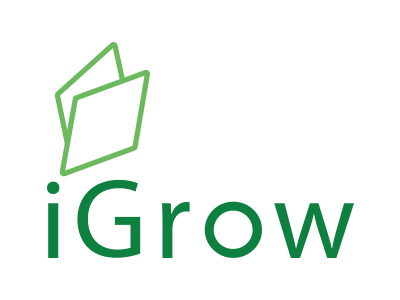
Welcome to iGrow News, Your Source for the World of Indoor Vertical Farming
Kimbal Musk: Food Is the Next Big Thing
Kimbal Musk: Food Is the Next Big Thing
Elliot Volkman
- Aug 10, 2017
Twenty years ago an internet pioneer made a fortune for being on the cutting edge of a booming industry, and today he is suggesting food will be the next big thing. Kimbal Musk, entrepreneur, venture capitalist, and environmentalist, and yes, sibling to Elon Musk, took the stage at last year’s Life is Beautiful to discuss the reality of food today and how the changing market can lead to large opportunities.
“We produce 30 percent more than we need to eat, in fact measured by the cheeseburger index, we are growing more than two-and-a-half cheeseburgers per person than we need. And the result is massive: obesity around the world 800 million in 1980 had obesity, today 2.1 billion people in the world are obese. And it’s a tragedy for those people and an economic disaster for the world,” said Musk.
According to Musk, the problem is not the food output overall, but industrial or processed foods. These foods are high in calories, lead to obesity, but at the same time lead to malnutrition for those who consume it. However, thanks to the internet, the world is becoming more informed about what Musk refers to as real food.
The Changing Supply and Demand of Real Food
Fast food chains are closing, and sales on microwavable and frozen foods are dropping. According to Musk, 45 percent of Americans want organic foods, but less than one percent of farms in the US are supply it. With information readily available, demand for organic food is rising, but there is still a separation based on age groups. More and more millennials want to see healthier local foods, are curious about where their food comes from, and want natural food. On the other hand, Musk says that baby boomers still see healthier food as slim shakes, fat-free, low-sugar, etc., which certainly has nothing to do with the mass amounts of marketing designed to convince people of such.
“The global software industry, which is where I started, is about a $400 billion industry. And while that sounds very big, it’s the size of the seafood market. When you look at food as a whole, it’s 10 percent of the global GDP and almost $5 trillion ($4.8T) in size. Think about all those friends you know of that mad a lot of money in software, multiply that by 10, that’s the opportunity in food,” said Musk.
In addition to the increase in demand, supply will see a change as well. In Iowa, 25 percent of the farmland is owned by a woman over the age of 75, and 26 percent is owned by a man over the age of 75. This means over the next 5-10 years there will be an avalanche of supply for farm land. Musk also highlights how 25 million acres of land are also used for ethanol, something the EPA has been looking into.
Although the EPA does not regular farm lands, Musk suggests this may change due to the increasing pollutants entering the global water supply as a result of nitrogen based fertilizers. If these changes to occur, and if ethanol producing farms are reduced, there will once again be a large supply of fertile farm lands.
Future Farming
The future of farming consists of as much technology as it does understanding the earth. From engineers building automated machines to do an otherwise unscalable skilled trade, to data scientists analyzing data from satellites regarding soil fertility, moisture, and crop harvest times, technologists will have an opportunity to take a piece of a booming industry. Musk ends his talk with a simple statement. For those who feel they missed out on the internet and .com boom of the past, real food is the opportunity they should pursue.
Life is Beautiful takes place in late September in downtown Las Vegas. Tickets are available now. More information, including the set times to expect each panel or activity, will be available on the website in the near future, but right now, you can browse all the events in the Life Is Beautiful lineup, from music, art, and food to ideas and comedy.
Tags: artisan foodsBusinessFoodKimbal MuskLIBLife Is BeautifulLife is Beautiful Festivalorganic foodStartupVideo
The Future Of Farming Is Here And It Is Happening In Lakewood
The Future Of Farming Is Here And It Is Happening In Lakewood
Infinite Harvest is growing crops in an efficient, environmental friendly way.
Tommy Romano walks through the grow room at Infinite Harvest, a vertical farm, Aug. 29, 2017 in Lakewood. Kathryn Scott,
By JOSEPH RIOS | jrios@denverpost.com | The Denver Post
September 5, 2017
Unless you’re a vertical farmer, the “fields” inside Infinite Harvest in Lakewood are unlike anything you’ve ever seen. Step inside under the glow of the blue LED lights and you might think you’re in a spaceship. Then you see the tens of thousands of plants growing in rows that stretch toward the ceiling.
Walk down the aisles of the 5,400-square-foot building, and you’re flanked by green, leafy plants growing on white tiers.
Infinite Harvest’s crops are grown in a controlled environment — lights, humidity, temperature, gases (think carbon dioxide), nutrients and fertigation, can all be regulated. Fertigation provides nutrients to plants and soil through an irrigation system.
“We can’t control the sun, but we can control the LED lights. The only thing unnatural (about our farming methods) is our ability to control the environment,” said founder Tommy Romano.
Infinite Harvest’s methods also differ in other ways from those used on many traditional farms, Romano said.
“We don’t use any pesticides or herbicides, no foliar sprays whatsoever. What you eat is 100 percent plant. We have a phrase that we pretty much use: We are ‘going beyond organic,’” Romano said.
“Going beyond organic” means producing crops in a way that is better for the environment, Romano said. He estimates Infinite Harvest uses 95 percent less water than a traditional farm with the same harvest.
“We bring the water right to the plants rather than letting it seep through the soil. We don’t spray, we don’t irrigate through sprinkler systems. We save a lot of water from that standpoint,” Romano said.
Infinite Harvest, which was 5 years old when it made Lakewood its home in 2014, is currently growing about 60,000 plants. Romano said it has the capacity to feed roughly 2 percent of the more than 140,000 people who live in Lakewood, based on average annual consumption rate. It’s owned by a group of shareholders interested in boosting efficiency in modern farming. One example of Infinite Harvest’s efficiency: It can grow and harvest year-round with no worry about weather damage.
“I don’t care if it’s the middle of January or the middle of July. You get the same thing,” said operations manager Nathan Lorne.
Infinite Harvest grows lettuce, kale, basil, arugula and other crops sold as fresh produce to local restaurants. Its harvests are also making their way into the kitchens of area schools. Buyers are interested in the farm-to-kitchen freshness, Lorne said.
“From the time we harvest it’s usually on someone’s lunch or dinner plate at the restaurants within 24 hours,” Romano said. “That freshness factor produces a lot more flavor.”
The business is attractive to employees too, because it offers year-round work rather than the seasonal work found at many traditional farms.
According to “Vertical Farming Market: Global Opportunity Analysis and Industry Forecast, 2017-2023,” a report by Research and Markets, the global vertical farming market is projected to reach $6.4 billion by 2023. In 2016, the global vertical farming market was valued at $1.5 billion.
“People are starting to understand that there is a demand for this. There is a viable business. We’re just still working on all of the kinks, technology-wise, and teaching the market more about this type of product,” Romano said.
Romano’s interest in feeding people in the distant future inspired his business. The former aerospace engineer focused on space habitat and colony design while working toward his master’s degree at the University of Colorado Boulder. While there, he wrote a thesis about how to feed a colony on Mars.
“I figured, well, if I can do this in such an adverse environment on Mars and produce healthy, sustainable crops, why aren’t we doing that here?” he said. “We have more people to feed here than we do on Mars.”
Nanochemistry Innovator Debuts GrowBlade™ Flat-Panel Growlights at NYC AgTech Week
Nanochemistry Innovator Debuts GrowBlade™ Flat-Panel Growlights at NYC AgTech Week
September 05, 2017 10:54 AM Eastern Daylight Time
SAN FRANCISCO--(BUSINESS WIRE)--Light Polymers, a nanochemistry startup with R&D operations in Silicon Valley, Taiwan and Korea, is debuting their GrowBlade™ flat-panel horticulture lighting at the third annual NYC AgTech Week.
Light Polymers is debuting their GrowBlade™ horticulture lighting at the annual NYC AgTech Week. #nycagtechweek
Tweet this
Hosted by the NYC Agriculture Technology Collective, NYC AgTech Week 2017 includes tours, workshops and presentations that engage attendees on the bleeding edge of urban agriculture knowledge and development. AgTech Week 2017 kicks off on September 16th followed by 6 days of events across the city. Light Polymers is also September’s featured sponsor for Agritecture, a leading urban agriculture blog and a founding member of the collective.
Light Polymers’ GrowBlade™ flat-panel grow lights are part of a new generation of LED lights that improve the productivity of multi-layer indoor cultivation for leafy greens and herbs, seedlings, clones, grafts and tissue culture. GrowBlade™ flat panels are made possible by our proprietary Crystallin® lyotropic coating and suspension chemistry which is water-based, lowering manufacturing costs.
“Our self-aligning coatings can be applied with high yield and low cost. The coating packs phosphor particles in a dense layer maximizing light conversion, allowing us to lower both production and operating costs. The result is GrowBlade™ light panels that are cheaper, thinner and more efficient than conventional grow lights. These advancements mean lower initial costs, lower operating costs and improved productivity for indoor farms,” said Sandor Schoichet, VP of Grow Products at Light Polymers.
About Light Polymers
Light Polymers is a nanochemistry company with deep domain knowledge of lyotropic liquid crystals, which have use in many applications including LCD and OLED flat panel displays, LED lighting, building materials and biomedical applications. Founded in 2013 in San Francisco, Light Polymers’ water-based coating and suspension chemistry is game-changing for a number of industries. For more information, visit http://www.lightpolymers.com/
About NYC AgTech Week 2017:
The Third Annual NYC AgTech Week will showcase the efforts of entrepreneurs, farmers and technologists who are advancing urban agriculture in New York City and beyond. The week commences with a brunch kick-off at Agritecture’s office at 40 Bushwick Ave and continues from September 16-21 at locations around the city. AgTech Week will feature farm tours, workshops, demos, networking and the ever popular Locavore Feast. Shown here is a recap video from the 2016 edition of NYC AgTech Week.
The Good, The Bad, And The Ugly of Container Farms
The Good, The Bad, And The Ugly of Container Farms
Chris MichaelFollow
Chris is the CEO at Bright Agrotech — The global leaders in vertical farming equipment design and technology. Creators of ZipGrow. www.zipgrow.com
It’s time to have an honest conversation about container farming.
There’s almost nothing that rouses more cheering here at the Bright Agrotech office than seeing new farmers make their first sale.
We love seeing photos of our farmers slinging salad at a farmers’ market or selfies with their cilantro.
At the end of the day, those moments are what power us to keep doing what we do. We love it. We revel in it.
And when it doesn’t work out, we mourn just as strongly as we cheered.
When a farmer decides to quit, or when they overestimate their market, or when their equipment fails — we feel that. It’s disheartening to see someone with so much passion give up their dream.
Over the last five years, we’ve seen a lot of new growers start farms of all kinds only to shut them down a few months or a few years later. Not only is this disappointing for the farmer, but it hampers the industry through the loss of valuable farms that were helping increase access to food.
An unfortunate trend we’ve seen recently is that too many of these losses are happening in one type of farming in particular: shipping container farms.
The common killer of container farms (or any modern farm that leverages technology) is unrealistic expectations about what the tech will do for them, how much their farms can produce, and what kind of labor is required to make it all work.
Don’t forget, even technologically advanced farming is still farming!
Leveraging the modularity of containerized farms can be a very powerful way to bring better food to local communities all around the world. There’s some serious potential here and it’s exciting stuff!
However, like any new venture, modern farmers need to know what goes into being successful and what challenges they need to prepare for in the process.
To help create realistic expectations, we need to talk honestly about the potential benefits and drawbacks of shipping container farms.
