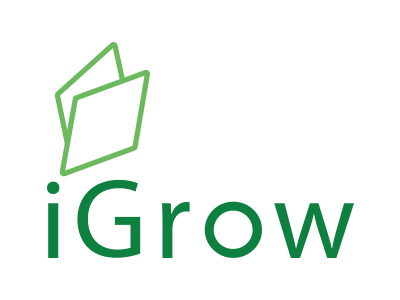
Welcome to iGrow News, Your Source for the World of Indoor Vertical Farming
A Man Waters Plants In A Rooftop Garden On Top of Le Bon Marché Department Store In Paris
A man waters plants in a rooftop garden on top of Le Bon Marché department store in Paris. Regis Duvignau/Reuters
Big Data Suggests Big Potential for Urban Farming
February 15, 2018 AMY CRAWFORD
A global analysis finds that urban agriculture could yield up to 10 percent of many food crops, plus a host of positive side benefits.
otham Greens’ boxed lettuces have been popping up on the shelves of high-end grocers in New York and the Upper Midwest since 2009, and with names like “Windy City Crunch,” “Queens Crisp,” and “Blooming Brooklyn Iceberg,” it’s clear the company is selling a story as much as it is selling salad.
Grown in hydroponic greenhouses on the rooftops of buildings in New York and Chicago, the greens are shipped to nearby stores and restaurants within hours of being harvested. That means a fresher product, less spoilage, and lower transportation emissions than a similar rural operation might have—plus, for the customer, the warm feeling of participating in a local food web.
“As a company, we want to connect urban residents to their food, with produce grown a few short miles from where you are,” said Viraj Puri, Gotham Greens’ co-founder, and CEO.
Gotham Greens’ appealing narrative and eight-figure annual revenues suggest a healthy future for urban agriculture. But while it makes intuitive sense that growing crops as close as possible to the people who will eat them is more environmentally friendly than shipping them across continents, evidence that urban agriculture is good for the environment has been harder to pin down.
A widely cited 2008 study by researchers at Carnegie Mellon University found that transportation from producer to store only accounts for 4 percent of food’s total greenhouse gas emissions, which calls into question the concern over “food miles.” Meanwhile, some forms of urban farming may be more energy-intensive than rural agriculture, especially indoor vertical farms that rely on artificial lighting and climate control.
An operation like Gotham Greens can recycle water through its hydroponic system, but outdoor farms such as the ones sprouting on vacant lots in Detroit usually require irrigation, a potential problem when many municipal water systems are struggling to keep up with demand. And many urban farms struggle financially; in a 2016 survey of urban farmers in the U.S., only one in three said they made a living from the farm.
Although cities and states have begun to loosen restrictions on urban agriculture, and even to encourage it with financial incentives, it has remained an open question whether growing food in cities is ultimately going to make them greener. Will the amount of food produced be worth the tradeoffs? A recent analysis of urban agriculture’s global potential, published in the journal Earth’s Future, has taken a big step toward an answer—and the news looks good for urban farming.
“Not only could urban agriculture account for several percent of global food production, but there are added co-benefits beyond that, and beyond the social impacts,” said Matei Georgescu, a professor of geographical sciences and urban planning at Arizona State University and a co-author of the study, along with other researchers at Arizona State, Google, China’s Tsinghua University, the University of California, Berkeley, and the University of Hawaii.
A MODIS Land Cover Type satellite image of the United States, similar to imagery analyzed by the researchers. Different colors indicate different land uses: red is urban; bright green is a deciduous broadleaf forest. (Obtained from https://lpdaac.usgs.gov/ maintained by the NASA EOSDIS Land Processes Distributed Active Archive Center, USGS/Earth Resources Observation and Science Center)
Using Google’s Earth Engine software, as well as population, meteorological, and other datasets, the researchers determined that, if fully implemented in cities around the world, urban agriculture could produce as much as 180 million metric tons of food a year—perhaps 10 percent of the global output of legumes, roots and tubers, and vegetable crops.
Those numbers are big. Researchers hope they encourage other scientists, as well as urban planners and local leaders, to begin to take urban agriculture more seriously as a potential force for sustainability.
The study also looks at “ecosystem services” associated with urban agriculture, including reduction of the urban heat-island effect, avoided stormwater runoff, nitrogen fixation, pest control, and energy savings. Taken together, these additional benefits make urban agriculture worth as much as $160 billion annually around the globe. The concept of ecosystem services has been around for decades, but it is growing in popularity as a way to account, in economic terms, for the benefits that humans gain from healthy ecosystems. Georgescu and his collaborators decided to investigate the potential ecosystem services that could be provided through widespread adoption of urban agriculture, something that had not been attempted before.
The team began with satellite imagery, using pre-existing analyses to determine which pixels in the images were likely to represent vegetation and urban infrastructure. Looking at existing vegetation in cities (it can be difficult to determine, from satellite imagery, what’s a park and what’s a farm), as well as suitable roofs, vacant land, and potential locations for vertical farms, they created a system for analyzing the benefits of so-called “natural capital”—here, that means soil and plants—on a global and country-wide scale.
Beyond the benefits we already enjoy from having street trees and parks in our cities, the researchers estimated that fully-realized urban agriculture could provide as much as 15 billion kilowatt hours of annual energy savings worldwide—equivalent to nearly half the power generated by solar panels in the U.S. It could also sequester up to 170,000 tons of nitrogen and prevent as much as 57 billion cubic meters of stormwater runoff, a major source of pollution in rivers and streams.
“We had no notion of what we would find until we developed the algorithm and the models and made the calculation,” Georgescu said. “And that work had never been done before. This is a benchmark study, and our hope with this work is that others now know what sort of data to look for.”
Robert Costanza, a professor of public policy at Australian National University, co-founded the International Society for Ecological Economics and researches sustainable urbanism and the economic relationship between humans and our environment. He called the study (in which he played no part) “a major advance.”
“This is the first global estimate of the potential for urban agriculture,” Costanza wrote in an email. “Urban agriculture will never feed the world, and this paper confirms that, but the important point is that natural capital in cities can be vastly improved and this would produce a range of benefits, not just food.”
“Urban agriculture will never feed the world … but the important point is that natural capital in cities can be vastly improved.”
Costanza said he would like to see the researchers’ big data approach become standard in urban planning, as a way to determine the best balance between urban infrastructure and green space—whether it’s farms, forests, parks, or wetlands. That is the researchers’ hope as well, and they’ve released their code to allow other scientists and urban planners to run their own data, especially at the local level.
“Somebody, maybe in Romania, say, could just plug their values in and that will produce local estimates,” Georgescu said. “If they have a grand vision of developing or expanding some city with X amount of available land where urban agriculture can be grown, they can now quantify these added co-benefits.”
That could be very valuable, said Sabina Shaikh, director of the Program on the Global Environment at the University of Chicago, who researches the urban environment and the economics of environmental policy.
“Ecosystem services is something that is very site-specific,” she said. “But this research may help people make comparisons a little bit better, particularly policymakers who want to think through, ‘What’s the benefit of a park vs. food production?’ or some combination of things. It doesn’t necessarily mean, because it has the additional benefit of food production, that a farm is going to be more highly valued than a park. But it gives policymakers another tool, another thing to consider.”
Meanwhile, policy in the U.S. and internationally is already changing to accommodate and encourage urban agriculture. California, for example, passed its Urban Agriculture Incentive Zones Act in 2014, allowing landowners who place urban plots into agricultural use to score valuable tax breaks. The idea has proven controversial—especially in housing-starved San Francisco. Beyond raising rents, critics have argued that urban agriculture, if it impedes the development of housing, could reduce density, contributing to the sort of sprawl that compels people to drive their cars more. Put urban farms in the wrong place, and an effort to reduce food’s carbon footprint could have the opposite effect.
On the other hand, businesses like Gotham Greens that aim to expand may still be hampered by zoning—Puri and his co-founders had to work with New York’s zoning authority to change regulations affecting greenhouses before they could open their first farm. As the company looks to add sites in other cities, the wide array of their zoning rules, utility access, and regulations will influence its decisions.
“I think we could benefit from the more cohesive policy,” Puri said, “but it’s also a very new industry. And then there are so many approaches to urban agriculture. How does a city approach something that is so broad and diverse at this stage?”
While more data about the potential ecosystem services and tradeoffs would surely help create a more navigable regulatory landscape, Puri, like others in his industry, is also something of an evangelist, eager to put in a word for urban farming’s less quantifiable benefits.
“I don’t believe that urban farming is ever going to replace more conventional farming,” he said. “I don’t think a city is going to be able to produce its entire food supply within city limits, but I think it can play a role in bringing people closer to their food, and in making our cities more diverse and interesting and green.”
About the Author
Amy Crawford has written for Boston magazine, the Boston Globe, Slate, and Smithsonian. She lives in Ann Arbor, Michigan.
The Underground Farm Delivering Rare Herbs to New York’s Top Chefs
The Underground Farm Delivering Rare Herbs to New York’s Top Chefs
Bespoke greens and flowers are grown-to-order in Manhattan.
FEBRUARY 14, 2018
Farm Manager Tom Rubino harvests marigolds at Farm.one. ALL PHOTOS: SARAH BLESENER
The sprouts and flowers are as recherché as they are delicious: nepitella, wood sorrel, papalo, micro cressida, afilia pea shoots. While diners may see garnish as little more than a sprig of green to fork aside, chefs see garnish in multiple dimensions—hue, flavor, texture, scent—and have exacting requirements in each. Meeting those requirements, which for millennia depended on the turn of the season or the whimsy of the weather, is now achieved in a Manhattan basement.
Farm.one is a blossoming underground vertical farm in the heart of Tribeca. Inside, farmers grow rare, bespoke, and chef-tailored micro-greens, herbs, and edible flowers for some of the most celebrated kitchens in New York. Several days a week, my job is to slalom through the city’s sidewalk traffic, turtle-backed with bags of the day’s harvest, and hand-deliver the morning’s pickings. (Consider this an official disclosure, although I am not an employee of the company.) Besides herbally gratifying chefs cloistered in the steam and aluminum of famous kitchens—and occasionally being gifted with the most delicious nibbles of my life—I’ve gotten a peek into what may well be the future of urban farming.
There are three clear perks of growing urban greens indoors: One, you can’t get much fresher than farm-to-fork in a few hours. Two, transportation emissions are no dirtier than the courier’s exhalations (Farm.one, at least, only delivers by bike, foot, or train). And three, by eluding meteorological vicissitude, growing to order is like strutting up and hand-sticking a dart right in the bullseye.
Preparing Red Veined Sorrel, a very popular micro known for its tart, bitter flavor and appearance.
Justin Chen, a sous chef at Jungsik, the two-Michelin star, Korean fusion joint, leans in to study the tangerine gem marigold stem pinched between his fingers. I ask what he looks for in Farm.one’s micro greens and flowers, which he occasionally sends back when they’re not “up to spec.” “Consistency,” he replies. In high-end dining, Chen adds, “There’s no room for error.” That’s why keeping tight control on the grow conditions at the farm is so critical.
Related Stories
New York City Officials Hunted Down 10 Food Poisoning Outbreaks Using YelpWild Boars Are Putting One of France's Smelliest Cheeses at RiskWhy Chuck E. Cheese's Has a Corporate Policy About Destroying Its Mascot’s Head
The tangerine gem marigold, a speck of a blossom no bigger than an iPhone home button, is for a petit four—that post-dessert, single-bite confectionary that seems to magically ablate from plate to memory in a single delicious swallow. Jungsik’s petit four looks fit for a centerpiece on a dollhouse dining table. The potted-plant-shaped bon-bon is made up of a dark chocolate shell lined with meyer-lemon caramel and ginger-and-white-chocolate ganache, and a tiny tangerine gem marigold flower sprouts out of the chocolate sable “soil.” If the flower were any bigger (the taste is subtle—like a sweetened tea with lemon) it would overpower the orchestral intricacy of the meyer lemon, caramel, and ginger chocolate. “The size,” Chen reiterates, “is what lets a chef correctly balance flavors [and] find visual symmetry in a dish.”
