth, temperature often is a big one. Nutrient content, volume of the soil, so there's other factors besides the light.
But, the quality of the light and the availability of the light, in terms of intensity, and spectrum. It's so cool to work with, because you're plant responds by really producing strong, vigorous plants.
So, while it might be, I could keep my plants in very cool growing conditions and it wouldn't be that the LEDs would speed them up, necessarily, if it affected the cold.
But, what I would see, because of the light, is these really stocky, sturdy plants with large mass. They're really thriving. You'll notice the difference if you side by side grow six tomatoes under the fluorescent and LEDs that are full spectrum because the fluorescent tend towards the blue, the plants elongate and much more left out and reaching for light.
And they are so vulnerable to that. When you put them under LEDs, it's so satisfying to see, wonderfully, stocky little seedlings.
It's really cool as a plant lover, it's really fun to grow under really high quality lighting.
UV: Can you talk about, I don't know how much interaction you have with people who are just getting started; maybe there are people who approach you tobuy but what do you see is the biggest mistakes that people make?
Or, biggest misconception about LED lighting?
Hedi: That is really something that we encounter a lot, actually. There's people who are trying to grow micro greens, there's people who are trying to grow herbs or medicines, or all kinds of things. And, I think there are three things that, kind of, continually repeat themselves.One is, the confusion about how to compare different lights, because in the past, when we use incandescent bulbs, we talk in sense of watts. And, then in terms of lumens.
But, actually watts don't matter with LEDs. That's not a good measure, because they beauty of the LEDs is that they hardly require any input of electricity, which is what watts are made of.
To have a really high output,so, you know, you can't compare an incandescent or a fluorescent wattage input with the output of the LED. It's just not a good measure. And lumens are a measure for human. So, shifting to where we're talking about the photosynthetic area of radiation that is emitted or hard value on things like that, that's a big challenge. And, the LED world does not adjust that well, we don't have a good standard for how we talk about light, lighting or label them. Although, that's coming, hopefully.
I want to make sure that I also touched on, there is a real big misconception among those who have been looking at LEDs, that they don't give off heat.
They actually do. A lot of the quality of the LED chip and it's mount, and the quality of the LED lamp itself, is how that heat is dealt with.
That's the critical thing with the LED.
So, there needs to be a really effective design to the way the LEDlamp is engineered so that the heat dissipates really quickly. And, that prolongs the life of the LED and the lives that it has good intensity.
So, I guess that is the third thing I would say is a big misconception. That an LED is an LED is an LED and that is not true.
There is high quality LEDs, that are really made by reputable manufacturers and there's cheap, crappy ones that come, trying to flood the market with something that looks much more affordable.
UV: If you wanted to set up a dead simple urban farming system, how would you do it?
Hedi: Well,I think the dead simple part is the hanging of the LEDs and determining what the footprint is going to be that you want to light up.
So, LEDs, the chips themselves, tend to be uni-directional, that's part of what makes them really efficient. They're not shooting light off out the back and sides, they're shooting it in the direction that you point them.
You can put lenses on them that broaden their footprint, their lighting, but whenever you do that,you're also then distributing their intensity over a greater area (and as a result, reducing intensity).
I think the key is, deciding how much space are you trying to light well. Then you want to be the one that rigs how the lights go up and down or do you want to get a system that already does that for you.
Because the beauty in the LED is that they're built well so they dissipate their heat well. You can have your plants, the canopy top over tops of your seedlings or whatever just a few centimeters from the LEDs themselves. That's where you're going to have the high intensity. That's the way that you want to give your plants maximum lighting. So, you need to either raise the plants up and down or lower the lights.
UV: Keeping the focus on the hanging mechanism, that's the key take away.
Hedi: That and then the quality of the LEDs that you're getting. So, if you're just getting a cheap one strip of LEDs, be aware that you can't put that down the middle of a big, wide tray and expect that it's going to light the outside edges.
UV: How do you make sure that you're on the right track (with LED quality)? Is there some kind of measure? On YouTube, you see people measure the intensity. What tools or what do you suggest for doing the quality assurance? Or, I guess coverage assurance?
Hedi: You can get a little PAR meter, its called. That would be your most accurate measure of how many photons are actually striking the leaf surface. And, those are fairly affordable, although it's more of an investment than I would call atypical do-it-yourself thing.
So, I guess I would advise that you either do some research and make sure that the company you're buying your LEDs from LED lamp is what they actually address how much output there is, in terms of the spectrum that the lights are giving.
The PAR value, and when they tell you what the output is, that they tell you how to measure that, how far away from the light that was. If it's a good, reputable company, they will tell you what the footprint is being lit beneath it.
I would just be leery if it seems like it's over stating what is possible with the LEDs, you know then I would just be leery. I've bought enough cheap ones in our prototyping work and before we started doing LED Habitats.
You end up investing more money than you wanted anyway on ones that you can't continue to use, if you've got really cheap ones. They just won't work.
UV: So, what are some of the, what are some of your favorite brands? What would you recommend? Obviously, besides your own system.
Hedi: We've been pretty impressed by some of the higher end lights. Like by kind. You know, I would have to actually give you a list of, the problem is that, the world that I work in because I've had the benefit of being in the University system. The lights that we've had really good luck with are very high end horticultural LEDs.
So, when we tried to go into the lower, more cost effective, like you'd bring into your home or something like that range, things like Aero Garden and stuff like that.
That's where we started running into problems and that was what drew us to do the LED Habitat (product creation).
I could try and come up with some responses for you. Mostly, I've had people send me pictures of other LED systems that they're trying to use and some other things.
Their little seedlings are all elongated and stretching and reaching for the light, I just haven't been very impressed yet.
UV: What do you see as the future, what is the next wave of technology that will downsize in (LED) cost so that they're more available to the average person?
Is there a new type of LED? Are there new blends? What do you see as the next big trend?
Hedi: Iwas really impressed at the first annual LED Light and Horticulture Conference that was in Chicago. I was really impressed by how much enthusiasm there was towards the place that LEDs will take in horticulture.
Certainly, high pressure sodium still is a big, important light source for indoor growing.
I think that it's clear that with this vertical farming movement, the fact that you can layer into tight spaces,the growing space and the lighting is just phenomenal. And, it's pretty exciting to look at some of the large scale projects that are taking place with vertical farming.
I'm sure that LED technology is going to continue to get better. I think already even, it's pretty affordable. I think that on a small scale, it's not that bad.
It'sworth it. I think that there are some really nice options for tabletop or counter top growing. Helping to supplement the freshness of what you're feeding your family and larger scale urban farming too.
UV: What is your favorite fruit or vegetable?
Hedi: My favorite fruit or vegetable? Wow. Okay, avocado.
UV: If you had to give just one sentence of advice to somebody starting urban or vertical farming or LEDs or not. What would that advice be just in one sentence?
Hedi: Start with greens. Doing like brassica family greens. They're super fast, easy to get to know and they're really rewarding and good for you.
UV: Okay What's the best advice you ever heard from maybe a mentor or somebody that you encountered in the academic setting?
Hedi: Soil matters. You know, we sometimes, especially in academia, but in general, get really arrogant. Thinking that we can deconstruct nature and understand it all.
So, having humility about things and learning from the natural world and recognizing that soil is part of the picture, and it matters.
Thanks Hedi!