In this article, we’re going to cover the main pros and cons of the (used) container form factor.
By speaking honestly about the good, the bad, and the ugly of container farms, we can help more aspiring farmers start businesses that positively impact their communities, now and in the future.
The good: What are the benefits of shipping container farms?
As of this writing, there are several hundred container farms parked in cities and backyards, parking lots and warehouses around the world.
They’ve been featured on TV, in newspapers, and by the internet’s top bloggers. Without a doubt, this type of farming has captured the interest of millions of people enchanted by the transformation of discarded containers into futuristic farms.
But does this farming form factor makes sense for farmers — those starting businesses growing and selling food?
The biggest “pros” of repurposed container farms are:
- They’re modular and easy to ship.
- They’re compact and self-contained.
- Used containers are cheap and available.
- Prices will continue to be driven down as competition increases.
Let’s dig into more details on the good side of shipping container farms.
Container farms are easy to transport
Farms built from used shipping containers are — as the name implies — easy to ship. Ideal, in fact.
The primary benefit of easy shipping is that manufacturers can set up shop where it’s cheap, then ship them directly to the farm site fully loaded and ready to grow.
There’s some serious potential there for setting up your farm quickly and starting to grow without having to worry about building a greenhouse or finding warehouse space.
Most of the benefit, however, stays with the manufacturer.
After all, why would a farmer who is establishing a farm to serve a local market need to move their farm that often? You could technically hire a crew with a crane to put in on a semi and move it across town if you felt so inclined, but why would you want to do that?
While the container farm is technically easier to move due to its form factor, we don’t advise planning a farm to be moved often.
Container farmers have a compact footprint
One benefit of growing in a container farm is that you don’t need a lot of land or a dedicated building to start.
That means modern farmers or program directors can now drop one of these behind a restaurant or in a school parking lot. In the end, the compact form opens up a lot of doors for producing food closer to where it’s consumed.
Keep in mind, however, that most container farms require a perfectly level platform to function (drainage lines need to flow in the right direction after all) and can require a cement pad.
Being able to park a farm anywhere you need food is an amazing achievement and therefore a big benefit of this form factor.
Containers are readily available
Used shipping containers are everywhere. Shipping companies have been using them for decades to ship all sorts of goods overseas, so millions of them are made.
When containers like refrigeration shipping containers break, they are often easier (and less expensive) to “retire” than to fix.
This still represents a loss for the shipping company, however, so they’re usually eager to sell whatever retired containers they can. Altogether, this makes used containers very inexpensive.
The good part for farmers is that these types of containers are cheap and available! That means for a few thousand bucks you can get the shell of your new farm to build out.
Future container farmers gain through value-based competition
Because the cost of acquiring used shipping containers is very low, there are more and more value-added companies getting into the space. The more companies there are, the more the price will decrease over time.
Obviously, a lower price point helps more aspiring farmers launch new businesses which will help to increase the supply of locally grown food around the world, which is good for everyone.
That said, investing your life savings into an inexpensive container farm may be a poor decision if you haven’t examined all the variables.
(Read on for more about the potential drawbacks of growing in a container.)
These four exciting benefits have never combined so well as in container farming. They represent an exciting area of development and accessibility to farming for people that were limited before.
The bad: What are the drawbacks of shipping container farms?
But while there are a lot of benefits to growing in a container, there are just as many drawbacks that aspiring modern farmers need to be aware of before applying for a loan or risking their 401k.
The core problem behind every drawback below is that shipping containers were not designed to grow food. And this puts growers at a disadvantage.
Because the intended purpose is absent in the fundamental design, everything required to outfit a container is a compromise.
The biggest potential drawbacks of container farms are:
- Environmental controls or lack thereof
- Structural integrity
- Antagonism between light, layout, and heat
- People and workflow issues (ergonomics)
- Misbalanced operational expense
- Low comparative output
Controlling the growing environment can be difficult in repurposed shipping containers
If managed well, there are many benefits to a controlled environment (year-round growing, more control over pests, etc.).
However, if environmental control is difficult in the facility, the same benefits become curses; conditions get out of control, humidity and heat accumulate, and pests thrive.
At any given time in an indoor farm…
- lights are generating heat.
- water is evaporating.
- plants are transpiring.
- gasses are accumulating and being exchanged.
- crop populations are fluctuating.
All the heat, humidity, and pests that result from these processes are amplified in a denser growing environment.
To make sure that controlled environment ag remains a blessing instead of a curse, environmental control must be understood and prioritized in the design of the farm.
But many container farms underestimate the complexity of controlling a growing environment consistently enough to produce a healthy crop reliably.
We’ve helped support dozens of farmers growing in repurposed containers who struggle with low productivity caused by poor environmental controls.
One farmer in particular has two containers less than a year old but have yet to reach even close to full production potential, or at least what was promised, because of humidity issues.
Insufficient lighting (constrained by heat as you’ll see below) and high humidity have resulted in low growth rates and rotting issues that are hard to compensate in the cramped space.
He’s in a very tough situation and we hate seeing this happen. Even though he’s added three new dehumidification devices, he still struggles to lower his humidity. As a result, his farm is vulnerable to disease like root rot which in a more purposefully-designed farm wouldn’t have been a problem.
That’s why it’s crucial that container farms purposefully provide adequate airflow, temperature controls, dehumidification, CO2, etc. to their units.
That’s a challenge for most repurposed shipping container farms simply because of the extreme constraints the structure provides.
Repurposed shipping containers can have structural integrity issues
An often overlooked danger of repurposed containers is the limits of their structural lifespan.
Remember, these things have been around the world a few times and battered by corrosive salt water, high winds, and many a forklift operator.
That means they were worn out well before they were made into farms.
This limits the life of the farm significantly. In extreme cases, the quality of the container can be so low that we’ve known farmers whose farms were condemned by the city — an enormous and painful blow when you’ve spent tens of thousands to start a farm.
If you go this route, please be sure you carefully inspect the structural integrity of your container! This industry will not move forward if passionate, local farmers like yourself are investing in farms that fail to function in a year or two.
Light, heat, and layout must be balanced appropriately in any indoor farm
The relationship between light and heat is a largely antagonist one.
Because light and heat are “coupled”, supplying the quality (i.e. intensity of light) needed for plants to grow to their full potential also increases the amount of heat in the growing environment.
Simply put: when light goes up, heat goes up with it. The problem is that plants like light, but they don’t like heat.
As we saw in the previous section on the importance of environmental controls, this delicate balance between light and heat is amplified in dense environments.
Because of their tight spacing, container farms face an interesting conundrum when it comes to this messy triangle. They need high-intensity lighting to grow their crops but don’t often have the space required to install adequate HVAC units to deal with the heat created by these lights.
The result? Many container farms sacrifice productivity by being forced to use less than adequate LED lights to avoid adversely affecting their plants with heat and humidity.
Thankfully, there are some container farms out there mitigating this antagonistic relationship with intent-informed design.
By building a container that’s intentionally designed and equipped to grow plants, companies like Modular Farms in Canada and several Chinese and Japanese container farm companies can manage their growing environments effectively (among other things like moving around and inspecting plants easily).
When doing your due diligence on any future indoor farming equipment, be sure to carefully inspect how the system deals with the antagonistic relationship between light and heat. If you provide the plants the proper light intensity, you’re going to be producing heat and this heat can throw your system into a tailspin if not managed effectively. Make sure you have a way to deal with it!
Remember, if you want to produce high quality crops consistently, you need high quality light. You are replacing the sun after all.
Ignoring human workflows is never a good idea
Farm environments aren’t just designed for plants. They also need to be designed for people. The problem with shipping containers is that they’re not designed for people and that poses some real issues for farmers.
There are two reasons to keep your farm labor-friendly: the first is that labor is money, and the second is that there’s nothing worse than working in a cramped, confined space for dozens of hours each week. It can be enough to drive you insane, or at the very least make you dread coming to work.
Ergonomics — or how efficiently your workplace is set up for workers — is also important, yet this isn’t something you really think about when shopping around for a farm. Our advice? Don’t neglect it!
With those two goals in mind, container farmers must ask and answer important questions about how people will interact with the container farm.
Can I see all my crops easily?”
“Could I work in here happily for several hours each day?”
“Can more than one person work comfortably in this farm?”
These are all questions to answer before making such a large investment.
The most practical way to feel out the workflow in your future farm is to visit a variety of container farms before buying one and see how they feel.
Talk to other farmers who’ve been farming for a while and get their feedback. You won’t regret it!
OPEX and CAPEX should be appropriately balanced
When it comes to starting a business, ignoring your market research or failing to fully understand your financial projections is just rolling the dice.
If you want to stay in business, you have to know you can earn a profit. (That’s why it’s critical every aspiring farmer conducts a feasibility study to assess the financial potential of your farm!)
And a major part of this research phase is understanding the right balance of capital expense and operating expense. Unfortunately, this is also where many new farmers can fall prey to being a little too frugal.
With roots in farming ourselves, we know the temptation to do things on the cheap. There’s something so seductive about scrapping a farm together with inexpensive components. But we also know that skimping on your initial investment may actually come back to bite you when it comes to the cost of running the farm.
Just remember that most of the time when you pay less upfront (CAPEX), you end up having higher costs as you run the business (OPEX). Pay more upfront, and the investment will keep operating costs lower in the future. Again, this isn’t always the case, but 9 times out of 10 it holds true.
The same goes for container farms, or any indoor farming equipment for that matter.
Container farms can be less expensive to set up than many other farms like greenhouse or warehouse operations, but the constraints of the container can drastically increase the cost of running your farm. Especially when you have to add or replace equipment that fails, and your labor costs go up because of the increased time spent performing daily tasks like inspections and harvesting.
Don’t forget you’re starting a commercial farm here, not a backyard garden, and your goal is to grow and sell good food.
If you’re starting a system that hinders productivity (both for plants and workers) and requires upgrades or expensive maintenance to operate, you’re actually hurting your ability to accomplish your goals.
At the end of the day, cheap is not actually that cheap.
Beware vanity metrics
Farmers almost always make money by selling pounds (or ounces) of produce. Rarely do they sell a number of plants rather than a weight.
That’s why it’s so dangerous to measure a system’s economic potential with metrics like “plant sites.” You may be able to grow an incredible number of plants per square foot, but if they’re small and unsalable then it’s a metric that at best is useless, and at worst is intentionally misleading. An example of this could be a microgreen tray with “1000 plant sites in 1.5 square feet!”
This means that biomass is the only truthful and non-subjective metric.
Remember, vertical farming is not about how much production you can possibly cram into a space. It’s about growing better food closer to market and maximizing your production as a function of the resources you invest, such as capital, light, water, energy, and labor.
The best way to measure the productive and economic potential of your future farm is to compare the capital expense divided by the pounds of produce. That will not only give you an idea of how much your system will yield, but will also allow you to conduct appropriate market research based on weight, not plant sites.
Again, while it’s possible some chefs or farmers’ market customers may buy a head of lettuce, the majority of your markets will want to know your price per pound or your price per ounce.
Like the simplified example used in the video above, imagine that one farm offers 2,000 lb/year of greens and costs $90k in capital expenses (i.e the price you pay for the farm, delivery, installation, and any modifications needed for it to perform when you plug it all in).
Another offers 4,000 lb/year of greens but costs $135k. The second option might take a little longer to pay off, but will be more profitable in the long run. (This is overly simplified so please do a feasibility study to get specific numbers!)
Remember, vertical farming is not about how much production you can possibly cram into a space. It’s about growing better food closer to market and maximizing your production as a function of the resources you invest, such as capital, light, water, energy, and labor.
The bottom line: Container farms can play a significant role in the future of our food system.
The world is begging for better food.