Red Veined Sorrel Seedlings being grown in Rock Wool Cubes.
One of the experts in charge of giving chefs the esculent tools to achieve such symmetry is farm manager Tom Rubino. Rubino walks the basement farms seven days a week, tweaking controls and sampling from the approximately 100 varieties of plants. His favorite is oxalis, a whale tail-shaped leaf that comes in beet purple or Irish green and has a puckering, citric flavor—something you seem to taste in your forehead as much as your mouth. “It tastes like grape skin,” Rubino says. “When I was a kid, I used to eat grape skins.”
The farm has between two and six levels of grow beds, and totals only about 1,500 square feet in three separate facilities. The plants either drop their roots directly in water, or into a grow medium—a coconut-husk concoction that gives the roots something to grip. Eliminating soil is just one of the ways to maximize and tightly control grow conditions. The farmers also tweak the pH of the water, adjust airflow and humidity, lock in the temperature, and toy with both the wattage and spectrum of the LED lights. They’re basically trying to outdo nature, not letting the plants “succumb to overcast skies,” Rubino tells me.
Shift Hand Manager Katherine Chester in the facility.
Like letting a dog off a leash in an open field, when you give a chef options, they tend to run with them. One chef wants only orange—not yellow or red—tangerine gems. Another wants clearly defined veins in the red-veined sorrel. Other demands include micro-cumin, Neon Rose Magic, Yarrow crowns, and nasturtiums with only purple rims.
On a December day, I watch Victor Amarilla admire those purple rims. But when he pops the little, lily-pad-looking leaf into his mouth, he frowns. “The flavor’s almost there,” he says. As the head chef at Le Turtle, the popular Chrystie Street French restaurant, he receives a twice-weekly delivery from Farm.one. To ensure the nasturtium pop enough, Rubino had to find the right seed for Le Turtle’s needs, and is now growing an exclusive small forest of nasturtium in one corner of the farm. The perfect nasturtium has a slight crunch, a slow, mouth-full wave of heat, and finishes with a flicker of pepper. When Amarilla gets a flavor he likes, he’s apt to pumps the air with his fists.
Petite Anise Hyssop Tops and Purple Oxalis Flowers from Farm.one placed on a dish.
Amarilla is not the only chef using farm.one to color his plates with edible whorls and frizz. One frozen day in late January, I watch chef Chris Owen, of the plant-based pizza restaurant Double Zero (part of the Matthew Kinney restaurant group), nibble on purslane, which he describes as a “juicy, cucumbery” wonder. He imagines aloud how it would taste on his chocolate cake. Little jade-looking purslane leaves inside sweet confections are the kinds of surprises that Owen likes to throw at Double Zero’s diners.
“Farm.one grabs things at the early stages of their lives, when they’re more interesting,” Owen tells me. He’s looking for red and pink flowers for his Valentine’s Day special—maybe some dianthus for his apple cider cheesecake. He also wants some acidic flavors, maybe some sorrel blossoms. As we chat, he sneaks me a bite from a tray of shiitake faux-bacon, which just came out of the wood-burning oven, and browses through a stack of farm.one samples encased in plastic clamshells.
Wood Sorrel Flowers are known for their bright yellow color and tart, slightly sweet flavor.
Double Zero’s aim is “to make vegan foods more accessible,” for which high-quality simplicity is critical, Owen explains. “Over-processing is a problem with veganism.” But be it vegan, classic French, fusion Korean, or omakase, pretty much whatever rare and delicious doodad or efflorescence you imagine can be grown in farm.one’s underground vertical fields.
“The first impression, and maybe 50 percent of the total experience in a restaurant is based on visuals,” Owen argues. Twice a week I deliver him a few dozen purple-and-yellow viola blossoms so he can make that first impression a kaleidoscopic one.
Gastro Obscura covers the world’s most wondrous food and drink.
Subscribe to the Atlas Obscura Newsletter and get our latest, delivered straight to your inbox.
© 2018 Atlas Obscura.
Sign up for our weekly email.
Urban Farming Platform Infarm Gets $25M Funding Endorsement
Berlin-based urban farming startup Infarm has received a rousing endorsement for its vertical, indoor farms in the form of cash. Like, lots of cash.
Urban Farming Platform Infarm Gets $25M Funding Endorsement
Photo Credit: Infarm
Berlin-based urban farming startup Infarm has received a rousing endorsement for its vertical, indoor farms in the form of cash. Like, lots of cash.
Balderton Capital was the leading investor in a Series A funding round, with other names such as Mons Investments, Cherry Ventures, and LocalGlobe claiming their stake in the promising indoor farming company. The round brings Infarm’s total funding to date to $35 million, and they plan on using the new capital to expand their international footprint in Paris, Copenhagen, London, and other German cities while improving upon their Berlin-based R&D headquarters.
The goal: 1,000 Infarm vertical farms in operation globally by 2019’s end.
Here’s how Infarm works. They conceived and control the glass-walled ‘vertical indoor farms’, allowing clients such as grocery stores and restaurants to place the Infarm incubator in their business. From there customer can pick their own herbs, lettuce, or other vegetables out for themselves, much like they would with any other fruit or vegetable. The difference is that they know Infarm produce is guaranteed fresh because they are picking the produce or herb from the incubator in which it’s grown.
Infarm’s techs and agricultural experts can manage their modules remotely, taking maintenance issues out of the hands of clients while using A.I. and a mass of analytical data to ensure that the produce is being grown as near to perfect as possible.
We collect 50,000 data points throughout a plant’s lifetime, Erez Galonska, cofounder and CTO explained, each farm acts as a data pipeline, sending information on plant growth to our platform 24/7 allowing it to learn, adjust, and optimize.
Each module can be controlled to establish the perfect amount of light, pH levels, temperature, and nutrients depending on what is being grown. The Infarm modules have been likened to their own contained, highly-controlled ecosystems, and Galonska has said that he hopes to create a world where seasonal changes and drought are irrelevant to one’s ability to produce food.
Infarm’s model makes too much sense for grocery stores, restaurants, and other establishments that waste countless funds throwing out over-ripe produce daily to overlook. It’s no wonder so many investors are willing to put their big bucks behind Galonska and his partners, brother Guy and Osnat Michaeli, and their one-of-a-kind urban farming platform.
The challenge [now] is in finding the right partners. Our initial focus is on supermarket chains, online food retailers, wholesalers, hotels, and other food-related businesses, for whom the superior quality and range of produce — with no fluctuation in costs — makes Infarm an attractive partner, Michaeli explains. In return, we can reintroduce the joy of growing to the urban population.
The Promise of Indoor, Hurricane-Proof ‘Vertical’ Farms
A worker rides a lift past stacks of vertical farming beds with LED lights
A worker at an indoor vertical farm in Newark, New JerseyMike Segar / Reuters
The Promise of Indoor, Hurricane-Proof ‘Vertical’ Farms
They might be an efficient way to produce food in a world withmore extreme weather—but only if growers can figure out a successful business model.
February 12, 2018, The Atlantic Daily | MEAGAN FLYNN
Federico Marques feared the worst for his farm as he watched live coverage of Hurricane Harvey ravaging fields across the Gulf Coast and inundating every pocket of Houston.
Marques was trapped at home during Harvey and could only monitor his crops from his couch, anxiously viewing footage from the farm’s single working indoor camera. “We couldn’t get in here for four days,” Marques said as he showed me around on an unseasonably warm afternoon this November. “I’m looking at all these aerial photos and thinking, ‘Oh my God, everything is underwater.’ When we finally got back, we had 10 inches of water on the floor—but we only lost maybe 5 percent of the product. The rest was perfectly fine.”
In a way, Harvey was a test for Moonflower Farms. Founded by Marques in December 2015, it was one of the state’s very first indoor “vertical” farms—where plants are stacked in trays on shelves, instead of laid out horizontally across larger plots of land. In these high-tech structures, plants don’t rely on sunlight or soil, rainwater or pesticides, but LED lights and minerals instead. The goal of vertical farms isn’t just to save space; it’s also to find a more economical way of producing food for the growing population—and to reduce the costs and consequences of getting that food to where people actually live.
Moonflower is in an industrial area about 15 miles south of downtown Houston, tucked away inside a relatively small, unassuming white shack. The small farm is housed in a 900-square-foot room with a 14-foot ceiling. There are hot-pink lights and a small irrigation system quietly feeding 20 varieties of micro-greens, which sprout up from a mineral-based substitute for soil called vermiculite. In Marques’s growing room, everything from the temperature to the lighting to the watering schedule has been engineered to replicate conventional outdoor farming, but without all the interruptions that plague it: seasonal changes, droughts, bitter cold, fires, and, of course, floods.
A Moonflower Farms employee checks on produce in the 900-square-foot growing room in southeast Houston. (Meagan Flynn / The Atlantic)
Houston has developed other vertical-farm concepts in the past two years. There’s Space City Farms, a backyard aeroponic vertical garden; Dream Harvest, a hydroponic system similar to Moonflower; and Acre in a Box, a literal take on the operation housed in a shipping container.
Acre in a Box’s founders—Andrew Abendshein, who works for an oil and gas trading firm in Houston, and Ana Buckman, a Rice University languages and creative-writing instructor—had no background in agriculture when they invested $80,000 in their first shipping-container farm. Abendshein said he has long had an interest in getting fresh produce to urban food deserts and hopes to one day start moving shipping-container vertical farms into those neighborhoods. For now, though, Acre in a Box’s two farms are hidden in the parking lot of an abandoned drill-bit factory at the end of a dead-end street in Houston’s East Downtown, a few blocks from where Houston’s two largest bayous intersect.
Harvey, and the deluge it brought, are exactly the kind of scenario that vertical farms are designed to withstand. Catastrophic flooding events like Harvey are only expected to become more frequent, and threats of food and water scarcity are projected to worsen in the years to come—all as the population grows. The United Nations projects that the world’s population will be 9.8 billion by 2050, with roughly two-thirds of those people living in urban areas, which aren’t exactly conducive to large-scale farming.
To meet the growing demand for food, the UN’s Food and Agriculture Organization estimates that there needs to be a 50 percent increase in global agriculture production—a distinct challenge, the UN warns, in the face of climate change and the growing need for water conservation. Vertical farms present a potential solution: There is no fertilizer runoff into the groundwater, fewer CO2 emissions from delivery trucks’ long journeys, and no land to till. They require only a fraction of the acreage and use only a fraction of the water—anywhere from 90 to 97 percent less—that traditional farms do.
“We are kind of at the beginning of a revolution,” Per Pinstrup-Andersen, a graduate-school professor at Cornell University’s College of Human Ecology, told me. “We’re at the beginning of a very rapid development in the use of indoor controlled facilities for producing vegetables and some fruits,” he said. “No matter what happens with climate change, you still have your controlled environment.”
The technology used for these farms has been around for decades. In fact, Marques began studying it in the 1990s after learning that NASA used it to grow plants in space. But only in the last several years has interest in using the technology for urban, commercial-scale agriculture picked up. Indoor farms have recently sprouted up in old warehouses, shipping containers, and small skyscrapers in New Jersey, South Korea, Germany, India, and Dubai—places where traditional farming is either difficult or impossible due to climate, population density, or the land itself. In Houston, sprawling commercial and residential developments were built on top of a swamp, making large-scale outdoor farming virtually impossible.