People have lost faith in labels and they’re sick of low quality food they see at the grocery store. They’re demanding fresher food, but can only get it if they have local farmers near them to supply it.
Container farms can play a significant role in solving this supply problem by helping more local farmers get started growing food much closer to market.
But not all container farms are created equal.
Repurposed containers, while a prize of pop culture, require too much compromise to be truly productive modern farming machines in the long run.
We have much more faith in custom built containers that practice intent-informed design and take a ground-up approach to environmental controls, labor workflows, and much more. They’re just much more efficient and effective at helping farmers accomplish their goals.
So while container farms have the potential to fundamentally change the game when it comes to growing better food closer to the markets that want it, these farms must survive to be impactful.
Why did we write this?
Our goal with this piece, like most of the articles we write, is to move the industry forward. Everything we do here at Bright is about helping the local farmer succeed and it pains us to see the opposite happen.
We believe that by being honest about the benefits and challenges, more farmers will start sustainable businesses and help supply the increasing demand for better food.
Do you have experience growing in a container? Do you have questions for those who do?
Note: Repurposed shipping containers and containers designed specifically for growing crops are fundamentally different. In most cases, the latter have mitigated the majority of these issues in the design phase.
Why Agtech Grows In Brooklyn
Aug. 30, 2017 12:59 pm
Why Agtech Grows In Brooklyn
We've seen an abundance of agtech activity in the borough. But why here?
A rooftop greenhouse in Brooklyn. (Photo courtesy of @oneminutemeal)
By Nina Sparling / CONTRIBUTOR
The Brooklyn landscape is going green — and not just on rooftop farms. Of late, the borough has seen an explosion of innovation about how to grow fresh, healthy food in the heart of the city.
Digging beds on rooftops and harvesting baby radishes under the summer sun is rather 2010. This year, Blue Planet Consulting will reveal its +farm — a build-it-yourself, modular hydroponic farm unit for the home. Agrilyst is refining its workflow and data management software for indoor farms to automate aspects of the industry. Re-Nuble brought its fertilizer for hydroponic and soil applications derived from wholesale food waste to market in late 2016.
The agriculture technology industry (agtech for short) has seen extraordinary growth in Brooklyn in the past several years. Local entrepreneurs are pushing the boundaries of what urban agriculture looks like despite the fact that New York appears an unexpected home for such disruption in farming space. Nevertheless, Brooklyn has become a fertile environment for the future of food.
But why Brooklyn and not, say, Bakersfield?
It started with farm-to-table. Eaters borough-wide (and further afield) started thinking about where food comes from. Michael Pollan pleaded citizens to “vote with your fork.” “Local” food rose to — and perhaps surpassed — the level of “organic.”
Consumers began to embrace what industry leaders like Dan Barber and Alice Waters had espoused for decades: Where food comes from matters. And Brooklyn has necessary ingredients like the intersection of passionate chefs and a thriving network of farms.
“It’s hard not to be inspired by that pulsing entrepreneurial spirit,” Meg Savage, head of business development at food mag Edible told Technical.ly. “This is a community that cares about it’s food and where it is coming from … and longing for more advances.”
Edenworks microgreens. (Courtesy photo)
For businesses in the agtech space, the consumer and demand side provides plentiful momentum for continued growth and innovation.
“Rather than having a burden on the food system creating this large carbon footprint of having to bring food from as far as California, people are interested in how can we grow the same thing here,” Tinia Pina, founder of the organic fertilizer company Re-nuble said in an interview.
But operators — the industry word for farmers — in the agtech space are thinking about supply, too. Projections suggest the global population will exceed 9.7 billion by 2050. With New York City populations predicted to grow 9.5 percent by 2040, many agtech companies are focused on how to provide fresh and healthy food in ever more dense urban environments. “There is definitely a need to have more resource efficient localized production, distribution and consumption of resources related to food,” said Pina.
Most companies growing high-tech crops focus on leafy greens and fresh herbs. In New York, this makes sense, suggested Allison Kopf, founder of Agrilyst. “We have an interesting agricultural economy where it is a really big agricultural state. But the things that New York can specialize in year-round is very limited because of the climate and different sort of seasonality.”
The first agtech companies cropped up in Brooklyn in the 2009–2011 period. Industry leaders like EdenWorks, Gotham Greens and AeroFarms played a key role in laying the groundwork for innovation. “Smaller companies are following suit based on the population and population needs,” said Liz Vaknin, cofounder of Our Name is Farm, a digital and experiential marketing company. “In general, Brooklyn is an open-minded type of place to test out concepts.”
Seeds. (Photo courtesy of @oneminutemeal)
The result is something like an ecosystem.
“Once you have investors and customers then you have technology companies that are interested in selling products to that industry,” said Kopf. “You have companies like us and others sprouting up. A lot of it had to do with the market opportunity that is New York and the supporting resources that needed to exist just sort of do exist [here].”
And ample room for innovation and development remains.
Agtech is still young. Many of the companies involved are just a few years old, if that. Excitement from investors is growing, but solid investment requires education and transparency.
“There is definitely room for more collaboration between operators,” said Re-Nuble’s Pina. “It’s hard, each farm has its own intellectual property that they’re trying to keep defensible so they can raise money. But in driving conversation with local stakeholders at the municipal and corporate levels, we need to work together to show how we can make the supply chain more sustainable.”
Funding is a major concern across the board. “We need intelligent capital especially on the loan side,” said Kopf of Agrilyst. “This is a massive infrastructure investment — far too often farms are trying to secure venture capital. But then banks have to understand the technology. Traditional farm loans don’t work the same way yet.”
Local policymakers are beginning to catch on. The Brooklyn Borough President’s office just announced $2 million in funding for an urban agriculture incubator. Further public infrastructure involvement could be a game changer. “If government money is available, the terms are going to be different than private equity money or venture capital funds,” said Vaknin. “All together, that kind of creates a perfect storm for robust growth.”
Edenworks microgreens. (Courtesy photo)
UK’s First Commercially Viable Vertical Farm Being Assembled
UK’s First Commercially Viable Vertical Farm Being Assembled
Food will be grown in a stacking system in a new building at Invergowrie
September 2, 2017
An indoor farm being built on the outskirts of Dundee is expected to be growing salad leaves and herbs by the end of the year.
The futuristic construction nearing completion at the James Hutton Institute (JHI) at Invergowrie will be the UK’s first commercially viable vertical farm.
It is being built by Intelligent Growth Solutions, (IGS) in collaboration with global automation business, Omron.
The company has just closed its facility at Guardbridge where it was working on prototype models which involved combining efficient smart lighting with automation and power to grow fresh produce in vertical towers.
IGS chief executive Henry Aykroyd said that the Guardbridge project had led to strong relationships with local universities and scientists at JHI who aimed to improve the plant science involved with this technology.
“Vertical farming allows us to provide the exact environmental conditions necessary for optimal plant growth,” he said.
“By adopting the principles of Total Controlled Environment Agriculture (TCEA), a system in which all aspects of the growing environment can be controlled, it is possible to eliminate variations in the growing environment, enabling the grower to produce consistent, high quality crops with minimal wastage, in any location, all year round.”
The company will initially be growing salad leaves and herbs and the long term goal is to grow a higher volume of lower value products such as tomatoes and cucumbers. IGS then aims to roll out the technology and create other vertical farms across the country.
Food will be grown in a stacking system with LED lighting, and nutrition will come via hydroponics. Mr Aykroyd saidautomation, energy reduction technology and advanced biological research would be the three key pillars to success.
He added: “Partnering with two leading experts, Omron and the James Hutton Institute, to deliver this provides the very best opportunity for a new approach to vertical farming.”
JHI chief executive Professor Colin Campbell said: “This initiative combines our world-leading knowledge of plant science at the James Hutton Institute and IGS’ entrepreneurship to develop efficient ways of growing plants on a small footprint with low energy and water input.”
nnicolson@thecourier.co.uk
Are You Really Ready To Start Your Urban Farm Operation?
Are You Really Ready To Start Your Urban Farm Operation?
AUGUST 15, 2017 | URBAN AG NEWS
By David Ceaser
So, you have been dreaming about starting an urban farm or are about to launch your new career with an indoor farm. You have gotten funding from friends and family (and Kickstarter) but have you really dotted all the i’s and crossed all the t’s as far as what challenges you will be taking on as you get your business up and running?
The truth is that many urban farming operations enter the business from one perspective. They may be started by a grower who knows a ton about growing but little about the business and legal end of things. Or, the operation may be started by someone with a business perspective who wants to see a farming operation thrive, but has little knowledge of the daily ins and outs of running a farm.
Many urban farms fail. It’s good to be as prepared as possible when starting out so you don’t repeat the same mistakes as others.
Here are some important things to think about before getting started. Any one of these roadblocks could delay your project for several months so it’s best to look at these things ahead of time rather than letting them derail your progress.
Zoning, code issues
Since urban agriculture (as it’s known today) is a relatively new field, many municipalities are unfamiliar with it and do not have any sort of code on the books for how to permit your project. If you can’t obtain a permit, then you can’t obtain a business license.
Your options will be to move your project to another location where it is permitted, permit under a different classification such as a food processing facility (if you can convince the planning department), work without a permit (there are work arounds depending on the location of the facility) or wait until legislation is updated. Many city planning departments will not be familiar with indoor agriculture projects so it is very valuable to do your homework first.
It is good to have at least basic drawings to show them how the facility will be laid out and will operate. It is also good to be familiar with cities that have urban farming legislation on the books so that you can show that to local planning departments as needed.
Business model
What is your business model? How will you make money? Will you sell your product wholesale? To restaurants? Direct to consumers? To supermarkets? At farmers markets?
Each of these particular customers may require certifications before they will purchase your product. These might be as simple to obtain as county ag permits or as complex and expensive as organic certification or regular tests for pathogens. It is important to know what your customers will ask of you beforehand so that you are prepared.
Water
Water is a key ingredient in your facility whether hydroponic or soil-based. Important questions to consider are: Can you use the existing municipal water? Will you need to invest in expensive filtering equipment to remove excessive salts or metals? Are there restrictions on water use (such as in California)? Are there disposal issues to be educated about regarding disposal of nutrient-rich water?
Growing medium
Hydroponic farming can be done with different growing media. Do you have a guaranteed supply of that medium, especially for operations where the medium is only used for a short period of time and replaced? If you are looking for organic certification, does the medium meet the requirements for certification? If not, what alternatives are there? If you are using soil, what tests do you need to do and what adjustments will you need to make to the soil?
Electricity, energy
If you are running an indoor farm, energy costs can be one of the most expensive budget items. Using lights and dehumidifiers can really be expensive.
Do you know what your power rates are? Do you know when power is most expensive? Do you know how much light your plants need ? Is the electricity in your area reliable or should you have a back up generator on hand? Do you know how much power your facility needs and how much does the property you are looking at offers? Is the existing electrical system up to code? How much will an upgrade cost?
Floors
If you are running an indoor facility, floor design is of key importance. You need to simultaneously design your floor for multiple factors such as being able to be cleaned easily, drainage, traction and bacterial control.
Input sourcing
Just like when you are baking bread, if you run out of flour, you have a big problem. The same is true with your farm. You will have numerous inputs and if any one of them runs out, your production will be slowed or might even stop. Make sure you have a reliable source for all your inputs and a reliable backup source just in case.
Controllers
So much of indoor farming and even aspects of outdoor farming are based on monitoring data and adjusting as necessary. What controllers will you use for your operation? How will you use the data that are being produced to your advantage?
Are you the type of person that feels more comfortable seeing everything in person and making adjustments on site or are you comfortable with making adjustments to your growing operation remotely? These questions are very important to think about before you get started so that production data can be easily understood and analyzed and the appropriate adjustments can be made to your operation when needed.
Perspective
When looking at your urban farming business, I have found it very valuable to analyze production and costs on a square foot basis. I have a background in real estate and using a square foot methodology has proven very valuable and easy to understand.
Full Cycle Planning
Many operations do intense planning for how to grow their product but don’t think about the best way to harvest and package until it is upon them. Unfortunately, harvesting and packaging can be very labor intensive and if not well planned beforehand, can turn a profitable venture into one that loses money. Talk with your buyers (especially supermarkets) about specific packaging needs they may have from the start and from there, plan a system that reduces labor costs whenever possible.
These are just some of the items that need to be thought about when launching an urban farming operation. There are many more that will undoubtedly arise based on your particular situation. If you are prepared with the ones listed above, it will significantly reduce headaches, time delays and money lost in your urban farming venture.
David Ceaser has over 20 years experience working with plants and agriculture in numerous capacities and countries. He has studied agroecology, horticulture and business along with several years working in real estate development. He currently does consulting work and operates a small outdoor urban farm specializing in herbs and salad greens. To contact David, please e-mail farmer@gsvfarm.com
The author would like to thank Will Kain for his time and insight in participating in this interview. Further gratitude goes to Chris Higgins of Hort Americas and the founder and editor of Urban Ag News.
Jim Pantaleo works to develop all aspects of indoor vertical farming and writes as an industry advocate.
Farming In A Shipping Container: It’s Happening In Grand Rapids
Farming In A Shipping Container: It’s Happening In Grand Rapids
POSTED 7:43 PM, AUGUST 29, 2017, BY JAMES GEMMELL
GRAND RAPIDS, Mich. — Imagine growing food indoors without water, sun or soil – and making a decent living doing so.
Green Collar Farms vertical crops
Green Collar Farms LLC says it is West Michigan’s first indoor hydroponic, vertical micro farm. That’s a 350-square-foot operation inside a re-purposed shipping container, located at 530 Second Street NW in Grand Rapids. Green Collar Farms was founded by Brian Harris, who says vertical farming is a sustainable enterprise that has the potential to grow local food and provide middle income-level jobs in urban areas.
“The ultimate goal,” says Harris, “is that a person could make a middle-income living out of the crops that go to your local farm-to-fork restaurant, and groceries.” He believes that could help grow a community’s vitality, not just grow crops. Under-used spaces like vacant warehouses or dormant garages and basements could be transformed into vertical farms.
The hydroponic farming uses L.E.D. technology that Harris says is 60 percent more efficient, per watt used, than sunlight. How can the plants grow inside a container with no sunlight? Harris says plants “see” light differently than people, who mostly observe it in yellows, greens and oranges. But plants see sunlight in red and blue, and interpret it in terms of radiation. So, the L.E.D.s that are used inside the shipping container are a red-and-blue combination. “So, it gives the plant the little bit of blue it needs to have to wake up in the morning. And the red is really what makes it stretch.”
Green Collar Farms uses automated Controlled Environment Agricultural (CEA) techniques to operate year-round, regardless of season. It can produce hyper-local greens and herbs with a yield equal to the output of a traditional two-acre farm – while using only 10 percent of the water. Green Collar is supplying hydroponic greens like kale, leaf lettuces and herbs to select restaurants in Grand Rapids. And Harris plans to expand distribution to local grocery stores, markets and even school cafeterias.
He figures that will benefit students. And that the L.E.D. technology will attract and introduce them to hydroponic vertical farming: “I think if you bring some kids in here, and they see these lights, it’s like Star Wars. And I think at that point, I’ve got them where I can start talking to them about the biology of plants. Start talking to them about engineering. Introduce them to the ‘what ifs’ of innovation.” He says that spark an interest in science, technology, engineering and math (STEM), as well as plant biology, agriculture and nutrition.
Harris envisions upscaling the vertical-farm concept up to 20,000 square feet, boosting the crop output significantly. He says that will really produce jobs: “At that point…you’re starting to employ hyper-local residents. You can introduce food (for) the under-served community. The idea here is, if we scale this up to the inner-city to provide them local jobs…”.
However, Harris recognizes that the indoor vertical farming has its limitations. “So, you’re not going to grow wheat, corn, barley…this is not an apple orchard…but there are lots of field crops that are grown in muck farms or other soil environments that are not necessarily optimal for the environment. You could bring those in to hyper-local. Because they’re typically consumed hyper-local.”
Japan’s SoftBank Is Investing Billions In The Technological Future
Japan’s SoftBank Is Investing Billions In The Technological Future
By Peter Rejcek | Aug 29, 2017
Remember the 1980s movie Brewster’s Millions, in which a minor league baseball pitcher (played by Richard Pryor) must spend $30 million in 30 days to inherit $300 million? Pryor goes on an epic spending spree for a bigger payoff down the road.
One of the world’s biggest public companies is making that film look like a weekend in the Hamptons. Japan’s SoftBank Group, led by its indefatigable CEO Masayoshi Son, is shooting to invest $100 billion over the next five years toward what the company calls the information revolution.
The newly-created SoftBank Vision Fund, with a handful of key investors, appears ready to almost single-handedly hack the technology revolution. Announced only last year, the fund had its first major close in May with $93 billion in committed capital. The rest of the money is expected to be raised this year.
The fund is unprecedented. Data firm CB Insights notes that the SoftBank Vision Fund, if and when it hits the $100 billion mark, will equal the total amountthat VC-backed companies received in all of 2016—$100.8 billion across 8,372 deals globally.
The money will go toward both billion-dollar corporations and startups, with a minimum $100 million buy-in. The focus is on core technologies like artificial intelligence, robotics and the Internet of Things.
Aside from being Japan’s richest man, Son is also a futurist who has predicted the singularity, the moment in time when machines will become smarter than humans and technology will progress exponentially. Son pegs the date as 2047. He appears to be hedging that bet in the biggest way possible.
Show Me the Money
Ostensibly a telecommunications company, SoftBank Group was founded in 1981 and started investing in internet technologies by the mid-1990s. Son infamously lost about $70 billion of his own fortune after the dot-com bubble burst around 2001. The company itself has a market cap of nearly $90 billion today, about half of where it was during the heydays of the internet boom.
The ups and downs did nothing to slake the company’s thirst for technology. It has made nine acquisitions and more than 130 investments since 1995. In 2017 alone, SoftBank has poured billions into nearly 30 companies and acquired three others. Some of those investments are being transferred to the massive SoftBank Vision Fund.
SoftBank is not going it alone with the new fund. More than half of the money—$60 billion—comes via the Middle East through Saudi Arabia’s Public Investment Fund ($45 billion) and Abu Dhabi’s Mubadala Investment Company ($15 billion). Other players at the table include Apple, Qualcomm, Sharp, Foxconn, and Oracle.
During a company conference in August, Son notes the SoftBank Vision Fund is not just about making money. “We don’t just want to be an investor just for the money game,” he says through a translator. “We want to make the information revolution. To do the information revolution, you can’t do it by yourself; you need a lot of synergy.”
Off to the Races
The fund has wasted little time creating that synergy. In July, its first official investment, not surprisingly, went to a company that specializes in artificial intelligence for robots—Brain Corp. The San Diego-based startup uses AI to turn manual machines into self-driving robots that navigate their environments autonomously. The first commercial application appears to be a really smart commercial-grade version that crosses a Roomba and Zamboni.
A second investment in July was a bit more surprising. SoftBank and its fund partners led a $200 million mega-round for Plenty, an agricultural tech company that promises to reshape farming by going vertical. Using IoT sensors and machine learning, Plenty claims its urban vertical farms can produce 350 times more vegetables than a conventional farm using 1 percent of the water.
Round Two
The spending spree continued into August.
The SoftBank Vision Fund led a $1.1 billion investment into a little-known biotechnology company called Roivant Sciences that goes dumpster diving for abandoned drugs and then creates subsidiaries around each therapy. For example, Axovant Sciences is devoted to neurology while Urovant focuses on urology. TechCrunch reports that Roivant is also creating a tech-focused subsidiary, called Datavant, that will use AI for drug discovery and other healthcare initiatives, such as designing clinical trials.
The AI angle may partly explain SoftBank’s interest in backing the biggest private placement in healthcare to date.
Also in August, SoftBank Vision Fund led a mix of $2.5 billion in primary and secondary capital investments into India’s largest private company in what was touted as the largest single investment in a private Indian company. Flipkart is an e-commerce company in the mold of Amazon.
The fund tacked on a $250 million investment round in August to Kabbage, an Atlanta-based startup in the alt-lending sector for small businesses. It ended big with a $4.4 billion investment into a co-working company called WeWork.
Betterment of Humanity
And those investments only include companies that SoftBank Vision Fund has backed directly.
SoftBank the company will offer—or has already turned over—previous investments to the Vision Fund in more than a half-dozen companies. Those assets include its shares in Nvidia, which produces chips for AI applications, and its first serious foray into autonomous driving with Nauto, a California startup that uses AI and high-tech cameras to retrofit vehicles to improve driving safety. The more miles the AI logs, the more it learns about safe and unsafe driving behaviors.
Other recent acquisitions, such as Boston Dynamics, a well-known US robotics company owned briefly by Google’s parent company Alphabet, will remain under the SoftBank Group umbrella for now.
This spending spree begs the question: What is the overall vision behind the SoftBank’s relentless pursuit of technology companies? A spokesperson for SoftBank told Singularity Hub that the “common thread among all of these companies is that they are creating the foundational platforms for the next stage of the information revolution.All of the companies, he adds, share SoftBank’s criteria of working toward “the betterment of humanity.”
While the SoftBank portfolio is diverse, from agtech to fintech to biotech, it’s obvious that SoftBank is betting on technologies that will connect the world in new and amazing ways. For instance, it wrote a $1 billion check last year in support of OneWeb, which aims to launch 900 satellites to bring internet to everyone on the planet. (It will also be turned over to the SoftBank Vision Fund.)
SoftBank also led a half-billion equity investment round earlier this year in a UK company called Improbable, which employs cloud-based distributed computing to create virtual worlds for gaming. The next step for the company is massive simulations of the real world that supports simultaneous users who can experience the same environment together(and another candidate for the SoftBank Vision Fund.)
Even something as seemingly low-tech as WeWork, which provides a desk or office in locations around the world, points toward a more connected planet.
In the end, the singularity is about bringing humanity together through technology. No one said it would be easy—or cheap.
Formerly the world’s only full-time journalist covering research in Antarctica, Peter became a freelance writer and digital nomad in 2015. Peter’s focus for the last decade has been on science journalism, but his interests and expertise include travel, outdoors, cycling, and Epicureanism (food and beer). Follow him at @poliepete.
Iowa Grocery Grows 10-15 lbs of Produce On Outdoor Vertical Garden – Every Week
Basil, lettuce, and mint flourish on the outdoor Grow Walls at Hy-Vee, installed by FFM in May this year. There’s no soil needed here: the plants are suspended in a growing medium made from recycled plastic bottles and grow in the sunlight.
Iowa Grocery Grows 10-15 lbs of Produce On Outdoor Vertical Garden – Every Week
under Agriculture, Eat & Drink, Features, Gardening and Plants, News
by Lacy Cooke
It doesn’t get much more local than this. In Davenport, Iowa, Hy-Veegrocery store commissioned Friday’s Fresh Market (FFM) to install and maintain two eight-tower Grow Walls, or hydroponic vertical gardens, on the outside of their store – which they then sell inside. Owner Andrew Freitag told Inhabitat they can obtain between 10 and 15 pounds of fresh produce every week, depending on the crop.
Basil, lettuce, and mint flourish on the outdoor Grow Walls at Hy-Vee, installed by FFM in May this year. There’s no soil needed here: the plants are suspended in a growing medium made from recycled plastic bottles and grow in the sunlight. FFM also installed a smaller Grow Wall inside the grocery store in the produce section. They maintain both systems, germinating seeds, transplanting, supplying nutrients and water, harvesting, and packaging the produce for sale in the store.