Marques and I hopped in his minivan and headed about a mile away from his garden to the site of the Moonflower Farms expansion, where men in hard hats were surveying the land. The new facility doesn’t look like much yet—just a large elevated mound of dirt with metal poles sticking out of it. But by the time it’s operational, Marques plans to have a 20,000-square-foot greenhouse that he expects will churn out 1,000 pounds of produce per day—compared with the 20 pounds that his tiny facility produces now. He currently sells to a couple dozen restaurants but plans to expand to regional and national distributors and local grocers once the new facility is up and running.
The elimination of long, cross-country transports to get the produce to grocery stores means consumers wind up with fresher food. Right now, Marques said, the time from harvest to table is sometimes only a matter of hours, which means that produce arrives in better shape and then lasts longer both in the store and in people’s homes. “If we can make this work in the city of Houston and produce 1,000 pounds a day or more of product—high-quality product that has three times the shelf life—then we have a good model that we can pretty much [take] to any city in the world and replicate,” Marques said.
The new greenhouse will operate like a research-and-development facility, helping Marques perfect a prototype that interested farmers around the world can use as a template. He already knows that he’ll need to make some changes. For starters, he’s not going to rely exclusively on LED lighting as he does now; instead he will mostly use sunlight, plugging in energy-efficient lighting as a supplement—a measure that will cut costs significantly. Marques said he has already had inquiries about this model from a food distributor in Cairo, where the arid climate and heavy reliance on imported crops make the food supply unpredictable. Marques says he has also talked to strawberry growers in Norway, where thousands of metric tons of strawberries are imported every year due to the short growing season. And he has heard from cattle farmers in Brazil, where the shrinking availability of pastureland and prohibitions on razing rainforests mean that some farmers may need to import grass to feed their cows.
Ana Buckman, Acre in a Box’s CFO, shows off kale that was later sent off to local businesses in Houston. (Meagan Flynn / The Atlantic)
Cutting the costs of building and maintaining the systems themselves will be crucial as vertical farms continue to evolve, according to Henry Gordon-Smith, the co-founder of the International Association for Vertical Farming and a consultant at the New York-based firm Agritecture. As a result of high costs, Gordon-Smith said, several vertical farms in North America have failed in recent years. That’s what happened at LocalGarden, a rooftop vertical farm in Vancouver that went bankrupt in 2014, and at PodPonics, a shipping-container vertical farm in Atlanta, where high labor and technology costs were consistently undermining return on investment.
Mike Nasseri, who was the harvest supervisor at LocalGarden, said that design flaws had inflated the endeavor’s operational and energy costs to the point that the farm couldn’t make enough money. Even though the farm had started small, Nasser said the crew decided to scale up too quickly to a commercial operation. To make matters worse, Nasseri said, the costs of the real estate in the middle of downtown Vancouver—a central location he said he would not recommend for new vertical farmers —were way too high. “That placement [in the middle of downtown] is basically the first way you can screw up,” Nasseri said.
Still, he’s a major proponent of vertical farming, primarily because of its environmental benefits. He’s now working at a startup called Ava Technologies, developing indoor “smart gardens,” essentially mini vertical farms that can fit on kitchen counters.
Gordon-Smith said the industry-wide goal going forward has to be to minimize the risk of failure, financial or otherwise, as much as possible in order to make vertical farming more accessible to the younger generation of produce growers, who have been moving steadily away from rural areas and toward cities over the past few decades. Still, he said, the failures serve as lessons for new investors as they continue to develop various types of vertical farms.
Like Marques, Abendshein, the founder of Acre in a Box, was stuck at home monitoring his produce from the couch during Harvey. But he knew he could rest assured that, as the waters raged, his produce was safe. Without land that could be ruined for an entire season, the worst that could happen, he thought, was that his farms would float away.
How Urban Farmers Are learning To Grow Food Without Soil Or Natural Light
Growing food in cities became popular in Europe and North America during and immediately after World War II.
How Urban Farmers Are learning To Grow Food Without Soil Or Natural Light
February 13, 2018
Mandy Zammit/Grow Up, Author provided
Author
- Silvio Caputo
Senior Lecturer, University of Portsmouth
Disclosure statement
Silvio Caputo does not work for, consult, own shares in or receive funding from any company or organization that would benefit from this article, and has disclosed no relevant affiliations beyond their academic appointment.
Partners
University of Portsmouth provides funding as a member of The Conversation UK.
Growing food in cities became popular in Europe and North America during and immediately after World War II. Urban farming provided citizens with food, at a time when resources were desperately scarce. In the decades that followed, parcels of land which had been given over to allotments and city farms were gradually taken up for urban development. But recently, there has been a renewed interest in urban farming – albeit for very different reasons than before.
As part of a recent research project investigating how urban farming is evolving across Europe, I found that in countries where growing food was embedded in the national culture, many people have started new food production projects. There was less uptake in countries such as Greece and Slovenia, where there was no tradition of urban farming. Yet a few community projects had recently been started in those places too.
Today’s urban farmers don’t just grow food to eat; they also see urban agriculture as a way of increasing the diversity of plants and animals in the city, bringing people from different backgrounds and age groups together, improving mental and physical health and regenerating derelict neighbourhoods.
Many new urban farming projects still struggle to find suitable green spaces. But people are finding inventive solutions; growing food in skips or on rooftops, on sites that are only temporarily free, or on raised beds in abandoned industrial yards. Growers are even using technologies such as hydroponics, aquaculture and aquaponics to make the most of unoccupied spaces.
Something fishy
Hydroponic systems were engineered as a highly space and resource efficient form of farming. Today, they represent a considerable source of industrially grown produce; one estimate suggests that, in 2016, the hydroponic vegetable market was worth about US$6.9 billion worldwide.
Hydroponics enable people to grow food without soil and natural light, using blocks of porous material where the plants’ roots grow, and artificial lighting such as low-energy LED. A study on lettuce production found that although hydroponic crops require significantly more energy than conventionally grown food, they also use less water and have considerably higher yields.
Growing hydroponic crops usually requires sophisticated technology, specialist skills and expensive equipment. But simplified versions can be affordable and easy to use.
They grow up so fast. Mandy Zammit/Grow Up, Author provided
Hemmaodlat is an organisation based in Malmö, in a neighbourhood primarily occupied by low-income groups and immigrants. The area is densely built, and there’s no green space available to grow food locally. Plus, the Swedish summer is short and not always ideal for growing crops. Instead, the organisation aims to promote hydroponic systems among local communities, as a way to grow fresh food using low-cost equipment.
The Bristol Fish Project is a community-supported aquaponics farm, which breeds fish and uses the organic waste they produce to fertilise plants grown hydroponically. GrowUp is another aquaponics venture located in an East London warehouse – they grow food and farm fish using only artificial light. Similarly, Growing Underground is an enterprise that produces crops in tunnels, which were originally built as air raid shelters during World War II in London.
The next big thing?
The potential to grow food in small spaces, under any environmental conditions, are certainly big advantages in an urban context. But these technologies also mean that the time spent outdoors, weathering the natural cycles of the seasons, is lost. Also, hydroponic systems require nutrients that are often synthesised chemically – although organic nutrients are now becoming available. Many urban farmers grow their food following organic principles, partly because the excessive use of chemical fertilisers is damaging soil fertilityand polluting groundwater.
To see whether these drawbacks would put urban growers off using hydroponic systems, my colleagues and I conducted a pilot study in Portsmouth. We installed small hydroponic units in two local community gardens, and interviewed volunteers and visitors to the gardens. Many of the people we spoke to were well informed about hydroponic technology, and knew that some of the vegetables sold in supermarkets today are produced with this system.
A simplified hydroponic frame in Portsmouth. Silvio Caputo/University of Portsmouth, Author provided
Many were fascinated by the idea of growing food without soil within their community projects, but at the same time reluctant to consume the produce because of the chemical nutrients used. A few interviewees were also uncomfortable with the idea that the food was not grown naturally. We intend to repeat this experiment in the near future, to see how public opinion changes over time.
And while we don’t think hydroponic systems can replace the enjoyment that growing food in soil can offer, they can save water and produce safe food, either indoors or outdoors, in a world with increasingly scarce resources. Learning to use these new technologies, and integrating them into existing projects, can only help to grow even more sustainable food.
As with many technological advancements, it could be that a period of slow acceptance will be followed by rapid, widespread uptake. Perhaps the fact that IKEA is selling portable hydroponic units, while hydroponic cabinets are on the market as components of kitchen systems, is a sign that this technology is primed to enter mainstream use.
Vertical Planting Establishes Roots In Laramie
An example of vertical gardens in downtown Laramie. (Photo taken by Seth Haack)
Vertical planting established more permanent roots in Laramie when the company Plenty, formerly Bright Agrotech, began construction on their new headquarters; providing jobs as well as fresh herbs in the community.
Rising from the ground in upright containers under controlled lighting and water systems, the latest trend in agriculture is featured just past the entrance of Washakie dining center and according to University of Wyoming researchers, vertical farming is here to stay.
“Plenty’s farms will be located near communities around the world, delivering industry-leading yields of delicious, locally-grown, backyard-fresh produce,” a Plenty spokesperson, Senior Communications Manager Patrick Mahoney stated in an email. “By shaving thousands of miles and weeks off the journey from farm to table, Plenty will transition agriculture to a reliable, predictable and resource-efficient model.”
The company was founded by Dr. Nate Storey, a UW alumnus.
“Nate Storey was a student of mine,” Extension Horticulture Specialist Karen Panter said. “He got all three of his degrees here in our department of plant sciences. The company includes engineers and computer experts and plant growth people and researchers and [Plenty’s] got some plant breeders now, there’s a lot of people working here in Laramie.”
Vertical farming allows for an increase in production per square foot, Panter said.
“So, there’s a limited amount of land that we can grow food on, limited resources, we have what growing people often refer to as ‘food deserts’ which are centers of urban settings with limited access to fresh produce,” Associate Professor of Agroecology Urszula Norton said. “And the fact that you can actually produce fresh green vegetables that don’t really take too many days and a way shorter period of time under optimum growth conditions.”
Indoor controlled conditions don’t experience drought, hail or other afflictions, resulting in a quicker growth turn around. The crops that are most compatible with vertical farming conditions tend to be leafy greens and some herbs, like lettuce and spinach.
“Plenty’s vertical towers can achieve industry-leading yields of fresh fruits and vegetables,” Mahoney stated in an email. “Up to 350 times greater per square foot than the field. Plants that get too big like tomatoes or that kind of thing just don’t work. The plants’ architecture is just completely wrong. It’s really hard to grow larger, longer, vining type plants.”
Norton, along with Liping Wang and other plant scientists, are in the midst of submitting a proposal to the National Science Foundation to better understand and improve on efficiency of water and energy using vertical farming settings.
“It is generally a proposal about learning more about where are we standing in terms of efficiency of vertical farming and how can we move it toward increasing effectiveness, efficiency, water use and energy,” Norton said. “My role would be pretty much to assess the growth yield and the quality of the produce.”
While the research and growth of vertical farming programs are certainly hot topics in the ag community, horizontal farming is not becoming obsolete by any means.
“[Vertical Farming is] not going to supplant traditional farming because there’s so many crops that can’t be grown in this type of system,” Panter said. “It’s not likely that we’ll be growing wheat or anything like that in this kind of a system, but for niche crops, it’s another tool to use.”