Related: Berlin grocery with vertical micro-farm reimagines the future of produce departments
FFM manager Chen Freitag told Inhabitat, “We see this disruptive technology becoming more and more popular in our future farming industry. It will help to improve the fresh food desert situation here in the Midwest tremendously and stimulate the local economy.”
The Grow Walls aren’t the only aspect of FFM’s business. They also cultivate indoor farms in shipping containers, using the same towers and irrigation system as a Grow Wall. Freitag said these farms consume around 90 percent less water than traditional methods, and since FFM can control the environment, produce grown inside the shipping container farms is more colorful and flavorful, with a higher nutrient content. She said FFM started pursuing hydroponics as a more efficient, sustainable way to grow fresh food, no matter the weather outside.
“Our goal is to improve the quality of life in our local communities,” Freitag told Inhabitat. “People here deserve to eat better, live better. We believe we are capable of being self-sufficient when it comes to fresh, local food year-round.”
One small Iowa company may not be able to change the entire agriculture industry right away; instead, Freitag said they focus on changing people’s daily lives with better food, and hope the industry evolves from there. “The earth is the resource account we cannot afford to overdraw,” she told Inhabitat. “We need to think about future generations: what we leave them to live with.”
Images via Lacy Cooke for Inhabitat
This Urban Farming Accelerator Wants To Let Thousands Of New Farms Bloom
08.23.17
This Urban Farming Accelerator Wants To Let Thousands Of New Farms Bloom
Kimbal Musk’s Square Roots is giving aspiring urban farmers their own shipping containers and helping them sprout a new business, in the hopes of creating a new agricultural system.
“We are successful if the farmers are successful. So we wake up every morning thinking: how can we help the farmers be more successful?” [Photo: courtesy Square Roots]
In a parking lot outside a former pharmaceutical factory in the Brooklyn neighborhood of Bedford-Stuyvesant, 10 entrepreneurs have spent the last nine and a half months learning how to take on the industrial food system through urban farming. Square Roots–a vertical farming accelerator co-founded by Kimbal Musk, with a campus of climate-controlled farms in shipping containers–is getting ready to graduate its first class.
With a new round of $5 million in seed funding, led by the Collaborative Fund, the accelerator is making plans to build new, larger campuses in other cities.
“Is it going to be one company that takes down the industrial food system, or is it going to be thousands of companies working together on a better food system?” [Photo: courtesy Square Roots]
In the program, each entrepreneur is temporarily given a single upgraded shipping container, filled with vertical growing towers, irrigation systems, and red and blue LED lights in a spectrum tuned to help grow greens. Then they spend roughly a year learning the skills to grow food–no prior experience is necessary–developing business plans and working with coaches and experts to improve their entrepreneurial skills. By the end, in theory, they’ll be ready to launch an urban farming business of their own.
Musk, who runs several health-focused restaurants and nonprofit school gardens (and is Elon’s brother), saw the need for a large network of well-trained young entrepreneurs who could quickly grow urban farming. “We wanted to come up with a model that scaled small urban farming, so literally every consumer of food can have a direct relationship with a farmer,” says Square Roots co-founder and CEO Tobias Peggs.
“We wanted to come up with a model that scaled small urban farming, so literally every consumer of food can have a direct relationship with a farmer.” [Photo: courtesy Square Roots]
“Is it going to be one company that takes down the industrial food system, or is it going to be thousands of companies working together on a better food system? We definitely believe the latter,” he says. “So part of the engine that we’ve created here is that by training these young people…at the end of that program, they’re armed with the tools that they need to go out and set up their own food business. The hope is there will be tens of thousands of new businesses that end up being formed.” The program offers mentorship and can help connect entrepreneurs to investors.
In a learn-by-doing model, everyone immediately starts farming. “When this first cohort joined on November 7, on that day, literally the farms were dropped from a truck onto the parking lot,” Peggs says. “Eight weeks later, we had our first farmers market in Bed-Stuy, where those people had learned to grow really tasty food. The whole system is kind of geared up to have a very fast learning curve.”
I think it’s important to expose people to urban farmers.” [Photo: courtesy Square Roots]
As they grow and sell greens during the program, the entrepreneurs make money; the accelerator keeps a portion of the profits to fund itself. “Our incentives are aligned,” he says. “We are successful if the farmers are successful. So we wake up every morning thinking: how can we help the farmers be more successful?” Even with a single shipping container farm, Peggs says that it’s possible to run a profitable business.
One pair of entrepreneurs worked together to launch a farm-to-desk delivery program that brings fresh greens to dozens of New York City offices. Another student is focused on growing greens for low-income neighborhoods. Someone else launched a business delivering produce to New Jersey while running her Square Roots farm. A former engineer is developing an improved lighting system for indoor farming and plans to launch an equipment business. Another entrepreneur used data analysis to perfect a growing recipe for heirloom basil, which he sells to restaurants and markets. (The accelerator’s layout, with modular growing containers, also allows it to study data about yield and quality and improve the technology for future students).
“What I found most valuable is you’re pretty much thrown into operating a business, and you learn as you go.”[Photo: courtesy Square Roots]
“The way that I learn is through experience and also through imitation,” says Nabeela Lakhani, one of the first class of entrepreneurs, who joined the accelerator after graduating from a public health and nutrition program. She had no prior farming experience. “What I found most valuable is you’re pretty much thrown into operating a business, and you learn as you go, which was perfect for me.”
Lakhani partnered with a SoHo restaurant, Chalk Point Kitchen, to become its “official farmer,” growing food on demand for the chef. The restaurant buys her entire yield from the shipping container, and Lakhani provides a year-round supply of produce. She also visits the restaurant once a week to wander around tables talking with customers.
[Photo: courtesy Square Roots]
“I think it’s important to expose people to urban farmers,” she says. “You should be friends with your farmer–that’s how local food should be. Just the way the chef comes out and says hi, I think it should be the norm that the farmer comes out and says hi. That builds trust between the consumer and the food system.”
The first cohort will graduate in October, and the accelerator is taking applications for its next class; in 2016, it had 500 applicants for 10 spots. In its new location in a yet-to-be announced city, it plans to have larger campuses with room for more students. The founders also hope to quickly launch in more locations. “It’s all stemming from the mission of real food for everyone,” says Peggs. “Ultimately, we want to put a Square Roots campus in every city in the U.S.”
ABOUT THE AUTHOR
Adele Peters is a staff writer at Fast Company who focuses on solutions to some of the world's largest problems, from climate change to homelessness. Previously, she worked with GOOD, BioLite, and the Sustainable Products and Solutions program at UC Berkeley.
Future Farm To Double Size and Ramp Up Baltimore Vertical Farming Project With Second Location
SOURCE: Future Farm Technologies, Inc. | August 24, 2017 08:00 ET
Future Farm To Double Size and Ramp Up Baltimore Vertical Farming Project With Second Location
VANCOUVER, BC--(Marketwired - Aug 24, 2017) - Future Farm Technologies Inc. (the "Company" or "Future Farm") (CSE: FFT) (OTCQB: FFRMF) announces an update with respect to its Baltimore farm. As previously announced, Future Farm signed a LOI to lease 25,000-sq ft of commercial space from Volunteers of America ("VOA") Chesapeake to accommodate a vertical farm in Baltimore, MD, which will distribute high value healthy produce to local area retail stores, restaurants, institutional non-profits and other buyers. The Company is pleased to announce that the facility's design and budget are now complete and a second location will double the size of the project to almost 50,000-sq ft and speed up the development.
The Company expects to gain site control of the second location in Baltimore within the next 7-10 days. This particular site is more accommodating to the Company's controlled environment agriculture ("CEA") technology requirements and requires less construction build-out. It is expected that this second location will be operational sooner than the original location and will therefore become Phase 1 of the Baltimore project.
As previously announced, Craig Stanley and CBO Financial will act as the Company's financial advisor with respect to New Market Tax Credits (NMTC) and will be arranging for $5,000,000 in NMTC-based financing for each phase of the Baltimore farms. The NMTC program is a $65 billion federal program designed to incentivize private investment in low-income communities. NMTCs are provided to financial institutions in exchange for equity investments that eligible businesses can use to subsidize project development costs. CBO Financial helps driven organizations, such as Future Farm, to finance facilities that will provide goods and services that benefit populations in need and revitalize communities.
"We are pleased to be working with CBO Financial and Volunteers of America Chesapeake on these projects and believe that their success will be a bellwether for public-private partnerships within the urban farming industry," says Mr. William Gildea, Future Farm's CEO and Chairman. "Our goal was always to create impactful social and corporate programs that are mutually beneficial for all involved, from the community, to the Company and our shareholders. Partnering with Volunteers of America and CBO Financial puts us in the position to achieve that goal."
"This approach to urban agriculture and community development is truly visionary and we are proud to be involved with such a meaningful project," says Tony Azola, General Contractor for Volunteers of America.
The primary objectives of both farms remain the same -- establish economical and environmentally friendly vertical farms; provide job training opportunities (specifically to the VOA's reentry program for ex-offenders in Baltimore, MD) as well as to the local community; provide therapeutic programs, which will be expanded to the disabled population; support entrepreneurship development; and establish a model for replication at other reentry and social services facilities.
One of the primary objectives of the projects is to provide opportunities to develop therapeutic programs involving all aspects of planting, growing/nurturing, harvesting and selling plants. The American Horticultural Therapy Association (AHTA) defines "Horticultural Therapy" as the "engagement of a person in gardening and plant-based activities, facilitated by a trained therapist, to achieve specific therapeutic treatment goals." AHTA believes that Horticultural Therapy (HT) is an active process, which occurs in the context of an established treatment plan where the process itself is considered the therapeutic activity rather than the end product. The therapeutic benefits of garden environments have been documented since ancient times. Today, HT is accepted as a beneficial and effective therapeutic modality and is widely used within a broad range of rehabilitative, vocational, and community settings. HT helps improve memory, cognitive abilities, task initiation, language skills, and socialization. In physical rehabilitation, HT can help strengthen muscles and improve coordination, balance, and endurance. In vocational HT settings, people learn to work independently, problem solve, and follow directions.
For further information, contact William Gildea, Director, at 617.834.9467.
On behalf of the Board,
Future Farm Technologies Inc.
William Gildea, CEO & Chairman
About Future Farm
The Company's business model includes developing and acquiring technologies that will position it as a leader in the evolution of Controlled Environment Agriculture (CEA) for the global production of various types of plants. Future Farm provides scalable, indoor CEA systems that utilize minimal land, water and energy regardless of climate, location or time of year and are customized to grow an abundance of crops close to consumers, therefore minimizing food miles and its impact to the environment. The Company holds an exclusive, worldwide license to use a patented vertical farming technology that, when compared to traditional plant production methods, generate yields up to 10 times greater per square foot of land. The contained system provides many other benefits including seed to sale security, scalability, consistency due to year-round production, cost control, product safety and purity by eliminating environmental variability.
The Company is also in the business of designing and distributing LED lighting solutions utilizing the COB and MCOB technology. The Company is focused on delivering cost efficient lighting to North America via advanced e-commerce sites the Company owns and operates. LEDCanada.com which caters to B2B customers is a supplier of the newest and highest demand LED solutions. The Company also owns and operates COBGrowlights.com which caters to both large and small agriculture green houses and controlled cultivation centers.
Neither the Canadian Securities Exchange nor its Market Regulator (as that term is defined in the policies of the Canadian Securities Exchange) accepts responsibility for the adequacy or accuracy of this release. The Canadian Securities Exchange has not in any way passed upon the merits of the proposed transaction and has neither approved nor disapproved the contents of this press release.
This news release may include forward-looking statements that are subject to risks and uncertainties. All statements within, other than statements of historical fact, are to be considered forward looking. Although the Company believes the expectations expressed in such forward-looking statements are based on reasonable assumptions, such statements are not guarantees of future performance and actual results or developments may differ materially from those in forward-looking statements. Factors that could cause actual results to differ materially from those in forward-looking statements include market prices, exploitation and exploration successes, continued availability of capital and financing, and general economic, market or business conditions. There can be no assurances that such statements will prove accurate and, therefore, readers are advised to rely on their own evaluation of such uncertainties. We do not assume any obligation to update any forward-looking statements except as required under the applicable laws.
CONTACT INFORMATION
William Gildea
CEO & Chairman
617-834-9467
bill@futurefarmtech.com
Purdue Student Startup Advances Automated Device With App To Grow Fresh Produce In home Hydroponic Appliance
August 24, 2017
Purdue Student Startup Advances Automated Device With App To Grow Fresh Produce In home Hydroponic Appliance
Scott Massey (left) and John Kissel (right) discuss two different grow-pods in front of their innovative hydroponic appliance called the Alpha III Pod. Massey founded Hydro Grow LLC to design and sell hydroponic, in-home appliances that produce fruits and vegetables. Their newest model, Alpha III Pod, incorporates advanced machine learning algorithms to create an ideal nutrient wash for each of the grow-pod’s plants. (Shannon Kane / Purdue Research Foundation image) Download image
WEST LAFAYETTE, Ind. – Purdue University students who developed an automated device to grow vegetables in consumer’s home have started a company to commercialize their technology and develop an improved third model.
Scott Massey and Ivan Ball, recent graduates of Purdue’s Polytechnic Institute, originally inspired by NASA-funded research into self-sufficient plant life systems, co-founded the company Hydro Grow LLC to commercialize their appliance. Others on the Hydro Grow team are James Carlson, a junior in the Department of Computer Science; and John Kissel, a past student of the Krannert School of Management.
Hydro Grow’s technology offers the Gropod, a self-sustainable refrigerator-sized unit capable of growing fresh produce in a consumer’s home. The system uses advanced machine learning algorithms, which allows the device to be aware of what plants are growing in it and adapt its environmental conditions to the specific preferences of that plant. After several prototypes, the company is developing an Alpha 3 model with improved functionality and a corresponding app.
Massey said the company’s mission is to eliminate consumer’s dependence on grocery stores.
“By 2050 the population is expected to grow to nearly 9 billion people, doubling the world’s food demand and water consumption,” he said. “Additionally, food deserts affect 23.5 million people in the United States. Half of these people are also low-income so if poorer communities do not have access to fresh produce, they are more likely to have health complications and additional expenses.”
Hydro Grow offers two services — a hydroponic appliance capable of growing produce, and seed pods from which the produce grows.
The Alpha 3 model is controlled by a user with the Hydro Grow app. The company will make the new model available to 10 to 30 early adopters.
“Users will be able to order the seed pods of their choice via our phone app, plug the seed pod into their system, update the phone application, and let the produce grow until it’s ready to harvest,” Ball said. “Users can remotely monitor the production of produce within each unit. The system will also have a clean cycle every few months that is activated via the phone application.”
Kissel said the company’s priority is to make the appliance as affordable as possible.
“Our most important goal is reducing the cost of the unit to make it a more sensible investment for most consumers,” he said. “Our system not only fills a need but can also help people who may have small gardens, by providing an alternative that produces 95 percent less waste and grows two to three times faster. Our feedback has been that people are ready for this product.”
A short video about Hydro Grow can be viewed at https://youtu.be/KE-nEQXHn0E.
Hydro Grow hopes to advance its technology as the company moves into its next stages of commercialization.
“We are progressing toward a robust system that can achieve optimal growth rates with the least amount of components and user maintenance,” Carlson said. “We hope to identify plastic or electrical manufacturing partners, with competitive pricing. We’re also working on a software development campaign to facilitate seedling orders on a ‘smart’ platform.”
Hydro Grow has raised over $80,000 through competitions to advance its technology. Hydro Grow hopes to collaborate with hydroponic nurseries in major cities to create and distribute seedpods. The company is also seeking investment funding.
“We’re actively looking for funding to achieve a full-scale commercial launch with our original equipment manufacturer. We hope to accomplish this launch by 2018,” Massey said. “We also are interested in taking on interns as the Hydro Grow’s business rapidly expands.”
About Purdue Foundry
The Purdue Foundry is an entrepreneurship and commercialization accelerator in Discovery Park's Burton D. Morgan Center for Entrepreneurship whose professionals help Purdue innovators create startups. Managed by the Purdue Research Foundation, the Purdue Foundry was named a top recipient at the 2016 Innovation and Economic Prosperity Universities Designation and Awards Program by the Association of Public and Land-grant Universities for its work in entrepreneurship. For more information about funding and investment opportunities in startups based on a Purdue innovation, contact the Purdue Foundry at foundry@prf.org.
Writer: Kelsey Henry, 765-588-3342, kehenry@prf.org
Purdue Research Foundation Contact: Hillary Henry, 765-588-3586, hkhenry@prf.org
Sources: Scott Massey, scott@hydrogrowllc.com
Ivan Ball, ivan@hydrogrowllc.com
Mobile Greenhouse Showcases Ontario's Indoor Crops
Mobile Greenhouse Showcases Ontario's Indoor Crops
By Andrew Coppolino, CBC News Posted: Aug 26, 2017 7:00 AM ET Last Updated: Aug 26, 2017 7:00 AM ET
NatureFresh Farms mobile greenhouse travels the U.S. and Canada promoting the commercial greenhouse crops industry. (NatureFresh Farms)
Andrew Coppolino
Food columnist, CBC Kitchener-Waterloo
Andrew Coppolino is a food columnist for CBC Radio in Waterloo Region. He was formerly restaurant reviewer with The Waterloo Region Record. He also contributes to Culinary Trends and Restaurant Report magazines in the U.S. and is the co-author of Cooking with Shakespeare. A couple of years of cooking as an apprentice chef in a restaurant kitchen helped him decide he wanted to work with food from the other side of the stove.
This summer, a mobile squad of cucumbers, tomatoes and green peppers have been travelling throughout Ontario and the United States with the objective of teaching the general public about greenhouse produce.
The one-of-a-kind roaming Greenhouse Education Centre is an initiative of NatureFresh, a Leamington, Ont., produce company that started in the greenhouse growing business in 1999.
Travelling from April to September, the educational unit – a 38-ft. trailer towed by a truck – is essentially a miniature version of a regular greenhouse. It's got a busy schedule of over 100 dates that showcase how produce is grown.
Though you've likely eaten more greenhouse produce than you might know, the balance of produce in Ontario is still grown outside.
For example, according to the Ministry of Agriculture, Food and Rural Affairs and the Ontario Greenhouse Vegetable Growers, in total in Ontario there are about 14,000 acres of tomatoes grown in fields, compared to approximately 1,000 acres of tomatoes grown in greenhouses.
Industry is growing
Greenhouse produce is, however, a growing industry, says Herman Fehr, manager of the NatureFresh mobile greenhouse.
"A lot of produce in grocery stores is greenhouse-grown, especially in the winter. It's an efficient way to grow. With the mobile education centre, people can see the full process of greenhouse growing from start to finish," Fehr said.
The mobile greenhouse has been in operation for three years and visits retail food outlets, summer camps and schools.
The company grows varieties of bell peppers, cucumbers and tomatoes in about 130 acres of greenhouses in Leamington, with 45 acres of tomato greenhouses in Delta, Ohio. The company is one of the largest greenhouse bell pepper growers in North America.
Sunset Produce, located in Kingsville, Ont., is another major greenhouse grower and has been around for six decades. In Waterloo region, Elmira's Own grows vine-ripened greenhouse tomatoes.
High yields, more energy, short distance
As a farming method, greenhouse production can yield as much as 14 times more tomatoes than conventional farming.
The closed-loop growing system of greenhouse facilities (demonstrated in the NatureFresh mobile greenhouse) saves water and requires less fertilizer and pesticides. They grow produce in a modified hydroponic system of recycled coconut fibre, and the mobile facility also has a bumblebee ecosystem, pollinators being an important – and at-risk – component to the growing cycle.
Compared to the five-month growing season of conventional farming, greenhouses have a stable environment that allows the producer to control the temperature and protect plants from harsh precipitation and damaging insects. It is a labour and energy intense process; however, the yields and quality of produce are also high, and transportation to local markets are shorter – much shorter than produce that travels here from the Central Valley of California.
More and more "indoor farms" are popping up in Europe and North America as communities face increasing numbers of retiring farmers, shrinking farmland, increasing costs, depleting soil and changing weather patterns. In Newark, New Jersey, AeroFarms, a "vertical farm," opened in an abandoned urban steel mill in 2015 and produces more than 1,000 tons of greens annually from its 70,000 sq.-ft. operation.
Food security
Whether greenhouse goods are the result of farming or "manufacturing," the reality is that we need to produce a lot of food as securely and inexpensively as possible, as populations continue to grow around the world.
Consumers get the benefit of a year-long supply of local produce grown by Ontario companies. Some of the input costs aside, the greenhouse environment is "a much more efficient way to grow," that gives customers good quality produce and minimizes the variables of what conventional farming faces, said Fehr.
"In a field, you're exposed to disease and pests and general environmental factors that a greenhouse grower really doesn't have to worry about."
You can visit the NatureFresh mobile greenhouse at Zehrs at 450 Erb Street West, Waterloo on Saturday, August 26, from 10 a.m. to 6 p.m. There's more information available at www.naturefresh.ca.
Buildings To Generate Their Own Power With Innovative Glass Blocks
News | August 15, 2017
Buildings To Generate Their Own Power With Innovative Glass Blocks
Buildings could soon be able to convert the sun’s energy into electricity without the need for solar panels, thanks to innovative new technology.
Image courtesy of Solar Squared
Buildings could soon be able to convert the sun's energy into electricity without the need for solar panels, thanks to innovative new technology.
Renewable Energy experts from the University of Exeter are developing a pioneering new technique that could accelerate the widespread introduction of net-zero energy buildings through the latest Building Integrated Photovoltaics (BIPV).
These products, similar to the solar tile created by Tesla, can become a part of a building’s architecture to generate electricity. The team have created an innovative glass block, which can be incorporated into the fabric of a building and is designed to collect solar energy and convert it to electricity.
It is thought that buildings consume more than forty percent of the electricity produced across the globe. This new technology would allow electricity to be produced at the site of use, whilst being seamlessly integrated into the building.
The blocks, called Solar Squared, are designed to fit seamlessly into either new buildings, or as part of renovations in existing properties. They are similar to existing glass blocks by allowing daylight to resonate around a property by replacing traditional bricks and mortar with transparent glass bricks.
Crucially, however, the Solar Squared blocks have intelligent optics that focus the incoming solar radiation onto small solar cells, enhancing the overall energy generated by each solar cell. The electricity generated will then be available to power the building, be stored or used to charge electric vehicles.
The Exeter team, which has created a start-up company Build Solar to market and produce the pioneering product, is now looking to encourage investment to carry out commercial testing of the product, and then aims to take it to market in 2018.
Dr Hasan Baig, founder of Build Solar and Research Fellow from the University of Exeter’s Environment and Sustainability Institute said: “BIPV is a growing industry with a 16% annual growth rate. Setting up a company, which can cater to this growing market shall prove beneficial for the UK economy in the long term.”
“We are aiming to build integrated, affordable, efficient and attractive solar technologies, which have the smallest impact on the local landscape. It’s an exciting venture and one that should capture the imagination of the construction industry, when looking to develop new office blocks and public buildings or infrastructure projects such as train stations and carparks,” said Professor Tapas Mallick, chief scientific advisor for Build Solar.