Evergreen Farm Wins Best Indoor Farming Innovation Award
Evergreen Farm Wins Best Indoor Farming Innovation Award
EverGreen Farm Oy participated in the Global Forum for Innovations in Agriculture (GFIA) at Abu Dhabi during the 5th and 6th of February, 2018, where it was presented with the Best Indoor Farming Innovation Award by the Minister of State, Her Excellency Mariam Bint Mohammed Saeed Hareb Al Mehairi, from the Abu Dhabi Food Control Authority.
During the conference H.E Mariam Bint Mohammed Saeed Hareb Al Mehairi stated “The Food Security Innovation Sessions are an ideal platform for joint action, aimed at putting the government and relevant sectors in a row to explore the future of food security and finding solutions to increase the contribution of the private sector in the food equation of the UAE. We cannot consider the issue of food security as an independent issue and separate from society, we must activate the role of all entities in addressing the challenges we face, taking into consideration that innovation is the key tool for improving food and agricultural production and essential for food security.”
Using the basic principle of hydroponics, Evergreen Farm Oy has developed an innovative vertical indoor farming technology that produces high-quality fruits and vegetables in a state-of-the-art, environmentally controlled, the multi-level indoor facility called the Direct Feed Vertical Hydroponics (DFVH) system.
"Best Indoor Farming Innovation" Award
Evergreen Farm Oy Wins "Best Indoor Farming Innovation" Award During the Global Forum for Innovations in Agriculture (GFIA)
The GFIA was founded in 2014 and it is the world’s largest series of events dedicated to showcasing innovations in sustainable agriculture across all types of food production. “The Global Forum for Innovations in Agriculture is based on the notion that the ongoing drive for innovation in the agriculture sector is the only way to feed 9 billion people sustainably by 2050,” said Nicolas Davison, Director of the Global Forum for Innovation in Agriculture.
Evergreen Farm Oy’s mission is to fundamentally transform agriculture by implementing the technologically advanced and easy-to-use DFVH system throughout the world. Thus, improving crop production while encouraging responsible, innovative farming methods that protect the environment and educate the community.
“We are extremely proud and thankful for the "Best Indoor Farming Innovation" award. We have now launched the first production-ready product portfolio, including both industrial and home units. After years of product development, we have got one step closer to our objective to make fresh, healthy, delicious, non-GMO, chemical and pesticide-free food accessible to everyone. While doing so, we also aim to improve the quality of life of local communities by providing job opportunities and a platform for growth and education, “ said Ali Amirlatifi, CEO of Evergreen Farm Oy.
Evergreen Farm is not only focusing on the technology for crop growth but also developing artificial intelligence (AI) based services to optimize production and accelerate our customers’ fruit and vegetable business entry into the markets. “With AI driven operations we can automate almost everything but also analyse global vegetable and fruit market automatically for our customer, “ thought Ali Amirlatifi.
For any inquiry to EverGreen Farm Oy please contact:
Ali Amirlatifi CEO, EverGreen Farm Oy
ali.amirlatifi@evergreenfarm.fi
Mobile: +358 50 390 3333
Website: www.evergreenfarm.eu
Evergreen Farm Oy is a Finnish company, located in Tampere. Evergreen Farm Oy is a technology company focused on providing clean sustainable food through agricultural innovation.
By offering the World highest yield per square meter as well as cubic meter, indoor protection from the elements, a variety of crops that go beyond leafy green, and the benefits of existing technology in robotics artificial intelligence and engineering, Evergreen Farm is sure to provide a solution to the food crisis and its associated environmental impacts.
Introduce Vertical Farming by Hydroponics and Aquaponics in Dry Arid Regions of India
It is known for everyone in India that the farming communities of the dry and arid regions of Central India mostly in the regions of Bundelkhand, Vidarbha and Marathwada have been struggling for a long time.
Introduce Vertical Farming by Hydroponics and Aquaponics in Dry Arid Regions of India
Independent started this petition to pmoindia and 4 others
It is known for everyone in India that the farming communities of the dry and arid regions of Central India mostly in the regions of Bundelkhand, Vidarbha and Marathwada have been struggling for a long time. Droughts and Farmer Suicides are rampant in Vidarbha and Marathwada. There were times when people have to eat even grass to kill their hunger in Bundelkhand. Unfortunately even though new technologies have been developed around the world to develop crops and food in most difficult situation, still these technologies have not reached these farmers who are in dire need of hope.
Hence I appeal to the Govt of India and the Ministry of Agriculture to introduce Vertical Farming by Hydroponics (and Aquaponics) to the farmers of these regions. Hydroponics is the method of growing plants without soil, using mineral nutrient solutions in a water solvent. This method can be used to grow plants in Vertical Towers and Stands without any need for soil.
Advantages of Vertical Farming using Hydroponics:
- No need for soil so can be set up in dry and arid regions.
- No effect of drought or storms or unseasonal rains.
- 80-90% less usage of water due to water recycling.
- Crops grow quickly hence improved productivity of 10-12 crops per year instead of 2-3 crops per year.
- Scope of Installing Solar Panels for Generation of Solar Electricity on top of Warehouse.
- Vertical Farms give more crops per acre. No limit of vertical expansion of farm.
Today, the advanced countries have been using these technologies for mass production of food for the people of their countries. Vertical Farming in Temperature Controlled Warehouses are now a proven and standard system for food production. Combined with installing Solar Panels on top of the roofs, these system can become a food production industry in itself and can bring the farming communities of Bundelkhand, Vidarbha and Marathwada out of Poverty. Since the plants being raised using Hydroponics are not dependent on soil, these can be setup in the dry and arid regions easily (and also anywhere in the country).
I am sure the ministry of agriculture must be aware of these technologies. I request the ministry and the Govt of India to urgently look at introducing Vertical Farming by Hydroponics in India. Not only it has the potential to eliminate poverty of the farming communities but also it can bring enough food for all the needy and the poor.
Hope the farmers of India can be benefitted and they come out of poverty quickly.
Regards
Souvik Jana
Panasonic Vertical Farm in Full Operation
February.5, 2018 - 23:28 — Evangeline_H 311 pageviews
Panasonic Vertical Farm in Full Operation; Special Horticultural LED Lighting Deployed to Increase Vegetable Production
Multinational electronics company Panasonic will start growing and marketing high-value vegetables in China from March 2018 with its vertical farm in Suzhou. Those vegetables will be made into salads and sold to up to 30 shops in Suzhou and Shanghai.
(Image: Panasonic)
In China, food safety has become more and more important. Panasonic claims monitoring and management at each stage will be thoroughly executed in hope to increase the sales in the Chinese market.
Panasonic in 2016 started running a vertical farm in its electronic component manufacturing subsidiary in Suzhou. The vertical farm, taking a 1,000 square meter area, is now officially in full operation.
The company aims to raise the plant production by 3 times to a monthly production of 9 tons.
Prices of the vegetables will be 2-2.5 times higher, compared with prices local plant growers set for their production. Those vegetables grown in the vertical farm were sold to merely two channels in Suzhou—the AEON MALL and the Izumiya Supermarket. In the future, Panasonic plans to approach local shops as well, broadening the channel to market its plant production to the Chinese community.
Panasonic uses special LED lighting to provide and adjust the light in the vertical farm to ensure the temperature, humidity, and the density of carbon dioxide are maintained at a certain level. That turns the farm an environment suitable to grow β-carotene-rich plants anytime of the year.
The company says the salads it offers are nutrient-rich and safe to eat, and looks for collaborations with local restaurants. It will also be working with local e-commerce companies to develop strategies to market both high-value vegetables and the equipment in the vertical farm.
People in China have become more aware of food safety after being affected by overuse of pesticides. The awareness towards vertical farms thus increased. Plant factories have been built in several regions in China since 2010.
At the early stage, these facilities were simply regarded as the demonstration of advanced plant production technology by governments and big corporations. Later on, more companies established their vertical farms once the government released more subsidies.
Establishments across the nation eventually scaled up, with the largest facility (approximately 9,000 square meters) that is able to produce 45 tons of vegetables on a monthly basis.
Growing Their Own At Corner Cafe
Growing Their Own At Corner Cafe
Cooking students soon will have fresh herbs to harvest
Natovia Talbot, a junior at Princeton Township, IL, High School, places bok choy seedlings into the new tower garden at the Corner Cafe in the Area Career Center’s Dolan Building next to the La Salle-Peru Township High School. The 5-foot tower circulates water and nutrients under artificial light to grow lettuce and herbs, which culinary arts students will harvest and use. Tracey MacLeod
- Jeff Dankert | February 6, 2018
Indoor growing technology is putting fresh herbs into the hands of culinary arts students.
A 5-foot tower garden is starting to green up in the dining area of the Corner Cafe, which is in the Area Career Center’s Dolan Building on the La Salle-Peru Township High School campus.
A few students took a break from the kitchen a few days ago to transplant lettuce, onion, chard, arugula, bok choy and basil into the tower. The plants were started in trays where each plant was labeled with a plastic spoon.
The tower herbage should be ready in a few weeks, said Susan Stiker, culinary arts instructor.
The students use many greens and herbs in the kitchen.
“Actually quite a bit. Kale, basil for pesto,” said Abby Nord, a junior at Princeton Township High School. The Area Career Center teaches students from several area high schools.
“Aren’t we going to try Chinese and use the bok choy with it?” said Natovia Talbot, also a junior at Princeton High.
The new gadget and the growing plants get frequent checks by the students.
“Every day when they come in, they check this first,” Stiker said.
The growing tower looks like high-tech hydroponics but the maker calls it aero-ponics because the plants are not sitting in the water.
Seeds are started in a synthetic medium called rockwool inside grow trays. The clumps of rockwool, bearing tiny seedlings, are transplanted into slotted pods on the outside of the tower cylinder. A rack surrounding the tower glows with three florescent light tubes, oriented vertically, to provide energy for photosynthesis. The lights are on for 14 hours and off for 10, Stiker said.
At the bottom of the tower cylinder is a 20-gallon water reservoir that holds dissolved fertilizers and nutrients. A pump circulates water up and drips it down along the inside, watering and feeding the clumps of rockwool and plant roots growing within. The watering is set on a timer.
“It cycles on for 15 minutes and is off for 45 minutes,” Stiker said.
Deborah Aldana checks the progress of celery, avocado and potato roots growing inside jars of water. These plants won’t go into the tower garden but are a demonstration of how vegetable roots can be used to grow new plants.
This project integrates with the educational buzzword, STEM — science, technology, engineering, and math. Preparing and cooking food has many STEM opportunities, Stiker said.
“I’m doing all of that STEM stuff all the time. That’s what this is,” she said, pointing to the tower. “Students looking to do an independent study, this would be a great thing. I had the kids research how to harvest and how to check the pH.”
The $900 apparatus came with all the equipment and supplies to get started. It was funded by a grant from the La Salle-Peru Township High School Foundation for Educational Enrichment.
The Corner Cafe is a restaurant with a fully-equipped kitchen and dining area for the public. Students prepare food to sell and for events. Students recently made pies for a buffet, prepared food for a group of eighth graders, made chili for a fundraiser and prepared Super Bowl snacks for staff.
Indoor garden towers are a thing among urbanites. The vertical design uses less space, such as a corner of the dining area inside the Corner Cafe.
“I knew I had to do something smaller here,” Stiker said.
Stiker got the idea from a middle school in Texas that was growing plants in an indoor tower. School gardens, indoors and outdoors, have taken off, she said.
“There are schools that actually supply their cafeteria,” Stiker said.
Streator Township High School students constructed six indoor plant towers that are now growing lettuce, said agricultural educator, Riley Hintzsche.
Streator students have a vegetable garden two blocks away and grow sweet corn on one-fourth of an acre outside of town. Students harvest the vegetables and donate them to the food pantry, he said.
“We do have some of the food classes use the produce occasionally as they need them,” Hintzsche said.
Jeff Dankert can be reached at (815) 220-6977 or lasallereporter@newstrib.com. Follow him on Twitter @NT_LaSalle.
Infarm Reinventing Food Supply With Vertical Urban Farms
Infarm Reinventing Food Supply With Vertical Urban Farms
By Katy Askew
06-Feb-2018
Infarm founders Osnat Michaeli and the brothers Erez and Guy Galonska have big ambitions for their urban farm model
German urban farming group Infarm aims to expand its network of urban farms to 1,000 locations throughout Europe by 2019.
Infarm was founded in 2013 by Osnat Michaeli and the brothers Erez and Guy Galonska. The company distributes what it describes as “smart modular farms” targeting urban areas.
Fusing vertical farming techniques with the internet of things technology and data science, the group aims to develop an “alternative food system” that is “resilient, transparent, and affordable”.
“Rather than asking ourselves how to fix the deficiencies in the current supply chain, we wanted to redesign the entire chain from start to finish; Instead of building large-scale farms outside of the city, optimising on a specific yield, and then distributing the produce, we decided it would be more effective to distribute the farms themselves and farm directly where people live and eat,” explained Erez Galonska, co-founder and CEO.
How it works
A single two meter squared farm unit can deliver an output of 1,200 plants per month.
Infarm’s indoor vertical farms are connected by the company’s central farming platform, creating what the company claims is a “first of its kind” urban farming network.
Each farm is a controlled ecosystem with growing recipes that tailor light, temperature, pH, and nutrients to ensure the maximum natural expression of each plant.
“We collect 50,000 data points throughout a plant’s lifetime,” Guy Galonska, co-founder and chief technical officer elaborated. “Each farm acts as a data pipeline, sending information on plant growth to our platform 24/7 allowing it to learn, adjust, and optimize.”
Infarm therefore not only distributes the vertical farming tech: the company operates as a service provider.
It can also personalize its farms to each customer’s needs, growing different varieties for different supermarket locations or equalizing the flavor of the produce to better suit the taste palate of a customer’s clientele.
Early success
Having introduced the concept two years ago, Infarm now operates more than 50 farms in supermarket aisles, restaurant kitchens and distribution centers throughout Berlin.
Infarm units can grow produce in retail locations
Infarm has integrated in-store farming into Edeka and Metro locations, partnering with two of Germany’s largest food retailers where it grows “dozens ” of herbs and leafy greens.
Infarm’s marketing project manager Peter Prautzsch told FoodNavigator that the company has already grown 300 different plants on its farms.
“Our modular and scaleable farms units are easily integrated into any given client space. We offer and operate both InStore and InHub installation,” he explained.
Infarm’s solutions also reach beyond addressing sustainability issues to deliver other benefits to its customers, he continued. “Cutting the supply chain to the minimum helps our produce to retain all of its nutrients and therefore an intense natural flavor. We considerably improve the safety and environmental footprint of each plant. We can offer a consistent supply, no matter the season [and] our farms create a unique and impactful customer experience.”
“We bring a world of choice right into your neighborhood without having to compromise on quality, safety, and taste. [...] B y eliminating the distance between farm and fork, we offer produce that has retained all of its nutrients and therefore, intense natural flavour," noted Osnat Michaeli, co-founder, and CMO.
Funding growth
Infarm announced yesterday (5 February) that it has completed a €20m series A funding round, which was led by an investment from Balderton Capital, alongside TriplePoint Capotal and Mons Investment as well as previous investors Cherry Ventures, QUIDIA and LocalGlobe.
Balderton Capital partner Daniel Waterhouse said that the investment vehicle believes Infarm can help develop a solution to some of the greatest challenges facing the food supply chain today.
“Urban living is growing unrelentingly across the world and societies are at a point where they have to confront the big existential questions such as how to feed their growing populations sustainably. Infarm is right at the forefront of a new wave of companies setting out to tackle the inefficiencies in the current food supply chain by making it possible to grow fresh produce right in the heart of our communities. We are delighted to be backing a company whose mission we believe in so passionately.”
The fresh wave of investment brings Infarm’s total capital raising to €24m, including a €2m grant awarded to the group by the European Commission as part of the Horizon 2020 program.
Overseas ambitions
Infarm will be launching in Paris, London, and Copenhagen this year, as well as extending to additional cities throughout Germany.
“This is the beginning of the urban farming revolution: it will redefine what it means to eat well, reshape the landscape of cities, and re-empower the people to take ownership of their food,” predicted Erez Galonska. “Our ambition is to reach cities as far as Seattle in the United States or Seoul, South Korea with our urban farming network.”
The new investment will be used to grow Infarm’s team into a global operation and to further develop its 5,000 square meter R&D center in Berlin. The center focuses on the promotion of biodiversity and further expanding the company’s product assortment; tomatoes, chilies, a variety of mushrooms, fruits and flowering vegetables are to be introduced next.
Balderton Capital Leads $25M Series A In ‘Urban Farming’ Platform Infarm
Infarm, a startup that has developed vertical farming tech for grocery stores, restaurants, and local distribution centres to bring fresh and artisan produce much closer to the consumer, has raised $25 million in Series A funding.
Infarm, a startup that has developed vertical farming tech for grocery stores, restaurants, and local distribution centres to bring fresh and artisan produce much closer to the consumer, has raised $25 million in Series A funding.
February 5, 2018 | Steve O'Hear (@sohear)
Balderton Capital Leads $25M Series A In ‘Urban Farming’ Platform Infarm
Infarm, a startup that has developed vertical farming tech for grocery stores, restaurants, and local distribution centres to bring fresh and artisan produce much closer to the consumer, has raised $25 million in Series A funding.
The round is led by London-based VC firm Balderton Capital, with participation from TriplePoint Capital, Mons Investments, and previous investors Cherry Ventures, QUADIA and LocalGlobe.
It brings the total raised by the Berlin-based company to $35 million, including a $2.5 million grant from the European Commission as part of the Horizon 2020 program.
Related Articles
Infarm wants to put a farm in every grocery store
Infarm says the new capital will be used for international expansion and to further develop its 5,000 sqm R&D centre in Berlin. This will include bringing its vertical farming system to Paris, London, and Copenhagen, in addition to other German cities later this year. The startup is targeting 1,000 farms to be operational across Europe by the end of 2019.
Founded in 2013 by Osnat Michaeli, and brothers Erez and Guy Galonska, Infarm has developed an “indoor vertical farming” system capable of growing anything from herbs, lettuce and other vegetables, and even fruit. It then places these modular farms in a variety of customer-facing city locations, such as grocery stores, restaurants, shopping malls, and schools, thus enabling the end-customer to actually pick the produce themselves.
The distributed system is designed to be infinitely scalable — you simply add more modules, space permitting — whilst the whole thing is cloud-based, meaning the farms can be monitored and controlled from Infarm’s central control centre. The whole thing is incredibly data-driven, a combination of IoT, Big Data and cloud analytics akin to “Farming-as-a-Service”.
The idea, the founding team told me back in June last year when I profiled the nascent company, isn’t just to produce fresher and better-tasting produce and re-introduce forgotten or rare varieties, but to disrupt the supply chain as a whole, which remains inefficient and produces a lot of waste.
“Behind our farms is a robust hardware and software platform for precision farming,” explained Michaeli. “Each farming unit is its own individual ecosystem, creating the exact environment our plants need to flourish. We are able to develop growing recipes that tailor the light spectrums, temperature, pH, and nutrients to ensure the maximum natural expression of each plant in terms of flavor, colour, and nutritional quality”.
Two years since launch, Infarm says it is now operating more than 50 farms across Berlin in supermarket aisles, restaurants kitchens, and distribution warehouses. This includes introducing in-store farming into EDEKA and METRO locations, two of Germany’s largest food retailers, in which dozens of “quality herbs and leafy greens” are grown and sold at what the startup describes as affordable prices.
Noteworthy, with an output of up to 1,200 plants per month from a single farm unit, Infarm claims it has already enabled some locations to become completely self-sufficient in their herb production.
“This is the beginning of the urban farming (r)evolution: it will redefine what it means to eat well, reshape the landscape of cities, and re-empower the people to take ownership of their food,” says Erez Galonska in a statement. “Our ambition is to reach cities as far as Seattle in the United States or Seoul, South Korea with our urban farming network”.
Pegasus Food Futures Will be Showcasing Their Pioneering Hydroponic Farming Capability At The Global Forum For Innovations in Agriculture, in Abu Dhabi on February 5th and 6th.
ABU DHABI, United Arab Emirates, February 1, 2018 /PRNewswire/
Pegasus Food Futures Will be Showcasing Their Pioneering Hydroponic Farming Capability At The Global Forum For Innovations in Agriculture, in Abu Dhabi on February 5th and 6th.
With the world population set to grow from 7.3 billion to 8.5 billion by 2030 and 11.2 billion by 2100, an agricultural solution to the growing food needs of the population is essential.
- Hydroponic farming is an innovative, soil-less system that uses up to 90% less water than conventional farming, uses less land producing high yields of sustainably high quality, reasonably priced crops.
- Farms in arid areas such as the Gulf Cooperation Council (GCC) countries can make the most of the long hours of sunlight, providing the region with crops and reducing the need to rely on expensive imports.
- Visit the Pegasus Food Futures stand at the Abu Dhabi Exhibition Centre and hear farming, technology and business specialist James Yau give an expert talk on Combining Operations and Finance to Provide Best Fit Solutions: Bringing the Offline of Traditional Farming Online at the Controlled Environments and Indoor Farming conference session at 11.30am on 5th February.
Leading owner and operator of hydroponic farming facilities in Europe, the Middle East and Africa, Pegasus Food Futures will be showcasing their pioneering hydroponic farming facilities at the Global Forum for Innovations in Agriculture (GFIA) Exhibition in Abu Dhabi on February 5th and 6th at the Abu Dhabi Exhibition Centre.
With the world population set to grow from current levels of 7.3 billion to 8.5 billion by 2030 and 11.2 billion by 2100, ensuring long-term food security has never been more important. Providing an affordable and reliable food source that is also environmentally sustainable is essential to meet the needs of the growing population. Pegasus Food Futures provides solutions for these global food supply challenges through its operations and innovations in farming, livestock, feedstock and food production.
Their primary goal is to provide security for our food and agricultural future. Through continued investment into hydroponic farming technology, techniques and innovation they aim to support food security by growing sustainable and consistent produce that offers consumers a high quality, reasonably priced and fresh harvest each and every time.
Hydroponics explained
The hydroponic system is a soil-less culture for crops in which water and nutrients are delivered directly to the roots of the plant, dispensing with the need for the plant to expend precious energy growing long roots through the soil to reach these vital ingredients. Produce is grown in advanced, environmentally- friendly greenhouses, equipped with technology that controls and monitors each plant's nutrient intake with optimum accuracy. The design of the hydroponic farming systems ensures that the system uses up to 90% less water than traditional agriculture. Not only does this preserve precious natural resources, it also helps to reduce costs. This is particularly important for farms located in arid regions like the GCC, where water is scarce. Hydroponic farms in such regions can make use of the long periods of natural sunlight and produce affordable crops that reduce the need for the region to rely on expensive imports. Moreover, the controlled conditions mean the crops require no pesticides and produce consistently high yields.
A hydroponic farm can continue functioning for more than 100 consecutive years, resulting in a secure, stable source of both food and employment for the local area.