The Build Solar team believe their blocks have better thermal insulation than traditional glass blocks, as well as providing power to the building. The patent pending technology is at prototype stage and the team are now in the process of fine-tuning their designs in order to test the technology at pilot sites.
Co-inventor and Exeter’s research commercialisation manager in Cornwall, Jim Williams, believes that the timing of the technology is favourable. “It’s now clear that the world is moving to a distributed energy system, of which a growing proportion is renewable. This, coupled with the shift to electric vehicles means that there are substantial opportunities for new ways of generating electricity at the point of use”.
For more information about, visit www.buildsolar.co.uk.
Bowery Farming Receives VC boost From Google, Others
Bowery Farming Receives VC boost From Google, Others
Jun 14, 2017, 1:31pm EDT Updated Jun 14, 2017, 3:17pm EDT
Anthony Noto | ReporterNew York Business Journal
In Feb. 2017, Bowery raised… more
COURTESY OF BOWERY
Irving Fain, CEO and… more
Bowery Farming Inc., the company known for growing the world’s first post-organic produce indoors, raised $20 million in new funding from General Catalyst and GGV Capital.
GV, or Google Ventures (NASDAQ: GOOG), also participated in the effort.
Bowery Farms is the innovator behind the scalable indoor vegetation system that can be… more
Prior to this round, Bowery Farming raised $7.5 million.
Previous investors include First Round Capital, Box Group, Lerer Hippeau Ventures, SV Angel, Homebrew, Flybridge, Red Swan, RRE, and Urban.us. Blue Apron founder and CEO Matt Salzberg, Plated chair Sally Robling, Gramercy Tavern co-founder Tom Colicchio and DigInn CEO Adam Eskin were also involved as angel investors.
To learn more about the new funding round and the current state of Bowery's produce business, we reached out to 37-year-old co-founder and CEO Irving Fain.
Here's what the Manhattan-based entrepreneur had to say:
How has the company expanded over the past couple years?
We raised our seed round in 2015. In a little over two years, we’ve assembled an incredible team of experts passionate about the problem we’re solving, developed BoweryOS — our proprietary software platform — from the ground up, and built a fully operational farm eight miles outside of New York City that supplies restaurants and grocery stores throughout the region. We are proud of what we’ve been able to accomplish so far, but there’s a lot more we want to accomplish.
Why is this funding round for Bowery Farming important?
This round will allow us to expand our operations, continue to innovate and invest in our proprietary technology, and hire world-class employees across the organization. We’re in the process of expanding our partnership with Whole Foods (NASDAQ: WFM) to serve more locations throughout the Tri-state area, and have already begun work on our next farm, which will allow us to deliver the freshest, purest produce to more people in urban areas.
We’re also actively hiring across the organization from engineering to agricultural science and business operations. It’s a great time to join our team!
Where can Bowery's produce be purchased?
Our produce is currently available at select Whole Foods and Foragers stores in the Tri-state area, and featured on the menus of Tom Colicchio’s New York restaurants Craft and Fowler & Wells. We’ve been getting great feedback from customers to-date, and are looking forward to expanding to serve more people in the Tri-state area in the near future.
What are some of the challenges that Bowery faces as a growing company?
There’s a clear need to improve traditional agriculture,which sits at the epicenter of so many global issues today. While indoor farming is still fairly new, we believe in the category and love that it is growing and helping to produce food in a way that’s better for us and our environment. This means we all win, and we’re excited to be the first to offer post-organic produce and to use BoweryOS — our proprietary operating system — to completely control our products from seed to store.
We also wholeheartedly believe in locally sourced food, and consider ourselves a local producer helping to meet an already high consumer demand for quality, local produce.
What are some of the high-tech approaches that Bowery takes?
By combining the benefits of the best local farms with advances made possible by technology, our indoor farms create the ideal conditions to grow the purest produce imaginable. We designed BoweryOS specifically to apply machine learning to vast amounts of data from advanced vision systems and an extensive network of sensors throughout our farm. This provides complete visibility into all the variables that drive growth at every stage in a plant's lifecycle, allows us to continuously monitor health and quality, and enables us to provide each plant with exactly what it needs and nothing more. It also drastically reduces the risk of human error and waste in the growing and harvesting processes. This precision is part of what allows us to be 100+ times more productive on the same footprint of land and use 95 percent less water than traditional agriculture.
How Local Roots Is Helping Solve The World's Food Waste Problem With Robots and Tech
How Local Roots Is Helping Solve The World's Food Waste Problem With Robots and Tech
August 22, 2017
By 2050, the world needs to feed an expected 9 billion mouths, but agricultural inefficiencies, food waste and climate change are limiting our capacity the feed the world of tomorrow. One Los Angeles company is trying to make inroads in this complex problem.
Ellestad is the CEO of Local Roots, a vertical farming company that uses technology to grow the equivalent of five acres of food in a 40-foot shipping container. They’re part of a growing wave of indoor farmers, who are using hydroponic technologies to raise food on a massive scale, at a fraction of the land required by conventional means.
Local Roots Butterhead lettuce growing inside of our TerraFarms™ | Courtesy of Local Roots
Los Angeles may seem like an uncanny place to start an indoor farming business, with its Mediterranean climate and year-round growing season. The city of Angels is surrounded by some of the most profitable agricultural lands in the continent. Over a third of the country's vegetables and two-thirds of the country's fruits and nuts are grown in the state.
“We’re sandwiched between Salinas, the Imperial Valley, and Mexico,” Eric Ellestad says, referring to places of rich agricultural productivity. “It doesn’t get any more competitive than this.” But, he is out to prove a point.
“The reason we chose Los Angeles is because it’s really the market that you need to prove that you can compete and that you can scale anywhere,” he says.
Based in Vernon just five miles south of downtown Los Angeles, Local Roots can grow 20 to 70 thousand pounds of food in just one shipping container. The operation can be powered entirely by solar energy and uses 99 percent less water than conventional farming techniques. All of the technology, from growing algorithms down to the PVC pipes are developed in-house, which makes them unique from their competitors. This move saves them money and makes their operation easily customizable to client needs.
Eric Ellestad with on of his TerraFarms | Clarissa Wei
“We realized that we were going to get trapped in a high price market if we just bought the available parts,” Ellestad says. “So we developed all our own technology and standardized those designs.”
Local Roots specializes in, though is not limited to, leafy greens like butter lettuce, arugula and all different sorts of kale. Every variety is programmed to its own algorithm and the efficiency of that makes it so that they can harvest every 12 days (versus 36 for conventional farming methods). The entire operation is confined to a warehouse in the industrial neighborhood of Vernon and has all the hallmarks of a tech start-up.
Ellestad himself comes from a venture capitalist background and secured one million dollars in funding for the company from venture capitalists, which was launched in 2013. Today they’re a team of 30 people, mostly young scientists and coders, who work in an adjacent air-conditioned office to the warehouse. The farmers, who harvest and propagate the plants, are dressed appropriately mostly in jeans and a T-shirt.
“We’re synthesizing conventional growing practices with technology. This means higher wages for our staff and that we can move more plants in the system,” he says.
Our proprietary red and blue LED lights that help the Butterhead lettuce grow at maximum efficiency | Courtesy of Local Roots
Currently, they have three shipping containers that can hold up to 16,000 plants. Nearly four years in, their client roster includes Space X, Mendocino Farms and Tender Greens. But this is simply a start. The grand ambition is to achieve an international reach.
“Our mission is to improve global health by building a better food system,” Ellestad says. “Simply being a produce company in Los Angeles doesn’t meet that goal.”
Farms emit about 13 percent of the world’s greenhouse gases, he notes. That and a growing world population — a projected 9.7 billion people by 2050 — are his primary motivations.
“We’ll need to grow 70 percent more food by 2050,” he says.
By automating the growing process, Local Roots is able to harvest in a third of time that it takes for a conventional farm to grow food. And of course, the greens are grown sans pesticides because everything is contained in a controlled environment.
Our proprietary red and blue LED lights that help the Butterhead lettuce grow at maximum efficiency | Courtesy of Local Roots
“We develop a model for each crop, determine the set of conditions, and get the most efficient production while still optimizing what the customer wants,” he says.
The technology does have its drawbacks, however. Vertical farming technology is mostly targeted toward leafy greens. Fruit and nut trees are not ideal in shipping containers, and major carbohydrates crops like rice and wheat cannot be supported in such an environment. Because the operation is held in a closed-loop system, vertical farming, unlike other alternative forms of agriculture like no-till farming, does not contribute to soil health and biodiversity.
Still, it’s a step forward in alleviating the pressures of feeding a growing population.
Check Out What Aeroasis Has Been Up To This Month
THE AUGUST NEWSLETTER!
Check Out What Aeroasis Has Been Up To This Month
Aeroasis has been hard at work reaching schools, school districts, & international partners in the AgTech industry to develop educational initiatives and social impact projects around the world.
We are currently talking to 2 new school districts about implementing our curriculum, and we hope to install a custom Smart Farm in over a dozen schools this semester alone!
BEYOND THE EXCITING PROGRESSIONS IN OUR EDUCATIONAL WORK, AEROASIS IS TALKING TO SEVERAL INTERESTED INVESTORS/PARTNERS ABOUT HELPING US LAUNCH OASIS MINI NEXT YEAR!
WE ARE ALSO WORKING ON SOMETHING REALLY BIG WITH A FEW STRATEGIC PARTNERS IN ASIA! MORE ON THAT SOON.
WE ARE HAPPY TO TALK TO ANYONE INTERESTED IN SHARING THEIR TIME, RESOURCES, OR NETWORK WITH US!
That's all for now, but thank you so much for your involvement and support in the growth of Aeroasis, and expect many more amazing things from us this year.
Let's Grow Together.
Urban Farming Incubator Square Roots Raises $5.4M
Founded by executive chairman Kimbal Musk (brother of Elon Musk, and board member at SpaceX, Tesla and Chipotle) and CEO Tobias Peggs (former CEO of Aviary), Square Roots launched a year ago in Brooklyn. Musk says it’s now accepting applicationsfor its second group of food entrepreneurs, selecting a city for its second location and it’s closed $5.4 million in seed funding.
Urban Farming Incubator Square Roots Raises $5.4M
Posted August 23, 2017 | By Anthony Ha (@anthonyha)
Square Roots isn’t your normal startup incubator. Sure, the people who participate are entrepreneurs — but instead of sitting at desks building new gadgets or smartphone apps, they’re growing food in hydroponic farms housed inside long, metal containers.
Founded by executive chairman Kimbal Musk (brother of Elon Musk, and board member at SpaceX, Tesla and Chipotle) and CEO Tobias Peggs (former CEO of Aviary), Square Roots launched a year ago in Brooklyn. Musk says it’s now accepting applicationsfor its second group of food entrepreneurs, selecting a city for its second location and it’s closed $5.4 million in seed funding.
That money includes $2 million from Collaborative Fund — Musk notes that the firm previously invested in Sweetgreen and Kickstarter, two very different companies that both work with Square Roots.
Each class of Square Roots selects 10 people who participate in a year long program where they’re trained in urban farming while also putting that training to use by growing food Square Roots facilities.
I had a chance to visit Square Roots’ Brooklyn location months ago, where I saw the former shipping containers that house the indoor farms. (The company says each container can produce more than 50 pounds of leafy greens per week while only requiring eight gallons of water per day.)
I enjoyed the contrast of the lush, warm indoor farms with the freezing New York winter outside, and I was impressed by the technology that Peggs showed me allowing the farmers to monitor the conditions inside. I also had a chance to meet some of the entrepreneurs themselves — they came from different backgrounds and were growing different crops, but they were united by an interest in rethinking food production.