The Global Forum for Innovations in Agriculture
Pegasus Food Futures will be exhibiting at GFIA on Feb 5th and 6th and the farming and business expert James Yau will be giving a talk on Combining Operations and Finance to Provide Best Fit Solutions: Bringing the Offline of Traditional Farming Online at the Controlled Environments and Indoor Farming conference session at 11.30am on 5th February.
James Yau has 20 years' experience in management consulting in North America and Asia. In early 2009, he established and operated more than 10 farms within Asia Pacific. In 2013, he founded a retail chain to sell safe, high quality food produce in Hong Kong. During 2016, he partnered with a well-established Hong Kong wholesale company and penetrated the south China region which now trades over 65 million kilos annually. With extensive knowledge of financing and operating farms combined with technological expertise, James offers a unique opportunity to learn about how to bring traditional farming online.
Exhibition attendees can visit the Pegasus Food Futures stand in B20 and attend James' talk in the Conference Theatre, with the session starting at 11:30 pm, Monday, 5 February.
Keep an eye on the Pegasus Food Futures social media channels from for updates, news and pictures from the show (Instagram @pegasusfoodfutures, Twitter @pegagsusff, Facebook @pegasusfoodfutures)
Currently, hydroponic farming comprises only 1% of world agriculture. There is huge room for expansion of this innovative, sustainable solution to the problem of the growing demand for food. Pegasus Food Futures are keen to expand their portfolio and will be on hand to talk to farmers and investors alike.
About hydroponic farming
The System
The Pegasus Food Futures System (PFFS) combines intellectual property, seed germination processes and bespoke nutrient formulas that produce superior crops compared to competitors. From 2013 this system has been refined and adapted with continued investment into innovation ensuring that Pegasus Food Futures remains the market leader in the Europe, Middle East and Africa.
With further farms under construction in Europe, the PFFS has been further modified through research and development, investing in people and recruiting new skills into the team. The system and team now have an impressive track record in hydroponic farming technology and the ability to produce a wide range of fresh salad items, soft fruits, herbs, and vegetables.
The PFFS needs to also incorporate other key elements which will ensure all of our farms work under a defined efficiency and produce a stable, sustainable, high quality produce each and every harvest.
The controlled environment
Having the right environment is essential for the hydroponic farm. Key elements to a proper environment include humidity, temperature, Carbon Dioxide (CO2), and air circulation/exchange. Most crops grow and bloom according to the amount of light they are given. Generally produce require 10-12 hours of sunlight per day. PFFS uses natural lighting (sunlight) and this is achieved by building our farms in locations where there is an abundance of natural sunlight throughout the year.
All living things need space in which to live, grow, and reproduce. Different crops have different spacing requirements so the growing frames are specifically designed for each crop that is grown.
The water that supplies the plants is tightly monitored and controlled, from the pH to the nutrient balance, which varies throughout the growing cycle. The PFFS uses a unique formula for nutrients, specific to each crop and stage of the growing cycle, enabling the ideal produce to be grown.
About Pegasus Food Futures
What's New?
In 2017 Pegasus Food Futures acquired farms in Abu Dhabi, Ras-Al-Khaimah and two sites in Portugal. For more highlights of 2017, visit: http://pegasusfoodfutures.com/highlights-of-2017/
Social media and web
Web: http://pegasusfoodfutures.com/
Investors: http://go.hydroponic-investment.com/invest
Instagram @pegasusfoodfutures, Twitter @pegagsusff, Facebook @pegasusfoodfutures
About GFIA
Cultivating Change.
Born with the belief that continuous innovation in agriculture is the only way to sustainably feed nine billion people by 2050, the Global Forum for Innovations in Agriculture has emerged as a global authority on sustainable food production, driving innovation through exhibitions and conferences across the Middle East, Europe and Africa. Since 2014, GFIA events have welcomed over 20,000 visitors and worked with over 50 globally significant partners committed to using the Forum as a catalyst for change.
Global Vision. Local Relevance.
Showcasing the latest game-changing innovations and technology, each GFIA exhibition and conference offers stakeholders a pioneering forum and marketplace to foster meaningful dialogue, collaboration, recognition and year-round action between regional food producers, buyers, innovators, policy makers and investors.
Abu Dhabi.
At the centre of the arid world and with a rapidly growing population, the MENA region's need to address food security is more urgent than almost anywhere else. Hosting a large exhibition and free conference programme, GFIA Abu Dhabi will present the latest innovations and technologies to regional food producers across six key areas: indoor farming and hydroponics; date palm production; aquatech; livestock and animal health; smart honey production; and sustainable crops.
Part of UAE Innovations Month, GFIA Abu Dhabi is held under the patronage of H.H. Sheikh Mansour bin Zayed Al Nahyan and enjoys strategic support from Abu Dhabi Food Control Authority and the UAE Ministry of Climate Change and Environment.
For more information, visit: http://innovationsinagriculture.com/
SOURCE Pegasus Food Futures
Living Greens Farm is Changing The Way Produce is Grown
Living Greens Farm is Changing The Way Produce is Grown
Living Greens Farm, located just south of the Twin Cities in Faribault, MN has developed its own patented aeroponic vertical growing system that, according to its own estimates, uses 200 times less land and 95 percent less water than traditional farming.
Launched in 2012, the company currently grows fresh lettuces, herbs and microgreens on vertical platforms indoors in its Faribault Industrial Park facility, without the use of herbicides or pesticides.
“We didn’t invent aeroponics,” said Dana Anderson, founder and president at Living Greens Farm. “But we invented how to commercialize it. We feel aeroponics is the fastest and most disease-resistant way to grow.”
Historically, farming has always been dependent upon the mercy of Mother Nature. But with this high-tech type of indoor farming, a computer controls all light, temperature, humidity and nutrients, thereby eliminating the uncertainties of day-to-day weather changes.
Plus, with aeroponics there is no growing medium like soil or water used; the plant roots are simply open to the air and regularly misted with a nutrient solution. Plants are initially grown outside of the machines before they are placed into the rows under the misting system technology, thus maximizing space and giving the plants the room they need to grow. The company has 10 patents for its traversing misting system, allowing it to grow more food in a much shorter amount of time.
“It’s proprietary technology that we invented here,” Anderson told The Product News. “We’ve invested five years of time and about $5 million into the research and development side of our business. Beyond the aeroponics piece, there was also the invention of the traversing misting system. There are many moving irrigation systems for field crops and it’s easy to understand when you see irrigation systems moving across a cornfield. But what we own is a moving irrigation system for roots and that allows for fewer nozzles and improved reliability. Instead of installing hundreds of thousands of nozzles in a full-scale facility, we just have to install hundreds.”
The company recently completed a major expansion project and added 30 more growing systems to its already existing 10 systems, so it will be producing substantially more produce. Normally, in 15 to 17 cycles per year, the farm harvests around 1,500 plants per cycle.
“We are building a rather large farm — one of the largest indoor farms in the world — in Faribault,” Anderson said. “It has four times more grow space, and larger expansion in terms of production because we are adding more grow lights, so we think it’s actually going to be more like a 10 times increase in total revenue and total sales and production. It’s 21,000-square-feet of grow space and that will produce about 1 million units, or heads of lettuce, per year. Aeroponics is very fast in germs of growing plants and it’s actually the fastest way to grow, according to NASA. That is a big deal for indoor farming because if you can grow four or five more cycles a year, that is of course more revenue per square foot — 40 percent more revenue per square foot of grow space — and that means the operation is more efficient.”
Living Greens Farm is definitely changing the way food is grown and it may eventually go worldwide, duplicating its Minnesota operation in other countries and producing additional types of crops. According to the company’s website, its goal is “to make the world a better place by growing healthy, sustainable, fresh produce.”
And Living Greens Farm Chief Executive Officer Dave Augustine said, “Things like this are totally necessary to feed the human population in the future.”
By Richard Lutes
Source: The Produce News
http://www.theproducenews.com/digital_editions/pn101617issue/index.html
Berlin Urban Farm-In-A-Box Raises $25 Million For European Expansion
The company, founded by three Israeli filmmakers-turned-entrepreneurs, plans to use the funds to roll out mini, in-store farms with Edeka, Germany’s largest supermarket chain. It is also working with Metro (B4B.DE), the country’s No.2 grocer.
Berlin Urban Farm-In-A-Box Raises $25 Million For European Expansion
February 5, 2018 Eric Auchard
FRANKFURT (Reuters) - Berlin-based urban farming start-up Infarm has raised $25 million to expand its indoor growing system - a soil-less technology better known for furtively growing marijuana - into major supermarket chains and restaurants across Europe.
The company, founded by three Israeli filmmakers-turned-entrepreneurs, plans to use the funds to roll out mini, in-store farms with Edeka, Germany’s largest supermarket chain. It is also working with Metro (B4B.DE), the country’s No.2 grocer.
Infarm wants to help cities become self-sufficient in food production, lowering farming’s environmental footprint.
A single, two-square-meter unit can be located in stores or dining rooms, or the same units can be chained together in central distribution centers to grow hundreds of different varieties of plants, each with its own micro-climate.
“We decided it would be more effective to distribute the farms themselves and farm directly where people live and eat,” Co-Founder and Chief Executive Erez Galonska said.
Industrial-scale U.S. rivals claim to be removing waste from long-distance agricultural supply chains, while Infarm is trying to break down the need for a supply chain itself, Osnat Michaeli, another co-founder, and Infarm’s chief marketing officer told Reuters.
Plenty Inc of South San Francisco, which operates vast indoor fields growing fruit, vegetables and herbs, raised $200 million in a 2017 round led by Softbank (9984.T) Vision Fund, marking the largest-ever agricultural tech venture funding.
Infarm said it will have 1,000 miniature urban farms operating across Europe by the middle of next year, starting with locations in Paris, London, Copenhagen and additional German cities by the end of 2018.
The compact plant growing system sits on stacked shelves, using hydroponics - a way of growing plants without soil - in a climate and LED-lighting controlled glass case. It grows everyday and exotic herbs like small-leaf Greek basil or Peruvian mint and leafy greens which customers are selling for prices at or below that of plastic-packaged herbs.
“We have replaced 15 grams of herbs in plastic boxes with living plants priced around 1.50 euros,” said Michaeli. “It’s the same type, similar price, but it’s alive.”
The new round of investment was led by Balderton Capital, one of Europe’s top early-stage venture investors, and joined by debt-financing firm Triple Point Capital and Mons Investments.
The company plans to invest further in its Berlin-based urban farm and research lab to expand its product catalog beyond some 200 herbs currently to include tomatoes, chillies, mushrooms, fruits and flowering vegetables, the company said.
Reporting by Eric Auchard; Editing by Kirsten Donovan
Our Standards:The Thomson Reuters Trust Principles.
What Does The Future of Conventional Agriculture Look Like? Does it Include Vertical Farming and Indoor AG?
Leading Japanese indoor ag tech companies to visit the heart of U.S. agricultural research and biotechnology community to attend controlled environment networking event.
What Does The Future of Conventional Agriculture Look Like? Does it Include Vertical Farming and Indoor AG?
Leading Japanese indoor ag tech companies to visit the heart of U.S. agricultural research and biotechnology community to attend controlled environment networking event.
If you are involved with the vertical farming or indoor agriculture industries, then you should plan on attending Ag Tech Worlds Collide. Scheduled for Feb. 21, 2018, at North Carolina State University, this event will tackle the big questions currently being addressed in the vertical farming and indoor agriculture industries worldwide.
Urban Ag News and the Japan Plant Factory Association in coordination with the Japanese Ministry of Economy, Trade and Industry are pleased to announce this joint networking event with U.S.-based agricultural organizations and operations. Participating Japanese organizations/companies include: Japan Plant Factory Association, Keystone Technology Inc., Shinnippou 808 Factory, Nihon Advanced Agri Corp., ESPEC MIC Corp. and MIRAI.
Presentations focus on CEA impact
Key presentations at this controlled environment agriculture (CEA) event will be made by Dr. Chieri Kubota, professor of controlled environment agriculture at The Ohio State University, and Dr. Ricardo Hernandez, assistant professor in the Department of Horticultural Sciences at North Carolina State University.
Dr. Kubota’s presentation will discuss “Optimizing input and output in controlled environment agriculture.” Dr. Kubota received a PhD. in horticultural engineering and M.S. in horticultural science from Chiba University in Japan. She worked for six years as a faculty member at Chiba University, 16 years in the School of Plant Sciences at the University of Arizona and recently joined the faculty at The Ohio State University. At Chiba University Dr. Kubota studied under and worked with Dr. Toyoki Kozai, one of the most published and greatest minds in indoor agriculture.
Dr. Kubota’s research program focuses on the development of science-based CEA technologies. She has been very active in interdisciplinary collaborations contributing to horticultural crop production under controlled environments. Her research includes value-added CEA crop production, vegetable grafting, hydroponic strawberry production and CEA LED lighting applications.
Dr. Hernandez will discuss “Using vertical farming/indoor ag to support traditional farming.” He is a faculty member in the Department of Horticultural Sciences in the area of horticultural energy at North Carolina State University. He has a B.S. in agronomy–crop consulting from New Mexico State University. His M.S. is in entomology–biological control from Texas A&M University. His PhD. is in plant sciences–plant physiology from the University of Arizona. He has a doctoral minor in entrepreneurship from the McGuire Center for Entrepreneurship, Eller School of Business and a minor in ag and biosystems engineering from the University of Arizona.
Dr. Hernandez’s research is focused on making CEA tools and techniques an integral part of sustainable agriculture and horticulture.
Event registration, location specifics
Ag Tech Worlds Collide will be held in the York Auditorium of the JC Raulston Arboretum in Raleigh, N.C. Entry to this event is $25 and includes morning coffee service and lunch. Attendance is limited and the event will sell out quickly. Click here to register.
Infarm Grows Produce In Supermarket Aisles
Infarm Grows Produce In Supermarket Aisles
There are more than 50 indoor vertical farms in Berlin alone
KEN SCHUCHTMANN
James Hurley
February 5, 2018, The Times
Retailers can earn brownie points with environmentally and ethically minded consumers already by boasting about selling local produce, but what if supermarkets could go one better and grow their own crops in-store?
It might sound fanciful, but some of Europe’s leading venture capitalists have invested $25 million in a start-up that produces vertical indoor “farms” that can be located in everything from supermarket aisles to restaurant kitchens, schools and distribution warehouses.
Infarm already operates more than 50 farms across Berlin and says that 1,000 units will be operational by 2019, including about 200 farms in London.
Erez Galonska, co-founder and chief executive of Infarm, said: “Rather than asking ourselves how to fix the deficiencies in the current supply chain, we wanted to redesign the entire chain from start to finish. We decided it would be more effective to farm directly where people live and eat.”
Infarm installations can be found in Edeka and Metro stores in Germany, two of the country’s largest grocers, with herbs and leafy greens being cultivated.
The company says that a single farm unit of two square metres can produce 1,200 plants per month and that some stores have become self-sufficient in herb production.
The plants are fed and nurtured by an internet-controlled system that uses sensors to monitor light, temperature, acidity, and nutrients for each crop.
Guy Galonska, co-founder of Infarm, said: “We collect 50,000 data points throughout a plant’s lifetime. Each farm acts as a data pipeline, sending information on plant growth to our platform, allowing it to learn, adjust, and optimise.” Thus different varieties of crops can be adapted for different supermarket locations to suit customer tastes.
Infarm was founded in 2013 by the Galonska brothers and Osnat Michaeli. Its vertical farms use “hydroponics”, a system that grows plants in oxygen and nutrient-enriched water instead of soil.
Osnat Michaeli, Erez Galonska and Guy Galonska have big plans
Erez Galonska said: “Our ambition is to reach cities as far as Seattle in the United States or Seoul, South Korea.”
The funding round was led by Balderton Capital, the London-based venture capital firm. The investment will help to pay for the planned international expansion.
Daniel Waterhouse, a partner at Balderton, said: “Urban living is growing unrelentingly across the world and societies are at a point where they have to confront big existential questions, such as how to feed their growing populations sustainably.
“ Infarm is right at the forefront of a new wave of companies setting out to tackle the inefficiencies in the food supply chain by making it possible to grow fresh produce right in the heart of our communities.”
Two Companies Taking A Vertical Leap In Newark
Two Companies Taking A Vertical Leap In Newark
By Sarah Fensom
Salad may not be the first thing that springs to mind when thinking of Newark. With its long history of environmental pollution and food deserts, Brick City is not a paragon of health.
Yet in recent years, it has embarked on a quest for wellness. In 2015, a ShopRite opened in the Central Ward, where there had previously been a scarcity of supermarkets. The following year, Newark Beth Israel Medical Center established the Beth Greenhouse, a small hydroponic farm that sells affordable produce in the South Ward.
In 2017, the former Hahne's department store building on Broad Street became home to Newark's first Whole Foods. And even former Newark mayor and current New Jersey senator Cory Booker has gone green, sharing snaps of his plant-based meals on social media and talking publicly about his veganism.
Getting in on the act are AeroFarms and Radicle Farm, two relatively new companies that are growing farm-fresh salad greens not in fields but in the city itself. The larger of the two, AeroFarms, runs several facilities in the Newark area, including a sustainable 70,000-square-foot vertical farm in a former steel plant in the Ironbound section. There, 2 million pounds of greens and herbs are produced each year, using an aeroponic growing method.
The other, Radicle Farm, operates in an 8,000-square-foot greenhouse in Branch Brook Park and grows greens hydroponically in horizontally-oriented plots using a method called nutrient film technique (NFT).
Both methods cut down on the environmental costs of field farming by using less water, less energy, and less space. Growing indoors allows the two companies to bypass fickle weather patterns and maintain the ideal conditions for their crops year-round, increasing both the yield and the freshness of their greens. AeroFarms and Radicle are showcasing two models for efficient, sustainable food growth, all the while helping to place Newark at the forefront of urban farming -- as unlikely as that may seem.
AeroFarms is the vanguard of the vanguard. Based on annual growing capacity, its Ironbound facility on Rome Street houses the largest indoor vertical farm in the world. With projects in development in China, the United Arab Emirates, and Europe, the company has its sights on the world but is still very focused on Newark.
"We embody Mayor Baraka's initiative 'Hire. Buy. Live.,' " says Marc Oshima, the chief marketing officer and a co-founder of AeroFarms. "In Newark alone, we have four farming operations and employ over 120 people -- 40 percent of which live in Newark, with 80 percent within a 15-mile radius."
The company's roots have spread throughout the city, with a research and development farm in a former downtown nightclub on Market Street; a 30,000-square-foot farm on Ferry Street, in what was once Inferno Limits, the paintball and laser-tag arena; and a smaller, 50-square-foot vertical farm in the dining hall of Phillips Academy. The school farm, which has been up and running since 2011, was a catalyst for the company to move its headquarters from Utica, N.Y., to Newark several years ago.
Later this year, AeroFarms is set to open a 78,000-square-foot vertical farm -- its biggest yet -- in Camden.
AeroFarms worked with RBH Group, the developers behind Teachers Village, on its Rome Street facility, with substantial backing from Goldman Sachs and Prudential Investment. (While it has raised some $50 million from investors, AeroFarms has yet to make a profit.)
"We looked at just about every ward and every property, and then we found the opportunity with RBH in the Ironbound and we thought it was somewhere we could make an impact," says Oshima. "There's a food desert right there."
One way AeroFarms is trying to stamp out food deserts is by giving Newark residents immediate access to their products, Oshima says.
"Wherever our farms are, people can come in and get greens all year round."
Many of the supermarkets that sell AeroFarms's retail brand Dream Greens (a 4.5 oz. package retails for $3.99) are extremely close to the farm, as well, reducing the toll that transportation takes on both the environment and the quality of the food.
The distribution center for ShopRite, one of AeroFarms's key partners, is just minutes from the Rome Street farm. "ShopRite puts a lot of emphasis on sourcing produce from local farms in the communities where our stores operate, and AeroFarms offers fresh produce we can source right here in Newark for our local ShopRite store," says Derrick Jenkins, vice president of produce and floral for ShopRite. "AeroFarms is a local business making an investment in Newark, and ShopRite believes it's important to support our neighbors and the city."
AeroFarms was co-founded by Oshima (the only Jersey native of the bunch), David Rosenberg, the company's CEO, and Ed Harwood, the chief science officer. Oshima and Rosenberg, who met in business school, formed a company called Just Greens in 2004. Research into the latest sustainable agricultural methods led them to Harwood, a former professor at Cornell's School of Agriculture, who was perfecting methods of aeroponic farming.
AeroFarms' patented growth method uses neither sun nor soil. The seeds rest on a special reusable cloth, developed by Harwood, which is made of BPA-free recycled plastic. They're housed in mobile modules that can be stacked many stories, effectively creating high-rises for plants.
Unlike with hydroponic methods, the seeds don't sit in water but are instead misted with a solution of nutrients, water, and oxygen deployed by a special nozzle (also developed by Harwood). Because the system is closed, fertilizer isn't leached into the waterways.
The method uses 95 percent less water than traditional farming and 40 percent less than hydroponics. In lieu of sunlight, energy-efficient LED lights supply the exact spectrum, intensity, and frequency that each individual plant needs for photosynthesis. This light system also ensures tyrannical control over each plant's texture, color, flavor, nutrition, shape, and size.
The farms also employ big data, monitoring more than 130,000 data points every harvest. Computer-generated algorithms enable the 250 varieties of greens and herbs the company grows to grow fast, some reaching maturity in two weeks, about half the time as those in the field.
Radicle Farm, though a much smaller operation than AeroFarms, also represents the future of farming. Co-founders Tony Gibbons and Jim Livengood started the company in Newark in 2014 and expanded quickly, adding a 50,000-square-foot facility in Utica in 2015.
Radicle grows a variety of microgreens, such as spinach, kale, tatsoi, and Russian mizuna, which have gained a reputation for their extraordinary flavor. As a measure to ensure freshness and maintain a diminutive carbon footprint, it keeps things exclusive, limiting its delivery zone to a 300-mile radius.
Before Radicle, Gibbons, a native of Maplewood, was immersed in the fine dining world, serving as the maitre d' at the celebrated Manhattan restaurant Gramercy Tavern for nearly a decade. He'd also dipped a toe into sustainable agriculture, establishing Garden State Urban Farms with his mother, Lorraine, in 2008 (together they helped launch the Beth Greenhouse).
Livengood, who grew up in South Orange, was a grant writer at the Liberty Science Center in Jersey City before joining up with Gibbons. While working on an indoor growing exhibition, he became fascinated by traditional agriculture's concerns and hydroponic agriculture's benefits.
"In terms of conserving water and land," says Livengood, "hydroponics sounded like an elegant solution."
He began looking for companies that were using hydroponic and sustainable growing methods and eventually found Gibbons.
When Garden State Urban Farms received a grant to turn the Branch Brook Park greenhouse into a working farm, the space hadn't been used in 20 years and was in bad shape.