Square Roots says its farmers are now distributing greens to more than 80 offices in New York City, and they’re also working with local restaurants.
“There is undoubtedly a lot of work ahead of us, and this funding will only help accelerate that,” Musk writes. “From hardware and software projects to help farmers grow more real food using fewer resources; to expanding our programming so we can support more entrepreneurs. We’re building a future where every person on the planet has a direct relationship with their farmer — who is producing locally grown food that people can trust.”
Will Zeal For Profits Hinder High-Tech Farming From Feeding People?
AUGUST 22, 2017 | NINA SPARLING
Will Zeal For Profits Hinder High-Tech Farming From Feeding People?
Part of the Sustainable Urban Masterplan for Shanghai, China by Except. Photo credit: Except / Flickr (CC BY-SA 2.0)
Vegetables grown on modular indoor farms in the hearts of cities may soon give roadside you-pick farms a run for their money. From produce ordered on-demand from smartphones to retrofitted shipping containers growing baby kale in the dead of urban winters, the future of farming looks ever more high-tech.
So-called vertical farming appeals to consumers devoted to clean eating and sustainable futures. Its potential to mitigate impending crises in the food system, like climate change, malnutrition and the challenge of feeding growing urban populations as the number of farmers drops worldwide, has attracted an array of investors and entrepreneurs. But can these typically venture-capital-backed businesses — which currently grow a tempting array of greens and herbs but little else— disrupt the massive and influential reach of big agriculture? That is far from certain.
An Urban Forest of Food
.In the future envisioned by Dr. Dickson Despommier, author of Vertical Farming: Feeding the World in the 21st Century, cities and the surrounding communities will house intensive agricultural production.
“They liken Manhattan to a forest of skyscrapers,” he told WhoWhatWhy, “I love that image because, yes, let’s make Manhattan imitate a real forest!”
He sees skyscrapers where basements harbor aquaculture tanks filled with tilapia, swimming laps under beds of microgreens whose roots take up the nutrients the fish waste provides. Heirloom tomatoes, sugar snap peas, and scotch bonnet peppers will grow on upper floors in beds programmed to provide ideal conditions through meticulous micronutrient dosage, light exposure and humidity controls.
A central column will house a massive freight elevator and utilities that allow the building to recycle the vast majority of its water. The behemoth will run on renewable energy. Vertical farmers share a common sentiment to, as Dr. Despommier put it, “get the hell off the grid.”
Investors and venture capitalists in the indoor agriculture space share his conviction. Many of the same companies that funded giants in the app-driven technology space underwrite vertical farm ventures: Bezos Expeditions, part of the empire of Amazon CEO Jeff Bezos, has invested in Plenty, a Silicon Valley-based vertical farming company. In June 2017, Plenty purchased Bright Agrotech, producer of the leading vertical farm hardware, the trademarked ZipGrow tower system. Square Roots, a Brooklyn vertical farm incubator and entrepreneurial space, is led by founder Kimbal Musk, the younger brother of Elon Musk of Tesla and SpaceX fame.
But the dream of this type of farming clashes with the way farming actually operates today. Agribusiness, supported by the federal government, is focused on raising a few cash crops. Of the $25 billion spent yearly on farm subsidies, 75 percent goes to just 10 percent of farmers. That 10% represents large scale commercial farms growing commodities for the global marketplace, raising livestock on feedlots, and turning considerable profits.
“People aren’t farming to raise food for people,” Despommier said, “they are raising crops to make money. It’s all about which crops the world needs rather than us.”
Federal support for agriculture was born in the 1930s to maintain a degree of stability in the business of farming commodity crops. A powerful lobby and a revolving door between industry and public office has reinforced this relationship between the government and agribusiness. The industry’s profits come both from turning heavily subsidized commodity crops like corn and soybeans into value-added goods like high fructose corn syrup and soy milk, and from exports into the global commodity marketplace.
This has been instrumental in creating a food system saturated with highly processed goods lacking in nutritional value. It does a poor job of nourishing people while providing an abundance of cheap calories. Moreover, it pads the pockets of a minority of farmers and transnational corporations like Bayer and ConAgra.
Inside AeroFarms
.Can the vertical farming industry challenge this hegemony? To see one of the new farms up close, I scheduled a visit to AeroFarms, a 78,000-square foot facility in Newark, New Jersey. I arrived at the site early in the morning. I found a landscape where nothing was growing. A massive off-white box constructed of corrugated metal siding sat set back from the sidewalk. It was unmarked.
Adjacent to the site at 212 Rome Street is US Route 1, the eastern boundary of Newark’s Ironbound District — named for the two railroads and two highways that define its limits. Behind the big white box was a massive shed filled with dirt, a wall covered in graffiti, and nothing else. Across the parking lot was a cinderblock bungalow with yellowed glass windows and an AeroFarms logo on the door. I peered through a window but saw no one.
Around the back of the sheet metal structure was an unmarked door. I opened it and found myself in a small room that welcomes workers and visitors alike. There I was greeted by Marc Oshima, the chief marketing officer of AeroFarms.
Before I could enter the heart of the operation, Oshima had me take off all jewelry, sign a food-safety compliance form, don a hairnet and navy-blue disposable lab coat, pass through a clean room, like the ones found in computer-chip factories, walk over rubber mats doused in sanitizer to remove harmful bacteria from the soles of my shoes, and finally wash my hands.
The procedure was an everyday routine for Oshima, the kind of executive who wears Oxfords with brightly colored laces and skips a tie. Several employees were getting to work around the same time and followed the same steps. We filed through a set of swinging doors and into one of the grow rooms.
Pictures of vertical farms often feature an array of magenta and cobalt-blue LED lights more reminiscent of a nightclub than a farm. These are for demonstration only: In reality, the beds are lit with LED light that appears bright white to the human eye, but in fact emits the pink and blue wavelengths that fuel microgreen growth. A few of the beds were unlit. The lights aren’t on all the time, Oshima explained. The grow room stays at an ambient 70 degrees. Huge fans whir in the background; nevertheless, the room smells like an aquarium and the air is similarly humid and dank.
The crops are planted in beds about 80 feet long and 5 feet wide. Farmers — who wear starched white lab coats — germinate the seeds in a reusable fabric. The seeds nestle into the off-white fleecy fiber that strikes a balance between breathability and structural integrity.
In newly-seeded beds, the sprouts perk up every half inch or so, stimulated by the intense light. When the greens are ready for harvest, the surface of the bed resembles a sea of green leaves. The plants’ roots dangle into a basin below, treated with a nutrient-dense mist and oxygen delivered through aeroponic technology. The mechanism that releases AeroFarms’ signature mist is hidden from view inside a black plastic tub called the solutions chamber.
The beds stack on top of one another into towers 12 stories or 36 feet into the air. Each vertical unit has its own computer that monitors all aspects of the plants’ growth. A control-panel box houses the wires, cables, and connections that feed into a touch screen displaying data for every inch of every bed.
Accordion platforms lift employees inspecting greens up into the air, where they perform maintenance tasks in response to computer-generated warning signs. This allows for directed and efficient crop management; human observation complements the digital monitoring. A machine harvests and packages the greens once they’ve reached baby maturity.
Infrastructure and Investment
Four external factors have driven investors’ interest in such plant factories: climate change, insecurity in the labor force, food safety, and increasingly urban populations. AeroFarms and its competitors claim to provide a comprehensive fix.
Given access to ample renewable energy to power the LED lights, the grow system can function with a great deal of independence from the environment. Its computer-controlled grow systems and automated harvesting and packaging chains mean the food supply need not rely on an uncertain workforce. The food safety measures that control who and what enters the growing facility reduce the risks of contamination and foodborne illness. AeroFarms — and its competitors — do not use agrichemicals such as pesticides and herbicides. And vertical farms can bring food production to the inner city.
Among indoor farmers, Dr. Despommier is a guiding light — but the vertical farms in operation today have yet to fulfill his vision. The kind of multi-use and agriculturally-diverse buildings he envisions would require significant investment to design and build. Estimates for multistory buildings hover in the hundreds of millions; retrofitting existing structures is cheaper but still represents a substantial investment.
AeroFarms’ beds may be vertical, but the entire operation sprawls out horizontally. It is, for now, more indoor farm than vertical farm. Its Dream Greens grow in the heart of Newark — a city that still rumbles with the aftershocks of deindustrialization and the environmental threats of industry — but funnel into distribution networks up and down the Eastern Seaboard. It doesn’t quite fit Despommier’s zero food-miles vision.
Leafy greens have become the poster child for efficient urban indoor agriculture. Unlike most other crops, farmers can sell the whole green plant, except for the roots. By contrast, a cherry tomato requires growth of the entire plant (stem, leaves, blossoms) before bearing fruit.
Whether indoor farming will prove viable for a range of crops is a basic, and unanswered, question. Imagine growing wheat, rice, corn, or soy in a system where photosynthesis (via artificial light) is expensive.
Getting Off the Grid
.
Solving the renewable energy problem is at the forefront of development for vertical farmers. AeroFarms uses hydropower and solar energy — it even has a farm in Saudi Arabia that pulls water out of the air through reverse-osmosis technology. But before cities can become energy-efficient urban jungles, engineers have to produce the means to get off the grid.
A rendering of what vertical farming might look like on Mars. Photo credit: NASA / Wikimedia
The drive to render indoor farming entirely independent of its environment has pushed the concepts behind vertical farming to the stratosphere — literally. Freight Farms, a company that upcycles shipping containers into portable vertical farms, just announced a partnership with Clemson University to explore deep-space applications of its technology. The collaboration is made possible through a NASA grant to explore a “Closed-Loop Living System for Deep-Space ECLSS with Immediate Applications for a Sustainable Planet.”
While container farms reach for outer space, cities will continue to urbanize at unprecedented rates. The droughts, floods and climate inconveniences that have already begun to exert pressure on commercial and family farmers alike will intensify.
Meanwhile, most of the the farmers raising food for people are small, conventional operations that struggle with minimal public support in a low-margin, high-risk business. Research and development funding for the majority of American farmers growing fresh fruits and vegetables is virtually nonexistent — families or individuals own almost 83% of the farms growing vegetables in the US.
The 2014 Farm Bill inaugurated microloan and grant programs for small and beginning farmers: whether funding for these programs will continue is up for debate as Congress considers the 2018 Farm Bill. Sonny Perdue, the current Secretary of Agriculture, is an agribusiness veteran.
Vertical farmers see themselves sidestepping both the vice-like grip of Big Ag and the insecurity of small-scale farming. They bring fresh, unprocessed foods to the hearts of cities independent of the industry lobby or the inconsistencies of farmers’ markets. Production is controlled and abundant enough to tap into existing supply chains. By distributing to supermarkets and online delivery platforms, they eliminate the distribution challenges many small farmers face. And, at least for the present, they receive ample funding from venture capital and private equity, untethered by the limits of public support.
Given the looming threat from climate change and ever increasing urban populations, it’s clear that both the current farm-to-table system and Big Ag fall short. Yet the new money from venture capitalists brings its own constraints. In fact, Despommier’s condemnation of agribusiness may best describe the conflict: behind their presentation as mission-driven companies passionate about making good food widely available, they are in it to make money.
There is little precedent for how the model will behave as companies scale up and diversify. Public investment in research and development could provide some answers. Calls to action range from implementing new urban agriculture and technology programs at universities to reworking city tax structures to support the new urban farmers through subsidies and tax credits. The growing urban and climate-insecure populations that vertical farmers hope to feed will need more than the production of leafy greens. But for now, the logic among vertical farmers amounts to a hale and hearty Let them eat kale.
Related front page panorama photo credit: Adapted by WhoWhatWhy from building (Cjacobs627 / Flickr – CC BY-SA 3.0) and VertiCrop System (Valcenteu / Wikimedia – CC BY-SA 3.0).