"It looked like Jumanji when I first went in there," says Gibbons. With an opportunity to transform the historic space, the duo didn't initially have business in mind.
"Our original goal was just to get it up and running," says Gibbons, "but then, because of how much room was available, we decided to launch Radicle and use the greenhouse as a commercial space."
Still, the operation is a relatively small one, with only five people -- most of whom come through training programs from halfway houses -- working in the space.
"It's important for us to work with the community and give our employees job skills," says Gibbons. "We hire a small number of people and train them to do a lot of things. Most of our employees can do 80 percent of what we do here."
The nutrient film technique that Gibbons and Livengood use in the greenhouse involves irrigating and fertilizing the plants with a recirculating solution that contains all of the nutrients necessary for proper growth. No soil is used; instead, the plants sit in long, pod-like channels with a shallow film of the solution lightly bathing their root systems. Because the fertilizer is contained within the growing system, it doesn't enter the local water table and harm the ecosystem.
The method uses only 10 percent of the water that field farming does. It also cuts down on the use of fossil fuels -- the minimal amount of machinery Radicle employs is powered electrically -- and space.
"It accounts for the needs of the plants, so they're not sprawling out, looking for water like they would in the field," says Livengood. "We can also grow more -- we get five times more yield per square foot because we're growing year-round, and the plants themselves grow two or three times as fast."
As with aeroponics, this hydroponic system can be used to grow any plant, but it is particularly efficient with greens. "Focusing on greens allowed us to start quickly," says Livengood.
Ensuring that their greens taste good is a priority for the Radicle crew, who are always experimenting with what they grow and with various blends in which their products can be sold.
"Selling mixes allows us to be creative with what we send our customers," says Gibbons. Their "Chef's Selection" blend, for example, combines red and green romaine lettuce with bitter mustard greens, as well as peppery arugula and mizunas. The result is a fiery mixture of piquant flavors.
The "Petal Power" adds a visual pop, with edible flowers joining beet greens, baby chard, and romaine.
This attention to look and flavor has helped Radicle develop a niche fan base among fine restaurants in New York and Jersey City.
"In the very beginning," says Gibbons, "we had success with restaurants in New Jersey that were Italian in an authentic way, which makes sense because Italian cooking is defined by going to the market and getting fresh food."
Arturo's, an osteria and pizzeria in Maplewood, was one of Radicle's first clients. "When they first started, their production was limited to primarily delivering to us and Gramercy Tavern," says Fred Shandler, the owner
of Arturo's. "To see how far they've grown and leveraged that experience into Radicle Farm is pretty impressive. Their product and overall operation are really solid. We'll regularly receive awesome basil or a micro green (that's delivered while still in its root system) and literally use it the same day."
Radicle sells its blends straight from the farm to consumers through Fresh Direct and several grocery stores across New Jersey, such as Whole Foods. A 4-ounce package sells at the same price point as AeroFarms's Dream Greens, $3.99.
Global Expansion Tipped For ‘Breakthrough’ Indoor Farming Venture
80 Acres Farms regards itself as a supply chain disruptor; choosing to focus on delivering high quality produce without the food miles by converting indoor urban spaces into ultra-efficient controlled environment agriculture (CEA) farms.
Global Expansion Tipped For ‘Breakthrough’ Indoor Farming Venture
by Gill McShane
30 January 2018
Samantha Bergman shows 80 Acres Farms' freshly picked lettuce at high-end U.S. retailer Dorothy Lane Market in Dayton, Ohio.
80 Acres Farms' shelf space at Clifton Market in Cincinnati, Ohio, which is just 2.4 miles from the company's farm.
Setting its sights on going global in the future, progressive indoor farming business 80 Acres Farms is about to launch on the mainstream U.S. market with a 12-month offer of locally-grown micro-greens, culinary herbs, leafy greens, tomatoes, cucumbers and peppers that have been bred, grown and harvested for nutrition and taste, rather than transportation. PBUK speaks with co-founders Mike Zelkind and Tisha Livingston, and their first major investor, Shawn Harris from start-up facilitator Orange Wings in the Netherlands.
80 Acres Farms regards itself as a supply chain disruptor; choosing to focus on delivering high quality produce without the food miles by converting indoor urban spaces into ultra-efficient controlled environment agriculture (CEA) farms.
Since its creation in late 2015, the company has worked tirelessly with major U.S. universities and Dutch technology company Priva to fine-tune its hydroponic growing systems. At a time when they saw other indoor growers facing challenges, 80 Acres Farms believes it has made phenomenal progress and is approaching a major breakthrough.
“This is the first real proven indoor farming business that is on the verge of getting the process completely right,” claims Harris. “We can now confidently say that we will be part of this game-changing trend to deliver fresh, healthy produce from around the corner.”
Harris invested in 80 Acres Farms in 2016 and sits on the board of directors. She set up her start-up accelerator Orange Wings after stepping down late last year as chief executive of another firm she founded – Nature’s Pride, Europe’s biggest exotic fruit and vegetable importer.
Having developed four urban indoor production sites with experienced growers in Ohio, Alabama, Arkansas and North Carolina, 80 Acres Farms has been selling its produce commercially for almost a year. In the last few months, Harris says the business has secured early commitments from some highly respected retailers and one of the biggest foodservice companies in the United States.
Using local depots, each production site will pick its produce at the peak stage of ripeness to deliver daily to local restaurants and various regional and national retailers located within 100 miles. Further details have yet to be disclosed.
Ultimately, 80 Acres Farms aims to deliver its accessible, nutritious, tasty and affordable local food concept to other parts of the world, particularly areas that are unable to either produce outdoors or in conventional greenhouses for 12 months of the year.
Disrupting the supply chain
According to company CEO Zelkind, the key factor that sets the business apart from others is the indoor status of its farms and its product mix, added to the fact that the team not only has food industry experience but has run food companies on a commercial scale.
Importantly, Zelkind says 80 Acres has built an indoor system that grows affordable produce all year round under a completely controlled environment.
“It’s the next generation of controlled environment agriculture,” he claims. “80 Acres grows products much faster than in the traditional outdoor environment or even in a greenhouse environment. We can control all the factors, like CO2 levels, and when and how much to deliberately stress the plant to get the right level of nutrition and flavour.”
Co-founders Zelkind and Livingston have spent decades running companies in the food industry. Before 80 Acres Farms, Zelkind was president and chief executive officer of Sager Creek Vegetable Company when it was a division of Del Monte Foods Inc., San Francisco, while Livingston was chief operating officer at the same firm.
In establishing 80 Acres Farms, the duo says they are bringing back the “backyard fresh taste” of produce to many communities around the United States all year-round.
Livingston points out that currently fresh produce often travels long distances.
“Because of these distances traveled, our food is now being bred, grown and harvested for transportation rather than nutrition and taste,” adds Zelkind. “80 Acres Farms drastically disrupts current produce supply chains.”
Indeed, being local to its customers in four U.S. states means 80 Acres Farms can pick produce when it’s ripe, and plant varieties that are bred for flavor and yield, rather than transportation and survival in an unpredictable environment.
“This is a huge differentiating point,” Livingston says. “We can deliver ‘just-picked’ quality produce to a retailer or restaurant year-round. We have partnered with and continue to partner with commercial and research institutions to gather nutritional information and to grow produce that has much more nutritional value.”
Thanks to the proximity to customers, Zelkind claims the products offered by 80 Acres Farms are also “more nutritious than most organics”. “We view ourselves as the next generation of organics,” he explains. “We don’t use pesticides – organic does.
“We are considering getting an organic certification but at this point, we are better than organic. We abide by most organic practices but we go way beyond what organic does. We are closer to the customer and we offer fresher products.”
Already, Zelkind explains that the first chef and consumer feedback is about how the produce offered by 80 Acres Farms is much tastier and fresh.
“I have visited stores with Mike and Tisha and I have heard customers talk about their experience with the products and the taste difference, which is why they keep coming back – it just makes you feel good,” Harris explains.
As such, Zelkind and Livingston believe the company’s target consumer market is wide open to anyone who likes high quality, fresh, tasty and pesticide-free produce, whether that be millennials or baby boomers.
Expansion plans
From its headquarters in Cincinnati, Ohio, 80 Acres Farms now plans to build many more sites across the US, while aiming to expand globally. Each individual farm will deliver a product mix driven by the needs of local customers. On top of that, the company is building its biggest farm that will use 100% renewable energy when completed.
“80 Acres has very ambitious goals, but there is a lot to prove before that kind of expansion is warranted,” Zelkind notes. “We believe in keeping our heads in the clouds and feet firmly planted in the mud!”
For now, that means scaling with its customer base and striving to delight its growing consumer base. To that end, 80 Acres Farms has an exciting R&D product portfolio in the pipeline that includes root crops, which will complement its current range of micro-greens, culinary herbs, leafy greens and vine crops such as tomatoes, cucumbers, peppers, and hops.
“No one has yet figured out how to grow vine crops profitably indoors, in a completely controlled environment,” Zelkind comments. “We are the first and only ones in the world doing it so far but we can do it better. That’s the most exciting part. That’s the challenge for the next few years.”
Of course, one of the drawbacks of indoor farming is that it isn’t possible yet to economically grow all fruits and vegetables. “You won’t be able to do so for a long time to come,” admits Zelkind. “But there is no intention to replace traditional farmers. 80 Acres wants to work with these farmers and supplement what they can grow locally.”
Getting the process right
While the concept of indoor agriculture is logical and straightforward when broken into its subunits, Zelkind says bringing together all the components is not simple.
Firstly, to achieve the optimal growing environment you need multi-disciplined engineering, an understanding of plant science, and good farming experience. Then to grow crops profitably you must be able to understand manufacturing practices, automation and how to scale production.
Once you have that, you need the ability to brand and sell your products in a crowded marketplace. Plus, to run and build the business, you need the right people with the right experience. To set up the farms in the first place also requires a great deal of capital investment.
So, starting in late 2015 with a small R&D facility, 80 Acres Farms teamed up with international academics and scientists to figure out how to grow high quality plants with the right nutrition and flavour levels in the most effective way.
Since then, the company has developed a strong in-house engineering team and a large pool of data analysts who manage a production system guided by various sensors and other technologies to understand and optimise plant growth and development.
Following much trial and error, 80 Acres Farms is now on the fourth iteration of its production systems, which are installed across its current production sites in four states of the US. From here on, the company remains committed to driving the industry forward.
“This is a new industry and we all have so much to learn,” concludes Zelkind.
What is Controlled Environment Agriculture?
Controlled Environment Agriculture (CEA) is designed to optimise the growing conditions for food and aquatic production in an enclosed area, such as a greenhouse or building.
By controlling variables, such as: light, carbon dioxide, temperature, humidity, water, nutrients and pH levels, plants receive the correct amounts of water and nutrients, which often results in greater yields, all year-round. Production technologies include: hydroponics, aquaculture and aquaponics.
CEA operations can vary from fully-automated glasshouses with computer controls for watering, lighting and ventilation, to low-tech facilities that use cloches or plastic film to cover rows of field-grown crops, or basic plastic-covered tunnels.
CEA focuses on raising efficiency and maximising resources, including: space, water, energy, labour and capital. Given its nature, CEA also reduces the incidences of pest and disease, and allows the grower to recycle inputs like water or nutrients.
80 Acres Farms has developed a CEA system for urban indoor buildings where it claims the growing environment is completely controlled and guided by sophisticated technology. The company uses hydroponic technology to locally produce year-round and pesticide-free commercial volumes of micro-greens, culinary herbs and leafy greens, as well as vine crops, such as tomatoes, cucumbers, peppers and hops.